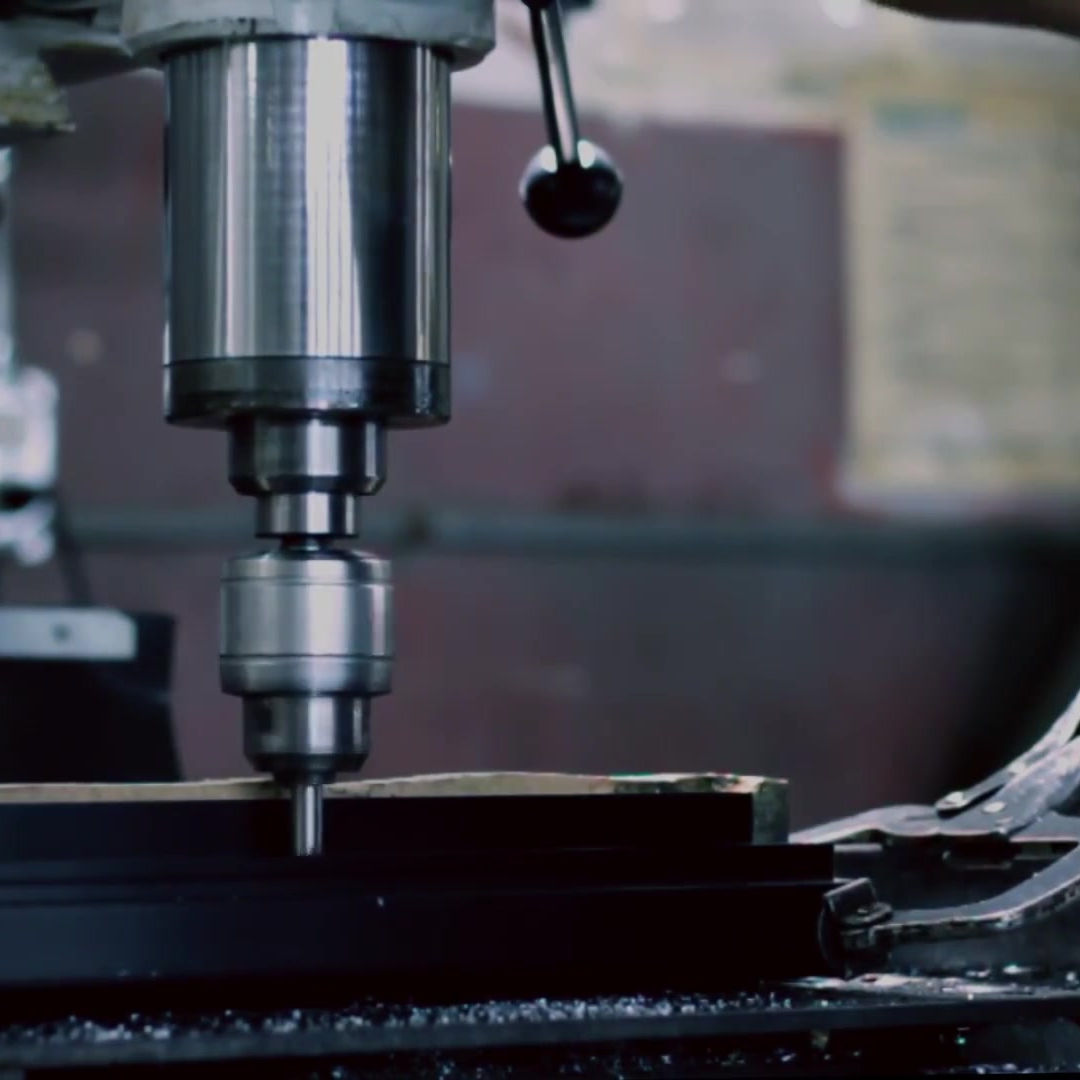
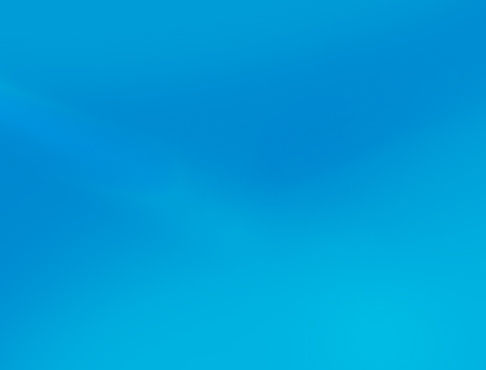
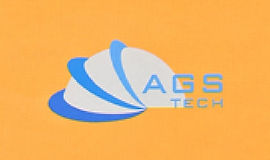
Wereldwijd op maat gemaakte fabrikant, integrator, consolidator, outsourcingpartner voor een breed scala aan producten en diensten.
Wij zijn uw one-stop-bron voor productie, fabricage, engineering, consolidatie, integratie, outsourcing van op maat gemaakte en off-shelf producten en diensten.
Choose your Language
-
Aangepaste productie
-
Binnenlandse en wereldwijde contractproductie
-
Uitbesteding van productie
-
Binnenlandse en wereldwijde inkoop
-
Consolidatie
-
Engineering-integratie
-
Ingenieursdiensten
Het type glasproductie dat wij aanbieden zijn containerglas, glasblazen, glasvezel & buizen & staven, huishoudelijk en industrieel glaswerk, lamp en bol, precisieglasgieten, optische componenten en assemblages, vlak & plaat & floatglas. We voeren zowel handmatig als machinaal vormen uit.
Onze populaire technische keramische productieprocessen zijn matrijzenpersen, isostatisch persen, heet isostatisch persen, heet persen, slipgieten, bandgieten, extrusie, spuitgieten, groene bewerking, sinteren of bakken, diamantslijpen, hermetische assemblages.
We raden u aan hier te klikken om:
DOWNLOAD onze schematische illustraties van glasvormings- en vormprocessen door AGS-TECH Inc.
Deze downloadbare bestanden met foto's en schetsen zullen u helpen de informatie die we u hieronder verstrekken beter te begrijpen.
• VERVAARDIGING VAN CONTAINERGLAS: We hebben zowel PRESS AND BLOW als BLOW AND BLOW-lijnen voor productie. In het blaas- en blaasproces laten we een klodder in een blanco mal vallen en vormen de nek door van bovenaf een slag van perslucht toe te passen. Direct daaropvolgend wordt een tweede keer perslucht vanuit de andere richting door de hals van de houder geblazen om de voorvorm van de fles te vormen. Deze voorvorm wordt vervolgens overgebracht naar de eigenlijke vorm, opnieuw verwarmd om zacht te worden en perslucht wordt toegepast om de voorvorm zijn uiteindelijke containervorm te geven. Meer expliciet wordt het onder druk gezet en tegen de wanden van de blaasvormholte geduwd om de gewenste vorm aan te nemen. Ten slotte wordt de vervaardigde glazen container overgebracht naar een gloeioven voor daaropvolgende heropwarming en verwijdering van spanningen die tijdens het vormen ontstaan en wordt op een gecontroleerde manier gekoeld. Bij de pers- en blaasmethode worden gesmolten klodders in een parisonvorm (blanco mal) gedaan en in de parisonvorm (blanco vorm) gedrukt. De blanco's worden vervolgens overgebracht naar blaasvormen en geblazen zoals hierboven beschreven onder "Blow and Blow-proces". Daaropvolgende stappen zoals gloeien en stressverlichting zijn vergelijkbaar of hetzelfde.
• GLASBLAZING : We hebben glasproducten vervaardigd door zowel conventioneel met de hand te blazen als door perslucht te gebruiken met geautomatiseerde apparatuur. Voor sommige bestellingen is conventioneel blazen noodzakelijk, zoals projecten met glaskunstwerk, of projecten die een kleiner aantal onderdelen vereisen met losse toleranties, prototyping / demoprojecten….etc. Conventioneel glasblazen omvat het dompelen van een holle metalen pijp in een pot met gesmolten glas en het roteren van de pijp om een bepaalde hoeveelheid glasmateriaal op te vangen. Het glas dat op de punt van de pijp wordt verzameld, wordt op plat ijzer gerold, naar wens gevormd, langwerpig, opnieuw verwarmd en met lucht geblazen. Als het klaar is, wordt het in een mal gestoken en wordt er lucht geblazen. De vormholte is nat om contact van het glas met metaal te voorkomen. De waterfilm fungeert als een kussen ertussen. Handmatig blazen is een arbeidsintensief langzaam proces en alleen geschikt voor prototyping of artikelen van hoge waarde, niet geschikt voor goedkope per stuk grote hoeveelheden bestellingen.
• VERVAARDIGING VAN HUISHOUDELIJK & INDUSTRIEEL GLASWERK: Met behulp van verschillende soorten glasmateriaal wordt een grote verscheidenheid aan glaswerk geproduceerd. Sommige glazen zijn hittebestendig en geschikt voor laboratoriumglaswerk, terwijl andere goed genoeg zijn om vele malen vaatwasmachinebestendig te zijn en geschikt zijn voor het maken van huishoudelijke producten. Met behulp van Westlake machines worden per dag tienduizenden stuks drinkglazen geproduceerd. Ter vereenvoudiging wordt gesmolten glas door vacuüm verzameld en in mallen gestoken om de voorvormen te maken. Vervolgens wordt er lucht in de mallen geblazen, deze worden overgebracht naar een andere mal en er wordt weer lucht geblazen en het glas krijgt zijn uiteindelijke vorm. Net als bij het met de hand blazen, worden deze mallen nat gehouden met water. Verder strekken maakt deel uit van de afwerkingsbewerking waarbij de nek wordt gevormd. Overtollig glas wordt weggebrand. Daarna volgt het hierboven beschreven gecontroleerde opwarm- en afkoelproces.
• GLASS TUBE & ROD VORMING: De belangrijkste processen die we gebruiken voor de productie van glazen buizen zijn de DANNER- en VELLO-processen. In het Danner-proces stroomt glas uit een oven en valt het op een schuine huls gemaakt van vuurvaste materialen. De huls wordt gedragen op een roterende holle as of blaaspijp. Het glas wordt dan om de huls gewikkeld en vormt een gladde laag die langs de huls en over de punt van de schacht stroomt. Bij buisvormen wordt lucht door een blaaspijp met holle punt geblazen en bij staafvormen gebruiken we massieve punten op de as. De buizen of staven worden dan over draagrollen getrokken. De afmetingen zoals wanddikte en diameter van de glazen buizen worden op de gewenste waarden ingesteld door de diameter van de huls en de blaasluchtdruk op een gewenste waarde in te stellen, de temperatuur, de stroomsnelheid van het glas en de treksnelheid aan te passen. Het fabricageproces van de Vello-glasbuis daarentegen omvat glas dat uit een oven en in een kom met een holle doorn of bel reist. Het glas gaat dan door de luchtruimte tussen de doorn en de kom en neemt de vorm aan van een buis. Daarna gaat het over rollen naar een trekmachine en wordt het gekoeld. Aan het einde van de koellijn vindt het snijden en de eindverwerking plaats. De buisafmetingen kunnen net als in het Danner-proces worden aangepast. Wanneer we het Danner- en het Vello-proces vergelijken, kunnen we zeggen dat het Vello-proces beter geschikt is voor de productie van grote hoeveelheden, terwijl het Danner-proces wellicht beter geschikt is voor nauwkeurige buisorders met een kleiner volume.
• VERWERKING VAN PLAAT & VLAK- & DRIJFGLAS : We hebben grote hoeveelheden vlakglas in diktes variërend van submilimeterdiktes tot enkele centimeters. Onze platte glazen zijn van bijna optische perfectie. Wij bieden glas aan met speciale coatings zoals optische coatings, waarbij chemische dampdepositietechniek wordt gebruikt om coatings zoals antireflectie- of spiegelcoating aan te brengen. Ook transparante geleidende coatings komen veel voor. Er zijn ook hydrofobe of hydrofiele coatings op glas en coatings die glas zelfreinigend maken. Geharde, kogelvrije en gelaagde glazen zijn nog andere populaire items. Wij snijden glas in gewenste vorm met gewenste toleranties. Andere secundaire bewerkingen zoals het buigen of buigen van vlakglas zijn beschikbaar.
• PRECISIE GLASVORMING: We gebruiken deze techniek meestal voor het vervaardigen van optische precisiecomponenten zonder de noodzaak van duurdere en tijdrovende technieken zoals slijpen, leppen en polijsten. Deze techniek is niet altijd voldoende om het beste van de beste optica te maken, maar in sommige gevallen, zoals consumentenproducten, digitale camera's en medische optica, kan het een minder dure goede optie zijn voor productie van grote volumes. Het heeft ook een voordeel ten opzichte van de andere glasvormende technieken waar complexe geometrieën vereist zijn, zoals in het geval van asferen. Het basisproces omvat het laden van de onderkant van onze matrijs met de glazen blanco, evacuatie van de proceskamer voor zuurstofverwijdering, bijna sluiten van de matrijs, snelle en isotherme verwarming van matrijs en glas met infrarood licht, verder sluiten van de matrijshelften om het verweekte glas langzaam en gecontroleerd tot de gewenste dikte te persen en tenslotte het glas af te koelen en de kamer te vullen met stikstof en het product te verwijderen. Nauwkeurige temperatuurregeling, sluitafstand van de mal, sluitkracht van de mal, aanpassing aan de uitzettingscoëfficiënten van de mal en het glasmateriaal zijn de sleutel in dit proces.
• VERVAARDIGING VAN OPTISCHE COMPONENTEN EN SAMENSTELLINGEN VAN GLAS: Naast precisieglasgieten, zijn er een aantal waardevolle processen die we gebruiken voor het maken van hoogwaardige optische componenten en samenstellingen voor veeleisende toepassingen. Slijpen, leppen en polijsten van optische kwaliteit glazen in fijne speciale schurende slurries is een kunst en wetenschap voor het maken van optische lenzen, prisma's, platte vlakken en meer. Oppervlakte vlakheid, golving, gladheid en defectvrije optische oppervlakken vereisen veel ervaring met dergelijke processen. Kleine veranderingen in de omgeving kunnen resulteren in producten die niet aan de specificaties voldoen en de productielijn stilleggen. Er zijn gevallen waarin een enkele veeg op het optische oppervlak met een schone doek ervoor kan zorgen dat een product aan de specificaties voldoet of de test niet doorstaat. Enkele populaire gebruikte glasmaterialen zijn gesmolten silica, kwarts, BK7. Ook de assemblage van dergelijke componenten vereist gespecialiseerde niche-ervaring. Soms worden speciale lijmen gebruikt. Soms is een techniek die optisch contact wordt genoemd echter de beste keuze en bevat geen materiaal tussen de bevestigde optische brillen. Het bestaat uit fysiek contact maken met vlakke oppervlakken om zonder lijm aan elkaar te bevestigen. In sommige gevallen worden mechanische afstandhouders, precisie glazen staven of kogels, klemmen of machinaal bewerkte metalen componenten gebruikt om de optische componenten op bepaalde afstanden en met bepaalde geometrische oriëntaties ten opzichte van elkaar te monteren. Laten we eens kijken naar enkele van onze populaire technieken voor het vervaardigen van hoogwaardige optica.
SLIJPEN & LAPPEN & POLIJSTEN: De ruwe vorm van de optische component wordt verkregen door het slijpen van een onbewerkte glas. Daarna worden leppen en polijsten uitgevoerd door de ruwe oppervlakken van de optische componenten te roteren en te wrijven tegen gereedschappen met de gewenste oppervlaktevormen. Slurries met kleine schurende deeltjes en vloeistof worden tussen de optiek en de vormgereedschappen gegoten. De grootte van de schurende deeltjes in dergelijke slurries kan worden gekozen in overeenstemming met de gewenste mate van vlakheid. De afwijkingen van kritische optische oppervlakken van gewenste vormen worden uitgedrukt in golflengten van het gebruikte licht. Onze hoge precisie-optieken hebben toleranties van tienden van een golflengte (Golflengte/10) of zelfs strakker is mogelijk. Naast het oppervlakteprofiel worden de kritische oppervlakken gescand en beoordeeld op andere oppervlaktekenmerken en defecten zoals afmetingen, krassen, spanen, putjes, vlekjes... enz. De strikte controle van de omgevingsomstandigheden in de optische productievloer en uitgebreide meet- en testvereisten met ultramoderne apparatuur maken dit een uitdagende industrietak.
• SECUNDAIRE PROCESSEN IN DE GLASPRODUCTIE: Nogmaals, we zijn alleen beperkt met uw verbeeldingskracht als het gaat om secundaire en afwerkingsprocessen van glas. Hier sommen we er enkele op:
-Coatings op glas (optisch, elektrisch, tribologisch, thermisch, functioneel, mechanisch...). We kunnen bijvoorbeeld de oppervlakte-eigenschappen van glas veranderen door het bijvoorbeeld warmte te laten weerkaatsen zodat het het interieur van gebouwen koel houdt, of eenzijdig infrarood-absorberend maken met behulp van nanotechnologie. Dit helpt de binnenkant van gebouwen warm te houden, omdat de buitenste oppervlaktelaag van glas de infrarode straling in het gebouw absorbeert en terug naar binnen uitstraalt.
-Ets op glas
-Toegepaste keramische etikettering (ACL)
-Gravure
- Vlam polijsten
-Chemisch polijsten
-kleuring
VERVAARDIGING VAN TECHNISCH KERAMIEK
• DIE PRESSING: Bestaat uit uniaxiale verdichting van korrelige poeders opgesloten in een matrijs
• HEET PERSEN: Vergelijkbaar met stansen, maar met toevoeging van temperatuur om de verdichting te verbeteren. Poeder of gecompacteerde voorvorm wordt in een grafietmatrijs geplaatst en uniaxiale druk wordt uitgeoefend terwijl de matrijs op hoge temperaturen wordt gehouden, zoals 2000 C. De temperaturen kunnen verschillen, afhankelijk van het type keramisch poeder dat wordt verwerkt. Voor gecompliceerde vormen en geometrieën kunnen andere latere bewerkingen nodig zijn, zoals diamantslijpen.
• ISOSTATISCH PERSEN : Korrelvormige poeders of geperste compacts worden in luchtdichte containers geplaatst en vervolgens in een gesloten drukvat met vloeistof erin. Daarna worden ze verdicht door de druk van het drukvat te verhogen. De vloeistof in het vat brengt de drukkrachten gelijkmatig over het gehele oppervlak van de luchtdichte container over. Het materiaal wordt dus uniform verdicht en neemt de vorm aan van zijn flexibele container en zijn interne profiel en kenmerken.
• HEET ISOSTATISCH PERSEN: Vergelijkbaar met isostatisch persen, maar naast een atmosfeer onder druk van gas, sinteren we het compact bij hoge temperatuur. Heet isostatisch persen resulteert in extra verdichting en verhoogde sterkte.
• SLIPGIET / AFVOERGIET : We vullen de mal met een suspensie van micrometergrote keramische deeltjes en dragervloeistof. Dit mengsel wordt "slip" genoemd. De mal heeft poriën en daarom wordt de vloeistof in het mengsel in de mal gefilterd. Als resultaat wordt een gietvorm gevormd op de binnenoppervlakken van de mal. Na het sinteren kunnen de onderdelen uit de mal worden gehaald.
• TAPEGIET: Wij vervaardigen keramische tapes door keramische slurries op vlakke bewegende drageroppervlakken te gieten. De slurries bevatten keramische poeders gemengd met andere chemicaliën voor bind- en transportdoeleinden. Als de oplosmiddelen verdampen, blijven er dichte en flexibele keramische platen achter die naar wens kunnen worden gesneden of gewalst.
• EXTRUSIEVORMING: Net als bij andere extrusieprocessen wordt een zacht mengsel van keramisch poeder met bindmiddelen en andere chemicaliën door een matrijs geleid om zijn dwarsdoorsnedevorm te verkrijgen en vervolgens op de gewenste lengte gesneden. Het proces wordt uitgevoerd met koude of verwarmde keramische mengsels.
• LAGE DRUK INJECTIEVORMING : We bereiden een mengsel van keramisch poeder met bindmiddelen en oplosmiddelen en verhitten het tot een temperatuur waarbij het gemakkelijk kan worden geperst en in de gereedschapsholte kan worden geperst. Zodra de vormcyclus is voltooid, wordt het onderdeel uitgeworpen en wordt de bindende chemische stof afgebrand. Door middel van spuitgieten kunnen we op een voordelige manier ingewikkelde onderdelen in hoge volumes verkrijgen. Gaten die een fractie van een millimeter op een 10 mm dikke wand zijn, zijn mogelijk, schroefdraad is mogelijk zonder verdere bewerking, toleranties zo krap als +/- 0,5% zijn mogelijk en zelfs lager wanneer onderdelen worden bewerkt , wanddiktes in de orde van 0,5 mm tot een lengte van 12,5 mm zijn mogelijk evenals wanddiktes van 6,5 mm tot een lengte van 150 mm.
• GROENE BEWERKING: Met dezelfde bewerkingsgereedschappen voor metaal kunnen we geperste keramische materialen machinaal bewerken terwijl ze nog zo zacht zijn als krijt. Toleranties van +/- 1% zijn mogelijk. Voor betere toleranties gebruiken we diamantslijpen.
• SINTEREN of VAKKEN : Sinteren maakt volledige verdichting mogelijk. Aanzienlijke krimp treedt op op de groene compacte onderdelen, maar dit is geen groot probleem, aangezien we rekening houden met deze dimensionale veranderingen bij het ontwerpen van het onderdeel en de tooling. Poederdeeltjes worden aan elkaar gehecht en porositeit veroorzaakt door het verdichtingsproces wordt grotendeels verwijderd.
• DIAMANT SLIJPEN: 's Werelds hardste materiaal “diamant” wordt gebruikt om harde materialen zoals keramiek te slijpen en er worden precisieonderdelen verkregen. Toleranties in het micrometerbereik en zeer gladde oppervlakken worden bereikt. Vanwege de kosten overwegen we deze techniek alleen als we het echt nodig hebben.
• HERMETIC ASSEMBLIES zijn die welke praktisch gezien geen uitwisseling van materie, vaste stoffen, vloeistoffen of gassen tussen interfaces toestaan. Hermetische afdichting is luchtdicht. Hermetische elektronische behuizingen zijn bijvoorbeeld behuizingen die de gevoelige binneninhoud van een verpakt apparaat onaangetast houden door vocht, verontreinigingen of gassen. Niets is 100% hermetisch, maar als we spreken van hermeticiteit bedoelen we dat in de praktijk, dat er hermeticiteit is in die mate dat de leksnelheid zo laag is dat de apparaten gedurende zeer lange tijd veilig zijn onder normale omgevingsomstandigheden. Onze hermetische assemblages bestaan uit metalen, glazen en keramische componenten, metaal-keramiek, keramisch-metaal-keramiek, metaal-keramiek-metaal, metaal op metaal, metaal-glas, metaal-glas-metaal, glas-metaal-glas, glas- metaal en glas op glas en alle andere combinaties van metaal-glas-keramiek binding. Zo kunnen we de keramische componenten met een metaalcoating coaten, zodat ze sterk aan andere componenten in de assemblage kunnen worden gehecht en een uitstekend afdichtend vermogen hebben. We hebben de knowhow om optische vezels of doorvoeropeningen met metaal te coaten en deze aan de behuizingen te solderen of te solderen, zodat er geen gassen in de behuizingen komen of lekken. Daarom worden ze gebruikt voor het vervaardigen van elektronische behuizingen om gevoelige apparaten in te kapselen en te beschermen tegen de buitenatmosfeer. Naast hun uitstekende afdichtingseigenschappen, andere eigenschappen zoals de thermische uitzettingscoëfficiënt, vervormingsweerstand, niet-ontgassend karakter, zeer lange levensduur, niet-geleidend karakter, thermische isolatie-eigenschappen, antistatisch karakter... enz. maken glas en keramische materialen de keuze voor bepaalde toepassingen. Informatie over onze fabriek voor de productie van keramisch-op-metaal fittingen, hermetische afdichting, vacuümdoorvoeren, hoog- en ultrahoogvacuüm- en vloeistofregelcomponenten vindt u hier:Hermetische componenten fabrieksbrochure