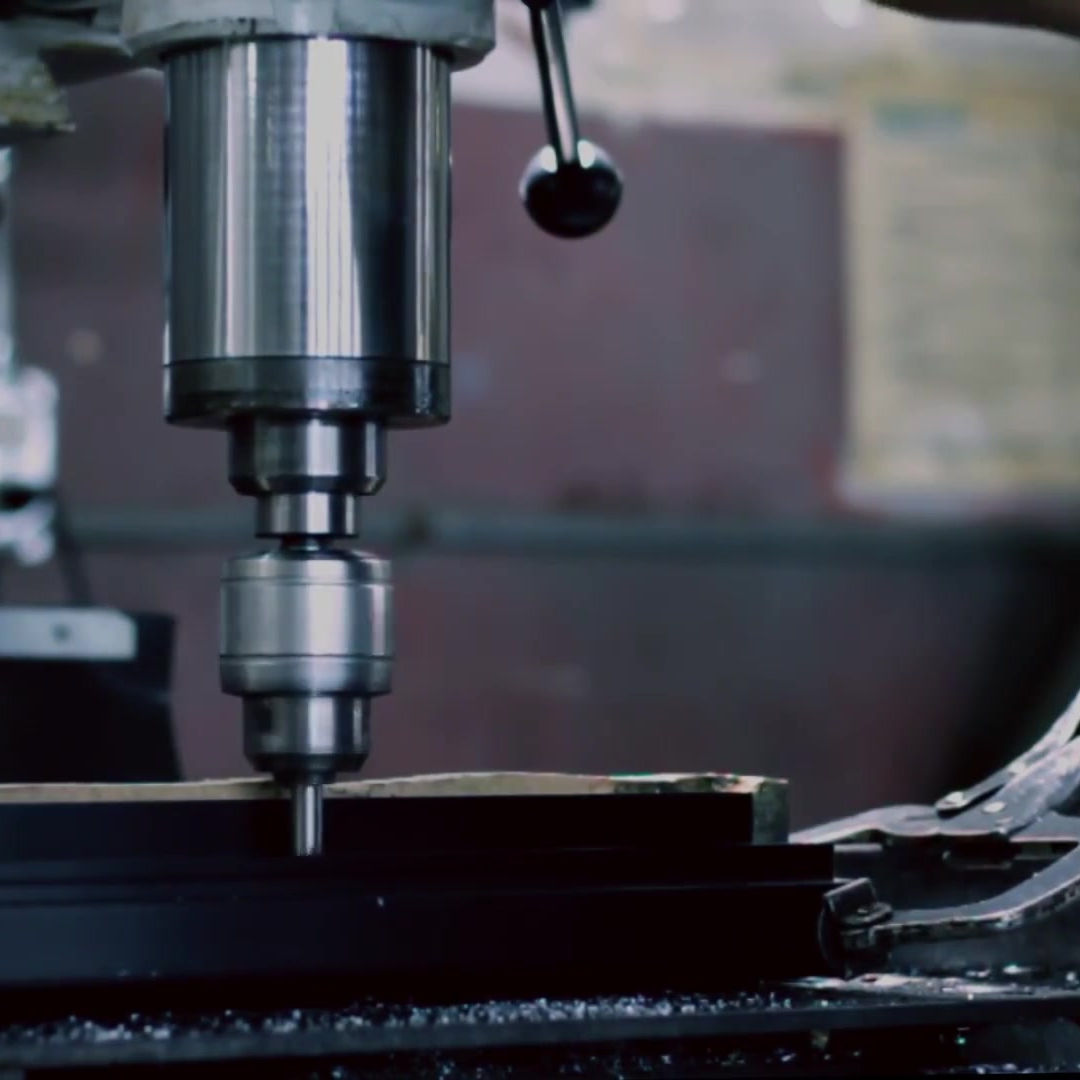
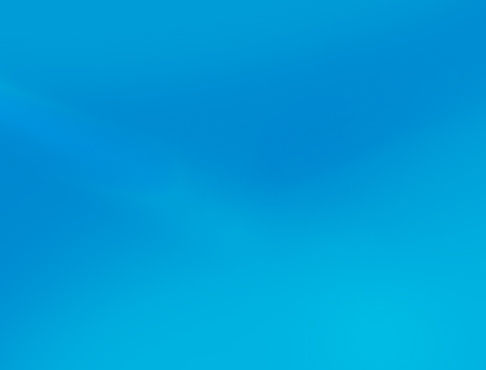
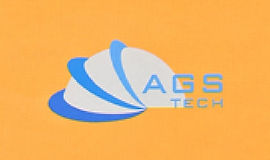
Globalny producent na zamówienie, integrator, konsolidator, partner outsourcingowy w zakresie szerokiej gamy produktów i usług.
Jesteśmy Twoim źródłem kompleksowej obsługi w zakresie produkcji, wytwarzania, inżynierii, konsolidacji, integracji, outsourcingu produktów i usług produkowanych na zamówienie oraz gotowych.
Choose your Language
-
Produkcja na zamówienie
-
Produkcja kontraktowa w kraju i na świecie
-
Outsourcing produkcji
-
Zamówienia krajowe i globalne
-
Konsolidacja
-
Integracja inżynierska
-
Usługi inżynieryjne
OBRÓBKA WYŁADOWNICZA ELEKTRYCZNEGO (EDM), określana również jako SPARK-EROSION or SPARK-EROSION or_cc781905-5cde-3194-bb3b-136bad5c- -136bad5cf58d_or EROZJA DRUTU, to a NON-CONVENTIONAL MANUFACTURING_cc781905-5cde-3194-bb3b-136proces, w którym uzyskuje się pożądany kształt i wyładowanie elektryczne iskier. Oferujemy również niektóre odmiany EDM, a mianowicie NO-WEAR EDM, DRUT EDM (WEDM), EDM GRINDING (EDG), EDM EDM, ELEKTRYCZNO-WYŁADOWCZE FREZOWANIE, micro-EDM, m-EDM_cc781905 -5cde-3194-bb3b-136bad5cf58d_and SZLIFOWANIE ELEKTROCHEMICZNE (ECDG). Nasze systemy EDM składają się z ukształtowanych narzędzi/elektrody i przedmiotu obrabianego podłączonych do zasilaczy prądu stałego i umieszczonych w nieprzewodzącym elektrycznie płynie dielektrycznym. Po 1940 r. obróbka elektroerozyjna stała się jedną z najważniejszych i najbardziej popularnych technologii produkcyjnych w przemyśle wytwórczym.
Gdy odległość między dwiema elektrodami jest zmniejszona, natężenie pola elektrycznego w objętości między elektrodami staje się w niektórych punktach większe niż siła dielektryka, który pęka, ostatecznie tworząc mostek dla przepływu prądu między dwiema elektrodami. Generowany jest intensywny łuk elektryczny, który powoduje znaczne nagrzewanie się części obrabianego przedmiotu i części materiału oprzyrządowania. W rezultacie materiał jest usuwany z obu elektrod. Jednocześnie płyn dielektryczny jest szybko podgrzewany, co powoduje odparowanie płynu w szczelinie łukowej. Gdy przepływ prądu ustaje lub jest zatrzymany, ciepło jest usuwane z pęcherzyka gazu przez otaczający płyn dielektryczny i pęcherzyk ulega kawitacji (zapada się). Fala uderzeniowa wytworzona przez zapadnięcie się bańki i przepływ płynu dielektrycznego wypłukuje zanieczyszczenia z powierzchni przedmiotu obrabianego i porywa stopiony materiał przedmiotu obrabianego do płynu dielektrycznego. Częstotliwość powtarzania tych wyładowań wynosi od 50 do 500 kHz, napięcia od 50 do 380 V i prądy od 0,1 do 500 amperów. Nowy ciekły dielektryk, taki jak oleje mineralne, nafta lub woda destylowana i dejonizowana, jest zwykle przenoszony do objętości międzyelektrodowej, unosząc cząstki stałe (w postaci gruzu) i przywracane są właściwości izolacyjne dielektryka. Po przepływie prądu różnica potencjałów między dwiema elektrodami zostaje przywrócona do wartości sprzed przebicia, więc może nastąpić nowe przebicie dielektryka ciekłego. Nasze nowoczesne maszyny elektroerozyjne (EDM) oferują ruchy sterowane numerycznie i są wyposażone w pompy i systemy filtrowania płynów dielektrycznych.
Obróbka elektroerozyjne (EDM) to metoda obróbki stosowana głównie w przypadku metali twardych lub tych, które byłyby bardzo trudne do obróbki konwencjonalnymi technikami. EDM zwykle pracuje z dowolnymi materiałami, które są przewodnikami elektrycznymi, chociaż zaproponowano również metody obróbki ceramiki izolacyjnej za pomocą EDM. Temperatura topnienia i utajone ciepło topnienia to właściwości, które determinują objętość usuwanego metalu podczas wyładowania. Im wyższe te wartości, tym wolniejsze tempo usuwania materiału. Ponieważ proces obróbki elektroerozyjnej nie wymaga żadnej energii mechanicznej, twardość, wytrzymałość i wytrzymałość przedmiotu obrabianego nie mają wpływu na szybkość usuwania. Częstotliwość rozładowania lub energia na wyładowanie, napięcie i prąd są zmieniane w celu kontrolowania szybkości usuwania materiału. Szybkość usuwania materiału i chropowatość powierzchni rosną wraz ze wzrostem gęstości prądu i spadkiem częstotliwości iskry. Możemy wycinać skomplikowane kontury lub wgłębienia we wstępnie utwardzonej stali za pomocą EDM bez konieczności obróbki cieplnej w celu ich zmiękczenia i ponownego utwardzenia. Metodę tę możemy zastosować z dowolnym metalem lub stopami metali, takimi jak tytan, hastelloy, kovar i inconel. Zastosowania procesu EDM obejmują kształtowanie narzędzi z polikrystalicznego diamentu. EDM jest uważany za nietradycyjną lub niekonwencjonalną metodę obróbki wraz z procesami takimi jak obróbka elektrochemiczna (ECM), cięcie strumieniem wody (WJ, AWJ), cięcie laserowe. Z drugiej strony konwencjonalne metody obróbki obejmują toczenie, frezowanie, szlifowanie, wiercenie i inne procesy, których mechanizm usuwania materiału opiera się zasadniczo na siłach mechanicznych. Elektrody do obróbki elektroerozyjnej (EDM) wykonane są ze stopów grafitu, mosiądzu, miedzi i miedzi z wolframem. Możliwe są średnice elektrod do 0,1 mm. Ponieważ zużycie narzędzia jest niepożądanym zjawiskiem, które ma negatywny wpływ na dokładność wymiarową w EDM, wykorzystujemy proces o nazwie NO-WEAR EDM, odwracając biegunowość i używając narzędzi miedzianych w celu zminimalizowania zużycia narzędzia.
Idealnie mówiąc, obróbkę elektroerozyjne (EDM) można uznać za serię przebicia i przywrócenia cieczy dielektrycznej między elektrodami. W rzeczywistości jednak usuwanie gruzu z obszaru międzyelektrodowego jest prawie zawsze częściowe. Powoduje to, że właściwości elektryczne dielektryka w obszarze międzyelektrodowym różnią się od ich wartości nominalnych i zmieniają się w czasie. Odległość między elektrodami (iskiernik) jest regulowana przez algorytmy sterowania używanej maszyny. Iskiernik w EDM może niestety czasami zostać zwarty przez zanieczyszczenia. System sterowania elektrody może nie reagować wystarczająco szybko, aby zapobiec zwarciu dwóch elektrod (narzędzia i przedmiotu obrabianego). To niepożądane zwarcie przyczynia się do usuwania materiału inaczej niż w idealnym przypadku. Przykładamy ogromną wagę do działania płukania w celu przywrócenia właściwości izolacyjnych dielektryka tak, aby prąd zawsze płynął w punkcie obszaru międzyelektrodowego, minimalizując tym samym możliwość niepożądanej zmiany kształtu (uszkodzenia) narzędzia-elektrody i obrabiany przedmiot. Aby uzyskać określoną geometrię, narzędzie EDM jest prowadzone po pożądanej ścieżce bardzo blisko obrabianego przedmiotu, bez dotykania go. Przywiązujemy najwyższą wagę do wydajności sterowania ruchem podczas użytkowania. W ten sposób ma miejsce duża liczba wyładowań prądowych/iskier, a każde z nich przyczynia się do usuwania materiału zarówno z narzędzia, jak i przedmiotu obrabianego, gdzie powstają małe kratery. Rozmiar kraterów jest funkcją parametrów technologicznych ustalonych dla konkretnego zadania, a wymiary mogą wahać się od nanoskali (tak jak w przypadku operacji mikro-EDM) do kilkuset mikrometrów w warunkach obróbki zgrubnej. Te małe kratery na narzędziu powodują stopniową erozję elektrody zwaną „zużyciem narzędzia”. Aby przeciwdziałać szkodliwemu wpływowi zużycia na geometrię przedmiotu obrabianego, stale wymieniamy narzędzie-elektrodę podczas obróbki. Czasami osiągamy to za pomocą stale wymienianego drutu jako elektrody (ten proces EDM jest również nazywany WIRE EDM ). Czasami używamy narzędzia-elektrody w taki sposób, że tylko niewielka jej część jest faktycznie zaangażowana w proces obróbki i ta część jest zmieniana na bieżąco. Tak jest na przykład w przypadku użycia wirującego dysku jako elektrody narzędziowej. Proces ten nazywa się EDM SZLIFOWANIE. Jeszcze inna technika, którą stosujemy, polega na użyciu zestawu elektrod o różnych rozmiarach i kształtach podczas tej samej operacji EDM, aby skompensować zużycie. Nazywamy tę technikę wieloelektrodową i jest ona najczęściej stosowana, gdy elektroda narzędziowa replikuje w negatywie pożądany kształt i jest przesuwana w kierunku półfabrykatu wzdłuż jednego kierunku, zwykle kierunku pionowego (tj. osi Z). Przypomina to zanurzenie narzędzia w cieczy dielektrycznej, w której zanurzony jest obrabiany przedmiot, i dlatego jest określane jako DIE-SINKING EDM (czasami nazywane_cc781905-5cde- 3194-bb3b-136bad5cf58d_CONVENTIONAL EDM or RAM EDM). Maszyny do tej operacji nazywają się SINKER EDM. Elektrody do tego typu EDM mają złożone formy. Jeśli ostateczną geometrię uzyskuje się za pomocą zwykle prostej elektrody poruszanej w kilku kierunkach i również podlega ona obrotom, nazywamy to EDM FREZOWANIE. Stopień zużycia jest ściśle uzależniony od parametrów technologicznych zastosowanych w operacji (biegunowość, prąd maksymalny, napięcie w obwodzie otwartym). Na przykład in micro-EDM, znany również jako m-EDM, parametry te są zwykle ustawiane na wartości, które powodują poważne zużycie. Dlatego zużycie jest poważnym problemem w tym obszarze, który minimalizujemy korzystając z naszego zgromadzonego know-how. Na przykład, aby zminimalizować zużycie elektrod grafitowych, generator cyfrowy, sterowany w ciągu milisekund, odwraca polaryzację podczas elektroerozji. Daje to efekt podobny do galwanizacji, która w sposób ciągły osadza zerodowany grafit z powrotem na elektrodzie. W innej metodzie, tak zwanym obwodzie „Zero Wear”, minimalizujemy częstotliwość rozpoczynania i zatrzymywania wyładowania, utrzymując je tak długo, jak to możliwe. Szybkość usuwania materiału w obróbce elektroerozyjnej można oszacować na podstawie:
MRR = 4 x 10 exp(4) x I x Tw exp (-1,23)
Tutaj MRR jest w mm3/min, I to prąd w amperach, Tw to temperatura topnienia obrabianego przedmiotu w K-273,15K. Exp oznacza wykładnik.
Z drugiej strony wskaźnik zużycia Wt elektrody można uzyskać z:
Wt = ( 1,1 x 10exp(11)) x I x Ttexp(-2,38)
Tutaj Wt jest w mm3/min, a Tt jest temperaturą topnienia materiału elektrody w K-273,15K
Ostatecznie stosunek zużycia przedmiotu obrabianego do elektrody R można uzyskać z:
R = 2,25 x Trex (-2,38)
Tutaj Tr jest stosunkiem temperatur topnienia przedmiotu obrabianego do elektrody.
SINKER EDM :
Elektrodrążarka wgłębna, określana również jako TYP WNĘKI EDM or VOLUME EDM, składa się z elektrody zanurzonej w płynie i przedmiocie obrabianym Elektroda i obrabiany przedmiot są podłączone do zasilania. Zasilacz generuje potencjał elektryczny między nimi. Gdy elektroda zbliża się do przedmiotu obrabianego, w płynie dochodzi do przebicia dielektryka, tworząc kanał plazmowy i przeskakuje mała iskra. Iskry zwykle uderzają pojedynczo, ponieważ jest wysoce nieprawdopodobne, aby różne miejsca w przestrzeni międzyelektrodowej miały identyczne lokalne właściwości elektryczne, które umożliwiłyby jednoczesne występowanie iskry we wszystkich takich miejscach. Setki tysięcy takich iskier wydarzają się w przypadkowych punktach między elektrodą a przedmiotem obrabianym na sekundę. Ponieważ metal nieszlachetny ulega erozji, a następnie zwiększa się szczelina iskrowa, elektroda jest automatycznie obniżana przez naszą maszynę CNC, dzięki czemu proces może być kontynuowany bez zakłóceń. Nasz sprzęt posiada cykle kontrolne znane jako „na czas” i „czas wolny”. Ustawienie czasu określa długość lub czas trwania iskry. Dłuższy czas wytwarza głębsze wgłębienie dla tej iskry i wszystkich kolejnych iskier dla tego cyklu, tworząc bardziej chropowate wykończenie przedmiotu obrabianego i odwrotnie. Czas wyłączenia to czas, w którym jedna iskra jest zastępowana przez inną. Dłuższy czas przestoju umożliwia przepłukanie płynu dielektrycznego przez dyszę w celu oczyszczenia zerodowanych zanieczyszczeń, unikając w ten sposób zwarcia. Te ustawienia są regulowane w mikrosekundach.
DRUT EDM :
In WIRE OBRÓBKA ELEKTRYCZNA (WEDM), zwana także WIRE-CUT EDM_cc781905-5cde-3194-bb3b-136bad5-336WIRE-bb5cF5cde-3194-bb3b-136bad5cf58d_WIRE-CUT EDM_cc781905-5cde-3194-bb3b-136bad5-336WIRE-bb5f5 cienki jednożyłowy metalowy drut z mosiądzu przechodzący przez obrabiany przedmiot, który jest zanurzony w zbiorniku z płynem dielektrycznym. Drut EDM jest ważną odmianą EDM. Czasami używamy elektrodrążarki drutowej do cięcia płyt o grubości do 300 mm oraz do wykonywania stempli, narzędzi i matryc z twardych metali, które są trudne do obróbki innymi metodami produkcyjnymi. W tym procesie, który przypomina cięcie konturowe piłą taśmową, drut, który jest stale podawany ze szpuli, jest utrzymywany pomiędzy górną i dolną prowadnicą diamentową. Sterowane CNC prowadnice poruszają się w płaszczyźnie x–y, a górna prowadnica może również poruszać się niezależnie w osi z–u–v, co daje możliwość wycinania stożkowych i przejściowych kształtów (takich jak okrąg na dole i kwadrat przy szczyt). Górna prowadnica może kontrolować ruchy osi w x–y–u–v–i–j–k–l–. Dzięki temu WEDM wycina bardzo skomplikowane i delikatne kształty. Przeciętny rzaz naszego sprzętu, który osiąga najlepszy koszt i czas obróbki, wynosi 0,335 mm przy użyciu drutu mosiężnego, miedzianego lub wolframowego Ø 0,25. Jednak górna i dolna prowadnica diamentowa naszego sprzętu CNC mają dokładność około 0,004 mm i mogą mieć ścieżkę cięcia lub szczelinę o wielkości zaledwie 0,021 mm przy użyciu drutu o średnicy 0,02 mm. Tak więc możliwe są naprawdę wąskie cięcia. Szerokość cięcia jest większa niż szerokość drutu, ponieważ iskrzenie występuje od boków drutu do przedmiotu obrabianego, powodując erozję. To „nacięcie” jest konieczne, w wielu zastosowaniach jest przewidywalne i dlatego można je skompensować (w mikro-EDM nie zdarza się to często). Szpule drutu są długie — 8 kg szpula drutu 0,25 mm ma nieco ponad 19 kilometrów długości. Średnica drutu może wynosić nawet 20 mikrometrów, a dokładność geometrii jest w okolicach +/- 1 mikrometra. Zazwyczaj używamy drutu tylko raz i poddajemy go recyklingowi, ponieważ jest stosunkowo niedrogi. Porusza się ze stałą prędkością od 0,15 do 9 m/min, a podczas cięcia utrzymywany jest stały rzaz (szczelina). W procesie wycinania drutem EDM używamy wody jako płynu dielektrycznego, kontrolując jego rezystywność i inne właściwości elektryczne za pomocą filtrów i jednostek dejonizujących. Woda wypłukuje cięte odpady ze strefy cięcia. Płukanie jest ważnym czynnikiem przy określaniu maksymalnej prędkości posuwu dla danej grubości materiału i dlatego utrzymujemy ją na stałym poziomie. Prędkość skrawania w drążeniu drutowym jest określana jako pole przekroju poprzecznego cięcia w jednostce czasu, np. 18 000 mm2/h dla stali narzędziowej D2 o grubości 50 mm. Liniowa prędkość skrawania w tym przypadku wynosiłaby 18 000/50 = 360 mm/godz. Szybkość usuwania materiału w drucianym EDM wynosi:
MRR = Vf xhxb
Tutaj MRR jest w mm3/min, Vf jest szybkością podawania drutu do przedmiotu obrabianego w mm/min, h jest grubością lub wysokością w mm, a b jest szczeliną, która wynosi:
b = dw + 2s
Tutaj dw jest średnicą drutu, a s jest odstępem między drutem a przedmiotem obrabianym w mm.
Wraz z węższymi tolerancjami, nasze nowoczesne wieloosiowe centra obróbkowe EDM do cięcia drutu posiadają dodatkowe funkcje, takie jak wiele głowic do jednoczesnego cięcia dwóch części, elementy sterujące zapobiegające zerwaniu drutu, automatyczne funkcje samogwintowania w przypadku zerwania drutu oraz zaprogramowane strategie obróbki w celu optymalizacji operacji, możliwości cięcia prostego i kątowego.
Wire-EDM oferuje nam niskie naprężenia szczątkowe, ponieważ nie wymaga dużych sił skrawania do usuwania materiału. Gdy energia/moc na impuls jest stosunkowo niska (jak w operacjach wykańczających), oczekuje się niewielkiej zmiany właściwości mechanicznych materiału ze względu na niskie naprężenia szczątkowe.
SZLIFOWANIE ELEKTRYCZNO-ELEKTRYCZNE (EDG) : Ściernice nie zawierają materiałów ściernych, są wykonane z grafitu lub mosiądzu. Powtarzające się iskry między obracającym się kołem a przedmiotem obrabianym usuwają materiał z powierzchni przedmiotu obrabianego. Szybkość usuwania materiału wynosi:
MRR = K x I
Tutaj MRR jest w mm3/min, I jest prądem w amperach, a K jest współczynnikiem materiału przedmiotu obrabianego w mm3/A-min. Często używamy szlifowania elektroerozyjnego do cięcia wąskich szczelin na elementach. Czasami łączymy proces EDG (Electrical-Discharge Grinding) z procesem EKG (Electrochemical Grinding), w którym materiał jest usuwany przez działanie chemiczne, wyładowania elektryczne z tarczy grafitowej rozbijają warstwę tlenku i są wypłukiwane przez elektrolit. Proces ten nazywa się ELEKTROCHEMICZNO-WYŁADOWCZE SZLIFOWANIE (ECDG). Mimo że proces ECDG zużywa stosunkowo więcej energii, jest procesem szybszym niż EDG. Tą techniką szlifujemy głównie narzędzia z węglików spiekanych.
Zastosowania obróbki elektroerozyjnej:
Produkcja prototypu:
Proces EDM wykorzystujemy w produkcji form, narzędzi i matryc, a także przy wykonywaniu prototypów i części produkcyjnych, szczególnie dla przemysłu lotniczego, samochodowego i elektronicznego, w których wielkość produkcji jest stosunkowo niewielka. W Sinker EDM elektroda grafitowa, miedziana wolframowa lub czysta miedź jest obrabiana w pożądany (negatywny) kształt i wprowadzana do przedmiotu obrabianego na końcu pionowego suwaka.
Wykonywanie wykrojników monet:
Do tworzenia matryc do produkcji biżuterii i odznak w procesie monet (stemplowania) matryca pozytywowa może być wykonana ze srebra próby 925, ponieważ (przy odpowiednich ustawieniach maszyny) matryca ulega znacznej erozji i jest używana tylko raz. Powstała matryca negatywowa jest następnie hartowana i używana w młotku spadowym do wytwarzania wytłoczonych płaskowników z wykrojów z brązu, srebra lub niskoodpornego stopu złota. W przypadku odznak te spłaszczenia mogą być dalej kształtowane do zakrzywionej powierzchni za pomocą innej matrycy. Ten typ EDM jest zwykle wykonywany zanurzony w dielektryku na bazie oleju. Gotowy przedmiot może być dalej uszlachetniany przez twarde (szkło) lub miękkie (farba) emaliowanie i/lub galwanicznie pokrywane czystym złotem lub niklem. Bardziej miękkie materiały, takie jak srebro, mogą być ręcznie grawerowane jako uszlachetnienie.
Wiercenie małych otworów:
W naszych wycinarkach drutowych EDM używamy EDM do wiercenia małych otworów, aby wykonać otwór przelotowy w obrabianym przedmiocie, przez który należy przewlec drut do operacji wycinania drutowego. Oddzielne głowice EDM przeznaczone specjalnie do wiercenia małych otworów są montowane na naszych wycinarkach drutowych, które umożliwiają erozję gotowych części dużych płyt hartowanych w razie potrzeby bez wstępnego wiercenia. Stosujemy również elektroerozyjne małe otwory do wiercenia rzędów otworów w krawędziach łopatek turbin stosowanych w silnikach odrzutowych. Przepływ gazu przez te małe otwory umożliwia silnikom stosowanie wyższych temperatur, niż byłoby to możliwe w innym przypadku. Wysokotemperaturowe, bardzo twarde, monokrystaliczne stopy, z których wykonane są te ostrza, sprawiają, że konwencjonalna obróbka tych otworów o wysokim wydłużeniu jest niezwykle trudna, a nawet niemożliwa. Inne obszary zastosowań EDM z małymi otworami to tworzenie mikroskopijnych otworów dla elementów układu paliwowego. Oprócz zintegrowanych głowic EDM wdrażamy samodzielne maszyny EDM do wiercenia małych otworów z osiami x–y do obróbki otworów nieprzelotowych lub przelotowych. EDM wierci otwory za pomocą długiej mosiężnej lub miedzianej elektrody rurowej, która obraca się w uchwycie przy stałym przepływie wody destylowanej lub dejonizowanej przepływającej przez elektrodę jako środek płuczący i dielektryk. Niektóre elektrodrążarki EDM do wiercenia małych otworów są w stanie przewiercić 100 mm miękkiej lub nawet hartowanej stali w czasie krótszym niż 10 sekund. W tej operacji wiercenia można wykonać otwory od 0,3 mm do 6,1 mm.
Obróbka z dezintegracją metalu:
Posiadamy również specjalne maszyny EDM przeznaczone do usuwania złamanych narzędzi (wierteł lub gwintowników) z obrabianych elementów. Proces ten nazywany jest „obróbką z dezintegracją metalu”.
Zalety i wady Obróbka elektroerozyjna:
Zalety EDM obejmują obróbkę:
- Złożone kształty, które w innym przypadku byłyby trudne do wykonania przy użyciu konwencjonalnych narzędzi skrawających
- Niezwykle twardy materiał z bardzo wąskimi tolerancjami
- Bardzo małe elementy obrabiane, w przypadku których konwencjonalne narzędzia tnące mogą uszkodzić część w wyniku nadmiernego nacisku narzędzia tnącego.
- Nie ma bezpośredniego kontaktu między narzędziem a obrabianym przedmiotem. Dzięki temu delikatne sekcje i słabe materiały mogą być obrabiane bez zniekształceń.
- Można uzyskać dobre wykończenie powierzchni.
- Bardzo drobne otwory można łatwo wywiercić.
Wady EDM obejmują:
- Wolne tempo usuwania materiału.
- Dodatkowy czas i koszt zużyty na wykonanie elektrod do EDM nurnika/nurnika.
- Odtworzenie ostrych narożników na obrabianym przedmiocie jest trudne ze względu na zużycie elektrody.
- Pobór mocy jest wysoki.
- Powstaje „Przecięcie”.
- Podczas obróbki dochodzi do nadmiernego zużycia narzędzia.
- Materiały nieprzewodzące elektrycznie mogą być obrabiane tylko przy określonej konfiguracji procesu.