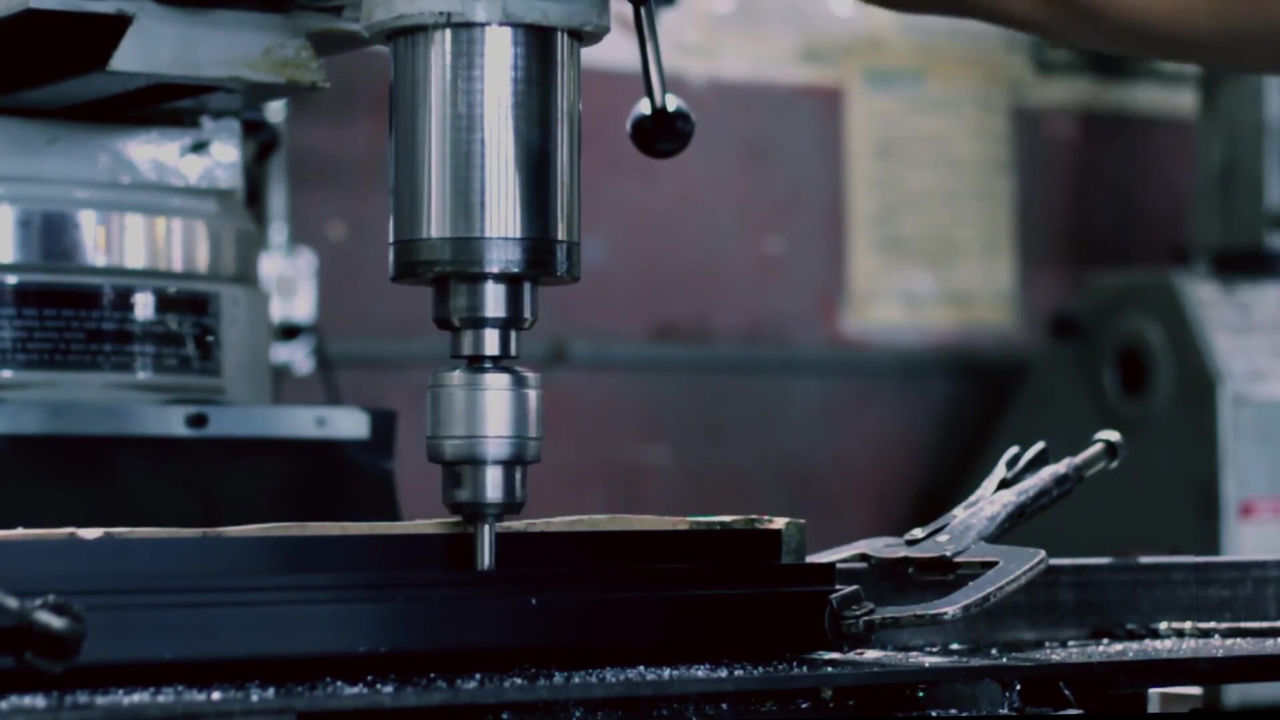
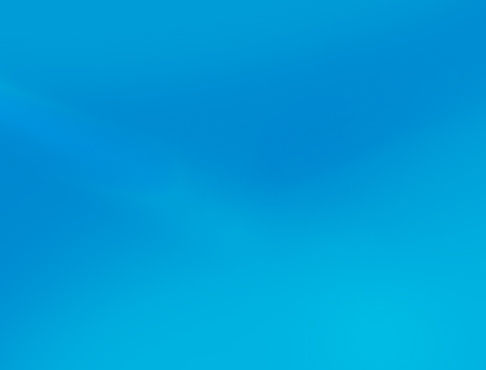
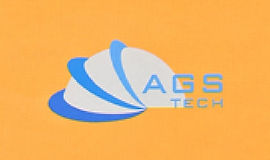
विश्वव्यापी कस्टम निर्माता, इन्टिग्रेटर, कन्सोलिडेटर, उत्पादन र सेवाहरूको विस्तृत विविधताका लागि आउटसोर्सिङ पार्टनर।
हामी उत्पादन, निर्माण, ईन्जिनियरिङ्, एकीकरण, एकीकरण, अनुकूलन निर्मित र अफ-शेल्फ उत्पादन र सेवाहरूको आउटसोर्सिङको लागि तपाईंको एक-स्टप स्रोत हौं।
आफ्नो भाषा छान्नुहोस्
-
कस्टम निर्माण
-
घरेलु र विश्वव्यापी अनुबंध निर्माण
-
उत्पादन आउटसोर्सिङ
-
घरेलु र विश्वव्यापी खरीद
-
Consolidation
-
इन्जिनियरिङ एकीकरण
-
इन्जिनियरिङ सेवाहरू
हामीले प्रस्ताव गर्ने मेटल फोर्जिङ प्रक्रियाहरूको प्रकार हो तातो र चिसो डाइ, ओपन डाइ र क्लोज्ड डाइ, इम्प्रेशन डाइ र फ्ल्याशलेस फोर्जिंग, cogging, फुलरिङ, एजिङ र प्रेसिजन फोर्जिङ, हेड शेपिङ, नजिकै , स्वेजिङ, अपसेट फोर्जिङ, मेटल हबिङ, प्रेस एण्ड रोल र रेडियल र ओर्बिटल र रिङ र आइसोथर्मल फोर्जिङ, कोइनिङ, रिभेटिङ्ग, मेटल बल फोर्जिङ, मेटल पियर्सिङ, साइजिङ, उच्च ऊर्जा दर फोर्जिङ।
हाम्रो पाउडर मेटालर्जी र पाउडर प्रशोधन प्रविधिहरू पाउडर प्रेसिङ र सिंटरिङ, गर्भाधान, घुसपैठ, तातो र चिसो आइसोस्टेटिक प्रेसिंग, मेटल इन्जेक्सन मोल्डिङ, रोल कम्प्याक्सन, पाउडर रोलिङ, पाउडर एक्सट्रुजन, लूज सिन्टरिङ, स्पार्क हट सिन्टरिङ, हो।
हामी तपाईंलाई यहाँ क्लिक गर्न सिफारिस गर्छौं
AGS-TECH Inc. द्वारा फोर्जिङ प्रक्रियाहरूको हाम्रो योजनाबद्ध चित्रणहरू डाउनलोड गर्नुहोस्।
AGS-TECH Inc. द्वारा पाउडर मेटलर्जी प्रक्रियाहरूको हाम्रो योजनाबद्ध चित्रण डाउनलोड गर्नुहोस्।
तस्बिरहरू र स्केचहरू भएका यी डाउनलोड गर्न मिल्ने फाइलहरूले तपाईंलाई हामीले तल उपलब्ध गराएको जानकारी अझ राम्ररी बुझ्न मद्दत गर्नेछ।
धातु फोर्जिङमा, कम्प्रेसिभ बलहरू लागू गरिन्छ र सामग्री विकृत हुन्छ र इच्छित आकार प्राप्त गरिन्छ। उद्योगमा सबैभन्दा सामान्य नक्कली सामग्रीहरू फलाम र इस्पात हुन्, तर धेरै अन्य जस्तै एल्युमिनियम, तामा, टाइटेनियम, म्याग्नेसियम पनि व्यापक रूपमा नक्कली छन्। नक्कली धातुका भागहरूले सिल गरिएको दरारहरू र बन्द खाली ठाउँहरू बाहेक अनाज संरचनाहरू सुधार गरेको छ, यसरी यस प्रक्रियाबाट प्राप्त भागहरूको बल बढी छ। फोर्जिङले भागहरू उत्पादन गर्दछ जुन कास्टिङ वा मेसिनिङद्वारा बनाइएका भागहरू भन्दा तिनीहरूको वजनको लागि महत्त्वपूर्ण रूपमा बलियो हुन्छ। नक्कली भागहरूलाई धातुको प्रवाहलाई अन्तिम आकारमा बनाएर आकार दिइएको हुनाले, धातुले दिशात्मक अनाज संरचना लिन्छ जसले भागहरूको उच्च शक्तिको लागि खाता बनाउँछ। अर्को शब्दमा भन्नुपर्दा, फोर्जिङ प्रक्रियाबाट प्राप्त भागहरूले साधारण कास्ट वा मेशिन पार्ट्सको तुलनामा राम्रो मेकानिकल गुणहरू प्रकट गर्दछ। मेटल फोर्जिङको तौल साना हल्का तौलका भागहरूदेखि लाखौं पाउण्डसम्म हुन सक्छ। हामी फोर्जिङहरू प्रायः यान्त्रिक रूपमा माग गर्ने अनुप्रयोगहरूको लागि उत्पादन गर्छौं जहाँ अटोमोटिभ पार्ट्स, गियरहरू, कार्य उपकरणहरू, हात उपकरणहरू, टर्बाइन शाफ्टहरू, मोटरसाइकल गियरहरू जस्ता भागहरूमा उच्च तनावहरू लागू हुन्छन्। टुलिङ र सेट-अप लागतहरू अपेक्षाकृत उच्च भएकाले, हामी यो उत्पादन प्रक्रियालाई उच्च मात्राको उत्पादन र कम भोल्युमका लागि तर एयरोस्पेस ल्यान्डिङ गियर जस्ता उच्च मूल्यका महत्वपूर्ण घटकहरूको लागि मात्र सिफारिस गर्छौं। टुलिङको लागत बाहेक, ठूलो परिमाणमा नक्कली भागहरूको निर्माणको समय केही साधारण मेशिन पार्ट्सको तुलनामा लामो हुन सक्छ, तर यो प्राविधिक भागहरूका लागि महत्त्वपूर्ण छ_ cc781905-5cde-3194-bb3b-136bad5cf58d_ बोल्ट, नट, विशेष अनुप्रयोग जस्ता असाधारण शक्ति चाहिन्छ। फास्टनर, मोटर वाहन, फोर्कलिफ्ट, क्रेन पार्ट्स।
• हट डाइ र कोल्ड डाइ फोर्जिङ: हट डाइ फोर्जिङ, नामले संकेत गरेझैं उच्च तापक्रममा गरिन्छ, त्यसैले लचकता उच्च हुन्छ र सामग्रीको बल कम हुन्छ। यसले सजिलै विरूपण र फोर्जिंग सुविधा दिन्छ। यसको विपरित, कोल्ड डाइ फोर्जिङ कम तापक्रममा गरिन्छ र उच्च बलहरू चाहिन्छ जसको परिणामले स्ट्रेन कडा बनाउँछ, राम्रो सतह समाप्त हुन्छ र उत्पादित भागहरूको शुद्धता हुन्छ।
• ओपन डाइ र इम्प्रेसन डाइ फोर्जिङ : ओपन डाइ फोर्जिङमा, डाइजले कम्प्रेस गरिएको सामग्रीलाई बाधा पुऱ्याउँदैन, जबकि इम्प्रेशनमा डाइ फोर्जिङले सामग्रीको प्रवाहलाई रोक्छ जबकि यसलाई इच्छित आकारमा बनाइन्छ। UPSET FORGING वा UPSETTING पनि भनिन्छ, जुन वास्तवमा उस्तै होइन तर एकदम मिल्दोजुल्दो प्रक्रिया हो, एक ओपन डाइ प्रक्रिया हो जहाँ कामको टुक्रा दुईवटा फ्ल्याट डाइहरू बीच स्यान्डविच गरिन्छ र कम्प्रेसिभ बलले यसको उचाइ घटाउँछ। उचाई reduced हुँदा, कार्य टुक्रा चौडाइ बढ्छ। हेडिङ, अपसेट फोर्जिङ प्रक्रियामा बेलनाकार स्टक समावेश हुन्छ जुन यसको अन्त्यमा अपसेट हुन्छ र यसको क्रस सेक्शन स्थानीय रूपमा बढाइन्छ। हेडिङमा स्टकलाई डाइ मार्फत खुवाइन्छ, नक्कली र त्यसपछि लम्बाइमा काटिन्छ। अपरेशनले उच्च मात्रामा फास्टनरहरू छिटो उत्पादन गर्न सक्षम छ। प्राय: यो चिसो काम गर्ने अपरेशन हो किनभने यो नङको छेउ, स्क्रू छेउ, नट र बोल्टहरू बनाउन प्रयोग गरिन्छ जहाँ सामग्रीलाई बलियो बनाउन आवश्यक छ। अर्को ओपन डाइ प्रक्रिया COGGING हो, जहाँ कार्य टुक्रालाई प्रत्येक चरणको साथ चरणहरूको श्रृंखलामा जाली गरिन्छ जसको परिणामस्वरूप सामग्रीको कम्प्रेसन हुन्छ र कार्य टुक्राको लम्बाइमा खुला डाईको पछिल्लो गति हुन्छ। प्रत्येक चरणमा, मोटाई घटाइन्छ र लम्बाइ सानो मात्रामा बढाइन्छ। प्रक्रिया स-साना पाइलाहरूमा आफ्नो पेन्सिल काट्ने एक नर्वस विद्यार्थी जस्तो देखिन्छ। फुलरिङ भनिने प्रक्रिया अर्को ओपन डाइ फोर्जिङ विधि हो जुन हामीले प्रायः अन्य मेटल फोर्जिङ कार्यहरू हुनु अघि कामको टुक्रामा सामग्री वितरण गर्न पहिलेको चरणको रूपमा प्रयोग गर्छौं। कामको टुक्रालाई धेरै फोर्जिङ operations आवश्यक हुँदा हामी यसलाई प्रयोग गर्छौं। अपरेशनमा, उत्तल सतहहरू विकृतसँग मर्नुहोस् र धातुको प्रवाह दुवै पक्षहरूमा निस्कन्छ। फुलरिङसँग मिल्दोजुल्दो प्रक्रिया, अर्कोतर्फ EDGING ले कार्य टुक्रालाई विकृत गर्न अवतल सतहहरूसँग खुला डाई समावेश गर्दछ। किनाराले पछिको फोर्जिङ अपरेसनहरूको लागि तयारी प्रक्रिया पनि दुवै पक्षबाट केन्द्रमा रहेको क्षेत्रमा प्रवाह बनाउँछ। इम्प्रेसन डाइ फोर्जिङ वा क्लोज्ड डाइ फोर्जिङ भनिन्छ जसलाई डाइ / मोल्ड प्रयोग गरिन्छ जसले सामग्रीलाई कम्प्रेस गर्छ र यसको प्रवाहलाई आफैंमा रोक्छ। डाइ बन्द हुन्छ र सामग्रीले डाइ / मोल्ड गुहाको आकार लिन्छ। PRECISION FORGING, विशेष उपकरण र मोल्ड आवश्यक पर्ने प्रक्रियाले कुनै वा धेरै थोरै फ्ल्यास बिना भागहरू उत्पादन गर्दछ। अन्य शब्दहरूमा, भागहरू नजिकको अन्तिम आयामहरू हुनेछन्। यस प्रक्रियामा सामग्रीको राम्रोसँग नियन्त्रित मात्रालाई ध्यानपूर्वक सम्मिलित गरिन्छ र मोल्ड भित्र राखिन्छ। हामी यो विधिलाई पातलो खण्डहरू, सानो सहनशीलता र मस्यौदा कोणहरूसँग जटिल आकारहरूका लागि प्रयोग गर्छौं र जब मात्राहरू मोल्ड र उपकरण लागतहरू उचित ठहराउन पर्याप्त हुन्छन्।
• फ्ल्यासलेस फोर्जिङ: वर्कपीसलाई डाइमा यसरी राखिएको छ कि कुनै पनि सामग्री फ्ल्यास बनाउनको लागि गुफाबाट बाहिर निस्कन सक्दैन। यसरी कुनै अवांछित फ्लैश ट्रिमिङ आवश्यक छैन। यो एक परिशुद्धता फोर्जिङ प्रक्रिया हो र यसैले प्रयोग गरिएको सामग्रीको मात्रामा नजिकको नियन्त्रण चाहिन्छ।
• मेटल स्वेगिङ वा रेडियल फोर्जिङ: कामको टुक्रालाई परिधिमा डाई र नक्कली गरी कार्य गरिन्छ। भित्री कामको टुक्रा ज्यामिति बनाउनको लागि मन्डरेल पनि प्रयोग गर्न सकिन्छ। स्वेजिङ सञ्चालनमा कार्य टुक्राले सामान्यतया प्रति सेकेन्ड धेरै स्ट्रोकहरू प्राप्त गर्दछ। स्वेजिंग द्वारा उत्पादित विशिष्ट वस्तुहरू पोइन्ट टिप उपकरणहरू, टेपर्ड बारहरू, स्क्रू ड्राइभरहरू हुन्।
• धातु छेड्ने: हामी यो अपरेशन बारम्बार भागहरु को निर्माण मा एक अतिरिक्त अपरेशन को रूप मा प्रयोग गर्दछ। प्वाल वा गुफा काम टुक्रा सतहमा छेडेर यसलाई नछोडिकन सिर्जना गरिन्छ। कृपया ध्यान दिनुहोस् कि छेदन ड्रिलिंग भन्दा फरक छ जसले प्वाल मार्फत परिणाम दिन्छ।
• हबिङ: इच्छित ज्यामितिको साथ एक पंचलाई कार्य टुक्रामा थिचिन्छ र इच्छित आकारको साथ गुहा बनाउँछ। हामी यसलाई HOB भन्छौं। अपरेशनमा उच्च दबाब समावेश छ र चिसोमा गरिन्छ। नतिजाको रूपमा सामग्री चिसो काम र तनाव कठोर छ। तसर्थ यो प्रक्रिया अन्य उत्पादन प्रक्रियाहरूको लागि मोल्ड, डाइ र गुहा निर्माणको लागि धेरै उपयुक्त छ। एकपटक हब बनाइसकेपछि, सजिलैसँग धेरै समान गुफाहरू एक-एक गरेर मेसिन नगरी निर्माण गर्न सकिन्छ।
• रोल फोर्जिङ वा रोल फारमिङ: धातुको भागलाई आकार दिन दुई विपरीत रोलहरू प्रयोग गरिन्छ। कामको टुक्रा रोलहरूमा खुवाइन्छ, रोलहरू घुमाउँछन् र कामलाई खाली ठाउँमा तान्छन्, त्यसपछि कामलाई रोलको ग्रुभ गरिएको भागबाट खुवाइन्छ र कम्प्रेसिभ बलहरूले सामग्रीलाई यसको इच्छित आकार दिन्छ। यो रोलिङ प्रक्रिया होइन तर फोर्जिंग प्रक्रिया हो, किनभने यो एक निरन्तर सञ्चालन भन्दा एक अलग छ। रोल ग्रोभ्समा रहेको ज्यामितिले सामग्रीलाई आवश्यक आकार र ज्यामितिमा फोर्ज गर्दछ। यो तातो प्रदर्शन गरिन्छ। फोर्जिङ प्रक्रिया भएको कारणले यसले उत्कृष्ट मेकानिकल गुणहरू भएका भागहरू उत्पादन गर्छ र त्यसैले हामी यसलाई Manufacturing अटोमोटिभ पार्ट्सहरू जस्तै शाफ्टहरू जसलाई कठिन कार्य वातावरणमा असाधारण सहनशीलता चाहिन्छ।
• ओर्बिटल फोर्जिङ: कार्य टुक्रा फोर्जिंग डाइ गुहामा राखिन्छ र माथिल्लो डाई द्वारा जाली गरिन्छ जुन एक झुकाव अक्षमा घुम्ने क्रममा कक्षीय मार्गमा यात्रा गर्दछ। प्रत्येक क्रान्तिमा, माथिल्लो डाईले सम्पूर्ण कार्य टुक्रामा कम्प्रेसिभ बलहरू प्रयोग गरेर पूरा गर्दछ। यी क्रान्तिहरू धेरै पटक दोहोर्याएर, पर्याप्त फोर्जिङ प्रदर्शन गरिन्छ। यस निर्माण प्रविधिको फाइदाहरू यसको कम आवाज सञ्चालन र कम बलहरू आवश्यक छन्। अर्को शब्दमा भन्नुपर्दा साना बलहरूसँग एक अक्षको वरिपरि भारी डाइलाई घुमाउन सकिन्छ जुन डाइसँग सम्पर्कमा रहेको कार्य टुक्राको खण्डमा ठूलो दबाब लागू गर्न सकिन्छ। डिस्क वा शंक्वाकार आकारका भागहरू कहिलेकाहीँ यस प्रक्रियाको लागि राम्रो फिट हुन्छन्।
• घण्टी फोर्जिङ: हामी प्रायः सिमलेस रिंगहरू निर्माण गर्न प्रयोग गर्छौं। स्टकलाई लम्बाइमा काटिएको छ, अपसेट गरिएको छ र त्यसपछि केन्द्रीय प्वाल सिर्जना गर्न सबै तरिकाले छेडिन्छ। त्यसपछि यसलाई म्यान्डरेलमा राखिन्छ र फोर्जिङ डाइले यसलाई माथिबाट हथौडा बनाउँछ जसरी इच्छित आयामहरू प्राप्त नभएसम्म औंठी बिस्तारै घुमाइन्छ।
• RIVETING: भागहरू जोड्नको लागि एक सामान्य प्रक्रिया, एक सीधा धातुको टुक्रा भागहरू मार्फत पूर्व बनाइएको प्वालहरूमा घुसाएर सुरु हुन्छ। त्यसपछि धातुको टुक्राको दुई छेउलाई माथिल्लो र तल्लो डाईको बीचको जोइन्ट निचोलेर नक्कली बनाइन्छ।
• कोइनिङ: मेकानिकल प्रेसद्वारा गरिएको अर्को लोकप्रिय प्रक्रिया, छोटो दूरीमा ठूलो बल प्रयोग गरी। नाम "सिक्का" धातुको सिक्काको सतहहरूमा नक्कली विवरणहरूबाट आएको हो। यो प्रायः उत्पादनको लागि परिष्करण प्रक्रिया हो जहाँ डाइ द्वारा लागू गरिएको ठूलो बलको परिणामको रूपमा सतहहरूमा राम्रो विवरणहरू प्राप्त हुन्छन् जसले यी विवरणहरूलाई कार्य टुक्रामा स्थानान्तरण गर्दछ।
• मेटल बल फोर्जिङ: बल बेरिङ जस्ता उत्पादनहरूलाई उच्च गुणस्तरको सटीक रूपमा निर्मित धातु बलहरू चाहिन्छ। SKEW ROLLING भनिने एउटा प्रविधिमा, हामी दुई विरोधी रोलहरू प्रयोग गर्छौं जुन स्टकलाई रोलहरूमा लगातार फिड गरिँदै गर्दा निरन्तर घुमिरहन्छन्। दुई रोलको एक छेउमा धातु गोलाहरू उत्पादनको रूपमा बाहिर निकालिन्छन्। मेटल बल फोर्जिङको लागि दोस्रो विधि भनेको मोल्ड गुहाको गोलाकार आकार लिई तिनीहरूको बीचमा राखिएको सामग्री स्टकलाई निचोड गर्ने डाइ प्रयोग गर्नु हो। प्रायः उत्पादन गरिएका बलहरूलाई उच्च गुणस्तरको उत्पादन बन्नको लागि परिष्करण र पालिश गर्ने जस्ता थप चरणहरू आवश्यक पर्दछ।
• ISOTHERMAL फोर्जिङ / हट डाइ फोर्जिङ : एक महँगो प्रक्रिया मात्र जब लाभ / लागत मूल्य जायज छ। तातो काम गर्ने प्रक्रिया जहाँ डाइलाई कामको टुक्राको रूपमा उही तापक्रममा तताइन्छ। मर्ने र काम गर्ने दुवैको तापक्रम एउटै भएकोले, त्यहाँ कुनै चिसो हुँदैन र धातुको प्रवाह विशेषताहरू सुधार हुन्छन्। अपरेशन सुपर मिश्र धातुहरू र निम्न फोर्जेबिलिटी र सामग्रीहरूका लागि उपयुक्त छ जसको
मेकानिकल गुणहरू सानो तापक्रम ढाँचा र परिवर्तनहरूप्रति धेरै संवेदनशील हुन्छन्।
• मेटल साइजिङ: यो चिसो परिष्करण प्रक्रिया हो। बल लागू गरिएको दिशा बाहेक सबै दिशाहरूमा सामग्री प्रवाह असीमित छ। नतिजाको रूपमा, धेरै राम्रो सतह समाप्त र सही आयाम प्राप्त गरिन्छ।
• HIGH ऊर्जा दर फोर्जिङ: यो प्रविधिमा पिस्टनको पाखुरामा जोडिएको माथिल्लो मोल्ड समावेश हुन्छ जुन इन्धन-हावा मिश्रणलाई spark द्वारा प्रज्वलित गर्दा द्रुत रूपमा धकेलिन्छ। यो कार इन्जिन मा पिस्टन को सञ्चालन जस्तै देखिन्छ। मोल्डले कामको टुक्रालाई धेरै छिटो हिर्काउँछ र त्यसपछि ब्याकप्रेसरको कारण धेरै छिटो आफ्नो मूल स्थितिमा फर्कन्छ। काम केहि मिलिसेकेन्ड भित्र नक्कली हुन्छ र त्यसैले काम चिसो हुन समय छैन। यो धेरै तापक्रम संवेदनशील मेकानिकल गुणहरू भएका भागहरू फोर्ज गर्नका लागि उपयोगी छ। अर्को शब्दमा भन्नुपर्दा प्रक्रिया यति छिटो छ कि भाग स्थिर तापक्रम अन्तर्गत बनाइन्छ र त्यहाँ मोल्ड/वर्क पीस इन्टरफेसहरूमा तापमान ढाँचा हुनेछैन।
• DIE FORGING मा, धातुलाई दुई मिल्दो स्टिल ब्लकहरू बीचमा विशेष आकारहरू राखिन्छ, जसलाई डाइ भनिन्छ। जब धातुलाई डाइको बीचमा ह्यामर गरिन्छ, यसले डाइमा भएका आकारहरू जस्तै आकार धारण गर्दछ। जब यो अन्तिम आकारमा पुग्छ, यसलाई चिसो पार्न बाहिर निकालिन्छ। यो प्रक्रियाले बलियो भागहरू उत्पादन गर्दछ जुन सटीक आकारको हुन्छ, तर विशेष डाइजको लागि ठूलो लगानी चाहिन्छ। अपसेट फोर्जिङले धातुको टुक्रालाई सपाट गरेर यसको व्यास बढाउँछ। यो सामान्यतया साना भागहरू बनाउन प्रयोग गरिन्छ, विशेष गरी बोल्ट र नङ जस्ता फास्टनरहरूमा टाउको बनाउन।
• पाउडर मेटलर्जी / पाउडर प्रशोधन: नामले संकेत गरेझैं, यसले पाउडरबाट निश्चित ज्यामिति र आकारहरूको ठोस भागहरू बनाउनको लागि निर्माण प्रक्रियाहरू समावेश गर्दछ। यदि यस उद्देश्यका लागि धातु पाउडरहरू प्रयोग गरिन्छ भने यो पाउडर धातु विज्ञानको क्षेत्र हो र यदि गैर-धातु पाउडरहरू प्रयोग गरिन्छ भने यो पाउडर प्रशोधन हो। ठोस भागहरू थिचेर र सिन्टेरिङ गरेर पाउडरबाट उत्पादन गरिन्छ।
POWDER PRESSING को प्रयोग पाउडरहरूलाई इच्छित आकारहरूमा कम्प्याक्ट गर्न प्रयोग गरिन्छ। पहिलो, प्राथमिक सामग्री भौतिक रूपमा पाउडर गरिएको छ, यसलाई धेरै साना व्यक्तिगत कणहरूमा विभाजन गर्दै। पाउडर मिश्रण डाइमा भरिन्छ र एक पंच पाउडर तिर सर्छ र इच्छित आकारमा कम्प्याक्ट गर्दछ। प्रायः कोठाको तापक्रममा प्रदर्शन गरिन्छ, पाउडर थिचेर ठोस भाग प्राप्त गरिन्छ र यसलाई हरियो कम्प्याक्ट भनिन्छ। बाइन्डर र स्नेहक सामान्यतया कम्प्याक्टेबिलिटी बढाउन प्रयोग गरिन्छ। हामी धेरै हजार टन क्षमताको साथ हाइड्रोलिक प्रेस प्रयोग गरेर पाउडर प्रेस बनाउन सक्षम छौं। साथै हामीसँग विपरित माथि र तल्लो मुक्काहरूका साथसाथै अत्यधिक जटिल भाग ज्यामितिहरूको लागि बहुविध कार्य प्रेसहरू छन्। एकरूपता जुन धेरै पाउडर धातु विज्ञान / पाउडर प्रशोधन प्लान्टहरूको लागि महत्त्वपूर्ण चुनौती हो AGS-TECH को लागि कुनै ठूलो समस्या होइन किनभने हाम्रो धेरै वर्षदेखि त्यस्ता भागहरू अनुकूलन निर्माणमा व्यापक अनुभव छ। बाक्लो भागहरूमा पनि जहाँ एकरूपताले चुनौती खडा गर्छ हामी सफल भएका छौं। यदि हामी तपाईंको परियोजनामा प्रतिबद्ध छौं भने, हामी तपाईंको भागहरू बनाउनेछौं। यदि हामीले कुनै सम्भावित जोखिमहरू देख्यौं भने, हामी तपाईंलाई in सूचित गर्नेछौं
अग्रिम।
POWDER SINTERING, जुन दोस्रो चरण हो, तापमानलाई एक निश्चित डिग्रीमा बढाउने र निश्चित समयको लागि त्यो स्तरमा तापक्रमको मर्मत समावेश गर्दछ ताकि दबाइएका भागमा पाउडर कणहरू एकसाथ बाँध्न सकून्। यसले धेरै बलियो बन्धन र कार्य टुक्राको सुदृढीकरणमा परिणाम दिन्छ। सिंटरिङ पाउडरको पग्लिने तापमानको नजिक हुन्छ। sintering को संकुचन को समयमा, सामाग्री बल, घनत्व, लचीलापन, थर्मल चालकता, विद्युत चालकता बढेको छ। हामीसँग सिन्टरिङका लागि ब्याच र निरन्तर भट्टीहरू छन्। हाम्रो क्षमताहरू मध्ये एउटा हामीले उत्पादन गर्ने पार्ट्सको पोरोसिटीको स्तर समायोजन गर्नु हो। उदाहरणका लागि, हामी भागहरूलाई केही हदसम्म छिद्रपूर्ण राखेर धातु फिल्टरहरू उत्पादन गर्न सक्षम छौं।
IMPREGNATION भनिने प्रविधि प्रयोग गरेर, हामी धातुको छिद्रहरू तेल जस्ता तरल पदार्थले भर्छौं। हामी उदाहरणका लागि तेल गर्भवती बियरिङहरू उत्पादन गर्छौं जुन स्व-लुब्रिकेटिङ हुन्छ। घुसपैठ प्रक्रियामा हामी आधार सामग्री भन्दा कम पग्लने बिन्दुको अर्को धातुले धातुको छिद्रहरू भर्छौं। मिश्रणलाई दुई धातुको पग्लिने तापक्रमको बीचमा तापक्रममा तताइन्छ। फलस्वरूप केही विशेष गुणहरू प्राप्त गर्न सकिन्छ। विशेष सुविधाहरू वा गुणहरू प्राप्त गर्न आवश्यक हुँदा वा कम प्रक्रिया चरणहरूमा भाग उत्पादन गर्न सकिन्छ जब हामी पाउडर निर्मित भागहरूमा मेसिनिङ र फोर्जिङ जस्ता माध्यमिक कार्यहरू पनि गर्छौं।
ISOSTATIC प्रेसिंग: यस प्रक्रियामा तरल दबाब भाग कम्प्याक्ट गर्न प्रयोग गरिन्छ। धातु पाउडरहरू सिल गरिएको लचिलो कन्टेनरबाट बनेको मोल्डमा राखिन्छ। आइसोस्टेटिक प्रेसिङमा, परम्परागत प्रेसिङमा देखिने अक्षीय दबाबको विपरीत, चारैतिरबाट दबाब प्रयोग गरिन्छ। आइसोस्टेटिक प्रेसिंगका फाइदाहरू भाग भित्र एकसमान घनत्व हो, विशेष गरी ठूला वा बाक्लो भागहरूको लागि, उच्च गुणहरू। यसको बेफाइदा लामो चक्र समय र अपेक्षाकृत कम ज्यामितीय सटीकता हो। कोल्ड आइसोस्ट्याटिक प्रेसिङ कोठाको तापक्रममा गरिन्छ र लचिलो मोल्ड रबर, पीभीसी वा युरेथेन वा समान सामग्रीबाट बनेको हुन्छ। दबाब र कम्प्याक्ट गर्न प्रयोग गरिने तरल पदार्थ तेल वा पानी हो। हरियो कम्प्याक्टको परम्परागत सिंटरिङले यसलाई पछ्याउँछ। अर्कोतर्फ तातो आइसोस्ट्याटिक प्रेसिङ उच्च तापक्रममा गरिन्छ र मोल्ड सामाग्री शीट मेटल वा सिरेमिक हो जसमा पर्याप्त उच्च पिघलने बिन्दु हुन्छ जसले तापक्रमलाई प्रतिरोध गर्दछ। दबाब दिने तरल पदार्थ सामान्यतया एक निष्क्रिय ग्यास हो। प्रेसिङ र सिंटरिङ अपरेसनहरू एक चरणमा प्रदर्शन गरिन्छ। पोरोसिटी लगभग पूर्ण रूपमा हटाइएको छ, एक समान grain संरचना प्राप्त भएको छ। तातो आइसोस्टेटिक प्रेसिङको फाइदा यो हो कि यसले कास्टिङ र फोर्जिङसँग तुलना गर्न मिल्ने भागहरू उत्पादन गर्न सक्छ जब कि कास्टिङ र फोर्जिङका लागि उपयुक्त नहुने सामग्रीहरू बनाउन सकिन्छ। तातो आइसोस्टेटिक प्रेसिंगको हानि यसको उच्च चक्र समय र त्यसैले लागत हो। यो कम भोल्युमको महत्वपूर्ण भागहरूको लागि उपयुक्त छ।
धातु इंजेक्शन मोल्डिंग: पातलो पर्खाल र विस्तृत ज्यामिति संग जटिल भागहरु उत्पादन को लागी धेरै उपयुक्त प्रक्रिया। साना भागहरूको लागि सबैभन्दा उपयुक्त। पाउडर र पोलिमर बाइन्डर मिलाइन्छ, तातो र मोल्डमा इन्जेक्सन गरिन्छ। पोलिमर बाइन्डरले पाउडर कणहरूको सतहहरू कोट गर्दछ। मोल्डिङ पछि, बाइन्डरलाई विलायक प्रयोग गरेर घुलनशीलको कम तापक्रम तापद्वारा हटाइन्छ।
रोल कम्प्याक्शन / पाउडर रोलिङ: पाउडरहरू लगातार स्ट्रिप वा पाना उत्पादन गर्न प्रयोग गरिन्छ। पाउडर फिडरबाट खुवाइन्छ र पाना वा स्ट्रिप्समा दुई घुम्ने रोलहरूद्वारा कम्प्याक्ट गरिन्छ। अपरेशन चिसो गरिन्छ। पानालाई सिन्टेरिङ भट्टीमा लगाइन्छ। sintering प्रक्रिया दोस्रो पटक दोहोर्याउन सकिन्छ।
पाउडर एक्सट्र्यूसन: ठूलो लम्बाइ र व्यास अनुपात भएका भागहरू पाउडरको साथ पातलो पाना धातु कन्टेनर बाहिर निकालेर निर्माण गरिन्छ।
लूज सिन्टरिङ: नामले संकेत गरेझैं, यो दबाबरहित कम्प्याक्शन र सिन्टरिङ विधि हो, धातु फिल्टरहरू जस्ता धेरै छिद्रपूर्ण भागहरू उत्पादन गर्नका लागि उपयुक्त। पाउडर कम्प्याक्ट नगरी मोल्ड गुहामा खुवाइन्छ।
लूज सिन्टरिङ: नामले संकेत गरेझैं, यो दबाबरहित कम्प्याक्शन र सिन्टरिङ विधि हो, धातु फिल्टरहरू जस्ता धेरै छिद्रपूर्ण भागहरू उत्पादन गर्नका लागि उपयुक्त। पाउडर कम्प्याक्ट नगरी मोल्ड गुहामा खुवाइन्छ।
स्पार्क सिन्टरिङ: पाउडरलाई मोल्डमा दुई विपरित पंचद्वारा संकुचित गरिन्छ र पंचमा उच्च शक्तिको विद्युतीय प्रवाह लगाइन्छ र तिनीहरूको बीचमा रहेको कम्प्याक्टेड पाउडर स्यान्डविच हुँदै जान्छ। उच्च प्रवाहले पाउडर कणहरूबाट सतह फिल्महरू जलाउँछ र उत्पन्न गर्मीको साथ तिनीहरूलाई सिंट गर्दछ। प्रक्रिया छिटो छ किनभने गर्मी बाहिरबाट लागू हुँदैन तर यसको सट्टा मोल्ड भित्रबाट उत्पन्न हुन्छ।
तातो थिच्ने: उच्च तापक्रम सहन सक्ने मोल्डमा पाउडरहरू एकै चरणमा थिचिन्छ र सिन्टर गरिन्छ। डाई कम्प्याक्ट हुने बित्तिकै यसमा पाउडर तातो लगाइन्छ। राम्रो शुद्धता र मेकानिकल गुणहरू यस विधि द्वारा प्राप्त यो एक आकर्षक विकल्प बनाउँछ। ग्रेफाइट जस्ता मोल्ड सामग्रीहरू प्रयोग गरेर अपवर्तक धातुहरूलाई पनि प्रशोधन गर्न सकिन्छ।