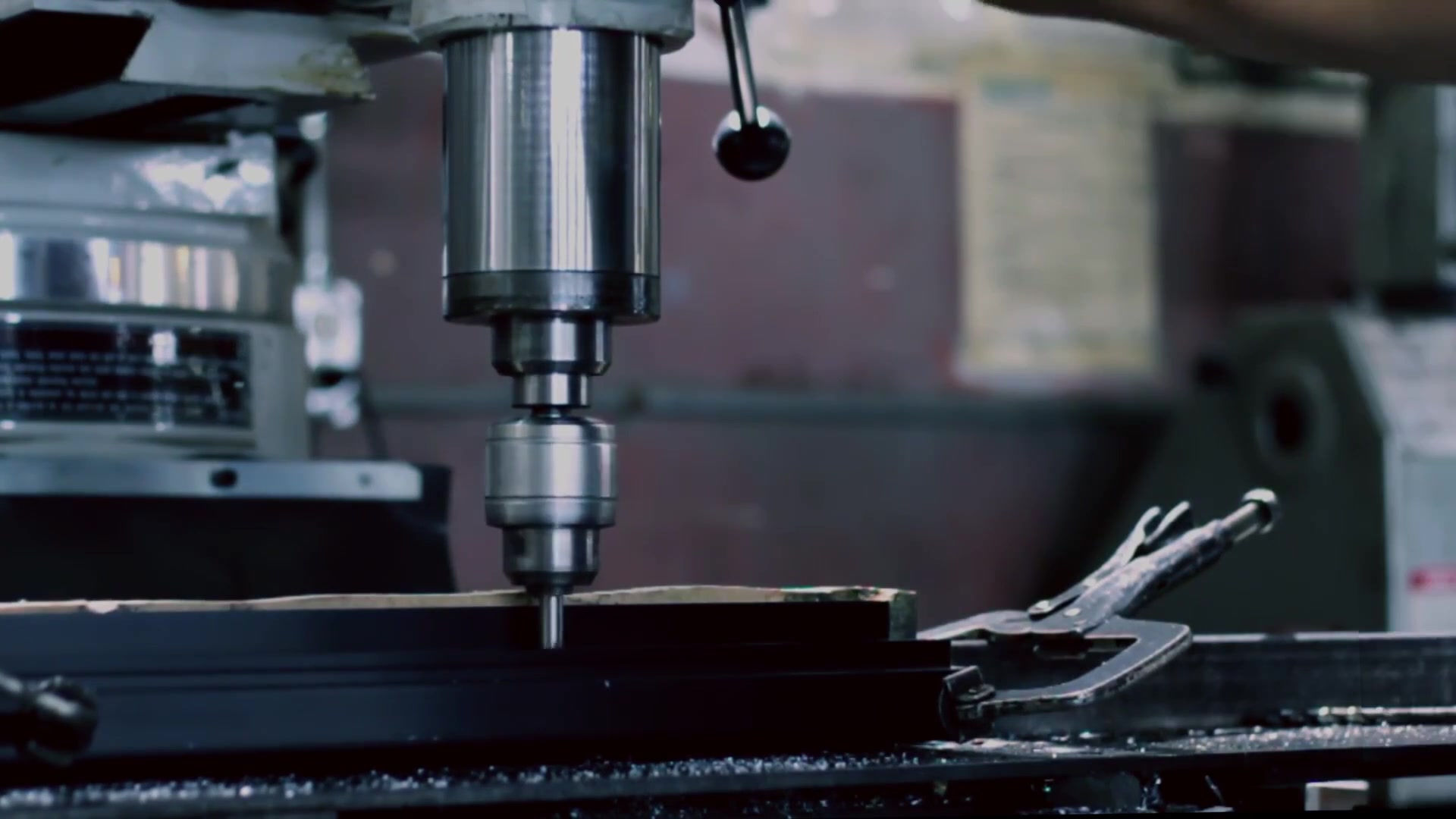
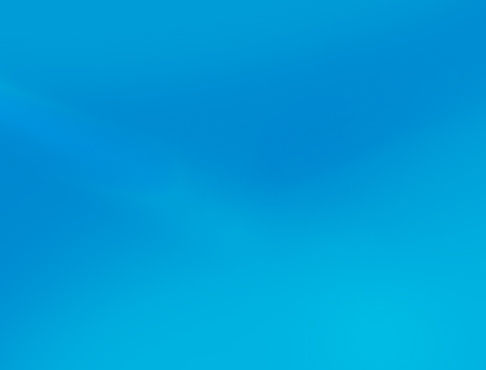
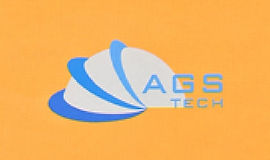
Глобалдык бажы өндүрүүчүсү, интегратор, консолидатор, өнүмдөрдүн жана кызматтардын кеңири түрү үчүн аутсорсинг өнөктөшү.
Биз сиздин өндүрүш, жасоо, инженерия, консолидация, интеграция, аутсорсинг үчүн бирдиктүү булагыбыз.
Тилиңизди тандаңыз
-
Ыңгайлаштырылган өндүрүш
-
Ата мекендик жана дүйнөлүк контракттык өндүрүш
-
Өндүрүштүк аутсорсинг
-
Ички жана дүйнөлүк сатып алуулар
-
Consolidation
-
Инженердик интеграция
-
Инженердик кызматтар
ELECTRICAL DISCHARGE MACHINING (EDM), also referred to as SPARK-EROSION or ELECTRODISCHARGE MACHINING, SPARK ERODING, DIE SINKING_cc781905-5cde-3194-bb3b -136bad5cf58d_or WIRE EROSION, is a NON-CONVENTIONAL MANUFACTURING process where erosion of metals takes place and desired shape is obtained using electrical discharges in the form учкундардын. Биз ошондой эле EDMдин кээ бир түрлөрүн сунуштайбыз, атап айтканда NO-WEAR EDM, WIRE EDM (WEDM), EDM GRINDING (EDG), DIE-SINKING EDM, ELECTRICAL-DISCHARGE MILLING, ELECTRICAL-DISCHARGE MILLING_18m5, -5cde-3194-bb3b-136bad5cf58d_and ЭЛЕКТРОХИМИЯЛЫК-РАЗГИЯЛЫК ТАРТУУ (ECDG). Биздин EDM системалары формадагы шаймандардан/электроддон жана туруктуу кубат булактарына туташтырылган жана электр өткөргүч эмес диэлектрдик суюктукка киргизилген даярдоо бөлүгүнөн турат. 1940-жылдан кийин электр разрядын иштетүү өндүрүш тармагындагы эң маанилүү жана популярдуу өндүрүш технологияларынын бири болуп калды.
Эки электроддун ортосундагы аралык азайганда, электроддордун ортосундагы көлөмдөгү электр талаасынын интенсивдүүлүгү кээ бир чекиттердеги диэлектриктин күчүнөн чоң болуп, ал үзүлүп, акыры эки электроддун ортосунда токтун өтүшү үчүн көпүрө түзүлөт. Интенсивдүү электр жаасы пайда болуп, олуттуу ысытуудан даярдалган материалдын бир бөлүгүн жана шаймандык материалдын бир бөлүгүн эритет. Натыйжада, материал эки электроддон алынып салынат. Ошол эле учурда диэлектрдик суюктук тез ысып, анын натыйжасында дога боштугунда суюктук бууланып кетет. Токтун агымы токтогондон кийин же ал токтогондон кийин айланадагы диэлектрдик суюктуктун жардамы менен газ көбүгүнөн жылуулук чыгарылат жана көбүк кавитацияланат (кыйрайт). Көбүктүн кыйрашынан пайда болгон сокку толкуну жана диэлектрдик суюктуктун агымы бөлүктүн бетинен калдыктарды агызып, эриген даяр материалды диэлектрдик суюктукка киргизет. Бул разряддардын кайталануу ылдамдыгы 50-500 кГц, чыңалуулар 50-380 В жана токтар 0,1 жана 500 Ампер арасында. Минералдык майлар, керосин же дистилденген жана деионизацияланган суу сыяктуу жаңы суюк диэлектрик, адатта, электроддор аралык көлөмдө катуу бөлүкчөлөрдү (таштандылар түрүндө) алып чыгып, диэлектриктин изоляциялык касиеттери калыбына келтирилет. Ток агымынан кийин эки электроддун ортосундагы потенциалдык айырма бузулууга чейинки абалга келет, ошондуктан жаңы суюк диэлектрик бузулушу мүмкүн. Биздин заманбап электрдик разряд машиналары (EDM) сандык башкарылуучу кыймылдарды сунуштайт жана диэлектрдик суюктуктар үчүн насостор жана чыпкалоо системалары менен жабдылган.
Электрдик разрядды иштетүү (EDM) - бул негизинен катуу металлдар үчүн колдонулган же кадимки ыкмалар менен иштетүү өтө кыйын болгон иштетүү ыкмасы. EDM, адатта, электр өткөргүчтөр болгон ар кандай материалдар менен иштейт, бирок изоляциялык керамикаларды EDM менен иштетүү ыкмалары да сунушталган. Эрүү температурасы жана эрүүнүн жашыруун жылуулугу бир разрядда алынган металлдын көлөмүн аныктоочу касиеттер болуп саналат. Бул баалуулуктар канчалык жогору болсо, материалды алып салуу ылдамдыгы ошончолук жайыраак болот. Электр разрядын иштетүү процесси эч кандай механикалык энергияны талап кылбагандыктан, даярдалган материалдын катуулугу, бекемдиги жана катуулугу алып салуу ылдамдыгына таасир этпейт. Разряддын жыштыгы же разряддагы энергия, чыңалуу жана ток материалды алып салуу ылдамдыгын көзөмөлдөө үчүн өзгөрөт. Токтун тыгыздыгынын жогорулашы жана учкундун жыштыгынын азайышы менен материалды алып салуу ылдамдыгы жана бетинин тегиздиги көбөйөт. Биз EDM аркылуу алдын ала катууланган болоттон жасалган татаал контурларды же көңдөйлөрдү жумшартуу жана кайра каттуу үчүн жылуулук менен дарылоонун зарылдыгы жок кесип алабыз. Бул ыкманы титан, хастеллой, ковар жана инконел сыяктуу каалаган металл же металл эритмелери менен колдоно алабыз. EDM процессинин колдонмолору поликристалдуу алмаз куралдарын калыптандырууну камтыйт. EDM электрохимиялык иштетүү (ECM), суу агымы менен кесүү (WJ, AWJ), лазердик кесүү сыяктуу процесстер менен бирге салттуу эмес же салттуу эмес иштетүү ыкмасы болуп эсептелет. Экинчи жагынан, кадимки иштетүү ыкмаларына токуу, фрезерлөө, майдалоо, бургулоо жана башка процесстер кирет, алардын материалды алып салуу механизми негизинен механикалык күчкө негизделген. Электр разряддуу механикалык иштетүү үчүн электроддор графиттен, латундан, жезден жана жез-вольфрам эритмесинен жасалат. Электроддун диаметри 0,1 мм ге чейин болушу мүмкүн. Аспаптын эскириши EDMдеги өлчөмдүк тактыкка терс таасирин тийгизүүчү каалабаган көрүнүш болгондуктан, биз полярдуулукту тескери өзгөртүү жана жез шаймандарды колдонуу менен шаймандардын эскирүүсүн азайтуу үчүн NO-WEAR EDM деп аталган процесстен пайдаланабыз.
Идеалында айтканда, электрдик разряддык иштетүүнү (EDM) электроддордун ортосундагы диэлектрдик суюктуктун бир катар бузулушу жана калыбына келтирилиши деп кароого болот. Чындыгында, электроддор аралык аймактан таштандыларды алып салуу дээрлик дайыма жарым-жартылай болот. Бул электроддор аралык аймактагы диэлектриктин электрдик касиеттери алардын номиналдык маанилеринен айырмаланып, убакыттын өтүшү менен өзгөрүп турат. Электроддор аралык аралык (учкун боштугу) колдонулган белгилүү машинанын башкаруу алгоритмдери менен жөнгө салынат. EDMдеги учкун боштугу, тилекке каршы, кээде сыныктар менен кыска туташуу болушу мүмкүн. Электроддун башкаруу системасы эки электроддун (куралдын жана даярдалган тетиктин) кыска туташуусуна жол бербөө үчүн жетиштүү тез реакция кылбай калышы мүмкүн. Бул керексиз кыска туташуу идеалдуу учурдан башкача материалды алып салууга өбөлгө түзөт. Биз диэлектриктин изоляциялык касиеттерин калыбына келтирүү үчүн, ток дайыма электроддор аралык аймактын чекитинде болуп турушу үчүн, шайман-электроддун формасынын (зыянынын) каалабаган өзгөрүү мүмкүнчүлүгүн минималдаштыруу үчүн өзгөчө маани беребиз. жана жумушчу бөлүгү. Белгилүү бир геометрияны алуу үчүн, EDM куралы керектүү жолду бойлото, ага тийбей туруп, ага абдан жакын багытталат. Ошентип, көп сандагы ток разряддары/учкундары пайда болуп, алардын ар бири кичинекей кратерлер пайда болгон аспаптан да, даярдалган материалдан да материалды алып салууга салым кошот. Кратерлердин өлчөмү конкреттүү жумуш үчүн коюлган технологиялык параметрлердин функциясы болуп саналат жана өлчөмдөр наношкаладан (мисалы, микро-EDM операцияларында) катаал шарттарда жүздөгөн микрометрлерге чейин өзгөрүшү мүмкүн. Аспаптын бул кичинекей кратерлери электроддун акырындык менен эрозиясына алып келет "куралдын эскириши". Даярдоочу тетиктин геометриясына эскирүүнүн зыяндуу таасирине каршы туруу үчүн биз механикалык иштетүү учурунда инструмент-электродду тынымсыз алмаштырып турабыз. Кээде биз буга үзгүлтүксүз алмаштырылган зымды электрод катары колдонуу менен жетишебиз (бул EDM процесси WIRE EDM деп аталат). Кээде биз инструмент-электродду ушундайча колдонобуз, анын бир аз гана бөлүгү иш жүзүндө иштетүү процессине катышат жана бул бөлүгү үзгүлтүксүз өзгөртүлүп турат. Бул, мисалы, айлануучу дискти инструмент-электрод катары колдонууда. Бул процесс деп аталат EDM ТАРТУУ. Биз колдонгон дагы бир ыкма эскирүүнүн ордун толтуруу үчүн бир эле EDM операциясы учурунда ар кандай өлчөмдөгү жана формадагы электроддордун топтомун колдонуудан турат. Биз муну көп электроддук техника деп атайбыз жана көбүнчө инструмент электрод каалаган формада терс репликацияланганда жана бир багытта, адатта вертикалдуу багыт боюнча (б.а. z огу) бланкты көздөй жылдырганда колдонулат. Бул аспаптын бөлүкчөсү чөмүлгөн диэлектрдик суюктукка чөгүп турган жерине окшош, ошондуктан ал DIE-SINKING EDM_cc781905-5cde-3194-bb6905-5cde-3194-bb6905d-деп аталат. 3194-bb3b-136bad5cf58d_CONVENTIONAL EDM or RAM EDM). Бул операция үчүн машиналар деп аталат SINKER EDM. EDM бул түрү үчүн электроддор татаал түрлөрү бар. Эгерде акыркы геометрия адатта жөнөкөй формадагы электроддун жардамы менен бир нече багытта жылдырылса жана ошондой эле айланууга дуушар болсо, биз аны EDM ФРЕЗЕРЛЕР деп атайбыз. Тозуунун көлөмү операцияда колдонулган технологиялык параметрлерге (полярдуулук, максималдуу ток, ачык чынжырдын чыңалуу) катуу көз каранды. Мисалы, in micro-EDM, ошондой эле m-EDM катары белгилүү, бул параметрлер адатта катуу эскирүүнү пайда кылган маанилерге коюлат. Ошондуктан, биз топтогон ноу-хауды колдонууну азайта турган бул чөйрөдөгү негизги көйгөй. Мисалы, графит электроддорунун эскиришин азайтуу үчүн, миллисекунд ичинде башкарылуучу санариптик генератор электр эрозиясы болуп жатканда полярдуулукту тескери кылат. Бул эрозияга учураган графитти кайра электродго тынымсыз түшүрүп турган электропластикага окшош эффектке алып келет. Башка ыкмада, ''Nol Wear'' деп аталган схемада биз разряддын канча убакытта башталып, токтой турганын азайтып, аны мүмкүн болушунча көпкө чейин өчүрөбүз. Электр разрядын иштетүүдө материалды алып салуу ылдамдыгын төмөнкүчө эсептөөгө болот:
MRR = 4 x 10 exp(4) x I x Tw exp (-1,23)
Бул жерде MRR мм3/мин, I ток Амперде, Tw - К-273,15Кда даярдалган эрүү температурасы. Экспонент көрсөткүчтү билдирет.
Башка жагынан алганда, электроддун эскирүү ылдамдыгын Wt төмөнкүдөн алууга болот:
Wt = (1,1 x 10exp(11) ) x I x Ttexp(-2,38)
Бул жерде Wt мм3/мин жана Tt электрод материалынын эрүү температурасы К-273,15К.
Акыр-аягы, R электрод менен даярдалган эскирүү катышын алууга болот:
R = 2,25 x Trexp(-2,38)
Бул жерде Tr — даяр материалдын эрүү чекиттеринин электродго болгон катышы.
SINKER EDM :
Sinker EDM, ошондой эле CAVITY TYPE EDM or_cc781905-5cde-3194 деп аталат. Электрод жана бөлүкчө электр булагы менен туташтырылган. Электр энергиясы бул экөөнүн ортосунда электр потенциалын жаратат. Электрод даярдалган тетикке жакындаган сайын суюктукта диэлектрдик бузулуу пайда болуп, плазма каналын пайда кылат жана кичинекей учкун секирип чыгат. Учкундар, адатта, бирден урайт, анткени электроддор аралык мейкиндиктеги ар кандай жерлердин бирдей локалдык электрдик мүнөздөмөлөргө ээ болушу өтө күмөндүү, бул учкундун бардык ушундай жерлерде бир убакта пайда болушуна мүмкүндүк берет. Бул учкундардын жүз миңдегени секундасына электрод менен даярдалган тетиктин ортосундагы туш келди чекиттерде пайда болот. Негизги металл эрозияга учурап, учкун боштугу чоңойгондо, процесс үзгүлтүксүз уланышы үчүн электрод биздин CNC машинабыз тарабынан автоматтык түрдө түшүрүлөт. Биздин жабдууларда ''өз убагында'' жана ''өчүрүү убактысы'' деп аталган башкаруу циклдери бар. Убакытты орнотуу учкундун узундугун же узактыгын аныктайт. Узак убакыт ошол учкун үчүн тереңирээк көңдөйдү жана ошол цикл үчүн кийинки бардык учкундарды жаратып, даярдалган бөлүгүндө одонораак жасалга жаратат жана тескерисинче. Өчүрүү убактысы - бул бир учкундун экинчиси менен алмаштырылган мезгили. Узак убакыттын өтүшү диэлектрдик суюктукка эрозияга учураган калдыктарды тазалоо үчүн саптама аркылуу агып өтүүгө мүмкүндүк берет, ошону менен кыска туташуунун алдын алат. Бул орнотуулар микро секунддарда жөнгө салынат.
WIRE EDM :
In WIRE ELECTRICAL DISCHARGE MACHINING (WEDM), also called WIRE-CUT EDM or WIRE CUTTING, we feed a диэлектрдик суюктуктун резервуарына чөмүлгөн жезден жасалган ичке бир жиптүү металл зым. Wire EDM EDM маанилүү вариация болуп саналат. Биз маал-маалы менен зым менен кесилген EDMди калыңдыгы 300 мм болгон плиталарды кесүү үчүн жана башка өндүрүш ыкмалары менен иштетүү кыйын болгон катуу металлдардан соккуларды, шаймандарды жана штамптарды жасоо үчүн колдонобуз. Тасма араа менен контурду кесүүгө окшош болгон бул процессте дайыма катушкадан азыктанган зым жогорку жана төмөнкү алмаз багыттоочуларынын ортосунда кармалат. CNC тарабынан башкарылуучу багыттоочулар x–y тегиздигинде кыймылдайт, ал эми үстүнкү жетектөөчү да z–u–v огунда өз алдынча кыймылдай алат, бул конустуу жана өтүүчү фигураларды (мисалы, астыңкы жагындагы тегерек жана төрт бурчтуу) кесүү мүмкүнчүлүгүн берет. үстү). Жогорку жетек x–y–u–v–i–j–k–l– огу кыймылдарын көзөмөлдөй алат. Бул WEDMге өтө татаал жана назик формаларды кесүүгө мүмкүндүк берет. Эң жакшы экономикалык чыгымды жана иштетүү убактысын камсыз кылган жабдууларыбыздын орточо кесүү керфи Ø 0,25 латунь, жез же вольфрам зымдарын колдонуу менен 0,335 мм. Бирок биздин CNC жабдууларыбыздын үстүнкү жана төмөнкү алмаз багыттары болжол менен 0,004 ммге чейин так жана Ø 0,02 мм зымды колдонуу менен 0,021 мм сыяктуу кичинекей кесүүчү жолго же керфке ээ болушу мүмкүн. Ошентип, чындап эле тар кесип болушу мүмкүн. Кесүүчү туурасы зымдын туурасынан чоңураак, анткени зымдын капталдарынан даярдалган бөлүгүнө чейин учкун чыгып, эрозияга алып келет. Бул '' ашыкча кесүү '' зарыл, көптөгөн тиркемелер үчүн аны алдын ала айтууга болот жана ошондуктан анын ордун толтурууга болот (микро-EDMде бул көп учурда андай эмес). Зым катушкалар узун — 0,25 мм зымдан турган 8 кг катушканын узундугу 19 километрден бир аз ашат. Зымдын диаметри 20 микрометрге чейин кичине болушу мүмкүн жана геометриянын тактыгы +/- 1 микрометрге жакын. Биз көбүнчө зымды бир жолу гана колдонобуз жана аны кайра иштетебиз, анткени ал салыштырмалуу арзан. Ал 0,15тен 9м/минге чейин туруктуу ылдамдыкта жүрөт жана кесүү учурунда туруктуу керф (уя) сакталат. Зым менен кесилген EDM процессинде биз диэлектрдик суюктук катары сууну колдонобуз, анын каршылыгын жана башка электрдик касиеттерин чыпкалар жана де-ионизаторлор менен көзөмөлдөйбүз. Суу кесилген калдыктарды кесүү зонасынан алыстатат. Аюу берилген материалдын калыңдыгы үчүн максималдуу тоют ылдамдыгын аныктоодо маанилүү фактор болуп саналат, ошондуктан биз аны ырааттуу сактайбыз. Зым EDM кесүү ылдамдыгы 50мм калыңдыгы D2 аспап болот үчүн 18,000 мм2/саат сыяктуу убакыт бирдигине кесилген кесилишинин аянты боюнча айтылат. Бул учурда сызыктуу кесүү ылдамдыгы 18,000/50 = 360 мм/саат болот зым EDMде материалды алып салуу ылдамдыгы:
MRR = Vf xhxb
Бул жерде MRR – мм3/мин, Vf – зымдын даярдалган бөлүгүнө берүү ылдамдыгы мм/мин, h – калыңдыгы же бийиктиги мм, ал эми b – керф, ал:
b = dw + 2s
Бул жерде dw зымдын диаметри, ал эми s - зым менен даяр материалдын ортосундагы боштук, мм.
Катуу толеранттуулук менен бирге, биздин заманбап көп октуу EDM зым кесүүчү иштетүү борборлорубуз бир эле учурда эки бөлүктү кесүү үчүн көп баштар, зымдын үзүлүшүн болтурбоо үчүн башкаруу элементтери, зым үзүлгөндө автоматтык өзүн-өзү жип чыгаруу функциялары жана программаланган функцияларды кошту. операцияны оптималдаштыруу үчүн иштетүү стратегиялары, түз жана бурчтук кесүү мүмкүнчүлүктөрү.
Wire-EDM бизге аз калдык стресстерди сунуш кылат, анткени ал материалды алып салуу үчүн жогорку кесүү күчтөрүн талап кылбайт. Импульстун энергиясы/кубаты салыштырмалуу төмөн болгондо (аяктоо операцияларындагыдай), калдык стресстердин аздыгынан материалдын механикалык касиеттери аз өзгөрүшү күтүлөт.
ЭЛЕКТРДИК разряддык майдалоо (EDG) : Жаргылчак дөңгөлөктөрүндө абразивдер жок, алар графиттен же жезден жасалган. Айлануучу дөңгөлөк менен даярдалган тетиктин ортосундагы кайталануучу учкундар материалды даярдайт. Материалды алып салуу көрсөткүчү:
MRR = K x I
Бул жерде MRR мм3/мин, I ток Амперде, ал эми К - мм3/А-мин боюнча даярдалган материалдын фактору. Тетиктердеги кууш тешиктерди кесүү үчүн биз электрдик разрядды майдалоону көп колдонобуз. Биз кээде EDG (Электрдик-разрядды майдалоо) процессин ЭКГ (Электрохимиялык майдалоо) процесси менен айкалыштырабыз, мында материал химиялык аракет менен алынып салынат, графит дөңгөлөктөн чыккан электрдик разряддар оксид пленкасын бузуп, электролит менен жууп кетет. Процесс деп аталат ЭЛЕКТРОХИМИЯЛЫК-разрядды майдалоо (ECDG). ECDG процесси салыштырмалуу көбүрөөк күч керектесе да, бул EDGге караганда ылдамыраак процесс. Көбүнчө карбид шаймандарын ушул ыкма менен майдалайбыз.
Электр разрядын иштетүүнүн колдонмолору:
Прототип өндүрүү:
Биз EDM процессин калыптарды жасоодо, инструменттерди жана калыптарды өндүрүүдө, ошондой эле прототипти жана өндүрүш бөлүктөрүн жасоодо, айрыкча өндүрүш көлөмү салыштырмалуу аз болгон аэрокосмостук, автомобиль жана электроника тармактарында колдонобуз. Sinker EDMде графит, жез вольфрам же таза жез электрод каалаган (терс) формада иштетилет жана вертикалдуу кочкордун учуна даярдалган бөлүгүнө берилет.
Монеталарды жасоо:
Зергерлик буюмдарды жана значокторду жасоо үчүн штамптарды монета (штамптоо) жолу менен жасоо үчүн позитивдүү мастер күмүштөн жасалышы мүмкүн, анткени (тиешелүү машина орнотуулары менен) мастер олуттуу эрозияга учурап, бир гана жолу колдонулат. Натыйжада пайда болгон терс калып, андан кийин катуулатылып, коло, күмүш же аз далилдүү алтын эритмесинин кесилген барак бланкаларынан штампталган батирлерди алуу үчүн тамчы балка менен колдонулат. Белгилер үчүн бул батирлер дагы башка штамп менен ийри бетине чейин формада болушу мүмкүн. EDM бул түрү, адатта, мунай негизделген диэлектрикке чөгүп жүзөгө ашырылат. Даяр объект катуу (айнек) же жумшак (боёк) эмалдоо жана/же таза алтын же никель менен электропластика жолу менен андан ары тазаланышы мүмкүн. Күмүш сыяктуу жумшак материалдарды кол менен оюп түшүрсө болот.
Чакан тешиктерди бургулоо:
Зым менен кесилген EDM машиналарыбызда биз кичинекей тешик бургулоочу EDMди колдонобуз, ал аркылуу зым менен кесилген EDM операциясы үчүн зымды жип өтүүчү тетикте тешик жасоо үчүн. Кичинекей тешиктерди бургулоо үчүн өзүнчө EDM баштары биздин зым кесүүчү машиналарыбызга орнотулган, бул чоң катууланган плиталардын даяр бөлүктөрү зарыл болгон учурда жана алдын ала бургулоосуз алардын эрозиясына жол берет. Ошондой эле биз реактивдүү кыймылдаткычтарда колдонулган турбинанын канаттарынын четтерине тешиктердин катарларын бургулоо үчүн EDM кичинекей тешиктерин колдонобуз. Бул кичинекей тешиктер аркылуу газ агымы кыймылдаткычтарга мүмкүн болушунча жогору температураларды колдонууга мүмкүндүк берет. Бул бычактар жасалган жогорку температурадагы, өтө катуу, монокристалл эритмелери, бул тешиктерди жогорку пропорциядагы кадимки иштетүүнү өтө кыйын жана ал тургай мүмкүн эмес кылат. Чакан тешик EDM үчүн башка колдонуу аймактары күйүүчү май системасынын компоненттери үчүн микроскопиялык тешиктерди түзүү болуп саналат. Интегралдык EDM баштарынан тышкары, биз сокур же тешиктер аркылуу x-y огу бар өз алдынча кичинекей тешик бургулоочу EDM машиналарын орнотобуз. EDM бургулары электрод аркылуу жуугуч жана диэлектрик катары аккан дистилденген же деионизацияланган суунун туруктуу агымы менен патрондо айланган узун жез же жез түтүк электрод менен тешиктерди ачат. Кээ бир майда тешик бургулоочу EDMs 10 секундага жетпеген убакытта 100 мм жумшак же ал тургай катууланган болотту теше алат. Бул бургулоо операциясында 0,3 ммден 6,1 ммге чейинки тешиктерге жетишүүгө болот.
Металлдарды майдалоону иштетүү:
Бизде ошондой эле сынган шаймандарды (бургулоо биттери же крандар) жумуш бөлүктөрүнөн алып салуу үчүн атайын EDM машиналары бар. Бул процесс ''металлдын ажыратуу процесси'' деп аталат.
Артыкчылыктары жана кемчиликтери Электр разрядын иштетүү:
EDM артыкчылыктары кайра иштетүү кирет:
- Кадимки кесүүчү шаймандар менен жасоо кыйынга турган татаал формалар
- Өтө катуу материал өтө жакын толеранттуулукка
- Кадимки кесүүчү шаймандар кесүүчү аспаптын ашыкча басымынан улам бөлүккө зыян келтириши мүмкүн болгон өтө кичинекей иш тетиктери.
- Аспап менен жумушчу тетиктин ортосунда түз байланыш жок. Ошондуктан назик бөлүмдөрдү жана алсыз материалдарды эч кандай бурмалоосуз иштетүүгө болот.
- Жакшы беттик бүтүрүү алууга болот.
- Абдан майда тешиктерди оңой бургулоого болот.
EDM кемчиликтери төмөнкүлөрдү камтыйт:
- материалды чыгаруунун жай темпи.
- Кочкор/чөгүч EDM үчүн электроддорду түзүү үчүн колдонулган кошумча убакыт жана чыгым.
- Дайындамадагы курч бурчтарды кайра чыгаруу электроддун эскирүүсүнөн улам кыйын.
- Электр энергиясын керектөө жогору.
- ''Overcut'' түзүлдү.
- Иштетүү учурунда аспаптын ашыкча эскириши пайда болот.
- Электр өткөргүч эмес материалдарды процесстин белгилүү бир орнотуусу менен гана иштетүүгө болот.