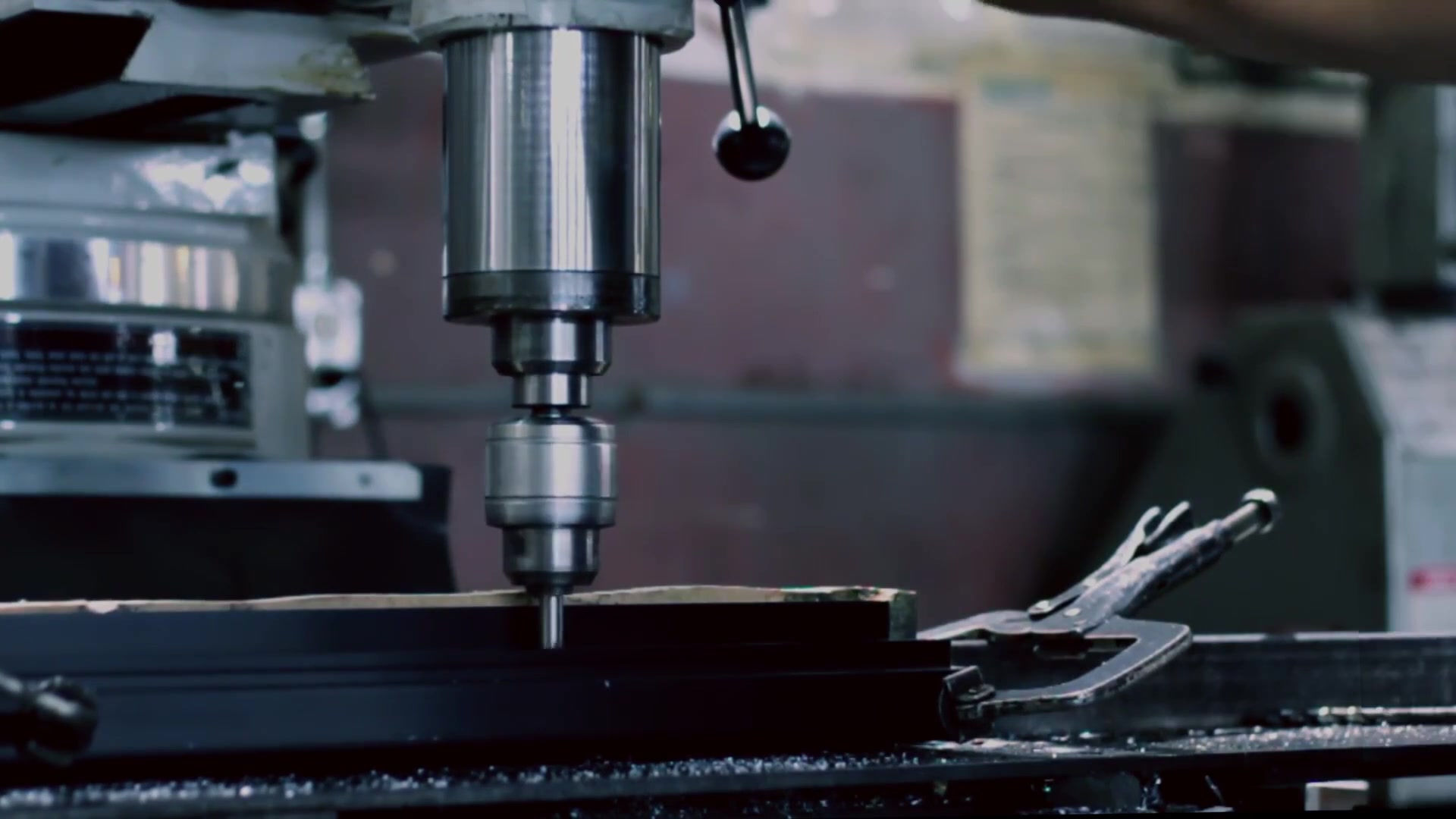
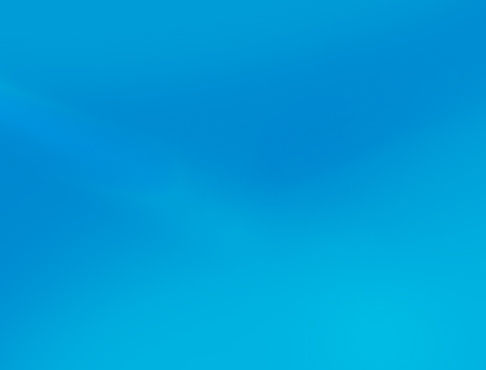
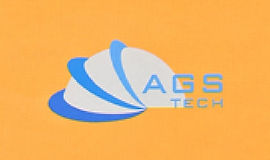
Produttore globale personalizzato, integratore, consolidatore, partner di outsourcing per un'ampia varietà di prodotti e servizi.
Siamo la tua fonte unica per la produzione, la fabbricazione, l'ingegnerizzazione, il consolidamento, l'integrazione, l'esternalizzazione di prodotti e servizi personalizzati e off-shelf.
Choose your Language
-
Produzione su misura
-
Produzione a contratto nazionale e globale
-
Esternalizzazione della produzione
-
Appalti nazionali e globali
-
Consolidamento
-
Integrazione ingegneristica
-
Servizi di ingegneria
Search Results
161 risultati trovati con una ricerca vuota
- Assemblaggi di parti fabbricati su misura, stampi in plastica, fusione di metalli, CNC
Parti prodotte su misura, assiemi, stampi in plastica, fusione, lavorazione CNC, estrusione, forgiatura di metalli, produzione di molle, assemblaggio di prodotti, PCBA, PCB AGS-TECH, Inc. è il tuo Produttore personalizzato globale, integratore, consolidatore, partner di outsourcing. Siamo la vostra fonte unica per la produzione, la fabbricazione, l'ingegneria, il consolidamento, l'outsourcing. Fill In your info if you you need custom design & development & prototyping & mass production: If filling out the form below is not possible or too difficult, we do accept your request by email also. Simply write us at sales@agstech.net Get a Price Quote on a custom designed, developed, prototyped or manufactured product. First name Last name Email Phone Product Name Your Application for the Product Quantity Needed Do you have a price target ? If you do have, please let us know your expected price: Give us more details if you want: Do you accept offshore manufacturing ? YES NO If you have any, upload product relevant files by clicking at the below link. Don't worry, the link below will pop up a new window for downloading your files. You will not navigate away from this current window. After uploading your files, close ONLY the Dropbox Window, but not this page. Make sure to fill out all spaces and click the submit button below. Files that will help us quote your specially tailored product are technical drawings, bill of materials, photos, sketches....etc. You can download more than one file. CLICK HERE TO UPLOAD FILES Request a Quote Thanks! We’ll send you a price quote shortly. PREVIOUS PAGE Siamo AGS-TECH Inc., il tuo punto di riferimento per la produzione, la fabbricazione, l'ingegneria, l'outsourcing e il consolidamento. Siamo l'integratore di ingegneria più diversificato al mondo che offre produzione personalizzata, sottoassiemi, assemblaggio di prodotti e servizi di ingegneria.
- Automazione e Sistemi Intelligenti, Intelligenza Artificiale, AI, IoT
Automazione e sistemi intelligenti, intelligenza artificiale, intelligenza artificiale, sistemi integrati, Internet delle cose, IoT, sistemi di controllo industriale, controllo automatico, Janz Automazione e sistemi intelligenti L'AUTOMAZIONE, denominata anche CONTROLLO AUTOMATICO, è l'uso di vari SISTEMI DI CONTROLLO per il funzionamento di apparecchiature come macchine di fabbrica, forni di trattamento termico e polimerizzazione, apparecchiature di telecomunicazione, ecc. con intervento umano minimo o ridotto. L'automazione si ottiene utilizzando vari mezzi tra cui meccanici, idraulici, pneumatici, elettrici, elettronici e informatici in combinazione. Un SISTEMA INTELLIGENTE d'altra parte è una macchina con un computer integrato connesso a Internet che ha la capacità di raccogliere e analizzare dati e comunicare con altri sistemi. I sistemi intelligenti richiedono sicurezza, connettività, capacità di adattamento ai dati attuali, capacità di monitoraggio e gestione a distanza. I SISTEMI EMBEDDED sono potenti e capaci di complesse elaborazioni e analisi dei dati solitamente specializzate per compiti rilevanti per la macchina host. I sistemi intelligenti sono ovunque nella nostra vita quotidiana. Esempi sono i semafori, i contatori intelligenti, i sistemi e le apparecchiature di trasporto, la segnaletica digitale. Alcuni prodotti di marca che vendiamo sono ATOP TECHNOLOGIES, JANZ TEC, KORENIX, ICP DAS, DFI-ITOX. AGS-TECH Inc. ti offre prodotti che puoi facilmente acquistare a magazzino e integrare nel tuo sistema di automazione o intelligente, nonché prodotti personalizzati progettati specificamente per la tua applicazione. In qualità di fornitore di INTEGRAZIONE ENGINEERING più diversificato, siamo orgogliosi della nostra capacità di fornire una soluzione per quasi tutte le esigenze di automazione o di sistema intelligente. Oltre ai prodotti, siamo qui per le vostre esigenze di consulenza e ingegneria. Scarica le nostre TECNOLOGIE ATOP depliant prodotto compatto (Scarica il prodotto ATOP Technologies List 2021) Scarica la nostra brochure sui prodotti compatti del marchio JANZ TEC Scarica la nostra brochure sui prodotti compatti del marchio KORENIX Scarica la nostra brochure sull'automazione delle macchine a marchio ICP DAS Scarica la nostra brochure sui prodotti per la comunicazione industriale e il networking del marchio ICP DAS Scarica la nostra brochure sui controller incorporati e DAQ del marchio ICP DAS Scarica la nostra brochure Industrial Touch Pad a marchio ICP DAS Scarica la nostra brochure sui moduli IO remoti e sulle unità di espansione IO a marchio ICP DAS Scarica le nostre schede PCI e schede IO del marchio ICP DAS Scarica la nostra brochure sui computer a scheda singola incorporati con marchio DFI-ITOX Scarica la brochure del ns PROGRAMMA DI PARTNERSHIP DI PROGETTAZIONE I sistemi di controllo industriale sono sistemi basati su computer per monitorare e controllare i processi industriali. Alcuni dei nostri SISTEMI DI CONTROLLO INDUSTRIALE (ICS) sono: - Sistemi di controllo di supervisione e acquisizione dati (SCADA): questi sistemi funzionano con segnali codificati su canali di comunicazione per fornire il controllo di apparecchiature remote, generalmente utilizzando un canale di comunicazione per stazione remota. I sistemi di controllo possono essere combinati con sistemi di acquisizione dati aggiungendo l'uso di segnali codificati su canali di comunicazione per acquisire informazioni sullo stato dell'apparecchiatura remota per funzioni di visualizzazione o registrazione. I sistemi SCADA sono diversi dagli altri sistemi ICS in quanto sono processi su larga scala che possono includere più siti su grandi distanze. I sistemi SCADA possono controllare i processi industriali come la produzione e la fabbricazione, i processi infrastrutturali come il trasporto di petrolio e gas, la trasmissione di energia elettrica e i processi basati su strutture come il monitoraggio e il controllo dei sistemi di riscaldamento, ventilazione e condizionamento dell'aria. - Sistemi di controllo distribuito (DCS): un tipo di sistema di controllo automatizzato distribuito in una macchina per fornire istruzioni a diverse parti della macchina. Contrariamente ad avere un dispositivo posizionato centralmente che controlla tutte le macchine, nei sistemi di controllo distribuito ogni sezione di una macchina ha il proprio computer che controlla il funzionamento. I sistemi DCS sono comunemente usati nelle apparecchiature di produzione, utilizzando protocolli di input e output per controllare la macchina. I sistemi di controllo distribuito in genere utilizzano processori progettati su misura come controller. Per la comunicazione vengono utilizzate sia le interconnessioni proprietarie che i protocolli di comunicazione standard. I moduli di ingresso e uscita sono le parti componenti di un DCS. I segnali di ingresso e di uscita possono essere analogici o digitali. I bus collegano il processore e i moduli tramite multiplexer e demultiplexer. Collegano anche i controller distribuiti con il controller centrale e l'interfaccia uomo-macchina. I DCS sono usati frequentemente in: -Impianti petrolchimici e chimici -Sistemi di centrali elettriche, caldaie, centrali nucleari -Sistemi di controllo ambientale -Sistemi di gestione delle acque -Impianti di lavorazione dei metalli - Controllori logici programmabili (PLC): un controllore logico programmabile è un piccolo computer con un sistema operativo integrato realizzato principalmente per controllare i macchinari. I sistemi operativi dei PLC sono specializzati per gestire gli eventi in arrivo in tempo reale. I controllori logici programmabili possono essere programmati. Viene scritto un programma per il PLC che attiva e disattiva le uscite in base alle condizioni di ingresso e al programma interno. I PLC hanno linee di ingresso in cui sono collegati sensori per notificare eventi (come temperatura superiore/inferiore a un certo livello, livello del liquido raggiunto, ecc.) e linee di uscita per segnalare qualsiasi reazione agli eventi in arrivo (come avviare il motore, aprire o chiudere una determinata valvola,… ecc.). Una volta che un PLC è stato programmato, può essere eseguito ripetutamente secondo necessità. I PLC si trovano all'interno di macchine in ambienti industriali e possono far funzionare macchine automatiche per molti anni con poco intervento umano. Sono progettati per ambienti difficili. I controllori logici programmabili sono ampiamente utilizzati nelle industrie basate sui processi, sono dispositivi a stato solido basati su computer che controllano apparecchiature e processi industriali. Anche se i PLC possono controllare i componenti di sistema utilizzati nei sistemi SCADA e DCS, sono spesso i componenti primari nei sistemi di controllo più piccoli. CLICK Product Finder-Locator Service PAGINA PRECEDENTE
- PCB, PCBA, assemblaggio di circuiti stampati, assemblaggio a montaggio superficiale, SMA
PCB - PCBA - Assemblaggio di circuiti stampati - Multistrato flessibile rigido - Assemblaggio a montaggio superficiale - SMA - AGS-TECH Inc. Produzione e assemblaggio di PCB e PCBA Noi offriamo: PCB: circuito stampato PCBA: Assemblaggio di circuiti stampati • Assemblaggi di circuiti stampati di tutti i tipi (PCB, rigidi, flessibili e multistrato) • Substrati o assemblaggio PCBA completo a seconda delle vostre esigenze. • Assemblaggio a foro passante e montaggio superficiale (SMA) Inviaci i tuoi file Gerber, BOM, specifiche dei componenti. Possiamo assemblare i vostri PCB e PCBA utilizzando i componenti esatti specificati, oppure possiamo offrirvi le nostre alternative corrispondenti. Siamo esperti nella spedizione di PCB e PCBA e ci assicureremo di imballarli in sacchetti antistatici per evitare danni elettrostatici. I PCB destinati agli ambienti estremi hanno spesso un rivestimento conforme, che viene applicato mediante immersione o spruzzatura dopo che i componenti sono stati saldati. Il rivestimento previene la corrosione e le correnti di dispersione o il cortocircuito dovuto alla condensa. I nostri rivestimenti conformi sono solitamente intingoli di soluzioni diluite di gomma siliconica, poliuretano, acrilico o resina epossidica. Alcuni sono tecnopolimeri spruzzati sul PCB in una camera a vuoto. Lo standard di sicurezza UL 796 copre i requisiti di sicurezza dei componenti per i circuiti stampati da utilizzare come componenti in dispositivi o apparecchi. I nostri test analizzano caratteristiche come infiammabilità, temperatura massima di esercizio, tracciamento elettrico, deviazione del calore e supporto diretto di parti elettriche sotto tensione. Le schede PCB possono utilizzare materiali di base organici o inorganici in forma singola o multistrato, rigida o flessibile. La costruzione dei circuiti può comprendere tecniche di conduttori incisi, stampati, pretagliati, pressati a filo, additivi e placcati. È possibile utilizzare componenti stampati. L'idoneità dei parametri del modello, della temperatura e dei limiti massimi di saldatura deve essere determinata in conformità con la costruzione e i requisiti del prodotto finale applicabili. Non aspettare, chiamaci per maggiori informazioni, assistenza alla progettazione, prototipi e produzione in serie. Se necessario, ci occuperemo noi di tutte le etichette, imballaggio, spedizione, importazione e dogana, stoccaggio e consegna. Di seguito è possibile scaricare le nostre brochure e cataloghi pertinenti per l'assemblaggio di PCB e PCBA: Capacità e tolleranze di processo generali per la produzione di PCB rigidi Capacità e tolleranze di processo generali per la produzione di PCB in alluminio Capacità e tolleranze di processo generali per la produzione di PCB flessibili e rigidi-flessibili Processi generali di fabbricazione di PCB Riepilogo generale del processo di produzione di PCBA per l'assemblaggio di circuiti stampati Panoramica dell'impianto di produzione di circuiti stampati Alcune altre brochure dei nostri prodotti che possiamo utilizzare nei vostri progetti di assemblaggio PCB e PCBA: Per scaricare il nostro catalogo di componenti e hardware di interconnessione pronti all'uso come terminali ad innesto rapido, spine e prese USB, micro pin e jack e altro, CLICCA QUI Morsettiere e connettori Catalogo Generale Morsettiere Dissipatori di calore standard Dissipatori di calore estrusi Easy Click dissipatori di calore un prodotto perfetto per assemblaggi PCB Dissipatori Super Power per sistemi elettronici di potenza medio-alta Dissipatori di calore con Super Fins Moduli LCD Catalogo Prese-Entrata-Connettori Scarica la brochure del ns PROGRAMMA DI PARTNERSHIP DI PROGETTAZIONE Se sei interessato alle nostre capacità di ingegneria e ricerca e sviluppo invece di operazioni e capacità di produzione, ti invitiamo a visitare il nostro sito di ingegneria http://www.ags-engineering.com CLICK Product Finder-Locator Service PAGINA PRECEDENTE
- Brasatura, saldatura, processi di giunzione, servizi di assemblaggio
Brasatura - Brasatura - Saldatura - Processi di giunzione - Servizi di assemblaggio - Sottoassiemi - Assiemi - Produzione personalizzata - AGS-TECH Inc. Brasatura & Saldatura Tra le molte tecniche di GIUNZIONE che impieghiamo nella produzione, viene data particolare enfasi a SALDATURA, BRASATURA, SALDATURA, INCOLLAGGIO ADESIVI E ASSEMBLAGGIO MECCANICO PERSONALIZZATO perché queste tecniche sono ampiamente utilizzate in applicazioni come la produzione di assemblaggi ermetici, la produzione di prodotti ad alta tecnologia e la sigillatura specializzata. Qui ci concentreremo sugli aspetti più specializzati di queste tecniche di giunzione in quanto sono legate alla produzione di prodotti e assemblaggi avanzati. SALDATURA A FUSIONE: Usiamo il calore per fondere e fondere i materiali. Il calore è fornito da elettricità o travi ad alta energia. I tipi di saldatura per fusione che impieghiamo sono SALDATURA A GAS OXYFUEL, SALDATURA AD ARCO, SALDATURA A FASCIO AD ALTA ENERGIA. SALDATURA A STATO SOLIDO: Uniamo le parti senza fusione e fusione. I nostri metodi di saldatura allo stato solido sono FREDDO, ULTRASUONI, RESISTENZA, FRICTION, EXPLOSION WELDING e DIFFUSION BONDING. BRASATURA E SALDATURA: Usano metalli d'apporto e ci danno il vantaggio di lavorare a temperature più basse rispetto alla saldatura, quindi meno danni strutturali ai prodotti. Informazioni sul nostro impianto di brasatura che produce raccordi da ceramica a metallo, tenuta ermetica, passanti per il vuoto, componenti per il controllo dei fluidi e per alto e ultra alto vuoto sono disponibili qui:Brochure della fabbrica di brasatura INCOLLAGGIO ADESIVI: A causa della diversità degli adesivi utilizzati nell'industria e anche della diversità delle applicazioni, abbiamo una pagina dedicata a questo. Per andare alla nostra pagina sull'incollaggio, fare clic qui. MONTAGGIO MECCANICO PERSONALIZZATO: Utilizziamo una varietà di elementi di fissaggio come bulloni, viti, dadi, rivetti. I nostri elementi di fissaggio non si limitano agli elementi di fissaggio standard standard. Progettiamo, sviluppiamo e produciamo elementi di fissaggio speciali realizzati con materiali non standard in modo che possano soddisfare i requisiti per applicazioni speciali. A volte si desidera la non conduttività elettrica o termica mentre a volte si desidera la conduttività. Per alcune applicazioni speciali, un cliente potrebbe desiderare elementi di fissaggio speciali che non possono essere rimossi senza distruggere il prodotto. Ci sono infinite idee e applicazioni. Abbiamo tutto per te, se non off-shelf possiamo svilupparlo rapidamente. Per andare alla nostra pagina sull'assemblaggio meccanico, fare clic qui . Esaminiamo le nostre varie tecniche di giunzione in modo più dettagliato. SALDATURA A GAS OXYFUEL (OFW): Utilizziamo un gas combustibile miscelato con ossigeno per produrre la fiamma di saldatura. Quando usiamo l'acetilene come combustibile e ossigeno, lo chiamiamo saldatura a gas ossiacetilenico. Nel processo di combustione del gas ossicombustibile si verificano due reazioni chimiche: C2H2 + O2 ------» 2CO + H2 + Riscald 2CO + H2 + 1,5 O2--------» 2 CO2 + H2O + Calore La prima reazione dissocia l'acetilene in monossido di carbonio e idrogeno producendo circa il 33% del calore totale generato. Il secondo processo sopra rappresenta un'ulteriore combustione dell'idrogeno e del monossido di carbonio mentre produce circa il 67% del calore totale. Le temperature nella fiamma sono comprese tra 1533 e 3573 Kelvin. La percentuale di ossigeno nella miscela di gas è importante. Se il contenuto di ossigeno è superiore alla metà, la fiamma diventa un agente ossidante. Questo è indesiderabile per alcuni metalli ma desiderabile per altri. Un esempio quando la fiamma ossidante è desiderabile sono le leghe a base di rame perché forma uno strato di passivazione sul metallo. Quando invece si riduce il contenuto di ossigeno, non è possibile la combustione completa e la fiamma diventa una fiamma riducente (carburante). Le temperature in una fiamma riducente sono più basse e quindi è adatto per processi come la saldatura e la brasatura. Anche altri gas sono potenziali combustibili, ma presentano alcuni svantaggi rispetto all'acetilene. Occasionalmente forniamo metalli d'apporto alla zona di saldatura sotto forma di barre di apporto o filo. Alcuni di essi sono rivestiti con fondente per ritardare l'ossidazione delle superfici e proteggere così il metallo fuso. Un ulteriore vantaggio che il flusso ci offre è la rimozione di ossidi e altre sostanze dalla zona di saldatura. Questo porta a un legame più forte. Una variante della saldatura a gas ossicombustibile è la SALDATURA A GAS A PRESSIONE, in cui i due componenti vengono riscaldati alla loro interfaccia utilizzando una torcia a gas ossiacetilenico e una volta che l'interfaccia inizia a fondere, la torcia viene estratta e viene applicata una forza assiale per premere insieme le due parti fino a quando l'interfaccia non si è solidificata. SALDATURA AD ARCO: Usiamo energia elettrica per produrre un arco tra la punta dell'elettrodo e le parti da saldare. L'alimentazione può essere AC o DC mentre gli elettrodi sono consumabili o non consumabili. Il trasferimento di calore nella saldatura ad arco può essere espresso dalla seguente equazione: H / l = ex VI / v Qui H è l'apporto termico, l è la lunghezza della saldatura, V e I sono la tensione e la corrente applicate, v è la velocità di saldatura ed e è l'efficienza del processo. Maggiore è l'efficienza "e", più vantaggiosamente viene utilizzata l'energia disponibile per fondere il materiale. La portata termica può anche essere espressa come: H = ux (Volume) = ux A xl Qui u è l'energia specifica per la fusione, A la sezione trasversale della saldatura e l la lunghezza della saldatura. Dalle due equazioni precedenti possiamo ottenere: v = ex VI / u A Una variante della saldatura ad arco è la SALDATURA AD ARCO METALLICO SHIELDED (SMAW) che costituisce circa il 50% di tutti i processi di saldatura industriale e di manutenzione. LA SALDATURA AD ARCO ELETTRICO (SALDATURA A STICK) viene eseguita toccando la punta di un elettrodo rivestito sul pezzo e ritirandolo rapidamente a una distanza sufficiente a mantenere l'arco. Chiamiamo questo processo anche saldatura a bastoncino perché gli elettrodi sono bastoncini sottili e lunghi. Durante il processo di saldatura, la punta dell'elettrodo fonde insieme al suo rivestimento e al metallo base in prossimità dell'arco. Una miscela di metallo di base, metallo dell'elettrodo e sostanze del rivestimento dell'elettrodo si solidifica nell'area di saldatura. Il rivestimento dell'elettrodo si disossida e fornisce un gas di protezione nella zona di saldatura, proteggendolo così dall'ossigeno nell'ambiente. Pertanto il processo è indicato come saldatura ad arco metallico schermato. Utilizziamo correnti comprese tra 50 e 300 Ampere e livelli di potenza generalmente inferiori a 10 kW per prestazioni di saldatura ottimali. Importante è anche la polarità della corrente continua (direzione del flusso di corrente). La polarità rettilinea in cui il pezzo è positivo e l'elettrodo è negativo è preferita nella saldatura di lamiere a causa della sua penetrazione ridotta e anche per giunti con giochi molto ampi. Quando abbiamo la polarità inversa, cioè l'elettrodo è positivo e il pezzo negativo, possiamo ottenere penetrazioni di saldatura più profonde. Con la corrente alternata, poiché disponiamo di archi pulsanti, possiamo saldare sezioni spesse utilizzando elettrodi di grande diametro e correnti massime. Il metodo di saldatura SMAW è adatto per spessori di pezzi da 3 a 19 mm e anche più utilizzando tecniche a più passate. La scoria formata sopra la saldatura deve essere rimossa utilizzando una spazzola metallica, in modo che non vi siano corrosione e rotture nell'area di saldatura. Questo ovviamente si aggiunge al costo della saldatura ad arco metallico schermato. Tuttavia, la SMAW è la tecnica di saldatura più popolare nell'industria e nei lavori di riparazione. SALDATURA AD ARCO SOMMERSO (SEGA): In questo processo proteggiamo l'arco di saldatura utilizzando materiali a flusso granulare come calce, silice, floruro di calcio, ossido di manganese….ecc. Il flusso granulare viene immesso nella zona di saldatura per gravità attraverso un ugello. Il flusso che ricopre la zona di saldatura fusa protegge in modo significativo da scintille, fumi, radiazioni UV, ecc. e funge da isolante termico, permettendo così al calore di penetrare in profondità nel pezzo. Il flusso non fuso viene recuperato, trattato e riutilizzato. Una bobina di nudo viene utilizzata come elettrodo e alimentata attraverso un tubo all'area di saldatura. Usiamo correnti comprese tra 300 e 2000 Ampere. Il processo di saldatura ad arco sommerso (SAW) è limitato alle posizioni orizzontali e piatte e alle saldature circolari se è possibile la rotazione della struttura circolare (come i tubi) durante la saldatura. Le velocità possono raggiungere i 5 m/min. Il processo SAW è adatto per lamiere spesse e consente saldature di alta qualità, tenaci, duttili e uniformi. La produttività, ovvero la quantità di materiale di saldatura depositato all'ora, è da 4 a 10 volte la quantità rispetto al processo SMAW. Un altro processo di saldatura ad arco, vale a dire il GAS METAL ARC WELDING (GMAW) o in alternativa denominato METAL INERT GAS WELDING (MIG) si basa sull'area di saldatura protetta da fonti esterne di gas come elio, argon, anidride carbonica ... ecc. Potrebbero essere presenti ulteriori disossidanti nel metallo dell'elettrodo. Il filo di consumo viene alimentato attraverso un ugello nella zona di saldatura. La fabbricazione che coinvolge metalli sia ferrosi che non ferrosi viene eseguita utilizzando la saldatura ad arco di metalli gassosi (GMAW). La produttività della saldatura è circa 2 volte quella del processo SMAW. Vengono utilizzate apparecchiature di saldatura automatizzate. Il metallo viene trasferito in uno dei tre modi seguenti in questo processo: "Trasferimento spray" comporta il trasferimento di diverse centinaia di piccole goccioline di metallo al secondo dall'elettrodo all'area di saldatura. Nel "trasferimento globulare", invece, vengono utilizzati gas ricchi di anidride carbonica e globuli di metallo fuso vengono spinti dall'arco elettrico. Le correnti di saldatura sono elevate e la penetrazione della saldatura è più profonda, la velocità di saldatura è maggiore rispetto al trasferimento a spruzzo. Pertanto il trasferimento globulare è migliore per la saldatura di sezioni più pesanti. Infine, nel metodo "Cortocircuito", la punta dell'elettrodo tocca il bagno di saldatura fuso, cortocircuitandolo mentre il metallo a velocità superiori a 50 goccioline/secondo viene trasferito in singole goccioline. Vengono utilizzate basse correnti e tensioni insieme a un filo più sottile. Le potenze utilizzate sono di circa 2 kW e le temperature relativamente basse, rendendo questo metodo adatto per lamiere sottili di spessore inferiore a 6 mm. Un'altra variazione del processo di SALDATURA AD ARCO FLUX-CORED (FCAW) è simile alla saldatura ad arco di metallo gas, tranne per il fatto che l'elettrodo è un tubo riempito di flusso. I vantaggi dell'utilizzo di elettrodi a flusso animato sono che producono archi più stabili, ci danno l'opportunità di migliorare le proprietà dei metalli di saldatura, la natura meno fragile e flessibile del suo flusso rispetto alla saldatura SMAW, i contorni di saldatura migliorati. Gli elettrodi animati autoprotetti contengono materiali che schermano la zona di saldatura dall'atmosfera. Usiamo circa 20 kW di potenza. Come il processo GMAW, anche il processo FCAW offre l'opportunità di automatizzare i processi per la saldatura continua ed è economico. È possibile sviluppare diverse sostanze chimiche dei metalli di saldatura aggiungendo varie leghe al nucleo di flusso. In ELECTROGAS WELDING (EGW) saldiamo i pezzi posizionati da bordo a bordo. A volte è anche chiamata SALDATURA DI TESTA. Il metallo di saldatura viene inserito in una cavità di saldatura tra due pezzi da unire. Lo spazio è racchiuso da due dighe raffreddate ad acqua per evitare che le scorie fuse fuoriescano. Le dighe vengono sollevate da azionamenti meccanici. Quando il pezzo può essere ruotato, possiamo utilizzare la tecnica della saldatura a elettrogas anche per la saldatura circonferenziale dei tubi. Gli elettrodi vengono alimentati attraverso un condotto per mantenere un arco continuo. Le correnti possono essere di circa 400 Ampere o 750 Ampere e livelli di potenza di circa 20 kW. I gas inerti provenienti da un elettrodo animato o da una sorgente esterna forniscono schermatura. Utilizziamo la saldatura a elettrogas (EGW) per metalli come acciai, titanio….ecc con spessori da 12mm a 75mm. La tecnica è adatta per grandi strutture. Tuttavia, in un'altra tecnica chiamata SALDATURA A ELETTROSLAG (ESW) l'arco si accende tra l'elettrodo e la parte inferiore del pezzo e viene aggiunto il flusso. Quando la scoria fusa raggiunge la punta dell'elettrodo, l'arco si spegne. L'energia viene continuamente fornita attraverso la resistenza elettrica delle scorie fuse. Possiamo saldare lamiere con spessori compresi tra 50 mm e 900 mm e anche superiori. Le correnti sono di circa 600 Ampere mentre le tensioni sono comprese tra 40 e 50 V. Le velocità di saldatura sono di circa 12-36 mm/min. Le applicazioni sono simili alla saldatura a elettrogas. Uno dei nostri processi con elettrodi non consumabili, la SALDATURA AD ARCO DI TUNGSTENO CON GAS (GTAW), nota anche come SALDATURA CON GAS INERTE DI TUNGSTENO (TIG), prevede la fornitura di un metallo d'apporto mediante un filo. Per giunti ravvicinati a volte non utilizziamo il metallo d'apporto. Nel processo TIG non utilizziamo il flusso, ma utilizziamo argon ed elio per la schermatura. Il tungsteno ha un alto punto di fusione e non viene consumato nel processo di saldatura TIG, quindi è possibile mantenere una corrente costante e spazi vuoti dell'arco. I livelli di potenza sono compresi tra 8 e 20 kW e le correnti a 200 Ampere (CC) o 500 Ampere (CA). Per l'alluminio e il magnesio utilizziamo la corrente alternata per la sua funzione di pulizia dell'ossido. Per evitare la contaminazione dell'elettrodo di tungsteno, evitiamo il suo contatto con metalli fusi. La saldatura ad arco di tungsteno a gas (GTAW) è particolarmente utile per la saldatura di metalli sottili. Le saldature GTAW sono di altissima qualità con una buona finitura superficiale. A causa del costo più elevato dell'idrogeno gassoso, una tecnica meno utilizzata è la SALDATURA A IDROGENO ATOMICO (AHW), in cui generiamo un arco tra due elettrodi di tungsteno in un'atmosfera schermante di gas idrogeno che scorre. L'AHW è anche un processo di saldatura ad elettrodo non consumabile. L'idrogeno biatomico H2 si scompone nella sua forma atomica vicino all'arco di saldatura dove le temperature sono superiori a 6273 Kelvin. Mentre si rompe, assorbe una grande quantità di calore dall'arco. Quando gli atomi di idrogeno colpiscono la zona di saldatura che è una superficie relativamente fredda, si ricombinano in forma biatomica e rilasciano il calore immagazzinato. L'energia può essere variata cambiando il pezzo in lavorazione alla distanza dell'arco. In un altro processo con elettrodi non consumabili, PLASMA ARC WELDING (PAW) abbiamo un arco plasma concentrato diretto verso la zona di saldatura. Le temperature raggiungono i 33.273 Kelvin in PAW. Un numero quasi uguale di elettroni e ioni costituisce il gas plasma. Un arco pilota a bassa corrente avvia il plasma che si trova tra l'elettrodo di tungsteno e l'orifizio. Le correnti di esercizio sono generalmente di circa 100 Ampere. Può essere alimentato un metallo d'apporto. Nella saldatura ad arco al plasma, la schermatura è ottenuta mediante un anello di schermatura esterno e utilizzando gas come argon ed elio. Nella saldatura ad arco al plasma, l'arco può trovarsi tra l'elettrodo e il pezzo o tra l'elettrodo e l'ugello. Questa tecnica di saldatura presenta i vantaggi rispetto ad altri metodi di maggiore concentrazione di energia, capacità di saldatura più profonda e più stretta, migliore stabilità dell'arco, velocità di saldatura più elevate fino a 1 metro/min, minore distorsione termica. Generalmente utilizziamo la saldatura ad arco plasma per spessori inferiori a 6 mm e talvolta fino a 20 mm per alluminio e titanio. SALDATURA A FASCIO AD ALTA ENERGIA: Un altro tipo di metodo di saldatura per fusione con saldatura a fascio di elettroni (EBW) e saldatura laser (LBW) in due varianti. Queste tecniche sono di particolare valore per il nostro lavoro di produzione di prodotti high-tech. Nella saldatura a fascio di elettroni, gli elettroni ad alta velocità colpiscono il pezzo e la loro energia cinetica viene convertita in calore. Lo stretto fascio di elettroni viaggia facilmente nella camera a vuoto. Generalmente utilizziamo l'alto vuoto nella saldatura a fascio elettronico. È possibile saldare piastre spesse fino a 150 mm. Non sono necessari gas di protezione, flusso o materiale di riempimento. I cannoni a raggi Elecron hanno una capacità di 100 kW. Sono possibili saldature profonde e strette con proporzioni elevate fino a 30 e piccole zone soggette a calore. Le velocità di saldatura possono raggiungere i 12 m/min. Nella saldatura a raggio laser utilizziamo laser ad alta potenza come fonte di calore. Raggi laser di soli 10 micron ad alta densità consentono una penetrazione profonda nel pezzo. Con la saldatura a raggio laser è possibile ottenere rapporti profondità-larghezza fino a 10. Utilizziamo sia laser pulsati che a onda continua, con il primo in applicazioni per materiali sottili e il secondo principalmente per pezzi spessi fino a circa 25 mm. I livelli di potenza sono fino a 100 kW. La saldatura a raggio laser non è adatta per materiali otticamente molto riflettenti. I gas possono essere utilizzati anche nel processo di saldatura. Il metodo di saldatura a raggio laser è adatto per l'automazione e la produzione ad alto volume e può offrire velocità di saldatura comprese tra 2,5 m/min e 80 m/min. Uno dei principali vantaggi offerti da questa tecnica di saldatura è l'accesso ad aree in cui non è possibile utilizzare altre tecniche. I raggi laser possono viaggiare facilmente in regioni così difficili. Non è necessario il vuoto come nella saldatura a fascio di elettroni. Saldature con buona qualità e resistenza, basso ritiro, bassa distorsione, bassa porosità possono essere ottenute con saldatura a raggio laser. I raggi laser possono essere facilmente manipolati e modellati utilizzando cavi in fibra ottica. La tecnica è quindi adatta per la saldatura di assiemi ermetici di precisione, pacchetti elettronici... ecc. Diamo un'occhiata alle nostre tecniche di SALDATURA A STATO SOLIDO. La SALDATURA A FREDDO (CW) è un processo in cui la pressione invece del calore viene applicata utilizzando stampi o rulli alle parti accoppiate. Nella saldatura a freddo, almeno una delle parti di accoppiamento deve essere duttile. I migliori risultati si ottengono con due materiali simili. Se i due metalli da unire con la saldatura a freddo sono dissimili si possono ottenere giunzioni deboli e fragili. Il metodo di saldatura a freddo è adatto per pezzi morbidi, duttili e di piccole dimensioni come collegamenti elettrici, bordi di contenitori termosensibili, nastri bimetallici per termostati... ecc. Una variante della saldatura a freddo è la saldatura a rulli (o saldatura a rulli), in cui la pressione viene applicata attraverso una coppia di rulli. A volte eseguiamo la saldatura a rulli a temperature elevate per una migliore resistenza interfacciale. Un altro processo di saldatura allo stato solido che utilizziamo è la SALDATURA A ULTRASUONI (USW), in cui i pezzi sono sottoposti a una forza normale statica ea sollecitazioni di taglio oscillanti. Le sollecitazioni di taglio oscillanti vengono applicate attraverso la punta di un trasduttore. La saldatura ad ultrasuoni distribuisce oscillazioni con frequenze da 10 a 75 kHz. In alcune applicazioni come la saldatura continua, utilizziamo un disco di saldatura rotante come punta. Le sollecitazioni di taglio applicate ai pezzi provocano piccole deformazioni plastiche, rompono gli strati di ossido, contaminanti e portano al legame allo stato solido. Le temperature coinvolte nella saldatura ad ultrasuoni sono molto al di sotto delle temperature del punto di fusione per i metalli e non avviene alcuna fusione. Usiamo spesso il processo di saldatura a ultrasuoni (USW) per materiali non metallici come la plastica. Nei termoplastici, tuttavia, le temperature raggiungono i punti di fusione. Un'altra tecnica popolare, nella SALDATURA PER FRICTION (FRW) il calore viene generato attraverso l'attrito all'interfaccia dei pezzi da unire. Nella saldatura ad attrito teniamo fermo uno dei pezzi mentre l'altro viene trattenuto in un'attrezzatura e ruotato a velocità costante. I pezzi vengono quindi portati in contatto sotto una forza assiale. La velocità di rotazione superficiale nella saldatura ad attrito può raggiungere in alcuni casi i 900 m/min. Dopo un sufficiente contatto interfacciale, il pezzo in rotazione viene arrestato improvvisamente e la forza assiale viene aumentata. La zona di saldatura è generalmente una regione stretta. La tecnica della saldatura ad attrito può essere utilizzata per unire parti solide e tubolari in diversi materiali. È possibile che si sviluppi un bagliore sull'interfaccia in FRW, ma questo lampo può essere rimosso mediante lavorazione secondaria o rettifica. Esistono variazioni del processo di saldatura per attrito. Ad esempio la “saldatura ad attrito inerziale” prevede un volano la cui energia cinetica rotazionale viene utilizzata per saldare le parti. La saldatura è completa quando il volano si ferma. La massa rotante può essere variata e quindi l'energia cinetica di rotazione. Un'altra variante è la "saldatura ad attrito lineare", in cui viene imposto un movimento alternativo lineare su almeno uno dei componenti da unire. Nella saldatura ad attrito lineare le parti non devono essere circolari, possono essere rettangolari, quadrate o di altra forma. Le frequenze possono essere nell'ordine delle decine di Hz, le ampiezze nell'intervallo dei millimetri e le pressioni nell'ordine delle decine o centinaia di MPa. Infine, la "saldatura per attrito e agitazione" è in qualche modo diversa dalle altre due spiegate sopra. Mentre nella saldatura ad attrito inerziale e nella saldatura ad attrito lineare il riscaldamento delle interfacce è ottenuto mediante attrito sfregando due superfici di contatto, nel metodo di saldatura ad attrito con agitazione un terzo corpo viene strofinato contro le due superfici da unire. Un utensile rotante di diametro compreso tra 5 e 6 mm viene portato a contatto con il giunto. Le temperature possono aumentare fino a valori compresi tra 503 e 533 Kelvin. Ha luogo il riscaldamento, la miscelazione e l'agitazione del materiale nel giunto. Usiamo la saldatura ad attrito su una varietà di materiali tra cui alluminio, plastica e compositi. Le saldature sono uniformi e la qualità è elevata con pori minimi. Nella saldatura ad agitazione ad attrito non vengono prodotti fumi o schizzi e il processo è ben automatizzato. SALDATURA A RESISTENZA (RW): Il calore necessario per la saldatura è prodotto dalla resistenza elettrica tra i due pezzi da unire. Nella saldatura a resistenza non vengono utilizzati flussi, gas di protezione o elettrodi consumabili. Il riscaldamento Joule avviene nella saldatura a resistenza e può essere espresso come: H = (Quadrato I) x R xtx K H è il calore generato in joule (watt-secondi), I la corrente in Ampere, R la resistenza in Ohm, t è il tempo in secondi in cui scorre la corrente. Il fattore K è minore di 1 e rappresenta la frazione di energia che non viene persa per irraggiamento e conduzione. Le correnti nei processi di saldatura a resistenza possono raggiungere livelli fino a 100.000 A, ma le tensioni sono in genere comprese tra 0,5 e 10 Volt. Gli elettrodi sono in genere realizzati in leghe di rame. Sia materiali simili che dissimili possono essere uniti mediante saldatura a resistenza. Esistono diverse varianti per questo processo: la "saldatura a punti di resistenza" prevede due elettrodi tondi opposti che entrano in contatto con le superfici della giunzione sovrapposta delle due lamiere. La pressione viene applicata fino allo spegnimento della corrente. La pepita di saldatura ha generalmente un diametro fino a 10 mm. La saldatura a punti a resistenza lascia segni di indentazione leggermente scoloriti nei punti di saldatura. La saldatura a punti è la nostra tecnica di saldatura a resistenza più popolare. Nella saldatura a punti vengono utilizzate varie forme di elettrodi per raggiungere aree difficili. La nostra attrezzatura per la saldatura a punti è controllata da CNC e dispone di più elettrodi che possono essere utilizzati contemporaneamente. Un'altra variante di "saldatura a resistenza continua" viene eseguita con elettrodi a ruota oa rullo che producono punti di saldatura continui ogni volta che la corrente raggiunge un livello sufficientemente alto nel ciclo di alimentazione CA. I giunti prodotti dalla saldatura a resistenza sono a tenuta di liquidi e gas. Velocità di saldatura di circa 1,5 m/min sono normali per lamiere sottili. Si possono applicare correnti intermittenti in modo da produrre punti di saldatura agli intervalli desiderati lungo la giunzione. Nella “saldatura a proiezione di resistenza” goffriamo una o più sporgenze (fossette) su una delle superfici del pezzo da saldare. Queste proiezioni possono essere rotonde o ovali. In questi punti goffrati che entrano in contatto con la parte di accoppiamento si raggiungono alte temperature localizzate. Gli elettrodi esercitano una pressione per comprimere queste proiezioni. Gli elettrodi nella saldatura a proiezione di resistenza hanno punte piatte e sono leghe di rame raffreddate ad acqua. Il vantaggio della saldatura a proiezione di resistenza è la nostra capacità di eseguire più saldature in una sola passata, quindi la maggiore durata dell'elettrodo, la capacità di saldare lamiere di vari spessori, la capacità di saldare dadi e bulloni alle lamiere. Lo svantaggio della saldatura a proiezione di resistenza è il costo aggiuntivo della goffratura delle fossette. Ancora un'altra tecnica, nella "saldatura flash", il calore viene generato dall'arco alle estremità dei due pezzi quando iniziano a entrare in contatto. Questo metodo può anche essere considerato in alternativa la saldatura ad arco. La temperatura all'interfaccia aumenta e il materiale si ammorbidisce. Viene applicata una forza assiale e si forma una saldatura nella regione ammorbidita. Dopo che la saldatura flash è completa, il giunto può essere lavorato per un aspetto migliore. La qualità della saldatura ottenuta mediante saldatura flash è buona. I livelli di potenza sono da 10 a 1500 kW. La saldatura flash è adatta per la giunzione da bordo a bordo di metalli simili o dissimili fino a 75 mm di diametro e lamiere con uno spessore compreso tra 0,2 mm e 25 mm. La "saldatura ad arco di perno" è molto simile alla saldatura flash. Il prigioniero come un bullone o un'asta filettata funge da elettrodo mentre viene unito a un pezzo come una piastra. Per concentrare il calore generato, prevenire l'ossidazione e trattenere il metallo fuso nella zona di saldatura, attorno al giunto viene posizionato un anello in ceramica monouso. Infine la “saldatura a percussione” un altro processo di saldatura a resistenza, utilizza un condensatore per fornire l'energia elettrica. Nella saldatura a percussione la potenza viene scaricata in pochi millisecondi di tempo sviluppando un elevato calore localizzato al giunto. Utilizziamo ampiamente la saldatura a percussione nell'industria manifatturiera elettronica, dove è necessario evitare il riscaldamento di componenti elettronici sensibili in prossimità del giunto. Una tecnica chiamata EXPLOSION WELDING prevede la detonazione di uno strato di esplosivo che viene posto su uno dei pezzi da unire. L'altissima pressione esercitata sul pezzo produce un'interfaccia turbolenta e ondulata e si verifica un incastro meccanico. Le forze di adesione nella saldatura esplosiva sono molto elevate. La saldatura per esplosione è un buon metodo per il rivestimento di lastre con metalli diversi. Dopo il rivestimento, le lastre possono essere laminate in sezioni più sottili. A volte utilizziamo la saldatura a esplosione per espandere i tubi in modo che vengano sigillati saldamente contro la piastra. Il nostro ultimo metodo nell'ambito della giunzione allo stato solido è DIFFUSION BONDING o DIFFUSION WELDING (DFW) in cui una buona giunzione si ottiene principalmente mediante la diffusione di atomi attraverso l'interfaccia. Anche una certa deformazione plastica all'interfaccia contribuisce alla saldatura. Le temperature coinvolte sono di circa 0,5 Tm dove Tm è la temperatura di fusione del metallo. La forza di adesione nella saldatura a diffusione dipende da pressione, temperatura, tempo di contatto e pulizia delle superfici di contatto. A volte utilizziamo metalli d'apporto nell'interfaccia. Il calore e la pressione sono richiesti nel legame per diffusione e sono forniti da resistenza elettrica o forno e pesi morti, pressa o altro. Metalli simili e dissimili possono essere uniti con saldatura a diffusione. Il processo è relativamente lento a causa del tempo impiegato dagli atomi per migrare. DFW può essere automatizzato ed è ampiamente utilizzato nella fabbricazione di parti complesse per l'industria aerospaziale, elettronica e medica. I prodotti fabbricati includono impianti ortopedici, sensori, elementi strutturali aerospaziali. L'incollaggio per diffusione può essere combinato con SUPERPLASTIC FORMING per realizzare strutture complesse in lamiera. Posizioni selezionate sui fogli vengono prima incollate per diffusione e quindi le regioni non legate vengono espanse in uno stampo usando la pressione dell'aria. Le strutture aerospaziali con un elevato rapporto rigidità/peso vengono prodotte utilizzando questa combinazione di metodi. Il processo combinato di saldatura a diffusione/formatura superplastica riduce il numero di parti richieste eliminando la necessità di elementi di fissaggio, produce parti a bassa sollecitazione altamente accurate in modo economico e con tempi di consegna brevi. BRASATURA: Le tecniche di brasatura e saldatura prevedono temperature inferiori a quelle richieste per la saldatura. Tuttavia, le temperature di brasatura sono superiori a quelle di saldatura. Nella brasatura un metallo d'apporto viene posizionato tra le superfici da unire e le temperature vengono portate alla temperatura di fusione del materiale d'apporto superiore a 723 Kelvin ma al di sotto delle temperature di fusione dei pezzi. Il metallo fuso riempie lo spazio a stretto contatto tra i pezzi. Il raffreddamento e la successiva solidificazione del metallo di limatura danno luogo a giunzioni forti. Nella saldobrasatura il metallo d'apporto si deposita sul giunto. Nella saldobrasatura viene utilizzato molto più metallo d'apporto rispetto alla brasatura. La torcia ossiacetilenica con fiamma ossidante viene utilizzata per depositare il metallo d'apporto nella saldobrasatura. A causa delle temperature più basse durante la brasatura, i problemi nelle zone colpite dal calore come la deformazione e le sollecitazioni residue sono minori. Minore è lo spazio libero nella brasatura, maggiore è la resistenza al taglio del giunto. La massima resistenza alla trazione viene tuttavia raggiunta con un gioco ottimale (un valore di picco). Al di sotto e al di sopra di questo valore ottimale, la resistenza alla trazione nella brasatura diminuisce. I giochi tipici nella brasatura possono essere compresi tra 0,025 e 0,2 mm. Utilizziamo una varietà di materiali per brasatura con forme diverse come pezzi, polvere, anelli, filo, nastro…..ecc. e può produrre queste prestazioni appositamente per il tuo design o la geometria del prodotto. Determiniamo anche il contenuto dei materiali di brasatura in base ai materiali di base e all'applicazione. Utilizziamo frequentemente flussi nelle operazioni di brasatura per rimuovere strati di ossido indesiderati e prevenire l'ossidazione. Per evitare la successiva corrosione, i flussi vengono generalmente rimossi dopo l'operazione di giunzione. AGS-TECH Inc. utilizza vari metodi di brasatura, tra cui: - Brasatura a torcia - Brasatura a forno - Brasatura ad induzione - Brasatura a resistenza - Brasatura ad immersione - Brasatura a infrarossi - Brasatura a diffusione - Fascio ad alta energia I nostri esempi più comuni di giunti brasati sono realizzati con metalli dissimili con una buona resistenza come punte in metallo duro, inserti, pacchetti ermetici optoelettronici, guarnizioni. SALDATURA : Questa è una delle nostre tecniche più utilizzate in cui la saldatura (metallo d'apporto) riempie il giunto come nella brasatura tra componenti strettamente aderenti. Le nostre saldature hanno punti di fusione inferiori a 723 Kelvin. Distribuiamo sia la saldatura manuale che automatizzata nelle operazioni di produzione. Rispetto alla brasatura, le temperature di saldatura sono inferiori. La saldatura non è molto adatta per applicazioni ad alta temperatura o ad alta resistenza. Utilizziamo saldature senza piombo e leghe stagno-piombo, stagno-zinco, piombo-argento, cadmio-argento, zinco-alluminio oltre ad altre leghe per la saldatura. Sia gli acidi e i sali a base di resine non corrosivi che quelli inorganici vengono utilizzati come disossidante nella saldatura. Utilizziamo flussi speciali per saldare metalli con bassa saldabilità. Nelle applicazioni in cui dobbiamo saldare materiali ceramici, vetro o grafite, placcamo prima le parti con un metallo adatto per una maggiore saldabilità. Le nostre tecniche di saldatura popolari sono: -Riflusso o incollare la saldatura - Saldatura ad onda - Saldatura a forno - Saldatura a torcia -Saldatura ad induzione - Saldatura a ferro -Saldatura a resistenza - Saldatura a immersione - Saldatura ad ultrasuoni - Saldatura a infrarossi La saldatura a ultrasuoni ci offre un vantaggio unico per cui la necessità di flussi viene eliminata grazie all'effetto di cavitazione ultrasonica che rimuove i film di ossido dalle superfici da unire. La saldatura a rifusione e a onda sono le nostre tecniche eccezionali a livello industriale per la produzione di grandi volumi nell'elettronica e quindi vale la pena spiegarle in modo più dettagliato. Nella saldatura a rifusione, utilizziamo paste semisolide che includono particelle di metallo saldato. La pasta viene posizionata sul giunto utilizzando un processo di retinatura o stencil. Nei circuiti stampati (PCB) utilizziamo frequentemente questa tecnica. Quando i componenti elettrici vengono posizionati su questi pad dalla pasta, la tensione superficiale mantiene allineati i pacchetti a montaggio superficiale. Dopo aver posizionato i componenti, riscaldiamo l'assieme in un forno in modo che avvenga la saldatura a rifusione. Durante questo processo, i solventi nella pasta evaporano, il flusso nella pasta viene attivato, i componenti vengono preriscaldati, le particelle di saldatura vengono sciolte e bagnano il giunto e infine l'assieme PCB viene raffreddato lentamente. La nostra seconda tecnica popolare per la produzione ad alto volume di schede PCB, vale a dire la saldatura ad onda, si basa sul fatto che le saldature fuse bagnano le superfici metalliche e formano buoni legami solo quando il metallo è preriscaldato. Un'onda laminare stazionaria di saldatura fusa viene prima generata da una pompa e i PCB preriscaldati e preflussi vengono convogliati sull'onda. La saldatura bagna solo le superfici metalliche esposte ma non bagna i pacchetti polimerici IC né i circuiti stampati rivestiti in polimero. Un getto di acqua calda ad alta velocità espelle la saldatura in eccesso dal giunto e impedisce la formazione di ponti tra i conduttori adiacenti. Nella saldatura ad onda di pacchetti a montaggio superficiale, li leghiamo prima adesivamente al circuito stampato prima di saldare. Anche in questo caso viene utilizzata la schermatura e lo stencil, ma questa volta per la resina epossidica. Dopo che i componenti sono stati posizionati nelle posizioni corrette, la resina epossidica viene polimerizzata, le schede vengono invertite e viene eseguita la saldatura ad onda. CLICK Product Finder-Locator Service PAGINA PRECEDENTE
- Microlavorazione, microlavorazione superficiale e di massa, microscala, MEMS
Microlavorazione - Microlavorazione superficiale e di massa - Produzione su microscala - MEMS - Accelerometri - AGS-TECH Inc. Produzione su microscala/Microproduzione/Microlavorazione/MEMS MICROFABBRICAZIONE, PRODUZIONE MICROSCALA, MICROFABBRICAZIONE or MICROMACHINING refers a microdispositivi e prodotti micron. A volte le dimensioni complessive di un prodotto microfabbricato possono essere maggiori, ma usiamo ancora questo termine per riferirci ai principi e ai processi coinvolti. Utilizziamo l'approccio della microproduzione per realizzare i seguenti tipi di dispositivi: Dispositivi microelettronici: esempi tipici sono i chip semiconduttori che funzionano in base a principi elettrici ed elettronici. Dispositivi micromeccanici: si tratta di prodotti di natura puramente meccanica come ingranaggi e cerniere molto piccoli. Dispositivi microelettromeccanici: utilizziamo tecniche di microproduzione per combinare elementi meccanici, elettrici ed elettronici su scale di lunghezza molto ridotte. La maggior parte dei nostri sensori rientra in questa categoria. Sistemi microelettromeccanici (MEMS): questi dispositivi microelettromeccanici incorporano anche un sistema elettrico integrato in un unico prodotto. I nostri prodotti commerciali più apprezzati in questa categoria sono accelerometri MEMS, sensori airbag e dispositivi a microspecchi digitali. A seconda del prodotto da fabbricare, utilizziamo uno dei seguenti principali metodi di microproduzione: MICROMACCHIATURA IN MASSA: Questo è un metodo relativamente più vecchio che utilizza incisioni dipendenti dall'orientamento su silicio monocristallino. L'approccio della microlavorazione di massa si basa sull'incisione su una superficie e sull'arresto su determinate facce di cristallo, regioni drogate e film mordenzabili per formare la struttura richiesta. I prodotti tipici che siamo in grado di microfabbricare utilizzando la tecnica della microlavorazione in massa sono: - Piccoli cantilever - Scanalature a V in silicone per allineamento e fissaggio di fibre ottiche. MICROMACCHIATURA DI SUPERFICIE: Sfortunatamente la microlavorazione di massa è limitata ai materiali a cristallo singolo, poiché i materiali policristallini non lavoreranno a velocità diverse in direzioni diverse utilizzando mordenzanti a umido. Pertanto la microlavorazione di superficie si distingue come alternativa alla microlavorazione di massa. Uno strato distanziatore o sacrificale come il vetro fosfosilicato viene depositato mediante processo CVD su un substrato di silicio. In generale, sullo strato distanziatore vengono depositati strati strutturali a film sottile di polisilicio, metallo, leghe metalliche, dielettrici. Usando tecniche di incisione a secco, gli strati di film sottile strutturale vengono modellati e l'incisione a umido viene utilizzata per rimuovere lo strato sacrificale, risultando così in strutture autoportanti come i cantilever. È anche possibile utilizzare combinazioni di tecniche di microlavorazione di massa e di superficie per trasformare alcuni progetti in prodotti. Prodotti tipici adatti alla microfabbricazione utilizzando una combinazione delle due tecniche di cui sopra: - Microlampade di dimensioni submillimetriche (nell'ordine di 0,1 mm) - Sensori di pressione - Micropompe - Micromotori - Attuatori - Dispositivi di microflusso di fluidi A volte, per ottenere strutture verticali elevate, la microfabbricazione viene eseguita su grandi strutture piatte orizzontalmente e quindi le strutture vengono ruotate o piegate in posizione verticale utilizzando tecniche come la centrifugazione o il microassemblaggio con sonde. Tuttavia, è possibile ottenere strutture molto alte in silicio monocristallino utilizzando il legame di fusione del silicio e l'attacco con ioni reattivi in profondità. Il processo di microproduzione di Deep Reactive Ion Etching (DRIE) viene eseguito su due wafer separati, quindi allineati e legati per fusione per produrre strutture molto alte che altrimenti sarebbero impossibili. PROCESSI DI MICROPRODUZIONE LIGA: Il processo LIGA combina litografia a raggi X, elettrodeposizione, stampaggio e generalmente prevede le seguenti fasi: 1. Sul substrato primario viene depositato uno strato di resist di polimetilmetacrilato (PMMA) spesso alcune centinaia di micron. 2. Il PMMA viene sviluppato utilizzando raggi X collimati. 3. Il metallo viene elettrodepositato sul substrato primario. 4. Il PMMA viene spogliato e rimane una struttura metallica autoportante. 5. Usiamo la struttura metallica rimanente come stampo ed eseguiamo lo stampaggio a iniezione di materie plastiche. Se si analizzano i cinque passaggi di base di cui sopra, utilizzando le tecniche di microproduzione / microlavorazione LIGA possiamo ottenere: - Strutture metalliche autoportanti - Strutture in plastica stampata ad iniezione - Utilizzando la struttura stampata a iniezione come grezzo, possiamo investire parti in metallo pressofuse o parti in ceramica slip-cast. I processi di microproduzione / microlavorazione LIGA richiedono tempo e sono costosi. Tuttavia, la microlavorazione LIGA produce questi stampi di precisione submicronici che possono essere utilizzati per replicare le strutture desiderate con evidenti vantaggi. La microproduzione LIGA può essere utilizzata ad esempio per fabbricare magneti in miniatura molto potenti da polveri di terre rare. Le polveri di terre rare vengono mescolate con un legante epossidico e pressate sullo stampo in PMMA, polimerizzate ad alta pressione, magnetizzate sotto forti campi magnetici e infine il PMMA viene sciolto lasciando dietro di sé i minuscoli potenti magneti di terre rare che sono una delle meraviglie di microproduzione / microlavorazione. Siamo anche in grado di sviluppare tecniche di microproduzione / microlavorazione MEMS multilivello attraverso il legame a diffusione su scala di wafer. Fondamentalmente possiamo avere geometrie sporgenti all'interno di dispositivi MEMS, utilizzando una procedura di incollaggio e rilascio a diffusione batch. Ad esempio, prepariamo due strati modellati ed elettroformati in PMMA con il PMMA successivamente rilasciato. Successivamente, i wafer vengono allineati faccia a faccia con i perni guida e si adattano a pressione insieme in una pressa a caldo. Lo strato sacrificale su uno dei substrati viene attaccato, il che si traduce in uno degli strati legato all'altro. Sono disponibili anche altre tecniche di microfabbricazione non basate su LIGA per la fabbricazione di varie strutture multistrato complesse. PROCESSI DI MICROFABBRICAZIONE SOLIDI A FORMA LIBERA: La microproduzione additiva viene utilizzata per la prototipazione rapida. Strutture 3D complesse possono essere ottenute con questo metodo di microlavorazione e non avviene alcuna rimozione di materiale. Il processo di microstereolitografia utilizza polimeri termoindurenti liquidi, un fotoiniziatore e una sorgente laser altamente focalizzata con un diametro di appena 1 micron e uno spessore dello strato di circa 10 micron. Questa tecnica di microfabbricazione è tuttavia limitata alla produzione di strutture polimeriche non conduttive. Un altro metodo di microfabbricazione, ovvero la "mascheratura istantanea" o anche noto come "fabbricazione elettrochimica" o EFAB prevede la produzione di una maschera elastomerica mediante fotolitografia. La maschera viene quindi premuta contro il substrato in un bagno di elettrodeposizione in modo che l'elastomero si adatti al substrato ed escluda la soluzione di placcatura nelle aree di contatto. Le aree non mascherate vengono elettrodeposte come immagine speculare della maschera. Utilizzando un riempitivo sacrificale, le forme 3D complesse vengono microfabbricate. Questo metodo di microfabbricazione / microlavorazione a "mascheramento istantaneo" consente anche di produrre sporgenze, archi, ecc. CLICK Product Finder-Locator Service PAGINA PRECEDENTE
- Durometro - Rockwell - Brinell - Vickers - Leeb - Microdurezza
Durometro - Rockwell - Brinell - Vickers - Leeb - Microdurezza - Universale - AGS-TECH Inc. Tester di durezza AGS-TECH Inc. offre una gamma completa di tester di durezza tra cui ROCKWELL, BRINELL, VICKERS, LEEB, KNOOP, MICROHARDNESS TESTER, UNIVERSAL HARDNESS TESTER, STRUMENTI PORTATILI PER PROVE DI DUREZZA, sistemi ottici e software per la misurazione, dati acquisizione e analisi, blocchetti di prova, penetratori, incudini e relativi accessori. Alcuni dei durometri di marca che vendiamo sono SADT, SINOAGE and MITECH. Per scaricare il catalogo delle nostre apparecchiature di misura e test a marchio SADT, CLICCA QUI. Per scaricare la brochure del nostro durometro portatile MITECH MH600, CLICCA QUI CLICCA QUI per scaricare la tabella di confronto dei prodotti tra i durometri MITECH Uno dei test più comuni per valutare le proprietà meccaniche dei materiali è il test di durezza. La durezza di un materiale è la sua resistenza alla rientranza permanente. Si può anche dire che la durezza è la resistenza di un materiale al graffio e all'usura. Esistono diverse tecniche per misurare la durezza dei materiali utilizzando varie geometrie e materiali. I risultati della misurazione non sono assoluti, sono più un indicatore comparativo relativo, perché i risultati dipendono dalla forma del penetratore e dal carico applicato. I nostri durometri portatili possono generalmente eseguire qualsiasi test di durezza sopra elencato. Possono essere configurati per particolari caratteristiche geometriche e materiali come interni dei fori, denti di ingranaggi, ecc. Esaminiamo brevemente i vari metodi di prova di durezza. BRINELL TEST : In questo test, una sfera di acciaio o carburo di tungsteno con un diametro di 10 mm viene pressata contro una superficie con un carico di 500, 1500 o 3000 Kg di forza. Il numero di durezza Brinell è il rapporto tra il carico e l'area curva della rientranza. Un test Brinell lascia diversi tipi di impronte sulla superficie a seconda delle condizioni del materiale testato. Ad esempio, sui materiali ricotti viene lasciato un profilo arrotondato mentre sui materiali lavorati a freddo si osserva un profilo spigoloso. Le sfere del penetratore in carburo di tungsteno sono consigliate per numeri di durezza Brinell superiori a 500. Per i materiali più duri si consiglia un carico di 1500 Kg o 3000 Kg in modo che le impronte lasciate siano sufficientemente grandi per una misurazione accurata. Poiché le impronte fatte dallo stesso penetratore a carichi diversi non sono geometricamente simili, il numero di durezza Brinell dipende dal carico utilizzato. Pertanto si dovrebbe sempre annotare il carico impiegato sui risultati del test. Il test Brinell è adatto per materiali con durezza da bassa a media. ROCKWELL TEST : In questo test viene misurata la profondità di penetrazione. Il penetratore viene premuto sulla superficie inizialmente con un carico minore e poi con un carico maggiore. La differenza nel debito di penetrazioneh è una misura della durezza. Esistono diverse scale di durezza Rockwell che impiegano carichi, materiali penetratori e geometrie diversi. Il numero di durezza Rockwell viene letto direttamente da un quadrante sulla macchina di prova. Ad esempio, se il numero di durezza è 55 utilizzando la scala C, viene scritto come 55 HRC. VICKERS TEST : A volte indicato anche come DIAMOND PYRAMID HARDNESS TEST, utilizza un penetratore diamantato a forma piramidale con carichi che vanno da 1 a 120 Kg. Il numero di durezza Vickers è dato da HV=1.854P / quadrato L. La L qui è la lunghezza diagonale della piramide di diamanti. Il test Vickers fornisce sostanzialmente lo stesso numero di durezza indipendentemente dal carico. Il test Vickers è adatto per testare materiali con un'ampia gamma di durezze, inclusi materiali molto duri. KNOOP TEST : In questo test utilizziamo un penetratore diamantato a forma di piramide allungata e carichi tra 25g e 5 Kg. Il numero di durezza Knoop è dato come HK=14.2P / quadrato L. Qui la lettera L è la lunghezza della diagonale allungata. La dimensione delle rientranze nei test Knoop è relativamente piccola, nell'intervallo da 0,01 a 0,10 mm. A causa di questo piccolo numero, la preparazione della superficie per il materiale è molto importante. I risultati del test dovrebbero citare il carico applicato perché il numero di durezza ottenuto dipende dal carico applicato. Poiché vengono utilizzati carichi leggeri, il test Knoop è considerato a MICROHARDNESS TEST. Il test Knoop è quindi adatto per campioni molto piccoli e sottili, materiali fragili come pietre preziose, vetro e carburi e persino per misurare la durezza dei singoli grani in un metallo. LEEB HARDNESS TEST : Si basa sulla tecnica del rimbalzo che misura la durezza Leeb. È un metodo facile e industrialmente popolare. Questo metodo portatile viene utilizzato principalmente per testare pezzi sufficientemente grandi al di sopra di 1 kg. Un corpo d'urto con una punta di prova in metallo duro viene spinto dalla forza della molla contro la superficie del pezzo. Quando il corpo d'urto colpisce il pezzo, si verifica una deformazione della superficie che comporterà la perdita di energia cinetica. Le misurazioni della velocità rivelano questa perdita di energia cinetica. Quando il corpo d'urto supera la bobina a una distanza precisa dalla superficie, viene indotta una tensione di segnale durante le fasi di impatto e di ritorno della prova. Queste tensioni sono proporzionali alla velocità. Utilizzando l'elaborazione elettronica del segnale si ottiene il valore di durezza Leeb dal display. Our PORTABLE HARDNESS TESTERS from SADT / HARTIP HARDNESS TESTER SADT HARTIP2000/HARTIP2000 D&DL : Si tratta di un innovativo durometro Leeb portatile con una nuova tecnologia brevettata, che rende HARTIP 2000 un misuratore di durezza con direzione di impatto ad angolo universale (UA). Non è necessario impostare la direzione dell'impatto quando si effettuano misurazioni con qualsiasi angolazione. Pertanto, HARTIP 2000 offre una precisione lineare rispetto al metodo di compensazione dell'angolo. HARTIP 2000 è anche un durometro a basso costo e ha molte altre caratteristiche. L'HARTIP2000 DL è dotato dell'esclusiva sonda D e DL 2 in 1 SADT. SADT HARTIP1800 Plus/1800 Plus D&DL : questo dispositivo è un misuratore di durezza per metalli palmare avanzato e all'avanguardia con molte nuove funzionalità. Utilizzando una tecnologia brevettata, SADT HARTIP1800 Plus è un prodotto di nuova generazione. Ha un'elevata precisione di +/-2 HL (o 0,3% @HL800) con display OLED ad alto contratto e ampio intervallo di temperatura ambientale (-40ºC~60ºC). Oltre a enormi memorie in 400 blocchi con 360.000 dati, HARTIP1800 Plus può scaricare i dati misurati su PC e stamparli su mini-stampante tramite porta USB e in modalità wireless con modulo Bluetooth interno. La batteria può essere caricata semplicemente dalla porta USB. Ha una funzione di ricalibrazione e statica del cliente. HARTIP 1800 plus D&DL è dotato di sonda due in uno. Con l'esclusiva sonda due in uno, HARTIP1800plus D&DL può convertire tra sonda D e sonda DL semplicemente cambiando il corpo di impatto. È più economico che acquistarli singolarmente. Ha la stessa configurazione con HARTIP1800 plus tranne la sonda due in uno. SADT HARTIP1800 Basic/1800 Basic D&DL : questo è un modello base per HARTIP1800plus. Con la maggior parte delle funzioni principali di HARTIP1800 plus e un prezzo inferiore, HARTIP1800 Basic è una buona scelta per i clienti con budget limitato. HARTIP1800 Basic può anche essere equipaggiato con il nostro esclusivo dispositivo di impatto due in uno D/DL. SADT HARTIP 3000 : questo è un durometro digitale portatile per metalli avanzato con elevata precisione, ampio campo di misurazione e facilità d'uso. È adatto per testare la durezza di tutti i metalli, in particolare in loco, per componenti strutturali e assemblati di grandi dimensioni, ampiamente utilizzati nei settori energetico, petrolchimico, aerospaziale, automobilistico e della costruzione di macchine. SADT HARTIP1500/HARTIP1000 : questo è un durometro portatile integrato per metalli che combina dispositivo di impatto (sonda) e processore in un'unica unità. La dimensione è molto più piccola rispetto al dispositivo di impatto standard, il che consente all'HARTIP 1500/1000 di soddisfare non solo le normali condizioni di misurazione, ma può anche eseguire misurazioni in spazi ristretti. HARTIP 1500/1000 è adatto per testare la durezza di quasi tutti i materiali ferrosi e non ferrosi. Con la sua nuova tecnologia, la sua precisione è migliorata a un livello superiore rispetto al tipo standard. HARTIP 1500/1000 è uno dei durometri più economici della sua categoria. SISTEMA DI MISURAZIONE AUTOMATICA DELLA DUREZZA BRINELL / SADT HB SCALER : HB Scaler è un sistema di misurazione ottico che può misurare automaticamente la dimensione della rientranza dal tester di durezza Brinell e fornisce letture di durezza Brinell. Tutti i valori e le immagini di rientro possono essere salvati su PC. Con il software, tutti i valori possono essere elaborati e stampati come report. Our BENCH HARDNESS TESTER products from SADT_cc781905-5c36bad-31:5bb-5c3cd-31:5 TESTER DI DUREZZA ROCKWELL SADT HR-150A : Il tester di durezza Rockwell HR-150A ad azionamento manuale è noto per la sua perfezione e facilità d'uso. Questa macchina utilizza la forza di prova preliminare standard di 10 kgf e carichi principali di 60/100/150 chilogrammi, conforme allo standard internazionale Rockwell. Dopo ogni test, l'HR-150A mostra il valore di durezza Rockwell B o Rockwell C direttamente sul quadrante. La forza di prova preliminare deve essere applicata manualmente, seguita dall'applicazione del carico principale per mezzo della leva sul lato destro del durometro. Dopo lo scarico, il quadrante indica direttamente il valore di durezza richiesto con elevata precisione e ripetibilità. SADT HR-150DT TESTER DI DUREZZA MOTORIZZATO ROCKWELL : Questa serie di durometri è riconosciuta per la sua precisione e facilità d'uso, il cui funzionamento è completamente conforme allo standard internazionale Rockwell. A seconda della combinazione del tipo di penetratore e della forza di prova totale applicata, a ciascuna bilancia Rockwell viene assegnato un simbolo univoco. HR-150DT e HRM-45DT presentano entrambe le specifiche scale Rockwell di HRC e HRB su un quadrante. La forza appropriata deve essere regolata manualmente, utilizzando la manopola sul lato destro della macchina. Dopo l'applicazione della forza preliminare, l'HR150DT e l'HRM-45DT procederanno con un test completamente automatizzato: carico, attesa, scarico e alla fine visualizzerà la durezza. SADT HRS-150 TESTER DI DUREZZA DIGITALE ROCKWELL : Il tester di durezza Rockwell digitale HRS-150 è progettato per facilità d'uso e sicurezza di funzionamento. È conforme allo standard internazionale Rockwell. A seconda della combinazione del tipo di penetratore e della forza di prova totale applicata, a ciascuna bilancia Rockwell viene assegnato un simbolo univoco. L'HRS-150 mostrerà automaticamente la selezione di una specifica scala Rockwell sul display LCD e indicherà quale carico viene utilizzato. Il meccanismo del freno automatico integrato consente di applicare manualmente la forza di prova preliminare senza possibilità di errore. Dopo l'applicazione della forza preliminare, l'HRS-150 procederà con un test completamente automatico: caricamento, tempo di sosta, scarico e calcolo del valore di durezza e relativa visualizzazione. Collegato alla stampante in dotazione tramite un'uscita RS232, è possibile stampare tutti i risultati. Our BENCH TYPE SUPERFICIAL ROCKWELL HARDNESS TESTER products from SADT are: SADT HRM-45DT TESTER DI DUREZZA SUPERFICIALE ROCKWELL MOTORIZZATO : Questa serie di tester di durezza è riconosciuta per la sua precisione e facilità d'uso, offre prestazioni completamente conformi allo standard internazionale Rockwell. A seconda della combinazione del tipo di penetratore e della forza di prova totale applicata, a ciascuna bilancia Rockwell viene assegnato un simbolo univoco. HR-150DT e HRM-45DT presentano entrambe le specifiche scale Rockwell HRC e HRB su un quadrante. La forza appropriata deve essere regolata manualmente, utilizzando la manopola sul lato destro della macchina. Dopo l'applicazione della forza preliminare, l'HR150DT e l'HRM-45DT procederanno con un processo di prova completamente automatico: carico, sosta, scarico e alla fine visualizzeranno la durezza. SADT HRMS-45 SUPERFICIAL ROCKWELL HARDNESS TESTER : HRMS-45 Digital Superficial Rockwell Hardness Tester è un nuovo prodotto che integra tecnologie meccaniche ed elettroniche avanzate. Il doppio display dei diodi digitali LCD e LED, ne fanno una versione aggiornata del prodotto del tester Rockwell superficiale di tipo standard. Misura la durezza di metalli ferrosi, non ferrosi e materiali duri, strati cementati e nitrurati e altri strati trattati chimicamente. Viene anche utilizzato per la misura della durezza di pezzi sottili. SADT XHR-150 PLASTIC ROCKWELL HARDNESS TESTER : XHR-150 plastica Il tester di durezza Rockwell adotta un metodo di prova motorizzato, la forza di prova può essere caricata, mantenuta a abitazione e scaricata automaticamente. L'errore umano è ridotto al minimo e facile da usare. Viene utilizzato per misurare plastiche dure, gomme dure, alluminio, stagno, rame, acciaio dolce, resine sintetiche, materiali tribologici, ecc. Our BENCH TYPE VICKERS HARDNESS TESTER products from SADT are: SADT HVS-10/50 TESTER DI DUREZZA VICKERS A BASSO CARICO : Questo durometro Vicker's a basso carico con display digitale è un nuovo prodotto hi-tech che integra tecnologie meccaniche e fotoelettriche. In sostituzione dei tradizionali durometri Vicker's per carichi ridotti, è caratterizzato da un funzionamento semplice e una buona affidabilità, appositamente progettati per testare campioni o parti piccoli e sottili dopo il rivestimento della superficie. Adatto per istituti di ricerca, laboratori industriali e dipartimenti di controllo qualità, è uno strumento di prova di durezza ideale per scopi di ricerca e misurazione. Offre l'integrazione della tecnologia di programmazione del computer, il sistema di misurazione ottico ad alta risoluzione e la tecnica fotoelettrica, l'immissione di tasti funzione, la regolazione della sorgente luminosa, il modello di prova selezionabile, le tabelle di conversione, il tempo di mantenimento della pressione, l'immissione del numero di file e le funzioni di salvataggio dei dati. Dispone di un grande schermo LCD per visualizzare il modello di prova, la pressione di prova, la lunghezza della rientranza, i valori di durezza, il tempo di mantenimento della pressione e il numero di prove. Offre anche la registrazione della data, la registrazione dei risultati dei test e l'elaborazione dei dati, la funzione di output di stampa, tramite un'interfaccia RS232. SADT HV-10/50 TESTER DI DUREZZA VICKERS A BASSO CARICO : Questi durometri Vickers a basso carico sono nuovi prodotti hi-tech che integrano tecnologie meccaniche e fotoelettriche. Questi tester sono appositamente progettati per testare campioni e parti piccoli e sottili dopo il rivestimento superficiale. Adatto per istituti di ricerca, laboratori industriali e dipartimenti di controllo qualità. Le caratteristiche e le funzioni principali sono il controllo del microcomputer, la regolazione della sorgente luminosa tramite i tasti softkey, la regolazione del tempo di mantenimento della pressione e il display LED/LCD, il suo esclusivo dispositivo di conversione della misurazione e l'esclusivo dispositivo di lettura delle misurazioni monouso con microoculare che garantisce un facile utilizzo e un'elevata precisione. SADT HV-30 VICKERS HARDNESS TESTER : Il tester di durezza Vickers modello HV-30 è appositamente progettato per testare campioni piccoli e sottili e parti dopo il rivestimento superficiale. Adatti per istituti di ricerca, laboratori di fabbrica e dipartimenti di controllo qualità, sono strumenti ideali per prove di durezza per scopi di ricerca e test. Le caratteristiche e le funzioni principali sono il controllo del microcomputer, il meccanismo di caricamento e scaricamento automatico, la regolazione della sorgente luminosa tramite hardware, la regolazione del tempo di mantenimento della pressione (0~30 s), il dispositivo di conversione della misurazione unico e il dispositivo di lettura della misurazione una tantum del microoculare, garantendo una facile uso e alta precisione. Our TESTER DI DUREZZA MICRO TIPO DA BANCO products from SADT_cc781905-9cf5cde-areb33:cf5cde-bar SADT HV-1000 MICRO TESTER DI DUREZZA / HVS-1000 DIGITALE MICRO TESTER DI DUREZZA : Questo prodotto è particolarmente adatto per prove di durezza ad alta precisione di campioni piccoli e sottili come fogli, fogli, rivestimenti, prodotti ceramici e strati induriti. Per garantire una rientranza soddisfacente, l'HV1000 / HVS1000 è dotato di operazioni di carico e scarico automatiche, un meccanismo di caricamento molto preciso e un robusto sistema di leve. Il sistema controllato da microcomputer garantisce una misurazione della durezza assolutamente precisa con tempo di sosta regolabile. SADT DHV-1000 MICRO HARDNESS TESTER / DHV-1000Z DIGITAL VICKERS HARDNESS TESTER : Questi micro tester di durezza Vickers realizzati con un design unico e preciso sono in grado di produrre una rientranza più chiara e quindi una misurazione più accurata. Per mezzo di una lente 20 × e una lente 40 × lo strumento ha un campo di misura più ampio e un campo di applicazione più ampio. Dotato di un microscopio digitale, mostra sul suo schermo LCD i metodi di misurazione, la forza di prova, la lunghezza della rientranza, il valore di durezza, il tempo di permanenza della forza di prova e il numero delle misurazioni. Inoltre è dotato di un'interfaccia collegata ad una fotocamera digitale e ad una videocamera CCD. Questo tester è ampiamente utilizzato per misurare metalli ferrosi, metalli non ferrosi, sezioni sottili IC, rivestimenti, vetro, ceramica, pietre preziose, strati temprati e altro ancora. SADT DXHV-1000 MICRO TESTER DI DUREZZA DIGITALE : Questi micro durometri Vickers realizzati con un unico e preciso sono in grado di produrre una rientranza più chiara e quindi misurazioni più accurate. Per mezzo di una lente 20 × e una lente 40 ×, il tester ha un campo di misura più ampio e un campo di applicazione più ampio. Con un dispositivo di rotazione automatica (la torretta che gira automaticamente), l'operazione è diventata più semplice; e con interfaccia filettata, può essere collegato ad una fotocamera digitale e ad una videocamera CCD. Innanzitutto il dispositivo consente di utilizzare il touch screen LCD, consentendo così un controllo più umano dell'operazione. Il dispositivo dispone di funzionalità quali la lettura diretta delle misure, il facile cambio delle scale di durezza, il salvataggio dei dati, la stampa e il collegamento con l'interfaccia RS232. Questo tester è ampiamente utilizzato per misurare metalli ferrosi, metalli non ferrosi, sezioni sottili IC, rivestimenti, vetro, ceramica, pietre preziose; sezioni di plastica sottili, strati temprati e altro ancora. Our BENCH TYPE BRINELL HARDNESS TESTER / MULTI-PURPOSE HARDNESS TESTER products from SADT are: SADT HD9-45 SUPERFICIAL ROCKWELL & VICKERS OPTICAL HARDNESS TESTER : Questo dispositivo ha lo scopo di misurare la durezza di metalli ferrosi, non ferrosi, metalli duri, strati cementati e nitrurati e strati trattati chimicamente e pezzi sottili. SADT HBRVU-187.5 BRINELL ROCKWELL & VICKERS OPTICAL HARDNESS TESTER : questo strumento viene utilizzato per determinare la durezza Brinell, Rockwell e Vickers di metalli ferrosi, non ferrosi, metalli duri, strati cementati e strati trattati chimicamente. Può essere utilizzato in piante, istituti scientifici e di ricerca, laboratori e college. SADT HBRV-187.5 BRINELL ROCKWELL & VICKERS HARDNESS TESTER (NON OTTICO) : Questo strumento viene utilizzato per determinare la durezza Brinell, Rockwell e Vickers di metalli ferrosi, non ferrosi, metalli duri, strati cementati e strati trattati chimicamente. Può essere utilizzato in fabbriche, istituti scientifici e di ricerca, laboratori e college. Non è un durometro di tipo ottico. SADT HBE-3000A BRINELL HARDNESS TESTER : questo durometro Brinell automatico presenta un ampio campo di misura fino a 3000 Kgf con un'elevata precisione conforme allo standard DIN 51225/1. Durante il ciclo di prova automatico la forza applicata sarà controllata da un sistema ad anello chiuso che garantisce una forza costante sul pezzo, conforme alla norma DIN 50351. L'HBE-3000A è dotato di un microscopio da lettura con fattore di ingrandimento 20X e una risoluzione micrometrica di 0,005 mm. SADT HBS-3000 TESTER DI DUREZZA BRINELL DIGITALE : Questo tester di durezza Brinell digitale è un dispositivo all'avanguardia di nuova generazione. Può essere utilizzato per determinare la durezza Brinell di metalli ferrosi e non ferrosi. Il tester offre caricamento automatico elettronico, programmazione software per computer, misurazione ottica ad alta potenza, fotosensore e altre funzionalità. Ogni processo operativo e risultato del test può essere visualizzato sul suo grande schermo LCD. I risultati del test possono essere stampati. Il dispositivo è adatto per ambienti di produzione, college e istituzioni scientifiche. SADT MHB-3000 TESTER ELETTRONICO DIGITALE DI DUREZZA BRINELL : Questo strumento è un prodotto integrato che combina tecniche ottiche, meccaniche ed elettroniche, adottando una struttura meccanica precisa e un sistema a circuito chiuso controllato da computer. Lo strumento carica e scarica la forza di prova con il suo motore. Utilizzando un sensore di compressione con una precisione dello 0,5% per il feedback delle informazioni e la CPU per il controllo, lo strumento compensa automaticamente le forze di prova variabili. Dotato di un microoculare digitale sullo strumento, la lunghezza dell'indentazione può essere misurata direttamente. Tutti i dati di prova come il metodo di prova, il valore della forza di prova, la lunghezza della rientranza di prova, il valore di durezza e il tempo di permanenza della forza di prova possono essere visualizzati sullo schermo LCD. Non è necessario inserire il valore della lunghezza diagonale per il rientro e non è necessario cercare il valore di durezza dalla tabella di durezza. Pertanto i dati letti sono più accurati e il funzionamento di questo strumento è più semplice. Per dettagli e altre apparecchiature simili, visitare il nostro sito Web delle apparecchiature: http://www.sourceindustrialsupply.com CLICK Product Finder-Locator Service PAGINA PRECEDENTE
- Lavorazione al plasma, taglio al plasma HF, scriccatura al plasma, CNC, saldatura ad arco
Lavorazione al plasma - Taglio al plasma HF - Scriccatura al plasma - CNC - Saldatura ad arco al plasma - PAW - GTAW - AGS-TECH Inc. Lavorazione e taglio al plasma We use the PLASMA CUTTING and PLASMA MACHINING processes to cut and machine steel, aluminum, metals and other materials of diversi spessori utilizzando una torcia al plasma. Nel taglio al plasma (chiamato anche a volte PLASMA-ARC CUTTING), un gas inerte o aria compressa viene soffiato ad alta velocità da un ugello e contemporaneamente si forma un arco elettrico attraverso quel gas dall'ugello a la superficie viene tagliata, trasformando una parte di quel gas in plasma. Per semplificare, il plasma può essere descritto come il quarto stato della materia. I tre stati della materia sono solido, liquido e gas. Per un esempio comune, l'acqua, questi tre stati sono ghiaccio, acqua e vapore. La differenza tra questi stati riguarda i loro livelli di energia. Quando aggiungiamo energia sotto forma di calore al ghiaccio, si scioglie e forma acqua. Quando aggiungiamo più energia, l'acqua vaporizza sotto forma di vapore. Aggiungendo più energia al vapore, questi gas vengono ionizzati. Questo processo di ionizzazione fa sì che il gas diventi elettricamente conduttivo. Chiamiamo questo gas ionizzato elettricamente conduttivo un "plasma". Il plasma è molto caldo e fonde il metallo da tagliare e allo stesso tempo soffia via il metallo fuso dal taglio. Usiamo il plasma per il taglio di materiali sottili e spessi, ferrosi e non ferrosi. Le nostre torce manuali possono solitamente tagliare lastre d'acciaio fino a 2 pollici di spessore e le nostre torce controllate da computer più potenti possono tagliare l'acciaio fino a 6 pollici di spessore. Le taglierine al plasma producono un cono molto caldo e localizzato con cui tagliare, e sono quindi molto adatte per il taglio di lamiere in forme curve e angolate. Le temperature generate nel taglio ad arco plasma sono molto elevate e circa 9673 Kelvin nella torcia al plasma di ossigeno. Questo ci offre un processo veloce, una larghezza di taglio ridotta e una buona finitura superficiale. Nei nostri sistemi che utilizzano elettrodi di tungsteno, il plasma è inerte, formato utilizzando gas argon, argon-H2 o azoto. Tuttavia, a volte utilizziamo anche gas ossidanti, come aria o ossigeno, e in questi sistemi l'elettrodo è in rame con afnio. Il vantaggio di una torcia al plasma ad aria è che utilizza l'aria invece di gas costosi, riducendo così potenzialmente i costi complessivi di lavorazione. Le nostre HF-TYPE PLASMA CUTTING machines utilizzano una scintilla ad alta frequenza e alta tensione per ionizzare l'aria attraverso la testa della torcia e avviare archi. Le nostre taglierine al plasma HF non richiedono che la torcia sia a contatto con il materiale del pezzo all'inizio e sono adatte per applicazioni che coinvolgono COMPUTER NUMERICAL CONTROL (CNC) cutting. Altri produttori utilizzano macchine primitive che richiedono il contatto della punta con il metallo madre per iniziare e quindi si verifica la separazione del gap. Queste taglierine al plasma più primitive sono più suscettibili alla punta di contatto e ai danni dello schermo all'avvio. Le nostre PILOT-ARC TYPE PLASMA machines utilizzano un processo in due fasi per la produzione di plasma, senza la necessità di un contatto iniziale. Nella prima fase, viene utilizzato un circuito ad alta tensione e bassa corrente per inizializzare una piccolissima scintilla ad alta intensità all'interno del corpo della torcia, generando una piccola sacca di gas plasma. Questo è chiamato arco pilota. L'arco pilota ha un percorso elettrico di ritorno integrato nella testa della torcia. L'arco pilota viene mantenuto e preservato fino a quando non viene portato in prossimità del pezzo. Lì l'arco pilota accende l'arco di taglio plasma principale. Gli archi di plasma sono estremamente caldi e sono nell'intervallo di 25.000 °C = 45.000 °F. Un metodo più tradizionale che utilizziamo anche è OXYFUEL-GAS CUTTING (OFC) dove utilizziamo una torcia come nella saldatura. L'operazione viene utilizzata nel taglio di acciaio, ghisa e acciaio fuso. Il principio del taglio nel taglio con ossitaglio si basa sull'ossidazione, la combustione e la fusione dell'acciaio. Le larghezze di taglio nel taglio del gas ossitaglio sono comprese tra 1,5 e 10 mm. Il processo ad arco di plasma è stato visto come un'alternativa al processo di ossitaglio. Il processo ad arco plasma differisce dal processo a ossicombustibile in quanto funziona utilizzando l'arco per fondere il metallo mentre nel processo a ossicombustibile l'ossigeno ossida il metallo e il calore della reazione esotermica fonde il metallo. Pertanto, a differenza del processo ossicombustibile, il processo al plasma può essere applicato per il taglio di metalli che formano ossidi refrattari come acciaio inossidabile, alluminio e leghe non ferrose. PLASMA GOUGING un processo simile al taglio al plasma, viene in genere eseguito con la stessa attrezzatura del taglio al plasma. Invece di tagliare il materiale, la scriccatura al plasma utilizza una diversa configurazione della torcia. L'ugello della torcia e il diffusore di gas sono generalmente diversi e viene mantenuta una distanza tra torcia e pezzo più lunga per soffiare via il metallo. La scriccatura al plasma può essere utilizzata in varie applicazioni, inclusa la rimozione di una saldatura per la rilavorazione. Alcune delle nostre taglierine al plasma sono integrate nella tavola CNC. I tavoli CNC hanno un computer per controllare la testa della torcia per produrre tagli netti e netti. La nostra moderna attrezzatura al plasma CNC è in grado di eseguire il taglio multiasse di materiali spessi e offre opportunità per saldature complesse che altrimenti non sarebbero possibili. Le nostre taglierine ad arco plasma sono altamente automatizzate attraverso l'uso di controlli programmabili. Per i materiali più sottili, preferiamo il taglio laser al taglio plasma, principalmente a causa delle superiori capacità di taglio dei fori del nostro laser cutter. Utilizziamo anche macchine per il taglio al plasma CNC verticali, offrendoci un ingombro ridotto, una maggiore flessibilità, una maggiore sicurezza e un funzionamento più rapido. La qualità del bordo tagliato al plasma è simile a quella ottenuta con i processi di taglio ossitaglio. Tuttavia, poiché il processo al plasma taglia per fusione, una caratteristica è il maggiore grado di fusione verso la parte superiore del metallo con conseguente arrotondamento del bordo superiore, scarsa ortogonalità del bordo o smussatura sul bordo tagliato. Utilizziamo nuovi modelli di torce plasma con un ugello più piccolo e un arco plasma più sottile per migliorare la costrizione dell'arco per produrre un riscaldamento più uniforme nella parte superiore e inferiore del taglio. Questo ci permette di ottenere una precisione quasi laser sul taglio al plasma e sui bordi lavorati. I nostri HIGH TOLERANCE PLASMA ARC CUTTING (HTPAC) systems funzionano con un plasma altamente ristretto. La messa a fuoco del plasma si ottiene costringendo il plasma generato dall'ossigeno a vorticare quando entra nell'orifizio del plasma e un flusso secondario di gas viene iniettato a valle dell'ugello del plasma. Abbiamo un campo magnetico separato che circonda l'arco. Questo stabilizza il getto di plasma mantenendo la rotazione indotta dal gas vorticoso. Combinando il controllo CNC di precisione con queste torce più piccole e sottili, siamo in grado di produrre parti che richiedono poca o nessuna finitura. Le velocità di rimozione del materiale nella lavorazione al plasma sono molto più elevate rispetto ai processi di lavorazione a scarica elettrica (EDM) e lavorazione a raggio laser (LBM) e le parti possono essere lavorate con una buona riproducibilità. LA SALDATURA AD ARCO AL PLASMA (PAW) è un processo simile alla saldatura ad arco di tungsteno a gas (GTAW). L'arco elettrico si forma tra un elettrodo generalmente in tungsteno sinterizzato e il pezzo. La differenza fondamentale rispetto a GTAW è che in PAW, posizionando l'elettrodo all'interno del corpo della torcia, l'arco plasma può essere separato dall'involucro del gas di protezione. Il plasma viene quindi forzato attraverso un ugello di rame a foro sottile che restringe l'arco e il plasma in uscita dall'orifizio ad alte velocità e temperature che si avvicinano a 20.000 °C. La saldatura ad arco al plasma è un progresso rispetto al processo GTAW. Il processo di saldatura PAW utilizza un elettrodo di tungsteno non consumabile e un arco ristretto attraverso un ugello di rame a foro sottile. PAW può essere utilizzato per unire tutti i metalli e le leghe saldabili con GTAW. Diverse variazioni di base del processo PAW sono possibili variando la corrente, la portata del gas plasma e il diametro dell'orifizio, tra cui: Microplasma (< 15 Ampere) Modalità di fusione (15–400 ampere) Modalità buco della serratura (>100 Ampere) Nella saldatura ad arco plasma (PAW) otteniamo una maggiore concentrazione di energia rispetto a GTAW. È possibile ottenere una penetrazione profonda e stretta, con una profondità massima da 12 a 18 mm (da 0,47 a 0,71 pollici) a seconda del materiale. Una maggiore stabilità dell'arco consente una lunghezza dell'arco molto più lunga (distanziamento) e una tolleranza molto maggiore alle variazioni della lunghezza dell'arco. Come svantaggio, tuttavia, PAW richiede apparecchiature relativamente costose e complesse rispetto a GTAW. Anche la manutenzione della torcia è fondamentale e più impegnativa. Altri svantaggi di PAW sono: le procedure di saldatura tendono ad essere più complesse e meno tolleranti alle variazioni di adattamento, ecc. L'abilità dell'operatore richiesta è leggermente superiore a quella di GTAW. È necessaria la sostituzione dell'orifizio. CLICK Product Finder-Locator Service PAGINA PRECEDENTE
- Trattamento e modifica delle superfici - Ingegneria delle superfici - Indurimento
Trattamento e modifica delle superfici - Ingegneria delle superfici - Indurimento - Plasma - Laser - Impianto di ioni - Elaborazione a fascio di elettroni presso AGS-TECH Trattamenti e modifiche superficiali Le superfici coprono tutto. Il fascino e le funzioni che le superfici dei materiali ci forniscono sono della massima importanza. Therefore SURFACE TREATMENT and SURFACE MODIFICATION are among our everyday industrial operations. Il trattamento e la modifica della superficie migliorano le proprietà della superficie e possono essere eseguiti come operazione di finitura finale o prima di un'operazione di rivestimento o giunzione. I processi di trattamento e modifica della superficie (indicati anche come SURFACE ENGINEERING) , adattare le superfici di materiali e prodotti a: - Controllo attrito e usura - Migliora la resistenza alla corrosione - Migliorare l'adesione dei rivestimenti successivi o delle parti unite - Modificare le proprietà fisiche conducibilità, resistività, energia superficiale e riflessione - Modificare le proprietà chimiche delle superfici introducendo gruppi funzionali - Cambia dimensioni - Modificare l'aspetto, ad es. colore, rugosità... ecc. - Pulire e/o disinfettare le superfici Utilizzando il trattamento e la modifica della superficie, è possibile migliorare le funzioni e la durata dei materiali. I nostri comuni metodi di trattamento e modifica delle superfici possono essere suddivisi in due categorie principali: Trattamento e modifica delle superfici che ricoprono le superfici: Rivestimenti organici: I rivestimenti organici applicano vernici, cementi, laminati, polveri fuse e lubrificanti sulle superfici dei materiali. Rivestimenti inorganici: i nostri rivestimenti inorganici popolari sono galvanica, placcatura autocatalitica (placcature senza elettrolisi), rivestimenti di conversione, spray termici, immersione a caldo, riporto duro, fusione in forno, rivestimenti a film sottile come SiO2, SiN su metallo, vetro, ceramica, ecc. Il trattamento superficiale e le modifiche che coinvolgono i rivestimenti sono spiegati in dettaglio nel relativo sottomenu, per favoreclicca qui Rivestimenti funzionali / Rivestimenti decorativi / Film sottile / Film spesso Trattamento e modifica delle superfici che alterano le superfici: qui in questa pagina ci concentreremo su questi. Non tutte le tecniche di trattamento e modifica delle superfici che descriviamo di seguito sono su scala micro o nanometrica, ma ne parleremo comunque brevemente poiché gli obiettivi e i metodi di base sono simili in misura significativa a quelli che si trovano sulla scala della microproduzione. Tempra: tempra superficiale selettiva mediante laser, fiamma, induzione e fascio di elettroni. Trattamenti ad alta energia: alcuni dei nostri trattamenti ad alta energia includono l'impianto di ioni, la smaltatura e la fusione laser e il trattamento con fasci di elettroni. Trattamenti di diffusione sottile: i processi di diffusione sottile includono ferritico-nitrocarburazione, boronizzazione, altri processi di reazione ad alta temperatura come TiC, VC. Trattamenti di diffusione pesante: i nostri processi di diffusione pesante includono la cementazione, la nitrurazione e la carbonitrurazione. Trattamenti superficiali speciali: Trattamenti speciali come trattamenti criogenici, magnetici e sonici interessano sia le superfici che i materiali sfusi. I processi di tempra selettiva possono essere effettuati mediante fiamma, induzione, fascio di elettroni, fascio laser. I substrati di grandi dimensioni vengono induriti in profondità utilizzando l'indurimento alla fiamma. La tempra a induzione invece viene utilizzata per le piccole parti. L'indurimento del laser e del fascio di elettroni a volte non si distingue da quelli nei riporti duri o nei trattamenti ad alta energia. Questi processi di trattamento superficiale e modifica sono applicabili solo agli acciai che hanno un contenuto di carbonio e leghe sufficiente per consentire l'indurimento da raffreddamento. Ghise, acciai al carbonio, acciai per utensili e acciai legati sono adatti per questo trattamento superficiale e metodo di modifica. Le dimensioni delle parti non vengono alterate in modo significativo da questi trattamenti superficiali di indurimento. La profondità di indurimento può variare da 250 micron all'intera profondità della sezione. Tuttavia, nel caso della sezione intera, la sezione deve essere sottile, inferiore a 25 mm (1 in), o piccola, poiché i processi di indurimento richiedono un rapido raffreddamento dei materiali, a volte entro un secondo. Questo è difficile da ottenere in pezzi di grandi dimensioni, e quindi in grandi sezioni, solo le superfici possono essere indurite. Come un popolare trattamento di superficie e processo di modifica, induriamo molle, lame di coltelli e lame chirurgiche tra molti altri prodotti. I processi ad alta energia sono metodi di trattamento e modifica delle superfici relativamente nuovi. Le proprietà delle superfici vengono modificate senza modificare le dimensioni. I nostri popolari processi di trattamento delle superfici ad alta energia sono il trattamento con raggio di elettroni, l'impianto di ioni e il trattamento con raggio laser. Trattamento del fascio di elettroni: il trattamento della superficie del fascio di elettroni altera le proprietà della superficie mediante riscaldamento e raffreddamento rapidi, nell'ordine di 10Exp6 gradi centigradi/sec (10exp6 Fahrenheit/sec) in una regione molto superficiale a circa 100 micron vicino alla superficie del materiale. Il trattamento a fascio di elettroni può essere utilizzato anche nel riporto duro per produrre leghe superficiali. Impianto ionico: questo metodo di trattamento e modifica della superficie utilizza un fascio di elettroni o plasma per convertire atomi di gas in ioni con energia sufficiente e impiantare/inserire gli ioni nel reticolo atomico del substrato, accelerato da bobine magnetiche in una camera a vuoto. Il vuoto consente agli ioni di muoversi liberamente nella camera. La mancata corrispondenza tra gli ioni impiantati e la superficie del metallo crea difetti atomici che induriscono la superficie. Trattamento del raggio laser: come il trattamento e la modifica della superficie del raggio di elettroni, il trattamento del raggio laser altera le proprietà della superficie mediante riscaldamento rapido e raffreddamento rapido in una regione molto superficiale vicino alla superficie. Questo metodo di trattamento e modifica della superficie può essere utilizzato anche nel riporto duro per produrre leghe di superficie. Un know-how nei dosaggi implantari e nei parametri di trattamento ci consente di utilizzare queste tecniche di trattamento superficiale ad alta energia nei nostri impianti di fabbricazione. Trattamenti di superficie a diffusione sottile: La nitrocarburazione ferritica è un processo di cementazione che diffonde azoto e carbonio nei metalli ferrosi a temperature subcritiche. La temperatura di lavorazione è solitamente a 565 gradi centigradi (1049 Fahrenheit). A questa temperatura gli acciai e le altre leghe ferrose si trovano ancora in una fase ferritica, vantaggiosa rispetto ad altri processi di cementazione che avvengono nella fase austenitica. Il processo viene utilizzato per migliorare: •resistenza allo sfregamento •proprietà di fatica •resistenza alla corrosione Durante il processo di indurimento si verificano pochissime deformazioni di forma grazie alle basse temperature di lavorazione. La boronizzazione è il processo in cui il boro viene introdotto in un metallo o una lega. È un processo di indurimento e modifica della superficie mediante il quale gli atomi di boro vengono diffusi sulla superficie di un componente metallico. Di conseguenza la superficie contiene boruri metallici, come boruri di ferro e boruri di nichel. Allo stato puro questi boruri hanno una durezza e una resistenza all'usura estremamente elevate. Le parti metalliche boronizzate sono estremamente resistenti all'usura e spesso dureranno fino a cinque volte di più rispetto ai componenti trattati con trattamenti termici convenzionali come tempra, cementazione, nitrurazione, nitrocarburazione o tempra a induzione. Trattamento e modifica della superficie a diffusione pesante: se il contenuto di carbonio è basso (ad esempio meno dello 0,25%), è possibile aumentare il contenuto di carbonio della superficie per l'indurimento. La parte può essere trattata termicamente mediante tempra in un liquido o raffreddata in aria ferma a seconda delle proprietà desiderate. Questo metodo consentirà solo un indurimento locale sulla superficie, ma non nel nucleo. Questo a volte è molto desiderabile perché consente una superficie dura con buone proprietà di usura come negli ingranaggi, ma ha un nucleo interno resistente che funzionerà bene sotto carico d'urto. In una delle tecniche di trattamento e modifica della superficie, vale a dire la carburazione, aggiungiamo carbonio alla superficie. Esponiamo la parte ad un'atmosfera ricca di carbonio ad una temperatura elevata e permettiamo alla diffusione di trasferire gli atomi di carbonio nell'acciaio. La diffusione avverrà solo se l'acciaio ha un basso contenuto di carbonio, perché la diffusione funziona sul principio del differenziale delle concentrazioni. Carburazione del pacco: le parti vengono imballate in un mezzo ad alto tenore di carbonio come polvere di carbonio e riscaldate in una fornace per 12-72 ore a 900 gradi centigradi (1652 Fahrenheit). A queste temperature viene prodotto gas CO che è un forte agente riducente. La reazione di riduzione avviene sulla superficie dell'acciaio rilasciando carbonio. Il carbonio viene poi diffuso in superficie grazie all'elevata temperatura. Il carbonio sulla superficie è compreso tra lo 0,7% e l'1,2% a seconda delle condizioni di processo. La durezza raggiunta è di 60 - 65 RC. La profondità della cassa carburata varia da circa 0,1 mm fino a 1,5 mm. La cementazione a pacco richiede un buon controllo dell'uniformità della temperatura e della costanza nel riscaldamento. Carburazione a gas: in questa variante di trattamento superficiale, il monossido di carbonio (CO) viene fornito gas a un forno riscaldato e la reazione di riduzione della deposizione di carbonio avviene sulla superficie delle parti. Questo processo risolve la maggior parte dei problemi di carburazione del pacco. Una preoccupazione, tuttavia, è il contenimento sicuro del gas CO. Carburazione liquida: le parti in acciaio sono immerse in un bagno ricco di carbonio fuso. La nitrurazione è un trattamento superficiale e un processo di modifica che comporta la diffusione dell'azoto sulla superficie dell'acciaio. L'azoto forma nitruri con elementi come alluminio, cromo e molibdeno. Le parti sono trattate termicamente e temperate prima della nitrurazione. Le parti vengono quindi pulite e riscaldate in un forno in un'atmosfera di ammoniaca dissociata (contenente N e H) per 10-40 ore a 500-625 gradi centigradi (932 - 1157 Fahrenheit). L'azoto si diffonde nell'acciaio e forma leghe di nitruro. Questo penetra fino a una profondità di 0,65 mm. Il case è molto duro e la distorsione è bassa. Poiché la cassa è sottile, la levigatura superficiale non è consigliata e quindi il trattamento superficiale di nitrurazione potrebbe non essere un'opzione per superfici con requisiti di finitura molto lisci. Il trattamento superficiale di carbonitrurazione e il processo di modifica sono più adatti per gli acciai legati a basso tenore di carbonio. Nel processo di carbonitrurazione, sia il carbonio che l'azoto vengono diffusi in superficie. Le parti vengono riscaldate in un'atmosfera di idrocarburo (come metano o propano) miscelato con ammoniaca (NH3). In poche parole, il processo è un mix di carburazione e nitrurazione. Il trattamento superficiale di carbonitrurazione viene eseguito a temperature di 760 - 870 gradi centigradi (1400 - 1598 Fahrenheit), quindi viene spento in un'atmosfera di gas naturale (senza ossigeno). Il processo di carbonitrurazione non è adatto per parti di alta precisione a causa delle distorsioni intrinseche. La durezza raggiunta è simile alla cementazione (60 - 65 RC) ma non così alta come la nitrurazione (70 RC). La profondità della cassa è compresa tra 0,1 e 0,75 mm. La cassa è ricca di Nitruri e di Martensite. È necessario un successivo rinvenimento per ridurre la fragilità. Speciali trattamenti superficiali e processi di modifica sono nelle prime fasi di sviluppo e la loro efficacia non è ancora stata dimostrata. Sono: Trattamento criogenico: generalmente applicato su acciai temprati, raffreddare lentamente il substrato a circa -166 gradi centigradi (-300 Fahrenheit) per aumentare la densità del materiale e quindi aumentare la resistenza all'usura e la stabilità dimensionale. Trattamento delle vibrazioni: intendono alleviare lo stress termico accumulato nei trattamenti termici attraverso le vibrazioni e aumentare la durata dell'usura. Trattamento magnetico: intendono alterare l'allineamento degli atomi nei materiali attraverso i campi magnetici e, si spera, migliorare la durata dell'usura. L'efficacia di queste speciali tecniche di trattamento e modifica delle superfici deve ancora essere provata. Anche queste tre tecniche sopra influiscono sul materiale sfuso oltre alle superfici. CLICK Product Finder-Locator Service PAGINA PRECEDENTE
- Lavorazione a elettroerosione, elettroerosione, lavorazione a scintilla, a tuffo
Lavorazione a elettroerosione - EDM - Lavorazione a scintilla - A tuffo - Erosione a filo - Produzione personalizzata - AGS-TECH Inc. Lavorazione elettroerosione, fresatura a scarica elettrica e rettifica ELECTRICAL DISCHARGE MACHINING (EDM), also referred to as SPARK-EROSION or ELECTRODISCHARGE MACHINING, SPARK ERODING, DIE SINKING_cc781905-5cde-3194-bb3b -136bad5cf58d_or WIRE EROSION, is a NON-CONVENTIONAL MANUFACTURING process where erosion of metals takes place and desired shape is obtained using electrical discharges in the form di scintille. Offriamo anche alcune varietà di elettroerosione, vale a dire NO-WEAR EDM, WIRE EDM (WEDM), EDM RETTIFICA (EDG), EDM A TUBO, FRESATURA A SCARICA ELETTRICA, micro-EDM, m-EDM_cc781905 -5cde-3194-bb3b-136bad5cf58d_and RETTIFICA A SCARICA ELETTROCHIMICA (ECDG). I nostri sistemi di elettroerosione sono costituiti da utensili/elettrodi sagomati e il pezzo da lavorare collegato ad alimentatori CC e inserito in un fluido dielettrico elettricamente non conduttivo. Dopo il 1940 la lavorazione a scarica elettrica è diventata una delle tecnologie di produzione più importanti e apprezzate nelle industrie manifatturiere. Quando la distanza tra i due elettrodi si riduce, l'intensità del campo elettrico nel volume tra gli elettrodi diventa maggiore della forza del dielettrico in alcuni punti, che si rompe, formando eventualmente un ponte per il flusso di corrente tra i due elettrodi. Viene generato un intenso arco elettrico che provoca un riscaldamento significativo per fondere una parte del pezzo in lavorazione e parte del materiale dell'utensileria. Di conseguenza, il materiale viene rimosso da entrambi gli elettrodi. Allo stesso tempo, il fluido dielettrico viene riscaldato rapidamente, provocando l'evaporazione del fluido nell'intercapedine dell'arco. Una volta che il flusso di corrente si interrompe o viene interrotto, il calore viene rimosso dalla bolla di gas dal fluido dielettrico circostante e la bolla cavita (collassa). L'onda d'urto creata dal collasso della bolla e dal flusso di fluido dielettrico irriga i detriti dalla superficie del pezzo in lavorazione e trascina tutto il materiale fuso del pezzo in lavorazione nel fluido dielettrico. La frequenza di ripetizione di queste scariche è compresa tra 50 e 500 kHz, tensioni tra 50 e 380 V e correnti tra 0,1 e 500 Ampere. Nuovo dielettrico liquido come oli minerali, cherosene o acqua distillata e deionizzata viene solitamente convogliato nel volume interelettrodico portando via le particelle solide (sotto forma di detriti) e vengono ripristinate le proprietà isolanti del dielettrico. Dopo un flusso di corrente, la differenza di potenziale tra i due elettrodi viene ripristinata a quella che era prima della rottura, quindi può verificarsi una nuova rottura del dielettrico liquido. Le nostre moderne macchine per elettroerosione (EDM) offrono movimenti a controllo numerico e sono dotate di pompe e sistemi di filtraggio dei fluidi dielettrici. La lavorazione a scarica elettrica (EDM) è un metodo di lavorazione utilizzato principalmente per i metalli duri o quelli che sarebbero molto difficili da lavorare con le tecniche convenzionali. L'EDM funziona tipicamente con qualsiasi materiale che sia conduttore elettrico, sebbene siano stati proposti anche metodi per la lavorazione della ceramica isolante con l'EDM. Il punto di fusione e il calore latente di fusione sono proprietà che determinano il volume di metallo rimosso per scarica. Più alti sono questi valori, più lenta è la velocità di rimozione del materiale. Poiché il processo di lavorazione a scarica elettrica non comporta alcuna energia meccanica, la durezza, la resistenza e la tenacità del pezzo non influiscono sulla velocità di asportazione. Frequenza di scarica o energia per scarica, la tensione e la corrente vengono variate per controllare i tassi di rimozione del materiale. La velocità di rimozione del materiale e la rugosità superficiale aumentano all'aumentare della densità di corrente e alla diminuzione della frequenza delle scintille. Possiamo tagliare contorni o cavità intricati nell'acciaio pretemprato utilizzando l'elettroerosione senza la necessità di un trattamento termico per ammorbidirli e temprarli nuovamente. Possiamo usare questo metodo con qualsiasi metallo o lega metallica come titanio, hastelloy, kovar e inconel. Le applicazioni del processo EDM includono la sagomatura di utensili diamantati policristallini. L'EDM è considerato un metodo di lavorazione non tradizionale o non convenzionale insieme a processi come la lavorazione elettrochimica (ECM), il taglio a getto d'acqua (WJ, AWJ), il taglio laser. D'altra parte i metodi di lavorazione convenzionali includono tornitura, fresatura, rettifica, foratura e altri processi il cui meccanismo di rimozione del materiale si basa essenzialmente su forze meccaniche. Gli elettrodi per elettroerosione (EDM) sono realizzati in grafite, ottone, rame e leghe di rame-tungsteno. Sono possibili diametri degli elettrodi fino a 0,1 mm. Poiché l'usura dell'utensile è un fenomeno indesiderato che influisce negativamente sulla precisione dimensionale nell'EDM, sfruttiamo un processo chiamato NO-WEAR EDM, invertendo la polarità e utilizzando utensili in rame per ridurre al minimo l'usura dell'utensile. Idealmente, la lavorazione a scarica elettrica (EDM) può essere considerata una serie di rottura e ripristino del liquido dielettrico tra gli elettrodi. In realtà, però, la rimozione dei detriti dalla zona interelettrodi è quasi sempre parziale. Ciò fa sì che le proprietà elettriche del dielettrico nell'area interelettrodi siano diverse dai loro valori nominali e variano nel tempo. La distanza tra gli elettrodi, (spark-gap), è regolata dagli algoritmi di controllo della specifica macchina utilizzata. Lo spinterometro nell'EDM a volte può purtroppo essere cortocircuitato dai detriti. Il sistema di controllo dell'elettrodo potrebbe non reagire in modo sufficientemente rapido da impedire il cortocircuito dei due elettrodi (utensile e pezzo). Questo cortocircuito indesiderato contribuisce alla rimozione del materiale in modo diverso dal caso ideale. Diamo la massima importanza all'azione di flussaggio al fine di ripristinare le proprietà isolanti del dielettrico in modo che la corrente avvenga sempre nel punto dell'area interelettrodo, riducendo così al minimo la possibilità di cambio di forma indesiderato (danneggiamento) dell'utensile-elettrodo e pezzo. Per ottenere una geometria specifica, l'utensile EDM viene guidato lungo il percorso desiderato molto vicino al pezzo senza toccarlo, Prestiamo la massima attenzione alle prestazioni del controllo del movimento in uso. In questo modo si verifica un gran numero di scariche/scintille di corrente e ciascuna contribuisce alla rimozione di materiale sia dall'utensile che dal pezzo, dove si formano piccoli crateri. La dimensione dei crateri è funzione dei parametri tecnologici impostati per lo specifico lavoro da svolgere e le dimensioni possono variare dalla nanoscala (come nel caso delle operazioni di microelettroerosione) a alcune centinaia di micrometri in condizioni di sgrossatura. Questi piccoli crateri sull'utensile provocano una graduale erosione dell'elettrodo detta “usura utensile”. Per contrastare l'effetto dannoso dell'usura sulla geometria del pezzo, sostituiamo continuamente l'utensile-elettrodo durante un'operazione di lavorazione. A volte si ottiene questo risultato utilizzando un filo continuamente sostituito come elettrodo (questo processo EDM è anche chiamato WIRE EDM ). A volte utilizziamo l'utensile-elettrodo in modo tale che solo una piccola parte di esso sia effettivamente impegnata nel processo di lavorazione e questa parte venga cambiata regolarmente. Questo è, ad esempio, il caso quando si utilizza un disco rotante come elettrodo utensile. Questo processo è chiamato EDM GRINDING. Un'altra tecnica che utilizziamo consiste nell'utilizzare un set di elettrodi con dimensioni e forme diverse durante la stessa operazione di elettroerosione per compensare l'usura. Chiamiamo questa tecnica a elettrodi multipli ed è più comunemente usata quando l'elettrodo dello strumento replica in negativo la forma desiderata e viene fatto avanzare verso il grezzo lungo un'unica direzione, solitamente la direzione verticale (cioè l'asse z). Questo assomiglia all'affondamento dell'utensile nel liquido dielettrico in cui è immerso il pezzo, e quindi è indicato come DIE-SINKING EDM (a volte chiamato_cc781905-5cde- 3194-bb3b-136bad5cf58d_CONVENTIONAL EDM or RAM EDM). Le macchine per questa operazione si chiamano SINKER EDM. Gli elettrodi per questo tipo di elettroerosione hanno forme complesse. Se la geometria finale è ottenuta utilizzando un elettrodo di forma solitamente semplice spostato lungo più direzioni ed è anche soggetto a rotazioni, lo chiamiamo EDM MILLING. La quantità di usura è strettamente dipendente dai parametri tecnologici utilizzati nell'operazione (polarità, corrente massima, tensione a circuito aperto). Ad esempio, in micro-EDM, noto anche come m-EDM, questi parametri sono generalmente impostati su valori che generano una forte usura. Pertanto, l'usura è un problema importante in quell'area che riduciamo al minimo utilizzando il nostro know-how accumulato. Ad esempio, per ridurre al minimo l'usura degli elettrodi di grafite, un generatore digitale, controllabile in millisecondi, inverte la polarità quando avviene l'elettroerosione. Ciò si traduce in un effetto simile alla galvanica che deposita continuamente la grafite erosa sull'elettrodo. In un altro metodo, un cosiddetto circuito "Zero Wear", riduciamo al minimo la frequenza con cui la scarica inizia e si arresta, mantenendola accesa il più a lungo possibile. La velocità di rimozione del materiale nella lavorazione a scarica elettrica può essere stimata da: MRR = 4 x 10 exp(4) x I x Tw exp (-1,23) Qui MRR è in mm3/min, I è la corrente in Ampere, Tw è il punto di fusione del pezzo in K-273,15K. L'exp sta per esponente. D'altra parte, il tasso di usura Wt dell'elettrodo può essere ottenuto da: Peso = ( 1,1 x 10exp(11) ) x I x Ttexp(-2,38) Qui Wt è in mm3/min e Tt è il punto di fusione del materiale dell'elettrodo in K-273,15K Infine, il rapporto di usura del pezzo rispetto all'elettrodo R può essere ottenuto da: R = 2,25 x Trexp(-2,38) Qui Tr è il rapporto tra i punti di fusione del pezzo in lavorazione e l'elettrodo. SINKER EDM : EDM a tuffo, indicato anche come CAVITY TYPE EDM or VOLUME EDM, è costituito da un elettrodo e un liquido isolante. L'elettrodo e il pezzo sono collegati a una fonte di alimentazione. L'alimentatore genera un potenziale elettrico tra i due. Quando l'elettrodo si avvicina al pezzo, si verifica una rottura dielettrica nel fluido, formando un canale plasma, e una piccola scintilla salta. Le scintille di solito scompaiono una alla volta perché è altamente improbabile che posizioni diverse nello spazio tra gli elettrodi abbiano caratteristiche elettriche locali identiche che consentirebbero la formazione simultanea di una scintilla in tutte queste posizioni. Centinaia di migliaia di queste scintille si verificano in punti casuali tra l'elettrodo e il pezzo al secondo. Quando il metallo di base si erode e lo spinterometro aumenta, l'elettrodo viene abbassato automaticamente dalla nostra macchina CNC in modo che il processo possa continuare senza interruzioni. La nostra attrezzatura ha cicli di controllo noti come "on time" e "off time". L'impostazione del tempo di accensione determina la durata o la durata della scintilla. Un tempo più lungo produce una cavità più profonda per quella scintilla e tutte le successive scintille per quel ciclo, creando una finitura più ruvida sul pezzo e viceversa. Il tempo di spegnimento è il periodo di tempo in cui una scintilla viene sostituita da un'altra. Un tempo di spegnimento più lungo consente al fluido dielettrico di fluire attraverso un ugello per ripulire i detriti erosi, evitando così un cortocircuito. Queste impostazioni vengono regolate in micro secondi. FILO EDM : In WIRE ELECTRICAL DISCHARGE MACHINING (WEDM), also called WIRE-CUT EDM or WIRE CUTTING, we feed a sottile filo metallico di ottone a filo singolo attraverso il pezzo, che è immerso in un serbatoio di fluido dielettrico. L'elettroerosione a filo è un'importante variazione dell'elettroerosione. Occasionalmente utilizziamo l'elettroerosione a filo per tagliare lamiere spesse fino a 300 mm e per realizzare punzoni, utensili e matrici da metalli duri difficili da lavorare con altri metodi di produzione. In questo processo che ricorda il taglio di contorni con una sega a nastro, il filo, che viene costantemente alimentato da una bobina, viene trattenuto tra le guide diamantate superiori e inferiori. Le guide controllate dal CNC si muovono nel piano x–y e la guida superiore può anche muoversi indipendentemente nell'asse z–u–v, dando vita alla possibilità di tagliare forme affusolate e di transizione (come cerchio sul fondo e quadrato in la cima). La guida superiore può controllare i movimenti degli assi in x–y–u–v–i–j–k–l–. Ciò consente al WEDM di tagliare forme molto intricate e delicate. Il taglio medio della nostra attrezzatura che consente di ottenere il miglior costo economico e tempo di lavorazione è di 0,335 mm utilizzando filo di ottone, rame o tungsteno Ø 0,25. Tuttavia, le guide diamantate superiori e inferiori delle nostre apparecchiature CNC hanno una precisione di circa 0,004 mm e possono avere un percorso di taglio o un taglio di taglio piccolo fino a 0,021 mm utilizzando un filo di Ø 0,02 mm. Quindi sono possibili tagli davvero stretti. La larghezza di taglio è maggiore della larghezza del filo perché si verificano scintille dai lati del filo al pezzo, causando erosione. Questo ''overcut'' è necessario, per molte applicazioni è prevedibile e quindi può essere compensato (in micro-EDM questo non è spesso il caso). Le bobine di filo sono lunghe: una bobina da 8 kg di filo da 0,25 mm è lunga poco più di 19 chilometri. Il diametro del filo può arrivare fino a 20 micrometri e la precisione della geometria è di circa +/- 1 micrometro. Generalmente utilizziamo il filo una sola volta e lo ricicliamo perché è relativamente economico. Viaggia a una velocità costante da 0,15 a 9 m/min e durante un taglio viene mantenuto un taglio (scanalatura) costante. Nel processo di elettroerosione a filo utilizziamo l'acqua come fluido dielettrico, controllandone la resistività e altre proprietà elettriche con filtri e unità deionizzatori. L'acqua allontana i detriti tagliati dalla zona di taglio. Il lavaggio è un fattore importante nel determinare la velocità di avanzamento massima per un determinato spessore del materiale e quindi lo manteniamo coerente. La velocità di taglio nell'elettroerosione a filo è espressa in termini di area della sezione trasversale tagliata per unità di tempo, ad esempio 18.000 mm2/ora per acciaio per utensili D2 di 50 mm di spessore. La velocità di taglio lineare per questo caso sarebbe 18.000/50 = 360 mm/ora La velocità di rimozione del materiale nell'elettroerosione a filo è: MRR = Vf xhxb Qui MRR è in mm3/min, Vf è la velocità di avanzamento del filo nel pezzo in mm/min, h è lo spessore o l'altezza in mm e b è il taglio, che è: b = dw + 2 s Qui dw è il diametro del filo e s è la distanza tra filo e pezzo in mm. Oltre a tolleranze più strette, i nostri moderni centri di lavoro per il taglio del filo EDM multiasse hanno aggiunto funzionalità come testine multiple per il taglio di due parti contemporaneamente, controlli per prevenire la rottura del filo, funzioni di autofilettatura automatica in caso di rottura del filo e strategie di lavorazione per ottimizzare le operazioni, capacità di taglio rettilineo e angolare. Wire-EDM ci offre basse sollecitazioni residue, perché non richiede forze di taglio elevate per la rimozione del materiale. Quando l'energia/potenza per impulso è relativamente bassa (come nelle operazioni di finitura), è previsto un piccolo cambiamento nelle proprietà meccaniche di un materiale a causa delle basse sollecitazioni residue. RETTIFICA A SCARICHE ELETTRICHE (EDG) : Le mole non contengono abrasivi, sono in grafite o ottone. Scintille ripetute tra la ruota rotante e il pezzo in lavorazione rimuovono il materiale dalle superfici del pezzo. Il tasso di rimozione del materiale è: MRR = K x I Qui MRR è in mm3/min, I è la corrente in Ampere e K è il fattore materiale del pezzo in mm3/A-min. Usiamo spesso la rettifica a scarica elettrica per segare fessure strette sui componenti. A volte combiniamo il processo EDG (Electrical-Discharge Grinding) con il processo ECG (Electrochemical Grinding) in cui il materiale viene rimosso per azione chimica, le scariche elettriche dalla ruota di grafite rompono il film di ossido e lavano via dall'elettrolita. Il processo è chiamato ELECTROCHEMICAL-DISCHARGE GRINDING (ECDG). Anche se il processo ECDG consuma relativamente più energia, è un processo più veloce dell'EDG. Lavoriamo principalmente utensili in metallo duro con questa tecnica. Applicazioni della lavorazione di scariche elettriche: Produzione di prototipi: Utilizziamo il processo EDM nella produzione di stampi, utensili e stampi, nonché per la realizzazione di prototipi e parti di produzione, in particolare per i settori aerospaziale, automobilistico ed elettronico in cui le quantità di produzione sono relativamente basse. In Sinker EDM, un elettrodo di grafite, rame, tungsteno o rame puro viene lavorato nella forma desiderata (negativa) e inserito nel pezzo in lavorazione all'estremità di un pistone verticale. Creazione di dadi per monete: Per la creazione di stampi per la produzione di gioielli e distintivi mediante il processo di conio (stampaggio), il master positivo può essere realizzato in argento sterling, poiché (con impostazioni della macchina appropriate) il master è notevolmente eroso e viene utilizzato solo una volta. La matrice negativa risultante viene quindi indurita e utilizzata in un martello a caduta per produrre piani stampati da fogli grezzi ritagliati di bronzo, argento o leghe d'oro a bassa resistenza. Per i distintivi questi appartamenti possono essere ulteriormente sagomati su una superficie curva da un altro dado. Questo tipo di elettroerosione viene solitamente eseguito immerso in un dielettrico a base di olio. L'oggetto finito può essere ulteriormente rifinito mediante smaltatura dura (vetro) o morbida (vernice) e/o galvanizzata con oro zecchino o nichel. I materiali più morbidi come l'argento possono essere incisi a mano come raffinatezza. Foratura di piccoli fori: Sulle nostre macchine per elettroerosione a filo, utilizziamo l'elettroerosione a fori piccoli per realizzare un foro passante in un pezzo attraverso il quale infilare il filo per l'operazione di elettroerosione a filo. Teste per elettroerosione separate, specifiche per la perforazione di piccoli fori, sono montate sulle nostre macchine per il taglio del filo che consentono alle grandi lastre temprate di avere parti finite erose secondo necessità e senza preforatura. Utilizziamo anche l'elettroerosione a fori piccoli per praticare file di fori nei bordi delle pale delle turbine utilizzate nei motori a reazione. Il flusso di gas attraverso questi piccoli fori consente ai motori di utilizzare temperature più elevate di quanto altrimenti possibile. Le leghe monocristalline ad alta temperatura, molto dure, di cui sono fatte queste lame rendono estremamente difficile e persino impossibile la lavorazione convenzionale di questi fori con proporzioni elevate. Altre aree di applicazione per l'EDM a piccoli fori sono la creazione di orifizi microscopici per i componenti del sistema di alimentazione. Oltre alle teste per elettroerosione integrate, impieghiamo macchine per elettroerosione a piccoli fori autonome con assi x–y per la lavorazione di fori ciechi o passanti. L'elettroerosione esegue fori con un elettrodo a tubo lungo in ottone o rame che ruota in un mandrino con un flusso costante di acqua distillata o deionizzata che scorre attraverso l'elettrodo come agente di lavaggio e dielettrico. Alcuni elettroerosioni per perforazione di piccoli fori sono in grado di perforare 100 mm di acciaio dolce o addirittura temprato in meno di 10 secondi. In questa operazione di perforazione è possibile ottenere fori compresi tra 0,3 mm e 6,1 mm. Lavorazione di disintegrazione del metallo: Disponiamo inoltre di macchine per elettroerosione speciali con lo scopo specifico di rimuovere gli utensili rotti (punte o maschi) dai pezzi in lavorazione. Questo processo è chiamato "lavorazione per disintegrazione dei metalli". Vantaggi e svantaggi Lavorazione a scarica elettrica: I vantaggi dell'elettroerosione includono la lavorazione di: - Forme complesse che altrimenti sarebbero difficili da produrre con utensili da taglio convenzionali - Materiale estremamente duro con tolleranze molto strette - Pezzi molto piccoli in cui gli utensili da taglio convenzionali possono danneggiare la parte a causa della pressione eccessiva dell'utensile da taglio. - Non vi è alcun contatto diretto tra utensile e pezzo da lavorare. Pertanto sezioni delicate e materiali deboli possono essere lavorati senza alcuna distorsione. - Si può ottenere una buona finitura superficiale. - I fori molto fini possono essere facilmente praticati. Gli svantaggi dell'EDM includono: - Il lento tasso di rimozione del materiale. - Il tempo e il costo aggiuntivi utilizzati per la creazione di elettrodi per elettroerosione a pistone/a tuffo. - La riproduzione di spigoli vivi sul pezzo è difficile a causa dell'usura degli elettrodi. - Il consumo di energia è elevato. - Si forma ''Sovrasquadro''. - Durante la lavorazione si verifica un'usura eccessiva dell'utensile. - I materiali elettricamente non conduttivi possono essere lavorati solo con un'impostazione specifica del processo. CLICK Product Finder-Locator Service PAGINA PRECEDENTE
- Telaio per computer, rack, scaffali, rack da 19 pollici, rack da 23 pollici, custodia
Telaio per computer - Rack - Ripiani - Rack da 19 pollici - Rack da 23 pollici - Produzione di custodie per computer e strumenti - AGS-TECH Inc. Chassis, Rack, Supporti per Computer Industriali We offer you the most durable and reliable INDUSTRIAL COMPUTER CHASSIS, RACKS, MOUNTS, RACK MOUNT INSTRUMENTS and RACK MOUNTED SYSTEMS, SUBRACK, SHELF, 19 INCH & 23 INCH RACKS, FULL SİZE and HALF RACKS, OPEN and CLOSED RACK, MOUNTING HARDWARE, STRUCTURAL AND SUPPORT COMPONENTS, RAILS and SLIDES, TWO andFOUR POST RACKS that meet international and industry standards. Oltre ai nostri prodotti standard, siamo in grado di costruire qualsiasi chassis, rack e supporto su misura. Alcuni dei marchi che abbiamo in stock sono BELKIN, HEWLETT PACKARD, KENDALL HOWARD, GREAT LAKES, APC, RITTAL, LIEBERT, RALOY, SHARK RACK, UPSITE TECHNOLOGIES. Fare clic qui per scaricare il nostro telaio industriale a marchio DFI-ITOX Fare clic qui per scaricare il nostro chassis plug-in serie 06 da AGS-Electronics Fare clic qui per scaricare la nostra custodia per strumenti della serie 01 System-I da AGS-Electronics Fare clic qui per scaricare la nostra custodia per strumenti della serie 05 System-V da AGS-Electronics Per scegliere un telaio, un rack o un supporto di grado industriale adatto, vai al nostro negozio di computer industriali FACENDO CLIC QUI. Scarica la brochure del ns PROGRAMMA DI PARTNERSHIP DI PROGETTAZIONE Ecco una terminologia chiave che dovrebbe essere utile a scopo di riferimento: A RACK UNIT or U (meno comunemente indicato come RU) è un'unità di misura utilizzata per descrivere l'altezza delle apparecchiature destinate al montaggio in a_cc781905-5cde-3194-bb3b -136bad5cf58d_19 pollici rack o a 23 pollici rack (La dimensione da 19 pollici si riferisce alla larghezza dell'attrezzatura telaio di montaggio nel rack, ovvero la larghezza dell'apparecchiatura che può essere montata all'interno del rack). Un'unità rack è alta 44,45 mm (1,75 pollici). La dimensione di un pezzo di attrezzatura montata su rack è spesso descritta come un numero in ''U''. Ad esempio, un'unità rack viene spesso definita ''1U'', 2 unità rack come ''2U'' e così via. Un tipico full size rack is 44U, il che significa che contiene poco più di 6 piedi di attrezzatura. Nell'informatica e nell'informatica, tuttavia, half-rack descrive tipicamente un'unità alta 1U e profonda la metà di un rack a 4 montanti (come uno switch di rete , router, switch KVM o server), in modo tale che due unità possano essere montate in 1U di spazio (una montata nella parte anteriore del rack e una nella parte posteriore). Quando viene utilizzato per descrivere l'armadio rack stesso, il termine mezzo rack indica in genere un armadio rack alto 24U. Un pannello frontale o un pannello di riempimento in un rack non è un multiplo esatto di 44,45 mm (1,75 pollici). Per lasciare spazio tra i componenti adiacenti montati su rack, un pannello ha un'altezza inferiore di 1⁄32 pollici (0,031 pollici o 0,79 mm) rispetto al numero completo di unità rack. Pertanto, un pannello frontale 1U sarebbe alto 1,719 pollici (43,66 mm). Un rack da 19 pollici è un telaio o un contenitore standardizzato per il montaggio di più moduli apparecchiature. Ogni modulo ha un pannello frontale largo 19 pollici (482,6 mm), inclusi bordi o alette che sporgono su ciascun lato che consentono di fissare il modulo al telaio del rack con viti. Le apparecchiature progettate per essere collocate in un rack sono generalmente descritte come rack-mount, strumento per montaggio su rack, sistema montato su rack, chassis con montaggio su rack, subrack, montabile su rack o, occasionalmente, semplicemente su scaffale. Un rack da 23 pollici viene utilizzato per alloggiare telefono (principalmente), computer, audio e altre apparecchiature, sebbene sia meno comune del rack da 19 pollici. La dimensione indica la larghezza del frontalino per l'apparecchiatura installata. L'unità rack misura la spaziatura verticale ed è comune a entrambi i rack da 19 e 23 pollici (580 mm). La spaziatura dei fori è su centri da 1 pollice (25 mm) (standard Western Electric) o la stessa dei rack da 19 pollici (480 mm) (spaziatura 15,9 mm/0,625 pollici). CLICK Product Finder-Locator Service PAGINA PRECEDENTE
- Microfabbricazione, Nanofabbricazione, Mesofabbricazione AGS-TECH Inc.
Microfabbricazione, Nanofabbricazione, Mesofabbricazione - Elettronica e Magnetica Ottica e Rivestimenti, Film Sottile, Nanotubi, MEMS, Fabbricazione su Microscala Produzione su nanoscala, microscala e mesoscala Leggi di più Our NANOMANUFACTURING, MICROMANUFACTURING and MESOMANUFACTURING processes can be categorized as: Trattamenti e modifiche superficiali Rivestimenti Funzionali / Rivestimenti Decorativi / Film sottile/film spesso Produzione su scala nanometrica / Produzione su nanoscala Produzione su microscala / Produzione su microscala / Microlavorazione Produzione su mesoscala / Produzione su mesoscala Microelettronica e Produzione di semiconduttori e Fabbricazione Dispositivi microfluidici Manufacturing Produzione di micro-ottica Micro Assemblaggio e Imballaggio Litografia morbida In ogni prodotto intelligente progettato oggi, si può considerare un elemento che aumenterà l'efficienza, la versatilità, ridurrà il consumo di energia, ridurrà gli sprechi, aumenterà la durata del prodotto e quindi sarà rispettoso dell'ambiente. A tal fine, AGS-TECH si sta concentrando su una serie di processi e prodotti che possono essere incorporati in dispositivi e apparecchiature per raggiungere questi obiettivi. Ad esempio, low-friction FUNCTIONAL COATINGS può ridurre il consumo energetico. Alcuni altri esempi di rivestimento funzionale sono rivestimenti resistenti ai graffi, anti-wetting SURFACE TREATMENTS e rivestimenti (idrofobici), trattamenti superficiali (idrofili) che promuovono l'umidità, rivestimenti antimicotici, rivestimenti in carbonio simil diamante per utensili da taglio e incisione, THIN FILMrivestimenti elettronici, rivestimenti magnetici a film sottile, rivestimenti ottici multistrato. Produciamo componenti su scale di lunghezza nanometrica. In pratica si tratta di operazioni di fabbricazione al di sotto della scala micrometrica. La nanoproduzione è ancora agli inizi rispetto alla microproduzione, tuttavia la tendenza è in quella direzione e la nanoproduzione è sicuramente molto importante per il prossimo futuro. Alcune applicazioni della nanoproduzione oggi sono i nanotubi di carbonio come fibre di rinforzo per materiali compositi nei telai delle biciclette, mazze da baseball e racchette da tennis. I nanotubi di carbonio, a seconda dell'orientamento della grafite nel nanotubo, possono agire come semiconduttori o conduttori. I nanotubi di carbonio hanno una capacità di trasporto di corrente molto elevata, 1000 volte superiore a quella dell'argento o del rame. Un'altra applicazione della nanoproduzione è la ceramica in nanofase. Utilizzando le nanoparticelle nella produzione di materiali ceramici, possiamo aumentare contemporaneamente sia la resistenza che la duttilità della ceramica. Fare clic sul sottomenu per ulteriori informazioni. MICROSCALE MANUFACTURING or MICROMANUFACTURING si riferisce ai nostri processi di fabbricazione e fabbricazione non visibili a occhio nudo. I termini microproduzione, microelettronica, sistemi microelettromeccanici non si limitano a scale di lunghezza così ridotte, ma suggeriscono invece un materiale e una strategia di produzione. Nelle nostre operazioni di microproduzione, alcune delle tecniche più diffuse che utilizziamo sono la litografia, l'incisione a umido ea secco, il rivestimento a film sottile. Un'ampia varietà di sensori e attuatori, sonde, testine magnetiche per dischi rigidi, chip microelettronici, dispositivi MEMS come accelerometri e sensori di pressione, tra gli altri, vengono prodotti utilizzando tali metodi di microproduzione. Troverai informazioni più dettagliate su questi nei sottomenu. MESOSCALE MANUFACTURING or MESOMANUFACTURING si riferisce ai nostri processi per protesi acustiche e orologi, dispositivi medici estremamente piccoli come apparecchi acustici e piccoli dispositivi medici motori. La produzione su mesoscala si sovrappone sia alla macro che alla microproduzione. Torni in miniatura, con motore da 1,5 Watt e dimensioni di 32 x 25 x 30,5 mm e pesi di 100 grammi, sono stati fabbricati utilizzando metodi di produzione su mesoscala. Utilizzando tali torni, l'ottone è stato lavorato fino a un diametro di 60 micron e rugosità superficiale dell'ordine di un micron o due. Anche altre macchine utensili in miniatura come fresatrici e presse sono state prodotte utilizzando la mesofabbricazione. In MICROELECTRONICS MANUFACTURING usiamo le stesse tecniche della microproduzione. I nostri substrati più popolari sono il silicio e vengono utilizzati anche altri come l'arseniuro di gallio, il fosfuro di indio e il germanio. Pellicole/rivestimenti di molti tipi e in particolare rivestimenti conduttivi e isolanti a film sottile sono utilizzati nella fabbricazione di dispositivi e circuiti microelettronici. Questi dispositivi sono solitamente ottenuti da multistrato. Gli strati isolanti sono generalmente ottenuti per ossidazione come SiO2. I droganti (sia p che n) sono comuni e parti dei dispositivi sono drogate per alterarne le proprietà elettroniche e ottenere regioni di tipo p e n. Usando la litografia come la fotolitografia ultravioletta, profonda o ultravioletta estrema, o la litografia a raggi X, a fascio di elettroni trasferiamo i motivi geometrici che definiscono i dispositivi da una fotomaschera/maschera alle superfici del substrato. Questi processi di litografia vengono applicati più volte nella microproduzione di chip microelettronici al fine di ottenere le strutture richieste nella progettazione. Vengono inoltre effettuati processi di incisione mediante i quali vengono rimossi interi film o particolari sezioni di film o substrato. In breve, utilizzando vari passaggi di deposizione, incisione e litografia multipla otteniamo le strutture multistrato sui substrati semiconduttori di supporto. Dopo che i wafer sono stati lavorati e molti circuiti sono stati microfabbricati su di essi, le parti ripetitive vengono tagliate e si ottengono stampi singoli. Ogni die viene successivamente legato, confezionato e testato e diventa un prodotto microelettronico commerciale. Alcuni dettagli in più sulla produzione di microelettronica possono essere trovati nel nostro sottomenu, tuttavia l'argomento è molto ampio e quindi ti invitiamo a contattarci nel caso avessi bisogno di informazioni specifiche sul prodotto o maggiori dettagli. Le nostre operazioni MICROFLUIDICS MANUFACTURING sono finalizzate alla fabbricazione di dispositivi e sistemi in cui vengono gestiti piccoli volumi di fluidi. Esempi di dispositivi microfluidici sono dispositivi di micropropulsione, sistemi lab-on-a-chip, dispositivi microtermici, testine di stampa a getto d'inchiostro e altro ancora. In microfluidica abbiamo a che fare con il controllo e la manipolazione precisi di fluidi vincolati a regioni sub-millimetriche. I fluidi vengono spostati, miscelati, separati ed elaborati. Nei sistemi microfluidici i fluidi vengono movimentati e controllati sia attivamente utilizzando minuscole micropompe e microvalvole e simili, sia sfruttando passivamente le forze capillari. Con i sistemi lab-on-a-chip, i processi normalmente eseguiti in laboratorio vengono miniaturizzati su un singolo chip al fine di migliorare l'efficienza e la mobilità, nonché di ridurre i volumi di campioni e reagenti. Abbiamo la capacità di progettare dispositivi microfluidici per te e offrire prototipazione microfluidica e microproduzione su misura per le tue applicazioni. Un altro campo promettente nella microfabbricazione è MICRO-OPTICS MANUFACTURING. La micro-ottica consente la manipolazione della luce e la gestione di fotoni con strutture e componenti a scala micro e submicronica. La micro-ottica ci consente di interfacciare il mondo macroscopico in cui viviamo con il mondo microscopico dell'elaborazione dati opto e nanoelettronica. I componenti e i sottosistemi micro-ottici trovano ampie applicazioni nei seguenti campi: Tecnologia dell'informazione: in micro-display, micro-proiettori, archiviazione dati ottica, microcamere, scanner, stampanti, fotocopiatrici...ecc. Biomedicina: diagnostica mininvasiva/point of care, monitoraggio del trattamento, sensori di microimaging, impianti retinici. Illuminazione: sistemi basati su LED e altre sorgenti luminose efficienti Sistemi di sicurezza e sicurezza: sistemi di visione notturna a infrarossi per applicazioni automobilistiche, sensori ottici di impronte digitali, scanner retinici. Comunicazione ottica e telecomunicazioni: in interruttori fotonici, componenti in fibra ottica passivi, amplificatori ottici, sistemi di interconnessione mainframe e personal computer Strutture intelligenti: nei sistemi di rilevamento basati su fibra ottica e molto altro In qualità di fornitore di integrazione ingegneristica più diversificata, siamo orgogliosi della nostra capacità di fornire una soluzione per quasi tutte le esigenze di consulenza, ingegneria, reverse engineering, prototipazione rapida, sviluppo prodotto, produzione, fabbricazione e assemblaggio. Dopo aver microfabbricato i nostri componenti, molto spesso dobbiamo continuare con MICRO ASSEMBLY & PACKAGING. Ciò comporta processi come l'attacco di filiere, l'incollaggio di fili, la connettorizzazione, la sigillatura ermetica dei pacchetti, il rilevamento, il test di prodotti imballati per l'affidabilità ambientale ... ecc. Dopo la microproduzione di dispositivi su uno stampo, lo attacchiamo a una base più robusta per garantire l'affidabilità. Frequentemente utilizziamo cementi epossidici speciali o leghe eutettiche per legare lo stampo alla sua confezione. Dopo che il chip o il die è stato legato al suo substrato, lo colleghiamo elettricamente ai cavi del pacchetto usando il wire bonding. Un metodo consiste nell'utilizzare fili d'oro molto sottili dalla confezione che porta a cuscinetti di incollaggio situati attorno al perimetro della filiera. Infine dobbiamo fare il confezionamento finale del circuito collegato. A seconda dell'applicazione e dell'ambiente operativo, sono disponibili una varietà di pacchetti standard e personalizzati per dispositivi elettronici, elettro-ottici e microelettromeccanici microprodotti. Un'altra tecnica di microproduzione che utilizziamo è SOFT LITHOGRAPHY, un termine utilizzato per una serie di processi per il trasferimento di modelli. In tutti i casi è necessario uno stampo master che viene microfabbricato utilizzando metodi di litografia standard. Utilizzando lo stampo principale, produciamo un motivo/timbro elastomerico. Una variante della litografia morbida è la "stampa a microcontatto". Il timbro in elastomero è rivestito con un inchiostro e premuto contro una superficie. I picchi del motivo entrano in contatto con la superficie e viene trasferito uno strato sottile di circa 1 monostrato di inchiostro. Questo monostrato a film sottile funge da maschera per l'incisione a umido selettiva. Una seconda variante è il "moulding microtransfer", in cui le rientranze dello stampo in elastomero sono riempite con precursore di polimero liquido e spinte contro una superficie. Una volta che il polimero si indurisce, rimuoviamo lo stampo, lasciando il motivo desiderato. Infine, una terza variante è il "microstampaggio in capillari", in cui il motivo del timbro in elastomero è costituito da canali che utilizzano forze capillari per aspirare un polimero liquido nel timbro dal suo lato. Fondamentalmente, una piccola quantità del polimero liquido viene posta adiacente ai canali capillari e le forze capillari trascinano il liquido nei canali. Il polimero liquido in eccesso viene rimosso e il polimero all'interno dei canali viene lasciato indurire. Lo stampo per timbri viene staccato e il prodotto è pronto. Puoi trovare maggiori dettagli sulle nostre tecniche di microproduzione di litografia morbida cliccando sul relativo sottomenu a lato di questa pagina. Se sei principalmente interessato alle nostre capacità di ingegneria e ricerca e sviluppo anziché alle capacità di produzione, ti invitiamo a visitare anche il nostro sito Web di ingegneria http://www.ags-engineering.com Leggi di più Leggi di più Leggi di più Leggi di più Leggi di più Leggi di più Leggi di più Leggi di più Leggi di più CLICK Product Finder-Locator Service PAGINA PRECEDENTE
- Filtri e prodotti di filtrazione e membrane, AGS-TECH
AGS-TECH fornisce filtri, prodotti di filtrazione e membrane fabbricati su misura e standard, inclusi filtri per la purificazione dell'aria, filtri in schiuma ceramica, filtri a carbone attivo, filtri HEPA, media prefiltranti e filtri grossolani, filtri in rete metallica e in tessuto, filtri per olio e filtri carburante e gas. Filtri e prodotti di filtrazione e membrane Forniamo filtri, prodotti di filtrazione e membrane per applicazioni industriali e di consumo. I prodotti includono: - Filtri a base di carbone attivo - Filtri in rete metallica planari realizzati su specifica del cliente - Filtri a rete metallica di forma irregolare realizzati su specifica del cliente. - Altri tipi di filtri come aria, olio, filtri carburante. - Filtri ceramici in schiuma e membrane ceramiche per varie applicazioni industriali in petrolchimica, produzione chimica, farmaceutica... ecc. - Camera bianca ad alte prestazioni e filtri HEPA. Disponiamo di filtri all'ingrosso pronti all'ingrosso, prodotti per la filtrazione e membrane con varie dimensioni e specifiche. Produciamo e forniamo anche filtri e membrane secondo le specifiche dei clienti. I nostri prodotti filtranti sono conformi agli standard internazionali come gli standard CE, UL e ROHS. Clicca sui link sotto per selezionare il prodotto di filtraggio di tuo interesse. Filtri a carbone attivo Il carbone attivo chiamato anche carbone attivo, è una forma di carbone lavorato per avere pori piccoli e a basso volume che aumentano la superficie disponibile per l'adsorbimento o reazioni chimiche. A causa del suo alto grado di microporosità, solo un grammo di carbone attivo ha una superficie superiore a 1.300 m2 (14.000 piedi quadrati). Un livello di attivazione sufficiente per un'utile applicazione di carbone attivo può essere ottenuto unicamente da un'elevata area superficiale; tuttavia, un ulteriore trattamento chimico spesso migliora le proprietà di adsorbimento. Il carbone attivo è ampiamente utilizzato nei filtri per la purificazione dei gas, nei filtri per la decaffeinizzazione, nell'estrazione di metalli e purificazione, filtrazione e purificazione dell'acqua, medicinali, trattamento delle acque reflue, filtri dell'aria in maschere antigas e respiratori, filtri per aria compressa , filtraggio di bevande alcoliche come vodka e whisky dalle impurità organiche che possono influenzare taste, odor e_50d_odor e_500 colore tra molte altre applicazioni.7881cf58d_odor e_500 colore -5cde-3194-bb3b-136bad5cf58d_Activated carbon is viene utilizzato in vari tipi di filtri, più comunemente in filtri a pannello, tessuto non tessuto, filtri a cartuccia....ecc. Puoi scaricare le brochure dei nostri filtri a carboni attivi dai link sottostanti. - Filtri di purificazione dell'aria (include tipo piegato e filtri dell'aria a carbone attivo a forma di V) Filtri a membrana in ceramica I filtri a membrana in ceramica sono inorganici, idrofili e sono ideali per applicazioni estreme di nano, ultra e microfiltrazione che richiedono longevità, tolleranze di pressione/temperatura superiori e resistenza ai solventi aggressivi. I filtri a membrana in ceramica sono fondamentalmente filtri di ultrafiltrazione o microfiltrazione, utilizzati per trattare le acque reflue e l'acqua a temperature più elevate. I filtri a membrana in ceramica sono prodotti da materiali inorganici come ossido di alluminio, carburo di silicio, ossido di titanio e ossido di zirconio. Il materiale del nucleo poroso della membrana viene prima formato attraverso il processo di estrusione che diventa la struttura di supporto per la membrana ceramica. Quindi vengono applicati rivestimenti sulla faccia interna o sulla faccia filtrante con le stesse particelle di ceramica o talvolta con particelle diverse, a seconda dell'applicazione. Ad esempio, se il materiale del nucleo è ossido di alluminio, utilizziamo anche particelle di ossido di alluminio come rivestimento. La dimensione delle particelle di ceramica utilizzate per il rivestimento, così come il numero di rivestimento applicato, determinerà la dimensione dei pori della membrana e le caratteristiche di distribuzione. Dopo aver depositato il rivestimento sul nucleo, avviene la sinterizzazione ad alta temperatura all'interno di un forno, rendendo lo strato di membrana parte integrante di la struttura di supporto del nucleo. Questo ci fornisce una superficie molto resistente e dura. Questo legame sinterizzato garantisce una vita molto lunga per la membrana. Siamo in grado di produrre filtri a membrana in ceramica per te dalla gamma di microfiltrazione alla gamma di ultrafiltrazione variando il numero di rivestimenti e utilizzando la giusta dimensione delle particelle per il rivestimento. Le dimensioni standard dei pori possono variare da 0,4 micron a 0,01 micron. I filtri a membrana in ceramica sono come il vetro, molto duri e durevoli, a differenza delle membrane polimeriche . Pertanto i filtri a membrana in ceramica offrono una resistenza meccanica molto elevata. I filtri a membrana ceramica sono chimicamente inerti e possono essere utilizzati ad un flusso molto elevato rispetto alle membrane polimeriche. I filtri a membrana in ceramica possono essere puliti energicamente e sono termicamente stabili. I filtri a membrana in ceramica hanno una vita operativa molto lunga, all'incirca da tre a quattro volte maggiore rispetto alle membrane polimeriche. Rispetto ai filtri polimerici, i filtri ceramici sono molto costosi, perché le applicazioni di filtrazione ceramica iniziano dove finiscono le applicazioni polimeriche. I filtri a membrana in ceramica hanno varie applicazioni, principalmente nel trattamento di acque e acque reflue molto difficili da trattare, o dove sono coinvolte operazioni ad alta temperatura. Ha anche vaste applicazioni nel petrolio e nel gas, nel riciclaggio delle acque reflue, come pretrattamento per RO e per la rimozione di metalli precipitati da qualsiasi processo di precipitazione, per la separazione di petrolio e acqua, industria alimentare e delle bevande, microfiltrazione del latte, chiarificazione di succhi di frutta , bonifica e raccolta di nano polveri e catalizzatori, nell'industria farmaceutica, nell'industria mineraria dove si devono trattare i bacini di decantazione dei rifiuti. Offriamo filtri a membrana in ceramica a canale singolo o multiplo. Sia la produzione standard che quella personalizzata sono offerte da AGS-TECH Inc. Filtri in schiuma ceramica Filtro in schiuma ceramica is a hard schiuma realizzato da ceramica . Le schiume polimeriche a cellula aperta sono impregnate internamente con ceramic liquami e poi licenziato in a forno , lasciando solo materiale ceramico. Le schiume possono essere costituite da diversi materiali ceramici come ossido di alluminio , una comune ceramica per alte temperature. Filtri in schiuma ceramica get isolanti dai molti minuscoli vuoti riempiti d'aria all'interno dei vuoti materiali. I filtri in schiuma ceramica sono utilizzati per filtrazione di leghe metalliche fuse, assorbimento di inquinanti ambientali e come substrato per catalizzatori richiede un'ampia superficie interna. Filtri ceramici in schiuma sono ceramiche temprate con sacche d'aria o altri gas intrappolati in_ccb-37819055cde-31905555 -136bad5cf58d_pori in tutto il corpo del materiale. Questi materiali possono essere fabbricati dal 94 al 96% di aria in volume con resistenze alle alte temperature come 1700 °C. Since most ceramics sono già ossidi o altri composti inerti, non c'è pericolo di ossidazione o riduzione del materiale nei filtri in schiuma ceramica. - Brochure sui filtri in schiuma ceramica - Guida per l'utente del filtro in schiuma ceramica Filtri HEPA HEPA è un tipo di filtro dell'aria e l'abbreviazione sta per High-Efficiency Particulate Arrestance (HEPA). I filtri che soddisfano lo standard HEPA hanno molte applicazioni in camere bianche, strutture mediche, automobili, aerei e abitazioni. I filtri HEPA devono soddisfare determinati standard di efficienza come quelli stabiliti dal Dipartimento dell'Energia degli Stati Uniti (DOE). Per qualificarsi come HEPA secondo gli standard del governo degli Stati Uniti, un filtro dell'aria deve rimuovere dall'aria che passa attraverso 99,97% delle particelle di dimensioni 0,3 µm. La resistenza minima del filtro HEPA al flusso d'aria o alla caduta di pressione è generalmente specificata come 300 pascal (0,044 psi) alla sua portata nominale. La filtrazione HEPA funziona con mezzi meccanici e non assomiglia ai metodi di filtrazione ionica e ozono che utilizzano rispettivamente ioni negativi e gas ozono. Pertanto, le possibilità di potenziali effetti collaterali polmonari come asma e allergie sono molto inferiori con i sistemi di filtraggio HEPA. I filtri HEPA sono utilizzati anche negli aspirapolvere di alta qualità per proteggere efficacemente gli utenti da asma e allergie, perché il filtro HEPA intrappola le particelle fini come pollini e feci di acari della polvere che provocano sintomi di allergia e asma. Contattaci se desideri avere la nostra opinione sull'utilizzo dei filtri HEPA per una particolare applicazione o progetto. You can scarica le nostre brochure di prodotto per i filtri HEPA standard sotto. Se non riesci a trovare la dimensione o la forma giusta di cui hai bisogno, saremo lieti di progettare e produrre filtri HEPA personalizzati per la tua applicazione speciale. - Filtri di purificazione dell'aria (include filtri HEPA) Filtri grossolani e media prefiltrante I filtri grossolani e i mezzi di prefiltrazione vengono utilizzati per bloccare i detriti di grandi dimensioni. Sono di fondamentale importanza perché sono economici e proteggono i filtri più costosi di grado superiore dalla contaminazione con particolato grossolano e contaminanti. Senza filtri grossolani e mezzi di prefiltraggio, il costo del filtraggio sarebbe stato molto più alto poiché avremmo dovuto cambiare i filtri fini molto più frequentemente. La maggior parte dei nostri filtri grossolani e dei nostri mezzi di prefiltrazione sono realizzati in fibre sintetiche con diametri e dimensioni dei pori controllati. I materiali filtranti grossolani includono il popolare materiale poliestere. Il grado di efficienza del filtraggio è un parametro importante da verificare prima di scegliere un particolare filtro grosso/media filtrante. Altri parametri e caratteristiche da verificare sono se il mezzo di prefiltraggio è lavabile, riutilizzabile, valore di arresto, resistenza al flusso di aria o fluido, flusso d'aria nominale, polvere e particolato capacità di tenuta, resistenza alla temperatura, infiammabilità , caratteristiche della caduta di pressione, dimensional e specifiche relative alla forma... ecc. Contattaci per un parere prima di scegliere i filtri grossolani e i mezzi prefiltranti giusti per i tuoi prodotti e sistemi. - Brochure su rete metallica e tela (include informazioni sulle nostre capacità di produzione di reti metalliche e filtri in tessuto. Tela metallica e non metallica può essere utilizzata come filtri grossolani e mezzi di prefiltrazione in alcune applicazioni) - Filtri di purificazione dell'aria (include filtri grossolani e media prefiltrante per l'aria) Filtri olio, carburante, gas, aria e acqua AGS-TECH Inc. progetta e produce filtri per olio, carburante, gas, aria e acqua in base alle esigenze del cliente per macchinari industriali, automobili, motoscafi, motocicli... ecc. I filtri dell'olio sono progettati per rimuovere i contaminanti da olio motore , olio di trasmissione , olio lubrificante , olio idraulico . I filtri dell'olio sono utilizzati in molti tipi diversi di macchine idrauliche . Anche la produzione di petrolio, l'industria dei trasporti e gli impianti di riciclaggio utilizzano filtri per olio e carburante nei loro processi di produzione. OEM gli ordini sono i benvenuti, etichettiamo, serigrafia, olio per marcatura laser, carburante, gas, aria e acqua filtri in base alle tue esigenze, applichiamo i tuoi loghi sul prodotto e sul pacchetto in base alle tue esigenze e richieste. Se lo si desidera, i materiali dell'alloggiamento per i filtri di olio, carburante, gas, aria e acqua possono essere personalizzati in base alla propria applicazione particolare. Le informazioni sui nostri filtri standard per olio, carburante, gas, aria e acqua possono essere scaricate di seguito. - Olio - Carburante - Gas - Aria - Catalogo Selezione Filtri Acqua per Auto, Moto, Camion e Autobus - Filtri di purificazione dell'aria Membrane A membrane è una barriera selettiva; permette ad alcune cose di passare ma ne blocca altre. Tali cose possono essere molecole, ioni o altre piccole particelle. Generalmente, le membrane polimeriche vengono utilizzate per separare, concentrare o frazionare un'ampia varietà di liquidi. Le membrane fungono da sottile barriera tra i fluidi miscibili che consentono il trasporto preferenziale di uno o più componenti di alimentazione quando viene applicata una forza motrice, come un differenziale di pressione. Offriamo una suite di membrane di nanofiltrazione, ultrafiltrazione e microfiltrazione progettate per fornire flusso e reiezione ottimali e possono essere personalizzate per soddisfare i requisiti esclusivi di applicazioni di processo specifiche. Membrane i sistemi di filtrazione sono il cuore di molti processi di separazione. La selezione della tecnologia, la progettazione delle apparecchiature e la qualità di fabbricazione sono tutti fattori critici per il successo finale di un progetto. Per iniziare, è necessario selezionare la corretta configurazione della membrana. Contattaci per ricevere aiuto nei tuoi progetti. PAGINA PRECEDENTE