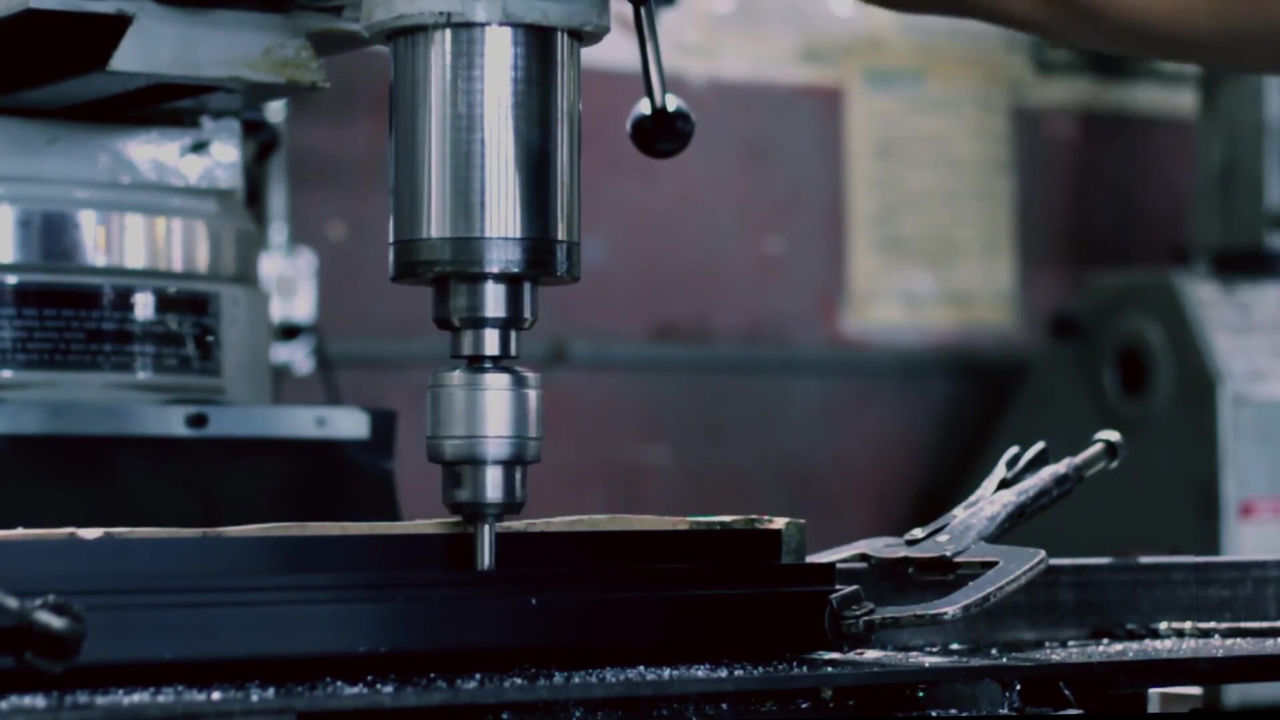
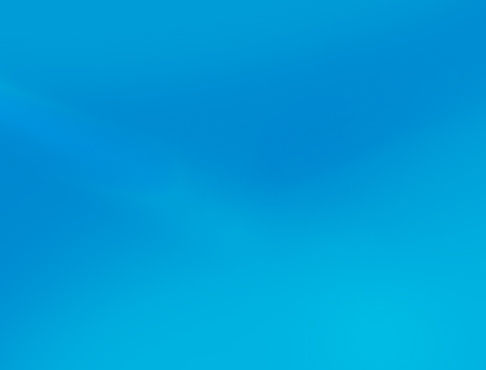
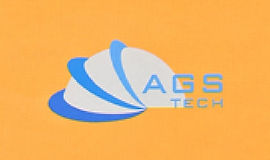
विश्वव्यापी कस्टम निर्माता, इन्टिग्रेटर, कन्सोलिडेटर, उत्पादन र सेवाहरूको विस्तृत विविधताका लागि आउटसोर्सिङ पार्टनर।
हामी उत्पादन, निर्माण, ईन्जिनियरिङ्, एकीकरण, एकीकरण, अनुकूलन निर्मित र अफ-शेल्फ उत्पादन र सेवाहरूको आउटसोर्सिङको लागि तपाईंको एक-स्टप स्रोत हौं।
आफ्नो भाषा छान्नुहोस्
-
कस्टम निर्माण
-
घरेलु र विश्वव्यापी अनुबंध निर्माण
-
उत्पादन आउटसोर्सिङ
-
घरेलु र विश्वव्यापी खरीद
-
Consolidation
-
इन्जिनियरिङ एकीकरण
-
इन्जिनियरिङ सेवाहरू
हाम्रो कस्टम कास्टिङ र मेसिनिङ प्रविधिहरू खर्चयोग्य र गैर-व्यययोग्य कास्टिङ, लौह र ननफेरस कास्टिङ, बालुवा, डाइ, केन्द्रापसारक, निरन्तर, सिरेमिक मोल्ड, लगानी, हराएको फोम, नजिक-नेट-आकार, स्थायी मोल्ड (गुरुत्वाकर्षण डाइ कास्टिङ), प्लास्टर हुन्। मोल्ड (प्लास्टर कास्टिङ) र शेल कास्टिङ, परम्परागत र सीएनसी उपकरणहरू प्रयोग गरेर मिलिङ र टर्निङद्वारा उत्पादित मेसिन पार्ट्स, उच्च थ्रुपुट सस्तो साना परिशुद्धता पार्ट्सका लागि स्विस टाइप मेसिनिङ, फास्टनरहरूको लागि स्क्रू मेसिनिङ, गैर-परम्परागत मेसिनिङ। कृपया ध्यान दिनुहोस् कि धातुहरू र धातु मिश्रहरू बाहेक, हामी सिरेमिक, गिलास र प्लास्टिकका कम्पोनेन्टहरू पनि मेशिन गर्छौं साथै केही अवस्थामा जब मोल्ड निर्माण आकर्षक छैन वा विकल्प छैन। पोलिमर सामग्रीको मेसिनिङको लागि हामीसँग विशेष अनुभव चाहिन्छ किनभने चुनौतीपूर्ण प्लास्टिक र रबर तिनीहरूको नरमता, गैर-कठोरता... आदिका कारण। सिरेमिक र गिलासको मेसिनिङको लागि, कृपया गैर-परम्परागत निर्माणमा हाम्रो पृष्ठ हेर्नुहोस्। AGS-TECH Inc. ले हल्का र भारी कास्टिङ दुवै उत्पादन र आपूर्ति गर्दछ। हामीले बोयलर, हीट एक्सचेन्जर, अटोमोबाइल, माइक्रोमोटर, विन्ड टर्बाइन, फूड प्याकेजिङ उपकरण र थपका लागि मेटल कास्टिङ र मेसिन पार्ट्स आपूर्ति गर्दै आएका छौं। हामी तपाईंलाई यहाँ क्लिक गर्न सिफारिस गर्छौं AGS-TECH Inc द्वारा मेसिनिङ र कास्टिङ प्रक्रियाहरूको हाम्रो योजनाबद्ध चित्रणहरू डाउनलोड गर्नुहोस्।
यसले तपाईलाई हामीले तल प्रदान गरिरहेको जानकारी राम्रोसँग बुझ्न मद्दत गर्नेछ। हामीले विस्तृत रूपमा प्रस्ताव गर्ने केही विभिन्न प्रविधिहरू हेरौं:
• एक्सपेन्डेबल मोल्ड कास्टिङ: यो फराकिलो वर्गले अस्थायी र पुन: प्रयोग गर्न नसकिने मोल्डहरू समावेश गर्ने विधिहरूलाई जनाउँछ। उदाहरणहरू बालुवा, प्लास्टर, खोल, लगानी (लोस्ट-म्याम पनि भनिन्छ) र प्लास्टर कास्टिङ हुन्।
• बालुवा कास्टिङ: एउटा प्रक्रिया जहाँ बालुवा मोल्ड सामग्रीको रूपमा प्रयोग गरिन्छ। एक धेरै पुरानो विधि र अझै पनि धेरै लोकप्रिय हदसम्म कि धातु कास्टिंग उत्पादन को बहुमत यस प्रविधि द्वारा बनाईएको हो। कम उत्पादनमा पनि कम लागत। साना र ठूला पार्ट्स निर्माणको लागि उपयुक्त। यो प्रविधि धेरै थोरै लगानीमा दिन वा हप्ता भित्र पार्ट्स निर्माण गर्न प्रयोग गर्न सकिन्छ। ओसिलो बालुवा माटो, बाइन्डर वा विशेष तेल प्रयोग गरेर एकसाथ बाँधिएको छ। बालुवा सामान्यतया मोल्ड बक्सहरूमा समावेश गरिन्छ र गुफा र गेट प्रणाली मोडेल वरिपरि बालुवा कम्प्याक्ट गरेर सिर्जना गरिन्छ। प्रक्रियाहरू हुन्:
1.) मोल्ड बनाउन बालुवामा मोडेल राख्ने
2.) गेटिङ प्रणालीमा मोडेल र बालुवाको समावेश
3.) मोडेल हटाउने
४.) पग्लिएको धातुले मोल्ड गुहा भर्ने
5.) धातु को शीतलन
6.) बालुवा मोल्ड तोड्ने र कास्टिङ हटाउने
• प्लास्टर मोल्ड कास्टिङ: बालुवा ढाल्ने जस्तै, र बालुवाको सट्टा, प्लास्टर अफ पेरिस मोल्ड सामग्रीको रूपमा प्रयोग भइरहेको छ। बालुवा कास्टिङ र सस्तो जस्ता छोटो उत्पादन नेतृत्व समय। राम्रो आयामी सहिष्णुता र सतह समाप्त। यसको प्रमुख हानि यो हो कि यो केवल कम पिघलने बिन्दु धातुहरु जस्तै एल्युमिनियम र जस्ता संग प्रयोग गर्न सकिन्छ।
• शेल मोल्ड कास्टिङ: बालुवा कास्टिङ जस्तै। बालुवा कास्टिङ प्रक्रियामा जस्तै बालुवाले भरिएको फ्लास्कको सट्टा बालुवाको कडा खोल र थर्मोसेटिंग राल बाइन्डरद्वारा प्राप्त मोल्ड गुहा। बालुवा द्वारा कास्ट गर्न उपयुक्त लगभग कुनै पनि धातु शेल मोल्डिंग द्वारा कास्ट गर्न सकिन्छ। प्रक्रिया निम्न रूपमा संक्षेप गर्न सकिन्छ:
1.) खोल मोल्ड को निर्माण। बालुवा कास्टिङमा प्रयोग गरिएको बालुवाको तुलनामा प्रयोग गरिएको बालुवा धेरै सानो दानाको आकारको हुन्छ। राम्रो बालुवा थर्मोसेटिंग राल संग मिश्रित छ। खोल हटाउन सजिलो बनाउन धातुको ढाँचालाई पार्टिङ एजेन्टसँग लेपित गरिएको छ। त्यसपछि धातुको ढाँचा तताइन्छ र बालुवाको मिश्रणलाई तातो कास्टिङ ढाँचामा छिद्रो पारिन्छ वा उडाइन्छ। ढाँचाको सतहमा पातलो खोल बनाउँछ। यस खोलको मोटाईलाई बालुवा राल मिश्रण धातुको ढाँचासँग सम्पर्कमा रहेको समयको लम्बाइ फरक गरेर समायोजन गर्न सकिन्छ। त्यसपछि खुकुलो बालुवा खोलिएको ढाँचा बाँकी राखेर हटाइन्छ।
2.) अर्को, खोल र ढाँचालाई ओभनमा तताइन्छ ताकि खोल कडा हुन्छ। कडाई पूरा भएपछि, खोललाई ढाँचामा निर्मित पिनहरू प्रयोग गरेर ढाँचाबाट बाहिर निकालिन्छ।
3.) त्यस्ता दुईवटा गोलाहरू ग्लुइङ वा क्ल्याम्पिङद्वारा एकसाथ जोडिन्छन् र पूर्ण मोल्ड बनाउँछन्। अब शेल मोल्ड कन्टेनरमा सम्मिलित गरिएको छ जसमा कास्टिङ प्रक्रियाको क्रममा बालुवा वा धातु शट द्वारा समर्थित छ।
4.) अब तातो धातु खोल मोल्ड मा खन्याउन सकिन्छ।
शेल कास्टिङका फाइदाहरू धेरै राम्रो सतह फिनिश भएका उत्पादनहरू, उच्च आयामी शुद्धताका साथ जटिल भागहरू निर्माण गर्ने सम्भावना, स्वचालित गर्न सजिलो प्रक्रिया, ठूलो मात्रा उत्पादनको लागि किफायती।
बेफाइदाहरू हुन् मोल्डहरूलाई राम्रो भेन्टिलेसन आवश्यक हुन्छ किनभने ग्यासहरू सिर्जना हुन्छन् जब पग्लिएको धातुले बाइन्डर केमिकललाई सम्पर्क गर्दछ, थर्मोसेटिंग रेसिनहरू र धातुको ढाँचाहरू महँगो हुन्छन्। धातु ढाँचाको लागतको कारणले, प्रविधि कम मात्रा उत्पादन रनको लागि राम्रोसँग उपयुक्त नहुन सक्छ।
• इन्भेस्टमेन्ट कास्टिङ (LOST-WAX CASTING को रूपमा पनि चिनिन्छ): धेरै पुरानो प्रविधि र उच्च शुद्धता, दोहोरिने क्षमता, बहुमुखी प्रतिभा र धेरै धातुहरू, दुर्दम्य सामग्री र विशेष उच्च प्रदर्शन मिश्र धातुहरूबाट गुणस्तरीय भागहरू निर्माण गर्नका लागि उपयुक्त। साना र ठूला आकारका भागहरू उत्पादन गर्न सकिन्छ। केही अन्य विधिहरूसँग तुलना गर्दा महँगो प्रक्रिया, तर प्रमुख फाइदा भनेको नजिकको नेट आकार, जटिल रूप र विवरणहरूको साथ भागहरू उत्पादन गर्ने सम्भावना हो। त्यसोभए लागत केहि हदसम्म पुन: कार्य र मेसिनिंग को उन्मूलन द्वारा अफसेट छ केहि अवस्थामा। यद्यपि त्यहाँ भिन्नताहरू हुन सक्छन्, यहाँ सामान्य लगानी कास्टिङ प्रक्रियाको सारांश छ:
१.) मोम वा प्लास्टिकबाट मौलिक मास्टर ढाँचाको सिर्जना। प्रत्येक कास्टिङलाई एउटा ढाँचा चाहिन्छ किनभने यी प्रक्रियामा नष्ट हुन्छन्। ढाँचा जसबाट ढाँचाहरू बनाइन्छ पनि आवश्यक छ र अधिकतर समय मोल्ड कास्ट वा मेसिन गरिएको छ। किनभने मोल्ड खोल्न आवश्यक छैन, जटिल कास्टिङहरू प्राप्त गर्न सकिन्छ, धेरै मोम ढाँचाहरू रूखको हाँगाहरू जस्तै जडान गर्न सकिन्छ र एकसाथ खन्याउन सकिन्छ, यसरी धातु वा धातु मिश्रको एकल खन्याइबाट धेरै भागहरूको उत्पादन सक्षम पार्छ।
2.) त्यसपछि, ढाँचालाई धेरै राम्रो दाना भएको सिलिका, पानी, बाइन्डरहरू मिलेर बनेको दुर्दम्य स्लरीसँग डुबाइन्छ वा खन्याइन्छ। यसले ढाँचाको सतहमा सिरेमिक तहमा परिणाम दिन्छ। ढाँचामा अपवर्तक कोट सुख्खा र कडा गर्न छोडिन्छ। यो चरण हो जहाँ नाम लगानी कास्टिङबाट आउँछ: रिफ्रेक्ट्री स्लरी मोम ढाँचामा लगानी गरिन्छ।
3.) यस चरणमा, कडा सिरेमिक मोल्डलाई उल्टो र तताइन्छ ताकि मोम पग्लन्छ र मोल्डबाट बाहिर निस्कन्छ। धातु कास्टिङको लागि गुफा पछाडि छोडिएको छ।
4.) मोम बाहिर भएपछि, सिरेमिक मोल्डलाई अझ बढी तापक्रममा तताइन्छ जसले मोल्डलाई बलियो बनाउँछ।
5.) सबै जटिल खण्डहरू भरेर तातो मोल्डमा धातु कास्टिङ खन्याइन्छ।
6.) कास्टिङलाई ठोस बनाउन अनुमति दिइएको छ
7.) अन्तमा सिरेमिक मोल्ड भाँचिन्छ र उत्पादित भागहरू रूखबाट काटिन्छ।
यहाँ लगानी कास्टिङ प्लान्ट ब्रोशरको लिङ्क छ
• बाष्पीकरण ढाँचा कास्टिङ: प्रक्रियाले पोलिस्टाइरिन फोम जस्ता सामग्रीबाट बनेको ढाँचा प्रयोग गर्दछ जुन तातो पग्लिएको धातु मोल्डमा खन्याइँदा वाष्पीकरण हुन्छ। यस प्रक्रियाका दुई प्रकार छन्: LOST FOAM CASTING जसले अनबन्डेड बालुवा प्रयोग गर्दछ र पूर्ण मोल्ड कास्टिङ जसले बन्धित बालुवा प्रयोग गर्दछ। यहाँ सामान्य प्रक्रिया चरणहरू छन्:
1.) polystyrene जस्ता सामग्रीबाट ढाँचा निर्माण गर्नुहोस्। जब ठूलो मात्रामा उत्पादन गरिनेछ, ढाँचा मोल्ड गरिएको छ। यदि भागमा जटिल आकार छ भने, त्यस्ता फोम सामग्रीका धेरै खण्डहरू ढाँचा बनाउनको लागि सँगै पालन गर्न आवश्यक पर्दछ। कास्टिङमा राम्रो सतह फिनिश सिर्जना गर्न हामी प्राय: ढाँचालाई दुर्दम्य कम्पाउन्डसँग कोट गर्छौं।
2.) ढाँचा त्यसपछि मोल्डिंग बालुवा मा राखिएको छ।
3.) पग्लिएको धातुलाई मोल्डमा खन्याइन्छ, फोमको ढाँचालाई वाष्पीकरण गर्दै, अर्थात् धेरैजसो अवस्थामा यो मोल्ड गुहाबाट बग्दा पोलिस्टाइरिन।
४.) पग्लिएको धातुलाई बालुवाको मोल्डमा कडा बनाउन छोडिन्छ।
5.) यो कडा भएपछि, हामी कास्टिङ हटाउँछौं।
केही अवस्थामा, हामीले उत्पादन गर्ने उत्पादनलाई ढाँचा भित्र कोर चाहिन्छ। बाष्पीकरणीय कास्टिङमा, मोल्ड गुहामा कोर राख्न र सुरक्षित गर्न आवश्यक छैन। यो प्रविधि धेरै जटिल ज्यामितिहरूको निर्माणको लागि उपयुक्त छ, यसलाई उच्च मात्रा उत्पादनको लागि सजिलै स्वचालित गर्न सकिन्छ, र कास्ट भागमा कुनै विभाजन रेखाहरू छैनन्। आधारभूत प्रक्रिया सरल र कार्यान्वयन गर्न किफायती छ। ठुलो मात्राको उत्पादनको लागि, पोलिस्टीरिनबाट ढाँचाहरू उत्पादन गर्न डाइ वा मोल्ड आवश्यक पर्ने हुनाले, यो केही महँगो हुन सक्छ।
• गैर-विस्तारयोग्य मोल्ड कास्टिङ: यो व्यापक श्रेणीले प्रत्येक उत्पादन चक्र पछि मोल्डलाई सुधार गर्न आवश्यक पर्दैन। उदाहरणहरू स्थायी, मर, निरन्तर र केन्द्रापसारक कास्टिङ हुन्। पुनरावृत्ति प्राप्त हुन्छ र भागहरू NEAR NET SHAPE को रूपमा चित्रण गर्न सकिन्छ।
• स्थायी मोल्ड कास्टिङ: धातुबाट बनेको पुन: प्रयोज्य मोल्डहरू बहु कास्टिङका लागि प्रयोग गरिन्छ। स्थायी मोल्ड सामान्यतया हजारौं पटक प्रयोग गर्न सकिन्छ यो बाहिर जानु अघि। गुरुत्वाकर्षण, ग्यासको दबाब वा भ्याकुम सामान्यतया मोल्ड भर्न प्रयोग गरिन्छ। मोल्डहरू (जसलाई डाइ पनि भनिन्छ) सामान्यतया फलाम, स्टिल, सिरेमिक वा अन्य धातुहरूबाट बनेको हुन्छ। सामान्य प्रक्रिया हो:
1.) मेसिन र मोल्ड सिर्जना गर्नुहोस्। एकै ठाउँमा मिल्ने र खोल्न र बन्द गर्न सकिने दुईवटा धातुका ब्लकहरूबाट मोल्ड बनाउनु सामान्य कुरा हो। दुबै भाग सुविधाहरू साथै गेटिङ प्रणाली सामान्यतया कास्टिङ मोल्डमा मिसिन गरिन्छ।
2.) आन्तरिक मोल्ड सतहहरू दुर्दम्य सामग्रीहरू समावेश गरी स्लरीले लेपित हुन्छन्। यसले तातो प्रवाहलाई नियन्त्रण गर्न मद्दत गर्दछ र कास्ट भागलाई सजिलै हटाउनको लागि स्नेहकको रूपमा कार्य गर्दछ।
3.) अर्को, स्थायी मोल्ड आधा बन्द छन् र मोल्ड तताइन्छ।
4.) पग्लिएको धातु मोल्डमा खन्याइन्छ र स्थिरताको लागि छोडिन्छ।
5.) धेरै चिसो हुनु अघि, हामी मोल्ड आधा खोल्दा इजेक्टरहरू प्रयोग गरेर स्थायी मोल्डबाट भाग हटाउँछौं।
हामी प्रायः जस्ता र एल्युमिनियम जस्ता कम पिघलने बिन्दु धातुहरूको लागि स्थायी मोल्ड कास्टिङ प्रयोग गर्छौं। स्टिल कास्टिङका लागि, हामी मोल्ड सामग्रीको रूपमा ग्रेफाइट प्रयोग गर्छौं। हामी कहिलेकाहीँ स्थायी मोल्ड भित्र कोर प्रयोग गरेर जटिल ज्यामितिहरू प्राप्त गर्छौं। यस प्रविधिका फाइदाहरू द्रुत शीतलन, गुणहरूमा एकरूपता, राम्रो शुद्धता र सतह समाप्ति, कम अस्वीकार दरहरू, प्रक्रियालाई स्वचालित गर्ने सम्भावना र आर्थिक रूपमा उच्च मात्रा उत्पादन गर्ने राम्रो मेकानिकल गुणहरूका साथ कास्टिंगहरू हुन्। हानिहरू उच्च प्रारम्भिक सेटअप लागतहरू हुन् जसले यसलाई कम भोल्युम सञ्चालनका लागि अनुपयुक्त बनाउँदछ, र निर्मित भागहरूको आकारमा सीमितताहरू।
• डाइ कास्टिङ: डाइलाई मेसिनमा लगाइन्छ र पग्लिएको धातुलाई उच्च दबाबमा मोल्ड क्याभिटीहरूमा धकेलिन्छ। दुबै अलौह र लौह धातु डाइ कास्टिङ सम्भव छ। प्रक्रिया विवरणहरू, अत्यन्त पातलो पर्खालहरू, आयामी स्थिरता र राम्रो सतह फिनिशको साथ साना देखि मध्यम आकारका भागहरूको उच्च मात्रा उत्पादन रनहरूको लागि उपयुक्त छ। AGS-TECH Inc. यस प्रविधिको प्रयोग गरेर 0.5 मिमी जति सानो पर्खाल मोटाई निर्माण गर्न सक्षम छ। स्थायी मोल्ड कास्टिङमा जस्तै, मोल्डमा दुई भागहरू समावेश हुनुपर्दछ जुन उत्पादन गरिएको भाग हटाउनको लागि खोल्न र बन्द गर्न सकिन्छ। प्रत्येक चक्र संग धेरै कास्टिङ को उत्पादन सक्षम गर्न एक डाइ कास्टिङ मोल्ड मा धेरै गुहा हुन सक्छ। डाइ कास्टिङ मोल्डहरू धेरै भारी हुन्छन् र तिनीहरूले उत्पादन गरेका भागहरू भन्दा धेरै ठूला हुन्छन्, त्यसैले महँगो पनि हुन्छ। हामी हाम्रा ग्राहकहरूको लागि नि:शुल्क मर्मत र प्रतिस्थापन गर्छौं जबसम्म उनीहरूले हामीबाट आफ्ना भागहरू पुन: क्रमबद्ध गर्छन्। हाम्रो मृत्यु धेरै लाख चक्र दायरा मा लामो जीवनकाल छ।
यहाँ आधारभूत सरलीकृत प्रक्रिया चरणहरू छन्:
1.) सामान्यतया स्टिलबाट मोल्डको उत्पादन
2.) डाई कास्टिङ मेसिनमा मोल्ड स्थापना गरियो
3.) पिस्टनले जटिल विशेषताहरू र पातलो पर्खालहरू भरेर डाई क्याभिटीहरूमा पग्लिएको धातुलाई प्रवाह गर्न बाध्य पार्छ।
४.) पग्लिएको धातुले मोल्ड भरेपछि, कास्टिङलाई दबाबमा कडा बनाइन्छ
5.) मोल्ड खोलिएको छ र इजेक्टर पिनको सहायताले कास्टिङ हटाइन्छ।
6.) अब खाली डाईलाई फेरि लुब्रिकेट गरिन्छ र अर्को चक्रको लागि क्ल्याम्प गरिन्छ।
डाइ कास्टिङमा, हामी प्रायः इन्सर्ट मोल्डिङ प्रयोग गर्छौं जहाँ हामी मोल्डमा थप भाग समावेश गर्छौं र यसको वरिपरि धातु कास्ट गर्छौं। दृढता पछि, यी भागहरू कास्ट उत्पादनको भाग बन्छन्। डाइ कास्टिङका फाइदाहरू भागहरूको राम्रो मेकानिकल गुणहरू, जटिल सुविधाहरूको सम्भावना, राम्रो विवरण र राम्रो सतह समाप्त, उच्च उत्पादन दरहरू, सजिलो स्वचालन हो। बेफाइदाहरू हुन्: उच्च डाई र उपकरण लागतको कारण कम भोल्युमको लागि उपयुक्त छैन, कास्ट गर्न सकिने आकारहरूमा सीमितताहरू, इजेक्टर पिनको सम्पर्कको कारणले कास्ट पार्टहरूमा सानो गोल चिन्हहरू, पार्टिङ लाइनमा निचोडिएको धातुको पातलो फ्ल्यास, आवश्यकता डाइ बीचको विभाजन रेखामा भेन्टहरूका लागि, पानीको परिसंचरण प्रयोग गरेर मोल्डको तापक्रम कम राख्न आवश्यक छ।
• सेन्ट्रिफ्यूगल कास्टिङ: घूर्णन अक्षमा घुम्ने मोल्डको केन्द्रमा पग्लिएको धातु खन्याइन्छ। केन्द्रापसारक बलहरूले धातुलाई परिधितिर फ्याँक्छ र मोल्ड घुमिरहँदा यसलाई बलियो हुन दिइन्छ। दुबै तेर्सो र ठाडो अक्ष परिक्रमा प्रयोग गर्न सकिन्छ। गोलाकार भित्री सतहहरू र अन्य गैर-गोलाकार आकारहरू भएका भागहरू कास्ट गर्न सकिन्छ। प्रक्रिया निम्न रूपमा संक्षेप गर्न सकिन्छ:
1.) पग्लिएको धातु केन्द्रापसारक मोल्डमा खन्याइन्छ। मोल्डको कताईको कारण धातु त्यसपछि बाहिरी पर्खालहरूमा बाध्य हुन्छ।
2.) मोल्ड घुमाउँदा, धातु कास्टिङ कडा हुन्छ
सेन्ट्रीफ्यूगल कास्टिङ पाइप जस्ता खोक्रो बेलनाकार भागहरू उत्पादन गर्न उपयुक्त प्रविधि हो, स्प्रू, राइजर र गेटिङ एलिमेन्टहरू आवश्यक पर्दैन, सतहको राम्रो फिनिश र विस्तृत सुविधाहरू, कुनै संकुचन समस्याहरू छैनन्, धेरै ठूला व्यास भएका लामो पाइपहरू उत्पादन गर्ने सम्भावना, उच्च दर उत्पादन क्षमता। ।
• निरन्तर कास्टिङ (स्ट्र्यान्ड कास्टिङ): धातुको निरन्तर लम्बाइ कास्ट गर्न प्रयोग गरिन्छ। मूलतः पग्लिएको धातुलाई मोल्डको दुई आयामी प्रोफाइलमा कास्ट गरिन्छ तर यसको लम्बाइ अनिश्चित हुन्छ। नयाँ पिघलाएको धातुलाई निरन्तर मोल्डमा खुवाइन्छ किनकि कास्टिङ समयसँगै यसको लम्बाइ बढ्दै तल तर्फ जान्छ। तामा, स्टिल, आल्मुनियम जस्ता धातुहरूलाई निरन्तर कास्टिङ प्रक्रिया प्रयोग गरेर लामो स्ट्र्यान्डमा कास्ट गरिन्छ। प्रक्रियामा विभिन्न कन्फिगरेसनहरू हुन सक्छन् तर सामान्यलाई निम्न रूपमा सरलीकृत गर्न सकिन्छ:
1.) पग्लिएको धातु राम्रोसँग गणना गरिएको मात्रा र प्रवाह दरमा मोल्डको माथि रहेको कन्टेनरमा खन्याइन्छ र पानी चिसो मोल्डबाट बग्छ। मोल्डमा खन्याइएको धातु कास्टिङ मोल्डको फेदमा राखिएको स्टार्टर बारमा ठोस हुन्छ। यो स्टार्टर बारले रोलरहरूलाई सुरुमा समात्न केही दिन्छ।
2.) लामो धातु स्ट्र्यान्ड एक स्थिर गति मा रोलर द्वारा बोकिन्छ। रोलरहरूले मेटल स्ट्र्यान्डको प्रवाहको दिशालाई ठाडोबाट तेर्सोमा परिवर्तन गर्दछ।
3.) लगातार कास्टिङले निश्चित तेर्सो दूरी पार गरिसकेपछि, कास्टिङसँग चल्ने टर्च वा आराले यसलाई चाँडै इच्छित लम्बाइमा काट्छ।
निरन्तर कास्टिङ प्रक्रियालाई रोलिङ प्रक्रियासँग एकीकृत गर्न सकिन्छ, जहाँ आइ-बीमहरू, टी-बीमहरू... आदि उत्पादन गर्न लगातार कास्ट मेटललाई सिधै रोलिङ मिलमा खुवाउन सकिन्छ। निरन्तर कास्टिङले सम्पूर्ण उत्पादनमा समान गुणहरू उत्पादन गर्दछ, यसको उच्च घनत्व दर छ, सामग्रीको धेरै कम हानिको कारण लागत घटाउँछ, एक प्रक्रिया प्रदान गर्दछ जहाँ धातुको लोडिङ, खन्याउने, ठोसीकरण, काट्ने र कास्टिङ हटाउने सबै निरन्तर सञ्चालनमा हुन्छन्। यसरी उच्च उत्पादकता दर र उच्च गुणस्तरको परिणाम। एक प्रमुख विचार उच्च प्रारम्भिक लगानी, सेटअप लागत र ठाउँ आवश्यकताहरु हो।
• मेसिनिङ सेवाहरू: हामी तीन, चार र पाँच - अक्ष मेसिनिङ प्रस्ताव गर्छौं। हामीले प्रयोग गर्ने मेसिनिङ प्रक्रियाहरूको प्रकार टर्निङ, मिलिङ, ड्रिलिङ, बोरिङ, ब्रोचिङ, प्लानिङ, SAWING, ग्राइन्डिङ, ल्यापिङ, पालिसिङ र गैर-परम्परागत मेशिनिङहरू हुन् जुन हाम्रो वेबसाइटको फरक मेनु अन्तर्गत थप विस्तार गरिएको छ। हाम्रा धेरैजसो उत्पादनका लागि, हामी सीएनसी मेसिनहरू प्रयोग गर्छौं। यद्यपि केही अपरेशनहरूको लागि परम्परागत प्रविधिहरू राम्रो फिट हुन्छन् र त्यसैले हामी तिनीहरूमा पनि भर पर्छौं। हाम्रो मेसिनिंग क्षमताहरू सम्भव उच्चतम स्तरमा पुग्छन् र केहि धेरै माग भएका भागहरू AS9100 प्रमाणित प्लान्टमा निर्मित हुन्छन्। जेट इन्जिन ब्लेडहरूलाई उच्च विशिष्ट उत्पादन अनुभव र सही उपकरण चाहिन्छ। एयरोस्पेस उद्योगसँग धेरै कडा मापदण्डहरू छन्। जटिल ज्यामितीय संरचना भएका केही कम्पोनेन्टहरू पाँच अक्ष मेसिनिङद्वारा सजिलैसँग निर्मित हुन्छन्, जुन हाम्रो लगायत केही मेसिनिङ प्लान्टहरूमा मात्र पाइन्छ। हाम्रो एयरोस्पेस प्रमाणित प्लान्टसँग एयरोस्पेस उद्योगको व्यापक कागजात आवश्यकताहरूको पालना गर्ने आवश्यक अनुभव छ।
टर्निङ अपरेसनहरूमा, वर्कपीस घुमाइन्छ र काट्ने उपकरण विरुद्ध सारियो। यस प्रक्रियाका लागि लेथ नामक मेसिन प्रयोग भइरहेको छ।
मिलिङमा, मिलिङ मेसिन भनिने मेसिनमा वर्कपीसको विरुद्धमा काट्ने किनारहरू ल्याउन घुम्ने उपकरण हुन्छ।
ड्रिलिंग कार्यहरूमा काट्ने किनारहरू सहित घुम्ने कटर समावेश हुन्छ जसले वर्कपीससँग सम्पर्कमा प्वालहरू उत्पादन गर्दछ। ड्रिल प्रेस, खराद वा मिल सामान्यतया प्रयोग गरिन्छ।
बोरिङ सञ्चालनहरूमा प्वाललाई थोरै ठुलो बनाउन र शुद्धतामा सुधार गर्नको लागि एकल झुकेको टिप भएको उपकरणलाई स्पिनिङ वर्कपीसको कुनै नराम्रो प्वालमा सारिन्छ। यो राम्रो परिष्करण उद्देश्यका लागि प्रयोग गरिन्छ।
ब्रोचिङमा ब्रोचको एउटा पासमा रहेको वर्कपीसबाट सामग्री हटाउन दाँत भएको औजार समावेश हुन्छ। रैखिक ब्रोचिंगमा, ब्रोच काटलाई प्रभाव पार्न वर्कपीसको सतहमा रेखीय रूपमा दौडन्छ, जबकि रोटरी ब्रोचिंगमा, ब्रोच घुमाइएको हुन्छ र अक्ष सममित आकार काट्न वर्कपीसमा थिचिन्छ।
SWISS TYPE MACHINING हाम्रो मूल्यवान प्रविधिहरू मध्ये एक हो जुन हामीले साना उच्च परिशुद्धता भागहरूको उच्च मात्रा निर्माणको लागि प्रयोग गर्छौं। स्विस-प्रकारको खराद प्रयोग गरेर हामी सस्तो, जटिल, सटीक भागहरू बदल्छौं। परम्परागत खरादहरू जस्तो नभई जहाँ वर्कपीसलाई स्थिर राखिन्छ र उपकरण चलाइन्छ, स्विस-प्रकार घुमाउने केन्द्रहरूमा, वर्कपीसलाई Z-अक्षमा सार्न अनुमति दिइन्छ र उपकरण स्थिर हुन्छ। स्विस-प्रकारको मेसिनिङमा, बार स्टकलाई मेसिनमा राखिन्छ र z-अक्षमा गाईड बुशिङको माध्यमबाट अगाडि बढाइन्छ, केवल मेशिन गर्नको लागि भागलाई उजागर गर्दछ। यस तरिकाले कडा पकड सुनिश्चित गरिएको छ र शुद्धता धेरै उच्च छ। प्रत्यक्ष उपकरणहरूको उपलब्धताले गाइड बुशिंगबाट सामग्रीको प्रगतिको रूपमा मिल र ड्रिल गर्ने अवसर प्रदान गर्दछ। स्विस-प्रकारको उपकरणको Y-अक्षले पूर्ण मिलिङ क्षमताहरू प्रदान गर्दछ र निर्माणमा धेरै समय बचत गर्दछ। यसबाहेक, हाम्रा मेसिनहरूमा ड्रिलहरू र बोरिङ उपकरणहरू छन् जुन भागमा काम गर्दछ जब यो सब स्पिन्डलमा राखिन्छ। हाम्रो स्विस-प्रकार मेसिनिङ क्षमताले हामीलाई एकल सञ्चालनमा पूर्ण स्वचालित पूर्ण मेसिनिङ अवसर दिन्छ।
मेसिनिङ AGS-TECH Inc. व्यवसायको सबैभन्दा ठूलो खण्डहरू मध्ये एक हो। हामी या त यसलाई प्राथमिक अपरेसनको रूपमा प्रयोग गर्छौं वा कुनै भाग कास्टिङ वा बाहिर निकालेपछि माध्यमिक अपरेशनको रूपमा प्रयोग गर्छौं ताकि सबै रेखाचित्र विनिर्देशहरू पूरा हुन्छन्।
• सर्फेस फिनिसिङ सेवाहरू: हामी सतहको उपचार र सतह फिनिशिङको एक विशाल विविधता प्रदान गर्दछौं जस्तै टाँसिएको सतह बढाउनको लागि, पातलो अक्साइड तह जम्मा गर्ने कोटिंग, स्यान्ड ब्लास्टिङ, केम-फिल्म, एनोडाइजिंग, नाइट्राइडिङ, पाउडर कोटिंग, स्प्रे कोटिंग। , विभिन्न उन्नत धातुकरण र कोटिंग प्रविधिहरू सहित स्पटरिङ, इलेक्ट्रोन बीम, वाष्पीकरण, प्लेटिङ, हार्ड कोटिंग्स जस्तै कार्बन (DLC) वा ड्रिलिंग र काट्ने उपकरणहरूको लागि टाइटेनियम कोटिंग।
• उत्पादन मार्किङ र लेबलिङ सेवाहरू: हाम्रा धेरै ग्राहकहरूलाई चिन्ह लगाउने र लेबलिङ, लेजर चिन्ह लगाउने, धातुका भागहरूमा नक्काशी गर्न आवश्यक छ। यदि तपाइँसँग त्यस्तो कुनै आवश्यकता छ भने, हामी तपाइँको लागि कुन विकल्प उत्तम हुनेछ छलफल गरौं।
यहाँ केहि सामान्यतया प्रयोग हुने धातु कास्ट उत्पादनहरू छन्। यी अफ-द-शेल्फ भएको हुनाले, यी मध्ये कुनै पनि तपाईंको आवश्यकताहरू फिट भएमा तपाईंले मोल्ड लागतहरूमा बचत गर्न सक्नुहुन्छ: