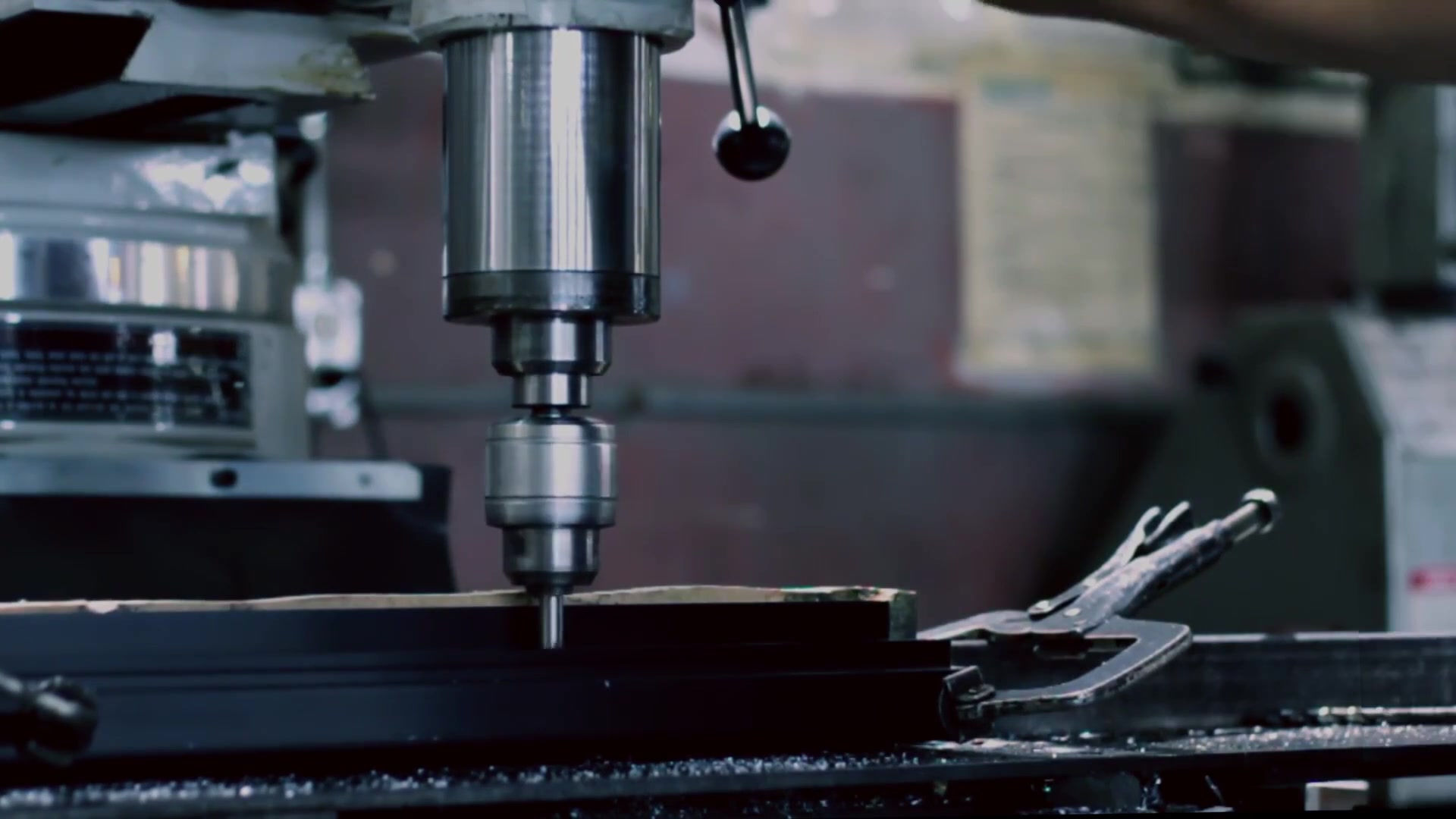
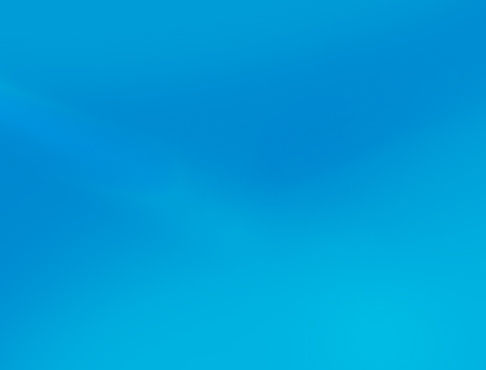
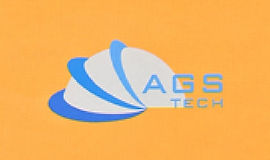
ਗਲੋਬਲ ਕਸਟਮ ਮੈਨੂਫੈਕਚਰਰ, ਇੰਟੀਗਰੇਟਰ, ਕੰਸੋਲੀਡੇਟਰ, ਉਤਪਾਦਾਂ ਅਤੇ ਸੇਵਾਵਾਂ ਦੀ ਵਿਭਿੰਨ ਕਿਸਮਾਂ ਲਈ ਆਊਟਸੋਰਸਿੰਗ ਪਾਰਟਨਰ।
ਅਸੀਂ ਨਿਰਮਾਣ, ਨਿਰਮਾਣ, ਇੰਜੀਨੀਅਰਿੰਗ, ਇਕਸਾਰਤਾ, ਏਕੀਕਰਣ, ਕਸਟਮ ਨਿਰਮਿਤ ਅਤੇ ਆਫ-ਸ਼ੈਲਫ ਉਤਪਾਦਾਂ ਅਤੇ ਸੇਵਾਵਾਂ ਦੀ ਆਊਟਸੋਰਸਿੰਗ ਲਈ ਤੁਹਾਡੇ ਇੱਕ-ਸਟਾਪ ਸਰੋਤ ਹਾਂ।
ਆਪਣੀ ਭਾਸ਼ਾ ਚੁਣੋ
-
ਕਸਟਮ ਨਿਰਮਾਣ
-
ਘਰੇਲੂ ਅਤੇ ਗਲੋਬਲ ਕੰਟਰੈਕਟ ਮੈਨੂਫੈਕਚਰਿੰਗ
-
ਨਿਰਮਾਣ ਆਊਟਸੋਰਸਿੰਗ
-
ਘਰੇਲੂ ਅਤੇ ਗਲੋਬਲ ਖਰੀਦਦਾਰੀ
-
ਇਕਸੁਰਤਾ
-
ਇੰਜੀਨੀਅਰਿੰਗ ਏਕੀਕਰਣ
-
ਇੰਜੀਨੀਅਰਿੰਗ ਸੇਵਾਵਾਂ
Search Results
164 results found with an empty search
- Transmission Components, Belts, Chains, Cable Drives, Pulleys,AGS-TECH
Transmission Components, Belts, Chains and Cable Drives, Conventional & Grooved or Serrated, Positive Drive, Pulleys ਬੈਲਟਸ ਅਤੇ ਚੇਨ ਅਤੇ ਕੇਬਲ ਡਰਾਈਵ ਅਸੈਂਬਲੀ AGS-TECH Inc. ਤੁਹਾਨੂੰ ਬੈਲਟਸ ਅਤੇ ਚੇਨਾਂ ਅਤੇ ਕੇਬਲ ਡਰਾਈਵ ਅਸੈਂਬਲੀ ਸਮੇਤ ਪਾਵਰ ਟ੍ਰਾਂਸਮਿਸ਼ਨ ਕੰਪੋਨੈਂਟਸ ਦੀ ਪੇਸ਼ਕਸ਼ ਕਰਦਾ ਹੈ। ਸਾਲਾਂ ਦੇ ਸੁਧਾਈ ਦੇ ਨਾਲ, ਸਾਡੀਆਂ ਰਬੜ, ਚਮੜੇ ਅਤੇ ਹੋਰ ਬੈਲਟ ਡਰਾਈਵਾਂ ਹਲਕੇ ਅਤੇ ਵਧੇਰੇ ਸੰਖੇਪ ਹੋ ਗਈਆਂ ਹਨ, ਜੋ ਘੱਟ ਕੀਮਤ 'ਤੇ ਵੱਧ ਭਾਰ ਚੁੱਕਣ ਦੇ ਸਮਰੱਥ ਹਨ। ਇਸੇ ਤਰ੍ਹਾਂ, ਸਾਡੀਆਂ ਚੇਨ ਡਰਾਈਵਾਂ ਸਮੇਂ ਦੇ ਨਾਲ ਬਹੁਤ ਵਿਕਾਸ ਵਿੱਚੋਂ ਲੰਘੀਆਂ ਹਨ ਅਤੇ ਉਹ ਸਾਡੇ ਗਾਹਕਾਂ ਨੂੰ ਕਈ ਫਾਇਦੇ ਪ੍ਰਦਾਨ ਕਰਦੀਆਂ ਹਨ। ਚੇਨ ਡਰਾਈਵਾਂ ਦੀ ਵਰਤੋਂ ਕਰਨ ਦੇ ਕੁਝ ਫਾਇਦੇ ਹਨ ਉਹਨਾਂ ਦੀ ਮੁਕਾਬਲਤਨ ਅਪ੍ਰਬੰਧਿਤ ਸ਼ਾਫਟ ਸੈਂਟਰ ਦੂਰੀ, ਸੰਖੇਪਤਾ, ਅਸੈਂਬਲੀ ਦੀ ਸੌਖ, ਤਿਲਕਣ ਜਾਂ ਕ੍ਰੀਪ ਤੋਂ ਬਿਨਾਂ ਤਣਾਅ ਵਿੱਚ ਲਚਕੀਲਾਪਣ, ਉੱਚ-ਤਾਪਮਾਨ ਵਾਲੇ ਵਾਤਾਵਰਣ ਵਿੱਚ ਕੰਮ ਕਰਨ ਦੀ ਯੋਗਤਾ। ਸਾਡੀਆਂ ਕੇਬਲ ਡਰਾਈਵਾਂ ਹੋਰ ਕਿਸਮਾਂ ਦੇ ਪ੍ਰਸਾਰਣ ਭਾਗਾਂ ਨਾਲੋਂ ਕੁਝ ਐਪਲੀਕੇਸ਼ਨਾਂ ਵਿੱਚ ਸਾਦਗੀ ਵਰਗੇ ਫਾਇਦੇ ਵੀ ਪੇਸ਼ ਕਰਦੀਆਂ ਹਨ। ਦੋਵੇਂ ਆਫ-ਸ਼ੈਲਫ ਬੈਲਟ, ਚੇਨ ਅਤੇ ਕੇਬਲ ਡਰਾਈਵਾਂ ਦੇ ਨਾਲ-ਨਾਲ ਕਸਟਮ ਫੈਬਰੀਕੇਟਿਡ ਅਤੇ ਅਸੈਂਬਲ ਕੀਤੇ ਸੰਸਕਰਣ ਉਪਲਬਧ ਹਨ। ਅਸੀਂ ਇਹਨਾਂ ਟ੍ਰਾਂਸਮਿਸ਼ਨ ਕੰਪੋਨੈਂਟਸ ਨੂੰ ਤੁਹਾਡੀ ਐਪਲੀਕੇਸ਼ਨ ਲਈ ਸਹੀ ਆਕਾਰ ਵਿੱਚ ਅਤੇ ਸਭ ਤੋਂ ਢੁਕਵੀਂ ਸਮੱਗਰੀ ਤੋਂ ਤਿਆਰ ਕਰ ਸਕਦੇ ਹਾਂ। ਬੈਲਟ ਅਤੇ ਬੈਲਟ ਡਰਾਈਵ: - ਪਰੰਪਰਾਗਤ ਫਲੈਟ ਬੈਲਟਾਂ: ਇਹ ਸਾਦੇ ਫਲੈਟ ਬੈਲਟਾਂ ਹਨ, ਬਿਨਾਂ ਦੰਦਾਂ, ਖੋਖਿਆਂ ਜਾਂ ਸੀਰੇਸ਼ਨਾਂ ਦੇ। ਫਲੈਟ ਬੈਲਟ ਡਰਾਈਵਾਂ ਲਚਕਤਾ, ਚੰਗੀ ਸਦਮਾ ਸਮਾਈ, ਉੱਚ ਰਫਤਾਰ 'ਤੇ ਕੁਸ਼ਲ ਪਾਵਰ ਟ੍ਰਾਂਸਮਿਸ਼ਨ, ਘਬਰਾਹਟ ਪ੍ਰਤੀਰੋਧ, ਘੱਟ ਕੀਮਤ ਦੀ ਪੇਸ਼ਕਸ਼ ਕਰਦੀਆਂ ਹਨ। ਵੱਡੀਆਂ ਬੈਲਟਾਂ ਬਣਾਉਣ ਲਈ ਬੈਲਟਾਂ ਨੂੰ ਕੱਟਿਆ ਜਾਂ ਜੋੜਿਆ ਜਾ ਸਕਦਾ ਹੈ। ਪਰੰਪਰਾਗਤ ਫਲੈਟ ਬੈਲਟਾਂ ਦੇ ਹੋਰ ਫਾਇਦੇ ਇਹ ਹਨ ਕਿ ਉਹ ਪਤਲੇ ਹੁੰਦੇ ਹਨ, ਉਹ ਉੱਚ ਸੈਂਟਰੀਫਿਊਗਲ ਲੋਡ ਦੇ ਅਧੀਨ ਨਹੀਂ ਹੁੰਦੇ ਹਨ (ਛੋਟੀਆਂ ਪੁੱਲੀਆਂ ਦੇ ਨਾਲ ਉੱਚ ਰਫਤਾਰ ਦੇ ਸੰਚਾਲਨ ਲਈ ਵਧੀਆ ਬਣਾਉਂਦੇ ਹਨ)। ਦੂਜੇ ਪਾਸੇ ਉਹ ਉੱਚ ਬੇਅਰਿੰਗ ਲੋਡ ਲਗਾਉਂਦੇ ਹਨ ਕਿਉਂਕਿ ਫਲੈਟ ਬੈਲਟਾਂ ਨੂੰ ਉੱਚ ਤਣਾਅ ਦੀ ਲੋੜ ਹੁੰਦੀ ਹੈ। ਫਲੈਟ ਬੈਲਟ ਡਰਾਈਵਾਂ ਦੇ ਹੋਰ ਨੁਕਸਾਨ ਫਿਸਲਣ, ਰੌਲੇ-ਰੱਪੇ ਵਾਲੇ ਸੰਚਾਲਨ ਅਤੇ ਸੰਚਾਲਨ ਦੀ ਘੱਟ ਅਤੇ ਮੱਧਮ ਗਤੀ 'ਤੇ ਮੁਕਾਬਲਤਨ ਘੱਟ ਕੁਸ਼ਲਤਾ ਹੋ ਸਕਦੇ ਹਨ। ਸਾਡੇ ਕੋਲ ਦੋ ਕਿਸਮਾਂ ਦੀਆਂ ਪਰੰਪਰਾਗਤ ਬੈਲਟਾਂ ਹਨ: ਪ੍ਰਬਲ ਅਤੇ ਗੈਰ-ਮਜਬੂਤ। ਮਜਬੂਤ ਬੈਲਟਾਂ ਦੀ ਬਣਤਰ ਵਿੱਚ ਇੱਕ ਟੈਂਸਿਲ ਮੈਂਬਰ ਹੁੰਦਾ ਹੈ। ਰਵਾਇਤੀ ਫਲੈਟ ਬੈਲਟ ਚਮੜੇ, ਰਬੜਾਈਜ਼ਡ ਫੈਬਰਿਕ ਜਾਂ ਕੋਰਡ, ਗੈਰ-ਮਜਬੂਤ ਰਬੜ ਜਾਂ ਪਲਾਸਟਿਕ, ਫੈਬਰਿਕ, ਮਜਬੂਤ ਚਮੜੇ ਦੇ ਰੂਪ ਵਿੱਚ ਉਪਲਬਧ ਹਨ। ਚਮੜੇ ਦੀਆਂ ਪੇਟੀਆਂ ਲੰਬੀ ਉਮਰ, ਲਚਕਤਾ, ਰਗੜ ਦੇ ਸ਼ਾਨਦਾਰ ਗੁਣਾਂਕ, ਆਸਾਨ ਮੁਰੰਮਤ ਦੀ ਪੇਸ਼ਕਸ਼ ਕਰਦੀਆਂ ਹਨ। ਹਾਲਾਂਕਿ ਚਮੜੇ ਦੀਆਂ ਬੈਲਟਾਂ ਮੁਕਾਬਲਤਨ ਮਹਿੰਗੀਆਂ ਹੁੰਦੀਆਂ ਹਨ, ਬੇਲਟ ਡਰੈਸਿੰਗ ਅਤੇ ਸਫਾਈ ਦੀ ਲੋੜ ਹੁੰਦੀ ਹੈ, ਅਤੇ ਮਾਹੌਲ 'ਤੇ ਨਿਰਭਰ ਕਰਦੇ ਹੋਏ ਉਹ ਸੁੰਗੜ ਸਕਦੇ ਹਨ ਜਾਂ ਖਿੱਚ ਸਕਦੇ ਹਨ। ਰਬੜਾਈਜ਼ਡ ਫੈਬਰਿਕ ਜਾਂ ਕੋਰਡ ਬੈਲਟ ਨਮੀ, ਐਸਿਡ ਅਤੇ ਅਲਕਲਿਸ ਪ੍ਰਤੀ ਰੋਧਕ ਹੁੰਦੇ ਹਨ। ਰਬਰਾਈਜ਼ਡ ਫੈਬਰਿਕ ਬੈਲਟ ਕਪਾਹ ਜਾਂ ਸਿੰਥੈਟਿਕ ਬਤਖ ਦੇ ਰਬੜ ਦੇ ਨਾਲ ਬਣੇ ਹੁੰਦੇ ਹਨ ਅਤੇ ਸਭ ਤੋਂ ਵੱਧ ਕਿਫ਼ਾਇਤੀ ਹੁੰਦੇ ਹਨ। ਰਬੜ ਵਾਲੀਆਂ ਕੋਰਡ ਬੈਲਟਾਂ ਵਿੱਚ ਰਬੜ-ਪ੍ਰੇਗਨੇਟਿਡ ਕੋਰਡਜ਼ ਦੀ ਇੱਕ ਲੜੀ ਹੁੰਦੀ ਹੈ। ਰਬੜਾਈਜ਼ਡ ਕੋਰਡ ਬੈਲਟ ਉੱਚ ਤਣਾਅ ਵਾਲੀ ਤਾਕਤ ਅਤੇ ਮਾਮੂਲੀ ਆਕਾਰ ਅਤੇ ਪੁੰਜ ਦੀ ਪੇਸ਼ਕਸ਼ ਕਰਦੇ ਹਨ। ਗੈਰ-ਮਜਬੂਤ ਰਬੜ ਜਾਂ ਪਲਾਸਟਿਕ ਬੈਲਟ ਲਾਈਟ-ਡਿਊਟੀ, ਘੱਟ-ਸਪੀਡ ਡਰਾਈਵ ਐਪਲੀਕੇਸ਼ਨਾਂ ਲਈ ਫਿੱਟ ਹਨ। ਗੈਰ-ਮਜਬੂਤ ਰਬੜ ਅਤੇ ਪਲਾਸਟਿਕ ਦੀਆਂ ਬੈਲਟਾਂ ਨੂੰ ਉਹਨਾਂ ਦੀਆਂ ਪੁਲੀਆਂ ਦੇ ਉੱਪਰ ਜਗ੍ਹਾ ਵਿੱਚ ਖਿੱਚਿਆ ਜਾ ਸਕਦਾ ਹੈ। ਪਲਾਸਟਿਕ ਦੇ ਗੈਰ-ਮਜਬੂਤ ਬੈਲਟ ਰਬੜ ਦੇ ਬੈਲਟਾਂ ਦੇ ਮੁਕਾਬਲੇ ਉੱਚ ਸ਼ਕਤੀ ਦਾ ਸੰਚਾਰ ਕਰ ਸਕਦੇ ਹਨ। ਮਜਬੂਤ ਚਮੜੇ ਦੀਆਂ ਬੈਲਟਾਂ ਵਿੱਚ ਚਮੜੇ ਦੇ ਉੱਪਰ ਅਤੇ ਹੇਠਾਂ ਦੀਆਂ ਪਰਤਾਂ ਦੇ ਵਿਚਕਾਰ ਸੈਂਡਵਿਚ ਕੀਤੇ ਪਲਾਸਟਿਕ ਟੈਂਸਿਲ ਮੈਂਬਰ ਹੁੰਦੇ ਹਨ। ਅੰਤ ਵਿੱਚ, ਸਾਡੇ ਫੈਬਰਿਕ ਬੈਲਟਾਂ ਵਿੱਚ ਸੂਤੀ ਦਾ ਇੱਕ ਟੁਕੜਾ ਜਾਂ ਬੱਤਖ ਨੂੰ ਜੋੜਿਆ ਅਤੇ ਲੰਬਕਾਰੀ ਟਾਂਕਿਆਂ ਦੀਆਂ ਕਤਾਰਾਂ ਨਾਲ ਸਿਲਾਈ ਹੋ ਸਕਦੀ ਹੈ। ਫੈਬਰਿਕ ਬੈਲਟ ਇਕਸਾਰ ਤਰੀਕੇ ਨਾਲ ਟਰੈਕ ਕਰਨ ਅਤੇ ਤੇਜ਼ ਰਫ਼ਤਾਰ 'ਤੇ ਕੰਮ ਕਰਨ ਦੇ ਯੋਗ ਹਨ। - ਗਰੂਵਡ ਜਾਂ ਸੇਰੇਟਿਡ ਬੈਲਟਸ (ਜਿਵੇਂ ਕਿ V-ਬੈਲਟਸ): ਇਹ ਕਿਸੇ ਹੋਰ ਕਿਸਮ ਦੇ ਟ੍ਰਾਂਸਮਿਸ਼ਨ ਉਤਪਾਦ ਦੇ ਫਾਇਦੇ ਪ੍ਰਦਾਨ ਕਰਨ ਲਈ ਸੋਧੀਆਂ ਗਈਆਂ ਮੂਲ ਫਲੈਟ ਬੈਲਟਾਂ ਹਨ। ਇਹ ਸਮਤਲ ਬੈਲਟਾਂ ਹਨ ਜਿਨ੍ਹਾਂ ਦੇ ਹੇਠਾਂ ਲੰਮੀ ਤੌਰ 'ਤੇ ਰਿਬਡ ਹੁੰਦੇ ਹਨ। ਪੌਲੀ-ਵੀ ਬੈਲਟ ਲੰਮੀ ਤੌਰ 'ਤੇ ਟੇਨਸਾਈਲ ਸੈਕਸ਼ਨ ਦੇ ਨਾਲ ਸੈਰੇਟਿਡ ਫਲੈਟ ਬੈਲਟ ਅਤੇ ਟਰੈਕਿੰਗ ਅਤੇ ਕੰਪਰੈਸ਼ਨ ਦੇ ਉਦੇਸ਼ਾਂ ਲਈ ਨਾਲ ਲੱਗਦੇ V-ਆਕਾਰ ਦੇ ਗਰੂਵਜ਼ ਦੀ ਇੱਕ ਲੜੀ ਦੇ ਨਾਲ ਹੁੰਦੇ ਹਨ। ਪਾਵਰ ਸਮਰੱਥਾ ਬੈਲਟ ਦੀ ਚੌੜਾਈ 'ਤੇ ਨਿਰਭਰ ਕਰਦੀ ਹੈ। ਵੀ-ਬੈਲਟ ਉਦਯੋਗ ਦਾ ਵਰਕ ਹਾਰਸ ਹੈ ਅਤੇ ਲਗਭਗ ਕਿਸੇ ਵੀ ਲੋਡ ਪਾਵਰ ਦੇ ਪ੍ਰਸਾਰਣ ਲਈ ਕਈ ਤਰ੍ਹਾਂ ਦੇ ਮਿਆਰੀ ਆਕਾਰਾਂ ਅਤੇ ਕਿਸਮਾਂ ਵਿੱਚ ਉਪਲਬਧ ਹਨ। V-ਬੈਲਟ ਡਰਾਈਵਾਂ 1500 ਤੋਂ 6000 ਫੁੱਟ/ਮਿੰਟ ਦੇ ਵਿਚਕਾਰ ਚੰਗੀ ਤਰ੍ਹਾਂ ਕੰਮ ਕਰਦੀਆਂ ਹਨ, ਹਾਲਾਂਕਿ ਤੰਗ V-ਬੈਲਟ 10,000 ਫੁੱਟ/ਮਿੰਟ ਤੱਕ ਕੰਮ ਕਰਨਗੀਆਂ। ਵੀ-ਬੈਲਟ ਡਰਾਈਵਾਂ 3 ਤੋਂ 5 ਸਾਲ ਦੀ ਲੰਮੀ ਉਮਰ ਦੀ ਪੇਸ਼ਕਸ਼ ਕਰਦੀਆਂ ਹਨ ਅਤੇ ਵੱਡੇ ਸਪੀਡ ਅਨੁਪਾਤ ਦੀ ਆਗਿਆ ਦਿੰਦੀਆਂ ਹਨ, ਉਹ ਸਥਾਪਤ ਕਰਨ ਅਤੇ ਹਟਾਉਣ ਲਈ ਆਸਾਨ ਹੁੰਦੀਆਂ ਹਨ, ਬੈਲਟ ਡਰਾਈਵਰ ਅਤੇ ਸੰਚਾਲਿਤ ਸ਼ਾਫਟਾਂ ਵਿਚਕਾਰ ਸ਼ਾਂਤ ਸੰਚਾਲਨ, ਘੱਟ ਰੱਖ-ਰਖਾਅ, ਚੰਗੀ ਸਦਮਾ ਸਮਾਈ ਦੀ ਪੇਸ਼ਕਸ਼ ਕਰਦੀਆਂ ਹਨ। V-ਬੈਲਟਾਂ ਦਾ ਨੁਕਸਾਨ ਉਹਨਾਂ ਦੀ ਕੁਝ ਸਲਿੱਪ ਅਤੇ ਕ੍ਰੀਪ ਹੈ ਅਤੇ ਇਸਲਈ ਉਹ ਸਭ ਤੋਂ ਵਧੀਆ ਹੱਲ ਨਹੀਂ ਹੋ ਸਕਦੇ ਜਿੱਥੇ ਸਮਕਾਲੀ ਗਤੀ ਦੀ ਲੋੜ ਹੁੰਦੀ ਹੈ। ਸਾਡੇ ਕੋਲ ਉਦਯੋਗਿਕ, ਆਟੋਮੋਟਿਵ ਅਤੇ ਖੇਤੀਬਾੜੀ ਪੱਟੀਆਂ ਹਨ। ਸਟਾਕਡ ਸਟੈਂਡਰਡ ਲੰਬਾਈ ਦੇ ਨਾਲ-ਨਾਲ ਕਸਟਮ ਲੰਬਾਈ ਦੀਆਂ ਬੈਲਟਾਂ ਉਪਲਬਧ ਹਨ। ਸਾਰੇ ਸਟੈਂਡਰਡ V-ਬੈਲਟ ਕਰਾਸ ਸੈਕਸ਼ਨ ਸਟਾਕ ਤੋਂ ਉਪਲਬਧ ਹਨ। ਇੱਥੇ ਟੇਬਲ ਹਨ ਜਿੱਥੇ ਤੁਸੀਂ ਅਣਜਾਣ ਮਾਪਦੰਡਾਂ ਦੀ ਗਣਨਾ ਕਰ ਸਕਦੇ ਹੋ ਜਿਵੇਂ ਕਿ ਬੈਲਟ ਦੀ ਲੰਬਾਈ, ਬੈਲਟ ਸੈਕਸ਼ਨ (ਚੌੜਾਈ ਅਤੇ ਮੋਟਾਈ) ਬਸ਼ਰਤੇ ਤੁਸੀਂ ਆਪਣੇ ਸਿਸਟਮ ਦੇ ਕੁਝ ਮਾਪਦੰਡਾਂ ਨੂੰ ਜਾਣਦੇ ਹੋ ਜਿਵੇਂ ਕਿ ਡਰਾਈਵਿੰਗ ਅਤੇ ਸੰਚਾਲਿਤ ਪੁਲੀ ਵਿਆਸ, ਪੁਲੀ ਦੇ ਵਿਚਕਾਰ ਕੇਂਦਰ ਦੀ ਦੂਰੀ ਅਤੇ ਪੁਲੀ ਦੀ ਰੋਟੇਸ਼ਨਲ ਸਪੀਡ। ਤੁਸੀਂ ਅਜਿਹੀਆਂ ਟੇਬਲਾਂ ਦੀ ਵਰਤੋਂ ਕਰ ਸਕਦੇ ਹੋ ਜਾਂ ਸਾਨੂੰ ਤੁਹਾਡੇ ਲਈ ਸਹੀ V-ਬੈਲਟ ਚੁਣਨ ਲਈ ਕਹਿ ਸਕਦੇ ਹੋ। - ਸਕਾਰਾਤਮਕ ਡਰਾਈਵ ਬੈਲਟ (ਟਾਈਮਿੰਗ ਬੈਲਟ): ਇਹ ਬੈਲਟ ਵੀ ਫਲੈਟ ਕਿਸਮ ਦੇ ਹੁੰਦੇ ਹਨ ਜਿਨ੍ਹਾਂ ਦੇ ਅੰਦਰਲੇ ਘੇਰੇ 'ਤੇ ਬਰਾਬਰ ਦੂਰੀ ਵਾਲੇ ਦੰਦਾਂ ਦੀ ਲੜੀ ਹੁੰਦੀ ਹੈ। ਸਕਾਰਾਤਮਕ ਡਰਾਈਵ ਜਾਂ ਟਾਈਮਿੰਗ ਬੈਲਟਾਂ ਫਲੈਟ ਬੈਲਟਾਂ ਦੇ ਫਾਇਦਿਆਂ ਨੂੰ ਚੇਨਾਂ ਅਤੇ ਗੀਅਰਾਂ ਦੀਆਂ ਸਕਾਰਾਤਮਕ-ਪਕੜ ਵਿਸ਼ੇਸ਼ਤਾਵਾਂ ਨਾਲ ਜੋੜਦੀਆਂ ਹਨ। ਸਕਾਰਾਤਮਕ ਡਰਾਈਵ ਬੈਲਟ ਕੋਈ ਫਿਸਲਣ ਜਾਂ ਸਪੀਡ ਭਿੰਨਤਾਵਾਂ ਨੂੰ ਪ੍ਰਗਟ ਨਹੀਂ ਕਰਦੇ ਹਨ। ਗਤੀ ਅਨੁਪਾਤ ਦੀ ਇੱਕ ਵਿਆਪਕ ਲੜੀ ਸੰਭਵ ਹੈ. ਬੇਅਰਿੰਗ ਲੋਡ ਘੱਟ ਹਨ ਕਿਉਂਕਿ ਉਹ ਘੱਟ ਤਣਾਅ 'ਤੇ ਕੰਮ ਕਰ ਸਕਦੇ ਹਨ। ਹਾਲਾਂਕਿ ਉਹ ਪੁਲੀਜ਼ ਵਿੱਚ ਗਲਤ ਅਲਾਈਨਮੈਂਟ ਲਈ ਵਧੇਰੇ ਸੰਵੇਦਨਸ਼ੀਲ ਹੁੰਦੇ ਹਨ। - ਪੁਲੀਜ਼, ਸ਼ੀਵਜ਼, ਬੈਲਟਾਂ ਲਈ ਹੱਬ: ਫਲੈਟ, ਰਿਬਡ (ਸੈਰੇਟਿਡ) ਅਤੇ ਸਕਾਰਾਤਮਕ ਡਰਾਈਵ ਬੈਲਟਾਂ ਦੇ ਨਾਲ ਵੱਖ-ਵੱਖ ਕਿਸਮਾਂ ਦੀਆਂ ਪਲਲੀਆਂ ਦੀ ਵਰਤੋਂ ਕੀਤੀ ਜਾਂਦੀ ਹੈ। ਅਸੀਂ ਉਨ੍ਹਾਂ ਸਾਰਿਆਂ ਦਾ ਨਿਰਮਾਣ ਕਰਦੇ ਹਾਂ। ਸਾਡੀਆਂ ਜ਼ਿਆਦਾਤਰ ਫਲੈਟ ਬੈਲਟ ਪੁਲੀਜ਼ ਲੋਹੇ ਦੀ ਕਾਸਟਿੰਗ ਦੁਆਰਾ ਬਣਾਈਆਂ ਜਾਂਦੀਆਂ ਹਨ, ਪਰ ਸਟੀਲ ਦੇ ਸੰਸਕਰਣ ਵੱਖ-ਵੱਖ ਰਿਮ ਅਤੇ ਹੱਬ ਸੰਜੋਗਾਂ ਵਿੱਚ ਵੀ ਉਪਲਬਧ ਹਨ। ਸਾਡੀਆਂ ਫਲੈਟ-ਬੈਲਟ ਪਲਲੀਆਂ ਵਿੱਚ ਠੋਸ, ਸਪੋਕਡ ਜਾਂ ਸਪਲਿਟ ਹੱਬ ਹੋ ਸਕਦੇ ਹਨ ਜਾਂ ਅਸੀਂ ਤੁਹਾਡੀ ਇੱਛਾ ਅਨੁਸਾਰ ਨਿਰਮਾਣ ਕਰ ਸਕਦੇ ਹਾਂ। Ribbed ਅਤੇ ਸਕਾਰਾਤਮਕ-ਡਰਾਈਵ ਬੈਲਟ ਵੱਖ-ਵੱਖ ਸਟਾਕ ਆਕਾਰਾਂ ਅਤੇ ਚੌੜਾਈ ਵਿੱਚ ਉਪਲਬਧ ਹਨ। ਬੈਲਟ ਨੂੰ ਡਰਾਈਵ 'ਤੇ ਰੱਖਣ ਲਈ ਟਾਈਮਿੰਗ-ਬੈਲਟ ਡਰਾਈਵ ਵਿੱਚ ਘੱਟੋ-ਘੱਟ ਇੱਕ ਪੁਲੀ ਨੂੰ ਫਲੈਂਜ ਕੀਤਾ ਜਾਣਾ ਚਾਹੀਦਾ ਹੈ। ਲੰਬੇ ਸੈਂਟਰ ਡਰਾਈਵ ਪ੍ਰਣਾਲੀਆਂ ਲਈ, ਇਹ ਸਿਫਾਰਸ਼ ਕੀਤੀ ਜਾਂਦੀ ਹੈ ਕਿ ਦੋਵੇਂ ਪਲੀਆਂ ਨੂੰ ਫਲੈਂਜ ਕੀਤਾ ਜਾਵੇ। ਸ਼ੀਵ ਪੁਲੀਜ਼ ਦੇ ਗਰੋਵਡ ਪਹੀਏ ਹੁੰਦੇ ਹਨ ਅਤੇ ਆਮ ਤੌਰ 'ਤੇ ਲੋਹੇ ਦੀ ਕਾਸਟਿੰਗ, ਸਟੀਲ ਬਣਾਉਣ ਜਾਂ ਪਲਾਸਟਿਕ ਮੋਲਡਿੰਗ ਦੁਆਰਾ ਨਿਰਮਿਤ ਹੁੰਦੇ ਹਨ। ਆਟੋਮੋਟਿਵ ਅਤੇ ਖੇਤੀਬਾੜੀ ਸ਼ੀਵ ਬਣਾਉਣ ਲਈ ਸਟੀਲ ਬਣਾਉਣਾ ਢੁਕਵੀਂ ਪ੍ਰਕਿਰਿਆ ਹੈ। ਅਸੀਂ ਨਿਯਮਤ ਅਤੇ ਡੂੰਘੇ ਖੰਭਿਆਂ ਨਾਲ ਸ਼ੀਵ ਪੈਦਾ ਕਰਦੇ ਹਾਂ। ਜਦੋਂ ਵੀ-ਬੈਲਟ ਇੱਕ ਕੋਣ 'ਤੇ ਸ਼ੀਵ ਵਿੱਚ ਦਾਖਲ ਹੁੰਦੀ ਹੈ, ਤਾਂ ਡੂੰਘੀਆਂ ਸ਼ੀਵੀਆਂ ਚੰਗੀ ਤਰ੍ਹਾਂ ਢੁਕਵੀਆਂ ਹੁੰਦੀਆਂ ਹਨ, ਜਿਵੇਂ ਕਿ ਕੁਆਰਟਰ-ਟਰਨ ਡਰਾਈਵਾਂ ਵਿੱਚ ਹੁੰਦਾ ਹੈ। ਡੂੰਘੇ ਗਰੂਵ ਲੰਬਕਾਰੀ-ਸ਼ਾਫਟ ਡਰਾਈਵਾਂ ਅਤੇ ਐਪਲੀਕੇਸ਼ਨਾਂ ਲਈ ਵੀ ਢੁਕਵੇਂ ਹਨ ਜਿੱਥੇ ਬੈਲਟਾਂ ਦੀ ਵਾਈਬ੍ਰੇਸ਼ਨ ਸਮੱਸਿਆ ਹੋ ਸਕਦੀ ਹੈ। ਸਾਡੀਆਂ ਆਈਡਲਰ ਪਲਲੀਆਂ ਗਰੂਵਡ ਸ਼ੀਵਜ਼ ਜਾਂ ਫਲੈਟ ਪਲਲੀਜ਼ ਹੁੰਦੀਆਂ ਹਨ ਜੋ ਮਕੈਨੀਕਲ ਪਾਵਰ ਸੰਚਾਰਿਤ ਨਹੀਂ ਕਰਦੀਆਂ ਹਨ। ਆਈਡਲਰ ਪੁਲੀਜ਼ ਜ਼ਿਆਦਾਤਰ ਬੈਲਟਾਂ ਨੂੰ ਕੱਸਣ ਲਈ ਵਰਤੀਆਂ ਜਾਂਦੀਆਂ ਹਨ। - ਸਿੰਗਲ ਅਤੇ ਮਲਟੀਪਲ ਬੈਲਟ ਡਰਾਈਵ: ਸਿੰਗਲ ਬੈਲਟ ਡਰਾਈਵ ਵਿੱਚ ਇੱਕ ਸਿੰਗਲ ਗਰੂਵ ਹੁੰਦਾ ਹੈ ਜਦੋਂ ਕਿ ਮਲਟੀਪਲ ਬੈਲਟ ਡਰਾਈਵਾਂ ਵਿੱਚ ਮਲਟੀਪਲ ਗਰੂਵ ਹੁੰਦੇ ਹਨ। ਹੇਠਾਂ ਸੰਬੰਧਿਤ ਰੰਗਦਾਰ ਟੈਕਸਟ 'ਤੇ ਕਲਿੱਕ ਕਰਕੇ ਤੁਸੀਂ ਸਾਡੇ ਕੈਟਾਲਾਗ ਡਾਊਨਲੋਡ ਕਰ ਸਕਦੇ ਹੋ: - ਪਾਵਰ ਟ੍ਰਾਂਸਮਿਸ਼ਨ ਬੈਲਟਸ (ਵੀ-ਬੈਲਟਸ, ਟਾਈਮਿੰਗ ਬੈਲਟਸ, ਰਾਅ ਐਜ ਬੈਲਟਸ, ਲਪੇਟੀਆਂ ਬੈਲਟਾਂ ਅਤੇ ਸਪੈਸ਼ਲਿਟੀ ਬੈਲਟਸ ਸ਼ਾਮਲ ਹਨ) - ਕਨਵੇਅਰ ਬੈਲਟਸ - ਵਿ- ਪੁਲੀਜ਼ - ਟਾਈਮਿੰਗ ਪੁਲੀਜ਼ ਚੇਨ ਅਤੇ ਚੇਨ ਡਰਾਈਵਜ਼: ਸਾਡੀ ਪਾਵਰ ਟਰਾਂਸਮਿਸ਼ਨ ਚੇਨਾਂ ਦੇ ਕੁਝ ਫਾਇਦੇ ਹਨ ਜਿਵੇਂ ਕਿ ਮੁਕਾਬਲਤਨ ਅਪ੍ਰਬੰਧਿਤ ਸ਼ਾਫਟ ਸੈਂਟਰ ਦੂਰੀ, ਆਸਾਨ ਅਸੈਂਬਲੀ, ਕੰਪੈਕਟਨੈੱਸ, ਬਿਨਾਂ ਤਿਲਕਣ ਜਾਂ ਕ੍ਰੀਪ ਦੇ ਤਣਾਅ ਦੇ ਅਧੀਨ ਲਚਕੀਲੇਪਨ, ਉੱਚ ਤਾਪਮਾਨਾਂ ਵਿੱਚ ਕੰਮ ਕਰਨ ਦੀ ਸਮਰੱਥਾ। ਇੱਥੇ ਸਾਡੀਆਂ ਚੇਨਾਂ ਦੀਆਂ ਪ੍ਰਮੁੱਖ ਕਿਸਮਾਂ ਹਨ: - ਡੀਟੈਚ ਕਰਨ ਯੋਗ ਚੇਨ: ਸਾਡੀਆਂ ਵੱਖ ਕਰਨ ਯੋਗ ਚੇਨਾਂ ਅਕਾਰ, ਪਿੱਚ ਅਤੇ ਅੰਤਮ ਤਾਕਤ ਅਤੇ ਆਮ ਤੌਰ 'ਤੇ ਕਮਜ਼ੋਰ ਲੋਹੇ ਜਾਂ ਸਟੀਲ ਤੋਂ ਬਣਾਈਆਂ ਜਾਂਦੀਆਂ ਹਨ। 0.902 (23 ਮਿਲੀਮੀਟਰ) ਤੋਂ 4.063 ਇੰਚ (103 ਮਿਲੀਮੀਟਰ) ਪਿੱਚ ਅਤੇ ਅੰਤਮ ਤਾਕਤ 700 ਤੋਂ 17,000 lb/ਵਰਗ ਇੰਚ ਤੱਕ ਅਕਾਰ ਦੀ ਇੱਕ ਰੇਂਜ ਵਿੱਚ ਬਣਾਈਆਂ ਜਾਂਦੀਆਂ ਹਨ। ਦੂਜੇ ਪਾਸੇ ਸਾਡੀਆਂ ਵੱਖ ਕਰਨ ਯੋਗ ਸਟੀਲ ਦੀਆਂ ਚੇਨਾਂ 0.904 ਇੰਚ (23 ਮਿ.ਮੀ.) ਤੋਂ ਲੈ ਕੇ ਲਗਭਗ 3.00 ਇੰਚ (76 ਮਿ.ਮੀ.) ਪਿੱਚ ਦੇ ਆਕਾਰਾਂ ਵਿੱਚ ਬਣੀਆਂ ਹਨ, 760 ਤੋਂ 5000 lb/ਵਰਗ ਇੰਚ ਤੱਕ ਅੰਤਮ ਤਾਕਤ ਦੇ ਨਾਲ।_cc781905-5cde-3194-3194-3. 136bad5cf58d_ - ਪਿੰਟਲ ਚੇਨ: ਇਹ ਚੇਨਾਂ ਭਾਰੀ ਲੋਡ ਅਤੇ ਥੋੜੀ ਉੱਚੀ ਗਤੀ ਲਈ ਲਗਭਗ 450 ਫੁੱਟ/ਮਿੰਟ (2.2 ਮੀਟਰ/ਸੈਕੰਡ) ਲਈ ਵਰਤੀਆਂ ਜਾਂਦੀਆਂ ਹਨ। ਪਿੰਟਲ ਚੇਨਜ਼ ਵਿਅਕਤੀਗਤ ਕਾਸਟ ਲਿੰਕਾਂ ਨਾਲ ਬਣੀਆਂ ਹੁੰਦੀਆਂ ਹਨ, ਜਿਸ ਵਿੱਚ ਔਫਸੈੱਟ ਸਾਈਡਬਾਰਾਂ ਦੇ ਨਾਲ ਪੂਰੇ, ਗੋਲ ਬੈਰਲ ਸਿਰੇ ਹੁੰਦੇ ਹਨ। ਇਹ ਚੇਨ ਲਿੰਕ ਸਟੀਲ ਦੀਆਂ ਪਿੰਨਾਂ ਨਾਲ ਆਪਸ ਵਿੱਚ ਜੁੜੇ ਹੋਏ ਹਨ। ਇਹ ਚੇਨ ਪਿਚ ਵਿੱਚ ਲਗਭਗ 1.00 ਇੰਚ (25 ਮਿਲੀਮੀਟਰ) ਤੋਂ 6.00 ਇੰਚ (150 ਮਿਲੀਮੀਟਰ) ਤੱਕ ਅਤੇ ਅੰਤਮ ਸ਼ਕਤੀਆਂ 3600 ਤੋਂ 30,000 lb/ਵਰਗ ਇੰਚ ਦੇ ਵਿਚਕਾਰ ਹੁੰਦੀਆਂ ਹਨ। - ਆਫਸੈੱਟ-ਸਾਈਡਬਾਰ ਚੇਨਜ਼: ਇਹ ਨਿਰਮਾਣ ਮਸ਼ੀਨਰੀ ਦੀਆਂ ਡਰਾਈਵ ਚੇਨਾਂ ਵਿੱਚ ਪ੍ਰਸਿੱਧ ਹਨ। ਇਹ ਚੇਨਾਂ 1000 ਫੁੱਟ/ਮਿੰਟ ਦੀ ਸਪੀਡ 'ਤੇ ਕੰਮ ਕਰਦੀਆਂ ਹਨ ਅਤੇ ਲਗਭਗ 250 ਐਚਪੀ ਤੱਕ ਲੋਡ ਸੰਚਾਰਿਤ ਕਰਦੀਆਂ ਹਨ। ਆਮ ਤੌਰ 'ਤੇ ਹਰੇਕ ਲਿੰਕ ਵਿੱਚ ਦੋ ਆਫਸੈੱਟ ਸਾਈਡਬਾਰ, ਇੱਕ ਬੁਸ਼ਿੰਗ, ਇੱਕ ਰੋਲਰ, ਇੱਕ ਪਿੰਨ, ਇੱਕ ਕੋਟਰ ਪਿੰਨ ਹੁੰਦਾ ਹੈ। - ਰੋਲਰ ਚੇਨਜ਼: ਇਹ 0.25 (6 ਮਿਲੀਮੀਟਰ) ਤੋਂ 3.00 (75 ਮਿਲੀਮੀਟਰ) ਇੰਚ ਦੀਆਂ ਪਿੱਚਾਂ ਵਿੱਚ ਉਪਲਬਧ ਹਨ। ਸਿੰਗਲ-ਚੌੜਾਈ ਵਾਲੇ ਰੋਲਰ ਚੇਨਾਂ ਦੀ ਅੰਤਮ ਤਾਕਤ 925 ਤੋਂ 130,000 lb/ਵਰਗ ਇੰਚ ਦੇ ਵਿਚਕਾਰ ਹੁੰਦੀ ਹੈ। ਰੋਲਰ ਚੇਨਾਂ ਦੇ ਮਲਟੀਪਲ-ਚੌੜਾਈ ਵਾਲੇ ਸੰਸਕਰਣ ਉਪਲਬਧ ਹਨ ਅਤੇ ਉੱਚ ਸਪੀਡ 'ਤੇ ਵਧੇਰੇ ਸ਼ਕਤੀ ਸੰਚਾਰਿਤ ਕਰਦੇ ਹਨ। ਮਲਟੀਪਲ-ਚੌੜਾਈ ਵਾਲੇ ਰੋਲਰ ਚੇਨ ਵੀ ਘੱਟ ਸ਼ੋਰ ਨਾਲ ਨਿਰਵਿਘਨ ਕਾਰਵਾਈ ਦੀ ਪੇਸ਼ਕਸ਼ ਕਰਦੀਆਂ ਹਨ। ਰੋਲਰ ਚੇਨਾਂ ਨੂੰ ਰੋਲਰ ਲਿੰਕਾਂ ਅਤੇ ਪਿੰਨ ਲਿੰਕਾਂ ਤੋਂ ਇਕੱਠਾ ਕੀਤਾ ਜਾਂਦਾ ਹੈ। ਕੋਟਰ ਪਿੰਨ ਨੂੰ ਵੱਖ ਕਰਨ ਯੋਗ ਸੰਸਕਰਣ ਰੋਲਰ ਚੇਨਾਂ ਵਿੱਚ ਵਰਤਿਆ ਜਾਂਦਾ ਹੈ। ਰੋਲਰ ਚੇਨ ਡਰਾਈਵਾਂ ਦੇ ਡਿਜ਼ਾਈਨ ਲਈ ਵਿਸ਼ੇ ਦੀ ਮੁਹਾਰਤ ਦੀ ਲੋੜ ਹੁੰਦੀ ਹੈ। ਜਦੋਂ ਕਿ ਬੈਲਟ ਡਰਾਈਵਾਂ ਲੀਨੀਅਰ ਸਪੀਡ 'ਤੇ ਅਧਾਰਤ ਹੁੰਦੀਆਂ ਹਨ, ਚੇਨ ਡਰਾਈਵਾਂ ਛੋਟੇ ਸਪਰੋਕੇਟ ਦੀ ਰੋਟੇਸ਼ਨਲ ਸਪੀਡ 'ਤੇ ਅਧਾਰਤ ਹੁੰਦੀਆਂ ਹਨ, ਜੋ ਕਿ ਜ਼ਿਆਦਾਤਰ ਸਥਾਪਨਾਵਾਂ ਵਿੱਚ ਸੰਚਾਲਿਤ ਮੈਂਬਰ ਹੁੰਦੀ ਹੈ। ਹਾਰਸ ਪਾਵਰ ਰੇਟਿੰਗਾਂ ਅਤੇ ਰੋਟੇਸ਼ਨਲ ਸਪੀਡ ਤੋਂ ਇਲਾਵਾ, ਚੇਨ ਡਰਾਈਵਾਂ ਦਾ ਡਿਜ਼ਾਈਨ ਕਈ ਹੋਰ ਕਾਰਕਾਂ 'ਤੇ ਅਧਾਰਤ ਹੈ। - ਡਬਲ-ਪਿਚ ਚੇਨਜ਼: ਅਸਲ ਵਿੱਚ ਰੋਲਰ ਚੇਨਾਂ ਦੇ ਸਮਾਨ ਹੈ ਸਿਵਾਏ ਇਸ ਤੋਂ ਇਲਾਵਾ ਕਿ ਪਿੱਚ ਦੁੱਗਣੀ ਲੰਬੀ ਹੈ। - ਇਨਵਰਟਡ ਟੂਥ (ਸਾਈਲੈਂਟ) ਚੇਨਜ਼: ਹਾਈ ਸਪੀਡ ਚੇਨ ਜ਼ਿਆਦਾਤਰ ਪ੍ਰਾਈਮ ਮੂਵਰ, ਪਾਵਰ-ਟੇਕਆਫ ਡਰਾਈਵ ਲਈ ਵਰਤੀਆਂ ਜਾਂਦੀਆਂ ਹਨ। ਇਨਵਰਟਡ ਟੂਥ ਚੇਨ ਡਰਾਈਵ 1200 ਐਚਪੀ ਤੱਕ ਸ਼ਕਤੀਆਂ ਨੂੰ ਸੰਚਾਰਿਤ ਕਰ ਸਕਦੀਆਂ ਹਨ ਅਤੇ ਦੰਦਾਂ ਦੇ ਲਿੰਕਾਂ ਦੀ ਇੱਕ ਲੜੀ ਨਾਲ ਬਣੀਆਂ ਹੁੰਦੀਆਂ ਹਨ, ਵਿਕਲਪਿਕ ਤੌਰ 'ਤੇ ਪਿੰਨ ਜਾਂ ਸੰਯੁਕਤ ਹਿੱਸਿਆਂ ਦੇ ਸੁਮੇਲ ਨਾਲ ਇਕੱਠੀਆਂ ਹੁੰਦੀਆਂ ਹਨ। ਸੈਂਟਰ-ਗਾਈਡ ਚੇਨ ਵਿੱਚ ਸਪ੍ਰੋਕੇਟ ਵਿੱਚ ਗਰੂਵਜ਼ ਨੂੰ ਸ਼ਾਮਲ ਕਰਨ ਲਈ ਗਾਈਡ ਲਿੰਕ ਹੁੰਦੇ ਹਨ, ਅਤੇ ਸਾਈਡ-ਗਾਈਡ ਚੇਨ ਵਿੱਚ ਸਪ੍ਰੋਕੇਟ ਦੇ ਪਾਸਿਆਂ ਨੂੰ ਸ਼ਾਮਲ ਕਰਨ ਲਈ ਗਾਈਡ ਹੁੰਦੇ ਹਨ। - ਬੀਡ ਜਾਂ ਸਲਾਈਡਰ ਚੇਨ: ਇਹਨਾਂ ਚੇਨਾਂ ਦੀ ਵਰਤੋਂ ਹੌਲੀ ਸਪੀਡ ਡਰਾਈਵਾਂ ਲਈ ਅਤੇ ਮੈਨੂਅਲ ਓਪਰੇਸ਼ਨਾਂ ਵਿੱਚ ਵੀ ਕੀਤੀ ਜਾਂਦੀ ਹੈ। ਹੇਠਾਂ ਸੰਬੰਧਿਤ ਰੰਗਦਾਰ ਟੈਕਸਟ 'ਤੇ ਕਲਿੱਕ ਕਰਕੇ ਤੁਸੀਂ ਸਾਡੇ ਕੈਟਾਲਾਗ ਡਾਊਨਲੋਡ ਕਰ ਸਕਦੇ ਹੋ: - ਡਰਾਈਵਿੰਗ ਚੇਨ - ਕਨਵੇਅਰ ਚੇਨਜ਼ - ਵੱਡੀ ਪਿੱਚ ਕਨਵੇਅਰ ਚੇਨਜ਼ - ਸਟੀਲ ਰੋਲਰ ਚੇਨਜ਼ - ਲਹਿਰਾਉਣ ਵਾਲੀਆਂ ਚੇਨਾਂ - ਮੋਟਰਸਾਈਕਲ ਚੇਨ - ਖੇਤੀਬਾੜੀ ਮਸ਼ੀਨ ਚੇਨ - Sprockets: ਸਾਡੇ ਮਿਆਰੀ sprockets ANSI ਮਿਆਰਾਂ ਦੇ ਅਨੁਕੂਲ ਹਨ। ਪਲੇਟ ਸਪ੍ਰੋਕੇਟ ਫਲੈਟ, ਹਬਲ ਰਹਿਤ ਸਪ੍ਰੋਕੇਟ ਹੁੰਦੇ ਹਨ। ਸਾਡੇ ਛੋਟੇ ਅਤੇ ਦਰਮਿਆਨੇ ਆਕਾਰ ਦੇ ਹੱਬ ਸਪਰੋਕੇਟਸ ਨੂੰ ਬਾਰ ਸਟਾਕ ਜਾਂ ਫੋਰਜਿੰਗ ਤੋਂ ਬਦਲਿਆ ਜਾਂਦਾ ਹੈ ਜਾਂ ਬਾਰ-ਸਟਾਕ ਹੱਬ ਨੂੰ ਇੱਕ ਗਰਮ-ਰੋਲਡ ਪਲੇਟ ਵਿੱਚ ਵੈਲਡਿੰਗ ਕਰਕੇ ਬਣਾਇਆ ਜਾਂਦਾ ਹੈ। AGS-TECH Inc. ਸਲੇਟੀ-ਲੋਹੇ ਦੀਆਂ ਕਾਸਟਿੰਗਾਂ, ਕਾਸਟ ਸਟੀਲ ਅਤੇ ਵੇਲਡ ਹੱਬ ਕੰਸਟ੍ਰਕਸ਼ਨ, ਸਿੰਟਰਡ ਪਾਊਡਰ ਮੈਟਲ, ਮੋਲਡ ਜਾਂ ਮਸ਼ੀਨਡ ਪਲਾਸਟਿਕ ਤੋਂ ਤਿਆਰ ਕੀਤੇ ਸਪਰੋਕੇਟਸ ਦੀ ਸਪਲਾਈ ਕਰ ਸਕਦਾ ਹੈ। ਉੱਚ ਰਫਤਾਰ 'ਤੇ ਸੁਚਾਰੂ ਸੰਚਾਲਨ ਲਈ, ਸਪਰੋਕੇਟਸ ਦੇ ਆਕਾਰ ਦੀ ਸਹੀ ਚੋਣ ਜ਼ਰੂਰੀ ਹੈ। ਸਪੇਸ ਸੀਮਾਵਾਂ ਬੇਸ਼ੱਕ ਇੱਕ ਅਜਿਹਾ ਕਾਰਕ ਹੈ ਜਿਸਨੂੰ ਅਸੀਂ ਇੱਕ ਸਪਰੋਕੇਟ ਦੀ ਚੋਣ ਕਰਦੇ ਸਮੇਂ ਅਣਡਿੱਠ ਨਹੀਂ ਕਰ ਸਕਦੇ। ਇਹ ਸਿਫ਼ਾਰਸ਼ ਕੀਤੀ ਜਾਂਦੀ ਹੈ ਕਿ ਡਰਾਈਵਡ ਸਪ੍ਰੋਕੇਟ ਅਤੇ ਡਰਾਈਵਰ ਦਾ ਅਨੁਪਾਤ 6:1 ਤੋਂ ਵੱਧ ਨਹੀਂ ਹੋਣਾ ਚਾਹੀਦਾ ਹੈ, ਅਤੇ ਡਰਾਈਵਰ 'ਤੇ ਚੇਨ ਰੈਪ 120 ਡਿਗਰੀ ਹੈ। ਛੋਟੇ ਅਤੇ ਵੱਡੇ ਸਪਰੋਕੇਟਸ, ਚੇਨ ਦੀ ਲੰਬਾਈ ਅਤੇ ਚੇਨ ਟੈਂਸ਼ਨ ਵਿਚਕਾਰ ਕੇਂਦਰ ਦੀ ਦੂਰੀ ਨੂੰ ਵੀ ਕੁਝ ਸਿਫ਼ਾਰਸ਼ ਕੀਤੇ ਇੰਜੀਨੀਅਰਿੰਗ ਗਣਨਾਵਾਂ ਅਤੇ ਦਿਸ਼ਾ-ਨਿਰਦੇਸ਼ਾਂ ਅਨੁਸਾਰ ਚੁਣਿਆ ਜਾਣਾ ਚਾਹੀਦਾ ਹੈ ਨਾ ਕਿ ਬੇਤਰਤੀਬੇ ਤੌਰ 'ਤੇ। ਹੇਠਾਂ ਰੰਗੀਨ ਟੈਕਸਟ 'ਤੇ ਕਲਿੱਕ ਕਰਕੇ ਸਾਡੇ ਕੈਟਾਲਾਗ ਡਾਊਨਲੋਡ ਕਰੋ: - ਸਪਰੋਕੇਟਸ ਅਤੇ ਪਲੇਟ ਵ੍ਹੀਲਜ਼ - ਟ੍ਰਾਂਸਮਿਸ਼ਨ ਬੁਸ਼ਿੰਗਜ਼ - ਚੇਨ ਕਪਲਿੰਗ - ਚੇਨ ਲਾਕ ਕੇਬਲ ਡ੍ਰਾਈਵਜ਼: ਇਹਨਾਂ ਦੇ ਕੁਝ ਮਾਮਲਿਆਂ ਵਿੱਚ ਬੈਲਟਾਂ ਅਤੇ ਚੇਨ ਡ੍ਰਾਈਵਾਂ ਨਾਲੋਂ ਆਪਣੇ ਫਾਇਦੇ ਹਨ। ਕੇਬਲ ਡਰਾਈਵਾਂ ਬੈਲਟਾਂ ਦੇ ਸਮਾਨ ਕਾਰਜ ਨੂੰ ਪੂਰਾ ਕਰ ਸਕਦੀਆਂ ਹਨ ਅਤੇ ਕੁਝ ਐਪਲੀਕੇਸ਼ਨਾਂ ਵਿੱਚ ਲਾਗੂ ਕਰਨ ਲਈ ਸਰਲ ਅਤੇ ਵਧੇਰੇ ਆਰਥਿਕ ਵੀ ਹੋ ਸਕਦੀਆਂ ਹਨ। ਉਦਾਹਰਨ ਲਈ, ਸਿੰਕ੍ਰੋਮੇਸ਼ ਕੇਬਲ ਡਰਾਈਵਾਂ ਦੀ ਇੱਕ ਨਵੀਂ ਲੜੀ ਰਵਾਇਤੀ ਰੱਸੀਆਂ, ਸਧਾਰਨ ਕੇਬਲਾਂ ਅਤੇ ਕੋਗ ਡਰਾਈਵਾਂ ਨੂੰ ਬਦਲਣ ਲਈ ਸਕਾਰਾਤਮਕ ਟ੍ਰੈਕਸ਼ਨ ਲਈ ਤਿਆਰ ਕੀਤੀ ਗਈ ਹੈ, ਖਾਸ ਕਰਕੇ ਤੰਗ ਥਾਂਵਾਂ ਵਿੱਚ। ਨਵੀਂ ਕੇਬਲ ਡਰਾਈਵ ਨੂੰ ਇਲੈਕਟ੍ਰਾਨਿਕ ਸਾਜ਼ੋ-ਸਾਮਾਨ ਜਿਵੇਂ ਕਿ ਕਾਪੀ ਕਰਨ ਵਾਲੀਆਂ ਮਸ਼ੀਨਾਂ, ਪਲਾਟਰਾਂ, ਟਾਈਪਰਾਈਟਰਾਂ, ਪ੍ਰਿੰਟਰਾਂ, ਆਦਿ ਵਿੱਚ ਉੱਚ ਸਟੀਕ ਸਥਿਤੀ ਪ੍ਰਦਾਨ ਕਰਨ ਲਈ ਡਿਜ਼ਾਇਨ ਕੀਤਾ ਗਿਆ ਹੈ। ਨਵੀਂ ਕੇਬਲ ਡਰਾਈਵ ਦੀ ਇੱਕ ਮੁੱਖ ਵਿਸ਼ੇਸ਼ਤਾ ਇਸਦੀ 3D ਸਰਪੈਂਟੀਨ ਸੰਰਚਨਾਵਾਂ ਵਿੱਚ ਵਰਤਣ ਦੀ ਸਮਰੱਥਾ ਹੈ ਜੋ ਇਸਨੂੰ ਸਮਰੱਥ ਬਣਾਉਂਦੀ ਹੈ। ਬਹੁਤ ਛੋਟੇ ਡਿਜ਼ਾਈਨ. ਸਿੰਕ੍ਰੋਮੇਸ਼ ਕੇਬਲਾਂ ਨੂੰ ਰੱਸਿਆਂ ਨਾਲ ਤੁਲਨਾ ਕਰਨ 'ਤੇ ਘੱਟ ਤਣਾਅ ਨਾਲ ਵਰਤਿਆ ਜਾ ਸਕਦਾ ਹੈ ਇਸ ਤਰ੍ਹਾਂ ਬਿਜਲੀ ਦੀ ਖਪਤ ਘਟਦੀ ਹੈ। ਬੈਲਟਾਂ, ਚੇਨ ਅਤੇ ਕੇਬਲ ਡਰਾਈਵਾਂ 'ਤੇ ਸਵਾਲਾਂ ਅਤੇ ਰਾਏ ਲਈ AGS-TECH ਨਾਲ ਸੰਪਰਕ ਕਰੋ। CLICK Product Finder-Locator Service ਪਿਛਲੇ ਸਫ਼ੇ
- Rapid Prototyping, Desktop Manufacturing, Additive Manufacturing, FDM
Rapid Prototyping, Desktop Manufacturing, Additive Manufacturing, Stereolithography, Polyjet, Fused Deposition Modeling, Selective Laser Sintering, FDM, SLS ਐਡਿਟਿਵ ਅਤੇ ਰੈਪਿਡ ਮੈਨੂਫੈਕਚਰਿੰਗ ਹਾਲ ਹੀ ਦੇ ਸਾਲਾਂ ਵਿੱਚ, ਅਸੀਂ ਰੈਪਿਡ ਮੈਨੂਫੈਕਚਰਿੰਗ ਜਾਂ ਰੈਪਿਡ ਪ੍ਰੋਟੋਟਾਈਪਿੰਗ ਦੀ ਮੰਗ ਵਿੱਚ ਵਾਧਾ ਦੇਖਿਆ ਹੈ। ਇਸ ਪ੍ਰਕਿਰਿਆ ਨੂੰ ਡੈਸਕਟੌਪ ਮੈਨੂਫੈਕਚਰਿੰਗ ਜਾਂ ਫਰੀ-ਫਾਰਮ ਫੈਬਰੀਕੇਸ਼ਨ ਵੀ ਕਿਹਾ ਜਾ ਸਕਦਾ ਹੈ। ਮੂਲ ਰੂਪ ਵਿੱਚ ਇੱਕ ਹਿੱਸੇ ਦਾ ਇੱਕ ਠੋਸ ਭੌਤਿਕ ਮਾਡਲ ਸਿੱਧਾ ਇੱਕ ਤਿੰਨ ਅਯਾਮੀ CAD ਡਰਾਇੰਗ ਤੋਂ ਬਣਾਇਆ ਜਾਂਦਾ ਹੈ। ਅਸੀਂ ਇਹਨਾਂ ਵੱਖ-ਵੱਖ ਤਕਨੀਕਾਂ ਲਈ ADDITIVE MANUFACTURING ਸ਼ਬਦ ਦੀ ਵਰਤੋਂ ਕਰਦੇ ਹਾਂ ਜਿੱਥੇ ਅਸੀਂ ਲੇਅਰਾਂ ਵਿੱਚ ਹਿੱਸੇ ਬਣਾਉਂਦੇ ਹਾਂ। ਏਕੀਕ੍ਰਿਤ ਕੰਪਿਊਟਰ ਦੁਆਰਾ ਸੰਚਾਲਿਤ ਹਾਰਡਵੇਅਰ ਅਤੇ ਸੌਫਟਵੇਅਰ ਦੀ ਵਰਤੋਂ ਕਰਕੇ ਅਸੀਂ ਐਡੀਟਿਵ ਨਿਰਮਾਣ ਕਰਦੇ ਹਾਂ। ਸਾਡੀਆਂ ਤੇਜ਼ ਪ੍ਰੋਟੋਟਾਈਪਿੰਗ ਅਤੇ ਨਿਰਮਾਣ ਤਕਨੀਕਾਂ ਹਨ ਸਟੀਰੀਓਲੀਥੋਗ੍ਰਾਫੀ, ਪੋਲੀਜੈੱਟ, ਫਿਊਜ਼ਡ-ਡਿਪੋਜ਼ਿਸ਼ਨ ਮਾਡਲਿੰਗ, ਚੋਣਵੇਂ ਲੇਜ਼ਰ ਸਿੰਟਰਿੰਗ, ਇਲੈਕਟ੍ਰੋਨ ਬੀਮ ਮੈਲਟਿੰਗ, ਤਿੰਨ-ਅਯਾਮੀ ਪ੍ਰਿੰਟਿੰਗ, ਡਾਇਰੈਕਟ ਮੈਨੂਫੈਕਚਰਿੰਗ, ਆਰ. ਅਸੀਂ ਸਿਫ਼ਾਰਿਸ਼ ਕਰਦੇ ਹਾਂ ਕਿ ਤੁਸੀਂ ਇੱਥੇ ਕਲਿੱਕ ਕਰੋAGS-TECH Inc. ਦੁਆਰਾ ਐਡਿਟਿਵ ਮੈਨੂਫੈਕਚਰਿੰਗ ਅਤੇ ਰੈਪਿਡ ਮੈਨੂਫੈਕਚਰਿੰਗ ਪ੍ਰਕਿਰਿਆਵਾਂ ਦੇ ਸਾਡੇ ਯੋਜਨਾਬੱਧ ਚਿੱਤਰਾਂ ਨੂੰ ਡਾਉਨਲੋਡ ਕਰੋ ਇਹ ਤੁਹਾਨੂੰ ਉਸ ਜਾਣਕਾਰੀ ਨੂੰ ਬਿਹਤਰ ਤਰੀਕੇ ਨਾਲ ਸਮਝਣ ਵਿੱਚ ਮਦਦ ਕਰੇਗਾ ਜੋ ਅਸੀਂ ਤੁਹਾਨੂੰ ਹੇਠਾਂ ਪ੍ਰਦਾਨ ਕਰ ਰਹੇ ਹਾਂ। ਰੈਪਿਡ ਪ੍ਰੋਟੋਟਾਈਪਿੰਗ ਸਾਨੂੰ ਪ੍ਰਦਾਨ ਕਰਦੀ ਹੈ: 1.) ਇੱਕ 3D / CAD ਸਿਸਟਮ ਦੀ ਵਰਤੋਂ ਕਰਦੇ ਹੋਏ ਇੱਕ ਮਾਨੀਟਰ 'ਤੇ ਸੰਕਲਪਿਕ ਉਤਪਾਦ ਡਿਜ਼ਾਈਨ ਨੂੰ ਵੱਖ-ਵੱਖ ਕੋਣਾਂ ਤੋਂ ਦੇਖਿਆ ਜਾਂਦਾ ਹੈ। 2.) ਗੈਰ-ਧਾਤੂ ਅਤੇ ਧਾਤੂ ਪਦਾਰਥਾਂ ਤੋਂ ਪ੍ਰੋਟੋਟਾਈਪਾਂ ਦਾ ਨਿਰਮਾਣ ਅਤੇ ਕਾਰਜਸ਼ੀਲ, ਤਕਨੀਕੀ ਅਤੇ ਸੁਹਜ ਦੇ ਪਹਿਲੂਆਂ ਤੋਂ ਅਧਿਐਨ ਕੀਤਾ ਜਾਂਦਾ ਹੈ। 3.) ਬਹੁਤ ਘੱਟ ਸਮੇਂ ਵਿੱਚ ਘੱਟ ਕੀਮਤ ਵਾਲੀ ਪ੍ਰੋਟੋਟਾਈਪਿੰਗ ਨੂੰ ਪੂਰਾ ਕੀਤਾ ਜਾਂਦਾ ਹੈ. ਐਡੀਟਿਵ ਮੈਨੂਫੈਕਚਰਿੰਗ ਨੂੰ ਇੱਕ-ਦੂਜੇ ਦੇ ਉੱਪਰ ਵਿਅਕਤੀਗਤ ਟੁਕੜਿਆਂ ਨੂੰ ਸਟੈਕ ਕਰਕੇ ਅਤੇ ਬੰਨ੍ਹ ਕੇ ਰੋਟੀ ਦੀ ਇੱਕ ਰੋਟੀ ਬਣਾਉਣ ਦੇ ਸਮਾਨ ਕੀਤਾ ਜਾ ਸਕਦਾ ਹੈ। ਦੂਜੇ ਸ਼ਬਦਾਂ ਵਿੱਚ, ਉਤਪਾਦ ਨੂੰ ਟੁਕੜੇ ਦੁਆਰਾ ਟੁਕੜਾ, ਜਾਂ ਪਰਤ ਦਰ ਪਰਤ ਇੱਕ ਦੂਜੇ ਉੱਤੇ ਜਮ੍ਹਾਂ ਕੀਤਾ ਜਾਂਦਾ ਹੈ। ਜ਼ਿਆਦਾਤਰ ਹਿੱਸੇ ਘੰਟਿਆਂ ਦੇ ਅੰਦਰ ਤਿਆਰ ਕੀਤੇ ਜਾ ਸਕਦੇ ਹਨ। ਇਹ ਤਕਨੀਕ ਚੰਗੀ ਹੈ ਜੇਕਰ ਪੁਰਜ਼ੇ ਬਹੁਤ ਜਲਦੀ ਲੋੜੀਂਦੇ ਹਨ ਜਾਂ ਜੇ ਲੋੜੀਂਦੀ ਮਾਤਰਾ ਘੱਟ ਹੈ ਅਤੇ ਇੱਕ ਉੱਲੀ ਅਤੇ ਟੂਲਿੰਗ ਬਣਾਉਣਾ ਬਹੁਤ ਮਹਿੰਗਾ ਹੈ ਅਤੇ ਸਮਾਂ ਲੱਗਦਾ ਹੈ। ਹਾਲਾਂਕਿ ਇੱਕ ਹਿੱਸੇ ਦੀ ਕੀਮਤ ਮਹਿੰਗੇ ਕੱਚੇ ਮਾਲ ਕਾਰਨ ਮਹਿੰਗੀ ਹੈ। • ਸਟੀਰੀਓਲੀਥੋਗ੍ਰਾਫੀ: ਇਸ ਤਕਨੀਕ ਨੂੰ STL ਵੀ ਕਿਹਾ ਜਾਂਦਾ ਹੈ, ਇੱਕ ਲੇਜ਼ਰ ਬੀਮ ਨੂੰ ਫੋਕਸ ਕਰਕੇ ਇੱਕ ਤਰਲ ਫੋਟੋਪੋਲੀਮਰ ਨੂੰ ਇੱਕ ਖਾਸ ਆਕਾਰ ਵਿੱਚ ਠੀਕ ਕਰਨ ਅਤੇ ਸਖ਼ਤ ਕਰਨ 'ਤੇ ਅਧਾਰਤ ਹੈ। ਲੇਜ਼ਰ ਫੋਟੋਪੋਲੀਮਰ ਨੂੰ ਪੋਲੀਮਰਾਈਜ਼ ਕਰਦਾ ਹੈ ਅਤੇ ਇਸ ਨੂੰ ਠੀਕ ਕਰਦਾ ਹੈ। ਫੋਟੋਪੋਲੀਮਰ ਮਿਸ਼ਰਣ ਦੀ ਸਤਹ ਦੇ ਨਾਲ ਪ੍ਰੋਗ੍ਰਾਮਡ ਸ਼ਕਲ ਦੇ ਅਨੁਸਾਰ ਯੂਵੀ ਲੇਜ਼ਰ ਬੀਮ ਨੂੰ ਸਕੈਨ ਕਰਨ ਨਾਲ ਹਿੱਸਾ ਇੱਕ ਦੂਜੇ ਦੇ ਸਿਖਰ 'ਤੇ ਕੈਸਕੇਡ ਕੀਤੇ ਵਿਅਕਤੀਗਤ ਟੁਕੜਿਆਂ ਵਿੱਚ ਹੇਠਾਂ ਤੋਂ ਉੱਪਰ ਪੈਦਾ ਹੁੰਦਾ ਹੈ। ਸਿਸਟਮ ਵਿੱਚ ਪ੍ਰੋਗਰਾਮ ਕੀਤੇ ਜਿਓਮੈਟਰੀਜ਼ ਨੂੰ ਪ੍ਰਾਪਤ ਕਰਨ ਲਈ ਲੇਜ਼ਰ ਸਪਾਟ ਦੀ ਸਕੈਨਿੰਗ ਨੂੰ ਕਈ ਵਾਰ ਦੁਹਰਾਇਆ ਜਾਂਦਾ ਹੈ। ਭਾਗ ਦੇ ਪੂਰੀ ਤਰ੍ਹਾਂ ਤਿਆਰ ਹੋਣ ਤੋਂ ਬਾਅਦ, ਇਸਨੂੰ ਪਲੇਟਫਾਰਮ ਤੋਂ ਹਟਾ ਦਿੱਤਾ ਜਾਂਦਾ ਹੈ, ਅਲਟਰਾਸੋਨਿਕ ਤਰੀਕੇ ਨਾਲ ਅਤੇ ਅਲਕੋਹਲ ਬਾਥ ਨਾਲ ਸਾਫ਼ ਕੀਤਾ ਜਾਂਦਾ ਹੈ। ਅੱਗੇ, ਇਹ ਯਕੀਨੀ ਬਣਾਉਣ ਲਈ ਕਿ ਪੌਲੀਮਰ ਪੂਰੀ ਤਰ੍ਹਾਂ ਠੀਕ ਹੋ ਗਿਆ ਹੈ ਅਤੇ ਸਖ਼ਤ ਹੋ ਗਿਆ ਹੈ, ਇਹ ਕੁਝ ਘੰਟਿਆਂ ਲਈ ਯੂਵੀ ਕਿਰਨਾਂ ਦੇ ਸੰਪਰਕ ਵਿੱਚ ਆਉਂਦਾ ਹੈ। ਪ੍ਰਕਿਰਿਆ ਨੂੰ ਸੰਖੇਪ ਕਰਨ ਲਈ, ਇੱਕ ਪਲੇਟਫਾਰਮ ਜੋ ਇੱਕ ਫੋਟੋਪੋਲੀਮਰ ਮਿਸ਼ਰਣ ਵਿੱਚ ਡੁਬੋਇਆ ਜਾਂਦਾ ਹੈ ਅਤੇ ਇੱਕ ਯੂਵੀ ਲੇਜ਼ਰ ਬੀਮ ਨੂੰ ਲੋੜੀਂਦੇ ਹਿੱਸੇ ਦੀ ਸ਼ਕਲ ਦੇ ਅਨੁਸਾਰ ਸਰਵੋ-ਨਿਯੰਤਰਣ ਪ੍ਰਣਾਲੀ ਦੁਆਰਾ ਨਿਯੰਤਰਿਤ ਅਤੇ ਮੂਵ ਕੀਤਾ ਜਾਂਦਾ ਹੈ ਅਤੇ ਭਾਗ ਨੂੰ ਪਰਤ ਦੁਆਰਾ ਪੋਲੀਮਰ ਪਰਤ ਨੂੰ ਫੋਟੋਕੁਰ ਕਰਕੇ ਪ੍ਰਾਪਤ ਕੀਤਾ ਜਾਂਦਾ ਹੈ। ਬੇਸ਼ੱਕ ਪੈਦਾ ਕੀਤੇ ਹਿੱਸੇ ਦੇ ਅਧਿਕਤਮ ਮਾਪ ਸਟੀਰੀਓਲਿਥੋਗ੍ਰਾਫੀ ਉਪਕਰਣ ਦੁਆਰਾ ਨਿਰਧਾਰਤ ਕੀਤੇ ਜਾਂਦੇ ਹਨ। • ਪੋਲੀਜੇਟ : ਇੰਕਜੈੱਟ ਪ੍ਰਿੰਟਿੰਗ ਦੇ ਸਮਾਨ, ਪੌਲੀਜੈੱਟ ਵਿੱਚ ਸਾਡੇ ਕੋਲ ਅੱਠ ਪ੍ਰਿੰਟ ਹੈਡ ਹਨ ਜੋ ਬਿਲਡ ਟ੍ਰੇ ਉੱਤੇ ਫੋਟੋਪੋਲੀਮਰ ਜਮ੍ਹਾਂ ਕਰਦੇ ਹਨ। ਜੈੱਟਾਂ ਦੇ ਨਾਲ ਰੱਖੀ ਅਲਟਰਾਵਾਇਲਟ ਰੋਸ਼ਨੀ ਹਰ ਪਰਤ ਨੂੰ ਤੁਰੰਤ ਠੀਕ ਕਰਦੀ ਹੈ ਅਤੇ ਸਖ਼ਤ ਕਰ ਦਿੰਦੀ ਹੈ। ਪੌਲੀਜੈੱਟ ਵਿੱਚ ਦੋ ਸਮੱਗਰੀਆਂ ਦੀ ਵਰਤੋਂ ਕੀਤੀ ਜਾਂਦੀ ਹੈ। ਪਹਿਲੀ ਸਮੱਗਰੀ ਅਸਲ ਮਾਡਲ ਦੇ ਨਿਰਮਾਣ ਲਈ ਹੈ. ਦੂਜੀ ਸਮੱਗਰੀ, ਇੱਕ ਜੈੱਲ ਵਰਗੀ ਰਾਲ ਸਹਾਇਤਾ ਲਈ ਵਰਤੀ ਜਾਂਦੀ ਹੈ। ਇਹ ਦੋਵੇਂ ਸਮੱਗਰੀ ਪਰਤ ਦਰ ਪਰਤ ਜਮ੍ਹਾ ਕੀਤੀ ਜਾਂਦੀ ਹੈ ਅਤੇ ਨਾਲ ਹੀ ਠੀਕ ਹੋ ਜਾਂਦੀ ਹੈ। ਮਾਡਲ ਦੇ ਪੂਰਾ ਹੋਣ ਤੋਂ ਬਾਅਦ, ਸਹਾਇਤਾ ਸਮੱਗਰੀ ਨੂੰ ਜਲਮਈ ਘੋਲ ਨਾਲ ਹਟਾ ਦਿੱਤਾ ਜਾਂਦਾ ਹੈ। ਵਰਤੇ ਗਏ ਰੈਜ਼ਿਨ ਸਟੀਰੀਓਲੀਥੋਗ੍ਰਾਫੀ (STL) ਦੇ ਸਮਾਨ ਹਨ। ਪੌਲੀਜੈੱਟ ਦੇ ਸਟੀਰੀਓਲੀਥੋਗ੍ਰਾਫੀ ਨਾਲੋਂ ਹੇਠਾਂ ਦਿੱਤੇ ਫਾਇਦੇ ਹਨ: 1.) ਪੁਰਜ਼ਿਆਂ ਦੀ ਸਫਾਈ ਦੀ ਕੋਈ ਲੋੜ ਨਹੀਂ। 2.) ਪੋਸਟ-ਪ੍ਰੋਸੈਸ ਇਲਾਜ ਦੀ ਕੋਈ ਲੋੜ ਨਹੀਂ 3.) ਛੋਟੀ ਪਰਤ ਮੋਟਾਈ ਸੰਭਵ ਹੈ ਅਤੇ ਇਸ ਤਰ੍ਹਾਂ ਅਸੀਂ ਬਿਹਤਰ ਰੈਜ਼ੋਲਿਊਸ਼ਨ ਪ੍ਰਾਪਤ ਕਰਦੇ ਹਾਂ ਅਤੇ ਵਧੀਆ ਪੁਰਜ਼ੇ ਬਣਾ ਸਕਦੇ ਹਾਂ। • ਫਿਊਜ਼ਡ ਡਿਪੋਜ਼ਿਸ਼ਨ ਮਾਡਲਿੰਗ: FDM ਦੇ ਰੂਪ ਵਿੱਚ ਵੀ ਸੰਖੇਪ ਰੂਪ ਵਿੱਚ, ਇਸ ਵਿਧੀ ਵਿੱਚ ਇੱਕ ਰੋਬੋਟ-ਨਿਯੰਤਰਿਤ ਐਕਸਟਰੂਡਰ ਹੈੱਡ ਇੱਕ ਮੇਜ਼ ਉੱਤੇ ਦੋ ਸਿਧਾਂਤ ਦਿਸ਼ਾਵਾਂ ਵਿੱਚ ਘੁੰਮਦਾ ਹੈ। ਕੇਬਲ ਨੂੰ ਲੋੜ ਅਨੁਸਾਰ ਹੇਠਾਂ ਅਤੇ ਉੱਚਾ ਕੀਤਾ ਜਾਂਦਾ ਹੈ। ਸਿਰ 'ਤੇ ਗਰਮ ਡਾਈ ਦੀ ਛੱਤ ਤੋਂ, ਇੱਕ ਥਰਮੋਪਲਾਸਟਿਕ ਫਿਲਾਮੈਂਟ ਬਾਹਰ ਕੱਢਿਆ ਜਾਂਦਾ ਹੈ ਅਤੇ ਇੱਕ ਸ਼ੁਰੂਆਤੀ ਪਰਤ ਇੱਕ ਫੋਮ ਫਾਊਂਡੇਸ਼ਨ 'ਤੇ ਜਮ੍ਹਾ ਕੀਤੀ ਜਾਂਦੀ ਹੈ। ਇਹ ਐਕਸਟਰੂਡਰ ਹੈਡ ਦੁਆਰਾ ਪੂਰਾ ਕੀਤਾ ਜਾਂਦਾ ਹੈ ਜੋ ਇੱਕ ਪੂਰਵ-ਨਿਰਧਾਰਤ ਮਾਰਗ ਦੀ ਪਾਲਣਾ ਕਰਦਾ ਹੈ. ਸ਼ੁਰੂਆਤੀ ਪਰਤ ਤੋਂ ਬਾਅਦ, ਸਾਰਣੀ ਨੂੰ ਨੀਵਾਂ ਕੀਤਾ ਜਾਂਦਾ ਹੈ ਅਤੇ ਬਾਅਦ ਦੀਆਂ ਪਰਤਾਂ ਇੱਕ ਦੂਜੇ ਦੇ ਉੱਪਰ ਜਮ੍ਹਾਂ ਹੁੰਦੀਆਂ ਹਨ. ਕਈ ਵਾਰ ਜਦੋਂ ਇੱਕ ਗੁੰਝਲਦਾਰ ਹਿੱਸੇ ਦਾ ਨਿਰਮਾਣ ਕੀਤਾ ਜਾਂਦਾ ਹੈ, ਤਾਂ ਸਹਾਇਤਾ ਢਾਂਚਿਆਂ ਦੀ ਲੋੜ ਹੁੰਦੀ ਹੈ ਤਾਂ ਜੋ ਜਮ੍ਹਾ ਕੁਝ ਦਿਸ਼ਾਵਾਂ ਵਿੱਚ ਜਾਰੀ ਰਹਿ ਸਕੇ। ਇਹਨਾਂ ਮਾਮਲਿਆਂ ਵਿੱਚ, ਇੱਕ ਸਹਾਇਕ ਸਮੱਗਰੀ ਨੂੰ ਇੱਕ ਪਰਤ ਉੱਤੇ ਫਿਲਾਮੈਂਟ ਦੀ ਘੱਟ ਸੰਘਣੀ ਵਿੱਥ ਦੇ ਨਾਲ ਬਾਹਰ ਕੱਢਿਆ ਜਾਂਦਾ ਹੈ ਤਾਂ ਜੋ ਇਹ ਮਾਡਲ ਸਮੱਗਰੀ ਨਾਲੋਂ ਕਮਜ਼ੋਰ ਹੋਵੇ। ਇਹ ਸਹਾਇਤਾ ਢਾਂਚਿਆਂ ਨੂੰ ਬਾਅਦ ਵਿੱਚ ਭਾਗ ਦੇ ਪੂਰਾ ਹੋਣ ਤੋਂ ਬਾਅਦ ਭੰਗ ਜਾਂ ਤੋੜਿਆ ਜਾ ਸਕਦਾ ਹੈ। ਐਕਸਟਰੂਡਰ ਡਾਈ ਮਾਪ ਐਕਸਟਰੂਡ ਲੇਅਰਾਂ ਦੀ ਮੋਟਾਈ ਨਿਰਧਾਰਤ ਕਰਦੇ ਹਨ। FDM ਪ੍ਰਕਿਰਿਆ ਤਿਰਛੇ ਬਾਹਰੀ ਜਹਾਜ਼ਾਂ 'ਤੇ ਸਟੈਪਡ ਸਤਹਾਂ ਵਾਲੇ ਹਿੱਸੇ ਪੈਦਾ ਕਰਦੀ ਹੈ। ਜੇ ਇਹ ਖੁਰਦਰਾਪਣ ਅਸਵੀਕਾਰਨਯੋਗ ਹੈ, ਤਾਂ ਇਹਨਾਂ ਨੂੰ ਸਮਤਲ ਕਰਨ ਲਈ ਰਸਾਇਣਕ ਭਾਫ਼ ਪਾਲਿਸ਼ ਜਾਂ ਗਰਮ ਟੂਲ ਦੀ ਵਰਤੋਂ ਕੀਤੀ ਜਾ ਸਕਦੀ ਹੈ। ਇੱਥੋਂ ਤੱਕ ਕਿ ਇੱਕ ਪਾਲਿਸ਼ਿੰਗ ਮੋਮ ਵੀ ਇਹਨਾਂ ਕਦਮਾਂ ਨੂੰ ਖਤਮ ਕਰਨ ਅਤੇ ਵਾਜਬ ਜਿਓਮੈਟ੍ਰਿਕ ਸਹਿਣਸ਼ੀਲਤਾ ਪ੍ਰਾਪਤ ਕਰਨ ਲਈ ਇੱਕ ਪਰਤ ਸਮੱਗਰੀ ਵਜੋਂ ਉਪਲਬਧ ਹੈ। • ਸਿਲੈਕਟਿਵ ਲੇਜ਼ਰ ਸਿੰਟਰਿੰਗ: SLS ਵਜੋਂ ਵੀ ਦਰਸਾਇਆ ਜਾਂਦਾ ਹੈ, ਇਹ ਪ੍ਰਕਿਰਿਆ ਕਿਸੇ ਵਸਤੂ ਵਿੱਚ ਚੋਣਵੇਂ ਰੂਪ ਵਿੱਚ ਇੱਕ ਪੋਲੀਮਰ, ਵਸਰਾਵਿਕ ਜਾਂ ਧਾਤੂ ਪਾਊਡਰ ਦੇ ਸਿੰਟਰਿੰਗ 'ਤੇ ਅਧਾਰਤ ਹੈ। ਪ੍ਰੋਸੈਸਿੰਗ ਚੈਂਬਰ ਦੇ ਹੇਠਾਂ ਦੋ ਸਿਲੰਡਰ ਹਨ: ਇੱਕ ਪਾਰਟ-ਬਿਲਡ ਸਿਲੰਡਰ ਅਤੇ ਇੱਕ ਪਾਊਡਰ-ਫੀਡ ਸਿਲੰਡਰ। ਪਹਿਲੇ ਹਿੱਸੇ ਨੂੰ ਹੌਲੀ-ਹੌਲੀ ਹੇਠਾਂ ਕੀਤਾ ਜਾਂਦਾ ਹੈ ਜਿੱਥੇ ਸਿੰਟਰਡ ਹਿੱਸਾ ਬਣ ਰਿਹਾ ਹੁੰਦਾ ਹੈ ਅਤੇ ਬਾਅਦ ਵਾਲੇ ਹਿੱਸੇ ਨੂੰ ਰੋਲਰ ਵਿਧੀ ਰਾਹੀਂ ਪਾਰਟ-ਬਿਲਡ ਸਿਲੰਡਰ ਨੂੰ ਪਾਊਡਰ ਸਪਲਾਈ ਕਰਨ ਲਈ ਲਗਾਤਾਰ ਵਧਾਇਆ ਜਾਂਦਾ ਹੈ। ਪਹਿਲਾਂ ਪਾਰਟ-ਬਿਲਡ ਸਿਲੰਡਰ ਵਿੱਚ ਪਾਊਡਰ ਦੀ ਇੱਕ ਪਤਲੀ ਪਰਤ ਜਮ੍ਹਾ ਕੀਤੀ ਜਾਂਦੀ ਹੈ, ਫਿਰ ਇੱਕ ਲੇਜ਼ਰ ਬੀਮ ਉਸ ਪਰਤ 'ਤੇ ਫੋਕਸ ਕੀਤੀ ਜਾਂਦੀ ਹੈ, ਇੱਕ ਖਾਸ ਕਰਾਸ ਸੈਕਸ਼ਨ ਨੂੰ ਟਰੇਸਿੰਗ ਅਤੇ ਪਿਘਲਾਉਣਾ/ਸਿੰਟਰਿੰਗ, ਜੋ ਫਿਰ ਇੱਕ ਠੋਸ ਬਣ ਜਾਂਦੀ ਹੈ। ਪਾਊਡਰ ਉਹ ਖੇਤਰ ਹਨ ਜੋ ਲੇਜ਼ਰ ਬੀਮ ਦੁਆਰਾ ਨਹੀਂ ਮਾਰਦੇ ਹਨ ਢਿੱਲੇ ਰਹਿੰਦੇ ਹਨ ਪਰ ਫਿਰ ਵੀ ਠੋਸ ਹਿੱਸੇ ਦਾ ਸਮਰਥਨ ਕਰਦੇ ਹਨ। ਫਿਰ ਪਾਊਡਰ ਦੀ ਇੱਕ ਹੋਰ ਪਰਤ ਜਮ੍ਹਾਂ ਕੀਤੀ ਜਾਂਦੀ ਹੈ ਅਤੇ ਭਾਗ ਨੂੰ ਪ੍ਰਾਪਤ ਕਰਨ ਲਈ ਪ੍ਰਕਿਰਿਆ ਨੂੰ ਕਈ ਵਾਰ ਦੁਹਰਾਇਆ ਜਾਂਦਾ ਹੈ. ਅੰਤ ਵਿੱਚ, ਢਿੱਲੇ ਪਾਊਡਰ ਦੇ ਕਣਾਂ ਨੂੰ ਹਿਲਾ ਦਿੱਤਾ ਜਾਂਦਾ ਹੈ. ਇਹ ਸਾਰੇ ਨਿਰਮਾਣ ਕੀਤੇ ਜਾ ਰਹੇ ਹਿੱਸੇ ਦੇ 3D CAD ਪ੍ਰੋਗਰਾਮ ਦੁਆਰਾ ਤਿਆਰ ਹਦਾਇਤਾਂ ਦੀ ਵਰਤੋਂ ਕਰਕੇ ਇੱਕ ਪ੍ਰਕਿਰਿਆ-ਨਿਯੰਤਰਣ ਕੰਪਿਊਟਰ ਦੁਆਰਾ ਕੀਤੇ ਜਾਂਦੇ ਹਨ। ਕਈ ਸਮੱਗਰੀ ਜਿਵੇਂ ਕਿ ਪੌਲੀਮਰ (ਜਿਵੇਂ ਕਿ ਏ.ਬੀ.ਐੱਸ., ਪੀ.ਵੀ.ਸੀ., ਪੋਲਿਸਟਰ), ਮੋਮ, ਧਾਤਾਂ ਅਤੇ ਉਚਿਤ ਪੌਲੀਮਰ ਬਾਈਂਡਰ ਵਾਲੇ ਵਸਰਾਵਿਕ ਪਦਾਰਥ ਜਮ੍ਹਾ ਕੀਤੇ ਜਾ ਸਕਦੇ ਹਨ। • ਇਲੈਕਟ੍ਰੋਨ-ਬੀਮ MELTING : ਚੋਣਵੇਂ ਲੇਜ਼ਰ ਸਿੰਟਰਿੰਗ ਦੇ ਸਮਾਨ, ਪਰ ਵੈਕਿਊਮ ਵਿੱਚ ਪ੍ਰੋਟੋਟਾਈਪ ਬਣਾਉਣ ਲਈ ਟਾਈਟੇਨੀਅਮ ਜਾਂ ਕੋਬਾਲਟ ਕ੍ਰੋਮ ਪਾਊਡਰ ਨੂੰ ਪਿਘਲਣ ਲਈ ਇਲੈਕਟ੍ਰੌਨ ਬੀਮ ਦੀ ਵਰਤੋਂ ਕਰਨਾ। ਸਟੇਨਲੈਸ ਸਟੀਲ, ਅਲਮੀਨੀਅਮ ਅਤੇ ਤਾਂਬੇ ਦੇ ਮਿਸ਼ਰਣਾਂ 'ਤੇ ਇਸ ਪ੍ਰਕਿਰਿਆ ਨੂੰ ਕਰਨ ਲਈ ਕੁਝ ਵਿਕਾਸ ਕੀਤੇ ਗਏ ਹਨ। ਜੇ ਪੈਦਾ ਕੀਤੇ ਹਿੱਸਿਆਂ ਦੀ ਥਕਾਵਟ ਸ਼ਕਤੀ ਨੂੰ ਵਧਾਉਣ ਦੀ ਲੋੜ ਹੈ, ਤਾਂ ਅਸੀਂ ਇੱਕ ਸੈਕੰਡਰੀ ਪ੍ਰਕਿਰਿਆ ਦੇ ਤੌਰ 'ਤੇ ਹਿੱਸੇ ਦੇ ਨਿਰਮਾਣ ਤੋਂ ਬਾਅਦ ਗਰਮ ਆਈਸੋਸਟੈਟਿਕ ਪ੍ਰੈੱਸਿੰਗ ਦੀ ਵਰਤੋਂ ਕਰਦੇ ਹਾਂ। • ਤਿੰਨ-ਅਯਾਮੀ ਪ੍ਰਿੰਟਿੰਗ: 3DP ਦੁਆਰਾ ਵੀ ਦਰਸਾਇਆ ਗਿਆ ਹੈ, ਇਸ ਤਕਨੀਕ ਵਿੱਚ ਇੱਕ ਪ੍ਰਿੰਟ ਹੈੱਡ ਇੱਕ ਅਕਾਰਗਨਿਕ ਬਾਈਂਡਰ ਨੂੰ ਗੈਰ-ਧਾਤੂ ਜਾਂ ਧਾਤੂ ਪਾਊਡਰ ਦੀ ਇੱਕ ਪਰਤ ਉੱਤੇ ਜਮ੍ਹਾਂ ਕਰਦਾ ਹੈ। ਪਾਊਡਰ ਬੈੱਡ ਨੂੰ ਲੈ ਕੇ ਜਾਣ ਵਾਲਾ ਪਿਸਟਨ ਲਗਾਤਾਰ ਘਟਾਇਆ ਜਾਂਦਾ ਹੈ ਅਤੇ ਹਰ ਪੜਾਅ 'ਤੇ ਬਾਈਂਡਰ ਨੂੰ layer ਪਰਤ ਦੁਆਰਾ ਜਮ੍ਹਾਂ ਕੀਤਾ ਜਾਂਦਾ ਹੈ ਅਤੇ ਬਾਈਂਡਰ ਦੁਆਰਾ ਫਿਊਜ਼ ਕੀਤਾ ਜਾਂਦਾ ਹੈ। ਵਰਤੇ ਗਏ ਪਾਊਡਰ ਸਾਮੱਗਰੀ ਪੌਲੀਮਰ ਮਿਸ਼ਰਣ ਅਤੇ ਰੇਸ਼ੇ, ਫਾਊਂਡਰੀ ਰੇਤ, ਧਾਤਾਂ ਹਨ। ਵੱਖ-ਵੱਖ ਬਾਈਂਡਰ ਹੈੱਡਾਂ ਅਤੇ ਵੱਖ-ਵੱਖ ਰੰਗਾਂ ਦੇ ਬਾਈਂਡਰਾਂ ਦੀ ਵਰਤੋਂ ਨਾਲ ਅਸੀਂ ਵੱਖ-ਵੱਖ ਰੰਗਾਂ ਨੂੰ ਪ੍ਰਾਪਤ ਕਰ ਸਕਦੇ ਹਾਂ। ਇਹ ਪ੍ਰਕਿਰਿਆ ਇੰਕਜੈੱਟ ਪ੍ਰਿੰਟਿੰਗ ਵਰਗੀ ਹੈ ਪਰ ਇੱਕ ਰੰਗਦਾਰ ਸ਼ੀਟ ਪ੍ਰਾਪਤ ਕਰਨ ਦੀ ਬਜਾਏ ਅਸੀਂ ਇੱਕ ਰੰਗੀਨ ਤਿੰਨ-ਅਯਾਮੀ ਵਸਤੂ ਪ੍ਰਾਪਤ ਕਰਦੇ ਹਾਂ। ਪੈਦਾ ਹੋਏ ਹਿੱਸੇ ਪੋਰਸ ਹੋ ਸਕਦੇ ਹਨ ਅਤੇ ਇਸਲਈ ਇਸਦੀ ਘਣਤਾ ਅਤੇ ਤਾਕਤ ਵਧਾਉਣ ਲਈ ਸਿੰਟਰਿੰਗ ਅਤੇ ਧਾਤ ਦੀ ਘੁਸਪੈਠ ਦੀ ਲੋੜ ਹੋ ਸਕਦੀ ਹੈ। ਸਿੰਟਰਿੰਗ ਬਾਈਂਡਰ ਨੂੰ ਸਾੜ ਦੇਵੇਗੀ ਅਤੇ ਧਾਤ ਦੇ ਪਾਊਡਰਾਂ ਨੂੰ ਇਕੱਠੇ ਫਿਊਜ਼ ਕਰ ਦੇਵੇਗੀ। ਧਾਤੂਆਂ ਜਿਵੇਂ ਕਿ ਸਟੀਲ, ਅਲਮੀਨੀਅਮ, ਟਾਈਟੇਨੀਅਮ ਦੀ ਵਰਤੋਂ ਹਿੱਸੇ ਬਣਾਉਣ ਲਈ ਕੀਤੀ ਜਾ ਸਕਦੀ ਹੈ ਅਤੇ ਘੁਸਪੈਠ ਸਮੱਗਰੀ ਵਜੋਂ ਅਸੀਂ ਆਮ ਤੌਰ 'ਤੇ ਤਾਂਬੇ ਅਤੇ ਕਾਂਸੀ ਦੀ ਵਰਤੋਂ ਕਰਦੇ ਹਾਂ। ਇਸ ਤਕਨੀਕ ਦੀ ਖ਼ੂਬਸੂਰਤੀ ਇਹ ਹੈ ਕਿ ਗੁੰਝਲਦਾਰ ਅਤੇ ਚਲਦੀਆਂ ਅਸੈਂਬਲੀਆਂ ਵੀ ਬਹੁਤ ਜਲਦੀ ਬਣਾਈਆਂ ਜਾ ਸਕਦੀਆਂ ਹਨ। ਉਦਾਹਰਨ ਲਈ ਇੱਕ ਗੇਅਰ ਅਸੈਂਬਲੀ, ਇੱਕ ਸੰਦ ਦੇ ਤੌਰ ਤੇ ਇੱਕ ਰੈਂਚ ਬਣਾਇਆ ਜਾ ਸਕਦਾ ਹੈ ਅਤੇ ਇਸ ਵਿੱਚ ਹਿਲਾਉਣ ਅਤੇ ਮੋੜਨ ਵਾਲੇ ਹਿੱਸੇ ਵਰਤੇ ਜਾਣ ਲਈ ਤਿਆਰ ਹੋਣਗੇ। ਅਸੈਂਬਲੀ ਦੇ ਵੱਖੋ-ਵੱਖਰੇ ਹਿੱਸਿਆਂ ਨੂੰ ਵੱਖ-ਵੱਖ ਰੰਗਾਂ ਨਾਲ ਤਿਆਰ ਕੀਤਾ ਜਾ ਸਕਦਾ ਹੈ ਅਤੇ ਸਾਰੇ ਇੱਕ ਹੀ ਸ਼ਾਟ ਵਿੱਚ।ਮੈਟਲ 3D ਪ੍ਰਿੰਟਿੰਗ ਬੇਸਿਕਸ • ਡਾਇਰੈਕਟ ਮੈਨੂਫੈਕਚਰਿੰਗ ਅਤੇ ਰੈਪਿਡ ਟੂਲਿੰਗ: ਡਿਜ਼ਾਇਨ ਮੁਲਾਂਕਣ ਤੋਂ ਇਲਾਵਾ, ਸਮੱਸਿਆ ਦਾ ਨਿਪਟਾਰਾ ਅਸੀਂ ਉਤਪਾਦਾਂ ਦੇ ਸਿੱਧੇ ਨਿਰਮਾਣ ਜਾਂ ਉਤਪਾਦਾਂ ਵਿੱਚ ਸਿੱਧੀ ਵਰਤੋਂ ਲਈ ਤੇਜ਼ ਪ੍ਰੋਟੋਟਾਈਪਿੰਗ ਦੀ ਵਰਤੋਂ ਕਰਦੇ ਹਾਂ। ਦੂਜੇ ਸ਼ਬਦਾਂ ਵਿੱਚ, ਤੇਜ਼ ਪ੍ਰੋਟੋਟਾਈਪਿੰਗ ਨੂੰ ਰਵਾਇਤੀ ਪ੍ਰਕਿਰਿਆਵਾਂ ਵਿੱਚ ਸ਼ਾਮਲ ਕੀਤਾ ਜਾ ਸਕਦਾ ਹੈ ਤਾਂ ਜੋ ਉਹਨਾਂ ਨੂੰ ਬਿਹਤਰ ਅਤੇ ਵਧੇਰੇ ਪ੍ਰਤੀਯੋਗੀ ਬਣਾਇਆ ਜਾ ਸਕੇ। ਉਦਾਹਰਨ ਲਈ, ਤੇਜ਼ ਪ੍ਰੋਟੋਟਾਈਪਿੰਗ ਪੈਟਰਨ ਅਤੇ ਮੋਲਡ ਪੈਦਾ ਕਰ ਸਕਦੀ ਹੈ। ਤੇਜ਼ੀ ਨਾਲ ਪ੍ਰੋਟੋਟਾਈਪਿੰਗ ਓਪਰੇਸ਼ਨਾਂ ਦੁਆਰਾ ਬਣਾਏ ਗਏ ਪਿਘਲਣ ਅਤੇ ਬਲਣ ਵਾਲੇ ਪੌਲੀਮਰ ਦੇ ਪੈਟਰਨ ਨੂੰ ਨਿਵੇਸ਼ ਕਾਸਟਿੰਗ ਲਈ ਇਕੱਠਾ ਕੀਤਾ ਜਾ ਸਕਦਾ ਹੈ ਅਤੇ ਨਿਵੇਸ਼ ਕੀਤਾ ਜਾ ਸਕਦਾ ਹੈ। ਜ਼ਿਕਰ ਕਰਨ ਲਈ ਇਕ ਹੋਰ ਉਦਾਹਰਨ ਹੈ 3DP ਦੀ ਵਰਤੋਂ ਵਸਰਾਵਿਕ ਕਾਸਟਿੰਗ ਸ਼ੈੱਲ ਬਣਾਉਣ ਲਈ ਅਤੇ ਸ਼ੈੱਲ ਕਾਸਟਿੰਗ ਓਪਰੇਸ਼ਨਾਂ ਲਈ ਇਸਦੀ ਵਰਤੋਂ ਕਰਨਾ ਹੈ। ਇੱਥੋਂ ਤੱਕ ਕਿ ਇੰਜੈਕਸ਼ਨ ਮੋਲਡ ਅਤੇ ਮੋਲਡ ਇਨਸਰਟਸ ਵੀ ਤੇਜ਼ ਪ੍ਰੋਟੋਟਾਈਪਿੰਗ ਦੁਆਰਾ ਤਿਆਰ ਕੀਤੇ ਜਾ ਸਕਦੇ ਹਨ ਅਤੇ ਕੋਈ ਵੀ ਕਈ ਹਫ਼ਤਿਆਂ ਜਾਂ ਮਹੀਨਿਆਂ ਦੇ ਮੋਲਡ ਬਣਾਉਣ ਦੇ ਲੀਡ ਟਾਈਮ ਨੂੰ ਬਚਾ ਸਕਦਾ ਹੈ। ਸਿਰਫ਼ ਲੋੜੀਂਦੇ ਹਿੱਸੇ ਦੀ ਇੱਕ CAD ਫਾਈਲ ਦਾ ਵਿਸ਼ਲੇਸ਼ਣ ਕਰਕੇ, ਅਸੀਂ ਸੌਫਟਵੇਅਰ ਦੀ ਵਰਤੋਂ ਕਰਕੇ ਟੂਲ ਜਿਓਮੈਟਰੀ ਤਿਆਰ ਕਰ ਸਕਦੇ ਹਾਂ। ਇੱਥੇ ਸਾਡੀਆਂ ਕੁਝ ਪ੍ਰਸਿੱਧ ਤੇਜ਼ ਟੂਲਿੰਗ ਵਿਧੀਆਂ ਹਨ: RTV (ਰੂਮ-ਟੈਂਪਰਚਰ ਵੁਲਕਨਾਈਜ਼ਿੰਗ) ਮੋਲਡਿੰਗ / ਯੂਰੇਥੇਨ ਕਾਸਟਿੰਗ: ਤੇਜ਼ੀ ਨਾਲ ਪ੍ਰੋਟੋਟਾਈਪ ਦੀ ਵਰਤੋਂ ਕਰਕੇ ਲੋੜੀਂਦੇ ਹਿੱਸੇ ਦਾ ਪੈਟਰਨ ਬਣਾਉਣ ਲਈ ਵਰਤਿਆ ਜਾ ਸਕਦਾ ਹੈ। ਫਿਰ ਇਸ ਪੈਟਰਨ ਨੂੰ ਇੱਕ ਵਿਭਾਜਨ ਏਜੰਟ ਨਾਲ ਕੋਟ ਕੀਤਾ ਜਾਂਦਾ ਹੈ ਅਤੇ ਤਰਲ RTV ਰਬੜ ਨੂੰ ਮੋਲਡ ਦੇ ਅੱਧੇ ਹਿੱਸੇ ਬਣਾਉਣ ਲਈ ਪੈਟਰਨ ਉੱਤੇ ਡੋਲ੍ਹਿਆ ਜਾਂਦਾ ਹੈ। ਅੱਗੇ, ਇਹ ਮੋਲਡ ਅੱਧੇ ਮੋਲਡ ਤਰਲ urethanes ਨੂੰ ਇੰਜੈਕਸ਼ਨ ਕਰਨ ਲਈ ਵਰਤੇ ਜਾਂਦੇ ਹਨ। ਮੋਲਡ ਦਾ ਜੀਵਨ ਛੋਟਾ ਹੁੰਦਾ ਹੈ, ਸਿਰਫ਼ 0 ਜਾਂ 30 ਚੱਕਰਾਂ ਵਾਂਗ ਪਰ ਛੋਟੇ ਬੈਚ ਦੇ ਉਤਪਾਦਨ ਲਈ ਕਾਫ਼ੀ ਹੁੰਦਾ ਹੈ। ACES (Acetal Clear Epoxy Solid) ਇੰਜੈਕਸ਼ਨ ਮੋਲਡਿੰਗ : ਤੇਜ਼ ਪ੍ਰੋਟੋਟਾਈਪਿੰਗ ਤਕਨੀਕਾਂ ਜਿਵੇਂ ਕਿ ਸਟੀਰੀਓਲੀਥੋਗ੍ਰਾਫੀ ਦੀ ਵਰਤੋਂ ਕਰਦੇ ਹੋਏ, ਅਸੀਂ ਇੰਜੈਕਸ਼ਨ ਮੋਲਡ ਤਿਆਰ ਕਰਦੇ ਹਾਂ। ਇਹ ਮੋਲਡ ਖੁੱਲੇ ਸਿਰੇ ਵਾਲੇ ਸ਼ੈੱਲ ਹੁੰਦੇ ਹਨ ਜੋ ਇਪੌਕਸੀ, ਐਲੂਮੀਨੀਅਮ ਨਾਲ ਭਰੇ ਇਪੌਕਸੀ ਜਾਂ ਧਾਤਾਂ ਵਰਗੀਆਂ ਸਮੱਗਰੀਆਂ ਨਾਲ ਭਰਨ ਦੀ ਆਗਿਆ ਦਿੰਦੇ ਹਨ। ਦੁਬਾਰਾ ਮੋਲਡ ਲਾਈਫ ਦਸਾਂ ਜਾਂ ਵੱਧ ਤੋਂ ਵੱਧ ਸੈਂਕੜੇ ਹਿੱਸਿਆਂ ਤੱਕ ਸੀਮਿਤ ਹੈ। ਸਪਰੇਅਡ ਮੈਟਲ ਟੂਲਿੰਗ ਪ੍ਰਕਿਰਿਆ: ਅਸੀਂ ਤੇਜ਼ ਪ੍ਰੋਟੋਟਾਈਪਿੰਗ ਦੀ ਵਰਤੋਂ ਕਰਦੇ ਹਾਂ ਅਤੇ ਇੱਕ ਪੈਟਰਨ ਬਣਾਉਂਦੇ ਹਾਂ। ਅਸੀਂ ਪੈਟਰਨ ਦੀ ਸਤ੍ਹਾ 'ਤੇ ਜ਼ਿੰਕ-ਅਲਮੀਨੀਅਮ ਮਿਸ਼ਰਤ ਦਾ ਛਿੜਕਾਅ ਕਰਦੇ ਹਾਂ ਅਤੇ ਇਸ ਨੂੰ ਕੋਟ ਕਰਦੇ ਹਾਂ। ਧਾਤ ਦੀ ਪਰਤ ਵਾਲਾ ਪੈਟਰਨ ਫਿਰ ਇੱਕ ਫਲਾਸਕ ਦੇ ਅੰਦਰ ਰੱਖਿਆ ਜਾਂਦਾ ਹੈ ਅਤੇ ਇੱਕ ਇਪੌਕਸੀ ਜਾਂ ਐਲੂਮੀਨੀਅਮ ਨਾਲ ਭਰੇ ਇਪੌਕਸੀ ਨਾਲ ਘੜੇ ਵਿੱਚ ਰੱਖਿਆ ਜਾਂਦਾ ਹੈ। ਅੰਤ ਵਿੱਚ, ਇਸਨੂੰ ਹਟਾ ਦਿੱਤਾ ਜਾਂਦਾ ਹੈ ਅਤੇ ਦੋ ਅਜਿਹੇ ਮੋਲਡ ਅੱਧੇ ਪੈਦਾ ਕਰਕੇ ਅਸੀਂ ਇੰਜੈਕਸ਼ਨ ਮੋਲਡਿੰਗ ਲਈ ਇੱਕ ਪੂਰਾ ਮੋਲਡ ਪ੍ਰਾਪਤ ਕਰਦੇ ਹਾਂ। ਇਹਨਾਂ ਮੋਲਡਾਂ ਦੀ ਉਮਰ ਲੰਬੀ ਹੁੰਦੀ ਹੈ, ਕੁਝ ਮਾਮਲਿਆਂ ਵਿੱਚ ਸਮੱਗਰੀ ਅਤੇ ਤਾਪਮਾਨ ਦੇ ਅਧਾਰ ਤੇ ਇਹ ਹਜ਼ਾਰਾਂ ਵਿੱਚ ਹਿੱਸੇ ਪੈਦਾ ਕਰ ਸਕਦੇ ਹਨ। ਕੀਲਟੂਲ ਪ੍ਰਕਿਰਿਆ: ਇਹ ਤਕਨੀਕ 100,000 ਤੋਂ 10 ਮਿਲੀਅਨ ਸਾਈਕਲ ਲਾਈਫ ਦੇ ਨਾਲ ਮੋਲਡ ਤਿਆਰ ਕਰ ਸਕਦੀ ਹੈ। ਤੇਜ਼ ਪ੍ਰੋਟੋਟਾਈਪਿੰਗ ਦੀ ਵਰਤੋਂ ਕਰਕੇ ਅਸੀਂ ਇੱਕ RTV ਮੋਲਡ ਤਿਆਰ ਕਰਦੇ ਹਾਂ। ਉੱਲੀ ਨੂੰ ਅੱਗੇ ਇੱਕ ਮਿਸ਼ਰਣ ਨਾਲ ਭਰਿਆ ਜਾਂਦਾ ਹੈ ਜਿਸ ਵਿੱਚ A6 ਟੂਲ ਸਟੀਲ ਪਾਊਡਰ, ਟੰਗਸਟਨ ਕਾਰਬਾਈਡ, ਪੋਲੀਮਰ ਬਾਈਂਡਰ ਅਤੇ ਇਲਾਜ ਲਈ ਦਿੱਤਾ ਜਾਂਦਾ ਹੈ। ਇਸ ਮੋਲਡ ਨੂੰ ਫਿਰ ਪੋਲੀਮਰ ਨੂੰ ਸਾੜਨ ਅਤੇ ਧਾਤ ਦੇ ਪਾਊਡਰ ਨੂੰ ਫਿਊਜ਼ ਕਰਨ ਲਈ ਗਰਮ ਕੀਤਾ ਜਾਂਦਾ ਹੈ। ਅਗਲਾ ਕਦਮ ਫਾਈਨਲ ਮੋਲਡ ਬਣਾਉਣ ਲਈ ਤਾਂਬੇ ਦੀ ਘੁਸਪੈਠ ਹੈ। ਜੇ ਲੋੜ ਹੋਵੇ, ਤਾਂ ਵਧੀਆ ਆਯਾਮੀ ਸ਼ੁੱਧਤਾ ਲਈ ਉੱਲੀ 'ਤੇ ਮਸ਼ੀਨਿੰਗ ਅਤੇ ਪਾਲਿਸ਼ਿੰਗ ਵਰਗੇ ਸੈਕੰਡਰੀ ਓਪਰੇਸ਼ਨ ਕੀਤੇ ਜਾ ਸਕਦੇ ਹਨ। _cc781905-5cde-3194-bb3b-1358cd_5 CLICK Product Finder-Locator Service ਪਿਛਲੇ ਸਫ਼ੇ
- Composites, Composite Materials Manufacturing, Fiber Reinforced
Composites, Composite Materials Manufacturing, Particle and Fiber Reinforced, Cermets, Ceramic & Metal Composite, Glass Fiber Reinforced Polymer, Lay-Up Process ਕੰਪੋਜ਼ਿਟ ਅਤੇ ਕੰਪੋਜ਼ਿਟ ਮੈਟੀਰੀਅਲ ਮੈਨੂਫੈਕਚਰਿੰਗ ਸਾਧਾਰਨ ਤੌਰ 'ਤੇ ਪਰਿਭਾਸ਼ਿਤ ਕੀਤਾ ਗਿਆ ਹੈ, ਮਿਸ਼ਰਿਤ ਜਾਂ ਮਿਸ਼ਰਿਤ ਪਦਾਰਥ ਵੱਖੋ-ਵੱਖਰੀਆਂ ਭੌਤਿਕ ਜਾਂ ਰਸਾਇਣਕ ਵਿਸ਼ੇਸ਼ਤਾਵਾਂ ਵਾਲੀਆਂ ਦੋ ਜਾਂ ਕਈ ਸਮੱਗਰੀਆਂ ਵਾਲੀ ਸਮੱਗਰੀ ਹਨ, ਪਰ ਜਦੋਂ ਉਹ ਸੰਯੁਕਤ ਸਮੱਗਰੀ ਬਣਦੇ ਹਨ ਤਾਂ ਉਹ ਸਮੱਗਰੀ ਬਣ ਜਾਂਦੇ ਹਨ ਜੋ ਸੰਘਟਕ ਸਮੱਗਰੀ ਤੋਂ ਵੱਖਰੀ ਹੁੰਦੀ ਹੈ। ਸਾਨੂੰ ਇਹ ਦੱਸਣ ਦੀ ਲੋੜ ਹੈ ਕਿ ਸੰਘਟਕ ਸਮੱਗਰੀ ਬਣਤਰ ਵਿੱਚ ਵੱਖਰੀ ਅਤੇ ਵੱਖਰੀ ਰਹਿੰਦੀ ਹੈ। ਇੱਕ ਸੰਯੁਕਤ ਸਮੱਗਰੀ ਦੇ ਨਿਰਮਾਣ ਵਿੱਚ ਟੀਚਾ ਇੱਕ ਉਤਪਾਦ ਪ੍ਰਾਪਤ ਕਰਨਾ ਹੈ ਜੋ ਇਸਦੇ ਭਾਗਾਂ ਨਾਲੋਂ ਉੱਤਮ ਹੈ ਅਤੇ ਹਰੇਕ ਹਿੱਸੇ ਦੀਆਂ ਲੋੜੀਂਦੀਆਂ ਵਿਸ਼ੇਸ਼ਤਾਵਾਂ ਨੂੰ ਜੋੜਦਾ ਹੈ। ਇੱਕ ਉਦਾਹਰਨ ਦੇ ਤੌਰ ਤੇ; ਤਾਕਤ, ਘੱਟ ਵਜ਼ਨ ਜਾਂ ਘੱਟ ਕੀਮਤ ਕੰਪੋਜ਼ਿਟ ਨੂੰ ਡਿਜ਼ਾਈਨ ਕਰਨ ਅਤੇ ਬਣਾਉਣ ਦੇ ਪਿੱਛੇ ਪ੍ਰੇਰਕ ਹੋ ਸਕਦੀ ਹੈ। ਕੰਪੋਜ਼ਿਟਸ ਦੀ ਕਿਸਮ ਜੋ ਅਸੀਂ ਪੇਸ਼ ਕਰਦੇ ਹਾਂ ਉਹ ਹਨ ਕਣ-ਮਜਬੂਤ ਕੰਪੋਜ਼ਿਟਸ, ਫਾਈਬਰ-ਰੀਇਨਫੋਰਸਡ ਕੰਪੋਜ਼ਿਟਸ ਜਿਸ ਵਿੱਚ ਸਿਰੇਮਿਕ-ਮੈਟ੍ਰਿਕਸ / ਪੋਲੀਮਰ-ਮੈਟ੍ਰਿਕਸ / ਮੈਟਲ-ਮੈਟ੍ਰਿਕਸ / ਕਾਰਬਨ-ਕਾਰਬਨ / ਹਾਈਬ੍ਰਿਡ ਕੰਪੋਜ਼ਿਟਸ, ਸਟ੍ਰਕਚਰਲ ਅਤੇ ਲੈਮੀਨੇਟਡ ਅਤੇ ਸੈਂਡਵਿਚ-ਸਟ੍ਰਕਚਰਡ ਕੰਪੋਜ਼ਿਟਸ ਅਤੇ ਨੈਨੋਕੰਪੋਜ਼ਿਟਸ ਸ਼ਾਮਲ ਹਨ। ਫੈਬਰੀਕੇਸ਼ਨ ਤਕਨੀਕਾਂ ਜੋ ਅਸੀਂ ਕੰਪੋਜ਼ਿਟ ਮਟੀਰੀਅਲ ਮੈਨੂਫੈਕਚਰਿੰਗ ਵਿੱਚ ਲਾਗੂ ਕਰਦੇ ਹਾਂ ਉਹ ਹਨ: ਪਲਟਰੂਸ਼ਨ, ਪ੍ਰੀਪ੍ਰੇਗ ਪ੍ਰੋਡਕਸ਼ਨ ਪ੍ਰਕਿਰਿਆਵਾਂ, ਐਡਵਾਂਸਡ ਫਾਈਬਰ ਪਲੇਸਮੈਂਟ, ਫਿਲਾਮੈਂਟ ਵਿੰਡਿੰਗ, ਟੇਲਰਡ ਫਾਈਬਰ ਪਲੇਸਮੈਂਟ, ਫਾਈਬਰਗਲਾਸ ਸਪਰੇਅ ਲੇਅ-ਅਪ ਪ੍ਰਕਿਰਿਆ, ਟੂਫਟਿੰਗ, ਲੈਨਕਸਾਈਡ ਪ੍ਰਕਿਰਿਆ, ਜ਼ੈੱਡ-ਪਿਨਿੰਗ। ਬਹੁਤ ਸਾਰੀਆਂ ਮਿਸ਼ਰਿਤ ਸਮੱਗਰੀਆਂ ਦੋ ਪੜਾਵਾਂ ਤੋਂ ਬਣੀਆਂ ਹੁੰਦੀਆਂ ਹਨ, ਮੈਟ੍ਰਿਕਸ, ਜੋ ਨਿਰੰਤਰ ਹੁੰਦਾ ਹੈ ਅਤੇ ਦੂਜੇ ਪੜਾਅ ਨੂੰ ਘੇਰਦਾ ਹੈ; ਅਤੇ ਖਿੰਡੇ ਹੋਏ ਪੜਾਅ ਜੋ ਮੈਟ੍ਰਿਕਸ ਨਾਲ ਘਿਰਿਆ ਹੋਇਆ ਹੈ। ਅਸੀਂ ਸਿਫ਼ਾਰਿਸ਼ ਕਰਦੇ ਹਾਂ ਕਿ ਤੁਸੀਂ ਇੱਥੇ ਕਲਿੱਕ ਕਰੋAGS-TECH Inc ਦੁਆਰਾ ਕੰਪੋਜ਼ਿਟਸ ਅਤੇ ਕੰਪੋਜ਼ਿਟ ਮਟੀਰੀਅਲ ਮੈਨੂਫੈਕਚਰਿੰਗ ਦੇ ਸਾਡੇ ਯੋਜਨਾਬੱਧ ਚਿੱਤਰਾਂ ਨੂੰ ਡਾਉਨਲੋਡ ਕਰੋ। ਇਹ ਤੁਹਾਨੂੰ ਉਸ ਜਾਣਕਾਰੀ ਨੂੰ ਬਿਹਤਰ ਤਰੀਕੇ ਨਾਲ ਸਮਝਣ ਵਿੱਚ ਮਦਦ ਕਰੇਗਾ ਜੋ ਅਸੀਂ ਤੁਹਾਨੂੰ ਹੇਠਾਂ ਪ੍ਰਦਾਨ ਕਰ ਰਹੇ ਹਾਂ। • ਕਣ-ਮਜਬੂਤ ਕੰਪੋਜ਼ਿਟਸ: ਇਸ ਸ਼੍ਰੇਣੀ ਵਿੱਚ ਦੋ ਕਿਸਮਾਂ ਦੇ ਹੁੰਦੇ ਹਨ: ਵੱਡੇ-ਕਣ ਕੰਪੋਜ਼ਿਟ ਅਤੇ ਫੈਲਾਅ-ਮਜਬੂਤ ਕੰਪੋਜ਼ਿਟਸ। ਪਿਛਲੀ ਕਿਸਮ ਵਿੱਚ, ਕਣ-ਮੈਟ੍ਰਿਕਸ ਪਰਸਪਰ ਕ੍ਰਿਆਵਾਂ ਨੂੰ ਪਰਮਾਣੂ ਜਾਂ ਅਣੂ ਪੱਧਰ 'ਤੇ ਨਹੀਂ ਮੰਨਿਆ ਜਾ ਸਕਦਾ ਹੈ। ਇਸ ਦੀ ਬਜਾਏ ਨਿਰੰਤਰ ਮਕੈਨਿਕਸ ਵੈਧ ਹੈ। ਦੂਜੇ ਪਾਸੇ, ਫੈਲਾਅ-ਮਜਬੂਤ ਕੰਪੋਜ਼ਿਟਸ ਵਿੱਚ ਕਣ ਆਮ ਤੌਰ 'ਤੇ ਨੈਨੋਮੀਟਰ ਰੇਂਜਾਂ ਦੇ ਦਸਾਂ ਵਿੱਚ ਬਹੁਤ ਛੋਟੇ ਹੁੰਦੇ ਹਨ। ਵੱਡੇ ਕਣ ਕੰਪੋਜ਼ਿਟ ਦੀ ਇੱਕ ਉਦਾਹਰਨ ਪੋਲੀਮਰ ਹੈ ਜਿਸ ਵਿੱਚ ਫਿਲਰ ਸ਼ਾਮਲ ਕੀਤੇ ਗਏ ਹਨ। ਫਿਲਰ ਸਮੱਗਰੀ ਦੀਆਂ ਵਿਸ਼ੇਸ਼ਤਾਵਾਂ ਨੂੰ ਸੁਧਾਰਦੇ ਹਨ ਅਤੇ ਕੁਝ ਪੌਲੀਮਰ ਵਾਲੀਅਮ ਨੂੰ ਵਧੇਰੇ ਕਿਫਾਇਤੀ ਸਮੱਗਰੀ ਨਾਲ ਬਦਲ ਸਕਦੇ ਹਨ। ਦੋ ਪੜਾਵਾਂ ਦੇ ਵਾਲੀਅਮ ਫਰੈਕਸ਼ਨ ਕੰਪੋਜ਼ਿਟ ਦੇ ਵਿਹਾਰ ਨੂੰ ਪ੍ਰਭਾਵਿਤ ਕਰਦੇ ਹਨ। ਧਾਤ, ਪੌਲੀਮਰ ਅਤੇ ਵਸਰਾਵਿਕਸ ਨਾਲ ਵੱਡੇ ਕਣ ਕੰਪੋਜ਼ਿਟ ਵਰਤੇ ਜਾਂਦੇ ਹਨ। CERMETS ਵਸਰਾਵਿਕ/ਧਾਤੂ ਮਿਸ਼ਰਣਾਂ ਦੀਆਂ ਉਦਾਹਰਣਾਂ ਹਨ। ਸਾਡਾ ਸਭ ਤੋਂ ਆਮ ਸਰਮੇਟ ਸੀਮਿੰਟਡ ਕਾਰਬਾਈਡ ਹੈ। ਇਸ ਵਿੱਚ ਰਿਫ੍ਰੈਕਟਰੀ ਕਾਰਬਾਈਡ ਸਿਰੇਮਿਕ ਜਿਵੇਂ ਕਿ ਕੋਬਾਲਟ ਜਾਂ ਨਿਕਲ ਵਰਗੀ ਧਾਤੂ ਦੇ ਮੈਟ੍ਰਿਕਸ ਵਿੱਚ ਟੰਗਸਟਨ ਕਾਰਬਾਈਡ ਕਣ ਹੁੰਦੇ ਹਨ। ਇਹ ਕਾਰਬਾਈਡ ਕੰਪੋਜ਼ਿਟ ਕਠੋਰ ਸਟੀਲ ਲਈ ਕਟਿੰਗ ਟੂਲ ਵਜੋਂ ਵਿਆਪਕ ਤੌਰ 'ਤੇ ਵਰਤੇ ਜਾਂਦੇ ਹਨ। ਕਠੋਰ ਕਾਰਬਾਈਡ ਕਣ ਕੱਟਣ ਦੀ ਕਾਰਵਾਈ ਲਈ ਜ਼ਿੰਮੇਵਾਰ ਹੁੰਦੇ ਹਨ ਅਤੇ ਉਹਨਾਂ ਦੀ ਕਠੋਰਤਾ ਨੂੰ ਨਕਲੀ ਧਾਤੂ ਮੈਟ੍ਰਿਕਸ ਦੁਆਰਾ ਵਧਾਇਆ ਜਾਂਦਾ ਹੈ। ਇਸ ਤਰ੍ਹਾਂ ਅਸੀਂ ਇੱਕ ਸਿੰਗਲ ਕੰਪੋਜ਼ਿਟ ਵਿੱਚ ਦੋਵਾਂ ਸਮੱਗਰੀਆਂ ਦੇ ਫਾਇਦੇ ਪ੍ਰਾਪਤ ਕਰਦੇ ਹਾਂ। ਇੱਕ ਵੱਡੇ ਕਣ ਮਿਸ਼ਰਣ ਦੀ ਇੱਕ ਹੋਰ ਆਮ ਉਦਾਹਰਨ ਹੈ ਜੋ ਅਸੀਂ ਵਰਤਦੇ ਹਾਂ ਕਾਰਬਨ ਬਲੈਕ ਕਣਾਂ ਨੂੰ ਵੁਲਕੇਨਾਈਜ਼ਡ ਰਬੜ ਵਿੱਚ ਮਿਲਾਇਆ ਜਾਂਦਾ ਹੈ ਤਾਂ ਜੋ ਉੱਚ ਤਨਾਅ ਸ਼ਕਤੀ, ਕਠੋਰਤਾ, ਅੱਥਰੂ ਅਤੇ ਘਬਰਾਹਟ ਪ੍ਰਤੀਰੋਧ ਦੇ ਨਾਲ ਮਿਸ਼ਰਤ ਪ੍ਰਾਪਤ ਕੀਤਾ ਜਾ ਸਕੇ। ਇੱਕ ਫੈਲਾਅ-ਮਜਬੂਤ ਮਿਸ਼ਰਣ ਦੀ ਇੱਕ ਉਦਾਹਰਨ ਹੈ ਧਾਤਾਂ ਅਤੇ ਧਾਤ ਦੇ ਮਿਸ਼ਰਤ ਇੱਕ ਬਹੁਤ ਹੀ ਸਖ਼ਤ ਅਤੇ ਅਟੱਲ ਪਦਾਰਥ ਦੇ ਬਰੀਕ ਕਣਾਂ ਦੇ ਇੱਕਸਾਰ ਫੈਲਾਅ ਦੁਆਰਾ ਮਜ਼ਬੂਤ ਅਤੇ ਸਖ਼ਤ ਹੁੰਦੇ ਹਨ। ਜਦੋਂ ਅਲਮੀਨੀਅਮ ਮੈਟਲ ਮੈਟ੍ਰਿਕਸ ਵਿੱਚ ਬਹੁਤ ਛੋਟੇ ਅਲਮੀਨੀਅਮ ਆਕਸਾਈਡ ਫਲੇਕਸ ਸ਼ਾਮਲ ਕੀਤੇ ਜਾਂਦੇ ਹਨ ਤਾਂ ਅਸੀਂ ਸਿੰਟਰਡ ਅਲਮੀਨੀਅਮ ਪਾਊਡਰ ਪ੍ਰਾਪਤ ਕਰਦੇ ਹਾਂ ਜਿਸ ਵਿੱਚ ਉੱਚ-ਤਾਪਮਾਨ ਦੀ ਤਾਕਤ ਹੁੰਦੀ ਹੈ। • ਫਾਈਬਰ-ਰੀਇਨਫੋਰਸਡ ਕੰਪੋਜ਼ਿਟਸ: ਕੰਪੋਜ਼ਿਟਸ ਦੀ ਇਹ ਸ਼੍ਰੇਣੀ ਅਸਲ ਵਿੱਚ ਸਭ ਤੋਂ ਮਹੱਤਵਪੂਰਨ ਹੈ। ਪ੍ਰਾਪਤ ਕਰਨ ਦਾ ਟੀਚਾ ਪ੍ਰਤੀ ਯੂਨਿਟ ਭਾਰ ਉੱਚ ਤਾਕਤ ਅਤੇ ਕਠੋਰਤਾ ਹੈ। ਇਹਨਾਂ ਮਿਸ਼ਰਣਾਂ ਵਿੱਚ ਫਾਈਬਰ ਦੀ ਰਚਨਾ, ਲੰਬਾਈ, ਸਥਿਤੀ ਅਤੇ ਇਕਾਗਰਤਾ ਇਹਨਾਂ ਸਮੱਗਰੀਆਂ ਦੀਆਂ ਵਿਸ਼ੇਸ਼ਤਾਵਾਂ ਅਤੇ ਉਪਯੋਗਤਾ ਨੂੰ ਨਿਰਧਾਰਤ ਕਰਨ ਵਿੱਚ ਮਹੱਤਵਪੂਰਨ ਹੈ। ਫਾਈਬਰਾਂ ਦੇ ਤਿੰਨ ਸਮੂਹ ਹਨ ਜਿਨ੍ਹਾਂ ਦੀ ਅਸੀਂ ਵਰਤੋਂ ਕਰਦੇ ਹਾਂ: ਮੁੱਛਾਂ, ਫਾਈਬਰ ਅਤੇ ਤਾਰਾਂ। WHISKERS ਬਹੁਤ ਪਤਲੇ ਅਤੇ ਲੰਬੇ ਸਿੰਗਲ ਕ੍ਰਿਸਟਲ ਹੁੰਦੇ ਹਨ। ਉਹ ਸਭ ਤੋਂ ਮਜ਼ਬੂਤ ਸਮੱਗਰੀਆਂ ਵਿੱਚੋਂ ਹਨ। ਗ੍ਰੇਫਾਈਟ, ਸਿਲੀਕਾਨ ਨਾਈਟਰਾਈਡ, ਐਲੂਮੀਨੀਅਮ ਆਕਸਾਈਡ ਦੀਆਂ ਕੁਝ ਉਦਾਹਰਣਾਂ ਹਨ। ਦੂਜੇ ਪਾਸੇ FIBERS ਜ਼ਿਆਦਾਤਰ ਪੌਲੀਮਰ ਜਾਂ ਵਸਰਾਵਿਕ ਹਨ ਅਤੇ ਪੌਲੀਕ੍ਰਿਸਟਲਾਈਨ ਜਾਂ ਅਮੋਰਫਸ ਅਵਸਥਾ ਵਿੱਚ ਹਨ। ਤੀਸਰਾ ਸਮੂਹ ਬਰੀਕ ਤਾਰਾਂ ਹਨ ਜਿਨ੍ਹਾਂ ਦਾ ਵਿਆਸ ਮੁਕਾਬਲਤਨ ਵੱਡੇ ਹੁੰਦਾ ਹੈ ਅਤੇ ਅਕਸਰ ਸਟੀਲ ਜਾਂ ਟੰਗਸਟਨ ਦੇ ਹੁੰਦੇ ਹਨ। ਵਾਇਰ ਰੀਇਨਫੋਰਸਡ ਕੰਪੋਜ਼ਿਟ ਦੀ ਇੱਕ ਉਦਾਹਰਣ ਕਾਰ ਦੇ ਟਾਇਰ ਹਨ ਜੋ ਰਬੜ ਦੇ ਅੰਦਰ ਸਟੀਲ ਤਾਰ ਨੂੰ ਸ਼ਾਮਲ ਕਰਦੇ ਹਨ। ਮੈਟ੍ਰਿਕਸ ਸਮੱਗਰੀ 'ਤੇ ਨਿਰਭਰ ਕਰਦਿਆਂ, ਸਾਡੇ ਕੋਲ ਹੇਠਾਂ ਦਿੱਤੇ ਕੰਪੋਜ਼ਿਟ ਹਨ: ਪੌਲੀਮਰ-ਮੈਟ੍ਰਿਕਸ ਕੰਪੋਜ਼ਿਟਸ: ਇਹ ਇੱਕ ਪੌਲੀਮਰ ਰੈਜ਼ਿਨ ਅਤੇ ਫਾਈਬਰਸ ਦੇ ਬਣੇ ਹੁੰਦੇ ਹਨ ਜਿਵੇਂ ਕਿ ਮਜ਼ਬੂਤੀ ਸਮੱਗਰੀ। ਇਹਨਾਂ ਦਾ ਇੱਕ ਉਪ ਸਮੂਹ ਗਲਾਸ ਫਾਈਬਰ-ਰੀਇਨਫੋਰਸਡ ਪੋਲੀਮਰ (GFRP) ਕੰਪੋਜ਼ਿਟਸ ਵਿੱਚ ਇੱਕ ਪੌਲੀਮਰ ਮੈਟ੍ਰਿਕਸ ਦੇ ਅੰਦਰ ਨਿਰੰਤਰ ਜਾਂ ਬੰਦ ਗਲਾਸ ਫਾਈਬਰ ਹੁੰਦੇ ਹਨ। ਗਲਾਸ ਉੱਚ ਤਾਕਤ ਦੀ ਪੇਸ਼ਕਸ਼ ਕਰਦਾ ਹੈ, ਇਹ ਕਿਫ਼ਾਇਤੀ ਹੈ, ਫਾਈਬਰਾਂ ਵਿੱਚ ਬਣਾਉਣਾ ਆਸਾਨ ਹੈ, ਅਤੇ ਰਸਾਇਣਕ ਤੌਰ 'ਤੇ ਅੜਿੱਕਾ ਹੈ। ਨੁਕਸਾਨ ਉਹਨਾਂ ਦੀ ਸੀਮਤ ਕਠੋਰਤਾ ਅਤੇ ਕਠੋਰਤਾ ਹਨ, ਸੇਵਾ ਦਾ ਤਾਪਮਾਨ ਸਿਰਫ 200 - 300 ਸੈਂਟੀਗਰੇਡ ਤੱਕ ਹੈ। ਫਾਈਬਰਗਲਾਸ ਆਟੋਮੋਟਿਵ ਬਾਡੀਜ਼ ਅਤੇ ਟ੍ਰਾਂਸਪੋਰਟੇਸ਼ਨ ਸਾਜ਼ੋ-ਸਾਮਾਨ, ਸਮੁੰਦਰੀ ਵਾਹਨਾਂ, ਸਟੋਰੇਜ ਕੰਟੇਨਰਾਂ ਲਈ ਢੁਕਵਾਂ ਹੈ। ਇਹ ਸੀਮਤ ਕਠੋਰਤਾ ਦੇ ਕਾਰਨ ਏਰੋਸਪੇਸ ਜਾਂ ਪੁਲ ਬਣਾਉਣ ਲਈ ਢੁਕਵੇਂ ਨਹੀਂ ਹਨ। ਦੂਜੇ ਉਪ ਸਮੂਹ ਨੂੰ ਕਾਰਬਨ ਫਾਈਬਰ-ਰੀਇਨਫੋਰਸਡ ਪੋਲੀਮਰ (CFRP) ਕੰਪੋਜ਼ਿਟ ਕਿਹਾ ਜਾਂਦਾ ਹੈ। ਇੱਥੇ, ਪੌਲੀਮਰ ਮੈਟਰਿਕਸ ਵਿੱਚ ਕਾਰਬਨ ਸਾਡੀ ਫਾਈਬਰ ਸਮੱਗਰੀ ਹੈ। ਕਾਰਬਨ ਇਸਦੇ ਉੱਚ ਵਿਸ਼ੇਸ਼ ਮਾਡਿਊਲਸ ਅਤੇ ਤਾਕਤ ਅਤੇ ਉੱਚ ਤਾਪਮਾਨਾਂ 'ਤੇ ਇਹਨਾਂ ਨੂੰ ਬਣਾਈ ਰੱਖਣ ਦੀ ਸਮਰੱਥਾ ਲਈ ਜਾਣਿਆ ਜਾਂਦਾ ਹੈ। ਕਾਰਬਨ ਫਾਈਬਰ ਸਾਨੂੰ ਸਟੈਂਡਰਡ, ਇੰਟਰਮੀਡੀਏਟ, ਹਾਈ ਅਤੇ ਅਲਟਰਾਹਾਈ ਟੈਂਸਿਲ ਮੋਡਿਊਲੀ ਦੀ ਪੇਸ਼ਕਸ਼ ਕਰ ਸਕਦੇ ਹਨ। ਇਸ ਤੋਂ ਇਲਾਵਾ, ਕਾਰਬਨ ਫਾਈਬਰ ਵਿਭਿੰਨ ਭੌਤਿਕ ਅਤੇ ਮਕੈਨੀਕਲ ਵਿਸ਼ੇਸ਼ਤਾਵਾਂ ਦੀ ਪੇਸ਼ਕਸ਼ ਕਰਦੇ ਹਨ ਅਤੇ ਇਸਲਈ ਵਿਭਿੰਨ ਕਸਟਮ ਅਨੁਕੂਲਿਤ ਇੰਜੀਨੀਅਰਿੰਗ ਐਪਲੀਕੇਸ਼ਨਾਂ ਲਈ ਢੁਕਵਾਂ ਹੈ। CFRP ਕੰਪੋਜ਼ਿਟਸ ਨੂੰ ਖੇਡਾਂ ਅਤੇ ਮਨੋਰੰਜਨ ਸਾਜ਼ੋ-ਸਾਮਾਨ, ਦਬਾਅ ਵਾਲੇ ਜਹਾਜ਼ਾਂ ਅਤੇ ਏਰੋਸਪੇਸ ਸਟ੍ਰਕਚਰਲ ਕੰਪੋਨੈਂਟਸ ਬਣਾਉਣ ਲਈ ਮੰਨਿਆ ਜਾ ਸਕਦਾ ਹੈ। ਫਿਰ ਵੀ, ਇੱਕ ਹੋਰ ਉਪ-ਸਮੂਹ, ਅਰਾਮਿਡ ਫਾਈਬਰ-ਰੀਇਨਫੋਰਸਡ ਪੋਲੀਮਰ ਕੰਪੋਜ਼ਿਟਸ ਵੀ ਉੱਚ-ਤਾਕਤ ਅਤੇ ਮਾਡੂਲਸ ਸਮੱਗਰੀ ਹਨ। ਉਹਨਾਂ ਦੀ ਤਾਕਤ ਤੋਂ ਭਾਰ ਅਨੁਪਾਤ ਬਹੁਤ ਜ਼ਿਆਦਾ ਹੈ। ਅਰਾਮਿਡ ਫਾਈਬਰਸ ਨੂੰ ਵਪਾਰਕ ਨਾਮ ਕੇਵਲਰ ਅਤੇ ਨੋਮੈਕਸ ਦੁਆਰਾ ਵੀ ਜਾਣਿਆ ਜਾਂਦਾ ਹੈ। ਤਣਾਅ ਦੇ ਅਧੀਨ ਉਹ ਹੋਰ ਪੌਲੀਮੇਰਿਕ ਫਾਈਬਰ ਸਮੱਗਰੀਆਂ ਨਾਲੋਂ ਵਧੀਆ ਪ੍ਰਦਰਸ਼ਨ ਕਰਦੇ ਹਨ, ਪਰ ਉਹ ਸੰਕੁਚਨ ਵਿੱਚ ਕਮਜ਼ੋਰ ਹੁੰਦੇ ਹਨ। ਅਰਾਮਿਡ ਫਾਈਬਰ ਸਖ਼ਤ, ਪ੍ਰਭਾਵ ਰੋਧਕ, ਕ੍ਰੀਪ ਅਤੇ ਥਕਾਵਟ ਰੋਧਕ, ਉੱਚ ਤਾਪਮਾਨਾਂ 'ਤੇ ਸਥਿਰ, ਮਜ਼ਬੂਤ ਐਸਿਡ ਅਤੇ ਬੇਸਾਂ ਨੂੰ ਛੱਡ ਕੇ ਰਸਾਇਣਕ ਤੌਰ 'ਤੇ ਅੜਿੱਕੇ ਹੁੰਦੇ ਹਨ। ਅਰਾਮਿਡ ਫਾਈਬਰਸ ਦੀ ਵਰਤੋਂ ਖੇਡਾਂ ਦੇ ਸਮਾਨ, ਬੁਲੇਟਪਰੂਫ ਵੇਸਟਾਂ, ਟਾਇਰਾਂ, ਰੱਸੀਆਂ, ਫਾਈਬਰ ਆਪਟਿਕ ਕੇਬਲ ਸ਼ੀਟਾਂ ਵਿੱਚ ਕੀਤੀ ਜਾਂਦੀ ਹੈ। ਹੋਰ ਫਾਈਬਰ ਰੀਨਫੋਰਸਮੈਂਟ ਸਮੱਗਰੀ ਮੌਜੂਦ ਹੈ ਪਰ ਘੱਟ ਡਿਗਰੀ ਲਈ ਵਰਤੀ ਜਾਂਦੀ ਹੈ। ਇਹ ਮੁੱਖ ਤੌਰ 'ਤੇ ਬੋਰਾਨ, ਸਿਲੀਕਾਨ ਕਾਰਬਾਈਡ, ਐਲੂਮੀਨੀਅਮ ਆਕਸਾਈਡ ਹਨ। ਦੂਜੇ ਪਾਸੇ ਪੌਲੀਮਰ ਮੈਟਰਿਕਸ ਸਮੱਗਰੀ ਵੀ ਨਾਜ਼ੁਕ ਹੈ। ਇਹ ਕੰਪੋਜ਼ਿਟ ਦਾ ਵੱਧ ਤੋਂ ਵੱਧ ਸੇਵਾ ਤਾਪਮਾਨ ਨਿਰਧਾਰਤ ਕਰਦਾ ਹੈ ਕਿਉਂਕਿ ਪੌਲੀਮਰ ਵਿੱਚ ਆਮ ਤੌਰ 'ਤੇ ਪਿਘਲਣ ਅਤੇ ਡਿਗਰੇਡੇਸ਼ਨ ਦਾ ਤਾਪਮਾਨ ਘੱਟ ਹੁੰਦਾ ਹੈ। ਪੋਲੀਸਟਰ ਅਤੇ ਵਿਨਾਇਲ ਐਸਟਰ ਵਿਆਪਕ ਤੌਰ 'ਤੇ ਪੋਲੀਮਰ ਮੈਟ੍ਰਿਕਸ ਵਜੋਂ ਵਰਤੇ ਜਾਂਦੇ ਹਨ। ਰੈਜ਼ਿਨ ਦੀ ਵਰਤੋਂ ਵੀ ਕੀਤੀ ਜਾਂਦੀ ਹੈ ਅਤੇ ਉਹਨਾਂ ਕੋਲ ਸ਼ਾਨਦਾਰ ਨਮੀ ਪ੍ਰਤੀਰੋਧ ਅਤੇ ਮਕੈਨੀਕਲ ਵਿਸ਼ੇਸ਼ਤਾਵਾਂ ਹੁੰਦੀਆਂ ਹਨ। ਉਦਾਹਰਨ ਲਈ ਪੌਲੀਮਾਈਡ ਰਾਲ ਲਗਭਗ 230 ਡਿਗਰੀ ਸੈਲਸੀਅਸ ਤੱਕ ਵਰਤੀ ਜਾ ਸਕਦੀ ਹੈ। ਧਾਤੂ-ਮੈਟ੍ਰਿਕਸ ਕੰਪੋਜ਼ਿਟਸ: ਇਹਨਾਂ ਸਮੱਗਰੀਆਂ ਵਿੱਚ ਅਸੀਂ ਇੱਕ ਨਕਲੀ ਧਾਤੂ ਮੈਟ੍ਰਿਕਸ ਦੀ ਵਰਤੋਂ ਕਰਦੇ ਹਾਂ ਅਤੇ ਸੇਵਾ ਦਾ ਤਾਪਮਾਨ ਆਮ ਤੌਰ 'ਤੇ ਉਹਨਾਂ ਦੇ ਭਾਗਾਂ ਤੋਂ ਵੱਧ ਹੁੰਦਾ ਹੈ। ਜਦੋਂ ਪੌਲੀਮਰ-ਮੈਟ੍ਰਿਕਸ ਕੰਪੋਜ਼ਿਟਸ ਦੀ ਤੁਲਨਾ ਕੀਤੀ ਜਾਂਦੀ ਹੈ, ਤਾਂ ਇਹਨਾਂ ਵਿੱਚ ਉੱਚ ਸੰਚਾਲਨ ਤਾਪਮਾਨ ਹੋ ਸਕਦਾ ਹੈ, ਜਲਣਸ਼ੀਲ ਨਹੀਂ ਹੋ ਸਕਦਾ ਹੈ, ਅਤੇ ਜੈਵਿਕ ਤਰਲ ਪਦਾਰਥਾਂ ਦੇ ਵਿਰੁੱਧ ਬਿਹਤਰ ਡਿਗਰੇਡੇਸ਼ਨ ਪ੍ਰਤੀਰੋਧ ਹੋ ਸਕਦਾ ਹੈ। ਹਾਲਾਂਕਿ ਉਹ ਵਧੇਰੇ ਮਹਿੰਗੇ ਹਨ. ਮਜਬੂਤ ਕਰਨ ਵਾਲੀਆਂ ਸਮੱਗਰੀਆਂ ਜਿਵੇਂ ਕਿ ਮੁੱਛਾਂ, ਕਣ, ਨਿਰੰਤਰ ਅਤੇ ਨਿਰੰਤਰ ਫਾਈਬਰ; ਅਤੇ ਮੈਟ੍ਰਿਕਸ ਸਮੱਗਰੀ ਜਿਵੇਂ ਕਿ ਤਾਂਬਾ, ਐਲੂਮੀਨੀਅਮ, ਮੈਗਨੀਸ਼ੀਅਮ, ਟਾਈਟੇਨੀਅਮ, ਸੁਪਰ ਅਲਾਏ ਆਮ ਤੌਰ 'ਤੇ ਵਰਤੇ ਜਾ ਰਹੇ ਹਨ। ਉਦਾਹਰਨ ਐਪਲੀਕੇਸ਼ਨਾਂ ਐਲੂਮੀਨੀਅਮ ਆਕਸਾਈਡ ਅਤੇ ਕਾਰਬਨ ਫਾਈਬਰਾਂ ਨਾਲ ਮਜਬੂਤ ਐਲੂਮੀਨੀਅਮ ਅਲੌਏ ਮੈਟਰਿਕਸ ਦੇ ਬਣੇ ਇੰਜਣ ਦੇ ਹਿੱਸੇ ਹਨ। ਸਿਰੇਮਿਕ-ਮੈਟ੍ਰਿਕਸ ਕੰਪੋਜ਼ਿਟਸ: ਵਸਰਾਵਿਕ ਸਮੱਗਰੀਆਂ ਉਹਨਾਂ ਦੀ ਸ਼ਾਨਦਾਰ ਉੱਚ ਤਾਪਮਾਨ ਭਰੋਸੇਯੋਗਤਾ ਲਈ ਜਾਣੀਆਂ ਜਾਂਦੀਆਂ ਹਨ। ਹਾਲਾਂਕਿ ਇਹ ਬਹੁਤ ਭੁਰਭੁਰਾ ਹਨ ਅਤੇ ਫ੍ਰੈਕਚਰ ਦੀ ਕਠੋਰਤਾ ਲਈ ਘੱਟ ਮੁੱਲ ਹਨ। ਇੱਕ ਸਿਰੇਮਿਕ ਦੇ ਕਣਾਂ, ਫਾਈਬਰਾਂ ਜਾਂ ਮੂਛਾਂ ਨੂੰ ਦੂਜੇ ਦੇ ਮੈਟਰਿਕਸ ਵਿੱਚ ਜੋੜ ਕੇ ਅਸੀਂ ਉੱਚ ਫ੍ਰੈਕਚਰ ਕਠੋਰਤਾ ਨਾਲ ਕੰਪੋਜ਼ਿਟਸ ਨੂੰ ਪ੍ਰਾਪਤ ਕਰਨ ਦੇ ਯੋਗ ਹੁੰਦੇ ਹਾਂ। ਇਹ ਏਮਬੈਡਡ ਸਾਮੱਗਰੀ ਮੂਲ ਰੂਪ ਵਿੱਚ ਕੁਝ ਵਿਧੀਆਂ ਦੁਆਰਾ ਮੈਟ੍ਰਿਕਸ ਦੇ ਅੰਦਰ ਦਰਾੜ ਦੇ ਪ੍ਰਸਾਰ ਨੂੰ ਰੋਕਦੀ ਹੈ ਜਿਵੇਂ ਕਿ ਦਰਾੜ ਦੇ ਟਿਪਸ ਨੂੰ ਵਿਗਾੜਨਾ ਜਾਂ ਦਰਾੜ ਦੇ ਚਿਹਰਿਆਂ ਵਿੱਚ ਪੁਲ ਬਣਾਉਣਾ। ਇੱਕ ਉਦਾਹਰਨ ਦੇ ਤੌਰ 'ਤੇ, ਐਲੂਮੀਨਾ ਜੋ ਕਿ SiC ਵਿਸਕਰ ਨਾਲ ਮਜਬੂਤ ਕੀਤੇ ਜਾਂਦੇ ਹਨ, ਹਾਰਡ ਮੈਟਲ ਅਲੌਇਸ ਮਸ਼ੀਨਿੰਗ ਲਈ ਕੱਟਣ ਵਾਲੇ ਟੂਲ ਇਨਸਰਟਸ ਵਜੋਂ ਵਰਤੇ ਜਾਂਦੇ ਹਨ। ਇਹ ਸੀਮਿੰਟਡ ਕਾਰਬਾਈਡਾਂ ਦੇ ਮੁਕਾਬਲੇ ਬਿਹਤਰ ਪ੍ਰਦਰਸ਼ਨ ਨੂੰ ਪ੍ਰਗਟ ਕਰ ਸਕਦੇ ਹਨ। ਕਾਰਬਨ-ਕਾਰਬਨ ਕੰਪੋਜ਼ਿਟਸ : ਰੀਨਫੋਰਸਮੈਂਟ ਅਤੇ ਮੈਟ੍ਰਿਕਸ ਦੋਵੇਂ ਕਾਰਬਨ ਹਨ। ਉਹਨਾਂ ਕੋਲ 2000 ਸੈਂਟੀਗਰੇਡ ਤੋਂ ਵੱਧ ਤਾਪਮਾਨਾਂ 'ਤੇ ਉੱਚ ਟੈਂਸਿਲ ਮੋਡਿਊਲੀ ਅਤੇ ਤਾਕਤ, ਕ੍ਰੀਪ ਪ੍ਰਤੀਰੋਧ, ਉੱਚ ਫ੍ਰੈਕਚਰ ਕਠੋਰਤਾ, ਘੱਟ ਥਰਮਲ ਵਿਸਥਾਰ ਗੁਣਾਂਕ, ਉੱਚ ਥਰਮਲ ਸੰਚਾਲਨਤਾਵਾਂ ਹਨ। ਇਹ ਵਿਸ਼ੇਸ਼ਤਾਵਾਂ ਉਹਨਾਂ ਨੂੰ ਉਹਨਾਂ ਐਪਲੀਕੇਸ਼ਨਾਂ ਲਈ ਆਦਰਸ਼ ਬਣਾਉਂਦੀਆਂ ਹਨ ਜਿਹਨਾਂ ਨੂੰ ਥਰਮਲ ਸਦਮਾ ਪ੍ਰਤੀਰੋਧ ਦੀ ਲੋੜ ਹੁੰਦੀ ਹੈ। ਕਾਰਬਨ-ਕਾਰਬਨ ਕੰਪੋਜ਼ਿਟਸ ਦੀ ਕਮਜ਼ੋਰੀ ਹਾਲਾਂਕਿ ਉੱਚ ਤਾਪਮਾਨਾਂ 'ਤੇ ਆਕਸੀਕਰਨ ਦੇ ਵਿਰੁੱਧ ਇਸਦੀ ਕਮਜ਼ੋਰੀ ਹੈ। ਵਰਤੋਂ ਦੀਆਂ ਖਾਸ ਉਦਾਹਰਣਾਂ ਹਨ ਗਰਮ-ਪ੍ਰੈਸਿੰਗ ਮੋਲਡ, ਐਡਵਾਂਸਡ ਟਰਬਾਈਨ ਇੰਜਣ ਕੰਪੋਨੈਂਟ ਨਿਰਮਾਣ। ਹਾਈਬ੍ਰਿਡ ਕੰਪੋਜ਼ਿਟਸ: ਇੱਕ ਮੈਟ੍ਰਿਕਸ ਵਿੱਚ ਦੋ ਜਾਂ ਦੋ ਤੋਂ ਵੱਧ ਵੱਖ-ਵੱਖ ਕਿਸਮਾਂ ਦੇ ਫਾਈਬਰ ਮਿਲਾਏ ਜਾਂਦੇ ਹਨ। ਇਸ ਤਰ੍ਹਾਂ ਕੋਈ ਵੀ ਵਿਸ਼ੇਸ਼ਤਾ ਦੇ ਸੁਮੇਲ ਨਾਲ ਨਵੀਂ ਸਮੱਗਰੀ ਤਿਆਰ ਕਰ ਸਕਦਾ ਹੈ। ਇੱਕ ਉਦਾਹਰਨ ਹੈ ਜਦੋਂ ਕਾਰਬਨ ਅਤੇ ਕੱਚ ਦੇ ਫਾਈਬਰ ਦੋਨਾਂ ਨੂੰ ਇੱਕ ਪੌਲੀਮੇਰਿਕ ਰਾਲ ਵਿੱਚ ਸ਼ਾਮਲ ਕੀਤਾ ਜਾਂਦਾ ਹੈ। ਕਾਰਬਨ ਫਾਈਬਰ ਘੱਟ ਘਣਤਾ ਦੀ ਕਠੋਰਤਾ ਅਤੇ ਤਾਕਤ ਪ੍ਰਦਾਨ ਕਰਦੇ ਹਨ ਪਰ ਮਹਿੰਗੇ ਹੁੰਦੇ ਹਨ। ਦੂਜੇ ਪਾਸੇ ਕੱਚ ਸਸਤਾ ਹੈ ਪਰ ਕਾਰਬਨ ਫਾਈਬਰਾਂ ਦੀ ਕਠੋਰਤਾ ਦੀ ਘਾਟ ਹੈ। ਗਲਾਸ-ਕਾਰਬਨ ਹਾਈਬ੍ਰਿਡ ਮਿਸ਼ਰਣ ਮਜ਼ਬੂਤ ਅਤੇ ਸਖ਼ਤ ਹੈ ਅਤੇ ਘੱਟ ਕੀਮਤ 'ਤੇ ਤਿਆਰ ਕੀਤਾ ਜਾ ਸਕਦਾ ਹੈ। ਫਾਈਬਰ-ਰੀਇਨਫੋਰਸਡ ਕੰਪੋਜ਼ਿਟਸ ਦੀ ਪ੍ਰੋਸੈਸਿੰਗ: ਲਗਾਤਾਰ ਫਾਈਬਰ-ਰੀਇਨਫੋਰਸਡ ਪਲਾਸਟਿਕ ਲਈ ਇੱਕੋ ਦਿਸ਼ਾ ਵਿੱਚ ਇੱਕਸਾਰ ਵੰਡੇ ਫਾਈਬਰਾਂ ਦੇ ਨਾਲ ਅਸੀਂ ਹੇਠ ਲਿਖੀਆਂ ਤਕਨੀਕਾਂ ਦੀ ਵਰਤੋਂ ਕਰਦੇ ਹਾਂ। ਪਲਟ੍ਰਯੂਸ਼ਨ: ਲਗਾਤਾਰ ਲੰਬਾਈ ਅਤੇ ਲਗਾਤਾਰ ਕਰਾਸ-ਸੈਕਸ਼ਨਾਂ ਦੀਆਂ ਡੰਡੀਆਂ, ਬੀਮ ਅਤੇ ਟਿਊਬਾਂ ਦਾ ਨਿਰਮਾਣ ਕੀਤਾ ਜਾਂਦਾ ਹੈ। ਲਗਾਤਾਰ ਫਾਈਬਰ ਰੋਵਿੰਗਾਂ ਨੂੰ ਥਰਮੋਸੈਟਿੰਗ ਰਾਲ ਨਾਲ ਪ੍ਰੇਗਨੇਟ ਕੀਤਾ ਜਾਂਦਾ ਹੈ ਅਤੇ ਉਹਨਾਂ ਨੂੰ ਲੋੜੀਂਦੇ ਆਕਾਰ ਵਿੱਚ ਬਣਾਉਣ ਲਈ ਇੱਕ ਸਟੀਲ ਡਾਈ ਦੁਆਰਾ ਖਿੱਚਿਆ ਜਾਂਦਾ ਹੈ। ਅੱਗੇ, ਉਹ ਇਸਦੇ ਅੰਤਮ ਰੂਪ ਨੂੰ ਪ੍ਰਾਪਤ ਕਰਨ ਲਈ ਇੱਕ ਸਟੀਕਸ਼ਨ ਮਸ਼ੀਨਡ ਕਿਊਰਿੰਗ ਡਾਈ ਵਿੱਚੋਂ ਲੰਘਦੇ ਹਨ। ਕਿਉਂਕਿ ਕਿਉਰਿੰਗ ਡਾਈ ਨੂੰ ਗਰਮ ਕੀਤਾ ਜਾਂਦਾ ਹੈ, ਇਹ ਰੈਜ਼ਿਨ ਮੈਟ੍ਰਿਕਸ ਨੂੰ ਠੀਕ ਕਰਦਾ ਹੈ। ਪੁੱਲਰ ਡੀਜ਼ ਰਾਹੀਂ ਸਮੱਗਰੀ ਖਿੱਚਦੇ ਹਨ। ਸੰਮਿਲਿਤ ਖੋਖਲੇ ਕੋਰਾਂ ਦੀ ਵਰਤੋਂ ਕਰਕੇ, ਅਸੀਂ ਟਿਊਬਾਂ ਅਤੇ ਖੋਖਲੇ ਜਿਓਮੈਟਰੀਜ਼ ਪ੍ਰਾਪਤ ਕਰਨ ਦੇ ਯੋਗ ਹੁੰਦੇ ਹਾਂ। ਪਲਟਰੂਸ਼ਨ ਵਿਧੀ ਸਵੈਚਾਲਿਤ ਹੈ ਅਤੇ ਸਾਨੂੰ ਉੱਚ ਉਤਪਾਦਨ ਦਰਾਂ ਦੀ ਪੇਸ਼ਕਸ਼ ਕਰਦੀ ਹੈ. ਉਤਪਾਦ ਦੀ ਕੋਈ ਵੀ ਲੰਬਾਈ ਪੈਦਾ ਕਰਨੀ ਸੰਭਵ ਹੈ। ਪ੍ਰੀਪ੍ਰੈਗ ਉਤਪਾਦਨ ਪ੍ਰਕਿਰਿਆ: ਪ੍ਰੀਪ੍ਰੈਗ ਇੱਕ ਨਿਰੰਤਰ-ਫਾਈਬਰ ਰੀਨਫੋਰਸਮੈਂਟ ਹੈ ਜੋ ਅੰਸ਼ਕ ਤੌਰ 'ਤੇ ਠੀਕ ਕੀਤੇ ਗਏ ਪੋਲੀਮਰ ਰਾਲ ਨਾਲ ਪ੍ਰੀਪ੍ਰੈਗਨੇਟ ਕੀਤੀ ਜਾਂਦੀ ਹੈ। ਇਹ ਢਾਂਚਾਗਤ ਕਾਰਜਾਂ ਲਈ ਵਿਆਪਕ ਤੌਰ 'ਤੇ ਵਰਤਿਆ ਜਾਂਦਾ ਹੈ। ਸਮੱਗਰੀ ਟੇਪ ਦੇ ਰੂਪ ਵਿੱਚ ਆਉਂਦੀ ਹੈ ਅਤੇ ਇੱਕ ਟੇਪ ਦੇ ਰੂਪ ਵਿੱਚ ਭੇਜੀ ਜਾਂਦੀ ਹੈ. ਨਿਰਮਾਤਾ ਇਸ ਨੂੰ ਸਿੱਧੇ ਤੌਰ 'ਤੇ ਢਾਲਦਾ ਹੈ ਅਤੇ ਬਿਨਾਂ ਕਿਸੇ ਰਾਲ ਨੂੰ ਜੋੜਨ ਦੀ ਲੋੜ ਤੋਂ ਪੂਰੀ ਤਰ੍ਹਾਂ ਠੀਕ ਕਰਦਾ ਹੈ। ਕਿਉਂਕਿ ਪ੍ਰੀਪ੍ਰੈਗਸ ਕਮਰੇ ਦੇ ਤਾਪਮਾਨ 'ਤੇ ਠੀਕ ਕਰਨ ਵਾਲੀਆਂ ਪ੍ਰਤੀਕ੍ਰਿਆਵਾਂ ਵਿੱਚੋਂ ਗੁਜ਼ਰਦੇ ਹਨ, ਇਸ ਲਈ ਉਹਨਾਂ ਨੂੰ 0 ਸੈਂਟੀਗ੍ਰੇਡ ਜਾਂ ਘੱਟ ਤਾਪਮਾਨ 'ਤੇ ਸਟੋਰ ਕੀਤਾ ਜਾਂਦਾ ਹੈ। ਵਰਤੋਂ ਤੋਂ ਬਾਅਦ ਬਾਕੀ ਬਚੀਆਂ ਟੇਪਾਂ ਨੂੰ ਘੱਟ ਤਾਪਮਾਨ 'ਤੇ ਵਾਪਸ ਸਟੋਰ ਕੀਤਾ ਜਾਂਦਾ ਹੈ। ਥਰਮੋਪਲਾਸਟਿਕ ਅਤੇ ਥਰਮੋਸੈਟਿੰਗ ਰੈਜ਼ਿਨ ਵਰਤੇ ਜਾਂਦੇ ਹਨ ਅਤੇ ਕਾਰਬਨ, ਅਰਾਮਿਡ ਅਤੇ ਕੱਚ ਦੇ ਮਜ਼ਬੂਤੀ ਵਾਲੇ ਫਾਈਬਰ ਆਮ ਹਨ। ਪ੍ਰੀਪ੍ਰੈਗਸ ਦੀ ਵਰਤੋਂ ਕਰਨ ਲਈ, ਕੈਰੀਅਰ ਬੈਕਿੰਗ ਪੇਪਰ ਨੂੰ ਪਹਿਲਾਂ ਹਟਾ ਦਿੱਤਾ ਜਾਂਦਾ ਹੈ ਅਤੇ ਫਿਰ ਪ੍ਰੀਪ੍ਰੇਗ ਟੇਪ ਨੂੰ ਟੂਲ ਵਾਲੀ ਸਤ੍ਹਾ (ਲੇਅ-ਅਪ ਪ੍ਰਕਿਰਿਆ) 'ਤੇ ਰੱਖ ਕੇ ਨਿਰਮਾਣ ਕੀਤਾ ਜਾਂਦਾ ਹੈ। ਲੋੜੀਦੀ ਮੋਟਾਈ ਪ੍ਰਾਪਤ ਕਰਨ ਲਈ ਕਈ ਪਲਾਈਆਂ ਰੱਖੀਆਂ ਜਾ ਸਕਦੀਆਂ ਹਨ। ਅਕਸਰ ਅਭਿਆਸ ਇੱਕ ਕਰਾਸ-ਪਲਾਈ ਜਾਂ ਐਂਗਲ-ਪਲਾਈ ਲੈਮੀਨੇਟ ਬਣਾਉਣ ਲਈ ਫਾਈਬਰ ਸਥਿਤੀ ਨੂੰ ਬਦਲਣਾ ਹੈ। ਅੰਤ ਵਿੱਚ ਇਲਾਜ ਲਈ ਗਰਮੀ ਅਤੇ ਦਬਾਅ ਲਾਗੂ ਕੀਤਾ ਜਾਂਦਾ ਹੈ। ਹੈਂਡ ਪ੍ਰੋਸੈਸਿੰਗ ਦੇ ਨਾਲ-ਨਾਲ ਸਵੈਚਲਿਤ ਪ੍ਰਕਿਰਿਆਵਾਂ ਦੀ ਵਰਤੋਂ ਪ੍ਰੀਪ੍ਰੈਗਸ ਅਤੇ ਲੇਅ-ਅਪ ਨੂੰ ਕੱਟਣ ਲਈ ਕੀਤੀ ਜਾਂਦੀ ਹੈ। ਫਿਲਾਮੈਂਟ ਵਿੰਡਿੰਗ : ਲਗਾਤਾਰ ਰੀਨਫੋਰਸਿੰਗ ਫਾਈਬਰ ਇੱਕ ਖੋਖਲੇ ਅਤੇ ਆਮ ਤੌਰ 'ਤੇ ਚੱਕਰਵਾਤੀ ਆਕਾਰ ਦੀ ਪਾਲਣਾ ਕਰਨ ਲਈ ਇੱਕ ਪੂਰਵ-ਨਿਰਧਾਰਤ ਪੈਟਰਨ ਵਿੱਚ ਸਹੀ ਸਥਿਤੀ ਵਿੱਚ ਹੁੰਦੇ ਹਨ। ਰੇਸ਼ੇ ਪਹਿਲਾਂ ਇੱਕ ਰਾਲ ਦੇ ਇਸ਼ਨਾਨ ਵਿੱਚੋਂ ਲੰਘਦੇ ਹਨ ਅਤੇ ਫਿਰ ਇੱਕ ਸਵੈਚਾਲਿਤ ਪ੍ਰਣਾਲੀ ਦੁਆਰਾ ਇੱਕ ਮੰਡਰੇਲ ਉੱਤੇ ਜ਼ਖ਼ਮ ਹੁੰਦੇ ਹਨ। ਕਈ ਵਾਰੀ ਦੁਹਰਾਓ ਦੇ ਬਾਅਦ ਲੋੜੀਂਦੀ ਮੋਟਾਈ ਪ੍ਰਾਪਤ ਕੀਤੀ ਜਾਂਦੀ ਹੈ ਅਤੇ ਇਲਾਜ ਕਮਰੇ ਦੇ ਤਾਪਮਾਨ 'ਤੇ ਜਾਂ ਇੱਕ ਓਵਨ ਦੇ ਅੰਦਰ ਕੀਤਾ ਜਾਂਦਾ ਹੈ। ਹੁਣ ਮੈਂਡਰਲ ਨੂੰ ਹਟਾ ਦਿੱਤਾ ਗਿਆ ਹੈ ਅਤੇ ਉਤਪਾਦ ਨੂੰ ਢਾਹ ਦਿੱਤਾ ਗਿਆ ਹੈ. ਫਿਲਾਮੈਂਟ ਵਾਇਨਿੰਗ ਫਾਈਬਰਾਂ ਨੂੰ ਘੇਰੇ, ਹੈਲੀਕਲ ਅਤੇ ਧਰੁਵੀ ਪੈਟਰਨਾਂ ਵਿੱਚ ਘੁਮਾ ਕੇ ਬਹੁਤ ਉੱਚ ਤਾਕਤ-ਤੋਂ-ਵਜ਼ਨ ਅਨੁਪਾਤ ਦੀ ਪੇਸ਼ਕਸ਼ ਕਰ ਸਕਦੀ ਹੈ। ਇਸ ਤਕਨੀਕ ਦੀ ਵਰਤੋਂ ਕਰਕੇ ਪਾਈਪਾਂ, ਟੈਂਕਾਂ, ਕੇਸਿੰਗਾਂ ਦਾ ਨਿਰਮਾਣ ਕੀਤਾ ਜਾਂਦਾ ਹੈ। • ਸਟ੍ਰਕਚਰਲ ਕੰਪੋਜ਼ਿਟਸ: ਆਮ ਤੌਰ 'ਤੇ ਇਹ ਸਮਰੂਪ ਅਤੇ ਸੰਯੁਕਤ ਸਮੱਗਰੀ ਦੋਵਾਂ ਦੇ ਬਣੇ ਹੁੰਦੇ ਹਨ। ਇਸਲਈ ਇਹਨਾਂ ਦੇ ਗੁਣਾਂ ਨੂੰ ਇਸ ਦੇ ਤੱਤ ਦੇ ਤੱਤ ਸਮੱਗਰੀ ਅਤੇ ਜਿਓਮੈਟ੍ਰਿਕਲ ਡਿਜ਼ਾਈਨ ਦੁਆਰਾ ਨਿਰਧਾਰਤ ਕੀਤਾ ਜਾਂਦਾ ਹੈ। ਇੱਥੇ ਮੁੱਖ ਕਿਸਮਾਂ ਹਨ: ਲੈਮਿਨਾਰ ਕੰਪੋਜ਼ਿਟਸ: ਇਹ ਢਾਂਚਾਗਤ ਸਮੱਗਰੀ ਦੋ-ਅਯਾਮੀ ਸ਼ੀਟਾਂ ਜਾਂ ਤਰਜੀਹੀ ਉੱਚ-ਤਾਕਤ ਦਿਸ਼ਾਵਾਂ ਵਾਲੇ ਪੈਨਲਾਂ ਨਾਲ ਬਣੀ ਹੁੰਦੀ ਹੈ। ਲੇਅਰਾਂ ਨੂੰ ਸਟੈਕ ਕੀਤਾ ਜਾਂਦਾ ਹੈ ਅਤੇ ਇਕੱਠੇ ਸੀਮਿੰਟ ਕੀਤਾ ਜਾਂਦਾ ਹੈ। ਦੋ ਲੰਬਕਾਰੀ ਧੁਰਿਆਂ ਵਿੱਚ ਉੱਚ-ਤਾਕਤ ਦਿਸ਼ਾਵਾਂ ਨੂੰ ਬਦਲ ਕੇ, ਅਸੀਂ ਦੋ-ਅਯਾਮੀ ਸਮਤਲ ਵਿੱਚ ਦੋਵਾਂ ਦਿਸ਼ਾਵਾਂ ਵਿੱਚ ਉੱਚ-ਤਾਕਤ ਵਾਲਾ ਮਿਸ਼ਰਣ ਪ੍ਰਾਪਤ ਕਰਦੇ ਹਾਂ। ਲੇਅਰਾਂ ਦੇ ਕੋਣਾਂ ਨੂੰ ਵਿਵਸਥਿਤ ਕਰਕੇ ਕੋਈ ਤਰਜੀਹੀ ਦਿਸ਼ਾਵਾਂ ਵਿੱਚ ਤਾਕਤ ਦੇ ਨਾਲ ਇੱਕ ਕੰਪੋਜ਼ਿਟ ਬਣਾ ਸਕਦਾ ਹੈ। ਆਧੁਨਿਕ ਸਕੀ ਇਸ ਤਰੀਕੇ ਨਾਲ ਬਣਾਈ ਜਾਂਦੀ ਹੈ। ਸੈਂਡਵਿਚ ਪੈਨਲ: ਇਹ ਢਾਂਚਾਗਤ ਮਿਸ਼ਰਣ ਹਲਕੇ ਹਨ ਪਰ ਫਿਰ ਵੀ ਉੱਚ ਕਠੋਰਤਾ ਅਤੇ ਤਾਕਤ ਹੈ। ਸੈਂਡਵਿਚ ਪੈਨਲਾਂ ਵਿੱਚ ਇੱਕ ਕਠੋਰ ਅਤੇ ਮਜ਼ਬੂਤ ਸਮੱਗਰੀ ਜਿਵੇਂ ਕਿ ਅਲਮੀਨੀਅਮ ਦੇ ਮਿਸ਼ਰਣ, ਫਾਈਬਰ ਰੀਇਨਫੋਰਸਡ ਪਲਾਸਟਿਕ ਜਾਂ ਸਟੀਲ ਅਤੇ ਬਾਹਰੀ ਸ਼ੀਟਾਂ ਦੇ ਵਿਚਕਾਰ ਇੱਕ ਕੋਰ ਤੋਂ ਬਣੀ ਦੋ ਬਾਹਰੀ ਸ਼ੀਟਾਂ ਹੁੰਦੀਆਂ ਹਨ। ਕੋਰ ਨੂੰ ਹਲਕਾ ਹੋਣਾ ਚਾਹੀਦਾ ਹੈ ਅਤੇ ਜ਼ਿਆਦਾਤਰ ਸਮਾਂ ਲਚਕਤਾ ਦਾ ਘੱਟ ਮਾਡਿਊਲਸ ਹੁੰਦਾ ਹੈ। ਪ੍ਰਸਿੱਧ ਮੂਲ ਸਮੱਗਰੀ ਸਖ਼ਤ ਪੌਲੀਮੇਰਿਕ ਫੋਮ, ਲੱਕੜ ਅਤੇ ਹਨੀਕੌਂਬ ਹਨ। ਸੈਂਡਵਿਚ ਪੈਨਲਾਂ ਦੀ ਵਰਤੋਂ ਉਸਾਰੀ ਉਦਯੋਗ ਵਿੱਚ ਛੱਤ ਸਮੱਗਰੀ, ਫਰਸ਼ ਜਾਂ ਕੰਧ ਸਮੱਗਰੀ ਦੇ ਤੌਰ ਤੇ ਅਤੇ ਏਰੋਸਪੇਸ ਉਦਯੋਗਾਂ ਵਿੱਚ ਵੀ ਕੀਤੀ ਜਾਂਦੀ ਹੈ। • ਨੈਨੋਕੰਪੋਜ਼ਿਟਸ: ਇਹ ਨਵੀਂ ਸਮੱਗਰੀ ਇੱਕ ਮੈਟ੍ਰਿਕਸ ਵਿੱਚ ਏਮਬੇਡ ਕੀਤੇ ਨੈਨੋਜ਼ਾਈਜ਼ਡ ਕਣਾਂ ਦੇ ਕਣਾਂ ਦੇ ਹੁੰਦੇ ਹਨ। ਨੈਨੋਕੰਪੋਜ਼ਿਟਸ ਦੀ ਵਰਤੋਂ ਕਰਕੇ ਅਸੀਂ ਰਬੜ ਦੀਆਂ ਸਮੱਗਰੀਆਂ ਦਾ ਨਿਰਮਾਣ ਕਰ ਸਕਦੇ ਹਾਂ ਜੋ ਹਵਾ ਦੇ ਪ੍ਰਵੇਸ਼ ਲਈ ਬਹੁਤ ਵਧੀਆ ਰੁਕਾਵਟਾਂ ਹਨ ਜਦੋਂ ਕਿ ਉਹਨਾਂ ਦੀਆਂ ਰਬੜ ਦੀਆਂ ਵਿਸ਼ੇਸ਼ਤਾਵਾਂ ਨੂੰ ਬਦਲਿਆ ਨਹੀਂ ਜਾਂਦਾ। CLICK Product Finder-Locator Service ਪਿਛਲੇ ਸਫ਼ੇ
- Joining & Assembly & Fastening Processes, Welding, Brazing, Soldering
Joining & Assembly & Fastening Processes, Welding, Brazing, Soldering, Sintering, Adhesive Bonding, Press Fitting, Wave and Reflow Solder Process, Torch Furnace ਜੁੜਨਾ ਅਤੇ ਅਸੈਂਬਲੀ ਅਤੇ ਫਸਟਨਿੰਗ ਪ੍ਰਕਿਰਿਆਵਾਂ ਅਸੀਂ ਤੁਹਾਡੇ ਨਿਰਮਿਤ ਹਿੱਸਿਆਂ ਨੂੰ ਜੋੜਦੇ, ਇਕੱਠੇ ਕਰਦੇ ਅਤੇ ਬੰਨ੍ਹਦੇ ਹਾਂ ਅਤੇ ਉਹਨਾਂ ਨੂੰ ਵੈਲਡਿੰਗ, ਬ੍ਰਾਜ਼ਿੰਗ, ਸੋਲਡਰਿੰਗ, ਸਿਨਟਰਿੰਗ, ਅਡੈਸਿਵ ਬਾਂਡਿੰਗ, ਫਾਸਟਨਿੰਗ, ਪ੍ਰੈੱਸ ਫਿਟਿੰਗ ਦੀ ਵਰਤੋਂ ਕਰਕੇ ਤਿਆਰ ਜਾਂ ਅਰਧ-ਤਿਆਰ ਉਤਪਾਦਾਂ ਵਿੱਚ ਬਦਲਦੇ ਹਾਂ। ਸਾਡੀਆਂ ਕੁਝ ਸਭ ਤੋਂ ਪ੍ਰਸਿੱਧ ਵੈਲਡਿੰਗ ਪ੍ਰਕਿਰਿਆਵਾਂ ਹਨ ਚਾਪ, ਆਕਸੀਫਿਊਲ ਗੈਸ, ਪ੍ਰਤੀਰੋਧ, ਪ੍ਰੋਜੈਕਸ਼ਨ, ਸੀਮ, ਅਪਸੈੱਟ, ਪਰਕਸ਼ਨ, ਸੋਲਿਡ ਸਟੇਟ, ਇਲੈਕਟ੍ਰੋਨ ਬੀਮ, ਲੇਜ਼ਰ, ਥਰਮਿਟ, ਇੰਡਕਸ਼ਨ ਵੈਲਡਿੰਗ। ਸਾਡੀਆਂ ਪ੍ਰਸਿੱਧ ਬ੍ਰੇਜ਼ਿੰਗ ਪ੍ਰਕਿਰਿਆਵਾਂ ਟਾਰਚ, ਇੰਡਕਸ਼ਨ, ਫਰਨੇਸ ਅਤੇ ਡਿਪ ਬ੍ਰੇਜ਼ਿੰਗ ਹਨ। ਸਾਡੇ ਸੋਲਡਰਿੰਗ ਦੇ ਤਰੀਕੇ ਆਇਰਨ, ਹਾਟ ਪਲੇਟ, ਓਵਨ, ਇੰਡਕਸ਼ਨ, ਡਿਪ, ਵੇਵ, ਰੀਫਲੋ ਅਤੇ ਅਲਟਰਾਸੋਨਿਕ ਸੋਲਡਰਿੰਗ ਹਨ। ਚਿਪਕਣ ਵਾਲੇ ਬੰਧਨ ਲਈ ਅਸੀਂ ਅਕਸਰ ਥਰਮੋਪਲਾਸਟਿਕਸ ਅਤੇ ਥਰਮੋ-ਸੈਟਿੰਗ, ਈਪੌਕਸੀਜ਼, ਫੀਨੋਲਿਕਸ, ਪੌਲੀਯੂਰੇਥੇਨ, ਅਡੈਸਿਵ ਅਲਾਏ ਦੇ ਨਾਲ-ਨਾਲ ਕੁਝ ਹੋਰ ਰਸਾਇਣਾਂ ਅਤੇ ਟੇਪਾਂ ਦੀ ਵਰਤੋਂ ਕਰਦੇ ਹਾਂ। ਅੰਤ ਵਿੱਚ ਸਾਡੀਆਂ ਫਾਸਟਨਿੰਗ ਪ੍ਰਕਿਰਿਆਵਾਂ ਵਿੱਚ ਨੇਲਿੰਗ, ਪੇਚਿੰਗ, ਨਟ ਅਤੇ ਬੋਲਟ, ਰਿਵੇਟਿੰਗ, ਕਲਿੰਚਿੰਗ, ਪਿੰਨਿੰਗ, ਸਿਲਾਈ ਅਤੇ ਸਟੈਪਲਿੰਗ ਅਤੇ ਪ੍ਰੈਸ ਫਿਟਿੰਗ ਸ਼ਾਮਲ ਹੁੰਦੇ ਹਨ। • ਵੈਲਡਿੰਗ: ਵੈਲਡਿੰਗ ਵਿੱਚ ਕੰਮ ਦੇ ਟੁਕੜਿਆਂ ਨੂੰ ਪਿਘਲਾ ਕੇ ਸਮੱਗਰੀ ਨੂੰ ਜੋੜਨਾ ਅਤੇ ਫਿਲਰ ਸਮੱਗਰੀ ਨੂੰ ਪੇਸ਼ ਕਰਨਾ ਸ਼ਾਮਲ ਹੁੰਦਾ ਹੈ, ਜੋ ਪਿਘਲੇ ਹੋਏ ਵੇਲਡ ਪੂਲ ਵਿੱਚ ਵੀ ਸ਼ਾਮਲ ਹੁੰਦਾ ਹੈ। ਜਦੋਂ ਖੇਤਰ ਠੰਢਾ ਹੋ ਜਾਂਦਾ ਹੈ, ਅਸੀਂ ਇੱਕ ਮਜ਼ਬੂਤ ਜੋੜ ਪ੍ਰਾਪਤ ਕਰਦੇ ਹਾਂ। ਕੁਝ ਮਾਮਲਿਆਂ ਵਿੱਚ ਦਬਾਅ ਪਾਇਆ ਜਾਂਦਾ ਹੈ। ਵੈਲਡਿੰਗ ਦੇ ਉਲਟ, ਬ੍ਰੇਜ਼ਿੰਗ ਅਤੇ ਸੋਲਡਰਿੰਗ ਓਪਰੇਸ਼ਨਾਂ ਵਿੱਚ ਵਰਕਪੀਸ ਦੇ ਵਿਚਕਾਰ ਹੇਠਲੇ ਪਿਘਲਣ ਵਾਲੇ ਬਿੰਦੂ ਵਾਲੀ ਸਮੱਗਰੀ ਦਾ ਸਿਰਫ ਪਿਘਲਣਾ ਸ਼ਾਮਲ ਹੁੰਦਾ ਹੈ, ਅਤੇ ਵਰਕਪੀਸ ਪਿਘਲਦੇ ਨਹੀਂ ਹਨ। ਅਸੀਂ ਸਿਫ਼ਾਰਿਸ਼ ਕਰਦੇ ਹਾਂ ਕਿ ਤੁਸੀਂ ਇੱਥੇ ਕਲਿੱਕ ਕਰੋAGS-TECH Inc ਦੁਆਰਾ ਵੈਲਡਿੰਗ ਪ੍ਰਕਿਰਿਆਵਾਂ ਦੇ ਸਾਡੇ ਯੋਜਨਾਬੱਧ ਚਿੱਤਰਾਂ ਨੂੰ ਡਾਉਨਲੋਡ ਕਰੋ। ਇਹ ਤੁਹਾਨੂੰ ਉਸ ਜਾਣਕਾਰੀ ਨੂੰ ਬਿਹਤਰ ਤਰੀਕੇ ਨਾਲ ਸਮਝਣ ਵਿੱਚ ਮਦਦ ਕਰੇਗਾ ਜੋ ਅਸੀਂ ਤੁਹਾਨੂੰ ਹੇਠਾਂ ਪ੍ਰਦਾਨ ਕਰ ਰਹੇ ਹਾਂ। ARC ਵੈਲਡਿੰਗ ਵਿੱਚ, ਅਸੀਂ ਇੱਕ ਇਲੈਕਟ੍ਰਿਕ ਚਾਪ ਬਣਾਉਣ ਲਈ ਇੱਕ ਪਾਵਰ ਸਪਲਾਈ ਅਤੇ ਇੱਕ ਇਲੈਕਟ੍ਰੋਡ ਦੀ ਵਰਤੋਂ ਕਰਦੇ ਹਾਂ ਜੋ ਧਾਤਾਂ ਨੂੰ ਪਿਘਲਦਾ ਹੈ। ਵੈਲਡਿੰਗ ਪੁਆਇੰਟ ਨੂੰ ਇੱਕ ਢਾਲਣ ਵਾਲੀ ਗੈਸ ਜਾਂ ਭਾਫ਼ ਜਾਂ ਹੋਰ ਸਮੱਗਰੀ ਦੁਆਰਾ ਸੁਰੱਖਿਅਤ ਕੀਤਾ ਜਾਂਦਾ ਹੈ। ਇਹ ਪ੍ਰਕਿਰਿਆ ਵੈਲਡਿੰਗ ਆਟੋਮੋਟਿਵ ਪਾਰਟਸ ਅਤੇ ਸਟੀਲ ਢਾਂਚੇ ਲਈ ਪ੍ਰਸਿੱਧ ਹੈ। ਸ਼ੈਲਡਡ ਮੈਟਲ ਆਰਕ ਵੈਲਡਿੰਗ (SMAW) ਜਾਂ ਸਟਿੱਕ ਵੈਲਡਿੰਗ ਵਜੋਂ ਵੀ ਜਾਣੀ ਜਾਂਦੀ ਹੈ, ਇੱਕ ਇਲੈਕਟ੍ਰੋਡ ਸਟਿੱਕ ਨੂੰ ਬੇਸ ਸਮੱਗਰੀ ਦੇ ਨੇੜੇ ਲਿਆਇਆ ਜਾਂਦਾ ਹੈ ਅਤੇ ਉਹਨਾਂ ਦੇ ਵਿਚਕਾਰ ਇੱਕ ਇਲੈਕਟ੍ਰਿਕ ਚਾਪ ਉਤਪੰਨ ਹੁੰਦਾ ਹੈ। ਇਲੈਕਟ੍ਰੋਡ ਡੰਡੇ ਪਿਘਲ ਜਾਂਦੇ ਹਨ ਅਤੇ ਫਿਲਰ ਸਮੱਗਰੀ ਵਜੋਂ ਕੰਮ ਕਰਦੇ ਹਨ। ਇਲੈਕਟ੍ਰੋਡ ਵਿੱਚ ਪ੍ਰਵਾਹ ਵੀ ਹੁੰਦਾ ਹੈ ਜੋ ਸਲੈਗ ਦੀ ਇੱਕ ਪਰਤ ਵਜੋਂ ਕੰਮ ਕਰਦਾ ਹੈ ਅਤੇ ਵਾਸ਼ਪਾਂ ਨੂੰ ਛੱਡਦਾ ਹੈ ਜੋ ਢਾਲਣ ਵਾਲੀ ਗੈਸ ਵਜੋਂ ਕੰਮ ਕਰਦੇ ਹਨ। ਇਹ ਵੇਲਡ ਖੇਤਰ ਨੂੰ ਵਾਤਾਵਰਣ ਦੇ ਗੰਦਗੀ ਤੋਂ ਬਚਾਉਂਦੇ ਹਨ। ਕੋਈ ਹੋਰ ਫਿਲਰ ਨਹੀਂ ਵਰਤੇ ਜਾ ਰਹੇ ਹਨ। ਇਸ ਪ੍ਰਕਿਰਿਆ ਦੇ ਨੁਕਸਾਨ ਹਨ ਇਸਦੀ ਸੁਸਤੀ, ਇਲੈਕਟ੍ਰੋਡਸ ਨੂੰ ਅਕਸਰ ਬਦਲਣ ਦੀ ਲੋੜ, ਵਹਾਅ ਤੋਂ ਪੈਦਾ ਹੋਣ ਵਾਲੇ ਬਚੇ ਹੋਏ ਸਲੈਗ ਨੂੰ ਦੂਰ ਕਰਨ ਦੀ ਲੋੜ। ਬਹੁਤ ਸਾਰੀਆਂ ਧਾਤਾਂ ਜਿਵੇਂ ਕਿ ਲੋਹਾ, ਸਟੀਲ, ਨਿਕਲ, ਐਲੂਮੀਨੀਅਮ, ਤਾਂਬਾ... ਆਦਿ। welded ਕੀਤਾ ਜਾ ਸਕਦਾ ਹੈ. ਇਸਦੇ ਫਾਇਦੇ ਇਸ ਦੇ ਸਸਤੇ ਸੰਦ ਅਤੇ ਵਰਤੋਂ ਵਿੱਚ ਸੌਖ ਹਨ. ਗੈਸ ਮੈਟਲ ਆਰਕ ਵੈਲਡਿੰਗ (GMAW) ਜਿਸਨੂੰ ਮੈਟਲ-ਇਨਰਟ ਗੈਸ (MIG) ਵੀ ਕਿਹਾ ਜਾਂਦਾ ਹੈ, ਸਾਡੇ ਕੋਲ ਇੱਕ ਖਪਤਯੋਗ ਇਲੈਕਟ੍ਰੋਡ ਵਾਇਰ ਫਿਲਰ ਅਤੇ ਇੱਕ ਅੜਿੱਕਾ ਜਾਂ ਅੰਸ਼ਕ ਤੌਰ 'ਤੇ ਅਯੋਗ ਗੈਸ ਦੀ ਨਿਰੰਤਰ ਖੁਰਾਕ ਹੁੰਦੀ ਹੈ ਜੋ ਵੇਲਡ ਖੇਤਰ ਦੇ ਵਾਤਾਵਰਣ ਦੂਸ਼ਿਤ ਹੋਣ ਦੇ ਵਿਰੁੱਧ ਤਾਰ ਦੇ ਦੁਆਲੇ ਵਗਦੀ ਹੈ। ਸਟੀਲ, ਅਲਮੀਨੀਅਮ ਅਤੇ ਹੋਰ ਗੈਰ-ਫੈਰਸ ਧਾਤਾਂ ਨੂੰ ਵੇਲਡ ਕੀਤਾ ਜਾ ਸਕਦਾ ਹੈ। MIG ਦੇ ਫਾਇਦੇ ਉੱਚ ਵੈਲਡਿੰਗ ਸਪੀਡ ਅਤੇ ਚੰਗੀ ਗੁਣਵੱਤਾ ਹਨ. ਨੁਕਸਾਨ ਇਸਦੇ ਗੁੰਝਲਦਾਰ ਉਪਕਰਣ ਹਨ ਅਤੇ ਹਵਾ ਵਾਲੇ ਬਾਹਰੀ ਵਾਤਾਵਰਣ ਵਿੱਚ ਚੁਣੌਤੀਆਂ ਦਾ ਸਾਹਮਣਾ ਕਰਨਾ ਪੈਂਦਾ ਹੈ ਕਿਉਂਕਿ ਸਾਨੂੰ ਵੈਲਡਿੰਗ ਖੇਤਰ ਦੇ ਆਲੇ ਦੁਆਲੇ ਸ਼ੀਲਡਿੰਗ ਗੈਸ ਨੂੰ ਸਥਿਰ ਰੱਖਣਾ ਪੈਂਦਾ ਹੈ। GMAW ਦੀ ਇੱਕ ਪਰਿਵਰਤਨ ਫਲਕਸ-ਕੋਰਡ ਆਰਕ ਵੈਲਡਿੰਗ (FCAW) ਹੈ ਜਿਸ ਵਿੱਚ ਫਲੈਕਸ ਸਮੱਗਰੀ ਨਾਲ ਭਰੀ ਇੱਕ ਵਧੀਆ ਧਾਤ ਦੀ ਟਿਊਬ ਹੁੰਦੀ ਹੈ। ਕਈ ਵਾਰ ਟਿਊਬ ਦੇ ਅੰਦਰ ਦਾ ਵਹਾਅ ਵਾਤਾਵਰਣ ਦੀ ਗੰਦਗੀ ਤੋਂ ਸੁਰੱਖਿਆ ਲਈ ਕਾਫੀ ਹੁੰਦਾ ਹੈ। ਡੁੱਬੀ ਚਾਪ ਵੈਲਡਿੰਗ (SAW) ਵਿਆਪਕ ਤੌਰ 'ਤੇ ਇੱਕ ਸਵੈਚਲਿਤ ਪ੍ਰਕਿਰਿਆ ਹੈ, ਜਿਸ ਵਿੱਚ ਲਗਾਤਾਰ ਤਾਰ ਫੀਡਿੰਗ ਅਤੇ ਚਾਪ ਸ਼ਾਮਲ ਹੁੰਦਾ ਹੈ ਜੋ ਫਲੈਕਸ ਕਵਰ ਦੀ ਇੱਕ ਪਰਤ ਦੇ ਹੇਠਾਂ ਮਾਰਿਆ ਜਾਂਦਾ ਹੈ। ਉਤਪਾਦਨ ਦੀਆਂ ਦਰਾਂ ਅਤੇ ਗੁਣਵੱਤਾ ਉੱਚੀਆਂ ਹਨ, ਵੈਲਡਿੰਗ ਸਲੈਗ ਆਸਾਨੀ ਨਾਲ ਬੰਦ ਹੋ ਜਾਂਦੀ ਹੈ, ਅਤੇ ਸਾਡੇ ਕੋਲ ਧੂੰਏਂ ਤੋਂ ਮੁਕਤ ਕੰਮ ਦਾ ਮਾਹੌਲ ਹੈ। ਨੁਕਸਾਨ ਇਹ ਹੈ ਕਿ ਇਸਦੀ ਵਰਤੋਂ ਸਿਰਫ parts ਨੂੰ ਕੁਝ ਖਾਸ ਸਥਿਤੀਆਂ ਵਿੱਚ ਵੇਲਡ ਕਰਨ ਲਈ ਕੀਤੀ ਜਾ ਸਕਦੀ ਹੈ। ਗੈਸ ਟੰਗਸਟਨ ਆਰਕ ਵੈਲਡਿੰਗ (GTAW) ਜਾਂ ਟੰਗਸਟਨ-ਇਨਰਟ ਗੈਸ ਵੈਲਡਿੰਗ (TIG) ਵਿੱਚ ਅਸੀਂ ਇੱਕ ਵੱਖਰੇ ਫਿਲਰ ਅਤੇ ਅੜਿੱਕੇ ਜਾਂ ਅੜਿੱਕੇ ਗੈਸਾਂ ਦੇ ਨਾਲ ਇੱਕ ਟੰਗਸਟਨ ਇਲੈਕਟ੍ਰੋਡ ਦੀ ਵਰਤੋਂ ਕਰਦੇ ਹਾਂ। ਜਿਵੇਂ ਕਿ ਅਸੀਂ ਜਾਣਦੇ ਹਾਂ ਕਿ ਟੰਗਸਟਨ ਵਿੱਚ ਇੱਕ ਉੱਚ ਪਿਘਲਣ ਵਾਲਾ ਬਿੰਦੂ ਹੈ ਅਤੇ ਇਹ ਬਹੁਤ ਉੱਚ ਤਾਪਮਾਨਾਂ ਲਈ ਇੱਕ ਬਹੁਤ ਢੁਕਵੀਂ ਧਾਤ ਹੈ। TIG ਵਿੱਚ ਟੰਗਸਟਨ ਉੱਪਰ ਦੱਸੇ ਗਏ ਹੋਰ ਤਰੀਕਿਆਂ ਦੇ ਉਲਟ ਖਪਤ ਨਹੀਂ ਕੀਤੀ ਜਾਂਦੀ। ਇੱਕ ਹੌਲੀ ਪਰ ਇੱਕ ਉੱਚ ਗੁਣਵੱਤਾ ਵਾਲੀ ਵੈਲਡਿੰਗ ਤਕਨੀਕ ਪਤਲੀ ਸਮੱਗਰੀ ਦੀ ਵੈਲਡਿੰਗ ਵਿੱਚ ਹੋਰ ਤਕਨੀਕਾਂ ਨਾਲੋਂ ਫਾਇਦੇਮੰਦ ਹੈ। ਬਹੁਤ ਸਾਰੀਆਂ ਧਾਤਾਂ ਲਈ ਅਨੁਕੂਲ. ਪਲਾਜ਼ਮਾ ਆਰਕ ਵੈਲਡਿੰਗ ਸਮਾਨ ਹੈ ਪਰ ਚਾਪ ਬਣਾਉਣ ਲਈ ਪਲਾਜ਼ਮਾ ਗੈਸ ਦੀ ਵਰਤੋਂ ਕਰਦਾ ਹੈ। ਪਲਾਜ਼ਮਾ ਆਰਕ ਵੈਲਡਿੰਗ ਵਿੱਚ ਚਾਪ GTAW ਦੀ ਤੁਲਨਾ ਵਿੱਚ ਮੁਕਾਬਲਤਨ ਵਧੇਰੇ ਕੇਂਦ੍ਰਿਤ ਹੈ ਅਤੇ ਇਸਦੀ ਵਰਤੋਂ ਬਹੁਤ ਜ਼ਿਆਦਾ ਗਤੀ 'ਤੇ ਧਾਤ ਦੀ ਮੋਟਾਈ ਦੀ ਵਿਸ਼ਾਲ ਸ਼੍ਰੇਣੀ ਲਈ ਕੀਤੀ ਜਾ ਸਕਦੀ ਹੈ। GTAW ਅਤੇ ਪਲਾਜ਼ਮਾ ਆਰਕ ਵੈਲਡਿੰਗ ਨੂੰ ਘੱਟ ਜਾਂ ਘੱਟ ਸਮਾਨ ਸਮੱਗਰੀਆਂ 'ਤੇ ਲਾਗੂ ਕੀਤਾ ਜਾ ਸਕਦਾ ਹੈ। OXY-FUEL / OXYFUEL ਵੈਲਡਿੰਗ ਨੂੰ oxyacetylene welding, oxy welding ਵੀ ਕਿਹਾ ਜਾਂਦਾ ਹੈ, ਵੈਲਡਿੰਗ ਲਈ ਗੈਸ ਬਾਲਣ ਅਤੇ ਆਕਸੀਜਨ ਦੀ ਵਰਤੋਂ ਕਰਕੇ ਗੈਸ ਵੈਲਡਿੰਗ ਕੀਤੀ ਜਾਂਦੀ ਹੈ। ਕਿਉਂਕਿ ਕੋਈ ਇਲੈਕਟ੍ਰਿਕ ਪਾਵਰ ਦੀ ਵਰਤੋਂ ਨਹੀਂ ਕੀਤੀ ਜਾਂਦੀ ਇਹ ਪੋਰਟੇਬਲ ਹੈ ਅਤੇ ਜਿੱਥੇ ਬਿਜਲੀ ਨਹੀਂ ਹੈ ਉੱਥੇ ਵਰਤੀ ਜਾ ਸਕਦੀ ਹੈ। ਇੱਕ ਵੈਲਡਿੰਗ ਟਾਰਚ ਦੀ ਵਰਤੋਂ ਕਰਦੇ ਹੋਏ ਅਸੀਂ ਇੱਕ ਸਾਂਝੇ ਪਿਘਲੇ ਹੋਏ ਧਾਤ ਦੇ ਪੂਲ ਨੂੰ ਬਣਾਉਣ ਲਈ ਟੁਕੜਿਆਂ ਅਤੇ ਫਿਲਰ ਸਮੱਗਰੀ ਨੂੰ ਗਰਮ ਕਰਦੇ ਹਾਂ। ਕਈ ਈਂਧਨ ਵਰਤੇ ਜਾ ਸਕਦੇ ਹਨ ਜਿਵੇਂ ਕਿ ਐਸੀਟਿਲੀਨ, ਗੈਸੋਲੀਨ, ਹਾਈਡ੍ਰੋਜਨ, ਪ੍ਰੋਪੇਨ, ਬਿਊਟੇਨ... ਆਦਿ। ਆਕਸੀ-ਈਂਧਨ ਵੈਲਡਿੰਗ ਵਿੱਚ ਅਸੀਂ ਦੋ ਕੰਟੇਨਰਾਂ ਦੀ ਵਰਤੋਂ ਕਰਦੇ ਹਾਂ, ਇੱਕ ਬਾਲਣ ਲਈ ਅਤੇ ਦੂਜਾ ਆਕਸੀਜਨ ਲਈ। ਆਕਸੀਜਨ ਬਾਲਣ ਨੂੰ ਆਕਸੀਡਾਈਜ਼ ਕਰਦੀ ਹੈ (ਇਸ ਨੂੰ ਸਾੜ ਦਿੰਦੀ ਹੈ)। ਪ੍ਰਤੀਰੋਧ ਵੈਲਡਿੰਗ: ਇਸ ਕਿਸਮ ਦੀ ਵੈਲਡਿੰਗ ਜੂਲ ਹੀਟਿੰਗ ਦਾ ਫਾਇਦਾ ਉਠਾਉਂਦੀ ਹੈ ਅਤੇ ਉਸ ਸਥਾਨ 'ਤੇ ਗਰਮੀ ਪੈਦਾ ਹੁੰਦੀ ਹੈ ਜਿੱਥੇ ਇੱਕ ਨਿਸ਼ਚਤ ਸਮੇਂ ਲਈ ਬਿਜਲੀ ਦਾ ਕਰੰਟ ਲਗਾਇਆ ਜਾਂਦਾ ਹੈ। ਉੱਚ ਧਾਰਾਵਾਂ ਧਾਤ ਵਿੱਚੋਂ ਲੰਘਦੀਆਂ ਹਨ। ਇਸ ਸਥਾਨ 'ਤੇ ਪਿਘਲੀ ਹੋਈ ਧਾਤ ਦੇ ਪੂਲ ਬਣਦੇ ਹਨ। ਪ੍ਰਤੀਰੋਧਕ ਿਲਵਿੰਗ ਵਿਧੀਆਂ ਉਹਨਾਂ ਦੀ ਕੁਸ਼ਲਤਾ, ਘੱਟ ਪ੍ਰਦੂਸ਼ਣ ਸਮਰੱਥਾ ਦੇ ਕਾਰਨ ਪ੍ਰਸਿੱਧ ਹਨ। ਹਾਲਾਂਕਿ ਨੁਕਸਾਨ ਇਹ ਹਨ ਕਿ ਸਾਜ਼ੋ-ਸਾਮਾਨ ਦੀ ਲਾਗਤ ਮੁਕਾਬਲਤਨ ਮਹੱਤਵਪੂਰਨ ਹੈ ਅਤੇ ਮੁਕਾਬਲਤਨ ਪਤਲੇ ਕੰਮ ਦੇ ਟੁਕੜਿਆਂ ਦੀ ਅੰਦਰੂਨੀ ਸੀਮਾ ਹੈ। ਸਪੌਟ ਵੈਲਡਿੰਗ ਇੱਕ ਪ੍ਰਮੁੱਖ ਕਿਸਮ ਦੀ ਪ੍ਰਤੀਰੋਧਕ ਵੈਲਡਿੰਗ ਹੈ। ਇੱਥੇ ਅਸੀਂ ਸ਼ੀਟਾਂ ਨੂੰ ਇਕੱਠੇ ਕਲੈਂਪ ਕਰਨ ਲਈ ਦੋ ਤਾਂਬੇ ਦੇ ਇਲੈਕਟ੍ਰੋਡਾਂ ਦੀ ਵਰਤੋਂ ਕਰਕੇ ਦੋ ਜਾਂ ਦੋ ਤੋਂ ਵੱਧ ਓਵਰਲੈਪਿੰਗ ਸ਼ੀਟਾਂ ਜਾਂ ਕੰਮ ਦੇ ਟੁਕੜਿਆਂ ਨੂੰ ਜੋੜਦੇ ਹਾਂ ਅਤੇ ਉਹਨਾਂ ਵਿੱਚੋਂ ਇੱਕ ਉੱਚ ਕਰੰਟ ਪਾਸ ਕਰਦੇ ਹਾਂ। ਤਾਂਬੇ ਦੇ ਇਲੈਕਟ੍ਰੋਡ ਦੇ ਵਿਚਕਾਰ ਦੀ ਸਮੱਗਰੀ ਗਰਮ ਹੋ ਜਾਂਦੀ ਹੈ ਅਤੇ ਉਸ ਸਥਾਨ 'ਤੇ ਇੱਕ ਪਿਘਲਾ ਹੋਇਆ ਪੂਲ ਪੈਦਾ ਹੁੰਦਾ ਹੈ। ਫਿਰ ਕਰੰਟ ਨੂੰ ਰੋਕ ਦਿੱਤਾ ਜਾਂਦਾ ਹੈ ਅਤੇ ਤਾਂਬੇ ਦੇ ਇਲੈਕਟ੍ਰੋਡ ਟਿਪਸ ਵੇਲਡ ਦੀ ਸਥਿਤੀ ਨੂੰ ਠੰਡਾ ਕਰਦੇ ਹਨ ਕਿਉਂਕਿ ਇਲੈਕਟ੍ਰੋਡ ਪਾਣੀ ਨੂੰ ਠੰਢਾ ਕਰਦੇ ਹਨ। ਸਹੀ ਸਮੱਗਰੀ ਅਤੇ ਮੋਟਾਈ ਲਈ ਸਹੀ ਮਾਤਰਾ ਵਿੱਚ ਗਰਮੀ ਨੂੰ ਲਾਗੂ ਕਰਨਾ ਇਸ ਤਕਨੀਕ ਲਈ ਮੁੱਖ ਹੈ, ਕਿਉਂਕਿ ਜੇਕਰ ਗਲਤ ਤਰੀਕੇ ਨਾਲ ਲਾਗੂ ਕੀਤਾ ਜਾਂਦਾ ਹੈ ਤਾਂ ਜੋੜ ਕਮਜ਼ੋਰ ਹੋ ਜਾਵੇਗਾ। ਸਪਾਟ ਵੈਲਡਿੰਗ ਵਿੱਚ ਵਰਕਪੀਸ, ਊਰਜਾ ਕੁਸ਼ਲਤਾ, ਆਟੋਮੇਸ਼ਨ ਦੀ ਸੌਖ ਅਤੇ ਬਕਾਇਆ ਉਤਪਾਦਨ ਦਰਾਂ, ਅਤੇ ਕਿਸੇ ਵੀ ਫਿਲਰ ਦੀ ਲੋੜ ਨਾ ਹੋਣ ਦੇ ਫਾਇਦੇ ਹਨ। ਨੁਕਸਾਨ ਇਹ ਹੈ ਕਿ ਕਿਉਂਕਿ ਵੈਲਡਿੰਗ ਲਗਾਤਾਰ ਸੀਮ ਬਣਾਉਣ ਦੀ ਬਜਾਏ ਥਾਂਵਾਂ 'ਤੇ ਹੁੰਦੀ ਹੈ, ਇਸ ਲਈ ਸਮੁੱਚੀ ਤਾਕਤ ਹੋਰ ਵੈਲਡਿੰਗ ਤਰੀਕਿਆਂ ਦੇ ਮੁਕਾਬਲੇ ਮੁਕਾਬਲਤਨ ਘੱਟ ਹੋ ਸਕਦੀ ਹੈ। ਦੂਜੇ ਪਾਸੇ ਸੀਮ ਵੈਲਡਿੰਗ ਸਮਾਨ ਸਮੱਗਰੀ ਦੀਆਂ ਫੇਇੰਗ ਸਤਹਾਂ 'ਤੇ ਵੇਲਡ ਪੈਦਾ ਕਰਦੀ ਹੈ। ਸੀਮ ਬੱਟ ਜਾਂ ਓਵਰਲੈਪ ਜੋੜ ਹੋ ਸਕਦਾ ਹੈ। ਸੀਮ ਵੈਲਡਿੰਗ ਇੱਕ ਸਿਰੇ ਤੋਂ ਸ਼ੁਰੂ ਹੁੰਦੀ ਹੈ ਅਤੇ ਹੌਲੀ-ਹੌਲੀ ਦੂਜੇ ਸਿਰੇ ਤੱਕ ਜਾਂਦੀ ਹੈ। ਇਹ ਵਿਧੀ ਵੇਲਡ ਖੇਤਰ ਵਿੱਚ ਦਬਾਅ ਅਤੇ ਕਰੰਟ ਲਾਗੂ ਕਰਨ ਲਈ ਤਾਂਬੇ ਤੋਂ ਦੋ ਇਲੈਕਟ੍ਰੋਡਾਂ ਦੀ ਵਰਤੋਂ ਵੀ ਕਰਦੀ ਹੈ। ਡਿਸਕ ਦੇ ਆਕਾਰ ਦੇ ਇਲੈਕਟ੍ਰੋਡ ਸੀਮ ਲਾਈਨ ਦੇ ਨਾਲ ਨਿਰੰਤਰ ਸੰਪਰਕ ਦੇ ਨਾਲ ਘੁੰਮਦੇ ਹਨ ਅਤੇ ਇੱਕ ਨਿਰੰਤਰ ਵੇਲਡ ਬਣਾਉਂਦੇ ਹਨ। ਇੱਥੇ ਵੀ, ਇਲੈਕਟ੍ਰੋਡ ਨੂੰ ਪਾਣੀ ਦੁਆਰਾ ਠੰਢਾ ਕੀਤਾ ਜਾਂਦਾ ਹੈ. ਵੇਲਡ ਬਹੁਤ ਮਜ਼ਬੂਤ ਅਤੇ ਭਰੋਸੇਮੰਦ ਹਨ. ਹੋਰ ਤਰੀਕੇ ਪ੍ਰੋਜੈਕਸ਼ਨ, ਫਲੈਸ਼ ਅਤੇ ਅਪਸੈਟ ਵੈਲਡਿੰਗ ਤਕਨੀਕ ਹਨ। ਸਾਲਿਡ-ਸਟੇਟ ਵੈਲਡਿੰਗ ਉੱਪਰ ਦੱਸੇ ਗਏ ਪਿਛਲੇ ਤਰੀਕਿਆਂ ਨਾਲੋਂ ਥੋੜੀ ਵੱਖਰੀ ਹੈ। ਮੇਲ ਖਾਂਦੀਆਂ ਧਾਤਾਂ ਦੇ ਪਿਘਲਣ ਦੇ ਤਾਪਮਾਨ ਤੋਂ ਘੱਟ ਤਾਪਮਾਨ 'ਤੇ ਅਤੇ ਮੈਟਲ ਫਿਲਰ ਦੀ ਵਰਤੋਂ ਕੀਤੇ ਬਿਨਾਂ ਹੁੰਦਾ ਹੈ। ਕੁਝ ਪ੍ਰਕਿਰਿਆਵਾਂ ਵਿੱਚ ਦਬਾਅ ਵਰਤਿਆ ਜਾ ਸਕਦਾ ਹੈ। ਵੱਖੋ-ਵੱਖਰੇ ਢੰਗ ਹਨ ਕੋਐਕਸਟਰਿਊਸ਼ਨ ਵੈਲਡਿੰਗ ਜਿੱਥੇ ਵੱਖੋ-ਵੱਖਰੀਆਂ ਧਾਤਾਂ ਨੂੰ ਇੱਕੋ ਡਾਈ ਰਾਹੀਂ ਬਾਹਰ ਕੱਢਿਆ ਜਾਂਦਾ ਹੈ, ਕੋਲਡ ਪ੍ਰੈਸ਼ਰ ਵੈਲਡਿੰਗ ਜਿੱਥੇ ਅਸੀਂ ਉਨ੍ਹਾਂ ਦੇ ਪਿਘਲਣ ਵਾਲੇ ਬਿੰਦੂਆਂ ਦੇ ਹੇਠਾਂ ਨਰਮ ਮਿਸ਼ਰਤ ਮਿਸ਼ਰਣਾਂ ਨੂੰ ਜੋੜਦੇ ਹਾਂ, ਵਿਸਤ੍ਰਿਤ ਵੇਲਡ ਲਾਈਨਾਂ ਤੋਂ ਬਿਨਾਂ ਇੱਕ ਤਕਨੀਕ ਨੂੰ ਡਿਫਿਊਜ਼ਨ ਵੈਲਡਿੰਗ, ਵੱਖੋ-ਵੱਖਰੇ ਪਦਾਰਥਾਂ ਨੂੰ ਮੁੜ ਤੋਂ ਵੱਖ ਕਰਨ ਵਾਲੀਆਂ ਸਮੱਗਰੀਆਂ ਨੂੰ ਜੋੜਨ ਲਈ ਵਿਸਫੋਟ ਵੈਲਡਿੰਗ। ਸਟੀਲਜ਼, ਇਲੈਕਟ੍ਰੋਮੈਗਨੈਟਿਕ ਪਲਸ ਵੈਲਡਿੰਗ ਜਿੱਥੇ ਅਸੀਂ ਇਲੈਕਟ੍ਰੋਮੈਗਨੈਟਿਕ ਬਲਾਂ ਦੁਆਰਾ ਟਿਊਬਾਂ ਅਤੇ ਸ਼ੀਟਾਂ ਨੂੰ ਤੇਜ਼ ਕਰਦੇ ਹਾਂ, ਫੋਰਜ ਵੈਲਡਿੰਗ ਜਿਸ ਵਿੱਚ ਧਾਤਾਂ ਨੂੰ ਉੱਚ ਤਾਪਮਾਨਾਂ ਤੱਕ ਗਰਮ ਕਰਨਾ ਅਤੇ ਉਹਨਾਂ ਨੂੰ ਇਕੱਠੇ ਹਥੌੜਾ ਕਰਨਾ ਸ਼ਾਮਲ ਹੁੰਦਾ ਹੈ, ਫਰੀਕਸ਼ਨ ਵੈਲਡਿੰਗ ਜਿੱਥੇ ਕਾਫ਼ੀ ਰਗੜ ਨਾਲ ਵੈਲਡਿੰਗ ਕੀਤੀ ਜਾਂਦੀ ਹੈ, ਰਗੜਨਾ ਜੋ ਕਿ ਰੋਟ-ਰੋਟ ਨਹੀਂ ਕਰਦੀ ਹੈ ਸੰਯੁਕਤ ਲਾਈਨ ਨੂੰ ਪਾਰ ਕਰਦੇ ਹੋਏ ਖਪਤਯੋਗ ਟੂਲ, ਹੌਟ ਪ੍ਰੈਸ਼ਰ ਵੈਲਡਿੰਗ ਜਿੱਥੇ ਅਸੀਂ ਵੈਕਿਊਮ ਜਾਂ ਅੜਿੱਕੇ ਗੈਸਾਂ ਵਿੱਚ ਪਿਘਲਣ ਵਾਲੇ ਤਾਪਮਾਨ ਤੋਂ ਹੇਠਾਂ ਉੱਚੇ ਤਾਪਮਾਨਾਂ 'ਤੇ ਧਾਤਾਂ ਨੂੰ ਇਕੱਠੇ ਦਬਾਉਂਦੇ ਹਾਂ, ਗਰਮ ਆਈਸੋਸਟੈਟਿਕ ਪ੍ਰੈਸ਼ਰ ਵੈਲਡਿੰਗ ਇੱਕ ਪ੍ਰਕਿਰਿਆ ਜਿੱਥੇ ਅਸੀਂ ਇੱਕ ਭਾਂਡੇ ਦੇ ਅੰਦਰ ਅੜਤ ਗੈਸਾਂ ਦੀ ਵਰਤੋਂ ਕਰਕੇ ਦਬਾਅ ਪਾਉਂਦੇ ਹਾਂ, ਰੋਲ ਵੈਲਡਿੰਗ ਜਿੱਥੇ ਅਸੀਂ ਜੁੜਦੇ ਹਾਂ। ਵੱਖੋ-ਵੱਖਰੀਆਂ ਸਮੱਗਰੀਆਂ ਨੂੰ ਵਿਚਕਾਰ ਧੱਕ ਕੇ ਦੋ ਘੁੰਮਦੇ ਪਹੀਏ, ਅਲਟ੍ਰਾਸੋਨਿਕ ਵੈਲਡਿੰਗ ਜਿੱਥੇ ਪਤਲੀ ਧਾਤ ਜਾਂ ਪਲਾਸਟਿਕ ਦੀਆਂ ਚਾਦਰਾਂ ਨੂੰ ਉੱਚ ਫ੍ਰੀਕੁਐਂਸੀ ਵਾਈਬ੍ਰੇਸ਼ਨਲ ਊਰਜਾ ਦੀ ਵਰਤੋਂ ਕਰਕੇ ਵੇਲਡ ਕੀਤਾ ਜਾਂਦਾ ਹੈ। ਸਾਡੀਆਂ ਹੋਰ ਵੈਲਡਿੰਗ ਪ੍ਰਕਿਰਿਆਵਾਂ ਡੂੰਘੇ ਪ੍ਰਵੇਸ਼ ਅਤੇ ਤੇਜ਼ ਪ੍ਰਕਿਰਿਆ ਦੇ ਨਾਲ ਇਲੈਕਟ੍ਰੌਨ ਬੀਮ ਵੈਲਡਿੰਗ ਹਨ ਪਰ ਇੱਕ ਮਹਿੰਗਾ ਤਰੀਕਾ ਹੋਣ ਕਰਕੇ ਅਸੀਂ ਇਸਨੂੰ ਵਿਸ਼ੇਸ਼ ਮਾਮਲਿਆਂ ਲਈ ਮੰਨਦੇ ਹਾਂ, ਇਲੈਕਟ੍ਰੋਸਲੈਗ ਵੈਲਡਿੰਗ ਇੱਕ ਢੰਗ ਹੈ ਜੋ ਭਾਰੀ ਮੋਟੀਆਂ ਪਲੇਟਾਂ ਅਤੇ ਸਟੀਲ ਦੇ ਕੰਮ ਦੇ ਟੁਕੜਿਆਂ ਲਈ ਢੁਕਵਾਂ ਹੈ, ਇੰਡਕਸ਼ਨ ਵੈਲਡਿੰਗ ਜਿੱਥੇ ਅਸੀਂ ਇਲੈਕਟ੍ਰੋਮੈਗਨੈਟਿਕ ਇੰਡਕਸ਼ਨ ਦੀ ਵਰਤੋਂ ਕਰਦੇ ਹਾਂ ਅਤੇ ਸਾਡੇ ਇਲੈਕਟ੍ਰਿਕਲੀ ਕੰਡਕਟਿਵ ਜਾਂ ਫੇਰੋਮੈਗਨੈਟਿਕ ਵਰਕਪੀਸ ਨੂੰ ਗਰਮ ਕਰੋ, ਲੇਜ਼ਰ ਬੀਮ ਵੈਲਡਿੰਗ ਵੀ ਡੂੰਘੀ ਪ੍ਰਵੇਸ਼ ਅਤੇ ਤੇਜ਼ ਪ੍ਰੋਸੈਸਿੰਗ ਦੇ ਨਾਲ ਪਰ ਇੱਕ ਮਹਿੰਗਾ ਤਰੀਕਾ, ਲੇਜ਼ਰ ਹਾਈਬ੍ਰਿਡ ਵੈਲਡਿੰਗ ਜੋ LBW ਨੂੰ GMAW ਨਾਲ ਉਸੇ ਵੈਲਡਿੰਗ ਹੈੱਡ ਵਿੱਚ ਜੋੜਦੀ ਹੈ ਅਤੇ 2 ਮਿਲੀਮੀਟਰ ਦੇ ਪਾੜੇ ਨੂੰ ਪੂਰਾ ਕਰਨ ਦੇ ਸਮਰੱਥ ਹੈ, LDWESS that ਇਸ ਵਿੱਚ ਇੱਕ ਇਲੈਕਟ੍ਰਿਕ ਡਿਸਚਾਰਜ ਸ਼ਾਮਲ ਹੁੰਦਾ ਹੈ ਜਿਸ ਤੋਂ ਬਾਅਦ ਲਾਗੂ ਕੀਤੇ ਦਬਾਅ ਨਾਲ ਸਮੱਗਰੀ ਨੂੰ ਫੋਜੀ ਕੀਤਾ ਜਾਂਦਾ ਹੈ, ਥਰਮਿਟ ਵੈਲਡਿੰਗ ਜਿਸ ਵਿੱਚ ਅਲਮੀਨੀਅਮ ਅਤੇ ਆਇਰਨ ਆਕਸਾਈਡ ਪਾਊਡਰਾਂ ਵਿਚਕਾਰ ਐਕਸੋਥਰਮਿਕ ਪ੍ਰਤੀਕ੍ਰਿਆ ਸ਼ਾਮਲ ਹੁੰਦੀ ਹੈ।, ਖਪਤਯੋਗ ਇਲੈਕਟ੍ਰੋਡਾਂ ਦੇ ਨਾਲ ਇਲੈਕਟ੍ਰੋਗੈਸ ਵੈਲਡਿੰਗ ਅਤੇ ਲੰਬਕਾਰੀ ਸਥਿਤੀ ਵਿੱਚ ਕੇਵਲ ਸਟੀਲ ਨਾਲ ਵਰਤੀ ਜਾਂਦੀ ਹੈ, ਅਤੇ ਅੰਤ ਵਿੱਚ ਸਟੱਡ ਨਾਲ ਬੇਸ ਨੂੰ ਜੋੜਨ ਲਈ STUD ARC ਵੈਲਡਿੰਗ। ਗਰਮੀ ਅਤੇ ਦਬਾਅ ਨਾਲ ਸਮੱਗਰੀ. ਅਸੀਂ ਸਿਫ਼ਾਰਿਸ਼ ਕਰਦੇ ਹਾਂ ਕਿ ਤੁਸੀਂ ਇੱਥੇ ਕਲਿੱਕ ਕਰੋAGS-TECH Inc ਦੁਆਰਾ ਬ੍ਰੇਜ਼ਿੰਗ, ਸੋਲਡਰਿੰਗ ਅਤੇ ਅਡੈਸਿਵ ਬੰਧਨ ਪ੍ਰਕਿਰਿਆਵਾਂ ਦੇ ਸਾਡੇ ਯੋਜਨਾਬੱਧ ਚਿੱਤਰਾਂ ਨੂੰ ਡਾਉਨਲੋਡ ਕਰੋ ਇਹ ਤੁਹਾਨੂੰ ਉਸ ਜਾਣਕਾਰੀ ਨੂੰ ਬਿਹਤਰ ਤਰੀਕੇ ਨਾਲ ਸਮਝਣ ਵਿੱਚ ਮਦਦ ਕਰੇਗਾ ਜੋ ਅਸੀਂ ਤੁਹਾਨੂੰ ਹੇਠਾਂ ਪ੍ਰਦਾਨ ਕਰ ਰਹੇ ਹਾਂ। • ਬ੍ਰੇਜ਼ਿੰਗ: ਅਸੀਂ ਦੋ ਜਾਂ ਦੋ ਤੋਂ ਵੱਧ ਧਾਤਾਂ ਨੂੰ ਉਹਨਾਂ ਦੇ ਪਿਘਲਣ ਵਾਲੇ ਬਿੰਦੂਆਂ ਦੇ ਉੱਪਰ ਉਹਨਾਂ ਦੇ ਵਿਚਕਾਰ ਫਿਲਰ ਧਾਤਾਂ ਨੂੰ ਗਰਮ ਕਰਕੇ ਅਤੇ ਫੈਲਣ ਲਈ ਕੇਸ਼ੀਲ ਕਿਰਿਆ ਦੀ ਵਰਤੋਂ ਕਰਕੇ ਜੋੜਦੇ ਹਾਂ। ਇਹ ਪ੍ਰਕਿਰਿਆ ਸੋਲਡਰਿੰਗ ਵਰਗੀ ਹੈ ਪਰ ਫਿਲਰ ਨੂੰ ਪਿਘਲਣ ਲਈ ਸ਼ਾਮਲ ਤਾਪਮਾਨ ਬਰੇਜ਼ਿੰਗ ਵਿੱਚ ਵੱਧ ਹੁੰਦਾ ਹੈ। ਵੈਲਡਿੰਗ ਦੀ ਤਰ੍ਹਾਂ, ਫਲੈਕਸ ਫਿਲਰ ਸਮੱਗਰੀ ਨੂੰ ਵਾਯੂਮੰਡਲ ਦੇ ਗੰਦਗੀ ਤੋਂ ਬਚਾਉਂਦਾ ਹੈ। ਠੰਢਾ ਹੋਣ ਤੋਂ ਬਾਅਦ ਵਰਕਪੀਸ ਇਕੱਠੇ ਮਿਲ ਜਾਂਦੇ ਹਨ. ਪ੍ਰਕਿਰਿਆ ਵਿੱਚ ਹੇਠਾਂ ਦਿੱਤੇ ਮੁੱਖ ਕਦਮ ਸ਼ਾਮਲ ਹੁੰਦੇ ਹਨ: ਚੰਗੀ ਫਿੱਟ ਅਤੇ ਕਲੀਅਰੈਂਸ, ਬੇਸ ਸਮੱਗਰੀ ਦੀ ਸਹੀ ਸਫਾਈ, ਸਹੀ ਫਿਕਸਚਰਿੰਗ, ਸਹੀ ਪ੍ਰਵਾਹ ਅਤੇ ਵਾਯੂਮੰਡਲ ਦੀ ਚੋਣ, ਅਸੈਂਬਲੀ ਨੂੰ ਗਰਮ ਕਰਨਾ ਅਤੇ ਅੰਤ ਵਿੱਚ ਬ੍ਰੇਜ਼ਡ ਅਸੈਂਬਲੀ ਦੀ ਸਫਾਈ। ਸਾਡੀਆਂ ਕੁਝ ਬ੍ਰੇਜ਼ਿੰਗ ਪ੍ਰਕਿਰਿਆਵਾਂ ਟਾਰਚ ਬ੍ਰੇਜ਼ਿੰਗ ਹਨ, ਇੱਕ ਪ੍ਰਸਿੱਧ ਵਿਧੀ ਜੋ ਹੱਥੀਂ ਜਾਂ ਸਵੈਚਲਿਤ ਢੰਗ ਨਾਲ ਕੀਤੀ ਜਾਂਦੀ ਹੈ। ਇਹ ਘੱਟ ਵਾਲੀਅਮ ਉਤਪਾਦਨ ਆਰਡਰ ਅਤੇ ਵਿਸ਼ੇਸ਼ ਕੇਸਾਂ ਲਈ ਢੁਕਵਾਂ ਹੈ। ਬਰੇਜ਼ ਕੀਤੇ ਜਾ ਰਹੇ ਜੋੜ ਦੇ ਨੇੜੇ ਗੈਸ ਦੀਆਂ ਲਾਟਾਂ ਦੀ ਵਰਤੋਂ ਕਰਕੇ ਹੀਟ ਲਾਗੂ ਕੀਤੀ ਜਾਂਦੀ ਹੈ। ਫਰਨੇਸ ਬ੍ਰੇਜ਼ਿੰਗ ਲਈ ਘੱਟ ਆਪਰੇਟਰ ਹੁਨਰ ਦੀ ਲੋੜ ਹੁੰਦੀ ਹੈ ਅਤੇ ਇਹ ਉਦਯੋਗਿਕ ਵੱਡੇ ਉਤਪਾਦਨ ਲਈ ਢੁਕਵੀਂ ਅਰਧ-ਆਟੋਮੈਟਿਕ ਪ੍ਰਕਿਰਿਆ ਹੈ। ਭੱਠੀ ਵਿੱਚ ਤਾਪਮਾਨ ਨਿਯੰਤਰਣ ਅਤੇ ਵਾਯੂਮੰਡਲ ਦਾ ਨਿਯੰਤਰਣ ਦੋਵੇਂ ਇਸ ਤਕਨੀਕ ਦੇ ਫਾਇਦੇ ਹਨ, ਕਿਉਂਕਿ ਪਹਿਲਾ ਸਾਨੂੰ ਨਿਯੰਤਰਿਤ ਗਰਮੀ ਦੇ ਚੱਕਰਾਂ ਅਤੇ ਸਥਾਨਕ ਹੀਟਿੰਗ ਨੂੰ ਖਤਮ ਕਰਨ ਦੇ ਯੋਗ ਬਣਾਉਂਦਾ ਹੈ ਜਿਵੇਂ ਕਿ ਟਾਰਚ ਬ੍ਰੇਜ਼ਿੰਗ ਵਿੱਚ ਹੁੰਦਾ ਹੈ, ਅਤੇ ਬਾਅਦ ਵਾਲੇ ਹਿੱਸੇ ਨੂੰ ਆਕਸੀਕਰਨ ਤੋਂ ਬਚਾਉਂਦਾ ਹੈ। ਜਿਗਿੰਗ ਦੀ ਵਰਤੋਂ ਕਰਕੇ ਅਸੀਂ ਨਿਰਮਾਣ ਲਾਗਤਾਂ ਨੂੰ ਘੱਟੋ-ਘੱਟ ਘਟਾਉਣ ਦੇ ਸਮਰੱਥ ਹਾਂ। ਨੁਕਸਾਨ ਉੱਚ ਬਿਜਲੀ ਦੀ ਖਪਤ, ਸਾਜ਼ੋ-ਸਾਮਾਨ ਦੀ ਲਾਗਤ ਅਤੇ ਹੋਰ ਚੁਣੌਤੀਪੂਰਨ ਡਿਜ਼ਾਈਨ ਵਿਚਾਰ ਹਨ। ਵੈਕਿਊਮ ਬ੍ਰੇਜ਼ਿੰਗ ਵੈਕਿਊਮ ਦੀ ਭੱਠੀ ਵਿੱਚ ਹੁੰਦੀ ਹੈ। ਤਾਪਮਾਨ ਦੀ ਇਕਸਾਰਤਾ ਬਣਾਈ ਰੱਖੀ ਜਾਂਦੀ ਹੈ ਅਤੇ ਅਸੀਂ ਬਹੁਤ ਘੱਟ ਬਕਾਇਆ ਤਣਾਅ ਦੇ ਨਾਲ ਪ੍ਰਵਾਹ ਮੁਕਤ, ਬਹੁਤ ਸਾਫ਼ ਜੋੜਾਂ ਨੂੰ ਪ੍ਰਾਪਤ ਕਰਦੇ ਹਾਂ। ਹੀਟ ਟ੍ਰੀਟਮੈਂਟ ਵੈਕਿਊਮ ਬ੍ਰੇਜ਼ਿੰਗ ਦੌਰਾਨ ਹੋ ਸਕਦੇ ਹਨ, ਕਿਉਂਕਿ ਹੌਲੀ ਹੀਟਿੰਗ ਅਤੇ ਕੂਲਿੰਗ ਚੱਕਰਾਂ ਦੌਰਾਨ ਮੌਜੂਦ ਘੱਟ ਬਚੇ ਹੋਏ ਤਣਾਅ ਦੇ ਕਾਰਨ। ਮੁੱਖ ਨੁਕਸਾਨ ਇਸਦੀ ਉੱਚ ਕੀਮਤ ਹੈ ਕਿਉਂਕਿ ਵੈਕਿਊਮ ਵਾਤਾਵਰਣ ਦੀ ਸਿਰਜਣਾ ਇੱਕ ਮਹਿੰਗੀ ਪ੍ਰਕਿਰਿਆ ਹੈ। ਫਿਰ ਵੀ ਇੱਕ ਹੋਰ ਤਕਨੀਕ ਡੀਆਈਪੀ ਬ੍ਰੇਜ਼ਿੰਗ ਫਿਕਸਚਰ ਵਾਲੇ ਹਿੱਸਿਆਂ ਨੂੰ ਜੋੜਦੀ ਹੈ ਜਿੱਥੇ ਮੇਲਣ ਵਾਲੀਆਂ ਸਤਹਾਂ 'ਤੇ ਬ੍ਰੇਜ਼ਿੰਗ ਮਿਸ਼ਰਣ ਲਾਗੂ ਕੀਤਾ ਜਾਂਦਾ ਹੈ। ਇਸ ਤੋਂ ਬਾਅਦ ਫਿਕਸਚਰ ਵਾਲੇ ਹਿੱਸਿਆਂ ਨੂੰ ਪਿਘਲੇ ਹੋਏ ਲੂਣ ਜਿਵੇਂ ਕਿ ਸੋਡੀਅਮ ਕਲੋਰਾਈਡ (ਟੇਬਲ ਲੂਣ) ਦੇ ਇਸ਼ਨਾਨ ਵਿੱਚ ਡੁਬੋਇਆ ਜਾਂਦਾ ਹੈ ਜੋ ਤਾਪ ਟ੍ਰਾਂਸਫਰ ਮਾਧਿਅਮ ਅਤੇ ਪ੍ਰਵਾਹ ਵਜੋਂ ਕੰਮ ਕਰਦਾ ਹੈ। ਹਵਾ ਨੂੰ ਬਾਹਰ ਰੱਖਿਆ ਗਿਆ ਹੈ ਅਤੇ ਇਸਲਈ ਕੋਈ ਆਕਸਾਈਡ ਨਹੀਂ ਬਣਦਾ ਹੈ। ਇੰਡਕਸ਼ਨ ਬ੍ਰੇਜ਼ਿੰਗ ਵਿੱਚ ਅਸੀਂ ਇੱਕ ਫਿਲਰ ਮੈਟਲ ਦੁਆਰਾ ਸਮੱਗਰੀ ਨੂੰ ਜੋੜਦੇ ਹਾਂ ਜਿਸਦਾ ਪਿਘਲਣ ਦਾ ਬਿੰਦੂ ਅਧਾਰ ਸਮੱਗਰੀ ਨਾਲੋਂ ਘੱਟ ਹੁੰਦਾ ਹੈ। ਇੰਡਕਸ਼ਨ ਕੋਇਲ ਤੋਂ ਬਦਲਵਾਂ ਕਰੰਟ ਇੱਕ ਇਲੈਕਟ੍ਰੋਮੈਗਨੈਟਿਕ ਫੀਲਡ ਬਣਾਉਂਦਾ ਹੈ ਜੋ ਜਿਆਦਾਤਰ ਫੈਰਸ ਮੈਗਨੈਟਿਕ ਸਾਮੱਗਰੀ 'ਤੇ ਇੰਡਕਸ਼ਨ ਹੀਟਿੰਗ ਨੂੰ ਪ੍ਰੇਰਿਤ ਕਰਦਾ ਹੈ। ਵਿਧੀ ਚੋਣਵੇਂ ਹੀਟਿੰਗ, ਫਿਲਰਾਂ ਦੇ ਨਾਲ ਚੰਗੇ ਜੋੜਾਂ ਨੂੰ ਸਿਰਫ ਲੋੜੀਂਦੇ ਖੇਤਰਾਂ ਵਿੱਚ ਵਹਿਣ, ਥੋੜ੍ਹਾ ਆਕਸੀਕਰਨ ਪ੍ਰਦਾਨ ਕਰਦਾ ਹੈ ਕਿਉਂਕਿ ਕੋਈ ਵੀ ਅੱਗ ਮੌਜੂਦ ਨਹੀਂ ਹੈ ਅਤੇ ਕੂਲਿੰਗ ਤੇਜ਼, ਤੇਜ਼ ਹੀਟਿੰਗ, ਇਕਸਾਰਤਾ ਅਤੇ ਉੱਚ ਵਾਲੀਅਮ ਨਿਰਮਾਣ ਲਈ ਅਨੁਕੂਲਤਾ ਹੈ। ਸਾਡੀਆਂ ਪ੍ਰਕਿਰਿਆਵਾਂ ਨੂੰ ਤੇਜ਼ ਕਰਨ ਅਤੇ ਇਕਸਾਰਤਾ ਨੂੰ ਯਕੀਨੀ ਬਣਾਉਣ ਲਈ ਅਸੀਂ ਅਕਸਰ ਪ੍ਰੀਫਾਰਮ ਦੀ ਵਰਤੋਂ ਕਰਦੇ ਹਾਂ। ਸਿਰੇਮਿਕ ਤੋਂ ਮੈਟਲ ਫਿਟਿੰਗਸ, ਹਰਮੇਟਿਕ ਸੀਲਿੰਗ, ਵੈਕਿਊਮ ਫੀਡਥਰੂਜ਼, ਹਾਈ ਅਤੇ ਅਲਟਰਾਹਾਈ ਵੈਕਿਊਮ ਅਤੇ ਤਰਲ ਨਿਯੰਤਰਣ ਕੰਪੋਨੈਂਟਸ ਬਾਰੇ ਜਾਣਕਾਰੀ ਇੱਥੇ ਮਿਲ ਸਕਦੀ ਹੈ:_cc781905-5cf58d_ ਇੱਥੇ ਮਿਲ ਸਕਦੀ ਹੈ:ਬ੍ਰੇਜ਼ਿੰਗ ਫੈਕਟਰੀ ਬਰੋਸ਼ਰ • ਸੋਲਡਰਿੰਗ: ਸੋਲਡਰਿੰਗ ਵਿੱਚ ਸਾਡੇ ਕੋਲ ਕੰਮ ਦੇ ਟੁਕੜਿਆਂ ਦਾ ਪਿਘਲਣਾ ਨਹੀਂ ਹੁੰਦਾ ਹੈ, ਪਰ ਜੋੜਾਂ ਵਿੱਚ ਵਹਿਣ ਵਾਲੇ ਜੋੜਨ ਵਾਲੇ ਹਿੱਸਿਆਂ ਨਾਲੋਂ ਘੱਟ ਪਿਘਲਣ ਵਾਲੇ ਬਿੰਦੂ ਵਾਲੀ ਇੱਕ ਫਿਲਰ ਮੈਟਲ ਹੁੰਦੀ ਹੈ। ਸੋਲਡਰਿੰਗ ਵਿਚ ਫਿਲਰ ਮੈਟਲ ਬ੍ਰੇਜ਼ਿੰਗ ਨਾਲੋਂ ਘੱਟ ਤਾਪਮਾਨ 'ਤੇ ਪਿਘਲ ਜਾਂਦੀ ਹੈ। ਅਸੀਂ ਸੋਲਡਰਿੰਗ ਲਈ ਲੀਡ-ਮੁਕਤ ਅਲਾਏ ਦੀ ਵਰਤੋਂ ਕਰਦੇ ਹਾਂ ਅਤੇ ਅਸੀਂ RoHS ਦੀ ਪਾਲਣਾ ਕਰਦੇ ਹਾਂ ਅਤੇ ਵੱਖ-ਵੱਖ ਐਪਲੀਕੇਸ਼ਨਾਂ ਅਤੇ ਲੋੜਾਂ ਲਈ ਸਾਡੇ ਕੋਲ ਸਿਲਵਰ ਅਲਾਏ ਵਰਗੀਆਂ ਵੱਖ-ਵੱਖ ਅਤੇ ਢੁਕਵੀਂ ਅਲਾਏ ਹਨ। ਸੋਲਡਰਿੰਗ ਸਾਨੂੰ ਜੋੜਾਂ ਦੀ ਪੇਸ਼ਕਸ਼ ਕਰਦਾ ਹੈ ਜੋ ਗੈਸ ਅਤੇ ਤਰਲ-ਤੰਗ ਹੁੰਦੇ ਹਨ। ਸਾਫਟ ਸੋਲਡਰਿੰਗ ਵਿੱਚ, ਸਾਡੀ ਫਿਲਰ ਧਾਤ ਦਾ ਪਿਘਲਣ ਦਾ ਬਿੰਦੂ 400 ਸੈਂਟੀਗਰੇਡ ਤੋਂ ਘੱਟ ਹੁੰਦਾ ਹੈ, ਜਦੋਂ ਕਿ ਸਿਲਵਰ ਸੋਲਡਰਿੰਗ ਅਤੇ ਬ੍ਰੇਜ਼ਿੰਗ ਵਿੱਚ ਸਾਨੂੰ ਉੱਚ ਤਾਪਮਾਨ ਦੀ ਲੋੜ ਹੁੰਦੀ ਹੈ। ਸੌਫਟ ਸੋਲਡਰਿੰਗ ਘੱਟ ਤਾਪਮਾਨਾਂ ਦੀ ਵਰਤੋਂ ਕਰਦੀ ਹੈ ਪਰ ਉੱਚੇ ਤਾਪਮਾਨਾਂ 'ਤੇ ਐਪਲੀਕੇਸ਼ਨਾਂ ਦੀ ਮੰਗ ਲਈ ਮਜ਼ਬੂਤ ਜੋੜਾਂ ਦਾ ਨਤੀਜਾ ਨਹੀਂ ਹੁੰਦਾ। ਦੂਜੇ ਪਾਸੇ, ਸਿਲਵਰ ਸੋਲਡਰਿੰਗ ਲਈ, ਟਾਰਚ ਦੁਆਰਾ ਪ੍ਰਦਾਨ ਕੀਤੇ ਗਏ ਉੱਚ ਤਾਪਮਾਨਾਂ ਦੀ ਲੋੜ ਹੁੰਦੀ ਹੈ ਅਤੇ ਸਾਨੂੰ ਉੱਚ ਤਾਪਮਾਨ ਦੀਆਂ ਐਪਲੀਕੇਸ਼ਨਾਂ ਲਈ ਢੁਕਵੇਂ ਮਜ਼ਬੂਤ ਜੋੜਾਂ ਦੀ ਲੋੜ ਹੁੰਦੀ ਹੈ। ਬ੍ਰੇਜ਼ਿੰਗ ਲਈ ਸਭ ਤੋਂ ਵੱਧ ਤਾਪਮਾਨ ਦੀ ਲੋੜ ਹੁੰਦੀ ਹੈ ਅਤੇ ਆਮ ਤੌਰ 'ਤੇ ਟਾਰਚ ਦੀ ਵਰਤੋਂ ਕੀਤੀ ਜਾਂਦੀ ਹੈ। ਕਿਉਂਕਿ ਬ੍ਰੇਜ਼ਿੰਗ ਜੋੜ ਬਹੁਤ ਮਜ਼ਬੂਤ ਹੁੰਦੇ ਹਨ, ਇਹ ਲੋਹੇ ਦੀਆਂ ਭਾਰੀ ਵਸਤੂਆਂ ਦੀ ਮੁਰੰਮਤ ਲਈ ਇੱਕ ਚੰਗੇ ਉਮੀਦਵਾਰ ਹਨ। ਸਾਡੀਆਂ ਨਿਰਮਾਣ ਲਾਈਨਾਂ ਵਿੱਚ ਅਸੀਂ ਮੈਨੂਅਲ ਹੈਂਡ ਸੋਲਡਰਿੰਗ ਦੇ ਨਾਲ-ਨਾਲ ਸਵੈਚਲਿਤ ਸੋਲਡਰ ਲਾਈਨਾਂ ਦੀ ਵਰਤੋਂ ਕਰਦੇ ਹਾਂ। INDUCTION ਸੋਲਡਰਿੰਗ ਇੰਡਕਸ਼ਨ ਹੀਟਿੰਗ ਦੀ ਸਹੂਲਤ ਲਈ ਇੱਕ ਤਾਂਬੇ ਦੇ ਕੋਇਲ ਵਿੱਚ ਉੱਚ ਆਵਿਰਤੀ AC ਕਰੰਟ ਦੀ ਵਰਤੋਂ ਕਰਦੀ ਹੈ। ਕਰੰਟ ਸੋਲਡ ਕੀਤੇ ਹਿੱਸੇ ਵਿੱਚ ਪ੍ਰੇਰਿਤ ਹੁੰਦੇ ਹਨ ਅਤੇ ਨਤੀਜੇ ਵਜੋਂ ਉੱਚ ਪ੍ਰਤੀਰੋਧ joint 'ਤੇ ਗਰਮੀ ਪੈਦਾ ਹੁੰਦੀ ਹੈ। ਇਹ ਗਰਮੀ ਫਿਲਰ ਧਾਤ ਨੂੰ ਪਿਘਲਾ ਦਿੰਦੀ ਹੈ। ਫਲੈਕਸ ਵੀ ਵਰਤਿਆ ਜਾਂਦਾ ਹੈ। ਇੰਡਕਸ਼ਨ ਸੋਲਡਰਿੰਗ ਸਾਈਕਲਿੰਡਰਾਂ ਅਤੇ ਪਾਈਪਾਂ ਨੂੰ ਉਹਨਾਂ ਦੇ ਦੁਆਲੇ ਕੋਇਲਾਂ ਨੂੰ ਲਪੇਟ ਕੇ ਇੱਕ ਨਿਰੰਤਰ ਪ੍ਰਕਿਰਿਆ ਵਿੱਚ ਸੋਲਡਰ ਕਰਨ ਦਾ ਇੱਕ ਵਧੀਆ ਤਰੀਕਾ ਹੈ। ਗ੍ਰੇਫਾਈਟ ਅਤੇ ਵਸਰਾਵਿਕਸ ਵਰਗੀਆਂ ਕੁਝ ਸਮੱਗਰੀਆਂ ਨੂੰ ਸੋਲਡਰ ਕਰਨਾ ਵਧੇਰੇ ਮੁਸ਼ਕਲ ਹੁੰਦਾ ਹੈ ਕਿਉਂਕਿ ਇਸ ਲਈ ਸੋਲਡਰਿੰਗ ਤੋਂ ਪਹਿਲਾਂ ਇੱਕ ਢੁਕਵੀਂ ਧਾਤ ਨਾਲ ਵਰਕਪੀਸ ਦੀ ਪਲੇਟਿੰਗ ਦੀ ਲੋੜ ਹੁੰਦੀ ਹੈ। ਇਹ ਇੰਟਰਫੇਸ਼ੀਅਲ ਬੰਧਨ ਦੀ ਸਹੂਲਤ ਦਿੰਦਾ ਹੈ। ਅਸੀਂ ਖਾਸ ਤੌਰ 'ਤੇ ਹਰਮੇਟਿਕ ਪੈਕੇਜਿੰਗ ਐਪਲੀਕੇਸ਼ਨਾਂ ਲਈ ਅਜਿਹੀਆਂ ਸਮੱਗਰੀਆਂ ਨੂੰ ਸੋਲਡਰ ਕਰਦੇ ਹਾਂ। ਅਸੀਂ ਜ਼ਿਆਦਾਤਰ ਵੇਵ ਸੋਲਡਰਿੰਗ ਦੀ ਵਰਤੋਂ ਕਰਕੇ ਆਪਣੇ ਪ੍ਰਿੰਟ ਕੀਤੇ ਸਰਕਟ ਬੋਰਡਾਂ (ਪੀਸੀਬੀ) ਨੂੰ ਉੱਚ ਮਾਤਰਾ ਵਿੱਚ ਬਣਾਉਂਦੇ ਹਾਂ। ਸਿਰਫ ਪ੍ਰੋਟੋਟਾਈਪਿੰਗ ਦੇ ਉਦੇਸ਼ਾਂ ਦੀ ਥੋੜ੍ਹੀ ਮਾਤਰਾ ਲਈ ਅਸੀਂ ਸੋਲਡਰਿੰਗ ਆਇਰਨ ਦੀ ਵਰਤੋਂ ਕਰਕੇ ਹੈਂਡ ਸੋਲਡਰਿੰਗ ਦੀ ਵਰਤੋਂ ਕਰਦੇ ਹਾਂ। ਅਸੀਂ ਥਰੋ-ਹੋਲ ਦੇ ਨਾਲ-ਨਾਲ ਸਤਹ ਮਾਊਂਟ ਪੀਸੀਬੀ ਅਸੈਂਬਲੀਆਂ (ਪੀਸੀਬੀਏ) ਦੋਵਾਂ ਲਈ ਵੇਵ ਸੋਲਡਰਿੰਗ ਦੀ ਵਰਤੋਂ ਕਰਦੇ ਹਾਂ। ਇੱਕ ਅਸਥਾਈ ਗੂੰਦ ਸਰਕਟ ਬੋਰਡ ਨਾਲ ਜੁੜੇ ਹਿੱਸਿਆਂ ਨੂੰ ਰੱਖਦਾ ਹੈ ਅਤੇ ਅਸੈਂਬਲੀ ਨੂੰ ਇੱਕ ਕਨਵੇਅਰ 'ਤੇ ਰੱਖਿਆ ਜਾਂਦਾ ਹੈ ਅਤੇ ਇੱਕ ਉਪਕਰਣ ਦੁਆਰਾ ਚਲਦਾ ਹੈ ਜਿਸ ਵਿੱਚ ਪਿਘਲੇ ਹੋਏ ਸੋਲਡਰ ਹੁੰਦੇ ਹਨ। ਪਹਿਲਾਂ ਪੀਸੀਬੀ ਫਲੈਕਸ ਹੁੰਦਾ ਹੈ ਅਤੇ ਫਿਰ ਪ੍ਰੀਹੀਟਿੰਗ ਜ਼ੋਨ ਵਿੱਚ ਦਾਖਲ ਹੁੰਦਾ ਹੈ। ਪਿਘਲਾ ਹੋਇਆ ਸੋਲਡਰ ਇੱਕ ਪੈਨ ਵਿੱਚ ਹੁੰਦਾ ਹੈ ਅਤੇ ਇਸਦੀ ਸਤ੍ਹਾ 'ਤੇ ਖੜ੍ਹੀਆਂ ਲਹਿਰਾਂ ਦਾ ਪੈਟਰਨ ਹੁੰਦਾ ਹੈ। ਜਦੋਂ ਪੀਸੀਬੀ ਇਹਨਾਂ ਤਰੰਗਾਂ ਉੱਤੇ ਚਲਦਾ ਹੈ, ਤਾਂ ਇਹ ਤਰੰਗਾਂ ਪੀਸੀਬੀ ਦੇ ਹੇਠਲੇ ਹਿੱਸੇ ਨਾਲ ਸੰਪਰਕ ਕਰਦੀਆਂ ਹਨ ਅਤੇ ਸੋਲਡਰਿੰਗ ਪੈਡਾਂ ਨਾਲ ਚਿਪਕ ਜਾਂਦੀਆਂ ਹਨ। ਸੋਲਡਰ ਸਿਰਫ਼ ਪਿੰਨਾਂ ਅਤੇ ਪੈਡਾਂ 'ਤੇ ਹੀ ਰਹਿੰਦਾ ਹੈ ਅਤੇ ਪੀਸੀਬੀ 'ਤੇ ਨਹੀਂ। ਪਿਘਲੇ ਹੋਏ ਸੋਲਡਰ ਵਿੱਚ ਤਰੰਗਾਂ ਨੂੰ ਚੰਗੀ ਤਰ੍ਹਾਂ ਨਿਯੰਤਰਿਤ ਕੀਤਾ ਜਾਣਾ ਚਾਹੀਦਾ ਹੈ ਤਾਂ ਜੋ ਕੋਈ ਛਿੜਕਾਅ ਨਾ ਹੋਵੇ ਅਤੇ ਵੇਵ ਟਾਪ ਬੋਰਡਾਂ ਦੇ ਅਣਚਾਹੇ ਖੇਤਰਾਂ ਨੂੰ ਛੂਹਣ ਅਤੇ ਦੂਸ਼ਿਤ ਨਾ ਕਰਨ। ਰੀਫਲੋ ਸੋਲਡਰਿੰਗ ਵਿੱਚ, ਅਸੀਂ ਬੋਰਡਾਂ ਵਿੱਚ ਇਲੈਕਟ੍ਰਾਨਿਕ ਭਾਗਾਂ ਨੂੰ ਅਸਥਾਈ ਤੌਰ 'ਤੇ ਜੋੜਨ ਲਈ ਇੱਕ ਸਟਿੱਕੀ ਸੋਲਡਰ ਪੇਸਟ ਦੀ ਵਰਤੋਂ ਕਰਦੇ ਹਾਂ। ਫਿਰ ਬੋਰਡਾਂ ਨੂੰ ਤਾਪਮਾਨ ਨਿਯੰਤਰਣ ਦੇ ਨਾਲ ਇੱਕ ਰੀਫਲੋ ਓਵਨ ਵਿੱਚ ਪਾ ਦਿੱਤਾ ਜਾਂਦਾ ਹੈ। ਇੱਥੇ ਸੋਲਡਰ ਪਿਘਲਦਾ ਹੈ ਅਤੇ ਭਾਗਾਂ ਨੂੰ ਪੱਕੇ ਤੌਰ 'ਤੇ ਜੋੜਦਾ ਹੈ। ਅਸੀਂ ਇਸ ਤਕਨੀਕ ਦੀ ਵਰਤੋਂ ਸਤਹ ਮਾਊਂਟ ਕੰਪੋਨੈਂਟਸ ਦੇ ਨਾਲ-ਨਾਲ ਹੋਲ ਕੰਪੋਨੈਂਟਾਂ ਲਈ ਵੀ ਕਰਦੇ ਹਾਂ। ਬੋਰਡ 'ਤੇ ਇਲੈਕਟ੍ਰਾਨਿਕ ਕੰਪੋਨੈਂਟਸ ਨੂੰ ਉਹਨਾਂ ਦੀ ਵੱਧ ਤੋਂ ਵੱਧ ਤਾਪਮਾਨ ਸੀਮਾਵਾਂ ਤੋਂ ਵੱਧ ਗਰਮ ਕਰਕੇ ਉਹਨਾਂ ਦੇ ਵਿਨਾਸ਼ ਤੋਂ ਬਚਣ ਲਈ ਉਚਿਤ ਤਾਪਮਾਨ ਨਿਯੰਤਰਣ ਅਤੇ ਓਵਨ ਦੇ ਤਾਪਮਾਨ ਦਾ ਸਮਾਯੋਜਨ ਜ਼ਰੂਰੀ ਹੈ। ਰੀਫਲੋ ਸੋਲਡਰਿੰਗ ਦੀ ਪ੍ਰਕਿਰਿਆ ਵਿੱਚ ਸਾਡੇ ਕੋਲ ਅਸਲ ਵਿੱਚ ਇੱਕ ਵੱਖਰੇ ਥਰਮਲ ਪ੍ਰੋਫਾਈਲ ਦੇ ਨਾਲ ਕਈ ਖੇਤਰ ਜਾਂ ਪੜਾਅ ਹੁੰਦੇ ਹਨ, ਜਿਵੇਂ ਕਿ ਪ੍ਰੀਹੀਟਿੰਗ ਸਟੈਪ, ਥਰਮਲ ਸੋਕਿੰਗ ਸਟੈਪ, ਰੀਫਲੋ ਅਤੇ ਕੂਲਿੰਗ ਸਟੈਪ। ਇਹ ਵੱਖ-ਵੱਖ ਕਦਮ ਪ੍ਰਿੰਟਿਡ ਸਰਕਟ ਬੋਰਡ ਅਸੈਂਬਲੀਆਂ (PCBA) ਦੇ ਨੁਕਸਾਨ ਤੋਂ ਮੁਕਤ ਰੀਫਲੋ ਸੋਲਡਰਿੰਗ ਲਈ ਜ਼ਰੂਰੀ ਹਨ। ULTRASONIC SOLDERING ਵਿਲੱਖਣ ਸਮਰੱਥਾਵਾਂ ਵਾਲੀ ਇੱਕ ਹੋਰ ਅਕਸਰ ਵਰਤੀ ਜਾਣ ਵਾਲੀ ਤਕਨੀਕ ਹੈ- ਇਸਦੀ ਵਰਤੋਂ ਕੱਚ, ਵਸਰਾਵਿਕ ਅਤੇ ਗੈਰ-ਧਾਤੂ ਸਮੱਗਰੀ ਨੂੰ ਸੋਲਡ ਕਰਨ ਲਈ ਕੀਤੀ ਜਾ ਸਕਦੀ ਹੈ। ਉਦਾਹਰਨ ਲਈ ਫੋਟੋਵੋਲਟੇਇਕ ਪੈਨਲ ਜੋ ਗੈਰ-ਧਾਤੂ ਹਨ, ਨੂੰ ਇਲੈਕਟ੍ਰੋਡ ਦੀ ਲੋੜ ਹੁੰਦੀ ਹੈ ਜੋ ਇਸ ਤਕਨੀਕ ਦੀ ਵਰਤੋਂ ਕਰਕੇ ਚਿਪਕਾਏ ਜਾ ਸਕਦੇ ਹਨ। ਅਲਟਰਾਸੋਨਿਕ ਸੋਲਡਰਿੰਗ ਵਿੱਚ, ਅਸੀਂ ਇੱਕ ਗਰਮ ਸੋਲਡਰਿੰਗ ਟਿਪ ਨੂੰ ਤੈਨਾਤ ਕਰਦੇ ਹਾਂ ਜੋ ਅਲਟਰਾਸੋਨਿਕ ਵਾਈਬ੍ਰੇਸ਼ਨਾਂ ਨੂੰ ਵੀ ਬਾਹਰ ਕੱਢਦਾ ਹੈ। ਇਹ ਵਾਈਬ੍ਰੇਸ਼ਨ ਪਿਘਲੇ ਹੋਏ ਸੋਲਡਰ ਸਮੱਗਰੀ ਦੇ ਨਾਲ ਸਬਸਟਰੇਟ ਦੇ ਇੰਟਰਫੇਸ 'ਤੇ cavitation ਬੁਲਬੁਲੇ ਪੈਦਾ ਕਰਦੇ ਹਨ। cavitation ਦੀ ਵਿਸਫੋਟਕ ਊਰਜਾ ਆਕਸਾਈਡ ਸਤਹ ਨੂੰ ਸੋਧਦੀ ਹੈ ਅਤੇ ਗੰਦਗੀ ਅਤੇ ਆਕਸਾਈਡ ਨੂੰ ਹਟਾਉਂਦੀ ਹੈ। ਇਸ ਸਮੇਂ ਦੌਰਾਨ ਇੱਕ ਮਿਸ਼ਰਤ ਪਰਤ ਵੀ ਬਣ ਜਾਂਦੀ ਹੈ। ਬੰਧਨ ਸਤਹ 'ਤੇ ਸੋਲਡਰ ਆਕਸੀਜਨ ਨੂੰ ਸ਼ਾਮਲ ਕਰਦਾ ਹੈ ਅਤੇ ਸ਼ੀਸ਼ੇ ਅਤੇ ਸੋਲਡਰ ਦੇ ਵਿਚਕਾਰ ਇੱਕ ਮਜ਼ਬੂਤ ਸਾਂਝਾ ਬੰਧਨ ਦੇ ਗਠਨ ਨੂੰ ਸਮਰੱਥ ਬਣਾਉਂਦਾ ਹੈ। ਡਿਪ ਸੋਲਡਰਿੰਗ ਨੂੰ ਸਿਰਫ ਛੋਟੇ ਪੈਮਾਨੇ ਦੇ ਉਤਪਾਦਨ ਲਈ ਢੁਕਵਾਂ ਵੇਵ ਸੋਲਡਰਿੰਗ ਦਾ ਇੱਕ ਸਰਲ ਸੰਸਕਰਣ ਮੰਨਿਆ ਜਾ ਸਕਦਾ ਹੈ। ਪਹਿਲੀ ਸਫਾਈ ਦਾ ਪ੍ਰਵਾਹ ਦੂਜੀਆਂ ਪ੍ਰਕਿਰਿਆਵਾਂ ਵਾਂਗ ਲਾਗੂ ਕੀਤਾ ਜਾਂਦਾ ਹੈ। ਮਾਊਂਟ ਕੀਤੇ ਭਾਗਾਂ ਵਾਲੇ PCBs ਨੂੰ ਹੱਥੀਂ ਜਾਂ ਅਰਧ-ਆਟੋਮੈਟਿਕ ਢੰਗ ਨਾਲ ਪਿਘਲੇ ਹੋਏ ਸੋਲਡਰ ਵਾਲੇ ਟੈਂਕ ਵਿੱਚ ਡੁਬੋਇਆ ਜਾਂਦਾ ਹੈ। ਪਿਘਲਾ ਹੋਇਆ ਸੋਲਡਰ ਬੋਰਡ 'ਤੇ ਸੋਲਡਰ ਮਾਸਕ ਦੁਆਰਾ ਅਸੁਰੱਖਿਅਤ ਧਾਤੂ ਖੇਤਰਾਂ ਨਾਲ ਚਿਪਕ ਜਾਂਦਾ ਹੈ। ਉਪਕਰਣ ਸਧਾਰਨ ਅਤੇ ਸਸਤੇ ਹਨ. • ਚਿਪਕਣ ਵਾਲਾ ਬੰਧਨ: ਇਹ ਇੱਕ ਹੋਰ ਪ੍ਰਸਿੱਧ ਤਕਨੀਕ ਹੈ ਜਿਸਦੀ ਅਸੀਂ ਅਕਸਰ ਵਰਤੋਂ ਕਰਦੇ ਹਾਂ ਅਤੇ ਇਸ ਵਿੱਚ ਗੂੰਦ, ਐਪੌਕਸੀਜ਼, ਪਲਾਸਟਿਕ ਏਜੰਟ ਜਾਂ ਹੋਰ ਰਸਾਇਣਾਂ ਦੀ ਵਰਤੋਂ ਕਰਦੇ ਹੋਏ ਸਤਹਾਂ ਨੂੰ ਜੋੜਨਾ ਸ਼ਾਮਲ ਹੁੰਦਾ ਹੈ। ਬੰਧਨ ਜਾਂ ਤਾਂ ਘੋਲਨ ਵਾਲੇ ਨੂੰ ਭਾਫ਼ ਬਣਾ ਕੇ, ਗਰਮੀ ਦੇ ਇਲਾਜ ਦੁਆਰਾ, ਯੂਵੀ ਰੋਸ਼ਨੀ ਦੇ ਇਲਾਜ ਦੁਆਰਾ, ਦਬਾਅ ਦੇ ਇਲਾਜ ਦੁਆਰਾ ਜਾਂ ਇੱਕ ਨਿਸ਼ਚਤ ਸਮੇਂ ਦੀ ਉਡੀਕ ਕਰਕੇ ਪੂਰਾ ਕੀਤਾ ਜਾਂਦਾ ਹੈ। ਸਾਡੀਆਂ ਉਤਪਾਦਨ ਲਾਈਨਾਂ ਵਿੱਚ ਕਈ ਉੱਚ ਪ੍ਰਦਰਸ਼ਨ ਗੂੰਦ ਵਰਤੇ ਜਾਂਦੇ ਹਨ। ਸਹੀ ਢੰਗ ਨਾਲ ਤਿਆਰ ਕੀਤੀ ਐਪਲੀਕੇਸ਼ਨ ਅਤੇ ਇਲਾਜ ਪ੍ਰਕਿਰਿਆਵਾਂ ਦੇ ਨਾਲ, ਚਿਪਕਣ ਵਾਲੇ ਬੰਧਨ ਦੇ ਨਤੀਜੇ ਵਜੋਂ ਬਹੁਤ ਘੱਟ ਤਣਾਅ ਵਾਲੇ ਬਾਂਡ ਹੋ ਸਕਦੇ ਹਨ ਜੋ ਮਜ਼ਬੂਤ ਅਤੇ ਭਰੋਸੇਮੰਦ ਹੁੰਦੇ ਹਨ। ਚਿਪਕਣ ਵਾਲੇ ਬਾਂਡ ਵਾਤਾਵਰਨ ਦੇ ਕਾਰਕਾਂ ਜਿਵੇਂ ਕਿ ਨਮੀ, ਗੰਦਗੀ, ਖੋਰ, ਵਾਈਬ੍ਰੇਸ਼ਨ... ਆਦਿ ਦੇ ਵਿਰੁੱਧ ਚੰਗੇ ਰੱਖਿਅਕ ਹੋ ਸਕਦੇ ਹਨ। ਚਿਪਕਣ ਵਾਲੇ ਬੰਧਨ ਦੇ ਫਾਇਦੇ ਹਨ: ਉਹਨਾਂ ਨੂੰ ਉਹਨਾਂ ਸਮੱਗਰੀਆਂ 'ਤੇ ਲਾਗੂ ਕੀਤਾ ਜਾ ਸਕਦਾ ਹੈ ਜਿਨ੍ਹਾਂ ਨੂੰ ਸੋਲਡਰ, ਵੇਲਡ ਜਾਂ ਬ੍ਰੇਜ਼ ਕਰਨਾ ਔਖਾ ਹੋਵੇਗਾ। ਇਹ ਗਰਮੀ ਸੰਵੇਦਨਸ਼ੀਲ ਸਮੱਗਰੀ ਲਈ ਵੀ ਤਰਜੀਹੀ ਹੋ ਸਕਦਾ ਹੈ ਜੋ ਵੈਲਡਿੰਗ ਜਾਂ ਹੋਰ ਉੱਚ ਤਾਪਮਾਨ ਦੀਆਂ ਪ੍ਰਕਿਰਿਆਵਾਂ ਦੁਆਰਾ ਨੁਕਸਾਨੇ ਜਾਣਗੇ। ਚਿਪਕਣ ਵਾਲੇ ਹੋਰ ਫਾਇਦੇ ਇਹ ਹਨ ਕਿ ਉਹਨਾਂ ਨੂੰ ਅਨਿਯਮਿਤ ਆਕਾਰ ਦੀਆਂ ਸਤਹਾਂ 'ਤੇ ਲਾਗੂ ਕੀਤਾ ਜਾ ਸਕਦਾ ਹੈ ਅਤੇ ਹੋਰ ਤਰੀਕਿਆਂ ਦੀ ਤੁਲਨਾ ਵਿਚ ਬਹੁਤ ਘੱਟ ਮਾਤਰਾ ਵਿਚ ਅਸੈਂਬਲੀ ਭਾਰ ਵਧਾਇਆ ਜਾ ਸਕਦਾ ਹੈ। ਭਾਗਾਂ ਵਿੱਚ ਅਯਾਮੀ ਤਬਦੀਲੀਆਂ ਵੀ ਬਹੁਤ ਘੱਟ ਹਨ। ਕੁਝ ਗਲੂਆਂ ਵਿੱਚ ਸੂਚਕਾਂਕ ਨਾਲ ਮੇਲ ਖਾਂਦੀਆਂ ਵਿਸ਼ੇਸ਼ਤਾਵਾਂ ਹੁੰਦੀਆਂ ਹਨ ਅਤੇ ਰੌਸ਼ਨੀ ਜਾਂ ਆਪਟੀਕਲ ਸਿਗਨਲ ਦੀ ਤਾਕਤ ਨੂੰ ਮਹੱਤਵਪੂਰਨ ਤੌਰ 'ਤੇ ਘਟਾਏ ਬਿਨਾਂ ਆਪਟੀਕਲ ਹਿੱਸਿਆਂ ਦੇ ਵਿਚਕਾਰ ਵਰਤਿਆ ਜਾ ਸਕਦਾ ਹੈ। ਦੂਜੇ ਪਾਸੇ ਨੁਕਸਾਨ ਲੰਬੇ ਸਮੇਂ ਤੱਕ ਠੀਕ ਕਰਨ ਦੇ ਸਮੇਂ ਹਨ ਜੋ ਨਿਰਮਾਣ ਲਾਈਨਾਂ, ਫਿਕਸਚਰਿੰਗ ਲੋੜਾਂ, ਸਤਹ ਦੀ ਤਿਆਰੀ ਦੀਆਂ ਜ਼ਰੂਰਤਾਂ ਅਤੇ ਦੁਬਾਰਾ ਕੰਮ ਦੀ ਲੋੜ ਪੈਣ 'ਤੇ ਵੱਖ ਕਰਨ ਵਿੱਚ ਮੁਸ਼ਕਲ ਨੂੰ ਹੌਲੀ ਕਰ ਸਕਦੇ ਹਨ। ਸਾਡੇ ਜ਼ਿਆਦਾਤਰ ਅਡੈਸਿਵ ਬੰਧਨ ਕਾਰਜਾਂ ਵਿੱਚ ਹੇਠਾਂ ਦਿੱਤੇ ਕਦਮ ਸ਼ਾਮਲ ਹੁੰਦੇ ਹਨ: - ਸਤ੍ਹਾ ਦਾ ਇਲਾਜ: ਵਿਸ਼ੇਸ਼ ਸਫਾਈ ਪ੍ਰਕਿਰਿਆਵਾਂ ਜਿਵੇਂ ਕਿ ਡੀਓਨਾਈਜ਼ਡ ਪਾਣੀ ਦੀ ਸਫਾਈ, ਅਲਕੋਹਲ ਸਫਾਈ, ਪਲਾਜ਼ਮਾ ਜਾਂ ਕੋਰੋਨਾ ਸਫਾਈ ਆਮ ਹਨ। ਸਫਾਈ ਕਰਨ ਤੋਂ ਬਾਅਦ ਅਸੀਂ ਸਭ ਤੋਂ ਵਧੀਆ ਸੰਭਾਵਿਤ ਜੋੜਾਂ ਨੂੰ ਯਕੀਨੀ ਬਣਾਉਣ ਲਈ ਸਤ੍ਹਾ 'ਤੇ ਅਡੈਸ਼ਨ ਪ੍ਰਮੋਟਰ ਲਗਾ ਸਕਦੇ ਹਾਂ। -ਪਾਰਟ ਫਿਕਸਚਰਿੰਗ: ਅਡੈਸਿਵ ਐਪਲੀਕੇਸ਼ਨ ਦੇ ਨਾਲ-ਨਾਲ ਠੀਕ ਕਰਨ ਲਈ ਅਸੀਂ ਕਸਟਮ ਫਿਕਸਚਰ ਡਿਜ਼ਾਈਨ ਅਤੇ ਵਰਤਦੇ ਹਾਂ। - ਅਡੈਸਿਵ ਐਪਲੀਕੇਸ਼ਨ: ਅਸੀਂ ਕਈ ਵਾਰ ਮੈਨੂਅਲ ਦੀ ਵਰਤੋਂ ਕਰਦੇ ਹਾਂ, ਅਤੇ ਕਈ ਵਾਰ ਕੇਸ ਆਟੋਮੇਟਿਡ ਸਿਸਟਮ ਜਿਵੇਂ ਕਿ ਰੋਬੋਟਿਕਸ, ਸਰਵੋ ਮੋਟਰਾਂ, ਲੀਨੀਅਰ ਐਕਚੁਏਟਰਾਂ 'ਤੇ ਨਿਰਭਰ ਕਰਦੇ ਹੋਏ ਅਡੈਸਿਵਾਂ ਨੂੰ ਸਹੀ ਸਥਾਨ 'ਤੇ ਪਹੁੰਚਾਉਣ ਲਈ ਅਤੇ ਅਸੀਂ ਇਸਨੂੰ ਸਹੀ ਮਾਤਰਾ ਅਤੇ ਮਾਤਰਾ 'ਤੇ ਪਹੁੰਚਾਉਣ ਲਈ ਡਿਸਪੈਂਸਰਾਂ ਦੀ ਵਰਤੋਂ ਕਰਦੇ ਹਾਂ। -ਕਿਊਰਿੰਗ: ਅਡੈਸਿਵ 'ਤੇ ਨਿਰਭਰ ਕਰਦੇ ਹੋਏ, ਅਸੀਂ ਯੂਵੀ ਲਾਈਟਾਂ ਦੇ ਹੇਠਾਂ ਸਧਾਰਣ ਸੁਕਾਉਣ ਅਤੇ ਇਲਾਜ ਦੇ ਨਾਲ-ਨਾਲ ਇਲਾਜ ਦੀ ਵਰਤੋਂ ਕਰ ਸਕਦੇ ਹਾਂ ਜੋ ਓਵਨ ਵਿੱਚ ਉਤਪ੍ਰੇਰਕ ਜਾਂ ਗਰਮੀ ਦੇ ਇਲਾਜ ਦੇ ਤੌਰ 'ਤੇ ਕੰਮ ਕਰਦੇ ਹਨ ਜਾਂ ਜਿਗ ਅਤੇ ਫਿਕਸਚਰ 'ਤੇ ਮਾਊਂਟ ਕੀਤੇ ਰੋਧਕ ਹੀਟਿੰਗ ਤੱਤਾਂ ਦੀ ਵਰਤੋਂ ਕਰਦੇ ਹਨ। ਅਸੀਂ ਸਿਫ਼ਾਰਿਸ਼ ਕਰਦੇ ਹਾਂ ਕਿ ਤੁਸੀਂ ਇੱਥੇ ਕਲਿੱਕ ਕਰੋAGS-TECH Inc ਦੁਆਰਾ ਫਾਸਟਨਿੰਗ ਪ੍ਰਕਿਰਿਆਵਾਂ ਦੇ ਸਾਡੇ ਯੋਜਨਾਬੱਧ ਚਿੱਤਰਾਂ ਨੂੰ ਡਾਉਨਲੋਡ ਕਰੋ। ਇਹ ਤੁਹਾਨੂੰ ਉਸ ਜਾਣਕਾਰੀ ਨੂੰ ਬਿਹਤਰ ਤਰੀਕੇ ਨਾਲ ਸਮਝਣ ਵਿੱਚ ਮਦਦ ਕਰੇਗਾ ਜੋ ਅਸੀਂ ਤੁਹਾਨੂੰ ਹੇਠਾਂ ਪ੍ਰਦਾਨ ਕਰ ਰਹੇ ਹਾਂ। • ਫਾਸਟਨਿੰਗ ਪ੍ਰਕਿਰਿਆਵਾਂ: ਸਾਡੀਆਂ ਮਕੈਨੀਕਲ ਜੁਆਇਨਿੰਗ ਪ੍ਰਕਿਰਿਆਵਾਂ ਦੋ ਬ੍ਰੈਡ ਸ਼੍ਰੇਣੀਆਂ ਵਿੱਚ ਆਉਂਦੀਆਂ ਹਨ: ਫਾਸਟਨਰ ਅਤੇ ਇੰਟੈਗਰਲ ਜੋੜ। ਫਾਸਟਨਰਾਂ ਦੀਆਂ ਉਦਾਹਰਣਾਂ ਜੋ ਅਸੀਂ ਵਰਤਦੇ ਹਾਂ ਉਹ ਹਨ ਪੇਚ, ਪਿੰਨ, ਨਟ, ਬੋਲਟ, ਰਿਵੇਟਸ। ਸਾਡੇ ਦੁਆਰਾ ਵਰਤੇ ਜਾਣ ਵਾਲੇ ਅਟੁੱਟ ਜੋੜਾਂ ਦੀਆਂ ਉਦਾਹਰਨਾਂ ਹਨ ਸਨੈਪ ਅਤੇ ਸੁੰਗੜਨ ਵਾਲੇ ਫਿੱਟ, ਸੀਮ, ਕ੍ਰਿੰਪਸ। ਕਈ ਤਰ੍ਹਾਂ ਦੇ ਫਾਸਟਨਿੰਗ ਤਰੀਕਿਆਂ ਦੀ ਵਰਤੋਂ ਕਰਦੇ ਹੋਏ ਅਸੀਂ ਇਹ ਯਕੀਨੀ ਬਣਾਉਂਦੇ ਹਾਂ ਕਿ ਸਾਡੇ ਮਕੈਨੀਕਲ ਜੋੜ ਮਜ਼ਬੂਤ ਅਤੇ ਕਈ ਸਾਲਾਂ ਦੀ ਵਰਤੋਂ ਲਈ ਭਰੋਸੇਯੋਗ ਹਨ। SCREWS ਅਤੇ BOLTS ਵਸਤੂਆਂ ਨੂੰ ਇਕੱਠੇ ਰੱਖਣ ਅਤੇ ਪੋਜੀਸ਼ਨਿੰਗ ਲਈ ਸਭ ਤੋਂ ਵੱਧ ਵਰਤੇ ਜਾਣ ਵਾਲੇ ਫਾਸਟਨਰ ਹਨ। ਸਾਡੇ ਪੇਚ ਅਤੇ ਬੋਲਟ ASME ਮਿਆਰਾਂ ਨੂੰ ਪੂਰਾ ਕਰਦੇ ਹਨ। ਵੱਖ-ਵੱਖ ਕਿਸਮਾਂ ਦੇ ਪੇਚ ਅਤੇ ਬੋਲਟ ਤਾਇਨਾਤ ਕੀਤੇ ਗਏ ਹਨ ਜਿਸ ਵਿੱਚ ਹੈਕਸ ਕੈਪ ਸਕ੍ਰੂ ਅਤੇ ਹੈਕਸ ਬੋਲਟ, ਲੈਗ ਸਕ੍ਰੂ ਅਤੇ ਬੋਲਟ, ਡਬਲ ਐਂਡਡ ਪੇਚ, ਡੋਵਲ ਪੇਚ, ਆਈ ਪੇਚ, ਮਿਰਰ ਪੇਚ, ਸ਼ੀਟ ਮੈਟਲ ਪੇਚ, ਫਾਈਨ ਐਡਜਸਟਮੈਂਟ ਪੇਚ, ਸਵੈ-ਡ੍ਰਿਲਿੰਗ ਅਤੇ ਸਵੈ-ਟੈਪਿੰਗ ਪੇਚ ਸ਼ਾਮਲ ਹਨ। , ਸੈੱਟ ਪੇਚ, ਬਿਲਟ-ਇਨ ਵਾਸ਼ਰ ਵਾਲੇ ਪੇਚ,…ਅਤੇ ਹੋਰ। ਸਾਡੇ ਕੋਲ ਵੱਖ-ਵੱਖ ਸਕ੍ਰੂ ਹੈੱਡ ਕਿਸਮਾਂ ਹਨ ਜਿਵੇਂ ਕਿ ਕਾਊਂਟਰਸੰਕ, ਡੋਮ, ਗੋਲ, ਫਲੈਂਜਡ ਹੈੱਡ ਅਤੇ ਵੱਖ-ਵੱਖ ਪੇਚ ਡਰਾਈਵ ਕਿਸਮਾਂ ਜਿਵੇਂ ਕਿ ਸਲਾਟ, ਫਿਲਿਪਸ, ਵਰਗ, ਹੈਕਸ ਸਾਕਟ। ਦੂਜੇ ਪਾਸੇ ਇੱਕ RIVET ਇੱਕ ਸਥਾਈ ਮਕੈਨੀਕਲ ਫਾਸਟਨਰ ਹੈ ਜਿਸ ਵਿੱਚ ਇੱਕ ਨਿਰਵਿਘਨ ਬੇਲਨਾਕਾਰ ਸ਼ਾਫਟ ਅਤੇ ਇੱਕ ਪਾਸੇ ਇੱਕ ਸਿਰ ਹੁੰਦਾ ਹੈ। ਸੰਮਿਲਨ ਤੋਂ ਬਾਅਦ, ਰਿਵੇਟ ਦੇ ਦੂਜੇ ਸਿਰੇ ਨੂੰ ਵਿਗਾੜ ਦਿੱਤਾ ਜਾਂਦਾ ਹੈ ਅਤੇ ਇਸਦਾ ਵਿਆਸ ਫੈਲਾਇਆ ਜਾਂਦਾ ਹੈ ਤਾਂ ਜੋ ਇਹ ਜਗ੍ਹਾ 'ਤੇ ਰਹੇ। ਦੂਜੇ ਸ਼ਬਦਾਂ ਵਿੱਚ, ਇੰਸਟਾਲੇਸ਼ਨ ਤੋਂ ਪਹਿਲਾਂ ਇੱਕ ਰਿਵੇਟ ਦਾ ਇੱਕ ਸਿਰ ਹੁੰਦਾ ਹੈ ਅਤੇ ਇੰਸਟਾਲੇਸ਼ਨ ਤੋਂ ਬਾਅਦ ਇਸਦੇ ਦੋ ਹੁੰਦੇ ਹਨ। ਅਸੀਂ ਐਪਲੀਕੇਸ਼ਨ, ਤਾਕਤ, ਪਹੁੰਚਯੋਗਤਾ ਅਤੇ ਲਾਗਤ 'ਤੇ ਨਿਰਭਰ ਕਰਦੇ ਹੋਏ ਵੱਖ-ਵੱਖ ਕਿਸਮਾਂ ਦੇ ਰਿਵੇਟਸ ਸਥਾਪਿਤ ਕਰਦੇ ਹਾਂ ਜਿਵੇਂ ਕਿ ਠੋਸ/ਗੋਲ ਹੈੱਡ ਰਿਵੇਟਸ, ਸਟ੍ਰਕਚਰਲ, ਸੈਮੀ-ਟਿਊਬਲਰ, ਬਲਾਇੰਡ, ਆਸਕਰ, ਡਰਾਈਵ, ਫਲੱਸ਼, ਫਰੀਕਸ਼ਨ-ਲਾਕ, ਸਵੈ-ਵਿੰਨ੍ਹਣ ਵਾਲੇ ਰਿਵੇਟਸ। ਰਿਵੇਟਿੰਗ ਨੂੰ ਉਹਨਾਂ ਮਾਮਲਿਆਂ ਵਿੱਚ ਤਰਜੀਹ ਦਿੱਤੀ ਜਾ ਸਕਦੀ ਹੈ ਜਿੱਥੇ ਗਰਮੀ ਦੇ ਵਿਗਾੜ ਅਤੇ ਵੈਲਡਿੰਗ ਗਰਮੀ ਕਾਰਨ ਪਦਾਰਥਕ ਵਿਸ਼ੇਸ਼ਤਾਵਾਂ ਵਿੱਚ ਤਬਦੀਲੀ ਤੋਂ ਬਚਣ ਦੀ ਲੋੜ ਹੁੰਦੀ ਹੈ। ਰਿਵੇਟਿੰਗ ਹਲਕੇ ਭਾਰ ਅਤੇ ਖਾਸ ਤੌਰ 'ਤੇ ਸ਼ੀਅਰ ਬਲਾਂ ਦੇ ਵਿਰੁੱਧ ਚੰਗੀ ਤਾਕਤ ਅਤੇ ਧੀਰਜ ਦੀ ਪੇਸ਼ਕਸ਼ ਵੀ ਕਰਦੀ ਹੈ। ਟੈਨਸਾਈਲ ਲੋਡਾਂ ਦੇ ਵਿਰੁੱਧ ਹਾਲਾਂਕਿ ਪੇਚ, ਗਿਰੀਦਾਰ ਅਤੇ ਬੋਲਟ ਵਧੇਰੇ ਢੁਕਵੇਂ ਹੋ ਸਕਦੇ ਹਨ। ਕਲਿੰਚਿੰਗ ਪ੍ਰਕਿਰਿਆ ਵਿੱਚ ਅਸੀਂ ਸ਼ੀਟ ਧਾਤਾਂ ਨੂੰ ਜੋੜਨ ਦੇ ਵਿਚਕਾਰ ਇੱਕ ਮਕੈਨੀਕਲ ਇੰਟਰਲਾਕ ਬਣਾਉਣ ਲਈ ਵਿਸ਼ੇਸ਼ ਪੰਚ ਅਤੇ ਡਾਈ ਦੀ ਵਰਤੋਂ ਕਰਦੇ ਹਾਂ। ਪੰਚ ਸ਼ੀਟ ਮੈਟਲ ਦੀਆਂ ਪਰਤਾਂ ਨੂੰ ਡਾਈ ਕੈਵਿਟੀ ਵਿੱਚ ਧੱਕਦਾ ਹੈ ਅਤੇ ਨਤੀਜੇ ਵਜੋਂ ਇੱਕ ਸਥਾਈ ਜੋੜ ਬਣ ਜਾਂਦਾ ਹੈ। ਕਲਿੰਚਿੰਗ ਵਿੱਚ ਕੋਈ ਹੀਟਿੰਗ ਅਤੇ ਕੂਲਿੰਗ ਦੀ ਲੋੜ ਨਹੀਂ ਹੈ ਅਤੇ ਇਹ ਇੱਕ ਠੰਡੇ ਕੰਮ ਕਰਨ ਵਾਲੀ ਪ੍ਰਕਿਰਿਆ ਹੈ। ਇਹ ਇੱਕ ਆਰਥਿਕ ਪ੍ਰਕਿਰਿਆ ਹੈ ਜੋ ਕੁਝ ਮਾਮਲਿਆਂ ਵਿੱਚ ਸਪਾਟ ਵੈਲਡਿੰਗ ਨੂੰ ਬਦਲ ਸਕਦੀ ਹੈ। ਪਿਨਿੰਗ ਵਿੱਚ ਅਸੀਂ ਪਿੰਨਾਂ ਦੀ ਵਰਤੋਂ ਕਰਦੇ ਹਾਂ ਜੋ ਮਸ਼ੀਨ ਦੇ ਤੱਤ ਹੁੰਦੇ ਹਨ ਜੋ ਮਸ਼ੀਨ ਦੇ ਹਿੱਸਿਆਂ ਦੀ ਸਥਿਤੀ ਨੂੰ ਇੱਕ ਦੂਜੇ ਦੇ ਮੁਕਾਬਲੇ ਸੁਰੱਖਿਅਤ ਕਰਨ ਲਈ ਵਰਤੇ ਜਾਂਦੇ ਹਨ। ਮੁੱਖ ਕਿਸਮਾਂ ਹਨ ਕਲੀਵਿਸ ਪਿੰਨ, ਕੋਟਰ ਪਿੰਨ, ਸਪਰਿੰਗ ਪਿੰਨ, ਡੋਵਲ ਪਿੰਨ, and ਸਪਲਿਟ ਪਿੰਨ। ਸਟੈਪਲਿੰਗ ਵਿੱਚ ਅਸੀਂ ਸਟੈਪਲਿੰਗ ਬੰਦੂਕਾਂ ਅਤੇ ਸਟੈਪਲਾਂ ਦੀ ਵਰਤੋਂ ਕਰਦੇ ਹਾਂ ਜੋ ਕਿ ਦੋ-ਪੱਖੀ ਫਾਸਟਨਰ ਹਨ ਜੋ ਸਮੱਗਰੀ ਨੂੰ ਜੋੜਨ ਜਾਂ ਬੰਨ੍ਹਣ ਲਈ ਵਰਤੇ ਜਾਂਦੇ ਹਨ। ਸਟੈਪਲਿੰਗ ਦੇ ਹੇਠਾਂ ਦਿੱਤੇ ਫਾਇਦੇ ਹਨ: ਕਿਫਾਇਤੀ, ਸਰਲ ਅਤੇ ਵਰਤਣ ਲਈ ਤੇਜ਼, ਸਟੈਪਲਾਂ ਦੇ ਤਾਜ ਦੀ ਵਰਤੋਂ ਸਮੱਗਰੀ ਨੂੰ ਜੋੜਨ ਲਈ ਕੀਤੀ ਜਾ ਸਕਦੀ ਹੈ, ਸਟੈਪਲ ਦਾ ਤਾਜ ਇੱਕ ਕੇਬਲ ਵਰਗੇ ਟੁਕੜੇ ਨੂੰ ਬ੍ਰਿਜ ਕਰਨ ਅਤੇ ਇਸ ਨੂੰ ਪੰਕਚਰ ਜਾਂ ਬਿਨਾਂ ਕਿਸੇ ਸਤ੍ਹਾ 'ਤੇ ਬੰਨ੍ਹਣ ਦੀ ਸਹੂਲਤ ਪ੍ਰਦਾਨ ਕਰ ਸਕਦਾ ਹੈ। ਨੁਕਸਾਨਦੇਹ, ਮੁਕਾਬਲਤਨ ਆਸਾਨ ਹਟਾਉਣਾ. ਪ੍ਰੈੱਸ ਫਿਟਿੰਗ ਭਾਗਾਂ ਨੂੰ ਇਕੱਠੇ ਧੱਕ ਕੇ ਕੀਤੀ ਜਾਂਦੀ ਹੈ ਅਤੇ ਉਹਨਾਂ ਵਿਚਕਾਰ ਰਗੜ ਕੇ ਹਿੱਸਿਆਂ ਨੂੰ ਮਜ਼ਬੂਤ ਕਰਦਾ ਹੈ। ਇੱਕ ਵੱਡੇ ਸ਼ਾਫਟ ਅਤੇ ਇੱਕ ਛੋਟੇ ਆਕਾਰ ਦੇ ਮੋਰੀ ਵਾਲੇ ਪ੍ਰੈੱਸ ਫਿੱਟ ਹਿੱਸੇ ਆਮ ਤੌਰ 'ਤੇ ਦੋ ਤਰੀਕਿਆਂ ਵਿੱਚੋਂ ਇੱਕ ਦੁਆਰਾ ਇਕੱਠੇ ਕੀਤੇ ਜਾਂਦੇ ਹਨ: ਜਾਂ ਤਾਂ ਬਲ ਲਗਾ ਕੇ ਜਾਂ ਥਰਮਲ ਵਿਸਤਾਰ ਜਾਂ ਹਿੱਸਿਆਂ ਦੇ ਸੰਕੁਚਨ ਦਾ ਫਾਇਦਾ ਉਠਾ ਕੇ। ਜਦੋਂ ਇੱਕ ਫੋਰਸ ਲਗਾ ਕੇ ਇੱਕ ਪ੍ਰੈਸ ਫਿਟਿੰਗ ਸਥਾਪਤ ਕੀਤੀ ਜਾਂਦੀ ਹੈ, ਅਸੀਂ ਜਾਂ ਤਾਂ ਇੱਕ ਹਾਈਡ੍ਰੌਲਿਕ ਪ੍ਰੈਸ ਜਾਂ ਹੱਥਾਂ ਦੁਆਰਾ ਸੰਚਾਲਿਤ ਪ੍ਰੈਸ ਦੀ ਵਰਤੋਂ ਕਰਦੇ ਹਾਂ। ਦੂਜੇ ਪਾਸੇ ਜਦੋਂ ਪ੍ਰੈੱਸ ਫਿਟਿੰਗ ਥਰਮਲ ਵਿਸਤਾਰ ਦੁਆਰਾ ਸਥਾਪਿਤ ਕੀਤੀ ਜਾਂਦੀ ਹੈ ਤਾਂ ਅਸੀਂ ਲਿਫਾਫੇ ਵਾਲੇ ਹਿੱਸਿਆਂ ਨੂੰ ਗਰਮ ਕਰਦੇ ਹਾਂ ਅਤੇ ਗਰਮ ਹੋਣ 'ਤੇ ਉਨ੍ਹਾਂ ਨੂੰ ਆਪਣੀ ਜਗ੍ਹਾ 'ਤੇ ਇਕੱਠਾ ਕਰਦੇ ਹਾਂ। ਜਦੋਂ ਉਹ ਠੰਢੇ ਹੁੰਦੇ ਹਨ ਤਾਂ ਉਹ ਸੁੰਗੜ ਜਾਂਦੇ ਹਨ ਅਤੇ ਆਪਣੇ ਆਮ ਮਾਪਾਂ 'ਤੇ ਵਾਪਸ ਆ ਜਾਂਦੇ ਹਨ। ਇਸ ਦੇ ਨਤੀਜੇ ਵਜੋਂ ਇੱਕ ਚੰਗੀ ਪ੍ਰੈਸ ਫਿੱਟ ਹੁੰਦੀ ਹੈ। ਅਸੀਂ ਇਸਨੂੰ ਵਿਕਲਪਿਕ ਤੌਰ 'ਤੇ SHRINK-FITTING ਕਹਿੰਦੇ ਹਾਂ। ਅਜਿਹਾ ਕਰਨ ਦਾ ਦੂਜਾ ਤਰੀਕਾ ਹੈ ਅਸੈਂਬਲੀ ਤੋਂ ਪਹਿਲਾਂ ਲਿਫਾਫੇ ਵਾਲੇ ਹਿੱਸਿਆਂ ਨੂੰ ਠੰਡਾ ਕਰਨਾ ਅਤੇ ਫਿਰ ਉਹਨਾਂ ਨੂੰ ਉਹਨਾਂ ਦੇ ਮੇਲਣ ਵਾਲੇ ਹਿੱਸਿਆਂ ਵਿੱਚ ਸਲਾਈਡ ਕਰਨਾ। ਜਦੋਂ ਅਸੈਂਬਲੀ ਗਰਮ ਹੁੰਦੀ ਹੈ ਤਾਂ ਉਹ ਫੈਲ ਜਾਂਦੇ ਹਨ ਅਤੇ ਅਸੀਂ ਇੱਕ ਤੰਗ ਫਿਟ ਪ੍ਰਾਪਤ ਕਰਦੇ ਹਾਂ। ਇਹ ਬਾਅਦ ਵਾਲਾ ਤਰੀਕਾ ਉਹਨਾਂ ਮਾਮਲਿਆਂ ਵਿੱਚ ਤਰਜੀਹੀ ਹੋ ਸਕਦਾ ਹੈ ਜਿੱਥੇ ਹੀਟਿੰਗ ਸਮੱਗਰੀ ਦੀਆਂ ਵਿਸ਼ੇਸ਼ਤਾਵਾਂ ਨੂੰ ਬਦਲਣ ਦਾ ਖਤਰਾ ਪੈਦਾ ਕਰਦੀ ਹੈ। ਇਹਨਾਂ ਮਾਮਲਿਆਂ ਵਿੱਚ ਠੰਢਾ ਕਰਨਾ ਵਧੇਰੇ ਸੁਰੱਖਿਅਤ ਹੈ। ਨਿਊਮੈਟਿਕ ਅਤੇ ਹਾਈਡ੍ਰੌਲਿਕ ਕੰਪੋਨੈਂਟਸ ਅਤੇ ਅਸੈਂਬਲੀਆਂ • ਵਾਲਵ, ਹਾਈਡ੍ਰੌਲਿਕ ਅਤੇ ਨਿਊਮੈਟਿਕ ਕੰਪੋਨੈਂਟ ਜਿਵੇਂ ਕਿ ਓ-ਰਿੰਗ, ਵਾਸ਼ਰ, ਸੀਲ, ਗੈਸਕੇਟ, ਰਿੰਗ, ਸ਼ਿਮ। ਕਿਉਂਕਿ ਵਾਲਵ ਅਤੇ ਨਿਊਮੈਟਿਕ ਕੰਪੋਨੈਂਟਸ ਵੱਡੀ ਕਿਸਮ ਵਿੱਚ ਆਉਂਦੇ ਹਨ, ਅਸੀਂ ਇੱਥੇ ਹਰ ਚੀਜ਼ ਨੂੰ ਸੂਚੀਬੱਧ ਨਹੀਂ ਕਰ ਸਕਦੇ ਹਾਂ। ਤੁਹਾਡੀ ਅਰਜ਼ੀ ਦੇ ਭੌਤਿਕ ਅਤੇ ਰਸਾਇਣਕ ਵਾਤਾਵਰਣ 'ਤੇ ਨਿਰਭਰ ਕਰਦੇ ਹੋਏ, ਸਾਡੇ ਕੋਲ ਤੁਹਾਡੇ ਲਈ ਵਿਸ਼ੇਸ਼ ਉਤਪਾਦ ਹਨ। ਕਿਰਪਾ ਕਰਕੇ ਸਾਨੂੰ ਐਪਲੀਕੇਸ਼ਨ, ਕੰਪੋਨੈਂਟ ਦੀ ਕਿਸਮ, ਵਿਸ਼ੇਸ਼ਤਾਵਾਂ, ਵਾਤਾਵਰਣ ਦੀਆਂ ਸਥਿਤੀਆਂ ਜਿਵੇਂ ਕਿ ਦਬਾਅ, ਤਾਪਮਾਨ, ਤਰਲ ਜਾਂ ਗੈਸਾਂ ਬਾਰੇ ਦੱਸੋ ਜੋ ਤੁਹਾਡੇ ਵਾਲਵ ਅਤੇ ਨਿਊਮੈਟਿਕ ਭਾਗਾਂ ਦੇ ਸੰਪਰਕ ਵਿੱਚ ਹੋਣਗੇ; ਅਤੇ ਅਸੀਂ ਤੁਹਾਡੇ ਲਈ ਸਭ ਤੋਂ ਢੁਕਵਾਂ ਉਤਪਾਦ ਚੁਣਾਂਗੇ ਜਾਂ ਤੁਹਾਡੀ ਐਪਲੀਕੇਸ਼ਨ ਲਈ ਵਿਸ਼ੇਸ਼ ਤੌਰ 'ਤੇ ਇਸ ਦਾ ਨਿਰਮਾਣ ਕਰਾਂਗੇ। CLICK Product Finder-Locator Service ਪਿਛਲੇ ਸਫ਼ੇ
- Machine Elements Manufacturing, Gears, Gear Drives, Bearings, Keys, Splines
Machine Elements Manufacturing, Gears, Gear Drives, Bearings, Keys, Splines, Pins, Shafts, Seals, Fasteners, Clutch, Cams, Followers, Belts, Couplings, Shafts ਮਸ਼ੀਨ ਐਲੀਮੈਂਟਸ ਮੈਨੂਫੈਕਚਰਿੰਗ ਹੋਰ ਪੜ੍ਹੋ ਬੈਲਟਸ ਅਤੇ ਚੇਨ ਅਤੇ ਕੇਬਲ ਡਰਾਈਵ ਅਸੈਂਬਲੀ ਹੋਰ ਪੜ੍ਹੋ ਗੇਅਰਸ ਅਤੇ ਗੇਅਰ ਡਰਾਈਵ ਅਸੈਂਬਲੀ ਹੋਰ ਪੜ੍ਹੋ ਕਪਲਿੰਗਸ ਅਤੇ ਬੇਅਰਿੰਗਸ ਮੈਨੂਫੈਕਚਰਿੰਗ ਹੋਰ ਪੜ੍ਹੋ ਕੁੰਜੀਆਂ ਅਤੇ ਸਪਲਾਈਨਾਂ ਅਤੇ ਪਿੰਨਾਂ ਦਾ ਨਿਰਮਾਣ ਹੋਰ ਪੜ੍ਹੋ ਕੈਮ ਅਤੇ ਫਾਲੋਅਰਜ਼ ਅਤੇ ਲਿੰਕੇਜ ਅਤੇ ਰੈਚੇਟ ਵ੍ਹੀਲਜ਼ ਮੈਨੂਫੈਕਚਰਿੰਗ ਹੋਰ ਪੜ੍ਹੋ ਸ਼ਾਫਟ ਮੈਨੂਫੈਕਚਰਿੰਗ ਹੋਰ ਪੜ੍ਹੋ ਮਕੈਨੀਕਲ ਸੀਲ ਨਿਰਮਾਣ ਹੋਰ ਪੜ੍ਹੋ ਕਲਚ ਅਤੇ ਬ੍ਰੇਕ ਅਸੈਂਬਲੀ ਹੋਰ ਪੜ੍ਹੋ ਫਾਸਟਨਰ ਨਿਰਮਾਣ ਹੋਰ ਪੜ੍ਹੋ ਸਧਾਰਨ ਮਸ਼ੀਨ ਅਸੈਂਬਲੀ MACHINE ELEMENTS ਇੱਕ ਮਸ਼ੀਨ ਦੇ ਮੁਢਲੇ ਹਿੱਸੇ ਹਨ। ਇਹ ਤੱਤ ਤਿੰਨ ਬੁਨਿਆਦੀ ਕਿਸਮਾਂ ਦੇ ਹੁੰਦੇ ਹਨ: 1.) ਫਰੇਮ ਮੈਂਬਰ, ਬੇਅਰਿੰਗਸ, ਐਕਸਲਜ਼, ਸਪਲਾਈਨਸ, ਫਾਸਟਨਰ, ਸੀਲ ਅਤੇ ਲੁਬਰੀਕੈਂਟਸ ਸਮੇਤ ਢਾਂਚਾਗਤ ਭਾਗ। 2.) ਗੀਅਰ ਟ੍ਰੇਨਾਂ, ਬੈਲਟ ਜਾਂ ਚੇਨ ਡਰਾਈਵਾਂ, ਲਿੰਕੇਜ, ਕੈਮ ਅਤੇ ਫਾਲੋਅਰ ਸਿਸਟਮ, ਬ੍ਰੇਕ ਅਤੇ ਕਲਚ ਵਰਗੇ ਵੱਖ-ਵੱਖ ਤਰੀਕਿਆਂ ਨਾਲ ਅੰਦੋਲਨ ਨੂੰ ਨਿਯੰਤਰਿਤ ਕਰਨ ਵਾਲੇ ਤੰਤਰ। 3.) ਕੰਟਰੋਲ ਕੰਪੋਨੈਂਟ ਜਿਵੇਂ ਕਿ ਬਟਨ, ਸਵਿੱਚ, ਇੰਡੀਕੇਟਰ, ਸੈਂਸਰ, ਐਕਟੂਏਟਰ ਅਤੇ ਕੰਪਿਊਟਰ ਕੰਟਰੋਲਰ। ਜ਼ਿਆਦਾਤਰ ਮਸ਼ੀਨ ਤੱਤ ਜੋ ਅਸੀਂ ਤੁਹਾਨੂੰ ਪੇਸ਼ ਕਰਦੇ ਹਾਂ, ਉਹ ਆਮ ਆਕਾਰਾਂ ਲਈ ਮਾਨਕੀਕ੍ਰਿਤ ਹਨ, ਪਰ ਕਸਟਮ ਬਣਾਏ ਮਸ਼ੀਨ ਤੱਤ ਤੁਹਾਡੀਆਂ ਵਿਸ਼ੇਸ਼ ਐਪਲੀਕੇਸ਼ਨਾਂ ਲਈ ਵੀ ਉਪਲਬਧ ਹਨ। ਮਸ਼ੀਨ ਤੱਤਾਂ ਦੀ ਕਸਟਮਾਈਜ਼ੇਸ਼ਨ ਮੌਜੂਦਾ ਡਿਜ਼ਾਈਨਾਂ 'ਤੇ ਹੋ ਸਕਦੀ ਹੈ ਜੋ ਸਾਡੇ ਡਾਊਨਲੋਡ ਕਰਨ ਯੋਗ ਕੈਟਾਲਾਗ ਜਾਂ ਬਿਲਕੁਲ ਨਵੇਂ ਡਿਜ਼ਾਈਨ 'ਤੇ ਹਨ। ਮਸ਼ੀਨ ਤੱਤਾਂ ਦੀ ਪ੍ਰੋਟੋਟਾਈਪਿੰਗ ਅਤੇ ਨਿਰਮਾਣ ਨੂੰ ਅੱਗੇ ਵਧਾਇਆ ਜਾ ਸਕਦਾ ਹੈ ਜਦੋਂ ਇੱਕ ਡਿਜ਼ਾਇਨ ਦੋਵਾਂ ਧਿਰਾਂ ਦੁਆਰਾ ਮਨਜ਼ੂਰ ਹੋ ਜਾਂਦਾ ਹੈ। ਜੇਕਰ ਨਵੀਂ ਮਸ਼ੀਨ ਐਲੀਮੈਂਟਸ ਨੂੰ ਡਿਜ਼ਾਈਨ ਅਤੇ ਨਿਰਮਾਣ ਕਰਨ ਦੀ ਲੋੜ ਹੈ, ਤਾਂ ਸਾਡੇ ਗ੍ਰਾਹਕ ਜਾਂ ਤਾਂ ਸਾਨੂੰ ਆਪਣੇ ਖੁਦ ਦੇ ਬਲੂਪ੍ਰਿੰਟ ਈਮੇਲ ਕਰਦੇ ਹਨ ਅਤੇ ਅਸੀਂ ਮਨਜ਼ੂਰੀ ਲਈ ਉਹਨਾਂ ਦੀ ਸਮੀਖਿਆ ਕਰਦੇ ਹਾਂ, ਜਾਂ ਉਹ ਸਾਨੂੰ ਉਹਨਾਂ ਦੀ ਅਰਜ਼ੀ ਲਈ ਮਸ਼ੀਨ ਤੱਤਾਂ ਨੂੰ ਡਿਜ਼ਾਈਨ ਕਰਨ ਲਈ ਕਹਿੰਦੇ ਹਨ। ਬਾਅਦ ਦੇ ਮਾਮਲੇ ਵਿੱਚ ਅਸੀਂ ਆਪਣੇ ਗਾਹਕਾਂ ਤੋਂ ਸਾਰੇ ਇਨਪੁਟ ਦੀ ਵਰਤੋਂ ਕਰਦੇ ਹਾਂ ਅਤੇ ਮਸ਼ੀਨ ਦੇ ਤੱਤਾਂ ਨੂੰ ਡਿਜ਼ਾਈਨ ਕਰਦੇ ਹਾਂ ਅਤੇ ਮਨਜ਼ੂਰੀ ਲਈ ਸਾਡੇ ਗਾਹਕਾਂ ਨੂੰ ਅੰਤਿਮ ਰੂਪ ਵਿੱਚ ਬਲੂਪ੍ਰਿੰਟ ਭੇਜਦੇ ਹਾਂ। ਇੱਕ ਵਾਰ ਮਨਜ਼ੂਰੀ ਮਿਲਣ ਤੋਂ ਬਾਅਦ, ਅਸੀਂ ਪਹਿਲੇ ਲੇਖ ਤਿਆਰ ਕਰਦੇ ਹਾਂ ਅਤੇ ਬਾਅਦ ਵਿੱਚ ਅੰਤਮ ਡਿਜ਼ਾਈਨ ਦੇ ਅਨੁਸਾਰ ਮਸ਼ੀਨ ਦੇ ਤੱਤ ਤਿਆਰ ਕਰਦੇ ਹਾਂ। ਇਸ ਕੰਮ ਦੇ ਕਿਸੇ ਵੀ ਪੜਾਅ 'ਤੇ, ਜੇਕਰ ਕੋਈ ਖਾਸ ਮਸ਼ੀਨ ਤੱਤ ਡਿਜ਼ਾਇਨ ਖੇਤਰ ਵਿੱਚ ਅਸੰਤੁਸ਼ਟੀਜਨਕ ਪ੍ਰਦਰਸ਼ਨ ਕਰਦਾ ਹੈ (ਜੋ ਕਿ ਬਹੁਤ ਘੱਟ ਹੁੰਦਾ ਹੈ), ਅਸੀਂ ਪੂਰੇ ਪ੍ਰੋਜੈਕਟ ਦੀ ਸਮੀਖਿਆ ਕਰਦੇ ਹਾਂ ਅਤੇ ਲੋੜ ਅਨੁਸਾਰ ਸਾਡੇ ਗਾਹਕਾਂ ਨਾਲ ਸਾਂਝੇ ਤੌਰ 'ਤੇ ਬਦਲਾਅ ਕਰਦੇ ਹਾਂ। ਜਦੋਂ ਵੀ ਲੋੜ ਹੋਵੇ ਜਾਂ ਲੋੜ ਹੋਵੇ, ਮਸ਼ੀਨ ਐਲੀਮੈਂਟਸ ਜਾਂ ਕਿਸੇ ਹੋਰ ਉਤਪਾਦ ਦੇ ਡਿਜ਼ਾਈਨ ਲਈ ਸਾਡੇ ਗਾਹਕਾਂ ਨਾਲ ਗੈਰ-ਡਿਸਕਲੋਜ਼ਰ ਐਗਰੀਮੈਂਟ (NDA) 'ਤੇ ਹਸਤਾਖਰ ਕਰਨਾ ਸਾਡਾ ਮਿਆਰੀ ਅਭਿਆਸ ਹੈ। ਇੱਕ ਵਾਰ ਜਦੋਂ ਕਿਸੇ ਖਾਸ ਗਾਹਕ ਲਈ ਮਸ਼ੀਨ ਦੇ ਤੱਤ ਕਸਟਮ ਡਿਜ਼ਾਈਨ ਅਤੇ ਨਿਰਮਿਤ ਹੋ ਜਾਂਦੇ ਹਨ, ਤਾਂ ਅਸੀਂ ਇਸਨੂੰ ਇੱਕ ਉਤਪਾਦ ਕੋਡ ਨਿਰਧਾਰਤ ਕਰਦੇ ਹਾਂ ਅਤੇ ਉਹਨਾਂ ਨੂੰ ਸਿਰਫ਼ ਸਾਡੇ ਗਾਹਕ ਨੂੰ ਹੀ ਪੈਦਾ ਕਰਦੇ ਅਤੇ ਵੇਚਦੇ ਹਾਂ ਜੋ ਉਤਪਾਦ ਦਾ ਮਾਲਕ ਹੈ। ਅਸੀਂ ਵਿਕਸਤ ਟੂਲਾਂ, ਮੋਲਡਾਂ ਅਤੇ ਪ੍ਰਕਿਰਿਆਵਾਂ ਦੀ ਵਰਤੋਂ ਕਰਕੇ ਮਸ਼ੀਨ ਦੇ ਤੱਤਾਂ ਨੂੰ ਜਿੰਨੀ ਵਾਰ ਲੋੜ ਹੁੰਦੀ ਹੈ ਅਤੇ ਜਦੋਂ ਵੀ ਸਾਡੇ ਗਾਹਕ ਉਹਨਾਂ ਨੂੰ ਮੁੜ-ਕ੍ਰਮਬੱਧ ਕਰਦੇ ਹਨ, ਦੁਬਾਰਾ ਤਿਆਰ ਕਰਦੇ ਹਾਂ। ਦੂਜੇ ਸ਼ਬਦਾਂ ਵਿੱਚ, ਇੱਕ ਵਾਰ ਜਦੋਂ ਤੁਹਾਡੇ ਲਈ ਇੱਕ ਕਸਟਮ ਮਸ਼ੀਨ ਤੱਤ ਤਿਆਰ ਅਤੇ ਤਿਆਰ ਕੀਤਾ ਜਾਂਦਾ ਹੈ, ਤਾਂ ਬੌਧਿਕ ਸੰਪਤੀ ਦੇ ਨਾਲ-ਨਾਲ ਸਾਰੇ ਟੂਲਿੰਗ ਅਤੇ ਮੋਲਡ ਤੁਹਾਡੇ ਲਈ ਅਤੇ ਉਤਪਾਦਾਂ ਨੂੰ ਤੁਹਾਡੀ ਇੱਛਾ ਅਨੁਸਾਰ ਦੁਬਾਰਾ ਤਿਆਰ ਕੀਤੇ ਜਾਣ ਲਈ ਸਾਡੇ ਦੁਆਰਾ ਰਾਖਵੇਂ ਅਤੇ ਸਟਾਕ ਕੀਤੇ ਜਾਂਦੇ ਹਨ। ਅਸੀਂ ਆਪਣੇ ਗਾਹਕਾਂ ਨੂੰ ਇੰਜਨੀਅਰਿੰਗ ਸੇਵਾਵਾਂ ਦੀ ਪੇਸ਼ਕਸ਼ ਵੀ ਰਚਨਾਤਮਕ ਤੌਰ 'ਤੇ ਮਸ਼ੀਨ ਤੱਤਾਂ ਨੂੰ ਇੱਕ ਕੰਪੋਨੈਂਟ ਜਾਂ ਅਸੈਂਬਲੀ ਵਿੱਚ ਜੋੜ ਕੇ ਕਰਦੇ ਹਾਂ ਜੋ ਇੱਕ ਐਪਲੀਕੇਸ਼ਨ ਦੀ ਸੇਵਾ ਕਰਦਾ ਹੈ ਅਤੇ ਸਾਡੇ ਗਾਹਕਾਂ ਦੀਆਂ ਉਮੀਦਾਂ ਨੂੰ ਪੂਰਾ ਕਰਦਾ ਹੈ ਜਾਂ ਵੱਧ ਕਰਦਾ ਹੈ। ਸਾਡੇ ਮਸ਼ੀਨ ਤੱਤਾਂ ਨੂੰ ਬਣਾਉਣ ਵਾਲੇ ਪੌਦੇ ISO9001, QS9000 ਜਾਂ TS16949 ਦੁਆਰਾ ਯੋਗ ਹਨ। ਇਸ ਤੋਂ ਇਲਾਵਾ, ਸਾਡੇ ਜ਼ਿਆਦਾਤਰ ਉਤਪਾਦਾਂ ਵਿੱਚ CE ਜਾਂ UL ਮਾਰਕ ਹੁੰਦੇ ਹਨ ਅਤੇ ਅੰਤਰਰਾਸ਼ਟਰੀ ਤੌਰ 'ਤੇ ਸੰਬੰਧਿਤ ਮਿਆਰਾਂ ਜਿਵੇਂ ਕਿ ISO, SAE, ASME, DIN ਨੂੰ ਪੂਰਾ ਕਰਦੇ ਹਨ। ਸਾਡੇ ਮਸ਼ੀਨ ਤੱਤਾਂ ਬਾਰੇ ਵਿਸਤ੍ਰਿਤ ਜਾਣਕਾਰੀ ਪ੍ਰਾਪਤ ਕਰਨ ਲਈ ਕਿਰਪਾ ਕਰਕੇ ਸਬਮੇਨੂ 'ਤੇ ਕਲਿੱਕ ਕਰੋ ਜਿਸ ਵਿੱਚ ਸ਼ਾਮਲ ਹਨ: - ਬੈਲਟ, ਚੇਨ ਅਤੇ ਕੇਬਲ ਡਰਾਈਵ - ਗੇਅਰਸ ਅਤੇ ਗੇਅਰ ਡਰਾਈਵਾਂ - ਕਪਲਿੰਗ ਅਤੇ ਬੇਅਰਿੰਗਸ - ਕੁੰਜੀਆਂ ਅਤੇ ਸਪਲਾਇਨ ਅਤੇ ਪਿੰਨ - ਕੈਮ ਅਤੇ ਲਿੰਕੇਜ - ਸ਼ਾਫਟ - ਮਕੈਨੀਕਲ ਸੀਲ - ਉਦਯੋਗਿਕ ਕਲਚ ਅਤੇ ਬ੍ਰੇਕ - ਫਾਸਟਨਰ - ਸਧਾਰਨ ਮਸ਼ੀਨਾਂ ਅਸੀਂ ਆਪਣੇ ਗਾਹਕਾਂ, ਡਿਜ਼ਾਈਨਰਾਂ ਅਤੇ ਮਸ਼ੀਨ ਤੱਤਾਂ ਸਮੇਤ ਨਵੇਂ ਉਤਪਾਦਾਂ ਦੇ ਡਿਵੈਲਪਰਾਂ ਲਈ ਇੱਕ ਹਵਾਲਾ ਬਰੋਸ਼ਰ ਤਿਆਰ ਕੀਤਾ ਹੈ। ਤੁਸੀਂ ਮਸ਼ੀਨ ਕੰਪੋਨੈਂਟ ਡਿਜ਼ਾਈਨ ਵਿੱਚ ਕੁਝ ਆਮ ਤੌਰ 'ਤੇ ਵਰਤੇ ਜਾਣ ਵਾਲੇ ਸ਼ਬਦਾਂ ਤੋਂ ਆਪਣੇ ਆਪ ਨੂੰ ਜਾਣੂ ਕਰ ਸਕਦੇ ਹੋ: ਡਿਜ਼ਾਈਨਰਾਂ ਅਤੇ ਇੰਜੀਨੀਅਰਾਂ ਦੁਆਰਾ ਵਰਤੀਆਂ ਜਾਂਦੀਆਂ ਆਮ ਮਕੈਨੀਕਲ ਇੰਜੀਨੀਅਰਿੰਗ ਸ਼ਰਤਾਂ ਲਈ ਬਰੋਸ਼ਰ ਡਾਊਨਲੋਡ ਕਰੋ ਸਾਡੇ ਮਸ਼ੀਨ ਤੱਤ ਵੱਖ-ਵੱਖ ਖੇਤਰਾਂ ਵਿੱਚ ਐਪਲੀਕੇਸ਼ਨ ਲੱਭਦੇ ਹਨ ਜਿਵੇਂ ਕਿ ਉਦਯੋਗਿਕ ਮਸ਼ੀਨਰੀ, ਆਟੋਮੇਸ਼ਨ ਸਿਸਟਮ, ਟੈਸਟ ਅਤੇ ਮੈਟਰੋਲੋਜੀ ਸਾਜ਼ੋ-ਸਾਮਾਨ, ਆਵਾਜਾਈ ਉਪਕਰਣ, ਨਿਰਮਾਣ ਮਸ਼ੀਨਾਂ ਅਤੇ ਅਮਲੀ ਤੌਰ 'ਤੇ ਜਿੱਥੇ ਵੀ ਤੁਸੀਂ ਸੋਚ ਸਕਦੇ ਹੋ। AGS-TECH ਐਪਲੀਕੇਸ਼ਨ 'ਤੇ ਨਿਰਭਰ ਕਰਦੇ ਹੋਏ ਵੱਖ-ਵੱਖ ਸਮੱਗਰੀਆਂ ਤੋਂ ਮਸ਼ੀਨ ਤੱਤ ਵਿਕਸਿਤ ਅਤੇ ਤਿਆਰ ਕਰਦਾ ਹੈ। ਮਸ਼ੀਨ ਦੇ ਤੱਤਾਂ ਲਈ ਵਰਤੀਆਂ ਜਾਣ ਵਾਲੀਆਂ ਸਮੱਗਰੀਆਂ ਖਿਡੌਣਿਆਂ ਲਈ ਵਰਤੇ ਜਾਣ ਵਾਲੇ ਮੋਲਡ ਪਲਾਸਟਿਕ ਤੋਂ ਲੈ ਕੇ ਉਦਯੋਗਿਕ ਮਸ਼ੀਨਰੀ ਲਈ ਸਖ਼ਤ ਅਤੇ ਵਿਸ਼ੇਸ਼ ਤੌਰ 'ਤੇ ਕੋਟੇਡ ਸਟੀਲ ਤੱਕ ਹੋ ਸਕਦੀਆਂ ਹਨ। ਸਾਡੇ ਡਿਜ਼ਾਈਨਰ ਮਸ਼ੀਨ ਤੱਤਾਂ ਨੂੰ ਵਿਕਸਤ ਕਰਨ ਲਈ ਅਤਿ ਆਧੁਨਿਕ ਪੇਸ਼ੇਵਰ ਸੌਫਟਵੇਅਰ ਅਤੇ ਡਿਜ਼ਾਈਨ ਟੂਲ ਦੀ ਵਰਤੋਂ ਕਰਦੇ ਹਨ, ਵੇਰਵਿਆਂ ਨੂੰ ਧਿਆਨ ਵਿੱਚ ਰੱਖਦੇ ਹੋਏ ਜਿਵੇਂ ਕਿ ਗੀਅਰ ਦੰਦਾਂ ਵਿੱਚ ਕੋਣ, ਸ਼ਾਮਲ ਤਣਾਅ, ਪਹਿਨਣ ਦੀਆਂ ਦਰਾਂ... ਆਦਿ। ਕਿਰਪਾ ਕਰਕੇ ਸਾਡੇ ਸਬਮੇਨਸ ਵਿੱਚੋਂ ਸਕ੍ਰੋਲ ਕਰੋ ਅਤੇ ਇਹ ਦੇਖਣ ਲਈ ਸਾਡੇ ਉਤਪਾਦ ਬਰੋਸ਼ਰ ਅਤੇ ਕੈਟਾਲਾਗ ਡਾਊਨਲੋਡ ਕਰੋ ਕਿ ਕੀ ਤੁਸੀਂ ਆਪਣੀ ਐਪਲੀਕੇਸ਼ਨ ਲਈ ਸ਼ੈਲਫ ਮਸ਼ੀਨ ਦੇ ਤੱਤ ਲੱਭ ਸਕਦੇ ਹੋ। ਜੇਕਰ ਤੁਸੀਂ ਆਪਣੀ ਅਰਜ਼ੀ ਲਈ ਵਧੀਆ ਮੇਲ ਨਹੀਂ ਲੱਭ ਸਕਦੇ ਹੋ, ਤਾਂ ਕਿਰਪਾ ਕਰਕੇ ਸਾਨੂੰ ਦੱਸੋ ਅਤੇ ਅਸੀਂ ਤੁਹਾਡੇ ਨਾਲ ਮਸ਼ੀਨ ਤੱਤਾਂ ਨੂੰ ਵਿਕਸਤ ਕਰਨ ਅਤੇ ਬਣਾਉਣ ਲਈ ਕੰਮ ਕਰਾਂਗੇ ਜੋ ਤੁਹਾਡੀਆਂ ਜ਼ਰੂਰਤਾਂ ਨੂੰ ਪੂਰਾ ਕਰਨਗੇ। ਜੇਕਰ ਤੁਸੀਂ ਨਿਰਮਾਣ ਸਮਰੱਥਾਵਾਂ ਦੀ ਬਜਾਏ ਸਾਡੀਆਂ ਇੰਜੀਨੀਅਰਿੰਗ ਅਤੇ ਖੋਜ ਅਤੇ ਵਿਕਾਸ ਸਮਰੱਥਾਵਾਂ ਵਿੱਚ ਦਿਲਚਸਪੀ ਰੱਖਦੇ ਹੋ, ਤਾਂ ਅਸੀਂ ਤੁਹਾਨੂੰ ਸਾਡੀ ਵੈੱਬਸਾਈਟ 'ਤੇ ਜਾਣ ਲਈ ਸੱਦਾ ਦਿੰਦੇ ਹਾਂ।http://www.ags-engineering.com ਜਿੱਥੇ ਤੁਸੀਂ ਸਾਡੇ ਡਿਜ਼ਾਈਨ, ਉਤਪਾਦ ਵਿਕਾਸ, ਪ੍ਰਕਿਰਿਆ ਦੇ ਵਿਕਾਸ, ਇੰਜੀਨੀਅਰਿੰਗ ਸਲਾਹ ਸੇਵਾਵਾਂ ਅਤੇ ਹੋਰ ਬਾਰੇ ਵਧੇਰੇ ਵਿਸਤ੍ਰਿਤ ਜਾਣਕਾਰੀ ਪ੍ਰਾਪਤ ਕਰ ਸਕਦੇ ਹੋ। CLICK Product Finder-Locator Service ਪਿਛਲੇ ਸਫ਼ੇ
- Glass and Ceramic Manufacturing, Hermetic Packages, Seals, Bonding
Glass and Ceramic Manufacturing, Hermetic Packages Seals and Bonding, Tempered Bulletproof Glass, Blow Moulding, Optical Grade Glass, Conductive Glass, Molding ਗਲਾਸ ਅਤੇ ਸਿਰੇਮਿਕ ਬਣਾਉਣਾ ਅਤੇ ਆਕਾਰ ਦੇਣਾ ਅਸੀਂ ਜਿਸ ਕਿਸਮ ਦੇ ਕੱਚ ਦੇ ਨਿਰਮਾਣ ਦੀ ਪੇਸ਼ਕਸ਼ ਕਰਦੇ ਹਾਂ ਉਹ ਹਨ ਕੰਟੇਨਰ ਗਲਾਸ, ਗਲਾਸ ਬਲੋਇੰਗ, ਗਲਾਸ ਫਾਈਬਰ ਅਤੇ ਟਿਊਬਿੰਗ ਅਤੇ ਡੰਡੇ, ਘਰੇਲੂ ਅਤੇ ਉਦਯੋਗਿਕ ਕੱਚ ਦੇ ਸਮਾਨ, ਲੈਂਪ ਅਤੇ ਬਲਬ, ਸ਼ੁੱਧਤਾ ਗਲਾਸ ਮੋਲਡਿੰਗ, ਆਪਟੀਕਲ ਕੰਪੋਨੈਂਟਸ ਅਤੇ ਅਸੈਂਬਲੀਆਂ, ਫਲੈਟ ਅਤੇ ਸ਼ੀਟ ਅਤੇ ਫਲੋਟ ਗਲਾਸ। ਅਸੀਂ ਹੱਥ ਬਣਾਉਣ ਦੇ ਨਾਲ-ਨਾਲ ਮਸ਼ੀਨ ਬਣਾਉਣਾ ਵੀ ਕਰਦੇ ਹਾਂ। ਸਾਡੀਆਂ ਪ੍ਰਸਿੱਧ ਤਕਨੀਕੀ ਵਸਰਾਵਿਕ ਨਿਰਮਾਣ ਪ੍ਰਕਿਰਿਆਵਾਂ ਹਨ ਡਾਈ ਪ੍ਰੈੱਸਿੰਗ, ਆਈਸੋਸਟੈਟਿਕ ਪ੍ਰੈੱਸਿੰਗ, ਹੌਟ ਆਈਸੋਸਟੈਟਿਕ ਪ੍ਰੈੱਸਿੰਗ, ਹੌਟ ਪ੍ਰੈੱਸਿੰਗ, ਸਲਿਪ ਕਾਸਟਿੰਗ, ਟੇਪ ਕਾਸਟਿੰਗ, ਐਕਸਟਰਿਊਜ਼ਨ, ਇੰਜੈਕਸ਼ਨ ਮੋਲਡਿੰਗ, ਗ੍ਰੀਨ ਮਸ਼ੀਨਿੰਗ, ਸਿੰਟਰਿੰਗ ਜਾਂ ਫਾਇਰਿੰਗ, ਹੀਰਾ ਪੀਸਣਾ, ਹਰਮੇਟਿਕ ਅਸੈਂਬਲੀਆਂ। ਅਸੀਂ ਸਿਫ਼ਾਰਿਸ਼ ਕਰਦੇ ਹਾਂ ਕਿ ਤੁਸੀਂ ਇੱਥੇ ਕਲਿੱਕ ਕਰੋ AGS-TECH Inc ਦੁਆਰਾ ਗਲਾਸ ਬਣਾਉਣ ਅਤੇ ਆਕਾਰ ਦੇਣ ਦੀਆਂ ਪ੍ਰਕਿਰਿਆਵਾਂ ਦੇ ਸਾਡੇ ਯੋਜਨਾਬੱਧ ਚਿੱਤਰਾਂ ਨੂੰ ਡਾਊਨਲੋਡ ਕਰੋ। AGS-TECH Inc ਦੁਆਰਾ ਤਕਨੀਕੀ ਸਿਰੇਮਿਕ ਨਿਰਮਾਣ ਪ੍ਰਕਿਰਿਆਵਾਂ ਦੇ ਸਾਡੇ ਯੋਜਨਾਬੱਧ ਚਿੱਤਰਾਂ ਨੂੰ ਡਾਉਨਲੋਡ ਕਰੋ। ਫੋਟੋਆਂ ਅਤੇ ਸਕੈਚਾਂ ਵਾਲੀਆਂ ਇਹ ਡਾਊਨਲੋਡ ਕਰਨ ਯੋਗ ਫ਼ਾਈਲਾਂ ਤੁਹਾਨੂੰ ਹੇਠਾਂ ਦਿੱਤੀ ਜਾਣਕਾਰੀ ਨੂੰ ਬਿਹਤਰ ਤਰੀਕੇ ਨਾਲ ਸਮਝਣ ਵਿੱਚ ਤੁਹਾਡੀ ਮਦਦ ਕਰਨਗੀਆਂ। • ਕੰਟੇਨਰ ਗਲਾਸ ਮੈਨੂਫੈਕਚਰ: ਸਾਡੇ ਕੋਲ ਨਿਰਮਾਣ ਲਈ ਪ੍ਰੈੱਸ ਅਤੇ ਬਲੋ ਦੇ ਨਾਲ-ਨਾਲ ਬਲੋ ਅਤੇ ਬਲੋ ਲਾਈਨਾਂ ਹਨ। ਝਟਕੇ ਅਤੇ ਝਟਕੇ ਦੀ ਪ੍ਰਕਿਰਿਆ ਵਿੱਚ ਅਸੀਂ ਇੱਕ ਗੋਬ ਨੂੰ ਖਾਲੀ ਉੱਲੀ ਵਿੱਚ ਸੁੱਟ ਦਿੰਦੇ ਹਾਂ ਅਤੇ ਉੱਪਰੋਂ ਕੰਪਰੈੱਸਡ ਹਵਾ ਦਾ ਇੱਕ ਝਟਕਾ ਲਗਾ ਕੇ ਗਰਦਨ ਨੂੰ ਬਣਾਉਂਦੇ ਹਾਂ। ਇਸ ਤੋਂ ਤੁਰੰਤ ਬਾਅਦ, ਬੋਤਲ ਦਾ ਪ੍ਰੀ-ਫਾਰਮ ਬਣਾਉਣ ਲਈ ਕੰਪਰੈੱਸਡ ਹਵਾ ਨੂੰ ਦੂਜੀ ਵਾਰ ਕੰਟੇਨਰ ਗਰਦਨ ਰਾਹੀਂ ਦੂਜੀ ਦਿਸ਼ਾ ਤੋਂ ਉਡਾਇਆ ਜਾਂਦਾ ਹੈ। ਇਹ ਪ੍ਰੀ-ਫਾਰਮ ਫਿਰ ਅਸਲ ਮੋਲਡ ਵਿੱਚ ਤਬਦੀਲ ਕੀਤਾ ਜਾਂਦਾ ਹੈ, ਨਰਮ ਕਰਨ ਲਈ ਦੁਬਾਰਾ ਗਰਮ ਕੀਤਾ ਜਾਂਦਾ ਹੈ ਅਤੇ ਪ੍ਰੀ-ਫਾਰਮ ਨੂੰ ਇਸਦੇ ਅੰਤਮ ਕੰਟੇਨਰ ਦਾ ਆਕਾਰ ਦੇਣ ਲਈ ਸੰਕੁਚਿਤ ਹਵਾ ਲਾਗੂ ਕੀਤੀ ਜਾਂਦੀ ਹੈ। ਹੋਰ ਸਪੱਸ਼ਟ ਤੌਰ 'ਤੇ, ਇਸ ਨੂੰ ਲੋੜੀਂਦਾ ਆਕਾਰ ਲੈਣ ਲਈ ਬਲੋ ਮੋਲਡ ਕੈਵਿਟੀ ਦੀਆਂ ਕੰਧਾਂ ਦੇ ਵਿਰੁੱਧ ਦਬਾਅ ਅਤੇ ਧੱਕਿਆ ਜਾਂਦਾ ਹੈ। ਅੰਤ ਵਿੱਚ, ਨਿਰਮਿਤ ਕੱਚ ਦੇ ਕੰਟੇਨਰ ਨੂੰ ਬਾਅਦ ਵਿੱਚ ਦੁਬਾਰਾ ਗਰਮ ਕਰਨ ਅਤੇ ਮੋਲਡਿੰਗ ਦੌਰਾਨ ਪੈਦਾ ਹੋਏ ਤਣਾਅ ਨੂੰ ਹਟਾਉਣ ਲਈ ਇੱਕ ਐਨੀਲਿੰਗ ਓਵਨ ਵਿੱਚ ਤਬਦੀਲ ਕੀਤਾ ਜਾਂਦਾ ਹੈ ਅਤੇ ਇੱਕ ਨਿਯੰਤਰਿਤ ਢੰਗ ਨਾਲ ਠੰਡਾ ਕੀਤਾ ਜਾਂਦਾ ਹੈ। ਪ੍ਰੈੱਸ ਅਤੇ ਬਲੋ ਵਿਧੀ ਵਿੱਚ, ਪਿਘਲੇ ਹੋਏ ਗੋਬਾਂ ਨੂੰ ਪੈਰੀਸਨ ਮੋਲਡ (ਖਾਲੀ ਮੋਲਡ) ਵਿੱਚ ਪਾ ਦਿੱਤਾ ਜਾਂਦਾ ਹੈ ਅਤੇ ਪੈਰੀਸਨ ਆਕਾਰ (ਖਾਲੀ ਆਕਾਰ) ਵਿੱਚ ਦਬਾਇਆ ਜਾਂਦਾ ਹੈ। ਫਿਰ ਖਾਲੀ ਥਾਂਵਾਂ ਨੂੰ ਬਲੋ ਮੋਲਡ ਵਿੱਚ ਤਬਦੀਲ ਕਰ ਦਿੱਤਾ ਜਾਂਦਾ ਹੈ ਅਤੇ "ਬਲੋ ਐਂਡ ਬਲੋ ਪ੍ਰੋਸੈਸ" ਦੇ ਤਹਿਤ ਉੱਪਰ ਦੱਸੀ ਪ੍ਰਕਿਰਿਆ ਵਾਂਗ ਹੀ ਉਡਾ ਦਿੱਤਾ ਜਾਂਦਾ ਹੈ। ਐਨੀਲਿੰਗ ਅਤੇ ਤਣਾਅ ਤੋਂ ਛੁਟਕਾਰਾ ਪਾਉਣ ਵਰਗੇ ਅਗਲੇ ਪੜਾਅ ਸਮਾਨ ਜਾਂ ਸਮਾਨ ਹਨ। • ਗਲਾਸ ਬਲੋਇੰਗ: ਅਸੀਂ ਰਵਾਇਤੀ ਹੱਥਾਂ ਨਾਲ ਉਡਾਉਣ ਦੇ ਨਾਲ-ਨਾਲ ਸਵੈਚਲਿਤ ਉਪਕਰਨਾਂ ਨਾਲ ਕੰਪਰੈੱਸਡ ਹਵਾ ਦੀ ਵਰਤੋਂ ਕਰਦੇ ਹੋਏ ਕੱਚ ਦੇ ਉਤਪਾਦਾਂ ਦਾ ਨਿਰਮਾਣ ਕਰ ਰਹੇ ਹਾਂ। ਕੁਝ ਆਰਡਰਾਂ ਲਈ ਪਰੰਪਰਾਗਤ ਉਡਾਉਣ ਦੀ ਲੋੜ ਹੁੰਦੀ ਹੈ, ਜਿਵੇਂ ਕਿ ਗਲਾਸ ਆਰਟ ਵਰਕ ਨੂੰ ਸ਼ਾਮਲ ਕਰਨ ਵਾਲੇ ਪ੍ਰੋਜੈਕਟ, ਜਾਂ ਅਜਿਹੇ ਪ੍ਰੋਜੈਕਟ ਜਿਨ੍ਹਾਂ ਲਈ ਢਿੱਲੀ ਸਹਿਣਸ਼ੀਲਤਾ, ਪ੍ਰੋਟੋਟਾਈਪਿੰਗ / ਡੈਮੋ ਪ੍ਰੋਜੈਕਟਾਂ ਦੇ ਨਾਲ ਥੋੜ੍ਹੇ ਜਿਹੇ ਹਿੱਸਿਆਂ ਦੀ ਲੋੜ ਹੁੰਦੀ ਹੈ। ਰਵਾਇਤੀ ਸ਼ੀਸ਼ੇ ਨੂੰ ਉਡਾਉਣ ਵਿੱਚ ਇੱਕ ਖੋਖਲੇ ਧਾਤੂ ਦੀ ਪਾਈਪ ਨੂੰ ਪਿਘਲੇ ਹੋਏ ਕੱਚ ਦੇ ਇੱਕ ਘੜੇ ਵਿੱਚ ਡੁਬੋਣਾ ਅਤੇ ਕੱਚ ਦੀ ਸਮੱਗਰੀ ਦੀ ਕੁਝ ਮਾਤਰਾ ਨੂੰ ਇਕੱਠਾ ਕਰਨ ਲਈ ਪਾਈਪ ਨੂੰ ਘੁੰਮਾਉਣਾ ਸ਼ਾਮਲ ਹੁੰਦਾ ਹੈ। ਪਾਈਪ ਦੀ ਸਿਰੇ 'ਤੇ ਇਕੱਠੇ ਕੀਤੇ ਸ਼ੀਸ਼ੇ ਨੂੰ ਫਲੈਟ ਲੋਹੇ 'ਤੇ ਰੋਲ ਕੀਤਾ ਜਾਂਦਾ ਹੈ, ਲੋੜ ਅਨੁਸਾਰ ਆਕਾਰ ਦਿੱਤਾ ਜਾਂਦਾ ਹੈ, ਲੰਬਾ ਕੀਤਾ ਜਾਂਦਾ ਹੈ, ਦੁਬਾਰਾ ਗਰਮ ਕੀਤਾ ਜਾਂਦਾ ਹੈ ਅਤੇ ਹਵਾ ਵਿਚ ਉਡਾਇਆ ਜਾਂਦਾ ਹੈ। ਤਿਆਰ ਹੋਣ 'ਤੇ, ਇਸ ਨੂੰ ਇੱਕ ਉੱਲੀ ਵਿੱਚ ਪਾਇਆ ਜਾਂਦਾ ਹੈ ਅਤੇ ਹਵਾ ਉਡਾ ਦਿੱਤੀ ਜਾਂਦੀ ਹੈ। ਧਾਤ ਦੇ ਨਾਲ ਸ਼ੀਸ਼ੇ ਦੇ ਸੰਪਰਕ ਤੋਂ ਬਚਣ ਲਈ ਮੋਲਡ ਕੈਵਿਟੀ ਗਿੱਲੀ ਹੁੰਦੀ ਹੈ। ਪਾਣੀ ਦੀ ਫਿਲਮ ਉਹਨਾਂ ਵਿਚਕਾਰ ਇੱਕ ਗੱਦੀ ਵਾਂਗ ਕੰਮ ਕਰਦੀ ਹੈ। ਮੈਨੂਅਲ ਬਲੋਇੰਗ ਇੱਕ ਲੇਬਰ ਤੀਬਰ ਹੌਲੀ ਪ੍ਰਕਿਰਿਆ ਹੈ ਅਤੇ ਸਿਰਫ ਪ੍ਰੋਟੋਟਾਈਪਿੰਗ ਜਾਂ ਉੱਚ ਮੁੱਲ ਦੀਆਂ ਚੀਜ਼ਾਂ ਲਈ ਢੁਕਵੀਂ ਹੈ, ਪ੍ਰਤੀ ਟੁਕੜਾ ਉੱਚ ਵਾਲੀਅਮ ਆਰਡਰ ਲਈ ਸਸਤੇ ਨਹੀਂ ਹੈ। • ਘਰੇਲੂ ਅਤੇ ਉਦਯੋਗਿਕ ਗਲਾਸਵੇਅਰ ਦਾ ਨਿਰਮਾਣ: ਵੱਖ-ਵੱਖ ਕਿਸਮਾਂ ਦੀਆਂ ਕੱਚ ਦੀਆਂ ਸਮੱਗਰੀਆਂ ਦੀ ਵਰਤੋਂ ਕਰਕੇ ਕੱਚ ਦੇ ਸਾਮਾਨ ਦੀ ਇੱਕ ਵੱਡੀ ਕਿਸਮ ਤਿਆਰ ਕੀਤੀ ਜਾ ਰਹੀ ਹੈ। ਕੁਝ ਗਲਾਸ ਗਰਮੀ ਰੋਧਕ ਹੁੰਦੇ ਹਨ ਅਤੇ ਪ੍ਰਯੋਗਸ਼ਾਲਾ ਦੇ ਕੱਚ ਦੇ ਸਾਮਾਨ ਲਈ ਢੁਕਵੇਂ ਹੁੰਦੇ ਹਨ ਜਦੋਂ ਕਿ ਕੁਝ ਕਈ ਵਾਰ ਡਿਸ਼ਵਾਸ਼ਰਾਂ ਦਾ ਸਾਮ੍ਹਣਾ ਕਰਨ ਲਈ ਕਾਫੀ ਚੰਗੇ ਹੁੰਦੇ ਹਨ ਅਤੇ ਘਰੇਲੂ ਉਤਪਾਦ ਬਣਾਉਣ ਲਈ ਫਿੱਟ ਹੁੰਦੇ ਹਨ। ਵੈਸਟਲੇਕ ਮਸ਼ੀਨਾਂ ਦੀ ਵਰਤੋਂ ਕਰਕੇ ਪ੍ਰਤੀ ਦਿਨ ਪੀਣ ਵਾਲੇ ਗਲਾਸ ਦੇ ਹਜ਼ਾਰਾਂ ਟੁਕੜੇ ਤਿਆਰ ਕੀਤੇ ਜਾ ਰਹੇ ਹਨ। ਸਰਲ ਬਣਾਉਣ ਲਈ, ਪਿਘਲੇ ਹੋਏ ਸ਼ੀਸ਼ੇ ਨੂੰ ਵੈਕਿਊਮ ਦੁਆਰਾ ਇਕੱਠਾ ਕੀਤਾ ਜਾਂਦਾ ਹੈ ਅਤੇ ਪ੍ਰੀ-ਫਾਰਮ ਬਣਾਉਣ ਲਈ ਮੋਲਡਾਂ ਵਿੱਚ ਪਾਇਆ ਜਾਂਦਾ ਹੈ। ਫਿਰ ਹਵਾ ਨੂੰ ਉੱਲੀ ਵਿੱਚ ਉਡਾਇਆ ਜਾਂਦਾ ਹੈ, ਇਹ ਕਿਸੇ ਹੋਰ ਉੱਲੀ ਵਿੱਚ ਤਬਦੀਲ ਹੋ ਜਾਂਦੇ ਹਨ ਅਤੇ ਹਵਾ ਦੁਬਾਰਾ ਉੱਡ ਜਾਂਦੀ ਹੈ ਅਤੇ ਕੱਚ ਆਪਣਾ ਅੰਤਮ ਰੂਪ ਲੈ ਲੈਂਦਾ ਹੈ। ਹੱਥਾਂ ਨਾਲ ਉਡਾਉਣ ਵਾਂਗ, ਇਨ੍ਹਾਂ ਮੋਲਡਾਂ ਨੂੰ ਪਾਣੀ ਨਾਲ ਗਿੱਲਾ ਰੱਖਿਆ ਜਾਂਦਾ ਹੈ। ਅੱਗੇ ਖਿੱਚਣਾ ਫਿਨਿਸ਼ਿੰਗ ਓਪਰੇਸ਼ਨ ਦਾ ਹਿੱਸਾ ਹੈ ਜਿੱਥੇ ਗਰਦਨ ਦਾ ਗਠਨ ਕੀਤਾ ਜਾ ਰਿਹਾ ਹੈ। ਵਾਧੂ ਕੱਚ ਨੂੰ ਸਾੜ ਦਿੱਤਾ ਗਿਆ ਹੈ. ਇਸ ਤੋਂ ਬਾਅਦ ਉੱਪਰ ਵਰਣਿਤ ਨਿਯੰਤਰਿਤ ਰੀ-ਹੀਟਿੰਗ ਅਤੇ ਕੂਲਿੰਗ ਪ੍ਰਕਿਰਿਆ ਹੇਠਾਂ ਦਿੱਤੀ ਗਈ ਹੈ। • ਗਲਾਸ ਟਿਊਬ ਅਤੇ ਡੰਡੇ ਬਣਾਉਣਾ: ਕੱਚ ਦੀਆਂ ਟਿਊਬਾਂ ਦੇ ਨਿਰਮਾਣ ਲਈ ਅਸੀਂ ਜਿਨ੍ਹਾਂ ਮੁੱਖ ਪ੍ਰਕਿਰਿਆਵਾਂ ਦੀ ਵਰਤੋਂ ਕਰਦੇ ਹਾਂ ਉਹ ਡੈਨਰ ਅਤੇ ਵੇਲੋ ਪ੍ਰਕਿਰਿਆਵਾਂ ਹਨ। ਡੈਨਰ ਪ੍ਰਕਿਰਿਆ ਵਿੱਚ, ਇੱਕ ਭੱਠੀ ਵਿੱਚੋਂ ਕੱਚ ਵਹਿੰਦਾ ਹੈ ਅਤੇ ਰਿਫ੍ਰੈਕਟਰੀ ਸਮੱਗਰੀ ਦੀ ਬਣੀ ਇੱਕ ਝੁਕੀ ਹੋਈ ਆਸਤੀਨ 'ਤੇ ਡਿੱਗਦਾ ਹੈ। ਆਸਤੀਨ ਨੂੰ ਘੁੰਮਦੇ ਹੋਏ ਖੋਖਲੇ ਸ਼ਾਫਟ ਜਾਂ ਬਲੋਪਾਈਪ 'ਤੇ ਲਿਜਾਇਆ ਜਾਂਦਾ ਹੈ। ਫਿਰ ਕੱਚ ਨੂੰ ਆਸਤੀਨ ਦੇ ਦੁਆਲੇ ਲਪੇਟਿਆ ਜਾਂਦਾ ਹੈ ਅਤੇ ਆਸਤੀਨ ਦੇ ਹੇਠਾਂ ਅਤੇ ਸ਼ਾਫਟ ਦੇ ਸਿਰੇ 'ਤੇ ਵਹਿਣ ਵਾਲੀ ਇੱਕ ਨਿਰਵਿਘਨ ਪਰਤ ਬਣਾਉਂਦਾ ਹੈ। ਟਿਊਬ ਬਣਾਉਣ ਦੇ ਮਾਮਲੇ ਵਿੱਚ, ਹਵਾ ਨੂੰ ਖੋਖਲੇ ਟਿਪ ਨਾਲ ਬਲੋਪਾਈਪ ਰਾਹੀਂ ਉਡਾਇਆ ਜਾਂਦਾ ਹੈ, ਅਤੇ ਡੰਡੇ ਦੇ ਬਣਨ ਦੇ ਮਾਮਲੇ ਵਿੱਚ ਅਸੀਂ ਸ਼ਾਫਟ 'ਤੇ ਠੋਸ ਟਿਪਸ ਦੀ ਵਰਤੋਂ ਕਰਦੇ ਹਾਂ। ਫਿਰ ਟਿਊਬਾਂ ਜਾਂ ਡੰਡੇ ਨੂੰ ਚੁੱਕਣ ਵਾਲੇ ਰੋਲਰ ਉੱਤੇ ਖਿੱਚਿਆ ਜਾਂਦਾ ਹੈ। ਸ਼ੀਸ਼ੇ ਦੀਆਂ ਟਿਊਬਾਂ ਦੀ ਕੰਧ ਦੀ ਮੋਟਾਈ ਅਤੇ ਵਿਆਸ ਵਰਗੇ ਮਾਪਾਂ ਨੂੰ ਆਸਤੀਨ ਦੇ ਵਿਆਸ ਨੂੰ ਸੈਟ ਕਰਕੇ ਅਤੇ ਹਵਾ ਦੇ ਦਬਾਅ ਨੂੰ ਲੋੜੀਂਦੇ ਮੁੱਲ 'ਤੇ ਉਡਾ ਕੇ, ਤਾਪਮਾਨ, ਸ਼ੀਸ਼ੇ ਦੇ ਵਹਾਅ ਦੀ ਦਰ ਅਤੇ ਡਰਾਇੰਗ ਦੀ ਗਤੀ ਨੂੰ ਅਨੁਕੂਲਿਤ ਕਰਕੇ ਲੋੜੀਂਦੇ ਮੁੱਲਾਂ ਨਾਲ ਐਡਜਸਟ ਕੀਤਾ ਜਾਂਦਾ ਹੈ। ਦੂਜੇ ਪਾਸੇ ਵੇਲੋ ਗਲਾਸ ਟਿਊਬ ਨਿਰਮਾਣ ਪ੍ਰਕਿਰਿਆ ਵਿੱਚ ਕੱਚ ਸ਼ਾਮਲ ਹੁੰਦਾ ਹੈ ਜੋ ਇੱਕ ਭੱਠੀ ਵਿੱਚੋਂ ਬਾਹਰ ਨਿਕਲਦਾ ਹੈ ਅਤੇ ਇੱਕ ਖੋਖਲੇ ਮੰਡਰੇਲ ਜਾਂ ਘੰਟੀ ਦੇ ਨਾਲ ਇੱਕ ਕਟੋਰੇ ਵਿੱਚ ਜਾਂਦਾ ਹੈ। ਫਿਰ ਸ਼ੀਸ਼ਾ ਮੰਡਰੇਲ ਅਤੇ ਕਟੋਰੇ ਦੇ ਵਿਚਕਾਰ ਹਵਾ ਵਾਲੀ ਥਾਂ ਵਿੱਚੋਂ ਲੰਘਦਾ ਹੈ ਅਤੇ ਇੱਕ ਟਿਊਬ ਦਾ ਰੂਪ ਲੈਂਦਾ ਹੈ। ਇਸ ਤੋਂ ਬਾਅਦ ਇਹ ਰੋਲਰਾਂ ਉੱਤੇ ਇੱਕ ਡਰਾਇੰਗ ਮਸ਼ੀਨ ਤੱਕ ਜਾਂਦਾ ਹੈ ਅਤੇ ਠੰਡਾ ਹੁੰਦਾ ਹੈ। ਕੂਲਿੰਗ ਲਾਈਨ ਦੇ ਅੰਤ 'ਤੇ ਕੱਟਣ ਅਤੇ ਅੰਤਮ ਪ੍ਰੋਸੈਸਿੰਗ ਹੁੰਦੀ ਹੈ। ਟਿਊਬ ਦੇ ਮਾਪਾਂ ਨੂੰ ਉਸੇ ਤਰ੍ਹਾਂ ਐਡਜਸਟ ਕੀਤਾ ਜਾ ਸਕਦਾ ਹੈ ਜਿਵੇਂ ਕਿ ਡੈਨਰ ਪ੍ਰਕਿਰਿਆ ਵਿੱਚ. ਡੈਨਰ ਦੀ ਵੇਲੋ ਪ੍ਰਕਿਰਿਆ ਨਾਲ ਤੁਲਨਾ ਕਰਦੇ ਸਮੇਂ, ਅਸੀਂ ਕਹਿ ਸਕਦੇ ਹਾਂ ਕਿ ਵੇਲੋ ਪ੍ਰਕਿਰਿਆ ਵੱਡੀ ਮਾਤਰਾ ਦੇ ਉਤਪਾਦਨ ਲਈ ਇੱਕ ਬਿਹਤਰ ਫਿੱਟ ਹੈ ਜਦੋਂ ਕਿ ਡੈਨਰ ਪ੍ਰਕਿਰਿਆ ਸਟੀਕ ਛੋਟੇ ਵਾਲੀਅਮ ਟਿਊਬ ਆਰਡਰ ਲਈ ਬਿਹਤਰ ਫਿੱਟ ਹੋ ਸਕਦੀ ਹੈ। • ਸ਼ੀਟ ਅਤੇ ਫਲੈਟ ਅਤੇ ਫਲੋਟ ਗਲਾਸ ਦੀ ਪ੍ਰੋਸੈਸਿੰਗ: ਸਾਡੇ ਕੋਲ ਸਬਮਿਲੀਮੀਟਰ ਮੋਟਾਈ ਤੋਂ ਲੈ ਕੇ ਕਈ ਸੈਂਟੀਮੀਟਰ ਤੱਕ ਮੋਟਾਈ ਵਿੱਚ ਫਲੈਟ ਕੱਚ ਦੀ ਵੱਡੀ ਮਾਤਰਾ ਹੈ। ਸਾਡੇ ਫਲੈਟ ਗਲਾਸ ਲਗਭਗ ਆਪਟੀਕਲ ਸੰਪੂਰਨਤਾ ਦੇ ਹਨ. ਅਸੀਂ ਵਿਸ਼ੇਸ਼ ਕੋਟਿੰਗਾਂ ਜਿਵੇਂ ਕਿ ਆਪਟੀਕਲ ਕੋਟਿੰਗਜ਼ ਦੇ ਨਾਲ ਕੱਚ ਦੀ ਪੇਸ਼ਕਸ਼ ਕਰਦੇ ਹਾਂ, ਜਿੱਥੇ ਕਿ ਐਂਟੀ-ਰਿਫਲੈਕਸ਼ਨ ਜਾਂ ਮਿਰਰ ਕੋਟਿੰਗ ਵਰਗੀਆਂ ਕੋਟਿੰਗਾਂ ਲਗਾਉਣ ਲਈ ਰਸਾਇਣਕ ਭਾਫ਼ ਜਮ੍ਹਾ ਕਰਨ ਦੀ ਤਕਨੀਕ ਦੀ ਵਰਤੋਂ ਕੀਤੀ ਜਾਂਦੀ ਹੈ। ਪਾਰਦਰਸ਼ੀ ਕੰਡਕਟਿਵ ਕੋਟਿੰਗ ਵੀ ਆਮ ਹਨ। ਸ਼ੀਸ਼ੇ 'ਤੇ ਹਾਈਡ੍ਰੋਫੋਬਿਕ ਜਾਂ ਹਾਈਡ੍ਰੋਫਿਲਿਕ ਕੋਟਿੰਗ ਅਤੇ ਸ਼ੀਸ਼ੇ ਦੀ ਸਵੈ-ਸਫ਼ਾਈ ਕਰਨ ਵਾਲੀ ਕੋਟਿੰਗ ਵੀ ਉਪਲਬਧ ਹਨ। ਟੈਂਪਰਡ, ਬੁਲੇਟਪਰੂਫ ਅਤੇ ਲੈਮੀਨੇਟਡ ਗਲਾਸ ਅਜੇ ਹੋਰ ਪ੍ਰਸਿੱਧ ਚੀਜ਼ਾਂ ਹਨ। ਅਸੀਂ ਲੋੜੀਦੀ ਸਹਿਣਸ਼ੀਲਤਾ ਦੇ ਨਾਲ ਕੱਚ ਨੂੰ ਲੋੜੀਂਦੇ ਆਕਾਰ ਵਿੱਚ ਕੱਟਦੇ ਹਾਂ. ਹੋਰ ਸੈਕੰਡਰੀ ਓਪਰੇਸ਼ਨ ਜਿਵੇਂ ਕਿ ਕਰਵਿੰਗ ਜਾਂ ਝੁਕਣ ਵਾਲਾ ਫਲੈਟ ਗਲਾਸ ਉਪਲਬਧ ਹਨ। • ਸਟੀਕਸ਼ਨ ਗਲਾਸ ਮੋਲਡਿੰਗ: ਅਸੀਂ ਇਸ ਤਕਨੀਕ ਦੀ ਵਰਤੋਂ ਜਿਆਦਾਤਰ ਸਟੀਕਸ਼ਨ ਆਪਟੀਕਲ ਕੰਪੋਨੈਂਟ ਬਣਾਉਣ ਲਈ ਕਰਦੇ ਹਾਂ, ਬਿਨਾਂ ਜ਼ਿਆਦਾ ਮਹਿੰਗੀਆਂ ਅਤੇ ਸਮਾਂ ਲੈਣ ਵਾਲੀਆਂ ਤਕਨੀਕਾਂ ਜਿਵੇਂ ਕਿ ਪੀਸਣ, ਲੈਪਿੰਗ ਅਤੇ ਪਾਲਿਸ਼ਿੰਗ ਦੀ ਲੋੜ ਤੋਂ ਬਿਨਾਂ। ਇਹ ਤਕਨੀਕ ਹਮੇਸ਼ਾ ਸਭ ਤੋਂ ਵਧੀਆ ਆਪਟਿਕਸ ਬਣਾਉਣ ਲਈ ਕਾਫੀ ਨਹੀਂ ਹੁੰਦੀ ਹੈ, ਪਰ ਕੁਝ ਮਾਮਲਿਆਂ ਵਿੱਚ ਜਿਵੇਂ ਕਿ ਖਪਤਕਾਰ ਉਤਪਾਦ, ਡਿਜੀਟਲ ਕੈਮਰੇ, ਮੈਡੀਕਲ ਆਪਟਿਕਸ ਉੱਚ ਮਾਤਰਾ ਦੇ ਨਿਰਮਾਣ ਲਈ ਇਹ ਇੱਕ ਘੱਟ ਮਹਿੰਗਾ ਚੰਗਾ ਵਿਕਲਪ ਹੋ ਸਕਦਾ ਹੈ। ਇਸ ਦੇ ਨਾਲ ਹੀ ਸ਼ੀਸ਼ੇ ਬਣਾਉਣ ਦੀਆਂ ਹੋਰ ਤਕਨੀਕਾਂ ਦੇ ਮੁਕਾਬਲੇ ਇਸਦਾ ਫਾਇਦਾ ਹੈ ਜਿੱਥੇ ਗੁੰਝਲਦਾਰ ਜਿਓਮੈਟਰੀ ਦੀ ਲੋੜ ਹੁੰਦੀ ਹੈ, ਜਿਵੇਂ ਕਿ ਅਸਫੀਅਰਜ਼ ਦੇ ਮਾਮਲੇ ਵਿੱਚ। ਬੁਨਿਆਦੀ ਪ੍ਰਕਿਰਿਆ ਵਿੱਚ ਸਾਡੇ ਉੱਲੀ ਦੇ ਹੇਠਲੇ ਪਾਸੇ ਨੂੰ ਕੱਚ ਦੇ ਖਾਲੀ ਨਾਲ ਲੋਡ ਕਰਨਾ, ਆਕਸੀਜਨ ਹਟਾਉਣ ਲਈ ਪ੍ਰਕਿਰਿਆ ਚੈਂਬਰ ਨੂੰ ਖਾਲੀ ਕਰਨਾ, ਮੋਲਡ ਦੇ ਨੇੜੇ ਬੰਦ ਹੋਣਾ, ਇਨਫਰਾਰੈੱਡ ਰੋਸ਼ਨੀ ਨਾਲ ਡਾਈ ਅਤੇ ਕੱਚ ਦੀ ਤੇਜ਼ ਅਤੇ ਆਈਸੋਥਰਮਲ ਹੀਟਿੰਗ, ਮੋਲਡ ਦੇ ਅੱਧੇ ਹਿੱਸੇ ਨੂੰ ਹੋਰ ਬੰਦ ਕਰਨਾ ਸ਼ਾਮਲ ਹੈ। ਨਰਮ ਕੀਤੇ ਗਲਾਸ ਨੂੰ ਹੌਲੀ-ਹੌਲੀ ਇੱਕ ਨਿਯੰਤਰਿਤ ਢੰਗ ਨਾਲ ਲੋੜੀਦੀ ਮੋਟਾਈ ਤੱਕ ਦਬਾਉਣ ਲਈ, ਅਤੇ ਅੰਤ ਵਿੱਚ ਸ਼ੀਸ਼ੇ ਨੂੰ ਠੰਢਾ ਕਰਨ ਅਤੇ ਨਾਈਟ੍ਰੋਜਨ ਨਾਲ ਚੈਂਬਰ ਨੂੰ ਭਰਨ ਅਤੇ ਉਤਪਾਦ ਨੂੰ ਹਟਾਉਣ ਲਈ। ਸਹੀ ਤਾਪਮਾਨ ਨਿਯੰਤਰਣ, ਉੱਲੀ ਬੰਦ ਕਰਨ ਦੀ ਦੂਰੀ, ਉੱਲੀ ਬੰਦ ਕਰਨ ਦੀ ਸ਼ਕਤੀ, ਉੱਲੀ ਦੇ ਵਿਸਤਾਰ ਦੇ ਗੁਣਾਂ ਦਾ ਮੇਲ ਕਰਨਾ ਅਤੇ ਕੱਚ ਦੀ ਸਮੱਗਰੀ ਇਸ ਪ੍ਰਕਿਰਿਆ ਵਿੱਚ ਮੁੱਖ ਹਨ। • ਗਲਾਸ ਆਪਟੀਕਲ ਕੰਪੋਨੈਂਟਸ ਅਤੇ ਅਸੈਂਬਲੀਆਂ ਦਾ ਨਿਰਮਾਣ: ਸਟੀਕ ਗਲਾਸ ਮੋਲਡਿੰਗ ਤੋਂ ਇਲਾਵਾ, ਬਹੁਤ ਸਾਰੀਆਂ ਕੀਮਤੀ ਪ੍ਰਕਿਰਿਆਵਾਂ ਹਨ ਜਿਨ੍ਹਾਂ ਦੀ ਵਰਤੋਂ ਅਸੀਂ ਉੱਚ ਗੁਣਵੱਤਾ ਵਾਲੇ ਆਪਟੀਕਲ ਕੰਪੋਨੈਂਟਸ ਅਤੇ ਅਸੈਂਬਲੀਆਂ ਨੂੰ ਮੰਗਣ ਵਾਲੀਆਂ ਐਪਲੀਕੇਸ਼ਨਾਂ ਲਈ ਬਣਾਉਣ ਲਈ ਕਰਦੇ ਹਾਂ। ਆਪਟੀਕਲ ਗ੍ਰੇਡ ਦੇ ਗਲਾਸਾਂ ਨੂੰ ਬਾਰੀਕ ਵਿਸ਼ੇਸ਼ ਘਬਰਾਹਟ ਵਾਲੀਆਂ ਸਲਰੀਆਂ ਵਿੱਚ ਪੀਸਣਾ, ਲੈਪ ਕਰਨਾ ਅਤੇ ਪਾਲਿਸ਼ ਕਰਨਾ ਆਪਟੀਕਲ ਲੈਂਸ, ਪ੍ਰਿਜ਼ਮ, ਫਲੈਟ ਅਤੇ ਹੋਰ ਬਹੁਤ ਕੁਝ ਬਣਾਉਣ ਲਈ ਇੱਕ ਕਲਾ ਅਤੇ ਵਿਗਿਆਨ ਹੈ। ਸਤ੍ਹਾ ਦੀ ਸਮਤਲਤਾ, ਲਹਿਰਾਂ, ਨਿਰਵਿਘਨਤਾ ਅਤੇ ਨੁਕਸ ਰਹਿਤ ਆਪਟੀਕਲ ਸਤਹਾਂ ਨੂੰ ਅਜਿਹੀਆਂ ਪ੍ਰਕਿਰਿਆਵਾਂ ਦੇ ਨਾਲ ਬਹੁਤ ਸਾਰੇ ਅਨੁਭਵ ਦੀ ਲੋੜ ਹੁੰਦੀ ਹੈ। ਵਾਤਾਵਰਣ ਵਿੱਚ ਛੋਟੀਆਂ ਤਬਦੀਲੀਆਂ ਦੇ ਨਤੀਜੇ ਵਜੋਂ ਉਤਪਾਦ ਨਿਰਧਾਰਨ ਤੋਂ ਬਾਹਰ ਹੋ ਸਕਦੇ ਹਨ ਅਤੇ ਨਿਰਮਾਣ ਲਾਈਨ ਨੂੰ ਰੋਕ ਸਕਦੇ ਹਨ। ਅਜਿਹੇ ਮਾਮਲੇ ਹਨ ਜਿੱਥੇ ਇੱਕ ਸਾਫ਼ ਕੱਪੜੇ ਨਾਲ ਆਪਟੀਕਲ ਸਤਹ 'ਤੇ ਇੱਕ ਸਿੰਗਲ ਪੂੰਝਣ ਨਾਲ ਉਤਪਾਦ ਵਿਸ਼ੇਸ਼ਤਾਵਾਂ ਨੂੰ ਪੂਰਾ ਕਰ ਸਕਦਾ ਹੈ ਜਾਂ ਟੈਸਟ ਵਿੱਚ ਅਸਫਲ ਹੋ ਸਕਦਾ ਹੈ। ਵਰਤੀਆਂ ਜਾਣ ਵਾਲੀਆਂ ਕੁਝ ਪ੍ਰਸਿੱਧ ਕੱਚ ਦੀਆਂ ਸਮੱਗਰੀਆਂ ਫਿਊਜ਼ਡ ਸਿਲਿਕਾ, ਕੁਆਰਟਜ਼, BK7 ਹਨ। ਅਜਿਹੇ ਭਾਗਾਂ ਦੀ ਅਸੈਂਬਲੀ ਲਈ ਵਿਸ਼ੇਸ਼ ਵਿਸ਼ੇਸ਼ ਅਨੁਭਵ ਦੀ ਲੋੜ ਹੁੰਦੀ ਹੈ. ਕਈ ਵਾਰ ਵਿਸ਼ੇਸ਼ ਗੂੰਦ ਦੀ ਵਰਤੋਂ ਕੀਤੀ ਜਾਂਦੀ ਹੈ. ਹਾਲਾਂਕਿ, ਕਈ ਵਾਰ ਇੱਕ ਤਕਨੀਕ ਜਿਸਨੂੰ ਆਪਟੀਕਲ ਸੰਪਰਕ ਕਿਹਾ ਜਾਂਦਾ ਹੈ ਸਭ ਤੋਂ ਵਧੀਆ ਵਿਕਲਪ ਹੁੰਦਾ ਹੈ ਅਤੇ ਇਸ ਵਿੱਚ ਅਟੈਚਡ ਆਪਟੀਕਲ ਗਲਾਸਾਂ ਦੇ ਵਿਚਕਾਰ ਕੋਈ ਸਮੱਗਰੀ ਸ਼ਾਮਲ ਨਹੀਂ ਹੁੰਦੀ ਹੈ। ਇਸ ਵਿੱਚ ਗੂੰਦ ਦੇ ਬਿਨਾਂ ਇੱਕ ਦੂਜੇ ਨਾਲ ਜੁੜਨ ਲਈ ਸਮਤਲ ਸਤਹਾਂ ਨਾਲ ਸਰੀਰਕ ਤੌਰ 'ਤੇ ਸੰਪਰਕ ਕਰਨਾ ਸ਼ਾਮਲ ਹੈ। ਕੁਝ ਮਾਮਲਿਆਂ ਵਿੱਚ ਮਕੈਨੀਕਲ ਸਪੇਸਰ, ਸਟੀਕ ਸ਼ੀਸ਼ੇ ਦੀਆਂ ਰਾਡਾਂ ਜਾਂ ਗੇਂਦਾਂ, ਕਲੈਂਪ ਜਾਂ ਮਸ਼ੀਨੀ ਧਾਤ ਦੇ ਭਾਗਾਂ ਦੀ ਵਰਤੋਂ ਆਪਟੀਕਲ ਹਿੱਸਿਆਂ ਨੂੰ ਕੁਝ ਦੂਰੀਆਂ 'ਤੇ ਅਤੇ ਇੱਕ ਦੂਜੇ ਨਾਲ ਕੁਝ ਜਿਓਮੈਟ੍ਰਿਕ ਸਥਿਤੀਆਂ ਦੇ ਨਾਲ ਇਕੱਠੇ ਕਰਨ ਲਈ ਕੀਤੀ ਜਾ ਰਹੀ ਹੈ। ਆਉ ਅਸੀਂ ਹਾਈ ਐਂਡ ਆਪਟਿਕਸ ਦੇ ਨਿਰਮਾਣ ਲਈ ਸਾਡੀਆਂ ਕੁਝ ਪ੍ਰਸਿੱਧ ਤਕਨੀਕਾਂ ਦੀ ਜਾਂਚ ਕਰੀਏ। ਪੀਸਣਾ ਅਤੇ ਲੈਪਿੰਗ ਅਤੇ ਪਾਲਿਸ਼ਿੰਗ: ਆਪਟੀਕਲ ਕੰਪੋਨੈਂਟ ਦਾ ਮੋਟਾ ਆਕਾਰ ਕੱਚ ਨੂੰ ਖਾਲੀ ਪੀਸਣ ਨਾਲ ਪ੍ਰਾਪਤ ਕੀਤਾ ਜਾਂਦਾ ਹੈ। ਇਸ ਤੋਂ ਬਾਅਦ ਲੋੜੀਂਦੇ ਸਤਹ ਆਕਾਰਾਂ ਵਾਲੇ ਔਜ਼ਾਰਾਂ ਦੇ ਵਿਰੁੱਧ ਆਪਟੀਕਲ ਕੰਪੋਨੈਂਟਾਂ ਦੀਆਂ ਖੁਰਦਰੀ ਸਤਹਾਂ ਨੂੰ ਘੁੰਮਾ ਕੇ ਅਤੇ ਰਗੜ ਕੇ ਲੈਪਿੰਗ ਅਤੇ ਪਾਲਿਸ਼ਿੰਗ ਕੀਤੀ ਜਾਂਦੀ ਹੈ। ਆਪਟਿਕਸ ਅਤੇ ਸ਼ੇਪਿੰਗ ਟੂਲਸ ਦੇ ਵਿਚਕਾਰ ਛੋਟੇ-ਛੋਟੇ ਘਬਰਾਹਟ ਵਾਲੇ ਕਣਾਂ ਅਤੇ ਤਰਲ ਨਾਲ ਸਲਰੀਜ਼ ਡੋਲ੍ਹੀਆਂ ਜਾ ਰਹੀਆਂ ਹਨ। ਅਜਿਹੀਆਂ ਸਲਰੀਆਂ ਵਿੱਚ ਘਸਣ ਵਾਲੇ ਕਣਾਂ ਦੇ ਆਕਾਰ ਨੂੰ ਲੋੜੀਦੀ ਸਮਤਲਤਾ ਦੀ ਡਿਗਰੀ ਦੇ ਅਨੁਸਾਰ ਚੁਣਿਆ ਜਾ ਸਕਦਾ ਹੈ। ਲੋੜੀਂਦੇ ਆਕਾਰਾਂ ਤੋਂ ਨਾਜ਼ੁਕ ਆਪਟੀਕਲ ਸਤਹਾਂ ਦੇ ਭਟਕਣਾਂ ਨੂੰ ਵਰਤੇ ਜਾ ਰਹੇ ਪ੍ਰਕਾਸ਼ ਦੀ ਤਰੰਗ-ਲੰਬਾਈ ਦੇ ਰੂਪ ਵਿੱਚ ਦਰਸਾਇਆ ਗਿਆ ਹੈ। ਸਾਡੇ ਉੱਚ ਸਟੀਕਸ਼ਨ ਆਪਟਿਕਸ ਵਿੱਚ ਤਰੰਗ-ਲੰਬਾਈ ਦਾ ਦਸਵਾਂ ਹਿੱਸਾ (ਤਰੰਗ-ਲੰਬਾਈ/10) ਸਹਿਣਸ਼ੀਲਤਾ ਹੁੰਦੀ ਹੈ ਜਾਂ ਇਸ ਤੋਂ ਵੀ ਸਖਤ ਸੰਭਵ ਹੈ। ਸਤਹ ਪ੍ਰੋਫਾਈਲ ਤੋਂ ਇਲਾਵਾ, ਨਾਜ਼ੁਕ ਸਤਹਾਂ ਨੂੰ ਸਕੈਨ ਕੀਤਾ ਜਾਂਦਾ ਹੈ ਅਤੇ ਸਤਹ ਦੀਆਂ ਹੋਰ ਵਿਸ਼ੇਸ਼ਤਾਵਾਂ ਅਤੇ ਨੁਕਸ ਜਿਵੇਂ ਕਿ ਮਾਪ, ਸਕ੍ਰੈਚ, ਚਿਪਸ, ਟੋਏ, ਚਟਾਕ... ਆਦਿ ਲਈ ਮੁਲਾਂਕਣ ਕੀਤਾ ਜਾਂਦਾ ਹੈ। ਆਪਟੀਕਲ ਨਿਰਮਾਣ ਮੰਜ਼ਿਲ ਵਿੱਚ ਵਾਤਾਵਰਣ ਦੀਆਂ ਸਥਿਤੀਆਂ ਦਾ ਸਖਤ ਨਿਯੰਤਰਣ ਅਤੇ ਅਤਿ-ਆਧੁਨਿਕ ਉਪਕਰਣਾਂ ਦੇ ਨਾਲ ਵਿਆਪਕ ਮੈਟਰੋਲੋਜੀ ਅਤੇ ਟੈਸਟਿੰਗ ਲੋੜਾਂ ਇਸ ਨੂੰ ਉਦਯੋਗ ਦੀ ਇੱਕ ਚੁਣੌਤੀਪੂਰਨ ਸ਼ਾਖਾ ਬਣਾਉਂਦੀਆਂ ਹਨ। • ਗਲਾਸ ਨਿਰਮਾਣ ਵਿੱਚ ਸੈਕੰਡਰੀ ਪ੍ਰਕਿਰਿਆਵਾਂ: ਦੁਬਾਰਾ, ਅਸੀਂ ਸਿਰਫ ਤੁਹਾਡੀ ਕਲਪਨਾ ਨਾਲ ਹੀ ਸੀਮਿਤ ਹਾਂ ਜਦੋਂ ਇਹ ਕੱਚ ਦੀਆਂ ਸੈਕੰਡਰੀ ਅਤੇ ਮੁਕੰਮਲ ਪ੍ਰਕਿਰਿਆਵਾਂ ਦੀ ਗੱਲ ਆਉਂਦੀ ਹੈ। ਇੱਥੇ ਅਸੀਂ ਉਹਨਾਂ ਵਿੱਚੋਂ ਕੁਝ ਨੂੰ ਸੂਚੀਬੱਧ ਕਰਦੇ ਹਾਂ: -ਸ਼ੀਸ਼ੇ 'ਤੇ ਕੋਟਿੰਗ (ਆਪਟੀਕਲ, ਇਲੈਕਟ੍ਰੀਕਲ, ਟ੍ਰਾਈਬੋਲੋਜੀਕਲ, ਥਰਮਲ, ਫੰਕਸ਼ਨਲ, ਮਕੈਨੀਕਲ...) ਇੱਕ ਉਦਾਹਰਨ ਦੇ ਤੌਰ 'ਤੇ ਅਸੀਂ ਸ਼ੀਸ਼ੇ ਦੀਆਂ ਸਤਹ ਵਿਸ਼ੇਸ਼ਤਾਵਾਂ ਨੂੰ ਬਦਲ ਸਕਦੇ ਹਾਂ ਜਿਸ ਨਾਲ ਇਹ ਉਦਾਹਰਨ ਲਈ ਗਰਮੀ ਨੂੰ ਪ੍ਰਤੀਬਿੰਬਤ ਕਰਦਾ ਹੈ ਤਾਂ ਜੋ ਇਹ ਇਮਾਰਤ ਦੇ ਅੰਦਰਲੇ ਹਿੱਸੇ ਨੂੰ ਠੰਡਾ ਰੱਖੇ, ਜਾਂ ਨੈਨੋ ਤਕਨਾਲੋਜੀ ਦੀ ਵਰਤੋਂ ਕਰਕੇ ਇੱਕ ਪਾਸੇ ਇਨਫਰਾਰੈੱਡ ਨੂੰ ਸੋਖਣ ਵਾਲਾ ਬਣਾ ਸਕੇ। ਇਹ ਇਮਾਰਤਾਂ ਦੇ ਅੰਦਰਲੇ ਹਿੱਸੇ ਨੂੰ ਗਰਮ ਰੱਖਣ ਵਿੱਚ ਮਦਦ ਕਰਦਾ ਹੈ ਕਿਉਂਕਿ ਕੱਚ ਦੀ ਸਭ ਤੋਂ ਬਾਹਰੀ ਸਤਹ ਪਰਤ ਇਮਾਰਤ ਦੇ ਅੰਦਰ ਇਨਫਰਾਰੈੱਡ ਰੇਡੀਏਸ਼ਨ ਨੂੰ ਜਜ਼ਬ ਕਰ ਲੈਂਦੀ ਹੈ ਅਤੇ ਇਸਨੂੰ ਅੰਦਰ ਵੱਲ ਵਾਪਸ ਭੇਜ ਦਿੰਦੀ ਹੈ। -ਐੱਚਿੰਗ on ਗਲਾਸ -ਅਪਲਾਈਡ ਸਿਰੇਮਿਕ ਲੇਬਲਿੰਗ (ACL) - ਉੱਕਰੀ - ਫਲੇਮ ਪਾਲਿਸ਼ਿੰਗ - ਕੈਮੀਕਲ ਪਾਲਿਸ਼ਿੰਗ -ਸਟੇਨਿੰਗ ਤਕਨੀਕੀ ਵਸਰਾਵਿਕਸ ਦਾ ਨਿਰਮਾਣ • ਡਾਈ ਪ੍ਰੇਸਿੰਗ: ਇੱਕ ਡਾਈ ਵਿੱਚ ਸੀਮਤ ਦਾਣੇਦਾਰ ਪਾਊਡਰਾਂ ਦੀ ਇਕਸਾਰ ਸੰਕੁਚਿਤਤਾ ਹੁੰਦੀ ਹੈ • ਹੌਟ ਪ੍ਰੈੱਸਿੰਗ: ਡਾਈ ਪ੍ਰੈੱਸਿੰਗ ਦੇ ਸਮਾਨ ਹੈ ਪਰ ਘਣਤਾ ਨੂੰ ਵਧਾਉਣ ਲਈ ਤਾਪਮਾਨ ਦੇ ਜੋੜ ਨਾਲ। ਪਾਊਡਰ ਜਾਂ ਕੰਪੈਕਟਡ ਪ੍ਰੀਫਾਰਮ ਨੂੰ ਗ੍ਰੇਫਾਈਟ ਡਾਈ ਵਿੱਚ ਰੱਖਿਆ ਜਾਂਦਾ ਹੈ ਅਤੇ ਇੱਕ ਅਕਸ਼ੈਸ਼ੀਅਲ ਪ੍ਰੈਸ਼ਰ ਲਾਗੂ ਕੀਤਾ ਜਾਂਦਾ ਹੈ ਜਦੋਂ ਕਿ ਡਾਈ ਨੂੰ ਉੱਚ ਤਾਪਮਾਨਾਂ ਜਿਵੇਂ ਕਿ 2000 C 'ਤੇ ਰੱਖਿਆ ਜਾਂਦਾ ਹੈ। ਸਿਰੇਮਿਕ ਪਾਊਡਰ ਦੀ ਪ੍ਰਕਿਰਿਆ ਦੇ ਆਧਾਰ 'ਤੇ ਤਾਪਮਾਨ ਵੱਖਰਾ ਹੋ ਸਕਦਾ ਹੈ। ਗੁੰਝਲਦਾਰ ਆਕਾਰਾਂ ਅਤੇ ਜਿਓਮੈਟਰੀਜ਼ ਲਈ ਹੋਰ ਅਗਲੀ ਪ੍ਰਕਿਰਿਆ ਜਿਵੇਂ ਕਿ ਹੀਰਾ ਪੀਸਣ ਦੀ ਲੋੜ ਹੋ ਸਕਦੀ ਹੈ। • ਆਈਸੋਸਟੈਟਿਕ ਪ੍ਰੈੱਸਿੰਗ: ਦਾਣੇਦਾਰ ਪਾਊਡਰ ਜਾਂ ਡਾਈ ਪ੍ਰੈੱਸਡ ਕੰਪੈਕਟਾਂ ਨੂੰ ਏਅਰਟਾਈਟ ਕੰਟੇਨਰਾਂ ਵਿੱਚ ਅਤੇ ਫਿਰ ਅੰਦਰ ਤਰਲ ਦੇ ਨਾਲ ਇੱਕ ਬੰਦ ਦਬਾਅ ਵਾਲੇ ਭਾਂਡੇ ਵਿੱਚ ਰੱਖਿਆ ਜਾਂਦਾ ਹੈ। ਇਸ ਤੋਂ ਬਾਅਦ ਉਹਨਾਂ ਨੂੰ ਪ੍ਰੈਸ਼ਰ ਵੈਸਲ ਦੇ ਦਬਾਅ ਨੂੰ ਵਧਾ ਕੇ ਸੰਕੁਚਿਤ ਕੀਤਾ ਜਾਂਦਾ ਹੈ. ਭਾਂਡੇ ਦੇ ਅੰਦਰ ਦਾ ਤਰਲ ਏਅਰਟਾਈਟ ਕੰਟੇਨਰ ਦੇ ਪੂਰੇ ਸਤਹ ਖੇਤਰ 'ਤੇ ਦਬਾਅ ਬਲਾਂ ਨੂੰ ਇਕਸਾਰ ਰੂਪ ਵਿੱਚ ਤਬਦੀਲ ਕਰਦਾ ਹੈ। ਇਸ ਤਰ੍ਹਾਂ ਸਮੱਗਰੀ ਨੂੰ ਇਕਸਾਰ ਰੂਪ ਵਿੱਚ ਸੰਕੁਚਿਤ ਕੀਤਾ ਜਾਂਦਾ ਹੈ ਅਤੇ ਇਸਦੇ ਲਚਕਦਾਰ ਕੰਟੇਨਰ ਅਤੇ ਇਸਦੇ ਅੰਦਰੂਨੀ ਪ੍ਰੋਫਾਈਲ ਅਤੇ ਵਿਸ਼ੇਸ਼ਤਾਵਾਂ ਦਾ ਆਕਾਰ ਲੈਂਦਾ ਹੈ। • ਗਰਮ ਆਈਸੋਸਟੈਟਿਕ ਪ੍ਰੈੱਸਿੰਗ: ਆਈਸੋਸਟੈਟਿਕ ਪ੍ਰੈੱਸਿੰਗ ਦੇ ਸਮਾਨ, ਪਰ ਦਬਾਅ ਵਾਲੇ ਗੈਸ ਵਾਯੂਮੰਡਲ ਤੋਂ ਇਲਾਵਾ, ਅਸੀਂ ਉੱਚ ਤਾਪਮਾਨ 'ਤੇ ਕੰਪੈਕਟ ਨੂੰ ਸਿੰਟਰ ਕਰਦੇ ਹਾਂ। ਗਰਮ ਆਈਸੋਸਟੈਟਿਕ ਦਬਾਉਣ ਦੇ ਨਤੀਜੇ ਵਜੋਂ ਵਾਧੂ ਘਣਤਾ ਅਤੇ ਤਾਕਤ ਵਧਦੀ ਹੈ। • ਸਲਿਪ ਕਾਸਟਿੰਗ / ਡਰੇਨ ਕਾਸਟਿੰਗ: ਅਸੀਂ ਮਾਈਕ੍ਰੋਮੀਟਰ ਆਕਾਰ ਦੇ ਸਿਰੇਮਿਕ ਕਣਾਂ ਅਤੇ ਕੈਰੀਅਰ ਤਰਲ ਦੇ ਮੁਅੱਤਲ ਨਾਲ ਉੱਲੀ ਨੂੰ ਭਰਦੇ ਹਾਂ। ਇਸ ਮਿਸ਼ਰਣ ਨੂੰ "ਸਲਿੱਪ" ਕਿਹਾ ਜਾਂਦਾ ਹੈ। ਉੱਲੀ ਵਿੱਚ ਛੇਦ ਹੁੰਦੇ ਹਨ ਅਤੇ ਇਸਲਈ ਮਿਸ਼ਰਣ ਵਿੱਚ ਤਰਲ ਨੂੰ ਉੱਲੀ ਵਿੱਚ ਫਿਲਟਰ ਕੀਤਾ ਜਾਂਦਾ ਹੈ। ਨਤੀਜੇ ਵਜੋਂ, ਉੱਲੀ ਦੀਆਂ ਅੰਦਰੂਨੀ ਸਤਹਾਂ 'ਤੇ ਇੱਕ ਪਲੱਸਤਰ ਬਣਦਾ ਹੈ। ਸਿੰਟਰਿੰਗ ਤੋਂ ਬਾਅਦ, ਹਿੱਸਿਆਂ ਨੂੰ ਉੱਲੀ ਤੋਂ ਬਾਹਰ ਲਿਆ ਜਾ ਸਕਦਾ ਹੈ। • ਟੇਪ ਕਾਸਟਿੰਗ: ਅਸੀਂ ਸਮਤਲ ਚਲਦੀਆਂ ਕੈਰੀਅਰ ਸਤਹਾਂ 'ਤੇ ਵਸਰਾਵਿਕ ਸਲਰੀਆਂ ਨੂੰ ਕਾਸਟ ਕਰਕੇ ਸਿਰੇਮਿਕ ਟੇਪਾਂ ਦਾ ਨਿਰਮਾਣ ਕਰਦੇ ਹਾਂ। ਗੰਢਾਂ ਵਿੱਚ ਸਿਰੇਮਿਕ ਪਾਊਡਰ ਹੁੰਦੇ ਹਨ ਜੋ ਬਾਈਡਿੰਗ ਅਤੇ ਚੁੱਕਣ ਦੇ ਉਦੇਸ਼ਾਂ ਲਈ ਹੋਰ ਰਸਾਇਣਾਂ ਨਾਲ ਮਿਲਾਏ ਜਾਂਦੇ ਹਨ। ਜਿਵੇਂ ਕਿ ਘੋਲਨ ਵਾਲੇ ਭਾਫ਼ ਬਣ ਜਾਂਦੇ ਹਨ, ਵਸਰਾਵਿਕ ਦੀਆਂ ਸੰਘਣੀ ਅਤੇ ਲਚਕਦਾਰ ਚਾਦਰਾਂ ਪਿੱਛੇ ਰਹਿ ਜਾਂਦੀਆਂ ਹਨ ਜਿਨ੍ਹਾਂ ਨੂੰ ਲੋੜ ਅਨੁਸਾਰ ਕੱਟਿਆ ਜਾਂ ਰੋਲ ਕੀਤਾ ਜਾ ਸਕਦਾ ਹੈ। • ਬਾਹਰ ਕੱਢਣਾ: ਜਿਵੇਂ ਕਿ ਹੋਰ ਬਾਹਰ ਕੱਢਣ ਦੀਆਂ ਪ੍ਰਕਿਰਿਆਵਾਂ ਵਿੱਚ, ਬਾਈਂਡਰ ਅਤੇ ਹੋਰ ਰਸਾਇਣਾਂ ਦੇ ਨਾਲ ਸਿਰੇਮਿਕ ਪਾਊਡਰ ਦੇ ਇੱਕ ਨਰਮ ਮਿਸ਼ਰਣ ਨੂੰ ਇਸਦੇ ਅੰਤਰ-ਵਿਭਾਗੀ ਆਕਾਰ ਨੂੰ ਪ੍ਰਾਪਤ ਕਰਨ ਲਈ ਇੱਕ ਡਾਈ ਵਿੱਚੋਂ ਲੰਘਾਇਆ ਜਾਂਦਾ ਹੈ ਅਤੇ ਫਿਰ ਲੋੜੀਂਦੀ ਲੰਬਾਈ 'ਤੇ ਕੱਟਿਆ ਜਾਂਦਾ ਹੈ। ਇਹ ਪ੍ਰਕਿਰਿਆ ਠੰਡੇ ਜਾਂ ਗਰਮ ਵਸਰਾਵਿਕ ਮਿਸ਼ਰਣਾਂ ਨਾਲ ਕੀਤੀ ਜਾਂਦੀ ਹੈ। • ਲੋਅ ਪ੍ਰੈਸ਼ਰ ਇੰਜੈਕਸ਼ਨ ਮੋਲਡਿੰਗ: ਅਸੀਂ ਬਾਈਂਡਰ ਅਤੇ ਘੋਲਨ ਵਾਲੇ ਨਾਲ ਸਿਰੇਮਿਕ ਪਾਊਡਰ ਦਾ ਮਿਸ਼ਰਣ ਤਿਆਰ ਕਰਦੇ ਹਾਂ ਅਤੇ ਇਸਨੂੰ ਅਜਿਹੇ ਤਾਪਮਾਨ 'ਤੇ ਗਰਮ ਕਰਦੇ ਹਾਂ ਜਿੱਥੇ ਇਸਨੂੰ ਆਸਾਨੀ ਨਾਲ ਦਬਾਇਆ ਜਾ ਸਕਦਾ ਹੈ ਅਤੇ ਟੂਲ ਕੈਵਿਟੀ ਵਿੱਚ ਧੱਕਿਆ ਜਾ ਸਕਦਾ ਹੈ। ਇੱਕ ਵਾਰ ਮੋਲਡਿੰਗ ਚੱਕਰ ਪੂਰਾ ਹੋਣ ਤੋਂ ਬਾਅਦ, ਹਿੱਸੇ ਨੂੰ ਬਾਹਰ ਕੱਢ ਦਿੱਤਾ ਜਾਂਦਾ ਹੈ ਅਤੇ ਬਾਈਡਿੰਗ ਕੈਮੀਕਲ ਨੂੰ ਸਾੜ ਦਿੱਤਾ ਜਾਂਦਾ ਹੈ। ਇੰਜੈਕਸ਼ਨ ਮੋਲਡਿੰਗ ਦੀ ਵਰਤੋਂ ਕਰਦੇ ਹੋਏ, ਅਸੀਂ ਆਰਥਿਕ ਤੌਰ 'ਤੇ ਉੱਚ ਮਾਤਰਾ 'ਤੇ ਗੁੰਝਲਦਾਰ ਹਿੱਸੇ ਪ੍ਰਾਪਤ ਕਰ ਸਕਦੇ ਹਾਂ। ਛੇਕ ਜੋ ਕਿ ਇੱਕ 10mm ਮੋਟੀ ਕੰਧ 'ਤੇ ਇੱਕ ਮਿਲੀਮੀਟਰ ਦਾ ਇੱਕ ਛੋਟਾ ਜਿਹਾ ਹਿੱਸਾ ਹੈ, ਸੰਭਵ ਹਨ, ਧਾਗੇ ਬਿਨਾਂ ਮਸ਼ੀਨਿੰਗ ਦੇ ਸੰਭਵ ਹਨ, +/- 0.5% ਜਿੰਨੀ ਤੰਗ ਸਹਿਣਸ਼ੀਲਤਾ ਸੰਭਵ ਹੈ ਅਤੇ ਮਸ਼ੀਨ ਦੇ ਹਿੱਸੇ ਘੱਟ ਹੋਣ 'ਤੇ ਵੀ , 0.5mm ਤੋਂ 12.5mm ਦੀ ਲੰਬਾਈ ਦੇ ਕ੍ਰਮ ਵਿੱਚ ਕੰਧ ਦੀ ਮੋਟਾਈ ਸੰਭਵ ਹੈ ਅਤੇ ਨਾਲ ਹੀ 6.5mm ਤੋਂ 150mm ਦੀ ਲੰਬਾਈ ਤੱਕ ਕੰਧ ਦੀ ਮੋਟਾਈ ਸੰਭਵ ਹੈ। • ਗ੍ਰੀਨ ਮਸ਼ੀਨਿੰਗ: ਇੱਕੋ ਮੈਟਲ ਮਸ਼ੀਨਿੰਗ ਟੂਲ ਦੀ ਵਰਤੋਂ ਕਰਦੇ ਹੋਏ, ਅਸੀਂ ਦਬਾਈਆਂ ਗਈਆਂ ਵਸਰਾਵਿਕ ਸਮੱਗਰੀਆਂ ਨੂੰ ਮਸ਼ੀਨ ਕਰ ਸਕਦੇ ਹਾਂ ਜਦੋਂ ਉਹ ਅਜੇ ਵੀ ਚਾਕ ਵਾਂਗ ਨਰਮ ਹੁੰਦੇ ਹਨ। +/- 1% ਦੀ ਸਹਿਣਸ਼ੀਲਤਾ ਸੰਭਵ ਹੈ। ਬਿਹਤਰ ਸਹਿਣਸ਼ੀਲਤਾ ਲਈ ਅਸੀਂ ਹੀਰਾ ਪੀਸਣ ਦੀ ਵਰਤੋਂ ਕਰਦੇ ਹਾਂ। • ਸਿਨਟਰਿੰਗ ਜਾਂ ਫਾਇਰਿੰਗ: ਸਿੰਟਰਿੰਗ ਪੂਰੀ ਘਣਤਾ ਸੰਭਵ ਬਣਾਉਂਦੀ ਹੈ। ਹਰੇ ਕੰਪੈਕਟ ਭਾਗਾਂ 'ਤੇ ਮਹੱਤਵਪੂਰਨ ਸੰਕੁਚਨ ਹੁੰਦਾ ਹੈ, ਪਰ ਇਹ ਕੋਈ ਵੱਡੀ ਸਮੱਸਿਆ ਨਹੀਂ ਹੈ ਕਿਉਂਕਿ ਜਦੋਂ ਅਸੀਂ ਹਿੱਸੇ ਅਤੇ ਟੂਲਿੰਗ ਨੂੰ ਡਿਜ਼ਾਈਨ ਕਰਦੇ ਹਾਂ ਤਾਂ ਅਸੀਂ ਇਹਨਾਂ ਅਯਾਮੀ ਤਬਦੀਲੀਆਂ ਨੂੰ ਧਿਆਨ ਵਿੱਚ ਰੱਖਦੇ ਹਾਂ। ਪਾਊਡਰ ਕਣਾਂ ਨੂੰ ਆਪਸ ਵਿੱਚ ਜੋੜਿਆ ਜਾਂਦਾ ਹੈ ਅਤੇ ਕੰਪੈਕਸ਼ਨ ਪ੍ਰਕਿਰਿਆ ਦੁਆਰਾ ਪ੍ਰੇਰਿਤ ਪੋਰੋਸਿਟੀ ਬਹੁਤ ਹੱਦ ਤੱਕ ਹਟਾ ਦਿੱਤੀ ਜਾਂਦੀ ਹੈ.. • ਹੀਰਾ ਪੀਸਣਾ: ਦੁਨੀਆ ਦੀ ਸਭ ਤੋਂ ਕਠਿਨ ਸਮੱਗਰੀ "ਹੀਰੇ" ਦੀ ਵਰਤੋਂ ਸਿਰੇਮਿਕਸ ਵਰਗੀਆਂ ਸਖ਼ਤ ਸਮੱਗਰੀਆਂ ਨੂੰ ਪੀਸਣ ਲਈ ਕੀਤੀ ਜਾ ਰਹੀ ਹੈ ਅਤੇ ਸ਼ੁੱਧ ਹਿੱਸੇ ਪ੍ਰਾਪਤ ਕੀਤੇ ਜਾਂਦੇ ਹਨ। ਮਾਈਕ੍ਰੋਮੀਟਰ ਰੇਂਜ ਅਤੇ ਬਹੁਤ ਹੀ ਨਿਰਵਿਘਨ ਸਤਹਾਂ ਵਿੱਚ ਸਹਿਣਸ਼ੀਲਤਾ ਪ੍ਰਾਪਤ ਕੀਤੀ ਜਾ ਰਹੀ ਹੈ। ਇਸਦੇ ਖਰਚੇ ਦੇ ਕਾਰਨ, ਅਸੀਂ ਸਿਰਫ ਇਸ ਤਕਨੀਕ 'ਤੇ ਵਿਚਾਰ ਕਰਦੇ ਹਾਂ ਜਦੋਂ ਸਾਨੂੰ ਅਸਲ ਵਿੱਚ ਇਸਦੀ ਲੋੜ ਹੁੰਦੀ ਹੈ. • ਹਰਮੇਟਿਕ ਅਸੈਂਬਲੀਆਂ ਉਹ ਹੁੰਦੀਆਂ ਹਨ ਜੋ ਵਿਹਾਰਕ ਤੌਰ 'ਤੇ ਇੰਟਰਫੇਸ ਦੇ ਵਿਚਕਾਰ ਕਿਸੇ ਵੀ ਪਦਾਰਥ, ਠੋਸ, ਤਰਲ ਜਾਂ ਗੈਸਾਂ ਦੇ ਆਦਾਨ-ਪ੍ਰਦਾਨ ਦੀ ਆਗਿਆ ਨਹੀਂ ਦਿੰਦੀਆਂ। ਹਰਮੇਟਿਕ ਸੀਲਿੰਗ ਏਅਰਟਾਈਟ ਹੈ। ਉਦਾਹਰਨ ਲਈ ਹਰਮੇਟਿਕ ਇਲੈਕਟ੍ਰਾਨਿਕ ਐਨਕਲੋਜ਼ਰ ਉਹ ਹੁੰਦੇ ਹਨ ਜੋ ਨਮੀ, ਗੰਦਗੀ ਜਾਂ ਗੈਸਾਂ ਦੁਆਰਾ ਇੱਕ ਪੈਕ ਕੀਤੇ ਉਪਕਰਣ ਦੀ ਸੰਵੇਦਨਸ਼ੀਲ ਅੰਦਰੂਨੀ ਸਮੱਗਰੀ ਨੂੰ ਨੁਕਸਾਨ ਤੋਂ ਬਿਨਾਂ ਰੱਖਦੇ ਹਨ। ਕੋਈ ਵੀ ਚੀਜ਼ 100% ਹਰਮੇਟਿਕ ਨਹੀਂ ਹੈ, ਪਰ ਜਦੋਂ ਅਸੀਂ ਹਰਮੇਟੀਸਿਟੀ ਦੀ ਗੱਲ ਕਰਦੇ ਹਾਂ ਤਾਂ ਵਿਹਾਰਕ ਰੂਪ ਵਿੱਚ, ਸਾਡਾ ਮਤਲਬ ਹੈ ਕਿ ਇਸ ਹੱਦ ਤੱਕ ਹਰਮੇਟਿਕਤਾ ਹੈ ਕਿ ਲੀਕ ਦੀ ਦਰ ਇੰਨੀ ਘੱਟ ਹੈ ਕਿ ਉਪਕਰਣ ਬਹੁਤ ਲੰਬੇ ਸਮੇਂ ਲਈ ਆਮ ਵਾਤਾਵਰਣਕ ਸਥਿਤੀਆਂ ਵਿੱਚ ਸੁਰੱਖਿਅਤ ਹਨ। ਸਾਡੀਆਂ ਹਰਮੇਟਿਕ ਅਸੈਂਬਲੀਆਂ ਵਿੱਚ ਧਾਤ, ਕੱਚ ਅਤੇ ਵਸਰਾਵਿਕ ਹਿੱਸੇ, ਧਾਤ-ਵਸਰਾਵਿਕ, ਵਸਰਾਵਿਕ-ਧਾਤੂ-ਸਿਰੇਮਿਕ, ਧਾਤ-ਵਸਰਾਵਿਕ-ਧਾਤੂ, ਧਾਤ ਤੋਂ ਧਾਤ, ਧਾਤ-ਗਲਾਸ, ਧਾਤ-ਗਲਾਸ-ਧਾਤੂ, ਕੱਚ-ਧਾਤੂ-ਗਲਾਸ, ਕੱਚ- ਧਾਤ ਅਤੇ ਕੱਚ ਤੋਂ ਸ਼ੀਸ਼ੇ ਅਤੇ ਮੈਟਲ-ਗਲਾਸ-ਸੀਰੇਮਿਕ ਬੰਧਨ ਦੇ ਹੋਰ ਸਾਰੇ ਸੰਜੋਗ। ਅਸੀਂ ਉਦਾਹਰਨ ਲਈ ਵਸਰਾਵਿਕ ਹਿੱਸਿਆਂ ਨੂੰ ਧਾਤੂ ਕੋਟ ਕਰ ਸਕਦੇ ਹਾਂ ਤਾਂ ਜੋ ਉਹਨਾਂ ਨੂੰ ਅਸੈਂਬਲੀ ਵਿੱਚ ਹੋਰ ਹਿੱਸਿਆਂ ਨਾਲ ਮਜ਼ਬੂਤੀ ਨਾਲ ਬੰਨ੍ਹਿਆ ਜਾ ਸਕੇ ਅਤੇ ਸ਼ਾਨਦਾਰ ਸੀਲਿੰਗ ਸਮਰੱਥਾ ਹੋਵੇ। ਸਾਡੇ ਕੋਲ ਆਪਟੀਕਲ ਫਾਈਬਰਾਂ ਜਾਂ ਫੀਡਥਰੂਜ਼ ਨੂੰ ਧਾਤ ਨਾਲ ਕੋਟਿੰਗ ਕਰਨ ਅਤੇ ਉਹਨਾਂ ਨੂੰ ਦੀਵਾਰਾਂ ਵਿੱਚ ਸੋਲਡਰਿੰਗ ਜਾਂ ਬ੍ਰੇਜ਼ਿੰਗ ਕਰਨ ਦੀ ਜਾਣਕਾਰੀ ਹੈ, ਇਸਲਈ ਕੋਈ ਵੀ ਗੈਸਾਂ ਦੀਵਾਰਾਂ ਵਿੱਚ ਨਹੀਂ ਲੰਘਦੀਆਂ ਜਾਂ ਲੀਕ ਨਹੀਂ ਹੁੰਦੀਆਂ ਹਨ। ਇਸ ਲਈ ਇਹਨਾਂ ਦੀ ਵਰਤੋਂ ਸੰਵੇਦਨਸ਼ੀਲ ਯੰਤਰਾਂ ਨੂੰ ਘੇਰਨ ਅਤੇ ਉਹਨਾਂ ਨੂੰ ਬਾਹਰੀ ਵਾਯੂਮੰਡਲ ਤੋਂ ਬਚਾਉਣ ਲਈ ਇਲੈਕਟ੍ਰਾਨਿਕ ਘੇਰੇ ਬਣਾਉਣ ਲਈ ਕੀਤੀ ਜਾਂਦੀ ਹੈ। ਉਹਨਾਂ ਦੀਆਂ ਸ਼ਾਨਦਾਰ ਸੀਲਿੰਗ ਵਿਸ਼ੇਸ਼ਤਾਵਾਂ ਤੋਂ ਇਲਾਵਾ, ਹੋਰ ਵਿਸ਼ੇਸ਼ਤਾਵਾਂ ਜਿਵੇਂ ਕਿ ਥਰਮਲ ਵਿਸਥਾਰ ਗੁਣਾਂਕ, ਵਿਗਾੜ ਪ੍ਰਤੀਰੋਧ, ਗੈਰ-ਆਉਟਗੈਸਿੰਗ ਕੁਦਰਤ, ਬਹੁਤ ਲੰਬੀ ਉਮਰ, ਗੈਰ-ਸੰਚਾਲਕ ਕੁਦਰਤ, ਥਰਮਲ ਇਨਸੂਲੇਸ਼ਨ ਵਿਸ਼ੇਸ਼ਤਾਵਾਂ, ਐਂਟੀਸਟੈਟਿਕ ਕੁਦਰਤ ... ਆਦਿ। ਕੱਚ ਅਤੇ ਵਸਰਾਵਿਕ ਸਮੱਗਰੀ ਨੂੰ ਕੁਝ ਐਪਲੀਕੇਸ਼ਨਾਂ ਲਈ ਵਿਕਲਪ ਬਣਾਓ। ਵਸਰਾਵਿਕ ਤੋਂ ਧਾਤ ਦੀਆਂ ਫਿਟਿੰਗਾਂ, ਹਰਮੇਟਿਕ ਸੀਲਿੰਗ, ਵੈਕਿਊਮ ਫੀਡਥਰੂਜ਼, ਹਾਈ ਅਤੇ ਅਲਟਰਾਹਾਈ ਵੈਕਿਊਮ ਅਤੇ ਤਰਲ ਕੰਟਰੋਲ ਕੰਪੋਨੈਂਟਸ ਬਣਾਉਣ ਵਾਲੀ ਸਾਡੀ ਸਹੂਲਤ ਬਾਰੇ ਜਾਣਕਾਰੀ ਇੱਥੇ ਮਿਲ ਸਕਦੀ ਹੈ:ਹਰਮੇਟਿਕ ਕੰਪੋਨੈਂਟਸ ਫੈਕਟਰੀ ਬਰੋਸ਼ਰ CLICK Product Finder-Locator Service ਪਿਛਲੇ ਸਫ਼ੇ
- Wire & Spring Forming, Shaping, Welding, Assembly of Wires, Coil, CNC
Wire & Spring Forming, Shaping, Welding, Assembly of Wires, Coil Compression Extension Torsion Flat Springs, Custom Wires, Helical Springs at AGS-TECH Inc. ਤਾਰ ਅਤੇ ਬਸੰਤ ਸਰੂਪ ਅਸੀਂ ਕਸਟਮ ਤਾਰ, ਵਾਇਰ ਅਸੈਂਬਲੀ, ਲੋੜੀਂਦੇ 2D ਅਤੇ 3D ਆਕਾਰਾਂ ਵਿੱਚ ਬਣੀਆਂ ਤਾਰਾਂ, ਤਾਰ ਦੇ ਜਾਲ, ਜਾਲ, ਐਨਕਲੋਜ਼ਰ, ਟੋਕਰੀ, ਵਾੜ, ਵਾਇਰ ਸਪਰਿੰਗ, ਫਲੈਟ ਸਪਰਿੰਗ; torsion, ਕੰਪਰੈਸ਼ਨ, ਤਣਾਅ, ਫਲੈਟ ਸਪ੍ਰਿੰਗਸ ਅਤੇ ਹੋਰ. ਸਾਡੀਆਂ ਪ੍ਰਕਿਰਿਆਵਾਂ ਹਨ ਵਾਇਰ ਅਤੇ ਸਪਰਿੰਗ ਬਣਾਉਣਾ, ਵਾਇਰ ਡਰਾਇੰਗ, ਆਕਾਰ ਦੇਣਾ, ਮੋੜਨਾ, ਵੈਲਡਿੰਗ, ਬ੍ਰੇਜ਼ਿੰਗ, ਸੋਲਡਰਿੰਗ, ਵਿੰਨ੍ਹਣਾ, ਸਵੈਜਿੰਗ, ਡਰਿਲਿੰਗ, ਚੈਂਫਰਿੰਗ, ਗ੍ਰਾਈਡਿੰਗ, ਥਰਿੱਡਿੰਗ, ਕੋਟਿੰਗ, ਚਾਰਸਲਾਈਡ, ਸਲਾਈਡ ਬਣਾਉਣਾ, ਵਿੰਡਿੰਗ, ਕੋਇਲਿੰਗ, ਅਪਸੈਟਿੰਗ। ਅਸੀਂ ਸਿਫ਼ਾਰਿਸ਼ ਕਰਦੇ ਹਾਂ ਕਿ ਤੁਸੀਂ ਇੱਥੇ ਕਲਿੱਕ ਕਰੋ AGS-TECH Inc ਦੁਆਰਾ ਤਾਰ ਅਤੇ ਬਸੰਤ ਬਣਾਉਣ ਦੀਆਂ ਪ੍ਰਕਿਰਿਆਵਾਂ ਦੇ ਸਾਡੇ ਯੋਜਨਾਬੱਧ ਚਿੱਤਰਾਂ ਨੂੰ ਡਾਉਨਲੋਡ ਕਰੋ। ਫੋਟੋਆਂ ਅਤੇ ਸਕੈਚਾਂ ਵਾਲੀ ਇਹ ਡਾਉਨਲੋਡ ਕਰਨ ਯੋਗ ਫਾਈਲ ਤੁਹਾਡੀ ਜਾਣਕਾਰੀ ਨੂੰ ਬਿਹਤਰ ਤਰੀਕੇ ਨਾਲ ਸਮਝਣ ਵਿੱਚ ਤੁਹਾਡੀ ਮਦਦ ਕਰੇਗੀ ਜੋ ਅਸੀਂ ਤੁਹਾਨੂੰ ਹੇਠਾਂ ਪ੍ਰਦਾਨ ਕਰ ਰਹੇ ਹਾਂ। • ਵਾਇਰ ਡਰਾਇੰਗ: ਟੈਂਸਿਲ ਬਲਾਂ ਦੀ ਵਰਤੋਂ ਕਰਦੇ ਹੋਏ ਅਸੀਂ ਮੈਟਲ ਸਟਾਕ ਨੂੰ ਖਿੱਚਦੇ ਹਾਂ ਅਤੇ ਵਿਆਸ ਨੂੰ ਘਟਾਉਣ ਅਤੇ ਇਸਦੀ ਲੰਬਾਈ ਨੂੰ ਵਧਾਉਣ ਲਈ ਇਸਨੂੰ ਡਾਈ ਦੁਆਰਾ ਖਿੱਚਦੇ ਹਾਂ। ਕਈ ਵਾਰ ਅਸੀਂ ਮਰਨ ਦੀ ਲੜੀ ਦੀ ਵਰਤੋਂ ਕਰਦੇ ਹਾਂ। ਅਸੀਂ ਤਾਰ ਦੇ ਹਰ ਗੇਜ ਲਈ ਡਾਈ ਬਣਾਉਣ ਦੇ ਸਮਰੱਥ ਹਾਂ। ਉੱਚ ਤਣਾਅ ਵਾਲੀ ਤਾਕਤ ਦੀ ਸਮੱਗਰੀ ਦੀ ਵਰਤੋਂ ਕਰਕੇ ਅਸੀਂ ਬਹੁਤ ਪਤਲੀਆਂ ਤਾਰਾਂ ਖਿੱਚਦੇ ਹਾਂ। ਅਸੀਂ ਠੰਡੇ ਅਤੇ ਗਰਮ ਦੋਵੇਂ ਤਰ੍ਹਾਂ ਦੀਆਂ ਤਾਰਾਂ ਦੀ ਪੇਸ਼ਕਸ਼ ਕਰਦੇ ਹਾਂ। • ਵਾਇਰ ਬਣਾਉਣਾ: ਗੇਜਡ ਤਾਰ ਦੇ ਇੱਕ ਰੋਲ ਨੂੰ ਮੋੜਿਆ ਜਾਂਦਾ ਹੈ ਅਤੇ ਇੱਕ ਉਪਯੋਗੀ ਉਤਪਾਦ ਵਿੱਚ ਆਕਾਰ ਦਿੱਤਾ ਜਾਂਦਾ ਹੈ। ਸਾਡੇ ਕੋਲ ਸਾਰੇ ਗੇਜਾਂ ਤੋਂ ਤਾਰਾਂ ਬਣਾਉਣ ਦੀ ਸਮਰੱਥਾ ਹੈ, ਜਿਸ ਵਿੱਚ ਪਤਲੇ ਤਾਰਾਂ ਦੇ ਨਾਲ-ਨਾਲ ਮੋਟੀਆਂ ਤਾਰਾਂ ਜਿਵੇਂ ਕਿ ਆਟੋਮੋਬਾਈਲ ਚੈਸਿਸ ਦੇ ਹੇਠਾਂ ਸਪਰਿੰਗਜ਼ ਵਜੋਂ ਵਰਤੀਆਂ ਜਾਂਦੀਆਂ ਹਨ। ਸਾਜ਼-ਸਾਮਾਨ ਜੋ ਅਸੀਂ ਵਾਇਰ ਬਣਾਉਣ ਲਈ ਵਰਤਦੇ ਹਾਂ ਉਹ ਮੈਨੂਅਲ ਅਤੇ ਸੀਐਨਸੀ ਵਾਇਰ ਫਾਰਮਰ, ਕੋਇਲਰ, ਪਾਵਰ ਪ੍ਰੈਸ, ਫੋਰਸਲਾਇਡ, ਮਲਟੀ-ਸਲਾਈਡ ਹਨ। ਸਾਡੀਆਂ ਪ੍ਰਕਿਰਿਆਵਾਂ ਹਨ ਡਰਾਇੰਗ, ਮੋੜਨਾ, ਸਿੱਧਾ ਕਰਨਾ, ਚਪਟਾ ਕਰਨਾ, ਖਿੱਚਣਾ, ਕੱਟਣਾ, ਅਪਸੈਟਿੰਗ, ਸੋਲਡਰਿੰਗ ਅਤੇ ਵੈਲਡਿੰਗ ਅਤੇ ਬ੍ਰੇਜ਼ਿੰਗ, ਅਸੈਂਬਲੀ, ਕੋਇਲਿੰਗ, ਸਵੈਜਿੰਗ (ਜਾਂ ਵਿੰਗਿੰਗ), ਵਿੰਨ੍ਹਣਾ, ਵਾਇਰ ਥ੍ਰੈਡਿੰਗ, ਡ੍ਰਿਲਿੰਗ, ਚੈਂਫਰਿੰਗ, ਪੀਸਣਾ, ਕੋਟਿੰਗ ਅਤੇ ਸਤਹ ਦੇ ਇਲਾਜ। ਸਾਡੇ ਅਤਿ-ਆਧੁਨਿਕ ਉਪਕਰਣਾਂ ਨੂੰ ਕਿਸੇ ਵੀ ਆਕਾਰ ਅਤੇ ਤੰਗ ਸਹਿਣਸ਼ੀਲਤਾ ਦੇ ਬਹੁਤ ਗੁੰਝਲਦਾਰ ਡਿਜ਼ਾਈਨ ਵਿਕਸਿਤ ਕਰਨ ਲਈ ਸੈੱਟ-ਅੱਪ ਕੀਤਾ ਜਾ ਸਕਦਾ ਹੈ। ਅਸੀਂ ਤੁਹਾਡੀਆਂ ਤਾਰਾਂ ਲਈ ਵੱਖ-ਵੱਖ ਸਿਰੇ ਦੀਆਂ ਕਿਸਮਾਂ ਦੀ ਪੇਸ਼ਕਸ਼ ਕਰਦੇ ਹਾਂ. ਸਾਡੇ ਜ਼ਿਆਦਾਤਰ ਤਾਰ ਬਣਾਉਣ ਵਾਲੇ ਪ੍ਰੋਜੈਕਟਾਂ ਦੀ ਘੱਟੋ-ਘੱਟ ਤੋਂ ਜ਼ੀਰੋ ਟੂਲਿੰਗ ਲਾਗਤ ਹੁੰਦੀ ਹੈ। ਨਮੂਨਾ ਬਦਲਣ ਦਾ ਸਮਾਂ ਆਮ ਤੌਰ 'ਤੇ ਦਿਨ ਹੁੰਦਾ ਹੈ। ਵਾਇਰ ਫਾਰਮਾਂ ਦੇ ਡਿਜ਼ਾਈਨ/ਸੰਰਚਨਾ ਵਿੱਚ ਤਬਦੀਲੀਆਂ ਬਹੁਤ ਜਲਦੀ ਕੀਤੀਆਂ ਜਾ ਸਕਦੀਆਂ ਹਨ। • ਸਪਰਿੰਗ ਫਾਰਮਿੰਗ: AGS-TECH ਸਪ੍ਰਿੰਗਸ ਦੀ ਇੱਕ ਵੱਡੀ ਕਿਸਮ ਦਾ ਨਿਰਮਾਣ ਕਰਦਾ ਹੈ ਜਿਸ ਵਿੱਚ ਸ਼ਾਮਲ ਹਨ: -ਟੋਰਸ਼ਨ / ਡਬਲ ਟੋਰਸ਼ਨ ਸਪਰਿੰਗ -ਟੈਂਸ਼ਨ / ਕੰਪਰੈਸ਼ਨ ਸਪਰਿੰਗ -ਕੰਸਟੈਂਟ / ਵੇਰੀਏਬਲ ਸਪਰਿੰਗ -ਕੋਇਲ ਅਤੇ ਹੇਲੀਕਲ ਸਪਰਿੰਗ -Flat & Leaf Spring -ਬੈਲੈਂਸ ਸਪਰਿੰਗ -ਬੇਲੇਵਿਲ ਵਾਸ਼ਰ -ਨੈਗੇਟਰ ਸਪਰਿੰਗ -ਪ੍ਰਗਤੀਸ਼ੀਲ ਦਰ ਕੋਇਲ ਸਪਰਿੰਗ -ਵੇਵ ਸਪਰਿੰਗ -ਵੋਲਟ ਸਪਰਿੰਗ - ਟੇਪਰਡ ਸਪ੍ਰਿੰਗਸ -ਸਪਰਿੰਗ ਰਿੰਗਸ -ਕਲੌਕ ਸਪ੍ਰਿੰਗਸ -ਕਲਿੱਪਸ ਅਸੀਂ ਕਈ ਤਰ੍ਹਾਂ ਦੀਆਂ ਸਮੱਗਰੀਆਂ ਤੋਂ ਚਸ਼ਮੇ ਬਣਾਉਂਦੇ ਹਾਂ ਅਤੇ ਤੁਹਾਡੀ ਐਪਲੀਕੇਸ਼ਨ ਦੇ ਅਨੁਸਾਰ ਤੁਹਾਡੀ ਅਗਵਾਈ ਕਰ ਸਕਦੇ ਹਾਂ। ਸਭ ਤੋਂ ਆਮ ਸਾਮੱਗਰੀ ਹਨ ਸਟੇਨਲੈਸ ਸਟੀਲ, ਕਰੋਮ ਸਿਲੀਕਾਨ, ਉੱਚ-ਕਾਰਬਨ ਸਟੀਲ, ਤੇਲ-ਟੈਂਪਰਡ ਲੋ-ਕਾਰਬਨ, ਕ੍ਰੋਮ ਵੈਨੇਡੀਅਮ, ਫਾਸਫੋਰ ਕਾਂਸੀ, ਟਾਈਟੇਨੀਅਮ, ਬੇਰੀਲੀਅਮ ਤਾਂਬੇ ਦਾ ਮਿਸ਼ਰਤ, ਉੱਚ-ਤਾਪਮਾਨ ਵਸਰਾਵਿਕ। ਅਸੀਂ ਸਪ੍ਰਿੰਗਸ ਦੇ ਨਿਰਮਾਣ ਵਿੱਚ ਕਈ ਤਕਨੀਕਾਂ ਦੀ ਵਰਤੋਂ ਕਰਦੇ ਹਾਂ, ਜਿਸ ਵਿੱਚ ਸੀਐਨਸੀ ਕੋਇਲਿੰਗ, ਕੋਲਡ ਵਿੰਡਿੰਗ, ਗਰਮ ਵਿੰਡਿੰਗ, ਹਾਰਡਨਿੰਗ, ਫਿਨਿਸ਼ਿੰਗ ਸ਼ਾਮਲ ਹਨ। ਤਾਰ ਬਣਾਉਣ ਦੇ ਅਧੀਨ ਉੱਪਰ ਦੱਸੀਆਂ ਗਈਆਂ ਹੋਰ ਤਕਨੀਕਾਂ ਵੀ ਸਾਡੇ ਬਸੰਤ ਨਿਰਮਾਣ ਕਾਰਜਾਂ ਵਿੱਚ ਆਮ ਹਨ। • ਤਾਰਾਂ ਅਤੇ ਸਪ੍ਰਿੰਗਾਂ ਲਈ ਸੇਵਾਵਾਂ ਨੂੰ ਪੂਰਾ ਕਰਨਾ: ਅਸੀਂ ਤੁਹਾਡੀ ਪਸੰਦ ਅਤੇ ਲੋੜਾਂ ਦੇ ਆਧਾਰ 'ਤੇ ਤੁਹਾਡੇ ਉਤਪਾਦਾਂ ਨੂੰ ਕਈ ਤਰੀਕਿਆਂ ਨਾਲ ਪੂਰਾ ਕਰ ਸਕਦੇ ਹਾਂ। ਕੁਝ ਆਮ ਪ੍ਰਕਿਰਿਆਵਾਂ ਜੋ ਅਸੀਂ ਪੇਸ਼ ਕਰਦੇ ਹਾਂ ਉਹ ਹਨ: ਪੇਂਟਿੰਗ, ਪਾਊਡਰ ਕੋਟਿੰਗ, ਪਲੇਟਿੰਗ, ਵਿਨਾਇਲ ਡਿਪਿੰਗ, ਐਨੋਡਾਈਜ਼ਿੰਗ, ਤਣਾਅ ਤੋਂ ਰਾਹਤ, ਹੀਟ ਟ੍ਰੀਟਮੈਂਟ, ਸ਼ਾਟ ਪੀਨ, ਟਿੰਬਲ, ਕ੍ਰੋਮੇਟ, electroless nickel, passivation, bakakmeled plastic. , ਪਲਾਜ਼ਮਾ ਸਫਾਈ। CLICK Product Finder-Locator Service ਪਿਛਲੇ ਸਫ਼ੇ
- Sheet Metal Forming Fabrication, Stamping, Punching, Deep Drawing, CNC
Sheet Metal Forming and Fabrication, Stamping, Punching, Bending, Progressive Die, Spot Welding, Deep Drawing, Metal Blanking and Slitting at AGS-TECH Inc. ਸਟੈਂਪਿੰਗ ਅਤੇ ਸ਼ੀਟ ਮੈਟਲ ਫੈਬਰੀਕੇਸ਼ਨ ਅਸੀਂ ਸ਼ੀਟ ਮੈਟਲ ਸਟੈਂਪਿੰਗ, ਸ਼ੇਪਿੰਗ, ਫਾਰਮਿੰਗ, ਮੋੜਨਾ, ਪੰਚਿੰਗ, ਬਲੈਂਕਿੰਗ, ਸਲਿਟਿੰਗ, ਪਰਫੋਰੇਟਿੰਗ, ਨੌਚਿੰਗ, ਨਿਬਲਿੰਗ, ਸ਼ੇਵਿੰਗ, ਪ੍ਰੈਸਵਰਕਿੰਗ, ਫੈਬਰੀਕੇਸ਼ਨ, ਸਿੰਗਲ ਪੰਚ / ਸਿੰਗਲ ਸਟ੍ਰੋਕ ਡਾਈਜ਼ ਦੀ ਵਰਤੋਂ ਕਰਦੇ ਹੋਏ ਡੂੰਘੀ ਡਰਾਇੰਗ ਦੇ ਨਾਲ-ਨਾਲ ਪ੍ਰਗਤੀਸ਼ੀਲ ਡਾਈਜ਼ ਅਤੇ ਸਪਿਨਿੰਗ, ਰਬੜ ਬਣਾਉਣ ਅਤੇ ਬਣਾਉਣ ਦੀ ਪੇਸ਼ਕਸ਼ ਕਰਦੇ ਹਾਂ। hydroforming; ਵਾਟਰ ਜੈੱਟ, ਪਲਾਜ਼ਮਾ, ਲੇਜ਼ਰ, ਆਰਾ, ਲਾਟ ਦੀ ਵਰਤੋਂ ਕਰਕੇ ਸ਼ੀਟ ਮੈਟਲ ਕੱਟਣਾ; ਵੈਲਡਿੰਗ, ਸਪਾਟ ਵੈਲਡਿੰਗ ਦੀ ਵਰਤੋਂ ਕਰਦੇ ਹੋਏ ਸ਼ੀਟ ਮੈਟਲ ਅਸੈਂਬਲੀ; ਸ਼ੀਟ ਮੈਟਲ ਟਿਊਬ ਉਭਰਨਾ ਅਤੇ ਝੁਕਣਾ; ਸ਼ੀਟ ਮੈਟਲ ਸਰਫੇਸ ਫਿਨਿਸ਼ਿੰਗ ਜਿਸ ਵਿੱਚ ਡਿੱਪ ਜਾਂ ਸਪਰੇਅ ਪੇਂਟਿੰਗ, ਇਲੈਕਟ੍ਰੋਸਟੈਟਿਕ ਪਾਊਡਰ ਕੋਟਿੰਗ, ਐਨੋਡਾਈਜ਼ਿੰਗ, ਪਲੇਟਿੰਗ, ਸਪਟਰਿੰਗ ਅਤੇ ਹੋਰ ਬਹੁਤ ਕੁਝ ਸ਼ਾਮਲ ਹੈ। ਸਾਡੀਆਂ ਸੇਵਾਵਾਂ ਤੇਜ਼ ਸ਼ੀਟ ਮੈਟਲ ਪ੍ਰੋਟੋਟਾਈਪਿੰਗ ਤੋਂ ਲੈ ਕੇ ਉੱਚ ਵਾਲੀਅਮ ਨਿਰਮਾਣ ਤੱਕ ਹਨ। ਅਸੀਂ ਸਿਫ਼ਾਰਿਸ਼ ਕਰਦੇ ਹਾਂ ਕਿ ਤੁਸੀਂ ਇੱਥੇ ਕਲਿੱਕ ਕਰੋAGS-TECH Inc ਦੁਆਰਾ ਸ਼ੀਟ ਮੈਟਲ ਫੈਬਰੀਕੇਸ਼ਨ ਅਤੇ ਸਟੈਂਪਿੰਗ ਪ੍ਰਕਿਰਿਆਵਾਂ ਦੇ ਸਾਡੇ ਯੋਜਨਾਬੱਧ ਚਿੱਤਰਾਂ ਨੂੰ ਡਾਉਨਲੋਡ ਕਰੋ। ਇਹ ਤੁਹਾਨੂੰ ਉਸ ਜਾਣਕਾਰੀ ਨੂੰ ਬਿਹਤਰ ਤਰੀਕੇ ਨਾਲ ਸਮਝਣ ਵਿੱਚ ਮਦਦ ਕਰੇਗਾ ਜੋ ਅਸੀਂ ਤੁਹਾਨੂੰ ਹੇਠਾਂ ਪ੍ਰਦਾਨ ਕਰ ਰਹੇ ਹਾਂ। • ਸ਼ੀਟ ਮੈਟਲ ਕਟਿੰਗ: ਅਸੀਂ ਕਟੌਫ ਅਤੇ ਭਾਗਾਂ ਦੀ ਪੇਸ਼ਕਸ਼ ਕਰਦੇ ਹਾਂ। ਕਟੌਫ ਇੱਕ ਸਮੇਂ ਵਿੱਚ ਇੱਕ ਮਾਰਗ ਉੱਤੇ ਸ਼ੀਟ ਮੈਟਲ ਨੂੰ ਕੱਟਦੇ ਹਨ ਅਤੇ ਅਸਲ ਵਿੱਚ ਸਮੱਗਰੀ ਦੀ ਕੋਈ ਬਰਬਾਦੀ ਨਹੀਂ ਹੁੰਦੀ ਹੈ, ਜਦੋਂ ਕਿ ਭਾਗਾਂ ਨਾਲ ਆਕਾਰ ਨੂੰ ਸਹੀ ਢੰਗ ਨਾਲ ਨਹੀਂ ਬਣਾਇਆ ਜਾ ਸਕਦਾ ਹੈ ਅਤੇ ਇਸਲਈ ਸਮੱਗਰੀ ਦੀ ਕੁਝ ਮਾਤਰਾ ਬਰਬਾਦ ਹੁੰਦੀ ਹੈ। ਸਾਡੀਆਂ ਸਭ ਤੋਂ ਪ੍ਰਸਿੱਧ ਪ੍ਰਕਿਰਿਆਵਾਂ ਵਿੱਚੋਂ ਇੱਕ ਪੰਚਿੰਗ ਹੈ, ਜਿੱਥੇ ਸ਼ੀਟ ਮੈਟਲ ਤੋਂ ਗੋਲ ਜਾਂ ਹੋਰ ਆਕਾਰ ਦਾ ਇੱਕ ਟੁਕੜਾ ਕੱਟਿਆ ਜਾਂਦਾ ਹੈ। ਜੋ ਟੁਕੜਾ ਕੱਟਿਆ ਜਾਂਦਾ ਹੈ ਉਹ ਕੂੜਾ ਹੁੰਦਾ ਹੈ। ਪੰਚਿੰਗ ਦਾ ਇੱਕ ਹੋਰ ਸੰਸਕਰਣ ਸਲੋਟਿੰਗ ਹੈ, ਜਿੱਥੇ ਆਇਤਾਕਾਰ ਜਾਂ ਲੰਬੇ ਛੇਕਾਂ ਨੂੰ ਪੰਚ ਕੀਤਾ ਜਾਂਦਾ ਹੈ। ਦੂਜੇ ਪਾਸੇ ਬਲੈਂਕਿੰਗ ਪੰਚਿੰਗ ਵਾਂਗ ਹੀ ਪ੍ਰਕਿਰਿਆ ਹੈ, ਜਿਸ ਵਿੱਚ ਟੁਕੜੇ ਨੂੰ ਕੱਟੇ ਜਾਣ ਦੇ ਅੰਤਰ ਨਾਲ ਕੰਮ ਹੈ ਅਤੇ ਰੱਖਿਆ ਜਾਂਦਾ ਹੈ। ਫਾਈਨ ਬਲੈਂਕਿੰਗ, ਬਲੈਂਕਿੰਗ ਦਾ ਇੱਕ ਉੱਤਮ ਸੰਸਕਰਣ, ਨਜ਼ਦੀਕੀ ਸਹਿਣਸ਼ੀਲਤਾ ਅਤੇ ਸਿੱਧੇ ਨਿਰਵਿਘਨ ਕਿਨਾਰਿਆਂ ਨਾਲ ਕੱਟ ਬਣਾਉਂਦਾ ਹੈ ਅਤੇ ਵਰਕਪੀਸ ਦੀ ਸੰਪੂਰਨਤਾ ਲਈ ਸੈਕੰਡਰੀ ਓਪਰੇਸ਼ਨਾਂ ਦੀ ਲੋੜ ਨਹੀਂ ਹੁੰਦੀ ਹੈ। ਇਕ ਹੋਰ ਪ੍ਰਕਿਰਿਆ ਜਿਸ ਦੀ ਅਸੀਂ ਅਕਸਰ ਵਰਤੋਂ ਕਰਦੇ ਹਾਂ ਉਹ ਹੈ ਸਲਿਟਿੰਗ, ਜੋ ਕਿ ਇੱਕ ਸ਼ੀਅਰਿੰਗ ਪ੍ਰਕਿਰਿਆ ਹੈ ਜਿੱਥੇ ਸ਼ੀਟ ਮੈਟਲ ਨੂੰ ਸਿੱਧੇ ਜਾਂ ਕਰਵ ਮਾਰਗ ਵਿੱਚ ਦੋ ਵਿਰੋਧੀ ਗੋਲਾਕਾਰ ਬਲੇਡਾਂ ਦੁਆਰਾ ਕੱਟਿਆ ਜਾਂਦਾ ਹੈ। ਕੈਨ ਓਪਨਰ ਸਲਿਟਿੰਗ ਪ੍ਰਕਿਰਿਆ ਦੀ ਇੱਕ ਸਧਾਰਨ ਉਦਾਹਰਣ ਹੈ। ਸਾਡੇ ਲਈ ਇੱਕ ਹੋਰ ਪ੍ਰਸਿੱਧ ਪ੍ਰਕਿਰਿਆ ਪਰਫੋਰੇਟਿੰਗ ਹੈ, ਜਿੱਥੇ ਇੱਕ ਖਾਸ ਪੈਟਰਨ ਵਿੱਚ ਸ਼ੀਟ ਮੈਟਲ ਵਿੱਚ ਗੋਲ ਜਾਂ ਹੋਰ ਆਕਾਰ ਦੇ ਕਈ ਛੇਕ ਕੀਤੇ ਜਾਂਦੇ ਹਨ। ਇੱਕ ਛੇਦ ਵਾਲੇ ਉਤਪਾਦ ਲਈ ਇੱਕ ਖਾਸ ਉਦਾਹਰਨ ਤਰਲ ਪਦਾਰਥਾਂ ਲਈ ਬਹੁਤ ਸਾਰੇ ਛੇਕ ਵਾਲੇ ਧਾਤ ਦੇ ਫਿਲਟਰ ਹਨ। ਨੋਚਿੰਗ ਵਿੱਚ, ਇੱਕ ਹੋਰ ਸ਼ੀਟ ਮੈਟਲ ਕੱਟਣ ਦੀ ਪ੍ਰਕਿਰਿਆ, ਅਸੀਂ ਕਿਸੇ ਕੰਮ ਦੇ ਟੁਕੜੇ ਤੋਂ ਸਮੱਗਰੀ ਨੂੰ ਹਟਾਉਂਦੇ ਹਾਂ, ਕਿਨਾਰੇ ਤੋਂ ਸ਼ੁਰੂ ਕਰਦੇ ਹੋਏ ਜਾਂ ਕਿਤੇ ਹੋਰ ਅਤੇ ਅੰਦਰ ਵੱਲ ਕੱਟਦੇ ਹਾਂ ਜਦੋਂ ਤੱਕ ਲੋੜੀਦਾ ਆਕਾਰ ਪ੍ਰਾਪਤ ਨਹੀਂ ਹੋ ਜਾਂਦਾ। ਇਹ ਇੱਕ ਪ੍ਰਗਤੀਸ਼ੀਲ ਪ੍ਰਕਿਰਿਆ ਹੈ ਜਿੱਥੇ ਹਰੇਕ ਓਪਰੇਸ਼ਨ ਇੱਕ ਹੋਰ ਟੁਕੜੇ ਨੂੰ ਹਟਾਉਂਦਾ ਹੈ ਜਦੋਂ ਤੱਕ ਲੋੜੀਦਾ ਸਮਰੂਪ ਪ੍ਰਾਪਤ ਨਹੀਂ ਹੋ ਜਾਂਦਾ। ਛੋਟੀਆਂ ਉਤਪਾਦਨ ਦੀਆਂ ਦੌੜਾਂ ਲਈ ਅਸੀਂ ਕਈ ਵਾਰ ਇੱਕ ਮੁਕਾਬਲਤਨ ਹੌਲੀ ਪ੍ਰਕਿਰਿਆ ਦੀ ਵਰਤੋਂ ਕਰਦੇ ਹਾਂ ਜਿਸ ਨੂੰ ਨਿਬਲਿੰਗ ਕਿਹਾ ਜਾਂਦਾ ਹੈ ਜਿਸ ਵਿੱਚ ਇੱਕ ਵੱਡੇ ਵਧੇਰੇ ਗੁੰਝਲਦਾਰ ਕੱਟ ਬਣਾਉਣ ਲਈ ਓਵਰਲੈਪਿੰਗ ਛੇਕਾਂ ਦੇ ਬਹੁਤ ਸਾਰੇ ਤੇਜ਼ ਪੰਚ ਹੁੰਦੇ ਹਨ। ਪ੍ਰਗਤੀਸ਼ੀਲ ਕਟਿੰਗ ਵਿੱਚ ਅਸੀਂ ਇੱਕ ਸਿੰਗਲ ਕੱਟ ਜਾਂ ਇੱਕ ਖਾਸ ਜਿਓਮੈਟਰੀ ਪ੍ਰਾਪਤ ਕਰਨ ਲਈ ਵੱਖ-ਵੱਖ ਕਾਰਵਾਈਆਂ ਦੀ ਇੱਕ ਲੜੀ ਦੀ ਵਰਤੋਂ ਕਰਦੇ ਹਾਂ। ਅੰਤ ਵਿੱਚ ਇੱਕ ਸੈਕੰਡਰੀ ਪ੍ਰਕਿਰਿਆ ਨੂੰ ਸ਼ੇਵ ਕਰਨ ਨਾਲ ਸਾਨੂੰ ਪਹਿਲਾਂ ਹੀ ਕੀਤੇ ਗਏ ਕੱਟਾਂ ਦੇ ਕਿਨਾਰਿਆਂ ਨੂੰ ਬਿਹਤਰ ਬਣਾਉਣ ਵਿੱਚ ਮਦਦ ਮਿਲਦੀ ਹੈ। ਇਹ ਸ਼ੀਟ ਮੈਟਲ ਦੇ ਕੰਮ 'ਤੇ ਚਿਪਸ, ਮੋਟੇ ਕਿਨਾਰਿਆਂ ਨੂੰ ਕੱਟਣ ਲਈ ਵਰਤਿਆ ਜਾਂਦਾ ਹੈ। • ਸ਼ੀਟ ਮੈਟਲ ਬੈਂਡਿੰਗ: ਕੱਟਣ ਤੋਂ ਇਲਾਵਾ, ਮੋੜਨਾ ਇੱਕ ਜ਼ਰੂਰੀ ਪ੍ਰਕਿਰਿਆ ਹੈ ਜਿਸ ਤੋਂ ਬਿਨਾਂ ਅਸੀਂ ਜ਼ਿਆਦਾਤਰ ਉਤਪਾਦ ਤਿਆਰ ਨਹੀਂ ਕਰ ਸਕਾਂਗੇ। ਜਿਆਦਾਤਰ ਇੱਕ ਠੰਡਾ ਕੰਮ ਕਰਨ ਵਾਲਾ ਓਪਰੇਸ਼ਨ ਪਰ ਕਈ ਵਾਰ ਗਰਮ ਜਾਂ ਗਰਮ ਹੋਣ 'ਤੇ ਵੀ ਕੀਤਾ ਜਾਂਦਾ ਹੈ। ਅਸੀਂ ਇਸ ਓਪਰੇਸ਼ਨ ਲਈ ਜ਼ਿਆਦਾਤਰ ਸਮਾਂ ਡਾਈਸ ਦੀ ਵਰਤੋਂ ਕਰਦੇ ਹਾਂ ਅਤੇ ਦਬਾਉਂਦੇ ਹਾਂ। ਪ੍ਰਗਤੀਸ਼ੀਲ ਮੋੜ ਵਿੱਚ ਅਸੀਂ ਇੱਕ ਸਿੰਗਲ ਮੋੜ ਜਾਂ ਇੱਕ ਖਾਸ ਜਿਓਮੈਟਰੀ ਪ੍ਰਾਪਤ ਕਰਨ ਲਈ ਵੱਖ-ਵੱਖ ਪੰਚ ਅਤੇ ਡਾਈ ਓਪਰੇਸ਼ਨਾਂ ਦੀ ਇੱਕ ਲੜੀ ਦੀ ਵਰਤੋਂ ਕਰਦੇ ਹਾਂ। AGS-TECH ਕਈ ਤਰ੍ਹਾਂ ਦੀਆਂ ਝੁਕਣ ਦੀਆਂ ਪ੍ਰਕਿਰਿਆਵਾਂ ਦੀ ਵਰਤੋਂ ਕਰਦਾ ਹੈ ਅਤੇ ਵਰਕਪੀਸ ਸਮੱਗਰੀ, ਇਸਦੇ ਆਕਾਰ, ਮੋਟਾਈ, ਮੋੜ ਦੇ ਲੋੜੀਂਦੇ ਆਕਾਰ, ਘੇਰੇ, ਵਕਰ ਅਤੇ ਮੋੜ ਦਾ ਕੋਣ, ਮੋੜ ਦੀ ਸਥਿਤੀ, ਸੰਚਾਲਨ ਦੀ ਆਰਥਿਕਤਾ, ਨਿਰਮਿਤ ਹੋਣ ਵਾਲੀਆਂ ਮਾਤਰਾਵਾਂ ਦੇ ਅਧਾਰ ਤੇ ਚੋਣ ਕਰਦਾ ਹੈ ... ਆਦਿ ਅਸੀਂ V-BENDING ਦੀ ਵਰਤੋਂ ਕਰਦੇ ਹਾਂ ਜਿੱਥੇ ਇੱਕ V ਆਕਾਰ ਵਾਲਾ ਪੰਚ ਸ਼ੀਟ ਮੈਟਲ ਨੂੰ V ਆਕਾਰ ਦੇ ਡਾਈ ਵਿੱਚ ਧੱਕਦਾ ਹੈ ਅਤੇ ਇਸਨੂੰ ਮੋੜਦਾ ਹੈ। 90 ਡਿਗਰੀ ਸਮੇਤ, ਬਹੁਤ ਹੀ ਤੀਬਰ ਅਤੇ ਗੂੜ੍ਹੇ ਕੋਣਾਂ ਅਤੇ ਵਿਚਕਾਰ ਦੋਵਾਂ ਲਈ ਵਧੀਆ। ਵਾਈਪਿੰਗ ਡਾਈਜ਼ ਦੀ ਵਰਤੋਂ ਕਰਦੇ ਹੋਏ ਅਸੀਂ EDGE ਬੇਡਿੰਗ ਕਰਦੇ ਹਾਂ। ਸਾਡਾ ਸਾਜ਼ੋ-ਸਾਮਾਨ ਸਾਨੂੰ 90 ਡਿਗਰੀ ਤੋਂ ਵੀ ਵੱਡਾ ਕੋਣ ਪ੍ਰਾਪਤ ਕਰਨ ਦੇ ਯੋਗ ਬਣਾਉਂਦਾ ਹੈ। ਕਿਨਾਰੇ ਦੇ ਝੁਕਣ ਵਿੱਚ ਵਰਕਪੀਸ ਨੂੰ ਇੱਕ ਪ੍ਰੈਸ਼ਰ ਪੈਡ ਅਤੇ ਡਾਈ ਦੇ ਵਿਚਕਾਰ ਸੈਂਡਵਿਚ ਕੀਤਾ ਜਾਂਦਾ ਹੈ, ਮੋੜਨ ਲਈ ਖੇਤਰ ਡਾਈ ਕਿਨਾਰੇ 'ਤੇ ਸਥਿਤ ਹੁੰਦਾ ਹੈ ਅਤੇ ਬਾਕੀ ਵਰਕਪੀਸ ਨੂੰ ਸਪੇਸ ਜਿਵੇਂ ਇੱਕ ਕੰਟੀਲੀਵਰ ਬੀਮ ਉੱਤੇ ਰੱਖਿਆ ਜਾਂਦਾ ਹੈ। ਜਦੋਂ ਪੰਚ ਕੰਟੀਲੀਵਰ ਵਾਲੇ ਹਿੱਸੇ 'ਤੇ ਕੰਮ ਕਰਦਾ ਹੈ, ਤਾਂ ਇਹ ਡਾਈ ਦੇ ਕਿਨਾਰੇ 'ਤੇ ਝੁਕਿਆ ਹੋਇਆ ਹੈ। FLANGING ਇੱਕ ਕਿਨਾਰੇ ਨੂੰ ਝੁਕਣ ਦੀ ਪ੍ਰਕਿਰਿਆ ਹੈ ਜਿਸਦੇ ਨਤੀਜੇ ਵਜੋਂ 90 ਡਿਗਰੀ ਕੋਣ ਹੁੰਦਾ ਹੈ। ਓਪਰੇਸ਼ਨ ਦੇ ਮੁੱਖ ਟੀਚੇ ਤਿੱਖੇ ਕਿਨਾਰਿਆਂ ਨੂੰ ਖਤਮ ਕਰਨਾ ਅਤੇ ਭਾਗਾਂ ਨੂੰ ਜੋੜਨ ਨੂੰ ਸੌਖਾ ਬਣਾਉਣ ਲਈ ਜਿਓਮੈਟ੍ਰਿਕ ਸਤਹ ਪ੍ਰਾਪਤ ਕਰਨਾ ਹੈ। ਬੀਡਿੰਗ, ਇੱਕ ਹੋਰ ਆਮ ਕਿਨਾਰੇ ਨੂੰ ਝੁਕਣ ਦੀ ਪ੍ਰਕਿਰਿਆ ਇੱਕ ਹਿੱਸੇ ਦੇ ਕਿਨਾਰੇ ਉੱਤੇ ਇੱਕ ਕਰਲ ਬਣਾਉਂਦੀ ਹੈ। ਦੂਜੇ ਪਾਸੇ ਹੇਮਿੰਗ ਦਾ ਨਤੀਜਾ ਸ਼ੀਟ ਦੇ ਇੱਕ ਕਿਨਾਰੇ ਨਾਲ ਹੁੰਦਾ ਹੈ ਜੋ ਆਪਣੇ ਆਪ ਉੱਤੇ ਪੂਰੀ ਤਰ੍ਹਾਂ ਝੁਕਿਆ ਹੋਇਆ ਹੈ। ਸੀਮਿੰਗ ਵਿੱਚ, ਦੋ ਹਿੱਸਿਆਂ ਦੇ ਕਿਨਾਰੇ ਇੱਕ ਦੂਜੇ ਉੱਤੇ ਝੁਕੇ ਹੋਏ ਹਨ ਅਤੇ ਜੁੜਦੇ ਹਨ। ਦੂਜੇ ਪਾਸੇ ਡਬਲ ਸੀਮਿੰਗ ਵਾਟਰਟਾਈਟ ਅਤੇ ਏਅਰਟਾਈਟ ਸ਼ੀਟ ਮੈਟਲ ਜੋੜ ਪ੍ਰਦਾਨ ਕਰਦੀ ਹੈ। ਕਿਨਾਰੇ ਦੇ ਝੁਕਣ ਦੇ ਸਮਾਨ, ਇੱਕ ਪ੍ਰਕਿਰਿਆ ਜਿਸਨੂੰ ROTARY BENDING ਕਿਹਾ ਜਾਂਦਾ ਹੈ ਇੱਕ ਸਿਲੰਡਰ ਨੂੰ ਲੋੜੀਂਦੇ ਐਂਗਲ ਨਾਲ ਕੱਟ ਕੇ ਪੰਚ ਦੇ ਤੌਰ 'ਤੇ ਕੰਮ ਕਰਦਾ ਹੈ। ਜਿਵੇਂ ਕਿ ਬਲ ਪੰਚ ਨੂੰ ਸੰਚਾਰਿਤ ਕੀਤਾ ਜਾਂਦਾ ਹੈ, ਇਹ ਵਰਕਪੀਸ ਨਾਲ ਬੰਦ ਹੋ ਜਾਂਦਾ ਹੈ. ਸਿਲੰਡਰ ਦੀ ਝਰੀ ਕੰਟੀਲੀਵਰ ਵਾਲੇ ਹਿੱਸੇ ਨੂੰ ਲੋੜੀਂਦਾ ਕੋਣ ਦਿੰਦੀ ਹੈ। ਝਰੀ ਦਾ ਕੋਣ 90 ਡਿਗਰੀ ਤੋਂ ਛੋਟਾ ਜਾਂ ਵੱਡਾ ਹੋ ਸਕਦਾ ਹੈ। ਏਅਰ ਬੈਂਡਿੰਗ ਵਿੱਚ, ਸਾਨੂੰ ਇੱਕ ਕੋਣ ਵਾਲੀ ਨਾਰੀ ਰੱਖਣ ਲਈ ਹੇਠਲੇ ਡਾਈ ਦੀ ਲੋੜ ਨਹੀਂ ਹੁੰਦੀ ਹੈ। ਸ਼ੀਟ ਮੈਟਲ ਨੂੰ ਦੋ ਸਤਹਾਂ ਦੇ ਉਲਟ ਪਾਸੇ ਅਤੇ ਇੱਕ ਨਿਸ਼ਚਿਤ ਦੂਰੀ 'ਤੇ ਸਮਰਥਿਤ ਕੀਤਾ ਜਾਂਦਾ ਹੈ। ਪੰਚ ਫਿਰ ਸਹੀ ਸਥਾਨ 'ਤੇ ਇੱਕ ਬਲ ਲਾਗੂ ਕਰਦਾ ਹੈ ਅਤੇ ਵਰਕਪੀਸ ਨੂੰ ਮੋੜਦਾ ਹੈ। ਚੈਨਲ ਬੈਂਡਿੰਗ ਇੱਕ ਚੈਨਲ ਦੇ ਆਕਾਰ ਵਾਲੇ ਪੰਚ ਅਤੇ ਡਾਈ ਦੀ ਵਰਤੋਂ ਕਰਕੇ ਕੀਤੀ ਜਾਂਦੀ ਹੈ, ਅਤੇ U-BEND ਨੂੰ ਇੱਕ U-ਆਕਾਰ ਵਾਲੇ ਪੰਚ ਨਾਲ ਪ੍ਰਾਪਤ ਕੀਤਾ ਜਾਂਦਾ ਹੈ। ਆਫਸੈੱਟ ਬੈਂਡਿੰਗ ਸ਼ੀਟ ਮੈਟਲ 'ਤੇ ਆਫਸੈੱਟ ਪੈਦਾ ਕਰਦੀ ਹੈ। ਰੋਲ ਬੈਂਡਿੰਗ, ਮੋਟੇ ਕੰਮ ਅਤੇ ਧਾਤ ਦੀਆਂ ਪਲੇਟਾਂ ਦੇ ਵੱਡੇ ਟੁਕੜਿਆਂ ਨੂੰ ਮੋੜਨ ਲਈ ਵਧੀਆ ਤਕਨੀਕ, ਪਲੇਟਾਂ ਨੂੰ ਲੋੜੀਂਦੇ ਵਕਰਾਂ ਤੱਕ ਖਾਣ ਅਤੇ ਮੋੜਨ ਲਈ ਤਿੰਨ ਰੋਲਾਂ ਦੀ ਵਰਤੋਂ ਕਰਦੀ ਹੈ। ਰੋਲ ਵਿਵਸਥਿਤ ਕੀਤੇ ਗਏ ਹਨ ਤਾਂ ਜੋ ਕੰਮ ਦਾ ਲੋੜੀਦਾ ਮੋੜ ਪ੍ਰਾਪਤ ਕੀਤਾ ਜਾ ਸਕੇ. ਲੋੜੀਦਾ ਨਤੀਜਾ ਪ੍ਰਾਪਤ ਕਰਨ ਲਈ ਰੋਲ ਵਿਚਕਾਰ ਦੂਰੀ ਅਤੇ ਕੋਣ ਨੂੰ ਨਿਯੰਤਰਿਤ ਕੀਤਾ ਜਾਂਦਾ ਹੈ। ਇੱਕ ਚਲਣਯੋਗ ਰੋਲ ਵਕਰ ਨੂੰ ਨਿਯੰਤਰਿਤ ਕਰਨਾ ਸੰਭਵ ਬਣਾਉਂਦਾ ਹੈ। ਟਿਊਬ ਫਾਰਮਿੰਗ ਇੱਕ ਹੋਰ ਪ੍ਰਸਿੱਧ ਸ਼ੀਟ ਮੈਟਲ ਮੋੜਨ ਵਾਲਾ ਆਪਰੇਸ਼ਨ ਹੈ ਜਿਸ ਵਿੱਚ ਮਲਟੀਪਲ ਡਾਈਜ਼ ਸ਼ਾਮਲ ਹਨ। ਕਈ ਕਿਰਿਆਵਾਂ ਤੋਂ ਬਾਅਦ ਟਿਊਬਾਂ ਪ੍ਰਾਪਤ ਕੀਤੀਆਂ ਜਾਂਦੀਆਂ ਹਨ। ਕੋਰੋਗੇਸ਼ਨ ਨੂੰ ਮੋੜਨ ਦੇ ਕੰਮ ਦੁਆਰਾ ਵੀ ਕੀਤਾ ਜਾਂਦਾ ਹੈ। ਅਸਲ ਵਿੱਚ ਇਹ ਸ਼ੀਟ ਮੈਟਲ ਦੇ ਇੱਕ ਪੂਰੇ ਟੁਕੜੇ ਵਿੱਚ ਨਿਯਮਤ ਅੰਤਰਾਲਾਂ 'ਤੇ ਸਮਮਿਤੀ ਝੁਕਣਾ ਹੈ। ਕੋਰੇਗੇਟਿੰਗ ਲਈ ਵੱਖ-ਵੱਖ ਆਕਾਰਾਂ ਦੀ ਵਰਤੋਂ ਕੀਤੀ ਜਾ ਸਕਦੀ ਹੈ। ਕੋਰੇਗੇਟਿਡ ਸ਼ੀਟ ਮੈਟਲ ਵਧੇਰੇ ਸਖ਼ਤ ਹੈ ਅਤੇ ਝੁਕਣ ਦੇ ਵਿਰੁੱਧ ਬਿਹਤਰ ਵਿਰੋਧ ਹੈ ਅਤੇ ਇਸਲਈ ਉਸਾਰੀ ਉਦਯੋਗ ਵਿੱਚ ਐਪਲੀਕੇਸ਼ਨ ਹਨ। ਸ਼ੀਟ ਮੈਟਲ ਰੋਲ ਫਾਰਮਿੰਗ, ਇੱਕ ਨਿਰੰਤਰ ਨਿਰਮਾਣ ਪ੍ਰਕਿਰਿਆ ਨੂੰ ਰੋਲ ਦੀ ਵਰਤੋਂ ਕਰਦੇ ਹੋਏ ਇੱਕ ਖਾਸ ਜਿਓਮੈਟਰੀ ਦੇ ਕਰਾਸ ਭਾਗਾਂ ਨੂੰ ਮੋੜਨ ਲਈ ਲਗਾਇਆ ਜਾਂਦਾ ਹੈ ਅਤੇ ਕੰਮ ਨੂੰ ਕ੍ਰਮਵਾਰ ਪੜਾਵਾਂ ਵਿੱਚ ਮੋੜਿਆ ਜਾਂਦਾ ਹੈ, ਅੰਤਮ ਕੰਮ ਪੂਰਾ ਕਰਨ ਦੇ ਨਾਲ। ਕੁਝ ਮਾਮਲਿਆਂ ਵਿੱਚ ਇੱਕ ਰੋਲ ਅਤੇ ਕੁਝ ਮਾਮਲਿਆਂ ਵਿੱਚ ਰੋਲ ਦੀ ਇੱਕ ਲੜੀ ਲਗਾਈ ਜਾਂਦੀ ਹੈ। • ਸੰਯੁਕਤ ਸ਼ੀਟ ਮੈਟਲ ਕਟਿੰਗ ਅਤੇ ਬੈਂਡਿੰਗ ਪ੍ਰਕਿਰਿਆਵਾਂ: ਇਹ ਉਹ ਪ੍ਰਕਿਰਿਆਵਾਂ ਹਨ ਜੋ ਇੱਕੋ ਸਮੇਂ ਕੱਟ ਅਤੇ ਮੋੜਦੀਆਂ ਹਨ। PIERCING ਵਿੱਚ, ਇੱਕ ਨੁਕੀਲੇ ਪੰਚ ਦੀ ਵਰਤੋਂ ਕਰਕੇ ਇੱਕ ਛੇਕ ਬਣਾਇਆ ਜਾਂਦਾ ਹੈ। ਜਿਵੇਂ ਕਿ ਪੰਚ ਸ਼ੀਟ ਵਿੱਚ ਮੋਰੀ ਨੂੰ ਚੌੜਾ ਕਰਦਾ ਹੈ, ਸਮਗਰੀ ਇੱਕੋ ਸਮੇਂ ਮੋਰੀ ਲਈ ਇੱਕ ਅੰਦਰੂਨੀ ਫਲੈਂਜ ਵਿੱਚ ਝੁਕ ਜਾਂਦੀ ਹੈ। ਪ੍ਰਾਪਤ flange ਮਹੱਤਵਪੂਰਨ ਫੰਕਸ਼ਨ ਹੋ ਸਕਦਾ ਹੈ. ਦੂਜੇ ਪਾਸੇ LANCING ਓਪਰੇਸ਼ਨ ਇੱਕ ਉੱਚੀ ਜਿਓਮੈਟਰੀ ਬਣਾਉਣ ਲਈ ਸ਼ੀਟ ਨੂੰ ਕੱਟਦਾ ਅਤੇ ਮੋੜਦਾ ਹੈ। • ਧਾਤੂ ਟਿਊਬ ਬੁਲਜਿੰਗ ਅਤੇ ਬੈਂਡਿੰਗ: ਬਲਜਿੰਗ ਵਿੱਚ ਇੱਕ ਖੋਖਲੇ ਟਿਊਬ ਦੇ ਕੁਝ ਅੰਦਰੂਨੀ ਹਿੱਸੇ 'ਤੇ ਦਬਾਅ ਪਾਇਆ ਜਾਂਦਾ ਹੈ, ਜਿਸ ਨਾਲ ਟਿਊਬ ਬਾਹਰ ਵੱਲ ਵਧ ਜਾਂਦੀ ਹੈ। ਕਿਉਂਕਿ ਟਿਊਬ ਡਾਈ ਦੇ ਅੰਦਰ ਹੁੰਦੀ ਹੈ, ਬਲਜ ਜਿਓਮੈਟਰੀ ਨੂੰ ਡਾਈ ਦੀ ਸ਼ਕਲ ਦੁਆਰਾ ਨਿਯੰਤਰਿਤ ਕੀਤਾ ਜਾਂਦਾ ਹੈ। ਸਟ੍ਰੈਚ ਬੈਂਡਿੰਗ ਵਿੱਚ, ਇੱਕ ਧਾਤ ਦੀ ਟਿਊਬ ਨੂੰ ਟਿਊਬ ਦੇ ਧੁਰੇ ਦੇ ਸਮਾਨਾਂਤਰ ਬਲਾਂ ਅਤੇ ਟਿਊਬ ਨੂੰ ਇੱਕ ਫਾਰਮ ਬਲਾਕ ਉੱਤੇ ਖਿੱਚਣ ਲਈ ਮੋੜਨ ਵਾਲੀਆਂ ਤਾਕਤਾਂ ਦੀ ਵਰਤੋਂ ਕਰਕੇ ਖਿੱਚਿਆ ਜਾਂਦਾ ਹੈ। ਡ੍ਰਾ ਮੋੜਨ ਵਿੱਚ, ਅਸੀਂ ਟਿਊਬ ਨੂੰ ਇਸਦੇ ਸਿਰੇ ਦੇ ਨੇੜੇ ਇੱਕ ਰੋਟੇਟਿੰਗ ਫਾਰਮ ਬਲਾਕ ਵਿੱਚ ਕਲੈਂਪ ਕਰਦੇ ਹਾਂ ਜੋ ਘੁੰਮਦੇ ਸਮੇਂ ਟਿਊਬ ਨੂੰ ਮੋੜਦਾ ਹੈ। ਅੰਤ ਵਿੱਚ, ਕੰਪਰੈਸ਼ਨ ਬੈਂਡਿੰਗ ਵਿੱਚ ਟਿਊਬ ਨੂੰ ਇੱਕ ਸਥਿਰ ਫਾਰਮ ਬਲਾਕ ਵਿੱਚ ਜ਼ੋਰ ਨਾਲ ਫੜਿਆ ਜਾਂਦਾ ਹੈ, ਅਤੇ ਇੱਕ ਡਾਈ ਇਸਨੂੰ ਫਾਰਮ ਬਲਾਕ ਉੱਤੇ ਮੋੜ ਦਿੰਦੀ ਹੈ। • ਡੂੰਘੀ ਡਰਾਇੰਗ: ਸਾਡੇ ਸਭ ਤੋਂ ਪ੍ਰਸਿੱਧ ਓਪਰੇਸ਼ਨਾਂ ਵਿੱਚੋਂ ਇੱਕ ਵਿੱਚ, ਇੱਕ ਪੰਚ, ਇੱਕ ਮੈਚਿੰਗ ਡਾਈ ਅਤੇ ਇੱਕ ਖਾਲੀ ਹੋਲਡਰ ਦੀ ਵਰਤੋਂ ਕੀਤੀ ਜਾਂਦੀ ਹੈ। ਸ਼ੀਟ ਮੈਟਲ ਖਾਲੀ ਨੂੰ ਡਾਈ ਓਪਨਿੰਗ 'ਤੇ ਰੱਖਿਆ ਜਾਂਦਾ ਹੈ ਅਤੇ ਪੰਚ ਖਾਲੀ ਧਾਰਕ ਦੁਆਰਾ ਰੱਖੀ ਖਾਲੀ ਥਾਂ ਵੱਲ ਵਧਦਾ ਹੈ। ਇੱਕ ਵਾਰ ਜਦੋਂ ਉਹ ਸੰਪਰਕ ਵਿੱਚ ਆਉਂਦੇ ਹਨ, ਤਾਂ ਪੰਚ ਸ਼ੀਟ ਮੈਟਲ ਨੂੰ ਉਤਪਾਦ ਬਣਾਉਣ ਲਈ ਡਾਈ ਕੈਵਿਟੀ ਵਿੱਚ ਮਜਬੂਰ ਕਰਦਾ ਹੈ। ਡੂੰਘੀ ਡਰਾਇੰਗ ਓਪਰੇਸ਼ਨ ਕੱਟਣ ਵਰਗਾ ਹੈ, ਹਾਲਾਂਕਿ ਪੰਚ ਅਤੇ ਡਾਈ ਵਿਚਕਾਰ ਕਲੀਅਰੈਂਸ ਸ਼ੀਟ ਨੂੰ ਕੱਟਣ ਤੋਂ ਰੋਕਦੀ ਹੈ। ਸ਼ੀਟ ਨੂੰ ਡੂੰਘਾ ਖਿੱਚਿਆ ਗਿਆ ਹੈ ਅਤੇ ਕੱਟਿਆ ਨਹੀਂ ਗਿਆ ਹੈ ਨੂੰ ਯਕੀਨੀ ਬਣਾਉਣ ਵਾਲਾ ਇੱਕ ਹੋਰ ਕਾਰਕ ਡਾਈ ਅਤੇ ਪੰਚ 'ਤੇ ਗੋਲ ਕੋਨੇ ਹਨ ਜੋ ਕਟਾਈ ਅਤੇ ਕੱਟਣ ਤੋਂ ਰੋਕਦੇ ਹਨ। ਡੂੰਘੀ ਡਰਾਇੰਗ ਦੀ ਇੱਕ ਵੱਡੀ ਮਾਤਰਾ ਨੂੰ ਪ੍ਰਾਪਤ ਕਰਨ ਲਈ, ਇੱਕ ਰੀਡ੍ਰੌਇੰਗ ਪ੍ਰਕਿਰਿਆ ਨੂੰ ਤੈਨਾਤ ਕੀਤਾ ਜਾ ਰਿਹਾ ਹੈ ਜਿੱਥੇ ਬਾਅਦ ਵਿੱਚ ਇੱਕ ਡੂੰਘੀ ਡਰਾਇੰਗ ਉਸ ਹਿੱਸੇ 'ਤੇ ਹੁੰਦੀ ਹੈ ਜੋ ਪਹਿਲਾਂ ਹੀ ਇੱਕ ਡੂੰਘੀ ਡਰਾਇੰਗ ਪ੍ਰਕਿਰਿਆ ਵਿੱਚੋਂ ਗੁਜ਼ਰ ਚੁੱਕਾ ਹੈ। ਰਿਵਰਸ ਰੀਡਰਾਇੰਗ ਵਿੱਚ, ਡੂੰਘੇ ਖਿੱਚੇ ਗਏ ਹਿੱਸੇ ਨੂੰ ਉਲਟਾ ਕੀਤਾ ਜਾਂਦਾ ਹੈ ਅਤੇ ਉਲਟ ਦਿਸ਼ਾ ਵਿੱਚ ਖਿੱਚਿਆ ਜਾਂਦਾ ਹੈ। ਡੂੰਘੀ ਡਰਾਇੰਗ ਅਨਿਯਮਿਤ ਆਕਾਰ ਦੀਆਂ ਵਸਤੂਆਂ ਪ੍ਰਦਾਨ ਕਰ ਸਕਦੀ ਹੈ ਜਿਵੇਂ ਕਿ ਗੁੰਬਦਦਾਰ, ਟੇਪਰਡ ਜਾਂ ਸਟੈਪਡ ਕੱਪ, EMBOSSING ਵਿੱਚ ਅਸੀਂ ਇੱਕ ਡਿਜ਼ਾਈਨ ਜਾਂ ਸਕ੍ਰਿਪਟ ਨਾਲ ਸ਼ੀਟ ਮੈਟਲ ਨੂੰ ਪ੍ਰਭਾਵਿਤ ਕਰਨ ਲਈ ਇੱਕ ਨਰ ਅਤੇ ਮਾਦਾ ਡਾਈ ਜੋੜੇ ਦੀ ਵਰਤੋਂ ਕਰਦੇ ਹਾਂ। • SPINNING : ਇੱਕ ਓਪਰੇਸ਼ਨ ਜਿੱਥੇ ਇੱਕ ਫਲੈਟ ਜਾਂ ਪ੍ਰੀਫਾਰਮਡ ਵਰਕਪੀਸ ਨੂੰ ਘੁੰਮਦੇ ਹੋਏ ਮੈਂਡਰਲ ਅਤੇ ਟੇਲ ਸਟਾਕ ਦੇ ਵਿਚਕਾਰ ਰੱਖਿਆ ਜਾਂਦਾ ਹੈ ਅਤੇ ਇੱਕ ਟੂਲ ਕੰਮ 'ਤੇ ਸਥਾਨਕ ਦਬਾਅ ਨੂੰ ਲਾਗੂ ਕਰਦਾ ਹੈ ਕਿਉਂਕਿ ਇਹ ਹੌਲੀ-ਹੌਲੀ ਮੈਂਡਰਲ ਨੂੰ ਉੱਪਰ ਵੱਲ ਜਾਂਦਾ ਹੈ। ਨਤੀਜੇ ਵਜੋਂ, ਵਰਕਪੀਸ ਮੇਂਡਰੇਲ ਉੱਤੇ ਲਪੇਟਿਆ ਜਾਂਦਾ ਹੈ ਅਤੇ ਇਸਦਾ ਆਕਾਰ ਲੈਂਦਾ ਹੈ. ਅਸੀਂ ਇਸ ਤਕਨੀਕ ਦੀ ਵਰਤੋਂ ਡੂੰਘੀ ਡਰਾਇੰਗ ਦੇ ਵਿਕਲਪ ਵਜੋਂ ਕਰਦੇ ਹਾਂ ਜਿੱਥੇ ਆਰਡਰ ਦੀ ਮਾਤਰਾ ਛੋਟੀ ਹੁੰਦੀ ਹੈ, ਹਿੱਸੇ ਵੱਡੇ ਹੁੰਦੇ ਹਨ (20 ਫੁੱਟ ਤੱਕ ਵਿਆਸ) ਅਤੇ ਵਿਲੱਖਣ ਕਰਵ ਹੁੰਦੇ ਹਨ। ਹਾਲਾਂਕਿ ਪ੍ਰਤੀ ਟੁਕੜੇ ਦੀਆਂ ਕੀਮਤਾਂ ਆਮ ਤੌਰ 'ਤੇ ਉੱਚੀਆਂ ਹੁੰਦੀਆਂ ਹਨ, ਸੀਐਨਸੀ ਸਪਿਨਿੰਗ ਓਪਰੇਸ਼ਨ ਲਈ ਸੈੱਟ-ਅੱਪ ਲਾਗਤ ਡੂੰਘੀ ਡਰਾਇੰਗ ਦੇ ਮੁਕਾਬਲੇ ਘੱਟ ਹਨ। ਇਸਦੇ ਉਲਟ, ਡੂੰਘੀ ਡਰਾਇੰਗ ਲਈ ਸੈੱਟ-ਅੱਪ ਲਈ ਉੱਚ ਸ਼ੁਰੂਆਤੀ ਨਿਵੇਸ਼ ਦੀ ਲੋੜ ਹੁੰਦੀ ਹੈ, ਪਰ ਜਦੋਂ ਉੱਚ ਮਾਤਰਾ ਵਿੱਚ ਹਿੱਸੇ ਪੈਦਾ ਕੀਤੇ ਜਾਂਦੇ ਹਨ ਤਾਂ ਪ੍ਰਤੀ ਟੁਕੜੇ ਦੀ ਲਾਗਤ ਘੱਟ ਹੁੰਦੀ ਹੈ। ਇਸ ਪ੍ਰਕਿਰਿਆ ਦਾ ਇੱਕ ਹੋਰ ਸੰਸਕਰਣ ਸ਼ੀਅਰ ਸਪਿਨਿੰਗ ਹੈ, ਜਿੱਥੇ ਵਰਕਪੀਸ ਦੇ ਅੰਦਰ ਧਾਤ ਦਾ ਪ੍ਰਵਾਹ ਵੀ ਹੁੰਦਾ ਹੈ। ਧਾਤ ਦਾ ਪ੍ਰਵਾਹ ਵਰਕਪੀਸ ਦੀ ਮੋਟਾਈ ਨੂੰ ਘਟਾ ਦੇਵੇਗਾ ਕਿਉਂਕਿ ਪ੍ਰਕਿਰਿਆ ਕੀਤੀ ਜਾਂਦੀ ਹੈ. ਫਿਰ ਵੀ ਇਕ ਹੋਰ ਸੰਬੰਧਿਤ ਪ੍ਰਕਿਰਿਆ ਟਿਊਬ ਸਪਿਨਿੰਗ ਹੈ, ਜੋ ਕਿ ਸਿਲੰਡਰ ਵਾਲੇ ਹਿੱਸਿਆਂ 'ਤੇ ਲਾਗੂ ਹੁੰਦੀ ਹੈ। ਇਸ ਪ੍ਰਕਿਰਿਆ ਵਿੱਚ ਵੀ ਵਰਕਪੀਸ ਦੇ ਅੰਦਰ ਧਾਤ ਦਾ ਪ੍ਰਵਾਹ ਹੁੰਦਾ ਹੈ। ਇਸ ਤਰ੍ਹਾਂ ਮੋਟਾਈ ਘਟਾਈ ਜਾਂਦੀ ਹੈ ਅਤੇ ਟਿਊਬ ਦੀ ਲੰਬਾਈ ਵਧ ਜਾਂਦੀ ਹੈ। ਟੂਲ ਨੂੰ ਟਿਊਬ ਦੇ ਅੰਦਰ ਜਾਂ ਬਾਹਰ ਵਿਸ਼ੇਸ਼ਤਾਵਾਂ ਬਣਾਉਣ ਲਈ ਮੂਵ ਕੀਤਾ ਜਾ ਸਕਦਾ ਹੈ। • ਸ਼ੀਟ ਮੈਟਲ ਦੀ ਰਬੜ ਬਣਾਉਣਾ: ਰਬੜ ਜਾਂ ਪੌਲੀਯੂਰੀਥੇਨ ਸਮੱਗਰੀ ਨੂੰ ਇੱਕ ਕੰਟੇਨਰ ਡਾਈ ਵਿੱਚ ਪਾ ਦਿੱਤਾ ਜਾਂਦਾ ਹੈ ਅਤੇ ਕੰਮ ਦੇ ਟੁਕੜੇ ਨੂੰ ਰਬੜ ਦੀ ਸਤ੍ਹਾ 'ਤੇ ਰੱਖਿਆ ਜਾਂਦਾ ਹੈ। ਫਿਰ ਕੰਮ ਦੇ ਟੁਕੜੇ 'ਤੇ ਇੱਕ ਪੰਚ ਲਗਾਇਆ ਜਾਂਦਾ ਹੈ ਅਤੇ ਇਸਨੂੰ ਰਬੜ ਵਿੱਚ ਧੱਕਦਾ ਹੈ। ਕਿਉਂਕਿ ਰਬੜ ਦੁਆਰਾ ਪੈਦਾ ਹੋਣ ਵਾਲਾ ਦਬਾਅ ਘੱਟ ਹੁੰਦਾ ਹੈ, ਇਸ ਲਈ ਪੈਦਾ ਹੋਏ ਹਿੱਸਿਆਂ ਦੀ ਡੂੰਘਾਈ ਸੀਮਤ ਹੁੰਦੀ ਹੈ। ਕਿਉਂਕਿ ਟੂਲਿੰਗ ਦੀ ਲਾਗਤ ਘੱਟ ਹੈ, ਪ੍ਰਕਿਰਿਆ ਘੱਟ ਮਾਤਰਾ ਦੇ ਉਤਪਾਦਨ ਲਈ ਢੁਕਵੀਂ ਹੈ। • ਹਾਈਡਰੋਫਾਰਮਿੰਗ: ਰਬੜ ਬਣਾਉਣ ਦੇ ਸਮਾਨ, ਇਸ ਪ੍ਰਕਿਰਿਆ ਵਿੱਚ ਸ਼ੀਟ ਮੈਟਲ ਦੇ ਕੰਮ ਨੂੰ ਇੱਕ ਪੰਚ ਦੁਆਰਾ ਇੱਕ ਚੈਂਬਰ ਦੇ ਅੰਦਰ ਇੱਕ ਦਬਾਅ ਵਾਲੇ ਤਰਲ ਵਿੱਚ ਦਬਾਇਆ ਜਾਂਦਾ ਹੈ। ਸ਼ੀਟ ਮੈਟਲ ਦਾ ਕੰਮ ਪੰਚ ਅਤੇ ਰਬੜ ਦੇ ਡਾਇਆਫ੍ਰਾਮ ਦੇ ਵਿਚਕਾਰ ਸੈਂਡਵਿਚ ਕੀਤਾ ਜਾਂਦਾ ਹੈ। ਡਾਇਆਫ੍ਰਾਮ ਵਰਕਪੀਸ ਨੂੰ ਪੂਰੀ ਤਰ੍ਹਾਂ ਘੇਰ ਲੈਂਦਾ ਹੈ ਅਤੇ ਤਰਲ ਦਾ ਦਬਾਅ ਇਸ ਨੂੰ ਪੰਚ 'ਤੇ ਬਣਾਉਣ ਲਈ ਮਜਬੂਰ ਕਰਦਾ ਹੈ। ਇਸ ਤਕਨੀਕ ਨਾਲ ਡੂੰਘੀ ਡਰਾਇੰਗ ਪ੍ਰਕਿਰਿਆ ਦੇ ਮੁਕਾਬਲੇ ਬਹੁਤ ਡੂੰਘੇ ਡਰਾਅ ਵੀ ਪ੍ਰਾਪਤ ਕੀਤੇ ਜਾ ਸਕਦੇ ਹਨ। ਅਸੀਂ ਤੁਹਾਡੇ ਹਿੱਸੇ ਦੇ ਆਧਾਰ 'ਤੇ ਸਿੰਗਲ-ਪੰਚ ਡਾਈਜ਼ ਦੇ ਨਾਲ-ਨਾਲ ਪ੍ਰੋਜੇਸਿਵ ਡਾਈਜ਼ ਦਾ ਨਿਰਮਾਣ ਕਰਦੇ ਹਾਂ। ਸਿੰਗਲ ਸਟ੍ਰੋਕ ਸਟੈਂਪਿੰਗ ਡਾਈਜ਼ ਵੱਡੀ ਮਾਤਰਾ ਵਿੱਚ ਸਧਾਰਨ ਸ਼ੀਟ ਮੈਟਲ ਪਾਰਟਸ ਜਿਵੇਂ ਕਿ ਵਾੱਸ਼ਰ ਜਲਦੀ ਤਿਆਰ ਕਰਨ ਲਈ ਇੱਕ ਲਾਗਤ ਪ੍ਰਭਾਵਸ਼ਾਲੀ ਤਰੀਕਾ ਹੈ। ਪ੍ਰਗਤੀਸ਼ੀਲ ਡੀਜ਼ ਜਾਂ ਡੂੰਘੀ ਡਰਾਇੰਗ ਤਕਨੀਕ ਦੀ ਵਰਤੋਂ ਵਧੇਰੇ ਗੁੰਝਲਦਾਰ ਜਿਓਮੈਟਰੀ ਬਣਾਉਣ ਲਈ ਕੀਤੀ ਜਾਂਦੀ ਹੈ। ਤੁਹਾਡੇ ਕੇਸ 'ਤੇ ਨਿਰਭਰ ਕਰਦਿਆਂ, ਵਾਟਰਜੈੱਟ, ਲੇਜ਼ਰ ਜਾਂ ਪਲਾਜ਼ਮਾ ਕੱਟਣ ਦੀ ਵਰਤੋਂ ਤੁਹਾਡੇ ਸ਼ੀਟ ਮੈਟਲ ਦੇ ਹਿੱਸਿਆਂ ਨੂੰ ਸਸਤੇ, ਤੇਜ਼ ਅਤੇ ਸਹੀ ਢੰਗ ਨਾਲ ਬਣਾਉਣ ਲਈ ਕੀਤੀ ਜਾ ਸਕਦੀ ਹੈ। ਬਹੁਤ ਸਾਰੇ ਸਪਲਾਇਰਾਂ ਨੂੰ ਇਹਨਾਂ ਵਿਕਲਪਿਕ ਤਕਨੀਕਾਂ ਬਾਰੇ ਕੋਈ ਜਾਣਕਾਰੀ ਨਹੀਂ ਹੈ ਜਾਂ ਉਹਨਾਂ ਕੋਲ ਨਹੀਂ ਹੈ ਅਤੇ ਇਸ ਲਈ ਉਹ ਡਾਈਜ਼ ਅਤੇ ਟੂਲ ਬਣਾਉਣ ਦੇ ਲੰਬੇ ਅਤੇ ਮਹਿੰਗੇ ਤਰੀਕਿਆਂ ਵਿੱਚੋਂ ਲੰਘਦੇ ਹਨ ਜੋ ਸਿਰਫ਼ ਗਾਹਕਾਂ ਦਾ ਸਮਾਂ ਅਤੇ ਪੈਸਾ ਬਰਬਾਦ ਕਰਦੇ ਹਨ। ਜੇਕਰ ਤੁਹਾਨੂੰ ਕਸਟਮ ਬਿਲਟ ਸ਼ੀਟ ਮੈਟਲ ਕੰਪੋਨੈਂਟਸ ਦੀ ਲੋੜ ਹੈ ਜਿਵੇਂ ਕਿ ਐਨਕਲੋਜ਼ਰ, ਇਲੈਕਟ੍ਰਾਨਿਕ ਹਾਊਸਿੰਗ...ਆਦਿ ਦਿਨਾਂ ਦੇ ਅੰਦਰ ਜਿੰਨੀ ਜਲਦੀ, ਤਾਂ ਸਾਡੀ ਰੈਪਿਡ ਸ਼ੀਟ ਮੈਟਲ ਪ੍ਰੋਟੋਟਾਈਪਿੰਗ ਸੇਵਾ ਲਈ ਸਾਡੇ ਨਾਲ ਸੰਪਰਕ ਕਰੋ। CLICK Product Finder-Locator Service ਪਿਛਲਾ ਮੀਨੂ
- Forging and Powdered Metallurgy, Die Forging, Heading, Hot Forging
Forging and Powdered Metallurgy, Die Forging, Heading, Hot Forging, Impression Die, Near Net Shape, Swaging, Metal Hobbing, Riveting, Coining from AGS-TECH Inc. ਮੈਟਲ ਫੋਰਜਿੰਗ ਅਤੇ ਪਾਊਡਰ ਧਾਤੂ ਮੈਟਲ ਫੋਰਜਿੰਗ ਪ੍ਰਕਿਰਿਆਵਾਂ ਦੀ ਕਿਸਮ ਜੋ ਅਸੀਂ ਪੇਸ਼ ਕਰਦੇ ਹਾਂ ਉਹ ਹਨ ਗਰਮ ਅਤੇ ਠੰਡੇ ਡਾਈ, ਓਪਨ ਡਾਈ ਅਤੇ ਬੰਦ ਡਾਈ, ਇਮਪ੍ਰੈਸ਼ਨ ਡਾਈ ਅਤੇ ਫਲੈਸ਼ ਰਹਿਤ ਫੋਰਜਿੰਗ, cogging, ਫੁਲਰਿੰਗ, ਕਿਨਾਰਾ ਅਤੇ ਸ਼ੁੱਧਤਾ- ਫੋਰਜਿੰਗ, ਨੇੜੇ- , ਸਵੈਜਿੰਗ, ਅਪਸੈਟ ਫੋਰਜਿੰਗ, ਮੈਟਲ ਹੌਬਿੰਗ, ਪ੍ਰੈਸ ਅਤੇ ਰੋਲ ਅਤੇ ਰੇਡੀਅਲ ਅਤੇ ਔਰਬਿਟਲ ਅਤੇ ਰਿੰਗ ਅਤੇ ਆਈਸੋਥਰਮਲ ਫੋਰਜਿੰਗ, ਸਿੱਕਾ ਬਣਾਉਣਾ, ਰਿਵੇਟਿੰਗ, ਮੈਟਲ ਬਾਲ ਫੋਰਜਿੰਗ, ਮੈਟਲ ਪੀਅਰਸਿੰਗ, ਸਾਈਜ਼ਿੰਗ, ਉੱਚ ਊਰਜਾ ਦਰ ਫੋਰਜਿੰਗ। ਸਾਡੀਆਂ ਪਾਊਡਰ ਮੈਟਲੁਰਜੀ ਅਤੇ ਪਾਊਡਰ ਪ੍ਰੋਸੈਸਿੰਗ ਤਕਨੀਕਾਂ ਹਨ ਪਾਊਡਰ ਦਬਾਉਣ ਅਤੇ ਸਿੰਟਰਿੰਗ, ਗਰਭਪਾਤ, ਘੁਸਪੈਠ, ਗਰਮ ਅਤੇ ਠੰਡੇ ਆਈਸੋਸਟੈਟਿਕ ਪ੍ਰੈੱਸਿੰਗ, ਮੈਟਲ ਇੰਜੈਕਸ਼ਨ ਮੋਲਡਿੰਗ, ਰੋਲ ਕੰਪੈਕਸ਼ਨ, ਪਾਊਡਰ ਰੋਲਿੰਗ, ਪਾਊਡਰ ਐਕਸਟਰਿਊਸ਼ਨ, ਢਿੱਲੀ ਸਿੰਟਰਿੰਗ, ਸਪਾਰਕ ਹੌਟ ਸਿੰਟਰਿੰਗ, ਅਸੀਂ ਸਿਫ਼ਾਰਿਸ਼ ਕਰਦੇ ਹਾਂ ਕਿ ਤੁਸੀਂ ਇੱਥੇ ਕਲਿੱਕ ਕਰੋ AGS-TECH Inc. ਦੁਆਰਾ ਫੋਰਜਿੰਗ ਪ੍ਰਕਿਰਿਆਵਾਂ ਦੇ ਸਾਡੇ ਯੋਜਨਾਬੱਧ ਚਿੱਤਰਾਂ ਨੂੰ ਡਾਉਨਲੋਡ ਕਰੋ AGS-TECH Inc. ਦੁਆਰਾ ਪਾਊਡਰ ਮੈਟਾਲੁਰਜੀ ਪ੍ਰਕਿਰਿਆਵਾਂ ਦੇ ਸਾਡੇ ਯੋਜਨਾਬੱਧ ਚਿੱਤਰਾਂ ਨੂੰ ਡਾਉਨਲੋਡ ਕਰੋ ਫੋਟੋਆਂ ਅਤੇ ਸਕੈਚਾਂ ਵਾਲੀਆਂ ਇਹ ਡਾਊਨਲੋਡ ਕਰਨ ਯੋਗ ਫ਼ਾਈਲਾਂ ਤੁਹਾਨੂੰ ਹੇਠਾਂ ਦਿੱਤੀ ਜਾਣਕਾਰੀ ਨੂੰ ਬਿਹਤਰ ਤਰੀਕੇ ਨਾਲ ਸਮਝਣ ਵਿੱਚ ਤੁਹਾਡੀ ਮਦਦ ਕਰਨਗੀਆਂ। ਮੈਟਲ ਫੋਰਜਿੰਗ ਵਿੱਚ, ਸੰਕੁਚਿਤ ਬਲਾਂ ਨੂੰ ਲਾਗੂ ਕੀਤਾ ਜਾਂਦਾ ਹੈ ਅਤੇ ਸਮੱਗਰੀ ਨੂੰ ਵਿਗਾੜ ਦਿੱਤਾ ਜਾਂਦਾ ਹੈ ਅਤੇ ਲੋੜੀਦਾ ਆਕਾਰ ਪ੍ਰਾਪਤ ਕੀਤਾ ਜਾਂਦਾ ਹੈ। ਉਦਯੋਗ ਵਿੱਚ ਸਭ ਤੋਂ ਆਮ ਜਾਅਲੀ ਸਮੱਗਰੀ ਲੋਹਾ ਅਤੇ ਸਟੀਲ ਹਨ, ਪਰ ਕਈ ਹੋਰ ਜਿਵੇਂ ਕਿ ਅਲਮੀਨੀਅਮ, ਤਾਂਬਾ, ਟਾਈਟੇਨੀਅਮ, ਮੈਗਨੀਸ਼ੀਅਮ ਵੀ ਵਿਆਪਕ ਤੌਰ 'ਤੇ ਜਾਅਲੀ ਹਨ। ਜਾਅਲੀ ਧਾਤ ਦੇ ਹਿੱਸਿਆਂ ਨੇ ਸੀਲਬੰਦ ਚੀਰ ਅਤੇ ਬੰਦ ਖਾਲੀ ਥਾਵਾਂ ਤੋਂ ਇਲਾਵਾ ਅਨਾਜ ਦੇ ਢਾਂਚੇ ਵਿੱਚ ਸੁਧਾਰ ਕੀਤਾ ਹੈ, ਇਸ ਤਰ੍ਹਾਂ ਇਸ ਪ੍ਰਕਿਰਿਆ ਦੁਆਰਾ ਪ੍ਰਾਪਤ ਕੀਤੇ ਹਿੱਸਿਆਂ ਦੀ ਤਾਕਤ ਵੱਧ ਹੈ। ਫੋਰਜਿੰਗ ਉਹ ਹਿੱਸੇ ਪੈਦਾ ਕਰਦੀ ਹੈ ਜੋ ਕਾਸਟਿੰਗ ਜਾਂ ਮਸ਼ੀਨਿੰਗ ਦੁਆਰਾ ਬਣਾਏ ਗਏ ਹਿੱਸਿਆਂ ਨਾਲੋਂ ਆਪਣੇ ਭਾਰ ਲਈ ਮਹੱਤਵਪੂਰਨ ਤੌਰ 'ਤੇ ਮਜ਼ਬੂਤ ਹੁੰਦੇ ਹਨ। ਕਿਉਂਕਿ ਜਾਅਲੀ ਹਿੱਸਿਆਂ ਨੂੰ ਧਾਤ ਦੇ ਪ੍ਰਵਾਹ ਨੂੰ ਇਸਦੇ ਅੰਤਮ ਆਕਾਰ ਵਿੱਚ ਬਣਾ ਕੇ ਆਕਾਰ ਦਿੱਤਾ ਜਾਂਦਾ ਹੈ, ਇਸਲਈ ਧਾਤ ਇੱਕ ਦਿਸ਼ਾਤਮਕ ਅਨਾਜ ਬਣਤਰ ਨੂੰ ਲੈਂਦੀ ਹੈ ਜੋ ਹਿੱਸਿਆਂ ਦੀ ਉੱਚ ਤਾਕਤ ਲਈ ਖਾਤਾ ਹੈ। ਦੂਜੇ ਸ਼ਬਦਾਂ ਵਿੱਚ, ਫੋਰਜਿੰਗ ਪ੍ਰਕਿਰਿਆ ਦੁਆਰਾ ਪ੍ਰਾਪਤ ਕੀਤੇ ਹਿੱਸੇ ਸਧਾਰਨ ਕਾਸਟ ਜਾਂ ਮਸ਼ੀਨ ਵਾਲੇ ਹਿੱਸਿਆਂ ਦੇ ਮੁਕਾਬਲੇ ਬਿਹਤਰ ਮਕੈਨੀਕਲ ਵਿਸ਼ੇਸ਼ਤਾਵਾਂ ਨੂੰ ਪ੍ਰਗਟ ਕਰਦੇ ਹਨ। ਮੈਟਲ ਫੋਰਜਿੰਗ ਦਾ ਭਾਰ ਛੋਟੇ ਹਲਕੇ ਭਾਰ ਵਾਲੇ ਹਿੱਸਿਆਂ ਤੋਂ ਲੈ ਕੇ ਲੱਖਾਂ ਪੌਂਡ ਤੱਕ ਹੋ ਸਕਦਾ ਹੈ। ਅਸੀਂ ਜ਼ਿਆਦਾਤਰ ਮਸ਼ੀਨੀ ਤੌਰ 'ਤੇ ਮੰਗ ਕਰਨ ਵਾਲੀਆਂ ਐਪਲੀਕੇਸ਼ਨਾਂ ਲਈ ਫੋਰਜਿੰਗ ਤਿਆਰ ਕਰਦੇ ਹਾਂ ਜਿੱਥੇ ਆਟੋਮੋਟਿਵ ਪਾਰਟਸ, ਗੀਅਰਜ਼, ਕੰਮ ਕਰਨ ਵਾਲੇ ਟੂਲ, ਹੈਂਡ ਟੂਲ, ਟਰਬਾਈਨ ਸ਼ਾਫਟ, ਮੋਟਰਸਾਈਕਲ ਗੇਅਰ ਵਰਗੇ ਹਿੱਸਿਆਂ 'ਤੇ ਉੱਚ ਤਣਾਅ ਲਾਗੂ ਹੁੰਦਾ ਹੈ। ਕਿਉਂਕਿ ਟੂਲਿੰਗ ਅਤੇ ਸੈੱਟ-ਅੱਪ ਲਾਗਤਾਂ ਮੁਕਾਬਲਤਨ ਉੱਚੀਆਂ ਹਨ, ਅਸੀਂ ਇਸ ਨਿਰਮਾਣ ਪ੍ਰਕਿਰਿਆ ਦੀ ਸਿਫ਼ਾਰਿਸ਼ ਕਰਦੇ ਹਾਂ ਸਿਰਫ਼ ਉੱਚ ਵਾਲੀਅਮ ਉਤਪਾਦਨ ਲਈ ਅਤੇ ਘੱਟ ਵਾਲੀਅਮ ਪਰ ਉੱਚ ਮੁੱਲ ਦੇ ਨਾਜ਼ੁਕ ਹਿੱਸਿਆਂ ਜਿਵੇਂ ਕਿ ਏਰੋਸਪੇਸ ਲੈਂਡਿੰਗ ਗੀਅਰ ਲਈ। ਟੂਲਿੰਗ ਦੀ ਲਾਗਤ ਤੋਂ ਇਲਾਵਾ, ਵੱਡੀ ਮਾਤਰਾ ਦੇ ਜਾਅਲੀ ਪੁਰਜ਼ਿਆਂ ਲਈ ਨਿਰਮਾਣ ਦਾ ਸਮਾਂ ਕੁਝ ਸਧਾਰਨ ਮਸ਼ੀਨ ਵਾਲੇ ਪੁਰਜ਼ਿਆਂ ਦੀ ਤੁਲਨਾ ਵਿੱਚ ਲੰਬਾ ਹੋ ਸਕਦਾ ਹੈ, ਪਰ ਇਹ ਤਕਨੀਕ ਉਹਨਾਂ ਹਿੱਸਿਆਂ ਲਈ ਮਹੱਤਵਪੂਰਨ ਹੈ ਜਿਨ੍ਹਾਂ ਨੂੰ ਅਸਾਧਾਰਨ ਤਾਕਤ ਦੀ ਲੋੜ ਹੁੰਦੀ ਹੈ ਜਿਵੇਂ ਕਿ ਬੋਲਟ, ਨਟਸ, ਵਿਸ਼ੇਸ਼ ਐਪਲੀਕੇਸ਼ਨ। ਫਾਸਟਨਰ, ਆਟੋਮੋਟਿਵ, ਫੋਰਕਲਿਫਟ, ਕਰੇਨ ਦੇ ਹਿੱਸੇ। • ਹੌਟ ਡਾਈ ਅਤੇ ਕੋਲਡ ਡਾਈ ਫੋਰਜਿੰਗ: ਹੌਟ ਡਾਈ ਫੋਰਜਿੰਗ, ਜਿਵੇਂ ਕਿ ਨਾਮ ਤੋਂ ਭਾਵ ਹੈ ਉੱਚ ਤਾਪਮਾਨਾਂ 'ਤੇ ਕੀਤਾ ਜਾਂਦਾ ਹੈ, ਇਸ ਲਈ ਲਚਕੀਲਾਪਣ ਉੱਚ ਹੁੰਦਾ ਹੈ ਅਤੇ ਸਮੱਗਰੀ ਦੀ ਤਾਕਤ ਘੱਟ ਹੁੰਦੀ ਹੈ। ਇਹ ਆਸਾਨ ਵਿਗਾੜ ਅਤੇ ਫੋਰਜਿੰਗ ਦੀ ਸਹੂਲਤ ਦਿੰਦਾ ਹੈ। ਇਸ ਦੇ ਉਲਟ, ਕੋਲਡ ਡਾਈ ਫੋਰਜਿੰਗ ਘੱਟ ਤਾਪਮਾਨਾਂ 'ਤੇ ਕੀਤੀ ਜਾਂਦੀ ਹੈ ਅਤੇ ਇਸ ਲਈ ਉੱਚ ਬਲਾਂ ਦੀ ਲੋੜ ਹੁੰਦੀ ਹੈ ਜਿਸ ਦੇ ਨਤੀਜੇ ਵਜੋਂ ਤਣਾਅ ਸਖ਼ਤ, ਬਿਹਤਰ ਸਤਹ ਮੁਕੰਮਲ ਅਤੇ ਨਿਰਮਿਤ ਹਿੱਸਿਆਂ ਦੀ ਸ਼ੁੱਧਤਾ ਹੁੰਦੀ ਹੈ। • ਓਪਨ ਡਾਈ ਅਤੇ ਇਮਪ੍ਰੈਸ਼ਨ ਡਾਈ ਫੋਰਜਿੰਗ: ਓਪਨ ਡਾਈ ਫੋਰਜਿੰਗ ਵਿੱਚ, ਡਾਈਜ਼ ਸੰਕੁਚਿਤ ਕੀਤੀ ਜਾ ਰਹੀ ਸਮੱਗਰੀ ਨੂੰ ਰੋਕਦੇ ਨਹੀਂ ਹਨ, ਜਦੋਂ ਕਿ ਇਮਪ੍ਰੇਸ਼ਨ ਡਾਈ ਫੋਰਜਿੰਗ ਵਿੱਚ ਡਾਈਜ਼ ਦੇ ਅੰਦਰ ਕੈਵਿਟੀਜ਼ ਸਮੱਗਰੀ ਦੇ ਪ੍ਰਵਾਹ ਨੂੰ ਸੀਮਤ ਕਰਦੇ ਹਨ ਜਦੋਂ ਕਿ ਇਹ ਲੋੜੀਂਦੇ ਆਕਾਰ ਵਿੱਚ ਜਾਅਲੀ ਹੁੰਦੀ ਹੈ। UPSET FORGING ਜਾਂ ਇਸਨੂੰ UPSETTING ਵੀ ਕਿਹਾ ਜਾਂਦਾ ਹੈ, ਜੋ ਕਿ ਅਸਲ ਵਿੱਚ ਇੱਕੋ ਜਿਹੀ ਨਹੀਂ ਹੈ ਪਰ ਇੱਕ ਬਹੁਤ ਹੀ ਸਮਾਨ ਪ੍ਰਕਿਰਿਆ ਹੈ, ਇੱਕ ਓਪਨ ਡਾਈ ਪ੍ਰਕਿਰਿਆ ਹੈ ਜਿੱਥੇ ਕੰਮ ਦੇ ਟੁਕੜੇ ਨੂੰ ਦੋ ਫਲੈਟ ਡਾਈਜ਼ ਦੇ ਵਿਚਕਾਰ ਸੈਂਡਵਿਚ ਕੀਤਾ ਜਾਂਦਾ ਹੈ ਅਤੇ ਇੱਕ ਸੰਕੁਚਿਤ ਬਲ ਇਸਦੀ ਉਚਾਈ ਨੂੰ ਘਟਾਉਂਦਾ ਹੈ। ਜਿਵੇਂ ਕਿ ਉਚਾਈ ਹੈ reduced, ਕੰਮ ਦੇ ਟੁਕੜੇ ਦੀ ਚੌੜਾਈ ਵਧਦੀ ਹੈ। HEADING, ਇੱਕ ਪਰੇਸ਼ਾਨ ਫੋਰਜਿੰਗ ਪ੍ਰਕਿਰਿਆ ਵਿੱਚ ਸਿਲੰਡਰ ਸਟਾਕ ਸ਼ਾਮਲ ਹੁੰਦਾ ਹੈ ਜੋ ਇਸਦੇ ਅੰਤ ਵਿੱਚ ਪਰੇਸ਼ਾਨ ਹੁੰਦਾ ਹੈ ਅਤੇ ਇਸਦੇ ਕਰਾਸ ਸੈਕਸ਼ਨ ਨੂੰ ਸਥਾਨਕ ਤੌਰ 'ਤੇ ਵਧਾਇਆ ਜਾਂਦਾ ਹੈ। ਸਿਰਲੇਖ ਵਿੱਚ ਸਟਾਕ ਨੂੰ ਡਾਈ ਦੁਆਰਾ ਖੁਆਇਆ ਜਾਂਦਾ ਹੈ, ਜਾਅਲੀ ਅਤੇ ਫਿਰ ਲੰਬਾਈ ਵਿੱਚ ਕੱਟਿਆ ਜਾਂਦਾ ਹੈ। ਓਪਰੇਸ਼ਨ ਤੇਜ਼ੀ ਨਾਲ ਫਾਸਟਨਰਾਂ ਦੀ ਉੱਚ ਮਾਤਰਾ ਪੈਦਾ ਕਰਨ ਦੇ ਸਮਰੱਥ ਹੈ। ਜ਼ਿਆਦਾਤਰ ਇਹ ਇੱਕ ਠੰਡਾ ਕੰਮ ਕਰਨ ਵਾਲਾ ਓਪਰੇਸ਼ਨ ਹੁੰਦਾ ਹੈ ਕਿਉਂਕਿ ਇਹ ਨਹੁੰ ਸਿਰੇ, ਪੇਚ ਦੇ ਸਿਰੇ, ਨਟ ਅਤੇ ਬੋਲਟ ਬਣਾਉਣ ਲਈ ਵਰਤਿਆ ਜਾਂਦਾ ਹੈ ਜਿੱਥੇ ਸਮੱਗਰੀ ਨੂੰ ਮਜ਼ਬੂਤ ਕਰਨ ਦੀ ਲੋੜ ਹੁੰਦੀ ਹੈ। ਇੱਕ ਹੋਰ ਓਪਨ ਡਾਈ ਪ੍ਰਕਿਰਿਆ ਕੋਗਿੰਗ ਹੈ, ਜਿੱਥੇ ਕੰਮ ਦੇ ਟੁਕੜੇ ਨੂੰ ਹਰ ਪੜਾਅ ਦੇ ਨਾਲ ਕਦਮਾਂ ਦੀ ਇੱਕ ਲੜੀ ਵਿੱਚ ਜਾਅਲੀ ਬਣਾਇਆ ਜਾਂਦਾ ਹੈ ਜਿਸਦੇ ਨਤੀਜੇ ਵਜੋਂ ਸਮੱਗਰੀ ਦੀ ਸੰਕੁਚਨ ਹੁੰਦੀ ਹੈ ਅਤੇ ਵਰਕ ਪੀਸ ਦੀ ਲੰਬਾਈ ਦੇ ਨਾਲ ਓਪਨ ਡਾਈ ਦੀ ਅਗਲੀ ਗਤੀ ਹੁੰਦੀ ਹੈ। ਹਰ ਪੜਾਅ 'ਤੇ, ਮੋਟਾਈ ਘਟਾਈ ਜਾਂਦੀ ਹੈ ਅਤੇ ਲੰਬਾਈ ਥੋੜ੍ਹੀ ਜਿਹੀ ਵਧ ਜਾਂਦੀ ਹੈ। ਇਹ ਪ੍ਰਕਿਰਿਆ ਇੱਕ ਘਬਰਾਏ ਹੋਏ ਵਿਦਿਆਰਥੀ ਵਰਗੀ ਹੈ ਜੋ ਛੋਟੇ ਕਦਮਾਂ ਵਿੱਚ ਆਪਣੀ ਪੈਨਸਿਲ ਨੂੰ ਕੱਟਦਾ ਹੈ। ਫੁਲਰਿੰਗ ਨਾਮਕ ਇੱਕ ਪ੍ਰਕਿਰਿਆ ਇੱਕ ਹੋਰ ਓਪਨ ਡਾਈ ਫੋਰਜਿੰਗ ਵਿਧੀ ਹੈ ਜਿਸ ਨੂੰ ਅਸੀਂ ਅਕਸਰ ਹੋਰ ਮੈਟਲ ਫੋਰਜਿੰਗ ਓਪਰੇਸ਼ਨ ਹੋਣ ਤੋਂ ਪਹਿਲਾਂ ਵਰਕ ਪੀਸ ਵਿੱਚ ਸਮੱਗਰੀ ਨੂੰ ਵੰਡਣ ਲਈ ਇੱਕ ਪਹਿਲੇ ਕਦਮ ਵਜੋਂ ਤਾਇਨਾਤ ਕਰਦੇ ਹਾਂ। ਅਸੀਂ ਇਸਦੀ ਵਰਤੋਂ ਉਦੋਂ ਕਰਦੇ ਹਾਂ ਜਦੋਂ ਕੰਮ ਦੇ ਟੁਕੜੇ ਨੂੰ ਕਈ forging operations ਦੀ ਲੋੜ ਹੁੰਦੀ ਹੈ। ਓਪਰੇਸ਼ਨ ਵਿੱਚ, ਕਨਵੈਕਸ ਸਤਹਾਂ ਦੇ ਵਿਗਾੜ ਦੇ ਨਾਲ ਮਰੋ ਅਤੇ ਧਾਤ ਦਾ ਵਹਾਅ ਦੋਵਾਂ ਪਾਸਿਆਂ ਤੋਂ ਬਾਹਰ ਆ ਜਾਂਦਾ ਹੈ। ਫੁਲਰਿੰਗ ਦੇ ਸਮਾਨ ਪ੍ਰਕਿਰਿਆ, ਦੂਜੇ ਪਾਸੇ EDGING ਵਿੱਚ ਕੰਮ ਦੇ ਟੁਕੜੇ ਨੂੰ ਵਿਗਾੜਨ ਲਈ ਅਵਤਲ ਸਤਹਾਂ ਦੇ ਨਾਲ ਖੁੱਲ੍ਹੀ ਡਾਈ ਸ਼ਾਮਲ ਹੁੰਦੀ ਹੈ। ਕਿਨਾਰਾ ਵੀ ਬਾਅਦ ਦੇ ਫੋਰਜਿੰਗ ਓਪਰੇਸ਼ਨਾਂ ਲਈ ਇੱਕ ਤਿਆਰੀ ਦੀ ਪ੍ਰਕਿਰਿਆ ਹੈ ਜੋ ਸਮੱਗਰੀ ਨੂੰ ਦੋਵਾਂ ਪਾਸਿਆਂ ਤੋਂ ਕੇਂਦਰ ਵਿੱਚ ਇੱਕ ਖੇਤਰ ਵਿੱਚ ਵਹਾਅ ਦਿੰਦਾ ਹੈ। ਇਮਪ੍ਰੈਸ਼ਨ ਡਾਈ ਫੋਰਜਿੰਗ ਜਾਂ ਕਲੋਜ਼ਡ ਡਾਈ ਫੋਰਜਿੰਗ ਜਿਵੇਂ ਕਿ ਇਸਨੂੰ ਡਾਈ / ਮੋਲਡ ਦੀ ਵਰਤੋਂ ਵੀ ਕਿਹਾ ਜਾਂਦਾ ਹੈ ਜੋ ਸਮੱਗਰੀ ਨੂੰ ਸੰਕੁਚਿਤ ਕਰਦਾ ਹੈ ਅਤੇ ਇਸਦੇ ਪ੍ਰਵਾਹ ਨੂੰ ਆਪਣੇ ਅੰਦਰ ਸੀਮਤ ਕਰਦਾ ਹੈ। ਡਾਈ ਬੰਦ ਹੋ ਜਾਂਦੀ ਹੈ ਅਤੇ ਸਮੱਗਰੀ ਡਾਈ/ਮੋਲਡ ਕੈਵਿਟੀ ਦਾ ਰੂਪ ਲੈ ਲੈਂਦੀ ਹੈ। ਸ਼ੁੱਧਤਾ ਫੋਰਜਿੰਗ, ਇੱਕ ਪ੍ਰਕਿਰਿਆ ਜਿਸ ਵਿੱਚ ਵਿਸ਼ੇਸ਼ ਉਪਕਰਣਾਂ ਅਤੇ ਉੱਲੀ ਦੀ ਲੋੜ ਹੁੰਦੀ ਹੈ, ਬਿਨਾਂ ਜਾਂ ਬਹੁਤ ਘੱਟ ਫਲੈਸ਼ ਵਾਲੇ ਹਿੱਸੇ ਪੈਦਾ ਕਰਦੀ ਹੈ। ਦੂਜੇ ਸ਼ਬਦਾਂ ਵਿੱਚ, ਭਾਗਾਂ ਦੇ ਨੇੜੇ ਅੰਤਿਮ ਮਾਪ ਹੋਣਗੇ। ਇਸ ਪ੍ਰਕਿਰਿਆ ਵਿੱਚ ਸਮੱਗਰੀ ਦੀ ਇੱਕ ਚੰਗੀ ਤਰ੍ਹਾਂ ਨਿਯੰਤਰਿਤ ਮਾਤਰਾ ਨੂੰ ਧਿਆਨ ਨਾਲ ਪਾਇਆ ਜਾਂਦਾ ਹੈ ਅਤੇ ਉੱਲੀ ਦੇ ਅੰਦਰ ਰੱਖਿਆ ਜਾਂਦਾ ਹੈ। ਅਸੀਂ ਇਸ ਵਿਧੀ ਨੂੰ ਗੁੰਝਲਦਾਰ ਆਕਾਰਾਂ ਲਈ ਪਤਲੇ ਭਾਗਾਂ, ਛੋਟੇ ਸਹਿਣਸ਼ੀਲਤਾਵਾਂ ਅਤੇ ਡਰਾਫਟ ਐਂਗਲਾਂ ਲਈ ਲਾਗੂ ਕਰਦੇ ਹਾਂ ਅਤੇ ਜਦੋਂ ਮੋਲਡ ਅਤੇ ਸਾਜ਼ੋ-ਸਾਮਾਨ ਦੀ ਲਾਗਤ ਨੂੰ ਜਾਇਜ਼ ਠਹਿਰਾਉਣ ਲਈ ਮਾਤਰਾਵਾਂ ਕਾਫ਼ੀ ਵੱਡੀਆਂ ਹੁੰਦੀਆਂ ਹਨ। • ਫਲੈਸ਼ ਰਹਿਤ ਫੋਰਜਿੰਗ: ਵਰਕਪੀਸ ਨੂੰ ਡਾਈ ਵਿੱਚ ਇਸ ਤਰੀਕੇ ਨਾਲ ਰੱਖਿਆ ਜਾਂਦਾ ਹੈ ਕਿ ਕੋਈ ਵੀ ਸਮੱਗਰੀ ਫਲੈਸ਼ ਬਣਾਉਣ ਲਈ ਕੈਵਿਟੀ ਵਿੱਚੋਂ ਬਾਹਰ ਨਾ ਨਿਕਲ ਸਕੇ। ਇਸ ਲਈ ਕਿਸੇ ਅਣਚਾਹੇ ਫਲੈਸ਼ ਟ੍ਰਿਮਿੰਗ ਦੀ ਲੋੜ ਨਹੀਂ ਹੈ। ਇਹ ਇੱਕ ਸ਼ੁੱਧਤਾ ਬਣਾਉਣ ਦੀ ਪ੍ਰਕਿਰਿਆ ਹੈ ਅਤੇ ਇਸ ਲਈ ਵਰਤੀ ਗਈ ਸਮੱਗਰੀ ਦੀ ਮਾਤਰਾ ਦੇ ਨਜ਼ਦੀਕੀ ਨਿਯੰਤਰਣ ਦੀ ਲੋੜ ਹੁੰਦੀ ਹੈ। • ਮੈਟਲ ਸਵੈਗਿੰਗ ਜਾਂ ਰੇਡੀਅਲ ਫੋਰਜਿੰਗ: ਇੱਕ ਕੰਮ ਦੇ ਟੁਕੜੇ 'ਤੇ ਘੇਰਾਬੰਦੀ ਨਾਲ ਡਾਈ ਅਤੇ ਜਾਅਲੀ ਦੁਆਰਾ ਕਾਰਵਾਈ ਕੀਤੀ ਜਾਂਦੀ ਹੈ। ਅੰਦਰੂਨੀ ਕੰਮ ਦੇ ਟੁਕੜੇ ਦੀ ਜਿਓਮੈਟਰੀ ਨੂੰ ਬਣਾਉਣ ਲਈ ਇੱਕ ਮੈਂਡਰਲ ਦੀ ਵਰਤੋਂ ਵੀ ਕੀਤੀ ਜਾ ਸਕਦੀ ਹੈ। ਸਵੈਜਿੰਗ ਓਪਰੇਸ਼ਨ ਵਿੱਚ ਵਰਕ ਪੀਸ ਨੂੰ ਆਮ ਤੌਰ 'ਤੇ ਪ੍ਰਤੀ ਸਕਿੰਟ ਕਈ ਸਟ੍ਰੋਕ ਪ੍ਰਾਪਤ ਹੁੰਦੇ ਹਨ। ਸਵੈਗਿੰਗ ਦੁਆਰਾ ਪੈਦਾ ਕੀਤੀਆਂ ਆਮ ਚੀਜ਼ਾਂ ਪੁਆਇੰਟ ਟਿਪ ਟੂਲ, ਟੇਪਰਡ ਬਾਰ, ਸਕ੍ਰਿਊਡ੍ਰਾਈਵਰ ਹਨ। • ਧਾਤੂ ਵਿੰਨ੍ਹਣਾ: ਅਸੀਂ ਇਸ ਓਪਰੇਸ਼ਨ ਨੂੰ ਪੁਰਜ਼ਿਆਂ ਦੇ ਨਿਰਮਾਣ ਵਿੱਚ ਇੱਕ ਵਾਧੂ ਕਾਰਵਾਈ ਵਜੋਂ ਅਕਸਰ ਵਰਤਦੇ ਹਾਂ। ਕੰਮ ਦੇ ਟੁਕੜੇ ਦੀ ਸਤ੍ਹਾ 'ਤੇ ਇਸ ਨੂੰ ਤੋੜੇ ਬਿਨਾਂ ਵਿੰਨ੍ਹਣ ਨਾਲ ਇੱਕ ਮੋਰੀ ਜਾਂ ਕੈਵਿਟੀ ਬਣਾਈ ਜਾਂਦੀ ਹੈ। ਕਿਰਪਾ ਕਰਕੇ ਨੋਟ ਕਰੋ ਕਿ ਵਿੰਨ੍ਹਣਾ ਡ੍ਰਿਲਿੰਗ ਨਾਲੋਂ ਵੱਖਰਾ ਹੈ ਜਿਸਦਾ ਨਤੀਜਾ ਇੱਕ ਮੋਰੀ ਵਿੱਚ ਹੁੰਦਾ ਹੈ। • ਹੌਬਿੰਗ: ਲੋੜੀਦੀ ਜਿਓਮੈਟਰੀ ਵਾਲਾ ਇੱਕ ਪੰਚ ਵਰਕ ਪੀਸ ਵਿੱਚ ਦਬਾਇਆ ਜਾਂਦਾ ਹੈ ਅਤੇ ਲੋੜੀਂਦੇ ਆਕਾਰ ਦੇ ਨਾਲ ਇੱਕ ਕੈਵਿਟੀ ਬਣਾਉਂਦਾ ਹੈ। ਅਸੀਂ ਇਸ ਪੰਚ ਨੂੰ HOB ਕਹਿੰਦੇ ਹਾਂ। ਓਪਰੇਸ਼ਨ ਵਿੱਚ ਉੱਚ ਦਬਾਅ ਸ਼ਾਮਲ ਹੁੰਦਾ ਹੈ ਅਤੇ ਠੰਡੇ ਸਮੇਂ ਕੀਤਾ ਜਾਂਦਾ ਹੈ। ਨਤੀਜੇ ਵਜੋਂ ਸਮੱਗਰੀ ਠੰਡੀ ਹੁੰਦੀ ਹੈ ਅਤੇ ਤਣਾਅ ਸਖ਼ਤ ਹੋ ਜਾਂਦੀ ਹੈ। ਇਸ ਲਈ ਇਹ ਪ੍ਰਕਿਰਿਆ ਹੋਰ ਨਿਰਮਾਣ ਪ੍ਰਕਿਰਿਆਵਾਂ ਲਈ ਮੋਲਡ, ਡਾਈ ਅਤੇ ਕੈਵਿਟੀ ਬਣਾਉਣ ਲਈ ਬਹੁਤ ਢੁਕਵੀਂ ਹੈ। ਇੱਕ ਵਾਰ ਹੋਬ ਦਾ ਨਿਰਮਾਣ ਹੋ ਜਾਣ ਤੋਂ ਬਾਅਦ, ਕੋਈ ਵੀ ਇੱਕ-ਇੱਕ ਕਰਕੇ ਮਸ਼ੀਨ ਦੀ ਲੋੜ ਤੋਂ ਬਿਨਾਂ ਕਈ ਇੱਕੋ ਜਿਹੇ ਕੈਵਿਟੀਜ਼ ਨੂੰ ਆਸਾਨੀ ਨਾਲ ਬਣਾ ਸਕਦਾ ਹੈ। • ਰੋਲ ਫੋਰਜਿੰਗ ਜਾਂ ਰੋਲ ਫਾਰਮਿੰਗ: ਧਾਤ ਦੇ ਹਿੱਸੇ ਨੂੰ ਆਕਾਰ ਦੇਣ ਲਈ ਦੋ ਵਿਰੋਧੀ ਰੋਲ ਵਰਤੇ ਜਾਂਦੇ ਹਨ। ਕੰਮ ਦੇ ਟੁਕੜੇ ਨੂੰ ਰੋਲਾਂ ਵਿੱਚ ਖੁਆਇਆ ਜਾਂਦਾ ਹੈ, ਰੋਲ ਕੰਮ ਨੂੰ ਮੋੜਦੇ ਹਨ ਅਤੇ ਪਾੜੇ ਵਿੱਚ ਖਿੱਚਦੇ ਹਨ, ਕੰਮ ਨੂੰ ਫਿਰ ਰੋਲ ਦੇ ਗਰੋਵਡ ਹਿੱਸੇ ਦੁਆਰਾ ਖੁਆਇਆ ਜਾਂਦਾ ਹੈ ਅਤੇ ਸੰਕੁਚਿਤ ਬਲ ਸਮੱਗਰੀ ਨੂੰ ਇਸਦਾ ਲੋੜੀਂਦਾ ਆਕਾਰ ਦਿੰਦੇ ਹਨ। ਇਹ ਇੱਕ ਰੋਲਿੰਗ ਪ੍ਰਕਿਰਿਆ ਨਹੀਂ ਹੈ ਪਰ ਇੱਕ ਫੋਰਜਿੰਗ ਪ੍ਰਕਿਰਿਆ ਹੈ, ਕਿਉਂਕਿ ਇਹ ਇੱਕ ਨਿਰੰਤਰ ਕਾਰਵਾਈ ਦੀ ਬਜਾਏ ਇੱਕ ਵੱਖਰਾ ਹੈ। ਰੋਲ ਗਰੋਵਜ਼ 'ਤੇ ਜਿਓਮੈਟਰੀ ਸਮੱਗਰੀ ਨੂੰ ਲੋੜੀਂਦੇ ਆਕਾਰ ਅਤੇ ਜਿਓਮੈਟਰੀ ਲਈ ਤਿਆਰ ਕਰਦੀ ਹੈ। ਇਹ ਗਰਮ ਕੀਤਾ ਜਾਂਦਾ ਹੈ. ਫੋਰਜਿੰਗ ਪ੍ਰਕਿਰਿਆ ਹੋਣ ਦੇ ਕਾਰਨ ਇਹ ਸ਼ਾਨਦਾਰ ਮਕੈਨੀਕਲ ਵਿਸ਼ੇਸ਼ਤਾਵਾਂ ਵਾਲੇ ਹਿੱਸੇ ਪੈਦਾ ਕਰਦੀ ਹੈ ਅਤੇ ਇਸਲਈ ਅਸੀਂ ਇਸਨੂੰ ਨਿਰਮਾਣ ਆਟੋਮੋਟਿਵ ਪਾਰਟਸ ਜਿਵੇਂ ਕਿ ਸ਼ਾਫਟਾਂ ਲਈ ਵਰਤਦੇ ਹਾਂ ਜਿਨ੍ਹਾਂ ਨੂੰ ਸਖ਼ਤ ਕੰਮ ਦੇ ਮਾਹੌਲ ਵਿੱਚ ਅਸਧਾਰਨ ਧੀਰਜ ਰੱਖਣ ਦੀ ਲੋੜ ਹੁੰਦੀ ਹੈ। • ਔਰਬਿਟਲ ਫੋਰਜਿੰਗ: ਕੰਮ ਦੇ ਟੁਕੜੇ ਨੂੰ ਇੱਕ ਫੋਰਜਿੰਗ ਡਾਈ ਕੈਵਿਟੀ ਵਿੱਚ ਰੱਖਿਆ ਜਾਂਦਾ ਹੈ ਅਤੇ ਇੱਕ ਉਪਰਲੇ ਡਾਈ ਦੁਆਰਾ ਜਾਅਲੀ ਬਣਾਇਆ ਜਾਂਦਾ ਹੈ ਜੋ ਇੱਕ ਔਰਬਿਟਲ ਮਾਰਗ ਵਿੱਚ ਯਾਤਰਾ ਕਰਦਾ ਹੈ ਕਿਉਂਕਿ ਇਹ ਇੱਕ ਝੁਕੇ ਹੋਏ ਧੁਰੇ 'ਤੇ ਘੁੰਮਦਾ ਹੈ। ਹਰੇਕ ਕ੍ਰਾਂਤੀ 'ਤੇ, ਉਪਰਲਾ ਡਾਈ ਪੂਰੇ ਕੰਮ ਦੇ ਟੁਕੜੇ ਨੂੰ ਸੰਕੁਚਿਤ ਬਲਾਂ ਨੂੰ ਲਾਗੂ ਕਰਦਾ ਹੈ। ਇਹਨਾਂ ਕ੍ਰਾਂਤੀਆਂ ਨੂੰ ਕਈ ਵਾਰ ਦੁਹਰਾਉਣ ਨਾਲ, ਕਾਫ਼ੀ ਫੋਰਜਿੰਗ ਕੀਤੀ ਜਾਂਦੀ ਹੈ। ਇਸ ਨਿਰਮਾਣ ਤਕਨੀਕ ਦੇ ਫਾਇਦੇ ਇਸਦਾ ਘੱਟ ਸ਼ੋਰ ਸੰਚਾਲਨ ਅਤੇ ਲੋੜੀਂਦੇ ਘੱਟ ਬਲ ਹਨ। ਦੂਜੇ ਸ਼ਬਦਾਂ ਵਿੱਚ, ਛੋਟੀਆਂ ਤਾਕਤਾਂ ਦੇ ਨਾਲ ਇੱਕ ਡਾਈ ਦੇ ਸੰਪਰਕ ਵਿੱਚ ਆਉਣ ਵਾਲੇ ਵਰਕ ਪੀਸ ਦੇ ਇੱਕ ਹਿੱਸੇ 'ਤੇ ਵੱਡੇ ਦਬਾਅ ਨੂੰ ਲਾਗੂ ਕਰਨ ਲਈ ਇੱਕ ਧੁਰੇ ਦੇ ਦੁਆਲੇ ਇੱਕ ਭਾਰੀ ਡਾਈ ਨੂੰ ਘੁੰਮਾ ਸਕਦਾ ਹੈ। ਡਿਸਕ ਜਾਂ ਕੋਨਿਕਲ ਆਕਾਰ ਦੇ ਹਿੱਸੇ ਕਈ ਵਾਰ ਇਸ ਪ੍ਰਕਿਰਿਆ ਲਈ ਵਧੀਆ ਫਿਟ ਹੁੰਦੇ ਹਨ। • ਰਿੰਗ ਫੋਰਜਿੰਗ: ਅਸੀਂ ਅਕਸਰ ਸਹਿਜ ਰਿੰਗ ਬਣਾਉਣ ਲਈ ਵਰਤਦੇ ਹਾਂ। ਸਟਾਕ ਨੂੰ ਲੰਬਾਈ ਤੱਕ ਕੱਟਿਆ ਜਾਂਦਾ ਹੈ, ਪਰੇਸ਼ਾਨ ਕੀਤਾ ਜਾਂਦਾ ਹੈ ਅਤੇ ਫਿਰ ਇੱਕ ਕੇਂਦਰੀ ਮੋਰੀ ਬਣਾਉਣ ਲਈ ਸਾਰੇ ਤਰੀਕੇ ਨਾਲ ਵਿੰਨ੍ਹਿਆ ਜਾਂਦਾ ਹੈ। ਫਿਰ ਇਸਨੂੰ ਇੱਕ ਮੰਡਰੇਲ ਉੱਤੇ ਰੱਖਿਆ ਜਾਂਦਾ ਹੈ ਅਤੇ ਇੱਕ ਫੋਰਜਿੰਗ ਡਾਈ ਇਸ ਨੂੰ ਉੱਪਰੋਂ ਹਥੌੜੇ ਮਾਰਦਾ ਹੈ ਕਿਉਂਕਿ ਰਿੰਗ ਨੂੰ ਹੌਲੀ ਹੌਲੀ ਘੁੰਮਾਇਆ ਜਾਂਦਾ ਹੈ ਜਦੋਂ ਤੱਕ ਲੋੜੀਂਦੇ ਮਾਪ ਪ੍ਰਾਪਤ ਨਹੀਂ ਹੋ ਜਾਂਦੇ। • ਰਾਈਵਟਿੰਗ: ਪੁਰਜ਼ਿਆਂ ਨੂੰ ਜੋੜਨ ਦੀ ਇੱਕ ਆਮ ਪ੍ਰਕਿਰਿਆ, ਪੁਰਜ਼ਿਆਂ ਰਾਹੀਂ ਪਹਿਲਾਂ ਤੋਂ ਬਣੇ ਛੇਕਾਂ ਵਿੱਚ ਪਾਈ ਸਿੱਧੀ ਧਾਤ ਦੇ ਟੁਕੜੇ ਨਾਲ ਸ਼ੁਰੂ ਹੁੰਦੀ ਹੈ। ਇਸ ਤੋਂ ਬਾਅਦ ਧਾਤ ਦੇ ਟੁਕੜੇ ਦੇ ਦੋਵੇਂ ਸਿਰੇ ਉੱਪਰਲੇ ਅਤੇ ਹੇਠਲੇ ਡਾਈ ਦੇ ਵਿਚਕਾਰ ਜੋੜ ਨੂੰ ਨਿਚੋੜ ਕੇ ਜਾਅਲੀ ਕੀਤੇ ਜਾਂਦੇ ਹਨ। • ਸਿੱਕਾ ਬਣਾਉਣਾ: ਮਕੈਨੀਕਲ ਪ੍ਰੈੱਸ ਦੁਆਰਾ ਕੀਤੀ ਜਾਂਦੀ ਇੱਕ ਹੋਰ ਪ੍ਰਸਿੱਧ ਪ੍ਰਕਿਰਿਆ, ਥੋੜੀ ਦੂਰੀ 'ਤੇ ਵੱਡੀਆਂ ਸ਼ਕਤੀਆਂ ਨੂੰ ਲਗਾ ਕੇ। ਨਾਮ "ਸਿੱਕਾ" ਉਹਨਾਂ ਬਾਰੀਕ ਵੇਰਵਿਆਂ ਤੋਂ ਆਉਂਦਾ ਹੈ ਜੋ ਧਾਤ ਦੇ ਸਿੱਕਿਆਂ ਦੀਆਂ ਸਤਹਾਂ 'ਤੇ ਜਾਅਲੀ ਹੁੰਦੇ ਹਨ। ਇਹ ਜਿਆਦਾਤਰ ਉਤਪਾਦ ਲਈ ਇੱਕ ਮੁਕੰਮਲ ਪ੍ਰਕਿਰਿਆ ਹੈ ਜਿੱਥੇ ਡਾਈ ਦੁਆਰਾ ਲਾਗੂ ਕੀਤੇ ਗਏ ਵੱਡੇ ਬਲ ਦੇ ਨਤੀਜੇ ਵਜੋਂ ਸਤ੍ਹਾ 'ਤੇ ਵਧੀਆ ਵੇਰਵੇ ਪ੍ਰਾਪਤ ਕੀਤੇ ਜਾਂਦੇ ਹਨ ਜੋ ਇਹਨਾਂ ਵੇਰਵਿਆਂ ਨੂੰ ਕੰਮ ਦੇ ਟੁਕੜੇ ਵਿੱਚ ਤਬਦੀਲ ਕਰਦੇ ਹਨ। • ਮੈਟਲ ਬਾਲ ਫੋਰਜਿੰਗ: ਬਾਲ ਬੇਅਰਿੰਗਾਂ ਵਰਗੇ ਉਤਪਾਦਾਂ ਲਈ ਉੱਚ ਗੁਣਵੱਤਾ ਵਾਲੇ ਸਟੀਕ ਤੌਰ 'ਤੇ ਨਿਰਮਿਤ ਮੈਟਲ ਬਾਲਾਂ ਦੀ ਲੋੜ ਹੁੰਦੀ ਹੈ। SKEW ROLLING ਨਾਮਕ ਇੱਕ ਤਕਨੀਕ ਵਿੱਚ, ਅਸੀਂ ਦੋ ਵਿਰੋਧੀ ਰੋਲਾਂ ਦੀ ਵਰਤੋਂ ਕਰਦੇ ਹਾਂ ਜੋ ਲਗਾਤਾਰ ਘੁੰਮਦੇ ਰਹਿੰਦੇ ਹਨ ਕਿਉਂਕਿ ਸਟਾਕ ਨੂੰ ਲਗਾਤਾਰ ਰੋਲ ਵਿੱਚ ਖੁਆਇਆ ਜਾ ਰਿਹਾ ਹੈ। ਦੋ ਰੋਲ ਦੇ ਇੱਕ ਸਿਰੇ 'ਤੇ ਧਾਤ ਦੇ ਗੋਲਿਆਂ ਨੂੰ ਉਤਪਾਦ ਦੇ ਰੂਪ ਵਿੱਚ ਬਾਹਰ ਕੱਢਿਆ ਜਾਂਦਾ ਹੈ। ਮੈਟਲ ਬਾਲ ਫੋਰਜਿੰਗ ਲਈ ਇੱਕ ਦੂਜੀ ਵਿਧੀ ਡਾਈ ਦੀ ਵਰਤੋਂ ਕਰ ਰਹੀ ਹੈ ਜੋ ਉਹਨਾਂ ਦੇ ਵਿਚਕਾਰ ਰੱਖੇ ਸਮੱਗਰੀ ਸਟਾਕ ਨੂੰ ਘੁੱਟ ਕੇ ਮੋਲਡ ਕੈਵਿਟੀ ਦਾ ਗੋਲਾਕਾਰ ਆਕਾਰ ਲੈਂਦੀ ਹੈ। ਕਈ ਵਾਰ ਪੈਦਾ ਕੀਤੀਆਂ ਗੇਂਦਾਂ ਨੂੰ ਉੱਚ ਗੁਣਵੱਤਾ ਵਾਲੇ ਉਤਪਾਦ ਬਣਨ ਲਈ ਕੁਝ ਵਾਧੂ ਕਦਮਾਂ ਦੀ ਲੋੜ ਹੁੰਦੀ ਹੈ ਜਿਵੇਂ ਕਿ ਫਿਨਿਸ਼ਿੰਗ ਅਤੇ ਪਾਲਿਸ਼ ਕਰਨਾ। • ISOTHERMAL ਫੋਰਜਿੰਗ / ਹੌਟ ਡਾਈ ਫੋਰਜਿੰਗ : ਇੱਕ ਮਹਿੰਗੀ ਪ੍ਰਕਿਰਿਆ ਉਦੋਂ ਹੀ ਕੀਤੀ ਜਾਂਦੀ ਹੈ ਜਦੋਂ ਲਾਭ / ਲਾਗਤ ਮੁੱਲ ਜਾਇਜ਼ ਹੋਵੇ। ਇੱਕ ਗਰਮ ਕੰਮ ਕਰਨ ਦੀ ਪ੍ਰਕਿਰਿਆ ਜਿੱਥੇ ਡਾਈ ਨੂੰ ਕੰਮ ਦੇ ਟੁਕੜੇ ਦੇ ਬਰਾਬਰ ਤਾਪਮਾਨ 'ਤੇ ਗਰਮ ਕੀਤਾ ਜਾਂਦਾ ਹੈ। ਕਿਉਂਕਿ ਮਰਨ ਅਤੇ ਕੰਮ ਦੋਵੇਂ ਇੱਕੋ ਜਿਹੇ ਤਾਪਮਾਨ ਦੇ ਹੁੰਦੇ ਹਨ, ਕੋਈ ਕੂਲਿੰਗ ਨਹੀਂ ਹੁੰਦੀ ਹੈ ਅਤੇ ਧਾਤ ਦੇ ਵਹਾਅ ਦੀਆਂ ਵਿਸ਼ੇਸ਼ਤਾਵਾਂ ਵਿੱਚ ਸੁਧਾਰ ਹੁੰਦਾ ਹੈ। ਇਹ ਓਪਰੇਸ਼ਨ ਸੁਪਰ ਅਲੌਇਸ ਅਤੇ ਘਟੀਆ ਫੋਰਜੀਬਿਲਟੀ ਵਾਲੀਆਂ ਸਮੱਗਰੀਆਂ ਅਤੇ ਸਮੱਗਰੀਆਂ ਲਈ ਵਧੀਆ ਫਿੱਟ ਹੈ ਜਿਸਦੀ ਮਕੈਨੀਕਲ ਵਿਸ਼ੇਸ਼ਤਾਵਾਂ ਛੋਟੇ ਤਾਪਮਾਨ ਗਰੇਡੀਐਂਟ ਅਤੇ ਤਬਦੀਲੀਆਂ ਲਈ ਬਹੁਤ ਸੰਵੇਦਨਸ਼ੀਲ ਹੁੰਦੀਆਂ ਹਨ। • ਮੈਟਲ ਸਾਈਜ਼ਿੰਗ: ਇਹ ਇੱਕ ਠੰਡੀ ਮੁਕੰਮਲ ਪ੍ਰਕਿਰਿਆ ਹੈ। ਪਦਾਰਥ ਦਾ ਪ੍ਰਵਾਹ ਉਸ ਦਿਸ਼ਾ ਦੇ ਅਪਵਾਦ ਦੇ ਨਾਲ ਸਾਰੀਆਂ ਦਿਸ਼ਾਵਾਂ ਵਿੱਚ ਅਪ੍ਰਬੰਧਿਤ ਹੁੰਦਾ ਹੈ ਜਿਸ ਵਿੱਚ ਬਲ ਲਾਗੂ ਕੀਤਾ ਜਾਂਦਾ ਹੈ। ਨਤੀਜੇ ਵਜੋਂ, ਬਹੁਤ ਵਧੀਆ ਸਤਹ ਮੁਕੰਮਲ ਅਤੇ ਸਹੀ ਮਾਪ ਪ੍ਰਾਪਤ ਹੁੰਦੇ ਹਨ. • HIGH ਐਨਰਜੀ ਰੇਟ ਫੋਰਜਿੰਗ: ਤਕਨੀਕ ਵਿੱਚ ਇੱਕ ਪਿਸਟਨ ਦੀ ਬਾਂਹ ਨਾਲ ਜੁੜਿਆ ਇੱਕ ਉਪਰਲਾ ਮੋਲਡ ਸ਼ਾਮਲ ਹੁੰਦਾ ਹੈ ਜੋ ਇੱਕ ਐਸਪਾਰਕ ਦੁਆਰਾ ਬਾਲਣ-ਹਵਾ ਮਿਸ਼ਰਣ ਦੇ ਰੂਪ ਵਿੱਚ ਤੇਜ਼ੀ ਨਾਲ ਧੱਕਿਆ ਜਾਂਦਾ ਹੈ। ਇਹ ਇੱਕ ਕਾਰ ਇੰਜਣ ਵਿੱਚ ਪਿਸਟਨ ਦੇ ਸੰਚਾਲਨ ਵਰਗਾ ਹੈ. ਮੋਲਡ ਕੰਮ ਦੇ ਟੁਕੜੇ ਨੂੰ ਬਹੁਤ ਤੇਜ਼ੀ ਨਾਲ ਹਿੱਟ ਕਰਦਾ ਹੈ ਅਤੇ ਫਿਰ ਬੈਕਪ੍ਰੈਸ਼ਰ ਦੇ ਕਾਰਨ ਬਹੁਤ ਤੇਜ਼ੀ ਨਾਲ ਆਪਣੀ ਅਸਲ ਸਥਿਤੀ 'ਤੇ ਵਾਪਸ ਆ ਜਾਂਦਾ ਹੈ। ਕੰਮ ਕੁਝ ਮਿਲੀਸਕਿੰਟਾਂ ਵਿੱਚ ਜਾਅਲੀ ਹੋ ਜਾਂਦਾ ਹੈ ਅਤੇ ਇਸਲਈ ਕੰਮ ਨੂੰ ਠੰਢਾ ਹੋਣ ਦਾ ਸਮਾਂ ਨਹੀਂ ਮਿਲਦਾ। ਇਹ ਉਹਨਾਂ ਹਿੱਸਿਆਂ ਲਈ ਲਾਭਦਾਇਕ ਹੈ ਜਿਨ੍ਹਾਂ ਵਿੱਚ ਬਹੁਤ ਜ਼ਿਆਦਾ ਤਾਪਮਾਨ ਸੰਵੇਦਨਸ਼ੀਲ ਮਕੈਨੀਕਲ ਵਿਸ਼ੇਸ਼ਤਾਵਾਂ ਹੁੰਦੀਆਂ ਹਨ। ਦੂਜੇ ਸ਼ਬਦਾਂ ਵਿਚ ਇਹ ਪ੍ਰਕਿਰਿਆ ਇੰਨੀ ਤੇਜ਼ ਹੈ ਕਿ ਹਿੱਸਾ ਲਗਾਤਾਰ ਤਾਪਮਾਨ ਦੇ ਅਧੀਨ ਬਣਦਾ ਹੈ ਅਤੇ ਮੋਲਡ/ਵਰਕ ਪੀਸ ਇੰਟਰਫੇਸ 'ਤੇ ਤਾਪਮਾਨ ਗਰੇਡੀਐਂਟ ਨਹੀਂ ਹੋਵੇਗਾ। • ਡਾਈ ਫੋਰਜਿੰਗ ਵਿੱਚ, ਧਾਤ ਨੂੰ ਦੋ ਮੇਲ ਖਾਂਦੇ ਸਟੀਲ ਬਲਾਕਾਂ ਦੇ ਵਿਚਕਾਰ ਕੁੱਟਿਆ ਜਾਂਦਾ ਹੈ ਜਿਸ ਵਿੱਚ ਵਿਸ਼ੇਸ਼ ਆਕਾਰ ਹੁੰਦੇ ਹਨ, ਜਿਸਨੂੰ ਡਾਈ ਕਿਹਾ ਜਾਂਦਾ ਹੈ। ਜਦੋਂ ਧਾਤ ਨੂੰ ਡਾਈਜ਼ ਦੇ ਵਿਚਕਾਰ ਹਥੌੜਾ ਕੀਤਾ ਜਾਂਦਾ ਹੈ, ਤਾਂ ਇਹ ਉਹੀ ਆਕਾਰ ਧਾਰਨ ਕਰਦਾ ਹੈ ਜਿਵੇਂ ਕਿ ਡਾਈ ਵਿੱਚ ਆਕਾਰ ਹੁੰਦਾ ਹੈ। ਜਦੋਂ ਇਹ ਆਪਣੀ ਅੰਤਿਮ ਸ਼ਕਲ 'ਤੇ ਪਹੁੰਚ ਜਾਂਦਾ ਹੈ, ਤਾਂ ਇਸਨੂੰ ਠੰਡਾ ਕਰਨ ਲਈ ਬਾਹਰ ਕੱਢਿਆ ਜਾਂਦਾ ਹੈ। ਇਹ ਪ੍ਰਕਿਰਿਆ ਮਜ਼ਬੂਤ ਪੁਰਜ਼ੇ ਪੈਦਾ ਕਰਦੀ ਹੈ ਜੋ ਇੱਕ ਸਟੀਕ ਆਕਾਰ ਦੇ ਹੁੰਦੇ ਹਨ, ਪਰ ਵਿਸ਼ੇਸ਼ ਡਾਈਜ਼ ਲਈ ਇੱਕ ਵੱਡੇ ਨਿਵੇਸ਼ ਦੀ ਲੋੜ ਹੁੰਦੀ ਹੈ। ਅਪਸੈਟ ਫੋਰਜਿੰਗ ਧਾਤੂ ਦੇ ਟੁਕੜੇ ਨੂੰ ਸਮਤਲ ਕਰਕੇ ਉਸ ਦੇ ਵਿਆਸ ਨੂੰ ਵਧਾਉਂਦੀ ਹੈ। ਇਹ ਆਮ ਤੌਰ 'ਤੇ ਛੋਟੇ ਹਿੱਸੇ ਬਣਾਉਣ ਲਈ ਵਰਤਿਆ ਜਾਂਦਾ ਹੈ, ਖਾਸ ਤੌਰ 'ਤੇ ਬੋਲਟ ਅਤੇ ਨਹੁੰ ਵਰਗੇ ਫਾਸਟਨਰਾਂ 'ਤੇ ਸਿਰ ਬਣਾਉਣ ਲਈ। • ਪਾਊਡਰ ਮੈਟਲਰਜੀ / ਪਾਊਡਰ ਪ੍ਰੋਸੈਸਿੰਗ: ਜਿਵੇਂ ਕਿ ਨਾਮ ਤੋਂ ਭਾਵ ਹੈ, ਇਸ ਵਿੱਚ ਪਾਊਡਰਾਂ ਤੋਂ ਕੁਝ ਜਿਓਮੈਟਰੀ ਅਤੇ ਆਕਾਰਾਂ ਦੇ ਠੋਸ ਹਿੱਸੇ ਬਣਾਉਣ ਲਈ ਨਿਰਮਾਣ ਪ੍ਰਕਿਰਿਆਵਾਂ ਸ਼ਾਮਲ ਹੁੰਦੀਆਂ ਹਨ। ਜੇਕਰ ਇਸ ਮਕਸਦ ਲਈ ਮੈਟਲ ਪਾਊਡਰ ਵਰਤੇ ਜਾਂਦੇ ਹਨ ਤਾਂ ਇਹ ਪਾਊਡਰ ਧਾਤੂ ਵਿਗਿਆਨ ਦਾ ਖੇਤਰ ਹੈ ਅਤੇ ਜੇਕਰ ਗੈਰ-ਧਾਤੂ ਪਾਊਡਰ ਵਰਤੇ ਜਾਂਦੇ ਹਨ ਤਾਂ ਇਹ ਪਾਊਡਰ ਪ੍ਰੋਸੈਸਿੰਗ ਹੈ। ਠੋਸ ਹਿੱਸੇ ਦਬਾਉਣ ਅਤੇ ਸਿੰਟਰਿੰਗ ਦੁਆਰਾ ਪਾਊਡਰ ਤੋਂ ਪੈਦਾ ਕੀਤੇ ਜਾਂਦੇ ਹਨ। ਪਾਊਡਰ ਪ੍ਰੈੱਸਿੰਗ ਦੀ ਵਰਤੋਂ ਪਾਊਡਰਾਂ ਨੂੰ ਲੋੜੀਂਦੇ ਆਕਾਰਾਂ ਵਿੱਚ ਸੰਕੁਚਿਤ ਕਰਨ ਲਈ ਕੀਤੀ ਜਾਂਦੀ ਹੈ। ਪਹਿਲਾਂ, ਪ੍ਰਾਇਮਰੀ ਸਮੱਗਰੀ ਨੂੰ ਭੌਤਿਕ ਤੌਰ 'ਤੇ ਪਾਊਡਰ ਕੀਤਾ ਜਾਂਦਾ ਹੈ, ਇਸ ਨੂੰ ਕਈ ਛੋਟੇ ਵਿਅਕਤੀਗਤ ਕਣਾਂ ਵਿੱਚ ਵੰਡਦਾ ਹੈ। ਪਾਊਡਰ ਮਿਸ਼ਰਣ ਨੂੰ ਡਾਈ ਵਿੱਚ ਭਰਿਆ ਜਾਂਦਾ ਹੈ ਅਤੇ ਇੱਕ ਪੰਚ ਪਾਊਡਰ ਵੱਲ ਵਧਦਾ ਹੈ ਅਤੇ ਇਸਨੂੰ ਲੋੜੀਂਦੇ ਆਕਾਰ ਵਿੱਚ ਸੰਕੁਚਿਤ ਕਰਦਾ ਹੈ। ਜ਼ਿਆਦਾਤਰ ਕਮਰੇ ਦੇ ਤਾਪਮਾਨ 'ਤੇ ਕੀਤਾ ਜਾਂਦਾ ਹੈ, ਪਾਊਡਰ ਦਬਾਉਣ ਨਾਲ ਇੱਕ ਠੋਸ ਹਿੱਸਾ ਪ੍ਰਾਪਤ ਹੁੰਦਾ ਹੈ ਅਤੇ ਇਸਨੂੰ ਗ੍ਰੀਨ ਕੰਪੈਕਟ ਕਿਹਾ ਜਾਂਦਾ ਹੈ। ਬਾਈਂਡਰ ਅਤੇ ਲੁਬਰੀਕੈਂਟਸ ਦੀ ਵਰਤੋਂ ਆਮ ਤੌਰ 'ਤੇ ਸੰਖੇਪਤਾ ਨੂੰ ਵਧਾਉਣ ਲਈ ਕੀਤੀ ਜਾਂਦੀ ਹੈ। ਅਸੀਂ ਕਈ ਹਜ਼ਾਰ ਟਨ ਸਮਰੱਥਾ ਵਾਲੇ ਹਾਈਡ੍ਰੌਲਿਕ ਪ੍ਰੈਸਾਂ ਦੀ ਵਰਤੋਂ ਕਰਕੇ ਪਾਊਡਰ ਪ੍ਰੈਸ ਬਣਾਉਣ ਦੇ ਸਮਰੱਥ ਹਾਂ। ਨਾਲ ਹੀ ਸਾਡੇ ਕੋਲ ਵਿਰੋਧੀ ਟਾਪ ਅਤੇ ਤਲ ਪੰਚਾਂ ਦੇ ਨਾਲ ਡਬਲ ਐਕਸ਼ਨ ਪ੍ਰੈਸਾਂ ਦੇ ਨਾਲ-ਨਾਲ ਬਹੁਤ ਹੀ ਗੁੰਝਲਦਾਰ ਭਾਗ ਜਿਓਮੈਟਰੀ ਲਈ ਮਲਟੀਪਲ ਐਕਸ਼ਨ ਪ੍ਰੈਸ ਵੀ ਹਨ। ਇਕਸਾਰਤਾ ਜੋ ਕਿ ਬਹੁਤ ਸਾਰੇ ਪਾਊਡਰ ਧਾਤੂ / ਪਾਊਡਰ ਪ੍ਰੋਸੈਸਿੰਗ ਪਲਾਂਟਾਂ ਲਈ ਇੱਕ ਮਹੱਤਵਪੂਰਨ ਚੁਣੌਤੀ ਹੈ, AGS-TECH ਲਈ ਕੋਈ ਵੱਡੀ ਸਮੱਸਿਆ ਨਹੀਂ ਹੈ ਕਿਉਂਕਿ ਕਈ ਸਾਲਾਂ ਤੋਂ ਅਜਿਹੇ ਪੁਰਜ਼ਿਆਂ ਦੇ ਕਸਟਮ ਨਿਰਮਾਣ ਵਿੱਚ ਸਾਡੇ ਵਿਆਪਕ ਅਨੁਭਵ ਦੇ ਕਾਰਨ. ਸੰਘਣੇ ਹਿੱਸਿਆਂ ਦੇ ਬਾਵਜੂਦ ਜਿੱਥੇ ਇਕਸਾਰਤਾ ਇੱਕ ਚੁਣੌਤੀ ਹੈ, ਅਸੀਂ ਸਫਲ ਹੋਏ ਹਾਂ। ਜੇਕਰ ਅਸੀਂ ਤੁਹਾਡੇ ਪ੍ਰੋਜੈਕਟ ਲਈ ਵਚਨਬੱਧ ਹਾਂ, ਤਾਂ ਅਸੀਂ ਤੁਹਾਡੇ ਹਿੱਸੇ ਬਣਾਵਾਂਗੇ। ਜੇਕਰ ਅਸੀਂ ਕੋਈ ਸੰਭਾਵੀ ਜੋਖਮ ਦੇਖਦੇ ਹਾਂ, ਤਾਂ ਅਸੀਂ ਤੁਹਾਨੂੰ ਵਿੱਚ ਸੂਚਿਤ ਕਰਾਂਗੇ ਐਡਵਾਂਸ. ਪਾਊਡਰ ਸਿੰਟਰਿੰਗ, ਜੋ ਕਿ ਦੂਜਾ ਕਦਮ ਹੈ, ਵਿੱਚ ਤਾਪਮਾਨ ਨੂੰ ਇੱਕ ਨਿਸ਼ਚਿਤ ਡਿਗਰੀ ਤੱਕ ਵਧਾਉਣਾ ਅਤੇ ਇੱਕ ਨਿਸ਼ਚਿਤ ਸਮੇਂ ਲਈ ਉਸ ਪੱਧਰ 'ਤੇ ਤਾਪਮਾਨ ਨੂੰ ਸੰਭਾਲਣਾ ਸ਼ਾਮਲ ਹੁੰਦਾ ਹੈ ਤਾਂ ਜੋ ਦਬਾਏ ਗਏ ਹਿੱਸੇ ਵਿੱਚ ਪਾਊਡਰ ਦੇ ਕਣ ਆਪਸ ਵਿੱਚ ਜੁੜ ਸਕਣ। ਇਸ ਦੇ ਨਤੀਜੇ ਵਜੋਂ ਕੰਮ ਦੇ ਟੁਕੜੇ ਨੂੰ ਬਹੁਤ ਮਜ਼ਬੂਤ ਬੰਧਨ ਅਤੇ ਮਜ਼ਬੂਤੀ ਮਿਲਦੀ ਹੈ। ਸਿੰਟਰਿੰਗ ਪਾਊਡਰ ਦੇ ਪਿਘਲਣ ਦੇ ਤਾਪਮਾਨ ਦੇ ਨੇੜੇ ਹੁੰਦੀ ਹੈ। ਸਿੰਟਰਿੰਗ ਦੇ ਦੌਰਾਨ ਸੰਕੁਚਨ ਵਾਪਰਦਾ ਹੈ, ਸਮੱਗਰੀ ਦੀ ਤਾਕਤ, ਘਣਤਾ, ਲਚਕਤਾ, ਥਰਮਲ ਚਾਲਕਤਾ, ਬਿਜਲੀ ਚਾਲਕਤਾ ਵਧ ਜਾਂਦੀ ਹੈ। ਸਾਡੇ ਕੋਲ ਸਿੰਟਰਿੰਗ ਲਈ ਬੈਚ ਅਤੇ ਨਿਰੰਤਰ ਭੱਠੀਆਂ ਹਨ। ਸਾਡੀਆਂ ਯੋਗਤਾਵਾਂ ਵਿੱਚੋਂ ਇੱਕ ਸਾਡੇ ਦੁਆਰਾ ਪੈਦਾ ਕੀਤੇ ਗਏ ਹਿੱਸਿਆਂ ਦੀ ਪੋਰੋਸਿਟੀ ਦੇ ਪੱਧਰ ਨੂੰ ਅਨੁਕੂਲ ਕਰਨਾ ਹੈ। ਉਦਾਹਰਨ ਲਈ ਅਸੀਂ ਪੁਰਜ਼ਿਆਂ ਨੂੰ ਕੁਝ ਹੱਦ ਤੱਕ ਪੋਰਸ ਰੱਖ ਕੇ ਮੈਟਲ ਫਿਲਟਰ ਤਿਆਰ ਕਰਨ ਦੇ ਯੋਗ ਹਾਂ। IMPREGNATION ਨਾਮਕ ਤਕਨੀਕ ਦੀ ਵਰਤੋਂ ਕਰਦੇ ਹੋਏ, ਅਸੀਂ ਧਾਤੂ ਦੇ ਪੋਰਸ ਨੂੰ ਤੇਲ ਵਰਗੇ ਤਰਲ ਨਾਲ ਭਰਦੇ ਹਾਂ। ਅਸੀਂ ਉਦਾਹਰਨ ਲਈ ਤੇਲ ਨਾਲ ਭਰੇ ਹੋਏ ਬੇਅਰਿੰਗਾਂ ਦਾ ਉਤਪਾਦਨ ਕਰਦੇ ਹਾਂ ਜੋ ਸਵੈ-ਲੁਬਰੀਕੇਟਿੰਗ ਹੁੰਦੀਆਂ ਹਨ। ਘੁਸਪੈਠ ਦੀ ਪ੍ਰਕਿਰਿਆ ਵਿੱਚ ਅਸੀਂ ਇੱਕ ਧਾਤ ਦੇ ਪੋਰਸ ਨੂੰ ਅਧਾਰ ਸਮੱਗਰੀ ਨਾਲੋਂ ਘੱਟ ਪਿਘਲਣ ਵਾਲੇ ਬਿੰਦੂ ਵਾਲੀ ਇੱਕ ਹੋਰ ਧਾਤੂ ਨਾਲ ਭਰਦੇ ਹਾਂ। ਮਿਸ਼ਰਣ ਨੂੰ ਦੋ ਧਾਤਾਂ ਦੇ ਪਿਘਲਣ ਦੇ ਤਾਪਮਾਨ ਦੇ ਵਿਚਕਾਰ ਇੱਕ ਤਾਪਮਾਨ ਤੱਕ ਗਰਮ ਕੀਤਾ ਜਾਂਦਾ ਹੈ। ਨਤੀਜੇ ਵਜੋਂ ਕੁਝ ਵਿਸ਼ੇਸ਼ ਵਿਸ਼ੇਸ਼ਤਾਵਾਂ ਪ੍ਰਾਪਤ ਕੀਤੀਆਂ ਜਾ ਸਕਦੀਆਂ ਹਨ। ਅਸੀਂ ਅਕਸਰ ਸੈਕੰਡਰੀ ਓਪਰੇਸ਼ਨ ਵੀ ਕਰਦੇ ਹਾਂ ਜਿਵੇਂ ਕਿ ਪਾਊਡਰ ਨਿਰਮਿਤ ਹਿੱਸਿਆਂ 'ਤੇ ਮਸ਼ੀਨਿੰਗ ਅਤੇ ਫੋਰਜਿੰਗ ਜਦੋਂ ਵਿਸ਼ੇਸ਼ ਵਿਸ਼ੇਸ਼ਤਾਵਾਂ ਜਾਂ ਵਿਸ਼ੇਸ਼ਤਾਵਾਂ ਪ੍ਰਾਪਤ ਕਰਨ ਦੀ ਲੋੜ ਹੁੰਦੀ ਹੈ ਜਾਂ ਜਦੋਂ ਹਿੱਸੇ ਨੂੰ ਘੱਟ ਪ੍ਰਕਿਰਿਆ ਦੇ ਕਦਮਾਂ ਨਾਲ ਬਣਾਇਆ ਜਾ ਸਕਦਾ ਹੈ। ਆਈਸੋਸਟੈਟਿਕ ਪ੍ਰੈੱਸਿੰਗ: ਇਸ ਪ੍ਰਕਿਰਿਆ ਵਿੱਚ ਹਿੱਸੇ ਨੂੰ ਸੰਕੁਚਿਤ ਕਰਨ ਲਈ ਤਰਲ ਦਬਾਅ ਦੀ ਵਰਤੋਂ ਕੀਤੀ ਜਾਂਦੀ ਹੈ। ਧਾਤੂ ਪਾਊਡਰ ਇੱਕ ਸੀਲਬੰਦ ਲਚਕਦਾਰ ਕੰਟੇਨਰ ਦੇ ਬਣੇ ਇੱਕ ਉੱਲੀ ਵਿੱਚ ਰੱਖੇ ਜਾਂਦੇ ਹਨ। ਆਈਸੋਸਟੈਟਿਕ ਪ੍ਰੈੱਸਿੰਗ ਵਿੱਚ, ਚਾਰੇ ਪਾਸੇ ਤੋਂ ਦਬਾਅ ਲਾਗੂ ਕੀਤਾ ਜਾਂਦਾ ਹੈ, ਪਰੰਪਰਾਗਤ ਦਬਾਉਣ ਵਿੱਚ ਦਿਖਾਈ ਦੇਣ ਵਾਲੇ ਧੁਰੀ ਦਬਾਅ ਦੇ ਉਲਟ। ਆਈਸੋਸਟੈਟਿਕ ਪ੍ਰੈੱਸਿੰਗ ਦੇ ਫਾਇਦੇ ਹਿੱਸੇ ਦੇ ਅੰਦਰ ਇਕਸਾਰ ਘਣਤਾ ਹਨ, ਖਾਸ ਤੌਰ 'ਤੇ ਵੱਡੇ ਜਾਂ ਮੋਟੇ ਹਿੱਸਿਆਂ ਲਈ, ਉੱਤਮ ਵਿਸ਼ੇਸ਼ਤਾਵਾਂ। ਇਸਦਾ ਨੁਕਸਾਨ ਲੰਬੇ ਚੱਕਰ ਵਾਰ ਅਤੇ ਮੁਕਾਬਲਤਨ ਘੱਟ ਜਿਓਮੈਟ੍ਰਿਕ ਸ਼ੁੱਧਤਾਵਾਂ ਹਨ। ਕੋਲਡ ਆਈਸੋਸਟੈਟਿਕ ਪ੍ਰੈੱਸਿੰਗ ਕਮਰੇ ਦੇ ਤਾਪਮਾਨ 'ਤੇ ਕੀਤੀ ਜਾਂਦੀ ਹੈ ਅਤੇ ਲਚਕੀਲਾ ਮੋਲਡ ਰਬੜ, ਪੀਵੀਸੀ ਜਾਂ ਯੂਰੀਥੇਨ ਜਾਂ ਸਮਾਨ ਸਮੱਗਰੀ ਦਾ ਬਣਿਆ ਹੁੰਦਾ ਹੈ। ਦਬਾਅ ਬਣਾਉਣ ਅਤੇ ਸੰਕੁਚਿਤ ਕਰਨ ਲਈ ਵਰਤਿਆ ਜਾਣ ਵਾਲਾ ਤਰਲ ਤੇਲ ਜਾਂ ਪਾਣੀ ਹੈ। ਹਰੇ ਕੰਪੈਕਟ ਦੀ ਰਵਾਇਤੀ ਸਿੰਟਰਿੰਗ ਇਸ ਦੀ ਪਾਲਣਾ ਕਰਦੀ ਹੈ। ਦੂਜੇ ਪਾਸੇ ਗਰਮ ਆਈਸੋਸਟੈਟਿਕ ਪ੍ਰੈੱਸਿੰਗ ਉੱਚ ਤਾਪਮਾਨਾਂ 'ਤੇ ਕੀਤੀ ਜਾਂਦੀ ਹੈ ਅਤੇ ਉੱਲੀ ਦੀ ਸਮੱਗਰੀ ਸ਼ੀਟ ਮੈਟਲ ਜਾਂ ਸਿਰੇਮਿਕ ਹੁੰਦੀ ਹੈ ਜਿਸ ਵਿੱਚ ਉੱਚੇ ਪਿਘਲਣ ਵਾਲੇ ਬਿੰਦੂ ਹੁੰਦੇ ਹਨ ਜੋ ਤਾਪਮਾਨਾਂ ਦਾ ਵਿਰੋਧ ਕਰਦੇ ਹਨ। ਦਬਾਅ ਪਾਉਣ ਵਾਲਾ ਤਰਲ ਆਮ ਤੌਰ 'ਤੇ ਇੱਕ ਅੜਿੱਕਾ ਗੈਸ ਹੁੰਦਾ ਹੈ। ਦਬਾਉਣ ਅਤੇ ਸਿੰਟਰਿੰਗ ਓਪਰੇਸ਼ਨ ਇੱਕ ਕਦਮ ਵਿੱਚ ਕੀਤੇ ਜਾਂਦੇ ਹਨ. ਪੋਰੋਸਿਟੀ ਲਗਭਗ ਪੂਰੀ ਤਰ੍ਹਾਂ ਖਤਮ ਹੋ ਜਾਂਦੀ ਹੈ, ਇੱਕ ਯੂਨੀਫਾਰਮ grain ਢਾਂਚਾ ਪ੍ਰਾਪਤ ਹੁੰਦਾ ਹੈ। ਗਰਮ ਆਈਸੋਸਟੈਟਿਕ ਪ੍ਰੈੱਸਿੰਗ ਦਾ ਫਾਇਦਾ ਇਹ ਹੈ ਕਿ ਇਹ ਕਾਸਟਿੰਗ ਅਤੇ ਫੋਰਜਿੰਗ ਦੇ ਨਾਲ ਤੁਲਨਾਯੋਗ ਹਿੱਸੇ ਪੈਦਾ ਕਰ ਸਕਦਾ ਹੈ ਜਦੋਂ ਕਿ ਉਹ ਸਮੱਗਰੀ ਬਣਾਉਂਦੇ ਹਨ ਜੋ ਕਾਸਟਿੰਗ ਅਤੇ ਫੋਰਜਿੰਗ ਲਈ ਢੁਕਵੇਂ ਨਹੀਂ ਹਨ ਅਤੇ ਵਰਤਣ ਲਈ ਸੰਭਵ ਹਨ। ਗਰਮ ਆਈਸੋਸਟੈਟਿਕ ਦਬਾਉਣ ਦਾ ਨੁਕਸਾਨ ਇਸਦਾ ਉੱਚ ਚੱਕਰ ਸਮਾਂ ਅਤੇ ਇਸਲਈ ਲਾਗਤ ਹੈ। ਇਹ ਘੱਟ ਵਾਲੀਅਮ ਦੇ ਨਾਜ਼ੁਕ ਹਿੱਸਿਆਂ ਲਈ ਢੁਕਵਾਂ ਹੈ। ਧਾਤੂ ਇੰਜੈਕਸ਼ਨ ਮੋਲਡਿੰਗ: ਪਤਲੀਆਂ ਕੰਧਾਂ ਅਤੇ ਵਿਸਤ੍ਰਿਤ ਜਿਓਮੈਟਰੀ ਦੇ ਨਾਲ ਗੁੰਝਲਦਾਰ ਹਿੱਸੇ ਬਣਾਉਣ ਲਈ ਬਹੁਤ ਢੁਕਵੀਂ ਪ੍ਰਕਿਰਿਆ। ਛੋਟੇ ਹਿੱਸਿਆਂ ਲਈ ਸਭ ਤੋਂ ਢੁਕਵਾਂ. ਪਾਊਡਰ ਅਤੇ ਪੌਲੀਮਰ ਬਾਈਂਡਰ ਨੂੰ ਮਿਲਾਇਆ ਜਾਂਦਾ ਹੈ, ਗਰਮ ਕੀਤਾ ਜਾਂਦਾ ਹੈ ਅਤੇ ਇੱਕ ਉੱਲੀ ਵਿੱਚ ਇੰਜੈਕਟ ਕੀਤਾ ਜਾਂਦਾ ਹੈ। ਪੌਲੀਮਰ ਬਾਈਂਡਰ ਪਾਊਡਰ ਕਣਾਂ ਦੀਆਂ ਸਤਹਾਂ ਨੂੰ ਕੋਟ ਕਰਦਾ ਹੈ। ਮੋਲਡਿੰਗ ਤੋਂ ਬਾਅਦ, ਬਾਈਂਡਰ ਨੂੰ ਘੋਲਨ ਵਾਲੇ ਦੀ ਵਰਤੋਂ ਕਰਕੇ ਭੰਗ ਦੇ ਘੱਟ ਤਾਪਮਾਨ ਨੂੰ ਗਰਮ ਕਰਕੇ ਹਟਾ ਦਿੱਤਾ ਜਾਂਦਾ ਹੈ। ਰੋਲ ਕੰਪੈਕਸ਼ਨ / ਪਾਊਡਰ ਰੋਲਿੰਗ: ਪਾਊਡਰ ਦੀ ਵਰਤੋਂ ਲਗਾਤਾਰ ਪੱਟੀਆਂ ਜਾਂ ਸ਼ੀਟ ਬਣਾਉਣ ਲਈ ਕੀਤੀ ਜਾਂਦੀ ਹੈ। ਪਾਊਡਰ ਨੂੰ ਇੱਕ ਫੀਡਰ ਤੋਂ ਖੁਆਇਆ ਜਾਂਦਾ ਹੈ ਅਤੇ ਦੋ ਰੋਟੇਟਿੰਗ ਰੋਲ ਦੁਆਰਾ ਸ਼ੀਟ ਜਾਂ ਪੱਟੀਆਂ ਵਿੱਚ ਸੰਕੁਚਿਤ ਕੀਤਾ ਜਾਂਦਾ ਹੈ। ਓਪਰੇਸ਼ਨ ਠੰਡੇ ਕੀਤਾ ਜਾਂਦਾ ਹੈ. ਸ਼ੀਟ ਨੂੰ ਇੱਕ ਸਿੰਟਰਿੰਗ ਭੱਠੀ ਵਿੱਚ ਲਿਜਾਇਆ ਜਾਂਦਾ ਹੈ. ਸਿੰਟਰਿੰਗ ਪ੍ਰਕਿਰਿਆ ਨੂੰ ਦੂਜੀ ਵਾਰ ਦੁਹਰਾਇਆ ਜਾ ਸਕਦਾ ਹੈ। ਪਾਊਡਰ ਐਕਸਟਰਿਊਸ਼ਨ: ਵੱਡੀ ਲੰਬਾਈ ਤੋਂ ਵਿਆਸ ਦੇ ਅਨੁਪਾਤ ਵਾਲੇ ਹਿੱਸੇ ਪਾਊਡਰ ਦੇ ਨਾਲ ਇੱਕ ਪਤਲੇ ਸ਼ੀਟ ਮੈਟਲ ਕੰਟੇਨਰ ਨੂੰ ਬਾਹਰ ਕੱਢ ਕੇ ਤਿਆਰ ਕੀਤੇ ਜਾਂਦੇ ਹਨ। ਢਿੱਲੀ ਸਿੰਟਰਿੰਗ: ਜਿਵੇਂ ਕਿ ਨਾਮ ਤੋਂ ਭਾਵ ਹੈ, ਇਹ ਇੱਕ ਦਬਾਅ ਰਹਿਤ ਕੰਪੈਕਸ਼ਨ ਅਤੇ ਸਿੰਟਰਿੰਗ ਵਿਧੀ ਹੈ, ਜੋ ਕਿ ਧਾਤ ਦੇ ਫਿਲਟਰਾਂ ਵਰਗੇ ਬਹੁਤ ਹੀ ਧੁੰਦਲੇ ਹਿੱਸੇ ਬਣਾਉਣ ਲਈ ਢੁਕਵੀਂ ਹੈ। ਪਾਊਡਰ ਨੂੰ ਸੰਕੁਚਿਤ ਕੀਤੇ ਬਿਨਾਂ ਮੋਲਡ ਕੈਵਿਟੀ ਵਿੱਚ ਖੁਆਇਆ ਜਾਂਦਾ ਹੈ। ਢਿੱਲੀ ਸਿੰਟਰਿੰਗ: ਜਿਵੇਂ ਕਿ ਨਾਮ ਤੋਂ ਭਾਵ ਹੈ, ਇਹ ਇੱਕ ਦਬਾਅ ਰਹਿਤ ਕੰਪੈਕਸ਼ਨ ਅਤੇ ਸਿੰਟਰਿੰਗ ਵਿਧੀ ਹੈ, ਜੋ ਕਿ ਧਾਤ ਦੇ ਫਿਲਟਰਾਂ ਵਰਗੇ ਬਹੁਤ ਹੀ ਧੁੰਦਲੇ ਹਿੱਸੇ ਬਣਾਉਣ ਲਈ ਢੁਕਵੀਂ ਹੈ। ਪਾਊਡਰ ਨੂੰ ਸੰਕੁਚਿਤ ਕੀਤੇ ਬਿਨਾਂ ਮੋਲਡ ਕੈਵਿਟੀ ਵਿੱਚ ਖੁਆਇਆ ਜਾਂਦਾ ਹੈ। ਸਪਾਰਕ ਸਿੰਟਰਿੰਗ: ਪਾਊਡਰ ਨੂੰ ਦੋ ਵਿਰੋਧੀ ਪੰਚਾਂ ਦੁਆਰਾ ਮੋਲਡ ਵਿੱਚ ਸੰਕੁਚਿਤ ਕੀਤਾ ਜਾਂਦਾ ਹੈ ਅਤੇ ਪੰਚ ਉੱਤੇ ਇੱਕ ਉੱਚ ਸ਼ਕਤੀ ਵਾਲਾ ਇਲੈਕਟ੍ਰਿਕ ਕਰੰਟ ਲਗਾਇਆ ਜਾਂਦਾ ਹੈ ਅਤੇ ਉਹਨਾਂ ਦੇ ਵਿਚਕਾਰ ਸੈਂਡਵਿਚ ਕੀਤੇ ਸੰਕੁਚਿਤ ਪਾਊਡਰ ਵਿੱਚੋਂ ਦੀ ਲੰਘਦਾ ਹੈ। ਉੱਚ ਕਰੰਟ ਪਾਊਡਰ ਕਣਾਂ ਤੋਂ ਸਤ੍ਹਾ ਦੀਆਂ ਫਿਲਮਾਂ ਨੂੰ ਸਾੜ ਦਿੰਦਾ ਹੈ ਅਤੇ ਪੈਦਾ ਹੋਈ ਗਰਮੀ ਨਾਲ ਉਨ੍ਹਾਂ ਨੂੰ ਸਿੰਟਰ ਕਰਦਾ ਹੈ। ਇਹ ਪ੍ਰਕਿਰਿਆ ਤੇਜ਼ ਹੁੰਦੀ ਹੈ ਕਿਉਂਕਿ ਗਰਮੀ ਬਾਹਰੋਂ ਨਹੀਂ ਲਗਾਈ ਜਾਂਦੀ ਸਗੋਂ ਇਹ ਉੱਲੀ ਦੇ ਅੰਦਰੋਂ ਪੈਦਾ ਹੁੰਦੀ ਹੈ। ਗਰਮ ਪ੍ਰੈੱਸਿੰਗ: ਪਾਊਡਰ ਨੂੰ ਇੱਕ ਉੱਲੀ ਵਿੱਚ ਇੱਕ ਪੜਾਅ ਵਿੱਚ ਦਬਾਇਆ ਜਾਂਦਾ ਹੈ ਅਤੇ ਸਿੰਟਰ ਕੀਤਾ ਜਾਂਦਾ ਹੈ ਜੋ ਉੱਚ ਤਾਪਮਾਨ ਦਾ ਸਾਮ੍ਹਣਾ ਕਰ ਸਕਦਾ ਹੈ। ਜਿਵੇਂ ਹੀ ਡਾਈ ਕੰਪੈਕਟ ਹੋ ਜਾਂਦੀ ਹੈ, ਪਾਊਡਰ ਹੀਟ ਨੂੰ ਇਸ 'ਤੇ ਲਾਗੂ ਕੀਤਾ ਜਾਂਦਾ ਹੈ। ਇਸ ਵਿਧੀ ਦੁਆਰਾ ਪ੍ਰਾਪਤ ਕੀਤੀਆਂ ਚੰਗੀਆਂ ਸ਼ੁੱਧਤਾਵਾਂ ਅਤੇ ਮਕੈਨੀਕਲ ਵਿਸ਼ੇਸ਼ਤਾਵਾਂ ਇਸ ਨੂੰ ਇੱਕ ਆਕਰਸ਼ਕ ਵਿਕਲਪ ਬਣਾਉਂਦੀਆਂ ਹਨ। ਇੱਥੋਂ ਤੱਕ ਕਿ ਰਿਫ੍ਰੈਕਟਰੀ ਧਾਤਾਂ ਨੂੰ ਵੀ ਮੋਲਡ ਸਮੱਗਰੀ ਜਿਵੇਂ ਕਿ ਗ੍ਰੈਫਾਈਟ ਦੀ ਵਰਤੋਂ ਕਰਕੇ ਸੰਸਾਧਿਤ ਕੀਤਾ ਜਾ ਸਕਦਾ ਹੈ। CLICK Product Finder-Locator Service ਪਿਛਲਾ ਮੀਨੂ
- Plastic Rubber Metal Extrusions, Extrusion Dies, Aluminum Extruding
Plastic Rubber Metal Extrusions, Extrusion Dies, Aluminum Extruding, Pipe Tube Forming, Plastic Profiles, Metal Profiles Manufacturing, PVC at AGS-TECH Inc. Extrusions, Extruded ਉਤਪਾਦ, Extrudates ਅਸੀਂ ਇੱਕ ਨਿਸ਼ਚਿਤ ਕਰਾਸ ਸੈਕਸ਼ਨਲ ਪ੍ਰੋਫਾਈਲ ਜਿਵੇਂ ਕਿ ਟਿਊਬਾਂ, ਹੀਟ ਪਾਈਪਾਂ ਨਾਲ ਉਤਪਾਦ ਬਣਾਉਣ ਲਈ EXTRUSION process ਦੀ ਵਰਤੋਂ ਕਰਦੇ ਹਾਂ। ਭਾਵੇਂ ਕਿ ਬਹੁਤ ਸਾਰੀਆਂ ਸਮੱਗਰੀਆਂ ਨੂੰ ਬਾਹਰ ਕੱਢਿਆ ਜਾ ਸਕਦਾ ਹੈ, ਸਾਡੇ ਸਭ ਤੋਂ ਆਮ ਐਕਸਟਰਿਊਸ਼ਨ ਧਾਤ, ਪੋਲੀਮਰ / ਪਲਾਸਟਿਕ, ਵਸਰਾਵਿਕ ਦੇ ਬਣੇ ਹੁੰਦੇ ਹਨ ਜੋ ਕਿ ਠੰਡੇ, ਨਿੱਘੇ ਜਾਂ ਗਰਮ ਐਕਸਟਰਿਊਸ਼ਨ ਵਿਧੀ ਦੁਆਰਾ ਪ੍ਰਾਪਤ ਕੀਤੇ ਜਾਂਦੇ ਹਨ। ਜੇ ਬਹੁਵਚਨ ਹੋਵੇ ਤਾਂ ਅਸੀਂ ਬਾਹਰ ਕੱਢੇ ਹੋਏ ਹਿੱਸਿਆਂ ਨੂੰ ਐਕਸਟਰੂਡੇਟ ਜਾਂ ਐਕਸਟਰੂਡੇਟਸ ਕਹਿੰਦੇ ਹਾਂ। ਪ੍ਰਕਿਰਿਆ ਦੇ ਕੁਝ ਵਿਸ਼ੇਸ਼ ਸੰਸਕਰਣ ਜੋ ਅਸੀਂ ਵੀ ਕਰਦੇ ਹਾਂ ਉਹ ਹਨ ਓਵਰਜੈਕਿੰਗ, ਕੋਐਕਸਟ੍ਰੂਜ਼ਨ ਅਤੇ ਕੰਪਾਊਂਡ ਐਕਸਟਰਿਊਸ਼ਨ। ਅਸੀਂ ਸਿਫ਼ਾਰਿਸ਼ ਕਰਦੇ ਹਾਂ ਕਿ ਤੁਸੀਂ ਇੱਥੇ ਕਲਿੱਕ ਕਰੋ AGS-TECH Inc ਦੁਆਰਾ ਧਾਤੂ ਸਿਰੇਮਿਕ ਅਤੇ ਪਲਾਸਟਿਕ ਐਕਸਟਰਿਊਸ਼ਨ ਪ੍ਰਕਿਰਿਆਵਾਂ ਦੇ ਸਾਡੇ ਯੋਜਨਾਬੱਧ ਚਿੱਤਰਾਂ ਨੂੰ ਡਾਉਨਲੋਡ ਕਰੋ। ਇਹ ਤੁਹਾਨੂੰ ਉਸ ਜਾਣਕਾਰੀ ਨੂੰ ਬਿਹਤਰ ਤਰੀਕੇ ਨਾਲ ਸਮਝਣ ਵਿੱਚ ਮਦਦ ਕਰੇਗਾ ਜੋ ਅਸੀਂ ਤੁਹਾਨੂੰ ਹੇਠਾਂ ਪ੍ਰਦਾਨ ਕਰ ਰਹੇ ਹਾਂ। ਬਾਹਰ ਕੱਢਣ ਲਈ ਸਮੱਗਰੀ ਨੂੰ ਇੱਕ ਡਾਈ ਰਾਹੀਂ ਧੱਕਿਆ ਜਾਂ ਖਿੱਚਿਆ ਜਾਂਦਾ ਹੈ ਜਿਸ ਵਿੱਚ ਲੋੜੀਂਦਾ ਕਰਾਸ-ਸੈਕਸ਼ਨਲ ਪ੍ਰੋਫਾਈਲ ਹੁੰਦਾ ਹੈ। ਪ੍ਰਕਿਰਿਆ ਦੀ ਵਰਤੋਂ ਸ਼ਾਨਦਾਰ ਸਤਹ ਫਿਨਿਸ਼ ਦੇ ਨਾਲ ਗੁੰਝਲਦਾਰ ਕਰਾਸ-ਸੈਕਸ਼ਨ ਬਣਾਉਣ ਅਤੇ ਭੁਰਭੁਰਾ ਸਮੱਗਰੀ 'ਤੇ ਕੰਮ ਕਰਨ ਲਈ ਕੀਤੀ ਜਾ ਸਕਦੀ ਹੈ। ਕੋਈ ਵੀ ਇਸ ਪ੍ਰਕਿਰਿਆ ਦੀ ਵਰਤੋਂ ਕਰਕੇ ਕਿਸੇ ਵੀ ਲੰਬਾਈ ਦੇ ਹਿੱਸੇ ਪੈਦਾ ਕਰ ਸਕਦਾ ਹੈ। ਪ੍ਰਕਿਰਿਆ ਦੇ ਕਦਮਾਂ ਨੂੰ ਸਰਲ ਬਣਾਉਣ ਲਈ: 1.) ਗਰਮ ਜਾਂ ਗਰਮ ਐਕਸਟਰਿਊਸ਼ਨ ਵਿੱਚ ਸਮੱਗਰੀ ਨੂੰ ਗਰਮ ਕੀਤਾ ਜਾਂਦਾ ਹੈ ਅਤੇ ਪ੍ਰੈਸ ਵਿੱਚ ਇੱਕ ਕੰਟੇਨਰ ਵਿੱਚ ਲੋਡ ਕੀਤਾ ਜਾਂਦਾ ਹੈ। ਸਮੱਗਰੀ ਨੂੰ ਦਬਾਇਆ ਜਾਂਦਾ ਹੈ ਅਤੇ ਮਰਨ ਤੋਂ ਬਾਹਰ ਧੱਕ ਦਿੱਤਾ ਜਾਂਦਾ ਹੈ. 2.) ਪੈਦਾ ਕੀਤੇ ਐਕਸਟਰੂਡੇਟ ਨੂੰ ਸਿੱਧੇ ਕਰਨ ਲਈ ਖਿੱਚਿਆ ਜਾਂਦਾ ਹੈ, ਗਰਮੀ ਦਾ ਇਲਾਜ ਕੀਤਾ ਜਾਂਦਾ ਹੈ ਜਾਂ ਇਸ ਦੀਆਂ ਵਿਸ਼ੇਸ਼ਤਾਵਾਂ ਨੂੰ ਵਧਾਉਣ ਲਈ ਠੰਡੇ ਕੰਮ ਕੀਤਾ ਜਾਂਦਾ ਹੈ। ਦੂਜੇ ਪਾਸੇ COLD EXTRUSION ਕਮਰੇ ਦੇ ਤਾਪਮਾਨ 'ਤੇ ਲੱਗ ਜਾਂਦਾ ਹੈ ਅਤੇ ਇਸ ਦੇ ਫਾਇਦੇ ਘੱਟ ਹੁੰਦੇ ਹਨ, ਉੱਚੀ ਤਾਕਤ, ਉੱਚੀ ਆਕਸੀਡੇਸ਼ਨ ਦੇ ਨੇੜੇ ਅਤੇ ਚੰਗੀ ਆਕਸੀਡੇਸ਼ਨ। WARM EXTRUSION ਕਮਰੇ ਦੇ ਤਾਪਮਾਨ ਤੋਂ ਉੱਪਰ ਪਰ ਪੁਨਰ-ਸਥਾਪਨ ਬਿੰਦੂ ਤੋਂ ਹੇਠਾਂ ਕੀਤਾ ਜਾਂਦਾ ਹੈ। ਇਹ ਲੋੜੀਂਦੇ ਬਲਾਂ, ਲਚਕਤਾ ਅਤੇ ਪਦਾਰਥਕ ਵਿਸ਼ੇਸ਼ਤਾਵਾਂ ਲਈ ਸਮਝੌਤਾ ਅਤੇ ਸੰਤੁਲਨ ਦੀ ਪੇਸ਼ਕਸ਼ ਕਰਦਾ ਹੈ ਅਤੇ ਇਸਲਈ ਕੁਝ ਐਪਲੀਕੇਸ਼ਨਾਂ ਲਈ ਵਿਕਲਪ ਹੈ। HOT EXTRUSION ਸਮੱਗਰੀ ਦੇ ਰੀਕ੍ਰਿਸਟਾਲਾਈਜ਼ੇਸ਼ਨ ਤਾਪਮਾਨ ਤੋਂ ਉੱਪਰ ਹੁੰਦਾ ਹੈ। ਇਸ ਤਰ੍ਹਾਂ ਸਮੱਗਰੀ ਨੂੰ ਡਾਈ ਰਾਹੀਂ ਧੱਕਣਾ ਆਸਾਨ ਹੁੰਦਾ ਹੈ। ਹਾਲਾਂਕਿ ਸਾਜ਼-ਸਾਮਾਨ ਦੀ ਕੀਮਤ ਬਹੁਤ ਜ਼ਿਆਦਾ ਹੈ. ਇੱਕ ਐਕਸਟਰੂਡ ਪ੍ਰੋਫਾਈਲ ਜਿੰਨਾ ਗੁੰਝਲਦਾਰ ਹੈ, ਓਨਾ ਹੀ ਮਹਿੰਗਾ ਡਾਈ (ਟੂਲਿੰਗ) ਹੈ ਅਤੇ ਉਤਪਾਦਨ ਦੀ ਦਰ ਘੱਟ ਹੈ। ਡਾਈ ਕਰਾਸ ਸੈਕਸ਼ਨਾਂ ਦੇ ਨਾਲ-ਨਾਲ ਮੋਟਾਈ ਦੀਆਂ ਸੀਮਾਵਾਂ ਹਨ ਜੋ ਬਾਹਰ ਕੱਢਣ ਲਈ ਸਮੱਗਰੀ 'ਤੇ ਨਿਰਭਰ ਕਰਦੀਆਂ ਹਨ। ਐਕਸਟਰਿਊਸ਼ਨ ਡਾਈਜ਼ ਵਿੱਚ ਤਿੱਖੇ ਕੋਨੇ ਹਮੇਸ਼ਾ ਅਣਚਾਹੇ ਹੁੰਦੇ ਹਨ ਅਤੇ ਜਦੋਂ ਤੱਕ ਜ਼ਰੂਰੀ ਨਾ ਹੋਵੇ ਪਰਹੇਜ਼ ਕੀਤਾ ਜਾਣਾ ਚਾਹੀਦਾ ਹੈ। ਬਾਹਰ ਕੱਢੀ ਜਾ ਰਹੀ ਸਮੱਗਰੀ ਦੇ ਅਨੁਸਾਰ, ਅਸੀਂ ਪੇਸ਼ਕਸ਼ ਕਰਦੇ ਹਾਂ: • ਧਾਤੂ EXTRUSIONS : ਸਭ ਤੋਂ ਆਮ ਜੋ ਅਸੀਂ ਪੈਦਾ ਕਰਦੇ ਹਾਂ ਉਹ ਹਨ ਅਲਮੀਨੀਅਮ, ਪਿੱਤਲ, ਜ਼ਿੰਕ, ਤਾਂਬਾ, ਸਟੀਲ, ਟਾਈਟੇਨੀਅਮ, ਮੈਗਨੀਸ਼ੀਅਮ • ਪਲਾਸਟਿਕ EXTRUSION : ਪਲਾਸਟਿਕ ਪਿਘਲ ਜਾਂਦਾ ਹੈ ਅਤੇ ਇੱਕ ਨਿਰੰਤਰ ਪ੍ਰੋਫਾਈਲ ਵਿੱਚ ਬਣਦਾ ਹੈ। ਪ੍ਰੋਸੈਸ ਕੀਤੀਆਂ ਗਈਆਂ ਸਾਡੀਆਂ ਆਮ ਸਮੱਗਰੀਆਂ ਹਨ ਪੋਲੀਥੀਲੀਨ, ਨਾਈਲੋਨ, ਪੋਲੀਸਟੀਰੀਨ, ਪੌਲੀਵਿਨਾਇਲ ਕਲੋਰਾਈਡ, ਪੌਲੀਪ੍ਰੋਪਾਈਲੀਨ, ਏਬੀਐਸ ਪਲਾਸਟਿਕ, ਪੌਲੀਕਾਰਬੋਨੇਟ, ਐਕਰੀਲਿਕ। ਸਾਡੇ ਦੁਆਰਾ ਤਿਆਰ ਕੀਤੇ ਗਏ ਖਾਸ ਉਤਪਾਦਾਂ ਵਿੱਚ ਪਾਈਪ ਅਤੇ ਟਿਊਬਿੰਗ, ਪਲਾਸਟਿਕ ਦੇ ਫਰੇਮ ਸ਼ਾਮਲ ਹਨ। ਪ੍ਰਕ੍ਰਿਆ ਵਿੱਚ ਛੋਟੇ ਪਲਾਸਟਿਕ ਦੇ ਮਣਕਿਆਂ/ਰਾਲ ਨੂੰ ਹਾਪਰ ਤੋਂ ਬਾਹਰ ਕੱਢਣ ਵਾਲੀ ਮਸ਼ੀਨ ਦੇ ਬੈਰਲ ਵਿੱਚ ਗਰੈਵਿਟੀ ਖੁਆਈ ਜਾਂਦੀ ਹੈ। ਉਤਪਾਦ ਨੂੰ ਲੋੜੀਂਦੀਆਂ ਵਿਸ਼ੇਸ਼ਤਾਵਾਂ ਅਤੇ ਵਿਸ਼ੇਸ਼ਤਾਵਾਂ ਦੇਣ ਲਈ ਅਕਸਰ ਅਸੀਂ ਰੰਗੀਨ ਜਾਂ ਹੋਰ ਜੋੜਾਂ ਨੂੰ ਹੌਪਰ ਵਿੱਚ ਮਿਲਾਉਂਦੇ ਹਾਂ। ਗਰਮ ਬੈਰਲ ਵਿੱਚ ਦਾਖਲ ਹੋਣ ਵਾਲੀ ਸਮੱਗਰੀ ਨੂੰ ਘੁੰਮਣ ਵਾਲੇ ਪੇਚ ਦੁਆਰਾ ਬੈਰਲ ਨੂੰ ਅੰਤ ਵਿੱਚ ਛੱਡਣ ਅਤੇ ਪਿਘਲੇ ਹੋਏ ਪਲਾਸਟਿਕ ਵਿੱਚ ਗੰਦਗੀ ਨੂੰ ਹਟਾਉਣ ਲਈ ਸਕ੍ਰੀਨ ਪੈਕ ਵਿੱਚੋਂ ਲੰਘਣ ਲਈ ਮਜਬੂਰ ਕੀਤਾ ਜਾਂਦਾ ਹੈ। ਸਕਰੀਨ ਪੈਕ ਨੂੰ ਪਾਸ ਕਰਨ ਤੋਂ ਬਾਅਦ ਪਲਾਸਟਿਕ ਐਕਸਟਰਿਊਸ਼ਨ ਡਾਈ ਵਿੱਚ ਦਾਖਲ ਹੁੰਦਾ ਹੈ। ਡਾਈ ਮੂਵਿੰਗ ਨਰਮ ਪਲਾਸਟਿਕ ਨੂੰ ਇਸਦੀ ਪ੍ਰੋਫਾਈਲ ਸ਼ਕਲ ਦਿੰਦੀ ਹੈ ਜਦੋਂ ਇਹ ਲੰਘਦਾ ਹੈ। ਹੁਣ extrudate ਠੰਡਾ ਕਰਨ ਲਈ ਇੱਕ ਪਾਣੀ ਦੇ ਇਸ਼ਨਾਨ ਦੁਆਰਾ ਚਲਾ. ਹੋਰ ਤਕਨੀਕਾਂ AGS-TECH Inc. ਕਈ ਸਾਲਾਂ ਤੋਂ ਵਰਤ ਰਹੀ ਹੈ: • ਪਾਈਪ ਅਤੇ ਟਿਊਬਿੰਗ EXTRUSION : ਪਲਾਸਟਿਕ ਦੀਆਂ ਪਾਈਪਾਂ ਅਤੇ ਟਿਊਬਾਂ ਉਦੋਂ ਬਣਦੀਆਂ ਹਨ ਜਦੋਂ ਪਲਾਸਟਿਕ ਨੂੰ ਗੋਲ ਆਕਾਰ ਵਾਲੀ ਡਾਈ ਰਾਹੀਂ ਬਾਹਰ ਕੱਢਿਆ ਜਾਂਦਾ ਹੈ ਅਤੇ ਪਾਣੀ ਦੇ ਇਸ਼ਨਾਨ ਵਿੱਚ ਠੰਢਾ ਕੀਤਾ ਜਾਂਦਾ ਹੈ, ਫਿਰ ਲੰਬਾਈ ਤੱਕ ਕੱਟਿਆ ਜਾਂਦਾ ਹੈ ਜਾਂ ਕੋਇਲ / ਸਪੂਲ ਕੀਤਾ ਜਾਂਦਾ ਹੈ। ਸਾਫ਼ ਜਾਂ ਰੰਗਦਾਰ, ਧਾਰੀਦਾਰ, ਸਿੰਗਲ ਜਾਂ ਦੋਹਰੀ ਕੰਧ, ਲਚਕਦਾਰ ਜਾਂ ਸਖ਼ਤ, PE, PP, ਪੌਲੀਯੂਰੇਥੇਨ, ਪੀਵੀਸੀ, ਨਾਈਲੋਨ, ਪੀਸੀ, ਸਿਲੀਕੋਨ, ਵਿਨਾਇਲ ਜਾਂ ਹੋਰ, ਸਾਡੇ ਕੋਲ ਇਹ ਸਭ ਹੈ. ਸਾਡੇ ਕੋਲ ਸਟਾਕ ਕੀਤੀਆਂ ਟਿਊਬਾਂ ਦੇ ਨਾਲ-ਨਾਲ ਤੁਹਾਡੀਆਂ ਵਿਸ਼ੇਸ਼ਤਾਵਾਂ ਦੇ ਅਨੁਸਾਰ ਉਤਪਾਦਨ ਕਰਨ ਦੀ ਸਮਰੱਥਾ ਹੈ. AGS-TECH ਮੈਡੀਕਲ, ਇਲੈਕਟ੍ਰਿਕ ਅਤੇ ਇਲੈਕਟ੍ਰਾਨਿਕ, ਉਦਯੋਗਿਕ ਅਤੇ ਹੋਰ ਐਪਲੀਕੇਸ਼ਨਾਂ ਲਈ FDA, UL, ਅਤੇ LE ਲੋੜਾਂ ਲਈ ਟਿਊਬਿੰਗ ਬਣਾਉਂਦਾ ਹੈ। • ਓਵਰ ਜੈਕੇਟਿੰਗ / ਓਵਰ ਜੈਕੇਟਿੰਗ EXTRUSION : ਇਹ ਤਕਨੀਕ ਮੌਜੂਦਾ ਤਾਰ ਜਾਂ ਕੇਬਲ 'ਤੇ ਪਲਾਸਟਿਕ ਦੀ ਬਾਹਰੀ ਪਰਤ ਨੂੰ ਲਾਗੂ ਕਰਦੀ ਹੈ। ਸਾਡੀਆਂ ਇਨਸੂਲੇਸ਼ਨ ਤਾਰਾਂ ਇਸ ਵਿਧੀ ਨਾਲ ਬਣਾਈਆਂ ਜਾਂਦੀਆਂ ਹਨ। • COEXTRUSION : ਸਮੱਗਰੀ ਦੀਆਂ ਕਈ ਪਰਤਾਂ ਇੱਕੋ ਸਮੇਂ ਕੱਢੀਆਂ ਜਾਂਦੀਆਂ ਹਨ। ਮਲਟੀਪਲ ਲੇਅਰਾਂ ਨੂੰ ਮਲਟੀਪਲ ਐਕਸਟਰੂਡਰ ਦੁਆਰਾ ਡਿਲੀਵਰ ਕੀਤਾ ਜਾਂਦਾ ਹੈ। ਗਾਹਕ ਦੀਆਂ ਵਿਸ਼ੇਸ਼ਤਾਵਾਂ ਨੂੰ ਪੂਰਾ ਕਰਨ ਲਈ ਵੱਖ-ਵੱਖ ਪਰਤ ਮੋਟਾਈ ਨੂੰ ਐਡਜਸਟ ਕੀਤਾ ਜਾ ਸਕਦਾ ਹੈ. ਇਹ ਪ੍ਰਕਿਰਿਆ ਉਤਪਾਦ ਵਿੱਚ ਵੱਖ-ਵੱਖ ਕਾਰਜਸ਼ੀਲਤਾ ਵਾਲੇ ਕਈ ਪੌਲੀਮਰਾਂ ਦੀ ਵਰਤੋਂ ਕਰਨਾ ਸੰਭਵ ਬਣਾਉਂਦੀ ਹੈ। ਨਤੀਜੇ ਵਜੋਂ, ਕੋਈ ਵੀ ਵਿਸ਼ੇਸ਼ਤਾਵਾਂ ਦੀ ਇੱਕ ਸੀਮਾ ਨੂੰ ਅਨੁਕੂਲ ਬਣਾ ਸਕਦਾ ਹੈ। • ਮਿਸ਼ਰਣ ਐਕਸਟਰਿਊਸ਼ਨ: ਪਲਾਸਟਿਕ ਮਿਸ਼ਰਣ ਪ੍ਰਾਪਤ ਕਰਨ ਲਈ ਇੱਕ ਸਿੰਗਲ ਜਾਂ ਮਲਟੀਪਲ ਪੌਲੀਮਰਾਂ ਨੂੰ ਐਡਿਟਿਵ ਨਾਲ ਮਿਲਾਇਆ ਜਾਂਦਾ ਹੈ। ਸਾਡੇ ਟਵਿਨ-ਸਕ੍ਰੂ ਐਕਸਟਰੂਡਰ ਕੰਪਾਊਂਡਿੰਗ ਐਕਸਟਰੂਸ਼ਨ ਪੈਦਾ ਕਰਦੇ ਹਨ। ਐਕਸਟਰਿਊਸ਼ਨ ਡਾਈਜ਼ ਆਮ ਤੌਰ 'ਤੇ ਧਾਤ ਦੇ ਉੱਲੀ ਦੇ ਮੁਕਾਬਲੇ ਸਸਤੇ ਹੁੰਦੇ ਹਨ। ਜੇ ਤੁਸੀਂ ਇੱਕ ਛੋਟੇ ਜਾਂ ਦਰਮਿਆਨੇ ਆਕਾਰ ਦੇ ਐਕਸਟਰੂਜ਼ਨ ਡਾਈ ਐਕਸਟਰੂਡਿੰਗ ਐਲੂਮੀਨੀਅਮ ਲਈ ਕੁਝ ਹਜ਼ਾਰ ਡਾਲਰਾਂ ਤੋਂ ਵੱਧ ਦਾ ਭੁਗਤਾਨ ਕਰ ਰਹੇ ਹੋ, ਤਾਂ ਤੁਸੀਂ ਸ਼ਾਇਦ ਬਹੁਤ ਜ਼ਿਆਦਾ ਭੁਗਤਾਨ ਕਰ ਰਹੇ ਹੋ। ਅਸੀਂ ਇਹ ਨਿਰਧਾਰਤ ਕਰਨ ਵਿੱਚ ਮਾਹਰ ਹਾਂ ਕਿ ਕਿਹੜੀ ਤਕਨੀਕ ਤੁਹਾਡੀ ਐਪਲੀਕੇਸ਼ਨ ਲਈ ਸਭ ਤੋਂ ਵੱਧ ਲਾਗਤ ਪ੍ਰਭਾਵਸ਼ਾਲੀ, ਸਭ ਤੋਂ ਤੇਜ਼ ਅਤੇ ਸਭ ਤੋਂ ਢੁਕਵੀਂ ਹੈ। ਕਦੇ-ਕਦਾਈਂ ਬਾਹਰ ਕੱਢਣਾ ਅਤੇ ਫਿਰ ਕਿਸੇ ਹਿੱਸੇ ਨੂੰ ਮਸ਼ੀਨ ਕਰਨਾ ਤੁਹਾਨੂੰ ਬਹੁਤ ਸਾਰਾ ਨਕਦ ਬਚਾ ਸਕਦਾ ਹੈ। ਕੋਈ ਪੱਕਾ ਫ਼ੈਸਲਾ ਕਰਨ ਤੋਂ ਪਹਿਲਾਂ, ਪਹਿਲਾਂ ਸਾਨੂੰ ਸਾਡੀ ਰਾਏ ਪੁੱਛੋ। ਅਸੀਂ ਬਹੁਤ ਸਾਰੇ ਗਾਹਕਾਂ ਦੀ ਸਹੀ ਫੈਸਲੇ ਲੈਣ ਵਿੱਚ ਮਦਦ ਕੀਤੀ ਹੈ। ਕੁਝ ਵਿਆਪਕ ਤੌਰ 'ਤੇ ਵਰਤੇ ਜਾਣ ਵਾਲੇ ਮੈਟਲ ਐਕਸਟਰਿਊਸ਼ਨਾਂ ਲਈ, ਤੁਸੀਂ ਹੇਠਾਂ ਦਿੱਤੇ ਰੰਗਦਾਰ ਟੈਕਸਟ 'ਤੇ ਕਲਿੱਕ ਕਰਕੇ ਸਾਡੇ ਬਰੋਸ਼ਰ ਅਤੇ ਕੈਟਾਲਾਗ ਡਾਊਨਲੋਡ ਕਰ ਸਕਦੇ ਹੋ। ਜੇਕਰ ਇਹ ਤੁਹਾਡੀਆਂ ਜ਼ਰੂਰਤਾਂ ਨੂੰ ਪੂਰਾ ਕਰਨ ਵਾਲਾ ਇੱਕ ਆਫ-ਸ਼ੈਲਫ ਉਤਪਾਦ ਹੈ, ਤਾਂ ਇਹ ਵਧੇਰੇ ਕਿਫ਼ਾਇਤੀ ਹੋਵੇਗਾ। ਸਾਡੀ ਮੈਡੀਕਲ ਟਿਊਬ ਅਤੇ ਪਾਈਪ ਐਕਸਟਰਿਊਸ਼ਨ ਸਮਰੱਥਾਵਾਂ ਨੂੰ ਡਾਊਨਲੋਡ ਕਰੋ ਸਾਡੇ ਬਾਹਰ ਕੱਢੇ ਹੀਟ ਸਿੰਕ ਨੂੰ ਡਾਊਨਲੋਡ ਕਰੋ • EXTRUSIONS ਲਈ ਸੈਕੰਡਰੀ ਨਿਰਮਾਣ ਅਤੇ ਨਿਰਮਾਣ ਪ੍ਰਕਿਰਿਆਵਾਂ: ਵੈਲਯੂ ਐਡਿਡ ਪ੍ਰਕਿਰਿਆਵਾਂ ਵਿੱਚੋਂ ਜੋ ਅਸੀਂ ਐਕਸਟਰੂਡ ਉਤਪਾਦਾਂ ਲਈ ਪੇਸ਼ ਕਰਦੇ ਹਾਂ: - ਕਸਟਮ ਟਿਊਬ ਅਤੇ ਪਾਈਪ ਮੋੜਨਾ, ਬਣਾਉਣਾ ਅਤੇ ਆਕਾਰ ਦੇਣਾ, ਟਿਊਬ ਕੱਟੋਫ, ਟਿਊਬ ਦਾ ਅੰਤ ਬਣਾਉਣਾ, ਟਿਊਬ ਕੋਇਲਿੰਗ, ਮਸ਼ੀਨਿੰਗ ਅਤੇ ਫਿਨਿਸ਼ਿੰਗ, ਹੋਲ ਡਰਿਲਿੰਗ ਅਤੇ ਵਿੰਨ੍ਹਣਾ ਅਤੇ ਪੰਚਿੰਗ, -ਕਸਟਮ ਪਾਈਪ ਅਤੇ ਟਿਊਬ ਅਸੈਂਬਲੀ, ਟਿਊਬਲਰ ਅਸੈਂਬਲੀ, ਵੈਲਡਿੰਗ, ਬ੍ਰੇਜ਼ਿੰਗ ਅਤੇ ਸੋਲਡਰਿੰਗ -ਕਸਟਮ ਐਕਸਟਰਿਊਸ਼ਨ ਮੋੜਨਾ, ਬਣਾਉਣਾ ਅਤੇ ਆਕਾਰ ਦੇਣਾ -ਸਫ਼ਾਈ, ਡੀਗਰੇਸਿੰਗ, ਪਿਕਲਿੰਗ, ਪੈਸੀਵੇਸ਼ਨ, ਪਾਲਿਸ਼ਿੰਗ, ਐਨੋਡਾਈਜ਼ਿੰਗ, ਪਲੇਟਿੰਗ, ਪੇਂਟਿੰਗ, ਹੀਟ ਟ੍ਰੀਟਿੰਗ, ਐਨੀਲਿੰਗ ਅਤੇ ਸਖਤ, ਮਾਰਕਿੰਗ, ਉੱਕਰੀ ਅਤੇ ਲੇਬਲਿੰਗ, ਕਸਟਮ ਪੈਕੇਜਿੰਗ। CLICK Product Finder-Locator Service ਪਿਛਲੇ ਸਫ਼ੇ
- Casting and Machined Parts, CNC Manufacturing, Milling, Turning, Swiss
Casting and Machined Parts, CNC Manufacturing, Milling, Turning, Swiss Type Machining, Die Casting, Investment Casting, Lost Foam Cast Parts from AGS-TECH Inc. ਕਾਸਟਿੰਗ ਅਤੇ ਮਸ਼ੀਨਿੰਗ ਸਾਡੀਆਂ ਕਸਟਮ ਕਾਸਟਿੰਗ ਅਤੇ ਮਸ਼ੀਨਿੰਗ ਤਕਨੀਕਾਂ ਹਨ ਖਰਚੇ ਯੋਗ ਅਤੇ ਗੈਰ-ਖਰਚਣਯੋਗ ਕਾਸਟਿੰਗ, ਫੈਰਸ ਅਤੇ ਗੈਰ-ਫੈਰਸ ਕਾਸਟਿੰਗ, ਰੇਤ, ਡਾਈ, ਸੈਂਟਰਿਫਿਊਗਲ, ਨਿਰੰਤਰ, ਵਸਰਾਵਿਕ ਉੱਲੀ, ਨਿਵੇਸ਼, ਗੁਆਚਿਆ ਫੋਮ, ਨੇੜੇ-ਨੈੱਟ-ਆਕਾਰ, ਸਥਾਈ ਉੱਲੀ (ਗਰੈਵਿਟੀ ਡਾਈ ਕਾਸਟਿੰਗ), ਪਲਾਸਟਰ ਮੋਲਡ (ਪਲਾਸਟਰ ਕਾਸਟਿੰਗ) ਅਤੇ ਸ਼ੈੱਲ ਕਾਸਟਿੰਗ, ਪਰੰਪਰਾਗਤ ਦੇ ਨਾਲ-ਨਾਲ CNC ਉਪਕਰਣਾਂ ਦੀ ਵਰਤੋਂ ਕਰਕੇ ਮਿਲਿੰਗ ਅਤੇ ਮੋੜ ਦੁਆਰਾ ਤਿਆਰ ਕੀਤੇ ਗਏ ਮਸ਼ੀਨ ਵਾਲੇ ਹਿੱਸੇ, ਉੱਚ ਥ੍ਰੋਪੁੱਟ ਸਸਤੇ ਛੋਟੇ ਸ਼ੁੱਧਤਾ ਵਾਲੇ ਹਿੱਸਿਆਂ ਲਈ ਸਵਿਸ ਟਾਈਪ ਮਸ਼ੀਨਿੰਗ, ਫਾਸਟਨਰਾਂ ਲਈ ਪੇਚ ਮਸ਼ੀਨ, ਗੈਰ-ਰਵਾਇਤੀ ਮਸ਼ੀਨਿੰਗ। ਕਿਰਪਾ ਕਰਕੇ ਧਿਆਨ ਵਿੱਚ ਰੱਖੋ ਕਿ ਧਾਤਾਂ ਅਤੇ ਧਾਤੂ ਮਿਸ਼ਰਣਾਂ ਤੋਂ ਇਲਾਵਾ, ਅਸੀਂ ਵਸਰਾਵਿਕ, ਸ਼ੀਸ਼ੇ ਅਤੇ ਪਲਾਸਟਿਕ ਦੇ ਹਿੱਸਿਆਂ ਦੇ ਨਾਲ-ਨਾਲ ਕੁਝ ਮਾਮਲਿਆਂ ਵਿੱਚ ਮਸ਼ੀਨ ਬਣਾਉਂਦੇ ਹਾਂ ਜਦੋਂ ਇੱਕ ਉੱਲੀ ਬਣਾਉਣਾ ਪਸੰਦ ਨਹੀਂ ਹੁੰਦਾ ਜਾਂ ਵਿਕਲਪ ਨਹੀਂ ਹੁੰਦਾ। ਪੌਲੀਮਰ ਸਮੱਗਰੀ ਦੀ ਮਸ਼ੀਨਿੰਗ ਲਈ ਸਾਡੇ ਕੋਲ ਵਿਸ਼ੇਸ਼ ਤਜ਼ਰਬੇ ਦੀ ਲੋੜ ਹੁੰਦੀ ਹੈ ਕਿਉਂਕਿ ਪਲਾਸਟਿਕ ਅਤੇ ਰਬੜ ਦੀ ਚੁਣੌਤੀ ਉਹਨਾਂ ਦੀ ਨਰਮਤਾ, ਗੈਰ-ਕਠੋਰਤਾ... ਆਦਿ ਕਾਰਨ ਹੈ। ਵਸਰਾਵਿਕ ਅਤੇ ਕੱਚ ਦੀ ਮਸ਼ੀਨਿੰਗ ਲਈ, ਕਿਰਪਾ ਕਰਕੇ ਗੈਰ-ਰਵਾਇਤੀ ਫੈਬਰੀਕੇਸ਼ਨ 'ਤੇ ਸਾਡਾ ਪੰਨਾ ਦੇਖੋ। AGS-TECH Inc. ਹਲਕੇ ਅਤੇ ਭਾਰੀ ਕਾਸਟਿੰਗ ਦੋਵਾਂ ਦਾ ਨਿਰਮਾਣ ਅਤੇ ਸਪਲਾਈ ਕਰਦਾ ਹੈ। ਅਸੀਂ ਬਾਇਲਰ, ਹੀਟ ਐਕਸਚੇਂਜਰ, ਆਟੋਮੋਬਾਈਲ, ਮਾਈਕ੍ਰੋਮੋਟਰ, ਵਿੰਡ ਟਰਬਾਈਨ, ਫੂਡ ਪੈਕਜਿੰਗ ਉਪਕਰਣ ਅਤੇ ਹੋਰ ਲਈ ਮੈਟਲ ਕਾਸਟਿੰਗ ਅਤੇ ਮਸ਼ੀਨਡ ਪਾਰਟਸ ਦੀ ਸਪਲਾਈ ਕਰਦੇ ਰਹੇ ਹਾਂ। ਅਸੀਂ ਸਿਫ਼ਾਰਿਸ਼ ਕਰਦੇ ਹਾਂ ਕਿ ਤੁਸੀਂ ਇੱਥੇ ਕਲਿੱਕ ਕਰੋ AGS-TECH Inc ਦੁਆਰਾ ਮਸ਼ੀਨਿੰਗ ਅਤੇ ਕਾਸਟਿੰਗ ਪ੍ਰਕਿਰਿਆਵਾਂ ਦੇ ਸਾਡੇ ਯੋਜਨਾਬੱਧ ਚਿੱਤਰਾਂ ਨੂੰ ਡਾਊਨਲੋਡ ਕਰੋ। ਇਹ ਤੁਹਾਨੂੰ ਉਸ ਜਾਣਕਾਰੀ ਨੂੰ ਬਿਹਤਰ ਤਰੀਕੇ ਨਾਲ ਸਮਝਣ ਵਿੱਚ ਮਦਦ ਕਰੇਗਾ ਜੋ ਅਸੀਂ ਤੁਹਾਨੂੰ ਹੇਠਾਂ ਪ੍ਰਦਾਨ ਕਰ ਰਹੇ ਹਾਂ। ਆਉ ਅਸੀਂ ਵਿਸਤਾਰ ਵਿੱਚ ਪੇਸ਼ ਕੀਤੀਆਂ ਕੁਝ ਵੱਖ-ਵੱਖ ਤਕਨੀਕਾਂ ਨੂੰ ਵੇਖੀਏ: • ਐਕਸਪੇਂਡੇਬਲ ਮੋਲਡ ਕਾਸਟਿੰਗ: ਇਹ ਵਿਆਪਕ ਸ਼੍ਰੇਣੀ ਉਹਨਾਂ ਤਰੀਕਿਆਂ ਨੂੰ ਦਰਸਾਉਂਦੀ ਹੈ ਜਿਹਨਾਂ ਵਿੱਚ ਅਸਥਾਈ ਅਤੇ ਗੈਰ-ਮੁੜ ਵਰਤੋਂ ਯੋਗ ਮੋਲਡ ਸ਼ਾਮਲ ਹੁੰਦੇ ਹਨ। ਉਦਾਹਰਨਾਂ ਹਨ ਰੇਤ, ਪਲਾਸਟਰ, ਸ਼ੈੱਲ, ਨਿਵੇਸ਼ (ਜਿਸ ਨੂੰ ਗੁਆਚਿਆ-ਮੋਮ ਵੀ ਕਿਹਾ ਜਾਂਦਾ ਹੈ) ਅਤੇ ਪਲਾਸਟਰ ਕਾਸਟਿੰਗ। • ਰੇਤ ਦੀ ਕਾਸਟਿੰਗ: ਇੱਕ ਪ੍ਰਕਿਰਿਆ ਜਿਸ ਵਿੱਚ ਰੇਤ ਨੂੰ ਮੋਲਡ ਸਮੱਗਰੀ ਵਜੋਂ ਵਰਤਿਆ ਜਾਂਦਾ ਹੈ। ਇੱਕ ਬਹੁਤ ਪੁਰਾਣਾ ਤਰੀਕਾ ਹੈ ਅਤੇ ਅਜੇ ਵੀ ਇਸ ਹੱਦ ਤੱਕ ਬਹੁਤ ਮਸ਼ਹੂਰ ਹੈ ਕਿ ਇਸ ਤਕਨੀਕ ਦੁਆਰਾ ਪੈਦਾ ਕੀਤੇ ਗਏ ਜ਼ਿਆਦਾਤਰ ਧਾਤ ਦੀਆਂ ਕਾਸਟਿੰਗਾਂ ਕੀਤੀਆਂ ਜਾਂਦੀਆਂ ਹਨ। ਘੱਟ ਮਾਤਰਾ ਦੇ ਉਤਪਾਦਨ 'ਤੇ ਵੀ ਘੱਟ ਲਾਗਤ. ਛੋਟੇ ਅਤੇ ਵੱਡੇ ਹਿੱਸੇ ਦੇ ਨਿਰਮਾਣ ਲਈ ਉਚਿਤ. ਤਕਨੀਕ ਦੀ ਵਰਤੋਂ ਬਹੁਤ ਘੱਟ ਨਿਵੇਸ਼ ਨਾਲ ਦਿਨਾਂ ਜਾਂ ਹਫ਼ਤਿਆਂ ਦੇ ਅੰਦਰ ਹਿੱਸੇ ਬਣਾਉਣ ਲਈ ਕੀਤੀ ਜਾ ਸਕਦੀ ਹੈ। ਨਮੀ ਵਾਲੀ ਰੇਤ ਨੂੰ ਮਿੱਟੀ, ਬਾਈਂਡਰ ਜਾਂ ਵਿਸ਼ੇਸ਼ ਤੇਲ ਦੀ ਵਰਤੋਂ ਕਰਕੇ ਜੋੜਿਆ ਜਾਂਦਾ ਹੈ। ਰੇਤ ਆਮ ਤੌਰ 'ਤੇ ਮੋਲਡ ਬਕਸਿਆਂ ਵਿੱਚ ਹੁੰਦੀ ਹੈ ਅਤੇ ਕੈਵਿਟੀ ਅਤੇ ਗੇਟ ਸਿਸਟਮ ਮਾਡਲਾਂ ਦੇ ਆਲੇ ਦੁਆਲੇ ਰੇਤ ਨੂੰ ਸੰਕੁਚਿਤ ਕਰਕੇ ਬਣਾਇਆ ਜਾਂਦਾ ਹੈ। ਪ੍ਰਕਿਰਿਆਵਾਂ ਹਨ: 1.) ਮੋਲਡ ਬਣਾਉਣ ਲਈ ਮਾਡਲ ਨੂੰ ਰੇਤ ਵਿੱਚ ਰੱਖਣਾ 2.) ਇੱਕ ਗੇਟਿੰਗ ਪ੍ਰਣਾਲੀ ਵਿੱਚ ਮਾਡਲ ਅਤੇ ਰੇਤ ਨੂੰ ਸ਼ਾਮਲ ਕਰਨਾ 3.) ਮਾਡਲ ਨੂੰ ਹਟਾਉਣਾ 4.) ਪਿਘਲੇ ਹੋਏ ਧਾਤ ਨਾਲ ਮੋਲਡ ਕੈਵਿਟੀ ਨੂੰ ਭਰਨਾ 5.) ਧਾਤ ਦੀ ਠੰਢਕ 6.) ਰੇਤ ਦੇ ਉੱਲੀ ਨੂੰ ਤੋੜਨਾ ਅਤੇ ਕਾਸਟਿੰਗ ਨੂੰ ਹਟਾਉਣਾ • ਪਲਾਸਟਰ ਮੋਲਡ ਕਾਸਟਿੰਗ: ਰੇਤ ਦੀ ਕਾਸਟਿੰਗ ਦੇ ਸਮਾਨ, ਅਤੇ ਰੇਤ ਦੀ ਬਜਾਏ, ਪਲਾਸਟਰ ਆਫ਼ ਪੈਰਿਸ ਨੂੰ ਮੋਲਡ ਸਮੱਗਰੀ ਵਜੋਂ ਵਰਤਿਆ ਜਾ ਰਿਹਾ ਹੈ। ਛੋਟੇ ਉਤਪਾਦਨ ਦੇ ਲੀਡ ਟਾਈਮ ਜਿਵੇਂ ਕਿ ਰੇਤ ਕਾਸਟਿੰਗ ਅਤੇ ਸਸਤੀ। ਚੰਗੀ ਆਯਾਮੀ ਸਹਿਣਸ਼ੀਲਤਾ ਅਤੇ ਸਤਹ ਮੁਕੰਮਲ. ਇਸ ਦਾ ਮੁੱਖ ਨੁਕਸਾਨ ਇਹ ਹੈ ਕਿ ਇਸਦੀ ਵਰਤੋਂ ਐਲੂਮੀਨੀਅਮ ਅਤੇ ਜ਼ਿੰਕ ਵਰਗੀਆਂ ਘੱਟ ਪਿਘਲਣ ਵਾਲੀਆਂ ਧਾਤਾਂ ਨਾਲ ਹੀ ਕੀਤੀ ਜਾ ਸਕਦੀ ਹੈ। • ਸ਼ੈੱਲ ਮੋਲਡ ਕਾਸਟਿੰਗ: ਰੇਤ ਕਾਸਟਿੰਗ ਦੇ ਸਮਾਨ ਵੀ। ਰੇਤ ਨਾਲ ਭਰੇ ਫਲਾਸਕ ਦੀ ਬਜਾਏ ਰੇਤ ਦੇ ਕਠੋਰ ਸ਼ੈੱਲ ਅਤੇ ਥਰਮੋਸੈਟਿੰਗ ਰਾਲ ਬਾਈਂਡਰ ਦੁਆਰਾ ਪ੍ਰਾਪਤ ਕੀਤੀ ਮੋਲਡ ਕੈਵੀਟੀ ਜਿਵੇਂ ਕਿ ਰੇਤ ਕਾਸਟਿੰਗ ਪ੍ਰਕਿਰਿਆ ਵਿੱਚ ਹੁੰਦੀ ਹੈ। ਰੇਤ ਦੁਆਰਾ ਸੁੱਟੇ ਜਾਣ ਲਈ ਢੁਕਵੀਂ ਲਗਭਗ ਕੋਈ ਵੀ ਧਾਤ ਸ਼ੈੱਲ ਮੋਲਡਿੰਗ ਦੁਆਰਾ ਸੁੱਟੀ ਜਾ ਸਕਦੀ ਹੈ। ਪ੍ਰਕਿਰਿਆ ਨੂੰ ਇਸ ਤਰ੍ਹਾਂ ਸੰਖੇਪ ਕੀਤਾ ਜਾ ਸਕਦਾ ਹੈ: 1.) ਸ਼ੈੱਲ ਉੱਲੀ ਦਾ ਨਿਰਮਾਣ. ਰੇਤ ਦੀ ਕਾਸਟਿੰਗ ਵਿੱਚ ਵਰਤੀ ਜਾਂਦੀ ਰੇਤ ਦੀ ਤੁਲਨਾ ਵਿੱਚ ਵਰਤੀ ਗਈ ਰੇਤ ਬਹੁਤ ਛੋਟੇ ਅਨਾਜ ਦੇ ਆਕਾਰ ਦੀ ਹੁੰਦੀ ਹੈ। ਬਰੀਕ ਰੇਤ ਨੂੰ ਥਰਮੋਸੈਟਿੰਗ ਰਾਲ ਨਾਲ ਮਿਲਾਇਆ ਜਾਂਦਾ ਹੈ। ਸ਼ੈੱਲ ਨੂੰ ਹਟਾਉਣਾ ਆਸਾਨ ਬਣਾਉਣ ਲਈ ਧਾਤ ਦੇ ਪੈਟਰਨ ਨੂੰ ਇੱਕ ਵਿਭਾਜਨ ਏਜੰਟ ਨਾਲ ਕੋਟ ਕੀਤਾ ਜਾਂਦਾ ਹੈ। ਇਸ ਤੋਂ ਬਾਅਦ ਧਾਤ ਦੇ ਪੈਟਰਨ ਨੂੰ ਗਰਮ ਕੀਤਾ ਜਾਂਦਾ ਹੈ ਅਤੇ ਰੇਤ ਦੇ ਮਿਸ਼ਰਣ ਨੂੰ ਗਰਮ ਕਾਸਟਿੰਗ ਪੈਟਰਨ 'ਤੇ ਪੋਰਡ ਜਾਂ ਉਡਾ ਦਿੱਤਾ ਜਾਂਦਾ ਹੈ। ਪੈਟਰਨ ਦੀ ਸਤ੍ਹਾ 'ਤੇ ਇੱਕ ਪਤਲਾ ਸ਼ੈੱਲ ਬਣਦਾ ਹੈ। ਇਸ ਸ਼ੈੱਲ ਦੀ ਮੋਟਾਈ ਨੂੰ ਰੇਤ ਦੇ ਰਾਲ ਦੇ ਮਿਸ਼ਰਣ ਦੇ ਮੈਟਲ ਪੈਟਰਨ ਦੇ ਸੰਪਰਕ ਵਿੱਚ ਹੋਣ ਦੇ ਸਮੇਂ ਦੀ ਲੰਬਾਈ ਨੂੰ ਬਦਲ ਕੇ ਐਡਜਸਟ ਕੀਤਾ ਜਾ ਸਕਦਾ ਹੈ। ਢਿੱਲੀ ਰੇਤ ਨੂੰ ਫਿਰ ਸ਼ੈੱਲ ਦੇ ਢੱਕੇ ਪੈਟਰਨ ਦੇ ਨਾਲ ਹਟਾ ਦਿੱਤਾ ਜਾਂਦਾ ਹੈ। 2.) ਅੱਗੇ, ਸ਼ੈੱਲ ਅਤੇ ਪੈਟਰਨ ਨੂੰ ਇੱਕ ਓਵਨ ਵਿੱਚ ਗਰਮ ਕੀਤਾ ਜਾਂਦਾ ਹੈ ਤਾਂ ਜੋ ਸ਼ੈੱਲ ਸਖ਼ਤ ਹੋ ਜਾਵੇ। ਸਖ਼ਤ ਹੋਣ ਤੋਂ ਬਾਅਦ, ਸ਼ੈੱਲ ਨੂੰ ਪੈਟਰਨ ਵਿੱਚ ਬਣੇ ਪਿੰਨਾਂ ਦੀ ਵਰਤੋਂ ਕਰਕੇ ਪੈਟਰਨ ਤੋਂ ਬਾਹਰ ਕੱਢਿਆ ਜਾਂਦਾ ਹੈ। 3.) ਦੋ ਅਜਿਹੇ ਸ਼ੈੱਲ ਗਲੂਇੰਗ ਜਾਂ ਕਲੈਂਪਿੰਗ ਦੁਆਰਾ ਇਕੱਠੇ ਕੀਤੇ ਜਾਂਦੇ ਹਨ ਅਤੇ ਪੂਰਾ ਉੱਲੀ ਬਣਾਉਂਦੇ ਹਨ। ਹੁਣ ਸ਼ੈੱਲ ਮੋਲਡ ਨੂੰ ਇੱਕ ਕੰਟੇਨਰ ਵਿੱਚ ਪਾਇਆ ਜਾਂਦਾ ਹੈ ਜਿਸ ਵਿੱਚ ਕਾਸਟਿੰਗ ਪ੍ਰਕਿਰਿਆ ਦੌਰਾਨ ਇਸਨੂੰ ਰੇਤ ਜਾਂ ਧਾਤ ਦੇ ਸ਼ਾਟ ਦੁਆਰਾ ਸਮਰਥਤ ਕੀਤਾ ਜਾਂਦਾ ਹੈ। 4.) ਹੁਣ ਗਰਮ ਧਾਤ ਨੂੰ ਸ਼ੈੱਲ ਮੋਲਡ ਵਿੱਚ ਡੋਲ੍ਹਿਆ ਜਾ ਸਕਦਾ ਹੈ। ਸ਼ੈੱਲ ਕਾਸਟਿੰਗ ਦੇ ਫਾਇਦੇ ਬਹੁਤ ਵਧੀਆ ਸਤਹ ਮੁਕੰਮਲ ਹੋਣ ਵਾਲੇ ਉਤਪਾਦ ਹਨ, ਉੱਚ ਅਯਾਮੀ ਸ਼ੁੱਧਤਾ ਦੇ ਨਾਲ ਗੁੰਝਲਦਾਰ ਹਿੱਸਿਆਂ ਦੇ ਨਿਰਮਾਣ ਦੀ ਸੰਭਾਵਨਾ, ਪ੍ਰਕਿਰਿਆ ਨੂੰ ਸਵੈਚਲਿਤ ਕਰਨ ਲਈ ਆਸਾਨ, ਵੱਡੀ ਮਾਤਰਾ ਦੇ ਉਤਪਾਦਨ ਲਈ ਕਿਫ਼ਾਇਤੀ। ਨੁਕਸਾਨ ਇਹ ਹਨ ਕਿ ਮੋਲਡਾਂ ਨੂੰ ਗੈਸਾਂ ਦੇ ਕਾਰਨ ਚੰਗੀ ਹਵਾਦਾਰੀ ਦੀ ਲੋੜ ਹੁੰਦੀ ਹੈ ਜੋ ਉਦੋਂ ਬਣਦੀਆਂ ਹਨ ਜਦੋਂ ਪਿਘਲੀ ਹੋਈ ਧਾਤ ਬਾਈਂਡਰ ਕੈਮੀਕਲ ਨਾਲ ਸੰਪਰਕ ਕਰਦੀ ਹੈ, ਥਰਮੋਸੈਟਿੰਗ ਰੈਜ਼ਿਨ ਅਤੇ ਧਾਤ ਦੇ ਪੈਟਰਨ ਮਹਿੰਗੇ ਹੁੰਦੇ ਹਨ। ਧਾਤ ਦੇ ਪੈਟਰਨਾਂ ਦੀ ਲਾਗਤ ਦੇ ਕਾਰਨ, ਇਹ ਤਕਨੀਕ ਘੱਟ ਮਾਤਰਾ ਦੇ ਉਤਪਾਦਨ ਲਈ ਚੰਗੀ ਤਰ੍ਹਾਂ ਅਨੁਕੂਲ ਨਹੀਂ ਹੋ ਸਕਦੀ। • ਇਨਵੈਸਟਮੈਂਟ ਕਾਸਟਿੰਗ (ਲੌਸਟ-ਵੈਕਸ ਕਾਸਟਿੰਗ ਵੀ ਕਿਹਾ ਜਾਂਦਾ ਹੈ): ਬਹੁਤ ਪੁਰਾਣੀ ਤਕਨੀਕ ਅਤੇ ਬਹੁਤ ਸਾਰੀਆਂ ਧਾਤਾਂ, ਰਿਫ੍ਰੈਕਟਰੀ ਸਮੱਗਰੀ ਅਤੇ ਵਿਸ਼ੇਸ਼ ਉੱਚ ਪ੍ਰਦਰਸ਼ਨ ਵਾਲੇ ਮਿਸ਼ਰਣਾਂ ਤੋਂ ਉੱਚ ਸ਼ੁੱਧਤਾ, ਦੁਹਰਾਉਣਯੋਗਤਾ, ਬਹੁਪੱਖੀਤਾ ਅਤੇ ਇਕਸਾਰਤਾ ਦੇ ਨਾਲ ਗੁਣਵੱਤਾ ਵਾਲੇ ਹਿੱਸੇ ਬਣਾਉਣ ਲਈ ਢੁਕਵੀਂ ਹੈ। ਛੋਟੇ ਅਤੇ ਵੱਡੇ ਆਕਾਰ ਦੇ ਹਿੱਸੇ ਪੈਦਾ ਕੀਤੇ ਜਾ ਸਕਦੇ ਹਨ. ਇੱਕ ਮਹਿੰਗੀ ਪ੍ਰਕਿਰਿਆ ਜਦੋਂ ਕੁਝ ਹੋਰ ਤਰੀਕਿਆਂ ਨਾਲ ਤੁਲਨਾ ਕੀਤੀ ਜਾਂਦੀ ਹੈ, ਪਰ ਮੁੱਖ ਫਾਇਦਾ ਇਹ ਹੈ ਕਿ ਨੇੜੇ ਦੇ ਸ਼ੁੱਧ ਆਕਾਰ, ਗੁੰਝਲਦਾਰ ਰੂਪਾਂ ਅਤੇ ਵੇਰਵਿਆਂ ਦੇ ਨਾਲ ਹਿੱਸੇ ਬਣਾਉਣ ਦੀ ਸੰਭਾਵਨਾ ਹੈ। ਇਸ ਲਈ ਲਾਗਤ ਕੁਝ ਮਾਮਲਿਆਂ ਵਿੱਚ ਮੁੜ ਕੰਮ ਅਤੇ ਮਸ਼ੀਨਿੰਗ ਨੂੰ ਖਤਮ ਕਰਕੇ ਕੁਝ ਹੱਦ ਤੱਕ ਆਫਸੈੱਟ ਕੀਤੀ ਜਾਂਦੀ ਹੈ। ਭਾਵੇਂ ਭਿੰਨਤਾਵਾਂ ਹੋ ਸਕਦੀਆਂ ਹਨ, ਇੱਥੇ ਆਮ ਨਿਵੇਸ਼ ਕਾਸਟਿੰਗ ਪ੍ਰਕਿਰਿਆ ਦਾ ਸੰਖੇਪ ਹੈ: 1.) ਮੋਮ ਜਾਂ ਪਲਾਸਟਿਕ ਤੋਂ ਅਸਲੀ ਮਾਸਟਰ ਪੈਟਰਨ ਦੀ ਸਿਰਜਣਾ। ਹਰੇਕ ਕਾਸਟਿੰਗ ਨੂੰ ਇੱਕ ਪੈਟਰਨ ਦੀ ਲੋੜ ਹੁੰਦੀ ਹੈ ਕਿਉਂਕਿ ਇਹ ਪ੍ਰਕਿਰਿਆ ਵਿੱਚ ਨਸ਼ਟ ਹੋ ਜਾਂਦੇ ਹਨ। ਉੱਲੀ ਜਿਸ ਤੋਂ ਪੈਟਰਨ ਬਣਾਏ ਜਾਂਦੇ ਹਨ, ਦੀ ਵੀ ਲੋੜ ਹੁੰਦੀ ਹੈ ਅਤੇ ਜ਼ਿਆਦਾਤਰ ਸਮਾਂ ਉੱਲੀ ਨੂੰ ਕਾਸਟ ਜਾਂ ਮਸ਼ੀਨ ਕੀਤਾ ਜਾਂਦਾ ਹੈ। ਕਿਉਂਕਿ ਉੱਲੀ ਨੂੰ ਖੋਲ੍ਹਣ ਦੀ ਜ਼ਰੂਰਤ ਨਹੀਂ ਹੈ, ਗੁੰਝਲਦਾਰ ਕਾਸਟਿੰਗ ਪ੍ਰਾਪਤ ਕੀਤੀ ਜਾ ਸਕਦੀ ਹੈ, ਬਹੁਤ ਸਾਰੇ ਮੋਮ ਦੇ ਪੈਟਰਨ ਨੂੰ ਇੱਕ ਰੁੱਖ ਦੀਆਂ ਸ਼ਾਖਾਵਾਂ ਵਾਂਗ ਜੋੜਿਆ ਜਾ ਸਕਦਾ ਹੈ ਅਤੇ ਇੱਕਠੇ ਡੋਲ੍ਹਿਆ ਜਾ ਸਕਦਾ ਹੈ, ਇਸ ਤਰ੍ਹਾਂ ਧਾਤ ਜਾਂ ਧਾਤ ਦੇ ਮਿਸ਼ਰਤ ਮਿਸ਼ਰਣ ਦੇ ਇੱਕਲੇ ਡੋਲ੍ਹਣ ਤੋਂ ਕਈ ਹਿੱਸਿਆਂ ਦੇ ਉਤਪਾਦਨ ਨੂੰ ਸਮਰੱਥ ਬਣਾਇਆ ਜਾ ਸਕਦਾ ਹੈ। 2.) ਅੱਗੇ, ਪੈਟਰਨ ਨੂੰ ਬਹੁਤ ਬਾਰੀਕ ਦਾਣੇਦਾਰ ਸਿਲਿਕਾ, ਪਾਣੀ, ਬਾਈਂਡਰ ਨਾਲ ਬਣੀ ਰਿਫ੍ਰੈਕਟਰੀ ਸਲਰੀ ਨਾਲ ਡੁਬੋਇਆ ਜਾਂ ਡੋਲ੍ਹਿਆ ਜਾਂਦਾ ਹੈ। ਇਸ ਦੇ ਨਤੀਜੇ ਵਜੋਂ ਪੈਟਰਨ ਦੀ ਸਤ੍ਹਾ ਉੱਤੇ ਵਸਰਾਵਿਕ ਪਰਤ ਆ ਜਾਂਦੀ ਹੈ। ਪੈਟਰਨ 'ਤੇ ਰਿਫ੍ਰੈਕਟਰੀ ਕੋਟ ਨੂੰ ਸੁੱਕਣ ਅਤੇ ਸਖ਼ਤ ਹੋਣ ਲਈ ਛੱਡ ਦਿੱਤਾ ਜਾਂਦਾ ਹੈ। ਇਹ ਕਦਮ ਉਹ ਹੈ ਜਿੱਥੋਂ ਨਾਮ ਨਿਵੇਸ਼ ਕਾਸਟਿੰਗ ਆਉਂਦਾ ਹੈ: ਰਿਫ੍ਰੈਕਟਰੀ ਸਲਰੀ ਨੂੰ ਮੋਮ ਦੇ ਪੈਟਰਨ ਉੱਤੇ ਨਿਵੇਸ਼ ਕੀਤਾ ਜਾਂਦਾ ਹੈ। 3.) ਇਸ ਪੜਾਅ 'ਤੇ, ਕਠੋਰ ਵਸਰਾਵਿਕ ਉੱਲੀ ਨੂੰ ਉਲਟਾ ਕਰ ਦਿੱਤਾ ਜਾਂਦਾ ਹੈ ਅਤੇ ਗਰਮ ਕੀਤਾ ਜਾਂਦਾ ਹੈ ਤਾਂ ਜੋ ਮੋਮ ਪਿਘਲ ਜਾਵੇ ਅਤੇ ਉੱਲੀ ਤੋਂ ਬਾਹਰ ਨਿਕਲ ਜਾਵੇ। ਮੈਟਲ ਕਾਸਟਿੰਗ ਲਈ ਇੱਕ ਕੈਵਿਟੀ ਪਿੱਛੇ ਛੱਡੀ ਜਾਂਦੀ ਹੈ। 4.) ਮੋਮ ਦੇ ਬਾਹਰ ਹੋਣ ਤੋਂ ਬਾਅਦ, ਵਸਰਾਵਿਕ ਉੱਲੀ ਨੂੰ ਉੱਚ ਤਾਪਮਾਨ ਤੱਕ ਗਰਮ ਕੀਤਾ ਜਾਂਦਾ ਹੈ ਜਿਸ ਦੇ ਨਤੀਜੇ ਵਜੋਂ ਉੱਲੀ ਮਜ਼ਬੂਤ ਹੁੰਦੀ ਹੈ। 5.) ਧਾਤੂ ਕਾਸਟਿੰਗ ਨੂੰ ਸਾਰੇ ਗੁੰਝਲਦਾਰ ਭਾਗਾਂ ਨੂੰ ਭਰਨ ਵਾਲੇ ਗਰਮ ਉੱਲੀ ਵਿੱਚ ਡੋਲ੍ਹਿਆ ਜਾਂਦਾ ਹੈ। 6.) ਕਾਸਟਿੰਗ ਨੂੰ ਠੋਸ ਕਰਨ ਦੀ ਆਗਿਆ ਹੈ 7.) ਅੰਤ ਵਿੱਚ ਵਸਰਾਵਿਕ ਉੱਲੀ ਟੁੱਟ ਗਈ ਹੈ ਅਤੇ ਨਿਰਮਿਤ ਹਿੱਸੇ ਦਰਖਤ ਤੋਂ ਕੱਟੇ ਗਏ ਹਨ। ਇੱਥੇ ਨਿਵੇਸ਼ ਕਾਸਟਿੰਗ ਪਲਾਂਟ ਬਰੋਸ਼ਰ ਦਾ ਲਿੰਕ ਹੈ • ਈਵੇਪੋਰੇਟਿਵ ਪੈਟਰਨ ਕਾਸਟਿੰਗ: ਇਹ ਪ੍ਰਕਿਰਿਆ ਪੋਲੀਸਟੀਰੀਨ ਫੋਮ ਵਰਗੀ ਸਮੱਗਰੀ ਤੋਂ ਬਣੇ ਪੈਟਰਨ ਦੀ ਵਰਤੋਂ ਕਰਦੀ ਹੈ ਜੋ ਉੱਲੀ ਵਿੱਚ ਗਰਮ ਪਿਘਲੀ ਹੋਈ ਧਾਤ ਨੂੰ ਡੋਲ੍ਹਣ 'ਤੇ ਭਾਫ਼ ਬਣ ਜਾਂਦੀ ਹੈ। ਇਸ ਪ੍ਰਕਿਰਿਆ ਦੀਆਂ ਦੋ ਕਿਸਮਾਂ ਹਨ: LOST FOAM CASTING ਜੋ ਬੰਧਨ ਰਹਿਤ ਰੇਤ ਦੀ ਵਰਤੋਂ ਕਰਦੀ ਹੈ ਅਤੇ ਪੂਰੀ ਮੋਲਡ ਕਾਸਟਿੰਗ ਜੋ ਬੰਧੂਆ ਰੇਤ ਦੀ ਵਰਤੋਂ ਕਰਦੀ ਹੈ। ਇੱਥੇ ਆਮ ਪ੍ਰਕਿਰਿਆ ਦੇ ਕਦਮ ਹਨ: 1.) ਪੋਲੀਸਟੀਰੀਨ ਵਰਗੀ ਸਮੱਗਰੀ ਤੋਂ ਪੈਟਰਨ ਤਿਆਰ ਕਰੋ। ਜਦੋਂ ਵੱਡੀ ਮਾਤਰਾ ਦਾ ਨਿਰਮਾਣ ਕੀਤਾ ਜਾਵੇਗਾ, ਪੈਟਰਨ ਨੂੰ ਢਾਲਿਆ ਜਾਂਦਾ ਹੈ. ਜੇ ਹਿੱਸੇ ਦੀ ਗੁੰਝਲਦਾਰ ਸ਼ਕਲ ਹੈ, ਤਾਂ ਪੈਟਰਨ ਬਣਾਉਣ ਲਈ ਅਜਿਹੇ ਫੋਮ ਸਮੱਗਰੀ ਦੇ ਕਈ ਭਾਗਾਂ ਨੂੰ ਇਕੱਠੇ ਕਰਨ ਦੀ ਲੋੜ ਹੋ ਸਕਦੀ ਹੈ। ਅਸੀਂ ਅਕਸਰ ਕਾਸਟਿੰਗ 'ਤੇ ਚੰਗੀ ਸਤਹ ਫਿਨਿਸ਼ ਬਣਾਉਣ ਲਈ ਪੈਟਰਨ ਨੂੰ ਰਿਫ੍ਰੈਕਟਰੀ ਮਿਸ਼ਰਣ ਨਾਲ ਕੋਟ ਕਰਦੇ ਹਾਂ। 2.) ਪੈਟਰਨ ਫਿਰ ਮੋਲਡਿੰਗ ਰੇਤ ਵਿੱਚ ਪਾ ਦਿੱਤਾ ਗਿਆ ਹੈ. 3.) ਪਿਘਲੀ ਹੋਈ ਧਾਤ ਨੂੰ ਉੱਲੀ ਵਿੱਚ ਡੋਲ੍ਹਿਆ ਜਾਂਦਾ ਹੈ, ਫੋਮ ਪੈਟਰਨ ਨੂੰ ਵਾਸ਼ਪੀਕਰਨ ਕਰਦਾ ਹੈ, ਜਿਵੇਂ ਕਿ ਜ਼ਿਆਦਾਤਰ ਮਾਮਲਿਆਂ ਵਿੱਚ ਪੋਲੀਸਟਾਈਰੀਨ ਜਿਵੇਂ ਕਿ ਇਹ ਮੋਲਡ ਕੈਵਿਟੀ ਵਿੱਚੋਂ ਵਹਿੰਦਾ ਹੈ। 4.) ਪਿਘਲੀ ਹੋਈ ਧਾਤ ਨੂੰ ਸਖ਼ਤ ਹੋਣ ਲਈ ਰੇਤ ਦੇ ਉੱਲੀ ਵਿੱਚ ਛੱਡ ਦਿੱਤਾ ਜਾਂਦਾ ਹੈ। 5.) ਸਖ਼ਤ ਹੋਣ ਤੋਂ ਬਾਅਦ, ਅਸੀਂ ਕਾਸਟਿੰਗ ਨੂੰ ਹਟਾ ਦਿੰਦੇ ਹਾਂ. ਕੁਝ ਮਾਮਲਿਆਂ ਵਿੱਚ, ਸਾਡੇ ਦੁਆਰਾ ਬਣਾਏ ਗਏ ਉਤਪਾਦ ਨੂੰ ਪੈਟਰਨ ਦੇ ਅੰਦਰ ਇੱਕ ਕੋਰ ਦੀ ਲੋੜ ਹੁੰਦੀ ਹੈ। ਵਾਸ਼ਪੀਕਰਨ ਵਾਲੀ ਕਾਸਟਿੰਗ ਵਿੱਚ, ਮੋਲਡ ਕੈਵਿਟੀ ਵਿੱਚ ਇੱਕ ਕੋਰ ਨੂੰ ਰੱਖਣ ਅਤੇ ਸੁਰੱਖਿਅਤ ਕਰਨ ਦੀ ਕੋਈ ਲੋੜ ਨਹੀਂ ਹੈ। ਇਹ ਤਕਨੀਕ ਬਹੁਤ ਹੀ ਗੁੰਝਲਦਾਰ ਜਿਓਮੈਟਰੀਜ਼ ਦੇ ਨਿਰਮਾਣ ਲਈ ਢੁਕਵੀਂ ਹੈ, ਇਹ ਉੱਚ ਮਾਤਰਾ ਦੇ ਉਤਪਾਦਨ ਲਈ ਆਸਾਨੀ ਨਾਲ ਸਵੈਚਾਲਿਤ ਹੋ ਸਕਦੀ ਹੈ, ਅਤੇ ਕਾਸਟ ਵਾਲੇ ਹਿੱਸੇ ਵਿੱਚ ਕੋਈ ਵਿਭਾਜਨ ਲਾਈਨਾਂ ਨਹੀਂ ਹਨ। ਬੁਨਿਆਦੀ ਪ੍ਰਕਿਰਿਆ ਨੂੰ ਲਾਗੂ ਕਰਨ ਲਈ ਸਧਾਰਨ ਅਤੇ ਕਿਫ਼ਾਇਤੀ ਹੈ. ਵੱਡੀ ਮਾਤਰਾ ਦੇ ਉਤਪਾਦਨ ਲਈ, ਕਿਉਂਕਿ ਪੋਲੀਸਟੀਰੀਨ ਤੋਂ ਪੈਟਰਨ ਬਣਾਉਣ ਲਈ ਇੱਕ ਡਾਈ ਜਾਂ ਮੋਲਡ ਦੀ ਲੋੜ ਹੁੰਦੀ ਹੈ, ਇਹ ਕੁਝ ਮਹਿੰਗਾ ਹੋ ਸਕਦਾ ਹੈ। • ਗੈਰ-ਵਿਸਥਾਰਯੋਗ ਮੋਲਡ ਕਾਸਟਿੰਗ: ਇਹ ਵਿਆਪਕ ਸ਼੍ਰੇਣੀ ਉਹਨਾਂ ਤਰੀਕਿਆਂ ਨੂੰ ਦਰਸਾਉਂਦੀ ਹੈ ਜਿੱਥੇ ਹਰੇਕ ਉਤਪਾਦਨ ਚੱਕਰ ਤੋਂ ਬਾਅਦ ਉੱਲੀ ਨੂੰ ਸੁਧਾਰਨ ਦੀ ਲੋੜ ਨਹੀਂ ਹੁੰਦੀ ਹੈ। ਉਦਾਹਰਨਾਂ ਹਨ ਸਥਾਈ, ਡਾਈ, ਨਿਰੰਤਰ ਅਤੇ ਸੈਂਟਰਿਫਿਊਗਲ ਕਾਸਟਿੰਗ। ਦੁਹਰਾਉਣਯੋਗਤਾ ਪ੍ਰਾਪਤ ਕੀਤੀ ਜਾਂਦੀ ਹੈ ਅਤੇ ਭਾਗਾਂ ਨੂੰ ਨਜ਼ਦੀਕੀ ਨੈੱਟ ਆਕਾਰ ਵਜੋਂ ਦਰਸਾਇਆ ਜਾ ਸਕਦਾ ਹੈ। • ਸਥਾਈ ਮੋਲਡ ਕਾਸਟਿੰਗ: ਧਾਤੂ ਤੋਂ ਬਣੇ ਮੁੜ ਵਰਤੋਂ ਯੋਗ ਮੋਲਡ ਮਲਟੀਪਲ ਕਾਸਟਿੰਗ ਲਈ ਵਰਤੇ ਜਾਂਦੇ ਹਨ। ਇੱਕ ਸਥਾਈ ਉੱਲੀ ਨੂੰ ਆਮ ਤੌਰ 'ਤੇ ਇਸ ਦੇ ਖਤਮ ਹੋਣ ਤੋਂ ਪਹਿਲਾਂ ਹਜ਼ਾਰਾਂ ਵਾਰ ਵਰਤਿਆ ਜਾ ਸਕਦਾ ਹੈ। ਗਰੈਵਿਟੀ, ਗੈਸ ਦਾ ਦਬਾਅ ਜਾਂ ਵੈਕਿਊਮ ਆਮ ਤੌਰ 'ਤੇ ਉੱਲੀ ਨੂੰ ਭਰਨ ਲਈ ਵਰਤਿਆ ਜਾਂਦਾ ਹੈ। ਮੋਲਡ (ਜਿਸ ਨੂੰ ਡਾਈ ਵੀ ਕਿਹਾ ਜਾਂਦਾ ਹੈ) ਆਮ ਤੌਰ 'ਤੇ ਲੋਹੇ, ਸਟੀਲ, ਵਸਰਾਵਿਕ ਜਾਂ ਹੋਰ ਧਾਤਾਂ ਦੇ ਬਣੇ ਹੁੰਦੇ ਹਨ। ਆਮ ਪ੍ਰਕਿਰਿਆ ਹੈ: 1.) ਮਸ਼ੀਨ ਅਤੇ ਉੱਲੀ ਬਣਾਓ. ਦੋ ਧਾਤ ਦੇ ਬਲਾਕਾਂ ਵਿੱਚੋਂ ਉੱਲੀ ਨੂੰ ਮਸ਼ੀਨ ਕਰਨਾ ਆਮ ਗੱਲ ਹੈ ਜੋ ਇਕੱਠੇ ਫਿੱਟ ਹੁੰਦੇ ਹਨ ਅਤੇ ਖੋਲ੍ਹੇ ਅਤੇ ਬੰਦ ਕੀਤੇ ਜਾ ਸਕਦੇ ਹਨ। ਦੋਵੇਂ ਭਾਗਾਂ ਦੀਆਂ ਵਿਸ਼ੇਸ਼ਤਾਵਾਂ ਦੇ ਨਾਲ ਨਾਲ ਗੇਟਿੰਗ ਪ੍ਰਣਾਲੀ ਨੂੰ ਆਮ ਤੌਰ 'ਤੇ ਕਾਸਟਿੰਗ ਮੋਲਡ ਵਿੱਚ ਬਣਾਇਆ ਜਾਂਦਾ ਹੈ। 2.) ਅੰਦਰੂਨੀ ਉੱਲੀ ਦੀਆਂ ਸਤਹਾਂ ਨੂੰ ਰਿਫ੍ਰੈਕਟਰੀ ਸਮੱਗਰੀ ਨੂੰ ਸ਼ਾਮਲ ਕਰਨ ਵਾਲੀ ਸਲਰੀ ਨਾਲ ਕੋਟ ਕੀਤਾ ਜਾਂਦਾ ਹੈ। ਇਹ ਗਰਮੀ ਦੇ ਪ੍ਰਵਾਹ ਨੂੰ ਨਿਯੰਤਰਿਤ ਕਰਨ ਵਿੱਚ ਮਦਦ ਕਰਦਾ ਹੈ ਅਤੇ ਪਲੱਸਤਰ ਵਾਲੇ ਹਿੱਸੇ ਨੂੰ ਆਸਾਨੀ ਨਾਲ ਹਟਾਉਣ ਲਈ ਇੱਕ ਲੁਬਰੀਕੈਂਟ ਵਜੋਂ ਕੰਮ ਕਰਦਾ ਹੈ। 3.) ਅੱਗੇ, ਸਥਾਈ ਉੱਲੀ ਦੇ ਅੱਧੇ ਹਿੱਸੇ ਨੂੰ ਬੰਦ ਕਰ ਦਿੱਤਾ ਜਾਂਦਾ ਹੈ ਅਤੇ ਉੱਲੀ ਨੂੰ ਗਰਮ ਕੀਤਾ ਜਾਂਦਾ ਹੈ। 4.) ਪਿਘਲੀ ਹੋਈ ਧਾਤ ਨੂੰ ਉੱਲੀ ਵਿੱਚ ਡੋਲ੍ਹਿਆ ਜਾਂਦਾ ਹੈ ਅਤੇ ਸਥਿਰਤਾ ਲਈ ਛੱਡ ਦਿੱਤਾ ਜਾਂਦਾ ਹੈ। 5.) ਜ਼ਿਆਦਾ ਕੂਲਿੰਗ ਹੋਣ ਤੋਂ ਪਹਿਲਾਂ, ਜਦੋਂ ਮੋਲਡ ਦੇ ਅੱਧੇ ਖੁੱਲ੍ਹੇ ਹੁੰਦੇ ਹਨ ਤਾਂ ਅਸੀਂ ਈਜੇਕਟਰਾਂ ਦੀ ਵਰਤੋਂ ਕਰਕੇ ਸਥਾਈ ਉੱਲੀ ਤੋਂ ਹਿੱਸੇ ਨੂੰ ਹਟਾ ਦਿੰਦੇ ਹਾਂ। ਅਸੀਂ ਅਕਸਰ ਘੱਟ ਪਿਘਲਣ ਵਾਲੇ ਬਿੰਦੂ ਧਾਤਾਂ ਜਿਵੇਂ ਕਿ ਜ਼ਿੰਕ ਅਤੇ ਐਲੂਮੀਨੀਅਮ ਲਈ ਸਥਾਈ ਮੋਲਡ ਕਾਸਟਿੰਗ ਦੀ ਵਰਤੋਂ ਕਰਦੇ ਹਾਂ। ਸਟੀਲ ਕਾਸਟਿੰਗ ਲਈ, ਅਸੀਂ ਗ੍ਰਾਫਾਈਟ ਨੂੰ ਮੋਲਡ ਸਮੱਗਰੀ ਵਜੋਂ ਵਰਤਦੇ ਹਾਂ। ਅਸੀਂ ਕਈ ਵਾਰ ਸਥਾਈ ਮੋਲਡਾਂ ਦੇ ਅੰਦਰ ਕੋਰ ਦੀ ਵਰਤੋਂ ਕਰਕੇ ਗੁੰਝਲਦਾਰ ਜਿਓਮੈਟਰੀ ਪ੍ਰਾਪਤ ਕਰਦੇ ਹਾਂ। ਇਸ ਤਕਨੀਕ ਦੇ ਫਾਇਦੇ ਤੇਜ਼ ਕੂਲਿੰਗ, ਗੁਣਾਂ ਵਿੱਚ ਇਕਸਾਰਤਾ, ਚੰਗੀ ਸ਼ੁੱਧਤਾ ਅਤੇ ਸਤਹ ਦੀ ਸਮਾਪਤੀ, ਘੱਟ ਰੱਦ ਦਰਾਂ, ਪ੍ਰਕਿਰਿਆ ਨੂੰ ਸਵੈਚਾਲਤ ਕਰਨ ਦੀ ਸੰਭਾਵਨਾ ਅਤੇ ਆਰਥਿਕ ਤੌਰ 'ਤੇ ਉੱਚ ਮਾਤਰਾ ਪੈਦਾ ਕਰਨ ਦੁਆਰਾ ਪ੍ਰਾਪਤ ਕੀਤੀਆਂ ਚੰਗੀਆਂ ਮਕੈਨੀਕਲ ਵਿਸ਼ੇਸ਼ਤਾਵਾਂ ਵਾਲੇ ਕਾਸਟਿੰਗ ਹਨ। ਨੁਕਸਾਨ ਉੱਚ ਸ਼ੁਰੂਆਤੀ ਸੈੱਟਅੱਪ ਲਾਗਤਾਂ ਹਨ ਜੋ ਇਸਨੂੰ ਘੱਟ ਵਾਲੀਅਮ ਓਪਰੇਸ਼ਨਾਂ ਲਈ ਅਣਉਚਿਤ ਬਣਾਉਂਦੀਆਂ ਹਨ, ਅਤੇ ਨਿਰਮਿਤ ਹਿੱਸਿਆਂ ਦੇ ਆਕਾਰ 'ਤੇ ਸੀਮਾਵਾਂ ਹਨ। • ਡਾਈ ਕਾਸਟਿੰਗ: ਇੱਕ ਡਾਈ ਮਸ਼ੀਨ ਕੀਤੀ ਜਾਂਦੀ ਹੈ ਅਤੇ ਪਿਘਲੀ ਹੋਈ ਧਾਤ ਨੂੰ ਉੱਚ ਦਬਾਅ ਹੇਠ ਮੋਲਡ ਕੈਵਿਟੀਜ਼ ਵਿੱਚ ਧੱਕਿਆ ਜਾਂਦਾ ਹੈ। ਨਾਨਫੈਰਸ ਅਤੇ ਨਾਲ ਹੀ ਫੈਰਸ ਮੈਟਲ ਡਾਈ ਕਾਸਟਿੰਗ ਸੰਭਵ ਹਨ। ਇਹ ਪ੍ਰਕਿਰਿਆ ਵੇਰਵਿਆਂ, ਬਹੁਤ ਹੀ ਪਤਲੀਆਂ ਕੰਧਾਂ, ਅਯਾਮੀ ਇਕਸਾਰਤਾ ਅਤੇ ਚੰਗੀ ਸਤਹ ਫਿਨਿਸ਼ ਦੇ ਨਾਲ ਛੋਟੇ ਤੋਂ ਦਰਮਿਆਨੇ ਆਕਾਰ ਦੇ ਹਿੱਸਿਆਂ ਦੇ ਉੱਚ ਮਾਤਰਾ ਵਿੱਚ ਉਤਪਾਦਨ ਲਈ ਢੁਕਵੀਂ ਹੈ। AGS-TECH Inc. ਇਸ ਤਕਨੀਕ ਦੀ ਵਰਤੋਂ ਕਰਕੇ ਕੰਧ ਦੀ ਮੋਟਾਈ 0.5 ਮਿਲੀਮੀਟਰ ਤੱਕ ਬਣਾਉਣ ਦੇ ਸਮਰੱਥ ਹੈ। ਸਥਾਈ ਮੋਲਡ ਕਾਸਟਿੰਗ ਦੀ ਤਰ੍ਹਾਂ, ਉੱਲੀ ਵਿੱਚ ਦੋ ਅੱਧੇ ਹੋਣੇ ਚਾਹੀਦੇ ਹਨ ਜੋ ਪੈਦਾ ਹੋਏ ਹਿੱਸੇ ਨੂੰ ਹਟਾਉਣ ਲਈ ਖੁੱਲ੍ਹ ਅਤੇ ਬੰਦ ਹੋ ਸਕਦੇ ਹਨ। ਇੱਕ ਡਾਈ ਕਾਸਟਿੰਗ ਮੋਲਡ ਵਿੱਚ ਹਰੇਕ ਚੱਕਰ ਦੇ ਨਾਲ ਮਲਟੀਪਲ ਕਾਸਟਿੰਗ ਦੇ ਉਤਪਾਦਨ ਨੂੰ ਸਮਰੱਥ ਕਰਨ ਲਈ ਕਈ ਕੈਵਿਟੀਜ਼ ਹੋ ਸਕਦੀਆਂ ਹਨ। ਡਾਈ ਕਾਸਟਿੰਗ ਮੋਲਡ ਬਹੁਤ ਭਾਰੀ ਹੁੰਦੇ ਹਨ ਅਤੇ ਉਹਨਾਂ ਦੁਆਰਾ ਬਣਾਏ ਗਏ ਹਿੱਸਿਆਂ ਨਾਲੋਂ ਬਹੁਤ ਵੱਡੇ ਹੁੰਦੇ ਹਨ, ਇਸਲਈ ਮਹਿੰਗੇ ਵੀ ਹੁੰਦੇ ਹਨ। ਅਸੀਂ ਆਪਣੇ ਗ੍ਰਾਹਕਾਂ ਲਈ ਖਰਾਬ ਮਰਨ ਦੀ ਮੁਰੰਮਤ ਅਤੇ ਬਦਲਦੇ ਹਾਂ ਜਦੋਂ ਤੱਕ ਉਹ ਸਾਡੇ ਤੋਂ ਆਪਣੇ ਪੁਰਜ਼ਿਆਂ ਨੂੰ ਦੁਬਾਰਾ ਕ੍ਰਮਬੱਧ ਕਰਦੇ ਹਨ। ਸਾਡੇ ਮਰਨ ਵਾਲਿਆਂ ਦਾ ਕਈ ਲੱਖ ਚੱਕਰਾਂ ਦੀ ਸੀਮਾ ਵਿੱਚ ਲੰਮੀ ਉਮਰ ਹੁੰਦੀ ਹੈ। ਇੱਥੇ ਬੁਨਿਆਦੀ ਸਰਲ ਪ੍ਰਕਿਰਿਆ ਦੇ ਕਦਮ ਹਨ: 1.) ਆਮ ਤੌਰ 'ਤੇ ਸਟੀਲ ਤੋਂ ਉੱਲੀ ਦਾ ਉਤਪਾਦਨ 2.) ਡਾਈ ਕਾਸਟਿੰਗ ਮਸ਼ੀਨ 'ਤੇ ਮੋਲਡ ਲਗਾਇਆ ਗਿਆ 3.) ਪਿਸਟਨ ਪਿਘਲੀ ਹੋਈ ਧਾਤ ਨੂੰ ਗੁੰਝਲਦਾਰ ਵਿਸ਼ੇਸ਼ਤਾਵਾਂ ਅਤੇ ਪਤਲੀਆਂ ਕੰਧਾਂ ਨੂੰ ਭਰ ਕੇ ਡਾਈ ਕੈਵਿਟੀਜ਼ ਵਿੱਚ ਵਹਿਣ ਲਈ ਮਜਬੂਰ ਕਰਦਾ ਹੈ। 4.) ਪਿਘਲੇ ਹੋਏ ਧਾਤ ਨਾਲ ਉੱਲੀ ਨੂੰ ਭਰਨ ਤੋਂ ਬਾਅਦ, ਕਾਸਟਿੰਗ ਨੂੰ ਦਬਾਅ ਹੇਠ ਸਖ਼ਤ ਹੋਣ ਦਿੱਤਾ ਜਾਂਦਾ ਹੈ 5.) ਈਜੇਕਟਰ ਪਿੰਨ ਦੀ ਮਦਦ ਨਾਲ ਮੋਲਡ ਨੂੰ ਖੋਲ੍ਹਿਆ ਜਾਂਦਾ ਹੈ ਅਤੇ ਕਾਸਟਿੰਗ ਨੂੰ ਹਟਾ ਦਿੱਤਾ ਜਾਂਦਾ ਹੈ। 6.) ਹੁਣ ਖਾਲੀ ਡਾਈ ਨੂੰ ਦੁਬਾਰਾ ਲੁਬਰੀਕੇਟ ਕੀਤਾ ਜਾਂਦਾ ਹੈ ਅਤੇ ਅਗਲੇ ਚੱਕਰ ਲਈ ਕਲੈਂਪ ਕੀਤਾ ਜਾਂਦਾ ਹੈ। ਡਾਈ ਕਾਸਟਿੰਗ ਵਿੱਚ, ਅਸੀਂ ਅਕਸਰ ਇਨਸਰਟ ਮੋਲਡਿੰਗ ਦੀ ਵਰਤੋਂ ਕਰਦੇ ਹਾਂ ਜਿੱਥੇ ਅਸੀਂ ਮੋਲਡ ਵਿੱਚ ਇੱਕ ਵਾਧੂ ਹਿੱਸਾ ਸ਼ਾਮਲ ਕਰਦੇ ਹਾਂ ਅਤੇ ਇਸਦੇ ਦੁਆਲੇ ਧਾਤ ਨੂੰ ਸੁੱਟ ਦਿੰਦੇ ਹਾਂ। ਠੋਸ ਹੋਣ ਤੋਂ ਬਾਅਦ, ਇਹ ਹਿੱਸੇ ਕਾਸਟ ਉਤਪਾਦ ਦਾ ਹਿੱਸਾ ਬਣ ਜਾਂਦੇ ਹਨ। ਡਾਈ ਕਾਸਟਿੰਗ ਦੇ ਫਾਇਦੇ ਭਾਗਾਂ ਦੀਆਂ ਚੰਗੀਆਂ ਮਕੈਨੀਕਲ ਵਿਸ਼ੇਸ਼ਤਾਵਾਂ, ਗੁੰਝਲਦਾਰ ਵਿਸ਼ੇਸ਼ਤਾਵਾਂ ਦੀ ਸੰਭਾਵਨਾ, ਵਧੀਆ ਵੇਰਵੇ ਅਤੇ ਚੰਗੀ ਸਤਹ ਮੁਕੰਮਲ, ਉੱਚ ਉਤਪਾਦਨ ਦਰਾਂ, ਆਸਾਨ ਆਟੋਮੇਸ਼ਨ ਹਨ। ਨੁਕਸਾਨ ਹਨ: ਉੱਚ ਡਾਈ ਅਤੇ ਸਾਜ਼ੋ-ਸਾਮਾਨ ਦੀ ਲਾਗਤ ਦੇ ਕਾਰਨ ਘੱਟ ਵਾਲੀਅਮ ਲਈ ਬਹੁਤ ਢੁਕਵਾਂ ਨਹੀਂ, ਕਾਸਟ ਕੀਤੇ ਜਾ ਸਕਣ ਵਾਲੇ ਆਕਾਰਾਂ ਵਿੱਚ ਸੀਮਾਵਾਂ, ਇਜੈਕਟਰ ਪਿੰਨ ਦੇ ਸੰਪਰਕ ਦੇ ਨਤੀਜੇ ਵਜੋਂ ਪਲੱਸਤਰ ਵਾਲੇ ਹਿੱਸਿਆਂ 'ਤੇ ਛੋਟੇ ਗੋਲ ਨਿਸ਼ਾਨ, ਵਿਭਾਜਨ ਲਾਈਨ 'ਤੇ ਧਾਤ ਦੀ ਪਤਲੀ ਫਲੈਸ਼, ਲੋੜ ਡਾਈ ਦੇ ਵਿਚਕਾਰ ਵਿਭਾਜਨ ਲਾਈਨ ਦੇ ਨਾਲ ਵੈਂਟਾਂ ਲਈ, ਪਾਣੀ ਦੇ ਗੇੜ ਦੀ ਵਰਤੋਂ ਕਰਕੇ ਉੱਲੀ ਦੇ ਤਾਪਮਾਨ ਨੂੰ ਘੱਟ ਰੱਖਣ ਦੀ ਜ਼ਰੂਰਤ। • ਸੈਂਟਰਿਫਿਊਗਲ ਕਾਸਟਿੰਗ: ਪਿਘਲੀ ਹੋਈ ਧਾਤ ਨੂੰ ਰੋਟੇਸ਼ਨ ਦੇ ਧੁਰੇ 'ਤੇ ਘੁੰਮਦੇ ਉੱਲੀ ਦੇ ਕੇਂਦਰ ਵਿੱਚ ਡੋਲ੍ਹਿਆ ਜਾਂਦਾ ਹੈ। ਸੈਂਟਰਿਫਿਊਗਲ ਬਲ ਧਾਤ ਨੂੰ ਘੇਰੇ ਵੱਲ ਸੁੱਟ ਦਿੰਦੇ ਹਨ ਅਤੇ ਇਸ ਨੂੰ ਠੋਸ ਹੋਣ ਦਿੱਤਾ ਜਾਂਦਾ ਹੈ ਕਿਉਂਕਿ ਉੱਲੀ ਘੁੰਮਦੀ ਰਹਿੰਦੀ ਹੈ। ਹਰੀਜੱਟਲ ਅਤੇ ਵਰਟੀਕਲ ਧੁਰੀ ਰੋਟੇਸ਼ਨਾਂ ਦੀ ਵਰਤੋਂ ਕੀਤੀ ਜਾ ਸਕਦੀ ਹੈ। ਗੋਲ ਅੰਦਰੂਨੀ ਸਤਹਾਂ ਦੇ ਨਾਲ-ਨਾਲ ਹੋਰ ਗੈਰ-ਗੋਲ ਆਕਾਰਾਂ ਵਾਲੇ ਹਿੱਸੇ ਕਾਸਟ ਕੀਤੇ ਜਾ ਸਕਦੇ ਹਨ। ਪ੍ਰਕਿਰਿਆ ਨੂੰ ਇਸ ਤਰ੍ਹਾਂ ਸੰਖੇਪ ਕੀਤਾ ਜਾ ਸਕਦਾ ਹੈ: 1.) ਪਿਘਲੀ ਹੋਈ ਧਾਤ ਨੂੰ ਸੈਂਟਰਿਫਿਊਗਲ ਮੋਲਡ ਵਿੱਚ ਡੋਲ੍ਹਿਆ ਜਾਂਦਾ ਹੈ। ਫਿਰ ਧਾਤ ਨੂੰ ਉੱਲੀ ਦੇ ਕਤਾਈ ਕਾਰਨ ਬਾਹਰੀ ਕੰਧਾਂ ਵੱਲ ਧੱਕਿਆ ਜਾਂਦਾ ਹੈ। 2.) ਜਿਵੇਂ ਕਿ ਉੱਲੀ ਘੁੰਮਦੀ ਹੈ, ਧਾਤ ਦੀ ਕਾਸਟਿੰਗ ਸਖਤ ਹੋ ਜਾਂਦੀ ਹੈ ਸੈਂਟਰਿਫਿਊਗਲ ਕਾਸਟਿੰਗ ਪਾਈਪਾਂ ਵਰਗੇ ਖੋਖਲੇ ਸਿਲੰਡਰ ਵਾਲੇ ਹਿੱਸਿਆਂ ਦੇ ਉਤਪਾਦਨ ਲਈ ਇੱਕ ਢੁਕਵੀਂ ਤਕਨੀਕ ਹੈ, ਸਪ੍ਰੂਜ਼, ਰਾਈਜ਼ਰ ਅਤੇ ਗੇਟਿੰਗ ਐਲੀਮੈਂਟਸ ਦੀ ਕੋਈ ਲੋੜ ਨਹੀਂ, ਚੰਗੀ ਸਤਹ ਫਿਨਿਸ਼ ਅਤੇ ਵਿਸਤ੍ਰਿਤ ਵਿਸ਼ੇਸ਼ਤਾਵਾਂ, ਕੋਈ ਸੁੰਗੜਨ ਦੀ ਸਮੱਸਿਆ ਨਹੀਂ, ਬਹੁਤ ਵੱਡੇ ਵਿਆਸ ਵਾਲੀਆਂ ਲੰਬੀਆਂ ਪਾਈਪਾਂ ਬਣਾਉਣ ਦੀ ਸੰਭਾਵਨਾ, ਉੱਚ ਦਰ ਉਤਪਾਦਨ ਸਮਰੱਥਾ। . • ਨਿਰੰਤਰ ਕਾਸਟਿੰਗ (ਸਟ੍ਰੈਂਡ ਕਾਸਟਿੰਗ): ਧਾਤ ਦੀ ਇੱਕ ਨਿਰੰਤਰ ਲੰਬਾਈ ਨੂੰ ਕਾਸਟ ਕਰਨ ਲਈ ਵਰਤਿਆ ਜਾਂਦਾ ਹੈ। ਮੂਲ ਰੂਪ ਵਿੱਚ ਪਿਘਲੀ ਹੋਈ ਧਾਤ ਨੂੰ ਉੱਲੀ ਦੇ ਦੋ-ਅਯਾਮੀ ਪ੍ਰੋਫਾਈਲ ਵਿੱਚ ਸੁੱਟਿਆ ਜਾਂਦਾ ਹੈ ਪਰ ਇਸਦੀ ਲੰਬਾਈ ਅਨਿਸ਼ਚਿਤ ਹੁੰਦੀ ਹੈ। ਨਵੀਂ ਪਿਘਲੀ ਹੋਈ ਧਾਤ ਨੂੰ ਲਗਾਤਾਰ ਉੱਲੀ ਵਿੱਚ ਖੁਆਇਆ ਜਾਂਦਾ ਹੈ ਕਿਉਂਕਿ ਕਾਸਟਿੰਗ ਸਮੇਂ ਦੇ ਨਾਲ ਇਸਦੀ ਲੰਬਾਈ ਵਧਣ ਦੇ ਨਾਲ ਹੇਠਾਂ ਵੱਲ ਜਾਂਦੀ ਹੈ। ਤਾਂਬਾ, ਸਟੀਲ, ਅਲਮੀਨੀਅਮ ਵਰਗੀਆਂ ਧਾਤਾਂ ਨੂੰ ਲਗਾਤਾਰ ਕਾਸਟਿੰਗ ਪ੍ਰਕਿਰਿਆ ਦੀ ਵਰਤੋਂ ਕਰਦੇ ਹੋਏ ਲੰਬੇ ਤਾਰਾਂ ਵਿੱਚ ਸੁੱਟਿਆ ਜਾਂਦਾ ਹੈ। ਪ੍ਰਕਿਰਿਆ ਦੀਆਂ ਵੱਖ-ਵੱਖ ਸੰਰਚਨਾਵਾਂ ਹੋ ਸਕਦੀਆਂ ਹਨ ਪਰ ਆਮ ਨੂੰ ਇਸ ਤਰ੍ਹਾਂ ਸਰਲ ਬਣਾਇਆ ਜਾ ਸਕਦਾ ਹੈ: 1.) ਪਿਘਲੀ ਹੋਈ ਧਾਤ ਨੂੰ ਚੰਗੀ ਤਰ੍ਹਾਂ ਗਣਨਾ ਕੀਤੀ ਮਾਤਰਾ ਅਤੇ ਵਹਾਅ ਦਰਾਂ 'ਤੇ ਉੱਲੀ ਦੇ ਉੱਪਰ ਸਥਿਤ ਇੱਕ ਕੰਟੇਨਰ ਵਿੱਚ ਡੋਲ੍ਹਿਆ ਜਾਂਦਾ ਹੈ ਅਤੇ ਵਾਟਰ ਕੂਲਡ ਮੋਲਡ ਵਿੱਚੋਂ ਲੰਘਦਾ ਹੈ। ਉੱਲੀ ਵਿੱਚ ਪਾਈ ਗਈ ਧਾਤ ਦੀ ਕਾਸਟਿੰਗ ਮੋਲਡ ਦੇ ਤਲ 'ਤੇ ਰੱਖੀ ਇੱਕ ਸਟਾਰਟਰ ਬਾਰ ਵਿੱਚ ਠੋਸ ਹੋ ਜਾਂਦੀ ਹੈ। ਇਹ ਸਟਾਰਟਰ ਬਾਰ ਰੋਲਰਸ ਨੂੰ ਸ਼ੁਰੂ ਵਿੱਚ ਫੜਨ ਲਈ ਕੁਝ ਦਿੰਦਾ ਹੈ। 2.) ਲੰਬੇ ਧਾਤ ਦੇ ਸਟ੍ਰੈਂਡ ਨੂੰ ਰੋਲਰਾਂ ਦੁਆਰਾ ਇੱਕ ਸਥਿਰ ਗਤੀ ਨਾਲ ਲਿਜਾਇਆ ਜਾਂਦਾ ਹੈ। ਰੋਲਰ ਮੈਟਲ ਸਟ੍ਰੈਂਡ ਦੇ ਵਹਾਅ ਦੀ ਦਿਸ਼ਾ ਨੂੰ ਲੰਬਕਾਰੀ ਤੋਂ ਖਿਤਿਜੀ ਤੱਕ ਬਦਲਦੇ ਹਨ। 3.) ਲਗਾਤਾਰ ਕਾਸਟਿੰਗ ਦੇ ਇੱਕ ਨਿਸ਼ਚਿਤ ਲੇਟਵੀਂ ਦੂਰੀ ਦੀ ਯਾਤਰਾ ਕਰਨ ਤੋਂ ਬਾਅਦ, ਇੱਕ ਟਾਰਚ ਜਾਂ ਆਰਾ ਜੋ ਕਾਸਟਿੰਗ ਦੇ ਨਾਲ ਚਲਦਾ ਹੈ, ਇਸਨੂੰ ਲੋੜੀਂਦੀ ਲੰਬਾਈ ਤੱਕ ਤੇਜ਼ੀ ਨਾਲ ਕੱਟ ਦਿੰਦਾ ਹੈ। ਨਿਰੰਤਰ ਕਾਸਟਿੰਗ ਪ੍ਰਕਿਰਿਆ ਨੂੰ ਰੋਲਿੰਗ ਪ੍ਰਕਿਰਿਆ ਨਾਲ ਜੋੜਿਆ ਜਾ ਸਕਦਾ ਹੈ, ਜਿੱਥੇ ਆਈ-ਬੀਮ, ਟੀ-ਬੀਮ ਆਦਿ ਪੈਦਾ ਕਰਨ ਲਈ ਲਗਾਤਾਰ ਕਾਸਟ ਧਾਤ ਨੂੰ ਸਿੱਧੇ ਰੋਲਿੰਗ ਮਿੱਲ ਵਿੱਚ ਖੁਆਇਆ ਜਾ ਸਕਦਾ ਹੈ। ਨਿਰੰਤਰ ਕਾਸਟਿੰਗ ਪੂਰੇ ਉਤਪਾਦ ਵਿੱਚ ਇਕਸਾਰ ਵਿਸ਼ੇਸ਼ਤਾਵਾਂ ਪੈਦਾ ਕਰਦੀ ਹੈ, ਇਸਦੀ ਉੱਚ ਠੋਸਤਾ ਦਰ ਹੁੰਦੀ ਹੈ, ਸਮੱਗਰੀ ਦੇ ਬਹੁਤ ਘੱਟ ਨੁਕਸਾਨ ਕਾਰਨ ਲਾਗਤ ਘਟਾਉਂਦੀ ਹੈ, ਇੱਕ ਪ੍ਰਕਿਰਿਆ ਦੀ ਪੇਸ਼ਕਸ਼ ਕਰਦੀ ਹੈ ਜਿੱਥੇ ਧਾਤ ਨੂੰ ਲੋਡ ਕਰਨਾ, ਡੋਲਣਾ, ਠੋਸ ਬਣਾਉਣਾ, ਕੱਟਣਾ ਅਤੇ ਕਾਸਟਿੰਗ ਹਟਾਉਣਾ ਸਭ ਇੱਕ ਨਿਰੰਤਰ ਕਾਰਜ ਵਿੱਚ ਹੁੰਦਾ ਹੈ ਅਤੇ ਇਸ ਤਰ੍ਹਾਂ ਉੱਚ ਉਤਪਾਦਕਤਾ ਦਰ ਅਤੇ ਉੱਚ ਗੁਣਵੱਤਾ ਦੇ ਨਤੀਜੇ ਵਜੋਂ. ਇੱਕ ਪ੍ਰਮੁੱਖ ਵਿਚਾਰ ਹਾਲਾਂਕਿ ਉੱਚ ਸ਼ੁਰੂਆਤੀ ਨਿਵੇਸ਼, ਸੈੱਟਅੱਪ ਲਾਗਤਾਂ ਅਤੇ ਸਪੇਸ ਲੋੜਾਂ ਹਨ। • ਮਸ਼ੀਨਿੰਗ ਸੇਵਾਵਾਂ: ਅਸੀਂ ਤਿੰਨ, ਚਾਰ ਅਤੇ ਪੰਜ - ਐਕਸਿਸ ਮਸ਼ੀਨਿੰਗ ਦੀ ਪੇਸ਼ਕਸ਼ ਕਰਦੇ ਹਾਂ। ਮਸ਼ੀਨਿੰਗ ਪ੍ਰਕਿਰਿਆਵਾਂ ਦੀ ਕਿਸਮ ਜਿਸ ਦੀ ਅਸੀਂ ਵਰਤੋਂ ਕਰਦੇ ਹਾਂ ਉਹ ਹਨ ਟਰਨਿੰਗ, ਮਿਲਿੰਗ, ਡਰਿਲਿੰਗ, ਬੋਰਿੰਗ, ਬ੍ਰੋਚਿੰਗ, ਪਲੈਨਿੰਗ, ਸਾਵਿੰਗ, ਗ੍ਰਾਈਂਡਿੰਗ, ਲੈਪਿੰਗ, ਪਾਲਿਸ਼ਿੰਗ ਅਤੇ ਗੈਰ-ਰਵਾਇਤੀ ਮਸ਼ੀਨਾਂ ਜੋ ਸਾਡੀ ਵੈਬਸਾਈਟ ਦੇ ਇੱਕ ਵੱਖਰੇ ਮੀਨੂ ਦੇ ਹੇਠਾਂ ਵਿਸਤ੍ਰਿਤ ਹਨ। ਸਾਡੇ ਜ਼ਿਆਦਾਤਰ ਨਿਰਮਾਣ ਲਈ, ਅਸੀਂ ਸੀਐਨਸੀ ਮਸ਼ੀਨਾਂ ਦੀ ਵਰਤੋਂ ਕਰਦੇ ਹਾਂ. ਹਾਲਾਂਕਿ ਕੁਝ ਓਪਰੇਸ਼ਨਾਂ ਲਈ ਪਰੰਪਰਾਗਤ ਤਕਨੀਕਾਂ ਇੱਕ ਬਿਹਤਰ ਫਿਟ ਹਨ ਅਤੇ ਇਸ ਲਈ ਅਸੀਂ ਉਹਨਾਂ 'ਤੇ ਵੀ ਭਰੋਸਾ ਕਰਦੇ ਹਾਂ। ਸਾਡੀ ਮਸ਼ੀਨਿੰਗ ਸਮਰੱਥਾ ਉੱਚਤਮ ਪੱਧਰ 'ਤੇ ਪਹੁੰਚ ਜਾਂਦੀ ਹੈ ਅਤੇ ਕੁਝ ਸਭ ਤੋਂ ਵੱਧ ਮੰਗ ਵਾਲੇ ਹਿੱਸੇ AS9100 ਪ੍ਰਮਾਣਿਤ ਪਲਾਂਟ 'ਤੇ ਬਣਾਏ ਜਾਂਦੇ ਹਨ। ਜੈੱਟ ਇੰਜਣ ਬਲੇਡਾਂ ਲਈ ਬਹੁਤ ਹੀ ਵਿਸ਼ੇਸ਼ ਨਿਰਮਾਣ ਅਨੁਭਵ ਅਤੇ ਸਹੀ ਉਪਕਰਨ ਦੀ ਲੋੜ ਹੁੰਦੀ ਹੈ। ਏਰੋਸਪੇਸ ਉਦਯੋਗ ਦੇ ਬਹੁਤ ਸਖਤ ਮਾਪਦੰਡ ਹਨ। ਗੁੰਝਲਦਾਰ ਜਿਓਮੈਟ੍ਰਿਕਲ ਢਾਂਚੇ ਵਾਲੇ ਕੁਝ ਹਿੱਸੇ ਸਭ ਤੋਂ ਆਸਾਨੀ ਨਾਲ ਪੰਜ ਧੁਰੀ ਮਸ਼ੀਨਾਂ ਦੁਆਰਾ ਬਣਾਏ ਜਾਂਦੇ ਹਨ, ਜੋ ਕਿ ਸਾਡੇ ਸਮੇਤ ਕੁਝ ਮਸ਼ੀਨਿੰਗ ਪਲਾਂਟਾਂ ਵਿੱਚ ਹੀ ਪਾਏ ਜਾਂਦੇ ਹਨ। ਸਾਡੇ ਏਰੋਸਪੇਸ ਪ੍ਰਮਾਣਿਤ ਪਲਾਂਟ ਕੋਲ ਏਰੋਸਪੇਸ ਉਦਯੋਗ ਦੀ ਵਿਆਪਕ ਦਸਤਾਵੇਜ਼ੀ ਲੋੜਾਂ ਦੀ ਪਾਲਣਾ ਕਰਨ ਲਈ ਲੋੜੀਂਦਾ ਅਨੁਭਵ ਹੈ। ਟਰਨਿੰਗ ਓਪਰੇਸ਼ਨਾਂ ਵਿੱਚ, ਇੱਕ ਵਰਕਪੀਸ ਨੂੰ ਘੁੰਮਾਇਆ ਜਾਂਦਾ ਹੈ ਅਤੇ ਇੱਕ ਕੱਟਣ ਵਾਲੇ ਟੂਲ ਦੇ ਵਿਰੁੱਧ ਹਿਲਾਇਆ ਜਾਂਦਾ ਹੈ। ਇਸ ਪ੍ਰਕਿਰਿਆ ਲਈ ਲੇਥ ਨਾਮਕ ਮਸ਼ੀਨ ਦੀ ਵਰਤੋਂ ਕੀਤੀ ਜਾ ਰਹੀ ਹੈ। ਮਿਲਿੰਗ ਵਿੱਚ, ਮਿਲਿੰਗ ਮਸ਼ੀਨ ਨਾਮਕ ਇੱਕ ਮਸ਼ੀਨ ਵਿੱਚ ਇੱਕ ਵਰਕਪੀਸ ਦੇ ਵਿਰੁੱਧ ਸਹਿਣ ਲਈ ਕੱਟਣ ਵਾਲੇ ਕਿਨਾਰਿਆਂ ਨੂੰ ਲਿਆਉਣ ਲਈ ਇੱਕ ਰੋਟੇਟਿੰਗ ਟੂਲ ਹੁੰਦਾ ਹੈ। ਡ੍ਰਿਲੰਗ ਓਪਰੇਸ਼ਨਾਂ ਵਿੱਚ ਕੱਟਣ ਵਾਲੇ ਕਿਨਾਰਿਆਂ ਵਾਲਾ ਇੱਕ ਘੁੰਮਦਾ ਕਟਰ ਸ਼ਾਮਲ ਹੁੰਦਾ ਹੈ ਜੋ ਵਰਕਪੀਸ ਦੇ ਸੰਪਰਕ ਵਿੱਚ ਆਉਣ 'ਤੇ ਛੇਕ ਪੈਦਾ ਕਰਦਾ ਹੈ। ਡ੍ਰਿਲ ਪ੍ਰੈਸ, ਖਰਾਦ ਜਾਂ ਮਿੱਲਾਂ ਦੀ ਵਰਤੋਂ ਆਮ ਤੌਰ 'ਤੇ ਕੀਤੀ ਜਾਂਦੀ ਹੈ। ਬੋਰਿੰਗ ਓਪਰੇਸ਼ਨਾਂ ਵਿੱਚ ਮੋਰੀ ਨੂੰ ਥੋੜ੍ਹਾ ਵੱਡਾ ਕਰਨ ਅਤੇ ਸ਼ੁੱਧਤਾ ਵਿੱਚ ਸੁਧਾਰ ਕਰਨ ਲਈ ਇੱਕ ਕਤਾਈ ਵਾਲੇ ਵਰਕਪੀਸ ਵਿੱਚ ਇੱਕ ਮੋਰੀ ਹੋਈ ਨੋਕ ਵਾਲੇ ਇੱਕ ਟੂਲ ਨੂੰ ਇੱਕ ਮੋਟੇ ਮੋਰੀ ਵਿੱਚ ਭੇਜਿਆ ਜਾਂਦਾ ਹੈ। ਇਹ ਵਧੀਆ ਮੁਕੰਮਲ ਕਰਨ ਦੇ ਉਦੇਸ਼ਾਂ ਲਈ ਵਰਤਿਆ ਜਾਂਦਾ ਹੈ. ਬ੍ਰੋਚਿੰਗ ਵਿੱਚ ਬਰੋਚ (ਦੰਦਾਂ ਵਾਲਾ ਟੂਲ) ਦੇ ਇੱਕ ਪਾਸ ਵਿੱਚ ਵਰਕਪੀਸ ਤੋਂ ਸਮੱਗਰੀ ਨੂੰ ਹਟਾਉਣ ਲਈ ਦੰਦਾਂ ਵਾਲਾ ਟੂਲ ਸ਼ਾਮਲ ਹੁੰਦਾ ਹੈ। ਲੀਨੀਅਰ ਬ੍ਰੋਚਿੰਗ ਵਿੱਚ, ਬਰੋਚ ਕੱਟ ਨੂੰ ਪ੍ਰਭਾਵਤ ਕਰਨ ਲਈ ਵਰਕਪੀਸ ਦੀ ਇੱਕ ਸਤਹ ਦੇ ਵਿਰੁੱਧ ਰੇਖਿਕ ਤੌਰ 'ਤੇ ਚੱਲਦਾ ਹੈ, ਜਦੋਂ ਕਿ ਰੋਟਰੀ ਬ੍ਰੋਚਿੰਗ ਵਿੱਚ, ਇੱਕ ਧੁਰੀ ਸਮਮਿਤੀ ਆਕਾਰ ਨੂੰ ਕੱਟਣ ਲਈ ਬਰੋਚ ਨੂੰ ਘੁੰਮਾਇਆ ਜਾਂਦਾ ਹੈ ਅਤੇ ਵਰਕਪੀਸ ਵਿੱਚ ਦਬਾਇਆ ਜਾਂਦਾ ਹੈ। ਸਵਿਸ ਟਾਈਪ ਮਸ਼ੀਨਿੰਗ ਸਾਡੀ ਕੀਮਤੀ ਤਕਨੀਕਾਂ ਵਿੱਚੋਂ ਇੱਕ ਹੈ ਜੋ ਅਸੀਂ ਛੋਟੇ ਉੱਚ ਸ਼ੁੱਧਤਾ ਵਾਲੇ ਹਿੱਸਿਆਂ ਦੇ ਉੱਚ ਵਾਲੀਅਮ ਨਿਰਮਾਣ ਲਈ ਵਰਤਦੇ ਹਾਂ। ਸਵਿਸ-ਕਿਸਮ ਦੀ ਖਰਾਦ ਦੀ ਵਰਤੋਂ ਕਰਕੇ ਅਸੀਂ ਛੋਟੇ, ਗੁੰਝਲਦਾਰ, ਸਟੀਕ ਪੁਰਜ਼ਿਆਂ ਨੂੰ ਸਸਤੇ ਢੰਗ ਨਾਲ ਬਦਲਦੇ ਹਾਂ। ਰਵਾਇਤੀ ਖਰਾਦ ਦੇ ਉਲਟ ਜਿੱਥੇ ਵਰਕਪੀਸ ਨੂੰ ਸਥਿਰ ਰੱਖਿਆ ਜਾਂਦਾ ਹੈ ਅਤੇ ਟੂਲ ਚਲਦਾ ਰਹਿੰਦਾ ਹੈ, ਸਵਿਸ-ਕਿਸਮ ਦੇ ਮੋੜ ਕੇਂਦਰਾਂ ਵਿੱਚ, ਵਰਕਪੀਸ ਨੂੰ Z-ਧੁਰੇ ਵਿੱਚ ਜਾਣ ਦੀ ਇਜਾਜ਼ਤ ਦਿੱਤੀ ਜਾਂਦੀ ਹੈ ਅਤੇ ਟੂਲ ਸਥਿਰ ਹੁੰਦਾ ਹੈ। ਸਵਿਸ-ਕਿਸਮ ਦੀ ਮਸ਼ੀਨਿੰਗ ਵਿੱਚ, ਬਾਰ ਸਟਾਕ ਨੂੰ ਮਸ਼ੀਨ ਵਿੱਚ ਰੱਖਿਆ ਜਾਂਦਾ ਹੈ ਅਤੇ z-ਧੁਰੇ ਵਿੱਚ ਇੱਕ ਗਾਈਡ ਬੁਸ਼ਿੰਗ ਦੁਆਰਾ ਅੱਗੇ ਵਧਾਇਆ ਜਾਂਦਾ ਹੈ, ਸਿਰਫ ਮਸ਼ੀਨ ਕੀਤੇ ਜਾਣ ਵਾਲੇ ਹਿੱਸੇ ਦਾ ਪਰਦਾਫਾਸ਼ ਕਰਦਾ ਹੈ। ਇਸ ਤਰ੍ਹਾਂ ਇੱਕ ਸਖ਼ਤ ਪਕੜ ਯਕੀਨੀ ਬਣਾਈ ਜਾਂਦੀ ਹੈ ਅਤੇ ਸ਼ੁੱਧਤਾ ਬਹੁਤ ਜ਼ਿਆਦਾ ਹੁੰਦੀ ਹੈ। ਲਾਈਵ ਟੂਲਸ ਦੀ ਉਪਲਬਧਤਾ ਗਾਈਡ ਬੁਸ਼ਿੰਗ ਤੋਂ ਸਮੱਗਰੀ ਦੇ ਅੱਗੇ ਵਧਣ ਦੇ ਨਾਲ ਮਿਲ ਅਤੇ ਡ੍ਰਿਲ ਕਰਨ ਦਾ ਮੌਕਾ ਪ੍ਰਦਾਨ ਕਰਦੀ ਹੈ। ਸਵਿਸ-ਕਿਸਮ ਦੇ ਸਾਜ਼ੋ-ਸਾਮਾਨ ਦਾ Y-ਧੁਰਾ ਪੂਰੀ ਮਿਲਿੰਗ ਸਮਰੱਥਾ ਪ੍ਰਦਾਨ ਕਰਦਾ ਹੈ ਅਤੇ ਨਿਰਮਾਣ ਵਿੱਚ ਬਹੁਤ ਸਮਾਂ ਬਚਾਉਂਦਾ ਹੈ। ਇਸ ਤੋਂ ਇਲਾਵਾ, ਸਾਡੀਆਂ ਮਸ਼ੀਨਾਂ ਵਿਚ ਡ੍ਰਿਲਸ ਅਤੇ ਬੋਰਿੰਗ ਟੂਲ ਹਨ ਜੋ ਉਸ ਹਿੱਸੇ 'ਤੇ ਕੰਮ ਕਰਦੇ ਹਨ ਜਦੋਂ ਇਹ ਸਬ ਸਪਿੰਡਲ ਵਿਚ ਰੱਖੀ ਜਾਂਦੀ ਹੈ। ਸਾਡੀ ਸਵਿਸ-ਟਾਈਪ ਮਸ਼ੀਨਿੰਗ ਸਮਰੱਥਾ ਸਾਨੂੰ ਇੱਕ ਸਿੰਗਲ ਓਪਰੇਸ਼ਨ ਵਿੱਚ ਇੱਕ ਪੂਰੀ ਤਰ੍ਹਾਂ ਸਵੈਚਲਿਤ ਸੰਪੂਰਨ ਮਸ਼ੀਨਿੰਗ ਦਾ ਮੌਕਾ ਦਿੰਦੀ ਹੈ। ਮਸ਼ੀਨਿੰਗ AGS-TECH Inc. ਕਾਰੋਬਾਰ ਦੇ ਸਭ ਤੋਂ ਵੱਡੇ ਹਿੱਸਿਆਂ ਵਿੱਚੋਂ ਇੱਕ ਹੈ। ਅਸੀਂ ਜਾਂ ਤਾਂ ਇਸਨੂੰ ਇੱਕ ਪ੍ਰਾਇਮਰੀ ਓਪਰੇਸ਼ਨ ਦੇ ਤੌਰ ਤੇ ਜਾਂ ਕਿਸੇ ਹਿੱਸੇ ਨੂੰ ਕੱਢਣ ਜਾਂ ਕੱਢਣ ਤੋਂ ਬਾਅਦ ਇੱਕ ਸੈਕੰਡਰੀ ਓਪਰੇਸ਼ਨ ਦੇ ਤੌਰ ਤੇ ਵਰਤਦੇ ਹਾਂ ਤਾਂ ਜੋ ਸਾਰੀਆਂ ਡਰਾਇੰਗ ਵਿਸ਼ੇਸ਼ਤਾਵਾਂ ਨੂੰ ਪੂਰਾ ਕੀਤਾ ਜਾ ਸਕੇ। • ਸਰਫੇਸ ਫਿਨਿਸ਼ਿੰਗ ਸੇਵਾਵਾਂ: ਅਸੀਂ ਸਰਫੇਸ ਟਰੀਟਮੈਂਟ ਅਤੇ ਸਰਫੇਸ ਫਿਨਿਸ਼ਿੰਗ ਦੀ ਇੱਕ ਵਿਸ਼ਾਲ ਕਿਸਮ ਦੀ ਪੇਸ਼ਕਸ਼ ਕਰਦੇ ਹਾਂ ਜਿਵੇਂ ਕਿ ਅਡਿਸ਼ਨ ਨੂੰ ਵਧਾਉਣ ਲਈ ਸਤਹ ਕੰਡੀਸ਼ਨਿੰਗ, ਕੋਟਿੰਗ ਦੇ ਅਡਜਸ਼ਨ ਨੂੰ ਵਧਾਉਣ ਲਈ ਪਤਲੀ ਆਕਸਾਈਡ ਪਰਤ ਜਮ੍ਹਾ ਕਰਨਾ, ਸੈਂਡ ਬਲਾਸਟਿੰਗ, ਕੈਮ-ਫਿਲਮ, ਐਨੋਡਾਈਜ਼ਿੰਗ, ਨਾਈਟ੍ਰਾਈਡਿੰਗ, ਪਾਊਡਰ ਕੋਟਿੰਗ, ਸਪਰੇਅ ਕੋਟਿੰਗ। , ਵੱਖ-ਵੱਖ ਉੱਨਤ ਧਾਤੂਕਰਨ ਅਤੇ ਪਰਤ ਦੀਆਂ ਤਕਨੀਕਾਂ ਜਿਵੇਂ ਕਿ ਸਪਟਰਿੰਗ, ਇਲੈਕਟ੍ਰੋਨ ਬੀਮ, ਵਾਸ਼ਪੀਕਰਨ, ਪਲੇਟਿੰਗ, ਹਾਰਡ ਕੋਟਿੰਗ ਜਿਵੇਂ ਕਿ ਹੀਰਾ ਜਿਵੇਂ ਕਿ ਕਾਰਬਨ (DLC) ਜਾਂ ਡ੍ਰਿਲੰਗ ਅਤੇ ਕੱਟਣ ਵਾਲੇ ਸਾਧਨਾਂ ਲਈ ਟਾਈਟੇਨੀਅਮ ਕੋਟਿੰਗ। • ਉਤਪਾਦ ਮਾਰਕਿੰਗ ਅਤੇ ਲੇਬਲਿੰਗ ਸੇਵਾਵਾਂ: ਸਾਡੇ ਬਹੁਤ ਸਾਰੇ ਗਾਹਕਾਂ ਨੂੰ ਮਾਰਕਿੰਗ ਅਤੇ ਲੇਬਲਿੰਗ, ਲੇਜ਼ਰ ਮਾਰਕਿੰਗ, ਧਾਤ ਦੇ ਹਿੱਸਿਆਂ 'ਤੇ ਉੱਕਰੀ ਕਰਨ ਦੀ ਲੋੜ ਹੁੰਦੀ ਹੈ। ਜੇਕਰ ਤੁਹਾਨੂੰ ਅਜਿਹੀ ਕੋਈ ਲੋੜ ਹੈ, ਤਾਂ ਆਓ ਇਸ ਬਾਰੇ ਚਰਚਾ ਕਰੀਏ ਕਿ ਤੁਹਾਡੇ ਲਈ ਕਿਹੜਾ ਵਿਕਲਪ ਸਭ ਤੋਂ ਵਧੀਆ ਹੋਵੇਗਾ। ਇੱਥੇ ਕੁਝ ਆਮ ਤੌਰ 'ਤੇ ਵਰਤੇ ਜਾਂਦੇ ਮੈਟਲ ਕਾਸਟ ਉਤਪਾਦ ਹਨ। ਕਿਉਂਕਿ ਇਹ ਸ਼ੈਲਫ ਤੋਂ ਬਾਹਰ ਹਨ, ਜੇਕਰ ਇਹਨਾਂ ਵਿੱਚੋਂ ਕੋਈ ਵੀ ਤੁਹਾਡੀਆਂ ਜ਼ਰੂਰਤਾਂ ਨੂੰ ਪੂਰਾ ਕਰਦਾ ਹੈ ਤਾਂ ਤੁਸੀਂ ਮੋਲਡ ਲਾਗਤਾਂ ਨੂੰ ਬਚਾ ਸਕਦੇ ਹੋ: AGS-Electronics ਤੋਂ ਸਾਡੇ 11 ਸੀਰੀਜ਼ ਡਾਈ-ਕਾਸਟ ਐਲੂਮੀਨੀਅਮ ਬਾਕਸ ਨੂੰ ਡਾਊਨਲੋਡ ਕਰਨ ਲਈ ਇੱਥੇ ਕਲਿੱਕ ਕਰੋ CLICK Product Finder-Locator Service ਪਿਛਲੇ ਸਫ਼ੇ
- Custom Manufactured Parts, Assemblies, Plastic Mold, Casting,Machining
Custom Manufactured Parts, Assemblies, Plastic Mold, Rubber Molding, Metal Casting, CNC Machining, Turning, Milling, Electrical Electronic Optical Assembly PCBA ਕਸਟਮ ਨਿਰਮਿਤ ਪਾਰਟਸ ਅਤੇ ਅਸੈਂਬਲੀਆਂ ਅਤੇ ਉਤਪਾਦ ਹੋਰ ਪੜ੍ਹੋ ਪਲਾਸਟਿਕ ਅਤੇ ਰਬੜ ਦੇ ਮੋਲਡ ਅਤੇ ਮੋਲਡਿੰਗ ਹੋਰ ਪੜ੍ਹੋ ਕਾਸਟਿੰਗ ਅਤੇ ਮਸ਼ੀਨਿੰਗ ਹੋਰ ਪੜ੍ਹੋ Extrusions, Extruded ਉਤਪਾਦ ਹੋਰ ਪੜ੍ਹੋ ਸਟੈਂਪਿੰਗ ਅਤੇ ਸ਼ੀਟ ਮੈਟਲ ਫੈਬਰੀਕੇਸ਼ਨ ਹੋਰ ਪੜ ੍ਹੋ ਮੈਟਲ ਫੋਰਜਿੰਗ ਅਤੇ ਪਾਊਡਰ ਧਾਤੂ ਹੋਰ ਪੜ੍ਹੋ ਤਾਰ ਅਤੇ ਬਸੰਤ ਸਰੂਪ ਹੋਰ ਪੜ੍ਹੋ ਗਲਾਸ ਅਤੇ ਸਿਰੇਮਿਕ ਬਣਾਉਣਾ ਅਤੇ ਆਕਾਰ ਦੇਣਾ ਹੋਰ ਪੜ੍ਹੋ ਐਡਿਟਿਵ ਅਤੇ ਰੈਪਿਡ ਮੈਨੂਫੈਕਚਰਿੰਗ ਹੋਰ ਪੜ੍ਹੋ ਕੰਪੋਜ਼ਿਟ ਅਤੇ ਕੰਪੋਜ਼ਿਟ ਮੈਟੀਰੀਅਲ ਮੈਨੂਫੈਕਚਰਿੰਗ ਹੋਰ ਪੜ੍ਹੋ ਜੁੜਨਾ ਅਤੇ ਅਸੈਂਬਲੀ ਅਤੇ ਫਸਟਨਿੰਗ ਪ੍ਰਕਿਰਿਆਵਾਂ ਅਸੀਂ ਤੁਹਾਡੇ ਲਈ ਹਿੱਸੇ ਅਤੇ ਅਸੈਂਬਲੀਆਂ ਤਿਆਰ ਕਰਦੇ ਹਾਂ ਅਤੇ ਹੇਠ ਲਿਖੀਆਂ ਨਿਰਮਾਣ ਪ੍ਰਕਿਰਿਆਵਾਂ ਦੀ ਪੇਸ਼ਕਸ਼ ਕਰਦੇ ਹਾਂ: • ਪਲਾਸਟਿਕ ਅਤੇ ਰਬੜ ਦੇ ਮੋਲਡ ਅਤੇ ਮੋਲਡ ਕੀਤੇ ਹਿੱਸੇ। ਇੰਜੈਕਸ਼ਨ ਮੋਲਡਿੰਗ, ਥਰਮੋਫਾਰਮਿੰਗ, ਥਰਮੋਸੈਟ ਮੋਲਡਿੰਗ, ਵੈਕਿਊਮ ਮੋਲਡਿੰਗ, ਬਲੋ ਮੋਲਡਿੰਗ, ਰੋਟੇਸ਼ਨਲ ਮੋਲਡਿੰਗ, ਪੋਰ ਮੋਲਡਿੰਗ, ਇਨਸਰਟ ਮੋਲਡਿੰਗ ਅਤੇ ਹੋਰ। • ਪਲਾਸਟਿਕ, ਰਬੜ ਅਤੇ ਧਾਤ ਦੇ ਐਕਸਟਰਿਊਸ਼ਨ • ਮਿੱਲਿੰਗ ਅਤੇ ਟਰਨਿੰਗ ਤਕਨੀਕਾਂ, ਸਵਿਸ-ਕਿਸਮ ਦੀ ਮਸ਼ੀਨਿੰਗ ਦੁਆਰਾ ਤਿਆਰ ਕੀਤੇ ਗਏ ਫੈਰਸ ਅਤੇ ਨਾਨਫੈਰਸ ਕਾਸਟਿੰਗ ਅਤੇ ਮਸ਼ੀਨ ਵਾਲੇ ਹਿੱਸੇ। • ਪਾਊਡਰ ਧਾਤੂ ਹਿੱਸੇ • ਧਾਤੂ ਅਤੇ ਨਾਨਮੈਟਲ ਸਟੈਂਪਿੰਗਜ਼, ਸ਼ੀਟ ਮੈਟਲ ਬਣਾਉਣਾ, ਵੇਲਡ ਸ਼ੀਟ ਮੈਟਲ ਅਸੈਂਬਲੀਆਂ • ਠੰਡਾ ਅਤੇ ਗਰਮ ਫੋਰਜਿੰਗ • ਤਾਰਾਂ, ਵੇਲਡ ਵਾਇਰ ਅਸੈਂਬਲੀਆਂ, ਤਾਰ ਬਣਾਉਣਾ • ਵੱਖ-ਵੱਖ ਕਿਸਮਾਂ ਦੇ ਸਪਰਿੰਗ, ਸਪਰਿੰਗ ਫਾਰਮਿੰਗ • ਗੀਅਰ ਨਿਰਮਾਣ, ਗੀਅਰਬਾਕਸ, ਕਪਲਿੰਗ, ਕੀੜਾ, ਸਪੀਡ ਰੀਡਿਊਸਰ, ਸਿਲੰਡਰ, ਟਰਾਂਸਮਿਸ਼ਨ ਬੈਲਟਸ, ਟ੍ਰਾਂਸਮਿਸ਼ਨ ਚੇਨ, ਟ੍ਰਾਂਸਮਿਸ਼ਨ ਕੰਪੋਨੈਂਟਸ • ਕਸਟਮ ਟੈਂਪਰਡ ਅਤੇ ਬੁਲੇਟਪਰੂਫ ਗਲਾਸ ਨਾਟੋ ਅਤੇ ਫੌਜੀ ਮਿਆਰਾਂ ਦੇ ਅਨੁਕੂਲ • ਗੇਂਦਾਂ, ਬੇਅਰਿੰਗਾਂ, ਪੁਲੀ ਅਤੇ ਪੁਲੀ ਅਸੈਂਬਲੀਆਂ • ਵਾਲਵ ਅਤੇ ਨਿਊਮੈਟਿਕ ਕੰਪੋਨੈਂਟ ਜਿਵੇਂ ਕਿ ਓ-ਰਿੰਗ, ਵਾਸ਼ਰ ਅਤੇ ਸੀਲਾਂ • ਕੱਚ ਅਤੇ ਵਸਰਾਵਿਕ ਹਿੱਸੇ ਅਤੇ ਅਸੈਂਬਲੀਆਂ, ਵੈਕਿਊਮ ਪਰੂਫ ਅਤੇ ਹਰਮੇਟਿਕ ਕੰਪੋਨੈਂਟਸ, ਮੈਟਲ-ਸੀਰੇਮਿਕ ਅਤੇ ਸਿਰੇਮਿਕ-ਸੀਰੇਮਿਕ ਬੰਧਨ। • ਮਕੈਨੀਕਲ, ਆਪਟੋਮੈਕਨੀਕਲ, ਇਲੈਕਟ੍ਰੋਮਕੈਨੀਕਲ, ਆਪਟੋਇਲੈਕਟ੍ਰੋਨਿਕ ਅਸੈਂਬਲੀਆਂ ਦੀਆਂ ਕਈ ਕਿਸਮਾਂ। • ਧਾਤੂ-ਰਬੜ, ਧਾਤ-ਪਲਾਸਟਿਕ ਬੰਧਨ • ਪਾਈਪ ਅਤੇ ਟਿਊਬ, ਪਾਈਪ ਬਣਾਉਣਾ, ਮੋੜਨਾ ਅਤੇ ਕਸਟਮ ਪਾਈਪ ਅਸੈਂਬਲੀਆਂ, ਬੇਲੋ ਮੈਨੂਫੈਕਚਰਿੰਗ। • ਫਾਈਬਰਗਲਾਸ ਨਿਰਮਾਣ • ਵੱਖ-ਵੱਖ ਤਕਨੀਕਾਂ ਜਿਵੇਂ ਕਿ ਸਪਾਟ ਵੈਲਡਿੰਗ, ਲੇਜ਼ਰ ਵੈਲਡਿੰਗ, MIG, TIG ਦੀ ਵਰਤੋਂ ਕਰਦੇ ਹੋਏ ਵੈਲਡਿੰਗ। ਪਲਾਸਟਿਕ ਦੇ ਹਿੱਸੇ ਲਈ Ultrasonic ਿਲਵਿੰਗ. • ਸਤਹ ਦੇ ਉਪਚਾਰਾਂ ਅਤੇ ਸਤਹ ਦੇ ਮੁਕੰਮਲ ਹੋਣ ਦੀਆਂ ਬਹੁਤ ਸਾਰੀਆਂ ਕਿਸਮਾਂ ਜਿਵੇਂ ਕਿ ਅਡਜਸ਼ਨ ਨੂੰ ਵਧਾਉਣ ਲਈ ਸਤਹ ਕੰਡੀਸ਼ਨਿੰਗ, ਕੋਟਿੰਗ ਦੇ ਅਡਿਸ਼ਨ ਨੂੰ ਵਧਾਉਣ ਲਈ ਪਤਲੀ ਆਕਸਾਈਡ ਪਰਤ ਜਮ੍ਹਾ ਕਰਨਾ, ਸੈਂਡ ਬਲਾਸਟਿੰਗ, ਕੈਮ-ਫਿਲਮ, ਐਨੋਡਾਈਜ਼ਿੰਗ, ਨਾਈਟ੍ਰਾਈਡਿੰਗ, ਪਾਊਡਰ ਕੋਟਿੰਗ, ਸਪਰੇਅ ਕੋਟਿੰਗ, ਵੱਖ-ਵੱਖ ਉੱਨਤ ਮੈਟਾਲਾਈਜ਼ੇਸ਼ਨ ਅਤੇ ਕੋਟਿੰਗ ਤਕਨੀਕਾਂ। ਜਿਸ ਵਿੱਚ ਸਪਟਰਿੰਗ, ਇਲੈਕਟ੍ਰੋਨ ਬੀਮ, ਵਾਸ਼ਪੀਕਰਨ, ਪਲੇਟਿੰਗ, ਹਾਰਡ ਕੋਟਿੰਗਜ਼ ਜਿਵੇਂ ਕਿ ਹੀਰਾ ਜਿਵੇਂ ਕਿ ਕਾਰਬਨ (DLC) ਜਾਂ ਟਾਈਟੇਨੀਅਮ ਕੱਟਣ ਅਤੇ ਡ੍ਰਿਲਿੰਗ ਟੂਲਜ਼ ਸ਼ਾਮਲ ਹਨ। • ਮਾਰਕਿੰਗ ਅਤੇ ਲੇਬਲਿੰਗ, ਧਾਤ ਦੇ ਹਿੱਸਿਆਂ 'ਤੇ ਲੇਜ਼ਰ ਮਾਰਕਿੰਗ, ਪਲਾਸਟਿਕ ਅਤੇ ਰਬੜ ਦੇ ਹਿੱਸਿਆਂ 'ਤੇ ਛਪਾਈ ਡਿਜ਼ਾਈਨਰਾਂ ਅਤੇ ਇੰਜੀਨੀਅਰਾਂ ਦੁਆਰਾ ਵਰਤੀਆਂ ਜਾਂਦੀਆਂ ਆਮ ਮਕੈਨੀਕਲ ਇੰਜੀਨੀਅਰਿੰਗ ਸ਼ਰਤਾਂ ਲਈ ਬਰੋਸ਼ਰ ਡਾਊਨਲੋਡ ਕਰੋ ਅਸੀਂ ਤੁਹਾਡੀਆਂ ਖਾਸ ਵਿਸ਼ੇਸ਼ਤਾਵਾਂ ਅਤੇ ਲੋੜਾਂ ਦੇ ਅਨੁਸਾਰ ਉਤਪਾਦ ਬਣਾਉਂਦੇ ਹਾਂ। ਤੁਹਾਨੂੰ ਵਧੀਆ ਕੁਆਲਿਟੀ, ਡਿਲੀਵਰੀ ਅਤੇ ਕੀਮਤਾਂ ਦੀ ਪੇਸ਼ਕਸ਼ ਕਰਨ ਲਈ, ਅਸੀਂ ਚੀਨ, ਭਾਰਤ, ਤਾਈਵਾਨ, ਫਿਲੀਪੀਨਜ਼, ਦੱਖਣੀ ਕੋਰੀਆ, ਮਲੇਸ਼ੀਆ, ਸ਼੍ਰੀਲੰਕਾ, ਤੁਰਕੀ, ਅਮਰੀਕਾ, ਕੈਨੇਡਾ, ਜਰਮਨੀ, ਯੂਕੇ ਅਤੇ ਜਾਪਾਨ ਵਿੱਚ ਵਿਸ਼ਵ ਪੱਧਰ 'ਤੇ ਉਤਪਾਦ ਤਿਆਰ ਕਰਦੇ ਹਾਂ। ਇਹ ਸਾਨੂੰ ਕਿਸੇ ਵੀ ਹੋਰ ਕਸਟਮ ਨਿਰਮਾਤਾ ਨਾਲੋਂ ਵਧੇਰੇ ਮਜ਼ਬੂਤ ਅਤੇ ਵਿਸ਼ਵ ਪੱਧਰ 'ਤੇ ਵਧੇਰੇ ਪ੍ਰਤੀਯੋਗੀ ਬਣਾਉਂਦਾ ਹੈ। ਸਾਡੇ ਉਤਪਾਦ ISO9001:2000, QS9000, ISO14001, TS16949 ਪ੍ਰਮਾਣਿਤ ਵਾਤਾਵਰਣ ਵਿੱਚ ਨਿਰਮਿਤ ਹੁੰਦੇ ਹਨ ਅਤੇ CE, UL ਮਾਰਕ ਰੱਖਦੇ ਹਨ ਅਤੇ ਉਦਯੋਗ ਦੇ ਹੋਰ ਮਿਆਰਾਂ ਨੂੰ ਪੂਰਾ ਕਰਦੇ ਹਨ। ਇੱਕ ਵਾਰ ਜਦੋਂ ਅਸੀਂ ਤੁਹਾਡੇ ਪ੍ਰੋਜੈਕਟ ਲਈ ਨਿਯੁਕਤ ਹੋ ਜਾਂਦੇ ਹਾਂ, ਅਸੀਂ ਤੁਹਾਡੀ ਇੱਛਾ ਅਨੁਸਾਰ ਪੂਰੇ ਨਿਰਮਾਣ, ਅਸੈਂਬਲੀ, ਟੈਸਟਿੰਗ, ਯੋਗਤਾ, ਸ਼ਿਪਿੰਗ ਅਤੇ ਕਸਟਮ ਦਾ ਧਿਆਨ ਰੱਖ ਸਕਦੇ ਹਾਂ। ਜੇ ਤੁਸੀਂ ਤਰਜੀਹ ਦਿੰਦੇ ਹੋ, ਤਾਂ ਅਸੀਂ ਤੁਹਾਡੇ ਪੁਰਜ਼ਿਆਂ ਨੂੰ ਵੇਅਰਹਾਊਸ ਕਰ ਸਕਦੇ ਹਾਂ, ਕਸਟਮ ਕਿੱਟਾਂ ਨੂੰ ਇਕੱਠਾ ਕਰ ਸਕਦੇ ਹਾਂ, ਤੁਹਾਡੀ ਕੰਪਨੀ ਦੇ ਨਾਮ ਅਤੇ ਬ੍ਰਾਂਡ ਨੂੰ ਪ੍ਰਿੰਟ ਅਤੇ ਲੇਬਲ ਕਰ ਸਕਦੇ ਹਾਂ ਅਤੇ ਤੁਹਾਡੇ ਗਾਹਕਾਂ ਨੂੰ ਜਹਾਜ਼ ਸੁੱਟ ਸਕਦੇ ਹਾਂ। ਦੂਜੇ ਸ਼ਬਦਾਂ ਵਿੱਚ, ਜੇਕਰ ਤਰਜੀਹ ਦਿੱਤੀ ਜਾਵੇ ਤਾਂ ਅਸੀਂ ਤੁਹਾਡਾ ਵੇਅਰਹਾਊਸਿੰਗ ਅਤੇ ਵੰਡ ਕੇਂਦਰ ਵੀ ਹੋ ਸਕਦੇ ਹਾਂ। ਕਿਉਂਕਿ ਸਾਡੇ ਵੇਅਰਹਾਊਸ ਪ੍ਰਮੁੱਖ ਬੰਦਰਗਾਹਾਂ ਦੇ ਨੇੜੇ ਸਥਿਤ ਹਨ, ਇਹ ਸਾਨੂੰ ਲੌਜਿਸਟਿਕਲ ਫਾਇਦਾ ਦਿੰਦਾ ਹੈ। ਉਦਾਹਰਨ ਲਈ, ਜਦੋਂ ਤੁਹਾਡੇ ਉਤਪਾਦ ਇੱਕ ਪ੍ਰਮੁੱਖ USA ਸਮੁੰਦਰੀ ਬੰਦਰਗਾਹ 'ਤੇ ਪਹੁੰਚਦੇ ਹਨ, ਤਾਂ ਅਸੀਂ ਇਸਨੂੰ ਸਿੱਧੇ ਇੱਕ ਨੇੜਲੇ ਵੇਅਰਹਾਊਸ ਵਿੱਚ ਟ੍ਰਾਂਸਪੋਰਟ ਕਰ ਸਕਦੇ ਹਾਂ ਜਿੱਥੇ ਅਸੀਂ ਤੁਹਾਡੀ ਪਸੰਦ ਅਤੇ ਡ੍ਰੌਪ ਦੇ ਅਨੁਸਾਰ ਸਟੋਰ, ਅਸੈਂਬਲ, ਕਿੱਟਾਂ, ਰੀਲੇਬਲ, ਪ੍ਰਿੰਟ, ਪੈਕੇਜ ਕਰ ਸਕਦੇ ਹਾਂ। ਤੁਹਾਡੇ ਗਾਹਕਾਂ ਨੂੰ ਭੇਜੋ. ਅਸੀਂ ਨਾ ਸਿਰਫ਼ ਉਤਪਾਦਾਂ ਦੀ ਸਪਲਾਈ ਕਰਦੇ ਹਾਂ। ਸਾਡੀ ਕੰਪਨੀ ਕਸਟਮ ਕੰਟਰੈਕਟਸ 'ਤੇ ਕੰਮ ਕਰਦੀ ਹੈ ਜਿੱਥੇ ਅਸੀਂ ਤੁਹਾਡੀ ਸਾਈਟ 'ਤੇ ਆਉਂਦੇ ਹਾਂ, ਸਾਈਟ 'ਤੇ ਤੁਹਾਡੇ ਪ੍ਰੋਜੈਕਟ ਦਾ ਮੁਲਾਂਕਣ ਕਰਦੇ ਹਾਂ ਅਤੇ ਤੁਹਾਡੇ ਲਈ ਤਿਆਰ ਕੀਤਾ ਗਿਆ ਇੱਕ ਪ੍ਰੋਜੈਕਟ ਪ੍ਰਸਤਾਵ ਤਿਆਰ ਕਰਦੇ ਹਾਂ। ਅਸੀਂ ਫਿਰ ਪ੍ਰੋਜੈਕਟ ਨੂੰ ਲਾਗੂ ਕਰਨ ਲਈ ਆਪਣੀ ਤਜਰਬੇਕਾਰ ਟੀਮ ਭੇਜਦੇ ਹਾਂ। ਸਾਡੇ ਇੰਜਨੀਅਰਿੰਗ ਕੰਮ ਬਾਰੇ ਹੋਰ ਜਾਣਕਾਰੀ ਇਸ 'ਤੇ ਮਿਲ ਸਕਦੀ ਹੈ http://www.ags-engineering.com -ਅਸੀਂ ਉਦਯੋਗਿਕ ਪੱਧਰ 'ਤੇ ਛੋਟੇ ਪ੍ਰੋਜੈਕਟਾਂ ਦੇ ਨਾਲ-ਨਾਲ ਵੱਡੇ ਪ੍ਰੋਜੈਕਟ ਵੀ ਲੈਂਦੇ ਹਾਂ। ਪਹਿਲੇ ਕਦਮ ਦੇ ਤੌਰ 'ਤੇ, ਅਸੀਂ ਤੁਹਾਨੂੰ ਸਾਡੀ ਮਾਹਰ ਟੀਮ ਦੇ ਮੈਂਬਰਾਂ ਨਾਲ ਜਾਂ ਤਾਂ ਫ਼ੋਨ, ਟੈਲੀਕਾਨਫਰੈਂਸਿੰਗ ਜਾਂ MSN ਮੈਸੇਂਜਰ ਰਾਹੀਂ ਜੋੜ ਸਕਦੇ ਹਾਂ, ਤਾਂ ਜੋ ਤੁਸੀਂ ਕਿਸੇ ਮਾਹਰ ਨਾਲ ਸਿੱਧਾ ਸੰਪਰਕ ਕਰ ਸਕੋ, ਸਵਾਲ ਪੁੱਛ ਸਕੋ ਅਤੇ ਆਪਣੇ ਪ੍ਰੋਜੈਕਟ ਬਾਰੇ ਚਰਚਾ ਕਰ ਸਕੋ। ਸਾਨੂੰ ਕਾਲ ਕਰੋ ਅਤੇ ਜੇ ਲੋੜ ਪਈ ਤਾਂ ਅਸੀਂ ਆ ਕੇ ਤੁਹਾਨੂੰ ਮਿਲਾਂਗੇ। ਪਿਛਲੇ ਸਫ਼ੇ