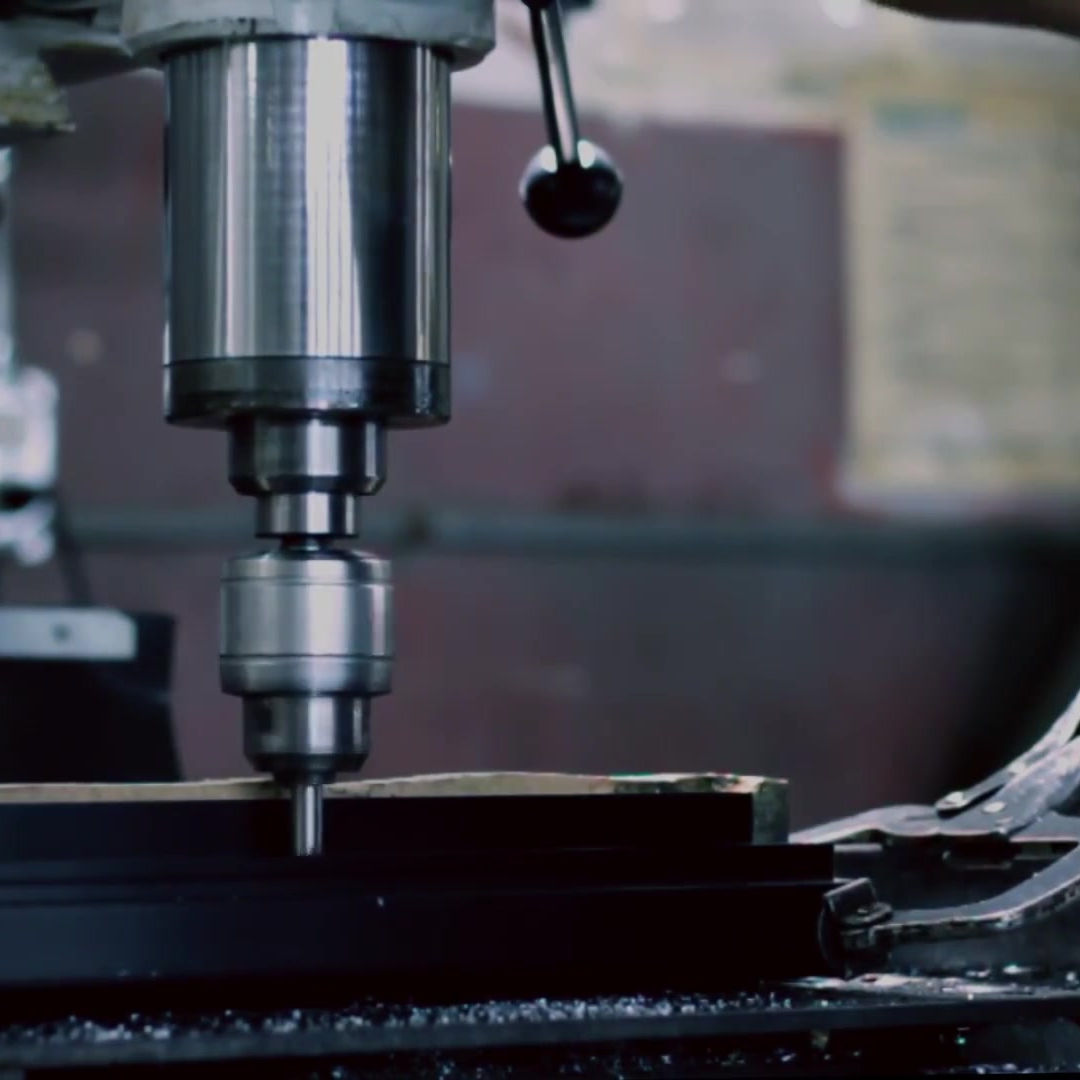
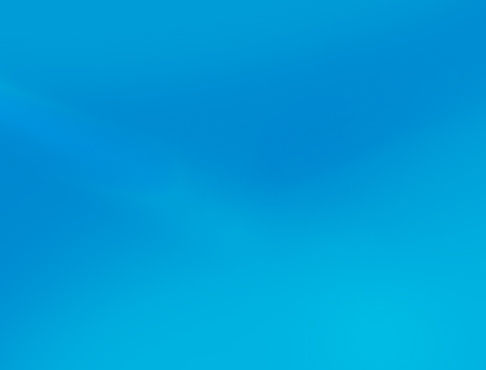
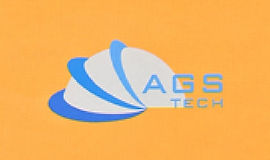
जागतिक कस्टम उत्पादक, इंटिग्रेटर, कंसोलिडेटर, उत्पादन आणि सेवांच्या विविधतेसाठी आउटसोर्सिंग भागीदार.
सानुकूल उत्पादित आणि ऑफ-शेल्फ उत्पादने आणि सेवांचे उत्पादन, फॅब्रिकेशन, अभियांत्रिकी, एकत्रीकरण, एकत्रीकरण, आउटसोर्सिंगसाठी आम्ही तुमचे एक-स्टॉप स्रोत आहोत.
तुमची भाषा निवडा
-
सानुकूल उत्पादन
-
देशांतर्गत आणि जागतिक करार निर्मिती
-
मॅन्युफॅक्चरिंग आउटसोर्सिंग
-
देशांतर्गत आणि जागतिक खरेदी
-
एकत्रीकरण
-
अभियांत्रिकी एकत्रीकरण
-
अभियांत्रिकी सेवा
उत्पादनामध्ये आम्ही वापरत असलेल्या अनेक जॉइनिंग तंत्रांपैकी वेल्डिंग, ब्रेझिंग, सोल्डरिंग, अॅडहेसिव्ह बाँडिंग आणि कस्टम मेकॅनिकल असेंबली यावर विशेष भर दिला जातो कारण ही तंत्रे हर्मेटिक असेंब्ली, हाय-टेक मॅन्युफॅक्चरिंग आणि मॅन्युफॅक्चरिंग उत्पादन यासारख्या अनुप्रयोगांमध्ये मोठ्या प्रमाणावर वापरली जातात. येथे आम्ही या सामील होण्याच्या तंत्रांच्या अधिक विशेष पैलूंवर लक्ष केंद्रित करू कारण ते प्रगत उत्पादनांच्या आणि असेंब्लींच्या निर्मितीशी संबंधित आहेत.
फ्यूजन वेल्डिंग: आम्ही सामग्री वितळण्यासाठी आणि एकत्र करण्यासाठी उष्णता वापरतो. उष्णता वीज किंवा उच्च-ऊर्जा बीमद्वारे पुरविली जाते. फ्यूजन वेल्डिंगचे प्रकार आम्ही उपयोजित करतो ते म्हणजे ऑक्सिफ्यूल गॅस वेल्डिंग, एआरसी वेल्डिंग, हाय-एनर्जी-बीम वेल्डिंग.
सॉलिड-स्टेट वेल्डिंग: आम्ही वितळणे आणि फ्यूजन न करता भाग जोडतो. आमच्या सॉलिड-स्टेट वेल्डिंग पद्धती म्हणजे कोल्ड, अल्ट्रासोनिक, रेझिस्टन्स, फ्रिक्शन, एक्सप्लोशन वेल्डिंग आणि डिफ्यूजन बाँडिंग.
ब्रॅझिंग आणि सोल्डरिंग: ते फिलर धातू वापरतात आणि आम्हाला वेल्डिंगपेक्षा कमी तापमानात काम करण्याचा फायदा देतात, त्यामुळे उत्पादनांचे कमी संरचनात्मक नुकसान होते. सिरेमिक ते मेटल फिटिंग्ज, हर्मेटिक सीलिंग, व्हॅक्यूम फीडथ्रू, उच्च आणि अतिउच्च व्हॅक्यूम आणि फ्लुइड कंट्रोल घटक उत्पादन करणाऱ्या आमच्या ब्रेझिंग सुविधेची माहिती येथे मिळू शकते:ब्रेझिंग फॅक्टरी ब्रोशर
अॅडहेसिव्ह बाँडिंग: उद्योगात वापरल्या जाणार्या अॅडझिव्हजच्या विविधतेमुळे आणि अॅप्लिकेशन्सच्या विविधतेमुळे, आमच्याकडे यासाठी एक समर्पित पृष्ठ आहे. चिकट बाँडिंगबद्दल आमच्या पृष्ठावर जाण्यासाठी, कृपया येथे क्लिक करा.
कस्टम मेकॅनिकल असेंब्ली: आम्ही बोल्ट, स्क्रू, नट, रिवेट्स यांसारखे विविध फास्टनर्स वापरतो. आमचे फास्टनर्स मानक ऑफ-शेल्फ फास्टनर्सपुरते मर्यादित नाहीत. आम्ही विशिष्ट फास्टनर्सची रचना, विकास आणि निर्मिती करतो जे अप्रमाणित सामग्रीपासून बनवले जातात जेणेकरून ते विशेष अनुप्रयोगांसाठी आवश्यकता पूर्ण करू शकतील. कधीकधी विद्युत किंवा उष्णता नॉन-कंडक्टिव्हिटी इच्छित असते तर कधीकधी चालकता. काही विशेष अनुप्रयोगांसाठी, ग्राहकाला विशेष फास्टनर्स हवे असतील जे उत्पादन नष्ट केल्याशिवाय काढले जाऊ शकत नाहीत. अंतहीन कल्पना आणि अनुप्रयोग आहेत. आमच्याकडे हे सर्व तुमच्यासाठी आहे, ऑफ-शेल्फ नसल्यास आम्ही ते त्वरीत विकसित करू शकतो. यांत्रिक असेंब्लीच्या आमच्या पृष्ठावर जाण्यासाठी, कृपया येथे क्लिक करा. आमच्या विविध सामील होण्याच्या तंत्रांचे अधिक तपशीलात परीक्षण करूया.
ऑक्सिफ्यूल गॅस वेल्डिंग (OFW): वेल्डिंगची ज्योत तयार करण्यासाठी आम्ही ऑक्सिजनमध्ये मिसळलेला इंधन वायू वापरतो. जेव्हा आपण इंधन आणि ऑक्सिजन म्हणून एसिटिलीन वापरतो, तेव्हा आपण त्याला ऑक्सिटिलीन गॅस वेल्डिंग म्हणतो. ऑक्सीइंधन वायूच्या ज्वलन प्रक्रियेत दोन रासायनिक अभिक्रिया घडतात:
C2H2 + O2 ------» 2CO + H2 + उष्णता
2CO + H2 + 1.5 O2 -------» 2 CO2 + H2O + उष्णता
पहिली प्रतिक्रिया कार्बन मोनॉक्साईड आणि हायड्रोजनमध्ये एसिटिलीनचे विघटन करते आणि एकूण उष्णतेच्या सुमारे 33% उत्पादन करते. वरील दुसरी प्रक्रिया हायड्रोजन आणि कार्बन मोनॉक्साईडचे पुढील ज्वलन दर्शवते आणि एकूण उष्णतेच्या सुमारे 67% उत्पादन करते. ज्वालामधील तापमान 1533 ते 3573 केल्विन दरम्यान असते. गॅस मिश्रणातील ऑक्सिजनची टक्केवारी महत्त्वाची आहे. ऑक्सिजनचे प्रमाण निम्म्यापेक्षा जास्त असल्यास, ज्योत ऑक्सिडायझिंग एजंट बनते. हे काही धातूंसाठी अवांछनीय आहे परंतु इतरांसाठी ते वांछनीय आहे. तांबे-आधारित मिश्रधातूंचे ऑक्सिडायझिंग ज्वाला इष्ट असते याचे उदाहरण कारण ते धातूवर एक निष्क्रियता थर बनवते. दुसरीकडे, जेव्हा ऑक्सिजनचे प्रमाण कमी होते, तेव्हा पूर्ण ज्वलन शक्य नसते आणि ज्योत कमी करणारी (कार्ब्युरिझिंग) ज्योत बनते. कमी करणार्या ज्वालाचे तापमान कमी असते आणि म्हणून ते सोल्डरिंग आणि ब्रेझिंग सारख्या प्रक्रियेसाठी योग्य असते. इतर वायू देखील संभाव्य इंधन आहेत, परंतु एसिटिलीनपेक्षा त्यांचे काही तोटे आहेत. कधीकधी आम्ही फिलर रॉड्स किंवा वायरच्या स्वरूपात वेल्ड झोनमध्ये फिलर धातू पुरवतो. त्यांपैकी काही पृष्ठभागांचे ऑक्सिडेशन थांबवण्यासाठी आणि अशा प्रकारे वितळलेल्या धातूचे संरक्षण करण्यासाठी फ्लक्सने लेपित केले जातात. वेल्ड झोनमधून ऑक्साईड आणि इतर पदार्थ काढून टाकणे हा फ्लक्सचा एक अतिरिक्त फायदा आहे. यामुळे बंध मजबूत होतात. ऑक्सीफ्युएल गॅस वेल्डिंगचा एक प्रकार म्हणजे प्रेशर गॅस वेल्डिंग, जिथे दोन घटक त्यांच्या इंटरफेसवर ऑक्सिटिलीन गॅस टॉर्च वापरून गरम केले जातात आणि एकदा इंटरफेस वितळण्यास सुरुवात झाली की, टॉर्च मागे घेतली जाते आणि दोन भाग एकत्र दाबण्यासाठी अक्षीय बल लागू केले जाते. इंटरफेस मजबूत होईपर्यंत.
एआरसी वेल्डिंग: इलेक्ट्रोडची टोक आणि वेल्डेड भाग यांच्यामध्ये चाप तयार करण्यासाठी आम्ही विद्युत उर्जेचा वापर करतो. विद्युत पुरवठा AC किंवा DC असू शकतो तर इलेक्ट्रोड एकतर उपभोग्य किंवा वापरण्यायोग्य नसतात. आर्क वेल्डिंगमध्ये उष्णता हस्तांतरण खालील समीकरणाद्वारे व्यक्त केले जाऊ शकते:
H / l = माजी VI / v
येथे H ही उष्णता इनपुट आहे, l ही वेल्डची लांबी आहे, V आणि I ही व्होल्टेज आणि विद्युतप्रवाह आहे, v ही वेल्डिंग गती आहे आणि e ही प्रक्रिया कार्यक्षमता आहे. "ई" कार्यक्षमता जितकी जास्त असेल तितकी उपलब्ध ऊर्जा सामग्री वितळण्यासाठी अधिक फायदेशीरपणे वापरली जाते. उष्णता इनपुट देखील याप्रमाणे व्यक्त केले जाऊ शकते:
H = ux (व्हॉल्यूम) = ux A xl
येथे u वितळण्यासाठी विशिष्ट ऊर्जा आहे, A वेल्डचा क्रॉस सेक्शन आणि l वेल्डची लांबी. वरील दोन समीकरणांमधून आपण मिळवू शकतो:
v = माजी VI / u ए
आर्क वेल्डिंगचा एक प्रकार म्हणजे शील्डेड मेटल आर्क वेल्डिंग (SMAW) जे सर्व औद्योगिक आणि देखभाल वेल्डिंग प्रक्रियेपैकी सुमारे 50% बनते. इलेक्ट्रिक आर्क वेल्डिंग (स्टिक वेल्डिंग) हे वर्कपीसला लेपित इलेक्ट्रोडच्या टोकाला स्पर्श करून आणि चाप राखण्यासाठी पुरेशा अंतरापर्यंत त्वरीत मागे घेऊन केले जाते. या प्रक्रियेला आम्ही स्टिक-वेल्डिंग असेही म्हणतो कारण इलेक्ट्रोड पातळ आणि लांब काड्या असतात. वेल्डिंग प्रक्रियेदरम्यान, इलेक्ट्रोडची टीप त्याच्या कोटिंगसह वितळते आणि कमानीच्या परिसरात बेस मेटल वितळते. बेस मेटल, इलेक्ट्रोड मेटल आणि इलेक्ट्रोड कोटिंगमधील पदार्थ यांचे मिश्रण वेल्ड क्षेत्रात घट्ट होते. इलेक्ट्रोडचे कोटिंग डीऑक्सिडाइझ करते आणि वेल्ड प्रदेशात एक संरक्षक वायू प्रदान करते, त्यामुळे वातावरणातील ऑक्सिजनपासून त्याचे संरक्षण होते. म्हणून या प्रक्रियेला शील्डेड मेटल आर्क वेल्डिंग असे संबोधले जाते. इष्टतम वेल्ड कार्यक्षमतेसाठी आम्ही 50 ते 300 अँपिअर आणि पॉवर लेव्हल 10 kW पेक्षा कमी प्रवाह वापरतो. डीसी प्रवाहाची ध्रुवीयता (वर्तमान प्रवाहाची दिशा) देखील महत्त्वाची आहे. सरळ ध्रुवीयता जेथे वर्कपीस सकारात्मक आहे आणि इलेक्ट्रोड ऋणात्मक आहे शीट मेटलच्या वेल्डिंगमध्ये त्याच्या उथळ प्रवेशामुळे आणि खूप रुंद अंतर असलेल्या सांध्यांसाठी देखील प्राधान्य दिले जाते. जेव्हा आपल्याकडे रिव्हर्स पोलॅरिटी असते, म्हणजे इलेक्ट्रोड पॉझिटिव्ह असते आणि वर्कपीस नकारात्मक असते तेव्हा आपण वेल्डचे सखोल प्रवेश करू शकतो. एसी करंटसह, आमच्याकडे स्पंदन करणारे आर्क्स असल्याने, आम्ही मोठ्या व्यासाचे इलेक्ट्रोड आणि जास्तीत जास्त करंट वापरून जाड भाग वेल्ड करू शकतो. SMAW वेल्डिंग पद्धत 3 ते 19 मिमी आणि त्याहूनही अधिक जाडीच्या वर्कपीससाठी एकाधिक-पास तंत्र वापरून योग्य आहे. वेल्डच्या वर तयार झालेला स्लॅग वायर ब्रश वापरून काढून टाकणे आवश्यक आहे, जेणेकरून वेल्डच्या ठिकाणी गंज आणि बिघाड होणार नाही. हे अर्थातच शील्ड मेटल आर्क वेल्डिंगच्या खर्चात भर घालते. तरीही SMAW हे उद्योग आणि दुरुस्तीच्या कामात सर्वात लोकप्रिय वेल्डिंग तंत्र आहे.
SUBMERGED ARC वेल्डिंग (SAW): या प्रक्रियेत आम्ही चुना, सिलिका, कॅल्शियम फ्लोराईड, मॅंगनीज ऑक्साईड... इत्यादी ग्रॅन्युलर फ्लक्स मटेरियल वापरून वेल्ड आर्कचे संरक्षण करतो. ग्रॅन्युलर फ्लक्स नोजलद्वारे गुरुत्वाकर्षण प्रवाहाद्वारे वेल्ड झोनमध्ये दिले जाते. वितळलेल्या वेल्ड झोनला झाकणारा प्रवाह स्पार्क्स, धुके, अतिनील किरणोत्सर्ग इत्यादीपासून लक्षणीयरीत्या संरक्षण करतो आणि थर्मल इन्सुलेटर म्हणून कार्य करतो, अशा प्रकारे उष्णता वर्कपीसमध्ये खोलवर जाऊ देतो. अनफ्यूज्ड फ्लक्स पुनर्प्राप्त केला जातो, उपचार केला जातो आणि पुन्हा वापरला जातो. बेअरची कॉइल इलेक्ट्रोड म्हणून वापरली जाते आणि वेल्डच्या क्षेत्रामध्ये ट्यूबद्वारे दिले जाते. आम्ही 300 आणि 2000 Amperes दरम्यानचा प्रवाह वापरतो. वेल्डिंग दरम्यान गोलाकार संरचनेचे (जसे की पाईप्स) रोटेशन शक्य असल्यास बुडलेल्या आर्क वेल्डिंग (एसएडब्ल्यू) प्रक्रिया आडव्या आणि सपाट पोझिशन्स आणि वर्तुळाकार वेल्ड्सपर्यंत मर्यादित आहे. वेग 5 मी/मिनिटापर्यंत पोहोचू शकतो. SAW प्रक्रिया जाड प्लेट्ससाठी योग्य आहे आणि त्याचा परिणाम उच्च-गुणवत्तेचा, कठीण, लवचिक आणि एकसमान वेल्डमध्ये होतो. उत्पादकता, म्हणजे प्रति तास जमा केलेल्या वेल्ड सामग्रीचे प्रमाण SMAW प्रक्रियेच्या तुलनेत 4 ते 10 पट आहे.
आणखी एक आर्क वेल्डिंग प्रक्रिया, म्हणजे गॅस मेटल आर्क वेल्डिंग (GMAW) किंवा पर्यायाने मेटल इनर्ट गॅस वेल्डिंग (MIG) म्हणून ओळखली जाते, हीलियम, आर्गॉन, कार्बन डायऑक्साइड सारख्या वायूंच्या बाह्य स्त्रोतांद्वारे संरक्षित केलेल्या वेल्ड क्षेत्रावर आधारित आहे. इलेक्ट्रोड मेटलमध्ये अतिरिक्त डीऑक्सिडायझर असू शकतात. उपभोगयोग्य वायर वेल्ड झोनमध्ये नोजलद्वारे दिले जाते. गॅस मेटल आर्क वेल्डिंग (GMAW) वापरून बॉट फेरस तसेच नॉनफेरस धातूंचा समावेश असलेले फॅब्रिकेशन केले जाते. वेल्डिंग उत्पादकता SMAW प्रक्रियेच्या सुमारे 2 पट आहे. स्वयंचलित वेल्डिंग उपकरणे वापरली जात आहेत. या प्रक्रियेत धातूचे तीनपैकी एका मार्गाने हस्तांतरण केले जाते: “स्प्रे ट्रान्सफर” मध्ये इलेक्ट्रोडपासून वेल्ड क्षेत्रामध्ये प्रति सेकंद शेकडो लहान धातूचे थेंब हस्तांतरित केले जातात. दुसरीकडे, "ग्लोब्युलर ट्रान्सफर" मध्ये, कार्बन डायऑक्साइड समृद्ध वायूंचा वापर केला जातो आणि वितळलेल्या धातूचे ग्लोब्यूल इलेक्ट्रिक आर्कद्वारे चालवले जातात. वेल्डिंग प्रवाह जास्त आहेत आणि वेल्डचा प्रवेश खोलवर आहे, वेल्डिंगचा वेग स्प्रे ट्रान्सफरपेक्षा जास्त आहे. अशा प्रकारे जड भाग वेल्डिंगसाठी गोलाकार हस्तांतरण अधिक चांगले आहे. शेवटी, "शॉर्ट सर्किटिंग" पद्धतीमध्ये, इलेक्ट्रोडची टीप वितळलेल्या वेल्ड पूलला स्पर्श करते, 50 थेंब/सेकंद पेक्षा जास्त दराने धातूच्या रूपात शॉर्ट सर्किट करते आणि वैयक्तिक थेंबांमध्ये स्थानांतरित होते. पातळ वायरसह कमी प्रवाह आणि व्होल्टेज वापरले जातात. वापरलेली शक्ती सुमारे 2 किलोवॅट आहे आणि तापमान तुलनेने कमी आहे, ही पद्धत 6 मिमी पेक्षा कमी जाडीच्या पातळ शीट्ससाठी योग्य बनवते.
FLUX-CORED ARC वेल्डिंग (FCAW) प्रक्रिया ही गॅस मेटल आर्क वेल्डिंगसारखीच आहे, इलेक्ट्रोड ही फ्लक्सने भरलेली ट्यूब आहे. कोरेड-फ्लक्स इलेक्ट्रोड्स वापरण्याचे फायदे म्हणजे ते अधिक स्थिर आर्क्स तयार करतात, आम्हाला वेल्ड धातूंचे गुणधर्म सुधारण्याची संधी देतात, SMAW वेल्डिंग, सुधारित वेल्डिंग कॉन्टूर्सच्या तुलनेत त्याच्या फ्लक्सचे कमी ठिसूळ आणि लवचिक स्वरूप. सेल्फ-शिल्डेड कोरेड इलेक्ट्रोड्समध्ये अशी सामग्री असते जी वेल्ड झोनला वातावरणापासून संरक्षण करते. आम्ही सुमारे 20 किलोवॅट पॉवर वापरतो. GMAW प्रक्रियेप्रमाणे, FCAW प्रक्रिया देखील सतत वेल्डिंगसाठी प्रक्रिया स्वयंचलित करण्याची संधी देते आणि ती किफायतशीर आहे. फ्लक्स कोरमध्ये विविध मिश्रधातू जोडून विविध वेल्ड मेटल रसायने विकसित केली जाऊ शकतात.
इलेक्ट्रोगॅस वेल्डिंग (EGW) मध्ये आम्ही तुकड्यांना काठावर वेल्ड करतो. याला कधीकधी बट वेल्डिंग असेही म्हणतात. जोडण्यासाठी दोन तुकड्यांमधील वेल्ड मेटल वेल्ड पोकळीत टाकले जाते. वितळलेला स्लॅग बाहेर पडू नये म्हणून जागा दोन वॉटर-कूल्ड डॅमने बंद केली आहे. यांत्रिक ड्राइव्हद्वारे धरणे वर हलवली जातात. जेव्हा वर्कपीस फिरवता येते, तेव्हा आम्ही पाईप्सच्या परिघीय वेल्डिंगसाठी इलेक्ट्रोगॅस वेल्डिंग तंत्र देखील वापरू शकतो. सतत चाप ठेवण्यासाठी इलेक्ट्रोड्स नालीतून दिले जातात. प्रवाह सुमारे 400Amperes किंवा 750 Amperes आणि उर्जा पातळी सुमारे 20 kW असू शकतात. फ्लक्स-कोरड इलेक्ट्रोड किंवा बाह्य स्त्रोतापासून उद्भवणारे निष्क्रिय वायू संरक्षण प्रदान करतात. आम्ही स्टील्स, टायटॅनियम इत्यादी धातूंसाठी इलेक्ट्रोगॅस वेल्डिंग (EGW) वापरतो. 12mm ते 75mm जाडी. तंत्र मोठ्या संरचनांसाठी योग्य आहे.
तरीही, इलेक्ट्रोस्लाग वेल्डिंग (ESW) नावाच्या दुसर्या तंत्रात इलेक्ट्रोड आणि वर्कपीसच्या तळाशी चाप प्रज्वलित केला जातो आणि फ्लक्स जोडला जातो. जेव्हा वितळलेला स्लॅग इलेक्ट्रोडच्या टोकापर्यंत पोहोचतो, तेव्हा चाप विझला जातो. वितळलेल्या स्लॅगच्या विद्युतीय प्रतिकाराद्वारे ऊर्जा सतत पुरवली जाते. आम्ही 50 मिमी आणि 900 मिमी आणि त्याहूनही जास्त जाडी असलेल्या प्लेट्स वेल्ड करू शकतो. प्रवाह सुमारे 600 अँपिअर आहेत तर व्होल्टेज 40 - 50 V च्या दरम्यान आहेत. वेल्डिंगचा वेग सुमारे 12 ते 36 मिमी/मिनिट आहे. ऍप्लिकेशन्स इलेक्ट्रोगॅस वेल्डिंगसारखेच आहेत.
आमच्या न वापरता येण्याजोग्या इलेक्ट्रोड प्रक्रियेपैकी एक, GAS TUNGSTEN ARC वेल्डिंग (GTAW) ज्याला टंगस्टन इनर्ट गॅस वेल्डिंग (TIG) देखील म्हणतात, त्यात वायरद्वारे फिलर मेटलचा पुरवठा समाविष्ट असतो. जवळून तंदुरुस्त जोड्यांसाठी कधीकधी आम्ही फिलर मेटल वापरत नाही. टीआयजी प्रक्रियेत आम्ही फ्लक्स वापरत नाही, परंतु संरक्षणासाठी आर्गॉन आणि हेलियम वापरतो. टंगस्टनचा वितळण्याचा बिंदू जास्त असतो आणि तो TIG वेल्डिंग प्रक्रियेत वापरला जात नाही, म्हणून स्थिर प्रवाह तसेच चाप अंतर राखले जाऊ शकते. पॉवर लेव्हल 8 ते 20 kW च्या दरम्यान आहेत आणि 200 अँपिअर (DC) किंवा 500 Ampere (AC) वर प्रवाह आहेत. अॅल्युमिनियम आणि मॅग्नेशियमसाठी आम्ही एसी करंट त्याच्या ऑक्साईड क्लीनिंग फंक्शनसाठी वापरतो. टंगस्टन इलेक्ट्रोडची दूषितता टाळण्यासाठी, आम्ही वितळलेल्या धातूंशी त्याचा संपर्क टाळतो. गॅस टंगस्टन आर्क वेल्डिंग (GTAW) विशेषतः पातळ धातू वेल्डिंगसाठी उपयुक्त आहे. जीटीएडब्ल्यू वेल्ड्स चांगल्या पृष्ठभागाच्या फिनिशसह अतिशय उच्च दर्जाचे असतात.
हायड्रोजन वायूच्या जास्त किमतीमुळे, कमी वारंवार वापरले जाणारे तंत्र म्हणजे ATOMIC HYDROGEN WELDING (AHW), जिथे आपण वाहत्या हायड्रोजन वायूच्या संरक्षणात्मक वातावरणात दोन टंगस्टन इलेक्ट्रोड्समध्ये एक चाप निर्माण करतो. AHW ही एक न वापरता येणारी इलेक्ट्रोड वेल्डिंग प्रक्रिया देखील आहे. डायटॉमिक हायड्रोजन वायू H2 त्याच्या अणुस्वरूपात वेल्डिंग आर्क जवळ मोडतो, जेथे तापमान 6273 केल्विनपेक्षा जास्त असते. तुटताना, ते कंसमधून मोठ्या प्रमाणात उष्णता शोषून घेते. जेव्हा हायड्रोजन अणू वेल्ड झोनवर आघात करतात जे तुलनेने थंड पृष्ठभाग असते तेव्हा ते डायटॉमिक स्वरूपात पुन्हा एकत्र होतात आणि साठवलेली उष्णता सोडतात. वर्कपीसला चाप अंतरापर्यंत बदलून ऊर्जा बदलली जाऊ शकते.
दुसर्या नॉन-कंझ्युमेबल इलेक्ट्रोड प्रक्रियेमध्ये, प्लाझ्मा एआरसी वेल्डिंग (पीएडब्ल्यू) आमच्याकडे वेल्ड झोनकडे निर्देशित केलेला प्लाझ्मा आर्क असतो. PAW मध्ये तापमान 33,273 केल्विनपर्यंत पोहोचते. जवळजवळ समान संख्येने इलेक्ट्रॉन आणि आयन प्लाझ्मा वायू बनवतात. कमी-वर्तमान पायलट आर्क प्लाझ्मा सुरू करतो जो टंगस्टन इलेक्ट्रोड आणि छिद्र यांच्या दरम्यान असतो. ऑपरेटिंग करंट्स साधारणतः 100 अँपिअरच्या आसपास असतात. एक फिलर मेटल दिले जाऊ शकते. प्लाझ्मा आर्क वेल्डिंगमध्ये, बाह्य संरक्षण रिंग आणि आर्गॉन आणि हेलियम सारख्या वायूंचा वापर करून शिल्डिंग पूर्ण केले जाते. प्लाझ्मा आर्क वेल्डिंगमध्ये, चाप इलेक्ट्रोड आणि वर्कपीस दरम्यान किंवा इलेक्ट्रोड आणि नोजल दरम्यान असू शकते. या वेल्डिंग तंत्राचे उच्च उर्जा एकाग्रता, सखोल आणि अरुंद वेल्डिंग क्षमता, चांगली चाप स्थिरता, 1 मीटर/मिनिट पर्यंत वेल्डिंगचा वेग, कमी थर्मल विकृती या इतर पद्धतींपेक्षा फायदे आहेत. आम्ही साधारणपणे 6 मिमी पेक्षा कमी जाडीसाठी आणि कधीकधी अॅल्युमिनियम आणि टायटॅनियमसाठी 20 मिमी पर्यंत प्लाझ्मा आर्क वेल्डिंग वापरतो.
हाय-एनर्जी-बीम वेल्डिंग: इलेक्ट्रॉन-बीम वेल्डिंग (EBW) आणि लेसर वेल्डिंग (LBW) या दोन प्रकारांसह फ्यूजन वेल्डिंग पद्धतीचा आणखी एक प्रकार. आमच्या उच्च-तंत्र उत्पादनांच्या निर्मितीसाठी ही तंत्रे विशेष महत्त्वाची आहेत. इलेक्ट्रॉन-बीम वेल्डिंगमध्ये, हाय स्पीड इलेक्ट्रॉन वर्कपीसवर धडकतात आणि त्यांची गतीज उर्जा उष्णतेमध्ये रूपांतरित होते. इलेक्ट्रॉनचे अरुंद किरण व्हॅक्यूम चेंबरमध्ये सहज प्रवास करतात. साधारणपणे आम्ही ई-बीम वेल्डिंगमध्ये उच्च व्हॅक्यूम वापरतो. 150 मिमी जाडीच्या प्लेट्स वेल्डेड केल्या जाऊ शकतात. कोणत्याही शील्डिंग गॅसेस, फ्लक्स किंवा फिलर सामग्रीची आवश्यकता नाही. इलेक्ट्रॉन बीम गनमध्ये 100 किलोवॅट क्षमता आहे. 30 पर्यंत उच्च गुणोत्तर असलेले खोल आणि अरुंद वेल्ड आणि लहान उष्णता-प्रभावित झोन शक्य आहेत. वेल्डिंगची गती 12 मी/मिनिटपर्यंत पोहोचू शकते. लेसर-बीम वेल्डिंगमध्ये आपण उष्णतेचा स्रोत म्हणून उच्च-शक्तीचे लेसर वापरतो. उच्च घनतेसह 10 मायक्रॉन इतके लहान लेझर बीम वर्कपीसमध्ये खोलवर प्रवेश करण्यास सक्षम करतात. लेसर-बीम वेल्डिंगसह खोली-ते-रुंदीचे प्रमाण 10 इतके शक्य आहे. आम्ही स्पंदित तसेच सतत वेव्ह लेसर दोन्ही वापरतो, आधीचे पातळ पदार्थांसाठी वापरतात आणि नंतरचे बहुतेक 25 मिमी पर्यंत जाड वर्कपीससाठी वापरतात. पॉवर पातळी 100 किलोवॅट पर्यंत आहे. लेसर बीम वेल्डिंग ऑप्टिकली अत्यंत परावर्तित सामग्रीसाठी योग्य नाही. वेल्डिंग प्रक्रियेत देखील वायूंचा वापर केला जाऊ शकतो. लेसर बीम वेल्डिंग पद्धत ऑटोमेशन आणि उच्च व्हॉल्यूम उत्पादनासाठी योग्य आहे आणि 2.5 मीटर/मिनिट आणि 80 मीटर/मिनिट दरम्यान वेल्डिंग गती देऊ शकते. या वेल्डिंग तंत्राचा एक मोठा फायदा म्हणजे इतर तंत्रे वापरता येत नसलेल्या भागात प्रवेश करणे. लेझर बीम अशा अवघड प्रदेशात सहज जाऊ शकतात. इलेक्ट्रॉन-बीम वेल्डिंगप्रमाणे व्हॅक्यूमची गरज नाही. लेसर बीम वेल्डिंगसह चांगल्या दर्जाचे आणि ताकद, कमी संकोचन, कमी विकृती, कमी छिद्रयुक्त वेल्ड्स मिळवता येतात. फायबर ऑप्टिक केबल्स वापरून लेझर बीम सहजपणे हाताळले जाऊ शकतात आणि आकार दिला जाऊ शकतात. हे तंत्र अचूक हर्मेटिक असेंब्ली, इलेक्ट्रॉनिक पॅकेजेस... इत्यादींच्या वेल्डिंगसाठी योग्य आहे.
चला आमचे सॉलिड स्टेट वेल्डिंग तंत्र पाहू. कोल्ड वेल्डिंग (CW) ही एक अशी प्रक्रिया आहे ज्यामध्ये उष्णतेऐवजी प्रेशर डायज किंवा रोल्स वापरून जोडलेल्या भागांवर लावला जातो. कोल्ड वेल्डिंगमध्ये, वीण भागांपैकी किमान एक लवचिक असणे आवश्यक आहे. दोन समान सामग्रीसह सर्वोत्तम परिणाम प्राप्त केले जातात. कोल्ड वेल्डिंगमध्ये जोडले जाणारे दोन धातू भिन्न असल्यास, आपल्याला कमकुवत आणि ठिसूळ सांधे होऊ शकतात. कोल्ड वेल्डिंग पद्धत मऊ, लवचिक आणि लहान वर्कपीससाठी योग्य आहे जसे की इलेक्ट्रिकल कनेक्शन, उष्णता संवेदनशील कंटेनरच्या कडा, थर्मोस्टॅट्ससाठी द्विधातु पट्ट्या... इ. कोल्ड वेल्डिंगची एक भिन्नता म्हणजे रोल बाँडिंग (किंवा रोल वेल्डिंग), जेथे रोलच्या जोडीद्वारे दबाव लागू केला जातो. कधीकधी आम्ही चांगल्या इंटरफेसियल मजबुतीसाठी भारदस्त तापमानात रोल वेल्डिंग करतो.
आम्ही वापरतो ती दुसरी सॉलिड स्टेट वेल्डिंग प्रक्रिया म्हणजे अल्ट्रासोनिक वेल्डिंग (यूएसडब्ल्यू), जिथे वर्कपीस स्थिर सामान्य शक्तीच्या अधीन असतात आणि ओसीलेटिंग शिअरिंग तणावाच्या अधीन असतात. ट्रान्सड्यूसरच्या टोकाद्वारे ओसीलेटिंग शीअरिंग स्ट्रेस लागू केले जातात. प्रचंड कंपनसंख्या असलेल्या (ध्वनिलहरी) वेल्डिंग 10 ते 75 kHz फ्रिक्वेन्सीसह दोलन तैनात करते. सीम वेल्डिंगसारख्या काही ऍप्लिकेशन्समध्ये, आम्ही टीप म्हणून फिरणारी वेल्डिंग डिस्क वापरतो. वर्कपीसवर लागू केलेल्या कातरणे तणावामुळे लहान प्लास्टिकचे विकृतीकरण होते, ऑक्साईडचे थर फुटतात, दूषित होतात आणि घन स्थितीचे बंधन निर्माण होते. प्रचंड कंपनसंख्या असलेल्या (ध्वनिलहरी) वेल्डिंगमध्ये सामील असलेले तापमान धातूंच्या वितळण्याच्या बिंदूच्या तापमानापेक्षा कमी असते आणि कोणतेही संलयन होत नाही. आम्ही वारंवार अल्ट्रासोनिक वेल्डिंग (USW) प्रक्रिया प्लास्टिक सारख्या नॉनमेटॅलिक सामग्रीसाठी वापरतो. थर्मोप्लास्टिकमध्ये, तापमान मात्र वितळण्याच्या बिंदूपर्यंत पोहोचते.
आणखी एक लोकप्रिय तंत्र, FRICTION वेल्डिंग (FRW) मध्ये जोडल्या जाणार्या वर्कपीसच्या इंटरफेसवर घर्षणाद्वारे उष्णता निर्माण केली जाते. घर्षण वेल्डिंगमध्ये आपण वर्कपीसपैकी एक स्थिर ठेवतो तर दुसरी वर्कपीस फिक्स्चरमध्ये धरून स्थिर गतीने फिरवली जाते. नंतर वर्कपीस अक्षीय शक्तीच्या अंतर्गत संपर्कात आणल्या जातात. घर्षण वेल्डिंगमध्ये रोटेशनची पृष्ठभागाची गती काही प्रकरणांमध्ये 900m/min पर्यंत पोहोचू शकते. पुरेशा इंटरफेसियल संपर्कानंतर, फिरणारी वर्कपीस अचानक थांबते आणि अक्षीय शक्ती वाढविली जाते. वेल्ड झोन हा साधारणपणे अरुंद प्रदेश असतो. घर्षण वेल्डिंग तंत्राचा वापर विविध प्रकारच्या सामग्रीपासून बनविलेले घन आणि ट्यूबलर भाग जोडण्यासाठी केला जाऊ शकतो. FRW मधील इंटरफेसवर काही फ्लॅश विकसित होऊ शकतात, परंतु हा फ्लॅश दुय्यम मशीनिंग किंवा ग्राइंडिंगद्वारे काढला जाऊ शकतो. घर्षण वेल्डिंग प्रक्रियेची भिन्नता अस्तित्वात आहे. उदाहरणार्थ "जडत्व घर्षण वेल्डिंग" मध्ये फ्लायव्हीलचा समावेश होतो ज्याची घूर्णन गतिज ऊर्जा भाग वेल्ड करण्यासाठी वापरली जाते. जेव्हा फ्लायव्हील थांबते तेव्हा वेल्ड पूर्ण होते. फिरणारे वस्तुमान वेगवेगळे असू शकते आणि त्यामुळे घूर्णन गतीज ऊर्जा. आणखी एक भिन्नता म्हणजे “रेखीय घर्षण वेल्डिंग”, जिथे जोडल्या जाणार्या घटकांपैकी किमान एका घटकावर रेखीय परस्पर गती लागू केली जाते. रेखीय घर्षण वेल्डिंगमध्ये भाग गोलाकार नसतात, ते आयताकृती, चौरस किंवा इतर आकाराचे असू शकतात. फ्रिक्वेन्सी दहापट Hz, मिलिमीटर श्रेणीतील मोठेपणा आणि दहापट किंवा शेकडो MPa मध्ये दाब असू शकतात. शेवटी “घर्षण स्टिअर वेल्डिंग” वर वर्णन केलेल्या इतर दोनपेक्षा काहीसे वेगळे आहे. जडत्वात घर्षण वेल्डिंग आणि रेखीय घर्षण वेल्डिंगमध्ये इंटरफेसचे गरम करणे घर्षणाद्वारे दोन संपर्क पृष्ठभागांना घासून साध्य केले जाते, तर घर्षण स्टिअर वेल्डिंग पद्धतीमध्ये तिसरा भाग जोडण्यासाठी दोन पृष्ठभागांवर घासले जाते. 5 ते 6 मिमी व्यासाचे एक फिरणारे साधन संयुक्तच्या संपर्कात आणले जाते. तापमान 503 ते 533 केल्विन दरम्यान वाढू शकते. सांध्यातील सामग्री गरम करणे, मिसळणे आणि ढवळणे हे घडते. आम्ही अॅल्युमिनियम, प्लास्टिक आणि कंपोझिटसह विविध सामग्रीवर घर्षण स्टिअर वेल्डिंग वापरतो. वेल्ड एकसमान असतात आणि किमान छिद्रांसह गुणवत्ता उच्च असते. घर्षण स्टिअर वेल्डिंगमध्ये कोणतेही धूर किंवा स्पॅटर तयार होत नाहीत आणि प्रक्रिया उत्तम प्रकारे स्वयंचलित आहे.
रेझिस्टन्स वेल्डिंग (RW): वेल्डिंगसाठी लागणारी उष्णता दोन वर्कपीसमध्ये जोडल्या जाणार्या विद्युत प्रतिरोधामुळे तयार होते. रेझिस्टन्स वेल्डिंगमध्ये कोणतेही फ्लक्स, शील्डिंग वायू किंवा उपभोग्य इलेक्ट्रोड वापरले जात नाहीत. जौल हीटिंग रेझिस्टन्स वेल्डिंगमध्ये होते आणि ते याप्रमाणे व्यक्त केले जाऊ शकते:
H = (चौरस I) x R xtx K
H ही ज्युल (वॅट-सेकंद) मध्ये निर्माण होणारी उष्णता आहे, अँपिअरमध्ये I विद्युत् प्रवाह आहे, ओहम्समध्ये R प्रतिरोधक आहे, टी म्हणजे विद्युत प्रवाह वाहणारी सेकंदात वेळ आहे. K हा घटक 1 पेक्षा कमी आहे आणि तो किरणोत्सर्ग आणि वहन यांद्वारे नष्ट होत नसलेल्या ऊर्जेचा अंश दर्शवतो. रेझिस्टन्स वेल्डिंग प्रक्रियेतील प्रवाह 100,000 A पर्यंत उच्च पातळीवर पोहोचू शकतात परंतु व्होल्टेज सामान्यतः 0.5 ते 10 व्होल्ट असतात. इलेक्ट्रोड सामान्यत: तांब्याच्या मिश्रधातूपासून बनलेले असतात. प्रतिरोध वेल्डिंगद्वारे समान आणि भिन्न सामग्री दोन्ही जोडल्या जाऊ शकतात. या प्रक्रियेसाठी अनेक भिन्नता अस्तित्त्वात आहेत: "प्रतिरोधक स्पॉट वेल्डिंग" मध्ये दोन शीटच्या लॅप जॉइंटच्या पृष्ठभागाशी संपर्क साधणारे दोन विरोधी गोल इलेक्ट्रोड समाविष्ट आहेत. विद्युत प्रवाह बंद होईपर्यंत दबाव लागू केला जातो. वेल्ड नगेटचा व्यास साधारणपणे 10 मिमी पर्यंत असतो. रेझिस्टन्स स्पॉट वेल्डिंग वेल्ड स्पॉट्सवर किंचित विकृत इंडेंटेशन चिन्ह सोडते. स्पॉट वेल्डिंग हे आमचे सर्वात लोकप्रिय प्रतिरोधक वेल्डिंग तंत्र आहे. कठीण भागात पोहोचण्यासाठी स्पॉट वेल्डिंगमध्ये विविध इलेक्ट्रोड आकार वापरले जातात. आमची स्पॉट वेल्डिंग उपकरणे सीएनसी नियंत्रित आहेत आणि त्यात एकाधिक इलेक्ट्रोड आहेत जे एकाच वेळी वापरले जाऊ शकतात. आणखी एक भिन्नता "प्रतिरोधक सीम वेल्डिंग" चाक किंवा रोलर इलेक्ट्रोडसह चालते जे जेव्हा AC पॉवर सायकलमध्ये करंट उच्च पातळीवर पोहोचते तेव्हा सतत स्पॉट वेल्ड तयार करतात. प्रतिकार सीम वेल्डिंगद्वारे उत्पादित सांधे द्रव आणि वायू घट्ट असतात. पातळ शीटसाठी सुमारे 1.5 मीटर/मिनिट वेल्डिंगचा वेग सामान्य आहे. एखादी व्यक्ती अधूनमधून प्रवाह लागू करू शकते जेणेकरून सीमच्या बाजूने इच्छित अंतराने स्पॉट वेल्ड्स तयार होतील. “रेझिस्टन्स प्रोजेक्शन वेल्डिंग” मध्ये आम्ही वेल्डेड करायच्या वर्कपीस पृष्ठभागांपैकी एकावर एक किंवा अधिक प्रोजेक्शन (डिंपल) एम्बॉस करतो. हे अंदाज गोल किंवा अंडाकृती असू शकतात. वीण भागाच्या संपर्कात आलेल्या या नक्षीदार स्थळांवर उच्च स्थानिक तापमान गाठले जाते. या प्रक्षेपणांना संकुचित करण्यासाठी इलेक्ट्रोड दबाव आणतात. रेझिस्टन्स प्रोजेक्शन वेल्डिंगमधील इलेक्ट्रोड्समध्ये सपाट टिपा असतात आणि ते वॉटर कूल्ड कॉपर मिश्र धातु असतात. रेझिस्टन्स प्रोजेक्शन वेल्डिंगचा फायदा म्हणजे एका स्ट्रोकमध्ये अनेक वेल्ड्स करण्याची आमची क्षमता, अशा प्रकारे विस्तारित इलेक्ट्रोडचे आयुष्य, विविध जाडीच्या शीट्स वेल्ड करण्याची क्षमता, शीटला नट आणि बोल्ट वेल्ड करण्याची क्षमता. रेझिस्टन्स प्रोजेक्शन वेल्डिंगचा तोटा म्हणजे डिंपल एम्बॉसिंगची अतिरिक्त किंमत. आणखी एक तंत्र, “फ्लॅश वेल्डिंग” मध्ये दोन वर्कपीसच्या टोकाला असलेल्या चापातून उष्णता निर्माण होते जेव्हा ते संपर्क करू लागतात. ही पद्धत वैकल्पिकरित्या आर्क वेल्डिंग देखील मानली जाऊ शकते. इंटरफेसचे तापमान वाढते आणि सामग्री मऊ होते. एक अक्षीय शक्ती लागू केली जाते आणि मऊ झालेल्या प्रदेशात वेल्ड तयार होते. फ्लॅश वेल्डिंग पूर्ण झाल्यानंतर, संयुक्त सुधारित स्वरूपासाठी मशीन केले जाऊ शकते. फ्लॅश वेल्डिंगद्वारे प्राप्त वेल्ड गुणवत्ता चांगली आहे. पॉवर पातळी 10 ते 1500 किलोवॅट आहे. फ्लॅश वेल्डिंग 75 मिमी व्यासापर्यंत आणि 0.2 मिमी ते 25 मिमी जाडीच्या शीट्सच्या समान किंवा भिन्न धातूंच्या काठापासून काठ जोडण्यासाठी योग्य आहे. "स्टड आर्क वेल्डिंग" हे फ्लॅश वेल्डिंगसारखेच आहे. बोल्ट किंवा थ्रेडेड रॉडसारखा स्टड प्लेटसारख्या वर्कपीसमध्ये जोडला जात असताना एक इलेक्ट्रोड म्हणून काम करतो. व्युत्पन्न उष्णता एकाग्र करण्यासाठी, ऑक्सिडेशन रोखण्यासाठी आणि वितळलेल्या धातूला वेल्ड झोनमध्ये टिकवून ठेवण्यासाठी, सांध्याभोवती एक डिस्पोजेबल सिरॅमिक रिंग ठेवली जाते. शेवटी “पर्क्यूशन वेल्डिंग” ही दुसरी रेझिस्टन्स वेल्डिंग प्रक्रिया, विद्युत उर्जेचा पुरवठा करण्यासाठी कॅपेसिटरचा वापर करते. पर्क्यूशन वेल्डिंगमध्ये पॉवर मिलिसेकंदांच्या आत सोडली जाते आणि संयुक्त ठिकाणी उच्च स्थानिक उष्णता विकसित होते. आम्ही इलेक्ट्रॉनिक्स उत्पादन उद्योगामध्ये पर्क्यूशन वेल्डिंगचा मोठ्या प्रमाणावर वापर करतो जेथे जॉइंटच्या परिसरातील संवेदनशील इलेक्ट्रॉनिक घटक गरम करण्याचे टाळावे लागते.
एक्सप्लोशन वेल्डिंग नावाच्या तंत्रामध्ये स्फोटकांच्या थराचा स्फोट होतो जो जोडल्या जाणार्या वर्कपीसपैकी एकावर ठेवला जातो. वर्कपीसवर खूप जास्त दबाव टाकल्याने एक अशांत आणि लहरी इंटरफेस तयार होतो आणि यांत्रिक इंटरलॉकिंग होते. स्फोटक वेल्डिंगमध्ये बाँडची ताकद खूप जास्त असते. भिन्न धातू असलेल्या प्लेट्सच्या क्लेडिंगसाठी विस्फोट वेल्डिंग ही एक चांगली पद्धत आहे. क्लेडिंग केल्यानंतर, प्लेट्स पातळ विभागात आणल्या जाऊ शकतात. काहीवेळा आम्ही विस्तारित नळ्यांसाठी स्फोट वेल्डिंग वापरतो जेणेकरून ते प्लेटच्या विरूद्ध घट्ट बंद केले जातील.
सॉलिड स्टेट जॉइनिंगच्या डोमेनमधील आमची शेवटची पद्धत म्हणजे डिफ्यूजन बाँडिंग किंवा डिफ्यूजन वेल्डिंग (डीएफडब्ल्यू) ज्यामध्ये मुख्यतः इंटरफेसमध्ये अणूंच्या प्रसाराद्वारे एक चांगला जॉइंट साध्य केला जातो. इंटरफेसमधील काही प्लास्टिक विकृती देखील वेल्डिंगमध्ये योगदान देते. अंतर्भूत तापमान सुमारे 0.5 Tm आहे जेथे Tm हे धातूचे वितळणारे तापमान आहे. डिफ्यूजन वेल्डिंगमधील बाँडची ताकद दबाव, तापमान, संपर्क वेळ आणि संपर्क पृष्ठभागांची स्वच्छता यावर अवलंबून असते. कधीकधी आम्ही इंटरफेसमध्ये फिलर धातू वापरतो. डिफ्यूजन बाँडिंगमध्ये उष्णता आणि दाब आवश्यक असतात आणि विद्युत प्रतिरोध किंवा भट्टी आणि मृत वजन, दाबा किंवा इतर द्वारे पुरवले जातात. डिफ्यूजन वेल्डिंगसह समान आणि भिन्न धातू जोडल्या जाऊ शकतात. अणूंचे स्थलांतर होण्यासाठी लागणाऱ्या वेळेमुळे ही प्रक्रिया तुलनेने मंद आहे. DFW स्वयंचलित असू शकते आणि एरोस्पेस, इलेक्ट्रॉनिक्स, वैद्यकीय उद्योगांसाठी जटिल भागांच्या निर्मितीमध्ये मोठ्या प्रमाणावर वापरले जाते. उत्पादित उत्पादनांमध्ये ऑर्थोपेडिक इम्प्लांट, सेन्सर्स, एरोस्पेस स्ट्रक्चरल सदस्यांचा समावेश आहे. कॉम्प्लेक्स शीट मेटल स्ट्रक्चर्स तयार करण्यासाठी डिफ्यूजन बाँडिंग सुपरप्लास्टिक फॉर्मिंगसह एकत्र केले जाऊ शकते. शीटवरील निवडलेली ठिकाणे प्रथम प्रसार बंधित असतात आणि नंतर बंध नसलेले क्षेत्र हवेचा दाब वापरून मोल्डमध्ये विस्तारित केले जातात. उच्च कडकपणा-ते-वजन गुणोत्तर असलेल्या एरोस्पेस संरचना या पद्धतींच्या संयोजनाचा वापर करून तयार केल्या जातात. डिफ्यूजन वेल्डिंग / सुपरप्लास्टिक बनवण्याच्या एकत्रित प्रक्रियेमुळे फास्टनर्सची गरज दूर करून आवश्यक भागांची संख्या कमी होते, परिणामी कमी ताण-तणाव असलेले अत्यंत अचूक भाग आर्थिकदृष्ट्या आणि कमी लीड वेळेसह मिळतात.
ब्रेझिंग: ब्रेझिंग आणि सोल्डरिंग तंत्रामध्ये वेल्डिंगसाठी आवश्यक तापमानापेक्षा कमी तापमानाचा समावेश होतो. ब्रेझिंग तापमान सोल्डरिंग तापमानापेक्षा जास्त असते. ब्रेझिंगमध्ये फिलर मेटल जोडल्या जाणार्या पृष्ठभागांमध्ये ठेवला जातो आणि फिलर मटेरिअलच्या वितळण्याच्या तपमानापर्यंत तापमान 723 केल्विनपेक्षा जास्त परंतु वर्कपीसच्या वितळण्याच्या तापमानापेक्षा कमी केले जाते. वितळलेला धातू वर्कपीसमधील जवळची जागा भरतो. फाइलर धातूचे थंड होणे आणि त्यानंतरचे घनीकरण यामुळे सांधे मजबूत होतात. ब्रेज वेल्डिंगमध्ये फिलर मेटल जॉइंटवर जमा केले जाते. ब्रेझिंगच्या तुलनेत ब्रेझ वेल्डिंगमध्ये अधिक फिलर मेटलचा वापर केला जातो. ऑक्सिडायझिंग फ्लेमसह ऑक्सिटिलीन टॉर्चचा वापर ब्रेज वेल्डिंगमध्ये फिलर मेटल जमा करण्यासाठी केला जातो. ब्रेझिंगमध्ये कमी तापमानामुळे, उष्णतेने प्रभावित झोनमधील समस्या जसे की वार्पिंग आणि अवशिष्ट ताण कमी होतात. ब्रेझिंगमधील क्लिअरन्स गॅप जितका लहान असेल तितकी सांध्याची कातरण्याची ताकद जास्त असते. जास्तीत जास्त तन्य शक्ती मात्र इष्टतम अंतरावर (एक शिखर मूल्य) गाठली जाते. या इष्टतम मूल्याच्या खाली आणि वर, ब्रेझिंगमधील तन्य शक्ती कमी होते. ब्रेझिंगमधील ठराविक मंजुरी 0.025 आणि 0.2 मिमी दरम्यान असू शकते. आम्ही परफॉर्म्स, पावडर, रिंग्ज, वायर, स्ट्रीप ….. इ. अशा विविध आकारांसह विविध प्रकारचे ब्रेझिंग साहित्य वापरतो. आणि आपल्या डिझाइन किंवा उत्पादन भूमितीसाठी हे प्रदर्शन तयार करू शकतात. आम्ही तुमच्या बेस मटेरियल आणि अॅप्लिकेशननुसार ब्रेझिंग मटेरियलची सामग्री देखील निर्धारित करतो. अवांछित ऑक्साईड स्तर काढून टाकण्यासाठी आणि ऑक्सिडेशन रोखण्यासाठी आम्ही ब्रेजिंग ऑपरेशनमध्ये वारंवार फ्लक्सचा वापर करतो. त्यानंतरचे गंज टाळण्यासाठी, सामान्यतः जॉइनिंग ऑपरेशननंतर फ्लक्सेस काढले जातात. AGS-TECH Inc. विविध ब्रेझिंग पद्धती वापरते, यासह:
- टॉर्च ब्रेझिंग
- फर्नेस ब्रेझिंग
- इंडक्शन ब्रेझिंग
- प्रतिकार ब्रेझिंग
- डिप ब्रेझिंग
- इन्फ्रारेड ब्रेझिंग
- प्रसार Brazing
- उच्च ऊर्जा बीम
कार्बाइड ड्रिल बिट्स, इन्सर्ट्स, ऑप्टोइलेक्ट्रॉनिक हर्मेटिक पॅकेजेस, सील यांसारख्या चांगल्या ताकदीसह भिन्न धातूंनी बनविलेले ब्रेझ्ड जोड्यांची आमची सर्वात सामान्य उदाहरणे.
सोल्डरिंग : हे आमच्या सर्वात वारंवार वापरल्या जाणार्या तंत्रांपैकी एक आहे जेथे सोल्डर (फिलर मेटल) जवळून फिटिंग घटकांमधील ब्रेझिंगप्रमाणे सांधे भरते. आमच्या सोल्डरचे वितळण्याचे बिंदू 723 केल्विनच्या खाली आहेत. आम्ही मॅन्युफॅक्चरिंग ऑपरेशन्समध्ये मॅन्युअल आणि ऑटोमेटेड सोल्डरिंग दोन्ही तैनात करतो. ब्रेझिंगच्या तुलनेत, सोल्डरिंग तापमान कमी आहे. सोल्डरिंग उच्च-तापमान किंवा उच्च-शक्ती अनुप्रयोगांसाठी फारसे योग्य नाही. आम्ही सोल्डरिंगसाठी शिसे-मुक्त सोल्डर तसेच टिन-लीड, टिन-जस्त, शिसे-चांदी, कॅडमियम-सिल्व्हर, झिंक-अॅल्युमिनियम मिश्र धातु वापरतो. सोल्डरिंगमध्ये नॉनकॉरोसिव्ह राळ-आधारित तसेच अजैविक ऍसिड आणि क्षार दोन्ही फ्लक्स म्हणून वापरले जातात. कमी सोल्डेबिलिटी असलेल्या धातूंना सोल्डर करण्यासाठी आम्ही विशेष फ्लक्स वापरतो. ज्या ऍप्लिकेशन्समध्ये आम्हाला सिरेमिक मटेरियल, काच किंवा ग्रेफाइट सोल्डर करावे लागते, आम्ही प्रथम भागांना सोल्डरबिलिटी वाढवण्यासाठी योग्य धातूने प्लेट करतो. आमची लोकप्रिय सोल्डरिंग तंत्रे आहेत:
-रिफ्लो किंवा पेस्ट सोल्डरिंग
-वेव्ह सोल्डरिंग
- फर्नेस सोल्डरिंग
- टॉर्च सोल्डरिंग
- इंडक्शन सोल्डरिंग
- लोह सोल्डरिंग
- प्रतिकार सोल्डरिंग
- डिप सोल्डरिंग
- अल्ट्रासोनिक सोल्डरिंग
- इन्फ्रारेड सोल्डरिंग
प्रचंड कंपनसंख्या असलेल्या (ध्वनिलहरी) सोल्डरिंगमुळे आम्हाला एक अनोखा फायदा मिळतो ज्यामध्ये अल्ट्रासोनिक पोकळ्या निर्माण होण्याच्या प्रभावामुळे फ्लक्सेसची गरज संपुष्टात येते ज्यामुळे ऑक्साईड फिल्म्स जोडल्या जात असलेल्या पृष्ठभागांवरून काढून टाकल्या जातात. रिफ्लो आणि वेव्ह सोल्डरिंग ही इलेक्ट्रॉनिक्समध्ये उच्च व्हॉल्यूम उत्पादनासाठी आमची औद्योगिकदृष्ट्या उत्कृष्ट तंत्रे आहेत आणि त्यामुळे अधिक तपशीलवार वर्णन करणे योग्य आहे. रिफ्लो सोल्डरिंगमध्ये, आम्ही सेमीसोलिड पेस्ट वापरतो ज्यात सोल्डर-मेटल कण असतात. स्क्रीनिंग किंवा स्टॅन्सिलिंग प्रक्रियेचा वापर करून पेस्ट संयुक्त वर ठेवली जाते. मुद्रित सर्किट बोर्ड (PCB) मध्ये आम्ही हे तंत्र वारंवार वापरतो. जेव्हा या पॅडवर पेस्टमधून इलेक्ट्रिकल घटक ठेवले जातात, तेव्हा पृष्ठभागावरील ताण पृष्ठभाग-माऊंट पॅकेजेस संरेखित ठेवतो. घटक ठेवल्यानंतर, आम्ही भट्टीत असेंब्ली गरम करतो जेणेकरून रिफ्लो सोल्डरिंग होते. या प्रक्रियेदरम्यान, पेस्टमधील सॉल्व्हेंट्सचे बाष्पीभवन होते, पेस्टमधील फ्लक्स सक्रिय केला जातो, घटक आधीपासून गरम केले जातात, सोल्डरचे कण वितळले जातात आणि संयुक्त ओले केले जातात आणि शेवटी पीसीबी असेंब्ली हळूहळू थंड केली जाते. पीसीबी बोर्डच्या उच्च व्हॉल्यूम उत्पादनासाठी आमचे दुसरे लोकप्रिय तंत्र, म्हणजे वेव्ह सोल्डरिंग या वस्तुस्थितीवर अवलंबून आहे की वितळलेले सोल्डर धातूचे पृष्ठभाग ओले करतात आणि जेव्हा धातू आधीपासून गरम केले जाते तेव्हाच चांगले बंध तयार होतात. वितळलेल्या सोल्डरची एक स्थायी लॅमिनार लहर प्रथम पंपाद्वारे तयार केली जाते आणि प्रीहेटेड आणि प्रीफ्लक्स केलेले पीसीबी लाटेवर पोहोचवले जातात. सोल्डर केवळ उघडलेल्या धातूच्या पृष्ठभागांना ओले करते परंतु IC पॉलिमर पॅकेजेस किंवा पॉलिमर-लेपित सर्किट बोर्डांना ओले करत नाही. गरम पाण्याच्या जेटचा उच्च-वेग संयुक्त पासून जास्त सोल्डर उडवतो आणि लगतच्या लीड्समधील ब्रिजिंग प्रतिबंधित करतो. सरफेस-माउंट पॅकेजेसच्या वेव्ह सोल्डरिंगमध्ये सोल्डरिंग करण्यापूर्वी आम्ही प्रथम त्यांना सर्किट बोर्डला चिकटवतो. पुन्हा स्क्रीनिंग आणि स्टॅन्सिलिंग वापरले जाते परंतु यावेळी इपॉक्सीसाठी. घटक त्यांच्या योग्य ठिकाणी ठेवल्यानंतर, इपॉक्सी बरा होतो, बोर्ड उलटे केले जातात आणि वेव्ह सोल्डरिंग होते.