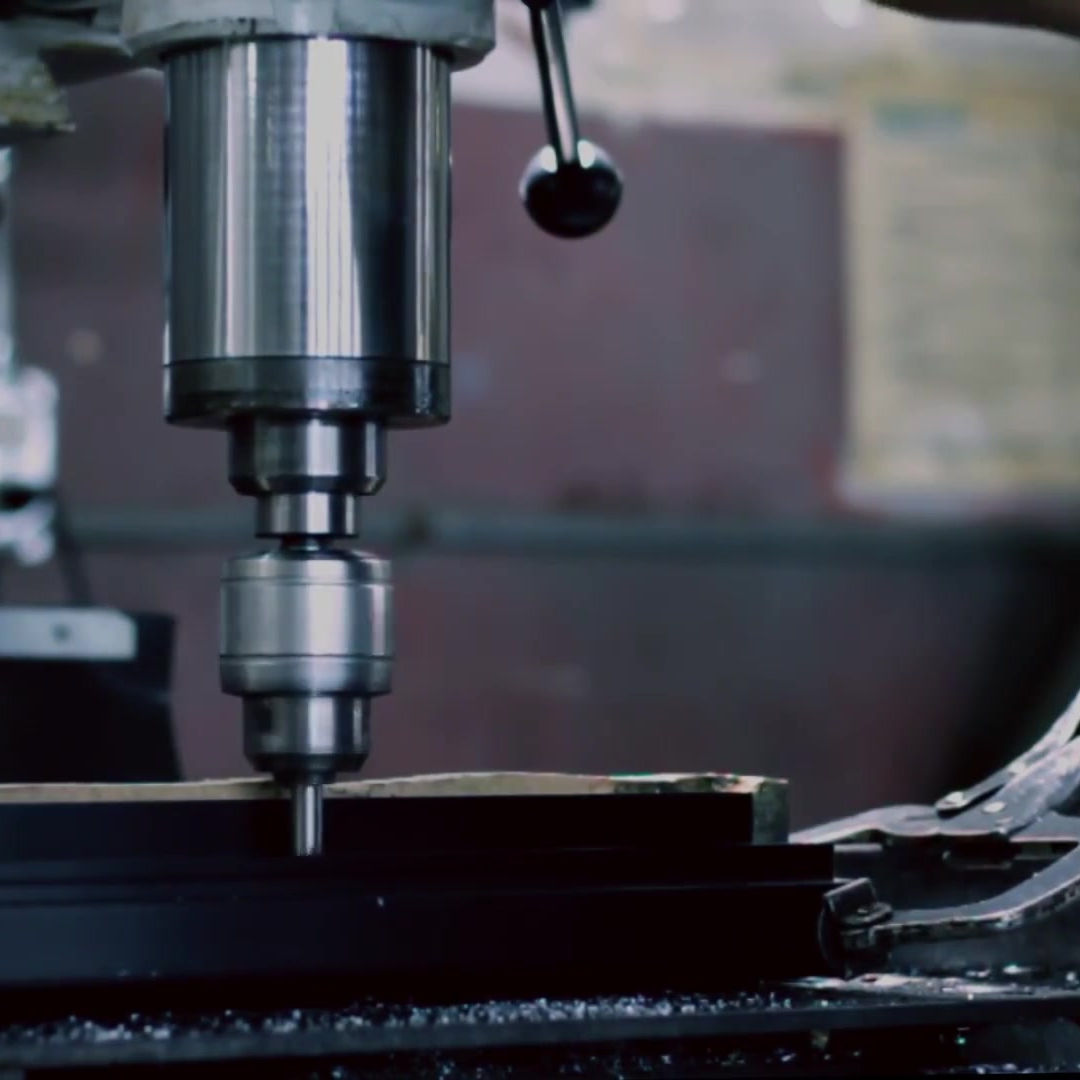
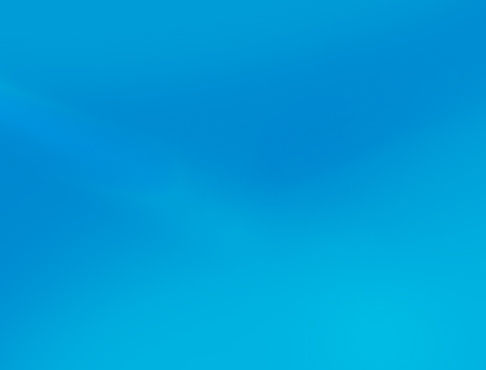
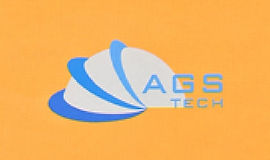
다양한 제품 및 서비스를 위한 글로벌 맞춤형 제조업체, 통합업체, 통합업체, 아웃소싱 파트너.
우리는 맞춤형 제조 및 기성 제품 및 서비스의 제조, 제조, 엔지니어링, 통합, 통합, 아웃소싱을 위한 원스톱 소스입니다.
Choose your Language
-
맞춤형 제조
-
국내 및 글로벌 계약 제조
-
제조 아웃소싱
-
국내 및 글로벌 조달
-
통합
-
엔지니어링 통합
-
엔지니어링 서비스
레이저 절단에 사용되는 레이저 CUTTING is a 5d_HIGH-ENERGY-BEAM MANUFACTURING_cc781903 In LASER BEAM MACHINING(LBM)에서 레이저 소스는 가공물의 표면에 광학 에너지를 집중시킵니다. 레이저 절단은 컴퓨터를 통해 고출력 레이저의 고집중 및 고밀도 출력을 절단할 재료로 향하게 합니다. 그런 다음 대상 재료는 녹거나, 타거나, 기화되거나 가스 제트에 의해 날아가 제어된 방식으로 가장자리에 고품질 표면 마감을 남깁니다. 당사의 산업용 레이저 절단기는 구조 및 배관 재료, 금속 및 비금속 공작물은 물론 평판 재료 절단에 적합합니다. 일반적으로 레이저 빔 가공 및 절단 공정에는 진공이 필요하지 않습니다. 레이저 절단 및 제조에 사용되는 여러 유형의 레이저가 있습니다. 펄스 또는 연속파 CO2 LASER 는 절단, 보링 및 조각에 적합합니다. The NEODYMIUM (Nd) and neodymium yttrium-aluminum-garnet (Nd-YAG) LASERS are identical 스타일과 응용 프로그램 만 다릅니다. 네오디뮴 Nd는 보링 작업에 사용되며 에너지는 높지만 반복 횟수가 적습니다. 반면에 Nd-YAG 레이저는 매우 높은 출력이 필요한 곳과 보링 및 조각에 사용됩니다. CO2 및 Nd/Nd-YAG 레이저 모두 LASER WELDING에 사용할 수 있습니다. 우리가 제조에 사용하는 다른 레이저로는 Nd:GLASS, RUBY 및 EXCIMER가 있습니다. LBM(Laser Beam Machining)에서는 다음 매개변수가 중요합니다. 가공물 표면의 반사율 및 열전도율, 비열 및 용융 및 증발 잠열. LBM(Laser Beam Machining) 공정의 효율성은 이러한 매개변수가 감소함에 따라 증가합니다. 절단 깊이는 다음과 같이 표현할 수 있습니다.
t ~ P / (vxd)
즉, 절단 깊이 "t"는 전원 입력 P에 비례하고 절단 속도 v 및 레이저 빔 스폿 직경 d에 반비례합니다. LBM으로 생산된 표면은 일반적으로 거칠고 열영향부가 있습니다.
이산화탄소(CO2) 레이저 절단 및 가공: DC 여기 CO2 레이저는 가스 혼합물을 통해 전류를 통과시켜 펌핑되는 반면 RF 여기 CO2 레이저는 여기를 위해 무선 주파수 에너지를 사용합니다. RF 방법은 비교적 새롭고 더 대중적입니다. DC 설계는 캐비티 내부에 전극이 필요하므로 전극 침식 및 광학 장치의 전극 재료 도금이 있을 수 있습니다. 이에 반해 RF 공진기는 외부 전극을 가지고 있어 이러한 문제가 발생하지 않는다. 당사는 연강, 알루미늄, 스테인리스강, 티타늄 및 플라스틱과 같은 다양한 재료의 산업용 절단에 CO2 레이저를 사용합니다.
YAG LASER CUTTING and MACHINING: 우리는 금속과 세라믹을 절단하고 스크라이빙하기 위해 YAG 레이저를 사용합니다. 레이저 발생기 및 외부 광학 장치는 냉각이 필요합니다. 폐열은 냉각제에 의해 생성되어 공기로 직접 전달됩니다. 물은 일반적으로 냉각기 또는 열 전달 시스템을 통해 순환되는 일반적인 냉각제입니다.
엑시머 레이저 절단 및 가공: 엑시머 레이저는 자외선 영역의 파장을 가진 일종의 레이저입니다. 정확한 파장은 사용된 분자에 따라 다릅니다. 예를 들어, 193 nm(ArF), 248 nm(KrF), 308 nm(XeCl), 353 nm(XeF)와 같은 파장은 괄호 안에 표시된 분자와 연관됩니다. 일부 엑시머 레이저는 조정 가능합니다. 엑시머 레이저는 가열이나 재료의 나머지 부분으로의 변화가 거의 없이 표면 재료의 매우 미세한 층을 제거할 수 있다는 매력적인 특성을 가지고 있습니다. 따라서 엑시머 레이저는 일부 폴리머 및 플라스틱과 같은 유기 재료의 정밀 미세 가공에 매우 적합합니다.
가스 보조 레이저 절단: 때로는 얇은 판재 절단을 위해 산소, 질소 또는 아르곤과 같은 가스 흐름과 함께 레이저 빔을 사용합니다. 이것은 a LASER-BEAM TORCH를 사용하여 수행됩니다. 스테인리스 스틸 및 알루미늄의 경우 질소를 사용하는 고압 불활성 가스 보조 레이저 절단을 사용합니다. 그 결과 용접성을 향상시키기 위해 산화물이 없는 모서리가 생성됩니다. 이러한 가스 흐름은 또한 공작물 표면에서 용융 및 기화된 재료를 날려 버립니다.
a LASER MICROJET CUTTING we에는 저압의 펄스 레이저 빔이 결합된 워터젯 유도 레이저가 있습니다. 광섬유와 유사하게 레이저 빔을 유도하기 위해 워터 제트를 사용하면서 레이저 절단을 수행하는 데 사용합니다. 레이저 마이크로젯의 장점은 물이 또한 파편을 제거하고 재료를 냉각시키며 더 높은 다이싱 속도, 평행 절단 및 전방향 절단 기능으로 기존의 '건식' 레이저 절단보다 더 빠르다는 것입니다.
우리는 레이저를 사용하여 절단하는 다양한 방법을 사용합니다. 방법 중 일부는 기화, 용융 및 취입, 용융 취입 및 연소, 열 응력 균열, 스크라이빙, 냉간 절단 및 연소, 안정화 레이저 절단입니다.
- 기화 절단: 집중된 빔이 재료 표면을 끓는점까지 가열하고 구멍을 만듭니다. 구멍은 흡수율을 갑자기 증가시키고 구멍을 빠르게 깊게 만듭니다. 구멍이 깊어지고 재료가 끓으면 생성된 증기가 용융된 벽을 침식하여 재료를 불어내고 구멍을 더욱 확대합니다. 목재, 탄소 및 열경화성 플라스틱과 같은 녹지 않는 재료는 일반적으로 이 방법으로 절단됩니다.
- 용융 및 중공 절단: 고압 가스를 사용하여 절단 영역에서 용융된 재료를 불어내어 필요한 동력을 줄입니다. 재료가 녹는점까지 가열된 다음 가스 제트가 용융된 재료를 커프에서 불어냅니다. 이렇게 하면 재료의 온도를 더 이상 올릴 필요가 없습니다. 우리는 이 기술로 금속을 절단합니다.
- 열응력균열: 취성재료는 열파괴에 민감하다. 빔이 표면에 집중되어 국부적인 가열 및 열팽창을 유발합니다. 그 결과 빔을 움직여 가이드될 수 있는 균열이 생깁니다. 우리는 유리 절단에 이 기술을 사용합니다.
- 실리콘 웨이퍼의 스텔스 다이싱: 실리콘 웨이퍼에서 마이크로 전자 칩의 분리는 펄스 Nd:YAG 레이저를 사용하여 스텔스 다이싱 프로세스에 의해 수행되며, 1064 nm의 파장은 실리콘의 전자 밴드 갭(1.11 eV 또는 1117nm). 이것은 반도체 장치 제조에서 널리 사용됩니다.
- 반응성 절단: 화염 절단이라고도 하는 이 기술은 산소 토치 절단과 유사할 수 있지만 점화원으로 레이저 빔을 사용합니다. 1mm 이상의 두께로 탄소강을 절단하거나 레이저 출력이 거의 없는 매우 두꺼운 강판을 절단하는 데 사용합니다.
PULSED LASERS 짧은 시간 동안 고출력 에너지 버스트를 제공하고 피어싱과 같은 일부 레이저 절단 공정 또는 매우 작은 구멍 또는 매우 낮은 절단 속도가 필요한 경우에 매우 효과적입니다. 일정한 레이저 빔을 대신 사용하면 열이 가공되는 전체 조각을 녹일 수 있는 지점에 도달할 수 있습니다. 당사의 레이저는 NC(수치 제어) 프로그램 제어에 따라 CW(연속파)를 펄스 또는 절단할 수 있습니다. 우리는 재료 제거율과 구멍 품질을 개선하기 위해 일련의 펄스 쌍을 방출하는 DOUBLE PULSE LASERS emit를 사용합니다. 첫 번째 펄스는 표면에서 재료를 제거하고 두 번째 펄스는 배출된 재료가 구멍 또는 절단면에 다시 부착되는 것을 방지합니다.
레이저 절단 및 가공의 공차 및 표면 조도가 뛰어납니다. 당사의 최신 레이저 절단기는 10마이크로미터 부근의 위치 정확도와 5마이크로미터의 반복성을 가지고 있습니다. 표준 거칠기 Rz는 시트 두께에 따라 증가하지만 레이저 출력 및 절단 속도에 따라 감소합니다. 레이저 절단 및 기계 가공 공정은 종종 0.001인치(0.025mm) 이내의 정밀한 공차를 달성할 수 있습니다. 부품 형상과 당사 기계의 기계적 기능은 최고의 공차 기능을 달성하도록 최적화되어 있습니다. 레이저 빔 절단으로 얻을 수 있는 표면 마감은 0.003mm에서 0.006mm 사이입니다. 일반적으로 0.025mm 직경의 구멍을 쉽게 만들 수 있으며 0.005mm의 작은 구멍과 50:1의 구멍 깊이 대 직경 비율이 다양한 재료로 생산되었습니다. 가장 단순하고 가장 표준적인 레이저 절단기는 탄소강 금속을 0.020–0.5인치(0.51–13mm) 두께로 절단하며 표준 톱질보다 최대 30배 더 빠릅니다.
레이저 빔 가공은 금속, 비금속 및 복합 재료의 드릴링 및 절단에 널리 사용됩니다. 기계적 절단에 비해 레이저 절단의 장점은 더 쉬운 작업 유지, 청결 및 공작물의 오염 감소를 포함합니다. 복합 재료의 연마 특성으로 인해 기존 방법으로는 가공하기 어렵지만 레이저 가공으로는 쉽게 가공할 수 있습니다. 레이저 빔은 공정 중에 마모되지 않기 때문에 얻은 정밀도가 더 좋을 수 있습니다. 레이저 시스템은 열 영향 영역이 작기 때문에 절단되는 재료가 뒤틀릴 가능성도 적습니다. 일부 재료의 경우 레이저 절단이 유일한 옵션일 수 있습니다. 레이저 빔 절단 공정은 유연하고 광섬유 빔 전달, 간단한 고정, 짧은 설정 시간, 3차원 CNC 시스템의 가용성으로 인해 레이저 절단 및 가공이 펀칭과 같은 다른 판금 제조 공정과 성공적으로 경쟁할 수 있습니다. 즉, 레이저 기술은 때때로 전반적인 효율성 향상을 위해 기계적 제조 기술과 결합될 수 있습니다.
판금의 레이저 절단은 플라즈마 절단에 비해 더 정확하고 에너지를 덜 사용하는 장점이 있지만 대부분의 산업용 레이저는 플라즈마가 할 수 있는 더 두꺼운 금속 두께를 절단할 수 없습니다. 6000와트와 같은 더 높은 출력에서 작동하는 레이저는 두꺼운 재료를 절단하는 능력에서 플라즈마 기계에 접근하고 있습니다. 그러나 이러한 6000와트 레이저 절단기의 자본 비용은 강판과 같은 두꺼운 재료를 절단할 수 있는 플라즈마 절단기의 자본 비용보다 훨씬 높습니다.
레이저 절단 및 가공의 단점도 있습니다. 레이저 절단은 높은 전력 소비를 수반합니다. 산업용 레이저 효율은 5%에서 15% 사이입니다. 특정 레이저의 전력 소비 및 효율은 출력 전력 및 작동 매개변수에 따라 달라집니다. 이것은 레이저 유형과 레이저가 현재 작업과 얼마나 잘 일치하는지에 따라 달라집니다. 특정 작업에 필요한 레이저 절단 출력의 양은 재료 유형, 두께, 사용된 공정(반응성/비활성) 및 원하는 절단 속도에 따라 다릅니다. 레이저 절단 및 기계 가공의 최대 생산 속도는 레이저 출력, 공정 유형(반응성 또는 비활성 여부), 재료 속성 및 두께를 포함한 여러 요인에 의해 제한됩니다.
In LASER ABLATION we 레이저 빔을 조사하여 고체 표면에서 물질을 제거합니다. 낮은 레이저 플럭스에서 재료는 흡수된 레이저 에너지에 의해 가열되고 증발하거나 승화됩니다. 높은 레이저 플럭스에서 재료는 일반적으로 플라즈마로 변환됩니다. 고출력 레이저는 단일 펄스로 넓은 부분을 청소합니다. 저출력 레이저는 영역 전체에 걸쳐 스캔될 수 있는 많은 작은 펄스를 사용합니다. 레이저 어블레이션에서는 펄스 레이저나 레이저 강도가 충분히 높은 경우 연속파 레이저 빔으로 재료를 제거합니다. 펄스 레이저는 매우 단단한 재료를 통해 매우 작고 깊은 구멍을 뚫을 수 있습니다. 매우 짧은 레이저 펄스는 재료를 매우 빠르게 제거하여 주변 재료가 매우 적은 열을 흡수하므로 섬세하거나 열에 민감한 재료에 레이저 드릴링을 수행할 수 있습니다. 레이저 에너지는 코팅에 의해 선택적으로 흡수될 수 있으므로 CO2 및 Nd:YAG 펄스 레이저를 사용하여 표면을 청소하고, 페인트와 코팅을 제거하거나, 기본 표면을 손상시키지 않고 페인팅할 표면을 준비할 수 있습니다.
We use LASER ENGRAVING and LASER MARKING to engrave or mark an object. 이 두 기술은 실제로 가장 널리 사용되는 응용 프로그램입니다. 잉크가 사용되지 않으며 전통적인 기계 조각 및 마킹 방법의 경우처럼 새겨진 표면과 접촉하고 마모되는 도구 비트가 포함되지 않습니다. 레이저 제판 및 마킹을 위해 특별히 설계된 재료에는 레이저에 민감한 폴리머와 특수 새 금속 합금이 포함됩니다. 레이저 마킹 및 조각 장비는 펀치, 핀, 스타일러스, 에칭 스탬프 등의 대체 장비에 비해 상대적으로 비싸지만 정확성, 재현성, 유연성, 자동화 용이성 및 온라인 적용으로 인해 더 대중화되었습니다. 다양한 제조 환경에서
마지막으로, 우리는 다른 여러 제조 작업에 레이저 빔을 사용합니다.
- LASER 용접
- LASER 열처리: 금속 및 세라믹의 표면 기계적 및 마찰 특성을 수정하기 위한 소규모 열처리.
- LASER SURFACE TREATMENT / MODIFICATION: 레이저는 코팅 증착 또는 접합 공정 전에 접착력을 향상시키기 위해 표면을 청소하고, 작용기를 도입하고, 표면을 수정하는 데 사용됩니다.