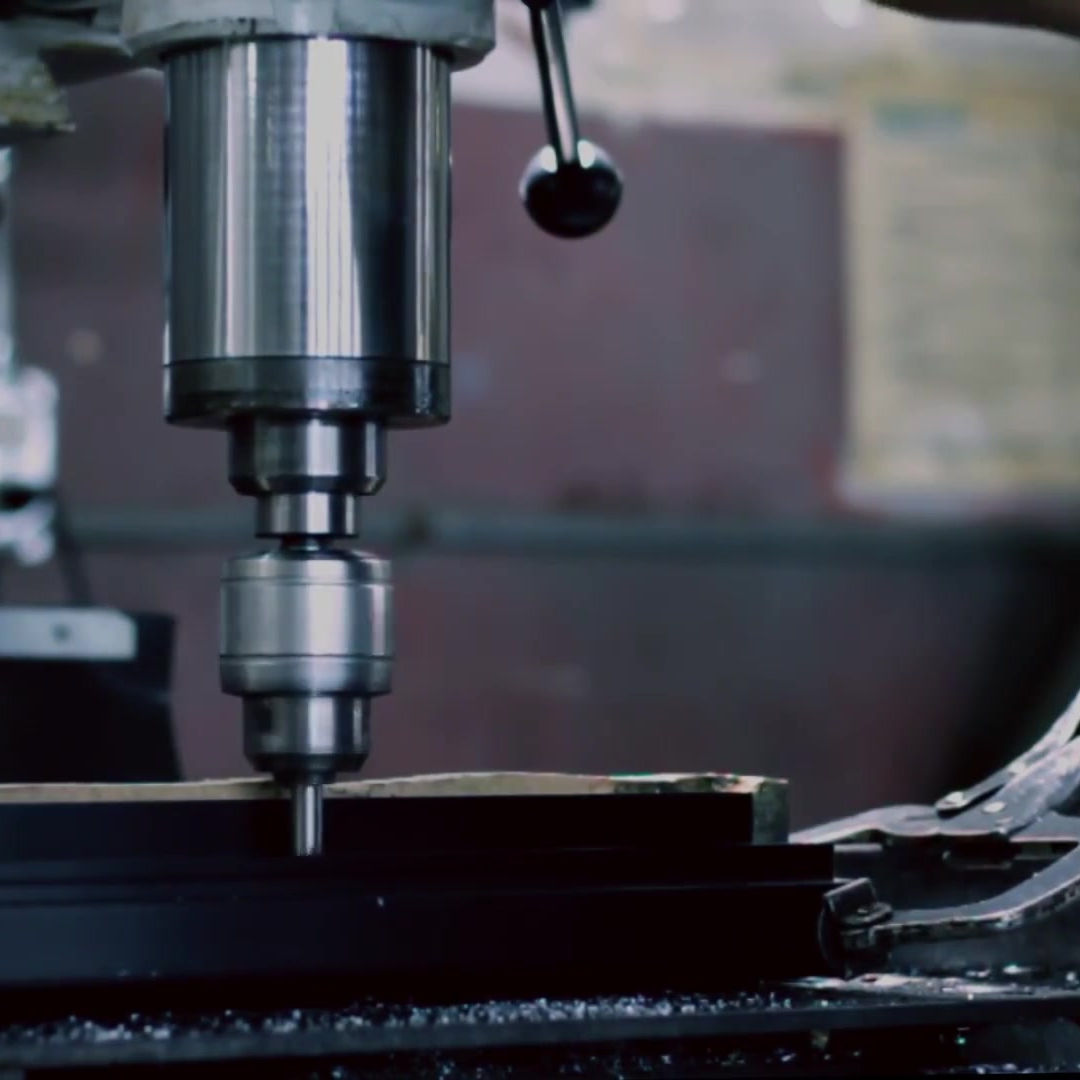
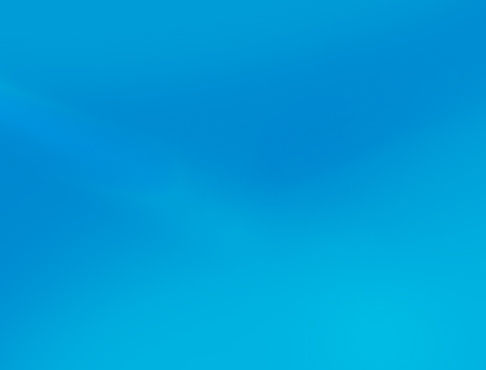
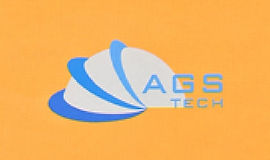
Globalny producent na zamówienie, integrator, konsolidator, partner outsourcingowy w zakresie szerokiej gamy produktów i usług.
Jesteśmy Twoim źródłem kompleksowej obsługi w zakresie produkcji, wytwarzania, inżynierii, konsolidacji, integracji, outsourcingu produktów i usług produkowanych na zamówienie oraz gotowych.
Choose your Language
-
Produkcja na zamówienie
-
Produkcja kontraktowa w kraju i na świecie
-
Outsourcing produkcji
-
Zamówienia krajowe i globalne
-
Konsolidacja
-
Integracja inżynierska
-
Usługi inżynieryjne
W ostatnich latach obserwujemy wzrost zapotrzebowania na RAPID MANUFACTURING lub RAPID PROTOTYPING. Proces ten można również nazwać DESKTOP MANUFACTURINGEM lub FABRICATION FABRICATION. Zasadniczo solidny fizyczny model części jest tworzony bezpośrednio z trójwymiarowego rysunku CAD. Używamy terminu ADDITIVE MANUFACTURING dla tych różnych technik, w których budujemy części warstwami. Wykorzystując zintegrowany sprzęt komputerowy i oprogramowanie, wykonujemy produkcję addytywną. Nasze techniki szybkiego prototypowania i produkcji to: STEREOLITOGRAFIA, POLYJET, MODELOWANIE STOSOWANE, SELEKTYWNE SPIEKANIE LASEROWE, TOPIENIE WIĄZKĄ ELEKTRONOWĄ, DRUK TRÓJWYMIAROWY, BEZPOŚREDNIA PRODUKCJA, SZYBKIE NARZĘDZIA. Zalecamy kliknięcie tutaj, abyPOBIERZ nasze schematyczne ilustracje wytwarzania przyrostowego i procesów szybkiego wytwarzania opracowane przez AGS-TECH Inc.
Pomoże Ci to lepiej zrozumieć informacje, które udostępniamy poniżej.
Szybkie prototypowanie zapewnia nam: 1.) Projekt koncepcyjny produktu jest oglądany pod różnymi kątami na monitorze za pomocą systemu 3D/CAD. 2.) Prototypy z materiałów niemetalicznych i metalowych są produkowane i badane pod kątem funkcjonalnym, technicznym i estetycznym. 3.) Prototypowanie niskokosztowe w bardzo krótkim czasie. Produkcja przyrostowa może być podobna do budowy bochenka chleba poprzez układanie i łączenie poszczególnych kromek jeden na drugim. Innymi słowy, produkt jest wytwarzany kawałek po kawałku lub nakładany na siebie warstwa po warstwie. Większość części można wyprodukować w ciągu kilku godzin. Technika jest dobra, jeśli części są potrzebne bardzo szybko lub jeśli potrzebne ilości są małe, a wykonanie formy i oprzyrządowania jest zbyt kosztowne i czasochłonne. Jednak koszt części jest wysoki ze względu na drogie surowce.
• STEREOLITOGRAFIA: Technika ta, określana również skrótem STL, polega na utwardzaniu i utwardzeniu ciekłego fotopolimeru do określonego kształtu poprzez skupienie na nim wiązki laserowej. Laser polimeryzuje fotopolimer i utwardza go. Dzięki skanowaniu wiązką lasera UV zgodnie z zaprogramowanym kształtem wzdłuż powierzchni mieszanki fotopolimerowej, część wytwarzana jest od dołu do góry w pojedynczych warstwach ułożonych kaskadowo jeden na drugim. Skanowanie plamki laserowej jest powtarzane wiele razy, aby uzyskać geometrie zaprogramowane w systemie. Po całkowitym wykonaniu części zdejmuje się ją z platformy, wyciera i czyści ultradźwiękowo oraz w kąpieli alkoholowej. Następnie przez kilka godzin jest wystawiony na działanie promieniowania UV, aby upewnić się, że polimer jest w pełni utwardzony i utwardzony. Podsumowując proces, platforma zanurzona w mieszaninie fotopolimerów i wiązka lasera UV są sterowane i przesuwane przez system serwosterowania zgodnie z kształtem pożądanej części, a część uzyskuje się poprzez fotoutwardzanie polimeru warstwa po warstwie. Oczywiście maksymalne wymiary produkowanej części określa sprzęt stereolitografii.
• POLYJET : Podobnie jak w przypadku druku atramentowego, w Polyjet mamy osiem głowic drukujących, które umieszczają fotopolimer na tacy roboczej. Światło ultrafioletowe umieszczone obok dysz natychmiast utwardza i utwardza każdą warstwę. W polyjet stosowane są dwa materiały. Pierwszy materiał służy do wykonania rzeczywistego modelu. Drugi materiał, żelowata żywica, służy do podparcia. Oba te materiały są nakładane warstwa po warstwie i jednocześnie utwardzane. Po ukończeniu modelu materiał nośnika usuwa się roztworem wodnym. Stosowane żywice są podobne do stereolitografii (STL). Polyjet ma następujące zalety w porównaniu ze stereolitografią: 1.) Nie ma potrzeby czyszczenia części. 2.) Nie ma potrzeby utwardzania po procesie 3.) Możliwe są mniejsze grubości warstw, dzięki czemu uzyskujemy lepszą rozdzielczość i możemy produkować drobniejsze części.
• MODELOWANIE STOSOWANEGO STANOWISKA: W tej metodzie, w skrócie FDM, głowica wytłaczarki sterowana przez robota porusza się w dwóch zasadniczych kierunkach po stole. W razie potrzeby lina jest opuszczana i podnoszona. Z otworu nagrzanej matrycy na głowicy wytłaczane jest włókno termoplastyczne i nakładana jest warstwa początkowa na podkład piankowy. Odbywa się to dzięki głowicy wytłaczarki, która porusza się z góry określoną ścieżką. Po pierwszej warstwie stół jest opuszczany, a kolejne warstwy układane są jedna na drugiej. Czasami przy wytwarzaniu skomplikowanej części potrzebne są struktury wspierające, aby osadzanie mogło być kontynuowane w określonych kierunkach. W takich przypadkach materiał podporowy jest wytłaczany z mniej gęstym odstępem filamentu na warstwie, dzięki czemu jest słabszy niż materiał modelowy. Te konstrukcje wsporcze można później rozpuścić lub odłamać po zakończeniu części. Wymiary matrycy wytłaczarki określają grubość wytłaczanych warstw. Proces FDM wytwarza części o stopniowanych powierzchniach na ukośnych płaszczyznach zewnętrznych. Jeśli ta chropowatość jest niedopuszczalna, do ich wygładzenia można użyć chemicznego polerowania parowego lub rozgrzanego narzędzia. Dostępny jest nawet wosk do polerowania jako materiał powlekający, aby wyeliminować te etapy i osiągnąć rozsądne tolerancje geometryczne.
• SELEKTYWNE SPIEKANIE LASEROWE: Proces ten, określany również jako SLS, opiera się na selektywnym spiekaniu proszków polimerowych, ceramicznych lub metalicznych w obiekcie. Dno komory przetwarzania ma dwa cylindry: cylinder częściowy i cylinder podający proszek. Pierwsza jest stopniowo obniżana do miejsca, w którym jest formowana spiekana część, a druga jest stopniowo podnoszona w celu dostarczenia proszku do cylindra do wytwarzania części poprzez mechanizm wałka. Najpierw cienka warstwa proszku jest osadzana w cylindrze do obróbki częściowej, a następnie wiązka lasera jest skupiana na tej warstwie, śledząc i topiąc/spiekając określony przekrój, który następnie zestala się w ciało stałe. Proszek to obszary, na które nie uderza wiązka laserowa, pozostają luźne, ale nadal podpierają twardą część. Następnie nakładana jest kolejna warstwa proszku i proces jest wielokrotnie powtarzany w celu uzyskania części. Na koniec strząsa się luźne cząsteczki proszku. Wszystko to realizowane jest przez komputer sterujący procesem za pomocą instrukcji generowanych przez program 3D CAD produkowanej części. Można osadzać różne materiały, takie jak polimery (takie jak ABS, PVC, poliester), wosk, metale i ceramikę z odpowiednimi spoiwami polimerowymi.
• ELECTRON-BEAM MELTING : Podobny do selektywnego spiekania laserowego, ale wykorzystujący wiązkę elektronów do topienia proszków tytanu lub chromu kobaltowego w celu wykonania prototypów w próżni. Wprowadzono pewne udoskonalenia, aby przeprowadzić ten proces na stalach nierdzewnych, aluminium i stopach miedzi. Jeśli trzeba zwiększyć wytrzymałość zmęczeniową produkowanych części, stosujemy prasowanie izostatyczne na gorąco po produkcji części jako proces wtórny.
• DRUK TRÓJWYMIAROWY: określany również jako 3DP, w tej technice głowica drukująca osadza nieorganiczne spoiwo na warstwie niemetalicznego lub metalicznego proszku. Tłok podtrzymujący złoże proszku jest stopniowo obniżany i na każdym etapie osadzane jest spoiwo warstwa po warstwie i stapiane przez spoiwo. Stosowane materiały proszkowe to mieszanki i włókna polimerów, piasek odlewniczy, metale. Stosując jednocześnie różne głowice bindujące i różne kolory binderów możemy uzyskać różne kolory. Proces ten jest podobny do drukowania atramentowego, ale zamiast kolorowego arkusza otrzymujemy kolorowy obiekt trójwymiarowy. Wytwarzane części mogą być porowate i dlatego mogą wymagać spiekania i infiltracji metalem w celu zwiększenia ich gęstości i wytrzymałości. Spiekanie spowoduje spalenie spoiwa i stopienie ze sobą proszków metali. Metale takie jak stal nierdzewna, aluminium, tytan mogą być używane do produkcji części, a jako materiały infiltracyjne powszechnie używamy miedzi i brązu. Piękno tej techniki polega na tym, że nawet skomplikowane i ruchome zespoły mogą być produkowane bardzo szybko. Na przykład zespół przekładni, klucz jako narzędzie może być wykonany i będzie miał części ruchome i obrotowe gotowe do użycia. Różne elementy zestawu mogą być wyprodukowane w różnych kolorach i wszystko w jednym ujęciu. Pobierz naszą broszurę na:Podstawy drukowania 3D w metalu
• BEZPOŚREDNIA PRODUKCJA i SZYBKIE NARZĘDZIA: Oprócz oceny projektu i rozwiązywania problemów stosujemy szybkie prototypowanie do bezpośredniego wytwarzania produktów lub bezpośredniego stosowania w produktach. Innymi słowy, szybkie prototypowanie można włączyć do konwencjonalnych procesów, aby uczynić je lepszymi i bardziej konkurencyjnymi. Na przykład szybkie prototypowanie może tworzyć wzory i formy. Wzory topniejącego i płonącego polimeru utworzonego w operacjach szybkiego prototypowania mogą być montowane do odlewania metodą traconego wosku i zainwestowane. Innym przykładem, o którym warto wspomnieć, jest zastosowanie 3DP do produkcji ceramicznej skorupy odlewniczej i wykorzystanie jej do operacji odlewania skorupy. Nawet formy wtryskowe i wkładki do form można wytwarzać za pomocą szybkiego prototypowania, co pozwala zaoszczędzić wiele tygodni lub miesięcy czasu realizacji formy. Analizując tylko plik CAD żądanej części, możemy wytworzyć geometrię narzędzia za pomocą oprogramowania. Oto niektóre z naszych popularnych metod szybkiego oprzyrządowania:
RTV (Wulkanizacja w temperaturze pokojowej) FORMOWANIE / ODLEWANIE URETANU: Przy użyciu szybkiego prototypowania można wykonać wzór żądanej części. Następnie ten wzór jest powlekany środkiem rozdzielającym i płynna guma RTV jest wylewana na wzór w celu wytworzenia połówek formy. Następnie te połówki formy są wykorzystywane do formowania wtryskowego ciekłych uretanów. Żywotność formy jest krótka, tylko 0 lub 30 cykli, ale wystarcza do produkcji małych partii.
ACES (Acetal Clear Epoxy Solid) FORMOWANIE WTRYSKOWE: Wykorzystując techniki szybkiego prototypowania, takie jak stereolitografia, produkujemy formy wtryskowe. Formy te to skorupy z otwartym końcem, aby umożliwić wypełnienie materiałami takimi jak żywica epoksydowa, żywica epoksydowa wypełniona aluminium lub metale. Ponownie żywotność formy jest ograniczona do dziesiątek lub maksymalnie setek części.
PROCES NATRYSKIWANIA METALI: Stosujemy szybkie prototypowanie i wykonujemy wzór. Na powierzchnię modelu natryskujemy stop cynkowo-aluminiowy i powlekamy go. Wzór z metalową powłoką jest następnie umieszczany w kolbie i zalewany żywicą epoksydową lub epoksydową wypełnioną aluminium. Na koniec zostaje ona usunięta i wytwarzając dwie takie połówki formy otrzymujemy kompletną formę do wtrysku. Formy te mają dłuższą żywotność, w niektórych przypadkach, w zależności od materiału i temperatury, mogą produkować tysiące części.
PROCES KEELTOOL: Ta technika umożliwia produkcję form o żywotności od 100 000 do 10 milionów cykli. Korzystając z szybkiego prototypowania produkujemy formę RTV. Forma jest następnie wypełniana mieszaniną składającą się z proszku stali narzędziowej A6, węglika wolframu, spoiwa polimerowego i pozostawiana do utwardzenia. Ta forma jest następnie podgrzewana, aby wypalić polimer i stopić proszki metalu. Następnym krokiem jest infiltracja miedzią w celu wytworzenia ostatecznej formy. W razie potrzeby na formie można wykonać dodatkowe operacje, takie jak obróbka skrawaniem i polerowanie, aby uzyskać lepszą dokładność wymiarową.