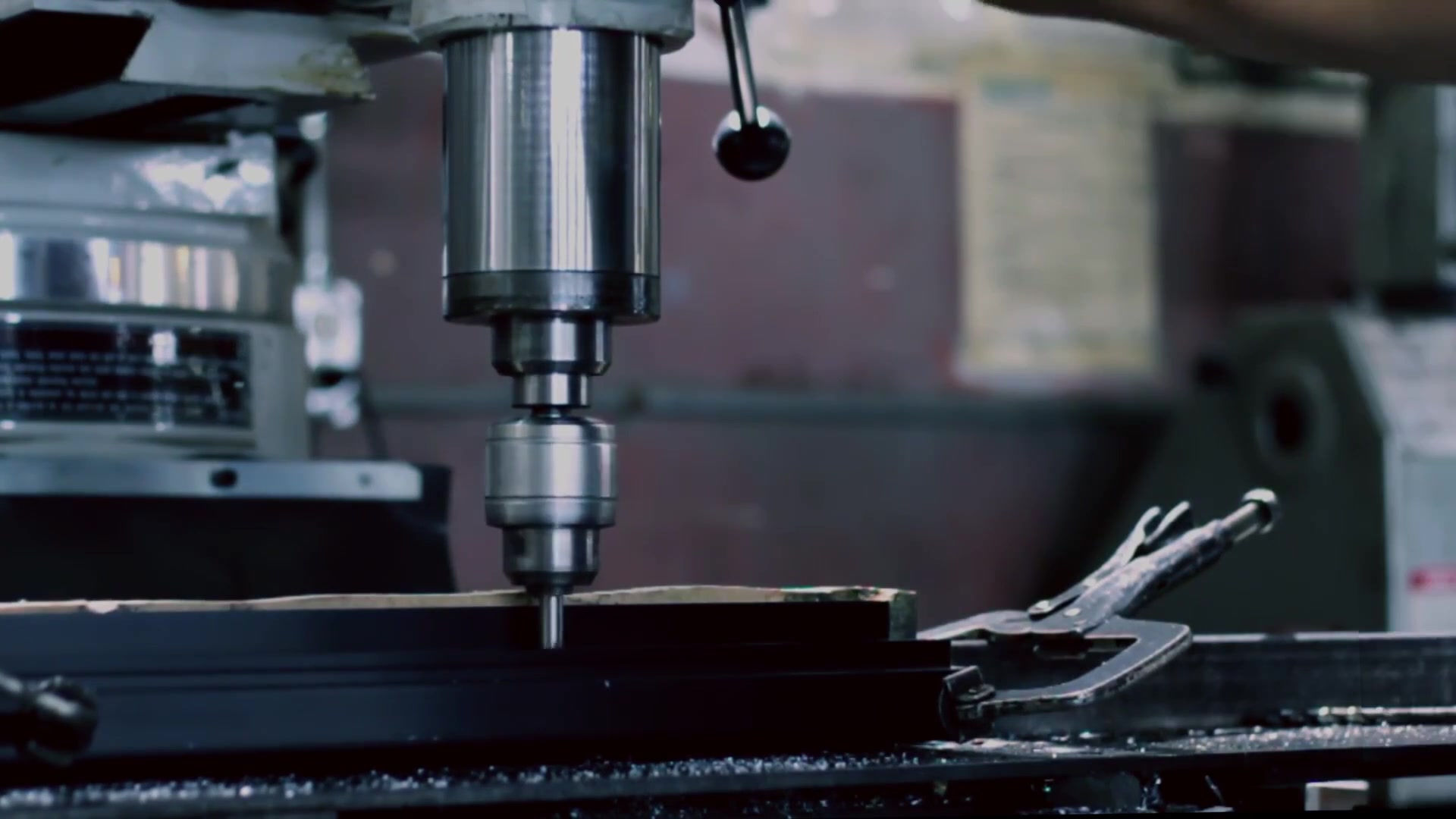
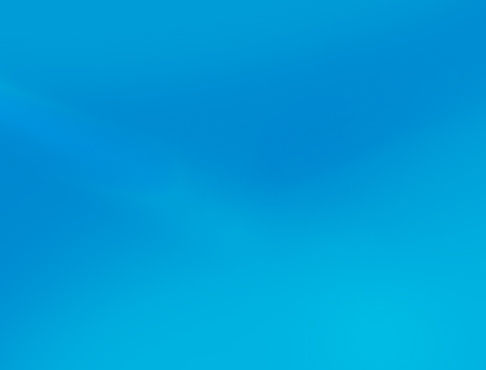
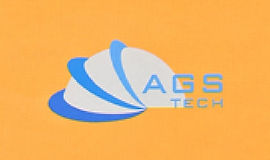
Pengeluar Tersuai Global, Penyepadu, Penyatuan, Rakan Kongsi Penyumberan Luar untuk Pelbagai Pelbagai Produk & Perkhidmatan.
Kami adalah sumber sehenti anda untuk pembuatan, fabrikasi, kejuruteraan, penyatuan, penyepaduan, penyumberan luar bagi produk & perkhidmatan buatan sendiri dan luar rak.
Pilih Bahasa anda
-
Pembuatan Tersuai
-
Pembuatan Kontrak Domestik & Global
-
Penyumberan Luar Pembuatan
-
Perolehan Domestik & Global
-
Consolidation
-
Integrasi Kejuruteraan
-
Perkhidmatan Kejuruteraan
Search Results
164 hasil ditemukan dengan carian kosong
- Machine Elements Manufacturing, Gears, Gear Drives, Bearings, Keys, Splines
Machine Elements Manufacturing, Gears, Gear Drives, Bearings, Keys, Splines, Pins, Shafts, Seals, Fasteners, Clutch, Cams, Followers, Belts, Couplings, Shafts Pembuatan Elemen Mesin Baca Lagi Tali Pinggang & Rantai & Pemasangan Pacuan Kabel Baca Lagi Pemasangan Gear & Gear Drive Baca Lagi Pembuatan Gandingan & Galas Baca Lagi Pembuatan Kunci & Spline & Pin Baca Lagi Cams & Followers & Linkages & Ratchet Wheels Manufacturing Baca Lagi Pembuatan Aci Baca Lagi Pembuatan Meterai Mekanikal Baca Lagi Pemasangan Klac & Brek Baca Lagi Pembuatan Pengikat Baca Lagi Perhimpunan Mesin Mudah ELEMEN MESIN adalah komponen asas mesin. Elemen ini terdiri daripada tiga jenis asas: 1.) Komponen struktur termasuk anggota rangka, galas, gandar, spline, pengikat, pengedap dan pelincir. 2.) Mekanisme mengawal pergerakan dalam pelbagai cara seperti gear train, belt atau chain drives, linkages, cam and follower systems, brek & clutch. 3.) Kawal komponen seperti butang, suis, penunjuk, penderia, penggerak dan pengawal komputer. Kebanyakan elemen mesin yang kami tawarkan kepada anda adalah diseragamkan kepada saiz biasa, tetapi elemen mesin tersuai juga tersedia untuk aplikasi khusus anda. Penyesuaian elemen mesin boleh berlaku pada reka bentuk sedia ada yang terdapat dalam katalog kami yang boleh dimuat turun atau pada reka bentuk serba baharu. Prototaip dan pembuatan elemen mesin boleh dibawa ke hadapan sebaik sahaja reka bentuk diluluskan oleh kedua-dua pihak. Jika elemen mesin baharu perlu direka & dihasilkan, pelanggan kami sama ada menghantar e-mel kepada kami pelan tindakan mereka sendiri dan kami menyemaknya untuk kelulusan, atau mereka meminta kami mereka bentuk elemen mesin untuk permohonan mereka. Dalam kes kedua, kami menggunakan semua input daripada pelanggan kami dan mereka bentuk elemen mesin dan menghantar pelan tindakan yang dimuktamadkan kepada pelanggan kami untuk kelulusan. Setelah diluluskan, kami menghasilkan artikel pertama dan seterusnya mengeluarkan elemen mesin mengikut reka bentuk akhir. Pada mana-mana peringkat kerja ini, sekiranya reka bentuk elemen mesin tertentu menunjukkan prestasi yang tidak memuaskan di lapangan (yang jarang berlaku), kami menyemak keseluruhan projek dan membuat perubahan bersama-sama dengan pelanggan kami mengikut keperluan. Adalah menjadi amalan standard kami untuk menandatangani perjanjian tidak mendedahkan (NDA) dengan pelanggan kami untuk reka bentuk elemen mesin atau sebarang produk lain apabila diperlukan atau diperlukan. Setelah elemen mesin untuk pelanggan tertentu direka dan dikilangkan tersuai, kami memberikan kod produk kepadanya dan hanya menghasilkan dan menjualnya kepada pelanggan kami yang memiliki produk tersebut. Kami mengeluarkan semula elemen mesin menggunakan alat, acuan dan prosedur yang dibangunkan seberapa banyak yang diperlukan dan setiap kali pelanggan kami memesannya semula. Dalam erti kata lain, sebaik sahaja elemen mesin tersuai direka dan dihasilkan untuk anda, harta intelek serta semua perkakas dan acuan akan disimpan dan disimpan selama-lamanya oleh kami untuk anda dan produk yang dikeluarkan semula mengikut kehendak anda. Kami juga menawarkan perkhidmatan kejuruteraan pelanggan kami dengan menggabungkan elemen mesin secara kreatif ke dalam komponen atau pemasangan yang menyediakan aplikasi dan memenuhi atau melebihi jangkaan pelanggan kami. Tumbuhan yang membuat elemen mesin kami layak oleh sama ada ISO9001, QS9000 atau TS16949. Di samping itu, kebanyakan produk kami mempunyai tanda CE atau UL dan memenuhi piawaian yang relevan di peringkat antarabangsa seperti ISO, SAE, ASME, DIN. Sila klik pada submenu untuk mendapatkan maklumat terperinci tentang elemen mesin kami termasuk: - Tali Pinggang, Rantai dan Pemacu Kabel - Gear dan Pemacu Gear - Gandingan & Galas - Kekunci & Spline & pin - Cam & Pautan - Aci - Meterai Mekanikal - Klac & Brek Industri - Pengikat - Mesin Mudah Kami telah menyediakan risalah rujukan untuk pelanggan, pereka dan pembangun produk baharu kami termasuk elemen mesin. Anda boleh membiasakan diri dengan beberapa istilah yang biasa digunakan dalam reka bentuk komponen mesin: Muat turun brosur untuk Syarat Kejuruteraan Mekanikal Biasa yang digunakan oleh Pereka dan Jurutera Elemen mesin kami menemui aplikasi dalam pelbagai bidang seperti jentera perindustrian, sistem automasi, peralatan ujian dan metrologi, peralatan pengangkutan, mesin pembinaan dan boleh dikatakan di mana-mana sahaja yang anda boleh fikirkan. AGS-TECH membangunkan dan mengeluarkan elemen mesin daripada pelbagai bahan bergantung pada aplikasi. Bahan yang digunakan untuk elemen mesin boleh terdiri daripada plastik acuan yang digunakan untuk mainan hingga kes yang dikeraskan dan keluli bersalut khas untuk jentera perindustrian. Pereka bentuk kami menggunakan perisian profesional dan alat reka bentuk terkini untuk membangunkan elemen mesin, dengan mengambil kira butiran seperti sudut dalam gigi gear, tegasan yang terlibat, kadar kehausan….dsb. Sila tatal melalui submenu kami dan muat turun brosur dan katalog produk kami untuk melihat sama ada anda boleh mencari elemen mesin luar rak untuk aplikasi anda. Jika anda tidak dapat mencari padanan yang sesuai untuk aplikasi anda, sila maklumkan kepada kami dan kami akan bekerjasama dengan anda untuk membangunkan dan mengeluarkan elemen mesin yang akan memenuhi keperluan anda. Jika anda kebanyakannya berminat dengan keupayaan kejuruteraan dan penyelidikan & pembangunan kami dan bukannya keupayaan pembuatan, maka kami menjemput anda untuk melawati laman web kami http://www.ags-engineering.com di mana anda boleh mendapatkan maklumat yang lebih terperinci tentang reka bentuk kami, pembangunan produk, pembangunan proses, perkhidmatan perundingan kejuruteraan dan banyak lagi CLICK Product Finder-Locator Service HALAMAN SEBELUMNYA
- Transmission Components, Belts, Chains, Cable Drives, Pulleys,AGS-TECH
Transmission Components, Belts, Chains and Cable Drives, Conventional & Grooved or Serrated, Positive Drive, Pulleys Tali Pinggang & Rantai & Pemasangan Pacuan Kabel AGS-TECH Inc. menawarkan kepada anda komponen penghantaran kuasa termasuk Tali Pinggang & Rantai & Pemasangan Pemacu Kabel. Dengan penambahbaikan bertahun-tahun, pemacu getah, kulit dan tali pinggang kami yang lain menjadi lebih ringan dan padat, mampu membawa beban yang lebih tinggi pada kos yang lebih rendah. Begitu juga, pemacu rantai kami telah melalui banyak pembangunan dari semasa ke semasa dan ia menawarkan beberapa kelebihan kepada pelanggan kami. Beberapa kelebihan menggunakan pemacu rantai adalah jarak pusat aci yang tidak terhad, kekompakan, kemudahan pemasangan, keanjalan dalam ketegangan tanpa gelincir atau rayapan, keupayaan untuk beroperasi dalam persekitaran suhu tinggi. Pemacu kabel kami juga menawarkan kelebihan seperti kesederhanaan dalam beberapa aplikasi berbanding jenis komponen penghantaran yang lain. Kedua-dua tali pinggang luar rak, pemacu rantai dan kabel serta versi fabrikasi dan pemasangan tersuai tersedia. Kami boleh mengeluarkan komponen penghantaran ini mengikut saiz yang sesuai untuk aplikasi anda dan daripada bahan yang paling sesuai. TALI TALI & TALI PINGGANG: - Tali Pinggang Rata Konvensional: Ini adalah tali pinggang rata biasa tanpa gigi, alur atau gerigi. Pemacu tali pinggang rata menawarkan fleksibiliti, penyerapan hentakan yang baik, penghantaran kuasa yang cekap pada kelajuan tinggi, rintangan lelasan, kos rendah. Tali pinggang boleh disambung atau disambungkan untuk membuat tali pinggang yang lebih besar. Kelebihan lain tali pinggang rata konvensional ialah ia nipis, ia tidak tertakluk kepada beban emparan yang tinggi (menjadikannya baik untuk operasi berkelajuan tinggi dengan takal kecil). Sebaliknya mereka mengenakan beban galas yang tinggi kerana tali pinggang rata memerlukan ketegangan yang tinggi. Kelemahan lain pemacu tali pinggang rata boleh tergelincir, operasi bising, dan kecekapan yang agak rendah pada kelajuan operasi rendah dan sederhana. Kami mempunyai dua jenis tali pinggang konvensional: Reinforced dan Non-Reinforced. Tali pinggang bertetulang mempunyai anggota tegangan dalam strukturnya. Tali pinggang rata konvensional boleh didapati sebagai kulit, fabrik atau tali getah, getah atau plastik tidak bertetulang, fabrik, kulit bertetulang. Tali pinggang kulit menawarkan jangka hayat yang panjang, fleksibiliti, pekali geseran yang sangat baik, pembaikan yang mudah. Walau bagaimanapun, tali pinggang kulit agak mahal, memerlukan pembalut dan pembersihan tali pinggang, dan bergantung pada suasana ia mungkin mengecut atau meregang. Fabrik bergetah atau tali pinggang tali tahan terhadap kelembapan, asid dan alkali. Tali pinggang kain bergetah diperbuat daripada lapisan kapas atau itik sintetik yang diresapi getah dan paling menjimatkan. Tali pinggang tali bergetah terdiri daripada satu siri lapis tali yang diresapi getah. Tali pinggang tali bergetah menawarkan kekuatan tegangan tinggi dan saiz dan jisim yang sederhana. Tali pinggang getah atau plastik tidak bertetulang sesuai untuk aplikasi pemacu berkelajuan rendah yang ringan. Tali pinggang getah dan plastik tidak bertetulang boleh diregangkan ke tempatnya di atas takalnya. Tali pinggang plastik tidak bertetulang boleh menghantar kuasa yang lebih tinggi berbanding dengan tali pinggang getah. Tali pinggang kulit bertetulang terdiri daripada anggota tegangan plastik yang diapit di antara lapisan atas dan bawah kulit. Akhir sekali, tali pinggang fabrik kami mungkin terdiri daripada sehelai kapas atau itik yang dilipat dan dijahit dengan barisan jahitan membujur. Tali pinggang fabrik dapat menjejak secara seragam dan beroperasi pada kelajuan tinggi. - Tali Pinggang Beralur atau Bergerigi (seperti Tali Pinggang V): Ini adalah tali pinggang rata asas yang diubah suai untuk memberikan kelebihan jenis produk penghantaran yang lain. Ini adalah tali pinggang rata dengan bahagian bawah rusuk membujur. Tali pinggang Poli-V ialah tali pinggang rata beralur membujur atau bergerigi dengan bahagian tegangan dan satu siri alur berbentuk V bersebelahan untuk tujuan pengesanan dan pemampatan. Kapasiti kuasa bergantung pada lebar tali pinggang. Tali pinggang V ialah tenaga kerja industri dan boleh didapati dalam pelbagai saiz dan jenis piawai untuk penghantaran hampir sebarang kuasa beban. Pemacu tali pinggang V beroperasi dengan baik antara 1500 hingga 6000 kaki/min, walau bagaimanapun tali pinggang V yang sempit akan beroperasi sehingga 10,000 kaki/min. Pemacu tali pinggang V menawarkan jangka hayat yang panjang seperti 3 hingga 5 tahun dan membenarkan nisbah kelajuan yang besar, ia mudah dipasang dan ditanggalkan, menawarkan operasi yang senyap, penyelenggaraan yang rendah, penyerapan hentakan yang baik antara pemandu tali pinggang dan aci yang digerakkan. Kelemahan tali pinggang V ialah gelinciran dan rayapan tertentu dan oleh itu ia mungkin bukan penyelesaian terbaik di mana kelajuan segerak diperlukan. Kami mempunyai tali pinggang perindustrian, automotif dan pertanian. Panjang standard yang disimpan serta panjang tali pinggang tersuai tersedia. Semua keratan rentas tali pinggang V standard boleh didapati daripada stok. Terdapat jadual di mana anda boleh mengira parameter yang tidak diketahui seperti panjang tali pinggang, bahagian tali pinggang (lebar & ketebalan) dengan syarat anda mengetahui beberapa parameter sistem anda seperti diameter takal pemanduan dan dipacu, jarak tengah antara takal dan kelajuan putaran takal. Anda boleh menggunakan jadual sedemikian atau meminta kami memilih tali pinggang V yang sesuai untuk anda. - Tali Pinggang Pemacu Positif (Timing Belt): Tali pinggang ini juga jenis rata dengan satu siri jarak gigi yang sama pada lilitan dalam. Pemacu positif atau tali pinggang masa menggabungkan kelebihan tali pinggang rata dengan ciri cengkaman positif rantai dan gear. Tali pinggang pemacu yang positif tidak mendedahkan kegelinciran atau variasi kelajuan. Pelbagai nisbah kelajuan adalah mungkin. Beban galas adalah rendah kerana ia boleh beroperasi pada tegangan rendah. Walau bagaimanapun, mereka lebih mudah terdedah kepada salah jajaran dalam takal. - Takal, Sheaves, Hab untuk Tali Pinggang: Jenis takal yang berbeza digunakan dengan tali pinggang pemacu rata, rusuk (bergerigi) dan positif. Kami mengeluarkan semuanya. Kebanyakan takal tali pinggang rata kami dibuat dengan tuangan besi, tetapi versi keluli juga tersedia dalam pelbagai kombinasi rim dan hab. Takal tali pinggang rata kami mungkin mempunyai hab pepejal, jejari atau belah atau kami boleh mengeluarkan mengikut kehendak anda. Tali pinggang bertali dan pemacu positif tersedia dalam pelbagai saiz dan lebar stok. Sekurang-kurangnya satu takal dalam pemacu tali pinggang pemasa mesti dibebibir untuk mengekalkan tali pinggang pada pemacu. Untuk sistem pemacu tengah yang panjang, adalah disyorkan untuk mempunyai kedua-dua takal bebibir. Sheaves ialah roda takal yang beralur dan biasanya dihasilkan dengan tuangan besi, pembentukan keluli atau acuan plastik. Pembentukan keluli adalah proses yang sesuai untuk mengeluarkan berkas automotif dan pertanian. Kami menghasilkan berkas dengan alur biasa dan dalam. Berkas beralur dalam amat sesuai apabila tali pinggang V memasuki berkas pada sudut, seperti yang berlaku dalam pemacu suku pusingan. Alur dalam juga sangat sesuai untuk pemacu aci menegak dan aplikasi di mana getaran tali pinggang boleh menjadi masalah. Takal pemalas kami ialah berkas beralur atau takal rata yang tidak berfungsi menghantar kuasa mekanikal. Takal pemalas digunakan kebanyakannya untuk mengetatkan tali pinggang. - Pemacu Tali Pinggang Tunggal dan Berbilang: Pemacu tali pinggang tunggal mempunyai alur tunggal manakala pemacu tali pinggang berbilang mempunyai berbilang alur. Dengan mengklik teks berwarna yang berkaitan di bawah anda boleh memuat turun katalog kami: - Tali Pinggang Penghantaran Kuasa (termasuk Tali Pinggang-V, Tali Pinggang Pemasa, Tali Pinggang Tepi Mentah, Tali Pinggang Berbalut dan Tali Pinggang Khusus) - Tali sawat - Takal V - Takal Masa RANTAI & PEMACU RANTAI: Rantai penghantaran kuasa kami mempunyai beberapa kelebihan seperti jarak pusat aci yang agak tidak terhad, pemasangan mudah, kekompakan, keanjalan di bawah ketegangan tanpa gelincir atau rayapan, keupayaan operasi di bawah suhu tinggi. Berikut adalah jenis utama rantai kami: - Rantai Boleh Cabut: Rantai boleh tanggal kami dibuat dalam pelbagai saiz, padang dan kekuatan muktamad dan secara amnya daripada besi atau keluli boleh ditempa. Rantai mudah dibentuk dibuat dalam julat saiz daripada 0.902 (23 mm) hingga 4.063 inci (103 mm) pic dan kekuatan muktamad dari 700 hingga 17,000 lb/inci persegi. Rantai keluli boleh tanggal kami sebaliknya dibuat dalam saiz dari 0.904 inci (23 mm) hingga kira-kira 3.00 inci (76 mm) dalam padang, dengan kekuatan muktamad dari 760 hingga 5000 lb/inci persegi._cc781905-5cde-3194-bb3b- 136bad5cf58d_ - Rantai Pintle: Rantai ini digunakan untuk beban yang lebih berat dan kelajuan lebih tinggi sedikit kepada kira-kira 450 kaki/min (2.2 m/saat). Rantai pintle diperbuat daripada pautan tuang individu yang mempunyai hujung tong bulat penuh dengan bar sisi offset. Pautan rantai ini digandingkan dengan pin keluli. Rantaian ini berjulat dalam nada daripada kira-kira 1.00 inci (25 mm) hingga 6.00 inci (150 mm) dan kekuatan muktamad antara 3600 hingga 30,000 lb/inci persegi. - Rantaian Bar Sisi Offset: Ini popular dalam rantaian pemacu jentera pembinaan. Rantai ini berfungsi pada kelajuan hingga 1000 kaki/min dan menghantar beban kepada kira-kira 250 hp. Secara amnya setiap pautan mempunyai dua bar sisi offset, satu sesendal, satu penggelek, satu pin, pin cotter. - Rantai Penggelek: Ia tersedia dalam pic dari 0.25 (6 mm) hingga 3.00 (75 mm) inci. Kekuatan muktamad rantai roller lebar tunggal berkisar antara 925 hingga 130,000 lb/inci persegi. Versi berbilang lebar rantai roller tersedia dan menghantar kuasa yang lebih besar pada kelajuan yang lebih tinggi. Rantai roller berbilang lebar juga menawarkan tindakan yang lebih lancar dengan bunyi yang berkurangan. Rantai penggelek dipasang daripada pautan penggelek dan pautan pin. Pin cotter digunakan dalam rantai roller versi boleh tanggal. Reka bentuk pemacu rantai roller memerlukan kepakaran subjek. Manakala pemacu tali pinggang adalah berdasarkan kelajuan linear, pemacu rantai adalah berdasarkan kelajuan putaran gegancu yang lebih kecil, yang merupakan dalam kebanyakan pemasangan ahli yang didorong. Selain penarafan kuasa kuda dan kelajuan putaran, reka bentuk pemacu rantai adalah berdasarkan banyak faktor lain. - Rantai Double-Pitch: Pada asasnya sama dengan rantai roller kecuali padang adalah dua kali lebih panjang. - Rantai Gigi Terbalik (Senyap): Rantai kelajuan tinggi digunakan kebanyakannya untuk penggerak utama, pemacu lepas landas. Pemacu rantai gigi terbalik boleh menghantar kuasa sehingga 1200 hp dan terdiri daripada satu siri pautan gigi, dipasang secara bergilir-gilir dengan sama ada pin atau gabungan komponen sambungan. Rantaian panduan tengah mempunyai pautan panduan untuk memasukkan alur dalam gegancu, dan rantai panduan sisi mempunyai panduan untuk memasukkan bahagian tepi gegancu. - Rantai Manik atau Gelangsar: Rantai ini digunakan untuk pemacu kelajuan perlahan dan juga dalam operasi manual. Dengan mengklik teks berwarna yang berkaitan di bawah anda boleh memuat turun katalog kami: - Rantaian Memandu - Rantai Penghantar - Rantai Penghantar Padang Besar - Rantai Penggelek Keluli Tahan Karat - Rantai Angkat - Rantai Motosikal - Rantai Mesin Pertanian - Sproket: Sproket standard kami mematuhi piawaian ANSI. Sproket plat adalah gegancu rata tanpa hub. Sproket hab bersaiz kecil dan sederhana kami dihidupkan daripada stok bar atau penempaan atau dibuat dengan mengimpal hab stok bar kepada plat gelek panas. AGS-TECH Inc. boleh membekalkan sproket yang dimesin daripada tuangan besi kelabu, keluli tuang dan pembinaan hab yang dikimpal, logam serbuk tersinter, plastik acuan atau dimesin. Untuk operasi yang lancar pada kelajuan tinggi, pemilihan saiz sproket yang betul adalah penting. Keterbatasan ruang sudah tentu merupakan faktor yang tidak boleh kita abaikan apabila memilih gegancu. Adalah disyorkan bahawa nisbah pemandu kepada sproket yang digerakkan hendaklah tidak lebih daripada 6:1, dan pembalut rantai pada pemandu ialah 120 darjah. Jarak tengah antara sproket yang lebih kecil dan lebih besar, panjang rantai dan ketegangan rantai juga mesti dipilih mengikut beberapa pengiraan & garis panduan kejuruteraan yang disyorkan dan bukan secara rawak. Muat turun katalog kami dengan mengklik teks berwarna di bawah: - Sproket dan Roda Plat - Sesendal Penghantaran - Gandingan Rantai - Kunci Rantai PEMACU KABEL: Ini mempunyai kelebihan berbanding tali pinggang dan pemacu rantai dalam beberapa kes. Pemacu kabel boleh mencapai fungsi yang sama seperti tali pinggang dan mungkin juga lebih mudah dan lebih ekonomi untuk dilaksanakan dalam sesetengah aplikasi. Sebagai contoh, siri baharu Pemacu Kabel Synchromesh direka bentuk untuk daya tarikan positif bagi menggantikan tali konvensional, kabel ringkas dan pemacu cog, terutamanya dalam ruang yang sempit. Pemacu kabel baharu direka bentuk untuk menyediakan penentududukan berketepatan tinggi dalam peralatan elektronik seperti mesin penyalin, plotter, mesin taip, pencetak,….. dsb. Ciri utama pemacu kabel baharu ialah keupayaannya untuk digunakan dalam konfigurasi serpentin 3D yang membolehkan reka bentuk yang sangat kecil. Kabel Synchromesh boleh digunakan dengan ketegangan yang lebih rendah jika dibandingkan dengan tali sekali gus mengurangkan penggunaan kuasa. Hubungi AGS-TECH untuk pertanyaan dan pendapat tentang tali pinggang, rantai dan pemacu kabel. CLICK Product Finder-Locator Service HALAMAN SEBELUMNYA
- Rapid Prototyping, Desktop Manufacturing, Additive Manufacturing, FDM
Rapid Prototyping, Desktop Manufacturing, Additive Manufacturing, Stereolithography, Polyjet, Fused Deposition Modeling, Selective Laser Sintering, FDM, SLS Pengilangan Aditif dan Pantas Dalam beberapa tahun kebelakangan ini, kami telah melihat peningkatan dalam permintaan untuk PEMBUATAN RAPID atau PROTOTAIP RAPID. Proses ini juga boleh dipanggil PEMBUATAN DESKTOP atau FABRIK BENTUK BEBAS. Pada asasnya model fizikal pepejal bahagian dibuat terus daripada lukisan CAD tiga dimensi. Kami menggunakan istilah PEMBUATAN TAMBAHAN untuk pelbagai teknik ini di mana kami membina bahagian dalam lapisan. Menggunakan perkakasan dan perisian yang dipacu komputer bersepadu, kami melaksanakan pembuatan bahan tambahan. Teknik prototaip dan pembuatan pantas kami ialah STEREOLITHOGRAFI, POLIJET, PEMODELAN PENEMPATAN BERFUS, PENSinteran LASER PILIH, PENCAIRAN RAK ELEKTRON, PERCETAKAN TIGA DIMENSI, PEMBUATAN LANGSUNG, PERALATAN CEPAT. Kami mengesyorkan anda klik di sini untukMUAT TURUN Ilustrasi Skema Pengilangan Aditif dan Proses Pengilangan Pantas kami oleh AGS-TECH Inc. Ini akan membantu anda memahami dengan lebih baik maklumat yang kami berikan kepada anda di bawah. Prototaip pantas memberikan kami: 1.) Reka bentuk produk konsep dilihat dari sudut yang berbeza pada monitor menggunakan sistem 3D / CAD. 2.) Prototaip daripada bahan bukan logam dan logam dihasilkan dan dikaji dari aspek fungsi, teknikal dan estetik. 3.) Prototaip kos rendah dalam masa yang singkat dapat dicapai. Pembuatan aditif boleh menyerupai pembinaan sebuku roti dengan menyusun dan mengikat kepingan individu di atas satu sama lain. Dalam erti kata lain, produk dihasilkan hirisan demi hirisan, atau lapisan demi lapisan didepositkan antara satu sama lain. Kebanyakan bahagian boleh dihasilkan dalam masa beberapa jam. Teknik ini bagus jika bahagian diperlukan sangat cepat atau jika kuantiti yang diperlukan adalah rendah dan membuat acuan dan perkakas terlalu mahal dan mengambil masa. Namun kos sesuatu bahagian mahal kerana bahan mentah yang mahal. • STEREOLITHOGRAFI : Teknik ini juga disingkatkan sebagai STL, adalah berdasarkan pengawetan dan pengerasan fotopolimer cecair kepada bentuk tertentu dengan memfokuskan pancaran laser padanya. Laser mempolimerkan fotopolimer dan menyembuhkannya. Dengan mengimbas pancaran laser UV mengikut bentuk yang diprogramkan di sepanjang permukaan campuran fotopolimer bahagian dihasilkan dari bawah ke atas dalam kepingan individu yang melata di atas satu sama lain. Pengimbasan titik laser diulang berkali-kali untuk mencapai geometri yang diprogramkan ke dalam sistem. Selepas bahagian itu dihasilkan sepenuhnya, ia dikeluarkan dari platform, dipadamkan dan dibersihkan secara ultrasonik dan dengan mandian alkohol. Seterusnya, ia terdedah kepada penyinaran UV selama beberapa jam untuk memastikan polimer sembuh sepenuhnya dan mengeras. Untuk meringkaskan proses, platform yang dicelup ke dalam campuran fotopolimer dan pancaran laser UV dikawal dan digerakkan melalui sistem kawalan servo mengikut bentuk bahagian yang diingini dan bahagian itu diperolehi dengan memfotokan lapisan polimer demi lapisan. Sudah tentu dimensi maksimum bahagian yang dihasilkan ditentukan oleh peralatan stereolitografi. • POLYJET : Sama seperti percetakan inkjet, dalam polyjet kami mempunyai lapan kepala cetakan yang mendepositkan fotopolimer pada dulang binaan. Cahaya ultraungu yang diletakkan di sebelah jet segera menyembuhkan dan mengeras setiap lapisan. Dua bahan digunakan dalam polyjet. Bahan pertama adalah untuk pembuatan model sebenar. Bahan kedua, resin seperti gel digunakan untuk sokongan. Kedua-dua bahan ini dimendapkan selapis demi selapis dan serentak disembuhkan. Selepas model siap, bahan sokongan dikeluarkan dengan larutan akueus. Resin yang digunakan adalah serupa dengan stereolitografi (STL). Polijet mempunyai kelebihan berikut berbanding stereolitografi: 1.) Tidak perlu membersihkan bahagian. 2.) Tidak perlu pengawetan selepas proses 3.) Ketebalan lapisan yang lebih kecil mungkin dan dengan itu kita mendapat resolusi yang lebih baik dan boleh mengeluarkan bahagian yang lebih halus. • PEMODELAN DEPOSISI BERFUS : Juga disingkatkan sebagai FDM, dalam kaedah ini kepala penyemperit dikawal robot bergerak dalam dua arah prinsip di atas meja. Kabel diturunkan dan dinaikkan mengikut keperluan. Dari orifis dadu yang dipanaskan pada kepala, filamen termoplastik diekstrusi dan lapisan awal diendapkan pada asas buih. Ini dicapai oleh kepala penyemperit yang mengikut laluan yang telah ditetapkan. Selepas lapisan awal, jadual diturunkan dan lapisan seterusnya didepositkan di atas satu sama lain. Kadangkala apabila membuat bahagian yang rumit, struktur sokongan diperlukan supaya pemendapan boleh diteruskan ke arah tertentu. Dalam kes ini, bahan sokongan diekstrusi dengan jarak filamen yang kurang padat pada lapisan supaya ia lebih lemah daripada bahan model. Struktur sokongan ini kemudiannya boleh dibubarkan atau dipecahkan selepas bahagian tersebut siap. Dimensi die extruder menentukan ketebalan lapisan tersemperit. Proses FDM menghasilkan bahagian dengan permukaan berpijak pada satah luar serong. Jika kekasaran ini tidak boleh diterima, penggilap wap kimia atau alat yang dipanaskan boleh digunakan untuk melicinkan ini. Malah lilin penggilap boleh didapati sebagai bahan salutan untuk menghapuskan langkah-langkah ini dan mencapai toleransi geometri yang munasabah. • PENSinteran LASER TERPILIH : Juga dilambangkan sebagai SLS, proses ini berdasarkan pensinteran polimer, seramik atau serbuk logam secara selektif ke dalam objek. Bahagian bawah ruang pemprosesan mempunyai dua silinder: Silinder bahagian binaan dan silinder suapan serbuk. Yang pertama diturunkan secara berperingkat ke tempat bahagian tersinter sedang dibentuk dan yang terakhir dinaikkan secara berperingkat untuk membekalkan serbuk kepada silinder binaan bahagian melalui mekanisme penggelek. Mula-mula lapisan nipis serbuk diendapkan dalam silinder binaan bahagian, kemudian pancaran laser ditumpukan pada lapisan itu, menjejak dan mencairkan/mensinter keratan rentas tertentu, yang kemudiannya menjadi pepejal. Serbuk adalah kawasan yang tidak terkena pancaran laser kekal longgar tetapi masih menyokong bahagian pepejal. Kemudian satu lagi lapisan serbuk disimpan dan proses diulang berkali-kali untuk mendapatkan bahagian tersebut. Pada akhirnya, zarah serbuk longgar digoncang. Semua ini dijalankan oleh komputer kawalan proses menggunakan arahan yang dihasilkan oleh program CAD 3D bagi bahagian yang dihasilkan. Pelbagai bahan seperti polimer (seperti ABS, PVC, poliester), lilin, logam dan seramik dengan pengikat polimer yang sesuai boleh disimpan. • ELECTRON-BEAM MELTING : Serupa dengan pensinteran laser terpilih, tetapi menggunakan pancaran elektron untuk mencairkan serbuk titanium atau kobalt krom untuk membuat prototaip dalam vakum. Beberapa perkembangan telah dibuat untuk melaksanakan proses ini pada keluli tahan karat, aluminium dan aloi kuprum. Jika kekuatan keletihan bahagian yang dihasilkan perlu ditingkatkan, kami menggunakan penekan isostatik panas selepas pembuatan bahagian sebagai proses sekunder. • CETAKAN TIGA DIMENSI : Juga dilambangkan dengan 3DP, dalam teknik ini kepala cetak mendepositkan pengikat bukan organik pada lapisan sama ada serbuk bukan logam atau logam. Omboh yang membawa katil serbuk diturunkan secara berperingkat dan pada setiap langkah pengikat dimendapkan lapisan mengikut lapisan dan dicantumkan oleh pengikat. Bahan serbuk yang digunakan ialah campuran polimer dan gentian, pasir faundri, logam. Menggunakan kepala pengikat yang berbeza secara serentak dan pengikat warna yang berbeza kita boleh memperoleh pelbagai warna. Prosesnya serupa dengan pencetakan inkjet tetapi bukannya mendapatkan helaian berwarna, kami memperoleh objek tiga dimensi berwarna. Bahagian yang dihasilkan mungkin berliang dan oleh itu mungkin memerlukan pensinteran dan penyusupan logam untuk meningkatkan ketumpatan dan kekuatannya. Pensinteran akan membakar pengikat dan menggabungkan serbuk logam bersama-sama. Logam seperti keluli tahan karat, aluminium, titanium boleh digunakan untuk membuat bahagian dan sebagai bahan penyusupan kita biasanya menggunakan tembaga dan gangsa. Keindahan teknik ini ialah pemasangan yang rumit dan bergerak boleh dihasilkan dengan cepat. Contohnya pemasangan gear, sepana sebagai alat boleh dibuat dan akan mempunyai bahagian bergerak dan pusing sedia untuk digunakan. Komponen pemasangan yang berbeza boleh dihasilkan dengan warna yang berbeza dan semuanya dalam satu pukulan. Muat turun risalah kami di:Asas Percetakan 3D Logam • PEMBUATAN LANGSUNG dan PERALATAN RAPID : Selain penilaian reka bentuk, penyelesaian masalah kami menggunakan prototaip pantas untuk pembuatan terus produk atau aplikasi terus ke dalam produk. Dalam erti kata lain, prototaip pantas boleh dimasukkan ke dalam proses konvensional untuk menjadikannya lebih baik dan lebih kompetitif. Contohnya, prototaip pantas boleh menghasilkan corak dan acuan. Corak polimer lebur dan terbakar yang dicipta oleh operasi prototaip pantas boleh dipasang untuk pemutus pelaburan dan dilaburkan. Contoh lain yang perlu disebutkan ialah menggunakan 3DP untuk menghasilkan cangkerang tuangan seramik dan menggunakannya untuk operasi tuangan cangkerang. Malah acuan suntikan dan sisipan acuan boleh dihasilkan dengan prototaip pantas dan seseorang boleh menjimatkan banyak minggu atau bulan masa utama membuat acuan. Dengan hanya menganalisis fail CAD bahagian yang dikehendaki, kami boleh menghasilkan geometri alat menggunakan perisian. Berikut ialah beberapa kaedah alat pantas kami yang popular: RTV (Room-Temperature Vulcanizing) MOLDING / URETHANE CASTING : Menggunakan prototaip pantas boleh digunakan untuk membuat corak bahagian yang dikehendaki. Kemudian corak ini disalut dengan agen pemisah dan getah RTV cecair dituangkan ke atas corak untuk menghasilkan bahagian acuan. Seterusnya, bahagian acuan ini digunakan untuk menyuntik uretana cecair acuan. Jangka hayat acuan adalah pendek, hanya seperti 0 atau 30 kitaran tetapi cukup untuk pengeluaran kelompok kecil. ACES (Acetal Clear Epoxy Solid) PENGABUHAN SUNTIKAN : Menggunakan teknik prototaip pantas seperti stereolitografi, kami menghasilkan acuan suntikan. Acuan ini adalah cangkerang dengan hujung terbuka untuk membolehkan pengisian dengan bahan seperti epoksi, epoksi berisi aluminium atau logam. Sekali lagi hayat acuan dihadkan kepada puluhan atau maksimum ratusan bahagian. PROSES PERALATAN LOGAM DISEMBUR : Kami menggunakan prototaip pantas dan membuat corak. Kami menyembur aloi zink-aluminium pada permukaan corak dan menyalutinya. Corak dengan salutan logam kemudiannya diletakkan di dalam kelalang dan disiram dengan epoksi atau epoksi berisi aluminium. Akhirnya, ia dikeluarkan dan dengan menghasilkan dua bahagian acuan sedemikian, kami memperoleh acuan lengkap untuk pengacuan suntikan. Acuan ini mempunyai hayat yang lebih lama, dalam beberapa kes bergantung pada bahan dan suhu ia boleh menghasilkan bahagian dalam ribuan. PROSES KEELTOOL : Teknik ini boleh menghasilkan acuan dengan hayat kitaran 100,000 hingga 10 Juta. Menggunakan prototaip pantas kami menghasilkan acuan RTV. Acuan seterusnya diisi dengan campuran yang terdiri daripada serbuk keluli alat A6, tungsten karbida, pengikat polimer dan biarkan untuk menyembuhkan. Acuan ini kemudiannya dipanaskan untuk membakar polimer dan serbuk logam untuk bercantum. Langkah seterusnya ialah penyusupan tembaga untuk menghasilkan acuan akhir. Jika perlu, operasi sekunder seperti pemesinan dan penggilapan boleh dilakukan pada acuan untuk ketepatan dimensi yang lebih baik. _cc781905-5cde-3194-bb3b-136bad_cf5 CLICK Product Finder-Locator Service HALAMAN SEBELUMNYA
- Joining & Assembly & Fastening Processes, Welding, Brazing, Soldering
Joining & Assembly & Fastening Processes, Welding, Brazing, Soldering, Sintering, Adhesive Bonding, Press Fitting, Wave and Reflow Solder Process, Torch Furnace Proses Mencantum & Memasang & Mengikat Kami menyertai, memasang dan mengikat bahagian kilang anda dan mengubahnya menjadi produk siap atau separuh siap menggunakan KIMPALAN, BRAZING, PEMATERIAN, PENSINTERAAN, IKATAN PELEKAT, PENGIKAT, PENYELESAIAN TEKAN. Beberapa proses kimpalan kami yang paling popular ialah arka, gas oxyfuel, rintangan, unjuran, jahitan, gangguan, perkusi, keadaan pepejal, pancaran elektron, laser, termit, kimpalan aruhan. Proses pematerian popular kami ialah obor, aruhan, relau dan pematerian celup. Kaedah pematerian kami ialah besi, plat panas, ketuhar, aruhan, celup, gelombang, aliran semula dan pematerian ultrasonik. Untuk ikatan pelekat kami kerap menggunakan termoplastik dan tetapan termo, epoksi, fenolik, poliuretana, aloi pelekat serta beberapa bahan kimia dan pita lain. Akhirnya proses pengikat kami terdiri daripada memaku, menskru, nat dan bolt, memukau, mencengkam, menyemat, mencantum & mencantum dan memasang tekan. • KIMPALAN : Kimpalan melibatkan penyambungan bahan dengan mencairkan kepingan kerja dan memasukkan bahan pengisi, yang juga bercantum dengan kolam kimpalan cair. Apabila kawasan itu sejuk, kami memperoleh sambungan yang kuat. Tekanan dikenakan dalam beberapa kes. Bertentangan dengan kimpalan, operasi pematerian dan pematerian hanya melibatkan peleburan bahan dengan takat lebur yang lebih rendah antara bahan kerja, dan bahan kerja tidak cair. Kami mengesyorkan anda klik di sini untukMUAT TURUN Ilustrasi Skema Proses Kimpalan kami oleh AGS-TECH Inc. Ini akan membantu anda memahami dengan lebih baik maklumat yang kami berikan kepada anda di bawah. Dalam KIMPALAN ARC, kami menggunakan bekalan kuasa dan elektrod untuk mencipta arka elektrik yang mencairkan logam. Titik kimpalan dilindungi oleh gas pelindung atau wap atau bahan lain. Proses ini popular untuk mengimpal bahagian automotif dan struktur keluli. Dalam kimpalan arka logam terlindung (SMAW) atau juga dikenali sebagai kimpalan kayu, kayu elektrod dirapatkan dengan bahan asas dan arka elektrik dijana di antaranya. Rod elektrod cair dan bertindak sebagai bahan pengisi. Elektrod juga mengandungi fluks yang bertindak sebagai lapisan sanga dan mengeluarkan wap yang bertindak sebagai gas pelindung. Ini melindungi kawasan kimpalan daripada pencemaran alam sekitar. Tiada pengisi lain digunakan. Kelemahan proses ini adalah kelambatannya, perlu menggantikan elektrod dengan kerap, keperluan untuk menghilangkan sanga sisa yang berasal dari fluks. Sebilangan logam seperti besi, keluli, nikel, aluminium, tembaga...dsb. Boleh dikimpal. Kelebihannya ialah alatnya yang murah dan kemudahan penggunaannya. Kimpalan arka logam gas (GMAW) juga dikenali sebagai gas lengai logam (MIG), kami mempunyai suapan berterusan pengisi wayar elektrod habis pakai dan gas lengai atau separa lengai yang mengalir di sekeliling wayar terhadap pencemaran alam sekitar kawasan kimpalan. Keluli, aluminium dan logam bukan ferus lain boleh dikimpal. Kelebihan MIG ialah kelajuan kimpalan yang tinggi dan kualiti yang baik. Kelemahannya ialah peralatannya yang rumit dan cabaran yang dihadapi dalam persekitaran luar berangin kerana kita perlu mengekalkan gas pelindung di sekitar kawasan kimpalan yang stabil. Variasi GMAW ialah kimpalan arka berteras fluks (FCAW) yang terdiri daripada tiub logam halus yang diisi dengan bahan fluks. Kadangkala fluks di dalam tiub adalah mencukupi untuk perlindungan daripada pencemaran alam sekitar. Kimpalan Arka Tenggelam (SAW) secara meluas merupakan proses automatik, melibatkan suapan wayar berterusan dan arka yang dipukul di bawah lapisan penutup fluks. Kadar pengeluaran dan kualiti adalah tinggi, sanga kimpalan mudah tanggal, dan kami mempunyai persekitaran kerja bebas asap rokok. Kelemahannya ialah ia hanya boleh digunakan untuk mengimpal parts dalam kedudukan tertentu. Dalam kimpalan arka tungsten gas (GTAW) atau kimpalan gas lengai tungsten (TIG) kami menggunakan elektrod Tungsten bersama-sama dengan pengisi berasingan dan gas lengai atau berhampiran lengai. Seperti yang kita tahu Tungsten mempunyai takat lebur yang tinggi dan ia adalah logam yang sangat sesuai untuk suhu yang sangat tinggi. Tungsten dalam TIG tidak digunakan bertentangan dengan kaedah lain yang dijelaskan di atas. Teknik kimpalan yang perlahan tetapi berkualiti tinggi berfaedah berbanding teknik lain dalam mengimpal bahan nipis. Sesuai untuk banyak logam. Kimpalan arka plasma adalah serupa tetapi menggunakan gas plasma untuk mencipta arka. Arka dalam kimpalan arka plasma secara relatifnya lebih tertumpu berbanding dengan GTAW dan boleh digunakan untuk julat ketebalan logam yang lebih luas pada kelajuan yang lebih tinggi. GTAW dan kimpalan arka plasma boleh digunakan pada lebih kurang bahan yang sama. OXY-FUEL / OXYFUEL WELDING juga dipanggil oxyacetylene welding, oxy welding, gas welding dijalankan menggunakan bahan api gas dan oksigen untuk kimpalan. Oleh kerana tiada kuasa elektrik digunakan, ia mudah alih dan boleh digunakan di tempat yang tiada bekalan elektrik. Menggunakan obor kimpalan kami memanaskan kepingan dan bahan pengisi untuk menghasilkan kolam logam lebur yang dikongsi. Pelbagai bahan api boleh digunakan seperti asetilena, petrol, hidrogen, propana, butana...dsb. Dalam kimpalan bahan api oksi kami menggunakan dua bekas, satu untuk bahan api dan satu lagi untuk oksigen. Oksigen mengoksidakan bahan api (membakarnya). KIMPALAN RINTANGAN: Kimpalan jenis ini mengambil kesempatan daripada pemanasan joule dan haba dijana di lokasi di mana arus elektrik digunakan untuk masa tertentu. Arus tinggi dialirkan melalui logam. Kolam logam cair terbentuk di lokasi ini. Kaedah kimpalan rintangan popular kerana kecekapannya, potensi pencemaran yang kecil. Walau bagaimanapun, kelemahan adalah kos peralatan yang agak ketara dan had yang wujud untuk bahan kerja yang agak nipis. KIMPALAN TITIK adalah salah satu jenis kimpalan rintangan yang utama. Di sini kami menggabungkan dua atau lebih kepingan atau kepingan kerja yang bertindih dengan menggunakan dua elektrod kuprum untuk mengapit kepingan bersama-sama dan mengalirkan arus tinggi melaluinya. Bahan antara elektrod kuprum menjadi panas dan kolam lebur terhasil di lokasi tersebut. Arus kemudiannya dihentikan dan hujung elektrod kuprum menyejukkan lokasi kimpalan kerana elektrod disejukkan dengan air. Penggunaan jumlah haba yang betul pada bahan dan ketebalan yang betul adalah kunci untuk teknik ini, kerana jika digunakan secara salah sendi akan menjadi lemah. Kimpalan titik mempunyai kelebihan kerana tidak menyebabkan ubah bentuk yang ketara pada bahan kerja, kecekapan tenaga, kemudahan automasi dan kadar pengeluaran yang cemerlang, dan tidak memerlukan sebarang pengisi. Kelemahannya ialah memandangkan kimpalan berlaku di tempat dan bukannya membentuk jahitan berterusan, kekuatan keseluruhan boleh menjadi lebih rendah berbanding kaedah kimpalan lain. KIMPALAN JAHITAN pula menghasilkan kimpalan pada permukaan faying bahan yang serupa. Jahitan boleh menjadi punggung atau sendi bertindih. Kimpalan jahitan bermula pada satu hujung dan bergerak secara progresif ke hujung yang lain. Kaedah ini juga menggunakan dua elektrod daripada kuprum untuk menggunakan tekanan dan arus ke kawasan kimpalan. Elektrod berbentuk cakera berputar dengan sentuhan berterusan di sepanjang garis jahitan dan membuat kimpalan berterusan. Di sini juga, elektrod disejukkan oleh air. Kimpalan sangat kuat dan boleh dipercayai. Kaedah lain ialah teknik kimpalan unjuran, kilat dan upset. KIMPALAN KEADAAN PEPEJ adalah sedikit berbeza daripada kaedah sebelumnya yang dijelaskan di atas. Penyatuan berlaku pada suhu di bawah suhu lebur logam yang dicantum dan tanpa menggunakan pengisi logam. Tekanan boleh digunakan dalam beberapa proses. Pelbagai kaedah ialah KIMPALAN COEXTRUSION di mana logam yang berbeza diekstrusi melalui acuan yang sama, KIMPALAN TEKANAN SEJUK di mana kami menggabungkan aloi lembut di bawah takat leburnya, KIMPALAN RESAPAN teknik tanpa garis kimpalan yang boleh dilihat, KIMPALAN LETUPAN untuk menyambung bahan yang berbeza, contohnya aloi tahan kakisan kepada struktur. keluli, KIMPALAN NADI ELEKTROMAGNET di mana kita mempercepatkan tiub dan kepingan dengan daya elektromagnet, KIMPALAN TEMPA yang terdiri daripada memanaskan logam ke suhu tinggi dan memalunya bersama-sama, KIMPALAN geseran di mana dengan kimpalan geseran yang mencukupi dilakukan, KIMPALAN KACAU GESARAN yang melibatkan putaran bukan- alat habis pakai yang melintasi garis sambungan, KIMPALAN TEKANAN PANAS di mana kami menekan logam bersama-sama pada suhu tinggi di bawah suhu lebur dalam vakum atau gas lengai, KIMPALAN TEKANAN ISOSTATIK PANAS proses di mana kami menggunakan tekanan menggunakan gas lengai di dalam vesel, KIMPALAN GULUNG tempat kami bercantum bahan yang berbeza dengan memaksa mereka antara dua roda berputar, KIMPALAN ULTRASONIK di mana kepingan logam atau plastik nipis dikimpal menggunakan tenaga getaran frekuensi tinggi. Proses kimpalan kami yang lain ialah KIMPALAN RAK ELEKTRON dengan penembusan dalam dan pemprosesan pantas tetapi sebagai kaedah yang mahal kami menganggapnya untuk kes-kes khas, KIMPALAN ELECTROSLAG kaedah yang sesuai untuk plat tebal berat dan kepingan kerja keluli sahaja, KIMPALAN ARUHAN di mana kami menggunakan aruhan elektromagnet dan memanaskan bahan kerja konduktif elektrik atau feromagnetik kami, KIMPALAN LASER BEAM juga dengan penembusan yang dalam dan pemprosesan yang cepat tetapi kaedah yang mahal, KIMPALAN HIBRID LASER yang menggabungkan LBW dengan GMAW dalam kepala kimpalan yang sama dan mampu merapatkan jurang 2 mm antara plat, KIMPALAN PERKUSI yang melibatkan pelepasan elektrik diikuti dengan menempa bahan dengan tekanan yang dikenakan, KIMPALAN TERMIT yang melibatkan tindak balas eksotermik antara serbuk aluminium dan oksida besi., KIMPALAN ELEKTROGAS dengan elektrod boleh guna dan digunakan dengan hanya keluli dalam kedudukan menegak, dan akhirnya KIMPALAN ARKA STUD untuk menyambung stud ke tapak bahan dengan haba dan tekanan. Kami mengesyorkan anda klik di sini untukMUAT TURUN Ilustrasi Skema kami bagi Proses Memateri, Memateri dan Ikatan Pelekat oleh AGS-TECH Inc Ini akan membantu anda memahami dengan lebih baik maklumat yang kami berikan kepada anda di bawah. • BRAZING : Kami menggabungkan dua atau lebih logam dengan memanaskan logam pengisi di antaranya di atas takat leburnya dan menggunakan tindakan kapilari untuk merebak. Prosesnya serupa dengan pematerian tetapi suhu yang terlibat untuk mencairkan pengisi lebih tinggi dalam pematerian. Seperti dalam kimpalan, fluks melindungi bahan pengisi daripada pencemaran atmosfera. Selepas menyejukkan bahan kerja dicantumkan bersama. Proses ini melibatkan langkah-langkah penting berikut: Kesesuaian dan kelegaan yang baik, pembersihan bahan asas yang betul, pemasangan yang betul, pemilihan fluks dan suasana yang betul, memanaskan pemasangan dan akhirnya pembersihan pemasangan yang dipateri. Beberapa proses pematerian kami ialah TORCH BRAZING, kaedah popular yang dijalankan secara manual atau secara automatik. Ia sesuai untuk pesanan pengeluaran volum rendah dan kes khusus. Haba digunakan menggunakan nyalaan gas berhampiran sambungan yang dipateri. PEMAPI TUNGKU memerlukan kurang kemahiran pengendali dan merupakan proses separa automatik yang sesuai untuk pengeluaran besar-besaran industri. Kedua-dua kawalan suhu dan kawalan atmosfera dalam relau adalah kelebihan teknik ini, kerana yang pertama membolehkan kita mengawal kitaran haba dan menghapuskan pemanasan tempatan seperti yang berlaku dalam pematerian obor, dan yang kedua melindungi bahagian tersebut daripada pengoksidaan. Menggunakan jigging kami mampu mengurangkan kos pembuatan ke tahap minimum. Kelemahannya ialah penggunaan kuasa yang tinggi, kos peralatan dan pertimbangan reka bentuk yang lebih mencabar. PEMBAZIRAN VACUUM berlaku dalam relau vakum. Keseragaman suhu dikekalkan dan kami memperoleh sambungan bebas fluks, sangat bersih dengan tegasan sisa yang sangat sedikit. Rawatan haba boleh berlaku semasa pematerian vakum, kerana tekanan sisa yang rendah semasa kitaran pemanasan dan penyejukan yang perlahan. Kelemahan utama adalah kosnya yang tinggi kerana penciptaan persekitaran vakum adalah proses yang mahal. Satu lagi teknik DIP BRAZING menggabungkan bahagian lekap di mana sebatian pematerian digunakan pada permukaan mengawan. Selepas itu bahagian fixtured dicelup ke dalam mandian garam cair seperti Sodium Chloride (garam meja) yang bertindak sebagai medium pemindahan haba dan fluks. Udara dikecualikan dan oleh itu tiada pembentukan oksida berlaku. Dalam INDUCTION BRAZING kita mencantumkan bahan dengan logam pengisi yang mempunyai takat lebur yang lebih rendah daripada bahan asas. Arus ulang alik dari gegelung aruhan mencipta medan elektromagnet yang mendorong pemanasan aruhan pada kebanyakan bahan magnet ferus. Kaedah ini menyediakan pemanasan terpilih, sambungan yang baik dengan pengisi hanya mengalir di kawasan yang dikehendaki, sedikit pengoksidaan kerana tiada nyalaan hadir dan penyejukan adalah pantas, pemanasan cepat, konsisten dan kesesuaian untuk pembuatan volum tinggi. Untuk mempercepatkan proses kami dan untuk memastikan konsistensi kami kerap menggunakan prabentuk. Maklumat tentang kemudahan pematerian kami yang menghasilkan kelengkapan seramik kepada logam, pengedap hermetik, suapan vakum, komponen kawalan vakum dan bendalir tinggi dan ultratinggi boleh didapati di sini:_cc781905-5cde-bad_5c94-5cde-3b51-5cde-3b51-5cde-3b58dBrosur Kilang Pateri • PEMATERIAN : Dalam pematerian kita tidak mempunyai peleburan kepingan kerja, tetapi logam pengisi dengan takat lebur yang lebih rendah daripada bahagian penyambung yang mengalir ke dalam penyambung. Logam pengisi dalam pematerian cair pada suhu yang lebih rendah daripada dalam pematerian. Kami menggunakan aloi bebas plumbum untuk pematerian dan mempunyai pematuhan RoHS dan untuk aplikasi dan keperluan yang berbeza kami mempunyai aloi yang berbeza dan sesuai seperti aloi perak. Pematerian menawarkan kepada kita sambungan yang kedap gas dan cecair. Dalam PEMATERIAN LEMBUT, logam pengisi kami mempunyai takat lebur di bawah 400 Celcius, manakala dalam PEMATERIAN PERAK dan BRAZING kami memerlukan suhu yang lebih tinggi. Pematerian lembut menggunakan suhu yang lebih rendah tetapi tidak menghasilkan sambungan yang kuat untuk aplikasi yang menuntut pada suhu tinggi. Penyolderan perak sebaliknya, memerlukan suhu tinggi yang disediakan oleh obor dan memberikan kita sambungan yang kuat sesuai untuk aplikasi suhu tinggi. Memateri memerlukan suhu tertinggi dan biasanya obor sedang digunakan. Oleh kerana sambungan pateri sangat kuat, ia adalah calon yang baik untuk membaiki objek besi berat. Dalam barisan pembuatan kami, kami menggunakan kedua-dua pematerian tangan manual dan juga talian pateri automatik. PEMATERIAN ARUHAN menggunakan arus AC frekuensi tinggi dalam gegelung kuprum untuk memudahkan pemanasan aruhan. Arus teraruh di bahagian yang dipateri dan akibatnya haba dijana pada rintangan tinggi joint. Haba ini mencairkan logam pengisi. Fluks juga digunakan. Pematerian aruhan adalah kaedah yang baik untuk memateri silinder dan paip dalam proses berterusan dengan membalut gegelung di sekelilingnya. Memateri beberapa bahan seperti grafit dan seramik adalah lebih sukar kerana ia memerlukan penyaduran bahan kerja dengan logam yang sesuai sebelum pematerian. Ini memudahkan ikatan antara muka. Kami menyolder bahan sedemikian terutamanya untuk aplikasi pembungkusan hermetik. Kami mengeluarkan papan litar bercetak (PCB) kami dalam jumlah tinggi kebanyakannya menggunakan PEMATERIAN GELOMBANG. Hanya untuk kuantiti kecil tujuan prototaip kami menggunakan pematerian tangan menggunakan besi pematerian. Kami menggunakan pematerian gelombang untuk kedua-dua lubang telus dan juga pemasangan PCB pelekap permukaan (PCBA). Gam sementara menyimpan komponen dilekatkan pada papan litar dan pemasangan diletakkan pada penghantar dan bergerak melalui peralatan yang mengandungi pateri cair. Mula-mula PCB difluks dan kemudian memasuki zon prapemanasan. Pateri cair berada di dalam kuali dan mempunyai corak gelombang berdiri di permukaannya. Apabila PCB bergerak di atas gelombang ini, gelombang ini menghubungi bahagian bawah PCB dan melekat pada pad pematerian. Pateri kekal pada pin dan pad sahaja dan bukan pada PCB itu sendiri. Gelombang dalam pateri cair perlu dikawal dengan baik supaya tiada percikan dan bahagian atas gelombang tidak menyentuh dan mencemarkan kawasan papan yang tidak diingini. Dalam REFLOW SOLDERING, kami menggunakan pes pateri melekit untuk memasang komponen elektronik pada papan sementara. Kemudian papan diletakkan melalui ketuhar aliran semula dengan kawalan suhu. Di sini pateri mencairkan dan menyambungkan komponen secara kekal. Kami menggunakan teknik ini untuk kedua-dua komponen pelekap permukaan dan juga untuk komponen lubang melalui. Kawalan suhu yang betul dan pelarasan suhu ketuhar adalah penting untuk mengelakkan kemusnahan komponen elektronik pada papan dengan memanaskannya melebihi had suhu maksimumnya. Dalam proses pematerian aliran semula, kami sebenarnya mempunyai beberapa kawasan atau peringkat setiap satu dengan profil terma yang berbeza, seperti langkah prapemanasan, langkah rendaman terma, langkah aliran semula dan penyejukan. Langkah-langkah berbeza ini adalah penting untuk pematerian aliran semula bebas kerosakan pada pemasangan papan litar bercetak (PCBA). PEMATERIAN ULTRASONIK ialah satu lagi teknik yang kerap digunakan dengan keupayaan unik- Ia boleh digunakan untuk memateri bahan kaca, seramik dan bukan logam. Contohnya panel fotovoltaik yang bukan logam memerlukan elektrod yang boleh dilekatkan menggunakan teknik ini. Dalam pematerian ultrasonik, kami menggunakan hujung pematerian yang dipanaskan yang juga mengeluarkan getaran ultrasonik. Getaran ini menghasilkan buih peronggaan pada antara muka substrat dengan bahan pateri cair. Tenaga letupan peronggaan mengubah suai permukaan oksida dan menghilangkan kotoran dan oksida. Pada masa ini lapisan aloi juga terbentuk. Pateri pada permukaan ikatan menggabungkan oksigen dan membolehkan pembentukan ikatan kongsi yang kuat antara kaca dan pateri. PEMATERIAN DIP boleh dianggap sebagai versi pematerian gelombang yang lebih ringkas sesuai untuk pengeluaran skala kecil sahaja. Fluks pembersihan pertama digunakan seperti dalam proses lain. PCB dengan komponen yang dipasang dicelup secara manual atau secara separa automatik ke dalam tangki yang mengandungi pateri cair. Pateri cair melekat pada kawasan logam terdedah tanpa perlindungan topeng pateri di papan. Peralatannya mudah dan murah. • IKATAN PELEKAT : Ini adalah satu lagi teknik popular yang sering kami gunakan dan ia melibatkan ikatan permukaan menggunakan gam, epoksi, agen plastik atau bahan kimia lain. Ikatan dicapai dengan sama ada menguap pelarut, dengan pengawetan haba, dengan pengawetan cahaya UV, dengan pengawetan tekanan atau menunggu masa tertentu. Pelbagai gam berprestasi tinggi digunakan dalam barisan pengeluaran kami. Dengan proses aplikasi dan pengawetan yang direka bentuk dengan betul, ikatan pelekat boleh menghasilkan ikatan tegasan yang sangat rendah yang kukuh dan boleh dipercayai. Ikatan pelekat boleh menjadi pelindung yang baik terhadap faktor persekitaran seperti lembapan, bahan cemar, pengakis, getaran…dsb. Kelebihan ikatan pelekat ialah: ia boleh digunakan pada bahan yang sebaliknya sukar untuk dipateri, dikimpal atau dipateri. Juga ia boleh menjadi lebih baik untuk bahan sensitif haba yang akan rosak oleh kimpalan atau proses suhu tinggi yang lain. Kelebihan lain pelekat adalah ia boleh digunakan pada permukaan berbentuk tidak sekata dan meningkatkan berat pemasangan dengan jumlah yang sangat kecil jika dibandingkan dengan kaedah lain. Juga perubahan dimensi dalam bahagian adalah sangat minimum. Sesetengah gam mempunyai ciri padanan indeks dan boleh digunakan di antara komponen optik tanpa mengurangkan kekuatan isyarat cahaya atau optik dengan ketara. Kelemahan sebaliknya ialah masa pengawetan yang lebih lama yang mungkin melambatkan talian pembuatan, keperluan lekapan, keperluan penyediaan permukaan dan kesukaran untuk ditanggalkan apabila kerja semula diperlukan. Kebanyakan operasi ikatan pelekat kami melibatkan langkah-langkah berikut: -Rawatan permukaan: Prosedur pembersihan khas seperti pembersihan air ternyahion, pembersihan alkohol, plasma atau pembersihan korona adalah perkara biasa. Selepas pembersihan, kami boleh menggunakan promoter lekatan pada permukaan untuk memastikan sambungan yang terbaik. -Pemasangan Bahagian: Untuk kedua-dua aplikasi pelekat dan juga untuk pengawetan kami mereka bentuk dan menggunakan lekapan tersuai. -Aplikasi Pelekat: Kami kadangkala menggunakan manual, dan kadangkala bergantung pada sistem automatik kotak seperti robotik, motor servo, penggerak linear untuk menghantar pelekat ke lokasi yang betul dan kami menggunakan dispenser untuk menghantarnya pada volum dan kuantiti yang betul. -Pengawetan: Bergantung pada pelekat, kami mungkin menggunakan pengeringan dan pengawetan ringkas serta pengawetan di bawah lampu UV yang bertindak sebagai pemangkin atau pengawetan haba dalam ketuhar atau menggunakan elemen pemanas rintangan yang dipasang pada jig dan lekapan. Kami mengesyorkan anda klik di sini untukMUAT TURUN Ilustrasi Skema Proses Pengikat kami oleh AGS-TECH Inc. Ini akan membantu anda memahami dengan lebih baik maklumat yang kami berikan kepada anda di bawah. • PROSES PENGIKAT : Proses penyambung mekanikal kami terbahagi kepada dua kategori brad: PENGikat dan SENDI SEPADU. Contoh pengikat yang kami gunakan ialah skru, pin, nat, bolt, rivet. Contoh sambungan integral yang kami gunakan ialah padanan snap dan kecut, jahitan, kelim. Menggunakan pelbagai kaedah pengikat, kami memastikan sambungan mekanikal kami kuat dan boleh dipercayai untuk penggunaan bertahun-tahun. Skru dan BOL ialah beberapa pengikat yang paling biasa digunakan untuk memegang objek bersama dan meletakkan kedudukan. Skru dan bolt kami memenuhi piawaian ASME. Pelbagai jenis skru dan bolt digunakan termasuk skru penutup hex dan bolt hex, skru lag dan bolt, skru dua hujung, skru dowel, skru mata, skru cermin, skru kepingan logam, skru pelarasan halus, penggerudian sendiri dan skru mengetuk sendiri , set skru, skru dengan pencuci terbina dalam,…dan banyak lagi. Kami mempunyai pelbagai jenis kepala skru seperti countersunk, kubah, bulat, kepala bebibir dan pelbagai jenis pemacu skru seperti slot, phillips, persegi, soket hex. A RIVET sebaliknya ialah pengikat mekanikal kekal yang terdiri daripada aci silinder licin dan kepala pada satu tangan. Selepas dimasukkan, hujung rivet yang satu lagi cacat dan diameternya dibesarkan supaya ia kekal di tempatnya. Dalam erti kata lain, sebelum pemasangan rivet mempunyai satu kepala dan selepas pemasangan ia mempunyai dua. Kami memasang pelbagai jenis rivet bergantung pada aplikasi, kekuatan, kebolehcapaian dan kos seperti rivet kepala pepejal/bulat, struktur, separa tiub, buta, oscar, pemacu, siram, kunci geseran, rivet penebuk diri. Riveting boleh diutamakan dalam kes di mana ubah bentuk haba dan perubahan sifat bahan akibat haba kimpalan perlu dielakkan. Riveting juga menawarkan berat ringan dan terutamanya kekuatan dan ketahanan yang baik terhadap daya ricih. Walau bagaimanapun, terhadap beban tegangan, skru, nat dan bolt mungkin lebih sesuai. Dalam proses CLINCHING kami menggunakan penebuk dan die khas untuk membentuk jalinan mekanikal antara kepingan logam yang dicantum. Pukulan itu menolak lapisan kepingan logam ke dalam rongga cetakan dan mengakibatkan pembentukan sendi kekal. Tiada pemanasan dan penyejukan tidak diperlukan dalam mencengkam dan ia adalah proses kerja yang sejuk. Ia adalah proses ekonomi yang boleh menggantikan kimpalan titik dalam beberapa kes. Dalam PINNING kami menggunakan pin yang merupakan elemen mesin yang digunakan untuk menjamin kedudukan bahagian mesin secara relatif antara satu sama lain. Jenis utama ialah pin clevis, pin cotter, pin spring, pin dowel, dan pin belah. Dalam STAPLING kami menggunakan senapang stapling dan staples yang merupakan pengikat serampang dua mata yang digunakan untuk menyambung atau mengikat bahan. Stapling mempunyai kelebihan berikut: Jimat, mudah dan cepat digunakan, mahkota staples boleh digunakan untuk merapatkan bahan yang diikat bersama, Mahkota staples boleh memudahkan merapatkan sekeping seperti kabel dan mengikatnya ke permukaan tanpa menusuk atau merosakkan, penyingkiran yang agak mudah. PRESS FITTING dilakukan dengan menolak bahagian bersama dan geseran antara bahagian tersebut mengikat bahagian tersebut. Bahagian muat tekan yang terdiri daripada aci bersaiz besar dan lubang bersaiz kecil biasanya dipasang dengan salah satu daripada dua kaedah: Sama ada dengan menggunakan daya atau mengambil kesempatan daripada pengembangan haba atau pengecutan bahagian. Apabila pemasangan penekan diwujudkan dengan menggunakan daya, kita sama ada menggunakan penekan hidraulik atau penekan yang dikendalikan tangan. Sebaliknya apabila pemasangan tekan diwujudkan oleh pengembangan haba, kami memanaskan bahagian yang menyelubungi dan memasangnya ke tempatnya semasa panas. Apabila mereka sejuk, mereka mengecut dan kembali ke dimensi normal mereka. Ini menghasilkan kesesuaian akhbar yang baik. Kami memanggil ini sebagai alternatif SHRINK-FITTING. Cara lain untuk melakukan ini ialah dengan menyejukkan bahagian yang diselubungi sebelum dipasang dan kemudian menggelongsorkannya ke bahagian mengawannya. Apabila perhimpunan memanaskan, ia mengembang dan kami mendapat kesesuaian yang ketat. Kaedah terakhir ini mungkin lebih baik dalam kes di mana pemanasan menimbulkan risiko menukar sifat bahan. Penyejukan adalah lebih selamat dalam kes tersebut. Komponen dan Pemasangan Pneumatik & Hidraulik • Injap, komponen hidraulik dan pneumatik seperti cincin-O, mesin basuh, pengedap, gasket, cincin, shim. Memandangkan injap dan komponen pneumatik datang dalam pelbagai jenis, kami tidak boleh menyenaraikan semuanya di sini. Bergantung pada persekitaran fizikal dan kimia aplikasi anda, kami mempunyai produk khas untuk anda. Sila nyatakan kepada kami aplikasi, jenis komponen, spesifikasi, keadaan persekitaran seperti tekanan, suhu, cecair atau gas yang akan bersentuhan dengan injap dan komponen pneumatik anda; dan kami akan memilih produk yang paling sesuai untuk anda atau mengeluarkannya khas untuk aplikasi anda. CLICK Product Finder-Locator Service HALAMAN SEBELUMNYA
- Composites, Composite Materials Manufacturing, Fiber Reinforced
Composites, Composite Materials Manufacturing, Particle and Fiber Reinforced, Cermets, Ceramic & Metal Composite, Glass Fiber Reinforced Polymer, Lay-Up Process Pembuatan Bahan Komposit & Komposit Secara ringkasnya, KOMPOSIT atau BAHAN KOMPOSIT ialah bahan yang terdiri daripada dua atau berbilang bahan dengan sifat fizikal atau kimia yang berbeza, tetapi apabila digabungkan ia menjadi bahan yang berbeza daripada bahan konstituen. Kita perlu menunjukkan bahawa bahan konstituen kekal berasingan dan berbeza dalam struktur. Matlamat dalam pembuatan bahan komposit adalah untuk mendapatkan produk yang lebih unggul daripada juzuknya dan menggabungkan ciri-ciri yang diingini setiap juzuk. Sebagai contoh; kekuatan, berat rendah atau harga yang lebih rendah mungkin menjadi pendorong di sebalik mereka bentuk dan menghasilkan komposit. Jenis komposit yang kami tawarkan ialah komposit bertetulang zarah, komposit bertetulang gentian termasuk komposit seramik-matriks / polimer-matriks / logam-matriks / karbon-karbon / hibrid, komposit berstruktur & berlapis & berstruktur sandwic dan komposit nano. Teknik fabrikasi yang kami gunakan dalam pembuatan bahan komposit ialah: Pultrusion, proses pengeluaran prepreg, penempatan gentian lanjutan, penggulungan filamen, penempatan gentian disesuaikan, proses susun semburan gentian kaca, tufting, proses lanxide, z-pinning. Banyak bahan komposit terdiri daripada dua fasa, matriks, yang berterusan dan mengelilingi fasa lain; dan fasa tersebar yang dikelilingi oleh matriks. Kami mengesyorkan anda klik di sini untukMUAT TURUN Ilustrasi Skema Pembuatan Komposit dan Bahan Komposit kami oleh AGS-TECH Inc. Ini akan membantu anda memahami dengan lebih baik maklumat yang kami berikan kepada anda di bawah. • KOMPOSIT BERTETULANG ZARAH : Kategori ini terdiri daripada dua jenis: Komposit zarah besar dan komposit diperkuatkan serakan. Dalam jenis terdahulu, interaksi zarah-matriks tidak boleh dirawat pada tahap atom atau molekul. Sebaliknya mekanik kontinum adalah sah. Sebaliknya, zarah komposit yang diperkuatkan serakan biasanya jauh lebih kecil dalam julat berpuluh-puluh nanometer. Contoh komposit zarah besar ialah polimer yang telah ditambah pengisi. Pengisi meningkatkan sifat bahan dan mungkin menggantikan beberapa isipadu polimer dengan bahan yang lebih menjimatkan. Pecahan isipadu dua fasa mempengaruhi tingkah laku komposit. Komposit zarah besar digunakan dengan logam, polimer dan seramik. CERMETS adalah contoh komposit seramik / logam. Cermet kami yang paling biasa ialah karbida bersimen. Ia terdiri daripada seramik karbida refraktori seperti zarah tungsten karbida dalam matriks logam seperti kobalt atau nikel. Komposit karbida ini digunakan secara meluas sebagai alat pemotong untuk keluli yang dikeraskan. Zarah karbida keras bertanggungjawab untuk tindakan pemotongan dan keliatannya dipertingkatkan oleh matriks logam mulur. Oleh itu, kami memperoleh kelebihan kedua-dua bahan dalam komposit tunggal. Satu lagi contoh biasa bagi komposit zarah besar yang kami gunakan ialah zarah hitam karbon dicampur dengan getah tervulkan untuk mendapatkan komposit dengan kekuatan tegangan tinggi, keliatan, rintangan koyakan dan lelasan. Contoh komposit yang diperkuatkan serakan ialah logam dan aloi logam yang dikuatkan dan dikeraskan oleh serakan seragam zarah halus bahan yang sangat keras dan lengai. Apabila kepingan aluminium oksida yang sangat kecil ditambah pada matriks logam aluminium, kami memperoleh serbuk aluminium tersinter yang mempunyai kekuatan suhu tinggi yang dipertingkatkan. • KOMPOSIT BERTETULANG FIBER: Kategori komposit ini sebenarnya adalah yang paling penting. Matlamat untuk dicapai ialah kekuatan tinggi dan kekakuan per unit berat. Komposisi gentian, panjang, orientasi dan kepekatan dalam komposit ini adalah penting dalam menentukan sifat dan kegunaan bahan ini. Terdapat tiga kumpulan gentian yang kami gunakan: misai, gentian dan wayar. WHISKERS adalah kristal tunggal yang sangat nipis dan panjang. Mereka adalah antara bahan yang paling kuat. Beberapa contoh bahan misai ialah grafit, silikon nitrida, aluminium oksida. FIBERS sebaliknya kebanyakannya polimer atau seramik dan berada dalam keadaan polihablur atau amorfus. Kumpulan ketiga ialah WIRES halus yang mempunyai diameter yang agak besar dan selalunya terdiri daripada keluli atau tungsten. Contoh komposit bertetulang dawai ialah tayar kereta yang menggabungkan dawai keluli di dalam getah. Bergantung pada bahan matriks, kami mempunyai komposit berikut: KOMPOSIT POLIMER-MATRIK : Ini diperbuat daripada resin polimer dan gentian sebagai bahan tetulang. Subkumpulan ini dipanggil Polimer Bertetulang Gentian Kaca (GFRP) Komposit mengandungi gentian kaca berterusan atau tidak selanjar dalam matriks polimer. Kaca menawarkan kekuatan yang tinggi, ia menjimatkan, mudah dibuat menjadi gentian, dan lengai secara kimia. Kelemahannya ialah ketegaran dan kekakuan yang terhad, suhu perkhidmatan hanya sehingga 200 – 300 Celcius. Gentian kaca sesuai untuk badan automotif dan peralatan pengangkutan, badan kenderaan marin, bekas penyimpanan. Ia tidak sesuai untuk aeroangkasa mahupun pembuatan jambatan kerana ketegaran yang terhad. Subkumpulan lain dipanggil Komposit Polimer Bertetulang Gentian Karbon (CFRP). Di sini, karbon ialah bahan gentian kami dalam matriks polimer. Karbon terkenal dengan modulus dan kekuatan spesifiknya yang tinggi serta keupayaannya untuk mengekalkannya pada suhu tinggi. Gentian karbon boleh menawarkan modul tegangan standard, pertengahan, tinggi dan ultratinggi kepada kami. Tambahan pula, gentian karbon menawarkan ciri fizikal dan mekanikal yang pelbagai dan oleh itu sesuai untuk pelbagai aplikasi kejuruteraan tersuai khusus. Komposit CFRP boleh dipertimbangkan untuk mengeluarkan peralatan sukan dan rekreasi, kapal tekanan dan komponen struktur aeroangkasa. Namun, subkumpulan lain, Komposit Polimer Bertetulang Gentian Aramid juga merupakan bahan berkekuatan tinggi dan modulus. Nisbah kekuatan kepada berat mereka sangat tinggi. Gentian aramid juga dikenali dengan nama dagang KEVLAR dan NOMEX. Di bawah ketegangan mereka berprestasi lebih baik daripada bahan gentian polimer lain, tetapi mereka lemah dalam pemampatan. Gentian aramid adalah tahan lasak, tahan hentaman, rayapan dan tahan lesu, stabil pada suhu tinggi, lengai secara kimia kecuali terhadap asid dan bes yang kuat. Gentian Aramid digunakan secara meluas dalam barangan sukan, jaket kalis peluru, tayar, tali, sarung kabel gentian optik. Bahan tetulang gentian lain wujud tetapi digunakan pada tahap yang lebih rendah. Ini adalah boron, silikon karbida, aluminium oksida terutamanya. Bahan matriks polimer sebaliknya juga kritikal. Ia menentukan suhu perkhidmatan maksimum komposit kerana polimer umumnya mempunyai suhu lebur dan degradasi yang lebih rendah. Poliester dan ester vinil digunakan secara meluas sebagai matriks polimer. Resin juga digunakan dan mereka mempunyai rintangan kelembapan dan sifat mekanikal yang sangat baik. Contohnya resin polimida boleh digunakan sehingga kira-kira 230 Darjah Celcius. KOMPOSIT LOGAM-MATRIK : Dalam bahan ini kita menggunakan matriks logam mulur dan suhu perkhidmatan secara amnya lebih tinggi daripada komponen konstituennya. Jika dibandingkan dengan komposit polimer-matriks, ini boleh mempunyai suhu operasi yang lebih tinggi, tidak mudah terbakar, dan mungkin mempunyai ketahanan degradasi yang lebih baik terhadap cecair organik. Walau bagaimanapun, mereka lebih mahal. Bahan tetulang seperti misai, zarah, gentian selanjar dan tak selanjar; dan bahan matriks seperti kuprum, aluminium, magnesium, titanium, aloi super sedang digunakan. Contoh aplikasi ialah komponen enjin yang diperbuat daripada matriks aloi aluminium yang diperkukuh dengan aluminium oksida dan gentian karbon. KOMPOSIT SERAMIK-MATRIK : Bahan seramik terkenal dengan kebolehpercayaan suhu tinggi yang sangat baik. Walau bagaimanapun ia sangat rapuh dan mempunyai nilai yang rendah untuk keliatan patah. Dengan memasukkan zarah, gentian atau misai satu seramik ke dalam matriks seramik yang lain, kami dapat mencapai komposit dengan keliatan patah yang lebih tinggi. Bahan terbenam ini pada asasnya menghalang perambatan retak di dalam matriks dengan beberapa mekanisme seperti memesongkan hujung retak atau membentuk jambatan merentasi muka retak. Sebagai contoh, alumina yang diperkukuh dengan misai SiC digunakan sebagai sisipan alat pemotong untuk pemesinan aloi logam keras. Ini boleh mendedahkan prestasi yang lebih baik berbanding dengan karbida bersimen. KOMPOSIT KARBON-KARBON : Kedua-dua tetulang dan juga matriks adalah karbon. Mereka mempunyai modulus tegangan tinggi dan kekuatan pada suhu tinggi melebihi 2000 Centigrade, rintangan rayapan, keliatan patah yang tinggi, pekali pengembangan haba yang rendah, kekonduksian haba yang tinggi. Ciri-ciri ini menjadikannya sesuai untuk aplikasi yang memerlukan rintangan kejutan haba. Kelemahan komposit karbon-karbon bagaimanapun adalah kelemahannya terhadap pengoksidaan pada suhu tinggi. Contoh penggunaan biasa ialah acuan penekan panas, pembuatan komponen enjin turbin termaju. KOMPOSIT HIBRID : Dua atau lebih jenis gentian berbeza dicampur dalam satu matriks. Oleh itu, seseorang boleh menyesuaikan bahan baru dengan gabungan sifat. Contohnya ialah apabila kedua-dua gentian karbon dan kaca digabungkan ke dalam resin polimer. Gentian karbon memberikan kekukuhan dan kekuatan ketumpatan rendah tetapi mahal. Kaca sebaliknya adalah murah tetapi tidak mempunyai kekakuan gentian karbon. Komposit hibrid kaca-karbon adalah lebih kuat dan lebih keras serta boleh dihasilkan pada kos yang lebih rendah. PEMPROSESAN KOMPOSIT BERTETULANG FIBER : Untuk plastik bertetulang gentian berterusan dengan gentian teragih seragam berorientasikan arah yang sama kami menggunakan teknik berikut. PULTRUSION: Rod, rasuk dan tiub dengan panjang berterusan dan keratan rentas malar dibuat. Roving gentian berterusan diresapi dengan resin termoset dan ditarik melalui acuan keluli untuk membentuknya kepada bentuk yang diingini. Seterusnya, mereka melalui acuan pengawetan yang dimesin ketepatan untuk mencapai bentuk terakhirnya. Oleh kerana acuan pengawetan dipanaskan, ia menyembuhkan matriks resin. Penarik menarik bahan melalui acuan. Menggunakan teras berongga yang dimasukkan, kami dapat memperoleh tiub dan geometri berongga. Kaedah pultrusion adalah automatik dan menawarkan kami kadar pengeluaran yang tinggi. Sebarang panjang produk boleh dihasilkan. PROSES PENGELUARAN PREPREG : Prepreg ialah tetulang gentian berterusan yang dipregnat dengan resin polimer yang telah diawet separa. Ia digunakan secara meluas untuk aplikasi struktur. Bahan itu datang dalam bentuk pita dan dihantar sebagai pita. Pengilang membentuknya secara langsung dan menyembuhkannya sepenuhnya tanpa perlu menambah sebarang resin. Oleh kerana prepreg mengalami tindak balas pengawetan pada suhu bilik, ia disimpan pada suhu 0 Celcius atau lebih rendah. Selepas digunakan, pita yang tinggal disimpan semula pada suhu rendah. Resin termoplastik dan termoset digunakan dan gentian tetulang karbon, aramid dan kaca adalah perkara biasa. Untuk menggunakan prepreg, kertas sandaran pembawa terlebih dahulu dikeluarkan dan kemudian fabrikasi dijalankan dengan meletakkan pita prepreg pada permukaan perkakas (proses lay-up). Beberapa lapisan boleh diletakkan untuk mendapatkan ketebalan yang dikehendaki. Amalan yang kerap dilakukan ialah menukar orientasi gentian untuk menghasilkan lamina lapis silang atau lapis sudut. Akhirnya haba dan tekanan dikenakan untuk pengawetan. Kedua-dua pemprosesan tangan serta proses automatik digunakan untuk memotong prepregs dan lay-up. PENGALITAN FILAMEN : Gentian pengukuhan berterusan diposisikan dengan tepat dalam corak yang telah ditetapkan untuk mengikut dan biasanya bentuk kitaran berongga. Gentian pertama melalui mandi resin dan kemudian dililit pada mandrel oleh sistem automatik. Selepas beberapa ulangan penggulungan, ketebalan yang dikehendaki diperolehi dan pengawetan dilakukan sama ada pada suhu bilik atau di dalam ketuhar. Sekarang mandrel dikeluarkan dan produk dirobohkan. Penggulungan filamen boleh menawarkan nisbah kekuatan kepada berat yang sangat tinggi dengan menggulung gentian dalam corak lilitan, heliks dan kutub. Paip, tangki, selongsong dihasilkan menggunakan teknik ini. • KOMPOSIT STRUKTUR : Umumnya ini terdiri daripada kedua-dua bahan homogen dan komposit. Oleh itu sifat-sifat ini ditentukan oleh bahan konstituen dan reka bentuk geometri unsur-unsurnya. Berikut adalah jenis utama: KOMPOSIT LAMINAR : Bahan struktur ini diperbuat daripada kepingan atau panel dua dimensi dengan arah kekuatan tinggi pilihan. Lapisan disusun dan disimen bersama. Dengan menukar arah kekuatan tinggi dalam dua paksi serenjang, kami memperoleh komposit yang mempunyai kekuatan tinggi dalam kedua-dua arah dalam satah dua dimensi. Dengan melaraskan sudut lapisan seseorang boleh menghasilkan komposit dengan kekuatan dalam arah pilihan. Ski moden dihasilkan dengan cara ini. PANEL SANDWICH : Komposit struktur ini ringan tetapi mempunyai kekukuhan dan kekuatan yang tinggi. Panel sandwic terdiri daripada dua helaian luar yang diperbuat daripada bahan kaku dan kuat seperti aloi aluminium, plastik atau keluli bertetulang gentian dan teras di antara kepingan luar. Teras perlu ringan dan kebanyakan masa mempunyai modulus keanjalan yang rendah. Bahan teras yang popular ialah busa polimer tegar, kayu dan sarang lebah. Panel sandwic digunakan secara meluas dalam industri pembinaan sebagai bahan bumbung, bahan lantai atau dinding, dan juga dalam industri aeroangkasa. • NANOKOMPOSIT : Bahan baharu ini terdiri daripada zarah zarah bersaiz nano yang tertanam dalam matriks. Menggunakan nanokomposit kita boleh mengeluarkan bahan getah yang merupakan penghalang yang sangat baik kepada penembusan udara sambil mengekalkan sifat getahnya tidak berubah. CLICK Product Finder-Locator Service HALAMAN SEBELUMNYA
- Glass and Ceramic Manufacturing, Hermetic Packages, Seals, Bonding
Glass and Ceramic Manufacturing, Hermetic Packages Seals and Bonding, Tempered Bulletproof Glass, Blow Moulding, Optical Grade Glass, Conductive Glass, Molding Pembentukan & Pembentukan Kaca & Seramik Jenis pembuatan kaca yang kami tawarkan ialah kaca bekas, tiupan kaca, gentian kaca & tiub & rod, barangan kaca domestik dan industri, lampu dan mentol, pengacuan kaca ketepatan, komponen dan pemasangan optik, kaca rata & kepingan & terapung. Kami melakukan kedua-dua membentuk tangan dan juga membentuk mesin. Proses pembuatan seramik teknikal kami yang popular ialah menekan mati, menekan isostatik, menekan isostatik panas, menekan panas, tuangan slip, tuangan pita, penyemperitan, pengacuan suntikan, pemesinan hijau, pensinteran atau penembakan, pengisaran berlian, pemasangan hermetik. Kami mengesyorkan anda klik di sini untuk MUAT TURUN Ilustrasi Skema Proses Pembentukan dan Pembentukan Kaca kami oleh AGS-TECH Inc. MUAT TURUN Ilustrasi Skema Proses Pembuatan Seramik Teknikal kami oleh AGS-TECH Inc. Fail yang boleh dimuat turun dengan foto dan lakaran ini akan membantu anda memahami dengan lebih baik maklumat yang kami berikan kepada anda di bawah. • PEMBUATAN KACA BEKAS: Kami telah mengautomasikan PRESS AND BLOW serta talian BLOW AND BLOW untuk pembuatan. Dalam proses pukulan dan pukulan kami menjatuhkan gob ke dalam acuan kosong dan membentuk leher dengan menggunakan tiupan udara termampat dari atas. Sejurus selepas ini, udara termampat ditiup kali kedua dari arah lain melalui leher bekas untuk membentuk pra-bentuk botol. Pra-bentuk ini kemudiannya dipindahkan ke acuan sebenar, dipanaskan semula untuk melembutkan dan udara termampat digunakan untuk memberikan pra-bentuk bentuk bekas terakhirnya. Lebih jelas, ia ditekan dan ditolak ke dinding rongga acuan tiupan untuk mengambil bentuk yang diingini. Akhir sekali, bekas kaca yang dikilang dipindahkan ke dalam ketuhar penyepuhlindapan untuk pemanasan semula dan penyingkiran tegasan yang dihasilkan semasa pengacuan dan disejukkan dalam cara terkawal. Dalam kaedah penekan dan pukulan, gob lebur dimasukkan ke dalam acuan parison (acuan kosong) dan ditekan ke dalam bentuk parison (bentuk kosong). Kosong kemudian dipindahkan ke acuan tiupan dan ditiup serupa dengan proses yang diterangkan di atas di bawah "Proses Tiupan dan Tiupan". Langkah seterusnya seperti penyepuhlindapan dan pelepasan tekanan adalah serupa atau sama. • GLASS BLOWING : Kami telah mengeluarkan produk kaca menggunakan tiupan tangan konvensional serta menggunakan udara termampat dengan peralatan automatik. Untuk beberapa pesanan, tiupan konvensional diperlukan, seperti projek yang melibatkan karya seni kaca, atau projek yang memerlukan bilangan bahagian yang lebih kecil dengan toleransi longgar, projek prototaip / demo….dsb. Tiupan kaca konvensional melibatkan mencelupkan paip logam berongga ke dalam periuk kaca cair dan memutarkan paip untuk mengumpul sejumlah bahan kaca. Kaca yang dikumpul di hujung paip digulung di atas besi rata, dibentuk seperti yang dikehendaki, memanjang, dipanaskan semula dan ditiup udara. Apabila siap, ia dimasukkan ke dalam acuan dan udara ditiup. Rongga acuan basah untuk mengelakkan sentuhan kaca dengan logam. Filem air bertindak seperti kusyen di antara mereka. Tiupan manual ialah proses perlahan yang intensif buruh dan hanya sesuai untuk prototaip atau item bernilai tinggi, tidak sesuai untuk pesanan volum tinggi yang murah bagi setiap keping. • PEMBUATAN PERANGKAT KACA DOMESTIK & INDUSTRI : Menggunakan pelbagai jenis bahan kaca pelbagai jenis barangan kaca sedang dihasilkan. Sesetengah cermin mata adalah kalis haba dan sesuai untuk barangan kaca makmal manakala sesetengahnya cukup baik untuk menahan mesin basuh pinggan mangkuk berkali-kali dan sesuai untuk membuat produk domestik. Menggunakan mesin Westlake, puluhan ribu keping gelas minuman dihasilkan setiap hari. Untuk memudahkan, kaca cair dikumpul dengan vakum dan dimasukkan ke dalam acuan untuk membuat pra-bentuk. Kemudian udara ditiup ke dalam acuan, ini dipindahkan ke acuan lain dan udara ditiup semula dan kaca mengambil bentuk terakhirnya. Seperti dalam tiupan tangan, acuan ini sentiasa basah dengan air. Regangan lanjut adalah sebahagian daripada operasi penamat di mana leher sedang dibentuk. Lebihan kaca hangus. Selepas itu proses pemanasan semula dan penyejukan terkawal yang diterangkan di atas berikut. • TIUB KACA & PEMBENTUKAN ROD : Proses utama yang kami gunakan untuk pembuatan tiub kaca ialah proses DANNER dan VELLO. Dalam Proses Danner, kaca dari relau mengalir dan jatuh pada lengan condong yang diperbuat daripada bahan tahan api. Lengan dibawa pada aci berongga berputar atau sumpitan. Kaca itu kemudiannya dibalut pada lengan dan membentuk lapisan licin mengalir ke bawah lengan dan di atas hujung aci. Dalam kes pembentukan tiub, udara ditiup melalui sumpitan dengan hujung berongga, dan dalam kes pembentukan rod kami menggunakan hujung pepejal pada aci. Tiub atau rod kemudian ditarik ke atas penggelek pembawa. Dimensi seperti ketebalan dinding dan diameter tiub kaca dilaraskan kepada nilai yang dikehendaki dengan menetapkan diameter lengan dan tekanan udara meniup ke nilai yang dikehendaki, melaraskan suhu, kadar aliran kaca dan kelajuan lukisan. Proses pembuatan tiub kaca Vello pula melibatkan kaca yang bergerak keluar dari relau dan ke dalam mangkuk dengan mandrel atau loceng berongga. Kaca itu kemudiannya melalui ruang udara antara mandrel dan mangkuk dan mengambil bentuk tiub. Selepas itu ia bergerak di atas penggelek ke mesin lukisan dan disejukkan. Pada penghujung garisan penyejukan pemotongan dan pemprosesan akhir berlaku. Dimensi tiub boleh dilaraskan sama seperti dalam proses Danner. Apabila membandingkan proses Danner dengan Vello, kita boleh mengatakan bahawa proses Vello adalah lebih sesuai untuk pengeluaran kuantiti yang banyak manakala proses Danner mungkin lebih sesuai untuk pesanan tiub volum lebih kecil yang tepat. • PEMPROSESAN LEMBARAN & KACA RATA & TERApung : Kami mempunyai sejumlah besar kaca rata dalam ketebalan antara ketebalan submilimeter hingga beberapa sentimeter. Cermin mata rata kami hampir sempurna optik. Kami menawarkan kaca dengan salutan khas seperti salutan optik, di mana teknik pemendapan wap kimia digunakan untuk meletakkan salutan seperti antipantulan atau salutan cermin. Juga salutan konduktif telus adalah perkara biasa. Juga tersedia ialah salutan hidrofobik atau hidrofilik pada kaca, dan salutan yang membuat pembersihan diri kaca. Cermin mata terbaja, kalis peluru dan berlamina merupakan barangan popular yang lain. Kami memotong kaca ke dalam bentuk yang dikehendaki dengan toleransi yang dikehendaki. Operasi sekunder lain seperti melengkung atau membengkokkan kaca rata tersedia. • PENGABUHAN KACA TEPAT : Kami menggunakan teknik ini kebanyakannya untuk menghasilkan komponen optik ketepatan tanpa memerlukan teknik yang lebih mahal dan memakan masa seperti pengisaran, lapping dan penggilap. Teknik ini tidak selalu mencukupi untuk membuat optik terbaik yang terbaik, tetapi dalam beberapa kes seperti produk pengguna, kamera digital, optik perubatan, ia boleh menjadi pilihan bagus yang lebih murah untuk pembuatan volum tinggi. Juga mempunyai kelebihan berbanding teknik membentuk kaca lain yang memerlukan geometri kompleks, seperti dalam kes asfera. Proses asas melibatkan pemuatan bahagian bawah acuan kami dengan kaca kosong, pemindahan ruang proses untuk penyingkiran oksigen, hampir penutupan acuan, pemanasan cepat dan isoterma die dan kaca dengan cahaya inframerah, penutupan selanjutnya bahagian acuan untuk menekan kaca yang dilembutkan perlahan-lahan dengan cara terkawal kepada ketebalan yang dikehendaki, dan akhirnya menyejukkan kaca dan mengisi ruang dengan nitrogen dan mengeluarkan produk. Kawalan suhu yang tepat, jarak penutupan acuan, daya tutup acuan, pemadanan pekali pengembangan acuan dan bahan kaca adalah kunci dalam proses ini. • PEMBUATAN KOMPONEN DAN ASET OPTIK KACA : Selain pengacuan kaca ketepatan, terdapat beberapa proses berharga yang kami gunakan untuk membuat komponen dan pemasangan optik berkualiti tinggi untuk aplikasi yang menuntut. Mengisar, menjilat dan menggilap cermin mata gred optik dalam buburan kasar khas yang halus adalah seni dan sains untuk membuat kanta optik, prisma, flat dan banyak lagi. Permukaan rata, bergelombang, licin dan permukaan optik bebas kecacatan memerlukan banyak pengalaman dengan proses sedemikian. Perubahan kecil dalam persekitaran boleh mengakibatkan produk keluar dari spesifikasi dan menghentikan barisan pembuatan. Terdapat kes di mana satu lap pada permukaan optik dengan kain bersih boleh menjadikan produk memenuhi spesifikasi atau gagal dalam ujian. Beberapa bahan kaca yang popular digunakan ialah silika bercantum, kuarza, BK7. Juga pemasangan komponen tersebut memerlukan pengalaman khusus khusus. Kadang-kadang gam khas digunakan. Walau bagaimanapun, kadangkala teknik yang dipanggil sentuhan optik adalah pilihan terbaik dan tidak melibatkan bahan di antara cermin mata optik yang dipasang. Ia terdiri daripada menyentuh permukaan rata secara fizikal untuk melekat antara satu sama lain tanpa gam. Dalam sesetengah kes, pengatur jarak mekanikal, rod atau bola kaca ketepatan, pengapit atau komponen logam dimesin digunakan untuk memasang komponen optik pada jarak tertentu dan dengan orientasi geometri tertentu antara satu sama lain. Mari kita periksa beberapa teknik popular kami untuk menghasilkan optik mewah. MENGISAR & MENGGUNAKAN & MENGGILAT : Bentuk kasar komponen optik diperolehi dengan mengisar kosong kaca. Selepas itu lapping dan penggilap dijalankan dengan memutar dan menggosok permukaan kasar komponen optik terhadap alat dengan bentuk permukaan yang dikehendaki. Buburan dengan zarah kasar dan bendalir kecil sedang dituangkan di antara optik dan alat membentuk. Saiz zarah kasar dalam buburan tersebut boleh dipilih mengikut tahap kerataan yang diingini. Sisihan permukaan optik kritikal daripada bentuk yang dikehendaki dinyatakan dari segi panjang gelombang cahaya yang digunakan. Optik berketepatan tinggi kami mempunyai sepersepuluh daripada toleransi panjang gelombang (Panjang Gelombang/10) atau mungkin lebih ketat. Selain profil permukaan, permukaan kritikal diimbas dan dinilai untuk ciri dan kecacatan permukaan lain seperti dimensi, calar, serpihan, lubang, bintik...dsb. Kawalan ketat terhadap keadaan persekitaran di tingkat pembuatan optik dan keperluan metrologi dan ujian yang meluas dengan peralatan terkini menjadikan ini cabang industri yang mencabar. • PROSES SEKUNDER DALAM PEMBUATAN KACA: Sekali lagi, kami hanya terhad dengan imaginasi anda apabila melibatkan proses sekunder dan kemasan kaca. Di sini kami menyenaraikan beberapa daripadanya: -Salutan pada kaca (optik, elektrik, tribologi, terma, berfungsi, mekanikal...). Sebagai contoh, kita boleh mengubah sifat permukaan kaca menjadikannya sebagai contoh memantulkan haba supaya ia terus membina dalaman sejuk, atau membuat satu sisi inframerah menyerap menggunakan nanoteknologi. Ini membantu memastikan bahagian dalam bangunan sentiasa hangat kerana lapisan permukaan paling luar kaca akan menyerap sinaran inframerah di dalam bangunan dan memancarkannya kembali ke bahagian dalam. -Goresan pada kaca -Pelabelan Seramik Gunaan (ACL) -Ukiran -Penggilap api -Penggilap kimia -Mewarna PEMBUATAN SERAMIK TEKNIKAL • DIE PRESSING : Terdiri daripada pemadatan uniaxial serbuk berbutir yang terkurung dalam dadu • TEKANAN PANAS : Sama seperti menekan mati tetapi dengan penambahan suhu untuk meningkatkan ketumpatan. Serbuk atau prabentuk yang dipadatkan diletakkan ke dalam die grafit dan tekanan uniaksial dikenakan manakala die disimpan pada suhu tinggi seperti 2000 C. Suhu boleh berbeza bergantung pada jenis serbuk seramik yang diproses. Untuk bentuk dan geometri yang rumit, pemprosesan seterusnya yang lain seperti pengisaran berlian mungkin diperlukan. • MENEKAN ISOSTATIK : Serbuk berbutir atau padat ditekan die diletakkan di dalam bekas kedap udara dan kemudian ke dalam bekas tekanan tertutup dengan cecair di dalamnya. Selepas itu ia dipadatkan dengan meningkatkan tekanan bejana tekanan. Cecair di dalam vesel memindahkan daya tekanan secara seragam ke atas seluruh kawasan permukaan bekas kedap udara. Oleh itu, bahan itu dipadatkan secara seragam dan mengambil bentuk bekas fleksibelnya serta profil dan ciri dalamannya. • MENEKAN ISOSTATIK PANAS : Sama seperti menekan isostatik, tetapi sebagai tambahan kepada atmosfera gas bertekanan, kami mensinter padat pada suhu tinggi. Penekanan isostatik panas menghasilkan ketumpatan tambahan dan peningkatan kekuatan. • SLIP CASTING / PARIT CASTING : Kami mengisi acuan dengan ampaian zarah seramik bersaiz mikrometer dan cecair pembawa. Campuran ini dipanggil "slip". Acuan mempunyai liang dan oleh itu cecair dalam campuran ditapis ke dalam acuan. Akibatnya, tuangan terbentuk pada permukaan dalaman acuan. Selepas pensinteran, bahagian boleh dikeluarkan dari acuan. • TUANG PITA : Kami mengeluarkan pita seramik dengan menuang buburan seramik pada permukaan pembawa bergerak rata. Buburan mengandungi serbuk seramik yang dicampur dengan bahan kimia lain untuk tujuan mengikat dan membawa. Apabila pelarut tersejat, kepingan seramik yang padat dan fleksibel ditinggalkan yang boleh dipotong atau digulung mengikut kehendak. • PEMBENTUKAN PENYEMPAT: Seperti dalam proses penyemperitan lain, campuran lembut serbuk seramik dengan pengikat dan bahan kimia lain disalurkan melalui acuan untuk memperoleh bentuk keratan rentasnya dan kemudian dipotong mengikut panjang yang dikehendaki. Proses ini dilakukan dengan campuran seramik sejuk atau dipanaskan. • PENGABUHAN SUNTIKAN BERTEKANAN RENDAH : Kami menyediakan campuran serbuk seramik dengan pengikat dan pelarut dan memanaskannya pada suhu yang mudah ditekan dan dipaksa ke dalam rongga alat. Setelah kitaran pengacuan selesai, bahagian itu dikeluarkan dan bahan kimia yang mengikat dibakar. Menggunakan pengacuan suntikan, kita boleh mendapatkan bahagian yang rumit pada jumlah yang tinggi secara ekonomi. Lubang iaitu pecahan kecil milimeter pada dinding setebal 10mm adalah mungkin, benang boleh dilakukan tanpa pemesinan semula, toleransi seketat +/- 0.5% adalah mungkin dan lebih rendah apabila bahagian dimesin , ketebalan dinding dalam urutan 0.5mm hingga panjang 12.5 mm adalah mungkin serta ketebalan dinding 6.5mm hingga panjang 150mm. • PEMESINAN HIJAU : Menggunakan alat pemesinan logam yang sama, kita boleh mesin bahan seramik yang ditekan semasa ia masih lembut seperti kapur. Toleransi +/- 1% adalah mungkin. Untuk toleransi yang lebih baik kami menggunakan pengisaran berlian. • SINTERING atau FIRING : Pensinteran memungkinkan ketumpatan penuh. Pengecutan yang ketara berlaku pada bahagian kompak hijau, tetapi ini bukan masalah besar kerana kami mengambil kira perubahan dimensi ini apabila kami mereka bentuk bahagian dan perkakas. Zarah serbuk diikat bersama dan keliangan yang disebabkan oleh proses pemadatan disingkirkan ke tahap yang besar.. • MENGISAR BERLIAN : Bahan "berlian" paling sukar di dunia sedang digunakan untuk mengisar bahan keras seperti seramik dan bahagian ketepatan diperoleh. Toleransi dalam julat mikrometer dan permukaan yang sangat licin sedang dicapai. Oleh kerana perbelanjaannya, kami hanya mempertimbangkan teknik ini apabila kami benar-benar memerlukannya. • PERHIMPUNAN HERMETIK adalah yang secara praktikalnya tidak membenarkan sebarang pertukaran jirim, pepejal, cecair atau gas antara antara muka. Pengedap hermetik adalah kedap udara. Sebagai contoh, kepungan elektronik hermetik adalah yang mengekalkan kandungan dalaman sensitif peranti yang dibungkus tanpa dicederakan oleh kelembapan, bahan cemar atau gas. Tiada yang 100% hermetic, tetapi apabila kita bercakap tentang hermeticity, kita bermaksud bahawa dari segi praktikal, terdapat hermeticity sehingga tahap kadar kebocoran adalah sangat rendah sehingga peranti selamat di bawah keadaan persekitaran biasa untuk masa yang sangat lama. Pemasangan hermetik kami terdiri daripada komponen logam, kaca dan seramik, logam-seramik, seramik-logam-seramik, logam-seramik-logam, logam kepada logam, logam-kaca, logam-kaca-logam, kaca-logam-kaca, kaca- logam dan kaca kepada kaca dan semua gabungan lain ikatan logam-kaca-seramik. Sebagai contoh, logam boleh melapisi komponen seramik supaya ia boleh diikat kuat dengan komponen lain dalam pemasangan dan mempunyai keupayaan pengedap yang sangat baik. Kami mempunyai pengetahuan tentang cara menyalut gentian optik atau suapan dengan logam dan memateri atau mematerikannya pada kepungan, supaya tiada gas melepasi atau bocor ke dalam kepungan. Oleh itu ia digunakan untuk pembuatan penutup elektronik untuk membungkus peranti sensitif dan melindunginya daripada atmosfera luar. Selain ciri-ciri pengedap yang sangat baik, sifat-sifat lain seperti pekali pengembangan haba, rintangan ubah bentuk, sifat tidak keluar gas, jangka hayat yang sangat lama, sifat tidak konduktif, sifat penebat haba, sifat antistatik...dsb. jadikan bahan kaca dan seramik sebagai pilihan untuk aplikasi tertentu. Maklumat mengenai kemudahan kami yang menghasilkan kelengkapan seramik kepada logam, pengedap hermetik, suapan vakum, komponen kawalan vakum dan bendalir tinggi dan ultratinggi boleh didapati di sini:Brosur Kilang Komponen Hermetik CLICK Product Finder-Locator Service HALAMAN SEBELUMNYA
- Wire & Spring Forming, Shaping, Welding, Assembly of Wires, Coil, CNC
Wire & Spring Forming, Shaping, Welding, Assembly of Wires, Coil Compression Extension Torsion Flat Springs, Custom Wires, Helical Springs at AGS-TECH Inc. Pembentukan Kawat & Spring Kami mengeluarkan wayar tersuai, pemasangan wayar, wayar yang dibentuk menjadi bentuk 2D dan 3D yang diingini, jaring dawai, jaringan, kandang, bakul, pagar, spring dawai, spring rata; kilasan, mampatan, ketegangan, spring rata dan banyak lagi. Proses kami ialah membentuk dawai dan spring, melukis wayar, membentuk, membengkok, mengimpal, memateri, memateri, menindik, menggoyang, menggerudi, chamfering, mengisar, menyulam, menyalut, empat gelongsor, membentuk slaid, penggulungan, penggulungan, menjengkelkan. Kami mengesyorkan anda klik di sini untuk MUAT TURUN Ilustrasi Skema Proses Pembentukan Wayar dan Spring kami oleh AGS-TECH Inc. Fail yang boleh dimuat turun dengan foto dan lakaran ini akan membantu anda memahami dengan lebih baik maklumat yang kami berikan kepada anda di bawah. • LUKISAN KAWAD : Dengan menggunakan daya tegangan, kami meregangkan stok logam dan menariknya melalui dadu untuk mengurangkan diameter dan menambah panjangnya. Kadang-kadang kita menggunakan satu siri mati. Kami mampu membuat acuan untuk setiap tolok wayar. Menggunakan bahan dengan kekuatan tegangan tinggi kami melukis wayar yang sangat nipis. Kami menawarkan wayar bekerja sejuk dan panas. • PEMBENTUKAN KAWAT : Segulung dawai yang diukur dibengkokkan dan dibentuk menjadi produk yang berguna. Kami mempunyai keupayaan untuk membentuk wayar daripada semua tolok, termasuk filamen nipis serta wayar tebal seperti yang digunakan sebagai spring di bawah casis kereta. Peralatan yang kami gunakan untuk membentuk wayar ialah pembentuk wayar manual dan CNC, gegelung, penekan kuasa, empat gelongsor, berbilang slaid. Proses kami ialah melukis, membengkok, meluruskan, merata, meregang, memotong, menjengkelkan, pematerian & kimpalan & pematerian, pemasangan, melingkar, swaging (atau sayap), menindik, benang dawai, menggerudi, chamfering, pengisaran, salutan dan rawatan permukaan. Peralatan tercanggih kami boleh disediakan untuk membangunkan reka bentuk yang sangat kompleks dalam sebarang bentuk dan toleransi yang ketat. Kami menawarkan pelbagai jenis hujung seperti hujung sfera, runcing atau chamfer untuk wayar anda. Kebanyakan projek membentuk wayar kami mempunyai kos perkakas yang minimum hingga sifar. Masa pemulihan sampel biasanya hari. Perubahan kepada reka bentuk/konfigurasi bentuk wayar boleh dibuat dengan cepat. • SPRING FORMING : AGS-TECH mengeluarkan pelbagai jenis spring termasuk: -Kilasan / Spring Torsion Berganda -Ketegangan / Spring Mampatan -Malar / Spring Berubah -Gegelung & Spring Heliks -Flat & Leaf Spring -Imbangan Spring -Pencuci Belleville -Negator Spring -Pegas Gegelung Kadar Progresif -Wave Spring -Volute Spring - Mata Air Tirus -Cincin Musim Bunga -Clock Springs -Klip Kami mengeluarkan mata air daripada pelbagai bahan dan boleh membimbing anda mengikut aplikasi anda. Bahan yang paling biasa ialah keluli tahan karat, silikon krom, keluli karbon tinggi, karbon rendah terbaja minyak, vanadium krom, gangsa fosfor, titanium, aloi tembaga berilium, seramik suhu tinggi. Kami menggunakan pelbagai teknik dalam pembuatan spring, termasuk CNC coiling, cold winding, hot winding, hardening, finishing. Teknik lain yang telah disebutkan di atas di bawah pembentukan wayar juga biasa dalam operasi pembuatan musim bunga kami. • PERKHIDMATAN PENAMAT untuk WIRES & SPRINGS : Kami boleh menyiapkan produk anda dalam pelbagai cara bergantung pada pilihan dan keperluan anda. Beberapa proses biasa yang kami tawarkan ialah: mengecat, menyalut serbuk, menyadur, mencelup vinil, menganodkan, melegakan tekanan, rawatan haba, pukulan peen, tumble, kromat, nikel tanpa elektrik, pempasifan, enamel bakar, lapisan plastik , pembersihan plasma. CLICK Product Finder-Locator Service HALAMAN SEBELUMNYA
- Sheet Metal Forming Fabrication, Stamping, Punching, Deep Drawing, CNC
Sheet Metal Forming and Fabrication, Stamping, Punching, Bending, Progressive Die, Spot Welding, Deep Drawing, Metal Blanking and Slitting at AGS-TECH Inc. Setem & Fabrikasi Logam Kepingan Kami menawarkan pengecapan logam lembaran, membentuk, membentuk, membengkok, menebuk, mengosongkan, menggorok, berlubang, torehan, menggigit, mencukur, kerja tekan, fabrikasi, lukisan dalam menggunakan pukulan tunggal / mati lejang tunggal serta dadu dan putaran progresif, pembentukan getah dan pembentukan hidro; pemotongan kepingan logam menggunakan pancutan air, plasma, laser, gergaji, nyalaan; pemasangan kepingan logam menggunakan kimpalan, kimpalan tempat; lembaran logam tiub membonjol dan membongkok; kemasan permukaan logam kepingan termasuk lukisan celup atau semburan, salutan serbuk elektrostatik, anodizing, penyaduran, sputtering dan banyak lagi. Perkhidmatan kami terdiri daripada prototaip logam kepingan pantas kepada pembuatan volum tinggi. Kami mengesyorkan anda klik di sini untukMUAT TURUN Ilustrasi Skema kami bagi Proses Fabrikasi dan Setem Lembaran Logam oleh AGS-TECH Inc. Ini akan membantu anda memahami dengan lebih baik maklumat yang kami berikan kepada anda di bawah. • POTONGAN LOGAM LEMBARAN : Kami menawarkan POTONGAN dan PERPISAHAN. Potongan memotong kepingan logam di atas satu laluan pada satu masa dan pada asasnya tiada pembaziran bahan, manakala dengan perpisahan bentuk tidak boleh diletakkan dengan tepat dan oleh itu sejumlah bahan terbuang. Salah satu proses kami yang paling popular ialah PUNCHING, di mana sekeping bahan bulat atau bentuk lain dipotong daripada kepingan logam. Sekeping yang dipotong adalah sisa. Satu lagi versi tebukan ialah SLOTTING, di mana lubang segi empat tepat atau memanjang ditebuk. BLANKING sebaliknya adalah proses yang sama seperti menumbuk, dengan perbezaan bahagian yang dipotong adalah kerja dan disimpan. FINE BLANKING, versi pengosongan yang unggul, menghasilkan potongan dengan toleransi rapat dan tepi licin lurus dan tidak memerlukan operasi kedua untuk kesempurnaan bahan kerja. Satu lagi proses yang kerap kami gunakan ialah SLITTING, iaitu proses ricih di mana kepingan logam dipotong oleh dua bilah bulat yang bertentangan dalam laluan lurus atau melengkung. Pembuka tin ialah contoh mudah proses menggorok. Satu lagi process yang popular bagi kami ialah PERFORATING, di mana banyak lubang bulat atau bentuk lain ditebuk dalam kepingan logam dalam corak tertentu. Contoh biasa untuk produk berlubang ialah penapis logam dengan banyak lubang untuk cecair. Dalam NOTCHING, satu lagi proses pemotongan kepingan logam, kami mengeluarkan bahan dari bahan kerja, bermula di tepi atau di tempat lain dan memotong ke dalam sehingga bentuk yang dikehendaki diperolehi. Ia adalah proses progresif di mana setiap operasi mengeluarkan sekeping lain sehingga kontur yang dikehendaki diperolehi. Untuk larian pengeluaran kecil kadangkala kami menggunakan proses yang agak perlahan dipanggil NIBBLING yang terdiri daripada banyak pukulan pantas lubang bertindih untuk membuat potongan yang lebih besar dan lebih kompleks. Dalam POTONGAN PROGRESIF kami menggunakan satu siri operasi yang berbeza untuk mendapatkan potongan tunggal atau geometri tertentu. Akhirnya MENCUKUR proses kedua membantu kami memperbaiki tepi potongan yang telah dibuat. Ia digunakan untuk memotong cip, tepi kasar pada kerja kepingan logam. • LEMBUNG LOGAM LEMBARAN : Selain pemotongan, lenturan adalah proses penting yang tanpanya kita tidak akan dapat menghasilkan kebanyakan produk. Selalunya operasi kerja sejuk tetapi kadangkala juga dilakukan semasa hangat atau panas. Kami menggunakan acuan dan menekan kebanyakan masa untuk operasi ini. Dalam PROGRESSIVE BENDING kami menggunakan satu siri operasi tebuk dan die yang berbeza untuk mendapatkan satu lengkok atau geometri tertentu. AGS-TECH menggunakan pelbagai proses lenturan dan membuat pilihan bergantung pada bahan bahan kerja, saiz, ketebalan, saiz lentur yang diingini, jejari, kelengkungan dan sudut lentur, lokasi lentur, ekonomi operasi, kuantiti yang akan dikeluarkan… dan lain-lain. Kami menggunakan V-BENDING di mana penebuk berbentuk V memaksa kepingan logam ke dalam cetakan berbentuk V dan membengkokkannya. Baik untuk kedua-dua sudut yang sangat akut dan tumpul dan di antaranya, termasuk 90 darjah. Menggunakan mengelap dies kita melakukan EDGE BENDING. Peralatan kami membolehkan kami memperoleh sudut yang lebih besar daripada 90 darjah. Dalam lenturan tepi, bahan kerja diapit di antara pad tekanan dan acuan, kawasan untuk lenturan terletak pada tepi acuan dan selebihnya bahan kerja dipegang di atas space seperti rasuk julur. Apabila pukulan bertindak pada bahagian julur, ia dibengkokkan di atas tepi dadu. FLANGING ialah proses lenturan tepi yang menghasilkan sudut 90 darjah. Matlamat utama operasi adalah penghapusan tepi tajam dan mendapatkan permukaan geometri untuk memudahkan penyambungan bahagian. BEADING, satu lagi proses lenturan tepi biasa membentuk lengkungan di atas tepi bahagian. HEMMING sebaliknya menghasilkan tepi helaian yang dibengkokkan sepenuhnya pada dirinya sendiri. Dalam SEAMING, tepi dua bahagian dibengkokkan antara satu sama lain dan bercantum. JAHITAN BERGANDA sebaliknya menyediakan sambungan kepingan logam kedap air dan kedap udara. Sama seperti lenturan tepi, proses yang dipanggil ROTARY BENDING menggunakan silinder dengan sudut yang dikehendaki dipotong dan berfungsi sebagai penebuk. Apabila daya dihantar ke pukulan, ia ditutup dengan bahan kerja. Alur silinder memberikan bahagian julur sudut yang dikehendaki. Alur boleh mempunyai sudut yang lebih kecil atau lebih besar daripada 90 darjah. Dalam LENTUN UDARA, kita tidak memerlukan acuan bawah untuk mempunyai alur bersudut. Lembaran logam disokong oleh dua permukaan pada sisi bertentangan dan pada jarak tertentu. Pukulan kemudian menggunakan daya di lokasi yang betul dan membengkokkan bahan kerja. LENTUN SALURAN dilakukan menggunakan tebuk dan die berbentuk saluran, dan U-BEND dicapai dengan tebukan berbentuk U. OFFSET BENDING menghasilkan offset pada kepingan logam. MELENTUR GULUNG, teknik yang baik untuk kerja tebal dan lenturan kepingan besar plat logam, menggunakan tiga gulung untuk menyuap dan membengkokkan plat ke kelengkungan yang dikehendaki. Gulung disusun supaya selekoh kerja yang dikehendaki diperolehi. Jarak dan sudut antara gulungan dikawal untuk mendapatkan hasil yang diingini. Gulungan boleh alih membolehkan anda mengawal kelengkungan. PEMBENTUKAN TIUB ialah satu lagi operasi lenturan kepingan logam popular yang melibatkan pelbagai die. Tiub diperolehi selepas beberapa tindakan. CORRUGATION juga dilakukan dengan operasi lenturan. Pada asasnya ia adalah lenturan simetri pada selang masa yang tetap merentasi keseluruhan kepingan logam. Pelbagai bentuk boleh digunakan untuk beralun. Lembaran logam beralun adalah lebih tegar dan mempunyai rintangan yang lebih baik terhadap lenturan dan oleh itu mempunyai aplikasi dalam industri pembinaan. PEMBENTUKAN GULUNG LOGAM LEMBARAN, proses pembuatan berterusan_cc781905-5cde-3194-bb3b-136bad5cf58d digunakan untuk membengkokkan keratan rentas geometri tertentu menggunakan gulungan dan kerja dibengkokkan dalam langkah berurutan, dengan gulungan akhir melengkapkan kerja. Dalam sesetengah kes satu gulung dan dalam beberapa kes satu siri gulung digunakan. • PROSES MEMOTONG & MELENTUR LOGAM LEMBARAN GABUNGAN : Ini adalah proses yang memotong dan membengkok pada masa yang sama. Dalam PIERCING, lubang dicipta menggunakan pukulan tajam. Apabila tebuk melebarkan lubang dalam helaian, bahan dibengkokkan serentak ke dalam bebibir dalaman untuk lubang. Bebibir yang diperoleh mungkin mempunyai fungsi penting. Operasi LANCING sebaliknya memotong dan membengkokkan helaian untuk mencipta geometri yang dinaikkan. • TIUB LOGAM MEMBONTONG DAN MELENTOK : Dalam MEMBENCANG beberapa bahagian dalaman tiub berongga bertekanan, menyebabkan tiub membonjol ke luar. Oleh kerana tiub berada di dalam dadu, geometri bonjolan dikawal oleh bentuk dadu. Dalam STRETCH BENDING, tiub logam diregangkan menggunakan daya selari dengan paksi tiub dan daya lentur untuk menarik tiub ke atas blok bentuk. Dalam DRAW BENDING, kami mengapit tiub berhampiran hujungnya pada blok bentuk berputar yang membengkokkan tiub semasa berputar. Akhir sekali, dalam MAMPATAN MAMPATAN tiub dipegang secara paksa pada blok bentuk tetap, dan dadu membengkokkannya di atas blok bentuk. • LUKISAN DALAM : Dalam salah satu operasi kami yang paling popular, pukulan, dadu padanan dan pemegang kosong digunakan. Lembaran logam kosong diletakkan di atas bukaan dadu dan penebuk bergerak ke arah kosong yang dipegang oleh pemegang kosong. Sebaik sahaja ia bersentuhan, tumbukan memaksa kepingan logam ke dalam rongga acuan untuk membentuk produk. Operasi lukisan dalam menyerupai pemotongan, namun kelegaan antara pukulan dan acuan menghalang helaian daripada dipotong. Faktor lain yang memastikan helaian dilukis dalam dan tidak dipotong ialah sudut bulat pada dadu dan penebuk yang menghalang pemotongan dan pemotongan. Untuk mencapai magnitud lukisan dalam yang lebih besar, proses RAWATAN SEMULA sedang digunakan di mana lukisan dalam seterusnya berlaku pada bahagian yang telah menjalani proses lukisan dalam. Dalam REVERSE RAWING, bahagian yang dilukis dalam terbalik dan dilukis ke arah yang bertentangan. Lukisan dalam boleh menyediakan objek berbentuk tidak sekata seperti cawan berkubah, tirus atau bertingkat, Dalam EMBOSSING kami menggunakan pasangan die lelaki dan perempuan untuk menarik perhatian kepingan logam dengan reka bentuk atau skrip. • SPINNING : Operasi di mana bahan kerja rata atau prabentuk dipegang di antara mandrel berputar dan stok ekor dan alat menggunakan tekanan setempat pada kerja sambil ia bergerak ke atas mandrel secara beransur-ansur. Akibatnya, bahan kerja dibalut di atas mandrel dan mengambil bentuknya. Kami menggunakan teknik ini sebagai alternatif kepada lukisan dalam di mana kuantiti pesanan adalah kecil, bahagiannya besar (diameter sehingga 20 kaki) dan mempunyai lengkung yang unik. Walaupun harga sekeping biasanya lebih tinggi, kos persediaan untuk operasi pemintalan CNC adalah rendah berbanding lukisan dalam. Sebaliknya, lukisan dalam memerlukan pelaburan awal yang tinggi untuk persediaan, tetapi kos setiap bahagian adalah rendah apabila kuantiti bahagian yang tinggi dihasilkan. Satu lagi versi proses ini ialah SHEAR SPINNING, di mana terdapat juga aliran logam dalam bahan kerja. Aliran logam akan mengurangkan ketebalan bahan kerja semasa proses dijalankan. Satu lagi proses yang berkaitan ialah TIUB SPINNING, yang digunakan pada bahagian silinder. Juga dalam proses ini terdapat aliran logam dalam bahan kerja. Ketebalan itu dikurangkan dan panjang tiub meningkat. Alat ini boleh dialihkan untuk mencipta ciri pada bahagian dalam atau luar tiub. • PEMBENTUKAN GETAH DARI LOGAM LEMBARAN : Getah atau bahan poliuretana dimasukkan ke dalam bekas bekas dan bahan kerja diletakkan di atas permukaan getah. Satu tumbukan kemudiannya dilakukan pada bahan kerja dan memaksanya masuk ke dalam getah. Oleh kerana tekanan yang dihasilkan oleh getah adalah rendah, kedalaman bahagian yang dihasilkan adalah terhad. Memandangkan kos perkakas adalah rendah, proses ini sesuai untuk pengeluaran kuantiti rendah. • PEMBENTUKAN HIDROFORMASI : Sama seperti pembentukan getah, dalam proses ini kerja kepingan logam ditekan dengan penebuk ke dalam cecair bertekanan di dalam ruang. Kerja kepingan logam diapit di antara penebuk dan diafragma getah. Diafragma mengelilingi bahan kerja sepenuhnya dan tekanan bendalir memaksanya terbentuk pada penebuk. Cabutan yang sangat dalam malah lebih dalam daripada proses lukisan dalam boleh diperolehi dengan teknik ini. Kami mengeluarkan die pukulan tunggal serta die progresif bergantung pada bahagian anda. Die stamping stroke tunggal ialah kaedah kos efektif untuk menghasilkan kuantiti besar bahagian kepingan logam mudah seperti pencuci dengan cepat. Die progresif atau teknik lukisan dalam digunakan untuk menghasilkan geometri yang lebih kompleks. Bergantung pada kes anda, waterjet, laser atau pemotongan plasma boleh digunakan untuk menghasilkan bahagian kepingan logam anda dengan murah, pantas dan tepat. Ramai pembekal tidak tahu tentang teknik alternatif ini atau tidak memilikinya dan oleh itu mereka melalui cara yang panjang dan mahal untuk membuat cetakan dan alat yang hanya membuang masa dan wang pelanggan. Jika anda memerlukan komponen kepingan logam tersuai yang dibina seperti penutup, perumah elektronik...dsb secepat dalam beberapa hari, kemudian hubungi kami untuk perkhidmatan PROTOTAIP LOGAM LEMBARAN RAPID kami. CLICK Product Finder-Locator Service MENU SEBELUMNYA
- Forging and Powdered Metallurgy, Die Forging, Heading, Hot Forging
Forging and Powdered Metallurgy, Die Forging, Heading, Hot Forging, Impression Die, Near Net Shape, Swaging, Metal Hobbing, Riveting, Coining from AGS-TECH Inc. Penempaan Logam & Metalurgi Serbuk Jenis proses PENEMPUAN LOGAM yang kami tawarkan ialah die panas dan sejuk, die terbuka dan die tertutup, die impression & penempaan tanpa kilat, cogging, fullering, edging and precision forging, near-net-shape, heading , swaging, tempaan kecewa, hobbing logam, tekan & guling & jejari & orbital & gelang & penempaan isoterma, syiling, rivet, penempaan bola logam, tindikan logam, saiz, penempaan kadar tenaga tinggi. Teknik METALURGI BEDAK dan BEDAK kami ialah menekan serbuk dan pensinteran, impregnasi, penyusupan, penekan isostatik panas dan sejuk, pengacuan suntikan logam, pemadatan gulung, penggulungan serbuk, penyemperitan serbuk, pensinteran longgar, pensinteran percikan, penekan panas. Kami mengesyorkan anda klik di sini untuk MUAT TURUN Ilustrasi Skema Proses Penempaan kami oleh AGS-TECH Inc. MUAT TURUN Ilustrasi Skema Proses Metalurgi Serbuk kami oleh AGS-TECH Inc. Fail yang boleh dimuat turun dengan foto dan lakaran ini akan membantu anda memahami dengan lebih baik maklumat yang kami berikan kepada anda di bawah. Dalam penempaan logam, daya mampatan dikenakan dan bahan berubah bentuk dan bentuk yang dikehendaki diperolehi. Bahan palsu yang paling biasa dalam industri adalah besi dan keluli, tetapi banyak lagi seperti aluminium, tembaga, titanium, magnesium juga ditempa secara meluas. Bahagian logam palsu telah menambah baik struktur bijian selain retakan tertutup dan ruang kosong tertutup, oleh itu kekuatan bahagian yang diperoleh melalui proses ini lebih tinggi. Penempaan menghasilkan bahagian yang dengan ketara lebih kuat untuk beratnya daripada bahagian yang dibuat dengan tuangan atau pemesinan. Memandangkan bahagian yang ditempa dibentuk dengan membuat aliran logam ke dalam bentuk terakhirnya, logam mengambil struktur butiran berarah yang menyumbang kepada kekuatan unggul bahagian tersebut. Dalam erti kata lain, bahagian yang diperoleh melalui proses penempaan mendedahkan sifat mekanikal yang lebih baik berbanding dengan bahagian tuangan atau mesin yang mudah. Berat penempaan logam boleh terdiri daripada bahagian ringan kecil hingga ratusan ribu paun. Kami mengeluarkan penempaan kebanyakannya untuk aplikasi yang menuntut secara mekanikal di mana tekanan tinggi dikenakan pada bahagian seperti bahagian automotif, gear, alatan kerja, alatan tangan, aci turbin, gear motosikal. Oleh kerana kos perkakas dan penyediaan agak tinggi, kami mengesyorkan proses pembuatan ini hanya untuk pengeluaran volum tinggi dan untuk komponen kritikal volum rendah tetapi bernilai tinggi seperti gear pendaratan aeroangkasa. Selain kos perkakas, masa utama pembuatan untuk bahagian tempa dalam kuantiti yang banyak boleh lebih lama berbanding dengan beberapa bahagian mesin yang ringkas, tetapi teknik ini penting untuk bahagian yang memerlukan kekuatan luar biasa seperti bolt, nat, aplikasi khas pengikat, automotif, forklift, bahagian kren. • HOT DIE dan COLD DIE FORGING : Penempaan die panas, seperti namanya dijalankan pada suhu tinggi, oleh itu kemuluran adalah tinggi dan kekuatan bahan rendah. Ini memudahkan ubah bentuk dan penempaan yang mudah. Sebaliknya, penempaan acuan sejuk dilakukan pada suhu yang lebih rendah dan memerlukan daya yang lebih tinggi yang mengakibatkan pengerasan terikan, kemasan permukaan yang lebih baik dan ketepatan bahagian yang dikeluarkan. • OPEN DIE dan IMPRESSION DIE FORGING : Dalam penempaan die terbuka, die tidak mengekang bahan yang dimampatkan, manakala dalam cetakan die menempa rongga dalam dies menyekat aliran bahan semasa ia ditempa mengikut bentuk yang dikehendaki. UPSET FORGING atau juga dipanggil UPSETTING, yang sebenarnya tidak sama tetapi proses yang hampir serupa, adalah proses die terbuka di mana bahan kerja diapit di antara dua dadu rata dan daya mampatan mengurangkan ketinggiannya. Apabila ketinggian adalah reduced, lebar bahan kerja bertambah. HEADING, proses penempaan kecewa melibatkan stok silinder yang terganggu pada hujungnya dan keratan rentasnya ditambah secara tempatan. Dalam tajuk stok disuap melalui acuan, dipalsukan dan kemudian dipotong mengikut panjang. Operasi ini mampu menghasilkan kuantiti pengikat yang tinggi dengan cepat. Kebanyakannya ia adalah operasi kerja sejuk kerana ia digunakan untuk membuat hujung paku, hujung skru, nat dan bolt di mana bahan perlu dikuatkan. Satu lagi proses die terbuka ialah COGGING, di mana bahan kerja ditempa dalam satu siri langkah dengan setiap langkah menghasilkan mampatan bahan dan gerakan seterusnya dari dadu terbuka sepanjang panjang bahan kerja. Pada setiap langkah, ketebalan dikurangkan dan panjang ditambah dengan jumlah yang kecil. Proses itu menyerupai pelajar yang gugup menggigit penselnya dalam beberapa langkah kecil. Proses yang dipanggil FULLERING ialah satu lagi kaedah penempaan acuan terbuka yang sering kami gunakan sebagai langkah awal untuk mengagihkan bahan dalam bahan kerja sebelum operasi penempaan logam lain berlaku. Kami menggunakannya apabila bahan kerja memerlukan beberapa forging operations. Dalam operasi, mati dengan permukaan cembung berubah bentuk dan menyebabkan logam mengalir keluar ke kedua-dua belah. Proses yang serupa dengan pemenuh, EDGING sebaliknya melibatkan acuan terbuka dengan permukaan cekung untuk mengubah bentuk bahan kerja. Tepi juga merupakan proses persediaan untuk operasi penempaan seterusnya menjadikan bahan mengalir dari kedua-dua belah ke kawasan di tengah. IMPRESSION DIE FORGING atau CLOSED DIE FORGING kerana ia juga dipanggil menggunakan acuan / acuan yang memampatkan bahan dan menyekat alirannya dalam dirinya. Die ditutup dan bahan mengambil bentuk die / rongga acuan. PECISION FORGING, proses yang memerlukan peralatan dan acuan khas, menghasilkan bahagian tanpa atau sangat sedikit kilat. Dalam erti kata lain, bahagian-bahagian akan mempunyai hampir dimensi akhir. Dalam proses ini jumlah bahan yang terkawal dengan teliti dimasukkan dan diletakkan di dalam acuan. Kami menggunakan kaedah ini untuk bentuk kompleks dengan bahagian nipis, had terima yang kecil dan sudut draf dan apabila kuantitinya cukup besar untuk mewajarkan kos acuan dan peralatan. • PENEMPUAN TAK KILAP : Bahan kerja diletakkan di dalam acuan sedemikian rupa sehingga tiada bahan boleh mengalir keluar dari rongga untuk membentuk kilat. Oleh itu, pemangkasan denyar yang tidak diingini tidak diperlukan. Ia adalah proses penempaan ketepatan dan oleh itu memerlukan kawalan rapi ke atas jumlah bahan yang digunakan. • METAL SWAGING atau RADIAL FORGING : Sekeping kerja digerakkan secara keliling oleh acuan dan ditempa. Mandrel juga boleh digunakan untuk menempa geometri bahan kerja dalaman. Dalam operasi swaging, bahan kerja biasanya menerima beberapa pukulan sesaat. Barangan biasa yang dihasilkan oleh swaging ialah alat hujung runcing, palang tirus, pemutar skru. • MENCUTIK LOGAM : Kami kerap menggunakan operasi ini sebagai operasi tambahan dalam pembuatan bahagian. Lubang atau rongga dicipta dengan menindik pada permukaan bahan kerja tanpa menembusinya. Sila ambil perhatian bahawa menindik adalah berbeza daripada menggerudi yang mengakibatkan lubang tembus. • HOBBING : Penebuk dengan geometri yang dikehendaki ditekan ke dalam bahan kerja dan mencipta rongga dengan bentuk yang diingini. Kami memanggil pukulan ini sebagai HOB. Operasi melibatkan tekanan tinggi dan dijalankan dalam keadaan sejuk. Akibatnya bahan itu bekerja sejuk dan terikan mengeras. Oleh itu proses ini sangat sesuai untuk pembuatan acuan, die dan kaviti untuk proses pembuatan lain. Sebaik sahaja dapur dikilangkan, seseorang boleh dengan mudah mengeluarkan banyak rongga yang serupa tanpa perlu memesinnya satu demi satu. • TEMPU GULUNG atau MEMBENTUK GULUNG : Dua gulungan bertentangan digunakan untuk membentuk bahagian logam. Bahan kerja dimasukkan ke dalam gulungan, gulungan berputar dan menarik kerja ke dalam celah, kerja kemudian disuap melalui bahagian beralur gulungan dan daya mampatan memberikan bahan bentuk yang diinginkan. Ia bukan proses rolling tetapi proses penempaan, kerana ia adalah diskret dan bukannya operasi berterusan. Geometri pada rumpun gulung menempa bahan kepada bentuk dan geometri yang diperlukan. Ia dilakukan panas. Kerana proses penempaan, ia menghasilkan bahagian dengan sifat mekanikal yang luar biasa dan oleh itu kami menggunakannya untuk menghasilkan bahagian automotif seperti aci yang perlu mempunyai ketahanan luar biasa dalam persekitaran kerja yang sukar. • PENEMPUAN ORBITAL : Bahan kerja dimasukkan ke dalam rongga acuan penempaan dan ditempa oleh acuan atas yang bergerak dalam laluan orbit semasa ia berputar pada paksi condong. Pada setiap pusingan, dadu atas selesai mengenakan daya mampatan ke seluruh bahan kerja. Dengan mengulangi revolusi ini beberapa kali, penempaan yang mencukupi dilakukan. Kelebihan teknik pembuatan ini adalah operasi hingar yang rendah dan daya yang lebih rendah diperlukan. Dalam erti kata lain dengan daya yang kecil seseorang boleh mengelilingi dadu berat di sekeliling paksi untuk mengenakan tekanan besar pada bahagian bahan kerja yang bersentuhan dengan dadu. Bahagian berbentuk cakera atau kon kadangkala sesuai untuk proses ini. • TEMPAKAN CINCIN : Kami kerap menggunakan untuk mengeluarkan cincin lancar. Stok dipotong mengikut panjang, kecewa dan kemudian ditebuk sehingga membuat lubang tengah. Kemudian ia diletakkan pada mandrel dan tukul acuan penempaan ia dari atas sambil cincin diputar perlahan-lahan sehingga dimensi yang dikehendaki diperolehi. • RIVETING : Proses biasa untuk menyambung bahagian, bermula dengan kepingan logam lurus yang dimasukkan ke dalam lubang yang telah dibuat melalui bahagian tersebut. Selepas itu kedua-dua hujung kepingan logam ditempa dengan memerah sambungan antara acuan atas dan bawah. • COINING : Satu lagi proses popular yang dijalankan oleh mesin penekan, menggunakan daya yang besar dalam jarak yang dekat. Nama "coining" berasal dari butiran halus yang dipalsukan pada permukaan syiling logam. Ia kebanyakannya merupakan proses penamat untuk produk di mana butiran halus diperoleh pada permukaan hasil daripada daya besar yang dikenakan oleh acuan yang memindahkan butiran ini ke bahan kerja. • TEMPUAN BOLA LOGAM : Produk seperti galas bebola memerlukan bebola logam berkualiti tinggi yang dihasilkan dengan tepat. Dalam satu teknik yang dipanggil SKEW ROLLING, kami menggunakan dua gulungan bertentangan yang berputar secara berterusan semasa stok dimasukkan secara berterusan ke dalam gulungan. Pada satu hujung dua gulung sfera logam dikeluarkan sebagai produk. Kaedah kedua untuk penempaan bola logam adalah menggunakan acuan yang memerah stok bahan yang diletakkan di antara mereka mengambil bentuk sfera rongga acuan. Selalunya bola yang dihasilkan memerlukan beberapa langkah tambahan seperti kemasan dan penggilap untuk menjadi produk berkualiti tinggi. • TEMPAKAN ISOTHERMAL / HOT DIE FORGING : Proses yang mahal dilakukan hanya apabila nilai manfaat / kos adalah wajar. Proses kerja panas di mana acuan dipanaskan pada suhu yang lebih kurang sama dengan bahan kerja. Oleh kerana kedua-dua mati dan kerja adalah kira-kira suhu yang sama, tiada penyejukan dan ciri-ciri aliran logam bertambah baik. Operasi ini sesuai untuk aloi super dan bahan dengan kebolehpalsuan rendah dan bahan yang sifat mekanikal sangat sensitif kepada kecerunan dan perubahan suhu yang kecil. • SAIZ LOGAM : Ia adalah proses kemasan sejuk. Aliran bahan tidak terhad dalam semua arah dengan pengecualian arah di mana daya dikenakan. Hasilnya, kemasan permukaan yang sangat baik dan dimensi yang tepat diperolehi. • PENEMPUAN KADAR TENAGA TINGGI : Teknik ini melibatkan acuan atas yang dipasang pada lengan omboh yang ditolak dengan pantas apabila campuran bahan api-udara dinyalakan oleh palam pencucuh. Ia menyerupai operasi piston dalam enjin kereta. Acuan terkena bahan kerja dengan sangat cepat dan kemudian kembali ke kedudukan asalnya dengan sangat cepat terima kasih kepada tekanan belakang. Kerja dipalsukan dalam beberapa milisaat dan oleh itu tiada masa untuk kerja itu menjadi sejuk. Ini berguna untuk bahagian yang sukar ditempa yang mempunyai sifat mekanikal yang sangat sensitif terhadap suhu. Dalam erti kata lain prosesnya sangat pantas sehingga bahagian itu terbentuk di bawah suhu malar sepanjang dan tidak akan ada kecerunan suhu pada antara muka acuan/bahan kerja. • Dalam DIE FORGING, logam dipukul di antara dua blok keluli yang sepadan dengan bentuk khas di dalamnya, dipanggil dies. Apabila logam dipalu di antara dadu, ia mempunyai bentuk yang sama seperti bentuk dalam dadu. Apabila ia mencapai bentuk akhir, ia dibawa keluar untuk menyejukkan. Proses ini menghasilkan bahagian yang kuat yang mempunyai bentuk yang tepat, tetapi memerlukan pelaburan yang lebih besar untuk die khusus. Penempaan kecewa meningkatkan diameter kepingan logam dengan meratakannya. Ia biasanya digunakan untuk membuat bahagian kecil, terutamanya untuk membentuk kepala pada pengikat seperti bolt dan paku. • BEDAK METALURGI / BEDAK PEMPROSESAN : Seperti namanya, ia melibatkan proses pembuatan untuk membuat bahagian pepejal geometri dan bentuk tertentu daripada serbuk. Jika serbuk logam digunakan untuk tujuan ini ia adalah bidang metalurgi serbuk dan jika serbuk bukan logam digunakan ia adalah pemprosesan serbuk. Bahagian pepejal dihasilkan daripada serbuk dengan menekan dan mensinter. POWDER PRESSING digunakan untuk memadatkan serbuk ke dalam bentuk yang diingini. Pertama, bahan utama adalah serbuk fizikal, membahagikannya kepada banyak zarah individu kecil. Campuran serbuk diisi ke dalam acuan dan pukulan bergerak ke arah serbuk dan padatkan ke dalam bentuk yang diingini. Kebanyakannya dilakukan pada suhu bilik, dengan serbuk menekan bahagian pepejal diperoleh dan ia dipanggil padat hijau. Pengikat dan pelincir biasanya digunakan untuk meningkatkan kebolehkompakan. Kami mampu membentuk penekan serbuk menggunakan penekan hidraulik dengan beberapa ribu tan kapasiti. Kami juga mempunyai penekan tindakan berganda dengan pukulan atas & bawah yang bertentangan serta tekanan berbilang tindakan untuk geometri bahagian yang sangat kompleks. Keseragaman yang merupakan cabaran penting bagi kebanyakan kilang metalurgi serbuk / pemprosesan serbuk bukanlah masalah besar bagi AGS-TECH kerana pengalaman kami yang luas dalam pembuatan tersuai bahagian tersebut selama bertahun-tahun. Walaupun dengan bahagian yang lebih tebal di mana keseragaman menimbulkan cabaran, kami telah berjaya. Jika kami komited dengan projek anda, kami akan membuat bahagian anda. Jika kami melihat sebarang potensi risiko, kami akan memaklumkan anda in advance. PENSINTARAN BEDAK, iaitu langkah kedua, melibatkan peningkatan suhu ke tahap tertentu dan pengekalan suhu pada tahap tersebut untuk masa tertentu supaya zarah serbuk di bahagian yang ditekan boleh terikat bersama. Ini menghasilkan ikatan yang lebih kuat dan pengukuhan bahan kerja. Pensinteran berlaku hampir dengan suhu lebur serbuk. Semasa pengecutan pensinteran akan berlaku, kekuatan bahan, ketumpatan, kemuluran, kekonduksian terma, kekonduksian elektrik meningkat. Kami mempunyai relau kelompok dan berterusan untuk pensinteran. Salah satu keupayaan kami ialah melaraskan tahap keliangan bahagian yang kami hasilkan. Sebagai contoh, kami dapat menghasilkan penapis logam dengan mengekalkan bahagian berliang pada tahap tertentu. Menggunakan teknik yang dipanggil IMPREGNATION, kami mengisi liang-liang dalam logam dengan cecair seperti minyak. Kami menghasilkan contohnya galas impregnated minyak yang pelincir sendiri. Dalam proses PENIPUSAN kita mengisi liang logam dengan logam lain yang takat lebur lebih rendah daripada bahan asas. Campuran dipanaskan pada suhu di antara suhu lebur kedua-dua logam. Hasilnya beberapa sifat istimewa boleh diperolehi. Kami juga kerap melakukan operasi sekunder seperti pemesinan dan penempaan pada bahagian yang dikeluarkan serbuk apabila ciri atau sifat khas perlu diperoleh atau apabila bahagian itu boleh dibuat dengan langkah proses yang kurang. MENEKAN ISOSTATIK : Dalam proses ini tekanan bendalir digunakan untuk memampatkan bahagian. Serbuk logam diletakkan dalam acuan yang diperbuat daripada bekas fleksibel yang tertutup. Dalam tekanan isostatik, tekanan dikenakan dari sekeliling, bertentangan dengan tekanan paksi yang dilihat dalam tekanan konvensional. Kelebihan menekan isostatik adalah ketumpatan seragam dalam bahagian, terutamanya untuk bahagian yang lebih besar atau lebih tebal, sifat unggul. Kelemahannya ialah masa kitaran yang panjang dan ketepatan geometri yang agak rendah. MENEKAN ISOSTATIK SEJUK dijalankan pada suhu bilik dan acuan fleksibel diperbuat daripada getah, PVC atau uretana atau bahan yang serupa. Bendalir yang digunakan untuk menekan dan memampatkan ialah minyak atau air. Pensinteran konvensional padat hijau mengikuti ini. MENEKAN ISOSTATIK PANAS sebaliknya dilakukan pada suhu tinggi dan bahan acuan adalah kepingan logam atau seramik dengan takat lebur yang cukup tinggi yang menahan suhu. Cecair tekanan biasanya merupakan gas lengai. Operasi menekan dan pensinteran dilakukan dalam satu langkah. Keliangan hampir tersingkir sepenuhnya, struktur seragam grain diperolehi. Kelebihan menekan isostatik panas ialah ia boleh menghasilkan bahagian yang setanding dengan tuangan dan penempaan digabungkan sambil membuat bahan yang tidak sesuai untuk tuangan dan penempaan boleh digunakan. Kelemahan menekan isostatik panas ialah masa kitarannya yang tinggi dan oleh itu kosnya. Ia sesuai untuk bahagian kritikal volum rendah. PENGABUHAN SUNTIKAN LOGAM : Proses yang sangat sesuai untuk menghasilkan bahagian kompleks dengan dinding nipis dan geometri terperinci. Paling sesuai untuk bahagian yang lebih kecil. Serbuk dan pengikat polimer dicampur, dipanaskan dan disuntik ke dalam acuan. Pengikat polimer menyaluti permukaan zarah serbuk. Selepas pengacuan, pengikat dikeluarkan dengan sama ada pemanasan suhu rendah terlarut menggunakan pelarut. PEMADATAN GULUNG / GELENGAN SERBUK : Serbuk digunakan untuk menghasilkan jalur atau kepingan berterusan. Serbuk disuap dari penyuap dan dipadatkan dengan dua gulungan berputar ke dalam kepingan atau jalur. Operasi dijalankan sejuk. Lembaran dibawa ke dalam relau pensinteran. Proses pensinteran boleh diulang kali kedua. PENYEMPAT SERBUK : Bahagian dengan nisbah panjang dan diameter yang besar dihasilkan dengan menyemperit bekas logam kepingan nipis dengan serbuk. PENSinteran LOOSE : Seperti namanya, ia adalah kaedah pemadatan dan pensinteran tanpa tekanan, sesuai untuk menghasilkan bahagian yang sangat berliang seperti penapis logam. Serbuk dimasukkan ke dalam rongga acuan tanpa padat. PENSinteran LOOSE : Seperti namanya, ia adalah kaedah pemadatan dan pensinteran tanpa tekanan, sesuai untuk menghasilkan bahagian yang sangat berliang seperti penapis logam. Serbuk dimasukkan ke dalam rongga acuan tanpa padat. PENSINTARAN SPARK : Serbuk dimampatkan dalam acuan dengan dua penebuk bertentangan dan arus elektrik kuasa tinggi dikenakan pada penebuk dan melalui serbuk padat yang diapit di antaranya. Arus tinggi membakar filem permukaan daripada zarah serbuk dan mensinterkannya dengan haba yang dihasilkan. Prosesnya cepat kerana haba tidak digunakan dari luar sebaliknya ia dihasilkan dari dalam acuan. MENEKAN PANAS : Serbuk ditekan dan disinter dalam satu langkah dalam acuan yang boleh menahan suhu tinggi. Semasa die memampatkan haba serbuk digunakan padanya. Ketepatan yang baik dan sifat mekanikal yang dicapai oleh kaedah ini menjadikannya pilihan yang menarik. Malah logam refraktori boleh diproses dengan menggunakan bahan acuan seperti grafit. CLICK Product Finder-Locator Service MENU SEBELUMNYA
- Casting and Machined Parts, CNC Manufacturing, Milling, Turning, Swiss
Casting and Machined Parts, CNC Manufacturing, Milling, Turning, Swiss Type Machining, Die Casting, Investment Casting, Lost Foam Cast Parts from AGS-TECH Inc. Pemutus dan Pemesinan Teknik tuangan dan pemesinan tersuai kami ialah tuangan yang boleh dibelanjakan dan tidak boleh dibelanjakan, tuangan ferus dan bukan ferus, pasir, die, emparan, berterusan, acuan seramik, pelaburan, buih hilang, bentuk hampir-jaring, acuan kekal (cetakan mati graviti), plaster acuan (cetakan plaster) dan tuangan cangkerang, bahagian dimesin yang dihasilkan dengan mengisar dan memusing menggunakan peralatan konvensional serta CNC, pemesinan jenis swiss untuk bahagian berkepersisan kecil yang boleh diproses tinggi, pemesinan skru untuk pengikat, pemesinan bukan konvensional. Sila ingat bahawa selain logam dan aloi logam, kami memesin komponen seramik, kaca dan plastik juga dalam beberapa kes apabila pembuatan acuan tidak menarik atau bukan pilihan. Pemesinan bahan polimer memerlukan pengalaman khusus yang kami miliki kerana plastik dan getah yang mencabar kerana kelembutannya, tidak tegar...dsb. Untuk pemesinan seramik dan kaca, sila lihat halaman kami di Fabrikasi Bukan Konvensional. AGS-TECH Inc. mengeluarkan dan membekalkan tuangan ringan dan berat. Kami telah membekalkan tuangan logam dan bahagian yang dimesin untuk dandang, penukar haba, kereta, mikromotor, turbin angin, peralatan pembungkusan makanan dan banyak lagi. Kami mengesyorkan anda klik di sini untuk MUAT TURUN Ilustrasi Skema Pemesinan dan Proses Casting kami oleh AGS-TECH Inc. Ini akan membantu anda memahami dengan lebih baik maklumat yang kami berikan kepada anda di bawah. Mari lihat beberapa teknik yang kami tawarkan secara terperinci: • TUANG ACUAN BOLEH DIBELI : Kategori luas ini merujuk kepada kaedah yang melibatkan acuan sementara dan tidak boleh diguna semula. Contohnya ialah pasir, plaster, cengkerang, pelaburan (juga dipanggil lost-wax) dan tuangan plaster. • TUANG PASIR : Satu proses di mana pasir digunakan sebagai bahan acuan. Kaedah yang sangat lama dan masih sangat popular sehingga sebahagian besar tuangan logam yang dihasilkan dibuat dengan teknik ini. Kos rendah walaupun pada pengeluaran kuantiti rendah. Sesuai untuk pembuatan bahagian kecil dan besar. Teknik ini boleh digunakan untuk mengeluarkan bahagian dalam beberapa hari atau minggu dengan pelaburan yang sangat sedikit. Pasir lembap diikat bersama menggunakan tanah liat, pengikat atau minyak khas. Pasir biasanya terkandung dalam kotak acuan dan rongga & sistem pintu dibuat dengan memampatkan pasir di sekeliling model. Proses-proses tersebut ialah: 1.) Meletakkan model dalam pasir untuk membuat acuan 2.) Penggabungan model dan pasir dalam sistem gating 3.) Penyingkiran model 4.) Mengisi rongga acuan dengan logam cair 5.) Penyejukan logam 6.) Memecahkan acuan pasir dan membuang tuangan • TUANG ACUAN PLASTER : Sama seperti tuangan pasir, dan bukannya pasir, plaster of paris digunakan sebagai bahan acuan. Masa utama pengeluaran yang singkat seperti tuangan pasir dan murah. Toleransi dimensi yang baik dan kemasan permukaan. Kelemahan utamanya ialah ia hanya boleh digunakan dengan logam takat lebur rendah seperti aluminium dan zink. • TUANG ACUAN KERANG : Juga serupa dengan tuangan pasir. Rongga acuan yang diperolehi oleh cangkerang pasir yang mengeras dan pengikat resin termoset dan bukannya kelalang yang diisi dengan pasir seperti dalam proses penuangan pasir. Hampir semua logam yang sesuai untuk dituang oleh pasir boleh dibuang melalui pengacuan cangkerang. Proses itu boleh diringkaskan sebagai: 1.) Pembuatan acuan cangkerang. Pasir yang digunakan mempunyai saiz butiran yang jauh lebih kecil jika dibandingkan dengan pasir yang digunakan dalam tuangan pasir. Pasir halus dicampur dengan resin termoset. Corak logam disalut dengan agen pemisah untuk memudahkan penyingkiran cangkerang. Selepas itu corak logam dipanaskan dan campuran pasir dituang atau ditiup ke atas corak tuangan panas. Cangkang nipis terbentuk pada permukaan corak. Ketebalan cangkerang ini boleh dilaraskan dengan mengubah tempoh masa campuran resin pasir bersentuhan dengan corak logam. Pasir yang longgar kemudiannya dikeluarkan dengan corak bersalut cangkerang yang tinggal. 2.) Seterusnya, cangkerang dan corak dipanaskan dalam ketuhar supaya cangkerang mengeras. Selepas pengerasan selesai, cangkerang dikeluarkan daripada corak menggunakan pin yang dibina ke dalam corak. 3.) Dua cengkerang sedemikian dicantumkan bersama dengan melekat atau mengapit dan membentuk acuan lengkap. Sekarang acuan cangkerang dimasukkan ke dalam bekas yang mana ia disokong oleh pasir atau pukulan logam semasa proses tuangan. 4.) Sekarang logam panas boleh dituangkan ke dalam acuan kulit. Kelebihan tuangan cangkerang adalah produk dengan kemasan permukaan yang sangat baik, kemungkinan pembuatan bahagian kompleks dengan ketepatan dimensi tinggi, proses mudah untuk mengautomasikan, menjimatkan untuk pengeluaran volum besar. Kelemahannya ialah acuan memerlukan pengudaraan yang baik kerana gas yang terhasil apabila logam cair menyentuh bahan kimia pengikat, resin termoset dan corak logam adalah mahal. Disebabkan oleh kos corak logam, teknik ini mungkin tidak sesuai untuk pengeluaran kuantiti yang rendah. • PELABURAN TUANG (juga dikenali sebagai LOST-WAX CASTING ): Juga teknik yang sangat lama dan sesuai untuk mengeluarkan bahagian berkualiti dengan ketepatan tinggi, kebolehulangan, serba boleh dan integriti daripada banyak logam, bahan refraktori dan aloi prestasi tinggi khas. Bahagian bersaiz kecil dan besar boleh dihasilkan. Proses yang mahal jika dibandingkan dengan beberapa kaedah lain, tetapi kelebihan utama adalah kemungkinan untuk menghasilkan bahagian dengan bentuk bersih yang hampir, kontur yang rumit dan butiran. Jadi kosnya agak diimbangi oleh penghapusan kerja semula dan pemesinan dalam beberapa kes. Walaupun terdapat variasi, berikut ialah ringkasan proses pemutus pelaburan am: 1.) Penciptaan corak induk asli daripada lilin atau plastik. Setiap tuangan memerlukan satu corak kerana ini dimusnahkan dalam proses. Acuan dari mana corak dihasilkan juga diperlukan dan kebanyakan masa acuan dituang atau dimesin. Oleh kerana acuan tidak perlu dibuka, tuangan yang kompleks boleh dicapai, banyak corak lilin boleh disambungkan seperti dahan pokok dan dituangkan bersama, sekali gus membolehkan pengeluaran berbilang bahagian daripada penuangan tunggal logam atau aloi logam. 2.) Seterusnya, corak dicelup atau dituangkan dengan buburan refraktori yang terdiri daripada silika berbutir sangat halus, air, pengikat. Ini menghasilkan lapisan seramik di atas permukaan corak. Lapisan refraktori pada corak dibiarkan kering dan mengeras. Langkah ini adalah asal nama pemutus pelaburan: Buburan refraktori dilaburkan ke atas corak lilin. 3.) Pada langkah ini, acuan seramik yang telah keras diterbalikkan dan dipanaskan supaya lilin cair dan mencurah keluar dari acuan. Satu rongga ditinggalkan untuk tuangan logam. 4.) Selepas lilin keluar, acuan seramik dipanaskan pada suhu yang lebih tinggi yang mengakibatkan pengukuhan acuan. 5.) Tuangan logam dituangkan ke dalam acuan panas mengisi semua bahagian yang rumit. 6.) Tuangan dibenarkan untuk memejal 7.) Akhirnya acuan seramik dipecahkan dan bahagian yang dikilang dipotong dari pokok. Berikut ialah pautan ke Risalah Loji Casting Pelaburan • TUANG CORAK SEJATAN : Prosesnya menggunakan corak yang diperbuat daripada bahan seperti busa polistirena yang akan tersejat apabila logam cair panas dituang ke dalam acuan. Terdapat dua jenis proses ini: LOST FOAM CASTING yang menggunakan pasir tidak terikat dan FULL MOLD CASTING yang menggunakan pasir terikat. Berikut adalah langkah-langkah proses umum: 1.) Menghasilkan corak daripada bahan seperti polisterin. Apabila kuantiti yang banyak akan dihasilkan, corak akan dibentuk. Jika bahagian mempunyai bentuk yang kompleks, beberapa bahagian bahan buih tersebut mungkin perlu dilekatkan bersama untuk membentuk corak. Kami sering menyalut corak dengan sebatian refraktori untuk menghasilkan kemasan permukaan yang baik pada tuangan. 2.) Corak kemudian dimasukkan ke dalam pasir acuan. 3.) Logam cair dituangkan ke dalam acuan, menyejat corak buih, iaitu polistirena dalam kebanyakan kes semasa ia mengalir melalui rongga acuan. 4.) Logam cair dibiarkan dalam acuan pasir untuk mengeras. 5.) Selepas ia mengeras, kita keluarkan tuangan. Dalam sesetengah kes, produk yang kami keluarkan memerlukan teras dalam corak. Dalam tuangan penyejatan, tidak perlu meletakkan dan mengamankan teras dalam rongga acuan. Teknik ini sesuai untuk pembuatan geometri yang sangat kompleks, ia boleh dengan mudah diautomatikkan untuk pengeluaran volum tinggi, dan tiada garisan perpisahan di bahagian tuang. Proses asasnya mudah dan menjimatkan untuk dilaksanakan. Untuk pengeluaran volum yang besar, kerana acuan atau acuan diperlukan untuk menghasilkan corak daripada polistirena, ini mungkin agak mahal. • TUANG ACUAN TIDAK BOLEH DIKELUAR : Kategori luas ini merujuk kepada kaedah di mana acuan tidak perlu diubahsuai selepas setiap kitaran pengeluaran. Contohnya ialah tuangan kekal, mati, berterusan dan emparan. Kebolehulangan diperoleh dan bahagian boleh dicirikan sebagai BENTUK BERSIH DEKAT. • TUANG ACUAN KEKAL : Acuan boleh guna semula yang diperbuat daripada logam digunakan untuk berbilang tuangan. Acuan kekal biasanya boleh digunakan untuk berpuluh-puluh ribu kali sebelum ia haus. Graviti, tekanan gas atau vakum biasanya digunakan untuk mengisi acuan. Acuan (juga dipanggil die) biasanya diperbuat daripada besi, keluli, seramik atau logam lain. Proses umum ialah: 1.) Mesin dan buat acuan. Adalah biasa untuk memesin acuan daripada dua blok logam yang sesuai bersama dan boleh dibuka dan ditutup. Kedua-dua ciri bahagian dan juga sistem gating biasanya dimesin ke dalam acuan tuangan. 2.) Permukaan acuan dalaman disalut dengan buburan yang menggabungkan bahan refraktori. Ini membantu mengawal aliran haba dan bertindak sebagai pelincir untuk memudahkan penyingkiran bahagian tuang. 3.) Seterusnya, bahagian acuan kekal ditutup dan acuan dipanaskan. 4.) Logam cair dituang ke dalam acuan dan biarkan diam untuk pemejalan. 5.) Sebelum banyak penyejukan berlaku, kami mengeluarkan bahagian dari acuan kekal menggunakan ejector apabila bahagian acuan dibuka. Kami kerap menggunakan tuangan acuan kekal untuk logam takat lebur rendah seperti zink dan aluminium. Untuk tuangan keluli, kami menggunakan grafit sebagai bahan acuan. Kami kadangkala memperoleh geometri kompleks menggunakan teras dalam acuan kekal. Kelebihan teknik ini ialah tuangan dengan sifat mekanikal yang baik diperolehi dengan penyejukan pantas, keseragaman sifat, ketepatan dan kemasan permukaan yang baik, kadar penolakan yang rendah, kemungkinan mengautomasikan proses dan menghasilkan volum yang tinggi secara ekonomi. Kelemahan ialah kos persediaan awal yang tinggi yang menjadikannya tidak sesuai untuk operasi volum rendah, dan had pada saiz bahagian yang dikeluarkan. • TUANG DIE : Sebuah dadu dimesin dan logam cair ditolak di bawah tekanan tinggi ke dalam rongga acuan. Tuangan die bukan ferus dan juga logam ferus adalah mungkin. Proses ini sesuai untuk pengeluaran kuantiti tinggi bahagian bersaiz kecil hingga sederhana dengan butiran, dinding yang sangat nipis, konsistensi dimensi dan kemasan permukaan yang baik. AGS-TECH Inc. mampu menghasilkan ketebalan dinding sekecil 0.5 mm menggunakan teknik ini. Seperti dalam tuangan acuan kekal, acuan perlu terdiri daripada dua bahagian yang boleh dibuka dan ditutup untuk penyingkiran bahagian yang dihasilkan. Acuan tuangan die mungkin mempunyai berbilang rongga untuk membolehkan pengeluaran berbilang tuangan dengan setiap kitaran. Acuan tuangan mati adalah sangat berat dan lebih besar daripada bahagian yang dihasilkannya, oleh itu juga mahal. Kami membaiki dan menggantikan mati yang usang secara percuma untuk pelanggan kami selagi mereka memesan semula alat ganti mereka daripada kami. Mati kita mempunyai jangka hayat yang panjang dalam julat beberapa ratus ribu kitaran. Berikut ialah langkah proses asas yang dipermudahkan: 1.) Pengeluaran acuan umumnya daripada keluli 2.) Acuan dipasang pada mesin die casting 3.) Omboh memaksa logam cair untuk mengalir dalam rongga die mengisi ciri-ciri rumit dan dinding nipis 4.) Selepas mengisi acuan dengan logam cair, tuangan dibiarkan mengeras di bawah tekanan 5.) Acuan dibuka dan tuangan dikeluarkan dengan bantuan pin ejektor. 6.) Sekarang die kosong dilincirkan semula dan diapit untuk kitaran seterusnya. Dalam tuangan die, kami kerap menggunakan acuan sisipan di mana kami memasukkan bahagian tambahan ke dalam acuan dan tuangkan logam di sekelilingnya. Selepas pemejalan, bahagian ini menjadi sebahagian daripada produk tuang. Kelebihan tuangan die ialah sifat mekanikal bahagian yang baik, kemungkinan ciri yang rumit, butiran halus dan kemasan permukaan yang baik, kadar pengeluaran yang tinggi, automasi yang mudah. Kelemahannya ialah: Tidak sesuai untuk isipadu rendah kerana kos cetakan dan peralatan yang tinggi, batasan dalam bentuk yang boleh dilemparkan, tanda bulat kecil pada bahagian tuang akibat sentuhan pin ejektor, kilat nipis logam yang terhimpit keluar pada garisan perpisahan, perlu untuk bolong di sepanjang garisan perpisahan antara acuan, keperluan untuk memastikan suhu acuan rendah menggunakan peredaran air. • TUANG ENTRIFUGAL : Logam cair dituang ke tengah acuan berputar pada paksi putaran. Daya sentrifugal melemparkan logam ke arah pinggir dan ia dibiarkan menjadi pejal apabila acuan terus berputar. Kedua-dua putaran paksi mendatar dan menegak boleh digunakan. Bahagian dengan permukaan dalam bulat serta bentuk bukan bulat lain boleh dilemparkan. Proses itu boleh diringkaskan sebagai: 1.) Logam cair dituang ke dalam acuan emparan. Logam kemudiannya dipaksa ke dinding luar kerana acuan berputar. 2.) Apabila acuan berputar, tuangan logam mengeras Tuang emparan adalah teknik yang sesuai untuk penghasilan bahagian silinder berongga seperti paip, tidak memerlukan sprue, risers dan elemen gating, kemasan permukaan yang baik dan ciri terperinci, tiada isu pengecutan, kemungkinan untuk menghasilkan paip panjang dengan diameter yang sangat besar, keupayaan pengeluaran kadar tinggi . • TUANG BERTERUSAN ( TUANG STRAND ) : Digunakan untuk menuang panjang berterusan logam. Pada asasnya logam cair dibuang ke dalam profil dua dimensi acuan tetapi panjangnya tidak tentu. Logam lebur baru sentiasa dimasukkan ke dalam acuan semasa tuangan bergerak ke bawah dengan panjangnya meningkat dengan masa. Logam seperti kuprum, keluli, aluminium dibuang ke dalam untaian panjang menggunakan proses tuangan berterusan. Proses ini mungkin mempunyai pelbagai konfigurasi tetapi yang biasa boleh dipermudahkan sebagai: 1.) Logam cair dituangkan ke dalam bekas yang terletak tinggi di atas acuan pada jumlah dan kadar alir yang dikira dengan baik dan mengalir melalui acuan yang disejukkan dengan air. Tuangan logam yang dituangkan ke dalam acuan mengeras kepada bar pemula yang diletakkan di bahagian bawah acuan. Bar permulaan ini memberikan penggelek sesuatu untuk dipegang pada mulanya. 2.) Helai logam panjang dibawa oleh penggelek pada kelajuan tetap. Penggelek juga menukar arah aliran helai logam dari menegak ke mendatar. 3.) Selepas tuangan berterusan telah menempuh jarak mendatar tertentu, obor atau gergaji yang bergerak bersama tuangan dengan pantas memotongnya ke panjang yang dikehendaki. Proses tuangan berterusan boleh disepadukan dengan PROSES GULANGAN, di mana logam tuangan berterusan boleh dimasukkan terus ke dalam kilang gelek untuk menghasilkan Rasuk-I, Rasuk-T….dsb. Tuangan berterusan menghasilkan sifat seragam di seluruh produk, ia mempunyai kadar pemejalan yang tinggi, mengurangkan kos akibat kehilangan bahan yang sangat rendah, menawarkan proses di mana pemuatan logam, penuangan, pemejalan, pemotongan dan penyingkiran tuangan semuanya berlaku dalam operasi berterusan dan sekali gus menghasilkan kadar produktiviti yang tinggi dan kualiti yang tinggi. Walau bagaimanapun, pertimbangan utama adalah pelaburan awal yang tinggi, kos persediaan dan keperluan ruang. • PERKHIDMATAN PEMESINAN : Kami menawarkan pemesinan tiga, empat dan lima paksi. Jenis proses pemesinan yang kami gunakan ialah MEMULIH, MENGIMPIL, MENGERUDI, MEMBORAN, MENEMPAK, MERANCANG, MENGGEMPAR, MENGISAR, MEMBENTUK, MENGIKAT dan PEMESINAN BUKAN TRADISIONAL yang dihuraikan dengan lebih lanjut di bawah menu berbeza laman web kami. Untuk kebanyakan pembuatan kami, kami menggunakan mesin CNC. Walau bagaimanapun untuk sesetengah operasi, teknik konvensional adalah lebih sesuai dan oleh itu kami juga bergantung padanya. Keupayaan pemesinan kami mencapai tahap tertinggi yang mungkin dan beberapa bahagian yang paling menuntut dihasilkan di kilang yang diperakui AS9100. Bilah enjin jet memerlukan pengalaman pembuatan yang sangat khusus dan peralatan yang betul. Industri aeroangkasa mempunyai piawaian yang sangat ketat. Sesetengah komponen dengan struktur geometri kompleks paling mudah dihasilkan oleh pemesinan lima paksi, yang hanya terdapat di beberapa loji pemesinan termasuk kami. Loji yang diperakui aeroangkasa kami mempunyai pengalaman yang diperlukan untuk mematuhi keperluan dokumentasi yang meluas bagi industri aeroangkasa. Dalam operasi TURNING, bahan kerja diputar dan digerakkan pada alat pemotong. Untuk proses ini mesin yang dipanggil pelarik sedang digunakan. Dalam PENGIMPIAN, mesin yang dipanggil mesin pengisar mempunyai alat berputar untuk membawa bahagian pemotongan kepada bahan kerja. Operasi menggerudi melibatkan pemotong berputar dengan tepi pemotong yang menghasilkan lubang apabila terkena bahan kerja. Mesin gerudi, mesin bubut atau kilang biasanya digunakan. Dalam operasi BORING, alat dengan satu hujung runcing bengkok dialihkan ke dalam lubang kasar dalam benda kerja berputar untuk membesarkan sedikit lubang dan meningkatkan ketepatan. Ia digunakan untuk tujuan kemasan halus. BROACHING melibatkan alat bergigi untuk mengeluarkan bahan dari bahan kerja dalam satu laluan broach (alat bergigi). Dalam broaching linear, broach berjalan secara linear terhadap permukaan bahan kerja untuk menghasilkan potongan, manakala dalam broaching berputar, broach diputar dan ditekan ke dalam bahan kerja untuk memotong bentuk simetri paksi. SWISS TYPE MACHINING ialah salah satu teknik berharga kami yang kami gunakan untuk pembuatan volum tinggi bahagian berketepatan tinggi yang kecil. Dengan menggunakan mesin pelarik jenis Swiss, kami menukar bahagian yang kecil, kompleks, ketepatan dengan murah. Tidak seperti mesin pelarik konvensional di mana bahan kerja disimpan dalam keadaan pegun dan alat bergerak, di pusat pusingan jenis Swiss, bahan kerja dibenarkan untuk bergerak dalam paksi Z dan alat adalah pegun. Dalam pemesinan jenis Swiss, stok bar disimpan di dalam mesin dan dimajukan melalui sesendal panduan dalam paksi z, hanya mendedahkan bahagian yang akan dimesin. Dengan cara ini cengkaman yang ketat dipastikan dan ketepatan adalah sangat tinggi. Ketersediaan alatan hidup memberi peluang untuk mengisar dan menggerudi apabila bahan bergerak dari sesendal pemandu. Paksi Y bagi peralatan jenis Swiss menyediakan keupayaan pengilangan penuh dan menjimatkan banyak masa dalam pembuatan. Tambahan pula, mesin kami mempunyai gerudi dan alat membosankan yang beroperasi pada bahagiannya apabila ia dipegang dalam gelendong kecil. Keupayaan pemesinan Swiss-Type kami memberi kami peluang pemesinan lengkap automatik sepenuhnya dalam satu operasi. Pemesinan ialah salah satu segmen terbesar perniagaan AGS-TECH Inc.. Kami sama ada menggunakannya sebagai operasi utama atau operasi sekunder selepas menuang atau menyemperit bahagian supaya semua spesifikasi lukisan dipenuhi. • PERKHIDMATAN KEMASAN PERMUKAAN : Kami menawarkan pelbagai jenis rawatan permukaan dan kemasan permukaan seperti penyaman permukaan untuk meningkatkan lekatan, mendepositkan lapisan oksida nipis untuk meningkatkan lekatan salutan, letupan pasir, filem kimia, anodizing, nitriding, salutan serbuk, salutan semburan , pelbagai teknik pemetaan dan salutan lanjutan termasuk sputtering, pancaran elektron, penyejatan, penyaduran, salutan keras seperti berlian seperti karbon (DLC) atau salutan titanium untuk alat penggerudian dan pemotongan. • PERKHIDMATAN PENANDA & PELABELAN PRODUK : Ramai pelanggan kami memerlukan penandaan dan pelabelan, penandaan laser, ukiran pada bahagian logam. Jika anda mempunyai sebarang keperluan sedemikian, izinkan kami membincangkan pilihan mana yang terbaik untuk anda. Berikut ialah beberapa produk tuangan logam yang biasa digunakan. Memandangkan ini adalah di luar rak, anda boleh menjimatkan kos acuan sekiranya mana-mana perkara ini sesuai dengan keperluan anda: KLIK DI SINI UNTUK MUAT TURUN Kotak Aluminium Die-cast 11 Siri kami daripada AGS-Electronics CLICK Product Finder-Locator Service HALAMAN SEBELUMNYA
- Custom Manufactured Parts, Assemblies, Plastic Mold, Casting,Machining
Custom Manufactured Parts, Assemblies, Plastic Mold, Rubber Molding, Metal Casting, CNC Machining, Turning, Milling, Electrical Electronic Optical Assembly PCBA Alat Ganti & Pemasangan & Produk Buatan Tersuai Baca Lagi Acuan dan Acuan Plastik & Getah Baca Lagi Pemutus dan Pemesinan Baca Lagi Penyemperitan, Produk Tersemperit Baca Lagi Setem & Fabrikasi Logam Kepingan Baca Lagi Penempaan Logam & Metalurgi Serbuk Baca Lagi Pembentukan Kawat & Spring Baca Lagi Pembentukan & Pembentukan Kaca & Seramik Baca Lagi Pengilangan Aditif dan Pantas Baca Lagi Pembuatan Bahan Komposit & Komposit Baca Lagi Proses Mencantum & Memasang & Mengikat Kami menghasilkan bahagian dan pemasangan untuk anda dan menawarkan proses pembuatan berikut: • Acuan plastik dan getah dan bahagian acuan. Pengacuan suntikan, pengacuan termoset, pengacuan termoset, pembentukan vakum, pengacuan tamparan, pengacuan putaran, pengacuan tuang, pengacuan sisipan dan lain-lain. • Penyemperitan plastik, getah dan logam • Tuangan ferus dan bukan ferus dan bahagian mesin yang dihasilkan dengan teknik pengilangan dan pemusingan, pemesinan jenis Swiss. • Bahagian metalurgi serbuk • Pengecapan logam dan bukan logam, pembentukan kepingan logam, pemasangan kepingan logam yang dikimpal • Penempaan sejuk dan panas • Wayar, pemasangan wayar dikimpal, pembentukan wayar • Pelbagai jenis spring, spring forming • Pembuatan gear, kotak gear, gandingan, cacing, pengurang kelajuan, silinder, tali pinggang penghantaran, rantai penghantaran, komponen penghantaran • Kaca terbaja tersuai dan kalis peluru mematuhi piawaian NATO dan ketenteraan • Pemasangan bebola, bearing, takal dan takal • Injap dan komponen pneumatik seperti cincin-O, mesin basuh dan pengedap • Bahagian dan pemasangan kaca dan seramik, komponen kalis vakum dan hermetik, ikatan logam-seramik dan seramik-seramik. • Pelbagai jenis pemasangan mekanikal, optomekanikal, elektromekanikal, optoelektronik. • Logam-getah, logam-plastik ikatan • Paip dan tiub, pembentukan paip, lenturan dan pemasangan paip tersuai, pembuatan bawah. • Pembuatan gentian kaca • Kimpalan menggunakan pelbagai teknik seperti kimpalan titik, kimpalan laser, MIG, TIG. Kimpalan ultrasonik untuk bahagian plastik. • Pelbagai jenis rawatan permukaan dan kemasan permukaan seperti penghawa dingin permukaan untuk meningkatkan lekatan, mendepositkan lapisan oksida nipis untuk meningkatkan lekatan salutan, letupan pasir, chem-film, anodizing, nitriding, salutan serbuk, salutan semburan, pelbagai teknik pemetaan dan salutan termaju termasuk sputtering, pancaran elektron, penyejatan, penyaduran, salutan keras seperti berlian seperti karbon (DLC) atau titanium untuk alat pemotong dan penggerudian. • Penandaan dan pelabelan, penandaan laser pada bahagian logam, cetakan pada bahagian plastik dan getah Muat turun brosur untuk Syarat Kejuruteraan Mekanikal Biasa yang digunakan oleh Pereka dan Jurutera Kami membina produk mengikut spesifikasi dan keperluan khusus anda. Untuk menawarkan kualiti, penghantaran dan harga terbaik kepada anda, kami mengeluarkan produk secara global di China, India, Taiwan, Filipina, Korea Selatan, Malaysia, Sri Lanka, Turki, Amerika Syarikat, Kanada, Jerman, UK dan Jepun. Ini menjadikan kami lebih kuat dan lebih berdaya saing di peringkat global berbanding mana-mana custom manufacturer lain. Produk kami dihasilkan dalam persekitaran yang diperakui ISO9001:2000, QS9000, ISO14001, TS16949 dan memiliki tanda CE, UL dan memenuhi piawaian industri yang lain. Sebaik sahaja kami dilantik untuk projek anda, kami boleh menguruskan keseluruhan pembuatan, pemasangan, ujian, kelayakan, penghantaran & kastam mengikut kehendak anda. Jika anda lebih suka, kami boleh menyimpan bahagian anda, memasang kit tersuai, mencetak dan melabel nama & jenama syarikat anda dan menghantar penghantaran kepada pelanggan anda. Dalam erti kata lain, kami boleh menjadi pusat pergudangan dan pengedaran anda juga jika mahu. Memandangkan gudang kami terletak berhampiran pelabuhan laut utama, ia memberi kami kelebihan logistik. Sebagai contoh, apabila produk anda tiba di pelabuhan utama Amerika Syarikat, kami boleh mengangkut terus ke gudang berdekatan di mana kami boleh menyimpan, memasang, membuat kit, melabel semula, mencetak, membungkus mengikut pilihan anda dan menjatuhkan hantar kepada pelanggan anda. Kami bukan sahaja membekalkan produk. Syarikat kami bekerja pada kontrak tersuai di mana kami datang ke tapak anda, menilai projek anda di tapak dan membangunkan cadangan projek yang direka khas untuk anda. Kami kemudian menghantar pasukan kami yang berpengalaman untuk melaksanakan projek tersebut. Maklumat lanjut tentang kerja kejuruteraan kami boleh didapati di http://www.ags-engineering.com -Kami mengambil projek kecil dan juga projek besar pada skala industri. Sebagai langkah pertama, kami boleh menghubungkan anda sama ada melalui telefon , telesidang atau messenger MSN kepada ahli pasukan pakar kami, supaya anda boleh berkomunikasi terus dengan pakar, bertanya soalan dan membincangkan projek anda. Hubungi kami dan jika perlu kami akan datang dan melawat anda. HALAMAN SEBELUMNYA
- Plastic And Rubber Molding | United States | AGS-TECH, Inc.
AGS-TECH Inc., Molding, Casting, Machining, Forging, Sheet Metal Fabrication, Mechanical Electrical Electronic Optical Assembly, PCBA, Powder Metallurgy, CNC AGS-TECH Inc. AGS-TECH Inc. Custom Manufacturing, Domestic & Global Outsourcing, Engineering Integration, Consolidation AGS-TECH Inc. 1/2 AGS-TECH, Inc. ialah anda: Pengeluar Tersuai Global, Penyepadu, Penyatuan, Rakan Kongsi Penyumberan Luar untuk Pelbagai Pelbagai Produk & Perkhidmatan. Kami adalah sumber sehenti anda untuk pembuatan, fabrikasi, kejuruteraan, penyatuan, penyumberan luar produk buatan sendiri dan luar rak. PERKHIDMATAN: Pembuatan Tersuai Pembuatan Kontrak Domestik & Global Penyumberan Luar Pembuatan Perolehan Domestik & Global Consolidation Integrasi Kejuruteraan MENGENAI AGS-TECH, Inc. - Pengeluar Tersuai Global Anda, Penyepadu Kejuruteraan, Penyatuan, Rakan Kongsi Penyumberan Luar AGS-TECH Inc. ialah pengilang, penyepadu kejuruteraan, pembekal global produk industri termasuk acuan, bahagian plastik dan getah acuan, tuangan, penyemperitan, fabrikasi kepingan logam, pengecapan & penempaan logam, pemesinan CNC, elemen mesin, metalurgi serbuk, seramik & membentuk kaca, membentuk dawai / spring, mencantum & memasang & pengikat, fabrikasi bukan konvensional, mikrofabrikasi, salutan nanoteknologi & filem nipis, komponen & pemasangan elektronik mekanikal & elektrik tersuai & PCB & PCBA & abah-abah kabel, komponen & pemasangan optik & gentian optik , peralatan ujian & metrologi seperti penguji kekerasan, mikroskop metalurgi, pengesan kerosakan ultrasonik, komputer industri, sistem terbenam, PC automasi & panel, komputer papan tunggal, peralatan kawalan kualiti. Selain produk, dengan kejuruteraan global, kejuruteraan terbalik, penyelidikan & pembangunan, pembangunan produk, pembuatan tambahan dan pantas, prototaip, keupayaan pengurusan projek kami menawarkan bantuan teknikal, logistik dan perniagaan untuk menjadikan anda lebih berdaya saing dan berjaya dalam pasaran global. Misi kami adalah mudah: Menjadikan pelanggan kami berjaya dan berkembang. bagaimana? Dengan menyediakan 1.) Kualiti Lebih Baik 2.) Harga Lebih Baik 3.) Penghantaran Lebih Baik........ semuanya daripada satu syarikat dan penyepadu dan pembekal kejuruteraan global yang paling pelbagai di dunia AGS-TECH Inc. Anda boleh memberikan cetak biru anda kepada kami dan kami boleh membuat acuan mesin, acuan dan alat untuk mengeluarkan bahagian anda. Kami menghasilkannya sama ada melalui pengacuan, tuangan, penyemperitan, penempaan, fabrikasi kepingan logam, pengecapan, metalurgi serbuk, pemesinan CNC, membentuk. Kami sama ada boleh menghantar alat ganti dan komponen kepada anda atau melakukan pemasangan, fabrikasi dan operasi pembuatan lengkap di kemudahan kami. Operasi pemasangan kami melibatkan produk mekanikal, optik, elektronik, gentian optik. Kami melakukan operasi penyambungan menggunakan pengikat, kimpalan, pematerian, pematerian, ikatan pelekat dan banyak lagi. Proses pengacuan kami adalah untuk pelbagai jenis plastik, getah, seramik, kaca, bahan metalurgi serbuk. Begitu juga tuangan, pemesinan CNC, penempaan, fabrikasi logam kepingan, dawai & proses membentuk spring kami yang melibatkan logam, aloi, plastik, seramik. Kami menawarkan operasi kemasan akhir seperti salutan & filem nipis dan tebal, pengisaran, lapping, penggilap dan banyak lagi. Keupayaan pembuatan kami melangkaui pemasangan mekanikal. Kami mengeluarkan komponen & pemasangan elektronik elektrik & PCB & PCBA & abah-abah kabel, komponen & pemasangan optik & gentian optik mengikut lukisan teknikal anda, fail BOM, Gerber. Pelbagai teknik pembuatan PCB dan PCBA termasuk pematerian aliran semula dan pematerian gelombang selain yang lain digunakan. Kami pakar dalam penyambungan ketepatan, penyambungan, pemasangan dan pengedap pakej dan produk optik elektronik dan gentian hermetik. Selain pemasangan mekanikal pasif dan aktif, kami memanfaatkan bahan dan teknik pematerian dan pematerian khas untuk mengeluarkan produk yang mematuhi Telcordia dan piawaian industri lain. Kami tidak terhad dengan pembuatan dan fabrikasi volum tinggi. Hampir setiap projek bermula dengan keperluan untuk kejuruteraan, kejuruteraan terbalik, penyelidikan & pembangunan, pembangunan produk, pembuatan aditif dan pesat, prototaip. Sebagai pengeluar tersuai global yang paling pelbagai di Dunia, penyepadu kejuruteraan, penyatuan, rakan kongsi penyumberan luar, kami mengalu-alukan anda walaupun anda hanya mempunyai idea. Kami membawa anda dari sana dan membantu anda pada semua fasa pembangunan produk lengkap dan kitaran pembuatan yang berjaya. Sama ada ia adalah fabrikasi logam kepingan pantas, pemesinan dan pengacuan acuan pantas, tuangan pantas, pemasangan PCB & PCBA pantas atau mana-mana teknik prototaip pantas disediakan untuk anda. Kami menawarkan anda di luar rak serta peralatan metrologi yang dikilangkan khas seperti penguji kekerasan, mikroskop metalurgi, pengesan kerosakan ultrasonik; komputer industri, sistem terbenam, automasi & PC panel, komputer papan tunggal dan peralatan kawalan kualiti yang digunakan secara meluas dalam kemudahan pembuatan dan perindustrian. Dengan menawarkan peralatan metrologi terkini dan komponen komputer industri, kami melengkapkan keperluan anda sebagai pengeluar dan pembekal sumber tunggal di mana anda boleh mendapatkan semua yang anda perlukan. Tanpa spektrum perkhidmatan kejuruteraan yang luas, kami tidak akan berbeza daripada kebanyakan pengeluar dan penjual lain dengan keupayaan pembuatan dan pemasangan tersuai terhad yang terdapat di pasaran. Jangka masa perkhidmatan kejuruteraan kami membezakan kami sebagai pengeluar tersuai yang paling pelbagai di Dunia, pengilang kontrak, penyepadu kejuruteraan, penyatuan dan rakan kongsi penyumberan luar. Perkhidmatan kejuruteraan boleh ditawarkan secara bersendirian atau sebagai sebahagian daripada pembangunan produk atau proses baharu, atau sebagai sebahagian daripada pembangunan produk atau proses sedia ada atau sebagai perkara lain yang terlintas di fikiran anda. Kami fleksibel dan perkhidmatan kejuruteraan kami boleh mengambil bentuk yang paling sesuai dengan keperluan dan keperluan anda. Penyampaian dan output perkhidmatan kejuruteraan kami dihadkan hanya oleh imaginasi anda dan boleh mengambil sebarang bentuk yang sesuai dengan anda. Bentuk keluaran yang paling biasa daripada perkhidmatan kejuruteraan kami ialah: Laporan perundingan, helaian ujian dan laporan, laporan pemeriksaan, pelan tindakan, lukisan kejuruteraan, lukisan pemasangan, senarai senarai bahan, lembaran data, simulasi, program perisian, grafik dan carta, output daripada khusus. optik, terma atau program perisian, sampel dan prototaip, model, demonstrasi…..dsb. Perkhidmatan kejuruteraan kami boleh dihantar dengan tandatangan atau beberapa tandatangan jurutera profesional bertauliah di negeri anda. Kadangkala beberapa jurutera profesional dari disiplin yang berbeza mungkin diperlukan untuk menandatangani kerja. Perkhidmatan kejuruteraan penyumberan luar kepada kami boleh memberi anda banyak faedah seperti penjimatan kos daripada mengupah jurutera atau jurutera sepenuh masa, dengan cepat mendapatkan jurutera pakar untuk berkhidmat kepada anda dalam tempoh masa dan bajet anda daripada mencari untuk mengupah seorang, memberikan anda keupayaan untuk berhenti projek dengan cepat sekiranya anda menyedari ia tidak boleh dilaksanakan (ini sangat mahal sekiranya anda mengupah dan memberhentikan jurutera anda sendiri), dengan cepat dapat menukar jurutera dari disiplin dan latar belakang yang berbeza memberikan anda keupayaan untuk bergerak pada bila-bila masa dan fasa projek anda…..dsb. Terdapat banyak faedah lain untuk perkhidmatan kejuruteraan penyumberan luar selain pembuatan dan pemasangan tersuai. Di laman web ini kami akan memberi tumpuan kepada pembuatan tersuai, pembuatan kontrak, pemasangan, penyepaduan, penyatuan dan penyumberan luar produk. Jika bahagian kejuruteraan perniagaan kami lebih menarik minat anda, anda boleh mendapatkan maklumat terperinci tentang perkhidmatan kejuruteraan kami dengan melawati http://www.ags-engineering.com Kami ialah AGS-TECH Inc., sumber sehenti anda untuk pembuatan & fabrikasi & kejuruteraan & penyumberan luar & penyatuan. Kami adalah penyepadu kejuruteraan yang paling pelbagai di Dunia yang menawarkan kepada anda pembuatan tersuai, pemasangan kecil, pemasangan produk dan perkhidmatan kejuruteraan. Contact Us First Name Last Name Email Write a message Submit Thanks for submitting!