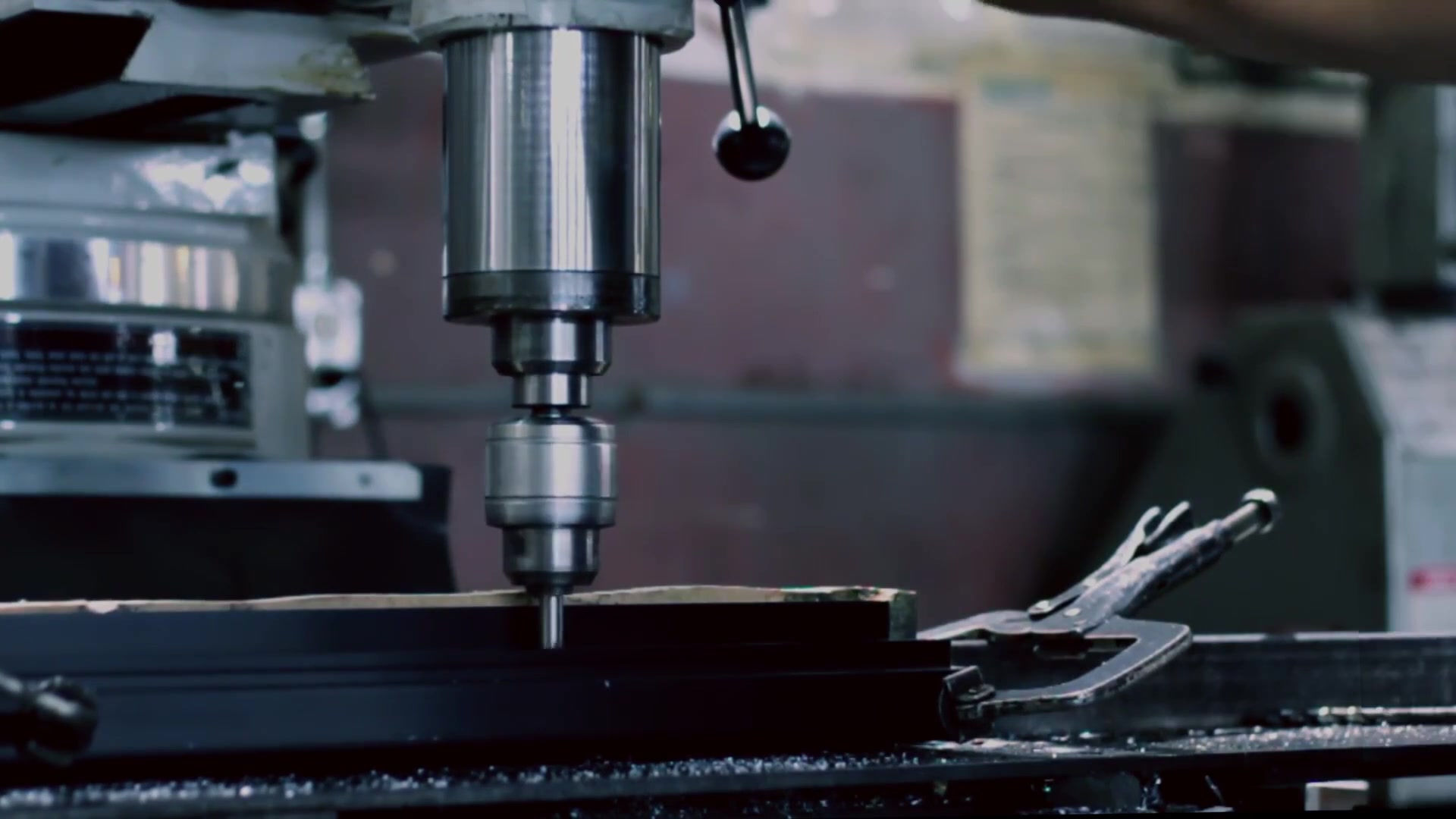
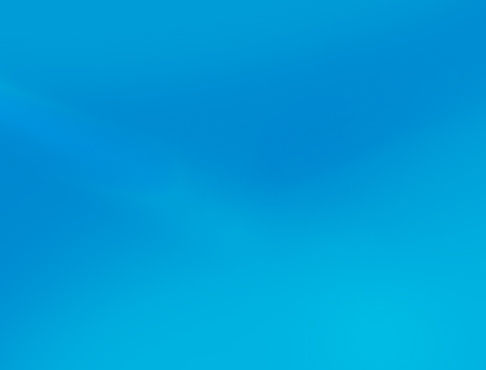
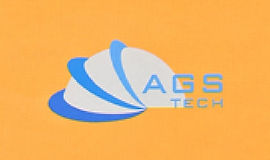
Globalny producent na zamówienie, integrator, konsolidator, partner outsourcingowy w zakresie szerokiej gamy produktów i usług.
Jesteśmy Twoim źródłem kompleksowej obsługi w zakresie produkcji, wytwarzania, inżynierii, konsolidacji, integracji, outsourcingu produktów i usług produkowanych na zamówienie oraz gotowych.
Choose your Language
-
Produkcja na zamówienie
-
Produkcja kontraktowa w kraju i na świecie
-
Outsourcing produkcji
-
Zamówienia krajowe i globalne
-
Konsolidacja
-
Integracja inżynierska
-
Usługi inżynieryjne
Produkcja i wytwarzanie mikroelektroniki i półprzewodników
Wiele z naszych technik i procesów nanoprodukcji, mikroprodukcji i mezoprodukcji wyjaśnionych w innych menu można wykorzystać do MICROELECTRONICS MANUFACTURING too. Jednak ze względu na znaczenie mikroelektroniki w naszych produktach, skoncentrujemy się tutaj na temat konkretnych zastosowań tych procesów. Procesy związane z mikroelektroniką są również powszechnie określane jako SEMICONDUCTOR FABRICATION processes. Nasze usługi w zakresie projektowania i wytwarzania półprzewodników obejmują:
- Projektowanie, rozwój i programowanie płyty FPGA
- Microelectronics usługi odlewnicze: projektowanie, prototypowanie i produkcja, usługi stron trzecich
- Przygotowanie płytek półprzewodnikowych: krojenie w kostkę, szlifowanie od tyłu, przerzedzanie, umieszczanie siatki, sortowanie matryc, pobieranie i umieszczanie, kontrola
- Projektowanie i produkcja opakowań mikroelektronicznych: zarówno gotowe, jak i niestandardowe projekty i produkcja
- Montaż i pakowanie i testowanie układów scalonych półprzewodników: łączenie matryc, drutów i chipów, hermetyzacja, montaż, znakowanie i branding
- Ramki wyprowadzeń do urządzeń półprzewodnikowych: zarówno gotowe, jak i niestandardowe projekty i produkcja
- Projektowanie i produkcja radiatorów dla mikroelektroniki: zarówno gotowe, jak i niestandardowe projekty i produkcja
- Projektowanie i produkcja czujników i siłowników: Zarówno projektowanie i produkcja gotowe, jak i niestandardowe
- Projektowanie i produkcja obwodów optoelektronicznych i fotonicznych
Pozwól nam bardziej szczegółowo zbadać mikroelektronikę i półprzewodniki oraz technologie testowe, abyś mógł lepiej zrozumieć oferowane przez nas usługi i produkty.
Projektowanie, rozwój i programowanie płyt FPGA: Programowalne macierze bramek (FPGA) to reprogramowalne układy krzemowe. W przeciwieństwie do procesorów, które można znaleźć w komputerach osobistych, programowanie FPGA polega na przeprogramowaniu samego układu w celu implementacji funkcjonalności użytkownika, zamiast uruchamiania aplikacji. Korzystając z gotowych bloków logicznych i programowalnych zasobów routingu, układy FPGA można skonfigurować tak, aby implementować niestandardowe funkcje sprzętowe bez użycia płytki stykowej i lutownicy. Zadania przetwarzania cyfrowego są wykonywane w oprogramowaniu i kompilowane do pliku konfiguracyjnego lub strumienia bitów, który zawiera informacje o tym, jak komponenty powinny być ze sobą połączone. Układy FPGA mogą być używane do implementacji dowolnej funkcji logicznej, którą mógłby wykonać układ ASIC i są całkowicie rekonfigurowalne i mogą otrzymać zupełnie inną „osobowość” poprzez ponowną kompilację innej konfiguracji obwodu. Układy FPGA łączą najlepsze części układów scalonych specyficznych dla aplikacji (ASIC) i systemów opartych na procesorach. Korzyści te obejmują:
• Szybsze czasy reakcji we/wy i specjalistyczna funkcjonalność
• Przekroczenie mocy obliczeniowej cyfrowych procesorów sygnałowych (DSP)
• Szybkie prototypowanie i weryfikacja bez procesu wytwarzania niestandardowego ASIC
• Implementacja niestandardowej funkcjonalności z niezawodnością dedykowanego sprzętu deterministycznego
• Możliwość rozbudowy w terenie, co eliminuje koszty przeprojektowania i konserwacji niestandardowych układów ASIC
Układy FPGA zapewniają szybkość i niezawodność, nie wymagając dużych nakładów, aby uzasadnić duże początkowe koszty niestandardowego projektu ASIC. Reprogramowalny krzem ma również taką samą elastyczność jak oprogramowanie działające w systemach opartych na procesorach i nie jest ograniczony liczbą dostępnych rdzeni przetwarzania. W przeciwieństwie do procesorów, układy FPGA mają prawdziwie równoległy charakter, więc różne operacje przetwarzania nie muszą konkurować o te same zasoby. Każde niezależne zadanie przetwarzania jest przypisane do dedykowanej sekcji układu i może działać autonomicznie bez wpływu innych bloków logicznych. W rezultacie dodanie większej ilości przetwarzania nie ma wpływu na wydajność jednej części aplikacji. Niektóre FPGA mają funkcje analogowe oprócz funkcji cyfrowych. Niektóre typowe funkcje analogowe to programowalna szybkość narastania i siła napędu na każdym pinie wyjściowym, co pozwala inżynierowi ustawić niskie szybkości na lekko obciążonych pinach, które w przeciwnym razie dzwoniłyby lub sprzęgałyby się niedopuszczalnie, oraz ustawić silniejsze, szybsze szybkości na mocno obciążonych pinach na wysokich prędkościach kanały, które w innym przypadku działałyby zbyt wolno. Inną stosunkowo powszechną cechą analogową są komparatory różnicowe na pinach wejściowych przeznaczone do podłączenia do różnicowych kanałów sygnalizacyjnych. Niektóre układy FPGA z mieszanym sygnałem mają zintegrowane peryferyjne przetworniki analogowo-cyfrowe (ADC) i przetworniki cyfrowo-analogowe (DAC) z blokami kondycjonowania sygnału analogowego, które pozwalają im działać jako system na chipie.
Krótko mówiąc, 5 najważniejszych zalet układów FPGA to:
1. Dobra wydajność
2. Krótki czas na rynek
3. Niski koszt
4. Wysoka niezawodność
5. Możliwość długoterminowej konserwacji
Dobra wydajność – dzięki możliwości przetwarzania równoległego, układy FPGA mają lepszą moc obliczeniową niż cyfrowe procesory sygnałowe (DSP) i nie wymagają sekwencyjnego wykonywania jako DSP i mogą osiągnąć więcej na cykl zegara. Sterowanie wejściami i wyjściami (I/O) na poziomie sprzętowym zapewnia krótsze czasy odpowiedzi i wyspecjalizowane funkcje, które ściśle odpowiadają wymaganiom aplikacji.
Krótki czas wprowadzenia na rynek — układy FPGA oferują elastyczność i możliwości szybkiego prototypowania, a tym samym krótszy czas wprowadzania na rynek. Nasi klienci mogą przetestować pomysł lub koncepcję i zweryfikować ją w sprzęcie bez przechodzenia przez długi i kosztowny proces produkcji niestandardowego projektu ASIC. Możemy wprowadzać zmiany przyrostowe i iterować projekt FPGA w ciągu godzin zamiast tygodni. Komercyjny, gotowy sprzęt jest również dostępny z różnymi typami wejść/wyjść już podłączonymi do programowalnego układu FPGA. Rosnąca dostępność narzędzi programowych wysokiego poziomu oferuje cenne rdzenie IP (wstępnie wbudowane funkcje) do zaawansowanego sterowania i przetwarzania sygnałów.
Niski koszt — Jednorazowe wydatki na inżynierię (NRE) niestandardowych projektów ASIC przewyższają koszty rozwiązań sprzętowych opartych na FPGA. Duża początkowa inwestycja w układy ASIC może być uzasadniona dla producentów OEM produkujących wiele chipów rocznie, jednak wielu użytkowników końcowych potrzebuje niestandardowej funkcjonalności sprzętowej dla wielu opracowywanych systemów. Nasz programowalny krzemowy układ FPGA oferuje coś bez kosztów produkcji lub długich czasów realizacji montażu. Wymagania systemowe często zmieniają się w czasie, a koszt wprowadzania zmian przyrostowych w projektach FPGA jest znikomy w porównaniu z dużymi kosztami ponownego rozkręcenia ASIC.
Wysoka niezawodność — narzędzia programowe zapewniają środowisko programistyczne, a obwody FPGA to prawdziwa implementacja wykonywania programu. Systemy oparte na procesorach zazwyczaj obejmują wiele warstw abstrakcji, aby ułatwić planowanie zadań i współdzielenie zasobów między wieloma procesami. Warstwa sterownika kontroluje zasoby sprzętowe, a system operacyjny zarządza przepustowością pamięci i procesora. Dla dowolnego rdzenia procesora, tylko jedna instrukcja może być wykonywana na raz, a systemy oparte na procesorach są nieustannie narażone na ryzyko, że zadania o krytycznym znaczeniu czasowe będą wyprzedzać się nawzajem. Układy FPGA, nie wykorzystujące systemów operacyjnych, stwarzają minimalne problemy z niezawodnością dzięki ich rzeczywistemu wykonywaniu równoległemu i deterministycznemu sprzętowi dedykowanemu do każdego zadania.
Możliwość długoterminowej konserwacji — układy FPGA można aktualizować w terenie i nie wymagają czasu ani kosztów związanych z przeprojektowaniem ASIC. Na przykład cyfrowe protokoły komunikacyjne mają specyfikacje, które mogą się zmieniać w czasie, a interfejsy oparte na ASIC mogą powodować problemy z konserwacją i kompatybilnością w przód. Wręcz przeciwnie, rekonfigurowalne układy FPGA mogą nadążyć za potencjalnie niezbędnymi przyszłymi modyfikacjami. W miarę dojrzewania produktów i systemów nasi klienci mogą wprowadzać ulepszenia funkcjonalne bez poświęcania czasu na przeprojektowanie sprzętu i modyfikację układów płytek.
Usługi odlewnicze mikroelektroniki: Nasze usługi odlewnicze mikroelektroniki obejmują projektowanie, prototypowanie i produkcję, usługi stron trzecich. Naszym klientom zapewniamy pomoc w całym cyklu rozwoju produktu - od wsparcia projektowego po prototypowanie i wsparcie produkcji chipów półprzewodnikowych. Naszym celem w zakresie usług wsparcia projektowania jest umożliwienie prawidłowego podejścia po raz pierwszy do projektów cyfrowych, analogowych i mieszanych sygnałów urządzeń półprzewodnikowych. Na przykład dostępne są specyficzne narzędzia symulacyjne MEMS. Fabryki, które mogą obsługiwać 6 i 8-calowe wafle dla zintegrowanych CMOS i MEMS, są do Twojej dyspozycji. Naszym klientom oferujemy wsparcie projektowe dla wszystkich głównych platform automatyzacji projektowania elektronicznego (EDA), dostarczając prawidłowe modele, zestawy do projektowania procesów (PDK), biblioteki analogowe i cyfrowe oraz wsparcie projektowania pod kątem produkcji (DFM). Oferujemy dwie opcje prototypowania dla wszystkich technologii: usługę Multi Product Wafer (MPW), w której kilka urządzeń jest przetwarzanych równolegle na jednym waflu, oraz usługę Multi Level Mask (MLM) z czterema poziomami maski narysowanymi na tej samej siatce. Są bardziej ekonomiczne niż pełny zestaw masek. Usługa MLM jest bardzo elastyczna w porównaniu do stałych terminów usługi MPW. Firmy mogą preferować outsourcing produktów półprzewodnikowych do odlewni mikroelektroniki z wielu powodów, takich jak potrzeba drugiego źródła, wykorzystanie zasobów wewnętrznych do innych produktów i usług, chęć odejścia od fabryk oraz zmniejszenie ryzyka i obciążenia związanego z prowadzeniem fabryki półprzewodników itp. AGS-TECH oferuje procesy wytwarzania mikroelektroniki na otwartej platformie, które można zmniejszyć do małych serii płytek, a także do produkcji masowej. W pewnych okolicznościach istniejące narzędzia mikroelektroniczne lub produkcyjne MEMS lub kompletne zestawy narzędzi mogą zostać przeniesione jako narzędzia wysłane lub sprzedane z fabryki do naszego fabryki, lub istniejąca mikroelektronika i produkty MEMS mogą zostać przeprojektowane przy użyciu technologii procesowych otwartej platformy i przeniesione do proces dostępny w naszej fabryce. Jest to szybsze i bardziej ekonomiczne niż niestandardowy transfer technologii. W razie potrzeby można jednak przenieść istniejące procesy produkcji mikroelektroniki/MEMS klienta.
Przygotowanie płytek półprzewodnikowych: Na życzenie klientów po mikrofabrykacji płytek półprzewodnikowych wykonujemy kostkowanie, szlifowanie od tyłu, przerzedzanie, umieszczanie siatki, sortowanie matryc, wybieranie i umieszczanie, operacje kontrolne na waflach półprzewodnikowych. Obróbka płytek półprzewodnikowych obejmuje metrologię pomiędzy różnymi etapami obróbki. Na przykład metody testowania cienkowarstwowego oparte na elipsometrii lub reflektometrii służą do ścisłej kontroli grubości tlenku bramki, a także grubości, współczynnika załamania i współczynnika ekstynkcji fotorezystu i innych powłok. Używamy sprzętu do testowania płytek półprzewodnikowych, aby sprawdzić, czy płytki nie zostały uszkodzone przez poprzednie etapy przetwarzania aż do testowania. Po zakończeniu procesów front-end półprzewodnikowe urządzenia mikroelektroniczne są poddawane różnorodnym testom elektrycznym w celu ustalenia, czy działają prawidłowo. Odsetek urządzeń mikroelektronicznych na płytce, które okazały się działać prawidłowo, nazywamy „wydajnością”. Testowanie chipów mikroelektronicznych na płytce odbywa się za pomocą testera elektronicznego, który dociska maleńkie sondy do chipa półprzewodnikowego. Zautomatyzowana maszyna znakuje każdy uszkodzony chip mikroelektroniczny kroplą barwnika. Dane testowe płytek są rejestrowane w centralnej komputerowej bazie danych, a układy półprzewodnikowe są sortowane do wirtualnych pojemników zgodnie z wcześniej określonymi limitami testowymi. Uzyskane dane binningu można przedstawić na wykresie lub zarejestrować na mapie waflowej w celu śledzenia defektów produkcyjnych i oznaczania uszkodzonych chipów. Mapa ta może być również wykorzystana podczas montażu i pakowania wafli. W testach końcowych układy mikroelektroniczne są ponownie testowane po zapakowaniu, ponieważ może brakować przewodów łączących lub wydajność analogowa może zostać zmieniona przez opakowanie. Po przetestowaniu płytki półprzewodnikowej, jej grubość jest zwykle zmniejszana przed nacięciem płytki, a następnie rozbiciem jej na poszczególne matryce. Proces ten nazywany jest kostką do płytek półprzewodnikowych. Do sortowania dobrych i złych matryc półprzewodnikowych używamy zautomatyzowanych maszyn typu „pick-and-place”, wyprodukowanych specjalnie dla przemysłu mikroelektronicznego. Opakowane są tylko dobre, nieoznakowane chipy półprzewodnikowe. Następnie w procesie mikroelektroniki w plastikowym lub ceramicznym procesie pakowania montujemy wykrojnik półprzewodnikowy, łączymy nakładki wykrojnikowe z kołkami na opakowaniu i uszczelniamy wykrojnik. Drobne złote druciki są używane do łączenia padów z pinami za pomocą zautomatyzowanych maszyn. Pakiet skali chipów (CSP) to kolejna technologia pakowania mikroelektroniki. Plastikowy podwójny pakiet in-line (DIP), podobnie jak większość pakietów, jest wielokrotnie większy niż rzeczywista matryca półprzewodnikowa umieszczona w środku, podczas gdy chipy CSP są prawie wielkości matrycy mikroelektronicznej; a CSP można skonstruować dla każdej kostki przed pokrojeniem w kostkę płytki półprzewodnikowej. Zapakowane chipy mikroelektroniczne są ponownie testowane, aby upewnić się, że nie zostały uszkodzone podczas pakowania i że proces łączenia matrycy z kołkiem został zakończony prawidłowo. Za pomocą laserów wytrawiamy nazwy chipów i numery na opakowaniu.
Projektowanie i produkcja opakowań mikroelektronicznych: Oferujemy zarówno gotowe, jak i niestandardowe projekty i produkcję pakietów mikroelektronicznych. W ramach tej usługi wykonywane jest również modelowanie i symulacja pakietów mikroelektronicznych. Modelowanie i symulacja zapewnia wirtualne projektowanie eksperymentów (DoE) w celu uzyskania optymalnego rozwiązania, zamiast testowania pakietów w terenie. Zmniejsza to koszty i czas produkcji, zwłaszcza w przypadku opracowywania nowych produktów w mikroelektronice. Ta praca daje nam również możliwość wyjaśnienia naszym klientom, w jaki sposób montaż, niezawodność i testowanie wpłyną na ich produkty mikroelektroniczne. Podstawowym celem opakowań mikroelektronicznych jest zaprojektowanie systemu elektronicznego, który spełni wymagania dla konkretnego zastosowania przy rozsądnych kosztach. Ze względu na wiele dostępnych opcji łączenia i umieszczania systemu mikroelektronicznego, wybór technologii pakowania dla danego zastosowania wymaga oceny eksperckiej. Kryteria wyboru pakietów mikroelektronicznych mogą obejmować niektóre z następujących sterowników technologii:
-Przewodność
-Dawać
-Koszt
-Właściwości rozpraszania ciepła
-Wydajność ekranowania elektromagnetycznego
-Wytrzymałość mechaniczna
-Niezawodność
Te względy projektowe dla pakietów mikroelektronicznych wpływają na szybkość, funkcjonalność, temperatury złącza, objętość, wagę i inne. Podstawowym celem jest wybór najbardziej opłacalnej, ale niezawodnej technologii połączeń wzajemnych. Wykorzystujemy wyrafinowane metody analityczne i oprogramowanie do projektowania pakietów mikroelektronicznych. Opakowania mikroelektroniczne zajmują się projektowaniem metod wytwarzania połączonych miniaturowych systemów elektronicznych i niezawodnością tych systemów. W szczególności pakowanie mikroelektroniki obejmuje kierowanie sygnałów przy zachowaniu integralności sygnału, dystrybucję masy i zasilania do półprzewodnikowych obwodów scalonych, rozpraszanie rozproszonego ciepła przy zachowaniu integralności strukturalnej i materiałowej oraz ochronę obwodu przed zagrożeniami środowiskowymi. Ogólnie rzecz biorąc, metody pakowania mikroelektronicznych układów scalonych obejmują użycie PWB ze złączami, które zapewniają rzeczywiste wejścia/wyjścia do obwodu elektronicznego. Tradycyjne podejścia do pakowania mikroelektroniki wymagają użycia pojedynczych opakowań. Główną zaletą pakietu jednoukładowego jest możliwość pełnego przetestowania mikroelektronicznego układu scalonego przed połączeniem go z leżącym poniżej podłożem. Takie zapakowane urządzenia półprzewodnikowe są montowane w otworach przelotowych lub montowane powierzchniowo do PWB. Opakowania mikroelektroniki montowane na powierzchni nie wymagają otworów przelotowych, aby przejść przez całą płytkę. Zamiast tego komponenty mikroelektroniczne montowane powierzchniowo można przylutować po obu stronach PWB, co zapewnia większą gęstość obwodów. Takie podejście nazywa się technologią montażu powierzchniowego (SMT). Dodanie pakietów typu Area-Array, takich jak układy typu ball-grid array (BGA) i pakiety chip-scale (CSP), sprawia, że SMT jest konkurencyjny w stosunku do technologii pakowania mikroelektroniki półprzewodników o największej gęstości. Nowsza technologia pakowania polega na dołączeniu więcej niż jednego urządzenia półprzewodnikowego do podłoża o dużej gęstości połączeń, które jest następnie montowane w dużej obudowie, zapewniając zarówno piny we/wy, jak i ochronę środowiska. Ta technologia modułu wielochipowego (MCM) charakteryzuje się ponadto technologiami podłoża używanymi do łączenia podłączonych układów scalonych. MCM-D reprezentuje osadzane cienkowarstwowe metalowe i dielektryczne wielowarstwy. Podłoża MCM-D mają najwyższą gęstość okablowania ze wszystkich technologii MCM dzięki wyrafinowanym technologiom przetwarzania półprzewodników. MCM-C odnosi się do wielowarstwowych „ceramicznych” podłoży, wypalanych z ułożonych w stos naprzemiennych warstw sitowych farb metalowych i niewypalanych arkuszy ceramicznych. Stosując MCM-C uzyskujemy umiarkowanie gęstą przepustowość okablowania. MCM-L odnosi się do wielowarstwowych podłoży wykonanych z ułożonych w stos metalizowanych „laminatów” PWB, które są indywidualnie wzorowane, a następnie laminowane. Kiedyś była to technologia połączeń o niskiej gęstości, jednak teraz MCM-L szybko zbliża się do gęstości technologii pakowania mikroelektroniki MCM-C i MCM-D. Bezpośrednia technologia pakowania mikroelektroniki (DCA) lub chip-on-board (COB) obejmuje montaż układów scalonych mikroelektroniki bezpośrednio do PWB. Plastikowa osłonka, którą „nakłada się” na goły układ scalony, a następnie utwardza, zapewnia ochronę środowiska. Układy scalone mikroelektroniki można łączyć z podłożem za pomocą metody flip-chip lub łączenia drutowego. Technologia DCA jest szczególnie ekonomiczna w przypadku systemów, które są ograniczone do 10 lub mniej półprzewodnikowych układów scalonych, ponieważ większa liczba chipów może wpływać na wydajność systemu, a przeróbki DCA mogą być trudne. Wspólną zaletą obu opcji pakowania DCA i MCM jest eliminacja poziomu połączeń półprzewodnikowych układów scalonych, co pozwala na bliższe zbliżenie (krótsze opóźnienia w transmisji sygnału) i zmniejszoną indukcyjność przewodów. Główną wadą obu metod jest trudność w zakupie w pełni przetestowanych mikroelektronicznych układów scalonych. Inne wady technologii DCA i MCM-L obejmują słabe zarządzanie termiczne dzięki niskiej przewodności cieplnej laminatów PWB oraz słaby współczynnik dopasowania współczynnika rozszerzalności cieplnej pomiędzy matrycą półprzewodnikową a podłożem. Rozwiązanie problemu niedopasowania rozszerzalności cieplnej wymaga podłoża przekładki, takiego jak molibden w przypadku matrycy spajanej drutem oraz podkład epoksydowy w przypadku matrycy typu flip-chip. Multichip carrier module (MCCM) łączy wszystkie pozytywne aspekty DCA z technologią MCM. MCCM to po prostu mały MCM na cienkim metalowym nośniku, który można połączyć lub mechanicznie przymocować do PWB. Metalowe dno działa zarówno jako rozpraszacz ciepła, jak i interposer naprężeń dla podłoża MCM. MCCM ma wyprowadzenia peryferyjne do łączenia przewodów, lutowania lub łączenia zakładek z PWB. Układy scalone z nieosłoniętymi półprzewodnikami są chronione materiałem typu „glob-top”. Kiedy skontaktujesz się z nami, omówimy Twoją aplikację i wymagania, aby wybrać najlepszą dla Ciebie opcję opakowania mikroelektroniki.
Montaż, pakowanie i testowanie półprzewodników IC: W ramach naszych usług w zakresie produkcji mikroelektroniki oferujemy łączenie matryc, drutów i chipów, hermetyzację, montaż, znakowanie i branding oraz testowanie. Aby chip półprzewodnikowy lub zintegrowany obwód mikroelektroniczny działał, musi być podłączony do systemu, którym będzie sterować lub który będzie dostarczał instrukcje. Zespół mikroelektroniki IC zapewnia połączenia do przesyłania zasilania i informacji między chipem a systemem. Odbywa się to poprzez podłączenie mikroukładu mikroelektronicznego do pakietu lub bezpośrednie podłączenie go do płytki drukowanej dla tych funkcji. Połączenia między chipem a opakowaniem lub płytką drukowaną (PCB) są realizowane za pomocą łączenia przewodów, montażu przez otwór lub flip chip. Jesteśmy liderem w branży w zakresie znajdowania rozwiązań w zakresie pakowania mikroelektroniki IC, aby spełnić złożone wymagania rynków bezprzewodowych i internetowych. Oferujemy tysiące różnych formatów i rozmiarów obudów, począwszy od tradycyjnych układów scalonych mikroelektroniki z ramką wyprowadzeniową do montażu przez otwór i powierzchniowego, po najnowsze rozwiązania w zakresie skalowania chipów (CSP) i układów siatki kulowej (BGA) wymagane w zastosowaniach o dużej liczbie pinów i dużej gęstości . Z magazynu dostępna jest szeroka gama pakietów, w tym CABGA (Chip Array BGA), CQFP, CTBGA (Chip Array Thin Core BGA), CVBGA (Very Thin Chip Array BGA), Flip Chip, LCC, LGA, MQFP, PBGA, PDIP, PLCC, PoP - Pakiet na opakowaniu, PoP TMV - Przez Mold Via, SOIC / SOJ, SSOP, TQFP, TSOP, WLP (Pakiet poziomu wafla)…..itd. Łączenie drutów za pomocą miedzi, srebra lub złota należy do popularnych w mikroelektronice. Drut miedziany (Cu) jest metodą łączenia krzemowych matryc półprzewodnikowych z zaciskami obudowy mikroelektroniki. Przy niedawnym wzroście ceny drutu złotego (Au), drut miedziany (Cu) jest atrakcyjnym sposobem zarządzania całkowitymi kosztami pakietu w mikroelektronice. Przypomina również drut złoty (Au) ze względu na podobne właściwości elektryczne. Indukcyjność i pojemność własna są prawie takie same dla drutu złotego (Au) i miedzianego (Cu) z przewodem miedzianym (Cu) o niższej rezystywności. W zastosowaniach mikroelektronicznych, w których rezystancja związana z drutem łączącym może negatywnie wpłynąć na wydajność obwodu, zastosowanie drutu miedzianego (Cu) może zapewnić poprawę. Druty miedziane, miedziane powlekane palladem (PCC) i ze stopów srebra (Ag) pojawiły się jako alternatywa dla drutów ze złotem ze względu na koszty. Druty miedziane są niedrogie i mają niską oporność elektryczną. Jednak twardość miedzi utrudnia jej zastosowanie w wielu zastosowaniach, takich jak te z kruchą strukturą podkładki spoiwa. W tych zastosowaniach Ag-Alloy oferuje właściwości podobne do złota, a jego koszt jest podobny do PCC. Drut ze stopu Ag jest bardziej miękki niż PCC, co skutkuje niższym rozpryskiem Al i mniejszym ryzykiem uszkodzenia podkładki wiązania. Drut ze stopu Ag jest najlepszym niedrogim zamiennikiem do zastosowań, które wymagają łączenia matrycy z matrycą, łączenia kaskadowego, bardzo drobnego rozstawu podkładek łączących i małych otworów podkładek łączących, ultra małej wysokości pętli. Zapewniamy pełen zakres usług testowania półprzewodników, w tym testowanie płytek półprzewodnikowych, różne rodzaje testów końcowych, testowanie na poziomie systemu, testowanie paskowe i kompletne usługi końcowe. Testujemy różne typy urządzeń półprzewodnikowych we wszystkich naszych rodzinach pakietów, w tym częstotliwości radiowe, sygnał analogowy i mieszany, cyfrowe, zarządzanie energią, pamięć i różne kombinacje, takie jak ASIC, moduły wieloukładowe, system w pakiecie (SiP) i ułożone w stos opakowania 3D, czujniki i urządzenia MEMS, takie jak akcelerometry i czujniki ciśnienia. Nasz sprzęt testowy i sprzęt kontaktowy są odpowiednie dla niestandardowych rozmiarów pakietów SiP, dwustronnych rozwiązań kontaktowych dla Package on Package (PoP), TMV PoP, gniazd FusionQuad, wielorzędowych MicroLeadFrame, drobnego słupka miedzianego. Sprzęt testowy i podłogi testowe są zintegrowane z narzędziami CIM / CAM, analizą plonów i monitorowaniem wydajności, aby zapewnić bardzo wysoką wydajność za pierwszym razem. Oferujemy naszym klientom liczne adaptacyjne procesy testowania mikroelektroniki oraz rozproszone przepływy testowe dla SiP i innych złożonych przepływów montażowych. AGS-TECH zapewnia pełen zakres konsultacji testowych, rozwoju i usług inżynieryjnych w całym cyklu życia produktów półprzewodnikowych i mikroelektronicznych. Rozumiemy unikalne rynki i wymagania testowe dla SiP, motoryzacji, sieci, gier, grafiki, komputerów, RF / bezprzewodowych. Procesy produkcji półprzewodników wymagają szybkich i precyzyjnie kontrolowanych rozwiązań znakowania. Prędkości znakowania ponad 1000 znaków na sekundę i głębokości penetracji materiału mniejsze niż 25 mikronów są powszechne w branży mikroelektroniki półprzewodnikowej przy użyciu zaawansowanych laserów. Jesteśmy w stanie znakować masy formowe, wafle, ceramikę i nie tylko przy minimalnym nakładzie ciepła i doskonałej powtarzalności. Używamy laserów z dużą dokładnością, aby znakować nawet najmniejsze części bez uszkodzeń.
Ramki wyprowadzeń do urządzeń półprzewodnikowych: Możliwe są zarówno gotowe, jak i niestandardowe projekty i produkcja. Ramki wyprowadzeniowe są wykorzystywane w procesach montażu urządzeń półprzewodnikowych i są zasadniczo cienkimi warstwami metalu, które łączą okablowanie z maleńkich zacisków elektrycznych na powierzchni mikroelektroniki półprzewodnikowej z obwodami wielkoskalowymi urządzeń elektrycznych i płytek drukowanych. Ramki wyprowadzeniowe są stosowane w prawie wszystkich pakietach mikroelektroniki półprzewodnikowej. Większość mikroelektronicznych układów scalonych jest wytwarzana przez umieszczenie półprzewodnikowego chipa krzemowego na ramie wyprowadzeń, a następnie spajanie drutem chipa z metalowymi wyprowadzeniami tej ramki wyprowadzeń, a następnie przykrycie chipa mikroelektroniki plastikową osłoną. To proste i stosunkowo niedrogie opakowanie dla mikroelektroniki jest nadal najlepszym rozwiązaniem dla wielu zastosowań. Ramki ołowiane są produkowane w długich taśmach, co pozwala na ich szybką obróbkę na zautomatyzowanych maszynach montażowych, a generalnie stosuje się dwa procesy produkcyjne: pewnego rodzaju fototrawienie i stemplowanie. W mikroelektronice konstrukcja ramek wyprowadzeniowych często wymaga niestandardowych specyfikacji i funkcji, projektów poprawiających właściwości elektryczne i termiczne oraz określonych wymagań dotyczących czasu cyklu. Posiadamy dogłębne doświadczenie w produkcji ramek ołowianych z mikroelektroniki dla wielu różnych klientów przy użyciu wspomaganego laserowo fototrawienia i stemplowania.
Projektowanie i produkcja radiatorów dla mikroelektroniki: zarówno gotowe, jak i niestandardowe projekty i produkcja. Wraz ze wzrostem rozpraszania ciepła z urządzeń mikroelektronicznych i zmniejszeniem ogólnych współczynników kształtu, zarządzanie termiczne staje się ważniejszym elementem projektowania produktów elektronicznych. Stała wydajność i oczekiwana żywotność sprzętu elektronicznego są odwrotnie proporcjonalne do temperatury komponentów sprzętu. Zależność między niezawodnością a temperaturą pracy typowego krzemowego urządzenia półprzewodnikowego pokazuje, że obniżenie temperatury odpowiada wykładniczemu wzrostowi niezawodności i oczekiwanej żywotności urządzenia. Dlatego długą żywotność i niezawodne działanie półprzewodnikowego komponentu mikroelektronicznego można osiągnąć poprzez efektywne kontrolowanie temperatury pracy urządzenia w granicach wyznaczonych przez konstruktorów. Radiatory to urządzenia, które zwiększają rozpraszanie ciepła z gorącej powierzchni, zwykle zewnętrznej obudowy elementu wytwarzającego ciepło, do chłodniejszego otoczenia, takiego jak powietrze. W poniższych dyskusjach zakłada się, że płynem chłodzącym jest powietrze. W większości sytuacji przenoszenie ciepła przez granicę między powierzchnią stałą a powietrzem chłodzącym jest najmniej wydajne w systemie, a granica faz ciało stałe-powietrze stanowi największą barierę dla rozpraszania ciepła. Radiator obniża tę barierę głównie poprzez zwiększenie powierzchni, która ma bezpośredni kontakt z chłodziwem. Pozwala to na rozproszenie większej ilości ciepła i/lub obniża temperaturę pracy urządzenia półprzewodnikowego. Podstawowym celem radiatora jest utrzymanie temperatury urządzenia mikroelektronicznego poniżej maksymalnej dopuszczalnej temperatury określonej przez producenta urządzenia półprzewodnikowego.
Potrafimy sklasyfikować radiatory ze względu na metody wytwarzania oraz ich kształty. Najpopularniejsze typy radiatorów chłodzonych powietrzem to:
- Tłoczenie: Blacha miedziana lub aluminiowa jest tłoczona w pożądane kształty. są stosowane w tradycyjnym chłodzeniu powietrzem komponentów elektronicznych i oferują ekonomiczne rozwiązanie problemów termicznych o niskiej gęstości. Nadają się do produkcji wielkoseryjnej.
- Wytłaczanie: Te radiatory umożliwiają tworzenie skomplikowanych dwuwymiarowych kształtów zdolnych do rozpraszania dużych obciążeń cieplnych. Mogą być cięte, obrabiane i dodawane opcje. Cięcie poprzeczne wytworzy wielokierunkowe, prostokątne radiatory żeberkowe, a zastosowanie ząbkowanych żeberek poprawia wydajność o około 10 do 20%, ale z wolniejszym tempem wytłaczania. Ograniczenia wytłaczania, takie jak wysokość żeber do szczeliny, zwykle dyktują elastyczność opcji projektowych. Typowy stosunek wysokości do szczeliny żeber wynoszący do 6 i minimalna grubość żeberek 1,3 mm są osiągalne przy użyciu standardowych technik wytłaczania. Dzięki specjalnym cechom konstrukcyjnym matrycy można uzyskać współczynnik kształtu 10 do 1 i grubość żeber 0,8 cala. Jednak wraz ze wzrostem współczynnika kształtu pogarsza się tolerancja wytłaczania.
- Żebra klejone / sfabrykowane: Większość radiatorów chłodzonych powietrzem jest ograniczona konwekcją, a ogólna wydajność cieplna radiatora chłodzonego powietrzem może często ulec znacznej poprawie, jeśli większa powierzchnia może być wystawiona na działanie strumienia powietrza. Te wysokowydajne radiatory wykorzystują przewodzącą ciepło żywicę epoksydową wypełnioną aluminium do łączenia płaskich żeber z rowkowaną płytą podstawy do wytłaczania. Proces ten pozwala na uzyskanie znacznie większego współczynnika wysokości płetwy do szczeliny od 20 do 40, znacznie zwiększając wydajność chłodzenia bez zwiększania zapotrzebowania na objętość.
- Odlewy: Procesy odlewania piaskowego, traconego wosku i odlewania ciśnieniowego aluminium lub miedzi / brązu są dostępne z lub bez wspomagania próżniowego. Używamy tej technologii do produkcji radiatorów z żebrami o wysokiej gęstości, które zapewniają maksymalną wydajność podczas korzystania z chłodzenia uderzeniowego.
- Składane lamele: Blacha falista z aluminium lub miedzi zwiększa powierzchnię i wydajność objętościową. Radiator jest następnie mocowany do płyty bazowej lub bezpośrednio do powierzchni grzewczej za pomocą żywicy epoksydowej lub lutowania twardego. Nie nadaje się do radiatorów o wysokim profilu ze względu na dostępność i wydajność żeber. W związku z tym umożliwia wytwarzanie radiatorów o wysokiej wydajności.
Wybierając odpowiedni radiator spełniający wymagane kryteria termiczne dla aplikacji mikroelektronicznych, musimy zbadać różne parametry, które wpływają nie tylko na wydajność samego radiatora, ale także na ogólną wydajność systemu. Wybór konkretnego typu radiatora w mikroelektronice zależy w dużej mierze od budżetu cieplnego dopuszczalnego dla radiatora oraz warunków zewnętrznych otaczających radiator. Nigdy nie ma jednej wartości oporu cieplnego przypisanej do danego radiatora, ponieważ opór cieplny zmienia się wraz z zewnętrznymi warunkami chłodzenia.
Projektowanie i produkcja czujników i siłowników: Dostępne są zarówno projekty i produkcja z półki, jak i na zamówienie. Oferujemy rozwiązania z gotowymi procesami dla czujników inercyjnych, czujników ciśnienia i ciśnienia względnego oraz czujników temperatury na podczerwień. Korzystając z naszych bloków IP dla akcelerometrów, czujników podczerwieni i czujników ciśnienia lub stosując projekt zgodnie z dostępnymi specyfikacjami i zasadami projektowania, możemy dostarczyć Ci urządzenia czujnikowe oparte na MEMS w ciągu kilku tygodni. Oprócz MEMS można wytwarzać inne typy konstrukcji czujników i siłowników.
Projektowanie i produkcja obwodów optoelektronicznych i fotonicznych: fotoniczny lub optyczny układ scalony (PIC) to urządzenie, które integruje wiele funkcji fotonicznych. Przypomina to elektroniczne układy scalone w mikroelektronice. Główna różnica między nimi polega na tym, że fotoniczny układ scalony zapewnia funkcjonalność sygnałów informacyjnych nałożonych na długości fal optycznych w widmie widzialnym lub bliskiej podczerwieni 850 nm-1650 nm. Techniki wytwarzania są podobne do tych stosowanych w mikroelektronicznych układach scalonych, w których fotolitografia jest wykorzystywana do modelowania płytek do wytrawiania i osadzania materiału. W przeciwieństwie do mikroelektroniki półprzewodnikowej, w której podstawowym urządzeniem jest tranzystor, nie ma jednego dominującego urządzenia w optoelektronice. Chipy fotoniczne obejmują niskostratne falowody interkonektowe, rozdzielacze mocy, wzmacniacze optyczne, modulatory optyczne, filtry, lasery i detektory. Urządzenia te wymagają różnych materiałów i technik wytwarzania, dlatego trudno jest zrealizować je wszystkie na jednym chipie. Nasze zastosowania fotonicznych układów scalonych dotyczą głównie komunikacji światłowodowej, obliczeń biomedycznych i fotonicznych. Przykładowe produkty optoelektroniczne, które możemy dla Ciebie zaprojektować i wyprodukować, to diody LED (diody elektroluminescencyjne), lasery diodowe, odbiorniki optoelektroniczne, fotodiody, moduły odległości laserowej, niestandardowe moduły laserowe i wiele innych.