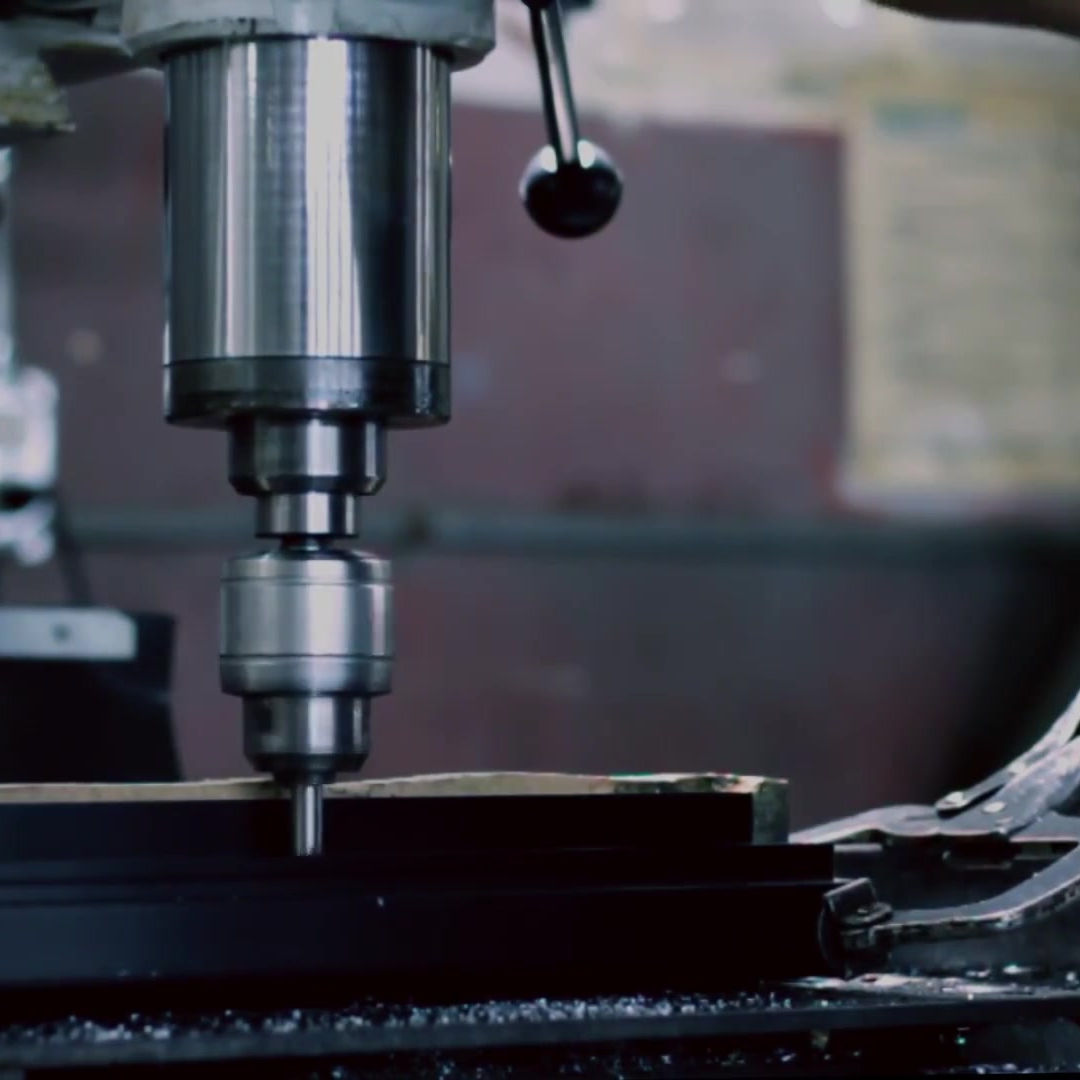
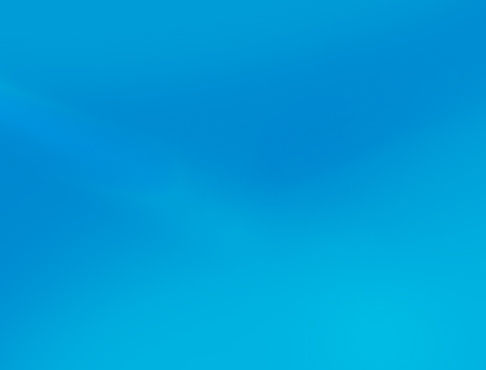
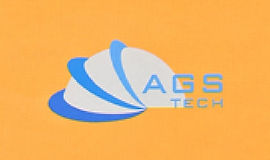
Hilberînerê Xwerû ya Gloverî, Integrator, Hevkar, Hevkarê Derveyî Ji bo Cûreyek Berfireh a Hilber û Karûbaran.
Em ji bo çêkirin, çêkirin, endezyarî, yekbûn, yekbûn, derxistina hilber û karûbarên xwerû yên çêkirî û yên li derveyî refê çavkaniya weya yek-rawest in. Ger hûn bixwazin, em di heman demê de etîketa taybet / spî hilberên we bi navê marqeya we nîşan didin.
Zimanê xwe hilbijêre
Hilberîna Xweser a Parçe, Pêkhatî, Meclîs, Berhemên Qediyayî, Makîne û Amûrên Pîşesaziyê
Hilberîna Peymana Navxweyî û Gerdûnî
Manufacturing Outsourcing
Kirîna Navxweyî, Gerdûnî ya Berhemên Pîşesazî
Etîketkirina taybet / Spî Hilberên xwe bi navê marqeya xwe nîşankirin
Karûbarên Dîtina Hilber & Cihgirtin
Sêwirana gerdûnî û Hevkariya Kanal
Endezyariya Entegrasyonê
Xizmetên Endezyariyê
Hevgirtina Gerdûnî, Warehousing, Logistics
Encamên Lêgerînê
164 results found with an empty search
- Global Product Finder Locator for Off Shelf Products
Global Product Finder Locator for Off Shelf Products AGS-TECH, Inc. ya we ye Çêkerê Xweseriya Gloverî, Integrator, Hevkar, Hevkarê Derveyî. Em ji bo çêkirin, çêkirin, endezyarî, hevgirtin, derxistina derve çavkaniya weya yek-rawest in. Heke hûn bi rastî hilbera ku hûn lê digerin dizanin, ji kerema xwe tabloya jêrîn dagirin Ger dagirtina forma li jêr ne mumkin an jî pir dijwar be, em daxwaza we bi e-nameyê jî qebûl dikin. Tenê ji me re binivîsin sales@agstech.net Get a Price Quote on a known brand, model, part number....etc. First name Last name Email Phone Product Name Product Make or Brand Please Enter Manufacturer Part Number if Known Please Enter SKU Code if You Know: Your Application for the Product Quantity Needed Do You have a price target ? If so, please let us know: Give us more details if you want: Condition of Product Needed New Used Does Not Matter Heke we hebe, pelên têkildar ên hilberê bi tikandina li ser lînka jêrîn barkirin. Xem neke, lînka jêrîn dê pencereyek nû ji bo daxistina pelên xwe vebike. Hûn ê ji vê pencereya heyî dûr nekevin. Piştî barkirina pelên xwe, TENÊ Pencera Dropboxê bigire, lê ne vê rûpelê. Bawer bikin ku hemî cîhan tije bikin û bişkojka şandina jêrîn bikirtînin. JI BO BAXKIRINA PÊLEYAN LI VIR bikirtînin Request a Quote Thanks! We’ll send you a price quote shortly. RÛPERA BERÊ Em AGS-TECH Inc., çavkaniya weya yek-stop ji bo çêkirin û çêkirin û endezyarî û jêderxistin û yekbûnek we ne. Em entegratora endezyariya herî cihêreng a Cîhanê ne ku hilberîna xwerû, binecivîn, komkirina hilberan û karûbarên endezyariyê pêşkêşî we dikin.
- Custom Made Products Data Entry
Custom Made Products Data Entry, Custom Manufactured Parts, Assemblies, Plastic Molds, Casting, CNC Machining, Extrusion, Metal Forging, Spring Manufacturing, Products Assembly, PCBA, PCB AGS-TECH, Inc. ya we ye Çêkerê Xweseriya Gloverî, Integrator, Hevkar, Hevkarê Derveyî. Em ji bo çêkirin, çêkirin, endezyarî, hevgirtin, derxistina derve çavkaniya weya yek-rawest in. Heke hûn hewceyê sêwirandin û pêşkeftina xwerû û prototîp û hilberîna girseyî hewce ne agahdariya xwe dagirin: Ger dagirtina forma li jêr ne mumkin an jî pir dijwar be, em daxwaza we bi e-nameyê jî qebûl dikin. Tenê ji me re binivîsin sales@agstech.net Get a Price Quote on a custom designed, developed, prototyped or manufactured product. First name Last name Email Phone Product Name Your Application for the Product Quantity Needed Do you have a price target ? If you do have, please let us know your expected price: Give us more details if you want: Do you accept offshore manufacturing ? YES NO Heke we hebe, pelên têkildar ên hilberê bi tikandina li ser lînka jêrîn barkirin. Xem neke, lînka jêrîn dê pencereyek nû ji bo daxistina pelên xwe vebike. Hûn ê ji vê pencereya heyî dûr nekevin. Piştî barkirina pelên xwe, TENÊ Pencera Dropboxê bigire, lê ne vê rûpelê. Bawer bikin ku hemî cîhan tije bikin û bişkojka şandina jêrîn bikirtînin. Pelên ku dê ji me re bibin alîkar ku em hilbera weya taybetî xêzkirî xêzkirinên teknîkî, fatûreya materyalan, wêne, xêzkirin ... hwd. Hûn dikarin ji yek pelê bêtir dakêşin. JI BO DAXISTINA PÊLEYAN LI VIR bikirtînin Request a Quote Thanks! We’ll send you a price quote shortly. RÛPERA BERÊ Em AGS-TECH Inc., çavkaniya weya yek-stop ji bo çêkirin û çêkirin û endezyarî û jêderxistin û yekbûnek we ne. Em entegratora endezyariya herî cihêreng a Cîhanê ne ku hilberîna xwerû, binecivîn, komkirina hilberan û karûbarên endezyariyê pêşkêşî we dikin.
- Wireless Components, Antenna, Radio Frequency Devices, RF Devices, HF
Wireless Components - Antenna - Radio Frequency Devices - RF Devices - Remote Sensing and Control - High Frequency Çêkirin & Civîna Amûrên RF û Wireless • Wireless components, devices and assemblies for remote sensing, remote control and communication. We can help you during the design, development, prototyping or mass production of various types of fixed, mobile, and portable two way radios, cellular telephones, GPS units, personal digital assistants (PDAs), smart and remote control equipment and wireless networking devices and instruments. We also have off-shelf wireless components and devices you can select from our brochures below. Antenna Brochure for 5G - LTE 4G - LPWA 3G - 2G - GPS - GNSS - WLAN - BT - Combo - ISM Barcode and Fixed Mount Scanners - RFID Products - Mobile Computers - Micro Kiosks OEM Technology (We private label these with your brand name and logo if you wish) Barcode Scanners (We private label these with your brand name and logo if you wish) High frequency devices product line (Band Pass Filters, Low Pass Filters, IPD, CPL, Balanced Filter, Diplexer, Balun, Chip Antenna...etc.) Microwave Flexible Cable Assembly Microwave and Milimeter Wave Test Accessories Brochure (Cable assemblies, VNA Test Assemblies, Mechanical Calibration Kits, RF Coaxial Adapters, Test Port Adapters, DC Blocks, NMD Connectors....etc.) Precision RF Adapter s Catalog (Coax RF, Microwave, mmWave Adapters such as SMA, SSMA, SMP, BNC, Type-N, 3.5 mm.....etc) Printers for Barcode Scanners and Mobile Computers (We private label these with your brand name and logo if you wish) RF Components Brochure for Coaxial Fixed Attenuators, Coaxial Terminations, DC Blocks, Coax Adapters, Waveguide Components, Power Dividers, RF Connectors, RF Tools. RF devices and high frequency inductors (Multilayer Ceramic Capacitors, Chip-Resistor, Disc Capacitors, RF & HF Inductor Varistors & SMD-Varistors, Chip Antenna, Filters, Coupler) RF and Microwave Components (Broadband 90/180 Degree Hybrid and Coupler, Broadband Power Divider, Filter, RF switch, Broadband Amplifier, Broadband Frequency Synthesizer) RFID Readers - Scanners - Encoders - Printers (We private label these with your brand name and logo if you wish) RF Product Overview Chart (RF Antenna, Multilayer Ceramic Filter, Multilayer Ceramic Balun, Ceramic Diplexer) Soft Ferrites - Cores - Toroids - EMI Suppression Products - RFID Transponders and Accessories Brochure Information on our facility producing ceramic to metal fittings, hermetic sealing, vacuum feedthroughs, high and ultrahigh vacuum components, BNC, SHV adapters and connectors, conductors and contact pins, connector terminals can be found here: Factory Brochure Dowload brochure for our DESIGN PARTNERSHIP PROGRAM We also participate in Third Party Resource Program and are a reseller of products offered by RF Digital ( Website: http://www.rfdigital.com ) , a company that manufactures an extensive line of fully integrated, low cost, high quality, high performance, configurable Wireless RF Transmitter, Receiver & Transceiver Modules, suitable for a wide range of applications. We participate in RF Digital's referral program as a Product Design and Development Company. Contact us to take advantage of our fully integrated, configurable Wireless RF Transmitter, Receiver & Transceiver Modules, High Frequency RF Devices, and most importantly of our consulting services regarding the implementation and application of these wireless components and devices and our engineering integration services. We can make you realize your new product development cycle by assisting you at every phase of the process, from concept to design to prototyping to first article manufacturing to mass production. • Some applications of wireless technology we can help you with are: - Wireless security systems - Remote control of consumer electronic devices or commercial equipment. - Cellular telephony (phones and modems): - WiFi - Wireless energy transfer - Radio communication devices - Short-range point-to-point communication devices such as wireless microphones, remote controls, IrDA, RFID (Radio Frequency Identification), Wireless USB, DSRC (Dedicated Short Range Communications), EnOcean, Near Field Communication, Wireless Sensor Networks : ZigBee, EnOcean; Personal area networks, Bluetooth, Ultra-wideband, wireless computer networks: Wireless Local Area Networks (WLAN), Wireless Metropolitan Area Networks (WMAN)...etc. More information on our engineering and research & development capabilities is available at our engineering site http://www.ags-engineering.com CLICK Product Finder-Locator Service RÛPERA BERÊ
- Micromanufacturing, Nanomanufacturing, Mesomanufacturing AGS-TECH Inc.
Micromanufacturing, Nanomanufacturing, Mesomanufacturing - Electronic & Magnetic Optical & Coatings, Thin Film, Nanotubes, MEMS, Microscale Fabrication Nanoscale & Microscale & Mesoscale Manufacturing Read More Our NANOMANUFACTURING, MICROMANUFACTURING and MESOMANUFACTURING processes can be categorized as: Surface Treatments and Modification Functional Coatings / Decorative Coatings / Thin Film / Thick Film Nanoscale Manufacturing / Nanomanufacturing Microscale Manufacturing / Micromanufacturing / Micromachining Mesoscale Manufacturing / Mesomanufacturing Microelectronics & Semiconductor Manufacturing and Fabrication Microfluidic Devices Manufacturing Micro-Optics Manufacturing Micro Assembly and Packaging Soft Lithography In every smart product designed today, one can consider an element that will increase efficiency, versatility, reduce power consumption, reduce waste, increase lifetime of the product and thus be environmentally friendly. For this purpose, AGS-TECH is focusing on a number of processes and products that can be incorporated into devices and equipment to achieve these goals. For example low-friction FUNCTIONAL COATINGS can reduce power consumption. Some other functional coating examples are scratch resistant coatings, anti-wetting SURFACE TREATMENTS and coatings (hydrophobic), wetness promoting (hydrophilic) surface treatment and coatings, anti-fungal coatings, diamond like carbon coatings for cutting and scribing tools, THIN FILMelectronic coatings, thin film magnetic coatings, multilayer optical coatings. In NANOMANUFACTURING or NANOSCALE MANUFACTURING, we produce parts at nanometer length scales. In practice it refers to manufacturing operations below micrometer scale. Nanomanufacturing is still in its infancy when compared to micromanufacturing, however the trend is in that direction and nanomanufacturing is definitely very important for the near future. Some applications of nanomanufacturing today are carbon nanotubes as reinforcing fibers for composite materials in bicycle frames, baseball bats and tennis racquets. Carbon nanotubes, depending on the orientation of the graphite in the nanotube, can act as semiconductors or conductors. Carbon nanotubes have very high current-carrying capability, 1000 times higher than silver or copper. Another application of nanomanufacturing is nanophase ceramics. By using nanoparticles in producing ceramic materials, we can simultaneously increase both the strength and ductility of the ceramic. Please click on the submenu for more information. MICROSCALE MANUFACTURING or MICROMANUFACTURING refers to our manufacturing and fabrication processes on a microscopic scale not visible to the naked eye. The terms micromanufacturing, microelectronics, microelectromechanical systems are not limited to such small length scales, but instead, suggest a material and manufacturing strategy. In our micromanufacturing operations some popular techniques we use are lithography, wet and dry etching, thin film coating. A wide variety of sensors & actuators, probes, magnetic hard-drive heads, microelectronic chips, MEMS devices such as accelerometers and pressure sensors among others are manufactured using such micromanufacturing methods. You will find more detailed information on these in the submenus. MESOSCALE MANUFACTURING or MESOMANUFACTURING refers to our processes for fabrication of miniature devices such as hearing aids, medical stents, medical valves, mechanical watches and extremely small motors. Mesoscale manufacturing overlaps both macro and micromanufacturing. Miniature lathes, with 1.5 Watt motor and dimensions of 32 x 25 x 30.5 mm and weights of 100 grams have been fabricated using mesoscale manufacturing methods. Using such lathes, brass has been machined to a diameter as small as 60 microns and surface roughnesses in the order of a micron or two. Other such miniature machine tools such as milling machines and presses have also been manufactured using mesomanufacturing. In MICROELECTRONICS MANUFACTURING we use the same techniques as in micromanufacturing. Our most popular substrates are silicon, and others like gallium arsenide, Indium Phosphide and Germanium are also used. Films/coatings of many types and especially conducting and insulating thin film coatings are used in the fabrication of microelectronic devices and circuits. These devices are usually obtained from multilayers. Insulating layers are generally obtained by oxidation such as SiO2. Dopants (both p and n) type are common and parts of the devices are doped in order to alter their electronic properties and obtain p and n type regions. Using lithography such as ultraviolet, deep or extreme ultraviolet photolithography, or X-ray, electron beam lithography we transfer geometric patterns defining the devices from a photomask/mask to the substrate surfaces. These lithography processes are applied several times in the micromanufacturing of microelectronic chips in order to achieve the required structures in the design. Also etching processes are carried out by which entire films or particular sections of films or substrate are removed. Briefly, by using various deposition, etching and multiple lithographic steps we obtain the multilayer structures on the supporting semiconductor substrates. After the wafers are processed and many circuits are microfabricated on them, the repetitive parts are cut and individual dies are obtained. Each die is thereafter wire bonded, packaged and tested and becomes a commercial microelectronic product. Some more details of microelectronics manufacturing can be found in our submenu, however the subject is very extensive and therefore we encourgae you to contact us in case you need product specific information or more details. Our MICROFLUIDICS MANUFACTURING operations are aimed at fabrication of devices and systems in which small volumes of fluids are handled. Examples of microfluidic devices are micro-propulsion devices, lab-on-a-chip systems, micro-thermal devices, inkjet printheads and more. In microfluidics we have to deal with the precise control and manipulation of fluids constrained to sub-milimeter regions. Fluids are moved, mixed, separated and processed. In microfluidic systems fluids are moved and controlled either actively using tiny micropumps and microvalves and the like or passively taking advantage of capillary forces. With lab-on-a-chip systems, processes which are normally carried out in a lab are miniaturized on a single chip in order to enhance efficiency and mobility as well as reduce sample and reagent volumes. We have the capability to design microfluidic devices for you and offer microfluidics prototyping & micromanufacturing custom tailored for your applications. Another promising field in microfabrication is MICRO-OPTICS MANUFACTURING. Micro-optics allows the manipulation of light and the management of photons with micron and sub-micron scale structures and components. Micro-optics allows us to interface the macroscopic world we live in with the microscopic world of opto- and nano-electronic data processing. Micro-optical components and subsystems find widespread applications in the following fields: Information technology: In micro-displays, micro-projectors, optical data storage, micro-cameras, scanners, printers, copiers…etc. Biomedicine: Minimally-invasive/point of care diagnostics, treatment monitoring, micro-imaging sensors, retinal implants. Lighting: Systems based on LEDs and other efficient light sources Safety and Security Systems: Infrared night vision systems for automotive applications, optical fingerprint sensors, retinal scanners. Optical Communication & Telecommunication: In photonic switches, passive fiber optic components, optical amplifiers, mainframe and personal computer interconnect systems Smart structures: In optical fiber-based sensing systems and much more As the most diverse engineering integration provider we pride ourselves with our capability to provide a solution for almost any consulting, engineering, reverse engineering, rapid prototyping, product development, manufacturing, fabrication and assembly needs. After micromanufacturing our components, very often we need to continue with MICRO ASSEMBLY & PACKAGING. This involves processes such as die attachment, wire bonding, connectorization, hermetic sealing of packages, probing, testing of packaged products for environmental reliability…etc. After micromanufacturing devices on a die, we attach the die to a more rugged foundation to ensure reliability. Frequently we use special epoxy cements or eutectic alloys to bond the die to its package. After the chip or die is bonded to its substrate, we connect it electrically to the package leads using wire bonding. One method is to use very thin gold wires from the package leads to bonding pads located around the perimeter of the die. Lastly we need to do the final packaging of the connected circuit. Depending on the application and operating environment, a variety of standard and custom manufactured packages are available for micromanufactured electronic, electro-optic, and microelectromechanical devices. Another micromanufacturing technique we use is SOFT LITHOGRAPHY, a term used for a number of processes for pattern transfer. A master mold is needed in all cases and is microfabricated using standard lithography methods. Using the master mold, we produce an elastomeric pattern / stamp. One variation of soft lithography is “microcontact printing”. The elastomer stamp is coated with an ink and pressed against a surface. The pattern peaks contact the surface and a thin layer of about 1 monolayer of the ink is transfered. This thin film monolayer acts as the mask for selective wet etching. A second variation is “microtransfer molding”, in which the recesses of the elastomer mold are filled with liquid polymer precursor and pushed against a surface. Once the polymer cures, we peel off the mold, leaving behind the desired pattern. Lastly a third variation is “micromolding in capillaries”, where the elastomer stamp pattern consists of channels that use capillary forces to wick a liquid polymer into the stamp from its side. Basically, a small amount of the liquid polymer is placed adjacent to the capillary channels and the capillary forces pull the liquid into the channels. Excess liquid polymer is removed and polymer inside the channels is allowed to cure. The stamp mold is peeled off and the product is ready. You can find more details about our soft lithography micromanufacturing techniques by clicking on the related submenu on the side of this page. If you are mostly interested in our engineering and research & development capabilities instead of manufacturing capabilities, then we invite you to also visit our engineering website http://www.ags-engineering.com Read More Read More Read More Read More Read More Read More Read More Read More Read More CLICK Product Finder-Locator Service RÛPERA BERÊ
- Computer Networking Equipment, Intermediate Systems, InterWorking Unit
Computer Networking Equipment - Intermediate Systems - InterWorking Unit - IWU - IS - Router - Bridge - Switch - Hub available from AGS-TECH Inc. Amûrên Torê, Amûrên Torê, Pergalên Navîn, Unit Interworking COMPUTER NETWORKING DEVICES are equipment that mediate data in computer networks. Computer networking devices are also called NETWORK EQUIPMENT, INTERMEDIATE SYSTEMS (IS) or INTERWORKING UNIT (IWU). Devices which are the last receiver or that generate data are called HOST or DATA TERMINAL EQUIPMENT. Among the high quality brands we offer are ATOP TECHNOLOGIES, JANZ TEC , ICP DAS and KORENIX. - ATOP TECHNOLOGIES compact product brochure - ATOP Technologies Product List 2021) - Barcode and Fixed Mount Scanners - RFID Products - Mobile Computers - Micro Kiosks OEM Technology (We private label these with your brand name and logo if you wish) - Barcode Scanners (We private label these with your brand name and logo if you wish) - CISCO Start Catalog (Networking Equipment, Switches, Wireless Controllers, Wireless Access Points (WAP), Cloud Managed Access Points, Routers) - Fixed Industrial Scanners (We private label these with your brand name and logo if you wish) - ICP DAS brand industrial communication and networking products brochure - ICP DAS brand industrial Ethernet switch for rugged environments - ICP DAS brand PACs Embedded Controllers & DAQ brochure - ICP DAS brand Industrial Touch Pad brochure - ICP DAS brand Remote IO Modules and IO Expansion Units brochure - ICP DAS brand PCI Boards and IO Cards - J ANZ TEC brand compact product brochure - Kiosk Systems (We private label these with your brand name and logo if you wish) - Kiosk Systems Accessories Guide (We private label these with your brand name and logo if you wish) - KORENIX brand compact product brochure - Mobile Computers for Enterprises (We private label these with your brand name and logo if you wish) - Printers for Barcode Scanners and Mobile Computers (We private label these with your brand name and logo if you wish) - RFID Readers - Scanners - Encoders - Printers (We private label these with your brand name and logo if you wish) To choose a suitable Industrial Grade Networking Device for your project, please go to our industrial computer store by CLICKING HERE. Dowload brochure for our DESIGN PARTNERSHIP PROGRAM Below is some fundamental information about networking devices that you may find useful. List of computer networking devices / Common basic networking devices: ROUTER: This is a specialized network device that determines the next network point where it can forward a data packet towards the destination of the packet. Unlike a gateway, it cannot interface different protocols. Works on OSI layer 3. BRIDGE: This is a device connecting multiple network segments along the data link layer. Works on OSI layer 2. SWITCH: This is a device that allocates traffic from one network segment to certain lines (intended destination(s)) which connect the segment to another network segment. So unlike a hub a switch splits the network traffic and sends it to different destinations rather than to all systems on the network. Works on OSI layer 2. HUB: Connects multiple Ethernet segments together and makes them act as a single segment. In other words, a hub provides bandwidth which is shared among all the objects. A hub is one of the most basic hardware devices that connects two or more Ethernet terminals in a network. Therefore, only one computer connected to the hub is able to transmit at a time, contrary to switches, which provide a dedicated connection between individual nodes. Works on OSI layer 1. REPEATER: This is a device to amplify and/or regenerate digital signals received while sending them from one part of a network to another. Works on OSI layer 1. Some of our HYBRID NETWORK devices: MULTILAYER SWITCH: This is a switch that besides switching on OSI layer 2, provides functionality at higher protocol layers. PROTOCOL CONVERTER: This is a hardware device that converts between two different types of transmissions, such as asynchronous and synchronous transmissions. BRIDGE ROUTER (B ROUTER): This piece of equipment combines router and bridge functionalities and therefore works on OSI layers 2 and 3. Here are some of our hardware and software components that most often are placed on the connection points of different networks, e.g. between internal and external networks: PROXY: This is a computer network service that allows clients to make indirect network connections to other network services FIREWALL: This is a piece of hardware and/or software placed on the network to prevent the type of communications that are forbidden by the network policy. NETWORK ADDRESS TRANSLATOR: Network services provided as hardware and/or software that convert internal to external network addresses and vice versa. Other popular hardware for establishing networks or dial-up connections: MULTIPLEXER: This device combines several electrical signals into a single signal. NETWORK INTERFACE CONTROLLER: A piece of computer hardware which allows the attached computer to communicate by network. WIRELESS NETWORK INTERFACE CONTROLLER: A piece of computer hardware which allows the attached computer to communicate by WLAN. MODEM: This is a device that modulates an analog ''carrier'' signal (such as sound), to encode digital information, and that also demodulates such a carrier signal to decode the transmitted information, as a computer communicating with another computer over the telephone network. ISDN TERMINAL ADAPTER (TA): This is a specialized gateway for Integrated Services Digital Network (ISDN) LINE DRIVER: This is a device that increases transmission distances by amplifying the signal. Base-band networks only. CLICK Product Finder-Locator Service RÛPERA BERÊ
- Filters & Filtration Products & Membranes, USA, AGS-TECH
AGS-TECH supplies off-the-shelf and custom manufactured filters, filtration products and membranes including air purification filters, ceramic foam filters, activated carbon filters, HEPA filters, pre-filtering media and coarse filters, wire mesh and cloth filters, oil & fuel & gas filters. Parzûn & Hilber û Parzûnên Parzûnê We supply filters, filtration products and membranes for industrial and consumer applications. Products include: - Activated carbon based filters - Planar wire mesh filters made to customer's specifications - Irregular shaped wire mesh filters made to customer's specifications. - Other type of filters such as air, oil, fuel filters. - Ceramic foam and ceramic membrane filters for various industrial applications in petrochemistry, chemical manufacturing, pharmaceuticals...etc. - High performance clean room and HEPA filters. We stock off-the-shelf wholesale filters, filtration products and membranes with various dimensions and specifications. We also manufacture and supply filters & membranes according to customers specifications. Our filter products comply with international standards such as CE, UL and ROHS standards. Please click on the links below to select the filtration product of your interest. Activated Carbon Filters Activated carbon also called activated charcoal, is a form of carbon processed to have small, low-volume pores that increase the surface area available for adsorption or chemical reactions. Due to its high degree of microporosity, just one gram of activated carbon has a surface area in excess of 1,300 m2 (14,000 sq ft). An activation level sufficient for useful application of activated carbon may be attained solely from high surface area; however, further chemical treatment often enhances adsorption properties. Activated carbon is widely used in filters for gas purification, filters for decaffeination, metal extraction & purification, filtration & purification of water, medicine, treatment of sewage, air filters in gas masks and respirators, compressed air filters, filtering of alcoholic beverages like vodka and whiskey from organic impurities which can affect taste, odor and color among many other applications. Activated carbon is being used in various types of filters, most commonly in panel filters, non-woven fabric, cartridge type filters....etc. You can download brochures of our activated carbon filters from the links below. - Air Purification Filters (includes folded type and V-shaped Activated Carbon Air Filters) Ceramic Membrane Filters Ceramic membrane filters are inorganic, hydrophilic, and are ideal for extreme nano-, ultra-, and micro-filtration applications that require longevity, superior pressure/temperature tolerances and resistance to aggressive solvents. Ceramic membrane filters are basically ultra-filtration or micro-filtration filters, used to treat wastewater and water at higher elevated temperatures. Ceramic membrane filters are produced from inorganic materials such as aluminum oxide, silicon carbide, titanium oxide, and zirconium oxide. The membrane porous core material is first formed through extrusion process which becomes the support structure for the ceramic membrane. Then coatings are applied to the inner face or the filtering face with the same ceramic particles or sometimes different particles, depending on the application. For example, if your core material is aluminum oxide, we also use aluminum oxide particles as the coating. The size of ceramic particles used for the coating, as well as the number of coating applied will determine the pore size of the membrane as well as the distribution characteristics. After depositing the coating to the core, high-temperature sintering takes place inside a furnace, making the membrane layer integral of the core support structure. This provides us a very durable and hard surface. This sintered bonding ensures a very long life for the membrane. We can custom manufacture ceramic membrane filters for you from micro-filtration range to ultra-filtration range by varying the number of coatings and by using the right particle size for the coating. Standard pore sizes can vary from 0.4 microns to .01 micron size. Ceramic membrane filters are like glass, very hard and durable, unlike polymeric membranes. Therefore ceramic membrane filters offer a very high mechanical strength. Ceramic membrane filters are chemically inert, and they can be used at a very high flux compared to polymeric membranes. Ceramic membrane filters can be vigorously cleaned and are thermally stable. Ceramic membrane filters have a very long operational life, roughly three to four times as long compared to the polymeric membranes. Compared to polymeric filters, ceramic filters are very expensive, because ceramic filtration applications start where the polymeric applications end. Ceramic membrane filters have various applications, mostly in treating very difficult to treat water and wastewater, or where high temperature operations are involved. It also has vast applications in oil and gas, wastewater recycling, as a pre‑treatment for RO, and for removing precipitated metals from any precipitation process, for oil & water separation, food and beverage industry, microfiltration of milk, clarification of fruit juice, reclamation and collection of nano powders and catalyzers, in the pharmaceutical industry, in mining where you have to treat the wasted tailing ponds. We offer single channel as well as multiple channel shaped ceramic membrane filters. Both off-the-shelf as well as custom manufacturing is offered to you by AGS-TECH Inc. Ceramic Foam Filters Ceramic foam filter is a tough foam made from ceramics . Open-cell polymer foams are internally impregnated with ceramic slurry and then fired in a kiln , leaving only ceramic material. The foams may consist of several ceramic materials such as aluminium oxide , a common high-temperature ceramic. Ceramic foam filters get insulating properties from the many tiny air-filled voids within the material. Ceramic foam filters are used for filtration of molten metal alloys, absorption of environmental pollutants , and as substrate for catalysts requiring large internal surface area. Ceramic foam filters are hardened ceramics with pockets of air or other gases trapped in pores throughout the body of the material. These materials can be fabricated as high as 94 to 96% air by volume with high temperature resistances such as 1700 °C. Since most ceramics are already oxides or other inert compounds, there is no danger of oxidation or reduction of the material in ceramic foam filters. - Ceramic Foam Filters Brochure - Ceramic Foam Filter User's Guide HEPA Filters HEPA is a type of air filter and the abbreviation stands for High-Efficiency Particulate Arrestance (HEPA). Filters meeting the HEPA standard have many applications in clean rooms, medical facilities, automobiles, aircraft and homes. HEPA filters must satisfy certain standards of efficiency such as those set by the United States Department of Energy (DOE). To qualify as HEPA by US government standards, an air filter must remove from the air that passes through 99.97% of particles that are sized 0.3 µm. HEPA filter's minimal resistance to airflow, or pressure drop, is generally specified as 300 pascals (0.044 psi) at its nominal flow rate. HEPA filtration works by mechanical means and does not resemble the Ionic and Ozone filtration methods which use negative ions and ozone gas respectively. Therefore, the chances of potential pulmonary side-effects like asthma and allergies is much lower with HEPA filtering systems. HEPA filters are also used in high quality vacuum cleaners effectively to protect users from asthma and allergies, because HEPA filter traps fine particles such as pollens and dust mite feces which trigger allergy and asthma symptoms. Contact us if you would like to get our opinion about using HEPA filters for a particular application or project. You can download our product brochures for off-the-shelf HEPA filters below. If you cannot find the right size or shape you would need we will be happy to design and manufacture custom HEPA filters for your special application. - Air Purification Filters (includes HEPA Filters) - Private Label Industrial Filters (We can put your company name and logo on these filters. Includes also HEPA filters) Coarse Filters & Pre-Filtering Media Coarse filters and pre-filtering media are used to block large debris. They are of critical importance because they are inexpensive and protect the more expensive higher grade filters from being contaminated with coarse particulates and contaminants. Without coarse filters and pre-filtering media, the cost of filtering would have been much much higher as we would need to change fine filters much more frequently. Most of our coarse filters and pre-filtering media are made of synthetic fibers with controlled diameters and pore sizes. Coarse filter materials include the popular material polyester. Filtering efficiency grade is an important parameter to check for before choosing a particular coarse filter / pre-filtering media. Other parameters and features to check for are whether the pre-filtering media is washable, reusable, arrestance value, resistance against air or fluid flow, rated air flow, dust and particulate holding capacity, temperature resistance, flammability, pressure drop characteristics, dimensional and shape related specification...etc. Contact us for opinion before choosing the right coarse filters & pre-filtering media for your products and systems. - Wire Mesh and Cloth Brochure (includes information on our wire mesh & cloth filters manufacturing capabilities. Metal and nonmetal wire cloth can be used as coarse filters and pre-filtering media in some applications) - Air Purification Filters (includes Coarse Filters & Pre-Filtering Media for air) Oil, Fuel, Gas, Air and Water Filters AGS-TECH Inc. designs and manufactures oil, fuel, gas, air and water filters according to customer's requirements for industrial machinery, automobiles, motorboats, motorcycles...etc. Oil filters are designed to remove contaminants from engine oil , transmission oil , lubricating oil , hydraulic oil . Oil filters are used in many different types of hydraulic machinery . Oil production, transportation industry, and recycling facilities also employ oil and fuel filters in their manufacturing processes. OEM orders are welcome, we label, silkscreen print, laser mark oil, fuel, gas, air and water filters according to your requirements, we put your logos on the product and package according to your needs and requirements. If desired, housing materials for your oil, fuel, gas, air, water filters can be customized depending on your particular application. Information about our standard off-the-shelf oil, fuel, gas, air and water filters can be downloaded below. - Air Purification Filters - Oil - Fuel - Gas - Air - Water Filters Selection Brochure for Automobiles, Motorcycles, Trucks and Buses - Private Label Industrial Filters (We can put your company name and logo on these filters) Membranes A membrane is a selective barrier; it allows some things to pass through but stops others. Such things may be molecules, ions, or other small particles. Generally, polymeric membranes are used to separate, concentrate, or fractionate a wide variety of liquids. Membranes serve as a thin barrier between miscible fluids that allow for preferential transport of one or more feed components when a driving force is applied, such as a pressure differential. We offer a suite of nanofiltration, ultrafiltration and microfiltration membranes that are engineered to provide optimal flux and rejection and can be customized to meet the unique requirements of specific process applications. Membrane filtration systems are the heart of many separation processes. Technology selection, equipment design, and fabrication quality are all critical factors in the ultimate success of a project. To start, the proper membrane configuration must be selected. Contact us for help in your projects. RÛPERA BERÊ
- Thermal Infrared Test Equipment, Thermal Camera, Differential Scanning
Thermal Infrared Test Equipment, Thermal Camera, Differential Scanning Calorimeter, Thermo Gravimetric Analyzer, Thermo Mechanical Analyzer, Dynamic Mechanical Amûrên Testê yên Termal û IR CLICK Product Finder-Locator Service Among the many THERMAL ANALYSIS EQUIPMENT, we focus our attention to the popular ones in industry, namely the DIFFERENTIAL SCANNING CALORIMETRY ( DSC ), THERMO-GRAVIMETRIC ANALYSIS ( TGA ), THERMO-MECHANICAL ANALYSIS ( TMA ), DILATOMETRY,DYNAMIC MECHANICAL ANALYSIS ( DMA ), DIFFERENTIAL THERMAL ANALYSIS ( DTA). Our INFRARED TEST EQUIPMENT involves THERMAL IMAGING INSTRUMENTS, INFRARED THERMOGRAPHERS, INFRARED CAMERAS. Some applications for our thermal imaging instruments are Electrical and Mechanical System Inspection, Electronic Component Inspection, Corrosion Damage and Metal Thinning, Flaw Detection. Please download catalogs from colored links below and let us know your prefered brand and model number of the product. You can purchase brand new or refurbished / used Thermal & IR Test Equipment from us: FLUKE Test Tools Catalog (includes Thermal Imagers, Thermometers) HAIDA Color Assessment Cabinet Private Label Hand Tools for Every Industry (This catalog contains a few thermal & IR test instruments. We can private label these hand tools if you wish. In other words, we can put your company name, brand and label on them. This way you can promote your brand by reselling these to your customers.) DIFFERENTIAL SCANNING CALORIMETERS (DSC) : A technique in which the difference in the amount of heat required to increase the temperature of a sample and reference is measured as a function of temperature. Both the sample and reference are maintained at nearly the same temperature throughout the experiment. The temperature program for a DSC analysis is established so that the sample holder temperature increases linearly as a function of time. The reference sample has a well-defined heat capacity over the range of temperatures to be scanned. DSC experiments provide as a result a curve of heat flux versus temperature or versus time. Differential scanning calorimeters are frequently used to study what happens to polymers when they're heated. The thermal transitions of a polymer can be studied using this technique. Thermal transitions are changes that take place in a polymer when they are heated. The melting of a crystalline polymer is an example. The glass transition is also a thermal transition. DSC thermal analysis is carried out for determining Thermal Phase Changes, Thermal Glass Transition Temperature (Tg), Crystalline Melt Temperatures, Endothermic Effects, Exothermic Effects, Thermal Stabilities, Thermal Formulation Stabilities, Oxidative Stabilities, Transition Phenomena, Solid State Structures. DSC analysis determines the Tg Glass Transition Temperature, temperature at which amorphous polymers or an amorphous part of a crystalline polymer go from a hard brittle state to a soft rubbery state, melting point, temperature at which a crystalline polymer melts, Hm Energy Absorbed (joules/gram), amount of energy a sample absorbs when melting, Tc Crystallization Point, temperature at which a polymer crystallizes upon heating or cooling, Hc Energy Released (joules/gram), amount of energy a sample releases when crystallizing. Differential Scanning Calorimeters can be used to determine the thermal properties of plastics, adhesives, sealants, metal alloys, pharmaceutical materials, waxes, foods, oils and lubricants and catalysts….etc. DIFFERENTIAL THERMAL ANALYZERS (DTA): An alternative technique to DSC. In this technique it is the heat flow to the sample and reference that remains the same instead of the temperature. When the sample and reference are heated identically, phase changes and other thermal processes cause a difference in temperature between the sample and reference. DSC measures the energy required to keep both the reference and the sample at the same temperature whereas DTA measures the difference in temperature between the sample and the reference when they are both put under the same heat. So they are similar techniques. THERMOMECHANICAL ANALYZER (TMA) : The TMA reveals the change in the dimensions of a sample as a function of temperature. One can regard TMA as a very sensitive micrometer. The TMA is a device that allows precise measurements of position and can be calibrated against known standards. A temperature control system consisting of a furnace, heat sink and a thermocouple surrounds the samples. Quartz, invar or ceramic fixtures hold the samples during tests. TMA measurements record changes caused by changes in the free volume of a polymer. Changes in free volume are volumetric changes in the polymer caused by the absorption or release of heat associated with that change; the loss of stiffness; increased flow; or by the change in relaxation time. The free volume of a polymer is known to be related to viscoelasticity, aging, penetration by solvents, and impact properties. The glass transition temperature Tg in a polymer corresponds to the expansion of the free volume allowing greater chain mobility above this transition. Seen as an inflection or bending in the thermal expansion curve, this change in the TMA can be seen to cover a range of temperatures. The glass transition temperature Tg is calculated by an agreed upon method. Perfect agreement is not immediately witnessed in the value of the Tg when comparing different methods, however if we carefully examine the agreed upon methods in determining the Tg values then we understand that there is actually good agreement. Besides its absolute value, the width of the Tg is also an indicator of changes in the material. TMA is a relatively simple technique to carry out. TMA is often used for measuring Tg of materials such as highly cross-linked thermoset polymers for which the Differential Scanning Calorimeter (DSC) is difficult to use. In addition to Tg, the coefficient of thermal expansion (CTE) is obtained from thermomechanical analysis. The CTE is calculated from the linear sections of the TMA curves. Another useful result the TMA can provide us is finding out the orientation of crystals or fibers. Composite materials may have three distinct thermal expansion coefficients in the x, y and z directions. By recording the CTE in x, y and z directions one may understand in which direction fibers or crystals are predominantly oriented. To measure the bulk expansion of the material a technique called DILATOMETRY can be used. The sample is immersed in a fluid such as silicon oil or Al2O3 powder in the dilatometer, run thru the temperature cycle and the expansions in all directions are converted to a vertical movement, which is measured by the TMA. Modern thermomechanical analyzers make this easy for users. If a pure liquid is used, the dilatometer is filled with that liquid instead of the silicon oil or alumina oxide. Using diamond TMA the users can run stress strain curves, stress relaxation experiments, creep-recovery and dynamic mechanical temperature scans. The TMA is an indispensible test equipment for industry and research. THERMOGRAVIMETRIC ANALYZERS ( TGA ) : Thermogravimetric Analysis is a technique where the mass of a substance or specimen is monitored as a function of temperature or time. The sample specimen is subjected to a controlled temperature program in a controlled atmosphere. The TGA measures a sample’s weight as it is heated or cooled in its furnace. A TGA instrument consists of a sample pan that is supported by a precision balance. That pan resides in a furnace and is heated or cooled during the test. The mass of the sample is monitored during the test. Sample environment is purged with an inert or a reactive gas. Thermogravimetric analyzers can quantify loss of water, solvent, plasticizer, decarboxylation, pyrolysis, oxidation, decomposition, weight % filler material, and weight % ash. Depending on the case, information may be obtained upon heating or cooling. A typical TGA thermal curve is displayed from left to right. If the TGA thermal curve descends, it indicates a weight loss. Modern TGAs are capable of conducting isothermal experiments. Sometimes the user may want to use a reactive sample purge gases, such as oxygen. When using oxygen as a purge gas user may want to switch gases from nitrogen to oxygen during the experiment. This technique is frequently used to identify the percent carbon in a material. Thermogravimetric analyzer can be used to compare two similar products, as a quality control tool to ensure products meet their material specifications, to ensure products meet safety standards, to determine carbon content, identifying counterfeit products, to identify safe operating temperatures in various gases, to enhance product formulation processes, to reverse engineer a product. Finally it is worth mentioning that combinations of a TGA with a GC/MS are available. GC is short for Gas Chromatography and MS is short for Mass Spectrometry. DYNAMIC MECHANICAL ANALYZER ( DMA) : This is a technique where a small sinusoidal deformation is applied to a sample of known geometry in a cyclic manner. The materials response to stress, temperature, frequency and other values is then studied. The sample can be subjected to a controlled stress or a controlled strain. For a known stress, the sample will deform a certain amount, depending on its stiffness. DMA measures stiffness and damping, these are reported as modulus and tan delta. Because we are applying a sinusoidal force, we can express the modulus as an in-phase component (the storage modulus), and an out of phase component (the loss modulus). The storage modulus, either E’ or G’, is the measure of the sample’s elastic behavior. The ratio of the loss to the storage is the tan delta and is called damping. It is considered a measure of the energy dissipation of a material. Damping varies with the state of the material, its temperature, and with the frequency. DMA is sometimes called DMTA standing for DYNAMIC MECHANICAL THERMAL ANALYZER. Thermomechanical Analysis applies a constant static force to a material and records the material dimensional changes as temperature or time varies. The DMA on the other hand, applies an oscillatory force at a set frequency to the sample and reports changes in stiffness and damping. DMA data provides us modulus information whereas the TMA data gives us the coefficient of thermal expansion. Both techniques detect transitions, but DMA is much more sensitive. Modulus values change with temperature and transitions in materials can be seen as changes in the E’ or tan delta curves. This includes glass transition, melting and other transitions that occur in the glassy or rubbery plateau which are indicators of subtle changes in the material. THERMAL IMAGING INSTRUMENTS, INFRARED THERMOGRAPHERS, INFRARED CAMERAS : These are devices that form an image using infrared radiation. Standard everyday cameras form images using visible light in the 450–750 nanometer wavelength range. Infrared cameras however operate in the infrared wavelength range as long as 14,000 nm. Generally, the higher an object's temperature, the more infrared radiation is emitted as black-body radiation. Infrared cameras work even in total darkness. Images from most infrared cameras have a single color channel because the cameras generally use an image sensor that does not distinguish different wavelengths of infrared radiation. To differentiate wavelengths color image sensors require a complex construction. In some test instruments these monochromatic images are displayed in pseudo-color, where changes in color are used rather than changes in intensity to display changes in the signal. The brightest (warmest) parts of images are customarily colored white, intermediate temperatures are colored red and yellow, and the dimmest (coolest) parts are colored black. A scale is generally shown next to a false color image to relate colors to temperatures. Thermal cameras have resolutions considerably lower than that of optical cameras, with values in the neighborhood of 160 x 120 or 320 x 240 pixels. More expensive infrared cameras can achieve a resolution of 1280 x 1024 pixels. There are two main categories of thermographic cameras: COOLED INFRARED IMAGE DETECTOR SYSTEMS and UNCOOLED INFRARED IMAGE DETECTOR SYSTEMS. Cooled thermographic cameras have detectors contained in a vacuum-sealed case and are cryogenically cooled. The cooling is necessary for the operation of the semiconductor materials used. Without cooling, these sensors would be flooded by their own radiation. Cooled infrared cameras are however expensive. Cooling requires much energy and is time-consuming, requiring several minutes of cooling time prior to working. Although the cooling apparatus is bulky and expensive, cooled infrared cameras offer users superior image quality compared to uncooled cameras. The better sensitivity of cooled cameras allows the use of lenses with higher focal length. Bottled nitrogen gas can be used for cooling. Uncooled thermal cameras use sensors operating at ambient temperature, or sensors stabilized at a temperature close to ambient using temperature control elements. Uncooled infrared sensors are not cooled to low temperatures and therefore do not require bulky and expensive cryogenic coolers. Their resolution and image quality however is lower as compared to cooled detectors. Thermographic cameras offer many opportunities. Overheating spots is power lines can be located and repaired. Electric circuitry can be observed and unusually hot spots can indicate problems such as short circuit. These cameras are also widely used in buildings and energy systems to locate places where there is significant heat loss so that better heat insulation can be considered at those points. Thermal imaging instruments serve as non-destructive test equipment. For details and other similar equipment, please visit our equipment website: http://www.sourceindustrialsupply.com RÛPERA BERÊ
- Camera Systems & Components, Optic Scanner, Optical Readers, CCD
Camera Systems - Components - Optic Scanner - Optical Readers - Imaging System - CCD - Optomechanical Systems - IR Cameras Hilberîn & Civîna Pergalên Kamera Xweserkirî AGS-TECH offers: • Camera systems, camera components and custom camera assemblies • Custom designed and manufactured optical scanners, readers, optical security product assemblies. • Precision optical, opto-mechanical and electro-optical assemblies integrating imaging and nonimaging optics, LED lighting, fiber optics and CCD cameras • Among the products our optical engineers have developed are: - Omni-directional periscope and camera for surveillance and security applications. 360 x 60º field of view high resolution image, no stitching required. - Inner cavity wide angle video camera - Super slim 0.6 mm diameter flexible video endoscope. All medical video couplers fit over standard endoscope eyepieces and are completely sealed and soakable. For our medical endoscope and camera systems, please visit: http://www.agsmedical.com - Video camera and coupler for semi-rigid endoscope - Eye-Q Videoprobe. Non-contact zoom videoprobe for coordinate measuring machines. - Optical spectrograph & IR imaging system (OSIRIS) for ODIN satellite. Our engineers worked on the flight unit assembly, alignment, integration and test. - Wind imaging interferometer (WINDII) for NASA upper atmosphere research satellite (UARS). Our engineers worked on consulting on assembly, integration and test. WINDII performance and operational lifetime far exceeded the design goals and requirements. Depending on your application, we will determine what dimensions, pixel count, resolution, wavelength sensitivity your camera application requires. We can build systems for you suitable for infrared, visible and other wavelengths. Contact us today to find out more. Dowload brochure for our DESIGN PARTNERSHIP PROGRAM Developing a customized camera system can take relatively longer lead times and cost more as compared to ready-to-use systems. Therefore please click on the blue links below to check whether any of our ready-to-use products fit your application: Barcode and Fixed Mount Scanners - RFID Products - Mobile Computers - Micro Kiosks OEM Technology (We private label these with your brand name and logo if you wish) Barcode Scanners (We private label these with your brand name and logo if you wish) Fixed Industrial Scanners (We private label these with your brand name and logo if you wish) Hikrobot Machine Vision Products Hikrobot Smart Machine Vision Products Hikrobot Machine Vision Standard Products Hikvision Logistic Vision Solutions Private Label Medical Endoscopes and Visualization Systems (We can put your company name and logo on these) Also make sure to download our comprehensive electric & electronic components catalog for off-shelf products by CLICKING HERE. CLICK Product Finder-Locator Service RÛPERA BERÊ
- Electric Discharge Machining, EDM, Spark Machining, Die Sinking
Electric Discharge Machining - EDM - Spark Machining - Die Sinking - Wire Erosion - Custom Manufacturing - AGS-TECH Inc. EDM Machining, Elektrîk-Daxistina Elektrîkê û Çêkirin ELECTRICAL DISCHARGE MACHINING (EDM), also referred to as SPARK-EROSION or ELECTRODISCHARGE MACHINING, SPARK ERODING, DIE SINKING or WIRE EROSION, is a NON-CONVENTIONAL MANUFACTURING process where erosion of metals takes place and desired shape is obtained using electrical discharges in the form of sparks. We also offer some varieties of EDM, namely NO-WEAR EDM, WIRE EDM (WEDM), EDM GRINDING (EDG), DIE-SINKING EDM, ELECTRICAL-DISCHARGE MILLING, micro-EDM, m-EDM and ELECTROCHEMICAL-DISCHARGE GRINDING (ECDG). Our EDM systems consist of shaped tools/electrode and the workpiece connected to DC power supplies and inserted in a electrically nonconducting dielectric fluid. After 1940 electrical discharge machining has become one of the most important and popular production technologies in manufacturing industries. When the distance between the two electrodes is reduced, the intensity of the electric field in the volume between the electrodes becomes greater than the strength of the dielectric in some points, which breaks, eventually forming a bridge for current to flow between the two electrodes. An intense electrical arc is generated causing significant heating to melt a portion of the workpiece and some of the tooling material. As a result, material is removed from both the electrodes. At the same time, the dielectric fluid is heated rapidly, resulting in evaporation of the fluid in the arc gap. Once the current flow stops or it is stopped heat is removed from the gas bubble by the surrounding dielectric fluid and the bubble cavitates (collapses). The shock wave created by the bubble’s collapse and the flow of dielectric fluid flush debris from the workpiece surface and entrain any molten workpiece material into the dielectric fluid. The repetition rate for these discharges are between 50 to 500 kHz, voltages between 50 to 380 V and currents between 0.1 and 500 Amperes. New liquid dielectric such as mineral oils, kerosene or distilled & deionized water is usually conveyed into the inter-electrode volume carrying away the solid particles (in the form of debris) and the insulating proprieties of the dielectric is restored. After a current flow, the potential difference between the two electrodes is restored to what it was before the breakdown, so a new liquid dielectric breakdown can occur. Our modern electrical discharge machines (EDM) offer numerically controlled movements and are equipped with pumps and filtering systems for the dielectric fluids. Electrical discharge machining (EDM) is a machining method mainly used for hard metals or those that would be very difficult to machine with conventional techniques. EDM typically works with any materials that are electrical conductors, although methods for machining insulating ceramics with EDM have also been proposed. The melting point and latent heat of melting are properties that determine the volume of metal removed per discharge. The higher these values, the slower the material removal rate. Because the electrical discharge machining process does not involve any mechanical energy, the hardness, strength, and toughness of the workpiece do not affect the removal rate. Discharge frequency or energy per discharge, the voltage and current are varied to control material removal rates. Rate of material removal and surface roughness increase with increasing current density and decreasing spark frequency. We can cut intricate contours or cavities in pre-hardened steel using EDM without the need for heat treatment to soften and re-harden them. We can use this method with any metal or metal alloys like titanium, hastelloy, kovar, and inconel. Applications of the EDM process include shaping of polycrystalline diamond tools. EDM is considered a non-traditional or non-conventional machining method along with processes such as electrochemical machining (ECM), water jet cutting (WJ, AWJ), laser cutting. On the other hand the conventional machining methods include turning, milling, grinding, drilling and other process whose material removal mechanism is essentially based on mechanical forces. Electrodes for electrical-discharge machining (EDM) are made of graphite, brass, copper and copper-tungsten alloy. Electrode diameters down to 0.1mm are possible. Since tool wear is an undesired phenomenon adversely affecting dimensional accuracy in EDM, we take advantage of a process called NO-WEAR EDM, by reversing polarity and using copper tools to minimize tool wear. Ideally speaking, the electrical-discharge machining (EDM) can be considered a series of breakdown and restoration of the dielectric liquid between the electrodes. In reality however, the removal of the debris from the inter-electrode area is almost always partial. This causes the electrical proprieties of the dielectric in the inter-electrodes area to be different from their nominal values and vary with time. The inter-electrode distance, (spark-gap), is adjusted by the control algorithms of the specific machine used. The spark-gap in EDM can unfortunately sometimes be short-circuited by the debris. The control system of the electrode may fail to react quickly enough to prevent the two electrodes (tool and workpiece) from short circuiting. This unwanted short circuit contributes to material removal differently from the ideal case. We pay utmost importance to flushing action in order to restore the insulating properties of the dielectric so that the current always happens in the point of the inter-electrode area, thereby minimizing the possibility of unwanted change of shape (damage) of the tool-electrode and workpiece. To obtain a specific geometry, the EDM tool is guided along the desired path very close to the workpiece without touching it, We pay utmost attention to the performance of motion control in use. This way, a large number of current discharges / sparks take place, and each contributes to the removal of material from both tool and workpiece, where small craters are formed. The size of the craters is a function of the technological parameters set for the specific job at hand and dimensions may range from the nanoscale (such as in the case of micro-EDM operations) to some hundreds of micrometers in roughing conditions. These small craters on the tool cause gradual erosion of the electrode called “tool wear”. To counteract the detrimental effect of the wear on the geometry of the workpiece we continuously replace the tool-electrode during a machining operation. Sometimes we achieve this by using a continuously replaced wire as electrode ( this EDM process is also called WIRE EDM ). Sometimes we use the tool-electrode in such a way that only a small portion of it is actually engaged in the machining process and this portion is changed on a regular basis. This is, for instance, the case when using a rotating disk as a tool-electrode. This process is called EDM GRINDING. Yet another technique we deploy consists of using a set of electrodes with different sizes and shapes during the same EDM operation to compensate for wear. We call this multiple electrode technique, and is most commonly used when the tool electrode replicates in negative the desired shape and is advanced towards the blank along a single direction, usually the vertical direction (i.e. z-axis). This resembles the sink of the tool into the dielectric liquid in which the workpiece is immersed, and therefore it is referred to as DIE-SINKING EDM (sometimes called CONVENTIONAL EDM or RAM EDM). The machines for this operation are called SINKER EDM. The electrodes for this type of EDM have complex forms. If the final geometry is obtained using a usually simple-shaped electrode moved along several directions and is also subject to rotations, we call it EDM MILLING. The amount of wear is strictly dependent on the technological parameters used in the operation ( polarity, maximum current, open circuit voltage). For example, in micro-EDM, also known as m-EDM, these parameters are usually set at values which generates severe wear. Therefore, wear is a major problem in that area which we minimize using our accumulated know-how. For example to minimize wear to graphite electrodes, a digital generator, controllable within milliseconds, reverses polarity as electro-erosion takes place. This results in an effect similar to electroplating that continuously deposits the eroded graphite back on the electrode. In another method, a so-called ''Zero Wear'' circuit we minimize how often the discharge starts and stops, keeping it on for as long a time as possible. The material removal rate in electrical-discharge machining can be estimated from: MRR = 4 x 10 exp(4) x I x Tw exp (-1.23) Here MRR is in mm3/min, I is current in Amperes, Tw is workpiece melting point in K-273.15K. The exp stands for exponent. On the other hand, the wear rate Wt of the electrode can be obtained from: Wt = ( 1.1 x 10exp(11) ) x I x Ttexp(-2.38) Here Wt is in mm3/min and Tt is melting point of the electrode material in K-273.15K Finally, the wear ratio of the workpiece to electrode R can be obtained from: R = 2.25 x Trexp(-2.38) Here Tr is the ratio of melting points of workpiece to electrode. SINKER EDM : Sinker EDM, also referred to as CAVITY TYPE EDM or VOLUME EDM, consists of an electrode and workpiece submerged in an insulating liquid. The electrode and workpiece are connected to a power supply. The power supply generates an electrical potential between the two. As the electrode approaches the workpiece, dielectric breakdown occurs in the fluid, forming a plasma channel, and a small spark jumps. The sparks usually strike one at a time because it is highly unlikely that different locations in the inter-electrode space have identical local electrical characteristics which would enable a spark to occur in all such locations simultaneously. Hundreds of thousands of these sparks happen at random points between the electrode and the workpiece per second. As the base metal erodes, and the spark gap subsequently increases, the electrode is lowered automatically by our CNC machine so that the process can continue uninterrupted. Our equipment has controlling cycles known as ''on time'' and ''off time''. The on time setting determines the length or duration of the spark. A longer on time produces a deeper cavity for that spark and all subsequent sparks for that cycle, creating a rougher finish on the workpiece and vice versa. The off time is the period of time that one spark is replaced by another. A longer off time permits the dielectric fluid to flush through a nozzle to clean out the eroded debris, thereby avoiding a short circuit. These settings are adjusted in micro seconds. WIRE EDM : In WIRE ELECTRICAL DISCHARGE MACHINING (WEDM), also called WIRE-CUT EDM or WIRE CUTTING, we feed a thin single-strand metal wire of brass through the workpiece, which is submerged in a tank of dielectric fluid. Wire EDM is an important variation of EDM. We occasionally use wire-cut EDM to cut plates as thick as 300mm and to make punches, tools, and dies from hard metals that are difficult to machine with other manufacturing methods. In this process which resembles to contour cutting with a band saw, the wire, which is constantly fed from a spool, is held between upper and lower diamond guides. The CNC-controlled guides move in the x–y plane and the upper guide can also move independently in the z–u–v axis, giving rise to the ability to cut tapered and transitioning shapes (such as circle on the bottom and square at the top). The upper guide can control axis movements in x–y–u–v–i–j–k–l–. This allows the WEDM to cut very intricate and delicate shapes. The average cutting kerf of our equipment that achieves the best economic cost and machining time is 0.335 mm using Ø 0.25 brass, copper or tungsten wire. However the upper and lower diamond guides of our CNC equipment are accurate to about 0.004 mm, and can have a cutting path or kerf as small as 0.021 mm using Ø 0.02 mm wire. So really narrow cuts are possible. The cutting width is greater than the width of the wire because sparking occurs from the sides of the wire to the workpiece, causing erosion. This ''overcut'' is necessary, for many applications it is predictable and therefore can be compensated for ( in micro-EDM this is not often the case). The wire spools are long—an 8 kg spool of 0.25 mm wire is just over 19 kilometers in length. Wire diameter can be as small as 20 micrometres and the geometry precision is in the neighborhood of +/- 1 micrometer. We generally use the wire only once and recycle it because it is relatively inexpensive. It travels at a constant velocity of 0.15 to 9m/min and a constant kerf (slot) is maintained during a cut. In the wire-cut EDM process we use water as the dielectric fluid, controlling its resistivity and other electrical properties with filters and de-ionizer units. The water flushes the cut debris away from the cutting zone. Flushing is an important factor in determining the maximum feed rate for a given material thickness and therefore we keep it consistent. Cutting speed in wire EDM is stated in terms of the cross-sectional area cut per unit time, such as 18,000 mm2/hr for 50mm thick D2 tool steel. The linear cutting speed for this case would be 18,000/50 = 360mm/hr The material removal rate in wire EDM is: MRR = Vf x h x b Here MRR is in mm3/min, Vf is the feed rate of the wire into workpiece in mm/min, h is thickness or height in mm, and b is the kerf, which is: b = dw + 2s Here dw is wire diameter and s is gap between wire and workpiece in mm. Along with tighter tolerances, our modern multi axis EDM wire-cutting machining centers have added features such as multi heads for cutting two parts at the same time, controls for preventing wire breakage, automatic self-threading features in case of wire breakage, and programmed machining strategies to optimize the operation, straight and angular cutting capabilities. Wire-EDM offers us low residual stresses, because it does not require high cutting forces for removal of material. When the energy/power per pulse is relatively low (as in finishing operations), little change in the mechanical properties of a material is expected due to low residual stresses. ELECTRICAL-DISCHARGE GRINDING (EDG) : The grinding wheels do not contain abrasives, they are made of graphite or brass. Repetitive sparks between the rotating wheel and workpiece remove material from workpiece surfaces. The material removal rate is: MRR = K x I Here MRR is in mm3/min, I is current in Amperes, and K is workpiece material factor in mm3/A-min. We frequently use electrical-discharge grinding to saw narrow slits on components. We sometimes combine EDG (Electrical-Discharge Grinding) process with ECG (Electrochemical Grinding) process where material is removed by chemical action, the electrical discharges from the graphite wheel breaking up the oxide film and washed away by the electrolyte. The process is called ELECTROCHEMICAL-DISCHARGE GRINDING (ECDG). Even though the ECDG process consumes relatively more power, it is a faster process than the EDG. We mostly grind carbide tools using this technique. Applications of Electrical Discharge Machining: Prototype production: We use the EDM process in mold-making, tool and die manufacturing, as well as for making prototype and production parts, especially for the aerospace, automobile and electronics industries in which production quantities are relatively low. In Sinker EDM, a graphite, copper tungsten or pure copper electrode is machined into the desired (negative) shape and fed into the workpiece on the end of a vertical ram. Coinage die making: For the creation of dies for producing jewelry and badges by the coinage (stamping) process, the positive master may be made from sterling silver, since (with appropriate machine settings) the master is significantly eroded and is used only once. The resultant negative die is then hardened and used in a drop hammer to produce stamped flats from cutout sheet blanks of bronze, silver, or low proof gold alloy. For badges these flats may be further shaped to a curved surface by another die. This type of EDM is usually performed submerged in an oil-based dielectric. The finished object may be further refined by hard (glass) or soft (paint) enameling and/or electroplated with pure gold or nickel. Softer materials such as silver may be hand engraved as a refinement. Drilling of Small Holes: On our wire-cut EDM machines, we use small hole drilling EDM to make a through hole in a workpiece through which to thread the wire for the wire-cut EDM operation. Separate EDM heads specifically for small hole drilling are mounted on our wire-cut machines which allow large hardened plates to have finished parts eroded from them as needed and without pre-drilling. We also use small hole EDM to drill rows of holes into the edges of turbine blades used in jet engines. Gas flow through these small holes allows the engines to use higher temperatures than otherwise possible. The high-temperature, very hard, single crystal alloys these blades are made of makes conventional machining of these holes with high aspect ratio extremely difficult and even impossible. Other application areas for small hole EDM is to create microscopic orifices for fuel system components. Besides the integrated EDM heads, we deploy stand-alone small hole drilling EDM machines with x–y axes to machine blind or through holes. EDM drills bore holes with a long brass or copper tube electrode that rotates in a chuck with a constant flow of distilled or deionized water flowing through the electrode as a flushing agent and dielectric. Some small-hole drilling EDMs are able to drill through 100 mm of soft or even hardened steel in less than 10 seconds. Holes between 0.3 mm and 6.1 mm can be achieved in this drilling operation. Metal disintegration machining: We also have special EDM machines for the specific purpose of removing broken tools (drill bits or taps) from work pieces. This process is called ''metal disintegration machining''. Advantages and Disadvantages Electrical-Discharge Machining: Advantages of EDM include machining of: - Complex shapes that would otherwise be difficult to produce with conventional cutting tools - Extremely hard material to very close tolerances - Very small work pieces where conventional cutting tools may damage the part from excess cutting tool pressure. - There is no direct contact between tool and work piece. Therefore delicate sections and weak materials can be machined without any distortion. - A good surface finish can be obtained. - Very fine holes can be easily drilled. Disadvantages of EDM include: - The slow rate of material removal. - The additional time and cost used for creating electrodes for ram/sinker EDM. - Reproducing sharp corners on the workpiece is difficult due to electrode wear. - Power consumption is high. - ''Overcut'' is formed. - Excessive tool wear occurs during machining. - Electrically non-conductive materials can be machined only with specific set-up of the process. CLICK Product Finder-Locator Service RÛPERA BERÊ
- Solar Power Modules, Rigid, Flexible Panels, Thin Film, Monocrystaline
Solar Power Modules - Rigid - Flexible Panels - Thin Film - Monocrystalline - Polycrystalline - Solar Connector available from AGS-TECH Inc. Çêkirin û Civîna Pergalên Enerjiya Rojê ya Xweserkirî Em peyda dikin: • Hucre û panelên hêza rojê, amûrên bi enerjiya rojê û meclîsên xwerû yên ji bo afirandina enerjiya alternatîf. Hucreyên hêza rojê dikarin ji bo amûrên xweser ên ku li deverên dûr têne bicîh kirin ji hêla xweya amûr an cîhazên xwe ve bibin çareseriya çêtirîn. Rakirina lênihêrîna zêde ya ji ber guheztina batterê, rakirina hewcedariya sazkirina kabloyên hêzê ji bo girêdana alavên we bi xetên elektrîkê yên sereke re dikare kirrûbirrek mezin bide hilberên we. Dema ku hûn amûrên bi tenê yên ku li deverên dûr têne bicîh kirin sêwirînin wê yekê bifikirin. Wekî din, enerjiya rojê dikare bi kêmkirina girêdana we ya bi enerjiya elektrîkê ya kirîn re drav bide we. Bînin bîra xwe, hucreyên enerjiya rojê dikarin maqûl an hişk bin. Lêkolîna sozdar li ser hucreyên rojê yên spray-li ser berdewam e. Enerjiya ku ji hêla amûrên rojê ve têne hilberandin bi gelemperî di pîlê de têne hilanîn an yekser piştî nifşê têne bikar anîn. Em dikarin ji bo projeyên we hucreyên rojê, panel, bataryayên rojê, guhêrbar, girêdanên enerjiya rojê, meclîsên kabloyê, tevahî kîtên hêza rojê peyda bikin. Em dikarin di qonaxa sêwirana cîhaza weya rojê de jî ji we re bibin alîkar. Bi hilbijartina pêkhateyên rast, celebê hucreya rojê ya rast û dibe ku bi karanîna lensên optîkî, prizma ...hwd. em dikarin hêza ku ji hêla şaneyên rojê ve têne hilberandin herî zêde bikin. Dema ku rûberên berdest ên li ser cîhaza we sînorkirî be, mezinkirina hêza rojê dikare bibe dijwariyek. Em pisporiya rast û amûrên sêwirana optîkî hene ku em bigihîjin vê yekê. Ji bo BERNAMEYA HEVKARÎYA DESIGN a me broşurê dakêşin Piştrast bikin ku kataloga meya pêkhateyên elektrîkî û elektronîkî yên berfereh ji bo hilberên li dorhêl dakêşin bi LI VIR BIKIRINA . Di vê katalogê de ji bo projeyên we yên têkildarî tavê hilberên wekî girêdanên tavê, batarî, veguherîner û hêj bêtir hene. Ger hûn nekarin wê li wir bibînin, bi me re têkilî daynin û em ê agahdariya li ser tiştên ku me hene ji we re bişînin. Ger hûn bi piranî ji hilber û pergalên enerjiya alternatîf ên nûjenkirî yên malî an jî kargêrî yên meya mezin eleqedar in, wê hingê em we vedixwînin ku biçin malpera meya enerjiyê http://www.ags-energy.com CLICK Product Finder-Locator Service RÛPERA BERÊ
- Soft Lithography - Microcontact Printing - Microtransfer Molding
Soft Lithography - Microcontact Printing - Microtransfer Molding - Micromolding in Capillaries - AGS-TECH Inc. - NM - USA Lîtografya nerm SOFT LITHOGRAPHY is a term used for a number of processes for pattern transfer. A master mold is needed in all cases and is microfabricated using standard lithography methods. Using the master mold, we produce an elastomeric pattern / stamp to be used in soft lithography. Elastomers used for this purpose need to be chemically inert, have good thermal stability, strength, durability, surface properties and be hygroscopic. Silicone rubber and PDMS (Polydimethylsiloxane) are two good candidate materials. These stamps can be used many times in soft lithography. One variation of soft lithography is MICROCONTACT PRINTING. The elastomer stamp is coated with an ink and pressed against a surface. The pattern peaks contact the surface and a thin layer of about 1 monolayer of the ink is transferred. This thin film monolayer acts as the mask for selective wet etching. A second variation is MICROTRANSFER MOLDING, in which the recesses of the elastomer mold are filled with liquid polymer precursor and pushed against a surface. Once the polymer cures after microtransfer molding, we peel off the mold, leaving behind the desired pattern. Lastly a third variation is MICROMOLDING IN CAPILLARIES, where the elastomer stamp pattern consists of channels that use capillary forces to wick a liquid polymer into the stamp from its side. Basically, a small amount of the liquid polymer is placed adjacent to the capillary channels and the capillary forces pull the liquid into the channels. Excess liquid polymer is removed and polymer inside the channels is allowed to cure. The stamp mold is peeled off and the product is ready. If the channel aspect ratio is moderate and the channel dimensions allowed depend on the liquid used, good pattern replication can be assured. The liquid used in micromolding in capillaries can be thermosetting polymers, ceramic sol-gel or suspensions of solids within liquid solvents. The micromolding in capillaries technique has been used in sensor manufacturing. Soft lithography is used to construct features measured on the micrometer to nanometer scale. Soft lithography has advantages over other forms of lithography like photolithography and electron beam lithography. The advantages include the following: • Lower cost in mass production than traditional photolithography • Suitability for applications in biotechnology and plastic electronics • Suitability for applications involving large or nonplanar (nonflat) surfaces • Soft lithography offers more pattern-transferring methods than traditional lithography techniques (more ''ink'' options) • Soft lithography does not need a photo-reactive surface to create nanostructures • With soft lithography we can achieve smaller details than photolithography in laboratory settings (~30 nm vs ~100 nm). The resolution depends on the mask used and can reach values down to 6 nm. MULTILAYER SOFT LITHOGRAPHY is a fabrication process in which microscopic chambers, channels, valves and vias are molded within bonded layers of elastomers. Using multilayer soft lithography devices consisting of multiple layers may be fabricated from soft materials. The softness of these materials allows the device areas to be reduced by more than two orders of magnitude compared with silicon-based devices. The other advantages of soft lithography, such as rapid prototyping, ease of fabrication, and biocompatibility, are also valid in multilayer soft lithography. We use this technique to build active microfluidic systems with on-off valves, switching valves, and pumps entirely out of elastomers. CLICK Product Finder-Locator Service RÛPERA BERÊ
- Holography - Holographic Glass Grating - AGS-TECH Inc. - New Mexico
Holography - Holographic Glass Grating - AGS-TECH Inc. - New Mexico - USA Hilberîna Hilber û Pergalên Holografîk Em stokên xwerû û her weha BERHEMÊN HOLOGRAPHY-ya xwerû sêwirandî û çêkirine peyda dikin, di nav de: • Nîşaneyên Hologramê 180, 270, 360 Derece/ Projekirina Dîmenî ya Bingeha Holografiyê • Nîşaneyên Hologramê yên 360 Degree yên Xwe-adhesive • Fîlma Pencereya 3D ji bo Reklama Nîşandanê • Pêşangeha Hologramê ya Full HD & Pêşandana Holographic 3D Pyramid Ji bo Reklamkirina Holografiyê • 3D Holographic Display Holocube Ji bo Reklama Holografiyê • Pergala Projekirina Holographic 3D • 3D Mesh Screen Holographic Screen • Fîlma Pêşniyara Paşî / Fîlma Pêşniyara Pêşiyê (bi lîsteyê) • Display Touch Interactive • Screen Projection Curved: Screen Projection Curved hilberek xwerû ye ku ji bo her xerîdar bi fermanê hatî çêkirin. Em ji bo ekranên simulatorên 3D yên çalak û pasîf û pêşandanên simulasyonê ekranên kelandî, dîmenderan çêdikin. • Berhemên optîkî yên holografîk ên wekî ewlekariya îsbatkirina nerm û çîpên rastbûna hilberê (çapkirina xwerû li gorî daxwaziya xerîdar) • Glass Glass Gratings ji bo sepanên xemilandî an nîgarkêşî û perwerdehiyê. Ji bo ku hûn di derheqê kapasîteyên endezyar û lêkolîn û pêşkeftinê de fêr bibin em we vedixwînin ku hûn biçin malpera meya endezyariyê http://www.ags-engineering.com CLICK Product Finder-Locator Service RÛPERA BERÊ