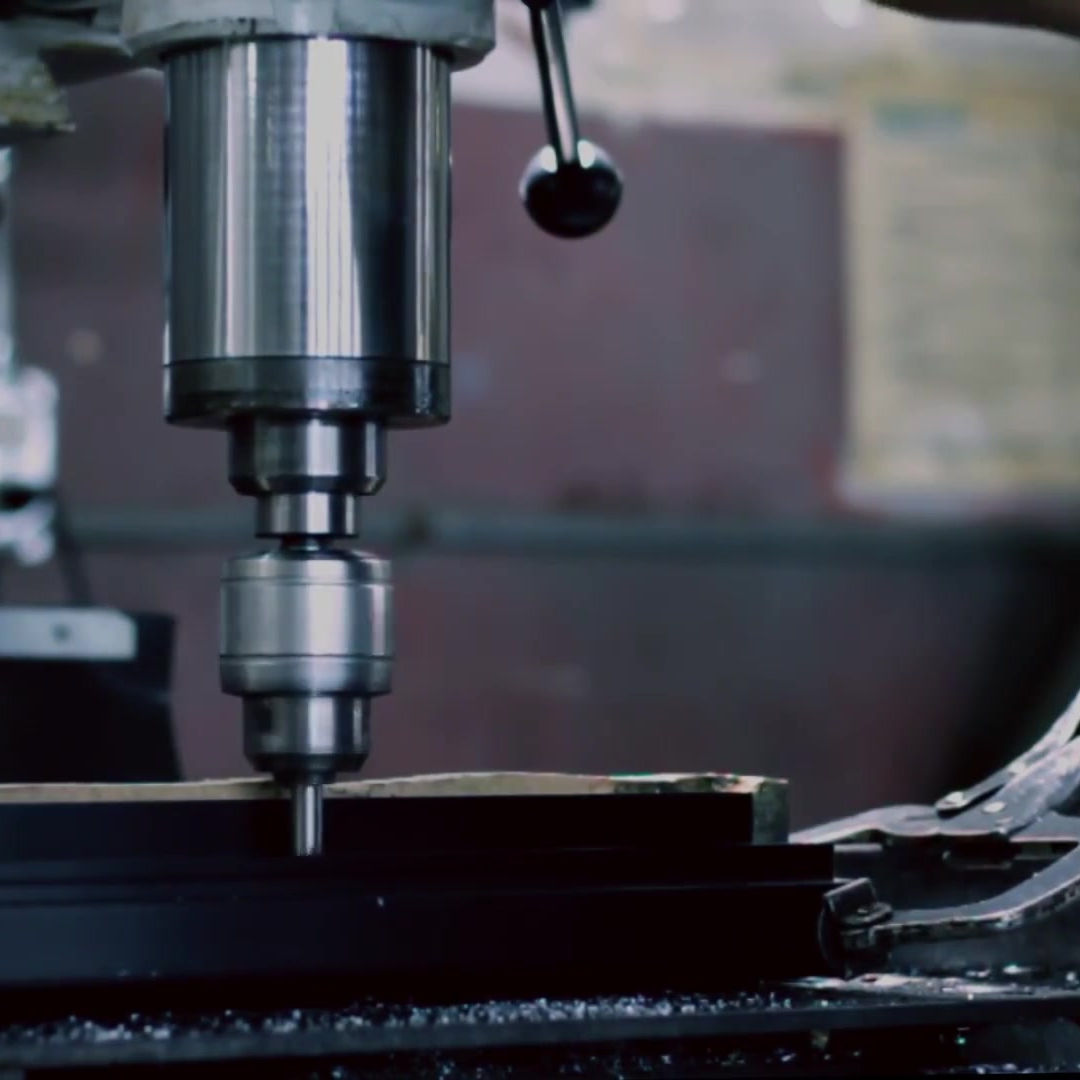
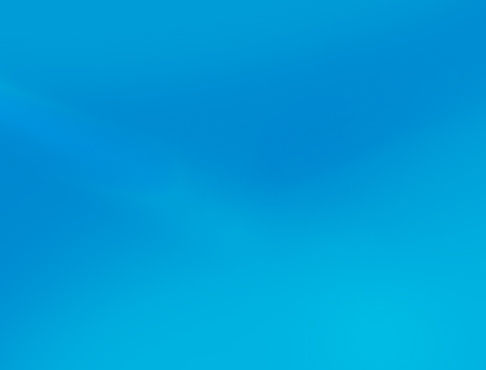
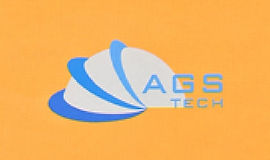
Wereldwijd op maat gemaakte fabrikant, integrator, consolidator, outsourcingpartner voor een breed scala aan producten en diensten.
Wij zijn uw one-stop-bron voor productie, fabricage, engineering, consolidatie, integratie, outsourcing van op maat gemaakte en off-shelf producten en diensten.
Choose your Language
-
Aangepaste productie
-
Binnenlandse en wereldwijde contractproductie
-
Uitbesteding van productie
-
Binnenlandse en wereldwijde inkoop
-
Consolidatie
-
Engineering-integratie
-
Ingenieursdiensten
Search Results
164 resultaten gevonden met een lege zoekopdracht
- Transmission Components, Belts, Chains, Cable Drives, Pulleys,AGS-TECH
Transmission Components, Belts, Chains and Cable Drives, Conventional & Grooved or Serrated, Positive Drive, Pulleys Riemen & Kettingen & Kabelaandrijving Montage AGS-TECH Inc. biedt u componenten voor krachtoverbrenging, waaronder riemen en kettingen en kabelaandrijving. Door jaren van verfijning zijn onze rubberen, leren en andere riemaandrijvingen lichter en compacter geworden, waardoor ze hogere belastingen kunnen dragen tegen lagere kosten. Evenzo hebben onze kettingaandrijvingen in de loop van de tijd veel ontwikkeling doorgemaakt en bieden ze onze klanten verschillende voordelen. Enkele voordelen van het gebruik van kettingaandrijvingen zijn hun relatief onbeperkte hartafstanden van de as, compactheid, gemakkelijke montage, elasticiteit in spanning zonder slip of kruip, vermogen om te werken in omgevingen met hoge temperaturen. Onze kabelaandrijvingen bieden ook voordelen zoals eenvoud in sommige toepassingen ten opzichte van andere soorten transmissiecomponenten. Zowel standaard riem-, ketting- en kabelaandrijvingen als op maat gemaakte en geassembleerde versies zijn beschikbaar. Wij kunnen deze transmissiecomponenten op de juiste maat voor uw toepassing en uit de meest geschikte materialen vervaardigen. RIEMEN & RIEMAANDRIJVINGEN: - Conventionele platte riemen: dit zijn gewone platte riemen zonder tanden, groeven of vertanding. Platte riemaandrijvingen bieden flexibiliteit, goede schokabsorptie, efficiënte krachtoverbrenging bij hoge snelheden, slijtvastheid, lage kosten. Riemen kunnen worden gesplitst of verbonden om grotere riemen te maken. Andere voordelen van conventionele platte riemen zijn dat ze dun zijn en niet onderhevig zijn aan hoge centrifugale belastingen (waardoor ze geschikt zijn voor bewerkingen op hoge snelheid met kleine riemschijven). Anderzijds leggen ze een hoge lagerbelasting op omdat platte riemen een hoge spanning vereisen. Andere nadelen van platte riemaandrijvingen kunnen slippen, lawaaierige werking en relatief lagere efficiëntie bij lage en matige werksnelheden zijn. We hebben twee soorten conventionele riemen: versterkt en niet-versterkt. Versterkte riemen hebben een trekelement in hun structuur. Conventionele platte riemen zijn verkrijgbaar als leer, met rubber beklede stof of koord, niet-versterkt rubber of kunststof, stof, versterkt leer. Leren riemen bieden een lange levensduur, flexibiliteit, uitstekende wrijvingscoëfficiënt en eenvoudige reparatie. Leren riemen zijn echter relatief duur, hebben een riem nodig en moeten worden schoongemaakt, en afhankelijk van de atmosfeer kunnen ze krimpen of uitrekken. Met rubber beklede weefsel- of koordriemen zijn bestand tegen vocht, zuren en logen. Riemen van rubberen stof zijn gemaakt van lagen katoen of synthetische eend geïmpregneerd met rubber en zijn het meest economisch. Met rubber beklede koordriemen bestaan uit een reeks lagen met rubber geïmpregneerde koorden. Met rubber beklede koordriemen bieden een hoge treksterkte en bescheiden afmetingen en massa. Niet-versterkte rubberen of plastic riemen zijn geschikt voor lichte toepassingen met lage snelheid. Niet-versterkte rubberen en plastic riemen kunnen op hun plaats worden gespannen over hun katrollen. Niet-versterkte kunststof riemen kunnen een hoger vermogen overbrengen in vergelijking met rubberen riemen. Versterkte leren riemen bestaan uit een plastic trekelement dat is ingeklemd tussen leren boven- en onderlagen. Tot slot kunnen onze stoffen riemen bestaan uit een enkel stuk katoen of eend, gevouwen en genaaid met rijen lengtesteken. Stoffen riemen kunnen uniform volgen en werken met hoge snelheid. - Gegroefde of getande riemen (zoals V-riemen): dit zijn platte riemen die zijn aangepast om de voordelen van een ander type transmissieproduct te bieden. Dit zijn platte riemen met een in de lengte geribbelde onderkant. Poly-V-riemen zijn in de lengterichting gegroefde of gekartelde platte riem met een trekgedeelte en een reeks aangrenzende V-vormige groeven voor tracking- en compressiedoeleinden. Het vermogen is afhankelijk van de bandbreedte. V-snaar is het werkpaard van de industrie en is verkrijgbaar in verschillende gestandaardiseerde maten en typen voor het overbrengen van bijna elk belastingsvermogen. V-riemaandrijvingen werken goed tussen 1500 en 6000 ft/min, maar smalle V-snaren werken tot 10.000 ft/min. V-riemaandrijvingen bieden een lange levensduur zoals 3 tot 5 jaar en maken grote snelheidsverhoudingen mogelijk, ze zijn eenvoudig te installeren en te verwijderen, bieden een stille werking, weinig onderhoud, goede schokabsorptie tussen riemaandrijving en aangedreven assen. Het nadeel van V-riemen is hun zekere slip en kruip en daarom zijn ze misschien niet de beste oplossing wanneer synchrone snelheden vereist zijn. We hebben industriële, automotive en agrarische riemen. Standaard lengtes op voorraad, evenals aangepaste lengtes van riemen zijn beschikbaar. Alle standaard V-riemdoorsneden zijn uit voorraad leverbaar. Er zijn tabellen waarin u onbekende parameters zoals riemlengte, riemsectie (breedte & dikte) kunt berekenen, mits u enkele parameters van uw systeem kent, zoals aandrijf- en aangedreven riemschijfdiameters, hartafstand tussen riemschijven en rotatiesnelheden van de riemschijven. U kunt dergelijke tabellen gebruiken of ons vragen om de juiste V-riem voor u te kiezen. Positieve aandrijfriemen (distributieriem): deze riemen zijn ook van het platte type met een reeks gelijkmatig verdeelde tanden aan de binnenomtrek. Positieve aandrijf- of tandriemen combineren de voordelen van platte riemen met de positieve grip-eigenschappen van kettingen en tandwielen. Positieve aandrijfriemen onthullen geen slip of snelheidsvariaties. Een breed scala aan snelheidsverhoudingen is mogelijk. Lagerbelastingen zijn laag omdat ze bij lage spanning kunnen werken. Ze zijn echter gevoeliger voor verkeerde uitlijning in katrollen. - Katrollen, schijven, naven voor riemen: Er worden verschillende soorten schijven gebruikt met platte, geribbelde (gekartelde) en positieve aandrijfriemen. We maken ze allemaal. De meeste van onze platte riemschijven worden gemaakt door gieten van ijzer, maar stalen versies zijn ook verkrijgbaar in verschillende velg- en naafcombinaties. Onze platte riemschijven kunnen massieve, gespaakte of gespleten naven hebben of we kunnen ze produceren zoals u dat wenst. Geribbelde en positief aangedreven riemen zijn verkrijgbaar in verschillende standaardmaten en breedtes. Ten minste één poelie in tandriemaandrijvingen moet worden geflensd om de riem op de aandrijving te houden. Voor lange centrale aandrijfsystemen wordt aanbevolen om beide poelies te flensen. Schijven zijn de gegroefde wielen van katrollen en worden over het algemeen vervaardigd door ijzergieten, staalvorming of kunststofgieten. Het vormen van staal is een geschikt proces om schijven voor auto's en landbouwmachines te vervaardigen. Wij produceren schijven met regelmatige en diepe groeven. Groefschijven zijn goed geschikt wanneer de V-riem schuin de schijf ingaat, zoals bij kwartslagaandrijvingen het geval is. Diepe groeven zijn ook zeer geschikt voor aandrijvingen met verticale as en toepassingen waar trillingen van riemen een probleem kunnen zijn. Onze spanpoelies zijn gegroefde schijven of platte poelies die niet dienen voor het overbrengen van mechanische kracht. Meelooprollen worden meestal gebruikt voor het aanspannen van riemen. - Enkele en meervoudige riemaandrijvingen: Enkele riemaandrijvingen hebben een enkele groef, terwijl meerdere riemaandrijvingen meerdere groeven hebben. Door hieronder op de betreffende gekleurde tekst te klikken kunt u onze catalogi downloaden: - Aandrijfriemen (inclusief V-riemen, tandriemen, onbewerkte riemen, gewikkelde riemen en speciale riemen) - Lopende banden - V-poelies - Timing Katrollen KETTINGEN & KETTINGAANDRIJVINGEN: Onze krachtoverbrengingskettingen hebben enkele voordelen, zoals relatief onbeperkte as-hartafstanden, eenvoudige montage, compactheid, elasticiteit onder spanning zonder slip of kruip, vermogen om onder hoge temperaturen te werken. Dit zijn de belangrijkste soorten van onze kettingen: - Afneembare kettingen: onze afneembare kettingen zijn gemaakt in verschillende maten, spoed en ultieme sterkte en over het algemeen van smeedbaar ijzer of staal. Kneedbare kettingen worden gemaakt in een reeks maten van 0,902 (23 mm) tot 4,063 inch (103 mm) spoed en ultieme sterkte van 700 tot 17.000 lb/square inch. Onze afneembare stalen kettingen daarentegen zijn gemaakt in maten van 0,904 inch (23 mm) tot ongeveer 3,00 inch (76 mm) in pitch, met een ultieme sterkte van 760 tot 5000 lb/square inch._cc781905-5cde-3194-bb3b- 136bad5cf58d_ - Egelkettingen: deze kettingen worden gebruikt voor zwaardere lasten en iets hogere snelheden tot ongeveer 2,2 m/sec. Egelkettingen zijn gemaakt van individuele gegoten schakels met een volledig, rond uiteinde met verspringende zijstangen. Deze kettingschakels zijn aan elkaar gekoppeld met stalen pinnen. Deze kettingen variëren in steek van ongeveer 1,00 inch (25 mm) tot 6,00 inch (150 mm) en ultieme sterktes tussen 3600 en 30.000 lb/square inch. - Offset-zijbalkkettingen: deze zijn populair in aandrijfkettingen van bouwmachines. Deze kettingen werken met snelheden tot 1000 ft/min en brengen lasten over tot ongeveer 250 pk. Over het algemeen heeft elke schakel twee versprongen zijbalken, een bus, een rol, een pen en een splitpen. - Rollenkettingen: ze zijn verkrijgbaar in stappen van 0,25 (6 mm) tot 3,00 (75 mm) inch. De ultieme sterkte van rollenkettingen met enkele breedte varieert van 925 tot 130.000 lb/square inch. Rollenkettingen met meerdere breedtes zijn beschikbaar en brengen meer kracht over bij hogere snelheden. Rollenkettingen met meerdere breedtes bieden ook een soepelere actie met minder geluid. Rollenkettingen worden samengesteld uit rolschakels en penschakels. Splitpennen worden gebruikt in afneembare rollenkettingen. Het ontwerpen van rollenkettingaandrijvingen vereist vakkennis. Waar riemaandrijvingen gebaseerd zijn op lineaire snelheden, zijn kettingaandrijvingen gebaseerd op de rotatiesnelheid van het kleinere tandwiel, dat in de meeste installaties het aangedreven onderdeel is. Naast het aantal pk's en het toerental, is het ontwerp van kettingaandrijvingen gebaseerd op vele andere factoren. - Dubbele steekkettingen: in principe hetzelfde als rollenkettingen, behalve dat de steek twee keer zo lang is. - Omgekeerde tand (stille) kettingen: kettingen met hoge snelheid die meestal worden gebruikt voor aandrijfmotoren en aftakassen. Kettingaandrijvingen met omgekeerde tanden kunnen vermogens tot 1200 pk overbrengen en bestaan uit een reeks tandschakels, afwisselend geassembleerd met pennen of een combinatie van gewrichtscomponenten. De ketting in het midden heeft geleidingsschakels om in groeven in het tandwiel te grijpen en de zijgeleidingsketting heeft geleiders om in de zijkanten van het tandwiel te grijpen. - Bead- of Slider-kettingen: deze kettingen worden gebruikt voor aandrijvingen met lage snelheid en ook voor handmatige bewerkingen. Door hieronder op de betreffende gekleurde tekst te klikken kunt u onze catalogi downloaden: - Aandrijfkettingen - Transportkettingen - Transportkettingen met grote steek - Rolkettingen van roestvrij staal - Hijskettingen - Motorkettingen - Landbouwmachinekettingen - Tandwielen: onze standaard tandwielen voldoen aan de ANSI-normen. Plaattandwielen zijn platte, naafloze tandwielen. Onze kleine en middelgrote naaftandwielen worden gedraaid uit stafmateriaal of smeedstukken of gemaakt door een stafmateriaalnaaf aan een warmgewalste plaat te lassen. AGS-TECH Inc. kan tandwielen leveren die zijn vervaardigd uit gietijzeren gietstukken, gegoten staal en gelaste naafconstructies, gesinterd poedermetaal, gegoten of machinaal bewerkte kunststoffen. Voor een soepele werking bij hoge snelheden is de juiste keuze van de maat van de tandwielen essentieel. Ruimtebeperkingen zijn natuurlijk een factor waar we niet omheen kunnen bij het kiezen van een tandwiel. Het wordt aanbevolen dat de verhouding tussen aandrijving en aangedreven tandwielen niet meer dan 6:1 is en dat de kettingomwikkeling op de aandrijving 120 graden is. Hartafstanden tussen de kleinere en grotere tandwielen, kettinglengtes en kettingspanning moeten ook worden gekozen volgens enkele aanbevolen technische berekeningen en richtlijnen en niet willekeurig. Download onze catalogi door hieronder op gekleurde tekst te klikken: - Tandwielen en plaatwielen - Transmissie bussen - Kettingkoppeling - Kettingsloten KABELAANDRIJVINGEN: Deze hebben in sommige gevallen hun voordelen ten opzichte van riemen en kettingaandrijvingen. Kabelaandrijvingen kunnen dezelfde functie vervullen als riemen en kunnen in sommige toepassingen ook eenvoudiger en voordeliger zijn om te implementeren. Een nieuwe serie Synchromesh-kabelaandrijvingen is bijvoorbeeld ontworpen voor positieve tractie om conventionele touwen, eenvoudige kabels en tandwielaandrijvingen te vervangen, vooral in krappe ruimtes. De nieuwe kabelaandrijving is ontworpen om zeer nauwkeurige positionering te bieden in elektronische apparatuur zoals kopieermachines, plotters, typemachines, printers, enz. Een belangrijk kenmerk van de nieuwe kabelaandrijving is de mogelijkheid om te worden gebruikt in 3D serpentineconfiguraties die extreem miniatuurontwerpen. Synchromesh-kabels kunnen worden gebruikt met een lagere spanning in vergelijking met touwen, waardoor het stroomverbruik wordt verminderd. Neem contact op met AGS-TECH voor vragen en meningen over riemen, ketting- en kabelaandrijvingen. CLICK Product Finder-Locator Service VORIGE PAGINA
- Joining & Assembly & Fastening Processes, Welding, Brazing, Soldering
Joining & Assembly & Fastening Processes, Welding, Brazing, Soldering, Sintering, Adhesive Bonding, Press Fitting, Wave and Reflow Solder Process, Torch Furnace Verbindings- en montage- en bevestigingsprocessen Wij verbinden, assembleren en bevestigen uw gefabriceerde onderdelen en verwerken ze tot eindproducten of halffabrikaten met behulp van LASSEN, SOLDEREN, SOLDEREN, SINTEREN, LIJMEN, BEVESTIGEN, PASSEN. Enkele van onze meest populaire lasprocessen zijn booglassen, autogeengas, weerstand, projectie, naad, stuiklassen, percussie, vaste toestand, elektronenstraal, laser, thermiet, inductielassen. Onze populaire soldeerprocessen zijn toorts-, inductie-, oven- en dompelsolderen. Onze soldeermethoden zijn ijzer, hete plaat, oven, inductie, dip, golf, reflow en ultrasoon solderen. Voor het lijmen gebruiken we vaak thermoplasten en thermoharders, epoxy's, fenolen, polyurethaan, lijmlegeringen en enkele andere chemicaliën en tapes. Tot slot bestaan onze bevestigingsprocessen uit spijkeren, schroeven, bouten en moeren, klinken, clinchen, pinnen, stikken & nieten en persen. • LASSEN : Lassen omvat het samenvoegen van materialen door de werkstukken te smelten en toevoegmateriaal toe te voegen, dat ook het gesmolten smeltbad verbindt. Als het gebied afkoelt, krijgen we een sterke verbinding. In sommige gevallen wordt druk uitgeoefend. In tegenstelling tot lassen, omvatten de soldeer- en soldeerbewerkingen alleen het smelten van een materiaal met een lager smeltpunt tussen de werkstukken, en werkstukken smelten niet. We raden u aan hier te klikken om:DOWNLOAD onze schematische illustraties van lasprocessen door AGS-TECH Inc. Dit zal u helpen de informatie die we u hieronder verstrekken beter te begrijpen. Bij ARC WELDING gebruiken we een voeding en een elektrode om een elektrische boog te creëren die de metalen doet smelten. Laspunt wordt beschermd door een beschermgas of damp of ander materiaal. Dit proces is populair voor het lassen van auto-onderdelen en staalconstructies. Bij afgeschermd metaalbooglassen (SMAW) of ook wel staaflassen genoemd, wordt een elektrodestaaf dicht bij het basismateriaal gebracht en daartussen wordt een elektrische boog gegenereerd. De elektrodestaaf smelt en fungeert als vulmateriaal. De elektrode bevat ook flux die fungeert als een laag slakken en dampen afgeeft die als beschermgas fungeren. Deze beschermen het lasgebied tegen milieuvervuiling. Er worden geen andere vulstoffen gebruikt. De nadelen van dit proces zijn de traagheid, de noodzaak om de elektroden vaak te vervangen, de noodzaak om de resterende slak die afkomstig is van het vloeimiddel weg te hakken. Een aantal metalen zoals ijzer, staal, nikkel, aluminium, koper... enz. Kan worden gelast. De voordelen zijn de goedkope tools en het gebruiksgemak. Gasmetaalbooglassen (GMAW), ook bekend als metaal-inert gas (MIG), we hebben een continue toevoer van een verbruikbare elektrodedraadvuller en een inert of gedeeltelijk inert gas dat rond de draad stroomt tegen omgevingsverontreiniging van het lasgebied. Staal, aluminium en andere non-ferro metalen kunnen worden gelast. De voordelen van MIG zijn hoge lassnelheden en een goede kwaliteit. De nadelen zijn de gecompliceerde uitrusting en de uitdagingen waarmee we worden geconfronteerd in winderige buitenomgevingen, omdat we het beschermgas rond het lasgebied stabiel moeten houden. Een variant van GMAW is flux-Cored Arc Welding (FCAW) dat bestaat uit een fijne metalen buis gevuld met fluxmaterialen. Soms is de flux in de buis voldoende om te beschermen tegen milieuverontreiniging. Ondergedompeld booglassen (SAW) is een algemeen geautomatiseerd proces, waarbij continue draadaanvoer en boog onder een laag fluxdekking wordt geslagen. De productiesnelheden en kwaliteit zijn hoog, lasslakken komen er makkelijk af en we hebben een rookvrije werkomgeving. Het nadeel is dat het alleen kan worden gebruikt om parts in bepaalde posities te lassen. Bij gas-wolfraambooglassen (GTAW) of wolfraam-inert gaslassen (TIG) gebruiken we een wolfraamelektrode samen met een aparte vulstof en inerte of bijna inerte gassen. Zoals we weten heeft Tungsten een hoog smeltpunt en is het een zeer geschikt metaal voor zeer hoge temperaturen. Het wolfraam in TIG wordt niet verbruikt in tegenstelling tot de andere hierboven toegelichte methoden. Een langzame maar hoogwaardige lastechniek die voordelig is boven andere technieken bij het lassen van dunne materialen. Geschikt voor veel metalen. Plasmabooglassen is vergelijkbaar, maar gebruikt plasmagas om de boog te creëren. De boog bij plasmabooglassen is relatief meer geconcentreerd in vergelijking met GTAW en kan worden gebruikt voor een breder scala aan metaaldiktes bij veel hogere snelheden. GTAW en plasmabooglassen kunnen op min of meer dezelfde materialen worden toegepast. OXY-FUEL / OXYFUEL WELDING ook wel oxyacetyleenlassen genoemd, autogeenlassen, gaslassen wordt uitgevoerd met gasbrandstoffen en zuurstof voor het lassen. Omdat er geen elektriciteit wordt gebruikt, is het draagbaar en kan het worden gebruikt waar er geen elektriciteit is. Met behulp van een lastoorts verhitten we de stukken en het vulmateriaal om een gemeenschappelijk smeltbad te produceren. Er kunnen verschillende brandstoffen worden gebruikt, zoals acetyleen, benzine, waterstof, propaan, butaan, enz. Bij autogeen lassen gebruiken we twee containers, één voor de brandstof en de andere voor zuurstof. De zuurstof oxideert de brandstof (verbrandt deze). WEERSTANDSLASSEN: Dit type lassen maakt gebruik van joule-verwarming en warmte wordt gegenereerd op de plaats waar gedurende een bepaalde tijd elektrische stroom wordt toegepast. Er worden hoge stromen door het metaal geleid. Op deze locatie worden plassen gesmolten metaal gevormd. Weerstandslasmethoden zijn populair vanwege hun efficiëntie en weinig vervuilingspotentieel. Nadelen zijn echter dat de uitrustingskosten relatief hoog zijn en de inherente beperking tot relatief dunne werkstukken. SPOT WELDING is een belangrijke vorm van weerstandslassen. Hier verbinden we twee of meer overlappende platen of werkstukken met behulp van twee koperen elektroden om de platen aan elkaar te klemmen en er een hoge stroom doorheen te laten gaan. Het materiaal tussen de koperelektroden warmt op en op die plek ontstaat een smeltbad. De stroom wordt dan gestopt en de koperen elektrodepunten koelen de laslocatie omdat de elektroden watergekoeld zijn. Het toepassen van de juiste hoeveelheid warmte op het juiste materiaal en de juiste dikte is de sleutel voor deze techniek, omdat bij verkeerde toepassing de voeg zwak zal zijn. Puntlassen heeft de voordelen dat het geen significante vervorming van werkstukken veroorzaakt, energie-efficiëntie, gemak van automatisering en uitstekende productiesnelheden, en dat er geen vulstoffen nodig zijn. Het nadeel is dat, aangezien het lassen op plaatsen plaatsvindt in plaats van een doorlopende naad te vormen, de algehele sterkte relatief lager kan zijn in vergelijking met andere lasmethoden. SEAM WELDING daarentegen produceert lassen op de faying-oppervlakken van vergelijkbare materialen. De naad kan een stompe of overlappende verbinding zijn. Naadlassen begint aan het ene uiteinde en gaat geleidelijk naar het andere. Deze methode maakt ook gebruik van twee elektroden van koper om druk en stroom uit te oefenen op het lasgebied. De schijfvormige elektroden roteren met constant contact langs de naadlijn en maken een continue las. Ook hier worden elektroden met water gekoeld. De lassen zijn zeer sterk en betrouwbaar. Andere methoden zijn projectie-, flits- en stuiklastechnieken. SOLID-STATE LASSEN is een beetje anders dan de voorgaande methoden die hierboven zijn uitgelegd. Coalescentie vindt plaats bij temperaturen onder de smelttemperatuur van de samengevoegde metalen en zonder gebruik van metaalvulmiddel. Bij sommige processen kan druk worden gebruikt. Verschillende methoden zijn CO-EXTRUSIELASSEN waarbij ongelijksoortige metalen door dezelfde matrijs worden geëxtrudeerd, KOUDEDRUKLASSEN waarbij we zachte legeringen onder hun smeltpunt verbinden, DIFFUSIELASSEN een techniek zonder zichtbare laslijnen, EXPLOSIELASSEN voor het verbinden van ongelijksoortige materialen, bijv. corrosiebestendige legeringen aan structurele staalsoorten, ELEKTROMAGNETISCH PULSLASSEN waarbij we buizen en platen versnellen door elektromagnetische krachten, SMEEDLASSEN dat bestaat uit het verhitten van de metalen tot hoge temperaturen en samenslaan, FRICTIELASSEN waarbij met voldoende wrijvingslassen wordt uitgevoerd, FRICTIEROERLASSEN waarbij een roterende niet- verbruiksgereedschap dat door de verbindingslijn gaat, HEET DRUKLASSEN waarbij we metalen samenpersen bij verhoogde temperaturen onder de smelttemperatuur in vacuüm of inerte gassen, HEET ISOSTATISCH DRUKLASSEN een proces waarbij we druk uitoefenen met behulp van inerte gassen in een vat, ROLLENLASSEN waar we samenkomen ongelijke materialen door ze tussen twee roterende wielen, ULTRASOON LASSEN waarbij dunne metalen of plastic platen worden gelast met behulp van hoogfrequente trillingsenergie. Onze andere lasprocessen zijn ELECTRON BEAM WELDING met diepe penetratie en snelle verwerking, maar omdat het een dure methode is, beschouwen we het voor speciale gevallen, ELEKTROSLAG WELDING een methode die alleen geschikt is voor zware dikke platen en werkstukken van staal, INDUCTIELASSEN waarbij we elektromagnetische inductie en onze elektrisch geleidende of ferromagnetische werkstukken verwarmen, LASERBEAM LASSEN ook met diepe penetratie en snelle verwerking maar een dure methode, LASER HYBRID WELDING dat LBW combineert met GMAW in dezelfde laskop en in staat is om openingen van 2 mm tussen platen te overbruggen, PERCUSSION WELDING dat omvat een elektrische ontlading gevolgd door het smeden van de materialen met toegepaste druk, THERMIT-LASSEN waarbij een exotherme reactie tussen aluminium en ijzeroxidepoeders plaatsvindt, ELEKTROGASLASSEN met verbruikselektroden en alleen gebruikt met staal in verticale positie, en ten slotte STUD ARC WELDING voor het verbinden van de bout met de basis materiaal met warmte en druk. We raden u aan hier te klikken om:DOWNLOAD onze schematische illustraties van soldeer-, soldeer- en lijmverbindingsprocessen door AGS-TECH Inc Dit zal u helpen de informatie die we u hieronder verstrekken beter te begrijpen. • BRAZING : We verbinden twee of meer metalen door vulmetalen ertussen te verhitten tot boven hun smeltpunt en door capillaire werking te gebruiken om zich te verspreiden. Het proces is vergelijkbaar met solderen, maar de temperaturen die nodig zijn om het vulmiddel te smelten zijn hoger bij het solderen. Net als bij lassen beschermt flux het vulmateriaal tegen atmosferische vervuiling. Na afkoeling worden de werkstukken samengevoegd. Het proces omvat de volgende belangrijke stappen: goede pasvorm en speling, juiste reiniging van basismaterialen, juiste bevestiging, juiste flux- en atmosfeerselectie, verwarming van de assemblage en tenslotte het reinigen van de gesoldeerde assemblage. Sommige van onze soldeerprocessen zijn TORCH BRAZING, een populaire methode die handmatig of op een geautomatiseerde manier wordt uitgevoerd. Het is geschikt voor productieorders met een laag volume en gespecialiseerde gevallen. Warmte wordt toegepast met behulp van gasvlammen in de buurt van de verbinding die wordt gesoldeerd. Ovensolderen vereist minder vaardigheid van de operator en is een semi-automatisch proces dat geschikt is voor industriële massaproductie. Zowel temperatuurregeling als regeling van de atmosfeer in de oven zijn voordelen van deze techniek, omdat de eerste ons in staat stelt om gecontroleerde warmtecycli te hebben en lokale verwarming te elimineren, zoals het geval is bij het solderen van de toorts, en de laatste het onderdeel beschermt tegen oxidatie. Met behulp van jigging zijn we in staat om de fabricagekosten tot een minimum te beperken. De nadelen zijn een hoog stroomverbruik, apparatuurkosten en meer uitdagende ontwerpoverwegingen. VACUM BRAZING vindt plaats in een vacuümoven. De gelijkmatigheid van de temperatuur wordt behouden en we verkrijgen vloeimiddelvrije, zeer schone verbindingen met zeer weinig restspanningen. Warmtebehandelingen kunnen plaatsvinden tijdens vacuümsolderen, vanwege de lage restspanningen die aanwezig zijn tijdens langzame verwarmings- en afkoelcycli. Het grootste nadeel zijn de hoge kosten omdat het creëren van een vacuümomgeving een duur proces is. Nog een andere techniek DIP-BRAZING verbindt vaste delen waar soldeermassa wordt aangebracht op pasvlakken. Daarna worden de fixtured onderdelen gedompeld in een bad van een gesmolten zout zoals natriumchloride (keukenzout) dat fungeert als een warmteoverdrachtsmedium en flux. Lucht is uitgesloten en er vindt dus geen oxidevorming plaats. Bij INDUCTIEBRAZING verbinden we materialen met een vulmetaal dat een lager smeltpunt heeft dan de basismaterialen. De wisselstroom van de inductiespoel creëert een elektromagnetisch veld dat inductieverwarming induceert op voornamelijk ferromagnetische materialen. De methode zorgt voor selectieve verwarming, goede verbindingen met vulstoffen die alleen in de gewenste gebieden stromen, weinig oxidatie omdat er geen vlammen aanwezig zijn en koeling is snel, snelle verwarming, consistentie en geschikt voor productie van grote volumes. Om onze processen te versnellen en consistentie te garanderen, gebruiken we vaak preforms. Informatie over onze soldeerfaciliteit die keramiek-op-metaal fittingen, hermetische afdichting, vacuümdoorvoeren, hoog- en ultrahoog vacuüm en vloeistofregelcomponenten produceert vindt u hier: Brochure soldeerfabriek • SOLDEREN : Bij het solderen hebben we geen smelten van de werkstukken, maar een vulmetaal met een lager smeltpunt dan de verbindende delen die in de voeg vloeien. Het vulmetaal bij het solderen smelt bij een lagere temperatuur dan bij het solderen. We gebruiken loodvrije legeringen voor het solderen en voldoen aan RoHS en voor verschillende toepassingen en vereisten hebben we verschillende en geschikte legeringen zoals zilverlegeringen. Solderen biedt ons verbindingen die gas- en vloeistofdicht zijn. Bij ZACHT SOLDEREN heeft ons vulmetaal een smeltpunt onder 400 Celsius, terwijl we bij ZILVER SOLDEREN en BRAZING hogere temperaturen nodig hebben. Zachtsolderen gebruikt lagere temperaturen maar resulteert niet in sterke verbindingen voor veeleisende toepassingen bij verhoogde temperaturen. Zilversolderen daarentegen vereist hoge temperaturen van de toorts en geeft ons sterke verbindingen die geschikt zijn voor toepassingen bij hoge temperaturen. Solderen vereist de hoogste temperaturen en meestal wordt een toorts gebruikt. Omdat soldeerverbindingen erg sterk zijn, zijn ze een goede kandidaat voor het repareren van zware ijzeren voorwerpen. In onze productielijnen gebruiken we zowel handmatig handmatig solderen als geautomatiseerde soldeerlijnen. INDUCTION SOLDERING gebruikt hoogfrequente wisselstroom in een koperen spoel om inductieverwarming te vergemakkelijken. Er worden stromen geïnduceerd in het gesoldeerde onderdeel en als resultaat wordt warmte gegenereerd bij de hoge weerstand joint. Door deze warmte smelt het vulmetaal. Flux wordt ook gebruikt. Inductiesolderen is een goede methode om cilinders en buizen in een continu proces te solderen door de spoelen eromheen te wikkelen. Het solderen van sommige materialen, zoals grafiet en keramiek, is moeilijker omdat de werkstukken vóór het solderen moeten worden geplateerd met een geschikt metaal. Dit vergemakkelijkt de grensvlakbinding. We solderen dergelijke materialen speciaal voor hermetische verpakkingstoepassingen. Wij vervaardigen onze printplaten (PCB's) in hoog volume, meestal met behulp van GOLFSOLDEREN. Alleen voor kleine hoeveelheden prototyping-doeleinden gebruiken we handsolderen met een soldeerbout. We gebruiken golfsolderen voor zowel through-hole als surface mount PCB-assemblies (PCBA). Een tijdelijke lijm houdt de componenten vast aan de printplaat en het geheel wordt op een transportband geplaatst en beweegt door een apparaat dat gesmolten soldeer bevat. Eerst wordt de printplaat gefluxt en komt dan in de voorverwarmingszone. Het gesmolten soldeer zit in een pan en heeft een patroon van staande golven op het oppervlak. Wanneer de printplaat over deze golven beweegt, komen deze golven in contact met de onderkant van de printplaat en kleven aan de soldeerpads. Het soldeer blijft alleen op pinnen en pads en niet op de print zelf. De golven in het gesmolten soldeer moeten goed worden gecontroleerd, zodat er geen spatten zijn en de golftoppen ongewenste delen van de platen niet raken en vervuilen. Bij REFLOW SOLDERING gebruiken we een kleverige soldeerpasta om de elektronische componenten tijdelijk op de printplaten te bevestigen. Vervolgens gaan de planken door een reflow-oven met temperatuurregeling. Hier smelt het soldeer en verbindt het de componenten permanent. We gebruiken deze techniek zowel voor opbouwcomponenten als voor doorlopende componenten. Een goede temperatuurregeling en aanpassing van de oventemperaturen is essentieel om vernietiging van elektronische componenten op het bord te voorkomen door oververhitting boven hun maximale temperatuurlimieten. In het proces van reflow-solderen hebben we in feite verschillende regio's of fasen met elk een duidelijk thermisch profiel, zoals voorverwarmstap, thermische inweekstap, reflow- en koelstappen. Deze verschillende stappen zijn essentieel voor een schadevrij reflow-solderen van printplaatassemblages (PCBA). ULTRASOON SOLDEREN is een andere veelgebruikte techniek met unieke mogelijkheden. Het kan worden gebruikt om glas, keramiek en niet-metalen materialen te solderen. Bijvoorbeeld fotovoltaïsche panelen die niet-metalen zijn, hebben elektroden nodig die met deze techniek kunnen worden bevestigd. Bij ultrasoon solderen zetten we een verwarmde soldeerpunt in die ook ultrasone trillingen afgeeft. Deze trillingen produceren cavitatiebellen op het grensvlak van het substraat met het gesmolten soldeermateriaal. De implosieve energie van cavitatie wijzigt het oxide-oppervlak en verwijdert het vuil en de oxiden. Gedurende deze tijd wordt ook een legeringslaag gevormd. Het soldeer op het hechtoppervlak neemt zuurstof op en maakt de vorming van een sterke gedeelde binding tussen het glas en het soldeer mogelijk. DIP SOLDEREN kan worden beschouwd als een eenvoudigere versie van golfsolderen die alleen geschikt is voor productie op kleine schaal. Eerste reinigingsvloeimiddel wordt toegepast zoals bij andere processen. PCB's met gemonteerde componenten worden handmatig of semi-automatisch gedompeld in een tank met gesmolten soldeer. Het gesmolten soldeer plakt aan de blootgestelde metalen delen die niet worden beschermd door een soldeermasker op het bord. De apparatuur is eenvoudig en goedkoop. • ADHESIVE LIJMING: Dit is een andere populaire techniek die we vaak gebruiken en het betreft het verlijmen van oppervlakken met behulp van lijm, epoxy, plastic middelen of andere chemicaliën. Hechting wordt bereikt door ofwel het oplosmiddel te verdampen, door warmte-uitharding, door UV-lichtuitharding, door drukuitharding of door een bepaalde tijd te wachten. In onze productielijnen worden verschillende hoogwaardige lijmen gebruikt. Met goed ontworpen applicatie- en uithardingsprocessen kan lijmverlijming resulteren in zeer sterke en betrouwbare verbindingen met zeer lage spanning. Lijmverbindingen kunnen goede beschermers zijn tegen omgevingsfactoren zoals vocht, verontreinigingen, corrosieve stoffen, trillingen, enz. Voordelen van lijmen zijn: ze kunnen worden toegepast op materialen die anders moeilijk te solderen, lassen of hardsolderen zouden zijn. Het kan ook de voorkeur hebben voor warmtegevoelige materialen die zouden worden beschadigd door lassen of andere processen bij hoge temperaturen. Andere voordelen van lijmen zijn dat ze op onregelmatig gevormde oppervlakken kunnen worden aangebracht en het gewicht van de montage met zeer kleine hoeveelheden kunnen verhogen in vergelijking met andere methoden. Ook maatveranderingen in onderdelen zijn zeer minimaal. Sommige lijmen hebben index-matching-eigenschappen en kunnen tussen optische componenten worden gebruikt zonder de licht- of optische signaalsterkte aanzienlijk te verminderen. Nadelen aan de andere kant zijn langere uithardingstijden die productielijnen kunnen vertragen, bevestigingsvereisten, vereisten voor oppervlaktevoorbereiding en moeilijkheid om te demonteren wanneer herbewerking nodig is. De meeste van onze lijmverbindingen omvatten de volgende stappen: - Oppervlaktebehandeling: speciale reinigingsprocedures zoals reiniging met gedeïoniseerd water, alcoholreiniging, plasma- of corona-reiniging komen vaak voor. Na reiniging kunnen we hechtingsbevorderaars op de oppervlakken aanbrengen om de best mogelijke verbindingen te garanderen. -Deelbevestiging: Voor zowel lijmtoepassing als voor uitharding ontwerpen en gebruiken we aangepaste armaturen. -Lijmtoepassing: we gebruiken soms handmatige, en soms, afhankelijk van het geval, geautomatiseerde systemen zoals robotica, servomotoren, lineaire actuatoren om de lijmen op de juiste locatie af te leveren en we gebruiken dispensers om het in het juiste volume en de juiste hoeveelheid te leveren. -Uitharding: Afhankelijk van de lijm kunnen we eenvoudig drogen en uitharden, maar ook uitharden onder UV-lampen die fungeren als katalysator of warmteuitharding in een oven of met behulp van resistieve verwarmingselementen die op mallen en armaturen zijn gemonteerd. We raden u aan hier te klikken om:DOWNLOAD onze schematische illustraties van bevestigingsprocessen door AGS-TECH Inc. Dit zal u helpen de informatie die we u hieronder verstrekken beter te begrijpen. • BEVESTIGINGSPROCESSEN: Onze mechanische verbindingsprocessen vallen in twee brad-categorieën: BEVESTIGINGSMIDDELEN en INTEGRALE VERBINDINGEN. Voorbeelden van bevestigingsmiddelen die wij gebruiken zijn schroeven, pennen, moeren, bouten, klinknagels. Voorbeelden van integrale verbindingen die we gebruiken zijn klik- en krimppassingen, naden, plooien. Met behulp van verschillende bevestigingsmethoden zorgen we ervoor dat onze mechanische verbindingen sterk en betrouwbaar zijn voor jarenlang gebruik. SCHROEVEN en BOUTEN zijn enkele van de meest gebruikte bevestigingsmiddelen om objecten bij elkaar te houden en te positioneren. Onze schroeven en bouten voldoen aan de ASME-normen. Er worden verschillende soorten schroeven en bouten gebruikt, waaronder zeskantbouten en zeskantbouten, houtdraadbouten en -bouten, tweezijdige schroeven, deuvelschroef, oogschroef, spiegelschroef, plaatschroef, fijnafstelschroef, zelfborende en zelftappende schroeven , stelschroef, schroeven met ingebouwde ringen,...en meer. We hebben verschillende typen schroefkoppen zoals verzonken, bolle, ronde, flenskop en verschillende typen schroefaandrijvingen zoals sleuf, kruiskop, vierkant, zeskant. Een RIVET daarentegen is een permanente mechanische sluiting bestaande uit een gladde cilindrische as en een kop enerzijds. Na het inbrengen wordt het andere uiteinde van de klinknagel vervormd en wordt de diameter vergroot zodat deze op zijn plaats blijft. Met andere woorden, vóór installatie heeft een klinknagel één kop en na installatie twee. We installeren verschillende soorten klinknagels, afhankelijk van de toepassing, sterkte, toegankelijkheid en kosten, zoals klinknagels met massieve/ronde kop, structurele, halfbuisvormige, blinde, oscar-, drive-, flush-, frictie-lock-, zelfborende klinknagels. Klinken kan de voorkeur hebben in gevallen waar warmtevervorming en verandering in materiaaleigenschappen als gevolg van laswarmte moeten worden vermeden. Klinken biedt ook een laag gewicht en vooral een goede sterkte en uithoudingsvermogen tegen schuifkrachten. Tegen trekbelastingen kunnen echter schroeven, moeren en bouten beter geschikt zijn. In het CLINCHING-proces gebruiken we speciale ponsen en matrijzen om een mechanische vergrendeling te vormen tussen plaatmetalen die worden samengevoegd. De pons duwt de lagen plaatmetaal in de matrijsholte en resulteert in de vorming van een permanente verbinding. Er is geen verwarming en geen koeling nodig bij het clinchen en het is een koud werkproces. Het is een economisch proces dat in sommige gevallen puntlassen kan vervangen. Bij PINNING gebruiken we pennen die machine-elementen zijn die worden gebruikt om posities van machineonderdelen ten opzichte van elkaar vast te zetten. De belangrijkste typen zijn gaffelpennen, splitpen, veerpennen, paspennen, en splitpen. Bij NIETEN gebruiken we nietpistolen en nietjes die tweeledige bevestigingsmiddelen zijn die worden gebruikt om materialen aan elkaar te verbinden of te binden. Nieten heeft de volgende voordelen: Economisch, eenvoudig en snel in gebruik, de kroon van de nietjes kan worden gebruikt om materialen tegen elkaar te overbruggen. schadelijke, relatief gemakkelijke verwijdering. PRESS FITTING wordt uitgevoerd door onderdelen tegen elkaar te duwen en de wrijving tussen hen maakt de onderdelen vast. Perspassingsonderdelen bestaande uit een overmaatse as en een ondermaats gat worden over het algemeen op twee manieren geassembleerd: ofwel door kracht uit te oefenen of door gebruik te maken van thermische uitzetting of samentrekking van de onderdelen. Wanneer een persfitting tot stand wordt gebracht door een kracht uit te oefenen, gebruiken we een hydraulische pers of een handbediende pers. Aan de andere kant, wanneer perspassing tot stand wordt gebracht door thermische uitzetting, verwarmen we de omhullende delen en assembleren ze op hun plaats terwijl ze heet zijn. Als ze afkoelen, krimpen ze en krijgen ze hun normale afmetingen terug. Dit resulteert in een goede perspassing. We noemen dit alternatief SHRINK-FITTING. De andere manier om dit te doen is door de omhulde delen vóór montage af te koelen en ze vervolgens in hun passende delen te schuiven. Als de assemblage opwarmt, zetten ze uit en krijgen we een strakke pasvorm. Deze laatste methode kan de voorkeur hebben in gevallen waar verwarming het risico met zich meebrengt dat de materiaaleigenschappen veranderen. Koelen is dan veiliger. Pneumatische en hydraulische componenten en assemblages • Kleppen, hydraulische en pneumatische componenten zoals O-ring, ring, afdichtingen, pakking, ring, shim. Omdat kleppen en pneumatische componenten er in een grote verscheidenheid zijn, kunnen we hier niet alles opnoemen. Afhankelijk van de fysische en chemische omgevingen van uw toepassing hebben wij wel speciale producten voor u. Geef ons alstublieft de toepassing, het type component, specificaties, omgevingscondities zoals druk, temperatuur, vloeistoffen of gassen die in contact komen met uw kleppen en pneumatische componenten; en we zullen het meest geschikte product voor u kiezen of het speciaal voor uw toepassing vervaardigen. CLICK Product Finder-Locator Service VORIGE PAGINA
- Machine Elements Manufacturing, Gears, Gear Drives, Bearings, Keys, Splines
Machine Elements Manufacturing, Gears, Gear Drives, Bearings, Keys, Splines, Pins, Shafts, Seals, Fasteners, Clutch, Cams, Followers, Belts, Couplings, Shafts Productie van machine-elementen Lees verder Riemen & Kettingen & Kabelaandrijving Montage Lees verder Tandwielen en tandwielaandrijving Lees verder Productie van koppelingen en lagers Lees verder Productie van sleutels & splines & pinnen Lees verder Nokken & Volgers & Koppelingen & Ratelwielen Productie Lees verder Productie van assen Lees verder Productie van mechanische afdichtingen Lees verder Koppeling & Rem Montage Lees verder Productie van bevestigingsmiddelen Lees verder Eenvoudige machinemontage MACHINE ELEMENTS zijn elementaire componenten van een machine. Deze elementen bestaan uit drie basistypen: 1.) Structurele componenten inclusief framedelen, lagers, assen, spiebanen, bevestigingsmiddelen, afdichtingen en smeermiddelen. 2.) Mechanismen die beweging op verschillende manieren regelen, zoals tandwieltreinen, riem- of kettingaandrijvingen, koppelingen, nokken- en volgsystemen, remmen en koppelingen. 3.) Besturingscomponenten zoals knoppen, schakelaars, indicatoren, sensoren, actuatoren en computercontrollers. De meeste machine-elementen die wij u aanbieden, zijn gestandaardiseerd op gangbare maten, maar op maat gemaakte machine-elementen zijn ook beschikbaar voor uw gespecialiseerde toepassingen. Aanpassing van machine-elementen kan plaatsvinden op bestaande ontwerpen die in onze downloadbare catalogi staan of op gloednieuwe ontwerpen. Prototyping en fabricage van machine-elementen kan worden voortgezet zodra een ontwerp door beide partijen is goedgekeurd. Als er nieuwe machine-elementen moeten worden ontworpen en geproduceerd, e-mailen onze klanten ons ofwel hun eigen blauwdrukken en we beoordelen ze ter goedkeuring, of ze vragen ons om machine-elementen te ontwerpen voor hun toepassing. In het laatste geval gebruiken we alle input van onze klanten en ontwerpen we de machine-elementen en sturen we de definitieve blauwdrukken ter goedkeuring naar onze klanten. Na goedkeuring produceren we de eerste artikelen en vervaardigen vervolgens de machine-elementen volgens het definitieve ontwerp. In elk stadium van dit werk, in het geval dat een bepaald ontwerp van een machine-element in het veld onbevredigend presteert (wat zeldzaam is), beoordelen we het hele project en brengen we samen met onze klanten wijzigingen aan als dat nodig is. Het is onze standaardpraktijk om geheimhoudingsovereenkomsten (NDA) met onze klanten te ondertekenen voor het ontwerp van machine-elementen of elk ander product wanneer dat nodig of vereist is. Zodra machine-elementen voor een bepaalde klant op maat zijn ontworpen en vervaardigd, kennen we er een productcode aan toe en produceren en verkopen we deze alleen aan onze klant die eigenaar is van het product. We reproduceren de machine-elementen met behulp van de ontwikkelde gereedschappen, matrijzen en procedures zo vaak als nodig is en wanneer onze klant ze opnieuw bestelt. Met andere woorden, zodra een op maat gemaakt machine-element voor u is ontworpen en geproduceerd, worden het intellectuele eigendom, evenals alle gereedschappen en mallen voor onbepaalde tijd door ons gereserveerd en opgeslagen voor u en de producten die worden gereproduceerd zoals u dat wilt. We bieden onze klanten ook technische diensten door machine-elementen op creatieve wijze te combineren tot een component of assemblage die een toepassing dient en die aan de verwachtingen van onze klanten voldoet of deze overtreft. Fabrieken die onze machine-elementen vervaardigen, zijn gekwalificeerd door ISO9001, QS9000 of TS16949. Bovendien hebben de meeste van onze producten een CE- of UL-markering en voldoen ze aan internationaal relevante normen zoals ISO, SAE, ASME, DIN. Klik op submenu's voor gedetailleerde informatie over onze machine-elementen, waaronder: - Riemen, kettingen en kabelaandrijvingen - Tandwielen en tandwielaandrijvingen - Koppelingen & Lagers - Sleutels & Splines & pinnen - Cams en koppelingen - Assen - Mechanische afdichtingen - Industriële koppeling en rem - Bevestigingsmiddelen - Simpele machines We hebben een referentiebrochure opgesteld voor onze klanten, ontwerpers en ontwikkelaars van nieuwe producten, waaronder machine-elementen. U kunt vertrouwd raken met enkele veelgebruikte termen in het ontwerp van machinecomponenten: Download brochure voor algemene termen voor werktuigbouwkunde die worden gebruikt door ontwerpers en ingenieurs Onze machine-elementen vinden toepassingen in een groot aantal gebieden, zoals industriële machines, automatiseringssystemen, test- en metrologieapparatuur, transportapparatuur, bouwmachines en praktisch overal waar u maar kunt bedenken. AGS-TECH ontwikkelt en produceert machine-elementen uit verschillende materialen, afhankelijk van de toepassing. Materialen die voor machine-elementen worden gebruikt, kunnen variëren van gegoten kunststoffen voor speelgoed tot gehard en speciaal gecoat staal voor industriële machines. Onze ontwerpers gebruiken ultramoderne professionele software en ontwerptools voor het ontwikkelen van machine-elementen, rekening houdend met details zoals hoeken in tandwieltanden, betrokken spanningen, slijtagesnelheden ... enz. Blader door onze submenu's en download onze productbrochures en catalogi om te zien of u kant-en-klare machine-elementen voor uw toepassing kunt vinden. Als u geen goede match voor uw toepassing kunt vinden, laat het ons dan weten en wij zullen met u samenwerken om machine-elementen te ontwikkelen en te produceren die aan uw behoeften voldoen. Als u vooral geïnteresseerd bent in onze engineering- en onderzoeks- en ontwikkelingsmogelijkheden in plaats van productiemogelijkheden, dan nodigen wij u uit om onze website te bezoeken http://www.ags-engineering.com waar u meer gedetailleerde informatie kunt vinden over ons ontwerp, productontwikkeling, procesontwikkeling, technische adviesdiensten en meer CLICK Product Finder-Locator Service VORIGE PAGINA
- Rapid Prototyping, Desktop Manufacturing, Additive Manufacturing, FDM
Rapid Prototyping, Desktop Manufacturing, Additive Manufacturing, Stereolithography, Polyjet, Fused Deposition Modeling, Selective Laser Sintering, FDM, SLS Additieve en snelle productie De laatste jaren zien we een toename van de vraag naar RAPID MANUFACTURING of RAPID PROTOTYPING. Dit proces kan ook DESKTOP MANUFACTURING of FREE-FORM FABRICATION worden genoemd. In principe wordt een solide fysiek model van een onderdeel rechtstreeks gemaakt van een driedimensionale CAD-tekening. We gebruiken de term ADDITIVE MANUFACTURING voor deze verschillende technieken waarbij we onderdelen in lagen bouwen. Met behulp van geïntegreerde computergestuurde hardware en software voeren we additive manufacturing uit. Onze snelle prototyping- en productietechnieken zijn STEREOLITHOGRAFIE, POLYJET, FUSED-DEPOSITION MODELING, SELECTIVE LASER SINTERING, ELEKTRONBEAM Smelten, DRIEDIMENSIONAAL PRINTEN, DIRECT MANUFACTURING, RAPID TOOLING. We raden u aan hier te klikken om:DOWNLOAD onze schematische illustraties van additieve productie en snelle productieprocessen door AGS-TECH Inc. Dit zal u helpen de informatie die we u hieronder verstrekken beter te begrijpen. Rapid prototyping biedt ons: 1.) Het conceptuele productontwerp wordt vanuit verschillende hoeken bekeken op een monitor met behulp van een 3D / CAD-systeem. 2.) Prototypes van niet-metalen en metalen materialen worden vervaardigd en bestudeerd vanuit functionele, technische en esthetische aspecten. 3.) Prototyping tegen lage kosten in een zeer korte tijd wordt bereikt. Additive manufacturing kan lijken op de constructie van een brood door afzonderlijke sneetjes op elkaar te stapelen en te lijmen. Met andere woorden, het product wordt plak voor plak vervaardigd, of laag voor laag op elkaar aangebracht. De meeste onderdelen kunnen binnen enkele uren worden geproduceerd. De techniek is goed als onderdelen heel snel nodig zijn of als de benodigde hoeveelheden laag zijn en het maken van een mal en gereedschap te duur en tijdrovend is. De kosten van een onderdeel zijn echter duur vanwege de dure grondstoffen. • STEREOLITHOGRAFIE: Deze techniek, ook wel afgekort als STL, is gebaseerd op het uitharden en uitharden van een vloeibaar fotopolymeer in een specifieke vorm door er een laserstraal op te focussen. De laser polymeriseert het fotopolymeer en hardt het uit. Door de UV-laserstraal volgens de geprogrammeerde vorm langs het oppervlak van het fotopolymeermengsel te scannen, wordt het onderdeel van onder naar boven geproduceerd in afzonderlijke plakjes die op elkaar vallen. Het scannen van de laserspot wordt vele malen herhaald om de in het systeem geprogrammeerde geometrieën te bereiken. Nadat het onderdeel volledig is vervaardigd, wordt het van het platform verwijderd, geblot en ultrasoon en met een alcoholbad gereinigd. Vervolgens wordt het een paar uur blootgesteld aan UV-straling om ervoor te zorgen dat het polymeer volledig is uitgehard en uitgehard. Om het proces samen te vatten, wordt een platform dat is gedompeld in een fotopolymeermengsel en een UV-laserstraal bestuurd en verplaatst door een servo-controlesysteem volgens de vorm van het gewenste onderdeel en het onderdeel wordt verkregen door het polymeer laag voor laag uit te harden. Uiteraard worden de maximale afmetingen van het geproduceerde onderdeel bepaald door de stereolithografische apparatuur. • POLYJET: Net als bij inkjetprinten, hebben we bij polyjet acht printkoppen die fotopolymeer op de buildtray deponeren. Ultraviolet licht dat naast de jets wordt geplaatst, hardt onmiddellijk uit en verhardt elke laag. In polyjet worden twee materialen gebruikt. Het eerste materiaal is voor het vervaardigen van het eigenlijke model. Het tweede materiaal, een gelachtige hars, wordt gebruikt voor ondersteuning. Deze beide materialen worden laag voor laag afgezet en gelijktijdig uitgehard. Na voltooiing van het model wordt het dragermateriaal verwijderd met een waterige oplossing. De gebruikte harsen zijn vergelijkbaar met stereolithografie (STL). De polyjet heeft de volgende voordelen ten opzichte van stereolithografie: 1.) Onderdelen reinigen is niet nodig. 2.) Nabehandeling niet nodig 3.) Kleinere laagdiktes zijn mogelijk en daardoor krijgen we een betere resolutie en kunnen we fijnere onderdelen vervaardigen. • FUSED DEPOSITION MODELING : Ook afgekort als FDM, bij deze methode beweegt een robotgestuurde extruderkop in twee principiële richtingen over een tafel. De kabel wordt indien nodig naar beneden en naar boven gebracht. Uit de opening van een verwarmde matrijs op de kop wordt een thermoplastisch filament geëxtrudeerd en een eerste laag wordt op een schuimbasis aangebracht. Dit wordt bereikt door de extruderkop die een vooraf bepaald pad volgt. Na de eerste laag wordt de tafel neergelaten en worden volgende lagen op elkaar gedeponeerd. Soms zijn bij het vervaardigen van een gecompliceerd onderdeel ondersteuningsstructuren nodig zodat de depositie in bepaalde richtingen kan doorgaan. In deze gevallen wordt een dragermateriaal geëxtrudeerd met een minder dichte afstand van filament op een laag, zodat het zwakker is dan het modelmateriaal. Deze draagstructuren kunnen later na voltooiing van het onderdeel worden opgelost of afgebroken. De afmetingen van de extrudermatrijs bepalen de dikte van de geëxtrudeerde lagen. Het FDM-proces produceert onderdelen met getrapte oppervlakken op schuine buitenvlakken. Als deze ruwheid onaanvaardbaar is, kan chemisch polijsten met damp of een verwarmd gereedschap worden gebruikt om deze glad te maken. Zelfs een polijstwas is beschikbaar als coatingmateriaal om deze stappen te elimineren en redelijke geometrische toleranties te bereiken. • SELECTIEVE LASER SINTERING: Ook wel aangeduid als SLS, is het proces gebaseerd op het selectief sinteren van een polymeer, keramiek of metaalpoeder in een object. De bodem van de verwerkingskamer heeft twee cilinders: een gedeeltelijk gebouwde cilinder en een poedertoevoercilinder. De eerstgenoemde wordt stapsgewijs neergelaten tot waar het gesinterde onderdeel wordt gevormd en de laatste wordt stapsgewijs omhoog gebracht om poeder via een rolmechanisme aan de deelcilinder toe te voeren. Eerst wordt een dunne laag poeder afgezet in de gedeeltelijk gebouwde cilinder, vervolgens wordt een laserstraal op die laag gefocust, waarbij een bepaalde dwarsdoorsnede wordt getraceerd en gesmolten / gesinterd, die vervolgens weer stolt tot een vaste stof. Het poeder is dat gebieden die niet door de laserstraal worden geraakt, los blijven maar wel het vaste gedeelte ondersteunen. Vervolgens wordt er nog een laag poeder aangebracht en wordt het proces vele malen herhaald om het onderdeel te verkrijgen. Op het einde worden de losse poederdeeltjes eraf geschud. Al deze worden uitgevoerd door een procesbesturingscomputer met behulp van instructies die worden gegenereerd door het 3D CAD-programma van het onderdeel dat wordt vervaardigd. Verschillende materialen zoals polymeren (zoals ABS, PVC, polyester), was, metalen en keramiek met geschikte polymeerbindmiddelen kunnen worden afgezet. • ELECTRON-BEAM MELTING: vergelijkbaar met selectief lasersinteren, maar met behulp van elektronenstraal om titanium- of kobaltchroompoeders te smelten om prototypes in vacuüm te maken. Er zijn enkele ontwikkelingen gedaan om dit proces uit te voeren op roestvast staal, aluminium en koperlegeringen. Als de vermoeiingssterkte van de geproduceerde onderdelen moet worden verhoogd, gebruiken we heet isostatisch persen na de fabricage van het onderdeel als secundair proces. • DRIEDIMENSIONAAL PRINTEN: Ook wel aangeduid met 3DP, bij deze techniek deponeert een printkop een anorganisch bindmiddel op een laag niet-metalen of metaalpoeder. Een zuiger die het poederbed draagt, wordt stapsgewijs neergelaten en bij elke stap wordt het bindmiddel laag voor laag gedeponeerd en door het bindmiddel versmolten. Gebruikte poedermaterialen zijn mengsels en vezels van polymeren, gietzand, metalen. Door gelijktijdig verschillende bindkoppen en verschillende kleuren bindmiddelen te gebruiken, kunnen we verschillende kleuren verkrijgen. Het proces is vergelijkbaar met inkjetprinten, maar in plaats van een gekleurd vel te verkrijgen, verkrijgen we een gekleurd driedimensionaal object. De geproduceerde onderdelen kunnen poreus zijn en kunnen daarom sinteren en metaalinfiltratie vereisen om de dichtheid en sterkte te vergroten. Sinteren zal het bindmiddel verbranden en de metaalpoeders samensmelten. Metalen zoals roestvrij staal, aluminium, titanium kunnen worden gebruikt om de onderdelen te maken en als infiltratiemateriaal gebruiken we meestal koper en brons. Het mooie van deze techniek is dat zelfs gecompliceerde en bewegende assemblages zeer snel kunnen worden vervaardigd. Er kan bijvoorbeeld een tandwielsamenstel, een moersleutel als gereedschap worden gemaakt en hebben bewegende en draaiende onderdelen klaar voor gebruik. Verschillende componenten van de assemblage kunnen in verschillende kleuren worden vervaardigd en allemaal in één keer. Download onze brochure op:Basisprincipes van 3D-printen van metaal • DIRECT MANUFACTURING en RAPID TOOLING: Naast ontwerpevaluatie, troubleshooting gebruiken we rapid prototyping voor directe fabricage van producten of directe toepassing in producten. Met andere woorden, rapid prototyping kan worden opgenomen in conventionele processen om ze beter en concurrerender te maken. Rapid prototyping kan bijvoorbeeld patronen en mallen produceren. Patronen van een smeltend en brandend polymeer gecreëerd door snelle prototyping-operaties kunnen worden geassembleerd voor investeringsgieten en geïnvesteerd. Een ander voorbeeld om te noemen is het gebruik van 3DP om een keramische gietschaal te produceren en die te gebruiken voor schaalgietbewerkingen. Zelfs spuitgietmatrijzen en matrijsinzetstukken kunnen worden geproduceerd door middel van rapid prototyping en men kan vele weken of maanden aan doorlooptijd voor het maken van matrijzen besparen. Door alleen een CAD-bestand van het gewenste onderdeel te analyseren, kunnen we de gereedschapsgeometrie softwarematig produceren. Hier zijn enkele van onze populaire snelle tooling-methoden: RTV (Room-Temperature Vulcanizing) MOLDING / URETHANE CASTING : Met behulp van rapid prototyping kan het patroon van het gewenste onderdeel worden gemaakt. Vervolgens wordt dit patroon gecoat met een scheidingsmiddel en wordt vloeibaar RTV-rubber over het patroon gegoten om de malhelften te produceren. Vervolgens worden deze matrijshelften gebruikt om vloeibare urethanen te spuitgieten. De levensduur van de mal is kort, slechts 0 of 30 cycli, maar voldoende voor productie in kleine series. ACES (Acetal Clear Epoxy Solid) INJECTIEMOLEN : Met behulp van rapid prototyping-technieken zoals stereolithografie produceren we spuitgietmatrijzen. Deze mallen zijn schalen met een open uiteinde om te kunnen vullen met materialen zoals epoxy, aluminium gevulde epoxy of metalen. Nogmaals, de levensduur van de mal is beperkt tot tientallen of maximaal honderden onderdelen. GESPUIT METALEN GEREEDSCHAPSPROCES: We gebruiken rapid prototyping en maken een patroon. We spuiten een zink-aluminium legering op het patroonoppervlak en coaten dit. Het patroon met de metalen coating wordt vervolgens in een kolf geplaatst en ingegoten met een epoxy of aluminium gevulde epoxy. Ten slotte wordt het verwijderd en door twee van dergelijke matrijshelften te produceren, verkrijgen we een complete matrijs voor spuitgieten. Deze mallen hebben een langere levensduur, in sommige gevallen kunnen ze, afhankelijk van het materiaal en de temperaturen, duizenden onderdelen produceren. KEELTOOL-PROCES: Deze techniek kan mallen produceren met 100.000 tot 10 miljoen levenscyclussen. Met behulp van rapid prototyping maken we een RTV-mal. Vervolgens wordt de mal gevuld met een mengsel bestaande uit A6 gereedschapsstaalpoeder, wolfraamcarbide, polymeerbindmiddel en laten uitharden. Deze mal wordt vervolgens verwarmd om het polymeer te laten afbranden en de metaalpoeders te laten smelten. De volgende stap is koperinfiltratie om de uiteindelijke mal te produceren. Indien nodig kunnen secundaire bewerkingen zoals machinale bewerking en polijsten op de mal worden uitgevoerd voor een betere maatnauwkeurigheid. CLICK Product Finder-Locator Service VORIGE PAGINA
- Composites, Composite Materials Manufacturing, Fiber Reinforced
Composites, Composite Materials Manufacturing, Particle and Fiber Reinforced, Cermets, Ceramic & Metal Composite, Glass Fiber Reinforced Polymer, Lay-Up Process Productie van composieten en composietmaterialen Eenvoudig gedefinieerd, COMPOSIETEN of SAMENGESTELDE MATERIALEN zijn materialen die bestaan uit twee of meerdere materialen met verschillende fysische of chemische eigenschappen, maar wanneer ze worden gecombineerd, worden ze een materiaal dat anders is dan de samenstellende materialen. We moeten erop wijzen dat de samenstellende materialen gescheiden en onderscheiden blijven in de structuur. Het doel bij het vervaardigen van een composietmateriaal is om een product te verkrijgen dat superieur is aan de bestanddelen en dat de gewenste eigenschappen van elk bestanddeel combineert. Als voorbeeld; sterkte, een laag gewicht of een lagere prijs kunnen de drijfveer zijn achter het ontwerpen en produceren van een composiet. Het type composieten dat wij aanbieden zijn deeltjesversterkte composieten, vezelversterkte composieten waaronder keramische matrix / polymeermatrix / metaalmatrix / koolstof-koolstof / hybride composieten, structurele & gelamineerde & sandwich-gestructureerde composieten en nanocomposieten. De fabricagetechnieken die we inzetten bij de fabricage van composietmaterialen zijn: Pultrusie, prepreg-productieprocessen, geavanceerde vezelplaatsing, filamentwikkeling, op maat gemaakte vezelplaatsing, glasvezelspray-lay-upproces, tuften, lanxide-proces, z-pinning. Veel composietmaterialen bestaan uit twee fasen, de matrix, die continu is en de andere fase omringt; en de gedispergeerde fase die wordt omgeven door de matrix. We raden u aan hier te klikken om:DOWNLOAD onze schematische illustraties van composieten en composietmaterialenproductie door AGS-TECH Inc. Dit zal u helpen de informatie die we u hieronder verstrekken beter te begrijpen. • MET DEELTJES VERSTERKTE COMPOSIETEN : Deze categorie bestaat uit twee typen: composieten met grote deeltjes en dispersieversterkte composieten. In het eerste type kunnen deeltjes-matrix-interacties niet worden behandeld op atomair of moleculair niveau. In plaats daarvan is continuümmechanica geldig. Aan de andere kant zijn in dispersieversterkte composieten deeltjes over het algemeen veel kleiner in het bereik van tientallen nanometers. Een voorbeeld van composiet met grote deeltjes zijn polymeren waaraan vulstoffen zijn toegevoegd. De vulstoffen verbeteren de eigenschappen van het materiaal en kunnen een deel van het polymeervolume vervangen door een zuiniger materiaal. De volumefracties van de twee fasen beïnvloeden het gedrag van het composiet. Grote deeltjes composieten worden gebruikt met metalen, polymeren en keramiek. De CERMETS zijn voorbeelden van keramiek/metaal composieten. Onze meest voorkomende cermet is gecementeerd carbide. Het bestaat uit vuurvast carbidekeramiek zoals wolfraamcarbidedeeltjes in een matrix van een metaal zoals kobalt of nikkel. Deze hardmetalen composieten worden veel gebruikt als snijgereedschap voor gehard staal. De harde carbidedeeltjes zijn verantwoordelijk voor de snijwerking en hun taaiheid wordt versterkt door de ductiele metalen matrix. Zo verkrijgen we de voordelen van beide materialen in één composiet. Een ander veelvoorkomend voorbeeld van een composiet met grote deeltjes die we gebruiken, zijn roetdeeltjes gemengd met gevulkaniseerd rubber om een composiet te verkrijgen met een hoge treksterkte, taaiheid, scheur- en slijtvastheid. Een voorbeeld van een dispersieversterkte composiet zijn metalen en metaallegeringen die zijn versterkt en gehard door de uniforme dispersie van fijne deeltjes van een zeer hard en inert materiaal. Wanneer zeer kleine aluminiumoxidevlokken aan de aluminiummetaalmatrix worden toegevoegd, verkrijgen we gesinterd aluminiumpoeder dat een verbeterde sterkte bij hoge temperaturen heeft. • VEZELVERSTERKTE COMPOSIETEN : Deze categorie composieten is in feite de belangrijkste. Het te bereiken doel is een hoge sterkte en stijfheid per gewichtseenheid. De vezelsamenstelling, lengte, oriëntatie en concentratie in deze composieten is cruciaal bij het bepalen van de eigenschappen en bruikbaarheid van deze materialen. Er zijn drie groepen vezels die we gebruiken: snorharen, vezels en draden. WHISKERS zijn zeer dunne en lange eenkristallen. Ze behoren tot de sterkste materialen. Enkele voorbeelden van whiskermaterialen zijn grafiet, siliciumnitride, aluminiumoxide. FIBERS daarentegen zijn meestal polymeren of keramiek en bevinden zich in polykristallijne of amorfe toestand. De derde groep zijn fijne DRADEN die relatief grote diameters hebben en vaak uit staal of wolfraam bestaan. Een voorbeeld van met draad versterkt composiet zijn autobanden waarin staaldraad in rubber is verwerkt. Afhankelijk van het matrixmateriaal hebben we de volgende composieten: POLYMER-MATRIX-COMPOSIETEN: Deze zijn gemaakt van een polymeerhars en vezels als versterkingsbestanddeel. Een subgroep hiervan, genaamd glasvezelversterkte polymeer (GFRP) composieten, bevat continue of discontinue glasvezels in een polymeermatrix. Glas biedt een hoge sterkte, is economisch, gemakkelijk te verwerken tot vezels en is chemisch inert. De nadelen zijn hun beperkte stijfheid en stijfheid, waarbij de gebruikstemperaturen slechts 200 – 300 Celsius bedragen. Glasvezel is geschikt voor carrosserieën en transportmiddelen, carrosserieën van scheepsvoertuigen, opslagcontainers. Vanwege de beperkte stijfheid zijn ze niet geschikt voor ruimtevaart of bruggenbouw. De andere subgroep heet Carbon Fiber-Reinforced Polymer (CFRP) Composite. Hier is koolstof ons vezelmateriaal in de polymeermatrix. Koolstof staat bekend om zijn hoge specifieke modulus en sterkte en zijn vermogen om deze bij hoge temperaturen te handhaven. Koolstofvezels kunnen ons standaard, intermediaire, hoge en ultrahoge trekmoduli bieden. Bovendien bieden koolstofvezels diverse fysieke en mechanische eigenschappen en zijn daarom geschikt voor verschillende op maat gemaakte technische toepassingen. CFRP-composieten kunnen worden overwogen om sport- en recreatieapparatuur, drukvaten en structurele componenten voor de ruimtevaart te vervaardigen. Nog een andere subgroep, de aramidevezelversterkte polymeercomposieten, zijn ook materialen met een hoge sterkte en modulus. Hun sterkte-gewichtsverhoudingen zijn opmerkelijk hoog. Aramidevezels zijn ook bekend onder de handelsnamen KEVLAR en NOMEX. Onder spanning presteren ze beter dan andere polymere vezelmaterialen, maar ze zijn zwak in compressie. Aramidevezels zijn taai, slagvast, kruip- en vermoeidheidsbestendig, stabiel bij hoge temperaturen, chemisch inert behalve tegen sterke zuren en basen. Aramidevezels worden veel gebruikt in sportartikelen, kogelvrije vesten, banden, touwen, glasvezelkabelmantels. Er bestaan andere vezelversterkende materialen, maar deze worden in mindere mate gebruikt. Dit zijn voornamelijk boor, siliciumcarbide en aluminiumoxide. Het polymeermatrixmateriaal aan de andere kant is ook kritisch. Het bepaalt de maximale gebruikstemperatuur van het composiet omdat het polymeer over het algemeen een lagere smelt- en afbraaktemperatuur heeft. Polyesters en vinylesters worden veel gebruikt als de polymeermatrix. Er worden ook harsen gebruikt en deze hebben een uitstekende vochtbestendigheid en mechanische eigenschappen. Polyimidehars kan bijvoorbeeld worden gebruikt tot ongeveer 230 graden Celsius. METAL-MATRIX COMPOSITES: In deze materialen gebruiken we een ductiele metalen matrix en de gebruikstemperaturen zijn over het algemeen hoger dan de samenstellende componenten. In vergelijking met polymeer-matrixcomposieten kunnen deze hogere bedrijfstemperaturen hebben, niet-ontvlambaar zijn en een betere weerstand tegen afbraak tegen organische vloeistoffen hebben. Ze zijn echter duurder. Versterkingsmaterialen zoals snorharen, deeltjes, continue en discontinue vezels; en matrixmaterialen zoals koper, aluminium, magnesium, titanium, superlegeringen worden algemeen gebruikt. Voorbeeldtoepassingen zijn motorcomponenten gemaakt van een aluminiumlegeringsmatrix versterkt met aluminiumoxide en koolstofvezels. CERAMIC-MATRIX COMPOSITES : Keramische materialen staan bekend om hun buitengewoon goede hoge temperatuurbetrouwbaarheid. Ze zijn echter erg bros en hebben lage waarden voor breuktaaiheid. Door deeltjes, vezels of snorharen van het ene keramiek in de matrix van het andere in te bedden, zijn we in staat composieten te bereiken met een hogere breuktaaiheid. Deze ingebedde materialen remmen in principe de scheurvoortplanting in de matrix door sommige mechanismen, zoals het afbuigen van de scheuruiteinden of het vormen van bruggen over scheurvlakken. Zo worden aluminiumoxiden die zijn versterkt met SiC-whiskers, gebruikt als snijgereedschapinzetstukken voor het bewerken van hardmetaallegeringen. Deze kunnen betere prestaties opleveren in vergelijking met gecementeerde carbiden. CARBON-CARBON COMPOSITES : Zowel de wapening als de matrix zijn van koolstof. Ze hebben hoge trekmoduli en sterke punten bij hoge temperaturen boven 2000 Celsius, kruipweerstand, hoge breuktaaiheden, lage thermische uitzettingscoëfficiënten, hoge thermische geleidbaarheid. Deze eigenschappen maken ze ideaal voor toepassingen die weerstand tegen thermische schokken vereisen. De zwakte van koolstof-koolstofcomposieten is echter de kwetsbaarheid ervan tegen oxidatie bij hoge temperaturen. Typische voorbeelden van gebruik zijn hete persvormen, geavanceerde fabricage van onderdelen van turbinemotoren. HYBRIDE COMPOSIETEN: Twee of meer verschillende soorten vezels worden gemengd in een enkele matrix. Zo kan men een nieuw materiaal op maat maken met een combinatie van eigenschappen. Een voorbeeld is wanneer zowel koolstof- als glasvezels worden opgenomen in een polymeerhars. Koolstofvezels bieden stijfheid en sterkte met een lage dichtheid, maar zijn duur. Het glas daarentegen is goedkoop, maar mist de stijfheid van koolstofvezels. Het hybride glas-koolstofcomposiet is sterker en taaier en kan tegen lagere kosten worden vervaardigd. VERWERKING VAN VEZELVERSTERKTE COMPOSIETEN : Voor continue vezelversterkte kunststoffen met gelijkmatig verdeelde vezels in dezelfde richting gebruiken we de volgende technieken. PULTRUSIE: Staven, balken en buizen van continue lengtes en constante doorsneden worden vervaardigd. Doorlopende vezelrovings zijn geïmpregneerd met een thermohardende hars en worden door een stalen matrijs getrokken om ze voor te vormen tot een gewenste vorm. Vervolgens gaan ze door een nauwkeurig bewerkte uithardingsmatrijs om hun uiteindelijke vorm te bereiken. Omdat de uithardingsmatrijs wordt verwarmd, hardt deze de harsmatrix uit. Trekkers trekken het materiaal door de matrijzen. Met behulp van ingestoken holle kernen zijn we in staat buizen en holle geometrieën te verkrijgen. De pultrusiemethode is geautomatiseerd en biedt ons hoge productiesnelheden. Elke lengte van het product is mogelijk om te produceren. PREPREG-PRODUCTIEPROCES : Prepreg is een continue vezelversterking die vooraf is geïmpregneerd met een gedeeltelijk uitgeharde polymeerhars. Het wordt veel gebruikt voor structurele toepassingen. Het materiaal wordt geleverd in tapevorm en wordt als tape verzonden. De fabrikant vormt het direct en hardt het volledig uit zonder de noodzaak om hars toe te voegen. Omdat prepregs uithardingsreacties ondergaan bij kamertemperatuur, worden ze bewaard bij 0 Celsius of lagere temperaturen. Na gebruik worden de resterende tapes weer bij lage temperaturen bewaard. Er worden thermoplastische en thermohardende harsen gebruikt en versterkingsvezels van koolstof, aramide en glas komen veel voor. Om prepregs te gebruiken, wordt eerst het rugpapier van de drager verwijderd en vervolgens wordt de fabricage uitgevoerd door de prepreg-tape op een bewerkt oppervlak te leggen (het oplegproces). Er kunnen meerdere lagen worden gelegd om de gewenste diktes te verkrijgen. Veel voorkomende praktijk is om de vezeloriëntatie af te wisselen om een kruislaag- of hoeklaaglaminaat te produceren. Ten slotte worden warmte en druk toegepast voor het uitharden. Zowel handmatige verwerking als geautomatiseerde processen worden gebruikt voor het snijden van prepregs en lay-up. FILAMENTWINDING: Doorlopende versterkende vezels worden nauwkeurig gepositioneerd in een vooraf bepaald patroon om een holle en meestal cyclindische vorm te volgen. De vezels gaan eerst door een harsbad en worden vervolgens door een geautomatiseerd systeem op een doorn gewikkeld. Na verschillende wikkelherhalingen worden de gewenste diktes verkregen en wordt de harding uitgevoerd bij kamertemperatuur of in een oven. Nu wordt de doorn verwijderd en wordt het product uit de vorm gehaald. Filamentwinding kan zeer hoge sterkte-gewichtsverhoudingen bieden door de vezels in omtreks-, spiraalvormige en polaire patronen te winden. Leidingen, tanks en omhulsels worden met deze techniek vervaardigd. • STRUCTURELE COMPOSIETEN : Deze bestaan doorgaans uit zowel homogene als composietmaterialen. Daarom worden de eigenschappen hiervan bepaald door de samenstellende materialen en het geometrische ontwerp van de elementen. Dit zijn de belangrijkste soorten: LAMINAIR COMPOSITES: Deze structurele materialen zijn gemaakt van tweedimensionale platen of panelen met voorkeursrichtingen met hoge sterkte. Lagen worden op elkaar gestapeld en gecementeerd. Door de richtingen met hoge sterkte in de twee loodrechte assen af te wisselen, verkrijgen we een composiet met hoge sterkte in beide richtingen in het tweedimensionale vlak. Door de hoeken van de lagen aan te passen kan men een composiet vervaardigen met sterkte in de gewenste richtingen. Moderne ski wordt op deze manier vervaardigd. SANDWICH PANELEN: Deze structurele composieten zijn lichtgewicht maar hebben toch een hoge stijfheid en sterkte. Sandwichpanelen bestaan uit twee buitenplaten gemaakt van een stijf en sterk materiaal zoals aluminiumlegeringen, vezelversterkte kunststoffen of staal en een kern tussen de buitenplaten. De kern moet lichtgewicht zijn en meestal een lage elasticiteitsmodulus hebben. Populaire kernmaterialen zijn hard polymeerschuim, hout en honingraten. Sandwichpanelen worden veel gebruikt in de bouwsector als dakbedekking, vloer- of wandmateriaal en ook in de lucht- en ruimtevaartindustrie. • NANOCOMPOSIETEN: deze nieuwe materialen bestaan uit deeltjes van nanogrootte die zijn ingebed in een matrix. Met behulp van nanocomposieten kunnen we rubbermaterialen vervaardigen die zeer goede barrières vormen voor luchtpenetratie terwijl hun rubbereigenschappen ongewijzigd blijven. CLICK Product Finder-Locator Service VORIGE PAGINA
- Glass and Ceramic Manufacturing, Hermetic Packages, Seals, Bonding
Glass and Ceramic Manufacturing, Hermetic Packages Seals and Bonding, Tempered Bulletproof Glass, Blow Moulding, Optical Grade Glass, Conductive Glass, Molding Vormen en vormen van glas en keramiek Het type glasproductie dat wij aanbieden zijn containerglas, glasblazen, glasvezel & buizen & staven, huishoudelijk en industrieel glaswerk, lamp en bol, precisieglasgieten, optische componenten en assemblages, vlak & plaat & floatglas. We voeren zowel handmatig als machinaal vormen uit. Onze populaire technische keramische productieprocessen zijn matrijzenpersen, isostatisch persen, heet isostatisch persen, heet persen, slipgieten, bandgieten, extrusie, spuitgieten, groene bewerking, sinteren of bakken, diamantslijpen, hermetische assemblages. We raden u aan hier te klikken om: DOWNLOAD onze schematische illustraties van glasvormings- en vormprocessen door AGS-TECH Inc. DOWNLOAD onze schematische illustraties van technische keramische productieprocessen door AGS-TECH Inc. Deze downloadbare bestanden met foto's en schetsen zullen u helpen de informatie die we u hieronder verstrekken beter te begrijpen. • VERVAARDIGING VAN CONTAINERGLAS: We hebben zowel PRESS AND BLOW als BLOW AND BLOW-lijnen voor productie. In het blaas- en blaasproces laten we een klodder in een blanco mal vallen en vormen de nek door van bovenaf een slag van perslucht toe te passen. Direct daaropvolgend wordt een tweede keer perslucht vanuit de andere richting door de hals van de houder geblazen om de voorvorm van de fles te vormen. Deze voorvorm wordt vervolgens overgebracht naar de eigenlijke vorm, opnieuw verwarmd om zacht te worden en perslucht wordt toegepast om de voorvorm zijn uiteindelijke containervorm te geven. Meer expliciet wordt het onder druk gezet en tegen de wanden van de blaasvormholte geduwd om de gewenste vorm aan te nemen. Ten slotte wordt de vervaardigde glazen container overgebracht naar een gloeioven voor daaropvolgende heropwarming en verwijdering van spanningen die tijdens het vormen ontstaan en wordt op een gecontroleerde manier gekoeld. Bij de pers- en blaasmethode worden gesmolten klodders in een parisonvorm (blanco mal) gedaan en in de parisonvorm (blanco vorm) gedrukt. De blanco's worden vervolgens overgebracht naar blaasvormen en geblazen zoals hierboven beschreven onder "Blow and Blow-proces". Daaropvolgende stappen zoals gloeien en stressverlichting zijn vergelijkbaar of hetzelfde. • GLASBLAZING : We hebben glasproducten vervaardigd door zowel conventioneel met de hand te blazen als door perslucht te gebruiken met geautomatiseerde apparatuur. Voor sommige bestellingen is conventioneel blazen noodzakelijk, zoals projecten met glaskunstwerk, of projecten die een kleiner aantal onderdelen vereisen met losse toleranties, prototyping / demoprojecten….etc. Conventioneel glasblazen omvat het dompelen van een holle metalen pijp in een pot met gesmolten glas en het roteren van de pijp om een bepaalde hoeveelheid glasmateriaal op te vangen. Het glas dat op de punt van de pijp wordt verzameld, wordt op plat ijzer gerold, naar wens gevormd, langwerpig, opnieuw verwarmd en met lucht geblazen. Als het klaar is, wordt het in een mal gestoken en wordt er lucht geblazen. De vormholte is nat om contact van het glas met metaal te voorkomen. De waterfilm fungeert als een kussen ertussen. Handmatig blazen is een arbeidsintensief langzaam proces en alleen geschikt voor prototyping of artikelen van hoge waarde, niet geschikt voor goedkope per stuk grote hoeveelheden bestellingen. • VERVAARDIGING VAN HUISHOUDELIJK & INDUSTRIEEL GLASWERK: Met behulp van verschillende soorten glasmateriaal wordt een grote verscheidenheid aan glaswerk geproduceerd. Sommige glazen zijn hittebestendig en geschikt voor laboratoriumglaswerk, terwijl andere goed genoeg zijn om vele malen vaatwasmachinebestendig te zijn en geschikt zijn voor het maken van huishoudelijke producten. Met behulp van Westlake machines worden per dag tienduizenden stuks drinkglazen geproduceerd. Ter vereenvoudiging wordt gesmolten glas door vacuüm verzameld en in mallen gestoken om de voorvormen te maken. Vervolgens wordt er lucht in de mallen geblazen, deze worden overgebracht naar een andere mal en er wordt weer lucht geblazen en het glas krijgt zijn uiteindelijke vorm. Net als bij het met de hand blazen, worden deze mallen nat gehouden met water. Verder strekken maakt deel uit van de afwerkingsbewerking waarbij de nek wordt gevormd. Overtollig glas wordt weggebrand. Daarna volgt het hierboven beschreven gecontroleerde opwarm- en afkoelproces. • GLASS TUBE & ROD VORMING: De belangrijkste processen die we gebruiken voor de productie van glazen buizen zijn de DANNER- en VELLO-processen. In het Danner-proces stroomt glas uit een oven en valt het op een schuine huls gemaakt van vuurvaste materialen. De huls wordt gedragen op een roterende holle as of blaaspijp. Het glas wordt dan om de huls gewikkeld en vormt een gladde laag die langs de huls en over de punt van de schacht stroomt. Bij buisvormen wordt lucht door een blaaspijp met holle punt geblazen en bij staafvormen gebruiken we massieve punten op de as. De buizen of staven worden dan over draagrollen getrokken. De afmetingen zoals wanddikte en diameter van de glazen buizen worden op de gewenste waarden ingesteld door de diameter van de huls en de blaasluchtdruk op een gewenste waarde in te stellen, de temperatuur, de stroomsnelheid van het glas en de treksnelheid aan te passen. Het fabricageproces van de Vello-glasbuis daarentegen omvat glas dat uit een oven en in een kom met een holle doorn of bel reist. Het glas gaat dan door de luchtruimte tussen de doorn en de kom en neemt de vorm aan van een buis. Daarna gaat het over rollen naar een trekmachine en wordt het gekoeld. Aan het einde van de koellijn vindt het snijden en de eindverwerking plaats. De buisafmetingen kunnen net als in het Danner-proces worden aangepast. Wanneer we het Danner- en het Vello-proces vergelijken, kunnen we zeggen dat het Vello-proces beter geschikt is voor de productie van grote hoeveelheden, terwijl het Danner-proces wellicht beter geschikt is voor nauwkeurige buisorders met een kleiner volume. • VERWERKING VAN PLAAT & VLAK- & DRIJFGLAS : We hebben grote hoeveelheden vlakglas in diktes variërend van submilimeterdiktes tot enkele centimeters. Onze platte glazen zijn van bijna optische perfectie. Wij bieden glas aan met speciale coatings zoals optische coatings, waarbij chemische dampdepositietechniek wordt gebruikt om coatings zoals antireflectie- of spiegelcoating aan te brengen. Ook transparante geleidende coatings komen veel voor. Er zijn ook hydrofobe of hydrofiele coatings op glas en coatings die glas zelfreinigend maken. Geharde, kogelvrije en gelaagde glazen zijn nog andere populaire items. Wij snijden glas in gewenste vorm met gewenste toleranties. Andere secundaire bewerkingen zoals het buigen of buigen van vlakglas zijn beschikbaar. • PRECISIE GLASVORMING: We gebruiken deze techniek meestal voor het vervaardigen van optische precisiecomponenten zonder de noodzaak van duurdere en tijdrovende technieken zoals slijpen, leppen en polijsten. Deze techniek is niet altijd voldoende om het beste van de beste optica te maken, maar in sommige gevallen, zoals consumentenproducten, digitale camera's en medische optica, kan het een minder dure goede optie zijn voor productie van grote volumes. Het heeft ook een voordeel ten opzichte van de andere glasvormende technieken waar complexe geometrieën vereist zijn, zoals in het geval van asferen. Het basisproces omvat het laden van de onderkant van onze matrijs met de glazen blanco, evacuatie van de proceskamer voor zuurstofverwijdering, bijna sluiten van de matrijs, snelle en isotherme verwarming van matrijs en glas met infrarood licht, verder sluiten van de matrijshelften om het verweekte glas langzaam en gecontroleerd tot de gewenste dikte te persen en tenslotte het glas af te koelen en de kamer te vullen met stikstof en het product te verwijderen. Nauwkeurige temperatuurregeling, sluitafstand van de mal, sluitkracht van de mal, aanpassing aan de uitzettingscoëfficiënten van de mal en het glasmateriaal zijn de sleutel in dit proces. • VERVAARDIGING VAN OPTISCHE COMPONENTEN EN SAMENSTELLINGEN VAN GLAS: Naast precisieglasgieten, zijn er een aantal waardevolle processen die we gebruiken voor het maken van hoogwaardige optische componenten en samenstellingen voor veeleisende toepassingen. Slijpen, leppen en polijsten van optische kwaliteit glazen in fijne speciale schurende slurries is een kunst en wetenschap voor het maken van optische lenzen, prisma's, platte vlakken en meer. Oppervlakte vlakheid, golving, gladheid en defectvrije optische oppervlakken vereisen veel ervaring met dergelijke processen. Kleine veranderingen in de omgeving kunnen resulteren in producten die niet aan de specificaties voldoen en de productielijn stilleggen. Er zijn gevallen waarin een enkele veeg op het optische oppervlak met een schone doek ervoor kan zorgen dat een product aan de specificaties voldoet of de test niet doorstaat. Enkele populaire gebruikte glasmaterialen zijn gesmolten silica, kwarts, BK7. Ook de assemblage van dergelijke componenten vereist gespecialiseerde niche-ervaring. Soms worden speciale lijmen gebruikt. Soms is een techniek die optisch contact wordt genoemd echter de beste keuze en bevat geen materiaal tussen de bevestigde optische brillen. Het bestaat uit fysiek contact maken met vlakke oppervlakken om zonder lijm aan elkaar te bevestigen. In sommige gevallen worden mechanische afstandhouders, precisie glazen staven of kogels, klemmen of machinaal bewerkte metalen componenten gebruikt om de optische componenten op bepaalde afstanden en met bepaalde geometrische oriëntaties ten opzichte van elkaar te monteren. Laten we eens kijken naar enkele van onze populaire technieken voor het vervaardigen van hoogwaardige optica. SLIJPEN & LAPPEN & POLIJSTEN: De ruwe vorm van de optische component wordt verkregen door het slijpen van een onbewerkte glas. Daarna worden leppen en polijsten uitgevoerd door de ruwe oppervlakken van de optische componenten te roteren en te wrijven tegen gereedschappen met de gewenste oppervlaktevormen. Slurries met kleine schurende deeltjes en vloeistof worden tussen de optiek en de vormgereedschappen gegoten. De grootte van de schurende deeltjes in dergelijke slurries kan worden gekozen in overeenstemming met de gewenste mate van vlakheid. De afwijkingen van kritische optische oppervlakken van gewenste vormen worden uitgedrukt in golflengten van het gebruikte licht. Onze hoge precisie-optieken hebben toleranties van tienden van een golflengte (Golflengte/10) of zelfs strakker is mogelijk. Naast het oppervlakteprofiel worden de kritische oppervlakken gescand en beoordeeld op andere oppervlaktekenmerken en defecten zoals afmetingen, krassen, spanen, putjes, vlekjes... enz. De strikte controle van de omgevingsomstandigheden in de optische productievloer en uitgebreide meet- en testvereisten met ultramoderne apparatuur maken dit een uitdagende industrietak. • SECUNDAIRE PROCESSEN IN DE GLASPRODUCTIE: Nogmaals, we zijn alleen beperkt met uw verbeeldingskracht als het gaat om secundaire en afwerkingsprocessen van glas. Hier sommen we er enkele op: -Coatings op glas (optisch, elektrisch, tribologisch, thermisch, functioneel, mechanisch...). We kunnen bijvoorbeeld de oppervlakte-eigenschappen van glas veranderen door het bijvoorbeeld warmte te laten weerkaatsen zodat het het interieur van gebouwen koel houdt, of eenzijdig infrarood-absorberend maken met behulp van nanotechnologie. Dit helpt de binnenkant van gebouwen warm te houden, omdat de buitenste oppervlaktelaag van glas de infrarode straling in het gebouw absorbeert en terug naar binnen uitstraalt. -Ets op glas -Toegepaste keramische etikettering (ACL) -Gravure - Vlam polijsten -Chemisch polijsten -kleuring VERVAARDIGING VAN TECHNISCH KERAMIEK • DIE PRESSING: Bestaat uit uniaxiale verdichting van korrelige poeders opgesloten in een matrijs • HEET PERSEN: Vergelijkbaar met stansen, maar met toevoeging van temperatuur om de verdichting te verbeteren. Poeder of gecompacteerde voorvorm wordt in een grafietmatrijs geplaatst en uniaxiale druk wordt uitgeoefend terwijl de matrijs op hoge temperaturen wordt gehouden, zoals 2000 C. De temperaturen kunnen verschillen, afhankelijk van het type keramisch poeder dat wordt verwerkt. Voor gecompliceerde vormen en geometrieën kunnen andere latere bewerkingen nodig zijn, zoals diamantslijpen. • ISOSTATISCH PERSEN : Korrelvormige poeders of geperste compacts worden in luchtdichte containers geplaatst en vervolgens in een gesloten drukvat met vloeistof erin. Daarna worden ze verdicht door de druk van het drukvat te verhogen. De vloeistof in het vat brengt de drukkrachten gelijkmatig over het gehele oppervlak van de luchtdichte container over. Het materiaal wordt dus uniform verdicht en neemt de vorm aan van zijn flexibele container en zijn interne profiel en kenmerken. • HEET ISOSTATISCH PERSEN: Vergelijkbaar met isostatisch persen, maar naast een atmosfeer onder druk van gas, sinteren we het compact bij hoge temperatuur. Heet isostatisch persen resulteert in extra verdichting en verhoogde sterkte. • SLIPGIET / AFVOERGIET : We vullen de mal met een suspensie van micrometergrote keramische deeltjes en dragervloeistof. Dit mengsel wordt "slip" genoemd. De mal heeft poriën en daarom wordt de vloeistof in het mengsel in de mal gefilterd. Als resultaat wordt een gietvorm gevormd op de binnenoppervlakken van de mal. Na het sinteren kunnen de onderdelen uit de mal worden gehaald. • TAPEGIET: Wij vervaardigen keramische tapes door keramische slurries op vlakke bewegende drageroppervlakken te gieten. De slurries bevatten keramische poeders gemengd met andere chemicaliën voor bind- en transportdoeleinden. Als de oplosmiddelen verdampen, blijven er dichte en flexibele keramische platen achter die naar wens kunnen worden gesneden of gewalst. • EXTRUSIEVORMING: Net als bij andere extrusieprocessen wordt een zacht mengsel van keramisch poeder met bindmiddelen en andere chemicaliën door een matrijs geleid om zijn dwarsdoorsnedevorm te verkrijgen en vervolgens op de gewenste lengte gesneden. Het proces wordt uitgevoerd met koude of verwarmde keramische mengsels. • LAGE DRUK INJECTIEVORMING : We bereiden een mengsel van keramisch poeder met bindmiddelen en oplosmiddelen en verhitten het tot een temperatuur waarbij het gemakkelijk kan worden geperst en in de gereedschapsholte kan worden geperst. Zodra de vormcyclus is voltooid, wordt het onderdeel uitgeworpen en wordt de bindende chemische stof afgebrand. Door middel van spuitgieten kunnen we op een voordelige manier ingewikkelde onderdelen in hoge volumes verkrijgen. Gaten die een fractie van een millimeter op een 10 mm dikke wand zijn, zijn mogelijk, schroefdraad is mogelijk zonder verdere bewerking, toleranties zo krap als +/- 0,5% zijn mogelijk en zelfs lager wanneer onderdelen worden bewerkt , wanddiktes in de orde van 0,5 mm tot een lengte van 12,5 mm zijn mogelijk evenals wanddiktes van 6,5 mm tot een lengte van 150 mm. • GROENE BEWERKING: Met dezelfde bewerkingsgereedschappen voor metaal kunnen we geperste keramische materialen machinaal bewerken terwijl ze nog zo zacht zijn als krijt. Toleranties van +/- 1% zijn mogelijk. Voor betere toleranties gebruiken we diamantslijpen. • SINTEREN of VAKKEN : Sinteren maakt volledige verdichting mogelijk. Aanzienlijke krimp treedt op op de groene compacte onderdelen, maar dit is geen groot probleem, aangezien we rekening houden met deze dimensionale veranderingen bij het ontwerpen van het onderdeel en de tooling. Poederdeeltjes worden aan elkaar gehecht en porositeit veroorzaakt door het verdichtingsproces wordt grotendeels verwijderd. • DIAMANT SLIJPEN: 's Werelds hardste materiaal “diamant” wordt gebruikt om harde materialen zoals keramiek te slijpen en er worden precisieonderdelen verkregen. Toleranties in het micrometerbereik en zeer gladde oppervlakken worden bereikt. Vanwege de kosten overwegen we deze techniek alleen als we het echt nodig hebben. • HERMETIC ASSEMBLIES zijn die welke praktisch gezien geen uitwisseling van materie, vaste stoffen, vloeistoffen of gassen tussen interfaces toestaan. Hermetische afdichting is luchtdicht. Hermetische elektronische behuizingen zijn bijvoorbeeld behuizingen die de gevoelige binneninhoud van een verpakt apparaat onaangetast houden door vocht, verontreinigingen of gassen. Niets is 100% hermetisch, maar als we spreken van hermeticiteit bedoelen we dat in de praktijk, dat er hermeticiteit is in die mate dat de leksnelheid zo laag is dat de apparaten gedurende zeer lange tijd veilig zijn onder normale omgevingsomstandigheden. Onze hermetische assemblages bestaan uit metalen, glazen en keramische componenten, metaal-keramiek, keramisch-metaal-keramiek, metaal-keramiek-metaal, metaal op metaal, metaal-glas, metaal-glas-metaal, glas-metaal-glas, glas- metaal en glas op glas en alle andere combinaties van metaal-glas-keramiek binding. Zo kunnen we de keramische componenten met een metaalcoating coaten, zodat ze sterk aan andere componenten in de assemblage kunnen worden gehecht en een uitstekend afdichtend vermogen hebben. We hebben de knowhow om optische vezels of doorvoeropeningen met metaal te coaten en deze aan de behuizingen te solderen of te solderen, zodat er geen gassen in de behuizingen komen of lekken. Daarom worden ze gebruikt voor het vervaardigen van elektronische behuizingen om gevoelige apparaten in te kapselen en te beschermen tegen de buitenatmosfeer. Naast hun uitstekende afdichtingseigenschappen, andere eigenschappen zoals de thermische uitzettingscoëfficiënt, vervormingsweerstand, niet-ontgassend karakter, zeer lange levensduur, niet-geleidend karakter, thermische isolatie-eigenschappen, antistatisch karakter... enz. maken glas en keramische materialen de keuze voor bepaalde toepassingen. Informatie over onze fabriek voor de productie van keramisch-op-metaal fittingen, hermetische afdichting, vacuümdoorvoeren, hoog- en ultrahoogvacuüm- en vloeistofregelcomponenten vindt u hier:Hermetische componenten fabrieksbrochure CLICK Product Finder-Locator Service VORIGE PAGINA
- Wire & Spring Forming, Shaping, Welding, Assembly of Wires, Coil, CNC
Wire & Spring Forming, Shaping, Welding, Assembly of Wires, Coil Compression Extension Torsion Flat Springs, Custom Wires, Helical Springs at AGS-TECH Inc. Draad- en veervormen Wij produceren op maat gemaakte draden, draadassemblage, draden gevormd in gewenste 2D- en 3D-vormen, draadnetten, gaas, behuizingen, mand, hek, draadveer, platte veer; torsie, compressie, spanning, platte veren en meer. Onze processen zijn draad- en veervormen, draadtrekken, vormen, buigen, lassen, solderen, solderen, doorboren, smeden, boren, afschuinen, slijpen, draadsnijden, coaten, fourslide, dia vormen, wikkelen, oprollen, schokken. We raden u aan hier te klikken om: DOWNLOAD onze schematische illustraties van draad- en veervormprocessen door AGS-TECH Inc. Dit downloadbare bestand met foto's en schetsen zal u helpen de informatie die we u hieronder verstrekken beter te begrijpen. • DRAADTEKENEN: Met behulp van trekkrachten rekken we de metalen voorraad uit en trekken deze door een matrijs om de diameter te verkleinen en de lengte te vergroten. Soms gebruiken we een reeks matrijzen. We zijn in staat om matrijzen te maken voor elke draaddikte. Met materiaal met een hoge treksterkte trekken we zeer dunne draden. Wij bieden zowel koud als warm bewerkte draden. • DRAADVORMING: Een rol gemetselde draad wordt gebogen en gevormd tot een bruikbaar product. We hebben de mogelijkheid om draden van alle diktes te vormen, inclusief dunne filamenten en dikke draden zoals die worden gebruikt als veren onder autochassis. Apparatuur die we gebruiken voor draadvorming zijn handmatige en CNC-draadvormers, haspel, krachtpersen, fourslide, multi-slide. Onze processen zijn tekenen, buigen, rechttrekken, pletten, strekken, snijden, stuiken, solderen & lassen & solderen, assembleren, oprollen, smeden (of vleugels), piercing, draadsnijden, boren, afschuinen, slijpen, coaten en oppervlaktebehandelingen. Onze state-of-the-art apparatuur kan worden ingesteld om zeer complexe ontwerpen van elke vorm en nauwe toleranties te ontwikkelen. We bieden verschillende soorten uiteinden achtige sferische, puntige of afgeschuinde uiteinden voor uw draden. De meeste van onze draadvormprojecten hebben minimale tot nul gereedschapskosten. Voorbeeld doorlooptijden zijn over het algemeen dagen. Wijzigingen in ontwerp/configuratie van draadvormen kunnen zeer snel worden aangebracht. • VEERVORMING: AGS-TECH produceert een grote verscheidenheid aan veren, waaronder: -Torsie / dubbele torsieveer -Spanning / Drukveer -Constante / variabele veer -Spiraal & Spiraalvormige Lente -Platte en bladveer - Evenwichtsveer -Belleville Wasmachine -Negatorveer -Progressieve snelheid spiraalveer -Golf lente -Voluutveer - Taps toelopende veren -Lenteringen -Klokveren -Klipjes Wij vervaardigen veren uit verschillende materialen en kunnen u begeleiden op basis van uw toepassing. De meest voorkomende materialen zijn roestvrij staal, chroomsilicium, koolstofstaal, oliegehard koolstofarm, chroom-vanadium, fosforbrons, titanium, beryllium-koperlegering, keramiek op hoge temperatuur. Bij het vervaardigen van veren gebruiken wij verschillende technieken, waaronder CNC-spoelen, koud wikkelen, warm wikkelen, harden, afwerken. Andere technieken die hierboven al onder draadvormen zijn genoemd, zijn ook gebruikelijk in onze verenproductie. • AFWERKINGSDIENSTEN voor DRADEN & VEREN : We kunnen uw producten op vele manieren afwerken, afhankelijk van uw keuze en behoeften. Enkele veel voorkomende processen die wij aanbieden zijn: verven, poedercoaten, plateren, vinyl dompelen, anodiseren, spanningsverlichting, warmtebehandeling, shot peen, tuimelen, chromaat, elektroloos nikkel, passiveren, gebakken email, plastic coating , plasmareiniging. CLICK Product Finder-Locator Service VORIGE PAGINA
- Sheet Metal Forming Fabrication, Stamping, Punching, Deep Drawing, CNC
Sheet Metal Forming and Fabrication, Stamping, Punching, Bending, Progressive Die, Spot Welding, Deep Drawing, Metal Blanking and Slitting at AGS-TECH Inc. Stempels en plaatbewerking Wij bieden plaatwerk stampen, vormgeven, vormen, buigen, ponsen, stansen, snijden, perforeren, kerven, knabbelen, scheren, persbewerking, fabricage, dieptrekken met behulp van enkele pons / enkele slag matrijzen evenals progressieve matrijzen en spinnen, rubber vormen en hydrovormen; plaatwerk snijden met waterstraal, plasma, laser, zaag, vlam; plaatwerk montage door middel van lassen, puntlassen; plaatwerk buis uitpuilen en buigen; oppervlakteafwerking van plaatmetaal inclusief dompel- of spuitverf, elektrostatische poedercoating, anodiseren, plateren, sputteren en meer. Onze diensten variëren van snelle prototyping van plaatwerk tot productie in grote volumes. We raden u aan hier te klikken om:DOWNLOAD onze schematische illustraties van plaatbewerkings- en stempelprocessen door AGS-TECH Inc. Dit zal u helpen de informatie die we u hieronder verstrekken beter te begrijpen. • PLAATWERK SNIJDEN: Wij bieden AFSNIJDERS en AFSCHEIDINGEN. Cutoffs snijden het plaatmetaal over één pad tegelijk en er is in principe geen verspilling van materiaal, terwijl bij scheidingen de vorm niet precies kan worden genesteld en daarom een bepaalde hoeveelheid materiaal wordt verspild. Een van onze meest populaire processen is PONSEN, waarbij een stuk materiaal rond of een andere vorm uit plaatwerk wordt gesneden. Het stuk dat eruit wordt gesneden, is afval. Een andere versie van ponsen is SLOTTING, waarbij rechthoekige of langwerpige gaten worden geponst. BLANKEREN daarentegen is hetzelfde proces als ponsen, met het onderscheid dat het stuk dat wordt uitgesneden het werk is en wordt bewaard. FINE BLANKING, een superieure versie van blanking, creëert sneden met nauwe toleranties en rechte gladde randen en vereist geen secundaire bewerkingen voor perfectie van het werkstuk. Een ander proces dat we vaak gebruiken, is SLITTING, een knipproces waarbij plaatmetaal wordt gesneden door twee tegenover elkaar liggende cirkelvormige bladen in een recht of gebogen pad. Blikopener is een eenvoudig voorbeeld van het snijproces. Een ander populair process voor ons is PERFORATING, waarbij veel ronde of andere vormen in plaatstaal in een bepaald patroon worden geponst. Een typisch voorbeeld van een geperforeerd product zijn metalen filters met veel gaten voor vloeistoffen. Bij NOTCHING, een ander snijproces van plaatstaal, verwijderen we materiaal van een werkstuk, beginnend bij de rand of elders en snijden naar binnen totdat de gewenste vorm is verkregen. Het is een progressief proces waarbij elke bewerking een ander stuk verwijdert totdat de gewenste contour is verkregen. Voor kleine productieruns gebruiken we soms een relatief langzamer proces, NIBBLING genaamd, dat bestaat uit veel snelle ponsen van overlappende gaten om een grotere, complexere snede te maken. Bij PROGRESSIEF SNIJDEN gebruiken we een reeks verschillende bewerkingen om een enkele snede of een bepaalde geometrie te verkrijgen. Tenslotte SCHEREN een secundair proces helpt ons om de randen van reeds gemaakte sneden te verbeteren. Het wordt gebruikt voor het afsnijden van spanen, ruwe randen op plaatwerk. • PLAATBEWERKING : Naast snijden is buigen een essentieel proces zonder welke we de meeste producten niet zouden kunnen produceren. Meestal een koude bewerking maar soms ook uitgevoerd als warm of heet. We gebruiken matrijzen en persen meestal voor deze bewerking. Bij PROGRESSIVE BENDING gebruiken we een reeks verschillende pons- en matrijsbewerkingen om een enkele buiging of een bepaalde geometrie te verkrijgen. AGS-TECH maakt gebruik van verschillende buigprocessen en maakt de keuze afhankelijk van het materiaal van het werkstuk, de grootte, dikte, gewenste buiggrootte, straal, kromming en buighoek, plaats van buiging, zuinigheid, te vervaardigen hoeveelheden… enz. We gebruiken V-BENDING waarbij een V-vormige pons het plaatmetaal in de V-vormige matrijs dwingt en het buigt. Goed voor zowel zeer scherpe als stompe hoeken en daartussenin, inclusief 90 graden. Met behulp van wissers voeren we EDGE BENDING uit. Onze apparatuur stelt ons in staat om hoeken te verkrijgen die zelfs groter zijn dan 90 graden. Bij het buigen van de randen wordt het werkstuk tussen een drukkussen en de matrijs geplaatst, het gebied voor het buigen bevindt zich op de matrijsrand en de rest van het werkstuk wordt over space als een vrijdragende balk gehouden. Wanneer de stempel op het vrijdragende gedeelte inwerkt, wordt deze over de rand van de matrijs gebogen. FLANGING is een randbuigproces dat resulteert in een hoek van 90 graden. De belangrijkste doelen van de operatie zijn het elimineren van scherpe randen en het verkrijgen van geometrische oppervlakken om het verbinden van onderdelen te vergemakkelijken. BEADING, een ander veelvoorkomend randbuigproces, vormt een krul over de rand van een onderdeel. HEMMING daarentegen resulteert in een rand van de plaat die volledig omgebogen is. Bij SEAMING worden de randen van twee delen op elkaar omgebogen en samengevoegd. DUBBELE NAADWERKING daarentegen zorgt voor waterdichte en luchtdichte plaatwerkverbindingen. Net als bij het buigen van randen, zet een proces dat ROTARY BENDING wordt genoemd, een cilinder in met de gewenste hoek uitgesneden en dient als de pons. Als de kracht op de stempel wordt overgebracht, sluit deze met het werkstuk. De groef van de cilinder geeft het vrijdragende gedeelte de gewenste hoek. De groef kan een hoek hebben die kleiner of groter is dan 90 graden. Bij AIR BENDING hebben we de onderste matrijs niet nodig om een schuine groef te hebben. Het plaatwerk wordt ondersteund door twee oppervlakken aan weerszijden en op een bepaalde afstand. De pons oefent dan een kracht uit op de juiste plaats en buigt het werkstuk. KANAALBUIGING wordt uitgevoerd met behulp van een kanaalvormige pons en matrijs, en U-BEND wordt bereikt met een U-vormige pons. OFFSET BENDING produceert offsets op het plaatwerk. ROLL BENDING, een techniek die goed is voor dik werk en het buigen van grote stukken metalen platen, maakt gebruik van drie rollen om de platen aan te voeren en te buigen tot de gewenste krommingen. Rollen zijn zo gerangschikt dat de gewenste buiging van het werk wordt verkregen. De afstand en hoek tussen de rollen wordt gecontroleerd om het gewenste resultaat te verkrijgen. Een beweegbare rol maakt het mogelijk om de kromming te controleren. TUBE FORMING is een andere populaire buigbewerking voor plaatwerk waarbij meerdere matrijzen betrokken zijn. Tubes worden verkregen na meerdere acties. CORRUGATIE wordt ook uitgevoerd door buigbewerkingen. In feite is het de symmetrische buiging met regelmatige tussenpozen over een heel stuk plaatwerk. Voor het golfen kunnen verschillende vormen worden gebruikt. Golfplaat is stijver en beter bestand tegen buigen en heeft daarom toepassingen in de bouw. PLAATMETAL ROLL FORMING, een continu manufacturing proces wordt ingezet om dwarsdoorsneden van een bepaalde geometrie te buigen met behulp van rollen en het werk wordt in opeenvolgende stappen gebogen, waarbij de laatste rol het werk voltooit. In sommige gevallen wordt een enkele rol en in sommige gevallen een serie rollen gebruikt. • GECOMBINEERDE SNIJ- & BUIGPROCESSEN VAN PLAATWERK: Dit zijn de processen die tegelijkertijd snijden en buigen. In PIERCING wordt een gat gemaakt met behulp van een puntige pons. Terwijl de pons het gat in de plaat verwijdt, wordt het materiaal tegelijkertijd gebogen tot een interne flens voor het gat. De verkregen flens kan belangrijke functies hebben. De LANCING-bewerking daarentegen snijdt en buigt de plaat om een verhoogde geometrie te creëren. • BULGING EN BULGING METALEN BUIS : Bij BULGING wordt een deel van een holle buis inwendig onder druk gezet, waardoor de buis naar buiten uitpuilt. Omdat de buis zich in een matrijs bevindt, wordt de uitstulpingsgeometrie bepaald door de vorm van de matrijs. Bij STRETCH BENDING wordt een metalen buis uitgerekt met krachten evenwijdig aan de as van de buis en buigkrachten om de buis over een vormblok te trekken. In DRAW BENDING klemmen we de buis aan het uiteinde vast aan een roterend vormblok dat de buis buigt tijdens het draaien. Ten slotte wordt bij COMPRESSION BENDING de buis met kracht tegen een vast vormblok gehouden en een matrijs buigt deze over het vormblok. • DIEPE TEKENING: Bij een van onze meest populaire bewerkingen worden een pons, een bijpassende matrijs en een blanco houder gebruikt. De plaatmetalen plano wordt over de matrijsopening geplaatst en de stempel beweegt naar de plano die door de planohouder wordt vastgehouden. Zodra ze in contact komen, dwingt de pons het plaatmetaal in de matrijsholte om het product te vormen. Dieptrekbewerking lijkt op snijden, maar de speling tussen de stempel en de matrijs verhindert dat de plaat wordt gesneden. Een andere factor die ervoor zorgt dat de plaat diepgetrokken is en niet gesneden, zijn de afgeronde hoeken op de matrijs en pons die het afknippen en snijden voorkomen. Om tot een grotere omvang van het dieptrekken te komen, wordt een HERDRAWING-proces ingezet waarbij een aansluitend dieptrekken plaatsvindt op een onderdeel dat al een dieptrekproces heeft ondergaan. Bij REVERSE REDRAWING wordt het diepgetrokken deel omgedraaid en in de tegenovergestelde richting getekend. Dieptrekken kan onregelmatig gevormde objecten opleveren, zoals koepelvormige, taps toelopende of getrapte kopjes, In EMBOSSING gebruiken we een mannelijk en vrouwelijk matrijspaar om indruk te maken op het plaatwerk met een ontwerp of script. • SPINNING : Een bewerking waarbij een vlak of voorgevormd werkstuk tussen een roterende doorn en losse kop wordt gehouden en een gereedschap plaatselijke druk uitoefent op het werkstuk terwijl het geleidelijk op de doorn omhoog beweegt. Hierdoor wordt het werkstuk om de doorn gewikkeld en krijgt het zijn vorm. We gebruiken deze techniek als alternatief voor dieptrekken waarbij de hoeveelheid van een bestelling klein is, de onderdelen groot zijn (diameters tot 20 voet) en unieke rondingen hebben. Hoewel de prijzen per stuk over het algemeen hoger zijn, zijn de instelkosten voor CNC-spinbewerking laag in vergelijking met dieptrekken. Integendeel, dieptrekken vereist een hoge initiële investering voor het opzetten, maar de kosten per stuk zijn laag wanneer een grote hoeveelheid onderdelen wordt geproduceerd. Een andere versie van dit proces is SHEAR SPINNING, waarbij er ook metaalstroom in het werkstuk is. De metaalstroom zal de dikte van het werkstuk verminderen terwijl het proces wordt uitgevoerd. Nog een ander gerelateerd proces is TUBE SPINNING, dat wordt toegepast op cilindrische onderdelen. Ook bij dit proces is er metaalstroom in het werkstuk. De dikte wordt dus verminderd en de lengte van de buis wordt vergroot. De tool kan worden verplaatst om functies aan de binnen- of buitenkant van de tube te maken. • RUBBERVORMING VAN PLAATMETAL : Rubber of polyurethaan wordt in een matrijs geplaatst en het werkstuk wordt op het oppervlak van het rubber geplaatst. Vervolgens wordt er een stoot op het werkstuk uitgeoefend en wordt het in het rubber geduwd. Omdat de door het rubber gegenereerde druk laag is, is de diepte van de geproduceerde onderdelen beperkt. Omdat de gereedschapskosten laag zijn, is het proces geschikt voor productie in kleine hoeveelheden. • HYDROVORMING: Net als bij het vormen van rubber, wordt bij dit proces plaatwerk door een pons in een vloeistof onder druk in een kamer geperst. Het plaatwerk zit ingeklemd tussen de pons en een rubberen membraan. Het diafragma omringt het werkstuk volledig en de druk van de vloeistof dwingt het om zich op de stempel te vormen. Met deze techniek kan zeer diep worden getrokken, zelfs dieper dan bij het dieptrekproces. Afhankelijk van uw onderdeel vervaardigen wij zowel enkelvoudige stempels als progressieve matrijzen. Stempelmatrijzen met één slag zijn een kosteneffectieve methode om snel grote hoeveelheden eenvoudige plaatmetalen onderdelen zoals ringen te produceren. Progressieve matrijzen of de dieptrektechniek worden gebruikt voor het vervaardigen van complexere geometrieën. Afhankelijk van uw situatie kunt u met waterstraal-, laser- of plasmasnijden uw plaatwerkdelen goedkoop, snel en nauwkeurig produceren. Veel leveranciers hebben geen idee van deze alternatieve technieken of hebben deze niet en daarom doorlopen ze langdurige en dure manieren om matrijzen en gereedschappen te maken die klanten alleen maar tijd en geld verspillen. Als u binnen enkele dagen op maat gemaakte plaatwerkcomponenten zoals behuizingen, elektronische behuizingen enz. nodig heeft, neem dan contact met ons op voor onze RAPID SHEET METAL PROTOTYPING-service. CLICK Product Finder-Locator Service VORIGE MENU
- Forging and Powdered Metallurgy, Die Forging, Heading, Hot Forging
Forging and Powdered Metallurgy, Die Forging, Heading, Hot Forging, Impression Die, Near Net Shape, Swaging, Metal Hobbing, Riveting, Coining from AGS-TECH Inc. Metaalsmeden en poedermetallurgie Het type metaalsmeedprocessen dat we aanbieden zijn warme en koude matrijs, open matrijs en gesloten matrijs, afdrukmatrijs en flitsloze smeedstukken, cogging, volvullen, randen en precisiesmeedwerk, bijna-netvorm, kop , smeden, overstuur smeden, metalen hobbing, pers & rol & radiaal & orbitaal & ring & isotherme smeedstukken, munten, klinken, metalen kogel smeden, metalen piercing, maatvoering, smeden met hoge energiesnelheid. Onze POEDERMETALLURGIE en POEDERVERWERKING technieken zijn poederpersen en sinteren, impregneren, infiltratie, warm en koud isostatisch persen, metaal spuitgieten, rolverdichting, poederwalsen, poederextrusie, los sinteren, vonken sinteren, heet persen. We raden u aan hier te klikken om: DOWNLOAD onze schematische illustraties van smeedprocessen door AGS-TECH Inc. DOWNLOAD onze schematische illustraties van poedermetallurgieprocessen door AGS-TECH Inc. Deze downloadbare bestanden met foto's en schetsen zullen u helpen de informatie die we u hieronder verstrekken beter te begrijpen. Bij het smeden van metaal worden drukkrachten uitgeoefend en wordt het materiaal vervormd en wordt de gewenste vorm verkregen. De meest voorkomende gesmede materialen in de industrie zijn ijzer en staal, maar tal van andere zoals aluminium, koper, titanium en magnesium worden ook op grote schaal gesmeed. Gesmede metalen onderdelen hebben verbeterde korrelstructuren naast afgedichte scheuren en gesloten lege ruimtes, dus de sterkte van onderdelen die door dit proces worden verkregen, is hoger. Smeden produceert onderdelen die aanzienlijk sterker zijn voor hun gewicht dan onderdelen die zijn gemaakt door gieten of machinaal bewerken. Omdat gesmede onderdelen worden gevormd door het metaal in zijn uiteindelijke vorm te laten vloeien, krijgt het metaal een gerichte korrelstructuur die verantwoordelijk is voor de superieure sterkte van de onderdelen. Met andere woorden, onderdelen verkregen door het smeedproces onthullen betere mechanische eigenschappen in vergelijking met eenvoudige gegoten of machinaal bewerkte onderdelen. Het gewicht van metalen smeedstukken kan variëren van kleine lichtgewicht onderdelen tot honderdduizenden ponden. Wij vervaardigen smeedstukken, voornamelijk voor mechanisch veeleisende toepassingen waarbij hoge spanningen worden uitgeoefend op onderdelen zoals auto-onderdelen, tandwielen, uitrustingsstukken, handgereedschap, turbineassen, motoruitrusting. Omdat de gereedschaps- en installatiekosten relatief hoog zijn, raden we dit fabricageproces alleen aan voor productie in grote volumes en voor kritische componenten met een laag volume, maar met een hoge waarde, zoals landingsgestellen in de ruimtevaart. Naast de gereedschapskosten kunnen de productiedoorlooptijden voor gesmede onderdelen in grote hoeveelheden langer zijn in vergelijking met sommige eenvoudig bewerkte onderdelen, maar de techniek is cruciaal voor onderdelen die buitengewone sterkte vereisen, zoals bouten, moeren, speciale toepassingen bevestigingsmiddelen, automotive, heftruck, kraanonderdelen. • HOT DIE EN KOUDE DIE SMEDEN : Heet smeedwerk, zoals de naam al aangeeft, wordt uitgevoerd bij hoge temperaturen, de ductiliteit is daarom hoog en de sterkte van het materiaal laag. Dit vergemakkelijkt gemakkelijk vervormen en smeden. Integendeel, koud smeden wordt uitgevoerd bij lagere temperaturen en vereist hogere krachten, wat resulteert in spanningsverharding, betere oppervlakteafwerking en nauwkeurigheid van de vervaardigde onderdelen. • OPEN DIE en IMPRESSIE SMEED : Bij het smeden met open matrijzen, beperken de matrijzen het materiaal dat wordt samengeperst niet, terwijl bij het smeden van de indrukstempel de holtes in de matrijzen de materiaalstroom beperken terwijl het in de gewenste vorm wordt gesmeed. UPSET FORGING of ook UPSETTING genoemd, wat eigenlijk niet hetzelfde is, maar een zeer vergelijkbaar proces, is een open matrijsproces waarbij het werkstuk tussen twee platte matrijzen wordt geklemd en een drukkracht de hoogte ervan vermindert. Naarmate de hoogte is reduced, neemt de werkstukbreedte toe. HEADING, een gestuikt smeedproces omvat een cilindrisch materiaal dat aan het uiteinde wordt gestuikt en waarvan de dwarsdoorsnede lokaal wordt vergroot. Bij de kop wordt de bouillon door de matrijs gevoerd, gesmeed en vervolgens op lengte gesneden. De operatie is in staat om snel grote hoeveelheden bevestigingsmiddelen te produceren. Meestal is het een koude bewerking omdat het wordt gebruikt om spijkeruiteinden, schroefuiteinden, moeren en bouten te maken waar het materiaal moet worden versterkt. Een ander open matrijsproces is COGGING, waarbij het werkstuk in een reeks stappen wordt gesmeed, waarbij elke stap resulteert in compressie van het materiaal en de daaropvolgende beweging van de open matrijs over de lengte van het werkstuk. Bij elke stap wordt de dikte verminderd en de lengte met een kleine hoeveelheid vergroot. Het proces lijkt op een nerveuze student die in kleine stapjes op zijn potlood bijt. Een proces dat FULLERING wordt genoemd, is een andere smeedmethode met open matrijs die we vaak gebruiken als een eerdere stap om het materiaal in het werkstuk te verdelen voordat andere metaalsmeedbewerkingen plaatsvinden. We gebruiken het wanneer het werkstuk meerdere forging operations vereist. Tijdens de bewerking vervormt de matrijs met convexe oppervlakken en laat het metaal naar beide kanten uitstromen. Een soortgelijk proces als volvullen, EDGING daarentegen omvat een open matrijs met concave oppervlakken om het werkstuk te vervormen. Randen is ook een voorbereidend proces voor daaropvolgende smeedbewerkingen, waardoor het materiaal van beide kanten naar een gebied in het midden stroomt. IMPRESSION DIE FORGING of CLOSED DIE FORGING zoals het ook wordt genoemd, maakt gebruik van een matrijs / mal die het materiaal samendrukt en de stroming in zichzelf beperkt. De matrijs sluit en het materiaal neemt de vorm aan van de matrijs/vormholte. PRECISIESMEDING, een proces dat speciale apparatuur en gietvorm vereist, produceert onderdelen zonder of met zeer weinig flits. Met andere woorden, de onderdelen zullen bijna de uiteindelijke afmetingen hebben. Bij dit proces wordt een goed gecontroleerde hoeveelheid materiaal zorgvuldig in de mal ingebracht en gepositioneerd. We zetten deze methode in voor complexe vormen met dunne secties, kleine toleranties en diepgangshoeken en wanneer de hoeveelheden groot genoeg zijn om de mal- en apparatuurkosten te rechtvaardigen. • FLASHLOOS SMEDEN: Het werkstuk wordt zo in de matrijs geplaatst dat er geen materiaal uit de holte kan stromen om een flits te vormen. Er is dus geen ongewenst trimmen van de flitser nodig. Het is een nauwkeurig smeedproces en vereist dus nauwkeurige controle van de hoeveelheid gebruikt materiaal. • METALEN SWAGING of RADIAAL SMEDEN: Een werkstuk wordt langs de omtrek bewerkt door een matrijs en gesmeed. Een doorn kan ook worden gebruikt om de inwendige geometrie van het werkstuk te smeden. Bij het smeden krijgt het werkstuk typisch meerdere slagen per seconde. Typische items die door smeden worden geproduceerd, zijn gereedschappen met een puntige punt, taps toelopende staven, schroevendraaiers. • METALEN PIERCING : We gebruiken deze bewerking vaak als extra bewerking bij de fabricage van onderdelen. Een gat of holte wordt gemaakt met een piercing op het werkstukoppervlak zonder er doorheen te breken. Houd er rekening mee dat piercing anders is dan boren, wat resulteert in een doorgaand gat. • AFHALEN : Een stempel met de gewenste geometrie wordt in het werkstuk gedrukt en creëert een holte met de gewenste vorm. We noemen deze stoot een HOB. De operatie gaat gepaard met hoge drukken en wordt koud uitgevoerd. Hierdoor wordt het materiaal koud bewerkt en rekgehard. Daarom is dit proces zeer geschikt voor het vervaardigen van matrijzen, matrijs en holtes voor andere fabricageprocessen. Als de kookplaat eenmaal is vervaardigd, kan men gemakkelijk veel identieke holtes maken zonder ze één voor één te hoeven bewerken. • ROLSMEDEN of ROLVORMING : Twee tegenover elkaar liggende rollen worden gebruikt om het metalen onderdeel te vormen. Het werkstuk wordt in de rollen gevoerd, de rollen draaien en trekken het werk in de spleet, het werk wordt vervolgens door het gegroefde gedeelte van de rollen gevoerd en de drukkrachten geven het materiaal de gewenste vorm. Het is geen walsproces maar een smeedproces, omdat het eerder een discrete dan een continue bewerking is. De geometrie op de walsgroeven smeedt het materiaal tot de gewenste vorm en geometrie. Het wordt warm uitgevoerd. Omdat het een smeedproces is, produceert het onderdelen met uitstekende mechanische eigenschappen en daarom gebruiken we het voor het vervaardigen van auto-onderdelen zoals assen die buitengewoon uithoudingsvermogen moeten hebben in zware werkomgevingen. • ORBITAAL SMEEDING: het werkstuk wordt in een smeedmatrijsholte geplaatst en gesmeed door een bovenste matrijs die in een orbitale baan beweegt terwijl deze op een schuine as draait. Bij elke omwenteling voltooit de bovenste matrijs het uitoefenen van drukkrachten op het gehele werkstuk. Door deze omwentelingen een aantal keren te herhalen wordt er voldoende gesmeed. De voordelen van deze fabricagetechniek zijn de geluidsarme werking en de lagere benodigde krachten. Met andere woorden, met kleine krachten kan men een zware matrijs rond een as laten draaien om grote druk uit te oefenen op een deel van het werkstuk dat in contact is met de matrijs. Schijf- of conisch gevormde delen passen soms goed bij dit proces. • RINGSMEEDING: wij maken regelmatig gebruik van naadloze ringen. De voorraad wordt op lengte gesneden, verstoord en vervolgens helemaal doorboord om een centraal gat te creëren. Vervolgens wordt het op een doorn geplaatst en een smeedmatrijs hamert het van bovenaf terwijl de ring langzaam wordt geroteerd totdat de gewenste afmetingen zijn verkregen. • KLINKEN: een veelgebruikt proces voor het verbinden van onderdelen, begint met een recht metalen stuk dat in vooraf gemaakte gaten door de onderdelen wordt gestoken. Daarna worden de twee uiteinden van het metalen stuk gesmeed door in de verbinding tussen een bovenste en onderste matrijs te knijpen. • MUNTEN : Een ander populair proces dat wordt uitgevoerd door een mechanische pers, waarbij grote krachten over een korte afstand worden uitgeoefend. De naam "munten" komt van de fijne details die op de oppervlakken van metalen munten zijn gesmeed. Het is meestal een afwerkingsproces voor een product waarbij fijne details op de oppervlakken worden verkregen als gevolg van de grote kracht die wordt uitgeoefend door de matrijs die deze details op het werkstuk overbrengt. • METALEN KOGEL SMEDEN: Producten zoals kogellagers vereisen nauwkeurig vervaardigde metalen kogels van hoge kwaliteit. Bij één techniek, SKEW ROLLING genaamd, gebruiken we twee tegenover elkaar liggende rollen die continu roteren terwijl het materiaal continu in de rollen wordt gevoerd. Aan het ene uiteinde van de twee rollen worden metalen bollen als product uitgeworpen. Een tweede methode voor het smeden van metalen kogels is het gebruik van een matrijs die de materiaalvoorraad die ertussen is geplaatst, samendrukt en de bolvorm van de vormholte aanneemt. Vaak hebben de geproduceerde ballen enkele extra stappen nodig, zoals afwerken en polijsten, om een product van hoge kwaliteit te worden. • ISOTHERMISCH SMEEDING / HEET DIESMEDEWERK: Een duur proces dat alleen wordt uitgevoerd als het voordeel / de kostenwaarde gerechtvaardigd is. Een heet werkproces waarbij de matrijs wordt verwarmd tot ongeveer dezelfde temperatuur als het werkstuk. Omdat zowel de matrijs als het werkstuk ongeveer dezelfde temperatuur hebben, is er geen koeling en worden de vloei-eigenschappen van het metaal verbeterd. De bewerking is geschikt voor superlegeringen en materialen met inferieure smeedbaarheid en materialen waarvan mechanische eigenschappen zijn erg gevoelig voor kleine temperatuurgradiënten en veranderingen. • METAL SIZING: Het is een koud afwerkingsproces. De materiaalstroom is onbeperkt in alle richtingen, met uitzondering van de richting waarin de kracht wordt uitgeoefend. Hierdoor wordt een zeer goede oppervlakteafwerking en nauwkeurige maatvoering verkregen. • HOOG ENERGIEVERSLAG SMEDEN: Bij deze techniek wordt een bovenste mal bevestigd aan de arm van een zuiger die snel wordt ingedrukt wanneer een brandstof-luchtmengsel wordt ontstoken door een bougie. Het lijkt op de werking van zuigers in een automotor. De mal raakt het werkstuk zeer snel en keert daarna dankzij de tegendruk zeer snel terug naar zijn oorspronkelijke positie. Het werk is binnen enkele milliseconden gesmeed en daardoor is er geen tijd om het werk af te koelen. Dit is handig voor moeilijk te smeden onderdelen met zeer temperatuurgevoelige mechanische eigenschappen. Met andere woorden, het proces is zo snel dat het onderdeel overal onder constante temperatuur wordt gevormd en er geen temperatuurgradiënten zijn bij de matrijs/werkstuk-interfaces. • In DIE FORGING wordt metaal geslagen tussen twee bijpassende stalen blokken met speciale vormen erin, die matrijzen genoemd. Wanneer het metaal tussen de matrijzen wordt gehamerd, neemt het dezelfde vorm aan als de vormen in de matrijs. Als het zijn definitieve vorm heeft bereikt, wordt het eruit gehaald om af te koelen. Dit proces produceert sterke onderdelen met een precieze vorm, maar vereist een grotere investering voor de gespecialiseerde matrijzen. Verstoord smeden vergroot de diameter van een stuk metaal door het plat te maken. Het wordt over het algemeen gebruikt om kleine onderdelen te maken, vooral om koppen te vormen op bevestigingsmiddelen zoals bouten en spijkers. • POEDERMETALLURGIE / POEDERVERWERKING : Zoals de naam al aangeeft, gaat het om productieprocessen voor het maken van vaste delen met bepaalde geometrieën en vormen uit poeders. Als metaalpoeders voor dit doel worden gebruikt, is dat het gebied van poedermetallurgie en als niet-metaalpoeders worden gebruikt, is het poederverwerking. Door persen en sinteren worden vaste delen uit poeders gemaakt. POWDER PRESSING wordt gebruikt om poeders in de gewenste vormen te persen. Ten eerste wordt het primaire materiaal fysiek verpoederd, waardoor het in vele kleine individuele deeltjes wordt verdeeld. Poedermengsel wordt in de matrijs gevuld en een pons beweegt naar het poeder toe en comprimeert het in de gewenste vorm. Meestal uitgevoerd bij kamertemperatuur, met poederpersen wordt een vast deel verkregen en dit wordt groen compact genoemd. Bindmiddelen en smeermiddelen worden vaak gebruikt om de verdichtbaarheid te verbeteren. We zijn in staat om poederpersen te vormen met behulp van hydraulische persen met een capaciteit van enkele duizenden tonnen. We hebben ook dubbelwerkende persen met tegengestelde boven- en onderponsen, evenals meervoudige actiepersen voor zeer complexe onderdeelgeometrieën. Uniformiteit, een belangrijke uitdaging voor veel poedermetallurgie / poederverwerkingsfabrieken, is voor AGS-TECH geen groot probleem vanwege onze jarenlange ervaring in het op maat vervaardigen van dergelijke onderdelen. Ook met dikkere onderdelen waar uniformiteit een uitdaging vormt zijn we erin geslaagd. Als we ons inzetten voor uw project, maken we uw onderdelen. Als we mogelijke risico's zien, zullen we u informeren in voorschot. POEDERSINTERING, de tweede stap, houdt in dat de temperatuur tot op zekere hoogte wordt verhoogd en gedurende een bepaalde tijd op dat niveau wordt gehouden, zodat de poederdeeltjes in het geperste deel aan elkaar kunnen hechten. Dit resulteert in veel sterkere bindingen en versterking van het werkstuk. Het sinteren vindt plaats dicht bij de smelttemperatuur van het poeder. Tijdens het sinteren zal krimp optreden, materiaalsterkte, dichtheid, ductiliteit, thermische geleidbaarheid, elektrische geleidbaarheid worden verhoogd. We hebben batch- en continue ovens voor sinteren. Een van onze mogelijkheden is het aanpassen van de porositeit van de onderdelen die we produceren. We kunnen bijvoorbeeld metalen filters maken door de onderdelen tot op zekere hoogte poreus te houden. Met behulp van een techniek genaamd IMPREGNATIE, vullen we de poriën in het metaal met een vloeistof zoals olie. We produceren bijvoorbeeld met olie geïmpregneerde lagers die zelfsmerend zijn. In het INFILTRATIE-proces vullen we de poriën van een metaal met een ander metaal met een lager smeltpunt dan het basismateriaal. Het mengsel wordt verwarmd tot een temperatuur tussen de smelttemperaturen van de twee metalen. Hierdoor kunnen enkele bijzondere eigenschappen worden verkregen. We voeren ook vaak secundaire bewerkingen uit, zoals machinale bewerking en smeden van in poedervorm vervaardigde onderdelen wanneer speciale kenmerken of eigenschappen moeten worden verkregen of wanneer het onderdeel kan worden vervaardigd met minder processtappen. ISOSTATISCH PERSEN: In dit proces wordt vloeistofdruk gebruikt om het onderdeel te verdichten. Metaalpoeders worden in een mal geplaatst die is gemaakt van een verzegelde flexibele container. Bij isostatisch persen wordt druk uitgeoefend van rondom, in tegenstelling tot axiale druk die wordt waargenomen bij conventioneel persen. De voordelen van isostatisch persen zijn uniforme dichtheid binnen het onderdeel, vooral voor grotere of dikkere onderdelen, superieure eigenschappen. Het nadeel is lange cyclustijden en relatief lage geometrische nauwkeurigheid. KOUD ISOSTATISCH PERSEN wordt uitgevoerd bij kamertemperatuur en de flexibele mal is gemaakt van rubber, PVC of urethaan of soortgelijke materialen. Vloeistof die wordt gebruikt voor het onder druk brengen en verdichten is olie of water. Conventioneel sinteren van de groene compact volgt dit. HEET ISOSTATISCH PERSEN daarentegen wordt uitgevoerd bij hoge temperaturen en het vormmateriaal is plaatmetaal of keramiek met een voldoende hoog smeltpunt dat bestand is tegen de temperaturen. Drukvloeistof is meestal een inert gas. De pers- en sinterbewerkingen worden in één stap uitgevoerd. Porositeit wordt bijna volledig geëlimineerd, een uniforme grain structuur wordt verkregen. Het voordeel van heet isostatisch persen is dat het onderdelen kan produceren die vergelijkbaar zijn met gieten en smeden gecombineerd, terwijl materialen kunnen worden gebruikt die niet geschikt zijn voor gieten en smeden. Nadeel van heet isostatisch persen is de hoge cyclustijd en dus de kosten. Het is geschikt voor kritische onderdelen met een laag volume. METAALINJECTIEVORMING: Zeer geschikt proces voor het produceren van complexe onderdelen met dunne wanden en gedetailleerde geometrieën. Meest geschikt voor kleinere onderdelen. Poeders en polymeerbindmiddel worden gemengd, verwarmd en in een mal gespoten. Het polymeer bindmiddel bedekt de oppervlakken van de poederdeeltjes. Na het vormen wordt het bindmiddel verwijderd door ofwel verwarming bij lage temperatuur of opgelost met behulp van een oplosmiddel. ROLLENVERDICHTING / POEDER ROLLEN : Poeders worden gebruikt om doorlopende stroken of vellen te produceren. Poeder wordt vanuit een feeder toegevoerd en door twee roterende rollen verdicht tot vellen of stroken. De operatie wordt koud uitgevoerd. De plaat wordt in een sinteroven gebracht. Het sinterproces kan een tweede keer worden herhaald. POEDEREXTRUSIE: Onderdelen met een grote verhouding tussen lengte en diameter worden vervaardigd door een dunne metalen container met poeder te extruderen. LOS SINTEREN: Zoals de naam al aangeeft, is het een drukloze verdichtings- en sintermethode, geschikt voor het produceren van zeer poreuze onderdelen zoals metalen filters. Poeder wordt zonder verdichting in de vormholte gevoerd. LOS SINTEREN: Zoals de naam al aangeeft, is het een drukloze verdichtings- en sintermethode, geschikt voor het produceren van zeer poreuze onderdelen zoals metalen filters. Poeder wordt zonder verdichting in de vormholte gevoerd. SPARK SINTERING: Het poeder wordt in de mal gecomprimeerd door twee tegengestelde ponsen en een elektrische stroom met hoog vermogen wordt op de pons aangebracht en gaat door het verdichte poeder dat ertussen zit. De hoge stroom brandt oppervlaktefilms van de poederdeeltjes weg en sintert ze met de gegenereerde warmte. Het proces is snel omdat warmte niet van buitenaf wordt toegepast, maar in plaats daarvan wordt gegenereerd vanuit de matrijs. HEET PERSEN : De poeders worden in een enkele stap geperst en gesinterd in een mal die bestand is tegen de hoge temperaturen. Terwijl de matrijs compacter wordt, wordt de poederwarmte erop toegepast. De goede nauwkeurigheid en mechanische eigenschappen die door deze methode worden bereikt, maken het een aantrekkelijke optie. Zelfs vuurvaste metalen kunnen worden verwerkt met behulp van malmaterialen zoals grafiet. CLICK Product Finder-Locator Service VORIGE MENU
- Plastic Rubber Metal Extrusions, Extrusion Dies, Aluminum Extruding
Plastic Rubber Metal Extrusions, Extrusion Dies, Aluminum Extruding, Pipe Tube Forming, Plastic Profiles, Metal Profiles Manufacturing, PVC at AGS-TECH Inc. Extrusies, geëxtrudeerde producten, extrudaten We gebruiken het EXTRUSION proces om producten te vervaardigen met een vast dwarsdoorsnedeprofiel zoals buizen, pijpen en koellichamen. Hoewel veel materialen kunnen worden geëxtrudeerd, zijn onze meest voorkomende extrusies gemaakt van metaal, polymeren / plastic, keramiek verkregen door koude, warme of warme extrusiemethode. We noemen de geëxtrudeerde delen extrudaat of extrudaten als het meervoud is. Sommige gespecialiseerde versies van het proces dat we ook uitvoeren, zijn overjacketing, co-extrusie en samengestelde extrusie. We raden u aan hier te klikken om DOWNLOAD onze schematische illustraties van metaalkeramiek en kunststof extrusieprocessen door AGS-TECH Inc. Dit zal u helpen de informatie die we u hieronder verstrekken beter te begrijpen. Bij extrusie wordt te extruderen materiaal door een matrijs geduwd of getrokken die het gewenste dwarsdoorsnedeprofiel heeft. Het proces kan worden gebruikt om complexe doorsneden met een uitstekende oppervlakteafwerking te vervaardigen en om op bros materiaal te werken. Met dit proces kan men onderdelen van elke lengte produceren. Om de processtappen te vereenvoudigen: 1.) Bij warme of hete extrusies wordt het materiaal verwarmd en in een container in de pers geladen. Het materiaal wordt geperst en uit de matrijs geduwd. 2.) Geproduceerd extrudaat wordt uitgerekt om te strekken, met warmte behandeld of koud bewerkt om de eigenschappen ervan te verbeteren. Aan de andere kant COLD EXTRUSION vindt plaats bij ongeveer kamertemperatuur en heeft de voordelen van minder oxidatie, hoge sterkte, nauwere toleranties, goede oppervlakteafwerking en echtheid. WARM EXTRUSION wordt uitgevoerd boven kamertemperatuur maar onder het herkristallisatiepunt. Het biedt een compromis en balans voor de vereiste krachten, ductiliteit en materiaaleigenschappen en is daarom de keuze voor sommige toepassingen. HOT EXTRUSION vindt plaats boven de herkristallisatietemperatuur van het materiaal. Op deze manier is het gemakkelijker om het materiaal door de matrijs te duwen. De kosten van de apparatuur zijn echter hoog. Hoe complexer een geëxtrudeerd profiel, hoe duurder de matrijs (gereedschap) en hoe lager de productiesnelheid. Zowel de matrijsdwarsdoorsneden als de dikten hebben beperkingen die afhankelijk zijn van het te extruderen materiaal. Scherpe hoeken in extrusiematrijzen zijn altijd ongewenst en moeten worden vermeden tenzij noodzakelijk. Afhankelijk van het materiaal dat wordt geëxtrudeerd, bieden wij: • METALEN EXTRUSIES : De meest voorkomende die we produceren zijn aluminium, messing, zink, koper, staal, titanium, magnesium • PLASTIC EXTRUSION : Kunststof wordt gesmolten en gevormd tot een doorlopend profiel. Onze gebruikelijke materialen die worden verwerkt, zijn polyethyleen, nylon, polystyreen, polyvinylchloride, polypropyleen, ABS-kunststof, polycarbonaat, acryl. Typische producten die wij vervaardigen zijn buizen en buizen, kunststof kozijnen. Tijdens het proces worden kleine plastic kralen / hars door de zwaartekracht vanuit de trechter in het vat van de extrusiemachine gevoerd. Vaak mengen we ook kleurstoffen of andere toevoegingen in de trechter om het product de gewenste specificaties en eigenschappen te geven. Het materiaal dat het verwarmde vat binnenkomt, wordt door de roterende schroef gedwongen om het vat aan het einde te verlaten en door het zeefpakket te bewegen om verontreinigingen in het gesmolten plastic te verwijderen. Na het passeren van het zeefpakket komt het plastic in de extrusiematrijs. De matrijs geeft het bewegende zachte plastic zijn profielvorm als het er doorheen gaat. Nu gaat het extrudaat door een waterbad om af te koelen. Andere technieken die AGS-TECH Inc. al vele jaren gebruikt, zijn: • PIPE & TUBING EXTRUSION : Kunststof buizen en pijpen worden gevormd wanneer kunststof wordt geëxtrudeerd door een ronde vormmatrijs en afgekoeld in een waterbad, vervolgens op lengte gesneden of opgerold / opgespoeld. Helder of gekleurd, gestreept, enkel- of dubbelwandig, flexibel of stijf, PE, PP, polyurethaan, PVC, nylon, PC, siliconen, vinyl of anders, we hebben het allemaal. Wij hebben zowel buizen op voorraad als de mogelijkheid om volgens uw specificaties te produceren. AGS-TECH produceert buizen volgens de FDA-, UL- en LE-vereisten voor medische, elektrische en elektronische, industriële en andere toepassingen. • OVERJACKETING / OVERJACKETING EXTRUSION : Deze techniek brengt een buitenste laag plastic aan op bestaande draad of kabel. Onze isolatiedraden worden met deze methode vervaardigd. • COEXTRUSION : Meerdere materiaallagen worden gelijktijdig geëxtrudeerd. De meerdere lagen worden geleverd door meerdere extruders. De verschillende laagdiktes kunnen worden aangepast aan de wensen van de klant. Dit proces maakt het mogelijk om meerdere polymeren met elk een andere functionaliteit in het product te gebruiken. Hierdoor kan men een scala aan eigenschappen optimaliseren. • COMPOUND EXTRUSIE: Een enkele of meerdere polymeren worden gemengd met additieven om een plastic verbinding te verkrijgen. Onze dubbelschroefsextruders produceren samengestelde extrusies. Extrusiematrijzen zijn over het algemeen goedkoop in vergelijking met metalen mallen. Als u veel meer dan een paar duizend dollar betaalt voor een kleine of middelgrote extrusiematrijs die aluminium extrudeert, betaalt u waarschijnlijk te veel. Wij zijn experts in het bepalen welke techniek het meest kosteneffectief, het snelst en het meest geschikt is voor uw toepassing. Soms kan het extruderen en vervolgens bewerken van een onderdeel u veel geld besparen. Vraag ons eerst onze mening voordat u een definitieve beslissing neemt. We hebben veel klanten geholpen de juiste beslissingen te nemen. Voor enkele veelgebruikte metalen extrusies kunt u onze brochures en catalogi downloaden door op de gekleurde tekst hieronder te klikken. Als het een kant-en-klaar product is dat aan uw eisen voldoet, is het voordeliger. Download onze extrusiemogelijkheden voor medische buizen en pijpen Download onze geëxtrudeerde koellichamen • SECUNDAIRE PRODUCTIE- EN FABRICAGEPROCESSEN VOOR EXTRUSIES : Onder de processen met toegevoegde waarde die we aanbieden voor geëxtrudeerde producten zijn: -Aangepaste buis & pijp buigen, vormen en vormgeven, buis afsnijden, buisuiteinde vormen, buis oprollen, machinale bewerking en afwerking, gat boren & piercing & ponsen, -Aangepaste pijp- en buisassemblages, buismontage, lassen, solderen en solderen -Aangepaste extrusie buigen, vormen en vormgeven -Reinigen, ontvetten, beitsen, passiveren, polijsten, anodiseren, plateren, schilderen, warmtebehandeling, gloeien en uitharden, markeren, graveren en labelen, verpakking op maat. CLICK Product Finder-Locator Service VORIGE PAGINA
- Casting and Machined Parts, CNC Manufacturing, Milling, Turning, Swiss
Casting and Machined Parts, CNC Manufacturing, Milling, Turning, Swiss Type Machining, Die Casting, Investment Casting, Lost Foam Cast Parts from AGS-TECH Inc. Gieten en verspanen Onze op maat gemaakte giet- en bewerkingstechnieken zijn vervangbare en niet-verbruikbare gietstukken, ferro- en non-ferrogietwerk, zand, matrijs, centrifugaal, continu, keramische mal, investering, verloren schuim, bijna-netvorm, permanente mal (zwaartekrachtgieten), gips mal (gipsgietwerk) en schaalgietstukken, bewerkte onderdelen geproduceerd door frezen en draaien met behulp van zowel conventionele als CNC-apparatuur, zwitserse bewerking voor hoge doorvoer, goedkope kleine precisieonderdelen, schroefbewerking voor bevestigingsmiddelen, niet-conventionele bewerking. Houd er rekening mee dat we naast metalen en metaallegeringen ook keramiek, glas en kunststof onderdelen bewerken in sommige gevallen wanneer het vervaardigen van een mal niet aantrekkelijk of niet de optie is. Het bewerken van polymeermaterialen vereist de gespecialiseerde ervaring die we hebben vanwege de uitdaging die kunststoffen en rubber met zich meebrengen vanwege hun zachtheid, niet-stijfheid ... enz. Voor het bewerken van keramiek en glas, zie onze pagina over niet-conventionele fabricage. AGS-TECH Inc. produceert en levert zowel lichtgewicht als zware gietstukken. We leveren metalen gietstukken en bewerkte onderdelen voor ketels, warmtewisselaars, auto's, micromotoren, windturbines, voedselverpakkingsapparatuur en meer. We raden u aan hier te klikken om DOWNLOAD onze schematische illustraties van bewerkings- en gietprocessen door AGS-TECH Inc. Dit zal u helpen de informatie die we u hieronder verstrekken beter te begrijpen. Laten we eens kijken naar enkele van de verschillende technieken die we aanbieden in detail: • EXPENDABLE MOLD CASTING: Deze brede categorie verwijst naar methoden waarbij tijdelijke en niet-herbruikbare mallen worden gebruikt. Voorbeelden zijn zand, gips, schelpen, inbedmassa (ook wel verloren was genoemd) en gipsafgietsel. • ZANDGIETEN: een proces waarbij zand als malmateriaal wordt gebruikt. Een zeer oude methode en nog steeds erg populair in de mate dat de meeste metalen gietstukken met deze techniek worden gemaakt. Lage kosten, zelfs bij lage productie. Geschikt voor de productie van kleine en grote onderdelen. De techniek kan worden gebruikt om onderdelen binnen enkele dagen of weken te vervaardigen met zeer weinig investeringen. Het vochtige zand wordt met klei, bindmiddelen of speciale oliën aan elkaar gehecht. Zand zit over het algemeen in vormbakken en spouw- en poortsystemen worden gecreëerd door het zand rond modellen te verdichten. De processen zijn: 1.) Het model in zand plaatsen om de mal te maken 2.) Opname van model en zand in een poortsysteem 3.) Model verwijderen 4.) Vullen van vormholte met gesmolten metaal 5.) Afkoeling van het metaal 6.) Het breken van de zandvorm en het verwijderen van het gietstuk • GIPSGIETEN: Vergelijkbaar met zandgieten, en in plaats van zand wordt gips uit Parijs gebruikt als malmateriaal. Korte productiedoorlooptijden zoals zandgieten en goedkoop. Goede maattoleranties en oppervlakteafwerking. Het grote nadeel is dat het alleen kan worden gebruikt met metalen met een laag smeltpunt, zoals aluminium en zink. • SHELL MOLD CASTING : Ook vergelijkbaar met zandgieten. Vormholte verkregen door geharde schaal van zand en thermohardend harsbindmiddel in plaats van een kolf gevuld met zand zoals bij het zandgietproces. Vrijwel elk metaal dat geschikt is om met zand te worden gegoten, kan worden gegoten door middel van schaalvormen. Het proces kan worden samengevat als: 1.) Vervaardiging van de schaalvorm. Het gebruikte zand heeft een veel kleinere korrelgrootte in vergelijking met zand dat wordt gebruikt bij het zandgieten. Het fijne zand wordt gemengd met thermohardende hars. Het metalen patroon is gecoat met een scheidingsmiddel om het verwijderen van de schaal gemakkelijker te maken. Daarna wordt het metaalpatroon verwarmd en wordt het zandmengsel geporeerd of geblazen op het hete gietpatroon. Een dunne schaal vormt zich op het oppervlak van het patroon. De dikte van deze schaal kan worden aangepast door de tijdsduur dat het zandharsmengsel in contact is met het metaalpatroon te variëren. Het losse zand wordt vervolgens verwijderd terwijl het met schelpen bedekte patroon overblijft. 2.) Vervolgens worden de schaal en het patroon in een oven verwarmd zodat de schaal hard wordt. Nadat het uitharden is voltooid, wordt de schaal uit het patroon geworpen met behulp van pinnen die in het patroon zijn ingebouwd. 3.) Twee van dergelijke schalen worden door lijmen of klemmen aan elkaar geassembleerd en vormen de volledige mal. Nu wordt de schaalvorm in een container gestoken waarin deze tijdens het gietproces wordt ondersteund door zand of metaalschot. 4.) Nu kan het hete metaal in de schaalvorm worden gegoten. Voordelen van schaalgieten zijn producten met een zeer goede oppervlakteafwerking, de mogelijkheid om complexe onderdelen te vervaardigen met een hoge maatnauwkeurigheid, het proces is eenvoudig te automatiseren, economisch voor de productie van grote volumes. Nadelen zijn dat de mallen een goede ventilatie vereisen vanwege gassen die ontstaan wanneer gesmolten metaal in contact komt met het bindmiddel, de thermohardende harsen en metaalpatronen zijn duur. Vanwege de kosten van metaalpatronen is de techniek mogelijk niet geschikt voor productieruns met een kleine hoeveelheid. • INVESTERINGSGIET (ook bekend als LOST-WAX CASTING): Ook een zeer oude techniek en geschikt voor het vervaardigen van kwaliteitsonderdelen met hoge nauwkeurigheid, herhaalbaarheid, veelzijdigheid en integriteit van vele metalen, vuurvaste materialen en speciale hoogwaardige legeringen. Zowel kleine als grote onderdelen kunnen worden geproduceerd. Een duur proces in vergelijking met sommige van de andere methoden, maar het grote voordeel is de mogelijkheid om onderdelen te produceren met een bijna netvorm, ingewikkelde contouren en details. De kosten worden dus enigszins gecompenseerd door de eliminatie van nabewerking en bewerking in sommige gevallen. Hoewel er variaties kunnen zijn, is hier een samenvatting van het algemene gietproces voor investeringen: 1.) Creatie van origineel masterpatroon van was of plastic. Elk gietstuk heeft één patroon nodig, omdat deze tijdens het proces worden vernietigd. Er is ook een mal nodig waaruit patronen worden vervaardigd en meestal wordt de mal gegoten of machinaal bewerkt. Omdat de mal niet geopend hoeft te worden, kunnen complexe gietstukken worden bereikt, kunnen veel waspatronen worden verbonden als de takken van een boom en samen worden gegoten, waardoor de productie van meerdere onderdelen mogelijk wordt door één keer gieten van het metaal of de metaallegering. 2.) Vervolgens wordt het patroon ondergedompeld of gegoten met een vuurvaste slurry bestaande uit zeer fijnkorrelige silica, water, bindmiddelen. Dit resulteert in een keramische laag over het oppervlak van het patroon. De vuurvaste laag op het patroon laat men drogen en uitharden. Deze stap is waar de naam investeringsgieten vandaan komt: vuurvaste slurry wordt geïnvesteerd over het waspatroon. 3.) Bij deze stap wordt de geharde keramische mal ondersteboven gekeerd en verwarmd zodat de was smelt en uit de mal stroomt. Er blijft een holte achter voor het metalen gietstuk. 4.) Nadat de was eruit is, wordt de keramische mal verwarmd tot een nog hogere temperatuur, wat resulteert in versteviging van de mal. 5.) Metaalgietwerk wordt in de hete vorm gegoten en vult alle ingewikkelde secties. 6.) Gieten mag stollen 7.) Ten slotte wordt de keramische mal gebroken en worden gefabriceerde onderdelen uit de boom gesneden. Hier is een link naar de brochure over investeringsgietinstallaties: • VERDAMPINGSPATROON GIETEN: Het proces maakt gebruik van een patroon gemaakt van een materiaal zoals polystyreenschuim dat zal verdampen wanneer heet gesmolten metaal in de mal wordt gegoten. Er zijn twee soorten van dit proces: LOST FOAM CASTING waarbij gebruik wordt gemaakt van niet-gebonden zand en FULL MOLD CASTING waarbij gebruik wordt gemaakt van gebonden zand. Dit zijn de algemene processtappen: 1.) Vervaardig het patroon van een materiaal zoals polystyreen. Wanneer er grote hoeveelheden worden vervaardigd, wordt het patroon gegoten. Als een onderdeel een complexe vorm heeft, moeten mogelijk meerdere secties van dergelijk schuimmateriaal aan elkaar worden gehecht om het patroon te vormen. We coaten het patroon vaak met een vuurvaste verbinding om een goede oppervlakteafwerking op het gietstuk te creëren. 2.) Het patroon wordt vervolgens in vormzand gelegd. 3.) Het gesmolten metaal wordt in de mal gegoten, waarbij het schuimpatroon, dwz polystyreen in de meeste gevallen, verdampt als het door de malholte stroomt. 4.) Het gesmolten metaal wordt in de zandvorm gelaten om uit te harden. 5.) Nadat het is uitgehard, verwijderen we het gietstuk. In sommige gevallen vereist het product dat we vervaardigen een kern binnen het patroon. Bij verdampingsgieten is het niet nodig om een kern in de vormholte te plaatsen en vast te zetten. De techniek is geschikt voor het vervaardigen van zeer complexe geometrieën, kan eenvoudig worden geautomatiseerd voor productie van grote volumes en er zijn geen scheidingslijnen in het gegoten onderdeel. Het basisproces is eenvoudig en economisch te implementeren. Voor productie van grote volumes, aangezien een matrijs of mal nodig is om de patronen van polystyreen te produceren, kan dit enigszins kostbaar zijn. • NIET-UITBREIDBARE VORMGIETEN: Deze brede categorie verwijst naar methoden waarbij de mal niet na elke productiecyclus hoeft te worden hervormd. Voorbeelden zijn permanent, matrijs-, continu- en centrifugaalgieten. Herhaalbaarheid wordt verkregen en onderdelen kunnen worden gekarakteriseerd als NEAR NET SHAPE. • PERMANENTE VORMGIETEN : Herbruikbare vormen van metaal worden gebruikt voor meerdere gietstukken. Een permanente mal kan over het algemeen tienduizenden keren worden gebruikt voordat deze verslijt. Over het algemeen worden zwaartekracht, gasdruk of vacuüm gebruikt om de mal te vullen. Mallen (ook wel matrijs genoemd) zijn over het algemeen gemaakt van ijzer, staal, keramiek of andere metalen. Het algemene proces is: 1.) Machine en maak de mal. Het is gebruikelijk om de mal uit twee metalen blokken te maken die in elkaar passen en kunnen worden geopend en gesloten. Zowel de onderdeelkenmerken als het poortsysteem worden over het algemeen machinaal in de gietvorm gefreesd. 2.) De interne matrijsoppervlakken zijn gecoat met een suspensie waarin vuurvaste materialen zijn verwerkt. Dit helpt de warmtestroom te beheersen en werkt als smeermiddel voor gemakkelijke verwijdering van het gegoten onderdeel. 3.) Vervolgens worden de permanente matrijshelften gesloten en wordt de matrijs verwarmd. 4.) Gesmolten metaal wordt in de vorm gegoten en stil gelaten om te stollen. 5.) Voordat er veel afkoeling plaatsvindt, verwijderen we het onderdeel uit de permanente mal met behulp van uitwerpers wanneer de malhelften worden geopend. Voor metalen met een laag smeltpunt, zoals zink en aluminium, gebruiken we vaak permanent gieten. Voor stalen gietstukken gebruiken we grafiet als malmateriaal. Soms verkrijgen we complexe geometrieën met behulp van kernen in permanente mallen. Voordelen van deze techniek zijn gietstukken met goede mechanische eigenschappen verkregen door snelle afkoeling, uniformiteit in eigenschappen, goede nauwkeurigheid en oppervlakteafwerking, lage uitvalpercentages, mogelijkheid om het proces te automatiseren en economisch hoge volumes te produceren. Nadelen zijn de hoge initiële installatiekosten die het ongeschikt maken voor bewerkingen met een laag volume, en beperkingen op de grootte van de vervaardigde onderdelen. • DIE CASTING: Een matrijs wordt machinaal bewerkt en gesmolten metaal wordt onder hoge druk in de vormholten geduwd. Zowel non-ferro als ferro metalen spuitgieten zijn mogelijk. Het proces is geschikt voor grote oplagen van kleine tot middelgrote onderdelen met details, extreem dunne wanden, maatvastheid en een goede oppervlakteafwerking. AGS-TECH Inc. is in staat om met deze techniek wanddiktes tot 0,5 mm te vervaardigen. Net als bij permanent gieten, moet de mal uit twee helften bestaan die kunnen openen en sluiten om het geproduceerde onderdeel te verwijderen. Een spuitgietvorm kan meerdere holtes hebben om de productie van meerdere gietstukken bij elke cyclus mogelijk te maken. Spuitgietmatrijzen zijn erg zwaar en veel groter dan de onderdelen die ze produceren, dus ook duur. We repareren en vervangen versleten matrijzen gratis voor onze klanten, zolang ze hun onderdelen bij ons nabestellen. Onze matrijzen hebben een lange levensduur in het bereik van enkele honderdduizenden cycli. Dit zijn de basis vereenvoudigde processtappen: 1.) Productie van de mal in het algemeen van staal 2.) Schimmel geïnstalleerd op spuitgietmachine; 3.) De zuiger dwingt gesmolten metaal in de matrijsholten te stromen en vult de ingewikkelde functies en dunne wanden in 4.) Na het vullen van de mal met het gesmolten metaal, wordt het gietstuk onder druk gehard 5.) De mal wordt geopend en het gietstuk wordt verwijderd met behulp van uitwerppennen. 6.) Nu wordt de lege matrijs opnieuw gesmeerd en vastgeklemd voor de volgende cyclus. Bij het spuitgieten gebruiken we vaak insert molding, waarbij we een extra onderdeel in de mal verwerken en het metaal eromheen gieten. Na stollen worden deze delen onderdeel van het gegoten product. Voordelen van spuitgieten zijn goede mechanische eigenschappen van de onderdelen, mogelijkheid van ingewikkelde functies, fijne details en goede oppervlakteafwerking, hoge productiesnelheden, eenvoudige automatisering. Nadelen zijn: Niet erg geschikt voor een laag volume vanwege de hoge matrijs- en apparatuurkosten, beperkingen in de vormen die kunnen worden gegoten, kleine ronde markeringen op gegoten onderdelen als gevolg van contact met uitwerppennen, dunne flits van metaal dat eruit wordt geperst bij de scheidingslijn, noodzaak voor ventilatieopeningen langs de scheidingslijn tussen de matrijs, noodzaak om de maltemperaturen laag te houden met behulp van watercirculatie. • CENTRIFUGAAL GIETEN : Gesmolten metaal wordt in het midden van de roterende mal gegoten op de rotatie-as. Centrifugale krachten werpen het metaal naar de periferie en het laat het stollen terwijl de mal blijft draaien. Zowel horizontale als verticale asrotaties kunnen worden gebruikt. Onderdelen met ronde binnenvlakken en andere niet-ronde vormen kunnen worden gegoten. Het proces kan worden samengevat als: 1.) Gesmolten metaal wordt in een centrifugaalvorm gegoten. Het metaal wordt vervolgens door het ronddraaien van de mal naar de buitenmuren geperst. 2.) Terwijl de mal draait, wordt het metalen gietstuk hard Centrifugaal gieten is een geschikte techniek voor de productie van holle cilindrische onderdelen zoals pijpen, geen behoefte aan sprues, risers en poortelementen, goede oppervlakteafwerking en gedetailleerde eigenschappen, geen krimpproblemen, mogelijkheid om lange pijpen met zeer grote diameters te produceren, hoge productiecapaciteit . • CONTINU GIETEN ( STRAND CASTING ) : Wordt gebruikt om een ononderbroken stuk metaal te gieten. In principe wordt het gesmolten metaal gegoten in een tweedimensionaal profiel van de mal, maar de lengte ervan is onbepaald. Er wordt constant nieuw gesmolten metaal in de mal gevoerd terwijl het gietstuk naar beneden beweegt en de lengte ervan met de tijd toeneemt. Metalen zoals koper, staal en aluminium worden in lange strengen gegoten met behulp van een continu gietproces. Het proces kan verschillende configuraties hebben, maar de algemene kan worden vereenvoudigd als: 1.) Gesmolten metaal wordt gegoten in een container die zich hoog boven de mal bevindt met goed berekende hoeveelheden en stroomsnelheden en stroomt door de watergekoelde mal. Het metalen gietstuk dat in de mal wordt gegoten, stolt tot een startstaaf die op de bodem van de mal wordt geplaatst. Deze startstang geeft de rollen in eerste instantie iets om aan vast te grijpen. 2.) De lange metalen streng wordt met een constante snelheid door rollen gedragen. De rollen veranderen ook de richting van de stroom van metaalstreng van verticaal naar horizontaal. 3.) Nadat het continugieten een bepaalde horizontale afstand heeft afgelegd, snijdt een toorts of zaag die met het gietstuk meebeweegt het snel op de gewenste lengte. Het continugietproces kan worden geïntegreerd met ROLLING PROCESS, waarbij het continu gegoten metaal rechtstreeks in een walserij kan worden ingevoerd om I-Beams, T-Beams ... enz. te produceren. Continu gieten produceert uniforme eigenschappen door het hele product, het heeft een hoge stollingssnelheid, verlaagt de kosten door een zeer laag materiaalverlies, biedt een proces waarbij het laden van metaal, gieten, stollen, snijden en verwijderen van het gietstuk allemaal plaatsvinden in een continue bewerking en wat resulteert in een hoge productiviteit en hoge kwaliteit. Een belangrijke overweging is echter de hoge initiële investering, installatiekosten en benodigde ruimte. • BEWERKINGSDIENSTEN: Wij bieden drie-, vier- en vijfassige bewerkingen aan. De soort bewerkingsprocessen die wij gebruiken zijn DRAAIEN, FREZEN, BOREN, KOOREN, BRAAKKEN, SCHAFFEN, ZAGEN, SLIJPEN, LAPPEN, POLIJSTEN en NIET-TRADITIONEEL BEWERKEN dat verder wordt uitgewerkt in een ander menu van onze website. Voor het grootste deel van onze productie gebruiken we CNC-machines. Voor sommige operaties passen conventionele technieken echter beter en daarom vertrouwen we er ook op. Onze bewerkingsmogelijkheden bereiken het hoogst mogelijke niveau en sommige meest veeleisende onderdelen worden vervaardigd in een AS9100-gecertificeerde fabriek. Schoepen voor straalmotoren vereisen zeer gespecialiseerde productie-ervaring en de juiste apparatuur. De lucht- en ruimtevaartindustrie heeft zeer strikte normen. Sommige componenten met complexe geometrische structuren kunnen het gemakkelijkst worden vervaardigd door middel van vijfassige bewerking, wat alleen in sommige bewerkingsfabrieken, waaronder de onze, wordt aangetroffen. Onze lucht- en ruimtevaart gecertificeerde fabriek heeft de nodige ervaring om te voldoen aan de uitgebreide documentatie-eisen van de lucht- en ruimtevaartindustrie. Bij DRAAIEN-bewerkingen wordt een werkstuk geroteerd en tegen een snijgereedschap bewogen. Voor dit proces wordt een machine genaamd draaibank gebruikt. In FREZEN heeft een machine die freesmachine wordt genoemd, een roterend gereedschap om snijkanten tegen een werkstuk aan te brengen. BOORbewerkingen omvatten een roterende frees met snijkanten die gaten produceert bij contact met het werkstuk. Over het algemeen worden boorpersen, draaibanken of molens gebruikt. Bij BORING-bewerkingen wordt een gereedschap met een enkele gebogen puntige punt in een ruw gat in een draaiend werkstuk bewogen om het gat iets te vergroten en de nauwkeurigheid te verbeteren. Het wordt gebruikt voor fijne afwerkingsdoeleinden. BRAAKKEN betreft een getand gereedschap om materiaal van een werkstuk te verwijderen in één doorgang van het aansnijden (getand gereedschap). Bij lineair brootsen loopt de broots lineair tegen een oppervlak van het werkstuk om de snede te bewerkstelligen, terwijl bij roterend brootsen de broots wordt geroteerd en in het werkstuk wordt gedrukt om een assymmetrische vorm te snijden. ZWITSERSE TYPE BEWERKING is een van onze waardevolle technieken die we gebruiken voor de productie van grote hoeveelheden kleine, zeer nauwkeurige onderdelen. Met behulp van een Zwitserse draaibank draaien we kleine, complexe precisieonderdelen goedkoop. In tegenstelling tot conventionele draaibanken waar het werkstuk stationair wordt gehouden en het gereedschap in beweging wordt gehouden, mag het werkstuk in Zwitserse draaicentra in de Z-as bewegen en staat het gereedschap stil. Bij de bewerking van het Zwitserse type wordt het stafmateriaal in de machine vastgehouden en door een geleidebus in de z-as voortbewogen, waardoor alleen het te bewerken gedeelte wordt blootgelegd. Op deze manier is een stevige grip verzekerd en is de nauwkeurigheid zeer hoog. De beschikbaarheid van onder spanning staande gereedschappen biedt de mogelijkheid om te frezen en te boren terwijl het materiaal uit de geleidingsbus komt. De Y-as van de apparatuur van het Zwitserse type biedt volledige freesmogelijkheden en bespaart veel tijd bij de productie. Bovendien hebben onze machines boren en kottergereedschappen die op het onderdeel werken wanneer het in de subspil wordt gehouden. Onze bewerkingscapaciteit van het Zwitserse type geeft ons een volledig geautomatiseerde complete bewerkingsmogelijkheid in één enkele bewerking. Verspaning is een van de grootste segmenten van de activiteiten van AGS-TECH Inc. We gebruiken het als primaire bewerking of als secundaire bewerking na het gieten of extruderen van een onderdeel, zodat aan alle tekeningspecificaties wordt voldaan. • OPPERVLAKTE AFWERKINGSDIENSTEN: We bieden een grote verscheidenheid aan oppervlaktebehandelingen en oppervlakteafwerking, zoals oppervlaktebehandeling om de hechting te verbeteren, het afzetten van een dunne oxidelaag om de hechting van de coating te verbeteren, zandstralen, chem-film, anodiseren, nitreren, poedercoaten, spraycoaten , diverse geavanceerde metallisatie- en coatingtechnieken waaronder sputteren, elektronenstraal, verdamping, plating, harde coatings zoals diamantachtige koolstof (DLC) of titaniumcoating voor boor- en snijgereedschappen. • PRODUCTMARKERING & ETIKETTERINGSDIENSTEN: Veel van onze klanten hebben behoefte aan markering en etikettering, lasermarkering, gravure op metalen onderdelen. Als u een dergelijke behoefte heeft, laten we dan bespreken welke optie het beste voor u is. Hier zijn enkele veelgebruikte metalen gegoten producten. Omdat deze kant-en-klaar zijn, kunt u besparen op matrijskosten als een van deze aan uw eisen voldoet: KLIK HIER OM onze 11-serie gegoten aluminium dozen van AGS-Electronics te downloaden CLICK Product Finder-Locator Service VORIGE PAGINA
- Custom Manufactured Parts, Assemblies, Plastic Mold, Casting,Machining
Custom Manufactured Parts, Assemblies, Plastic Mold, Rubber Molding, Metal Casting, CNC Machining, Turning, Milling, Electrical Electronic Optical Assembly PCBA Op maat gemaakte onderdelen & Assemblies en producten Lees verder Kunststof en rubberen mallen en vormen Lees verder Gieten en verspanen Lees verder Extrusies, geëxtrudeerde producten Lees verder Stempels en plaatbewerking Lees verder Metaalsmeden en poedermetallurgie Lees verder Draad- en veervormen Lees verder Vormen en vormen van glas en keramiek Lees verder Additieve en snelle productie Lees verder Productie van composieten en composietmaterialen Lees verder Verbindings- en montage- en bevestigingsprocessen Wij produceren onderdelen en samenstellingen voor u en bieden de volgende productieprocessen aan: • Kunststof en rubberen mallen en vormdelen. Spuitgieten, thermovormen, thermoharden, vacuümvormen, blaasvormen, rotatiegieten, gietvormen, insert molding en andere. • Kunststof, rubber en metalen profielen • Ferro- en non-ferrogietstukken en bewerkte onderdelen geproduceerd door middel van frees- en draaitechnieken, bewerking van het Zwitserse type. • Onderdelen voor poedermetallurgie • Metalen en niet-metalen stempels, plaatbewerking, gelaste plaatwerkassemblages • Koud en warm smeden • Draden, gelaste draadassemblages, draadvorming • Verschillende soorten veren, veervormend • Tandwielproductie, versnellingsbak, koppeling, worm, snelheidsreductiemiddel, cilinder, transmissieriemen, transmissiekettingen, transmissiecomponenten • Op maat gehard en kogelvrij glas dat voldoet aan de NAVO- en militaire normen • Kogels, lagers, katrollen en katrolassemblages • Kleppen en pneumatische componenten zoals O-ring, ring en afdichtingen • Glas- en keramische onderdelen en samenstellingen, vacuümdichte en hermetische componenten, metaal-keramiek en keramisch-keramiek verlijming. • Verschillende soorten mechanische, optomechanische, elektromechanische, opto-elektronische samenstellingen. • Metaal-rubber, metaal-kunststof binding • Pijpen en buizen, pijpvormen, buigen en op maat gemaakte pijpassemblages, balgproductie. • Glasvezelproductie • Lassen met verschillende technieken zoals puntlassen, laserlassen, MIG, TIG. Ultrasoon lassen van kunststof onderdelen. • Grote verscheidenheid aan oppervlaktebehandelingen en oppervlakteafwerkingen zoals oppervlaktebehandeling om de hechting te verbeteren, het afzetten van een dunne oxidelaag om de hechting van de coating te verbeteren, zandstralen, chem-film, anodiseren, nitreren, poedercoaten, spraycoaten, verschillende geavanceerde metallisatie- en coatingtechnieken inclusief sputteren, elektronenstraal, verdamping, plating, harde coatings zoals diamantachtige koolstof (DLC) of titanium voor snij- en boorgereedschap. • Markering en etikettering, lasermarkering op metalen onderdelen, bedrukking op kunststof en rubberen onderdelen Download brochure voor algemene termen voor werktuigbouwkunde die worden gebruikt door ontwerpers en ingenieurs Wij bouwen producten volgens uw specifieke specificaties en eisen. Om u de beste kwaliteit, levering en prijzen te bieden, vervaardigen wij producten wereldwijd in China, India, Taiwan, de Filippijnen, Zuid-Korea, Maleisië, Sri Lanka, Turkije, de VS, Canada, Duitsland, het VK en Japan. Dit maakt ons veel sterker en wereldwijd concurrerender dan elke andere custom manufacturer. Onze producten worden vervaardigd in ISO9001:2000, QS9000, ISO14001, TS16949 gecertificeerde omgevingen en beschikken over CE-, UL-markering en voldoen aan andere industrienormen. Zodra we voor uw project zijn aangesteld, kunnen we de volledige productie, montage, testen, kwalificatie, verzending en douane verzorgen zoals u dat wilt. Als u wilt, kunnen we uw onderdelen opslaan, aangepaste kits samenstellen, uw bedrijfsnaam en merk afdrukken en labelen en naar uw klanten verzenden. Met andere woorden, wij kunnen desgewenst ook uw warehousing en distributiecentrum zijn. Omdat onze magazijnen zich in de buurt van grote zeehavens bevinden, geeft dit ons logistiek voordeel. Wanneer uw producten bijvoorbeeld aankomen in een grote Amerikaanse zeehaven, kunnen we het rechtstreeks naar een nabijgelegen magazijn transporteren waar we kunnen opslaan, assembleren, kits maken, opnieuw labelen, afdrukken, verpakken volgens uw keuze en drop verzenden naar uw klanten. Wij leveren niet alleen producten. Ons bedrijf werkt aan aangepaste contracten waarbij we naar uw locatie komen, uw project ter plaatse evalueren en een projectvoorstel op maat voor u ontwikkelen. Vervolgens sturen we ons ervaren team om het project uit te voeren. Meer informatie over onze engineering vindt u op: http://www.ags-engineering.com -We nemen zowel kleine projecten als grote projecten op industriële schaal aan. Als eerste stap kunnen we u via telefoon, teleconferentie of MSN-messenger doorverbinden met onze deskundige teamleden, zodat u rechtstreeks met een deskundige kunt communiceren, vragen kunt stellen en uw project kunt bespreken. Bel ons en indien nodig komen we bij u langs. VORIGE PAGINA