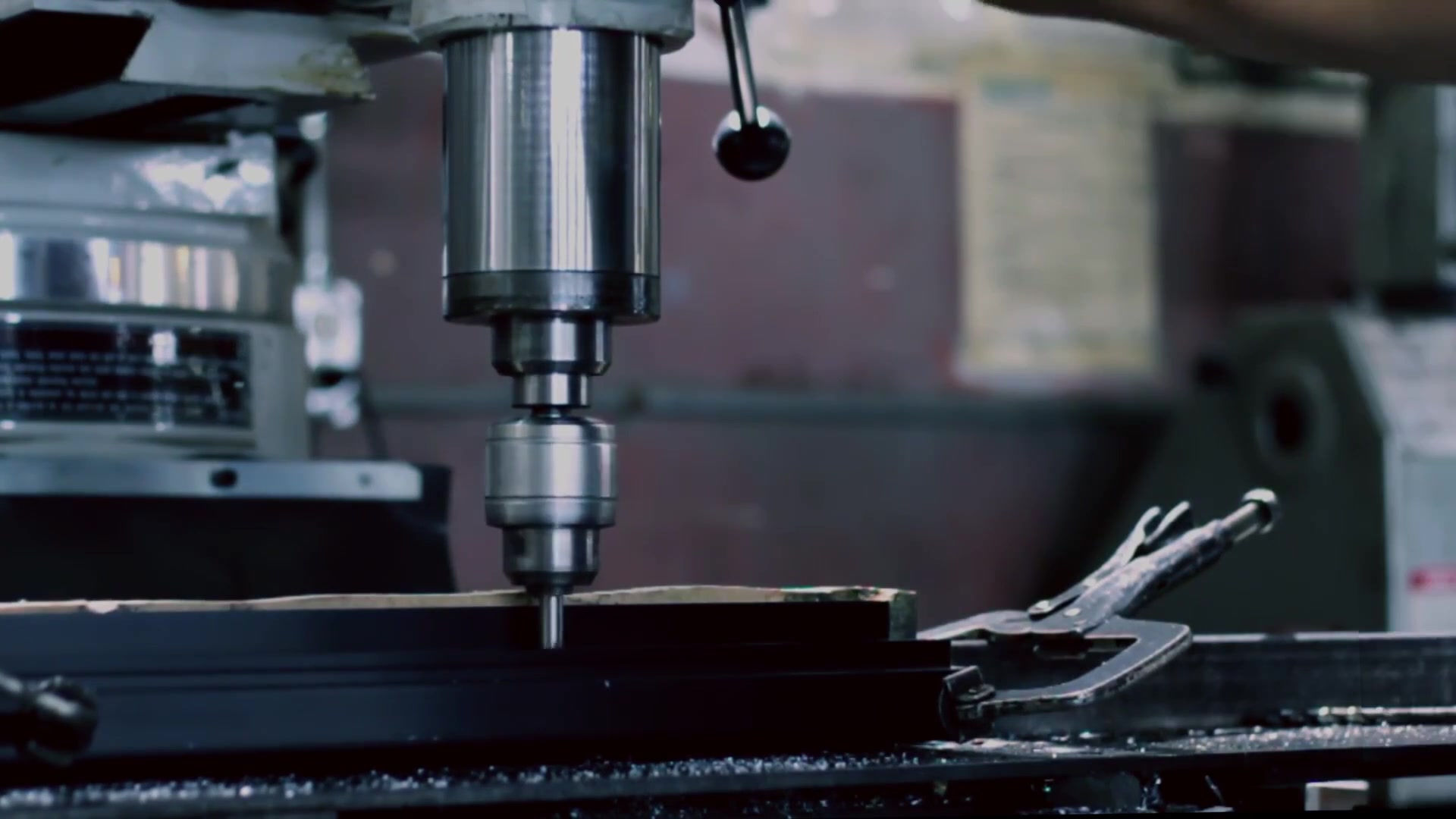
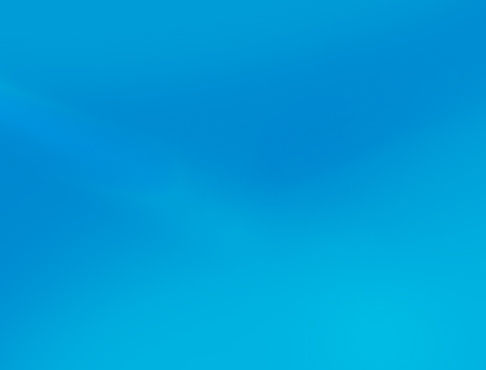
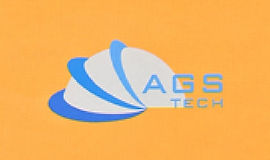
Globális egyedi gyártó, integrátor, konszolidátor, kiszervezési partner a termékek és szolgáltatások széles skálájához.
Mi vagyunk az Ön egyablakos forrása a gyártás, gyártás, tervezés, konszolidáció, integráció, egyedi gyártású és késztermékek és szolgáltatások kiszervezése terén.
Choose your Language
-
Egyedi gyártás
-
Belföldi és globális szerződéses gyártás
-
Gyártási outsourcing
-
Belföldi és globális beszerzés
-
Consolidation
-
Mérnöki integráció
-
Mérnöki szolgáltatások
Search Results
164 találat üres kereséssel
- Embedded Systems, Embedded Computer, Industrial Computers, Janz Tec
Embedded Systems - Embedded Computer - Industrial Computers - Janz Tec - Korenix - AGS-TECH Inc. - New Mexico - USA Beágyazott rendszerek és számítógépek A BEÉPÜLT RENDSZER egy olyan számítógépes rendszer, amelyet egy nagyobb rendszeren belüli meghatározott vezérlési funkciókra terveztek, gyakran valós idejű számítási korlátokkal. Egy komplett eszköz részeként van beágyazva, amely gyakran hardvert és mechanikai részeket is tartalmaz. Ezzel szemben az általános célú számítógépeket, például a személyi számítógépeket (PC) úgy tervezték, hogy rugalmasak legyenek, és a végfelhasználói igények széles körét kielégítsék. A beágyazott rendszer architektúrája egy szabványos PC-re orientált, így a BEÉPÜLT PC csak azokból az összetevőkből áll, amelyekre az adott alkalmazáshoz valóban szüksége van. A beágyazott rendszerek számos ma általánosan használt eszközt vezérelnek. A BEÁGYÁLT SZÁMÍTÓGÉPEK között kínálunk ATOP TECHNOLOGIES, JANZ TEC, KORENIX TECHNOLOGY, DFI-ITOX és más termékmodelleket. Beágyazott számítógépeink robusztus és megbízható rendszerek ipari használatra, ahol az állásidő katasztrofális lehet. Energiahatékonyak, nagyon rugalmasak a használat során, moduláris felépítésűek, kompaktak, nagy teljesítményűek, mint egy komplett számítógép, ventilátor- és zajmentesek. Beágyazott számítógépeink kiváló hőmérséklet-, tömítettség-, ütés- és rezgésállósággal bírnak zord környezetben, és széles körben használják gép- és gyárépítésben, erőművekben, erőművekben, közlekedési és szállítási iparban, orvosi, orvosbiológiai, bioműszeriparban, autóiparban, katonai, bányászatban, haditengerészetben. , tengeri, űrhajózási és egyéb. Töltse le ATOP TECHNOLOGIES kompakt termékismertetőnket (Az ATOP Technologies termékének letöltése: List 2021) Töltse le JANZ TEC modell kompakt termékismertetőnket Töltse le KORENIX modell kompakt termékismertetőnket Töltse le DFI-ITOX modell beágyazott rendszerek brosúránkat Töltse le a DFI-ITOX modell beágyazott egylapos számítógépek brosúráját Töltse le a DFI-ITOX típusú számítógépes modulok brosúráját Töltse le ICP DAS modell PACs beágyazott vezérlők és DAQ brosúránkat Ipari számítástechnikai üzletünkhöz KATTINTSON IDE. Íme néhány az általunk kínált legnépszerűbb beágyazott számítógépek: Beágyazott PC Intel ATOM Z510/530 technológiával Ventilátor nélküli beágyazott PC Beágyazott PC-rendszer Freescale i.MX515-tel Robusztus-beágyazott-PC-rendszerek Moduláris beágyazott PC-rendszerek HMI rendszerek és ventilátor nélküli ipari kijelzőmegoldások Kérjük, mindig ne feledje, hogy az AGS-TECH Inc. bevett MÉRNÖKI INTEGRÁTOR és EGYEDI GYÁRTÓ. Ezért, ha valami egyedi gyártásra van szüksége, kérjük, jelezze felénk, és mi kínálunk Önnek egy kulcsrakész megoldást, amely leveszi a rejtvényt az asztaláról és megkönnyíti a munkáját. Brosúra letöltése számunkra TERVEZÉSI PARTNERSÉGI PROGRAM Röviden bemutatjuk partnereinket, akik ezeket a beágyazott számítógépeket készítik: JANZ TEC AG: A Janz Tec AG 1982 óta az elektronikai szerelvények és komplett ipari számítógépes rendszerek vezető gyártója. A vállalat beágyazott számítástechnikai termékeket, ipari számítógépeket és ipari kommunikációs eszközöket fejleszt az ügyfelek igényei szerint. Minden JANZ TEC terméket kizárólag Németországban gyártanak a legmagasabb minőségben. A több mint 30 éves piaci tapasztalattal a Janz Tec AG képes megfelelni az egyéni vevői igényeknek – ez a koncepció fázisától kezdődik, és az alkatrészek fejlesztésén és gyártásán át egészen a szállításig tart. A Janz Tec AG szabványokat állít fel a beágyazott számítástechnika, ipari PC, ipari kommunikáció és egyedi tervezés területén. A Janz Tec AG alkalmazottai beágyazott számítógép-összetevőket és rendszereket terveznek, fejlesztenek és gyártanak világszabványok alapján, amelyek egyedileg igazodnak az ügyfelek egyedi igényeihez. A Janz Tec beágyazott számítógépeinek további előnyei a hosszú távú rendelkezésre állás és a lehető legjobb minőség, valamint az optimális ár/teljesítmény arány. A Janz Tec beágyazott számítógépeket mindig akkor használják, ha a velük szemben támasztott követelmények miatt rendkívül robusztus és megbízható rendszerekre van szükség. A moduláris felépítésű és kompakt Janz Tec ipari számítógépek kevés karbantartást igényelnek, energiatakarékosak és rendkívül rugalmasak. A Janz Tec beágyazott rendszerek számítógépes architektúrája egy szabványos PC-re orientált, így a beágyazott PC csak azokból a komponensekből áll, amelyekre az adott alkalmazáshoz valóban szüksége van. Ez lehetővé teszi a teljesen független használatot olyan környezetben, ahol a szolgáltatás egyébként rendkívül költséges lenne. Annak ellenére, hogy beágyazott számítógépek, sok Janz Tec termék olyan erős, hogy képes helyettesíteni egy komplett számítógépet. A Janz Tec márkájú beágyazott számítógépek előnyei a ventilátor nélküli működés és az alacsony karbantartási igény. A Janz Tec beágyazott számítógépeit gép- és üzemépítésben, energia- és energiatermelésben, szállításban és közlekedésben, orvostechnikában, autóiparban, gyártás- és gyártástechnikában és sok más ipari alkalmazásban használják. Az egyre nagyobb teljesítményű processzorok lehetővé teszik a Janz Tec beágyazott PC használatát még akkor is, ha ezen iparágak különösen összetett követelményei vannak. Ennek egyik előnye a sok fejlesztő által ismert hardverkörnyezet és a megfelelő szoftverfejlesztői környezetek elérhetősége. A Janz Tec AG megszerzi a szükséges tapasztalatokat saját beágyazott számítógépes rendszereinek fejlesztésében, amelyek szükség esetén az ügyfelek igényeihez igazíthatók. A Janz Tec tervezői a beágyazott számítástechnikai szektorban az alkalmazásnak és az egyedi vevői igényeknek megfelelő optimális megoldásra helyezik a hangsúlyt. A Janz Tec AG-nak mindig is az volt a célja, hogy kiváló minőséget biztosítson a rendszerek számára, masszív kialakítást a hosszú távú használatra, valamint kivételes ár-teljesítmény arányt. A beágyazott számítógépes rendszerekben jelenleg használt modern processzorok a Freescale Intel Core i3/i5/i7, i.MX5x és Intel Atom, Intel Celeron és Core2Duo. Ezenkívül a Janz Tec ipari számítógépei nem csak szabványos interfészekkel vannak felszerelve, mint például Ethernet, USB és RS 232, hanem egy CANbus interfész is elérhető a felhasználó számára. A Janz Tec beágyazott számítógép gyakran ventilátor nélkül van, ezért a legtöbb esetben CompactFlash adathordozóval is használható, így karbantartásmentes. CLICK Product Finder-Locator Service ELŐZŐ OLDAL
- Nanomanufacturing, Nanoparticles, Nanotubes, Nanocomposites, CNT
Nanomanufacturing - Nanoparticles - Nanotubes - Nanocomposites - Nanophase Ceramics - CNT - AGS-TECH Inc. - New Mexico Nanoméretű gyártás / Nanogyártás Nanométeres méretarányú alkatrészeink és termékeink NANOSKÁLÚ GYÁRTÁS / NANOGYÁRTÁS felhasználásával készülnek. Ez a terület még gyerekcipőben jár, de nagy ígéreteket rejt a jövőre nézve. Molekulárisan megtervezett eszközök, gyógyszerek, pigmentek stb. fejlesztés alatt áll, és partnereinkkel azon dolgozunk, hogy a versenytársak előtt maradjunk. Íme néhány a jelenleg kínált kereskedelmi forgalomban kapható termékek közül: SZÉN NANOTÚVOK NANORÉSZÉKEK NANOFÁZIS KERÁMIA CARBON BLACK REINFORCEMENT gumihoz és polimerekhez NANOCOMPOSITES teniszlabdákban, baseball ütőkben, motorkerékpárokban és kerékpárokban MÁGNESES NANOPARTICLES adattároláshoz NANOPARTICLE katalizátorok A nanoanyagok a négy típus bármelyike lehetnek, nevezetesen fémek, kerámiák, polimerek vagy kompozitok. Általában a NANOSTRUCTURES kisebb, mint 100 nanométer. A nanogyártásban két megközelítés egyikét alkalmazzuk. Példaként, felülről lefelé irányuló megközelítésünkben szilícium ostyát veszünk, litográfiás, nedves és száraz maratási módszereket alkalmazunk apró mikroprocesszorok, érzékelők, szondák megalkotásához. Másrészt az alulról felfelé építkező nanogyártási megközelítésünkben atomokat és molekulákat használunk apró eszközök felépítéséhez. Az anyag bizonyos fizikai és kémiai jellemzői szélsőséges változásokat tapasztalhatnak, amikor a részecskeméret megközelíti az atomi méretet. Az átlátszatlan anyagok makroszkopikus állapotukban átlátszóvá válhatnak nanoméretükben. A makroállapotban kémiailag stabil anyagok nanoméretükben éghetővé válhatnak, az elektromosan szigetelő anyagok pedig vezetővé válhatnak. Jelenleg a következők találhatók az általunk kínált kereskedelmi termékek között: CARBON NANOTUBE (CNT) ESZKÖZÖK / NANOTUBES: A szén nanocsöveket a grafit csőszerű formáiként tudjuk megjeleníteni, amelyekből nanoméretű eszközöket lehet építeni. CVD, grafit lézeres ablációja, szén-ív kisülés használható szén nanocső eszközök előállítására. A nanocsövek az egyfalú nanocsövek (SWNT) és a többfalú nanocsövek (MWNT) kategóriába sorolhatók, és más elemekkel adalékolhatók. A szén nanocsövek (CNT-k) a szén nanoszerkezetű allotrópjai, amelyek hosszúság-átmérő aránya nagyobb, mint 10 000 000, és akár 40 000 000 vagy még magasabb is lehet. Ezek a hengeres szénmolekulák olyan tulajdonságokkal rendelkeznek, amelyek potenciálisan hasznosak lehetnek a nanotechnológia, az elektronika, az optika, az építészet és az anyagtudomány egyéb területein. Rendkívüli szilárdsággal és egyedülálló elektromos tulajdonságokkal rendelkeznek, és hatékony hővezetők. A nanocsövek és a gömb alakú buckyballok a fullerén szerkezeti család tagjai. A hengeres nanocsőnek általában legalább az egyik vége a buckyball szerkezet félgömbjével van lezárva. A nanocső elnevezés a méretéből származik, mivel a nanocső átmérője néhány nanométer nagyságrendű, hossza legalább néhány milliméter. A nanocső kötésének természetét orbitális hibridizáció írja le. A nanocsövek kémiai kötése teljes egészében sp2 kötésekből áll, hasonlóan a grafithoz. Ez a kötőszerkezet erősebb, mint a gyémántokban található sp3 kötések, és egyedülálló szilárdságot biztosít a molekulák számára. A nanocsövek természetesen kötelekbe illeszkednek, amelyeket a Van der Waals erők tartanak össze. Nagy nyomás alatt a nanocsövek összeolvadhatnak, egyes sp2 kötéseket sp3 kötésekre cserélve, ami lehetőséget ad erős, korlátlan hosszúságú vezetékek előállítására nagynyomású nanocsövek összekapcsolásával. A szén nanocsövek szilárdsága és rugalmassága potenciálisan felhasználhatóvá teszi más nanoméretű szerkezetek szabályozásában. Egyfalú nanocsöveket állítottak elő 50 és 200 GPa közötti szakítószilárdsággal, és ezek az értékek megközelítőleg egy nagyságrenddel nagyobbak, mint a szénszálaké. A rugalmassági modulusértékek 1 tetrapascal (1000 GPa) nagyságrendűek, a törési feszültségek körülbelül 5% és 20% közöttiek. A szén nanocsövek kiemelkedő mechanikai tulajdonságai miatt kemény ruhákban és sportfelszerelésekben, harci kabátokban használjuk őket. A szén nanocsövek szilárdsága a gyémánthoz hasonló, és ruhákba fonják őket, hogy szúrás- és golyóálló ruházatot hozzanak létre. CNT molekulák térhálósításával a polimer mátrixba való beépítés előtt szuper nagy szilárdságú kompozit anyagot alakíthatunk ki. Ennek a CNT kompozitnak a szakítószilárdsága 20 millió psi (138 GPa) nagyságrendű lehet, ami forradalmasítja a mérnöki tervezést, ahol kis tömegre és nagy szilárdságra van szükség. A szén nanocsövek szokatlan áramvezetési mechanizmusokat is feltárnak. Attól függően, hogy a hatszögletű egységek a grafénsíkban (azaz a csőfalak) a cső tengelyéhez viszonyítva milyen orientációjúak, a szén nanocsövek fémként vagy félvezetőként is viselkedhetnek. Vezetőként a szén nanocsövek nagyon nagy elektromos áramot szállítanak. Egyes nanocsövek az ezüst vagy a réz áramsűrűségének 1000-szeresét is képesek hordozni. A polimerekbe beépített szén nanocsövek javítják a statikus elektromosság kisülési képességét. Ezt az autók és repülőgépek üzemanyag-vezetékeiben, valamint a hidrogénüzemű járművek hidrogéntároló tartályainak gyártásában alkalmazzák. A szén nanocsövekről kimutatták, hogy erős elektron-fonon rezonanciát mutatnak, ami azt jelzi, hogy bizonyos egyenáramú (DC) előfeszítések és adalékolási feltételek mellett az áramuk és az átlagos elektronsebesség, valamint a csövön lévő elektronkoncentráció terahertz frekvencián oszcillál. Ezek a rezonanciák felhasználhatók terahertzes források vagy érzékelők készítésére. Tranzisztorokat és nanocsöves integrált memóriaáramköröket mutattak be. A szén nanocsöveket edényként használják a gyógyszerek szervezetbe történő szállítására. A nanocső lehetővé teszi a gyógyszeradag csökkentését az eloszlás lokalizálásával. Ez gazdaságilag is életképes az alacsonyabb mennyiségű felhasznált gyógyszer miatt. A gyógyszert rögzíteni lehet a nanocső oldalához, vagy hátra lehet húzni, vagy a gyógyszert ténylegesen a nanocső belsejébe lehet helyezni. Az ömlesztett nanocsövek a nanocsövek meglehetősen rendezetlen töredékeinek tömege. Előfordulhat, hogy az ömlesztett nanocsövek húzószilárdsága nem éri el az egyedi csövekhez hasonló szakítószilárdságot, de az ilyen kompozitok ennek ellenére számos alkalmazáshoz elegendő folyáshatárt biztosíthatnak. Az ömlesztett szén nanocsöveket kompozit szálként használják polimerekben, hogy javítsák az ömlesztett termék mechanikai, termikus és elektromos tulajdonságait. A szén nanocsövekből álló átlátszó, vezetőképes filmekkel helyettesítik az indium-ón-oxidot (ITO). A szén nanocső fóliák mechanikailag robusztusabbak, mint az ITO fóliák, így ideálisak nagy megbízhatóságú érintőképernyőkhöz és rugalmas kijelzőkhöz. A szén nanocső filmekből készült, nyomtatható vízbázisú tintákat kívánják helyettesíteni az ITO-val. A nanocsöves filmek ígéretesek a számítógépek, mobiltelefonok, ATM-ek stb. kijelzőiben való felhasználásra. Nanocsöveket használtak az ultrakondenzátorok javítására. A hagyományos ultrakondenzátorokban használt aktív szénben sok kis üreges tér található, méreteloszlással, amelyek együttesen nagy felületet képeznek az elektromos töltések tárolására. Mivel azonban a töltés elemi töltésekké, azaz elektronokká kvantálódik, és ezek mindegyike minimális helyet igényel, az elektróda felületének nagy része nem áll rendelkezésre tárolásra, mert az üregek túl kicsik. A nanocsövekből készült elektródákkal a tervek szerint méretre szabják a tereket, csak néhány túl nagy vagy túl kicsi, és ebből következően a kapacitás növelhető. Egy kifejlesztett napelem szén nanocső komplexet használ, amely szén nanocsövekből és apró széngolyócskákkal (más néven fullerénekkel) kombinálva kígyószerű struktúrákat alkot. A buckyballok befogják az elektronokat, de nem tudják áramlásra késztetni az elektronokat. Amikor a napfény gerjeszti a polimereket, a buckyballs megragadja az elektronokat. A rézhuzalként viselkedő nanocsövek ezután képesek lesznek az elektronok vagy az áram áramlására. NANORÉSZecskék: A nanorészecskék hídnak tekinthetők az ömlesztett anyagok és az atomi vagy molekuláris struktúrák között. Az ömlesztett anyag általában állandó fizikai tulajdonságokkal rendelkezik, méretétől függetlenül, de nanoméretben ez gyakran nem így van. Méretfüggő tulajdonságok figyelhetők meg, mint például a félvezető részecskékben lévő kvantumzáródás, egyes fémrészecskék felületi plazmonrezonanciája és mágneses anyagokban a szuperparamágnesesség. Az anyagok tulajdonságai megváltoznak, ahogy méretük nanoméretűre csökken, és ahogy az atomok százalékos aránya a felszínen jelentőssé válik. A mikrométernél nagyobb ömlesztett anyagok esetében a felületen lévő atomok százalékos aránya nagyon kicsi az anyagban lévő atomok teljes számához képest. A nanorészecskék eltérő és kiemelkedő tulajdonságai részben abból adódnak, hogy az anyag felületének szempontjai dominálnak a tulajdonságokban, nem pedig a tömbtulajdonságok. Például az ömlesztett réz hajlítása a rézatomok/ -klaszterek körülbelül 50 nm-es skálán történő mozgásával történik. Az 50 nm-nél kisebb réz nanorészecskéket szuperkemény anyagoknak tekintik, amelyek nem mutatnak ugyanolyan alakíthatóságot és hajlékonyságot, mint az ömlesztett réz. A tulajdonságok megváltoztatása nem mindig kívánatos. A 10 nm-nél kisebb ferroelektromos anyagok szobahőmérsékletű hőenergiával képesek megváltoztatni mágnesezési irányukat, így használhatatlanok a memória tárolására. A nanorészecskék szuszpenziói azért lehetségesek, mert a részecskefelület és az oldószer kölcsönhatása elég erős ahhoz, hogy leküzdje a sűrűségbeli különbségeket, ami nagyobb részecskék esetén általában azt eredményezi, hogy az anyag vagy elsüllyed, vagy lebeg a folyadékban. A nanorészecskék váratlan látható tulajdonságokkal rendelkeznek, mivel elég kicsik ahhoz, hogy behatárolják elektronjaikat és kvantumhatásokat hozzanak létre. Például az arany nanorészecskék mélyvöröstől feketéig jelennek meg oldatban. A nagy felület/térfogat arány csökkenti a nanorészecskék olvadási hőmérsékletét. A nanorészecskék nagyon magas felület/térfogat aránya a diffúzió hajtóereje. A szinterezés alacsonyabb hőmérsékleten, rövidebb idő alatt mehet végbe, mint nagyobb részecskék esetében. Ez nem befolyásolhatja a végtermék sűrűségét, azonban az áramlási nehézségek és a nanorészecskék agglomerálódási hajlama problémákat okozhat. A titán-dioxid nanorészecskék jelenléte öntisztító hatást kölcsönöz, és nanotartományú méretük miatt a részecskék nem láthatók. A cink-oxid nanorészecskék UV-blokkoló tulajdonságokkal rendelkeznek, és a fényvédő krémekhez adják őket. Az agyag nanorészecskék vagy a korom polimer mátrixokba beépítve növelik a megerősítést, erősebb műanyagot kínálva, magasabb üvegesedési hőmérséklettel. Ezek a nanorészecskék kemények, és tulajdonságaikat adják a polimernek. A textilszálakhoz tapadt nanorészecskék okos és funkcionális ruházatot hozhatnak létre. NANOFÁZIS KERÁMIA: A nanoméretű részecskék felhasználásával a kerámia anyagok gyártásában egyszerre és jelentős mértékben növelhetjük a szilárdságot és a hajlékonyságot. A nanofázisú kerámiákat katalízisre is használják magas felület/terület arányuk miatt. A nanofázisú kerámia részecskéket, mint például a SiC, szintén használják fémek, például alumíniummátrix megerősítésére. Ha olyan nanogyártási alkalmazásra gondol, amely hasznos lehet vállalkozása számára, tudassa velünk, és fogadja visszajelzésünket. Ezeket megtervezzük, prototípusainkkal, gyártjuk, teszteljük és eljuttatjuk Önnek. Nagy értéket tulajdonítunk a szellemi tulajdon védelmének, és különleges intézkedéseket tehetünk az Ön számára, hogy ne másolják le a mintáit és a termékeit. Nanotechnológiai tervezőink és nanogyártó mérnökeink a világ legjobbjai közé tartoznak, és ugyanazok az emberek, akik a világ legfejlettebb és legkisebb eszközeit fejlesztették ki. CLICK Product Finder-Locator Service ELŐZŐ OLDAL
- Mesomanufacturing,Mesoscale Manufacturing,Miniature Device Fabrication
Mesomanufacturing - Mesoscale Manufacturing - Miniature Device Fabrication - Tiny Motors - AGS-TECH Inc. - New Mexico Mesoscale Manufacturing / Mesomanufacturing Hagyományos gyártási technikákkal olyan „makroméretű” szerkezeteket állítunk elő, amelyek viszonylag nagyok és szabad szemmel is láthatóak. A MESOMANUFACTURING azonban miniatűr eszközökhöz gyártunk alkatrészeket. A mezogyártásra más néven is hivatkoznak: MESOSCALE MANUFACTURING or_cce-54cf58d_or_cc781-de A mezogyártás átfedi mind a makro-, mind a mikrogyártást. A mezogyártásra példák a hallókészülékek, sztentek, nagyon kicsi motorok. A mezogyártásban az első megközelítés a makrogyártási folyamatok lecsökkentése. Például egy apró esztergagép néhány tucat milliméteres méretekkel és egy 1,5 W-os, 100 grammos motorral jó példa a mezogyártásra, ahol a méretcsökkentés megtörtént. A második megközelítés a mikrogyártási folyamatok bővítése. Például a LIGA folyamatok felskálázhatók, és beléphetnek a mezogyártás birodalmába. Mezogyártási folyamataink áthidalják a szakadékot a szilícium alapú MEMS eljárások és a hagyományos miniatűr megmunkálás között. A mezoskálás eljárásokkal két- és háromdimenziós alkatrészeket lehet előállítani, amelyek mikron méretű jellemzőkkel rendelkeznek hagyományos anyagokból, például rozsdamentes acélból, kerámiából és üvegből. A jelenleg rendelkezésünkre álló mezogyártási eljárások közé tartozik a fókuszált ionsugaras (FIB) porlasztás, a mikromarás, a mikroesztergálás, az excimer lézeres abláció, a femto-másodperces lézeres abláció és a mikroelektromos kisüléses (EDM) megmunkálás. Ezek a mezoskálás eljárások szubtraktív megmunkálási technológiát (azaz anyageltávolítást) alkalmaznak, míg a LIGA eljárás egy additív mezoskálás eljárás. A mezogyártási folyamatok eltérő képességekkel és teljesítményspecifikációkkal rendelkeznek. Az érdeklődésre számot tartó megmunkálási teljesítmény specifikációk közé tartozik a minimális elemméret, a jellemző tolerancia, a jellemző helyének pontossága, a felületi minőség és az anyageltávolítási sebesség (MRR). Lehetőségünk van olyan elektromechanikus alkatrészek mezogyártására, amelyekhez mezoskálájú alkatrészekre van szükség. A szubtraktív mezogyártási eljárásokkal előállított mezoskálájú részek egyedi tribológiai tulajdonságokkal rendelkeznek az anyagok sokfélesége és a különböző mezogyártási folyamatok által előállított felületi viszonyok miatt. Ezek a szubtraktív mezoskálás megmunkálási technológiák a tisztasággal, az összeszereléssel és a tribológiával kapcsolatos aggályokat vetnek fel bennünk. A tisztaság létfontosságú a mezo-megmunkálás során, mivel a mezo-megmunkálási folyamat során keletkező mezoméretű szennyeződés és törmelék szemcsemérete összemérhető a mezoskálás jellemzőkkel. A mezoskálás marás és esztergálás forgácsokat és sorjakat hozhat létre, amelyek eltömíthetik a lyukakat. A felület morfológiája és a felületkiképzés feltételei nagymértékben változnak a mezogyártási módszertől függően. A mezoméretű alkatrészeket nehéz kezelni és beállítani, ami az összeszerelést olyan kihívássá teszi, amelyet a legtöbb versenytársunk nem tud leküzdeni. A mezogyártásban jóval magasabb hozammutatóink, mint versenytársaink, ami azt az előnyt jelenti, hogy jobb árakat tudunk kínálni. MESOSCALE FORGÁSI FOLYAMATOK: Főbb mezogyártási technikáink a fókuszált ionsugár (FIB), mikromarás és mikroesztergálás, lézeres mezo-megmunkálás, mikro-EDM (elektromos kisüléses megmunkálás) Mezogyártás fókuszált ionsugárral (FIB), mikromarással és mikroesztergálással: A FIB gallium ionsugaras bombázással porlasztja ki az anyagot a munkadarabból. A munkadarabot egy sor precíziós fokozatra szerelik fel, és egy vákuumkamrába helyezik a galliumforrás alatt. A vákuumkamrában lévő transzlációs és forgási fokozatok a munkadarabon különböző helyeket tesznek elérhetővé a gallium ionok nyalábja számára a FIB mezogyártáshoz. Hangolható elektromos mező pásztázza a sugarat, hogy lefedjen egy előre meghatározott vetített területet. A nagyfeszültségű potenciál miatt a gallium-ionforrás felgyorsul, és ütközik a munkadarabbal. Az ütközések leválasztják az atomokat a munkadarabról. A FIB mezo-megmunkálási folyamat eredménye lehet egy közeli függőleges metszet. Egyes rendelkezésünkre álló FIB-k sugárátmérője akár 5 nanométer is lehet, így a FIB mezoskálájú, sőt mikroméretű gép is lehet. Mikro-marószerszámokat nagy pontosságú marógépekre szerelünk alumínium megmunkálási csatornákra. A FIB segítségével mikroesztergaszerszámokat készíthetünk, amelyeket aztán esztergagépen használhatunk finom menetes rudak előállítására. Más szóval, a FIB kemény szerszámok megmunkálására is használható a közvetlen mezo-megmunkálási jellemzők mellett a munkadarab végére. A lassú anyageltávolítási sebesség miatt a FIB nem praktikus a nagy elemek közvetlen megmunkálására. A kemény szerszámok azonban lenyűgöző sebességgel képesek eltávolítani az anyagot, és elég tartósak több órás megmunkálási időhöz. Ennek ellenére a FIB praktikus olyan összetett háromdimenziós formák közvetlen mezo-megmunkálására, amelyek nem igényelnek jelentős anyagleválasztási sebességet. Az expozíció hossza és a beesési szög nagymértékben befolyásolhatja a közvetlenül megmunkált elemek geometriáját. Lézeres mezogyártás: Excimer lézereket használnak mezogyártáshoz. Az excimer lézer nanomásodperces ultraibolya fény impulzusokkal megmunkálja az anyagot. A munkadarab precíziós transzlációs szakaszokra van felszerelve. Egy vezérlő koordinálja a munkadarab mozgását az álló UV lézersugárhoz képest, és koordinálja az impulzusok tüzelését. A mezo-megmunkálási geometriák meghatározására maszkvetítési technika használható. A maszkot a sugár kiterjesztett részébe helyezik be, ahol a lézer áramlása túl alacsony a maszk eltávolításához. A maszk geometriája a lencsén keresztül nagyítás nélkül ki van vetítve a munkadarabra. Ez a megközelítés több furat (tömb) egyidejű megmunkálására is használható. Excimer és YAG lézereink akár 12 mikron méretű polimerek, kerámiák, üvegek és fémek megmunkálására is használhatók. Az UV hullámhossz (248 nm) és a munkadarab közötti jó csatolás a lézeres mezogyártás/mezo-megmunkálás során függőleges csatornafalakat eredményez. A tisztább lézeres mezo-megmunkálási megközelítés a Ti-zafír femtoszekundumos lézer használata. Az ilyen mezogyártási folyamatok kimutatható törmelékei nanoméretű részecskék. A femtoszekundumos lézerrel mély, egy mikron méretű elemek mikrogyárthatók. A femtoszekundumos lézeres ablációs eljárás egyedülálló abban, hogy az atomi kötéseket bontja meg a termikusan abláló anyag helyett. A femtoszekundumos lézeres mezo-megmunkálási / mikromegmunkálási eljárásnak kiemelt helye van a mezogyártásban, mert tisztább, mikronképes, és nem anyagspecifikus. Mezogyártás Micro-EDM-mel (elektromos kisüléses megmunkálás): Az elektrokisüléses megmunkálás szikraeróziós folyamaton keresztül távolítja el az anyagot. Mikro-EDM gépeink akár 25 mikron átmérőjű tulajdonságokat is képesek előállítani. A süllyesztő és a vezetékes mikro-EDM gép esetében a jellemző méretének meghatározásánál a két fő szempont az elektróda mérete és a túlnyúló rés. 10 mikronnál valamivel nagyobb átmérőjű elektródákat használnak, amelyek átmérője néhány mikron. Egy összetett geometriájú elektróda létrehozása a süllyesztő szikraforgácsoló géphez know-how-t igényel. A grafit és a réz egyaránt népszerű elektródaanyagként. Egy bonyolult süllyesztő EDM elektróda előállításának egyik módja a mezoskálás részhez a LIGA eljárás alkalmazása. A réz, mint elektróda anyaga LIGA formákba bevonható. A réz LIGA elektródát ezután fel lehet szerelni a süllyesztő szikraforgácsoló gépre, hogy egy alkatrészt más anyagból, például rozsdamentes acélból vagy kovarból lehessen legyártani. Egyetlen mezogyártási folyamat sem elegendő minden művelethez. Egyes mezoskálás folyamatok szélesebb körűek, mint mások, de mindegyik folyamatnak megvan a maga rése. Legtöbbször különféle anyagokra van szükségünk a mechanikai alkatrészek teljesítményének optimalizálása érdekében, és kényelmesek vagyunk a hagyományos anyagokkal, például a rozsdamentes acéllal, mivel ezek az anyagok hosszú múltra tekintenek vissza, és az évek során nagyon jól jellemezték őket. A mezogyártási folyamatok lehetővé teszik számunkra a hagyományos anyagok felhasználását. A szubtraktív mezoskálás megmunkálási technológiák bővítik anyagbázisunkat. A mezogyártás egyes anyagkombinációinál problémát jelenthet a kiütés. Minden adott mezoskálás megmunkálási folyamat egyedileg befolyásolja a felület érdességét és morfológiáját. A mikromarás és mikroesztergálás sorját és részecskéket képezhet, amelyek mechanikai problémákat okozhatnak. A Micro-EDM olyan újraöntött réteget hagyhat maga után, amely különleges kopási és súrlódási jellemzőkkel bír. A mezoskálájú részek közötti súrlódási hatások korlátozott érintkezési pontokkal rendelkezhetnek, és a felületi érintkezési modellekkel nem modellezhetők pontosan. Néhány mezoskálás megmunkálási technológia, mint például a mikro-EDM, meglehetősen kiforrott, szemben másokkal, mint például a femtoszekundumos lézeres mezo-megmunkálás, amelyek még további fejlesztést igényelnek. CLICK Product Finder-Locator Service ELŐZŐ OLDAL
- Micro-Optics - Micro-Optical - Microoptical - Wafer Level Optics
Micro-Optics, Micro-Optical, Microoptical, Wafer Level Optics, Gratings, Fresnel Lenses, Lens Array, Micromirrors, Micro Reflectors, Collimators, Aspheres, LED Mikro-optika gyártás A mikrogyártás egyik területe, amelyben részt veszünk, a MICRO-OPTICS GYÁRTÁS. A mikrooptika lehetővé teszi a fény manipulálását és a fotonok kezelését mikron és szubmikron léptékű szerkezetekkel és komponensekkel. A MICRO-OPTICAL COMPONENTS és az SUBSYSTEMS egyes alkalmazásai: Információtechnológia: Mikrokijelzőkben, mikroprojektorokban, optikai adattárolókban, mikrokamerákban, szkennerekben, nyomtatókban, fénymásolókban stb. Biomedicina: Minimálisan invazív/pontos ellátási diagnosztika, kezelés monitorozása, mikro-képalkotó szenzorok, retina implantátumok, mikroendoszkópok. Világítás: LED-eken és más hatékony fényforrásokon alapuló rendszerek Biztonsági és biztonsági rendszerek: Infravörös éjjellátó rendszerek autóipari alkalmazásokhoz, optikai ujjlenyomat-érzékelők, retinaszkennerek. Optikai kommunikáció és telekommunikáció: fotonikus kapcsolókban, passzív száloptikai alkatrészekben, optikai erősítőkben, nagyszámítógépekben és személyi számítógépek összekapcsolási rendszereiben Intelligens szerkezetek: optikai szál alapú érzékelő rendszerekben és még sok másban Az általunk gyártott és szállított mikrooptikai alkatrészek és alrendszerek típusai a következők: - Wafer Level optika - Törőoptika - Diffrakciós optika - Szűrők - Rácsok - Számítógéppel generált hologramok - Hibrid mikrooptikai alkatrészek - Infravörös mikrooptika - Polimer mikrooptika - Optikai MEMS - Monolitikusan és diszkréten integrált mikro-optikai rendszerek A legszélesebb körben használt mikro-optikai termékeink közül néhány: - Bi-konvex és plano-konvex lencsék - Achromat lencsék - Golyós lencsék - Vortex lencsék - Fresnel lencsék - Multifokális lencse - Hengeres lencsék - Graded Index (GRIN) lencsék - Mikro-optikai prizmák - Aszférák - Aszférák tömbjei - Kollimátorok - Mikro-lencse tömbök - Diffrakciós rácsok - Dróthálós polarizátorok - Mikro-optikai digitális szűrők - Impulzus-kompressziós rácsok - LED modulok - Gerendaformázók - Nyaláb mintavevő - Gyűrűgenerátor - Mikro-optikai homogenizátorok / diffúzorok - Multispot sugárosztók - Kettős hullámhosszú sugárkombinátorok - Mikro-optikai összeköttetések - Intelligens mikrooptikai rendszerek - Képalkotó mikrolencsék - Mikrotükrök - Mikro reflektorok - Mikro-optikai ablakok - Dielektromos maszk - Írisz rekeszizom Adunk néhány alapvető információt ezekről a mikro-optikai termékekről és alkalmazásaikról: GOLYÓLENCSÉK: A golyóslencsék teljesen gömb alakú mikro-optikai lencsék, amelyeket leggyakrabban fényszálak be- és kikapcsolására használnak. Számos mikro-optikai golyós lencsét szállítunk, és saját specifikációi szerint is le tudjuk gyártani. Kvarcból készült golyós lencséink kiváló UV- és IR-áteresztéssel rendelkeznek 185 nm és >2000 nm között, zafír lencséink pedig magasabb törésmutatóval rendelkeznek, ami nagyon rövid gyújtótávolságot tesz lehetővé a kiváló szálcsatolás érdekében. Más anyagból és átmérőjű mikro-optikai golyós lencsék is kaphatók. A szálcsatolási alkalmazások mellett a mikro-optikai golyós lencséket objektív lencsékként használják endoszkópiában, lézeres mérőrendszerekben és vonalkód-leolvasásban. Másrészt a mikro-optikai félgömb lencsék egyenletes fényeloszlást biztosítanak, és széles körben használják LED-kijelzőkben és közlekedési lámpákban. MIKROOPTIKAI ASZFÉRÁK és MÖBÖK: Az aszférikus felületek profilja nem gömb alakú. Az aszférák használata csökkentheti a kívánt optikai teljesítmény eléréséhez szükséges optikák számát. A gömb- vagy aszférikus görbületű mikro-optikai lencsetömbök népszerű alkalmazásai a képalkotás és a megvilágítás, valamint a lézerfény hatékony kollimációja. Egyetlen aszférikus mikrolencse-tömb helyettesítése egy összetett többlencsés rendszerrel nem csak kisebb méretet, könnyebb súlyt, kompakt geometriát és alacsonyabb költséget eredményez az optikai rendszerben, hanem jelentősen javítja optikai teljesítményét is, például jobb képminőséget. Az aszférikus mikrolencsék és mikrolencse-tömbök gyártása azonban kihívást jelent, mivel a makroméretű aszférákhoz használt hagyományos technológiák, mint például az egypontos gyémántmarás és a termikus visszafolyatás, nem képesek bonyolult mikro-optikai lencseprofilt meghatározni olyan kis területen, mint több. több tíz mikrométerig. Rendelkezünk az ilyen mikro-optikai szerkezetek olyan fejlett technikák felhasználásával történő előállításához szükséges know-how-val, mint a femtoszekundumos lézerek. MIKROOPTIKAI ACHROMÁT LENCSÉK: Ezek a lencsék ideálisak a színkorrekciót igénylő alkalmazásokhoz, míg az aszférikus lencséket a szférikus aberráció korrigálására tervezték. Az akromatikus lencse vagy akromata olyan lencse, amelyet a kromatikus és gömbi aberráció hatásainak korlátozására terveztek. A mikro-optikai akromatikus lencsék olyan korrekciókat hajtanak végre, amelyek két hullámhosszt (például vörös és kék színt) állítanak fókuszba ugyanazon a síkon. HENGERES LENCSÉK: Ezek a lencsék a fényt egy vonalra fókuszálják, nem pedig pontra, ahogy azt egy gömb alakú lencsék tennék. A hengeres lencse ívelt felülete vagy lapjai egy henger metszetei, és a rajta áthaladó képet a lencse felületének metszéspontjával párhuzamos egyenesre és egy azt érintő síkra fókuszálják. A hengeres lencse erre a vonalra merőleges irányban összenyomja a képet, és a vele párhuzamos irányban (az érintősíkban) változatlanul hagyja. Apró mikrooptikai változatok állnak rendelkezésre, amelyek alkalmasak mikrooptikai környezetben való használatra, kompakt méretű száloptikai komponenseket, lézerrendszereket és mikro-optikai eszközöket igényelnek. MIKROOPTIKAI ABLAKOK és LAKÁSOK: A szigorú tűréskövetelményeknek megfelelő milimetrikus mikro-optikai ablakok állnak rendelkezésre. Bármely optikai minőségű szemüvegből egyedi igény szerint le tudjuk gyártani őket. Sokféle mikro-optikai ablakot kínálunk különböző anyagokból, mint például olvasztott szilícium-dioxid, BK7, zafír, cink-szulfid stb. átvitellel az UV-től a közepes IR tartományig. KÉPKÉPZŐ MIKROLENCSEK: A mikrolencsék kisméretű lencsék, amelyek átmérője általában egy milliméternél (mm) kisebb, és legfeljebb 10 mikrométer. A képalkotó lencséket a képalkotó rendszerekben lévő objektumok megtekintésére használják. A képalkotó lencséket képalkotó rendszerekben arra használják, hogy egy vizsgált tárgy képét a kamera érzékelőjére fókuszálják. Az objektívtől függően a képalkotó lencsék használhatók a parallaxis vagy a perspektíva hiba eltávolítására. Állítható nagyítást, látómezőt és gyújtótávolságot is kínálnak. Ezek a lencsék lehetővé teszik, hogy egy tárgyat többféleképpen is megtekintsen, hogy szemléltesse bizonyos jellemzőket vagy jellemzőket, amelyek bizonyos alkalmazásokban kívánatosak lehetnek. MIKROMÜKRÖK: A mikrotükör eszközök mikroszkopikusan kisméretű tükrökön alapulnak. A tükrök mikroelektromechanikai rendszerek (MEMS). Ezeknek a mikro-optikai eszközöknek az állapotát úgy szabályozzák, hogy feszültséget kapcsolnak a két elektróda közé a tükörtömbök körül. Digitális mikrotükör eszközöket használnak a videoprojektorokban, az optikát és a mikrotükör eszközöket pedig a fény eltérítésére és szabályozására. MIKROOPTIKAI KOLLIMÁTOROK ÉS KOLLIMÁTORKÖZÖK: Különféle mikro-optikai kollimátorok kaphatók készen. Az igényes alkalmazásokhoz szükséges mikro-optikai kissugaras kollimátorok lézerfúziós technológiával készülnek. A szál vége közvetlenül a lencse optikai középpontjához van olvasztva, ezáltal megszűnik az epoxi az optikai úton. A mikro-optikai kollimátorlencse felületét ezután lézerrel polírozzák az ideális alak milliomod hüvelyknyi pontosságára. A kis sugárnyalábú kollimátorok kollimált gerendákat állítanak elő milliméter alatti sugár derékkal. A mikro-optikai kissugaras kollimátorokat jellemzően 1064, 1310 vagy 1550 nm hullámhosszon használják. GRIN objektív alapú mikro-optikai kollimátorok, valamint kollimátor tömb és kollimátor száltömb összeállítások is kaphatók. MIKROOPTIKAI FRESNEL LENCSÉK: A Fresnel-objektív egy olyan kompakt objektív, amelyet arra terveztek, hogy lehetővé tegye nagy rekesznyílású és rövid gyújtótávolságú objektívek készítését anélkül, hogy tömege és térfogata olyan anyagmennyiséget igényelne, amely egy hagyományos kialakítású objektívhez lenne szükséges. A Fresnel-lencsék sokkal vékonyabbak, mint a hasonló hagyományos lencsék, néha lapos lap formájában. A Fresnel-lencse több ferde fényt képes befogni egy fényforrásból, így a fény nagyobb távolságból is látható. A Fresnel-lencse a hagyományos lencsékhez képest csökkenti a szükséges anyagmennyiséget azáltal, hogy a lencsét koncentrikus gyűrű alakú részekre osztja. Mindegyik szakaszban a teljes vastagság csökken egy egyenértékű egyszerű lencséhez képest. Ezt úgy tekinthetjük, mint egy szabványos lencse folytonos felületének felosztását azonos görbületű felületek halmazára, amelyek között fokozatos megszakadások vannak. A mikrooptikai Fresnel lencsék koncentrikusan ívelt felületeken törés útján fókuszálják a fényt. Ezek a lencsék nagyon vékonyak és könnyűek. A mikro-optikai Fresnel lencsék lehetőségeket kínálnak az optikában a nagy felbontású röntgen alkalmazásokhoz, átmenő lapos optikai összekapcsolási lehetőségeket. Számos gyártási módszerünk van, beleértve a mikroöntést és a mikromegmunkálást, hogy mikro-optikai Fresnel lencséket és tömböket állítsunk elő kifejezetten az Ön alkalmazásaihoz. Pozitív Fresnel lencsét tervezhetünk kollimátorként, kollektorként vagy két véges konjugátummal. A mikro-optikai Fresnel lencséket általában a szférikus aberrációkra korrigálják. A mikrooptikai pozitív lencsék fémezhetők második felületi reflektorként, a negatív lencsék pedig fémezhetők első felületi reflektorként való használatra. MIKROOPTIKAI PRIZMÁK: A precíziós mikrooptikai termékcsaládunk szabványos bevonatos és bevonat nélküli mikroprizmákat tartalmaz. Alkalmasak lézerforrásokhoz és képalkotó alkalmazásokhoz. Mikro-optikai prizmáink szubmiméteres méretűek. Bevonatos mikro-optikai prizmáink tükörreflektorként is használhatók a bejövő fény tekintetében. A bevonat nélküli prizmák tükrökként szolgálnak az egyik rövid oldalra beeső fény számára, mivel a beeső fény teljes mértékben visszaverődik a hipotenuzuson belülről. Mikro-optikai prizmáink példái közé tartoznak a derékszögű prizmák, a sugárosztó kocka szerelvények, az Amici prizmák, a K-prizmák, a Dove prizmák, a tetőprizmák, a sarokkockák, a pentaprizmák, a rombusz prizmák, a Bauernfeind prizmák, a diszpergáló prizmák, a Refl. Kínálunk továbbá akrilból, polikarbonátból és egyéb műanyagokból melegdomborítással készült fényvezető és vakító optikai mikroprizmákat lámpákban és lámpatestekben, LED-ekben való alkalmazásokhoz. Rendkívül hatékony, erős fényvezető precíz prizmafelületek, támogatják a világítótesteket, hogy megfeleljenek az irodai vakítás-elhárító előírásoknak. További egyedi prizmaszerkezetek is lehetségesek. Mikroprizmák és mikroprizmatömbök ostyaszinten is lehetségesek mikrogyártási technikák alkalmazásával. DIFRAKCIÓS RÁCSOK: Diffrakciós mikro-optikai elemek (DOE) tervezését és gyártását kínáljuk. A diffrakciós rács egy periodikus szerkezetű optikai alkatrész, amely a fényt több, különböző irányba haladó nyalábra osztja és szórja szét. Ezen sugarak iránya a rács távolságától és a fény hullámhosszától függ, így a rács diszpergáló elemként működik. Ez teszi a rácsot alkalmas elemmé monokromátorokban és spektrométerekben való használatra. Az ostya alapú litográfiával olyan diffrakciós mikro-optikai elemeket állítunk elő, amelyek kivételes hő-, mechanikai és optikai jellemzőkkel rendelkeznek. A mikrooptika ostyaszintű feldolgozása kiváló gyártási megismételhetőséget és gazdaságos teljesítményt biztosít. A diffrakciós mikrooptikai elemekhez rendelkezésre álló anyagok közül néhány kristálykvarc, olvasztott szilícium-dioxid, üveg, szilícium és szintetikus hordozók. A diffrakciós rácsok olyan alkalmazásokban hasznosak, mint a spektrális elemzés/spektroszkópia, MUX/DEMUX/DWDM, precíziós mozgásvezérlés, például optikai kódolókban. A litográfiai technikák lehetővé teszik precíziós mikro-optikai rácsok gyártását szigorúan szabályozott horonytávolsággal. Az AGS-TECH egyedi és raktári kiviteleket is kínál. ÖRÖGLENCSÉK: Lézeres alkalmazásokban szükség van a Gauss-sugarat fánk alakú energiagyűrűvé alakítani. Ezt Vortex lencsékkel érik el. Egyes alkalmazások a litográfiában és a nagyfelbontású mikroszkópiában találhatók. Polimer üvegen Vortex fázisú lemezek is kaphatók. MIKROOPTIKAI HOMOGENIZÁLÓK / DIFFÚZOROK: Mikro-optikai homogenizátoraink és diffúzoraink gyártásához számos technológiát alkalmaznak, beleértve a dombornyomást, a tervezett diffúzor filmeket, a maratott diffúzorokat és a HiLAM diffúzorokat. A lézerfoltok a koherens fény véletlenszerű interferenciájából eredő optikai jelenségek. Ezt a jelenséget a detektortömbök modulációs átviteli függvényének (MTF) mérésére használják. A mikrolencsés diffúzorokról kimutatták, hogy hatékony mikrooptikai eszközök a foltok létrehozásához. SUGÁRFORMÁZÓK: A mikro-optikai sugárformázó olyan optika vagy optikakészlet, amely a lézersugár intenzitáseloszlását és térbeli alakját is egy adott alkalmazáshoz kívánatosabbá alakítja. A Gauss-szerű vagy nem egyenletes lézersugarat gyakran lapos felső sugárrá alakítják át. A sugárformázó mikrooptikát az egymódusú és többmódusú lézersugarak alakítására és manipulálására használják. Nyalábformázó mikrooptikánk kör, négyzet, egyenes, hatszögletű vagy vonal alakú formákat biztosít, és homogenizálja a gerendát (lapos tetejű), vagy egyedi intenzitású mintázatot biztosít az alkalmazás követelményeinek megfelelően. Törő, diffrakciós és fényvisszaverő mikro-optikai elemeket gyártottak a lézersugár formálására és homogenizálására. A többfunkciós mikro-optikai elemeket tetszőleges lézersugár-profilok különféle geometriájúvá alakítására használják, mint például homogén folttömb vagy vonalminta, lézerfénylap vagy lapos felső intenzitású profilok. A finomsugaras alkalmazási példák a vágás és a kulcslyukhegesztés. A szélessugaras alkalmazási példák a vezetőhegesztés, keményforrasztás, hőkezelés, vékonyréteg-eltávolítás, lézeres kivágás. IMPULZUS TÖMÖRÍTÉSI RÁCSOK: Az impulzustömörítés egy hasznos technika, amely kihasználja az impulzus időtartama és az impulzus spektrális szélessége közötti kapcsolatot. Ez lehetővé teszi a lézerimpulzusok erősítését a lézerrendszer optikai komponensei által előírt normál károsodási küszöbérték felett. Léteznek lineáris és nemlineáris technikák az optikai impulzusok időtartamának csökkentésére. Számos módszer létezik az optikai impulzusok időleges tömörítésére/lerövidítésére, azaz az impulzus időtartamának csökkentésére. Ezek a módszerek általában a pikoszekundumos vagy femtoszekundumos régióban kezdődnek, vagyis már az ultrarövid impulzusok tartományában. MULTISPOT NYALÉK OSZTÓK: A diffrakciós elemekkel történő sugárfelosztás akkor kívánatos, ha egy elem több nyaláb előállításához szükséges, vagy ha nagyon pontos optikai teljesítmény-leválasztásra van szükség. Pontos pozicionálás is elérhető, például lyukak létrehozása egyértelműen meghatározott és pontos távolságokban. Vannak többpontos elemeink, sugármintavevő elemeink, több fókuszú elemeink. Diffraktív elem segítségével a kollimált beeső nyalábokat több sugárnyalábra osztják. Ezek az optikai sugarak azonos intenzitásúak és azonos szöget zárnak be egymással. Vannak egydimenziós és kétdimenziós elemeink is. Az 1D-s elemek egyenes vonal mentén osztják el a gerendákat, míg a 2D-s elemek például 2 x 2 vagy 3 x 3 foltokból álló mátrixban elrendezett nyalábokat és hatszögletű foltokkal rendelkező elemeket hoznak létre. Mikro-optikai változatok is elérhetők. NYALÁR MINTAVÉTELŐ ELEMEK: Ezek az elemek rácsok, amelyeket nagy teljesítményű lézerek beépített monitorozására használnak. Nyalábméréshez a ± első diffrakciós sorrend használható. Erősségük lényegesen alacsonyabb, mint a távolsági sugáré, és egyedi tervezésűek. Magasabb diffrakciós sorrend is használható még kisebb intenzitású mérésekhez. Ezzel a módszerrel a nagy teljesítményű lézerek intenzitásbeli változásai és sugárprofiljának változásai megbízhatóan nyomon követhetők. MULTI-FÓKUSZUS ELEMEK: Ezzel a diffrakciós elemmel több fókuszpont is létrehozható az optikai tengely mentén. Ezeket az optikai elemeket érzékelőkben, szemészetben, anyagfeldolgozásban használják. Mikro-optikai változatok is elérhetők. MIKROOPTIKAI ÖSSZEFÜGGÉSEK: Az optikai összeköttetések váltották fel az elektromos rézvezetékeket az összekapcsolási hierarchia különböző szintjein. A mikrooptikai távközlés előnyeinek a számítógép hátlapjára, a nyomtatott áramköri lapra, az inter-chip és on-chip összekapcsolási szintjére való eljuttatásának egyik lehetősége a szabad helyű, műanyagból készült mikro-optikai összekötő modulok alkalmazása. Ezek a modulok nagy összesített kommunikációs sávszélességet képesek hordozni több ezer pont-pont optikai kapcsolaton keresztül négyzetcentiméteres területen. Forduljon hozzánk, ha a számítógép hátlapjához, a nyomtatott áramköri laphoz, a chipek közötti és az on-chip összeköttetési szintekhez különálló, valamint személyre szabott mikro-optikai összekötőket szeretne kapni. INTELLIGENS MIKROOPTIKAI RENDSZEREK: Az intelligens mikro-optikai fénymodulokat okostelefonokban és okoseszközökben használják LED-vaku alkalmazásokhoz, optikai összeköttetésekben adatátvitelhez szuperszámítógépekben és távközlési berendezésekben, miniatürizált megoldásként közeli infravörös sugárzás kialakításához, detektáláshoz a játékokban alkalmazásokhoz és a természetes felhasználói felületeken a gesztusvezérlés támogatásához. Az érzékelő optoelektronikai modulokat számos termékalkalmazáshoz használják, például a környezeti fényhez és az okostelefonok közelségérzékelőihez. Intelligens képalkotó mikro-optikai rendszereket használnak az elsődleges és az előlapi kamerákhoz. Személyre szabott intelligens mikro-optikai rendszereket is kínálunk nagy teljesítménnyel és gyárthatósággal. LED MODULOK: LED chipjeinket, matricáinkat és moduljainkat megtalálja oldalunkon Világítási és világítási alkatrészek gyártása ide kattintva. VEZETÉKRÁCS POLARIZÁTOROK: Ezek a beeső sugárra merőleges síkban elhelyezett finom, párhuzamos fémhuzalok szabályos sorából állnak. A polarizációs irány merőleges a vezetékekre. A mintás polarizátorok polarimetriában, interferometriában, 3D-s kijelzőkben és optikai adattárolásban alkalmazhatók. A vezetékes rácsos polarizátorokat széles körben használják infravörös alkalmazásokban. Másrészt a mikromintázatú huzalrácsos polarizátorok korlátozott térbeli felbontással és látható hullámhosszon gyenge teljesítményükkel rendelkeznek, érzékenyek a hibákra, és nem könnyen kiterjeszthetők nemlineáris polarizációkra. A pixeles polarizátorok mikromintázatú nanohuzalos rácsokat használnak. A pixeles mikro-optikai polarizátorok kamerákkal, síktömbökkel, interferométerekkel és mikrobolométerekkel illeszthetők anélkül, hogy mechanikus polarizátorkapcsolókra lenne szükség. Élénk képek, amelyek megkülönböztetik a látható és az IR hullámhosszú polarizációt, egyidejűleg, valós időben rögzíthetők, így gyors, nagy felbontású képek készíthetők. A pixeles mikro-optikai polarizátorok tiszta 2D és 3D képeket tesznek lehetővé még gyenge fényviszonyok között is. Két-, három- és négyállapotú képalkotó készülékekhez kínálunk mintás polarizátorokat. Mikro-optikai változatok is elérhetők. FOKOZATOS INDEX (GRIN) LENCSÉK: Egy anyag törésmutatójának (n) fokozatos változtatásával sík felületű lencséket lehet előállítani, vagy olyan lencséket lehet előállítani, amelyek nem rendelkeznek a hagyományos gömb alakú lencséknél jellemző aberrációkkal. A gradiens-index (GRIN) lencsék fénytörési gradiense lehet gömb alakú, axiális vagy radiális. Nagyon kicsi mikro-optikai változatok is elérhetők. MIKROOPTIKUS DIGITÁLIS SZŰRŐK: A digitális semleges sűrűségű szűrők a megvilágítási és vetítőrendszerek intenzitásprofiljának szabályozására szolgálnak. Ezek a mikrooptikai szűrők jól meghatározott fém abszorber mikrostruktúrákat tartalmaznak, amelyek véletlenszerűen oszlanak el egy olvasztott szilícium-dioxid hordozón. Ezeknek a mikro-optikai alkatrészeknek a tulajdonságai a nagy pontosság, a nagy átlátszó apertúra, a magas károsodási küszöb, a szélessávú csillapítás a DUV-tól az IR hullámhosszig, jól meghatározott egy- vagy kétdimenziós átviteli profilok. Egyes alkalmazások lágy élű nyílások, intenzitásprofilok pontos korrekciója megvilágítási vagy vetítőrendszerekben, változó csillapítású szűrők nagy teljesítményű lámpákhoz és kiterjesztett lézersugarak. Testreszabhatjuk a szerkezetek sűrűségét és méretét, hogy pontosan megfeleljenek az alkalmazás által megkövetelt átviteli profiloknak. MULTI-HULLÁMÚ NYALÓS KOMBINÁTOROK: A többhullámú nyalábkombinátorok két különböző hullámhosszú LED-kollimátort egyesítenek egyetlen kollimált sugárban. Több kombináló is kaszkádozható, hogy kettőnél több LED-kollimátor forrást kombináljon. A nyalábkombinátorok nagy teljesítményű dikroikus sugárosztókból készülnek, amelyek két hullámhosszt kombinálnak >95%-os hatékonysággal. Nagyon kicsi mikro-optikai változatok is elérhetők. CLICK Product Finder-Locator Service ELŐZŐ OLDAL
- Camera Systems & Components, Optic Scanner, Optical Readers, CCD
Camera Systems - Components - Optic Scanner - Optical Readers - Imaging System - CCD - Optomechanical Systems - IR Cameras Egyedi kamerarendszerek gyártása és összeszerelése Az AGS-TECH a következőket kínálja: • Kamerarendszerek, kameraalkatrészek és egyedi kameraegységek • Egyedi tervezésű és gyártású optikai szkennerek, olvasók, optikai biztonsági termékegységek. • Precíziós optikai, opto-mechanikai és elektro-optikai szerelvények, amelyek integrálják a képalkotó és nem képalkotó optikát, a LED-es világítást, a száloptikát és a CCD kamerákat • Optikai mérnökeink által kifejlesztett termékek közül a következők: - Omni-directional periszkóp és kamera megfigyelési és biztonsági alkalmazásokhoz. 360 x 60º-os látómező nagy felbontású kép, nincs szükség varrásra. - Belső üreges, széles látószögű videokamera - Szupervékony, 0,6 mm átmérőjű, rugalmas video endoszkóp. Minden orvosi videocsatoló illeszkedik a szabványos endoszkóp okulárokhoz, és teljesen tömített és átitatható. Orvosi endoszkóp- és kamerarendszereinkért keresse fel a következő címet: http://www.agsmedical.com - Videokamera és csatlakozó félmerev endoszkóphoz - Eye-Q Videoprobe. Érintkezés nélküli zoom videoszonda koordináta mérőgépekhez. - Optikai spektrográf és infravörös képalkotó rendszer (OSIRIS) ODIN műholdhoz. Mérnökeink a repülési egység összeszerelésén, beállításán, integrációján és tesztelésén dolgoztak. - Szélképes interferométer (WINDII) a NASA felső légköri kutatóműholdjához (UARS). Mérnökeink az összeszereléssel, az integrációval és a teszteléssel kapcsolatos tanácsadáson dolgoztak. A WINDII teljesítménye és élettartama messze meghaladta a tervezési célokat és követelményeket. Alkalmazásától függően meghatározzuk, hogy milyen méreteket, pixelszámot, felbontást és hullámhossz-érzékenységet igényel a kamera alkalmazása. Kiépítünk Önnek infravörös, látható és egyéb hullámhosszúságú rendszereket. További információért lépjen kapcsolatba velünk még ma. Brosúra letöltése számunkra TERVEZÉSI PARTNERSÉGI PROGRAM Győződjön meg arról is, hogy IDE KATTINTVA töltse le átfogó elektromos és elektronikus alkatrészek katalógusunkat a késztermékekhez. CLICK Product Finder-Locator Service ELŐZŐ OLDAL
- Surface Treatment and Modification - Surface Engineering - Hardening
Surface Treatment and Modification - Surface Engineering - Hardening - Plasma - Laser - Ion Implantation - Electron Beam Processing at AGS-TECH Felületkezelések és módosítások A felületek mindent beborítanak. Az anyagfelületek vonzereje és funkciói rendkívül fontosak számunkra. Therefore SURFACE TREATMENT and SURFACE MODIFICATION are among our everyday industrial operations. A felületkezelés és módosítás a felületi tulajdonságok javulását eredményezi, és akár végső befejező műveletként, akár bevonási vagy ragasztási művelet előtt is elvégezhető. Felületkezelési és módosítási folyamatok (más néven SURFACE ENGINEERING) , az anyagok és termékek felületeit a következőkre szabja: - A súrlódás és a kopás szabályozása - Javítja a korrózióállóságot - Javítja a későbbi bevonatok vagy az összeillesztett részek tapadását - A fizikai tulajdonságok megváltoztatása: vezetőképesség, ellenállás, felületi energia és visszaverődés - A felületek kémiai tulajdonságainak megváltoztatása funkciós csoportok bevezetésével - Méretek módosítása - A megjelenés megváltoztatása, pl. szín, érdesség stb. - Tisztítsa meg és/vagy fertőtlenítse a felületeket Felületkezeléssel és módosítással javítható az anyagok funkciója és élettartama. Általános felületkezelési és módosítási módszereink két nagy csoportra oszthatók: Felületkezelés és a felületeket lefedő módosítások: Szerves bevonatok: A szerves bevonatok festékeket, cementeket, laminátumokat, olvasztott porokat és kenőanyagokat visznek fel az anyagok felületére. Szervetlen bevonatok: Népszerű szervetlen bevonataink a galvanizálás, autokatalitikus bevonat (elektromos bevonat), konverziós bevonatok, hőpermetek, melegbemerítés, keménybevonatok, kemencében történő olvasztás, vékonyréteg-bevonatok, mint például SiO2, SiN fémen, üvegen, kerámián stb. A felületkezelést és a bevonatokkal járó módosításokat a kapcsolódó almenüben kérjük részletesen ismertetnikattintson ide Funkcionális bevonatok / Dekoratív bevonatok / Vékony fólia / Vastag fólia Felületkezelés és módosítások, amelyek megváltoztatják a felületeket: Ezen az oldalon ezekre fogunk koncentrálni. Az alábbiakban ismertetett felületkezelési és -módosítási technikák közül nem mindegyik van mikro- vagy nanoléptékű, de röviden említést teszünk róluk, mivel az alapvető célok és módszerek jelentős mértékben hasonlóak a mikrogyártási léptékűekhez. Edzés: Szelektív felületkeményítés lézerrel, lánggal, indukcióval és elektronsugárral. Nagy energiájú kezelések: Nagy energiájú kezeléseink közé tartozik az ionimplantáció, a lézeres üvegezés és fúzió, valamint az elektronsugaras kezelés. Vékony diffúziós kezelések: A vékony diffúziós eljárások közé tartozik a ferrites-nitrokarburizálás, a bórozás és más magas hőmérsékletű reakciófolyamatok, mint például a TiC, VC. Erős diffúziós kezelések: Erős diffúziós folyamataink közé tartozik a karburálás, a nitridálás és a karbonitridálás. Speciális felületkezelések: Az olyan speciális kezelések, mint a kriogén, mágneses és szonikus kezelések mind a felületekre, mind az ömlesztett anyagokra hatással vannak. A szelektív keményedési folyamatok végrehajthatók lánggal, indukcióval, elektronsugárral, lézersugárral. A nagy aljzatokat lángkeményítéssel mélykeményítik. Az indukciós edzést viszont kis alkatrészekhez használják. A lézer- és elektronsugaras edzést néha nem különböztetik meg a keményburkolatoknál vagy a nagy energiájú kezeléseknél alkalmazottaktól. Ezek a felületkezelési és módosítási eljárások csak olyan acélokra alkalmazhatók, amelyek elegendő szén- és ötvözettartalommal rendelkeznek ahhoz, hogy lehetővé tegyék az edzést. Az öntöttvas, szénacél, szerszámacél és ötvözött acél alkalmas erre a felületkezelési és módosítási módszerre. Az alkatrészek méreteit ezek a keményedő felületkezelések nem változtatják meg jelentősen. Az edzés mélysége 250 mikrontól a teljes metszetmélységig változhat. A teljes metszet esetében azonban a metszetnek vékonynak, 25 mm-nél (1 hüvelyknél) kisebbnek vagy kicsinek kell lennie, mivel a keményedési folyamatokhoz az anyagok gyors lehűlése szükséges, néha egy másodpercen belül. Ez nagy munkadaraboknál nehezen valósítható meg, ezért nagy szakaszokon csak a felületek edzhetők. Népszerű felületkezelési és módosítási eljárásként rugókat, késpengéket és sebészeti pengék edzését számos egyéb termék mellett végezzük. A nagyenergiájú eljárások viszonylag új felületkezelési és módosítási módszerek. A felületek tulajdonságai a méretek megváltoztatása nélkül változnak. Népszerű, nagy energiájú felületkezelési eljárásaink az elektronsugaras kezelés, az ionimplantáció és a lézersugaras kezelés. Elektronsugaras kezelés: Az elektronsugaras felületkezelés gyors melegítéssel és gyors hűtéssel megváltoztatja a felület tulajdonságait – 10 Exp6 Celsius/sec (10exp6 Fahrenheit/sec) nagyságrendben egy nagyon sekély, 100 mikron körüli területen az anyag felületéhez közel. Az elektronsugaras kezelés kemény felületkezelésben is alkalmazható felületi ötvözetek előállítására. Ionbeültetés: Ez a felületkezelési és -módosító módszer elektronsugarat vagy plazmát használ a gázatomok megfelelő energiájú ionokká történő átalakítására, és az ionok beültetésére/behelyezésére a szubsztrát atomrácsába, vákuumkamrában mágnestekercsekkel felgyorsítva. A vákuum megkönnyíti az ionok szabad mozgását a kamrában. A beültetett ionok és a fém felülete közötti eltérés atomi hibákat hoz létre, amelyek megkeményítik a felületet. Lézersugaras kezelés: Az elektronsugaras felületkezeléshez és -módosításhoz hasonlóan a lézersugaras kezelés is megváltoztatja a felület tulajdonságait gyors melegítéssel és gyors hűtéssel egy nagyon sekély területen a felszín közelében. Ez a felületkezelési és -módosítási módszer a keményítésnél is használható felületi ötvözetek előállítására. Az implantátum adagolásával és kezelési paramétereivel kapcsolatos know-how lehetővé teszi számunkra, hogy ezeket a nagy energiájú felületkezelési technikákat gyártóüzemeinkben alkalmazzuk. Vékony diffúziós felületkezelések: A ferrites nitrokarburizálás olyan keményedési eljárás, amely a nitrogént és a szenet vasfémekké diffundálja a kritikus alatti hőmérsékleten. A feldolgozási hőmérséklet általában 565 Celsius-fok (1049 Fahrenheit). Ezen a hőmérsékleten az acélok és más vasötvözetek még ferrites fázisban vannak, ami előnyös az ausztenites fázisban előforduló egyéb keményedési folyamatokhoz képest. Az eljárást a következők javítására használják: •kopásállóság •fáradási tulajdonságok •korrozióállóság Az alacsony feldolgozási hőmérsékletnek köszönhetően nagyon kis alaktorzulás lép fel az edzési folyamat során. A bórozás az a folyamat, amelyben a bórt egy fémbe vagy ötvözetbe juttatják. Ez egy felületkeményítési és -módosítási eljárás, amelynek során a bóratomokat egy fémkomponens felületére diffundálják. Ennek eredményeként a felület fém-boridokat, például vas-boridokat és nikkel-boridokat tartalmaz. Ezek a boridok tiszta állapotukban rendkívül nagy keménységgel és kopásállósággal rendelkeznek. A bórozott fém alkatrészek rendkívül kopásállóak, és gyakran akár ötször tovább tartanak, mint a hagyományos hőkezeléssel, például keményítéssel, karburizálással, nitridálással, nitrokarburizálással vagy indukciós edzéssel kezelt alkatrészek. Erős diffúziós felületkezelés és módosítás: Ha a széntartalom alacsony (pl. 0,25% alatt), akkor a felület széntartalmát növelhetjük az edzéshez. Az alkatrész a kívánt tulajdonságoktól függően hőkezelhető folyadékban történő hűtéssel vagy csendes levegőn hűthető. Ez a módszer csak a felületen teszi lehetővé a helyi keményedést, a magban nem. Ez néha nagyon kívánatos, mert kemény felületet tesz lehetővé, jó kopási tulajdonságokkal, mint a fogaskerekek esetében, de szívós belső magja van, amely ütési terhelés alatt is jól működik. Az egyik felületkezelési és -módosító technikánál, nevezetesen a karburálásnál szenet adunk a felülethez. Az alkatrészt szénben gazdag atmoszférának tesszük ki emelt hőmérsékleten, és lehetővé tesszük a diffúziót, hogy a szénatomok átkerüljenek az acélba. A diffúzió csak akkor megy végbe, ha az acél alacsony széntartalmú, mert a diffúzió a koncentrációkülönbség elvén működik. Csomagolási karburálás: Az alkatrészeket magas széntartalmú közegbe, például szénporba csomagolják, és kemencében 12-72 órán át 900 Celsius-fok (1652 Fahrenheit) hőmérsékleten hevítik. Ezen a hőmérsékleten CO gáz keletkezik, amely erős redukálószer. A redukciós reakció az acél felületén megy végbe, amely szenet szabadít fel. A szén ezután a magas hőmérsékletnek köszönhetően a felületbe diffundál. A felületi szén mennyisége a folyamat körülményeitől függően 0,7-1,2%. Az elért keménység 60-65 RC. A karburált ház mélysége körülbelül 0,1 mm-től 1,5 mm-ig terjed. A csomagolóanyag-karburálás megköveteli a hőmérséklet egyenletességének és a fűtés konzisztenciájának megfelelő szabályozását. Gázkarburálás: A felületkezelés ezen változatánál a szén-monoxid (CO) gázt egy fűtött kemencébe vezetik, és a szén lerakódásának redukciós reakciója az alkatrészek felületén megy végbe. Ez a folyamat megoldja a csomagkarburálás legtöbb problémáját. Az egyik gond azonban a CO-gáz biztonságos elszigetelése. Folyékony karburálás: Az acél alkatrészeket olvadt szénben gazdag fürdőbe merítik. A nitridálás egy felületkezelési és -módosítási folyamat, amely magában foglalja a nitrogén diffúzióját az acél felületébe. A nitrogén nitrideket képez olyan elemekkel, mint az alumínium, króm és molibdén. Az alkatrészeket nitridálás előtt hőkezelik és temperálják. Az alkatrészeket ezután megtisztítják és kemencében (N-t és H-t tartalmazó) disszociált ammónia atmoszférájában hevítik 10-40 órán át 500-625 Celsius-fok (932-1157 Fahrenheit) hőmérsékleten. A nitrogén bediffundál az acélba és nitridötvözeteket képez. Ez akár 0,65 mm mélységig behatol. A tok nagyon kemény és csekély a torzítás. Mivel a ház vékony, a felület csiszolása nem javasolt, ezért a nitridálásos felületkezelés nem biztos, hogy választható a nagyon sima felületkezelést igénylő felületeken. A karbonitridáló felületkezelési és módosítási eljárás a legalkalmasabb az alacsony széntartalmú ötvözött acélokhoz. A karbonitridálás során a szén és a nitrogén egyaránt diffundálódik a felületbe. Az alkatrészeket ammóniával (NH3) kevert szénhidrogén (például metán vagy propán) atmoszférában hevítik. Egyszerűen fogalmazva, a folyamat a karburálás és a nitridálás keveréke. A karbonitridáló felületkezelést 760-870 Celsius-fok (1400-1598 Fahrenheit) hőmérsékleten hajtják végre, majd földgáz (oxigénmentes) atmoszférában lehűtik. A karbonitridálási eljárás nem alkalmas nagy pontosságú alkatrészekhez a benne rejlő torzulások miatt. Az elért keménység hasonló a karburáláshoz (60-65 RC), de nem olyan magas, mint a nitridálásnál (70 RC). A tok mélysége 0,1 és 0,75 mm között van. A tok nitridekben és martenzitben gazdag. A ridegség csökkentése érdekében utólagos temperálásra van szükség. A speciális felületkezelési és módosítási eljárások a fejlesztés korai szakaszában járnak, hatékonyságuk egyelőre nem bizonyított. Ők: Kriogén kezelés: Általában edzett acélokon alkalmazzák, lassan hűtse le az aljzatot körülbelül -166 Celsius fokra (-300 Fahrenheit), hogy növelje az anyag sűrűségét, és ezáltal növelje a kopásállóságot és a méretstabilitást. Vibrációs kezelés: Céljuk, hogy enyhítsék a hőkezelések során felhalmozódott hőfeszültséget a vibráció révén, és növeljék a kopás élettartamát. Mágneses kezelés: Ezek célja, hogy a mágneses mezők hatására megváltoztassák az anyagok atomjainak felépítését, és remélhetőleg javítsák a kopási élettartamot. Ezeknek a speciális felületkezelési és módosítási technikáknak a hatékonysága még bizonyításra vár. A fenti három technika a felületeken kívül az ömlesztett anyagot is érinti. CLICK Product Finder-Locator Service ELŐZŐ OLDAL
- Plasma Machining, HF Plasma Cutting, Plasma Gouging, CNC, Arc Welding
Plasma Machining - HF Plasma Cutting - Plasma Gouging - CNC - Plasma Arc Welding - PAW - GTAW - AGS-TECH Inc. - New Mexico Plazma megmunkálás és vágás We use the PLASMA CUTTING and PLASMA MACHINING processes to cut and machine steel, aluminum, metals and other materials of Különböző vastagságok plazmaégő segítségével. A plazmavágásnál (más néven PLAZMA-ARC CUTTING) inert gázt vagy sűrített levegőt fújnak ki nagy sebességgel a fúvókából, és ezzel egyidejűleg elektromos ív képződik ezen a gázon a fúvókától a fúvókáig. a felületet vágják, és ennek a gáznak egy részét plazmává alakítják. Leegyszerűsítve a plazmát az anyag negyedik halmazállapotaként írhatjuk le. Az anyag három halmazállapota szilárd, folyékony és gáz. Egy általános példa, a víz esetében ez a három állapot a jég, a víz és a gőz. A különbség ezen állapotok között az energiaszintjükben van. Amikor hő formájában energiát adunk a jéghez, az megolvad és vizet képez. Ha több energiát adunk hozzá, a víz gőz formájában elpárolog. Ha több energiát adunk a gőzhöz, ezek a gázok ionizálódnak. Ez az ionizációs folyamat hatására a gáz elektromosan vezetővé válik. Ezt az elektromosan vezető, ionizált gázt „plazmának” nevezzük. A plazma nagyon forró és megolvasztja a vágandó fémet, és egyúttal kifújja az olvadt fémet a vágásról. Plazmát használunk vékony és vastag, vas- és színesfém anyagok vágására egyaránt. Kézi fáklyáink általában 2 hüvelyk vastag acéllemezt, erősebb számítógép-vezérlésű zseblámpáink pedig 6 hüvelyk vastag acélt képesek vágni. A plazmavágók nagyon forró és lokalizált kúpot hoznak létre a vágáshoz, ezért nagyon alkalmasak ívelt és szögletes formájú fémlemezek vágására. A plazmaíves vágás során keletkező hőmérséklet nagyon magas, 9673 Kelvin körüli az oxigén plazmafáklyában. Ez gyors folyamatot, kis vágásszélességet és jó felületi minőséget biztosít számunkra. Volfrámelektródákat használó rendszereinkben a plazma inert, vagy argon, argon-H2 vagy nitrogéngázok felhasználásával keletkezik. Azonban néha oxidáló gázokat is használunk, például levegőt vagy oxigént, és ezekben a rendszerekben az elektróda réz és hafnium. A levegős plazmafáklyák előnye, hogy levegőt használ a drága gázok helyett, így potenciálisan csökkenti a megmunkálás teljes költségét. A mi HF-TÍPUSÚ PLAZMA VÁGÁS gépeink nagyfrekvenciás ívet és ívet indítanak el a levegő magas ionáramának a fején keresztül. A nagyfrekvenciás plazmavágóink nem igénylik, hogy a pisztoly érintkezésbe kerüljön a munkadarab anyagával az elején, és alkalmasak az alábbi alkalmazásokhoz: SZÁMÍTÓGÉP SZÁMVEZÉRLÉS (CNC)_cc781905-54cbt5cbt53cb6-3. Más gyártók primitív gépeket használnak, amelyeknek a csúcsnak az alapfémmel való érintkezése szükséges az induláshoz, majd megtörténik a rés elválasztása. Ezek a primitívebb plazmavágók érzékenyebbek az érintkezési csúcs és az árnyékolás sérülésére indításkor. A mi PILOT-ARC TÍPUSÚ PLASMA gépeink kétlépéses folyamatot használnak a kezdeti érintkezés nélküli plazma előállításához. Az első lépésben egy nagyfeszültségű, kisáramú áramkört használnak egy nagyon kicsi, nagy intenzitású szikra inicializálására a fáklya testében, ami egy kis plazmagáz zsebet hoz létre. Ezt pilótaívnek hívják. A pilótaívnek egy visszatérő elektromos útja van a fáklyafejbe beépítve. A pilótaív mindaddig megmarad és megőrződik, amíg a munkadarab közelébe nem kerül. Ott a pilotív meggyújtja a fő plazmavágó ívet. A plazmaívek rendkívül forróak, és a 25 000 °C = 45 000 °F tartományba esnek. Egy hagyományosabb módszer, amelyet szintén alkalmazunk, a OXYFUEL-GAS CUTTING (OFC) ch, ahol a hegesztésben is használjuk. A műveletet acél, öntöttvas és acélöntvény vágására használják. A vágás elve az oxigén-gáz vágásnál az acél oxidációján, égésén és megolvasztásán alapul. Az oxigén-gáz vágásnál a vágásszélesség 1,5 és 10 mm között van. A plazmaíves eljárást az oxigén-üzemanyag eljárás alternatívájának tekintették. A plazmaíves eljárás abban különbözik az oxigén-üzemanyag eljárástól, hogy az ív segítségével megolvasztja a fémet, míg az oxigén-üzemanyag eljárásban az oxigén oxidálja a fémet, és az exoterm reakcióból származó hő megolvasztja a fémet. Ezért az oxigén-üzemanyag eljárással ellentétben a plazma-eljárás alkalmazható olyan fémek vágására, amelyek tűzálló oxidokat képeznek, mint például a rozsdamentes acél, az alumínium és a színesfém ötvözetek. PLAZMA GOUGING a plazmavágáshoz hasonló eljárás, jellemzően ugyanazzal a berendezéssel történik, mint a plazmavágás. Az anyag vágása helyett a plazmamarás egy másik pisztoly konfigurációt használ. A pisztoly fúvókája és a gázbefúvó általában eltérő, és hosszabb a pisztoly és a munkadarab közötti távolság a fém elfújásához. A plazmamarás különféle alkalmazásokban használható, beleértve a hegesztés eltávolítását az újrafeldolgozáshoz. Néhány plazmavágónk a CNC asztalba van beépítve. A CNC asztalok számítógéppel rendelkeznek a fáklyafej vezérlésére, hogy tiszta éles vágásokat készítsenek. Modern CNC plazma berendezéseink vastag anyagok többtengelyes vágására is alkalmasak, és olyan összetett hegesztési varratokat tesznek lehetővé, amelyek egyébként nem lehetségesek. Plazmaívvágóink nagymértékben automatizáltak a programozható vezérlők használatával. Vékonyabb anyagoknál előnyben részesítjük a lézervágást a plazmavágással szemben, leginkább lézervágónk kiváló lyukvágó képességei miatt. Függőleges CNC plazmavágó gépeket is alkalmazunk, amelyek kisebb helyigényt, nagyobb rugalmasságot, nagyobb biztonságot és gyorsabb működést kínálnak számunkra. A plazmavágási él minősége hasonló az oxigén-üzemanyag vágási eljárásokkal elérthez. Mivel azonban a plazma eljárás olvasztással vág, jellemző a fém teteje felé irányuló nagyobb mértékű olvadás, ami a felső él lekerekítését, rossz élszögletességét vagy a vágott él ferdeségét eredményezi. Kisebb fúvókával és vékonyabb plazmaívvel rendelkező plazmaégők új modelljeit használjuk, hogy javítsuk az ívszűkületet, hogy egyenletesebb melegítést érjünk el a vágás tetején és alján. Ezzel közel lézeres pontosságot érhetünk el a plazmavágott és megmunkált éleken. A mi MAGAS TŰRÉS PLAZMAÍVVÁGÁS (HTPAC) rendszereink erősen konzisztens plazmával működnek A plazma fókuszálását úgy érik el, hogy az oxigén által termelt plazmát örvényre kényszerítik, amikor belép a plazmanyílásba, és egy másodlagos gázáramot fecskendeznek be a plazmafúvóka után. Külön mágneses mező veszi körül az ívet. Ez stabilizálja a plazmasugarat az örvénylő gáz által kiváltott forgás fenntartásával. A precíziós CNC vezérlést ezekkel a kisebb és vékonyabb pisztolyokkal kombinálva képesek vagyunk olyan alkatrészeket gyártani, amelyek kevés vagy egyáltalán nem igényelnek feldolgozást. Az anyageltávolítási sebesség a plazma-megmunkálásban sokkal magasabb, mint az elektromos kisütési megmunkálási (EDM) és a lézersugaras megmunkálási (LBM) folyamatokban, és az alkatrészek jó reprodukálhatósággal megmunkálhatók. A PLAZMA ÍVHEGESZTÉS (PAW) a gázvolfrámíves hegesztéshez (GTAW) hasonló eljárás. Az elektromos ív egy általában szinterezett volfrámból készült elektróda és a munkadarab között jön létre. A legfontosabb különbség a GTAW-hoz képest az, hogy a PAW-ban az elektródának a fáklya testén belüli elhelyezésével a plazmaív elválasztható a védőgáz burkától. A plazmát ezután egy finom furatú rézfúvókán keresztül nyomják át, amely nagy sebességgel és 20 000 °C-ot megközelítő hőmérsékleten szűkíti az ívet és a nyíláson kilépő plazmát. A plazmaívhegesztés előrelépést jelent a GTAW eljáráshoz képest. A PAW hegesztési eljárás egy nem fogyó wolfram elektródát és egy finom furatú réz fúvókán keresztül szűkített ívet használ. A PAW használható minden olyan fém és ötvözet összekapcsolására, amely GTAW-val hegeszthető. Számos alapvető PAW-folyamatvariáció lehetséges az áramerősség, a plazmagáz áramlási sebességének és a nyílás átmérőjének változtatásával, beleértve: Mikroplazma (< 15 A) Beolvadási mód (15–400 Amper) Kulcslyuk mód (>100 Amper) A plazmaíves hegesztésnél (PAW) nagyobb energiakoncentrációt kapunk a GTAW-hoz képest. Mély és keskeny behatolás érhető el, a maximális mélység 12-18 mm (0,47-0,71 hüvelyk) az anyagtól függően. A nagyobb ívstabilitás sokkal hosszabb ívhosszt tesz lehetővé (kiállás), és sokkal nagyobb tolerancia az ívhossz-változásokkal szemben. Hátránya azonban, hogy a PAW viszonylag drága és összetett berendezést igényel a GTAW-hoz képest. A fáklya karbantartása is kritikus és nagyobb kihívást jelent. A PAW további hátrányai a következők: A hegesztési eljárások általában bonyolultabbak és kevésbé tűrik az illesztések stb. eltéréseit. A kezelői szakértelem valamivel több, mint a GTAW esetében. A nyílás cseréje szükséges. CLICK Product Finder-Locator Service ELŐZŐ OLDAL
- Microelectronics Manufacturing, Semiconductor Fabrication, Foundry, IC
Microelectronics Manufacturing, Semiconductor Fabrication - Foundry - FPGA - IC Assembly Packaging - AGS-TECH Inc. Mikroelektronika és félvezető gyártás és gyártás A többi menüben ismertetett nanogyártási, mikrogyártási és mezogyártási technikáink és folyamataink közül sok használható a következőhöz: MICROELECTRONICS MANUFACTURING_cc781905-94f6bbd8. A mikroelektronika termékeinkben betöltött jelentőségéből adódóan azonban itt ezen eljárások tárgyspecifikus alkalmazásaira koncentrálunk. A mikroelektronikával kapcsolatos folyamatokat széles körben emlegetik: SEMICONDUCTOR FABRICATION processes. Félvezető mérnöki tervezési és gyártási szolgáltatásaink a következők: - FPGA kártya tervezés, fejlesztés és programozás - Microelectronics öntödei szolgáltatások: Tervezés, prototípus-készítés és gyártás, harmadik féltől származó szolgáltatások - Félvezető ostya előkészítése: Kockavágás, hátcsiszolás, soványítás, irányzék elhelyezés, kockaválogatás, szedés és elhelyezés, ellenőrzés - Mikroelektronikus csomagolás tervezése és gyártása: mind kész, mind egyedi tervezés és gyártás - Félvezető IC összeszerelés és csomagolás és tesztelés: Die, huzal és chip kötés, tokozás, összeszerelés, jelölés és márkajelzés - Ólomkeretek félvezető eszközökhöz: mind kész, mind egyedi tervezés és gyártás - Hűtőbordák tervezése és gyártása mikroelektronikához: mind kész, mind egyedi tervezés és gyártás - Érzékelők és működtető szerkezetek tervezése és gyártása: Mind kész, mind egyedi tervezés és gyártás - Optoelektronikai és fotonikus áramkörök tervezése és gyártása Vizsgáljuk meg részletesebben a mikroelektronikai és félvezetőgyártási és tesztelési technológiákat, hogy jobban megértse az általunk kínált szolgáltatásokat és termékeket. FPGA kártya tervezése és fejlesztése és programozása: Field-programable gate array (FPGA-k) újraprogramozható szilícium chipek. Ellentétben a személyi számítógépekben található processzorokkal, az FPGA programozása magát a chipet újrahuzalozza, hogy megvalósítsa a felhasználói funkciókat, nem pedig szoftveralkalmazást. Előre beépített logikai blokkok és programozható útválasztási erőforrások segítségével az FPGA chipek konfigurálhatók egyéni hardverfunkciók megvalósítására kenyérsütő és forrasztópáka használata nélkül. A digitális számítási feladatokat szoftverben hajtják végre, és konfigurációs fájlba vagy bitfolyamba fordítják le, amely információkat tartalmaz arról, hogyan kell az összetevőket összekötni. Az FPGA-k bármilyen logikai funkció megvalósítására használhatók, amelyet egy ASIC végrehajthat, és teljesen újrakonfigurálható, és teljesen más „személyiséget” adhat egy másik áramköri konfiguráció újrafordításával. Az FPGA-k egyesítik az alkalmazás-specifikus integrált áramkörök (ASIC) és a processzor alapú rendszerek legjobb részeit. Ezek az előnyök a következők: • Gyorsabb I/O válaszidő és speciális funkciók • A digitális jelprocesszorok (DSP-k) számítási teljesítményének túllépése • Gyors prototípuskészítés és ellenőrzés az egyedi ASIC gyártási folyamata nélkül • Egyedi funkcionalitás megvalósítása a dedikált determinisztikus hardver megbízhatóságával • Helyszínen frissíthető, kiküszöbölve az egyedi ASIC újratervezés és karbantartás költségeit Az FPGA-k gyorsaságot és megbízhatóságot biztosítanak anélkül, hogy nagy mennyiségre lenne szükségük, ami indokolná az egyedi ASIC-tervezés nagy előzetes költségeit. Az újraprogramozható szilícium is ugyanolyan rugalmassággal rendelkezik, mint a processzor alapú rendszereken futó szoftver, és nem korlátozza a rendelkezésre álló feldolgozómagok száma. A processzorokkal ellentétben az FPGA-k valóban párhuzamos jellegűek, így a különböző feldolgozási műveleteknek nem kell versenyezniük ugyanazon erőforrásokért. Minden független feldolgozási feladat a chip egy dedikált részéhez van hozzárendelve, és önállóan működhet anélkül, hogy bármilyen más logikai blokk befolyásolná. Ennek eredményeként az alkalmazás egy részének teljesítménye nincs hatással, ha további feldolgozást ad hozzá. Egyes FPGA-k a digitális funkciókon kívül analóg funkciókkal is rendelkeznek. Néhány gyakori analóg jellemző a programozható elfordulási sebesség és a meghajtó erőssége minden kimeneti érintkezőn, ami lehetővé teszi a mérnök számára, hogy lassú sebességet állítson be az enyhén terhelt érintkezőkön, amelyek egyébként elfogadhatatlanul csengenének vagy párosodnának, valamint hogy erősebb, gyorsabb sebességet állítson be a nagy sebességű érintkezőkön. csatornák, amelyek egyébként túl lassan futnának. Egy másik viszonylag gyakori analóg jellemző a differenciálösszehasonlítók a bemeneti érintkezőkön, amelyeket úgy terveztek, hogy differenciális jelzőcsatornákhoz csatlakozzanak. Egyes vegyes jelű FPGA-k integrált perifériás analóg-digitális konverterekkel (ADC-kkel) és digitális-analóg átalakítókkal (DAC-okkal) rendelkeznek analóg jelkondicionáló blokkokkal, amelyek lehetővé teszik, hogy rendszerként működjenek a chipen. Röviden, az FPGA chipek 5 legfontosabb előnye: 1. Jó teljesítmény 2. Rövid piacra jutási idő 3. Alacsony költség 4. Nagy megbízhatóság 5. Hosszú távú karbantartási képesség Jó teljesítmény – A párhuzamos feldolgozásra való képességüknek köszönhetően az FPGA-k jobb számítási teljesítménnyel rendelkeznek, mint a digitális jelfeldolgozók (DSP-k), és nem igényelnek szekvenciális végrehajtást DSP-ként, és órajelenként többet tudnak teljesíteni. A bemenetek és kimenetek (I/O) hardverszintű vezérlése gyorsabb válaszidőt és speciális funkcionalitást biztosít az alkalmazási követelményeknek megfelelően. Rövid piacra kerülési idő – Az FPGA-k rugalmasságot és gyors prototípus-készítési lehetőségeket kínálnak, így rövidebb a piacra kerülési idő. Ügyfeleink tesztelhetnek egy ötletet vagy koncepciót, és ellenőrizhetik azt hardveren anélkül, hogy az egyedi ASIC tervezés hosszú és költséges gyártási folyamatán mennének keresztül. Inkrementális változtatásokat hajthatunk végre, és hetek helyett órákon belül iterálhatunk egy FPGA-tervet. Kereskedelmi kész hardver is elérhető különböző típusú I/O-kkal, amelyek már csatlakoztatva vannak a felhasználó által programozható FPGA chiphez. A magas szintű szoftvereszközök növekvő elérhetősége értékes IP magokat (előre beépített funkciókat) kínál a fejlett vezérléshez és jelfeldolgozáshoz. Alacsony költség – Az egyedi ASIC tervezések nem ismétlődő tervezési (NRE) költségei meghaladják az FPGA-alapú hardvermegoldásokét. Az ASIC-ekbe való nagy kezdeti beruházás indokolt lehet az évente sok chipet gyártó OEM-ek számára, azonban sok végfelhasználónak egyedi hardverfunkciókra van szüksége a fejlesztés alatt álló számos rendszerhez. Programozható szilícium FPGA-nk gyártási költségek és hosszú összeszerelési idő nélkül kínál valamit. A rendszerkövetelmények gyakran változnak az idő múlásával, és az FPGA-tervek fokozatos változtatásainak költsége elhanyagolható az ASIC újrapörgésének költségeihez képest. Nagy megbízhatóság – A szoftvereszközök biztosítják a programozási környezetet, az FPGA áramkör pedig a programvégrehajtás valódi megvalósítását jelenti. A processzor alapú rendszerek általában több absztrakciós réteget foglalnak magukban, hogy segítsék a feladatok ütemezését és az erőforrások megosztását több folyamat között. Az illesztőprogram-réteg vezérli a hardvererőforrásokat, az operációs rendszer pedig a memóriát és a processzor sávszélességét. Egy adott processzormag esetében egyszerre csak egy utasítás hajtható végre, és a processzor alapú rendszerek folyamatosan fennállnak annak a veszélye, hogy az időkritikus feladatok megelőzik egymást. Az FPGA-k, amelyek nem használnak operációs rendszereket, minimális megbízhatósági aggályokat vetnek fel valódi párhuzamos végrehajtásukkal és minden feladathoz determinisztikus hardverrel. Hosszú távú karbantartási képesség – Az FPGA chipek helyben frissíthetők, és nem igényelnek időt és költséget az ASIC újratervezéséhez. A digitális kommunikációs protokolloknak például olyan specifikációi vannak, amelyek idővel változhatnak, az ASIC-alapú interfészek pedig karbantartási és előrehaladási kompatibilitási kihívásokat okozhatnak. Éppen ellenkezőleg, az újrakonfigurálható FPGA chipek lépést tudnak tartani a potenciálisan szükséges jövőbeni módosításokkal. Ahogy a termékek és a rendszerek érnek, ügyfeleink funkcionális fejlesztéseket hajthatnak végre anélkül, hogy időt kellene fordítaniuk a hardver újratervezésére és az alaplapok elrendezésének módosítására. Mikroelektronikai öntödei szolgáltatások: Mikroelektronikai öntödei szolgáltatásaink magukban foglalják a tervezést, a prototípus-készítést és a gyártást, valamint harmadik féltől származó szolgáltatásokat. Ügyfeleinknek segítséget nyújtunk a teljes termékfejlesztési ciklusban – a tervezési támogatástól a félvezető chipek prototípus-készítéséig és gyártási támogatásáig. Célunk a tervezést támogató szolgáltatások terén, hogy lehetővé tegyük az első alkalommal megfelelő megközelítést a félvezető eszközök digitális, analóg és vegyes jelű tervezésénél. Például MEMS-specifikus szimulációs eszközök állnak rendelkezésre. Az integrált CMOS-hoz és MEMS-hez 6 és 8 hüvelykes ostyák kezelésére alkalmas fabok az Ön szolgálatában állnak. Ügyfeleinknek tervezési támogatást kínálunk az összes főbb elektronikus tervezési automatizálási (EDA) platformhoz, megfelelő modelleket, folyamattervező készleteket (PDK), analóg és digitális könyvtárakat, valamint tervezési gyártási (DFM) támogatást biztosítunk. Minden technológiához két prototípus-készítési lehetőséget kínálunk: a Multi Product Wafer (MPW) szolgáltatást, ahol több készüléket dolgoznak fel párhuzamosan egy ostyán, és a Multi Level Mask (MLM) szolgáltatást, amelyben négy maszkszintet rajzolnak ugyanarra az irányzékra. Ezek gazdaságosabbak, mint a teljes maszkkészlet. Az MLM szolgáltatás rendkívül rugalmas az MPW szolgáltatás fix dátumaihoz képest. A vállalatok több okból is előnyben részesíthetik a félvezető termékek kiszervezését a mikroelektronikai öntödékkel szemben, többek között a második forrás szükségessége, a belső erőforrások más termékekhez és szolgáltatásokhoz való felhasználása, a mesékre való hajlandóság, valamint a félvezetőgyárak üzemeltetésével járó kockázatok és terhek csökkentése stb. Az AGS-TECH nyílt platformú mikroelektronikai gyártási folyamatokat kínál, amelyek kicsinyíthetők kis szeletsorozatokhoz, valamint tömeggyártáshoz. Bizonyos körülmények között meglévő mikroelektronikai vagy MEMS gyártási eszközei vagy komplett szerszámkészletei szállított szerszámként vagy értékesített szerszámokként átvihetők az Ön gyárából a gyári telephelyünkre, vagy meglévő mikroelektronikai és MEMS termékei újratervezhetők nyílt platformos folyamattechnológiák segítségével, és áthelyezhetők gyárunkban elérhető folyamat. Ez gyorsabb és gazdaságosabb, mint az egyedi technológia transzfer. Igény esetén azonban az ügyfél meglévő mikroelektronikai / MEMS gyártási folyamatai átadhatók. Félvezető ostya előkészítés: Ha a vásárlók kívánják az ostyák mikrogyártása után, félkonduktor ostyákon kockázást, hátcsiszolást, soványítást, szálas elhelyezést, szeletelést, szeletelést és ellenőrzést végzünk. A félvezető lapka-feldolgozás metrológiát foglal magában a különböző feldolgozási lépések között. Például ellipszometrián vagy reflektometrián alapuló vékonyréteg-vizsgálati módszereket használnak a kapu-oxid vastagságának, valamint a fotoreziszt és más bevonatok vastagságának, törésmutatójának és kioltási együtthatójának szigorú szabályozására. Félvezető lapkát vizsgáló berendezéssel ellenőrizzük, hogy a lapkák nem sérültek-e meg a korábbi feldolgozási lépések során egészen a tesztelésig. Az elülső folyamatok befejezése után a félvezető mikroelektronikai eszközöket különféle elektromos teszteknek vetik alá annak megállapítására, hogy megfelelően működnek-e. A mikroelektronikai eszközök arányát az ostyán megfelelően teljesítőnek találtuk „hozamként”. Az ostyán lévő mikroelektronikai chipek tesztelése elektronikus teszterrel történik, amely apró szondákat nyom a félvezető chiphez. Az automata gép minden rossz mikroelektronikai chipet megjelöl egy csepp festékkel. Az ostya tesztadatokat egy központi számítógépes adatbázisba naplózzák, a félvezető chipeket pedig virtuális rekeszekbe rendezik az előre meghatározott teszthatárok szerint. Az eredményül kapott binning adatok grafikonon ábrázolhatók vagy naplózhatók egy wafer térképen a gyártási hibák nyomon követésére és a rossz chipek megjelölésére. Ez a térkép az ostya összeszerelése és csomagolása során is használható. A végső tesztelés során a mikroelektronikai chipeket a csomagolás után újra tesztelik, mert hiányozhatnak a kötőhuzalok, vagy az analóg teljesítményt megváltoztathatja a csomagolás. A félvezető lapka tesztelése után jellemzően lecsökkentik a vastagságát, mielőtt az ostyát bevágják, majd egyedi szerszámokra törik. Ezt a folyamatot félvezető szelet kockázásnak nevezik. Kifejezetten a mikroelektronikai ipar számára gyártott automata gyűjtőgépeket használjuk a jó és rossz félvezető szerszámok szétválogatására. Csak a jó, jelöletlen félvezető chipeket csomagolják. Ezt követően a mikroelektronikai műanyag vagy kerámia csomagolási eljárás során felszereljük a félvezető szerszámot, a szerszámbetéteket a csomagoláson lévő csapokhoz csatlakoztatjuk, majd lezárjuk a szerszámot. Apró aranyhuzalokat használnak arra, hogy automata gépekkel csatlakoztassák a párnákat a csapokhoz. A chip-skálás csomag (CSP) egy másik mikroelektronikai csomagolási technológia. A műanyag dual in-line tok (DIP), mint a legtöbb csomag, többszöröse a benne elhelyezett tényleges félvezető szerszámnak, míg a CSP chipek csaknem akkorák, mint a mikroelektronikai szerszám; és a félvezető lapka felkockázása előtt minden matricához készíthető egy CSP. A becsomagolt mikroelektronikai chipeket újra tesztelik, hogy megbizonyosodjanak arról, hogy nem sérülnek-e meg a csomagolás során, és hogy a vágótűk közötti összekapcsolási folyamat megfelelően befejeződött. Lézerek segítségével ezután rámaratjuk a chipek nevét és számát a csomagolásra. Mikroelektronikai csomagok tervezése és gyártása: Kínálunk kész és egyedi tervezést és mikroelektronikai csomagok gyártását is. A szolgáltatás részeként mikroelektronikai csomagok modellezése és szimulációja is megvalósul. A modellezés és szimuláció biztosítja a virtuális kísérlettervezést (DoE) az optimális megoldás elérése érdekében, ahelyett, hogy a csomagokat a helyszínen tesztelné. Ez csökkenti a költségeket és a gyártási időt, különösen a mikroelektronikai új termékek fejlesztése esetén. Ez a munka lehetőséget ad arra is, hogy elmagyarázzuk ügyfeleinknek, hogy az összeszerelés, a megbízhatóság és a tesztelés milyen hatással lesz mikroelektronikai termékeikre. A mikroelektronikai csomagolás elsődleges célja egy olyan elektronikus rendszer megtervezése, amely ésszerű költségek mellett megfelel az adott alkalmazás követelményeinek. A mikroelektronikai rendszer összekapcsolásának és elhelyezésének számos lehetősége miatt az adott alkalmazáshoz szükséges csomagolási technológia kiválasztása szakértői értékelést igényel. A mikroelektronikai csomagok kiválasztási kritériumai közé tartozhatnak a következő technológiai illesztőprogramok: - Vezetékezhetőség -Hozam -Költség - Hőelvezetési tulajdonságok - Elektromágneses árnyékolási teljesítmény - Mechanikai szívósság -Megbízhatóság A mikroelektronikai csomagokra vonatkozó tervezési szempontok befolyásolják a sebességet, a funkcionalitást, a csomóponti hőmérsékletet, a térfogatot, a súlyt és még sok mást. Az elsődleges cél a legköltséghatékonyabb, ugyanakkor megbízható összekapcsolási technológia kiválasztása. Kifinomult elemzési módszereket és szoftvereket használunk a mikroelektronikai csomagok tervezéséhez. A mikroelektronikai csomagolás az összekapcsolt miniatűr elektronikus rendszerek gyártására szolgáló módszerek tervezésével és e rendszerek megbízhatóságával foglalkozik. Pontosabban, a mikroelektronikai csomagolás magában foglalja a jelek továbbítását a jelek integritásának megőrzése mellett, a föld és a tápfeszültség elosztását a félvezető integrált áramkörök között, a disszipált hő eloszlását, miközben megőrzi a szerkezeti és anyagi integritást, és megvédi az áramkört a környezeti veszélyektől. Általában a mikroelektronikai IC-k csomagolásának módszerei egy PWB-t használnak olyan csatlakozókkal, amelyek a valós I/O-kat biztosítják egy elektronikus áramkör számára. A hagyományos mikroelektronikai csomagolási megközelítések egyetlen csomagolás használatát jelentik. Az egychipes csomag fő előnye a mikroelektronikai IC teljes körű tesztelése, mielőtt összekapcsolná az alatta lévő hordozóval. Az ilyen csomagolt félvezető eszközöket vagy átmenő furattal vagy felülettel szerelik fel a PWB-re. A felületre szerelt mikroelektronikai csomagoknál nincs szükség átmenő lyukak átmenésére a teljes kártyán. Ehelyett a felületre szerelt mikroelektronikai alkatrészek a PWB mindkét oldalára forraszthatók, ami nagyobb áramkörsűrűséget tesz lehetővé. Ezt a megközelítést felületi szerelési technológiának (SMT) nevezik. A területtömb stílusú csomagok, például a golyós rácstömbök (BGA-k) és a chip-scale csomagok (CSP-k) hozzáadása versenyképessé teszi az SMT-t a legnagyobb sűrűségű félvezető mikroelektronikai csomagolási technológiákkal szemben. Egy újabb csomagolási technológia magában foglalja egynél több félvezető eszköz rögzítését egy nagy sűrűségű összekötő hordozóra, amelyet azután egy nagy csomagba szerelnek, így biztosítva az I/O érintkezőket és a környezet védelmét. Ezt a multichip modul (MCM) technológiát a csatolt IC-k összekapcsolására használt hordozótechnológiák is jellemzik. Az MCM-D leválasztott vékonyrétegű fémet és dielektromos többrétegű rétegeket képvisel. Az MCM-D hordozók az összes MCM technológia közül a legnagyobb huzalozási sűrűséggel rendelkeznek a kifinomult félvezető-feldolgozási technológiáknak köszönhetően. Az MCM-C többrétegű „kerámia” szubsztrátumokra utal, amelyeket szitált fémfestékek és nem égetett kerámialapok egymásra rakott váltakozó rétegeiből égetnek ki. Az MCM-C használatával közepesen sűrű huzalozási kapacitást kapunk. Az MCM-L olyan többrétegű szubsztrátumokra vonatkozik, amelyek egymásra rakott, fémezett PWB „laminátumokból” készülnek, amelyeket egyedileg mintáznak, majd laminálnak. Korábban alacsony sűrűségű összekapcsolási technológia volt, most azonban az MCM-L gyorsan megközelíti az MCM-C és MCM-D mikroelektronikai csomagolási technológiák sűrűségét. Közvetlen chipcsatlakozás (DCA) vagy chip-on-board (COB) mikroelektronikai csomagolási technológia magában foglalja a mikroelektronikai IC-k közvetlenül a PWB-re történő felszerelését. Egy műanyag kapszulázó, amelyet a csupasz IC fölé „gömbölyítenek”, majd kikeményítenek, környezetvédelmet biztosít. A mikroelektronikai IC-k flip-chip vagy huzalkötési módszerekkel csatlakoztathatók a hordozóhoz. A DCA technológia különösen gazdaságos azoknál a rendszereknél, amelyek legfeljebb 10 félvezető IC-t tartalmaznak, mivel a nagyobb számú chip befolyásolhatja a rendszer teljesítményét, és a DCA-szerelvényeket nehéz lehet átdolgozni. Mind a DCA, mind az MCM csomagolási opciók közös előnye a félvezető IC-csomag összekapcsolási szintjének kiküszöbölése, ami közelebbi közelséget (rövidebb jelátviteli késleltetést) és csökkentett vezetékinduktivitást tesz lehetővé. Mindkét módszer elsődleges hátránya a teljesen tesztelt mikroelektronikai IC-k beszerzésének nehézsége. A DCA és MCM-L technológiák további hátrányai közé tartozik a rossz hőkezelés a PWB laminátumok alacsony hővezető képességének és a félvezető szerszám és a hordozó közötti rossz hőtágulási együtthatónak köszönhetően. A hőtágulási eltérési probléma megoldásához szükség van egy közbeiktatott szubsztrátumra, például molibdénre a huzalkötésű szerszámhoz és egy alátöltő epoxira a flip-chip matricákhoz. A többcsipes hordozó modul (MCCM) a DCA minden pozitív aspektusát egyesíti az MCM technológiával. Az MCCM egyszerűen egy kis MCM egy vékony fém hordozón, amely ragasztható vagy mechanikusan rögzíthető PWB-hez. A fém fenék hőelvezetőként és feszültség-közvetítőként is működik az MCM hordozó számára. Az MCCM perifériás vezetékekkel rendelkezik a huzalkötéshez, forrasztáshoz vagy füles rögzítéshez a PWB-hez. A csupasz félvezető IC-ket glob-top anyag védi. Amikor felveszi velünk a kapcsolatot, megbeszéljük az Ön kérelmét és követelményeit, hogy kiválaszthassuk az Önnek legmegfelelőbb mikroelektronikai csomagolási lehetőséget. Félvezető IC összeszerelés és csomagolás és tesztelés: Mikroelektronikai gyártási szolgáltatásaink részeként matricák, huzalok és chipek ragasztását, tokozását, összeszerelését, jelölését és márkajelzését, tesztelését kínáljuk. A félvezető chip vagy az integrált mikroelektronikai áramkör működéséhez csatlakoztatni kell ahhoz a rendszerhez, amelyet vezérelni fog, vagy amelyhez utasításokat ad. A mikroelektronikai IC-szerelvény biztosítja a tápellátást és az információátvitelt a chip és a rendszer között. Ez úgy érhető el, hogy a mikroelektronikai chipet egy csomaghoz csatlakoztatják, vagy közvetlenül a PCB-hez csatlakoztatják ezekhez a funkciókhoz. A chip és a csomagolás vagy a nyomtatott áramköri lap (PCB) közötti kapcsolatok huzalkötéssel, átmenő lyukkal vagy flip chip-szerelvényen keresztül történnek. Iparági vezető szerepet töltünk be a mikroelektronikai IC csomagolási megoldások megtalálásában, amelyek megfelelnek a vezeték nélküli és internetes piacok összetett követelményeinek. Több ezer különböző csomagformátumot és -méretet kínálunk, a hagyományos ólomvázas mikroelektronikai IC-csomagoktól az átmenő és felületi szereléshez, a legújabb chipskálás (CSP) és golyós rácstömb (BGA) megoldásokig, amelyek nagy tűszámú és nagy sűrűségű alkalmazásokhoz szükségesek. . Csomagok széles választéka áll rendelkezésre raktárról, beleértve a CABGA (Chip Array BGA), CQFP, CTBGA (Chip Array Thin Core BGA), CVBGA (Very Thin Chip Array BGA), Flip Chip, LCC, LGA, MQFP, PBGA, PDIP, PLCC, PoP - Csomag a csomagon, PoP TMV - Mold Via, SOIC / SOJ, SSOP, TQFP, TSOP, WLP (Wafer Level Package)… stb. A réz, ezüst vagy arany felhasználásával végzett huzalkötés a mikroelektronikában a legnépszerűbbek közé tartozik. A réz (Cu) huzal a szilícium félvezető matricák és a mikroelektronikai csomag termináljainak csatlakoztatásának egyik módja. Az arany (Au) huzal költségének közelmúltbeli növekedése miatt a réz (Cu) huzal vonzó módja a mikroelektronikai csomagok teljes költségének kezelésének. Hasonló elektromos tulajdonságai miatt arany (Au) huzalra is hasonlít. Az öninduktivitás és az önkapacitás közel azonos az arany (Au) és réz (Cu) huzalnál, alacsonyabb ellenállású réz (Cu) huzalnál. A mikroelektronikai alkalmazásokban, ahol a kötőhuzal miatti ellenállás negatívan befolyásolhatja az áramkör teljesítményét, a réz (Cu) huzal használata javíthat. A réz, palládium bevonatú réz (PCC) és ezüst (Ag) ötvözethuzalok a költségek miatt jelentek meg az aranykötésű huzalok alternatívájaként. A réz alapú vezetékek olcsók és alacsony az elektromos ellenállásuk. A réz keménysége azonban megnehezíti a használatát számos alkalmazásban, például a törékeny kötőbetét-szerkezeteknél. Ezekhez az alkalmazásokhoz az Ag-Alloy az aranyhoz hasonló tulajdonságokat kínál, míg költsége hasonló a PCC-éhoz. Az Ag-ötvözet huzal lágyabb, mint a PCC, ami alacsonyabb Al-Splash-t és kisebb kötési párna sérülésének kockázatát eredményezi. Az Ag-Alloy huzal a legjobb alacsony költségű csere olyan alkalmazásokhoz, amelyeknél szükség van a préskötésre, vízesés-kötésre, ultrafinom kötési osztástávolságra és kis kötési párnanyílásokra, ultra alacsony hurokmagasságra. A félvezetőtesztelési szolgáltatások teljes skáláját kínáljuk, beleértve az ostyatesztelést, a különböző típusú végső tesztelést, a rendszerszintű tesztelést, a szalagtesztelést és a teljes vonalvégi szolgáltatásokat. Különféle félvezető eszköztípusokat tesztelünk minden csomagcsaládunkban, beleértve a rádiófrekvenciás, analóg és vegyes jeleket, digitális, energiagazdálkodást, memóriát és különféle kombinációkat, mint például az ASIC, a többchip modulok, a System-in-Package (SiP) és halmozott 3D csomagolás, érzékelők és MEMS-eszközök, például gyorsulásmérők és nyomásérzékelők. Teszt hardverünk és érintkező berendezéseink alkalmasak egyedi csomagméretű SiP-hez, kétoldalas érintkezési megoldásokhoz Package on Package (PoP), TMV PoP, FusionQuad aljzatokhoz, többsoros MicroLeadFrame-hez, Fine-Pitch Copper Pillarhoz. A tesztberendezések és a tesztpadlók CIM/CAM eszközökkel, hozamelemzéssel és teljesítményfigyeléssel vannak integrálva, hogy első alkalommal nagyon magas hatékonyságú hozamot érjenek el. Számos adaptív mikroelektronikai tesztfolyamatot kínálunk ügyfeleink számára, és elosztott tesztfolyamatokat kínálunk a SiP és más összetett összeállítási folyamatokhoz. Az AGS-TECH teszttanácsadási, fejlesztési és mérnöki szolgáltatások teljes skáláját nyújtja az Ön félvezető- és mikroelektronikai termékeinek teljes életciklusa során. Tisztában vagyunk a SiP, az autóipar, a hálózatépítés, a játékok, a grafika, a számítástechnika, az RF / vezeték nélküli szolgáltatások egyedi piacaival és tesztelési követelményeivel. A félvezető gyártási folyamatok gyors és pontosan ellenőrzött jelölési megoldásokat igényelnek. Az 1000 karakter/másodperc feletti jelölési sebesség és a 25 mikronnál kisebb anyagbehatolási mélység gyakori a fejlett lézereket használó félvezető mikroelektronikai iparban. Minimális hőbevitellel és tökéletes ismételhetőség mellett képesek vagyunk öntőformák, ostyák, kerámiák és egyéb anyagok jelölésére. Nagy pontosságú lézereket használunk a legkisebb alkatrészek sérülésmentes megjelölésére is. Ólomkeretek félvezető eszközökhöz: Mind kész, mind egyedi tervezés és gyártás lehetséges. Az ólomkereteket a félvezető eszközök összeszerelési folyamataiban használják, és lényegében vékony fémrétegek, amelyek a félvezető mikroelektronikai felületén lévő apró elektromos kivezetések vezetékeit kötik össze az elektromos eszközök és PCB-k nagyméretű áramköreivel. Az ólomkereteket szinte minden félvezető mikroelektronikai csomagban használják. A legtöbb mikroelektronikai IC-csomag úgy készül, hogy a félvezető szilícium chipet egy ólomkeretre helyezik, majd a chipet az ólomváz fém vezetékeihez kötik, majd a mikroelektronikai chipet műanyag borítással fedik le. Ez az egyszerű és viszonylag olcsó mikroelektronikai csomagolás még mindig a legjobb megoldás számos alkalmazáshoz. Az ólomkereteket hosszú szalagokban állítják elő, ami lehetővé teszi, hogy gyorsan feldolgozzák őket automata összeszerelő gépeken, és általában két gyártási eljárást alkalmaznak: valamilyen fotómaratást és bélyegzést. A mikroelektronikai ólomkeretek tervezésében gyakran igény van testreszabott specifikációkra és jellemzőkre, olyan kialakításokra, amelyek javítják az elektromos és termikus tulajdonságokat, valamint konkrét ciklusidő-követelményeket. Mélyreható tapasztalattal rendelkezünk a mikroelektronikai ólomkeretek gyártásában egy sor ügyfél számára, lézerrel segített fényképmaratással és bélyegzéssel. Mikroelektronikai hűtőbordák tervezése és gyártása: mind kész, mind egyedi tervezés és gyártás. A mikroelektronikai eszközök hőelvezetésének növekedésével és az általános formai tényezők csökkenésével a hőkezelés egyre fontosabb eleme lesz az elektronikai terméktervezésnek. Az elektronikus berendezések teljesítményének állandósága és várható élettartama fordítottan arányos a berendezés alkatrészeinek hőmérsékletével. Egy tipikus szilícium félvezető eszköz megbízhatósága és üzemi hőmérséklete közötti kapcsolat azt mutatja, hogy a hőmérséklet csökkenése az eszköz megbízhatóságának és várható élettartamának exponenciális növekedésének felel meg. Ezért a félvezető mikroelektronikai alkatrész hosszú élettartama és megbízható teljesítménye érhető el az eszköz üzemi hőmérsékletének hatékony szabályozásával a tervezők által meghatározott határokon belül. A hűtőbordák olyan eszközök, amelyek fokozzák a hőeloszlást egy forró felületről, általában egy hőtermelő alkatrész külső házáról, egy hidegebb környezetbe, például levegőbe. A következő tárgyalásokhoz a levegőt feltételezzük hűtőfolyadéknak. A legtöbb esetben a hőátadás a szilárd felület és a hűtőfolyadék levegője közötti határfelületen a legkevésbé hatékony a rendszeren belül, és a szilárd-levegő határfelület jelenti a legnagyobb akadályt a hőelvezetésben. A hűtőborda főként a hűtőközeggel közvetlenül érintkező felület növelésével csökkenti ezt az akadályt. Ez lehetővé teszi több hő elvezetését és/vagy csökkenti a félvezető eszköz működési hőmérsékletét. A hűtőborda elsődleges célja, hogy a mikroelektronikai eszköz hőmérsékletét a félvezető eszköz gyártója által meghatározott maximálisan megengedhető hőmérséklet alatt tartsa. A hűtőbordákat a gyártási módok és azok alakja szerint osztályozhatjuk. A léghűtéses hűtőbordák leggyakoribb típusai a következők: - Bélyegzések: A réz- vagy alumíniumlemezeket a kívánt formára préselik. elektronikus alkatrészek hagyományos léghűtésére használják, és gazdaságos megoldást kínálnak az alacsony sűrűségű termikus problémákra. Nagy volumenű gyártásra alkalmasak. - Extrudálás: Ezek a hűtőbordák lehetővé teszik a kidolgozott, kétdimenziós formák kialakítását, amelyek képesek nagy hőterhelést elvezetni. Vághatók, megmunkálhatók, és opciók adhatók hozzá. A keresztmetszet mindenirányú, téglalap alakú bordás hűtőbordákat eredményez, és a fogazott bordák beépítése körülbelül 10-20%-kal javítja a teljesítményt, de lassabb extrudálási sebességgel. Az extrudálási korlátok, például a borda magasságától a résig terjedő bordavastagság általában megszabják a tervezési lehetőségek rugalmasságát. Normál extrudálási technikákkal elérhető a tipikus bordamagasság-rés méretarány akár 6, és a minimális bordavastagság 1,3 mm. 10:1 oldalarány és 0,8 hüvelykes bordavastagság érhető el a speciális formatervezési jellemzőkkel. A méretarány növekedésével azonban az extrudálási tűrés sérül. - Ragasztott/gyártott bordák: A legtöbb léghűtéses hűtőbordának a konvekciója korlátozott, és a léghűtéses hűtőbordák általános hőteljesítménye gyakran jelentősen javítható, ha nagyobb felületet lehet kitenni a légáramnak. Ezek a nagy teljesítményű hűtőbordák hővezető, alumíniummal töltött epoxit használnak a sík bordák rögzítéséhez egy hornyolt extrudált alaplemezhez. Ez az eljárás sokkal nagyobb, 20-40-as bordamagasság-rés oldalarányt tesz lehetővé, jelentősen növelve a hűtőteljesítményt anélkül, hogy a térfogatra lenne szükség. - Öntvények: A homok, viasz és présöntési eljárások alumíniumhoz vagy rézhez/bronzhoz elérhetők vákuum segítségével vagy anélkül. Ezt a technológiát nagy sűrűségű tűbordás hűtőbordák gyártására használjuk, amelyek maximális teljesítményt biztosítanak ütközőhűtés esetén. - Hajtogatott bordák: Az alumíniumból vagy rézből készült hullámlemez növeli a felületet és a térfogati teljesítményt. A hűtőbordát ezután vagy egy alaplaphoz, vagy közvetlenül a fűtőfelülethez rögzítik epoxi vagy keményforrasztás útján. Nem alkalmas nagy profilú hűtőbordákhoz a rendelkezésre állás és a borda hatékonysága miatt. Így lehetővé teszi nagy teljesítményű hűtőbordák gyártását. A mikroelektronikai alkalmazásokhoz szükséges termikus kritériumoknak megfelelő hűtőborda kiválasztásakor számos olyan paramétert kell megvizsgálnunk, amelyek nemcsak magát a hűtőborda teljesítményét, hanem a rendszer általános teljesítményét is befolyásolják. Egy adott típusú hűtőborda kiválasztása a mikroelektronikában nagymértékben függ a hűtőborda számára megengedett hőköltségvetéstől és a hűtőbordát körülvevő külső körülményektől. Egy adott hűtőbordához soha nincs egyetlen hőellenállási érték hozzárendelve, mivel a hőellenállás a külső hűtési körülményektől függően változik. Érzékelők és működtetők tervezése és gyártása: Mind kész, mind egyedi tervezés és gyártás elérhető. Használatra kész folyamatokkal rendelkező megoldásokat kínálunk inerciális érzékelőkhöz, nyomás- és relatív nyomásérzékelőkhöz, valamint infravörös hőmérséklet-érzékelő eszközökhöz. Ha IP blokkjainkat gyorsulásmérőkhöz, infravörös és nyomásérzékelőkhöz használjuk, vagy az Ön terveit a rendelkezésre álló specifikációk és tervezési szabályok szerint alkalmazzuk, heteken belül kiszállítjuk Önnek a MEMS alapú érzékelőeszközöket. A MEMS mellett más típusú érzékelő- és működtetőszerkezetek is gyárthatók. Optoelektronikai és fotonikus áramkörök tervezése és gyártása: A fotonikus vagy optikai integrált áramkör (PIC) olyan eszköz, amely több fotonikus funkciót integrál. A mikroelektronika elektronikus integrált áramköreihez hasonlítható. A fő különbség a kettő között az, hogy a fotonikus integrált áramkör funkcionalitást biztosít a látható spektrumban vagy a közeli infravörös 850-1650 nm-es optikai hullámhosszakra kibocsátott információs jelekhez. A gyártási technikák hasonlóak a mikroelektronikai integrált áramkörökben használtakhoz, ahol a fotolitográfiát ostyák mintázására használják maratáshoz és anyaglerakáshoz. A félvezető mikroelektronikától eltérően, ahol az elsődleges eszköz a tranzisztor, az optoelektronikában nincs egyetlen domináns eszköz. A fotonikus chipek közé tartoznak az alacsony veszteségű összekötő hullámvezetők, teljesítményosztók, optikai erősítők, optikai modulátorok, szűrők, lézerek és detektorok. Ezek az eszközök sokféle anyagot és gyártási technikát igényelnek, ezért nehéz mindezt egyetlen chipen megvalósítani. A fotonikus integrált áramkörök alkalmazása elsősorban a száloptikai kommunikáció, az orvosbiológiai és a fotonikus számítástechnika területén található. Néhány példa az Ön számára tervezhető és gyártható optoelektronikai termékekre: LED-ek (Light Emitting Diodes), dióda lézerek, optoelektronikai vevők, fotodiódák, lézertávolság-modulok, testreszabott lézermodulok és még sok más. CLICK Product Finder-Locator Service ELŐZŐ OLDAL