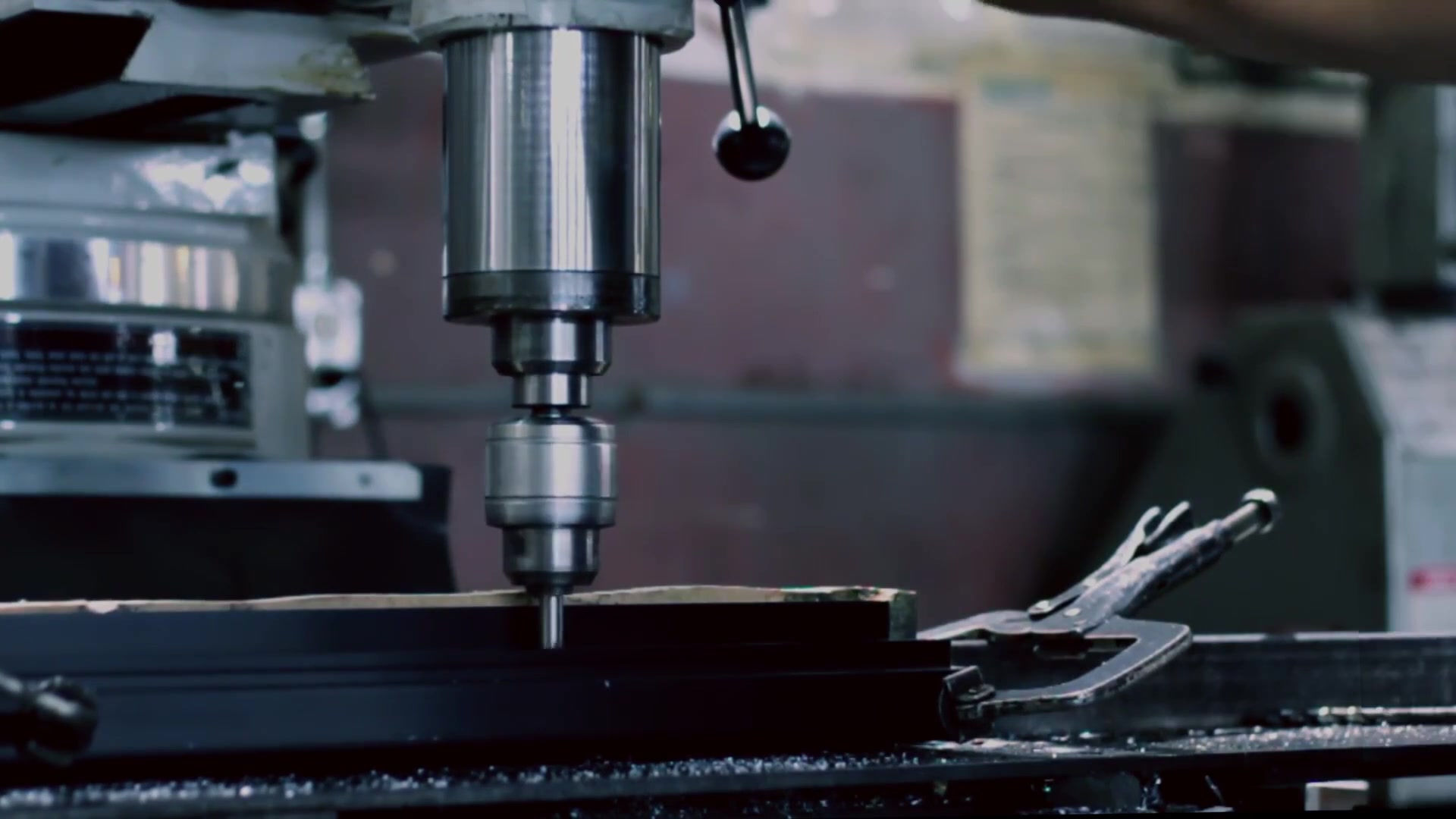
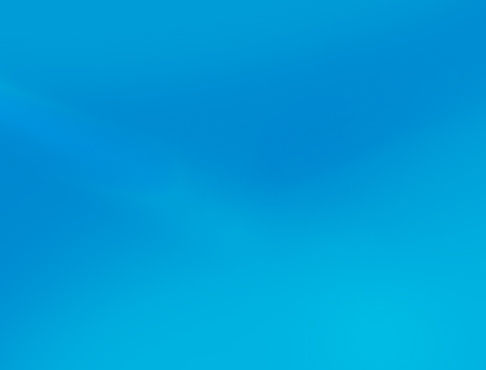
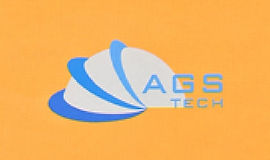
जागतिक कस्टम उत्पादक, इंटिग्रेटर, कंसोलिडेटर, उत्पादन आणि सेवांच्या विविधतेसाठी आउटसोर्सिंग भागीदार.
सानुकूल उत्पादित आणि ऑफ-शेल्फ उत्पादने आणि सेवांचे उत्पादन, फॅब्रिकेशन, अभियांत्रिकी, एकत्रीकरण, एकत्रीकरण, आउटसोर्सिंगसाठी आम्ही तुमचे एक-स्टॉप स्रोत आहोत.
तुमची भाषा निवडा
-
सानुकूल उत्पादन
-
देशांतर्गत आणि जागतिक करार निर्मिती
-
मॅन्युफॅक्चरिंग आउटसोर्सिंग
-
देशांतर्गत आणि जागतिक खरेदी
-
एकत्रीकरण
-
अभियांत्रिकी एकत्रीकरण
-
अभियांत्रिकी सेवा
ELECTRICAL DISCHARGE MACHINING (EDM), also referred to as SPARK-EROSION or ELECTRODISCHARGE MACHINING, SPARK ERODING, DIE SINKING_cc781905-5cde-3194-bb3b -136bad5cf58d_or WIRE EROSION, is a NON-CONVENTIONAL MANUFACTURING process where erosion of metals takes place and desired shape is obtained using electrical discharges in the form ठिणग्यांचा. आम्ही EDM चे काही प्रकार देखील ऑफर करतो, namely NO-WEAR EDM, WIRE EDM (WEDM), EDM ग्राइंडिंग (EDG), DIE-SINKING EDM, electrical-DISCHARGEM7, mcc-MCCEDM5, micro-MCCEDM58 -5cde-3194-bb3b-136bad5cf58d_and ELECTROCHEMICAL-डिस्चार्ज ग्राइंडिंग (ECDG). आमच्या EDM सिस्टीममध्ये आकाराची साधने/इलेक्ट्रोड आणि DC पॉवर सप्लायशी जोडलेली वर्कपीस आणि इलेक्ट्रिकली नॉन-कंडक्टिंग डायलेक्ट्रिक फ्लुइडमध्ये घातलेली असते. 1940 नंतर इलेक्ट्रिकल डिस्चार्ज मशीनिंग हे उत्पादन उद्योगांमध्ये सर्वात महत्वाचे आणि लोकप्रिय उत्पादन तंत्रज्ञान बनले आहे.
जेव्हा दोन इलेक्ट्रोड्समधील अंतर कमी होते, तेव्हा इलेक्ट्रोड्समधील व्हॉल्यूममधील विद्युत क्षेत्राची तीव्रता काही बिंदूंमध्ये डायलेक्ट्रिकच्या ताकदीपेक्षा जास्त होते, जे तुटते आणि अखेरीस दोन इलेक्ट्रोड्समध्ये विद्युत प्रवाहासाठी एक पूल तयार होतो. एक तीव्र विद्युत चाप तयार होतो ज्यामुळे वर्कपीसचा काही भाग आणि काही टूलिंग सामग्री वितळते. परिणामी, दोन्ही इलेक्ट्रोडमधून सामग्री काढून टाकली जाते. त्याच वेळी, डायलेक्ट्रिक द्रव वेगाने गरम होतो, परिणामी आर्क गॅपमध्ये द्रवपदार्थाचे बाष्पीभवन होते. एकदा विद्युत प्रवाह थांबला किंवा तो थांबला की आसपासच्या डायलेक्ट्रिक द्रवाद्वारे गॅस बबलमधून उष्णता काढून टाकली जाते आणि बबल पोकळी निर्माण करतो (कोसतो). बुडबुडे कोसळल्यामुळे आणि वर्कपीसच्या पृष्ठभागावरून डायलेक्ट्रिक फ्लुइड फ्लश डेब्रिजच्या प्रवाहामुळे निर्माण झालेली शॉक वेव्ह आणि कोणतीही वितळलेली वर्कपीस सामग्री डायलेक्ट्रिक द्रवपदार्थात प्रवेश करते. या डिस्चार्जचा पुनरावृत्ती दर 50 ते 500 kHz, 50 ते 380 V मधील व्होल्टेज आणि 0.1 आणि 500 Amperes दरम्यानचा प्रवाह आहे. नवीन द्रव डायलेक्ट्रिक जसे की खनिज तेल, केरोसीन किंवा डिस्टिल्ड आणि डिआयनाइज्ड पाणी सामान्यत: आंतर-इलेक्ट्रोड व्हॉल्यूममध्ये पोहोचवले जाते जे घन कण (भंगाराच्या स्वरूपात) काढून टाकते आणि डायलेक्ट्रिकचे इन्सुलेट गुणधर्म पुनर्संचयित केले जातात. विद्युत् प्रवाहानंतर, दोन इलेक्ट्रोडमधील संभाव्य फरक ब्रेकडाउनच्या आधीच्या स्थितीत पुनर्संचयित केला जातो, त्यामुळे नवीन द्रव डायलेक्ट्रिक ब्रेकडाउन होऊ शकते. आमची आधुनिक इलेक्ट्रिकल डिस्चार्ज मशीन (EDM) संख्यात्मकरित्या नियंत्रित हालचाली देतात आणि डायलेक्ट्रिक द्रवांसाठी पंप आणि फिल्टरिंग सिस्टमसह सुसज्ज आहेत.
इलेक्ट्रिकल डिस्चार्ज मशीनिंग (EDM) ही एक मशीनिंग पद्धत आहे जी मुख्यतः कठोर धातूंसाठी वापरली जाते किंवा ज्यांना पारंपारिक तंत्रांसह मशीन करणे खूप कठीण असते. EDM सामान्यत: विद्युत वाहक असलेल्या कोणत्याही सामग्रीसह कार्य करते, जरी EDM सह इन्सुलेट सिरेमिक मशीनिंग करण्याच्या पद्धती देखील प्रस्तावित केल्या गेल्या आहेत. हळुवार बिंदू आणि वितळण्याची सुप्त उष्णता हे गुणधर्म आहेत जे प्रत्येक डिस्चार्ज काढून टाकलेल्या धातूचे प्रमाण निर्धारित करतात. ही मूल्ये जितकी जास्त असतील तितकी सामग्री काढण्याची गती कमी होईल. इलेक्ट्रिकल डिस्चार्ज मशीनिंग प्रक्रियेमध्ये कोणतीही यांत्रिक ऊर्जा समाविष्ट नसल्यामुळे, वर्कपीसची कडकपणा, ताकद आणि कडकपणा काढण्याच्या दरावर परिणाम करत नाही. डिस्चार्ज वारंवारता किंवा ऊर्जा प्रति डिस्चार्ज, व्होल्टेज आणि करंट सामग्री काढण्याचे दर नियंत्रित करण्यासाठी भिन्न असतात. सामग्री काढण्याचा दर आणि पृष्ठभागाचा खडबडीतपणा वाढत्या वर्तमान घनतेसह आणि स्पार्क वारंवारता कमी होत आहे. आम्ही EDM वापरून प्री-कठोर स्टीलमधील गुंतागुंतीचे आकृतिबंध किंवा पोकळी कापून त्यांना मऊ आणि पुन्हा कडक करण्यासाठी उष्मा उपचार न करता करू शकतो. आपण ही पद्धत टायटॅनियम, हॅस्टेलॉय, कोवर आणि इनकोनेल सारख्या कोणत्याही धातू किंवा धातूच्या मिश्रधातूंसह वापरू शकतो. EDM प्रक्रियेच्या ऍप्लिकेशन्समध्ये पॉलीक्रिस्टलाइन डायमंड टूल्सचा आकार देणे समाविष्ट आहे. इलेक्ट्रोकेमिकल मशीनिंग (ECM), वॉटर जेट कटिंग (WJ, AWJ), लेझर कटिंग यासारख्या प्रक्रियांसह EDM ही अपारंपारिक किंवा अपारंपरिक मशीनिंग पद्धत मानली जाते. दुसरीकडे पारंपारिक मशीनिंग पद्धतींमध्ये टर्निंग, मिलिंग, ग्राइंडिंग, ड्रिलिंग आणि इतर प्रक्रिया समाविष्ट आहेत ज्याची सामग्री काढण्याची यंत्रणा मूलत: यांत्रिक शक्तींवर आधारित आहे. इलेक्ट्रिकल-डिस्चार्ज मशीनिंग (EDM) साठी इलेक्ट्रोड्स ग्रेफाइट, पितळ, तांबे आणि तांबे-टंगस्टन मिश्रधातूपासून बनलेले असतात. इलेक्ट्रोड व्यास 0.1 मिमी पर्यंत कमी करणे शक्य आहे. टूल वेअर ही एक अवांछित घटना असल्यामुळे EDM मधील मितीय अचूकतेवर विपरित परिणाम होतो, आम्ही ध्रुवीयता उलट करून आणि तांबे टूल्स वापरून, कमी करण्यासाठी NO-WEAR EDM नावाच्या प्रक्रियेचा लाभ घेतो.
तद्वतच, इलेक्ट्रिकल-डिस्चार्ज मशीनिंग (EDM) ही इलेक्ट्रोड्समधील डायलेक्ट्रिक लिक्विडचे ब्रेकडाउन आणि पुनर्संचयित करण्याची मालिका मानली जाऊ शकते. तथापि, प्रत्यक्षात, आंतर-इलेक्ट्रोड क्षेत्रातून मोडतोड काढणे जवळजवळ नेहमीच अर्धवट असते. यामुळे आंतर-इलेक्ट्रोड क्षेत्रातील डायलेक्ट्रिकचे विद्युत गुणधर्म त्यांच्या नाममात्र मूल्यांपेक्षा भिन्न असतात आणि वेळेनुसार बदलतात. इंटर-इलेक्ट्रोड अंतर, (स्पार्क-गॅप), वापरलेल्या विशिष्ट मशीनच्या नियंत्रण अल्गोरिदमद्वारे समायोजित केले जाते. EDM मधील स्पार्क-गॅप दुर्दैवाने कधीकधी मोडतोडमुळे शॉर्ट सर्किट होऊ शकते. दोन इलेक्ट्रोड्स (टूल आणि वर्कपीस) शॉर्ट सर्किटिंगपासून रोखण्यासाठी इलेक्ट्रोडची नियंत्रण प्रणाली त्वरीत प्रतिक्रिया देण्यास अयशस्वी होऊ शकते. हे अवांछित शॉर्ट सर्किट आदर्श केसपेक्षा वेगळ्या पद्धतीने सामग्री काढून टाकण्यास योगदान देते. डायलेक्ट्रिकचे इन्सुलेटिंग गुणधर्म पुनर्संचयित करण्यासाठी आम्ही फ्लशिंग क्रियेला अत्यंत महत्त्व देतो जेणेकरून विद्युत प्रवाह नेहमी इंटर-इलेक्ट्रोड क्षेत्राच्या बिंदूमध्ये होतो, ज्यामुळे टूल-इलेक्ट्रोडच्या आकारात अवांछित बदल (नुकसान) होण्याची शक्यता कमी होते. आणि वर्कपीस. विशिष्ट भूमिती प्राप्त करण्यासाठी, EDM साधन वर्कपीसला स्पर्श न करता त्याच्या अगदी जवळ इच्छित मार्गावर मार्गदर्शन केले जाते, आम्ही वापरात असलेल्या गती नियंत्रणाच्या कार्यक्षमतेकडे अत्यंत लक्ष देतो. अशा प्रकारे, मोठ्या प्रमाणात वर्तमान डिस्चार्ज / स्पार्क्स होतात आणि प्रत्येक साधन आणि वर्कपीस दोन्हीमधून सामग्री काढून टाकण्यास हातभार लावते, जेथे लहान खड्डे तयार होतात. क्रेटर्सचा आकार हा हातातील विशिष्ट कामासाठी सेट केलेल्या तांत्रिक पॅरामीटर्सचे कार्य आहे आणि परिमाणे नॅनोस्केल (जसे की मायक्रो-EDM ऑपरेशन्सच्या बाबतीत) पासून काही शेकडो मायक्रोमीटरपर्यंत खडबडीत स्थितीत असू शकतात. टूलवरील हे छोटे खड्डे "टूल वेअर" नावाच्या इलेक्ट्रोडची हळूहळू धूप करतात. वर्कपीसच्या भूमितीवरील पोशाखांच्या हानिकारक प्रभावाचा प्रतिकार करण्यासाठी आम्ही मशीनिंग ऑपरेशन दरम्यान टूल-इलेक्ट्रोड सतत बदलतो. काहीवेळा आम्ही इलेक्ट्रोड म्हणून सतत बदललेली वायर वापरून हे साध्य करतो (या EDM प्रक्रियेला WIRE EDM देखील म्हणतात). काहीवेळा आपण टूल-इलेक्ट्रोड अशा प्रकारे वापरतो की त्याचा फक्त एक छोटासा भाग मशीनिंग प्रक्रियेत गुंतलेला असतो आणि हा भाग नियमितपणे बदलला जातो. हे, उदाहरणार्थ, टूल-इलेक्ट्रोड म्हणून फिरणारी डिस्क वापरताना केस. या प्रक्रियेला EDM ग्राइंडिंग म्हणतात. तरीही आम्ही उपयोजित केलेल्या दुसर्या तंत्रात पोशाखांची भरपाई करण्यासाठी समान EDM ऑपरेशन दरम्यान भिन्न आकार आणि आकारांसह इलेक्ट्रोडचा संच वापरणे समाविष्ट आहे. आम्ही याला मल्टिपल इलेक्ट्रोड तंत्र म्हणतो, आणि जेव्हा टूल इलेक्ट्रोड इच्छित आकारात नकारात्मक प्रतिकृती बनवते आणि एका दिशेने, सामान्यतः उभ्या दिशेने (म्हणजे z-अक्ष) रिकाम्या दिशेने प्रगत केले जाते तेव्हा सर्वात जास्त वापरले जाते. हे डायलेक्ट्रिक द्रवामध्ये टूलच्या सिंकसारखे दिसते ज्यामध्ये वर्कपीस विसर्जित केली जाते आणि म्हणून त्याला DIE-SINKING EDM_cc781905-5cbb6-31-31_5cde-31_time_cc781905-5cde-31-31_cd-time_cc781905 म्हणतात 3194-bb3b-136bad5cf58d_CONVENTIONAL EDM or_cc781905-5cde-3194-bb3b-136bad5cf58d). या ऑपरेशनसाठी मशीन्सना SINKER EDM म्हणतात. या प्रकारच्या EDM साठी इलेक्ट्रोड्समध्ये जटिल फॉर्म असतात. जर अंतिम भूमिती सामान्यत: साध्या-आकाराच्या इलेक्ट्रोडचा वापर करून प्राप्त केली गेली असेल ज्याला अनेक दिशांनी हलवले जाते आणि ते रोटेशनच्या अधीन देखील असेल, तर आम्ही त्याला EDM मिलिंग म्हणतो. परिधानाचे प्रमाण ऑपरेशनमध्ये वापरल्या जाणार्या तांत्रिक पॅरामीटर्सवर कठोरपणे अवलंबून असते (ध्रुवीयता, कमाल वर्तमान, ओपन सर्किट व्होल्टेज). उदाहरणार्थ, in micro-EDM, ज्याला m-EDM म्हणून देखील ओळखले जाते, हे पॅरामीटर्स सामान्यतः गंभीर जेन व्हॅल्यूवर सेट केले जातात. म्हणून, परिधान ही त्या क्षेत्रातील एक मोठी समस्या आहे जी आपण आपल्या संचित माहितीचा वापर करून कमी करतो. उदाहरणार्थ, ग्रेफाइट इलेक्ट्रोडचा पोशाख कमी करण्यासाठी, डिजिटल जनरेटर, मिलिसेकंदांमध्ये नियंत्रित करता येण्याजोगा, इलेक्ट्रो-इरोशन होत असताना ध्रुवीयता उलट करतो. याचा परिणाम इलेक्ट्रोप्लेटिंग सारखाच परिणाम होतो जो सतत खोडलेला ग्रेफाइट इलेक्ट्रोडवर परत जमा करतो. दुसर्या पद्धतीत, तथाकथित ''झिरो वेअर'' सर्किट आपण स्त्राव किती वेळा सुरू होतो आणि थांबतो हे कमी करतो, शक्य तितक्या जास्त वेळ चालू ठेवतो. इलेक्ट्रिकल-डिस्चार्ज मशीनिंगमधील सामग्री काढण्याच्या दराचा अंदाज यावरून लावला जाऊ शकतो:
MRR = 4 x 10 exp(4) x I x Tw exp (-1.23)
येथे MRR mm3/min मध्ये आहे, I amperes मध्ये चालू आहे, Tw K-273.15K मध्ये वर्कपीस मेल्टिंग पॉइंट आहे. exp म्हणजे घातांक.
दुसरीकडे, इलेक्ट्रोडचा पोशाख दर Wt यावरून मिळू शकतो:
Wt = ( 1.1 x 10exp(11) ) x I x Ttexp(-2.38)
येथे Wt mm3/min मध्ये आहे आणि Tt हा K-273.15K मध्ये इलेक्ट्रोड सामग्रीचा वितळणारा बिंदू आहे
शेवटी, वर्कपीसचे इलेक्ट्रोड आर ते परिधान गुणोत्तर यावरून मिळू शकते:
R = 2.25 x Trex(-2.38)
येथे Tr हे वर्कपीसच्या वितळण्याचे बिंदू आणि इलेक्ट्रोडचे गुणोत्तर आहे.
SINKER EDM :
Sinker EDM, also referred to as CAVITY TYPE EDM or VOLUME EDM, consists of an electrode and workpiece submerged in an insulating liquid. इलेक्ट्रोड आणि वर्कपीस वीज पुरवठ्याशी जोडलेले आहेत. वीज पुरवठा या दोघांमध्ये विद्युत क्षमता निर्माण करतो. जसजसे इलेक्ट्रोड वर्कपीसजवळ येतो तसतसे द्रवपदार्थामध्ये डायलेक्ट्रिक ब्रेकडाउन होते, प्लाझ्मा चॅनेल बनते आणि एक लहान ठिणगी उडी मारते. ठिणग्या सामान्यत: एका वेळी एकच प्रहार करतात कारण आंतर-इलेक्ट्रोड स्पेसमधील भिन्न स्थानांमध्ये समान स्थानिक विद्युत वैशिष्ट्ये असण्याची शक्यता फारच कमी असते ज्यामुळे अशा सर्व ठिकाणी एकाच वेळी ठिणगी पडू शकते. इलेक्ट्रोड आणि वर्कपीस दरम्यान प्रति सेकंद यादृच्छिक बिंदूंवर या शेकडो हजारो ठिणग्या होतात. जसजसे बेस मेटल क्षीण होते आणि त्यानंतर स्पार्क गॅप वाढत जाते, तसतसे आमच्या CNC मशीनद्वारे इलेक्ट्रोड आपोआप कमी केला जातो जेणेकरून प्रक्रिया अखंडपणे चालू ठेवता येईल. आमच्या उपकरणांमध्ये '' वेळेवर '' आणि '' ऑफ टाइम '' म्हणून ओळखल्या जाणार्या नियंत्रित चक्र आहेत. ऑन टाइम सेटिंग स्पार्कची लांबी किंवा कालावधी ठरवते. जास्त वेळ त्या स्पार्कसाठी सखोल पोकळी निर्माण करतो आणि त्या सायकलसाठी त्यानंतरच्या सर्व स्पार्क तयार करतो, ज्यामुळे वर्कपीसवर अधिक खडबडीत फिनिश तयार होते आणि त्याउलट. ऑफ टाईम म्हणजे एक ठिणगी दुसर्याने बदलण्याचा कालावधी. जास्त वेळ मिटलेला मलबा साफ करण्यासाठी डायलेक्ट्रिक द्रवपदार्थाला नोजलमधून फ्लश करण्यास परवानगी देतो, ज्यामुळे शॉर्ट सर्किट टाळता येते. या सेटिंग्ज सूक्ष्म सेकंदांमध्ये समायोजित केल्या जातात.
वायर EDM :
In WIRE ELECTRICAL DISCHARGE MACHINING (WEDM), also called WIRE-CUT EDM or WIRE CUTTING, we feed a वर्कपीसमधून पितळाची पातळ सिंगल-स्ट्रँड मेटल वायर, जी डायलेक्ट्रिक द्रवपदार्थाच्या टाकीमध्ये बुडविली जाते. वायर EDM हा EDM चा एक महत्वाचा फरक आहे. आम्ही अधूनमधून 300 मिमी जाड प्लेट्स कापण्यासाठी आणि इतर उत्पादन पद्धतींसह मशीनसाठी कठीण असलेल्या कठीण धातूपासून पंच, टूल्स आणि डाय बनवण्यासाठी वायर-कट EDM वापरतो. बँड सॉच्या सहाय्याने कंटूर कटिंग सारखी दिसणारी या प्रक्रियेत, स्पूलमधून सतत दिलेली वायर, वरच्या आणि खालच्या डायमंड मार्गदर्शकांमध्ये धरली जाते. सीएनसी-नियंत्रित मार्गदर्शक x–y विमानात फिरतात आणि वरचा मार्गदर्शक देखील z–u–v अक्षात स्वतंत्रपणे फिरू शकतो, ज्यामुळे टॅपर्ड आणि संक्रमण आकार कापण्याची क्षमता वाढते (जसे की तळाशी वर्तुळ आणि चौरस अव्वल). वरचा मार्गदर्शक x–y–u–v–i–j–k–l– मध्ये अक्षाच्या हालचाली नियंत्रित करू शकतो. हे WEDM ला अतिशय गुंतागुंतीचे आणि नाजूक आकार कापण्यास अनुमती देते. Ø 0.25 ब्रास, तांबे किंवा टंगस्टन वायर वापरून आमच्या उपकरणांचे सरासरी कटिंग केर्फ जे सर्वोत्तम आर्थिक खर्च आणि मशीनिंग वेळ मिळवते ते 0.335 मिमी आहे. तथापि, आमच्या CNC उपकरणांचे वरचे आणि खालचे डायमंड मार्गदर्शक सुमारे 0.004 मिमी पर्यंत अचूक आहेत, आणि Ø 0.02 मिमी वायर वापरून कटिंग पथ किंवा 0.021 मिमी इतका लहान कर्फ असू शकतो. त्यामुळे खरोखर अरुंद कट शक्य आहेत. कटिंगची रुंदी वायरच्या रुंदीपेक्षा जास्त असते कारण वायरच्या बाजूपासून वर्कपीसपर्यंत स्पार्किंग होते, ज्यामुळे धूप होते. हे ''ओव्हरकट'' आवश्यक आहे, बर्याच ऍप्लिकेशन्ससाठी ते अंदाज करण्यायोग्य आहे आणि म्हणून त्याची भरपाई केली जाऊ शकते (मायक्रो-EDM मध्ये असे सहसा होत नाही). वायर स्पूल लांब असतात - 0.25 मिमी वायरचा 8 किलोचा स्पूल फक्त 19 किलोमीटर लांबीचा असतो. वायरचा व्यास 20 मायक्रोमीटर इतका लहान असू शकतो आणि भूमितीची अचूकता +/- 1 मायक्रोमीटरच्या शेजारी आहे. आम्ही साधारणपणे वायर फक्त एकदाच वापरतो आणि ती रिसायकल करतो कारण ती तुलनेने स्वस्त आहे. ते 0.15 ते 9m/मिनिट या स्थिर गतीने प्रवास करते आणि कट करताना एक स्थिर कर्फ (स्लॉट) राखला जातो. वायर-कट EDM प्रक्रियेमध्ये आम्ही पाण्याचा वापर डायलेक्ट्रिक द्रव म्हणून करतो, त्याची प्रतिरोधकता आणि इतर विद्युत गुणधर्म फिल्टर आणि डी-आयोनायझर युनिट्ससह नियंत्रित करतो. पाणी कटिंग झोनपासून कट मोडतोड दूर करते. दिलेल्या सामग्रीच्या जाडीसाठी जास्तीत जास्त फीड रेट ठरवण्यासाठी फ्लशिंग हा एक महत्त्वाचा घटक आहे आणि म्हणून आम्ही ते सातत्य ठेवतो. वायर EDM मधील कटिंग स्पीड प्रति युनिट वेळेच्या क्रॉस-सेक्शनल एरिया कटच्या संदर्भात सांगितले जाते, जसे की 50 मिमी जाड D2 टूल स्टीलसाठी 18,000 mm2/तास. या केससाठी रेखीय कटिंग गती 18,000/50 = 360mm/hr असेल वायर EDM मधील सामग्री काढण्याचा दर आहे:
MRR = Vf xhxb
येथे MRR mm3/min मध्ये आहे, Vf हा वर्कपीसमध्ये mm/min मध्ये वायरचा फीड रेट आहे, h हा मिमीमध्ये जाडी किंवा उंची आहे आणि b हा कर्फ आहे, जे आहे:
b = dw + 2s
येथे dw हा वायरचा व्यास आहे आणि s हा वायर आणि वर्कपीसमधील अंतर मिमीमध्ये आहे.
कडक सहिष्णुतेसह, आमच्या आधुनिक मल्टी अॅक्सिस EDM वायर-कटिंग मशीनिंग सेंटर्समध्ये एकाच वेळी दोन भाग कापण्यासाठी मल्टी हेड्स, वायर तुटणे टाळण्यासाठी नियंत्रणे, वायर तुटण्याच्या बाबतीत स्वयंचलित सेल्फ-थ्रेडिंग वैशिष्ट्ये आणि प्रोग्राम केलेली वैशिष्ट्ये जोडली आहेत. ऑपरेशन ऑप्टिमाइझ करण्यासाठी मशीनिंग धोरण, सरळ आणि टोकदार कटिंग क्षमता.
वायर-ईडीएम आम्हाला कमी अवशिष्ट ताण देतात, कारण सामग्री काढून टाकण्यासाठी उच्च कटिंग फोर्सची आवश्यकता नसते. जेव्हा प्रति नाडी ऊर्जा/शक्ती तुलनेने कमी असते (फिनिशिंग ऑपरेशन्सप्रमाणे), कमी अवशिष्ट ताणांमुळे सामग्रीच्या यांत्रिक गुणधर्मांमध्ये थोडासा बदल अपेक्षित असतो.
इलेक्ट्रिकल-डिस्चार्ज ग्राइंडिंग (EDG) : ग्राइंडिंग चाकांमध्ये अपघर्षक नसतात, ते ग्रेफाइट किंवा पितळाचे बनलेले असतात. फिरणारे चाक आणि वर्कपीस दरम्यान पुनरावृत्ती होणार्या ठिणग्या वर्कपीसच्या पृष्ठभागावरील सामग्री काढून टाकतात. सामग्री काढण्याची दर आहे:
MRR = K x I
येथे MRR mm3/min मध्ये आहे, I amperes मध्ये करंट आहे आणि K mm3/A-min मध्ये वर्कपीस मटेरियल फॅक्टर आहे. घटकांवर अरुंद स्लिट्स पाहण्यासाठी आम्ही वारंवार इलेक्ट्रिकल-डिस्चार्ज ग्राइंडिंगचा वापर करतो. आम्ही कधीकधी EDG (इलेक्ट्रिकल-डिस्चार्ज ग्राइंडिंग) प्रक्रिया ECG (इलेक्ट्रोकेमिकल ग्राइंडिंग) प्रक्रियेसह एकत्र करतो जिथे सामग्री रासायनिक क्रियेद्वारे काढून टाकली जाते, ग्रेफाइट व्हीलमधून विद्युत डिस्चार्ज ऑक्साईड फिल्मला तोडते आणि इलेक्ट्रोलाइटद्वारे वाहून जाते. प्रक्रियेला ELECTROCHEMICAL-DISCHARGE ग्राइंडिंग (ECDG) म्हणतात. जरी ECDG प्रक्रिया तुलनेने जास्त उर्जा वापरते, तरीही ती EDG पेक्षा वेगवान प्रक्रिया आहे. या तंत्राचा वापर करून आम्ही बहुतेक कार्बाइड टूल्स पीसतो.
इलेक्ट्रिकल डिस्चार्ज मशीनिंगचे अनुप्रयोग:
प्रोटोटाइप उत्पादन:
आम्ही ईडीएम प्रक्रिया मोल्ड मेकिंग, टूल आणि डाय मॅन्युफॅक्चरिंगमध्ये वापरतो, तसेच प्रोटोटाइप आणि उत्पादन भाग बनवण्यासाठी, विशेषत: एरोस्पेस, ऑटोमोबाईल आणि इलेक्ट्रॉनिक्स उद्योगांसाठी ज्यामध्ये उत्पादनाचे प्रमाण तुलनेने कमी आहे. सिंकर EDM मध्ये, ग्रेफाइट, तांबे टंगस्टन किंवा शुद्ध तांबे इलेक्ट्रोड इच्छित (ऋण) आकारात तयार केले जाते आणि उभ्या रॅमच्या शेवटी वर्कपीसमध्ये दिले जाते.
नाणे तयार करणे:
नाणे (स्टॅम्पिंग) प्रक्रियेद्वारे दागिने आणि बॅज तयार करण्यासाठी, सकारात्मक मास्टर स्टर्लिंग चांदीपासून बनविला जाऊ शकतो, कारण (योग्य मशीन सेटिंग्जसह) मास्टर लक्षणीयरीत्या खोडलेला आहे आणि फक्त एकदाच वापरला जातो. परिणामी निगेटिव्ह डाय नंतर कडक केला जातो आणि कांस्य, चांदी किंवा कमी प्रुफ सोन्याच्या मिश्र धातुच्या कटआउट शीट ब्लँक्समधून स्टँप केलेले फ्लॅट तयार करण्यासाठी ड्रॉप हॅमरमध्ये वापरला जातो. बॅजसाठी हे फ्लॅट्स आणखी एका डायद्वारे वक्र पृष्ठभागावर आकारले जाऊ शकतात. या प्रकारचा EDM सहसा तेल-आधारित डायलेक्ट्रिकमध्ये बुडवून केला जातो. तयार वस्तू कठोर (काच) किंवा मऊ (पेंट) इनॅमलिंग आणि/किंवा शुद्ध सोने किंवा निकेलने इलेक्ट्रोप्लेट करून अधिक परिष्कृत केली जाऊ शकते. परिष्करण म्हणून चांदीसारखी मऊ सामग्री हाताने कोरलेली असू शकते.
लहान छिद्रे पाडणे:
आमच्या वायर-कट EDM मशीनवर, आम्ही वर्कपीसमध्ये थ्रू होल बनवण्यासाठी लहान छिद्र ड्रिलिंग EDM वापरतो ज्याद्वारे वायर-कट EDM ऑपरेशनसाठी वायर थ्रेड करण्यासाठी. आमच्या वायर-कट मशिनवर विशेषत: लहान छिद्र ड्रिलिंगसाठी वेगळे EDM हेड बसवले जातात जे मोठ्या कडक प्लेट्सना आवश्यकतेनुसार आणि प्री-ड्रिलिंगशिवाय त्यांच्यापासून तयार झालेले भाग खोडून काढू देतात. आम्ही जेट इंजिनमध्ये वापरल्या जाणार्या टर्बाइन ब्लेडच्या कडांमध्ये छिद्रांच्या पंक्ती ड्रिल करण्यासाठी लहान छिद्र EDM देखील वापरतो. या लहान छिद्रांमधून वायूचा प्रवाह इंजिनांना शक्यतोपेक्षा जास्त तापमान वापरण्याची परवानगी देतो. उच्च-तापमान, अतिशय कठोर, एकल क्रिस्टल मिश्र धातुंनी बनलेले हे ब्लेड उच्च गुणोत्तर असलेल्या या छिद्रांचे पारंपारिक मशीनिंग अत्यंत कठीण आणि अशक्य बनवते. लहान छिद्र EDM साठी इतर अनुप्रयोग क्षेत्र म्हणजे इंधन प्रणाली घटकांसाठी सूक्ष्म छिद्र तयार करणे. एकात्मिक EDM हेड्स व्यतिरिक्त, आम्ही स्वतंत्रपणे लहान छिद्र ड्रिलिंग EDM मशीन्स x–y अक्षांसह मशीनच्या अंधांवर किंवा छिद्रांमधून तैनात करतो. EDM ड्रिलमध्ये लांब पितळ किंवा तांबे ट्यूब इलेक्ट्रोडसह भोक पाडतात जे फ्लशिंग एजंट आणि डायलेक्ट्रिक म्हणून इलेक्ट्रोडमधून वाहणाऱ्या डिस्टिल्ड किंवा डीआयोनाइज्ड पाण्याच्या सतत प्रवाहासह चकमध्ये फिरतात. काही लहान-होल ड्रिलिंग EDMs 10 सेकंदांपेक्षा कमी वेळेत 100 मिमी मऊ किंवा अगदी कडक स्टीलमधून ड्रिल करण्यास सक्षम असतात. या ड्रिलिंग ऑपरेशनमध्ये 0.3 मिमी आणि 6.1 मिमी दरम्यान छिद्रे मिळवता येतात.
धातू विघटन मशीनिंग:
कामाच्या तुकड्यांमधून तुटलेली साधने (ड्रिल बिट्स किंवा टॅप) काढण्याच्या विशिष्ट हेतूसाठी आमच्याकडे विशेष EDM मशीन देखील आहेत. या प्रक्रियेला ''धातूचे विघटन मशिनिंग'' म्हणतात.
इलेक्ट्रिकल-डिस्चार्ज मशीनिंगचे फायदे आणि तोटे:
EDM च्या फायद्यांमध्ये मशीनिंग समाविष्ट आहे:
- जटिल आकार जे अन्यथा पारंपरिक कटिंग साधनांसह तयार करणे कठीण होईल
- अगदी जवळच्या सहनशीलतेसाठी अत्यंत कठीण सामग्री
- खूप लहान कामाचे तुकडे जेथे पारंपारिक कटिंग टूल्स जास्त कटिंग टूलच्या दाबाने भाग खराब करू शकतात.
- टूल आणि वर्क पीस यांच्यात थेट संपर्क नाही. म्हणून नाजूक विभाग आणि कमकुवत साहित्य कोणत्याही विकृतीशिवाय मशीन केले जाऊ शकते.
- चांगली पृष्ठभागाची समाप्ती मिळू शकते.
- अतिशय बारीक छिद्रे सहजपणे ड्रिल करता येतात.
EDM च्या तोट्यांमध्ये हे समाविष्ट आहे:
- सामग्री काढून टाकण्याचा मंद दर.
- रॅम/सिंकर EDM साठी इलेक्ट्रोड तयार करण्यासाठी वापरलेला अतिरिक्त वेळ आणि खर्च.
- इलेक्ट्रोडच्या पोशाखांमुळे वर्कपीसवर तीक्ष्ण कोपऱ्यांचे पुनरुत्पादन करणे कठीण आहे.
- वीज वापर जास्त आहे.
- ''ओव्हरकट'' तयार होतो.
- मशिनिंग दरम्यान जास्त प्रमाणात टूल पोशाख होतो.
- इलेक्ट्रिकली नॉन-कंडक्टिव्ह सामग्री केवळ प्रक्रियेच्या विशिष्ट सेट-अपसह मशीन केली जाऊ शकते.