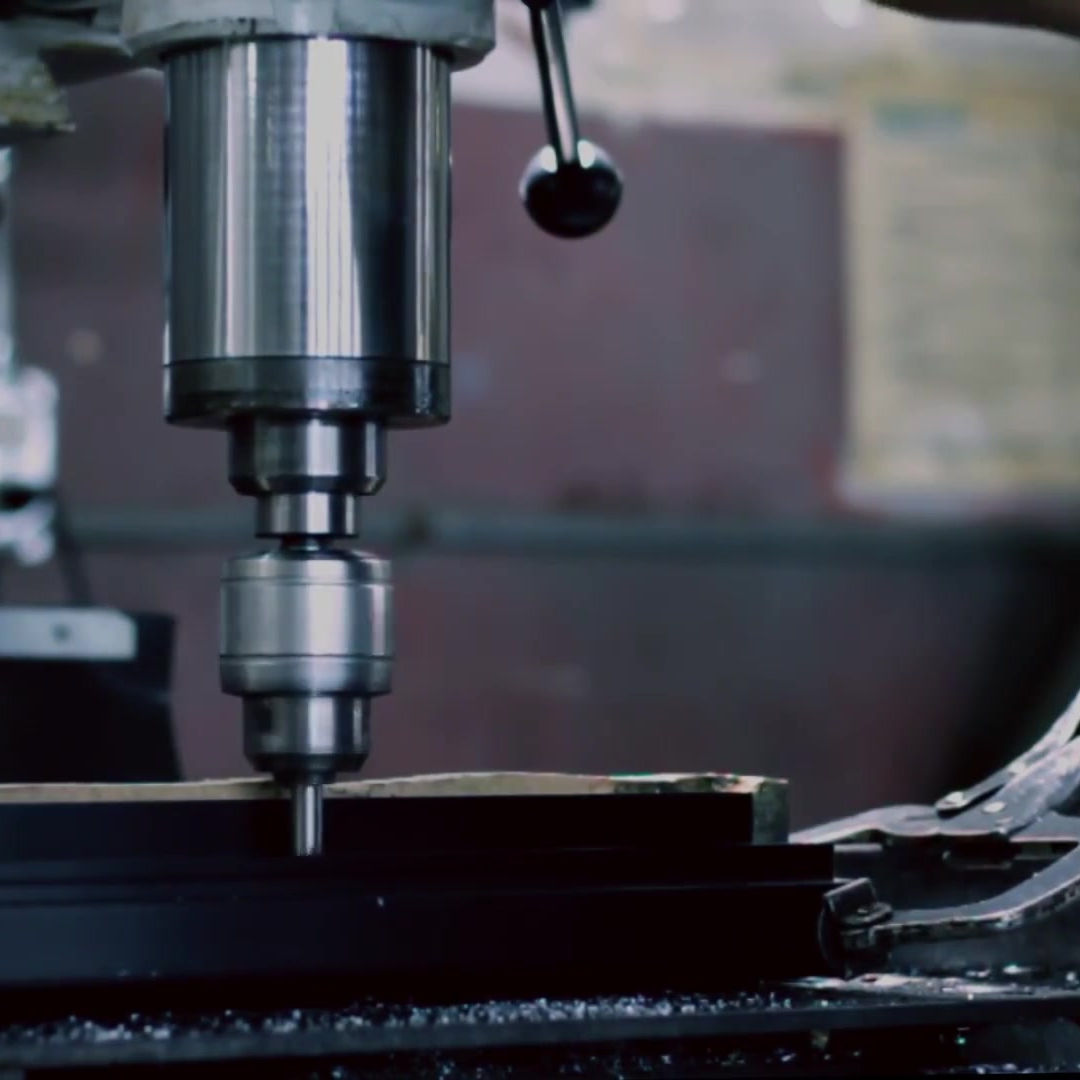
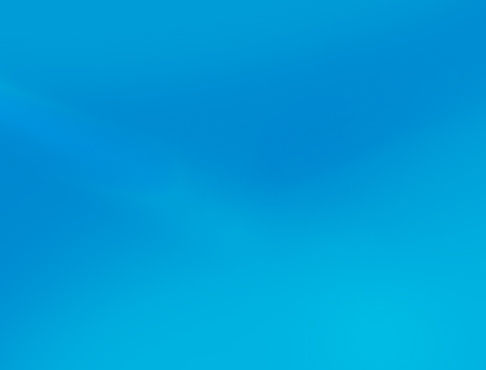
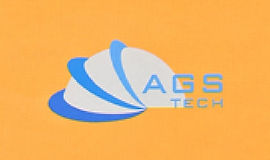
Hilberînerê Xwerû ya Gloverî, Integrator, Hevkar, Hevkarê Derveyî Ji bo Cûreyek Berfireh a Hilber û Karûbaran.
Em ji bo çêkirin, çêkirin, endezyarî, yekbûn, yekbûn, derxistina hilber û karûbarên xwerû yên çêkirî û yên li derveyî refê çavkaniya weya yek-rawest in. Ger hûn bixwazin, em di heman demê de etîketa taybet / spî hilberên we bi navê marqeya we nîşan didin.
Zimanê xwe hilbijêre
Hilberîna Xweser a Parçe, Pêkhatî, Meclîs, Berhemên Qediyayî, Makîne û Amûrên Pîşesaziyê
Hilberîna Peymana Navxweyî û Gerdûnî
Manufacturing Outsourcing
Kirîna Navxweyî, Gerdûnî ya Berhemên Pîşesazî
Etîketkirina taybet / Spî Hilberên xwe bi navê marqeya xwe nîşankirin
Karûbarên Dîtina Hilber & Cihgirtin
Sêwirana gerdûnî û Hevkariya Kanal
Endezyariya Entegrasyonê
Xizmetên Endezyariyê
Hevgirtina Gerdûnî, Warehousing, Logistics
Encamên Lêgerînê
164 results found with an empty search
- Fiber Optic Test Instruments, Optical Fiber Testing, OTDR, Loss Meter
Fiber Optic Test Instruments - Optical Fiber Testing - OTDR - Loss Meter - Fiber Cleaver - from AGS-TECH Inc. - NM - USA Amûrên Testê yên Fiber Optîk AGS-TECH Inc. offers the following FIBER OPTIC TEST and METROLOGY INSTRUMENTS : - OPTICAL FIBER SPLICER & FUSION SPLICER & FIBER CLEAVER - OTDR & OPTICAL TIME DOMAIN REFLECTOMETER - AUDIO FIBER CABLE DETECTOR - AUDIO FIBER CABLE DETECTOR - OPTICAL POWER METER - LASER SOURCE - VISUAL FAULT LOCATOR - PON POWER METER - FIBER IDENTIFIER - OPTICAL LOSS TESTER - OPTICAL TALK SET - OPTICAL VARIABLE ATTENUATOR - INSERTION / RETURN LOSS TESTER - E1 BER TESTER - FTTH TOOLS You can download our product catalogs and brochures below to choose a suitable fiber optic test equipment for your needs or you may tell us what you need and we will match something suitable for you. We do have in stock brand new as well as refurbished or used but still very good fiber optic instruments. All our equipment is under warranty. Please download our related brochures and catalogs by clicking the colored text below: ANRITSU Electronic Measuring Instruments EXFO Optical Testing Solutions for Manufacturing and R&D EXFO Data Center Solution Guide EXFO Remote Fiber Testing and Monitoring EXFO Test Solutions for Submarine Networks EXFO Quick Guide to Testing FTTH EXFO Fiber Deep and Remote PHY Test Solutions EXFO OTDR and iOLM Selection Guide EXFO Spectral Testing of Active Systems EXFO Network Equipment Manufacturers End-to End Solutions EXFO Expert-Level Field Test Solutions EXFO Mobile Backhaul End to End Network Assessment EXFO High-Speed Product Portfolio EXFO 40G Testing Solutions TRIBRER Handheld Optical Fiber Instruments and Tools You can purchase brand new, refurbished or used equipment from us at the most competitive discounted prices. Simply choose the product from the downloadable catalogs and let us know the product name, product code and relevant information and we will send you our best quote. What distinguishes AGS-TECH Inc. from other suppliers is our wide spectrum of ENGINEERING INTEGRATION and CUSTOM MANUFACTURING capabilities. Therefore, please let us know if you need a custom jig, a custom automation system designed specifically for your fiber optic testing needs. We can modify existing equipment or integrate various components to build a turn-key solution to your engineering needs. It will be our pleasure to briefly summarize and provide information about the main concepts in the realm of FIBER OPTIC TESTING. FIBER STRIPPING & CLEAVING & SPLICING : There are two major types of splicing, FUSION SPLICING and MECHANICAL SPLICING. In industry and high volume manufacturing, fusion splicing is the most widely used technique as it provides for the lowest loss and least reflectance, as well as providing the strongest and most reliable fiber joints. Fusion splicing machines can splice a single fiber or a ribbon of multiple fibers at one time. Most single mode splices are fusion type. Mechanical splicing on the other hand is mostly used for temporary restoration and mostly for multimode splicing. Fusion splicing requires higher capital expenses as compared to mechanical splicing because it requires a fusion splicer. Consistent low loss splices can only be achieved using proper techniques and keeping equipment in good condition. Cleanliness is vital. FIBER STRIPPERS should be kept clean and in good condition and be replaced when nicked or worn. FIBER CLEAVERS are also vital for good splices as one has to have good cleaves on both fibers. Fusion splicers need proper maintenance and fusing parameters need to be set for the fibers being spliced. OTDR & OPTICAL TIME DOMAIN REFLECTOMETER : This instrument is used to test the performance of new fiber optic links and detect problems with existing fiber links. OTDR traces are graphical signatures of a fiber's attenuation along its length. The optical time domain reflectometer (OTDR) injects an optical pulse into one end of the fiber and analyzes the returning backscattered and reflected signal. A technician at one end of the fiber span can measure and localize attenuation, event loss, reflectance, and optical return loss. Examining non-uniformities in the OTDR trace we can evaluate the performance of the link components such as cables, connectors and splices as well as the quality of the installation. Such fiber tests assure us that the workmanship and quality of the installation meet the design and warranty specifications. OTDR traces help characterize individual events that can often be invisible when conducting only loss/length testing. Only with a complete fiber certification, installers can fully understand the quality of a fiber installation. OTDRs are also used for testing and maintaining fiber plant performance. OTDR allows us to see more details impacted by the cabling installation. OTDR maps the cabling and can illustrate termination quality, location of faults. An OTDR provides advanced diagnostics to isolate a point of failure that may hinder network performance. OTDRs allow discovery of problems or potential problems along the length of a channel that may affect long term reliability. OTDRs characterize features such as attenuation uniformity and attenuation rate, segment length, location and insertion loss of connectors and splices, and other events such as sharp bends that may have been incurred during installation of cables. An OTDR detects, locates, and measures events on fiber links and requires access to only one end of the fiber. Here is a summary of what a typical OTDR can measure: Attenuation (also known as fiber loss): Expressed in dB or dB/km, attenuation represents the loss or the rate of loss between two points along the fiber span. Event Loss: The difference in the optical power level before and after an event, expressed in dB. Reflectance: The ratio of reflected power to incident power of an event, expressed as a negative dB value. Optical Return Loss (ORL): The ratio of the reflected power to the incident power from a fiber optic link or system, expressed as a positive dB value. OPTICAL POWER METERS : These meters measure average optical power out of an optical fiber. Removable connector adapters are used in optical power meters so that various models of fiber optic connectors can be used. Semiconductor detectors inside power meters have sensitivities that vary with the wavelength of light. Therefore they are calibrated at typical fiber optic wavelengths such as 850, 1300 and 1550 nm. Plastic Optical Fiber or POF meters on the other hand are calibrated at 650 and 850 nm. Power meters are sometimes calibrated to read in dB (Decibel) referenced to one miliwatt of optical power. Some power meters however are calibrated in relative dB scale, which is well suited for loss measurements because the reference value may be set to “0 dB” on the output of the test source. Rare but occasionally lab meters measure in linear units such as miliwatts, nanowatts….etc. Power meters cover a very broad dynamic range 60 dB. However most optical power and loss measurements are made in the range 0 dBm to (-50 dBm). Special power meters with higher power ranges of up to +20 dBm are used for testing fiber amplifiers and analog CATV systems. Such higher power levels are needed to assure the proper functioning of such commercial systems. Some laboratory type meters on the other hand can measure at very low power levels down to (-70 dBm) or even lower, because in research and development engineers frequently have to deal with weak signals. Continuous wave (CW) test sources are used frequently for loss measurements. Power meters measure the time average of the optical power instead of the peak power. Fiber optic power meters should be recalibrated frequently by labs with NIST traceable calibration systems. Regardless of price, all power meters have similar inaccuracies typically in the neighborhood of +/-5%. This uncertainty is caused by the variability in coupling efficiency at the adapters/connectors, reflections at polished connector ferrules, unknown source wavelengths, nonlinearities in electronic signal conditioning circuitry of the meters and detector noise at low signal levels. FIBER OPTIC TEST SOURCE / LASER SOURCE : An operator needs a test source as well as a FO power meter in order to make measurements of optical loss or attenuation in fibers, cables and connectors. The test source must be chosen for compatibility with the type of fiber in use and the wavelength desired for performing the test. Sources are either LED's or lasers similar to those used as transmitters in actual fiber optic systems. LED's are generally used for testing multimode fiber and lasers for singlemode fibers. For some tests such as measuring spectral attenuation of fiber, a variable wavelength source is used, which is usually a tungsten lamp with a monochromator to vary the output wavelength. OPTICAL LOSS TEST SETS : Sometimes also refered to as ATTENUATION METERS, these are instruments made of fiber optic power meters and sources which are used to measure the loss of fibers, connectors and connectorized cables. Some optical loss test sets have individual source outputs and meters like a separate power meter and test source, and have two wavelengths from one source output (MM: 850/1300 or SM:1310/1550) Some of them offer bidirectional testing on a single fiber and some have two bidirectional ports. The combination instrument which contains both a meter and a source may be less convenient than an individual source and power meter. This is the case when the ends of the fiber and cable are usually separated by long distances, which would require two optical loss test sets instead of one source and one meter. Some instruments also have a single port for bidirectional measurements. VISUAL FAULT LOCATOR : These are simple instruments that inject visible wavelength light into the system and one can visually trace the fiber from transmitter to receiver to insure correct orientation and continuity. Some visual fault locators have powerful visible light sources such as a HeNe laser or visible diode laser and therefore high loss points can be made visible. Most applications center around short cables such as used in telecommunication central offices to connect to the fiber optic trunk cables. Since the visual fault locator covers the range where OTDRs are not useful, it is complementary instrument to the OTDR in cable troubleshooting. Systems with powerful light sources will work on buffered fiber and jacketed single fiber cable if the jacket is not opaque to the visible light. The yellow jacket of singlemode fibers and orange jacket of multimode fibers will usually pass the visible light. With most multifiber cables this instrument cannot be used. Many cable breaks, macrobending losses caused by kinks in the fiber, bad splices….. can be detected visually with these instruments. These instruments have a short range, typically 3-5 km, due to high attenuation of visible wavelengths in fibers. FIBER IDENTIFIER : Fiber Optic technicians need to identify a fiber in a splice closure or at a patch panel. If one carefully bends a singlemode fiber enough to cause loss, the light that couples out can also be detected by a large area detector. This technique is used in fiber identifiers to detect a signal in the fiber at transmission wavelengths. A fiber identifier generally functions as a receiver, is able to discriminate between no signal, a high speed signal and a 2 kHz tone. By specifically looking for a 2 kHz signal from a test source that is coupled into the fiber, the instrument can identify a specific fiber in a large multifiber cable. This is essential in fast and speedy splicing and restoration processes. Fiber identifiers can be used with buffered fibers and jacketed single fiber cables. FIBER OPTIC TALKSET : Optical talk sets are useful for fiber installation and testing. They transmit voice over fiber optic cables that are installed and allow the technician splicing or testing the fiber to communicate effectively. Talksets are even more useful when walkie-talkies and telephones are not available in remote locations where splicing is being done and in buildings with thick walls where radio waves will not penetrate through. Talksets are most effectively used by setting up the talksets on one fiber and leaving them in operation while testing or splicing work is done. This way there will always be a communications link between the work crews and will facilitate deciding which fibers to work with next. The continuous communications capability will minimize misunderstandings, mistakes and will speed up the process. Talksets include those for networking multi-party communications, especially helpful in restorations, and system talksets for use as intercoms in installed systems. Combination testers and talksets are also available commercially. To this date, unfortunately different manufacturers' talksets can not communicate with each other. VARIABLE OPTICAL ATTENUATOR : Variable Optical Attenuators allow the technician to manually vary the attenuation of the signal in the fiber as it is transmitted through the device. VOAs can be used to balance the signal strengths in fiber circuits or to balance an optical signal when evaluating the dynamic range of the measurement system. Optical attenuators are commonly used in fiber optic communications to test power level margins by temporarily adding a calibrated amount of signal loss, or installed permanently to properly match transmitter and receiver levels. There are fixed, step-wise variable, and continuously variable VOAs commercially available. Variable optical test attenuators generally use a variable neutral density filter. This offers the advantages of being stable, wavelength insensitive, mode insensitive, and a large dynamic range. A VOA may be either manually or motor controlled. Motor control provides users a distinct productivity advantage, since commonly used test sequences can be run automatically. The most accurate variable attenuators have thousands of calibration points, resulting in excellent overall accuracy. INSERTION / RETURN LOSS TESTER : In fiber optics, Insertion Loss is the loss of signal power resulting from the insertion of a device in a transmission line or optical fiber and is usually expressed in decibels (dB). If the power transmitted to the load before insertion is PT and the power received by the load after insertion is PR, then the insertion loss in dB is given by: IL = 10 log10(PT/PR) Optical Return Loss is the ratio of the light reflected back from a device under test, Pout, to the light launched into that device, Pin, usually expressed as a negative number in dB. RL = 10 log10(Pout/Pin) Loss may be caused by reflections and scattering along the fiber network due to contributors such as dirty connectors, broken optical fibers, poor connector mating. Commercial optical return loss (RL) & insertion loss (IL) testers are high performance loss test stations that are designed specially for optical fibre testing, lab testing and passive components production. Some integrate three different tests modes in one test station, working as a stable laser source, optical power meter and a return loss meter. The RL and IL measurements are displayed on two separate LCD screens, whilst in return loss test model, the unit will automatically and synchronously set the same wavelength for the light source and power meter. These instruments come complete with FC, SC, ST and universal adaptors. E1 BER TESTER : Bit error rate (BER) tests allow technicians to test cables and diagnose signal problems in the field. One can configure individual T1 channel groups to run an independent BER test, set one local serial port to Bit error rate test (BERT) mode while the remaining local serial ports continue to transmit and receive normal traffic. The BER test checks communication between the local and the remote ports. When running a BER test, the system expects to receive the same pattern that it is transmitting. If traffic is not being transmitted or received, technicians create a back-to-back loopback BER test on the link or in the network, and send out a predictable stream to ensure that they receive the same data that was transmitted. To determine whether the remote serial port returns the BERT pattern unchanged, technicians must manually enable network loopback at the remote serial port while they configure a BERT pattern to be used in the test at specified time intervals on the local serial port. Later they can display and analyze the total number of error bits transmitted and the total number of bits received on the link. Error statistics can be retrieved anytime during the BER test. AGS-TECH Inc. offers E1 BER (Bit Error Rate) testers that are compact, multi-functional and handheld instruments, specially designed for R&D, production, installation and maintenance of SDH, PDH, PCM, and DATA protocol conversion. They feature self-check and keyboard testing, extensive error and alarm generation, detection and indication. Our testers provide smart menu navigation and have a large color LCD screen allowing test results to be displayed clearly. Test results can be downloaded and printed using product software included in the package. E1 BER Testers are ideal devices for fast problem resolution, E1 PCM line access, maintenance and acceptance testing. FTTH – FIBER TO THE HOME TOOLS : Among the tools we offer are single and multihole fiber strippers, fiber tubing cutter, wire stripper, Kevlar cutter, fiber cable slitter, single fiber protection sleeve, fiber microscope, fiber connector cleaner, connector heating oven, crimping tool, pen type fiber cutter, ribbon fiber buff stripper, FTTH tool bag, portable fiber optic polishing machine. If you haven't found something that fits your needs and would like to search further for other similar equipment, please visit our equipment website: http://www.sourceindustrialsupply.com CLICK Product Finder-Locator Service RÛPERA BERÊ
- Clutch, Brake, Friction Clutches, Belt Clutch, Dog & Hydraulic Clutch
Clutch, Brake, Friction Clutches, Belt Clutch, Dog Clutch, Hydraulic Clutch, Electromagnetic Clutch, Overruning Clutch, Wrap Spring Clutch, Frictional Brake Clutch & Brake Meclîsa CLUTCHES are a type of coupling that permit shafts to be connected or disconnected as desired. A CLUTCH is a mechanical device that transmits power and motion from one component (the driving member) to another (the driven member) when engaged, but can be disengaged when desired. Clutches are used whenever the transmission of power or motion needs to be controlled either in amount or over time (for example electric screwdrivers use clutches to limit how much torque is transmitted through; automobile clutches control transmitted engine power to the wheels). In simplest applications, clutches are employed in devices which have two rotating shafts (drive shaft or line shaft). In these devices, one shaft is typically attached to a motor or other type of power unit (the driving member) while the other shaft (the driven member) provides output power for work to be done. As an example, in a torque-controlled drill, one shaft is driven by a motor and the other drives a drill chuck. The clutch connects the two shafts so that they may be locked together and spin at the same speed (engaged), locked together but spinning at different speeds (slipping), or unlocked and spinning at different speeds (disengaged). We offer the following types of clutches: FRICTION CLUTCHES: - Multiple plate clutch - Wet & dry - Centrifugal - Cone clutch - Torque limiter BELT CLUTCH DOG CLUTCH HYDRAULIC CLUTCH ELECTROMAGNETIC CLUTCH OVERRUNING CLUTCH (FREEWHEEL) WRAP-SPRING CLUTCH Contact us for clutch assemblies to be used in your manufacturing line for motorcycles, automobiles, trucks, trailers, lawn movers, industrial machines...etc. BRAKES: A BRAKE is a mechanical device inhibiting motion. Most commonly brakes use friction to convert kinetic energy into heat, though other methods of energy conversion may also be employed. Regenerative braking converts much of the energy to electrical energy, which may be stored in batteries for later use. Eddy current brakes use magnetic fields to convert kinetic energy into electric current in the brake disc, fin, or rail, which is subsequently converted into heat. Other methods of brake systems convert kinetic energy into potential energy in such stored forms as pressurized air or pressurized oil. There are braking methods that transform kinetic energy into different forms, such as transferring the energy to a rotating flywheel. Generic Types of brakes we offer are: FRICTIONAL BRAKE PUMPING BRAKE ELECTROMAGNETIC BRAKE We have the capability to design and fabricate custom clutch and break systems tailored to your application. - Download our catalog for Powder Clutches and Brakes and Tension Control System by CLICKING HERE - Download our catalog for Non-Excited Brakes by CLICKING HERE Click on the links below to download our catalog for: - Air Disk and Air Shaft Brakes & Clutches and Safety Disc Spring Brakes - pages 1 to 35 - Air Disk and Air Shaft Brakes & Clutches and Safety Disc Spring Brakes - pages 36 to 71 - Air Disk and Air Shaft Brakes & Clutches and Safety Disc Spring Brakes - pages 72 to 86 - Electromagnetic Clutch and Brakes CLICK Product Finder-Locator Service RÛPERA BERÊ
- Brazing, Soldering, Welding, Joining Processes, Assembly Services
Brazing - Soldering - Welding - Joining Processes - Assembly Services - Subassemblies - Assemblies - Custom Manufacturing - AGS-TECH Inc. - NM - USA Brazing & Soldering & Welding Among the many JOINING techniques we deploy in manufacturing, special emphasis is given to WELDING, BRAZING, SOLDERING, ADHESIVE BONDING and CUSTOM MECHANICAL ASSEMBLY because these techniques are widely used in applications like manufacturing of hermetic assemblies, high-tech product manufacturing and specialized sealing. Here we will concentrate on the more specialized aspects of these joining techniques as they are related to manufacturing of advanced products and assemblies. FUSION WELDING: We use heat to melt and coalesce materials. Heat is supplied by electricity or high-energy beams. The types of fusion welding we deploy are OXYFUEL GAS WELDING, ARC WELDING, HIGH-ENERGY-BEAM WELDING. SOLID-STATE WELDING: We join parts without melting and fusion. Our solid-state welding methods are COLD, ULTRASONIC, RESISTANCE, FRICTION, EXPLOSION WELDING and DIFFUSION BONDING. BRAZING & SOLDERING: They use filler metals and give us the advantage of working at lower temperatures than in welding, thus less structural damage to products. Information on our brazing facility producing ceramic to metal fittings, hermetic sealing, vacuum feedthroughs, high and ultrahigh vacuum and fluid control components can be found here: Brazing Factory Brochure Brazing Machines (We private label these with your brand name and logo if you wish. This way you can promote your brand name when you resell these machines to your customers) ADHESIVE BONDING: Because of the diversity of adhesives used in industry and also diversity of applications, we have a dedicated page for this. To go to our page about adhesive bonding, please click here. CUSTOM MECHANICAL ASSEMBLY: We use a variety of fasteners such as bolts, screws, nuts, rivets. Our fasteners are not limited to standard off-shelf fasteners. We design, develop and manufacture specialty fasteners that are made from nonstandard materials so they can meet requirements for special applications. Sometimes electrical or heat non-conductivity is desired whereas sometimes conductivity. For some special applications, a customer may want special fasteners that cannot be removed without destroying the product. There are endless ideas and applications. We have it all for you, if not off-shelf we can quickly develop it. To go to our page on mechanical assembly, please click here . Let us examine our various joining techniques in more details. OXYFUEL GAS WELDING (OFW): We use a fuel gas mixed with oxygen to produce the welding flame. When we use acetylene as the fuel and oxygen, we call it oxyacetylene gas welding. Two chemical reactions occur in the oxyfuel gas combustion process: C2H2 + O2 ------» 2CO + H2 + Heat 2CO + H2 + 1.5 O2--------» 2 CO2 + H2O + Heat The first reaction dissociates the acetylene into carbon monoxide and hydrogen while producing about 33% of the total heat generated. The second process above represents further combustion of the hydrogen and carbon monoxide while producing about 67% of the total heat. Temperatures in the flame are between 1533 to 3573 Kelvin. The oxygen percentage in the gas mixture is important. If the oxygen content is more than half, the flame becomes an oxidizing agent. This is undesirable for some metals but desirable for others. An example when oxidizing flame is desirable is copper-based alloys because it forms a passivation layer over the metal. On the other hand, when the oxygen content is reduced, full combustion is not possible and the flame becomes a reducing (carburizing) flame. The temperatures in a reducing flame are lower and therefore it is suitable for processes like soldering and brazing. Other gases are also potential fuels, but they have some disadvantages over acetylene. Occasionally we supply filler metals to the weld zone in the form of filler rods or wire. Some of them are coated with flux to retard oxidation of surfaces and thus protecting the molten metal. An additional benefit the flux gives us is the removal of oxides and other substances from the weld zone. This leads to stronger bonding. A variation of the oxyfuel gas welding is the PRESSURE GAS WELDING, where the two components are heated at their interface using oxyacetylene gas torch and once the interface starts to melt, the torch is withdrawn and an axial force is applied to press the two parts together until the interface is solidified. ARC WELDING: We use electrical energy to produce an arc between the electrode tip and parts to be welded. The power supply can be AC or DC while the electrodes are either consumable or nonconsumable. Heat transfer in arc welding can be expressed by the following equation: H / l = e x V I / v Here H is the heat input, l is the weld length, V and I are the voltage and current applied, v is the welding speed and e is the process efficiency. The higher the efficiency “e” the more beneficially the available energy is used to melt the material. The heat input can also be expressed as : H = u x (Volume) = u x A x l Here u is the specific energy for melting, A the cross section of the weld and l the weld length. From the two equations above we can obtain: v = e x V I / u A A variation of arc welding is the SHIELDED METAL ARC WELDING (SMAW) which constitutes about 50% of all industrial and maintenance welding processes. ELECTRIC ARC WELDING (STICK WELDING) is performed by touching the tip of a coated electrode to the workpiece and quickly withdrawing it to a distance sufficient to maintain the arc. We call this process also stick-welding because the electrodes are thin and long sticks. During the welding process, the tip of the electrode melts along with its coating and the base metal in the vicinity of the arc. A mixture of the base metal, electrode metal and substances from the electrode coating solidify in the weld area. The coating of the electrode deoxidizes and provides a shielding gas in the weld region, thus protecting it from the oxygen in the environment. Therefore the process is referred to as shielded metal arc welding. We use currents between 50 and 300 Amperes and power levels generally less than 10 kW for optimum weld performance. Also of importance is the polarity of the DC current (direction of current flow). Straight polarity where the workpiece is positive and the electrode is negative is preferred in welding of sheet metals because of its shallow penetration and also for joints with very wide gaps. When we have reverse polarity, i.e. the electrode is positive and workpiece negative we can achieve deeper weld penetrations. With AC current, since we have pulsating arcs, we can weld thick sections using large diameter electrodes and maximum currents. The SMAW welding method is suitable for workpiece thicknesses of 3 to 19 mm and even more using multiple-pass techniques. The slag formed on top of the weld needs to be removed using a wire brush, so that there is no corrosion and failure at the weld area. This of course adds to the cost of shielded metal arc welding. Nevertheless the SMAW is the most popular welding technique in industry and repair work. SUBMERGED ARC WELDING (SAW): In this process we shield the weld arc using granular flux materials like lime, silica, calcium floride, manganese oxide….etc. The granular flux is fed into the weld zone by gravity flow through a nozzle. The flux covering the molten weld zone significantly protects from sparks, fumes, UV radiation….etc and acts as a thermal insulator, thus letting heat penetrate deep into workpiece. The unfused flux is recovered, treated and reused. A coil of bare is used as electrode and fed through a tube to the area of weld. We use currents between 300 and 2000 Amperes. The submerged arc welding (SAW) process is limited to horizontal and flat positions and circular welds if rotation of the circular structure (such as pipes) is possible during welding. Speeds can reach 5 m/min. The SAW process is suitable for thick plates and results in high-quality, tough, ductile and uniform welds. The productivity, that is the amount of weld material deposited per hour is 4 to 10 times the amount as compared to the SMAW process. Another arc welding process, namely the GAS METAL ARC WELDING (GMAW) or alternatively referred to as METAL INERT GAS WELDING (MIG) is based on the weld area being shielded by external sources of gases like helium, argon, carbon dioxide….etc. There may be additional deoxidizers present in the electrode metal. Consumable wire is fed through a nozzle into the weld zone. Fabrication involving bot ferrous as well as nonferrous metals is carried out using gas metal arc welding (GMAW). Welding productivity is about 2 times that of the SMAW process. Automated welding equipment is being used. Metal is transferred in one of three ways in this process: “Spray Transfer” involves transfer of several hundred small metal droplets per second from electrode to the weld area. In “Globular Transfer” on the other hand, carbon dioxide rich gases are used and globules of molten metal are propelled by the electric arc. Welding currents are high and weld penetration deeper, welding speed greater than in spray transfer. Thus the globular transfer is better for welding heavier sections. Finally, in the “Short Circuiting” method, the electrode tip touches the molten weld pool, short circuiting it as metal at rates over 50 droplets/second is transferred in individual droplets. Low currents and voltages are used along with thinner wire. Powers used are about 2 kW and temperatures relatively low, making this method suitable for thin sheets less than 6mm thickness. Another variation the FLUX-CORED ARC WELDING (FCAW) process is similar to gas metal arc welding, except that the electrode is a tube filled with flux. The advantages of using cored-flux electrodes is that they produce more stable arcs, give us the opportunity to improve properties of weld metals, less brittle and flexible nature of its flux as compared to SMAW welding, improved welding contours. Self-shielded cored electrodes contain materials that shield the weld zone against the atmosphere. We use about 20 kW power. Like the GMAW process, the FCAW process also offers the opportunity to automate processes for continuous welding, and it is economical. Different weld metal chemistries can be developed by adding various alloys to the flux core. In ELECTROGAS WELDING (EGW) we weld the pieces placed edge to edge. It is sometimes also called BUTT WELDING. Weld metal is put into a weld cavity between two pieces to be joined. The space is enclosed by two water-cooled dams to keep the molten slag from pouring out. The dams are moved up by mechanical drives. When workpiece can be rotated, we can use the electrogas welding technique for circumferential welding of pipes too. Electrodes are fed through a conduit to keep a continuous arc. Currents can be around 400Amperes or 750 Amperes and power levels around 20 kW. Inert gases originating from either a flux-cored electrode or external source provide shielding. We use the electrogas welding (EGW) for metals such as steels, titanium….etc with thicknesses from 12mm to 75mm. The technique is a good fit for large structures. Yet, in another technique called ELECTROSLAG WELDING (ESW) the arc is ignited between the electrode and the bottom of the workpiece and flux is added. When molten slag reaches the electrode tip, the arc is extinguished. Energy is continuously supplied through the electrical resistance of the molten slag. We can weld plates with thicknesses between 50 mm and 900 mm and even higher. Currents are around 600 Ampere while voltages are between 40 – 50 V. The welding speeds are around 12 to 36 mm/min. Applications are similar to electrogas welding. One of our nonconsumable electrode processes, the GAS TUNGSTEN ARC WELDING (GTAW) also known as TUNGSTEN INERT GAS WELDING (TIG) involves the supply of a filler metal by a wire. For closely-fit joints sometimes we do not use the filler metal. In the TIG process we do not use flux, but use argon and helium for shielding. Tungsten has a high melting point and is not consumed in the TIG welding process, therefore constant current as well as arc gaps can be maintained. Power levels are between 8 to 20 kW and currents at either 200 Ampere (DC) or 500 Ampere (AC). For aluminum and magnesium we use AC current for its oxide cleaning function. To avoid contamination of the tungsten electrode, we avoid its contact with molten metals. Gas Tungsten Arc Welding (GTAW) is especially useful for welding thin metals. GTAW welds are of very high quality with good surface finish. Due to the higher cost of hydrogen gas, a less frequently used technique is ATOMIC HYDROGEN WELDING (AHW), where we generate an arc between two tungsten electrodes in a shielding atmosphere of flowing hydrogen gas. The AHW is also a nonconsumable electrode welding process. The diatomic hydrogen gas H2 breaks down into its atomic form near the welding arc where temperatures are over 6273 Kelvin. While breaking down, it absorbs large amount of heat from the arc. When the hydrogen atoms strike the weld zone which is a relatively cold surface, they recombine into diatomic form and release the stored heat. Energy can be varied by changing the workpiece to arc distance. In another nonconsumable electrode process, PLASMA ARC WELDING (PAW) we have a concentrated plasma arc directed toward the weld zone. The temperatures reach 33,273 Kelvin in PAW. A nearly equal number of electrons and ions make up the plasma gas. A low-current pilot arc initiates the plasma which is between the tungsten electrode and orifice. Operating currents are generally around 100 Amperes. A filler metal may be fed. In plasma arc welding, shielding is accomplished by an outer shielding ring and using gases such as argon and helium. In plasma arc welding, the arc may be between the electrode and workpiece or between the electrode and nozzle. This welding technique has the advantages over other methods of higher energy concentration, deeper and narrower welding capability, better arc stability, higher welding speeds up to 1 meter/min, less thermal distortion. We generally use plasma arc welding for thicknesses less than 6 mm and sometimes up to 20 mm for aluminum and titanium. HIGH-ENERGY-BEAM WELDING: Another type of fusion welding method with electron-beam welding (EBW) and laser welding (LBW) as two variants. These techniques are of particular value for our high-tech products manufacturing work. In electron-beam welding, high speed electrons strike the workpiece and their kinetic energy is converted to heat. The narrow beam of electrons travel easily in the vacuum chamber. Generally we use high vacuum in e-beam welding. Plates as thick as 150 mm can be welded. No shielding gases, flux or filler material is needed. Elecron beam guns have 100 kW capacities. Deep and narrow welds with high aspect ratios up to 30 and small heat-affected zones are possible. Welding speeds can reach 12 m/min. In laser-beam welding we use high-power lasers as the source of heat. Laser beams as small as 10 microns with high density enable deep penetration into the workpiece. Depth-to-width ratios as much as 10 is possible with laser-beam welding. We use both pulsed as well as continuous wave lasers, with the former in applications for thin materials and the latter mostly for thick workpieces up to about 25 mm. Power levels are up to 100 kW. The laser beam welding is not well suited for optically very reflective materials. Gases may also be used in the welding process. The laser beam welding method is well fit for automation & high volume manufacturing and can offer welding speeds between 2.5 m/min and 80 m/min. One major advantage this welding technique offers is access to areas where other techniques cannot be used. Laser beams can easily travel to such difficult regions. No vacuum as in electron-beam welding is needed. Welds with good quality & strength, low shrinkage, low distortion, low porosity can be obtained with laser beam welding. Laser beams can be easily manipulated and shaped using fiber optic cables. The technique is thus well suitable for welding of precision hermetic assemblies, electronic packages…etc. Let us look at our SOLID STATE WELDING techniques. COLD WELDING (CW) is a process where pressure instead of heat is applied using dies or rolls to the parts that are mated. In cold welding, at least one of the mating parts needs to be ductile. Best results are obtained with two similar materials. If the two metals to be joined with cold welding are dissimilar, we may get weak and brittle joints. The cold welding method is well suited for soft, ductile and small workpieces such as electrical connections, heat sensitive container edges, bimetallic strips for thermostats…etc. One variation of cold welding is roll bonding (or roll welding), where the pressure is applied through a pair of rolls. Sometimes we perform roll welding at elevated temperatures for better interfacial strength. Another solid state welding process we use is the ULTRASONIC WELDING (USW), where the workpieces are subjected to a static normal force and oscillating shearing stresses. The oscillating shearing stresses are applied through the tip of a transducer. Ultrasonic welding deploys oscillations with frequencies from 10 to 75 kHz. In some applications such as seam welding, we use a rotating welding disk as the tip. Shearing stresses applied to the workpieces cause small plastic deformations, break up oxide layers, contaminants and lead to solid state bonding. Temperatures involved in ultrasonic welding are way below melting point temperatures for metals and no fusion takes place. We frequently use the ultrasonic welding (USW) process for nonmetallic materials like plastics. In thermoplastics, the temperatures do reach melting points however. Another popular technique, in FRICTION WELDING (FRW) the heat is generated through friction at the interface of the workpieces to be joined. In friction welding we keep one of the workpieces stationary while the other workpiece is held in a fixture and rotated at a constant speed. The workpieces are then brought into contact under an axial force. The surface speed of rotation in friction welding may reach 900m/min in some cases. After sufficient interfacial contact, the rotating workpiece is brought to a sudden stop and the axial force is increased. The weld zone is generally a narrow region. The friction welding technique can be used to join solid and tubular parts made of a variety of materials. Some flash may develop at the interface in FRW, but this flash can be removed by secondary machining or grinding. Variations of the friction welding process exist. For example “inertia friction welding” involves a flywheel whose rotational kinetic energy is used to weld the parts. The weld is complete when the flywheel comes to a stop. The rotating mass can be varied and thus the rotational kinetic energy. Another variation is “linear friction welding”, where linear reciprocating motion is imposed on at least one of the components to be joined. In linear friction welding parts do not have to be circular, they can be rectangular, square or of other shape. Frequencies can be in the tens of Hz, amplitudes in the millimeters range and pressures in the tens or hundreds of MPa. Finally “friction stir welding” is somewhat different than the other two explained above. Whereas in inertia friction welding and linear friction welding heating of interfaces is achieved through friction by rubbing two contacting surfaces, in the friction stir welding method a third body is rubbed against the two surfaces to be joined. A rotating tool of 5 to 6 mm diameter is brought into contact with the joint. The temperatures can increase to values between 503 to 533 Kelvin. Heating, mixing and stirring of the material in the joint takes place. We use the friction stir welding on a variety of materials including aluminum, plastics and composites. Welds are uniform and quality is high with minimum pores. No fumes or spatter are produced in friction stir welding and the process is well automated. RESISTANCE WELDING (RW): The heat required for welding is produced by the electrical resistance between the two workpieces to be joined. No flux, shielding gases or consumable electrodes are used in resistance welding. Joule heating takes place in resistance welding and can be expressed as: H = (Square I) x R x t x K H is heat generated in joules (watt-seconds), I current in Amperes, R resistance in Ohms, t is the time in seconds the current flows through. The factor K is less than 1 and represents the fraction of energy that is not lost through radiation and conduction. Currents in resistance welding processes can reach levels as high as 100,000 A but voltages are typically 0.5 to 10 Volts. Electrodes are typically made of copper alloys. Both similar and dissimilar materials can be joined by resistance welding. Several variations exist for this process: “Resistance spot welding” involves two opposing round electrodes contacting the surfaces of the lap joint of the two sheets. Pressure is applied until current is turned off. The weld nugget is generally up to 10 mm in diameter. Resistance spot welding leaves slightly discolored indentation marks at weld spots. Spot welding is our most popular resistance welding technique. Various electrode shapes are used in spot welding in order to reach difficult areas. Our spot welding equipment is CNC controlled and has multiple electrodes that can be used simultaneously. Another variation “resistance seam welding” is carried out with wheel or roller electrodes that produce continuous spot welds whenever the current reaches a sufficiently high level in the AC power cycle. Joints produced by resistance seam welding are liquid and gas tight. Welding speeds of about 1.5 m/min are normal for thin sheets. One may apply intermittent currents so that spot welds are produced at desired intervals along the seam. In “resistance projection welding” we emboss one or more projections (dimples) on one of the workpiece surfaces to be welded. These projections may be round or oval. High localized temperatures are reached at these embossed spots that come into contact with the mating part. Electrodes exert pressure to compress these projections. Electrodes in resistance projection welding have flat tips and are water cooled copper alloys. The advantage of resistance projection welding is our ability to a number of welds in one stroke, thus the extended electrode life, capability to weld sheets of various thicknesses, capability to weld nuts and bolts to sheets. Disadvantage of resistance projection welding is the added cost of embossing the dimples. Yet another technique, in “flash welding” heat is generated from the arc at the ends of the two workpieces as they begin to make contact. This method may also alternatively considered arc welding. The temperature at the interface rises, and material softens. An axial force is applied and a weld is formed at the softened region. After the flash welding is complete, the joint can be machined for improved appearance. Weld quality obtained by flash welding is good. Power levels are 10 to 1500 kW. Flash welding is suitable for edge-to-edge joining of similar or dissimilar metals up to 75 mm diameter and sheets between 0.2 mm to 25 mm thickness. “Stud arc welding” is very similar to flash welding. The stud such as a bolt or threaded rod serves as one electrode while being joined to a workpiece such as a plate. To concentrate the generated heat, prevent oxidation and retain the molten metal in the weld zone, a disposable ceramic ring is placed around the joint. Finally “percussion welding” another resistance welding process, utilizes a capacitor to supply the electrical energy. In percussion welding the power is discharged within milliseconds of time very quickly developing high localized heat at the joint. We use percussion welding widely in the electronics manufacturing industry where heating of sensitive electronic components in the vicinity of the joint has to be avoided. A technique called EXPLOSION WELDING involves detonation of a layer of explosive that is put over one of the workpieces to be joined. The very high pressure exerted on the workpiece produces a turbulent and wavy interface and mechanical interlocking takes place. Bond strengths in explosive welding are very high. Explosion welding is a good method for cladding of plates with dissimilar metals. After cladding, the plates may be rolled into thinner sections. Sometimes we use explosion welding for expanding tubes so that they get sealed tightly against the plate. Our last method within the domain of solid state joining is DIFFUSION BONDING or DIFFUSION WELDING (DFW) in which a good joint is achieved mainly by diffusion of atoms across the interface. Some plastic deformation at the interface also contributes to the welding. Temperatures involved are around 0.5 Tm where Tm is melting temperature of the metal. Bond strength in diffusion welding depends on pressure, temperature, contact time and cleanliness of contacting surfaces. Sometimes we use filler metals at the interface. Heat and pressure are required in diffusion bonding and are supplied by electrical resistance or furnace and dead weights, press or else. Similar and dissimilar metals can be joined with diffusion welding. The process is relatively slow due to the time it takes for atoms to migrate. DFW can be automated and is widely used in the fabrication of complex parts for the aerospace, electronics, medical industries. Products manufactured include orthopedic implants, sensors, aerospace structural members. Diffusion bonding can be combined with SUPERPLASTIC FORMING to fabricate complex sheet metal structures. Selected locations on sheets are first diffusion bonded and then the unbonded regions are expanded into a mold using air pressure. Aerospace structures with high stiffness-to-weight ratios are manufactured using this combination of methods. The diffusion welding / superplastic forming combined process reduces the number of parts required by eliminating the need for fasteners, results in low-stress highly accurate parts economically and with short lead times. BRAZING: The brazing and soldering techniques involve lower temperatures than those required for welding. Brazing temperatures are higher than soldering temperatures however. In brazing a filler metal is placed between the surfaces to be joined and temperatures are raised to the melting temperature of the filler material above 723 Kelvin but below the melting temperatures of the workpieces. The molten metal fills the closely fitting space between workpieces. Cooling and subsequent solidification of the filer metal results in strong joints. In braze welding the filler metal is deposited at the joint. Considerably more filler metal is used in braze welding compared to brazing. Oxyacetylene torch with oxidizing flame is used to deposit the filler metal in braze welding. Due to lower temperatures in brazing, problems at heat affected zones such as warping and residual stresses are less. The smaller the clearance gap in brazing the higher is the shear strength of the joint. Maximum tensile strength however is achieved at an optimum gap (a peak value). Below and above this optimum value, the tensile strength in brazing decreases. Typical clearances in brazing can be between 0.025 and 0.2 mm. We use a variety of brazing materials with different shapes such as performs, powder, rings, wire, strip…..etc. and can manufacture these performs specially for your design or product geometry. We do also determine the content of the brazing materials according to your base materials and application. We frequently use fluxes in brazing operations to remove unwanted oxide layers and prevent oxidation. To avoid subsequent corrosion, fluxes are generally removed after the joining operation. AGS-TECH Inc. uses various brazing methods, including: - Torch Brazing - Furnace Brazing - Induction Brazing - Resistance Brazing - Dip Brazing - Infrared Brazing - Diffusion Brazing - High Energy Beam Our most common examples of brazed joints are made of dissimilar metals with good strength such as carbide drill bits, inserts, optoelectronic hermetic packages, seals. SOLDERING : This is one of our most frequently used techniques where the solder (filler metal) fills the joint as in brazing between closely fitting components. Our solders have melting points below 723 Kelvin. We deploy both manual and automated soldering in manufacturing operations. Compared to brazing, soldering temperatures are lower. Soldering is not very suitable for high-temperature or high-strength applications. We use lead-free solders as well as tin-lead, tin-zinc, lead-silver, cadmium-silver, zinc-aluminum alloys besides others for soldering. Both noncorrosive resin-based as well as inorganic acids and salts are used as flux in soldering. We use special fluxes to solder metals with low solderability. In applications where we have to solder ceramic materials, glass or graphite, we first plate the parts with a suitable metal for increased solderability. Our popular soldering techniques are: -Reflow or Paste Soldering -Wave Soldering -Furnace Soldering -Torch Soldering -Induction Soldering -Iron Soldering -Resistance Soldering -Dip soldering -Ultrasonic Soldering -Infrared Soldering Ultrasonic soldering offers us a unique advantage whereby the need for fluxes is eliminated due to ultrasonic cavitation effect which removes oxide films from the surfaces being joined. Reflow and Wave soldering are our industrially outstanding techniques for high volume manufacturing in electronics and therefore worth explaining in greater detail. In reflow soldering, we use semisolid pastes that include solder-metal particles. The paste is placed onto the joint using a screening or stenciling process. In printed circuit boards (PCB) we frequently use this technique. When electrical components are placed onto these pads from paste, the surface tension keeps the surface-mount packages aligned. After placing the components, we heat the assembly in a furnace so the reflow soldering takes place. During this process, the solvents in the paste evaporate, the flux in the paste is activated, the components are preheated, the solder particles are melted and wet the joint, and finally the PCB assembly is cooled slowly. Our second popular technique for high volume production of PCB boards, namely wave soldering relias on the fact that molten solders wet metal surfaces and form good bonds only when the metal is preheated. A standing laminar wave of molten solder is first generated by a pump and the preheated and prefluxed PCBs are conveyed over the wave. The solder wets only exposed metal surfaces but does not wet the IC polymer packages nor the polymer-coated circuit boards. A high-velocity of hot water jet blows excess solder from the joint and prevents bridging between adjacent leads. In wave soldering of surface-mount packages we first adhesively bond them to the circuit board before soldering. Again screening and stenciling is used but this time for epoxy. After the components are placed in their correct locations, the epoxy is cured, the boards are inverted and wave soldering takes place. CLICK Product Finder-Locator Service RÛPERA BERÊ
- Micro-Optics - Micro-Optical - Microoptical - Wafer Level Optics
Micro-Optics, Micro-Optical, Microoptical, Wafer Level Optics, Gratings, Fresnel Lenses, Lens Array, Micromirrors, Micro Reflectors, Collimators, Aspheres, LED Micro-Optics Manufacturing One of the fields in microfabrication we are involved in is MICRO-OPTICS MANUFACTURING. Micro-optics allows the manipulation of light and the management of photons with micron and sub-micron scale structures and components. Some applications of MICRO-OPTICAL COMPONENTS and SUBSYSTEMS are: Information technology: In micro-displays, micro-projectors, optical data storage, micro-cameras, scanners, printers, copiers…etc. Biomedicine: Minimally-invasive/point of care diagnostics, treatment monitoring, micro-imaging sensors, retinal implants, micro-endoscopes. Lighting: Systems based on LEDs and other efficient light sources Safety and Security Systems: Infrared night vision systems for automotive applications, optical fingerprint sensors, retinal scanners. Optical Communication & Telecommunication: In photonic switches, passive fiber optic components, optical amplifiers, mainframe and personal computer interconnect systems Smart structures: In optical fiber-based sensing systems and much more The types of micro-optical components and subsystems we manufacture and supply are: - Wafer Level Optics - Refractive Optics - Diffractive Optics - Filters - Gratings - Computer Generated Holograms - Hybrid Microoptical Components - Infrared Micro-Optics - Polymer Micro-Optics - Optical MEMS - Monolithically and Discretely Integrated Micro-Optic Systems Some of our most widely used micro-optical products are: - Bi-convex and plano-convex lenses - Achromat lenses - Ball lenses - Vortex Lenses - Fresnel Lenses - Multifocal Lens - Cylindrical Lenses - Graded Index (GRIN) Lenses - Micro-Optical Prisms - Aspheres - Arrays of Aspheres - Collimators - Micro-Lens Arrays - Diffraction Gratings - Wire-Grid Polarizers - Micro-Optic Digital Filters - Pulse Compression Gratings - LED Modules - Beam Shapers - Beam Sampler - Ring Generator - Micro-Optical Homogenizers / Diffusers - Multispot Beam Splitters - Dual Wavelength Beam Combiners - Micro-Optical Interconnects - Intelligent Micro-Optics Systems - Imaging Microlenses - Micromirrors - Micro Reflectors - Micro-Optical Windows - Dielectric Mask - Iris Diaphragms Let us provide you some basic information about these micro-optical products and their applications: BALL LENSES: Ball lenses are completely spherical micro-optic lenses most commonly used to couple light in and out of fibers. We supply a range of micro-optic stock ball lenses and can manufacture also to your own specifications. Our stock ball lenses from quartz have excellent UV and IR transmission between 185nm to >2000nm, and our sapphire lenses have a higher refractive index, allowing a very short focal length for excellent fiber coupling. Micro-optical ball lenses from other materials and diameters are available. Besides fiber coupling applications, micro-optical ball lenses are used as objective lenses in endoscopy, laser measurement systems and bar-code scanning. On the other hand, micro-optic half ball lenses offer uniform dispersion of light and are widely used in LED displays and traffic lights. MICRO-OPTICAL ASPHERES and ARRAYS: Aspheric surfaces have a non-spherical profile. Use of aspheres can reduce the number of optics required to reach a desired optical performance. Popular applications for micro-optical lens arrays with spherical or aspherical curvature are imaging and illumination and the effective collimation of laser light. Substitution of a single aspheric microlens array for a complex multilens system results not only in smaller size, lighter weight, compact geometry, and lower cost of an optical system, but also in significant improvement of its optical performance such as better imaging quality. However, the fabrication of aspheric microlenses and microlens arrays is challenging, because conventional technologies used for macro-sized aspheres like single-point diamond milling and thermal reflow are not capable of defining a complicated micro-optic lens profile in an area as small as several to tens of micrometers. We possess the know-how of producing such micro-optical structures using advanced techniques such as femtosecond lasers. MICRO-OPTICAL ACHROMAT LENSES: These lenses are ideal for applications requiring color correction, while aspheric lenses are designed to correct spherical aberration. An achromatic lens or achromat is a lens that is designed to limit the effects of chromatic and spherical aberration. Micro-optical achromatic lenses make corrections to bring two wavelengths (such as red and blue colors) into focus on the same plane. CYLINDRICAL LENSES: These lenses focus light into a line instead of a point, as a spherical lens would. The curved face or faces of a cylindrical lens are sections of a cylinder, and focus the image passing through it into a line parallel to the intersection of the surface of the lens and a plane tangent to it. The cylindrical lens compresses the image in the direction perpendicular to this line, and leaves it unaltered in the direction parallel to it (in the tangent plane). Tiny micro-optical versions are available which are suitable for use in micro optical environments, requiring compact-size fiber optical components, laser systems, and micro-optical devices. MICRO-OPTICAL WINDOWS and FLATS: Milimetric micro-optical windows meeting tight tolerance requirements are available. We can custom manufacture them to your specifications from any of the optical grade glasses. We offer a variety of micro-optical windows made of different materials such as fused silica, BK7, sapphire, zinc sulphide….etc. with transmission from UV to middle IR range. IMAGING MICROLENSES: Microlenses are small lenses, generally with a diameter less than a millimetre (mm) and as small as 10 micrometres. Imaging Lenses are used to view objects in imaging systems. Imaging Lenses are used in imaging systems to focus an image of an examined object onto a camera sensor. Depending on the lens, imaging lenses can be used to remove parallax or perspective error. They can also offer adjustable magnifications, field of views, and focal lengths. These lenses allow an object to be viewed in several ways to illustrate certain features or characteristics that may be desirable in certain applications. MICROMIRRORS: Micromirror devices are based on microscopically small mirrors. The mirrors are Microelectromechanical systems (MEMS). The states of these micro-optical devices are controlled by applying a voltage between the two electrodes around the mirror arrays. Digital micromirror devices are used in video projectors and optics and micromirror devices are used for light deflection and control. MICRO-OPTIC COLLIMATORS & COLLIMATOR ARRAYS: A variety of micro-optical collimators are available off-the-shelf. Micro-optical small beam collimators for demanding applications are produced using laser fusion technology. The fiber end is directly fused to the optical center of the lens, thereby eliminated epoxy within the optical path. The micro-optic collimator lens surface is then laser polished to within a millionth of an inch of the ideal shape. Small Beam collimators produce collimated beams with beam waists under a millimeter. Micro-optical small beam collimators are typically used at 1064, 1310 or 1550 nm wavelengths. GRIN lens based micro-optic collimators are also available as well as collimator array and collimator fiber array assemblies. MICRO-OPTICAL FRESNEL LENSES: A Fresnel lens is a type of compact lens designed to allow the construction of lenses of large aperture and short focal length without the mass and volume of material that would be required by a lens of conventional design. A Fresnel lens can be made much thinner than a comparable conventional lens, sometimes taking the form of a flat sheet. A Fresnel lens can capture more oblique light from a light source, thus allowing the light to be visible over greater distances. The Fresnel lens reduces the amount of material required compared to a conventional lens by dividing the lens into a set of concentric annular sections. In each section, the overall thickness is decreased compared to an equivalent simple lens. This can be viewed as dividing the continuous surface of a standard lens into a set of surfaces of the same curvature, with stepwise discontinuities between them. Micro-optic Fresnel lenses focus light by refraction in a set of concentric curved surfaces. These lenses can be made very thin and lightweight. Micro-optical Fresnel lenses offer opportunities in optics for highresolution Xray applications, throughwafer optical interconnection capabilities. We have a number of fabrication methods including micromolding and micromachining to manufacture micro-optical Fresnel lenses and arrays specifically for your applications. We can design a positive Fresnel lens as a collimator, collector or with two finite conjugates. Micro-Optical Fresnel lenses are usually corrected for spherical aberrations. Micro-optic positive lenses can be metalized for use as a second surface reflector and negative lenses can be metalized for use as a first surface reflector. MICRO-OPTICAL PRISMS: Our line of precision micro-optics includes standard coated and uncoated micro prisms. They are suitable for use with laser sources and imaging applications. Our micro-optical prisms have submilimeter dimensions. Our coated micro-optical prisms can also be used as mirror reflectors with respect to incoming light. Uncoated prisms act as mirrors for light incident on one of the short sides since incident light is totally internally reflected at the hypotenuse. Examples of our micro-optical prism capabilities include right angle prisms, beamsplitter cube assemblies, Amici prisms, K-prisms, Dove prisms, Roof prisms, Cornercubes, Pentaprisms, Rhomboid prisms, Bauernfeind prisms, Dispersing prisms, Reflecting prisms. We also offer light guiding and de-glaring optical micro-prisms made from acrylic, polycarbonate and other plastic materials by hot embossing manufacturing process for applications in lamps and luminaries, LEDs. They are highly efficient, strong light guiding precise prism surfaces, support luminaries to fulfill office regulations for de-glaring. Additional customized prism structures are possible. Microprisms and microprism arrays on wafer level are also possible using microfabrication techniques. DIFFRACTION GRATINGS: We offer design and manufacture of diffractive micro-optical elements (DOEs). A diffraction grating is an optical component with a periodic structure, which splits and diffracts light into several beams travelling in different directions. The directions of these beams depend on the spacing of the grating and the wavelength of the light so that the grating acts as the dispersive element. This makes grating a suitable element to be used in monochromators and spectrometers. Using wafer-based lithography, we produce diffractive micro-optical elements with exceptional thermal, mechanical and optical performance characteristics. Wafer-level processing of micro-optics provides excellent manufacturing repeatability and economic output. Some of the available materials for diffractive micro-optical elements are crystal-quartz, fused-silica, glass, silicon and synthetic substrates. Diffraction gratings are useful in applications such as spectral analysis / spectroscopy, MUX/DEMUX/DWDM, precision motion control such as in optical encoders. Lithography techniques make the fabrication of precision micro-optical gratings with tightly-controlled groove spacings possible. AGS-TECH offers both custom and stock designs. VORTEX LENSES: In laser applications there is a need to convert a Gaussian beam to a donut-shaped energy ring. This is achieved using Vortex lenses. Some applications are in lithography and high-resolution microscopy. Polymer on glass Vortex phase plates are also available. MICRO-OPTICAL HOMOGENIZERS / DIFFUSERS: A variety of technologies are used to fabricate our micro-optical homogenizers and diffusers, including embossing, engineered diffuser films, etched diffusers, HiLAM diffusers. Laser Speckle is the optical phenomena resulting from the random interference of coherent light. This phenomenon is utilized to measure the Modulation Transfer Function (MTF) of detector arrays. Microlens diffusers are shown to be efficient micro-optic devices for speckle generation. BEAM SHAPERS: A micro-optic beam shaper is an optic or a set of optics that transforms both the intensity distribution and the spatial shape of a laser beam to something more desirable for a given application. Frequently, a Gaussian-like or non-uniform laser beam is transformed to a flat top beam. Beam shaper micro-optics are used to shape and manipulate single mode and multi-mode laser beams. Our beam shaper micro-optics provide circular, square, rectilinear, hexagonal or line shapes, and homogenize the beam (flat top) or provide a custom intensity pattern according to the requirements of the application. Refractive, diffractive and reflective micro-optical elements for laser beam shaping and homogenizing have been manufactured. Multifunctional micro-optical elements are used for shaping arbitrary laser beam profiles into a variety of geometries like, a homogeneous spot array or line pattern, a laser light sheet or flat-top intensity profiles. Fine beam application examples are cutting and keyhole welding. Broad beam application examples are conduction welding, brazing, soldering, heat treatment, thin film ablation, laser peening. PULSE COMPRESSION GRATINGS: Pulse compression is a useful technique that takes advantage of the relationship between pulse duration and spectral width of a pulse. This enables the amplification of laser pulses above the normal damage threshold limits imposed by the optical components in the laser system. There are linear and nonlinear techniques for reducing the durations of optical pulses. There is variety of methods for temporally compressing / shortening optical pulses, i.e., reducing the pulse duration. These methods generally start in the picosecond or femtosecond region, i.e. already in the regime of ultrashort pulses. MULTISPOT BEAM SPLITTERS: Beam splitting by means of diffractive elements is desirable when one element is required to produce several beams or when very exact optical power separation is required. Precise positioning can also be achieved, for example, to create holes at clearly defined and accurate distances. We have Multi-Spot Elements, Beam Sampler Elements, Multi-Focus Element. Using a diffractive element, collimated incident beams are split into several beams. These optical beams have equal intensity and equal angle to one another. We have both one-dimensional and two-dimensional elements. 1D elements split beams along a straight line whereas 2D elements produce beams arranged in a matrix of, for example, 2 x 2 or 3 x 3 spots and elements with spots that are arranged hexagonally. Micro-optical versions are available. BEAM SAMPLER ELEMENTS: These elements are gratings that are used for inline monitoring of high power lasers. The ± first diffraction order can be used for beam measurements. Their intensity is significantly lower than that of the main beam and can be custom designed. Higher diffraction orders can also be used for measurement with even lower intensity. Variations in intensity and changes in the beam profile of high power lasers can be reliably monitored inline using this method. MULTI-FOCUS ELEMENTS: With this diffractive element several focal points can be created along the optical axis. These optical elements are used in sensors, ophthalmology, material processing. Micro-optical versions are available. MICRO-OPTICAL INTERCONNECTS: Optical interconnects have been replacing electrical copper wires at the different levels in the interconnect hierarchy. One of the possibilities to bring the advantages of micro-optics telecommunications to the computer backplane, the printed circuit board, the inter-chip and on-chip interconnect level, is to use free-space micro-optical interconnect modules made of plastic. These modules are capable of carrying high aggregate communication bandwidth through thousands of point-to-point optical links on a footprint of a square centimeter. Contact us for off-shelf as well as custom tailored micro-optical interconnects for computer backplane, the printed circuit board, the inter-chip and on-chip interconnect levels. INTELLIGENT MICRO-OPTICS SYSTEMS: Intelligent micro-optic light modules are used in smart phones and smart devices for LED flash applications, in optical interconnects for transporting data in supercomputers and telecommunications equipment, as miniaturized solutions for near-infrared beam shaping, detection in gaming applications and for supporting gesture control in natural user interfaces. Sensing opto-electronic modules are used for a number of product applications such as ambient light and proximity sensors in smart phones. Intelligent imaging micro-optic systems are used for primary and front-facing cameras. We offer also customized intelligent micro-optical systems with high performance and manufacturability. LED MODULES: You can find our LED chips, dies and modules on our page Lighting & Illumination Components Manufacturing by clicking here. WIRE-GRID POLARIZERS: These consist of a regular array of fine parallel metallic wires, placed in a plane perpendicular to the incident beam. The polarization direction is perpendicular to the wires. Patterned polarizers have applications in polarimetry, interferometry, 3D displays, and optical data storage. Wire-grid polarizers are extensively used in infrared applications. On the other hand micropatterned wire-grid polarizers have limited spatial resolution and poor performance at visible wavelengths, are susceptible to defects and cannot be easily extended to non-linear polarizations. Pixelated polarizers use an array of micro-patterned nanowire grids. The pixelated micro-optical polarizers can be aligned with cameras, plane arrays, interferometers, and microbolometers without the need for mechanical polarizer switches. Vibrant images distinguishing between multiple polarizations across the visible and IR wavelengths can be captured simultaneously in real-time enabling fast, high resolution images. Pixelated micro-optical polarizers also enable clear 2D and 3D images even in low-light conditions. We offer patterned polarizers for two, three and four-state imaging devices. Micro-optical versions are available. GRADED INDEX (GRIN) LENSES: Gradual variation of the refractive index (n) of a material can be used to produce lenses with flat surfaces, or lenses that do not have the aberrations typically observed with traditional spherical lenses. Gradient-index (GRIN) lenses may have a refraction gradient that is spherical, axial, or radial. Very small micro-optical versions are available. MICRO-OPTIC DIGITAL FILTERS: Digital neutral density filters are used to control the intensity profiles of illumination and projection systems. These micro-optic filters contain well-defined metal absorber micro-structures that are randomly distributed on a fused silica substrate. Properties of these micro-optical components are high accuracy, large clear aperture, high damage threshold, broadband attenuation for DUV to IR wavelengths, well defined one or two dimensional transmission profiles. Some applications are soft edge apertures, precise correction of intensity profiles in illumination or projection systems, variable attenuation filters for high-power lamps and expanded laser beams. We can customize the density and size of the structures to meet precisely the transmission profiles required by the application. MULTI-WAVELENGTH BEAM COMBINERS: Multi-Wavelength beam combiners combine two LED collimators of different wavelengths into a single collimated beam. Multiple combiners can be cascaded to combine more than two LED collimator sources. Beam combiners are made of high-performance dichroic beam splitters that combine two wavelengths with >95% efficiency. Very small micro-optic versions are available. CLICK Product Finder-Locator Service RÛPERA BERÊ
- Customized Optomechanical Assemblies | agstech
Optomechanical Components & Assemblies, Beam Expander, Interferometers, Polarizers, Prism and Cube Assembly, Medical & Industrial Video Coupler, Optic Mounts Meclîsên Optomekanîkî yên Xweserkirî AGS-TECH is a supplier of: • Custom optomechanical assemblies like beam expander, beamsplitter, interferometry, etalon, filter, isolator, polarizer, prism and cube assembly, optical mounts, telescope, binocular, metallurgical microscope, digital camera adapters for microscope and telescope, medical and industrial video couplers, special custom designed illumination systems. Among the optomechanical products our engineers have developed are: - A portable metallurgical microscope which can be set as upright or inverted. - A gravure inspection microscope. - Digital camera adapters for microscope and telescope. Standard adapters fit all popular digital camera models and can be customized if required. - Medical and industrial video couplers. All medical video couplers fit over standard endoscope eyepieces and are completely sealed and soakable. - Night vision goggles - Automotive mirrors Automotive Mirrors Brochure (Click on the left blue link to download) Optical Components Brochure (Click on the left blue link to download) - in this you can find our free space optical components and subassemblies we use when we design and manufacture optomechanical assembly for special applications. We combine and assemble these optical components with precision machined metal parts to build our customers optomechanical products. We use special bonding and attachment techniques and materials for rigid, reliable and long life assembly. In some cases we deploy ''optical contacting'' technique where we bring extremely flat and clean surfaces together and join them without using any glues or epoxies. Our optomechanical assemblies are sometimes passively assembled and sometimes active assembly takes place where we use lasers and detectors to make sure the parts are properly aligned prior to fixing them in place. Even under extensive environmental cycling in special chambers such as high temperature/low temperature; high humidity/low humidity chambers, our assemblies remain intact and keep working. All our raw materials for optomechanical assembly are procured from World famous sources such as Corning and Schott. Private Label Medical Endoscopes and Visualization Systems (We can put your company name and logo on these) CLICK Product Finder-Locator Service RÛPERA BERÊ
- Nanomanufacturing, Nanoparticles, Nanotubes, Nanocomposites, CNT
Nanomanufacturing - Nanoparticles - Nanotubes - Nanocomposites - Nanophase Ceramics - CNT - AGS-TECH Inc. - New Mexico Çêkirina Nanoscale / Nanomanufacturing Our nanometer length scale parts and products are produced using NANOSCALE MANUFACTURING / NANOMANUFACTURING. This area is still in its infancy, but holds great promises for the future. Molecularly engineered devices, medicines, pigments…etc. are being developed and we are working with our partners to stay ahead of the competition. The following are some of the commercially available products we currently offer: CARBON NANOTUBES NANOPARTICLES NANOPHASE CERAMICS CARBON BLACK REINFORCEMENT for rubber and polymers NANOCOMPOSITES in tennis balls, baseball bats, motorcycles and bikes MAGNETIC NANOPARTICLES for data storage NANOPARTICLE catalytic converters Nanomaterials may be any one of the four types, namely metals, ceramics, polymers or composites. Generally, NANOSTRUCTURES are less than 100 nanometers. In nanomanufacturing we take one of two approaches. As an example, in our top-down approach we take a silicon wafer, use lithography, wet and dry etching methods to construct tiny microprocessors, sensors, probes. On the other hand, in our bottom-up nanomanufacturing approach we use atoms and molecules to build tiny devices. Some of the physical and chemical characteristics exhibited by matter may experience extreme changes as particle size approaches atomic dimensions. Opaque materials in their macroscopic state may become transparent in their nanoscale. Materials that are chemically stable in macrostate may become combustible in their nanoscale and electrically insulating materials may become conductors. Currently the following are among the commercial products we are able to offer: CARBON NANOTUBE (CNT) DEVICES / NANOTUBES: We can visualize carbon nanotubes as tubular forms of graphite from which nanoscale devices can be constructed. CVD, laser ablation of graphite, carbon-arc discharge can be used to produce carbon nanotube devices. Nanotubes are categorized as single-walled nanotubes (SWNTs) and multi-walled nanotubes (MWNTs) and can be doped with other elements. Carbon nanotubes (CNTs) are allotropes of carbon with a nanostructure that can have a length-to-diameter ratio greater than 10,000,000 and as high as 40,000,000 and even higher. These cylindrical carbon molecules have properties that make them potentially useful in applications in nanotechnology, electronics, optics, architecture and other fields of materials science. They exhibit extraordinary strength and unique electrical properties, and are efficient conductors of heat. Nanotubes and spherical buckyballs are members of the fullerene structural family. The cylindrical nanotube usually has at least one end capped with a hemisphere of the buckyball structure. The name nanotube is derived from its size, since the diameter of a nanotube is in the order of a few nanometers, with lengths of at least several millimeters. The nature of the bonding of a nanotube is described by orbital hybridization. The chemical bonding of nanotubes is composed entirely of sp2 bonds, similar to those of graphite. This bonding structure, is stronger than the sp3 bonds found in diamonds, and provides the molecules with their unique strength. Nanotubes naturally align themselves into ropes held together by Van der Waals forces. Under high pressure, nanotubes can merge together, trading some sp2 bonds for sp3 bonds, giving the possibility of producing strong, unlimited-length wires through high-pressure nanotube linking. The strength and flexibility of carbon nanotubes makes them of potential use in controlling other nanoscale structures. Single-walled nanotubes with tensile strengths between 50 and 200 GPa have been produced, and these values are approximately an order of magnitude greater than for carbon fibers. Elastic modulus values are on the order of 1 Tetrapascal (1000 GPa) with fracture strains between about 5% to 20%. The outstanding mechanical properties of the carbon nanotubes makes us use them in tough clothes and sports gear, combat jackets. Carbon nanotubes have strength comparable to diamond, and they are weaved into clothes to create stab-proof and bulletproof clothing. By cross-linking CNT molecules prior to incorporation in a polymer matrix we can form a super high strength composite material. This CNT composite could have a tensile strength on the order of 20 million psi (138 GPa), revolutionizing engineering design where low weight and high strength is required. Carbon nanotubes reveal also unusual current conduction mechanisms. Depending on the orientation of the hexagonal units in the graphene plane (i.e. tube walls) with the tube axis, the carbon nanotubes may behave either as metals or semiconductors. As conductors, carbon nanotubes have very high electrical current-carrying capability. Some nanotubes may be able to carry current densities over 1000 times that of silver or copper. Carbon nanotubes incorporated into polymers improve their static electricity discharge capability. This has applications in automobile and airplane fuel lines and production of hydrogen storage tanks for hydrogen-powered vehicles. Carbon nanotubes have shown to exhibit strong electron-phonon resonances, which indicate that under certain direct current (DC) bias and doping conditions their current and the average electron velocity, as well as the electron concentration on the tube oscillate at terahertz frequencies. These resonances can be used to make terahertz sources or sensors. Transistors and nanotube integrated memory circuits have been demonstrated. The carbon nanotubes are used as a vessel for transporting drugs into the body. The nanotube allows for the drug dosage to be lowered by localizing its distribution. This is also economically viable due to lower amounts of drugs being used.. The drug can be either attached to the side of the nanotube or trailed behind, or the drug can actually be placed inside the nanotube. Bulk nanotubes are a mass of rather unorganized fragments of nanotubes. Bulk nanotube materials may not reach tensile strengths similar to that of individual tubes, but such composites may nevertheless yield strengths sufficient for many applications. Bulk carbon nanotubes are being used as composite fibers in polymers to improve the mechanical, thermal and electrical properties of the bulk product. Transparent, conductive films of carbon nanotubes are being considered to replace indium tin oxide (ITO). Carbon nanotube films are mechanically more robust than ITO films, making them ideal for high reliability touch screens and flexible displays. Printable water-based inks of carbon nanotube films are desired to replace ITO. Nanotube films show promise for use in displays for computers, cell phones, ATMs….etc. Nanotubes have been used to improve ultracapacitors. The activated charcoal used in conventional ultracapacitors has many small hollow spaces with a distribution of sizes, which create together a large surface to store electric charges. However as charge is quantized into elementary charges, i.e. electrons, and each of these needs a minimum space, a large fraction of the electrode surface is not available for storage because the hollow spaces are too small. With electrodes made of nanotubes, the spaces are planned to be tailored to size, with only a few being too large or too small and consequently the capacity to be increased. A solar cell developed uses a carbon nanotube complex, made of carbon nanotubes combined with tiny carbon buckyballs (also called Fullerenes) to form snake-like structures. Buckyballs trap electrons, but they can't make electrons flow. When sunlight excites the polymers, the buckyballs grab the electrons. Nanotubes, behaving like copper wires, will then be able to make the electrons or current flow. NANOPARTICLES: Nanoparticles can be considered a bridge between bulk materials and atomic or molecular structures. A bulk material generally has constant physical properties throughout regardless of its size, but at the nanoscale this is often not the case. Size-dependent properties are observed such as quantum confinement in semiconductor particles, surface plasmon resonance in some metal particles and superparamagnetism in magnetic materials. Properties of materials change as their size is reduced to nanoscale and as the percentage of atoms at the surface becomes significant. For bulk materials larger than a micrometer the percentage of atoms at the surface is very small compared to the total number of atoms in the material. The different and outstanding properties of nanoparticles are partly due to the aspects of the surface of the material dominating the properties in lieu of the bulk properties. For example, the bending of bulk copper occurs with movement of copper atoms/clusters at about the 50 nm scale. Copper nanoparticles smaller than 50 nm are considered super hard materials that do not exhibit the same malleability and ductility as bulk copper. The change in properties is not always desirable. Ferroelectric materials smaller than 10 nm can switch their magnetization direction using room temperature thermal energy, making them useless for memory storage. Suspensions of nanoparticles are possible because the interaction of the particle surface with the solvent is strong enough to overcome differences in density, which for larger particles usually results in a material either sinking or floating in a liquid. Nanoparticles have unexpected visible properties because they are small enough to confine their electrons and produce quantum effects. For example gold nanoparticles appear deep red to black in solution. The large surface area to volume ratio reduces the melting temperatures of nanoparticles. The very high surface area to volume ratio of nanoparticles is a driving force for diffusion. Sintering can take place at lower temperatures, in less time than for larger particles. This should not affect the density of the final product, however flow difficulties and the tendency of nanoparticles to agglomerate can cause issues. The presence of Titanium Dioxide nanoparticles impart a self-cleaning effect, and the size being nanorange, the particles can't be seen. Zinc Oxide nanoparticles have UV blocking properties and are added to sunscreen lotions. Clay nanoparticles or carbon black when incorporated into polymer matrices increase reinforcement, offering us stronger plastics, with higher glass transition temperatures. These nanoparticles are hard, and impart their properties to the polymer. Nanoparticles attached to textile fibers can create smart and functional clothing. NANOPHASE CERAMICS: Using nanoscale particles in the production of ceramic materials we can have simultaneous and major increase in both strength and ductility. Nanophase ceramics are also utilized for catalysis because of their high surface-to-area ratios. Nanophase ceramic particles such as SiC are also used as reinforcement in metals such as aluminum matrix. If you can think of an application for nanomanufacturing useful for your business, let us know and receive our input. We can design, prototype, manufacture, test and deliver these to you. We put great value in intellectual property protection and can make special arrangements for you to ensure your designs and products are not copied. Our nanotechnology designers and nanomanufacturing engineers are some of the best in the World and they are the same people who developed some of the World's most advanced and smallest devices. Click on blue colored text below to download product catalogs and brochures: - Private Label Nano Surface Protection Car Care Products We can label these products with your name and logo if you wish - Private Label Nano Surface Industrial Products We can label these products with your name and logo if you wish - Private Label Nano Surface Protection Marine Products We can label these products with your name and logo if you wish - Private Label Nano Surface Protection Products We can label these products with your name and logo if you wish CLICK Product Finder-Locator Service RÛPERA BERÊ
- Microelectronics Manufacturing, Semiconductor Fabrication, Foundry, IC
Microelectronics Manufacturing, Semiconductor Fabrication - Foundry - FPGA - IC Assembly Packaging - AGS-TECH Inc. Mîkroelektronîk & Çêkirin û Çêkirin Semiconductor Many of our nanomanufacturing, micromanufacturing and mesomanufacturing techniques and processes explained under the other menus can be used for MICROELECTRONICS MANUFACTURING too. However due to the importance of microelectronics in our products, we will concentrate on the subject specific applications of these processes here. Microelectronics related processes are also widely referred to as SEMICONDUCTOR FABRICATION processes. Our semiconductor engineering design and fabrication services include: - FPGA board design, development and programming - Microelectronics foundry services: Design, prototyping and manufacturing, third-party services - Semiconductor wafer preparation: Dicing, backgrinding, thinning, reticle placement, die sorting, pick and place, inspection - Microelectronic package design and fabrication: Both off-shelf and custom design and fabrication - Semiconductor IC assembly & packaging & test: Die, wire and chip bonding, encapsulation, assembly, marking and branding - Lead frames for semiconductor devices: Both off-shelf and custom design and fabrication - Design and fabrication of heat sinks for microelectronics: Both off-shelf and custom design and fabrication - Sensor & actuator design and fabrication: Both off-shelf and custom design and fabrication - Optoelectronic & photonic circuits design and fabrication Let us examine the microelectronics and semiconductor fabrication and test technologies in more detail so you can better understand the services and products we are offering. FPGA Board Design & Development and Programming: Field-programmable gate arrays (FPGAs) are reprogrammable silicon chips. Contrary to processors that you find in personal computers, programming an FPGA rewires the chip itself to implement user’s functionality rather than running a software application. Using prebuilt logic blocks and programmable routing resources, FPGA chips can be configured to implement custom hardware functionality without using a breadboard and soldering iron. Digital computing tasks are carried out in software and compiled down to a configuration file or bitstream that contains information on how the components should be wired together. FPGAs can be used to implement any logical function that an ASIC could perform and are completely reconfigurable and can be given a completely different “personality” by recompiling a different circuit configuration. FPGAs combine the best parts of application-specific integrated circuits (ASICs) and processor-based systems. These benefits include the following: • Faster I/O response times and specialized functionality • Exceeding the computing power of digital signal processors (DSPs) • Rapid prototyping and verification without the fabrication process of custom ASIC • Implementation of custom functionality with the reliability of dedicated deterministic hardware • Field-upgradable eliminating the expense of custom ASIC re-design and maintenance FPGAs provide speed and reliability, without requiring high volumes to justify the large upfront expense of custom ASIC design. Reprogrammable silicon also has the same flexibility of software running on processor-based systems, and it is not limited by the number of processing cores available. Unlike processors, FPGAs are truly parallel in nature, so different processing operations do not have to compete for the same resources. Each independent processing task is assigned to a dedicated section of the chip, and can function autonomously without any influence from other logic blocks. As a result, the performance of one part of the application is not affected when more processing is added on. Some FPGAs have analog features in addition to digital functions. Some common analog features are programmable slew rate and drive strength on each output pin, allowing the engineer to set slow rates on lightly loaded pins that would otherwise ring or couple unacceptably, and to set stronger, faster rates on heavily loaded pins on high-speed channels that would otherwise run too slowly. Another relatively common analog feature is differential comparators on input pins designed to be connected to differential signaling channels. Some mixed signal FPGAs have integrated peripheral analog-to-digital converters (ADCs) and digital-to-analog converters (DACs) with analog signal conditioning blocks that allow them to operate as a system-on-a-chip. Briefly, the top 5 benefits of FPGA chips are: 1. Good Performance 2. Short Time to Market 3. Low Cost 4. High Reliability 5. Long-Term Maintenance Capability Good Performance – With their capability of accommodating parallel processing, FPGAs have better computing power than digital signal processors (DSPs) and do not require sequential execution as DSPs and can accomplish more per clock cycles. Controlling inputs and outputs (I/O) at the hardware level provides faster response times and specialized functionality to closely match application requirements. Short Time to market - FPGAs offer flexibility and rapid prototyping capabilities and thus shorter time-to-market. Our customers can test an idea or concept and verify it in hardware without going through the long and expensive fabrication process of custom ASIC design. We can implement incremental changes and iterate on an FPGA design within hours instead of weeks. Commercial off-the-shelf hardware is also available with different types of I/O already connected to a user-programmable FPGA chip. The growing availability of high-level software tools offer valuable IP cores (prebuilt functions) for advanced control and signal processing. Low Cost—The nonrecurring engineering (NRE) expenses of custom ASIC designs exceed that of FPGA-based hardware solutions. The large initial investment in ASICs can be justified for OEMs producing many chips per year, however many end users need custom hardware functionality for the many systems in development. Our programmable silicon FPGA offers you something with no fabrication costs or long lead times for assembly. System requirements frequently change over time, and the cost of making incremental changes to FPGA designs is negligible when compared to the large expense of respinning an ASIC. High Reliability - Software tools provide the programming environment and FPGA circuitry is a true implementation of program execution. Processor-based systems generally involve multiple layers of abstraction to help task scheduling and share resources among multiple processes. The driver layer controls hardware resources and the OS manages memory and processor bandwidth. For any given processor core, only one instruction can execute at a time, and processor-based systems are continually at risk of time-critical tasks preempting one another. FPGAs, do not use OSs, pose minimum reliability concerns with their true parallel execution and deterministic hardware dedicated to every task. Long-term Maintenance Capability - FPGA chips are field-upgradable and do not require the time and cost involved with redesigning ASIC. Digital communication protocols, for example, have specifications that can change over time, and ASIC-based interfaces may cause maintenance and forward-compatibility challenges. To the contrary, reconfigurable FPGA chips can keep up with potentially necessary future modifications. As products and systems mature, our customers can make functional enhancements without spending time redesigning hardware and modifying the board layouts. Microelectronics Foundry Services: Our microelectronics foundry services include design, prototyping and manufacturing, third-party services. We provide our customers with assistance throughout the entire product development cycle - from design support to prototyping and manufacturing support of semiconductor chips. Our objective in design support services is to enable a first-time right approach for digital, analog, and mixed-signal designs of semiconductor devices. For example, MEMS specific simulation tools are available. Fabs that can handle 6 and 8 inch wafers for integrated CMOS and MEMS are at your service. We offer our clients design support for all major electronic design automation (EDA) platforms, supplying correct models, process design kits (PDK), analog and digital libraries, and design for manufacturing (DFM) support. We offer two prototyping options for all technologies: the Multi Product Wafer (MPW) service, where several devices are processed in parallel on one wafer, and the Multi Level Mask (MLM) service with four mask levels drawn on the same reticle. These are more economical than the full mask set. The MLM service is highly flexible compared to the fixed dates of the MPW service. Companies may prefer outsourcing semiconductor products to a microelectronics foundry for a number of reasons including the need for a second source, using internal resources for other products and services, willingness to go fabless and decrease risk and burden of running a semiconductor fab…etc. AGS-TECH offers open-platform microelectronics fabrication processes that can be scaled down for small wafer runs as well as mass manufacturing. Under certain circumstances, your existing microelectronics or MEMS fabrication tools or complete tool sets can be transferred as consigned tools or sold tools from your fab into our fab site, or your existing microelectronics and MEMS products can be redesigned using open platform process technologies and ported to a process available at our fab. This is faster and more economical than a custom technology transfer. If desired however customer’s existing microelectronics / MEMS fabrication processes may be transferred. Semiconductor Wafer Preparation: If desired by customers after wafers are microfabricated, we carry out dicing, backgrinding, thinning, reticle placement, die sorting, pick and place, inspection operations on semiconductor wafers. Semiconductor wafer processing involves metrology in between the various processing steps. For example, thin film test methods based on ellipsometry or reflectometry, are used to tightly control the thickness of gate oxide, as well as the thickness, refractive index and extinction coefficient of photoresist and other coatings. We use semiconductor wafer test equipment to verify that the wafers haven't been damaged by previous processing steps up until testing. Once the front-end processes have been completed, the semiconductor microelectronic devices are subjected to a variety of electrical tests to determine if they function properly. We refer to the proportion of microelectronics devices on the wafer found to perform properly as the “yield”. Testing of microelectronics chips on the wafer are carried out with an electronic tester that presses tiny probes against the semiconductor chip. The automated machine marks each bad microelectronics chip with a drop of dye. Wafer test data is logged into a central computer database and semiconductor chips are sorted into virtual bins according to predetermined test limits. The resulting binning data can be graphed, or logged, on a wafer map to trace manufacturing defects and mark bad chips. This map can also be used during wafer assembly and packaging. In final testing, microelectronics chips are tested again after packaging, because bond wires may be missing, or analog performance may be altered by the package. After a semiconductor wafer is tested, it is typically reduced in thickness before the wafer is scored and then broken into individual dies. This process is called semiconductor wafer dicing. We use automated pick-and-place machines specially manufactured for microelectronics industry to sort out the good and bad semiconductor dies. Only the good, unmarked semiconductor chips are packaged. Next, in the microelectronics plastic or ceramic packaging process we mount the semiconductor die, connect the die pads to the pins on the package, and seal the die. Tiny gold wires are used to connect the pads to the pins using automated machines. Chip scale package (CSP) is another microelectronics packaging technology. A plastic dual in-line package (DIP), like most packages, is multiple times larger than the actual semiconductor die placed inside, whereas CSP chips are nearly the size of the microelectronics die; and a CSP can be constructed for each die before the semiconductor wafer is diced. The packaged microelectronics chips are re-tested to make sure that they are not damaged during packaging and that the die-to-pin interconnect process was completed correctly. Using lasers we then etch the chip names and numbers on the package. Microelectronic Package Design and Fabrication: We offer both off-shelf and custom design and fabrication of microelectronic packages. As part of this service, modeling and simulation of microelectronic packages is also carried out. Modeling and simulation ensures virtual Design of Experiments (DoE) to achieve the optimal solution, rather than testing packages on the field. This reduces the cost and production time, especially for new product development in microelectronics. This work also gives us the opportunity to explain our customers how the assembly, reliability and testing will impact their microelectronic products. The primary objective of microelectronic packaging is to design an electronic system that will satisfy the requirements for a particular application at a reasonable cost. Because of the many options available to interconnect and house a microelectronics system, the choice of a packaging technology for a given application needs expert evaluation. Selection criteria for microelectronics packages may include some of the following technology drivers: -Wireability -Yield -Cost -Heat dissipation properties -Electromagnetic shielding performance -Mechanical toughness -Reliability These design considerations for microelectronics packages affect speed, functionality, junction temperatures, volume, weight and more. The primary goal is to select the most cost-effective yet reliable interconnection technology. We use sophisticated analysis methods and software to design microelectronics packages. Microelectronics packaging deals with the design of methods for the fabrication of interconnected miniature electronic systems and the reliability of those systems. Specifically, microelectronics packaging involves routing of signals while maintaining signal integrity, distributing ground and power to semiconductor integrated circuits, dispersing dissipated heat while maintaining structural and material integrity, and protecting the circuit from environmental hazards. Generally, methods for packaging microelectronics ICs involve the use of a PWB with connectors that provide the real-world I/Os to an electronic circuit. Traditional microelectronics packaging approaches involve the use of single packages. The main advantage of a single-chip package is the ability to fully test the microelectronics IC before interconnecting it to the underlying substrate. Such packaged semiconductor devices are either through-hole mounted or surface mounted to the PWB. Surface-mounted microelectronics packages do not require via holes to go through the entire board. Instead, surface-mounted microelectronics components can be soldered to both sides of the PWB, enabling higher circuit density. This approach is called surface-mount technology (SMT). The addition of area-array–style packages such as ball-grid arrays (BGAs) and chip-scale packages (CSPs) is making SMT competitive with the highest-density semiconductor microelectronics packaging technologies. A newer packaging technology involves the attachment of more than one semiconductor device onto a high-density interconnection substrate, which is then mounted in a large package, providing both I/O pins and environmental protection. This multichip module (MCM) technology is further characterized by the substrate technologies used to interconnect the attached ICs. MCM-D represents deposited thin film metal and dielectric multilayers. MCM-D substrates have the highest wiring densities of all MCM technologies thanks to the sophisticated semiconductor processing technologies. MCM-C refers to multilayered “ceramic” substrates, fired from stacked alternating layers of screened metal inks and unfired ceramic sheets. Using MCM-C we obtain a moderately dense wiring capacity. MCM-L refers to multilayer substrates made from stacked, metallized PWB “laminates,” that are individually patterned and then laminated. It used to be a low-density interconnect technology, however now MCM-L is quickly approaching the density of MCM-C and MCM-D microelectronics packaging technologies. Direct chip attach (DCA) or chip-on-board (COB) microelectronics packaging technology involves mounting the microelectronics ICs directly to the PWB. A plastic encapsulant, which is “globbed” over the bare IC and then cured, provides environmental protection. Microelectronics ICs can be interconnected to the substrate using either flip-chip, or wire bonding methods. DCA technology is particularly economical for systems that are limited to 10 or fewer semiconductor ICs, since larger numbers of chips can affect system yield and DCA assemblies can be difficult to rework. An advantage common to both the DCA and MCM packaging options is the elimination of the semiconductor IC package interconnection level, which allows closer proximity (shorter signal transmission delays) and reduced lead inductance. The primary disadvantage with both methods is the difficulty in purchasing fully tested microelectronics ICs. Other disadvantages of DCA and MCM-L technologies include poor thermal management thanks to the low thermal conductivity of PWB laminates and a poor coefficient of thermal expansion match between the semiconductor die and the substrate. Solving the thermal expansion mismatch problem requires an interposer substrate such as molybdenum for wire bonded die and an underfill epoxy for flip-chip die. The multichip carrier module (MCCM) combines all the positive aspects of DCA with MCM technology. The MCCM is simply a small MCM on a thin metal carrier that can be bonded or mechanically attached to a PWB. The metal bottom acts as both a heat dissipater and a stress interposer for the MCM substrate. The MCCM has peripheral leads for wire bonding, soldering, or tab bonding to a PWB. Bare semiconductor ICs are protected using a glob-top material. When you contact us, we will discuss your application and requirements to choose the best microelectronics packaging option for you. Semiconductor IC Assembly & Packaging & Test: As part of our microelectronics fabrication services we offer die, wire and chip bonding, encapsulation, assembly, marking and branding, testing. For a semiconductor chip or integrated microelectronics circuit to function, it needs to be connected to the system that it will control or provide instructions to. Microelectronics IC assembly does provide the connections for power and information transfer between the chip and the system. This is accomplished by connecting the microelectronics chip to a package or directly connecting it to the PCB for these functions. Connections between the chip and the package or printed circuit board (PCB) are via wire bonding, thru-hole or flip chip assembly. We are an industry leader in finding microelectronics IC packaging solutions to meet the complex requirements of the wireless and internet markets. We offer thousands of different package formats and sizes, ranging from traditional leadframe microelectronics IC packages for thru-hole and surface mount, to the latest chip scale (CSP) and ball grid array (BGA) solutions required in high pin count and high density applications. A wide variety of packages are available from stock including CABGA (Chip Array BGA), CQFP, CTBGA (Chip Array Thin Core BGA), CVBGA (Very Thin Chip Array BGA), Flip Chip, LCC, LGA, MQFP, PBGA, PDIP, PLCC, PoP - Package on Package, PoP TMV - Through Mold Via, SOIC / SOJ, SSOP, TQFP, TSOP, WLP (Wafer Level Package)…..etc. Wire bonding using copper, silver or gold are among the popular in microelectronics. Copper (Cu) wire has been a method of connecting silicon semiconductor dies to the microelectronics package terminals. With recent increase in gold (Au) wire cost, copper (Cu) wire is an attractive way to manage overall package cost in microelectronics. It also resembles gold (Au) wire due to its similar electrical properties. Self inductance and self capacitance are almost the same for gold (Au) and copper (Cu) wire with copper (Cu) wire having lower resistivity. In microelectronics applications where resistance due to bond wire can negatively impact circuit performance, using copper (Cu) wire can offer improvement. Copper, Palladium Coated Copper (PCC) and Silver (Ag) alloy wires have emerged as alternatives to gold bond wires due to cost. Copper-based wires are inexpensive and have low electrical resistivity. However, the hardness of copper makes it difficult to use in many applications such as those with fragile bond pad structures. For these applications, Ag-Alloy offers properties similar to those of gold while its cost is similar to that of PCC. Ag-Alloy wire is softer than PCC resulting in lower Al-Splash and lower risk of bond pad damage. Ag-Alloy wire is the best low cost replacement for applications that need die-to-die bonding, waterfall bonding, ultra-fine bond pad pitch and small bond pad openings, ultra low loop height. We provide a complete range of semiconductor testing services including wafer testing, various types of final testing, system level testing, strip testing and complete end-of-line services. We test a variety of semiconductor device types across all of our package families including radio frequency, analog and mixed signal, digital, power management, memory and various combinations such as ASIC, multi chip modules, System-in-Package (SiP), and stacked 3D packaging, sensors and MEMS devices such as accelerometers and pressure sensors. Our test hardware and contacting equipment are suitable for custom package size SiP, dual-sided contacting solutions for Package on Package (PoP), TMV PoP, FusionQuad sockets, multiple-row MicroLeadFrame, Fine-Pitch Copper Pillar. Test equipment and test floors are integrated with CIM / CAM tools, yield analysis and performance monitoring to deliver very high efficiency yield the first time. We offer numerous adaptive microelectronics test processes for our customers and offer distributed test flows for SiP and other complex assembly flows. AGS-TECH provides a full range of test consultation, development and engineering services across your entire semiconductor and microelectronics product lifecycle. We understand the unique markets and testing requirements for SiP, automotive, networking, gaming, graphics, computing, RF / wireless. Semiconductor manufacturing processes require fast and precisely controlled marking solutions. Marking speeds over 1000 characters/second and material penetration depths less than 25 microns are common in semiconductor microelectronics industry using advanced lasers. We are capable of marking mold compounds, wafers, ceramics and more with minimal heat input and perfect repeatability. We use lasers with high accuracy to mark even the smallest parts without damage. Lead frames for Semiconductor Devices: Both off-shelf and custom design and fabrication are possible. Lead frames are utilized in the semiconductor device assembly processes, and are essentially thin layers of metal that connect the wiring from tiny electrical terminals on the semiconductor microelectronics surface to the large-scale circuitry on electrical devices and PCBs. Lead frames are used in almost all semiconductor microelectronics packages. Most microelectronics IC packages are made by placing the semiconductor silicon chip on a lead frame, then wire bonding the chip to the metal leads of that lead frame, and subsequently covering the microelectronics chip with plastic cover. This simple and relatively low cost microelectronics packaging is still the best solution for many applications. Lead frames are produced in long strips, which allows them to be quickly processed on automated assembly machines, and generally two manufacturing processes are used: photo etching of some sort and stamping. In microelectronics lead frame design often demand is for customized specifications and features, designs that enhance electrical and thermal properties, and specific cycle time requirements. We have in-depth experience of microelectronics lead frame manufacturing for an array of different customers using laser assisted photo etching and stamping. Design and fabrication of heat sinks for microelectronics: Both off-shelf and custom design and fabrication. With the increase in heat dissipation from microelectronics devices and the reduction in overall form factors, thermal management becomes a more a more important element of electronic product design. The consistency in performance and life expectancy of electronic equipment are inversely related to the component temperature of the equipment. The relationship between the reliability and the operating temperature of a typical silicon semiconductor device shows that a reduction in the temperature corresponds to an exponential increase in the reliability and life expectancy of the device. Therefore, long life and reliable performance of a semiconductor microelectronics component may be achieved by effectively controlling the device operating temperature within the limits set by the designers. Heat sinks are devices that enhance heat dissipation from a hot surface, usually the outer case of a heat generating component, to a cooler ambient such as air. For the following discussions, air is assumed to be the cooling fluid. In most situations, heat transfer across the interface between the solid surface and the coolant air is the least efficient within the system, and the solid-air interface represents the greatest barrier for heat dissipation. A heat sink lowers this barrier mainly by increasing the surface area that is in direct contact with the coolant. This allows more heat to be dissipated and/or lowers the semiconductor device operating temperature. The primary purpose of a heat sink is to maintain the microelectronics device temperature below the maximum allowable temperature specified by the semiconductor device manufacturer. We can classify heat sinks in terms of manufacturing methods and their shapes. The most common types of air-cooled heat sinks include: - Stampings: Copper or aluminum sheet metals are stamped into desired shapes. they are used in traditional air cooling of electronic components and offer an economical solution to low density thermal problems. They are suitable for high volume production. - Extrusion: These heat sinks allow the formation of elaborate two-dimensional shapes capable of dissipating large heat loads. They may be cut, machined, and options added. A cross-cutting will produce omnidirectional, rectangular pin fin heat sinks, and incorporating serrated fins improves the performance by approximately 10 to 20%, but with a slower extrusion rate. Extrusion limits, such as the fin height-to-gap fin thickness, usually dictate the flexibility in design options. Typical fin height-to-gap aspect ratio of up to 6 and a minimum fin thickness of 1.3mm, are attainable with standard extrusion techniques. A 10 to 1 aspect ratio and a fin thickness of 0.8″can be obtained with special die design features. However, as the aspect ratio increases, the extrusion tolerance is compromised. - Bonded/Fabricated Fins: Most air cooled heat sinks are convection limited, and the overall thermal performance of an air cooled heat sink can often be improved significantly if more surface area can be exposed to the air stream. These high performance heat sinks utilize thermally conductive aluminum-filled epoxy to bond planar fins onto a grooved extrusion base plate. This process allows for a much greater fin height-to-gap aspect ratio of 20 to 40, significantly increasing the cooling capacity without increasing the need for volume. - Castings: Sand, lost wax and die casting processes for aluminum or copper / bronze are available with or without vacuum assistance. We use this technology for fabrication of high density pin fin heat sinks which provide maximum performance when using impingement cooling. - Folded Fins: Corrugated sheet metal from aluminum or copper increases surface area and the volumetric performance. The heat sink is then attached to either a base plate or directly to the heating surface via epoxy or brazing. It is not suitable for high profile heat sinks on account of the availability and fin efficiency. Hence, it allows high performance heat sinks to be fabricated. In selecting an appropriate heat sink meeting the required thermal criteria for your microelectronics applications, we need to examine various parameters that affect not only the heat sink performance itself, but also the overall performance of the system. The choice of a particular type of heat sink in microelectronics depends largely to the thermal budget allowed for the heat sink and external conditions surrounding the heat sink. There is never a single value of thermal resistance assigned to a given heat sink, since the thermal resistance varies with external cooling conditions. Sensor & Actuator Design and Fabrication: Both off-shelf and custom design and fabrication are available. We offer solutions with ready-to-use processes for inertial sensors, pressure and relative pressure sensors and IR temperature sensor devices. By using our IP blocks for accelerometers, IR and pressure sensors or applying your design according to available specifications and design rules, we can have MEMS based sensor devices delivered to you within weeks. Besides MEMS, other types of sensor and actuator structures can be fabricated. Optoelectronic & photonic circuits design and fabrication: A photonic or optical integrated circuit (PIC) is a device that integrates multiple photonic functions. It can be resembled to electronic integrated circuits in microelectronics. The major difference between the two is that a photonic integrated circuit provides functionality for information signals imposed on optical wavelengths in the visible spectrum or near infrared 850 nm-1650 nm. Fabrication techniques are similar to those used in microelectronics integrated circuits where photolithography is used to pattern wafers for etching and material deposition. Unlike semiconductor microelectronics where the primary device is the transistor, there is no single dominant device in optoelectronics. Photonic chips include low loss interconnect waveguides, power splitters, optical amplifiers, optical modulators, filters, lasers and detectors. These devices require a variety of different materials and fabrication techniques and therefore it is difficult to realize all of them on a single chip. Our applications of photonic integrated circuits are mainly in the areas of fiber-optic communication, biomedical and photonic computing. Some example optoelectronic products we can design and fabricate for you are LEDs (Light Emitting Diodes), diode lasers, optoelectronic receivers, photodiodes, laser distance modules, customized laser modules and more. CLICK Product Finder-Locator Service RÛPERA BERÊ
- Glass Cutting Shaping Tools , USA , AGS-TECH Inc.
Glass Cutting Shaping Tools offered by AGS-TECH, Inc. We supply high quality diamond wheel series, diamond wheel for solar glass, diamond wheel for CNC machine, peripheral diamond wheel, cup & bowl shape diamond wheels, resin wheel series, polishing wheel series, felt wheel, stone wheel, coating removal wheel... Glass Cutting Shaping Tools Please click on the Glass Cutting and Shaping Tools of interest below to download related brochure. Diamond Wheel Series Diamond Wheel for Solar Glass Diamond Wheel for CNC Machine Peripheral Diamond Wheel Cup & Bowl Shape Diamond Wheel Resin Wheel Series Polishing Wheel Series 10S Polishing Wheel Felt Wheel Stone Wheel Coating Removal Wheel BD Polishing Wheel BK Polishing Wheel 9R Ploshing Wheel Polishing Material series Cerium Oxide Series Glass Drill Series Glass Tool Series Other Glass Tools Glass Plier Glass Suction & Lifter Grinding Tool Power Tool UV,Testing Tool Sandblast Fittings Series Machine Fittings Series Cutting Discs Glass Cutters Ungrouped Price of our glass cutting shaping tools depends on model and quantity of order. If you would like us to design and/or manufacture glass cutting and shaping tools specifically for you, please either provide us detailed blueprints, or ask us for help. We will then design, prototype and manufacture them specially for you. Since we carry a wide variety of glass cutting, drilling, grinding, polishing and shaping products with different dimensions, applications and material; it is impossible to list them here. We encourage you to email or call us so we can determine which product is the best fit for you. When contacting us, please inform us about: - Intended application - Material grade preferred - Dimensions - Finishing requirements - Packaging requirements - Labeling requirements - Quantity of your planned order & estimated yearly demand Private Label Auto Glass Repair and Replacement Systems We can private label these hand tools if you wish. In other words, we can put your company name, brand and label on them. This way you can promote your brand by reselling these to your customers. Private Label Hand Tools for Every Industry This catalog contains a few glass cutting and shaping tools. We can private label these hand tools if you wish. In other words, we can put your company name, brand and label on them. This way you can promote your brand by reselling these to your customers. Private Label Power Tool Accessories This brochure includes some glass cutting and shaping tools. We can private label these hand tools if you wish. In other words, we can put your company name, brand and label on them. This way you can promote your brand by reselling these to your customers. Private Label Power Tools for Every Industry This catalog contains some glass cutting and shaping tools. We can private label these hand tools if you wish. In other words, we can put your company name, brand and label on them. This way you can promote your brand by reselling these to your customers. VIRÊ bikirtînin da ku kapasîteyên me yên teknîkî û rêbernameya referansê dakêşin ji bo birîna taybetmendî, sondajê, rijandin, çêkirin, şikilandin, pîvazkirina amûrên ku di bijîjkî, diranan, amûrên rast, mêtina metal, çêkirina mirinê û sepanên din ên pîşesaziyê de têne bikar anîn. CLICK Product Finder-Locator Service Li vir bikirtînin da ku biçin Menuya Amûrên Birîn, Xalkirin, Xirkirin, Lapkirin, Paqijkirin, Diçandin û Teşekirin. Ref. Kod: OICASANHUA
- Microwave Components & Subassembly, Microwave Circuits, RF Transformer
Microwave Components - Subassembly - Microwave Circuits - RF Transformer - LNA - Mixer - Fixed Attenuator - AGS-TECH Pêkhateyên Mîkropêl û Pergalên Hilberîn & Civîn We manufacture and supply: Microwave electronics including silicon microwave diodes, dot touch diodes, schottky diodes, PIN diodes, varactor diodes, step recovery diodes, microwave integrated circuits, splitters/combiners, mixers, directional couplers, detectors, I/Q modulators, filters, fixed attenuators, RF transformers, simulation phase shifters, LNA, PA, switches, attenuators, and limiters. We also custom manufacture microwave subassemblies and assemblies according to users' requirements. Please download our microwave components and systems brochures from the links below: Antenna Brochure for 5G - LTE 4G - LPWA 3G - 2G - GPS - GNSS - WLAN - BT - Combo - ISM Barcode and Fixed Mount Scanners - RFID Products - Mobile Computers - Micro Kiosks OEM Technology (We private label these with your brand name and logo if you wish) Barcode Scanners (We private label these with your brand name and logo if you wish) Microwave Flexible Cable Assembly Microwave and Milimeter Wave Test Accessories Brochure (Cable assemblies, VNA Test Assemblies, Mechanical Calibration Kits, RF Coaxial Adapters, Test Port Adapters, DC Blocks, NMD Connectors....etc.) Microwave Waveguides - Coaxial Components - Milimeterwave Antennas (Straight Waveguide, Waveguide Bend, Waveguide to Coaxial Adapter, Directional Couplers, Waveguide Tee, Circulators, Isolators......etc.) Printers for Barcode Scanners and Mobile Computers (We private label these with your brand name and logo if you wish) RF and Microwave Components (Broadband 90/180 Degree Hybrid and Coupler, Broadband Power Divider, Filter, RF switch, Broadband Amplifier, Broadband Frequency Synthesizer) RFID Readers - Scanners - Encoders - Printers (We private label these with your brand name and logo if you wish) Soft Ferrites - Cores - Toroids - EMI Suppression Products - RFID Transponders and Accessories Brochure Dowload brochure for our DESIGN PARTNERSHIP PROGRAM Microwaves are electromagnetic waves with wavelengths ranging from 1 mm to 1 m, or frequencies between 0.3 GHz and 300 GHz.The microwave range includes ultra-high frequency (UHF) (0.3–3 GHz), super high frequency (SHF) (3–30 GHz), and extremely high frequency (EHF) (30–300 GHz) signals. Uses of microwave technology: COMMUNICATION SYSTEMS: Before the invention of fiber optic transmission technology, most long distance telephone calls were carried via microwave point-to-point links through sites like the AT&T Long Lines. Starting in the early 1950s, frequency division multiplexing was used to send up to 5,400 telephone channels on each microwave radio channel, with as many as ten radio channels combined into one antenna for the hop to the next site, that was up to 70 km away. Wireless LAN protocols, such as Bluetooth and the IEEE 802.11 specifications, also use microwaves in the 2.4 GHz ISM band, although 802.11a uses ISM band and U-NII frequencies in the 5 GHz range. Licensed long-range (up to about 25 km) Wireless Internet Access services can be found in many countries in the 3.5–4.0 GHz range (not in the USA however). Metropolitan Area Networks: MAN protocols, such as WiMAX (Worldwide Interoperability for Microwave Access) based in the IEEE 802.16 specification. The IEEE 802.16 specification was designed to operate between 2 to 11 GHz frequencies. The commercial implementations are in the 2.3GHz, 2.5 GHz, 3.5 GHz and 5.8 GHz frequency ranges. Wide Area Mobile Broadband Wireless Access: MBWA protocols based on standards specifications such as IEEE 802.20 or ATIS/ANSI HC-SDMA (e.g. iBurst) are designed to operate between 1.6 and 2.3 GHz to give mobility and in-building penetration characteristics similar to mobile phones but with much much greater spectral efficiency. Some of the lower microwave frequency spectrum is used on Cable TV and Internet access on coaxial cable as well as broadcast television. Also some mobile phone networks, like GSM, also use lower microwave frequencies. Microwave radio is used in broadcasting and telecommunication transmissions because, due to their short wavelength, highly directive antennas are smaller and therefore more practical than they would be at lower frequencies (longer wavelengths). There is also more bandwidth in the microwave spectrum than in the rest of the radio spectrum; the usable bandwidth below 300 MHz is less than 300 MHz while many GHz can be used above 300 MHz. Typically, microwaves are used in television news to transmit a signal from a remote location to a television station in a specially equipped van. The C, X, Ka, or Ku Bands of the microwave spectrum are used in the operation of most satellite communications systems. These frequencies allow large bandwidth while avoiding the crowded UHF frequencies and staying below the atmospheric absorption of EHF frequencies. Satellite TV either operates in the C band for the traditional large dish Fixed Satellite Service or Ku band for Direct Broadcast Satellite. Military communication systems run primarily over X or Ku Band links, with Ka band being used for Milstar. REMOTE SENSING: Radars use microwave frequency radiation to detect the range, speed, and other characteristics of remote objects. Radars are widely used for applications including air traffic control, navigation of ships, and traffic speed limit control. Besides ultrasonic decices, sometimes Gunn diode oscillators and waveguides are used as motion detectors for automatic door openers. Much of radio astronomy uses microwave technology. NAVIGATION SYSTEMS: Global Navigation Satellite Systems (GNSS) including the American Global Positioning System (GPS), the Chinese Beidou and the Russian GLONASS broadcast navigational signals in various bands between about 1.2 GHz and 1.6 GHz. POWER: A microwave oven passes (non-ionizing) microwave radiation (at a frequency near 2.45 GHz) through food, causing dielectric heating by absorption of energy in the water, fats and sugar contained in the food. Microwave ovens became common following development of inexpensive cavity magnetrons. Microwave heating is widely used in industrial processes for drying and curing products. Many semiconductor processing techniques use microwaves to generate plasma for purposes such as reactive ion etching (RIE) and plasma-enhanced chemical vapor deposition (PECVD). Microwaves can be used to transmit power over long distances. NASA worked in the 1970s and early 1980s to research the possibilities of using Solar Power Satellite (SPS) systems with large solar arrays that would beam power down to the Earth's surface via microwaves. Some light weaponry uses millimeter waves to heat a thin layer of human skin to an intolerable temperature to make the targeted person move away. A two-second burst of the 95 GHz focused beam heats the skin to a temperature of 130 °F (54 °C) at a depth of 1/64th of an inch (0.4 mm). The United States Air Force and Marines use this type of Active Denial System. If your interest is in engineering and research & development, please visit our engineering site http://www.ags-engineering.com CLICK Product Finder-Locator Service RÛPERA BERÊ
- Automation Robotic Systems Manufacturing | agstech
Motion Control, Positioning, Motorized Stage, Actuator, Gripper, Servo Amplifier, Hardware Software Interface Card, Translation Stages, Rotary Table,Servo Motor Otomasyon & Hilberîn û Civîna Pergalên Robotîk Being an engineering integrator, we can provide you AUTOMATION SYSTEMS including: • Motion control and positioning assemblies, motors, motion controller, servo amplifier, motorized stage, lift stage, goniometers, drives, actuators, grippers, direct drive air bearing spindles, hardware-software interface cards and software, custom built pick and place systems, custom built automated inspection systems assembled from translation/rotary stages and cameras, custom built robots, custom automation systems. We also supply manual positioner, manual tilt, rotary or linear stage for simpler applications. A large selection of linear and rotary tables/slides/stages that utilize brushless linear direct-drive servomotors, as well as ball screw models driven with brush or brushless rotary motors are available. Air bearing systems are also an option in automation. Depending on your automation requirements and application, we choose translation stages with suitable travel distance, speed, accuracy, resolution, repeatability, load capacity, in-position stability, reliability...etc. Again, depending on your automation application we can supply you either a purely linear or linear/rotary combination stage. We can manufacture special fixtures, tools and combine them with your motion control hardware to turn them into a complete turnkey automation solution for you. If you require also assistance with installing drivers, code writing for specially developed software with user friendly interface, we can send our experienced automation engineer to your site on a contract basis. Our engineer can directly communicate with you on a daily basis so that at the end you have a custom tailored automation system free of bugs and meeting your expectations. Goniometers: For high-accuracy angular alignment of optical components. The design utilizes direct-drive noncontact motor technology. When used with the multiplier, it provides a positioning speed of 150 degrees per second. So whether you are thinking of an automation system with a moving camera, taking snapshots of a product and analyzing the images acquired to determine a product defect, or whether you are trying to reduce manufacturing leadtimes by integrating a pick and place robot to your automated manufacturing, call us, contact us and you will be glad with the solutions we can provide you. ROBOTS and COBOTS Here are brochures of some off-shelf robots you can download. If you wish we can build you customized robots and cobots that will better fit your needs and applications. We can either redesign and modify existing robot platforms or make new designs for you. Click on blue colored text below to download catalogs: - Collaborative Robots - Customized Agricultural Robots - Customized Commercial Places Robots - Customized Health Care and Hospital Robots - Customized Warehousing Robots - Customized Robots for a Variety of Applications - Food and Beverage Delivery Robot-A302-A302D - Hospital Delivery Robot A801 - Indoor Delivery Robots A301-A301A - Indoor Delivery Robot A305 - Mobile Robot Platform A001 - Robotic Laser Welding Workstation - Robotics Product Brochure - Robotics Workstations - Robot Palletizing Workstation - Robotic Vending Machine A406 - Security Robot A602 - Selection Guide of Industrial Robot Platforms - Small Objects Transfer Robot A503 - Warehouse Logistics Robots A201-A201A - Welding Robots Brochure OTHER ALTERNATIVE ROBOTS and COBOTS No one design or product meets every customer's needs. Below are downloadable brochures for our other products. - Hikrobot Mobile Robots Catalog - Hikvision Logistic Vision Solutions AUTOMATION COMPONENTS AND SPARE PARTS Click on highlighted text to download brochures and catalogs of products you can use as accessories, spare components in building automation systems, robots and cobots: - Barcode and Fixed Mount Scanners - RFID Products - Mobile Computers - Micro Kiosks OEM Technology (We private label these with your brand name and logo if you wish) - Barcode Scanners (We private label these with your brand name and logo if you wish) - Fixed Industrial Scanners (We private label these with your brand name and logo if you wish) - Hikrobot Machine Vision Products - Hikrobot Smart Machine Vision Products - Hikrobot Machine Vision Standard Products - Kinco automation products, including HMI, stepper system, ED servo, CD servo, PLC, field bus. - Kiosk Systems (We private label these with your brand name and logo if you wish) - Kiosk Systems Accessories Guide (We private label these with your brand name and logo if you wish) - Linear Bearings, Die-Set Flange Mount Bearings, Pillow Blocks, Square Bearings and various Shafts & Slides for motion control - Mobile Computers for Enterprises (We private label these with your brand name and logo if you wish) - Motor Starter with UL and CE Certification NS2100111-1158052 - Printers for Barcode Scanners and Mobile Computers (We private label these with your brand name and logo if you wish) - Process Automation Solutions (We private label these with your brand name and logo if you wish) - RFID Readers - Scanners - Encoders - Printers (We private label these with your brand name and logo if you wish) - Vandal-Proof IP65/IP67/IP68 Keyboards, Keypads, Pointing Devices, ATM Pinpads, Medical & Military Keyboards and other similar Rugged Computer Peripherals Download brochure for our CUSTOM MACHINE AND EQUIPMENT MANUFACTURING Dowload brochure for our DESIGN PARTNERSHIP PROGRAM If you are looking for industrial computers, embedded computers, panel PC for your automation system, we invite you to visit our industrial computers store at http://www.agsindustrialcomputers.com If you would like to obtain more information about our engineering and research & development capabilities besides manufacturing capabilities, then we invite you to visit our engineering site http://www.ags-engineering.com CLICK Product Finder-Locator Service RÛPERA BERÊ
- Functional Decorative Coatings - Thin Film - Thick Films - AR Coating
Functional & Decorative Coatings, Thin Film, Thick Films, Antireflective and Reflective Mirror Coating - AGS-TECH Inc. Kişandinên Fonksiyonî / Kulîlkên Dekoratîf / Fîlma nazik / Fîlma stûr A COATING is a covering that is applied to the surface of an object. Coatings can be in the form of THIN FILM (less than 1 micron thick) or THICK FILM (over 1 micron thick). Based on the purpose of applying the coating we can offer you DECORATIVE COATINGS and/or FUNCTIONAL COATINGS, or both. Sometimes we apply functional coatings to change the surface properties of the substrate, such as adhesion, wettability, corrosion resistance, or wear resistance. In some other cases such as in semiconductor device fabrication, we apply the functional coatings to add a completely new property such as magnetization or electrical conductivity which become an essential part of the finished product. Our most popular FUNCTIONAL COATINGS are: Adhesive Coatings: Examples are adhesive tape, iron-on fabric. Other functional adhesive coatings are applied to change the adhesion properties, such as non-stick PTFE coated cooking pans, primers that encourage subsequent coatings to adhere well. Tribological Coatings: These functional coatings relate to the principles of friction, lubrication and wear. Any product where one material slides or rubs over another is affected by complex tribological interactions. Products like hip implants and other artificial prosthesis are lubricated in certain ways whereas other products are unlubricated as in high temperature sliding components where conventional lubricants can not be used. The formation of compacted oxide layers have been proven to protect against wear of such sliding mechanical parts. Tribological functional coatings have huge benefits in industry, minimizing wear of machine elements, minimizing wear and tolerance deviations in manufacturing tools such as dies and moulds, minimizing power requirements and making machinery and equipment more energy efficient. Optical Coatings: Examples are Anti-reflective (AR) coatings, reflective coatings for mirrors, UV- absorbent coatings for protection of eyes or for increasing the life of the substrate, tinting used in some colored lighting, tinted glazing and sunglasses. Catalytic Coatings such as applied on self-cleaning glass. Light-Sensitive Coatings used to make products such as photographic films Protective Coatings: Paints can be considered protecting the products besides being decorative in purpose. Hard anti-scratch coatings on plastics and other materials are one of our most widely used functional coatings to reduce scratching, improve wear resistance, …etc. Anti-corrosion coatings such as plating are also very popular. Other protective functional coatings are put on waterproof fabric and paper, antimicrobial surface coatings on surgical tools and implants. Hydrophilic / Hydrophobic Coatings: Wetting (hydrophilic) and unwetting (hydrophobic) functional thin and thick films are important in applications where water absorption is either desired or undesired. Using advanced technology we can alter your product surfaces, to make them either easily wettable or unwettable. Typical applications are in textiles, dressings, leather boots, pharmaceutical or surgical products. Hydrophilic nature refers to a physical property of a molecule that can transiently bond with water (H2O) through hydrogen bonding. This is thermodynamically favorable, and makes these molecules soluble not only in water, but also in other polar solvents. Hydrophilic and hydrophobic molecules are also known as polar molecules and nonpolar molecules, respectively. Magnetic Coatings: These functional coatings add magnetic properties such as is the case for magnetic floppy disks, cassettes, magnetic stripes, magnetooptic storage, inductive recording media, magnetoresist sensors, and thin-film heads on products. Magnetic thin films are sheets of magnetic material with thicknesses of a few micrometers or less, used primarily in the electronics industry. Magnetic thin films can be single-crystal, polycrystalline, amorphous, or multilayered functional coatings in the arrangement of their atoms. Both ferro- and ferrimagnetic films are used. The ferromagnetic functional coatings are usually transition-metal-based alloys. For example, permalloy is a nickel-iron alloy. The ferrimagnetic functional coatings, such as garnets or the amorphous films, contain transition metals such as iron or cobalt and rare earths and the ferrimagnetic properties are advantageous in magnetooptic applications where a low overall magnetic moment can be achieved without a significant change in the Curie temperature. Some sensor elements function on the principle of change in electrical properties, such as the electrical resistance, with a magnetic field. In semiconductor technology, the magnetoresist head used in disk storage technology functions with this principle. Very large magnetoresist signals (giant magnetoresistance) are observed in magnetic multilayers and composites containing a magnetic and nonmagnetic material. Electrical or Electronic Coatings: These functional coatings add electrical or electronic properties such as conductivity to manufacture products such as resistors, insulation properties such as in the case of magnet wire coatings used in transformers. DECORATIVE COATINGS: When we speak of decorative coatings the options are only limited by your imagination. Both thick and thin film type coatings have been successfully engineered and applied in the past to our customers products. Regardless of the difficulty in the geometric shape and material of the substrate and application conditions, we are always capable to formulate the chemistry, physical aspects such as exact Pantone code of color and application method for your desired decorative coatings. Complex patterns involving shapes or different colors are also possible. We can make your plastic polymer parts look metallic. We can color anodize extrusions with various patterns and it won’t even look anodized. We can mirror coat an oddly-shaped part. Furthermore decorative coatings can be formulated that will also act as functional coatings at the same time. Any of the below mentioned thin and thick film deposition techniques used for functional coatings can be deployed for decorative coatings. Here are some of our popular decorative coatings: - PVD Thin Film Decorative Coatings - Electroplated Decorative Coatings - CVD and PECVD Thin Film Decorative Coatings - Thermal Evaporation Decorative Coatings - Roll-to-Roll Decorative Coating - E-Beam Oxide Interference Decorative Coatings - Ion Plating - Cathodic Arc Evaporation for Decorative Coatings - PVD + Photolithography, Heavy Gold Plating on PVD - Aerosol Coatings for Glass Coloring - Anti-tarnish Coating - Decorative Copper-Nickel-Chrome Systems - Decorative Powder Coating - Decorative Painting, Custom Tailored Paint Formulations using Pigments, Fillers, Colloidal Silica Dispersant...etc. If you contact us with your requirements for decorative coatings, we can provide you our expert opinion. We have advanced tools such as color readers, color comparators….etc. to guarantee consistent quality of your coatings. THIN and THICK FILM COATING PROCESSES: Here are the most widely used of our techniques. Electro-Plating / Chemical Plating (hard chromium, chemical nickel) Electroplating is the process of plating one metal onto another by hydrolysis, for decorative purposes, corrosion prevention of a metal or other purposes. Electroplating lets us use inexpensive metals such as steel or zinc or plastics for the bulk of the product and then apply different metals on the outside in the form of a film for better appearance, protection, and for other properties desired for the product. Electroless plating, also known as chemical plating, is a non-galvanic plating method that involves several simultaneous reactions in an aqueous solution, which occur without the use of external electrical power. The reaction is accomplished when hydrogen is released by a reducing agent and oxidized, thus producing a negative charge on the surface of the part. Advantages of these thin and thick films are good corrosion resistance, low processing temperature, possibility to deposit in bore holes, slots… etc. Disadvantages are the limited selection of coating materials, relatively soft nature of the coatings, environmentally polluting treatment baths that are needed including chemicals such as cyanide, heavy metals, fluorides, oils, limited accuracy of surface replication. Diffusion Processes (Nitriding, nitrocarburization, boronizing, phosphating, etc.) In heat treatment furnaces, the diffused elements usually originate from gases reacting at high temperatures with the metal surfaces. This can be a pure thermal and chemical reaction as a consequence of the thermal dissociation of the gases. In some cases, diffused elements originate from solids. The advantages of these thermochemical coating processes are good corrosion resistance, good reproducibility. The disadvantages of these are being relatively soft coatings, limited selection of base material (which must be suitable for nitriding), long processing times, environmental and health hazards involved, requirement of post-treatment. CVD (Chemical Vapor Deposition) CVD is a chemical process used to produce high quality, high-performance, solid coatings. The process produces thin films too. In a typical CVD, the substrates are exposed to one or more volatile precursors, that react and/or decompose on the substrate surface to produce the desired thin film. Advantages of these thin & thick films are their high wear resistance, potential to economically produce thicker coatings, suitability for bore holes, slots ….etc. Disadvantages of CVD processes are their high processing temperatures, difficulty or impossibility of coatings with multiple metals (such as TiAlN), rounding of edges, use of environmentally hazardous chemicals. PACVD / PECVD (Plasma-Assisted Chemical Vapor Deposition) PACVD is also called PECVD standing for Plasma Enhanced CVD. Whereas in a PVD coating process the thin & thick film materials are evaporated from a solid form, in PECVD the coating results from a gas phase. Precursor gasses are cracked in the plasma to become available for the coating. Advantages of this thin and thick film deposition technique is that significantly lower process temperatures are possible as compared to CVD, precise coatings are deposited. Disadvantages of PACVD are that it has only limited suitability for bore holes, slots etc. PVD (Physical Vapor Deposition) PVD processes are a variety of purely physical vacuum deposition methods used to deposit thin films by the condensation of a vaporized form of the desired film material onto workpiece surfaces. Sputtering and evaporative coatings are examples of PVD. Advantages are that no environmentally damaging materials and emissions are produced, a large variety of coatings can be produced, coating temperatures are below the final heat treatment temperature of most steels, precisely reproducible thin coatings, high wear resistance, low frictional coefficient. Disadvantages are bore holes, slots ...etc. can only be coated down to a depth equal to the diameter or width of the opening, corrosion resistant only under certain conditions, and for obtaining uniform film thicknesses, parts must be rotated during deposition. The adhesion of functional and decorative coatings are substrate dependent. Furthermore, the lifetime of thin and thick film coatings depends on environmental parameters such as humidity, temperature...etc. Therefore, before considering a functional or decorative coating, contact us for our opinion. We can choose the most suitable coating materials and coating technique that fits your substrates and application and deposit them under the strictest quality standards. Contact AGS-TECH Inc. for details of thin and thick film deposition capabilities. Do you need design assistance ? Do you need prototypes ? Do you need mass manufacturing ? We are here to help you. Click on blue colored text below to download product catalogs and brochures: - Private Label Nano Surface Protection Car Care Products We can label these products with your name and logo if you wish - Private Label Nano Surface Industrial Products We can label these products with your name and logo if you wish - Private Label Nano Surface Protection Marine Products We can label these products with your name and logo if you wish - Private Label Nano Surface Protection Products We can label these products with your name and logo if you wish CLICK Product Finder-Locator Service RÛPERA BERÊ
- Fiber Optic Components, Splicing Enclosures, FTTH Node, CATV Products
Fiber Optic Components - Splicing Enclosures - FTTH Node - Fiber Distribution Box - Optical Platform - CATV Products - Telecommunication Optics - AGS-TECH Inc. Berhemên Fiber Optîk We supply: • Fiber optic connectors, adapters, terminators, pigtails, patchcords, connector faceplates, shelves, communication racks, fiber distribution box, splicing enclosure, FTTH node, optical platform, fiber optic taps, splitters-combiners, fixed and variable optical attenuators, optical switch, DWDM, MUX/DEMUX, EDFA, Raman amplifiers and other amplifiers, isolator, circulator, gain flattener, custom fiberoptic assembly for telecommunication systems, optical waveguide devices, CATV products • Lasers and photodetectors, PSD (Position Sensitive Detectors), quadcells • Fiber optic assemblies for industrial applications (illumination, light delivery or inspection of pipe interiors, crevices, cavities, body interiors....). • Fiberoptic assemblies for medical applications (see our site http://www.agsmedical.com for medical endoscopes and couplers). Among the products our engineers have developed is a super slim 0.6 mm diameter flexible video endoscope, and a fiber end inspection interferometer. The interferometer was developed by our engineers for in-process and final inspection in manufacturing of fiber connectors. We use special bonding and attachment techniques and materials for rigid, reliable and long life assemblies. Even under extensive environmental cycling such as high temperature/low temperature; high humidity/low humidity our assemblies remain intact and keep working. Download our catalog for passive fiber optic components Download our catalog for active fiber optic products Download our catalog for free space optical components and assemblies Private Label Medical Endoscopes and Visualization Systems (We can put your company name and logo on these) CLICK Product Finder-Locator Service RÛPERA BERÊ