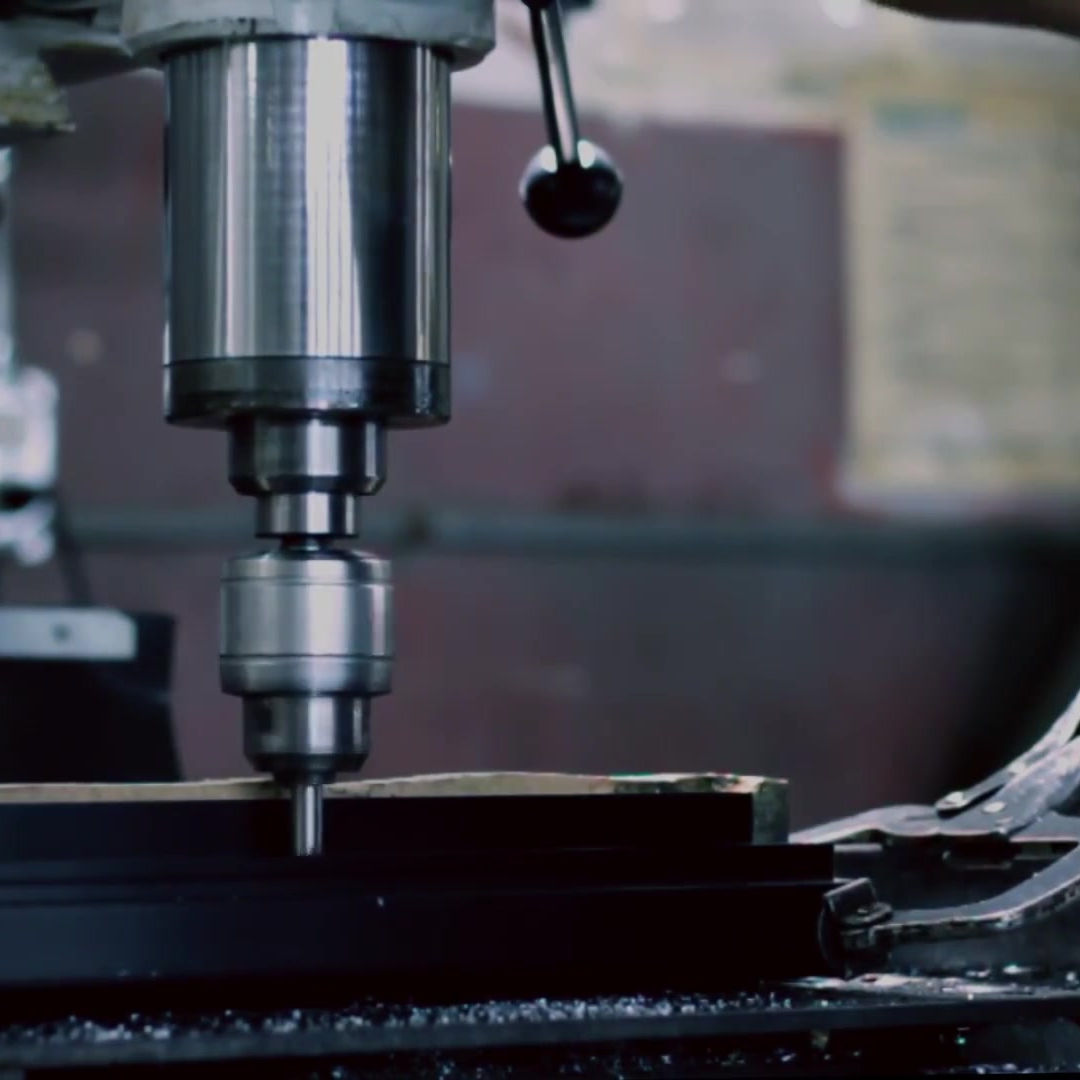
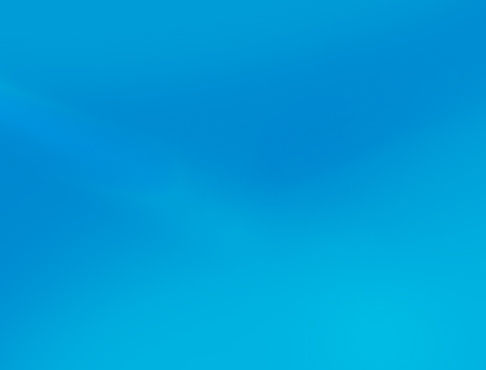
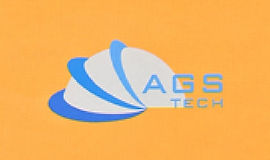
Globális egyedi gyártó, integrátor, konszolidátor, kiszervezési partner a termékek és szolgáltatások széles skálájához.
Mi vagyunk az Ön egyablakos forrása a gyártás, gyártás, tervezés, konszolidáció, integráció, egyedi gyártású és késztermékek és szolgáltatások kiszervezése terén.
Choose your Language
-
Egyedi gyártás
-
Belföldi és globális szerződéses gyártás
-
Gyártási outsourcing
-
Belföldi és globális beszerzés
-
Consolidation
-
Mérnöki integráció
-
Mérnöki szolgáltatások
ELECTRICAL DISCHARGE MACHINING (EDM), also referred to as SPARK-EROSION or ELECTRODISCHARGE MACHINING, SPARK ERODING, DIE SINKING_cc781905-5cde-3194-bb3b -136bad5cf58d_or WIRE EROSION, is a NON-CONVENTIONAL MANUFACTURING process where erosion of metals takes place and desired shape is obtained using electrical discharges in the form a szikráktól. A szikraforgácsolás néhány fajtáját is kínáljuk, nevezetesen kopásmentes szikraforgácsolás, huzalszikraforgácsolás (WEDM), szikraforgácsoló köszörülés (EDG), süllyesztõ szikraforgácsoló szikraforgácsoló szikraforgácsolás, ELEKTROMOS KIÜLÍTÉSŰ MARÁS, m-1-0-9MCC7 -5cde-3194-bb3b-136bad5cf58d_and ELEKTROKÉMIAI KIBOCSOLÁS (ECDG). EDM rendszereink formázott szerszámokból/elektródákból és egyenáramú tápegységekhez csatlakoztatott, elektromosan nem vezető dielektromos folyadékba helyezett munkadarabból állnak. 1940 után az elektromos kisülésű megmunkálás az egyik legfontosabb és legnépszerűbb gyártási technológiává vált a feldolgozóiparban.
Ha a két elektróda közötti távolságot csökkentjük, az elektródák közötti térfogatban az elektromos tér intenzitása egyes pontokon nagyobb lesz, mint a dielektrikum erőssége, amely elszakad, és végül hidat képez a két elektróda közötti áram áramlásához. Erős elektromos ív keletkezik, ami jelentős felmelegedést okoz a munkadarab egy részének és a szerszámanyag egy részének megolvadásához. Ennek eredményeként mindkét elektródáról eltávolítják az anyagot. Ugyanakkor a dielektromos folyadék gyorsan felmelegszik, ami a folyadék elpárologtatását eredményezi az ívrésben. Amint az áram áramlása leáll vagy leáll, a környező dielektromos folyadék hőt távolít el a gázbuborékból, és a buborék kavitálódik (összeesik). A buborék összeomlása és a dielektromos folyadék áramlása által keltett lökéshullám leöblíti a törmeléket a munkadarab felületéről, és magával ragad minden megolvadt munkadarab anyagot a dielektromos folyadékba. Ezeknek a kisüléseknek az ismétlési gyakorisága 50 és 500 kHz között van, a feszültségek 50 és 380 V között, az áramok pedig 0,1 és 500 amper között vannak. Az új folyékony dielektrikum, mint például ásványolajok, kerozin vagy desztillált és ionmentesített víz rendszerint az elektródák közötti térfogatba kerül, és elszállítja a szilárd részecskéket (törmelék formájában), és helyreáll a dielektrikum szigetelő tulajdonságai. Egy áram áramlása után a két elektróda közötti potenciálkülönbség visszaáll a leállás előtti értékre, így új folyékony dielektrikum törés léphet fel. Modern elektromos kisülési gépeink (EDM) numerikusan vezérelt mozgásokat kínálnak, és szivattyúkkal és szűrőrendszerekkel vannak felszerelve a dielektromos folyadékok számára.
Az elektromos kisüléses megmunkálás (EDM) egy olyan megmunkálási módszer, amelyet főként keményfémekhez használnak, vagy olyanokat, amelyeket hagyományos technikákkal nagyon nehéz megmunkálni. Az EDM általában minden olyan anyaggal működik, amely elektromos vezető, bár javasoltak módszereket szigetelő kerámiák EDM-mel történő megmunkálására is. Az olvadáspont és az olvadás látens hője olyan tulajdonságok, amelyek meghatározzák a kisülésenként eltávolított fém térfogatát. Minél magasabbak ezek az értékek, annál lassabb az anyageltávolítási sebesség. Mivel az elektromos kisüléses megmunkálási folyamat nem igényel mechanikai energiát, a munkadarab keménysége, szilárdsága és szívóssága nem befolyásolja az eltávolítási sebességet. A kisülési frekvencia vagy a kisülésenkénti energia, a feszültség és az áramerősség változtatható az anyageltávolítási sebesség szabályozására. Az anyagleválasztás sebessége és a felületi érdesség az áramsűrűség növekedésével és a szikrafrekvencia csökkenésével nő. Bonyolult kontúrokat vagy üregeket vághatunk előre edzett acélból szikraforgácsolással anélkül, hogy hőkezelésre lenne szükség a lágyításhoz és újrakeményítéshez. Ezt a módszert bármilyen fémmel vagy fémötvözetekkel, például titánnal, hastelloy-val, kovarral és inconel-lel használhatjuk. Az EDM eljárás alkalmazásai közé tartozik a polikristályos gyémántszerszámok formázása. Az EDM-et nem hagyományos vagy nem hagyományos megmunkálási módszernek tekintik, olyan folyamatokkal együtt, mint az elektrokémiai megmunkálás (ECM), a vízsugaras vágás (WJ, AWJ), a lézervágás. Másrészt a hagyományos megmunkálási eljárások közé tartozik az esztergálás, marás, köszörülés, fúrás és egyéb olyan eljárások, amelyek anyagleválasztási mechanizmusa alapvetően mechanikai erőkön alapul. Az elektromos kisüléses megmunkáláshoz (EDM) használt elektródák grafitból, sárgarézből, rézből és réz-volfrám ötvözetből készülnek. Az elektróda átmérője 0,1 mm-ig lehetséges. Mivel a szerszámkopás olyan nemkívánatos jelenség, amely hátrányosan befolyásolja a szikraforgácsolás méretpontosságát, kihasználjuk a NO-WEAR EDM eljárást a polaritás megfordításával és rézszerszámok használatával a szerszámkopás minimalizálása érdekében.
Ideális esetben az elektromos kisüléses megmunkálás (EDM) az elektródák közötti dielektromos folyadék lebontásának és helyreállításának sorozatának tekinthető. A valóságban azonban a törmelék eltávolítása az elektródák közötti területről szinte mindig részleges. Emiatt a dielektrikum elektromos tulajdonságai az elektródák közötti területen eltérnek a névleges értéküktől, és idővel változnak. Az elektródák közötti távolságot (szikraköz) az adott gép vezérlési algoritmusai állítják be. Az EDM szikraközét sajnos néha rövidre zárhatja a törmelék. Előfordulhat, hogy az elektróda vezérlőrendszere nem reagál elég gyorsan ahhoz, hogy megakadályozza a két elektróda (a szerszám és a munkadarab) rövidzárlatát. Ez a nem kívánt rövidzárlat az ideális esettől eltérően járul hozzá az anyag eltávolításához. Kiemelten fontosnak tartjuk az öblítést, hogy helyreállítsuk a dielektrikum szigetelő tulajdonságait, hogy az áram mindig az elektródák közötti terület pontján történjen, ezáltal minimalizálva a szerszám-elektróda nem kívánt alakváltozásának (károsodásának) lehetőségét. és munkadarab. Egy adott geometria elérése érdekében az EDM-szerszámot a kívánt pályán a munkadarabhoz nagyon közel vezetik, anélkül, hogy hozzáérnénk. A használat során kiemelt figyelmet fordítunk a mozgásvezérlés teljesítményére. Így nagyszámú áramkisülés/szikra jön létre, és mindegyik hozzájárul az anyag eltávolításához mind a szerszámról, mind a munkadarabról, ahol kis kráterek keletkeznek. A kráterek mérete az adott feladathoz beállított technológiai paraméterek függvénye, és méretei a nanoméretűtől (például mikro-EDM műveletek esetén) a nagyolási körülmények között több száz mikrométerig terjedhetnek. Ezek a kis kráterek a szerszámon az elektróda fokozatos erózióját okozzák, az úgynevezett „szerszámkopást”. A kopásnak a munkadarab geometriájára gyakorolt káros hatásának ellensúlyozására a megmunkálás során folyamatosan cseréljük a szerszám-elektródát. Néha ezt úgy érjük el, hogy egy folyamatosan cserélt vezetéket használunk elektródaként (ezt az EDM eljárást WIRE EDM néven is nevezik). Néha úgy használjuk a szerszámelektródát, hogy csak egy kis része vesz részt ténylegesen a megmunkálási folyamatban, és ezt a részt rendszeresen cseréljük. Ez a helyzet például akkor, ha egy forgó korongot használnak szerszámelektródaként. Ennek a folyamatnak a neve EDM GRINDING. Egy másik, általunk alkalmazott technika abból áll, hogy ugyanazon szikraforgácsolási művelet során különböző méretű és alakú elektródákat használunk a kopás kompenzálására. Ezt a többelektródos technikát nevezzük, és leggyakrabban akkor alkalmazzák, amikor a szerszámelektróda negatívan replikálja a kívánt alakot, és egyetlen irányban, általában a függőleges irányban (azaz a z-tengelyen) halad a nyersdarab felé. Ez hasonlít a szerszámnak abba a dielektromos folyadékba való süllyesztőjéhez, amelybe a munkadarab belemerül, ezért a következő néven: DIE-SINKING EDM_cc781905-5cde-31914-5ccdd 3194-bb3b-136bad5cf58d_HAGYOMÁNYOS EDM or RAM). Az ehhez a művelethez szükséges gépek neve: SINKER EDM. Az ilyen típusú szikraforgácsoláshoz használt elektródák összetett formájúak. Ha a végső geometriát egy általában egyszerű formájú, több irányban mozgatott elektródával kapjuk meg, amely szintén elfordulásnak van kitéve, ezt EDM MARÁSNAK nevezzük. A kopás mértéke szigorúan függ az üzemeltetés során alkalmazott technológiai paraméterektől (polaritás, maximális áramerősség, szakadási feszültség). Például az in micro-EDM, más néven m-EDM, ezek a paraméterek általában olyan értékekre vannak beállítva, amelyek súlyos kopást okoznak. Ezért a kopás komoly probléma ezen a területen, amelyet felhalmozott know-how-nkkal minimalizálunk. Például a grafitelektródák kopásának minimalizálása érdekében egy ezredmásodperceken belül vezérelhető digitális generátor megfordítja a polaritást, amikor elektroerózió történik. Ez a galvanizáláshoz hasonló hatást eredményez, amely az erodált grafitot folyamatosan visszahelyezi az elektródára. Egy másik módszernél, az úgynevezett ''Zero Wear'' áramkörnél minimalizáljuk a kisülés megindulásának és leállásának gyakoriságát, és a lehető leghosszabb ideig bekapcsolva tartjuk. Az elektromos kisüléses megmunkálásnál az anyageltávolítási sebesség a következőképpen becsülhető meg:
MRR = 4 x 10 exp(4) x I x Tw exp (-1,23)
Itt az MRR mm3/perc, az I áramerősség Amperben, Tw a munkadarab olvadáspontja K-273,15K-ban. Az exp a kitevőt jelenti.
Másrészről az elektróda kopási sebessége Wt a következőképpen számolható:
Wt = ( 1,1 x 10exp(11) ) x I x Ttexp(-2,38)
Itt Wt mm3/perc-ben, Tt pedig az elektróda anyagának olvadáspontja K-273,15K-ban
Végül a munkadarab és az R elektróda kopási arányát a következőkből kaphatjuk meg:
R = 2,25 x Trex (-2,38)
Itt Tr a munkadarab és az elektróda olvadáspontjának aránya.
SINKER EDM :
Sinker EDM, más néven: CAVITY TYPE EDM or_cc781905-9cce-136bad5cf58d_or_cc781905-9c. Az elektróda és a munkadarab egy áramforráshoz csatlakozik. A tápegység elektromos potenciált generál a kettő között. Ahogy az elektróda közeledik a munkadarabhoz, a folyadékban dielektromos lebomlás következik be, plazmacsatorna képződik, és egy kis szikra ugrik. A szikrák általában egyenként csapnak le, mert nagyon valószínűtlen, hogy az elektródák közötti tér különböző helyei azonos helyi elektromos jellemzőkkel rendelkezzenek, ami lehetővé tenné, hogy az összes ilyen helyen egyidejűleg szikra keletkezzen. Az elektróda és a munkadarab között másodpercenként több százezer szikra keletkezik véletlenszerű pontokon. Ahogy az alapfém erodálódik, és a szikraköz növekszik, az elektródát a CNC gépünk automatikusan leengedi, hogy a folyamat megszakítás nélkül folytatódhasson. Berendezésünk vezérlőciklusokkal rendelkezik, amelyek „bekapcsolási idő” és „kikapcsolási idő” néven ismertek. A bekapcsolási idő beállítása határozza meg a szikra hosszát vagy időtartamát. A hosszabb üzemidő mélyebb üreget hoz létre a szikra számára, és minden további szikrát a ciklushoz, durvább felületet hozva létre a munkadarabon és fordítva. A kikapcsolási idő az az időtartam, ameddig az egyik szikrát egy másik váltja fel. A hosszabb kikapcsolási idő lehetővé teszi, hogy a dielektromos folyadék átmosódjon egy fúvókán, hogy eltávolítsa az erodált törmeléket, elkerülve ezzel a rövidzárlatot. Ezek a beállítások mikro másodpercek alatt módosíthatók.
WIRE EDM :
In WIRE ELECTRICAL DISCHARGE MACHINING (WEDM), also called WIRE-CUT EDM or WIRE CUTTING, we feed a vékony egyszálú sárgaréz fémhuzal a munkadarabon keresztül, amelyet dielektromos folyadék tartályba merítenek. A huzalos szikraforgácsolás az EDM egyik fontos változata. Alkalmanként huzalra vágott szikraforgácsot használunk akár 300 mm vastag lemezek vágására, valamint lyukasztók, szerszámok és matricák készítésére olyan keményfémekből, amelyeket más gyártási módszerekkel nehéz megmunkálni. Ebben a szalagfűrésszel végzett kontúrvágáshoz hasonló folyamatban a huzal, amelyet folyamatosan egy orsóból táplálnak, a felső és az alsó gyémántvezetők között tartják. A CNC-vezérelt vezetők az x–y síkban mozognak, a felső vezető pedig függetlenül is mozoghat a z–u–v tengelyben, ami lehetővé teszi kúpos és átmeneti alakzatok (például kör alul és négyzet A csúcs). A felső vezető az x–y–u–v–i–j–k–l– tengelymozgásokat tudja szabályozni. Ez lehetővé teszi, hogy a WEDM nagyon bonyolult és finom formákat vágjon. A legjobb gazdaságos költséget és megmunkálási időt elérő berendezéseink átlagos vágási bevágása 0,335 mm Ø 0,25 sárgaréz-, réz- vagy volfrámhuzallal. CNC-berendezéseink felső és alsó gyémántvezetőinek pontossága körülbelül 0,004 mm, és 0,02 mm-es Ø 0,02 mm-es huzal használatával akár 0,021 mm-es vágási út vagy bevágás is lehet. Tehát nagyon szűk vágások lehetségesek. A vágási szélesség nagyobb, mint a huzal szélessége, mert a huzal oldalaitól a munkadarabig szikra keletkezik, ami eróziót okoz. Ez a "túlvágás" szükséges, sok alkalmazásnál kiszámítható, és ezért kompenzálható (mikro-EDM-ben ez nem gyakran fordul elő). A huzaltekercsek hosszúak – egy 8 kg-os 0,25 mm-es huzal orsója valamivel több, mint 19 kilométer. A huzal átmérője akár 20 mikrométer is lehet, a geometria pontossága pedig +/- 1 mikrométer körül van. Általában csak egyszer használjuk a vezetéket, és újrahasznosítjuk, mert viszonylag olcsó. Állandó 0,15-9 m/perc sebességgel halad, és a vágás során állandó bevágás (rés) marad fenn. A huzalvágásos szikraforgácsolási folyamat során dielektromos folyadékként vizet használunk, amelynek ellenállását és egyéb elektromos tulajdonságait szűrőkkel és ionmentesítő egységekkel szabályozzuk. A víz kiöblíti a vágott törmeléket a vágási zónából. Az öblítés fontos tényező az adott anyagvastagság maximális előtolási sebességének meghatározásában, ezért azt állandóan tartjuk. A huzal szikraforgácsolásában a vágási sebességet az egységnyi idő alatti vágási keresztmetszeti felületben adják meg, például 18 000 mm2/óra 50 mm vastag D2 szerszámacél esetén. A lineáris vágási sebesség ebben az esetben 18 000/50 = 360 mm/óra. Az anyageltávolítási sebesség a huzal szikraforgácsolásánál:
MRR = Vf xhxb
Itt MRR mm3/perc-ben, Vf a huzal előtolása a munkadarabhoz mm/percben, h a vastagság vagy magasság mm-ben, b pedig a bevágás, ami:
b = dw + 2s
Itt dw a huzal átmérője, s pedig a huzal és a munkadarab közötti távolság mm-ben.
A szigorúbb tűréshatárok mellett modern, többtengelyes EDM huzalvágó megmunkáló központjaink olyan funkciókkal egészültek ki, mint például több fej két alkatrész egyidejű vágására, kezelőszervek a huzaltörés megelőzésére, automatikus önbefűzési funkciók huzaltörés esetén, és programozott megmunkálási stratégiák a művelet, az egyenes és szögletes vágási képességek optimalizálására.
A Wire-EDM alacsony maradó feszültséget kínál számunkra, mivel nem igényel nagy forgácsolóerőt az anyag eltávolításához. Ha az impulzusonkénti energia/teljesítmény viszonylag alacsony (mint a befejező műveleteknél), akkor az alacsony maradó feszültségek miatt kevés változás várható az anyag mechanikai tulajdonságaiban.
ELEKTROMOS KÖSZÖRÉS (EDG) : A csiszolókorongok nem tartalmaznak csiszolóanyagot, grafitból vagy sárgarézből készülnek. A forgó kerék és a munkadarab között ismétlődő szikrák eltávolítják az anyagot a munkadarab felületeiről. Az anyageltávolítási sebesség:
MRR = K x I
Itt az MRR mm3/perc, az I az áramerősség Amperben, a K pedig a munkadarab anyagtényezője mm3/A-percben. Gyakran használunk elektromos kisüléses köszörülést az alkatrészeken lévő keskeny rések fűrészelésére. Néha kombináljuk az EDG (elektromos kisülési csiszolás) eljárást az EKG (elektrokémiai köszörülés) eljárással, ahol az anyagot kémiai úton távolítják el, a grafitkorong elektromos kisülései felbontják az oxidfilmet, és az elektrolit elmossa. Az eljárás neve ELECTROCHEMICAL-DSHARGE GRINDING (ECDG). Annak ellenére, hogy az ECDG folyamat viszonylag több energiát fogyaszt, gyorsabb, mint az EDG. Főleg keményfém szerszámokat csiszolunk ezzel a technikával.
Az elektromos kisüléses megmunkálás alkalmazásai:
Prototípus gyártás:
Az EDM-eljárást öntőforma-, szerszám- és szerszámgyártásban, valamint prototípus- és gyártási alkatrészek készítésében használjuk, különösen a repülőgép-, autó- és elektronikai iparban, ahol a gyártási mennyiségek viszonylag alacsonyak. A Sinker szikraforgácsolásnál egy grafit, réz wolfram vagy tiszta réz elektródát a kívánt (negatív) alakra forgácsolnak, és egy függőleges nyomószár végén a munkadarabba táplálják.
Pénzverő szerszámkészítés:
Ékszerek és jelvények pénzverési (bélyegzési) eljárással történő előállításához a pozitív mester készíthető ezüstből, mivel (megfelelő gépbeállításokkal) a mester jelentősen erodálódik, és csak egyszer kerül felhasználásra. Az így kapott negatív szerszámot ezután megkeményítik, és leejtő kalapácsban használják fel bélyegzett lapok előállítására bronzból, ezüstből vagy alacsony szilárdságú aranyötvözetből készült kivágott lapokból. Jelvények esetében ezeket a lapokat egy másik szerszámmal íves felületre tovább lehet formálni. Az ilyen típusú szikraforgácsolást általában olajalapú dielektrikumba merítve végzik. A kész tárgy tovább finomítható kemény (üveg) vagy lágy (festék) zománcozással és/vagy galvanizálható tiszta arannyal vagy nikkellel. A lágyabb anyagok, például az ezüst, finomításként kézzel gravírozhatók.
Kis lyukak fúrása:
Huzalra vágott szikraforgácsoló gépeinken kis lyukfúró szikraforgácsolást használunk, hogy átmenő lyukat készítsünk a munkadarabon, amelyen keresztül a huzalt átfűzzük a huzalvágásos szikraforgácsolási művelethez. Kifejezetten kis lyukak fúrásához külön szikraforgácsoló fejek vannak felszerelve drótvágó gépeinkre, amelyek lehetővé teszik, hogy a nagy edzett lemezekről szükség szerint és előfúrás nélkül lekophassanak a kész alkatrészekről. Kis lyukú szikraforgácsolót is használunk, hogy lyuksorokat fúrjunk a sugárhajtóművekben használt turbinalapátok széleibe. A gázáramlás ezeken a kis lyukakon keresztül lehetővé teszi, hogy a motorok magasabb hőmérsékletet használjanak, mint az egyébként lehetséges. A magas hőmérsékletű, nagyon kemény, egykristály ötvözetek, amelyekből ezek a pengék készülnek, rendkívül megnehezítik, sőt lehetetlenné teszik a nagy oldalarányú furatok hagyományos megmunkálását. A kis lyukú szikraforgácsolás további alkalmazási területei az üzemanyagrendszer alkatrészei számára mikroszkopikus nyílások létrehozása. Az integrált szikraforgácsoló fejek mellett önálló kis lyukfúró szikraforgácsoló gépeket alkalmazunk x-y tengellyel zsák- vagy átmenő furatok megmunkálására. Az EDM hosszú sárgaréz vagy rézcső elektródával fúrja a lyukakat, amelyek egy tokmányban forognak, miközben állandó áramlású desztillált vagy ionmentesített víz folyik át az elektródán öblítőszerként és dielektrikumként. Egyes kis lyukakat fúró szikraforgácsolók 100 mm-es lágy vagy akár edzett acélon is kevesebb mint 10 másodperc alatt képesek átfúrni. Ezzel a fúrási művelettel 0,3 mm és 6,1 mm közötti furatok készíthetők.
Fémbontásos megmunkálás:
Vannak speciális szikraforgácsoló gépeink is, amelyek kifejezetten a törött szerszámok (fúrószárak vagy menetfúrók) munkadarabokról történő eltávolítására szolgálnak. Ezt a folyamatot "fémszéteszesítő megmunkálásnak" nevezik.
Az elektromos kisüléses megmunkálás előnyei és hátrányai:
Az EDM előnyei közé tartozik a következők megmunkálása:
- Összetett formák, amelyeket egyébként nehéz lenne hagyományos vágószerszámokkal előállítani
- Rendkívül kemény anyag, nagyon szűk tűréshatárig
- Nagyon kicsi munkadarabok, ahol a hagyományos vágószerszámok károsíthatják az alkatrészt a vágószerszám túlnyomása miatt.
- Nincs közvetlen érintkezés a szerszám és a munkadarab között. Ezért a kényes szakaszok és a gyenge anyagok torzítás nélkül megmunkálhatók.
- Jó felületminőség érhető el.
- Nagyon finom lyukak könnyen fúrhatók.
Az EDM hátrányai a következők:
- Az anyageltávolítás lassú üteme.
- A nyomószár/süllyesztő szikraforgácsoló elektródák létrehozásához felhasznált többletidő és költség.
- Az éles sarkok reprodukálása a munkadarabon az elektródák kopása miatt nehézkes.
- Magas az áramfogyasztás.
- "Overcut" jön létre.
- A megmunkálás során túlzott szerszámkopás lép fel.
- Elektromosan nem vezető anyagokat csak meghatározott folyamatbeállítás mellett lehet megmunkálni.