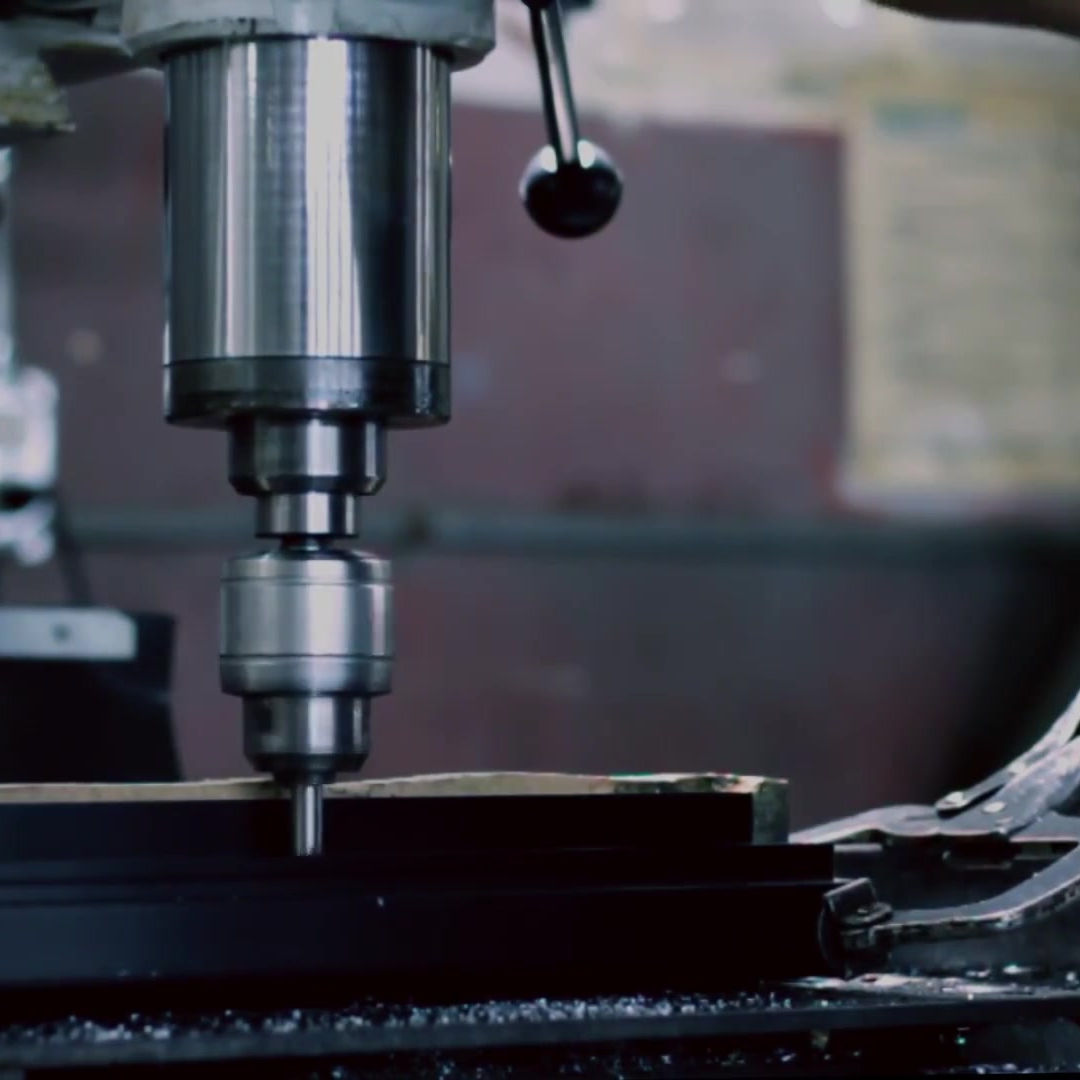
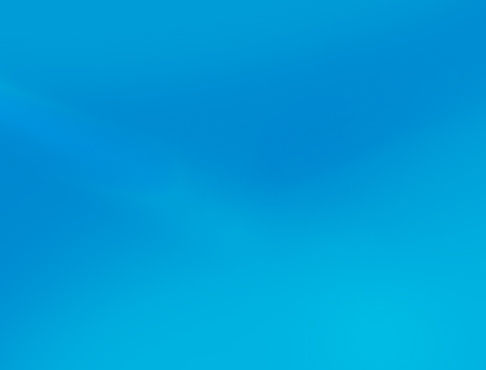
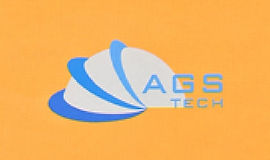
विश्वव्यापी कस्टम निर्माता, इन्टिग्रेटर, कन्सोलिडेटर, उत्पादन र सेवाहरूको विस्तृत विविधताका लागि आउटसोर्सिङ पार्टनर।
हामी उत्पादन, निर्माण, ईन्जिनियरिङ्, एकीकरण, एकीकरण, अनुकूलन निर्मित र अफ-शेल्फ उत्पादन र सेवाहरूको आउटसोर्सिङको लागि तपाईंको एक-स्टप स्रोत हौं।
आफ्नो भाषा छान्नुहोस्
-
कस्टम निर्माण
-
घरेलु र विश्वव्यापी अनुबंध निर्माण
-
उत्पादन आउटसोर्सिङ
-
घरेलु र विश्वव्यापी खरीद
-
Consolidation
-
इन्जिनियरिङ एकीकरण
-
इन्जिनियरिङ सेवाहरू
ELECTRICAL DISCHARGE MACHINING (EDM), also referred to as SPARK-EROSION or ELECTRODISCHARGE MACHINING, SPARK ERODING, DIE SINKING_cc781905-5cde-3194-bb3b -136bad5cf58d_or WIRE EROSION, is a NON-CONVENTIONAL MANUFACTURING process where erosion of metals takes place and desired shape is obtained using electrical discharges in the form स्पार्क्स को। हामी EDM का केही प्रकारहरू पनि प्रस्ताव गर्छौं, जस्तै NO-WEAR EDM, WIRE EDM (WEDM), EDM GRINDING (EDG), DIE-SINKING EDM, ELECTRICAL-DISCHARGEDM, m5-cc-MILLEDM, micro-DISCHARGEEDM5 -5cde-3194-bb3b-136bad5cf58d_and ELECTROCHEMICAL-DISCHARGE GRINDING (ECDG)। हाम्रो EDM प्रणालीहरूमा आकारको उपकरण/इलेक्ट्रोड र DC पावर सप्लाईमा जोडिएको वर्कपीस र विद्युतीय रूपमा ननकन्डक्टिङ डाइलेक्ट्रिक फ्लुइडमा सम्मिलित हुन्छ। 1940 पछि इलेक्ट्रिकल डिस्चार्ज मेसिनिंग उत्पादन उद्योगहरूमा सबैभन्दा महत्त्वपूर्ण र लोकप्रिय उत्पादन प्रविधिहरू मध्ये एक भएको छ।
जब दुई इलेक्ट्रोडहरू बीचको दूरी कम हुन्छ, इलेक्ट्रोडहरू बीचको भोल्युममा विद्युतीय क्षेत्रको तीव्रता केही बिन्दुहरूमा डाइइलेक्ट्रिकको बल भन्दा बढी हुन्छ, जुन टुट्छ, अन्ततः दुई इलेक्ट्रोडहरू बीचको प्रवाहको लागि पुल बनाउँछ। वर्कपीसको एक भाग र केही टुलिङ सामाग्री पगाल्न महत्त्वपूर्ण तताउने कारणले तीव्र विद्युतीय चाप उत्पन्न हुन्छ। नतिजाको रूपमा, सामग्री दुवै इलेक्ट्रोडबाट हटाइन्छ। एकै समयमा, डाइइलेक्ट्रिक फ्लुइड चाप ग्याप मा तरल को वाष्पीकरण को परिणामस्वरूप, चाँडै तताइएको छ। एक पटक हालको प्रवाह बन्द भएपछि वा यो बन्द भएपछि वरपरको डाइइलेक्ट्रिक फ्लुइडले ग्यासको बबलबाट तातो हटाउँछ र बबल गुफाहरू (पत्न सक्छ)। बबलको पतन र वर्कपीस सतहबाट डाइइलेक्ट्रिक फ्लुइड फ्लश मलबेको प्रवाह र कुनै पनि पग्लिएको वर्कपीस सामग्रीलाई डाइइलेक्ट्रिक फ्लुइडमा प्रवेशद्वारा सिर्जना गरिएको सदमेको लहर। यी डिस्चार्जहरूको पुनरावृत्ति दर 50 देखि 500 kHz, 50 देखि 380 V बीचको भोल्टेज र 0.1 र 500 Amperes को बीचमा प्रवाहहरू छन्। नयाँ तरल डाइइलेक्ट्रिक जस्तै खनिज तेल, मट्टितेल वा डिस्टिल्ड र डिआयनाइज्ड पानी सामान्यतया इन्टर-इलेक्ट्रोड भोल्युममा ठोस कणहरू (भग्नावशेषको रूपमा) लैजान्छ र डाइलेक्ट्रिकको इन्सुलेट विशेषताहरू पुनर्स्थापित गरिन्छ। हालको प्रवाह पछि, दुई इलेक्ट्रोडहरू बीचको सम्भावित भिन्नता ब्रेकडाउन अघि के थियो भनेर पुनर्स्थापित हुन्छ, त्यसैले नयाँ तरल डाइलेक्ट्रिक ब्रेकडाउन हुन सक्छ। हाम्रो आधुनिक विद्युतीय डिस्चार्ज मेसिन (EDM) ले संख्यात्मक रूपमा नियन्त्रित चालहरू प्रदान गर्दछ र डाइलेक्ट्रिक तरल पदार्थहरूको लागि पम्पहरू र फिल्टरिङ प्रणालीहरूसँग सुसज्जित छन्।
इलेक्ट्रिकल डिस्चार्ज मेसिनिङ (EDM) एक मेसिनिङ विधि हो जुन मुख्यतया कडा धातुहरूका लागि प्रयोग गरिन्छ वा जुन परम्परागत प्रविधिहरूसँग मेसिन गर्न धेरै गाह्रो हुन्छ। EDM ले सामान्यतया कुनै पनि सामग्रीहरूसँग काम गर्दछ जुन विद्युतीय कन्डक्टरहरू हुन्, यद्यपि EDM सँग इन्सुलेट सिरेमिकहरू मेसिन गर्ने तरिकाहरू पनि प्रस्तावित गरिएको छ। पग्लने बिन्दु र पिघलिएको अव्यक्त ताप गुणहरू हुन् जसले प्रति डिस्चार्ज हटाइएको धातुको मात्रा निर्धारण गर्दछ। यी मानहरू जति उच्च हुन्छन्, सामग्री हटाउने दर त्यति नै ढिलो हुन्छ। किनभने विद्युतीय डिस्चार्ज मेसिनिङ प्रक्रियाले कुनै मेकानिकल ऊर्जा समावेश गर्दैन, वर्कपीसको कठोरता, बल र कठोरताले हटाउने दरलाई असर गर्दैन। डिस्चार्ज फ्रिक्वेन्सी वा ऊर्जा प्रति डिस्चार्ज, भोल्टेज र वर्तमान सामग्री हटाउने दरहरू नियन्त्रण गर्न भिन्न हुन्छन्। हालको घनत्व बढ्दै र स्पार्क फ्रिक्वेन्सी घट्दै गर्दा सामाग्री हटाउने दर र सतहको नरमपन बढ्छ। हामी ईडीएम प्रयोग गरेर पूर्व-कठोर स्टिलमा जटिल रूपरेखा वा गुहाहरू काट्न सक्छौं र तिनीहरूलाई नरम गर्न र पुन: कडा बनाउन तातो उपचारको आवश्यकता बिना। हामी यो विधि कुनै पनि धातु वा धातु मिश्र धातु जस्तै टाइटेनियम, हेस्टेलोय, कोभर, र इनकोनेल प्रयोग गर्न सक्छौं। EDM प्रक्रियाको अनुप्रयोगहरूले पोलीक्रिस्टलाइन हीरा उपकरणहरूको आकार समावेश गर्दछ। EDM लाई इलेक्ट्रोकेमिकल मेशिनिङ (ECM), वाटर जेट कटिङ (WJ, AWJ), लेजर काट्ने जस्ता प्रक्रियाहरूसँग गैर-परम्परागत वा गैर-परम्परागत मेसिनिङ विधि मानिन्छ। अर्कोतर्फ परम्परागत मेसिनिङ विधिहरूमा टर्निङ, मिलिङ, ग्राइन्डिङ, ड्रिलिङ र अन्य प्रक्रियाहरू समावेश हुन्छन् जसको सामग्री हटाउने मेकानिज्म अनिवार्य रूपमा मेकानिकल बलहरूमा आधारित हुन्छ। इलेक्ट्रिकल-डिस्चार्ज मेसिन (EDM) को लागि इलेक्ट्रोडहरू ग्रेफाइट, पीतल, तामा र तामा-टंगस्टन मिश्रबाट बनेका हुन्छन्। इलेक्ट्रोड व्यास ०.१ मिमी सम्म सम्भव छ। उपकरण पहिरनले EDM मा आयामी शुद्धतालाई प्रतिकूल रूपमा असर गर्ने एक अवांछित घटना भएकोले, हामी ध्रुवतालाई उल्टाएर र तामाका उपकरणहरू प्रयोग गरेर मिनिमिङ गर्नका लागि NO-WEAR EDM नामक प्रक्रियाको फाइदा लिन्छौं।
आदर्श रूपमा भन्नुपर्दा, इलेक्ट्रिकल-डिस्चार्ज मेसिनिङ (EDM) लाई इलेक्ट्रोडहरू बीचको डाइलेक्ट्रिक तरलको ब्रेकडाउन र पुनर्स्थापनाको श्रृंखला मान्न सकिन्छ। यद्यपि वास्तविकतामा, अन्तर-इलेक्ट्रोड क्षेत्रबाट मलबे हटाउने लगभग सधैं आंशिक हुन्छ। यसले अन्तर-इलेक्ट्रोड क्षेत्रमा डाइलेक्ट्रिकको विद्युतीय विशेषताहरू तिनीहरूको नाममात्र मानहरू भन्दा फरक हुन र समयसँगै भिन्न हुने कारण दिन्छ। अन्तर-इलेक्ट्रोड दूरी, (स्पार्क-ग्याप), प्रयोग गरिएको विशिष्ट मेसिनको नियन्त्रण एल्गोरिदम द्वारा समायोजित हुन्छ। EDM मा स्पार्क-गैप दुर्भाग्यवश कहिलेकाहीं मलबे द्वारा छोटो सर्किट हुन सक्छ। इलेक्ट्रोडको नियन्त्रण प्रणालीले दुई इलेक्ट्रोड (उपकरण र वर्कपीस) लाई छोटो सर्किटिङबाट रोक्नको लागि छिटो प्रतिक्रिया गर्न असफल हुन सक्छ। यो अवांछित सर्ट सर्किटले आदर्श केस भन्दा फरक रूपमा सामग्री हटाउन योगदान गर्दछ। हामी डाइइलेक्ट्रिकको इन्सुलेट गुणहरू पुनर्स्थापना गर्न फ्लशिङ कार्यलाई अत्यन्तै महत्त्व दिन्छौं ताकि करेन्ट सधैं अन्तर-इलेक्ट्रोड क्षेत्रको बिन्दुमा हुन्छ, जसले गर्दा उपकरण-इलेक्ट्रोडको आकार (क्षति) को अनावश्यक परिवर्तनको सम्भावना कम हुन्छ। र workpiece। एक विशिष्ट ज्यामिति प्राप्त गर्नको लागि, EDM उपकरणले यसलाई नछोइकन वर्कपीसको धेरै नजिक इच्छित मार्गमा निर्देशित गरिन्छ, हामी प्रयोगमा गति नियन्त्रणको प्रदर्शनमा अत्यन्त ध्यान दिन्छौं। यस तरिकाले, वर्तमान डिस्चार्ज / स्पार्कहरूको ठूलो संख्या हुन्छ, र प्रत्येकले उपकरण र वर्कपीस दुवैबाट सामग्री हटाउन योगदान गर्दछ, जहाँ साना क्रेटरहरू गठन हुन्छन्। क्रेटरहरूको साइज हातमा रहेको विशिष्ट कार्यको लागि सेट गरिएको प्राविधिक मापदण्डहरूको कार्य हो र आयामहरू नानोस्केल (जस्तै माइक्रो-ईडीएम अपरेसनहरूको मामलामा) देखि रफिंग अवस्थामा केही सयौं माइक्रोमिटरसम्म हुन सक्छन्। उपकरणमा रहेका यी साना क्रेटरहरूले इलेक्ट्रोडको बिस्तारै क्षरण गराउँछ जसलाई "उपकरण पहिरन" भनिन्छ। वर्कपीसको ज्यामितिमा पहिरनको हानिकारक प्रभावलाई प्रतिरोध गर्न हामी मेशिन सञ्चालनको क्रममा उपकरण-इलेक्ट्रोडलाई निरन्तर बदल्छौं। कहिलेकाहीँ हामी इलेक्ट्रोडको रूपमा निरन्तर प्रतिस्थापन गरिएको तार प्रयोग गरेर यो प्राप्त गर्छौं (यो EDM प्रक्रियालाई WIRE EDM पनि भनिन्छ)। कहिलेकाहीँ हामी उपकरण-इलेक्ट्रोडलाई यसरी प्रयोग गर्छौं कि यसको सानो भाग मात्र मेसिनिङ प्रक्रियामा संलग्न हुन्छ र यो भाग नियमित रूपमा परिवर्तन हुन्छ। यो, उदाहरणका लागि, उपकरण-इलेक्ट्रोड रूपमा घुमाउने डिस्क प्रयोग गर्दा मामला हो। यो प्रक्रिया भनिन्छ EDM GRINDING। हामीले प्रयोग गर्ने अर्को प्रविधिले पहिरनको क्षतिपूर्ति गर्न एउटै EDM सञ्चालनको क्रममा विभिन्न साइज र आकारहरूसँग इलेक्ट्रोडहरूको सेट प्रयोग गर्दछ। हामी यसलाई मल्टिपल इलेक्ट्रोड टेक्निक भन्छौं, र सामान्यतया प्रयोग गरिन्छ जब उपकरण इलेक्ट्रोडले नकारात्मक इच्छित आकारमा प्रतिकृति बनाउँछ र एकल दिशामा खाली दिशामा उन्नत हुन्छ, सामान्यतया ठाडो दिशा (जस्तै z-अक्ष)। यो डाइइलेक्ट्रिक तरलमा उपकरणको सिङ्कसँग मिल्दोजुल्दो छ जसमा वर्कपीस डुबाइएको छ, र त्यसैले यसलाई DIE-SINKING EDM_cc781905-5cbb6-bad31_31_time_cc781905-5cde-31_31_5cde-3194-5cf58d_DIE-SINKING भनिन्छ। 3194-bb3b-136bad5cf58d_CONVENTIONAL EDM or_cc781905-5cde-3194-bb3b-136bad5cf58d)। यस सञ्चालनका लागि मेसिनहरूलाई SINKER EDM भनिन्छ। यस प्रकारको EDM को लागि इलेक्ट्रोडहरू जटिल रूपहरू छन्। यदि अन्तिम ज्यामिति सामान्यतया साधारण आकारको इलेक्ट्रोड प्रयोग गरेर धेरै दिशाहरूमा सारियो र घुमाउने विषय पनि हो भने, हामी यसलाई EDM मिलिङ भन्छौं। पहिरनको मात्रा अपरेशनमा प्रयोग हुने प्राविधिक मापदण्डहरूमा कडा रूपमा निर्भर हुन्छ (ध्रुवता, अधिकतम वर्तमान, खुला सर्किट भोल्टेज)। उदाहरणका लागि, in micro-EDM, जसलाई m-EDM पनि भनिन्छ, यी प्यारामिटरहरू सामान्यतया गम्भीर मानहरू सेट हुन्छन्। तसर्थ, पहिरन त्यो क्षेत्रमा एक प्रमुख समस्या हो जुन हामीले हाम्रो संचित ज्ञान कसरी प्रयोग गरेर कम गर्छौं। उदाहरणका लागि, ग्रेफाइट इलेक्ट्रोडको पहिरन कम गर्न मिलिसेकेन्ड भित्र नियन्त्रण गर्न सकिने डिजिटल जेनेरेटरले इलेक्ट्रो-इरोसन हुने बित्तिकै ध्रुवतालाई उल्टाउँछ। यसले इलेक्ट्रोप्लेटिंग जस्तै प्रभाव पार्छ जसले लगातार क्षय भएको ग्रेफाइटलाई इलेक्ट्रोडमा फिर्ता जम्मा गर्दछ। अर्को विधिमा, तथाकथित ''शून्य पहिरन'' सर्किटमा हामीले डिस्चार्ज कति पटक सुरु हुन्छ र रोक्छ, यसलाई सकेसम्म लामो समयसम्म चलाएर राख्छौं। विद्युतीय-डिस्चार्ज मेसिनमा सामग्री हटाउने दर निम्नबाट अनुमान गर्न सकिन्छ:
MRR = 4 x 10 exp(4) x I x Tw exp (-1.23)
यहाँ MRR mm3/min मा छ, म एम्पीयरमा वर्तमान छु, Tw K-273.15K मा workpiece पिघलाउने बिन्दु हो। एक्सपोनेन्ट को लागि खडा छ।
अर्कोतर्फ, इलेक्ट्रोडको पहिरन दर Wt बाट प्राप्त गर्न सकिन्छ:
Wt = ( 1.1 x 10exp(11) ) x I x Ttexp (-2.38)
यहाँ Wt mm3/min मा छ र Tt K-273.15K मा इलेक्ट्रोड सामग्रीको पग्लने बिन्दु हो।
अन्तमा, इलेक्ट्रोड R मा workpiece को पहिरन अनुपात बाट प्राप्त गर्न सकिन्छ:
R = 2.25 x Trex(-2.38)
यहाँ Tr इलेक्ट्रोडमा workpiece को पिघलने बिन्दुहरूको अनुपात हो।
SINKER EDM :
बोन्डरको एडीएम, पनि AS_CC781905-5- B BB3B-138- bb3b-138- bb3b-138- bb3b-138- BB38- BB3PHEDED AMB4819094840948409484840948409409484094848484848409484094848484094848194094848409484848409484094094.ve-804840948409484840940948484094819484840948194094840940941940948409- इलेक्ट्रोड र workpiece एक पावर आपूर्ति जोडिएको छ। बिजुली आपूर्तिले दुई बीचको विद्युतीय क्षमता उत्पन्न गर्दछ। जब इलेक्ट्रोड वर्कपीसमा पुग्छ, तरल पदार्थमा डाइलेक्ट्रिक ब्रेकडाउन हुन्छ, प्लाज्मा च्यानल बनाउँछ, र सानो स्पार्क जम्प हुन्छ। स्पार्कहरू सामान्यतया एक पटकमा प्रहार गर्छन् किनभने अन्तर-इलेक्ट्रोड स्पेसमा विभिन्न स्थानहरूमा समान स्थानीय विद्युतीय विशेषताहरू हुने सम्भावना धेरै छैन जसले त्यस्ता सबै स्थानहरूमा एकैसाथ स्पार्क निस्कन सक्षम बनाउँछ। यी हजारौं स्पार्कहरू इलेक्ट्रोड र वर्कपीस प्रति सेकेन्डको बीचमा अनियमित बिन्दुहरूमा हुन्छन्। आधारभूत धातु घट्दै जाँदा, र स्पार्क ग्याप पछि बढ्दै जाँदा, हाम्रो CNC मेसिनद्वारा इलेक्ट्रोड स्वचालित रूपमा घटाइन्छ ताकि प्रक्रिया निर्बाध रूपमा जारी रहन सकोस्। हाम्रा उपकरणहरूमा ''समयमा'' र ''अफ टाइम'' भनेर चिनिने नियन्त्रक चक्रहरू छन्। टाइम सेटिङले स्पार्कको लम्बाइ वा अवधि निर्धारण गर्दछ। लामो समयले त्यो स्पार्कको लागि गहिरो गुहा र त्यस चक्रको लागि सबै पछिका स्पार्कहरू उत्पादन गर्दछ, जसले वर्कपीसमा रउर फिनिश सिर्जना गर्दछ र यसको विपरित। अफ टाइम भनेको समयको अवधि हो जुन एक स्पार्क अर्को द्वारा प्रतिस्थापित हुन्छ। लामो समयको बन्द समयले क्षय भएको मलबे सफा गर्नको लागि नोजल मार्फत डाइलेक्ट्रिक फ्लुइडलाई फ्लस गर्न अनुमति दिन्छ, जसले गर्दा सर्ट सर्किटबाट बच्न। यी सेटिङहरू माइक्रो सेकेन्डमा समायोजित हुन्छन्।
WIRE EDM :
In WIRE ELECTRICAL DISCHARGE MACHINING (WEDM), also called WIRE-CUT EDM or WIRE CUTTING, we feed a वर्कपीस मार्फत पीतलको पातलो सिंगल-स्ट्र्यान्ड धातुको तार, जुन डाइलेक्ट्रिक फ्लुइडको ट्याङ्कीमा डुबेको हुन्छ। तार EDM EDM को एक महत्त्वपूर्ण भिन्नता हो। हामी कहिलेकाहीं 300mm जति बाक्लो प्लेटहरू काट्न र अन्य उत्पादन विधिहरूसँग मेसिन गर्न गाह्रो हुने कडा धातुहरूबाट पञ्चहरू, औजारहरू र डाइहरू बनाउन तार-कट EDM प्रयोग गर्छौं। यस प्रक्रियामा जुन ब्यान्ड आरको साथ कन्टूर काट्ने जस्तो देखिन्छ, तार, जुन स्पूलबाट निरन्तर खुवाइन्छ, माथिल्लो र तल्लो हीरा गाइडहरू बीचमा राखिन्छ। सीएनसी-नियन्त्रित गाइडहरू x–y प्लेनमा सार्न सक्छन् र माथिल्लो गाइडले पनि z–u–v अक्षमा स्वतन्त्र रूपमा सार्न सक्छ, जसले ट्यापर्ड र ट्रान्जिसन आकारहरू (जस्तै तलको सर्कल र स्क्वायरमा काट्ने क्षमतालाई जन्म दिन्छ। शीर्ष)। माथिल्लो गाईडले x–y–u–v–i–j–k–l– मा अक्ष आन्दोलनहरू नियन्त्रण गर्न सक्छ। यसले WEDM लाई धेरै जटिल र नाजुक आकारहरू काट्न अनुमति दिन्छ। Ø ०.२५ ब्रास, तामा वा टंगस्टन तार प्रयोग गरेर उत्तम आर्थिक लागत र मेसिनिङ समय प्राप्त गर्ने हाम्रो उपकरणको औसत काट्ने कर्फ ०.३३५ एमएम हो। यद्यपि हाम्रो सीएनसी उपकरणको माथिल्लो र तल्लो हीरा गाइडहरू लगभग ०.००४ एमएमसम्म सही छन्, र Ø ०.०२ एमएम तार प्रयोग गरेर ०.०२१ मिमी जति सानो काट्ने मार्ग वा कर्फ हुन सक्छ। त्यसैले साँच्चै साँघुरो कटौती सम्भव छ। काट्ने चौडाइ तारको चौडाइ भन्दा ठूलो छ किनभने तारको छेउबाट वर्कपीसमा स्पार्किङ हुन्छ, जसले क्षरण निम्त्याउँछ। यो ''ओभरकट'' आवश्यक छ, धेरै अनुप्रयोगहरूको लागि यो अनुमानित छ र त्यसैले क्षतिपूर्ति गर्न सकिन्छ (माइक्रो-ईडीएममा यो प्रायः केस हुँदैन)। तार स्पूलहरू लामो हुन्छन् - 0.25 मिमी तारको 8 किलोग्राम स्पूलको लम्बाइ 19 किलोमिटर मात्र हुन्छ। तारको व्यास २० माइक्रोमिटर जति सानो हुन सक्छ र ज्यामिति परिशुद्धता +/- १ माइक्रोमिटरको छेउमा छ। हामी सामान्यतया तार एक पटक मात्र प्रयोग गर्छौं र यसलाई पुन: प्रयोग गर्छौं किनभने यो अपेक्षाकृत सस्तो छ। यो 0.15 देखि 9m/मिनेट को एक स्थिर वेग मा यात्रा गर्दछ र एक स्थिर कर्फ (स्लट) एक कट समयमा राखिएको छ। तार-कट EDM प्रक्रियामा हामी पानीलाई डाइइलेक्ट्रिक फ्लुइडको रूपमा प्रयोग गर्छौं, यसको प्रतिरोधात्मकता र अन्य विद्युतीय गुणहरूलाई फिल्टर र डी-आयनाइजर एकाइहरू नियन्त्रण गर्दै। पानीले काटिएको फोहोरलाई काट्ने क्षेत्रबाट टाढा लैजान्छ। दिइएको सामग्री मोटाईको लागि अधिकतम फिड दर निर्धारण गर्न फ्लशिंग एक महत्त्वपूर्ण कारक हो र त्यसैले हामी यसलाई निरन्तर राख्छौं। तार EDM मा काट्ने गति प्रति एकाइ समय काटिएको क्रस-सेक्शनल क्षेत्रको सन्दर्भमा भनिन्छ, जस्तै 18,000 mm2/hr 50mm बाक्लो D2 उपकरण स्टीलको लागि। यस केसको लागि रैखिक काट्ने गति 18,000/50 = 360mm/hr हुनेछ तार EDM मा सामग्री हटाउने दर हो:
MRR = Vf xhxb
यहाँ MRR mm3/min मा छ, Vf mm/min मा workpiece मा तारको फिड दर हो, h मोटाई वा उचाइ मिमी हो, र b कर्फ हो, जुन हो:
b = dw + 2s
यहाँ dw तारको व्यास हो र s तार र वर्कपीस बीचको ग्याप मिमीमा हो।
कडा सहिष्णुताको साथसाथै, हाम्रो आधुनिक बहु अक्ष EDM तार काट्ने मेसिनिङ केन्द्रहरूले एकै समयमा दुई भागहरू काट्नको लागि बहु हेडहरू, तार भाँच्नबाट रोक्नको लागि नियन्त्रणहरू, तार फुटेको अवस्थामा स्वचालित स्व-थ्रेडिङ सुविधाहरू, र प्रोग्राम गरिएका सुविधाहरू थपेका छन्। अपरेशन, सीधा र कोणीय काट्ने क्षमताहरू अनुकूलन गर्न मेसिनिंग रणनीतिहरू।
तार-EDM ले हामीलाई कम अवशिष्ट तनावहरू प्रदान गर्दछ, किनकि यसले सामग्री हटाउन उच्च काटन बलहरू आवश्यक पर्दैन। जब प्रति पल्स उर्जा/शक्ति अपेक्षाकृत कम हुन्छ (जस्तै परिष्करण कार्यहरूमा), कम अवशिष्ट तनावका कारण सामग्रीको मेकानिकल गुणहरूमा थोरै परिवर्तन अपेक्षित हुन्छ।
ELECTRICAL-DISCHARGE GRINDING (EDG) : ग्राइन्डिङ पाङ्ग्राहरूमा एब्रेसिभहरू हुँदैनन्, तिनीहरू ग्रेफाइट वा पीतलबाट बनेका हुन्छन्। घुम्ने पाङ्ग्रा र workpiece बीचको दोहोरिने स्पार्कहरूले workpiece सतहहरूबाट सामग्री हटाउँदछ। सामग्री हटाउने दर हो:
MRR = K x I
यहाँ MRR mm3/min मा छ, I Amperes मा वर्तमान छ, र K mm3/A-min मा workpiece सामग्री कारक हो। हामी प्राय: कम्पोनेन्टहरूमा साँघुरो स्लिटहरू देख्नको लागि इलेक्ट्रिकल-डिस्चार्ज ग्राइन्डिङ प्रयोग गर्छौं। हामीले कहिलेकाहीँ EDG (विद्युतीय-डिस्चार्ज ग्राइंडिङ) प्रक्रियालाई ECG (इलेक्ट्रोकेमिकल ग्राइन्डिङ) प्रक्रियासँग जोड्छौं जहाँ सामग्रीलाई रासायनिक क्रियाद्वारा हटाइन्छ, ग्रेफाइट ह्वीलबाट निस्कने विद्युतीय डिस्चार्जले अक्साइड फिल्मलाई तोड्छ र इलेक्ट्रोलाइटद्वारा धुन्छ। प्रक्रिया भनिन्छ ELECTROCHEMICAL-DISCHARGE GRINDING (ECDG)। यद्यपि ECDG प्रक्रियाले अपेक्षाकृत अधिक शक्ति खपत गर्छ, यो EDG भन्दा छिटो प्रक्रिया हो। हामी प्राय: यो प्रविधि प्रयोग गरेर कार्बाइड उपकरणहरू पीस्छौं।
इलेक्ट्रिकल डिस्चार्ज मेसिनिंग को आवेदन:
प्रोटोटाइप उत्पादन:
हामी EDM प्रक्रियालाई मोल्ड बनाउने, उपकरण र डाइ निर्माणमा प्रयोग गर्छौं, साथै प्रोटोटाइप र उत्पादन भागहरू बनाउनका लागि, विशेष गरी एयरोस्पेस, अटोमोबाइल र इलेक्ट्रोनिक्स उद्योगहरूको लागि जहाँ उत्पादन मात्रा अपेक्षाकृत कम छ। सिङ्कर ईडीएममा, ग्रेफाइट, तामाको टंगस्टन वा शुद्ध तामाको इलेक्ट्रोडलाई इच्छित (नकारात्मक) आकारमा मिसाइन्छ र ठाडो रामको अन्त्यमा वर्कपीसमा खुवाइन्छ।
सिक्का मर्ने निर्माण:
सिक्का (स्टाम्पिङ) प्रक्रियाद्वारा गहना र ब्याजहरू उत्पादन गर्नको लागि डाइजको सिर्जनाको लागि, सकारात्मक मास्टर स्टर्लिंग चाँदीबाट बनाइन्छ, किनकि (उपयुक्त मेसिन सेटिङहरूसँग) मास्टर महत्त्वपूर्ण रूपमा क्षय भएको छ र एक पटक मात्र प्रयोग गरिन्छ। नतिजाको नकारात्मक डाइलाई त्यसपछि कडा बनाइन्छ र कांस्य, चाँदी, वा कम प्रमाण सुनको मिश्र धातुको कटआउट शीट खाली ठाउँबाट स्ट्याम्प गरिएको फ्ल्याटहरू उत्पादन गर्न ड्रप ह्यामरमा प्रयोग गरिन्छ। ब्याजहरूका लागि यी फ्ल्याटहरूलाई अर्को डाइद्वारा घुमाउरो सतहमा आकार दिन सकिन्छ। यस प्रकारको EDM सामान्यतया तेलमा आधारित डाइलेक्ट्रिकमा डुबेर गरिन्छ। तयार वस्तुलाई कडा (ग्लास) वा नरम (पेन्ट) इनेमिलिङ र/वा शुद्ध सुन वा निकलले इलेक्ट्रोप्लेट गरेर थप परिष्कृत गर्न सकिन्छ। चाँदी जस्ता नरम सामग्रीहरू परिष्करणको रूपमा हात कुँदिएको हुन सक्छ।
साना प्वालहरू ड्रिलिंग:
हाम्रो तार-कट EDM मेसिनहरूमा, हामी तार-कट EDM सञ्चालनको लागि तार थ्रेड गर्न वर्कपीसमा थ्रु होल बनाउनको लागि सानो प्वाल ड्रिलिंग EDM प्रयोग गर्छौं। विशेष गरी सानो प्वाल ड्रिलिंगका लागि छुट्टै EDM हेडहरू हाम्रा तार काट्ने मेसिनहरूमा माउन्ट गरिएका छन् जसले ठूला कडा प्लेटहरूलाई आवश्यकता अनुसार र पूर्व-ड्रिलिंग बिना नै ती टुक्राहरू मेटाउन अनुमति दिन्छ। हामी जेट इन्जिनहरूमा प्रयोग हुने टर्बाइन ब्लेडको किनारमा प्वालहरूको पङ्क्तिहरू ड्रिल गर्न सानो प्वाल EDM प्रयोग गर्छौं। यी साना प्वालहरू मार्फत ग्यास प्रवाहले इन्जिनहरूलाई अन्यथा सम्भव भन्दा उच्च तापक्रम प्रयोग गर्न अनुमति दिन्छ। उच्च-तापमान, धेरै कडा, एकल क्रिस्टल मिश्र धातुबाट बनेका यी ब्लेडहरूले उच्च पक्ष अनुपातका साथ यी प्वालहरूको परम्परागत मेसिनिङ अत्यन्त गाह्रो र असम्भव पनि बनाउँछ। सानो प्वाल EDM को लागी अन्य अनुप्रयोग क्षेत्रहरु ईन्धन प्रणाली घटकहरु को लागी माइक्रोस्कोपिक ओरिफिसहरु को निर्माण गर्न को लागी छ। एकीकृत EDM हेडहरू बाहेक, हामी स्ट्यान्ड-अलोन सानो प्वाल ड्रिलिंग EDM मेशिनहरू x–y अक्षहरूको साथ मेशिन अन्धा वा प्वालहरू मार्फत तैनात गर्छौं। EDM ड्रिलहरूले लामो ब्रास वा तामाको ट्यूब इलेक्ट्रोडको साथ प्वालहरू बोर्छ जुन फ्लशिंग एजेन्ट र डाइलेक्ट्रिकको रूपमा इलेक्ट्रोडबाट बहने डिस्टिल्ड वा डिआयनाइज्ड पानीको निरन्तर प्रवाहको साथ चकमा घुम्छ। केही सानो प्वाल ड्रिलिंग EDM हरू 10 सेकेन्ड भन्दा कममा 100 मिमी नरम वा कडा इस्पात मार्फत ड्रिल गर्न सक्षम छन्। यस ड्रिलिंग कार्यमा ०.३ मिमी र ६.१ मिमी बीचको प्वालहरू प्राप्त गर्न सकिन्छ।
धातु विघटन मेसिन:
हामीसँग कामका टुक्राहरूबाट टुक्रा टुक्राहरू (ड्रिल बिट वा ट्यापहरू) हटाउने विशेष उद्देश्यका लागि विशेष EDM मेसिनहरू पनि छन्। यो प्रक्रियालाई "धातु विघटन मेसिनिङ" भनिन्छ।
इलेक्ट्रिकल डिस्चार्ज मेसिनिंगका फाइदाहरू र हानिहरू:
EDM का फाइदाहरूमा मेसिनिंग समावेश छ:
- जटिल आकारहरू जुन अन्यथा पारंपरिक काटन उपकरणहरूसँग उत्पादन गर्न गाह्रो हुनेछ
- धेरै नजिकको सहिष्णुताको लागि अत्यन्त कठिन सामग्री
- धेरै साना कार्य टुक्राहरू जहाँ परम्परागत काट्ने उपकरणहरूले अतिरिक्त काट्ने उपकरणको दबाबबाट भागलाई क्षति पुर्याउन सक्छ।
- उपकरण र कार्य टुक्रा बीच कुनै सीधा सम्पर्क छैन। त्यसैले नाजुक खण्डहरू र कमजोर सामग्रीहरू कुनै विकृति बिना मेसिन गर्न सकिन्छ।
- राम्रो सतह समाप्त प्राप्त गर्न सकिन्छ।
- धेरै राम्रो प्वालहरू सजिलै ड्रिल गर्न सकिन्छ।
EDM को बेफाइदाहरू समावेश छन्:
- सामग्री हटाउने ढिलो दर।
- RAM/sinker EDM को लागि इलेक्ट्रोडहरू सिर्जना गर्न प्रयोग गरिएको अतिरिक्त समय र लागत।
- इलेक्ट्रोड पहिरनको कारण वर्कपीसमा तीखो कुनाहरू पुन: उत्पादन गर्न गाह्रो छ।
- बिजुली खपत उच्च छ।
- ''ओभरकट'' गठन भएको छ।
- मेसिनिङको समयमा अत्यधिक उपकरण लगाउने हुन्छ।
- विद्युतीय रूपमा गैर प्रवाहकीय सामग्रीहरू प्रक्रियाको विशिष्ट सेट-अपको साथ मात्र मेसिन गर्न सकिन्छ।