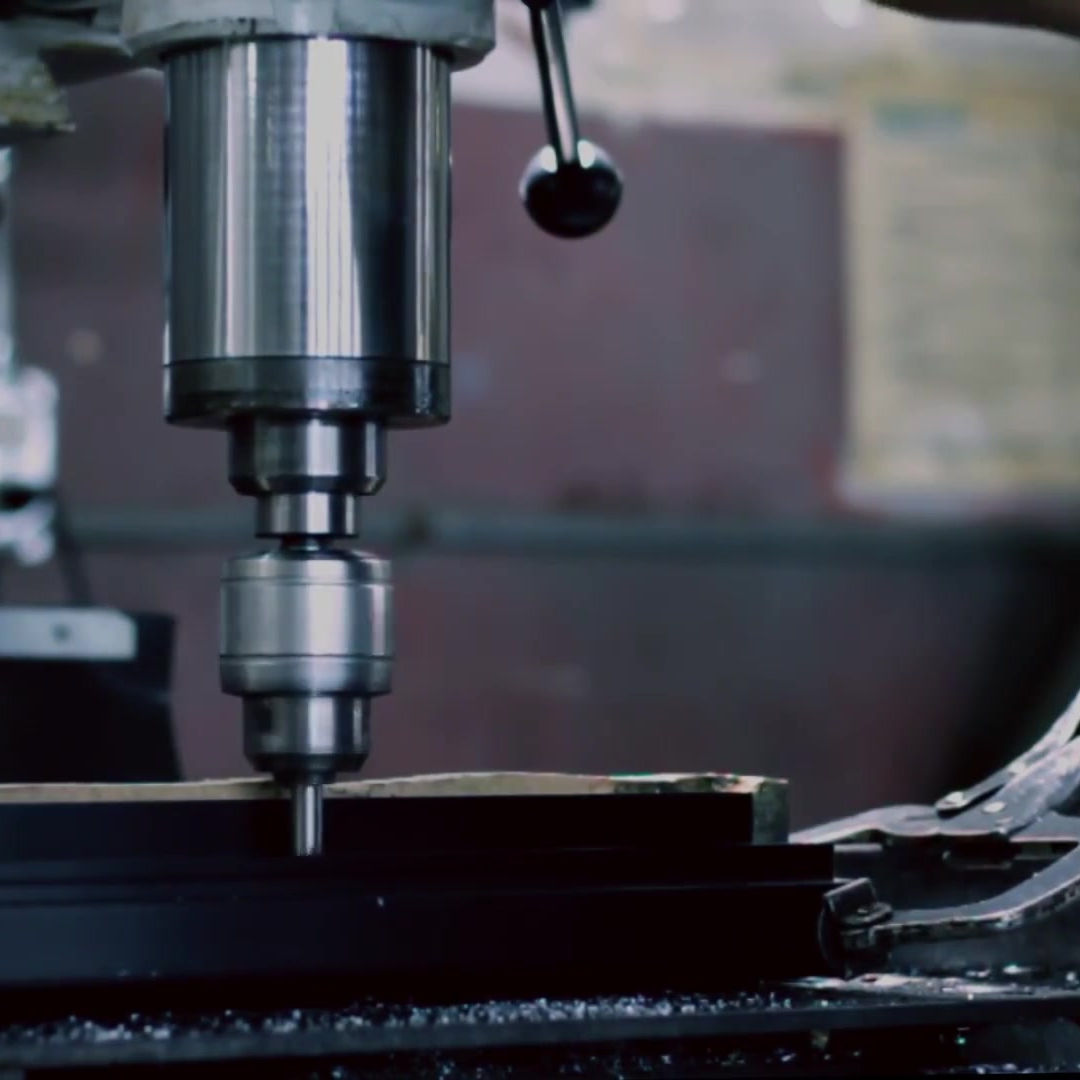
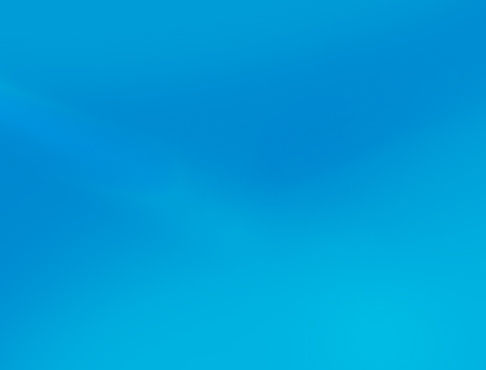
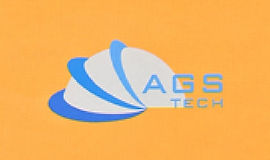
विश्वव्यापी कस्टम निर्माता, इन्टिग्रेटर, कन्सोलिडेटर, उत्पादन र सेवाहरूको विस्तृत विविधताका लागि आउटसोर्सिङ पार्टनर।
हामी उत्पादन, निर्माण, ईन्जिनियरिङ्, एकीकरण, एकीकरण, अनुकूलन निर्मित र अफ-शेल्फ उत्पादन र सेवाहरूको आउटसोर्सिङको लागि तपाईंको एक-स्टप स्रोत हौं।
आफ्नो भाषा छान्नुहोस्
-
कस्टम निर्माण
-
घरेलु र विश्वव्यापी अनुबंध निर्माण
-
उत्पादन आउटसोर्सिङ
-
घरेलु र विश्वव्यापी खरीद
-
Consolidation
-
इन्जिनियरिङ एकीकरण
-
इन्जिनियरिङ सेवाहरू
हामीले उत्पादनमा प्रयोग गर्ने धेरै ज्वाइनिङ प्रविधिहरू मध्ये, वेल्डिङ, ब्राजिङ, सोल्डरिङ, टाँसेको बन्धन र कस्टम मेकानिकल एसेम्बलीलाई विशेष जोड दिइन्छ किनभने यी प्रविधिहरू हर्मेटिक एसेम्बलीहरू, उच्च प्रविधियुक्त उत्पादनहरू र समुद्री उत्पादनहरू उत्पादन गर्ने जस्ता अनुप्रयोगहरूमा व्यापक रूपमा प्रयोग गरिन्छ। यहाँ हामी यी जोड्ने प्रविधिहरूको थप विशेष पक्षहरूमा ध्यान केन्द्रित गर्नेछौं किनभने तिनीहरू उन्नत उत्पादनहरू र सम्मेलनहरूको निर्माणसँग सम्बन्धित छन्।
फ्युजन वेल्डिङ: हामी सामग्रीहरू पग्लन र मिलाउन ताप प्रयोग गर्छौं। गर्मी बिजुली वा उच्च ऊर्जा बीम द्वारा आपूर्ति गरिन्छ। हामीले प्रयोग गर्ने फ्युजन वेल्डिङका प्रकारहरू ओक्सीफुल ग्यास वेल्डिङ, एआरसी वेल्डिङ, उच्च ऊर्जा-बीम वेल्डिङ हुन्।
सोलिड-स्टेट वेल्डिङ: हामी पग्लन र फ्युजन बिना भागहरू जोड्छौं। हाम्रो ठोस-राज्य वेल्डिंग विधिहरू कोल्ड, अल्ट्रासोनिक, प्रतिरोध, घर्षण, विस्फोट वेल्डिंग र डिफ्यूजन बन्डिङ हुन्।
ब्राजिङ र सोल्डरिङ: तिनीहरूले फिलर धातुहरू प्रयोग गर्छन् र हामीलाई वेल्डिङको तुलनामा कम तापक्रममा काम गर्ने फाइदा दिन्छन्, जसले गर्दा उत्पादनहरूमा कम संरचनात्मक क्षति हुन्छ। सिरेमिक देखि मेटल फिटिंग, हर्मेटिक सील, भ्याकुम फिडथ्रु, उच्च र अति उच्च भ्याकुम र फ्लुइड कन्ट्रोल कम्पोनेन्टहरू उत्पादन गर्ने हाम्रो ब्राजिङ सुविधाको जानकारी यहाँ पाउन सकिन्छ:Brazing कारखाना ब्रोशर
टाँसिएको बन्धन: उद्योगमा प्रयोग हुने चिपकाउने र अनुप्रयोगहरूको विविधताको कारणले गर्दा, हामीसँग यसको लागि समर्पित पृष्ठ छ। टाँस्ने बन्धनको बारेमा हाम्रो पृष्ठमा जानको लागि, कृपया यहाँ क्लिक गर्नुहोस्।
कस्टम मेकानिकल एसेम्बली: हामी बोल्ट, स्क्रू, नट, रिभेट्स जस्ता विभिन्न फास्टनरहरू प्रयोग गर्छौं। हाम्रा फास्टनरहरू मानक अफ-शेल्फ फास्टनरहरूमा सीमित छैनन्। हामी विशेष फास्टनरहरू डिजाइन, विकास र निर्माण गर्छौं जुन गैर-मानक सामग्रीबाट बनाइन्छ ताकि तिनीहरूले विशेष अनुप्रयोगहरूको लागि आवश्यकताहरू पूरा गर्न सकून्। कहिलेकाहीं विद्युतीय वा गर्मी गैर-चालकता चाहिन्छ भने कहिलेकाहीं चालकता। केहि विशेष अनुप्रयोगहरूको लागि, ग्राहकले विशेष फास्टनरहरू चाहन सक्छ जुन उत्पादनलाई नष्ट नगरी हटाउन सकिँदैन। त्यहाँ अनन्त विचार र अनुप्रयोगहरू छन्। हामीसँग यो सबै तपाईंको लागि छ, यदि अफ-शेल्फ होइन भने हामी यसलाई द्रुत रूपमा विकास गर्न सक्छौं। मेकानिकल असेंबलीमा हाम्रो पृष्ठमा जानको लागि, कृपया यहाँ क्लिक गर्नुहोस्। हामी थप विवरणहरूमा हाम्रो विभिन्न सामेल हुने प्रविधिहरूको जाँच गरौं।
OXYFUEL ग्यास वेल्डिङ (OFW): हामी वेल्डिङको ज्वाला उत्पादन गर्न अक्सिजनसँग मिसाइएको इन्धन ग्यास प्रयोग गर्छौं। जब हामी एसिटिलीनलाई ईन्धन र अक्सिजनको रूपमा प्रयोग गर्छौं, हामी यसलाई अक्स्यासेटिलीन ग्यास वेल्डिङ भन्छौं। अक्सि इन्धन ग्यास दहन प्रक्रियामा दुई रासायनिक प्रतिक्रियाहरू हुन्छन्:
C2H2 + O2 ------» 2CO + H2 + ताप
2CO + H2 + 1.5 O2 -------» 2 CO2 + H2O + ताप
पहिलो प्रतिक्रियाले एसिटिलीनलाई कार्बन मोनोअक्साइड र हाइड्रोजनमा पृथक गर्छ जबकि कुल तापको लगभग 33% उत्पादन गर्छ। माथिको दोस्रो प्रक्रियाले हाइड्रोजन र कार्बन मोनोअक्साइडको थप दहनलाई प्रतिनिधित्व गर्दछ जबकि कुल तापको लगभग 67% उत्पादन गर्दछ। ज्वालाको तापक्रम १५३३ देखि ३५७३ केल्भिनको बीचमा हुन्छ। ग्याँस मिश्रणमा अक्सिजन प्रतिशत महत्त्वपूर्ण छ। यदि अक्सिजन सामग्री आधा भन्दा बढी छ भने, ज्वाला एक अक्सिडाइजिंग एजेन्ट हुन्छ। यो केहि धातुहरु को लागी अवांछनीय छ तर अरु को लागी वांछनीय छ। एक उदाहरण जब अक्सिडाइजिंग ज्वाला वांछनीय हुन्छ तामा-आधारित मिश्र धातु हो किनभने यसले धातुमा एक निष्क्रिय तह बनाउँछ। अर्कोतर्फ, जब अक्सिजन सामग्री कम हुन्छ, पूर्ण दहन सम्भव छैन र ज्वाला घटाउने (carburizing) ज्वाला हुन्छ। घटाउने ज्वालामा तापक्रम कम हुन्छ र त्यसैले यो सोल्डरिङ र ब्रेजिङ जस्ता प्रक्रियाहरूको लागि उपयुक्त हुन्छ। अन्य ग्याँसहरू पनि सम्भावित इन्धन हुन्, तर तिनीहरूसँग एसिटिलीनमा केही बेफाइदाहरू छन्। कहिलेकाहीँ हामी फिलर रड वा तारको रूपमा वेल्ड जोनमा फिलर धातुहरू आपूर्ति गर्छौं। तिनीहरूमध्ये केही सतहहरूको अक्सीकरणलाई रोक्न र यसरी पग्लिएको धातुलाई सुरक्षित गर्न फ्लक्ससँग लेपित हुन्छन्। फ्लक्सले हामीलाई दिने एउटा अतिरिक्त फाइदा भनेको वेल्ड जोनबाट अक्साइड र अन्य पदार्थहरू हटाउनु हो। यसले बलियो बन्धनमा जान्छ। अक्सिफुल ग्यास वेल्डिङको भिन्नता प्रेसर ग्यास वेल्डिङ हो, जहाँ दुईवटा कम्पोनेन्टहरू आफ्नो इन्टरफेसमा अक्स्यासेटिलीन ग्यास टर्च प्रयोग गरेर तताइन्छ र एक पटक इन्टरफेस पग्लन थालेपछि, टर्च फिर्ता लिइन्छ र दुई भागहरूलाई सँगै थिच्न अक्षीय बल प्रयोग गरिन्छ। इन्टरफेस ठोस नभएसम्म।
एआरसी वेल्डिङ: हामी इलेक्ट्रोड टिप र वेल्डेड हुने भागहरू बीच एक चाप उत्पादन गर्न विद्युत ऊर्जा प्रयोग गर्छौं। विद्युत आपूर्ति AC वा DC हुन सक्छ जबकि इलेक्ट्रोडहरू उपभोगयोग्य वा गैर उपभोगयोग्य हुन्छन्। चाप वेल्डिंग मा गर्मी स्थानान्तरण निम्न समीकरण द्वारा व्यक्त गर्न सकिन्छ:
H / l = पूर्व VI / v
यहाँ H तातो इनपुट हो, l वेल्ड लम्बाइ हो, V र I भोल्टेज र वर्तमान लागू हुन्छ, v वेल्डिंग गति हो र e प्रक्रिया दक्षता हो। दक्षता "e" जति उच्च हुन्छ, त्यति नै लाभदायक रूपमा उपलब्ध ऊर्जा सामग्री पग्लन प्रयोग गरिन्छ। ताप इनपुट निम्न रूपमा व्यक्त गर्न सकिन्छ:
H = ux (भोल्युम) = ux A xl
यहाँ u पग्लनेको लागि विशिष्ट ऊर्जा हो, A वेल्डको क्रस सेक्शन र l वेल्ड लम्बाइ। माथिका दुई समीकरणहरूबाट हामी प्राप्त गर्न सक्छौं:
v = पूर्व VI / u A
आर्क वेल्डिङको भिन्नता भनेको ढालिएको धातु आर्क वेल्डिङ (SMAW) हो जसले सबै औद्योगिक र मर्मतसम्भार वेल्डिङ प्रक्रियाहरूको लगभग 50% गठन गर्दछ। विद्युतीय चाप वेल्डिङ (स्टिक वेल्डिङ) लेपित इलेक्ट्रोडको टुप्पोलाई वर्कपीसमा छोएर र चापलाई कायम राख्न पर्याप्त दूरीमा तुरुन्तै फिर्ता लिएर गरिन्छ। यस प्रक्रियालाई हामी स्टिक-वेल्डिङ पनि भन्छौं किनभने इलेक्ट्रोडहरू पातलो र लामो स्टिक हुन्छन्। वेल्डिङ प्रक्रियाको क्रममा, इलेक्ट्रोडको टिप यसको कोटिंग र चापको वरपरको आधार धातुसँगै पग्लन्छ। आधार धातु, इलेक्ट्रोड धातु र इलेक्ट्रोड कोटिंगबाट पदार्थहरूको मिश्रण वेल्ड क्षेत्रमा ठोस हुन्छ। इलेक्ट्रोडको कोटिंगले वेल्ड क्षेत्रमा डिअक्सिडाइज गर्दछ र एक सुरक्षा ग्याँस प्रदान गर्दछ, यसरी यसलाई वातावरणमा अक्सिजनबाट बचाउँछ। यसैले प्रक्रियालाई ढाल धातु आर्क वेल्डिंग भनिन्छ। हामी इष्टतम वेल्ड कार्यसम्पादनको लागि 50 र 300 एम्पियर र शक्ति स्तर सामान्यतया 10 kW भन्दा कम बीचको प्रवाहहरू प्रयोग गर्छौं। DC वर्तमान (वर्तमान प्रवाहको दिशा) को ध्रुवता पनि महत्त्वपूर्ण छ। सीधा ध्रुवता जहाँ वर्कपीस सकारात्मक छ र इलेक्ट्रोड नकारात्मक छ पाना धातुको वेल्डिंगमा यसको उथल प्रवेशको कारण र धेरै फराकिलो अन्तर भएका जोडहरूका लागि प्राथमिकता दिइन्छ। जब हामीसँग उल्टो ध्रुवता हुन्छ, अर्थात् इलेक्ट्रोड सकारात्मक हुन्छ र वर्कपीस नकारात्मक हुन्छ हामी गहिरो वेल्ड प्रवेश प्राप्त गर्न सक्छौं। एसी करन्टको साथ, हामीसँग पल्सेटिंग आर्क्स भएकोले, हामी ठूला व्यास इलेक्ट्रोडहरू र अधिकतम करेन्टहरू प्रयोग गरेर बाक्लो खण्डहरू वेल्ड गर्न सक्छौं। SMAW वेल्डिङ विधि 3 देखि 19 mm को workpiece मोटाई को लागी उपयुक्त छ र धेरै-पास प्रविधिहरु को प्रयोग गरेर। वेल्डको शीर्षमा बनेको स्ल्यागलाई तार ब्रश प्रयोग गरेर हटाउन आवश्यक छ, ताकि वेल्ड क्षेत्रमा कुनै क्षय र विफलता नहोस्। यो अवश्य पनि ढाल धातु आर्क वेल्डिंग को लागत मा थप्छ। यद्यपि SMAW उद्योग र मर्मत कार्यमा सबैभन्दा लोकप्रिय वेल्डिङ प्रविधि हो।
SUBMERGED ARC welding (SAW): यस प्रक्रियामा हामी लेम, सिलिका, क्याल्सियम फ्लोराइड, म्याङ्गनीज अक्साइड... आदि जस्ता दानेदार फ्लक्स सामग्रीहरू प्रयोग गरेर वेल्ड आर्कलाई ढाल्छौं। दानेदार प्रवाहलाई नोजल मार्फत गुरुत्वाकर्षण प्रवाहद्वारा वेल्ड क्षेत्रमा खुवाइन्छ। पग्लिएको वेल्ड जोनलाई ढाक्ने फ्लक्सले स्पार्क, धुवाँ, पराबैंगनी विकिरण आदिबाट महत्वपूर्ण रूपमा सुरक्षा गर्छ र थर्मल इन्सुलेटरको रूपमा काम गर्छ, जसले गर्दा तापलाई वर्कपीसमा गहिरो छिर्न दिन्छ। अनफ्युज्ड फ्लक्स पुन: प्राप्त, उपचार र पुन: प्रयोग गरिन्छ। बेयरको कुण्डललाई इलेक्ट्रोडको रूपमा प्रयोग गरिन्छ र ट्यूब मार्फत वेल्डको क्षेत्रमा खुवाइन्छ। हामी 300 र 2000 एम्पीयर बीच करंटहरू प्रयोग गर्छौं। जलमग्न आर्क वेल्डिङ (SAW) प्रक्रिया तेर्सो र समतल स्थिति र गोलाकार वेल्डहरूमा सीमित छ यदि वेल्डिङको क्रममा गोलाकार संरचना (जस्तै पाइपहरू) को घुमाउन सम्भव छ। गति 5 मि/मिनेट पुग्न सक्छ। SAW प्रक्रिया बाक्लो प्लेटहरूको लागि उपयुक्त छ र उच्च-गुणस्तर, कडा, नरम र समान वेल्डहरूमा परिणाम दिन्छ। उत्पादकता, प्रति घण्टा जम्मा गरिएको वेल्ड सामग्रीको मात्रा SMAW प्रक्रियाको तुलनामा 4 देखि 10 गुणा मात्रा हो।
अर्को चाप वेल्डिङ प्रक्रिया, जस्तै ग्यास मेटल एआरसी वेल्डिङ (GMAW) वा वैकल्पिक रूपमा मेटल इनर्ट ग्यास वेल्डिङ (MIG) भनेर चिनिने वेल्ड क्षेत्रमा आधारित छ जसलाई हेलियम, आर्गन, कार्बन डाइअक्साइड जस्ता ग्यासहरूको बाह्य स्रोतहरूद्वारा ढालिएको छ। इलेक्ट्रोड धातुमा अतिरिक्त डिअक्सिडाइजरहरू हुन सक्छन्। उपभोगयोग्य तार एक नोजल मार्फत वेल्ड क्षेत्रमा खुवाइन्छ। ग्यास मेटल आर्क वेल्डिङ (GMAW) को प्रयोग गरेर बोट फेरस र अलौह धातुहरू समावेश गरी निर्माण गरिन्छ। वेल्डिङ उत्पादकता SMAW प्रक्रियाको करिब २ गुणा हो। स्वचालित वेल्डिङ उपकरण प्रयोग भइरहेको छ। यस प्रक्रियामा धातु तीन मध्ये एक तरिकामा स्थानान्तरण गरिन्छ: "स्प्रे ट्रान्सफर" मा इलेक्ट्रोडबाट वेल्ड क्षेत्रमा प्रति सेकेन्ड धेरै सय साना धातुका थोपाहरू स्थानान्तरण समावेश हुन्छ। अर्कोतर्फ, "ग्लोबुलर ट्रान्सफर" मा, कार्बन डाइअक्साइड युक्त ग्यासहरू प्रयोग गरिन्छ र पिघलाएको धातुको ग्लोब्युलहरू विद्युतीय चापद्वारा चलाइन्छ। वेल्डिङ धाराहरू उच्च छन् र वेल्ड प्रवेश गहिरो, स्प्रे स्थानान्तरण भन्दा बढी वेल्डिङ गति। यसरी भारी खण्डहरू वेल्डिंगको लागि ग्लोबुलर स्थानान्तरण राम्रो छ। अन्तमा, "सर्ट सर्किटिङ" विधिमा, इलेक्ट्रोड टिपले पग्लिएको वेल्ड पूललाई छुन्छ, यसलाई धातुको रूपमा ५० थोपा/सेकेन्ड भन्दा बढी दरमा व्यक्तिगत थोपाहरूमा स्थानान्तरण गरिन्छ। कम प्रवाह र भोल्टेजहरू पातलो तारको साथ प्रयोग गरिन्छ। प्रयोग गरिएको पावरहरू लगभग 2 kW र तापमान अपेक्षाकृत कम छन्, यो विधि 6mm भन्दा कम मोटाई पातलो पानाहरूको लागि उपयुक्त बनाउँछ।
अर्को भिन्नता FLUX-CORED ARC welding (FCAW) प्रक्रिया ग्यास मेटल आर्क वेल्डिङ जस्तै छ, बाहेक इलेक्ट्रोड फ्लक्सले भरिएको ट्यूब हो। कोरेड-फ्लक्स इलेक्ट्रोडहरू प्रयोग गर्ने फाइदाहरू यो हो कि तिनीहरूले अधिक स्थिर आर्कहरू उत्पादन गर्छन्, हामीलाई SMAW वेल्डिंग, सुधारिएको वेल्डिंग रूपरेखाको तुलनामा वेल्ड धातुहरूको गुणहरू, कम भंगुर र यसको फ्लक्सको लचिलो प्रकृति सुधार गर्ने अवसर दिन्छ। सेल्फ-शिल्डेड कोरेड इलेक्ट्रोडहरूले वायुमण्डल विरुद्ध वेल्ड जोनलाई ढाल्ने सामग्रीहरू समावेश गर्दछ। हामी लगभग 20 किलोवाट शक्ति प्रयोग गर्छौं। GMAW प्रक्रिया जस्तै, FCAW प्रक्रियाले निरन्तर वेल्डिङका लागि प्रक्रियाहरू स्वचालित गर्ने अवसर पनि प्रदान गर्दछ, र यो किफायती छ। फ्लक्स कोरमा विभिन्न मिश्र धातुहरू थपेर विभिन्न वेल्ड धातु रसायनहरू विकास गर्न सकिन्छ।
ELECTROGAS WELDING (EGW) मा हामी टुक्राहरूलाई किनारामा जोडेर जोड्छौं। यसलाई कहिलेकाहीँ बट वेल्डिङ पनि भनिन्छ। वेल्ड धातुलाई जोड्नका लागि दुई टुक्राहरू बीचको वेल्ड गुहामा राखिन्छ। पग्लिएको स्ल्यागलाई खन्याउनबाट जोगाउन ठाउँलाई दुईवटा पानी-चिसो बाँधले घेरिएको छ। बाँधहरू मेकानिकल ड्राइभहरूद्वारा माथि सारियो। जब workpiece घुमाउन सकिन्छ, हामी पाइप को परिधि वेल्डिंग को लागी इलेक्ट्रोग्यास वेल्डिंग प्रविधि पनि प्रयोग गर्न सक्छौं। इलेक्ट्रोडहरू निरन्तर चाप राख्नको लागि नालीबाट खुवाइन्छ। धाराहरू 400Amperes वा 750 Amperes र 20 kW वरिपरि पावर स्तर हुन सक्छ। फ्लक्स-कोर्ड इलेक्ट्रोड वा बाह्य स्रोतबाट उत्पन्न हुने निष्क्रिय ग्यासहरूले सुरक्षा प्रदान गर्दछ। हामी 12mm देखि 75mm सम्म मोटाई भएको स्टील्स, टाइटेनियम आदि जस्ता धातुहरूको लागि इलेक्ट्रोग्यास वेल्डिङ (EGW) प्रयोग गर्छौं। यो प्रविधि ठूला संरचनाहरूको लागि उपयुक्त छ।
यद्यपि, इलेक्ट्रोस्लाग वेल्डिङ (ESW) भनिने अर्को प्रविधिमा इलेक्ट्रोड र वर्कपीसको तल्लो भागको बीचमा चाप प्रज्वलित गरिन्छ र फ्लक्स थपिन्छ। जब पग्लिएको स्ल्याग इलेक्ट्रोड टिपमा पुग्छ, चाप निभिन्छ। पग्लिएको स्ल्यागको विद्युतीय प्रतिरोध मार्फत ऊर्जा निरन्तर आपूर्ति गरिन्छ। हामी ५० एमएम र ९०० एमएम र त्यसभन्दा माथिको मोटाईका प्लेटहरू वेल्ड गर्न सक्छौँ। धाराहरू लगभग 600 एम्पियर छन् जबकि भोल्टेजहरू 40 - 50 V को बीचमा छन्। वेल्डिङको गति लगभग 12 देखि 36 मिमी/मिनेट हुन्छ। आवेदन इलेक्ट्रोग्यास वेल्डिंग जस्तै छन्।
हाम्रो गैर-उपभोग्य इलेक्ट्रोड प्रक्रियाहरू मध्ये एक, GAS TUNGSTEN ARC WELDING (GTAW) जसलाई TUNGSTEN INERT GAS WELDING (TIG) पनि भनिन्छ जसमा तारद्वारा फिलर धातुको आपूर्ति समावेश हुन्छ। नजिकबाट फिट जोड्नका लागि कहिलेकाहीँ हामी फिलर मेटल प्रयोग गर्दैनौं। TIG प्रक्रियामा हामी फ्लक्स प्रयोग गर्दैनौं, तर ढालको लागि आर्गन र हेलियम प्रयोग गर्छौं। टंगस्टनको उच्च पिघलने बिन्दु छ र TIG वेल्डिंग प्रक्रियामा खपत हुँदैन, त्यसैले स्थिर वर्तमान र चाप खाली ठाउँहरू कायम राख्न सकिन्छ। पावर स्तरहरू 8 देखि 20 kW र 200 Ampere (DC) वा 500 Ampere (AC) मा प्रवाहहरू छन्। एल्युमिनियम र म्याग्नेसियमको लागि हामी यसको अक्साइड सफाई कार्यको लागि एसी करन्ट प्रयोग गर्छौं। टंगस्टन इलेक्ट्रोडको प्रदूषणबाट बच्न, हामी पग्लिएको धातुहरूसँग यसको सम्पर्कबाट बच्न सक्छौं। ग्यास टंगस्टन आर्क वेल्डिंग (GTAW) विशेष गरी पातलो धातुहरू वेल्डिंगको लागि उपयोगी छ। GTAW वेल्डहरू राम्रो सतह फिनिशको साथ धेरै उच्च गुणस्तरका छन्।
हाइड्रोजन ग्यासको उच्च लागतको कारण, कम प्रयोग हुने प्रविधि एटोमिक हाइड्रोजन वेल्डिङ (एएचडब्ल्यू) हो, जहाँ हामी बगिरहेको हाइड्रोजन ग्यासको ढाल वातावरणमा दुई टंगस्टन इलेक्ट्रोडहरू बीच चाप उत्पन्न गर्छौं। AHW पनि एक गैर-उपभोग्य इलेक्ट्रोड वेल्डिंग प्रक्रिया हो। डायटोमिक हाइड्रोजन ग्याँस H2 वेल्डिंग आर्कको नजिक यसको परमाणु रूपमा टुक्रन्छ जहाँ तापमान 6273 केल्भिन भन्दा बढी हुन्छ। बिच्छेद गर्दा, यसले चापबाट ठूलो मात्रामा तातो अवशोषित गर्दछ। जब हाइड्रोजन परमाणुहरूले वेल्ड जोनमा प्रहार गर्दछ जुन तुलनात्मक रूपमा चिसो सतह हो, तिनीहरू डायटोमिक फारममा पुन: संयोजित हुन्छन् र भण्डार गरिएको तापलाई छोड्छन्। वर्कपीसलाई चाप दूरीमा परिवर्तन गरेर ऊर्जा फरक हुन सक्छ।
अर्को गैर-उपभोगयोग्य इलेक्ट्रोड प्रक्रियामा, प्लाज्मा एआरसी वेल्डिङ (PAW) हामीसँग वेल्ड क्षेत्रतर्फ निर्देशित प्लाज्मा आर्क छ। PAW मा तापमान 33,273 केल्भिन पुग्छ। इलेक्ट्रोन र आयनहरूको लगभग बराबर संख्याले प्लाज्मा ग्यास बनाउँछ। कम-वर्तमान पायलट आर्कले प्लाज्मा सुरु गर्छ जुन टंगस्टन इलेक्ट्रोड र ओरिफिसको बीचमा हुन्छ। सञ्चालन प्रवाह सामान्यतया 100 Amperes को आसपास छ। एक फिलर धातु खुवाउन सकिन्छ। प्लाज्मा आर्क वेल्डिङमा, बाहिरी ढाल रिंग र आर्गन र हेलियम जस्ता ग्यासहरू प्रयोग गरेर ढाललाई पूरा गरिन्छ। प्लाज्मा आर्क वेल्डिङमा, चाप इलेक्ट्रोड र वर्कपीस वा इलेक्ट्रोड र नोजलको बीचमा हुन सक्छ। यो वेल्डिङ प्रविधिमा उच्च ऊर्जा एकाग्रता, गहिरो र साँघुरो वेल्डिङ क्षमता, राम्रो चाप स्थिरता, 1 मिटर/मिनेटसम्म उच्च वेल्डिङ गति, कम थर्मल विरूपणका अन्य विधिहरूमा फाइदाहरू छन्। हामी सामान्यतया प्लाज्मा आर्क वेल्डिङ 6 मिमी भन्दा कम मोटाई र कहिलेकाहीं एल्युमिनियम र टाइटेनियमको लागि 20 मिमी सम्म प्रयोग गर्छौं।
उच्च-ऊर्जा-बीम वेल्डिङ: इलेक्ट्रोन-बीम वेल्डिंग (EBW) र लेजर वेल्डिङ (LBW) दुई प्रकारका रूपमा फ्यूजन वेल्डिङ विधिको अर्को प्रकार। यी प्रविधिहरू हाम्रो उच्च-टेक उत्पादनहरू निर्माण कार्यको लागि विशेष मूल्यका छन्। इलेक्ट्रोन-बीम वेल्डिङमा, उच्च गतिको इलेक्ट्रोनहरूले वर्कपीसलाई प्रहार गर्दछ र तिनीहरूको गतिज ऊर्जा तापमा रूपान्तरण हुन्छ। इलेक्ट्रोनहरूको साँघुरो बीम भ्याकुम चेम्बरमा सजिलैसँग यात्रा गर्दछ। सामान्यतया हामी ई-बीम वेल्डिङमा उच्च भ्याकुम प्रयोग गर्छौं। 150 मिमी जति बाक्लो प्लेटहरू वेल्डेड गर्न सकिन्छ। कुनै ढाल ग्याँस, फ्लक्स वा फिलर सामग्री आवश्यक पर्दैन। इलेक्ट्रोन बीम गनमा १०० किलोवाट क्षमता हुन्छ। गहिरो र साँघुरो वेल्डहरू उच्च पक्ष अनुपात 30 सम्म र साना ताप-प्रभावित क्षेत्रहरू सम्भव छन्। वेल्डिङ गति 12 मीटर / मिनेट पुग्न सक्छ। लेजर-बिम वेल्डिङमा हामी गर्मीको स्रोतको रूपमा उच्च-शक्ति लेजरहरू प्रयोग गर्छौं। उच्च घनत्व भएको १० माइक्रोन जति सानो लेजर बीमले वर्कपीसमा गहिरो प्रवेश सक्षम पार्छ। लेजर-बीम वेल्डिङको साथ 10 सम्मको गहिराई-देखि-चौडाइ अनुपात सम्भव छ। हामी पल्स्ड र लगातार वेभ लेजर दुवै प्रयोग गर्छौं, पहिले पातलो सामग्रीका लागि र पछिल्लो प्रायः 25 मिमी सम्मको बाक्लो वर्कपीसका लागि प्रयोग गरिन्छ। पावर स्तरहरू 100 kW सम्म छन्। लेजर बीम वेल्डिंग अप्टिकली धेरै परावर्तित सामग्रीहरूको लागि राम्रोसँग उपयुक्त छैन। वेल्डिङ प्रक्रियामा ग्यासहरू पनि प्रयोग गर्न सकिन्छ। लेजर बीम वेल्डिङ विधि स्वचालन र उच्च मात्रा निर्माणको लागि राम्रोसँग फिट छ र 2.5 m/min र 80 m/min बीच वेल्डिङ गति प्रस्ताव गर्न सक्छ। यो वेल्डिङ प्रविधिले प्रदान गर्ने एउटा प्रमुख फाइदा अन्य प्रविधिहरू प्रयोग गर्न नसकिने क्षेत्रहरूमा पहुँच हो। लेजर किरणहरू सजिलैसँग त्यस्ता कठिन क्षेत्रहरूमा जान सक्छन्। इलेक्ट्रोन-बीम वेल्डिङमा जस्तै कुनै भ्याकुम आवश्यक छैन। लेजर बीम वेल्डिङबाट राम्रो गुणस्तर र बल, कम संकुचन, कम विरूपण, कम पोरोसिटी भएका वेल्डहरू प्राप्त गर्न सकिन्छ। लेजर बीमहरू सजिलैसँग हेरफेर गर्न सकिन्छ र फाइबर अप्टिक केबलहरू प्रयोग गरेर आकार दिन सकिन्छ। यो प्रविधि सटीक हर्मेटिक असेंबलीहरू, इलेक्ट्रोनिक प्याकेजहरू ... आदिको वेल्डिंगको लागि राम्रोसँग उपयुक्त छ।
हाम्रो ठोस राज्य वेल्डिङ प्रविधिहरू हेरौं। कोल्ड वेल्डिङ (CW) एक प्रक्रिया हो जहाँ तातोको सट्टा दबाब प्रयोग गरी मिलाइएका भागहरूमा डाइज वा रोलहरू प्रयोग गरिन्छ। चिसो वेल्डिंगमा, कम्तिमा एक मिलन भागहरू नरम हुनु आवश्यक छ। सबै भन्दा राम्रो परिणाम दुई समान सामग्री संग प्राप्त गरिन्छ। यदि चिसो वेल्डिङमा जोडिने दुई धातुहरू भिन्न छन् भने, हामी कमजोर र भंगुर जोडहरू पाउन सक्छौं। चिसो वेल्डिङ विधि नरम, नरम र साना वर्कपीसहरू जस्तै बिजुली जडानहरू, तातो संवेदनशील कन्टेनर किनारहरू, थर्मोस्टेटहरूका लागि बाइमेटलिक स्ट्रिपहरू... आदिका लागि उपयुक्त छ। चिसो वेल्डिङको एउटा भिन्नता रोल बन्डिङ (वा रोल वेल्डिङ) हो, जहाँ रोलको जोडी मार्फत दबाब लागू गरिन्छ। कहिलेकाहीँ हामी राम्रो इन्टरफेसियल बलको लागि उच्च तापक्रममा रोल वेल्डिङ गर्छौं।
हामीले प्रयोग गर्ने अर्को ठोस राज्य वेल्डिङ प्रक्रिया अल्ट्रासोनिक वेल्डिङ (USW) हो, जहाँ वर्कपीसहरू स्थिर सामान्य बल र ओसिलेटिंग कतरण तनावको अधीनमा हुन्छन्। ट्रान्सड्यूसरको टुप्पो मार्फत ओसिलिटिंग कतरण तनावहरू लागू गरिन्छ। अल्ट्रासोनिक वेल्डिङले 10 देखि 75 kHz सम्मको फ्रिक्वेन्सीको साथ दोलनहरू तैनात गर्दछ। सिम वेल्डिङ जस्ता केही अनुप्रयोगहरूमा, हामी टिपको रूपमा घुमाउने वेल्डिङ डिस्क प्रयोग गर्छौं। वर्कपीसहरूमा लागू हुने छाँट्ने तनावले प्लास्टिकको सानो विकृति निम्त्याउँछ, अक्साइड तहहरू, दूषित पदार्थहरू तोड्छ र ठोस अवस्था बन्धनमा नेतृत्व गर्दछ। अल्ट्रासोनिक वेल्डिङमा संलग्न तापक्रम धातुहरूको लागि पिघलने बिन्दुको तापक्रमभन्दा तल हुन्छ र कुनै फ्युजन हुँदैन। हामी बारम्बार अल्ट्रासोनिक वेल्डिंग (USW) प्रक्रिया प्लास्टिक जस्ता गैर-मेटालिक सामग्रीहरूको लागि प्रयोग गर्छौं। थर्मोप्लास्टिकमा तापक्रम पग्लने बिन्दुमा पुग्छ।
अर्को लोकप्रिय प्रविधि, FRICTION WELDING (FRW) मा जोडिने वर्कपीसको इन्टरफेसमा घर्षणको माध्यमबाट ताप उत्पन्न हुन्छ। घर्षण वेल्डिङमा हामी एउटा वर्कपीसलाई स्थिर राख्छौं जबकि अर्को वर्कपीसलाई फिक्स्चरमा राखिन्छ र स्थिर गतिमा घुमाइन्छ। त्यसपछि workpieces एक अक्षीय बल अन्तर्गत सम्पर्कमा ल्याइन्छ। घर्षण वेल्डिङमा घुमाउने सतह गति केही अवस्थामा 900m/min पुग्न सक्छ। पर्याप्त इन्टरफेसियल सम्पर्क पछि, घुमाउने वर्कपीस अचानक रोकिन्छ र अक्षीय बल बढाइन्छ। वेल्ड जोन सामान्यतया साँघुरो क्षेत्र हो। घर्षण वेल्डिंग प्रविधि विभिन्न प्रकारका सामग्रीबाट बनेको ठोस र ट्यूबलर भागहरू जोड्न प्रयोग गर्न सकिन्छ। केही फ्ल्यास FRW मा इन्टरफेसमा विकास हुन सक्छ, तर यो फ्ल्यास माध्यमिक मेसिन वा पीस द्वारा हटाउन सकिन्छ। घर्षण वेल्डिंग प्रक्रियाको भिन्नताहरू अवस्थित छन्। उदाहरण को लागी "जडता घर्षण वेल्डिंग" मा फ्लाईव्हील समावेश छ जसको परिक्रमा गतिज ऊर्जा भागहरु वेल्ड गर्न को लागी प्रयोग गरिन्छ। फ्लाईव्हील बन्द हुँदा वेल्ड पूरा हुन्छ। घुम्ने पिण्ड विविध हुन सक्छ र यसरी घुम्ने गतिज ऊर्जा। अर्को भिन्नता "रैखिक घर्षण वेल्डिंग" हो, जहाँ कम्तिमा एक कम्पोनेन्टलाई जोड्न रैखिक पारस्परिक गति लागू गरिन्छ। रैखिक घर्षण वेल्डिंग भागहरूमा गोलाकार हुनु हुँदैन, तिनीहरू आयताकार, वर्ग वा अन्य आकारको हुन सक्छन्। फ्रिक्वेन्सीहरू हर्ट्जको दशौं, मिलिमिटर दायरामा एम्प्लिच्युडहरू र दश वा सयौं एमपीएमा दबाबहरू हुन सक्छन्। अन्तमा "घर्षण हलचल वेल्डिंग" माथि वर्णन गरिएका अन्य दुई भन्दा केही फरक छ। जहाँ जडत्व घर्षण वेल्डिंग र रैखिक घर्षण वेल्डिंगमा इन्टरफेसहरूको तापक्रम घर्षणको माध्यमबाट दुईवटा सम्पर्क सतहहरूलाई रगडेर प्राप्त गरिन्छ, घर्षण हलचल वेल्डिंग विधिमा तेस्रो बडी जोडिने दुईवटा सतहहरू विरुद्ध रगडिन्छ। ५ देखि ६ मिलिमिटर व्यासको घुमाउने उपकरणलाई जोडसँग सम्पर्कमा ल्याइएको छ। तापमान 503 देखि 533 केल्भिन बीचको मानहरूमा बढ्न सक्छ। तातो, मिश्रण र संयुक्त मा सामग्री को हलचल स्थान लिन्छ। हामी एल्युमिनियम, प्लास्टिक र कम्पोजिटहरू सहित विभिन्न सामग्रीहरूमा घर्षण हलचल वेल्डिंग प्रयोग गर्छौं। वेल्डहरू समान छन् र न्यूनतम छिद्रहरूको साथ गुणस्तर उच्च छ। घर्षण हलचल वेल्डिंगमा कुनै धुवाँ वा स्प्याटर उत्पादन हुँदैन र प्रक्रिया राम्रोसँग स्वचालित हुन्छ।
प्रतिरोध वेल्डिंग (RW): वेल्डिङको लागि आवश्यक ताप दुई वर्कपीसहरू बीचको विद्युतीय प्रतिरोधद्वारा जोडिने गरी उत्पादन गरिन्छ। प्रतिरोध वेल्डिङमा कुनै फ्लक्स, सिल्डिङ ग्याँस वा उपभोग्य इलेक्ट्रोडहरू प्रयोग हुँदैनन्। जुल तताउने प्रतिरोध वेल्डिंग मा स्थान लिन्छ र व्यक्त गर्न सकिन्छ:
H = (वर्ग I) x R xtx K
H जूल (वाट-सेकेन्ड) मा उत्पन्न हुने ताप हो, एम्पीयरमा I प्रवाह, ओम्समा R प्रतिरोध, t सेकेन्डमा प्रवाहको समय हो। कारक K 1 भन्दा कम छ र ऊर्जा को अंश को प्रतिनिधित्व गर्दछ जुन विकिरण र प्रवाह को माध्यम बाट हराएको छैन। प्रतिरोध वेल्डिंग प्रक्रियाहरूमा प्रवाहहरू 100,000 A सम्म उच्च स्तरमा पुग्न सक्छ तर भोल्टेजहरू सामान्यतया 0.5 देखि 10 भोल्ट हुन्छन्। इलेक्ट्रोडहरू सामान्यतया तामा मिश्रबाट बनेका हुन्छन्। दुवै समान र भिन्न सामग्री प्रतिरोध वेल्डिंग द्वारा सामेल गर्न सकिन्छ। यस प्रक्रियाको लागि धेरै भिन्नताहरू अवस्थित छन्: "प्रतिरोध स्पट वेल्डिंग" मा दुईवटा पानाहरूको ल्याप संयुक्तको सतहहरूलाई सम्पर्क गर्ने दुई विरोधी गोल इलेक्ट्रोडहरू समावेश छन्। वर्तमान बन्द नभएसम्म दबाब लागू हुन्छ। वेल्ड नगेट सामान्यतया 10 मिमी सम्म व्यासमा हुन्छ। रेजिस्टेन्स स्पट वेल्डिङले वेल्ड स्पटहरूमा अलिकति रङ्गीन इन्डेन्टेसन चिन्हहरू छोड्छ। स्पट वेल्डिंग हाम्रो सबैभन्दा लोकप्रिय प्रतिरोध वेल्डिंग प्रविधि हो। कठिन क्षेत्रहरूमा पुग्न स्पट वेल्डिङमा विभिन्न इलेक्ट्रोड आकारहरू प्रयोग गरिन्छ। हाम्रो स्पट वेल्डिङ उपकरण सीएनसी नियन्त्रित छ र धेरै इलेक्ट्रोडहरू छन् जुन एकै साथ प्रयोग गर्न सकिन्छ। अर्को भिन्नता "रेजिस्टेन्स सीम वेल्डिंग" ह्वील वा रोलर इलेक्ट्रोडको साथ गरिन्छ जसले AC पावर चक्रमा करेन्ट पर्याप्त उच्च स्तरमा पुग्दा निरन्तर स्पट वेल्डहरू उत्पादन गर्दछ। प्रतिरोधी सीम वेल्डिंग द्वारा उत्पादित जोडहरू तरल र ग्यास तंग छन्। पातलो पानाहरूको लागि लगभग 1.5 m/min को वेल्डिंग गति सामान्य छ। एकले रुकाउने धाराहरू लागू गर्न सक्छ ताकि स्पट वेल्डहरू सीमको साथ इच्छित अन्तरालहरूमा उत्पादन गरिन्छ। "प्रतिरोध प्रक्षेपण वेल्डिंग" मा हामी वेल्डेड गर्न को लागी workpiece सतहहरु मध्ये एक मा एक वा धेरै प्रक्षेपण (डिम्पल) एम्बोस गर्छौं। यी अनुमानहरू गोलाकार वा अंडाकार हुन सक्छन्। उच्च स्थानीयकृत तापमान यी एम्बोस्ड स्पटहरूमा पुग्छ जुन संभोग भागको सम्पर्कमा आउँछ। इलेक्ट्रोडहरूले यी अनुमानहरूलाई कम्प्रेस गर्न दबाब दिन्छ। प्रतिरोधी प्रक्षेपण वेल्डिङमा इलेक्ट्रोडहरू समतल टिपहरू छन् र पानी चिसो तामा मिश्रहरू छन्। प्रतिरोध प्रक्षेपण वेल्डिंगको फाइदा भनेको एक स्ट्रोकमा धेरै वेल्डहरू गर्ने हाम्रो क्षमता हो, यसरी विस्तारित इलेक्ट्रोड जीवन, विभिन्न मोटाईका पानाहरू वेल्ड गर्ने क्षमता, पानाहरूमा नट र बोल्टहरू वेल्ड गर्ने क्षमता। प्रतिरोधी प्रक्षेपण वेल्डिङको बेफाइदा भनेको डिम्पल एम्बोसिङको थप लागत हो। अझै अर्को प्रविधि, "फ्ल्याश वेल्डिङ" मा दुई वर्कपीसको छेउमा रहेको चापबाट ताप उत्पन्न हुन्छ जब तिनीहरू सम्पर्क गर्न थाल्छन्। यो विधि पनि वैकल्पिक रूपमा चाप वेल्डिंग मान्न सकिन्छ। इन्टरफेसमा तापमान बढ्छ, र सामग्री नरम हुन्छ। एक अक्षीय बल लागू गरिन्छ र नरम क्षेत्रमा वेल्ड बनाइन्छ। फ्ल्यास वेल्डिंग पूरा भएपछि, संयुक्त सुधारिएको उपस्थितिको लागि मेसिन गर्न सकिन्छ। फ्ल्यास वेल्डिंग द्वारा प्राप्त वेल्ड गुणस्तर राम्रो छ। पावर स्तरहरू 10 देखि 1500 kW छन्। फ्ल्यास वेल्डिङ 75 मिमी व्यास सम्म र 0.2 मिमी देखि 25 मिमी मोटाई बीचको पानाहरू समान वा भिन्न धातुहरू जोड्नको लागि उपयुक्त छ। "स्टड आर्क वेल्डिंग" फ्लैश वेल्डिंग जस्तै धेरै समान छ। बोल्ट वा थ्रेडेड रड जस्ता स्टडले प्लेट जस्ता वर्कपीसमा जोडिएको बेला एक इलेक्ट्रोडको रूपमा काम गर्दछ। उत्पन्न तापलाई केन्द्रित गर्न, अक्सिडेशन रोक्न र पग्लिएको धातुलाई वेल्ड जोनमा राख्न, एक डिस्पोजेबल सिरेमिक रिंग जोडिएको वरिपरि राखिएको छ। अन्तमा "पर्कसन वेल्डिंग" अर्को प्रतिरोध वेल्डिंग प्रक्रिया, बिजुली ऊर्जा आपूर्ति गर्न एक क्यापेसिटर प्रयोग गर्दछ। पर्कसन वेल्डिङमा पावर मिलिसेकेन्ड भित्रै जोइन्टमा उच्च लोकलाइज्ड तापको विकास गरेर धेरै चाँडै डिस्चार्ज हुन्छ। हामी इलेक्ट्रोनिक्स उत्पादन उद्योगमा व्यापक रूपमा पर्कसन वेल्डिङ प्रयोग गर्छौं जहाँ जोडको वरपरका संवेदनशील इलेक्ट्रोनिक कम्पोनेन्टहरू तताउनबाट जोगिनु पर्छ।
EXPLOSION WELDING भनिने प्रविधीमा विस्फोटक पदार्थको तहलाई विस्फोट गराइन्छ जसलाई जोड्नको लागि वर्कपीसहरू मध्ये एकमा राखिन्छ। वर्कपीसमा लगाइएको धेरै उच्च दबाबले एक अशान्त र लहरा इन्टरफेस उत्पादन गर्दछ र मेकानिकल इन्टरलकिङ हुन्छ। विस्फोटक वेल्डिंगमा बन्ड बलहरू धेरै उच्च छन्। विस्फोट वेल्डिंग फरक धातुहरू संग प्लेट को क्लेडिंग को लागी एक राम्रो तरीका हो। क्लेडिङ पछि, प्लेटहरू पातलो खण्डहरूमा घुमाउन सकिन्छ। कहिलेकाहीँ हामी ट्यूबहरू विस्तार गर्नको लागि विस्फोट वेल्डिंग प्रयोग गर्दछौं ताकि तिनीहरू प्लेटको बिरूद्ध कडा रूपमा बन्द हुन्छन्।
ठोस अवस्था जोड्ने डोमेन भित्रको हाम्रो अन्तिम विधि डिफ्यूजन बन्डिङ वा डिफ्यूजन वेल्डिङ (DFW) हो जसमा मुख्यतया इन्टरफेसमा परमाणुहरू फैलाएर राम्रो जोइन्ट प्राप्त गरिन्छ। इन्टरफेसमा केहि प्लास्टिक विरूपण पनि वेल्डिंग मा योगदान गर्दछ। संलग्न तापमान लगभग 0.5 Tm छ जहाँ Tm धातुको पग्लने तापमान हो। डिफ्यूजन वेल्डिङमा बन्ड बल दबाब, तापमान, सम्पर्क समय र सम्पर्क सतहहरूको सरसफाइमा निर्भर गर्दछ। कहिलेकाहीँ हामी इन्टरफेसमा फिलर धातुहरू प्रयोग गर्छौं। डिफ्युजन बन्धनमा ताप र दबाब आवश्यक हुन्छ र विद्युतीय प्रतिरोध वा भट्टी र मृत वजन, प्रेस वा अन्य द्वारा आपूर्ति गरिन्छ। समान र भिन्न धातुहरू प्रसार वेल्डिंगसँग जोड्न सकिन्छ। परमाणुहरू माइग्रेट हुनको लागि समयको कारण प्रक्रिया अपेक्षाकृत ढिलो छ। DFW स्वचालित हुन सक्छ र एयरोस्पेस, इलेक्ट्रोनिक्स, चिकित्सा उद्योगहरूको लागि जटिल भागहरूको निर्माणमा व्यापक रूपमा प्रयोग गरिन्छ। उत्पादन गरिएका उत्पादनहरूमा आर्थोपेडिक प्रत्यारोपण, सेन्सर, एयरोस्पेस संरचनात्मक सदस्यहरू समावेश छन्। जटिल पाना धातु संरचनाहरू बनाउनको लागि डिफ्यूजन बन्डिङलाई सुपरप्लास्टिक फारमिङसँग जोड्न सकिन्छ। पानाहरूमा चयन गरिएका स्थानहरू पहिले डिफ्युजन बन्डेड हुन्छन् र त्यसपछि अनबन्डेड क्षेत्रहरूलाई हावाको चाप प्रयोग गरेर मोल्डमा विस्तार गरिन्छ। उच्च कठोरता-देखि-वजन अनुपात भएका एयरोस्पेस संरचनाहरू विधिहरूको यो संयोजन प्रयोग गरेर निर्माण गरिन्छ। फैलावट वेल्डिंग / सुपरप्लास्टिक गठन संयुक्त प्रक्रियाले फास्टनरहरूको आवश्यकतालाई हटाएर आवश्यक भागहरूको संख्या घटाउँछ, आर्थिक रूपमा र छोटो नेतृत्व समयको साथ कम तनाव अत्यधिक सटीक भागहरूमा परिणाम दिन्छ।
ब्राजिङ: ब्राजिङ र सोल्डरिङ प्रविधिहरूमा वेल्डिङका लागि आवश्यकभन्दा कम तापक्रम समावेश हुन्छ। यद्यपि ब्राजिङको तापक्रम सोल्डरिङ तापक्रमभन्दा बढी हुन्छ। ब्रेजिङमा फिलर मेटल जोड्नका लागि सतहहरू बीचमा राखिन्छ र तापक्रम फिलर सामग्रीको पग्लने तापक्रम 723 केल्भिन भन्दा माथि तर वर्कपीसहरूको पग्लने तापक्रमभन्दा कम हुन्छ। पग्लिएको धातुले वर्कपीसहरू बीचको नजिकको फिटिंग ठाउँ भर्छ। फाइलर धातुको शीतलता र पछिको ठोसीकरणले बलियो जोडहरूमा परिणाम दिन्छ। ब्रेज वेल्डिङमा फिलर मेटल जोइन्टमा जम्मा हुन्छ। ब्राजिङको तुलनामा ब्राज वेल्डिङमा धेरै फिलर मेटल प्रयोग गरिन्छ। अक्सिडाइजिंग ज्वालाको साथ अक्स्यासेटिलीन टर्च ब्राज वेल्डिंगमा फिलर मेटल जम्मा गर्न प्रयोग गरिन्छ। ब्रेजिङमा कम तापक्रमको कारण, तातो प्रभावित क्षेत्रमा समस्याहरू जस्तै वार्पिङ र अवशिष्ट तनावहरू कम हुन्छन्। ब्रेजिङमा क्लियरेन्स ग्याप जति सानो हुन्छ त्यति नै जोडको शियर बल बढी हुन्छ। यद्यपि अधिकतम तन्य शक्ति इष्टतम अन्तर (एक शिखर मान) मा प्राप्त गरिन्छ। यस इष्टतम मानको तल र माथि, ब्रेजिङमा तन्य शक्ति घट्छ। ब्रेजिङमा सामान्य निकासीहरू ०.०२५ र ०.२ मिमी बीचमा हुन सक्छन्। हामी विभिन्न आकारहरू जस्तै परफर्म्स, पाउडर, रिङ्, तार, स्ट्रिप ….. इत्यादिका विभिन्न प्रकारका ब्राजिङ सामग्रीहरू प्रयोग गर्छौं। र तपाईंको डिजाइन वा उत्पादन ज्यामितिको लागि विशेष रूपमा यी प्रदर्शनहरू निर्माण गर्न सक्छ। हामी तपाईंको आधार सामग्री र अनुप्रयोग अनुसार ब्रेजिङ सामग्रीको सामग्री पनि निर्धारण गर्छौं। हामीले अनावश्यक अक्साइड तहहरू हटाउन र अक्सिडेशन रोक्नको लागि ब्रेजिङ कार्यहरूमा प्रायः फ्लक्सहरू प्रयोग गर्छौं। पछिको क्षरणबाट बच्नको लागि, फ्लक्सहरू सामान्यतया जडान अपरेशन पछि हटाइन्छ। AGS-TECH Inc. सहित विभिन्न ब्रेजिङ विधिहरू प्रयोग गर्दछ:
- टर्च ब्रेजिङ
- फर्नेस ब्राजिङ
- इन्डक्शन ब्रेजिङ
- प्रतिरोध ब्राजिंग
- डिप ब्रेजिङ
- इन्फ्रारेड ब्राजिङ
- प्रसार ब्रेजिंग
- उच्च ऊर्जा बीम
कार्बाइड ड्रिल बिटहरू, इन्सर्टहरू, अप्टोइलेक्ट्रोनिक हर्मेटिक प्याकेजहरू, सिलहरू जस्ता राम्रो शक्ति भएका भिन्न धातुहरूबाट बनेका ब्राज्ड जोडहरूका हाम्रा सबैभन्दा सामान्य उदाहरणहरू।
सोल्डरिङ: यो हाम्रो प्रायः प्रयोग हुने प्रविधिहरू मध्ये एक हो जहाँ सोल्डर (फिलर मेटल) ले जोडलाई नजिकबाट फिट गर्ने कम्पोनेन्टहरू बीच ब्रेजिङमा भर्दछ। हाम्रो सोल्डरसँग 723 केल्भिन भन्दा कम पिघलने बिन्दुहरू छन्। हामी निर्माण कार्यहरूमा म्यानुअल र स्वचालित सोल्डरिङ दुवै तैनाथ गर्छौं। ब्राजिङको तुलनामा, सोल्डरिङ तापमान कम छ। उच्च-तापमान वा उच्च-शक्ति अनुप्रयोगहरूको लागि सोल्डरिंग धेरै उपयुक्त छैन। हामी सोल्डरिङका लागि सिसा-रहित सोल्डरहरू साथै टिन-लीड, टिन-जस्ता, लिड-सिल्भर, क्याडमियम-सिल्भर, जस्ता-आल्मुनियम मिश्र धातुहरू प्रयोग गर्छौं। दुवै noncorrosive राल आधारित साथ साथै अकार्बनिक एसिड र लवण सोल्डरिंग मा प्रवाह को रूप मा प्रयोग गरिन्छ। हामी कम सोल्डरबिलिटी भएका धातुहरू सोल्डर गर्न विशेष फ्लक्सहरू प्रयोग गर्छौं। एप्लिकेसनहरूमा जहाँ हामीले सिरेमिक सामग्री, गिलास वा ग्रेफाइट सोल्डर गर्नुपर्दछ, हामी पहिले सोल्डरबिलिटी बढाउन उपयुक्त धातुको साथ भागहरू प्लेट गर्छौं। हाम्रो लोकप्रिय सोल्डरिंग प्रविधिहरू हुन्:
- रिफ्लो वा टाँस्ने सोल्डरिंग
- वेभ सोल्डरिंग
- फर्नेस सोल्डरिंग
- टर्च सोल्डरिंग
- इन्डक्शन सोल्डरिंग
- आइरन सोल्डरिंग
- प्रतिरोध सोल्डरिंग
- डिप सोल्डरिंग
- अल्ट्रासोनिक सोल्डरिंग
- इन्फ्रारेड सोल्डरिंग
अल्ट्रासोनिक सोल्डरिङले हामीलाई एक अद्वितीय फाइदा प्रदान गर्दछ जसमा अल्ट्रासोनिक cavitation प्रभावका कारण फ्लक्सहरूको आवश्यकता हटाइएको छ जसले जोडिएको सतहहरूबाट अक्साइड फिल्महरू हटाउँछ। रिफ्लो र वेभ सोल्डरिङ इलेक्ट्रोनिक्समा उच्च मात्राको उत्पादनका लागि हाम्रो औद्योगिक रूपमा उत्कृष्ट प्रविधिहरू हुन् र त्यसैले विस्तृत रूपमा व्याख्या गर्न लायक छन्। रिफ्लो सोल्डरिङमा, हामी सोल्डर-मेटल कणहरू समावेश गर्ने सेमिसोलिड पेस्टहरू प्रयोग गर्छौं। पेस्ट एक स्क्रीनिंग वा स्टेंसिलिङ प्रक्रिया प्रयोग गरेर संयुक्त मा राखिएको छ। मुद्रित सर्किट बोर्डहरू (PCB) मा हामी प्राय: यो प्रविधि प्रयोग गर्छौं। जब विद्युतीय कम्पोनेन्टहरू यी प्याडहरूमा टाँसिएर राखिन्छ, सतह तनावले सतह-माउन्ट प्याकेजहरूलाई पङ्क्तिबद्ध राख्छ। कम्पोनेन्टहरू राखेपछि, हामी भट्टीमा असेंबलीलाई तताउँछौं ताकि रिफ्लो सोल्डरिङ हुन्छ। यस प्रक्रियाको क्रममा, पेस्टमा रहेका विलायकहरू वाष्पीकरण हुन्छन्, पेस्टमा फ्लक्स सक्रिय हुन्छ, कम्पोनेन्टहरू पहिले तताइन्छ, सोल्डर कणहरू पग्लिन्छन् र जोडलाई भिजाइन्छ, र अन्तमा PCB असेंबली बिस्तारै चिसो हुन्छ। PCB बोर्डहरूको उच्च मात्रा उत्पादनको लागि हाम्रो दोस्रो लोकप्रिय प्रविधि, अर्थात् वेभ सोल्डरिङ यस तथ्यमा निर्भर गर्दछ कि पिघलेको सोल्डरले धातुको सतहहरू भिजेको छ र धातुलाई पहिले तताउँदा मात्र राम्रो बन्धन बनाउँछ। पग्लिएको सोल्डरको स्थायी लामिनार तरंग पहिले पम्पद्वारा उत्पन्न हुन्छ र प्रि-हेटेड र प्रीफ्लक्स पीसीबीहरू तरंगमा पठाइन्छ। सोल्डरले खुला धातु सतहहरू मात्र भिजाउँछ तर IC पोलिमर प्याकेजहरू वा पोलिमर-लेपित सर्किट बोर्डहरूलाई भिजाउँदैन। तातो पानीको जेटको उच्च-वेगले जोडबाट थप सोल्डर उडाउँछ र छेउछाउको लिडहरू बीचको पुललाई रोक्छ। सतह-माउन्ट प्याकेजहरूको वेभ सोल्डरिङमा हामीले सोल्डरिङ गर्नुअघि तिनीहरूलाई टाँसेर सर्किट बोर्डमा बाँध्छौं। फेरि स्क्रिनिङ र स्टेन्सिलिङ प्रयोग गरिन्छ तर यो पटक epoxy को लागि। कम्पोनेन्टहरू तिनीहरूको सही स्थानहरूमा राखेपछि, इपोक्सी ठीक हुन्छ, बोर्डहरू उल्टो हुन्छन् र तरंग सोल्डरिङ हुन्छ।