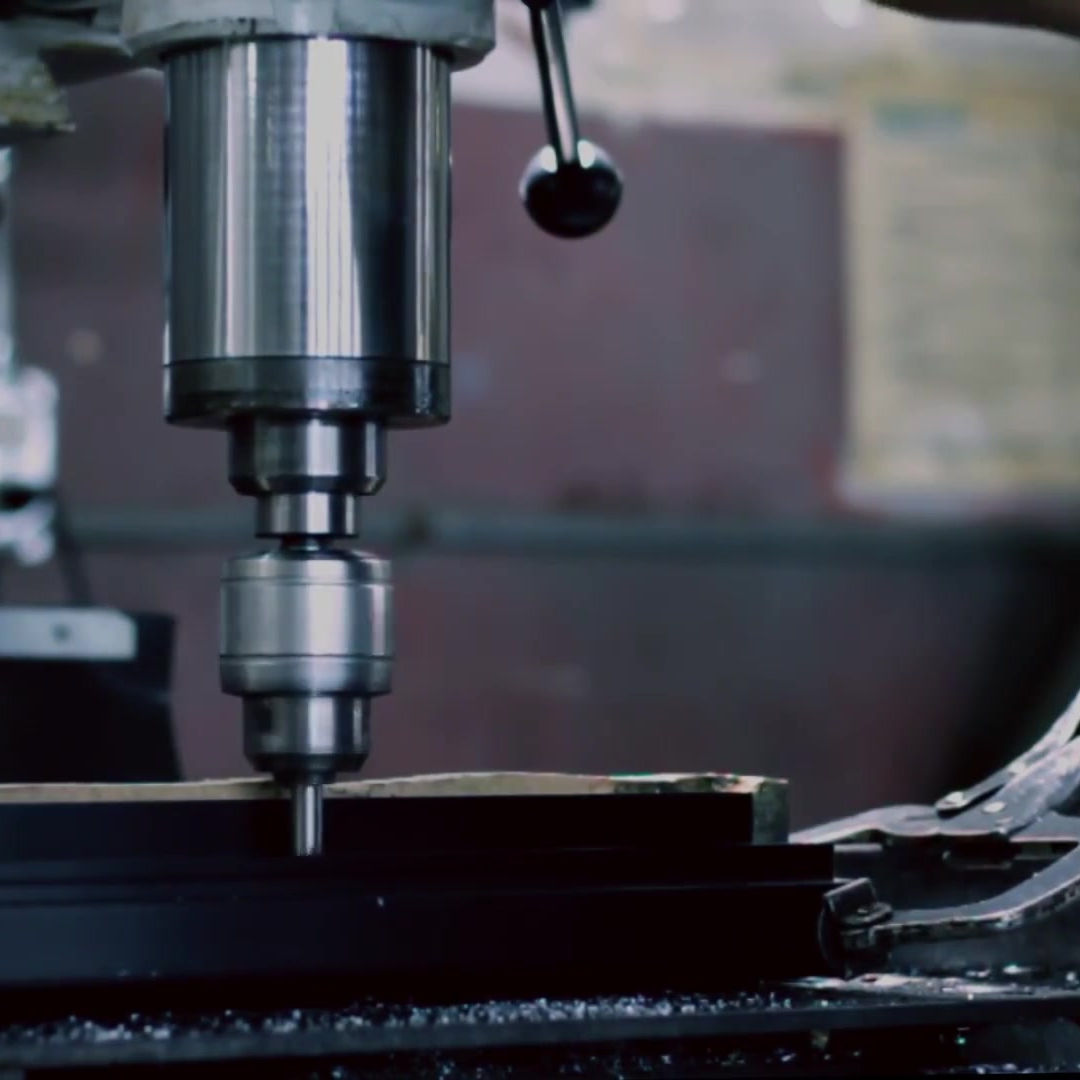
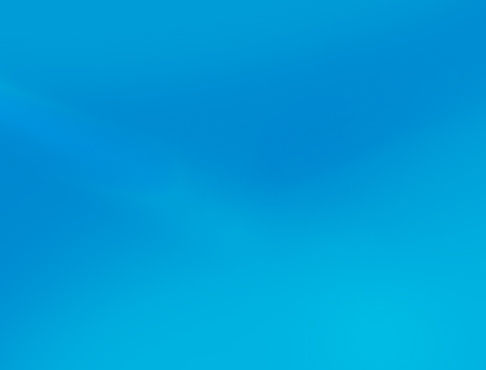
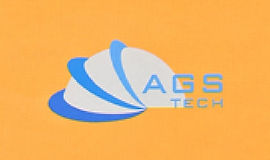
다양한 제품 및 서비스를 위한 글로벌 맞춤형 제조업체, 통합업체, 통합업체, 아웃소싱 파트너.
우리는 맞춤형 제조 및 기성 제품 및 서비스의 제조, 제조, 엔지니어링, 통합, 통합, 아웃소싱을 위한 원스톱 소스입니다.
Choose your Language
-
맞춤형 제조
-
국내 및 글로벌 계약 제조
-
제조 아웃소싱
-
국내 및 글로벌 조달
-
통합
-
엔지니어링 통합
-
엔지니어링 서비스
Search Results
공란으로 164개 검색됨
- Transmission Components, Belts, Chains, Cable Drives, Pulleys,AGS-TECH
Transmission Components, Belts, Chains and Cable Drives, Conventional & Grooved or Serrated, Positive Drive, Pulleys 벨트 및 체인 및 케이블 드라이브 어셈블리 AGS-TECH Inc.는 벨트 및 체인 및 케이블 드라이브 어셈블리를 포함한 동력 전달 부품을 제공합니다. 수년간의 개선을 통해 당사의 고무, 가죽 및 기타 벨트 드라이브는 더 가볍고 더 작아져 더 낮은 비용으로 더 높은 하중을 운반할 수 있습니다. 마찬가지로, 우리의 체인 드라이브는 시간이 지남에 따라 많은 발전을 이루었으며 고객에게 몇 가지 이점을 제공합니다. 체인 드라이브 사용의 몇 가지 장점은 상대적으로 제한되지 않은 샤프트 중심 거리, 소형화, 조립 용이성, 슬립 또는 크리프 없는 인장 탄성, 고온 환경에서 작동할 수 있는 능력입니다. 당사의 케이블 드라이브는 또한 다른 유형의 전송 구성요소에 비해 일부 애플리케이션에서 단순성과 같은 이점을 제공합니다. 기성품 벨트, 체인 및 케이블 드라이브와 맞춤형 제작 및 조립 버전을 모두 사용할 수 있습니다. 우리는 이러한 전송 구성 요소를 귀하의 응용 분야에 적합한 크기와 가장 적합한 재료로 제조할 수 있습니다. 벨트 및 벨트 드라이브: - 기존 평벨트: 톱니, 홈 또는 톱니가 없는 평벨트입니다. 평벨트 드라이브는 유연성, 우수한 충격 흡수, 고속에서 효율적인 동력 전달, 내마모성, 저렴한 비용을 제공합니다. 벨트를 접합하거나 연결하여 더 큰 벨트를 만들 수 있습니다. 기존 평벨트의 또 다른 장점은 얇아서 높은 원심력을 받지 않는다는 것입니다(작은 풀리로 고속 작업에 적합함). 반면 평벨트는 높은 장력을 필요로 하기 때문에 높은 베어링 하중을 가합니다. 평벨트 구동장치의 다른 단점은 저속 및 중급 작동 속도에서 미끄러짐, 시끄러운 작동 및 상대적으로 낮은 효율일 수 있습니다. 기존 벨트에는 강화 및 비보강의 두 가지 유형이 있습니다. 강화 벨트는 구조에 인장 부재가 있습니다. 기존의 평벨트는 가죽, 고무 처리된 직물 또는 코드, 비보강 고무 또는 플라스틱, 직물, 강화 가죽으로 제공됩니다. 가죽 벨트는 긴 수명, 유연성, 우수한 마찰 계수, 쉬운 수리를 제공합니다. 그러나 가죽 벨트는 상대적으로 비싸고 벨트 드레싱과 청소가 필요하며 환경에 따라 줄어들거나 늘어날 수 있습니다. 고무 처리된 직물 또는 코드 벨트는 습기, 산 및 알칼리에 강합니다. 고무 처리된 패브릭 벨트는 고무가 함침된 면 또는 합성 오리의 겹으로 구성되며 가장 경제적입니다. 고무 처리된 코드 벨트는 고무가 함침된 일련의 코드 플라이로 구성됩니다. 고무 처리된 코드 벨트는 높은 인장 강도와 적당한 크기와 질량을 제공합니다. 비강화 고무 또는 플라스틱 벨트는 경량, 저속 드라이브 애플리케이션에 적합합니다. 강화되지 않은 고무 및 플라스틱 벨트는 풀리 위에 제자리에 고정될 수 있습니다. 플라스틱 비보강 벨트는 고무 벨트에 비해 더 높은 동력을 전달할 수 있습니다. 강화 가죽 벨트는 가죽 상단과 하단 레이어 사이에 끼워진 플라스틱 인장 부재로 구성됩니다. 마지막으로, 우리의 패브릭 벨트는 한 줄의 면이나 오리를 접고 세로 스티치로 꿰매어 구성할 수 있습니다. 패브릭 벨트는 균일하게 추적하고 고속으로 작동할 수 있습니다. - 홈이 있는 벨트 또는 톱니 모양의 벨트(예: V-벨트): 다른 유형의 변속기 제품의 장점을 제공하도록 수정된 기본 평벨트입니다. 세로로 골이 있는 밑면이 있는 평벨트입니다. Poly-V 벨트는 인장 단면과 추적 및 압축 목적을 위한 일련의 인접한 V자형 홈이 있는 세로 홈 또는 톱니 모양의 평벨트입니다. 전력 용량은 벨트 너비에 따라 다릅니다. V-벨트는 산업계의 주력 제품이며 거의 모든 부하 전력의 전송을 위해 다양한 표준화된 크기 및 유형으로 제공됩니다. V-벨트 드라이브는 1500~6000피트/분 사이에서 잘 작동하지만 좁은 V-벨트는 최대 10,000피트/분에서 작동합니다. V-벨트 드라이브는 3~5년과 같은 긴 수명을 제공하고 큰 속도 비율을 허용하며 설치 및 제거가 용이하며 조용한 작동, 낮은 유지보수, 벨트 드라이버와 종동 샤프트 사이의 우수한 충격 흡수를 제공합니다. V-벨트의 단점은 특정 슬립과 크리프가 있기 때문에 동기 속도가 필요한 최고의 솔루션이 아닐 수 있습니다. 우리는 산업, 자동차 및 농업 벨트를 보유하고 있습니다. 표준 길이와 맞춤 길이의 벨트를 사용할 수 있습니다. 모든 표준 V-벨트 단면은 재고로 제공됩니다. 구동 및 종동 풀리 직경, 풀리 사이의 중심 거리 및 풀리 회전 속도와 같은 시스템 매개변수를 알고 있다면 벨트 길이, 벨트 단면(너비 및 두께)과 같은 알려지지 않은 매개변수를 계산할 수 있는 테이블이 있습니다. 이러한 테이블을 사용하거나 귀하에게 적합한 V-벨트를 선택하도록 요청할 수 있습니다. - 포지티브 구동 벨트(타이밍 벨트): 이 벨트도 내부 둘레에 일련의 균일한 간격의 톱니가 있는 플랫 유형입니다. 포지티브 드라이브 또는 타이밍 벨트는 평벨트의 장점과 체인 및 기어의 포지티브 그립 특성을 결합합니다. 포지티브 구동 벨트는 미끄러짐이나 속도 변화를 나타내지 않습니다. 다양한 속도 비율이 가능합니다. 베어링 하중은 낮은 장력으로 작동할 수 있기 때문에 낮습니다. 그러나 풀리의 정렬 불량에 더 취약합니다. - 풀리, 도르래, 벨트용 허브: 다양한 유형의 풀리가 플랫, 리브(톱니형) 및 포지티브 구동 벨트와 함께 사용됩니다. 우리는 그것들을 모두 제조합니다. 대부분의 평벨트 풀리는 주철로 만들어지지만 강철 버전도 다양한 림과 허브 조합으로 제공됩니다. 당사의 평벨트 풀리에는 솔리드, 스포크 또는 분할 허브가 있거나 원하는 대로 제조할 수 있습니다. 늑골이 있는 포지티브 구동 벨트는 다양한 크기와 너비로 제공됩니다. 벨트를 드라이브에 유지하려면 타이밍 벨트 드라이브에서 적어도 하나의 풀리를 플랜지로 고정해야 합니다. 긴 센터 드라이브 시스템의 경우 두 풀리 모두 플랜지를 사용하는 것이 좋습니다. 도르래는 도르래의 홈이 있는 바퀴이며 일반적으로 철 주조, 강철 성형 또는 플라스틱 성형으로 제조됩니다. 강철 성형은 자동차 및 농업용 단을 제조하는 데 적합한 공정입니다. 우리는 규칙적이고 깊은 홈이 있는 단을 생산합니다. 깊은 홈 도르래는 1/4 회전 드라이브의 경우와 같이 V-벨트가 도르래에 비스듬히 들어갈 때 적합합니다. 깊은 홈은 수직 샤프트 드라이브와 벨트의 진동이 문제가 될 수 있는 응용 분야에도 적합합니다. 우리의 아이들러 도르래는 기계적 동력을 전달하는 역할을 하지 않는 홈이 있는 도르래 또는 플랫 도르래입니다. 아이들러 풀리는 주로 벨트를 조일 때 사용됩니다. - 단일 및 다중 벨트 드라이브: 단일 벨트 드라이브에는 단일 홈이 있는 반면 다중 벨트 드라이브에는 다중 홈이 있습니다. 아래의 관련 컬러 텍스트를 클릭하면 카탈로그를 다운로드할 수 있습니다. - 동력 전달 벨트(V-Belt, Timing Belt, Raw Edge Belt, Wrapped Belt, Specialty Belt 포함) - 컨베이어 벨트 - V 풀리 - 타이밍 풀리 CHAINS & CHAIN DRIVES: 당사의 동력 전달 체인은 비교적 자유로운 축 중심 거리, 쉬운 조립, 소형, 슬립 또는 크리프 없는 인장 하에서의 탄성, 고온에서의 작동 능력과 같은 몇 가지 장점이 있습니다. 체인의 주요 유형은 다음과 같습니다. - 탈착식 사슬: 당사의 탈착식 사슬은 다양한 크기, 피치 및 극한 강도로 만들어지며 일반적으로 가단성 철 또는 강철로 만들어집니다. 가단성 체인은 0.902(23mm) ~ 4.063인치(103mm) 피치의 다양한 크기와 700 ~ 17,000lb/square inch의 극한 강도로 만들어집니다. 반면에 당사의 탈착식 강철 체인은 0.904인치(23mm)에서 약 3.00인치(76mm) 피치의 크기로 만들어지며 최대 강도는 760~5000lb/square inch입니다._cc781905-5cde-3194-bb3b- 136나쁜5cf58d_ - 핀틀 체인: 이 체인은 더 무거운 하중과 약 450피트/분(2.2m/초)의 약간 더 높은 속도에 사용됩니다. 핀틀 체인은 오프셋 사이드바가 있는 전체 라운드 배럴 엔드가 있는 개별 캐스트 링크로 만들어집니다. 이 체인 링크는 강철 핀으로 연결됩니다. 이러한 체인의 피치 범위는 약 1.00인치(25mm)에서 6.00인치(150mm)이며 극한 강도는 3600~30,000lb/square inch입니다. - 오프셋 사이드바 체인: 건설 기계의 구동 체인에 널리 사용됩니다. 이 체인은 분당 1000피트의 속도로 작동하고 약 250마력의 하중을 전달합니다. 일반적으로 각 링크에는 두 개의 오프셋 사이드바, 하나의 부싱, 하나의 롤러, 하나의 핀, 코터 핀이 있습니다. - 롤러 체인: 0.25(6mm) ~ 3.00(75mm) 인치의 피치로 제공됩니다. 단일 너비 롤러 체인의 최대 강도는 925~130,000lb/square inch입니다. 롤러 체인의 다중 너비 버전을 사용할 수 있으며 더 높은 속도에서 더 큰 힘을 전달합니다. 다중 너비 롤러 체인은 또한 소음을 줄이면서 더 부드러운 동작을 제공합니다. 롤러 체인은 롤러 링크와 핀 링크로 조립됩니다. 분리형 롤러 체인에는 코터 핀이 사용됩니다. 롤러 체인 드라이브의 설계에는 해당 분야의 전문 지식이 필요합니다. 벨트 드라이브는 선형 속도를 기반으로 하는 반면 체인 드라이브는 대부분의 설치에서 피동 멤버인 작은 스프로킷의 회전 속도를 기반으로 합니다. 마력 등급 및 회전 속도 외에도 체인 드라이브의 설계는 다른 많은 요소를 기반으로 합니다. - 더블피치체인 : 피치가 2배인 것을 제외하고는 기본적으로 롤러체인과 동일하다. - 역치(침묵) 체인: 주로 원동기, 동력인출장치 구동에 사용되는 고속 체인. 역 톱니 체인 드라이브는 최대 1200hp의 동력을 전달할 수 있으며 일련의 톱니 링크로 구성되며 핀 또는 조인트 구성 요소의 조합으로 교대로 조립됩니다. 센터 가이드 체인에는 스프로킷의 홈과 맞물리는 가이드 링크가 있고, 사이드 가이드 체인에는 스프로킷의 측면과 맞물리는 가이드가 있습니다. - 비드 또는 슬라이더 체인: 이 체인은 저속 드라이브 및 수동 작업에 사용됩니다. 아래의 관련 컬러 텍스트를 클릭하면 카탈로그를 다운로드할 수 있습니다. - 구동 체인 - 컨베이어 체인 - 대형 피치 컨베이어 체인 - 스테인리스 스틸 롤러 체인 - 호이스팅 체인 - 오토바이 체인 - 농업 기계 사슬 - 스프로킷: 당사의 표준 스프로킷은 ANSI 표준을 따릅니다. 플레이트 스프로킷은 평평하고 허브가 없는 스프로킷입니다. 당사의 중소형 허브 스프로킷은 스톡바 또는 단조품으로 만들거나 스톡바 허브를 열간 압연 플레이트에 용접하여 만듭니다. AGS-TECH Inc.는 회주철 주물, 주강 및 용접 허브 구조, 소결 분말 금속, 성형 또는 기계 플라스틱으로 가공된 스프로킷을 공급할 수 있습니다. 고속에서 원활한 작동을 위해서는 적절한 스프라켓 사이즈 선택이 필수적입니다. 물론 공간 제한은 스프로킷을 선택할 때 무시할 수 없는 요소입니다. 구동 스프로킷과 구동 스프로킷의 비율은 6:1 이하이고 드라이버의 체인 랩은 120도가 되도록 권장합니다. 더 작은 스프로킷과 더 큰 스프로킷 사이의 중심 거리, 체인 길이 및 체인 장력도 무작위가 아닌 권장 엔지니어링 계산 및 지침에 따라 선택해야 합니다. 아래 컬러 텍스트를 클릭하여 카탈로그를 다운로드하십시오. - 스프로킷 및 플레이트 휠 - 변속기 부싱 - 체인 커플링 - 체인 잠금 장치 케이블 드라이브: 어떤 경우에는 벨트 및 체인 드라이브보다 장점이 있습니다. 케이블 드라이브는 벨트와 동일한 기능을 수행할 수 있으며 일부 애플리케이션에서 구현하는 것이 더 간단하고 경제적일 수도 있습니다. 예를 들어, 새로운 Synchromesh 케이블 드라이브 시리즈는 특히 좁은 공간에서 기존 로프, 단순 케이블 및 코그 드라이브를 대체하는 확실한 견인력을 위해 설계되었습니다. 새 케이블 드라이브는 복사기, 플로터, 타자기, 프린터 등과 같은 전자 장비에서 고정밀 위치 지정을 제공하도록 설계되었습니다. 새 케이블 드라이브의 주요 기능은 3D 구불구불한 구성에서 사용할 수 있다는 것입니다. 극도로 미니어처 디자인. Synchromesh 케이블은 로프에 비해 낮은 장력으로 사용할 수 있으므로 전력 소비를 줄일 수 있습니다. 벨트, 체인 및 케이블 드라이브에 대한 질문과 의견은 AGS-TECH에 문의하십시오. CLICK Product Finder-Locator Service 이전 페이지
- Rapid Prototyping, Desktop Manufacturing, Additive Manufacturing, FDM
Rapid Prototyping, Desktop Manufacturing, Additive Manufacturing, Stereolithography, Polyjet, Fused Deposition Modeling, Selective Laser Sintering, FDM, SLS 적층 및 신속한 제조 최근 몇 년 동안 RAPID MANUFACTURING 또는 RAPID PROTOTYPING에 대한 수요가 증가했습니다. 이 프로세스는 DESKTOP MANUFACTURING 또는 FREE-FORM FABRICATION이라고도 합니다. 기본적으로 부품의 견고한 물리적 모델은 3차원 CAD 도면에서 직접 만들어집니다. 우리는 부품을 레이어로 만드는 이러한 다양한 기술에 대해 적층 제조라는 용어를 사용합니다. 통합된 컴퓨터 구동 하드웨어 및 소프트웨어를 사용하여 적층 제조를 수행합니다. 당사의 신속한 프로토타이핑 및 제조 기술은 STEREOLITHOGRAPHY, POLYJET, FUSED-DEPOSITION MODELING, SELECTIVE LASER SINTERING, ELECTRON BEAM MELTING, THREE-DIMENSIONAL PRINTING, DIRECT MANUFACTURING, RAPID TOOLING입니다. 여기를 클릭하는 것이 좋습니다.AGS-TECH Inc.의 적층 제조 및 신속한 제조 공정의 개략도를 다운로드하십시오. 이렇게 하면 아래에서 제공하는 정보를 더 잘 이해하는 데 도움이 됩니다. Rapid prototyping은 다음을 제공합니다. 1.) 개념적 제품 디자인은 3D/CAD 시스템을 사용하여 모니터에서 다양한 각도에서 봅니다. 2.) 비금속 및 금속 재료의 프로토타입을 제조하고 기능적, 기술적, 미적 측면에서 연구합니다. 3.) 매우 짧은 시간에 저가의 프로토타이핑이 가능합니다. 적층 제조는 개별 조각을 서로 쌓고 결합하여 한 덩어리의 빵을 만드는 것과 유사할 수 있습니다. 즉, 제품은 슬라이스로 제조되거나 서로 적층되어 적층됩니다. 대부분의 부품은 몇 시간 내에 생산할 수 있습니다. 이 기술은 부품이 매우 빨리 필요하거나 필요한 양이 적고 금형과 도구를 만드는 데 너무 비싸고 시간이 걸리는 경우에 좋습니다. 하지만 비싼 원자재로 인해 부품비가 비싸다. • STEREOLITHOGRAPHY : STL이라고도 하는 이 기술은 액체 포토폴리머에 레이저 빔을 집중시켜 특정 모양으로 경화 및 경화시키는 기술입니다. 레이저는 포토폴리머를 중합하여 경화시킵니다. 포토폴리머 혼합물의 표면을 따라 프로그래밍된 모양에 따라 UV 레이저 빔을 스캔함으로써 부품은 서로의 위에 계단식으로 연결된 개별 슬라이스로 아래에서 위로 생성됩니다. 레이저 스폿의 스캐닝은 시스템에 프로그래밍된 형상을 달성하기 위해 여러 번 반복됩니다. 부품이 완전히 제조된 후 플랫폼에서 제거하고 초음파 및 알코올 욕조로 닦아내고 세척합니다. 다음으로 폴리머가 완전히 경화되고 경화되었는지 확인하기 위해 몇 시간 동안 UV 조사에 노출됩니다. 이 과정을 요약하자면, 포토폴리머 혼합물에 담근 플랫폼과 UV 레이저 빔이 제어되고 서보 제어 시스템을 통해 원하는 부품의 모양에 따라 이동되며 부품은 폴리머 층을 광경화하여 얻습니다. 물론 생산된 부품의 최대 치수는 광조형 장비에 의해 결정됩니다. • POLYJET: 잉크젯 인쇄와 유사하게, 폴리젯에는 빌드 트레이에 포토폴리머를 증착하는 8개의 프린트 헤드가 있습니다. 제트와 함께 배치된 자외선은 각 층을 즉시 경화시키고 경화시킵니다. 폴리젯에는 두 가지 재료가 사용됩니다. 첫 번째 재료는 실제 모델을 제작하기 위한 것입니다. 두 번째 재료인 젤 같은 수지가 지지체로 사용됩니다. 이 두 재료는 층별로 증착되고 동시에 경화됩니다. 모델 완성 후 지지체 물질을 수용액으로 제거합니다. 사용된 수지는 STL(stereolithography)과 유사합니다. 폴리젯은 광조형에 비해 다음과 같은 장점이 있습니다. 1.) 부품을 청소할 필요가 없습니다. 2.) 후처리 경화가 필요 없음 3.) 더 얇은 층 두께가 가능하므로 더 나은 해상도를 얻고 더 미세한 부품을 제조할 수 있습니다. • FUSED DEPOSITION MODELING : FDM으로도 약칭되는 이 방법에서는 로봇 제어 압출기 헤드가 테이블 위에서 두 가지 기본 방향으로 이동합니다. 필요에 따라 케이블을 내리고 올립니다. 헤드의 가열된 다이 오리피스에서 열가소성 필라멘트가 압출되고 초기 레이어가 폼 기초에 증착됩니다. 이것은 미리 결정된 경로를 따르는 압출기 헤드에 의해 수행됩니다. 초기 레이어 후에 테이블이 낮아지고 후속 레이어가 서로 위에 증착됩니다. 때로는 복잡한 부품을 제조할 때 특정 방향으로 증착이 계속될 수 있도록 지지 구조가 필요합니다. 이러한 경우 지지재는 층에 필라멘트의 간격이 덜 조밀하게 압출되어 모델재보다 약합니다. 이러한 지지 구조는 나중에 부품이 완성된 후 분해되거나 분리될 수 있습니다. 압출기 다이 치수는 압출된 층의 두께를 결정합니다. FDM 공정은 비스듬한 외부 평면에 계단이 있는 표면이 있는 부품을 생산합니다. 이 거칠기가 허용되지 않는 경우 화학 증기 연마 또는 가열 도구를 사용하여 매끄럽게 할 수 있습니다. 이러한 단계를 제거하고 합리적인 기하 공차를 달성하기 위해 연마 왁스도 코팅 재료로 사용할 수 있습니다. • 선택적 레이저 소결: SLS라고도 하는 이 공정은 고분자, 세라믹 또는 금속 분말을 대상물에 선택적으로 소결하는 것을 기반으로 합니다. 처리 챔버의 바닥에는 부품 제작 실린더와 분말 공급 실린더의 두 개의 실린더가 있습니다. 전자는 소결 부품이 형성되는 곳까지 점진적으로 낮아지고 후자는 롤러 메커니즘을 통해 부품 제작 실린더에 분말을 공급하기 위해 점진적으로 올라갑니다. 먼저 부품 제작 실린더에 얇은 분말 층이 증착된 다음 레이저 빔이 해당 층에 집중되어 특정 단면을 추적 및 용융/소결한 다음 고체로 재응고됩니다. 파우더는 레이저 빔이 닿지 않는 영역이 느슨하게 남아 있지만 여전히 단단한 부분을 지지합니다. 그런 다음 또 다른 분말 층이 증착되고 이 과정을 여러 번 반복하여 부품을 얻습니다. 마지막에 느슨한 분말 입자를 털어냅니다. 이 모든 작업은 제조 중인 부품의 3D CAD 프로그램에서 생성된 지침을 사용하여 프로세스 제어 컴퓨터에 의해 수행됩니다. 폴리머(ABS, PVC, 폴리에스터 등), 왁스, 금속 및 세라믹과 같은 다양한 재료를 적절한 폴리머 바인더로 증착할 수 있습니다. • ELECTRON-BEAM MELTING : 선택적 레이저 소결과 유사하지만 전자빔을 사용하여 티타늄 또는 코발트 크롬 분말을 녹여 진공에서 프로토타입을 만듭니다. 스테인리스강, 알루미늄 및 구리 합금에 이 공정을 수행하기 위해 일부 개발이 이루어졌습니다. 생산된 부품의 피로 강도를 높여야 하는 경우 부품 제조에 이어 열간 등방압 프레스를 2차 공정으로 사용합니다. • 3차원 인쇄: 3DP라고도 하는 이 기술에서 프린트 헤드는 비금속 또는 금속 분말 층에 무기 바인더를 증착합니다. 분말 베드를 운반하는 피스톤이 점차 낮아지고 각 단계에서 바인더가 층별로 적층되고 바인더에 의해 융합됩니다. 사용된 분말 재료는 폴리머 블렌드 및 섬유, 주조 모래, 금속입니다. 다른 바인더 헤드를 동시에 사용하고 다른 색상 바인더를 사용하면 다양한 색상을 얻을 수 있습니다. 이 과정은 잉크젯 인쇄와 유사하지만 컬러 시트를 얻는 대신 컬러 3차원 물체를 얻습니다. 생산된 부품은 다공성일 수 있으므로 밀도와 강도를 높이기 위해 소결 및 금속 침투가 필요할 수 있습니다. 소결은 바인더를 태우고 금속 분말을 함께 융합시킵니다. 스테인레스 스틸, 알루미늄, 티타늄과 같은 금속은 부품을 만드는 데 사용할 수 있으며 침투 재료로는 일반적으로 구리와 청동을 사용합니다. 이 기술의 장점은 복잡하고 움직이는 어셈블리도 매우 빠르게 제조할 수 있다는 것입니다. 예를 들어, 기어 어셈블리, 도구로서의 렌치를 만들 수 있으며 사용할 준비가 된 움직이는 부품과 회전 부품을 갖게 됩니다. 어셈블리의 여러 구성 요소를 한 번에 다양한 색상으로 제조할 수 있습니다. 다음에서 브로셔 다운로드:금속 3D 프린팅 기초 • DIRECT MANUFACTURING 및 RAPID TOOLING : 설계 평가 외에도 문제 해결을 위해 제품을 직접 제조하거나 제품에 직접 적용하기 위해 Rapid prototyping을 사용합니다. 즉, 신속한 프로토타이핑을 기존 프로세스에 통합하여 더 우수하고 경쟁력 있게 만들 수 있습니다. 예를 들어, 신속한 프로토타이핑은 패턴과 금형을 생성할 수 있습니다. 신속한 프로토타이핑 작업으로 생성된 용융 및 연소 폴리머의 패턴은 매몰 주조를 위해 조립되고 매몰될 수 있습니다. 언급할 또 다른 예는 3DP를 사용하여 세라믹 주조 쉘을 생산하고 쉘 주조 작업에 사용하는 것입니다. 사출 금형 및 금형 인서트도 신속한 프로토타이핑으로 생산할 수 있으며 금형 제작 리드 타임을 몇 주 또는 몇 달 절약할 수 있습니다. 원하는 부품의 CAD 파일만 분석하면 소프트웨어를 사용하여 도구 형상을 생성할 수 있습니다. 다음은 인기 있는 빠른 툴링 방법 중 일부입니다. RTV(Room-Temperature Vulcanizing) MOLDING / URETHANE CASTING : Rapid prototyping을 이용하여 원하는 부품의 패턴을 만들 수 있습니다. 그런 다음 이 패턴을 이형제로 코팅하고 액체 RTV 고무를 패턴 위에 부어서 몰드 반쪽을 생성합니다. 다음으로, 이 금형 반쪽은 액체 우레탄을 사출 성형하는 데 사용됩니다. 금형 수명은 0 또는 30 사이클처럼 짧지만 소량 생산에는 충분합니다. ACES(Acetal Clear Epoxy Solid) 사출 성형 : 광조형과 같은 쾌속 조형 기술을 사용하여 사출 금형을 생산합니다. 이 몰드는 에폭시, 알루미늄 충전 에폭시 또는 금속과 같은 재료로 채울 수 있도록 끝이 열린 쉘입니다. 다시 금형 수명은 수십 또는 최대 수백 개의 부품으로 제한됩니다. SPRAYED METAL TOOLING PROCESS : 우리는 빠른 프로토 타이핑을 사용하여 패턴을 만듭니다. 패턴 표면에 아연-알루미늄 합금을 분사하고 코팅합니다. 그런 다음 금속 코팅된 패턴을 플라스크 내부에 놓고 에폭시 또는 알루미늄으로 채워진 에폭시로 포팅합니다. 마지막으로 제거하고 두 개의 반쪽 금형을 생산하여 사출 성형을 위한 완전한 금형을 얻습니다. 이 금형은 재료와 온도에 따라 더 긴 수명을 가지며 수천 개의 부품을 생산할 수 있습니다. KEELTOOL PROCESS : 이 기술은 100,000~1000만 사이클 수명의 금형을 생산할 수 있습니다. 신속한 프로토타이핑을 사용하여 RTV 금형을 생산합니다. 다음으로 금형은 A6 공구강 분말, 텅스텐 카바이드, 폴리머 바인더로 구성된 혼합물로 채워지고 경화됩니다. 그런 다음 이 몰드를 가열하여 폴리머를 태우고 금속 분말을 융합시킵니다. 다음 단계는 최종 금형을 생산하기 위한 구리 침투입니다. 필요한 경우 더 나은 치수 정확도를 위해 금형에서 기계가공 및 연마와 같은 2차 작업을 수행할 수 있습니다. _cc781905-5cde-3194-bb3b-136bad5cf5 CLICK Product Finder-Locator Service 이전 페이지
- Joining & Assembly & Fastening Processes, Welding, Brazing, Soldering
Joining & Assembly & Fastening Processes, Welding, Brazing, Soldering, Sintering, Adhesive Bonding, Press Fitting, Wave and Reflow Solder Process, Torch Furnace 결합 및 조립 및 고정 프로세스 WELDING, BRAZING, SOLDERING, SINTERING, ADHESIVE BONDING, FASTENING, PRESS FITTING을 사용하여 제조 부품을 결합, 조립 및 고정하고 완제품 또는 반제품으로 변환합니다. 가장 널리 사용되는 용접 공정 중 일부는 아크, 산소 연료 가스, 저항, 투영, 이음매, 업셋, 충격, 고체 상태, 전자빔, 레이저, 써밋, 유도 용접입니다. 우리의 인기 있는 브레이징 공정은 토치, 인덕션, 퍼니스 및 딥 브레이징입니다. 우리의 납땜 방법은 철, 핫 플레이트, 오븐, 인덕션, 딥, 웨이브, 리플로 및 초음파 납땜입니다. 접착 결합을 위해 우리는 열가소성 수지 및 열경화성, 에폭시, 페놀, 폴리우레탄, 접착 합금 및 기타 화학 물질 및 테이프를 자주 사용합니다. 마지막으로 우리의 고정 프로세스는 못 박기, 나사 고정, 너트와 볼트, 리벳 팅, 클린칭, 고정, 스티칭 및 스테이플링 및 압입으로 구성됩니다. • WELDING : 용접은 가공물을 녹이고 용가재를 도입하여 재료를 접합하는 것으로 용융된 용접 풀도 합류합니다. 해당 지역이 식으면 강한 관절을 얻습니다. 경우에 따라 압력이 가해집니다. 용접과 달리 브레이징 및 솔더링 작업은 공작물 사이의 융점이 낮은 재료의 용융만 포함하며 공작물은 용융되지 않습니다. 여기를 클릭하는 것이 좋습니다.AGS-TECH Inc.의 용접 공정 개략도를 다운로드하십시오. 이렇게 하면 아래에서 제공하는 정보를 더 잘 이해하는 데 도움이 됩니다. 아크 용접에서는 전원 공급 장치와 전극을 사용하여 금속을 녹이는 전기 아크를 생성합니다. 용접점은 차폐 가스, 증기 또는 기타 재료로 보호됩니다. 이 공정은 자동차 부품 및 철강 구조물 용접에 널리 사용됩니다. shelded metal arc welding(SMAW) 또는 스틱 용접이라고도 하는 용접에서 전극 스틱을 모재에 가까이 가져오고 전극 스틱 사이에 전기 아크가 생성됩니다. 전극봉이 녹아서 충전재 역할을 합니다. 전극은 또한 슬래그 층으로 작용하고 차폐 가스로 작용하는 증기를 방출하는 플럭스를 포함합니다. 이는 환경 오염으로부터 용접 영역을 보호합니다. 다른 필러는 사용되지 않습니다. 이 공정의 단점은 속도가 느리고 전극을 자주 교체해야 하며 플럭스에서 발생하는 잔류 슬래그를 제거해야 한다는 것입니다. 철, 강철, 니켈, 알루미늄, 구리 등의 여러 금속. 용접할 수 있습니다. 장점은 저렴한 도구와 사용 용이성입니다. 금속 불활성 가스(MIG)라고도 하는 가스 금속 아크 용접(GMAW)은 용접 영역의 환경 오염에 대해 와이어 주위를 흐르는 불활성 또는 부분적으로 불활성 가스와 소모성 전극 와이어 필러를 지속적으로 공급합니다. 강철, 알루미늄 및 기타 비철금속을 용접할 수 있습니다. MIG의 장점은 높은 용접 속도와 우수한 품질입니다. 단점은 용접 영역 주변의 차폐 가스를 안정적으로 유지해야 하기 때문에 바람이 많이 부는 실외 환경에서 직면하는 복잡한 장비와 문제입니다. GMAW의 변형은 플럭스 재료로 채워진 미세한 금속 튜브로 구성된 플럭스 코어드 아크 용접(FCAW)입니다. 때로는 튜브 내부의 플럭스가 환경 오염으로부터 보호하기에 충분합니다. 서브머지드 아크 용접(SAW)은 광범위하게 자동화된 프로세스로, 연속 와이어 공급 및 플럭스 커버 층 아래에서 발생하는 아크를 포함합니다. 생산율과 품질이 높고 용접 슬래그가 쉽게 떨어져 나가며 연기가 나지 않는 작업 환경을 갖추고 있습니다. 단점은 특정 위치에서 parts를 용접하는 데에만 사용할 수 있다는 것입니다. 가스 텅스텐 아크 용접(GTAW) 또는 텅스텐-비활성 가스 용접(TIG)에서 우리는 별도의 필러 및 불활성 또는 거의 불활성 가스와 함께 텅스텐 전극을 사용합니다. 우리가 알고 있듯이 텅스텐은 융점이 높으며 매우 높은 온도에 매우 적합한 금속입니다. TIG의 텅스텐은 위에서 설명한 다른 방법과 달리 소비되지 않습니다. 얇은 재료의 용접에서 다른 기술에 비해 느리지만 고품질의 용접 기술입니다. 많은 금속에 적합합니다. 플라즈마 아크 용접은 유사하지만 플라즈마 가스를 사용하여 아크를 생성합니다. 플라즈마 아크 용접의 아크는 GTAW에 비해 상대적으로 더 집중되어 있으며 훨씬 빠른 속도로 더 넓은 범위의 금속 두께에 사용할 수 있습니다. GTAW 및 플라즈마 아크 용접은 다소 동일한 재료에 적용될 수 있습니다. OXY-FUEL / OXYFUEL WELDING 옥시아세틸렌 용접이라고도 하며, 산소 용접, 가스 용접은 용접용 가스 연료와 산소를 사용하여 수행됩니다. 전력을 사용하지 않기 때문에 휴대용으로 전기가 없는 곳에서도 사용할 수 있습니다. 용접 토치를 사용하여 조각과 충전재를 가열하여 공유 용융 금속 풀을 생성합니다. 아세틸렌, 가솔린, 수소, 프로판, 부탄 등 다양한 연료를 사용할 수 있습니다. 순산소 용접에서 우리는 두 개의 용기를 사용합니다. 하나는 연료용이고 다른 하나는 산소용입니다. 산소는 연료를 산화시킵니다(연소). RESISTANCE WELDING: joule heating을 이용하여 전류가 인가되는 위치에서 일정 시간 열을 발생시키는 용접 방식입니다. 높은 전류가 금속을 통과합니다. 이 위치에서 용융 금속 풀이 형성됩니다. 저항 용접 방법은 효율성과 오염 가능성이 적기 때문에 널리 사용됩니다. 그러나 단점은 장비 비용이 상대적으로 중요하고 상대적으로 얇은 공작물에 대한 고유한 한계입니다. 스폿 용접은 저항 용접의 주요 유형 중 하나입니다. 여기서 우리는 두 개 이상의 구리 전극을 사용하여 두 개 이상의 겹치는 시트 또는 공작물을 결합하여 시트를 함께 고정하고 높은 전류를 통과시킵니다. 구리 전극 사이의 물질이 가열되고 그 위치에 용융 풀이 생성됩니다. 그런 다음 전류가 멈추고 전극이 수냉식이므로 구리 전극 팁이 용접 위치를 냉각시킵니다. 올바른 재료와 두께에 적절한 양의 열을 가하는 것이 이 기술의 핵심입니다. 잘못 적용하면 접합부가 약해지기 때문입니다. 스폿 용접은 공작물에 큰 변형을 일으키지 않고 에너지 효율이 높고 자동화가 쉽고 생산 속도가 우수하며 필러가 필요하지 않은 장점이 있습니다. 단점은 용접이 연속적인 이음매를 형성하지 않고 스폿에서 이루어지기 때문에 전체 강도가 다른 용접 방법에 비해 상대적으로 낮을 수 있다는 것입니다. 반면에 SEAM WELDING은 유사한 재료의 접합 표면에서 용접을 생성합니다. 솔기는 맞대기 또는 겹침 조인트가 될 수 있습니다. 심 용접은 한쪽 끝에서 시작하여 다른 쪽 끝으로 점진적으로 이동합니다. 이 방법은 또한 두 개의 구리 전극을 사용하여 용접 영역에 압력과 전류를 가합니다. 디스크 모양의 전극은 솔기 라인을 따라 일정한 접촉으로 회전하고 연속 용접을 합니다. 여기에서도 전극은 물로 냉각됩니다. 용접은 매우 강력하고 신뢰할 수 있습니다. 다른 방법으로는 프로젝션, 플래시 및 업셋 용접 기술이 있습니다. SOLID-STATE WELDING은 위에서 설명한 이전 방법과 약간 다릅니다. 유착은 금속 충전재를 사용하지 않고 결합된 금속의 용융 온도보다 낮은 온도에서 발생합니다. 일부 공정에서는 압력이 사용될 수 있습니다. 다양한 방법으로는 이종 금속을 동일한 다이를 통해 압출하는 공압출 용접, 융점 이하의 연질 합금을 접합하는 냉압 용접, 용접선이 보이지 않는 확산 용접, 내식성 합금과 같은 이종 재료를 구조에 접합하는 폭발 용접이 있습니다. 강, 강관과 판재를 전자기력으로 가속하는 ELECTROMAGNETIC PULSE WELDING, 금속을 고온으로 가열하여 함께 망치질하는 FORGE WELDING, 충분한 마찰로 용접하는 FRICTION WELDING, 회전하지 않고 회전하는 FRICTION STIR WELDING 접합선을 가로지르는 소모품 도구, 진공 또는 불활성 가스에서 용융 온도 이하의 고온에서 금속을 함께 누르는 HOT PRESSURE WELDING, 용기 내부의 불활성 가스를 사용하여 압력을 가하는 공정 HOT ISOSTATIC PRESSURE WELDING, 접합하는 ROLL WELDING 서로 다른 재료를 강제로 두 개의 회전 바퀴, 고주파 진동 에너지를 사용하여 얇은 금속 또는 플라스틱 시트를 용접하는 ULTRASONIC WELDING. 다른 용접 공정으로는 깊은 용입과 빠른 가공을 하는 ELECTRON BEAM WELDING이지만 특수한 경우에는 고가라고 생각하는 ELECTROSLAG WELDING, 두꺼운 후판과 철재에만 적합한 ELECTROSLAG WELDING, 전자기 유도를 사용하는 INDUCTION WELDING 등이 있습니다. 우리의 전기 전도성 또는 강자성 공작물을 가열, 깊은 침투와 빠른 처리 그러나 고가의 방법을 사용하는 LASER BEAM WELDING, 동일한 용접 헤드에서 LBW와 GMAW를 결합하고 플레이트 사이의 2mm 간격을 연결할 수 있는 LASER HYBRID WELDING, PERCUSSION WELDING 방전 후 압력을 가하여 재료를 단조하는 방법, 알루미늄과 산화철 분말 사이의 발열 반응을 포함하는 THERMIT WELDING, 소모성 전극을 사용하고 수직 위치에 강철만 사용하는 ELECTROGAS WELDING, 마지막으로 스터드를 베이스에 접합하기 위한 STUD ARC WELDING이 포함됩니다. 열과 압력이 있는 재료. 여기를 클릭하는 것이 좋습니다.AGS-TECH Inc의 브레이징, 납땜 및 접착 본딩 공정의 개략도를 다운로드하십시오. 이렇게 하면 아래에서 제공하는 정보를 더 잘 이해하는 데 도움이 됩니다. • BRAZING : 두 개 이상의 금속을 융점 이상으로 가열하고 모세관 현상을 이용하여 두 개 이상의 금속을 접합합니다. 이 공정은 납땜과 유사하지만 충전재를 녹이는 데 관련된 온도는 납땜에서 더 높습니다. 용접과 마찬가지로 플럭스는 대기 오염으로부터 충전재를 보호합니다. 냉각 후 공작물이 함께 결합됩니다. 이 프로세스에는 다음과 같은 주요 단계가 포함됩니다. 적절한 맞춤 및 간극, 기본 재료의 적절한 세척, 적절한 고정, 적절한 플럭스 및 분위기 선택, 어셈블리 가열 및 최종적으로 납땜 어셈블리의 세척. 당사의 일부 납땜 공정은 수동 또는 자동 방식으로 수행되는 인기 있는 방법인 TORCH BRAZING입니다. 소량 생산 주문 및 특수 케이스에 적합합니다. 납땜되는 접합부 근처에 가스 화염을 사용하여 열이 가해집니다. Furnace BRAZING은 작업자의 기술이 덜 필요하고 산업용 대량 생산에 적합한 반자동 공정입니다. 퍼니스의 온도 제어와 분위기 제어는 모두 이 기술의 장점입니다. 전자는 토치 브레이징의 경우처럼 열 사이클을 제어하고 국부 가열을 제거할 수 있고 후자는 부품을 산화로부터 보호하기 때문입니다. 지깅을 사용하여 제조 비용을 최소화할 수 있습니다. 단점은 높은 전력 소비, 장비 비용 및 더 까다로운 설계 고려 사항입니다. VACUUM BRAZING은 진공 용광로에서 이루어집니다. 온도 균일성이 유지되고 잔류 응력이 거의 없는 플럭스가 없고 매우 깨끗한 조인트를 얻을 수 있습니다. 열처리는 느린 가열 및 냉각 주기 동안 존재하는 낮은 잔류 응력 때문에 진공 브레이징 중에 발생할 수 있습니다. 가장 큰 단점은 진공 환경을 만드는 데 비용이 많이 들기 때문에 비용이 많이 든다는 것입니다. 또 다른 기술 DIP BRAZING은 접합면에 브레이징 화합물이 적용되는 고정 부품을 결합합니다. 그 후 fixtured 부품을 열 전달 매체 및 플럭스로 작용하는 염화나트륨(식염)과 같은 용융염 욕조에 담근다. 공기가 배제되어 산화물 형성이 일어나지 않습니다. 인덕션 브레이징에서는 모재보다 융점이 낮은 용가재로 재료를 접합합니다. 유도 코일의 교류는 대부분 철 자성 재료에 유도 가열을 유도하는 전자기장을 생성합니다. 이 방법은 선택적인 가열, 충전제가 원하는 영역에만 흐르는 양호한 접합부, 화염이 존재하지 않고 냉각이 빠르기 때문에 산화가 적음, 빠른 가열, 일관성 및 대량 제조에 대한 적합성을 제공합니다. 공정 속도를 높이고 일관성을 보장하기 위해 우리는 프리폼을 자주 사용합니다. 세라믹-금속 피팅, 밀폐 밀봉, 진공 피드스루, 고진공 및 초고진공 및 유체 제어 부품을 생산하는 당사의 브레이징 시설에 대한 정보는 여기에서 확인할 수 있습니다._cc781905-5cde-3194-bb3b-136d_브레이징 공장 브로셔 • SOLDERING : 솔더링에서는 가공물이 녹는 것이 아니라 접합부로 흘러 들어가는 접합부보다 융점이 낮은 용가재가 있습니다. 납땜에서 용가재는 납땜보다 낮은 온도에서 녹습니다. 우리는 납땜을 위해 무연 합금을 사용하고 RoHS를 준수하며 다양한 애플리케이션 및 요구 사항에 대해 은 합금과 같은 다양하고 적합한 합금을 보유하고 있습니다. 납땜은 기체 및 액체가 새지 않는 접합부를 제공합니다. SOFT SOLDERING에서 우리의 용가재는 섭씨 400도 미만의 융점을 갖는 반면 SILVER SOLDERING 및 BRAZING에서는 더 높은 온도가 필요합니다. 소프트 솔더링은 더 낮은 온도를 사용하지만 고온에서 까다로운 애플리케이션을 위한 강한 접합을 생성하지 않습니다. 반면에 은 납땜은 토치에 의해 제공되는 고온이 필요하고 고온 응용 분야에 적합한 강한 접합부를 제공합니다. 브레이징에는 가장 높은 온도가 필요하며 일반적으로 토치가 사용됩니다. 브레이징 조인트는 매우 강하기 때문에 무거운 철 물체를 수리하기에 좋은 후보입니다. 우리의 제조 라인에서는 수동 수동 납땜과 자동 납땜 라인을 모두 사용합니다. INDUCTION SOLDERING은 유도 가열을 촉진하기 위해 구리 코일에서 고주파 AC 전류를 사용합니다. 납땜 부분에 전류가 유도되어 고저항 joint에서 열이 발생합니다. 이 열은 용가재를 녹입니다. 플럭스도 사용됩니다. 유도 납땜은 코일을 감아 연속 공정으로 실린더와 파이프를 납땜하는 좋은 방법입니다. 흑연 및 세라믹과 같은 일부 재료를 납땜하는 것은 납땜 전에 적절한 금속으로 공작물을 도금해야 하기 때문에 더 어렵습니다. 이것은 계면 결합을 용이하게 합니다. 우리는 특히 밀폐 포장 응용 분야를 위해 이러한 재료를 납땜합니다. 우리는 주로 WAVE SOLDERING을 사용하여 인쇄 회로 기판(PCB)을 대량 생산합니다. 소량의 프로토 타이핑 목적으로만 우리는 납땜 인두를 사용하여 손 납땜을 사용합니다. 우리는 스루홀과 표면 실장 PCB 어셈블리(PCBA) 모두에 웨이브 솔더링을 사용합니다. 임시 접착제는 부품이 회로 기판에 부착된 상태를 유지하고 어셈블리가 컨베이어에 배치되고 용융 땜납이 포함된 장비를 통해 이동합니다. 먼저 PCB가 플럭스화된 다음 예열 영역으로 들어갑니다. 용융 땜납은 팬에 있고 표면에 정상파 패턴이 있습니다. PCB가 이 파동 위로 이동할 때 이 파동이 PCB 바닥에 닿아 납땜 패드에 달라붙습니다. 솔더는 핀과 패드에만 남아 있고 PCB 자체에는 남아 있지 않습니다. 용융 땜납의 파도는 튀지 않고 파도 꼭대기가 보드의 원하지 않는 부분을 만지거나 오염시키지 않도록 잘 제어되어야 합니다. REFLOW SOLDERING에서는 점착성 솔더 페이스트를 사용하여 전자 부품을 보드에 임시로 부착합니다. 그런 다음 보드는 온도 조절 기능이 있는 리플로 오븐을 통과합니다. 여기에서 땜납이 녹고 구성 요소를 영구적으로 연결합니다. 우리는 이 기술을 표면 실장 부품과 관통 구멍 부품 모두에 사용합니다. 적절한 온도 제어 및 오븐 온도 조정은 기판의 전자 부품이 최대 온도 한계 이상으로 과열되어 파손되는 것을 방지하는 데 필수적입니다. 리플 로우 솔더링 과정에서 실제로 예열 단계, 열 흡수 단계, 리플 로우 및 냉각 단계와 같은 뚜렷한 열 프로파일을 가진 여러 영역 또는 단계가 있습니다. 이러한 다양한 단계는 PCBA(인쇄 회로 기판 어셈블리)의 손상 없는 리플로 납땜에 필수적입니다. ULTRASONIC SOLDERING은 독특한 기능을 가진 자주 사용되는 또 다른 기술입니다. 유리, 세라믹 및 비금속 재료를 납땜하는 데 사용할 수 있습니다. 예를 들어 비금속인 광전지 패널에는 이 기술을 사용하여 부착할 수 있는 전극이 필요합니다. 초음파 납땜에서는 초음파 진동도 방출하는 가열된 납땜 팁을 배치합니다. 이러한 진동은 기판과 용융 솔더 재료의 계면에서 캐비테이션 거품을 생성합니다. 캐비테이션의 파열 에너지는 산화물 표면을 수정하고 먼지와 산화물을 제거합니다. 이 시간 동안 합금 층이 또한 형성됩니다. 결합 표면의 땜납은 산소를 포함하고 유리와 땜납 사이에 강한 공유 결합을 형성할 수 있습니다. DIP SOLDERING은 소규모 생산에만 적합한 웨이브 솔더링의 간단한 버전으로 간주될 수 있습니다. 첫 번째 세척 플럭스는 다른 공정과 마찬가지로 적용됩니다. 부품이 장착된 PCB는 수동 또는 반자동 방식으로 용융 땜납이 들어 있는 탱크에 담근다. 녹은 솔더는 기판의 솔더 마스크로 보호되지 않은 노출된 금속 영역에 달라붙습니다. 장비가 간단하고 저렴합니다. • ADHESIVE BONDING : 이것은 우리가 자주 사용하는 또 다른 대중적인 기술이며 접착제, 에폭시, 플라스틱 에이전트 또는 기타 화학 물질을 사용하여 표면을 접착하는 것과 관련됩니다. 결합은 용매 증발, 열 경화, UV 광 경화, 압력 경화 또는 특정 시간 대기에 의해 수행됩니다. 당사의 생산 라인에는 다양한 고성능 접착제가 사용됩니다. 적절하게 설계된 적용 및 경화 공정을 통해 접착 결합은 강력하고 신뢰할 수 있는 매우 낮은 응력 결합을 생성할 수 있습니다. 접착제는 습기, 오염 물질, 부식성, 진동 등의 환경 요인에 대한 좋은 보호 장치가 될 수 있습니다. 접착 결합의 장점은 다음과 같습니다. 그렇지 않으면 납땜, 용접 또는 납땜하기 어려운 재료에 적용할 수 있습니다. 또한 용접 또는 기타 고온 공정에 의해 손상되는 열에 민감한 재료에 적합할 수 있습니다. 접착제의 다른 장점은 불규칙한 모양의 표면에 적용할 수 있고 다른 방법과 비교할 때 매우 적은 양으로 조립 중량을 증가시킬 수 있다는 것입니다. 또한 부품의 치수 변화가 매우 적습니다. 일부 접착제는 굴절률 일치 특성을 가지며 빛 또는 광학 신호 강도를 크게 감소시키지 않으면서 광학 부품 사이에 사용할 수 있습니다. 반면에 단점은 경화 시간이 길어 제조 라인, 고정 장치 요구 사항, 표면 준비 요구 사항 및 재작업이 필요할 때 분해하기 어려운 속도를 늦출 수 있습니다. 대부분의 접착 접합 작업에는 다음 단계가 포함됩니다. -표면 처리: 탈이온수 세척, 알코올 세척, 플라즈마 또는 코로나 세척과 같은 특수 세척 절차가 일반적입니다. 청소 후 가능한 한 최상의 접합을 보장하기 위해 표면에 접착 촉진제를 적용할 수 있습니다. -부품 고정: 접착제 도포와 경화 모두를 위해 맞춤형 고정 장치를 설계하고 사용합니다. -접착제 적용: 우리는 때로는 수동을 사용하고 때로는 로봇 공학, 서보 모터, 선형 액추에이터와 같은 자동화 시스템을 사용하여 접착제를 올바른 위치에 전달하고 디스펜서를 사용하여 적절한 양과 양으로 전달합니다. -경화: 접착제에 따라 단순 건조 및 경화, 촉매 역할을 하는 UV 광선 하에서의 경화 또는 오븐에서 열경화 또는 지그 및 고정구에 장착된 저항 발열체를 사용하는 경화를 사용할 수 있습니다. 여기를 클릭하는 것이 좋습니다.AGS-TECH Inc.의 고정 프로세스 개략도를 다운로드하십시오. 이렇게 하면 아래에서 제공하는 정보를 더 잘 이해하는 데 도움이 됩니다. • FASTENING PROCESSES: 당사의 기계적 결합 프로세스는 FASTENERS 및 INTEGRAL JOINTS의 두 가지 브래드 범주로 나뉩니다. 우리가 사용하는 패스너의 예로는 나사, 핀, 너트, 볼트, 리벳이 있습니다. 우리가 사용하는 일체형 조인트의 예로는 스냅 및 열박음, 솔기, 크림프가 있습니다. 다양한 고정 방법을 사용하여 기계식 조인트가 수년 동안 견고하고 신뢰할 수 있는지 확인합니다. 나사와 볼트는 물체를 함께 고정하고 위치를 지정하는 데 가장 일반적으로 사용되는 패스너입니다. 당사의 나사와 볼트는 ASME 표준을 충족합니다. 육각 캡 나사 및 육각 볼트, 래그 나사 및 볼트, 양단 나사, 맞춤 나사, 아이 나사, 미러 나사, 판금 나사, 미세 조정 나사, 셀프 드릴링 및 셀프 태핑 나사 등 다양한 유형의 나사 및 볼트가 배치됩니다. , 고정 나사, 내장 와셔가 있는 나사 등… 접시머리, 돔, 원형, 플랜지 머리와 같은 다양한 나사 머리 유형과 슬롯, 필립스, 사각형, 육각 소켓과 같은 다양한 나사 드라이브 유형이 있습니다. 다른 한편으로 A RIVET은 한편으로는 매끄러운 원통형 샤프트와 헤드로 구성된 영구 기계식 패스너입니다. 삽입 후 리벳의 다른 쪽 끝이 변형되고 직경이 확장되어 제자리에 유지됩니다. 즉, 리벳을 설치하기 전에는 헤드가 하나이고 설치 후에는 헤드가 두 개입니다. 솔리드/라운드 헤드 리벳, 구조용, 반관형, 블라인드, 오스카, 드라이브, 플러시, 마찰 잠금, 셀프 피어싱 리벳 등 용도, 강도, 접근성 및 비용에 따라 다양한 유형의 리벳을 설치합니다. 용접 열로 인한 열 변형 및 재료 특성의 변화를 피해야 하는 경우 리벳팅이 선호될 수 있습니다. 리벳팅은 또한 경량이며 특히 전단력에 대한 우수한 강도와 내구성을 제공합니다. 그러나 인장 하중에 대해서는 나사, 너트 및 볼트가 더 적합할 수 있습니다. CLINCHING 공정에서 우리는 접합되는 판금 사이에 기계적 인터록을 형성하기 위해 특수 펀치와 다이를 사용합니다. 펀치는 판금 층을 다이 캐비티로 밀어넣고 영구 조인트를 형성합니다. 클린칭 시 가열 및 냉각이 필요하지 않으며 냉간 가공 공정입니다. 경우에 따라 스폿 용접을 대체할 수 있는 경제적인 공정입니다. PINNING에서 우리는 기계 부품의 상대적인 위치를 고정하는 데 사용되는 기계 요소인 핀을 사용합니다. 주요 유형은 클레비스 핀, 분할 핀, 스프링 핀, 맞춤 핀, 및 분할 핀입니다. 스테이플링에서는 재료를 결합하거나 묶는 데 사용되는 두 갈래 패스너인 스테이플링 건과 스테이플을 사용합니다. 스테이플링에는 다음과 같은 장점이 있습니다. 경제적이고 간단하며 사용이 빠릅니다. 스테이플의 크라운을 사용하여 서로 맞댐된 재료를 연결할 수 있습니다. 스테이플의 크라운을 사용하면 케이블과 같은 조각을 쉽게 연결하여 구멍을 뚫거나 표면에 고정할 수 있습니다. 손상, 비교적 쉬운 제거. PRESS FITTING은 부품을 서로 밀어서 수행하며 부품 간의 마찰로 부품이 고정됩니다. 오버사이즈 샤프트와 언더사이즈 구멍으로 구성된 압입 부품은 일반적으로 힘을 가하거나 부품의 열팽창 또는 수축을 이용하는 두 가지 방법 중 하나로 조립됩니다. 힘을 가해 압입을 할 때 유압프레스나 수동프레스를 사용합니다. 반면에 열팽창에 의해 압입이 이루어지면 우리는 둘러싸는 부품을 가열하고 뜨거울 때 제자리에 조립합니다. 냉각되면 수축하고 원래 크기로 돌아갑니다. 그 결과 압입이 잘 됩니다. 우리는 이것을 SHRINK-FITTING이라고 부릅니다. 이 작업을 수행하는 다른 방법은 조립 전에 엔벨로프 부품을 냉각한 다음 짝을 이루는 부품으로 밀어 넣는 것입니다. 조립품이 예열되면 팽창하여 꽉 끼게 됩니다. 이 후자의 방법은 가열이 재료 특성을 변경할 위험이 있는 경우에 선호될 수 있습니다. 이러한 경우 냉각이 더 안전합니다. 공압 및 유압 부품 및 어셈블리 • 밸브, O-링, 와셔, 씰, 개스킷, 링, 심과 같은 유압 및 공압 부품. 밸브와 공압 부품은 매우 다양하기 때문에 여기에 모든 것을 나열할 수는 없습니다. 응용 프로그램의 물리적 및 화학적 환경에 따라 특수 제품이 있습니다. 밸브 및 공압 부품과 접촉하게 될 압력, 온도, 액체 또는 가스와 같은 애플리케이션, 구성 요소 유형, 사양, 환경 조건을 지정하십시오. 그리고 우리는 귀하에게 가장 적합한 제품을 선택하거나 귀하의 응용 분야에 맞게 특별히 제조할 것입니다. CLICK Product Finder-Locator Service 이전 페이지
- Composites, Composite Materials Manufacturing, Fiber Reinforced
Composites, Composite Materials Manufacturing, Particle and Fiber Reinforced, Cermets, Ceramic & Metal Composite, Glass Fiber Reinforced Polymer, Lay-Up Process 복합재료 및 복합재료 제조 간단히 정의하면 COMPOSITES 또는 COMPOSITE MATERIALS는 물리적 또는 화학적 특성이 다른 두 가지 이상의 재료로 구성된 재료이지만 결합하면 구성 재료와 다른 재료가 됩니다. 우리는 구성 재료가 구조에서 분리되고 구별된다는 점을 지적할 필요가 있습니다. 복합재료 제조의 목적은 구성성분보다 우수하고 각 구성성분이 원하는 특성을 결합한 제품을 얻는 것입니다. 예로서; 강도, 낮은 무게 또는 낮은 가격은 복합 재료를 설계하고 생산하는 동기가 될 수 있습니다. 우리가 제공하는 복합 재료의 유형은 입자 강화 복합 재료, 세라믹-매트릭스/폴리머-매트릭스/금속-매트릭스/탄소-탄소/하이브리드 복합 재료를 포함한 섬유 강화 복합 재료, 구조 및 적층 및 샌드위치 구조 복합 재료 및 나노 복합 재료입니다. 복합 재료 제조에 사용하는 제조 기술은 다음과 같습니다. 많은 복합 재료는 연속적이고 다른 상을 둘러싸는 두 개의 상으로 구성됩니다. 및 매트릭스에 의해 둘러싸인 분산상. 여기를 클릭하는 것이 좋습니다.AGS-TECH Inc.의 복합 재료 및 복합 재료 제조 개략도를 다운로드하십시오. 이렇게 하면 아래에서 제공하는 정보를 더 잘 이해하는 데 도움이 됩니다. • PARTICLE-REINFORCED COMPOSITES : 이 범주는 두 가지 유형으로 구성됩니다. 전자의 경우 입자-기질 상호작용은 원자 또는 분자 수준에서 처리할 수 없습니다. 대신 연속체 역학이 유효합니다. 반면에, 분산 강화 복합 재료에서 입자는 일반적으로 수십 나노미터 범위에서 훨씬 더 작습니다. 큰 입자 합성물의 예는 충전제가 추가된 폴리머입니다. 충전제는 재료의 특성을 개선하고 폴리머 부피의 일부를 보다 경제적인 재료로 대체할 수 있습니다. 두 단계의 체적 분율은 합성물의 거동에 영향을 줍니다. 큰 입자 합성물은 금속, 폴리머 및 세라믹과 함께 사용됩니다. CERMETS는 세라믹/금속 복합 재료의 예입니다. 우리의 가장 일반적인 서멧은 초경합금입니다. 그것은 코발트 또는 니켈과 같은 금속 매트릭스에 텅스텐 카바이드 입자와 같은 내화 카바이드 세라믹으로 구성됩니다. 이러한 초경 복합재는 경화강의 절삭 공구로 널리 사용됩니다. 경질 카바이드 입자는 절단 작업을 담당하며 연성 금속 매트릭스에 의해 인성이 향상됩니다. 따라서 우리는 단일 복합 재료에서 두 재료의 장점을 얻습니다. 우리가 사용하는 큰 입자 합성물의 또 다른 일반적인 예는 높은 인장 강도, 인성, 인열 및 내마모성을 갖는 합성물을 얻기 위해 가황 고무와 혼합된 카본 블랙 미립자입니다. 분산 강화 복합재의 예로는 매우 단단하고 불활성인 물질의 미세 입자가 균일하게 분산되어 강화 및 경화된 금속 및 금속 합금이 있습니다. 매우 작은 산화알루미늄 플레이크가 알루미늄 금속 매트릭스에 추가되면 고온 강도가 향상된 소결 알루미늄 분말을 얻을 수 있습니다. • FIBER-REINFORCED COMPOSITES : 이 복합소재 카테고리는 사실 가장 중요합니다. 달성 목표는 단위 중량당 고강도 및 강성입니다. 이러한 복합 재료의 섬유 구성, 길이, 방향 및 농도는 이러한 재료의 특성과 유용성을 결정하는 데 중요합니다. 우리가 사용하는 섬유에는 위스커, 섬유 및 와이어의 세 가지 그룹이 있습니다. WHISKERS는 매우 얇고 긴 단결정입니다. 그들은 가장 강력한 재료 중 하나입니다. 일부 예시적인 위스커 재료는 흑연, 질화규소, 산화알루미늄입니다. 반면에 FIBERS는 대부분 폴리머 또는 세라믹이며 다결정 또는 비정질 상태입니다. 세 번째 그룹은 비교적 큰 직경을 가지며 강철이나 텅스텐으로 구성된 가는 와이어입니다. 와이어 강화 합성물의 예로는 고무 내부에 강철 와이어를 통합한 자동차 타이어가 있습니다. 매트릭스 재료에 따라 다음과 같은 합성물이 있습니다. POLYMER-MATRIX COMPOSITES : 고분자 수지와 섬유를 보강재로 사용하여 만든 복합재료입니다. 유리 섬유 강화 폴리머(GFRP) 복합 재료라고 하는 이들의 하위 그룹은 폴리머 매트릭스 내에 연속 또는 불연속 유리 섬유를 포함합니다. 유리는 강도가 높고 경제적이며 섬유로 제작하기 쉬우며 화학적으로 불활성입니다. 단점은 제한된 강성과 강성, 서비스 온도가 섭씨 200~300도에 불과하다는 것입니다. 유리 섬유는 자동차 차체 및 운송 장비, 선박 차체, 보관 용기에 적합합니다. 그들은 제한된 강성으로 인해 항공 우주 또는 교량 제작에 적합하지 않습니다. 다른 하위 그룹은 탄소 섬유 강화 폴리머(CFRP) 복합재라고 합니다. 여기에서 탄소는 폴리머 매트릭스의 섬유 재료입니다. 탄소는 높은 비탄성률과 강도 및 고온에서 이를 유지하는 능력으로 유명합니다. 탄소 섬유는 표준, 중간, 고 및 초고 인장 계수를 제공할 수 있습니다. 또한 탄소 섬유는 다양한 물리적 및 기계적 특성을 제공하므로 다양한 맞춤형 엔지니어링 응용 프로그램에 적합합니다. CFRP 복합 재료는 스포츠 및 레크리에이션 장비, 압력 용기 및 항공 우주 구조 구성 요소를 제조하는 것으로 간주될 수 있습니다. 그러나 또 다른 하위 그룹인 Aramid Fiber-Reinforced Polymer Composites도 고강도 및 모듈러스 재료입니다. 중량 대비 강도 비율이 매우 높습니다. 아라미드 섬유는 상품명 KEVLAR 및 NOMEX로도 알려져 있습니다. 장력 상태에서는 다른 고분자 섬유 재료보다 성능이 우수하지만 압축에는 약합니다. 아라미드 섬유는 강하고, 충격에 강하고, 크리프와 피로에 강하고, 고온에서 안정하며, 강산과 염기를 제외하고는 화학적으로 불활성입니다. 아라미드 섬유는 스포츠 용품, 방탄 조끼, 타이어, 로프, 광섬유 케이블 시트에 널리 사용됩니다. 다른 섬유 강화 재료가 존재하지만 덜 사용됩니다. 이들은 주로 붕소, 탄화규소, 산화알루미늄입니다. 반면에 폴리머 매트릭스 재료도 중요합니다. 폴리머는 일반적으로 용융 및 분해 온도가 더 낮기 때문에 복합재의 최대 사용 온도를 결정합니다. 폴리에스터와 비닐 에스터는 고분자 매트릭스로 널리 사용됩니다. 수지도 사용되며 우수한 내습성과 기계적 특성을 가지고 있습니다. 예를 들어 폴리이미드 수지는 약 섭씨 230도까지 사용할 수 있습니다. METAL-MATRIX COMPOSITES: 이 재료에서 우리는 연성 금속 매트릭스를 사용하며 사용 온도는 일반적으로 구성 요소보다 높습니다. 폴리머-매트릭스 복합물과 비교할 때, 이들은 더 높은 작동 온도를 가질 수 있고, 불연성일 수 있으며, 유기 유체에 대한 더 나은 분해 저항성을 가질 수 있습니다. 그러나 그들은 더 비쌉니다. 위스커, 미립자, 연속 및 불연속 섬유와 같은 강화 재료; 구리, 알루미늄, 마그네슘, 티타늄, 초합금과 같은 매트릭스 재료가 일반적으로 사용됩니다. 적용 예는 알루미늄 산화물과 탄소 섬유로 강화된 알루미늄 합금 매트릭스로 만든 엔진 부품입니다. CERAMIC-MATRIX COMPOSITES : 세라믹 재료는 뛰어난 고온 신뢰성으로 유명합니다. 그러나 그들은 매우 부서지기 쉽고 파괴 인성 값이 낮습니다. 한 세라믹의 미립자, 섬유 또는 위스커를 다른 세라믹의 매트릭스에 포함함으로써 더 높은 파괴 인성을 가진 복합 재료를 얻을 수 있습니다. 이러한 내장된 재료는 기본적으로 균열 팁을 편향시키거나 균열면을 가로질러 브리지를 형성하는 것과 같은 일부 메커니즘에 의해 매트릭스 내부의 균열 전파를 억제합니다. 예를 들어, SiC 위스커로 강화된 알루미나는 경금속 합금 가공을 위한 절삭 공구 인서트로 사용됩니다. 이들은 초경합금에 비해 더 나은 성능을 나타낼 수 있습니다. CARBON-CARBON COMPOSITES : 보강재와 매트릭스 모두 탄소입니다. 그들은 높은 인장 계수와 섭씨 2000도 이상의 고온에서 강도, 크리프 저항, 높은 파괴 인성, 낮은 열팽창 계수, 높은 열전도도를 가지고 있습니다. 이러한 특성으로 인해 열 충격 저항이 필요한 응용 분야에 이상적입니다. 그러나 탄소-탄소 복합 재료의 약점은 고온에서의 산화에 대한 취약성입니다. 사용의 일반적인 예는 핫 프레스 금형, 고급 터빈 엔진 부품 제조입니다. HYBRID COMPOSITES : 두 가지 이상의 서로 다른 종류의 섬유가 하나의 매트릭스에 혼합되어 있습니다. 따라서 속성의 조합으로 새로운 재료를 맞춤화할 수 있습니다. 탄소 섬유와 유리 섬유가 모두 고분자 수지에 통합된 경우가 그 예입니다. 탄소 섬유는 밀도가 낮고 강도가 높지만 값이 비쌉니다. 반면에 유리는 저렴하지만 탄소 섬유의 강성이 부족합니다. 유리-탄소 하이브리드 복합 재료는 더 강하고 단단하며 더 저렴한 비용으로 제조할 수 있습니다. 섬유 강화 복합 재료의 가공 : 섬유가 같은 방향으로 균일하게 분포되어 있는 연속 섬유 강화 플라스틱의 경우 다음 기술을 사용합니다. PULTRUSION: 연속적인 길이와 일정한 단면의 막대, 빔 및 튜브가 제조됩니다. 연속 섬유 조방사는 열경화성 수지로 함침되고 강철 다이를 통해 당겨져 원하는 모양으로 예비 성형됩니다. 다음으로 정밀 가공된 경화 다이를 통과하여 최종 모양을 얻습니다. 경화 다이가 가열되기 때문에 수지 매트릭스가 경화됩니다. 풀러는 다이를 통해 재료를 끌어옵니다. 삽입된 중공 코어를 사용하여 튜브 및 중공 형상을 얻을 수 있습니다. 인발 방식은 자동화되어 높은 생산 속도를 제공합니다. 어떤 길이의 제품도 제작 가능합니다. PREPREG 생산 공정 : Prepreg는 부분적으로 경화된 고분자 수지가 사전 함침된 연속 섬유 보강재입니다. 구조용으로 널리 사용됩니다. 재료는 테이프 형태로 제공되며 테이프로 배송됩니다. 제조사에서 직접 성형하여 수지를 추가할 필요 없이 완전히 경화시킵니다. 프리프레그는 상온에서 경화반응을 일으키기 때문에 섭씨 0도 이하에서 보관한다. 사용 후 남은 테이프는 저온에서 다시 보관됩니다. 열가소성 수지 및 열경화성 수지가 사용되며 탄소, 아라미드 및 유리의 강화 섬유가 일반적입니다. 프리프레그를 사용하려면 먼저 캐리어 백킹지를 제거한 다음 프리프레그 테이프를 공구 표면에 놓는 방식으로 제작합니다(레이업 공정). 원하는 두께를 얻기 위해 여러 겹을 쌓을 수 있습니다. 교차 플라이 또는 앵글 플라이 라미네이트를 생성하기 위해 섬유 방향을 교대로 사용하는 경우가 많습니다. 마지막으로 열과 압력을 가하여 경화합니다. 프리프레그 절단 및 레이업에는 수작업 가공과 자동화 공정이 모두 사용됩니다. FILAMENT WINDING : 연속 강화 섬유는 중공 및 일반적으로 원통 모양을 따르도록 미리 결정된 패턴으로 정확하게 배치됩니다. 섬유는 먼저 수지 수조를 통과한 다음 자동화 시스템에 의해 맨드릴에 감깁니다. 여러 번 감으면 원하는 두께가 얻어지고 실온이나 오븐 내부에서 경화가 수행됩니다. 이제 맨드릴이 제거되고 제품이 탈형됩니다. 필라멘트 권선은 원주, 나선형 및 극성 패턴으로 섬유를 감아 매우 높은 강도 대 중량 비율을 제공할 수 있습니다. 파이프, 탱크, 케이싱은 이 기술을 사용하여 제조됩니다. • 구조적 복합재 : 일반적으로 균질 및 복합재로 구성됩니다. 따라서 이들의 속성은 구성 재료와 요소의 기하학적 디자인에 의해 결정됩니다. 주요 유형은 다음과 같습니다. LAMINAR COMPOSITES : 이 구조 재료는 선호하는 고강도 방향을 가진 2차원 시트 또는 패널로 만들어집니다. 레이어가 쌓이고 함께 접착됩니다. 두 개의 수직 축에서 고강도 방향을 번갈아 가며 2차원 평면에서 양방향으로 고강도 합성물을 얻습니다. 층의 각도를 조정하여 원하는 방향으로 강도를 갖는 복합재를 제조할 수 있습니다. 현대 스키는 이렇게 제조됩니다. SANDWICH PANELS : 구조용 복합재료는 가벼우면서도 높은 강성과 강도를 가지고 있습니다. 샌드위치 패널은 알루미늄 합금, 섬유 강화 플라스틱 또는 강철과 같은 뻣뻣하고 강한 재료로 만들어진 두 개의 외부 시트와 외부 시트 사이의 코어로 구성됩니다. 코어는 가벼워야 하고 대부분의 경우 낮은 탄성 계수를 가져야 합니다. 인기 있는 핵심 재료는 경질 폴리머 폼, 목재 및 벌집입니다. 샌드위치 패널은 건축 산업에서 지붕 재료, 바닥 또는 벽 재료로 널리 사용되며 항공 우주 산업에서도 사용됩니다. • 나노복합체(NANOCOMPOSITES): 이 새로운 재료는 매트릭스에 내장된 나노크기 입자 입자로 구성됩니다. 나노복합체를 사용하여 고무 특성을 변경하지 않고 유지하면서 공기 침투에 대한 매우 우수한 장벽을 만드는 고무 재료를 제조할 수 있습니다. CLICK Product Finder-Locator Service 이전 페이지
- Machine Elements Manufacturing, Gears, Gear Drives, Bearings, Keys, Splines
Machine Elements Manufacturing, Gears, Gear Drives, Bearings, Keys, Splines, Pins, Shafts, Seals, Fasteners, Clutch, Cams, Followers, Belts, Couplings, Shafts 기계 부품 제조 더 읽어보기 벨트 및 체인 및 케이블 드라이브 어셈블리 더 읽어보기 기어 및 기어 드라이브 어셈블리 더 읽어보기 커플링 및 베어링 제조 더 읽어보기 키 및 스플라인 및 핀 제조 더 읽어보기 캠 및 팔로워 및 링키지 및 래칫 휠 제조 더 읽어보기 샤프트 제조 더 읽어보기 메카니컬 씰 제조 더 읽어보기 클러치 및 브레이크 어셈블리 더 읽어보기 패스너 제조 더 읽어보기 단순 기계 조립 MACHINE ELEMENTS 는 기계의 기본 구성 요소입니다. 이러한 요소는 세 가지 기본 유형으로 구성됩니다. 1.) 프레임 부재, 베어링, 차축, 스플라인, 패스너, 씰 및 윤활유를 포함한 구조적 구성요소. 2.) 기어 트레인, 벨트 또는 체인 드라이브, 링키지, 캠 및 팔로워 시스템, 브레이크 및 클러치와 같은 다양한 방식으로 움직임을 제어하는 메커니즘. 3.) 버튼, 스위치, 표시기, 센서, 액추에이터 및 컴퓨터 컨트롤러와 같은 제어 구성 요소. 우리가 제공하는 대부분의 기계 요소는 일반적인 크기로 표준화되어 있지만 맞춤형 기계 요소도 특수 응용 분야에 사용할 수 있습니다. 기계 요소의 사용자 정의는 다운로드 가능한 카탈로그에 있는 기존 설계 또는 완전히 새로운 설계에 대해 수행할 수 있습니다. 기계 요소의 프로토타이핑 및 제조는 설계가 양 당사자의 승인을 받으면 계속 진행할 수 있습니다. 새로운 기계 요소를 설계 및 제조해야 하는 경우 고객은 자체 청사진을 이메일로 보내 승인을 위해 검토하거나 응용 프로그램에 사용할 기계 요소를 설계하도록 요청합니다. 후자의 경우 우리는 고객의 모든 입력을 사용하고 기계 요소를 설계하고 승인을 위해 최종 청사진을 고객에게 보냅니다. 승인을 받으면 첫 번째 제품을 생산하고 최종 설계에 따라 기계 요소를 제조합니다. 이 작업의 모든 단계에서 특정 기계 요소 설계가 현장에서 불만족스럽게 수행되는 경우(드문 경우임), 전체 프로젝트를 검토하고 필요에 따라 고객과 공동으로 변경합니다. 필요하거나 필요할 때마다 기계 요소 또는 기타 제품의 설계를 위해 고객과 NDA(비공개 계약)에 서명하는 것이 당사의 표준 관행입니다. 특정 고객을 위한 기계 요소가 맞춤 설계 및 제조되면 제품 코드를 할당하고 해당 제품을 소유한 고객에게만 생산 및 판매합니다. 고객이 재주문할 때마다 개발된 도구, 금형 및 절차를 사용하여 필요한 만큼 여러 번 기계 요소를 재현합니다. 다시 말해, 맞춤형 기계 요소가 귀하를 위해 설계 및 생산되면 귀하와 귀하가 원하는 대로 복제된 제품을 위해 지적 재산과 모든 툴링 및 금형을 무기한으로 예약하고 비축합니다. 또한 기계 요소를 응용 프로그램을 제공하고 고객의 기대를 충족하거나 초과하는 구성 요소 또는 어셈블리에 창의적으로 결합하여 고객에게 엔지니어링 서비스를 제공합니다. 당사의 기계 요소를 제조하는 공장은 ISO9001, QS9000 또는 TS16949 인증을 받았습니다. 또한 당사 제품의 대부분은 CE 또는 UL 마크가 있으며 ISO, SAE, ASME, DIN과 같은 국제 관련 표준을 충족합니다. 다음을 포함한 당사 기계 요소에 대한 자세한 정보를 얻으려면 하위 메뉴를 클릭하십시오. - 벨트, 체인 및 케이블 드라이브 - 기어 및 기어 드라이브 - 커플링 및 베어링 - 키 및 스플라인 및 핀 - 캠 및 링키지 - 샤프트 - 메카니컬 씰 - 산업용 클러치 및 브레이크 - 패스너 - 심플머신 우리는 기계 요소를 포함한 신제품의 고객, 설계자 및 개발자를 위한 참조 브로셔를 준비했습니다. 기계 구성 요소 설계에서 일반적으로 사용되는 몇 가지 용어에 익숙해질 수 있습니다. 설계자와 엔지니어가 사용하는 일반적인 기계 공학 용어에 대한 브로셔 다운로드 당사의 기계 요소는 산업 기계, 자동화 시스템, 테스트 및 계측 장비, 운송 장비, 건설 기계 및 생각할 수 있는 거의 모든 분야와 같은 다양한 분야에서 응용 프로그램을 찾습니다. AGS-TECH는 응용 분야에 따라 다양한 재료로 기계 요소를 개발 및 제조합니다. 기계 요소에 사용되는 재료는 장난감에 사용되는 성형 플라스틱에서 산업 기계용 케이스 경화 및 특수 코팅 강철에 이르기까지 다양합니다. 당사의 설계자는 기어 톱니의 각도, 관련된 응력, 마모율 등의 세부 사항을 고려하여 기계 요소를 개발하기 위해 최첨단 전문 소프트웨어 및 설계 도구를 사용합니다. 하위 메뉴를 스크롤하고 제품 브로셔와 카탈로그를 다운로드하여 응용 분야에 맞는 기성 기계 요소를 찾을 수 있는지 확인하십시오. 귀하의 응용 분야에 적합한 제품을 찾을 수 없는 경우 저희에게 알려주시면 귀하의 요구를 충족할 기계 요소를 개발 및 제조하기 위해 귀하와 협력할 것입니다. 제조 능력 대신 당사의 엔지니어링 및 연구 개발 기능에 주로 관심이 있으시면 당사 웹사이트 를 방문하시기 바랍니다.http://www.ags-engineering.com 여기서 당사의 설계, 제품 개발, 프로세스 개발, 엔지니어링 컨설팅 서비스 등에 대한 자세한 정보를 찾을 수 있습니다. CLICK Product Finder-Locator Service 이전 페이지
- Glass and Ceramic Manufacturing, Hermetic Packages, Seals, Bonding
Glass and Ceramic Manufacturing, Hermetic Packages Seals and Bonding, Tempered Bulletproof Glass, Blow Moulding, Optical Grade Glass, Conductive Glass, Molding 유리 및 세라믹 성형 및 성형 우리가 제공하는 유리 제조 유형은 용기 유리, 유리 블로잉, 유리 섬유 및 튜브 및 막대, 가정용 및 산업용 유리 제품, 램프 및 전구, 정밀 유리 몰딩, 광학 부품 및 어셈블리, 평판 및 시트 및 플로트 유리입니다. 핸드포밍과 머신포밍을 동시에 진행합니다. 당사의 인기 있는 기술 세라믹 제조 공정은 다이 프레싱, 등압 프레싱, 열간 정수압 프레싱, 열간 프레싱, 슬립 캐스팅, 테이프 캐스팅, 압출, 사출 성형, 그린 가공, 소결 또는 소성, 다이아몬드 연삭, 밀폐 어셈블리입니다. 여기를 클릭하는 것이 좋습니다. AGS-TECH Inc.의 유리 성형 및 성형 공정의 개략도를 다운로드하십시오. AGS-TECH Inc.의 기술 세라믹 제조 공정의 개략도를 다운로드하십시오. 사진과 스케치가 포함된 다운로드 가능한 파일은 아래에서 제공하는 정보를 더 잘 이해하는 데 도움이 됩니다. • CONTAINER GLASS MANUFACTURE: 우리는 자동화된 PRESS 및 BLOW 뿐만 아니라 BLOW 및 BLOW 제조 라인을 보유하고 있습니다. 블로우 및 블로우 공정에서 블랭크 몰드에 덩어리를 떨어뜨리고 상단에서 압축 공기를 불어 넣어 넥을 형성합니다. 그 직후에 압축 공기는 용기 목을 통해 다른 방향에서 두 번째로 불어서 병의 프리폼을 형성합니다. 그런 다음 이 프리폼을 실제 몰드로 옮기고 다시 가열하여 부드럽게 하고 압축 공기를 가하여 프리폼의 최종 용기 모양을 만듭니다. 보다 명시적으로, 압력을 가하고 블로우 몰드 캐비티의 벽에 밀어 넣어 원하는 모양을 취합니다. 마지막으로, 제조된 유리 용기는 후속 재가열 및 성형 중에 생성된 응력 제거를 위해 어닐링 오븐으로 옮겨지고 제어된 방식으로 냉각됩니다. 프레스 및 블로우 방식에서는 녹은 덩어리를 패리슨 몰드(블랭크 몰드)에 넣고 패리슨 형상(블랭크 형상)으로 프레스합니다. 그런 다음 블랭크를 블로우 몰드로 옮기고 "블로우 및 블로우 프로세스"에서 위에서 설명한 프로세스와 유사하게 블로우합니다. 어닐링 및 응력 완화와 같은 후속 단계는 유사하거나 동일합니다. • GLASS BLOWING : 기존의 Hand Blowing과 압축공기를 이용한 자동화 설비를 이용한 Glass 제품을 생산하고 있습니다. 일부 주문의 경우 유리 예술 작품과 관련된 프로젝트 또는 허용 오차가 느슨한 적은 수의 부품이 필요한 프로젝트, 프로토타이핑/데모 프로젝트 등의 기존 블로잉이 필요합니다. 기존의 유리 블로잉은 속이 빈 금속 파이프를 용융 유리 냄비에 담그고 파이프를 회전하여 유리 재료를 일정량 모으는 것을 포함합니다. 파이프의 끝 부분에 수집된 유리는 평평한 철 위에 굴려 원하는 모양으로 만들고 길게 늘이고 다시 가열하고 공기를 불어넣습니다. 준비되면 금형에 삽입하고 공기를 불어 넣습니다. 금형 캐비티는 유리와 금속의 접촉을 피하기 위해 젖었습니다. 물막은 그들 사이에서 쿠션 역할을 합니다. 수동 블로잉은 노동 집약적인 느린 프로세스이며 프로토타이핑 또는 고가의 품목에만 적합하며 저렴한 개당 대량 주문에는 적합하지 않습니다. • 국내 및 산업용 유리제품 제조 : 다양한 종류의 유리재료를 사용하여 다양한 유리제품이 생산되고 있습니다. 일부 유리는 내열성이 있어 실험실 유리 제품에 적합하지만 일부는 식기 세척기를 여러 번 견딜 수 있을 만큼 충분히 좋으며 국내 제품을 만드는 데 적합합니다. Westlake 기계를 사용하여 하루에 수만 개의 술잔이 생산되고 있습니다. 단순화하기 위해 용융 유리를 진공으로 수집하고 금형에 삽입하여 프리폼을 만듭니다. 그런 다음 공기를 주형으로 불어넣고 다른 주형으로 옮기고 공기를 다시 불어 유리의 최종 형태를 취합니다. 손으로 부는 것과 마찬가지로 이 금형은 물에 젖은 상태로 유지됩니다. 추가 스트레칭은 목이 형성되는 마무리 작업의 일부입니다. 초과 유리가 타 버립니다. 그 후 위에서 설명한 제어된 재가열 및 냉각 프로세스가 다음과 같습니다. • GLASS TUBE & ROD FORMING : 당사가 Glass Tube 제조에 사용하는 주요 공정은 DANNER 및 VELLO 공정입니다. Danner 공정에서는 용광로에서 나온 유리가 내화 재료로 만들어진 경사진 슬리브 위로 흐르고 떨어집니다. 슬리브는 회전하는 중공축 또는 송풍관에 장착됩니다. 그런 다음 유리는 슬리브 주위를 감싸고 슬리브 아래로 그리고 샤프트 팁 위로 흐르는 매끄러운 층을 형성합니다. 튜브 성형의 경우 중공 팁이 있는 블로우 파이프를 통해 공기를 불어넣고 로드 성형의 경우 샤프트에 솔리드 팁을 사용합니다. 그런 다음 튜브 또는 막대가 운반 롤러 위로 당겨집니다. 슬리브의 직경을 설정하고 공기압을 원하는 값으로 불어넣고 온도, 유리의 유속 및 드로잉 속도를 조정하여 유리관의 벽 두께 및 직경과 같은 치수를 원하는 값으로 조정합니다. 반면에 Vello 유리관 제조 공정에는 유리가 용광로에서 나와 속이 빈 맨드릴 또는 벨이 있는 보울로 이동하는 과정이 포함됩니다. 그런 다음 유리는 맨드릴과 보울 사이의 공기 공간을 통과하여 튜브 모양을 취합니다. 그런 다음 롤러를 통해 드로잉 머신으로 이동하고 냉각됩니다. 냉각 라인의 끝에서 절단 및 최종 처리가 이루어집니다. 튜브 치수는 Danner 프로세스와 마찬가지로 조정할 수 있습니다. Danner와 Vello 공정을 비교할 때 Vello 공정은 대량 생산에 더 적합하고 Danner 공정은 정밀한 소량 튜브 주문에 더 적합할 수 있다고 말할 수 있습니다. • SHEET & FLAT & FLOAT GLASS 가공 : 우리는 밀리미터 이하의 두께에서 수 센티미터에 이르는 두께의 판유리를 대량으로 보유하고 있습니다. 우리의 평면 안경은 거의 광학적으로 완벽합니다. 우리는 화학 기상 증착 기술을 사용하여 반사 방지 또는 미러 코팅과 같은 코팅을 적용하는 광학 코팅과 같은 특수 코팅이 된 유리를 제공합니다. 또한 투명 전도성 코팅이 일반적입니다. 또한 유리의 소수성 또는 친수성 코팅과 유리 자체 세척을 만드는 코팅도 사용할 수 있습니다. 강화 유리, 방탄 유리 및 접합 유리는 또 다른 인기 품목입니다. 원하는 공차로 원하는 모양으로 유리를 자릅니다. 평판 유리를 구부리거나 구부리는 것과 같은 다른 2차 작업을 사용할 수 있습니다. • PRECISION GLASS MOLDING : 연삭, 래핑 및 폴리싱과 같은 더 비싸고 시간 소모적인 기술이 필요 없이 정밀 광학 부품을 제조하는 데 주로 이 기술을 사용합니다. 이 기술은 최고의 광학 제품을 만드는 데 항상 충분하지 않지만 소비자 제품, 디지털 카메라, 의료 광학과 같은 일부 경우에는 대량 제조에 더 저렴하고 좋은 옵션이 될 수 있습니다. 또한 비구면의 경우와 같이 복잡한 형상이 필요한 다른 유리 성형 기술에 비해 이점이 있습니다. 기본 공정에는 유리 블랭크가 있는 금형의 아래쪽 로딩, 산소 제거를 위한 공정 챔버 비우기, 금형의 거의 닫힘, 적외선으로 다이와 유리의 빠른 등온 가열, 금형 반쪽의 추가 폐쇄가 포함됩니다. 연화된 유리를 원하는 두께로 제어된 방식으로 천천히 누르고, 마지막으로 유리를 냉각시키고 챔버를 질소로 채우고 생성물을 제거한다. 정확한 온도 제어, 금형 폐쇄 거리, 금형 폐쇄력, 금형 및 유리 재료의 팽창 계수 일치가 이 프로세스의 핵심입니다. • 유리 광학 부품 및 조립품의 제조: 정밀 유리 성형 외에도 까다로운 응용 분야를 위한 고품질 광학 부품 및 조립품을 제조하는 데 사용하는 귀중한 공정이 많이 있습니다. 정밀한 특수 연마 슬러리에서 광학 등급 유리의 그라인딩, 래핑 및 폴리싱은 광학 렌즈, 프리즘, 플랫 등을 만들기 위한 예술이자 과학입니다. 표면 평탄도, 물결 모양, 부드러움 및 결함이 없는 광학 표면은 이러한 프로세스에 대한 많은 경험을 필요로 합니다. 환경의 작은 변화로 인해 사양을 벗어난 제품이 생성되고 제조 라인이 중단될 수 있습니다. 깨끗한 천으로 광학 표면을 한 번 닦아도 제품이 사양을 충족하거나 테스트에 실패하는 경우가 있습니다. 사용되는 일부 인기 있는 유리 재료는 용융 실리카, 석영, BK7입니다. 또한 이러한 구성 요소의 조립에는 전문적인 틈새 경험이 필요합니다. 때로는 특수 접착제가 사용됩니다. 그러나 때로는 광학 접촉이라고 하는 기술이 최선의 선택이며 부착된 광학 유리 사이에 재료가 포함되지 않습니다. 접착제 없이 서로 부착하기 위해 물리적으로 접촉하는 평평한 표면으로 구성됩니다. 어떤 경우에는 기계적 스페이서, 정밀 유리 막대 또는 볼, 클램프 또는 기계 가공된 금속 부품이 광학 부품을 특정 거리에서 서로에 대해 특정 기하학적 방향으로 조립하는 데 사용됩니다. 고급 광학 제품을 제조하는 데 널리 사용되는 몇 가지 기술을 살펴보겠습니다. GRINDING & LAPPING & POLISHING : Glass Blank를 연마하여 광학 부품의 거친 형상을 얻습니다. 그런 다음 원하는 표면 모양을 가진 도구에 대해 광학 부품의 거친 표면을 회전하고 문질러 래핑 및 연마를 수행합니다. 미세한 연마 입자와 유체가 포함된 슬러리가 광학 장치와 성형 도구 사이에 붓고 있습니다. 이러한 슬러리의 연마 입자 크기는 원하는 평탄도에 따라 선택할 수 있습니다. 원하는 모양에서 중요한 광학 표면의 편차는 사용되는 빛의 파장으로 표현됩니다. 당사의 고정밀 광학 장치는 10분의 1 파장(Wavelength/10) 허용 오차를 가지거나 더 엄격하게 허용됩니다. 표면 프로파일 외에도 중요한 표면을 스캔하고 치수, 스크래치, 칩, 구덩이, 반점 등의 다른 표면 특징 및 결함을 평가합니다. 광학 제조 현장의 환경 조건을 엄격하게 제어하고 첨단 장비를 사용한 광범위한 계측 및 테스트 요구 사항을 통해 이 분야는 까다로운 산업 분야입니다. • 유리 제조의 2차 공정: 다시 말하지만, 우리는 유리의 2차 및 마감 공정과 관련하여 상상력이 제한적입니다. 다음은 그 중 일부를 나열합니다. -유리 코팅(광학, 전기, 마찰, 열, 기능, 기계...). 예를 들어 유리의 표면 특성을 변경하여 열을 반사하여 건물 내부를 시원하게 유지하거나 나노 기술을 사용하여 한 면이 적외선을 흡수하도록 할 수 있습니다. 유리의 가장 바깥쪽 표면층이 건물 내부의 적외선을 흡수하고 다시 내부로 방출하기 때문에 건물 내부를 따뜻하게 유지하는 데 도움이 됩니다. -에칭 on glass -응용 세라믹 라벨링(ACL) -조각 - 화염 연마 -화학 연마 -더럽히는 것 테크니컬 세라믹 제조 • DIE PRESSING : 금형에 갇힌 입상분말의 일축압축으로 구성 • HOT PRESSING : 다이 프레스와 유사하지만 밀도를 높이기 위해 온도를 추가합니다. 분말 또는 압축된 프리폼을 흑연 다이에 넣고 다이를 2000C와 같은 고온에서 유지하면서 단축 압력을 가합니다. 온도는 처리되는 세라믹 분말의 유형에 따라 다를 수 있습니다. 복잡한 모양과 형상의 경우 다이아몬드 연삭과 같은 다른 후속 처리가 필요할 수 있습니다. • ISOSTATIC PRESSING : 입상 분말 또는 다이 프레스 압축물을 밀폐 용기에 넣은 다음 내부에 액체가 들어 있는 밀폐된 압력 용기에 넣습니다. 그 후 그들은 압력 용기의 압력을 증가시켜 압축됩니다. 용기 내부의 액체는 밀폐 용기의 전체 표면적에 균일하게 압력을 전달합니다. 따라서 재료는 균일하게 압축되고 유연한 용기의 모양과 내부 프로파일 및 기능을 취합니다. • HOT ISOSTATIC PRESSING : Isostatic Press와 유사하나 가압된 가스분위기 외에 고온에서 소결한다. 열간 등방압 프레싱은 밀도를 높이고 강도를 높입니다. • SLIP CASTING / DRAIN CASTING : 마이크로미터 크기의 세라믹 입자 현탁액과 캐리어 액체로 금형을 채웁니다. 이 혼합물을 "슬립"이라고 합니다. 금형에는 기공이 있으므로 혼합물의 액체가 금형으로 여과됩니다. 결과적으로 금형의 내부 표면에 캐스트가 형성됩니다. 소결 후 부품을 금형에서 꺼낼 수 있습니다. • TAPE CASTING : 평평하게 움직이는 캐리어 표면에 세라믹 슬러리를 캐스팅하여 세라믹 테이프를 제조합니다. 슬러리에는 결합 및 운반 목적으로 다른 화학 물질과 혼합된 세라믹 분말이 포함되어 있습니다. 용매가 증발함에 따라 원하는 대로 자르거나 말릴 수 있는 조밀하고 유연한 세라믹 시트가 남게 됩니다. • 압출 성형 : 다른 압출 공정과 마찬가지로 세라믹 분말과 바인더 및 기타 화학 물질의 부드러운 혼합물을 금형을 통과하여 단면 모양을 얻은 다음 원하는 길이로 절단합니다. 이 과정은 차갑거나 가열된 세라믹 혼합물로 수행됩니다. • 저압 사출 성형: 세라믹 분말과 바인더 및 솔벤트의 혼합물을 준비하고 쉽게 눌러 도구 구멍으로 밀어 넣을 수 있는 온도로 가열합니다. 성형 주기가 완료되면 부품이 배출되고 결합 화학 물질이 연소됩니다. 사출 성형을 사용하여 복잡한 부품을 경제적으로 대량으로 얻을 수 있습니다. 10mm 두께의 벽에 밀리미터의 아주 작은 부분인 구멍 , 추가 가공 없이 나사산 가능, +/- 0.5% 정도의 공차가 가능하며 부품 가공 시 더 낮음 , 벽 두께는 0.5mm에서 길이 12.5mm까지 가능하며 벽 두께는 6.5mm에서 길이 150mm까지 가능합니다. • 녹색 가공 : 동일한 금속 가공 도구를 사용하여 프레스 세라믹 재료를 초크처럼 부드럽지만 가공할 수 있습니다. +/- 1%의 허용 오차가 가능합니다. 더 나은 공차를 위해 다이아몬드 연삭을 사용합니다. • SINTERING or FIRING : Sintering은 완전한 치밀화를 가능하게 한다. 그린 컴팩트 부품에서 상당한 수축이 발생하지만 부품 및 툴링을 설계할 때 이러한 치수 변화를 고려하기 때문에 큰 문제는 아닙니다. 분말 입자가 서로 결합되어 압축 공정으로 인한 다공성이 크게 제거됩니다.. • DIAMOND GRINDING : 세계에서 가장 단단한 재료인 '다이아몬드'를 세라믹과 같은 단단한 재료를 연마하는 데 사용하며 정밀 부품을 얻습니다. 마이크로미터 범위의 허용 오차와 매우 매끄러운 표면이 달성되고 있습니다. 비용 때문에 우리는 이 기술이 정말로 필요할 때만 고려합니다. • 밀폐형 어셈블리는 실질적으로 인터페이스 사이에서 물질, 고체, 액체 또는 기체의 교환을 허용하지 않는 어셈블리입니다. 기밀 밀봉은 기밀입니다. 예를 들어 밀폐형 전자 인클로저는 패키지 장치의 민감한 내부 내용물을 습기, 오염 물질 또는 가스에 의해 손상되지 않도록 유지하는 인클로저입니다. 100% 밀폐된 것은 없지만, 밀폐성에 대해 이야기할 때 누출률이 너무 낮아 기기가 정상적인 환경 조건에서 매우 오랜 시간 동안 안전할 정도로 밀폐성이 있다는 것을 의미합니다. 당사의 밀폐형 어셈블리는 금속, 유리 및 세라믹 부품, 금속-세라믹, 세라믹-금속-세라믹, 금속-세라믹-금속, 금속 대 금속, 금속-유리, 금속-유리-금속, 유리-금속-유리, 유리-로 구성됩니다. 금속 및 유리 대 유리 및 기타 금속-유리-세라믹 결합의 모든 조합. 예를 들어 세라믹 구성 요소를 금속 코팅하여 어셈블리의 다른 구성 요소에 강력하게 결합하고 우수한 밀봉 기능을 가질 수 있습니다. 광섬유 또는 피드스루를 금속으로 코팅하고 인클로저에 납땜 또는 납땜하는 노하우를 보유하여 인클로저로 가스가 통과하거나 누출되지 않습니다. 따라서 민감한 장치를 캡슐화하고 외부 대기로부터 보호하기 위해 전자 인클로저를 제조하는 데 사용됩니다. 우수한 밀봉 특성 외에도 열팽창 계수, 변형 저항, 비 가스 방출 특성, 매우 긴 수명, 비전도성 특성, 단열 특성, 정전기 방지 특성 등의 기타 특성. 특정 용도에 유리 및 세라믹 재료를 선택하십시오. 세라믹-금속 피팅, 밀폐 밀봉, 진공 피드스루, 고진공 및 초고진공 및 유체 제어 구성 요소를 생산하는 당사 시설에 대한 정보는 여기에서 확인할 수 있습니다.밀폐 부품 공장 브로셔 CLICK Product Finder-Locator Service 이전 페이지
- Wire & Spring Forming, Shaping, Welding, Assembly of Wires, Coil, CNC
Wire & Spring Forming, Shaping, Welding, Assembly of Wires, Coil Compression Extension Torsion Flat Springs, Custom Wires, Helical Springs at AGS-TECH Inc. 와이어 및 스프링 성형 우리는 맞춤형 와이어, 와이어 어셈블리, 원하는 2D 및 3D 모양으로 형성된 와이어, 와이어 그물, 메쉬, 인클로저, 바구니, 울타리, 와이어 스프링, 플랫 스프링을 제조합니다. 비틀림, 압축, 인장, 플랫 스프링 등. 우리의 프로세스는 와이어 및 스프링 성형, 와이어 드로잉, 성형, 굽힘, 용접, 브레이징, 납땜, 피어싱, 스웨이징, 드릴링, 챔퍼링, 연삭, 스레딩, 코팅, 포슬라이드, 슬라이드 성형, 와인딩, 코일링, 업세팅입니다. 여기를 클릭하는 것이 좋습니다. AGS-TECH Inc.의 와이어 및 스프링 성형 공정의 개략도를 다운로드하십시오. 사진과 스케치가 포함된 이 다운로드 가능한 파일은 아래에서 제공하는 정보를 더 잘 이해하는 데 도움이 됩니다. • 와이어 드로잉: 인장력을 사용하여 금속 스톡을 늘리고 다이를 통해 끌어 직경을 줄이고 길이를 늘립니다. 때때로 우리는 일련의 다이를 사용합니다. 우리는 모든 와이어 게이지에 대해 다이를 만들 수 있습니다. 인장 강도가 높은 재료를 사용하여 매우 가는 와이어를 그립니다. 우리는 냉간 및 열간 작업 와이어를 모두 제공합니다. • WIRE FORMING : 게이지 와이어 롤을 구부려서 유용한 제품으로 만듭니다. 우리는 가는 필라멘트뿐만 아니라 자동차 섀시 아래 스프링으로 사용되는 것과 같은 두꺼운 와이어를 포함하여 모든 게이지에서 와이어를 형성할 수 있는 능력을 보유하고 있습니다. 와이어 포밍에 사용하는 장비는 수동 및 CNC 와이어 포머, 코일러, 파워 프레스, 포슬라이드, 멀티슬라이드입니다. 당사의 프로세스는 드로잉, 벤딩, 스트레이트닝, 플랫화, 스트레칭, 절단, 업세팅, 납땜 및 용접 및 브레이징, 조립, 코일링, 스웨이징(또는 날개), 피어싱, 와이어 스레딩, 드릴링, 모따기, 연삭, 코팅 및 표면 처리입니다. 당사의 최첨단 장비는 모든 모양과 엄격한 허용 오차의 매우 복잡한 설계를 개발하도록 설정할 수 있습니다. 우리는 와이어에 대해 다양한 끝 유형 like 구형, 뾰족한 끝 또는 모따기 끝을 제공합니다. 대부분의 와이어 포밍 프로젝트는 툴링 비용이 최소에서 0입니다. 샘플 처리 시간은 일반적으로 며칠입니다. 와이어 형태의 디자인/구성을 매우 빠르게 변경할 수 있습니다. • SPRING FORMING : AGS-TECH는 다음과 같은 다양한 스프링을 제조합니다. - 토션 / 더블 토션 스프링 - 인장/압축 스프링 - 일정/가변 스프링 -코일 & 헬리컬 스프링 -플랫 & 리프 스프링 -밸런스 스프링 - 벨빌 세탁기 -네게이터 스프링 -프로그레시브 레이트 코일 스프링 - 웨이브 스프링 -볼류트 스프링 -테이퍼 스프링 -스프링 링 -시계 스프링 -클립 우리는 다양한 재료로 스프링을 제조하고 귀하의 응용 분야에 따라 귀하를 안내할 수 있습니다. 가장 일반적인 재료는 스테인레스 스틸, 크롬 실리콘, 고탄소강, 오일 템퍼링된 저탄소, 크롬 바나듐, 인청동, 티타늄, 베릴륨 구리 합금, 고온 세라믹입니다. CNC 코일링, 콜드 와인딩, 핫 와인딩, 경화, 마무리 등 다양한 기술을 스프링 제조에 사용합니다. 와이어 성형에 대해 위에서 이미 언급한 다른 기술도 스프링 제조 작업에서 일반적입니다. • WIRES & SPRINGS 마감 서비스 : 귀하의 선택과 필요에 따라 다양한 방법으로 제품을 마감할 수 있습니다. 우리가 제공하는 몇 가지 일반적인 공정은 다음과 같습니다. 페인팅, 분체 도장, 도금, 비닐 침지, 아노다이징, 응력 완화, 열처리, 쇼트 핀, 텀블, 크롬산염, 무전해 니켈, 패시베이션, 구운 에나멜, 플라스틱 코팅 , 플라즈마 세정. CLICK Product Finder-Locator Service 이전 페이지
- Sheet Metal Forming Fabrication, Stamping, Punching, Deep Drawing, CNC
Sheet Metal Forming and Fabrication, Stamping, Punching, Bending, Progressive Die, Spot Welding, Deep Drawing, Metal Blanking and Slitting at AGS-TECH Inc. 스탬핑 및 판금 제작 우리는 판금 스탬핑, 성형, 성형, 굽힘, 펀칭, 블랭킹, 슬리팅, 천공, 노칭, 니블링, 면도, 프레스 가공, 제작, 싱글 펀치/싱글 스트로크 다이를 사용한 딥 드로잉, 프로그레시브 다이 및 스피닝, 고무 성형 및 하이드로포밍; 워터젯, 플라즈마, 레이저, 톱, 화염을 사용한 판금 절단; 용접, 스폿 용접을 사용한 판금 조립; 판금 튜브 팽창 및 굽힘; 딥 또는 스프레이 페인팅, 정전기 분말 코팅, 아노다이징, 도금, 스퍼터링 등을 포함한 판금 표면 마감. 당사의 서비스는 신속한 판금 프로토타이핑에서 대량 제조에 이르기까지 다양합니다. 여기를 클릭하는 것이 좋습니다.AGS-TECH Inc.의 판금 제조 및 스탬핑 공정의 개략도를 다운로드하십시오. 이렇게 하면 아래에서 제공하는 정보를 더 잘 이해하는 데 도움이 됩니다. • 판금 절단 : 절단 및 절단을 제공합니다. 컷오프는 한 번에 한 경로에 걸쳐 판금을 절단하고 기본적으로 재료 낭비가 없는 반면, 분할을 사용하면 모양이 정확하게 자리잡을 수 없으므로 특정 양의 재료가 낭비됩니다. 가장 인기 있는 공정 중 하나는 판금에서 원형 또는 다른 모양의 재료 조각을 잘라내는 펀칭입니다. 잘린 부분은 낭비입니다. 펀칭의 또 다른 버전은 직사각형 또는 길쭉한 구멍이 펀칭되는 SLOTTING입니다. BLANKING은 펀칭과 동일한 과정으로 잘라낸 부분을 구분하여 작업하며 보관합니다. 블랭킹의 우수한 버전인 FINE BLANKING은 정밀한 공차와 직선형 매끄러운 모서리로 절단을 생성하고 공작물의 완성을 위한 2차 작업이 필요하지 않습니다. 우리가 자주 사용하는 또 다른 공정은 SLITTING입니다. 이는 판금이 직선 또는 곡선 경로에서 두 개의 반대 원형 블레이드에 의해 절단되는 전단 공정입니다. 캔따개는 슬리팅 프로세스의 간단한 예입니다. 우리를 위한 또 다른 인기 있는 process는 원형 또는 기타 모양의 많은 구멍이 특정 패턴으로 판금에 펀칭되는 PERFORATING입니다. 다공 제품의 전형적인 예는 유체용 구멍이 많은 금속 필터입니다. 또 다른 판금 절단 공정인 노칭(NOCHING)에서는 가장자리 또는 다른 곳에서 시작하여 공작물에서 재료를 제거하고 원하는 모양이 얻어질 때까지 안쪽으로 절단합니다. 원하는 윤곽을 얻을 때까지 각 작업에서 다른 조각을 제거하는 점진적 프로세스입니다. 소규모 생산 실행의 경우 더 크고 복잡한 절단을 만들기 위해 겹치는 구멍의 많은 빠른 펀치로 구성된 NIBBLING이라는 비교적 느린 프로세스를 사용하는 경우가 있습니다. PROGRESSIVE CUTTING에서는 단일 절단 또는 특정 형상을 얻기 위해 일련의 다양한 작업을 사용합니다. 마지막으로 2차 공정을 면도하면 이미 만들어진 절단면의 가장자리를 개선하는 데 도움이 됩니다. 판금 작업의 칩, 거친 모서리 절단에 사용됩니다. • SHEET METAL BENDING : 절단 외에 절곡은 우리가 대부분의 제품을 생산할 수 없는 필수적인 공정입니다. 대부분 냉간 작업이지만 때로는 따뜻하거나 더울 때도 수행됩니다. 우리는 이 작업을 위해 대부분의 시간을 다이와 프레스를 사용합니다. 프로그레시브 벤딩에서는 단일 벤드 또는 특정 형상을 얻기 위해 일련의 다른 펀치 및 다이 작업을 사용합니다. AGS-TECH는 다양한 굽힘 공정을 사용하며 공작물 재료, 크기, 두께, 원하는 굽힘 크기, 반경, 곡률 및 굽힘 각도, 굽힘 위치, 작동 경제성, 제조 수량 등에 따라 선택합니다. 등. V자형 펀치가 판금을 V자형 다이에 밀어넣고 구부리는 V-BENDING을 사용합니다. 90도를 포함하여 매우 예각과 둔각과 그 사이에 모두 좋습니다. 와이핑 다이를 사용하여 EDGE BENDING을 수행합니다. 우리 장비를 사용하면 90도보다 더 큰 각도를 얻을 수 있습니다. 에지 벤딩에서 공작물은 압력 패드와 다이 사이에 끼어 있으며, 벤딩 영역은 다이 에지에 있고 나머지 공작물은 캔틸레버 빔과 같은 space like 위에 유지됩니다. 펀치가 캔틸레버 부분에 작용하면 다이 가장자리 위로 구부러집니다. FLANGING은 90도 각도를 생성하는 가장자리 굽힘 공정입니다. 작업의 주요 목표는 날카로운 모서리를 제거하고 부품을 쉽게 결합할 수 있도록 기하학적 표면을 얻는 것입니다. BEADING, 또 다른 일반적인 모서리 굽힘 공정은 부품의 모서리에 컬을 형성합니다. 반면에 HEMMING은 시트의 가장자리가 완전히 구부러지는 결과를 가져옵니다. SEAMING에서는 두 부분의 가장자리가 서로 구부러져 결합됩니다. 반면에 DOUBLE SEAMING은 방수 및 기밀 판금 조인트를 제공합니다. 에지 벤딩과 유사하게 ROTARY BENDING이라는 프로세스는 원하는 각도로 절단된 실린더를 배치하고 펀치 역할을 합니다. 힘이 펀치에 전달되면 공작물과 함께 닫힙니다. 실린더의 홈은 캔틸레버 부분에 원하는 각도를 제공합니다. 홈은 90도보다 작거나 큰 각도를 가질 수 있습니다. AIR BENDING에서는 각진 홈이 있는 하부 다이가 필요하지 않습니다. 판금은 2개의 표면에 의해 반대 측면과 특정 거리에서 지지됩니다. 그런 다음 펀치는 올바른 위치에 힘을 가하고 공작물을 구부립니다. CHANNEL BENDING은 Channel 모양의 Punch와 Die를 이용하여 수행하며 U-BEND는 U자형 Punch를 이용하여 수행한다. 오프셋 굽힘은 판금에 오프셋을 생성합니다. 롤 벤딩(ROLL BENDING)은 큰 금속판의 두꺼운 작업과 굽힘에 적합한 기술로 3개의 롤을 사용하여 원하는 곡률로 판을 이송하고 구부립니다. 롤은 작업의 원하는 굽힘이 얻어지도록 배열됩니다. 롤 사이의 거리와 각도를 제어하여 원하는 결과를 얻습니다. 움직일 수 있는 롤로 곡률을 제어할 수 있습니다. TUBE FORMING은 여러 다이와 관련된 또 다른 인기 있는 판금 굽힘 작업입니다. 튜브는 여러 작업 후에 얻을 수 있습니다. CORRUGATION은 굽힘 작업으로도 수행됩니다. 기본적으로 전체 판금 조각에 걸쳐 일정한 간격으로 대칭 굽힘입니다. 주름에 다양한 모양을 사용할 수 있습니다. 골판지 금속판은 더 단단하고 굽힘에 대한 저항성이 더 우수하므로 건설 산업에 응용할 수 있습니다. SHEET METAL ROLL FORMING, 연속 manufacturing 공정은 롤을 사용하여 특정 형상의 단면을 구부리기 위해 배포되고 작업은 순차적 단계로 구부러지며 최종 롤이 작업을 완료합니다. 어떤 경우에는 단일 롤과 어떤 경우에는 일련의 롤이 사용됩니다. • COMBINED SHEET METAL CUTTING & BENDING 공정 : 절단과 절곡을 동시에 하는 공정입니다. PIERCING에서는 뾰족한 펀치를 사용하여 구멍을 만듭니다. 펀치가 시트의 구멍을 넓힐 때 재료는 구멍의 내부 플랜지로 동시에 구부러집니다. 얻은 플랜지는 중요한 기능을 가질 수 있습니다. 반면 LANCING 작업은 시트를 자르고 구부려 융기된 형상을 만듭니다. • METAL TUBE BULGING 및 BENDING : BULGING에서는 속이 빈 튜브의 내부 일부에 압력이 가해져 튜브가 바깥쪽으로 부풀어 오릅니다. 튜브가 다이 내부에 있기 때문에 벌지 형상은 다이의 모양에 의해 제어됩니다. STRETCH BENDING에서 금속 튜브는 튜브의 축에 평행한 힘과 굽힘 힘을 사용하여 늘어납니다. DRAW BENDING에서 우리는 회전하는 동안 튜브를 구부리는 회전하는 형태 블록에 끝 근처의 튜브를 고정합니다. 마지막으로 COMPRESSION BENDING에서 튜브는 고정된 형태의 블록에 힘으로 고정되고 다이는 그것을 형태의 블록 위로 구부립니다. • 딥 드로잉: 가장 널리 사용되는 작업 중 하나에서 펀치, 매칭 다이 및 블랭크 홀더가 사용됩니다. 판금 블랭크가 다이 개구부 위에 배치되고 펀치가 블랭크 홀더에 의해 고정된 블랭크 쪽으로 이동합니다. 일단 접촉하면 펀치가 판금을 다이 공동으로 밀어 넣어 제품을 형성합니다. 딥 드로잉 작업은 절단과 유사하지만 펀치와 다이 사이의 간격은 시트가 절단되는 것을 방지합니다. 시트가 딥 드로잉되고 절단되지 않도록 보장하는 또 다른 요소는 전단 및 절단을 방지하는 다이와 펀치의 둥근 모서리입니다. 더 큰 규모의 딥 드로잉을 달성하기 위해 이미 딥 드로잉 프로세스를 거친 부품에 후속 딥 드로잉이 수행되는 REDRAWING 프로세스가 배포됩니다. REVERSE REDRAWING에서는 딥 드로잉 부분을 뒤집어 반대 방향으로 그립니다. 딥 드로잉은 돔형, 테이퍼형 또는 계단형 컵과 같은 불규칙한 모양의 물체를 제공할 수 있습니다. EMBOSSING에서는 암수 다이 쌍을 사용하여 디자인이나 스크립트로 판금에 깊은 인상을 남깁니다. • SPINNING : 평평하거나 미리 형성된 공작물을 회전하는 맨드릴과 심압대 사이에 잡고 도구가 맨드릴 위로 점차적으로 이동하면서 공작물에 국부적인 압력을 가하는 작업입니다. 결과적으로 공작물이 맨드릴 위에 감겨서 모양이 잡힙니다. 주문량이 적고 부품이 크며(직경이 최대 20피트) 고유한 곡선이 있는 딥 드로잉의 대안으로 이 기술을 사용합니다. 개당 가격은 일반적으로 높지만 CNC 회전 작업의 설정 비용은 딥 드로잉에 비해 저렴합니다. 반대로 딥드로잉은 초기 셋업에 많은 투자가 필요하지만 부품을 많이 생산할 때 개당 비용이 저렴합니다. 이 공정의 또 다른 버전은 전단 회전(SHEAR SPINNING)으로, 공작물 내에서 금속 흐름도 있습니다. 금속 흐름은 프로세스가 수행됨에 따라 공작물의 두께를 감소시킵니다. 또 다른 관련 공정은 원통형 부품에 적용되는 TUBE SPINNING입니다. 또한 이 과정에서 공작물 내부에 금속 흐름이 있습니다. 따라서 두께가 감소하고 튜브의 길이가 증가합니다. 도구를 이동하여 튜브 내부 또는 외부에 피쳐를 생성할 수 있습니다. • RUBBER FORMING OF SHEET METAL : 고무나 폴리우레탄 소재를 용기 금형에 넣고 고무 표면에 가공물을 올려놓는 방식. 그런 다음 펀치가 공작물에 작용하여 고무에 밀어 넣습니다. 고무에 의해 발생하는 압력이 낮기 때문에 생산되는 부품의 깊이가 제한됩니다. 툴링 비용이 저렴하여 소량 생산에 적합합니다. • HYDROFORMING : 고무 성형과 유사하게 이 공정에서 판금 가공물을 펀치로 눌러 챔버 내부의 가압 액체에 넣습니다. 판금 작업은 펀치와 고무 다이어프램 사이에 끼워져 있습니다. 다이어프램은 공작물을 완전히 둘러싸고 유체의 압력으로 인해 공작물이 펀치에 형성됩니다. 이 기술을 사용하면 딥 드로잉 프로세스보다 더 깊은 매우 딥 드로잉을 얻을 수 있습니다. 당사는 고객의 부품에 따라 단일 펀치 다이와 프로그레시브 다이를 제조합니다. 단일 스트로크 스탬핑 다이는 와셔와 같은 단순한 판금 부품을 대량으로 빠르게 생산하기 위한 비용 효율적인 방법입니다. 프로그레시브 다이 또는 딥 드로잉 기술은 보다 복잡한 형상을 제조하는 데 사용됩니다. 귀하의 경우에 따라 워터젯, 레이저 또는 플라즈마 절단을 사용하여 판금 부품을 저렴하고 빠르고 정확하게 생산할 수 있습니다. 많은 공급업체는 이러한 대체 기술에 대해 전혀 모르고 있거나 가지고 있지 않기 때문에 고객의 시간과 비용만 낭비하는 금형과 도구를 만드는 데 길고 값비싼 방법을 사용합니다. 인클로저, 전자 하우징... 등과 같은 맞춤형 판금 구성 요소가 필요한 경우 빠른 시간 내에 당사에 연락하여 신속한 판금 프로토타이핑 서비스를 받으십시오. CLICK Product Finder-Locator Service 이전 메뉴
- Forging and Powdered Metallurgy, Die Forging, Heading, Hot Forging
Forging and Powdered Metallurgy, Die Forging, Heading, Hot Forging, Impression Die, Near Net Shape, Swaging, Metal Hobbing, Riveting, Coining from AGS-TECH Inc. 금속 단조 및 분말 야금 우리가 제공하는 금속 단조 공정의 유형은 열간 및 냉간 다이, 개방형 다이 및 폐쇄형 다이, 인상 다이 및 플래시리스 단조, cogging, 풀러링, 에징 및 정밀 단조, 거의 그물 모양, 헤딩입니다. , 스웨이징, 업셋 단조, 금속 호빙, 프레스 및 롤 및 방사형 및 궤도 및 링 및 등온 단조, 코이닝, 리벳팅, 금속 볼 단조, 금속 피어싱, 사이징, 고에너지 단조. 당사의 분말 야금 및 분말 처리 기술은 분말 압축 및 소결, 함침, 침투, 열간 및 냉간 등방압 압축, 금속 사출 성형, 롤 압축, 분말 압연, 분말 압출, 느슨한 소결, 불꽃 소결, 고온 압축입니다. 여기를 클릭하는 것이 좋습니다. AGS-TECH Inc.의 단조 공정 개략도를 다운로드하십시오. AGS-TECH Inc.의 분말 야금 공정 개략도를 다운로드하십시오. 사진과 스케치가 포함된 다운로드 가능한 파일은 아래에서 제공하는 정보를 더 잘 이해하는 데 도움이 됩니다. 금속 단조에서는 압축력이 가해지고 재료가 변형되어 원하는 모양이 얻어집니다. 산업에서 가장 일반적인 단조 재료는 철과 강철이지만 알루미늄, 구리, 티타늄, 마그네슘과 같은 수많은 다른 재료도 널리 단조됩니다. 단조 금속 부품은 밀봉된 균열 및 폐쇄된 빈 공간 외에도 결정립 구조가 개선되어 이 공정으로 얻은 부품의 강도가 더 높습니다. 단조는 주조 또는 기계 가공으로 만든 부품보다 무게에 비해 훨씬 더 강한 부품을 생산합니다. 단조 부품은 금속을 최종 형상으로 흐르게 하여 성형되기 때문에 금속은 부품의 우수한 강도를 설명하는 방향성 결정립 구조를 취합니다. 즉, 단조 공정으로 얻은 부품은 단순 주조 부품이나 기계 부품에 비해 기계적 특성이 더 우수합니다. 금속 단조의 무게는 작은 경량 부품에서 수십만 파운드에 이르기까지 다양합니다. 우리는 주로 자동차 부품, 기어, 작업 도구, 수공구, 터빈 샤프트, 오토바이 기어와 같은 부품에 높은 응력이 가해지는 기계적으로 까다로운 응용 분야를 위한 단조품을 제조합니다. 툴링 및 설정 비용이 상대적으로 높기 때문에 이 제조 공정은 대량 생산 및 항공우주 랜딩 기어와 같은 소량이지만 고가치 중요 부품에만 권장됩니다. 툴링 비용 외에도 대량 단조 부품의 제조 리드 타임은 일부 단순 가공 부품에 비해 더 길 수 있지만 기술은 볼트, 너트, 특수 적용과 같이 특별한 강도를 요구하는 부품에 중요합니다 패스너, 자동차, 지게차, 크레인 부품. • HOT DIE 및 COLD DIE 단조 : 열간 단조는 이름에서 알 수 있듯이 고온에서 수행되므로 연성은 높고 재료의 강도는 낮습니다. 이는 변형 및 단조를 용이하게 합니다. 반대로 냉간 다이 단조는 더 낮은 온도에서 수행되고 더 높은 힘이 필요하므로 변형 경화, 더 나은 표면 조도 및 제조 부품의 정확도가 발생합니다. • OPEN DIE 및 IMPRESSION DIE FORGING : 개방형 단조에서 금형은 압축되는 재료를 구속하지 않는 반면, 인상 금형 단조에서는 금형 내의 공동이 원하는 모양으로 단조되는 동안 재료 흐름을 제한합니다. 실제로 동일하지는 않지만 매우 유사한 공정인 UPSET FORGING 또는 UPSETTING이라고도 하는 는 공작물이 두 개의 플랫 다이 사이에 끼워지고 압축력이 높이를 줄이는 개방형 다이 공정입니다. 높이가 reduced에 따라 공작물 너비가 증가합니다. HEADING, 업셋 단조 공정에는 끝 부분이 업셋되고 단면이 국부적으로 증가하는 원통형 스톡이 포함됩니다. 제목에서 스톡은 다이를 통해 공급되고 단조된 다음 길이로 절단됩니다. 이 작업은 많은 양의 패스너를 빠르게 생산할 수 있습니다. 재료를 강화해야 하는 못 끝, 나사 끝, 너트 및 볼트를 만드는 데 사용되기 때문에 주로 냉간 가공입니다. 또 다른 개방형 다이 공정은 COGGING으로, 각 단계에서 공작물이 일련의 단계로 단조되어 재료가 압축되고 공작물 길이를 따라 열린 다이가 후속적으로 움직입니다. 각 단계에서 두께가 줄어들고 길이가 조금씩 늘어납니다. 그 과정은 신경질적인 학생이 작은 걸음으로 연필을 물어뜯는 것과 비슷합니다. 풀러링(FULLERING)이라는 프로세스는 다른 금속 단조 작업이 수행되기 전에 공작물에 재료를 분배하기 위한 초기 단계로 자주 사용하는 또 다른 개방형 다이 단조 방법입니다. 공작물에 여러 forging operations가 필요할 때 사용합니다. 작업 시 볼록면이 있는 다이가 변형되어 금속이 양쪽으로 유출됩니다. 풀러링과 유사한 프로세스인 EDGING은 반면에 가공물을 변형시키기 위해 오목한 표면이 있는 개방형 다이를 포함합니다. 테두리는 또한 후속 단조 작업을 위한 준비 프로세스로 재료가 양쪽에서 중앙 영역으로 흐르게 합니다. IMPRESSION DIE FORGING 또는 CLOSED DIE FORGING이라고도 하는 CLOSED DIE FORGING은 재료를 압축하고 자체 내부의 흐름을 제한하는 다이/몰드를 사용합니다. 다이가 닫히고 재료가 다이/몰드 캐비티의 형태를 취합니다. PRECISION FORGING은 특별한 장비와 금형을 필요로 하는 공정으로 Flash가 없거나 아주 적은 부품을 생산합니다. 즉, 부품은 최종 치수에 가깝습니다. 이 과정에서 잘 조절된 양의 재료가 조심스럽게 삽입되어 금형 내부에 배치됩니다. 우리는 이 방법을 얇은 단면, 작은 공차 및 구배 각도가 있는 복잡한 모양과 금형 및 장비 비용을 정당화할 만큼 충분히 큰 경우에 사용합니다. • 플래시리스 단조: 재료가 캐비티 밖으로 흘러나와 플래시를 형성할 수 없도록 공작물을 다이에 배치합니다. 따라서 원하지 않는 플래시 트리밍이 필요하지 않습니다. 정밀 단조 공정이므로 재료 사용량의 세심한 관리가 필요합니다. • METAL SWAGING 또는 RADIAL 단조 : 공작물을 금형에 의해 원주방향으로 가공하여 단조합니다. 맨드릴을 사용하여 내부 공작물 형상을 단조할 수도 있습니다. 스웨이징 작업에서 공작물은 일반적으로 초당 여러 스트로크를 받습니다. 스웨이징으로 생산되는 대표적인 품목은 뾰족한 팁 도구, 테이퍼 바, 스크루드라이버입니다. • METAL PIRCING : 부품 제조시 추가적인 작업으로 자주 사용하는 작업입니다. 구멍이나 캐비티는 뚫지 않고 공작물 표면에 피어싱으로 생성됩니다. 피어싱은 관통 구멍이 생기는 드릴링과 다릅니다. • 호빙(HOBBING) : 원하는 형상의 펀치가 공작물에 눌러지고 원하는 모양의 캐비티가 생성됩니다. 우리는 이 펀치를 HOB라고 부릅니다. 작업에는 고압이 포함되며 저온에서 수행됩니다. 결과적으로 재료는 냉간 가공되고 변형 경화됩니다. 따라서 이 공정은 다른 제조 공정을 위한 금형, 다이 및 캐비티 제조에 매우 적합합니다. 호브가 제작되면 하나씩 가공할 필요 없이 동일한 캐비티를 여러 개 쉽게 제작할 수 있습니다. • ROLL FORGING 또는 ROLL FORMING : 두 개의 대향 롤을 사용하여 금속 부품을 성형합니다. 가공물이 롤에 공급되고 롤이 회전하여 틈새로 가공물을 당기고 가공물이 롤의 홈이 있는 부분을 통해 공급되고 압축력이 재료에 원하는 모양을 부여합니다. 압연 공정이 아니라 단조 공정이기 때문에 연속 작업이 아닌 개별 작업입니다. 롤 그로브의 형상은 재료를 필요한 모양과 형상으로 단조합니다. 뜨겁게 수행됩니다. 단조 공정이기 때문에 기계적 특성이 뛰어난 부품을 생산하므로 샤프트와 같은 거친 작업 환경에서 탁월한 내구성이 필요한 자동차 부품 제조에 사용합니다. • ORBITAL FORGING : 공작물을 단조 금형 캐비티에 넣고 경사 축을 중심으로 회전하면서 궤도 경로를 이동하는 상부 금형에 의해 단조됩니다. 각 회전에서 상부 다이는 전체 공작물에 압축력을 가하는 것을 완료합니다. 이러한 회전을 여러 번 반복함으로써 충분한 단조가 수행됩니다. 이 제조 기술의 장점은 저소음 작동과 더 적은 힘이 필요하다는 것입니다. 다시 말해서 작은 힘으로 축을 중심으로 무거운 다이를 회전시켜 다이와 접촉하는 공작물 부분에 큰 압력을 가할 수 있습니다. 디스크 또는 원추형 부품이 때때로 이 프로세스에 적합합니다. • RING FORGING : 이음매 없는 링을 만드는 데 자주 사용합니다. 스톡을 길이로 자르고 뒤집은 다음 중앙 구멍을 만들기 위해 끝까지 뚫습니다. 그런 다음 맨드릴에 놓고 원하는 치수가 얻어질 때까지 링을 천천히 회전시키면서 단조 다이가 위에서 망치질을 합니다. • 리벳팅: 부품을 결합하는 일반적인 프로세스는 부품을 통해 미리 만들어진 구멍에 삽입된 직선 금속 조각으로 시작합니다. 그 후 금속 조각의 두 끝은 상부 및 하부 다이 사이의 조인트를 압착하여 단조됩니다. • COINING : 짧은 거리에 큰 힘을 가하는 기계적 프레스에 의해 수행되는 또 다른 대중적인 공정. 주화(coining)라는 이름은 금속 주화의 표면에 세세한 부분을 단조하여 만든 것입니다. 대부분 제품의 마무리 공정으로, 이러한 세부 사항을 가공물에 전달하는 다이에 의해 가해지는 큰 힘의 결과로 표면에 미세한 세부 사항이 얻어집니다. • METAL BALL 단조 : 볼베어링과 같은 제품은 정밀하게 제작된 고품질의 금속구를 필요로 합니다. SKEW ROLLING이라는 기술에서는 스톡이 롤에 지속적으로 공급될 때 연속적으로 회전하는 두 개의 반대 롤을 사용합니다. 두 롤의 한쪽 끝에서 금속 구체가 제품으로 배출됩니다. 금속 볼 단조의 두 번째 방법은 금형 캐비티의 구형을 취하여 그 사이에 배치된 재료 스톡을 압착하는 다이를 사용하는 것입니다. 종종 생산된 볼은 고품질 제품이 되기 위해 마무리 및 연마와 같은 몇 가지 추가 단계가 필요합니다. • 등온 단조 / 열간 단조 : 편익/비용 가치가 정당할 때만 수행되는 고가의 공정. 금형이 공작물과 거의 같은 온도로 가열되는 열간 가공 공정. 금형과 공작물의 온도가 거의 같기 때문에 냉각이 없고 금속의 유동 특성이 향상됩니다. 작업은 초합금 및 단조성이 떨어지는 재료 및 재료에 적합합니다. 기계적 특성은 작은 온도 구배 및 변화에 매우 민감합니다. • METAL SIZING : 냉간 마무리 공정입니다. 재료의 흐름은 힘이 가해지는 방향을 제외하고 모든 방향으로 제한되지 않습니다. 결과적으로 매우 우수한 표면 조도와 정확한 치수를 얻을 수 있습니다. • HIGH ENERGY RATE FORGY 단조: 이 기술은 연료-공기 혼합물이 점화 플러그에 의해 점화될 때 빠르게 밀어지는 피스톤 암에 부착된 상부 금형을 포함합니다. 이는 자동차 엔진의 피스톤 작동과 유사합니다. 금형은 공작물에 매우 빠르게 부딪힌 다음 배압 덕분에 매우 빠르게 원래 위치로 돌아갑니다. 작업은 몇 밀리초 이내에 위조되므로 작업이 식을 시간이 없습니다. 이것은 매우 온도에 민감한 기계적 특성을 갖는 단조하기 어려운 부품에 유용합니다. 즉, 공정이 너무 빨라서 부품이 전체에 걸쳐 일정한 온도에서 형성되고 금형/가공물 인터페이스에 온도 구배가 없을 것입니다. • DIE FORGING에서 금속은 금형이라고 하는 특별한 모양을 가진 두 개의 일치하는 강철 블록 사이에서 두들겨집니다. 금속이 다이 사이에서 두드려지면 다이의 모양과 같은 모양이 됩니다. 최종 모양이 되면 꺼내서 식힙니다. 이 프로세스는 정확한 모양의 강력한 부품을 생산하지만 특수 다이에 더 많은 투자가 필요합니다. 업셋 단조는 금속 조각을 평평하게 하여 직경을 증가시킵니다. 일반적으로 작은 부품을 만드는 데 사용되며 특히 볼트 및 못과 같은 패스너에 머리를 형성하는 데 사용됩니다. • POWDER METALLURGY / POWDER PROCESSING : 이름에서 알 수 있듯 분말로 특정 형상과 모양의 단단한 부품을 만드는 제조 공정을 포함합니다. 이 목적으로 금속 분말을 사용하는 경우 분말 야금의 영역이고 비금속 분말을 사용하는 경우 분말 가공입니다. 고체 부품은 압축 및 소결을 통해 분말에서 생산됩니다. POWDER PRESSING은 분말을 원하는 모양으로 압축하는 데 사용됩니다. 첫째, 주요 물질은 물리적으로 분말화되어 여러 개의 작은 개별 입자로 나뉩니다. 분말 혼합물이 다이에 채워지고 펀치가 분말 쪽으로 이동하여 원하는 모양으로 압축합니다. 대부분 상온에서 가루로 압착하여 단단한 부분을 얻어서 성형체라고 합니다. 결합제 및 윤활제는 압축성을 향상시키기 위해 일반적으로 사용됩니다. 수천 톤의 유압 프레스를 사용하여 분말 프레스 성형이 가능합니다. 또한 상반된 펀치와 바텀 펀치가 있는 더블 액션 프레스와 매우 복잡한 부품 형상을 위한 멀티 액션 프레스가 있습니다. 많은 분말 야금/분말 가공 공장에서 중요한 문제인 균일성은 AGS-TECH에서 수년간 이러한 부품을 맞춤 제작한 광범위한 경험 때문에 큰 문제가 아닙니다. 균일성이 문제가 되는 두꺼운 부품에서도 우리는 성공했습니다. 우리가 당신의 프로젝트에 전념하면 당신의 부품을 만들 것입니다. 잠재적인 위험이 발견되면 in 에 알려드리겠습니다. 전진. 2단계인 POWDER SINTERING은 프레스된 부분의 분말 입자가 서로 결합할 수 있도록 일정 온도까지 온도를 올리고 그 온도를 일정 시간 유지하는 과정입니다. 이것은 훨씬 더 강한 결합과 공작물의 강화를 초래합니다. 소결은 분말의 용융 온도 근처에서 발생합니다. 소결하는 동안 수축이 일어나고 재료의 강도, 밀도, 연성, 열전도도, 전기전도도가 증가합니다. 우리는 소결을 위한 배치 및 연속로가 있습니다. 우리의 능력 중 하나는 우리가 생산하는 부품의 다공성 수준을 조정하는 것입니다. 예를 들어 부품을 어느 정도 다공성으로 유지하여 금속 필터를 생산할 수 있습니다. IMPREGNATION이라는 기술을 사용하여 금속의 구멍을 오일과 같은 유체로 채웁니다. 예를 들어 자체 윤활성 오일 함침 베어링을 생산합니다. INFILTRATION 공정에서 우리는 금속의 기공을 모재보다 융점이 낮은 다른 금속으로 채웁니다. 혼합물은 두 금속의 용융 온도 사이의 온도로 가열됩니다. 그 결과 몇 가지 특별한 속성을 얻을 수 있습니다. 우리는 또한 특수한 특징이나 특성을 얻어야 하거나 더 적은 공정 단계로 부품을 제조할 수 있는 경우 분말 제조 부품에 기계가공 및 단조와 같은 2차 작업을 자주 수행합니다. ISOSTATIC PRESSING: 이 프로세스에서 유체 압력이 부품을 압축하는 데 사용됩니다. 금속 분말을 밀봉된 유연한 용기로 만든 금형에 넣습니다. 등방압 프레스에서는 기존의 프레스에서 볼 수 있는 축방향 압력과 달리 사방에서 압력이 가해집니다. 등방압 프레싱의 장점은 부품 내 균일한 밀도, 특히 더 크거나 두꺼운 부품의 경우 우수한 특성입니다. 단점은 긴 사이클 시간과 상대적으로 낮은 기하학적 정확도입니다. COLD ISOSTATIC PRESSING은 상온에서 이루어지며 유연한 몰드는 고무, PVC, 우레탄 또는 이와 유사한 재질로 만들어집니다. 가압 및 압착에 사용되는 유체는 오일 또는 물입니다. 그린 콤팩트의 통상적인 소결은 이것을 따른다. 반면에 HOT ISOSTATIC PRESSING은 고온에서 수행되며 금형 재료는 온도에 견딜 수 있을 만큼 충분히 높은 융점을 가진 판금 또는 세라믹입니다. 가압 유체는 일반적으로 불활성 기체입니다. 프레싱 및 소결 작업이 한 단계로 수행됩니다. 다공성이 거의 완전히 제거되고 uniform grain 구조가 얻어집니다. 열간 등압 프레스의 장점은 주조와 단조에 적합하지 않은 재료를 사용할 수 있게 하면서 주조와 단조를 합친 것과 비슷한 부품을 생산할 수 있다는 것입니다. 열간 등방압 프레스의 단점은 사이클 시간이 길어 비용이 많이 든다는 것입니다. 낮은 볼륨의 중요한 부분에 적합합니다. 금속 사출 성형 : 얇은 벽과 상세한 형상을 가진 복잡한 부품을 생산하는 데 매우 적합한 공정입니다. 작은 부품에 가장 적합합니다. 분말과 폴리머 바인더를 혼합, 가열하여 금형에 주입합니다. 폴리머 바인더는 분말 입자의 표면을 코팅합니다. 성형 후, 용제를 사용하여 용해된 것을 저온 가열하여 바인더를 제거한다. ROLL COMPACTION / POWDER ROLLING : 분말은 연속 스트립 또는 시트를 생산하는 데 사용됩니다. 분말은 피더에서 공급되고 두 개의 회전 롤에 의해 시트 또는 스트립으로 압축됩니다. 수술은 차갑게 수행됩니다. 시트는 소결로로 운반됩니다. 소결 과정은 2회 반복될 수 있다. 분말 압출 : 얇은 판금 용기에 분말을 압출하여 길이 대 직경 비율이 큰 부품을 제조합니다. LOOSE SINTERING : 이름에서 알 수 있듯이 압력이 없는 압축 소결 방식으로 금속 필터와 같이 다공성이 매우 높은 부품을 생산하는 데 적합합니다. 분말은 압축하지 않고 금형 캐비티에 공급됩니다. LOOSE SINTERING : 이름에서 알 수 있듯이 압력이 없는 압축 소결 방식으로 금속 필터와 같이 다공성이 매우 높은 부품을 생산하는 데 적합합니다. 분말은 압축하지 않고 금형 캐비티에 공급됩니다. SPARK SINTERING : 두 개의 대향 펀치에 의해 분말이 금형 내에서 압축되고 펀치에 고전력 전류가 인가되어 그 사이에 끼워진 압축 분말을 통과합니다. 고전류는 분말 입자에서 표면 필름을 태우고 생성된 열로 소결합니다. 열이 외부에서 가해지지 않고 금형 내부에서 열이 발생하기 때문에 공정이 빠릅니다. HOT PRESSING : 고온에 견딜 수 있는 금형에서 분말을 1단계로 압착, 소결합니다. 다이가 압축됨에 따라 분말 열이 다이에 가해집니다. 이 방법으로 얻은 우수한 정확도와 기계적 특성은 매력적인 옵션입니다. 내화 금속도 흑연과 같은 주형 재료를 사용하여 가공할 수 있습니다. CLICK Product Finder-Locator Service 이전 메뉴
- Plastic Rubber Metal Extrusions, Extrusion Dies, Aluminum Extruding
Plastic Rubber Metal Extrusions, Extrusion Dies, Aluminum Extruding, Pipe Tube Forming, Plastic Profiles, Metal Profiles Manufacturing, PVC at AGS-TECH Inc. 압출, 압출 제품, 압출 우리는 EXTRUSION process를 사용하여 튜브, 파이프 및 방열판과 같은 고정된 단면 프로파일을 가진 제품을 제조합니다. 많은 재료를 압출할 수 있지만 가장 일반적인 압출은 금속, 폴리머/플라스틱, 세라믹으로 만들어집니다. 압출된 부품을 압출물 또는 복수인 경우 압출물이라고 합니다. 우리가 수행하는 프로세스의 일부 특수 버전은 오버재킷, 공압출 및 복합 압출입니다. to 여기를 클릭하는 것이 좋습니다.AGS-TECH Inc.의 금속 세라믹 및 플라스틱 압출 공정의 개략도를 다운로드하십시오. 이렇게 하면 아래에서 제공하는 정보를 더 잘 이해하는 데 도움이 됩니다. 압출에서 압출될 재료는 원하는 단면 프로파일을 갖는 다이를 통해 밀거나 당겨집니다. 이 공정은 표면 마감이 우수한 복잡한 단면을 제조하고 취성 재료에 대한 작업에 사용할 수 있습니다. 이 프로세스를 사용하여 원하는 길이의 부품을 생산할 수 있습니다. 프로세스 단계를 단순화하려면: 1.) 따뜻하거나 뜨거운 압출에서 재료는 가열되어 프레스의 용기에 로드됩니다. 재료를 눌러 다이에서 밀어냅니다. 2.) 생산된 압출물을 펴서 펴거나 열처리하거나 냉간가공하여 물성을 높인다. 반면에 COLD EXTRUSION takes는 실온 부근에서 발생하며 산화가 적고 견뢰도가 좋고 표면 조도가 우수하며 표면 조도가 더 가깝습니다. WARM EXTRUSION 는 실온 이상이지만 재결정화점 이하에서 수행됩니다. 필요한 힘, 연성 및 재료 특성에 대한 절충안과 균형을 제공하므로 일부 응용 분야에서 선택됩니다. HOT EXTRUSION 재료의 재결정 온도 이상에서 발생합니다. 이렇게 하면 다이를 통해 재료를 더 쉽게 밀어낼 수 있습니다. 그러나 장비 비용이 높습니다. 압출 프로파일이 더 복잡할수록 다이(툴링) 비용이 더 많이 들고 생산 속도는 더 낮아집니다. 다이 단면과 두께에는 압출할 재료에 따라 제한이 있습니다. 압출 다이의 날카로운 모서리는 항상 바람직하지 않으며 필요한 경우가 아니면 피해야 합니다. 압출되는 재료에 따라 다음을 제공합니다. • METAL EXTRUSIONS : 우리가 생산하는 가장 일반적인 것은 알루미늄, 황동, 아연, 구리, 강철, 티타늄, 마그네슘입니다. • PLASTIC EXTRUSION : 플라스틱이 용융되어 연속 프로파일로 형성됩니다. 가공되는 우리의 일반적인 재료는 폴리에틸렌, 나일론, 폴리스티렌, 폴리염화비닐, 폴리프로필렌, ABS 플라스틱, 폴리카보네이트, 아크릴입니다. 우리가 제조하는 일반적인 제품에는 파이프 및 튜브, 플라스틱 프레임이 포함됩니다. 이 과정에서 작은 플라스틱 비드/수지는 호퍼에서 압출기의 배럴로 중력이 공급됩니다. 종종 우리는 제품에 필요한 사양과 특성을 제공하기 위해 착색제 또는 기타 첨가제를 호퍼에 혼합합니다. 가열된 배럴에 들어가는 재료는 회전하는 나사에 의해 강제로 배럴의 끝 부분을 떠나 용융 플라스틱의 오염 물질을 제거하기 위해 스크린 팩을 통해 이동합니다. 스크린 팩을 통과한 후 플라스틱은 압출 다이에 들어갑니다. 다이는 움직이는 부드러운 플라스틱이 통과할 때 프로파일 모양을 제공합니다. 이제 압출물은 냉각을 위해 수조를 거칩니다. AGS-TECH Inc.가 수년 동안 사용해 온 기타 기술은 다음과 같습니다. • PIPE & TUBING EXTRUSION : 플라스틱 파이프와 튜브는 플라스틱이 원형 다이를 통해 압출되고 수조에서 냉각된 다음 길이로 절단되거나 코일/감기될 때 형성됩니다. 투명 또는 유색, 줄무늬, 단일 또는 이중 벽, 유연 또는 경질, PE, PP, 폴리우레탄, PVC, 나일론, PC, 실리콘, 비닐 또는 기타 모든 것이 있습니다. 우리는 귀하의 사양에 따라 생산할 수있는 기능뿐만 아니라 튜브도 보유하고 있습니다. AGS-TECH는 의료, 전기 및 전자, 산업 및 기타 응용 분야에 대한 FDA, UL 및 LE 요구 사항에 따라 튜브를 제조합니다. • OVERJACKETING / OVER JACKETING EXTRUSION : 이 기술은 기존 와이어 또는 케이블에 외부 플라스틱 층을 적용합니다. 당사의 절연 전선은 이 방법으로 제조됩니다. • COEXTRUSION : 재료의 여러 레이어가 동시에 압출됩니다. 여러 레이어는 여러 압출기에 의해 전달됩니다. 다양한 층 두께는 고객 사양에 맞게 조정할 수 있습니다. 이 프로세스를 통해 제품에서 각각 다른 기능을 갖는 여러 폴리머를 사용할 수 있습니다. 결과적으로 다양한 속성을 최적화할 수 있습니다. • COMPOUND EXTRUSION: 단일 또는 다중 폴리머를 첨가제와 혼합하여 플라스틱 화합물을 얻습니다. 당사의 이축 압출기는 컴파운딩 압출을 생산합니다. 압출 다이는 일반적으로 금속 금형에 비해 저렴합니다. 알루미늄을 압출하는 중소형 압출 다이에 수천 달러 이상을 지불하고 있다면 아마도 너무 많은 비용을 지불하고 있는 것입니다. 우리는 귀하의 응용 분야에 가장 비용 효율적이고 빠르며 가장 적합한 기술을 결정하는 전문가입니다. 때로는 부품을 압출하고 기계가공하면 많은 현금을 절약할 수 있습니다. 확고한 결정을 내리기 전에 먼저 의견을 물어보십시오. 우리는 많은 고객들이 올바른 결정을 내릴 수 있도록 도왔습니다. 널리 사용되는 일부 금속 압출물의 경우 아래 컬러 텍스트를 클릭하여 브로셔 및 카탈로그를 다운로드할 수 있습니다. 요구 사항을 충족하는 기성품이라면 더 경제적입니다. 의료용 튜브 및 파이프 압출 기능 다운로드 압출 방열판 다운로드 • 압출 성형용 2차 제조 및 가공 공정 : 압출 제품에 제공하는 부가가치 프로세스는 다음과 같습니다. - 맞춤형 튜브 및 파이프 벤딩, 성형 및 성형, 튜브 컷오프, 튜브 엔드 성형, 튜브 코일링, 기계 가공 및 마무리, 홀 드릴링 및 피어싱 및 펀칭, - 맞춤형 파이프 및 튜브 어셈블리, 관형 어셈블리, 용접, 브레이징 및 납땜 - 맞춤형 압출 벤딩, 성형 및 성형 - 세척, 탈지, 산세척, 부동태화, 연마, 아노다이징, 도금, 페인팅, 열처리, 어닐링 및 경화, 마킹, 조각 및 라벨링, 맞춤형 포장. CLICK Product Finder-Locator Service 이전 페이지
- Casting and Machined Parts, CNC Manufacturing, Milling, Turning, Swiss
Casting and Machined Parts, CNC Manufacturing, Milling, Turning, Swiss Type Machining, Die Casting, Investment Casting, Lost Foam Cast Parts from AGS-TECH Inc. 주조 및 가공 당사의 맞춤형 주조 및 가공 기술은 소모품 및 비소모성 주조, 철 및 비철 주조, 모래, 다이, 원심, 연속, 세라믹 몰드, 매몰, 로스트 폼, 그물에 가까운 형상, 영구 몰드(중력 다이캐스팅), 석고입니다. 몰드(석고 주조) 및 쉘 주물, 밀링 및 선삭 가공으로 생산되는 가공 부품, 기존 및 CNC 장비, 높은 처리량을 위한 스위스 유형 가공 저렴한 소형 정밀 부품, 패스너용 나사 가공, 비전통적 가공. 금형 제조가 매력적이지 않거나 옵션이 아닌 경우 금속 및 금속 합금 외에도 세라믹, 유리 및 플라스틱 부품도 가공한다는 점을 염두에 두십시오. 폴리머 재료의 가공은 플라스틱과 고무의 부드러움, 비강성 등으로 인해 어려움을 겪기 때문에 전문적인 경험이 필요합니다. 세라믹 및 유리 가공에 대해서는 비전통 가공 페이지를 참조하십시오. AGS-TECH Inc.는 경량 및 중량 주물을 모두 제조 및 공급합니다. 보일러, 열교환기, 자동차, 마이크로 모터, 풍력 터빈, 식품 포장 장비 등의 금속 주물 및 가공 부품을 공급하고 있습니다. to 여기를 클릭하는 것이 좋습니다.AGS-TECH Inc.의 가공 및 주조 공정의 개략도를 다운로드하십시오. 이렇게 하면 아래에서 제공하는 정보를 더 잘 이해하는 데 도움이 됩니다. 당사가 제공하는 다양한 기술 중 일부를 자세히 살펴보겠습니다. • EXPENDABLE MOLD CASTING : 이 광범위한 범주는 임시 및 재사용할 수 없는 금형을 포함하는 방법을 나타냅니다. 예로는 모래, 석고, 조개, 매몰(로스트 왁스라고도 함) 및 석고 주조가 있습니다. • SAND CASTING : 모래를 주형재료로 사용하는 공정. 매우 오래된 방법이며 생산되는 금속 주물 대부분이 이 기술로 만들어질 정도로 여전히 매우 인기가 있습니다. 소량 생산에도 저비용. 소형 및 대형 부품 제조에 적합합니다. 이 기술은 아주 적은 투자로 며칠 또는 몇 주 안에 부품을 제조하는 데 사용할 수 있습니다. 축축한 모래는 점토, 바인더 또는 특수 오일을 사용하여 함께 결합됩니다. 일반적으로 모래는 금형 상자에 담겨 있으며 모형 주위에 모래를 압축하여 캐비티 & 게이트 시스템을 만듭니다. 프로세스는 다음과 같습니다. 1.) 모형을 만들기 위해 모래에 모형을 놓기 2.) 게이팅 시스템에 모델과 모래의 통합 3.) 모델 제거 4.) 용융 금속으로 금형 캐비티 채우기 5.) 금속 냉각 6.) 샌드 몰드 파괴 및 주물 제거 • PLASTER MOLD CASTING : 샌드캐스팅과 유사하며, 샌드 대신 파리의 석고를 형재로 사용한다. 모래 주조와 같이 생산 리드 타임이 짧고 저렴합니다. 치수 공차 및 표면 마감이 우수합니다. 주요 단점은 알루미늄 및 아연과 같은 저융점 금속에만 사용할 수 있다는 것입니다. • SHELL MOLD CASTING : 또한 샌드캐스팅과 유사하다. 모래 주조 공정에서와 같이 모래로 채워진 플라스크 대신 모래 껍질과 열경화성 수지 바인더를 경화시켜 얻은 금형 캐비티. 모래로 주조하기에 적합한 거의 모든 금속은 쉘 몰딩으로 주조할 수 있습니다. 프로세스는 다음과 같이 요약할 수 있습니다. 1.) 쉘 몰드의 제조. 사용되는 모래는 모래 주조에 사용되는 모래와 비교할 때 훨씬 작은 입자 크기입니다. 고운 모래는 열경화성 수지와 혼합됩니다. 금속 패턴은 이형제로 코팅되어 쉘을 쉽게 제거할 수 있습니다. 그 후 금속 패턴이 가열되고 모래 혼합물이 열간 주조 패턴에 구멍을 뚫거나 취입됩니다. 패턴의 표면에 얇은 껍질이 형성됩니다. 이 쉘의 두께는 모래 수지 혼합물이 금속 패턴과 접촉하는 시간의 길이를 변경하여 조정할 수 있습니다. 그런 다음 느슨한 모래는 껍질로 덮인 패턴이 남아있는 상태로 제거됩니다. 2.) 다음으로 껍질과 패턴을 오븐에서 가열하여 껍질을 굳힙니다. 경화가 완료되면 패턴에 내장된 핀을 사용하여 패턴에서 쉘이 배출됩니다. 3.) 두 개의 이러한 쉘은 접착 또는 클램핑으로 함께 조립되어 완전한 금형을 구성합니다. 이제 쉘 몰드는 주조 과정에서 모래 또는 금속 샷으로 지지되는 용기에 삽입됩니다. 4.) 이제 뜨거운 금속을 쉘 몰드에 부을 수 있습니다. 쉘 캐스팅의 장점은 표면 조도가 매우 우수한 제품, 높은 치수 정확도로 복잡한 부품을 제조할 수 있는 가능성, 공정 자동화가 용이하고 대량 생산에 경제적이라는 점입니다. 단점은 용융 금속이 바인더 화학 물질과 접촉할 때 생성되는 가스로 인해 금형이 통풍이 잘되어야 하고 열경화성 수지 및 금속 패턴이 비싸다는 것입니다. 금속 패턴의 비용으로 인해 이 기술은 소량 생산에 적합하지 않을 수 있습니다. • 투자 주조(로스트 왁스 주조라고도 함): 또한 매우 오래된 기술이며 많은 금속, 내화 재료 및 특수 고성능 합금으로 높은 정확도, 반복성, 다양성 및 무결성을 갖춘 고품질 부품을 제조하는 데 적합합니다. 소형 부품은 물론 대형 부품도 생산할 수 있습니다. 다른 방법과 비교할 때 비용이 많이 들지만 주요 이점은 거의 그물 모양, 복잡한 윤곽 및 세부 사항을 가진 부품을 생산할 수 있다는 것입니다. 따라서 경우에 따라 재작업 및 기계 가공을 제거함으로써 비용이 다소 상쇄됩니다. 변형이 있을 수 있지만 다음은 일반적인 매몰 주조 프로세스를 요약한 것입니다. 1.) 왁스 또는 플라스틱에서 원래의 마스터 패턴 생성. 각 주조에는 프로세스에서 파괴되므로 하나의 패턴이 필요합니다. 패턴이 제조되는 금형도 필요하며 대부분의 경우 금형을 주조하거나 가공합니다. 금형을 열 필요가 없기 때문에 복잡한 주조가 가능하고 많은 왁스 패턴을 나무 가지처럼 연결하고 함께 부을 수 있으므로 금속 또는 금속 합금을 한 번 부어 여러 부품을 생산할 수 있습니다. 2.) 다음으로, 패턴은 매우 미세한 입자의 실리카, 물, 결합제로 구성된 내화성 슬러리에 담그거나 붓습니다. 그 결과 패턴 표면 위에 세라믹 층이 생깁니다. 패턴의 내화 코트는 건조되고 경화됩니다. 이 단계에서 매몰 주조라는 이름이 유래되었습니다. 내화 슬러리가 왁스 패턴 위에 매몰됩니다. 3.) 이 단계에서 경화된 세라믹 몰드를 뒤집어 가열하여 왁스를 녹여 몰드에서 쏟아냅니다. 금속 주조를 위해 구멍이 남습니다. 4.) 왁스가 제거된 후 세라믹 몰드는 더 높은 온도로 가열되어 몰드가 강화됩니다. 5.) 모든 복잡한 섹션을 채우는 뜨거운 금형에 금속 주조를 붓습니다. 6.) 주조가 굳어질 수 있습니다. 7.) 마지막으로 세라믹 몰드를 부수고 제조된 부품을 나무에서 잘라냅니다. 투자 주조 플랜트 브로셔에 대한 링크입니다. • EVAPORATIVE PATTERN CASTING : 뜨거운 용융 금속을 금형에 부으면 증발하는 폴리스티렌 폼과 같은 재료로 만든 패턴을 사용합니다. 이 공정에는 결합되지 않은 모래를 사용하는 LOST FOAM CASTING과 결합된 모래를 사용하는 FULL MOLD CASTING의 두 가지 유형이 있습니다. 다음은 일반적인 프로세스 단계입니다. 1.) 폴리스티렌과 같은 재료로 패턴을 제조합니다. 대량 생산시 패턴을 성형합니다. 부품의 모양이 복잡한 경우 이러한 폼 재료의 여러 섹션을 함께 접착하여 패턴을 형성해야 할 수 있습니다. 우리는 종종 주물에 좋은 표면 마감을 만들기 위해 내화 화합물로 패턴을 코팅합니다. 2.) 그런 다음 패턴을 주물 모래에 넣습니다. 3.) 용융 금속을 금형에 붓고 발포 패턴, 즉 대부분의 경우 폴리스티렌이 금형 캐비티를 통해 흐를 때 증발합니다. 4.) 용융 금속은 경화를 위해 모래 주형에 남아 있습니다. 5.) 경화 후 주물을 제거합니다. 어떤 경우에는 우리가 제조하는 제품에 패턴 내에 코어가 필요합니다. 증발 주조에서는 금형 캐비티에 코어를 배치하고 고정할 필요가 없습니다. 이 기술은 매우 복잡한 형상의 제조에 적합하며 대량 생산을 위해 쉽게 자동화할 수 있으며 주조 부품에 파팅 라인이 없습니다. 기본 프로세스는 간단하고 경제적으로 구현됩니다. 대량 생산의 경우 폴리스티렌에서 패턴을 생산하기 위해 다이 또는 몰드가 필요하기 때문에 다소 비용이 많이 들 수 있습니다. • NON-EXPANDABLE MOLD CASTING : 이 광범위한 범주는 각 생산 주기 후에 금형을 개질할 필요가 없는 방법을 나타냅니다. 영구, 다이, 연속 및 원심 주조가 그 예입니다. 반복성을 확보하고 부품을 NEAR NET SHAPE로 특성화할 수 있습니다. • 영구금형 주물 : 금속으로 만든 재사용 가능한 주형을 다중 주물에 사용합니다. 영구 금형은 일반적으로 마모되기 전에 수만 번 사용할 수 있습니다. 중력, 가스 압력 또는 진공은 일반적으로 금형을 채우는 데 사용됩니다. 금형(다이라고도 함)은 일반적으로 철, 강철, 세라믹 또는 기타 금속으로 만들어집니다. 일반적인 프로세스는 다음과 같습니다. 1.) 금형을 가공하고 만듭니다. 함께 맞고 열리고 닫힐 수 있는 두 개의 금속 블록으로 금형을 가공하는 것이 일반적입니다. 부품 형상과 게이팅 시스템은 일반적으로 주조 금형으로 가공됩니다. 2.) 내부 금형 표면은 내화 재료를 포함하는 슬러리로 코팅됩니다. 이는 열 흐름을 제어하는 데 도움이 되며 주조 부품을 쉽게 제거할 수 있도록 윤활제 역할을 합니다. 3.) 다음으로 영구 금형 반쪽을 닫고 금형을 가열합니다. 4.) 용융 금속을 주형에 붓고 응고를 위해 그대로 둡니다. 5.) 많은 냉각이 일어나기 전에 금형 반쪽이 열렸을 때 이젝터를 사용하여 영구 금형에서 부품을 제거합니다. 아연, 알루미늄과 같은 저융점 금속에는 영구 주형을 자주 사용합니다. 강철 주물의 경우 흑연을 주형 재료로 사용합니다. 우리는 때때로 영구 금형 내의 코어를 사용하여 복잡한 형상을 얻습니다. 이 기술의 장점은 급속 냉각으로 얻은 우수한 기계적 특성, 특성의 균일성, 우수한 정확도 및 표면 마감, 낮은 불량률, 공정 자동화 가능성 및 경제적으로 대량 생산이 가능한 주물입니다. 단점은 초기 설정 비용이 높아 소량 작업에 적합하지 않고 제조되는 부품 크기에 제한이 있다는 것입니다. • DIE CASTING : 금형을 가공하여 용융된 금속을 고압으로 금형 캐비티로 밀어 넣습니다. 비철금속 및 철금속 다이캐스팅 모두 가능합니다. 이 프로세스는 세부 사항, 매우 얇은 벽, 치수 일관성 및 우수한 표면 마감을 가진 중소 규모 부품의 대량 생산에 적합합니다. AGS-TECH Inc.는 이 기술을 사용하여 0.5mm만큼 얇은 벽 두께를 제조할 수 있습니다. 영구 주형 주조에서와 같이 주형은 생산된 부품을 제거하기 위해 열고 닫을 수 있는 두 개의 반쪽으로 구성되어야 합니다. 다이 캐스팅 몰드는 각 사이클에서 여러 주조를 생산할 수 있도록 여러 공동을 가질 수 있습니다. 다이캐스팅 몰드는 그들이 생산하는 부품보다 매우 무겁고 훨씬 크기 때문에 비용도 많이 듭니다. 우리는 고객이 부품을 재주문하는 한 고객을 위해 마모된 다이를 무료로 수리 및 교체합니다. 우리의 다이는 수십만 사이클 범위에서 긴 수명을 가지고 있습니다. 다음은 기본 간소화된 프로세스 단계입니다. 1.) 일반적으로 강철로 금형 제작 2.) 다이캐스팅 기계에 설치된 금형 3.) 피스톤은 복잡한 형상과 얇은 벽을 채우는 다이 캐비티에서 용융 금속을 강제로 흐르게 합니다. 4.) 주형에 용탕을 채운 후 압력을 가하여 주물을 경화시킨다. 5.) 이젝터 핀을 사용하여 금형을 열고 주물을 제거합니다. 6.) 이제 빈 다이에 다시 윤활유를 바르고 다음 사이클을 위해 고정합니다. 다이캐스팅에서는 금형에 추가 부품을 통합하고 그 주위에 금속을 주조하는 인서트 성형을 자주 사용합니다. 응고 후 이러한 부품은 주조 제품의 일부가 됩니다. 다이캐스팅의 장점은 부품의 우수한 기계적 특성, 복잡한 기능의 가능성, 미세한 세부 사항 및 우수한 표면 마감, 높은 생산 속도, 쉬운 자동화입니다. 단점: 높은 다이 및 장비 비용, 주조할 수 있는 모양의 제한, 이젝터 핀의 접촉으로 인한 주조 부품의 작은 둥근 자국, 파팅 라인에서 압착된 얇은 금속 플래시로 인해 소량에는 적합하지 않음 다이 사이의 파팅 라인을 따라 있는 벤트의 경우 물 순환을 사용하여 금형 온도를 낮게 유지해야 합니다. • CENTRIFUGAL CASTING : 회전축에서 회전하는 금형의 중심에 용탕을 붓는다. 원심력은 금속을 주변으로 던지고 금형이 계속 회전하면서 굳게 됩니다. 수평 및 수직 축 회전을 모두 사용할 수 있습니다. 내부 표면이 둥근 부품과 기타 원형이 아닌 모양이 있는 부품을 주조할 수 있습니다. 프로세스는 다음과 같이 요약할 수 있습니다. 1.) 용융 금속을 원심 금형에 붓습니다. 그런 다음 금형의 회전으로 인해 금속이 외벽으로 밀려납니다. 2.) 금형이 회전함에 따라 금속 주조물이 경화됩니다. 원심 주조는 파이프와 같은 중공 원통형 부품의 생산에 적합한 기술이며, 스프루, 라이저 및 게이팅 요소가 필요하지 않으며, 우수한 표면 조도 및 세부 기능, 수축 문제가 없고, 매우 큰 직경의 긴 파이프를 생산할 수 있는 가능성, 고속 생산 능력 . • CONTINUOUS CASTING ( STRAND CASTING ) : 금속을 연속적으로 주조할 때 사용합니다. 기본적으로 용탕은 금형의 2차원 프로파일로 주조되지만 그 길이는 불확실합니다. 시간이 지남에 따라 길이가 증가하면서 주조물이 아래쪽으로 이동함에 따라 새로운 용융 금속이 지속적으로 주형에 공급됩니다. 구리, 강철, 알루미늄과 같은 금속은 연속 주조 공정을 사용하여 긴 가닥으로 주조됩니다. 프로세스에는 다양한 구성이 있을 수 있지만 일반적인 구성은 다음과 같이 단순화할 수 있습니다. 1.) 용융 금속을 잘 계산된 양과 유속으로 금형 위 높은 곳에 위치한 용기에 붓고 수냉식 금형을 통해 흐릅니다. 주형에 부어진 금속 주조물은 주형 바닥에 배치된 스타터 바에 응고됩니다. 이 스타터 바는 롤러가 처음에 잡을 수 있도록 해줍니다. 2.) 긴 금속 가닥은 롤러에 의해 일정한 속도로 운반됩니다. 롤러는 또한 금속 가닥의 흐름 방향을 수직에서 수평으로 변경합니다. 3.) 연속주조가 일정한 수평거리를 이동한 후, 주물과 함께 움직이는 토치나 톱이 재빨리 원하는 길이로 절단한다. 연속 주조 공정은 연속 주조 금속을 압연기에 직접 공급하여 I-빔, T-빔 등을 생산할 수 있는 압연 공정과 통합될 수 있습니다. 연속주조는 제품 전반에 걸쳐 균일한 물성을 생성하고, 응고율이 높고, 재료 손실이 매우 적어 비용을 절감하고, 금속의 로딩, 주입, 응고, 절단 및 주조 제거가 모두 연속 작업으로 일어나는 공정을 제공하며, 따라서 높은 생산성과 높은 품질을 제공합니다. 그러나 주요 고려 사항은 높은 초기 투자, 설치 비용 및 공간 요구 사항입니다. • 가공 서비스 : 3축, 4축, 5축 가공을 제공합니다. 우리가 사용하는 가공 프로세스 유형은 선삭, 밀링, 드릴링, 보링, 브로칭, 플래닝, 톱질, 연삭, 래핑, 폴리싱 및 비전통 가공이며 당사 웹사이트의 다른 메뉴에서 자세히 설명합니다. 대부분의 제조에는 CNC 기계를 사용합니다. 그러나 일부 작업의 경우 기존 기술이 더 적합하므로 저희도 이를 사용합니다. 당사의 가공 능력은 가능한 최고 수준에 도달하며 가장 까다로운 일부 부품은 AS9100 인증 공장에서 제조됩니다. 제트 엔진 블레이드에는 고도로 전문화된 제조 경험과 올바른 장비가 필요합니다. 항공 우주 산업에는 매우 엄격한 기준이 있습니다. 복잡한 기하학적 구조를 가진 일부 구성 요소는 당사를 포함한 일부 기계 공장에서만 볼 수 있는 5축 가공으로 가장 쉽게 제조됩니다. 당사의 항공 우주 인증 공장은 항공 우주 산업의 광범위한 문서 요구 사항을 준수하는 데 필요한 경험을 보유하고 있습니다. 선삭 작업에서 공작물은 절삭 공구에 대해 회전하고 이동합니다. 이 프로세스를 위해 선반이라는 기계가 사용됩니다. 밀링에서 밀링 머신이라고 하는 기계에는 절삭날이 공작물에 닿도록 하는 회전 도구가 있습니다. 드릴링 작업에는 공작물과 접촉할 때 구멍을 생성하는 절삭날이 있는 회전 커터가 포함됩니다. 드릴 프레스, 선반 또는 밀이 일반적으로 사용됩니다. 보링 작업에서는 끝이 구부러진 단일 도구가 회전하는 공작물의 거친 구멍으로 이동하여 구멍을 약간 확대하고 정확도를 향상시킵니다. 정밀한 마감용으로 사용됩니다. 브로치(BROACHING)에는 브로치(톱니가 있는 도구)의 한 패스로 공작물에서 재료를 제거하는 톱니형 도구가 포함됩니다. 선형 브로칭에서는 브로치가 가공물의 표면에 대해 선형으로 실행되어 절단이 수행되는 반면, 로터리 브로칭에서는 브로치가 회전되어 공작물에 눌러져 축 대칭 모양을 절단합니다. SWISS TYPE MACHINING은 소형 고정밀 부품의 대량 생산에 사용하는 귀중한 기술 중 하나입니다. 스위스형 선반을 사용하여 작고 복잡한 정밀 부품을 저렴하게 가공합니다. 공작물이 정지 상태로 유지되고 공구가 움직이는 기존 선반과 달리 스위스형 터닝 센터에서는 공작물이 Z축으로 이동하고 공구가 고정되어 있습니다. 스위스식 가공에서 봉재는 기계에 고정되고 z축의 가이드 부싱을 통해 전진하여 가공할 부분만 노출됩니다. 이렇게 하면 꽉 쥐고 정확도가 매우 높아집니다. 라이브 도구의 가용성은 가이드 부싱에서 재료가 진행됨에 따라 밀링 및 드릴링할 기회를 제공합니다. 스위스형 장비의 Y축은 완전한 밀링 기능을 제공하고 제조 시간을 크게 절약합니다. 또한 당사 기계에는 부품이 서브 스핀들에 고정되어 있을 때 부품에서 작동하는 드릴 및 보링 도구가 있습니다. 당사의 Swiss-Type 가공 기능은 단일 작업으로 완전 자동화된 완전한 가공 기회를 제공합니다. 가공은 AGS-TECH Inc. 사업의 가장 큰 부분 중 하나입니다. 모든 도면 사양이 충족되도록 부품을 주조 또는 압출한 후 1차 작업 또는 2차 작업으로 사용합니다. • SURFACE FINISHING SERVICES : 접착력을 향상시키기 위한 표면처리, 코팅의 접착력을 높이기 위한 얇은 산화막 증착, 샌드 블라스팅, 케미컬필름, 아노다이징, 질화, 분체도장, 스프레이 코팅 등 다양한 표면처리 및 표면처리를 제공합니다. , 스퍼터링, 전자빔, 증발, 도금, 다이아몬드 라이크 카본(DLC)과 같은 경질 코팅 또는 드릴링 및 절삭 공구용 티타늄 코팅을 포함한 다양한 고급 금속화 및 코팅 기술. • 제품 마킹 및 라벨링 서비스 : 많은 고객이 금속 부품에 마킹 및 라벨링, 레이저 마킹, 조각을 요구합니다. 그러한 필요가 있는 경우 어떤 옵션이 귀하에게 가장 적합한지 논의해 보겠습니다. 다음은 일반적으로 사용되는 금속 주조 제품 중 일부입니다. 이들은 기성품이므로 요구 사항에 맞는 경우 금형 비용을 절약할 수 있습니다. 여기를 클릭하여 AGS-Electronics의 11 시리즈 다이캐스트 알루미늄 상자를 다운로드하십시오. CLICK Product Finder-Locator Service 이전 페이지
- Custom Manufactured Parts, Assemblies, Plastic Mold, Casting,Machining
Custom Manufactured Parts, Assemblies, Plastic Mold, Rubber Molding, Metal Casting, CNC Machining, Turning, Milling, Electrical Electronic Optical Assembly PCBA 주문 제작 부품 & 어셈블리 및 제품 더 읽어보기 플라스틱 및 고무 몰드 및 몰딩 더 읽어보기 주조 및 가공 더 읽어보기 압출, 압출 제품 더 읽어보기 스탬핑 및 판금 제작 더 읽어보기 금속 단조 및 분말 야금 더 읽어보기 와이어 및 스프링 성형 더 읽어보기 유리 및 세라믹 성형 및 성형 더 읽어보기 적층 및 신속한 제조 더 읽어보기 복합재료 및 복합재료 제조 더 읽어보기 결합 및 조립 및 고정 프로세스 당사는 귀하를 위해 부품 및 어셈블리를 생산하고 다음과 같은 제조 공정을 제공합니다. • 플라스틱 및 고무 몰드 및 성형 부품. 사출 성형, 열 성형, 열경화성 성형, 진공 성형, 중공 성형, 회전 성형, 주입 성형, 인서트 성형 및 기타. • 플라스틱, 고무 및 금속 압출 • 밀링 및 터닝 기술, 스위스식 기계 가공으로 생산되는 철 및 비철 주조 및 가공 부품. • 분말 야금 부품 • 금속 및 비금속 스탬핑, 판금 성형, 용접 판금 어셈블리 • 냉간 단조 • 와이어, 용접 와이어 어셈블리, 와이어 성형 • 다양한 유형의 스프링, 스프링 성형 • 기어 제조, 기어박스, 커플링, 웜, 감속기, 실린더, 변속기 벨트, 변속기 체인, 변속기 부품 • NATO 및 군사 표준을 준수하는 맞춤형 강화 및 방탄 유리 • 볼, 베어링, 풀리 및 풀리 어셈블리 • 밸브 및 O-링, 와셔 및 씰과 같은 공압 부품 • 유리 및 세라믹 부품 및 어셈블리, 진공 방지 및 밀폐 구성 요소, 금속-세라믹 및 세라믹-세라믹 접합. • 다양한 유형의 기계, 광기계, 전기기계, 광전자 어셈블리. • 금속-고무, 금속-플라스틱 접합 • 파이프 및 튜브, 파이프 성형, 벤딩 및 맞춤형 파이프 어셈블리, 벨로우즈 제조. • 유리 섬유 제조 • 스폿 용접, 레이저 용접, MIG, TIG 등의 다양한 기술을 사용한 용접. 플라스틱 부품의 초음파 용접. • 접착력 향상을 위한 표면 처리, 코팅 접착력 향상을 위한 얇은 산화막 증착, 샌드 블라스팅, 화학 필름, 아노다이징, 질화, 분말 코팅, 스프레이 코팅, 다양한 고급 금속화 및 코팅 기술과 같은 다양한 표면 처리 및 표면 마감 처리 절단 및 드릴링 도구용 스퍼터링, 전자빔, 증발, 도금, 다이아몬드 라이크 카본(DLC) 또는 티타늄과 같은 하드 코팅을 포함합니다. • 마킹 및 라벨링, 금속 부품 레이저 마킹, 플라스틱 및 고무 부품 인쇄 설계자와 엔지니어가 사용하는 일반적인 기계 공학 용어에 대한 브로셔 다운로드 우리는 귀하의 특정 사양과 요구 사항에 따라 제품을 제작합니다. 최고의 품질, 배송 및 가격을 제공하기 위해 우리는 중국, 인도, 대만, 필리핀, 한국, 말레이시아, 스리랑카, 터키, 미국, 캐나다, 독일, 영국 및 일본에서 전 세계적으로 제품을 제조합니다. 이것은 우리를 다른 어떤 custom manufacturer보다 훨씬 더 강력하고 전 세계적으로 더 경쟁력 있게 만듭니다. 당사의 제품은 ISO9001:2000, QS9000, ISO14001, TS16949 인증 환경에서 제조되며 CE, UL 마크를 보유하고 기타 산업 표준을 충족합니다. 귀하의 프로젝트에 임명되면 귀하가 원하는 대로 전체 제조, 조립, 테스트, 자격, 배송 및 통관을 처리할 수 있습니다. 원하는 경우 부품을 보관하고 맞춤형 키트를 조립하고 회사 이름 및 브랜드를 인쇄 및 라벨링하고 고객에게 직송할 수 있습니다. 즉, 원하는 경우 창고 및 유통 센터가 될 수도 있습니다. 우리 창고는 주요 항구 근처에 있기 때문에 물류 이점을 제공합니다. 예를 들어, 귀하의 제품이 미국의 주요 항구에 도착하면 귀하의 선택에 따라 제품을 보관, 조립, 키트 제작, 라벨 재지정, 인쇄, 포장 및 드롭할 수 있는 가까운 창고로 직접 운송할 수 있습니다. 고객에게 배송합니다. 우리는 제품만 공급하지 않습니다. 우리 회사는 귀하의 사이트에 와서 귀하의 프로젝트를 현장에서 평가하고 귀하를 위해 설계된 맞춤형 프로젝트 제안서를 개발하는 맞춤형 계약을 진행합니다. 그런 다음 경험이 풍부한 팀을 보내 프로젝트를 구현합니다. 엔지니어링 작업에 대한 자세한 내용은 다음에서 찾을 수 있습니다. http://www.ags-engineering.com - 우리는 산업 규모의 대규모 프로젝트뿐만 아니라 소규모 프로젝트도 수행합니다. 첫 번째 단계로 전화, 원격 회의 또는 MSN 메신저를 통해 전문가 팀 구성원과 연결하여 전문가와 직접 소통하고 질문하고 프로젝트에 대해 논의할 수 있습니다. 전화 주시면 방문 드리겠습니다. 이전 페이지