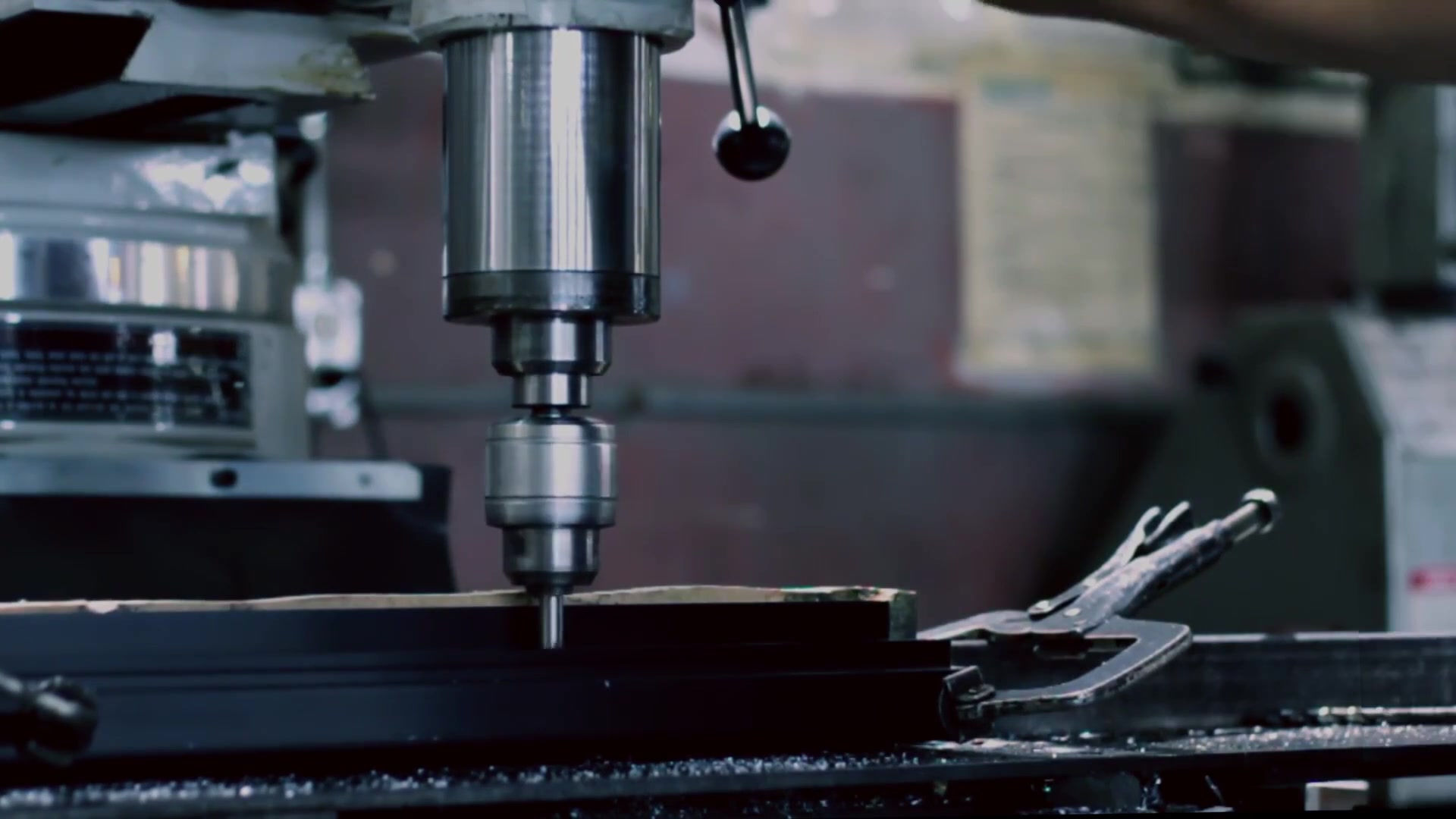
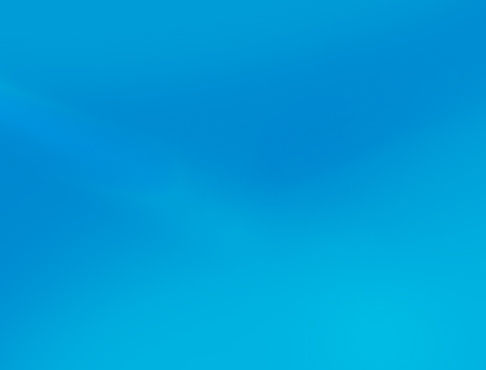
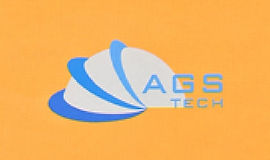
다양한 제품 및 서비스를 위한 글로벌 맞춤형 제조업체, 통합업체, 통합업체, 아웃소싱 파트너.
우리는 맞춤형 제조 및 기성 제품 및 서비스의 제조, 제조, 엔지니어링, 통합, 통합, 아웃소싱을 위한 원스톱 소스입니다.
Choose your Language
-
맞춤형 제조
-
국내 및 글로벌 계약 제조
-
제조 아웃소싱
-
국내 및 글로벌 조달
-
통합
-
엔지니어링 통합
-
엔지니어링 서비스
ELECTRICAL DISCHARGE MACHINING (EDM), also referred to as SPARK-EROSION or ELECTRODISCHARGE MACHINING, SPARK ERODING, DIE SINKING_cc781905-5cde-3194-bb3b -136bad5cf58d_or WIRE EROSION, is a NON-CONVENTIONAL MANUFACTURING process where erosion of metals takes place and desired shape is obtained using electrical discharges in the form 스파크. 우리는 또한 몇 가지 종류의 EDM, 즉 NO-WEAR EDM, WIRE EDM(WEDM), EDM GRINDING(EDG), DIE-SINKING EDM, ELECTRICAL-DISCHARGE MILLING,7ccm-E900 -5cde-3194-bb3b-136bad5cf58d_and ELECTROCHEMICAL-DISCHARGE 연마(ECDG). 당사의 EDM 시스템은 형상 도구/전극 및 DC 전원 공급 장치에 연결되고 전기적으로 비전도성 유전체 유체에 삽입된 공작물로 구성됩니다. 1940년 이후 방전 가공은 제조 산업에서 가장 중요하고 인기 있는 생산 기술 중 하나가 되었습니다.
두 전극 사이의 거리가 줄어들면 전극 사이의 체적에 있는 전기장의 세기가 일부 지점에서 유전체의 세기보다 커지며, 이것이 끊어지고 결국 두 전극 사이에 전류가 흐르는 다리가 형성됩니다. 강한 전기 아크가 생성되어 상당한 가열로 공작물의 일부와 일부 공구 재료가 녹습니다. 결과적으로 두 전극에서 재료가 제거됩니다. 동시에 유전체 유체가 빠르게 가열되어 아크 갭에서 유체가 증발합니다. 전류 흐름이 중지되거나 중지되면 주변 유전체 유체에 의해 가스 거품에서 열이 제거되고 거품이 공동화(붕괴)합니다. 기포의 붕괴와 유전체 유체의 흐름에 의해 생성된 충격파는 공작물 표면에서 파편을 씻어내고 용융된 공작물 재료를 유전체 유체로 동반합니다. 이러한 방전의 반복률은 50~500kHz, 전압은 50~380V, 전류는 0.1~500A입니다. 광유, 등유 또는 증류수 및 탈이온수와 같은 새로운 액체 유전체는 일반적으로 고체 입자(잔해 형태)를 운반하는 전극 간 부피로 전달되고 유전체의 절연 특성이 복원됩니다. 전류가 흐르면 두 전극 사이의 전위차가 파괴되기 전의 상태로 복원되어 새로운 액체 절연 파괴가 발생할 수 있습니다. 당사의 최신 방전 기계(EDM)는 수치 제어된 움직임을 제공하며 유전성 유체용 펌프 및 여과 시스템이 장착되어 있습니다.
방전 가공(EDM)은 주로 경금속 또는 기존 기술로 가공하기 매우 어려운 금속에 사용되는 가공 방법입니다. EDM으로 절연 세라믹을 가공하는 방법도 제안되었지만 EDM은 일반적으로 전기 전도체인 모든 재료와 함께 작동합니다. 용융점과 용융 잠열은 방전당 제거되는 금속의 부피를 결정하는 특성입니다. 이 값이 높을수록 재료 제거 속도가 느려집니다. 방전 가공 공정에는 기계적 에너지가 필요하지 않기 때문에 가공물의 경도, 강도 및 인성은 제거율에 영향을 미치지 않습니다. 방전 주파수 또는 방전당 에너지, 전압 및 전류는 재료 제거율을 제어하기 위해 변경됩니다. 재료 제거율과 표면 거칠기는 전류 밀도가 증가하고 스파크 주파수가 감소함에 따라 증가합니다. EDM을 사용하여 사전 경화된 강철의 복잡한 윤곽이나 공동을 연화하고 다시 경화시키기 위한 열처리 없이 절단할 수 있습니다. 티타늄, 하스텔로이, 코바르 및 인코넬과 같은 금속 또는 금속 합금에 이 방법을 사용할 수 있습니다. EDM 공정의 적용에는 다결정 다이아몬드 공구의 성형이 포함됩니다. EDM은 전기화학가공(ECM), 워터젯 절단(WJ, AWJ), 레이저 절단과 같은 공정과 함께 비전통적 또는 비전통적 가공 방법으로 간주됩니다. 다른 한편으로, 기존의 기계가공 방법은 선삭, 밀링, 연삭, 드릴링 및 재료 제거 메커니즘이 본질적으로 기계적 힘에 기초하는 기타 공정을 포함합니다. 방전 가공(EDM)용 전극은 흑연, 황동, 구리 및 구리-텅스텐 합금으로 만들어집니다. 전극 직경은 0.1mm까지 가능합니다. 공구 마모는 EDM의 치수 정확도에 부정적인 영향을 미치는 바람직하지 않은 현상이므로 극성을 반대로 하고 구리 공구를 사용하여 공구 마모를 최소화함으로써 NO-WEAR EDM이라는 프로세스를 활용합니다.
이상적으로 말하면 방전 가공(EDM)은 전극 사이의 유전체 액체의 일련의 고장 및 복원으로 간주될 수 있습니다. 그러나 실제로 전극간 영역에서 파편을 제거하는 것은 거의 항상 부분적입니다. 이로 인해 전극 간 영역의 유전체의 전기적 특성이 공칭 값과 다르고 시간에 따라 변합니다. 전극 간 거리(스파크 갭)는 사용된 특정 기계의 제어 알고리즘에 의해 조정됩니다. EDM의 스파크 갭은 불행하게도 때때로 파편에 의해 단락될 수 있습니다. 전극의 제어 시스템은 두 전극(공구 및 공작물)이 단락되는 것을 방지할 만큼 충분히 빠르게 반응하지 않을 수 있습니다. 이 원치 않는 단락은 이상적인 경우와 다르게 재료 제거에 기여합니다. 항상 전극간 영역에 전류가 흐르도록 유전체의 절연성을 회복시켜 공구-전극의 원치 않는 형태 변화(손상) 가능성을 최소화하기 위해 플러싱 작용을 가장 중요하게 생각합니다. 및 공작물. 특정 형상을 얻기 위해 EDM 도구는 공작물에 닿지 않고 공작물에 매우 가까운 원하는 경로를 따라 안내되며 사용 중인 모션 제어 성능에 최대한 주의를 기울입니다. 이러한 방식으로 많은 전류 방전/스파크가 발생하고 각각은 작은 크레이터가 형성되는 공구와 공작물 모두에서 재료를 제거하는 데 기여합니다. 크레이터의 크기는 당면한 특정 작업에 대해 설정된 기술 매개변수의 함수이며 크기는 나노스케일(예: 마이크로 EDM 작업의 경우)에서 황삭 조건에서 수백 마이크로미터까지 다양합니다. 공구의 이러한 작은 크레이터는 "공구 마모"라고 하는 전극의 점진적인 침식을 유발합니다. 공작물의 형상에 대한 마모의 해로운 영향을 상쇄하기 위해 가공 작업 중에 공구 전극을 지속적으로 교체합니다. 때때로 우리는 지속적으로 교체된 와이어를 전극으로 사용하여 이를 달성합니다(이 EDM 프로세스는 WIRE EDM 라고도 함). 때때로 우리는 공구 전극의 일부만 실제로 가공 공정에 참여하고 이 부분이 정기적으로 변경되는 방식으로 도구 전극을 사용합니다. 예를 들어 회전 디스크를 도구 전극으로 사용하는 경우입니다. 이 프로세스를 EDM 연삭이라고 합니다. 우리가 배포하는 또 다른 기술은 마모를 보상하기 위해 동일한 EDM 작업 중에 크기와 모양이 다른 전극 세트를 사용하는 것입니다. 우리는 이것을 다중 전극 기술이라고 부르며, 도구 전극이 원하는 모양의 음으로 복제되고 단일 방향, 일반적으로 수직 방향(즉, z축)을 따라 블랭크 쪽으로 전진할 때 가장 일반적으로 사용됩니다. 이것은 공작물이 잠긴 유전체 액체로의 도구 싱크와 유사하므로 다음과 같이 표시됩니다. 3194-bb3b-136bad5cf58d_CONVENTIONAL EDM or RAM EDM 이 작업을 위한 기계는 SINKER EDM이라고 합니다. 이러한 유형의 EDM용 전극은 복잡한 형태를 가지고 있습니다. 여러 방향을 따라 이동하는 일반적으로 단순한 모양의 전극을 사용하여 최종 형상을 얻었고 회전도 적용되는 경우 이를 EDM 밀링이라고 합니다. 마모 정도는 작동에 사용된 기술 매개변수(극성, 최대 전류, 개방 회로 전압)에 따라 엄격하게 달라집니다. 예를 들어, in micro-EDM( m-EDM이라고도 함)에서 이러한 매개변수는 일반적으로 심각한 마모를 생성하는 값으로 설정됩니다. 따라서 마모는 축적된 노하우를 사용하여 최소화하는 부분에서 큰 문제입니다. 예를 들어 흑연 전극의 마모를 최소화하기 위해 밀리초 이내에 제어할 수 있는 디지털 발전기는 전기 침식이 일어날 때 극성을 반전시킵니다. 이는 전극에 침식된 흑연을 계속해서 침착시키는 전기도금과 유사한 효과를 가져온다. 또 다른 방법으로 소위 ''제로 마모'' 회로는 방전이 시작되고 중지되는 빈도를 최소화하여 가능한 한 오랫동안 방전을 유지합니다. 방전 가공에서 재료 제거율은 다음과 같이 추정할 수 있습니다.
MRR = 4 x 10 exp(4) x I x Tw exp(-1.23)
여기서 MRR은 mm3/min, I는 전류(암페어), Tw는 공작물 융점(K-273.15K)입니다. exp는 지수를 의미합니다.
한편, 전극의 마모율 W는 다음과 같이 구할 수 있습니다.
중량 = ( 1.1 x 10exp(11) ) x I x Ttexp(-2.38)
여기서 Wt는 mm3/min 단위이고 Tt는 K-273.15K 단위의 전극 재료의 융점입니다.
마지막으로 전극 R에 대한 공작물의 마모 비율은 다음과 같이 얻을 수 있습니다.
R = 2.25 x Trex(-2.38)
여기서 Tr은 전극에 대한 공작물의 융점 비율입니다.
싱커 EDM :
싱커 EDM, 라고도 CAVITY TYPE EDM or_cc781905-5cde-5로 구성되어 있습니다. 전극과 공작물은 전원 공급 장치에 연결됩니다. 전원 공급 장치는 둘 사이에 전위를 생성합니다. 전극이 공작물에 접근함에 따라 유체에서 절연 파괴가 발생하여 플라즈마 채널을 형성하고 작은 스파크 점프가 발생합니다. 스파크는 일반적으로 한 번에 하나씩 발생합니다. 그 이유는 전극간 공간의 다른 위치가 동일한 모든 위치에서 동시에 스파크를 발생시킬 수 있는 동일한 국부적 전기적 특성을 가질 가능성이 거의 없기 때문입니다. 초당 수십만 개의 스파크가 전극과 공작물 사이의 임의의 지점에서 발생합니다. 모재가 침식되고 스파크 갭이 연속적으로 증가함에 따라 전극은 CNC 기계에 의해 자동으로 낮아져 프로세스가 중단 없이 계속될 수 있습니다. 당사 장비에는 ''시간' 및 '오프 시간''으로 알려진 제어 주기가 있습니다. 켜짐 시간 설정은 스파크의 길이 또는 지속 시간을 결정합니다. 시간이 길수록 해당 스파크와 해당 사이클에 대한 모든 후속 스파크에 대해 더 깊은 캐비티가 생성되어 공작물에 거친 마무리가 생성되고 그 반대의 경우도 마찬가지입니다. 오프 시간은 하나의 스파크가 다른 스파크로 교체되는 시간입니다. 더 긴 오프 시간은 유전체 유체가 노즐을 통해 흘러내리도록 하여 침식된 파편을 청소하여 단락을 방지합니다. 이러한 설정은 마이크로 초 단위로 조정됩니다.
와이어 EDM :
In WIRE ELECTRICAL DISCHARGE MACHINING (WEDM), also called WIRE-CUT EDM or WIRE CUTTING, we feed a 유전체 유체 탱크에 잠긴 공작물을 통해 황동의 얇은 단일 가닥 금속 와이어. 와이어 EDM은 EDM의 중요한 변형입니다. 우리는 때때로 와이어 컷 EDM을 사용하여 300mm 두께의 판을 절단하고 다른 제조 방법으로 기계로 가공하기 어려운 경금속으로 펀치, 도구 및 다이를 만듭니다. 띠톱으로 윤곽을 절단하는 것과 유사한 이 과정에서 스풀에서 지속적으로 공급되는 와이어가 상부 및 하부 다이아몬드 가이드 사이에 고정됩니다. CNC 제어 가이드는 x-y 평면에서 이동하고 상단 가이드는 z-u-v 축에서 독립적으로 이동할 수 있어 테이퍼 및 전환 모양(예: 바닥의 원 및 상단). 상부 가이드는 x–y–u–v–i–j–k–l–의 축 이동을 제어할 수 있습니다. 이를 통해 WEDM은 매우 복잡하고 섬세한 모양을 절단할 수 있습니다. 최고의 경제적 비용과 가공 시간을 달성하는 장비의 평균 절단 커프는 Ø 0.25 황동, 구리 또는 텅스텐 와이어를 사용하여 0.335mm입니다. 그러나 당사 CNC 장비의 상부 및 하부 다이아몬드 가이드는 약 0.004mm까지 정확하며 Ø 0.02mm 와이어를 사용하여 0.021mm만큼 작은 절단 경로 또는 커프를 가질 수 있습니다. 따라서 정말 좁은 절단이 가능합니다. 와이어의 측면에서 가공물까지 스파크가 발생하여 침식의 원인이 되기 때문에 절단 폭이 와이어의 폭보다 큽니다. 이 '오버컷'은 많은 응용 분야에서 필요하며 예측 가능하므로 보상할 수 있습니다(마이크로 EDM에서는 자주 발생하지 않음). 와이어 스풀은 깁니다. 0.25mm 와이어의 8kg 스풀은 길이가 19km가 조금 넘습니다. 와이어 직경은 20마이크로미터만큼 작을 수 있으며 기하학적 정밀도는 +/- 1마이크로미터에 가깝습니다. 우리는 일반적으로 와이어를 한 번만 사용하고 상대적으로 저렴하기 때문에 재활용합니다. 0.15~9m/min의 일정한 속도로 이동하며 절단 중에 일정한 절단(슬롯)이 유지됩니다. 와이어 컷 EDM 공정에서 우리는 물을 유전체 유체로 사용하여 필터와 탈이온화 장치로 물의 저항과 기타 전기적 특성을 제어합니다. 물은 절단 영역에서 절단 파편을 씻어냅니다. 플러싱은 주어진 재료 두께에 대한 최대 이송 속도를 결정하는 중요한 요소이므로 이를 일관되게 유지합니다. 와이어 EDM의 절단 속도는 50mm 두께의 D2 공구강의 경우 18,000mm2/hr과 같이 단위 시간당 절단된 단면적으로 표시됩니다. 이 경우 선형 절단 속도는 18,000/50 = 360mm/hr입니다. 와이어 EDM의 재료 제거율은 다음과 같습니다.
MRR = Vf xhxb
여기서 MRR은 mm3/min, Vf는 공작물로 들어가는 와이어의 이송 속도(mm/min), h는 두께 또는 높이(mm), b는 커프(kerf)입니다.
b = dw + 2s
여기서 dw는 와이어 직경이고 s는 와이어와 공작물 사이의 간격(mm)입니다.
더 엄격한 공차와 함께 현대적인 다축 EDM 와이어 절단 머시닝 센터에는 두 부품을 동시에 절단하기 위한 멀티 헤드, 와이어 파손 방지 제어, 와이어 파손 시 자동 셀프 스레딩 기능 및 프로그래밍된 기능과 같은 기능이 추가되었습니다. 작업, 직선 및 각진 절단 기능을 최적화하기 위한 가공 전략.
Wire-EDM은 재료 제거에 높은 절삭 부하가 필요하지 않기 때문에 낮은 잔류 응력을 제공합니다. 펄스당 에너지/전력이 상대적으로 낮으면(마무리 작업에서와 같이) 낮은 잔류 응력으로 인해 재료의 기계적 특성에 거의 변화가 없을 것으로 예상됩니다.
전기 방전 연삭(EDG) : 연삭 휠에는 연마제가 포함되어 있지 않으며 흑연 또는 황동으로 만들어집니다. 회전하는 휠과 공작물 사이의 반복적인 스파크는 공작물 표면에서 재료를 제거합니다. 재료 제거율은 다음과 같습니다.
MRR = K x I
여기에서 MRR은 mm3/min 단위, I는 전류 단위 암페어, K는 mm3/A-min 단위의 공작물 재료 계수입니다. 부품의 좁은 슬릿을 보기 위해 방전 연삭을 자주 사용합니다. 우리는 때때로 EDG(Electrical-Discharge Grinding) 공정과 화학 작용에 의해 물질이 제거되는 ECG(Electrochemical Grinding) 공정을 결합합니다. 프로세스는 ELECTROCHEMICAL-DISCHARGE GRINDING(ECDG)이라고 합니다. ECDG 프로세스는 상대적으로 더 많은 전력을 소비하지만 EDG보다 빠른 프로세스입니다. 우리는 주로 이 기술을 사용하여 초경 공구를 연삭합니다.
방전 가공의 응용:
시제품 생산:
우리는 특히 생산량이 상대적으로 적은 항공우주, 자동차 및 전자 산업을 위해 금형 제작, 도구 및 다이 제조는 물론 프로토타입 및 생산 부품을 만드는 데 EDM 공정을 사용합니다. Sinker EDM에서 흑연, 구리 텅스텐 또는 순수 구리 전극은 원하는(음의) 모양으로 가공되어 수직 램의 끝에서 공작물로 공급됩니다.
주화 다이 만들기:
주화(스탬핑) 공정으로 보석과 배지를 생산하기 위한 다이를 만드는 경우, 포지티브 마스터는 순은으로 만들 수 있습니다. 왜냐하면 (적절한 기계 설정으로) 마스터가 크게 침식되어 한 번만 사용되기 때문입니다. 그 결과 생성된 네거티브 다이는 경화되고 드롭 해머로 사용되어 청동, 은 또는 낮은 증거 금 합금의 컷아웃 시트 블랭크에서 스탬핑된 플랫을 생성합니다. 배지의 경우 이러한 플랫은 다른 다이에 의해 곡면으로 더 성형될 수 있습니다. 이러한 유형의 EDM은 일반적으로 유성 유전체에 잠겨 수행됩니다. 완성된 물체는 경질(유리) 또는 연질(페인트) 에나멜 및/또는 순금 또는 니켈로 전기도금하여 더욱 정제할 수 있습니다. 은과 같은 더 부드러운 재료는 정교하게 손으로 조각할 수 있습니다.
작은 구멍 드릴링:
와이어 절단 EDM 기계에서 우리는 작은 구멍 드릴링 EDM을 사용하여 와이어 절단 EDM 작업을 위해 와이어를 끼울 공작물에 관통 구멍을 만듭니다. 특별히 작은 구멍 드릴링을 위한 별도의 EDM 헤드가 와이어 컷 기계에 장착되어 있어 사전 드릴링 없이 필요에 따라 큰 경화 플레이트에서 완성 부품이 부식되도록 합니다. 우리는 또한 작은 구멍 EDM을 사용하여 제트 엔진에 사용되는 터빈 블레이드의 가장자리에 구멍을 뚫습니다. 이 작은 구멍을 통한 가스 흐름은 엔진이 가능한 것보다 더 높은 온도를 사용할 수 있도록 합니다. 이 블레이드는 고온의 매우 단단한 단결정 합금으로 만들어지기 때문에 종횡비가 높은 이러한 구멍의 기존 기계가공이 매우 어렵고 심지어 불가능합니다. 작은 구멍 EDM의 다른 응용 분야는 연료 시스템 구성 요소를 위한 미세한 구멍을 만드는 것입니다. 통합 EDM 헤드 외에도 블라인드 또는 관통 홀을 가공하기 위해 x–y 축이 있는 독립형 소형 홀 드릴링 EDM 장비를 배포합니다. EDM은 플러싱 에이전트 및 유전체로 전극을 통해 흐르는 일정한 증류수 또는 탈이온수 흐름과 함께 척에서 회전하는 긴 황동 또는 구리 튜브 전극으로 구멍을 뚫습니다. 일부 작은 구멍 드릴링 EDM은 10초 이내에 연강 또는 경화강의 100mm를 드릴링할 수 있습니다. 이 드릴링 작업에서 0.3mm와 6.1mm 사이의 구멍을 얻을 수 있습니다.
금속 분해 가공:
우리는 또한 공작물에서 부러진 도구(드릴 비트 또는 탭)를 제거하기 위한 특정 목적을 위한 특수 EDM 기계를 보유하고 있습니다. 이 공정을 '금속 분해 가공''이라고 합니다.
장점 및 단점 방전 가공:
EDM의 장점은 다음과 같은 가공을 포함합니다.
- 기존의 절삭 공구로 생산하기 어려운 복잡한 형상
- 공차에 매우 가까운 매우 단단한 재료
- 기존의 절삭 공구가 과도한 절삭 공구 압력으로 부품을 손상시킬 수 있는 매우 작은 공작물.
- 공구와 공작물이 직접 접촉하지 않습니다. 따라서 섬세한 단면과 약한 재료를 왜곡 없이 가공할 수 있습니다.
- 우수한 표면조도를 얻을 수 있다.
- 아주 미세한 구멍을 쉽게 뚫을 수 있습니다.
EDM의 단점은 다음과 같습니다.
- 재료 제거 속도가 느림.
- ram/sinker EDM용 전극을 만드는 데 사용되는 추가 시간과 비용.
- 전극 마모로 인해 공작물의 날카로운 모서리 재현이 어렵습니다.
- 소비전력이 높다.
- '오버컷'이 형성됩니다.
- 가공 중 과도한 공구 마모가 발생합니다.
- 전기적으로 비전도성인 재료는 특정 프로세스 설정으로만 가공할 수 있습니다.