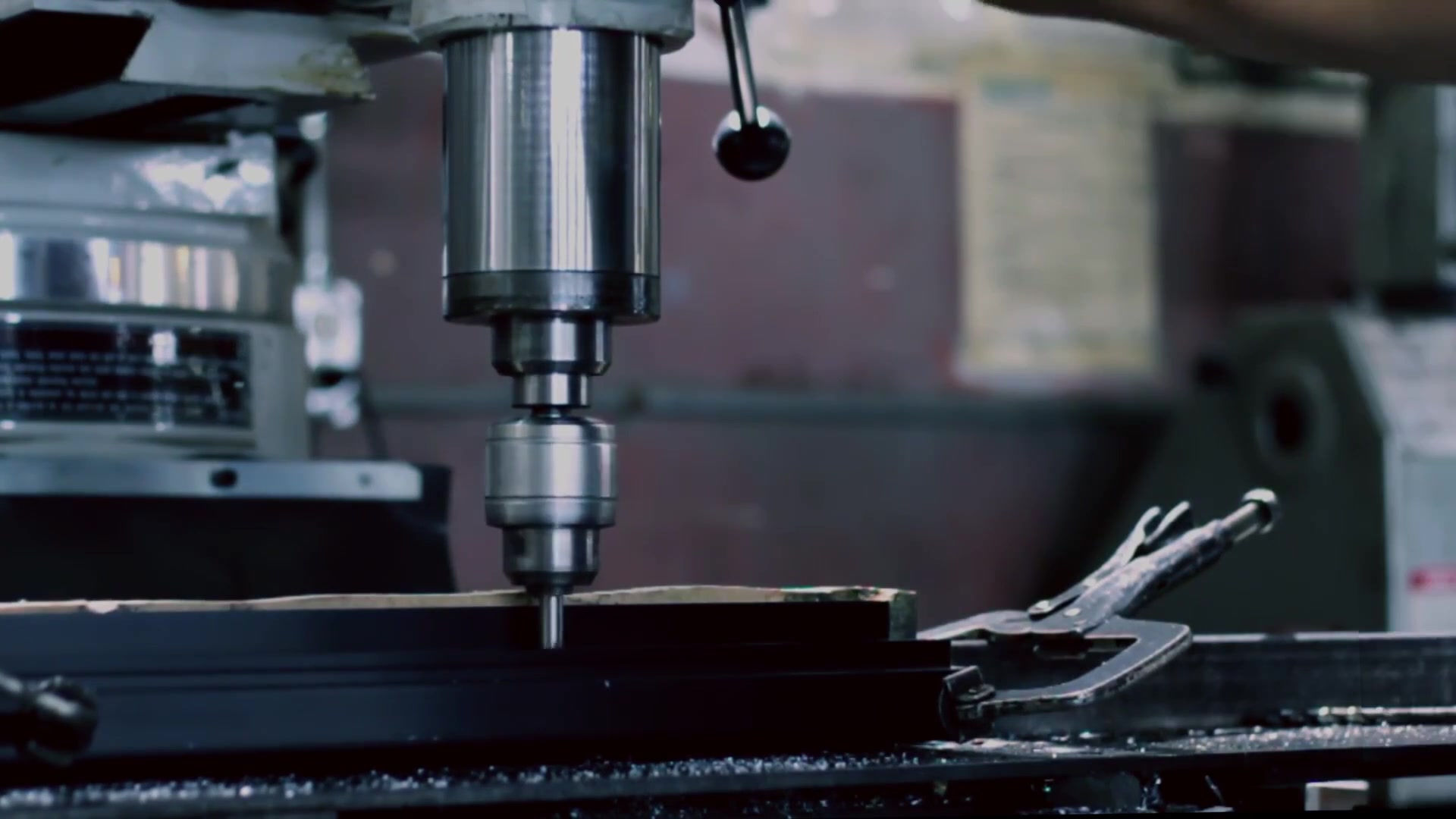
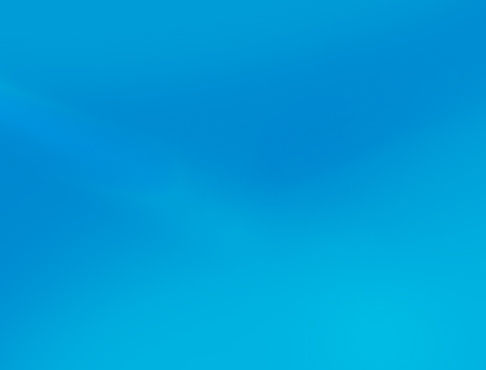
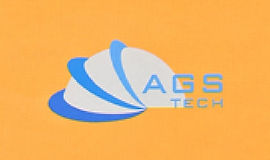
Дэлхийн захиалгат үйлдвэрлэгч, интегратор, нэгтгэгч, олон төрлийн бүтээгдэхүүн, үйлчилгээний аутсорсингийн түнш.
Бид захиалгаар үйлдвэрлэсэн болон бэлэн бус бүтээгдэхүүн, үйлчилгээг үйлдвэрлэх, үйлдвэрлэх, инженерчлэх, нэгтгэх, нэгтгэх, аутсорсинг хийх нэг цэгийн эх үүсвэр юм.
Хэлээ сонгоно уу
-
Захиалгат үйлдвэрлэл
-
Дотоодын болон дэлхийн гэрээт үйлдвэрлэл
-
Үйлдвэрлэлийн аутсорсинг
-
Дотоодын болон дэлхийн худалдан авалт
-
Consolidation
-
Инженерийн интеграци
-
Инженерийн үйлчилгээ
ELECTRICAL DISCHARGE MACHINING (EDM), also referred to as SPARK-EROSION or ELECTRODISCHARGE MACHINING, SPARK ERODING, DIE SINKING_cc781905-5cde-3194-bb3b -136bad5cf58d_or WIRE EROSION, is a NON-CONVENTIONAL MANUFACTURING process where erosion of metals takes place and desired shape is obtained using electrical discharges in the form оч. Мөн бид EDM-ийн зарим сортуудыг санал болгож байна, тухайлбал NO-WEAR EDM, WIRE EDM (WEDM), EDM NUNNDING (EDG), DIE-SINKING EDM, ЦАХИЛГААН-ЦАХИЛГААН-ЦАХИЛГААН-ЦАХИЛГААН-ЦАХИЛГААН-ЦАХИЛГААН-ЦАХИЛГААН-ЦАХИЛГААН-ЦАХИЛГААН-ЦАХИЛГААН-ЦАСГАЛТАЙ тээрэмдэх,18-Mccm5, -5cde-3194-bb3b-136bad5cf58d_and ЦАХИЛГААН ХИМИЙН-ЦАХИЛГААН БУСДАГ НУНТАХ (ECDG). Манай EDM системүүд нь тогтмол гүйдлийн тэжээлийн эх үүсвэрт холбогдсон, цахилгаан дамжуулдаггүй диэлектрик шингэнд суурилуулсан хэлбэртэй багаж/электрод ба ажлын хэсгээс бүрдэнэ. 1940 оноос хойш цахилгаан цэнэгийн боловсруулалт нь үйлдвэрлэлийн салбарт хамгийн чухал бөгөөд түгээмэл үйлдвэрлэлийн технологийн нэг болжээ.
Хоёр электродын хоорондох зай багасах үед электродуудын хоорондох эзэлхүүн дэх цахилгаан талбайн эрчим нь зарим цэгүүдийн диэлектрикийн хүчнээс их болж, энэ нь тасарч, эцэст нь хоёр электродын хооронд гүйдэл гүйх гүүр болдог. Хүчтэй цахилгаан нум үүсдэг бөгөөд энэ нь ажлын хэсэг болон багаж хэрэгслийн зарим хэсгийг хайлахад ихээхэн халах шалтгаан болдог. Үүний үр дүнд материалыг электродоос хоёуланг нь арилгадаг. Үүний зэрэгцээ диэлектрик шингэнийг хурдан халааж, нумын завсар дахь шингэний ууршилт үүсдэг. Гүйдлийн урсгал зогссон эсвэл зогссоны дараа хүрээлэн буй диэлектрик шингэний тусламжтайгаар хийн бөмбөлөгөөс дулааныг зайлуулж, бөмбөлөг хөндийрч (нурдаг). Бөмбөлөг нурж, диэлектрик шингэний урсгалаас үүссэн цочролын долгион нь ажлын хэсгийн гадаргуугаас хог хаягдлыг зайлж, хайлсан бэлдэцийг диэлектрик шингэн рүү оруулна. Эдгээр цэнэгийн давтамжийн давтамж нь 50-500 кГц, хүчдэл 50-380 В, гүйдэл нь 0.1-500 ампер байна. Ашигт малтмалын тос, керосин эсвэл нэрмэл, ионгүйжүүлсэн ус гэх мэт шинэ шингэн диэлектрикийг ихэвчлэн хатуу хэсгүүдийг (хог хаягдал хэлбэрээр) зайлуулж, электрод хоорондын эзэлхүүн рүү шилжүүлж, диэлектрикийн тусгаарлагч шинж чанарыг сэргээдэг. Гүйдлийн урсгалын дараа хоёр электродын хоорондох боломжит ялгаа нь эвдрэлийн өмнөх байдалд сэргээгддэг тул шингэн диэлектрикийн шинэ эвдрэл үүсч болно. Манай орчин үеийн цахилгаан цэнэгийн машинууд (EDM) нь тоон удирдлагатай хөдөлгөөнийг санал болгодог бөгөөд диэлектрик шингэний насос, шүүлтүүрийн системээр тоноглогдсон байдаг.
Цахилгаан гүйдлийн боловсруулалт (EDM) нь ихэвчлэн хатуу металл эсвэл ердийн техникээр боловсруулахад маш хэцүү байдаг механик боловсруулалтын арга юм. EDM нь ихэвчлэн цахилгаан дамжуулагч бүхий ямар ч материалтай ажилладаг боловч EDM-ээр тусгаарлагч керамик боловсруулах аргуудыг санал болгосон. Хайлах цэг ба хайлалтын далд дулаан нь нэг гадагшлуулсан металлын хэмжээг тодорхойлдог шинж чанарууд юм. Эдгээр утгууд өндөр байх тусам материалыг зайлуулах хурд багасна. Цахилгаан гүйдэл боловсруулах процесс нь механик энерги шаарддаггүй тул ажлын хэсгийн хатуулаг, бат бөх, бат бөх чанар нь зайлуулах хурдад нөлөөлдөггүй. Цэнэглэх давтамж эсвэл цэнэг тутамд эрчим хүч, хүчдэл ба гүйдэл нь материалыг зайлуулах хурдыг хянахын тулд өөр өөр байдаг. Материалыг зайлуулах хурд ба гадаргуугийн тэгш бус байдал нь гүйдлийн нягтрал нэмэгдэж, оч давтамж буурах тусам нэмэгддэг. Урьдчилан хатууруулсан гангаар хийсэн нарийн төвөгтэй контур эсвэл хөндийг бид дулааны боловсруулалтгүйгээр EDM ашиглан зүсэж, зөөлрүүлж, дахин хатууруулах боломжтой. Бид энэ аргыг титан, хастеллой, ковар, инконел гэх мэт ямар ч металл эсвэл металл хайлштай ашиглаж болно. EDM процессын хэрэглээнд поликристал алмаазан багажийг хэлбэржүүлэх орно. EDM нь цахилгаан химийн боловсруулалт (ECM), усны тийрэлтэт зүсэлт (WJ, AWJ), лазер зүсэлт зэрэг процессуудын хамт уламжлалт бус эсвэл уламжлалт бус боловсруулалтын арга гэж тооцогддог. Нөгөөтэйгүүр, боловсруулах уламжлалт аргууд нь эргэлт, тээрэмдэх, нунтаглах, өрөмдөх болон бусад процессуудыг багтаадаг бөгөөд материалыг зайлуулах механизм нь үндсэндээ механик хүч дээр суурилдаг. Цахилгаан гүйдэл боловсруулах (EDM) электродууд нь бал чулуу, гууль, зэс, зэс-волфрамын хайлшаар хийгдсэн байдаг. Электродын диаметр нь 0.1 мм хүртэл байж болно. Багажны элэгдэл нь EDM-ийн хэмжээсийн нарийвчлалд сөргөөр нөлөөлдөг хүсээгүй үзэгдэл тул бид туйлшралыг эргүүлж, зэс багаж ашиглан багажийн элэгдлийг багасгахын тулд NO-WEAR EDM гэж нэрлэгддэг процессын давуу талыг ашигладаг.
Тохиромжтойгоор хэлэхэд, цахилгаан цэнэгийн боловсруулалт (EDM) нь электродуудын хоорондох диэлектрик шингэнийг хэд хэдэн удаа задлах, сэргээх үйл явц гэж үзэж болно. Гэвч бодит байдал дээр электрод хоорондын талбайгаас хог хаягдлыг зайлуулах нь бараг үргэлж хэсэгчилсэн байдаг. Энэ нь электрод хоорондын бүсийн диэлектрикийн цахилгаан шинж чанар нь нэрлэсэн утгаасаа ялгаатай бөгөөд цаг хугацааны явцад өөрчлөгддөг. Электрод хоорондын зай (оч зай) нь ашигласан тусгай машины хяналтын алгоритмаар тохируулагддаг. Харамсалтай нь EDM дахь оч зай нь заримдаа хог хаягдлаас болж богино холболт үүсдэг. Электродын хяналтын систем нь хоёр электродыг (багаж ба ажлын хэсэг) богино холболтоос урьдчилан сэргийлэхийн тулд хурдан хариу үйлдэл үзүүлэхгүй байж магадгүй юм. Энэхүү хүсээгүй богино холболт нь хамгийн тохиромжтой тохиолдлоос өөрөөр материалыг зайлуулахад хувь нэмэр оруулдаг. Бид диэлектрикийн тусгаарлах шинж чанарыг сэргээхийн тулд гүйдэл нь электрод хоорондын хэсгийн цэгт байнга үүсэж, улмаар багаж-электродын хэлбэр (гэмтэл) -ийг хүсээгүй өөрчлөх боломжийг багасгахын тулд угаах үйл ажиллагаанд онцгой ач холбогдол өгдөг. болон ажлын хэсэг. Тодорхой геометрийг олж авахын тулд EDM хэрэгслийг ажлын хэсэгт хүрэлгүйгээр хүссэн зам дагуу чиглүүлдэг. Бид ашиглалтын явцад хөдөлгөөний удирдлагын гүйцэтгэлд онцгой анхаарал хандуулдаг. Ингэснээр олон тооны гүйдэл / оч гарч ирдэг бөгөөд тэдгээр нь жижиг тогоонууд үүсдэг багаж хэрэгсэл болон ажлын хэсгээс материалыг зайлуулахад хувь нэмэр оруулдаг. Тогоонуудын хэмжээ нь тухайн ажилд зориулагдсан технологийн параметрүүдээс хамаардаг бөгөөд хэмжээсүүд нь нано хэмжээстээс (жишээ нь микро-EDM үйлдлийн хувьд) барзгар нөхцөлд хэдэн зуун микрометр хүртэл хэлбэлзэж болно. Багаж дээрх эдгээр жижиг тогоонууд нь "багажийн элэгдэл" гэж нэрлэгддэг электродын аажмаар элэгдэлд хүргэдэг. Ажлын хэсгийн геометрийн элэгдэлд үзүүлэх сөрөг нөлөөг арилгахын тулд бид механик боловсруулалтын явцад багаж-электродыг байнга сольж байдаг. Заримдаа бид үүнийг тасралтгүй солих утсыг электрод болгон ашиглах замаар олж авдаг (энэхүү EDM процессыг мөн WIRE EDM гэж нэрлэдэг). Заримдаа бид багаж-электродыг ийм байдлаар ашигладаг бөгөөд үүний зөвхөн багахан хэсэг нь боловсруулах үйл явцад оролцдог бөгөөд энэ хэсэг нь тогтмол өөрчлөгддөг. Энэ нь жишээлбэл, эргэдэг дискийг багаж-электрод болгон ашиглах тохиолдол юм. Энэ процессыг EDM нунтаглах гэж нэрлэдэг. Бидний ашигладаг өөр нэг арга бол элэгдлийг нөхөхийн тулд ижил EDM үйл ажиллагааны явцад янз бүрийн хэмжээ, хэлбэртэй электродуудыг ашиглах явдал юм. Бид үүнийг олон электродын техник гэж нэрлэдэг бөгөөд багажны электрод нь хүссэн хэлбэрээ сөрөг байдлаар хуулбарлаж, нэг чиглэлд, ихэвчлэн босоо чиглэлд (жишээ нь, z тэнхлэг) хоосон зай руу урагшлах үед ихэвчлэн ашиглагддаг. Энэ нь ажлын хэсгийг дүрэх диэлектрик шингэнд багажны угаалтууртай төстэй бөгөөд иймээс үүнийг DIE-SINKING EDM_cc781905-5cde-3194-bb58905d(adm) гэж нэрлэдэг 3194-bb3b-136bad5cf58d_ЕРӨНХИЙ EDM or RAM EDM). Энэ үйлдлийг гүйцэтгэх машинуудыг SINKER EDM гэж нэрлэдэг. Энэ төрлийн EDM-ийн электродууд нь нарийн төвөгтэй хэлбэртэй байдаг. Хэрэв эцсийн геометрийг хэд хэдэн чиглэлд хөдөлсөн энгийн хэлбэртэй электродыг ашиглан олж авсан бөгөөд эргэлтэнд ордог бол бид үүнийг EDM тээрэмдэх гэж нэрлэдэг. Элэгдлийн хэмжээ нь үйл ажиллагаанд ашигласан технологийн параметрүүдээс шууд хамаардаг (туйлшрал, хамгийн их гүйдэл, нээлттэй хэлхээний хүчдэл). Жишээлбэл, micro-EDM, мөн m-EDM гэгддэг эдгээр параметрүүдийг ихэвчлэн ноцтой элэгдэл үүсгэдэг утгуудаар тохируулдаг. Иймээс элэгдэл бол бидний хуримтлуулсан ноу-хаугийн хэрэглээг багасгахад хүргэдэг гол асуудал юм. Жишээлбэл, графит электродын элэгдлийг багасгахын тулд миллисекундэд удирдаж болох дижитал генератор нь цахилгаан элэгдэл үүсэх үед туйлшралыг эргүүлдэг. Үүний үр дүнд элэгдэлд орсон бал чулууг электрод дээр байнга хадгалдаг цахилгаанаар бүрэхтэй төстэй нөлөө үзүүлдэг. Өөр нэг аргын хувьд "Тэг элэгдлийн" гэж нэрлэгддэг хэлхээний хувьд бид ялгадас хэр олон удаа эхэлж зогсохыг багасгаж, аль болох удаан байлгадаг. Цахилгаан гүйдэл боловсруулах явцад материалыг зайлуулах хурдыг дараахь байдлаар тооцоолж болно.
MRR = 4 x 10 exp(4) x I x Tw exp (-1.23)
Энд MRR нь мм3/мин, I гүйдэл Ампераар, Tw нь K-273.15K дахь ажлын хэсэг хайлах цэг юм. Exp гэдэг нь экспонент гэсэн үг юм.
Нөгөө талаас электродын элэгдлийн хурд Wt-ийг дараахь зүйлээс авч болно.
Wt = ( 1.1 x 10exp(11) ) x I x Ttexp(-2.38)
Энд Wt нь мм3/мин, Tt нь электродын материалын хайлах цэг нь K-273.15K байна.
Эцэст нь, бэлдэц болон электрод R-ийн элэгдлийн харьцааг дараахь байдлаар авч болно.
R = 2.25 x Trexp(-2.38)
Энд Tr нь ажлын хэсгийн хайлах цэгүүдийн электрод ба электродын харьцаа юм.
SINKER EDM :
Sinker EDM, мөн CAVITY TYPE EDM or_cc781905-5cde-3194-bb3b-5cde-3194-bb3b-136bad5cf58d гэж нэрлэдэг. Электрод ба ажлын хэсэг нь цахилгаан тэжээлд холбогдсон байна. Цахилгаан хангамж нь хоёрын хооронд цахилгаан потенциал үүсгэдэг. Электрод нь ажлын хэсэг рүү ойртох үед шингэн дэх диэлектрикийн эвдрэл үүсч, плазмын суваг үүсч, жижиг оч үсрэх болно. Электрод хоорондын зай дахь өөр өөр байршил нь ижил орон нутгийн цахилгаан шинж чанартай байх нь тийм ч их биш тул оч нь ихэвчлэн нэг нэгээр нь очдог. Эдгээр хэдэн зуун мянган оч нь секундэд электрод ба ажлын хэсгийн хооронд санамсаргүй цэгүүдэд тохиолддог. Суурь металл элэгдэж, дараа нь очны цоорхой нэмэгдэхийн хэрээр электродыг манай CNC машин автоматаар буулгадаг бөгөөд ингэснээр процесс тасралтгүй үргэлжлэх болно. Манай төхөөрөмжид ''цагаа'' ба ''унтраах'' гэж нэрлэгддэг хяналтын циклүүд байдаг. Цагийн тохиргоо нь оч үүсэх урт эсвэл үргэлжлэх хугацааг тодорхойлдог. Удаан хугацааны туршид энэ оч болон дараагийн бүх оч нь илүү гүн хөндий үүсгэж, ажлын хэсэг дээр илүү барзгар өнгөлгөө үүсгэдэг ба эсрэгээр. Унтраах хугацаа гэдэг нь нэг оч нөгөө очоор солигдох хугацаа юм. Илүү урт хугацаа нь диэлектрик шингэнийг хошуугаар урсгаж, элэгдэлд орсон хог хаягдлыг цэвэрлэх боломжийг олгодог бөгөөд ингэснээр богино холболт үүсэхээс сэргийлдэг. Эдгээр тохиргоог микро секундын дотор тохируулдаг.
WIRE EDM :
In WIRE ELECTRICAL DISCHARGE MACHINING (WEDM), also called WIRE-CUT EDM or WIRE CUTTING, we feed a диэлектрик шингэний саванд живсэн бэлдэцийг дамжин гуулин нимгэн нэг судалтай металл утас. Утасны EDM нь EDM-ийн чухал хувилбар юм. Бид хааяа утсаар зүссэн EDM-ийг 300 мм хүртэл зузаантай хавтанг хайчилж, бусад үйлдвэрлэлийн аргаар боловсруулахад хэцүү хатуу металлаар цоолтуур, багаж хэрэгсэл, хэвийг хийдэг. Туузан хөрөө ашиглан контур зүсэхтэй төстэй энэ процесст дамараас байнга тэжээгддэг утсыг дээд ба доод алмазан чиглүүлэгчийн хооронд барина. CNC удирдлагатай хөтөч нь x-y хавтгайд хөдөлж, дээд чиглүүлэгч нь мөн z-u-v тэнхлэгт бие даан хөдөлж, нарийссан болон шилжилтийн хэлбэрийг (доод талын тойрог, дөрвөлжин гэх мэт) зүсэх чадварыг бий болгодог. шилдэг). Дээд талын хөтөч нь x–y–u–v–i–j–k–l– тэнхлэгийн хөдөлгөөнийг хянах боломжтой. Энэ нь WEDM-д маш нарийн төвөгтэй, нарийн дүрсийг зүсэх боломжийг олгодог. Манай тоног төхөөрөмжийн хамгийн сайн эдийн засгийн өртөг, боловсруулах хугацаа нь дунджаар Ø 0.25 гууль, зэс эсвэл вольфрам утас ашиглан 0.335 мм-ийн зүсэлттэй байдаг. Гэсэн хэдий ч манай CNC төхөөрөмжийн дээд ба доод алмазан хөтөч нь ойролцоогоор 0.004 мм-ийн нарийвчлалтай бөгөөд Ø 0.02 мм утсаар огтлох зам эсвэл 0.021 мм хүртэл жижиг зүсэлттэй байж болно. Тиймээс үнэхээр нарийн зүсэлт хийх боломжтой. Утасны хажуу талаас ажлын хэсэг хүртэл оч гарч, элэгдэл үүсгэдэг тул огтлох өргөн нь утасны өргөнөөс их байна. Энэ ''хэт таслах'' нь зайлшгүй шаардлагатай бөгөөд олон програмын хувьд үүнийг урьдчилан таамаглах боломжтой тул нөхөн төлж болно (микро-EDM-д энэ нь тийм ч их тохиолддоггүй). Утасны дамар нь урт - 0.25 мм-ийн утастай 8 кг дамар нь 19 гаруй километр урт юм. Утасны диаметр нь 20 микрометрээс бага байж болох ба геометрийн нарийвчлал нь +/- 1 микрометрийн ойролцоо байна. Бид ерөнхийдөө утсыг нэг удаа ашигладаг бөгөөд харьцангуй хямд учраас дахин боловсруулдаг. Энэ нь 0.15-аас 9м/мин тогтмол хурдтайгаар хөдөлдөг ба зүсэлтийн үед тогтмол цоорхой (холт) хадгалагдана. Утас хайчлах EDM процесст бид усыг диэлектрик шингэн болгон ашиглаж, түүний эсэргүүцэл болон бусад цахилгаан шинж чанарыг шүүлтүүр, ионгүйжүүлэгч төхөөрөмжөөр хянадаг. Ус нь зүссэн хог хаягдлыг зүссэн бүсээс зайлуулдаг. Угаах нь тухайн материалын зузаанын хамгийн их тэжээлийн хурдыг тодорхойлоход чухал хүчин зүйл болдог тул бид үүнийг тогтвортой байлгадаг. Утасны EDM дахь зүсэлтийн хурдыг нэгж хугацаанд огтлох хөндлөн огтлолын талбайгаар илэрхийлнэ, тухайлбал 50 мм зузаантай D2 багажны гангийн хувьд 18,000 мм2/цаг. Энэ тохиолдолд шугаман зүсэх хурд нь 18,000/50 = 360 мм/цаг байх болно Утасны EDM дахь материалыг зайлуулах хурд нь:
MRR = Vf xhxb
Энд MRR нь мм3/мин, Vf нь утсыг ажлын хэсэг рүү дамжуулах хурдыг мм/мин, h нь зузаан эсвэл өндөр мм, b нь эрф бөгөөд энэ нь:
b = dw + 2s
Энд dw нь утасны диаметр, s нь утас ба ажлын хэсгийн хоорондох зайг мм-ээр илэрхийлнэ.
Илүү хатуу хүлцлийн зэрэгцээ орчин үеийн олон тэнхлэгтэй EDM утас хайчлах машин боловсруулах төвүүд нь хоёр хэсгийг зэрэг огтлох олон толгой, утас тасрахаас урьдчилан сэргийлэх удирдлага, утас тасрах үед автоматаар өөрөө залгах функцүүд, программчлагдсан зэрэг функцуудыг нэмсэн. үйл ажиллагааг оновчтой болгохын тулд боловсруулах стратеги, шулуун ба өнцгийн зүсэх чадвар.
Wire-EDM нь материалыг зайлуулахын тулд огтлох хүч шаарддаггүй тул үлдэгдэл багатай стрессийг санал болгодог. Нэг импульсийн эрчим хүч/хүч харьцангуй бага байх үед (дуусгах үйл ажиллагаатай адил) үлдэгдэл стресс багатай тул материалын механик шинж чанарт бага зэрэг өөрчлөлт гарах болно.
ЦАХИЛГААН-ЦАСГАЛТАЙ НУНТГАХ (EDG) : Нунтаглагч дугуй нь зүлгүүрийн бодис агуулаагүй, бал чулуу эсвэл гуулинаар хийгдсэн байдаг. Эргэдэг дугуй ба ажлын хэсгийн хооронд дахин давтагдах оч нь ажлын хэсгийн гадаргуугаас материалыг зайлуулдаг. Материалыг зайлуулах хурд нь:
MRR = K x I
Энд MRR нь мм3/мин, I гүйдэл Ампераар, K нь мм3/А-мин-ээр ажлын хэсгийн материалын хүчин зүйл юм. Бид эд ангиудын нарийн ан цавыг хөрөөдөхийн тулд цахилгаан цэнэгийн нунтаглах аргыг ихэвчлэн ашигладаг. Бид заримдаа EDG (цахилгаан ялгадас нунтаглах) процессыг ЭКГ (цахилгаан химийн нунтаглах) процесстой хослуулдаг бөгөөд энэ нь химийн үйлчлэлээр материалыг зайлуулж, бал чулуун дугуйнаас үүссэн цахилгаан ялгадас нь ислийн хальсыг задалж, электролитээр угаадаг. Уг процессыг ЦАХИЛГААН ХИМИЙН-ЦАХИЛГААНЫ ҮНТГЭХ (ECDG) гэж нэрлэдэг. Хэдийгээр ECDG процесс нь харьцангуй их эрчим хүч зарцуулдаг ч энэ нь EDG-ээс илүү хурдан процесс юм. Энэ техникийг ашиглан бид ихэвчлэн карбидын багажийг нунтагладаг.
Цахилгаан цэнэгийн боловсруулалтын хэрэглээ:
Прототип үйлдвэрлэл:
Бид EDM процессыг хэвний үйлдвэрлэл, багаж хэрэгсэл, хэвний үйлдвэрлэлд ашигладаг, мөн эх загвар, үйлдвэрлэлийн эд анги, ялангуяа үйлдвэрлэлийн хэмжээ харьцангуй бага байдаг сансар, автомашин, электроникийн үйлдвэрүүдэд ашигладаг. Sinker EDM-д бал чулуу, зэс гянт болд эсвэл цэвэр зэс электродыг хүссэн (сөрөг) хэлбэрт оруулж, босоо хуцны төгсгөлд ажлын хэсэг рүү оруулдаг.
Зоосны хэв хийх:
Зоос урлах (тамгалах) аргаар үнэт эдлэл, тэмдэг үйлдвэрлэх хэвийг бий болгохын тулд мастер нь мэдэгдэхүйц элэгдэлд орсон тул (машины зохих тохиргоотой) зөвхөн нэг удаа ашигладаг тул эерэг мастерийг мөнгөн мөнгөнөөс хийж болно. Үүний үр дүнд үүссэн сөрөг хэвийг хатууруулж, дуслын алхаар хүрэл, мөнгө эсвэл бага бат бөх алтны хайлшаар хийсэн зүсмэл хуудаснаас тамгатай хавтгай үйлдвэрлэдэг. Тэмдгийн хувьд эдгээр хавтгайг өөр хэвээр муруй гадаргуутай болгож болно. Энэ төрлийн EDM нь ихэвчлэн газрын тос дээр суурилсан диэлектрик дотор живж хийгддэг. Дууссан объектыг хатуу (шил) эсвэл зөөлөн (будаг) пааландах ба/эсвэл цэвэр алт эсвэл никельээр бүрэх замаар илүү боловсронгуй болгож болно. Мөнгө гэх мэт илүү зөөлөн материалыг гараар сийлбэрлэн сайжруулж болно.
Жижиг цооног өрөмдөх:
Манай утсаар зүссэн EDM машинууд дээр бид жижиг цооногийн өрөмдлөгийн EDM-ийг ашиглан ажлын хэсэгт нүх гаргаж, утсаар зүссэн EDM үйл ажиллагаанд зориулж утсыг дамжуулдаг. Жижиг цооног өрөмдөхөд зориулагдсан тусдаа EDM толгойг манай утсан зүсэгч машинууд дээр суурилуулсан бөгөөд энэ нь том хэмжээний хатуурсан хавтангууд нь шаардлагатай үед болон урьдчилсан өрөмдлөггүйгээр тэдгээрээс элэгдэж дуусах боломжийг олгодог. Бид мөн жижиг цооног EDM ашиглан тийрэлтэт хөдөлгүүрт ашигладаг турбины ирний ирмэг дээр эгнээ цооног өрөмдөхөд ашигладаг. Эдгээр жижиг нүхээр дамжих хийн урсгал нь хөдөлгүүрүүдэд өөр боломжоос илүү өндөр температурыг ашиглах боломжийг олгодог. Эдгээр ирээр хийсэн өндөр температурт, маш хатуу, дан болор хайлш нь өндөр харьцаатай эдгээр нүхийг ердийн аргаар боловсруулахад маш хэцүү, бүр боломжгүй болгодог. Жижиг нүхний EDM-ийн бусад хэрэглээний талбарууд нь түлшний системийн бүрэлдэхүүн хэсгүүдийн бичил нүхийг бий болгох явдал юм. Нэгдсэн EDM толгойнуудаас гадна бид х-y тэнхлэг бүхий бие даасан жижиг цооног өрөмдөх EDM машинуудыг машин сохор эсвэл нүхэнд байрлуулдаг. EDM өрөмдлөг нь угаагч бодис, диэлектрик байдлаар электродоор урсаж буй нэрмэл эсвэл ионгүйжүүлсэн усны тогтмол урсгалтай патрон дотор эргэлддэг урт гуулин эсвэл зэс хоолойн электрод бүхий цооногууд юм. Зарим жижиг цооногийн өрөмдлөгийн EDM нь 100 мм-ийн зөөлөн эсвэл бүр хатуурсан ганг 10 секундээс бага хугацаанд өрөмдөх чадвартай. Энэ өрөмдлөгийн явцад 0.3 мм-ээс 6.1 мм-ийн нүх гаргах боломжтой.
Металл задралын боловсруулалт:
Бид мөн ажлын хэсгүүдээс эвдэрсэн багаж хэрэгслийг (өрөмдлөгийн хошуу эсвэл цорго) зайлуулах тусгай зориулалтын EDM машинуудтай. Энэ процессыг ''металл задралын боловсруулалт'' гэж нэрлэдэг.
Давуу болон сул талууд Цахилгаан гүйдэл боловсруулах:
EDM-ийн давуу талууд нь дараахь зүйлийг боловсруулах явдал юм.
- Уламжлалт зүсэгч хэрэгслээр үйлдвэрлэхэд хэцүү байх нарийн төвөгтэй хэлбэрүүд
- Хэт хатуу материал, маш ойрхон хүлцэл
- Маш жижиг ажлын хэсгүүд нь ердийн зүсэх хэрэгсэл нь зүсэх хэрэгслийн илүүдэл даралтаас болж эд ангийг гэмтээж болно.
- Багаж ба ажлын хэсэг хооронд шууд холбоо байхгүй. Тиймээс нарийн зүсэлт, сул материалыг ямар ч гажуудалгүйгээр боловсруулах боломжтой.
- Гадаргуугийн сайн өнгөлгөө авах боломжтой.
- Маш нарийн нүхийг амархан өрөмдөж болно.
EDM-ийн сул талууд нь:
- Материалыг зайлуулах хурд бага.
- Ram/sinker EDM-д электрод бүтээхэд зарцуулсан нэмэлт цаг, зардал.
- Ажлын хэсэг дээр хурц өнцөг үүсгэх нь электродын элэгдлээс болж хэцүү байдаг.
- Эрчим хүчний хэрэглээ өндөр.
-''Overcut'' бий болсон.
- Машины боловсруулалтын явцад багаж хэрэгслийн хэт элэгдэл үүсдэг.
- Цахилгаан дамжуулдаггүй материалыг зөвхөн тодорхой үйл явцын дагуу боловсруулж болно.