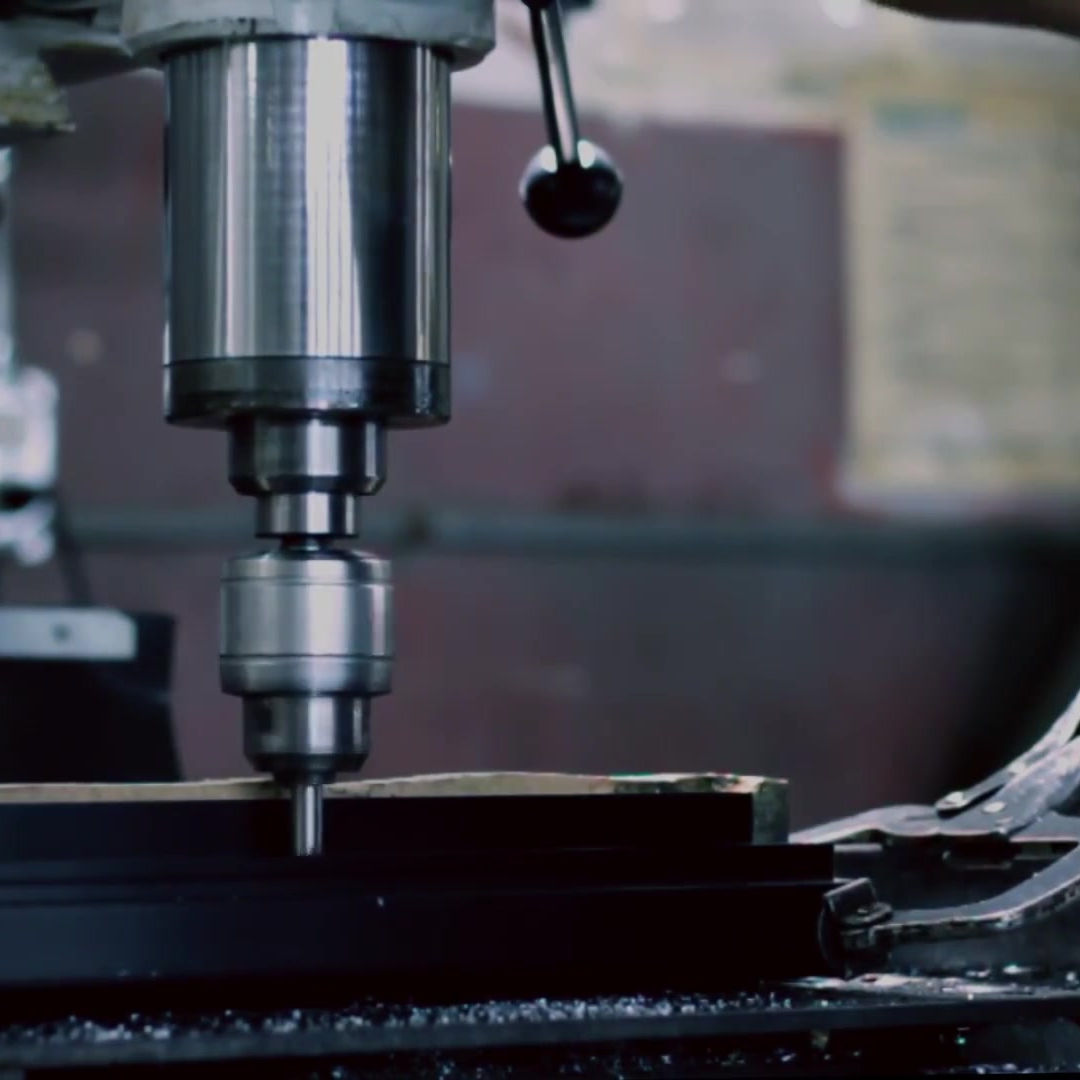
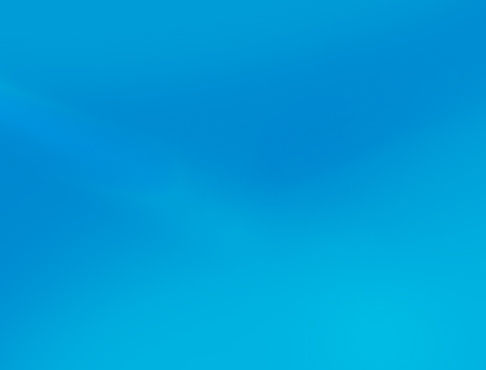
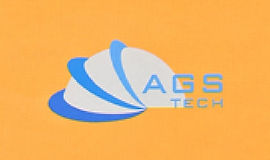
Hilberînerê Xwerû ya Gloverî, Integrator, Hevkar, Hevkarê Derveyî Ji bo Cûreyek Berfireh a Hilber û Karûbaran.
Em ji bo çêkirin, çêkirin, endezyarî, yekbûn, yekbûn, derxistina hilber û karûbarên xwerû yên çêkirî û yên li derveyî refê çavkaniya weya yek-rawest in. Ger hûn bixwazin, em di heman demê de etîketa taybet / spî hilberên we bi navê marqeya we nîşan didin.
Zimanê xwe hilbijêre
Hilberîna Xweser a Parçe, Pêkhatî, Meclîs, Berhemên Qediyayî, Makîne û Amûrên Pîşesaziyê
Hilberîna Peymana Navxweyî û Gerdûnî
Manufacturing Outsourcing
Kirîna Navxweyî, Gerdûnî ya Berhemên Pîşesazî
Etîketkirina taybet / Spî Hilberên xwe bi navê marqeya xwe nîşankirin
Karûbarên Dîtina Hilber & Cihgirtin
Sêwirana gerdûnî û Hevkariya Kanal
Endezyariya Entegrasyonê
Xizmetên Endezyariyê
Hevgirtina Gerdûnî, Warehousing, Logistics
Encamên Lêgerînê
164 results found with an empty search
- Display, Touchscreen, Monitors, LED, OLED, LCD, PDP, HMD, VFD, ELD
Display - Touchscreen - Monitors - LED - OLED - LCD - PDP - HMD - VFD - ELD - SED - Flat Panel Displays - AGS-TECH Inc. Pêşandan & Touchscreen & Monitor Çêkirin û Civînê We offer: • Custom displays including LED, OLED, LCD, PDP, VFD, ELD, SED, HMD, Laser TV, flat panel display of required dimensions and electro-optic specifications. Please click on highlighted text to download relevant brochures for our display, touchscreen, and monitor products. - Catalog for Vandal-Proof IP65/IP67/IP68 Keyboards, Keypads, Pointing Devices, ATM Pinpads, Medical & Military Keyboards and other similar Rugged Computer Peripherals - Kiosk Systems (We private label these with your brand name and logo if you wish) - Kiosk Systems Accessories Guide (We private label these with your brand name and logo if you wish) - LED display panels - LCD modules - Mobile Computers for Enterprises (We private label these with your brand name and logo if you wish) - Process Automation Solutions (This brochure includes some industrial display products. We private label these with your brand name and logo if you wish) Download our brochure for TRu Multi-Touch Monitors. This monitor product line consists of a range of desktop, open frame, slim line and large format multi-touch displays - from 15” to 70''. Built for quality, responsiveness, visual appeal, and durability, TRu Multi-Touch Monitors complement any multi-touch interactive solution. Click here for pricing If you would like to have LCD modules specially designed & manufactured according to your requirements, please fill out and email us: Custom design form for LCD modules If you would like to have LCD panels specially designed & manufactured according to your requirements, please fill out and email us: Custom design form for LCD panels • Custom touchscreen ( such as iPod ) • Among the custom products our engineers have developed are: - A contrast measuring station for liquid crystal displays. - A computerized centering station for television projection lenses Panels / Displays are electronic screens used to view data and / or graphics and are available in a variety of sizes and technologies. Here are the meanings of abbreviated terms related to display, touchscreen and monitor devices: LED: Light Emitting Diode LCD: Liquid Crystal Display PDP: Plasma Display Panel VFD: Vacuum Fluorescent Display OLED: Organic Light Emitting Diode ELD: Electroluminescent Display SED: Surface-conduction Electron-emitter Display HMD: Head Mounted Display A significant benefit of OLED display over liquid crystal display (LCD) is that OLED does not require a backlight to function. Therefore OLED display draws far less power and, when powered from a battery, can operate longer as compared to LCD. Because there is no need for a backlight, an OLED display can be much thinner than an LCD panel. However, degradation of OLED materials has limited their use as display, touchscreen and monitor. ELD works by exciting atoms by passing an electric current through them, and causing ELD to emit photons. By varying the material being excited, the colour of the emitted light can be changed. ELD is constructed using flat, opaque electrode strips running parallel to each other, covered by a layer of electroluminescent material, followed by another layer of electrodes, running perpendicular to the bottom layer. The top layer must be transparent in order to let light go through and escape. At each intersection, the material lights, thereby creating a pixel. ELDs are sometimes used as backlights in LCDs. They are also useful for creating soft ambient light, and for low-colour, high-contrast screens. A surface-conduction electron-emitter display (SED) is a flat panel display technology that uses surface conduction electron emitters for each individual display pixel. The surface conduction emitter emits electrons that excite a phosphor coating on the display panel, similar to cathode ray tube (CRT) televisions. In other words, SEDs use tiny cathode ray tubes behind every single pixel instead of one tube for the whole display, and can combine the slim form factor of LCDs and plasma displays with the superior viewing angles, contrast, black levels, color definition and pixel response time of CRTs. It is also widely claimed that SEDs consume less power than LCD displays. A head-mounted display or Helmet mounted display, both abbreviated 'HMD', is a display device, worn on the head or as part of a helmet, that has a small display optic in front of one or each eye. A typical HMD has either one or two small displays with lenses and semi-transparent mirrors embedded in a helmet, eye-glasses or visor. The display units are small and may include CRT, LCDs, Liquid Crystal on Silicon, or OLED. Sometimes multiple micro-displays are deployed to increase total resolution and field of view. HMDs differ in whether they can display just a computer generated image (CGI), show live images from the real world or a combination of both. Most HMDs display only a computer-generated image, sometimes referred to as a virtual image. Some HMDs allow superimposing a CGI upon a real-world view. This is sometimes referred to as augmented reality or mixed reality. Combining real-world view with CGI can be done by projecting the CGI through a partially reflective mirror and viewing the real world directly. For partially reflective mirrors, check our page on Passive Optical Components. This method is often called Optical See-Through. Combining real-world view with CGI can also be done electronically by accepting video from a camera and mixing it electronically with CGI. This method is often called Video See-Through. Major HMD applications include military, governmental (fire, police, etc.) and civilian/commercial (medicine, video gaming, sports, etc.). Military, police and firefighters use HMDs to display tactical information such as maps or thermal imaging data while viewing the real scene. HMDs are integrated into the cockpits of modern helicopters and fighter aircraft. They are fully integrated with the pilot's flying helmet and may include protective visors, night vision devices and displays of other symbols and information. Engineers and scientists use HMDs to provide stereoscopic views of CAD (Computer Aided Design) schematics. These systems are also used in the maintenance of complex systems, as they can give a technician an effectively ''x-ray vision'' by combining computer graphics such as system diagrams and imagery with the technician's natural vision. There are also applications in surgery, wherein a combination of radiographic data (CAT scans and MRI imaging) is combined with the surgeon's natural view of the operation. Examples of lower cost HMD devices can be seen with 3D games and entertainment applications. Such systems allow 'virtual' opponents to peek from real windows as a player moves about. Other interesting developments in display, touchscreen and monitor technologies AGS-TECH is interested are: Laser TV: Laser illumination technology remained too costly to be used in commercially viable consumer products and too poor in performance to replace lamps except in some rare ultra-high-end projectors. More recently however, companies demonstrated their laser illumination source for projection displays and a prototype rear-projection ''laser TV''. The first commercial Laser TV and subsequently others have been unveiled. First audiences who were shown reference clips from popular movies reported that they were blown away by a Laser TV's hitherto unseen color-display prowess. Some people even describe it as being too intense to the point of seeming artificial. Some other future display technologies will likely include carbon nanotubes and nanocrystal displays using quantum dots to make vibrant and flexible screens. As always, if you provide us details of your requirement and application, we can design and custom manufacture displays, touchscreens and monitors for you. Click here to download brochure of our Panel Meters - OICASCHINT Dowload brochure for our DESIGN PARTNERSHIP PROGRAM More information on our engineering work can be found on: http://www.ags-engineering.com CLICK Product Finder-Locator Service RÛPERA BERÊ
- Micro Assembly & Packaging - Micromechanical Fasteners - Self Assembly
Micro Assembly & Packaging - Micromechanical Fasteners - Self Assembly - Adhesive Micromechanical Fastening - AGS-TECH Inc. - New Mexico - USA Meclisa mîkro û pakkirinê We have already summarized our MICRO ASSEMBLY & PACKAGING services and products related specifically to microelectronics on our page Microelectronics Manufacturing / Semiconductor Fabrication. Here we will concentrate on more generic and universal micro assembly & packaging techniques we use for all kinds of products including mechanical, optical, microelectronic, optoelectronic and hybrid systems consisting of a combination of these. The techniques we discuss here are more versatile and can be considered to be used in more unusual and nonstandard applications. In other words the micro assembly & packaging techniques discussed here are our tools that help us to think “out of the box”. Here are some of our extraordinary micro assembly & packaging methods: - Manual micro assembly & packaging - Automated micro assembly & packaging - Self assembly methods such as fluidic self-assembly - Stochastic micro assembly using vibration, gravitational or electrostatic forces or else. - Use of micromechanical fasteners - Adhesive micromechanical fastening Let us explore some of our versatile extraordinary microassembly & packaging techniques in more detail. MANUAL MICRO ASSEMBLY & PACKAGING: Manual operations can be cost prohibitive and require a level of precision that can be impractical for an operator due to the strain it causes in the eyes and dexterity limitations associated with assembling such miniature parts under a microscope. However, for low volume special applications manual micro assembly may be the best option because it does not necessarily require the design and construction of automated micro assembly systems. AUTOMATED MICRO ASSEMBLY & PACKAGING: Our micro assembly systems are designed to make assembly easier and more cost effective, enabling the development of new applications for micro machine technologies. We can micro-assemble devices and components in the microns level dimensions using robotic systems. Here are some of our automated micro assembly & packaging equipment and capabilities: • Top notch motion control equipment including a robotic workcell with nanometric position resolution • Fully automated CAD-driven workcells for micro assembly • Fourier optics methods to generate synthetic microscope images from CAD drawings to test image processing routines under varying magnifications and depths of field (DOF) • Custom designing and production capability of micro tweezers, manipulators and actuators for precision micro assembly and packaging • Laser interferometers • Strain gages for force feedback • Real-time computer vision to control servo mechanisms and motors for the micro-alignment and micro-assembly of parts with sub-micron tolerances • Scanning Electron Microscopes (SEM) and Transmission Electron Microscopes (TEM) • 12 degrees of freedom nano manipulator Our automated micro assembly process can place multiple gears or other components on multiple posts or locations in a single step. Our micromanipulation capabilities are enormous. We are here to help you with non-standard extraordinary ideas. MICRO & NANO SELF ASSEMBLY METHODS: In self-assembly processes a disordered system of pre-existing components forms an organized structure or pattern as a consequence of specific, local interactions among the components, without external direction. The self-assembling components experience only local interactions and typically obey a simple set of rules that govern how they combine. Even though this phenomenon is scale-independent and can be utilized for self-constructing and manufacturing systems at nearly every scale, our focus is on micro self assembly and nano self assembly. For building microscopic devices, one of the most promising ideas is to exploit the process of self-assembly. Complex structures can be created by combining building blocks under natural circumstances. To give an example, a method is established for micro assembly of multiple batches of micro components onto a single substrate. The substrate is prepared with hydrophobic coated gold binding sites. To perform micro assembly, a hydrocarbon oil is applied to the substrate and wets exclusively the hydrophobic binding sites in water. Micro components are then added to the water, and assembled on the oil-wetted binding sites. Even more, micro assembly can be controlled to take place on desired binding sites by using an electrochemical method to deactivate specific substrate binding sites. By repeatedly applying this technique, different batches of micro components can be sequentially assembled to a single substrate. After the micro assembly procedure, electroplating takes place to establish electrical connections for micro assembled components. STOCHASTIC MICRO ASSEMBLY: In parallel micro assembly, where parts are assembled simultaneously, there is deterministic and stochastic micro assembly. In the deterministic micro assembly, the relationship between the part and its destination on the substrate is known in advance. In the stochastic micro assembly on the other hand, this relationship is unknown or random. Parts do self-assemble in stochastic processes driven by some motive force. In order for the micro self-assembly to take place, there need to be bonding forces, the bonding needs to occur selectively, and micro assembling parts need to be able to move so they can get together. Stochastic micro assembly is many times accompanied by vibrations, electrostatic, microfluidic or other forces that act on the components. Stochastic micro assembly is especially useful when the building blocks are smaller, because the handling of the individual components becomes more of a challenge. Stochastic self-assembly can be observed in nature as well. MICROMECHANICAL FASTENERS: At the micro scale, conventional types of fasteners like screws and hinges will not easily work due to present fabrication constraints and large friction forces. Micro snap fasteners on the other hand work more easily in micro assembly applications. Micro snap fasteners are deformable devices consisting of pairs of mating surfaces that snap together during micro assembly. Because of the simple and linear assembly motion, snap fasteners have a wide range of applications in micro assembly operations, such as devices with multiple or layered components, or micro opto-mechanical plugs, sensors with memory. Other micro assembly fasteners are “key-lock” joints and “inter-lock” joints. Key-lock joints consist of the insertion of a “key” on one micro-part, into a mating slot on another micro-part. Locking into position is achieved by translating the first micro-part within the other. Inter-lock joints are created by the perpendicular insertion of one micro-part with a slit, into another micro-part with a slit. The slits create an interference fit and are permanent once the micro-parts are joined. ADHESIVE MICROMECHANICAL FASTENING: Adhesive mechanical fastening is used to construct 3D micro devices. The fastening process includes self-alignment mechanisms and adhesive bonding. Self-alignment mechanisms are deployed in adhesive micro assembly to increase the positioning accuracy. A micro probe bonded to a robotic micromanipulator picks up and accurately deposits adhesive to target locations. Curing light hardens the adhesive. The cured adhesive keeps the micro assembled parts into their positions and provides strong mechanical joints. Using conductive adhesive, a reliable electrical connection can be obtained. The adhesive mechanical fastening only requires simple operations, and can result in reliable connections and high positioning accuracies, which are important in automatic microassembly. To demonstrate the feasibility of this method, many three-dimensional MEMS devices have been micro assembled, including a 3D rotary optical switch. CLICK Product Finder-Locator Service RÛPERA BERÊ
- Cable & Connector Assembly, Wire Harness, Cable Management Accessories
Cable Assembly - Wire Harness - Cable Management Accessories - Connectorization - Cable Fan Out - Interconnects Civîn û Têkiliyên Kabloya Elektrîk & Elektronîkî We offer: • Various kinds of wires, cables, cable assembly and cable management accessories, unshielded or shielded cable for power distribution, high voltage, low signal, telecommunications…etc., inteconnects and interconnect components. • Connectors, plugs, adaptors and mating sleeves, connectorized patch panel, splicing enclosure. Cable Termination Products Brochure (Tubing, Insulation, Protection, Heat Shrinkable, Cable Repair, Breakout Boots, Clamps, Cable Ties and Clips, Wire Markers, Tapes, Cable End Caps, Distribution Slots) Custom Specialized Cable Assemblies Brochure for Lighting, Touch Technology, Industrial Electronics, Security, White Goods, Aerospace, Military, Telecom, Medical & Sterilizable, Renewable Energy...etc. Download our catalog for off-shelf interconnect components and hardware, please CLICK HERE. IGOYE Brand Solar Products Catalog Includes Solar Connectors & Cables, EV Charging Sockets. Microwave Flexible Cable Assembly Microwave and Milimeter Wave Test Accessories Brochure (Cable assemblies, VNA Test Assemblies, Mechanical Calibration Kits, RF Coaxial Adapters, Test Port Adapters, DC Blocks, NMD Connectors....etc.) Precision RF Adapters Catalog Private Label Low-Voltage Cables (We can put your name and logo on these, so you can market your name when you sell or install these cables) Private Label Low-Voltage Cables & Accessories for AV - DataCom - CATV - Security - LAN - Electrical (We can put your name and logo on these, so you can market your name when you sell or install these cables) Receptacles-Power Entry-Connectors Catalogue RF Components Brochure for Coaxial Fixed Attenuators, Coaxial Terminations, DC Blocks, Coax Adapters, Waveguide Components, Power Dividers, RF Connectors, RF Tools. Terminal Blocks and Connectors Terminal Blocks General Catalogue - Information on our facility producing ceramic to metal fittings, hermetic sealing, vacuum feedthroughs, high and ultrahigh vacuum components, BNC, SHV adapters and connectors, conductors and contact pins, connector terminals can be found here: Factory Brochure Dowload brochure for our DESIGN PARTNERSHIP PROGRAM Interconnects and cable assembly products come in a large variety. Please specify us the type, application, specification sheets if available and we will offer you the most suitable product. We can custom tailor these for you in case it is not an off-the-shelf product. Our cable assemblies and interconnects are CE or UL marked by authorized organizations and comply with industry regulations and standards such as IEEE, IEC, ISO...etc. To find out more about our engineering and research & development capabilities instead of manufacturing operations, we invite you to visit our engineering site http://www.ags-engineering.com CLICK Product Finder-Locator Service RÛPERA BERÊ
- Plasma Machining, HF Plasma Cutting, Plasma Gouging, CNC, Arc Welding
Plasma Machining - HF Plasma Cutting - Plasma Gouging - CNC - Plasma Arc Welding - PAW - GTAW - AGS-TECH Inc. - New Mexico Çêkirina Plasma û Çêkirin We use the PLASMA CUTTING and PLASMA MACHINING processes to cut and machine steel, aluminum, metals and other materials of different thicknesses using a plasma torch. In plasma-cutting (also sometimes called PLASMA-ARC CUTTING), an inert gas or compressed air is blown at high speed out of a nozzle and simultaneously an electrical arc is formed through that gas from the nozzle to the surface being cut, turning a portion of that gas to plasma. To simplify, plasma can be described as the fourth state of matter. The three states of matter are solid, liquid and gas. For a common example, water, these three states are ice, water and steam. The difference between these states relates to their energy levels. When we add energy in the form of heat to ice, it melts and forms water. When we add more energy, the water vaporizes in the form of steam. By adding more energy to steam these gases become ionized. This ionization process causes the gas to become electrically conductive. We call this electrically conductive, ionized gas a “plasma”. The plasma is very hot and melts the metal being cut and at the same time blowing the molten metal away from the cut. We use plasma for cutting thin and thick, ferrous and nonferrous materials alike. Our hand-held torches can usually cut up to 2 inches thick steel plate, and our stronger computer-controlled torches can cut steel up to 6 inches thick. Plasma cutters produce a very hot and localized cone to cut with, and are therefore very suitable for cutting metal sheets in curved and angled shapes. The temperatures generated in plasma-arc cutting are very high and around 9673 Kelvin in the oxygen plasma torch. This offers us a fast process, small kerf width, and good surface finish. In our systems using tungsten electrodes, the plasma is inert, formed using either argon, argon-H2 or nitrogen gases. However, we also use sometimes oxidizing gases, such as air or oxygen, and in those systems the electrode is copper with hafnium. The advantage of an air plasma torch is that it uses air instead of expensive gases, thus potentially reducing overall cost of machining . Our HF-TYPE PLASMA CUTTING machines use a high-frequency, high-voltage spark to ionize the air through the torch head and initiate arcs. Our HF plasma cutters do not require the torch to be in contact with the workpiece material at the start, and are suitable for applications involving COMPUTER NUMERICAL CONTROL (CNC) cutting. Other manufacturers are using primitive machines that require tip contact with the parent metal to start and then the gap separation occurs. These more primitive plasma cutters are more susceptible to contact tip and shield damage at starting. Our PILOT-ARC TYPE PLASMA machines use a two step process for producing plasma, without the need for initial contact. In the first step, a high-voltage, low current circuit is used to initialize a very small high-intensity spark within the torch body, generating a small pocket of plasma gas. This is called the pilot arc. The pilot arc has a return electrical path built into the torch head. The pilot arc is maintained and preserved until it is brought into proximity of the workpiece. There the pilot arc ignites the main plasma cutting arc. Plasma arcs are extremely hot and are in the range of 25,000 °C = 45,000 °F. A more traditional method we also deploy is OXYFUEL-GAS CUTTING (OFC) where we use a torch as in welding. The operation is used in cutting of steel, cast iron and cast steel. The principle of cutting in oxyfuel-gas cutting is based on oxidation, burning and melting of the steel. Kerf widths in oxyfuel-gas cutting are in the neighborhood of 1.5 to 10mm. The plasma arc process has been seen as an alternative to the oxy-fuel process. The plasma-arc process differs from the oxy-fuel process in that it operates by using the arc to melt the metal whereas in the oxy-fuel process, the oxygen oxidizes the metal and the heat from the exothermic reaction melts the metal. Therefore, unlike the oxy-fuel process, the plasma-process can be applied for cutting metals which form refractory oxides such as stainless steel, aluminium, and non-ferrous alloys. PLASMA GOUGING a similar process to plasma cutting, is typically performed with the same equipment as plasma cutting. Instead of cutting the material, plasma gouging uses a different torch configuration. The torch nozzle and gas diffuser is usually different, and a longer torch-to-workpiece distance is maintained for blowing away metal. Plasma gouging can be used in various applications, including removing a weld for rework. Some of our plasma cutters are built in to the CNC table. CNC tables have a computer to control the torch head to produce clean sharp cuts. Our modern CNC plasma equipment is capable of multi-axis cutting of thick materials and allowing opportunities for complex welding seams that are not possible otherwise. Our plasma-arc cutters are highly automated through the use of programmable controls. For thinner materials, we prefer laser cutting to plasma cutting, mostly because of our laser cutter's superior hole-cutting abilities. We also deploy vertical CNC plasma cutting machines, offering us a smaller footprint, increased flexibility, better safety and faster operation. The quality of the plasma cut edge is similar to that achieved with the oxy-fuel cutting processes. However, because the plasma process cuts by melting, a characteristic feature is the greater degree of melting towards the top of the metal resulting in top edge rounding, poor edge squareness or a bevel on the cut edge. We use new models of plasma torches with a smaller nozzle and a thinner plasma arc to improve arc constriction to produce more uniform heating at the top and bottom of the cut. This allows us to obtain near-laser precision on plasma cut and machined edges. Our HIGH TOLERANCE PLASMA ARC CUTTING (HTPAC) systems operate with a highly constricted plasma. Focusing of the plasma is achieved by forcing the oxygen generated plasma to swirl as it enters the plasma orifice and a secondary flow of gas is injected downstream of the plasma nozzle. We have a separate magnetic field surrounding the arc. This stabilises the plasma jet by maintaining the rotation induced by the swirling gas. By combining precision CNC control with these smaller and thinner torches we are capable to produce parts that require little or no finishing. Material removal rates in plasma-machining are much higher than in the Electric-Discharge-Machining (EDM) and Laser-Beam-Machining (LBM) processes, and parts can be machined with good reproducibility. PLASMA ARC WELDING (PAW) is a process similar to gas tungsten arc welding (GTAW). The electric arc is formed between an electrode generally made of sintered tungsten and the workpiece. The key difference from GTAW is that in PAW, by positioning the electrode within the body of the torch, the plasma arc can be separated from the shielding gas envelope. The plasma is then forced through a fine-bore copper nozzle which constricts the arc and the plasma exiting the orifice at high velocities and temperatures approaching 20,000 °C. Plasma arc welding is an advancement over the GTAW process. The PAW welding process uses a non-consumable tungsten electrode and an arc constricted through a fine-bore copper nozzle. PAW can be used to join all metals and alloys that are weldable with GTAW. Several basic PAW process variations are possible by varying the current, plasma gas flow rate, and the orifice diameter, including: Micro-plasma (< 15 Amperes) Melt-in mode (15–400 Amperes) Keyhole mode (>100 Amperes) In plasma arc welding (PAW) we obtain a greater energy concentration as compared to GTAW. Deep and narrow penetration is achievable, with a maximum depth of 12 to 18 mm (0.47 to 0.71 in) depending on the material. Greater arc stability allows a much longer arc length (stand-off), and much greater tolerance to arc length changes. As a disadvantage however, PAW requires relatively expensive and complex equipment as compared to GTAW. Also the torch maintenance is critical and more challenging. Other disadvantages of PAW are: Welding procedures tend to be more complex and less tolerant to variations in fit-up, etc. Operator skill required is a little more than for GTAW. Orifice replacement is necessary. CLICK Product Finder-Locator Service RÛPERA BERÊ
- Mesomanufacturing,Mesoscale Manufacturing,Miniature Device Fabrication
Mesomanufacturing - Mesoscale Manufacturing - Miniature Device Fabrication - Tiny Motors - AGS-TECH Inc. - New Mexico Hilberîna Mesoscale / Mesomanufacturing With conventional production techniques we produce “macroscale” structures that are relatively large and visible to the naked eye. With MESOMANUFACTURING however we produce components for miniature devices. Mesomanufacturing is also referred to as MESOSCALE MANUFACTURING or MESO-MACHINING. Mesomanufacturing overlaps both macro and micromanufacturing. Examples of mesomanufacturing are hearing aides, stents, very small motors. The first approach in mesomanufacturing is to scale macromanufacturing processes down. For example a tiny lathe with dimensions in the few dozen millimeters and a motor of 1.5W weighing 100 grams is a good example of mesomanufacturing where downscaling has taken place. The second approach is to scale micromanufacturing processes up. As an example LIGA processes can be upscaled and enter the realm of mesomanufacturing. Our mesomanufacturing processes are bridging the gap between silicon-based MEMS processes and conventional miniature machining. Mesoscale processes can fabricate two and three-dimensional parts having micron size features in traditional materials such as stainless steels, ceramics, and glass. Mesomanufacturing processes that are currently available to us include, focused ion beam (FIB) sputtering, micro-milling, micro-turning, excimer laser ablation, femto-second laser ablation, and micro electro-discharge (EDM) machining. These mesoscale processes employ subtractive machining technologies (i.e., material removal), whereas the LIGA process, is an additive mesoscale process. Mesomanufacturing processes have different capabilities and performance specifications. Machining performance specifications of interest include minimum feature size, feature tolerance, feature location accuracy, surface finish, and material removal rate (MRR). We have the capability of mesomanufacturing electro-mechanical components that require mesoscale parts. The mesoscale parts fabricated by subtractive mesomanufacturing processes have unique tribological properties because of the variety of materials and the surface conditions produced by the different mesomanufacturing processes. These subtractive mesoscale machining technologies bring us concerns related to cleanliness, assembly, and tribology. Cleanliness is vital in mesomanufacturing because mesoscale dirt and debris particle size created during the meso-machining process can be comparable to mesoscale features. Mesoscale milling and turning can create chips and burrs that can block holes. Surface morphology and surface finish conditions vary greatly depending on the mesomanufacturing method. Mesoscale parts are difficult to handle and align which makes assembly a challenge which most of our competitors are unable to overcome. Our yield rates in mesomanufacturing is far higher than our competitors which gives us the advantage of being able to offer better prices. MESOSCALE MACHINING PROCESSES: Our major mesomanufacturing techniques are Focused Ion Beam (FIB), Micro-milling, & Micro-turning, laser meso-machining, Micro-EDM (electro-discharge machining) Mesomanufacturing using focused Ion Beam (FIB), Micro-milling, & Micro-turning: The FIB sputters material from a workpiece by Gallium ion beam bombardment. The workpiece is mounted to a set of precision stages and is placed in a vacuum chamber underneath the source of Gallium. The translation and rotation stages in the vacuum chamber make various locations on the work piece available to the beam of Gallium ions for FIB mesomanufacturing. A tunable electric field scans the beam to cover a pre-defined projected area. A high voltage potential causes a source of Gallium ions to accelerate and collide with the work piece. The collisions strip away atoms from the work piece. The result of the FIB meso-machining process can be the creation of a near vertical facets. Some FIBs available to us have beam diameters as small as 5 nanometers, making the FIB a mesoscale and even microscale capable machine. We mount micro-milling tools on high precision milling machines to machine channels in aluminum. Using FIB we can fabricate micro-turning tools which can then be used on a lathe to fabricate finely threaded rods. In other words, FIB can be used to machine hard tooling besides directly meso-machining features onto the end work piece. The slow material removal rate has rendered the FIB as impractical for directly machining large features. The hard tools, however, can remove material at an impressive rate and are durable enough for several hours of machining time. Nevertheless, the FIB is practical for directly meso-machining complex three dimensional shapes that do not require a substantial material removal rate. Length of exposure and angle of incidence can greatly affect the geometry of directly machined features. Laser Mesomanufacturing: Excimer lasers are used for mesomanufacturing. The excimer laser machines material by pulsing it with nanosecond pulses of ultraviolet light. The work piece is mounted to precision translational stages. A controller coordinates the motion of the work piece relative to the stationary UV laser beam and coordinates the firing of the pulses. A mask projection technique can be used to define meso-machining geometries. The mask is inserted into the expanded part of the beam where the laser fluence is too low to ablate the mask. The mask geometry is de-magnified through the lens and projected onto the work piece. This approach can be used for machining multiple holes (arrays) simultaneously. Our excimer and YAG lasers can be used to machine polymers, ceramics, glass and metals having feature sizes as small as 12 microns. Good coupling between the UV wavelength (248 nm) and the workpiece in laser mesomanufacturing / meso-machining results in vertical channel walls. A cleaner laser meso-machining approach is to use a Ti-sapphire femtosecond laser. The detectable debris from such mesomanufacturing processes are nano-sized particles. Deep one micron-size features can be microfabricated using the femtosecond laser. The femtosecond laser ablation process is unique in that it breaks atomic bonds instead of thermally ablating material. The femtosecond laser meso-machining / micromachining process has a special place in mesomanufacturing because it is cleaner, micron capable, and it is not material specific. Mesomanufacturing using Micro-EDM (electro-discharge machining): Electro-discharge machining removes material through a spark erosion process. Our micro-EDM machines can produce features as small as 25 microns. For the sinker and the wire micro-EDM machine, the two major considerations for determining feature size are the electrode size and the over-bum gap. Electrodes little over 10 microns in diameter and over-bum as little as a few microns are being used. Creating an electrode having a complex geometry for the sinker EDM machine requires know-how. Both graphite and copper are popular as electrode materials. One approach to fabricating a complicated sinker EDM electrode for a mesoscale part is to use the LIGA process. Copper, as the electrode material, can be plated into LIGA molds. The copper LIGA electrode can then be mounted onto the sinker EDM machine for mesomanufacturing a part in a different material such as stainless steel or kovar. No one mesomanufacturing process is sufficient for all operations. Some mesoscale processes are more wide reaching than others, but each process has its niche. Most of the time we require a variety of materials to optimize performance of mechanical components and are comfortable with traditional materials such as stainless steel because these materials have a long history and have been very well characterized through the years. Mesomanufacturing processes allow us to use traditional materials. Subtractive mesoscale machining technologies expand our material base. Galling may be an-issue with some material combinations in mesomanufacturing. Each particular mesoscale machining process uniquely affects the surface roughness and morphology. Micro-milling and micro-turning may generate burrs and particles that can cause mechanical problems. Micro-EDM may leave a recast layer that can have particular wear and friction characteristics. Friction effects between mesoscale parts may have limited points of contact and are not accurately modeled by surface contact models. Some mesoscale machining technologies, such as micro-EDM, are fairly mature, as opposed to others, such as femtosecond laser meso-machining, which still require additional development. CLICK Product Finder-Locator Service RÛPERA BERÊ
- Optical Displays, Screen, Monitors Manufacturing - AGS-TECH Inc.
Optical Displays, Screen, Monitors, Touch Panel Manufacturing Çêkirin & Civîna Dîmender, Dîmender, Çavdêrên Optîkî Ji bo BERNAMEYA HEVKARÎYA DESIGN a me broşurê dakêşin CLICK Product Finder-Locator Service RÛPERA BERÊ
- Electronic Components, Diodes, Transistors, Thermoelectric Cooler, TEC
Electronic Components, Diodes, Transistors - Resistors, Thermoelectric Cooler, Heating Elements, Capacitors, Inductors, Driver, Device Sockets and Adapters Pêkhatin û Meclîsên Elektrîk & Elektronîkî As a custom manufacturer and engineering integrator, AGS-TECH can supply you the following ELECTRONIC COMPONENTS and ASSEMBLIES: • Active and passive electronic components, devices, subassemblies and finished products. We can either use the electronic components in our catalogs and brochures listed below or use your prefered manufacturers components in your electronic products assembly. Some of the electronic components and assembly can be custom tailored according to your needs and requirements. If your order quantities justify, we can have the manufacturing plant produce according to your specifications. You can scroll down and download our brochures of interest by clicking on highlighted text: Antenna Brochure for 5G - LTE 4G - LPWA 3G - 2G - GPS - GNSS - WLAN - BT - Combo - ISM Chip resistors Chip resistors product line Custom Specialized Cable Assemblies Brochure for Lighting, Touch Technology, Industrial Electronics, Security, White Goods, Aerospace, Military, Telecom, Medical & Sterilizable, Renewable Energy...etc. Diodes and rectifiers Disc capacitors catalog High frequency devices product line (Band Pass Filters, Low Pass Filters, IPD, CPL, Balanced Filter, Diplexer, Balun, Chip Antenna...etc.) Microwave Flexible Cable Assembly Microwave and Milimeter Wave Test Accessories Brochure (Cable assemblies, VNA Test Assemblies, Mechanical Calibration Kits, RF Coaxial Adapters, Test Port Adapters, DC Blocks, NMD Connectors....etc.) Microwave Waveguides - Coaxial Components - Milimeterwave Antennas (Straight Waveguide, Waveguide Bend, Waveguide to Coaxial Adapter, Directional Couplers, Waveguide Tee, Circulators, Isolators......etc.) Multilayer ceramic capacitors MLCC catalog Multilayer ceramic capacitors MLCC product line Off-shelf interconnect components and hardware Precision RF Adapter s Catalog (Coax RF, Microwave, mmWave Adapters such as SMA, SSMA, SMP, BNC, Type-N, 3.5 mm.....etc) RF Components Brochure for Coaxial Fixed Attenuators, Coaxial Terminations, DC Blocks, Coax Adapters, Waveguide Components, Power Dividers, RF Connectors, RF Tools. RF devices and high frequency inductors (Multilayer Ceramic Capacitors, Chip-Resistor, Disc Capacitors, RF & HF Inductor Varistors & SMD-Varistors, Chip Antenna, Filters, Coupler) RF and Microwave Components (Broadband 90/180 Degree Hybrid and Coupler, Broadband Power Divider, Filter, RF switch, Broadband Amplifier, Broadband Frequency Synthesizer) RF Product Overview Chart (RF Antenna, Multilayer Ceramic Filter, Multilayer Ceramic Balun, Ceramic Diplexer) Soft Ferrites - Cores - Toroids - EMI Suppression Products - RFID Transponders and Accessories Brochure Terminal Blocks and Connectors Terminal Blocks General Catalogue Receptacles-Power Entry-Connectors Catalogue Vandal-Proof IP65/IP67/IP68 Keyboards, Keypads, Pointing Devices, ATM Pinpads, Medical & Military Keyboards and other similar Rugged Computer Peripherals Varistors Varistors product overview Yaren Model MOSFET - SCR - FRD - Voltage Control Devices - Bipolar Transistors Zeasset Model Electrolytic Capacitors • Other electronic components and assembly we have been providing are pressure sensors, temperature sensors, conductivity sensors, proximity sensors, humidity sensors, speed sensor, shock sensor, chemical sensor, inclination sensor, load cell, strain gauges. To download related catalogs and brochures of these, please click on colored text: Coding system for off-shelf strain gauges Digital Temperature Transmitter UTI2 Digital Temperature Transmitter UTI6 Din Rail Mounted Temperature Transmitters UTB11 Electronic Temperature Switch UTS2 Explosive Proof Temperature Transmitter UTB4 Integrated Temperature Transmitter UTB8 Intelligent Temperature Transmitter UTI5 Load cells, weight sensors, load gauges, transducers and transmitters Pressure sensors, pressure gauges, transducers and transmitters Process Automation Solutions (We private label these with your brand name and logo if you wish) Proximity sensors Sensors & Analytical Measurement Systems for Liquid Analysis (We private label these with your brand name and logo if you wish) Sensors & Analytical Measurement Systems for Optical OEM Applications in Liquid Analysis (We private label these with your brand name and logo if you wish) Sensors & Analytical Measurement Systems for pH Testing (We private label these with your brand name and logo if you wish) Smart Temperature Transmitter UTB-101 Sockets and accessories of proximity sensors Strain Gauges for Stress Analysis Temperature Humidity Transmitters Temperature Pressure Integration Transmitter UTB5 Thermal Resistor Temperature Transducer UTC1 (-50~+600 C) Thermal Resistor Temperature Transducer UTC2 (-40~+200 C) Wireless Digital Temperature Gauge UTI7 • Chip level micrometer scale tiny Microelectromechanical Systems (MEMS) based devices such as micropumps, micromirrors, micromotors, microfluidic devices. • Integrated Circuits (IC) • Switching elements, switch, relay, contactor, circuit breaker Contactors with UL and CE Certification NC1100111-1042532 Contactors with UL and CE Certification NC2100111-1044422 Contactors with UL and CE Certifications NC6100111-1040002 Definite Purpose Contactor with UL and CE Certifications NCK3100111-1052422 Electronic Overload Relay with UL and CE Certification NRE8100111-1143132 Miniature Circuit Breakers with UL and CE Certification NB1100111-1114242 Miniature Power Relay with UL and CE Certification JQX-10F100111-1153432 Miniature Power Relay with UL and CE Certifications JQX-13F100111-1154072 Miniature Power Relay with UL and CE Certification JTX100111-1155122 Miniature Power Relay with UL and CE Certification MK100111-1155402 Miniature Power Relay with UL and CE Certification NJX-13FW100111-1152352 Push button and rotary switches & control boxes Sub-Miniature Power Relay with UL and CE Certification JQC-3F100111-1153132 Thermal Overload Relay with UL and CE Certification NR2100111-1144062 • Electric fans and coolers for installation in electronic and industrial devices • Heating elements, thermoelectric coolers (TEC) Easy Click heat sinks Extruded heat sinks Heat sinks with Super Fins Standard heat sinks Super cooling plates Super Power heat sinks for medium - high power electronic systems Waterless cooling plates • We supply Electronic Enclosures for protection of your electronic components and assembly. Besides these off-shelf electronic enclosures, we do custom injection mold and thermoform electronic enclosures that fit your technical drawings. Please download from links below: Economic 17 Series Hand Held Enclosures Tibox Model Enclosures and Cabinets 01 Series Instrument Case System-I 02 Series Plastic and Aluminum Instrument Case Systems II 03 Series Plastic and Steel Enclosures 05 Series Instrument Case System-V 08 Series Plastic Cases 10 Series Sealed Plastic Enclosures 11 Series Die-cast Aluminium Boxes 14 Series PLC Enclosures 15 Series Modular Plastic Enclosures 16 Series DIN rail module enclosures 18 Series Special Plastic Enclosures 19 Series Desktop Enclosures 20 Series Wall-Mounting Enclosures 21 Series Card Reader Enclosures 24 Series DIN Plastic Enclosures 31 Series Potting and Power Supply Enclosures 37 Series Plastic Equipment Cases • Telecommunication and datacommunication products, lasers, receivers, transceivers, transponders, modulators, amplifiers. CATV products such as CAT3, CAT5, CAT5e, CAT6, CAT7 cables, CATV splitters. • Laser components and assembly • Acoustic components and assemblies, recording electronics - These catalogs contain only some brands we sell. We also have generic brand names and other brands with similar good quality for you to choose from. Dowload brochure for our DESIGN PARTNERSHIP PROGRAM - Contact us for your special electronic assembly requests. We integrate various components & products and manufacture complex assemblies. We can either design it for you or assemble according to your design. Reference Code: OICASANLY CLICK Product Finder-Locator Service RÛPERA BERÊ
- Surface Treatment and Modification - Surface Engineering - Hardening
Surface Treatment and Modification - Surface Engineering - Hardening - Plasma - Laser - Ion Implantation - Electron Beam Processing at AGS-TECH Tedawiyên Rûyê û Guhertin Surfaces cover everything. The appeal and functions material surfaces provide us are of utmost importance. Therefore SURFACE TREATMENT and SURFACE MODIFICATION are among our everyday industrial operations. Surface treatment & modification leads to enhanced surface properties and can be performed either as a final finishing operation or prior to a coating or joining operation. The processes of surface treatments and modification (also referred to as SURFACE ENGINEERING), tailor the surfaces of materials and products to: - Control friction and wear - Improve corrosion resistance - Enhance adhesion of subsequent coatings or joined parts - Change physical properties conductivity, resistivity, surface energy and reflection - Change chemical properties of surfaces by introducing functional groups - Change dimensions - Change the appearance, e.g., color, roughness…etc. - Clean and / or disinfect the surfaces Using surface treatment and modification, the functions and service lives of materials can be improved. Our common surface treatment and modification methods can be divided into two major categories: Surface Treatment and Modification That Covers Surfaces: Organic Coatings: The organic coatings apply paints, cements, laminates, fused powders and lubricants on the surfaces of materials. Inorganic Coatings: Our popular inorganic coatings are electroplating, autocatalytic plating (electroless platings), conversion coatings, thermal sprays, hot dipping, hardfacing, furnace fusing, thin film coatings such as SiO2, SiN on metal, glass, ceramics,….etc. Surface treatment and modification involving coatings is explained in detail under the related submenu, please click here Functional Coatings / Decorative Coatings / Thin Film / Thick Film Surface Treatment and Modification That Alters Surfaces: Here on this page we will concentrate on these. Not all of the surface treatment and modification techniques we describe below are on the micro or nano-scale, but we will nevertheless mention about them briefly since the basic objectives and methods are similar to significant extent to those that are on the micromanufacturing scale. Hardening: Selective surface hardening by laser, flame, induction and electron beam. High Energy Treatments: Some of our high energy treatments include ion implantation, laser glazing & fusion, and electron beam treatment. Thin Diffusion Treatments: Thin diffusion processes include ferritic-nitrocarburizing, boronizing, other high temperature reaction processes such as TiC, VC. Heavy Diffusion Treatments: Our heavy diffusion processes include carburizing, nitriding, and carbonitriding. Special Surface Treatments: Special treatments such as cryogenic, magnetic, and sonic treatments affect both the surfaces and the bulk materials. The selective hardening processes can be carried out by flame, induction, electron beam, laser beam. Large substrates are deep hardened using flame hardening. Induction hardening on the other hand is used for small parts. Laser and electron beam hardening are sometimes not distinguished from those in hardfacings or high-energy treatments. These surface treatment and modification processes are applicable only to steels that have sufficient carbon and alloy content to allow quench hardening. Cast irons, carbon steels, tool steels, and alloy steels are suitable for this surface treatment and modification method. Dimensions of parts are not significantly altered by these hardening surface treatments. Depth of hardening can vary from 250 microns to the whole section depth. However, in the whole section case, the section must be thin, less than 25 mm (1 in), or small, since the hardening processes require a rapid cooling of materials, sometimes within a second. This is difficult to achieve in large workpieces, and therefore in large sections, only the surfaces can be hardened. As a popular surface treatment and modification process we harden springs, knife blades, and surgical blades among many other products. High-energy processes are relatively new surface treatment and modification methods. Properties of surfaces are changed without changing the dimensions. Our popular high-energy surface treatment processes are electron beam treatment, ion implantation, and laser beam treatment. Electron Beam Treatment: Electron beam surface treatment alters the surface properties by rapid heating and rapid cooling — in the order of 10Exp6 Centigrade/sec (10exp6 Fahrenheit/sec) in a very shallow region around 100 microns near the material surface. Electron beam treatment can also be used in hardfacing to produce surface alloys. Ion Implantation: This surface treatment and modification method uses electron beam or plasma to convert gas atoms to ions with sufficient energy, and implant/insert the ions into atomic lattice of the substrate, accelerated by magnetic coils in a vacuum chamber. Vacuum makes it easier for ions to move freely in the chamber. The mismatch between implanted ions and the surface of the metal creates atomic defects that hardens the surface. Laser Beam Treatment: Like the electron beam surface treatment and modification, laser beam treatment alters the surface properties by rapid heating and rapid cooling in a very shallow region near the surface. This surface treatment & modification method can also be used in hardfacing to produce surface alloys. A know-how in Implant dosages and treatment parameters makes it possible for us to use these high energy surface treatment techniques in our fabrication plants. Thin Diffusion Surface Treatments: Ferritic nitrocarburizing is a case hardening process that diffuses nitrogen and carbon into ferrous metals at sub-critical temperatures. The processing temperature is usually at 565 Centigrade (1049 Fahrenheit). At this temperature steels and other ferrous alloys are still in a ferritic phase, which is advantageous compared to other case hardening processes that occur in the austenitic phase. The process is used to improve: •scuffing resistance •fatigue properties •corrosion resistance Very little shape distortion occurs during the hardening process thanks to the low processing temperatures. Boronizing, is the process where boron is introduced to a metal or alloy. It is a surface hardening and modification process by which boron atoms are diffused into the surface of a metal component. As a result the surface contains metal borides, such as iron borides and nickel borides. In their pure state these borides have extremely high hardness and wear resistance. Boronized metal parts are extremely wear resistant and will often last up to five times longer than components treated with conventional heat treatments such as hardening, carburizing, nitriding, nitrocarburizing or induction hardening. Heavy Diffusion Surface Treatment and Modification: If the carbon content is low (less than 0.25% for example) then we can increase the carbon content of the surface for hardening. The part can be either heat-treated by quenching in a liquid or cooled in still air depending on the properties desired. This method will only allow local hardening on the surface, but not in the core. This is sometimes very desirable because it allows for a hard surface with good wear properties as in gears, but has a tough inner core that will perform well under impact loading. In one of the surface treatment and modification techniques, namely Carburizing we add carbon to the surface. We expose the part to a Carbon rich atmosphere at an elevated temperature and allow diffusion to transfer the Carbon atoms into the steel. Diffusion will happen only if the steel has low carbon content, because diffusion works on the differential of the concentrations principle. Pack Carburizing: Parts are packed in a high carbon medium such as carbon powder and heated in a furnace for 12 to 72 hours at 900 Centigrade (1652 Fahrenheit). At these temperatures CO gas is produced which is a strong reducing agent. The reduction reaction occurs on the surface of the steel releasing carbon. The carbon is then diffused into the surface thanks to the high temperature. The Carbon on the surface is 0.7% to 1.2% depending on process conditions. The hardness achieved is 60 - 65 RC. The depth of the carburized case ranges from about 0.1 mm up to 1.5 mm. Pack carburizing requires good control of temperature uniformity and consistency in heating. Gas Carburizing: In this variant of surface treatment, Carbon Monoxide (CO) gas is supplied to a heated furnace and the reduction reaction of deposition of carbon takes place on the surface of the parts. This process overcomes most of the problems of pack carburizing. One concern however is the safe containment of the CO gas. Liquid Carburizing: The steel parts are immersed in a molten carbon rich bath. Nitriding is a surface treatment and modification process involving diffusion of Nitrogen into the surface of steel. Nitrogen forms Nitrides with elements such as Aluminum, Chromium, and Molybdenum. The parts are heat-treated and tempered before nitriding. The parts are then cleaned and heated in a furnace in an atmosphere of dissociated Ammonia (containing N and H) for 10 to 40 hours at 500-625 Centigrade (932 - 1157 Fahrenheit). Nitrogen diffuses into the steel and forms nitride alloys. This penetrates to a depth of up to 0.65 mm. The case is very hard and distortion is low. Since the case is thin, surface grinding is not recommended and therefore nitriding surface treatment may not be an option for surfaces with very smooth finishing requirements. Carbonitriding surface treatment and modification process is most suitable for low carbon alloy steels. In the carbonitriding process, both Carbon and Nitrogen are diffused into the surface. The parts are heated in an atmosphere of a hydrocarbon (such as methane or propane) mixed with Ammonia (NH3). Simply put, the process is a mix of Carburizing and Nitriding. Carbonitriding surface treatment is performed at temperatures of 760 - 870 Centigrade (1400 - 1598 Fahrenheit), It is then quenched in a natural gas (Oxygen free) atmosphere. The carbonitriding process is not suitable for high precision parts due to the distortions that are inherent. The hardness achieved is similar to carburizing (60 - 65 RC) but not as high as Nitriding (70 RC). The case depth is between 0.1 and 0.75 mm. The case is rich in Nitrides as well as Martensite. Subsequent tempering is needed to reduce brittleness. Special surface treatment and modification processes are in the early stages of development and their effectiveness is as yet unproven. They are: Cryogenic Treatment: Generally applied on hardened steels, slowly cool down the substrate to about -166 Centigrade (-300 Fahrenheit) to increase the density of the material and thus increase the wear resistance and dimension stability. Vibration Treatment: These intend to relieve thermal stress built-up in heat treatments through vibrations and increase the wear life. Magnetic Treatment: These intend to alter the line-up of atoms in materials through magnetic fields and hopefully improve the wear life. The effectiveness of these special surface treatment and modification techniques still remains to be proven. Also these three techniques above affect the bulk material besides surfaces. Please download our catalogs and brochures by clicking on the blue colored text below: - Private Label Nano Surface Protection Car Care Products We can label these products with your name and logo if you wish - Private Label Nano Surface Protection Industrial Products We can label these products with your name and logo if you wish - Private Label Nano Surface Protection Marine Products We can label these products with your name and logo if you wish - Private Label Nano Surface Protection Products We can label these products with your name and logo if you wish CLICK Product Finder-Locator Service RÛPERA BERÊ