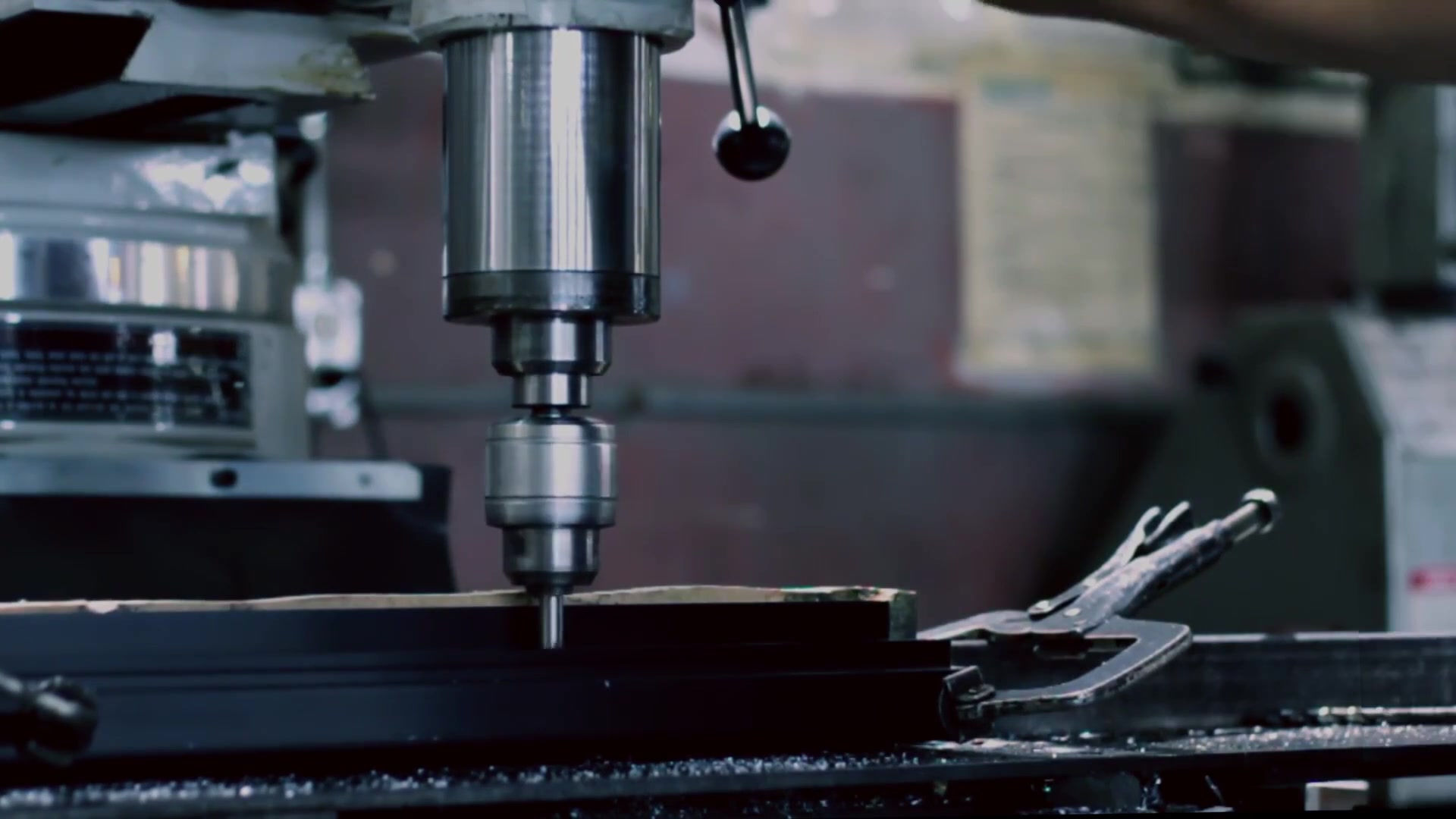
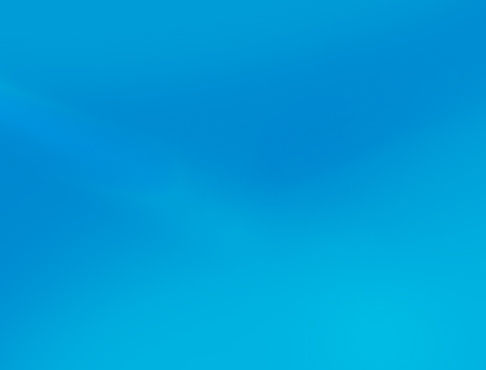
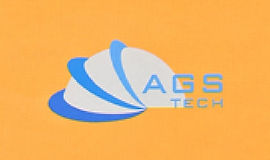
Globális egyedi gyártó, integrátor, konszolidátor, kiszervezési partner a termékek és szolgáltatások széles skálájához.
Mi vagyunk az Ön egyablakos forrása a gyártás, gyártás, tervezés, konszolidáció, integráció, egyedi gyártású és késztermékek és szolgáltatások kiszervezése terén.
Choose your Language
-
Egyedi gyártás
-
Belföldi és globális szerződéses gyártás
-
Gyártási outsourcing
-
Belföldi és globális beszerzés
-
Consolidation
-
Mérnöki integráció
-
Mérnöki szolgáltatások
Search Results
164 találat üres kereséssel
- Transmission Components, Belts, Chains, Cable Drives, Pulleys,AGS-TECH
Transmission Components, Belts, Chains and Cable Drives, Conventional & Grooved or Serrated, Positive Drive, Pulleys Szíjak és láncok és kábelmeghajtó egység Az AGS-TECH Inc. erőátviteli alkatrészeket kínál, beleértve a szíjakat és láncokat, valamint a kábelmeghajtó egységet. Évek óta tartó tökéletesítésnek köszönhetően gumi-, bőr- és egyéb szíjhajtásaink könnyebbek és kompaktabbak lettek, és alacsonyabb költségek mellett nagyobb terhelést is képesek elbírni. Hasonlóképpen, lánchajtásaink is sokat fejlődtek az idők során, és számos előnnyel járnak ügyfeleinknek. A lánchajtások használatának néhány előnye a viszonylag korlátlan tengelyközéptávolság, kompaktság, könnyű összeszerelés, csúszás vagy kúszás nélküli feszítési rugalmasság, magas hőmérsékletű környezetben való működés. Kábelmeghajtóink olyan előnyöket is kínálnak, mint például az egyszerűség bizonyos alkalmazásokban más típusú átviteli alkatrészekkel szemben. Rendelkezésre állnak a polcról kapható szíj-, lánc- és kábelhajtások, valamint egyedi gyártású és összeszerelt változatok is. Ezeket a sebességváltó alkatrészeket az Ön alkalmazásának megfelelő méretre és a legmegfelelőbb anyagokból tudjuk legyártani. SZÍJAK ÉS SZÍJHAJTÁSOK: - Hagyományos lapos szíjak: ezek sima lapos övek fogak, hornyok vagy fogazat nélkül. A lapos szíjhajtások rugalmasságot, jó lengéscsillapítást, hatékony erőátvitelt nagy sebességnél, kopásállóságot és alacsony költséget kínálnak. A szíjak összeilleszthetők vagy összekapcsolhatók nagyobb szíjak készítéséhez. A hagyományos lapos szíjak további előnye, hogy vékonyak, nincsenek kitéve nagy centrifugális terhelésnek (így alkalmasak kis tárcsákkal végzett nagy sebességű műveletekre). Másrészt nagy csapágyterhelést jelentenek, mivel a lapos szíjak nagy feszültséget igényelnek. A lapos szíjhajtások további hátrányai lehetnek a csúszás, a zajos működés, valamint a viszonylag alacsonyabb hatásfok alacsony és közepes sebesség mellett. Kétféle hagyományos szíjank van: megerősített és nem megerősített. A megerősített szíjak szerkezetében húzótag van. A hagyományos lapos övek bőr, gumírozott szövet vagy zsinór, nem erősített gumi vagy műanyag, szövet, megerősített bőr formájában kaphatók. A bőr övek hosszú élettartamot, rugalmasságot, kiváló súrlódási együtthatót és könnyű javítást kínálnak. A bőr övek azonban viszonylag drágák, övkötést és tisztítást igényelnek, és a légkörtől függően összezsugorodhatnak vagy megnyúlhatnak. A gumírozott szövet vagy zsinór övek ellenállnak a nedvességnek, savaknak és lúgoknak. A gumírozott szövetszíjak gumival impregnált pamut vagy szintetikus kacsarétegekből állnak, és a leggazdaságosabbak. A gumírozott zsinórszíjak egy sor gumival impregnált zsinórrétegből állnak. A gumírozott zsinórhevederek nagy szakítószilárdságot, szerény méretet és tömeget kínálnak. A nem megerősített gumi vagy műanyag szíjak alkalmasak a könnyű, alacsony fordulatszámú hajtási alkalmazásokhoz. A nem erősített gumi és műanyag szíjak a helyükre feszíthetők a szíjtárcsáik felett. A nem erősített műanyag szíjak nagyobb teljesítményt képesek továbbítani, mint a gumihevederek. A megerősített bőr övek egy műanyag húzóelemből állnak, amely a bőr felső és alsó rétegei között helyezkedik el. Végül a szövetöveink egyetlen pamut- vagy kacsadarabból állhatnak, amelyet összehajtogatnak és hosszanti öltéssorokkal varrnak. A szövetszíjak képesek egyenletesen követni és nagy sebességgel működni. - Hornyolt vagy fogazott szíjak (például ékszíjak): Ezek alapvető lapos szíjak, amelyeket úgy módosítottak, hogy más típusú erőátviteli termékek előnyeit biztosítsák. Ezek lapos övek hosszirányban bordázott alsó oldallal. A poli-V szíjak hosszirányú hornyolt vagy fogazott lapos szíj húzószakaszokkal és egy sor szomszédos V-alakú hornygal, nyomkövetési és összenyomási célokra. A teljesítmény a szíj szélességétől függ. Az ékszíj az ipar igáslója, és számos szabványos méretben és típusban kapható szinte bármilyen terhelési teljesítmény átvitelére. Az ékszíjhajtások 1500 és 6000 láb/perc között jól működnek, a keskeny ékszíjak azonban akár 10 000 láb/perc sebességgel is működnek. Az ékszíjhajtások hosszú élettartamot, például 3-5 évet kínálnak, és nagy fordulatszám-arányt tesznek lehetővé, könnyen szerelhetők és eltávolíthatók, csendes működést, alacsony karbantartási igényt, jó lengéscsillapítást biztosítanak a szíjhajtó és a hajtott tengelyek között. Az ékszíjak hátránya a bizonyos csúszás és kúszás, ezért nem biztos, hogy a legjobb megoldás ott, ahol szinkron sebességre van szükség. Ipari, autóipari és mezőgazdasági szíjaink vannak. Rendelkezésre állnak standard hosszúságok, valamint egyedi hosszúságú övek. Minden szabványos ékszíj keresztmetszet raktárról elérhető. Vannak táblázatok, ahol kiszámíthatja az ismeretlen paramétereket, például a szíj hosszát, a szíj szakaszát (szélesség és vastagság), feltéve, hogy ismeri a rendszer néhány paraméterét, például a hajtó- és hajtott szíjtárcsák átmérőjét, a szíjtárcsák közötti távolságot és a szíjtárcsák forgási sebességét. Használhat ilyen asztalokat, vagy kérhet tőlünk, hogy válasszuk ki a megfelelő ékszíjat. - Pozitív hajtószíjak (vezérműszíj): Ezek a szíjak szintén lapos típusúak, és a belső kerületén egyenletesen elhelyezett fogakkal rendelkeznek. A pozitív hajtás vagy vezérműszíjak egyesítik a lapos szíjak előnyeit a láncok és fogaskerekek pozitív tapadási jellemzőivel. A pozitív hajtószíjak nem mutatnak kicsúszást vagy sebességváltozást. A sebesség arányok széles skálája lehetséges. A csapágyak terhelése kicsi, mert alacsony feszültség mellett is működhetnek. Ezek azonban érzékenyebbek a szíjtárcsák eltolódására. - Szíjtárcsák, tárcsák, szíjagyak: Különböző típusú szíjtárcsákat használnak lapos, bordás (fogazott) és pozitív hajtószíjakkal. Mindet mi gyártjuk. Lapos szíjtárcsáink többsége vasöntéssel készül, de acél változatok is kaphatók különféle felni és agy kombinációkban. Lapos szíjtárcsáink lehetnek tömör, küllős vagy osztott agyúak, vagy tetszés szerint gyártjuk. A bordás és pozitív hajtószíjak különféle készletméretekben és -szélességekben kaphatók. A vezérműszíj-hajtásokban legalább egy szíjtárcsát karimásnak kell lennie, hogy a szíj a hajtáson maradjon. Hosszú középső hajtásrendszereknél javasolt mindkét szíjtárcsa karimás kialakítása. A tárcsák a csigák hornyolt kerekei, és általában vasöntéssel, acélformázással vagy műanyag fröccsöntéssel készülnek. Az acélalakítás alkalmas eljárás autóipari és mezőgazdasági tárcsák gyártására. Szabályos és mély hornyú tárcsákat gyártunk. A mélyhornyú tárcsák jól használhatók, ha az ékszíj ferdén lép be a tárcsába, mint például a negyedfordulatú hajtásoknál. A mély hornyok kiválóan alkalmasak függőleges tengelyű hajtásokhoz és olyan alkalmazásokhoz is, ahol a szíjak vibrációja problémát jelenthet. Féktárcsáink hornyos vagy lapos tárcsák, amelyek nem szolgálnak mechanikai erőátvitelt. A feszítőgörgőket leginkább a szíjak meghúzására használják. - Egy- és többszíjhajtások: Az egyszíjhajtásoknak egyetlen hornya van, míg a több szíjhajtásnak több hornya van. Az alábbi színes szövegre kattintva letöltheti katalógusainkat: - Erőátviteli szíjak (beleértve az ékszíjakat, a vezérműszíjakat, a nyers élszíjakat, a becsomagolt szíjakat és a speciális szíjakat) - Futószalag - V-szíjtárcsák - Időzítő tárcsák LÁNCOK ÉS LÁNCHAJTÁSOK: Erőátviteli láncainknak van néhány előnye, mint például a viszonylag korlátlan tengelyközéptávolság, könnyű összeszerelés, tömörség, csúszás vagy csúszás nélküli feszített rugalmasság, magas hőmérsékleten való működés. Íme láncaink főbb típusai: - Levehető láncok: Levehető láncaink többféle méretben, emelkedésben és végszilárdságban készülnek, általában temperöntvényből vagy acélból. Az alakítható láncok 0,902 (23 mm) és 4,063 hüvelyk (103 mm) közötti mérettartományban készülnek, és 700 és 17 000 font/négyzethüvelyk közötti végszilárdságban. Levehető acélláncaink viszont 0,904 hüvelyk (23 mm) és körülbelül 3,00 hüvelyk (76 mm) közötti méretben készülnek, a végső szilárdság pedig 760 és 5000 font/négyzethüvelyk között van._cc781905-5cde-3194-bb3b- 136bad5cf58d_ - Pintle láncok: Ezeket a láncokat nagyobb terhelésekhez és valamivel nagyobb sebességekhez használják, körülbelül 450 láb/percig (2,2 m/sec). A csapszeges láncok egyedi öntött láncszemekből készülnek, teljes, kerek csővéggel, eltolt oldallécekkel. Ezek a láncszemek acélcsapokkal vannak összekapcsolva. Ezeknek a láncoknak a osztása körülbelül 1,00 hüvelyk (25 mm) és 6,00 hüvelyk (150 mm) között van, a végső szilárdságuk pedig 3600 és 30 000 font/négyzethüvelyk között van. - Offset-oldalsó láncok: Ezek népszerűek az építőipari gépek hajtóláncaiban. Ezek a láncok 1000 láb/perc sebességgel működnek, és körülbelül 250 LE terhelést adnak át. Általában minden láncszemnek két eltolt oldalrúdja van, egy persely, egy görgő, egy csap, egy sasszeg. - Görgős láncok: 0,25 (6 mm) és 3,00 (75 mm) hüvelyk közötti osztásközökben kaphatók. Az egyszélességű görgős láncok végső szilárdsága 925 és 130 000 font/négyzethüvelyk között van. A görgős láncok többféle szélességű változata is elérhető, és nagyobb sebességnél nagyobb teljesítményt ad át. A többszörös szélességű görgős láncok simább működést tesznek lehetővé, csökkentett zaj mellett. A görgős láncok görgős láncszemekből és csapszegekből állnak össze. A sasszegeket a levehető változatú görgősláncokban használják. A görgős lánchajtások tervezése szakértelmet igényel. Míg a szíjhajtások lineáris sebességeken alapulnak, a lánchajtások a kisebb lánckerék forgási sebességén alapulnak, amely a legtöbb esetben a hajtott elem. A lóerő-értékeken és a fordulatszámon kívül a lánchajtások tervezése sok más tényezőn is alapul. - Kettős osztású láncok: Alapvetően ugyanaz, mint a görgős láncok, kivéve, hogy a menetemelkedés kétszer olyan hosszú. - Fordított fogú (csendes) láncok: Nagy sebességű láncok, amelyeket főként erőgépekhez, teljesítményleadó hajtásokhoz használnak. A fordított foglánc-hajtások akár 1200 LE teljesítményt is továbbíthatnak, és egy sor fogláncból állnak, amelyek felváltva vannak összeszerelve csapokkal vagy csuklós alkatrészek kombinációjával. A középső vezetőlánc vezetőszemei a lánckerék hornyaihoz kapcsolódnak, az oldalsó vezetőlánc pedig vezetőkkel rendelkezik a lánckerék oldalaihoz. - Gyöngy- vagy csúszóláncok: Ezeket a láncokat lassú sebességű hajtásokhoz és kézi műveletekhez is használják. Az alábbi színes szövegre kattintva letöltheti katalógusainkat: - Vezetőláncok - Szállítószalagok - Nagy dőlésszögű szállítószalagok - Rozsdamentes acél görgős láncok - Emelőláncok - Motorkerékpár láncok - Mezőgazdasági gépláncok - Lánckerekek: Szabványos lánckerekeink megfelelnek az ANSI szabványoknak. A lemezes lánckerekek lapos, kerékagy nélküli lánckerekek. Kis és közepes méretű kerékagy lánckerekeinket rúdanyagból vagy kovácsolásból esztergálják, vagy egy rúd-agy melegen hengerelt lemezre hegesztésével készítik. Az AGS-TECH Inc. szürkevas öntvényből, öntött acélból és hegesztett agyszerkezetekből, szinterezett fémporból, öntött vagy megmunkált műanyagokból gyártott lánckerekeket tud szállítani. A nagy sebességű zökkenőmentes működéshez elengedhetetlen a lánckerekek megfelelő méretének kiválasztása. A helykorlátozás természetesen olyan tényező, amelyet nem hagyhatunk figyelmen kívül a lánckerék kiválasztásakor. Javasoljuk, hogy a meghajtó és a hajtott lánckerekek aránya ne legyen nagyobb 6:1-nél, és a lánc tekercselése a meghajtón 120 fok. A kisebb és nagyobb lánckerekek közötti középtávolságot, a lánc hosszát és a lánc feszességét szintén néhány javasolt műszaki számítás és irányelv alapján kell megválasztani, nem pedig véletlenszerűen. Töltse le katalógusainkat az alábbi színes szövegre kattintva: - Lánckerekek és lemezkerekek - Sebességváltó perselyek - Lánccsatlakozás - Lánczárak KÁBELMEGHAJTÁSOK: Ezeknek bizonyos esetekben megvannak az előnyei a szíj- és lánchajtásokhoz képest. A kábelmeghajtók ugyanazt a funkciót látják el, mint a szíjak, és egyes alkalmazásokban egyszerűbbek és gazdaságosabbak is lehetnek. Például a Synchromesh Cable Drives új sorozatát pozitív tapadásra tervezték, hogy helyettesítsék a hagyományos köteleket, egyszerű kábeleket és fogaskerekes meghajtókat, különösen szűk helyeken. Az új kábelmeghajtót úgy tervezték, hogy nagy pontosságú pozicionálást biztosítson elektronikus berendezésekben, például másológépekben, plotterekben, írógépekben, nyomtatókban stb. Az új kábelmeghajtó egyik legfontosabb jellemzője, hogy 3D szerpentin konfigurációkban is használható. rendkívül miniatűr minták. A szinkronkábelek a kötelekhez képest kisebb feszültséggel használhatók, így csökken az energiafogyasztás. Szíjakkal, lánc- és kábelhajtásokkal kapcsolatos kérdéseivel és véleményével kapcsolatban forduljon az AGS-TECH-hez. CLICK Product Finder-Locator Service ELŐZŐ OLDAL
- Joining & Assembly & Fastening Processes, Welding, Brazing, Soldering
Joining & Assembly & Fastening Processes, Welding, Brazing, Soldering, Sintering, Adhesive Bonding, Press Fitting, Wave and Reflow Solder Process, Torch Furnace Csatlakoztatási és összeszerelési és rögzítési eljárások HEGESZTÉS, FORRSZÍTÁS, SZINTEREZÉS, RAGASZTÁS, RÖGZÍTÉS, SAJTÁSSZERELÉS segítségével összeillesztjük, összeszereljük, rögzítjük és kész- vagy félkész termékké alakítjuk. Legnépszerűbb hegesztési eljárásaink közé tartozik az ív-, oxi-üzemanyag-, ellenállás-, vetítés-, varrat-, felborítás-, ütő-, szilárdtest-, elektronsugár-, lézer-, termit-, indukciós hegesztés. Népszerű keményforrasztási eljárásaink a pisztolyos, az indukciós, a kemencés és a merítőforrasztás. Forrasztási módszereink vas-, főzőlap-, sütő-, indukciós, merítési, hullámos, visszafolyós és ultrahangos forrasztás. Ragasztáshoz gyakran használunk hőre lágyuló és hőre keményedő műanyagokat, epoxikat, fenolokat, poliuretánt, ragasztó ötvözeteket, valamint néhány egyéb vegyszert és szalagot. Végül a rögzítési folyamataink szegezésből, csavarozásból, anyákból és csavarokból, szegecselésből, rögzítésből, tűzésből, varrásból és tűzésből, valamint présillesztésből állnak. • HEGESZTÉS: A hegesztés során az anyagokat a munkadarabok megolvasztásával és töltőanyagok bejuttatásával kötik össze, amelyek az olvadt hegesztőmedencét is összekapcsolják. Amikor a terület lehűl, erős kötést kapunk. Bizonyos esetekben nyomást alkalmaznak. A hegesztéssel ellentétben a keményforrasztási műveletek csak egy alacsonyabb olvadáspontú anyag megolvasztását jelentik a munkadarabok között, és a munkadarabok nem olvadnak meg. Javasoljuk, hogy kattintson ideTöltsd le az AGS-TECH Inc. által készített hegesztési folyamatok sematikus illusztrációit. Ez segít jobban megérteni az alább közölt információkat. Az ÍVHEGESZTÉS során tápegységet és elektródát használunk a fémeket megolvasztó elektromos ív létrehozására. A hegesztési pontot védőgáz, gőz vagy más anyag védi. Ez az eljárás népszerű autóalkatrészek és acélszerkezetek hegesztésénél. A shelded metal ívhegesztésnél (SMAW) vagy más néven pálcás hegesztésnél egy elektródapálcát visznek az alapanyag közelébe, és közöttük elektromos ív keletkezik. Az elektróda rúd megolvad és töltőanyagként működik. Az elektróda folyasztószert is tartalmaz, amely salakrétegként működik, és gőzöket bocsát ki, amelyek védőgázként működnek. Ezek megvédik a hegesztési területet a környezeti szennyeződésektől. Más töltőanyagot nem használnak. Ennek az eljárásnak a hátránya a lassúsága, az elektródák gyakori cseréjének szükségessége, a fluxusból származó maradék salak leforgácsolásának szükségessége. Számos fém, például vas, acél, nikkel, alumínium, réz stb. Hegeszthető. Előnye az olcsó eszközök és a könnyű használat. A gázos fémíves hegesztés (GMAW), más néven fém-inert gáz (MIG), folyamatos betáplálást biztosít a fogyóelektródos huzaltöltőanyagból és egy inert vagy részben inert gázból, amely a huzal körül áramlik a hegesztési tartomány környezeti szennyeződése ellen. Acél, alumínium és más színesfémek hegeszthetők. A MIG előnyei a nagy hegesztési sebesség és a jó minőség. Hátránya a bonyolult felszereltség és a szeles kültéri kihívások, mert stabilan kell tartanunk a hegesztési terület körüli védőgázt. A GMAW egy változata a folyasztószeres ívhegesztés (FCAW), amely egy finom fémcsőből áll, amely folyasztószerekkel van megtöltve. Néha a cső belsejében lévő fluxus elegendő a környezeti szennyeződések elleni védelemhez. A merülőíves hegesztés (SAW) széles körben automatizált folyamat, amely magában foglalja a folyamatos huzal-adagolást és az ívet, amelyet egy folyasztószer-réteg alá ütnek. A gyártási arányok és a minőség magas, a hegesztési salak könnyen leválik, füstmentes munkakörnyezetünk van. Hátránya, hogy csak bizonyos pozíciókban használható alkatrészek hegesztésére. Gáz-volframíves hegesztésnél (GTAW) vagy volfrám-inert gázhegesztésnél (TIG) wolframelektródát használunk külön töltőanyaggal és inert vagy közel inert gázokkal. Mint tudjuk, a volfrámnak magas olvadáspontja van, és nagyon alkalmas fém nagyon magas hőmérsékletekhez. A TIG-ben lévő volfrám nem kerül felhasználásra a fent ismertetett többi módszerrel ellentétben. Lassú, de jó minőségű hegesztési technika, amely előnyös a vékony anyagok hegesztésének más technikáival szemben. Számos fémhez alkalmas. A plazmaívhegesztés hasonló, de plazmagázt használ az ív létrehozásához. A plazmaívhegesztésnél az ív viszonylag koncentráltabb a GTAW-hoz képest, és szélesebb fémvastagság-tartományban használható sokkal nagyobb sebességgel. A GTAW és a plazmaívhegesztés többé-kevésbé ugyanazon anyagokon alkalmazható. OXY-FUEL / OXYFUEL HEGESZTÉS, amit oxiacetilén hegesztésnek is neveznek, oxi-hegesztés, gázhegesztés gázüzemanyag és oxigén hegesztéssel történik. Mivel nem használnak elektromos áramot, hordozható, és ott is használható, ahol nincs áram. Hegesztőpisztoly segítségével felmelegítjük a darabokat és a töltőanyagot, így közös olvadt fémmedencét állítunk elő. Különféle üzemanyagok használhatók, például acetilén, benzin, hidrogén, propán, bután stb. Az oxigén-üzemanyag hegesztésnél két tartályt használunk, az egyiket az üzemanyagnak, a másikat az oxigénnek. Az oxigén oxidálja az üzemanyagot (elégeti). ELLENÁLLÁS HEGESZTÉS: Ez a fajta hegesztés kihasználja a joule melegítés előnyeit, és hő keletkezik azon a helyen, ahol egy bizonyos ideig elektromos áramot alkalmaznak. Nagy áramok haladnak át a fémen. Ezen a helyen olvadt fém medencék képződnek. Az ellenálláshegesztési módszerek hatékonyságuk, csekély szennyezési potenciáljuk miatt népszerűek. A hátrányok azonban a viszonylag jelentős berendezések költségei és a viszonylag vékony munkadarabokra vonatkozó korlátozás. A PONTHEGESZTÉS az ellenálláshegesztés egyik fő típusa. Itt két vagy több átfedő lapot vagy munkadarabot kapcsolunk össze úgy, hogy két rézelektródával összefogjuk a lapokat, és nagy áramot vezetünk át rajtuk. A rézelektródák közötti anyag felmelegszik, és ezen a helyen olvadt medence keletkezik. Ezután az áram leáll, és a rézelektróda csúcsai lehűtik a hegesztési helyet, mivel az elektródák vízhűtésesek. Ennél a technikánál kulcsfontosságú a megfelelő mennyiségű hő alkalmazása a megfelelő anyagra és vastagságra, mert ha rosszul alkalmazzák, a hézag gyenge lesz. A ponthegesztés előnye, hogy nem okoz jelentős deformációt a munkadarabokon, energiahatékonyság, könnyű automatizálás és kiemelkedő gyártási sebesség, és nincs szükség töltőanyagra. Hátránya, hogy mivel a hegesztés nem folytonos varratként, hanem pontokban történik, az összszilárdság viszonylag alacsonyabb lehet más hegesztési módszerekkel összehasonlítva. A SEAM WELDING ezzel szemben varratokat hoz létre hasonló anyagok elválasztó felületein. A varrás lehet tompa vagy átlapoló illesztés. A varrathegesztés az egyik végén kezdődik, és fokozatosan halad át a másik felé. Ez a módszer két rézelektródát is használ, hogy nyomást és áramot fejtsen ki a hegesztési tartományra. A korong alakú elektródák állandó érintkezéssel forognak a varratvonal mentén, és folyamatos hegesztést hoznak létre. Az elektródákat itt is víz hűti. A hegesztési varratok nagyon erősek és megbízhatóak. További módszerek a vetítés, a villanás és a felhajtható hegesztési technikák. A SZILÁRDÁLLÁSÚ HEGESZTÉS egy kicsit eltér a fentebb ismertetett korábbi módszerektől. Az összeolvadás az összekapcsolt fémek olvadáspontja alatti hőmérsékleten megy végbe, fém töltőanyag használata nélkül. Egyes folyamatokban nyomást lehet alkalmazni. Különböző módszerek a KOEXTRÚZIÓS HEGESZTÉS, ahol különböző fémeket extrudálnak ugyanazon a szerszámon keresztül, a HIDEGNYOMÁSÚ HEGESZTÉS, amikor lágy ötvözeteket az olvadáspontjuk alatt kötünk össze, a DIFFÚZIÓS HEGESZTÉS egy látható hegesztési vonalak nélküli technika, a ROBBANÁSI HEGESZTÉS különböző szerkezeti anyagok, pl. korrózióálló anyagok összekapcsolására. acélok, ELEKTROMÁGNESES IMPULZUSHEGESZTÉS, ahol csöveket, lemezeket elektromágneses erővel gyorsítunk, kovácsolt HEGESZTÉS, amely a fémek magas hőmérsékletre való hevítéséből és egymáshoz kalapálásából áll, DRIKCIÓS HEGESZTÉS, ahol kellő súrlódásos hegesztést végeznek, DRIKCIÓS HEGESZTÉS, amely forgó nem fogyószerszám, amely áthalad a csatlakozási vonalon, FORGÓNYOMÁSÚ HEGESZTÉS ahol emelt, olvadási hőmérséklet alatti hőmérsékleten, vákuumban vagy közömbös gázokban fémeket préselünk össze, FORRÓ IZOTATIKUS NYOMÁSHEGESZTÉS olyan eljárás, ahol nyomást alkalmazunk inert gázok felhasználásával egy edény belsejében, ROLL HEGESZTÉS, ahol egyesítjük különböző anyagokat egymás között kényszerítve két forgó kerék, ULTRAHANGOS HEGESZTÉS ahol vékony fém vagy műanyag lemezeket hegesztenek nagyfrekvenciás rezgési energiával. További hegesztési eljárásaink a mély behatolású, gyors megmunkálású, de költséges módszernek számító ELEKTRONSugaras HEGESZTÉS speciális esetekre, az ELEKTROLAG HEGESZTÉS nehéz vastag lemezek és csak acél munkadarabok megmunkálására alkalmas módszer, az INDUKCIÓS HEGESZTÉS ahol elektromágneses indukciót alkalmazunk, ill. melegítsük fel elektromosan vezető vagy ferromágneses munkadarabjainkat, LÉZERSUGÁR HEGESZTÉS szintén mély behatolású és gyors feldolgozással, de költséges módszer, LÉZER HIBRID HEGESZTÉS, amely az LBW-t a GMAW-val kombinálja ugyanabban a hegesztőfejben, és képes áthidalni a lemezek közötti 2 mm-es hézagokat, ÜTŐHEGESZTÉS magában foglalja az elektromos kisülést, majd az anyagok kovácsolását alkalmazott nyomással, a HERMIT HEGESZTÉST, amely exoterm reakciót foglal magában az alumínium és a vas-oxid porok között., ELEKTROGÁZHEGESZTÉS fogyóelektródákkal, és csak függőleges helyzetben használják acélt, végül pedig a CSÜK ÍVHEGESZTÉSE a csap és az alap összekapcsolásához. anyag hővel és nyomással. Javasoljuk, hogy kattintson ideTöltsd le az AGS-TECH Inc. által készített keményforrasztási, forrasztási és ragasztási folyamatok vázlatos illusztrációit Ez segít jobban megérteni az alább közölt információkat. • FORRRASZTÁS: Két vagy több fémet úgy kapcsolunk össze, hogy a köztük lévő töltőanyagot olvadáspontjuk fölé hevítjük, és kapilláris hatást alkalmazunk a szétterítéshez. Az eljárás hasonló a forrasztáshoz, de a töltőanyag megolvadásához szükséges hőmérséklet magasabb a keményforrasztásnál. A hegesztéshez hasonlóan a fluxus megvédi a töltőanyagot a légköri szennyeződésektől. Lehűlés után a munkadarabokat összeillesztjük. A folyamat a következő kulcslépésekből áll: Jó illeszkedés és hézag, az alapanyagok megfelelő tisztítása, megfelelő rögzítés, megfelelő folyasztószer és légkör kiválasztása, a szerelvény felmelegítése és végül a keményforrasztott szerkezet tisztítása. Néhány keményforrasztási eljárásunk a TORCH BRAZING, egy népszerű módszer, amelyet manuálisan vagy automatizáltan hajtanak végre. Alkalmas kis volumenű gyártási rendelésekre és speciális esetekre. A hőt gázlángokkal alkalmazzák a keményforrasztási hézag közelében. A KEMÉNÉS FORRASZTÁSA kevesebb kezelői jártasságot igényel, és egy félautomata folyamat, amely alkalmas ipari tömeggyártásra. Mind a hőmérséklet-szabályozás, mind a kemence légkörének szabályozása ennek a technikának az előnye, mert az előbbi lehetővé teszi, hogy szabályozott hőciklust biztosítsunk, és kiküszöböljük a helyi felmelegedést, ahogy az a fáklyás keményforrasztásnál, az utóbbi pedig megvédi az alkatrészt az oxidációtól. A jigging segítségével minimálisra tudjuk csökkenteni a gyártási költségeket. Hátránya a nagy energiafogyasztás, a berendezés költségei és a nagyobb kihívást jelentő tervezési szempontok. A VÁKUUMFORRASZTÁS vákuumkemencében történik. A hőmérséklet egyenletes marad, és folyasztószermentes, nagyon tiszta kötéseket kapunk, nagyon kis maradék feszültségekkel. A hőkezelések a vákuumforrasztás során történhetnek, mivel a lassú fűtési és hűtési ciklusok során alacsony maradó feszültségek jelentkeznek. A fő hátrány a magas költség, mivel a vákuumkörnyezet létrehozása költséges folyamat. Egy másik technika a DIP BRAZING rögzíti a rögzített részeket, ahol keményforrasztó keveréket visznek fel az illeszkedő felületekre. Ezt követően a fixturált részeket olvadt só, például nátrium-klorid (asztali só) fürdőbe mártják, amely hőátadó közegként és fluxusként működik. Levegő kizárva, ezért nem oxidálódik. Az INDUKCIÓS FORRASZTÁS során az anyagokat olyan töltőfémmel kötjük össze, amelynek olvadáspontja alacsonyabb, mint az alapanyagoké. Az indukciós tekercs váltakozó árama elektromágneses teret hoz létre, amely indukciós melegítést indukál a többnyire vastartalmú mágneses anyagokon. A módszer szelektív melegítést, jó hézagokat biztosít a töltőanyagokkal, amelyek csak a kívánt területeken áramlanak, csekély oxidációt biztosít, mivel nincs láng és a hűtés gyors, gyors felmelegedés, konzisztencia és alkalmas nagy mennyiségű gyártásra. Folyamataink felgyorsítása és a következetesség biztosítása érdekében gyakran használunk előformákat. A kerámia-fém szerelvényeket, hermetikus tömítést, vákuumátvezetéseket, magas és ultramagas vákuum- és folyadékszabályozó alkatrészeket gyártó keményforrasztóüzemünkkel kapcsolatos információk itt találhatók:_cc781905-31-14cdebbbad_5cdebbbad.Forrasztógyári prospektus • FORRASZTÁS: A forrasztásnál nem a munkadarabok olvadásáról van szó, hanem a kötésbe befolyó töltőfémről, amelynek olvadáspontja alacsonyabb, mint az összekötő részeké. A töltőanyag a forrasztásnál alacsonyabb hőmérsékleten olvad meg, mint a keményforrasztásnál. A forrasztáshoz ólommentes ötvözeteket használunk, és megfelelünk az RoHS-nek, és különböző alkalmazásokhoz és követelményekhez különböző és megfelelő ötvözeteink vannak, mint például az ezüstötvözet. A forrasztás gáz- és folyadéktömör csatlakozásokat kínál számunkra. LÁGYFORRASZTÁSBAN a töltőfém olvadáspontja 400 Celsius-fok alatt van, míg EZÜSTFORRASZTÁSBAN és FORRRASZTÁSBAN magasabb hőmérsékletre van szükségünk. A lágyforrasztás alacsonyabb hőmérsékletet használ, de nem eredményez erős kötéseket az igényes alkalmazásokhoz magas hőmérsékleten. Az ezüstforrasztás viszont magas hőmérsékletet igényel, amelyet a fáklya biztosít, és erős kötéseket biztosít, amelyek alkalmasak magas hőmérsékletű alkalmazásokhoz. A keményforrasztás a legmagasabb hőmérsékletet igényli, és általában égőt használnak. Mivel a keményforrasztó hézagok nagyon erősek, jó jelöltek nehéz vastárgyak javítására. Gyártósorainkon kézi kézi forrasztást és automatizált forrasztósorokat egyaránt alkalmazunk. INDUCTION FORRASZTÁS nagyfrekvenciás váltakozó áramot használ egy réztekercsben, hogy megkönnyítse az indukciós fűtést. A forrasztott részben áramok indukálódnak, és ennek eredményeként hő keletkezik a nagy ellenállású csuklón. Ez a hő megolvasztja a töltőfémet. Fluxust is használnak. Az indukciós forrasztás jó módszer a körhengerek és csövek folyamatos forrasztására úgy, hogy a tekercseket körbetekerjük. Egyes anyagok, például grafit és kerámia forrasztása nehezebb, mert ehhez a forrasztás előtt a munkadarabokat megfelelő fémmel kell bevonni. Ez megkönnyíti a határfelületi kötést. Az ilyen anyagokat kifejezetten hermetikus csomagolási alkalmazásokhoz forrasztjuk. Nyomtatott áramköri lapjainkat (NYÁK) nagy mennyiségben gyártjuk, többnyire HULLÁMFORRASZTÁSSAL. Csak kis mennyiségű prototípus készítéséhez használunk kézi forrasztást forrasztópáka segítségével. Hullámforrasztást alkalmazunk mind átmenőfuratokhoz, mind felületre szerelhető PCB-szerelvényekhez (PCBA). Egy ideiglenes ragasztó tartja az alkatrészeket az áramköri laphoz rögzítve, és a szerelvény egy szállítószalagra kerül, és egy olvadt forrasztóanyagot tartalmazó berendezésen mozog. Először a NYÁK-ot folyósítják, majd belép az előmelegítő zónába. Az olvadt forrasztóanyag egy serpenyőben van, és a felületén állóhullámok mintázata van. Amikor a PCB áthalad ezeken a hullámokon, ezek a hullámok érintkeznek a NYÁK aljával, és hozzátapadnak a forrasztólapokhoz. A forrasztóanyag csak a csapokon és a betéteken marad, magán a PCB-n nem. Az olvadt forrasztóanyagban lévő hullámokat jól szabályozni kell, hogy ne fröccsenjen ki, és a hullámok teteje ne érjen hozzá és ne szennyezze be a táblák nem kívánt területeit. A REFLOW SOLDERING során ragadós forrasztópasztát használunk az elektronikus alkatrészek ideiglenes rögzítésére a lapokra. Ezután a táblákat egy visszafolyó kemencén helyezik át hőmérséklet-szabályozással. Itt a forraszanyag megolvad és tartósan összeköti az alkatrészeket. Ezt a technikát mind a felületre szerelhető, mind az átmenő furatú alkatrészekhez használjuk. A megfelelő hőmérséklet-szabályozás és a sütő hőmérsékletének beállítása elengedhetetlen ahhoz, hogy elkerüljük az elektronikus alkatrészek tönkremenetelét a maximális hőmérsékleti határérték fölé történő túlmelegedés következtében. Az újrafolyós forrasztás folyamatában valójában több régiónk vagy szakaszunk van, amelyek mindegyike külön termikus profillal rendelkezik, mint például az előmelegítési lépés, a termikus áztatási lépés, az újrafolyatás és a hűtés lépései. Ezek a különböző lépések elengedhetetlenek a nyomtatott áramköri kártya szerelvények (PCBA) sérülésmentes újrafolyási forrasztásához. ULTRAHANGOS FORRASZTÁS egy másik gyakran használt technika, egyedülálló képességekkel. Üveg, kerámia és nem fémes anyagok forrasztására használható. Például a nem fémes fotovoltaikus panelekhez elektródák szükségesek, amelyeket ezzel a technikával lehet rögzíteni. Az ultrahangos forrasztásnál fűtött forrasztócsúcsot alkalmazunk, amely ultrahangos rezgéseket is kibocsát. Ezek a rezgések kavitációs buborékokat hoznak létre a hordozó és az olvadt forrasztóanyag határfelületén. A kavitáció implozív energiája módosítja az oxidfelületet, eltávolítja a szennyeződéseket és az oxidokat. Ez idő alatt ötvözetréteg is képződik. A kötőfelületen lévő forrasztóanyag oxigént tartalmaz, és lehetővé teszi az üveg és a forraszanyag közötti erős megosztott kötés kialakítását. A MERTÉSFORRASZTÁS a hullámforrasztás egyszerűbb, csak kisüzemi gyártásra alkalmas változatának tekinthető. Az első tisztítófolyasztószert más eljárásokhoz hasonlóan alkalmazzák. A beépített alkatrészekkel rendelkező PCB-ket kézzel vagy félautomata módon olvadt forrasztóanyagot tartalmazó tartályba mártják. Az olvadt forrasztóanyag hozzátapad a szabaddá vált fémes területekhez, amelyeket nem véd a táblán lévő forrasztómaszk. A berendezés egyszerű és olcsó. • RAGASZTÁS: Ez egy másik népszerű technika, amelyet gyakran használunk, és a felületek ragasztóval, epoxival, műanyaggal vagy más vegyszerekkel történő ragasztását foglalja magában. A ragasztás vagy az oldószer elpárologtatásával, hőkezeléssel, UV-fényben történő térhálósítással, nyomásos térhálósítással vagy egy bizonyos idő várakozásával történik. Gyártósorainkon különféle nagy teljesítményű ragasztókat használnak. Megfelelően megtervezett felhordási és kikeményedési folyamatokkal a ragasztós kötés nagyon alacsony feszültségű kötéseket eredményezhet, amelyek erősek és megbízhatóak. A ragasztóanyag jó védelmet nyújthat a környezeti tényezőkkel szemben, mint például a nedvesség, szennyeződések, korrozív anyagok, vibráció stb. A ragasztás előnyei: olyan anyagokra is felhordható, amelyek egyébként nehezen forraszthatók, hegeszthetők vagy keményforraszthatók. Előnyös lehet olyan hőérzékeny anyagoknál is, amelyek hegesztés vagy más magas hőmérsékletű folyamatok károsodnának. A ragasztók további előnye, hogy szabálytalan alakú felületekre is felvihetők, és más módszerekkel összehasonlítva nagyon kis mértékben növelik az összeszerelés súlyát. Az alkatrészek méretváltozásai is nagyon minimálisak. Egyes ragasztók indexillesztő tulajdonságokkal rendelkeznek, és használhatók az optikai alkatrészek között anélkül, hogy jelentősen csökkentené a fény vagy az optikai jel erősségét. Másrészt a hátrányok a hosszabb kikeményedési idők, amelyek lelassíthatják a gyártási folyamatokat, a rögzítési követelményeket, a felület-előkészítési követelményeket és a szétszerelési nehézségeket, amikor újrafeldolgozásra van szükség. A legtöbb ragasztási műveletünk a következő lépésekből áll: -Felületkezelés: Gyakoriak a speciális tisztítási eljárások, mint például az ioncserélt vizes tisztítás, alkoholos tisztítás, plazma vagy koronatisztítás. Tisztítás után tapadást elősegítő anyagokat vihetünk fel a felületekre, hogy a lehető legjobb hézagokat biztosítsuk. - Alkatrészrögzítés: Mind a ragasztós felhordáshoz, mind a kikeményítéshez egyedi rögzítőelemeket tervezünk és használunk. - Ragasztó alkalmazás: Néha kézi, esettől függően pedig automatizált rendszereket használunk, mint például robotika, szervomotorok, lineáris aktuátorok, hogy a ragasztókat a megfelelő helyre szállítsuk, és adagolókat használunk a megfelelő mennyiségben és mennyiségben történő szállításhoz. - Kikeményedés: A ragasztóanyagtól függően alkalmazhatunk egyszerű szárítást és térhálósodást, valamint UV-fény alatti térhálósítást, amely katalizátorként működik, vagy hőkeményedést kemencében, vagy rezisztív fűtőelemeket használunk, amelyek rögzítőelemekre és szerelvényekre vannak felszerelve. Javasoljuk, hogy kattintson ideTöltsd le az AGS-TECH Inc. által készített rögzítési folyamatok sematikus illusztrációit. Ez segít jobban megérteni az alább közölt információkat. • RÖGZÍTÉSI FOLYAMATOK: A mechanikus illesztési eljárásaink két szegélykategóriára oszlanak: RÖGZÍTŐK és INTEGRAL KÖZÖSSÉGEK. Példák az általunk használt kötőelemekre: csavarok, csapok, anyák, csavarok, szegecsek. Példák az általunk használt integrált illesztésekre: bepattanó és zsugorodó illesztések, varratok, krimpelések. Különféle rögzítési módokkal biztosítjuk, hogy mechanikus kötéseink erősek és megbízhatóak legyenek hosszú éveken át. A CSAVAROK és a CSAVAROK a leggyakrabban használt rögzítőelemek tárgyak összetartására és elhelyezésére. Csavarjaink és csavarjaink megfelelnek az ASME szabványoknak. Különféle típusú csavarokat és csavarokat alkalmaznak, beleértve a hatlapfejű csavarokat és hatlapfejű csavarokat, a késcsavarokat és csavarokat, a kétvégű csavarokat, a tiplik csavarokat, a szemcsavarokat, a tükörcsavarokat, a fémlemez csavarokat, a finombeállító csavarokat, az önfúró és önmetsző csavarokat , rögzítőcsavar, csavarok beépített alátéttel stb. Különféle csavarfejtípusokkal rendelkezünk, mint például süllyesztett, kupola, kerek, karimás fej és különféle csavarmeghajtó típusok, például hornyos, philips, négyzet alakú, hatlapú foglalat. A RIVET másrészt egy állandó mechanikus rögzítő, amely egy sima hengeres tengelyből és egy fejből áll. A behelyezés után a szegecs másik vége deformálódik és átmérője kitágul, hogy a helyén maradjon. Más szóval, a beszerelés előtt a szegecsnek egy feje van, a beszerelés után pedig kettő. Különféle típusú szegecseket szerelünk be az alkalmazástól, szilárdságtól, hozzáférhetőségtől és költségtől függően, mint például tömör/kerekfejű szegecsek, szerkezeti, félcsöves, vak-, oscar-, meghajtó-, süllyesztett-, súrlódó-, önszúró-szegecsek. A szegecselés olyan esetekben előnyös, amikor el kell kerülni a hegesztési hő hatására bekövetkező hődeformációt és az anyagtulajdonságok megváltozását. A szegecselés könnyű súlyt és különösen jó szilárdságot és tartósságot biztosít a nyíróerők ellen. A húzó terhelések ellen azonban a csavarok, anyák és csavarok alkalmasabbak lehetnek. A CLINCHING folyamatban speciális lyukasztót és szerszámot használunk, hogy mechanikus reteszelést hozzunk létre az összeillesztendő fémlemezek között. A lyukasztó a fémlemez rétegeit a szerszámüregbe tolja, és állandó kötést eredményez. A csiszoláshoz nincs szükség fűtésre és hűtésre, és ez egy hideg munkafolyamat. Ez egy gazdaságos eljárás, amely bizonyos esetekben helyettesítheti a ponthegesztést. A PINNING során csapokat használunk, amelyek gépelemek, amelyek a gépalkatrészek egymáshoz viszonyított helyzetének rögzítésére szolgálnak. A főbb típusok a csapszegek, a sasszegek, a rugós csapok, a tiplicsapok, a és a hasított csapszegek. A TŰZÉS során tűzőpisztolyokat és kapcsokat használunk, amelyek kétágú rögzítőelemek, amelyek anyagok összekapcsolására vagy megkötésére szolgálnak. A tűzésnek a következő előnyei vannak: Gazdaságos, egyszerű és gyors a használata, a kapcsok koronája használható egymáshoz tapasztott anyagok áthidalására, A kapocskorona megkönnyíti egy darab kábelszerű áthidalását és a felülethez történő rögzítését anélkül, hogy kilyukadna, ill. káros, viszonylag könnyen eltávolítható. A PRESS FITTING az alkatrészek egymáshoz tolásával történik, és a köztük lévő súrlódás rögzíti az alkatrészeket. A túlméretezett tengelyből és egy alulméretezett furatból álló présillesztett alkatrészeket általában két módszer egyikével szerelik össze: Vagy erő alkalmazásával, vagy az alkatrészek hőtágulásának vagy összehúzódásának kihasználásával. Ha erőkifejtéssel présszerelvényt alakítunk ki, akkor vagy hidraulikus prést, vagy kézi működtetésű prést használunk. Másrészt a présillesztés hőtágulással történő kialakításánál a burkoló részeket felmelegítjük és melegen a helyükre szereljük. Amikor lehűlnek, összehúzódnak, és visszatérnek normál méretükhöz. Ez jó préselést eredményez. Ezt más néven SZUGORÓSZERELÉS-nek nevezzük. Ennek másik módja az, hogy összeszerelés előtt lehűtjük a burkolt részeket, majd becsúsztatjuk azokat az illeszkedő részeikbe. Amikor a szerelvény felmelegszik, kitágulnak, és szoros illeszkedést kapunk. Ez utóbbi módszer előnyösebb lehet olyan esetekben, amikor a melegítés az anyagtulajdonságok megváltozásának kockázatát hordozza magában. Ilyen esetekben a hűtés biztonságosabb. Pneumatikus és hidraulikus alkatrészek és szerelvények • Szelepek, hidraulikus és pneumatikus alkatrészek, például O-gyűrű, alátét, tömítések, tömítés, gyűrű, alátét. Mivel a szelepek és pneumatikus alkatrészek nagy választékban kaphatók, nem tudunk itt mindent felsorolni. Az alkalmazás fizikai és kémiai környezetétől függően speciális termékeink vannak az Ön számára. Kérjük, adja meg az alkalmazást, az alkatrész típusát, specifikációit, környezeti feltételeket, például nyomást, hőmérsékletet, folyadékokat vagy gázokat, amelyek érintkezésbe kerülnek a szelepekkel és pneumatikus alkatrészekkel; és kiválasztjuk az Önnek legmegfelelőbb terméket, vagy kifejezetten az Ön alkalmazására gyártjuk. CLICK Product Finder-Locator Service ELŐZŐ OLDAL
- Rapid Prototyping, Desktop Manufacturing, Additive Manufacturing, FDM
Rapid Prototyping, Desktop Manufacturing, Additive Manufacturing, Stereolithography, Polyjet, Fused Deposition Modeling, Selective Laser Sintering, FDM, SLS Adalékanyag és gyors gyártás Az elmúlt években megnőtt a kereslet a RAPID MANUFACTURING vagy RAPID PROTOTYPING iránt. Ezt a folyamatot ASZTALI GYÁRTÁSNAK vagy SZABADFORMÚ GYÁRTÁSNAK is nevezhetjük. Alapvetően egy alkatrész szilárd fizikai modellje közvetlenül egy háromdimenziós CAD-rajzból készül. Az ADDITIVE MANUFACTURING kifejezést használjuk ezekre a különféle technikákra, ahol az alkatrészeket rétegesen építjük fel. Integrált számítógép-vezérelt hardver és szoftver segítségével additív gyártást végzünk. Gyors prototípus-készítési és gyártási technikáink a következők: SZTEREOLITOGRÁFIA, POLYJET, OLVASZTÁSÚ MODELLEZÉS, SZELEKTÍV LÉZERES SZINTEREZÉS, ELEKTRONSUGÁRZÁS, HÁROMDIMENZIÓS NYOMTATÁS, KÖZVETLEN GYÁRTÁS, GYORS SZERSZÁMZÁS. Javasoljuk, hogy kattintson ideTöltsd le sematikus illusztrációinkat az additív gyártásról és a gyors gyártási folyamatokról az AGS-TECH Inc.-től. Ez segít jobban megérteni az alább közölt információkat. A gyors prototípuskészítés a következőket nyújtja számunkra: 1.) A koncepcionális terméktervezést egy monitoron, 3D / CAD rendszer segítségével különböző szögekből tekintjük meg. 2.) Nemfémes és fémes anyagokból prototípusok gyártása és tanulmányozása funkcionális, műszaki és esztétikai szempontból. 3.) Alacsony költségű prototípuskészítés nagyon rövid idő alatt megvalósul. Az additív gyártás egy kenyér elkészítéséhez hasonlítható úgy, hogy az egyes szeleteket egymásra rakják és ragasztják. Más szavakkal, a terméket szeletről szeletre, vagy rétegről rétegre egymásra rakva állítják elő. A legtöbb alkatrész órákon belül elkészíthető. A technika akkor jó, ha nagyon gyorsan van szükség az alkatrészekre, vagy ha kevés a szükséges mennyiség, és a forma és a szerszámok elkészítése túl költséges és időigényes. Az alkatrész költsége azonban drága a drága alapanyagok miatt. • SZTEREOLITOGRÁFIA: Ez a STL-nek is nevezett technika egy folyékony fotopolimer lézersugár fókuszálásával egy meghatározott formára való kikeményítésén és keményítésén alapul. A lézer polimerizálja a fotopolimert és kikeményíti. Az UV lézersugarat a programozott alakzatnak megfelelően a fotopolimer keverék felülete mentén pásztázva alulról felfelé, egymásra zuhanó egyes szeletekben állítják elő. A lézerpont szkennelését sokszor megismételjük, hogy elérjük a rendszerbe programozott geometriákat. Miután az alkatrészt teljesen legyártották, eltávolítják a platformról, felitatják és ultrahanggal és alkoholfürdővel megtisztítják. Ezután néhány órára UV-sugárzásnak teszik ki, hogy megbizonyosodjanak arról, hogy a polimer teljesen kikeményedett és megkeményedett. Összefoglalva a folyamatot, egy fotopolimer keverékbe mártott platformot és egy UV lézersugarat vezérelnek és mozgatnak egy szervovezérlő rendszeren keresztül a kívánt alkatrész alakjának megfelelően, és az alkatrészt a polimer rétegről rétegre történő fotokeményítésével állítják elő. Természetesen a gyártott alkatrész maximális méreteit a sztereolitográfiai berendezés határozza meg. • POLYJET: A tintasugaras nyomtatáshoz hasonlóan a polyjet nyomtatófejeknél is nyolc nyomtatófej található, amelyek fotopolimert helyeznek fel az építőtálcára. A fúvókák mellé helyezett ultraibolya fény minden réteget azonnal kikeményedik és megkeményedik. A polyjetben két anyagot használnak. Az első anyag a tényleges modell gyártására szolgál. A második anyag, egy gélszerű gyantát használnak alátámasztásra. Mindkét anyagot rétegről rétegre rakják le, és egyidejűleg kikeményítik. A modell elkészítése után a hordozóanyagot vizes oldattal eltávolítjuk. A használt gyanták hasonlóak a sztereolitográfiához (STL). A polyjet a következő előnyökkel rendelkezik a sztereolitográfiával szemben: 1.) Nincs szükség az alkatrészek tisztítására. 2.) Nincs szükség utókezelésre 3.) Kisebb rétegvastagság is lehetséges, így jobb felbontást kapunk és finomabb alkatrészeket tudunk gyártani. • FUSED DEPOSITION MODELING: FDM-nek is nevezik, ennél a módszernél a robot által vezérelt extruderfej két alapvető irányban mozog egy asztal felett. A kábelt szükség szerint leengedjük és felemeljük. A fejen lévő fűtött szerszám nyílásából hőre lágyuló szálat extrudálnak, és egy kezdeti réteget helyeznek fel egy hab alapra. Ezt az extruderfej hajtja végre, amely előre meghatározott útvonalon halad. A kezdeti réteg után az asztalt leeresztik, és a következő rétegeket egymásra rakják. Egy bonyolult alkatrész gyártásakor néha tartószerkezetekre van szükség, hogy a lerakódás bizonyos irányban folytatódhasson. Ezekben az esetekben a hordozóanyagot kevésbé sűrű filamentközökkel extrudálják egy rétegen, így az gyengébb, mint a modellanyag. Ezek a tartószerkezetek az alkatrész elkészülte után később feloldhatók vagy letörhetők. Az extruder szerszám méretei meghatározzák az extrudált rétegek vastagságát. Az FDM eljárás lépcsős felületű alkatrészeket állít elő ferde külső síkon. Ha ez az érdesség elfogadhatatlan, vegyi gőzpolírozás vagy fűtött szerszám használható ezek simítására. Még egy polírozó viasz is rendelkezésre áll bevonóanyagként, hogy kiküszöbölje ezeket a lépéseket és ésszerű geometriai tűréseket érjen el. • SZELEKTÍV LÉZERES SZINTEREZÉS: SLS-nek is nevezik, az eljárás polimer, kerámia vagy fémporok szelektív zsugorításán alapul egy tárgyba. A feldolgozókamra alján két henger található: egy részfelépítésű henger és egy poradagoló henger. Az előbbit fokozatosan leengedjük oda, ahol a szinterezett rész képződik, az utóbbit pedig fokozatosan felemeljük, hogy egy görgős mechanizmuson keresztül port szállítson az alkatrész-hengerbe. Először egy vékony porréteget raknak le a részből álló hengerben, majd egy lézersugarat erre a rétegre fókuszálnak, nyomon követve és megolvasztva / szinterezve egy adott keresztmetszetet, amely ezután szilárd anyaggá szilárdul. A por olyan területek, amelyeket nem ér el a lézersugár, laza marad, de továbbra is támogatja a szilárd részt. Ezután egy újabb porréteget raknak le, és a folyamatot többször megismételve megkapják az alkatrészt. A végén a laza porszemcséket lerázzuk. Mindezt folyamatirányító számítógép hajtja végre a gyártandó alkatrész 3D CAD programja által generált utasítások segítségével. Különféle anyagok, mint például polimerek (például ABS, PVC, poliészter), viasz, fémek és kerámiák, megfelelő polimer kötőanyagokkal lerakhatók. • ELECTRON-BEAM OLVASZTÁS: Hasonló a szelektív lézeres szinterezéshez, de elektronsugarat használnak a titán vagy kobaltkrómpor olvasztására, hogy vákuumban prototípusokat készítsenek. Néhány fejlesztés történt ennek az eljárásnak a rozsdamentes acélokon, alumíniumon és rézötvözeteken való végrehajtására. Ha az előállított alkatrészek kifáradási szilárdságát növelni kell, másodlagos eljárásként az alkatrészgyártást követő melegizosztatikus préselést alkalmazzuk. • HÁROMDIMENZIÓS NYOMTATÁS: 3DP-vel is jelölve, ennél a technikánál a nyomtatófej szervetlen kötőanyagot visz fel egy nemfémes vagy fémpor rétegre. A porágyat hordozó dugattyú fokozatosan leereszkedik, és minden lépésben a kötőanyagot rétegenként rakják le, és a kötőanyag megolvasztja. A felhasznált poranyagok polimer keverékek és rostok, öntödei homok, fémek. Különböző kötőfejek egyidejű és különböző színű kötőanyagokkal többféle színt kaphatunk. Az eljárás hasonló a tintasugaras nyomtatáshoz, de a színes lap készítése helyett egy színes, háromdimenziós objektumot kapunk. Az előállított alkatrészek porózusak lehetnek, ezért szinterezést és fémbeszivárgást igényelhetnek a sűrűség és a szilárdság növelése érdekében. A szinterezés leégeti a kötőanyagot, és összeolvad a fémporokkal. Fémek, például rozsdamentes acél, alumínium, titán felhasználhatók az alkatrészek gyártásához, és infiltrációs anyagként általában rezet és bronzot használunk. Ennek a technikának az a szépsége, hogy a bonyolult és mozgó szerelvények is nagyon gyorsan előállíthatók. Például egy fogaskerék-szerelvény, egy csavarkulcs, mint szerszám készíthető, és mozgó és forgó alkatrészei készen állnak a használatra. Az összeállítás különböző alkatrészei különböző színekkel és egy csapásra gyárthatók. Töltse le brosúránkat a következő címen:Fém 3D nyomtatás alapjai • KÖZVETLEN GYÁRTÁS és GYORS SZERSZÁMZÁS: A tervezés kiértékelése és hibaelhárítása mellett gyors prototípusokat alkalmazunk a termékek közvetlen gyártásához vagy a termékekben való közvetlen alkalmazáshoz. Más szóval, a gyors prototípuskészítést be lehet építeni a hagyományos folyamatokba, hogy jobbak és versenyképesebbek legyenek. Például a gyors prototípuskészítés mintákat és formákat hozhat létre. Az olvadó és égető polimer mintái, amelyeket gyors prototípuskészítési műveletekkel hoztak létre, összeállíthatók beruházási öntéshez és befektethetők. Egy másik megemlítendő példa a 3DP használata kerámiaöntvényhéj előállítására, és ennek felhasználása héjöntési műveletekhez. Még fröccsöntő formák és formabetétek is előállíthatók gyors prototípuskészítéssel, és sok hetes vagy hónapos formakészítési időt takaríthatunk meg. Ha csak a kívánt alkatrész CAD fájlját elemezzük, akkor szoftver segítségével elkészíthetjük a szerszámgeometriát. Íme néhány népszerű gyors szerszámozási módszerünk: RTV (szobahőmérsékletű vulkanizálás) FORMÁZÁS / URETÁNÖNTÉS: Gyors prototípuskészítéssel elkészíthető a kívánt alkatrész mintája. Ezután ezt a mintát vonják be elválasztószerrel, és folyékony RTV gumit öntenek a mintára, hogy elkészítsék a formafeleket. Ezután ezeket a formafeleket folyékony uretánok fröccsöntésére használják. Az öntőforma élettartama rövid, csak 0 vagy 30 ciklus, de elegendő kis tételes gyártáshoz. ACES (acetál tiszta epoxi szilárd) Fröccsöntés: Gyors prototípus-készítési technikák, például sztereolitográfia segítségével fröccsöntő formákat gyártunk. Ezek a formák nyitott végű héjak, amelyek lehetővé teszik az olyan anyagokkal való feltöltést, mint az epoxi, az alumíniummal töltött epoxi vagy a fémek. A penész élettartama ismét több tíz vagy legfeljebb száz alkatrészre korlátozódik. SZÓRALT FÉM SZERSZÁMOLÁSI FOLYAMAT: Gyors prototípuskészítést és mintát készítünk. A mintafelületre cink-alumínium ötvözetet szórunk és bevonjuk. A fémbevonattal ellátott mintát ezután egy lombikba helyezik, és epoxival vagy alumíniummal töltött epoxival öntik be. Végül eltávolítják, és két ilyen formafelet készítve egy komplett fröccsöntési formát kapunk. Ezeknek a formáknak hosszabb élettartamuk van, bizonyos esetekben az anyagtól és a hőmérséklettől függően több ezer darab alkatrészt készíthetnek. KEELTOOL ELJÁRÁS: Ezzel a technikával 100 000-10 millió ciklus élettartamú formákat lehet előállítani. Gyors prototípuskészítéssel RTV formát készítünk. Ezután a formát megtöltjük A6-os szerszámacél porból, volfrám-karbidból és polimer kötőanyagból álló keverékkel, és hagyjuk kikeményedni. Ezt az öntőformát ezután felmelegítik, hogy a polimer leégjen, és a fémporok megolvadjanak. A következő lépés a réz beszivárgása a végső forma előállításához. Szükség esetén másodlagos műveletek, például megmunkálás és polírozás is elvégezhető a formán a jobb méretpontosság érdekében. _cc781905-5cde-3194-bb3b-136bad_cf58bad CLICK Product Finder-Locator Service ELŐZŐ OLDAL
- Composites, Composite Materials Manufacturing, Fiber Reinforced
Composites, Composite Materials Manufacturing, Particle and Fiber Reinforced, Cermets, Ceramic & Metal Composite, Glass Fiber Reinforced Polymer, Lay-Up Process Kompozitok és kompozit anyagok gyártása Egyszerűen definiálva a KOMPOZITOK vagy KOMPOZIT ANYAGOK olyan anyagok, amelyek két vagy több anyagból állnak, eltérő fizikai vagy kémiai tulajdonságokkal, de kombinálva olyan anyaggá válnak, amely különbözik az alkotó anyagoktól. Rá kell mutatnunk, hogy az alkotó anyagok a szerkezetben különállóak és különállóak maradnak. A kompozit anyagok gyártása során az a cél, hogy olyan terméket kapjunk, amely felülmúlja az összetevőit, és egyesíti az egyes összetevők kívánt tulajdonságait. Mint például; szilárdság, kis súly vagy alacsonyabb ár lehet a motiváló tényező a kompozit tervezése és gyártása mögött. Az általunk kínált kompozit típusok részecske-erősítésű kompozitok, szálerősítésű kompozitok, beleértve a kerámia-mátrix / polimer-mátrix / fém-mátrix / szén-szén / hibrid kompozitokat, szerkezeti és laminált és szendvics-szerkezetű kompozitokat és nanokompozitokat. A kompozit anyagok gyártásában alkalmazott gyártási technikák a következők: Pultruzió, prepreg gyártási eljárások, fejlett szálelhelyezés, száltekercselés, testreszabott szálelhelyezés, üvegszálas permetezési eljárás, tuftelés, lanxid eljárás, z-tűzés. Sok kompozit anyag két fázisból áll, a mátrixból, amely folytonos és körülveszi a másik fázist; és a diszpergált fázist, amelyet a mátrix vesz körül. Javasoljuk, hogy kattintson ideTöltsd le sematikus illusztrációinkat az AGS-TECH Inc. által gyártott kompozitokról és kompozit anyagokról. Ez segít jobban megérteni az alább közölt információkat. • RÉSZECSKEL MEGERŐSÍTETT KOMPOZITOK: Ez a kategória két típusból áll: nagy szemcsés kompozitok és diszperziósan erősített kompozitok. Az előbbi típusnál a részecske-mátrix kölcsönhatások sem atomi, sem molekuláris szinten nem kezelhetők. Ehelyett a kontinuum mechanika érvényes. Másrészt a diszperziós szilárdságú kompozitokban a részecskék általában sokkal kisebbek, több tíz nanométeres tartományban. A nagy szemcsés kompozit példája a polimerek, amelyekhez töltőanyagokat adtak. A töltőanyagok javítják az anyag tulajdonságait, és a polimer térfogatának egy részét gazdaságosabb anyaggal helyettesíthetik. A két fázis térfogati hányada befolyásolja a kompozit viselkedését. A nagy szemcsés kompozitokat fémekkel, polimerekkel és kerámiákkal használják. A CERMETS a kerámia/fém kompozitok példái. A legelterjedtebb cermetünk a keményfém. Tűzálló karbid kerámiából, például volfrám-karbid részecskékből áll egy fém mátrixában, például kobaltban vagy nikkelben. Ezeket a keményfém kompozitokat széles körben használják vágószerszámként edzett acélhoz. A kemény karbid részecskék felelősek a forgácsolásért, szívósságukat pedig a képlékeny fémmátrix fokozza. Így mindkét anyag előnyeit egyetlen kompozitban kapjuk meg. Az általunk használt nagy részecskékből álló kompozitok másik gyakori példája a korom részecskék, amelyeket vulkanizált gumival keverünk össze, így nagy szakítószilárdságú, szívósságú, szakítószilárdságú és kopásállóságú kompozitot kapunk. A diszperziós szilárdságú kompozitra példa a fémek és fémötvözetek, amelyeket egy nagyon kemény és inert anyag finom részecskéinek egyenletes diszperziójával erősítettek meg és edzettek. Ha nagyon kis alumínium-oxid-pelyheket adunk az alumínium-fémmátrixhoz, szinterezett alumíniumport kapunk, amely fokozott magas hőmérsékleti szilárdsággal rendelkezik. • SZÁLLAL MEGERŐSÍTETT KOMPOZITOK: A kompozitok ezen kategóriája valójában a legfontosabb. Az elérendő cél a nagy szilárdság és merevség egységsúlyra vonatkoztatva. A szálak összetétele, hossza, orientációja és koncentrációja ezekben a kompozitokban kritikus fontosságú ezen anyagok tulajdonságainak és hasznosságának meghatározásában. Három szálcsoportot használunk: bajusz, rost és huzal. A WHISKERS nagyon vékony és hosszú egykristályok. A legerősebb anyagok közé tartoznak. Néhány példa a whisker anyagokra a grafit, szilícium-nitrid, alumínium-oxid. A FIBRES viszont többnyire polimerek vagy kerámiák, és polikristályos vagy amorf állapotban vannak. A harmadik csoport a finomhuzalok, amelyek viszonylag nagy átmérőjűek, és gyakran acélból vagy volfrámból állnak. A dróttal megerősített kompozit példája az autógumik, amelyek acélhuzalt tartalmaznak a gumi belsejében. A mátrix anyagától függően a következő kompozitokat kínáljuk: POLIMER-MATRIX KOMPOZITOK: Ezek polimer gyantából és szálakból készülnek, mint erősítő összetevő. Ezeknek az üvegszállal megerősített polimer (GFRP) kompozitok egy alcsoportja folytonos vagy nem folytonos üvegszálakat tartalmaz egy polimer mátrixon belül. Az üveg nagy szilárdságú, gazdaságos, könnyen szálká alakítható és kémiailag semleges. Hátránya korlátozott merevségük és merevségük, az üzemi hőmérséklet csak 200-300 Celsius fokig terjed. Az üvegszál alkalmas autókarosszériákhoz és szállítóeszközökhöz, tengeri járművek karosszériájához, tárolókonténerekhez. A korlátozott merevség miatt nem alkalmasak űrrepülésre vagy hidak készítésére. A másik alcsoport a Carbon Fiber-Reforced Polymer (CFRP) kompozit. Itt a szén a szálanyagunk a polimer mátrixban. A szén magas fajlagos modulusáról és szilárdságáról ismert, valamint arról, hogy képes ezeket magas hőmérsékleten fenntartani. A szénszálak szabványos, közepes, nagy és ultranagy szakítószilárdságú modulokat kínálnak számunkra. Ezen túlmenően a szénszálak változatos fizikai és mechanikai jellemzőket kínálnak, ezért alkalmasak különféle egyedi mérnöki alkalmazásokhoz. A CFRP kompozitok sport- és szabadidős felszerelések, nyomástartó edények és repülőgép-szerkezeti alkatrészek gyártására is alkalmasak. Egy másik alcsoport, az aramidszál-erősítésű polimer kompozitok szintén nagy szilárdságú és modulusú anyagok. Erősség-tömeg arányuk kiemelkedően magas. Az aramid szálak KEVLAR és NOMEX márkanéven is ismertek. Feszültség alatt jobban teljesítenek, mint más polimer szálas anyagok, de tömörítésük gyengébb. Az aramid szálak szívósak, ütésállóak, kúszás- és kifáradásállóak, magas hőmérsékleten stabilak, kémiailag semlegesek, kivéve az erős savakkal és lúgokkal szemben. Az aramid szálakat széles körben használják sportszerekben, golyóálló mellényekben, gumiabroncsokban, kötelekben, száloptikai kábelköpenyekben. Más szálerősítő anyagok is léteznek, de ezeket kisebb mértékben használják. Ezek elsősorban a bór, a szilícium-karbid, az alumínium-oxid. Másrészt a polimer mátrix anyaga szintén kritikus. Ez határozza meg a kompozit maximális üzemi hőmérsékletét, mivel a polimer általában alacsonyabb olvadási és bomlási hőmérséklettel rendelkezik. A poliésztereket és a vinil-észtereket széles körben használják polimer mátrixként. Gyantákat is használnak, amelyek kiváló nedvességállósággal és mechanikai tulajdonságokkal rendelkeznek. Például a poliimid gyanta körülbelül 230 Celsius-fokig használható. FÉM-MÁTRIX KOMPOZITOK: Ezekben az anyagokban képlékeny fémmátrixot használunk, és az üzemi hőmérsékletek általában magasabbak, mint az alkotóelemeik. A polimer-mátrix kompozitokhoz képest ezek magasabb üzemi hőmérsékletűek, nem gyúlékonyak, és jobban ellenállnak a szerves folyadékokkal szemben. Ezek azonban drágábbak. Erősítő anyagok, például bordák, részecskék, folytonos és nem folytonos szálak; és mátrix anyagokat, például réz, alumínium, magnézium, titán, szuperötvözetek általánosan használják. Alkalmazási példák: alumínium-oxiddal és szénszálakkal megerősített alumíniumötvözet mátrixból készült motoralkatrészek. KERÁMIA-MATRIX KOMPOZITOK: A kerámia anyagok kiemelkedően jó magas hőmérsékleti megbízhatóságukról ismertek. Mindazonáltal nagyon törékenyek, és alacsony a törési szilárdságuk. Az egyik kerámia részecskéinek, rostjainak vagy bajuszainak beágyazásával egy másik kerámia mátrixába nagyobb törési szilárdságú kompozitokat érhetünk el. Ezek a beágyazott anyagok alapvetően gátolják a repedések terjedését a mátrixon belül bizonyos mechanizmusok révén, mint például a repedéscsúcsok eltérítése vagy a repedések felületein átívelő hidak kialakítása. Például a szilícium-karbid bordákkal megerősített alumínium-oxidokat vágószerszám-betétként használják keményfémötvözetek megmunkálásához. Ezek jobb teljesítményt mutatnak a cementált karbidokhoz képest. SZÉN-SZÉN KOMPOZITOK: Mind az erősítés, mind a mátrix karbon. Nagy szakítószilárdságuk van 2000 Celsius-fok feletti magas hőmérsékleten, kúszásállóságuk, nagy törési szilárdságuk, alacsony hőtágulási együtthatójuk és nagy hővezető képességük van. Ezek a tulajdonságok ideálissá teszik azokat a hősokkállóságot igénylő alkalmazásokhoz. A szén-szén kompozitok gyengesége azonban a magas hőmérsékleten történő oxidációval szembeni sebezhetőségük. Tipikus példák a felhasználásra a forró présformák, a fejlett turbinamotor-alkatrészek gyártása. HIBRID KOMPOZITOK: Két vagy több különböző típusú szálat kevernek össze egyetlen mátrixban. Így a tulajdonságok kombinációjával új anyagot lehet szabni. Példa erre, amikor szén- és üvegszálakat is beépítenek egy polimer gyantába. A szénszálak alacsony sűrűségű merevséget és szilárdságot biztosítanak, de drágák. Az üveg viszont olcsó, de hiányzik belőle a szénszál merevsége. Az üveg-szén hibrid kompozit erősebb és szívósabb, és alacsonyabb költséggel gyártható. SZÁLLAL ERŐSÍTETT KOMPOZITOK FELDOLGOZÁSA: Folytonos szálerősítésű műanyagokhoz, amelyekben egyenletes eloszlású, azonos irányba orientált szálak a következő technikákat alkalmazzuk. PULTRUZIÓ: Folyamatos hosszúságú és állandó keresztmetszetű rudakat, gerendákat és csöveket gyártanak. A folytonos szálas előfonatokat hőre keményedő gyantával impregnálják, és egy acél szerszámon keresztül húzzák a kívánt alakra. Ezután egy precíziósan megmunkált keményítőszerszámon mennek keresztül, hogy elérjék végső formáját. Mivel a keményítőszerszámot felmelegítik, a gyantamátrixot kikeményíti. A lehúzók áthúzzák az anyagot a matricákon. A behelyezett üreges magok segítségével csöveket és üreges geometriákat tudunk előállítani. A pultrúziós módszer automatizált, és magas termelési arányt kínál számunkra. Bármilyen hosszúságú termék gyártható. PREPREG GYÁRTÁSI FOLYAMAT: A Prepreg egy részlegesen kikeményedett polimer gyantával előimpregnált folytonos szálerősítő. Széles körben használják szerkezeti alkalmazásokhoz. Az anyag szalag formájában érkezik, és szalagként szállítják. A gyártó közvetlenül megformázza, és gyanta hozzáadása nélkül teljesen kikeményedik. Mivel a prepregek szobahőmérsékleten térhálósodási reakciókon mennek keresztül, 0 Celsius-fok vagy ennél alacsonyabb hőmérsékleten tárolják őket. Használat után a megmaradt szalagokat alacsony hőmérsékleten tároljuk. Hőre lágyuló és hőre keményedő gyantákat használnak, és gyakoriak a szén, aramid és üveg erősítőszálai. A prepreg használatához először eltávolítják a hordozó hátlappapírt, majd a gyártást úgy végzik el, hogy a prepreg szalagot egy szerszámozott felületre fektetik (a lay-up folyamat). A kívánt vastagság eléréséhez több réteget is fel lehet rakni. Gyakori gyakorlat az, hogy a szálak orientációját váltogatják kereszt- vagy szögrétegű laminátum előállításához. Végül hőt és nyomást alkalmazunk a kikeményítéshez. Mind a kézi megmunkálást, mind az automatizált folyamatokat alkalmazzák a prepregek vágásához és a felrakáshoz. FILAMENT TEKERCSELÉSE: A folytonos erősítő szálak pontosan vannak elrendezve egy előre meghatározott mintában, hogy kövessék az üreges és általában a kör alakú formát. A szálak először egy gyantafürdőn mennek keresztül, majd egy automata rendszerrel feltekerik egy tüskére. Többszöri tekercselés után megkapjuk a kívánt vastagságot, és a térhálósítást szobahőmérsékleten vagy kemencében végezzük. Most a tüskét eltávolítjuk, és a terméket szétszereljük. A száltekercselés nagyon magas szilárdság/tömeg arányt kínálhat a szálak kerületi, spirális és poláris mintázatú tekercselésével. A csövek, tartályok, burkolatok ezzel a technikával készülnek. • SZERKEZETI KOMPOZITOK: Általában ezek homogén és kompozit anyagokból állnak. Ezért ezek tulajdonságait az alkotó anyagok és az elemek geometriai kialakítása határozza meg. Íme a főbb típusok: LAMINÁRIS KOMPOZITOK: Ezek a szerkezeti anyagok kétdimenziós lapokból vagy panelekből készülnek, előnyösen nagy szilárdságú irányokkal. A rétegeket egymásra rakják és összeragasztják. A két merőleges tengely nagy szilárdságú irányainak váltogatásával olyan kompozitot kapunk, amely a kétdimenziós síkban mindkét irányban nagy szilárdságú. A rétegek szögeinek beállításával a kívánt irányban szilárdságú kompozit készíthető. A modern sílécek így készülnek. SZendvicspanelek: Ezek a szerkezeti kompozitok könnyűek, de mégis nagy merevséggel és szilárdsággal rendelkeznek. A szendvicspanelek két külső lemezből állnak, amelyek merev és erős anyagból, például alumíniumötvözetből, szálerősítésű műanyagból vagy acélból készülnek, a külső lapok között pedig egy mag. A magnak könnyűnek kell lennie, és legtöbbször alacsony rugalmassági modulussal kell rendelkeznie. A népszerű maganyagok a merev polimer habok, a fa és a méhsejt. A szendvicspaneleket széles körben használják az építőiparban tetőfedő anyagként, padló- vagy falanyagként, valamint a repülőgépiparban is. • NANOKOMPOZITOK: Ezek az új anyagok mátrixba ágyazott nanoméretű részecskékből állnak. Nanokompozitok felhasználásával olyan gumianyagokat állíthatunk elő, amelyek nagyon jól gátolják a levegő behatolását, miközben a gumi tulajdonságai változatlanok. CLICK Product Finder-Locator Service ELŐZŐ OLDAL
- Machine Elements Manufacturing, Gears, Gear Drives, Bearings, Keys, Splines
Machine Elements Manufacturing, Gears, Gear Drives, Bearings, Keys, Splines, Pins, Shafts, Seals, Fasteners, Clutch, Cams, Followers, Belts, Couplings, Shafts Gépelemek gyártása Olvass tovább Szíjak és láncok és kábelmeghajtó egység Olvass tovább Fogaskerekek és hajtóművek Olvass tovább Tengelykapcsolók és csapágyak gyártása Olvass tovább Keys & Splines & Pins gyártása Olvass tovább Bütykök és követők, összeköttetések és racsnis kerekek gyártása Olvass tovább Tengelyek gyártása Olvass tovább Mechanikus tömítések gyártása Olvass tovább Tengelykapcsoló és fék szerelvény Olvass tovább Rögzítőelemek gyártása Olvass tovább Egyszerű gépek összeszerelése A GÉPELEMEK a gép elemi alkatrészei. Ezek az elemek három alapvető típusból állnak: 1.) Szerkezeti elemek, beleértve a keretelemeket, csapágyakat, tengelyeket, bordákat, rögzítőelemeket, tömítéseket és kenőanyagokat. 2.) A mozgást különféle módokon vezérlő mechanizmusok, mint például fogaskerekek, szíj- vagy lánchajtások, tengelykapcsolók, bütykös és követő rendszerek, fékek és tengelykapcsolók. 3.) Vezérlőelemek, például gombok, kapcsolók, indikátorok, érzékelők, működtetők és számítógép-vezérlők. Az általunk kínált gépelemek többsége általános méretekre van szabványosítva, de egyedi gyártású gépelemek is rendelkezésre állnak speciális alkalmazásokhoz. A gépelemek testreszabása történhet a letölthető katalógusainkban szereplő meglévő terveken vagy vadonatúj terveken. A prototípus és a gépelemek gyártása továbbvihető, ha a tervet mindkét fél jóváhagyta. Ha új gépelemeket kell tervezni és gyártani, ügyfeleink vagy e-mailben elküldik nekünk a saját terveiket és mi átnézzük azokat jóváhagyás céljából, vagy kérnek tőlünk, hogy tervezzünk gépelemeket az alkalmazásukhoz. Utóbbi esetben ügyfeleink minden inputját felhasználjuk, és a gépelemeket megtervezzük és a véglegesített tervrajzokat jóváhagyásra elküldjük ügyfeleinknek. A jóváhagyás után az első cikkeket, majd a végleges terv szerint gyártjuk le a gépelemeket. A munka bármely szakaszában, ha egy adott gépelem terv nem megfelelően teljesít a terepen (ami ritka), a teljes projektet átnézzük, és szükség esetén megrendelőinkkel közösen módosítjuk. Bevett gyakorlatunk, hogy szükség esetén titoktartási megállapodást (NDA) kötünk ügyfeleinkkel a gépelemek vagy bármely más termék tervezésére vonatkozóan. Miután egy adott vásárló gépelemeit egyedi tervezéssel és gyártással végeztük, termékkódot rendelünk hozzá, és csak a terméket birtokló ügyfelünknek gyártjuk és értékesítjük. A gépelemeket a kifejlesztett szerszámokkal, öntőformákkal és eljárásokkal sokszorosítjuk, ahányszor szükség van rá, és amikor ügyfelünk újrarendeli. Más szóval, miután egy egyedi gépelemet megterveztek és gyártottak az Ön számára, a szellemi tulajdont, valamint az összes szerszámot és formát lefoglaljuk és korlátlan ideig raktáron tartjuk az Ön számára, és a termékeket az Ön kívánsága szerint reprodukáljuk. Ügyfeleinknek mérnöki szolgáltatásokat is kínálunk a gépelemek kreatív kombinálásával olyan alkatrészré vagy összeállításba, amely egy alkalmazást szolgál ki, és megfelel vagy meghaladja ügyfeleink elvárásait. A gépelemeinket gyártó üzemek ISO9001, QS9000 vagy TS16949 minősítéssel rendelkeznek. Ezenkívül a legtöbb termékünk rendelkezik CE vagy UL jelöléssel, és megfelel a nemzetközileg releváns szabványoknak, mint például az ISO, SAE, ASME, DIN. Kérjük, kattintson az almenükre, hogy részletes információkat kapjon gépelemeinkről, beleértve: - Szíjak, láncok és kábelmeghajtók - Fogaskerekek és hajtóművek - Tengelykapcsolók és csapágyak - Keys & Splines & csapok - Cams & Linkages - Aknák - Mechanikus tömítések - Ipari tengelykapcsoló és fék - Rögzítőelemek - Egyszerű gépek Ügyfeleink, tervezőink és gépelemeket is tartalmazó új termékek fejlesztői számára referencia brosúrát készítettünk. Megismerhet néhány gyakran használt kifejezést a gépalkatrészek tervezésében: Töltse le a tervezők és mérnökök által használt általános gépészeti kifejezések brosúráját Gépelemeink számos területen megtalálhatók, mint például az ipari gépek, automatizálási rendszerek, teszt- és méréstechnikai berendezések, szállítóeszközök, építőipari gépek és gyakorlatilag bárhol, ahol csak eszébe jut. Az AGS-TECH az alkalmazástól függően különféle anyagokból fejleszt és gyárt gépelemeket. A gépelemekhez használt anyagok a játékokhoz használt öntött műanyagoktól az ipari gépekhez használt, edzett és speciális bevonatú acélokig terjedhetnek. Tervezőink a legmodernebb professzionális szoftvereket és tervezőeszközöket használják a gépelemek fejlesztéséhez, figyelembe véve az olyan részleteket, mint a fogaskerekek fogainak szögei, feszültségek, kopási arányok stb. Kérjük, görgessen át almenüinket, és töltse le termékprospektusainkat és katalógusainkat, hogy megtudja, megtalálja-e az alkalmazásához szükséges kész gépelemeket. Ha nem talál megfelelőt az alkalmazásához, kérjük, jelezze felénk, és együttműködünk Önnel az Ön igényeinek megfelelő gépelemek fejlesztésében és legyártásában. Ha leginkább a gyártási képességeink helyett a mérnöki és kutatás-fejlesztési képességeink érdeklik, akkor kérjük, látogassa meg weboldalunkat http://www.ags-engineering.com ahol részletesebb információkat talál a tervezésről, termékfejlesztésről, folyamatfejlesztésről, mérnöki tanácsadási szolgáltatásainkról és egyebekről CLICK Product Finder-Locator Service ELŐZŐ OLDAL
- Glass and Ceramic Manufacturing, Hermetic Packages, Seals, Bonding
Glass and Ceramic Manufacturing, Hermetic Packages Seals and Bonding, Tempered Bulletproof Glass, Blow Moulding, Optical Grade Glass, Conductive Glass, Molding Üveg és kerámia formázás és formázás Az általunk kínált üveggyártás típusa: konténerüveg, üvegfúvás, üvegszál- és cső- és rúd, háztartási és ipari üvegáru, lámpa és izzó, precíziós üvegöntés, optikai alkatrészek és szerelvények, sík- és lemez- és floatüveg. Mind a kézi, mind a gépi alakítást végezzük. Népszerű műszaki kerámiagyártási eljárásaink a préselés, izosztatikus préselés, melegizosztatikus préselés, melegsajtolás, csúszóöntés, szalagöntés, extrudálás, fröccsöntés, zöld megmunkálás, szinterezés vagy égetés, gyémántcsiszolás, hermetikus összeállítások. Javasoljuk, hogy kattintson ide Töltsd le az AGS-TECH Inc. által készített üvegformázó és -formázó folyamatok sematikus illusztrációit. Töltsd le az AGS-TECH Inc. műszaki kerámiagyártási folyamatainak sematikus illusztrációit. Ezek a fotókat és vázlatokat tartalmazó letölthető fájlok segítenek jobban megérteni az alábbiakban közölt információkat. • KONTÉNERES ÜVEG GYÁRTÁS: A gyártáshoz automatizált PRESS ÉS FLOW, valamint FÚVÓ ÉS FÚVÓ soraink vannak. A fúvási és fúvási folyamat során egy golyót beleejtünk az üres formába, és felülről sűrített levegő fújásával kialakítjuk a nyakat. Közvetlenül ezt követően a sűrített levegőt másodszor fújják át a másik irányból a tartály nyakán keresztül, hogy kialakítsák a palack előformáját. Ezt az előformát azután átvisszük a tényleges formába, felmelegítjük, hogy meglágyuljon, és sűrített levegőt alkalmazunk, hogy az előforma végleges formáját kapja. Pontosabban, nyomás alá helyezik, és a fúvóforma üregének falaihoz nyomják, hogy felvegye kívánt formáját. Végül a legyártott üvegtartályt egy izzítókemencébe helyezik át az ezt követő újramelegítés és az öntés során keletkező feszültségek eltávolítása céljából, és szabályozott módon lehűtik. A préselési és fúvásos módszerrel az olvadt golyókat egy parison formába (blank formába) helyezik, és a parison formába (üres forma) préselik. A nyersdarabokat ezután fúvóformákba helyezik, és a fent „Fúvási és fúvási eljárás” részben leírt eljáráshoz hasonlóan fújják. Az ezt követő lépések, például a lágyítás és a stresszoldás hasonlóak vagy azonosak. • ÜVEGFÚVÁS: Üvegtermékeket gyártunk hagyományos kézi fúvással, valamint automatizált berendezésekkel sűrített levegővel. Egyes megrendeléseknél hagyományos fúvás szükséges, mint például üvegművészeti alkotások, vagy kisebb számú, laza tűréssel rendelkező alkatrészt igénylő projektek, prototípus/demó projektek stb. A hagyományos üvegfúvás során egy üreges fémcsövet belemerítenek egy olvadt üvegedénybe, és a csövet forgatják az üveganyag bizonyos mennyiségének összegyűjtésére. A csővégen összegyűlt üveget laposvasra hengereljük, tetszőlegesen formázzuk, meghosszabbítjuk, felmelegítjük és levegővel fújjuk. Ha kész, formába szúrjuk és levegőt fújunk. A formaüreg nedves, hogy elkerüljük az üveg fémmel való érintkezését. A vízfilm párnaként működik közöttük. A kézi fúvás munkaigényes lassú folyamat, és csak prototípusok vagy nagy értékű cikkek készítésére alkalmas, olcsó darabonkénti nagy volumenű megrendelésekre nem. • HÁZTARTÁSI ÉS IPARI ÜVEGÁRUK GYÁRTÁSA: Különféle üveganyagok felhasználásával sokféle üvegáru készül. Egyes poharak hőállóak és alkalmasak laboratóriumi üvegedények készítésére, míg vannak, amelyek elég jók a mosogatógépben való többszöri kibíráshoz, és alkalmasak háztartási termékek készítésére. A Westlake gépek használatával naponta több tízezer darab ivópohár készül. Az egyszerűsítés kedvéért az olvadt üveget vákuum segítségével gyűjtik össze, és formákba helyezik az előformák elkészítéséhez. Ezután levegőt fújnak a formákba, ezeket átteszik egy másik formába és újra levegőt fújnak, és az üveg elnyeri végleges formáját. A kézi fúváshoz hasonlóan ezeket a formákat vízzel nedvesen tartják. A további nyújtás a befejező művelet része, ahol a nyak kialakítása történik. A felesleges üveg leégett. Ezt követően a fent leírt szabályozott újramelegítési és hűtési folyamat következik. • ÜVEGCSÖVEK ÉS RÚDAK ALAKÍTÁSA: Az üvegcsövek gyártásához használt fő eljárások a DANNER és a VELLO eljárások. A Danner-eljárás során a kemencéből származó üveg folyik, és egy tűzálló anyagokból készült ferde hüvelyre esik. A hüvely forgó üreges tengelyen vagy fúvócsövön van hordva. Ezután az üveget a hüvely köré tekerik, és sima réteget képeznek, amely lefolyik a hüvelyen és a szár hegyén. Csőalakítás esetén üreges hegyű fúvócsövön keresztül fújják át a levegőt, rúdformázásnál pedig tömör csúcsokat használunk a tengelyen. A csöveket vagy rudakat ezután hordozógörgőkre kell húzni. Az üvegcsövek falvastagságának és átmérőjének méreteit a kívánt értékekre állítjuk be a hüvely átmérőjének és a légnyomásnak a kívánt értékre állításával, a hőmérséklet, az üveg áramlási sebességének és a húzás sebességének beállításával. A Vello üvegcső gyártási folyamata viszont olyan üvegből áll, amely kijut a kemencéből egy edénybe egy üreges tüskével vagy haranggal. Az üveg ezután áthalad a tüske és a tál közötti légteren, és cső alakot ölt. Ezt követően görgőkön keresztül egy húzógéphez jut, és lehűtik. A hűtősor végén a vágás és a végső feldolgozás történik. A cső méretei a Danner eljáráshoz hasonlóan állíthatók. A Danner-Vello-eljárás összehasonlításakor elmondható, hogy a Vello-eljárás jobban illeszkedik a nagy mennyiségű gyártáshoz, míg a Danner-eljárás jobban illeszkedik a precíz, kisebb volumenű csőrendelésekhez. • LEMEZ- ÉS SÍK- ÉS ÚSZTÓÜVEG FELDOLGOZÁSA: Nagy mennyiségű síküvegünk van, vastagságuk szubmilmétertől néhány centiméterig terjed. Lapos szemüvegeink szinte optikailag tökéletesek. Speciális bevonattal ellátott üvegeket kínálunk, például optikai bevonattal, ahol kémiai gőzleválasztásos technikát alkalmaznak olyan bevonatok felvitelére, mint a tükröződésgátló vagy tükörbevonat. Szintén gyakoriak az átlátszó, vezetőképes bevonatok. Rendelkezésre állnak továbbá hidrofób vagy hidrofil bevonatok az üvegen, valamint olyan bevonat, amely az üveget öntisztítóvá teszi. Az edzett, golyóálló és laminált üvegek is népszerű termékek. Az üveget a kívánt formára vágjuk a kívánt tűréshatárokkal. Más másodlagos műveletek, például síküveg hajlítása vagy hajlítása is elérhető. • PRECÍZIÓS ÜVEGÖNTÉS: Ezt a technikát leginkább precíziós optikai alkatrészek gyártására használjuk, anélkül, hogy szükség lenne drágább és időigényesebb technikákra, mint például csiszolás, átlapolás és polírozás. Ez a technika nem mindig elegendő a legjobb optikák legjobbjának elkészítéséhez, de bizonyos esetekben, mint a fogyasztói termékek, digitális fényképezőgépek, orvosi optikák, olcsóbb megoldás lehet nagy volumenű gyártáshoz. Emellett előnye van a többi üvegformázó technikával szemben, ahol összetett geometriákra van szükség, például aszférák esetében. Az alapfolyamat magában foglalja a formánk alsó oldalának megtöltését az üveglappal, a folyamatkamra kiürítését az oxigén eltávolításához, a forma közeli záródását, a szerszám és az üveg gyors és izoterm felmelegítését infravörös fénnyel, a formafelek további zárását. a meglágyult üveget lassan, szabályozott módon a kívánt vastagságig préselni, végül az üveget lehűteni, a kamrát nitrogénnel feltölteni és a terméket eltávolítani. Ebben a folyamatban kulcsfontosságú a pontos hőmérsékletszabályozás, a szerszámzárási távolság, a szerszámzáró erő, a forma és az üveganyag tágulási együtthatóinak összehangolása. • OPTIKAI ÜVEG ALKATRÉSZEK ÉS ÖSSZETÉTELEK GYÁRTÁSA: A precíziós üvegöntés mellett számos értékes eljárást alkalmazunk magas színvonalú optikai alkatrészek és szerelvények előállítására, igényes alkalmazásokhoz. Az optikai minőségű üvegek csiszolása, lelapolása és polírozása finom speciális csiszoló iszapokban művészet és tudomány az optikai lencsék, prizmák, laposüvegek és egyebek előállításához. A felületi síkság, hullámosság, simaság és hibamentes optikai felületek sok tapasztalatot igényelnek az ilyen eljárásokban. A környezetben bekövetkezett kis változások a specifikációkon túli termékeket eredményezhetnek, és leállíthatják a gyártósort. Vannak esetek, amikor az optikai felület egyetlen tiszta ronggyal történő letörlésével a termék megfelel a specifikációknak, vagy nem sikerül a teszten. Néhány népszerű üveganyag az olvasztott szilícium-dioxid, kvarc, BK7. Az ilyen alkatrészek összeszerelése is speciális szaktudást igényel. Néha speciális ragasztókat használnak. Néha azonban az optikai érintkezésnek nevezett technika a legjobb választás, és nem használ semmilyen anyagot a csatlakoztatott optikai üvegek közé. Fizikailag érintkező sík felületekből áll, amelyek ragasztó nélkül rögzíthetők egymáshoz. Egyes esetekben mechanikus távtartókat, precíziós üvegrudakat vagy golyókat, bilincseket vagy megmunkált fém alkatrészeket használnak az optikai alkatrészek bizonyos távolságra és bizonyos geometriai orientációjú egymáshoz való összeszerelésére. Vizsgáljuk meg néhány népszerű technikánkat csúcskategóriás optika gyártására. KÖSZÖLÉS ÉS FELÉPÍTÉS ÉS POLÍROZÁS: Az optikai alkatrész durva formáját egy üres üveg csiszolásával kapjuk. Ezt követően az optikai alkatrészek durva felületének forgatásával és dörzsölésével történik a lapolás és polírozás a kívánt felületi formájú szerszámokhoz. Az optika és a formázó szerszámok közé apró csiszolórészecskéket és folyadékot tartalmazó szuszpenziót öntenek. Az ilyen szuszpenziókban a csiszolószemcsék mérete a kívánt síkosság mértéke szerint választható meg. A kritikus optikai felületek kívánt alaktól való eltérését a használt fény hullámhosszaiban fejezzük ki. Nagy pontosságú optikánk tized hullámhosszú (Wavelength/10) tűréssel rendelkezik, vagy ennél is szűkebb. A felületi profilon kívül a kritikus felületeket szkenneljük és értékeljük egyéb felületi jellemzők és hibák, például méretek, karcolások, forgácsok, gödrök, foltok stb. szempontjából. A környezeti feltételek szigorú ellenőrzése az optikai gyártási padlóban, valamint a kiterjedt metrológiai és tesztelési követelmények a legmodernebb berendezésekkel teszik ezt az ipar kihívást jelentő ágává. • MÁSODLAGOS FOLYAMATOK AZ ÜVEGGYÁRTÁSBAN: Ismét csak az Ön fantáziája szab határt, amikor az üveg másodlagos és befejező folyamatairól van szó. Íme néhány közülük: - Üvegbevonatok (optikai, elektromos, tribológiai, termikus, funkcionális, mechanikai...). Például megváltoztathatjuk az üveg felületi tulajdonságait úgy, hogy például visszaveri a hőt, hogy hűvösen tartsa az épület belsejét, vagy nanotechnológiával infravörös elnyelővé tehetjük az egyik oldalát. Ez segít melegen tartani az épületek belsejét, mivel az üveg legkülső felületi rétege elnyeli az infravörös sugárzást az épületen belül, és visszasugározza azt a belső térbe. -maratás on üveg - Alkalmazott kerámia címkézés (ACL) -Metszés -Lángpolírozás - Vegyi polírozás -Festés MŰSZAKI KERÁMIA GYÁRTÁSA • KONCENTRÁLÁS: A szerszámba zárt szemcsés porok egytengelyű tömörítéséből áll. • HOT PRESSING: Hasonló a préseléshez, de hőmérséklet hozzáadásával fokozza a tömörítést. A port vagy a tömörített előformát grafit szerszámba helyezik, és egytengelyű nyomást alkalmaznak, miközben a szerszámot magas hőmérsékleten, például 2000 C-on tartják. A hőmérséklet eltérő lehet a feldolgozott kerámiapor típusától függően. Bonyolult formák és geometriák esetén további utólagos feldolgozásra, például gyémántcsiszolásra lehet szükség. • IZOZTATIKUS PRESSZELÉS: A szemcsés por- vagy préselt tömörítéseket légmentesen záródó edényekbe helyezik, majd zárt nyomástartó edénybe, amelyben folyadék van. Ezt követően a nyomástartó edény nyomásának növelésével tömörítik őket. Az edényben lévő folyadék egyenletesen adja át a nyomást a légmentesen záródó tartály teljes felületén. Az anyag így egyenletesen tömörül, és felveszi a rugalmas tartály alakját, valamint belső profilját és jellemzőit. • MELEG IZOSZTATIKUS PRESSING : Hasonlóan az izosztatikus préseléshez, de a nyomás alatti gázatmoszféra mellett magas hőmérsékleten szintereljük a tömörítést. A forró izosztatikus préselés további tömörítést és nagyobb szilárdságot eredményez. • CSÚSZTÓÖNTÉS / DRAIN ÖNTÉS: A formát mikrométer méretű kerámiaszemcsékből és hordozófolyadékból álló szuszpenzióval töltjük meg. Ezt a keveréket „csúszásnak” nevezik. A forma pórusos, ezért a keverékben lévő folyadékot a formába szűrik. Ennek eredményeként az öntőforma belső felületein öntvény képződik. Szinterezés után az alkatrészeket ki lehet venni a formából. • SZALAGÖNTÉS: Kerámia szalagokat gyártunk úgy, hogy kerámia iszapot öntünk sík mozgó hordozófelületekre. Az iszapok kerámiaporokat tartalmaznak, amelyeket más vegyszerekkel kevernek össze megkötési és szállítási célokra. Ahogy az oldószer elpárolog, sűrű és rugalmas kerámialapok maradnak hátra, amelyeket tetszés szerint vághatunk vagy hengerelhetünk. • EXTRÚZIÓS FORMÁZÁS: Más extrudálási eljárásokhoz hasonlóan a kerámiapor kötőanyagokkal és egyéb vegyszerekkel alkotott lágy keverékét egy szerszámon vezetik át, hogy elnyerje keresztmetszeti alakját, majd a kívánt hosszúságúra vágják. A folyamat hideg vagy melegített kerámia keverékekkel történik. • ALACSONY NYOMÁSÚ Fröccsöntés: Kerámiapor keveréket készítünk kötőanyagokkal és oldószerekkel, és olyan hőmérsékletre hevítjük, hogy könnyen benyomható és a szerszám üregébe kényszeríthető. Amint a formázási ciklus befejeződött, az alkatrész kilökődik, és a kötőanyag leég. Fröccsöntéssel nagy mennyiségben, gazdaságosan tudunk bonyolult alkatrészeket előállítani. A lyukak, amelyek a milliméter apró töredékét teszik ki 10 mm vastag falon, lehetségesek, menetek további megmunkálás nélkül is lehetségesek, +/- 0,5%-os tűrések lehetségesek, de megmunkáláskor még ennél is alacsonyabbak. 0,5 mm-től 12,5 mm-ig terjedő falvastagságok, valamint 6,5 mm-től 150 mm-es hosszig terjedő falvastagságok lehetségesek. • ZÖLD MEGMUNKÁLÁS : Ugyanazokkal a fémmegmunkáló szerszámokkal megmunkálhatjuk a préselt kerámia anyagokat, amíg azok még puhaak, mint a kréta. +/- 1%-os tűrés lehetséges. A jobb tűrés érdekében gyémántcsiszolást alkalmazunk. • SZINTEREZÉS vagy ÉGEZÉS: A szinterezés lehetővé teszi a teljes tömörítést. Jelentős zsugorodás lép fel a zöld kompakt alkatrészeken, de ez nem nagy probléma, hiszen az alkatrész és a szerszámok tervezésénél figyelembe vesszük ezeket a méretváltozásokat. A porszemcsék egymáshoz kötődnek, és a tömörítési folyamat által kiváltott porozitás nagymértékben eltűnik. • GYÉMÁNTKÖSZÖRÉS: A világ legkeményebb anyagát, a „gyémántot” kemény anyagok, például kerámiák csiszolására használják, és precíziós alkatrészeket állítanak elő. Mikrométeres tűrések és nagyon sima felületek érhetők el. Költsége miatt csak akkor vesszük figyelembe ezt a technikát, amikor valóban szükségünk van rá. • A HERMETIKUS EGYSÉGEK azok, amelyek gyakorlatilag nem teszik lehetővé az anyagok, szilárd anyagok, folyadékok vagy gázok cseréjét a határfelületek között. A hermetikus tömítés légmentes. Például a hermetikus elektronikus házak azok, amelyek a becsomagolt készülék érzékeny belső tartalmát nedvességtől, szennyeződésektől vagy gázoktól sértetlenül tartják. Semmi sem 100%-ban hermetikus, de amikor hermetikusról beszélünk, akkor gyakorlatilag azt értjük, hogy olyan mértékben van hermetikus, hogy a szivárgás mértéke olyan alacsony, hogy a készülékek normál környezeti körülmények között nagyon hosszú ideig biztonságosak. Hermetikus szerelvényeink fém, üveg és kerámia alkatrészekből állnak, fém-kerámia, kerámia-fém-kerámia, fém-kerámia-fém, fém-fém, fém-üveg, fém-üveg-fém, üveg-fém-üveg, üveg- fém és üveg az üveghez és a fém-üvegkerámia kötés minden egyéb kombinációja. Például fémmel bevonhatjuk a kerámia alkatrészeket, így azok erősen kötődhetnek a szerelvény többi alkatrészéhez, és kiváló tömítőképességgel rendelkeznek. Az optikai szálak vagy átvezetések fémmel való bevonásával és a burkolatokhoz való forrasztásával vagy keményforrasztásával kapcsolatos know-how-val rendelkezünk, így a gázok nem jutnak át vagy szivárognak be a házakba. Ezért elektronikus burkolatok gyártására használják őket, hogy az érzékeny eszközöket tokba zárják és megvédjék őket a külső légkörtől. A kiváló tömítési tulajdonságaikon kívül egyéb tulajdonságok, mint például a hőtágulási együttható, deformációállóság, gázmentesség, nagyon hosszú élettartam, nem vezetőképesség, hőszigetelő tulajdonságok, antisztatikus tulajdonságok stb. bizonyos alkalmazásokhoz az üveg és a kerámia anyagokat válasszák. A kerámia-fém szerelvényeket, hermetikus tömítést, vákuum átvezetéseket, magas és ultramagas vákuum- és folyadékszabályozási alkatrészeket gyártó létesítményünkkel kapcsolatos információkat itt találja:Hermetic Components Factory Brosúra CLICK Product Finder-Locator Service ELŐZŐ OLDAL
- Wire & Spring Forming, Shaping, Welding, Assembly of Wires, Coil, CNC
Wire & Spring Forming, Shaping, Welding, Assembly of Wires, Coil Compression Extension Torsion Flat Springs, Custom Wires, Helical Springs at AGS-TECH Inc. Huzal és rugó alakítás Gyártunk egyedi huzalokat, huzalösszeállítást, kívánt 2D és 3D formára formált vezetékeket, dróthálókat, hálót, burkolatokat, kosarat, kerítést, drótrugót, lapos rugót; csavarás, összenyomás, feszítés, lapos rugók és így tovább. Eljárásaink a következők: huzal- és rugóalakítás, huzalhúzás, alakítás, hajlítás, hegesztés, keményforrasztás, forrasztás, lyukasztás, hengerezés, fúrás, élletörés, köszörülés, menetvágás, bevonat, négycsúszás, csúszás, tekercselés, tekercselés, felborítás. Javasoljuk, hogy kattintson ide Töltsd le az AGS-TECH Inc. huzal- és rugóalakítási folyamatainak sematikus illusztrációit. Ez a fotókat és vázlatokat tartalmazó letölthető fájl segít jobban megérteni az alábbiakban közölt információkat. • HUROZÁS: Húzóerők segítségével megnyújtjuk a fémanyagot és áthúzzuk egy szerszámon, hogy csökkentsük az átmérőt és növeljük a hosszát. Néha egy sor szerszámot használunk. Képesek vagyunk matricákat készíteni minden vezetékhosszhoz. Nagy szakítószilárdságú anyag felhasználásával nagyon vékony huzalokat húzunk. Hidegen és melegen megmunkált vezetékeket egyaránt kínálunk. • DRÓTALAKÍTÁS: Egy tekercs méretű huzalt meghajlítanak és hasznos termékké formálják. Lehetőségünk van vezetékek kialakítására minden mérőeszközből, beleértve a vékony szálakat, valamint a vastag vezetékeket, például az autók alváza alatti rugóként használtakat. A huzalalakításhoz használt berendezések a kézi és CNC huzalformázók, tekercselők, erőgépek, négyszán, többcsúszka. Eljárásaink a következők: húzás, hajlítás, egyengetés, simítás, nyújtás, vágás, felborítás, forrasztás és hegesztés és keményforrasztás, összeszerelés, tekercselés, húzás (vagy szárnyozás), átszúrás, huzalmenet, fúrás, letörés, köszörülés, bevonat és felületkezelés. Csúcstechnológiás berendezéseink bármilyen formájú és szűk tűréshatárú nagyon összetett tervek kialakítására beállíthatók. Különféle végtípusokat kínálunk szerű gömb alakú, hegyes vagy lesarkított végeket vezetékeihez. A legtöbb huzalformázó projektünk minimális vagy nulla szerszámköltséggel jár. A minták átfutási ideje általában nap. A huzalformák kialakításának/konfigurációjának módosítása nagyon gyorsan elvégezhető. • RUGÓALAKÍTÁS: Az AGS-TECH rugók széles választékát gyártja, beleértve: - Torziós / Dupla torziós rugó - Feszítő / nyomórugó - Állandó / Változó rugó -Tekercs és csavarrugó - Lapos és lapos rugó - Balance Spring -Belleville mosógép -Negátor tavasz -Progresszív sebességű tekercsrugó - Hullám tavasz -Volute Spring -Kúpos rugók - Tavaszi gyűrűk -Clock Springs -Klipek Különféle anyagokból gyártunk rugókat, és az alkalmazásodnak megfelelően tudunk segíteni. A leggyakoribb anyagok a rozsdamentes acél, króm-szilícium, magas széntartalmú acél, olajos temperált alacsony széntartalmú acél, króm-vanádium, foszforbronz, titán, berillium rézötvözet, magas hőmérsékletű kerámia. A rugók gyártása során különféle technikákat alkalmazunk, beleértve a CNC tekercselést, hideg tekercselést, meleg tekercselést, edzést, simítást. A huzalformázásnál fentebb már említett egyéb technikák is gyakoriak rugós gyártási műveleteink során. • KIVITELEZÉSI SZOLGÁLTATÁSOK VEZETÉKEKNEK ÉS RUGÓKHOZ: Termékeit sokféleképpen tudjuk befejezni az Ön választásától és igényeitől függően. Néhány elterjedt eljárás, amit kínálunk: festés, porfestés, bevonat, vinilbemerítés, eloxálás, feszültségmentesítés, hőkezelés, sörét, simítás, kromát, electroless nikkel, passziválás, sült zománc, műanyag bevonat , plazma tisztítás. CLICK Product Finder-Locator Service ELŐZŐ OLDAL
- Sheet Metal Forming Fabrication, Stamping, Punching, Deep Drawing, CNC
Sheet Metal Forming and Fabrication, Stamping, Punching, Bending, Progressive Die, Spot Welding, Deep Drawing, Metal Blanking and Slitting at AGS-TECH Inc. Bélyegzés és fémlemez gyártás Kínálunk fémlemez sajtolást, alakítást, alakítást, hajlítást, lyukasztást, vágást, hasítást, perforálást, bevágást, rágcsálást, borotválkozást, préselést, gyártást, mélyhúzást egy-/egylöketű szerszámokkal, valamint progresszív matricákat és fonást, gumialakítást és hidroformálás; lemezvágás vízsugár, plazma, lézer, fűrész, láng segítségével; lemezszerelés hegesztéssel, ponthegesztéssel; fémlemezcső kidudorodása és hajlítása; fémlemez felületkezelés, beleértve a mártással vagy szórással történő festést, az elektrosztatikus porfestést, az eloxálást, a bevonatot, a porlasztást és egyebeket. Szolgáltatásaink a gyors fémlemez prototípuskészítéstől a nagy volumenű gyártásig terjednek. Javasoljuk, hogy kattintson ideTöltsd le az AGS-TECH Inc. által készített lemezgyártási és bélyegzési folyamatok sematikus illusztrációit. Ez segít jobban megérteni az alábbiakban közölt információkat. • LEMEZVÁGÁS: VÁGÁST és VÁLASZTÁST kínálunk. A levágások egy-egy pályán vágják le a fémlemezt, és alapvetően nincs anyagpazarlás, az elválasztásoknál viszont nem lehet pontosan beágyazni a formát, így bizonyos mennyiségű anyag elvész. Az egyik legkedveltebb eljárásunk a LYUKGÁS, amikor a fémlemezből kör alakú vagy más alakú anyagdarabot vágunk ki. A kivágott darab hulladék. A lyukasztás másik változata a SLOTTING, ahol téglalap alakú vagy hosszúkás lyukakat ütnek ki. A BLANKOLÁS ezzel szemben ugyanaz a folyamat, mint a lyukasztás, azzal a különbséggel, hogy a kivágott darab megkülönbözteti a munkát és a megtartást. A FINE BLANKING, a kivágás kiváló változata, szoros tűréssel és egyenes sima élekkel vágásokat hoz létre, és nincs szükség másodlagos műveletekre a munkadarab tökéletesítéséhez. Egy másik gyakran használt eljárás a HAJTÁS, amely egy nyírási eljárás, ahol a fémlemezt két egymással szemben lévő körkéssel vágják egyenes vagy íves úton. A konzervnyitó egy egyszerű példa a hasítási folyamatra. Egy másik nálunk népszerű eljárás a PERFORÁLÁS, ahol sok kerek vagy más alakú lyukat lyukasztanak a fémlemezbe meghatározott mintázatban. A perforált termékek tipikus példája a fémszűrők sok lyukkal a folyadékok számára. A NOTCHING, egy másik fémlemez vágási eljárás során a munkadarab szélétől vagy máshonnan eltávolítjuk az anyagot, és befelé vágjuk, amíg el nem érjük a kívánt formát. Ez egy progresszív folyamat, ahol minden művelet egy újabb darabot távolít el, amíg a kívánt kontúrt el nem éri. Kisebb gyártási sorozatok esetén néha egy viszonylag lassabb eljárást alkalmazunk, amelyet NIBBLING-nek neveznek, és amely számos, egymást átfedő lyukak gyors kilyukasztásából áll, hogy nagyobb, összetettebb vágást készítsünk. A PROGRESSIVE CUTTING során különböző műveletek sorozatát alkalmazzuk egyetlen vágás vagy egy bizonyos geometria eléréséhez. Végül a borotválkozás egy másodlagos folyamat segít javítani a már elkészített vágások éleit. A forgácsok, durva élek levágására használják lemezmunkákon. • LEMEZHAJLÍTÁS: A vágás mellett a hajlítás elengedhetetlen folyamat, amely nélkül a legtöbb terméket nem tudnánk előállítani. Többnyire hidegen megmunkálási művelet, de néha melegen vagy melegen is végrehajtják. Ehhez a művelethez a legtöbb esetben szerszámokat és prést használunk. A PROGRESSZÍV HAJLÍTÁS során különféle lyukasztási és stancolási műveleteket alkalmazunk egyetlen hajlítás vagy egy bizonyos geometria eléréséhez. Az AGS-TECH különféle hajlítási eljárásokat alkalmaz, és a választást a munkadarab anyagától, méretétől, vastagságától, kívánt hajlítási méretétől, sugarától, görbületétől és hajlítási szögétől, a hajlítás helyétől, a művelet gazdaságosságától, a gyártási mennyiségtől függően választja… stb. V-hajlítást használunk, ahol egy V alakú lyukasztó a fémlemezt a V alakú szerszámba kényszeríti és meghajlítja. Nagyon hegyes és tompaszögekhez, valamint a közöttük lévő szögekhez is jó, beleértve a 90 fokot is. Törlőszerszámok segítségével EDGE BENDINGET végzünk. Berendezéseink lehetővé teszik, hogy akár 90 foknál nagyobb szögeket is elérjünk. Élhajlításnál a munkadarabot egy nyomópárna és a matrica közé helyezik, a hajlítási terület a szerszám élén található, és a munkadarab többi részét a space konzolos gerendához hasonlóan tartják. Amikor a lyukasztó a konzolos részre hat, az a szerszám széle fölé hajlik. A FLANGING egy élhajlítási eljárás, amely 90 fokos szöget eredményez. A művelet fő célja az éles élek kiküszöbölése és az alkatrészek összekapcsolását megkönnyítő geometriai felületek kialakítása. A GYÖNTÖZÉS, egy másik gyakori élhajlítási eljárás, amely az alkatrész szélén felgöndörödik. A BESZÉRÍTÉS viszont azt eredményezi, hogy a lap széle teljesen magára van hajlítva. A VARRASZTÁS során két rész élét egymásra hajlítják és összeillesztik. A KETTŐS VARRASZTÁS viszont víz- és légmentes fémlemez csatlakozásokat biztosít. Hasonlóan az élhajlításhoz, a ROTARY BENDING nevű eljárás során egy hengert használnak, amely a kívánt szögben van kivágva és lyukasztóként szolgál. Ahogy az erő átadódik a lyukasztóra, az a munkadarabbal együtt záródik. A henger hornya a kívánt szöget adja a konzolos résznek. A horony szöge lehet kisebb vagy nagyobb, mint 90 fok. A AIR BENDING során nincs szükségünk arra, hogy az alsó szerszámnak ferde hornya legyen. A fémlemezt két felület támasztja alá egymással ellentétes oldalon és bizonyos távolságban. A lyukasztó ezután erőt fejt ki a megfelelő helyen, és meghajlítja a munkadarabot. A CHANNEL BENDING csatorna alakú lyukasztóval és matricával történik, az U-BEND pedig egy U alakú lyukasztóval. OFFSET BENDING eltolásokat hoz létre a fémlemezen. A ROLL BENDING egy olyan technika, amely alkalmas vastag megmunkáláshoz és nagy fémlemezdarabok hajlításához, három tekercset használ a lemezek kívánt görbületére történő adagolásához és hajlításához. A tekercsek úgy vannak elrendezve, hogy a munka kívánt hajlítását elérjék. A hengerek közötti távolságot és szöget szabályozzák a kívánt eredmény elérése érdekében. A mozgatható tekercs lehetővé teszi a görbület szabályozását. A TUBE FORMING egy másik népszerű fémlemez hajlítási művelet, amely több szerszámot is magában foglal. A csöveket több művelet után kapjuk meg. A HULLÁZÁS hajlítási műveletekkel is történik. Alapvetően ez a szimmetrikus hajlítás szabályos időközönként egy teljes fémlemezen. A hullámosításhoz különféle formák használhatók. A hullámos fémlemez merevebb és jobban ellenáll a hajlításnak, ezért az építőiparban alkalmazható. LEMEZhengeralakítás, egy folyamatos gyártási eljárást alkalmaznak egy bizonyos geometriájú keresztmetszet hengerek segítségével történő hajlítására, és a munka szekvenciális lépésekben hajlításra kerül, az utolsó tekercs pedig befejezi a munkát. Egyes esetekben egyetlen tekercset, néhány esetben pedig több tekercset alkalmaznak. • KOMBINÁLT LEMEZVÁGÁSI ÉS HAJLÍTÁSI FOLYAMATOK: Ezek azok a folyamatok, amelyek egyszerre vágnak és hajlítanak. A PIERCING során egy lyukat hoznak létre egy hegyes lyukasztó segítségével. Ahogy a lyukasztó kiszélesíti a lyukat a lapon, az anyag egyidejűleg a lyuk belső karimájává hajlik. A kapott karimának fontos funkciói lehetnek. A LANCING művelet ezzel szemben levágja és meghajlítja a lapot, hogy megemelt geometriát hozzon létre. • FÉM CSŐ KIDUDRODÁSA ÉS HAJLÍTÁSA: A KIDUDRODÁS során az üreges cső egyes belső részei nyomás alatt állnak, ami a cső kidudorodását okozza. Mivel a cső a szerszám belsejében van, a kidudorodási geometriát a szerszám alakja szabályozza. A STRETCH BENDING során egy fémcsövet a cső tengelyével párhuzamos erők és hajlító erők segítségével megfeszítenek, hogy a csövet egy formatömb fölé húzzák. A DRAW BENDING során a csövet a végéhez közel rögzítjük egy forgó formatömbhöz, amely forgás közben hajlítja a csövet. Végül a NYOMÁSOS HAJLÍTÁS során a csövet erővel egy rögzített formázótömbhöz tartják, és egy szerszám hajlítja a formatömb fölé. • MÉLYRAJZÁS: Az egyik legnépszerűbb műveletünkben lyukasztót, hozzáillő szerszámot és üres tartót használunk. A fémlemez nyersdarabot a szerszámnyílás fölé helyezik, és a lyukasztó a nyersdarabtartó által tartott nyersdarab felé mozog. Miután érintkezésbe kerülnek, a lyukasztó a fémlemezt a szerszámüregbe kényszeríti a termék kialakításához. A mélyhúzási művelet a vágáshoz hasonlít, azonban a lyukasztó és a szerszám közötti hézag megakadályozza a lap elvágását. Egy másik tényező, amely biztosítja a lemez mélyhúzását és nem vágását, a szerszám és a lyukasztó lekerekített sarkai, amelyek megakadályozzák a nyírást és a vágást. A mélyhúzás nagyobb mértékű elérése érdekében egy REDRAWING folyamatot alkalmaznak, ahol egy következő mélyrajzolás történik egy olyan alkatrészen, amely már átesett egy mélyhúzási folyamaton. A REVERSE REDRAWING során a mélyen húzott részt megfordítják és az ellenkező irányba húzzák. A mélyrajzolás szabálytalan alakú tárgyakat, például kupolás, kúpos vagy lépcsős csészéket biztosíthat, A EMBOSSING-ban férfi és női matricapárt használunk, hogy lenyűgözzük a fémlemezt egy tervvel vagy forgatókönyvvel. • SPINNING : Olyan művelet, amelyben egy lapos vagy előre kialakított munkadarabot a forgó tüske és a farokrész között tartanak, és egy szerszám helyi nyomást fejt ki a munkára, miközben fokozatosan felfelé mozog a tüskén. Ennek eredményeként a munkadarab a tüskére tekerve felveszi a formáját. Ezt a technikát a mélyhúzás alternatívájaként használjuk, ahol a rendelési mennyiség kicsi, az alkatrészek nagyok (20 láb átmérőig) és egyedi ívekkel rendelkeznek. Annak ellenére, hogy a darabonkénti árak általában magasabbak, a CNC-fonás üzembe helyezési költségei alacsonyak a mélyhúzáshoz képest. Éppen ellenkezőleg, a mélyhúzás nagy kezdeti beruházást igényel a beállításhoz, de a darabonkénti költség alacsony, ha nagy mennyiségű alkatrészt gyártanak. Ennek a folyamatnak egy másik változata a NYÍRÁSOS FORGÁS, ahol a munkadarabon belül fémáramlás is van. A fémáramlás csökkenti a munkadarab vastagságát a folyamat során. Egy másik kapcsolódó eljárás a TUBE SPINNING, amelyet hengeres részeken alkalmaznak. Ebben a folyamatban is van fémáramlás a munkadarabon belül. Így a vastagság csökken, és a cső hossza megnő. Az eszköz mozgatásával funkciókat hozhat létre a cső belső vagy külső oldalán. • FÉMLEMEZ GUMIALAKÍTÁSA: A gumit vagy poliuretánt egy tartályszerszámba helyezik, és a munkadarabot a gumi felületére helyezik. Ezután egy ütést gyakorolnak a munkadarabra, és belenyomják a gumiba. Mivel a gumi által keltett nyomás alacsony, a gyártott alkatrészek mélysége korlátozott. Mivel a szerszámköltségek alacsonyak, az eljárás kis mennyiségű gyártásra alkalmas. • HIDROFORMÁZÁS: A gumialakításhoz hasonlóan ebben a folyamatban a fémlemezt lyukasztó nyomás alatt lévő folyadékká préselik egy kamrában. A fémlemez munkadarab a lyukasztó és a gumimembrán közé kerül. A membrán teljesen körülveszi a munkadarabot, és a folyadék nyomása rákényszeríti, hogy a lyukasztón kialakuljon. Ezzel a technikával a mélyhúzásnál is mélyebb húzások érhetők el. Gyártunk egylyukasztó szerszámokat, valamint progresszív matricákat, az Ön részétől függően. Az egylöketű sajtolószerszámok költséghatékony módszer nagy mennyiségű egyszerű fémlemez alkatrészek, például alátétek gyors előállítására. Bonyolultabb geometriák gyártásához progresszív szerszámokat vagy mélyhúzási technikát alkalmaznak. Esetétől függően vízsugaras, lézeres vagy plazmavágással olcsón, gyorsan és pontosan készítheti elő fémlemez alkatrészeit. Sok beszállítónak fogalma sincs ezekről az alternatív technikákról, vagy nincs is velük, ezért hosszadalmas és költséges szerszámok és szerszámok készítésének módjai vannak, amivel csak az ügyfelek időt és pénzt pazarolnak. Ha egyedi gyártású fémlemez alkatrészekre van szüksége, mint például házak, elektronikai házak stb., akár néhány napon belül, akkor vegye fel velünk a kapcsolatot a GYORS LEMEZ PROTOTÍPOZÁSI szolgáltatásunkért. CLICK Product Finder-Locator Service ELŐZŐ MENÜ
- Forging and Powdered Metallurgy, Die Forging, Heading, Hot Forging
Forging and Powdered Metallurgy, Die Forging, Heading, Hot Forging, Impression Die, Near Net Shape, Swaging, Metal Hobbing, Riveting, Coining from AGS-TECH Inc. Fémkovácsolás és porkohászat Az általunk kínált FÉMKOVÍTÁSI eljárások a következők: hideg és meleg sajtolószerszám, nyitott és zárt sajtolószerszám, nyomószerszám és vaku nélküli kovácsolás, cogging, fullering, élezés és precíziós kovácsolás, hálóközeli alakzat , hajlítás, kovácsolás, fém kovácsolás, préselés és tekercselés, radiális és orbitális és gyűrűs és izoterm kovácsolás, éremelés, szegecselés, fémgolyós kovácsolás, fémlyukasztás, méretezés, nagy energiájú kovácsolás. PORKOHÁSZATI és PORFELDOLGOZÁSI technikáink a porpréselés és szinterezés, impregnálás, infiltráció, meleg- és hideg izosztatikus préselés, fém fröccsöntés, hengeres tömörítés, porhengerlés, porextrudálás, laza szinterezés, szikraszinterelés, melegsajtolás. Javasoljuk, hogy kattintson ide Töltsd le az AGS-TECH Inc. kovácsolási folyamatainak sematikus illusztrációit. Töltsd le sematikus illusztrációinkat a porkohászati folyamatokról az AGS-TECH Inc.-től. Ezek a fotókat és vázlatokat tartalmazó letölthető fájlok segítenek jobban megérteni az alábbiakban közölt információkat. A fémkovácsolásnál nyomóerők fejtenek ki, és az anyag deformálódik és a kívánt formát kapják. Az iparban a legelterjedtebb kovácsolt anyagok a vas és az acél, de számos más anyagot, például alumíniumot, rezet, titánt, magnéziumot is széles körben kovácsolnak. A kovácsolt fém alkatrészek a tömített repedések és zárt üres terek mellett javított szemcseszerkezettel rendelkeznek, így az így nyert alkatrészek szilárdsága nagyobb. A kovácsolással olyan alkatrészeket állítanak elő, amelyek súlyukhoz képest jelentősen erősebbek, mint az öntéssel vagy megmunkálással készült alkatrészek. Mivel a kovácsolt alkatrészeket úgy alakítják ki, hogy a fémet a végső formába folyjanak, a fém olyan irányított szemcseszerkezetet vesz fel, amely az alkatrészek kiváló szilárdságát magyarázza. Más szóval, a kovácsolási eljárással előállított alkatrészek jobb mechanikai tulajdonságokat mutatnak, mint az egyszerű öntött vagy megmunkált alkatrészek. A fémkovácsolt anyagok súlya a kis könnyű alkatrészektől a több százezer fontig terjedhet. A kovácsolt anyagokat főként mechanikailag megerőltető alkalmazásokhoz gyártjuk, ahol nagy igénybevételek érik autóalkatrészeket, hajtóműveket, munkaeszközöket, kéziszerszámokat, turbinatengelyeket, motorkerékpár-felszereléseket. Mivel a szerszámozási és beállítási költségek viszonylag magasak, ezt a gyártási eljárást csak nagy volumenű gyártáshoz és kis mennyiségű, de nagy értékű kritikus alkatrészekhez, például repülőgép-futóművekhez ajánljuk. A szerszámköltség mellett a nagy mennyiségű kovácsolt alkatrészek gyártási ideje hosszabb lehet néhány egyszerű megmunkált alkatrészéhez képest, de a technika kulcsfontosságú az olyan alkatrészek esetében, amelyek rendkívüli szilárdságot igényelnek, mint például csavarok, anyák, speciális alkalmazás. kötőelemek, autóipari, targonca, daru alkatrészek. • HOT DIE és COLD DIE kovácsolás: A forró sajtolást, ahogy a neve is sugallja, magas hőmérsékleten végzik, ezért a hajlékonyság magas és az anyag szilárdsága alacsony. Ez megkönnyíti a deformációt és a kovácsolást. Ellenkezőleg, a hideg sajtolást alacsonyabb hőmérsékleten végzik, és nagyobb erőket igényel, ami húzószilárdságot, jobb felületminőséget és a gyártott alkatrészek pontosságát eredményezi. • NYITOTT SZERKESZTŐ és LENYOMÁSOS KOVÁCSÍTÁS: Nyílt sajtolószerszám-kovácsolásnál a matricák nem korlátozzák az összenyomandó anyagot, míg a nyomószerszám-kovácsolásnál a szerszámon belüli üregek korlátozzák az anyagáramlást, miközben a kívánt formára kovácsolják. UPSET FORGING vagy más néven UPSETTING, ami valójában nem ugyanaz, de nagyon hasonló folyamat, a egy nyitott szerszámos eljárás, ahol a munkadarabot két lapos szerszám közé szorítják, és nyomóerő csökkenti a magasságát. Ahogy a magasság reduced, a munkadarab szélessége nő. FEJEZET, a felborított kovácsolási folyamat során hengeres idomanyagot használnak, amely a végén fel van törve, és a keresztmetszete helyben megnő. A fejlécben az alapanyagot a szerszámon keresztül táplálják, kovácsolják, majd hosszra vágják. A művelet nagy mennyiségű rögzítőelem gyors előállítására képes. Többnyire hidegmegmunkálási művelet, mert szögvégek, csavarvégek, anyák és csavarok készítésére használják, ahol az anyagot meg kell erősíteni. Egy másik nyitott szerszámeljárás a COGGING, ahol a munkadarabot lépések sorozatában kovácsolják, minden egyes lépésben az anyag összenyomódását és a nyitott szerszám ezt követő mozgását eredményezi a munkadarab hosszában. Minden lépésnél a vastagság csökken, a hossz pedig kis mértékben nő. A folyamat egy ideges diákhoz hasonlít, aki kis lépésekkel végig harapja a ceruzáját. A FULLERING nevű eljárás egy másik nyitott szerszámos kovácsolási módszer, amelyet gyakran alkalmazunk korábbi lépésként az anyag elosztására a munkadarabban, mielőtt más fémkovácsolási műveleteket végeznének. Akkor használjuk, ha a munkadarab több kovácsolási műveletet igényel. A művelet során a domború felületű szerszám deformálódik, és fémkiáramlást okoz mindkét oldalra. A telítéshez hasonló folyamat, a SZÉLELÉS ezzel szemben homorú felületű nyitott szerszámot tartalmaz a munkadarab deformálásához. A szegélyezés egyben a későbbi kovácsolási műveletek előkészítő folyamata is arra készteti az anyagot, hogy mindkét oldalról a közepén lévő területre áramoljon. A LENYOMÁSOS KOVOCÍTÁS vagy a ZÁRT FORGÁSKOVÍTÁS, ahogyan ezt is nevezik, olyan szerszámot/formát használ, amely összenyomja az anyagot és korlátozza annak áramlását magában. A szerszám bezárul, és az anyag felveszi a szerszám/formaüreg alakját. A PRECÍZIÓS KOVÁCSÍTÁS, egy speciális felszerelést és formát igénylő eljárás, olyan alkatrészeket állít elő, amelyeknél nincs vagy nagyon kevés a villanás. Más szóval, az alkatrészek közel végleges méretekkel rendelkeznek. Ebben a folyamatban egy jól ellenőrzött mennyiségű anyagot óvatosan helyeznek be és helyeznek el a formába. Ezt a módszert olyan összetett formák esetén alkalmazzuk, amelyek vékony metszetekkel, kis tűrésekkel és merülési szögekkel rendelkeznek, és amikor a mennyiségek elég nagyok ahhoz, hogy indokolják a szerszám- és berendezésköltségeket. • HANGMENTES KOVÁCSÍTÁS: A munkadarabot úgy helyezik a szerszámba, hogy az üregből semmilyen anyag ne tudjon kifolyni, hogy vakut képezzen. Így nincs szükség nem kívánt vakuvágásra. Ez egy precíziós kovácsolási eljárás, ezért a felhasznált anyag mennyiségének szigorú ellenőrzését igényli. • FÉM HAJTÁS vagy RADIÁLIS KOVÍTÁS: A munkadarabot a kerület mentén stancolják és kovácsolják. A belső munkadarab geometriájának kovácsolásához tüske is használható. A lengési művelet során a munkadarab másodpercenként általában több ütést kap. A hegesztéssel előállított tipikus elemek a hegyes hegyű szerszámok, kúpos rudak, csavarhúzók. • FÉM PIRCING: Ezt a műveletet gyakran alkalmazzuk kiegészítő műveletként az alkatrészek gyártása során. A munkadarab felületén átszúrással lyuk vagy üreg keletkezik anélkül, hogy áttörne rajta. Kérjük, vegye figyelembe, hogy a szúrás különbözik a fúrástól, amely átmenő lyukat eredményez. • HOBBING: A kívánt geometriájú lyukasztót benyomják a munkadarabba, és a kívánt alakú üreget hoznak létre. Ezt az ütést főzőlapnak hívjuk. A művelet nagy nyomással jár, és hidegen hajtják végre. Ennek eredményeként az anyagot hidegen megmunkálják és húzásra keményedik. Ezért ez az eljárás nagyon alkalmas öntőformák, szerszámok és üregek gyártására más gyártási folyamatokhoz. A főzőlap gyártása után könnyen elkészíthető sok egyforma üreg anélkül, hogy egyenként meg kellene dolgozni őket. • TEkercs-kovácsolás vagy TEkercsalakítás: Két egymással szemben lévő hengert használnak a fémrész formálására. A munkadarabot betáplálják a tekercsekbe, a hengerek elfordítják és behúzzák a munkát a résbe, majd a munkadarabot a hengerek hornyolt részén továbbítják, és a nyomóerők adják az anyagnak a kívánt formát. Ez nem hengerlési folyamat, hanem kovácsolás, mert ez inkább diszkrét, mint folyamatos művelet. A tekercshornyokon lévő geometria a kívánt formára és geometriára kovácsolja az anyagot. Melegen hajtják végre. A kovácsolási eljárásnak köszönhetően kiemelkedő mechanikai tulajdonságokkal rendelkező alkatrészeket állít elő, ezért használjuk autóalkatrészek, például tengelyek gyártására, amelyeknek rendkívüli állóképességre van szükségük nehéz munkakörülmények között. • ORBITAL KOVÁCSOLÁS: A munkadarabot egy kovácsolószerszám üregébe helyezik, és egy felső szerszámmal kovácsolják, amely egy pályapályán halad, miközben egy ferde tengelyen forog. Minden fordulatnál a felső szerszám befejezi a nyomóerők kifejtését a teljes munkadarabra. Ezeket a fordulatokat többször megismételve elegendő kovácsolást hajtanak végre. Ennek a gyártási technikának az előnye az alacsony zajszint és a kisebb erőkifejtés. Más szóval, kis erőkkel meg lehet forgatni egy nehéz szerszámot egy tengely körül, hogy nagy nyomást fejtsünk ki a munkadarabnak a szerszámmal érintkező szakaszára. A tárcsa vagy kúp alakú részek néha jól illeszkednek ehhez a folyamathoz. • GYŰRŰ KOVÁCSÍTÁS: Gyakran használjuk varrat nélküli gyűrűk gyártására. A készletet a hosszra vágják, felborítják, majd végig átszúrják, hogy egy központi lyukat hozzon létre. Ezután tüskére teszik, és egy kovácsolószerszám felülről kalapálja, miközben a gyűrűt lassan forgatják, amíg el nem érik a kívánt méreteket. • SZEGECSÍTÉS: Az alkatrészek összeillesztésének elterjedt folyamata egy egyenes fémdarabbal kezdődik, amelyet előre elkészített lyukakba helyeznek az alkatrészeken keresztül. Ezt követően a fémdarab két végét megkovácsolják egy felső és alsó szerszám közötti csatlakozás összenyomásával. • ÉMÉLÉS: Egy másik népszerű eljárás, amelyet mechanikus préssel hajtanak végre, és nagy erőket fejt ki kis távolságon. Az „érmék” elnevezés a fémérmék felületére kovácsolt finom részletekből származik. Ez többnyire egy olyan termék megmunkálási folyamata, ahol finom részleteket nyernek a felületeken a szerszám által kifejtett nagy erő hatására, amely ezeket a részleteket a munkadarabra továbbítja. • FÉMGOLYÓKOVÍTÁS: Az olyan termékekhez, mint a golyóscsapágyak, kiváló minőségű, pontosan gyártott fémgolyókra van szükség. Az egyik technika, az úgynevezett SKEW ROLLING, két egymással szemben lévő hengert használunk, amelyek folyamatosan forognak, miközben az alapanyagot folyamatosan adagolják a tekercsekbe. A két tekercs egyik végén fémgömbök lökődnek ki termékként. A fémgolyós kovácsolás másik módszere a szerszám használata, amely a közéjük helyezett anyagkészletet a formaüreg gömb alakú formáját öltve összenyomja. Az előállított labdákhoz gyakran további lépésekre van szükség, például kikészítésre és polírozásra, hogy kiváló minőségű termékké váljanak. • IZORMÁLIS KOVÁCSÍTÁS / FORRÓ KOVÍTÁS: drága eljárás, amelyet csak akkor hajtanak végre, ha a haszon/költség értéke indokolt. Meleg megmunkálási folyamat, ahol a szerszámot körülbelül a munkadarab hőmérsékletére melegítik fel. Mivel mind a szerszám, mind a munka körülbelül azonos hőmérsékletű, nincs hűtés, és a fém áramlási jellemzői javulnak. A művelet jól illeszkedik szuperötvözetekhez és gyengébb kovácsolhatóságú anyagokhoz, valamint olyan anyagokhoz, amelyek a mechanikai tulajdonságok nagyon érzékenyek a kis hőmérsékleti gradiensekre és változásokra. • FÉM MÉRETEZÉS: Hideg kikészítési eljárás. Az anyagáramlás minden irányban korlátlan, kivéve azt az irányt, amelyben az erőt kifejtik. Ennek eredményeként nagyon jó felületminőség és pontos méretek érhetők el. • MAGAS ENERGIÁJÁBAN KOVÁCSOLÁS: A technika egy dugattyú karjára erősített felső szerszámot foglal magában, amelyet gyorsan tolnak, miközben az üzemanyag-levegő keveréket egy gyújtógyertya meggyújtja. Ez hasonlít az autómotorok dugattyúinak működésére. A forma nagyon gyorsan hozzáütődik a munkadarabhoz, majd az ellennyomásnak köszönhetően nagyon gyorsan visszatér eredeti helyzetébe. A mű néhány ezredmásodperc alatt megkovácsolódik, ezért nincs ideje kihűlni. Ez olyan nehezen kovácsolható alkatrészeknél hasznos, amelyek nagyon hőmérsékletérzékeny mechanikai tulajdonságokkal rendelkeznek. Más szóval a folyamat olyan gyors, hogy az alkatrészt végig állandó hőmérsékleten alakítják ki, és a forma/munkadarab határfelületein nem lesz hőmérséklet-gradiens. • A DIE FORGING során a fémet két egymáshoz illeszkedő acéltömb közé verik, amelyekben speciális formák vannak, úgynevezett matricák. Ha a fémet a matricák közé kalapálják, akkor ugyanolyan alakot vesz fel, mint a szerszámban lévő formák. Amikor eléri végleges formáját, kivesszük hűlni. Ez az eljárás erős alkatrészeket állít elő, amelyek precíz alakúak, de nagyobb befektetést igényelnek a speciális szerszámok esetében. A felborított kovácsolás megnöveli a fémdarab átmérőjét azáltal, hogy lelapítja. Általában kis alkatrészek készítésére használják, különösen kötőelemek, például csavarok és szögek fejének kialakítására. • PORKOHÁZAT / PORFELDOLGOZÁS: Ahogy a neve is sugallja, bizonyos geometriájú és alakú szilárd részek porokból történő előállítására szolgáló gyártási folyamatokat foglalja magában. Ha fémporokat használnak erre a célra, az a porkohászat területe, ha pedig nem fémporokat, akkor a porfeldolgozás. A szilárd alkatrészeket porokból állítják elő préseléssel és szintereléssel. A POR PRESSING a porok kívánt formájú tömörítésére szolgál. Először is, az elsődleges anyagot fizikailag porítják, és sok kis egyedi részecskére osztják. A porkeveréket a szerszámba töltik, és egy lyukasztó a por felé haladva a kívánt formára tömöríti. Többnyire szobahőmérsékleten végezzük, porsajtolással szilárd alkatrészt kapunk, amit zöld tömörítésnek neveznek. A tömöríthetőség javítására általában kötőanyagokat és kenőanyagokat használnak. Több ezer tonnás kapacitású hidraulikus prések segítségével porpréselésre is képesek vagyunk. Vannak kettős működésű prések is egymással szemben lévő felső és alsó ütésekkel, valamint többszörös működésű prések a rendkívül összetett alkatrészgeometriákhoz. Az egységesség, amely számos porkohászati / porfeldolgozó üzem számára fontos kihívás, nem jelent nagy problémát az AGS-TECH számára, mivel az ilyen alkatrészek egyedi gyártásában sok éves tapasztalatunk van. Még a vastagabb részekkel is sikerrel jártunk, ahol az egységesség kihívást jelent. Ha elkötelezzük magunkat a projektje mellett, elkészítjük alkatrészeit. Ha bármilyen lehetséges kockázatot látunk, értesítjük in advance. A PORSZINTERELÉS, amely a második lépés, magában foglalja a hőmérséklet egy bizonyos fokig történő emelését és a hőmérséklet ezen a szinten tartását egy bizonyos ideig, hogy a préselt részben lévő porszemcsék egymáshoz kapcsolódhassanak. Ez sokkal erősebb kötéseket és a munkadarab erősítését eredményezi. A szinterezés a por olvadáspontjához közel megy végbe. A szinterezés során zsugorodás lép fel, nő az anyag szilárdsága, sűrűsége, alakíthatósága, hővezető képessége, elektromos vezetőképessége. A szinterezéshez szakaszos és folyamatos kemencék is vannak. Az egyik lehetőségünk az általunk gyártott alkatrészek porozitási szintjének beállítása. Például képesek vagyunk fémszűrőket előállítani úgy, hogy az alkatrészeket bizonyos mértékig porózusan tartjuk. Az IMPREGNATION nevű technikával feltöltjük a fém pórusait folyadékkal, például olajjal. Gyártunk például olajjal impregnált, önkenő csapágyakat. Az INFILTRÁCIÓS eljárás során a fém pórusait egy másik, az alapanyagnál alacsonyabb olvadáspontú fémmel töltjük ki. A keveréket a két fém olvadáspontja közötti hőmérsékletre melegítjük. Ennek eredményeként néhány különleges tulajdonság érhető el. Gyakran végzünk másodlagos műveleteket is, például megmunkálást és kovácsolást a porral gyártott alkatrészeken, amikor különleges tulajdonságokat vagy tulajdonságokat kell elérni, vagy ha az alkatrész kevesebb feldolgozási lépéssel előállítható. IZOZTATIKUS PRESSING: Ebben a folyamatban a folyadéknyomást használják az alkatrész tömörítésére. A fémporokat egy lezárt, rugalmas tartályból készült formába helyezik. Az izosztatikus préselésnél a nyomást mindenütt fejtik ki, ellentétben a hagyományos préselésnél tapasztalt axiális nyomással. Az izosztatikus préselés előnyei az alkatrészen belüli egyenletes sűrűség, különösen nagyobb vagy vastagabb alkatrészeknél, kiváló tulajdonságok. Hátránya a hosszú ciklusidők és a viszonylag alacsony geometriai pontosság. A HIDEG IZOZTATIKUS PRESSZELÉS szobahőmérsékleten történik, és a rugalmas forma gumiból, PVC-ből vagy uretánból vagy hasonló anyagokból készül. A nyomás alá helyezéshez és tömörítéshez használt folyadék olaj vagy víz. A zöld kompakt hagyományos szinterezése ezt követi. A FORRÓ izosztatikus PRÉSZELÉS viszont magas hőmérsékleten történik, és a forma anyaga fémlemez vagy kerámia, amelynek olvadáspontja elég magas ahhoz, hogy ellenálljon a hőmérsékletnek. A nyomófolyadék általában inert gáz. A préselési és szinterezési műveletek egy lépésben történnek. A porozitás szinte teljesen megszűnik, egységes szemcseszerkezetet kapunk. A melegizosztatikus préselés előnye, hogy az öntéssel és kovácsolással kombinált alkatrészeket képes előállítani, miközben olyan anyagokat is felhasználhat, amelyek nem alkalmasak öntésre és kovácsolásra. A forró izosztatikus préselés hátránya a hosszú ciklusidő és ebből adódóan a költsége. Alacsony hangerejű kritikus részekhez alkalmas. FÉM Fröccsöntés: Nagyon alkalmas eljárás vékony falú és részletes geometriájú, összetett alkatrészek előállítására. Kisebb alkatrészekhez leginkább alkalmas. A porokat és a polimer kötőanyagot összekeverik, felmelegítik és egy formába fecskendezik. A polimer kötőanyag bevonja a porszemcsék felületét. A formázás után a kötőanyagot alacsony hőmérsékletű melegítéssel vagy oldószerrel oldva távolítják el. TEkercstömörítés / PORhengerlés: A porokat folyamatos szalagok vagy lapok előállítására használják. A port egy adagolóból táplálják be, és két forgó hengerrel tömörítik lapokká vagy csíkokká. A művelet hidegen történik. A lapot szinterező kemencébe viszik. A szinterezési folyamat másodszor is megismételhető. POREXTRÚZIÓ: A nagy hosszúság/átmérő arányú alkatrészeket vékony fémlemez tartály porral történő extrudálásával állítják elő. LAZA SZINTEREZÉS: Ahogy a neve is sugallja, ez egy nyomásmentes tömörítési és szinterezési módszer, amely alkalmas nagyon porózus alkatrészek, például fémszűrők előállítására. A port tömörítés nélkül adagolják a formaüregbe. LAZA SZINTEREZÉS: Ahogy a neve is sugallja, ez egy nyomásmentes tömörítési és szinterezési módszer, amely alkalmas nagyon porózus alkatrészek, például fémszűrők előállítására. A port tömörítés nélkül adagolják a formaüregbe. SZINTERELÉS: A port a formában két egymással szemben lévő lyukasztó összenyomja, és nagy teljesítményű elektromos áramot alkalmaznak a lyukasztóra, és áthalad a közöttük lévő tömörített port. A nagy áramerősség leégeti a felületi filmeket a porszemcsékről, és a keletkező hővel szinterezi azokat. A folyamat gyors, mivel a hőt nem kívülről juttatják el, hanem a formán belülről termelik. MELEGPRÉSELÉS: A porokat egyetlen lépésben préselik és szinterelik egy olyan szerszámban, amely ellenáll a magas hőmérsékletnek. Ahogy a szerszám tömörül, porhőt alkalmaznak rá. Az ezzel a módszerrel elért jó pontosság és mechanikai tulajdonságok vonzó opcióvá teszik. Még a tűzálló fémek is megmunkálhatók penészanyagokkal, például grafittal. CLICK Product Finder-Locator Service ELŐZŐ MENÜ
- Plastic Rubber Metal Extrusions, Extrusion Dies, Aluminum Extruding
Plastic Rubber Metal Extrusions, Extrusion Dies, Aluminum Extruding, Pipe Tube Forming, Plastic Profiles, Metal Profiles Manufacturing, PVC at AGS-TECH Inc. Extrudálások, extrudált termékek, extrudált termékek A EXTRUSION eljárást használjuk rögzített keresztmetszeti profilú termékek, például csövek, csövek és hőelvezetők gyártására. Annak ellenére, hogy sok anyag extrudálható, legelterjedtebb extrudálásaink fémből, polimerekből/műanyagból, kerámiából készülnek, amelyet hideg, meleg vagy meleg extrudálással nyernek. Az extrudált részeket extrudátumnak vagy extrudátumnak nevezzük, ha többes számban. Az általunk is végrehajtott eljárás néhány speciális változata a borítás, a koextrudálás és az összetett extrudálás. Javasoljuk, hogy kattintson ide: Töltsd le az AGS-TECH Inc. által készített fémkerámia és műanyag extrudálási folyamatok sematikus illusztrációit. Ez segít jobban megérteni az alábbiakban közölt információkat. Az extrudálás során az extrudálandó anyagot a kívánt keresztmetszeti profillal rendelkező szerszámon keresztül tolják vagy húzzák. Az eljárással kiváló felületi minőséggel rendelkező komplex keresztmetszeteket lehet készíteni, illetve rideg anyagokon megmunkálni. Ezzel az eljárással bármilyen hosszúságú alkatrész gyártható. A folyamat lépéseinek egyszerűsítése érdekében: 1.) Meleg vagy meleg extrudálásnál az anyagot felmelegítik és a présben egy edénybe töltik. Az anyagot préselik és kinyomják a szerszámból. 2.) Az előállított extrudátumot egyengetéshez nyújtják, hőkezelik vagy hidegen megmunkálják a tulajdonságainak javítása érdekében. Másrészt a COLD EXTRUSION körülbelül szobahőmérsékleten játszódik le, és előnye a nagy felületi szilárdság, a kevésbé oxidálható. A WARM EXTRUSION szobahőmérséklet felett, de az átkristályosodási pont alatt történik. Kompromisszumot és egyensúlyt kínál a szükséges erők, hajlékonyság és anyagtulajdonságok tekintetében, ezért bizonyos alkalmazásokhoz megfelelő választás. A HOT EXTRUSION az anyag átkristályosodási hőmérséklete felett történik. Így könnyebb átnyomni az anyagot a szerszámon. A berendezés költsége azonban magas. Minél összetettebb egy extrudált profil, annál költségesebb a szerszám (szerszám) és annál alacsonyabb a gyártási sebesség. A szerszám keresztmetszete és vastagsága az extrudálandó anyagtól függ. Az extrudáló szerszámok éles sarkai mindig nemkívánatosak, és szükség esetén kerülendők. Az extrudálandó anyagtól függően a következőket kínáljuk: • FÉM EXTRUSIONS : Leggyakrabban az alumínium, sárgaréz, cink, réz, acél, titán, magnézium • MŰANYAG EXTRUSION : A műanyagot megolvasztják és folytonos profilt alakítanak ki. Gyakori feldolgozott anyagaink a polietilén, nejlon, polisztirol, polivinil-klorid, polipropilén, ABS műanyag, polikarbonát, akril. Az általunk gyártott tipikus termékek közé tartoznak a csövek, valamint a műanyag keretek. A folyamat során a kisméretű műanyag gyöngyöket/gyantát gravitációs erővel táplálják a garatból az extrudálógép hordójába. Gyakran színezékeket vagy egyéb adalékanyagokat is keverünk a tartályba, hogy a termék a kívánt specifikációkat és tulajdonságokat biztosítsa. A fűtött hordóba belépő anyagot a forgócsavar arra kényszeríti, hogy elhagyja a hengert a végén, és áthaladjon a szitacsomagon, hogy eltávolítsa az olvadt műanyagban lévő szennyeződéseket. Miután áthaladt a szitacsomagon, a műanyag belép az extrudáló szerszámba. A szerszám áthaladva adja a mozgó puha műanyag profilformáját. Most az extrudátum vízfürdőn megy keresztül a hűtéshez. Az AGS-TECH Inc. sok éve használt egyéb technikák a következők: • PIPE & TUBING EXTRUSION : Műanyag csövek és csövek akkor keletkeznek, amikor a műanyagot egy kerek formázószerszámon keresztül extrudálják, és vízfürdőben lehűtik, majd hosszra vágják vagy feltekerik/tekerik. Átlátszó vagy színes, csíkos, egy- vagy kétfalú, rugalmas vagy merev, PE, PP, poliuretán, PVC, nejlon, PC, szilikon, vinil vagy más, nálunk minden megtalálható. Van raktáron csövek, valamint az Ön specifikációi szerinti gyártási képességünk. Az AGS-TECH az FDA, UL és LE követelményeinek megfelelő csöveket gyárt orvosi, elektromos és elektronikus, ipari és egyéb alkalmazásokhoz. • OVERJACKETING / OVER JACKETING EXTRUSION : Ez a technika egy külső műanyag réteget visz fel a meglévő vezetékre vagy kábelre. Szigetelő vezetékeink ezzel a módszerrel készülnek. • COEXTRUSION : Egyszerre több anyagréteget extrudálnak. A több réteget több extruder szállítja. A különböző rétegvastagságok az ügyfél specifikációinak megfelelően állíthatók. Ez az eljárás lehetővé teszi több polimer alkalmazását, amelyek mindegyike eltérő funkcióval rendelkezik a termékben. Ennek eredményeként egy sor tulajdonság optimalizálható. • VEGYÜLET EXTRÚZIÓ: Egy vagy több polimert kevernek össze adalékanyagokkal, hogy műanyag keveréket kapjanak. Ikercsigás extrudereink összetett extrudálást készítenek. Az extrudáló szerszámok általában olcsók a fémformákhoz képest. Ha néhány ezer dollárnál jóval többet fizet egy kis vagy közepes méretű, alumíniumot extrudáló extrudáló szerszámért, valószínűleg túl sokat fizet. Szakértők vagyunk annak meghatározásában, hogy melyik technika a legköltséghatékonyabb, leggyorsabb és legmegfelelőbb az Ön alkalmazásához. Néha egy alkatrész extrudálásával, majd megmunkálásával sok pénzt takaríthat meg. Mielőtt határozott döntést hozna, először kérdezze meg véleményünket. Sok ügyfelünknek segítettünk a helyes döntések meghozatalában. Néhány széles körben használt fémextrudáláshoz az alábbi színes szövegre kattintva letöltheti prospektusainkat és katalógusainkat. Ha ez egy késztermék, amely megfelel az Ön igényeinek, akkor gazdaságosabb lesz. Töltse le orvosi csövek és csőextrudálási képességeinket Töltse le extrudált hűtőbordáinkat • AZ EXTRUSIONS MÁSODLAG GYÁRTÁSI ÉS GYÁRTÁSI ELJÁRÁSAI: Az extrudált termékekhez kínált értéknövelt eljárások közül a következőket kínáljuk: - Egyedi csövek és csövek hajlítása, alakítása és alakítása, csővágás, csővég formázás, csőtekercselés, megmunkálás és kikészítés, lyukfúrás és lyukasztás és lyukasztás, -Egyedi cső- és csőszerelvények, csőszerelvények, hegesztés, keményforrasztás -Egyedi extrudálás hajlítás, alakítás és formázás -Tisztítás, zsírtalanítás, pácolás, passziválás, polírozás, eloxálás, bevonat, festés, hőkezelés, izzítás és edzés, jelölés, gravírozás és címkézés, egyedi csomagolás. CLICK Product Finder-Locator Service ELŐZŐ OLDAL
- Casting and Machined Parts, CNC Manufacturing, Milling, Turning, Swiss
Casting and Machined Parts, CNC Manufacturing, Milling, Turning, Swiss Type Machining, Die Casting, Investment Casting, Lost Foam Cast Parts from AGS-TECH Inc. Öntés és megmunkálás Egyedi öntési és megmunkálási technikáink a fogyó és nem elhasználható öntvények, vas- és színesfém öntvények, homok-, sajtoló-, centrifugális, folytonos, kerámiaformák, befektetések, veszett hab, hálóhoz közeli forma, tartós forma (gravitációs öntés), vakolat öntőforma (gipszöntés) és héjöntvények, megmunkált alkatrészek marással és esztergálással hagyományos valamint CNC berendezésekkel, svájci típusú megmunkálás nagy áteresztőképességű olcsó kis precíziós alkatrészekhez, csavaros megmunkálás kötőelemekhez, nem hagyományos megmunkálás. Kérjük, vegye figyelembe, hogy a fémek és fémötvözetek mellett kerámia, üveg és műanyag alkatrészeket is megmunkálunk bizonyos esetekben, amikor a formagyártás nem tetszetős, vagy nem lehetséges. A polimer anyagok megmunkálása speciális tapasztalatot igényel, mivel a műanyagok és a gumi kihívást jelentenek lágyságuk, nem merevségük stb. miatt. A kerámia és üveg megmunkálásához tekintse meg a nem hagyományos gyártás oldalunkat. Az AGS-TECH Inc. könnyű és nehéz öntvényeket egyaránt gyárt és szállít. Fémöntvényeket és megmunkált alkatrészeket szállítunk kazánokhoz, hőcserélőkhöz, autókhoz, mikromotorokhoz, szélturbinákhoz, élelmiszer-csomagoló berendezésekhez és egyebekhez. Javasoljuk, hogy kattintson ide: Töltsd le az AGS-TECH Inc. megmunkálási és öntési folyamatainak sematikus illusztrációit. Ez segít jobban megérteni az alábbiakban közölt információkat. Nézzünk meg néhányat az általunk kínált különféle technikák közül: • KIADHATÓ FORMÁKÖNTÉS: Ez a tág kategória olyan módszerekre vonatkozik, amelyek ideiglenes és nem újrafelhasználható formákat foglalnak magukban. Ilyen például a homok, a vakolat, a héj, a befektetés (más néven elveszett viasz) és a gipszöntés. • HOMOKÖNTÉS: Olyan eljárás, amelyben homokot használnak formaanyagként. Nagyon régi módszer és még mindig nagyon népszerű, mivel az előállított fémöntvények többsége ezzel a technikával készül. Alacsony költség még kis mennyiségben is. Alkalmas kis és nagy alkatrészek gyártására. A technikával napokon vagy heteken belül nagyon kis befektetéssel alkatrészeket lehet gyártani. A nedves homokot agyaggal, kötőanyagokkal vagy speciális olajokkal kötik össze. A homokot általában a formadobozok tartalmazzák, és az üregeket és kapurendszereket a homok modellek körüli tömörítésével hozzák létre. A folyamatok a következők: 1.) A modell homokba helyezése a forma elkészítéséhez 2.) Modell és homok beépítése kapurendszerbe 3.) Modell eltávolítása 4.) Formaüreg kitöltése olvadt fémmel 5.) A fém hűtése 6.) A homokforma feltörése és az öntvény eltávolítása • GIPSZÖNTÉS: A homoköntéshez hasonlóan, homok helyett párizsi vakolatot használnak formaanyagként. Rövid gyártási átfutási idők, például homoköntés és olcsó. Jó mérettűrések és felületi minőség. Legnagyobb hátránya, hogy csak alacsony olvadáspontú fémekkel, például alumíniummal és cinkkel használható. • SHELL MOLD CASTING: Hasonlóan a homoköntéshez. Formaüreg, amelyet megkeményített homokhéjjal és hőre keményedő gyanta kötőanyaggal nyernek a homokkal töltött lombik helyett, mint a homoköntési eljárásnál. Szinte minden homokkal öntésre alkalmas fém önthető héjalakítással. A folyamat a következőképpen foglalható össze: 1.) A héjforma gyártása. A felhasznált homok szemcsemérete sokkal kisebb, mint a homoköntéshez használt homok. A finom homokot hőre keményedő gyantával keverjük össze. A fémmintázat elválasztószerrel van bevonva, hogy megkönnyítse a héj eltávolítását. Ezt követően a fémmintát felmelegítik, és a homokkeveréket pórusos formában vagy ráfújják a forró öntési mintára. A minta felületén vékony héj képződik. Ennek a héjnak a vastagsága beállítható a homokgyanta keverékének a fémmintával való érintkezési időtartamának változtatásával. A laza homokot ezután eltávolítjuk, a héjjal borított minta megmarad. 2.) Ezután a héjat és a mintát sütőben felmelegítjük, hogy a héj megkeményedjen. A keményedés befejezése után a héjat a mintába épített csapok segítségével kilökődik a mintából. 3.) Két ilyen héjat ragasztással vagy befogással összeillesztünk, és alkotják a teljes formát. Most a héjformát egy tartályba helyezik, amelyben az öntési folyamat során homok vagy fémlövés támasztja alá. 4.) Most a forró fémet önthetjük a héjformába. A héjöntés előnyei a nagyon jó felületkezelésű termékek, nagy méretpontosságú összetett alkatrészek gyártásának lehetősége, a folyamat könnyen automatizálható, gazdaságos nagy volumenű gyártáshoz. Hátránya, hogy az öntőformák jó szellőzést tesznek szükségessé, mivel az olvadt fém a kötőanyaggal érintkezve keletkező gázok miatt drágák a hőre keményedő gyanták és a fémmintázatok. A fémminták költsége miatt előfordulhat, hogy a technika nem alkalmas kis mennyiségű gyártásra. • BEFEKTETÉSI ÖNTÉS (más néven LOST-WAX CASTING): Szintén nagyon régi technika, és alkalmas minőségi alkatrészek nagy pontosságú, ismételhetőségű, sokoldalú és integritású gyártására számos fémből, tűzálló anyagokból és speciális, nagy teljesítményű ötvözetekből. Kis és nagy méretű alkatrészek is gyárthatók. A többi módszerhez képest költséges eljárás, de nagy előnye a közel háló alakú, bonyolult kontúrú és részletekkel rendelkező alkatrészek előállításának lehetősége. Így a költségeket némileg ellensúlyozza az utómunkálatok és megmunkálások kiiktatása bizonyos esetekben. Bár lehetnek eltérések, íme egy összefoglaló az általános befektetési öntés folyamatáról: 1.) Eredeti mesterminta készítése viaszból vagy műanyagból. Minden öntvényhez egy minta kell, mivel ezek a folyamat során megsemmisülnek. Olyan öntőformára is szükség van, amelyből mintákat gyártanak, és a formát legtöbbször öntik vagy megmunkálják. Mivel a formát nem kell kinyitni, összetett öntvények érhetők el, sok viaszminta összekapcsolható, mint a fa ágai, és összeönthetők, így a fém vagy fémötvözet egyetlen öntésével több alkatrész is előállítható. 2.) Ezután a mintát bemártjuk vagy leöntjük nagyon finom szemcsés szilícium-dioxidból, vízből, kötőanyagokból álló tűzálló iszappal. Ez kerámiaréteget eredményez a minta felületén. A mintán lévő tűzálló bevonatot hagyjuk megszáradni és megkeményedni. Ebből a lépésből származik a befektetési öntés elnevezés: A tűzálló hígtrágyát a viaszmintára helyezik. 3.) Ennél a lépésnél a megkeményedett kerámia formát fejjel lefelé fordítjuk és felmelegítjük, hogy a viasz megolvadjon és kifolyjon a formából. A fémöntvény számára egy üreg marad hátra. 4.) A viasz kiürülése után a kerámia formát még magasabb hőmérsékletre melegítjük, ami a forma megerősödését eredményezi. 5.) A fémöntvényt a forró formába öntik, kitöltve az összes bonyolult szakaszt. 6.) Az öntést hagyjuk megszilárdulni 7.) Végül a kerámia formát feltörjük, és a fáról levágjuk a legyártott részeket. Itt található egy link az Investment Casting Plant Brosúrához • PÁROLGÁSOS MINTÁZÁS: Az eljárás olyan anyagból, például polisztirolhabból készült mintát használ, amely elpárolog, amikor forró olvadt fémet öntenek a formába. Ennek a folyamatnak két típusa van: LOST HABÖNTÉS, amely nem kötött homokot használ, és TELJES FORMÁNYÖNTÉS, amely ragasztott homokot használ. Íme az általános folyamat lépései: 1.) Készítse elő a mintát olyan anyagból, mint a polisztirol. Ha nagy mennyiséget gyártanak, a mintát formázzák. Ha az alkatrész összetett alakú, előfordulhat, hogy több ilyen habanyag-szakaszt kell összeragasztani a minta kialakításához. Gyakran vonjuk be a mintát tűzálló keverékkel, hogy jó felületi minőséget hozzunk létre az öntvényen. 2.) Ezután a mintát formázó homokba helyezzük. 3.) Az olvadt fémet a formába öntik, a habmintát, azaz a legtöbb esetben a polisztirolt elpárologtatják, miközben átfolyik a formaüregen. 4.) Az olvadt fémet a homokformában hagyjuk megkeményedni. 5.) Miután megszilárdult, eltávolítjuk az öntvényt. Bizonyos esetekben az általunk gyártott terméknek magra van szüksége a mintán belül. Párolgásos öntésnél nincs szükség mag elhelyezésére és rögzítésére a formaüregben. A technika nagyon összetett geometriák gyártására alkalmas, nagy volumenű gyártáshoz könnyen automatizálható, az öntött alkatrészben nincsenek elválasztó vonalak. Az alapfolyamat egyszerű és gazdaságos végrehajtani. Nagy mennyiségű gyártás esetén, mivel a minták polisztirolból történő előállításához szerszámra vagy öntőformára van szükség, ez némileg költséges lehet. • NEM HAJSZÍTHATÓ FORMÁBANÖNTÉS: Ez a tág kategória azokra a módszerekre vonatkozik, ahol a formát nem kell megreformálni minden gyártási ciklus után. Ilyen például a permanens, fröccsöntés, folyamatos és centrifugális öntés. Megismételhetőség érhető el, és az alkatrészeket NEAR NET SHAPE-ként jellemezhetjük. • ÁLLANDÓ FORMAÖNTÉS: A fémből készült újrafelhasználható formákat többszörös öntéshez használják. Az állandó penész általában több tízezer alkalommal használható, mielőtt elhasználódik. A forma kitöltésére általában gravitációt, gáznyomást vagy vákuumot használnak. A formák (más néven matricák) általában vasból, acélból, kerámiából vagy más fémekből készülnek. Az általános folyamat a következő: 1.) Géppel és készítsd el a formát. Gyakori, hogy a formát két egymáshoz illeszkedő, nyitható és zárható fémtömbből készítik. Mind az alkatrész jellemzői, mind a kapurendszer általában az öntőformába van bedolgozva. 2.) A belső formafelületeket tűzálló anyagokat tartalmazó iszappal vonják be. Ez segít szabályozni a hőáramlást, és kenőanyagként működik az öntött rész egyszerű eltávolításához. 3.) Ezután az állandó formafelet lezárjuk, és a formát felmelegítjük. 4.) Az olvadt fémet a formába öntjük, és hagyjuk állni, hogy megszilárduljon. 5.) Mielőtt nagymértékben lehűlne, eltávolítjuk az alkatrészt az állandó formából egy kidobó segítségével, amikor a formafelet kinyitjuk. Gyakran alkalmazunk állandó öntést alacsony olvadáspontú fémekhez, például cinkhez és alumíniumhoz. Acélöntvényekhez formaanyagként grafitot használunk. Néha összetett geometriákat kapunk állandó formákban lévő magok felhasználásával. Ennek a technikának a előnyei a gyors hűtéssel elért jó mechanikai tulajdonságokkal rendelkező öntvények, a tulajdonságok egyenletessége, a jó pontosság és a felületi minőség, az alacsony selejtezési arány, a folyamat automatizálásának és a nagy mennyiségek gazdaságos előállításának lehetősége. Hátránya a magas kezdeti beállítási költségek, amelyek alkalmatlanná teszik kis mennyiségű műveletekre, valamint a gyártott alkatrészek méretének korlátai. • PÖLCSÖNTÉS: A szerszámot megmunkálják, és az olvadt fémet nagy nyomás alatt a formaüregekbe nyomják. Színes és vasfém présöntvények egyaránt lehetségesek. Az eljárás alkalmas kis és közepes méretű, részletgazdag, rendkívül vékony falú, méretkonzisztens és jó felületkezelésű alkatrészek nagy mennyiségű gyártására. Az AGS-TECH Inc. ezzel a technikával akár 0,5 mm-es falvastagság gyártására is képes. Az állandó öntési formához hasonlóan a formának két félből kell állnia, amelyek nyithatók és zárhatók az előállított alkatrész eltávolításához. Egy fröccsöntő öntőforma több üreggel is rendelkezhet, hogy minden ciklusban több öntvényt lehessen gyártani. A présöntőformák nagyon nehezek és sokkal nagyobbak, mint az általuk gyártott alkatrészek, ezért drágák is. Ügyfeleink számára díjmentesen javítjuk és cseréljük az elhasználódott szerszámokat mindaddig, amíg alkatrészeiket tőlünk rendelik. Szerszámaink hosszú élettartamúak, több százezer ciklusban. Íme az egyszerűsített folyamat alapvető lépései: 1.) A forma gyártása általában acélból 2.) Présöntőgépre szerelt forma 3.) A dugattyú arra kényszeríti az olvadt fémet, hogy a szerszámüregekben áramoljon, kitöltve a bonyolult vonásokat és vékony falakat. 4.) Az öntőforma megolvadt fémmel való megtöltése után az öntvényt nyomás alatt hagyjuk megkeményedni 5.) Kidobócsapok segítségével a formát kinyitjuk és az öntvényt eltávolítjuk. 6.) Most újra meg kell kenni az üres szerszámot, és rögzíteni kell a következő ciklushoz. A fröccsöntés során gyakran alkalmazunk lapkás öntést, ahol egy további alkatrészt építünk be a formába, és körbeöntjük a fémet. Megszilárdulás után ezek az alkatrészek az öntött termék részévé válnak. A présöntés előnyei az alkatrészek jó mechanikai tulajdonságai, a bonyolult jellemzők lehetősége, a finom részletek és a jó felületi minőség, a magas gyártási sebesség, az egyszerű automatizálás. Hátrányok: Kis térfogatra nem nagyon alkalmas a magas szerszám- és berendezésköltség miatt, az önthető alakzatok korlátai, az öntött részeken a kilökőcsapok érintkezéséből adódó kis kerek foltok, az elválási vonalnál kinyomódó vékony fémhullám, szükség a szerszámok közötti elválasztó vonal mentén lévő szellőzőnyílások esetében a formahőmérsékletet alacsonyan kell tartani vízkeringetéssel. • CENTRIFUGÁLIS ÖNTÉS: Az olvadt fémet a forgó forma közepébe öntik a forgástengelyen. A centrifugális erők a fémet a perem felé hajítják, és hagyják megszilárdulni, miközben a forma folyamatosan forog. Vízszintes és függőleges tengelyforgatások is használhatók. Kerek belső felületű alkatrészek, valamint egyéb nem kerek formájú alkatrészek önthetők. A folyamat a következőképpen foglalható össze: 1.) Az olvadt fémet centrifugális formába öntik. A fém ezután a forma forgásának következtében a külső falakhoz szorul. 2.) Ahogy a forma forog, a fémöntvény megkeményedik A centrifugális öntés megfelelő technika üreges hengeres alkatrészek, például csövek gyártására, nincs szükség csövekre, felszállókra és kapuelemekre, jó felületminőség és részletgazdag jellemzők, nincs zsugorodási probléma, lehetőség nagyon nagy átmérőjű hosszú csövek gyártására, nagy gyártási kapacitás . • FOLYAMATOS ÖNTÉS (FOLYAMATOS ÖNTÉS): Folyamatos hosszúságú fém öntésére szolgál. Alapvetően az olvadt fémet a forma kétdimenziós profiljába öntik, de a hossza meghatározatlan. Folyamatosan új olvadt fém kerül a formába, miközben az öntvény lefelé halad, és hossza idővel növekszik. A fémeket, mint a réz, acél, alumínium, folyamatos öntési eljárással hosszú szálakká öntik. A folyamat különféle konfigurációkkal rendelkezhet, de a közös a következőképpen egyszerűsíthető: 1.) Az olvadt fémet jól kiszámított mennyiségben és áramlási sebességgel a forma felett magasan elhelyezett edénybe öntik, és átfolynak a vízhűtéses formán. A formába öntött fémöntvény a forma alján elhelyezett indítórúdká szilárdul. Ez az indítóléc ad a görgőknek valamit, amibe kezdetben meg kell ragadni. 2.) A hosszú fémszálat görgők hordják állandó sebességgel. A görgők a fémszál áramlási irányát is változtatják függőlegesről vízszintesre. 3.) Miután a folyamatos öntés megtett egy bizonyos vízszintes távolságot, az öntéssel együtt mozgó fáklya vagy fűrész gyorsan levágja a kívánt hosszúságra. A folyamatos öntési folyamat integrálható a ROLLING PROCESS-szal, ahol a folyamatosan öntött fém közvetlenül egy hengerműbe adagolható I-gerendák, T-gerendák stb. A folyamatos öntés egyenletes tulajdonságokat hoz létre az egész termékben, nagy a megszilárdulási sebessége, csökkenti a költségeket a nagyon alacsony anyagveszteség miatt, olyan eljárást kínál, amelyben a fém betöltése, az öntés, a megszilárdítás, a vágás és az öntés eltávolítása folyamatos működésben történik, így magas termelékenységi rátát és kiváló minőséget eredményez. Fontos szempont azonban a magas kezdeti beruházás, a telepítési költségek és a helyigény. • GYÁRTÁSI SZOLGÁLTATÁSOK: Három-, négy- és öttengelyes megmunkálást kínálunk. Az általunk használt megmunkálási folyamatok típusai: ESZTERGÁLÁS, MARÁS, FÚRÁS, FÚRÁS, TÖRÍTÉS, GYALULÁS, FŰRÉSZÉS, KÖSZÖRÉS, LÉPÍTÉS, POLÍROZÁS és NEM HAGYOMÁNYOS MEGMUNKÁLÁS, amelyet honlapunk egy másik menüpontja alatt részletezünk. Gyártásunk nagy részében CNC gépeket használunk. Néhány művelethez azonban a hagyományos technikák jobban illeszkednek, ezért mi is támaszkodunk rájuk. Megmunkálási képességeink a lehető legmagasabb szintet érik el, és néhány legigényesebb alkatrészt AS9100 tanúsítvánnyal rendelkező üzemben gyártanak. A sugárhajtómű-lapátok speciális gyártási tapasztalatot és megfelelő felszerelést igényelnek. A repülőgépiparnak nagyon szigorú szabványai vannak. Egyes összetett geometriai szerkezetű alkatrészeket legkönnyebben öttengelyes megmunkálással lehet előállítani, ami csak néhány megmunkáló üzemben található meg, köztük a miénk is. Repülőgép-tanúsítvánnyal rendelkező üzemünk rendelkezik a szükséges tapasztalattal, hogy megfeleljen a repülőgépipar kiterjedt dokumentációs követelményeinek. ESZTERGÁLÁSI műveletek során a munkadarabot elforgatják és egy vágószerszámmal szemben mozgatják. Ehhez a folyamathoz egy esztergagépet használnak. A MARÁS során a marógépnek nevezett gépnek van egy forgó szerszáma, amely a vágóéleket a munkadarabhoz támasztja. A FÚRÁSI műveletek egy forgó vágóéllel rendelkeznek, amely a munkadarabbal érintkezve lyukakat hoz létre. Általában fúrópréseket, esztergagépeket vagy marókat használnak. FÚRÁSI műveleteknél egyetlen hajlított hegyű szerszámot a forgó munkadarab durva furatába mozgatnak, hogy kissé megnagyobbítsák a furatot és javítsák a pontosságot. Finom befejező célokra használják. A TÖRÍTÉS egy fogazott szerszámot foglal magában, amely az anyagot a munkadarabból a préselés egy menetében eltávolítja (fogazott szerszám). Lineáris kimetszésnél a bélyeg lineárisan fut a munkadarab felületén a vágás érdekében, míg a forgófúrásnál a bélyeg elforgatja és belepréselődik a munkadarabba, hogy tengelyszimmetrikus alakot vágjon. A SWISS TYPE MACHINING az egyik értékes technikánk, amelyet kis, nagy pontosságú alkatrészek nagy volumenű gyártásához használunk. Svájci típusú esztergagéppel kicsi, összetett, precíziós alkatrészeket esztergálunk olcsón. Ellentétben a hagyományos esztergagépekkel, ahol a munkadarabot helyben tartják és a szerszámot mozgatják, a svájci típusú esztergaközpontokban a munkadarab a Z tengelyben mozoghat, a szerszám pedig álló helyzetben van. A svájci típusú megmunkálásnál a rúdkészletet a gépben tartják, és a z tengelyen lévő vezetőperselyen keresztül továbbítják, így csak a megmunkálandó részt szabadítják fel. Így biztosítható a szoros fogás és nagyon nagy a pontosság. Az éles szerszámok rendelkezésre állása lehetőséget ad a marásra és fúrásra, ahogy az anyag előrehalad a vezetőperselyből. A svájci típusú berendezés Y tengelye teljes marási képességet biztosít, és jelentős időt takarít meg a gyártás során. Ezenkívül gépeink fúrókkal és fúrószerszámokkal rendelkeznek, amelyek akkor dolgoznak az alkatrészen, amikor az alkatrészt az alorsóban tartják. Swiss-Type megmunkálási képességünk teljesen automatizált, teljes megmunkálási lehetőséget biztosít számunkra egyetlen műveletben. A megmunkálás az AGS-TECH Inc. üzletágának egyik legnagyobb szegmense. Vagy elsődleges műveletként, vagy másodlagos műveletként használjuk egy alkatrész öntése vagy extrudálása után, hogy minden rajzi előírás teljesüljön. • FELÜLETKIEMELÉSI SZOLGÁLTATÁSOK: Felületkezelések és felületkezelések széles választékát kínáljuk, mint például felületkezelés a tapadás fokozására, vékony oxidréteg felhordása a bevonat tapadásának fokozására, homokfúvás, vegyi film, eloxálás, nitridálás, porfestés, szórással történő bevonat , különféle fejlett fémezési és bevonási technikák, beleértve a porlasztást, elektronsugarat, párologtatást, bevonatot, kemény bevonatokat, például gyémántszerű szén (DLC) vagy titán bevonatot fúró- és vágószerszámokhoz. • TERMÉKJELÖLÉSI ÉS CÍMKÉZÉSI SZOLGÁLTATÁSOK: Sok ügyfelünk igényel jelölést és címkézést, lézeres jelölést, gravírozást a fém alkatrészeken. Ha van ilyen igénye, beszéljük meg, melyik megoldás lenne a legmegfelelőbb az Ön számára. Íme néhány gyakran használt fémöntvény termék. Mivel ezek készen állnak, megtakaríthatja a penészköltségeket, ha ezek közül bármelyik megfelel az Ön igényeinek: KATTINTSON IDE AZ AGS-Electronics 11-es sorozatú présöntött alumíniumdobozaink letöltéséhez CLICK Product Finder-Locator Service ELŐZŐ OLDAL
- Custom Manufactured Parts, Assemblies, Plastic Mold, Casting,Machining
Custom Manufactured Parts, Assemblies, Plastic Mold, Rubber Molding, Metal Casting, CNC Machining, Turning, Milling, Electrical Electronic Optical Assembly PCBA Egyedi gyártású alkatrészek & Assemblies & Products Olvass tovább Műanyag és gumi öntőformák és öntőformák Olvass tovább Öntés és megmunkálás Olvass tovább Extrudálások, extrudált termékek Olvass tovább Bélyegzés és fémlemez gyártás Olvass tovább Fémkovácsolás és porkohászat Olvass tovább Huzal és rugó alakítás Olvass tovább Üveg és kerámia formázás és formázás Olvass tovább Adalékanyag és gyors gyártás Olvass tovább Kompozitok és kompozit anyagok gyártása Olvass tovább Csatlakoztatási és összeszerelési és rögzítési eljárások Alkatrészeket és szerelvényeket gyártunk Önnek, és a következő gyártási folyamatokat kínáljuk: • Műanyag és gumi öntőformák és öntött alkatrészek. Fröccsöntés, hőformázás, hőre keményedő fröccsöntés, vákuumformázás, fúvósajtolás, rotációs fröccsöntés, öntés, betétes fröccsöntés és mások. • Műanyag, gumi és fém extrudálás • Vas- és színesfém öntvények és megmunkált alkatrészek marási és esztergálási technikával, svájci típusú megmunkálással. • Porkohászati alkatrészek • Fém- és nemfém sajtolás, lemezalakítás, hegesztett lemezszerelvények • Hideg és meleg kovácsolás • Huzalok, hegesztett huzalszerelvények, huzalformázás • Különféle rugók, rugóformázó • Fogaskerekek gyártása, sebességváltó, tengelykapcsoló, csiga, sebességcsökkentő, henger, hajtószíjak, hajtóműláncok, erőátviteli alkatrészek • Egyedi edzett és golyóálló üveg, amely megfelel a NATO és katonai szabványoknak • Golyók, csapágyak, szíjtárcsák és szíjtárcsák • Szelepek és pneumatikus alkatrészek, például O-gyűrű, alátét és tömítések • Üveg és kerámia alkatrészek és szerelvények, vákuumálló és hermetikus alkatrészek, fém-kerámia és kerámia-kerámia kötés. • Különféle mechanikai, optomechanikai, elektromechanikus, optoelektronikai szerelvények. • Fém-gumi, fém-műanyag kötés • Cső és cső, csőalakítás, hajlítás és egyedi csőszerelvények, harmonikagyártás. • Üvegszál gyártás • Hegesztés különféle technikákkal, mint például ponthegesztés, lézerhegesztés, MIG, AWI. Ultrahangos hegesztés műanyag alkatrészekhez. • Felületkezelések és felületkezelések széles választéka, például felületkezelés a tapadás fokozására, vékony oxidréteg felhordása a bevonat tapadásának fokozására, homokfúvás, vegyi film, eloxálás, nitridálás, porbevonat, szórással történő bevonat, különféle fejlett fémezési és bevonási technikák ideértve a porlasztást, az elektronsugarat, a párologtatást, a bevonatot, a kemény bevonatokat, mint például a gyémántszerű szén (DLC) vagy a titán vágó- és fúrószerszámokhoz. • Jelölés és címkézés, lézeres jelölés fém alkatrészeken, nyomtatás műanyag és gumi alkatrészeken Töltse le a tervezők és mérnökök által használt általános gépészeti kifejezések brosúráját Termékeinket az Ön egyedi specifikációi és követelményei szerint készítjük. Annak érdekében, hogy a legjobb minőséget, szállítást és árakat kínáljuk Önnek, világszerte gyártunk termékeket Kínában, Indiában, Tajvanon, a Fülöp-szigeteken, Dél-Koreában, Malajziában, Srí Lankán, Törökországban, az Egyesült Államokban, Kanadában, Németországban, az Egyesült Királyságban és Japánban. Ezáltal sokkal erősebbek és globálisan versenyképesebbek vagyunk, mint bármely más custom gyártó. Termékeinket ISO9001:2000, QS9000, ISO14001, TS16949 tanúsítvánnyal rendelkező környezetben gyártjuk, és CE, UL jelöléssel és más iparági szabványoknak is megfelelnek. Miután kineveztünk az Ön projektjére, a teljes gyártást, összeszerelést, tesztelést, minősítést, szállítást és vámkezelést igény szerint elvégezhetjük. Ha úgy szeretné, raktározzuk az alkatrészeket, összeállítjuk az egyedi készleteket, kinyomtatjuk és felcímkézzük cége nevét és márkáját, és kiszállítjuk ügyfeleinek. Más szóval, igény szerint raktározási és elosztási központja is lehetünk. Mivel raktáraink a főbb tengeri kikötők közelében találhatók, ez logisztikai előnyt jelent számunkra. Például, amikor a termékei megérkeznek egy nagyobb amerikai tengeri kikötőbe, akkor közvetlenül egy közeli raktárba szállíthatjuk, ahol tárolhatjuk, összeállíthatjuk, készleteket készíthetünk, átcímkézhetünk, nyomtathatunk, csomagolhatunk az Ön választása szerint és ledobhatjuk. szállítsa ügyfeleinek. Nem csak termékeket szállítunk. Cégünk egyedi szerződések alapján dolgozik, ahol az Ön telephelyére érkezünk, a helyszínen értékeljük projektjét, és egyedi projektjavaslatot készítünk Önnek. Ezt követően tapasztalt csapatunkat küldjük a projekt megvalósítására. Mérnöki munkánkkal kapcsolatos további információk a címen találhatók http://www.ags-engineering.com -Kis projekteket, valamint nagy ipari projekteket is vállalunk. Első lépésként telefonon, telekonferencián vagy MSN messengeren keresztül összeköthetjük szakértői csapatunk tagjaival, így közvetlenül kommunikálhat egy szakértővel, kérdéseket tehet fel és megvitathatja projektjét. Hívjon minket, és ha szükséges, eljövünk és meglátogatunk. ELŐZŐ OLDAL