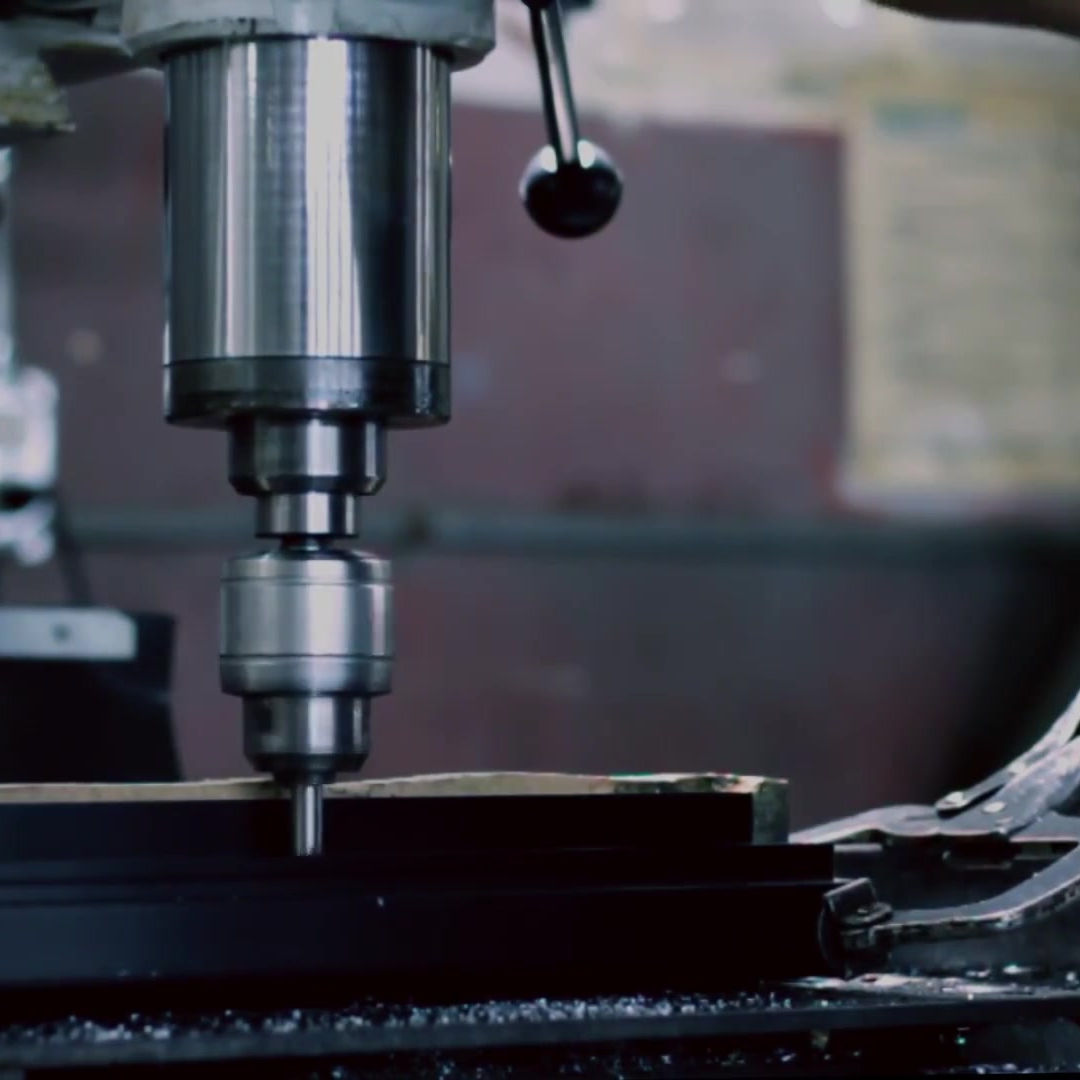
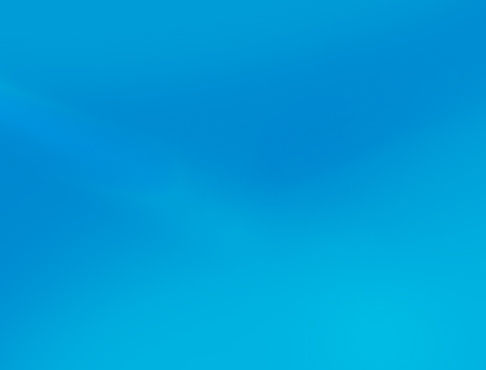
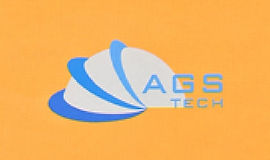
Globalni proizvođač po narudžbi, integrator, konsolidator, vanjski partner za široku paletu proizvoda i usluga.
Mi smo vaš sveobuhvatni izvor za proizvodnju, izradu, inženjering, konsolidaciju, integraciju, outsourcing proizvoda i usluga proizvedenih po narudžbi i proizvoda i usluga izvan police.
Odaberite svoj jezik
-
Proizvodnja po narudžbi
-
Domaća i globalna ugovorna proizvodnja
-
Outsourcing proizvodnje
-
Domaća i globalna nabava
-
Konsolidacija
-
Inženjerska integracija
-
Inženjerske usluge
Search Results
164 rezultata pronađena s praznim pretraživanjem
- Transmission Components, Belts, Chains, Cable Drives, Pulleys,AGS-TECH
Transmission Components, Belts, Chains and Cable Drives, Conventional & Grooved or Serrated, Positive Drive, Pulleys Pojasevi, lanci i pogonski sklop kabela AGS-TECH Inc. nudi vam komponente za prijenos snage uključujući remene i lance te pogonski sklop kabela. S godinama usavršavanja, naši gumeni, kožni i drugi remenski pogoni postali su lakši i kompaktniji, sposobni nositi veća opterećenja po nižoj cijeni. Slično tome, naši lančani prijenosi prošli su kroz mnogo razvoja tijekom vremena i našim kupcima nude nekoliko prednosti. Neke prednosti korištenja lančanih pogona su njihove relativno neograničene udaljenosti središta osovine, kompaktnost, jednostavnost montaže, elastičnost u napetosti bez klizanja ili puzanja, sposobnost rada u okruženjima s visokim temperaturama. Naši kabelski pogoni također nude prednosti kao što je jednostavnost u nekim primjenama u odnosu na druge vrste komponenti prijenosa. Dostupni su i remenski, lančani i kabelski pogoni, kao i prilagođeno izrađene i sastavljene verzije. Možemo proizvesti ove komponente prijenosa do prave veličine za vašu primjenu i od najprikladnijih materijala. REMENI I REMENSKI POGONI: - Konvencionalni ravni remeni: Ovo su obični ravni remeni bez zubaca, utora ili nazubljenih dijelova. Pogoni s plosnatim remenom nude fleksibilnost, dobru apsorpciju udarca, učinkovit prijenos snage pri velikim brzinama, otpornost na abraziju, nisku cijenu. Pojasevi se mogu spajati ili spajati kako bi se napravili veći pojasevi. Druge prednosti konvencionalnih ravnih remena su tanki, nisu podložni velikim centrifugalnim opterećenjima (što ih čini dobrim za rad pri velikim brzinama s malim remenicama). S druge strane, oni nameću velika nosiva opterećenja jer ravni remeni zahtijevaju veliku napetost. Drugi nedostaci prijenosa s ravnim remenom mogu biti proklizavanje, bučan rad i relativno niža učinkovitost pri niskim i umjerenim brzinama rada. Imamo dvije vrste konvencionalnih remena: ojačane i neojačane. Ojačani pojasevi u svojoj strukturi imaju vlačni element. Konvencionalni ravni remeni dostupni su kao koža, gumirana tkanina ili uže, nearmirana guma ili plastika, tkanina, ojačana koža. Kožni remeni nude dug vijek trajanja, fleksibilnost, izvrstan koeficijent trenja, lako popravljanje. Međutim, kožni remeni su relativno skupi, potrebno ih je dotjerivati i čistiti, a ovisno o atmosferi mogu se skupiti ili rastegnuti. Pojasevi od gumirane tkanine ili užadi otporni su na vlagu, kiseline i lužine. Pojasevi od gumirane tkanine sastoje se od slojeva pamuka ili sintetičke patke impregnirane gumom i najekonomičniji su. Gumirani pojasevi od užadi sastoje se od niza slojeva užadi impregniranih gumom. Gumirani pojasevi nude visoku vlačnu čvrstoću i skromnu veličinu i masu. Neojačani gumeni ili plastični remeni prikladni su za lagane pogone s malim brzinama. Neojačani gumeni i plastični remeni mogu se rastegnuti na svoje mjesto preko svojih remenica. Plastični neojačani remeni mogu prenijeti veću snagu u usporedbi s gumenim remenima. Ojačani kožni pojasevi sastoje se od plastičnog zateznog elementa u sendviču između gornjeg i donjeg sloja kože. Konačno, naši pojasevi od tkanine mogu se sastojati od jednog komada pamuka ili patke presavijenog i prošivenog redovima uzdužnih šavova. Pojasevi od tkanine mogu ravnomjerno pratiti i raditi velikom brzinom. - Užlijebljeni ili nazubljeni remeni (kao što su klinasti remeni): Ovo su osnovni ravni remeni modificirani da pruže prednosti druge vrste prijenosnog proizvoda. To su plosnati pojasevi s uzdužno rebrastom donjom stranom. Poly-V remeni su uzdužno užljebljeni ili nazubljeni ravni remeni s rastezljivim presjekom i nizom susjednih utora u obliku slova V za potrebe praćenja i kompresije. Kapacitet snage ovisi o širini remena. Klinasti remen je radni konj industrije i dostupan je u nizu standardiziranih veličina i vrsta za prijenos gotovo svake snage opterećenja. Pogoni s klinastim remenom dobro rade između 1500 i 6000 ft/min, međutim uski klinasti remeni radit će do 10 000 ft/min. Pogoni s klinastim remenom nude dug životni vijek od 3 do 5 godina i omogućuju velike omjere brzine, lako se postavljaju i uklanjaju, nude tihi rad, nisko održavanje, dobru apsorpciju udara između pogonskog remena i pogonskih vratila. Nedostatak klinastih remena je njihovo izvjesno klizanje i puzanje i stoga možda nisu najbolje rješenje tamo gdje su potrebne sinkrone brzine. Imamo industrijske, automobilske i poljoprivredne trake. Dostupne su standardne duljine remena na zalihama kao i prilagođene duljine remena. Svi standardni presjeci klinastih remena dostupni su na skladištu. Postoje tablice u kojima možete izračunati nepoznate parametre kao što su duljina remena, presjek remena (širina i debljina) pod uvjetom da znate neke parametre vašeg sustava kao što su promjeri pogonskih i gonjenih remenica, središnja udaljenost između remenica i brzine rotacije remenica. Možete koristiti takve tablice ili nas zamoliti da odaberemo pravi klinasti remen za vas. - Pogonski remeni (zupčasti remen): Ovi remeni su također ravnog tipa s nizom ravnomjerno raspoređenih zuba na unutarnjem obodu. Pozitivni pogon ili zupčasti remen kombiniraju prednosti plosnatog remena s karakteristikama pozitivnog prianjanja lanaca i zupčanika. Pozitivni pogonski remeni ne otkrivaju proklizavanje ili varijacije brzine. Moguć je širok raspon omjera brzine. Opterećenja ležajeva su niska jer mogu raditi pri maloj napetosti. Međutim, oni su osjetljiviji na neusklađenost remenica. - Koloturnice, remenice, glavčine za remenje: Različite vrste remenica koriste se s ravnim, rebrastim (nazubljenim) i pozitivnim pogonskim remenima. Sve ih proizvodimo. Većina naših remenica s ravnim remenom izrađena je lijevanjem željeza, no dostupne su i izvedbe od čelika u različitim kombinacijama naplatka i glavčine. Naše remenice s ravnim remenima mogu imati čvrste, žbičaste ili podijeljene glavčine ili ih možemo proizvesti po vašoj želji. Rebrasti i pozitivni pogonski remeni dostupni su u različitim veličinama i širinama. Najmanje jedna remenica u pogonima s razvodnim remenom mora imati prirubnicu kako bi remen ostao na pogonu. Za sustave dugog središnjeg pogona, preporuča se da obje remenice imaju prirubnicu. Snopovi su užljebljeni kotači remenica i općenito se proizvode lijevanjem željeza, oblikovanjem čelika ili plastičnim kalupljenjem. Oblikovanje čelika prikladan je postupak za proizvodnju automobilskih i poljoprivrednih snopa. Proizvodimo snopove s pravilnim i dubokim utorima. Korunice s dubokim utorima dobro su prikladne kada klinasti remen ulazi u kolut pod kutom, kao što je slučaj kod pogona s četvrtinom okretaja. Duboki utori također su prikladni za pogone s okomitim vratilima i primjene gdje vibracije remena mogu biti problem. Naše pomoćne remenice su žljebovi ili ravne remenice koje ne služe za prijenos mehaničke snage. Prazne remenice koriste se uglavnom za zatezanje remena. - Pogoni s jednim i više remena: Pogoni s jednim remenom imaju jedan utor, dok pogoni s više remena imaju više utora. Klikom na odgovarajući tekst u boji ispod možete preuzeti naše kataloge: - Remeni za prijenos snage (uključujući V-remene, zupčaste remene, remene s neobrađenim rubovima, omotane remene i specijalne remene) - Pokretne trake - V-remenice - Razvodne remenice LANCI & LANČANI POGONI: Naši lanci za prijenos snage imaju neke prednosti kao što su relativno neograničeni razmaci središta osovine, jednostavno sastavljanje, kompaktnost, elastičnost pod napetostima bez klizanja ili puzanja, sposobnost rada na visokim temperaturama. Ovo su glavne vrste naših lanaca: - Odvojivi lanci: Naši odvojivi lanci izrađuju se u različitim veličinama, nagibima i krajnjoj čvrstoći i općenito od temperanog željeza ili čelika. Savitljivi lanci izrađuju se u rasponu veličina od 0,902 (23 mm) do 4,063 inča (103 mm) koraka i krajnje čvrstoće od 700 do 17 000 lb/kvadratnom inču. S druge strane, naši odvojivi čelični lanci izrađuju se u veličinama od 0,904 inča (23 mm) do oko 3,00 inča (76 mm) u koraku, s krajnjom čvrstoćom od 760 do 5000 lb/kvadratnom inču._cc781905-5cde-3194-bb3b- 136bad5cf58d_ - Pintle lanci: Ovi se lanci koriste za teža opterećenja i nešto veće brzine do oko 450 stopa/min (2,2 m/sek). Lanci s iglama izrađeni su od pojedinačnih lijevanih karika s punim, okruglim završetkom cijevi s pomaknutim bočnim prečkama. Ove karike lanca međusobno su spojene čeličnim klinovima. Ovi lanci imaju raspon koraka od oko 1,00 inča (25 mm) do 6,00 inča (150 mm) i krajnje čvrstoće između 3600 do 30 000 lb/kvadratnom inču. - Lanci s pomaknutom stranom: popularni su u pogonskim lancima građevinskih strojeva. Ovi lanci rade pri brzinama do 1000 ft/min i prenose opterećenja do oko 250 KS. Općenito, svaka karika ima dvije pomaknute bočne šipke, jednu čahuru, jedan valjak, jednu osovinicu, rascjepku. - Valjkasti lanci: Dostupni su u razmacima od 0,25 (6 mm) do 3,00 (75 mm) inča. Krajnja čvrstoća lanaca s valjcima s jednom širinom kreće se između 925 i 130 000 lb/kvadratnom inču. Dostupne su verzije valjkastih lanaca s više širina i prenose veću snagu pri većim brzinama. Lanci s valjcima višestruke širine također nude glatkiju radnju uz smanjenu buku. Valjkasti lanci sastavljeni su od valjkastih karika i karika. Rascjepke se koriste u rastavljivim valjkastim lancima. Dizajn lančanih pogona valjka zahtijeva stručno znanje. Dok se remenski prijenosi temelje na linearnim brzinama, lančani se temelje na brzini rotacije manjeg lančanika, koji je u većini instalacija pogonski član. Osim konjskih snaga i brzine vrtnje, dizajn lančanih pogona temelji se na mnogim drugim čimbenicima. - Lanci s dvostrukim usponom: U osnovi isti kao i lanci s valjcima osim što je korak dvaput duži. - Lanci s obrnutim zubima (tihi): Lanci velike brzine koji se uglavnom koriste za primarne pogone, pogone izvoda snage. Lančani pogoni s obrnutim zupcima mogu prenijeti snagu do 1200 KS i sastoje se od niza zupčastih karika, naizmjenično sastavljenih s klinovima ili kombinacijom spojnih komponenti. Središnji lanac za vođenje ima vodeće karike za uključivanje utora u lančaniku, a bočni lanac za vođenje ima vodilice za uključivanje strana lančanika. - Zrnasti ili klizni lanci: Ovi se lanci koriste za spore pogone i također u ručnim operacijama. Klikom na odgovarajući tekst u boji ispod možete preuzeti naše kataloge: - Pogonski lanci - Transportni lanci - Transportni lanci velikog koraka - Valjkasti lanci od nehrđajućeg čelika - Lanci za podizanje - Lanci za motocikle - Lanci za poljoprivredne strojeve - Lančanici: Naši standardni lančanici u skladu su s ANSI standardima. Pločasti lančanici su ravni lančanici bez glavčine. Naši mali i srednji lančanici glavčine izrađeni su od šipke ili otkovaka ili izrađeni zavarivanjem glavčine šipke na vruće valjanu ploču. AGS-TECH Inc. može isporučiti lančanike izrađene od odljevaka od sivog željeza, lijevanog čelika i zavarenih konstrukcija glavčina, sinteriranog metala u prahu, lijevane ili strojno obrađene plastike. Za neometan rad pri velikim brzinama bitan je pravilan odabir veličine lančanika. Ograničenje prostora je naravno faktor koji ne možemo zanemariti pri odabiru lančanika. Preporuča se da omjer pogonskih i pogonskih lančanika ne bude veći od 6:1, a omotač lanca na pokretaču je 120 stupnjeva. Središnje udaljenosti između manjeg i većeg lančanika, duljina lanca i napetost lanca također se moraju odabrati u skladu s nekim preporučenim inženjerskim proračunima i smjernicama, a ne nasumično. Preuzmite naše kataloge klikom na tekst u boji ispod: - Zupčanici i pločasti kotači - Čahure prijenosa - Lančana spojka - lančane brave KABELSKI POGONI: Oni u nekim slučajevima imaju svoje prednosti u odnosu na remenske i lančane pogone. Kabelski pogoni mogu ostvariti istu funkciju kao remeni, a mogu biti i jednostavniji i ekonomičniji za implementaciju u nekim primjenama. Na primjer, nova serija Synchromesh Cable Drives dizajnirana je za pozitivnu vuču koja zamjenjuje konvencionalne užadi, jednostavne sajle i zupčaste pogone, posebno u tijesnim prostorima. Novi kabelski pogon dizajniran je za pružanje visoke preciznosti pozicioniranja u elektroničkoj opremi kao što su strojevi za kopiranje, crtači, pisaći strojevi, pisači,….. itd. Ključna značajka novog kabelskog pogona je njegova sposobnost da se koristi u 3D zmijolikim konfiguracijama koje omogućuju izuzetno minijaturnih dizajna. Sinhromatski kabeli mogu se koristiti s manjom napetosti u usporedbi s užadima čime se smanjuje potrošnja energije. Kontaktirajte AGS-TECH za pitanja i mišljenje o remenima, lančanim i kabelskim pogonima. CLICK Product Finder-Locator Service PRETHODNA STRANICA
- Composites, Composite Materials Manufacturing, Fiber Reinforced
Composites, Composite Materials Manufacturing, Particle and Fiber Reinforced, Cermets, Ceramic & Metal Composite, Glass Fiber Reinforced Polymer, Lay-Up Process Kompoziti i proizvodnja kompozitnih materijala Jednostavno definirani, KOMPOZITI ili KOMPOZITNI MATERIJALI su materijali koji se sastoje od dva ili više materijala s različitim fizičkim ili kemijskim svojstvima, ali kada se kombiniraju postaju materijal koji se razlikuje od sastavnih materijala. Moramo istaknuti da sastavni materijali ostaju odvojeni i različiti u strukturi. Cilj u proizvodnji kompozitnog materijala je dobiti proizvod koji je bolji od svojih sastojaka i kombinira željena svojstva svakog sastojka. Kao primjer; snaga, mala težina ili niža cijena mogu biti motivacija iza dizajniranja i proizvodnje kompozita. Vrsta kompozita koje nudimo su kompoziti ojačani česticama, kompoziti ojačani vlaknima uključujući kompozite keramičke matrice/polimerne matrice/metalne matrice/ugljik-ugljik/hibridne kompozite, strukturne i laminirane kompozite i kompozite sendvič strukture te nanokompozite. Tehnike izrade koje primjenjujemo u proizvodnji kompozitnih materijala su: pultruzija, procesi proizvodnje preprega, napredno postavljanje vlakana, namotavanje filamenta, prilagođeno postavljanje vlakana, postupak postavljanja raspršivanjem staklenih vlakana, tufting, lanksidni postupak, z-pinning. Mnogi kompozitni materijali sastoje se od dvije faze, matrice, koja je kontinuirana i okružuje drugu fazu; i disperzne faze koja je okružena matriksom. Preporučujemo da kliknete ovdje zaPREUZMITE naše shematske ilustracije kompozita i proizvodnje kompozitnih materijala od strane AGS-TECH Inc. To će vam pomoći da bolje razumijete informacije koje vam pružamo u nastavku. • KOMPOZITI OJAČANI ČESTICAMA: Ova se kategorija sastoji od dvije vrste: kompoziti s velikim česticama i kompoziti ojačani disperzijom. U prvom tipu, interakcije čestica-matrica ne mogu se tretirati na atomskoj ili molekularnoj razini. Umjesto toga vrijedi mehanika kontinuuma. S druge strane, u kompozitima ojačanim disperzijom čestice su općenito mnogo manje u rasponima desetaka nanometara. Primjer kompozita velikih čestica su polimeri kojima su dodana punila. Punila poboljšavaju svojstva materijala i mogu zamijeniti dio polimernog volumena s ekonomičnijim materijalom. Volumni udjeli dviju faza utječu na ponašanje kompozita. Kompoziti velikih čestica koriste se s metalima, polimerima i keramikom. KERMETI su primjeri keramičkih/metalnih kompozita. Naš najčešći kermet je cementni karbid. Sastoji se od vatrostalne karbidne keramike kao što su čestice volfram karbida u matrici metala kao što je kobalt ili nikal. Ovi karbidni kompoziti naširoko se koriste kao alati za rezanje kaljenog čelika. Čestice tvrdog karbida odgovorne su za djelovanje rezanja, a njihova žilavost je poboljšana duktilnom metalnom matricom. Tako dobivamo prednosti oba materijala u jednom kompozitu. Još jedan uobičajeni primjer kompozita s velikim česticama koji koristimo su čestice čađe pomiješane s vulkaniziranom gumom kako bi se dobio kompozit visoke vlačne čvrstoće, žilavosti, otpornosti na trganje i abraziju. Primjer kompozita ojačanog disperzijom su metali i metalne legure ojačani i očvrsnuti jednolikom disperzijom finih čestica vrlo tvrdog i inertnog materijala. Kada se vrlo male ljuskice aluminijevog oksida dodaju metalnoj matrici aluminija, dobivamo sinterirani aluminijski prah koji ima povećanu čvrstoću na visokim temperaturama. • KOMPOZITI OJAČANI VLAKNIMA: Ova kategorija kompozita je zapravo najvažnija. Cilj koji treba postići je visoka čvrstoća i krutost po jedinici težine. Sastav vlakana, duljina, orijentacija i koncentracija u ovim kompozitima ključni su za određivanje svojstava i korisnosti ovih materijala. Tri su skupine vlakana koje koristimo: brkovi, vlakna i žice. BRISOVI su vrlo tanki i dugi monokristali. Među najjačim su materijalima. Neki primjeri materijala za brkove su grafit, silicijev nitrid, aluminijev oksid. VLAKNA su s druge strane uglavnom polimeri ili keramika i nalaze se u polikristalnom ili amorfnom stanju. Treća skupina su fine ŽICE koje imaju relativno velike promjere i često se sastoje od čelika ili volframa. Primjer kompozita ojačanog žicom su automobilske gume koje sadrže čeličnu žicu unutar gume. Ovisno o materijalu matrice, imamo sljedeće kompozite: POLIMER-MATRIČNI KOMPOZITI: Izrađuju se od polimerne smole i vlakana kao sastojka za pojačanje. Podskupina ovih zvanih polimernih kompozita ojačanih staklenim vlaknima (GFRP) sadrži kontinuirana ili diskontinuirana staklena vlakna unutar polimerne matrice. Staklo nudi visoku čvrstoću, ekonomično je, lako se proizvodi u vlakna i kemijski je inertno. Nedostaci su njihova ograničena krutost i krutost, radne temperature su samo do 200 – 300 Celzijusa. Stakloplastika je prikladna za karoserije automobila i transportnu opremu, karoserije brodskih vozila, kontejnere za skladištenje. Nisu prikladni za zrakoplovstvo niti za izradu mostova zbog ograničene krutosti. Druga podskupina naziva se polimerni kompozit ojačan ugljičnim vlaknima (CFRP). Ovdje je ugljik naš vlaknasti materijal u polimernoj matrici. Ugljik je poznat po svom visokom specifičnom modulu i čvrstoći i sposobnosti da ih održava na visokim temperaturama. Karbonska vlakna nam mogu ponuditi standardne, srednje, visoke i ultravisoke vlačne module. Nadalje, ugljična vlakna nude različite fizičke i mehaničke karakteristike i stoga su prikladna za različite inženjerske primjene po mjeri. CFRP kompoziti mogu se smatrati za proizvodnju sportske i rekreacijske opreme, tlačnih posuda i konstrukcijskih komponenti za zrakoplovstvo. Ipak, druga podskupina, polimerni kompoziti ojačani aramidnim vlaknima također su materijali visoke čvrstoće i modula. Njihov omjer snage i težine je izuzetno visok. Aramidna vlakna poznata su i pod trgovačkim nazivima KEVLAR i NOMEX. Pod napetosti imaju bolje performanse od drugih materijala od polimernih vlakana, ali su slabi u kompresiji. Aramidna vlakna su čvrsta, otporna na udarce, puzanje i zamor, stabilna na visokim temperaturama, kemijski inertna osim protiv jakih kiselina i baza. Aramidna vlakna naširoko se koriste u sportskoj opremi, pancirnim prslucima, gumama, užadi, omotačima optičkih kabela. Postoje i drugi materijali za ojačanje vlaknima, ali se koriste u manjoj mjeri. To su uglavnom bor, silicijev karbid, aluminijev oksid. S druge strane, materijal polimerne matrice također je kritičan. Određuje maksimalnu radnu temperaturu kompozita jer polimer općenito ima nižu temperaturu taljenja i razgradnje. Poliesteri i vinil esteri naširoko se koriste kao polimerne matrice. Također se koriste smole koje imaju izvrsnu otpornost na vlagu i mehanička svojstva. Na primjer, poliimidna smola može se koristiti do oko 230 Celzijevih stupnjeva. KOMPOZITI METALNE MATRICE: U ovim materijalima koristimo duktilnu metalnu matricu, a radne temperature općenito su više nego njihove sastavne komponente. U usporedbi s kompozitima polimerne matrice, oni mogu imati više radne temperature, biti nezapaljivi i mogu imati bolju otpornost na razgradnju u organskim tekućinama. Međutim, oni su skuplji. Materijali za pojačanje kao što su vlakna, čestice, kontinuirana i diskontinuirana vlakna; i matrični materijali kao što su bakar, aluminij, magnezij, titan, superlegure se obično koriste. Primjeri primjene su komponente motora izrađene od matrice aluminijske legure ojačane aluminijevim oksidom i ugljičnim vlaknima. KOMPOZITI KERAMIKA-MATRICA: Keramički materijali poznati su po svojoj izvanredno dobroj pouzdanosti pri visokim temperaturama. Međutim, oni su vrlo krti i imaju niske vrijednosti za žilavost loma. Ugrađivanjem čestica, vlakana ili viskira jedne keramike u matricu druge možemo postići kompozite s većom otpornošću na lom. Ovi ugrađeni materijali u osnovi inhibiraju širenje pukotina unutar matrice nekim mehanizmima kao što je skretanje vrhova pukotina ili stvaranje mostova preko lica pukotina. Kao primjer, aluminijev oksid koji je ojačan SiC brkovima koristi se kao uložak alata za obradu tvrdih metalnih legura. Oni mogu pokazati bolje performanse u usporedbi s cementnim karbidima. KARBON-KARBON KOMPOZITI: I ojačanje kao i matrica su ugljik. Imaju visoke vlačne module i čvrstoće na visokim temperaturama iznad 2000 Celzijusa, otpornost na puzanje, visoku otpornost na lom, niske koeficijente toplinske ekspanzije, visoku toplinsku vodljivost. Ova svojstva ih čine idealnim za primjene koje zahtijevaju otpornost na toplinski udar. Međutim, slabost ugljik-ugljik kompozita je njihova osjetljivost na oksidaciju na visokim temperaturama. Tipični primjeri upotrebe su kalupi za vruće prešanje, proizvodnja naprednih komponenti turbinskih motora. HIBRIDNI KOMPOZITI: Dvije ili više različitih vrsta vlakana miješaju se u jednu matricu. Tako se može oblikovati novi materijal kombinacijom svojstava. Primjer je kada su i karbonska i staklena vlakna ugrađena u polimernu smolu. Karbonska vlakna daju krutost i snagu male gustoće, ali su skupa. Staklo je s druge strane jeftino, ali mu nedostaje krutost karbonskih vlakana. Staklo-ugljik hibridni kompozit je jači i čvršći i može se proizvoditi po nižoj cijeni. OBRADA KOMPOZITA OJAČANIH VLAKNIMA: Za kontinuiranu plastiku ojačanu vlaknima s ravnomjerno raspoređenim vlaknima usmjerenim u istom smjeru koristimo sljedeće tehnike. PULTRUZIJA: Izrađuju se šipke, grede i cijevi kontinuiranih duljina i konstantnih presjeka. Kontinuirana vlaknasta rovinga impregnirana su termoreaktivnom smolom i provučena kroz čeličnu matricu kako bi se prethodno oblikovala u željeni oblik. Zatim prolaze kroz precizno strojno izrađenu matricu za stvrdnjavanje kako bi postigli svoj konačni oblik. Budući da se matrica za stvrdnjavanje zagrijava, ona stvrdnjava matricu smole. Izvlakači izvlače materijal kroz matrice. Koristeći umetnute šuplje jezgre, možemo dobiti cijevi i šuplje geometrije. Metoda pultruzije je automatizirana i nudi nam visoke stope proizvodnje. Moguća je izrada bilo koje duljine proizvoda. PROIZVODNI PROCES PREPREGA: Prepreg je ojačanje od kontinuiranih vlakana prethodno impregnirano djelomično stvrdnutom polimernom smolom. Široko se koristi za strukturne primjene. Materijal dolazi u obliku trake i isporučuje se kao traka. Proizvođač ga izravno oblikuje i potpuno stvrdnjava bez potrebe za dodavanjem smole. Budući da se preprezi podvrgavaju reakcijama stvrdnjavanja na sobnoj temperaturi, skladište se na 0 C ili nižim temperaturama. Nakon upotrebe preostale trake pohranjuju se na niskim temperaturama. Koriste se termoplastične i termoreaktivne smole, a česta su i ojačavajuća vlakna od ugljika, aramida i stakla. Da bi se koristili prepregovi, najprije se uklanja noseći papir za podlogu, a zatim se izvodi izrada polaganjem prepreg trake na površinu obrađenu alatom (postupak postavljanja). Može se postaviti nekoliko slojeva kako bi se postigle željene debljine. Česta praksa je izmjenjivanje orijentacije vlakana kako bi se proizveo križni ili kutni laminat. Na kraju se primjenjuju toplina i pritisak za stvrdnjavanje. I ručna obrada kao i automatizirani procesi koriste se za rezanje preprega i postavljanje. NAMOTAVANJE FILAMENTA: Kontinuirana ojačavajuća vlakna točno su postavljena u unaprijed određeni uzorak kako bi slijedila šuplji i obično kružni oblik. Vlakna prvo prolaze kroz smolnu kupku, a zatim se pomoću automatiziranog sustava namotavaju na trn. Nakon nekoliko ponavljanja namotavanja postižu se željene debljine i stvrdnjavanje se izvodi na sobnoj temperaturi ili u pećnici. Sada je trn uklonjen i proizvod je izvađen iz kalupa. Namatanje filamenta može ponuditi vrlo visoke omjere čvrstoće i težine namotavanjem vlakana u obodnim, spiralnim i polarnim uzorcima. Cijevi, spremnici, kućišta proizvode se ovom tehnikom. • STRUKTURALNI KOMPOZITI: Općenito se sastoje od homogenih i kompozitnih materijala. Stoga su njihova svojstva određena sastavnim materijalima i geometrijskim dizajnom njegovih elemenata. Evo glavnih vrsta: LAMINARNI KOMPOZITI: Ovi strukturni materijali izrađeni su od dvodimenzionalnih listova ili ploča s preferiranim smjerovima visoke čvrstoće. Slojevi se slažu i cementiraju zajedno. Izmjenom smjerova visoke čvrstoće u dvije okomite osi dobivamo kompozit koji ima veliku čvrstoću u oba smjera u dvodimenzionalnoj ravnini. Podešavanjem kutova slojeva može se proizvesti kompozit čvrstoće u željenim smjerovima. Moderne skije se proizvode na ovaj način. SENDVIČ PANELI: Ovi strukturni kompoziti su lagani, ali ipak imaju veliku krutost i snagu. Sendvič paneli se sastoje od dvije vanjske ploče izrađene od krutog i jakog materijala poput aluminijskih legura, plastike ojačane vlaknima ili čelika i jezgre između vanjskih ploča. Jezgra mora biti lagana i većinu vremena mora imati nizak modul elastičnosti. Popularni osnovni materijali su krute polimerne pjene, drvo i saće. Sendvič paneli naširoko se koriste u građevinskoj industriji kao krovni materijal, podni ili zidni materijal, a također i u zrakoplovnoj industriji. • NANOKOMPOZITI: Ovi novi materijali sastoje se od čestica nano veličine umetnutih u matricu. Korištenjem nanokompozita možemo proizvesti gumene materijale koji su vrlo dobre barijere za prodor zraka, a istovremeno zadržavaju nepromijenjena svojstva gume. CLICK Product Finder-Locator Service PRETHODNA STRANICA
- Joining & Assembly & Fastening Processes, Welding, Brazing, Soldering
Joining & Assembly & Fastening Processes, Welding, Brazing, Soldering, Sintering, Adhesive Bonding, Press Fitting, Wave and Reflow Solder Process, Torch Furnace Postupci spajanja, montaže i pričvršćivanja Vaše proizvedene dijelove spajamo, sastavljamo i pričvršćujemo te ih pretvaramo u gotove ili poluproizvode ZAVARIVANJEM, TEMLJENJEM, LEMLJENJEM, SINTERANJEM, LIJEPLJENJEM, PRIČVRŠĆIVANJEM, PREŠANJEM. Neki od naših najpopularnijih postupaka zavarivanja su lučno, plinsko zavarivanje, otpor, projekcija, šav, zavarivanje, udarno zavarivanje, čvrsto stanje, elektronski snop, laser, termičko zavarivanje, indukcijsko zavarivanje. Naši popularni postupci lemljenja su lemljenje plamenikom, indukcijom, peći i lemljenje potapanjem. Naše metode lemljenja su željezo, vruća ploča, pećnica, indukcijsko lemljenje, lemljenje umakanjem, valovito lemljenje, reflow i ultrazvučno lemljenje. Za ljepljenje često koristimo termoplaste i termofiksatore, epokside, fenole, poliuretane, ljepljive legure kao i neke druge kemikalije i trake. Naposljetku, naši postupci pričvršćivanja sastoje se od zabijanja čavlima, zavrtanja, matica i vijaka, zakivanja, stezanja, zabadanja, šivanja i klamanja te presovanja. • ZAVARIVANJE: Zavarivanje uključuje spajanje materijala taljenjem radnih komada i uvođenjem dodatnih materijala, koji također spajaju rastaljenu zavarenu posudu. Kada se područje ohladi, dobivamo čvrst spoj. U nekim slučajevima primjenjuje se pritisak. Za razliku od zavarivanja, postupci tvrdog lemljenja uključuju samo taljenje materijala s nižim talištem između izradaka, a izratki se ne tale. Preporučujemo da kliknete ovdje zaPREUZMITE naše shematske ilustracije procesa zavarivanja tvrtke AGS-TECH Inc. To će vam pomoći da bolje razumijete informacije koje vam pružamo u nastavku. Kod LUČNOG ZAVARIVANJA koristimo izvor napajanja i elektrodu za stvaranje električnog luka koji topi metale. Mjesto zavarivanja zaštićeno je zaštitnim plinom ili parom ili drugim materijalom. Ovaj postupak je popularan za zavarivanje automobilskih dijelova i čeličnih konstrukcija. U shelded metal arc welding (SMAW) ili također poznatom kao štapno zavarivanje, štap elektrode se približava osnovnom materijalu i između njih se stvara električni luk. Šipka elektrode se topi i djeluje kao materijal za punjenje. Elektroda također sadrži fluks koji djeluje kao sloj troske i ispušta pare koje djeluju kao zaštitni plin. Oni štite područje zavara od kontaminacije okoliša. Ne koriste se druga punila. Nedostaci ovog procesa su njegova sporost, potreba za čestim mijenjanjem elektroda, potreba za uklanjanjem zaostale troske koja potječe od topitelja. Brojni metali kao što su željezo, čelik, nikal, aluminij, bakar… itd. Može se zavarivati. Njegove prednosti su jeftini alati i jednostavnost korištenja. Plinsko elektrolučno zavarivanje (GMAW) također poznato kao metalno-inertni plin (MIG), imamo kontinuirano punjenje potrošne elektrode za punjenje žice i inertnog ili djelomično inertnog plina koji teče oko žice protiv onečišćenja područja zavara iz okoline. Mogu se zavarivati čelik, aluminij i drugi obojeni metali. Prednosti MIG su velike brzine zavarivanja i dobra kvaliteta. Nedostaci su njegova komplicirana oprema i izazovi s kojima se suočavamo u vjetrovitim vanjskim okruženjima jer moramo održavati stabilnim zaštitni plin oko područja zavarivanja. Varijanta GMAW je elektrolučno zavarivanje punjenom jezgrom (FCAW) koje se sastoji od fine metalne cijevi ispunjene materijalima za pražnjenje. Ponekad je fluks unutar cijevi dovoljan za zaštitu od kontaminacije okoliša. Zavarivanje pod praškom (SAW) je uvelike automatizirani proces, uključuje kontinuirano dodavanje žice i električni luk koji se udara ispod sloja topitelja. Stope proizvodnje i kvaliteta su visoki, troska od zavarivanja se lako odvaja, a imamo radno okruženje bez dima. Nedostatak je što se može koristiti samo za zavarivanje dijelova u određenim položajima. Kod plinskolučnog zavarivanja volframom (GTAW) ili zavarivanja volframom i inertnim plinom (TIG) koristimo volframovu elektrodu zajedno s posebnim punilom i inertnim ili gotovo inertnim plinovima. Kao što znamo volfram ima visoko talište i vrlo je pogodan metal za vrlo visoke temperature. Volfram u TIG-u se ne troši za razliku od drugih gore objašnjenih metoda. Spora, ali kvalitetna tehnika zavarivanja koja ima prednost u odnosu na druge tehnike zavarivanja tankih materijala. Prikladno za mnoge metale. Zavarivanje plazma lukom je slično, ali koristi plazma plin za stvaranje luka. Luk u plazma zavarivanju relativno je koncentriraniji u usporedbi s GTAW i može se koristiti za širi raspon debljina metala pri mnogo većim brzinama. GTAW i plazma zavarivanje mogu se primijeniti na više-manje iste materijale. KISIKOSNO GORIVO / KISIKOSNO GORIVO ZAVARIVANJE koje se naziva i oksiacetilensko zavarivanje, kisikovo zavarivanje, plinsko zavarivanje provodi se korištenjem plinskih goriva i kisika za zavarivanje. Budući da se ne koristi električna energija, prenosiv je i može se koristiti tamo gdje nema struje. Pomoću plamenika za zavarivanje zagrijavamo komade i materijal za punjenje kako bismo proizveli zajednički bazen rastaljenog metala. Mogu se koristiti različita goriva kao što su acetilen, benzin, vodik, propan, butan… itd. Kod zavarivanja s kisikom koristimo dvije posude, jednu za gorivo, a drugu za kisik. Kisik oksidira gorivo (sagorijeva ga). OTPORNSKO ZAVARIVANJE: Ova vrsta zavarivanja koristi Joule zagrijavanje i toplina se stvara na mjestu gdje se električna struja primjenjuje određeno vrijeme. Visoke struje prolaze kroz metal. Na ovom mjestu nastaju bazeni rastaljenog metala. Metode otpornog zavarivanja popularne su zbog svoje učinkovitosti i malog potencijala onečišćenja. Međutim, nedostaci su relativno veliki troškovi opreme i inherentno ograničenje na relativno tanke radne dijelove. TOČKASTO ZAVARIVANJE jedna je od glavnih vrsta otpornog zavarivanja. Ovdje spajamo dva ili više listova ili radnih komada koji se preklapaju pomoću dviju bakrenih elektroda za spajanje listova zajedno i propuštanje jake struje kroz njih. Materijal između bakrenih elektroda se zagrijava i na tom se mjestu stvara rastaljena lokva. Struja se tada zaustavlja i vrhovi bakrenih elektroda hlade mjesto zavara jer se elektrode hlade vodom. Primjena prave količine topline na pravi materijal i debljinu ključna je za ovu tehniku, jer ako se primijeni pogrešno, spoj će biti slab. Točkasto zavarivanje ima prednosti jer ne uzrokuje značajne deformacije izradaka, energetsku učinkovitost, jednostavnost automatizacije i izvanredne proizvodne stope te ne zahtijeva nikakva punila. Nedostatak je taj što, budući da se zavarivanje odvija na mjestima, a ne da se formira kontinuirani šav, ukupna čvrstoća može biti relativno niža u usporedbi s drugim metodama zavarivanja. S druge strane, ZAVARIVANJE ŠAVOVA stvara zavare na dodirnim površinama sličnih materijala. Šav može biti sučeoni ili preklapajući. Zavarivanje šava počinje na jednom kraju i postupno prelazi na drugi. Ova metoda također koristi dvije elektrode od bakra za primjenu pritiska i struje na područje zavara. Elektrode u obliku diska rotiraju uz stalni kontakt duž linije šava i stvaraju kontinuirani zavar. I ovdje se elektrode hlade vodom. Varovi su vrlo čvrsti i pouzdani. Ostale metode su tehnike projiciranja, bljeskalice i tehnike zavarivanja uz zavarivanje. ZAVARIVANJE U ČVRSTOM STANJU malo je drugačije od prethodno objašnjenih metoda. Koalescencija se odvija na temperaturama nižim od temperature taljenja spojenih metala i bez upotrebe metalnog punila. Tlak se može koristiti u nekim procesima. Različite metode su KOEKSTRUZIJSKO ZAVARIVANJE gdje se različiti metali ekstrudiraju kroz istu matricu, HLADNO ZAVARIVANJE PRI TLAKU gdje spajamo meke legure ispod njihovih tališta, DIFUZIJSKO ZAVARIVANJE tehnika bez vidljivih linija zavara, EKSPLOZIJSKO ZAVARIVANJE za spajanje različitih materijala, npr. legura otpornih na koroziju sa konstrukcijskim čelika, ELEKTROMAGNETNO IMPULSNO ZAVARIVANJE gdje ubrzavamo cijevi i limove elektromagnetskim silama, KOVAČKO ZAVARIVANJE koje se sastoji od zagrijavanja metala na visoke temperature i njihovog spajanja čekićem, ZAVARIVANJE FRIKCIJOM gdje se izvodi zavarivanje trenjem uz dovoljno zavarivanje, ZAVARIVANJE TRANJEM S MJEŠANJEM koje uključuje rotirajući ne- potrošni alat koji prolazi kroz spojnu liniju, TOPLO TLAČNO ZAVARIVANJE gdje metale prešamo zajedno na povišenim temperaturama ispod temperature taljenja u vakuumu ili inertnim plinovima, VRUĆE IZOSTATIČKO TLAČNO ZAVARIVANJE postupak gdje primjenjujemo pritisak pomoću inertnih plinova unutar posude, ROLL WELDING gdje spajamo različite materijale gurajući ih između dva rotirajuća kotača, ULTRAZVUČNO ZAVARIVANJE gdje se tanki metalni ili plastični listovi zavaruju korištenjem visokofrekventne vibracijske energije. Naši drugi postupci zavarivanja su ZAVARIVANJE ELEKTRONSKIM ZRAKOM s dubokim prodiranjem i brzom obradom, ali budući da je skupa metoda, smatramo je za posebne slučajeve, ZAVARIVANJE ELEKTROTROSKOM metoda prikladna samo za teške debele ploče i radne komade čelika, INDUKCIJSKO ZAVARIVANJE gdje koristimo elektromagnetsku indukciju i zagrijavaju naše električno vodljive ili feromagnetske izratke, ZAVARIVANJE LASERSKIM ZRAKOM također s dubokim prodiranjem i brzom obradom, ali skupom metodom, LASERSKO HIBRIDNO ZAVARIVANJE koje kombinira LBW s GMAW u istoj glavi za zavarivanje i može premostiti razmake od 2 mm između ploča, UDARNO ZAVARIVANJE koje uključuje električno pražnjenje nakon čega slijedi kovanje materijala primijenjenim pritiskom, TERMITSKO ZAVARIVANJE koje uključuje egzotermnu reakciju između praha aluminija i željeznog oksida, ELEKTROPLINSKO ZAVARIVANJE s potrošnim elektrodama i koristi se samo s čelikom u okomitom položaju, i na kraju LUČNO ZAVARIVANJE STUPOVA za spajanje klina na bazu materijala toplinom i pritiskom. Preporučujemo da kliknete ovdje zaPREUZMITE naše shematske ilustracije postupaka lemljenja, lemljenja i lijepljenja od strane AGS-TECH Inc. To će vam pomoći da bolje razumijete informacije koje vam pružamo u nastavku. • LEMLJENJE: Spajamo dva ili više metala zagrijavanjem dodatnih metala između njih iznad njihovih tališta i korištenjem kapilarnog djelovanja za širenje. Proces je sličan lemljenju, ali su temperature potrebne za topljenje punila više kod lemljenja. Kao i kod zavarivanja, prašak štiti dodatni materijal od atmosferske kontaminacije. Nakon hlađenja obradaci se spajaju. Proces uključuje sljedeće ključne korake: dobro pristajanje i razmak, pravilno čišćenje osnovnih materijala, pravilno pričvršćivanje, pravilan izbor fluksa i atmosfere, zagrijavanje sklopa i konačno čišćenje lemljenog sklopa. Neki od naših postupaka lemljenja su LEMLJENJE BAKELOM, popularna metoda koja se izvodi ručno ili na automatizirani način. Pogodan je za narudžbe male količine proizvodnje i specijalizirane slučajeve. Toplina se primjenjuje plinskim plamenom u blizini spoja koji se lemi. LEMLJENJE U PEĆI zahtijeva manje vještine operatera i poluautomatski je postupak pogodan za industrijsku masovnu proizvodnju. I kontrola temperature i kontrola atmosfere u peći su prednosti ove tehnike, jer nam prva omogućuje kontrolirane toplinske cikluse i eliminira lokalno zagrijavanje kao što je slučaj kod lemljenja plamenikom, a druga štiti dio od oksidacije. Korištenjem jigginga sposobni smo svesti troškove proizvodnje na minimum. Nedostaci su velika potrošnja energije, troškovi opreme i zahtjevniji dizajn. VAKUUMSKO LEMLJENJE odvija se u vakuumskoj peći. Održava se jednolikost temperature i dobivamo vrlo čiste spojeve bez fluksa s vrlo malim zaostalim naprezanjima. Toplinska obrada može se odvijati tijekom lemljenja pod vakuumom, zbog niskih zaostalih naprezanja prisutnih tijekom sporih ciklusa zagrijavanja i hlađenja. Glavni nedostatak je njegova visoka cijena jer je stvaranje vakuumskog okruženja skup proces. Još jedna tehnika DIP BRAZING spaja čvrste dijelove gdje se smjesa za lemljenje nanosi na spojene površine. Nakon toga se fiksirani dijelovi uranjaju u kupku rastaljene soli kao što je natrijev klorid (kuhinjska sol) koji djeluje kao medij za prijenos topline i fluks. Zrak je isključen i stoga ne dolazi do stvaranja oksida. U INDUKCIJSKOM LEMLJENJU spajamo materijale dodatnim metalom koji ima nižu točku taljenja od osnovnih materijala. Izmjenična struja iz indukcijske zavojnice stvara elektromagnetsko polje koje inducira indukcijsko zagrijavanje većinom željeznih magnetskih materijala. Metoda osigurava selektivno zagrijavanje, dobre spojeve s punilima koja teku samo u željenim područjima, malu oksidaciju jer nema plamena i hlađenje je brzo, brzo zagrijavanje, konzistentnost i prikladnost za proizvodnju velikih količina. Kako bismo ubrzali naše procese i osigurali dosljednost, često koristimo predforme. Informacije o našem postrojenju za lemljenje koje proizvodi spojeve od keramike u metal, hermetičko brtvljenje, vakuumske prolaze, komponente za kontrolu visokog i ultravisokog vakuuma i tekućine možete pronaći ovdje: Brošura tvornice lemljenja • LEMLJENJE : Kod lemljenja nemamo taljenje radnih komada, već dodatni metal s nižim talištem od spojnih dijelova koji teče u spoj. Dodatni metal kod lemljenja se topi na nižoj temperaturi nego kod lemljenja. Koristimo legure bez olova za lemljenje i imamo RoHS usklađenost, a za različite primjene i zahtjeve imamo različite i prikladne legure kao što je legura srebra. Lemljenje nam nudi spojeve koji su nepropusni za plin i tekućinu. U MEKOM LEMLJENJU, naš dodatni metal ima točku taljenja ispod 400 Celzijevih stupnjeva, dok su u LEMLJENJU SREBROM i LEMLJENJU potrebne više temperature. Meko lemljenje koristi niže temperature, ali ne rezultira čvrstim spojevima za zahtjevne primjene na povišenim temperaturama. Lemljenje srebrom, s druge strane, zahtijeva visoke temperature koje osigurava plamenik i daje nam čvrste spojeve pogodne za primjenu na visokim temperaturama. Za lemljenje su potrebne najviše temperature i obično se koristi plamenik. Budući da su lemljeni spojevi vrlo čvrsti, dobri su kandidati za popravak teških željeznih predmeta. U našim proizvodnim linijama koristimo i ručno lemljenje kao i automatizirane linije za lemljenje. INDUKCIJSKO LEMLJENJE koristi izmjeničnu struju visoke frekvencije u bakrenoj zavojnici kako bi se olakšalo indukcijsko zagrijavanje. Struje se induciraju u zalemljenom dijelu i kao rezultat se stvara toplina na visokom otporu joint. Ova toplina topi dodatni metal. Također se koristi fluks. Indukcijsko lemljenje dobra je metoda za lemljenje cilindara i cijevi u kontinuiranom procesu omotavanjem zavojnica oko njih. Lemljenje nekih materijala kao što su grafit i keramika je teže jer zahtijeva oblaganje obradaka odgovarajućim metalom prije lemljenja. Ovo olakšava međufazno spajanje. Lemimo takve materijale posebno za primjene u hermetičkom pakiranju. Proizvodimo naše tiskane pločice (PCB) u velikim količinama uglavnom koristeći VALNO LEMLJENJE. Samo za male količine prototipova koristimo ručno lemljenje pomoću lemilice. Koristimo valovito lemljenje i za sklopove tiskanih pločica s otvorom i za površinsku montažu (PCBA). Privremeno ljepilo drži komponente pričvršćene na tiskanu ploču, a sklop se postavlja na pokretnu traku i kreće se kroz opremu koja sadrži rastaljeni lem. Prvo se PCB topi, a zatim ulazi u zonu predgrijavanja. Rastaljeni lem nalazi se u posudi i na površini ima uzorak stojnih valova. Kada se PCB pomiče preko ovih valova, ti valovi dodiruju dno PCB-a i lijepe se na podloge za lemljenje. Lem ostaje samo na iglama i jastučićima, a ne na samoj tiskanoj ploči. Valovi u rastaljenom lemu moraju biti dobro kontrolirani kako ne bi došlo do prskanja i kako vrhovi valova ne bi dodirivali i kontaminirali neželjena područja ploča. U REFLOW LEMLJENJU koristimo ljepljivu pastu za lemljenje za privremeno pričvršćivanje elektroničkih komponenti na ploče. Zatim se ploče stavljaju kroz reflow peć s kontrolom temperature. Ovdje se lem topi i trajno povezuje komponente. Ovu tehniku koristimo i za komponente za površinsku montažu kao i za komponente s provrtom. Odgovarajuća kontrola temperature i podešavanje temperature pećnice ključni su kako bi se izbjeglo uništavanje elektroničkih komponenti na ploči njihovim pregrijavanjem iznad njihovih maksimalnih temperaturnih ograničenja. U procesu reflow lemljenja zapravo imamo nekoliko regija ili faza od kojih svaka ima poseban toplinski profil, kao što su korak predgrijavanja, toplinski korak namakanja, reflow i koraci hlađenja. Ovi različiti koraci ključni su za lemljenje sklopova tiskanih ploča (PCBA) bez oštećenja. ULTRAZVUČNO LEMLJENJE još je jedna često korištena tehnika s jedinstvenim mogućnostima - može se koristiti za lemljenje stakla, keramike i nemetalnih materijala. Na primjer, fotonaponske ploče koje nisu metalne trebaju elektrode koje se mogu pričvrstiti ovom tehnikom. Kod ultrazvučnog lemljenja koristimo grijani vrh za lemljenje koji također emitira ultrazvučne vibracije. Ove vibracije stvaraju kavitacijske mjehuriće na granici supstrata i rastaljenog lemljenog materijala. Implozivna energija kavitacije modificira površinu oksida i uklanja prljavštinu i okside. Tijekom tog vremena također se formira sloj legure. Lem na površini za spajanje sadrži kisik i omogućuje stvaranje jake zajedničke veze između stakla i lema. DIP LEMLJENJE se može smatrati jednostavnijom verzijom valnog lemljenja prikladnom samo za malu proizvodnju. Prvi fluks za čišćenje primjenjuje se kao i u drugim procesima. PCB-ovi s montiranim komponentama uranjaju se ručno ili na poluautomatski način u spremnik koji sadrži rastaljeni lem. Otopljeni lem lijepi se za izložena metalna područja nezaštićena maskom za lemljenje na ploči. Oprema je jednostavna i jeftina. • LIJEPLJENJE : Ovo je još jedna popularna tehnika koju često koristimo, a uključuje lijepljenje površina pomoću ljepila, epoksida, plastičnih sredstava ili drugih kemikalija. Lijepljenje se postiže ili isparavanjem otapala, stvrdnjavanjem toplinom, stvrdnjavanjem UV svjetlom, stvrdnjavanjem pod pritiskom ili čekanjem određenog vremena. U našim proizvodnim linijama koriste se razna ljepila visokih performansi. S pravilno projektiranim postupcima nanošenja i stvrdnjavanja, lijepljenje može rezultirati jakim i pouzdanim vezama s vrlo malim stresom. Ljepljivi spojevi mogu biti dobra zaštita od čimbenika okoline kao što su vlaga, onečišćenja, korozivna sredstva, vibracije… itd. Prednosti lijepljenja ljepilom su: mogu se primijeniti na materijale koje bi inače bilo teško lemiti, zavarivati ili lemiti. Također može biti poželjniji za materijale osjetljive na toplinu koji bi se oštetili zavarivanjem ili drugim procesima visoke temperature. Druge prednosti ljepila su da se mogu nanositi na površine nepravilnog oblika i povećati težinu sklopa za vrlo vrlo male količine u usporedbi s drugim metodama. Također su promjene dimenzija u dijelovima vrlo minimalne. Neka ljepila imaju svojstva usklađivanja indeksa i mogu se koristiti između optičkih komponenti bez značajnog smanjenja svjetlosti ili jačine optičkog signala. S druge strane, nedostaci su dulja vremena otvrdnjavanja koja mogu usporiti proizvodne linije, zahtjevi za pričvršćivanje, zahtjevi za pripremu površine i poteškoće pri rastavljanju kada je potrebna ponovna obrada. Većina naših operacija lijepljenja ljepilom uključuje sljedeće korake: -Površinska obrada: Uobičajeni su posebni postupci čišćenja kao što su čišćenje deioniziranom vodom, čišćenje alkoholom, plazma ili korona čišćenje. Nakon čišćenja možemo nanijeti pospješivače prianjanja na površine kako bismo osigurali najbolje moguće spojeve. - Učvršćivanje dijelova: za nanošenje ljepila kao i za stvrdnjavanje dizajniramo i koristimo prilagođene učvršćivače. -Primjena ljepila: Ponekad koristimo ručne, a ponekad ovisno o slučaju automatizirane sustave kao što su robotika, servo motori, linearni aktuatori za isporuku ljepila na pravo mjesto i koristimo dozatore za isporuku u pravoj količini i količini. - Stvrdnjavanje: Ovisno o ljepilu, možemo koristiti jednostavno sušenje i stvrdnjavanje, kao i stvrdnjavanje pod UV svjetlima koja djeluju kao katalizator ili toplinsko stvrdnjavanje u pećnici ili korištenjem otpornih grijaćih elemenata montiranih na šablone i učvršćivače. Preporučujemo da kliknete ovdje zaPREUZMITE naše shematske ilustracije procesa pričvršćivanja tvrtke AGS-TECH Inc. To će vam pomoći da bolje razumijete informacije koje vam pružamo u nastavku. • PROCESI PRIČVRŠĆIVANJA: Naši postupci mehaničkog spajanja spadaju u dvije kategorije: SPOJNICI i INTEGRALNI SPOJEVI. Primjeri pričvrsnih elemenata koje koristimo su vijci, klinovi, matice, vijci, zakovice. Primjeri integralnih spojeva koje koristimo su uskočne i stezne spojeve, šavovi, stezanja. Korištenjem raznih metoda pričvršćivanja osiguravamo da su naši mehanički spojevi čvrsti i pouzdani za dugogodišnju upotrebu. VIJCI i VIJACI neki su od najčešće korištenih spojnih elemenata za držanje predmeta zajedno i pozicioniranje. Naši vijci i vijci zadovoljavaju ASME standarde. Primjenjuju se različite vrste vijaka i vijaka, uključujući šesterokutne vijke i šesterokutne vijke, vijke i vijke, dvostruke vijke, zatične vijke, očne vijke, zrcalne vijke, vijke za lim, vijke za fino podešavanje, samobušeće i samonarezne vijke , vijak za podešavanje, vijci s ugrađenim podloškama,…i više. Imamo različite tipove glava vijaka kao što su upušteni, kupolasti, okrugli, s prirubnicom i razne vrste vijaka kao što su prorez, križni, kvadratni, šesterokutni. RIVET s druge strane je trajni mehanički pričvršćivač koji se sastoji od glatke cilindrične osovine i glave s jedne strane. Nakon umetanja, drugi kraj zakovice se deformira i promjer mu se proširi tako da ostane na mjestu. Drugim riječima, prije ugradnje zakovica ima jednu glavu, a nakon ugradnje dvije. Ugrađujemo različite vrste zakovica ovisno o primjeni, čvrstoći, pristupačnosti i cijeni kao što su zakovice s punom/okruglom glavom, strukturalne, polu-cijevaste, slijepe, oscar, pogonske, ujednačene, frikcijske zakovice, samoprobijajuće. Zakivanje se može preferirati u slučajevima kada treba izbjeći toplinsku deformaciju i promjenu svojstava materijala uslijed topline zavarivanja. Zakivanje također nudi malu težinu i posebno dobru čvrstoću i otpornost na sile smicanja. Međutim, protiv vlačnih opterećenja vijci, matice i vijci mogu biti prikladniji. U postupku CLINCHING koristimo posebne izbijače i matrice za stvaranje mehaničkog spoja između limova koji se spajaju. Probijač gura slojeve metalnog lima u šupljinu matrice i rezultira stvaranjem trajnog spoja. U klinču nije potrebno grijanje i hlađenje i radi se o hladnom procesu rada. To je ekonomičan postupak koji u nekim slučajevima može zamijeniti točkasto zavarivanje. U PININGU koristimo klinove koji su strojni elementi koji služe za učvršćivanje položaja strojnih dijelova jedan u odnosu na drugi. Glavne vrste su klinovi, rascjepka, opružni klin, klinovi, i rascjepni klin. U STAPLING-u koristimo pištolje za klamanje i spajalice koje su dvokraki spojni elementi koji se koriste za spajanje ili vezanje materijala. Klamerica ima sljedeće prednosti: Ekonomično, jednostavno i brzo za korištenje, kruna spajalica može se koristiti za premošćivanje materijala spojenih zajedno, Kruna spajalice može olakšati premošćivanje komada poput kabela i njegovo pričvršćivanje na površinu bez probijanja ili štetno, relativno lako uklanjanje. PRESS FITTING se izvodi guranjem dijelova zajedno, a trenje između njih pričvršćuje dijelove. Dijelovi pritisnuti koji se sastoje od prevelike osovine i premale rupe općenito se sastavljaju na jedan od dva načina: ili primjenom sile ili iskorištavanjem prednosti toplinskog širenja ili skupljanja dijelova. Kada se prešani fiting uspostavlja primjenom sile, koristimo ili hidrauličku prešu ili prešu na ručni pogon. S druge strane, kada se prešani spoj uspostavi toplinskim širenjem, zagrijavamo dijelove koji omotaju i sastavljamo ih na svoje mjesto dok su vrući. Kada se ohlade skupljaju se i vraćaju u svoje normalne dimenzije. To rezultira dobrim pristajanjem za tisak. To alternativno nazivamo SHRINK FITTING. Drugi način da se to učini je hlađenje omotanih dijelova prije sastavljanja i zatim njihovo umetanje u njihove spojene dijelove. Kada se sklop zagrije, oni se šire i postižemo čvrsto prianjanje. Ova druga metoda može biti poželjnija u slučajevima kada zagrijavanje predstavlja rizik promjene svojstava materijala. Hlađenje je u tim slučajevima sigurnije. Pneumatske i hidrauličke komponente i sklopovi • Ventili, hidrauličke i pneumatske komponente kao što su O-prsten, podloška, brtve, brtva, prsten, podloška. Budući da ventili i pneumatske komponente dolaze u velikom izboru, ne možemo sve nabrojati ovdje. Ovisno o fizičkom i kemijskom okruženju vaše primjene, imamo posebne proizvode za vas. Navedite nam primjenu, vrstu komponente, specifikacije, uvjete okoline kao što su tlak, temperatura, tekućine ili plinovi koji će biti u kontaktu s vašim ventilima i pneumatskim komponentama; a mi ćemo odabrati najprikladniji proizvod za vas ili ga proizvesti posebno za vašu primjenu. CLICK Product Finder-Locator Service PRETHODNA STRANICA
- Machine Elements Manufacturing, Gears, Gear Drives, Bearings, Keys, Splines
Machine Elements Manufacturing, Gears, Gear Drives, Bearings, Keys, Splines, Pins, Shafts, Seals, Fasteners, Clutch, Cams, Followers, Belts, Couplings, Shafts Proizvodnja elemenata strojeva Čitaj više Pojasevi, lanci i pogonski sklop kabela Čitaj više Zupčanici i pogonski sklop zupčanika Čitaj više Proizvodnja spojnica i ležajeva Čitaj više Proizvodnja ključeva, klinova i klinova Čitaj više Bregovi, pratioci i veze i proizvodnja zapornih kotača Čitaj više Proizvodnja osovina Čitaj više Proizvodnja mehaničkih brtvi Čitaj više Sklop kvačila i kočnice Čitaj više Proizvodnja spojnih elemenata Čitaj više Sastavljanje jednostavnih strojeva ELEMENTI STROJA su elementarne komponente stroja. Ovi elementi se sastoje od tri osnovne vrste: 1.) Strukturalne komponente uključujući elemente okvira, ležajeve, osovine, klinove, pričvršćivače, brtve i maziva. 2.) Mehanizmi koji kontroliraju kretanje na razne načine kao što su zupčanici, remenski ili lančani prijenosi, poluge, bregasti i prateći sustavi, kočnice i kvačila. 3.) Upravljačke komponente poput gumba, prekidača, indikatora, senzora, pokretača i računalnih kontrolera. Većina strojnih elemenata koje vam nudimo standardizirana je na uobičajene veličine, ali strojni elementi izrađeni po narudžbi također su dostupni za vaše specijalizirane primjene. Prilagodba strojnih elemenata može se izvršiti na postojećim nacrtima koji se nalaze u našim katalozima za preuzimanje ili na potpuno novim nacrtima. Izrada prototipa i proizvodnja strojnih elemenata može se nastaviti nakon što obje strane odobre dizajn. Ako je potrebno dizajnirati i proizvesti nove elemente stroja, naši kupci nam ili e-poštom pošalju svoje vlastite nacrte i mi ih pregledamo radi odobrenja, ili nas zatraže da dizajniramo elemente stroja za njihovu primjenu. U potonjem slučaju koristimo sve podatke naših kupaca i dizajniramo elemente stroja te šaljemo finalizirane nacrte našim klijentima na odobrenje. Nakon odobrenja izrađujemo prve artikle, a zatim izrađujemo elemente stroja prema konačnom projektu. U bilo kojoj fazi ovog posla, u slučaju da se određeni element stroja ne pokaže zadovoljavajuće na terenu (što je rijetkost), pregledavamo cijeli projekt i po potrebi zajedno s našim klijentima radimo izmjene. Naša je standardna praksa da s našim klijentima potpišemo ugovore o tajnosti podataka (NDA) za dizajn strojnih elemenata ili bilo kojeg drugog proizvoda kad god je potrebno ili potrebno. Nakon što su elementi stroja za određenog kupca posebno dizajnirani i proizvedeni, mi mu dodjeljujemo šifru proizvoda i samo ih proizvodimo i prodajemo našem kupcu koji je vlasnik proizvoda. Reproduciramo elemente strojeva pomoću razvijenih alata, kalupa i postupaka onoliko puta koliko je potrebno i kad god ih naš kupac ponovno naruči. Drugim riječima, nakon što je prilagođeni strojni element dizajniran i proizveden za vas, intelektualno vlasništvo kao i svi alati i kalupi rezervirani su i skladišteni na neodređeno vrijeme za vas, a proizvodi se reproduciraju kako želite. Našim klijentima također nudimo inženjerske usluge kreativnim kombiniranjem strojnih elemenata u komponentu ili sklop koji služi aplikaciji i ispunjava ili premašuje očekivanja naših kupaca. Pogoni koji proizvode naše strojne elemente kvalificirani su prema ISO9001, QS9000 ili TS16949. Osim toga, većina naših proizvoda ima oznaku CE ili UL i zadovoljava međunarodno relevantne standarde kao što su ISO, SAE, ASME, DIN. Kliknite na podizbornike kako biste dobili detaljne informacije o elementima našeg stroja, uključujući: - Remeni, lanci i pogoni sajli - Zupčanici i zupčanički pogoni - Spojnice i ležajevi - Ključevi, klinovi i igle - Bregovi i veze - Osovine - Mehaničke brtve - Industrijska spojka i kočnica - Spojni elementi - Jednostavni strojevi Pripremili smo referentnu brošuru za naše kupce, dizajnere i programere novih proizvoda uključujući strojne elemente. Možete se upoznati s nekim često korištenim izrazima u dizajnu strojnih komponenti: Preuzmite brošuru za zajedničke pojmove strojarstva koje koriste dizajneri i inženjeri Naši elementi strojeva nalaze primjenu u raznim područjima kao što su industrijski strojevi, sustavi automatizacije, ispitna i mjeriteljska oprema, transportna oprema, građevinski strojevi i praktički svugdje čega se možete sjetiti. AGS-TECH razvija i proizvodi elemente strojeva od različitih materijala ovisno o namjeni. Materijali koji se koriste za elemente strojeva mogu varirati od lijevane plastike koja se koristi za igračke do kaljenog i posebno obloženog čelika za industrijske strojeve. Naši dizajneri koriste najsuvremeniji profesionalni softver i alate za dizajn za razvoj strojnih elemenata, uzimajući u obzir detalje kao što su kutovi u zubima zupčanika, uključena naprezanja, stope trošenja… itd. Molimo pregledajte naše podizbornike i preuzmite naše brošure i kataloge proizvoda kako biste vidjeli možete li pronaći gotove elemente strojeva za svoju primjenu. Ako ne možete pronaći odgovarajuću kombinaciju za svoju primjenu, javite nam i mi ćemo raditi s vama na razvoju i proizvodnji strojnih elemenata koji će ispuniti vaše potrebe. Ako ste većinom zainteresirani za naše inženjerske i istraživačke i razvojne sposobnosti umjesto za proizvodne mogućnosti, pozivamo vas da posjetite našu web stranicu http://www.ags-engineering.com gdje možete pronaći detaljnije informacije o našem dizajnu, razvoju proizvoda, razvoju procesa, uslugama inženjerskog savjetovanja i više CLICK Product Finder-Locator Service PRETHODNA STRANICA
- Rapid Prototyping, Desktop Manufacturing, Additive Manufacturing, FDM
Rapid Prototyping, Desktop Manufacturing, Additive Manufacturing, Stereolithography, Polyjet, Fused Deposition Modeling, Selective Laser Sintering, FDM, SLS Aditivna i brza proizvodnja Posljednjih godina vidjeli smo porast potražnje za BRZOM PROIZVODNJOM ili BRZOM IZRADOM PROTOTIPA. Ovaj proces se također može nazvati PROIZVODNJA STOLNIH RAČUNARA ili PROIZVODNJA SLOBODNOG OBLIKA. U osnovi čvrsti fizički model dijela izrađuje se izravno iz trodimenzionalnog CAD crteža. Koristimo izraz ADITIVNA PROIZVODNJA za ove različite tehnike gdje dijelove izrađujemo u slojevima. Koristeći integrirani računalno upravljani hardver i softver izvodimo aditivnu proizvodnju. Naše brze tehnike izrade prototipova i proizvodnje su STEREOLITOGRAFIJA, POLYJET, MODELIRANJE TALOŽENJEM, SELEKTIVNO LASERSKO SINTERANJE, TALJENJE ELEKTRONSKIM ZRAKOM, TRODIMENZIONALNI ISPIS, IZRAVNA PROIZVODNJA, BRZA IZRADA ALATA. Preporučujemo da kliknete ovdje zaPREUZMITE naše shematske ilustracije aditivne proizvodnje i brzih proizvodnih procesa tvrtke AGS-TECH Inc. To će vam pomoći da bolje razumijete informacije koje vam pružamo u nastavku. Brza izrada prototipa nam omogućuje: 1.) Konceptualni dizajn proizvoda gleda se iz različitih kutova na monitoru pomoću 3D / CAD sustava. 2.) Prototipovi od nemetalnih i metalnih materijala se izrađuju i proučavaju s funkcionalnog, tehničkog i estetskog aspekta. 3.) Izrada prototipa po niskoj cijeni u vrlo kratkom vremenu. Aditivna proizvodnja može se nalikovati izradi štruce kruha slaganjem i lijepljenjem pojedinačnih kriški jedne na drugu. Drugim riječima, proizvod se proizvodi krišku po krišku ili sloj po sloj koji se nanosi jedan na drugi. Većina dijelova može se proizvesti u roku od nekoliko sati. Tehnika je dobra ako su dijelovi potrebni vrlo brzo ili ako su potrebne količine male, a izrada kalupa i alata je preskupa i dugotrajna. Međutim, cijena dijela je skupa zbog skupih sirovina. • STEREOLITOGRAFIJA: Ova tehnika također skraćeno STL, temelji se na stvrdnjavanju tekućeg fotopolimera u određeni oblik fokusiranjem laserske zrake na njega. Laser polimerizira fotopolimer i stvrdnjava ga. Skeniranjem UV laserske zrake prema programiranom obliku duž površine fotopolimerne smjese, dio se proizvodi odozdo prema gore u pojedinačnim rezovima kaskadno postavljenim jedan na drugi. Skeniranje laserske točke ponavlja se mnogo puta kako bi se postigla geometrija programirana u sustavu. Nakon što je dio potpuno proizveden, uklanja se s platforme, upija i čisti ultrazvučno i alkoholnom kupkom. Zatim se izlaže UV zračenju nekoliko sati kako bi se osiguralo da je polimer potpuno otvrdnuo i očvrsnuo. Da sažmemo proces, platforma koja je umočena u fotopolimernu smjesu i UV laserska zraka se kontroliraju i pomiču kroz servo-kontrolni sustav u skladu s oblikom željenog dijela, a dio se dobiva fotostvrdnjavanjem polimera sloj po sloj. Naravno, maksimalne dimenzije proizvedenog dijela određene su opremom za stereolitografiju. • POLYJET: Slično inkjet ispisu, kod polijeta imamo osam ispisnih glava koje talože fotopolimer na ladicu za izradu. Ultraljubičasto svjetlo postavljeno uz mlaznice odmah stvrdnjava i stvrdnjava svaki sloj. U polijetu se koriste dva materijala. Prvi materijal je za izradu stvarnog modela. Drugi materijal, smola slična gelu, koristi se za potporu. Oba se materijala talože sloj po sloj i istovremeno stvrdnjavaju. Nakon završetka modela, potporni materijal se uklanja vodenom otopinom. Korištene smole slične su stereolitografiji (STL). Polyjet ima sljedeće prednosti u odnosu na stereolitografiju: 1.) Nema potrebe za čišćenjem dijelova. 2.) Nema potrebe za postprocesnim stvrdnjavanjem 3.) Moguće su manje debljine slojeva i tako dobivamo bolju rezoluciju i možemo proizvoditi finije dijelove. • MODELIRANJE TALOŽENJA : Također skraćeno kao FDM, u ovoj metodi glava ekstrudera kojom upravlja robot pomiče se u dva glavna smjera preko stola. Kabel se po potrebi spušta i podiže. Iz otvora grijane matrice na glavi, ekstrudira se termoplastična nit i početni sloj se nanosi na pjenastu podlogu. To se postiže glavom ekstrudera koja slijedi unaprijed zadanu putanju. Nakon početnog sloja, stol se spušta, a sljedeći slojevi se postavljaju jedan na drugi. Ponekad su pri proizvodnji kompliciranog dijela potrebne potporne strukture kako bi se taloženje moglo nastaviti u određenim smjerovima. U tim slučajevima, potporni materijal se ekstrudira s manje gustim razmakom niti na sloju tako da je slabiji od materijala modela. Ove potporne strukture mogu se kasnije rastvoriti ili odlomiti nakon završetka dijela. Dimenzije matrice ekstrudera određuju debljinu ekstrudiranih slojeva. FDM proces proizvodi dijelove sa stepenastim površinama na kosim vanjskim ravninama. Ako je ova hrapavost neprihvatljiva, može se koristiti poliranje kemijskom parom ili zagrijani alat za njihovo izravnavanje. Čak je i vosak za poliranje dostupan kao materijal za premazivanje kako bi se eliminirali ovi koraci i postigle razumne geometrijske tolerancije. • SELEKTIVNO LASERSKO SINTERANJE: Također se označava kao SLS, proces se temelji na sinterovanju polimera, keramike ili metalnog praha selektivno u predmet. Dno komore za obradu ima dva cilindra: djelomični cilindar i cilindar za dovod praha. Prvi se postupno spušta do mjesta gdje se oblikuje sinterirani dio, a drugi se postupno podiže kako bi dopremio prah u cilindar za izradu dijela kroz mehanizam valjka. Najprije se tanki sloj praha taloži u cilindar za izradu dijela, zatim se laserska zraka fokusira na taj sloj, ocrtavajući i otapajući/sinterujući određeni poprečni presjek, koji se zatim ponovno skrućuje u krutinu. Puder je područja koja nisu pogođena laserskom zrakom i ostaju labava, ali još uvijek podržavaju čvrsti dio. Zatim se nanosi još jedan sloj praha i postupak se ponavlja mnogo puta kako bi se dobio dio. Na kraju se otresu čestice pudera u prahu. Sve to provodi računalo za kontrolu procesa korištenjem uputa koje generira 3D CAD program dijela koji se proizvodi. Mogu se deponirati različiti materijali kao što su polimeri (kao što su ABS, PVC, poliester), vosak, metali i keramika s odgovarajućim polimernim vezivima. • ELEKTRONSKIM ZRAKOM TALJENJE : Slično selektivnom laserskom sinteriranju, ali korištenjem elektronskog snopa za taljenje praha titana ili kobaltnog kroma za izradu prototipova u vakuumu. Napravljena su određena poboljšanja za izvođenje ovog procesa na nehrđajućem čeliku, aluminiju i legurama bakra. Ako je potrebno povećati otpornost na zamor proizvedenih dijelova, kao sekundarni proces koristimo vruće izostatičko prešanje nakon proizvodnje dijelova. • TRODIMENZIONALNI ISPIS: Također označen kao 3DP, u ovoj tehnici ispisna glava taloži anorgansko vezivo na sloj nemetalnog ili metalnog praha. Klip koji nosi sloj praha postupno se spušta i u svakom koraku vezivo se taloži sloj po sloj i spaja vezivo. Praškasti materijali koji se koriste su mješavine polimera i vlakana, lijevački pijesak, metali. Istodobnom upotrebom različitih glava za uvezivače i uvezivača u različitim bojama možemo dobiti različite boje. Proces je sličan inkjet ispisu, ali umjesto obojenog lista dobivamo obojeni trodimenzionalni objekt. Proizvedeni dijelovi mogu biti porozni i stoga mogu zahtijevati sinteriranje i infiltraciju metala kako bi se povećala gustoća i čvrstoća. Sinteriranje će sagorjeti vezivo i spojiti metalne prahove. Metali kao što su nehrđajući čelik, aluminij, titan mogu se koristiti za izradu dijelova, a kao materijale za infiltraciju obično koristimo bakar i broncu. Ljepota ove tehnike je u tome što se čak i komplicirani i pokretni sklopovi mogu proizvesti vrlo brzo. Na primjer, može se izraditi sklop zupčanika, ključ kao alat koji će imati pokretne i okretne dijelove spremne za upotrebu. Različite komponente sklopa mogu se proizvesti u različitim bojama i sve u jednom kadru. Preuzmite našu brošuru na:Osnove metalnog 3D ispisa • IZRAVNA PROIZVODNJA i BRZA IZRADA ALATA: Osim procjene dizajna, rješavanja problema koristimo brzu izradu prototipova za izravnu proizvodnju proizvoda ili izravnu primjenu u proizvodima. Drugim riječima, brza izrada prototipova može se ugraditi u konvencionalne procese kako bi bili bolji i konkurentniji. Na primjer, brza izrada prototipa može proizvesti uzorke i kalupe. Uzorci polimera koji se tale i gore, stvoreni operacijama brze izrade prototipa, mogu se sastaviti za livenje u kalupe i uložiti. Još jedan primjer koji treba spomenuti je korištenje 3DP-a za proizvodnju ljuske za lijevanje keramike i korištenje toga za operacije lijevanja ljuske. Čak se i kalupi za injekcijsko ubrizgavanje i umetci za kalupe mogu proizvesti brzom izradom prototipova i mogu se uštedjeti tjedni ili mjeseci vremena za izradu kalupa. Samo analizom CAD datoteke željenog dijela možemo proizvesti geometriju alata pomoću softvera. Evo nekih od naših popularnih brzih metoda izrade alata: RTV (Vulkanizacija na sobnoj temperaturi) LIJEVANJE / LIJEVANJE URETANA: Korištenje brze izrade prototipa može se koristiti za izradu uzorka željenog dijela. Zatim se ovaj uzorak premaže sredstvom za razdvajanje i tekuća RTV guma se izlije preko uzorka kako bi se proizvele polovice kalupa. Zatim se ove polovice kalupa koriste za injekcijsko kalupljenje tekućih uretana. Vijek trajanja kalupa je kratak, samo 0 ili 30 ciklusa, ali dovoljno za proizvodnju malih serija. ACES (Acetal Clear Epoxy Solid) INJEKCIJSKO LIJEPANJE: Koristeći brze tehnike izrade prototipova kao što je stereolitografija, proizvodimo kalupe za injekcijsko prešanje. Ovi kalupi su školjke s otvorenim krajem kako bi se omogućilo punjenje materijalima poput epoksida, epoksida punjenog aluminijem ili metala. Ponovo je vijek trajanja kalupa ograničen na desetke ili maksimalno stotine dijelova. POSTUPAK IZRADE ALATA ZA METALE S PRŠANJEM: Koristimo brzu izradu prototipa i izrađujemo uzorak. Na površinu uzorka raspršimo leguru cink-aluminij i premažemo je. Uzorak s metalnim premazom se zatim stavlja u tikvicu i popunjava epoksidom ili epoksidom punjenim aluminijem. Na kraju se uklanja i izradom dvije takve polovice kalupa dobivamo kompletan kalup za injekcijsko prešanje. Ovi kalupi imaju duži vijek trajanja, u nekim slučajevima, ovisno o materijalu i temperaturama, mogu proizvesti dijelove u tisućama. KEELTOOL PROCES: Ova tehnika može proizvesti kalupe sa 100.000 do 10 milijuna životnih ciklusa. Korištenjem brze izrade prototipova proizvodimo RTV kalup. Kalup se zatim puni mješavinom koja se sastoji od praha alatnog čelika A6, volframovog karbida, polimernog veziva i ostavlja se da očvrsne. Ovaj kalup se zatim zagrijava kako bi se polimer sagorio i metalni prah stopio. Sljedeći korak je infiltracija bakra za proizvodnju konačnog kalupa. Ako je potrebno, sekundarne operacije kao što su strojna obrada i poliranje mogu se izvesti na kalupu za bolju točnost dimenzija. CLICK Product Finder-Locator Service PRETHODNA STRANICA
- Glass and Ceramic Manufacturing, Hermetic Packages, Seals, Bonding
Glass and Ceramic Manufacturing, Hermetic Packages Seals and Bonding, Tempered Bulletproof Glass, Blow Moulding, Optical Grade Glass, Conductive Glass, Molding Oblikovanje i oblikovanje stakla i keramike Vrste proizvodnje stakla koje nudimo su ambalažno staklo, puhanje stakla, staklena vlakna, cijevi i šipke, kućno i industrijsko stakleno posuđe, svjetiljke i žarulje, precizno oblikovanje stakla, optičke komponente i sklopovi, ravno i limeno i float staklo. Vršimo i ručno i strojno oblikovanje. Naši popularni procesi proizvodnje tehničke keramike su prešanje, izostatičko prešanje, vruće izostatičko prešanje, vruće prešanje, klizno lijevanje, lijevanje trakom, ekstruzija, injekcijsko prešanje, zelena strojna obrada, sinteriranje ili pečenje, brušenje dijamanata, hermetički sklopovi. Preporučujemo da kliknete ovdje za PREUZMITE naše shematske ilustracije procesa oblikovanja i oblikovanja stakla tvrtke AGS-TECH Inc. PREUZMITE naše shematske ilustracije procesa proizvodnje tehničke keramike tvrtke AGS-TECH Inc. Ove datoteke s fotografijama i skicama koje možete preuzeti pomoći će vam da bolje razumijete informacije koje vam dajemo u nastavku. • PROIZVODNJA KONTEJNERSKOG STAKLA: Imamo automatizirane linije PRESS AND BLOW kao i BLOW AND BLOW linije za proizvodnju. U procesu puhanja i puhanja ubacujemo kuglicu u prazan kalup i oblikujemo grlić primjenom puhanja komprimiranog zraka s vrha. Odmah nakon toga, komprimirani zrak se drugi put upuhuje iz drugog smjera kroz grlo spremnika da bi se formirao predoblik boce. Ovaj pred-oblik se zatim prenosi u stvarni kalup, ponovno zagrijava da omekša i primjenjuje se komprimirani zrak kako bi pred-oblik dobio konačni oblik posude. Eksplicitnije, pod pritiskom je i gura se uz stijenke šupljine kalupa za puhanje da poprimi željeni oblik. Na kraju, proizvedeni stakleni spremnik se prenosi u peć za žarenje radi naknadnog ponovnog zagrijavanja i uklanjanja naprezanja nastalih tijekom kalupljenja te se kontrolirano hladi. U metodi prešanja i puhanja, rastaljene kuglice se stavljaju u kalup za parčenje (prazni kalup) i prešaju u oblik parizona (prazan oblik). Praznine se zatim prenose u kalupe za puhanje i puhaju slično postupku opisanom gore pod “Postupak puhanja i puhanja”. Naknadni koraci kao što su žarenje i smanjenje naprezanja slični su ili isti. • PUHANJE STAKLA: proizvodili smo proizvode od stakla korištenjem konvencionalnog ručnog puhanja, kao i korištenjem komprimiranog zraka s automatiziranom opremom. Za neke narudžbe potrebno je konvencionalno puhanje, kao što su projekti koji uključuju umjetničke radove na staklu ili projekti koji zahtijevaju manji broj dijelova s labavim tolerancijama, izrada prototipova/demo projekti… itd. Konvencionalno puhanje stakla uključuje uranjanje šuplje metalne cijevi u posudu s rastaljenim staklom i rotiranje cijevi za prikupljanje određene količine staklenog materijala. Staklo skupljeno na vrhu cijevi se kotrlja na plosnato željezo, oblikuje po želji, izdužuje, ponovno zagrijava i puše zrak. Kad je gotov, stavlja se u kalup i puše zrak. Šupljina kalupa je mokra kako bi se izbjegao kontakt stakla s metalom. Vodeni film djeluje poput jastuka između njih. Ručno puhanje je radno intenzivan spor proces i prikladan samo za izradu prototipova ili predmeta visoke vrijednosti, nije prikladan za jeftine narudžbe velike količine po komadu. • PROIZVODNJA STAKLA ZA KUĆANSTVO I INDUSTRIJU: Korištenjem različitih vrsta staklenih materijala proizvodi se veliki izbor staklenih proizvoda. Neke su čaše otporne na toplinu i prikladne za laboratorijsko stakleno posuđe, dok su neke dovoljno dobre da izdrže pranje u perilici posuđa više puta i prikladne su za izradu domaćih proizvoda. Koristeći Westlake strojeve dnevno se proizvode deseci tisuća komada čaša za piće. Da pojednostavimo, rastaljeno staklo skuplja se vakuumom i umeće u kalupe za izradu predformi. Zatim se u kalupe upuhuje zrak, oni se prenose u drugi kalup i ponovno se upuhuje zrak i staklo poprima svoj konačni oblik. Kao kod ručnog puhanja, ovi se kalupi održavaju mokrim vodom. Daljnje rastezanje je dio završne operacije gdje se oblikuje vrat. Višak stakla je spaljen. Nakon toga slijedi gore opisani kontrolirani proces ponovnog zagrijavanja i hlađenja. • OBLIKOVANJE STAKLENE CIJEVI I ŠIPKE: Glavni procesi koje koristimo za proizvodnju staklenih cijevi su DANNER i VELLO procesi. U Dannerovom procesu staklo iz peći teče i pada na nagnuti rukavac izrađen od vatrostalnih materijala. Čahura se nosi na rotirajućoj šupljoj osovini ili puhalici. Staklo se zatim omota oko rukavca i formira glatki sloj koji teče niz rukav i preko vrha osovine. Kod oblikovanja cijevi zrak se upuhuje kroz puhaljku sa šupljim vrhom, a kod oblikovanja šipkom koristimo pune vrhove na osovini. Cijevi ili šipke se zatim povlače preko nosivih valjaka. Dimenzije poput debljine stjenke i promjera staklenih cijevi podešavaju se na željene vrijednosti postavljanjem promjera rukavca i tlaka zraka za puhanje na željenu vrijednost, podešavanjem temperature, protoka stakla i brzine izvlačenja. S druge strane, postupak proizvodnje staklene cijevi Vello uključuje staklo koje izlazi iz peći u zdjelu sa šupljim trnom ili zvonom. Staklo tada prolazi kroz zračni prostor između trna i posude i poprima oblik cijevi. Nakon toga putuje preko valjaka do stroja za izvlačenje i hladi se. Na kraju rashladne linije odvija se rezanje i završna obrada. Dimenzije cijevi mogu se prilagoditi baš kao u Danner procesu. Kada uspoređujemo Dannerov i Vello proces, možemo reći da je Vello postupak bolji za proizvodnju velikih količina, dok Dannerov postupak može biti bolji za precizne narudžbe cijevi manjeg volumena. • OBRADA LISTA I RAVNOG I FLOAT STAKLA : Imamo velike količine ravnog stakla u debljinama od submilimetarskih do nekoliko centimetara. Naša ravna stakla su gotovo optički savršena. Nudimo stakla s posebnim premazima kao što su optički premazi, gdje se tehnika kemijskog taloženja koristi za nanošenje premaza kao što su antirefleks ili zrcalni premaz. Uobičajene su i prozirne vodljive prevlake. Dostupni su i hidrofobni ili hidrofilni premazi na staklu, te premazi koji staklo čine samočistećim. Kaljena, neprobojna i laminirana stakla još su jedan od popularnih proizvoda. Režemo staklo u željeni oblik sa željenim tolerancijama. Dostupne su i druge sekundarne operacije poput krivljenja ili savijanja ravnog stakla. • PRECIZNO LIJEPENJE STAKLA: Ovu tehniku uglavnom koristimo za proizvodnju preciznih optičkih komponenti bez potrebe za skupljim i dugotrajnijim tehnikama poput brušenja, lapiranja i poliranja. Ova tehnika nije uvijek dovoljna za izradu najbolje od najbolje optike, ali u nekim slučajevima kao što su potrošački proizvodi, digitalni fotoaparati, medicinska optika može biti jeftinija dobra opcija za proizvodnju velikih količina. Također ima prednost u odnosu na druge tehnike oblikovanja stakla gdje su potrebne složene geometrije, kao što je slučaj s kuglicama. Osnovni proces uključuje punjenje donje strane našeg kalupa s staklenim sirovim materijalom, pražnjenje procesne komore za uklanjanje kisika, blizu zatvaranja kalupa, brzo i izotermno zagrijavanje kalupa i stakla infracrvenim svjetlom, daljnje zatvaranje polovica kalupa. polagano kontrolirano prešanje omekšanog stakla do željene debljine, te na kraju hlađenje stakla i punjenje komore dušikom te uklanjanje proizvoda. Precizna kontrola temperature, udaljenost zatvaranja kalupa, sila zatvaranja kalupa, usklađivanje koeficijenata širenja kalupa i staklenog materijala ključni su u ovom procesu. • PROIZVODNJA STAKLENIH OPTIČKIH KOMPONENTI I SKLOPOVA: Osim preciznog oblikovanja stakla, postoji niz vrijednih procesa koje koristimo za izradu visokokvalitetnih optičkih komponenti i sklopova za zahtjevne primjene. Brušenje, lapiranje i poliranje stakala optičke kvalitete u finim posebnim abrazivnim kašama je umjetnost i znanost za izradu optičkih leća, prizmi, ravnih i više. Ravnost površine, valovitost, glatkoća i optičke površine bez defekata zahtijevaju puno iskustva s takvim procesima. Male promjene u okruženju mogu rezultirati proizvodima izvan specifikacija i zaustaviti proizvodnu liniju. Postoje slučajevi u kojima samo jedno brisanje optičke površine čistom krpom može učiniti da proizvod zadovolji specifikacije ili padne na testu. Neki od popularnih staklenih materijala koji se koriste su taljeni silicij, kvarc, BK7. Također sastavljanje takvih komponenti zahtijeva specijalizirano iskustvo u niši. Ponekad se koriste posebna ljepila. Međutim, ponekad je tehnika koja se naziva optički kontakt najbolji izbor i ne uključuje nikakav materijal između pričvršćenih optičkih stakala. Sastoji se od fizičkog dodirivanja ravnih površina koje se pričvršćuju jedna na drugu bez ljepila. U nekim se slučajevima mehanički odstojnici, precizne staklene šipke ili kuglice, stezaljke ili strojno obrađene metalne komponente koriste za sastavljanje optičkih komponenti na određenim udaljenostima i s određenim geometrijskim usmjerenjima jedna prema drugoj. Ispitajmo neke od naših popularnih tehnika za proizvodnju vrhunske optike. BRUŠENJE & LEPANJE & POLIRANJE: Grubi oblik optičke komponente dobiva se brušenjem staklenog uzorka. Nakon toga se provodi lapiranje i poliranje rotiranjem i trljanjem grubih površina optičkih komponenti o alate sa željenim površinskim oblicima. Između optike i alata za oblikovanje ulijevaju se kaše sa sitnim abrazivnim česticama i tekućinom. Veličine abrazivnih čestica u takvim kašama mogu se odabrati prema željenom stupnju ravnosti. Odstupanja kritičnih optičkih površina od željenih oblika izražavaju se valnim duljinama svjetlosti koja se koristi. Naša visokoprecizna optika ima desetinu valne duljine (valna duljina/10) tolerancije ili je moguće čak i strože. Osim površinskog profila, kritične površine se skeniraju i ocjenjuju za druge površinske značajke i nedostatke kao što su dimenzije, ogrebotine, krhotine, rupe, točkice... itd. Čvrsta kontrola uvjeta okoline u pogonu optičke proizvodnje i opsežni mjeriteljski zahtjevi i zahtjevi za ispitivanje s najsuvremenijom opremom čine ovu granu industrije izazovnom. • SEKUNDARNI PROCESI U PROIZVODNJI STAKLA: Opet, ograničeni smo samo vašom maštom kada su u pitanju sekundarni i završni postupci stakla. Ovdje navodimo neke od njih: -Premazi na staklu (optički, električni, tribološki, toplinski, funkcionalni, mehanički...). Kao primjer, možemo promijeniti površinska svojstva stakla tako da ono, na primjer, reflektira toplinu tako da unutrašnjost zgrade održava hladnom, ili pomoću nanotehnologije učiniti jednu stranu infracrvenom koja apsorbira. To pomaže u održavanju topline u unutrašnjosti zgrada jer će krajnji vanjski površinski sloj stakla apsorbirati infracrveno zračenje unutar zgrade i zračiti ga natrag u unutrašnjost. -Graviranje na staklu - Primijenjeno keramičko označavanje (ACL) -Graviranje - Plameno poliranje -Kemijsko poliranje -Bojenje PROIZVODNJA TEHNIČKE KERAMIKE • PREŠANJE MATRE: Sastoji se od jednoosne kompakcije zrnatog praha zatvorenog u matrici • VRUĆE PREŠANJE: Slično prešanju, ali uz dodatak temperature za povećanje zgušnjavanja. Prah ili kompaktirani preform se stavlja u grafitnu matricu i primjenjuje se jednoosni pritisak dok se matrica drži na visokim temperaturama kao što je 2000 C. Temperature mogu biti različite ovisno o vrsti keramičkog praha koji se obrađuje. Za komplicirane oblike i geometrije može biti potrebna druga naknadna obrada kao što je dijamantsko brušenje. • IZOSTATIČKO PREŠANJE: granulirani prah ili prešani kompakti stavljaju se u hermetički zatvorene spremnike, a zatim u zatvorenu tlačnu posudu s tekućinom unutra. Nakon toga se zbijaju povećanjem tlaka u tlačnoj posudi. Tekućina unutar posude ravnomjerno prenosi sile pritiska po cijeloj površini hermetičkog spremnika. Materijal je na taj način ravnomjerno zbijen i poprima oblik svog fleksibilnog spremnika i svoj unutarnji profil i značajke. • VRUĆE IZOSTATIČKO PREŠANJE: Slično izostatičkom prešanju, ali osim atmosfere plina pod tlakom, sinteriramo kompakt na visokoj temperaturi. Vruće izostatičko prešanje rezultira dodatnim zgušnjavanjem i povećanom čvrstoćom. • KLIZNO LIJEVANJE / LIJEVANJE S DRENOM: Kalup punimo suspenzijom mikrometarskih keramičkih čestica i tekućine nosača. Ova smjesa se naziva "slip". Kalup ima pore i stoga se tekućina u smjesi filtrira u kalup. Kao rezultat toga, na unutarnjim površinama kalupa nastaje odljev. Nakon sinteriranja, dijelovi se mogu izvaditi iz kalupa. • LIJEVANJE TRAKA: Proizvodimo keramičke trake lijevanjem keramičkih kaša na ravne pokretne površine nosača. Kaše sadrže keramičke prahove pomiješane s drugim kemikalijama za vezivanje i nošenje. Kako otapala isparavaju, ostaju gusti i savitljivi listovi keramike koji se po želji mogu rezati ili smotati. • OBLIKOVANJE EKSTRUZIJOM: Kao i u drugim postupcima ekstruzije, meka mješavina keramičkog praha s vezivima i drugim kemikalijama prolazi kroz matricu kako bi dobila oblik poprečnog presjeka i zatim se reže na željene duljine. Proces se izvodi hladnim ili zagrijanim keramičkim smjesama. • NISKOTLAČNO INJEKCIJSKO LIJEPANJE: pripremamo smjesu keramičkog praha s vezivima i otapalima i zagrijavamo je do temperature na kojoj se lako može prešati i ugurati u šupljinu alata. Nakon što je ciklus kalupljenja dovršen, dio se izbacuje i vezivna kemikalija izgara. Koristeći injekcijsko prešanje, možemo ekonomično dobiti složene dijelove u velikim količinama. Moguće su rupe koje su maleni djelić milimetra na zidu debljine 10 mm, navoji su mogući bez daljnje strojne obrade, moguće su tolerancije od +/- 0,5%, pa čak i niže kada se dijelovi strojno obrađuju , moguće su debljine stijenke reda veličine od 0,5 mm do duljine od 12,5 mm, kao i debljine stijenke od 6,5 mm do duljine od 150 mm. • ZELENA STROJNA OBRADA: Koristeći iste alate za obradu metala, možemo obraditi prešane keramičke materijale dok su još mekani poput krede. Moguća su odstupanja od +/- 1%. Za bolje tolerancije koristimo dijamantno brušenje. • SINTERANJE ili PEČENJE: Sinteriranje omogućuje potpuno zgušnjavanje. Na zelenim kompaktnim dijelovima dolazi do značajnog skupljanja, ali to nije veliki problem budući da uzimamo u obzir te promjene dimenzija kada dizajniramo dio i alat. Čestice praha se međusobno povezuju i poroznost izazvana procesom zbijanja se u velikoj mjeri uklanja. • DIJAMANTNO BRUŠENJE: Najtvrđi materijal na svijetu “dijamant” koristi se za brušenje tvrdih materijala poput keramike i dobivaju se precizni dijelovi. Postižu se tolerancije u mikrometarskom području i vrlo glatke površine. Zbog skupoće, ovu tehniku razmatramo samo kada nam je stvarno potrebna. • HERMETIČKI SKLOPOVI su oni koji praktično govoreći ne dopuštaju nikakvu razmjenu tvari, krutina, tekućina ili plinova između sučelja. Hermetičko brtvljenje je hermetičko. Na primjer, hermetička elektronička kućišta su ona koja čuvaju osjetljivi unutarnji sadržaj pakiranog uređaja neoštećenim vlagom, zagađivačima ili plinovima. Ništa nije 100% hermetičko, ali kada govorimo o hermetičnosti, mislimo da u praktičnom smislu, da postoji hermetičnost do te mjere da je stopa curenja toliko niska da su uređaji sigurni u normalnim uvjetima okoline jako dugo vremena. Naši hermetički sklopovi sastoje se od metalnih, staklenih i keramičkih komponenti, metal-keramika, keramika-metal-keramika, metal-keramika-metal, metal na metal, metal-staklo, metal-staklo-metal, staklo-metal-staklo, staklo- metal i staklo na staklo i sve ostale kombinacije lijepljenja metal-staklo-keramika. Na primjer, možemo obložiti metalom keramičke komponente tako da se mogu čvrsto spojiti s drugim komponentama u sklopu i imaju izvrsnu sposobnost brtvljenja. Imamo znanje i iskustvo presvlačenja optičkih vlakana ili prolaza metalom i njihovog lemljenja na kućišta, tako da plinovi ne prolaze niti cure u kućišta. Stoga se koriste za proizvodnju elektroničkih kućišta za kapsuliranje osjetljivih uređaja i njihovu zaštitu od vanjske atmosfere. Osim izvrsnih svojstava brtvljenja, druga svojstva kao što su koeficijent toplinske ekspanzije, otpornost na deformacije, priroda bez ispuštanja plinova, vrlo dug životni vijek, nevodljiva priroda, svojstva toplinske izolacije, antistatička priroda... itd. učiniti staklene i keramičke materijale izborom za određene primjene. Informacije o našem pogonu za proizvodnju keramičkih i metalnih spojnica, hermetičkog brtvljenja, vakuumskih prolaza, visokog i ultravisokog vakuuma i komponenti za kontrolu tekućine možete pronaći ovdje:Brošura tvornice hermetičkih komponenti CLICK Product Finder-Locator Service PRETHODNA STRANICA
- Wire & Spring Forming, Shaping, Welding, Assembly of Wires, Coil, CNC
Wire & Spring Forming, Shaping, Welding, Assembly of Wires, Coil Compression Extension Torsion Flat Springs, Custom Wires, Helical Springs at AGS-TECH Inc. Oblikovanje žice i opruga Izrađujemo žice po narudžbi, montažu žice, žice oblikovane u željene 2D i 3D oblike, žičane mreže, mreže, ograde, košare, ograde, žičane opruge, ravne opruge; torzija, kompresija, napetost, ravne opruge i više. Naši procesi su oblikovanje žice i opruga, izvlačenje žice, oblikovanje, savijanje, zavarivanje, lemljenje, lemljenje, bušenje, savijanje, bušenje, skošenje, brušenje, narezivanje navoja, premazivanje, četveroklizno oblikovanje, namatanje, namotavanje, presvlačenje. Preporučujemo da kliknete ovdje za PREUZMITE naše shematske ilustracije procesa oblikovanja žice i opruga tvrtke AGS-TECH Inc. Ova datoteka s fotografijama i skicama koju možete preuzeti pomoći će vam da bolje razumijete informacije koje vam dajemo u nastavku. • IZVLAČENJE ŽICE: Koristeći vlačne sile rastežemo metalni dio i provlačimo ga kroz matricu kako bismo smanjili promjer i povećali njegovu duljinu. Ponekad koristimo niz matrica. Sposobni smo izraditi matrice za svaki promjer žice. Koristeći materijal visoke vlačne čvrstoće izvlačimo vrlo tanke žice. Nudimo i hladno i toplo obrađene žice. • OBLIKOVANJE ŽICE : Rola žice je savijena i oblikovana u koristan proizvod. Imamo sposobnost oblikovanja žica svih promjera, uključujući tanke filamente kao i debele žice poput onih koje se koriste kao opruge ispod šasije automobila. Oprema koju koristimo za oblikovanje žice su ručni i CNC strojevi za oblikovanje žice, namotavač, pogonske preše, fourslide, multi-slide. Naši procesi su izvlačenje, savijanje, ravnanje, ravnanje, rastezanje, rezanje, savijanje, lemljenje i zavarivanje i tvrdo lemljenje, sastavljanje, namotavanje, savijanje (ili krilo), probijanje, uvlačenje žice, bušenje, skošenje, brušenje, premazivanje i obrada površina. Naša najsuvremenija oprema može se postaviti za razvoj vrlo složenih dizajna bilo kojeg oblika i uskih tolerancija. Nudimo različite tipove krajeva poput sferičnih, šiljastih ili skošenih krajeva za vaše žice. Većina naših projekata oblikovanja žice ima minimalne do nulte troškove alata. Uzorak vremena obrade obično je danima. Promjene u dizajnu/konfiguraciji žičanih oblika mogu se napraviti vrlo brzo. • OBLIKOVANJE OPRUGA: AGS-TECH proizvodi veliki izbor opruga uključujući: -Torzijska/dvostruka torziona opruga -Vlačna/kompresivna opruga -Konstantna/varijabilna opruga - Zavojna i spiralna opruga -Ravna i lisnata opruga - Opruga ravnoteže -Belleville perilica -Negatorsko proljeće - Zavojna opruga progresivne brzine -Valovito proljeće -Voluta opruga - Konusne opruge - Proljetni prstenovi - Satne opruge - Isječci Proizvodimo opruge od raznih materijala i možemo vas uputiti prema vašoj primjeni. Najčešći materijali su nehrđajući čelik, krom silicij, čelik s visokim udjelom ugljika, niskougljični čelik kaljen u ulju, krom vanadij, fosforna bronca, titan, legura berilij bakra, keramika za visoke temperature. Koristimo različite tehnike u proizvodnji opruga, uključujući CNC namotavanje, hladno namotavanje, vruće namotavanje, kaljenje, završnu obradu. Druge tehnike koje smo već spomenuli pod oblikovanjem žice također su uobičajene u našim proizvodnim operacijama opruga. • USLUGE ZAVRŠNE OBRADE ŽICA I OPRUGA: Vaše proizvode možemo završiti na više načina, ovisno o vašem izboru i potrebama. Neki uobičajeni procesi koje nudimo su: bojanje, premazivanje prahom, pozlaćivanje, uranjanje vinilom, eloksiranje, uklanjanje naprezanja, toplinska obrada, shot peen, tumble, kromatiranje, električni nikl, pasivizacija, pečeni emajl, plastični premaz , čišćenje plazmom. CLICK Product Finder-Locator Service PRETHODNA STRANICA
- Forging and Powdered Metallurgy, Die Forging, Heading, Hot Forging
Forging and Powdered Metallurgy, Die Forging, Heading, Hot Forging, Impression Die, Near Net Shape, Swaging, Metal Hobbing, Riveting, Coining from AGS-TECH Inc. Kovanje metala i metalurgija praha Vrste procesa KOVANJA METALA koje nudimo su topli i hladni kalupi, otvoreni kalupi i zatvoreni kalupi, kalupi za otiskivanje i otkovci bez fleka, cogging, punilo, rubno i precizno kovanje, skoro neto oblik, naslov , prešanje, iskrivljeno kovanje, metalno glodanje, prešanje i valjanje, radijalno i orbitalno i prstenasto i izotermno kovanje, kovanje, zakivanje, kovanje metalnom kuglom, probijanje metala, dimenzioniranje, kovanje s visokom energetskom brzinom. Naše tehnike METALURGIJE PRAHA i OBRADE PRAHA su prešanje i sinteriranje praha, impregnacija, infiltracija, toplo i hladno izostatičko prešanje, brizganje metala, zbijanje u valjku, valjanje u prahu, ekstruzija praha, slobodno sinteriranje, sinteriranje iskrom, vruće prešanje. Preporučujemo da kliknete ovdje za PREUZMITE naše shematske ilustracije procesa kovanja tvrtke AGS-TECH Inc. PREUZMITE naše shematske ilustracije procesa metalurgije praha tvrtke AGS-TECH Inc. Ove datoteke s fotografijama i skicama koje možete preuzeti pomoći će vam da bolje razumijete informacije koje vam dajemo u nastavku. Kod kovanja metala djeluju tlačne sile te se materijal deformira i dobiva željeni oblik. Najčešći kovani materijali u industriji su željezo i čelik, ali brojni drugi kao što su aluminij, bakar, titan, magnezij također su naširoko kovani. Kovani metalni dijelovi imaju poboljšanu zrnastu strukturu osim zapečaćenih pukotina i zatvorenih praznih prostora, pa je čvrstoća dijelova dobivenih ovim postupkom veća. Kovanjem se proizvode dijelovi koji su znatno jači u odnosu na svoju težinu od dijelova izrađenih lijevanjem ili strojnom obradom. Budući da se kovani dijelovi oblikuju tako da metal teče u svoj konačni oblik, metal poprima usmjerenu strukturu zrna koja je odgovorna za vrhunsku čvrstoću dijelova. Drugim riječima, dijelovi dobiveni postupkom kovanja pokazuju bolja mehanička svojstva u usporedbi s jednostavnim lijevanim ili strojno obrađenim dijelovima. Težina metalnih otkovaka može varirati od malih laganih dijelova do stotina tisuća funti. Proizvodimo otkivke uglavnom za mehanički zahtjevne primjene gdje se primjenjuju velika naprezanja na dijelove kao što su automobilski dijelovi, zupčanici, radni alati, ručni alati, osovine turbina, oprema za motocikle. Budući da su troškovi alata i postavljanja relativno visoki, preporučujemo ovaj proizvodni proces samo za proizvodnju velike količine i za male količine, ali visoke vrijednosti kritičnih komponenti kao što je zrakoplovni stajni trap. Osim troškova alata, vrijeme proizvodnje za velike količine kovanih dijelova može biti dulje u usporedbi s nekim jednostavnim strojno obrađenim dijelovima, ali tehnika je presudna za dijelove koji zahtijevaju izvanrednu čvrstoću kao što su vijci, matice, posebna primjena pričvršćivači, dijelovi za automobile, viličare, dizalice. • KOVANJE VRUĆIM MATRANJEM i HLADNIM MATRANJEM: Kovanje vrućim kalupom, kao što naziv govori, provodi se na visokim temperaturama, stoga je duktilnost visoka, a čvrstoća materijala niska. To olakšava lako deformiranje i kovanje. Naprotiv, hladno kovanje se izvodi na nižim temperaturama i zahtijeva veće sile što rezultira deformacijskim otvrdnjavanjem, boljom završnom obradom površine i točnosti proizvedenih dijelova. • KOVANJE OTVORENOM MATRICOM i OTISKANJEM: Kod otvorenog kovanja, matrice ne ograničavaju komprimirani materijal, dok kod kovanja otiskom šupljine unutar matrica ograničavaju protok materijala dok se kuje u željeni oblik. UPSET FORGING ili također nazvan UPSETTING, što zapravo nije isti, ali vrlo sličan proces, je otvoreni proces matrice gdje se radni komad nalazi u sendviču između dva ravna matrica i sila pritiska smanjuje njegovu visinu. Kako se visina smanjuje, širina obratka se povećava. HEADING, proces kovanja sa savijanjem uključuje cilindrični materijal koji se savija na kraju i njegov presjek se lokalno povećava. U zaglavlju materijal prolazi kroz matricu, kuje se i zatim reže na željenu duljinu. Operacija je sposobna brzo proizvesti velike količine spojnih elemenata. Uglavnom je to operacija hladne obrade jer se koristi za izradu krajeva čavala, završetaka vijaka, matica i vijaka gdje materijal treba ojačati. Još jedan proces otvorene matrice je COGGING, gdje se radni komad kuje u nizu koraka pri čemu svaki korak rezultira kompresijom materijala i naknadnim kretanjem otvorene matrice duž duljine radnog komada. U svakom koraku, debljina se smanjuje, a duljina se malo povećava. Proces nalikuje nervoznom studentu koji cijelo vrijeme grize olovku malim koracima. Proces koji se zove FULLERING još je jedna otvorena metoda kovanja u kalupu koju često primjenjujemo kao raniji korak za raspodjelu materijala u radnom komadu prije nego što se izvedu druge operacije kovanja metala. Koristimo ga kada izradak zahtijeva nekoliko forging operacija. U radu se kalup s konveksnim površinama deformira i uzrokuje istjecanje metala na obje strane. Sličan proces fulleringu, EDGING s druge strane uključuje otvorenu matricu s konkavnim površinama za deformiranje radnog komada. Obrubljivanje također predstavlja pripremni proces za sljedeće operacije kovanja i čini da materijal teče s obje strane u područje u sredini. IMPRESSION DIE FORGING ili CLOSED DIE FORGING kako se još naziva koristi matricu/kalup koji sabija materijal i ograničava njegov protok unutar sebe. Matrica se zatvara i materijal poprima oblik šupljine kalupa/kalupa. PRECIZNO KOVANJE, proces koji zahtijeva posebnu opremu i kalup, proizvodi dijelove bez ili s vrlo malo bljeskanja. Drugim riječima, dijelovi će imati gotovo konačne dimenzije. U ovom procesu dobro kontrolirana količina materijala pažljivo se umeće i postavlja unutar kalupa. Ovu metodu koristimo za složene oblike s tankim presjecima, malim tolerancijama i kutovima nagiba i kada su količine dovoljno velike da opravdaju troškove kalupa i opreme. • KOVANJE BEZ FLASHLA: Izradak se postavlja u matricu na takav način da nikakav materijal ne može istjecati iz šupljine i formirati flash. Stoga nije potrebno neželjeno podrezivanje bljeskalicom. To je precizan proces kovanja i stoga zahtijeva strogu kontrolu količine upotrijebljenog materijala. • METALNO KOVANJE ili RADIJALNO KOVANJE: Na radni komad obodno djeluje matrica i kuje se. Trn se također može koristiti za kovanje unutarnje geometrije obratka. U operaciji savijanja radni komad obično prima nekoliko udaraca u sekundi. Tipični predmeti proizvedeni prešanjem su alati sa šiljastim vrhom, konusne šipke, odvijači. • PROBUŠANJE METALA: ovu operaciju često koristimo kao dodatnu operaciju u proizvodnji dijelova. Rupa ili šupljina stvara se bušenjem na površini radnog komada bez probijanja. Imajte na umu da se bušenje razlikuje od bušenja koje rezultira prolaznom rupom. • GLOBANJE: Probijač željene geometrije utiskuje se u radni komad i stvara šupljinu željenog oblika. Ovaj punč nazivamo HOB. Operacija uključuje visoke tlakove i provodi se na hladnoći. Kao rezultat, materijal je hladno obrađen i otvrdnut. Stoga je ovaj postupak vrlo prikladan za proizvodnju kalupa, kalupa i šupljina za druge proizvodne procese. Nakon što je ploča za kuhanje proizvedena, možete jednostavno proizvesti mnogo identičnih šupljina bez potrebe da ih strojno obrađujete jednu po jednu. • KOVANJE VALJKOM ili OBLIKOVANJE VALJKOM: Dva nasuprotna valjka koriste se za oblikovanje metalnog dijela. Radni komad se dovodi u valjke, valjci se okreću i povlače rad u procjep, rad se zatim dovodi kroz užljebljeni dio valjaka i sile pritiska daju materijalu željeni oblik. To nije proces valjanja, već proces kovanja, jer se radi o diskretnoj, a ne kontinuiranoj operaciji. Geometrija na valjcima kuje materijal u traženi oblik i geometriju. Izvodi se vruće. Budući da se radi o procesu kovanja, proizvodi dijelove s izvanrednim mehaničkim svojstvima i stoga ga koristimo za proizvodnju automobilskih dijelova kao što su osovine koje trebaju imati izvanrednu izdržljivost u teškim radnim okruženjima. • ORBITALNO KOVANJE: Radni komad se stavlja u šupljinu kalupa za kovanje i kuje pomoću gornjeg kalupa koji putuje u orbitalnoj putanji dok se okreće oko nagnute osi. Pri svakom okretaju gornja matrica dovršava vršenje sile pritiska na cijeli radni komad. Ponavljanjem ovih okretaja više puta, izvodi se dovoljan broj kovanja. Prednosti ove tehnike proizvodnje su niska buka rada i manje potrebne sile. Drugim riječima, malim se silama može okretati teška matrica oko osi kako bi se primijenili veliki pritisci na dio obratka koji je u kontaktu s matricom. Dijelovi diska ili stožastog oblika ponekad dobro odgovaraju ovom procesu. • KOVANJE PRSTENA: Često koristimo za proizvodnju bešavnog prstenja. Kundak se reže na duljinu, savija i zatim probuši do kraja kako bi se stvorila središnja rupa. Zatim se stavlja na trn i kalup za kovanje ga udara odozgo dok se prsten polako okreće dok se ne postignu željene dimenzije. • ZAKIVANJE: Uobičajeni postupak za spajanje dijelova, počinje ravnim metalnim komadom umetnutim u unaprijed napravljene rupe kroz dijelove. Nakon toga se dva kraja metalnog komada kuje stiskanjem spoja između gornje i donje matrice. • KOVANJE: Još jedan popularan proces koji se izvodi mehaničkom prešom, koja djeluje velikom silom na maloj udaljenosti. Naziv "kovanje" dolazi od finih detalja koji su iskovani na površini metalnih kovanica. To je uglavnom postupak završne obrade proizvoda gdje se dobivaju fini detalji na površinama kao rezultat velike sile koju primjenjuje matrica koja te detalje prenosi na radni komad. • KOVANJE METALNIH KUGLICA: proizvodi kao što su kuglični ležajevi zahtijevaju visokokvalitetne precizno izrađene metalne kuglice. U jednoj tehnici koja se zove SKEW ROLLING, koristimo dva nasuprotna valjka koja se neprekidno okreću dok se materijal neprestano ubacuje u valjke. Na jednom kraju dvaju valjaka metalne kugle se izbacuju kao proizvod. Druga metoda za kovanje metalnih kuglica je korištenje matrice koja istiskuje zalihu materijala postavljenu između njih poprimajući sferni oblik šupljine kalupa. Proizvedene lopte često zahtijevaju neke dodatne korake kao što su završna obrada i poliranje kako bi postale proizvod visoke kvalitete. • IZOTERMIČNO KOVANJE / TOPLO KOVANJE: Skup proces koji se izvodi samo kada je vrijednost koristi/troška opravdana. Vrući radni proces u kojem se matrica zagrijava na otprilike istu temperaturu kao i radni komad. Budući da i kalup i rad imaju približno istu temperaturu, nema hlađenja i karakteristike protoka metala su poboljšane. Operacija je dobra za super legure i materijale s lošijom kovanošću i materijale čiji mehanička svojstva vrlo su osjetljiva na male gradijente i promjene temperature. • DIMENZIONIRANJE METALA: To je postupak hladne dorade. Protok materijala je neograničen u svim smjerovima osim u smjeru u kojem se primjenjuje sila. Kao rezultat, dobivena je vrlo dobra obrada površine i točne dimenzije. • KOVANJE S VISOKOM ENERGETSKOM KOVANJEM: Tehnika uključuje gornji kalup pričvršćen na krak klipa koji se brzo gura dok se smjesa goriva i zraka pali pomoću svjećice. To podsjeća na rad klipova u automobilskom motoru. Kalup vrlo brzo udara u radni komad, a zatim se vrlo brzo vraća u prvobitni položaj zahvaljujući povratnom pritisku. Rad se kuje u roku od nekoliko milisekundi i stoga nema vremena da se rad ohladi. Ovo je korisno za dijelove koje je teško kovati i koji imaju mehanička svojstva vrlo osjetljiva na temperaturu. Drugim riječima, proces je toliko brz da se dio oblikuje pod konstantnom temperaturom tijekom cijele godine i neće biti temperaturnih gradijenata na sučeljima kalupa/radnog komada. • Kod KOVANJA, metal se tuče između dva odgovarajuća čelična bloka s posebnim oblicima u njima, koji se nazivaju matrice. Kada se metal zabije između matrica, poprima isti oblik kao oblici u matrici. Kad postigne svoj konačni oblik, izvadi se na hlađenje. Ovaj proces proizvodi snažne dijelove koji su preciznog oblika, ali zahtijeva veća ulaganja za specijalizirane matrice. Iskrivljeno kovanje povećava promjer komada metala spljoštavanjem. Općenito se koristi za izradu malih dijelova, posebno za oblikovanje glava na spojnim elementima poput vijaka i čavala. • METALURGIJA PRAHA/OBRADA PRAHA: Kao što naziv implicira, uključuje proizvodne procese za izradu čvrstih dijelova određenih geometrija i oblika od praha. Ako se u tu svrhu koriste metalni prahovi, to je područje metalurgije praha, a ako se koriste nemetalni prahovi, to je područje obrade praha. Čvrsti dijelovi se proizvode od praha prešanjem i sinteriranjem. PREŠANJE PRAHA koristi se za kompaktiranje praha u željene oblike. Prvo, primarni materijal se fizički usitnjava, dijeleći ga na mnogo malih pojedinačnih čestica. Mješavina praha se puni u matricu i bušilica se kreće prema prahu i zbija ga u željeni oblik. Uglavnom se izvodi na sobnoj temperaturi, prešanjem praha dobiva se čvrsti dio i naziva se zeleni kompakt. Veziva i maziva obično se koriste za povećanje kompaktnosti. Osposobljeni smo za prešanje praha pomoću hidrauličkih preša kapaciteta nekoliko tisuća tona. Također imamo dvostruke preše sa suprotnim gornjim i donjim probojcima, kao i višestruke preše za vrlo složene geometrije dijelova. Ujednačenost koja je važan izazov za mnoga postrojenja za metalurgiju praha / obradu praha nije veliki problem za AGS-TECH zbog našeg dugogodišnjeg iskustva u proizvodnji takvih dijelova po narudžbi. Čak i s debljim dijelovima gdje ujednačenost predstavlja izazov, uspjeli smo. Ako se posvetimo vašem projektu, izradit ćemo vaše dijelove. Ako uočimo potencijalne rizike, obavijestit ćemo vas in unaprijed. SINTERANJE PRAHA, koje je drugi korak, uključuje podizanje temperature do određenog stupnja i održavanje temperature na toj razini određeno vrijeme kako bi se čestice praha u prešanom dijelu međusobno povezale. To rezultira mnogo jačim vezama i ojačavanjem radnog komada. Sinteriranje se odvija blizu temperature taljenja praha. Tijekom sinteriranja dolazi do skupljanja, povećava se čvrstoća materijala, gustoća, duktilnost, toplinska vodljivost, električna vodljivost. Imamo šaržne i kontinuirane peći za sinteriranje. Jedna od naših mogućnosti je podešavanje razine poroznosti dijelova koje proizvodimo. Na primjer, u mogućnosti smo proizvesti metalne filtere održavajući dijelove poroznima do određenog stupnja. Koristeći tehniku zvanu IMPREGNACIJA, ispunjavamo pore u metalu tekućinom kao što je ulje. Proizvodimo na primjer ležajeve natopljene uljem koji su samopodmazujući. U procesu INFILTRACIJE ispunjavamo pore metala drugim metalom nižeg tališta od osnovnog materijala. Smjesa se zagrijava do temperature između temperatura taljenja dvaju metala. Kao rezultat mogu se dobiti neka posebna svojstva. Također često izvodimo sekundarne operacije kao što su strojna obrada i kovanje na dijelovima proizvedenim u prahu kada je potrebno postići posebna svojstva ili svojstva ili kada se dio može proizvesti s manje koraka procesa. IZOSTATIČKO PREŠANJE: U ovom procesu tlak tekućine se koristi za zbijanje dijela. Metalni prah se stavlja u kalup napravljen od zapečaćene fleksibilne posude. U izostatičkom prešanju, pritisak se primjenjuje sa svih strana, za razliku od aksijalnog pritiska koji se vidi kod konvencionalnog prešanja. Prednosti izostatičkog prešanja su jednolika gustoća unutar dijela, posebno za veće ili deblje dijelove, vrhunska svojstva. Njegov nedostatak su duga vremena ciklusa i relativno niska geometrijska točnost. HLADNO IZOSTATSKO PREŠANJE se provodi na sobnoj temperaturi, a fleksibilni kalup je izrađen od gume, PVC-a ili uretana ili sličnih materijala. Tekućina koja se koristi za stvaranje tlaka i zbijanje je ulje ili voda. Slijedi konvencionalno sinteriranje zelenog kompakta. S druge strane, VRUĆE IZOSTATIČKO PREŠANJE se provodi na visokim temperaturama, a materijal kalupa je metalni lim ili keramika s dovoljno visokom točkom taljenja koja je otporna na temperature. Tekućina za tlačenje obično je inertni plin. Operacije prešanja i sinteriranja izvode se u jednom koraku. Poroznost je gotovo potpuno eliminirana, dobivena je ujednačena zrnata struktura. Prednost vrućeg izostatičkog prešanja je u tome što se njime mogu proizvesti dijelovi koji se mogu usporediti s kombinacijom lijevanja i kovanja, dok se materijali koji nisu prikladni za lijevanje i kovanje mogu koristiti. Nedostatak vrućeg izostatičkog prešanja je njegovo dugo vrijeme ciklusa, a time i cijena. Pogodan je za kritične dijelove malog volumena. INJEKCIJSKO PREŠTANJE METALA: Vrlo prikladan postupak za proizvodnju složenih dijelova s tankim stijenkama i detaljnom geometrijom. Najprikladniji za manje dijelove. Prašci i polimerno vezivo se miješaju, zagrijavaju i ubrizgavaju u kalup. Polimerno vezivo oblaže površine čestica praha. Nakon kalupljenja, vezivo se uklanja grijanjem na niskoj temperaturi ili otapanjem pomoću otapala. KOMPAKCIJA U VALJU / VALJANJE PRAHA: Prahovi se koriste za proizvodnju kontinuiranih traka ili listova. Prah se dovodi iz dodavača i sabija pomoću dva rotirajuća valjka u listove ili trake. Operacija se izvodi hladno. Lim se nosi u peć za sinteriranje. Proces sinteriranja može se ponoviti drugi put. EKSTRUDIJA PRAHA: Dijelovi s velikim omjerom duljine i promjera proizvode se ekstrudiranjem spremnika tankog lima s prahom. LASOBNO SINTERANJE: Kao što naziv implicira, to je metoda sabijanja i sinteriranja bez pritiska, pogodna za proizvodnju vrlo poroznih dijelova kao što su metalni filtri. Prah se ubacuje u šupljinu kalupa bez sabijanja. LASOBNO SINTERANJE: Kao što naziv implicira, to je metoda sabijanja i sinteriranja bez pritiska, pogodna za proizvodnju vrlo poroznih dijelova kao što su metalni filtri. Prah se ubacuje u šupljinu kalupa bez sabijanja. SINTERANJE ISKROM: Prah se komprimira u kalupu pomoću dva suprotna probijača, a električna struja velike snage primjenjuje se na probijač i prolazi kroz zbijeni prah koji se nalazi između njih. Visoka struja spaljuje površinske filmove s čestica praha i sinteruje ih s generiranom toplinom. Proces je brz jer se toplina ne primjenjuje izvana, već se stvara iz kalupa. VRUĆE PREŠANJE: Prahovi se prešaju i sinteriraju u jednom koraku u kalupu koji može izdržati visoke temperature. Dok se matrica sabija, na nju se dovodi toplina praha. Dobra točnost i mehanička svojstva postignuta ovom metodom čine je atraktivnom opcijom. Čak se i vatrostalni metali mogu obraditi korištenjem kalupnih materijala kao što je grafit. CLICK Product Finder-Locator Service PRETHODNI JELOVNIK
- Sheet Metal Forming Fabrication, Stamping, Punching, Deep Drawing, CNC
Sheet Metal Forming and Fabrication, Stamping, Punching, Bending, Progressive Die, Spot Welding, Deep Drawing, Metal Blanking and Slitting at AGS-TECH Inc. Štancanje i proizvodnja limova Nudimo štancanje lima, oblikovanje, oblikovanje, savijanje, probijanje, izrezivanje, rezanje, perforiranje, urezivanje, grickanje, brijanje, prešanje, izradu, duboko izvlačenje korištenjem pojedinačnih probijača / jednostrukih matrica kao i progresivnih matrica i predenja, oblikovanja gume i hidroformiranje; rezanje lima vodenim mlazom, plazmom, laserom, pilom, plamenom; montaža lima zavarivanjem, točkastim zavarivanjem; ispupčenje i savijanje limene cijevi; završna obrada površine lima uključujući bojanje umakanjem ili prskanjem, elektrostatsko premazivanje prahom, eloksiranje, galvaniziranje, raspršivanje i više. Naše usluge sežu od brze izrade prototipa od metalnog lima do velike količine proizvodnje. Preporučujemo da kliknete ovdje zaPREUZMITE naše shematske ilustracije procesa proizvodnje limova i utiskivanja tvrtke AGS-TECH Inc. To će vam pomoći da bolje razumijete informacije koje vam dajemo u nastavku. • REZANJE LIMOVA : Nudimo ODSJEKE i ODJECKE. Odsjeci režu lim jednu po jednu putanju i uglavnom nema rasipanja materijala, dok se kod odvajanja oblik ne može precizno ugnijezditi pa se gubi određena količina materijala. Jedan od naših najpopularnijih postupaka je PROBACANJE, gdje se iz lima izrezuje komad materijala okruglog ili drugog oblika. Komad koji je izrezan je otpad. Druga inačica probijanja je PROBIRANJE, gdje se buše pravokutne ili izdužene rupe. S druge strane, BLANKIRANJE je isti proces kao i bušenje, s razlikom da je komad koji se izrezuje posao i čuva se. FINE BLANKING, vrhunska verzija brušenja, stvara rezove s malim tolerancijama i ravnim glatkim rubovima i ne zahtijeva sekundarne operacije za savršenstvo obratka. Još jedan postupak koji često koristimo je REZANJE, što je postupak rezanja u kojem se metalni lim reže s dvije nasuprotne kružne oštrice u ravnoj ili zakrivljenoj putanji. Otvarač za limenke jednostavan je primjer postupka rezanja. Još jedan popularan proces za nas je PERFORIRANJE, gdje se mnoge rupe okruglog ili drugog oblika buše u limu prema određenom uzorku. Tipičan primjer za perforirani proizvod su metalni filtri s mnogo rupa za tekućine. U NOTCHING-u, još jednom procesu rezanja lima, uklanjamo materijal s obratka, počevši od ruba ili negdje drugdje i režemo prema unutra dok se ne dobije željeni oblik. To je progresivan proces gdje se svakom operacijom uklanja još jedan komad dok se ne dobije željena kontura. Za male proizvodne serije ponekad koristimo relativno sporiji proces koji se zove NIBBLING koji se sastoji od mnogih brzih probijanja rupa koje se preklapaju kako bi se napravio veći i složeniji rez. U PROGRESIVNOM REZANJU koristimo niz različitih operacija kako bismo dobili jedan rez ili određenu geometriju. Konačno, BRIJANJE sekundarni proces pomaže nam poboljšati rubove već napravljenih posjekotina. Koristi se za rezanje strugotina, grubih rubova na limu. • SAVIJANJE LIMOVA: Osim rezanja, savijanje je bitan proces bez kojeg ne bismo mogli proizvesti većinu proizvoda. Uglavnom rad na hladnom, ali ponekad se također izvodi kada je toplo ili vruće. Većinu vremena za ovu operaciju koristimo matrice i prešu. U PROGRESIVNOM SAVIJANJU koristimo niz različitih operacija probijanja i matrica kako bismo dobili jedno savijanje ili određenu geometriju. AGS-TECH koristi različite postupke savijanja i odabire ovisno o materijalu obratka, njegovoj veličini, debljini, željenoj veličini savijanja, polumjeru, zakrivljenosti i kutu savijanja, mjestu savijanja, ekonomičnosti rada, količinama koje treba proizvesti… itd. Koristimo V-SAVIJANJE gdje probijač u obliku slova V gura lim u matricu u obliku slova V i savija ga. Dobar i za vrlo oštre i za tupe kutove i između, uključujući 90 stupnjeva. Koristeći matrice za brisanje izvodimo SAVIJANJE RUBA. Naša oprema nam omogućuje dobivanje kutova i većih od 90 stupnjeva. Kod savijanja ruba izradak je u sendviču između tlačne podloge i matrice, područje za savijanje nalazi se na rubu matrice, a ostatak izratka drži se iznad space poput konzolne grede. Kada probijač djeluje na konzolni dio, on se savija preko ruba matrice. FLANGING je postupak savijanja rubova koji rezultira kutom od 90 stupnjeva. Glavni ciljevi operacije su eliminacija oštrih rubova i dobivanje geometrijskih površina za lakše spajanje dijelova. BEADING, još jedan uobičajeni postupak savijanja rubova oblikuje uvojak preko ruba dijela. OBRUB, s druge strane, rezultira rubom plahte koji je potpuno savijen na sebe. Kod SEAMING-a, rubovi dvaju dijelova savijaju se jedan na drugi i spajaju. DVOSTRUKO ŠAVOVANJE s druge strane osigurava vodonepropusne i zrakonepropusne spojeve lima. Slično savijanju rubova, proces koji se naziva ROTACIJSKO SAVIJANJE postavlja cilindar s izrezanim željenim kutom koji služi kao bušilica. Kako se sila prenosi na izbijač, on se zatvara s izratkom. Utor cilindra daje konzolnom dijelu željeni kut. Utor može imati kut manji ili veći od 90 stupnjeva. U ZRAČNOM SAVIJANJU ne trebamo da donji kalup ima utor pod kutom. Lim se oslanja na dvije površine na suprotnim stranama i na određenom razmaku. Probijač zatim primjenjuje silu na pravom mjestu i savija izradak. KANALNO SAVIJANJE se izvodi pomoću proboja i matrice u obliku kanala, a U-SAVIJANJE se postiže probijačem u obliku slova U. OFFSET BENDING proizvodi odstupanja na limu. SAVIJANJE VALJKOM, tehnika dobra za debele radove i savijanje velikih komada metalnih ploča, koristi tri valjka za uvlačenje i savijanje ploča do željenih zakrivljenosti. Role se slažu tako da se dobije željena krivina rada. Udaljenost i kut između valjaka se kontroliraju kako bi se dobio željeni rezultat. Pokretni valjak omogućuje kontrolu zakrivljenosti. OBLIKOVANJE CIJEVI još je jedna popularna operacija savijanja lima koja uključuje više matrica. Cijevi se dobivaju nakon višestrukih radnji. VALOVANJE se također izvodi operacijama savijanja. U osnovi to je simetrično savijanje u pravilnim razmacima preko cijelog komada lima. Za valovitost se mogu koristiti različiti oblici. Valoviti lim je čvršći i ima bolju otpornost na savijanje te stoga ima primjenu u građevinskoj industriji. OBLIKOVANJE LIMA U ROLAMA, kontinuirani proizvodni proces primjenjuje se za savijanje poprečnih presjeka određene geometrije pomoću valjaka, a rad se savija u uzastopnim koracima, pri čemu posljednji valjak dovršava posao. U nekim slučajevima koristi se jedna rola, au nekim slučajevima niz rola. • KOMBINIRANI PROCESI REZANJA I SAVIJANJA LIMA: Ovo su procesi koji istovremeno režu i savijaju. Kod PIERCINGA, rupa se stvara šiljastim probojcem. Kako probijač širi rupu u limu, materijal se istovremeno savija u unutarnju prirubnicu za rupu. Dobivena prirubnica može imati važne funkcije. Operacija LANCING s druge strane reže i savija lim kako bi se stvorila uzdignuta geometrija. • ISPUBLJIVANJE I SAVIJANJE METALNE CIJEVI: Kod IZBURAVANJA neki unutarnji dio šuplje cijevi je pod pritiskom, uzrokujući izbočenje cijevi prema van. Budući da je cijev unutar matrice, geometrija ispupčenja je kontrolirana oblikom matrice. Kod SAVIJANJA RAZTEZANJEM, metalna cijev se rasteže korištenjem sila paralelnih s osi cijevi i sila savijanja kako bi se cijev povukla preko bloka oplate. Kod DRAW BENDING-a, cijev stežemo blizu njenog kraja za rotirajući blok koji savija cijev dok se rotira. Na kraju, kod KOMPRESIJSKOG SAVIJANJA cijev se drži silom na fiksni blok oplate, a matrica je savija preko bloka oplate. • DUBOKO IZVUČENJE: U jednoj od naših najpopularnijih operacija koriste se probijač, odgovarajuća matrica i držač za slijepo. Obradak od lima postavlja se preko otvora matrice i probijač se pomiče prema izrezku koji drži držač za ploču. Nakon što dođu u kontakt, probojac tjera metalni lim u šupljinu matrice kako bi se formirao proizvod. Operacija dubokog izvlačenja nalikuje rezanju, međutim razmak između bušilice i matrice sprječava rezanje lima. Još jedan čimbenik koji osigurava da je lim duboko izvučen, a ne rezan, su zaobljeni kutovi na matrici i bušilici koji sprječavaju rezanje i rezanje. Da bi se postigla veća veličina dubokog izvlačenja, primjenjuje se proces PONOVNOG CRTANJA gdje se naknadno duboko izvlačenje odvija na dijelu koji je već prošao proces dubokog izvlačenja. Kod REVERSE REDRAWING, duboko nacrtani dio se okreće i crta u suprotnom smjeru. Duboko izvlačenje može pružiti objekte nepravilnog oblika kao što su kupolaste, sužene ili stepenaste čašice, U UTISIVANJU koristimo par muških i ženskih matrica kako bismo metalni lim otisnuli dizajnom ili tekstom. • SPINNING : Operacija u kojoj se ravni ili prethodno oblikovani obradak drži između rotirajuće igle i zadnjeg trupa, a alat primjenjuje lokalizirani pritisak na rad dok se postupno pomiče uz iglu. Kao rezultat, obradak je omotan preko trna i poprima njegov oblik. Ovu tehniku koristimo kao alternativu dubokom izvlačenju gdje je količina narudžbe mala, dijelovi veliki (promjera do 20 stopa) i imaju jedinstvene krivulje. Iako su cijene po komadu općenito više, troškovi postavljanja za CNC predenje su niski u usporedbi s dubokim izvlačenjem. Naprotiv, duboko izvlačenje zahtijeva velika početna ulaganja za postavljanje, ali troškovi po komadu su niski kada se proizvodi velika količina dijelova. Druga inačica ovog procesa je POSMIČNO PREDENJE, gdje također postoji strujanje metala unutar izratka. Strujanje metala smanjit će debljinu izratka tijekom izvođenja procesa. Još jedan srodni proces je TUBE SPINNING koji se primjenjuje na cilindrične dijelove. Također u ovom procesu dolazi do strujanja metala unutar obratka. Debljina se tako smanjuje, a duljina cijevi povećava. Alat se može pomicati kako bi se stvorile značajke na unutarnjoj ili vanjskoj strani cijevi. • GUMENO OBLIKOVANJE LIMA: Guma ili poliuretanski materijal stavlja se u spremnik i radni komad se postavlja na površinu gume. Zatim se na radni komad djeluje udarcem i gura ga u gumu. Budući da je pritisak koji stvara guma nizak, dubina proizvedenih dijelova je ograničena. Budući da su troškovi alata niski, postupak je prikladan za proizvodnju malih količina. • HIDROFORMIRANJE: Slično oblikovanju gume, u ovom se procesu metalni lim utiskuje probijačem u tekućinu pod pritiskom unutar komore. Radni lim je u sendviču između proboja i gumene dijafragme. Dijafragma u potpunosti okružuje obradak i pritisak tekućine ga tjera da se oblikuje na izbijaču. Ovom se tehnikom mogu postići vrlo duboki crteži čak dublji nego u procesu dubokog crtanja. Proizvodimo matrice s jednim probijanjem kao i progresivne matrice ovisno o vašem dijelu. Jednostruke matrice za utiskivanje isplativa su metoda za brzu proizvodnju velikih količina jednostavnih dijelova od lima kao što su podloške. Progresivne matrice ili tehnika dubokog izvlačenja koriste se za izradu složenijih geometrija. Ovisno o vašem slučaju, rezanje vodenim mlazom, laserom ili plazmom može se koristiti za jeftinu, brzu i točnu izradu vaših dijelova od lima. Mnogi dobavljači nemaju pojma o ovim alternativnim tehnikama ili ih nemaju i stoga prolaze kroz dugotrajne i skupe načine izrade matrica i alata koji kupcima samo gube vrijeme i novac. Ako su vam potrebni dijelovi od lima izrađeni po narudžbi kao što su kućišta, elektronička kućišta... itd., i to u roku od nekoliko dana, kontaktirajte nas za našu uslugu BRZE IZRADE PROTOTIPA OD LIMA. CLICK Product Finder-Locator Service PRETHODNI JELOVNIK
- Plastic Rubber Metal Extrusions, Extrusion Dies, Aluminum Extruding
Plastic Rubber Metal Extrusions, Extrusion Dies, Aluminum Extruding, Pipe Tube Forming, Plastic Profiles, Metal Profiles Manufacturing, PVC at AGS-TECH Inc. Ekstruzije, ekstrudirani proizvodi, ekstrudati Koristimo proces EXTRUSION process za proizvodnju proizvoda s fiksnim profilom poprečnog presjeka kao što su cijevi, cijevi i hladnjaki. Iako se mnogi materijali mogu ekstrudirati, naši najčešći ekstruziji su izrađeni od metala, polimera/plastike, keramike dobiveni hladnom, toplom ili vrućom metodom ekstruzije. Ekstrudirane dijelove nazivamo ekstrudatom ili ekstrudatima u množini. Neke specijalizirane verzije procesa koje također izvodimo su presvlaka, koekstruzija i složena ekstruzija. Preporučujemo da kliknete ovdje na PREUZMITE naše shematske ilustracije procesa ekstruzije metalne keramike i plastike tvrtke AGS-TECH Inc. To će vam pomoći da bolje razumijete informacije koje vam dajemo u nastavku. Kod ekstruzije materijal koji se ekstrudira gura se ili izvlači kroz matricu koja ima željeni profil poprečnog presjeka. Proces se može koristiti za izradu složenih poprečnih presjeka s izvrsnom završnom obradom površine i za rad na krhkom materijalu. Ovim se postupkom mogu proizvesti dijelovi bilo koje duljine. Da biste pojednostavili korake procesa: 1.) Kod toplih ili vrućih ekstruzija materijal se zagrijava i stavlja u spremnik u preši. Materijal se preša i istiskuje iz matrice. 2.) Proizvedeni ekstrudat se rasteže radi ravnanja, toplinski ili hladno obrađuje radi poboljšanja njegovih svojstava. S druge strane COLD EXTRUSION odvija se na otprilike sobnoj temperaturi i ima prednosti manje oksidacije, visoke čvrstoće, manjih tolerancija, dobre završne obrade površine i postojanosti. WARM EXTRUSION izvodi se iznad sobne temperature, ali ispod točke rekristalizacije. Nudi kompromis i ravnotežu za potrebne sile, duktilnost i svojstva materijala i stoga je izbor za neke primjene. HOT EXTRUSION odvija se iznad temperature rekristalizacije materijala. Na taj način je lakše gurati materijal kroz matricu. Međutim, cijena opreme je visoka. Što je složeniji ekstrudirani profil, to je skuplji kalup (alat) i niža je stopa proizvodnje. Presjeci kalupa kao i debljine imaju ograničenja koja ovise o materijalu koji se ekstrudira. Oštri kutovi u kalupima za ekstruziju uvijek su nepoželjni i treba ih izbjegavati osim ako je neophodno. Prema materijalu koji se ekstrudira nudimo: • METALNI EKSTRUZIJE : Najčešći proizvodi koje proizvodimo su aluminij, mesing, cink, bakar, čelik, titan, magnezij • EKSTRUZIJA PLASTIKE : Plastika se topi i oblikuje u kontinuirani profil. Naši uobičajeni materijali koje obrađujemo su polietilen, najlon, polistiren, polivinil klorid, polipropilen, ABS plastika, polikarbonat, akril. Tipični proizvodi koje proizvodimo uključuju cijevi i cijevi, plastične okvire. U procesu se male plastične kuglice/smola gravitacijom unose iz spremnika u bačvu stroja za ekstruziju. Često također miješamo bojila ili druge aditive u spremnik kako bismo proizvodu dali potrebne specifikacije i svojstva. Rotirajući vijak tjera materijal koji ulazi u grijanu bačvu da napusti bačvu na kraju i kreće se kroz sito za uklanjanje kontaminanata u rastaljenoj plastici. Nakon što prođe sito, plastika ulazi u matricu za ekstruziju. Matrica daje pokretnoj mekoj plastici oblik profila dok prolazi kroz nju. Sada ekstrudat prolazi kroz vodenu kupelj radi hlađenja. Druge tehnike koje tvrtka AGS-TECH Inc. koristi dugi niz godina su: • EKSTRUZIJA CIJEVI I CIJEVI : Plastične cijevi i cijevi nastaju kada se plastika istisne kroz okruglu matricu za oblikovanje i ohladi u vodenoj kupelji, zatim izreže na određenu duljinu ili namota na kalem. Prozirni ili u boji, prugasti, s jednom ili dvije stijenke, fleksibilni ili kruti, PE, PP, poliuretan, PVC, najlon, PC, silikon, vinil ili drugi, imamo sve. Imamo opskrbljene cijevi kao i mogućnost proizvodnje prema vašim specifikacijama. AGS-TECH proizvodi cijevi prema zahtjevima FDA, UL i LE za medicinske, električne i elektroničke, industrijske i druge primjene. • PREKO JACKETING / OVER JACKETING EXTRUSION : Ova tehnika nanosi vanjski sloj plastike na postojeću žicu ili kabel. Naše izolacijske žice proizvode se ovom metodom. • COEXTRUSION : Više slojeva materijala se istiskuje istovremeno. Više slojeva isporučuje više ekstrudera. Različite debljine slojeva mogu se prilagoditi zahtjevima kupaca. Ovaj postupak omogućuje korištenje više polimera od kojih svaki ima različitu funkcionalnost u proizvodu. Kao rezultat toga, može se optimizirati niz svojstava. • EKSTRUDIJA SPOJEVA: jedan ili više polimera miješaju se s dodacima kako bi se dobila plastična smjesa. Naši dvopužni ekstruderi proizvode ekstruzije za miješanje. Kalupi za istiskivanje općenito su jeftini u usporedbi s metalnim kalupima. Ako plaćate puno više od nekoliko tisuća dolara za malu ili srednju matricu za ekstrudiranje aluminija, vjerojatno plaćate previše. Mi smo stručnjaci u određivanju koja je tehnika najisplativija, najbrža i najprikladnija za vašu primjenu. Ponekad vam ekstrudiranje i zatim strojna obrada dijela može uštedjeti mnogo novca. Prije donošenja čvrste odluke prvo nas pitajte za naše mišljenje. Pomogli smo mnogim kupcima da donesu ispravne odluke. Za neke naširoko korištene metalne ekstruzije možete preuzeti naše brošure i kataloge klikom na tekst u boji ispod. Ako je to gotov proizvod koji zadovoljava vaše zahtjeve, bit će ekonomičniji. Preuzmite naše mogućnosti ekstruzije medicinskih cijevi i cijevi Preuzmite naše ekstrudirane hladnjake • SEKUNDARNI PROCESI PROIZVODNJE I PROIZVODNJE ZA EKSTRUZIJE : Među procesima dodane vrijednosti koje nudimo za ekstrudirane proizvode su: -Savijanje cijevi i cijevi po narudžbi, oblikovanje i oblikovanje, rezanje cijevi, oblikovanje krajeva cijevi, namotavanje cijevi, strojna obrada i završna obrada, bušenje rupa, bušenje i probijanje, -Sklopovi cijevi i cijevi po narudžbi, cijevni sklopovi, zavarivanje, lemljenje i lemljenje -Prilagođeno ekstruzijsko savijanje, oblikovanje i oblikovanje -Čišćenje, odmašćivanje, dekapiranje, pasiviranje, poliranje, anodiziranje, pozlaćivanje, bojanje, toplinska obrada, žarenje i kaljenje, označavanje, graviranje i označavanje, pakiranje po narudžbi. CLICK Product Finder-Locator Service PRETHODNA STRANICA
- Casting and Machined Parts, CNC Manufacturing, Milling, Turning, Swiss
Casting and Machined Parts, CNC Manufacturing, Milling, Turning, Swiss Type Machining, Die Casting, Investment Casting, Lost Foam Cast Parts from AGS-TECH Inc. Lijevanje i strojna obrada Naše prilagođene tehnike lijevanja i strojne obrade su potrošni i jednokratni odljevci, željezni i neželjezni lijevi, pijesak, kalupi, centrifugalni, kontinuirani, keramički kalupi, ulaganje, izgubljena pjena, gotovo neto oblik, trajni kalupi (gravitacijski tlačni lijev), gips kalupi (gipsani odljevi) i odljevci ljuski, strojno obrađeni dijelovi proizvedeni glodanjem i tokarenjem pomoću konvencionalne kao i CNC opreme, švicarski tip strojne obrade za visoku propusnost, jeftini mali precizni dijelovi, obrada vijaka za spojne elemente, nekonvencionalna strojna obrada. Imajte na umu da osim metala i metalnih legura, strojno obrađujemo i keramičke, staklene i plastične komponente u nekim slučajevima kada izrada kalupa nije privlačna ili nije opcija. Strojna obrada polimernih materijala zahtijeva specijalizirano iskustvo koje imamo zbog izazova koji predstavljaju plastika i guma zbog svoje mekoće, nekrutosti... itd. Za strojnu obradu keramike i stakla pogledajte našu stranicu o nekonvencionalnoj izradi. AGS-TECH Inc. proizvodi i isporučuje lake i teške odljevke. Isporučujemo metalne odljevke i strojno obrađene dijelove za kotlove, izmjenjivače topline, automobile, mikromotore, vjetroturbine, opremu za pakiranje hrane i još mnogo toga. Preporučujemo da kliknete ovdje na PREUZMITE naše shematske ilustracije procesa strojne obrade i lijevanja tvrtke AGS-TECH Inc. To će vam pomoći da bolje razumijete informacije koje vam dajemo u nastavku. Pogledajmo detaljno neke od različitih tehnika koje nudimo: • LIJEVANJE U POTROŠNIM KALUPIMA: Ova široka kategorija odnosi se na metode koje uključuju privremene kalupe za jednokratnu upotrebu. Primjeri su pijesak, gips, ljuska, materijal za ulaganje (koji se naziva i izgubljeni vosak) i odljevak od gipsa. • LIJEVANJE U PIJESKU: proces u kojem se pijesak koristi kao materijal kalupa. Vrlo stara metoda i još uvijek vrlo popularna do te mjere da se većina proizvedenih metalnih odljevaka izrađuje ovom tehnikom. Niska cijena čak i pri maloj količini proizvodnje. Pogodan za proizvodnju malih i velikih dijelova. Tehnika se može koristiti za proizvodnju dijelova u roku od nekoliko dana ili tjedana uz vrlo malo ulaganja. Vlažni pijesak spaja se pomoću gline, veziva ili posebnih ulja. Pijesak se općenito nalazi u kalupnim kutijama, a sustav šupljina i vrata nastaje zbijanjem pijeska oko modela. Procesi su: 1.) Postavljanje modela u pijesak za izradu kalupa 2.) Ugradnja modela i pijeska u sustav okretanja 3.) Uklanjanje modela 4.) Ispunjavanje kalupne šupljine rastaljenim metalom 5.) Hlađenje metala 6.) Razbijanje pješčanog kalupa i skidanje odljevka • LIJEVANJE U KALUPU SAPSA: Slično lijevanju u pijesak, a umjesto pijeska, kao materijal za kalupe koristi se pariški gips. Kratko vrijeme proizvodnje poput lijevanja u pijesak i jeftino. Dobre tolerancije dimenzija i površinske obrade. Njegov glavni nedostatak je što se može koristiti samo s metalima niske točke taljenja kao što su aluminij i cink. • LIJEVANJE U KALUP ZA LJUSKE: Također slično lijevanju u pijesak. Šupljina kalupa dobivena stvrdnutom ljuskom od pijeska i vezivom od termoreaktivne smole umjesto posude ispunjene pijeskom kao u postupku lijevanja u pijesak. Gotovo svaki metal prikladan za lijevanje u pijesku može se lijevati ljuskastim kalupljenjem. Proces se može sažeti kao: 1.) Izrada kalupa za ljuske. Upotrijebljeni pijesak ima puno manju veličinu zrna u usporedbi s pijeskom koji se koristi za lijevanje u pijesak. Sitni pijesak pomiješan je s termoreaktivnom smolom. Metalni uzorak premazan je sredstvom za razdvajanje kako bi se olakšalo uklanjanje školjke. Nakon toga se metalni uzorak zagrijava, a mješavina pijeska se posipa ili upuhuje na vrući uzorak za lijevanje. Na površini uzorka formira se tanka ljuska. Debljina ove ljuske može se podesiti mijenjanjem vremena u kojem je mješavina smole pijeska u kontaktu s metalnim uzorkom. Rahli pijesak se zatim uklanja s preostalim uzorkom prekrivenim školjkama. 2.) Zatim se ljuska i šara zagriju u pećnici da se ljuska stvrdne. Nakon završetka stvrdnjavanja, školjka se izbacuje iz uzorka pomoću klinova ugrađenih u uzorak. 3.) Dvije takve ljuske spajaju se lijepljenjem ili stezanjem i čine kompletan kalup. Sada se kalup za ljusku umeće u spremnik u kojem se tijekom procesa lijevanja oslanja na pijesak ili metalnu česticu. 4.) Sada se vrući metal može izliti u kalup za ljusku. Prednosti ljuskavog lijevanja su proizvodi s vrlo dobrom završnom obradom površine, mogućnost izrade složenih dijelova s visokom preciznošću dimenzija, proces koji se lako automatizira, ekonomičan za proizvodnju velikih količina. Nedostaci su da kalupi zahtijevaju dobru ventilaciju zbog plinova koji se stvaraju kada rastaljeni metal dođe u kontakt s vezivnom kemikalijom, termoreaktivne smole i metalni uzorci su skupi. Zbog cijene metalnih uzoraka, tehnika možda neće dobro odgovarati za male količine proizvodnje. • LIJEVANJE PO TOVORU (također poznato kao LIJEVANJE IZ VOSKA): Također vrlo stara tehnika i prikladna za proizvodnju kvalitetnih dijelova visoke točnosti, ponovljivosti, svestranosti i cjelovitosti od mnogih metala, vatrostalnih materijala i posebnih legura visokih performansi. Mogu se proizvesti dijelovi malih i velikih dimenzija. Skup proces u usporedbi s nekim drugim metodama, ali glavna prednost je mogućnost proizvodnje dijelova gotovo neto oblika, zamršenih kontura i detalja. Dakle, trošak je donekle nadoknađen eliminacijom prerade i strojne obrade u nekim slučajevima. Iako mogu postojati varijacije, ovdje je sažetak općeg procesa lijevanja uloškom: 1.) Izrada originalnog glavnog uzorka od voska ili plastike. Svaki odljevak treba jedan uzorak jer se oni uništavaju u procesu. Također je potreban kalup iz kojeg se izrađuju uzorci, a najčešće se kalup lijeva ili obrađuje. Budući da kalup ne treba otvarati, mogu se postići složeni odljevci, mnogi voštani uzorci mogu se povezati poput grana drveta i izliti zajedno, čime se omogućuje izrada više dijelova iz jednog lijevanja metala ili metalne legure. 2.) Zatim se uzorak umoči ili prelije vatrostalnom smjesom koja se sastoji od vrlo fino zrnatog silicija, vode, veziva. To rezultira keramičkim slojem na površini uzorka. Vatrostalni premaz na uzorku ostavimo da se osuši i stvrdne. Od ovog koraka dolazi naziv livenje za ulaganje: Vatrostalna kaša se ulaže preko voštanog uzorka. 3.) U ovom koraku se stvrdnuti keramički kalup okreće naopako i zagrijava da se vosak otopi i izlije iz kalupa. Ostavljena je šupljina za metalni odljev. 4.) Nakon što je vosak izašao, keramički kalup se zagrijava na još višu temperaturu što rezultira učvršćivanjem kalupa. 5.) Metalni odljevak se ulijeva u vrući kalup ispunjavajući sve zamršene dijelove. 6.) Pusti se da se odljevak skrutne 7.) Konačno se keramički kalup lomi i proizvedeni dijelovi se režu sa stabla. Ovdje je poveznica na brošuru postrojenja za livenje u kalupe • LIJEVANJE ISPARIVAČKOG UZORCA: Proces koristi uzorak izrađen od materijala kao što je polistirenska pjena koja će ispariti kada se vrući rastaljeni metal izlije u kalup. Postoje dvije vrste ovog procesa: LIJEVANJE IZ GUBLJENE PJENE koje koristi nevezani pijesak i LIJEVANJE U PUNOM KALUPU koje koristi vezani pijesak. Evo općih koraka procesa: 1.) Izradite uzorak od materijala kao što je polistiren. Kada će se proizvoditi velike količine, uzorak se oblikuje. Ako dio ima složen oblik, nekoliko dijelova takvog pjenastog materijala možda će biti potrebno zalijepiti zajedno kako bi se formirao uzorak. Često premazujemo uzorak vatrostalnom smjesom kako bismo stvorili dobru završnu obradu površine odljevka. 2.) Uzorak se zatim stavlja u kalupni pijesak. 3.) Rastaljeni metal se ulijeva u kalup, isparavajući pjenasti uzorak, tj. polistiren u većini slučajeva dok teče kroz šupljinu kalupa. 4.) Rastaljeni metal ostavlja se u pješčanom kalupu da se stvrdne. 5.) Nakon što se stvrdne, skidamo odljev. U nekim slučajevima, proizvod koji proizvodimo zahtijeva jezgru unutar uzorka. Kod lijevanja isparavanjem nema potrebe za postavljanjem i pričvršćivanjem jezgre u šupljinu kalupa. Tehnika je prikladna za izradu vrlo složenih geometrija, može se lako automatizirati za proizvodnju velikih količina, au lijevanom dijelu nema rastavnih linija. Osnovni postupak je jednostavan i ekonomičan za provedbu. Za proizvodnju velikih količina, budući da je potrebna matrica ili kalup za izradu uzoraka od polistirena, to može biti donekle skupo. • LIJEVANJE U NEEKSPANDIDNOM KALUPU: Ova široka kategorija odnosi se na metode kod kojih se kalup ne mora reformirati nakon svakog proizvodnog ciklusa. Primjeri su trajno, kokilno, kontinuirano i centrifugalno lijevanje. Postiže se ponovljivost i dijelovi se mogu okarakterizirati kao BLIZU NETO OBLIKA. • TRAJNO LIJEVANJE U KALUP: Kalupi za višekratnu upotrebu izrađeni od metala koriste se za višestruke odljevke. Trajni kalup općenito se može koristiti desetke tisuća puta prije nego što se istroši. Gravitacija, tlak plina ili vakuum općenito se koriste za punjenje kalupa. Kalupi (koji se nazivaju i kalupi) općenito su izrađeni od željeza, čelika, keramike ili drugih metala. Opći proces je sljedeći: 1.) Strojno obradite i izradite kalup. Uobičajeno je obraditi kalup od dva metalna bloka koji pristaju zajedno i mogu se otvarati i zatvarati. I značajke dijela, kao i sustav zatvarača općenito se strojno obrađuju u kalup za lijevanje. 2.) Unutarnje površine kalupa obložene su kašom koja sadrži vatrostalne materijale. To pomaže u kontroli protoka topline i djeluje kao lubrikant za jednostavno uklanjanje lijevanog dijela. 3.) Zatim se trajne polovice kalupa zatvore i kalup se zagrijava. 4.) Rastaljeni metal se izlije u kalup i ostavi da se skrutne. 5.) Prije nego što dođe do većeg hlađenja, uklanjamo dio iz trajnog kalupa pomoću ejektora kada se polovice kalupa otvore. Često koristimo trajno lijevanje u kalupe za metale niske točke taljenja kao što su cink i aluminij. Za čelične odljevke koristimo grafit kao materijal za kalupe. Ponekad dobivamo složene geometrije pomoću jezgri unutar trajnih kalupa. Prednosti ove tehnike su odljevci s dobrim mehaničkim svojstvima dobivenim brzim hlađenjem, ujednačenost svojstava, dobra točnost i završna obrada površine, niske stope odbacivanja, mogućnost automatizacije procesa i ekonomična proizvodnja velikih količina. Nedostaci su visoki početni troškovi postavljanja koji ga čine neprikladnim za male količine rada i ograničenja u veličini proizvedenih dijelova. • LIJEVANJE U TLAKU: Kalup se strojno obrađuje i rastaljeni metal se pod visokim pritiskom gura u šupljine kalupa. Mogući su tlačni odljevci obojenih i željeznih metala. Proces je prikladan za velike količine proizvodnje malih do srednjih dijelova s detaljima, izuzetno tankim stijenkama, konzistentnošću dimenzija i dobrom završnom obradom površine. AGS-TECH Inc. je sposoban proizvesti zidove debljine od samo 0,5 mm koristeći ovu tehniku. Kao i kod trajnog lijevanja u kalupe, kalup se mora sastojati od dvije polovice koje se mogu otvarati i zatvarati radi uklanjanja proizvedenog dijela. Kalup za tlačni lijev može imati više šupljina kako bi se omogućila proizvodnja više odljevaka u svakom ciklusu. Kalupi za tlačni lijev su vrlo teški i puno veći od dijelova koje proizvode, stoga su i skupi. Popravljamo i zamjenjujemo istrošene matrice besplatno za naše klijente sve dok ponovno naruče svoje dijelove od nas. Naši matrice imaju dug životni vijek u rasponu od nekoliko stotina tisuća ciklusa. Ovo su osnovni pojednostavljeni koraci procesa: 1.) Proizvodnja kalupa općenito od čelika 2.) Kalup instaliran na stroju za tlačni lijev 3.) Klip tjera rastaljeni metal da teče u šupljinama kalupa ispunjavajući zamršene karakteristike i tanke stijenke 4.) Nakon punjenja kalupa rastaljenim metalom, odljevak se ostavlja da očvrsne pod pritiskom 5.) Kalup se otvara i odljevak vadi pomoću klinova za izbacivanje. 6.) Sada se prazna matrica ponovno podmazuje i pričvršćuje za sljedeći ciklus. U tlačnom lijevanju često koristimo umetnuto kalupljenje gdje ugrađujemo dodatni dio u kalup i lijevamo metal oko njega. Nakon skrućivanja ti dijelovi postaju dio lijevanog proizvoda. Prednosti tlačnog lijevanja su dobra mehanička svojstva dijelova, mogućnost zamršenih karakteristika, finih detalja i dobre površinske obrade, visoke proizvodne stope, laka automatizacija. Nedostaci su: Nije baš prikladno za mali volumen zbog visoke cijene matrice i opreme, ograničenja u oblicima koji se mogu lijevati, male okrugle oznake na lijevanim dijelovima koje proizlaze iz kontakta ejektorskih igala, tanki komadić metala istisnut na liniji razdvajanja, potreba za ventilacijske otvore duž linije razdvajanja između kalupa, potreba za održavanjem niske temperature kalupa pomoću cirkulacije vode. • CENTRIFUGALNO LIJEVANJE: Rastaljeni metal se ulijeva u središte rotirajućeg kalupa na osi rotacije. Centrifugalne sile bacaju metal prema periferiji i ostavljaju ga da se skrutne dok se kalup neprestano okreće. Mogu se koristiti i vodoravna i okomita rotacija osi. Mogu se lijevati dijelovi s okruglim unutarnjim površinama kao i drugi neokrugli oblici. Proces se može sažeti kao: 1.) Rastaljeni metal se ulijeva u centrifugalni kalup. Metal se zatim gura prema vanjskim stijenkama zbog vrtnje kalupa. 2.) Kako se kalup okreće, metalni odljevak se stvrdnjava Centrifugalno lijevanje je prikladna tehnika za proizvodnju šupljih cilindričnih dijelova kao što su cijevi, nema potrebe za kanalima, usponima i elementima za zatvaranje, dobra završna obrada površine i detaljne značajke, nema problema sa skupljanjem, mogućnost proizvodnje dugih cijevi s vrlo velikim promjerima, sposobnost visoke brzine proizvodnje . • KONTINUIRANI LIJEVANJE ( LIJEVANJE UŽAKA ): Koristi se za lijevanje metala u kontinuiranoj duljini. U osnovi se rastaljeni metal lijeva u dvodimenzionalni profil kalupa, ali je njegova duljina neodređena. Novi rastaljeni metal neprestano se dovodi u kalup dok odljevak putuje prema dolje, a njegova se duljina s vremenom povećava. Metali kao što su bakar, čelik, aluminij lijevaju se u dugačke niti pomoću procesa kontinuiranog lijevanja. Proces može imati različite konfiguracije, ali zajednička se može pojednostaviti kao: 1.) Rastaljeni metal se ulijeva u spremnik koji se nalazi visoko iznad kalupa u dobro izračunatim količinama i brzinama protoka te teče kroz vodom hlađeni kalup. Metalni odljevak izliven u kalup skrućuje se na početnu šipku postavljenu na dno kalupa. Ova početna traka daje valjcima nešto za što se u početku mogu uhvatiti. 2.) Dugu metalnu nit nose valjci konstantnom brzinom. Valjci također mijenjaju smjer toka metalne niti iz okomitog u vodoravni. 3.) Nakon što je kontinuirani odljev prešao određenu horizontalnu udaljenost, plamenik ili pila koja se kreće s odljevkom brzo ga reže na željene duljine. Proces kontinuiranog lijevanja može se integrirati s POSTUPKOM VALJANJA, gdje se kontinuirano lijevani metal može unijeti izravno u valjaonicu za proizvodnju I-greda, T-greda… itd. Kontinuirano lijevanje proizvodi ujednačena svojstva u cijelom proizvodu, ima visoku stopu skrućivanja, smanjuje troškove zbog vrlo malog gubitka materijala, nudi proces u kojem se punjenje metala, lijevanje, skrućivanje, rezanje i uklanjanje lijevanja odvijaju u kontinuiranom radu i što rezultira visokom stopom produktivnosti i visokom kvalitetom. Međutim, glavno razmatranje je veliko početno ulaganje, troškovi postavljanja i zahtjevi za prostorom. • USLUGE STROJNE OBRADE: Nudimo tri, četiri i pet osi strojne obrade. Vrste obradnih procesa koje koristimo su TOKARENJE, GLODANJE, BUŠENJE, PROBUŠIVANJE, PROVIRANJE, BLANJANJE, PILENJE, BRUŠENJE, LEPANJE, POLIRANJE i NETRADICIONALNA STROJNA OBRADA koja je dalje razrađena u drugom izborniku naše web stranice. Za većinu naše proizvodnje koristimo CNC strojeve. Međutim, za neke operacije konvencionalne tehnike bolje odgovaraju i stoga se oslanjamo i na njih. Naše mogućnosti strojne obrade dosežu najvišu moguću razinu, a neki najzahtjevniji dijelovi se proizvode u tvornici s certifikatom AS9100. Lopatice mlaznog motora zahtijevaju visoko specijalizirano iskustvo u proizvodnji i odgovarajuću opremu. Zrakoplovna industrija ima vrlo stroge standarde. Neke komponente sa složenom geometrijskom strukturom najlakše je proizvesti petoosnom strojnom obradom, koja se nalazi samo u nekim pogonima za strojnu obradu, uključujući i našu. Naša zrakoplovno-svemirska certificirana tvornica ima potrebno iskustvo u skladu s opsežnim dokumentacijskim zahtjevima zrakoplovne industrije. U operacijama TOKARENJE obradak se okreće i pomiče prema alatu za rezanje. Za ovaj proces koristi se stroj koji se zove strug. U GLODALJU, stroj koji se naziva glodalica ima rotirajući alat koji dovodi rezne rubove na radni komad. Operacije BUŠENJA uključuju rotirajući rezač s oštricama koje stvaraju rupe nakon kontakta s radnim komadom. Općenito se koriste bušilice, tokarilice ili glodalice. U operacijama BUŠENJA alat s jednim savijenim šiljastim vrhom pomiče se u grubu rupu u izratku koji se vrti kako bi se malo povećala rupa i poboljšala točnost. Koristi se za finu završnu obradu. PROVIRANJE uključuje nazubljeni alat za uklanjanje materijala s izratka u jednom prolazu provlačenja (nazubljeni alat). Kod linearnog provlačenja, provlaka ide linearno uz površinu obratka kako bi izvršila rez, dok se kod rotacijskog provlačenja provlaka okreće i utiskuje u obradak kako bi se izrezao oblik simetričan po osi. SWISS TYPE MACHINING je jedna od naših vrijednih tehnika koje koristimo za proizvodnju velikih količina malih i visoko preciznih dijelova. Koristeći tokarski stroj švicarskog tipa, jeftino tokarimo male, složene, precizne dijelove. Za razliku od konvencionalnih tokarilica kod kojih se obradak drži nepomično, a alat se kreće, u centrima za tokarenje švicarskog tipa izradak se može pomicati u Z-osi, a alat je nepomičan. U obradi švicarskog tipa, materijal šipke se drži u stroju i pomiče kroz čahuru za vođenje u osi z, izlažući samo dio koji se obrađuje. Na taj način je osiguran čvrsti stisak i vrlo visoka točnost. Dostupnost alata pod naponom daje mogućnost glodanja i bušenja kako materijal napreduje iz čahure vodilice. Y-os opreme švicarskog tipa pruža pune mogućnosti glodanja i štedi veliku količinu vremena u proizvodnji. Nadalje, naši strojevi imaju bušilice i alate za bušenje koji rade na dijelu kada se drži u pomoćnom vretenu. Naša mogućnost strojne obrade švicarskog tipa daje nam mogućnost potpuno automatizirane strojne obrade u jednoj operaciji. Strojna obrada je jedan od najvećih segmenata poslovanja AGS-TECH Inc. Koristimo ga ili kao primarnu operaciju ili kao sekundarnu operaciju nakon lijevanja ili ekstrudiranja dijela tako da su ispunjene sve specifikacije crteža. • USLUGE ZAVRŠNE OBRADE POVRŠINA: Nudimo veliki izbor površinskih obrada i završne obrade površine kao što je kondicioniranje površine za poboljšanje prianjanja, nanošenje tankog oksidnog sloja za poboljšanje prianjanja premaza, pjeskarenje, kemijski film, eloksiranje, nitriranje, premazivanje prahom, premazivanje raspršivanjem , razne napredne tehnike metalizacije i presvlačenja, uključujući raspršivanje, elektronski snop, isparavanje, galvanizaciju, tvrde prevlake kao što je dijamant poput ugljika (DLC) ili prevlaka od titana za alate za bušenje i rezanje. • USLUGE OZNAČAVANJA I OZNAČAVANJA PROIZVODA: Mnogi naši kupci zahtijevaju označavanje i označavanje, lasersko označavanje, graviranje na metalnim dijelovima. Ako imate bilo kakvu takvu potrebu, dopustite nam da razgovaramo koja bi opcija bila najbolja za vas. Ovdje su neki od često korištenih proizvoda od lijevanog metala. Budući da su gotove, možete uštedjeti na troškovima kalupa u slučaju da nešto od ovoga odgovara vašim zahtjevima: KLIKNITE OVDJE ZA PREUZIMANJE naših 11 serija kutija od tlačno lijevanog aluminija iz AGS-Electronics CLICK Product Finder-Locator Service PRETHODNA STRANICA
- Custom Manufactured Parts, Assemblies, Plastic Mold, Casting,Machining
Custom Manufactured Parts, Assemblies, Plastic Mold, Rubber Molding, Metal Casting, CNC Machining, Turning, Milling, Electrical Electronic Optical Assembly PCBA Dijelovi proizvedeni po narudžbi & Sklopovi i proizvodi Čitaj više Plastični i gumeni kalupi i kalupi Čitaj više Lijevanje i strojna obrada Čitaj više Ekstruzije, ekstrudirani proizvodi Čitaj više Štancanje i proizvodnja limova Čitaj više Kovanje metala i metalurgija praha Čitaj više Oblikovanje žice i opruga Čitaj više Oblikovanje i oblikovanje stakla i keramike Čitaj više Aditivna i brza proizvodnja Čitaj više Kompoziti i proizvodnja kompozitnih materijala Čitaj više Postupci spajanja, montaže i pričvršćivanja Proizvodimo dijelove i sklopove za vas i nudimo sljedeće proizvodne procese: • Plastični i gumeni kalupi i lijevani dijelovi. Injekcijsko prešanje, termooblikovanje, duroplastičko prešanje, vakuumsko oblikovanje, puhanje, rotacijsko prešanje, izlijevanje, umetanje u prešanje i drugo. • Ekstruzije od plastike, gume i metala • Odljevci od željeza i obojenih metala i strojno obrađeni dijelovi proizvedeni tehnikama glodanja i tokarenja, strojna obrada švicarskog tipa. • Dijelovi za metalurgiju praha • Štancanje metala i nemetala, oblikovanje lima, zavareni sklopovi lima • Hladno i toplo kovanje • Žice, sklopovi zavarene žice, oblikovanje žice • Razne vrste opruga, oblikovanje opruga • Proizvodnja zupčanika, mjenjač, spojka, puž, reduktor brzine, cilindar, prijenosni remeni, prijenosni lanci, komponente prijenosa • Prilagođeno kaljeno i neprobojno staklo u skladu s NATO i vojnim standardima • Kuglice, ležajevi, remenice i sklopovi remenica • Ventili i pneumatske komponente kao što su O-prsten, podloška i brtve • Stakleni i keramički dijelovi i sklopovi, vakumski otporne i hermetičke komponente, spajanje metal-keramika i keramika-keramika. • Razne vrste mehaničkih, optomehaničkih, elektromehaničkih, optoelektroničkih sklopova. • Veza metal-guma, metal-plastika • Cijevi, oblikovanje cijevi, savijanje i sklopovi cijevi po narudžbi, proizvodnja mijehova. • Proizvodnja stakloplastike • Zavarivanje različitim tehnikama kao što su točkasto zavarivanje, lasersko zavarivanje, MIG, TIG. Ultrazvučno zavarivanje plastičnih dijelova. • Veliki izbor površinskih obrada i završnih obrada površina kao što je kondicioniranje površine za poboljšanje prianjanja, nanošenje tankog oksidnog sloja za poboljšanje prianjanja premaza, pjeskarenje, kemijski film, eloksiranje, nitriranje, premazivanje prahom, premazivanje raspršivanjem, razne napredne tehnike metalizacije i premazivanja uključujući raspršivanje, elektronski snop, isparavanje, oplata, tvrde prevlake kao što je dijamant poput ugljika (DLC) ili titan za alate za rezanje i bušenje. • Označavanje i etiketiranje, lasersko označavanje na metalne dijelove, tisak na plastične i gumene dijelove Preuzmite brošuru za zajedničke pojmove strojarstva koje koriste dizajneri i inženjeri Izrađujemo proizvode prema vašim posebnim specifikacijama i zahtjevima. Kako bismo vam ponudili najbolju kvalitetu, dostavu i cijene, proizvode proizvodimo globalno u Kini, Indiji, Tajvanu, Filipinima, Južnoj Koreji, Maleziji, Šri Lanki, Turskoj, SAD-u, Kanadi, Njemačkoj, Velikoj Britaniji i Japanu. To nas čini puno jačim i globalno konkurentnijim od bilo kojeg drugog custom proizvođača. Naši proizvodi proizvedeni su u ISO9001:2000, QS9000, ISO14001, TS16949 certificiranim okruženjima te posjeduju oznaku CE, UL i zadovoljavaju druge industrijske standarde. Nakon što smo imenovani za vaš projekt, možemo se pobrinuti za cjelokupnu proizvodnju, montažu, testiranje, kvalifikaciju, otpremu i carinu po vašoj želji. Ako želite, možemo skladištiti vaše dijelove, sastaviti prilagođene setove, ispisati i označiti naziv i marku vaše tvrtke i isporučiti ih vašim kupcima. Drugim riječima, po želji možemo biti i vaš centar za skladištenje i distribuciju. S obzirom da se naša skladišta nalaze u blizini velikih morskih luka, to nam daje logističku prednost. Na primjer, kada vaši proizvodi stignu u veliku morsku luku SAD-a, možemo prevesti ih izravno u obližnje skladište gdje možemo pohraniti, sastaviti, izraditi komplete, ponovno označiti, ispisati, pakirati prema vašem izboru i ostaviti isporučite svojim kupcima. Ne isporučujemo samo proizvode. Naša tvrtka radi na prilagođenim ugovorima gdje dolazimo na vašu stranicu, procjenjujemo vaš projekt na licu mjesta i razvijamo prijedlog projekta prilagođen vama. Zatim šaljemo naš iskusni tim da provede projekt. Više informacija o našem inženjerskom radu možete pronaći na http://www.ags-engineering.com -Primamo male projekte, kao i velike projekte u industrijskim razmjerima. Kao prvi korak, možemo vas telefonom, telekonferencijom ili MSN messengerom povezati s članovima našeg stručnog tima, tako da možete izravno komunicirati sa stručnjakom, postavljati pitanja i razgovarati o svom projektu. Nazovite nas i po potrebi ćemo doći u posjet. PRETHODNA STRANICA