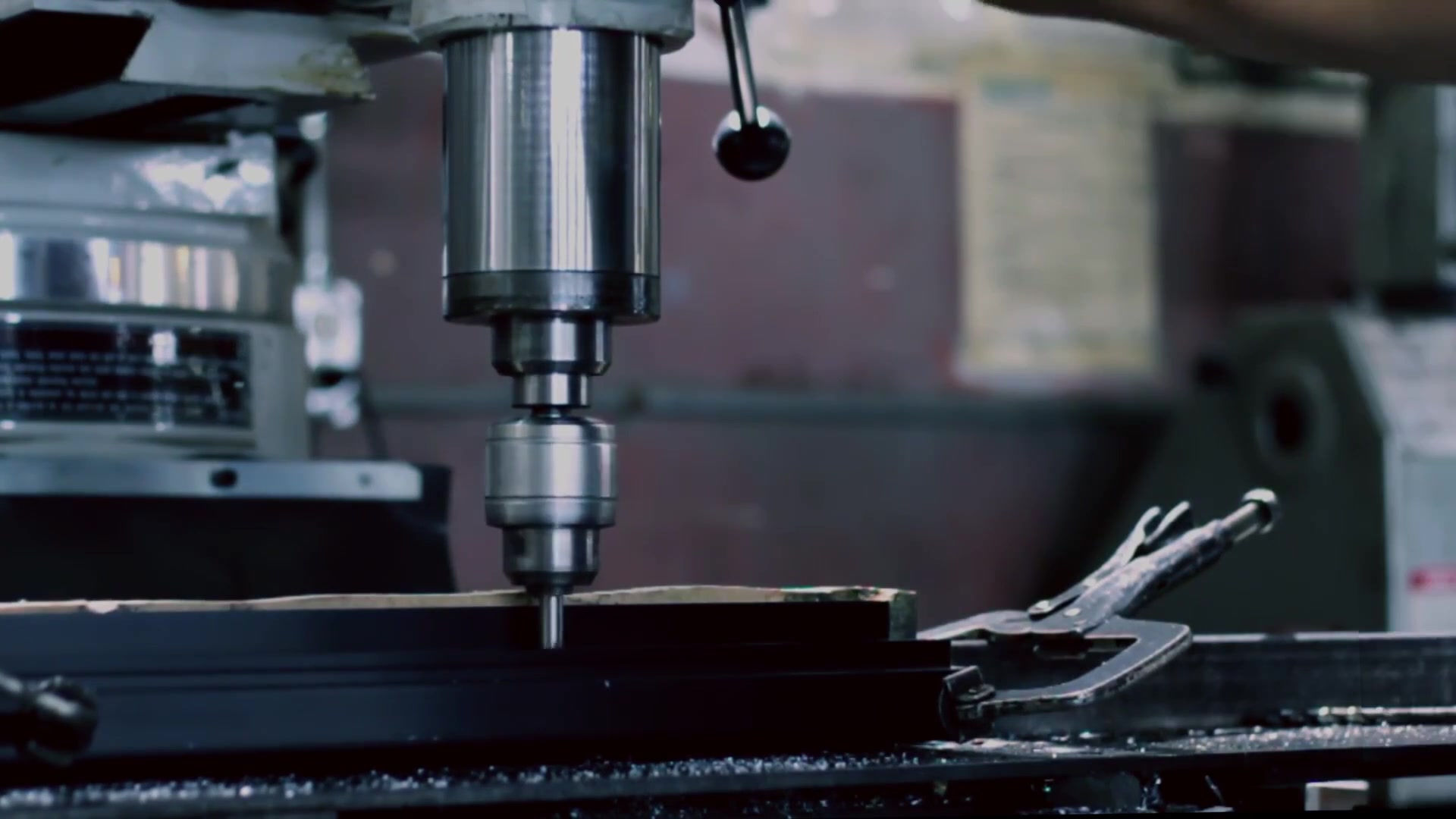
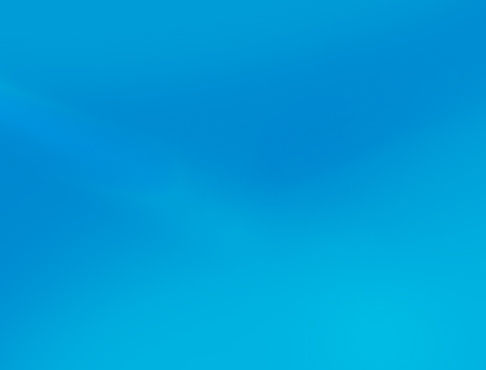
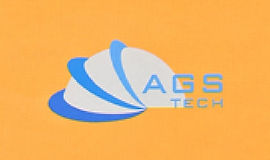
Produttore globale personalizzato, integratore, consolidatore, partner di outsourcing per un'ampia varietà di prodotti e servizi.
Siamo la tua fonte unica per la produzione, la fabbricazione, l'ingegnerizzazione, il consolidamento, l'integrazione, l'esternalizzazione di prodotti e servizi personalizzati e off-shelf.
Choose your Language
-
Produzione su misura
-
Produzione a contratto nazionale e globale
-
Esternalizzazione della produzione
-
Appalti nazionali e globali
-
Consolidamento
-
Integrazione ingegneristica
-
Servizi di ingegneria
Search Results
161 risultati trovati con una ricerca vuota
- Componenti di trasmissione, cinghie, catene, trasmissioni a cavo, pulegge, AGS-TECH
Componenti di trasmissione, cinghie, catene e trasmissioni a cavo, convenzionali e scanalate o dentate, trasmissione positiva, pulegge Cinghie e Catene e Assemblaggio di Trasmissione a Cavo AGS-TECH Inc. ti offre componenti per la trasmissione di potenza, tra cui cinghie e catene e assemblaggio di cavi. Con anni di perfezionamento, le nostre trasmissioni in gomma, pelle e altre cinghie sono diventate più leggere e compatte, in grado di trasportare carichi maggiori a costi inferiori. Allo stesso modo, le nostre trasmissioni a catena hanno subito molti sviluppi nel tempo e offrono ai nostri clienti numerosi vantaggi. Alcuni vantaggi dell'utilizzo di trasmissioni a catena sono gli interassi dell'albero relativamente illimitati, la compattezza, la facilità di montaggio, l'elasticità in tensione senza slittamento o scorrimento, la capacità di operare in ambienti ad alta temperatura. I nostri drive per cavi offrono anche vantaggi come la semplicità in alcune applicazioni rispetto ad altri tipi di componenti di trasmissione. Sono disponibili sia azionamenti a cinghia, a catena e a cavo, sia versioni fabbricate e assemblate su misura. Siamo in grado di produrre questi componenti di trasmissione nella misura giusta per la vostra applicazione e con i materiali più adatti. CINGHIE E TRASMISSIONI A CINGHIA: - Cinghie piatte convenzionali: sono cinghie piatte semplici senza denti, scanalature o dentellature. Le trasmissioni a cinghia piatta offrono flessibilità, buon assorbimento degli urti, trasmissione di potenza efficiente alle alte velocità, resistenza all'abrasione, basso costo. Le cinghie possono essere giuntate o collegate per creare cinghie più grandi. Altri vantaggi delle cinghie piatte convenzionali sono che sono sottili, non sono soggette a carichi centrifughi elevati (le rende adatte per operazioni ad alta velocità con piccole pulegge). D'altra parte impongono carichi portanti elevati perché le cinghie piatte richiedono un'elevata tensione. Altri svantaggi delle trasmissioni a cinghia piatta possono essere lo slittamento, il funzionamento rumoroso e le efficienze relativamente inferiori a velocità di funzionamento basse e moderate. Abbiamo due tipi di cinghie convenzionali: rinforzate e non rinforzate. Le cinghie rinforzate hanno un elemento di trazione nella loro struttura. Le cinghie piatte convenzionali sono disponibili in pelle, tessuto gommato o corda, gomma o plastica non rinforzata, tessuto, pelle rinforzata. Le cinghie in pelle offrono lunga durata, flessibilità, ottimo coefficiente di attrito, facile riparazione. Tuttavia, le cinture in pelle sono relativamente costose, necessitano di pulitura e pulizia delle cinture e, a seconda dell'atmosfera, possono restringersi o allungarsi. I nastri in tessuto gommato o in corda sono resistenti all'umidità, agli acidi e agli alcali. I nastri in tessuto gommato sono costituiti da strati di cotone o anatra sintetica impregnati di gomma e sono i più economici. I nastri in corda gommata sono costituiti da una serie di strati di corde impregnate di gomma. I nastri in corda gommata offrono un'elevata resistenza alla trazione e dimensioni e massa modeste. Le cinghie in gomma o plastica non rinforzate sono adatte per applicazioni di azionamento leggere ea bassa velocità. Le cinghie di gomma e plastica non rinforzate possono essere tese in posizione sopra le loro pulegge. Le cinghie in plastica non rinforzate possono trasmettere una potenza maggiore rispetto alle cinghie in gomma. Le cinghie in pelle rinforzata sono costituite da un elemento di trazione in plastica inserito tra gli strati superiore e inferiore in pelle. Infine, le nostre cinture in tessuto possono essere costituite da un unico pezzo di cotone o anatra piegato e cucito con file di punti longitudinali. I nastri in tessuto sono in grado di tracciare uniformemente e funzionare ad alta velocità. - Cinghie scanalate o seghettate (come cinghie trapezoidali): si tratta di cinghie piatte di base modificate per fornire i vantaggi di un altro tipo di prodotto di trasmissione. Si tratta di cinghie piatte con la parte inferiore a coste longitudinali. Le cinghie Poly-V sono cinghie piatte scanalate longitudinalmente o seghettate con sezione di trazione e una serie di scanalature a V adiacenti per scopi di tracciamento e compressione. La capacità di alimentazione dipende dalla larghezza del nastro. Le cinghie trapezoidali sono il cavallo di battaglia dell'industria e sono disponibili in una varietà di dimensioni e tipi standardizzati per la trasmissione di quasi tutte le potenze di carico. Le trasmissioni a cinghia trapezoidale funzionano bene tra 1500 e 6000 piedi/min, tuttavia le cinghie trapezoidali strette funzioneranno fino a 10.000 piedi/min. Le trasmissioni a cinghia trapezoidale offrono una lunga durata da 3 a 5 anni e consentono rapporti di velocità elevati, sono facili da installare e rimuovere, offrono un funzionamento silenzioso, bassa manutenzione, buon assorbimento degli urti tra la trasmissione della cinghia e gli alberi condotti. Lo svantaggio delle cinghie trapezoidali è il loro certo slittamento e scorrimento e quindi potrebbero non essere la soluzione migliore dove sono richieste velocità sincrone. Disponiamo di nastri industriali, automobilistici e agricoli. Sono disponibili lunghezze standard in stock e lunghezze personalizzate di cinghie. Tutte le sezioni trasversali standard della cinghia trapezoidale sono disponibili a magazzino. Esistono tabelle in cui è possibile calcolare parametri sconosciuti come la lunghezza della cinghia, la sezione della cinghia (larghezza e spessore) a condizione che si conoscano alcuni parametri del sistema come i diametri delle pulegge motrici e condotte, l'interasse tra le pulegge e le velocità di rotazione delle pulegge. Puoi utilizzare tali tabelle o chiederci di scegliere la cinghia trapezoidale giusta per te. - Cinghie di trasmissione positiva (cinghia dentata): queste cinghie sono anche di tipo piatto con una serie di denti equidistanti sulla circonferenza interna. Le cinghie di trasmissione o di distribuzione uniscono i vantaggi delle cinghie piatte con le caratteristiche di presa positiva di catene e ingranaggi. Le cinghie di trasmissione positive non rivelano slittamenti o variazioni di velocità. È possibile un'ampia gamma di rapporti di velocità. I carichi sui cuscinetti sono bassi perché possono funzionare a bassa tensione. Sono tuttavia più suscettibili ai disallineamenti nelle pulegge. - Pulegge, pulegge, mozzi per cinghie: vengono utilizzati diversi tipi di pulegge con cinghie di trasmissione piatte, scanalate (dentellate) e positive. Li produciamo tutti. La maggior parte delle nostre pulegge per cinghie piatte sono realizzate mediante fusione di ferro, ma le versioni in acciaio sono disponibili anche in varie combinazioni di cerchioni e mozzi. Le nostre pulegge per cinghie piatte possono avere mozzi pieni, a raggi o divisi oppure possiamo produrre come desideri. Le cinghie nervate ea trasmissione positiva sono disponibili in una varietà di misure e larghezze stock. Almeno una puleggia nelle trasmissioni a cinghia dentata deve essere flangiata per mantenere la cinghia sulla trasmissione. Per i sistemi di trasmissione a centro lungo, si consiglia di avere entrambe le pulegge flangiate. Le pulegge sono le ruote scanalate delle pulegge e sono generalmente prodotte mediante fusione di ferro, formatura dell'acciaio o stampaggio della plastica. La formatura dell'acciaio è un processo adatto per la produzione di pulegge per autoveicoli e agricoli. Produciamo covoni con scanalature regolari e profonde. Le pulegge a gola profonda sono adatte quando la cinghia trapezoidale entra nella puleggia ad angolo, come nel caso degli azionamenti a un quarto di giro. Le scanalature profonde sono adatte anche per azionamenti ad albero verticale e applicazioni in cui le vibrazioni delle cinghie possono essere un problema. Le nostre pulegge folli sono pulegge scanalate o pulegge piatte che non servono a trasmettere potenza meccanica. Le pulegge di rinvio sono utilizzate principalmente per il tensionamento delle cinghie. - Trasmissioni a cinghia singola e multipla: le trasmissioni a cinghia singola hanno una singola scanalatura mentre le trasmissioni a cinghia multipla hanno più scanalature. Cliccando sul relativo testo colorato di seguito è possibile scaricare i nostri cataloghi: - Cinghie di trasmissione di potenza (include cinghie trapezoidali, cinghie dentate, cinghie con bordo grezzo, cinghie avvolte e cinghie speciali) - Nastri trasportatori - Pulegge a V - Pulegge dentate CATENE E TRASMISSIONI A CATENA: Le nostre catene di trasmissione di potenza presentano alcuni vantaggi come interassi dell'albero relativamente illimitati, facilità di montaggio, compattezza, elasticità sotto tensione senza slittamento o scorrimento, capacità di funzionamento ad alte temperature. Ecco le principali tipologie delle nostre catene: - Catene staccabili: le nostre catene staccabili sono realizzate in una gamma di dimensioni, passo e massima resistenza e generalmente in ferro o acciaio malleabile. Le catene malleabili sono realizzate in una gamma di dimensioni da 0,902 (23 mm) a 4,063 pollici (103 mm) di passo e massima resistenza da 700 a 17.000 libbre/pollice quadrato. Le nostre catene rimovibili in acciaio, d'altra parte, sono realizzate in dimensioni da 0,904 pollici (23 mm) a circa 3,00 pollici (76 mm) di passo, con una resistenza massima da 760 a 5000 libbre/pollice quadrato._cc781905-5cde-3194-bb3b- 136bad5cf58d_ - Catene a perno: queste catene sono utilizzate per carichi più pesanti e velocità leggermente superiori a circa 450 piedi/min (2,2 m/sec). Le catene a perno sono realizzate con singole maglie fuse aventi l'estremità della canna rotonda e piena con barre laterali sfalsate. Queste maglie della catena sono accoppiate con perni in acciaio. Queste catene variano in passo da circa 1,00 pollici (25 mm) a 6,00 pollici (150 mm) e resistenze finali comprese tra 3600 e 30.000 libbre/pollice quadrato. - Catene con barra laterale sfalsata: sono popolari nelle catene di trasmissione delle macchine edili. Queste catene funzionano a velocità fino a 1000 piedi/min e trasmettono carichi a circa 250 CV. Generalmente ogni maglia ha due barre laterali sfalsate, una boccola, un rullo, un perno, una coppiglia. - Catene a rulli: sono disponibili con passi da 0,25 (6 mm) a 3,00 (75 mm) pollici. La massima resistenza delle catene a rulli a larghezza singola varia da 925 a 130.000 libbre/pollice quadrato. Sono disponibili versioni a più larghezze di catene a rulli che trasmettono maggiore potenza a velocità più elevate. Le catene a rulli a larghezza multipla offrono anche un'azione più fluida con una rumorosità ridotta. Le catene a rulli sono assemblate da maglie a rulli e maglie a perno. Le coppiglie sono utilizzate nelle catene a rulli in versione staccabile. La progettazione di trasmissioni a catena a rulli richiede competenza in materia. Mentre le trasmissioni a cinghia si basano su velocità lineari, le trasmissioni a catena si basano sulla velocità di rotazione della ruota dentata più piccola, che nella maggior parte delle installazioni è l'elemento condotto. Oltre alla potenza nominale e alla velocità di rotazione, la progettazione delle trasmissioni a catena si basa su molti altri fattori. - Catene a passo doppio: fondamentalmente le stesse delle catene a rulli, tranne per il fatto che il passo è lungo il doppio. - Catene a denti invertiti (silenziose): catene ad alta velocità utilizzate principalmente per motori primi, azionamenti a presa di forza. Le trasmissioni a catena a denti invertiti possono trasmettere potenze fino a 1200 CV e sono costituite da una serie di maglie dei denti, assemblate alternativamente con perni o una combinazione di componenti di giunzione. La catena con guida centrale ha maglie di guida per innestare le scanalature nella ruota dentata e la catena con guida laterale ha guide per impegnare i lati della ruota dentata. - Catene Bead o Slider: queste catene sono utilizzate per azionamenti a bassa velocità e anche nelle operazioni manuali. Cliccando sul relativo testo colorato di seguito è possibile scaricare i nostri cataloghi: - Catene motrici - Catene di trasporto - Catene di trasporto a passo largo - Catene a rulli in acciaio inossidabile - Catene di sollevamento - Catene da moto - Catene per macchine agricole - Pignoni: i nostri pignoni standard sono conformi agli standard ANSI. Le ruote dentate a piastra sono ruote dentate piatte e senza mozzo. I nostri pignoni con mozzo di piccole e medie dimensioni vengono torniti da barra o forgiati o realizzati saldando un mozzo da barra su una piastra laminata a caldo. AGS-TECH Inc. può fornire ruote dentate lavorate da getti di ghisa grigia, acciaio fuso e costruzioni di mozzi saldati, metallo in polvere sinterizzato, plastica stampata o lavorata. Per un funzionamento regolare ad alte velocità, è essenziale selezionare correttamente la dimensione dei pignoni. I limiti di spazio sono ovviamente un fattore che non possiamo ignorare quando si sceglie un pignone. Si raccomanda che il rapporto tra trascinatore e pignoni condotti non sia superiore a 6:1 e che l'avvolgimento della catena sul trascinatore sia di 120 gradi. Anche gli interassi tra i pignoni più piccoli e più grandi, le lunghezze della catena e la tensione della catena devono essere scelti in base ad alcuni calcoli e linee guida ingegneristici consigliati e non in modo casuale. Scarica i nostri cataloghi cliccando il testo colorato qui sotto: - Pignoni e ruote a piastre - Boccole di trasmissione - Accoppiamento a catena - Lucchetti a catena AZIONAMENTI PER CAVI: Questi hanno i loro vantaggi rispetto alle cinghie e alle trasmissioni a catena in alcuni casi. Gli azionamenti a cavo possono svolgere la stessa funzione delle cinghie e possono anche essere più semplici ed economici da implementare in alcune applicazioni. Ad esempio, una nuova serie di azionamenti per cavi sincronizzati è progettata per la trazione positiva in sostituzione di funi convenzionali, cavi semplici e azionamenti a cremagliera, soprattutto in spazi ristretti. Il nuovo cavo di azionamento è progettato per fornire un posizionamento di alta precisione in apparecchiature elettroniche come fotocopiatrici, plotter, macchine da scrivere, stampanti,….. ecc. Una caratteristica fondamentale del nuovo cavo di azionamento è la sua capacità di essere utilizzato in configurazioni a serpentina 3D che consentono disegni estremamente in miniatura. I cavi Synchromesh possono essere utilizzati con una tensione inferiore rispetto alle corde, riducendo così il consumo di energia. Contattare AGS-TECH per domande e opinioni su cinghie, catene e trasmissioni a cavo. CLICK Product Finder-Locator Service PAGINA PRECEDENTE
- Compositi, produzione di materiali compositi, rinforzati con fibre
Compositi, produzione di materiali compositi, rinforzati con particelle e fibre, cermet, compositi ceramici e metallici, polimeri rinforzati con fibre di vetro, processo di stratificazione Compositi e produzione di materiali compositi Definiti semplicemente, COMPOSITI o MATERIALI COMPOSITI sono materiali costituiti da due o più materiali con proprietà fisiche o chimiche diverse, ma quando combinati diventano un materiale diverso dai materiali costituenti. Occorre sottolineare che i materiali costitutivi restano separati e distinti nella struttura. L'obiettivo nella produzione di un materiale composito è quello di ottenere un prodotto che sia superiore ai suoi componenti e combini le caratteristiche desiderate di ogni componente. Come esempio; forza, peso ridotto o prezzo inferiore possono essere la motivazione dietro la progettazione e la produzione di un composito. Il tipo di compositi che offriamo sono compositi rinforzati con particelle, compositi rinforzati con fibre, inclusi compositi a matrice ceramica / matrice polimerica / matrice metallica / carbonio-carbonio / compositi ibridi, compositi strutturali e laminati e strutturati a sandwich e nanocompositi. Le tecniche di fabbricazione che impieghiamo nella produzione di materiali compositi sono: pultrusione, processi di produzione preimpregnati, posizionamento avanzato delle fibre, avvolgimento del filamento, posizionamento su misura delle fibre, processo di laminazione a spruzzo in fibra di vetro, tufting, processo lanxide, z-pinning. Molti materiali compositi sono costituiti da due fasi, la matrice, che è continua e circonda l'altra fase; e la fase dispersa che è circondata dalla matrice. Ti consigliamo di fare clic qui perSCARICA le nostre illustrazioni schematiche della produzione di compositi e materiali compositi di AGS-TECH Inc. Questo ti aiuterà a comprendere meglio le informazioni che ti forniamo di seguito. • COMPOSITI RINFORZATI CON PARTICELLE: Questa categoria è composta da due tipi: compositi a grandi particelle e compositi rinforzati con dispersione. Nel primo tipo, le interazioni particella-matrice non possono essere trattate a livello atomico o molecolare. Invece è valida la meccanica del continuo. D'altra parte, nei compositi rinforzati con dispersione le particelle sono generalmente molto più piccole nelle gamme di decine di nanometri. Un esempio di composito a particelle grandi sono i polimeri a cui sono stati aggiunti riempitivi. I riempitivi migliorano le proprietà del materiale e possono sostituire parte del volume del polimero con un materiale più economico. Le frazioni di volume delle due fasi influenzano il comportamento del composito. I compositi a grandi particelle vengono utilizzati con metalli, polimeri e ceramiche. I CERMETS sono esempi di compositi ceramica/metallo. Il nostro cermet più comune è il carburo cementato. È costituito da ceramica refrattaria al carburo come particelle di carburo di tungsteno in una matrice di un metallo come cobalto o nichel. Questi compositi in metallo duro sono ampiamente utilizzati come utensili da taglio per acciaio temprato. Le particelle di carburo duro sono responsabili dell'azione di taglio e la loro tenacità è esaltata dalla matrice metallica duttile. In questo modo otteniamo i vantaggi di entrambi i materiali in un unico composito. Un altro esempio comune di composito a grandi particelle che utilizziamo sono le particelle di nerofumo mescolate con gomma vulcanizzata per ottenere un composito con elevata resistenza alla trazione, tenacità, resistenza allo strappo e all'abrasione. Un esempio di composito rinforzato per dispersione sono i metalli e le leghe metalliche rinforzati e induriti dalla dispersione uniforme di particelle fini di un materiale molto duro e inerte. Quando vengono aggiunte scaglie di ossido di alluminio molto piccole alla matrice metallica di alluminio, otteniamo polvere di alluminio sinterizzato che ha una maggiore resistenza alle alte temperature. • COMPOSITI FIBRORINFORZATI: Questa categoria di compositi è infatti la più importante. L'obiettivo da raggiungere è un'elevata resistenza e rigidità per unità di peso. La composizione delle fibre, la lunghezza, l'orientamento e la concentrazione in questi compositi sono fondamentali per determinare le proprietà e l'utilità di questi materiali. Ci sono tre gruppi di fibre che utilizziamo: baffi, fibre e fili. I BATTINI sono monocristalli molto sottili e lunghi. Sono tra i materiali più resistenti. Alcuni esempi di materiali per baffi sono grafite, nitruro di silicio, ossido di alluminio. FIBERS invece sono per lo più polimeri o ceramiche e sono allo stato policristallino o amorfo. Il terzo gruppo è costituito da FILI fini che hanno diametri relativamente grandi e sono costituiti spesso da acciaio o tungsteno. Un esempio di composito rinforzato con filo sono i pneumatici per auto che incorporano filo di acciaio all'interno della gomma. A seconda del materiale della matrice, abbiamo i seguenti compositi: COMPOSITI A MATRICE POLIMERICA: Sono costituiti da una resina polimerica e fibre come ingrediente di rinforzo. Un sottogruppo di questi, chiamati compositi polimerici rinforzati con fibra di vetro (GFRP), contiene fibre di vetro continue o discontinue all'interno di una matrice polimerica. Il vetro offre un'elevata resistenza, è economico, facile da fabbricare in fibre ed è chimicamente inerte. Gli svantaggi sono la loro rigidità e rigidità limitate, le temperature di servizio sono solo fino a 200 – 300 gradi centigradi. La fibra di vetro è adatta per carrozzerie e attrezzature per il trasporto di automobili, carrozzerie di veicoli marini, container di stoccaggio. Non sono adatti per l'industria aerospaziale né per la costruzione di ponti a causa della rigidità limitata. L'altro sottogruppo è chiamato composito con polimero rinforzato con fibra di carbonio (CFRP). Qui, il carbonio è il nostro materiale in fibra nella matrice polimerica. Il carbonio è noto per il suo elevato modulo specifico e resistenza e per la sua capacità di mantenerli ad alte temperature. Le fibre di carbonio possono offrirci moduli di trazione standard, intermedi, alti e ultraelevati. Inoltre, le fibre di carbonio offrono diverse caratteristiche fisiche e meccaniche e quindi sono adatte a varie applicazioni ingegneristiche personalizzate. I compositi CFRP possono essere considerati per la produzione di attrezzature sportive e ricreative, recipienti a pressione e componenti strutturali aerospaziali. Ancora, un altro sottogruppo, i compositi polimerici rinforzati con fibra aramidica sono anche materiali ad alta resistenza e modulo. I loro rapporti forza/peso sono straordinariamente elevati. Le fibre aramidiche sono anche conosciute con i nomi commerciali KEVLAR e NOMEX. Sotto tensione si comportano meglio di altri materiali in fibra polimerica, ma sono deboli in compressione. Le fibre aramidiche sono tenaci, resistenti agli urti, allo scorrimento e alla fatica, stabili alle alte temperature, chimicamente inerti tranne che contro acidi e basi forti. Le fibre aramidiche sono ampiamente utilizzate in articoli sportivi, giubbotti antiproiettile, pneumatici, corde, guaine per cavi in fibra ottica. Esistono altri materiali di rinforzo in fibra, ma vengono utilizzati in misura minore. Questi sono principalmente boro, carburo di silicio, ossido di alluminio. Anche il materiale della matrice polimerica è critico. Determina la temperatura massima di servizio del composito perché il polimero ha generalmente una temperatura di fusione e degradazione inferiore. I poliesteri e gli esteri vinilici sono ampiamente utilizzati come matrice polimerica. Vengono utilizzate anche resine che hanno un'eccellente resistenza all'umidità e proprietà meccaniche. Ad esempio la resina poliimmidica può essere utilizzata fino a circa 230 gradi Celsius. COMPOSITI A MATRICE METALLICA : In questi materiali utilizziamo una matrice metallica duttile e le temperature di servizio sono generalmente superiori ai loro componenti costitutivi. Rispetto ai compositi a matrice polimerica, questi possono avere temperature operative più elevate, essere non infiammabili e possono avere una migliore resistenza alla degradazione contro i fluidi organici. Tuttavia sono più costosi. Materiali di rinforzo come baffi, particelle, fibre continue e discontinue; e vengono comunemente usati materiali di matrice come rame, alluminio, magnesio, titanio, superleghe. Esempi di applicazioni sono i componenti del motore realizzati con matrice in lega di alluminio rinforzata con ossido di alluminio e fibre di carbonio. COMPOSITI A MATRICE CERAMICA: I materiali ceramici sono noti per la loro eccezionale affidabilità alle alte temperature. Tuttavia sono molto fragili e hanno bassi valori di tenacità alla frattura. Incorporando particelle, fibre o baffi di una ceramica nella matrice di un'altra, siamo in grado di ottenere compositi con tenacità alla frattura più elevate. Questi materiali incorporati fondamentalmente inibiscono la propagazione della cricca all'interno della matrice mediante alcuni meccanismi come la deflessione delle punte delle cricche o la formazione di ponti attraverso le facce delle cricche. Ad esempio, le allumine rinforzate con baffi SiC vengono utilizzate come inserti per utensili da taglio per la lavorazione di leghe di metalli duri. Questi possono rivelare prestazioni migliori rispetto ai carburi cementati. COMPOSITI CARBONIO-CARBONIO: Sia il rinforzo che la matrice sono in carbonio. Hanno moduli e resistenze alla trazione elevati a temperature superiori a 2000 gradi centigradi, resistenza allo scorrimento, elevata tenacità alla frattura, bassi coefficienti di dilatazione termica, elevata conducibilità termica. Queste proprietà li rendono ideali per applicazioni che richiedono resistenza agli shock termici. Il punto debole dei compositi carbonio-carbonio è tuttavia la sua vulnerabilità all'ossidazione alle alte temperature. Esempi tipici di utilizzo sono gli stampi per stampaggio a caldo, la produzione avanzata di componenti di motori a turbina. COMPOSITI IBRIDI: Due o più diversi tipi di fibre sono mescolati in un'unica matrice. Si può così personalizzare un nuovo materiale con una combinazione di proprietà. Un esempio è quando sia le fibre di carbonio che quelle di vetro sono incorporate in una resina polimerica. Le fibre di carbonio forniscono rigidità e resistenza a bassa densità, ma sono costose. Il vetro invece è economico ma manca della rigidità delle fibre di carbonio. Il composito ibrido vetro-carbonio è più resistente e resistente e può essere prodotto a un costo inferiore. LAVORAZIONE DEI COMPOSITI FIBRORINFORZATI: Per i materiali plastici fibrorinforzati continui con fibre uniformemente distribuite orientate nella stessa direzione utilizziamo le seguenti tecniche. PULTRUSIONE: Vengono prodotti tondini, travi e tubi di lunghezza continua e sezione costante. I roving in fibra continua sono impregnati con una resina termoindurente e vengono tirati attraverso uno stampo in acciaio per preformarli alla forma desiderata. Successivamente, passano attraverso uno stampo di polimerizzazione lavorato con precisione per ottenere la sua forma finale. Poiché lo stampo di polimerizzazione viene riscaldato, polimerizza la matrice di resina. Gli estrattori aspirano il materiale attraverso gli stampi. Utilizzando le anime cave inserite, siamo in grado di ottenere tubi e geometrie cave. Il metodo di pultrusione è automatizzato e ci offre alti tassi di produzione. È possibile produrre qualsiasi lunghezza di prodotto. PROCESSO DI PRODUZIONE DEL PREPREG: Il prepreg è un rinforzo a fibra continua preimpregnato con una resina polimerica parzialmente indurita. È ampiamente utilizzato per applicazioni strutturali. Il materiale viene fornito sotto forma di nastro e viene spedito come nastro. Il produttore lo modella direttamente e lo polimerizza completamente senza la necessità di aggiungere alcuna resina. Poiché i preimpregnati subiscono reazioni di polimerizzazione a temperatura ambiente, vengono conservati a 0 gradi centigradi o temperature inferiori. Dopo l'uso, i nastri rimanenti vengono rimessi a basse temperature. Vengono utilizzate resine termoplastiche e termoindurenti e sono comuni fibre di rinforzo di carbonio, aramide e vetro. Per utilizzare i preimpregnati, la carta di supporto del supporto viene prima rimossa e quindi la fabbricazione viene eseguita stendendo il nastro preimpregnato su una superficie lavorata (il processo di laminazione). Possono essere posati più strati per ottenere gli spessori desiderati. La pratica frequente consiste nell'alternare l'orientamento della fibra per produrre un laminato a strati incrociati o angolari. Infine vengono applicati calore e pressione per l'indurimento. Sia la lavorazione manuale che i processi automatizzati vengono utilizzati per il taglio di preimpregnati e lay-up. AVVOLGIMENTO DEL FILAMENTO: le fibre di rinforzo continue sono accuratamente posizionate secondo uno schema predeterminato per seguire una forma cava e solitamente cilindrica. Le fibre passano prima in un bagno di resina e poi vengono avvolte su un mandrino da un sistema automatizzato. Dopo diverse ripetizioni di avvolgimento si ottengono gli spessori desiderati e la stagionatura viene eseguita a temperatura ambiente o all'interno di un forno. Ora il mandrino viene rimosso e il prodotto viene sformato. L'avvolgimento del filamento può offrire rapporti resistenza-peso molto elevati avvolgendo le fibre secondo schemi circonferenziali, elicoidali e polari. Tubi, serbatoi, involucri sono realizzati con questa tecnica. • COMPOSITI STRUTTURALI: Generalmente sono costituiti da materiali sia omogenei che compositi. Pertanto le proprietà di questi sono determinate dai materiali costitutivi e dal disegno geometrico dei suoi elementi. Ecco i tipi principali: COMPOSITI LAMINARI: Questi materiali strutturali sono costituiti da lastre o pannelli bidimensionali con direzioni preferenziali ad alta resistenza. Gli strati sono impilati e cementati insieme. Alternando le direzioni di alta resistenza nei due assi perpendicolari, otteniamo un composito che ha alta resistenza in entrambe le direzioni nel piano bidimensionale. Regolando gli angoli degli strati si può fabbricare un composito con forza nelle direzioni preferite. Lo sci moderno è prodotto in questo modo. PANNELLI SANDWICH: questi compositi strutturali sono leggeri ma hanno un'elevata rigidità e resistenza. I pannelli sandwich sono costituiti da due fogli esterni realizzati con un materiale rigido e resistente come leghe di alluminio, plastica rinforzata con fibre o acciaio e un'anima tra i fogli esterni. Il nucleo deve essere leggero e il più delle volte avere un basso modulo di elasticità. I materiali di base popolari sono schiume polimeriche rigide, legno e nido d'ape. I pannelli sandwich sono ampiamente utilizzati nel settore edile come materiale di copertura, materiale per pavimenti o pareti e anche nell'industria aerospaziale. • NANOCOMPOSITI: questi nuovi materiali sono costituiti da particelle di dimensioni nanometriche incorporate in una matrice. Usando i nanocompositi possiamo produrre materiali in gomma che sono ottime barriere alla penetrazione dell'aria mantenendo inalterate le loro proprietà della gomma. CLICK Product Finder-Locator Service PAGINA PRECEDENTE
- Processi di giunzione e assemblaggio e fissaggio, saldatura, brasatura, brasatura
Processi di giunzione, assemblaggio e fissaggio, saldatura, brasatura, brasatura, sinterizzazione, incollaggio adesivo, montaggio a pressione, processo di saldatura ad onda e rifusione, forno a torcia Processi di unione e assemblaggio e fissaggio Uniamo, montiamo e fissiamo i vostri manufatti e li trasformiamo in prodotti finiti o semilavorati mediante SALDATURA, BRASATURA, SALDATURA, SINTERIZZAZIONE, INCOLLAGGIO ADESIVI, FISSAGGIO, PRESS FITTING. Alcuni dei nostri processi di saldatura più diffusi sono l'arco, il gas ossitaglio, la resistenza, la proiezione, l'aggraffatura, il ribaltamento, la percussione, lo stato solido, il fascio di elettroni, il laser, la termita, la saldatura a induzione. I nostri processi di brasatura più diffusi sono la brasatura a torcia, a induzione, in forno e a immersione. I nostri metodi di saldatura sono ferro, piastra calda, forno, induzione, immersione, saldatura a onda, rifusione e saldatura ad ultrasuoni. Per l'incollaggio utilizziamo spesso materiali termoplastici e termoindurenti, epossidici, fenolici, poliuretanici, leghe adesive e altri prodotti chimici e nastri. Infine, i nostri processi di fissaggio consistono in chiodatura, avvitamento, dadi e bulloni, rivettatura, clinciatura, pinning, cucitura e pinzatura e montaggio a pressione. • SALDATURA : La saldatura comporta l'unione di materiali mediante la fusione dei pezzi da lavorare e l'introduzione di materiali di riempimento, che si uniscono anche al bagno di saldatura fuso. Quando la zona si raffredda, otteniamo una forte giunzione. In alcuni casi viene applicata pressione. Contrariamente alla saldatura, le operazioni di brasatura e saldatura comportano solo la fusione di un materiale con punto di fusione più basso tra i pezzi e i pezzi non fondono. Ti consigliamo di fare clic qui perSCARICA le nostre illustrazioni schematiche dei processi di saldatura di AGS-TECH Inc. Questo ti aiuterà a comprendere meglio le informazioni che ti forniamo di seguito. In ARC WELDING, utilizziamo un alimentatore e un elettrodo per creare un arco elettrico che fonde i metalli. Il punto di saldatura è protetto da gas o vapore di protezione o altro materiale. Questo processo è popolare per la saldatura di parti di automobili e strutture in acciaio. Nella saldatura ad arco metallico shelded (SMAW) o anche nota come saldatura stick, un elettrodo stick viene avvicinato al materiale di base e viene generato un arco elettrico tra di loro. L'asta dell'elettrodo fonde e funge da materiale di riempimento. L'elettrodo contiene anche un flusso che funge da strato di scorie ed emette vapori che fungono da gas di protezione. Questi proteggono l'area di saldatura dalla contaminazione ambientale. Non vengono utilizzati altri riempitivi. Gli svantaggi di questo processo sono la sua lentezza, la necessità di sostituire frequentemente gli elettrodi, la necessità di scheggiare le scorie residue provenienti dal flusso. Un certo numero di metalli come ferro, acciaio, nichel, alluminio, rame... ecc. Può essere saldato. I suoi vantaggi sono i suoi strumenti economici e la facilità d'uso. Saldatura ad arco di gas metallico (GMAW) nota anche come gas inerte metallico (MIG), abbiamo un'alimentazione continua di un riempitivo per filo di elettrodo consumabile e un gas inerte o parzialmente inerte che scorre attorno al filo contro la contaminazione ambientale della regione di saldatura. È possibile saldare acciaio, alluminio e altri metalli non ferrosi. I vantaggi di MIG sono elevate velocità di saldatura e buona qualità. Gli svantaggi sono le sue apparecchiature complicate e le sfide affrontate in ambienti esterni ventosi perché dobbiamo mantenere stabile il gas di protezione attorno all'area di saldatura. Una variazione di GMAW è la saldatura ad arco animato (FCAW) che consiste in un tubo di metallo sottile riempito con materiali di flusso. A volte il flusso all'interno del tubo è sufficiente per la protezione dalla contaminazione ambientale. La saldatura ad arco sommerso (SAW) è un processo ampiamente automatizzato, prevede l'alimentazione continua del filo e l'arco che viene colpito sotto uno strato di copertura del flusso. I tassi di produzione e la qualità sono elevati, le scorie di saldatura si staccano facilmente e disponiamo di un ambiente di lavoro privo di fumo. Lo svantaggio è che può essere utilizzato solo per saldare parts in determinate posizioni. Nella saldatura ad arco di tungsteno con gas (GTAW) o nella saldatura con gas inerte di tungsteno (TIG) utilizziamo un elettrodo di tungsteno insieme a un riempitivo separato e gas inerti o quasi inerti. Come sappiamo il tungsteno ha un alto punto di fusione ed è un metallo molto adatto per temperature molto elevate. Il tungsteno in TIG non viene consumato contrariamente agli altri metodi spiegati sopra. Una tecnica di saldatura lenta ma di alta qualità vantaggiosa rispetto ad altre tecniche di saldatura di materiali sottili. Adatto a molti metalli. La saldatura ad arco al plasma è simile ma utilizza gas plasma per creare l'arco. L'arco nella saldatura ad arco al plasma è relativamente più concentrato rispetto a GTAW e può essere utilizzato per una gamma più ampia di spessori metallici a velocità molto più elevate. GTAW e saldatura ad arco plasma possono essere applicati a materiali più o meno uguali. SALDATURA OXY-FUEL / OXYFUEL detta anche saldatura ossiacetilenica, la saldatura a gas viene eseguita utilizzando combustibili gassosi e ossigeno per la saldatura. Poiché non viene utilizzata energia elettrica, è portatile e può essere utilizzato dove non c'è elettricità. Utilizzando una torcia di saldatura riscaldiamo i pezzi e il materiale di riempimento per produrre un pool di metallo fuso condiviso. Possono essere utilizzati vari combustibili come acetilene, benzina, idrogeno, propano, butano, ecc. Nella saldatura a ossitaglio utilizziamo due contenitori, uno per il carburante e l'altro per l'ossigeno. L'ossigeno ossida il carburante (lo brucia). SALDATURA A RESISTENZA: Questo tipo di saldatura sfrutta il riscaldamento joule e il calore viene generato nel punto in cui viene applicata corrente elettrica per un certo tempo. Alte correnti passano attraverso il metallo. In questa posizione si formano pozze di metallo fuso. I metodi di saldatura a resistenza sono popolari grazie alla loro efficienza e al basso potenziale di inquinamento. Tuttavia, gli svantaggi sono i costi delle apparecchiature relativamente significativi e la limitazione intrinseca a pezzi relativamente sottili. La SALDATURA A PUNTI è uno dei principali tipi di saldatura a resistenza. Qui uniamo due o più fogli sovrapposti o pezzi da lavorare utilizzando due elettrodi di rame per bloccare insieme i fogli e far passare una corrente elevata attraverso di essi. Il materiale tra gli elettrodi di rame si riscalda e in quella posizione viene generata una pozza fusa. La corrente viene quindi interrotta e le punte degli elettrodi di rame raffreddano il punto di saldatura perché gli elettrodi sono raffreddati ad acqua. Applicare la giusta quantità di calore al materiale e allo spessore giusti è fondamentale per questa tecnica, perché se applicato in modo errato il giunto sarà debole. La saldatura a punti ha il vantaggio di non causare deformazioni significative ai pezzi, efficienza energetica, facilità di automazione e velocità di produzione eccezionali e non richiede riempitivi. Lo svantaggio è che poiché la saldatura avviene in punti piuttosto che formare una cucitura continua, la resistenza complessiva può essere relativamente inferiore rispetto ad altri metodi di saldatura. SEAM WELDING invece produce saldature sulle superfici di contatto di materiali simili. La cucitura può essere di testa o sovrapposta. La saldatura continua inizia da un'estremità e si sposta progressivamente all'altra. Questo metodo utilizza anche due elettrodi di rame per applicare pressione e corrente alla regione di saldatura. Gli elettrodi a forma di disco ruotano a contatto costante lungo la linea di giunzione e realizzano una saldatura continua. Anche in questo caso gli elettrodi sono raffreddati ad acqua. Le saldature sono molto forti e affidabili. Altri metodi sono le tecniche di proiezione, flash e saldatura a ribalta. LA SALDATURA A STATO SOLIDO è leggermente diversa dai metodi precedenti spiegati sopra. La coalescenza avviene a temperature inferiori alla temperatura di fusione dei metalli uniti e senza l'utilizzo di cariche metalliche. La pressione può essere utilizzata in alcuni processi. Vari metodi sono la SALDATURA PER COESTRUSIONE in cui metalli dissimili vengono estrusi attraverso lo stesso stampo, LA SALDATURA A PRESSIONE A FREDDO dove uniamo le leghe morbide al di sotto dei loro punti di fusione, LA SALDATURA PER DIFFUSIONE una tecnica senza linee di saldatura visibili, LA SALDATURA PER ESPLOSIONE per unire materiali dissimili, ad esempio leghe resistenti alla corrosione a strutture acciai, SALDATURA ELETTROMAGNETICA PULSATA dove acceleriamo tubi e lamiere mediante forze elettromagnetiche, SALDATURA FRIZIONE che consiste nel riscaldare i metalli ad alte temperature e martellarli insieme, SALDATURA PER FRIZIONE dove con sufficiente attrito si esegue la saldatura, SALDATURA PER FRIZIONE STIR che comporta una non rotazione utensile di consumo che attraversa la linea di giunzione, SALDATURA A PRESSIONE CALDA dove premiamo i metalli insieme a temperature elevate al di sotto della temperatura di fusione sotto vuoto o gas inerti, SALDATURA A PRESSIONE ISOSTATICA A CALDO un processo in cui applichiamo pressione utilizzando gas inerti all'interno di un recipiente, SALDATURA A RULLI dove ci uniamo materiali dissimili costringendoli tra di loro due ruote girevoli, SALDATURA A ULTRASUONI dove vengono saldate sottili lamine di metallo o plastica utilizzando energia vibrazionale ad alta frequenza. Gli altri nostri processi di saldatura sono la SALDATURA A FASCIO DI ELETTRONI con penetrazione profonda e lavorazione veloce ma essendo un metodo costoso lo consideriamo per casi speciali, la SALDATURA A ELETTROSLAG un metodo adatto per lamiere di grosso spessore e solo pezzi di acciaio, LA SALDATURA A INDUZIONE dove utilizziamo l'induzione elettromagnetica e riscaldare i nostri pezzi elettricamente conduttivi o ferromagnetici, SALDATURA A RAGGIO LASER anche con penetrazione profonda e lavorazione veloce ma un metodo costoso, SALDATURA IBRIDA LASER che combina LBW con GMAW nella stessa testa di saldatura e in grado di colmare giochi di 2 mm tra le piastre, SALDATURA A PERCUSSIONE che prevede una scarica elettrica seguita da forgiatura dei materiali con pressione applicata, SALDATURA TERMICA con reazione esotermica tra alluminio e polveri di ossido di ferro., SALDATURA ELETTROGAS con elettrodi consumabili e utilizzata con solo acciaio in posizione verticale, ed infine SALDATURA AD ARCO PERNO per unire il prigioniero alla base materiale con calore e pressione. Ti consigliamo di fare clic qui perSCARICA le nostre illustrazioni schematiche dei processi di brasatura, saldatura e incollaggio di AGS-TECH Inc Questo ti aiuterà a comprendere meglio le informazioni che ti forniamo di seguito. • BRASATURA : Uniamo due o più metalli riscaldando i metalli d'apporto tra di loro sopra i loro punti di fusione e usando l'azione capillare per diffonderli. Il processo è simile alla saldatura, ma le temperature necessarie per fondere il riempitivo sono più elevate durante la brasatura. Come nella saldatura, il flusso protegge il materiale di riempimento dalla contaminazione atmosferica. Dopo il raffreddamento i pezzi vengono uniti. Il processo prevede i seguenti passaggi chiave: buon adattamento e gioco, corretta pulizia dei materiali di base, corretto fissaggio, corretta selezione del flusso e dell'atmosfera, riscaldamento dell'assieme e infine la pulizia dell'assieme brasato. Alcuni dei nostri processi di brasatura sono TORCH BRAZING, un metodo diffuso eseguito manualmente o in modo automatizzato. È adatto per ordini di produzione a basso volume e casi specializzati. Il calore viene applicato utilizzando fiamme a gas vicino al giunto da brasare. LA BRASATURA A FORNO richiede meno abilità dell'operatore ed è un processo semiautomatico adatto alla produzione industriale di massa. Sia il controllo della temperatura che il controllo dell'atmosfera nel forno sono vantaggi di questa tecnica, perché il primo permette di avere cicli termici controllati ed eliminare il riscaldamento locale come nel caso della brasatura a cannello, mentre il secondo protegge il pezzo dall'ossidazione. Usando il jigging siamo in grado di ridurre al minimo i costi di produzione. Gli svantaggi sono l'elevato consumo energetico, i costi delle apparecchiature e considerazioni di progettazione più impegnative. LA BRASATURA SOTTOVUOTO avviene in un forno del vuoto. L'uniformità della temperatura viene mantenuta e otteniamo giunti esenti da flusso, molto puliti con pochissime sollecitazioni residue. I trattamenti termici possono avvenire durante la brasatura sotto vuoto, a causa delle basse sollecitazioni residue presenti durante i cicli lenti di riscaldamento e raffreddamento. Il principale svantaggio è il suo costo elevato perché la creazione di un ambiente sottovuoto è un processo costoso. Ancora un'altra tecnica DIP BRAZING unisce le parti fissate in cui il composto per brasatura viene applicato alle superfici di accoppiamento. Successivamente le parti fissate vengono immerse in un bagno di un sale fuso come il cloruro di sodio (sale da cucina) che funge da mezzo di trasferimento di calore e flusso. L'aria è esclusa e quindi non avviene la formazione di ossido. Nella BRASATURA A INDUZIONE uniamo i materiali mediante un metallo d'apporto che ha un punto di fusione inferiore rispetto ai materiali di base. La corrente alternata dalla bobina di induzione crea un campo elettromagnetico che induce il riscaldamento a induzione su materiali magnetici prevalentemente ferrosi. Il metodo fornisce un riscaldamento selettivo, buoni giunti con riempitivi che scorrono solo nelle aree desiderate, poca ossidazione perché non sono presenti fiamme e il raffreddamento è rapido, riscaldamento rapido, consistenza e idoneità per la produzione di grandi volumi. Per velocizzare i nostri processi e garantire la coerenza utilizziamo frequentemente le preforme. Informazioni sul nostro impianto di brasatura che produce raccordi da ceramica a metallo, tenuta ermetica, passanti per vuoto, componenti per il controllo dei fluidi e per alto e ultra alto vuoto sono disponibili qui: Brochure della fabbrica di brasatura • SALDATURA : Nella saldatura non abbiamo la fusione dei pezzi da lavorare, ma un metallo d'apporto con un punto di fusione inferiore rispetto alle parti di giunzione che scorre nel giunto. Il metallo d'apporto nella saldatura fonde a una temperatura inferiore rispetto alla brasatura. Utilizziamo leghe senza piombo per la saldatura e abbiamo la conformità RoHS e per diverse applicazioni e requisiti abbiamo leghe diverse e adatte come la lega d'argento. La saldatura ci offre giunti a tenuta di gas e liquidi. Nella SALDATURA DOLCE, il nostro metallo d'apporto ha un punto di fusione inferiore a 400 gradi centigradi, mentre nella SALDATURA D'ARGENTO e nella BRASATURA abbiamo bisogno di temperature più elevate. La saldatura dolce utilizza temperature più basse ma non si traduce in giunti forti per applicazioni impegnative a temperature elevate. La saldatura all'argento, invece, richiede alte temperature fornite dalla torcia e ci dà giunti robusti adatti ad applicazioni ad alta temperatura. La brasatura richiede le temperature più elevate e di solito viene utilizzata una torcia. Poiché i giunti di brasatura sono molto resistenti, sono buoni candidati per la riparazione di oggetti di ferro pesanti. Nelle nostre linee di produzione utilizziamo sia la saldatura manuale manuale che le linee di saldatura automatizzate. INDUCTION SOLDERING utilizza la corrente alternata ad alta frequenza in una bobina di rame per facilitare il riscaldamento a induzione. Le correnti sono indotte nella parte saldata e di conseguenza si genera calore all'alta resistenza joint. Questo calore scioglie il metallo d'apporto. Viene utilizzato anche il flusso. La saldatura a induzione è un buon metodo per saldare cilindri e tubi in un processo continuo avvolgendo le bobine attorno ad essi. La saldatura di alcuni materiali come la grafite e la ceramica è più difficile perché richiede la placcatura dei pezzi con un metallo adatto prima della saldatura. Ciò facilita il legame interfacciale. Saldiamo tali materiali soprattutto per applicazioni di imballaggio ermetico. Produciamo i nostri circuiti stampati (PCB) in grandi volumi utilizzando principalmente la SALDATURA A ONDA. Solo per piccole quantità di prototipazione utilizziamo la saldatura a mano utilizzando il saldatore. Utilizziamo la saldatura ad onda sia per i gruppi PCB a foro passante che per quelli a montaggio superficiale (PCBA). Una colla temporanea mantiene i componenti attaccati al circuito stampato e l'assieme viene posizionato su un nastro trasportatore e si muove attraverso un'apparecchiatura che contiene saldatura fusa. Prima il PCB viene flussato e poi entra nella zona di preriscaldamento. La saldatura fusa è in una padella e presenta un motivo di onde stazionarie sulla sua superficie. Quando il PCB si muove su queste onde, queste onde entrano in contatto con la parte inferiore del PCB e si attaccano ai pad di saldatura. La saldatura rimane solo su pin e pad e non sul PCB stesso. Le onde nella saldatura fusa devono essere ben controllate in modo che non vi siano schizzi e le parti superiori delle onde non tocchino e non contaminino le aree indesiderate delle schede. In REFLOW SOLDERING, utilizziamo una pasta saldante appiccicosa per fissare temporaneamente i componenti elettronici alle schede. Quindi le tavole vengono passate in un forno a rifusione con controllo della temperatura. Qui la saldatura si scioglie e collega i componenti in modo permanente. Utilizziamo questa tecnica sia per i componenti a montaggio superficiale che per i componenti a foro passante. Un corretto controllo della temperatura e regolazione delle temperature del forno è fondamentale per evitare la distruzione dei componenti elettronici sulla scheda surriscaldandoli oltre i loro limiti di temperatura massima. Nel processo di saldatura a rifusione abbiamo in realtà diverse regioni o stadi ciascuna con un profilo termico distinto, come la fase di preriscaldamento, la fase di ammollo termico, le fasi di rifusione e raffreddamento. Questi diversi passaggi sono essenziali per una saldatura a riflusso senza danni di assiemi di circuiti stampati (PCBA). LA SALDATURA A ULTRASUONI è un'altra tecnica usata frequentemente con capacità uniche: può essere utilizzata per saldare vetro, ceramica e materiali non metallici. Ad esempio i pannelli fotovoltaici che non sono metallici necessitano di elettrodi che possono essere fissati utilizzando questa tecnica. Nella saldatura a ultrasuoni, utilizziamo una punta di saldatura riscaldata che emette anche vibrazioni ultrasoniche. Queste vibrazioni producono bolle di cavitazione all'interfaccia del substrato con il materiale di saldatura fuso. L'energia implosiva della cavitazione modifica la superficie dell'ossido e rimuove lo sporco e gli ossidi. Durante questo periodo si forma anche uno strato di lega. La saldatura sulla superficie di unione incorpora ossigeno e consente la formazione di un forte legame condiviso tra il vetro e la saldatura. La SALDATURA A DIP può essere considerata una versione più semplice della saldatura ad onda adatta solo per la produzione su piccola scala. Il primo flusso di pulizia viene applicato come in altri processi. I PCB con componenti montati vengono immersi manualmente o in modo semiautomatico in un serbatoio contenente saldatura fusa. La saldatura fusa si attacca alle aree metalliche esposte non protette dalla maschera di saldatura sulla scheda. L'attrezzatura è semplice ed economica. • INCOLLAGGIO ADESIVO: questa è un'altra tecnica popolare che utilizziamo frequentemente e prevede l'incollaggio di superfici mediante colle, resine epossidiche, agenti plastici o altri prodotti chimici. L'incollaggio si ottiene evaporando il solvente, polimerizzando a caldo, polimerizzando con luce UV, polimerizzando a pressione o attendendo un certo tempo. Nelle nostre linee di produzione vengono utilizzate diverse colle ad alte prestazioni. Con un'applicazione adeguatamente progettata e processi di polimerizzazione, l'incollaggio può dare luogo a legami di sollecitazione molto bassi, forti e affidabili. I legami adesivi possono essere buoni protettori contro fattori ambientali come umidità, contaminanti, agenti corrosivi, vibrazioni... ecc. I vantaggi dell'incollaggio sono: possono essere applicati su materiali che altrimenti sarebbero difficili da saldare, saldare o brasare. Inoltre può essere preferibile per materiali sensibili al calore che verrebbero danneggiati dalla saldatura o da altri processi ad alta temperatura. Altri vantaggi degli adesivi sono che possono essere applicati su superfici di forma irregolare e aumentare il peso dell'assemblaggio di quantità molto molto piccole rispetto ad altri metodi. Anche i cambiamenti dimensionali nelle parti sono molto minimi. Alcune colle hanno proprietà di corrispondenza dell'indice e possono essere utilizzate tra i componenti ottici senza ridurre significativamente la potenza del segnale luminoso o ottico. Gli svantaggi sono invece i tempi di polimerizzazione più lunghi che possono rallentare le linee di produzione, i requisiti di fissaggio, i requisiti di preparazione della superficie e la difficoltà di smontare quando è necessaria una rilavorazione. La maggior parte delle nostre operazioni di incollaggio prevede i seguenti passaggi: -Trattamento della superficie: sono comuni procedure di pulizia speciali come la pulizia con acqua deionizzata, la pulizia con alcol, la pulizia al plasma o corona. Dopo la pulizia si possono applicare promotori di adesione sulle superfici per assicurare le migliori fughe possibili. -Fissaggio delle parti: sia per l'applicazione dell'adesivo che per la polimerizzazione progettiamo e utilizziamo dispositivi personalizzati. -Applicazione dell'adesivo: a volte utilizziamo sistemi manuali e, a seconda dei casi, automatizzati come robotica, servomotori, attuatori lineari per consegnare gli adesivi nella giusta posizione e utilizziamo distributori per consegnarli al giusto volume e quantità. - Indurimento: a seconda dell'adesivo, possiamo utilizzare una semplice essiccazione e indurimento, nonché l'indurimento sotto le luci UV che fungono da catalizzatore o l'indurimento termico in un forno o utilizzando elementi riscaldanti resistivi montati su maschere e dispositivi. Ti consigliamo di fare clic qui perSCARICA le nostre illustrazioni schematiche dei processi di fissaggio di AGS-TECH Inc. Questo ti aiuterà a comprendere meglio le informazioni che ti forniamo di seguito. • PROCESSI DI FISSAGGIO: I nostri processi di giunzione meccanica rientrano in due categorie di marca: FISSAGGI e GIUNTI INTEGRALI. Esempi di elementi di fissaggio che utilizziamo sono viti, perni, dadi, bulloni, rivetti. Esempi di giunti integrali che utilizziamo sono accoppiamenti a scatto e termoretraibili, cuciture, aggraffature. Utilizzando una varietà di metodi di fissaggio, ci assicuriamo che i nostri giunti meccanici siano robusti e affidabili per molti anni di utilizzo. VITI e BULLONI sono alcuni degli elementi di fissaggio più comunemente usati per tenere insieme gli oggetti e posizionarli. Le nostre viti e bulloni soddisfano gli standard ASME. Vengono utilizzati vari tipi di viti e bulloni, comprese viti a testa esagonale e bulloni esagonali, viti e bulloni a testa piatta, vite a doppia estremità, vite per tasselli, vite a occhiello, vite a specchio, vite per lamiera, vite di regolazione fine, viti autoperforanti e autofilettanti , vite di fermo, viti con rondelle integrate e altro ancora. Disponiamo di vari tipi di testa della vite come testa svasata, a cupola, rotonda, flangiata e vari tipi di vite come slot, phillips, quadrato, esagono incassato. A RIVET d'altra parte è un fissaggio meccanico permanente costituito da un albero cilindrico liscio e una testa da un lato. Dopo l'inserimento, l'altra estremità del rivetto si deforma e il suo diametro viene espanso in modo che rimanga in posizione. In altre parole, prima dell'installazione un rivetto ha una testa e dopo l'installazione ne ha due. Installiamo vari tipi di rivetti a seconda dell'applicazione, della forza, dell'accessibilità e del costo come rivetti a testa piena/tonda, strutturali, semitubolari, ciechi, oscar, drive, flush, friction-lock, autoperforanti. La rivettatura può essere preferita nei casi in cui è necessario evitare la deformazione termica e la modifica delle proprietà del materiale dovute al calore di saldatura. La rivettatura offre anche un peso leggero e soprattutto una buona resistenza e resistenza alle forze di taglio. Contro i carichi di trazione, tuttavia, possono essere più indicati viti, dadi e bulloni. Nel processo di CLINCHING utilizziamo punzoni e matrici speciali per formare un incastro meccanico tra le lamiere da unire. Il punzone spinge gli strati di lamiera nella cavità dello stampo e determina la formazione di un giunto permanente. Nella clinciatura non è richiesto né riscaldamento né raffreddamento ed è un processo di lavorazione a freddo. È un processo economico che in alcuni casi può sostituire la saldatura a punti. In PINNING utilizziamo perni che sono elementi della macchina utilizzati per fissare le posizioni delle parti della macchina l'una rispetto all'altra. I tipi principali sono perni con testa, coppiglia, perno a molla, perni di riferimento, e copiglia. In STAPLING utilizziamo pistole e graffette che sono dispositivi di fissaggio a due punte utilizzati per unire o rilegare i materiali. La graffatura presenta i seguenti vantaggi: Economica, semplice e veloce da usare, la corona delle graffette può essere utilizzata per unire materiali accostati, La corona della graffatura può facilitare il collegamento di un pezzo come un cavo e il fissaggio ad una superficie senza forare o rimozione dannosa e relativamente facile. Il PRESS FITTING viene eseguito spingendo le parti insieme e l'attrito tra di esse fissa le parti. Le parti a pressione costituite da un albero sovradimensionato e un foro sottodimensionato vengono generalmente assemblate con uno dei due metodi seguenti: applicando forza o sfruttando l'espansione o la contrazione termica delle parti. Quando si stabilisce un raccordo a pressare applicando una forza, utilizziamo una pressa idraulica o una pressa manuale. D'altra parte, quando il raccordo a pressare è stabilito dall'espansione termica, riscaldiamo le parti avvolgenti e le assembliamo al loro posto mentre sono calde. Quando si raffreddano si contraggono e tornano alle loro dimensioni normali. Ciò si traduce in una buona vestibilità a pressione. Chiamiamo questo in alternativa RACCORDO TERMORETRAIBILE. L'altro modo per farlo è raffreddare le parti avvolte prima del montaggio e quindi farle scorrere nelle parti di accoppiamento. Quando l'assieme si scalda si espandono e otteniamo una perfetta aderenza. Quest'ultimo metodo può essere preferibile nei casi in cui il riscaldamento comporta il rischio di modificare le proprietà del materiale. Il raffreddamento è più sicuro in questi casi. Componenti e assiemi pneumatici e idraulici • Valvole, componenti idraulici e pneumatici come O-ring, rondella, guarnizioni, guarnizione, anello, spessora. Poiché le valvole e i componenti pneumatici sono disponibili in una grande varietà, non possiamo elencare tutto qui. A seconda degli ambienti fisici e chimici della tua applicazione, abbiamo prodotti speciali per te. Specificateci l'applicazione, il tipo di componente, le specifiche, le condizioni ambientali come pressione, temperatura, liquidi o gas che verranno a contatto con le vostre valvole e componenti pneumatici; e noi sceglieremo il prodotto più adatto a te o lo realizzeremo appositamente per la tua applicazione. CLICK Product Finder-Locator Service PAGINA PRECEDENTE
- Prototipazione rapida, produzione desktop, produzione additiva, FDM
Prototipazione rapida, produzione desktop, produzione additiva, stereolitografia, Polyjet, modellazione a deposizione fusa, sinterizzazione laser selettiva, FDM, SLS Produzione additiva e rapida Negli ultimi anni abbiamo assistito a un aumento della domanda di RAPID MANUFACTURING o RAPID PROTOTYPING. Questo processo può anche essere chiamato FABBRICAZIONE DESKTOP o FABBRICAZIONE A FORMA LIBERA. Fondamentalmente un modello fisico solido di una parte viene realizzato direttamente da un disegno CAD tridimensionale. Utilizziamo il termine PRODUZIONE ADDITIVA per queste varie tecniche in cui costruiamo parti a strati. Utilizzando hardware e software integrati basati su computer eseguiamo la produzione additiva. Le nostre tecniche di prototipazione rapida e produzione sono STEREOLITOGRAFIA, POLYJET, MODELLAZIONE A DEPOSIZIONE FUSA, SINTERIZZAZIONE LASER SELETTIVA, FUSIONE DEL FASCIO DI ELETTRONI, STAMPA TRIDIMENSIONALE, PRODUZIONE DIRETTA, ATTREZZATURA RAPIDA. Ti consigliamo di fare clic qui perSCARICA le nostre illustrazioni schematiche di produzione additiva e processi di produzione rapida di AGS-TECH Inc. Questo ti aiuterà a comprendere meglio le informazioni che ti forniamo di seguito. La prototipazione rapida ci fornisce: 1.) Il design concettuale del prodotto viene visualizzato da diverse angolazioni su un monitor utilizzando un sistema 3D/CAD. 2.) I prototipi di materiali non metallici e metallici vengono realizzati e studiati sotto il profilo funzionale, tecnico ed estetico. 3.) Si realizza la prototipazione a basso costo in brevissimo tempo. La produzione additiva può essere simile alla costruzione di una pagnotta impilando e incollando le singole fette l'una sull'altra. In altre parole, il prodotto viene fabbricato fetta per fetta, o strato per strato depositato l'uno sull'altro. La maggior parte delle parti può essere prodotta in poche ore. La tecnica è buona se le parti sono necessarie molto rapidamente o se le quantità necessarie sono basse e la realizzazione di uno stampo e degli utensili è troppo costosa e richiede tempo. Tuttavia il costo di una parte è costoso a causa delle costose materie prime. • STEREOLITOGRAFIA: questa tecnica abbreviata anche in STL, si basa sulla polimerizzazione e sull'indurimento di un fotopolimero liquido in una forma specifica focalizzando un raggio laser su di esso. Il laser polimerizza il fotopolimero e lo polimerizza. Scansionando il raggio laser UV secondo la forma programmata lungo la superficie della miscela di fotopolimeri, il pezzo viene prodotto dal basso verso l'alto in singole fette sovrapposte l'una sull'altra. La scansione dello spot laser viene ripetuta più volte per ottenere le geometrie programmate nel sistema. Dopo che la parte è stata completamente prodotta, viene rimossa dalla piattaforma, asciugata e pulita a ultrasuoni e con bagno di alcol. Successivamente, viene esposto all'irradiazione UV per alcune ore per assicurarsi che il polimero sia completamente indurito e indurito. Per riassumere il processo, una piattaforma che viene immersa in una miscela di fotopolimeri e un raggio laser UV vengono controllati e spostati attraverso un sistema di servocontrollo in base alla forma della parte desiderata e la parte viene ottenuta fotopolimerizzando il polimero strato per strato. Naturalmente le dimensioni massime del pezzo prodotto sono determinate dall'attrezzatura per la stereolitografia. • POLYJET : Simile alla stampa a getto d'inchiostro, in Polyjet abbiamo otto testine di stampa che depositano il fotopolimero sul vassoio di stampa. La luce ultravioletta posta a fianco dei getti polimerizza e indurisce immediatamente ogni strato. Due materiali sono usati in polyjet. Il primo materiale è per la fabbricazione del modello vero e proprio. Il secondo materiale, una resina gelatinosa, viene utilizzato per il supporto. Entrambi questi materiali vengono depositati strato per strato e contemporaneamente polimerizzati. Dopo il completamento del modello, il materiale di supporto viene rimosso con una soluzione acquosa. Le resine utilizzate sono simili alla stereolitografia (STL). Il polyjet presenta i seguenti vantaggi rispetto alla stereolitografia: 1.) Non è necessario pulire le parti. 2.) Non c'è bisogno di polimerizzazione post-processo 3.) Sono possibili spessori di strato più piccoli e quindi otteniamo una migliore risoluzione e possiamo produrre parti più fini. • MODELLAZIONE A DEPOSIZIONE FUSA: abbreviata anche in FDM, in questo metodo una testa di estrusione controllata da robot si muove in due direzioni principali su un tavolo. Il cavo viene abbassato e sollevato secondo necessità. Dall'orifizio di una filiera riscaldata sulla testa, viene estruso un filamento termoplastico e viene depositato uno strato iniziale su una base di schiuma. Ciò è ottenuto dalla testa dell'estrusore che segue un percorso predeterminato. Dopo lo strato iniziale, il tavolo viene abbassato e gli strati successivi vengono depositati uno sopra l'altro. A volte, durante la produzione di una parte complicata, sono necessarie strutture di supporto in modo che la deposizione possa continuare in determinate direzioni. In questi casi, un materiale di supporto viene estruso con una spaziatura del filamento meno densa su uno strato in modo che sia più debole del materiale del modello. Queste strutture di supporto possono essere successivamente dissolte o interrotte dopo il completamento della parte. Le dimensioni della filiera dell'estrusore determinano lo spessore degli strati estrusi. Il processo FDM produce parti con superfici a gradini su piani esterni obliqui. Se questa rugosità è inaccettabile, è possibile utilizzare la lucidatura chimica a vapore o uno strumento riscaldato per levigarli. Anche una cera per lucidatura è disponibile come materiale di rivestimento per eliminare questi passaggi e ottenere tolleranze geometriche ragionevoli. • SINTERIZZAZIONE LASER SELETTIVA: Detta anche SLS, il processo si basa sulla sinterizzazione selettiva di un polimero, polvere di ceramica o metallo in un oggetto. Il fondo della camera di lavorazione ha due cilindri: un cilindro di costruzione parziale e un cilindro di alimentazione della polvere. Il primo viene abbassato in modo incrementale al punto in cui viene formata la parte sinterizzata e il secondo viene sollevato in modo incrementale per fornire polvere al cilindro di costruzione parziale attraverso un meccanismo a rulli. Prima viene depositato un sottile strato di polvere nel cilindro di costruzione parziale, quindi un raggio laser viene focalizzato su quello strato, tracciando e fondendo/sinterizzando una particolare sezione trasversale, che poi si risolidifica in un solido. La polvere è che le aree che non vengono colpite dal raggio laser rimangono libere ma supportano comunque la parte solida. Quindi viene depositato un altro strato di polvere e il processo ripetuto più volte per ottenere il pezzo. Alla fine, le particelle di polvere sciolta vengono scrollate via. Tutto ciò viene eseguito da un computer di controllo del processo utilizzando le istruzioni generate dal programma CAD 3D del pezzo in lavorazione. Possono essere depositati vari materiali come polimeri (come ABS, PVC, poliestere), cera, metalli e ceramica con opportuni leganti polimerici. • ELECTRON-BEAM MELTING : Simile alla sinterizzazione laser selettiva, ma utilizza un raggio di elettroni per fondere polveri di titanio o cromo cobalto per realizzare prototipi sotto vuoto. Sono stati fatti alcuni sviluppi per eseguire questo processo su acciai inossidabili, alluminio e leghe di rame. Se è necessario aumentare la resistenza alla fatica delle parti prodotte, utilizziamo la pressatura isostatica a caldo successiva alla produzione delle parti come processo secondario. • STAMPA TRIDIMENSIONALE: Indicata anche con 3DP, in questa tecnica una testina di stampa deposita un legante inorganico su uno strato di polvere non metallica o metallica. Un pistone che trasporta il letto di polvere viene abbassato in modo incrementale e ad ogni passaggio il legante viene depositato strato per strato e fuso dal legante. I materiali in polvere utilizzati sono miscele e fibre di polimeri, sabbia di fonderia, metalli. Usando diverse teste di legante contemporaneamente e diversi leganti di colore possiamo ottenere vari colori. Il processo è simile alla stampa a getto d'inchiostro ma invece di ottenere un foglio colorato otteniamo un oggetto tridimensionale colorato. Le parti prodotte possono essere porose e quindi possono richiedere la sinterizzazione e l'infiltrazione di metallo per aumentarne la densità e la resistenza. La sinterizzazione brucerà il legante e fonderà insieme le polveri metalliche. Metalli come acciaio inossidabile, alluminio, titanio possono essere utilizzati per realizzare le parti e come materiali di infiltrazione utilizziamo comunemente rame e bronzo. Il bello di questa tecnica è che anche gli assiemi complicati e mobili possono essere realizzati molto rapidamente. Ad esempio, è possibile realizzare un gruppo ingranaggi, una chiave inglese come strumento e avere parti mobili e girevoli pronte per essere utilizzate. Diversi componenti dell'assieme possono essere realizzati con colori diversi e tutti in un unico colpo. Scarica la nostra brochure su:Nozioni di base sulla stampa 3D in metallo • PRODUZIONE DIRETTA e ATTREZZATURA RAPIDA: oltre alla valutazione del progetto, alla risoluzione dei problemi, utilizziamo la prototipazione rapida per la produzione diretta di prodotti o l'applicazione diretta nei prodotti. In altre parole, la prototipazione rapida può essere incorporata nei processi convenzionali per renderli migliori e più competitivi. Ad esempio, la prototipazione rapida può produrre modelli e stampi. I modelli di un polimero fuso e bruciato creati da operazioni di prototipazione rapida possono essere assemblati per la colata a cera persa e rivestiti. Un altro esempio da menzionare è l'utilizzo di 3DP per produrre conchiglie di colata di ceramica e utilizzarle per le operazioni di colata in conchiglia. Anche stampi a iniezione e inserti per stampi possono essere prodotti mediante prototipazione rapida e si possono risparmiare molte settimane o mesi di tempo di realizzazione degli stampi. Analizzando solo un file CAD del pezzo desiderato, possiamo produrre la geometria dell'utensile tramite software. Ecco alcuni dei nostri metodi di attrezzaggio rapido più diffusi: STAMPAGGIO RTV ( Vulcanizzazione a temperatura ambiente) / COLATA DI URETANO : Utilizzando la prototipazione rapida è possibile realizzare il modello della parte desiderata. Quindi questo modello viene rivestito con un agente distaccante e la gomma RTV liquida viene versata sul modello per produrre le metà dello stampo. Successivamente, queste metà dello stampo vengono utilizzate per lo stampaggio a iniezione di uretani liquidi. La vita dello stampo è breve, solo come 0 o 30 cicli ma sufficiente per la produzione di piccoli lotti. STAMPAGGIO A INIEZIONE ACES (Acetal Clear Epoxy Solid): Utilizzando tecniche di prototipazione rapida come la stereolitografia, produciamo stampi a iniezione. Questi stampi sono gusci con un'estremità aperta per consentire il riempimento con materiali come resina epossidica, resina epossidica riempita di alluminio o metalli. Anche in questo caso la durata dello stampo è limitata a decine o al massimo centinaia di parti. PROCESSO DI UTENSILI PER METALLI SPRUZZATI: Utilizziamo la prototipazione rapida e realizziamo un modello. Spruzziamo una lega di zinco-alluminio sulla superficie del modello e la rivestiamo. Il motivo con il rivestimento in metallo viene quindi posizionato all'interno di una fiaschetta e imbottigliato con una resina epossidica o riempita di alluminio. Infine, viene rimosso e producendo due di questi semistampi otteniamo uno stampo completo per lo stampaggio ad iniezione. Questi stampi hanno una vita più lunga, in alcuni casi a seconda del materiale e delle temperature possono produrre migliaia di pezzi. PROCESSO KEELTOOL: questa tecnica può produrre stampi con cicli di vita da 100.000 a 10 milioni. Utilizzando la prototipazione rapida produciamo uno stampo RTV. Lo stampo viene quindi riempito con una miscela composta da polvere di acciaio per utensili A6, carburo di tungsteno, legante polimerico e lasciato indurire. Questo stampo viene quindi riscaldato per far bruciare il polimero e far fondere le polveri metalliche. Il passaggio successivo è l'infiltrazione di rame per produrre lo stampo finale. Se necessario, sullo stampo possono essere eseguite operazioni secondarie come la lavorazione a macchina e la lucidatura per una migliore precisione dimensionale. CLICK Product Finder-Locator Service PAGINA PRECEDENTE
- Machine Elements Manu, Gears, Gear Drives, Bearings, Keys, Splines
Produzione di elementi di macchine, ingranaggi, trasmissioni a ingranaggi, cuscinetti, chiavette, scanalature, perni, alberi, guarnizioni, elementi di fissaggio, frizione, camme, rulli, cinghie, giunti, alberi Produzione di elementi di macchine Leggi di più Cinghie e Catene e Assemblaggio di Trasmissione a Cavo Leggi di più Ingranaggi e gruppo trasmissione a ingranaggi Leggi di più Produzione di giunti e cuscinetti Leggi di più Produzione di chiavi e scanalature e perni Leggi di più Camme e follower e collegamenti e produzione di ruote a cricchetto Leggi di più Produzione di alberi Leggi di più Produzione di tenute meccaniche Leggi di più Frizione e gruppo freno Leggi di più Produzione di elementi di fissaggio Leggi di più Assemblaggio di macchine semplici MACHINE ELEMENTS sono componenti elementari di una macchina. Questi elementi sono costituiti da tre tipi fondamentali: 1.) Componenti strutturali inclusi elementi del telaio, cuscinetti, assi, scanalature, elementi di fissaggio, guarnizioni e lubrificanti. 2.) Meccanismi che controllano il movimento in vari modi come ingranaggi, trasmissioni a cinghia o a catena, collegamenti, sistemi a camme e seguicamma, freni e frizioni. 3.) Componenti di controllo come pulsanti, interruttori, indicatori, sensori, attuatori e controller del computer. La maggior parte degli elementi macchina che ti offriamo sono standardizzati su dimensioni comuni, ma sono disponibili anche elementi macchina personalizzati per le tue applicazioni specializzate. La personalizzazione degli elementi della macchina può avvenire su design esistenti che sono nei nostri cataloghi scaricabili o su design nuovi di zecca. La prototipazione e la produzione di elementi della macchina possono essere portate avanti una volta che un progetto è stato approvato da entrambe le parti. Se è necessario progettare e produrre nuovi elementi della macchina, i nostri clienti ci inviano via e-mail i propri progetti e li esaminiamo per l'approvazione, oppure ci chiedono di progettare elementi della macchina per la loro applicazione. In quest'ultimo caso utilizziamo tutti gli input dei nostri clienti, progettiamo gli elementi della macchina e inviamo i progetti finali ai nostri clienti per l'approvazione. Una volta approvati, produciamo i primi articoli e successivamente realizziamo gli elementi della macchina secondo il progetto definitivo. In qualsiasi fase di questo lavoro, nel caso in cui il progetto di un particolare elemento della macchina non funzioni in modo soddisfacente sul campo (cosa rara), esaminiamo l'intero progetto e apportiamo modifiche insieme ai nostri clienti secondo necessità. È nostra pratica standard firmare accordi di riservatezza (NDA) con i nostri clienti per la progettazione di elementi di macchine o qualsiasi altro prodotto quando necessario o richiesto. Una volta che gli elementi della macchina per un particolare cliente sono progettati e realizzati su misura, gli assegniamo un codice prodotto e li produciamo e vendiamo solo al nostro cliente che possiede il prodotto. Riproduciamo gli elementi della macchina utilizzando gli strumenti, gli stampi e le procedure sviluppati tutte le volte che è necessario e ogni volta che il nostro cliente li riordina. In altre parole, una volta che un elemento macchina personalizzato è stato progettato e prodotto per te, la proprietà intellettuale così come tutti gli utensili e gli stampi sono riservati e immagazzinati a tempo indeterminato da noi per te e per i prodotti riprodotti come desideri. Offriamo inoltre ai nostri clienti servizi di ingegneria combinando creativamente gli elementi della macchina in un componente o un assieme che serve un'applicazione e soddisfa o supera le aspettative dei nostri clienti. Gli impianti che fabbricano i nostri elementi macchina sono qualificati da ISO9001, QS9000 o TS16949. Inoltre, la maggior parte dei nostri prodotti ha il marchio CE o UL e soddisfa gli standard internazionali rilevanti come ISO, SAE, ASME, DIN. Fare clic sui sottomenu per ottenere informazioni dettagliate sugli elementi della nostra macchina, tra cui: - Cinghie, Catene e Passacavi - Ingranaggi e trasmissioni ad ingranaggi - Giunti e cuscinetti - Chiavi, scanalature e spille - Camme e collegamenti - Aste - Tenute meccaniche - Frizione e freno industriali - Elementi di fissaggio - Macchine semplici Abbiamo preparato una brochure di riferimento per i nostri clienti, progettisti e sviluppatori di nuovi prodotti, compresi gli elementi della macchina. Puoi familiarizzare con alcuni termini comunemente usati nella progettazione di componenti di macchine: Scarica la brochure per i termini comuni di ingegneria meccanica utilizzati da progettisti e ingegneri I nostri elementi per macchine trovano applicazioni in una varietà di campi come macchinari industriali, sistemi di automazione, apparecchiature di test e metrologia, apparecchiature di trasporto, macchine edili e praticamente ovunque tu possa pensare. AGS-TECH sviluppa e produce elementi di macchine di vari materiali a seconda dell'applicazione. I materiali utilizzati per gli elementi delle macchine possono variare dalla plastica stampata utilizzata per i giocattoli all'acciaio cementato e rivestito in modo speciale per i macchinari industriali. I nostri progettisti utilizzano software professionali all'avanguardia e strumenti di progettazione per lo sviluppo di elementi della macchina, prendendo in considerazione dettagli come gli angoli dei denti degli ingranaggi, le sollecitazioni coinvolte, i tassi di usura... ecc. Scorri i nostri sottomenu e scarica le nostre brochure e cataloghi dei prodotti per vedere se riesci a individuare gli elementi della macchina pronti all'uso per la tua applicazione. Se non riesci a trovare una buona corrispondenza per la tua applicazione, faccelo sapere e lavoreremo con te per sviluppare e produrre elementi della macchina che soddisfino le tue esigenze. Se sei principalmente interessato alle nostre capacità di ingegneria e ricerca e sviluppo anziché alle capacità di produzione, ti invitiamo a visitare il nostro sito Web http://www.ags-engineering.com dove puoi trovare informazioni più dettagliate sulla nostra progettazione, sviluppo prodotto, sviluppo dei processi, servizi di consulenza ingegneristica e altro ancora CLICK Product Finder-Locator Service PAGINA PRECEDENTE
- Formatura di fili e molle, sagomatura, saldatura, assemblaggio di fili, bobina, CNC
Formatura di fili e molle, sagomatura, saldatura, assemblaggio di fili, molle piatte di torsione di estensione di compressione della bobina, fili personalizzati, molle elicoidali presso AGS-TECH Inc. Formatura di fili e molle Produciamo fili personalizzati, assemblaggio di fili, fili formati nelle forme 2D e 3D desiderate, reti metalliche, reti, recinzioni, cestini, recinzioni, molle a filo, molle piatte; torsione, compressione, tensione, molle piatte e altro ancora. I nostri processi sono la formatura di fili e molle, la trafilatura, la sagomatura, la piegatura, la saldatura, la brasatura, la brasatura, la perforazione, la foggiatura, la foratura, la bisellatura, la rettifica, la filettatura, il rivestimento, il fourslide, la profilatura, l'avvolgimento, l'avvolgimento, il ribaltamento. Ti consigliamo di fare clic qui per SCARICA le nostre illustrazioni schematiche dei processi di formatura di fili e molle di AGS-TECH Inc. Questo file scaricabile con foto e schizzi ti aiuterà a comprendere meglio le informazioni che ti forniamo di seguito. • TRAFILATURA DEL FILO : Usando le forze di trazione allunghiamo il materiale metallico e lo trasciniamo attraverso una filiera per ridurre il diametro e aumentarne la lunghezza. A volte usiamo una serie di dadi. Siamo in grado di realizzare filiere per ogni calibro di filo. Utilizzando materiale ad alta resistenza alla trazione trafilamo fili molto sottili. Offriamo fili lavorati sia a freddo che a caldo. • FORMATURA DEL FILO: Un rotolo di filo calibrato viene piegato e modellato in un prodotto utile. Abbiamo la capacità di formare fili di tutti i calibri, inclusi filamenti sottili e fili spessi come quelli usati come molle sotto il telaio delle automobili. Le attrezzature che utilizziamo per la formatura del filo sono formatrici manuali e CNC, avvolgitori, presse elettriche, quattro slitte, multi-slitte. I nostri processi sono trafilatura, piegatura, raddrizzatura, appiattimento, allungamento, taglio, ricalcatura, saldatura e brasatura, assemblaggio, avvolgimento, foggiatura (o ala), perforazione, filettatura di fili, foratura, smussatura, rettifica, rivestimento e trattamenti superficiali. Le nostre apparecchiature all'avanguardia possono essere configurate per sviluppare progetti molto complessi di qualsiasi forma e tolleranze strette. Offriamo vari tipi di estremità come estremità sferiche, appuntite o smussate per i tuoi fili. La maggior parte dei nostri progetti di formatura del filo ha costi di attrezzaggio minimi o nulli. I tempi di consegna del campione sono generalmente giorni. Le modifiche alla progettazione/configurazione delle forme dei cavi possono essere apportate molto rapidamente. • FORMATURA MOLLE: AGS-TECH produce un'ampia varietà di molle tra cui: -Molla a torsione/doppia torsione - Molla di trazione/compressione -Molla costante/variabile - Bobina e molla elicoidale -Molla piatta e a balestra -Equilibrio Primavera -Lavatrice Belleville -Negatore Primavera -Molla elicoidale a velocità progressiva -Onda di primavera - Primavera a volute - Molle affusolate -Anelli di primavera -Molle dell'orologio -Clip Produciamo molle da una varietà di materiali e possiamo guidarvi in base alla vostra applicazione. I materiali più comuni sono acciaio inossidabile, silicio cromato, acciaio ad alto tenore di carbonio, acciaio temperato a basso tenore di carbonio, cromo vanadio, bronzo fosforoso, titanio, lega di rame al berillio, ceramica ad alta temperatura. Utilizziamo varie tecniche nella produzione di molle, tra cui avvolgimento CNC, avvolgimento a freddo, avvolgimento a caldo, tempra, finitura. Altre tecniche già menzionate sopra per la formatura del filo sono comuni anche nelle nostre operazioni di produzione di molle. • SERVIZI DI FINITURA per FILI E MOLLE: Possiamo rifinire i vostri prodotti in molti modi a seconda della vostra scelta e delle vostre esigenze. Alcuni processi comuni che offriamo sono: verniciatura, verniciatura a polvere, placcatura, immersione in vinile, anodizzazione, antistress, trattamento termico, pallinatura, burattatura, cromatura, electroless nichel, passivazione, smalto a forno, rivestimento plastico , pulizia al plasma. CLICK Product Finder-Locator Service PAGINA PRECEDENTE
- Fabbricazione di formatura di lamiere, stampaggio, punzonatura, imbutitura profonda, CNC
Formatura e fabbricazione di lamiere, stampaggio, punzonatura, piegatura, stampi progressivi, saldatura a punti, imbutitura profonda, tranciatura di metalli e taglio presso AGS-TECH Inc. Stampaggi e fabbricazione di lamiere Offriamo stampaggio lamiera, sagomatura, formatura, piegatura, punzonatura, tranciatura, taglio, perforazione, intaglio, roditura, rasatura, stampaggio, fabbricazione, imbutitura profonda utilizzando stampi a punzone singolo / corsa singola, nonché stampi progressivi e filatura, formatura gomma e idroformatura; taglio lamiera mediante getto d'acqua, plasma, laser, sega, fiamma; assemblaggio di lamiere mediante saldatura, saldatura a punti; rigonfiamento e piegatura di tubi in lamiera; finitura della superficie della lamiera, compresa la verniciatura a immersione o a spruzzo, la verniciatura a polvere elettrostatica, l'anodizzazione, la placcatura, lo sputtering e altro ancora. I nostri servizi spaziano dalla prototipazione rapida di lamiere alla produzione ad alto volume. Ti consigliamo di fare clic qui perSCARICA le nostre illustrazioni schematiche di fabbricazione di lamiere e processi di stampaggio di AGS-TECH Inc. Questo ti aiuterà a comprendere meglio le informazioni che ti stiamo fornendo di seguito. • TAGLIO LAMIERA : Offriamo TAGLI e PARTI DI RICAMBIO. I tagli tagliano la lamiera su un percorso alla volta e non c'è praticamente nessuno spreco di materiale, mentre con le troncature la forma non può essere annidata con precisione e quindi una certa quantità di materiale viene sprecata. Uno dei nostri processi più popolari è la PUNZONATURA, in cui un pezzo di materiale rotondo o di altra forma viene ritagliato da una lamiera. Il pezzo che viene ritagliato è un rifiuto. Un'altra versione della punzonatura è SLOTTING, dove vengono praticati fori rettangolari o allungati. La tranciatura invece è la stessa lavorazione della punzonatura, con la particolarità che il pezzo da ritagliare è il lavoro e viene mantenuto. FINE BLANKING, una versione superiore della tranciatura, crea tagli con tolleranze strette e bordi dritti lisci e non richiede operazioni secondarie per la perfezione del pezzo. Un altro processo che utilizziamo frequentemente è SLITTING, che è un processo di tranciatura in cui la lamiera viene tagliata da due lame circolari opposte in un percorso rettilineo o curvo. L'apriscatole è un semplice esempio del processo di taglio. Un altro popolare process per noi è PERFORATING, in cui molti fori rotondi o di altra forma vengono praticati nella lamiera secondo un determinato schema. Un tipico esempio di prodotto forato sono i filtri metallici con molti fori per i fluidi. In NOTCHING, un altro processo di taglio della lamiera, rimuoviamo materiale da un pezzo, partendo dal bordo o altrove e tagliando verso l'interno fino a ottenere la forma desiderata. È un processo progressivo in cui ogni operazione rimuove un altro pezzo fino a ottenere il contorno desiderato. Per piccole tirature a volte utilizziamo un processo relativamente più lento chiamato RODITURA che consiste in molti punzoni rapidi di fori sovrapposti per eseguire un taglio più grande e complesso. Nel TAGLIO PROGRESSIVO utilizziamo una serie di diverse operazioni per ottenere un unico taglio o una determinata geometria. Infine la RASATURA un processo secondario ci aiuta a migliorare i bordi dei tagli già eseguiti. Viene utilizzato per tagliare trucioli, spigoli vivi su lamiere. • PIEGATURA LAMIERA: Oltre al taglio, la piegatura è un processo essenziale senza il quale non saremmo in grado di produrre la maggior parte dei prodotti. Per lo più un'operazione di lavoro a freddo, ma a volte eseguita anche a caldo oa caldo. Usiamo stampi e premiamo la maggior parte del tempo per questa operazione. Nella PIEGATURA PROGRESSIVA utilizziamo una serie di diverse operazioni di punzonatura e matrice per ottenere una singola piega o una determinata geometria. AGS-TECH utilizza una varietà di processi di piegatura e fa la scelta in base al materiale del pezzo, alle sue dimensioni, spessore, dimensione di piegatura desiderata, raggio, curvatura e angolo di piegatura, posizione della piega, economia di funzionamento, quantità da produrre... eccetera. Utilizziamo V-BENDING in cui un punzone a V forza la lamiera nello stampo a V e lo piega. Buono sia per angoli molto acuti che ottusi e nel mezzo, inclusi 90 gradi. Usando le matrici di pulizia eseguiamo la PIEGATURA DEL BORDO. La nostra attrezzatura ci permette di ottenere angoli anche maggiori di 90 gradi. Nella piegatura del bordo, il pezzo è inserito tra un tampone di pressione e lo stampo, l'area per la piegatura si trova sul bordo dello stampo e il resto del pezzo è trattenuto nello spazio come una trave a sbalzo. Quando il punzone agisce sulla porzione a sbalzo, viene piegato oltre il bordo dello stampo. FLANGING è un processo di piegatura dei bordi che si traduce in un angolo di 90 gradi. Gli obiettivi principali dell'operazione sono l'eliminazione degli spigoli vivi e l'ottenimento di superfici geometriche per facilitare l'unione delle parti. BEADING, un altro comune processo di piegatura dei bordi forma un ricciolo sul bordo di una parte. L'ORLATURA invece risulta con un bordo del foglio che è completamente ripiegato su se stesso. In SEAMING, i bordi di due parti vengono piegati l'uno sull'altro e uniti. LA DOPPIA AGGANCIO invece fornisce giunti di lamiera a tenuta stagna ed ermetica. Simile alla piegatura dei bordi, un processo chiamato ROTARY BENDING distribuisce un cilindro con l'angolo desiderato ritagliato e funge da punzone. Quando la forza viene trasmessa al punzone, si chiude con il pezzo. La scanalatura del cilindro conferisce alla parte a sbalzo l'angolo desiderato. La scanalatura può avere un angolo minore o maggiore di 90 gradi. In AIR BENDING, non è necessario che lo stampo inferiore abbia una scanalatura angolata. La lamiera è supportata da due superfici sui lati opposti e ad una certa distanza. Il punzone applica quindi una forza nella posizione corretta e piega il pezzo. CHANNEL BENDING viene eseguita utilizzando un punzone e una matrice a forma di canale e U-BEND si ottiene con un punzone a forma di U. OFFSET BENDING produce offset sulla lamiera. LA PIEGATURA A RULLO, una tecnica adatta per lavori di grosso spessore e per la piegatura di grandi pezzi di lamiere metalliche, utilizza tre rulli per alimentare e piegare le lastre alle curvature desiderate. I rotoli sono disposti in modo da ottenere la piega desiderata del lavoro. La distanza e l'angolo tra i rotoli è controllata per ottenere il risultato desiderato. Un rullo mobile permette di controllare la curvatura. TUBE FORMING è un'altra popolare operazione di piegatura della lamiera che coinvolge più stampi. I tubi si ottengono dopo più azioni. LA CORRUGAZIONE viene eseguita anche mediante operazioni di piegatura. Fondamentalmente è la piegatura simmetrica a intervalli regolari su un intero pezzo di lamiera. Varie forme possono essere utilizzate per l'ondulazione. La lamiera grecata è più rigida e ha una migliore resistenza alla flessione e quindi trova applicazioni nel settore edile. LAMIERA RULLO FORMING, un processo di produzione continuo viene utilizzato per piegare sezioni trasversali di una certa geometria utilizzando rulli e il lavoro viene piegato in fasi sequenziali, con il rullo finale che completa il lavoro. In alcuni casi viene impiegato un singolo rullo e in alcuni casi una serie di rulli. • PROCESSI COMBINATI DI TAGLIO E PIEGATURA LAMIERA: Questi sono i processi che tagliano e piegano allo stesso tempo. In PIERCING, viene creato un foro usando un punzone appuntito. Quando il punzone allarga il foro nel foglio, il materiale viene piegato simultaneamente in una flangia interna per il foro. La flangia ottenuta può avere importanti funzioni. L'operazione PLANCIA invece taglia e piega la lamiera per creare una geometria in rilievo. • RIgonfiamento E PIEGATURA DEL TUBO METALLICO: Nel RIgonfiamento una parte interna di un tubo cavo viene pressurizzata, provocando il rigonfiamento del tubo verso l'esterno. Poiché il tubo si trova all'interno di una filiera, la geometria del rigonfiamento è controllata dalla forma della filiera. In STRETCH BENDING, un tubo di metallo viene allungato utilizzando forze parallele all'asse del tubo e forze di flessione per tirare il tubo su un blocco di forma. In DRAW BENDING, fissiamo il tubo vicino alla sua estremità a un blocco di forma rotante che piega il tubo durante la rotazione. Infine, nella PIEGATURA A COMPRESSIONE il tubo viene trattenuto con forza su un blocco di forma fisso e una matrice lo piega sopra il blocco di forma. • IMBOTTITURA PROFONDA: In una delle nostre operazioni più popolari, vengono utilizzati un punzone, una matrice di corrispondenza e un premilamiera. Lo sbozzato di lamiera viene posizionato sopra l'apertura dello stampo e il punzone si sposta verso lo sbozzato trattenuto dal premilamiera. Una volta entrati in contatto, il punzone spinge la lamiera nella cavità dello stampo per formare il prodotto. L'operazione di imbutitura è simile al taglio, tuttavia la distanza tra il punzone e la matrice impedisce il taglio del foglio. Un altro fattore che assicura che il foglio sia imbutito e non tagliato sono gli angoli arrotondati della matrice e del punzone che impediscono il taglio e il taglio. Per ottenere una maggiore entità dell'imbutitura, viene implementato un processo di REDRAWING in cui viene eseguita una successiva imbutitura su una parte che ha già subito un processo di imbutitura profonda. In REVERSE REDRAWING, la parte imbutita viene capovolta e disegnata nella direzione opposta. L'imbutitura profonda può fornire oggetti di forma irregolare come coppe a cupola, affusolate o a gradini, In EMBOSSING utilizziamo una coppia di fustelle maschio e femmina per imprimere sulla lamiera un disegno o una scritta. • SPINNING : un'operazione in cui un pezzo piatto o preformato viene trattenuto tra un mandrino rotante e una contropunta e un utensile applica una pressione localizzata al lavoro mentre si sposta gradualmente verso l'alto il mandrino. Di conseguenza, il pezzo viene avvolto sul mandrino e prende la sua forma. Usiamo questa tecnica come alternativa all'imbutitura dove la quantità di un ordine è piccola, le parti sono grandi (diametri fino a 20 piedi) e hanno curve uniche. Anche se i prezzi per pezzo sono generalmente più elevati, i costi di allestimento per l'operazione di filatura CNC sono bassi rispetto all'imbutitura. Al contrario, l'imbutitura richiede un investimento iniziale elevato per la messa a punto, ma i costi per pezzo sono bassi quando vengono prodotte quantità elevate di parti. Un'altra versione di questo processo è SHEAR SPINNING, dove c'è anche flusso di metallo all'interno del pezzo. Il flusso di metallo ridurrà lo spessore del pezzo durante l'esecuzione del processo. Ancora un altro processo correlato è TUBE SPINNING, che viene applicato su parti cilindriche. Anche in questo processo c'è flusso di metallo all'interno del pezzo. Lo spessore viene così ridotto e la lunghezza del tubo viene aumentata. Lo strumento può essere spostato per creare feature all'interno o all'esterno del tubo. • FORMATURA DELLA GOMMA DELLA LAMIERA: Il materiale in gomma o poliuretano viene inserito in una matrice contenitore e il pezzo da lavorare viene posizionato sulla superficie della gomma. Un punzone viene quindi azionato sul pezzo da lavorare e lo forza nella gomma. Poiché la pressione generata dalla gomma è bassa, la profondità delle parti prodotte è limitata. Poiché i costi degli utensili sono bassi, il processo è adatto per la produzione di piccole quantità. • IDROFORMAZIONE: Simile alla formatura della gomma, in questo processo la lamiera viene pressata da un punzone in un liquido pressurizzato all'interno di una camera. La lamiera è inserita tra il punzone e un diaframma di gomma. Il diaframma circonda completamente il pezzo e la pressione del fluido lo costringe a formarsi sul punzone. Con questa tecnica è possibile ottenere imbutiture molto profonde anche più profonde rispetto al processo di imbutitura profonda. Produciamo stampi a punzone singolo e stampi progressivi a seconda del pezzo. Gli stampi per stampaggio a corsa singola sono un metodo conveniente per produrre rapidamente grandi quantità di semplici parti in lamiera come le rondelle. Gli stampi progressivi o la tecnica di imbutitura profonda vengono utilizzati per la produzione di geometrie più complesse. A seconda del caso, è possibile utilizzare il taglio a getto d'acqua, laser o plasma per produrre le parti in lamiera in modo economico, rapido e preciso. Molti fornitori non hanno idea di queste tecniche alternative o non le hanno e quindi utilizzano metodi lunghi e costosi per realizzare stampi e strumenti che fanno sprecare ai clienti solo tempo e denaro. Se hai bisogno di componenti in lamiera personalizzati come custodie, custodie elettroniche... ecc. in pochi giorni, contattaci per il nostro servizio di PROTOTIPAZIONE RAPIDA DI LAMIERE. CLICK Product Finder-Locator Service MENÙ PRECEDENTE
- Forgiatura e Metallurgia delle Polveri, Forgiatura Stampi, Intestatura, Forgiatura a Caldo
Forgiatura e metallurgia delle polveri, forgiatura di stampi, intestazione, forgiatura a caldo, stampaggio a impronta, forma quasi netta, stampaggio, dentatura di metalli, rivettatura, coniatura da AGS-TECH Inc. Forgiatura dei metalli e metallurgia delle polveri Il tipo di processi di FORGIATURA METALLICA che offriamo sono stampi a caldo ea freddo, stampi aperti e chiusi, stampi per impronte e forgiati senza flash, cogging, follatura, bordatura e forgiatura di precisione, forma quasi rete, testata , forgiatura, forgiatura a rovescio, forgiatura di metalli, pressa e rullo e forgiatura radiale e orbitale e ad anello e isotermica, coniatura, rivettatura, forgiatura di sfere metalliche, perforazione di metalli, dimensionamento, forgiatura ad alto tasso di energia. Le nostre tecniche di METALLURGIA e LAVORAZIONE DELLE POLVERI sono la pressatura e la sinterizzazione delle polveri, l'impregnazione, l'infiltrazione, la pressatura isostatica a caldo ea freddo, lo stampaggio a iniezione dei metalli, la compattazione dei rulli, la laminazione delle polveri, l'estrusione delle polveri, la sinterizzazione sfusa, la sinterizzazione a scintilla, la pressatura a caldo. Ti consigliamo di fare clic qui per SCARICA le nostre illustrazioni schematiche dei processi di forgiatura di AGS-TECH Inc. SCARICA le nostre illustrazioni schematiche dei processi di metallurgia delle polveri di AGS-TECH Inc. Questi file scaricabili con foto e schizzi ti aiuteranno a comprendere meglio le informazioni che ti forniamo di seguito. Nella forgiatura dei metalli vengono applicate forze di compressione e il materiale viene deformato e si ottiene la forma desiderata. I materiali forgiati più comuni nell'industria sono il ferro e l'acciaio, ma anche numerosi altri come alluminio, rame, titanio, magnesio sono ampiamente forgiati. Le parti metalliche forgiate hanno strutture del grano migliorate oltre a fessure sigillate e spazi vuoti chiusi, quindi la resistenza delle parti ottenute con questo processo è maggiore. La forgiatura produce parti che sono significativamente più resistenti per il loro peso rispetto alle parti realizzate mediante fusione o lavorazione. Poiché le parti forgiate sono modellate facendo scorrere il metallo nella sua forma finale, il metallo assume una struttura a grana direzionale che spiega la resistenza superiore delle parti. In altre parole, le parti ottenute dal processo di forgiatura rivelano migliori proprietà meccaniche rispetto alle semplici parti fuse o lavorate. Il peso dei pezzi forgiati in metallo può variare da piccole parti leggere a centinaia di migliaia di libbre. Produciamo forgiati principalmente per applicazioni meccanicamente impegnative in cui vengono applicate sollecitazioni elevate su parti come parti di automobili, ingranaggi, strumenti di lavoro, utensili manuali, alberi di turbine, ingranaggi di motociclette. Poiché i costi di attrezzaggio e configurazione sono relativamente elevati, consigliamo questo processo di produzione solo per la produzione di volumi elevati e per componenti critici di basso volume ma di alto valore come il carrello di atterraggio aerospaziale. Oltre al costo degli utensili, i tempi di produzione per grandi quantità di pezzi forgiati possono essere più lunghi rispetto ad alcuni semplici pezzi lavorati, ma la tecnica è fondamentale per parti che richiedono una resistenza straordinaria come bulloni, dadi, applicazioni speciali elementi di fissaggio, automotive, carrelli elevatori, parti di gru. • STAMPAGGIO A CALDO e STAMPAGGIO A FREDDO: Lo stampaggio a caldo, come suggerisce il nome, viene eseguito ad alte temperature, la duttilità è quindi elevata e la resistenza del materiale bassa. Ciò facilita la deformazione e la forgiatura facili. Al contrario, la forgiatura a freddo viene eseguita a temperature più basse e richiede forze maggiori che si traducono in incrudimento, migliore finitura superficiale e precisione delle parti prodotte. • STAMPAGGIO APERTO e STAMPAGGIO A IMPRONTA: Nella forgiatura a stampo aperto, gli stampi non vincolano il materiale da comprimere, mentre nella forgiatura a stampo le cavità all'interno degli stampi limitano il flusso del materiale mentre viene forgiato nella forma desiderata. UPSET FORGING o anche chiamato UPSETTING, che in realtà non è lo stesso ma un processo molto simile, è un processo di stampo aperto in cui il pezzo è inserito tra due stampi piatti e una forza di compressione ne riduce l'altezza. Poiché l'altezza è ridotta, la larghezza del pezzo da lavorare aumenta. HEADING, un processo di forgiatura rovesciata prevede un grezzo cilindrico che viene ribaltato alla sua estremità e la sua sezione trasversale viene aumentata localmente. Nella testata lo stock viene alimentato attraverso lo stampo, forgiato e quindi tagliato a misura. L'operazione è in grado di produrre rapidamente elevate quantità di elementi di fissaggio. Per lo più è un'operazione di lavorazione a freddo perché viene utilizzata per realizzare punte di chiodi, estremità di viti, dadi e bulloni dove il materiale deve essere rinforzato. Un altro processo di stampo aperto è COGGING, in cui il pezzo da lavorare viene forgiato in una serie di passaggi con ogni passaggio che determina la compressione del materiale e il successivo movimento dello stampo aperto lungo la lunghezza del pezzo da lavorare. Ad ogni passaggio, lo spessore viene ridotto e la lunghezza viene leggermente aumentata. Il processo assomiglia a uno studente nervoso che morde la matita per tutto il tempo a piccoli passi. Un processo chiamato FULLERING è un altro metodo di forgiatura a stampo aperto che spesso utilizziamo come passaggio precedente per distribuire il materiale nel pezzo prima che avvengano altre operazioni di forgiatura dei metalli. Lo usiamo quando il pezzo richiede diverse operazioni di forging . Nell'operazione, la matrice con superfici convesse si deforma e fa fuoriuscire il metallo su entrambi i lati. Un processo simile alla follatura, BORDO d'altra parte prevede una matrice aperta con superfici concave per deformare il pezzo. Anche la bordatura, un processo preparatorio per le successive operazioni di forgiatura, fa fluire il materiale da entrambi i lati in un'area centrale. LA FORGIATURA A IMPRONTA o FORGIATURA CHIUSA come viene anche chiamata utilizza uno stampo/stampo che comprime il materiale e ne limita il flusso al suo interno. La trafila si chiude e il materiale prende la forma della trafila/cavità dello stampo. LA FORGIATURA DI PRECISIONE, un processo che richiede attrezzature e stampi speciali, produce pezzi con bagliore nullo o minimo. In altre parole, le parti avranno dimensioni quasi finali. In questo processo una quantità ben controllata di materiale viene accuratamente inserita e posizionata all'interno dello stampo. Utilizziamo questo metodo per forme complesse con sezioni sottili, tolleranze e angoli di sformo ridotti e quando le quantità sono sufficientemente grandi da giustificare i costi di stampi e attrezzature. • FORGIATURA FLASHLESS: Il pezzo viene posizionato nello stampo in modo tale che nessun materiale possa fuoriuscire dalla cavità per formare bave. Non è quindi necessario alcun taglio del flash indesiderato. È un processo di forgiatura di precisione e quindi richiede uno stretto controllo della quantità di materiale utilizzato. • FORGIATURA METALLICA o FORGIATURA RADIALE: Un pezzo viene lavorato circonferenzialmente da una matrice e forgiato. Un mandrino può anche essere utilizzato per forgiare la geometria interna del pezzo. Nell'operazione di pressatura il pezzo in lavorazione riceve tipicamente più colpi al secondo. Gli articoli tipici prodotti dalla forgiatura sono strumenti a punta appuntita, barre coniche, cacciaviti. • METAL PIERCING : Usiamo questa operazione frequentemente come operazione aggiuntiva nella produzione di parti. Viene creato un foro o una cavità perforando la superficie del pezzo senza sfondarla. Si prega di notare che la perforazione è diversa dalla perforazione che si traduce in un foro passante. • CREAZIONE A CREMAGLIERA: un punzone con la geometria desiderata viene premuto nel pezzo e crea una cavità con la forma desiderata. Chiamiamo questo pugno un HOB. L'operazione prevede alte pressioni e si effettua a freddo. Di conseguenza il materiale viene lavorato a freddo e indurito. Pertanto questo processo è molto adatto per la produzione di stampi, matrici e cavità per altri processi di produzione. Una volta prodotto il piano, è possibile realizzare facilmente molte cavità identiche senza la necessità di lavorarle una per una. • FORGIATURA A RULLI o FORGIATURA A RULLI: Per sagomare la parte metallica vengono utilizzati due rulli contrapposti. Il pezzo viene alimentato nei rulli, i rulli girano e tirano il pezzo nella fessura, il pezzo viene quindi alimentato attraverso la parte scanalata dei rulli e le forze di compressione conferiscono al materiale la forma desiderata. Non è un processo di laminazione ma un processo di forgiatura, perché è un'operazione discreta piuttosto che continua. La geometria sulle scanalature dei rulli forgia il materiale alla forma e alla geometria richieste. Si esegue a caldo. Poiché è un processo di forgiatura, produce parti con proprietà meccaniche eccezionali e quindi lo utilizziamo per produzione di parti automobilistiche come alberi che devono avere una durata straordinaria in ambienti di lavoro difficili. • FORGIATURA ORBITALE : Il pezzo da lavorare viene inserito in una cavità dello stampo di forgiatura e forgiato da uno stampo superiore che viaggia in un percorso orbitale mentre ruota su un asse inclinato. Ad ogni giro, lo stampo superiore completa esercitando forze di compressione sull'intero pezzo da lavorare. Ripetendo queste rivoluzioni un certo numero di volte, viene eseguita una forgiatura sufficiente. I vantaggi di questa tecnica di produzione sono il suo funzionamento a bassa rumorosità e le minori forze necessarie. In altre parole con piccole forze si può far ruotare uno stampo pesante attorno ad un asse per applicare grandi pressioni su una sezione del pezzo in lavorazione che è a contatto con lo stampo. A volte le parti a forma di disco o coniche si adattano bene a questo processo. • FORGIATURA DI ANELLI: Usiamo spesso per produrre anelli senza saldatura. Il brodo viene tagliato a misura, rovesciato e poi trafitto fino in fondo per creare un foro centrale. Quindi viene messo su un mandrino e uno stampo di forgiatura lo martella dall'alto mentre l'anello viene ruotato lentamente fino a ottenere le dimensioni desiderate. • RIVETTATURA: un processo comune per unire le parti, inizia con un pezzo di metallo diritto inserito in fori preformati attraverso le parti. Successivamente le due estremità del pezzo metallico vengono forgiate schiacciando il giunto tra uno stampo superiore e uno inferiore. • CONIATURA: un altro processo popolare eseguito dalla pressa meccanica, che esercita grandi forze su una breve distanza. Il nome “coniatura” deriva dai dettagli fini che vengono forgiati sulla superficie delle monete metalliche. Si tratta principalmente di un processo di finitura per un prodotto in cui si ottengono dettagli fini sulle superfici grazie alla grande forza applicata dalla matrice che trasferisce questi dettagli sul pezzo da lavorare. • FORGIATURA DI SFERE DI METALLO: prodotti come i cuscinetti a sfere richiedono sfere di metallo di alta qualità, fabbricate con precisione. In una tecnica chiamata SKEW ROLLING, utilizziamo due rulli opposti che ruotano continuamente mentre il materiale viene alimentato continuamente nei rulli. Ad un'estremità dei due rulli vengono espulse sfere di metallo come prodotto. Un secondo metodo per la forgiatura delle sfere di metallo è l'utilizzo di stampi che comprimono il materiale inserito tra di loro assumendo la forma sferica della cavità dello stampo. Spesso le palline prodotte richiedono alcuni passaggi aggiuntivi come la finitura e la lucidatura per diventare un prodotto di alta qualità. • FORGIATURA ISOTERMICA / STAMPAGGIO A CALDO: Un processo costoso eseguito solo quando il valore del beneficio/costo è giustificato. Un processo di lavorazione a caldo in cui gli stampi vengono riscaldati all'incirca alla stessa temperatura del pezzo in lavorazione. Poiché sia lo stampo che il lavoro hanno all'incirca la stessa temperatura, non c'è raffreddamento e le caratteristiche di flusso del metallo sono migliorate. L'operazione è adatta per superleghe e materiali con forgiabilità inferiore e materiali la cui le proprietà meccaniche sono molto sensibili a piccoli gradienti di temperatura e variazioni. • DIMENSIONAMENTO METALLO : E' un processo di finitura a freddo. Il flusso del materiale è illimitato in tutte le direzioni ad eccezione della direzione in cui viene applicata la forza. Di conseguenza, si ottengono un'ottima finitura superficiale e dimensioni accurate. • FORGIATURA AD ALTO TASSO DI ENERGIA: La tecnica prevede uno stampo superiore attaccato al braccio di un pistone che viene spinto rapidamente quando una miscela aria-carburante viene accesa da una candela. Assomiglia al funzionamento dei pistoni nel motore di un'auto. Lo stampo colpisce il pezzo molto velocemente e poi ritorna molto velocemente nella sua posizione originale grazie alla contropressione. Il lavoro viene forgiato nel giro di pochi millisecondi e quindi non c'è tempo per raffreddare il lavoro. Ciò è utile per parti difficili da forgiare con proprietà meccaniche molto sensibili alla temperatura. In altre parole, il processo è così veloce che la parte viene formata a temperatura costante e non ci saranno gradienti di temperatura sulle interfacce stampo/pezzo. • Nello STAMPAGGIO, il metallo viene battuto tra due blocchi di acciaio abbinati con forme speciali al loro interno, detti stampi. Quando il metallo viene martellato tra le trafile, assume la stessa forma delle forme della trafila. Quando raggiunge la sua forma finale, viene tirato fuori per raffreddare. Questo processo produce parti robuste che hanno una forma precisa, ma richiede un investimento maggiore per gli stampi specializzati. La forgiatura rovesciata aumenta il diametro di un pezzo di metallo appiattendolo. Viene generalmente utilizzato per realizzare piccole parti, in particolare per formare teste su elementi di fissaggio come bulloni e chiodi. • METALLURGIA DELLE POLVERI / LAVORAZIONE DELLE POLVERI: come suggerisce il nome, si tratta di processi di fabbricazione per realizzare parti solide di determinate geometrie e forme da polveri. Se le polveri metalliche vengono utilizzate per questo scopo, è il regno della metallurgia delle polveri e se vengono utilizzate polveri non metalliche è la lavorazione delle polveri. Le parti solide sono prodotte da polveri mediante pressatura e sinterizzazione. POWDER PRESSING viene utilizzato per compattare le polveri nelle forme desiderate. In primo luogo, il materiale primario viene fisicamente polverizzato, dividendolo in tante piccole particelle individuali. La miscela di polvere viene riempita nello stampo e un punzone si muove verso la polvere e la compatta nella forma desiderata. Eseguita prevalentemente a temperatura ambiente, con la pressatura delle polveri si ottiene una parte solida che prende il nome di green compact. Leganti e lubrificanti sono comunemente usati per migliorare la compattabilità. Siamo in grado di eseguire la formatura delle polveri mediante presse idrauliche con capacità di diverse migliaia di tonnellate. Inoltre abbiamo presse a doppia azione con punzoni superiori e inferiori contrapposti, nonché presse ad azione multipla per geometrie di pezzi altamente complesse. L'uniformità, che è una sfida importante per molti impianti di metallurgia/lavorazione delle polveri, non è un grosso problema per AGS-TECH, grazie alla nostra vasta esperienza pluriennale nella produzione personalizzata di tali parti. Anche con parti più spesse in cui l'uniformità rappresenta una sfida, ci siamo riusciti. Se ci impegniamo nel tuo progetto, realizzeremo le tue parti. Se vediamo potenziali rischi, ti informeremo in anticipo. La SINTERIZZAZIONE DELLA POLVERE, che è la seconda fase, prevede l'innalzamento della temperatura ad un certo grado e il mantenimento della temperatura a quel livello per un certo tempo in modo che le particelle di polvere nella parte stampata possano legarsi tra loro. Ciò si traduce in legami molto più forti e rafforzamento del pezzo in lavorazione. La sinterizzazione avviene vicino alla temperatura di fusione della polvere. Durante la sinterizzazione si verificherà un restringimento, la resistenza del materiale, la densità, la duttilità, la conduttività termica e la conduttività elettrica saranno aumentate. Disponiamo di forni batch e continui per la sinterizzazione. Una delle nostre capacità è regolare il livello di porosità delle parti che produciamo. Ad esempio siamo in grado di produrre filtri metallici mantenendo le parti in una certa misura porose. Usando una tecnica chiamata IMPREGNAZIONE, riempiamo i pori del metallo con un fluido come l'olio. Produciamo ad esempio cuscinetti impregnati d'olio che sono autolubrificanti. Nel processo di INFILTRAZIONE riempiamo i pori di un metallo con un altro metallo con punto di fusione inferiore al materiale di base. La miscela viene riscaldata a una temperatura compresa tra le temperature di fusione dei due metalli. Di conseguenza si possono ottenere alcune proprietà speciali. Eseguiamo spesso anche operazioni secondarie come la lavorazione a macchina e la forgiatura su parti prodotte in polvere quando è necessario ottenere caratteristiche o proprietà speciali o quando la parte può essere prodotta con meno fasi di processo. PRESSATURA ISOSTATICA: In questo processo la pressione del fluido viene utilizzata per compattare la parte. Le polveri metalliche vengono poste in uno stampo costituito da un contenitore flessibile sigillato. Nella pressatura isostatica, la pressione viene applicata da tutto intorno, contrariamente alla pressione assiale vista nella pressatura convenzionale. I vantaggi della pressatura isostatica sono la densità uniforme all'interno della parte, specialmente per le parti più grandi o più spesse, proprietà superiori. Il suo svantaggio sono i lunghi tempi di ciclo e le precisioni geometriche relativamente basse. Lo STAMPAGGIO ISOSTATICO A FREDDO viene effettuato a temperatura ambiente e lo stampo flessibile è realizzato in gomma, PVC o uretano o materiali simili. Il fluido utilizzato per pressurizzare e compattare è olio o acqua. Segue la sinterizzazione convenzionale del compatto verde. La PRESSATURA ISOSTATICA A CALDO invece viene eseguita ad alte temperature e il materiale dello stampo è lamiera o ceramica con punto di fusione sufficientemente alto da resistere alle temperature. Il fluido di pressurizzazione è solitamente un gas inerte. Le operazioni di pressatura e sinterizzazione vengono eseguite in un unico passaggio. La porosità viene quasi completamente eliminata, si ottiene una struttura uniform grain. Il vantaggio della pressatura isostatica a caldo è che può produrre parti paragonabili alla fusione e alla forgiatura combinate, rendendo possibile l'uso di materiali che non sono adatti per la fusione e la forgiatura. Lo svantaggio della pressatura isostatica a caldo è il suo tempo di ciclo elevato e quindi il costo. È adatto per parti critiche di basso volume. STAMPAGGIO A INIEZIONE DI METALLI : Processo molto adatto per la produzione di parti complesse con pareti sottili e geometrie dettagliate. Più adatto per parti più piccole. Le polveri e il legante polimerico vengono miscelati, riscaldati e iniettati in uno stampo. Il legante polimerico riveste le superfici delle particelle di polvere. Dopo lo stampaggio, il legante viene rimosso mediante riscaldamento a bassa temperatura o disciolto utilizzando un solvente. COMPATTAZIONE IN ROTOLI / LAMINAZIONE IN POLVERE: Le polveri vengono utilizzate per produrre nastri o fogli continui. La polvere viene alimentata da un alimentatore e compattata da due rulli rotanti in fogli o strisce. L'operazione viene eseguita a freddo. La lastra viene trasportata in un forno di sinterizzazione. Il processo di sinterizzazione può essere ripetuto una seconda volta. ESTRUSIONE IN POLVERE: Le parti con un rapporto lunghezza/diametro elevati vengono prodotte estrudendo un contenitore di lamiera sottile con polvere. SINTERIZZAZIONE ALLENTATA: Come suggerisce il nome, è un metodo di compattazione e sinterizzazione senza pressione, adatto per la produzione di parti molto porose come i filtri metallici. La polvere viene immessa nella cavità dello stampo senza compattarsi. SINTERIZZAZIONE ALLENTATA: Come suggerisce il nome, è un metodo di compattazione e sinterizzazione senza pressione, adatto per la produzione di parti molto porose come i filtri metallici. La polvere viene immessa nella cavità dello stampo senza compattarsi. SINTERIZZAZIONE A SCINTILLA: La polvere viene compressa nello stampo da due punzoni contrapposti e una corrente elettrica ad alta potenza viene applicata al punzone e passa attraverso la polvere compattata racchiusa tra di loro. L'elevata corrente brucia le pellicole superficiali dalle particelle di polvere e le sinterizza con il calore generato. Il processo è veloce perché il calore non viene applicato dall'esterno ma viene invece generato dall'interno dello stampo. PRESSATURA A CALDO: Le polveri vengono pressate e sinterizzate in un unico passaggio in uno stampo in grado di resistere alle alte temperature. Quando lo stampo si compatta, viene applicato il calore della polvere. La buona precisione e le proprietà meccaniche ottenute con questo metodo lo rendono un'opzione interessante. Anche i metalli refrattari possono essere lavorati utilizzando materiali per stampi come la grafite. CLICK Product Finder-Locator Service MENÙ PRECEDENTE
- Estrusioni di gomma plastica metallo, matrici di estrusione, estrusione di alluminio
Estrusioni di metallo in gomma plastica, matrici di estrusione, estrusione di alluminio, formatura di tubi per tubi, profili in plastica, produzione di profili in metallo, PVC presso AGS-TECH Inc. Estrusioni, prodotti estrusi, estrusi Utilizziamo il processo EXTRUSION per produrre prodotti con un profilo di sezione trasversale fisso come tubi, tubi e dissipatori di calore. Anche se molti materiali possono essere estrusi, le nostre estrusioni più comuni sono realizzate in metallo, polimeri/plastica, ceramica ottenute con metodo di estrusione a freddo, a caldo oa caldo. Chiamiamo le parti estruse estrudere o estrudere se plurale. Alcune versioni specializzate del processo che eseguiamo anche sono il rivestimento, la coestrusione e l'estrusione di composti. Ti consigliamo di fare clic qui per SCARICA le nostre illustrazioni schematiche dei processi di estrusione di metallo, ceramica e plastica di AGS-TECH Inc. Questo ti aiuterà a comprendere meglio le informazioni che ti stiamo fornendo di seguito. Nell'estrusione il materiale da estrudere viene spinto o trafilato attraverso uno stampo che ha il profilo della sezione trasversale desiderato. Il processo può essere utilizzato per produrre sezioni trasversali complesse con un'eccellente finitura superficiale e per lavorare su materiale fragile. Si può produrre qualsiasi lunghezza di parti utilizzando questo processo. Per semplificare le fasi del processo: 1.) Nelle estrusioni calde o calde il materiale viene riscaldato e caricato in un contenitore nella pressa. Il materiale viene pressato ed espulso dallo stampo. 2.) L'estruso prodotto viene stirato per essere raddrizzato, trattato termicamente o lavorato a freddo per esaltarne le proprietà. D'altra parte COLD EXTRUSION avviene a temperatura ambiente e presenta i vantaggi di minore ossidazione, elevata resistenza, tolleranze più strette, buona finitura superficiale e solidità. WARM EXTRUSION viene eseguito al di sopra della temperatura ambiente ma al di sotto del punto di ricristallizzazione. Offre un compromesso e un equilibrio per le forze richieste, la duttilità e le proprietà del materiale ed è quindi la scelta per alcune applicazioni. HOT EXTRUSION avviene al di sopra della temperatura di ricristallizzazione del materiale. In questo modo è più facile spingere il materiale attraverso lo stampo. Tuttavia il costo dell'attrezzatura è elevato. Più un profilo estruso è complesso, più costosa è la filiera (attrezzature) e minore è la velocità di produzione. Le sezioni trasversali dello stampo e gli spessori hanno limitazioni che dipendono dal materiale da estrudere. Gli spigoli vivi negli stampi per estrusione sono sempre indesiderabili e da evitare se non necessario. A seconda del materiale che viene estruso, offriamo: • ESTRUSIONI METALLICHE : Le più comuni che produciamo sono alluminio, ottone, zinco, rame, acciaio, titanio, magnesio • PLASTIC EXTRUSION : la plastica viene fusa e formata in un profilo continuo. I nostri materiali comuni lavorati sono polietilene, nylon, polistirene, polivinilcloruro, polipropilene, plastica ABS, policarbonato, acrilico. I prodotti tipici che produciamo includono tubi e tubazioni, telai in plastica. Nel processo, piccole perline di plastica/resina vengono alimentate per gravità dalla tramoggia nella canna della macchina di estrusione. Spesso mescoliamo anche coloranti o altri additivi nella tramoggia per conferire al prodotto le specifiche e le proprietà richieste. Il materiale che entra nella canna riscaldata è costretto dalla vite rotante a lasciare la canna all'estremità e a muoversi attraverso il setaccio per la rimozione dei contaminanti nella plastica fusa. Dopo aver superato lo schermo, la plastica entra nella filiera di estrusione. Lo stampo conferisce alla plastica morbida in movimento la sua forma di profilo mentre la attraversa. Ora l'estruso passa attraverso un bagno d'acqua per il raffreddamento. Altre tecniche che AGS-TECH Inc. utilizza da molti anni sono: • ESTRUSIONE DI TUBI E TUBI : i tubi e i tubi di plastica si formano quando la plastica viene estrusa attraverso uno stampo di sagomatura circolare e raffreddata a bagnomaria, quindi tagliata a misura o arrotolata/bobinata. Trasparente o colorato, rigato, a parete singola o doppia, flessibile o rigido, PE, PP, poliuretano, PVC, nylon, PC, silicone, vinile o altro, abbiamo tutto. Abbiamo immagazzinato tubi e la capacità di produrre secondo le vostre specifiche. AGS-TECH produce tubi secondo i requisiti FDA, UL e LE per applicazioni mediche, elettriche ed elettroniche, industriali e di altro tipo. • OVERJACKETING / OVER JACKETING EXTRUSION : questa tecnica applica uno strato esterno di plastica sul filo o cavo esistente. I nostri fili isolanti sono realizzati con questo metodo. • COEXTRUSION : più strati di materiale vengono estrusi contemporaneamente. Gli strati multipli vengono forniti da più estrusori. I vari spessori degli strati possono essere regolati per soddisfare le specifiche del cliente. Questo processo consente di utilizzare più polimeri ciascuno aventi una diversa funzionalità nel prodotto. Di conseguenza, è possibile ottimizzare una gamma di proprietà. • ESTRUSIONE DEL COMPOUND: Uno o più polimeri vengono miscelati con additivi per ottenere un composto plastico. I nostri estrusori bivite producono estrusioni di compounding. Gli stampi per estrusione sono generalmente economici rispetto agli stampi in metallo. Se stai pagando molto più di qualche migliaio di dollari per uno stampo per estrusione di alluminio estruso di piccole o medie dimensioni, probabilmente stai pagando troppo. Siamo esperti nel determinare quale tecnica è la più conveniente, più veloce e più adatta alla tua applicazione. A volte l'estrusione e la lavorazione di una parte possono farti risparmiare un sacco di soldi. Prima di prendere una decisione ferma, chiedici prima la nostra opinione. Abbiamo aiutato molti clienti a prendere le decisioni giuste. Per alcuni estrusi metallici ampiamente utilizzati, puoi scaricare le nostre brochure e cataloghi facendo clic sul testo colorato qui sotto. Se si tratta di un prodotto pronto all'uso che soddisfa le tue esigenze, sarà più economico. Scarica le nostre capacità di estrusione di tubi e tubi medicali Scarica i nostri dissipatori di calore estrusi • PROCESSI DI FABBRICAZIONE E FABBRICAZIONE SECONDARI PER ESTRUSIONI : Tra i processi a valore aggiunto che offriamo per i prodotti estrusi ci sono: - Piegatura, formatura e sagomatura di tubi e tubi personalizzati, taglio tubi, formatura estremità tubi, avvolgimento tubi, lavorazione e finitura, perforazione e perforazione e punzonatura, -Assemblaggi di tubi e tubi personalizzati, assemblaggio tubolare, saldatura, brasatura e brasatura - Piegatura, formatura e sagomatura dell'estrusione personalizzata -Pulizia, sgrassaggio, decapaggio, passivazione, lucidatura, anodizzazione, placcatura, verniciatura, trattamento termico, ricottura e tempra, marcatura, incisione ed etichettatura, packaging personalizzato. CLICK Product Finder-Locator Service PAGINA PRECEDENTE
- Pezzi fusi e lavorati, produzione CNC, fresatura, tornitura, Svizzera
Pezzi fusi e lavorati, produzione CNC, fresatura, tornitura, lavorazione di tipo svizzero, pressofusione, microfusione, pezzi fusi in schiuma persa di AGS-TECH Inc. Fusione e lavorazione Le nostre tecniche di colata e lavorazione personalizzate sono getti consumabili e non, getti ferrosi e non ferrosi, sabbia, stampi, centrifughi, continui, stampi in ceramica, rivestimento, schiuma persa, forma quasi netta, stampo permanente (pressofusione a gravità), gesso stampi (colata in gesso) e fusioni in conchiglia, parti lavorate prodotte mediante fresatura e tornitura utilizzando attrezzature convenzionali e CNC, lavorazione di tipo svizzero per pezzi di piccola precisione a basso costo ad alta produttività, lavorazione di viti per elementi di fissaggio, lavorazione non convenzionale. Tieni presente che, oltre a metalli e leghe metalliche, lavoriamo anche componenti in ceramica, vetro e plastica, in alcuni casi quando la produzione di uno stampo non è interessante o non è un'opzione. La lavorazione di materiali polimerici richiede l'esperienza specializzata che abbiamo a causa della sfida che la plastica e la gomma presentano a causa della loro morbidezza, non rigidità ... ecc. Per la lavorazione di ceramica e vetro, consultare la nostra pagina sulla fabbricazione non convenzionale. AGS-TECH Inc. produce e fornisce fusioni sia leggere che pesanti. Abbiamo fornito fusioni metalliche e parti lavorate per caldaie, scambiatori di calore, automobili, micromotori, turbine eoliche, attrezzature per l'imballaggio alimentare e altro ancora. Ti consigliamo di fare clic qui per SCARICA le nostre illustrazioni schematiche dei processi di lavorazione e colata di AGS-TECH Inc. Questo ti aiuterà a comprendere meglio le informazioni che ti stiamo fornendo di seguito. Vediamo nel dettaglio alcune delle varie tecniche che offriamo: • COLATA DELLO STAMPO ESAURIBILE: questa ampia categoria si riferisce a metodi che coinvolgono stampi temporanei e non riutilizzabili. Esempi sono sabbia, gesso, conchiglia, rivestimento (chiamato anche cera persa) e colata in gesso. • COLATA IN SABBIA: un processo in cui la sabbia viene utilizzata come materiale dello stampo. Un metodo molto antico e ancora molto diffuso nella misura in cui la maggior parte delle fusioni metalliche prodotte sono realizzate con questa tecnica. Basso costo anche a basse quantità di produzione. Adatto per la produzione di piccoli e grandi pezzi. La tecnica può essere utilizzata per produrre parti in pochi giorni o settimane con un investimento minimo. La sabbia umida viene legata insieme usando argilla, leganti o oli speciali. La sabbia è generalmente contenuta negli stampi e il sistema cavità e cancello viene creato compattando la sabbia attorno ai modelli. I processi sono: 1.) Posizionamento del modello nella sabbia per realizzare lo stampo 2.) Incorporazione di modello e sabbia in un sistema di gating 3.) Rimozione del modello 4.) Riempimento della cavità dello stampo con metallo fuso 5.) Raffreddamento del metallo 6.) Rottura dello stampo in sabbia e rimozione del getto • COLATA IN STAMPO IN GESSO: Simile alla colata in sabbia, e invece della sabbia, come materiale dello stampo viene utilizzato gesso di Parigi. Tempi di produzione brevi come colata in sabbia ed economici. Buone tolleranze dimensionali e finitura superficiale. Il suo principale svantaggio è che può essere utilizzato solo con metalli a basso punto di fusione come alluminio e zinco. • COLATA IN SHELL MOLD : Simile anche alla colata in sabbia. Cavità dello stampo ottenuta da guscio indurito di sabbia e legante di resina termoindurente al posto della muffola riempita di sabbia come nel processo di colata in sabbia. Quasi tutti i metalli adatti per essere fusi con la sabbia possono essere fusi mediante stampaggio a conchiglia. Il processo può essere riassunto come: 1.) Fabbricazione dello stampo a conchiglia. La sabbia utilizzata ha una granulometria molto più piccola rispetto alla sabbia utilizzata nella colata in sabbia. La sabbia fine viene miscelata con resina termoindurente. Il motivo in metallo è rivestito con un agente distaccante per facilitare la rimozione del guscio. Successivamente il modello di metallo viene riscaldato e la miscela di sabbia viene porosa o soffiata sul modello di colata a caldo. Un sottile guscio si forma sulla superficie del motivo. Lo spessore di questo guscio può essere regolato variando il tempo in cui la miscela di sabbia e resina è a contatto con il motivo metallico. La sabbia sciolta viene quindi rimossa con il rimanente motivo ricoperto di conchiglie. 2.) Successivamente, il guscio e il motivo vengono riscaldati in un forno in modo che il guscio si indurisca. Dopo che l'indurimento è completo, il guscio viene espulso dal modello utilizzando perni incorporati nel modello. 3.) Due di questi gusci vengono assemblati insieme mediante incollaggio o bloccaggio e costituiscono lo stampo completo. Ora lo stampo a conchiglia viene inserito in un contenitore in cui viene supportato da sabbia o graniglia di metallo durante il processo di colata. 4.) Ora il metallo caldo può essere versato nello stampo a conchiglia. I vantaggi della colata in conchiglia sono prodotti con un'ottima finitura superficiale, possibilità di produrre parti complesse con elevata precisione dimensionale, processo facile da automatizzare, economico per grandi volumi di produzione. Gli svantaggi sono che gli stampi richiedono una buona ventilazione a causa dei gas che si creano quando il metallo fuso entra in contatto con il legante chimico, le resine termoindurenti e i modelli di metallo sono costosi. A causa del costo dei modelli in metallo, la tecnica potrebbe non adattarsi bene a basse quantità di produzione. • COLATA A INVESTIMENTO (nota anche come FUSIONE A CERA PERSA): anche una tecnica molto antica e adatta alla produzione di parti di qualità con elevata precisione, ripetibilità, versatilità e integrità da molti metalli, materiali refrattari e leghe speciali ad alte prestazioni. Possono essere prodotte parti di piccole e grandi dimensioni. Un processo costoso rispetto ad alcuni degli altri metodi, ma il vantaggio principale è la possibilità di produrre parti con una forma quasi netta, contorni e dettagli intricati. Quindi il costo è in qualche modo compensato dall'eliminazione di rilavorazione e lavorazione in alcuni casi. Anche se possono esserci variazioni, ecco un riepilogo del processo generale di microfusione: 1.) Creazione di un modello master originale da cera o plastica. Ogni fusione ha bisogno di un modello poiché questi vengono distrutti nel processo. È anche necessario lo stampo da cui vengono prodotti i modelli e la maggior parte delle volte lo stampo viene colato o lavorato. Poiché lo stampo non deve essere aperto, è possibile ottenere fusioni complesse, molti modelli in cera possono essere collegati come i rami di un albero e fusi insieme, consentendo così la produzione di più parti da un'unica colata del metallo o della lega metallica. 2.) Successivamente, il modello viene immerso o versato sopra con un impasto liquido refrattario composto da silice a grana molto fine, acqua, leganti. Ciò si traduce in uno strato di ceramica sulla superficie del motivo. Il mantello refrattario sul disegno viene lasciato asciugare e indurire. Da questo passaggio deriva il nome della colata a cera persa: la sospensione refrattaria viene investita sul modello in cera. 3.) A questo punto, lo stampo in ceramica indurita viene capovolto e riscaldato in modo che la cera si sciolga e fuoriesca dallo stampo. Viene lasciata una cavità per la colata di metallo. 4.) Dopo che la cera è fuoriuscita, lo stampo in ceramica viene riscaldato a una temperatura ancora più elevata, il che si traduce in un rafforzamento dello stampo. 5.) La colata di metallo viene versata nello stampo caldo riempiendo tutte le sezioni complesse. 6.) La colata può solidificare 7.) Infine si rompe lo stampo in ceramica e si tagliano i manufatti dall'albero. Ecco un collegamento all'opuscolo dell'impianto di colata di investimento • COLATA DEL MODELLO EVAPORATIVO: il processo utilizza un modello realizzato con un materiale come il polistirene espanso che evaporerà quando il metallo fuso caldo viene versato nello stampo. Esistono due tipi di questo processo: LOST FOAM CASTING che utilizza sabbia non legata e FULL MOLD CASTING che utilizza sabbia legata. Ecco i passaggi generali del processo: 1.) Realizzare il modello da un materiale come il polistirolo. Quando verranno prodotte grandi quantità, il modello viene modellato. Se la parte ha una forma complessa, potrebbe essere necessario far aderire insieme diverse sezioni di tale materiale espanso per formare il motivo. Spesso ricopriamo il modello con un composto refrattario per creare una buona finitura superficiale sul getto. 2.) Il motivo viene quindi messo nella sabbia per modellare. 3.) Il metallo fuso viene colato nello stampo, facendo evaporare il modello di schiuma, nella maggior parte dei casi il polistirene mentre scorre attraverso la cavità dello stampo. 4.) Il metallo fuso viene lasciato indurire nello stampo di sabbia. 5.) Dopo che si è indurito, rimuoviamo il getto. In alcuni casi, il prodotto che produciamo richiede un nucleo all'interno del modello. Nella colata evaporativa, non è necessario posizionare e fissare un'anima nella cavità dello stampo. La tecnica è adatta per la produzione di geometrie molto complesse, può essere facilmente automatizzata per produzioni ad alto volume e non ci sono linee di divisione nella parte fusa. Il processo di base è semplice ed economico da implementare. Per la produzione di grandi volumi, poiché è necessario uno stampo o uno stampo per produrre i modelli dal polistirene, ciò può essere alquanto costoso. • COLATA IN STAMPO NON ESPANDIBILE: Questa ampia categoria si riferisce a metodi in cui lo stampo non ha bisogno di essere riformato dopo ogni ciclo di produzione. Esempi sono la colata permanente, in pressofusione, continua e centrifuga. Si ottiene la ripetibilità e le parti possono essere caratterizzate come NEAR NET SHAPE. • COLATA IN STAMPO PERMANENTE: Gli stampi riutilizzabili in metallo vengono utilizzati per fusioni multiple. Uno stampo permanente può generalmente essere utilizzato per decine di migliaia di volte prima che si esaurisca. La gravità, la pressione del gas o il vuoto sono generalmente utilizzati per riempire lo stampo. Gli stampi (chiamati anche stampi) sono generalmente realizzati in ferro, acciaio, ceramica o altri metalli. Il processo generale è: 1.) Lavorare e creare lo stampo. È comune lavorare lo stampo da due blocchi di metallo che si incastrano e possono essere aperti e chiusi. Sia le caratteristiche della parte che il sistema di iniezione sono generalmente lavorati nello stampo di colata. 2.) Le superfici interne dello stampo sono rivestite con un impasto liquido che incorpora materiali refrattari. Questo aiuta a controllare il flusso di calore e funge da lubrificante per una facile rimozione della parte fusa. 3.) Successivamente, le metà dello stampo permanente vengono chiuse e lo stampo viene riscaldato. 4.) Il metallo fuso viene colato nello stampo e lasciato riposare per la solidificazione. 5.) Prima che si verifichi molto raffreddamento, rimuoviamo la parte dallo stampo permanente utilizzando gli espulsori quando le metà dello stampo vengono aperte. Utilizziamo spesso la colata permanente in stampi per metalli a basso punto di fusione come zinco e alluminio. Per le fusioni in acciaio, utilizziamo la grafite come materiale per stampi. A volte otteniamo geometrie complesse utilizzando anime all'interno di stampi permanenti. I vantaggi di questa tecnica sono getti con buone proprietà meccaniche ottenute per raffreddamento rapido, uniformità delle proprietà, buona precisione e finitura superficiale, bassi tassi di scarto, possibilità di automatizzare il processo e produrre volumi elevati in modo economico. Gli svantaggi sono gli elevati costi di installazione iniziale che lo rendono inadatto per operazioni a basso volume e le limitazioni alle dimensioni delle parti prodotte. • PRESSOFUSIONE: uno stampo viene lavorato e il metallo fuso viene spinto ad alta pressione nelle cavità dello stampo. Sono possibili sia pressofusioni di metalli non ferrosi che ferrosi. Il processo è adatto per produzioni di grandi quantità di pezzi di piccole e medie dimensioni con dettagli, pareti estremamente sottili, consistenza dimensionale e buona finitura superficiale. AGS-TECH Inc. è in grado di produrre spessori di parete fino a 0,5 mm utilizzando questa tecnica. Come nella colata in stampo permanente, lo stampo deve essere costituito da due metà che possono aprirsi e chiudersi per la rimozione della parte prodotta. Uno stampo per pressofusione può avere più cavità per consentire la produzione di più getti con ogni ciclo. Gli stampi per pressofusione sono molto pesanti e molto più grandi delle parti che producono, quindi anche costosi. Ripariamo e sostituiamo gratuitamente le matrici usurate per i nostri clienti, a condizione che riordinino le loro parti da noi. I nostri stampi hanno una lunga durata nell'intervallo di diverse centinaia di migliaia di cicli. Di seguito sono riportati i passaggi di base del processo semplificato: 1.) Produzione dello stampo generalmente in acciaio 2.) Stampo installato su macchina per pressofusione 3.) Il pistone costringe il metallo fuso a fluire nelle cavità dello stampo riempiendo le caratteristiche intricate e le pareti sottili 4.) Dopo aver riempito lo stampo con il metallo fuso, la colata viene fatta indurire sotto pressione 5.) Lo stampo viene aperto e la colata rimossa con l'aiuto di perni di espulsione. 6.) Ora gli stampi vuoti vengono nuovamente lubrificati e bloccati per il ciclo successivo. Nella pressofusione, utilizziamo spesso lo stampaggio a inserti in cui incorporiamo una parte aggiuntiva nello stampo e fondiamo il metallo attorno ad esso. Dopo la solidificazione, queste parti diventano parte del prodotto colato. I vantaggi della pressofusione sono buone proprietà meccaniche delle parti, possibilità di caratteristiche complesse, dettagli fini e buona finitura superficiale, alti tassi di produzione, facile automazione. Gli svantaggi sono: Non molto adatto per bassi volumi a causa dell'elevato costo dello stampo e dell'attrezzatura, limitazioni nelle forme che possono essere fuse, piccoli segni rotondi sulle parti fuse risultanti dal contatto dei perni di espulsione, sottile lamella di metallo spremuta sulla linea di divisione, necessità per gli sfiati lungo la linea di separazione tra lo stampo, necessità di mantenere basse le temperature dello stampo utilizzando la circolazione dell'acqua. • COLATA CENTRIFUGA: Il metallo fuso viene colato al centro dello stampo rotante sull'asse di rotazione. Le forze centrifughe proiettano il metallo verso la periferia e viene lasciato solidificare mentre lo stampo continua a ruotare. È possibile utilizzare sia la rotazione dell'asse orizzontale che quella verticale. Possono essere colate parti con superfici interne rotonde e altre forme non rotonde. Il processo può essere riassunto come: 1.) Il metallo fuso viene versato nello stampo centrifugo. Il metallo viene quindi forzato alle pareti esterne a causa della filatura dello stampo. 2.) Quando lo stampo ruota, la colata di metallo si indurisce La colata centrifuga è una tecnica adatta per la produzione di parti cilindriche cave come tubi, nessuna necessità di materozze, colonne montanti ed elementi di iniezione, buona finitura superficiale e caratteristiche dettagliate, nessun problema di ritiro, possibilità di produrre tubi lunghi con diametri molto grandi, capacità di produzione elevata . • COLATA CONTINUA ( COLATA A STRAND ) : Usata per colare una lunghezza continua di metallo. Fondamentalmente il metallo fuso viene colato nel profilo bidimensionale dello stampo ma la sua lunghezza è indeterminata. Il nuovo metallo fuso viene costantemente alimentato nello stampo mentre la colata viaggia verso il basso con la sua lunghezza che aumenta con il tempo. Metalli come rame, acciaio, alluminio vengono fusi in lunghi fili utilizzando un processo di colata continua. Il processo può avere varie configurazioni ma quella comune può essere semplificata come: 1.) Il metallo fuso viene versato in un contenitore posizionato in alto sopra lo stampo a quantità e portate ben calcolate e scorre attraverso lo stampo raffreddato ad acqua. La colata metallica versata nello stampo solidifica su una barra di avviamento posta sul fondo dello stampo. Questa barra di avviamento offre ai rulli qualcosa a cui aggrapparsi inizialmente. 2.) Il lungo filo metallico è trasportato da rulli a velocità costante. I rulli cambiano anche la direzione del flusso del filo metallico da verticale a orizzontale. 3.) Dopo che la colata continua ha percorso una certa distanza orizzontale, una torcia o una sega che si muove con la colata la taglia rapidamente alla lunghezza desiderata. Il processo di colata continua può essere integrato con ROLLING PROCESS, dove il metallo colato in continuo può essere alimentato direttamente in un laminatoio per produrre I-Beams, T-Beams….ecc. La colata continua produce proprietà uniformi in tutto il prodotto, ha un alto tasso di solidificazione, riduce i costi grazie alla bassissima perdita di materiale, offre un processo in cui il caricamento del metallo, la colata, la solidificazione, il taglio e la rimozione della colata avvengono in un funzionamento continuo e con conseguente alto tasso di produttività e alta qualità. Una considerazione importante è tuttavia l'elevato investimento iniziale, i costi di installazione e i requisiti di spazio. • SERVIZI DI LAVORAZIONE: Offriamo lavorazioni a tre, quattro e cinque assi. I tipi di lavorazioni che utilizziamo sono TORNITURA, FRESATURA, FORATURA, ALESATURA, BROCCIA, PIALLATURA, SEGA, RETTIFICA, LAPPATURA, LUCIDATURA e LAVORAZIONE NON TRADIZIONALE che viene ulteriormente elaborata in un diverso menu del nostro sito web. Per la maggior parte della nostra produzione, utilizziamo macchine a controllo numerico. Tuttavia per alcune operazioni le tecniche convenzionali sono più adatte e quindi ci affidiamo anche a loro. Le nostre capacità di lavorazione raggiungono il livello più alto possibile e alcune parti più esigenti sono prodotte in uno stabilimento certificato AS9100. Le pale dei motori a reazione richiedono un'esperienza di produzione altamente specializzata e l'attrezzatura giusta. L'industria aerospaziale ha standard molto severi. Alcuni componenti con strutture geometriche complesse sono più facilmente realizzati mediante lavorazione a cinque assi, che si trova solo in alcuni impianti di lavorazione, compreso il nostro. Il nostro stabilimento certificato aerospaziale ha l'esperienza necessaria per soddisfare l'ampia richiesta di documentazione dell'industria aerospaziale. Nelle operazioni di TORNITURA, un pezzo viene ruotato e spostato contro un utensile da taglio. Per questo processo viene utilizzata una macchina chiamata tornio. In FRESATURA, una macchina chiamata fresatrice ha un utensile rotante per portare i taglienti in appoggio su un pezzo. Le operazioni di FORATURA prevedono una fresa rotante con taglienti che produce fori al contatto con il pezzo. Generalmente vengono utilizzati trapani, torni o frese. Nelle operazioni di ALESATURA un utensile con un'unica punta appuntita piegata viene spostato in un foro grezzo in un pezzo in lavorazione per allargare leggermente il foro e migliorare la precisione. Viene utilizzato per fini di finitura. BROCCIA comporta un utensile dentato per rimuovere materiale da un pezzo in un passaggio della broccia (utensile dentato). Nella brocciatura lineare, la broccia scorre linearmente contro una superficie del pezzo in lavorazione per effettuare il taglio, mentre nella brocciatura rotativa, la broccia viene ruotata e premuta nel pezzo in lavorazione per tagliare una forma simmetrica dell'asse. LA LAVORAZIONE DI TIPO SVIZZERO è una delle nostre preziose tecniche che utilizziamo per la produzione ad alto volume di piccoli pezzi di alta precisione. Utilizzando un tornio di tipo svizzero, torniamo a buon mercato pezzi piccoli, complessi e di precisione. A differenza dei torni convenzionali in cui il pezzo viene mantenuto fermo e l'utensile in movimento, nei centri di tornitura di tipo svizzero, il pezzo può muoversi sull'asse Z e l'utensile è fermo. Nella lavorazione di tipo svizzero, il grezzo della barra viene trattenuto nella macchina e fatto avanzare attraverso una boccola di guida nell'asse z, esponendo solo la parte da lavorare. In questo modo è assicurata una presa salda e la precisione è molto elevata. La disponibilità di utensili motorizzati offre l'opportunità di fresare e forare mentre il materiale avanza dalla boccola di guida. L'asse Y dell'attrezzatura di tipo svizzero offre capacità di fresatura complete e consente di risparmiare molto tempo nella produzione. Inoltre, le nostre macchine dispongono di trapani e utensili alesatori che operano sul pezzo quando è trattenuto nel contromandrino. La nostra capacità di lavorazione di tipo svizzero ci offre un'opportunità di lavorazione completa completamente automatizzata in un'unica operazione. La lavorazione meccanica è uno dei segmenti più grandi dell'attività di AGS-TECH Inc. La utilizziamo come operazione primaria o secondaria dopo la fusione o l'estrusione di una parte in modo da soddisfare tutte le specifiche del disegno. • SERVIZI DI FINITURA SUPERFICIALE: Offriamo una vasta gamma di trattamenti superficiali e finiture superficiali come condizionamento superficiale per migliorare l'adesione, deposito di uno strato di ossido sottile per migliorare l'adesione del rivestimento, sabbiatura, film chimico, anodizzazione, nitrurazione, verniciatura a polvere, verniciatura a spruzzo , varie tecniche avanzate di metallizzazione e rivestimento, tra cui sputtering, fascio di elettroni, evaporazione, placcatura, rivestimenti duri come il rivestimento in carbonio simil diamante (DLC) o titanio per utensili di perforazione e taglio. • SERVIZI DI MARCATURA ED ETICHETTATURA DEI PRODOTTI: Molti dei nostri clienti richiedono marcatura ed etichettatura, marcatura laser, incisione su parti metalliche. Se hai una tale esigenza, discutiamo quale opzione sarà la migliore per te. Ecco alcuni dei prodotti fusi in metallo comunemente usati. Dal momento che sono pronti all'uso, puoi risparmiare sui costi dello stampo nel caso in cui uno di questi soddisfi le tue esigenze: CLICCA QUI PER SCARICARE le nostre scatole in alluminio pressofuso serie 11 di AGS-Electronics CLICK Product Finder-Locator Service PAGINA PRECEDENTE
- Parti, assemblaggi, stampi in plastica, fusione, lavorazione su misura
Parti prodotte su misura, assiemi, stampi in plastica, stampaggio in gomma, fusione di metalli, lavorazione CNC, tornitura, fresatura, assemblaggio ottico elettronico elettrico PCBA Parti, assiemi e prodotti su misura Leggi di più Stampi e stampaggio plastica e gomma Leggi di più Fusione e lavorazione Leggi di più Estrusioni, prodotti estrusi Leggi di più Stampaggi e fabbricazione di lamiere Leggi di più Forgiatura dei metalli e metallurgia delle polveri Leggi di più Formatura di fili e molle Leggi di più Formatura e modellatura di vetro e ceramica Leggi di più Produzione additiva e rapida Leggi di più Compositi e produzione di materiali compositi Leggi di più Processi di unione e assemblaggio e fissaggio Produciamo per voi parti e assiemi e offriamo i seguenti processi di produzione: • Stampi in plastica e gomma e parti stampate. Stampaggio ad iniezione, termoformatura, termoindurente, formatura sottovuoto, soffiaggio, stampaggio rotazionale, stampaggio per colata, stampaggio inserti e altri. • Estrusioni di plastica, gomma e metallo • Getti ferrosi e non ferrosi e pezzi lavorati prodotti con tecniche di fresatura e tornitura, lavorazioni di tipo svizzero. • Parti di metallurgia delle polveri • Stampaggio di metalli e non, stampaggio lamiere, assemblaggi di lamiere saldate • Forgiatura a freddo ea caldo • Fili, assemblaggi di fili saldati, formatura di fili • Vari tipi di molle, a molla • Produzione ingranaggi, riduttori, giunti, vite senza fine, riduttori di velocità, cilindri, cinghie di trasmissione, catene di trasmissione, organi di trasmissione • Vetro temperato e antiproiettile conforme agli standard NATO e militari • Sfere, cuscinetti, pulegge e gruppi pulegge • Valvole e componenti pneumatici come O-ring, rondelle e guarnizioni • Parti e assiemi in vetro e ceramica, componenti a prova di vuoto ed ermetici, incollaggio metallo-ceramica e ceramica-ceramica. • Vari tipi di assiemi meccanici, optomeccanici, elettromeccanici, optoelettronici. • Incollaggio metallo-gomma, metallo-plastica • Tubi e tubi, formatura tubi, piegatura e assemblaggi di tubi personalizzati, produzione di soffietti. • Produzione di fibra di vetro • Saldatura con varie tecniche come saldatura a punti, saldatura laser, MIG, TIG. Saldatura ad ultrasuoni per parti in plastica. • Vasta varietà di trattamenti superficiali e finiture superficiali come condizionamento superficiale per migliorare l'adesione, deposito di un sottile strato di ossido per migliorare l'adesione del rivestimento, sabbiatura, film chimico, anodizzazione, nitrurazione, verniciatura a polvere, verniciatura a spruzzo, varie tecniche avanzate di metallizzazione e rivestimento compreso lo sputtering, il fascio di elettroni, l'evaporazione, la placcatura, i rivestimenti duri come il carbonio simile al diamante (DLC) o il titanio per utensili da taglio e perforazione. • Marcatura ed etichettatura, marcatura laser su parti metalliche, stampa su parti in plastica e gomma Scarica la brochure per i termini comuni di ingegneria meccanica utilizzati da progettisti e ingegneri Costruiamo prodotti secondo le vostre specifiche e requisiti particolari. Per offrirti la migliore qualità, consegna e prezzi, produciamo prodotti a livello globale in Cina, India, Taiwan, Filippine, Corea del Sud, Malesia, Sri Lanka, Turchia, Stati Uniti, Canada, Germania, Regno Unito e Giappone. Questo ci rende molto più forti e globalmente più competitivi di qualsiasi altro produttore custom manufacturer. I nostri prodotti sono fabbricati in ambienti certificati ISO9001:2000, QS9000, ISO14001, TS16949 e possiedono il marchio CE, UL e soddisfano altri standard del settore. Una volta che siamo stati nominati per il tuo progetto, possiamo occuparci dell'intera produzione, assemblaggio, collaudo, qualificazione, spedizione e dogana come desideri. Se preferisci, possiamo immagazzinare le tue parti, assemblare kit personalizzati, stampare ed etichettare il nome e il marchio della tua azienda e spedirli ai tuoi clienti. In altre parole, possiamo essere anche il tuo centro di deposito e distribuzione, se lo desideri. Poiché i nostri magazzini si trovano vicino ai principali porti marittimi, ciò ci offre un vantaggio logistico. Ad esempio, quando i tuoi prodotti arrivano in un importante porto marittimo degli Stati Uniti, possiamo trasportarli direttamente in un magazzino vicino dove possiamo immagazzinare, assemblare, realizzare kit, rietichettare, stampare, imballare secondo la tua scelta e consegnarli spedisci ai tuoi clienti Non forniamo solo prodotti. La nostra azienda lavora su contratti personalizzati dove veniamo presso la tua sede, valutiamo il tuo progetto in loco e sviluppiamo una proposta progettuale su misura per te. Quindi inviamo il nostro team di esperti per implementare il progetto. Maggiori informazioni sul nostro lavoro di ingegneria possono essere trovate su http://www.ags-engineering.com - Prendiamo piccoli progetti così come grandi progetti su scala industriale. Come primo passo, possiamo metterti in contatto tramite telefono, teleconferenza o MSN messenger con i membri del nostro team di esperti, in modo che tu possa comunicare direttamente con un esperto, porre domande e discutere il tuo progetto. Chiamaci e se necessario verremo a trovarti. PAGINA PRECEDENTE
- Assemblaggi di parti fabbricati su misura, stampi in plastica, fusione di metalli, CNC
Parti prodotte su misura, assiemi, stampi in plastica, fusione, lavorazione CNC, estrusione, forgiatura di metalli, produzione di molle, assemblaggio di prodotti, PCBA, PCB AGS-TECH, Inc. è il tuo Produttore personalizzato globale, integratore, consolidatore, partner di outsourcing. Siamo la vostra fonte unica per la produzione, la fabbricazione, l'ingegneria, il consolidamento, l'outsourcing. Parti e assiemi realizzati su misura Per saperne di più Produzione di elementi di macchine Per saperne di più Elementi di fissaggio, produzione di hardware per rigging Per saperne di più Produzione di utensili da taglio, foratura, sagomatura Per saperne di più Pneumatica, idraulica, prodotti per il vuoto Fabbricazione non convenzionale Per saperne di più Per saperne di più Produzione di Prodotti Straordinari Per saperne di più Produzione su nanoscala, microscala e mesoscala Per saperne di più Produzione elettrica ed elettronica Per saperne di più Produzione ottica, fibra ottica, optoelettronica Per saperne di più Integrazione ingegneristica Jigs, Fixtues, Tools Manufacturing Per saperne di più Per saperne di più Machines & Equipment Manufacturing Per saperne di più Industrial Test Equipment Per saperne di più Siamo AGS-TECH Inc., il tuo punto di riferimento per la produzione, la fabbricazione, l'ingegneria, l'outsourcing e il consolidamento. Siamo l'integratore di ingegneria più diversificato al mondo che offre produzione personalizzata, sottoassiemi, assemblaggio di prodotti e servizi di ingegneria.