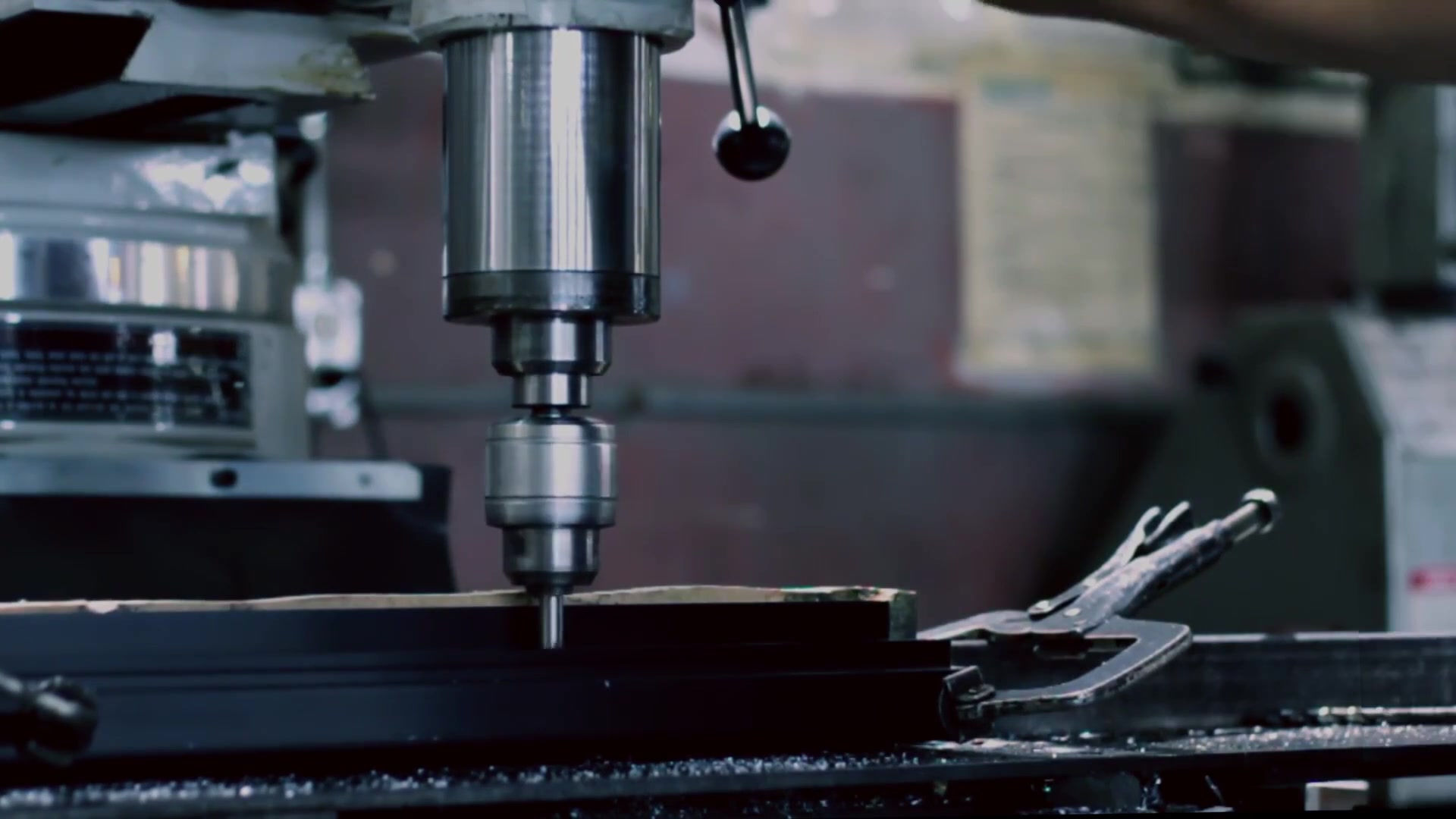
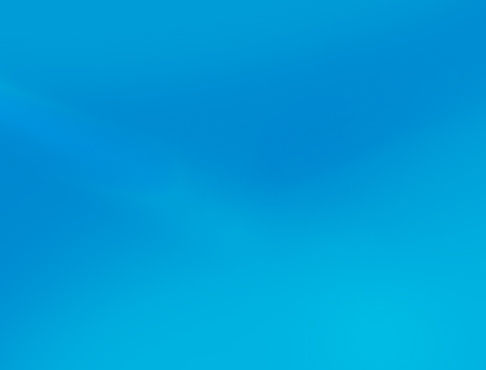
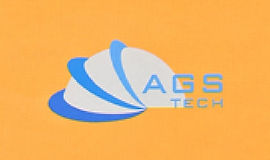
Produttore globale personalizzato, integratore, consolidatore, partner di outsourcing per un'ampia varietà di prodotti e servizi.
Siamo la tua fonte unica per la produzione, la fabbricazione, l'ingegnerizzazione, il consolidamento, l'integrazione, l'esternalizzazione di prodotti e servizi personalizzati e off-shelf.
Choose your Language
-
Produzione su misura
-
Produzione a contratto nazionale e globale
-
Esternalizzazione della produzione
-
Appalti nazionali e globali
-
Consolidamento
-
Integrazione ingegneristica
-
Servizi di ingegneria
Le nostre tecniche di colata e lavorazione personalizzate sono getti consumabili e non, getti ferrosi e non ferrosi, sabbia, stampi, centrifughi, continui, stampi in ceramica, rivestimento, schiuma persa, forma quasi netta, stampo permanente (pressofusione a gravità), gesso stampi (colata in gesso) e fusioni in conchiglia, parti lavorate prodotte mediante fresatura e tornitura utilizzando attrezzature convenzionali e CNC, lavorazione di tipo svizzero per pezzi di piccola precisione a basso costo ad alta produttività, lavorazione di viti per elementi di fissaggio, lavorazione non convenzionale. Tieni presente che, oltre a metalli e leghe metalliche, lavoriamo anche componenti in ceramica, vetro e plastica, in alcuni casi quando la produzione di uno stampo non è interessante o non è un'opzione. La lavorazione di materiali polimerici richiede l'esperienza specializzata che abbiamo a causa della sfida che la plastica e la gomma presentano a causa della loro morbidezza, non rigidità ... ecc. Per la lavorazione di ceramica e vetro, consultare la nostra pagina sulla fabbricazione non convenzionale. AGS-TECH Inc. produce e fornisce fusioni sia leggere che pesanti. Abbiamo fornito fusioni metalliche e parti lavorate per caldaie, scambiatori di calore, automobili, micromotori, turbine eoliche, attrezzature per l'imballaggio alimentare e altro ancora. Ti consigliamo di fare clic qui per SCARICA le nostre illustrazioni schematiche dei processi di lavorazione e colata di AGS-TECH Inc.
Questo ti aiuterà a comprendere meglio le informazioni che ti stiamo fornendo di seguito. Vediamo nel dettaglio alcune delle varie tecniche che offriamo:
• COLATA DELLO STAMPO ESAURIBILE: questa ampia categoria si riferisce a metodi che coinvolgono stampi temporanei e non riutilizzabili. Esempi sono sabbia, gesso, conchiglia, rivestimento (chiamato anche cera persa) e colata in gesso.
• COLATA IN SABBIA: un processo in cui la sabbia viene utilizzata come materiale dello stampo. Un metodo molto antico e ancora molto diffuso nella misura in cui la maggior parte delle fusioni metalliche prodotte sono realizzate con questa tecnica. Basso costo anche a basse quantità di produzione. Adatto per la produzione di piccoli e grandi pezzi. La tecnica può essere utilizzata per produrre parti in pochi giorni o settimane con un investimento minimo. La sabbia umida viene legata insieme usando argilla, leganti o oli speciali. La sabbia è generalmente contenuta negli stampi e il sistema cavità e cancello viene creato compattando la sabbia attorno ai modelli. I processi sono:
1.) Posizionamento del modello nella sabbia per realizzare lo stampo
2.) Incorporazione di modello e sabbia in un sistema di gating
3.) Rimozione del modello
4.) Riempimento della cavità dello stampo con metallo fuso
5.) Raffreddamento del metallo
6.) Rottura dello stampo in sabbia e rimozione del getto
• COLATA IN STAMPO IN GESSO: Simile alla colata in sabbia, e invece della sabbia, come materiale dello stampo viene utilizzato gesso di Parigi. Tempi di produzione brevi come colata in sabbia ed economici. Buone tolleranze dimensionali e finitura superficiale. Il suo principale svantaggio è che può essere utilizzato solo con metalli a basso punto di fusione come alluminio e zinco.
• COLATA IN SHELL MOLD : Simile anche alla colata in sabbia. Cavità dello stampo ottenuta da guscio indurito di sabbia e legante di resina termoindurente al posto della muffola riempita di sabbia come nel processo di colata in sabbia. Quasi tutti i metalli adatti per essere fusi con la sabbia possono essere fusi mediante stampaggio a conchiglia. Il processo può essere riassunto come:
1.) Fabbricazione dello stampo a conchiglia. La sabbia utilizzata ha una granulometria molto più piccola rispetto alla sabbia utilizzata nella colata in sabbia. La sabbia fine viene miscelata con resina termoindurente. Il motivo in metallo è rivestito con un agente distaccante per facilitare la rimozione del guscio. Successivamente il modello di metallo viene riscaldato e la miscela di sabbia viene porosa o soffiata sul modello di colata a caldo. Un sottile guscio si forma sulla superficie del motivo. Lo spessore di questo guscio può essere regolato variando il tempo in cui la miscela di sabbia e resina è a contatto con il motivo metallico. La sabbia sciolta viene quindi rimossa con il rimanente motivo ricoperto di conchiglie.
2.) Successivamente, il guscio e il motivo vengono riscaldati in un forno in modo che il guscio si indurisca. Dopo che l'indurimento è completo, il guscio viene espulso dal modello utilizzando perni incorporati nel modello.
3.) Due di questi gusci vengono assemblati insieme mediante incollaggio o bloccaggio e costituiscono lo stampo completo. Ora lo stampo a conchiglia viene inserito in un contenitore in cui viene supportato da sabbia o graniglia di metallo durante il processo di colata.
4.) Ora il metallo caldo può essere versato nello stampo a conchiglia.
I vantaggi della colata in conchiglia sono prodotti con un'ottima finitura superficiale, possibilità di produrre parti complesse con elevata precisione dimensionale, processo facile da automatizzare, economico per grandi volumi di produzione.
Gli svantaggi sono che gli stampi richiedono una buona ventilazione a causa dei gas che si creano quando il metallo fuso entra in contatto con il legante chimico, le resine termoindurenti e i modelli di metallo sono costosi. A causa del costo dei modelli in metallo, la tecnica potrebbe non adattarsi bene a basse quantità di produzione.
• COLATA A INVESTIMENTO (nota anche come FUSIONE A CERA PERSA): anche una tecnica molto antica e adatta alla produzione di parti di qualità con elevata precisione, ripetibilità, versatilità e integrità da molti metalli, materiali refrattari e leghe speciali ad alte prestazioni. Possono essere prodotte parti di piccole e grandi dimensioni. Un processo costoso rispetto ad alcuni degli altri metodi, ma il vantaggio principale è la possibilità di produrre parti con una forma quasi netta, contorni e dettagli intricati. Quindi il costo è in qualche modo compensato dall'eliminazione di rilavorazione e lavorazione in alcuni casi. Anche se possono esserci variazioni, ecco un riepilogo del processo generale di microfusione:
1.) Creazione di un modello master originale da cera o plastica. Ogni fusione ha bisogno di un modello poiché questi vengono distrutti nel processo. È anche necessario lo stampo da cui vengono prodotti i modelli e la maggior parte delle volte lo stampo viene colato o lavorato. Poiché lo stampo non deve essere aperto, è possibile ottenere fusioni complesse, molti modelli in cera possono essere collegati come i rami di un albero e fusi insieme, consentendo così la produzione di più parti da un'unica colata del metallo o della lega metallica.
2.) Successivamente, il modello viene immerso o versato sopra con un impasto liquido refrattario composto da silice a grana molto fine, acqua, leganti. Ciò si traduce in uno strato di ceramica sulla superficie del motivo. Il mantello refrattario sul disegno viene lasciato asciugare e indurire. Da questo passaggio deriva il nome della colata a cera persa: la sospensione refrattaria viene investita sul modello in cera.
3.) A questo punto, lo stampo in ceramica indurita viene capovolto e riscaldato in modo che la cera si sciolga e fuoriesca dallo stampo. Viene lasciata una cavità per la colata di metallo.
4.) Dopo che la cera è fuoriuscita, lo stampo in ceramica viene riscaldato a una temperatura ancora più elevata, il che si traduce in un rafforzamento dello stampo.
5.) La colata di metallo viene versata nello stampo caldo riempiendo tutte le sezioni complesse.
6.) La colata può solidificare
7.) Infine si rompe lo stampo in ceramica e si tagliano i manufatti dall'albero.
Ecco un collegamento all'opuscolo dell'impianto di colata di investimento
• COLATA DEL MODELLO EVAPORATIVO: il processo utilizza un modello realizzato con un materiale come il polistirene espanso che evaporerà quando il metallo fuso caldo viene versato nello stampo. Esistono due tipi di questo processo: LOST FOAM CASTING che utilizza sabbia non legata e FULL MOLD CASTING che utilizza sabbia legata. Ecco i passaggi generali del processo:
1.) Realizzare il modello da un materiale come il polistirolo. Quando verranno prodotte grandi quantità, il modello viene modellato. Se la parte ha una forma complessa, potrebbe essere necessario far aderire insieme diverse sezioni di tale materiale espanso per formare il motivo. Spesso ricopriamo il modello con un composto refrattario per creare una buona finitura superficiale sul getto.
2.) Il motivo viene quindi messo nella sabbia per modellare.
3.) Il metallo fuso viene colato nello stampo, facendo evaporare il modello di schiuma, nella maggior parte dei casi il polistirene mentre scorre attraverso la cavità dello stampo.
4.) Il metallo fuso viene lasciato indurire nello stampo di sabbia.
5.) Dopo che si è indurito, rimuoviamo il getto.
In alcuni casi, il prodotto che produciamo richiede un nucleo all'interno del modello. Nella colata evaporativa, non è necessario posizionare e fissare un'anima nella cavità dello stampo. La tecnica è adatta per la produzione di geometrie molto complesse, può essere facilmente automatizzata per produzioni ad alto volume e non ci sono linee di divisione nella parte fusa. Il processo di base è semplice ed economico da implementare. Per la produzione di grandi volumi, poiché è necessario uno stampo o uno stampo per produrre i modelli dal polistirene, ciò può essere alquanto costoso.
• COLATA IN STAMPO NON ESPANDIBILE: Questa ampia categoria si riferisce a metodi in cui lo stampo non ha bisogno di essere riformato dopo ogni ciclo di produzione. Esempi sono la colata permanente, in pressofusione, continua e centrifuga. Si ottiene la ripetibilità e le parti possono essere caratterizzate come NEAR NET SHAPE.
• COLATA IN STAMPO PERMANENTE: Gli stampi riutilizzabili in metallo vengono utilizzati per fusioni multiple. Uno stampo permanente può generalmente essere utilizzato per decine di migliaia di volte prima che si esaurisca. La gravità, la pressione del gas o il vuoto sono generalmente utilizzati per riempire lo stampo. Gli stampi (chiamati anche stampi) sono generalmente realizzati in ferro, acciaio, ceramica o altri metalli. Il processo generale è:
1.) Lavorare e creare lo stampo. È comune lavorare lo stampo da due blocchi di metallo che si incastrano e possono essere aperti e chiusi. Sia le caratteristiche della parte che il sistema di iniezione sono generalmente lavorati nello stampo di colata.
2.) Le superfici interne dello stampo sono rivestite con un impasto liquido che incorpora materiali refrattari. Questo aiuta a controllare il flusso di calore e funge da lubrificante per una facile rimozione della parte fusa.
3.) Successivamente, le metà dello stampo permanente vengono chiuse e lo stampo viene riscaldato.
4.) Il metallo fuso viene colato nello stampo e lasciato riposare per la solidificazione.
5.) Prima che si verifichi molto raffreddamento, rimuoviamo la parte dallo stampo permanente utilizzando gli espulsori quando le metà dello stampo vengono aperte.
Utilizziamo spesso la colata permanente in stampi per metalli a basso punto di fusione come zinco e alluminio. Per le fusioni in acciaio, utilizziamo la grafite come materiale per stampi. A volte otteniamo geometrie complesse utilizzando anime all'interno di stampi permanenti. I vantaggi di questa tecnica sono getti con buone proprietà meccaniche ottenute per raffreddamento rapido, uniformità delle proprietà, buona precisione e finitura superficiale, bassi tassi di scarto, possibilità di automatizzare il processo e produrre volumi elevati in modo economico. Gli svantaggi sono gli elevati costi di installazione iniziale che lo rendono inadatto per operazioni a basso volume e le limitazioni alle dimensioni delle parti prodotte.
• PRESSOFUSIONE: uno stampo viene lavorato e il metallo fuso viene spinto ad alta pressione nelle cavità dello stampo. Sono possibili sia pressofusioni di metalli non ferrosi che ferrosi. Il processo è adatto per produzioni di grandi quantità di pezzi di piccole e medie dimensioni con dettagli, pareti estremamente sottili, consistenza dimensionale e buona finitura superficiale. AGS-TECH Inc. è in grado di produrre spessori di parete fino a 0,5 mm utilizzando questa tecnica. Come nella colata in stampo permanente, lo stampo deve essere costituito da due metà che possono aprirsi e chiudersi per la rimozione della parte prodotta. Uno stampo per pressofusione può avere più cavità per consentire la produzione di più getti con ogni ciclo. Gli stampi per pressofusione sono molto pesanti e molto più grandi delle parti che producono, quindi anche costosi. Ripariamo e sostituiamo gratuitamente le matrici usurate per i nostri clienti, a condizione che riordinino le loro parti da noi. I nostri stampi hanno una lunga durata nell'intervallo di diverse centinaia di migliaia di cicli.
Di seguito sono riportati i passaggi di base del processo semplificato:
1.) Produzione dello stampo generalmente in acciaio
2.) Stampo installato su macchina per pressofusione
3.) Il pistone costringe il metallo fuso a fluire nelle cavità dello stampo riempiendo le caratteristiche intricate e le pareti sottili
4.) Dopo aver riempito lo stampo con il metallo fuso, la colata viene fatta indurire sotto pressione
5.) Lo stampo viene aperto e la colata rimossa con l'aiuto di perni di espulsione.
6.) Ora gli stampi vuoti vengono nuovamente lubrificati e bloccati per il ciclo successivo.
Nella pressofusione, utilizziamo spesso lo stampaggio a inserti in cui incorporiamo una parte aggiuntiva nello stampo e fondiamo il metallo attorno ad esso. Dopo la solidificazione, queste parti diventano parte del prodotto colato. I vantaggi della pressofusione sono buone proprietà meccaniche delle parti, possibilità di caratteristiche complesse, dettagli fini e buona finitura superficiale, alti tassi di produzione, facile automazione. Gli svantaggi sono: Non molto adatto per bassi volumi a causa dell'elevato costo dello stampo e dell'attrezzatura, limitazioni nelle forme che possono essere fuse, piccoli segni rotondi sulle parti fuse risultanti dal contatto dei perni di espulsione, sottile lamella di metallo spremuta sulla linea di divisione, necessità per gli sfiati lungo la linea di separazione tra lo stampo, necessità di mantenere basse le temperature dello stampo utilizzando la circolazione dell'acqua.
• COLATA CENTRIFUGA: Il metallo fuso viene colato al centro dello stampo rotante sull'asse di rotazione. Le forze centrifughe proiettano il metallo verso la periferia e viene lasciato solidificare mentre lo stampo continua a ruotare. È possibile utilizzare sia la rotazione dell'asse orizzontale che quella verticale. Possono essere colate parti con superfici interne rotonde e altre forme non rotonde. Il processo può essere riassunto come:
1.) Il metallo fuso viene versato nello stampo centrifugo. Il metallo viene quindi forzato alle pareti esterne a causa della filatura dello stampo.
2.) Quando lo stampo ruota, la colata di metallo si indurisce
La colata centrifuga è una tecnica adatta per la produzione di parti cilindriche cave come tubi, nessuna necessità di materozze, colonne montanti ed elementi di iniezione, buona finitura superficiale e caratteristiche dettagliate, nessun problema di ritiro, possibilità di produrre tubi lunghi con diametri molto grandi, capacità di produzione elevata .
• COLATA CONTINUA ( COLATA A STRAND ) : Usata per colare una lunghezza continua di metallo. Fondamentalmente il metallo fuso viene colato nel profilo bidimensionale dello stampo ma la sua lunghezza è indeterminata. Il nuovo metallo fuso viene costantemente alimentato nello stampo mentre la colata viaggia verso il basso con la sua lunghezza che aumenta con il tempo. Metalli come rame, acciaio, alluminio vengono fusi in lunghi fili utilizzando un processo di colata continua. Il processo può avere varie configurazioni ma quella comune può essere semplificata come:
1.) Il metallo fuso viene versato in un contenitore posizionato in alto sopra lo stampo a quantità e portate ben calcolate e scorre attraverso lo stampo raffreddato ad acqua. La colata metallica versata nello stampo solidifica su una barra di avviamento posta sul fondo dello stampo. Questa barra di avviamento offre ai rulli qualcosa a cui aggrapparsi inizialmente.
2.) Il lungo filo metallico è trasportato da rulli a velocità costante. I rulli cambiano anche la direzione del flusso del filo metallico da verticale a orizzontale.
3.) Dopo che la colata continua ha percorso una certa distanza orizzontale, una torcia o una sega che si muove con la colata la taglia rapidamente alla lunghezza desiderata.
Il processo di colata continua può essere integrato con ROLLING PROCESS, dove il metallo colato in continuo può essere alimentato direttamente in un laminatoio per produrre I-Beams, T-Beams….ecc. La colata continua produce proprietà uniformi in tutto il prodotto, ha un alto tasso di solidificazione, riduce i costi grazie alla bassissima perdita di materiale, offre un processo in cui il caricamento del metallo, la colata, la solidificazione, il taglio e la rimozione della colata avvengono in un funzionamento continuo e con conseguente alto tasso di produttività e alta qualità. Una considerazione importante è tuttavia l'elevato investimento iniziale, i costi di installazione e i requisiti di spazio.
• SERVIZI DI LAVORAZIONE: Offriamo lavorazioni a tre, quattro e cinque assi. I tipi di lavorazioni che utilizziamo sono TORNITURA, FRESATURA, FORATURA, ALESATURA, BROCCIA, PIALLATURA, SEGA, RETTIFICA, LAPPATURA, LUCIDATURA e LAVORAZIONE NON TRADIZIONALE che viene ulteriormente elaborata in un diverso menu del nostro sito web. Per la maggior parte della nostra produzione, utilizziamo macchine a controllo numerico. Tuttavia per alcune operazioni le tecniche convenzionali sono più adatte e quindi ci affidiamo anche a loro. Le nostre capacità di lavorazione raggiungono il livello più alto possibile e alcune parti più esigenti sono prodotte in uno stabilimento certificato AS9100. Le pale dei motori a reazione richiedono un'esperienza di produzione altamente specializzata e l'attrezzatura giusta. L'industria aerospaziale ha standard molto severi. Alcuni componenti con strutture geometriche complesse sono più facilmente realizzati mediante lavorazione a cinque assi, che si trova solo in alcuni impianti di lavorazione, compreso il nostro. Il nostro stabilimento certificato aerospaziale ha l'esperienza necessaria per soddisfare l'ampia richiesta di documentazione dell'industria aerospaziale.
Nelle operazioni di TORNITURA, un pezzo viene ruotato e spostato contro un utensile da taglio. Per questo processo viene utilizzata una macchina chiamata tornio.
In FRESATURA, una macchina chiamata fresatrice ha un utensile rotante per portare i taglienti in appoggio su un pezzo.
Le operazioni di FORATURA prevedono una fresa rotante con taglienti che produce fori al contatto con il pezzo. Generalmente vengono utilizzati trapani, torni o frese.
Nelle operazioni di ALESATURA un utensile con un'unica punta appuntita piegata viene spostato in un foro grezzo in un pezzo in lavorazione per allargare leggermente il foro e migliorare la precisione. Viene utilizzato per fini di finitura.
BROCCIA comporta un utensile dentato per rimuovere materiale da un pezzo in un passaggio della broccia (utensile dentato). Nella brocciatura lineare, la broccia scorre linearmente contro una superficie del pezzo in lavorazione per effettuare il taglio, mentre nella brocciatura rotativa, la broccia viene ruotata e premuta nel pezzo in lavorazione per tagliare una forma simmetrica dell'asse.
LA LAVORAZIONE DI TIPO SVIZZERO è una delle nostre preziose tecniche che utilizziamo per la produzione ad alto volume di piccoli pezzi di alta precisione. Utilizzando un tornio di tipo svizzero, torniamo a buon mercato pezzi piccoli, complessi e di precisione. A differenza dei torni convenzionali in cui il pezzo viene mantenuto fermo e l'utensile in movimento, nei centri di tornitura di tipo svizzero, il pezzo può muoversi sull'asse Z e l'utensile è fermo. Nella lavorazione di tipo svizzero, il grezzo della barra viene trattenuto nella macchina e fatto avanzare attraverso una boccola di guida nell'asse z, esponendo solo la parte da lavorare. In questo modo è assicurata una presa salda e la precisione è molto elevata. La disponibilità di utensili motorizzati offre l'opportunità di fresare e forare mentre il materiale avanza dalla boccola di guida. L'asse Y dell'attrezzatura di tipo svizzero offre capacità di fresatura complete e consente di risparmiare molto tempo nella produzione. Inoltre, le nostre macchine dispongono di trapani e utensili alesatori che operano sul pezzo quando è trattenuto nel contromandrino. La nostra capacità di lavorazione di tipo svizzero ci offre un'opportunità di lavorazione completa completamente automatizzata in un'unica operazione.
La lavorazione meccanica è uno dei segmenti più grandi dell'attività di AGS-TECH Inc. La utilizziamo come operazione primaria o secondaria dopo la fusione o l'estrusione di una parte in modo da soddisfare tutte le specifiche del disegno.
• SERVIZI DI FINITURA SUPERFICIALE: Offriamo una vasta gamma di trattamenti superficiali e finiture superficiali come condizionamento superficiale per migliorare l'adesione, deposito di uno strato di ossido sottile per migliorare l'adesione del rivestimento, sabbiatura, film chimico, anodizzazione, nitrurazione, verniciatura a polvere, verniciatura a spruzzo , varie tecniche avanzate di metallizzazione e rivestimento, tra cui sputtering, fascio di elettroni, evaporazione, placcatura, rivestimenti duri come il rivestimento in carbonio simil diamante (DLC) o titanio per utensili di perforazione e taglio.
• SERVIZI DI MARCATURA ED ETICHETTATURA DEI PRODOTTI: Molti dei nostri clienti richiedono marcatura ed etichettatura, marcatura laser, incisione su parti metalliche. Se hai una tale esigenza, discutiamo quale opzione sarà la migliore per te.
Ecco alcuni dei prodotti fusi in metallo comunemente usati. Dal momento che sono pronti all'uso, puoi risparmiare sui costi dello stampo nel caso in cui uno di questi soddisfi le tue esigenze:
CLICCA QUI PER SCARICARE le nostre scatole in alluminio pressofuso serie 11 di AGS-Electronics