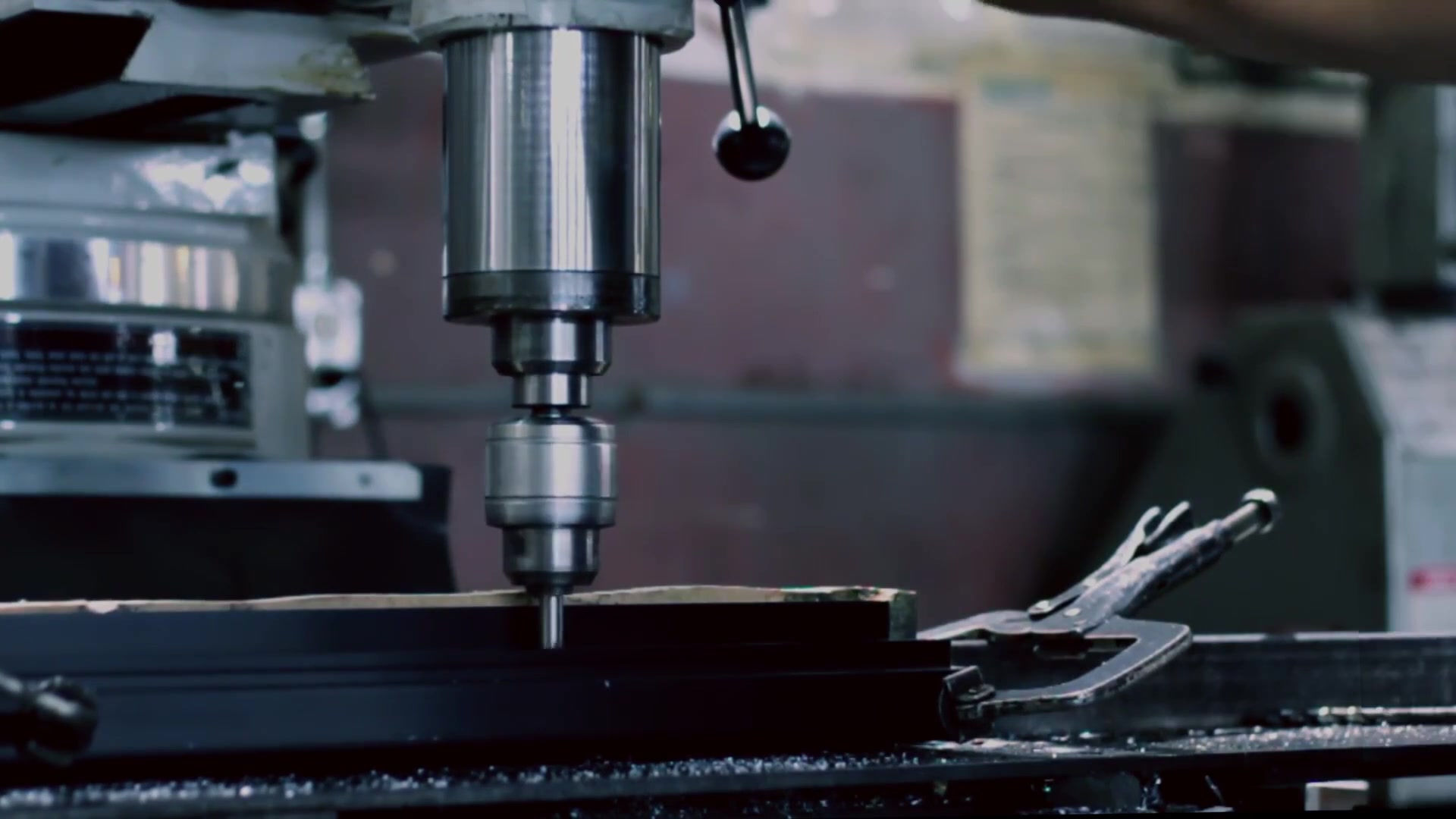
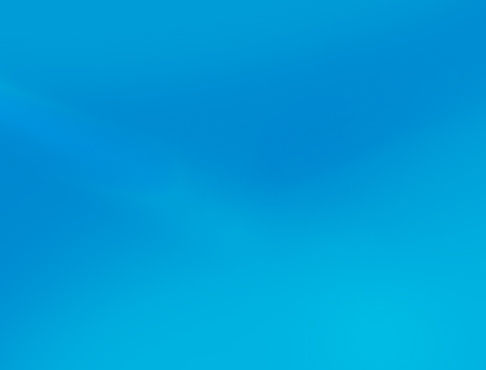
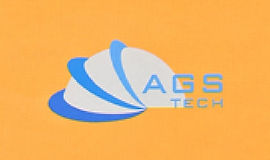
Globális egyedi gyártó, integrátor, konszolidátor, kiszervezési partner a termékek és szolgáltatások széles skálájához.
Mi vagyunk az Ön egyablakos forrása a gyártás, gyártás, tervezés, konszolidáció, integráció, egyedi gyártású és késztermékek és szolgáltatások kiszervezése terén.
Choose your Language
-
Egyedi gyártás
-
Belföldi és globális szerződéses gyártás
-
Gyártási outsourcing
-
Belföldi és globális beszerzés
-
Consolidation
-
Mérnöki integráció
-
Mérnöki szolgáltatások
Search Results
164 találat üres kereséssel
- Global Product Finder Locator for Off Shelf Products
Global Product Finder Locator for Off Shelf Products Az AGS-TECH, Inc. az Ön Globális egyedi gyártó, integrátor, konszolidátor, kiszervezési partner. Mi vagyunk az Ön egyablakos forrása a gyártás, a gyártás, a tervezés, a konszolidáció és a kiszervezés terén. If you exactly know the product you are searching, please fill out the table below If filling out the form below is not possible or too difficult, we do accept your request by email also. Simply write us at sales@agstech.net Get a Price Quote on a known brand, model, part number....etc. First name Last name Email Phone Product Name Product Make or Brand Please Enter Manufacturer Part Number if Known Please Enter SKU Code if You Know: Your Application for the Product Quantity Needed Do You have a price target ? If so, please let us know: Give us more details if you want: Condition of Product Needed New Used Does Not Matter If you have any, upload product relevant files by clicking at the below link. Don't worry, the link below will pop up a new window for downloading your files. You will not navigate away from this current window. After uploading your files, close ONLY the Dropbox Window, but not this page. Make sure to fill out all spaces and click the submit button below. CLICK HERE TO UPLOAD FILES Request a Quote Thanks! We’ll send you a price quote shortly. PREVIOUS PAGE Mi vagyunk az AGS-TECH Inc., az Ön egyablakos forrása a gyártáshoz és a gyártáshoz, a tervezéshez, a kiszervezéshez és a konszolidációhoz. Mi vagyunk a világ legváltozatosabb mérnöki integrátora, amely egyedi gyártást, részösszeszerelést, termékek összeszerelését és mérnöki szolgáltatásokat kínál Önnek.
- Custom Made Products Data Entry
Custom Made Products Data Entry, Custom Manufactured Parts, Assemblies, Plastic Molds, Casting, CNC Machining, Extrusion, Metal Forging, Spring Manufacturing, Products Assembly, PCBA, PCB Az AGS-TECH, Inc. az Ön Globális egyedi gyártó, integrátor, konszolidátor, kiszervezési partner. Mi vagyunk az Ön egyablakos forrása a gyártás, a gyártás, a tervezés, a konszolidáció és a kiszervezés terén. Fill In your info if you you need custom design & development & prototyping & mass production: If filling out the form below is not possible or too difficult, we do accept your request by email also. Simply write us at sales@agstech.net Get a Price Quote on a custom designed, developed, prototyped or manufactured product. First name Last name Email Phone Product Name Your Application for the Product Quantity Needed Do you have a price target ? If you do have, please let us know your expected price: Give us more details if you want: Do you accept offshore manufacturing ? YES NO If you have any, upload product relevant files by clicking at the below link. Don't worry, the link below will pop up a new window for downloading your files. You will not navigate away from this current window. After uploading your files, close ONLY the Dropbox Window, but not this page. Make sure to fill out all spaces and click the submit button below. Files that will help us quote your specially tailored product are technical drawings, bill of materials, photos, sketches....etc. You can download more than one file. CLICK HERE TO UPLOAD FILES Request a Quote Thanks! We’ll send you a price quote shortly. PREVIOUS PAGE Mi vagyunk az AGS-TECH Inc., az Ön egyablakos forrása a gyártáshoz és a gyártáshoz, a tervezéshez, a kiszervezéshez és a konszolidációhoz. Mi vagyunk a világ legváltozatosabb mérnöki integrátora, amely egyedi gyártást, részösszeszerelést, termékek összeszerelését és mérnöki szolgáltatásokat kínál Önnek.
- Industrial & Specialty & Functional Textiles, Hydrophobic - Hydrophillic Textile Materials, Flame Resistant, Antibasterial, Antifungal, Antistatic Fabrics, Filtering Cloths, Biocompatible Fabric
Industrial & Specialty & Functional Textiles, Hydrophobic - Hydrophillic Textile Materials, Flame Resistant Textiles, Antibasterial, Antifungal, Antistatic, UC Protective Fabrics, Filtering Clothes, Textiles for Surgery, Biocompatible Fabric Ipari és speciális és funkcionális textíliák Számunkra csak a speciális és funkcionális textíliák és szövetek és az ezekből készült termékek érdekelnek, amelyek egy adott alkalmazást szolgálnak. Kiemelkedő értékű műszaki textíliákról van szó, amelyeket néha műszaki textíliáknak és szöveteknek is neveznek. Szőtt, valamint nem szőtt szövetek és kendők számos alkalmazáshoz elérhetők. Az alábbiakban felsorolunk néhány főbb ipari, speciális és funkcionális textíliát, amelyek termékfejlesztési és gyártási körünkbe tartoznak. Készek vagyunk együttműködni Önnel az Ön termékeinek tervezésében, fejlesztésében és gyártásában: Hidrofób (víztaszító) és hidrofil (vízelnyelő) textilanyagok Rendkívüli szilárdságú textíliák és szövetek, tartósság és kemény környezeti feltételekkel szembeni ellenálló képesség (például golyóálló, nagy hőálló, alacsony hőmérsékletnek ellenálló, lángálló, közömbös vagy ellenáll a korrozív folyadékoknak és gázoknak, képződés….) Antibakteriális és gombaellenes textíliák és szövetek UV védő Elektromosan vezető és nem vezető textíliák és szövetek Antisztatikus szövetek az ESD szabályozáshoz… stb. Speciális optikai tulajdonságokkal és hatásokkal rendelkező textíliák és szövetek (fluoreszkáló… stb.) Speciális szűrőképességű textíliák, szövetek és kendők, szűrőgyártás Ipari textíliák, például légcsatorna szövetek, közbélések, megerősítések, hajtószíjak, gumierősítők (szállítószalagok, nyomattakarók, zsinórok), textíliák szalagokhoz és csiszolóanyagokhoz. Textíliák az autóipar számára (tömlők, övek, légzsákok, betétek, gumiabroncsok) Textíliák építőipari, építőipari és infrastrukturális termékekhez (betonszövet, geomembránok és szövetbetét) Kompozit többfunkciós textíliák különböző rétegekkel vagy különböző funkciókat biztosító alkatrészekkel. Az aktív szénből készült textíliák infusion on poliészter szálak pamut kézérzetet, szagvédelmet és UV-kezelést biztosítanak. Alakmemóriás polimerekből készült textíliák Textíliák sebészeti és sebészeti implantátumokhoz, biokompatibilis szövetek Felhívjuk figyelmét, hogy az Ön igényeinek és specifikációinak megfelelő termékeket tervezünk, tervezünk és gyártunk. Készítünk termékeket az Ön specifikációi szerint, vagy igény esetén segítünk a megfelelő anyagok kiválasztásában és a termék tervezésében. ELŐZŐ OLDAL
- Accessories, Modules, Carrier Boards | agstech
Industrial Computer Accessories, PCI, Peripheral Component Interconnect, Multichannel Analog & Digital Input Output Modules, Relay Module, Printer Interface Tartozékok, modulok, hordozólapok ipari számítógépekhez A PERIPHERAL DEVICE egy gazdagéphez csatlakozik, de nem része annak, és többé-kevésbé a gazdagéptől függ. Kibővíti a gazdagép képességeit, de nem része a központi számítógép-architektúrának. Ilyenek például a számítógépes nyomtatók, képszkennerek, szalagos meghajtók, mikrofonok, hangszórók, webkamerák és digitális fényképezőgépek. A perifériás eszközök a számítógép portjain keresztül csatlakoznak a rendszeregységhez. HAGYOMÁNYOS PCI (A PCI jelentése PERIPHERAL COMPONENT, a számítógépes INTERCONNECT helyi busz szabvány része) a hardver PCI eszközök csatlakoztatásához. Ezek az eszközök magára az alaplapra szerelt integrált áramkör formájában is megjelenhetnek, az úgynevezett a planar device_cc781905-5cde-3194-bb3b-136bad5cf58dsdsd_de-PCI-ben card amely belefér egy nyílásba. We carry name brands such as JANZ TEC, DFI-ITOX and KORENIX. Töltse le JANZ TEC márkájú kompakt termékismertetőnket Töltse le KORENIX márkájú kompakt termékismertetőnket Töltse le ICP DAS márkájú ipari kommunikációs és hálózati termékekről szóló prospektusunkat Töltse le ICP DAS márkájú PACs beágyazott vezérlők és DAQ brosúránkat Töltse le ICP DAS márkájú ipari érintőpad prospektusunkat Töltse le ICP DAS márkájú Távoli IO modulok és IO bővítőegységek brosúránkat Töltse le ICP DAS márkájú PCI kártyáinkat és IO kártyáinkat Töltse le DFI-ITOX márkájú ipari számítógép-perifériánkat Töltse le DFI-ITOX márkájú grafikus kártyáinkat Töltse le a DFI-ITOX márkájú ipari alaplapok prospektusunkat Töltse le a DFI-ITOX márkájú beágyazott egylapos számítógépekről szóló prospektusunkat Töltse le DFI-ITOX márkájú számítógépes fedélzeti modulok brosúránkat Töltse le DFI-ITOX márkájú beágyazott operációs rendszer szolgáltatásainkat Projektjeihez megfelelő alkatrész vagy tartozék kiválasztása. kérjük, látogasson el ipari számítástechnikai üzletünkbe IDE KATTINTVA. Brosúra letöltése számunkra TERVEZÉSI PARTNERSÉGI PROGRAM Ipari számítógépekhez kínálunk néhány alkatrészt és tartozékot: - Többcsatornás analóg és digitális bemeneti modulok : Több száz különböző 1-, 4-, 2-csatornás modult kínálunk. Kompakt méretük van, és ez a kis méret megkönnyíti a szűk helyeken való használatát. Egy 12 mm-es (0,47 hüvelyk) széles modulban akár 16 csatorna is elhelyezhető. A csatlakozások dugaszolhatóak, biztonságosak és erősek, megkönnyítve a cserét a kezelő számára, míg a rugónyomás-technológia folyamatos működést biztosít még olyan súlyos környezeti feltételek mellett is, mint ütés/rezgés, hőmérséklet-ciklus stb. Többcsatornás analóg és digitális bemeneti kimeneti moduljaink rendkívül rugalmasak, így a I/O system_cc781905-5cde-3194-bb3b-136bad5cf58d minden egyes csomópontja digitálisan be- és konfigurálható. mások könnyen kombinálhatók. Könnyen kezelhetők, a moduláris sínre szerelhető modulkialakítás könnyű és szerszámmentes kezelést és módosítást tesz lehetővé. Színes jelölők segítségével azonosítják az egyes I/O modulok funkcionalitását, a modul oldalára nyomtatják a terminálkiosztást és a műszaki adatokat. Moduláris rendszereink terepi buszfüggetlenek. - Multichannel relay modules : A relé egy elektromos árammal vezérelt kapcsoló. A relék lehetővé teszik egy kisfeszültségű kisáramú áramkör számára a nagyfeszültségű/nagyáramú készülék biztonságos kapcsolását. Példaként használhatunk egy elemes kisméretű fényérzékelő áramkört a nagy hálózati tápellátású lámpák relé segítségével történő vezérlésére. A relé kártyák vagy modulok kereskedelmi forgalomban kapható áramköri kártyák, amelyek relékkel, LED-jelzőkkel, hátsó EMF-gátló diódákkal és praktikus becsavarható csatlakozókkal vannak felszerelve feszültségbemenetekhez, legalább NC, NO, COM csatlakozásokhoz a relén. A rajtuk lévő több pólus lehetővé teszi több eszköz egyidejű be- és kikapcsolását. A legtöbb ipari projekt egynél több relét igényel. Therefore multi-channel or also known as multiple relay boards are offered. Ugyanazon az áramköri lapon 2-16 relé lehet. A relé kártyák számítógéppel közvetlenül is vezérelhetők USB- vagy soros kapcsolaton keresztül. Relay boards távirányító PC-ről távolról csatlakoztatható LAN-hoz vagy internethez. szoftver. - Nyomtató interfész: A nyomtató interfész hardver és szoftver kombinációja, amely lehetővé teszi a nyomtató és a számítógép közötti kommunikációt. A hardveres interfészt portnak hívják, és minden nyomtatónak van legalább egy interfésze. Egy interfész több összetevőből áll, beleértve a kommunikációs típust és az interfész szoftvert. Nyolc fő kommunikációs típus létezik: 1. Serial : Through serial connections computers send one bit of information at a time, one after another . A kommunikációs paramétereket, például paritást, baudot mindkét entitáson be kell állítani a kommunikáció előtt. 2. Parallel : Parallel communication is more popular with printers because it is faster compared to serial communication . A párhuzamos típusú kommunikációt használó nyomtatók nyolc bitet kapnak egyszerre nyolc különálló vezetéken. A Parallel DB25 csatlakozást használ a számítógép oldalán és egy furcsa alakú 36 tűs csatlakozást a nyomtató oldalán. A és automatikusan felismeri az új eszközöket. 4. Network : Also commonly referred to as Ethernet, network connections_cc781905-5cde-3194-bb3b A 136bad5cf58d_ általánosak a hálózati lézernyomtatókon. Más típusú nyomtatók is alkalmazzák ezt a csatlakozási módot. Ezek a nyomtatók hálózati csatolókártyával (NIC) és ROM-alapú szoftverrel rendelkeznek, amely lehetővé teszi számukra a hálózatokkal, szerverekkel és munkaállomásokkal való kommunikációt. 5. Infrared : Infrared transmissions are wireless transmissions that use infrared radiation of the electromagnetic spectrum. Az infravörös fogadó lehetővé teszi, hogy eszközei (laptopok, PDA-k, kamerák stb.) csatlakozzanak a nyomtatóhoz, és infravörös jeleken keresztül nyomtatási parancsokat küldjenek. 6. Small Computer System Interface (known as SCSI) : Laser printers and some others use SCSI interfaces_cc781905 -5cde-3194-bb3b-136bad5cf58d_a PC-re, mivel megvan a százszoros láncolás előnyei, ahol több eszköz is lehet egyetlen SCSI kapcsolaton. Megvalósítása egyszerű. 7. IEEE 1394 Firewire : A Firewire egy nagy sebességű kapcsolat, amelyet széles körben használnak a nagy sávú digitális videószerkesztéshez és egyéb követelményekhez Ez az interfész jelenleg 800 Mbps maximális átviteli sebességű és 3,2 Gbps sebességig képes eszközöket támogat. 8. Wireless : A vezeték nélküli a jelenleg népszerű technológia, mint például az infravörös és a bluetooth. Az információkat vezeték nélkül, rádióhullámok segítségével továbbítják a levegőben, és a készülék fogadja. A Bluetooth a számítógépek és perifériái közötti kábelek cseréjére szolgál, és általában kis, körülbelül 10 méteres távolságban működnek. A fenti kommunikációs típusok közül a szkennerek többnyire USB, Parallel, SCSI, IEEE 1394/FireWire szabványt használnak. - Inkrementális kódoló modul : Az inkrementális jeladók helymeghatározási és motorsebesség-visszacsatolási alkalmazásokban használatosak. Az inkrementális jeladók kiváló sebesség- és távolságvisszajelzést adnak. Mivel kevés érzékelőről van szó, a incremental encoder systems egyszerűek és gazdaságosak. A növekményes jeladót az korlátozza, hogy csak változási információkat szolgáltat, ezért a kódolónak referenciaeszközre van szüksége a mozgás kiszámításához. Inkrementális jeladó moduljaink sokoldalúak és testreszabhatók, hogy megfeleljenek a különféle alkalmazásoknak, például nagy igénybevételnek kitett alkalmazásokhoz, mint például a cellulóz- és papíripar, valamint az acélipar; ipari alkalmazások, például textil-, élelmiszer-, italipar és könnyű/szervo-alkalmazások, például robotika, elektronika, félvezetőipar. - Teljes CAN vezérlő a MODULbus Sockets számára: A Controller Area Network, rövidítve: CAN_cc781905-5cf58d_CAN_cc781905-5cf58d_CAN_cc781905-5cf58d_CAN_cc781905-5cf5-6-ba3b_c-c-d_ Az első beágyazott rendszerekben a modulok egyetlen MCU-t tartalmaztak, amely egyetlen vagy több egyszerű funkciót is végrehajtott, mint például az érzékelő szintjének leolvasása ADC-n keresztül, és egy egyenáramú motor vezérlése. Ahogy a funkciók bonyolultabbá váltak, a tervezők elosztott modularchitektúrákat alkalmaztak, és a funkciókat több MCU-ban valósították meg ugyanazon a PCB-n. A példa szerint egy összetett modulnak a fő MCU-ja lenne, amely az összes rendszerfunkciót, diagnosztikát és hibamentességet látná el, míg egy másik MCU egy BLDC motorvezérlő funkciót kezelne. Ezt az általános célú MCU-k alacsony költségű széles körű elérhetősége tette lehetővé. A mai járművekben, amikor a funkciók egy járműben, nem pedig egy modulon belül oszlanak meg, a nagy hibatűrő képesség, a modulok közötti kommunikációs protokoll szükségessége a CAN megtervezéséhez és az autóipari piacon való bevezetéséhez vezetett. A Full CAN Controller az üzenetszűrés, valamint a hardverben történő üzenetelemzés széles körű megvalósítását biztosítja, így felszabadítja a CPU-t attól a feladattól, hogy minden fogadott üzenetre válaszoljon. A teljes CAN vezérlők konfigurálhatók úgy, hogy csak akkor szakítsák meg a CPU-t, ha azok az üzenetek, amelyek azonosítói be vannak állítva elfogadási szűrőként a vezérlőben. A teljes CAN vezérlők több üzenetobjektummal is be vannak állítva, amelyeket postafiókoknak neveznek, és amelyek specifikus üzenetinformációkat tárolhatnak, például a CPU számára kapott azonosítót és adatbájtokat. A CPU ebben az esetben bármikor lekérné az üzenetet, azonban be kell fejeznie a feladatot, mielőtt ugyanazon üzenet frissítése érkezik, és felülírja a postafiók aktuális tartalmát. Ezt a forgatókönyvet a CAN vezérlők végső típusa oldja meg. Extended Full CAN controllers Extended Full CAN controllers amellett, hogy a kapott FI hardver további funkcionalitást biztosít a hardverhez. Egy ilyen megvalósítás lehetővé teszi ugyanannak az üzenetnek egynél több példányának tárolását a CPU megszakítása előtt, így megakadályozza a nagyfrekvenciás üzenetek információvesztését, vagy akár lehetővé teszi, hogy a CPU hosszabb ideig a fő modul funkciójára összpontosítson. Teljes CAN vezérlőnk MODULbus socketekhez a következő szolgáltatásokat kínálja: Intel 82527 Full CAN vezérlő, támogatja a V 2.0 A és A 2.0 B CAN protokollt, ISO/DIS 11898-2, 9 tűs D-SUB csatlakozó, Opciók Elszigetelt CAN interfész, A támogatott operációs rendszerek a Windows, Windows CE, Linux, QNX, VxWorks. - Intelligens CAN vezérlő MODULbus Sockets-hez : Ügyfeleinknek helyi intelligenciát kínálunk MC68332-vel, 256 kB SRAM / 16 bit széles, 64 kB SRAM / 16 bit széles, 64 kB SD RAM, 1 1 ISO8 8 bites DPRAM / 1 1 9 6 bites DPRAM 2, 9 tűs D-SUB csatlakozó, ICANOS firmware beépített, MODULbus+ kompatibilis, olyan opciók, mint izolált CAN interfész, CANopen elérhető, támogatott operációs rendszerek: Windows, Windows CE, Linux, QNX, VxWorks. - Intelligent MC68332 Based VMEbus Computer : VMEbus standing for VersaModular Eurocard bus is a computer data path or bus system that is used in industrial, commercial és katonai alkalmazások világszerte. A VMEbust forgalomirányító rendszerekben, fegyverzetvezérlő rendszerekben, távközlési rendszerekben, robotikában, adatgyűjtésben, videó képalkotásban stb. használják. A VMEbus rendszerek jobban ellenállnak az ütéseknek, a vibrációnak és a hosszabb hőmérsékletnek, mint az asztali számítógépekben használt szabványos buszrendszerek. Ez ideálissá teszi őket zord környezetben. Dupla euro-kártya faktorból (6U) , A32/24/16:D16/08 VMEbus master; A24:D16/08 slave interfész, 3 MODULbus I/O aljzat, előlap és MODULbus I/O vonalak P2 csatlakozása, programozható MC68332 MCU 21 MHz-el, fedélzeti rendszervezérlő első slot érzékeléssel, megszakításkezelő IRQ 1 – 5, megszakítás generátor bármelyik 7-ből, 1 MB SRAM főmemória, legfeljebb 1 MB EPROM, legfeljebb 1 MB FLASH EPROM, 256 kB kétportos akkumulátoros pufferelt SRAM, akkumulátorral pufferelt valós idejű óra 2 kB SRAM-mal, RS232 soros port, időszakos megszakítási időzítő (belső az MC68332-hez), watchdog időzítő (belső az MC68332-hez), DC/DC átalakító az analóg modulok ellátásához. Az opciók 4 MB SRAM főmemória. A támogatott operációs rendszer a VxWorks. - Intelligent PLC Link Concept (3964R) : A programmable logic controller or briefly PLC_cc781905-5cde-3194 -bb3b-136bad5cf58d_egy digitális számítógép, amelyet ipari elektromechanikus folyamatok automatizálására használnak, például gépek vezérlésére a gyári összeszerelő sorokon, vidámparkokban vagy világítótestekben. A PLC Link egy protokoll a memóriaterület egyszerű megosztására két PLC között. A PLC Link nagy előnye, hogy távoli I/O egységként használható PLC-kkel. Intelligens PLC Link koncepciónk 3964® kommunikációs eljárást kínál, üzenetküldési interfészt a gazdagép és a firmware között szoftver-illesztőprogramon keresztül, a gazdagépen lévő alkalmazásokat a soros vonali kapcsolat másik állomásával való kommunikációhoz, a 3964® protokoll szerinti soros adatkommunikációt, a szoftver-illesztőprogramok elérhetőségét. különféle operációs rendszerekhez. - Intelligens Profibus DP Slave Interface : A ProfiBus egy üzenetküldési formátum, amelyet kifejezetten a gyári és épületautomatizálási alkalmazások nagysebességű soros I/O-jához terveztek. A ProfiBus egy nyílt szabvány, és az RS485 és az európai EN50170 elektromos specifikáció alapján a ma működő leggyorsabb FieldBusként ismert. A DP utótag a „decentralizált periféria”-ra vonatkozik, amely a központi vezérlővel gyors soros adatkapcsolaton keresztül csatlakoztatott elosztott I/O eszközök leírására szolgál. Éppen ellenkezőleg, a fent leírt programozható logikai vezérlő vagy PLC bemeneti/kimeneti csatornái általában központilag vannak elrendezve. A fő vezérlő (master) és I/O csatornái (slave) közötti hálózati busz bevezetésével decentralizáltuk az I/O-t. A ProfiBus rendszer buszmestert használ az RS485 soros buszon több-drop módon elosztott slave eszközök lekérdezésére. A ProfiBus slave minden olyan perifériaeszköz (például I/O jelátalakító, szelep, hálózati meghajtó vagy más mérőeszköz), amely feldolgozza az információkat és elküldi a kimenetét a masternek. A slave egy passzívan működő állomás a hálózaton, mivel nem rendelkezik busz hozzáférési jogokkal, és csak a fogadott üzeneteket tudja nyugtázni, vagy kérésre válaszüzeneteket küldeni a masternek. Fontos megjegyezni, hogy minden ProfiBus slave prioritása azonos, és minden hálózati kommunikáció a mastertől származik. Összefoglalva: A ProfiBus DP egy nyílt szabvány, amely az EN 50170 szabványon alapul, ez az eddigi leggyorsabb Fieldbus szabvány akár 12 Mb adatátviteli sebességgel, plug and play működést tesz lehetővé, üzenetenként akár 244 bájt bemeneti/kimeneti adatot tesz lehetővé, legfeljebb 126 állomás csatlakozhat az autóbuszhoz, és legfeljebb 32 állomás buszszakaszonként. Our Intelligent Profibus DP Slave Interfész A Janz Tec VMOD-PROF minden funkciót kínál az egyenáramú szervomotorok motorvezérléséhez, programozható digitális PID szűrőt, sebességet, célpozíciót és szűrőparamétereket mozgás közben, változtatható interfészeket impulzus bemenet, programozható host megszakítások, 12 bites D/A konverter, 32 bites pozíció, sebesség és gyorsulás regiszterek. Támogatja a Windows, Windows CE, Linux, QNX és VxWorks operációs rendszereket. - MODULbus hordozókártya 3 U VMEbus rendszerekhez : Ez a rendszer 3 U VMEbus nem intelligens hordozókártyát kínál MODULbushoz, egyetlen euro-kártya formátumtényező (3 U), A24/16:D16/08 VMEbus slave interfész, 1 aljzat MODULbus I/O-hoz, jumper választható megszakítási szint 1-7 és vektoros megszakítás, rövid I/O vagy szabványos címzés, csak egy VME-helyet igényel, támogatja a MODULbus+azonosító mechanizmust, előlapi csatlakozó I/O jelek (modulok által biztosított). Választható DC/DC átalakító az analóg modul tápellátásához. Támogatott operációs rendszerek: Linux, QNX, VxWorks. - MODULbus hordozókártya 6 U-s VMEbus rendszerekhez : Ez a rendszer 6U VMEbus nem intelligens hordozókártyát kínál MODULbushoz, dupla euro-kártya, A24/D16 VMEbus szolga interfész MODUL-buszhoz, 4 plug-os M socket I/O, az egyes MODULbus I/O-któl eltérő vektorok, 2 kB rövid I/O vagy szabványos címtartomány, csak egy VME-helyre, előlapra és I/O-vonalak P2-csatlakozására van szüksége. Választható DC/DC átalakító az analóg modulok tápellátásához. Támogatott operációs rendszerek: Linux, QNX, VxWorks. - MODULbus Carrier Board For PCI Systems : Our MOD-PCI carrier boards offer non-intelligent PCI with two MODULbus+ sockets, extended height short form faktor, 32 bites PCI 2.2 célinterfész (PLX 9030), 3.3V / 5V PCI interfész, csak egy PCI-busz foglalat, a 0. MODULbus aljzat előlapi csatlakozója elérhető a PCI busz keretén. Másrészt, a mi MOD-PCI4 kártyáink nem Intelligens PCI-busz-busz-tényezős PCI-busz-busz hordozó kártyával, négy M-hosszú 2-es hosszúságú CI-busz-magassággal rendelkeznek. (PLX 9052), 5 V PCI interfész, csak egy PCI foglalat foglalt, a 0. MODULbus aljzat előlapi csatlakozója elérhető az ISAbus konzolnál, az 1. MODULbus aljzat I/O csatlakozója 16 tűs laposkábel csatlakozón az ISA konzolnál. - Motorvezérlő egyenáramú szervomotorokhoz : Mechanikai rendszerek gyártói, áram- és energiaipari vállalat, számos autóipari és szolgáltatói terület, valamint egyéb közlekedési és szolgáltatói berendezések gyártója nyugodt szívvel használhatják berendezéseinket, mert hajtástechnológiájukhoz robusztus, megbízható és méretezhető hardvert kínálunk. Motorvezérlőink moduláris felépítése lehetővé teszi, hogy a emPC systems alapú megoldásokat kínáljunk, amelyek rendkívül rugalmasan és készen állnak az ügyfelek igényeihez. Képesek vagyunk olyan interfészeket tervezni, amelyek gazdaságosak és alkalmasak az egyszerű egytengelyestől a több szinkronizált tengelyig terjedő alkalmazásokhoz. Moduláris és kompakt emPC-ink kiegészíthetők a skálázható emVIEW displays .5”-os integrált rendszerektől az egyszerű spektrumú alkalmazásoktól (jelenleg 5”-ig terjedő széles spektrumú rendszerekig) kezelői interfész rendszerek. EmPC rendszereink különböző teljesítményosztályokban és méretekben állnak rendelkezésre. Nincsenek ventilátoraik, és kompakt flash adathordozókkal dolgoznak. Our emCONTROL soft PLC environment can be used as a fully fledged, real-time control system enabling both simple as well as complex DRIVE ENGINEERING_cc781905-5cde -3194-bb3b-136bad5cf58d_elvégzendő feladatok. Az emPC-nket személyre szabjuk az Ön egyedi igényeinek megfelelően. - Soros interfész modul : A soros interfész modul egy olyan eszköz, amely egy címezhető zónabemenetet hoz létre. Kapcsolódást kínál egy címezhető buszhoz és egy felügyelt zóna bemenetet. Amikor a zóna bemenet nyitva van, a modul állapotadatokat küld a központnak, jelezve a nyitott helyzetet. Amikor a zóna bemenet rövidre van zárva, a modul állapotadatokat küld a központnak, jelezve a rövidre zárt állapotot. Ha a zóna bemenet normális, a modul adatokat küld a központnak, jelezve a normál állapotot. A felhasználók a helyi billentyűzeten láthatják az érzékelő állapotát és riasztásait. A központ üzenetet is küldhet a távfelügyeletnek. A soros interfész modul használható riasztórendszerekben, épületirányítási és energiagazdálkodási rendszerekben. A soros interfész modulok fontos előnyökkel járnak, csökkentve a telepítési időt speciális kialakításukkal, címezhető zónabemenettel, csökkentve a teljes rendszer összköltségét. A kábelezés minimális, mivel a modul adatkábelét nem kell külön-külön elvezetni a központhoz. A kábel egy címezhető busz, amely lehetővé teszi számos eszköz csatlakoztatását a kábelezés és a központhoz való csatlakozás előtt feldolgozás céljából. Áramot takarít meg, és alacsony áramigénye miatt minimálisra csökkenti a további tápegységek szükségességét. - VMEbus Prototyping Board : VDEV-IO kártyáink dupla Eurocard V/Bus6 interfésszel, V/Bus6 interfésszel, A cap interfész1 V/Busz interfésszel (6U) , 8 címtartomány elődekódolása, vektorregiszter, nagy mátrixmező környező sávval a GND/Vcc számára, 8 felhasználó által definiálható LED az előlapon. CLICK Product Finder-Locator Service ELŐZŐ OLDAL
- Mesh & Wire, USA, AGS-TECH Inc.
We supply wire and wire mesh, galvanized wires, metal wire, black annealed wire, wire mesh filters, wire cloth, perforated metal mesh, wire mesh fence and panels, conveyor belt mesh, wire mesh containers and customized wire mesh products to your specifications. Mesh & Wire Huzal- és hálótermékeket szállítunk, beleértve a horganyzott vashuzalokat, PVC-bevonatú vaskötőhuzalokat, dróthálót, dróthálót, kerítéshuzalokat, szállítószalag-hálót, perforált fémhálót. A készen kapható drótháló termékeinken kívül egyedi gyártású hálót és metal huzaltermékeket is végzünk az Ön specifikációi és igényei szerint. Vágjuk a kívánt méretre, címkézzük és csomagoljuk az ügyfél igényei szerint. Kérjük, kattintson az alábbi almenükre, ha többet szeretne megtudni egy adott drót- és hálótermékről. Horganyzott vezetékek és fémhuzalok Ezeket a vezetékeket számos alkalmazásban használják az iparban. Például a horganyzott vashuzalokat gyakran használják kötözési és rögzítési célokra, mint jelentős szakítószilárdságú köteleket. Ezek a fémhuzalok lehetnek tűzihorganyzottak és fémes megjelenésűek, vagy lehetnek PVC bevonatúak és színesek. A szögesdrótok különféle borotvatípusokkal rendelkeznek, és arra szolgálnak, hogy a behatolókat a korlátozott területeken kívül tartsák. Különféle huzalmérők kaphatók raktárról. Hosszú vezetékek tekercsben érkeznek. Ha a mennyiség indokolja, lehetséges, hogy az Ön által kívánt hosszban és tekercsméretben le tudjuk gyártani. A horganyzott huzalok, Metal Wires, szögesdrót egyedi címkézése és csomagolása lehetséges. Brosúrák letöltése: - Fémhuzalok - Horganyzott - Fekete lágyított Drótháló szűrők Ezek többnyire vékony rozsdamentes acél dróthálóból készülnek, és széles körben használják az iparban szűrőként folyadékok, porok, porok... stb. szűrésére. A dróthálós szűrők vastagsága néhány milliméteres tartományba esik. Az AGS-TECH elérte az 1 mm-nél kisebb huzalátmérőjű drótháló gyártását katonai haditengerészeti világítórendszerek elektromágneses árnyékolásához. A vevői specifikációk szerinti méretekkel dróthálószűrőket gyártunk. A négyzet, a kerek és az ovális geometriák általában használatosak. Szűrőink huzalátmérőjét és hálószámát Ön választhatja meg. Méretre vágjuk és bekeretezzük a széleket, hogy a szűrőháló ne torzuljon vagy sérüljön. Drótháló szűrőink nagy teherbírással, hosszú élettartammal, erős és megbízható élekkel rendelkeznek. Dróthálós szűrőink néhány felhasználási területe a vegyipar, gyógyszeripar, sörfőzés, italgyártás, elektromágneses árnyékolás, autóipar, mechanikai alkalmazások stb. - Drótháló és szövet prospektus (a dróthálós szűrőket tartalmazza) Perforált fémháló Perforált fémhálós lemezeinket horganyzott acélból, alacsony széntartalmú acélból, rozsdamentes acélból, rézlemezekből, nikkellemezekből vagy az Ön megrendelői igénye szerint gyártjuk. Különféle lyuk formák és minták tetszés szerint bélyegezhetők. Perforált fémhálónk sima, tökéletes felületi síkságot, szilárdságot és tartósságot kínál, és számos alkalmazásra alkalmas. A perforált fémháló szállításával számos iparág és alkalmazás igényeit kielégítettük, beleértve a beltéri hangszigetelést, a hangtompítógyártást, a bányászatot, az orvostudományt, az élelmiszer-feldolgozást, a szellőzést, a mezőgazdasági raktározást, a mechanikai védelmet és még sok mást. Hívjon minket még ma. Örömmel vágjuk, bélyegezzük, hajlítjuk, elkészítjük perforált fémhálóját az Ön specifikációi és igényei szerint. - Drótháló és szövet prospektus (perforált fémhálót tartalmaz) Dróthálós kerítés és panelek és megerősítés A dróthálót széles körben használják az építőiparban, a tereprendezésben, a lakásfelújításban, a kertészetben, az útépítésben stb., a drótháló népszerű alkalmazásai kerítésként és merevítő panelként az építőiparban._cc781905-5c-3194-3194- bb3b-136bad5cf58d_Tekintse meg alább letölthető prospektusainkat, hogy kiválaszthassa a hálónyílás, a huzalmérő, a szín és a felület kívánt modelljét. Minden dróthálós kerítésünk, panelünk és erősítő termékünk megfelel a nemzetközi ipari szabványoknak. Raktárról számos dróthálós kerítésszerkezet áll rendelkezésre. - Drótháló és szövet prospektus (Információt tartalmaz a kerítésünkről és a panelekről, valamint a megerősítésről) Szállítószalag háló Szállítószalaghálóink általában megerősített hálóból, rozsdamentes acélhuzalból, rozsdamentes vashuzalból, nikrómhuzalból, lövedékhuzalból készülnek. A szállítószalaghálók alkalmazása szűrőként, szállítószalagként és vegyiparban kőolaj, kohászat, élelmiszeripar, gyógyszeripar, üvegipar, alkatrészek szállítása üzemen vagy létesítményen belül... stb. A legtöbb szállítószalag-háló szövési stílusa a rugóra való hajlítás, majd a huzal behelyezése. A huzal átmérője általában: 0,8-2,5 mm A huzalvastagság általában: 5-13,2 mm A gyakori színek általában a következők: Silver Általában a szélesség 0,4-3 m, a hossza pedig 0,5-100 m A szállítószalag hálója hőálló A lánc típusa, a szállítószalag háló szélessége és hossza a testreszabható paraméterek közé tartozik. - Drótháló és szövet prospektus (általános információkat tartalmaz a képességeinkről) Testreszabott drótháló termékek (például kábeltálcák, kengyel stb.) Dróthálóból és perforált fémhálóból számos egyedi terméket tudunk gyártani, mint például kábeltálcák, keverők, Faraday ketrecek és EM árnyékoló szerkezetek, drótkosarak és -tálcák, építészeti tárgyak, műtárgyak, húsiparban használt acél dróthálós kesztyűk sérülések elleni védelemre...stb. Testreszabott dróthálóink, perforált fémeink és expandált fémeink méretre vághatók és lelapíthatók a kívánt alkalmazáshoz. A lapított dróthálót általában gépvédőként, szellőzőképernyőként, égőszűrőként, biztonsági képernyőként, folyadékelvezető képernyőként, mennyezeti panelként és sok más alkalmazásként használják. Testreszabott perforált fémeket készíthetünk furatformákkal és -méretekkel, hogy megfeleljenek az Ön projekt- és termékkövetelményeinek. A perforált fémek felhasználása sokoldalú. Bevonatos dróthálót is tudunk biztosítani. A bevonatok javíthatják a testre szabott dróthálótermékek tartósságát, és rozsdaálló védőréteget is biztosíthatnak. A rendelkezésre álló egyedi drótháló bevonatok közé tartozik a porbevonat, az elektropolírozás, a tüzihorganyzás, a nylon, a festés, az alumíniumozás, az elektrogalvanizálás, a PVC, a kevlár stb. Akár drótból szőtt testreszabott dróthálóként, akár sajtolt és lyukasztott és lapított fémlemezből perforált lemezként, testreszabott termékkövetelményeiért forduljon az AGS-TECH hoz. - Drótháló és szövet prospektus (Rengeteg információt tartalmaz a személyre szabott drótháló-gyártási képességeinkről) - Dróthálós kábeltálcák és kosarak prospektus (a prospektusban szereplő termékeken kívül egyedi kábeltálcákat is kaphat az Ön specifikációi szerint) - Drótháló konténer árajánlat tervezési űrlap (Kattintson a letöltéshez, töltse ki és küldjön nekünk e-mailt) ELŐZŐ OLDAL
- Pneumatic and Hydraulic Actuators - Accumulators - AGS-TECH Inc. - NM
Pneumatic and Hydraulic Actuators - Accumulators - AGS-TECH Inc. - NM Működtetők Akkumulátorok Az AGS-TECH a PNEUMATIKUS és HIDRAULIKUS AKTUÁTOROK vezető gyártója és szállítója az összeszereléshez, csomagoláshoz, robotikához és ipari automatizáláshoz. Aktoraink teljesítményükről, rugalmasságukról és rendkívül hosszú élettartamukról ismertek, és örömmel fogadják a különféle típusú működési környezetek kihívásait. Szállítunk még HIDRAULIKUS AKKUMULÁTOROK , amelyek olyan eszközök, amelyekben a potenciális energia a gáz vagy a rugó által súlyemelésre kerül, vagy a potenciális energiát súlyemelésként tárolja. viszonylag összenyomhatatlan folyadékkal szemben. Pneumatikus és hidraulikus hajtóművek és akkumulátorok gyors szállítása csökkenti a raktározási költségeit, és a gyártási ütemtervének megfelelően. AKTUÁTOROK: A működtető egy olyan típusú motor, amely egy mechanizmus vagy rendszer mozgatásáért vagy vezérléséért felelős. A hajtóműveket energiaforrás működteti. A hidraulikus hajtóműveket hidraulikus folyadéknyomással, a pneumatikus hajtóműveket pedig pneumatikus nyomással működtetik, és ezt az energiát mozgássá alakítják. Az aktuátorok olyan mechanizmusok, amelyekkel a vezérlőrendszer a környezetre hat. A vezérlőrendszer lehet rögzített mechanikus vagy elektronikus rendszer, szoftver alapú rendszer, személy vagy bármilyen más bemenet. A hidraulikus működtetők hengeres vagy folyadékmotorból állnak, amely hidraulikus erőt használ a mechanikai működés megkönnyítésére. A mechanikus mozgás lineáris, forgó vagy oszcilláló mozgást eredményezhet. Mivel a folyadékokat szinte lehetetlen összenyomni, a hidraulikus működtetők jelentős erőket fejthetnek ki. A hidraulikus működtetők azonban korlátozottan gyorsulhatnak. Az aktuátor hidraulikus hengere egy üreges hengeres csőből áll, amelyen egy dugattyú csúszhat. Az egyszeres működésű hidraulikus működtetőkben a folyadéknyomás csak a dugattyú egyik oldalán érvényesül. A dugattyú csak egy irányba tud mozogni, és általában rugót használnak a dugattyú visszatérő löketének biztosítására. Kettős működésű működtetőket használnak, ha nyomást gyakorolnak a dugattyú mindkét oldalán; a dugattyú két oldala közötti nyomáskülönbség a dugattyút az egyik vagy a másik oldalra mozgatja. A pneumatikus működtetők a vákuum vagy a nagy nyomású sűrített levegő által képzett energiát lineáris vagy forgó mozgássá alakítják át. A pneumatikus működtetők lehetővé teszik nagy erők létrehozását viszonylag kis nyomásváltozásokból. Ezeket az erőket gyakran használják a szelepeknél a membránok mozgatására, hogy befolyásolják a folyadék áramlását a szelepen keresztül. A pneumatikus energia azért kívánatos, mert gyorsan reagál indításkor és leállításkor, mivel az áramforrást nem kell tartalékban tárolni a működéshez. Az aktuátorok ipari alkalmazásai közé tartozik az automatizálás, a logikai és sorrendvezérlés, a rögzítőelemek és a nagy teljesítményű mozgásvezérlés. Másrészt az indítószerkezetek autóipari alkalmazásai magukban foglalják a szervokormányt, az elektromos fékeket, a hidraulikus fékeket és a szellőzésvezérlőket. A működtetők repülési alkalmazásai közé tartoznak a repülésvezérlő rendszerek, a kormányzásvezérlő rendszerek, a légkondicionáló és a fékvezérlő rendszerek. A PNEUMATIKUS és HIDRAULIKUS AKTUÁTOROK ÖSSZEHASONLÍTÁSA: A pneumatikus lineáris hajtóművek egy üreges hengerben található dugattyúból állnak. A külső kompresszor vagy kézi szivattyú nyomása mozgatja a dugattyút a henger belsejében. A nyomás növekedésével a működtető hengere a dugattyú tengelye mentén mozog, lineáris erőt hozva létre. A dugattyú visszatér eredeti helyzetébe vagy visszarugózó erő hatására, vagy a dugattyú másik oldalára áramló folyadék hatására. A hidraulikus lineáris hajtóművek a pneumatikus működtetőkhöz hasonlóan működnek, de a szivattyúból összenyomhatatlan folyadék, nem pedig túlnyomásos levegő mozgatja a hengert. A pneumatikus hajtóművek előnyei az egyszerűségükből fakadnak. A pneumatikus alumínium működtetők többségének maximális nyomása 150 psi, a furat mérete 1/2 és 8 hüvelyk között van, ami körülbelül 30 és 7500 font közötti erővé alakítható. Ezzel szemben az acél pneumatikus működtetők maximális nyomása 250 psi, a furat mérete 1/2 és 14 hüvelyk között van, és 50 és 38 465 lb közötti erőket generálnak. A pneumatikus hajtóművek precíz lineáris mozgást biztosítanak, például 0,1 pontossággal. hüvelyk és ismételhetőség 0,001 hüvelyken belül. A pneumatikus hajtóművek tipikus alkalmazásai a szélsőséges hőmérsékletű területek, például -40 F és 250 F között. Levegőt használva a pneumatikus működtetők elkerülik a veszélyes anyagok használatát. A pneumatikus hajtóművek megfelelnek a robbanásvédelmi és gépbiztonsági követelményeknek, mivel motorhiányuk miatt nem okoznak mágneses interferenciát. A pneumatikus hajtóművek költsége alacsony a hidraulikus hajtóművekhez képest. A pneumatikus működtetők szintén könnyűek, minimális karbantartást igényelnek, és tartós alkatrészekkel rendelkeznek. Másrészt a pneumatikus hajtóműveknek vannak hátrányai: a nyomásveszteségek és a levegő összenyomhatósága miatt a pneumatika kevésbé hatékony, mint a többi lineáris mozgási módszer. Az alacsonyabb nyomáson végzett műveletek kisebb erőkkel és lassabb sebességgel járnak. A kompresszornak folyamatosan működnie kell és nyomást kell gyakorolnia akkor is, ha semmi sem mozog. A hatékony működés érdekében a pneumatikus hajtóműveket egy adott feladathoz kell méretezni, és nem használhatók más alkalmazásokhoz. A pontos szabályozáshoz és hatékonysághoz arányos szabályozókra és szelepekre van szükség, ami költséges és bonyolult. Annak ellenére, hogy a levegő könnyen hozzáférhető, szennyeződhet olajjal vagy kenéssel, ami leálláshoz és karbantartáshoz vezethet. A sűrített levegő fogyóeszköz, amelyet meg kell vásárolni. A hidraulikus működtetők viszont masszívak és nagy erejű alkalmazásokhoz alkalmasak. 25-ször nagyobb erőt képesek kifejteni, mint az azonos méretű pneumatikus működtetők, és akár 4000 psi nyomással működnek. A hidraulikus motorok lóerő/tömeg aránya 1-2 LE/lb-vel nagyobb, mint a pneumatikus motoroké. A hidraulikus működtetők állandó erőt és nyomatékot tudnak tartani anélkül, hogy a szivattyú több folyadékot vagy nyomást szolgáltatna, mivel a folyadékok összenyomhatatlanok. A hidraulikus hajtóművek szivattyúi és motorjai jelentős távolságra helyezhetők el, még mindig minimális teljesítményveszteség mellett. Azonban a hidraulikából folyadék szivárog, ami csökkenti a hatékonyságot. A hidraulikafolyadék szivárgása tisztasági problémákhoz, valamint a környező alkatrészek és területek esetleges károsodásához vezet. A hidraulikus működtetőkhöz sok kiegészítő alkatrészre van szükség, például folyadéktartályokra, motorokra, szivattyúkra, kioldószelepekre és hőcserélőkre, zajcsökkentő berendezésekre. Ennek eredményeként a hidraulikus lineáris mozgásrendszerek nagyok és nehezen befogadhatók. AKKUMULÁTOROK: Ezeket folyékony energiaellátó rendszerekben használják az energia felhalmozására és a lüktetések kisimítására. Az akkumulátorokat használó hidraulikus rendszerek kisebb folyadékszivattyúkat is használhatnak, mivel az akkumulátorok a szivattyúból tárolják az energiát alacsony igényű időszakokban. Ez az energia azonnali felhasználásra áll rendelkezésre, igény esetén annyiszor szabadul fel, mint amennyit a szivattyú önmagában biztosítana. Az akkumulátorok túlfeszültség- vagy pulzációcsillapítóként is működhetnek a hidraulikus kalapácsok csillapításával, csökkentve a hidraulikus körben lévő erőhengerek gyors működése vagy hirtelen indítása és leállása által okozott ütéseket. Az akkumulátoroknak négy fő típusa van: 1.) Súlyterhelésű dugattyús típusú akkumulátorok, 2.) Membrán típusú akkumulátorok, 3.) Rugós típusú akkumulátorok és 4.) Hidropneumatikus dugattyús típusú akkumulátorok. A súllyal terhelt típus sokkal nagyobb és kapacitásához képest nehezebb, mint a modern dugattyús és tömlős típusok. Mind a súlyterhelésű, mind a mechanikus rugós típust ma nagyon ritkán használják. A hidropneumatikus típusú akkumulátorok rugós párnaként gázt használnak hidraulikafolyadékkal együtt, a gázt és a folyadékot vékony membrán vagy dugattyú választja el egymástól. Az akkumulátorok a következő funkciókkal rendelkeznek: -Energia tároló - Lüktetések elnyelése - Üzemi lökések csillapítása -Kiegészítő szivattyú szállítás - Nyomás fenntartása -Adagolóként működnek A hidropneumatikus akkumulátorok gázt és hidraulikafolyadékot tartalmaznak. A folyadéknak csekély dinamikus energiatároló képessége van. A hidraulikafolyadék relatív összenyomhatatlansága azonban ideálissá teszi folyadékellátó rendszerekhez, és gyors választ ad az energiaigényre. A gáz viszont, amely az akkumulátorban lévő hidraulikafolyadék partnere, nagy nyomásra és kis térfogatra sűríthető. A sűrített gázban a potenciális energia tárolódik, hogy szükség esetén felszabaduljon. A dugattyús típusú akkumulátorokban a sűrített gázban lévő energia nyomást fejt ki a gázt és a hidraulikus folyadékot elválasztó dugattyúra. A dugattyú pedig a folyadékot a hengerből a rendszerbe és arra a helyre kényszeríti, ahol hasznos munkát kell végezni. A legtöbb folyadékenergia-alkalmazásban szivattyúkat használnak a hidraulikus rendszerben felhasználandó vagy tárolható teljesítmény előállítására, és a szivattyúk ezt a teljesítményt pulzáló áramlásban adják le. A dugattyús szivattyú, amelyet általában nagyobb nyomásokhoz használnak, pulzációkat produkál, amelyek károsak a nagynyomású rendszerre. A rendszerben megfelelően elhelyezett akkumulátor jelentősen tompítja ezeket a nyomásingadozásokat. Sok folyadék-alkalmazásban a hidraulikus rendszer hajtott tagja hirtelen leáll, nyomáshullámot hozva létre, amely visszakerül a rendszeren. Ez a lökéshullám a normál üzemi nyomásnál többszörös csúcsnyomást fejleszthet ki, és rendszerhiba vagy zavaró zaj forrása lehet. Az akkumulátorban lévő gázcsillapító hatás minimálisra csökkenti ezeket a lökéshullámokat. Egy példa erre az alkalmazásra a rázkódás elnyelése, amelyet egy hidraulikus homlokrakodó rakodókanarájának hirtelen leállítása okoz. Az energia tárolására képes akkumulátor kiegészítheti a folyadékszivattyút a rendszer áramellátásában. A szivattyú a munkaciklus üresjárati szakaszaiban tárolja a potenciális energiát az akkumulátorban, és az akkumulátor ezt a tartalékteljesítményt visszaadja a rendszernek, amikor a ciklus vész- vagy csúcsteljesítményt igényel. Ez lehetővé teszi a rendszer számára, hogy kisebb szivattyúkat használjon, ami költség- és energiamegtakarítást eredményez. Nyomásváltozások figyelhetők meg a hidraulikus rendszerekben, amikor a folyadékot emelkedő vagy csökkenő hőmérsékletnek teszik ki. Emellett nyomásesések is előfordulhatnak a hidraulikafolyadékok szivárgása miatt. Az akkumulátorok az ilyen nyomásváltozásokat kis mennyiségű hidraulikus folyadék szállításával vagy fogadásával kompenzálják. Abban az esetben, ha a fő áramforrás meghibásodna vagy leállna, az akkumulátorok kiegészítő áramforrásként működnének, fenntartva a nyomást a rendszerben. Végül az akkumulátorok nyomás alatti folyadékok, például kenőolajok adagolására használhatók. Kérjük, kattintson az alábbi kiemelt szövegre, hogy letöltse termékismertetőinket aktuátorokhoz és akkumulátorokhoz: - Pneumatikus hengerek - YC sorozatú hidraulikus henger - akkumulátorok az AGS-TECH Inc.-től CLICK Product Finder-Locator Service ELŐZŐ OLDAL
- Brushes, Brush Manufacturing, USA, AGS-TECH
AGS-TECH Inc. supplies off-the-shelf as well as custom manufactured brushes. Many types are offered including industrial brush, agricultural brushes, municipal brushes, copper wire brush, zig zag brush, roller brush, side brushes, metal polishing brush, window cleaning brushes, heavy industrial scrubbing brush...etc. Kefék és ecsetek gyártása Az AGS-TECH szakértőkkel rendelkezik a tisztító- és feldolgozóberendezés-gyártók kefék tanácsadásában, tervezésében és gyártásában. Együttműködünk Önnel, hogy innovatív, egyedi ecsettervezési megoldásokat kínáljunk. Az ecset prototípusait még a mennyiségi gyártás megkezdése előtt fejlesztik. Segítünk Önnek a kiváló minőségű kefék tervezésében, fejlesztésében és gyártásában az optimális gépteljesítmény érdekében. A termékek szinte bármilyen méretben előállíthatók, amit szeretne, vagy az alkalmazásnak megfelelő. A kefe sörtéi is különböző hosszúságúak és anyagúak lehetnek. Az alkalmazástól függően természetes és szintetikus sörtéket és anyagokat is használunk keféinkben. Néha olyan kész ecsetet tudunk ajánlani Önnek, amely megfelel az Ön alkalmazásának és igényeinek. Csak tudassa velünk igényeit, és mi segítünk Önnek. Néhány kefetípus, amelyet szállítani tudunk Önnek: Ipari kefék Mezőgazdasági ecsetek Zöldségkefék Városi ecsetek Réz drótkefe Cikk-zag ecsetek Görgős ecset Oldalsó kefék Görgős kefék Lemezkefék Kör alakú ecsetek Gyűrűkefék és távtartók Tisztító kefék Szállítószalag tisztító kefe Polírozó ecsetek Fém polírozó ecset Ablaktisztító kefék Üveggyártó kefék Trommel szitakefék Strip ecsetek Ipari hengerkefék Változó sörtéjű kefék Változtatható és állítható sörtéjű kefék Szintetikus szálú ecset Természetes szálú ecset Lath Brush Nehéz ipari súrolókefék Speciális kereskedelmi kefék Ha részletes tervrajzai vannak a legyártandó ecsetekrõl, az tökéletes. Csak küldje el nekünk értékelésre. Ha nincs tervrajza, nincs gond. A legtöbb projekthez kezdetben elegendő lehet az ecset mintája, fényképe vagy kézzel készített vázlata. Speciális sablonokat küldünk Önnek, amelyek kitöltik az Ön igényeit és adatait, hogy helyesen tudjuk értékelni, megtervezni és legyártani termékét. Sablonjainkban olyan részletekkel kapcsolatban vannak kérdéseink, mint például: Ecset arc hossza Cső hossza Cső belső és külső átmérője A lemez belső és külső átmérője A lemez vastagsága Kefe átmérője Ecset magassága Csomó átmérője Sűrűség A sörték anyaga és színe Sörte átmérő Ecsetminta és kitöltési minta (kétsoros spirális, kétsoros csík, teljes kitöltés stb.) Választott kefehajtás Alkalmazások kefékhez (élelmiszerek, gyógyszerek, fémek polírozása, ipari tisztítás stb.) Keféivel olyan tartozékokat szállítunk, mint a betéttartók, horgas alátétek, a szükséges tartozékok, lemezmeghajtók, meghajtócsatlakozók stb. Ha nem ismeri ezeket az ecsetspecifikációkat, ismét nincs probléma. Végigvezetjük Önt a tervezési folyamat során. ELŐZŐ OLDAL
- Industrial Chemicals, Industrial Consumables, Aerosols, Sprays, Industrial Chemical Agents
Industrial Chemicals, Industrial Consumables, Aerosols, Sprays, Industrial Chemical Agents Ipari és speciális és funkcionális textíliák Számunkra csak a speciális és funkcionális textíliák és szövetek és az ezekből készült termékek érdekelnek, amelyek egy adott alkalmazást szolgálnak. Kiemelkedő értékű műszaki textíliákról van szó, amelyeket néha műszaki textíliáknak és szöveteknek is neveznek. Szőtt, valamint nem szőtt szövetek és kendők számos alkalmazáshoz elérhetők. Az alábbiakban felsorolunk néhány főbb ipari, speciális és funkcionális textíliát, amelyek termékfejlesztési és gyártási körünkbe tartoznak. Készek vagyunk együttműködni Önnel az Ön termékeinek tervezésében, fejlesztésében és gyártásában: Hidrofób (víztaszító) és hidrofil (vízelnyelő) textilanyagok Rendkívüli szilárdságú textíliák és szövetek, tartósság és kemény környezeti feltételekkel szembeni ellenálló képesség (például golyóálló, nagy hőálló, alacsony hőmérsékletnek ellenálló, lángálló, közömbös vagy ellenáll a korrozív folyadékoknak és gázoknak, képződés….) Antibakteriális és gombaellenes textíliák és szövetek UV védő Elektromosan vezető és nem vezető textíliák és szövetek Antisztatikus szövetek az ESD szabályozáshoz… stb. Speciális optikai tulajdonságokkal és hatásokkal rendelkező textíliák és szövetek (fluoreszkáló… stb.) Speciális szűrőképességű textíliák, szövetek és kendők, szűrőgyártás Ipari textíliák, például légcsatorna szövetek, közbélések, megerősítések, hajtószíjak, gumierősítők (szállítószalagok, nyomattakarók, zsinórok), textíliák szalagokhoz és csiszolóanyagokhoz. Textíliák az autóipar számára (tömlők, övek, légzsákok, betétek, gumiabroncsok) Textíliák építőipari, építőipari és infrastrukturális termékekhez (betonszövet, geomembránok és szövetbetét) Kompozit többfunkciós textíliák különböző rétegekkel vagy különböző funkciókat biztosító alkatrészekkel. Az aktív szénből készült textíliák infusion on poliészter szálak pamut kézérzetet, szagvédelmet és UV-kezelést biztosítanak. Alakmemóriás polimerekből készült textíliák Textíliák sebészeti és sebészeti implantátumokhoz, biokompatibilis szövetek Felhívjuk figyelmét, hogy az Ön igényeinek és specifikációinak megfelelő termékeket tervezünk, tervezünk és gyártunk. Készítünk termékeket az Ön specifikációi szerint, vagy igény esetén segítünk a megfelelő anyagok kiválasztásában és a termék tervezésében. ELŐZŐ OLDAL
- Power & Energy, Power Supply, Wind Generator, Hydro Turbine, Solar
Power & Energy Components and Systems Power Supply - Wind Generator - Hydro Turbine - Solar Module Assembly - Rechargeable Battery - AGS-TECH Elektromos energia és energia alkatrészek és rendszerek gyártása és összeszerelése AGS-TECH kellékek: • Egyedi tápegységek (távközlés, ipari áramellátás, kutatás). Meglévő tápegységeinket, transzformátorainkat az Ön igényeinek megfelelően módosíthatjuk, vagy az Ön igényeinek és követelményeinek megfelelő tápegységeket tervezhetünk, gyárthatunk és összeszerelhetünk. Mind a huzaltekercses, mind a szilárdtest tápegységek kaphatók. Egyedi transzformátor és tápegység ház kialakítás fém és polimer típusú anyagokból elérhető. Egyedi címkézést, csomagolást is kínálunk, és kérésre megszerezzük az UL, CE jelölés, FCC megfelelőséget. • Szélenergia-generátorok alternatív energia előállítására és önálló távoli berendezések, lakóterületek, ipari épületek és mások energiaellátására. A szélenergia az egyik legnépszerűbb alternatív energiatrend azokban a földrajzi régiókban, ahol sok és erős a szél. A szélenergia-generátorok bármilyen méretűek lehetnek, a kis tetőtéri generátoroktól a nagy szélturbinákig, amelyek teljes lakó- vagy ipari területeket képesek táplálni. A megtermelt energiát általában akkumulátorokban tárolják, amelyek táplálják a létesítményt. Ha többletenergia keletkezik, azt vissza lehet adni az elektromos hálózatnak (hálózatnak). Néha a szélenergia-generátorok képesek az energia egy töredékét szolgáltatni, de így is jelentős villanyszámla megtakarítást eredményez bizonyos időszakokban. A szélerőművek néhány éven belül megtéríthetik beruházási költségeiket. • Napelemek és napelemek (rugalmas és merev). Folyamatban vannak a kutatások a rápermetezett napelemekkel kapcsolatban. A napenergia az egyik legnépszerűbb alternatív energiatrend azokban a földrajzi régiókban, ahol sok és erős a napsütés. A napelem panelek bármilyen méretűek lehetnek, a kis számítógépes laptop méretű panelektől a nagy, lépcsőzetes tetőtéri panelekig, amelyek egész lakó- vagy ipari területet képesek ellátni. A megtermelt energiát általában akkumulátorokban tárolják, amelyek táplálják a létesítményt. Ha többletenergia keletkezik, azt vissza lehet adni a hálózatnak. Néha a napelem panelek képesek az energia egy töredékét ellátni, de akárcsak a szélenergia-generátorok esetében, ez is jelentős villanyszámla megtakarítást eredményez hosszú időn keresztül. Napjainkban a napelem panelek költsége alacsony szintet ért el, ami könnyen kivitelezhetővé teszi még olyan területeken is, ahol alacsony a napsugárzás. Kérjük, ne feledje, hogy az Egyesült Államok, Kanada és az EU legtöbb közösségében, önkormányzatában kormányzati ösztönzők és alternatív energiaprojektek támogatása létezik. Ennek részleteiben tudunk segíteni, így a befektetésének egy részét visszakapja az önkormányzati vagy állami hatóságoktól. • Hosszú élettartamú újratölthető akkumulátorokat is szállítunk. Egyedi gyártású akkumulátorokat és akkumulátortöltőket kínálunk arra az esetre, ha alkalmazásának valami szokatlanra lenne szüksége. Egyes ügyfeleink új termékei vannak a piacon, és szeretnének megbizonyosodni arról, hogy ügyfeleik cserealkatrészeket, köztük akkumulátorokat vásárolnak tőlük. Ezekben az esetekben egy új akkumulátor-kialakítás biztosíthatja, hogy Ön folyamatosan bevételt termeljen az akkumulátorok értékesítéséből, mert az Ön saját tervezésű lesz, és semmilyen más, már kapható akkumulátor nem fér bele a termékbe. A lítium-ion akkumulátorok manapság népszerűvé váltak az autóiparban és másokban. Az elektromos autók sikere nagyban függ az akkumulátoroktól. A csúcskategóriás akkumulátorok egyre nagyobb jelentőséget kapnak a szénhidrogén alapú energiaválság elmélyülésével. Az alternatív energiaforrások, például a szél- és a napenergia fejlesztése további hajtóerők, amelyek növelik az újratölthető akkumulátorok iránti keresletet. Az alternatív energiaforrásokból nyert energiát tárolni kell, hogy szükség esetén felhasználható legyen. WEHO modell kapcsoló tápegységek katalógusa Puha ferritek - Magok - Toroidok - EMI-elnyomó termékek - RFID transzponderek és tartozékok prospektus Brosúra letöltése számunkra TERVEZÉSI PARTNERSÉGI PROGRAM Ha leginkább megújuló alternatív energiatermékeink iránt érdeklődik, akkor látogassa meg megújuló energia oldalunkat http://www.ags-energy.com Ha mérnöki, kutatási és fejlesztési lehetőségeink is érdeklik, kérjük, látogassa meg mérnöki oldalunkat http://www.ags-engineering.com CLICK Product Finder-Locator Service ELŐZŐ OLDAL
- Solar Power Modules, Rigid, Flexible Panels, Thin Film, Monocrystaline
Solar Power Modules - Rigid - Flexible Panels - Thin Film - Monocrystalline - Polycrystalline - Solar Connector available from AGS-TECH Inc. Egyedi napelemes rendszerek gyártása és összeszerelése Mi szállítjuk: • Napelemek és panelek, napenergiával működő eszközök és egyedi szerelvények alternatív energia előállításához. A napelemek a legjobb megoldást jelenthetik a távoli területeken elhelyezett, önálló berendezésekhez, amelyek önellátásáról gondoskodnak. Az akkumulátorcsere miatti magas karbantartási igények kiküszöbölése, a tápkábelek beszerelésének megszüntetése a berendezés fő vezetékekhez való csatlakoztatásához nagy marketing lökést adhat termékeinek. Gondoljon erre, amikor önálló berendezést tervez távoli területeken. Ezenkívül a napenergiával pénzt takaríthat meg azáltal, hogy csökkenti a vásárolt elektromos energiától való függőségét. Ne feledje, hogy a napelemek lehetnek rugalmasak vagy merevek. Ígéretes kutatások folynak a rápermetezett napelemekkel kapcsolatban. A napelemes eszközök által termelt energiát általában akkumulátorokban tárolják, vagy közvetlenül a generálás után felhasználják. Projektjeihez napelemeket, paneleket, napelemeket, invertereket, napenergia csatlakozókat, kábelszerelvényeket, teljes napelem készleteket tudunk szállítani. A napelemes készülék tervezési fázisában is tudunk segíteni. A megfelelő alkatrészek kiválasztásával, a megfelelő napelem típussal és esetleg optikai lencsék, prizmák... stb. maximalizálhatjuk a napelemek által termelt energia mennyiségét. Kihívást jelenthet a napenergia maximalizálása, ha az eszközön rendelkezésre álló felületek korlátozottak. Ennek eléréséhez megfelelő szaktudással és optikai tervezőeszközeinkkel rendelkezünk. Brosúra letöltése számunkra TERVEZÉSI PARTNERSÉGI PROGRAM IDE KATTINTVA töltse le átfogó elektromos és elektronikus alkatrészek katalógusunkat a késztermékekhez . Ebben a katalógusban olyan termékek találhatók, mint a napelemes csatlakozók, akkumulátorok, átalakítók és egyebek a napenergiával kapcsolatos projektjeihez. Ha nem találja ott, vegye fel velünk a kapcsolatot, és elküldjük Önnek a rendelkezésre álló információkat. Ha leginkább nagyszabású hazai vagy közüzemi méretű megújuló alternatív energiatermékeink és rendszereink, köztük napelemes rendszereink iránt érdeklődik, kérjük, látogassa meg energetikai oldalunkat http://www.ags-energy.com CLICK Product Finder-Locator Service ELŐZŐ OLDAL
- Brazing, Soldering, Welding, Joining Processes, Assembly Services
Brazing - Soldering - Welding - Joining Processes - Assembly Services - Subassemblies - Assemblies - Custom Manufacturing - AGS-TECH Inc. - NM - USA Forrasztás és hegesztés Az általunk a gyártásban alkalmazott számos ÖSSZEFOGLALÁSI technika közül kiemelt hangsúlyt kap a HEGESZTÉS, FORRSZÍTÁS, RAGASZTÁS és EGYEDI MECHANIKAI ÖSSZESZERELÉS, mert ezeket a technikákat széles körben alkalmazzák olyan alkalmazásokban, mint a hermetikus szerelvények gyártása, a high-tech termékgyártás és a speciális tömítés. Itt ezeknek az illesztési technikáknak a speciálisabb aspektusaira koncentrálunk, mivel ezek a fejlett termékek és szerelvények gyártásához kapcsolódnak. FÚZIÓS HEGESZTÉS: Hőt használunk az anyagok olvasztására és egyesítésére. A hőt elektromos árammal vagy nagyenergiájú gerendákkal biztosítják. Az általunk alkalmazott fúziós hegesztés típusok: OXYFUEL GÁZHEGESZTÉS, ÍVHEGESZTÉS, NAGYENERGIÁJÚ HEGESZTÉS. SZILÁRDHEZETŐ HEGESZTÉS: Az alkatrészeket olvasztás és ömlesztés nélkül egyesítjük. Szilárdtest-hegesztési módszereink a HIDEG, ULTRAHANGOS, ELLENÁLLÁS, SÚRLÁS, ROBBANÁS HEGESZTÉS és DIFFÚZIÓS RAGASZTÁS. FORRASZTÁS ÉS FORRASZTÁS: Töltőfémeket használnak, és azt az előnyt biztosítják, hogy alacsonyabb hőmérsékleten dolgozunk, mint a hegesztésnél, így kevesebb szerkezeti sérülés keletkezik a termékeken. A kerámia-fém idomokat, hermetikus tömítést, vákuumátvezetéseket, magas és ultramagas vákuum- és folyadékszabályozási alkatrészeket gyártó keményforrasztóüzemünkkel kapcsolatos információkat itt találja:Forrasztógyári prospektus RAGASZTÁS: Az iparban használt ragasztók és az alkalmazások sokfélesége miatt külön oldalunk van erre. A ragasztással foglalkozó oldalunk megtekintéséhez kattintson ide. EGYEDI MECHANIKAI ÖSSZESZERELÉS: Különféle rögzítőelemeket használunk, például csavarokat, csavarokat, anyákat, szegecseket. Rögzítőink nem korlátozódnak a szokásos, polcról kapható kötőelemekre. Speciális kötőelemeket tervezünk, fejlesztünk és gyártunk, amelyek nem szabványos anyagokból készülnek, hogy megfeleljenek a speciális alkalmazások követelményeinek. Néha elektromos vagy hő nem vezetőképesség kívánatos, míg néha vezetőképesség. Egyes speciális alkalmazásokhoz az ügyfélnek olyan speciális rögzítőelemekre van szüksége, amelyeket nem lehet eltávolítani a termék tönkretétele nélkül. Végtelen sok ötlet és alkalmazás létezik. Nálunk mindent megtalálsz, ha nem készen, gyorsan kifejlesztjük. A mechanikus összeszereléssel foglalkozó oldalunk megtekintéséhez kattintson ide . Nézzük meg részletesebben a különféle illesztési technikáinkat. OXYFUEL GAS HEGESZTÉS (OFW): A hegesztési láng előállításához oxigénnel kevert fűtőgázt használunk. Ha acetilént használunk tüzelőanyagként és oxigénként, azt oxiacetilén gázhegesztésnek nevezzük. Az oxigéngáz égési folyamatában két kémiai reakció megy végbe: C2H2 + O2 ------» 2CO + H2 + Hő 2CO + H2 + 1,5 O2--------» 2 CO2 + H2O + Hő Az első reakció során az acetilént szén-monoxidra és hidrogénre disszociálják, miközben a teljes hőtermelés mintegy 33%-át állítják elő. A fenti második eljárás a hidrogén és a szén-monoxid további elégetését jelenti, miközben a teljes hő mintegy 67%-át állítják elő. A láng hőmérséklete 1533 és 3573 Kelvin között van. A gázkeverék oxigénszázaléka fontos. Ha az oxigéntartalom több mint a fele, akkor a láng oxidálószerré válik. Ez egyes fémeknél nemkívánatos, mások számára viszont kívánatos. Egy példa arra, amikor az oxidáló láng kívánatos, a rézalapú ötvözetek, mivel passziváló réteget képeznek a fémen. Másrészt, ha az oxigéntartalom csökken, a teljes égés nem lehetséges, és a láng redukáló (karburáló) lánggá válik. A redukáló láng hőmérséklete alacsonyabb, ezért alkalmas olyan eljárásokra, mint a forrasztás és keményforrasztás. Más gázok is potenciális tüzelőanyagok, de van néhány hátrányuk az acetilénhez képest. Alkalmanként töltőrudak vagy huzalok formájában töltőfémeket szállítunk a hegesztési zónába. Némelyikük folyasztószerrel van bevonva, hogy késleltesse a felületek oxidációját, és így védje az olvadt fémet. A fluxus további előnye az oxidok és egyéb anyagok eltávolítása a hegesztési zónából. Ez erősebb kötődéshez vezet. Az oxigéngázos hegesztés egy változata a NYOMÁSOS GÁZHEGESZTÉS, ahol a két komponenst a határfelületükön hevítik fel oxiacetilén gázpisztoly segítségével, és amint a határfelület elkezd olvadni, a pisztolyt kihúzzák, és axiális erőt alkalmaznak a két rész összenyomására. amíg a felület megszilárdul. ÍVHEGESZTÉS: Az elektromos energiát használva ívet hozunk létre az elektróda csúcsa és a hegesztendő részek között. A tápegység lehet AC vagy DC, míg az elektródák fogyaszthatók vagy nem fogyaszthatók. Az ívhegesztés hőátadása a következő egyenlettel fejezhető ki: H / l = ex VI / v Itt H a hőbevitel, l a hegesztési varrat hossza, V és I az alkalmazott feszültség és áram, v a hegesztési sebesség és e a folyamat hatékonysága. Minél nagyobb az „e” hatásfok, annál előnyösebben hasznosul a rendelkezésre álló energia az anyag olvasztására. A hőbevitel a következőképpen is kifejezhető: H = ux (térfogat) = ux A xl Itt u az olvadás fajlagos energiája, A a varrat keresztmetszete és l a varrat hossza. A fenti két egyenletből a következőket kaphatjuk: v = ex VI / u A Az ívhegesztés egy változata a SHIELDED METAL ARC WELDING (SMAW), amely az összes ipari és karbantartási hegesztési folyamat mintegy 50%-át teszi ki. AZ ELEKTROMOS ÍVHEGESZTÉS (STAC HEGESZTÉS) úgy történik, hogy a bevonatos elektróda hegyét hozzáérinti a munkadarabhoz, és gyorsan visszahúzza az ív fenntartásához elegendő távolságra. Ezt az eljárást pálcás hegesztésnek is nevezzük, mivel az elektródák vékony és hosszú pálcikák. A hegesztési folyamat során az elektróda hegye a bevonattal és az ív közelében lévő nem nemesfémmel együtt megolvad. Az alapfém, az elektródfém és az elektródabevonatból származó anyagok keveréke megszilárdul a hegesztési területen. Az elektróda bevonata dezoxidálódik és védőgázt képez a hegesztési tartományban, így megvédi a környezet oxigénjétől. Ezért az eljárást árnyékolt fém ívhegesztésnek nevezik. Az optimális hegesztési teljesítmény érdekében 50 és 300 amper közötti áramerősséget és általában 10 kW-nál kisebb teljesítményszintet használunk. Szintén fontos az egyenáram polaritása (az áram áramlási iránya). Az egyenes polaritás, ahol a munkadarab pozitív, az elektróda pedig negatív, előnyös a fémlemezek hegesztésénél a sekély behatolása miatt, valamint a nagyon széles hézagokkal rendelkező kötéseknél is. Fordított polaritás esetén, azaz az elektróda pozitív és a munkadarab negatív, akkor mélyebb hegesztési behatolást érhetünk el. Váltakozó árammal, mivel pulzáló íveink vannak, vastag szakaszokat tudunk hegeszteni nagy átmérőjű elektródákkal és maximális áramerősségekkel. Az SMAW hegesztési módszer 3-19 mm-es és még ennél is nagyobb vastagságú munkadarabokhoz alkalmas többszörös menetes technikával. A hegesztési varrat tetején keletkezett salakot drótkefével kell eltávolítani, hogy ne legyen korrózió és tönkremenetel a hegesztési helyen. Ez természetesen növeli az árnyékolt fém ívhegesztés költségeit. Ennek ellenére az SMAW a legnépszerűbb hegesztési technika az iparban és a javítási munkákban. MERÜLT ÍVHEGESZTÉS (FŰRÉSZ): Ebben a folyamatban a hegesztési ívet szemcsés folyasztószerekkel árnyékoljuk, mint például mész, szilícium-dioxid, kalcium-fluorid, mangán-oxid stb. A szemcsés folyasztószert egy fúvókán keresztül gravitációs áramlással táplálják a hegesztési zónába. Az olvadt hegesztési zónát lefedő fluxus jelentősen véd a szikrától, füsttől, UV sugárzástól stb., és hőszigetelőként működik, így a hő mélyen behatol a munkadarabba. A meg nem ömlesztett fluxust visszanyerjük, kezeljük és újra felhasználjuk. Egy csupasz tekercset használnak elektródaként, és egy csövön keresztül a hegesztési területre vezetik. 300 és 2000 amper közötti áramot használunk. A merülőíves hegesztési (SAW) eljárás vízszintes és lapos helyzetekre és körhegesztésekre korlátozódik, ha a hegesztés során a kör alakú szerkezet (például csövek) elfordulása lehetséges. A sebesség elérheti az 5 m/perc-et. A SAW eljárás vastag lemezekhez alkalmas, és kiváló minőségű, szívós, képlékeny és egyenletes hegesztést eredményez. A termelékenység, vagyis az óránként felvitt hegesztési anyag mennyisége 4-10-szerese az SMAW eljáráshoz képest. Egy másik ívhegesztési eljárás, nevezetesen a GAS METAL ARC WELDING (GMAW) vagy más néven METAL INERT GAS WELDING (MIG) azon alapul, hogy a hegesztési területet külső gázforrások, például hélium, argon, szén-dioxid stb. védik. Az elektródfémben további deoxidálószerek is lehetnek. A fogyóhuzalt egy fúvókán keresztül vezetik be a hegesztési zónába. A vas- és színesfémeket egyaránt tartalmazó gyártás gázíves fémívhegesztéssel (GMAW) történik. A hegesztési termelékenység körülbelül kétszerese az SMAW-eljárásénak. Automatizált hegesztőberendezéseket használnak. A fémet ebben a folyamatban háromféleképpen továbbítják: „Spray Transfer”: másodpercenként több száz kis fémcsepp átvitele az elektródáról a hegesztési területre. A „globuláris átvitelben” viszont szén-dioxidban gazdag gázokat használnak, és az olvadt fémgömböket az elektromos ív hajtja. A hegesztőáramok nagyok, a hegesztési varrat mélyebb behatolása, a hegesztési sebesség nagyobb, mint a permetezésnél. Így a gömb alakú átvitel jobb a nehezebb szakaszok hegesztéséhez. Végül a „rövidzárlatos” módszernél az elektróda csúcsa hozzáér az olvadt hegesztési medencéhez, rövidre zárva azt, miközben a fém 50 csepp/másodperc feletti sebességgel kerül át az egyes cseppekben. Alacsony áramot és feszültséget vékonyabb vezetékkel együtt használnak. A felhasznált teljesítmény körülbelül 2 kW és a hőmérséklet viszonylag alacsony, így ez a módszer alkalmas 6 mm-nél kisebb vékony lemezekhez. A FLUX-CORED ARC WELDING (FCAW) eljárás egy másik változata hasonló a gázos fémívhegesztéshez, azzal a különbséggel, hogy az elektróda egy folyasztószerrel töltött cső. A mag-folyasztószeres elektródák használatának előnye, hogy stabilabb íveket hoznak létre, lehetőséget adnak a hegesztett fémek tulajdonságainak javítására, az SMAW-hegesztéshez képest kevésbé rideg és rugalmas folyasztószer, jobb hegesztési kontúrok. Az önárnyékolt magelektródák olyan anyagokat tartalmaznak, amelyek védik a hegesztési zónát a légkörtől. Kb. 20 kW teljesítményt használunk. A GMAW eljáráshoz hasonlóan az FCAW eljárás is lehetőséget kínál a folyamatos hegesztési folyamatok automatizálására, és gazdaságos. Különböző hegesztési fémek kémiája fejleszthető ki különböző ötvözetek hozzáadásával a folyasztószermaghoz. Az ELECTROGAS WELDING (EGW) során az egymás mellett elhelyezett darabokat hegesztjük. Néha TOMPHEGESZTÉSnek is nevezik. A hegesztett fémet egy hegesztési üregbe helyezik két összekapcsolandó darab közé. A teret két vízhűtéses gát veszi körül, hogy az olvadt salak ne ömljön ki. A gátak mozgatása mechanikus hajtásokkal történik. Ha a munkadarab forgatható, akkor az elektrogázos hegesztési technikát csövek kerületi hegesztésére is használhatjuk. Az elektródákat egy vezetéken keresztül vezetik be a folyamatos ív fenntartása érdekében. Az áramerősség körülbelül 400 Amper vagy 750 Amper, a teljesítményszint pedig körülbelül 20 kW. A fluxusmagos elektródából vagy külső forrásból származó inert gázok árnyékolást biztosítanak. Az elektrogázos hegesztést (EGW) használjuk fémekhez, például acélokhoz, titánhoz stb. 12-75 mm vastagságban. A technika jól illeszkedik nagyméretű szerkezetekhez. Mégis, egy másik technikában, az ELECTROSLAG WELDING (ESW) néven, az ívet meggyújtják az elektróda és a munkadarab alja között, és hozzáadják a fluxust. Amikor az olvadt salak eléri az elektróda csúcsát, az ív kialszik. Az energiaellátás az olvadt salak elektromos ellenállásán keresztül folyamatosan történik. 50 mm és 900 mm közötti vastagságú lemezeket is tudunk hegeszteni. Az áramerősség körülbelül 600 Amper, míg a feszültség 40-50 V között van. A hegesztési sebesség 12-36 mm/perc. Az alkalmazások hasonlóak az elektrogázhegesztéshez. Egyik nem fogyó elektródával kapcsolatos eljárásunk, a GAS TUNGSTEN ARC WELDING (GTAW), más néven TUNGSTEN INERT GAS WELDING (TIG), magában foglalja a töltőfém huzalon történő ellátását. A szorosan illeszkedő hézagokhoz néha nem használunk töltőfémet. A TIG folyamatban nem folyasztószert használunk, hanem argont és héliumot használunk az árnyékoláshoz. A volfrám magas olvadáspontú, és a TIG hegesztési folyamat során nem fogyasztják, így az állandó áram és az ívhézag is fenntartható. A teljesítményszint 8 és 20 kW között van, az áramerősség pedig 200 Amper (DC) vagy 500 Amper (AC). Alumínium és magnézium esetében AC áramot használunk az oxidtisztító funkcióhoz. A volfrámelektróda szennyeződésének elkerülése érdekében kerüljük az olvadt fémekkel való érintkezést. A Gas Tungsten Arc Welding (GTAW) különösen vékony fémek hegesztésére alkalmas. A GTAW varratok nagyon jó minőségűek, jó felületi minőséggel. A hidrogéngáz magasabb költsége miatt ritkábban alkalmazott technika az ATOMIC HYDROGEN WELDING (AHW), ahol áramló hidrogéngáz árnyékoló atmoszférájában ívet hozunk létre két volfrámelektróda között. Az AHW egy nem fogyó elektródahegesztési eljárás is. A H2 kétatomos hidrogéngáz atomformájára bomlik a hegesztési ív közelében, ahol a hőmérséklet meghaladja a 6273 Kelvint. Lebomlása során nagy mennyiségű hőt vesz fel az ívből. Amikor a hidrogénatomok nekiütköznek a hegesztési zónának, amely egy viszonylag hideg felület, akkor újra kétatomos formává egyesülnek, és felszabadítják a tárolt hőt. Az energia változtatható a munkadarab ívtávolságra való változtatásával. Egy másik nem fogyó elektróda eljárásban, a PLASMA ARC WELDING (PAW) során koncentrált plazmaívet irányítunk a hegesztési zóna felé. A hőmérséklet PAW-ban eléri a 33 273 Kelvint. Közel azonos számú elektron és ion alkotja a plazmagázt. Egy kisáramú pilotív indítja el a plazmát, amely a volfrámelektróda és a nyílás között van. Az üzemi áramok általában 100 amper körül mozognak. Töltőfém adagolható. A plazmaíves hegesztésnél az árnyékolást egy külső árnyékoló gyűrű és gázok, például argon és hélium felhasználásával valósítják meg. A plazmaívhegesztésnél az ív lehet az elektróda és a munkadarab, vagy az elektróda és a fúvóka között. Ennek a hegesztési technikának az előnyei a többi módszerhez képest nagyobb energiakoncentráció, mélyebb és keskenyebb hegesztési képesség, jobb ívstabilitás, nagyobb hegesztési sebesség akár 1 méter/percig, kisebb hőtorzulás. Általában plazmaívhegesztést alkalmazunk 6 mm-nél kisebb vastagságoknál, esetenként pedig 20 mm-es vastagságnál alumínium és titán esetében. NAGYENERGIÁJÚ HEGESZTÉS: Egy másik típusú fúziós hegesztési módszer, két változatként elektronsugaras hegesztéssel (EBW) és lézerhegesztéssel (LBW). Ezek a technikák különösen értékesek csúcstechnológiás termékeink gyártása során. Az elektronsugaras hegesztés során nagy sebességű elektronok ütköznek a munkadarabba, és mozgási energiájuk hővé alakul. A keskeny elektronnyaláb könnyen halad a vákuumkamrában. Az e-sugaras hegesztésnél általában nagyvákuumot használunk. 150 mm vastag lemezek hegeszthetők. Nincs szükség védőgázra, folyasztószerre vagy töltőanyagra. Az elektronsugaras fegyverek 100 kW teljesítményűek. Mély és keskeny hegesztések lehetségesek akár 30-ig terjedő nagy oldalaránnyal és kis hőhatású zónákkal. A hegesztési sebesség elérheti a 12 m/perc értéket. A lézersugaras hegesztésnél nagy teljesítményű lézereket használunk hőforrásként. A 10 mikronos nagy sűrűségű lézersugarak mélyen behatolnak a munkadarabba. A lézersugaras hegesztéssel akár 10-es mélység-szélesség arány is elérhető. Mind pulzáló, mind folyamatos hullámú lézereket használunk, az előbbit vékony anyagokhoz, az utóbbit pedig leginkább 25 mm-es vastagságú munkadarabokhoz. A teljesítményszint 100 kW-ig terjed. A lézersugaras hegesztés nem alkalmas optikailag nagyon visszaverő anyagokhoz. A hegesztési folyamat során gázok is használhatók. A lézersugaras hegesztési módszer jól illeszkedik az automatizáláshoz és a nagy volumenű gyártáshoz, és 2,5 m/perc és 80 m/perc közötti hegesztési sebességet kínál. Ennek a hegesztési technikának az egyik fő előnye, hogy olyan területekhez is hozzáférhet, ahol más technikák nem használhatók. A lézersugarak könnyen eljuthatnak ilyen nehéz területekre. Nincs szükség vákuumra, mint az elektronsugaras hegesztésnél. A lézersugaras hegesztéssel jó minőségű és szilárdságú, alacsony zsugorodású, alacsony torzítású, alacsony porozitású hegesztések érhetők el. A lézersugarak könnyen kezelhetők és formázhatók száloptikai kábelekkel. A technika tehát kiválóan alkalmas precíziós hermetikus szerelvények, elektronikai csomagok stb. hegesztésére. Nézzük meg a SZILÁRDÁLLÁSÚ HEGESZTÉSI technikáinkat. A HIDEGHEGESZTÉS (CW) egy olyan folyamat, ahol hő helyett nyomást alkalmaznak szerszámok vagy hengerek segítségével a párosított részekre. Hideghegesztésnél legalább az egyik illeszkedő alkatrésznek képlékenynek kell lennie. A legjobb eredményt két hasonló anyaggal lehet elérni. Ha a hideghegesztéssel összekötendő két fém különbözik, akkor gyenge és törékeny kötéseket kaphatunk. A hideghegesztési módszer jól alkalmazható puha, képlékeny és kisméretű munkadarabokhoz, például elektromos csatlakozásokhoz, hőérzékeny tartályélekhez, bimetál szalagokhoz termosztátokhoz stb. A hideghegesztés egyik változata a tekercskötés (vagy tekercshegesztés), ahol a nyomást egy hengerpáron keresztül fejtik ki. Néha a hengeres hegesztést magasabb hőmérsékleten végezzük a jobb felületi szilárdság érdekében. Egy másik általunk használt szilárdtest-hegesztési eljárás az ULTRAHANGOS HEGESZTÉS (USW), ahol a munkadarabokat statikus normálerő és oszcilláló nyírófeszültségek érik. Az oszcilláló nyírófeszültségeket egy átalakító hegyén keresztül fejtik ki. Az ultrahangos hegesztés 10-75 kHz frekvenciájú rezgéseket alkalmaz. Egyes alkalmazásokban, például varrathegesztésnél, forgó hegesztőtárcsát használunk hegyként. A munkadarabokra ható nyírófeszültségek kis képlékeny alakváltozásokat okoznak, felbontják az oxidrétegeket, szennyeződéseket és szilárdtest-kötéshez vezetnek. Az ultrahangos hegesztésnél alkalmazott hőmérséklet jóval a fémek olvadáspontja alatt van, és nem történik fúzió. Gyakran használjuk az ultrahangos hegesztési (USW) eljárást nemfémes anyagokhoz, például műanyagokhoz. A hőre lágyuló műanyagokban azonban a hőmérséklet eléri az olvadáspontot. Egy másik népszerű technika, a DRICTION WELDING (FRW) során a hő súrlódás révén keletkezik az összekapcsolandó munkadarabok határfelületén. A dörzshegesztésnél az egyik munkadarabot álló helyzetben tartjuk, míg a másik munkadarabot egy rögzítőben tartjuk és állandó sebességgel forgatjuk. Ezután a munkadarabokat axiális erő hatására érintkezésbe hozzuk. A felületi forgási sebesség dörzshegesztésnél egyes esetekben elérheti a 900 m/perc értéket. Elegendő határfelületi érintkezés után a forgó munkadarab hirtelen leáll, és az axiális erő megnő. A hegesztési zóna általában egy szűk terület. A súrlódó hegesztési technika különféle anyagokból készült tömör és cső alakú alkatrészek összekapcsolására használható. Az FRW-ben előfordulhat némi vaku az interfészen, de ez a vaku eltávolítható másodlagos megmunkálással vagy köszörüléssel. A súrlódó hegesztési eljárásnak vannak változatai. Például a „tehetetlenségi súrlódásos hegesztés” egy lendkereket foglal magában, amelynek forgási kinetikus energiáját használják fel az alkatrészek hegesztésére. A hegesztés akkor fejeződik be, amikor a lendkerék megáll. A forgó tömeg és így a forgási mozgási energia változtatható. Egy másik változat a „lineáris súrlódásos hegesztés”, ahol lineáris oda-vissza mozgást gyakorolnak legalább az egyik összeillesztendő alkatrészre. A lineáris dörzshegesztésnél az alkatrészeknek nem kell kör alakúaknak lenniük, lehetnek téglalap alakúak, négyzet alakúak vagy más alakúak. A frekvenciák tíz Hz-ben, az amplitúdók milliméteres tartományban, a nyomások pedig tíz- vagy száz MPa-ban lehetnek. Végül a „súrlódó keverős hegesztés” némileg eltér a fentebb ismertetett másik kettőtől. Míg a tehetetlenségi súrlódásos hegesztésnél és a lineáris súrlódásos hegesztésnél a határfelületek felmelegítése súrlódás révén valósul meg két érintkező felület dörzsölésével, addig a súrlódó keverős hegesztésnél egy harmadik testet dörzsölnek a két összekapcsolandó felülethez. Egy 5-6 mm átmérőjű forgó szerszám érintkezik a kötéssel. A hőmérséklet 503 és 533 Kelvin közötti értékekre emelkedhet. A hézagban az anyag melegítése, keverése és keverése történik. A súrlódó keverős hegesztést különféle anyagokon alkalmazzuk, beleértve az alumíniumot, a műanyagokat és a kompozitokat. A hegesztési varratok egységesek, minősége kiváló, minimális pórusokkal. A súrlódó keverőhegesztés során nem keletkeznek gőzök vagy fröccsenések, és a folyamat jól automatizált. ELLENÁLLÁS HEGESZTÉS (RW): A hegesztéshez szükséges hőt a két összeillesztendő munkadarab közötti elektromos ellenállás termeli. Az ellenálláshegesztés során nem használnak folyasztószert, védőgázt vagy fogyó elektródákat. A Joule-melegítés ellenálláshegesztésben történik, és a következőképpen fejezhető ki: H = (I. négyzet) x R xtx K H a keletkező hő joule-ban (watt-másodpercben), I áram Amperben, R ellenállás ohmban, t az áram átfolyási ideje másodpercben. A K tényező kisebb, mint 1, és az energia azon hányadát jelenti, amely nem vész el a sugárzás és a vezetés során. Az ellenállás-hegesztési folyamatokban az áramok elérhetik a 100 000 A-t is, de a feszültségek általában 0,5-10 Volt. Az elektródák jellemzően rézötvözetből készülnek. Ellenálláshegesztéssel hasonló és eltérő anyagok is összekapcsolhatók. Ennek az eljárásnak számos változata létezik: Az „ellenállási ponthegesztés” két egymással szemben lévő kerek elektródát foglal magában, amelyek érintkeznek a két lap átlapolt csatlakozásának felületeivel. A nyomást addig alkalmazzák, amíg az áramot le nem kapcsolják. A hegesztési rög általában legfeljebb 10 mm átmérőjű. Az ellenállási ponthegesztés enyhén elszíneződött bemélyedésnyomokat hagy a hegesztési pontokon. A ponthegesztés a legnépszerűbb ellenállás-hegesztési technikánk. A ponthegesztésben különféle elektródaformákat használnak a nehéz területek elérése érdekében. Ponthegesztő berendezésünk CNC vezérlésű, és több elektródával rendelkezik, amelyek egyidejűleg használhatók. Az „ellenállási varrathegesztés” egy másik változata kerék- vagy görgős elektródákkal történik, amelyek folyamatos ponthegesztést hoznak létre, amikor az áram eléri a kellően magas szintet a váltakozó áramú tápciklusban. Az ellenállási hegesztéssel előállított kötések folyadék- és gáztömörek. A körülbelül 1,5 m/perc hegesztési sebesség normális vékony lemezeknél. Alkalmazhatunk szakaszos áramokat, így a ponthegesztések a varrat mentén kívánt időközönként jönnek létre. Az „ellenállási vetületi hegesztésnél” egy vagy több kiemelkedést (gödröcskét) domborítunk a hegesztendő munkadarab egyik felületére. Ezek a kiemelkedések lehetnek kerekek vagy oválisak. Ezeken a dombornyomott helyeken, amelyek érintkezésbe kerülnek az illeszkedő résszel, magas helyi hőmérséklet érhető el. Az elektródák nyomást fejtenek ki, hogy összenyomják ezeket a kiemelkedéseket. Az ellenállás-kivetítő hegesztésben használt elektródák lapos hegyűek, és vízhűtéses rézötvözetekből állnak. Az ellenállás-kivetítő hegesztés előnye, hogy egy lökettel több hegesztést tudunk elvégezni, ezáltal meghosszabbodik az elektródák élettartama, különböző vastagságú lemezek hegeszthetősége, valamint anyák és csavarok lemezre hegeszthetősége. Az ellenállás-kivetítő hegesztés hátránya a mélyedések domborításának többletköltsége. Egy másik technika, a „villanóhegesztés” során a két munkadarab végén lévő ívből hő keletkezik, amikor azok érintkezni kezdenek. Ez a módszer alternatív megoldásként ívhegesztésnek is tekinthető. A határfelület hőmérséklete emelkedik, és az anyag meglágyul. Axiális erőt fejtenek ki, és hegesztési varrat keletkezik a lágyított tartományban. A villanóhegesztés befejezése után a kötés megmunkálható a jobb megjelenés érdekében. A villanóhegesztéssel kapott hegesztési minőség jó. A teljesítményszint 10-1500 kW. A villanóhegesztés alkalmas hasonló vagy eltérő fémek 75 mm átmérőig és 0,2 mm és 25 mm közötti vastagságú lemezek élek közötti összekötésére. A „csapos ívhegesztés” nagyon hasonlít a villanóhegesztéshez. A csap, például egy csavar vagy menetes rúd egy elektródaként szolgál, miközben egy munkadarabhoz, például egy lemezhez csatlakozik. A keletkező hő koncentrálása, az oxidáció megelőzése és az olvadt fém hegesztési zónában való megtartása érdekében eldobható kerámiagyűrűt helyeznek a kötés köré. Végül az „ütőhegesztés” egy másik ellenálláshegesztési eljárás, amely kondenzátort használ az elektromos energia ellátására. Ütőhegesztésnél a teljesítmény ezredmásodperceken belül lemerül, nagyon gyorsan nagy helyi hőt fejlesztve a csatlakozásnál. Az ütős hegesztést széles körben alkalmazzuk az elektronikai gyártóiparban, ahol kerülni kell az érzékeny elektronikai alkatrészek felmelegedését a csatlakozás közelében. A ROBBANÁSI HEGESZTÉSnek nevezett technika magában foglalja egy robbanóanyag-réteg felrobbantását, amelyet az összeillesztendő munkadarabok egyikére helyeznek. A munkadarabra kifejtett nagyon nagy nyomás turbulens és hullámos felületet hoz létre, és mechanikus reteszelés történik. A robbanásveszélyes hegesztésnél a kötési szilárdság nagyon magas. A robbantásos hegesztés jó módszer a lemezek különböző fémekkel történő burkolására. A burkolat után a lemezeket vékonyabb részekre lehet hengerelni. Néha robbantásos hegesztést alkalmazunk a csövek kiterjesztésére, hogy azok szorosan a lemezhez tapadjanak. Utolsó módszerünk a szilárdtest-illesztés tartományán belül a DIFFÚZIÓS KÖTÖTÉS vagy DIFFÚZIÓS HEGESZTÉS (DFW), amelyben a jó kötést főként az atomok határfelületi diffúziójával érjük el. A felületen előforduló képlékeny alakváltozás is hozzájárul a hegesztéshez. Az érintett hőmérséklet körülbelül 0,5 Tm, ahol Tm a fém olvadáspontja. A diffúziós hegesztés kötési szilárdsága a nyomástól, a hőmérséklettől, az érintkezési időtől és az érintkező felületek tisztaságától függ. Néha töltőfémeket használunk a határfelületen. Hőre és nyomásra van szükség a diffúziós kötésnél, és elektromos ellenállással vagy kemencével és önsúlyokkal, préssel vagy mással biztosítják. Hasonló és eltérő fémek diffúziós hegesztéssel is összekapcsolhatók. A folyamat viszonylag lassú az atomok migrációjához szükséges idő miatt. A DFW automatizálható, és széles körben használják összetett alkatrészek gyártásában a repülőgépiparban, az elektronikában és az orvosi iparban. A gyártott termékek között ortopédiai implantátumok, érzékelők, repülőgép-szerkezeti elemek találhatók. A diffúziós kötés kombinálható a SZUPERPLASTIC FORMING-mal összetett fémlemez szerkezetek készítéséhez. A lapok kiválasztott helyeit először diffúziós ragasztással kötik össze, majd a nem ragasztott részeket légnyomással formába expandálják. A módszerek ezen kombinációjával nagy merevség/tömeg arányú repülőgép- és űrszerkezeteket gyártanak. A diffúziós hegesztés / szuperplasztikus alakítás kombinált eljárása csökkenti a szükséges alkatrészek számát azáltal, hogy nincs szükség kötőelemekre, alacsony feszültségű, rendkívül pontos alkatrészeket eredményez gazdaságosan és rövid átfutási idővel. FORRÁS: A keményforrasztási technikák alacsonyabb hőmérsékletet igényelnek, mint a hegesztéshez szükséges. A keményforrasztási hőmérséklet azonban magasabb, mint a forrasztási hőmérséklet. A keményforrasztás során az összeillesztendő felületek közé töltőanyagot helyeznek, és a hőmérsékletet a töltőanyag olvadási hőmérsékletére 723 Kelvin fölé, de a munkadarabok olvadási hőmérséklete alá emelik. Az olvadt fém kitölti a munkadarabok közötti szorosan illeszkedő teret. A reszelőfém lehűtése és ezt követő megszilárdulása erős kötéseket eredményez. A keményforrasztó hegesztésnél a töltőanyag a csatlakozásnál lerakódik. A keményforrasztásnál lényegesen több töltőfémet használnak fel, mint a keményforrasztásnál. Az oxidáló lánggal rendelkező oxi-acetilén pisztolyt keményforrasztó hegesztésnél a töltőfém leválasztására használják. A keményforrasztásnál alacsonyabb hőmérsékletnek köszönhetően kisebbek a problémák a hő által érintett zónákban, mint például a vetemedés és a maradék feszültség. Minél kisebb a hézag a keményforrasztásnál, annál nagyobb a kötés nyírószilárdsága. A maximális szakítószilárdság azonban optimális résnél (csúcsérték) érhető el. Ezen optimális érték alatt és felett a keményforrasztás szakítószilárdsága csökken. A tipikus hézagok keményforrasztásnál 0,025 és 0,2 mm között lehetnek. Különféle formájú keményforrasztási anyagokat használunk, mint például forrasztó, por, gyűrűk, huzal, szalag stb. és ezeket kifejezetten az Ön tervezési vagy termékgeometriájának megfelelően tudja legyártani. Meghatározzuk a keményforrasztó anyagok tartalmát is az Ön alapanyagának és felhasználásának megfelelően. A keményforrasztási műveleteknél gyakran használunk folyasztószereket a nem kívánt oxidrétegek eltávolítására és az oxidáció megelőzésére. A későbbi korrózió elkerülése érdekében a folyasztószereket általában az illesztési művelet után eltávolítják. Az AGS-TECH Inc. különféle keményforrasztási módszereket alkalmaz, többek között: - Fáklyaforrasztás - Kemencés keményforrasztás - Indukciós keményforrasztás - Ellenállási keményforrasztás - Merítési keményforrasztás - Infravörös keményforrasztás - Diffúziós keményforrasztás - High Energy Beam A leggyakrabban használt keményforrasztott kötéseink jó szilárdságú, eltérő fémekből készülnek, mint például keményfém fúrószárak, betétek, optoelektronikus hermetikus tokok, tömítések. FORRASZTÁS: Ez az egyik leggyakrabban használt technikánk, ahol a forrasztóanyag (töltőfém) kitölti a hézagot, mint a szorosan illeszkedő alkatrészek közötti keményforrasztáskor. Forraszanyagaink olvadáspontja 723 Kelvin alatt van. A gyártási műveletekben kézi és automatizált forrasztást egyaránt alkalmazunk. A keményforrasztáshoz képest a forrasztási hőmérséklet alacsonyabb. A forrasztás nem nagyon alkalmas magas hőmérsékletű vagy nagy szilárdságú alkalmazásokhoz. Forrasztáshoz ólommentes forrasztóanyagokat, valamint ón-ólom, ón-cink, ólom-ezüst, kadmium-ezüst, cink-alumínium ötvözeteket használunk. Mind a nem korrozív gyantaalapú, mind a szervetlen savakat és sókat folyasztószerként használják a forrasztáshoz. Speciális folyasztószereket használunk alacsony forraszthatóságú fémek forrasztásához. Azokban az alkalmazásokban, ahol kerámia anyagokat, üveget vagy grafitot kell forrasztanunk, először az alkatrészeket megfelelő fémmel bevonjuk a jobb forraszthatóság érdekében. Népszerű forrasztási technikáink a következők: - Reflow vagy Paste forrasztás - Hullámforrasztás -Kemence forrasztás - Fáklya forrasztás - Indukciós forrasztás - Vasforrasztás - Ellenállásos forrasztás - Merítési forrasztás - Ultrahangos forrasztás - Infravörös forrasztás Az ultrahangos forrasztás egyedülálló előnyt kínál számunkra, mivel az ultrahangos kavitációs hatásnak köszönhetően nincs szükség folyasztószerre, amely eltávolítja az oxidfilmeket az összekapcsolandó felületekről. A Reflow és Wave forrasztás iparilag kiemelkedő technikáink az elektronikai nagy volumenű gyártáshoz, ezért érdemes részletesebben elmagyarázni. Az újrafolyós forrasztásnál félszilárd pasztákat használunk, amelyek forrasztófém részecskéket tartalmaznak. A pasztát szita- vagy sablonozási eljárással helyezik az illesztésre. A nyomtatott áramköri lapoknál (PCB) gyakran alkalmazzuk ezt a technikát. Amikor elektromos alkatrészeket helyeznek ezekre a pasztából készült párnákra, a felületi feszültség egy vonalban tartja a felületre szerelhető csomagokat. Az alkatrészek elhelyezése után a szerelvényt kemencében felmelegítjük, így megtörténik a visszafolyó forrasztás. A folyamat során a pasztában lévő oldószerek elpárolognak, a pasztában lévő fluxus aktiválódik, az alkatrészek előmelegednek, a forrasztási részecskék megolvasztják és nedvesítik a kötést, végül a PCB-szerelvény lassan lehűl. Második népszerű technikánk a nyomtatott áramköri lapok nagy volumenű gyártására, nevezetesen a hullámforrasztás azon a tényen alapul, hogy az olvadt forrasztóanyagok nedvesítik a fémfelületeket, és csak akkor hoznak létre jó kötést, ha a fémet előmelegítik. Az olvadt forrasztóanyag álló lamináris hullámát először egy szivattyú generálja, és az előmelegített és előmelegített PCB-ket a hullámon továbbítják. A forrasztás csak a szabaddá vált fémfelületeket nedvesíti, de nem nedvesíti az IC polimer csomagokat, sem a polimer bevonatú áramköri lapokat. A nagy sebességű forró vízsugár kifújja a felesleges forrasztást a csatlakozásból, és megakadályozza a szomszédos vezetékek közötti áthidalást. A felületre szerelhető csomagok hullámforrasztásánál először ragasztjuk őket az áramköri lapra a forrasztás előtt. Ismét szűrést és stencilezést alkalmaznak, de ezúttal epoxira. Miután az alkatrészeket a megfelelő helyükre helyezték, az epoxi megkeményedik, a táblákat felfordítják, és megtörténik a hullámforrasztás. CLICK Product Finder-Locator Service ELŐZŐ OLDAL
- Electric Discharge Machining, EDM, Spark Machining, Die Sinking
Electric Discharge Machining - EDM - Spark Machining - Die Sinking - Wire Erosion - Custom Manufacturing - AGS-TECH Inc. EDM megmunkálás, elektromos kisülési marás és köszörülés ELECTRICAL DISCHARGE MACHINING (EDM), also referred to as SPARK-EROSION or ELECTRODISCHARGE MACHINING, SPARK ERODING, DIE SINKING_cc781905-5cde-3194-bb3b -136bad5cf58d_or WIRE EROSION, is a NON-CONVENTIONAL MANUFACTURING process where erosion of metals takes place and desired shape is obtained using electrical discharges in the form a szikráktól. A szikraforgácsolás néhány fajtáját is kínáljuk, nevezetesen kopásmentes szikraforgácsolás, huzalszikraforgácsolás (WEDM), szikraforgácsoló köszörülés (EDG), süllyesztõ szikraforgácsoló szikraforgácsoló szikraforgácsolás, ELEKTROMOS KIÜLÍTÉSŰ MARÁS, m-1-0-9MCC7 -5cde-3194-bb3b-136bad5cf58d_and ELEKTROKÉMIAI KIBOCSOLÁS (ECDG). EDM rendszereink formázott szerszámokból/elektródákból és egyenáramú tápegységekhez csatlakoztatott, elektromosan nem vezető dielektromos folyadékba helyezett munkadarabból állnak. 1940 után az elektromos kisülésű megmunkálás az egyik legfontosabb és legnépszerűbb gyártási technológiává vált a feldolgozóiparban. Ha a két elektróda közötti távolságot csökkentjük, az elektródák közötti térfogatban az elektromos tér intenzitása egyes pontokon nagyobb lesz, mint a dielektrikum erőssége, amely elszakad, és végül hidat képez a két elektróda közötti áram áramlásához. Erős elektromos ív keletkezik, ami jelentős felmelegedést okoz a munkadarab egy részének és a szerszámanyag egy részének megolvadásához. Ennek eredményeként mindkét elektródáról eltávolítják az anyagot. Ugyanakkor a dielektromos folyadék gyorsan felmelegszik, ami a folyadék elpárologtatását eredményezi az ívrésben. Amint az áram áramlása leáll vagy leáll, a környező dielektromos folyadék hőt távolít el a gázbuborékból, és a buborék kavitálódik (összeesik). A buborék összeomlása és a dielektromos folyadék áramlása által keltett lökéshullám leöblíti a törmeléket a munkadarab felületéről, és magával ragad minden megolvadt munkadarab anyagot a dielektromos folyadékba. Ezeknek a kisüléseknek az ismétlési gyakorisága 50 és 500 kHz között van, a feszültségek 50 és 380 V között, az áramok pedig 0,1 és 500 amper között vannak. Az új folyékony dielektrikum, mint például ásványolajok, kerozin vagy desztillált és ionmentesített víz rendszerint az elektródák közötti térfogatba kerül, és elszállítja a szilárd részecskéket (törmelék formájában), és helyreáll a dielektrikum szigetelő tulajdonságai. Egy áram áramlása után a két elektróda közötti potenciálkülönbség visszaáll a leállás előtti értékre, így új folyékony dielektrikum törés léphet fel. Modern elektromos kisülési gépeink (EDM) numerikusan vezérelt mozgásokat kínálnak, és szivattyúkkal és szűrőrendszerekkel vannak felszerelve a dielektromos folyadékok számára. Az elektromos kisüléses megmunkálás (EDM) egy olyan megmunkálási módszer, amelyet főként keményfémekhez használnak, vagy olyanokat, amelyeket hagyományos technikákkal nagyon nehéz megmunkálni. Az EDM általában minden olyan anyaggal működik, amely elektromos vezető, bár javasoltak módszereket szigetelő kerámiák EDM-mel történő megmunkálására is. Az olvadáspont és az olvadás látens hője olyan tulajdonságok, amelyek meghatározzák a kisülésenként eltávolított fém térfogatát. Minél magasabbak ezek az értékek, annál lassabb az anyageltávolítási sebesség. Mivel az elektromos kisüléses megmunkálási folyamat nem igényel mechanikai energiát, a munkadarab keménysége, szilárdsága és szívóssága nem befolyásolja az eltávolítási sebességet. A kisülési frekvencia vagy a kisülésenkénti energia, a feszültség és az áramerősség változtatható az anyageltávolítási sebesség szabályozására. Az anyagleválasztás sebessége és a felületi érdesség az áramsűrűség növekedésével és a szikrafrekvencia csökkenésével nő. Bonyolult kontúrokat vagy üregeket vághatunk előre edzett acélból szikraforgácsolással anélkül, hogy hőkezelésre lenne szükség a lágyításhoz és újrakeményítéshez. Ezt a módszert bármilyen fémmel vagy fémötvözetekkel, például titánnal, hastelloy-val, kovarral és inconel-lel használhatjuk. Az EDM eljárás alkalmazásai közé tartozik a polikristályos gyémántszerszámok formázása. Az EDM-et nem hagyományos vagy nem hagyományos megmunkálási módszernek tekintik, olyan folyamatokkal együtt, mint az elektrokémiai megmunkálás (ECM), a vízsugaras vágás (WJ, AWJ), a lézervágás. Másrészt a hagyományos megmunkálási eljárások közé tartozik az esztergálás, marás, köszörülés, fúrás és egyéb olyan eljárások, amelyek anyagleválasztási mechanizmusa alapvetően mechanikai erőkön alapul. Az elektromos kisüléses megmunkáláshoz (EDM) használt elektródák grafitból, sárgarézből, rézből és réz-volfrám ötvözetből készülnek. Az elektróda átmérője 0,1 mm-ig lehetséges. Mivel a szerszámkopás olyan nemkívánatos jelenség, amely hátrányosan befolyásolja a szikraforgácsolás méretpontosságát, kihasználjuk a NO-WEAR EDM eljárást a polaritás megfordításával és rézszerszámok használatával a szerszámkopás minimalizálása érdekében. Ideális esetben az elektromos kisüléses megmunkálás (EDM) az elektródák közötti dielektromos folyadék lebontásának és helyreállításának sorozatának tekinthető. A valóságban azonban a törmelék eltávolítása az elektródák közötti területről szinte mindig részleges. Emiatt a dielektrikum elektromos tulajdonságai az elektródák közötti területen eltérnek a névleges értéküktől, és idővel változnak. Az elektródák közötti távolságot (szikraköz) az adott gép vezérlési algoritmusai állítják be. Az EDM szikraközét sajnos néha rövidre zárhatja a törmelék. Előfordulhat, hogy az elektróda vezérlőrendszere nem reagál elég gyorsan ahhoz, hogy megakadályozza a két elektróda (a szerszám és a munkadarab) rövidzárlatát. Ez a nem kívánt rövidzárlat az ideális esettől eltérően járul hozzá az anyag eltávolításához. Kiemelten fontosnak tartjuk az öblítést, hogy helyreállítsuk a dielektrikum szigetelő tulajdonságait, hogy az áram mindig az elektródák közötti terület pontján történjen, ezáltal minimalizálva a szerszám-elektróda nem kívánt alakváltozásának (károsodásának) lehetőségét. és munkadarab. Egy adott geometria elérése érdekében az EDM-szerszámot a kívánt pályán a munkadarabhoz nagyon közel vezetik, anélkül, hogy hozzáérnénk. A használat során kiemelt figyelmet fordítunk a mozgásvezérlés teljesítményére. Így nagyszámú áramkisülés/szikra jön létre, és mindegyik hozzájárul az anyag eltávolításához mind a szerszámról, mind a munkadarabról, ahol kis kráterek keletkeznek. A kráterek mérete az adott feladathoz beállított technológiai paraméterek függvénye, és méretei a nanoméretűtől (például mikro-EDM műveletek esetén) a nagyolási körülmények között több száz mikrométerig terjedhetnek. Ezek a kis kráterek a szerszámon az elektróda fokozatos erózióját okozzák, az úgynevezett „szerszámkopást”. A kopásnak a munkadarab geometriájára gyakorolt káros hatásának ellensúlyozására a megmunkálás során folyamatosan cseréljük a szerszám-elektródát. Néha ezt úgy érjük el, hogy egy folyamatosan cserélt vezetéket használunk elektródaként (ezt az EDM eljárást WIRE EDM néven is nevezik). Néha úgy használjuk a szerszámelektródát, hogy csak egy kis része vesz részt ténylegesen a megmunkálási folyamatban, és ezt a részt rendszeresen cseréljük. Ez a helyzet például akkor, ha egy forgó korongot használnak szerszámelektródaként. Ennek a folyamatnak a neve EDM GRINDING. Egy másik, általunk alkalmazott technika abból áll, hogy ugyanazon szikraforgácsolási művelet során különböző méretű és alakú elektródákat használunk a kopás kompenzálására. Ezt a többelektródos technikát nevezzük, és leggyakrabban akkor alkalmazzák, amikor a szerszámelektróda negatívan replikálja a kívánt alakot, és egyetlen irányban, általában a függőleges irányban (azaz a z-tengelyen) halad a nyersdarab felé. Ez hasonlít a szerszámnak abba a dielektromos folyadékba való süllyesztőjéhez, amelybe a munkadarab belemerül, ezért a következő néven: DIE-SINKING EDM_cc781905-5cde-31914-5ccdd 3194-bb3b-136bad5cf58d_HAGYOMÁNYOS EDM or RAM). Az ehhez a művelethez szükséges gépek neve: SINKER EDM. Az ilyen típusú szikraforgácsoláshoz használt elektródák összetett formájúak. Ha a végső geometriát egy általában egyszerű formájú, több irányban mozgatott elektródával kapjuk meg, amely szintén elfordulásnak van kitéve, ezt EDM MARÁSNAK nevezzük. A kopás mértéke szigorúan függ az üzemeltetés során alkalmazott technológiai paraméterektől (polaritás, maximális áramerősség, szakadási feszültség). Például az in micro-EDM, más néven m-EDM, ezek a paraméterek általában olyan értékekre vannak beállítva, amelyek súlyos kopást okoznak. Ezért a kopás komoly probléma ezen a területen, amelyet felhalmozott know-how-nkkal minimalizálunk. Például a grafitelektródák kopásának minimalizálása érdekében egy ezredmásodperceken belül vezérelhető digitális generátor megfordítja a polaritást, amikor elektroerózió történik. Ez a galvanizáláshoz hasonló hatást eredményez, amely az erodált grafitot folyamatosan visszahelyezi az elektródára. Egy másik módszernél, az úgynevezett ''Zero Wear'' áramkörnél minimalizáljuk a kisülés megindulásának és leállásának gyakoriságát, és a lehető leghosszabb ideig bekapcsolva tartjuk. Az elektromos kisüléses megmunkálásnál az anyageltávolítási sebesség a következőképpen becsülhető meg: MRR = 4 x 10 exp(4) x I x Tw exp (-1,23) Itt az MRR mm3/perc, az I áramerősség Amperben, Tw a munkadarab olvadáspontja K-273,15K-ban. Az exp a kitevőt jelenti. Másrészről az elektróda kopási sebessége Wt a következőképpen számolható: Wt = ( 1,1 x 10exp(11) ) x I x Ttexp(-2,38) Itt Wt mm3/perc-ben, Tt pedig az elektróda anyagának olvadáspontja K-273,15K-ban Végül a munkadarab és az R elektróda kopási arányát a következőkből kaphatjuk meg: R = 2,25 x Trex (-2,38) Itt Tr a munkadarab és az elektróda olvadáspontjának aránya. SINKER EDM : Sinker EDM, más néven: CAVITY TYPE EDM or_cc781905-9cce-136bad5cf58d_or_cc781905-9c. Az elektróda és a munkadarab egy áramforráshoz csatlakozik. A tápegység elektromos potenciált generál a kettő között. Ahogy az elektróda közeledik a munkadarabhoz, a folyadékban dielektromos lebomlás következik be, plazmacsatorna képződik, és egy kis szikra ugrik. A szikrák általában egyenként csapnak le, mert nagyon valószínűtlen, hogy az elektródák közötti tér különböző helyei azonos helyi elektromos jellemzőkkel rendelkezzenek, ami lehetővé tenné, hogy az összes ilyen helyen egyidejűleg szikra keletkezzen. Az elektróda és a munkadarab között másodpercenként több százezer szikra keletkezik véletlenszerű pontokon. Ahogy az alapfém erodálódik, és a szikraköz növekszik, az elektródát a CNC gépünk automatikusan leengedi, hogy a folyamat megszakítás nélkül folytatódhasson. Berendezésünk vezérlőciklusokkal rendelkezik, amelyek „bekapcsolási idő” és „kikapcsolási idő” néven ismertek. A bekapcsolási idő beállítása határozza meg a szikra hosszát vagy időtartamát. A hosszabb üzemidő mélyebb üreget hoz létre a szikra számára, és minden további szikrát a ciklushoz, durvább felületet hozva létre a munkadarabon és fordítva. A kikapcsolási idő az az időtartam, ameddig az egyik szikrát egy másik váltja fel. A hosszabb kikapcsolási idő lehetővé teszi, hogy a dielektromos folyadék átmosódjon egy fúvókán, hogy eltávolítsa az erodált törmeléket, elkerülve ezzel a rövidzárlatot. Ezek a beállítások mikro másodpercek alatt módosíthatók. WIRE EDM : In WIRE ELECTRICAL DISCHARGE MACHINING (WEDM), also called WIRE-CUT EDM or WIRE CUTTING, we feed a vékony egyszálú sárgaréz fémhuzal a munkadarabon keresztül, amelyet dielektromos folyadék tartályba merítenek. A huzalos szikraforgácsolás az EDM egyik fontos változata. Alkalmanként huzalra vágott szikraforgácsot használunk akár 300 mm vastag lemezek vágására, valamint lyukasztók, szerszámok és matricák készítésére olyan keményfémekből, amelyeket más gyártási módszerekkel nehéz megmunkálni. Ebben a szalagfűrésszel végzett kontúrvágáshoz hasonló folyamatban a huzal, amelyet folyamatosan egy orsóból táplálnak, a felső és az alsó gyémántvezetők között tartják. A CNC-vezérelt vezetők az x–y síkban mozognak, a felső vezető pedig függetlenül is mozoghat a z–u–v tengelyben, ami lehetővé teszi kúpos és átmeneti alakzatok (például kör alul és négyzet A csúcs). A felső vezető az x–y–u–v–i–j–k–l– tengelymozgásokat tudja szabályozni. Ez lehetővé teszi, hogy a WEDM nagyon bonyolult és finom formákat vágjon. A legjobb gazdaságos költséget és megmunkálási időt elérő berendezéseink átlagos vágási bevágása 0,335 mm Ø 0,25 sárgaréz-, réz- vagy volfrámhuzallal. CNC-berendezéseink felső és alsó gyémántvezetőinek pontossága körülbelül 0,004 mm, és 0,02 mm-es Ø 0,02 mm-es huzal használatával akár 0,021 mm-es vágási út vagy bevágás is lehet. Tehát nagyon szűk vágások lehetségesek. A vágási szélesség nagyobb, mint a huzal szélessége, mert a huzal oldalaitól a munkadarabig szikra keletkezik, ami eróziót okoz. Ez a "túlvágás" szükséges, sok alkalmazásnál kiszámítható, és ezért kompenzálható (mikro-EDM-ben ez nem gyakran fordul elő). A huzaltekercsek hosszúak – egy 8 kg-os 0,25 mm-es huzal orsója valamivel több, mint 19 kilométer. A huzal átmérője akár 20 mikrométer is lehet, a geometria pontossága pedig +/- 1 mikrométer körül van. Általában csak egyszer használjuk a vezetéket, és újrahasznosítjuk, mert viszonylag olcsó. Állandó 0,15-9 m/perc sebességgel halad, és a vágás során állandó bevágás (rés) marad fenn. A huzalvágásos szikraforgácsolási folyamat során dielektromos folyadékként vizet használunk, amelynek ellenállását és egyéb elektromos tulajdonságait szűrőkkel és ionmentesítő egységekkel szabályozzuk. A víz kiöblíti a vágott törmeléket a vágási zónából. Az öblítés fontos tényező az adott anyagvastagság maximális előtolási sebességének meghatározásában, ezért azt állandóan tartjuk. A huzal szikraforgácsolásában a vágási sebességet az egységnyi idő alatti vágási keresztmetszeti felületben adják meg, például 18 000 mm2/óra 50 mm vastag D2 szerszámacél esetén. A lineáris vágási sebesség ebben az esetben 18 000/50 = 360 mm/óra. Az anyageltávolítási sebesség a huzal szikraforgácsolásánál: MRR = Vf xhxb Itt MRR mm3/perc-ben, Vf a huzal előtolása a munkadarabhoz mm/percben, h a vastagság vagy magasság mm-ben, b pedig a bevágás, ami: b = dw + 2s Itt dw a huzal átmérője, s pedig a huzal és a munkadarab közötti távolság mm-ben. A szigorúbb tűréshatárok mellett modern, többtengelyes EDM huzalvágó megmunkáló központjaink olyan funkciókkal egészültek ki, mint például több fej két alkatrész egyidejű vágására, kezelőszervek a huzaltörés megelőzésére, automatikus önbefűzési funkciók huzaltörés esetén, és programozott megmunkálási stratégiák a művelet, az egyenes és szögletes vágási képességek optimalizálására. A Wire-EDM alacsony maradó feszültséget kínál számunkra, mivel nem igényel nagy forgácsolóerőt az anyag eltávolításához. Ha az impulzusonkénti energia/teljesítmény viszonylag alacsony (mint a befejező műveleteknél), akkor az alacsony maradó feszültségek miatt kevés változás várható az anyag mechanikai tulajdonságaiban. ELEKTROMOS KÖSZÖRÉS (EDG) : A csiszolókorongok nem tartalmaznak csiszolóanyagot, grafitból vagy sárgarézből készülnek. A forgó kerék és a munkadarab között ismétlődő szikrák eltávolítják az anyagot a munkadarab felületeiről. Az anyageltávolítási sebesség: MRR = K x I Itt az MRR mm3/perc, az I az áramerősség Amperben, a K pedig a munkadarab anyagtényezője mm3/A-percben. Gyakran használunk elektromos kisüléses köszörülést az alkatrészeken lévő keskeny rések fűrészelésére. Néha kombináljuk az EDG (elektromos kisülési csiszolás) eljárást az EKG (elektrokémiai köszörülés) eljárással, ahol az anyagot kémiai úton távolítják el, a grafitkorong elektromos kisülései felbontják az oxidfilmet, és az elektrolit elmossa. Az eljárás neve ELECTROCHEMICAL-DSHARGE GRINDING (ECDG). Annak ellenére, hogy az ECDG folyamat viszonylag több energiát fogyaszt, gyorsabb, mint az EDG. Főleg keményfém szerszámokat csiszolunk ezzel a technikával. Az elektromos kisüléses megmunkálás alkalmazásai: Prototípus gyártás: Az EDM-eljárást öntőforma-, szerszám- és szerszámgyártásban, valamint prototípus- és gyártási alkatrészek készítésében használjuk, különösen a repülőgép-, autó- és elektronikai iparban, ahol a gyártási mennyiségek viszonylag alacsonyak. A Sinker szikraforgácsolásnál egy grafit, réz wolfram vagy tiszta réz elektródát a kívánt (negatív) alakra forgácsolnak, és egy függőleges nyomószár végén a munkadarabba táplálják. Pénzverő szerszámkészítés: Ékszerek és jelvények pénzverési (bélyegzési) eljárással történő előállításához a pozitív mester készíthető ezüstből, mivel (megfelelő gépbeállításokkal) a mester jelentősen erodálódik, és csak egyszer kerül felhasználásra. Az így kapott negatív szerszámot ezután megkeményítik, és leejtő kalapácsban használják fel bélyegzett lapok előállítására bronzból, ezüstből vagy alacsony szilárdságú aranyötvözetből készült kivágott lapokból. Jelvények esetében ezeket a lapokat egy másik szerszámmal íves felületre tovább lehet formálni. Az ilyen típusú szikraforgácsolást általában olajalapú dielektrikumba merítve végzik. A kész tárgy tovább finomítható kemény (üveg) vagy lágy (festék) zománcozással és/vagy galvanizálható tiszta arannyal vagy nikkellel. A lágyabb anyagok, például az ezüst, finomításként kézzel gravírozhatók. Kis lyukak fúrása: Huzalra vágott szikraforgácsoló gépeinken kis lyukfúró szikraforgácsolást használunk, hogy átmenő lyukat készítsünk a munkadarabon, amelyen keresztül a huzalt átfűzzük a huzalvágásos szikraforgácsolási művelethez. Kifejezetten kis lyukak fúrásához külön szikraforgácsoló fejek vannak felszerelve drótvágó gépeinkre, amelyek lehetővé teszik, hogy a nagy edzett lemezekről szükség szerint és előfúrás nélkül lekophassanak a kész alkatrészekről. Kis lyukú szikraforgácsolót is használunk, hogy lyuksorokat fúrjunk a sugárhajtóművekben használt turbinalapátok széleibe. A gázáramlás ezeken a kis lyukakon keresztül lehetővé teszi, hogy a motorok magasabb hőmérsékletet használjanak, mint az egyébként lehetséges. A magas hőmérsékletű, nagyon kemény, egykristály ötvözetek, amelyekből ezek a pengék készülnek, rendkívül megnehezítik, sőt lehetetlenné teszik a nagy oldalarányú furatok hagyományos megmunkálását. A kis lyukú szikraforgácsolás további alkalmazási területei az üzemanyagrendszer alkatrészei számára mikroszkopikus nyílások létrehozása. Az integrált szikraforgácsoló fejek mellett önálló kis lyukfúró szikraforgácsoló gépeket alkalmazunk x-y tengellyel zsák- vagy átmenő furatok megmunkálására. Az EDM hosszú sárgaréz vagy rézcső elektródával fúrja a lyukakat, amelyek egy tokmányban forognak, miközben állandó áramlású desztillált vagy ionmentesített víz folyik át az elektródán öblítőszerként és dielektrikumként. Egyes kis lyukakat fúró szikraforgácsolók 100 mm-es lágy vagy akár edzett acélon is kevesebb mint 10 másodperc alatt képesek átfúrni. Ezzel a fúrási művelettel 0,3 mm és 6,1 mm közötti furatok készíthetők. Fémbontásos megmunkálás: Vannak speciális szikraforgácsoló gépeink is, amelyek kifejezetten a törött szerszámok (fúrószárak vagy menetfúrók) munkadarabokról történő eltávolítására szolgálnak. Ezt a folyamatot "fémszéteszesítő megmunkálásnak" nevezik. Az elektromos kisüléses megmunkálás előnyei és hátrányai: Az EDM előnyei közé tartozik a következők megmunkálása: - Összetett formák, amelyeket egyébként nehéz lenne hagyományos vágószerszámokkal előállítani - Rendkívül kemény anyag, nagyon szűk tűréshatárig - Nagyon kicsi munkadarabok, ahol a hagyományos vágószerszámok károsíthatják az alkatrészt a vágószerszám túlnyomása miatt. - Nincs közvetlen érintkezés a szerszám és a munkadarab között. Ezért a kényes szakaszok és a gyenge anyagok torzítás nélkül megmunkálhatók. - Jó felületminőség érhető el. - Nagyon finom lyukak könnyen fúrhatók. Az EDM hátrányai a következők: - Az anyageltávolítás lassú üteme. - A nyomószár/süllyesztő szikraforgácsoló elektródák létrehozásához felhasznált többletidő és költség. - Az éles sarkok reprodukálása a munkadarabon az elektródák kopása miatt nehézkes. - Magas az áramfogyasztás. - "Overcut" jön létre. - A megmunkálás során túlzott szerszámkopás lép fel. - Elektromosan nem vezető anyagokat csak meghatározott folyamatbeállítás mellett lehet megmunkálni. CLICK Product Finder-Locator Service ELŐZŐ OLDAL