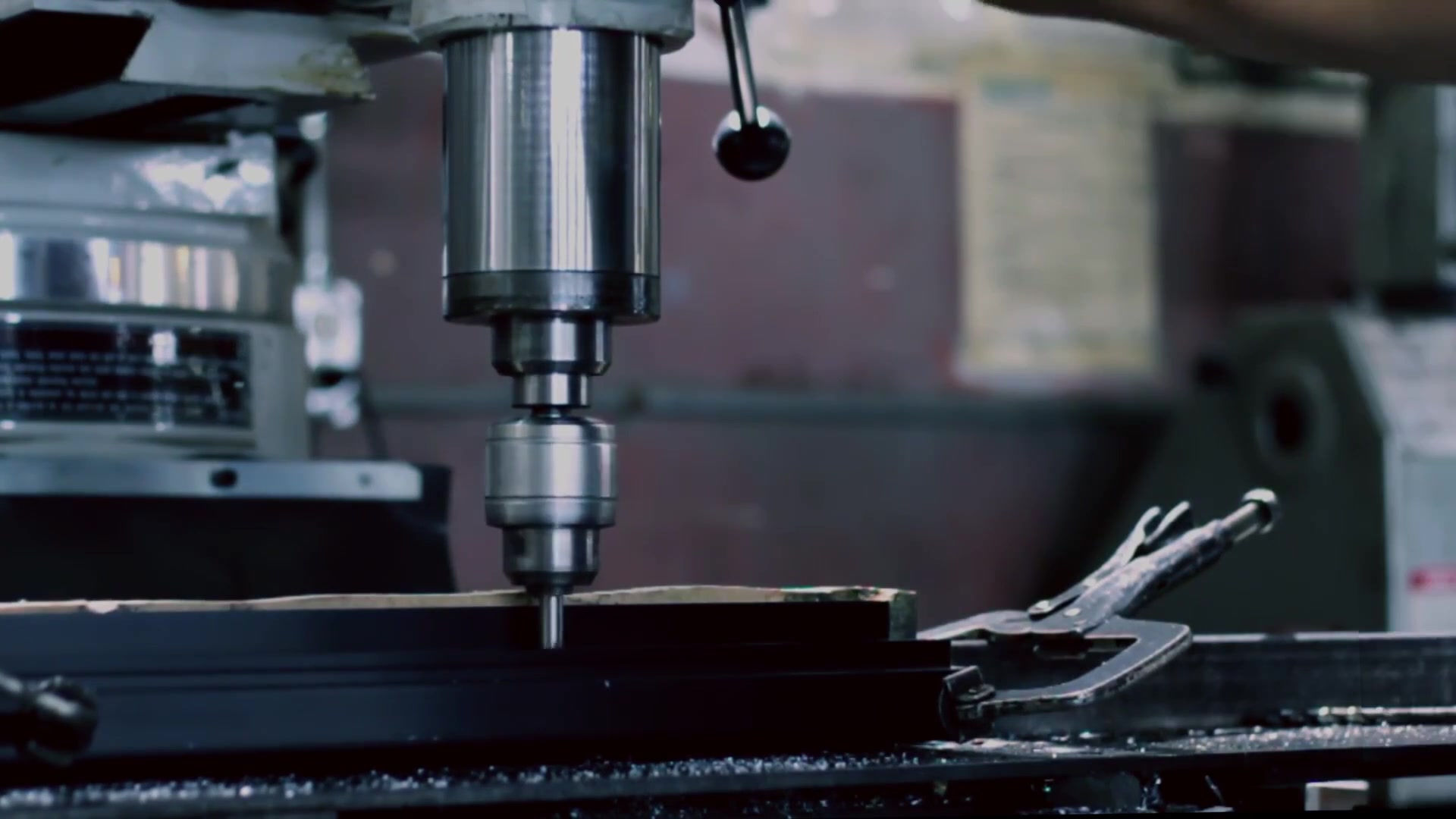
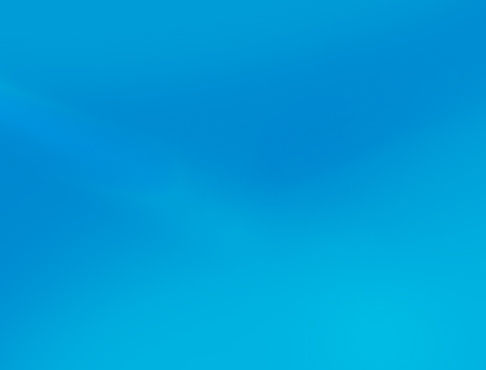
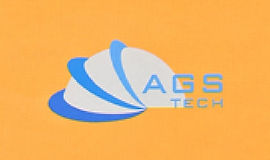
יצרן מותאם אישית גלובלי, אינטגרטור, מאחד, שותף מיקור חוץ עבור מגוון רחב של מוצרים ושירותים.
אנחנו המקור היחיד שלך לייצור, ייצור, הנדסה, איחוד, אינטגרציה, מיקור חוץ של מוצרים ושירותי מדף מיוצרים בהתאמה אישית.
בחר את השפה שלך
-
ייצור בהתאמה אישית
-
ייצור חוזים מקומי וגלובלי
-
מיקור חוץ של ייצור
-
רכש מקומי וגלובלי
-
Consolidation
-
אינטגרציה הנדסית
-
שרותי הנדסה
Search Results
נמצאו 164 תוצאות בלי מונחי חיפוש
- Global Product Finder Locator for Off Shelf Products
Global Product Finder Locator for Off Shelf Products AGS-TECH, Inc. הוא שלך יצרן מותאם אישית גלובלי, אינטגרטור, קונסולידטור, שותף מיקור חוץ. אנחנו המקור היחיד שלך לייצור, ייצור, הנדסה, איחוד, מיקור חוץ. If you exactly know the product you are searching, please fill out the table below If filling out the form below is not possible or too difficult, we do accept your request by email also. Simply write us at sales@agstech.net Get a Price Quote on a known brand, model, part number....etc. First name Last name Email Phone Product Name Product Make or Brand Please Enter Manufacturer Part Number if Known Please Enter SKU Code if You Know: Your Application for the Product Quantity Needed Do You have a price target ? If so, please let us know: Give us more details if you want: Condition of Product Needed New Used Does Not Matter If you have any, upload product relevant files by clicking at the below link. Don't worry, the link below will pop up a new window for downloading your files. You will not navigate away from this current window. After uploading your files, close ONLY the Dropbox Window, but not this page. Make sure to fill out all spaces and click the submit button below. CLICK HERE TO UPLOAD FILES Request a Quote Thanks! We’ll send you a price quote shortly. PREVIOUS PAGE אנחנו AGS-TECH Inc., המקור היחיד שלך לייצור וייצור והנדסה ומיקור חוץ ואיחוד. אנחנו האינטגרטור ההנדסי המגוון ביותר בעולם המציע לך ייצור בהתאמה אישית, תת-הרכבה, הרכבה של מוצרים ושירותי הנדסה.
- Custom Made Products Data Entry
Custom Made Products Data Entry, Custom Manufactured Parts, Assemblies, Plastic Molds, Casting, CNC Machining, Extrusion, Metal Forging, Spring Manufacturing, Products Assembly, PCBA, PCB AGS-TECH, Inc. הוא שלך יצרן מותאם אישית גלובלי, אינטגרטור, קונסולידטור, שותף מיקור חוץ. אנחנו המקור היחיד שלך לייצור, ייצור, הנדסה, איחוד, מיקור חוץ. Fill In your info if you you need custom design & development & prototyping & mass production: If filling out the form below is not possible or too difficult, we do accept your request by email also. Simply write us at sales@agstech.net Get a Price Quote on a custom designed, developed, prototyped or manufactured product. First name Last name Email Phone Product Name Your Application for the Product Quantity Needed Do you have a price target ? If you do have, please let us know your expected price: Give us more details if you want: Do you accept offshore manufacturing ? YES NO If you have any, upload product relevant files by clicking at the below link. Don't worry, the link below will pop up a new window for downloading your files. You will not navigate away from this current window. After uploading your files, close ONLY the Dropbox Window, but not this page. Make sure to fill out all spaces and click the submit button below. Files that will help us quote your specially tailored product are technical drawings, bill of materials, photos, sketches....etc. You can download more than one file. CLICK HERE TO UPLOAD FILES Request a Quote Thanks! We’ll send you a price quote shortly. PREVIOUS PAGE אנחנו AGS-TECH Inc., המקור היחיד שלך לייצור וייצור והנדסה ומיקור חוץ ואיחוד. אנחנו האינטגרטור ההנדסי המגוון ביותר בעולם המציע לך ייצור בהתאמה אישית, תת-הרכבה, הרכבה של מוצרים ושירותי הנדסה.
- Hardness Tester - Rockwell - Brinell - Vickers - Leeb - Microhardness
Hardness Tester - Rockwell - Brinell - Vickers - Leeb - Microhardness - Universal - AGS-TECH Inc. - New Mexico - USA בודקי קשיות AGS-TECH Inc. מחזיקה במלאי מגוון מקיף של בודקי קשיות כולל ROCKWELL, BRINELL, VICKERS, LEEB, KNOOP, MICROHHARDNESS TESTERS, UNIVERSAL HardNESSTHNESS TESTERS, מערכות UNIVERSAL HardnestABLEESTINGSTRUM ומדידות נתונים עבור מערכות בדיקות תקינות TESTRtical, רכישה וניתוח, בלוקים לבדיקה, מכנסיים, סדים ואביזרים נלווים. כמה מבוחני הקשיות של שמות המותג שאנו מוכרים הם SADT, SINOAGE and_cc781905-53dbb-31905-53d_cc781905-531cdb31905-51cdb31905-531cd_bcf5cf31cd-53cdb31905-531cdb31905-51cd_5cf5cf58cd_511905-531cdb31905-531cdb31905-51c. להורדת קטלוג למטרולוגיה וציוד בדיקה של המותג SADT שלנו, אנא לחץ כאן. להורדת חוברת עבור בודק הקשיות הנייד שלנו MITECH MH600, אנא לחץ כאן לחץ כאן להורדת טבלת השוואת מוצרים בין בודקי קשיות MITECH אחת הבדיקות הנפוצות ביותר להערכת התכונות המכניות של חומרים היא בדיקת הקשיות. קשיות של חומר היא עמידותו בפני הזחה קבועה. אפשר גם לומר שקשיות היא עמידות החומר בפני שריטות ובלאי. ישנן מספר טכניקות למדידת קשיות החומרים באמצעות גיאומטריות וחומרים שונים. תוצאות המדידה אינן מוחלטות, הן מהוות יותר אינדיקטור השוואתי יחסי, מכיוון שהתוצאות תלויות בצורת המפתח ובעומס המופעל. בודקי הקשיות הניידים שלנו יכולים בדרך כלל להריץ כל בדיקת קשיות המפורטת לעיל. ניתן להגדיר אותם עבור תכונות וחומרים גיאומטריים מסוימים כגון פנים חורים, שיניים ציוד וכו '. הבה נעבור בקצרה על שיטות בדיקת הקשיות השונות. BRINELL TEST : בבדיקה זו, כדור פלדה או טונגסטן קרביד בקוטר 10 מ"מ נלחץ על משטח עם עומס של 500, 1500 או 3000 ק"ג כוח. מספר קשיות ברינל הוא היחס בין העומס לאזור המעוקל של הזחה. בדיקת ברינל מותירה אחריה סוגים שונים של טביעות על פני השטח בהתאם למצב החומר הנבדק. לדוגמה, על חומרים מחושלים נותר מאחור פרופיל מעוגל ואילו בחומרים שעברו עבודה קרה אנו רואים פרופיל חד. כדורי טונגסטן קרביד מומלצים למספרי קשיות ברינל הגבוהים מ-500. לחומרי עבודה קשים יותר מומלץ עומס של 1500 ק"ג או 3000 ק"ג כדי שהחריצים שנותרו מאחור יהיו גדולים מספיק למדידה מדויקת. בגלל העובדה שהטביעות שנעשות על ידי אותו שקע בעומסים שונים אינם דומים מבחינה גיאומטרית, מספר הקשיות של Brinell תלוי בעומס המשמש. לכן יש לשים לב תמיד לעומס המופעל על תוצאות הבדיקה. מבחן Brinell מתאים היטב לחומרים בין קשיות נמוכה עד בינונית. ROCKWELL TEST : בבדיקה זו נמדד עומק החדירה. המשטח נלחץ על פני השטח בתחילה בעומס מינורי ולאחר מכן בעומס גדול. ההבדל בחוב החדירה הוא מדד לקשיות. קיימים מספר סולמות קשיות של רוקוול המשתמשים בעומסים שונים, בחומרי שקע ובגיאומטריות שונות. מספר הקשיות של Rockwell נקרא ישירות מחוגה במכונת הבדיקה. לדוגמה, אם מספר הקשיות הוא 55 באמצעות סולם C, הוא כתוב כ-55 HRC. VICKERS TEST : לפעמים מכונה גם the DIAMOND PYRAMID HARDNESS TEST, זה משתמש ב-0 diamond a diamond tond-2 מספר הקשיות של ויקרס ניתן על ידי HV=1.854P / ריבוע L. ה-L כאן הוא האורך האלכסוני של פירמידת היהלום. מבחן Vickers נותן בעצם את אותו מספר קשיות ללא קשר לעומס. מבחן Vickers מתאים לבדיקת חומרים בעלי טווח קשיות רחב כולל חומרים קשים מאוד. KNOOP TEST : בבדיקה זו, אנו משתמשים במכנס יהלום בצורת פירמידה מוארכת ועומס בין 25 גרם ל- 5 ק"ג. מספר קשיות Knoop ניתן כ-HK=14.2P / ריבוע L. כאן האות L היא אורך האלכסון המוארך. גודל החריצים בבדיקות Knoop קטן יחסית, בטווח של 0.01 עד 0.10 מ"מ. בשל מספר קטן זה הכנת פני השטח לחומר חשובה מאוד. תוצאות הבדיקה צריכות לציין את העומס המופעל מכיוון שמספר הקשיות המתקבל תלוי בעומס המופעל. מכיוון שמשתמשים בעומסים קלים, מבחן Knoop נחשב ל-a MICROHARDNESS TEST. לכן בדיקת Knoop מתאימה לדגימות קטנות מאוד ודקות, לחומרים שבירים כמו אבני חן, זכוכית וקרבידים ואפילו למדידת קשיות של גרגרים בודדים במתכת. LEEB HARDNESS TEST : הוא מבוסס על טכניקת ריבאונד המודדת את קשיות Leeb. זוהי שיטה קלה ופופולרית מבחינה תעשייתית. שיטה ניידת זו משמשת בעיקר לבדיקת חלקי עבודה גדולים מספיק מעל 1 ק"ג. גוף פגיעה עם קצה בדיקה מתכת קשה מונע על ידי כוח קפיץ כנגד משטח העבודה. כאשר גוף הפגיעה פוגע בחומר העבודה, מתרחש עיוות פני השטח אשר יגרום לאובדן אנרגיה קינטית. מדידות מהירות חושפות הפסד זה באנרגיה קינטית. כאשר גוף הפגיעה עובר סליל במרחק מדויק מהמשטח, מתח אות מושרה במהלך שלבי הפגיעה והריבאונד של הבדיקה. מתחים אלה פרופורציונליים למהירות. באמצעות עיבוד אותות אלקטרוני מקבלים את ערך קשיות Leeb מהתצוגה. Our PORTABLE HARDNESS TESTERS from SADT / HARTIP HARDNESS TESTER SADT HARTIP2000/HARTIP2000 D&DL : זהו בודק קשיות Leeb נייד חדשני עם טכנולוגיה חדשה רשומה בפטנט, מה שהופך את HARTIP 2000 לבוחן זווית אוניברסלי (UA) כיוון פגיעות. אין צורך להגדיר את כיוון ההשפעה בעת ביצוע מדידות בכל זווית. לכן, HARTIP 2000 מציע דיוק ליניארי בהשוואה לשיטת פיצוי הזווית. HARTIP 2000 הוא גם בודק קשיות חוסך בעלויות ויש לו תכונות רבות אחרות. ה-HARTIP2000 DL מצויד ב-SADT ייחודי מסוג D ו-DL 2-in-1. SADT HARTIP1800 Plus/1800 Plus D&DL : מכשיר זה הוא בודק קשיות מתכת מתקדם מתקדם בגודל כף היד עם תכונות חדשות רבות. באמצעות טכנולוגיה מוגנת בפטנט, SADT HARTIP1800 Plus הוא מוצר מהדור החדש. יש לו דיוק גבוה של +/-2 HL (או 0.3% @HL800) עם תצוגת OLED בחוזה גבוה וטווח טמפרטורות סביבתי רחב (-40ºC~60ºC). מלבד זיכרונות ענק ב-400 בלוקים עם נתונים של 360,000, HARTIP1800 Plus יכול להוריד נתונים נמדדים למחשב ולתדפיס למיני מדפסת באמצעות יציאת USB ובאופן אלחוטי עם מודול שן כחולה פנימי. ניתן לטעון את הסוללה פשוט מיציאת USB. יש לו פונקציית כיול מחדש של הלקוח וסטטיקה. HARTIP 1800 plus D&DL מצויד בבדיקה של שניים באחד. עם בדיקה ייחודית של שניים באחד, HARTIP1800plus D&DL יכול להמיר בין בדיקה D לבדיקה DL פשוט על ידי שינוי גוף הפגיעה. זה יותר חסכוני מאשר לקנות אותם בנפרד. יש לו אותה תצורה עם HARTIP1800 plus למעט בדיקה שניים באחד. SADT HARTIP1800 Basic/1800 Basic D&DL : זהו דגם בסיסי עבור HARTIP1800plus. עם רוב פונקציות הליבה של HARTIP1800 plus ומחיר נמוך יותר, HARTIP1800 Basic הוא בחירה טובה ללקוח עם תקציב מוגבל. ניתן לצייד את HARTIP1800 Basic גם במכשיר ההשפעה הייחודי שלנו D/DL דו-באחד. SADT HARTIP 3000 : זהו בודק קשיות מתכת דיגיטלי מתקדם עם דיוק גבוה, טווח מדידה רחב וקלות תפעול. הוא מתאים לבדיקת קשיות כל המתכות במיוחד באתר עבור רכיבים מבניים ומורכבים גדולים, הנמצאים בשימוש נרחב בתעשיות החשמל, הפטרוכימיה, התעופה והחלל, הרכב ובניית מכונות. SADT HARTIP1500/HARTIP1000 : זהו בודק קשיות מתכת כף יד משולב המשלב התקן השפעה (בדיקה) ומעבד ליחידה אחת. הגודל קטן בהרבה ממכשיר ההשפעה הסטנדרטי, המאפשר ל-HARTIP 1500/1000 לעמוד לא רק בתנאי מדידה רגילים, אלא גם לבצע מדידות במקומות צרים. HARTIP 1500/1000 מתאים לבדיקת קשיות כמעט של כל החומרים הברזליים והלא ברזליים. עם הטכנולוגיה החדשה שלו, הדיוק שלו משתפר לרמה גבוהה יותר מהסוג הסטנדרטי. HARTIP 1500/1000 הוא אחד מבוחני הקשיות החסכוניים ביותר בכיתה שלו. מערכת מדידה אוטומטית לקריאת קשיות BRINELL / SADT HB SCALER : HB Scaler היא מערכת מדידה אופטית שיכולה למדוד אוטומטית את גודל השקע מבוחן קשיות Brinell ומעניקה לבדיקת קשיות Brinell. ניתן לשמור את כל הערכים ותמונות ההזחה במחשב. בעזרת התוכנה ניתן לעבד את כל הערכים ולהדפיס אותם כדוח. Our BENCH HARDNESS TESTER products from SADT are: SADT HR-150A ROCKWELL HARDNESS TESTER : בודק הקשיות HR-150A Rockwell המופעל באופן ידני ידוע בשלמותו ובקלות התפעול שלו. מכונה זו משתמשת בכוח הבדיקה המקדים הסטנדרטי של 10kgf ובעומסים עיקריים של 60/100/150 קילוגרמים תוך התאמה לתקן Rockwell הבינלאומי. לאחר כל בדיקה, ה-HR-150A מציג את ערך הקשיות של Rockwell B או Rockwell C ישירות על מחוון החוגה. יש להפעיל את כוח הבדיקה המקדים באופן ידני, ולאחר מכן הפעלת העומס העיקרי באמצעות הידית בצד ימין של בודק הקשיות. לאחר הפריקה, החוגה מציינת את ערך הקשיות המבוקש ישירות עם דיוק וחזרה גבוהים. SADT HR-150DT MOTORIZED ROCKWELL HARDNESS TESTER : סדרה זו של בודקי קשיות מוכרת בזכות הדיוק וקלות התפעול שלהם, מתפקדים בהתאם לחלוטין לתקן Rockwell הבינלאומי. בהתאם לשילוב של סוג ההזחה וכוח הבדיקה הכולל המופעל, ניתן סמל ייחודי לכל סולם Rockwell. HR-150DT ו-HRM-45DT כוללים את שני מאזני Rockwell ספציפיים של HRC ו-HRB על חוגה. יש לכוונן את הכוח המתאים באופן ידני, באמצעות החוגה בצד ימין של המכונה. לאחר הפעלת הכוח המקדים, ה-HR150DT ו-HRM-45DT ימשיכו בבדיקה אוטומטית לחלוטין: טעינה, המתנה, פריקה, ובסופה יציגו את הקשיות. SADT HRS-150 DIGITAL ROCKWELL HARDNESS TESTER : בודק הקשיות הדיגיטלי של Rockwell HRS-150 מיועד לקלות שימוש ובטיחות תפעול. זה תואם את תקן Rockwell הבינלאומי. בהתאם לשילוב של סוג ההזחה וכוח הבדיקה הכולל המופעל, ניתן סמל ייחודי לכל סולם Rockwell. ה-HRS-150 יציג אוטומטית את הבחירה שלך בסולם Rockwell ספציפי על תצוגת ה-LCD, ויציין באיזה עומס נעשה שימוש. מנגנון הבלם האוטומטי המשולב מאפשר להפעיל את כוח הבדיקה המקדים באופן ידני ללא אפשרות לשגיאה. לאחר הפעלת הכוח המקדים, ה-HRS-150 ימשיך בבדיקה אוטומטית לחלוטין: טעינה, זמן שהייה, פריקה וחישוב ערך הקשיות והתצוגה שלו. מחובר למדפסת המצורפת דרך פלט RS232, אפשר להדפיס את כל התוצאות. Our BENCH TYPE SUPERFICIAL ROCKWELL HARDNESS TESTER products from SADT are: SADT HRM-45DT MOTORIZED SUPERFICIAL ROCKWELL HARDNESS TESTER : בודקי קשיות מסדרה זו מוכרים בזכות הדיוק וקלות ההפעלה שלהם, פועלים בהתאם לתקן הבינלאומי של Rockwell. בהתאם לשילוב של סוג ההזחה וכוח הבדיקה הכולל המופעל, ניתן סמל ייחודי לכל סולם Rockwell. HR-150DT ו-HRM-45DT כוללים את שני מאזני Rockwell הספציפיים HRC ו-HRB על חוגה. יש לכוונן את הכוח המתאים באופן ידני, באמצעות החוגה בצד ימין של המכונה. לאחר הפעלת הכוח המקדים, ה-HR150DT וה-HRM-45DT ימשיכו בתהליך בדיקה אוטומטי לחלוטין: טעינה, השהייה, פריקה ובסופו יציג את הקשיות. SADT HRMS-45 SUPERFICIAL ROCKWELL HARDNESS TESTER : HRMS-45 Digital Superficial Rockwell Hardness Tester הוא מוצר חדשני המשלב טכנולוגיות מכניות ואלקטרוניות מתקדמות. התצוגה הכפולה של דיודות LCD ו-LED דיגיטליות, הופכות אותה לגרסת מוצר משודרגת של בודק Rockwell שטחי מסוג סטנדרטי. הוא מודד את הקשיות של מתכות ברזליות, לא ברזליות וחומרים קשים, שכבות מקרבות וחנקות ושכבות אחרות שעברו טיפול כימי. הוא משמש גם למדידת קשיות של חתיכות דקות. SADT XHR-150 PLASTIC ROCKWELL HARDNESS TESTER : בודק קשיות פלסטיק XHR-150 Rockwell מאמץ שיטת בדיקה ממונעת, ניתן להעמיס את כוח הבדיקה, לפרוק אותו באופן אוטומטי ולפרוק אותו בבית. טעויות אנוש ממוזערות וקלות לתפעול. הוא משמש למדידת פלסטיק קשיח, גומיות קשות, אלומיניום, פח, נחושת, פלדה רכה, שרפים סינתטיים, חומרים טריבוליים וכו'. Our BENCH TYPE VICKERS HARDNESS TESTER products from SADT are: SADT HVS-10/50 LOW LOAD VICKERS HARDNESS TESTER : בודק הקשיות של Vicker בעל עומס נמוך עם תצוגה דיגיטלית הוא מוצר היי-טק חדש המשלב טכנולוגיות מכניות ופוטואלקטריות. כתחליף לבוחני הקשיות המסורתיים של Vicker עם עומס קטן, הוא כולל תפעול קל ואמינות טובה, אשר תוכנן במיוחד לבדיקת דוגמאות קטנות ודקות או חלקים לאחר ציפוי פני השטח. מתאים למכוני מחקר, מעבדות תעשייתיות ומחלקות QC, זהו מכשיר אידיאלי לבדיקת קשיות למטרות מחקר ומדידה. הוא מציע שילוב של טכנולוגיית תכנות מחשבים, מערכת מדידה אופטית ברזולוציה גבוהה וטכניקה פוטו-אלקטרית, כניסת מפתח רך, התאמת מקור אור, דגם בדיקה לבחירה, טבלאות המרה, זמן החזקת לחץ, קלט מספר קובץ ופונקציות שמירת נתונים. יש לו מסך LCD גדול כדי להציג את דגם הבדיקה, לחץ הבדיקה, אורך ההזחה, ערכי הקשיות, זמן החזקת הלחץ ומספרי הבדיקות. מציע גם רישום תאריך, רישום תוצאות בדיקה ועיבוד נתונים, פונקציית פלט הדפסה, דרך ממשק RS232. SADT HV-10/50 LOW LOAD VICKERS HARDNESS TESTER : בודקי הקשיות של Vickers בעומס נמוך הם מוצרי היי-טק חדשים המשלבים טכנולוגיות מכניות ופוטואלקטריות. בודקים אלו תוכננו במיוחד לבדיקת דוגמאות וחלקים קטנים ודקים לאחר ציפוי פני השטח. מתאים למכוני מחקר, מעבדות תעשייתיות ומחלקות QC. תכונות ופונקציות עיקריות הן בקרת מיקרו-מחשב, התאמת מקור האור באמצעות מקשי רכים, התאמת זמן החזקת הלחץ ותצוגת LED/LCD, מכשיר המרת המדידה הייחודי שלו ומכשיר קריאת מדידה חד פעמי של עינית מיקרו המבטיח שימוש קל ודיוק גבוה. SADT HV-30 VICKERS HARDNESS TESTER : בודק הקשיות HV-30 דגם Vickers תוכנן במיוחד לבדיקת דגימות וחלקים קטנים ודקים לאחר ציפוי פני השטח. מתאימים למכוני מחקר, מעבדות מפעל ומחלקות QC, אלו הם מכשירי בדיקת קשיות אידיאליים למטרות מחקר ובדיקה. תכונות ופונקציות עיקריות הן בקרת מחשב מיקרו, מנגנון טעינה ופריקה אוטומטיים, התאמה של מקור תאורה באמצעות חומרה, התאמה של זמן החזקת לחץ (0~30 שניות), התקן המרת מדידה ייחודי ומכשיר קריאת מדידה חד פעמי מיקרו עינית, המבטיח קלה שימוש ודיוק גבוה. Our BENCH TYPE MICRO HARDNESS TESTER products from SADT are: SADT HV-1000 MICRO HARDNESS TESTER / HVS-1000 DIGITAL MICRO HARDNESS TESTER : מוצר זה מתאים במיוחד לבדיקת קשיות דיוק גבוהה של מוצרים קטנים ודקים, דגימות של חומרי ציפוי, דגימות. ושכבות מוקשות. כדי להבטיח הזחה משביעת רצון, ה-HV1000 / HVS1000 כולל פעולות טעינה ופריקה אוטומטיות, מנגנון טעינה מדויק מאוד ומערכת מנוף חזקה. המערכת מבוקרת המיקרו-מחשב מבטיחה מדידת קשיות מדויקת לחלוטין עם זמן שהייה מתכוונן. SADT DHV-1000 MICRO HARDNESS TESTER / DHV-1000Z DIGITAL VICKERS HARDNESS TESTER : בודקי קשיות המיקרו Vickers אלה המיוצרים עם עיצוב ייחודי ומדויק של מדידת שקעים ומדויקת, מסוגלים לייצר יותר מדידת שקעים ומדויקת. באמצעות עדשת 20 × ועדשת 40 × למכשיר יש שדה מדידה רחב יותר וטווח יישום רחב יותר. מצויד במיקרוסקופ דיגיטלי, על מסך ה-LCD שלו הוא מציג את שיטות המדידה, כוח הבדיקה, אורך השקע, ערך הקשיות, זמן השהייה של כוח הבדיקה וכן מספר המדידות. בנוסף, הוא מצויד בממשק המקושר למצלמה דיגיטלית ומצלמת וידאו CCD. בודק זה נמצא בשימוש נרחב למדידת מתכות ברזליות, מתכות לא ברזליות, חתכים דקים IC, ציפויים, זכוכית, קרמיקה, אבנים יקרות, שכבות מוקשות למרווה ועוד. SADT DXHV-1000 DIGITAL MICRO HARDNESS TESTER : בודקי קשיות מיקרו Vickers אלה העשויים עם ייחודיות ומדויקות מסוגלים לייצר חריטה ברורה יותר ומכאן מדידות מדויקות יותר. באמצעות עדשת 20 × ועדשת 40 × לבודק יש שדה מדידה רחב יותר וטווח יישום רחב יותר. עם מכשיר מסתובב אוטומטי (הצריח המסתובב אוטומטית), הפעולה הפכה לקלה יותר; ועם ממשק מושחל, ניתן לקשר אותו למצלמה דיגיטלית ומצלמת וידאו CCD. ראשית המכשיר מאפשר להשתמש במסך המגע ה-LCD, ובכך מאפשר שליטה אנושית יותר בפעולה. למכשיר יכולות כמו קריאה ישירה של המידות, שינוי קל של מאזני הקשיות, שמירת הנתונים, ההדפסה והחיבור לממשק RS232. בודק זה נמצא בשימוש נרחב למדידת מתכות ברזליות, מתכות לא ברזליות, חלקים דקים IC, ציפויים, זכוכית, קרמיקה, אבנים יקרות; חלקי פלסטיק דקים, מרווה שכבות מוקשות ועוד. Our BENCH TYPE BRINELL HARDNESS TESTER / MULTI-PURPOSE HARDNESS TESTER products from SADT are: SADT HD9-45 SUPERFICIAL ROCKWELL & VICKERS OPTICAL HARDNESS TESTER : התקן זה משרת את המטרה של מדידת הקשיות של מתכות ברזליות, לא ברזליות, מתכות קשות בשכבות ומתכות כימיות מרובות ומתכות קשות. SADT HBRVU-187.5 BRINELL ROCKWELL & VICKERS OPTICAL HARDNESS TESTER : מכשיר זה משמש לקביעת הקשיות של Brinell, Rockwell ו-Vickers של שכבות ברזליות, מתכת לא-ברזלית ושכבות כימיות קשות. זה יכול לשמש במפעלים, מכוני מדעי ומחקר, מעבדות ומכללות. SADT HBRV-187.5 BRINELL ROCKWELL & VICKERS HARDNESS Tester (לא אופטי) : מכשיר זה משמש לקביעת קשיות Brinell, Rockwell ו-Vickers של מתכת לא-ברזלית, שכבות ברזליות, מתכת קשה. ושכבות שעברו טיפול כימי. זה יכול לשמש במפעלים, מכוני מדעי ומחקר, מעבדות ומכללות. זה לא בודק קשיות מסוג אופטי. SADT HBE-3000A BRINELL HARDNESS TESTER : בודק קשיות Brinell אוטומטי זה כולל טווח מדידה רחב של עד 3000 Kgf עם דיוק גבוה התואם לתקן DIN/11225. במהלך מחזור הבדיקה האוטומטי הכוח המופעל יהיה נשלט על ידי מערכת לולאה סגורה המבטיחה כוח קבוע על חלק העבודה, בהתאם לתקן DIN 50351. ה-HBE-3000A מגיע לחלוטין עם מיקרוסקופ קריאה עם מקדם הגדלה של 20X ורזולוציית מיקרומטר של 0.005 מ"מ. SADT HBS-3000 DIGITAL BRINELL HARDNESS TESTER : בודק קשיות ברינל דיגיטלי זה הוא מכשיר חדיש מהדור החדש. זה יכול לשמש כדי לקבוע את קשיות ברינל של מתכות ברזליות ולא ברזליות. הבוחן מציע טעינה אוטומטית אלקטרונית, תכנות תוכנת מחשב, מדידה אופטית בעוצמה גבוהה, חיישן פוטו ותכונות נוספות. ניתן להציג כל תהליך תפעולי ותוצאת בדיקה על מסך ה-LCD הגדול שלו. ניתן להדפיס את תוצאות הבדיקה. המכשיר מתאים לסביבות ייצור, מכללות ומוסדות מדעיים. SADT MHB-3000 DIGITAL ELECTRONIC BRINELL HARDNESS TESTER : מכשיר זה הוא מוצר משולב המשלב טכניקות אופטיות, מכניות ואלקטרוניות, תוך אימוץ מבנה מכני סגור מדויק ומערכת ממוחשבת. המכשיר טוען ופורק את כוח הבדיקה עם המנוע שלו. באמצעות חיישן דחיסה דיוק של 0.5% למשוב המידע וה-CPU לשליטה, המכשיר מפצה אוטומטית על כוחות הבדיקה המשתנים. מצויד בעינית מיקרו דיגיטלית על המכשיר, ניתן למדוד את אורך ההזחה directly. כל נתוני הבדיקה כגון שיטת הבדיקה, ערך כוח הבדיקה, אורך כניסת הבדיקה, ערך הקשיות וזמן השהייה של כוח הבדיקה יכולים להיות מוצגים על מסך ה-LCD. אין צורך להזין את ערך האורך האלכסוני עבור ההזחה ואין צורך לחפש את ערך הקשיות מטבלת הקשיות. לכן נתוני הקריאה מדויקים יותר והתפעול של מכשיר זה קל יותר. לפרטים וציוד דומה אחר, אנא בקר באתר הציוד שלנו: http://www.sourceindustrialsupply.com CLICK Product Finder-Locator Service עמוד קודם
- Computer Chassis, Racks, Shelves, 19 inch Rack, 23 inch Rack, Case
Computer Chassis - Racks - Shelves - 19 inch Rack - 23 inch Rack - Computer and Instrument Case Manufacturing - AGS-TECH Inc. - New Mexico - USA שלדה, מתלים, תושבות למחשבים תעשייתיים אנו מציעים לך את העמידה ביותר והאמינה ביותר_CC781905-5CDE-3194-BB3B-136BAD5CF58D_ שלדות מחשב, מתלים, MOTRTS, MONT MONT INSTRUMENS_CC781905-5CDE-3194-BB3B-136BD5CF5D_AND_AND_ANDE INCH & 23 INCH RACKS, FULL SİZE and HALF RACKS, OPEN and CLOSED RACK, MOUNTING HARDWARE, STRUCTURAL AND SUPPORT COMPONENTS, RAILS and SLIDES, TWO andFOUR POST RACKS that meet international and industry standards. מלבד מוצרי המדף שלנו, אנו מסוגלים לבנות לך כל שלדה, מתלים ותליונים המותאמים במיוחד. חלק משמות המותגים שיש לנו במלאי הם BELKIN, HEWLETT PACKARD, KENDALL HOWARD, GREAT LAKES, APC, RITTAL, LIEBERT, RALOY, SHARK TECHNOLOGIES, UPSITE . לחץ כאן כדי להוריד מארז תעשייתי של מותג DFI-ITOX לחץ כאן כדי להוריד את מארז 06 Plug-in שלנו מבית AGS-Electronics לחץ כאן כדי להוריד את 01 Instrument Case System-I שלנו מבית AGS-Electronics לחץ כאן כדי להוריד את מכשיר נרתיק מסדרת 05 שלנו מבית AGS-Electronics לבחירת שלדה, מתלה או מתקן מתאים בדרגה תעשייתית, אנא עברו לחנות המחשבים התעשייתית שלנו על ידי לחיצה כאן. הורד חוברת עבורנו תוכנית שותפות עיצוב הנה כמה מינוח מפתח שאמור להיות שימושי למטרות עיון: A RACK UNIT or U (המכונה פחות RU) היא יחידת מידה המשמשת לתיאור גובהו של 731905-900 ציוד להרכבה של 730-40-9 -136bad5cf58d_19-inch rack or a 23-inch rack (The 19-inch or 23-inch dimension refers to the width of the equipment מסגרת הרכבה במדף כלומר רוחב הציוד שניתן להרכבה בתוך המתלה). יחידת מתלה אחת בגובה 1.75 אינץ' (44.45 מ"מ). גודלו של ציוד המותקן על מתלה מתואר לעתים קרובות כמספר ב-''U''. לדוגמה, יחידת מתלה אחת מכונה לעתים קרובות ''1U'', 2 יחידות מתלה כ-''2U'' וכן הלאה. מתלה טיפוסי גודל מלא is 44U, מה שאומר שהוא מחזיק קצת יותר מ-6 רגל של ציוד. עם זאת, בתחום המחשוב וטכנולוגיית המידע, half-rack מתאר בדרך כלל יחידה שגובהה 1U מרשת וחצי (מתג 4 עמודים , נתב, מתג KVM או שרת), כך שניתן להרכיב שתי יחידות בשטח של 1U (אחת מותקנת בקדמת המתלה ואחת מאחור). כאשר משתמשים בו לתיאור מארז המתלה עצמו, המונח חצי מתלה פירושו בדרך כלל מארז מתלה בגובה 24U. פאנל קדמי או פאנל מילוי במדף אינם מכפיל מדויק של 1.75 אינץ' (44.45 מ"מ). כדי לאפשר מרווח בין רכיבים סמוכים להתקנה, גובה הפאנל הוא ב-1⁄32 אינץ' (0.031 אינץ' או 0.79 מ"מ) ממה שהמספר המלא של יחידות המתלה מרמז. לפיכך, פאנל קדמי 1U יהיה בגובה 1.719 אינץ' (43.66 מ"מ). מתלה 19 אינץ' הוא מסגרת או מארז סטנדרטיים להרכבת מודולי ציוד מרובים. לכל מודול יש פאנל קדמי ברוחב 19 אינץ' (482.6 מ"מ), כולל קצוות או אוזניים הבולטים מכל צד המאפשרים להדק את המודול למסגרת המתלה באמצעות ברגים. ציוד המיועד להצבה במדף מתואר בדרך כלל כ rack-mount, מכשיר לתלייה על מתלה, מערכת מותקנת על מתלה, מארז לתלייה על מתלה, תת מתלה, מתלה מתלה, או מדי פעם פשוט מדף. מתלה בגודל 23 אינץ' משמש לאחסון טלפון (בעיקר), מחשב, אודיו וציוד אחר, אם כי הוא פחות נפוץ מאשר מתלה 19 אינץ'. הגודל מציין את רוחב לוח הפנים עבור הציוד המותקן. יחידת המתלה היא מדד של מרווח אנכי והיא משותפת הן למתלים 19 והן 23 אינץ' (580 מ"מ). מרווח החורים הוא על מרכזים של 1 אינץ' (25 מ"מ) (תקן ווסטרן אלקטריק), או זהה לזה של מתלים 19 אינץ' (480 מ"מ) (מרווח של 0.625 אינץ' / 15.9 מילימטרים). CLICK Product Finder-Locator Service עמוד קודם
- Industrial Leather Products, USA, AGS-TECH Inc.
Industrial leather products including honing and sharpening belts, leather transmission belts, sewing machine leather treadle belt, leather tool organizers and holders, leather gun holsters, leather steering wheel covers and more. מוצרי עור תעשייתיים מוצרי עור תעשייתיים המיוצרים כוללים: - חגורות חידוד וחידוד עור - חגורות הילוכים מעור - חגורת עור למכונת תפירה - ארגוניות ומחזיקי כלי עור - נרתיקי אקדח מעור עור הוא מוצר טבעי עם תכונות יוצאות דופן ההופכות אותו להתאמה טובה ליישומים רבים. חגורות עור תעשייתיות משמשות בשידורי כוח, כחגורות משטח עור למכונת תפירה, כמו גם הידוק, אבטחה, חידוד והשחזה של להבי מתכת בין רבים אחרים. מלבד חגורות העור התעשייתיות שלנו המופיעות בחוברות שלנו, ניתן לייצר עבורכם גם חגורות אינסופיות ואורכים/רוחבים מיוחדים. יישומים של עור תעשייתי כוללים חגורת עור שטוחה להעברת כוח וחגורת עור עגולה למכונות תפירה תעשייתיות. Industrial leather is one of the oldest types of manufactured products. Our Vegetable Tanned Industrial leathers are pit tanned for חודשים רבים ולבוש בכבדות עם תערובת של שמנים ומשומנים כדי להעניק את החוזק האולטימטיבי שלו. ניתן לייצר את עורות הכרום התעשייתיים שלנו בדרכים שונות,_cc781905-5cde-31954-63bd oil dry עבור יציקה. We_cc781905-5cde-3194-bb3b-158_badther טמפרטורה משומשת ל-5cde-3194-bb3b-158_badreter מאוד עמידה בשימוש בטמפרטורה גבוהה 5cf58d_we_cc781905-5cde. 3194-bb3b-136bad5cf58d_and packings. Our35191cath_Our31905-5cde-3194-bb3b-136bad5cf58d_Our35193d-9319418199419941999411111111111111111111111111111111111111111111 ED עם מאפייני שחיקה יוצאי דופן ._CC781905-5CDE-3194-BB3B-136BAD5CF58D_VARIOUS SHORE קשיות. קיימים יישומים רבים אחרים של מוצרי עור תעשייתיים, כולל מארגני כלים לבישים, מחזיקי כלים, חוטי עור, כיסויי הגה... וכו'. אנחנו כאן כדי לעזור לך בפרויקטים שלך. שרטוט, סקיצה, תמונה או דוגמה יכולים לשרת אותנו כדי להבין את צרכי המוצר שלך. אנחנו יכולים לייצר את מוצר העור התעשייתי לפי העיצוב שלך, או שנוכל לעזור לך בעבודת העיצוב שלך ולאחר שתאשר את העיצוב הסופי, נוכל לייצר עבורך את המוצר. מכיוון שאנו מספקים מגוון רחב של מוצרי עור תעשייתיים עם ממדים, יישומים וציון חומרים שונים; אי אפשר לרשום את כולם כאן. אנו ממליצים לך לשלוח אימייל או להתקשר אלינו כדי שנוכל לקבוע איזה מוצר מתאים לך ביותר. בעת יצירת קשר, אנא הקפד ליידע אותנו לגבי: - האפליקציה שלך למוצרי העור התעשייתיים - דרגת חומר רצויה ודרושה - ממדים - סיים - דרישות אריזה - דרישות תיוג - כמות עמוד קודם
- Display, Touchscreen, Monitors, LED, OLED, LCD, PDP, HMD, VFD, ELD
Display - Touchscreen - Monitors - LED - OLED - LCD - PDP - HMD - VFD - ELD - SED - Flat Panel Displays - AGS-TECH Inc. ייצור והרכבה של תצוגה ומסך מגע ומסך אנחנו מציעים: • צגים מותאמים אישית הכוללים LED, OLED, LCD, PDP, VFD, ELD, SED, HMD, Laser TV, צג שטוח במידות הנדרשות ומפרטים אלקטרו-אופטיים. אנא לחץ על הטקסט המודגש כדי להוריד עלונים רלוונטיים עבור מוצרי התצוגה, מסך המגע והצג שלנו. לוחות תצוגת LED מודולי LCD הורד את החוברת שלנו עבור מסכי TRu Multi-Touch. קו מוצרי צג זה מורכב ממגוון של תצוגות שולחניות, מסגרת פתוחה, קו דק וצגי מולטי-טאץ' בפורמט גדול - מ-15 אינץ' ועד 70 אינץ'. צגי TRu Multi-Touch בנויים לאיכות, היענות, משיכה ויזואלית ועמידות משלימים כל פתרון אינטראקטיבי רב-מגע. לחץ כאן לתמחור אם ברצונך לקבל מודולי LCD שתוכננו וייוצרו במיוחד בהתאם לדרישות שלך, אנא מלא ושלח לנו דוא"ל: טופס עיצוב מותאם אישית עבור מודולי LCD אם ברצונך לקבל לוחות LCD שתוכננו וייוצרו במיוחד בהתאם לדרישות שלך, אנא מלא ושלח לנו דוא"ל: טופס עיצוב מותאם אישית עבור לוחות LCD • מסך מגע מותאם אישית (כגון iPod) • בין המוצרים המותאמים אישית שהמהנדסים שלנו פיתחו הם: - תחנת מדידת ניגודיות עבור צגי גביש נוזלי. - עמדת ריכוז ממוחשבת לעדשות הקרנת טלוויזיה פאנלים / צגים הם מסכים אלקטרוניים המשמשים לצפייה בנתונים ו/או גרפיקה וזמינים במגוון גדלים וטכנולוגיות. להלן המשמעויות של מונחים מקוצרים הקשורים להתקני תצוגה, מסך מגע וצג: LED: דיודה פולטת אור LCD: תצוגת גביש נוזלי PDP: לוח תצוגת פלזמה VFD: תצוגת פלורסנט ואקום OLED: דיודה פולטת אור אורגנית ELD: צג אלקטרולומינסצנטי SED: תצוגת פולט אלקטרונים עם מוליכת פני השטח HMD: תצוגת ראש יתרון משמעותי של תצוגת OLED על פני תצוגת גביש נוזלי (LCD) הוא ש-OLED אינו דורש תאורה אחורית כדי לתפקד. לכן תצוגת OLED שואבת הרבה פחות חשמל, וכאשר היא מופעלת מסוללה, היא יכולה לפעול זמן רב יותר בהשוואה ל-LCD. מכיוון שאין צורך בתאורה אחורית, תצוגת OLED יכולה להיות הרבה יותר דקה מפאנל LCD. עם זאת, השפלה של חומרי OLED הגבילה את השימוש בהם כתצוגה, מסך מגע וכצג. ELD פועל על ידי מרגש אטומים על ידי העברת זרם חשמלי דרכם, וגורם ל-ELD לפלוט פוטונים. על ידי שינוי החומר הנרגש, ניתן לשנות את צבע האור הנפלט. ELD בנויה באמצעות רצועות אלקטרודות שטוחות ואטומות הפועלות במקביל זו לזו, מכוסות בשכבה של חומר אלקטרו-אורני, ואחריהן שכבה נוספת של אלקטרודות, העוברות בניצב לשכבה התחתונה. השכבה העליונה חייבת להיות שקופה על מנת לתת לאור לעבור ולברוח. בכל צומת החומר נדלק ובכך יוצר פיקסל. ELD משמשים לפעמים כתאורות אחוריות במסכי LCD. הם שימושיים גם ליצירת אור סביבה רך, ולמסכים בעלי ניגודיות בצבע נמוך. תצוגת אלקטרונים פולטת הולכה משטחית (SED) היא טכנולוגיית תצוגה שטוחה המשתמשת בפולטות אלקטרונים הולכה על פני השטח עבור כל פיקסל תצוגה בודד. פולט ההולכה על פני השטח פולט אלקטרונים המעוררים ציפוי זרחני על לוח התצוגה, בדומה לטלוויזיות של שפופרת קרן קתודית (CRT). במילים אחרות, מכשירי SED משתמשים בשפופרות זעירות של קרני קתודיות מאחורי כל פיקסל בודד במקום צינור אחד עבור כל התצוגה, ויכולים לשלב את גורם הצורה הדק של צגי LCD וצגי פלזמה עם זוויות הצפייה המעולות, הניגודיות, רמות השחור, הגדרת הצבע והפיקסל. זמן תגובה של CRTs. כמו כן, נטען באופן נרחב שמכשירי SED צורכים פחות חשמל מאשר צגי LCD. צג צמוד לראש או צג רכוב על קסדה, שניהם בקיצור 'HMD', הוא מכשיר תצוגה, המולבש על הראש או כחלק מקסדה, בעל אופטיקה קטנה לתצוגה מול עין אחת או כל אחת. ל-HMD טיפוסי יש צג קטן אחד או שניים עם עדשות ומראות שקופות למחצה המוטבעות בקסדה, במשקפי ראייה או במגן. יחידות התצוגה קטנות ועשויות לכלול CRT, LCDs, Liquid Crystal on Silicon או OLED. לפעמים מיקרו-מסכים מרובים נפרסים כדי להגדיל את הרזולוציה הכוללת ואת שדה הראייה. HMDs נבדלים זה מזה אם הם יכולים להציג רק תמונה שנוצרה על ידי מחשב (CGI), להציג תמונות חיות מהעולם האמיתי או שילוב של שניהם. רוב HMDs מציגים רק תמונה שנוצרה על ידי מחשב, המכונה לפעמים תמונה וירטואלית. חלק מה-HMDs מאפשרים להצמיד CGI על תפיסת עולם אמיתי. זה מכונה לפעמים מציאות רבודה או מציאות מעורבת. שילוב של תצוגת עולם אמיתי עם CGI יכול להיעשות על ידי הקרנת ה-CGI דרך מראה רפלקטיבית חלקית וצפייה ישירה בעולם האמיתי. למראות מחזירות חלקית, עיין בעמוד שלנו בנושא רכיבים אופטיים פסיביים. שיטה זו נקראת לעתים קרובות אופטית שקופה. שילוב של תצוגת עולם אמיתי עם CGI יכול להיעשות גם באופן אלקטרוני על ידי קבלת וידאו ממצלמה וערבוב אלקטרוני עם CGI. שיטה זו נקראת לעתים קרובות Video See-Through. יישומי HMD העיקריים כוללים צבא, ממשלתי (כבאות, משטרה וכו') ואזרחי/מסחרי (רפואה, משחקי וידאו, ספורט וכו'). צבא, משטרה וכבאים משתמשים ב-HMDs כדי להציג מידע טקטי כגון מפות או נתוני הדמיה תרמית תוך כדי צפייה בסצנה האמיתית. מטוסי HMD משולבים בתאי הטייס של מסוקים ומטוסי קרב מודרניים. הם משולבים במלואם עם קסדת הטייס של הטייס ועשויים לכלול מגני מגן, התקני ראיית לילה ותצוגות של סמלים ומידע אחרים. מהנדסים ומדענים משתמשים ב-HMDs כדי לספק תצוגות סטריאוסקופיות של סכימות CAD (Computer Aided Design). מערכות אלו משמשות גם בתחזוקה של מערכות מורכבות, שכן הן יכולות להעניק לטכנאי ''ראיית רנטגן'' בצורה יעילה על ידי שילוב גרפיקה ממוחשבת כגון דיאגרמות מערכת ותמונות עם הראייה הטבעית של הטכנאי. ישנם גם יישומים בכירורגיה, בהם שילוב של נתונים רדיוגרפיים (סריקות CAT והדמיית MRI) משולב עם הראייה הטבעית של המנתח על הניתוח. ניתן לראות דוגמאות למכשירי HMD בעלות נמוכה יותר עם משחקי תלת מימד ויישומי בידור. מערכות כאלה מאפשרות ליריבים "וירטואליים" להציץ מחלונות אמיתיים בזמן ששחקן נע. פיתוחים מעניינים נוספים בטכנולוגיות תצוגה, מסך מגע ומסכים ש-AGS-TECH מעוניינת הם: טלוויזיה בלייזר: טכנולוגיית תאורת הלייזר נותרה יקרה מכדי לשמש במוצרי צריכה ראויים מבחינה מסחרית ודלה מדי בביצועים מכדי להחליף מנורות למעט מקרנים נדירים במיוחד. עם זאת, לאחרונה, חברות הדגימו את מקור תאורת הלייזר שלהן עבור תצוגות הקרנה ואב-טיפוס ''טלוויזיית לייזר'' עם הקרנה אחורית. ה- Laser TV המסחרי הראשון ולאחר מכן אחרים נחשפו. קהלים ראשונים שהוצגו להם קטעי רפרנס מסרטים פופולריים דיווחו שהם נדהמו מיכולת התצוגה הצבעונית של טלוויזיית לייזר שלא נראתה עד כה. יש אנשים שאפילו מתארים את זה כאינטנסיבי מדי עד כדי כך שהוא נראה מלאכותי. כמה טכנולוגיות תצוגה עתידיות אחרות יכללו ככל הנראה ננו-צינורות פחמן ותצוגות ננו-גביש באמצעות נקודות קוונטיות כדי ליצור מסכים תוססים וגמישים. כמו תמיד, אם תספק לנו פרטים על הדרישה והיישום שלך, נוכל לעצב ולייצר צגים, מסכי מגע ומסכים בהתאמה אישית עבורך. לחץ כאן להורדת חוברת של מדי הפנל שלנו - OICASCHINT הורד חוברת עבורנו תוכנית שותפות עיצוב מידע נוסף על עבודת ההנדסה שלנו ניתן למצוא בכתובת: http://www.ags-engineering.com CLICK Product Finder-Locator Service עמוד קודם
- Electric Discharge Machining, EDM, Spark Machining, Die Sinking
Electric Discharge Machining - EDM - Spark Machining - Die Sinking - Wire Erosion - Custom Manufacturing - AGS-TECH Inc. עיבוד שבבי EDM, כרסום וטחינה חשמלית-פריקה ELECTRICAL DISCHARGE MACHINING (EDM), also referred to as SPARK-EROSION or ELECTRODISCHARGE MACHINING, SPARK ERODING, DIE SINKING_cc781905-5cde-3194-bb3b -136bad5cf58d_or WIRE EROSION, is a NON-CONVENTIONAL MANUFACTURING process where erosion of metals takes place and desired shape is obtained using electrical discharges in the form של ניצוצות. אנו מציעים גם כמה סוגים של EDM, כלומר NO-WEAR EDM, WIRE EDM (WEDM), EDM GRINDING (EDG), EDM-Sinking EDM, EDM-Sinking EDM, ELECTRICAL-DESCHARGE TILLING, mc-19EDMcc, micro-EDM_cc -5cde-3194-bb3b-136bad5cf58d_and ELECTROCHEMICAL-DISCHARGE GRINDING (ECDG). מערכות ה-EDM שלנו מורכבות מכלים/אלקטרודה מעוצבים ומחומר העבודה המחוברים לספקי כוח DC ומוכנסים בנוזל דיאלקטרי שאינו מוליך חשמלית. לאחר 1940 הפכה עיבוד שבבי פריקה חשמלית לאחת מטכנולוגיות הייצור החשובות והפופולריות ביותר בתעשיות הייצור. כאשר המרחק בין שתי האלקטרודות מצטמצם, עוצמת השדה החשמלי בנפח בין האלקטרודות הופכת גדולה יותר מחוזק הדיאלקטרי בחלק מהנקודות, אשר נשבר, ובסופו של דבר יוצר גשר לזרימת זרם בין שתי האלקטרודות. נוצרת קשת חשמלית עזה הגורמת לחימום משמעותי להמיס חלק מחומר העבודה וחלק מחומר העבודה. כתוצאה מכך, חומר מוסר משתי האלקטרודות. במקביל, הנוזל הדיאלקטרי מחומם במהירות, וכתוצאה מכך אידוי של הנוזל במרווח הקשת. ברגע שזרימת הזרם נעצרת או שהיא נעצרת חום מוסר מבועת הגז על ידי הנוזל הדיאלקטרי שמסביב והבועה מתנתקת (קורסת). גל ההלם שנוצר כתוצאה מהתמוטטות הבועה וזרימת הנוזל הדיאלקטרי שוטף פסולת ממשטח היצירה ומכניס כל חומר מותך של חומר העבודה לתוך הנוזל הדיאלקטרי. קצב החזרות לפריקות אלו הוא בין 50 ל-500 קילו-הרץ, מתחים בין 50 ל-380 וולט וזרמים בין 0.1 ל-500 אמפר. דיאלקטרי נוזלי חדש, כגון שמנים מינרליים, נפט או מים מזוקקים ודה-יוניים, מועברים בדרך כלל לתוך נפח הבין-אלקטרודות כשהוא נושא את החלקיקים המוצקים (בצורה של פסולת) ותכונות הבידוד של הדיאלקטרי משוחזרות. לאחר זרימת זרם, הפרש הפוטנציאלים בין שתי האלקטרודות משוחזר למה שהיה לפני ההתמוטטות, כך שיכול להתרחש התמוטטות דיאלקטרי נוזלי חדש. מכונות הפריקה החשמליות המודרניות שלנו (EDM) מציעות תנועות מבוקרות מספרית ומצוידות במשאבות ומערכות סינון לנוזלים הדיאלקטריים. עיבוד פריקה חשמלית (EDM) היא שיטת עיבוד המשמשת בעיקר למתכות קשות או כאלה שיהיה קשה מאוד לעבד אותן בטכניקות קונבנציונליות. EDM עובד בדרך כלל עם כל חומר שהם מוליכים חשמליים, אם כי הוצעו גם שיטות לעיבוד קרמיקה בידודית עם EDM. נקודת ההיתוך והחום הסמוי של ההיתוך הם מאפיינים שקובעים את נפח המתכת שהוצאה בכל פריקה. ככל שערכים אלו גבוהים יותר, כך קצב הסרת החומר איטי יותר. מכיוון שתהליך עיבוד הפריקה החשמלית אינו כרוך באנרגיה מכנית כלשהי, הקשיות, החוזק והקשיחות של חומר העבודה אינם משפיעים על קצב ההסרה. תדירות פריקה או אנרגיה לכל פריקה, המתח והזרם משתנים כדי לשלוט בקצבי הסרת החומר. קצב הסרת החומר וחספוס פני השטח גדלים עם הגדלת צפיפות הזרם וירידה בתדירות הניצוץ. אנו יכולים לחתוך קווי מתאר או חללים מורכבים בפלדה מוקשה מראש באמצעות EDM ללא צורך בטיפול בחום כדי לרכך ולהקשיח אותם מחדש. אנו יכולים להשתמש בשיטה זו עם כל מתכת או סגסוגות מתכת כמו טיטניום, hastelloy, kovar, ו-inconel. יישומים של תהליך EDM כוללים עיצוב של כלי יהלום רב גבישי. EDM נחשבת לשיטת עיבוד שבבי לא מסורתית או לא קונבנציונלית יחד עם תהליכים כמו עיבוד אלקטרוכימי (ECM), חיתוך סילון מים (WJ, AWJ), חיתוך לייזר. מצד שני שיטות העיבוד הקונבנציונליות כוללות חריטה, כרסום, שחיקה, קידוח ועוד תהליך שמנגנון הסרת החומרים שלהם מבוסס בעיקרו על כוחות מכניים. אלקטרודות לעיבוד עיבוד חשמלי (EDM) עשויות גרפיט, פליז, נחושת וסגסוגת נחושת-טונגסטן. קוטרים של אלקטרודה עד 0.1 מ"מ אפשריים. מכיוון שחיקת הכלים היא תופעה לא רצויה המשפיעה לרעה על דיוק הממדים ב-EDM, אנו מנצלים את היתרונות של תהליך שנקרא NO-WEAR EDM, על ידי היפוך קוטביות ושימוש בכלי נחושת כדי למזער את שחיקת הכלים. באופן אידיאלי, עיבוד פריקה חשמלית (EDM) יכול להיחשב כסדרה של התמוטטות ושיקום של הנוזל הדיאלקטרי בין האלקטרודות. אולם במציאות, הסרת הפסולת מאזור הבין-אלקטרודות היא כמעט תמיד חלקית. זה גורם לתכונות החשמליות של הדיאלקטרי באזור הבין-אלקטרודות להיות שונות מהערכים הנומינליים שלהן ומשתנות עם הזמן. המרחק בין האלקטרודות, (פער ניצוץ), מותאם על ידי אלגוריתמי הבקרה של המכונה הספציפית שבה נעשה שימוש. פער הניצוצות ב-EDM יכול למרבה הצער לפעמים להיות קצר על ידי הפסולת. מערכת הבקרה של האלקטרודה עלולה להיכשל בתגובה מהירה מספיק כדי למנוע משתי האלקטרודות (כלי וחומר עבודה) לקצר. קצר חשמלי לא רצוי זה תורם להסרת חומר באופן שונה מהמקרה האידיאלי. אנו מקדישים חשיבות מרבית לפעולת השטיפה על מנת לשחזר את תכונות הבידוד של הדיאלקטרי כך שהזרם יתרחש תמיד בנקודה של אזור הבין-אלקטרודות, ובכך למזער את האפשרות של שינוי צורה (נזק) לא רצוי של הכלי-אלקטרודה. וחומר עבודה. כדי להשיג גיאומטריה ספציפית, כלי ה-EDM מונחה לאורך הנתיב הרצוי קרוב מאוד לחומר העבודה מבלי לגעת בו, אנו מקדישים תשומת לב מרבית לביצועי בקרת התנועה בשימוש. כך מתרחשות מספר רב של פריקות/ניצוצות זרם, וכל אחת מהן תורמת להסרת החומר הן מהכלי והן מחומר העבודה, שם נוצרים מכתשים קטנים. גודל המכתשים הוא פונקציה של הפרמטרים הטכנולוגיים שנקבעו לעבודה הספציפית שעל הפרק, והממדים עשויים לנוע בין ננו-סקאלה (כגון במקרה של פעולות מיקרו-EDM) ועד כמה מאות מיקרומטרים בתנאי חיספוס. המכתשים הקטנים הללו על הכלי גורמים לשחיקה הדרגתית של האלקטרודה הנקראת "בלאי הכלים". כדי לנטרל את ההשפעה המזיקה של הבלאי על הגיאומטריה של חומר העבודה, אנו מחליפים ללא הרף את האלקטרודה של הכלי במהלך פעולת עיבוד שבבי. לפעמים אנו משיגים זאת על ידי שימוש בחוט שהוחלף ברציפות כאלקטרודה (תהליך EDM זה נקרא גם WIRE EDM ). לפעמים אנו משתמשים בכלי-אלקטרודה בצורה כזו שרק חלק קטן ממנה עוסק בפועל בתהליך העיבוד והחלק הזה משתנה על בסיס קבוע. זה, למשל, המקרה כאשר משתמשים בדיסק מסתובב כאלקטרודה לכלי. תהליך זה נקרא EDM GRINDING. טכניקה נוספת שאנו פורסים מורכבת משימוש בסט של אלקטרודות בגדלים וצורות שונות במהלך אותה פעולת EDM כדי לפצות על שחיקה. אנו קוראים לזה טכניקת אלקטרודות מרובות, והיא משמשת לרוב כאשר אלקטרודת הכלי משכפלת בשלילה את הצורה הרצויה ומתקדמת לעבר הריק לאורך כיוון יחיד, בדרך כלל הכיוון האנכי (כלומר ציר z). זה דומה לשקוע של הכלי בנוזל הדיאלקטרי שבו טבול חומר העבודה, ולכן הוא מכונה DIE-SINKING EDM_cc781905-5cde-3194-bb3b-15scde 3194-bb3b-136bad5cf58d_CONVENTIONAL EDM or RAM EDM). המכונות לפעולה זו נקראות SINKER EDM. לאלקטרודות לסוג זה של EDM יש צורות מורכבות. אם הגיאומטריה הסופית מתקבלת באמצעות אלקטרודה בעלת צורה פשוטה בדרך כלל הנעה לאורך מספר כיוונים ונתונה גם לסיבובים, אנו קוראים לזה EDM MILLING. כמות הבלאי תלויה אך ורק בפרמטרים הטכנולוגיים המשמשים בפעולה (קוטביות, זרם מרבי, מתח מעגל פתוח). לדוגמה, in micro-EDM, הידוע גם בשם m-EDM, פרמטרים אלו נקבעים בדרך כלל בערכים חמורים שיוצרים שחיקה חמורה. לכן, בלאי הוא בעיה מרכזית באותו תחום שאנו ממזערים באמצעות הידע המצטבר שלנו. לדוגמה, כדי למזער שחיקה של אלקטרודות גרפיט, גנרטור דיגיטלי, הניתן לשליטה תוך אלפיות שניות, הופך את הקוטביות כאשר מתרחשת שחיקה אלקטרו. כתוצאה מכך נוצרת השפעה דומה לציפוי האלקטרוני שמפקיד את הגרפיט הנשחק בחזרה על האלקטרודה. בשיטה אחרת, מעגל שנקרא ''Zero Wear'' אנו ממזערים את התדירות שבה הפריקה מתחילה ונפסקת, ומשאירים אותה דולקת למשך זמן רב ככל האפשר. ניתן להעריך את קצב הסרת החומר בעיבוד שבבי פריקה חשמלית מתוך: MRR = 4 x 10 exp(4) x I x Tw exp (-1.23) כאן MRR הוא ב-mm3/min, I הוא זרם באמפר, Tw הוא נקודת התכה של חלקי העבודה ב-K-273.15K. ה-ex מייצג אקספוננט. מצד שני, ניתן לקבל את קצב הבלאי Wt של האלקטרודה מ: Wt = ( 1.1 x 10exp(11) ) x I x Ttexp(-2.38) כאן Wt הוא ב-mm3/min ו-Tt היא נקודת ההתכה של חומר האלקטרודה ב-K-273.15K לבסוף, ניתן לקבל את יחס הבלאי של חומר העבודה לאלקטרודה R מ: R = 2.25 x Trexp(-2.38) כאן Tr הוא היחס בין נקודות ההתכה של חלק העבודה לאלקטרודה. SINKER EDM : Sinker EDM, המכונה גם CAVITY TYPE EDM or_cc781905-94cde-electronic work an-5cde31905-94cde, EDM or_cc781905-94cde-electronic workflow an-f3d3d5111905-94cde-5cde האלקטרודה וחומר העבודה מחוברים לאספקת חשמל. ספק הכוח מייצר פוטנציאל חשמלי בין השניים. כאשר האלקטרודה מתקרבת לחומר העבודה, מתרחשת התמוטטות דיאלקטרית בנוזל, ויוצרת תעלת פלזמה, וניצוץ קטן קופץ. הניצוצות בדרך כלל פוגעים בזה אחר זה מכיוון שאין זה סביר ביותר שלמיקומים שונים בחלל הבין-אלקטרודות יש מאפיינים חשמליים מקומיים זהים שיאפשרו לניצוץ להתרחש בכל המיקומים הללו בו זמנית. מאות אלפי ניצוצות אלו קורים בנקודות אקראיות בין האלקטרודה לחומר העבודה בשנייה. כאשר המתכת הבסיסית נשחקת, ומרווח הניצוץ גדל לאחר מכן, האלקטרודה יורדת אוטומטית על ידי מכונת ה-CNC שלנו כך שהתהליך יכול להמשיך ללא הפרעה. לציוד שלנו יש מחזורי שליטה הידועים כ''בזמן'' ו''זמן כבוי''. הגדרת זמן ההפעלה קובעת את אורך או משך הניצוץ. זמן ארוך יותר מייצר חלל עמוק יותר עבור אותו ניצוץ וכל הניצוצות הבאים עבור אותו מחזור, יוצר גימור גס יותר על חומר העבודה ולהיפך. זמן הכיבוי הוא פרק הזמן שבו ניצוץ אחד מוחלף באחר. זמן הפסקה ארוך יותר מאפשר לנוזל הדיאלקטרי לשטוף דרך זרבובית כדי לנקות את הפסולת הנשחקת, ובכך למנוע קצר חשמלי. הגדרות אלו מותאמות תוך מיקרו שניות. WIRE EDM : In WIRE ELECTRICAL DISCHARGE MACHINING (WEDM), also called WIRE-CUT EDM or WIRE CUTTING, we feed a חוט מתכת דק של פליז דרך חומר העבודה, שקוע במיכל נוזל דיאלקטרי. Wire EDM הוא וריאציה חשובה של EDM. מדי פעם אנו משתמשים ב-EDM בחיתוך חוט כדי לחתוך צלחות בעובי של עד 300 מ"מ וליצור חבטות, כלים וקוביות ממתכות קשות שקשה לעבד אותן בשיטות ייצור אחרות. בתהליך זה הדומה לחיתוך קווי מתאר עם מסור פס, החוט, המוזן כל הזמן מסליל, מוחזק בין מובילי יהלום עליונים ותחתונים. המנחים הנשלטים על ידי CNC נעים במישור x–y והמוביל העליון יכול גם לנוע באופן עצמאי בציר z–u–v, מה שמוביל ליכולת לחתוך צורות מחודדות ומעבר (כגון עיגול בתחתית וריבוע ב החלק העליון). המנחה העליון יכול לשלוט בתנועות הציר ב-x–y–u–v–i–j–k–l–. זה מאפשר ל-WEDM לחתוך צורות מאוד מורכבות ועדינות. חוט החיתוך הממוצע של הציוד שלנו המשיג את העלות הכלכלית ואת זמן העיבוד הטובים ביותר הוא 0.335 מ"מ באמצעות Ø 0.25 חוטי פליז, נחושת או טונגסטן. עם זאת, מובילי היהלומים העליונים והתחתונים של ציוד ה-CNC שלנו מדוייקים עד ל-0.004 מ"מ בערך, ויכולים להיות בעלי נתיב חיתוך או חוט קטן עד 0.021 מ"מ באמצעות חוט Ø 0.02 מ"מ. אז אפשר לחתוך ממש צר. רוחב החיתוך גדול מרוחב החוט מכיוון שנוצר ניצוצות מצידי החוט לחומר העבודה, הגורם לשחיקה. ''חיתוך יתר'' זה הכרחי, עבור יישומים רבים הוא ניתן לחיזוי ולכן ניתן לפצות עליו (במיקרו-EDM זה לא קורה לעתים קרובות). סלילי החוטים ארוכים - סליל של 8 ק"ג של חוט 0.25 מ"מ באורך של קצת יותר מ-19 ק"מ. קוטר החוט יכול להיות קטן עד 20 מיקרומטר ודיוק הגיאומטריה הוא בסביבה של +/- 1 מיקרומטר. בדרך כלל אנו משתמשים בחוט רק פעם אחת וממחזרים אותו מכיוון שהוא זול יחסית. הוא נוסע במהירות קבועה של 0.15 עד 9 מ'/דקה ונשמר חריץ (חריץ) קבוע במהלך החתך. בתהליך חיתוך תיל אנו משתמשים במים כנוזל הדיאלקטרי, שולטים בהתנגדות שלו ובתכונות חשמליות אחרות באמצעות מסננים ויחידות דה-יוניזטור. המים שוטפים את הפסולת החתוכה מאזור החיתוך. שטיפה היא גורם חשוב בקביעת קצב ההזנה המקסימלי עבור עובי חומר נתון ולכן אנו שומרים על עקביות. מהירות חיתוך ב-EDM של חוט מצוינת במונחים של שטח חתך חתך ליחידת זמן, כגון 18,000 מ"מ לשעה עבור פלדת כלי D2 בעובי 50 מ"מ. מהירות החיתוך הליניארית עבור מקרה זה תהיה 18,000/50 = 360 מ"מ לשעה. קצב הסרת החומר ב-EDM חוט הוא: MRR = Vf xhxb כאן MRR הוא ב-mm3/min, Vf הוא קצב ההזנה של החוט לתוך חלק העבודה ב-mm/min, h הוא עובי או גובה ב-mm, ו-b הוא ה-cerf, כלומר: b = dw + 2s כאן dw הוא קוטר החוט ו-s הוא הפער בין החוט לחומר העבודה במ"מ. יחד עם סובלנות הדוקה יותר, מרכזי העיבוד הרב-ציריים המודרניים שלנו לחיתוך חוט EDM הוסיפו תכונות כמו רב ראשים לחיתוך שני חלקים בו-זמנית, בקרות למניעת שבירת חוט, תכונות הברגה עצמית אוטומטית במקרה של שבירת חוט, ומתוכנתות אסטרטגיות עיבוד כדי לייעל את הפעולה, יכולות חיתוך ישר וזוויתי. Wire-EDM מציע לנו מתחים שיוריים נמוכים, מכיוון שהוא אינו דורש כוחות חיתוך גבוהים להסרת החומר. כאשר האנרגיה/הספק לפולס נמוכים יחסית (כמו בפעולות גימור), צפוי שינוי קטן בתכונות המכניות של חומר עקב מתחים שיוריים נמוכים. שחיקה חשמלית (EDG) : גלגלי השחזה אינם מכילים חומרים שוחקים, הם עשויים גרפיט או פליז. ניצוצות חוזרים ונשנים בין הגלגל המסתובב לחומר העבודה מסירים חומר ממשטחי העבודה. קצב הסרת החומר הוא: MRR = K x I כאן MRR הוא ב-mm3/min, I הוא זרם באמפר, ו-K הוא גורם חומרי עבודה ב-mm3/A-min. אנו משתמשים לעתים קרובות בטחינת פריקה חשמלית כדי לנסר חריצים צרים ברכיבים. לעיתים אנו משלבים תהליך EDG (Electrical-Discharge Grinding) עם תהליך ECG (Electrochemical Grinding) שבו חומר מוסר על ידי פעולה כימית, הפרשות החשמליות מגלגל הגרפיט מפרקות את סרט התחמוצת ונשטפות על ידי האלקטרוליט. התהליך נקרא ELECTROCHEMICAL-DISCHARGE GRINDING (ECDG). למרות שתהליך ה-ECDG צורך יחסית יותר חשמל, זהו תהליך מהיר יותר מה-EDG. אנו טוחנים בעיקר כלי קרביד בטכניקה זו. יישומים של עיבוד שבבי פריקה חשמלית: ייצור אב טיפוס: אנו משתמשים בתהליך ה-EDM בייצור תבניות, ייצור כלים ומוות, כמו גם לייצור אב טיפוס וחלקי ייצור, במיוחד עבור תעשיות התעופה והחלל, הרכב והאלקטרוניקה שבהן כמויות הייצור נמוכות יחסית. ב-Sinker EDM, אלקטרודת גרפיט, נחושת טונגסטן או נחושת טהורה מעובדת במכונה לצורה הרצויה (שלילית) ומוכנסת לחומר העבודה בקצה כבש אנכי. יצירת קוביות מטבעות: ליצירת קוביות לייצור תכשיטים ותגים בתהליך המטבעות (הטבעה), המאסטר החיובי עשוי להיות עשוי מכסף סטרלינג, שכן (עם הגדרות מכונה מתאימות) המאסטר נשחק באופן משמעותי ונעשה בו שימוש פעם אחת בלבד. לאחר מכן, התבנית הנגטיבית שנוצרה מוקשחת ומשמשת בפטיש טיפה לייצור חלקים מוטבעים מחלקי גיליון חתוכים של ברונזה, כסף או סגסוגת זהב בעלת הוכחה נמוכה. עבור תגים ניתן לעצב את הדירות הללו למשטח מעוקל על ידי קובייה אחרת. סוג זה של EDM מבוצע בדרך כלל שקוע בדיאלקטרי מבוסס שמן. האובייקט המוגמר עשוי להיות מעודן יותר על ידי אמייל קשיח (זכוכית) או רך (צבע) ו/או מצופה אלקטרוניקה בזהב טהור או ניקל. חומרים רכים יותר כגון כסף עשויים להיות חרוטים ביד כעידון. קידוח חורים קטנים: במכונות EDM לחתוך חוט שלנו, אנו משתמשים ב-EDM לקידוח חורים קטנים כדי ליצור חור דרך בחומר עבודה שדרכו ניתן להשחיל את החוט לפעולת ה-EDM החתוכה. ראשי EDM נפרדים במיוחד עבור קידוח חורים קטנים מותקנים על מכונות החיתוך החוט שלנו המאפשרות לצלחות גדולות מוקשחות לשחוק מהן חלקים מוגמרים לפי הצורך וללא קידוח מוקדם. אנו משתמשים גם ב-EDM עם חורים קטנים כדי לקדוח שורות של חורים בקצוות של להבי טורבינה המשמשים במנועי סילון. זרימת גז דרך החורים הקטנים הללו מאפשרת למנועים להשתמש בטמפרטורות גבוהות יותר ממה שאפשר אחרת. הסגסוגות החד-גבישיות בטמפרטורה גבוהה, קשיחה מאוד, מהן עשויים להבים, הופכת את העיבוד הקונבנציונלי של חורים אלה עם יחס רוחב-גובה לקשה ביותר ואף בלתי אפשרי. אזורי יישום אחרים עבור חור קטן EDM הוא ליצור פתחים מיקרוסקופיים עבור רכיבי מערכת הדלק. מלבד ראשי ה-EDM המשולבים, אנו פורסים מכונות EDM לקידוח חורים קטנים עצמאיים עם צירי x-y למכונה עיוורת או דרך חורים. קדחי EDM מקדחים חורים עם אלקטרודה ארוכה של צינור פליז או נחושת המסתובבת בצ'אק עם זרימה קבועה של מים מזוקקים או דה-יוניונים הזורמים דרך האלקטרודה כחומר שטיפה ודיאלקטרי. כמה EDMs לקידוח חורים קטנים מסוגלים לקדוח דרך 100 מ"מ של פלדה רכה או אפילו מוקשה בפחות מ-10 שניות. ניתן להשיג חורים בין 0.3 מ"מ ל-6.1 מ"מ בפעולת קידוח זו. עיבוד שבבי לפירוק מתכת: יש לנו גם מכונות EDM מיוחדות למטרות ספציפיות של הסרת כלים שבורים (מקדחים או ברזים) מחתיכות עבודה. תהליך זה נקרא ''עיבוד עיבוד מתכת''. יתרונות וחסרונות עיבוד שבבי פריקה חשמלית: היתרונות של EDM כוללים עיבוד שבבי של: - צורות מורכבות שאחרת יהיה קשה לייצר עם כלי חיתוך קונבנציונליים - חומר קשה במיוחד לסובלנות קרובה מאוד - חלקי עבודה קטנים מאוד שבהם כלי חיתוך קונבנציונליים עלולים לגרום נזק לחלק כתוצאה מלחץ יתר של כלי החיתוך. - אין מגע ישיר בין הכלי לפריט העבודה. לכן ניתן לעבד קטעים עדינים וחומרים חלשים ללא כל עיוות. - ניתן לקבל גימור משטח טוב. - ניתן לקדוח בקלות חורים עדינים מאוד. החסרונות של EDM כוללים: - הקצב האיטי של הסרת החומר. - הזמן והעלות הנוספים המשמשים ליצירת אלקטרודות ל-RAM/Sinker EDM. - קשה לשחזר פינות חדות על חומר העבודה עקב בלאי אלקטרודות. - צריכת החשמל גבוהה. - נוצר ''חיתוך יתר''. - בלאי יתר של הכלים מתרחש במהלך העיבוד. - חומרים שאינם מוליכים חשמלית ניתנים לעיבוד רק עם הגדרה ספציפית של התהליך. CLICK Product Finder-Locator Service עמוד קודם
- Brazing, Soldering, Welding, Joining Processes, Assembly Services
Brazing - Soldering - Welding - Joining Processes - Assembly Services - Subassemblies - Assemblies - Custom Manufacturing - AGS-TECH Inc. - NM - USA הלחמה והלחמה וריתוך בין טכניקות ההצטרפות הרבות שאנו נוקטים בייצור, ניתן דגש מיוחד על ריתוך, הלחמה, הלחמה, הדבקה דבקה והרכבה מכנית מותאמת אישית מכיוון שטכניקות אלו נמצאות בשימוש נרחב ביישומים כמו ייצור של מכלולים הרמטיים, ייצור מוצרי היי-טק ואיטום מיוחד. כאן נתרכז בהיבטים המיוחדים יותר של טכניקות הצטרפות אלה, שכן הם קשורים לייצור מוצרים ומכלולים מתקדמים. ריתוך היתוך: אנו משתמשים בחום כדי להמיס ולהתלכד חומרים. החום מסופק על ידי חשמל או קרני אנרגיה גבוהה. סוגי ריתוך היתוך שאנו פורסים הם ריתוך גז OXYFUEL, ריתוך קשת, ריתוך קרן גבוה. ריתוך במצב מוצק: אנו מחברים חלקים ללא התכה והיתוך. שיטות הריתוך במצב מוצק שלנו הן COLD, ULTRASonic, התנגדות, חיכוך, ריתוך פיצוץ והדבקה בפיזור. הלחמה והלחמה: הם משתמשים במתכות מילוי ומעניקים לנו את היתרון של עבודה בטמפרטורות נמוכות יותר מאשר בריתוך, ובכך פחות נזק מבני למוצרים. מידע על מתקן ההלחמה שלנו לייצור אביזרי קרמיקה למתכת, איטום הרמטי, הזנת ואקום, ואקום גבוה ואולטרה גבוה ורכיבי בקרת נוזלים ניתן למצוא כאן:חוברת מפעל הלחמה הדבקת דבק: בגלל מגוון הדבקים המשמשים בתעשייה וגם מגוון היישומים, יש לנו דף ייעודי לכך. למעבר לדף שלנו בנושא הדבקה, אנא לחץ כאן. הרכבה מכנית מותאמת אישית: אנו משתמשים במגוון מחברים כגון ברגים, ברגים, אומים, מסמרות. המחברים שלנו אינם מוגבלים למחברי מדף סטנדרטיים. אנו מתכננים, מפתחים ומייצרים מחברים מיוחדים העשויים מחומרים לא סטנדרטיים כדי שיוכלו לעמוד בדרישות ליישומים מיוחדים. לפעמים רצויה אי מוליכות חשמלית או חום ולפעמים מוליכות. עבור יישומים מיוחדים מסוימים, ייתכן שלקוח ירצה מחברים מיוחדים שלא ניתן להסירם מבלי להרוס את המוצר. יש אינסוף רעיונות ויישומים. יש לנו הכל בשבילך, אם לא מהמדף נוכל לפתח אותו במהירות. למעבר לעמוד שלנו בנושא הרכבה מכנית, אנא לחץ כאן . הבה נבחן את טכניקות ההצטרפות השונות שלנו בפירוט רב יותר. ריתוך גז OXYFUEL (OFW): אנו משתמשים בגז דלק מעורבב עם חמצן כדי לייצר את להבת הריתוך. כאשר אנו משתמשים באצטילן כדלק וחמצן, אנו קוראים לזה ריתוך גז אוקסיאצטילן. שתי תגובות כימיות מתרחשות בתהליך שריפת גז החמצן: C2H2 + O2 ------» 2CO + H2 + חום 2CO + H2 + 1.5 O2--------» 2 CO2 + H2O + חום התגובה הראשונה מפרקת את האצטילן לפחמן חד חמצני ומימן תוך הפקת כ-33% מסך החום שנוצר. התהליך השני לעיל מייצג בעירה נוספת של המימן והפחמן החד חמצני תוך הפקת כ-67% מכלל החום. הטמפרטורות בלהבה הן בין 1533 ל-3573 קלווין. אחוז החמצן בתערובת הגז חשוב. אם תכולת החמצן היא יותר ממחצית, הלהבה הופכת לחומר מחמצן. זה לא רצוי עבור מתכות מסוימות אך רצוי עבור אחרות. דוגמה כאשר רצוי להבה מחמצנת היא סגסוגות על בסיס נחושת מכיוון שהיא יוצרת שכבת פסיבציה על המתכת. לעומת זאת, כאשר תכולת החמצן מצטמצמת, לא מתאפשרת בעירה מלאה והלהבה הופכת ללהבה מצמצמת (מקרבת). הטמפרטורות בלהבה מפחיתה נמוכות יותר ולכן היא מתאימה לתהליכים כמו הלחמה והלחמה. גזים אחרים הם גם דלקים פוטנציאליים, אבל יש להם כמה חסרונות על פני אצטילן. מדי פעם אנו מספקים מתכות מילוי לאזור הריתוך בצורה של מוטות מילוי או חוט. חלקם מצופים בשטף כדי לעכב חמצון של משטחים ובכך להגן על המתכת המותכת. יתרון נוסף שהשטף נותן לנו הוא סילוק תחמוצות וחומרים אחרים מאזור הריתוך. זה מוביל לחיבור חזק יותר. וריאציה של ריתוך גז oxyfuel היא ריתוך גז PRESSURE, שבו שני הרכיבים מחוממים בממשק שלהם באמצעות לפיד גז אוקסיאצטילן וברגע שהממשק מתחיל להימס, הלפיד נסוג ומופעל כוח צירי כדי ללחוץ את שני החלקים יחד. עד שהממשק מתמצק. ריתוך קשת: אנו משתמשים באנרגיה חשמלית כדי לייצר קשת בין קצה האלקטרודה לחלקים שיש לרתך. ספק הכוח יכול להיות AC או DC בעוד האלקטרודות הן מתכלות או בלתי מתכלות. ניתן לבטא העברת חום בריתוך קשת באמצעות המשוואה הבאה: H / l = ex VI / v כאן H הוא קלט החום, l הוא אורך הריתוך, V ו-I הם המתח והזרם המופעלים, v היא מהירות הריתוך ו-e היא יעילות התהליך. ככל שהיעילות "e" גבוהה יותר, כך נעשה שימוש מועיל יותר באנרגיה הזמינה להמסת החומר. ניתן לבטא את כניסת החום גם כך: H = ux (נפח) = ux A xl כאן u היא האנרגיה הספציפית להתכה, A חתך הריתוך ו-l אורך הריתוך. משתי המשוואות לעיל נוכל לקבל: v = ex VI / u A וריאציה של ריתוך קשת הוא ריתוך מתכת SHIELDED METAL ARC WELDING (SMAW) המהווה כ-50% מכלל תהליכי הריתוך התעשייתי והתחזוקה. ריתוך חשמלי בקשת (ELECTRIC WELDING) מתבצע על ידי נגיעה בקצה האלקטרודה המצופה בחומר העבודה ומשיכתו במהירות למרחק מספיק כדי לשמור על הקשת. אנו קוראים לתהליך הזה גם ריתוך מקל מכיוון שהאלקטרודות הן מקלות דקים וארוכים. במהלך תהליך הריתוך, קצה האלקטרודה נמס יחד עם הציפוי שלה והמתכת הבסיסית בסביבת הקשת. תערובת של המתכת הבסיסית, מתכת האלקטרודה וחומרים מציפוי האלקטרודה מתמצקת באזור הריתוך. ציפוי האלקטרודה משחרר את החמצון ומספק גז מגן באזור הריתוך ובכך מגן עליו מפני החמצן בסביבה. לכן התהליך מכונה ריתוך קשת מתכת מוגנת. אנו משתמשים בזרמים בין 50 ל-300 אמפר וברמות הספק בדרך כלל פחות מ-10 קילוואט לביצועי ריתוך מיטביים. ישנה חשיבות גם לקוטביות של זרם ה-DC (כיוון זרימת הזרם). קוטביות ישרה שבה חומר העבודה חיובי והאלקטרודה שלילית מועדפת בריתוך של מתכות בגלל חדירתה הרדודה וגם לחיבורים עם מרווחים רחבים מאוד. כאשר יש לנו קוטביות הפוכה, כלומר האלקטרודה היא חיובית וחומר שלילי, נוכל להשיג חדירות ריתוך עמוקות יותר. עם זרם AC, מכיוון שיש לנו קשתות פועם, אנו יכולים לרתך קטעים עבים באמצעות אלקטרודות בקוטר גדול וזרמים מקסימליים. שיטת ריתוך SMAW מתאימה לעוביים של 3 עד 19 מ"מ ואף יותר באמצעות טכניקות ריבוי מעברים. את הסיגים שנוצרו על גבי הריתוך יש להסיר באמצעות מברשת תיל, כדי שלא תהיה קורוזיה וכשל באזור הריתוך. זה כמובן מוסיף לעלות של ריתוך בקשת מתכת מסוככת. עם זאת, ה-SMAW היא טכניקת הריתוך הפופולרית ביותר בתעשייה ובעבודות תיקונים. ריתוך קשת שקוע (מסור): בתהליך זה אנו מגנים על קשת הריתוך באמצעות חומרי שטף גרגירים כמו סיד, סיליקה, סידן פלוריד, תחמוצת מנגן וכו'. השטף הגרגירי מוזן לאזור הריתוך על ידי זרימת כוח הכבידה דרך זרבובית. השטף המכסה את אזור הריתוך המותך מגן באופן משמעותי מפני ניצוצות, אדים, קרינת UV וכו' ופועל כמבודד תרמי, ובכך נותן לחום לחדור עמוק לתוך חלק העבודה. השטף שלא התמזג מוחזר, מטופל ועושה שימוש חוזר. סליל חשוף משמש כאלקטרודה ומוזן דרך צינור לאזור הריתוך. אנו משתמשים בזרמים בין 300 ל-2000 אמפר. תהליך ריתוך קשת שקוע (SAW) מוגבל למצבים אופקיים ושטוחים ולריתוכים מעגליים אם סיבוב המבנה העגול (כגון צינורות) אפשרי במהלך הריתוך. המהירויות יכולות להגיע ל-5 מ' לדקה. תהליך ה-SAW מתאים לצלחות עבות ומביא לריתוך איכותי, קשיח, רקיע ואחיד. הפרודוקטיביות, כלומר כמות חומר הריתוך המופקד בשעה היא פי 4 עד 10 מהכמות בהשוואה לתהליך SMAW. תהליך ריתוך קשת נוסף, כלומר ריתוך גז מתכת GAS (GMAW) או לחילופין המכונה METAL INERT GAS WELDING (MIG) מבוסס על אזור הריתוך המוגן על ידי מקורות חיצוניים של גזים כמו הליום, ארגון, פחמן דו חמצני וכו'. יתכנו חומרים משחררי חמצון נוספים במתכת האלקטרודה. חוט מתכלה מוזן דרך זרבובית לתוך אזור הריתוך. ייצור הכולל מתכות ברזליות כמו גם מתכות לא ברזליות מתבצע באמצעות ריתוך גז מתכת קשת (GMAW). פרודוקטיביות הריתוך היא בערך פי 2 מתהליך SMAW. נעשה שימוש בציוד ריתוך אוטומטי. מתכת מועברת באחת משלוש דרכים בתהליך זה: "העברת ספריי" כוללת העברה של כמה מאות טיפות מתכת קטנות בשנייה מאלקטרודה לאזור הריתוך. ב"העברה כדורית" לעומת זאת, נעשה שימוש בגזים עשירים בפחמן דו חמצני וכדוריות של מתכת מותכת מונעות על ידי הקשת החשמלית. זרמי ריתוך גבוהים וחדירת ריתוך עמוקה יותר, מהירות ריתוך גבוהה יותר מאשר בהעברת ריסוס. לפיכך ההעברה הכדורית טובה יותר לריתוך קטעים כבדים יותר. לבסוף, בשיטת "קצר חשמלי", קצה האלקטרודה נוגע בבריכת הריתוך המותך, מקצר אותה כמתכת בקצבים של מעל 50 טיפות לשנייה מועברת בטיפות בודדות. זרמים ומתחים נמוכים משמשים יחד עם חוט דק יותר. ההספקים המשמשים הם כ-2 קילוואט והטמפרטורות נמוכות יחסית, מה שהופך שיטה זו למתאימה ליריעות דקות בעובי של פחות מ-6 מ"מ. וריאציה נוספת של תהליך FLUX-CORED ARC WELDING (FCAW) דומה לריתוך קשת מתכת בגז, אלא שהאלקטרודה היא צינור מלא בשטף. היתרונות של שימוש באלקטרודות עם שטף ליבות הוא שהן מייצרות קשתות יציבות יותר, נותנות לנו את ההזדמנות לשפר את המאפיינים של מתכות ריתוך, אופי פחות שביר וגמיש של השטף שלה בהשוואה לריתוך SMAW, קווי מתאר ריתוך משופרים. אלקטרודות מכוסות ליבה עצמיות מכילות חומרים המגנים על אזור הריתוך מפני האטמוספרה. אנו משתמשים בהספק של כ-20 קילוואט. כמו תהליך GMAW, גם תהליך FCAW מציע הזדמנות להפוך תהליכים לריתוך מתמשך לאוטומטי, וזה חסכוני. ניתן לפתח כימיות שונות של מתכת ריתוך על ידי הוספת סגסוגות שונות לליבת השטף. ב- ELECTROGAS WELDING (EGW) אנו מרתכים את החלקים הממוקמים מקצה לקצה. לפעמים זה נקרא גם ריתוך בטן. מתכת ריתוך מוכנסת לתוך חלל ריתוך בין שני חלקים לחיבור. החלל מוקף בשני סכרים מקוררים במים כדי למנוע מהסיגים המותכים לשפוך החוצה. הסכרים מוזזים על ידי כוננים מכניים. כאשר ניתן לסובב חומר עבודה, אנו יכולים להשתמש בטכניקת ריתוך אלקטרוגז גם לריתוך היקפי של צינורות. אלקטרודות מוזנות דרך צינור כדי לשמור על קשת רציפה. זרמים יכולים להיות בסביבות 400 אמפר או 750 אמפר ורמות הספק בסביבות 20 קילוואט. גזים אינרטיים שמקורם מאלקטרודה עם ליבת שטף או מקור חיצוני מספקים מיגון. אנו משתמשים בריתוך אלקטרוגז (EGW) עבור מתכות כגון פלדה, טיטניום וכו' בעוביים של 12 מ"מ עד 75 מ"מ. הטכניקה מתאימה למבנים גדולים. עם זאת, בטכניקה אחרת הנקראת ELECTROSLAG WELDING (ESW) הקשת מוצתת בין האלקטרודה לתחתית חומר העבודה ומתווסף שטף. כאשר סיגים מותכים מגיעים לקצה האלקטרודה, הקשת נכבית. אנרגיה מסופקת באופן רציף דרך ההתנגדות החשמלית של הסיגים המותכים. אנו יכולים לרתך צלחות בעוביים שבין 50 מ"מ ל-900 מ"מ ואף יותר. הזרמים הם בסביבות 600 אמפר בעוד המתחים הם בין 40 - 50 וולט. מהירויות הריתוך נעות בסביבות 12 עד 36 מ"מ לדקה. יישומים דומים לריתוך אלקטרוגז. אחד מתהליכי האלקטרודה הבלתי מתכלים שלנו, GAS TUNGSTEN ARC WELDING (GTAW) הידוע גם בשם TUNGSTEN INERT GAS WELDING (TIG) כולל אספקה של מתכת מילוי באמצעות חוט. עבור מפרקים בהתאמה הדוקה, לפעמים אנחנו לא משתמשים במתכת המילוי. בתהליך TIG אנחנו לא משתמשים בשטף, אלא משתמשים בארגון והליום למיגון. לטונגסטן יש נקודת התכה גבוהה ואינו נצרך בתהליך ריתוך TIG, לכן ניתן לשמור על זרם קבוע כמו גם פערי קשת. רמות ההספק נעות בין 8 ל-20 קילוואט וזרמים של 200 אמפר (DC) או 500 אמפר (AC). עבור אלומיניום ומגנזיום אנו משתמשים בזרם AC לפונקציית ניקוי התחמוצת שלו. כדי למנוע זיהום של אלקטרודת הטונגסטן, אנו נמנעים ממגע שלה עם מתכות מותכות. ריתוך קשת טונגסטן בגז (GTAW) שימושי במיוחד לריתוך מתכות דקות. ריתוך GTAW הם באיכות גבוהה מאוד עם גימור משטח טוב. בשל העלות הגבוהה יותר של גז מימן, טכניקה שפחות נפוצה היא ריתוך מימן אטומי (ATOMIC HYDROGEN WELDING), שבו אנו יוצרים קשת בין שתי אלקטרודות טונגסטן באווירת מיגון של גז מימן זורם. ה-AHW הוא גם תהליך ריתוך אלקטרודות שאינו מתכלה. גז המימן הדיאטומי H2 מתפרק לצורתו האטומית ליד קשת הריתוך שבה הטמפרטורות הן מעל 6273 קלווין. בזמן פירוק, הוא סופג כמות גדולה של חום מהקשת. כאשר אטומי המימן פוגעים באזור הריתוך שהוא משטח קר יחסית, הם מתחברים מחדש לצורה דו-אטומית ומשחררים את החום המאוחסן. ניתן לשנות את האנרגיה על ידי שינוי חומר העבודה למרחק קשת. בתהליך אחר של אלקטרודה שאינה מתכלה, ריתוך PLASMA ARC (PAW) יש לנו קשת פלזמה מרוכזת המכוונת לכיוון אזור הריתוך. הטמפרטורות מגיעות ל-33,273 קלווין ב-PAW. מספר כמעט שווה של אלקטרונים ויונים מרכיבים את גז הפלזמה. קשת פיילוט עם זרם נמוך יוזמת את הפלזמה שנמצאת בין אלקטרודת הטונגסטן לפתח. זרמי הפעולה הם בדרך כלל סביב 100 אמפר. ניתן להזין מתכת מילוי. בריתוך קשת פלזמה, המיגון מתבצע על ידי טבעת מיגון חיצונית ושימוש בגזים כגון ארגון והליום. בריתוך קשת פלזמה, הקשת עשויה להיות בין האלקטרודה לחומר העבודה או בין האלקטרודה והזרבובית. לטכניקת ריתוך זו היתרונות על פני שיטות אחרות של ריכוז אנרגיה גבוה יותר, יכולת ריתוך עמוקה וצרה יותר, יציבות קשת טובה יותר, מהירויות ריתוך גבוהות יותר עד 1 מטר/דקה, פחות עיוות תרמי. בדרך כלל אנו משתמשים בריתוך קשת פלזמה בעוביים של פחות מ-6 מ"מ ולעיתים עד 20 מ"מ עבור אלומיניום וטיטניום. ריתוך קרן אנרגיה גבוהה: סוג נוסף של שיטת ריתוך היתוך עם ריתוך קרן אלקטרונים (EBW) וריתוך לייזר (LBW) כשתי גרסאות. לטכניקות אלו יש ערך מיוחד עבור עבודת ייצור מוצרי ההייטק שלנו. בריתוך קרן אלקטרונים, אלקטרונים במהירות גבוהה פוגעים בחומר העבודה והאנרגיה הקינטית שלהם מומרת לחום. אלומת האלקטרונים הצרה נעה בקלות בתא הוואקום. בדרך כלל אנו משתמשים בוואקום גבוה בריתוך קרן אלקטרוני. ניתן לרתך צלחות בעובי של עד 150 מ"מ. אין צורך בגזי מגן, שטף או חומר מילוי. לתותחי אלקרון יש קיבולת של 100 קילוואט. ריתוכים עמוקים וצרים עם יחסי גובה-רוחב גבוהים של עד 30 ואזורים קטנים מושפעי חום אפשריים. מהירויות ריתוך יכולות להגיע ל-12 מ' לדקה. בריתוך קרן לייזר אנו משתמשים בלייזרים בעלי הספק גבוה כמקור החום. קרני לייזר קטנות עד 10 מיקרון עם צפיפות גבוהה מאפשרות חדירה עמוקה לתוך חומר העבודה. יחסי עומק לרוחב אפשריים עד 10 עם ריתוך קרן לייזר. אנו משתמשים בלייזר גלים פולסים ורציפים, כאשר הראשון ביישומים לחומרים דקים והשני בעיקר עבור חלקי עבודה עבים עד כ-25 מ"מ. רמות ההספק הן עד 100 קילוואט. ריתוך קרן הלייזר אינו מתאים לחומרים מחזירי אור אופטית. גזים עשויים לשמש גם בתהליך הריתוך. שיטת הריתוך בקרן הלייזר מתאימה היטב לאוטומציה וייצור בנפח גבוה ויכולה להציע מהירויות ריתוך בין 2.5 מ' לדקה ל-80 מ' לדקה. יתרון מרכזי אחד שטכניקת ריתוך זו מציעה הוא גישה לאזורים שבהם לא ניתן להשתמש בטכניקות אחרות. קרני לייזר יכולות להגיע בקלות לאזורים קשים כאלה. אין צורך בוואקום כמו בריתוך קרן אלקטרונים. ניתן להשיג ריתוכים עם איכות וחוזק טוב, התכווצות נמוכה, עיוות נמוך, נקבוביות נמוכה עם ריתוך בקרן לייזר. ניתן לתפעל ולעצב בקלות קרני לייזר באמצעות כבלי סיבים אופטיים. לכן הטכניקה מתאימה היטב לריתוך של מכלולים הרמטיים מדויקים, אריזות אלקטרוניות וכו'. הבה נבחן את טכניקות הריתוך שלנו במצב מוצק. ריתוך קר (CW) הוא תהליך שבו לחץ במקום חום מופעל באמצעות קוביות או גלילים על החלקים המשודכים. בריתוך קר, לפחות אחד מהחלקים המתואמים צריך להיות רקיע. התוצאות הטובות ביותר מתקבלות עם שני חומרים דומים. אם שתי המתכות שיש לחבר בריתוך קר אינן דומות, אנו עלולים לקבל חיבורים חלשים ושבירים. שיטת הריתוך הקרה מתאימה היטב לחלקי עבודה רכים, רקיעים וקטנים כגון חיבורי חשמל, קצוות מיכלים רגישים לחום, פסים דו-מתכתיים לתרמוסטטים וכו'. וריאציה אחת של ריתוך קר היא ריתוך גליל (או ריתוך גליל), כאשר הלחץ מופעל דרך זוג גלילים. לפעמים אנו מבצעים ריתוך גליל בטמפרטורות גבוהות לחוזק הממשק טוב יותר. תהליך ריתוך מוצק נוסף שאנו משתמשים בו הוא הריתוך האולטראסוני (USW), שבו חלקי העבודה נתונים לכוח נורמלי סטטי ולמתחי גזירה מתנודדים. מתחי הגזירה המתנודדים מופעלים דרך קצהו של מתמר. ריתוך אולטראסוני פורס תנודות עם תדרים מ-10 עד 75 קילו-הרץ. ביישומים מסוימים כגון ריתוך תפר, אנו משתמשים בדיסק ריתוך מסתובב כקצה. מתחי הגזירה המופעלים על חלקי העבודה גורמים לעיוותים פלסטיים קטנים, מפרקים שכבות תחמוצת, מזהמים ומובילים להדבקה במצב מוצק. הטמפרטורות המעורבות בריתוך קולי הן הרבה מתחת לטמפרטורות נקודת ההיתוך עבור מתכות ולא מתרחש היתוך. אנו משתמשים לעתים קרובות בתהליך ריתוך קולי (USW) עבור חומרים לא מתכתיים כמו פלסטיק. עם זאת, בתרמופלסטיים, הטמפרטורות אכן מגיעות לנקודות התכה. טכניקה פופולרית נוספת, בריתוך FRICTION (FRW) החום נוצר באמצעות חיכוך בממשק של חלקי העבודה שיש לחבר. בריתוך חיכוך אנו שומרים על אחד מחלקי העבודה נייח בעוד החלק השני מוחזק במתקן ומסובב במהירות קבועה. לאחר מכן מביאים את חלקי העבודה למגע תחת כוח צירי. מהירות סיבוב פני השטח בריתוך חיכוך עשויה להגיע ל-900 מטר לדקה במקרים מסוימים. לאחר מגע מספיק משטחי, חומר העבודה המסתובב נעצר בפתאומיות והכוח הצירי מוגבר. אזור הריתוך הוא בדרך כלל אזור צר. ניתן להשתמש בטכניקת ריתוך החיכוך לחיבור חלקים מוצקים וצינוריים העשויים ממגוון חומרים. הבזק מסוים עשוי להתפתח בממשק ב-FRW, אך ניתן להסיר הבזק זה על ידי עיבוד משני או שחיקה. קיימות וריאציות של תהליך ריתוך החיכוך. לדוגמה "ריתוך חיכוך אינרציה" כולל גלגל תנופה שהאנרגיה הקינטית הסיבובית שלו משמשת לריתוך החלקים. הריתוך הושלם כאשר גלגל התנופה נעצר. ניתן לגוון את המסה המסתובבת ובכך את האנרגיה הקינטית הסיבובית. וריאציה נוספת היא "ריתוך חיכוך ליניארי", כאשר תנועה הדדית ליניארית מוטלת על לפחות אחד מהרכיבים שיש לחבר. בריתוך חיכוך ליניארי חלקים לא חייבים להיות מעגליים, הם יכולים להיות מלבניים, מרובעים או בעלי צורה אחרת. תדרים יכולים להיות בעשרות הרץ, אמפליטודות בטווח המילימטרים ולחצים בעשרות או מאות MPa. לבסוף "ריתוך בוחשת חיכוך" שונה במקצת מהשניים האחרים שהוסברו לעיל. בעוד בריתוך חיכוך אינרציה וריתוך חיכוך ליניארי חימום ממשקים מושג באמצעות חיכוך על ידי שפשוף שני משטחים מגע, בשיטת ריתוך בחיכוך ערעור גוף שלישי משופשף בשני המשטחים שיש לחבר. כלי מסתובב בקוטר של 5 עד 6 מ"מ מובא במגע עם המפרק. הטמפרטורות יכולות לעלות לערכים שבין 503 ל-533 קלווין. מתבצע חימום, ערבוב וערבוב של החומר במפרק. אנו משתמשים בריתוך בחיכוך על מגוון חומרים כולל אלומיניום, פלסטיק וחומרים מרוכבים. הריתוכים אחידים והאיכות גבוהה עם מינימום נקבוביות. לא מיוצרים אדים או ניתזים בריתוך בחיכוך והתהליך הוא אוטומטי היטב. ריתוך התנגדות (RW): החום הנדרש לריתוך מופק על ידי ההתנגדות החשמלית בין שני חלקי העבודה שיש לחבר. אין שימוש בשטף, גזי מגן או אלקטרודות מתכלות בריתוך התנגדות. חימום ג'ול מתרחש בריתוך התנגדות ויכול להתבטא כך: H = (ריבוע I) x R xtx K H הוא חום שנוצר בג'אול (וואט-שניות), זרם I באמפר, התנגדות R באוהם, t הוא הזמן בשניות שהזרם זורם דרכו. הגורם K קטן מ-1 ומייצג את חלק האנרגיה שלא אובד בקרינה והולכה. זרמים בתהליכי ריתוך התנגדות יכולים להגיע לרמות גבוהות של 100,000 A אך המתחים הם בדרך כלל 0.5 עד 10 וולט. אלקטרודות עשויות בדרך כלל מסגסוגות נחושת. ניתן לחבר חומרים דומים ולא דומים על ידי ריתוך התנגדות. קיימות מספר וריאציות לתהליך זה: "ריתוך נקודתי התנגדות" כולל שתי אלקטרודות עגולות מנוגדות המגעות עם המשטחים של מפרק הברכיים של שתי היריעות. לחץ מופעל עד כיבוי הזרם. קוטר גוש הריתוך הוא בדרך כלל עד 10 מ"מ. ריתוך נקודתי התנגדות משאיר סימני חריטה מעט דהויים בנקודות הריתוך. ריתוך נקודתי היא טכניקת ריתוך ההתנגדות הפופולרית ביותר שלנו. צורות אלקטרודות שונות משמשות בריתוך נקודתי על מנת להגיע לאזורים קשים. ציוד הריתוך הנקודתי שלנו נשלט CNC ויש לו מספר אלקטרודות שניתן להשתמש בהן בו זמנית. וריאציה נוספת של "ריתוך תפר התנגדות" מתבצעת עם אלקטרודות גלגל או רולר המייצרות ריתוכים נקודתיים רציפים בכל פעם שהזרם מגיע לרמה גבוהה מספיק במחזור הספק AC. המפרקים המיוצרים על ידי ריתוך תפר התנגדות הם אטומים לנוזל ולגז. מהירויות ריתוך של כ-1.5 מ' לדקה נורמליות עבור יריעות דקות. אפשר להחיל זרמים לסירוגין כך שריתוכים נקודתיים מיוצרים במרווחים רצויים לאורך התפר. ב"ריתוך הקרנת התנגדות" אנו מטביעים הבלטה אחת או יותר (גומות) על אחד ממשטחי העבודה שיש לרתך. הקרנות אלו עשויות להיות עגולות או סגלגלות. מגיעים לטמפרטורות מקומיות גבוהות בנקודות המובלטות הללו הבאות במגע עם חלק ההזדווגות. אלקטרודות מפעילות לחץ כדי לדחוס את ההקרנות הללו. לאלקטרודות בריתוך הקרנת התנגדות יש קצוות שטוחים והן סגסוגות נחושת מקוררות במים. היתרון של ריתוך הקרנת התנגדות הוא היכולת שלנו לבצע מספר ריתוכים במכה אחת, ובכך הארכת חיי האלקטרודה, יכולת ריתוך יריעות בעוביים שונים, יכולת ריתוך אוומים וברגים ליריעות. החיסרון של ריתוך הקרנת התנגדות הוא העלות הנוספת של הבלטה של הגומות. טכניקה נוספת, ב"ריתוך הבזק" נוצר חום מהקשת בקצות שני חלקי העבודה כשהם מתחילים ליצור מגע. שיטה זו עשויה גם לשקול לחילופין ריתוך קשת. הטמפרטורה בממשק עולה, והחומר מתרכך. מופעל כוח צירי ונוצר ריתוך באזור המרוכך. לאחר השלמת ריתוך הבזק, ניתן לעבד את המפרק לשיפור המראה. איכות הריתוך המתקבלת על ידי ריתוך הבזק טובה. רמות ההספק הן 10 עד 1500 קילוואט. ריתוך הבזק מתאים לחיבור מקצה לקצה של מתכות דומות או שונות בקוטר של עד 75 מ"מ ויריעות בעובי של 0.2 מ"מ עד 25 מ"מ. "ריתוך קשת חתיכים" דומה מאוד לריתוך הבזק. החתך כגון בורג או מוט הברגה משמש כאלקטרודה אחת בזמן שהוא מחובר לחומר עבודה כגון צלחת. כדי לרכז את החום שנוצר, למנוע חמצון ולשמור על המתכת המותכת באזור הריתוך, מונחת טבעת קרמית חד פעמית סביב המפרק. לבסוף "ריתוך הקשה" תהליך ריתוך התנגדות נוסף, משתמש בקבל כדי לספק את האנרגיה החשמלית. בריתוך הקשה הכוח נפרק תוך אלפיות שניות של זמן במהירות רבה ומפתח חום מקומי גבוה במפרק. אנו משתמשים בריתוך כלי הקשה נרחב בתעשיית ייצור האלקטרוניקה שבה יש להימנע מחימום של רכיבים אלקטרוניים רגישים בקרבת המפרק. טכניקה הנקראת EXPLOSION WELDING כוללת פיצוץ של שכבת חומר נפץ המונחת על אחד מחלקי העבודה שיש לחבר. הלחץ הגבוה מאוד המופעל על חומר העבודה מייצר ממשק סוער וגלי ומתרחשת חיבור מכני. חוזק הקשר בריתוך נפץ גבוה מאוד. ריתוך פיצוץ הוא שיטה טובה לחיפוי לוחות עם מתכות שונות. לאחר החיפוי, ניתן לגלגל את הצלחות לחלקים דקים יותר. לפעמים אנו משתמשים בריתוך פיצוץ להרחבת צינורות כך שהם ייאטמו בחוזקה כנגד הצלחת. השיטה האחרונה שלנו בתחום של הצטרפות מצב מוצק היא DIFFUSION BONDING או DIFFUSION WELDING (DFW) שבה חיבור טוב מושג בעיקר על ידי דיפוזיה של אטומים על פני הממשק. דפורמציה פלסטית מסוימת בממשק תורמת גם היא לריתוך. הטמפרטורות המעורבות הן בסביבות 0.5 Tm כאשר Tm היא טמפרטורת ההיתוך של המתכת. חוזק הקשר בריתוך דיפוזיה תלוי בלחץ, טמפרטורה, זמן מגע וניקיון משטחי מגע. לפעמים אנו משתמשים במתכות מילוי בממשק. חום ולחץ נדרשים בחיבור דיפוזיה והם מסופקים על ידי התנגדות חשמלית או תנור ומשקולות מתות, מכבש או אחר. ניתן לחבר מתכות דומות ולא דומות באמצעות ריתוך דיפוזיה. התהליך איטי יחסית בגלל הזמן שלוקח לאטומים להגירה. DFW יכול להיות אוטומטי ונמצא בשימוש נרחב בייצור חלקים מורכבים לתעשיות התעופה והחלל, האלקטרוניקה והרפואה. המוצרים המיוצרים כוללים שתלים אורטופדיים, חיישנים, חלקי מבנה תעופה וחלל. ניתן לשלב הדבקת דיפוזיה עם SUPERPLASTIC FORMING לייצור מבני מתכת מורכבים. מיקומים נבחרים על היריעות מחוברים תחילה בדיפוזיה ולאחר מכן מורחבים האזורים הלא מלוכדים לתוך תבנית באמצעות לחץ אוויר. מבני תעופה וחלל בעלי יחסי קשיחות-משקל גבוהים מיוצרים בשילוב שיטות זה. התהליך המשולב של ריתוך דיפוזיה / יצירת סופר-פלסטיק מפחית את מספר החלקים הנדרשים על-ידי ביטול הצורך במחברים, גורם לחלקים בעלי מתח נמוך ומדויק ביותר מבחינה כלכלית ועם זמני אספקה קצרים. הלחמה: טכניקות ההלחמה וההלחמה כרוכות בטמפרטורות נמוכות מאלה הנדרשות לריתוך. עם זאת, טמפרטורות ההלחמה גבוהות יותר מטמפרטורות ההלחמה. בהלחמה מונחת מתכת מילוי בין המשטחים לחיבור והטמפרטורות מועלות לטמפרטורת ההיתוך של חומר המילוי מעל 723 קלווין אך מתחת לטמפרטורות ההיתוך של חלקי העבודה. המתכת המותכת ממלאת את החלל המתאים בין חלקי העבודה. הקירור וההתמצקות לאחר מכן של מתכת הפילטר מביאים למפרקים חזקים. בריתוך הלחמה מתכת המילוי מופקדת במפרק. הרבה יותר מתכת מילוי משמשת בריתוך הלחמה בהשוואה להלחמה. לפיד אוקסיאצטילן עם להבה מחמצנת משמש להפקדת מתכת המילוי בריתוך הלחמה. בשל טמפרטורות נמוכות יותר בהלחמה, הבעיות באזורים מושפעי חום כמו עיוות ומתחים שיוריים פחותות. ככל שפער המרווח בהלחמה קטן יותר חוזק הגזירה של המפרק גבוה יותר. חוזק מתיחה מרבי עם זאת מושג בפער אופטימלי (ערך שיא). מתחת ומעל לערך אופטימלי זה, חוזק המתיחה בהלחמה פוחת. מרווחים אופייניים בהלחמה יכולים להיות בין 0.025 ל-0.2 מ"מ. אנו משתמשים במגוון של חומרי הלחמה בעלי צורות שונות כגון ביצועים, אבקה, טבעות, חוט, רצועה וכו'. והוא יכול לייצר ביצועים אלה במיוחד עבור העיצוב או הגיאומטריה של המוצר שלך. אנו גם קובעים את תכולת חומרי ההלחמה בהתאם לחומרי הבסיס והיישום שלך. אנו משתמשים לעתים קרובות בשטפים בפעולות הלחמה כדי להסיר שכבות תחמוצת לא רצויות ולמנוע חמצון. כדי למנוע קורוזיה לאחר מכן, שטפים מוסרים בדרך כלל לאחר פעולת ההצטרפות. AGS-TECH Inc משתמשת בשיטות הלחמה שונות, כולל: - הלחמת לפיד - הלחמת תנור - הלחמת אינדוקציה - הלחמת התנגדות - הלחמת טבילה - הלחמת אינפרא אדום - הלחמת דיפוזיה - קרן אנרגיה גבוהה הדוגמאות הנפוצות ביותר שלנו לחיבורים מולחמים עשויות ממתכות שונות בעלות חוזק טוב כגון מקדחי קרביד, תוספות, אריזות הרמטיות אופטואלקטרוניות, אטמים. הלחמה: זוהי אחת הטכניקות הנפוצות ביותר שלנו, שבה ההלחמה (מתכת המילוי) ממלאת את המפרק כמו בהלחמה בין רכיבים מתאימים. להלחמות שלנו יש נקודות התכה מתחת ל-723 קלווין. אנו פורסים הלחמה ידנית ואוטומטית בפעולות ייצור. בהשוואה להלחמה, טמפרטורות ההלחמה נמוכות יותר. הלחמה אינה מתאימה במיוחד ליישומים בטמפרטורה גבוהה או חוזק גבוה. אנו משתמשים בהלחמות ללא עופרת וכן בסגסוגות בדיל-עופרת, בדיל-אבץ, עופרת-כסף, קדמיום-כסף, אבץ-אלומיניום מלבד אחרים להלחמה. גם חומצות ומלחים לא-קורוזיביות, כמו גם חומצות אורגניות, משמשות כשטף בהלחמה. אנו משתמשים בשטפים מיוחדים להלחמת מתכות עם יכולת הלחמה נמוכה. ביישומים בהם עלינו להלחים חומרים קרמיים, זכוכית או גרפיט, אנו מצפים תחילה את החלקים במתכת מתאימה להגברת הלחמה. טכניקות ההלחמה הפופולריות שלנו הן: - הלחמה מחדש או הדבקה -הלחמת גל -הלחמת תנור -הלחמת לפיד -הלחמת אינדוקציה -הלחמת ברזל -הלחמת התנגדות -הלחמת טבילה -הלחמה אולטרה-סונית -הלחמה אינפרא אדום הלחמה אולטראסונית מעניקה לנו יתרון ייחודי לפיו הצורך בשטפים מתבטל עקב אפקט קוויטציה אולטרסאונד אשר מסיר סרטי תחמוצת מהמשטחים המחוברים. זרימה חוזרת והלחמת גל הן הטכניקות הבולטות שלנו מבחינה תעשייתית לייצור בנפח גבוה באלקטרוניקה, ולכן כדאי להסביר בפירוט רב יותר. בהלחמה חוזרת, אנו משתמשים במשחות מוצקות למחצה הכוללות חלקיקי הלחמה-מתכת. את המשחה מניחים על המפרק באמצעות תהליך הקרנה או שבלונה. במעגלים מודפסים (PCB) אנו משתמשים לעתים קרובות בטכניקה זו. כאשר מרכיבים חשמליים מונחים על רפידות אלה מהדבקה, מתח פני השטח שומר על אריזות ההרכבה על פני השטח מיושרות. לאחר הנחת הרכיבים, אנו מחממים את המכלול בכבשן כך שההלחמה החוזרת מתרחשת. במהלך תהליך זה, הממיסים שבמשחה מתאדים, השטף במשחה מופעל, הרכיבים מחוממים מראש, חלקיקי ההלחמה מומסים ומרטיבים את המפרק, ולבסוף מכלול ה-PCB מתקרר באיטיות. הטכניקה הפופולרית השנייה שלנו לייצור בנפח גבוה של לוחות PCB, כלומר הלחמת גלים מבוססת על העובדה שהלחמות מותכות מרטיבות משטחי מתכת ויוצרות קשרים טובים רק כאשר המתכת מחוממת מראש. גל למינרי עומד של הלחמה מותכת נוצר תחילה על ידי משאבה וה-PCB שחומם מראש ושטף מראש מועברים על הגל. ההלחמה מרטיבת רק משטחי מתכת חשופים אך אינה מרטיבת את אריזות הפולימר IC וגם לא את לוחות המעגלים המצופים בפולימר. מהירות גבוהה של סילון מים חמים מוציאה עודפי הלחמה מהמפרק ומונעת גישור בין מובילים סמוכים. בהלחמת גלים של חבילות מותקן על פני השטח, אנו מחברים אותן תחילה בהדבקה ללוח המעגלים לפני ההלחמה. שוב נעשה שימוש בסינון ובשבלונות אבל הפעם לאפוקסי. לאחר הנחת הרכיבים במיקומים הנכונים, האפוקסי מתרפא, הלוחות הופכים ומתבצעת הלחמת גלים. CLICK Product Finder-Locator Service עמוד קודם
- Micromanufacturing, Nanomanufacturing, Mesomanufacturing AGS-TECH Inc.
Micromanufacturing, Nanomanufacturing, Mesomanufacturing - Electronic & Magnetic Optical & Coatings, Thin Film, Nanotubes, MEMS, Microscale Fabrication ייצור בקנה מידה ננו, בקנה מידה בקנה מידה מזערי קרא עוד Our NANOMANUFACTURING, MICROMANUFACTURING and MESOMANUFACTURING processes can be categorized as: טיפולי שטח ושינויים ציפויים פונקציונליים / ציפויים דקורטיביים / סרט דק / סרט עבה ייצור בקנה מידה ננו / ייצור ננו ייצור בקנה מידה מיקרו / ייצור מיקרו / מיקרו-עיבוד Mesoscale Manufacturing / Mesomanufacturing מיקרואלקטרוניקה & ייצור מוליכים למחצה ויצור Microfluidic Devices Manufacturing ייצור מיקרו-אופטיקה מיקרו הרכבה ואריזה ליטוגרפיה רכה בכל מוצר חכם שמתוכנן כיום, ניתן לשקול אלמנט שיגדיל את היעילות, הרבגוניות, יפחית את צריכת החשמל, יצמצם בזבוז, יגדיל את חיי המוצר ובכך יהיה ידידותי לסביבה. לצורך כך, AGS-TECH מתמקדת במספר תהליכים ומוצרים הניתנים לשילוב במכשירים ובציוד להשגת מטרות אלו. לדוגמה low-friction FUNCTIONAL COATINGS יכול להפחית את צריכת החשמל. כמה דוגמאות אחרות לציפוי פונקציונלי הן ציפויים עמידים בפני שריטות, אנטי-הרטבה SURFACE TREATMENTS coating, ציפויים אנטי-פטרייתיים וציפויי משטחים (הידרופיליים) ציפויי פחמן כמו יהלומים עבור כלי חיתוך ושרטוט, THIN FILM ציפויים אלקטרוניים, ציפויים מגנטיים של סרט דק, ציפויים אופטיים רב שכבתיים. In NANOMANUFACTURING or_cc781905-5cde-3194-6_bb3NA אורך MANUFACTURING 3194-6_BAD NUSCAL אורך MANUF-3194-6BAD NUSCLE בפועל זה מתייחס לפעולות ייצור מתחת לקנה מידה מיקרומטר. ייצור ננו עדיין בחיתוליו בהשוואה לייצור מיקרו, אולם המגמה היא בכיוון הזה וייצור ננו הוא בהחלט חשוב מאוד לעתיד הקרוב. יישומים מסוימים של ייצור ננו כיום הם ננו-צינורות פחמן כסיבי חיזוק לחומרים מרוכבים במסגרות אופניים, מחבטות בייסבול ומחבטי טניס. ננו-צינוריות פחמן, בהתאם לכיוון הגרפיט בננו-צינור, יכולים לפעול כמוליכים למחצה או כמוליכים. לננו-צינוריות פחמן יש יכולת נשיאת זרם גבוהה מאוד, גבוהה פי 1000 מכסף או נחושת. יישום נוסף של ייצור ננו הוא קרמיקה ננו-פאזית. על ידי שימוש בננו-חלקיקים בייצור חומרים קרמיים, נוכל להגדיל בו זמנית את החוזק והגמישות של הקרמיקה. אנא לחץ על תפריט המשנה לקבלת מידע נוסף. Microscale Manufacturing_CC781905-5CDE-3194-BB3B-136BAD5CF58D_OR_CC781905-5CDE-3194-BB3B-136BAD5CF58D_MICRONALONEDERSORY_CC781905-5CDE-3119-BBISCORSOCSOCESOCESOCES. המונחים מיקרו-ייצור, מיקרו-אלקטרוניקה, מערכות מיקרו-אלקטרו-מכאניות אינם מוגבלים לסולמות אורך כה קטנים, אלא מציעים אסטרטגיית חומר וייצור. בפעולות המיקרו-ייצור שלנו כמה טכניקות פופולריות בהן אנו משתמשים הן ליתוגרפיה, תחריט רטוב ויבש, ציפוי סרט דק. מגוון רחב של חיישנים ומפעילים, בדיקות, ראשי כוננים קשיחים מגנטיים, שבבים מיקרואלקטרוניים, התקני MEMS כגון מדי תאוצה וחיישני לחץ, בין היתר, מיוצרים בשיטות מיקרו-ייצור כאלה. תוכל למצוא מידע מפורט יותר על אלה בתפריטי המשנה. MESOSCALE MANUFACTURING or MESOMANUFACTURING refers to our processes for fabrication of miniature devices such as hearing aids, medical stents, medical valves, mechanical watches and extremely small מנועים. ייצור בקנה מידה גדול חופף הן ייצור מאקרו והן מיקרו. מחרטות מיניאטוריות, עם מנוע 1.5 וואט וממדים של 32 x 25 x 30.5 מ"מ ומשקלים של 100 גרם, יוצרו בשיטות ייצור בקנה מידה מזוק. באמצעות מחרטות כאלה, פליז עבר עיבוד בקוטר קטן כמו 60 מיקרון וחספוס פני השטח בסדר גודל של מיקרון או שניים. כלי מכונות מיניאטוריים אחרים כגון מכונות כרסום ומכבשים יוצרו גם הם באמצעות ייצור משני. In MICROELECTRONICS MANUFACTURING אנו משתמשים באותן טכניקות כמו בייצור מיקרו. המצעים הפופולריים ביותר שלנו הם סיליקון, ואחרים כמו גליום ארסניד, אינדיום פוספיד וגרמניום משמשים גם הם. סרטים/ציפויים מסוגים רבים ובמיוחד ציפויי סרט דק מוליכים ומבודדים משמשים לייצור מכשירים ומעגלים מיקרואלקטרוניים. התקנים אלה מתקבלים בדרך כלל מרב שכבות. שכבות בידוד מתקבלות בדרך כלל על ידי חמצון כגון SiO2. דופטנטים (גם P וגם n) הם נפוצים וחלקים מהמכשירים מסוממים על מנת לשנות את המאפיינים האלקטרוניים שלהם ולהשיג אזורים מסוג p ו-n. באמצעות ליטוגרפיה כגון פוטוליתוגרפיה אולטרה סגולה, עמוקה או קיצונית אולטרה סגולה, או ליתוגרפיה של קרני רנטגן, קרן אלקטרונים אנו מעבירים דפוסים גיאומטריים המגדירים את המכשירים מפוטומסק/מסכה אל משטחי המצע. תהליכי ליתוגרפיה אלו מיושמים מספר פעמים בייצור מיקרו של שבבים מיקרואלקטרוניים על מנת להשיג את המבנים הנדרשים בתכנון. כמו כן מבוצעים תהליכי תחריט שבאמצעותם מסירים סרטים שלמים או קטעים מסוימים של סרטים או מצע. בקצרה, על ידי שימוש בתצהיר שונים, תחריט ושלבים ליטוגרפיים מרובים אנו משיגים את המבנים הרב-שכבתיים על מצעי המוליכים למחצה התומכים. לאחר עיבוד הפרוסים ומעגלים רבים מיוצרים עליהם במיקרו, החלקים החוזרים נחתכים ומתקבלים קוביות בודדות. לאחר מכן כל תבנית מחוברת בחוט, ארוזה ונבדקת והופכת למוצר מיקרואלקטרוני מסחרי. עוד כמה פרטים על ייצור מיקרואלקטרוניקה ניתן למצוא בתפריט המשנה שלנו, אולם הנושא הוא נרחב מאוד ולכן אנו מעודדים אותך ליצור איתנו קשר במקרה שאתה צריך מידע ספציפי למוצר או פרטים נוספים. Our MICROFLUIDICS MANUFACTURING פעולות מכוונות לייצור התקנים ומערכות של נוזלים שבהם מטופלים נפחים קטנים. דוגמאות להתקנים מיקרו-נוזליים הם התקני מיקרו הנעה, מערכות מעבדה-על-שבב, מכשירים מיקרו-תרמיים, ראשי הדפסה להזרקת דיו ועוד. במיקרופלואידיקה עלינו להתמודד עם שליטה ומניפולציה מדויקת של נוזלים המוגבלים לאזורים תת-מילימטרים. נוזלים מועברים, מערבבים, מופרדים ומעובדים. במערכות מיקרו-נוזליות נוזלים מועברים ונשלטים באופן אקטיבי באמצעות מיקרו-משאבות זעירות ומיקרו-שסתומים וכדומה או תוך ניצול פסיבי של כוחות נימיים. עם מערכות מעבדה-על-שבב, תהליכים המבוצעים בדרך כלל במעבדה ממוזערים על שבב בודד על מנת לשפר את היעילות והניידות וכן להפחית את נפחי הדגימות והריאגנטים. יש לנו את היכולת לעצב עבורך התקני מיקרו-נוזלים ולהציע אב טיפוס ומיקרו-ייצור בהתאמה אישית עבור היישומים שלך. תחום מבטיח נוסף בייצור מיקרו הוא MICRO-OPTICS MANUFACTURING. מיקרו-אופטיקה מאפשרת מניפולציה של אור וניהול פוטונים עם מבנים ורכיבים בקנה מידה של מיקרון ותת-מיקרון. מיקרו-אופטיקה מאפשרת לנו לממשק את העולם המקרוסקופי בו אנו חיים עם העולם המיקרוסקופי של עיבוד נתונים אופטו וננו-אלקטרוני. רכיבים ותתי מערכות מיקרו-אופטיים מוצאים יישומים נרחבים בתחומים הבאים: טכנולוגיית מידע: בתצוגות מיקרו, מיקרו מקרנים, אחסון נתונים אופטיים, מיקרו מצלמות, סורקים, מדפסות, מכונות צילום וכו'. ביו-רפואה: אבחון זעיר פולשני/נקודתי טיפול, ניטור טיפול, חיישני מיקרו הדמיה, השתלות רשתית. תאורה: מערכות המבוססות על לדים ושאר מקורות אור יעילים מערכות בטיחות ואבטחה: מערכות ראיית לילה אינפרא אדום ליישומי רכב, חיישני טביעות אצבע אופטיים, סורקי רשתית. תקשורת אופטית וטלקומוניקציה: במתגים פוטוניים, רכיבי סיבים אופטיים פסיביים, מגברים אופטיים, מיינפריים ומחשבים אישיים. מבנים חכמים: במערכות חישה מבוססות סיבים אופטיים ועוד ועוד כספקית האינטגרציה ההנדסית המגוון ביותר, אנו מתגאים ביכולתנו לספק מענה כמעט לכל צרכי ייעוץ, הנדסה, הנדסה הפוכה, יצירת אב טיפוס מהיר, פיתוח מוצר, ייצור, ייצור והרכבה. לאחר מיקרו-ייצור של הרכיבים שלנו, לעתים קרובות מאוד עלינו להמשיך עם MICRO ASSEMBLY & PACKAGING. זה כרוך בתהליכים כגון הצמדת קוביות, חיבור חוט, חיבור, איטום הרמטי של חבילות, בדיקה, בדיקת מוצרים ארוזים לאמינות סביבתית... וכו'. לאחר מיקרו-ייצור מכשירים על תבנית, אנו מחברים את התבנית לבסיס קשיח יותר כדי להבטיח אמינות. לעתים קרובות אנו משתמשים בצמנטים אפוקסי מיוחדים או סגסוגות אוקטיות כדי לחבר את התבנית לאריזה שלה. לאחר שהשבב או התבנית מחוברים למצע שלו, אנו מחברים אותו חשמלית למובילי האריזה באמצעות הדבקת חוטים. שיטה אחת היא להשתמש בחוטי זהב דקים מאוד מהחבילה המובילה לרפידות הדבקה הממוקמות סביב היקף התבנית. לבסוף עלינו לבצע את האריזה הסופית של המעגל המחובר. בהתאם ליישום ולסביבת ההפעלה, מגוון חבילות סטנדרטיות ומיוצרות בהתאמה אישית זמינות עבור מכשירים אלקטרוניים, אלקטרו-אופטיים ומיקרו-אלקטרו-מכניים. טכניקת מיקרו-ייצור נוספת בה אנו משתמשים היא SOFT LITHOGRAPHY, מונח המשמש למספר תהליכים להעברת דפוסים. יש צורך בתבנית מאסטר בכל המקרים והיא מיוצרת במיקרו בשיטות ליטוגרפיה סטנדרטיות. באמצעות תבנית המאסטר, אנו מייצרים דוגמה / חותמת אלסטומרי. וריאציה אחת של ליתוגרפיה רכה היא "הדפסת מיקרו מגע". חותמת האלסטומר מצופה בדיו ונלחצת על משטח. פסגות הדפוס מתקשרות עם פני השטח ומועברת שכבה דקה של כ-1 שכבה אחת של הדיו. שכבת סרט דק זה משמשת כמסכה לחריטה רטובה סלקטיבית. וריאציה שנייה היא "יציקת מיקרו-טרנספר", שבה ממלאים את השקעים של תבנית האלסטומר במבשר פולימר נוזלי ונדחפים אל משטח. לאחר שהפולימר מתרפא, אנו מקלפים את התבנית ומשאירים מאחור את התבנית הרצויה. לבסוף וריאציה שלישית היא "מיקרו-יציקה בנימים", כאשר תבנית חותמת האלסטומר מורכבת מתעלות המשתמשות בכוחות נימיים כדי לנפת פולימר נוזלי לתוך הבול מצידו. בעיקרון, כמות קטנה מהפולימר הנוזלי מונחת בסמוך לתעלות הנימים והכוחות הנימים מושכים את הנוזל לתוך התעלות. עודף פולימר נוזלי מוסר ומאפשר לפולימר בתוך התעלות להתרפא. מקלפים את תבנית החותמת והמוצר מוכן. תוכל למצוא פרטים נוספים על טכניקות מיקרו-ייצור הליטוגרפיות הרכות שלנו על ידי לחיצה על תפריט המשנה הקשור בצד דף זה. אם אתה מתעניין בעיקר ביכולות ההנדסה והמחקר והפיתוח שלנו במקום ביכולות הייצור, אז אנו מזמינים אותך לבקר גם באתר ההנדסה שלנו http://www.ags-engineering.com קרא עוד קרא עוד קרא עוד קרא עוד קרא עוד קרא עוד קרא עוד קרא עוד קרא עוד CLICK Product Finder-Locator Service עמוד קודם
- Adhesive Bonding - Adhesives - Sealing - Fastening - Joining
Adhesive Bonding - Adhesives - Sealing - Fastening - Joining Nonmetallic Materials - Optical Contacting - UV Bonding - Specialty Glue - Epoxy - Custom Assembly הדבקה ואיטום דבק והידוק והרכבה מכניים בהתאמה אישית בין שאר טכניקות ההצטרפות החשובות ביותר שלנו הן הדבקת דבק, הידוק מכני והרכבה, חיבור של חומרים לא מתכתיים. אנו מקדישים חלק זה לטכניקות ההצטרפות וההרכבה הללו בגלל חשיבותן בפעולות הייצור שלנו והתוכן הנרחב הקשור אליהן. הדבקת דבק: האם ידעת שיש אפוקסי מיוחדים שניתן להשתמש בהם לאיטום ברמה הרמטית כמעט? בהתאם לרמת האיטום הדרושה לך, אנו נבחר או נגבש עבורך חומר איטום. האם אתה יודע שגם חומרי איטום מסוימים ניתנים לריפוי בחום בעוד שאחרים דורשים רק אור UV כדי להתרפא? אם תסביר לנו את בקשתך, נוכל לגבש את האפוקסי המתאים לך. ייתכן שתדרוש משהו שהוא נטול בועות או משהו שתואם את מקדם ההתפשטות התרמי של חלקי ההזדווגות שלך. יש לנו הכל! צור איתנו קשר והסבר את בקשתך. לאחר מכן נבחר את החומר המתאים ביותר עבורך או נגבש פתרון בהתאמה אישית לאתגר שלך. החומרים שלנו מגיעים עם דוחות בדיקה, דפי מידע ואישורים. אנו מסוגלים להרכיב את הרכיבים שלך בצורה חסכונית מאוד ולשלוח לך מוצרים גמורים ואיכותיים שנבדקו. דבקים זמינים עבורנו בצורות שונות כגון נוזלים, תמיסות, משחות, אמולסיות, אבקה, סרט וסרטים. אנו משתמשים בשלושה סוגים בסיסיים של דבקים לתהליכי ההצטרפות שלנו: -דבקים טבעיים -דבקים אנאורגניים -דבקים אורגניים סינתטיים עבור יישומים נושאי עומס בייצור וייצור אנו משתמשים בדבקים בעלי חוזק לכידות גבוה, והם לרוב דבקים אורגניים סינתטיים, אשר עשויים להיות תרמופלסטיים או פולימרים תרמו-מקביעים. דבקים אורגניים סינתטיים הם הקטגוריה החשובה ביותר שלנו וניתן לסווג אותם כ: דבקים ריאקטיביים כימיים: דוגמאות פופולריות הן סיליקונים, פוליאוריטן, אפוקסי, פנולים, פוליאמידים, אנאירוביים כמו Loctite. דבקים רגישים ללחץ: דוגמאות נפוצות הן גומי טבעי, גומי ניטריל, פוליאקרילטים, גומי בוטיל. דבק Hot Melt: דוגמאות לכך הן תרמופלסטיים כמו אתילן-ויניל-אצטט קופולימרים, פוליאמידים, פוליאסטר, פוליאולפינים. דבקים חמים תגובתיים: יש להם חלק תרמוסטי המבוסס על הכימיה של urethane. דבקים לאידוי/דיפוזיה: הפופולריים הם ויניל, אקריליק, פנולים, פוליאוריטן, גומי סינתטי וגומי טבעי. דבקים מסוג סרט וסרט: דוגמאות הן ניילון-אפוקסיות, אלסטומר-אפוקסיות, ניטריל-פנולים, פוליאמידים. דבקים מושהים: אלה כוללים פוליוויניל אצטט, פוליסטירן, פוליאמידים. דבקים מוליכים חשמלית ותרמית: דוגמאות פופולריות הן אפוקסי, פוליאוריטן, סיליקונים, פוליאמידים. על פי הכימיה שלהם ניתן לסווג דבקים שאנו משתמשים בייצור כ: - מערכות דבק מבוססות אפוקסי: חוזק גבוה וסיבולת טמפרטורה גבוהה עד 473 קלווין אופייניים לאלה. חומרי מליטה ביציקות תבניות חול הם מסוג זה. - אקריליק: אלה מתאימים ליישומים הכוללים משטחים מלוכלכים מזוהמים. - מערכות דבק אנאירוביות: אשפרה על ידי מניעת חמצן. קשרים קשים ושבירים. - ציאנואקרילט: קווי קשר דקים עם זמני התייצבות מתחת לדקה. - Urethanes: אנו משתמשים בהם כחומרי איטום פופולריים בעלי קשיחות וגמישות גבוהים. - סיליקונים: ידועים בעמידותם בפני לחות וממיסים, השפעה גבוהה וחוזק קילוף. זמני ריפוי ארוכים יחסית של עד מספר ימים. כדי לייעל את המאפיינים בהדבקת דבק, אנו עשויים לשלב מספר דבקים. דוגמאות לכך הן מערכות דבק משולבות אפוקסי-סיליקון, ניטריל-פנולי. פוליאמידים ופוליבנזימידאזולים משמשים ביישומים בטמפרטורה גבוהה. חיבורי דבק עמידים היטב בכוחות גזירה, דחיסה ומתיחה, אך הם עלולים להיכשל בקלות כאשר הם נתונים לכוחות קילוף. לכן, בהדבקה דביקה עלינו להתחשב ביישום ולתכנן את המפרק בהתאם. הכנת פני השטח היא גם בעלת חשיבות קריטית בהדבקה. אנו מנקים, מטפלים ומשנים משטחים כדי להגביר את החוזק והאמינות של ממשקים בהדבקת דבק. שימוש בפריימרים מיוחדים, טכניקות תחריט רטוב ויבש כמו ניקוי פלזמה הן בין השיטות הנפוצות שלנו. שכבה מקדמת הידבקות כגון תחמוצת דקה עשויה לשפר את ההידבקות ביישומים מסוימים. הגדלת החספוס של פני השטח עשויה להיות מועילה גם לפני הדבקת הדבק, אך היא צריכה להיות מבוקרת היטב ולא מוגזמת מכיוון שחספוס מוגזם עלול לגרום ללכידת אוויר ולפיכך ממשק מלוכד דבק חלש יותר. אנו משתמשים בשיטות לא הרסניות לבדיקת האיכות והחוזק של המוצרים שלנו לאחר פעולות הדבקה. הטכניקות שלנו כוללות שיטות כגון השפעה אקוסטית, זיהוי IR, בדיקות אולטרסאונד. יתרונות הדבקה הם: -הדבקה יכולה לספק חוזק מבני, תפקוד איטום ובידוד, דיכוי רעידות ורעש. -הדבקה יכולה לבטל מתחים מקומיים בממשק על ידי ביטול הצורך בחיבור באמצעות מחברים או ריתוך. -בדרך כלל אין צורך בחורים להדבקה, ולכן המראה החיצוני של הרכיבים אינו מושפע. -ניתן לחבר חלקים דקים ושבירים בהדבקה ללא נזק וללא עלייה משמעותית במשקל. -ניתן להשתמש בחיבור דבק לחיבור חלקים העשויים מחומרים שונים מאוד בגדלים שונים באופן משמעותי. -ניתן להשתמש בחיבור דבק על רכיבים רגישים לחום בבטחה עקב טמפרטורות נמוכות מעורבות. עם זאת, ישנם חסרונות מסוימים עבור הדבקה ולקוחותינו צריכים לשקול אותם לפני סיום עיצובי המפרקים שלהם: -טמפרטורות השירות נמוכות יחסית עבור רכיבי חיבור דבק -הדבקה דבק עשויה לדרוש זמני הדבקה וריפוי ארוכים. - יש צורך בהכנת פני השטח בהדבקה. -במיוחד עבור מבנים גדולים זה עשוי להיות קשה לבדוק חיבורים מודבקים באופן לא הרסני. -הדבקה עשויה להוות דאגות מהימנות בטווח הארוך עקב השפלה, קורוזיה במתח, פירוק... וכדומה. אחד המוצרים הבולטים שלנו הוא דבק מוליך חשמלי, שיכול להחליף הלחמות על בסיס עופרת. חומרי מילוי כגון כסף, אלומיניום, נחושת, זהב הופכים את המשחות הללו למוליכות. חומרי מילוי יכולים להיות בצורת פתיתים, חלקיקים או חלקיקים פולימריים המצופים בסרטים דקים של כסף או זהב. חומרי מילוי יכולים גם לשפר מוליכות תרמית מלבד חשמל. הבה נמשיך בתהליכי ההצטרפות האחרים שלנו המשמשים בייצור מוצרים. הידוק מכאני והרכבה: הידוק מכני מציע לנו קלות ייצור, קלות הרכבה ופירוק, קלות הובלה, קלות החלפת חלקים, תחזוקה ותיקון, קלות בתכנון של מוצרים ניידים ומתכווננים, עלות נמוכה יותר. עבור הידוק אנו משתמשים: מחברים עם הברגה: ברגים, ברגים ואומים הם דוגמאות לכך. בהתאם ליישום שלך, אנו יכולים לספק לך אגוזים ודסקיות נעילה שתוכננו במיוחד עבור שיכוך רעידות. מסמרות: מסמרות הן בין השיטות הנפוצות ביותר שלנו לתהליכי חיבור והרכבה מכניים קבועים. מסמרות מונחות בחורים וקצותיהן מעוותים על ידי התהפכות. אנו מבצעים הרכבה באמצעות ניטים בטמפרטורת החדר וכן בטמפרטורות גבוהות. תפירה / הידוק / הידוק: פעולות הרכבה אלו נמצאות בשימוש נרחב בייצור והן בעצם זהות לאלו המשמשות בניירות וקרטון. ניתן לחבר ולהרכיב חומרים מתכתיים וגם חומרים שאינם מתכתיים במהירות ללא צורך בקדיחה מראש של חורים. תפירה: טכניקת חיבור מהירה זולה בה אנו משתמשים בהרחבה בייצור מיכלים ופחיות מתכת. הוא מבוסס על קיפול של שתי פיסות חומר דקות יחד. אפילו תפרים אטומים ואטומים למים אפשריים, במיוחד אם התפירה מתבצעת במשותף עם שימוש בחומרי איטום ודבקים. כיווץ: כיווץ היא שיטת הצטרפות שבה איננו משתמשים במחברים. מחברים חשמליים או סיבים אופטיים מותקנים לפעמים באמצעות כיווץ. בייצור בנפח גבוה, כיווץ הוא טכניקה הכרחית לחיבור והרכבה מהירים של רכיבים שטוחים וצינוריים כאחד. מחברים נצמדים: התאמות הצמד הן גם טכניקת הצטרפות חסכונית בהרכבה ובייצור. הם מאפשרים הרכבה ופירוק מהירים של רכיבים ומתאימים למוצרים ביתיים, צעצועים, רהיטים בין היתר. התאמת כיווץ ולחיצה: טכניקת הרכבה מכנית נוספת, כלומר התאמת כיווץ מבוססת על העיקרון של התפשטות תרמית דיפרנציאלית והתכווצות של שני רכיבים, בעוד בהתאמת לחיצה רכיב אחד נאלץ על פני אחר וכתוצאה מכך חוזק חיבור טוב. אנו משתמשים בהתאמת כיווץ באופן נרחב בהרכבה ובייצור של רתמות כבלים, והרכבת גלגלי שיניים ומצלמות על פירים. צירוף חומרים לא מתכתיים: ניתן לחמם ולהמיס תרמופלסטיים בממשקים שיש לחבר אותם ועל ידי יישום חיבור דבק בלחץ ניתן לבצע היתוך. לחילופין ניתן להשתמש בחומרי מילוי תרמופלסטיים מאותו סוג לתהליך ההצטרפות. חיבור של כמה פולימרים כגון פוליאתילן עשוי להיות קשה עקב חמצון. במקרים כאלה, ניתן להשתמש בגז מגן אינרטי כמו חנקן נגד חמצון. ניתן להשתמש במקורות חום חיצוניים וגם פנימיים בחיבור דבק של פולימרים. דוגמאות למקורות חיצוניים שבהם אנו משתמשים בדרך כלל בחיבור דבק של תרמופלסטיים הם אוויר חם או גזים, קרינת IR, כלים מחוממים, לייזרים, גופי חימום חשמליים התנגדות. חלק ממקורות החום הפנימיים שלנו הם ריתוך קולי וריתוך חיכוך. ביישומי הרכבה וייצור מסוימים אנו משתמשים בדבקים להדבקת פולימרים. לחלק מהפולימרים כמו PTFE (טפלון) או PE (פוליאתילן) יש אנרגיות שטח נמוכות ולכן מורחים תחילה פריימר לפני השלמת תהליך הדבקת הדבק עם דבק מתאים. טכניקה פופולרית נוספת בהצטרפות היא "תהליך Clearweld" שבו טונר מוחל לראשונה על ממשקי הפולימר. לאחר מכן מכוון לייזר אל הממשק, אך הוא אינו מחמם את הפולימר, אלא מחמם את הטונר. זה מאפשר לחמם רק ממשקים מוגדרים היטב וכתוצאה מכך ריתוכים מקומיים. טכניקות הצטרפות אלטרנטיביות אחרות בהרכבה של תרמופלסטיות הן שימוש במחברים, ברגים עם הקשה עצמית, מחברים משולבים. טכניקה אקזוטית בפעולות ייצור והרכבה היא הטמעת חלקיקים זעירים בגודל מיקרון לתוך הפולימר ושימוש בשדה אלקטרומגנטי בתדר גבוה כדי לחמם ולהמיס אותו באופן אינדוקטיבי בממשקים שיש לחברו. חומרים טרמוסיסטים לעומת זאת, אינם מתרככים או נמסים עם עלייה בטמפרטורות. לכן, חיבור דבק של פלסטיק תרמו-סטומי מבוצע בדרך כלל באמצעות תוספות מושחלות או יצוקות אחרות, מחברים מכניים והדבקת ממס. לגבי פעולות חיבור והרכבה הכוללות זכוכית וקרמיקה במפעלי הייצור שלנו, להלן מספר הערות נפוצות: במקרים בהם יש לחבר קרמיקה או זכוכית עם חומרים קשים לחיבור, החומרים הקרמיים או הזכוכית מצופים לעתים קרובות ב- מתכת שמתחברת אליהם בקלות, ואז מתחברת לחומר הקשה לחיבור. כאשר לקרמיקה או לזכוכית יש ציפוי מתכת דק ניתן להלחים אותם בקלות רבה יותר למתכות. לפעמים קרמיקה מחוברת ומורכבת יחד במהלך תהליך העיצוב שלה בעודה חמה, רכה ודביקה. ניתן להלחים קרבידים בקלות רבה יותר למתכות אם יש להם כחומר המטריצה חומר מקשר מתכתי כגון קובלט או סגסוגת ניקל-מוליבדן. אנו מלחמים כלי חיתוך מקרביד למחזיקי כלי פלדה. משקפיים מתחברים היטב אחד לשני ומתכות כשהם חמים ורכים. מידע על המתקן שלנו לייצור אביזרי קרמיקה למתכת, איטום הרמטי, הזנת ואקום, ואקום גבוה ואולטרה גבוה ורכיבי בקרת נוזלים ניתן למצוא כאן:חוברת מפעל הלחמה CLICK Product Finder-Locator Service עמוד קודם
- Tanks and Containers, USA, AGS-TECH Inc.
AGS-TECH offers off-shelf and custom manufactured tanks and containers of various sizes. We supply wire mesh cage containers, stainless, aluminum and metal tanks and containers, IBC tanks, plastic and polymer containers, fiberglass tanks, collapsible tanks. טנקים ומכולות אנו מספקים מיכלים ומיכלים לאחסון כימיקלים, אבקות, נוזלים וגז העשויים מפולימרים אינרטיים, נירוסטה... וכו'. יש לנו מכולות מתקפלות, מתגלגלות, מכולות הניתנות לערמה, מכולות מתקפלות, מכולות עם פונקציונליות שימושית נוספת המציאת יישומים בתעשיות רבות כגון בנייה, מזון, תרופות, כימיקלים, פטרוכימיה... וכו'. ספר לנו על הבקשה שלך ואנו נמליץ לך על המיכל המתאים ביותר. מיכלי נירוסטה או חומר אחר בנפח גדול מיוצרים לפי הזמנה ובהתאם למפרט שלך. מכולות קטנות יותר זמינות בדרך כלל מהמדף וגם מיוצרות בהתאמה אישית אם הכמויות שלך מצדיקות. אם הכמויות משמעותיות, נוכל לפוצץ או לסובב מיכלי פלסטיק ומיכלים לפי המפרט שלך. להלן הסוגים העיקריים של הטנקים והמכולות שלנו: מיכלי כלוב רשת תיל יש לנו מגוון של מיכלי כלוב רשת תיל במלאי ויכולים גם לייצר אותם בהתאמה אישית לפי המפרט והצרכים שלך. מיכלי כלוב רשת התיל שלנו כוללים מוצרים כגון: משטחי כלוב הניתנים לערמה מיכלי גליל רשת תיל מתקפלים מיכלי רשת תיל מתקפלים כל מיכלי כלובי רשת התיל שלנו עשויים מחומרי נירוסטה או פלדה עדינה באיכות הגבוהה ביותר והגרסאות הלא אל חלד מצופות נגד קורוזיה וריקבון בדרך כלל תוך שימוש ב_cc781905-5cde-3194-bb58bzin-cfcfcfcfcfcdc1365bcdcfcfcdc781905-5cde-3194-5cde-3194-bbcdcfcfcdc, ציפוי אבקה 3194-bb3b-136bad5cf58d_hot dip or_cc781905-5cde-3194-bb3b-136bad5cf58d. צבע הגימור הוא בדרך כלל zinc: לבן או צהוב; או מצופה אבקה לפי בקשתך. מיכלי כלוב רשת התיל שלנו מורכבים תחת נהלי בקרת איכות קפדניים ונבדקים עבור השפעה מכנית, כושר נשיאת משקל, עמידות, חוזק ואמינות לטווח ארוך. מיכלי כלוב רשת התיל שלנו תואמים לתקני איכות בינלאומיים כמו גם לתקני תחבורה אמריקאיים ובינלאומיים. מיכלי כלוב רשת תיל משמשים בדרך כלל כקופסאות אחסון ופחים, עגלות אחסון, עגלות הובלה וכו'. בבחירת מיכל לכלוב רשת תיל, אנא קחו בחשבון פרמטרים חשובים כמו כושר העמסה, משקל המיכל עצמו, מידות הרשת, מידות חיצוניות ופנימיות, האם אתם זקוקים למכולה מתקפלת שטוחה לצורך משלוח ואיחסון חסכוניים במקום, וכן אנא שקול גם כמה ממכולה מסוימת ניתן לטעון במיכל משלוח של 20 רגל או 40 רגל. השורה התחתונה היא מיכלי כלוב רשת תיל הם חלופה ארוכת טווח, חסכונית וידידותית לסביבה לאריזה חד פעמית. להלן חוברות להורדה של מוצרי מיכל רשת התיל שלנו. - טופס עיצוב הצעת מחיר למיכל רשת חוט (אנא לחץ כדי להוריד, למלא ולשלוח לנו דוא"ל) מיכלים ומכולות נירוסטה ומתכת מיכלי הנירוסטה והמתכת האחרים שלנו הם אידיאליים לאחסון קרמים ונוזלים. הם אידיאליים לתעשיות קוסמטיקה, תרופות ומזון ומשקאות ואחרות. They comply with European, American and international guidelines. Our stainless and metal tanks are easy to clean._cc781905-5cde-3194-bb3b- 136bad5cf58d_למכולות האלה יש בסיס יציב וניתן לחטא אותן ללא אזור שמירה. אנחנו יכולים להתאים את מיכלי הנירוסטה והמתכת שלנו עם כל סוגי האביזרים, כגון שילוב של ראש כביסה. המיכלים שלנו ניתנים ללחץ. הם ניתנים להתאמה בקלות למפעל ולמקום העבודה שלך. לחצי העבודה של המיכלים שלנו משתנים, אז הקפד להשוות את המפרט לצרכים שלך. גם מיכלי האלומיניום והמיכלים שלנו פופולריים מאוד בתעשייה. חלק מהדגמים ניידים עם גלגלים, אחרים ניתנים לערמה. יש לנו מיכלי אחסון של אבקה, גרגירים וכדורים שהם UN מאושרים להובלה של מוצרים מסוכנים. אנחנו יציבים לפי הצרכים שלך במיכל וללא בד יציבים בהתאם לצרכיך וללא בד. ומפרטים. מידות פנימיות וחיצוניות, עובי הדופן של מיכלי הנירוסטה והמתכת שלנו יכולים להשתנות בהתאם לדרישות שלך. מיכלים ומיכלי נירוסטה ואלומיניום מיכלים ומכולות הניתנים לערמה טנקים ומכולות על גלגלים IBC & GRV Tanks מיכלי אחסון של אבקות, גרגירים וכדורים מיכלים ומכולות מעוצבים ומיוצרים בהתאמה אישית אנא לחץ על הקישורים למטה כדי להוריד את החוברות שלנו עבור מכלים ומכולות נירוסטה ומתכת: טנקים ומכולות IBC מיכלים ומיכלים מפלסטיק ופולימר AGS-TECH מספקת מיכלים ומיכלים ממגוון עצום של חומרים פלסטיים ופולימריים. אנו ממליצים לך לפנות אלינו עם בקשתך ולציין את הדברים הבאים כדי שנוכל לצטט לך את המוצר המתאים ביותר. - יישום - דרגת חומר - ממדים - סיים - דרישות אריזה - כמות לדוגמה, חומרים פלסטיים שאושרו על ידי ה-FDA בדרגת מזון חשובים למיכלים מסוימים המאחסנים משקאות, דגנים, מיץ פירות... וכו'. מצד שני, אם אתה צריך מיכלים ומיכלים מפלסטיק ופולימר לאחסון כימיקלים או תרופות, יש חשיבות עליונה לאינרציות של החומר הפלסטי כנגד התוכן. פנו אלינו לקבלת חוות דעתנו על חומרים. אתה יכול גם להזמין מיכלים ומיכלי מדף מפלסטיק ופולימר מהברושורים below שלנו. אנא לחץ על הקישורים למטה כדי להוריד את החוברות שלנו עבור מיכלים ומיכלים מפלסטיק ופולימר: טנקים ומכולות IBC מיכלים ומכולות פיברגלס אנו מציעים טנקים ומיכלים העשויים מפיברגלס materials. מיכלי הפיברגלס והמכולות שלנו meet US & internationally_cc781905-5cde-bb-3b5d_construction standard for tank מיכלי פיברגלס ומכולות מיוצרים עם למינציות יצוקות במגע התואמות ל-ASTM 4097 ולמינטים פצועים נימה התואמים ל-ASTM 3299. שרפים מיוחדים המשמשים במיכלי פיברגלס 781905-5bc1905-5bc190353c190343513513535135313519035135135135135135135135190135135135190135135135190135135135190000000000000000000000000000000000000000000001 לגבי ריכוז, טמפרטורה והתנהגות קורוזיבית של המוצר המאוחסן. FDA מאושרת כמו גם שרפים מעכבי אש זמינים עבור יישומים מיוחדים. אנו ממליצים לך ליצור איתנו קשר עם בקשתך ולציין את הדברים הבאים כדי שנוכל להציע לך את המיכל והמיכל הפיברגלס המתאימים ביותר. - יישום - ציפיות ומפרטי חומר - ממדים - סיים - דרישות אריזה - נדרשת כמות נשמח לתת לך את דעתנו. אתה יכול גם להזמין מדף פיברגלס טנקים ומכולות מהברושורים below שלנו. אם אף אחד ממיכלי הפיברגלס והמיכלים בתיק המדף שלנו לא מספק אותך, אנא הודע לנו ונוכל לשקול ייצור מותאם אישית בהתאם לצרכים שלך. טנקים ומכולות מתקפלים מיכלי מים ומיכלים מתקפלים הם הבחירה הטובה ביותר שלך לאחסן נוזלים ביישומים שבהם חביות פלסטיק קטנות או לא פרקטיות ומכלים אחרים. כמו כן כאשר אתה צריך כמויות גדולות של מים או נוזל במהירות מבלי לבנות מיכל בטון או מתכת, המיכלים והמיכלים המתקפלים שלנו הם אידיאליים. כפי שהשם מרמז, מיכלים ומיכלים מתקפלים, הם מתקפלים, כלומר ניתן לכווץ אותם לאחר השימוש, לגלגל ולהפוך אותם לקומפקטיים מאוד וקטני נפח, קלים לאחסון ולהובלה כשהם ריקים. הם ניתנים לשימוש חוזר. אנו יכולים לספק לך כל גודל ודגם ובהתאם למפרט שלך. מאפיינים כלליים של הטנקים והמיכלים המתקפלים שלנו: - צבע: כחול, כתום, אפור, ירוק כהה, שחור וכו'. - חומר: PVC - קיבולת: בדרך כלל בין 200 ל-30000 ליטר - קל משקל, תפעול קל. - גודל אריזה מינימלי, קל להובלה ואחסון. - אין זיהום של water - חוזק גבוה של בד מצופה, adhesion עד 60 פאונד/אינץ'. - חוזק גבוה של התפרים מובטח עם המסה בתדירות גבוהה ואטומה באותו פוליאוריטן כמו גוף המיכל, כך שלמכלים יש יכולת מצוינת למנוע_cc781905-5cde-3b154-31905-5cde-31905-5cde-31905-31905-31905-5cde-31905-31954-31954-31954-31954-3194-5cde-31956 בטוח למים. יישומים עבור מיכלים ומיכלים מתקפלים: · אכסון זמני · איסוף מי גשמים · אחסון מים למגורים וציבוריים · יישומים לאחסון מים בהגנה · טיפול במים · אחסון והקלה לשעת חירום · השקיה · חברות בנייה בוחרות במיכלי מים PVC כדי לגשר על עומס מרבי · כיבוי אש אנו מקבלים גם הזמנות OEM. ניתן לקבל תיוג, אריזה והדפסת לוגו בהתאמה אישית. עמוד קודם
- Metal Stamping, Sheet Metal Fabrication, Zinc Plated Metal Stamped
Metal Stamping & Sheet Metal Fabrication, Zinc Plated Metal Stamped Parts, Wire and Spring Forming הטבעת מתכת וייצור יריעות מתכת חלקים מוטבעים בציפוי אבץ הטבעות מדויקות ויצירת תיל הטבעות מתכת מדויקות בציפוי אבץ חלקים מוטבעים מדויקים הטבעת מתכת מדויקת של AGS-TECH Inc ייצור מתכת על ידי AGS-TECH Inc. Sheet Metal Rapid Prototyping על ידי AGS-TECH Inc. הטבעה של מכונות כביסה בנפח גבוה פיתוח וייצור בית מסנן שמן מתכת מתכת ייצור רכיבי פח לפילטר שמן והרכבה מלאה ייצור והרכבה בהתאמה אישית של מוצרי פח ייצור אטם ראש על ידי AGS-TECH Inc. ייצור סט אטמים ב-AGS-TECH Inc. ייצור מארזי פח - AGS-TECH Inc חותמות בודדות ופרוגרסיביות פשוטות מבית AGS-TECH Inc. הטבעות ממתכת וסגסוגות מתכת - AGS-TECH Inc חלקי פח לפני סיום הפעולה גיבוש פח - מארז חשמלי - AGS-TECH Inc ייצור להבי חיתוך מצופים טיטניום עבור תעשיית המזון ייצור להבי גלישה לתעשיית אריזות מזון עמוד קודם