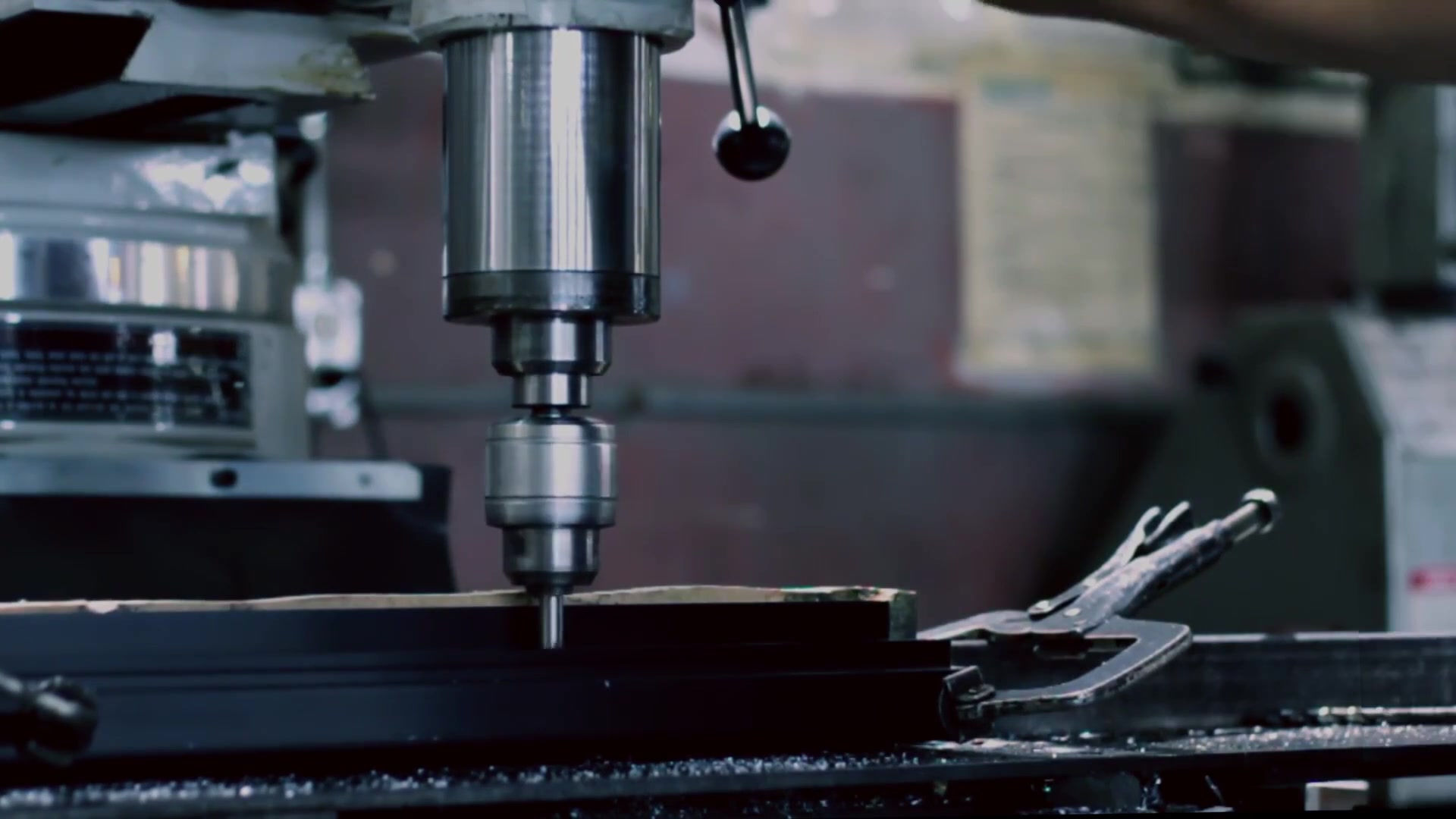
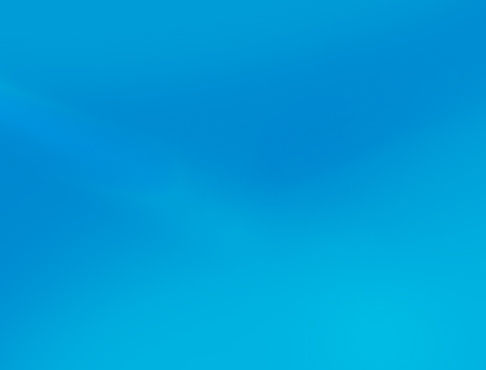
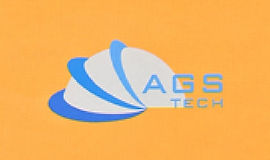
Wereldwijd op maat gemaakte fabrikant, integrator, consolidator, outsourcingpartner voor een breed scala aan producten en diensten.
Wij zijn uw one-stop-bron voor productie, fabricage, engineering, consolidatie, integratie, outsourcing van op maat gemaakte en off-shelf producten en diensten.
Choose your Language
-
Aangepaste productie
-
Binnenlandse en wereldwijde contractproductie
-
Uitbesteding van productie
-
Binnenlandse en wereldwijde inkoop
-
Consolidatie
-
Engineering-integratie
-
Ingenieursdiensten
ELEKTRISCHE ONTLADING MACHINING (EDM), ook wel aangeduid als SPARK-EROSION or_cc781905-5cde-3194-bb358d_bad5cINTROSION_CC781905-5cde-3194-bb3b-136bad5cf58d_or_cc781905-5cde-3194-bb358d_bad5cINTRO -136bad5cf58d_or WIRE EROSION, is a NON-CONVENTIONAL MANUFACTURING_cc781905-5cde-31945-bb358ds_cc781905-5cde-31945-bb358ds van vonken. We bieden ook enkele varianten van EDM aan, namelijk NO-WEAR EDM, WIRE EDM (WEDM), EDM GRINDING (EDG), DIE-SINKING EDM, ELECTRICAL-DISCHARGE FILLING, micro-EDM, m-EDM_cc781905 -5cde-3194-bb3b-136bad5cf58d_and ELECTROCHEMICAL-DISCHARGE SLIJPEN (ECDG). Onze EDM-systemen bestaan uit gevormde gereedschappen/elektroden en het werkstuk aangesloten op gelijkstroomvoedingen en ingebracht in een elektrisch niet-geleidende diëlektrische vloeistof. Na 1940 is machinale bewerking met elektrische ontlading een van de belangrijkste en meest populaire productietechnologieën in de verwerkende industrie geworden.
Wanneer de afstand tussen de twee elektroden wordt verkleind, wordt de intensiteit van het elektrische veld in het volume tussen de elektroden op sommige punten groter dan de sterkte van het diëlektricum, dat breekt en uiteindelijk een brug vormt waardoor stroom tussen de twee elektroden kan vloeien. Er wordt een intense elektrische boog gegenereerd die een aanzienlijke verwarming veroorzaakt om een deel van het werkstuk en een deel van het gereedschapsmateriaal te smelten. Hierdoor wordt materiaal van beide elektroden verwijderd. Tegelijkertijd wordt de diëlektrische vloeistof snel verwarmd, wat resulteert in verdamping van de vloeistof in de boogspleet. Zodra de stroom stopt of stopt, wordt warmte uit de gasbel verwijderd door de omringende diëlektrische vloeistof en caviteert de bel (klapt in). De schokgolf die wordt gecreëerd door het instorten van de bel en de stroom van diëlektrische vloeistof spoelt vuil van het werkstukoppervlak en voert eventueel gesmolten werkstukmateriaal mee in de diëlektrische vloeistof. De herhalingsfrequentie voor deze ontladingen ligt tussen 50 en 500 kHz, spanningen tussen 50 en 380 V en stromen tussen 0,1 en 500 Ampère. Nieuw vloeibaar diëlektricum, zoals minerale oliën, kerosine of gedestilleerd en gedeïoniseerd water, wordt gewoonlijk in het volume tussen de elektroden getransporteerd dat de vaste deeltjes (in de vorm van puin) wegvoert en de isolerende eigenschappen van het diëlektricum worden hersteld. Na het vloeien van een stroom wordt het potentiaalverschil tussen de twee elektroden hersteld tot wat het was vóór de doorslag, zodat een nieuwe vloeibare diëlektrische doorslag kan optreden. Onze moderne elektrische ontladingsmachines (EDM) bieden numeriek gestuurde bewegingen en zijn uitgerust met pompen en filtersystemen voor de diëlektrische vloeistoffen.
Verspanen met elektrische ontlading (EDM) is een bewerkingsmethode die voornamelijk wordt gebruikt voor harde metalen of metalen die met conventionele technieken zeer moeilijk te bewerken zijn. EDM werkt doorgaans met alle materialen die elektrische geleiders zijn, hoewel er ook methoden zijn voorgesteld voor het machinaal bewerken van isolerend keramiek met EDM. Het smeltpunt en de latente smeltwarmte zijn eigenschappen die bepalend zijn voor de hoeveelheid verwijderd metaal per ontlading. Hoe hoger deze waarden, hoe lager de materiaalverwijderingssnelheid. Omdat het bewerkingsproces met elektrische ontlading geen mechanische energie met zich meebrengt, hebben de hardheid, sterkte en taaiheid van het werkstuk geen invloed op de verwijderingssnelheid. Ontladingsfrequentie of energie per ontlading, de spanning en stroom worden gevarieerd om de materiaalverwijderingssnelheden te regelen. De mate van materiaalverwijdering en oppervlakteruwheid nemen toe met toenemende stroomdichtheid en afnemende vonkfrequentie. We kunnen ingewikkelde contouren of holtes in voorgehard staal snijden met behulp van EDM zonder dat een warmtebehandeling nodig is om ze zacht te maken en opnieuw te harden. We kunnen deze methode gebruiken met elk metaal of metaallegeringen zoals titanium, hastelloy, kovar en inconel. Toepassingen van het EDM-proces omvatten het vormen van polykristallijne diamantgereedschappen. EDM wordt beschouwd als een niet-traditionele of niet-conventionele bewerkingsmethode, samen met processen zoals elektrochemische bewerking (ECM), waterstraalsnijden (WJ, AWJ), lasersnijden. Aan de andere kant omvatten de conventionele bewerkingsmethoden draaien, frezen, slijpen, boren en andere processen waarvan het materiaalverwijderingsmechanisme in wezen gebaseerd is op mechanische krachten. Elektroden voor elektrische ontladingsbewerking (EDM) zijn gemaakt van grafiet, messing, koper en koper-wolfraamlegering. Elektrodediameters tot 0,1 mm zijn mogelijk. Aangezien gereedschapsslijtage een ongewenst fenomeen is dat de maatnauwkeurigheid in EDM nadelig beïnvloedt, maken we gebruik van een proces genaamd NO-WEAR EDM, door de polariteit om te keren en koperen gereedschappen te gebruiken om gereedschapsslijtage te minimaliseren.
Idealiter kan de elektrische ontladingsbewerking (EDM) worden beschouwd als een reeks afbraak en herstel van de diëlektrische vloeistof tussen de elektroden. In werkelijkheid is het verwijderen van het vuil uit het gebied tussen de elektroden echter bijna altijd gedeeltelijk. Dit zorgt ervoor dat de elektrische eigenschappen van het diëlektricum in het gebied tussen de elektroden verschillen van hun nominale waarden en met de tijd variëren. De afstand tussen de elektroden, (vonkbrug), wordt aangepast door de besturingsalgoritmen van de specifieke gebruikte machine. De vonkbrug in EDM kan helaas soms worden kortgesloten door het puin. Het regelsysteem van de elektrode reageert mogelijk niet snel genoeg om te voorkomen dat de twee elektroden (gereedschap en werkstuk) kortsluiten. Deze ongewenste kortsluiting draagt anders bij aan het verwijderen van materiaal dan in het ideale geval. We hechten het grootste belang aan de spoelactie om de isolerende eigenschappen van het diëlektricum te herstellen, zodat de stroom altijd plaatsvindt in het punt van het gebied tussen de elektroden, waardoor de mogelijkheid van ongewenste vormverandering (beschadiging) van de gereedschapselektrode wordt geminimaliseerd en werkstuk. Om een specifieke geometrie te verkrijgen, wordt het EDM-gereedschap langs het gewenste pad zeer dicht bij het werkstuk geleid zonder het aan te raken. We besteden de grootste aandacht aan de prestaties van de motion control in gebruik. Op deze manier vindt er een groot aantal stroomontladingen / vonken plaats, die elk bijdragen aan het verwijderen van materiaal van zowel gereedschap als werkstuk, waar kleine kraters worden gevormd. De grootte van de kraters is een functie van de technologische parameters die zijn ingesteld voor de specifieke taak en de afmetingen kunnen variëren van nanoschaal (zoals in het geval van micro-EDM-bewerkingen) tot enkele honderden micrometers in ruwe omstandigheden. Deze kleine kraters op het gereedschap veroorzaken een geleidelijke erosie van de elektrode die "gereedschapslijtage" wordt genoemd. Om het nadelige effect van de slijtage op de geometrie van het werkstuk tegen te gaan, vervangen we continu de gereedschapselektrode tijdens een bewerking. Soms bereiken we dit door een continu vervangen draad als elektrode te gebruiken (dit EDM-proces wordt ook wel WIRE EDM genoemd). Soms gebruiken we de gereedschapselektrode op zo'n manier dat slechts een klein deel ervan daadwerkelijk in het bewerkingsproces wordt betrokken en dit deel wordt regelmatig vervangen. Dit is bijvoorbeeld het geval bij het gebruik van een roterende schijf als gereedschapselektrode. Dit proces heet EDM GRINDING. Nog een andere techniek die we toepassen, bestaat uit het gebruik van een set elektroden met verschillende maten en vormen tijdens dezelfde EDM-operatie om slijtage te compenseren. We noemen deze techniek met meerdere elektroden en wordt het meest gebruikt wanneer de gereedschapselektrode de gewenste vorm negatief repliceert en in een enkele richting naar de blanco wordt voortbewogen, gewoonlijk de verticale richting (dwz de z-as). Dit lijkt op het wegzinken van het gereedschap in de diëlektrische vloeistof waarin het werkstuk is ondergedompeld, en wordt daarom aangeduid als DIE-SINKING EDM (soms genoemd_cc781905-5cde- 3194-bb3b-136bad5cf58d_CONVENTIONAL EDM or RAM EDM). De machines voor deze bewerking heten SINKER EDM. De elektroden voor dit type EDM hebben complexe vormen. Als de uiteindelijke geometrie wordt verkregen met behulp van een meestal eenvoudig gevormde elektrode die in verschillende richtingen wordt bewogen en ook onderhevig is aan rotaties, noemen we dit EDM MILLING. De mate van slijtage is strikt afhankelijk van de technologische parameters die bij de operatie worden gebruikt (polariteit, maximale stroom, nullastspanning). Bijvoorbeeld, in micro-EDM, ook bekend als m-EDM, worden deze parameters meestal ingesteld op waarden die ernstige slijtage veroorzaken. Slijtage is dan ook een groot probleem op dat gebied, dat we met onze opgebouwde knowhow tot een minimum beperken. Om bijvoorbeeld slijtage aan grafietelektroden te minimaliseren, keert een digitale generator, die binnen milliseconden kan worden bestuurd, de polariteit om wanneer elektro-erosie plaatsvindt. Dit resulteert in een effect vergelijkbaar met galvaniseren, waarbij het geërodeerde grafiet continu terug op de elektrode wordt afgezet. Bij een andere methode, een zogenaamd ''Zero Wear''-circuit, minimaliseren we hoe vaak de ontlading begint en stopt, en houden we deze zo lang mogelijk aan. De materiaalverwijderingssnelheid bij machinale bewerking met elektrische ontlading kan worden geschat op basis van:
MRR = 4 x 10 exp(4) x I x Tw exp (-1,23)
Hier is MRR in mm3/min, I is stroom in Ampère, Tw is het smeltpunt van het werkstuk in K-273,15K. De exp staat voor exponent.
Aan de andere kant kan de slijtagesnelheid Wt van de elektrode worden verkregen uit:
Wt = ( 1.1 x 10exp(11) ) x I x Ttexp(-2,38)
Hier is Wt in mm3/min en is Tt het smeltpunt van het elektrodemateriaal in K-273.15K
Ten slotte kan de slijtageverhouding van het werkstuk tot elektrode R worden verkregen uit:
R = 2,25 x Trex (-2,38)
Hier is Tr de verhouding van smeltpunten van werkstuk tot elektrode.
SINKER EDM :
Sinker EDM, ook wel CAVITY TYPE EDM or VOLUME EDM. De elektrode en het werkstuk zijn aangesloten op een voeding. De voeding genereert een elektrisch potentiaal tussen de twee. Wanneer de elektrode het werkstuk nadert, treedt er diëlektrische doorslag op in de vloeistof, waardoor een plasmakanaal wordt gevormd en een kleine vonk springt. De vonken slaan gewoonlijk één voor één in, omdat het hoogst onwaarschijnlijk is dat verschillende locaties in de ruimte tussen de elektroden identieke lokale elektrische eigenschappen hebben waardoor een vonk op al dergelijke locaties tegelijk zou kunnen optreden. Honderdduizenden van deze vonken gebeuren per seconde op willekeurige punten tussen de elektrode en het werkstuk. Naarmate het basismetaal erodeert en de vonkbrug vervolgens groter wordt, wordt de elektrode automatisch neergelaten door onze CNC-machine, zodat het proces ononderbroken kan doorgaan. Onze apparatuur heeft regelcycli die bekend staan als ''op tijd'' en ''uit tijd''. De aan-tijd instelling bepaalt de lengte of duur van de vonk. Een langere op tijd produceert een diepere holte voor die vonk en alle volgende vonken voor die cyclus, waardoor een ruwere afwerking op het werkstuk ontstaat en vice versa. De uitschakeltijd is de periode dat de ene vonk wordt vervangen door een andere. Een langere uitschakeltijd zorgt ervoor dat de diëlektrische vloeistof door een mondstuk kan spoelen om het geërodeerde vuil te verwijderen, waardoor kortsluiting wordt vermeden. Deze instellingen worden in microseconden aangepast.
DRAAD EDM :
In WIRE ELECTRICAL DISCHARGE MACHINING (WEDM), ook wel WIRE-CUT EDM_cc781905-5cde-3194-bb378UTTING_bad5c-de Cde-3194-bb3781905-1394-bb3b-136bad5cf58d_WIRE-CUT EDM_cc781905-5cde-3194-bb378UTTING_bad5c-de C dunne enkelstrengs metalen draad van messing door het werkstuk, dat is ondergedompeld in een tank met diëlektrische vloeistof. Draadvonken is een belangrijke variant van EDM. We gebruiken af en toe draadvonken om platen tot 300 mm dik te snijden en om ponsen, gereedschappen en matrijzen te maken van harde metalen die moeilijk te bewerken zijn met andere productiemethoden. Bij dit proces, dat lijkt op het snijden van contouren met een lintzaag, wordt de draad, die constant wordt gevoed vanaf een spoel, vastgehouden tussen de bovenste en onderste diamantgeleiders. De CNC-gestuurde geleiders bewegen in het x–y-vlak en de bovenste geleider kan ook onafhankelijk bewegen in de z–u–v-as, waardoor het mogelijk wordt om taps toelopende en overgangsvormen te snijden (zoals een cirkel aan de onderkant en vierkant bij de top). De bovenste geleider kan asbewegingen in x–y–u–v–i–j–k–l– regelen. Hierdoor kan de WEDM zeer ingewikkelde en delicate vormen snijden. De gemiddelde snijkerf van onze apparatuur die de beste economische kosten en bewerkingstijd bereikt, is 0,335 mm bij gebruik van Ø 0,25 messing-, koper- of wolfraamdraad. De bovenste en onderste diamantgeleiders van onze CNC-apparatuur zijn echter nauwkeurig tot ongeveer 0,004 mm en kunnen een snijpad of kerf hebben van slechts 0,021 mm bij gebruik van draad van Ø 0,02 mm. Dus echt smalle sneden zijn mogelijk. De snijbreedte is groter dan de breedte van de draad omdat er vonken ontstaan vanaf de zijkanten van de draad naar het werkstuk, waardoor erosie ontstaat. Deze ''overcut'' is nodig, voor veel toepassingen voorspelbaar en dus te compenseren (in micro-EDM is dit niet vaak het geval). De draadspoelen zijn lang - een spoel van 0,25 mm draad van 8 kg is iets meer dan 19 kilometer lang. De draaddiameter kan zo klein zijn als 20 micrometer en de geometrieprecisie ligt in de buurt van +/- 1 micrometer. Over het algemeen gebruiken we de draad maar één keer en recyclen we deze omdat het relatief goedkoop is. Het beweegt met een constante snelheid van 0,15 tot 9 m/min en een constante kerf (gleuf) wordt gehandhaafd tijdens een snede. In het wire-cut EDM-proces gebruiken we water als de diëlektrische vloeistof, waarbij we de soortelijke weerstand en andere elektrische eigenschappen regelen met filters en de-ionisatie-eenheden. Het water spoelt het snijafval weg van de snijzone. Spoelen is een belangrijke factor bij het bepalen van de maximale voedingssnelheid voor een bepaalde materiaaldikte en daarom houden we deze consistent. De snijsnelheid in draadvonken wordt aangegeven in termen van de dwarsdoorsnede die per tijdseenheid wordt gesneden, zoals 18.000 mm2/uur voor 50 mm dik D2-gereedschapsstaal. De lineaire snijsnelheid voor dit geval zou 18.000/50 = 360 mm/uur zijn. De materiaalverwijderingssnelheid in draadvonken is:
MRR = Vfxhxb
Hier is MRR in mm3/min, Vf is de voedingssnelheid van de draad in het werkstuk in mm/min, h is dikte of hoogte in mm, en b is de kerf, die is:
b = dw + 2s
Hier is dw de draaddiameter en s de opening tussen de draad en het werkstuk in mm.
Naast nauwere toleranties hebben onze moderne meerassige EDM-draadsnijbewerkingscentra extra functies zoals meerdere koppen voor het tegelijkertijd snijden van twee onderdelen, bedieningselementen om draadbreuk te voorkomen, automatische zelf-draadsnijfuncties in geval van draadbreuk en geprogrammeerde bewerkingsstrategieën om de bewerking, rechte en hoekige snijmogelijkheden te optimaliseren.
Wire-EDM biedt ons lage restspanningen, omdat er geen hoge snijkrachten nodig zijn voor het verwijderen van materiaal. Wanneer de energie/het vermogen per puls relatief laag is (zoals bij nabewerkingen), wordt door lage restspanningen weinig verandering in de mechanische eigenschappen van een materiaal verwacht.
ELEKTRISCH ONTLADEN SLIJPERS (EDG) : De slijpstenen bevatten geen schuurmiddelen, ze zijn gemaakt van grafiet of messing. Herhaalde vonken tussen het roterende wiel en het werkstuk verwijderen materiaal van het werkstukoppervlak. Het materiaalverwijderingspercentage is:
MRR = K x I
Hier is MRR in mm3/min, I is stroom in Ampère en K is werkstukmateriaalfactor in mm3/A-min. We gebruiken vaak elektrisch ontladingsslijpen om smalle spleten op componenten te zagen. We combineren soms het EDG-proces (Electrical-Discharge Grinding) met het ECG-proces (Electrochemical Grinding), waarbij materiaal wordt verwijderd door chemische actie, waarbij de elektrische ontladingen van het grafietwiel de oxidefilm breken en wegspoelen door de elektrolyt. Het proces heet ELECTROCHEMICAL-DISCHARGE GRINDING (ECDG). Hoewel het ECDG-proces relatief meer stroom verbruikt, is het een sneller proces dan de EDG. We slijpen meestal hardmetalen gereedschappen met deze techniek.
Toepassingen van elektrische ontladingsbewerking:
Prototype productie:
We gebruiken het EDM-proces bij het maken van matrijzen, de fabricage van gereedschappen en matrijzen, maar ook voor het maken van prototypen en productieonderdelen, met name voor de lucht- en ruimtevaart-, auto- en elektronica-industrie waar de productiehoeveelheden relatief laag zijn. Bij Sinker EDM wordt een grafiet-, koperwolfraam- of puur koperelektrode in de gewenste (negatieve) vorm gefreesd en aan het uiteinde van een verticale ram in het werkstuk gevoerd.
Munten sterven maken:
Voor het maken van matrijzen voor het produceren van sieraden en insignes door het muntproces (stempelen), kan de positieve master worden gemaakt van sterling zilver, omdat (met de juiste machine-instellingen) de master aanzienlijk is geërodeerd en slechts één keer wordt gebruikt. De resulterende negatieve matrijs wordt vervolgens gehard en gebruikt in een valhamer om gestempelde vlakken te produceren van uitgesneden plaatblanco's van brons, zilver of een laagbestendige goudlegering. Voor badges kunnen deze vlakken verder worden gevormd tot een gebogen oppervlak door een andere matrijs. Dit type EDM wordt meestal uitgevoerd ondergedompeld in een op olie gebaseerd diëlektricum. Het afgewerkte object kan verder worden verfijnd door hard (glas) of zacht (verf) emailleren en/of galvaniseren met puur goud of nikkel. Zachtere materialen zoals zilver kunnen als verfijning met de hand worden gegraveerd.
Boren van kleine gaten:
Op onze draadvonkmachines gebruiken we EDM voor het boren van kleine gaten om een doorgaand gat in een werkstuk te maken waar de draad doorheen wordt geleid voor de draadvonkbewerking. Afzonderlijke EDM-koppen speciaal voor het boren van kleine gaten zijn gemonteerd op onze draadsnijmachines, waardoor grote geharde platen waar nodig en zonder voorboren van afgewerkte onderdelen kunnen worden geërodeerd. We gebruiken ook EDM met kleine gaten om rijen gaten te boren in de randen van turbinebladen die in straalmotoren worden gebruikt. Door de gasstroom door deze kleine gaatjes kunnen de motoren hogere temperaturen gebruiken dan anders mogelijk zou zijn. De hoge temperatuur, zeer harde, eenkristallegeringen waarvan deze bladen zijn gemaakt, maken conventionele bewerking van deze gaten met een hoge aspectverhouding extreem moeilijk en zelfs onmogelijk. Andere toepassingsgebieden voor EDM met kleine gaten zijn het creëren van microscopisch kleine openingen voor brandstofsysteemcomponenten. Naast de geïntegreerde EDM-koppen, gebruiken we stand-alone EDM-machines voor het boren van kleine gaten met x–y-assen om blinde of doorlopende gaten te bewerken. EDM boort gaten met een lange koperen of koperen buiselektrode die in een boorkop draait met een constante stroom gedestilleerd of gedeïoniseerd water dat door de elektrode stroomt als spoelmiddel en diëlektricum. Sommige EDM's voor het boren van kleine gaten kunnen in minder dan 10 seconden door 100 mm zacht of zelfs gehard staal boren. Met deze boorbewerking kunnen gaten tussen 0,3 mm en 6,1 mm worden bereikt.
Metaal desintegratie bewerking:
We hebben ook speciale EDM-machines die specifiek zijn bedoeld om kapotte gereedschappen (boren of tappen) van werkstukken te verwijderen. Dit proces wordt ''metaaldesintegratiebewerking'' genoemd.
Voordelen en nadelen Elektrische ontladingsbewerking:
Voordelen van EDM zijn onder meer de bewerking van:
- Complexe vormen die anders moeilijk te maken zouden zijn met conventionele snijgereedschappen
- Extreem hard materiaal tot zeer nauwe toleranties
- Zeer kleine werkstukken waar conventionele snijgereedschappen het onderdeel kunnen beschadigen door overmatige snijgereedschapdruk.
- Er is geen direct contact tussen gereedschap en werkstuk. Daarom kunnen delicate secties en zwakke materialen zonder enige vervorming worden bewerkt.
- Er kan een goede oppervlakteafwerking worden verkregen.
- Zeer fijne gaten kunnen gemakkelijk worden geboord.
Nadelen van EDM zijn onder meer:
- De langzame snelheid van materiaalverwijdering.
- De extra tijd en kosten die worden gebruikt voor het maken van elektroden voor ram/zinker EDM.
- Het reproduceren van scherpe hoeken op het werkstuk is moeilijk door elektrodeslijtage.
- Stroomverbruik is hoog.
- ''Overcut'' wordt gevormd.
- Er treedt overmatige gereedschapsslijtage op tijdens de bewerking.
- Elektrisch niet-geleidende materialen kunnen alleen worden bewerkt met een specifieke opstelling van het proces.