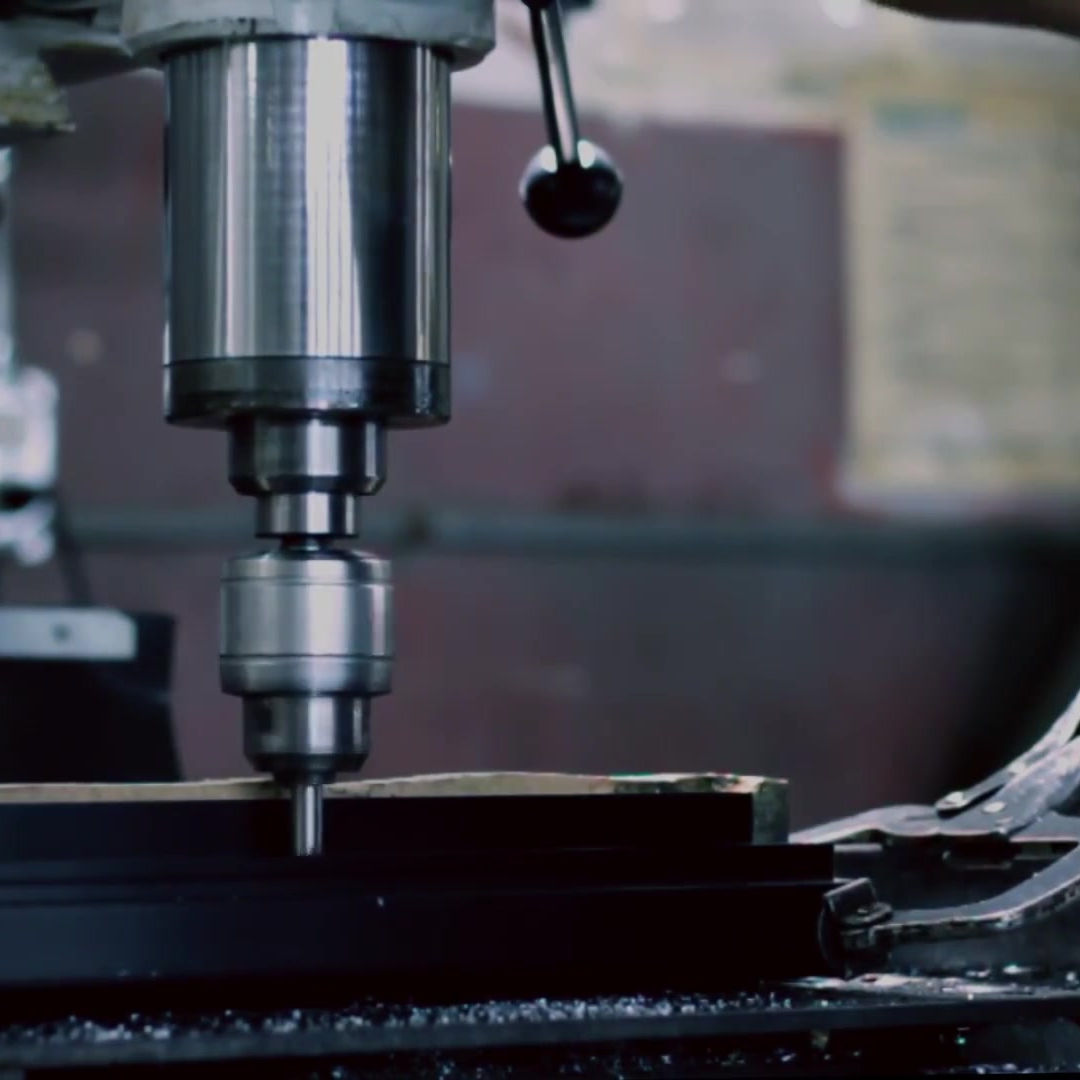
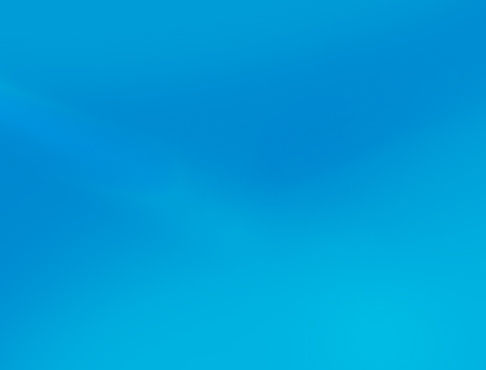
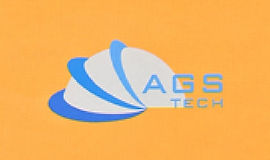
다양한 제품 및 서비스를 위한 글로벌 맞춤형 제조업체, 통합업체, 통합업체, 아웃소싱 파트너.
우리는 맞춤형 제조 및 기성 제품 및 서비스의 제조, 제조, 엔지니어링, 통합, 통합, 아웃소싱을 위한 원스톱 소스입니다.
Choose your Language
-
맞춤형 제조
-
국내 및 글로벌 계약 제조
-
제조 아웃소싱
-
국내 및 글로벌 조달
-
통합
-
엔지니어링 통합
-
엔지니어링 서비스
우리는 판금 스탬핑, 성형, 성형, 굽힘, 펀칭, 블랭킹, 슬리팅, 천공, 노칭, 니블링, 면도, 프레스 가공, 제작, 싱글 펀치/싱글 스트로크 다이를 사용한 딥 드로잉, 프로그레시브 다이 및 스피닝, 고무 성형 및 하이드로포밍; 워터젯, 플라즈마, 레이저, 톱, 화염을 사용한 판금 절단; 용접, 스폿 용접을 사용한 판금 조립; 판금 튜브 팽창 및 굽힘; 딥 또는 스프레이 페인팅, 정전기 분말 코팅, 아노다이징, 도금, 스퍼터링 등을 포함한 판금 표면 마감. 당사의 서비스는 신속한 판금 프로토타이핑에서 대량 제조에 이르기까지 다양합니다. 여기를 클릭하는 것이 좋습니다.AGS-TECH Inc.의 판금 제조 및 스탬핑 공정의 개략도를 다운로드하십시오.
이렇게 하면 아래에서 제공하는 정보를 더 잘 이해하는 데 도움이 됩니다.
• 판금 절단 : 절단 및 절단을 제공합니다. 컷오프는 한 번에 한 경로에 걸쳐 판금을 절단하고 기본적으로 재료 낭비가 없는 반면, 분할을 사용하면 모양이 정확하게 자리잡을 수 없으므로 특정 양의 재료가 낭비됩니다. 가장 인기 있는 공정 중 하나는 판금에서 원형 또는 다른 모양의 재료 조각을 잘라내는 펀칭입니다. 잘린 부분은 낭비입니다. 펀칭의 또 다른 버전은 직사각형 또는 길쭉한 구멍이 펀칭되는 SLOTTING입니다. BLANKING은 펀칭과 동일한 과정으로 잘라낸 부분을 구분하여 작업하며 보관합니다. 블랭킹의 우수한 버전인 FINE BLANKING은 정밀한 공차와 직선형 매끄러운 모서리로 절단을 생성하고 공작물의 완성을 위한 2차 작업이 필요하지 않습니다. 우리가 자주 사용하는 또 다른 공정은 SLITTING입니다. 이는 판금이 직선 또는 곡선 경로에서 두 개의 반대 원형 블레이드에 의해 절단되는 전단 공정입니다. 캔따개는 슬리팅 프로세스의 간단한 예입니다. 우리를 위한 또 다른 인기 있는 process는 원형 또는 기타 모양의 많은 구멍이 특정 패턴으로 판금에 펀칭되는 PERFORATING입니다. 다공 제품의 전형적인 예는 유체용 구멍이 많은 금속 필터입니다. 또 다른 판금 절단 공정인 노칭(NOCHING)에서는 가장자리 또는 다른 곳에서 시작하여 공작물에서 재료를 제거하고 원하는 모양이 얻어질 때까지 안쪽으로 절단합니다. 원하는 윤곽을 얻을 때까지 각 작업에서 다른 조각을 제거하는 점진적 프로세스입니다. 소규모 생산 실행의 경우 더 크고 복잡한 절단을 만들기 위해 겹치는 구멍의 많은 빠른 펀치로 구성된 NIBBLING이라는 비교적 느린 프로세스를 사용하는 경우가 있습니다. PROGRESSIVE CUTTING에서는 단일 절단 또는 특정 형상을 얻기 위해 일련의 다양한 작업을 사용합니다. 마지막으로 2차 공정을 면도하면 이미 만들어진 절단면의 가장자리를 개선하는 데 도움이 됩니다. 판금 작업의 칩, 거친 모서리 절단에 사용됩니다.
• SHEET METAL BENDING : 절단 외에 절곡은 우리가 대부분의 제품을 생산할 수 없는 필수적인 공정입니다. 대부분 냉간 작업이지만 때로는 따뜻하거나 더울 때도 수행됩니다. 우리는 이 작업을 위해 대부분의 시간을 다이와 프레스를 사용합니다. 프로그레시브 벤딩에서는 단일 벤드 또는 특정 형상을 얻기 위해 일련의 다른 펀치 및 다이 작업을 사용합니다. AGS-TECH는 다양한 굽힘 공정을 사용하며 공작물 재료, 크기, 두께, 원하는 굽힘 크기, 반경, 곡률 및 굽힘 각도, 굽힘 위치, 작동 경제성, 제조 수량 등에 따라 선택합니다. 등. V자형 펀치가 판금을 V자형 다이에 밀어넣고 구부리는 V-BENDING을 사용합니다. 90도를 포함하여 매우 예각과 둔각과 그 사이에 모두 좋습니다. 와이핑 다이를 사용하여 EDGE BENDING을 수행합니다. 우리 장비를 사용하면 90도보다 더 큰 각도를 얻을 수 있습니다. 에지 벤딩에서 공작물은 압력 패드와 다이 사이에 끼어 있으며, 벤딩 영역은 다이 에지에 있고 나머지 공작물은 캔틸레버 빔과 같은 space like 위에 유지됩니다. 펀치가 캔틸레버 부분에 작용하면 다이 가장자리 위로 구부러집니다. FLANGING은 90도 각도를 생성하는 가장자리 굽힘 공정입니다. 작업의 주요 목표는 날카로운 모서리를 제거하고 부품을 쉽게 결합할 수 있도록 기하학적 표면을 얻는 것입니다. BEADING, 또 다른 일반적인 모서리 굽힘 공정은 부품의 모서리에 컬을 형성합니다. 반면에 HEMMING은 시트의 가장자리가 완전히 구부러지는 결과를 가져옵니다. SEAMING에서는 두 부분의 가장자리가 서로 구부러져 결합됩니다. 반면에 DOUBLE SEAMING은 방수 및 기밀 판금 조인트를 제공합니다. 에지 벤딩과 유사하게 ROTARY BENDING이라는 프로세스는 원하는 각도로 절단된 실린더를 배치하고 펀치 역할을 합니다. 힘이 펀치에 전달되면 공작물과 함께 닫힙니다. 실린더의 홈은 캔틸레버 부분에 원하는 각도를 제공합니다. 홈은 90도보다 작거나 큰 각도를 가질 수 있습니다. AIR BENDING에서는 각진 홈이 있는 하부 다이가 필요하지 않습니다. 판금은 2개의 표면에 의해 반대 측면과 특정 거리에서 지지됩니다. 그런 다음 펀치는 올바른 위치에 힘을 가하고 공작물을 구부립니다. CHANNEL BENDING은 Channel 모양의 Punch와 Die를 이용하여 수행하며 U-BEND는 U자형 Punch를 이용하여 수행한다. 오프셋 굽힘은 판금에 오프셋을 생성합니다. 롤 벤딩(ROLL BENDING)은 큰 금속판의 두꺼운 작업과 굽힘에 적합한 기술로 3개의 롤을 사용하여 원하는 곡률로 판을 이송하고 구부립니다. 롤은 작업의 원하는 굽힘이 얻어지도록 배열됩니다. 롤 사이의 거리와 각도를 제어하여 원하는 결과를 얻습니다. 움직일 수 있는 롤로 곡률을 제어할 수 있습니다. TUBE FORMING은 여러 다이와 관련된 또 다른 인기 있는 판금 굽힘 작업입니다. 튜브는 여러 작업 후에 얻을 수 있습니다. CORRUGATION은 굽힘 작업으로도 수행됩니다. 기본적으로 전체 판금 조각에 걸쳐 일정한 간격으로 대칭 굽힘입니다. 주름에 다양한 모양을 사용할 수 있습니다. 골판지 금속판은 더 단단하고 굽힘에 대한 저항성이 더 우수하므로 건설 산업에 응용할 수 있습니다. SHEET METAL ROLL FORMING, 연속 manufacturing 공정은 롤을 사용하여 특정 형상의 단면을 구부리기 위해 배포되고 작업은 순차적 단계로 구부러지며 최종 롤이 작업을 완료합니다. 어떤 경우에는 단일 롤과 어떤 경우에는 일련의 롤이 사용됩니다.
• COMBINED SHEET METAL CUTTING & BENDING 공정 : 절단과 절곡을 동시에 하는 공정입니다. PIERCING에서는 뾰족한 펀치를 사용하여 구멍을 만듭니다. 펀치가 시트의 구멍을 넓힐 때 재료는 구멍의 내부 플랜지로 동시에 구부러집니다. 얻은 플랜지는 중요한 기능을 가질 수 있습니다. 반면 LANCING 작업은 시트를 자르고 구부려 융기된 형상을 만듭니다.
• METAL TUBE BULGING 및 BENDING : BULGING에서는 속이 빈 튜브의 내부 일부에 압력이 가해져 튜브가 바깥쪽으로 부풀어 오릅니다. 튜브가 다이 내부에 있기 때문에 벌지 형상은 다이의 모양에 의해 제어됩니다. STRETCH BENDING에서 금속 튜브는 튜브의 축에 평행한 힘과 굽힘 힘을 사용하여 늘어납니다. DRAW BENDING에서 우리는 회전하는 동안 튜브를 구부리는 회전하는 형태 블록에 끝 근처의 튜브를 고정합니다. 마지막으로 COMPRESSION BENDING에서 튜브는 고정된 형태의 블록에 힘으로 고정되고 다이는 그것을 형태의 블록 위로 구부립니다.
• 딥 드로잉: 가장 널리 사용되는 작업 중 하나에서 펀치, 매칭 다이 및 블랭크 홀더가 사용됩니다. 판금 블랭크가 다이 개구부 위에 배치되고 펀치가 블랭크 홀더에 의해 고정된 블랭크 쪽으로 이동합니다. 일단 접촉하면 펀치가 판금을 다이 공동으로 밀어 넣어 제품을 형성합니다. 딥 드로잉 작업은 절단과 유사하지만 펀치와 다이 사이의 간격은 시트가 절단되는 것을 방지합니다. 시트가 딥 드로잉되고 절단되지 않도록 보장하는 또 다른 요소는 전단 및 절단을 방지하는 다이와 펀치의 둥근 모서리입니다. 더 큰 규모의 딥 드로잉을 달성하기 위해 이미 딥 드로잉 프로세스를 거친 부품에 후속 딥 드로잉이 수행되는 REDRAWING 프로세스가 배포됩니다. REVERSE REDRAWING에서는 딥 드로잉 부분을 뒤집어 반대 방향으로 그립니다. 딥 드로잉은 돔형, 테이퍼형 또는 계단형 컵과 같은 불규칙한 모양의 물체를 제공할 수 있습니다. EMBOSSING에서는 암수 다이 쌍을 사용하여 디자인이나 스크립트로 판금에 깊은 인상을 남깁니다.
• SPINNING : 평평하거나 미리 형성된 공작물을 회전하는 맨드릴과 심압대 사이에 잡고 도구가 맨드릴 위로 점차적으로 이동하면서 공작물에 국부적인 압력을 가하는 작업입니다. 결과적으로 공작물이 맨드릴 위에 감겨서 모양이 잡힙니다. 주문량이 적고 부품이 크며(직경이 최대 20피트) 고유한 곡선이 있는 딥 드로잉의 대안으로 이 기술을 사용합니다. 개당 가격은 일반적으로 높지만 CNC 회전 작업의 설정 비용은 딥 드로잉에 비해 저렴합니다. 반대로 딥드로잉은 초기 셋업에 많은 투자가 필요하지만 부품을 많이 생산할 때 개당 비용이 저렴합니다. 이 공정의 또 다른 버전은 전단 회전(SHEAR SPINNING)으로, 공작물 내에서 금속 흐름도 있습니다. 금속 흐름은 프로세스가 수행됨에 따라 공작물의 두께를 감소시킵니다. 또 다른 관련 공정은 원통형 부품에 적용되는 TUBE SPINNING입니다. 또한 이 과정에서 공작물 내부에 금속 흐름이 있습니다. 따라서 두께가 감소하고 튜브의 길이가 증가합니다. 도구를 이동하여 튜브 내부 또는 외부에 피쳐를 생성할 수 있습니다.
• RUBBER FORMING OF SHEET METAL : 고무나 폴리우레탄 소재를 용기 금형에 넣고 고무 표면에 가공물을 올려놓는 방식. 그런 다음 펀치가 공작물에 작용하여 고무에 밀어 넣습니다. 고무에 의해 발생하는 압력이 낮기 때문에 생산되는 부품의 깊이가 제한됩니다. 툴링 비용이 저렴하여 소량 생산에 적합합니다.
• HYDROFORMING : 고무 성형과 유사하게 이 공정에서 판금 가공물을 펀치로 눌러 챔버 내부의 가압 액체에 넣습니다. 판금 작업은 펀치와 고무 다이어프램 사이에 끼워져 있습니다. 다이어프램은 공작물을 완전히 둘러싸고 유체의 압력으로 인해 공작물이 펀치에 형성됩니다. 이 기술을 사용하면 딥 드로잉 프로세스보다 더 깊은 매우 딥 드로잉을 얻을 수 있습니다.
당사는 고객의 부품에 따라 단일 펀치 다이와 프로그레시브 다이를 제조합니다. 단일 스트로크 스탬핑 다이는 와셔와 같은 단순한 판금 부품을 대량으로 빠르게 생산하기 위한 비용 효율적인 방법입니다. 프로그레시브 다이 또는 딥 드로잉 기술은 보다 복잡한 형상을 제조하는 데 사용됩니다.
귀하의 경우에 따라 워터젯, 레이저 또는 플라즈마 절단을 사용하여 판금 부품을 저렴하고 빠르고 정확하게 생산할 수 있습니다. 많은 공급업체는 이러한 대체 기술에 대해 전혀 모르고 있거나 가지고 있지 않기 때문에 고객의 시간과 비용만 낭비하는 금형과 도구를 만드는 데 길고 값비싼 방법을 사용합니다.
인클로저, 전자 하우징... 등과 같은 맞춤형 판금 구성 요소가 필요한 경우 빠른 시간 내에 당사에 연락하여 신속한 판금 프로토타이핑 서비스를 받으십시오.