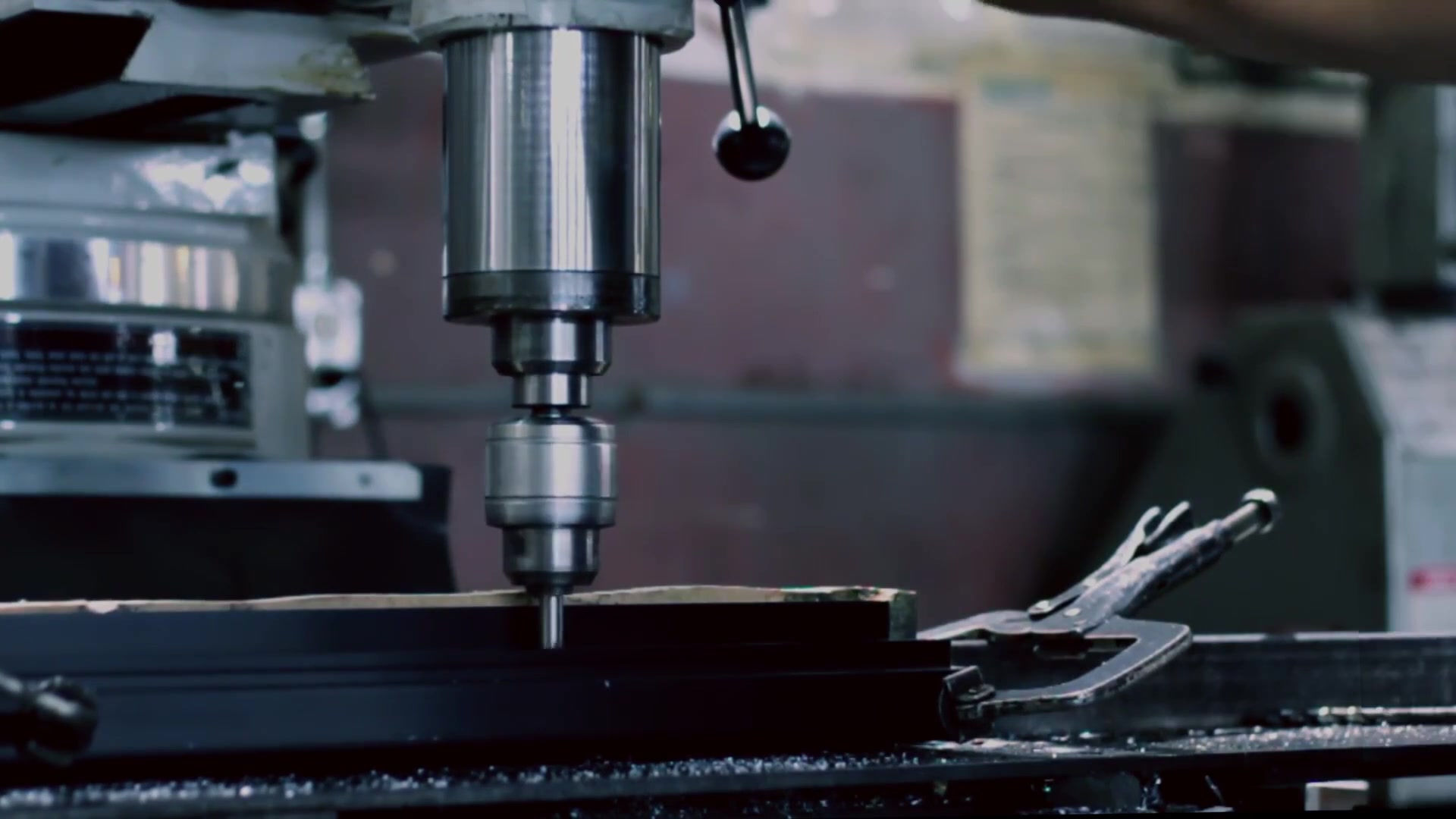
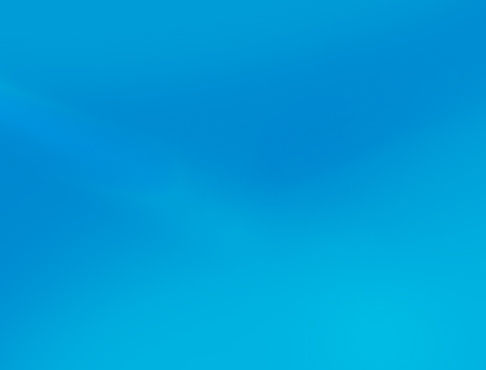
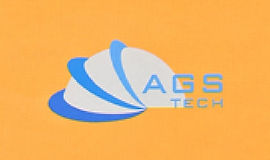
Globalny producent na zamówienie, integrator, konsolidator, partner outsourcingowy w zakresie szerokiej gamy produktów i usług.
Jesteśmy Twoim źródłem kompleksowej obsługi w zakresie produkcji, wytwarzania, inżynierii, konsolidacji, integracji, outsourcingu produktów i usług produkowanych na zamówienie oraz gotowych.
Choose your Language
-
Produkcja na zamówienie
-
Produkcja kontraktowa w kraju i na świecie
-
Outsourcing produkcji
-
Zamówienia krajowe i globalne
-
Konsolidacja
-
Integracja inżynierska
-
Usługi inżynieryjne
Wykonujemy na zamówienie formy z tworzyw sztucznych i gumy oraz elementy formowane metodą wtrysku, przetłoczenia, termoformowania, prasowania, formowania termoutwardzalnego, formowania próżniowego, rozdmuchu, formowania rotacyjnego, formowania wkładek, odlewania, łączenia metal z gumą i metal z tworzywem sztucznym, ultradźwiękowe spawanie, produkcja wtórna i procesy produkcyjne. Zalecamy kliknięcie tutaj, abyPOBIERZ nasze schematyczne ilustracje procesów formowania tworzyw sztucznych i gumy autorstwa AGS-TECH Inc.
Pomoże to lepiej zrozumieć informacje, które przekazujemy poniżej.
• FORMOWANIE WTRYSKOWE: Mieszanka termoutwardzalna jest podawana i wtryskiwana za pomocą szybkobieżnej śruby lub systemu tłoka. Formowanie wtryskowe może wytwarzać małe i średnie części w dużych ilościach ekonomicznie, można osiągnąć wąskie tolerancje, spójność między częściami i dobrą wytrzymałość. Ta technika jest najczęstszą metodą produkcji wyrobów z tworzyw sztucznych firmy AGS-TECH Inc. Nasze standardowe formy mają cykle rzędu 500 000 razy i są wykonane ze stali narzędziowej P20. Przy większych formach wtryskowych i głębszych wnękach spójność i twardość w całym materiale staje się jeszcze ważniejsza, dlatego używamy wyłącznie certyfikowanej stali narzędziowej najwyższej jakości od głównych dostawców z silnymi systemami identyfikowalności i zapewnienia jakości. Nie wszystkie stale narzędziowe P20 są takie same. Ich jakość może się różnić w zależności od dostawcy i kraju. Dlatego nawet do naszych form wtryskowych produkowanych w Chinach używamy stali narzędziowej sprowadzanej z USA, Niemiec i Japonii. Zgromadziliśmy wiedzę na temat zastosowania zmodyfikowanej chemii stali P20 do formowania wtryskowego produktów o powierzchniach wymagających bardzo wąskich tolerancji lustrzanych. Dzięki temu jesteśmy w stanie produkować nawet formy do soczewek optycznych. Innym rodzajem wymagającego wykończenia powierzchni są powierzchnie teksturowane. Wymagają one stałej twardości na całej powierzchni. Dlatego każda niejednorodność stali może skutkować niedoskonałą teksturą powierzchni. Z tego powodu część naszej stali używanej na takie formy zawiera specjalne elementy stopowe i jest odlewana przy użyciu zaawansowanych technik metalurgicznych. Miniaturowe części i koła zębate z tworzyw sztucznych to komponenty, które wymagają know-how w zakresie odpowiednich materiałów i procesów z tworzyw sztucznych, które zdobyliśmy przez lata. Dla firmy produkującej mikrosilniki produkujemy drobne, precyzyjne elementy z tworzyw sztucznych o wąskich tolerancjach. Nie każda firma zajmująca się formowaniem tworzyw sztucznych jest w stanie wyprodukować tak małe, dokładne części, ponieważ wymaga know-how, które zdobywa się dzięki wieloletniemu doświadczeniu w badaniach i rozwoju. Oferujemy różne rodzaje tej techniki formowania, w tym formowanie wtryskowe wspomagane gazem.
• FORMOWANIE WKŁADEK: Wkładki mogą być wstawiane w trakcie procesu formowania lub być wkładane po procesie formowania. Po włączeniu jako część procesu formowania, wkładki mogą być ładowane przez roboty lub przez operatora. Jeżeli wkładki są wprowadzane po operacji formowania, można je zwykle nakładać w dowolnym momencie po procesie formowania. Powszechnym procesem formowania wkładek jest proces formowania plastiku wokół wstępnie uformowanych wkładek metalowych. Na przykład złącza elektroniczne mają metalowe kołki lub elementy zamknięte w uszczelniającym materiale z tworzywa sztucznego. Zdobyliśmy wieloletnie doświadczenie w utrzymywaniu stałego czasu cyklu od strzału do strzału, nawet przy wstawianiu po formowaniu, ponieważ różnice w czasie cyklu między wtryskami będą skutkować niską jakością.
• THERMOSET MOLDING : Ta technika charakteryzuje się wymaganiem ogrzewania formy w porównaniu z chłodzeniem termoplastu. Części wytwarzane metodą formowania termoutwardzalnego są idealne do zastosowań wymagających wysokiej wytrzymałości mechanicznej, szerokiego zakresu temperatur i wyjątkowych właściwości dielektrycznych. Tworzywa termoutwardzalne można formować w dowolnym z trzech procesów formowania: prasowanie, formowanie wtryskowe lub formowanie transferowe. Sposób dostarczania materiału do wnęk formy odróżnia te trzy techniki. We wszystkich trzech procesach podgrzewana jest forma wykonana z miękkiej lub hartowanej stali narzędziowej. Forma jest chromowana, aby zmniejszyć zużycie formy i poprawić uwalnianie części. Części są wyrzucane za pomocą hydraulicznie uruchamianych sworzni wyrzutnika i grzybków powietrznych. Usuwanie części może być ręczne lub automatyczne. Elementy formowane termoutwardzalnie do zastosowań elektrycznych wymagają odporności na płynięcie i topienie w podwyższonych temperaturach. Jak wszyscy wiedzą, elementy elektryczne i elektroniczne nagrzewają się podczas pracy i tylko odpowiednie tworzywa sztuczne mogą być używane do zapewnienia bezpieczeństwa i długotrwałej pracy. Posiadamy doświadczenie w kwalifikacjach CE i UL komponentów z tworzyw sztucznych dla przemysłu elektronicznego.
• TRANSFER MOLDING : Odmierzona ilość materiału do formowania jest wstępnie podgrzewana i wkładana do komory zwanej zbiornikiem transferowym. Mechanizm znany jako tłok wtłacza materiał z garnka przez kanały znane jako system wlewu i kanału do wnęk formy. Podczas wkładania materiału forma pozostaje zamknięta i otwiera się tylko wtedy, gdy nadejdzie czas uwolnienia wyprodukowanej części. Utrzymywanie ścianek formy w temperaturze wyższej niż temperatura topnienia tworzywa sztucznego zapewnia szybki przepływ materiału przez wnęki. Używamy tej techniki często do:
- Do celów enkapsulacji, w których w części są formowane złożone metalowe wkładki
- Małe i średnie części o rozsądnie dużej objętości
- Gdy potrzebne są części o wąskich tolerancjach i potrzebne są materiały o niskim skurczu
- Potrzebna jest spójność, ponieważ technika formowania transferowego umożliwia spójne dostarczanie materiału
• TERMOFORMOWANIE: Jest to ogólny termin używany do opisania grupy procesów wytwarzania części z tworzyw sztucznych z płaskich arkuszy tworzywa sztucznego pod wpływem temperatury i ciśnienia. W tej technice arkusze z tworzywa sztucznego są podgrzewane i formowane na męskiej lub żeńskiej formie. Po uformowaniu są przycinane, aby stworzyć produkt użytkowy. Przycięty materiał jest ponownie przerabiany i poddawany recyklingowi. Zasadniczo istnieją dwa rodzaje procesów termoformowania, a mianowicie formowanie próżniowe i formowanie ciśnieniowe (które wyjaśniono poniżej). Koszty inżynierii i oprzyrządowania są niskie, a czas realizacji krótki. Dlatego ta metoda doskonale nadaje się do prototypowania i produkcji małoseryjnej. Niektóre tworzywa termoformowane to ABS, HIPS, HDPE, HMWPE, PP, PVC, PMMA, modyfikowany PETG. Proces jest odpowiedni dla dużych paneli, obudów i obudów i jest preferowany dla takich produktów niż formowanie wtryskowe ze względu na niższy koszt i szybsze wytwarzanie oprzyrządowania. Termoformowanie najlepiej nadaje się do części, których ważne cechy ograniczają się głównie do jednej z jego stron. Firma AGS-TECH Inc. jest jednak w stanie wykorzystać tę technikę wraz z dodatkowymi metodami, takimi jak przycinanie, produkcja i montaż, do produkcji części o krytycznych cechach on
obie strony.
• FORMOWANIE KOMPRESYJNE: Formowanie kompresyjne to proces formowania, w którym tworzywo sztuczne jest umieszczane bezpośrednio w ogrzanej metalowej formie, gdzie jest zmiękczane przez ciepło i zmuszane do dostosowania się do kształtu formy podczas zamykania formy. Kołki wypychaczy na dnie form szybko wyrzucają gotowe elementy z formy i proces jest zakończony. Jako materiał powszechnie stosuje się termoutwardzalne tworzywa sztuczne w postaci preform lub granulek. Do tej techniki nadają się również wzmocnienia z włókna szklanego o wysokiej wytrzymałości. Aby uniknąć nadmiernego wyładowania, materiał jest mierzony przed formowaniem. Zaletą formowania tłocznego jest możliwość formowania dużych, skomplikowanych części, co jest jedną z najtańszych metod formowania w porównaniu z innymi metodami, takimi jak formowanie wtryskowe; mało odpadów materiałowych. Z drugiej strony formowanie tłoczne często zapewnia słabą konsystencję produktu i stosunkowo trudną kontrolę wypływu. W porównaniu z formowaniem wtryskowym wytwarza się mniej linii dzianin i występuje mniejsza degradacja długości włókien. Formowanie tłoczne nadaje się również do produkcji bardzo dużych kształtów podstawowych w rozmiarach przekraczających możliwości technik wytłaczania. AGS-TECH wykorzystuje tę technikę do produkcji głównie części elektrycznych, obudów elektrycznych, obudów z tworzyw sztucznych, pojemników, gałek, uchwytów, kół zębatych, stosunkowo dużych części płaskich i umiarkowanie zakrzywionych. Posiadamy know-how w zakresie określania odpowiedniej ilości surowca w celu ekonomicznej eksploatacji i redukcji wyrzutu, dopasowywania odpowiedniej ilości energii i czasu nagrzewania materiału, doboru najbardziej odpowiedniej techniki nagrzewania dla każdego projektu, obliczania wymaganej siły dla optymalnego kształtowania materiału, zoptymalizowana konstrukcja formy do szybkiego chłodzenia po każdym cyklu prasowania.
• FORMOWANIE PRÓŻNIOWE (opisane również jako uproszczona wersja TERMOFORMOWANIA): Arkusz z tworzywa sztucznego jest podgrzewany do miękkości i układany na formie. Następnie przykładana jest próżnia i arkusz jest zasysany do formy. Po tym, jak arkusz przyjmie pożądany kształt formy, jest schładzany i wyrzucany z formy. AGS-TECH wykorzystuje zaawansowaną kontrolę pneumatyczną, cieplną i hydrofobową, aby osiągnąć wysokie prędkości produkcji poprzez formowanie próżniowe. Materiały odpowiednie do tej techniki to wytłaczane arkusze termoplastyczne, takie jak ABS, PETG, PS, PC, PVC, PP, PMMA, akryl. Metoda ta jest najbardziej odpowiednia do formowania części z tworzyw sztucznych, które są dość płytkie. Jednak produkujemy również stosunkowo głębokie części poprzez mechaniczne lub pneumatyczne rozciąganie formowalnego arkusza przed doprowadzeniem go do kontaktu z powierzchnią formy i przyłożeniem próżni. Typowe produkty formowane tą techniką to tace i pojemniki na stopy, obudowy, pudełka na kanapki, brodziki prysznicowe, plastikowe garnki, deski rozdzielcze samochodów. Ponieważ technika wykorzystuje niskie ciśnienia, można stosować niedrogie materiały na formy, a formy można wytwarzać niedrogo w krótkim czasie. Możliwa jest więc produkcja małoseryjna dużych części. W zależności od ilości produkcji funkcjonalność formy może zostać zwiększona, gdy potrzebna jest produkcja wielkoseryjna. Jesteśmy profesjonalistami w określaniu, jakiej jakości formy wymaga każdy projekt. Wytwarzanie niepotrzebnie skomplikowanej formy do niskoseryjnej produkcji byłoby stratą pieniędzy i zasobów klienta. Na przykład produkty, takie jak obudowy do dużych maszyn medycznych o wielkości produkcji w zakresie od 300 do 3000 jednostek rocznie, mogą być formowane próżniowo z grubych surowców, zamiast wytwarzać je kosztownymi technikami, takimi jak formowanie wtryskowe lub formowanie blach._cc781905- 5cde-3194-bb3b-136bad5cf58d_
• FORMOWANIE Z ROZDMUCHEM: Używamy tej techniki do wytwarzania pustych części z tworzywa sztucznego (także części szklanych). Preformę lub kształtkę wstępną, która jest kawałkiem plastiku przypominającego rurkę, mocuje się w formie i wdmuchuje się do niej sprężonym powietrzem przez otwór na jednym końcu. W efekcie plastikowa forma / kształtka zostaje wypchnięta na zewnątrz i nabiera kształtu wnęki formy. Po schłodzeniu i zestaleniu tworzywo sztuczne jest wyrzucane z gniazda formy. Istnieją trzy rodzaje tej techniki:
-Wytłaczanie z rozdmuchem
-Wtrysk z rozdmuchem
-Formowanie wtryskowe z rozciąganiem i rozdmuchiwaniem
Powszechnymi materiałami używanymi w tych procesach są PP, PE, PET, PVC. Typowymi przedmiotami wytwarzanymi tą techniką są plastikowe butelki, wiaderka, pojemniki.
• FORMOWANIE ROTACYJNE (zwane również ROTAMOULDINGiem lub ROTOMULDINGiem) to technika odpowiednia do wytwarzania pustych w środku wyrobów z tworzyw sztucznych. W formowaniu rotacyjnym ogrzewanie, topienie, kształtowanie i chłodzenie następuje po umieszczeniu polimeru w formie. Nie stosuje się ciśnienia zewnętrznego. Formowanie rotacyjne jest ekonomiczne przy wytwarzaniu dużych produktów, koszty form są niskie, produkty są wolne od naprężeń, brak linii spoin polimerowych, niewiele ograniczeń projektowych do pokonania. Proces rotomouldingu rozpoczyna się od załadowania formy, czyli kontrolowana ilość proszku polimerowego jest umieszczana w formie, zamykana i ładowana do pieca. Wewnątrz pieca odbywa się drugi etap procesu: ogrzewanie i fuzja. Forma obraca się wokół dwóch osi ze stosunkowo małą prędkością, następuje nagrzewanie, a stopiony proszek polimerowy topi się i przykleja do ścianek formy. Następnie, w trzecim etapie, następuje chłodzenie i zestalanie polimeru wewnątrz formy. Wreszcie etap rozładunku obejmuje otwarcie formy i usunięcie produktu. Te cztery etapy procesu są następnie wielokrotnie powtarzane. Niektóre materiały stosowane w formowaniu rotacyjnym to LDPE, PP, EVA, PVC. Typowe wytwarzane produkty to duże wyroby z tworzyw sztucznych, takie jak SPA, zjeżdżalnie dla dzieci, duże zabawki, duże pojemniki, zbiorniki na deszczówkę, pachołki, kajaki i kajaki...itd. Ponieważ produkty formowane rotacyjnie mają zazwyczaj duże geometrie i są kosztowne w transporcie, ważnym punktem do zapamiętania w formowaniu rotacyjnym jest rozważenie projektów, które ułatwiają układanie produktów w stosy przed wysyłką. W razie potrzeby pomagamy naszym klientom w fazie projektowania.
• WYLEWANIE : Ta metoda jest stosowana, gdy trzeba wyprodukować wiele przedmiotów. Wydrążony blok jest używany jako forma i wypełniany przez proste wlanie do niego płynnego materiału, takiego jak stopiony materiał termoplastyczny lub mieszanina żywicy i utwardzacza. W ten sposób wytwarza się części lub inną formę. Ciecz, taka jak plastik, jest następnie pozostawiana do stwardnienia i przybiera kształt gniazda formy. Materiały ze środków antyadhezyjnych są powszechnie stosowane do uwalniania części z formy. Formowanie odlewów jest również czasami określane jako zalewanie tworzywem sztucznym lub odlewanie uretanowe. Używamy tego procesu do niedrogiego wytwarzania produktów w kształcie posągów, ozdób… itd., produktów, które nie wymagają doskonałej jednorodności ani doskonałych właściwości materiałowych, a jedynie kształtu przedmiotu. Czasami wykonujemy formy silikonowe do celów prototypowania. Niektóre z naszych niskonakładowych projektów są przetwarzane przy użyciu tej techniki. Formowanie wylewowe może być również wykorzystywane do produkcji części szklanych, metalowych i ceramicznych. Ponieważ koszty ustawienia i oprzyrządowania są minimalne, rozważamy tę technikę zawsze, gdy produkcja wielu w małej ilości
pozycje o minimalnych wymaganiach tolerancji znajdują się na stole. W przypadku produkcji wielkoseryjnej technika formowania przez odlewanie generalnie nie jest odpowiednia, ponieważ jest powolna, a zatem kosztowna, gdy trzeba wyprodukować duże ilości. Istnieją jednak wyjątki, w których formowanie przez wylewanie może być wykorzystywane do produkcji dużych ilości, takie jak mieszanki do zalewania formowania wylewania do hermetyzacji komponentów i zespołów elektronicznych i elektrycznych w celu izolacji i ochrony.
• FORMOWANIE GUMY – ODLEWANIE – USŁUGI OBRÓBKI : Produkujemy na zamówienie elementy gumowe z kauczuku naturalnego i syntetycznego przy użyciu niektórych z wyżej wyjaśnionych procesów. Możemy dostosować twardość i inne właściwości mechaniczne do Twojego zastosowania. Włączając inne dodatki organiczne lub nieorganiczne, możemy zwiększyć stabilność cieplną części gumowych, takich jak kulki do czyszczenia w wysokiej temperaturze. Różne inne właściwości gumy można modyfikować według potrzeb i potrzeb. Zapewniamy również, że nie używamy toksycznych lub niebezpiecznych materiałów do produkcji zabawek lub innych wyrobów formowanych z elastomerów/elastomerów. Zapewniamy
Karty charakterystyki substancji niebezpiecznych (MSDS), raporty zgodności, certyfikaty materiałowe i inne dokumenty, takie jak zgodność naszych materiałów i produktów z dyrektywą ROHS. W razie potrzeby w certyfikowanych laboratoriach rządowych lub zatwierdzonych przez rząd przeprowadza się dodatkowe testy specjalne. Od wielu lat produkujemy gumowe dywaniki samochodowe, małe gumowe figurki i zabawki.
• DRUGORZĘDNY MANUFACTURING & WYTWARZANIE PROCESY: Na koniec należy pamiętać o dużej różnorodności procesów powlekania wtórnego wyrobów z tworzyw sztucznych do zastosowań typu lustrzanego lub nadawania plastikowi metalicznego połysku. Zgrzewanie ultradźwiękowe to kolejny przykład wtórnego procesu oferowanego dla elementów z tworzyw sztucznych. Jeszcze trzecim przykładem procesu wtórnego na tworzywach sztucznych może być obróbka powierzchni przed powlekaniem w celu zwiększenia przyczepności powłoki. Wiadomo, że zderzaki samochodowe korzystają z tego wtórnego procesu. Klejenie metal-guma, łączenie metal-plastik to inne powszechne procesy, z którymi mamy do czynienia. Oceniając Twój projekt, możemy wspólnie określić, które procesy wtórne będą najbardziej odpowiednie dla Twojego produktu.
Oto niektóre z powszechnie stosowanych produktów z tworzyw sztucznych. Ponieważ są one gotowe, możesz zaoszczędzić na kosztach form, jeśli którykolwiek z nich spełni Twoje wymagania.
Kliknij tutaj, aby pobrać nasze uszczelnione plastikowe obudowy serii 10 firmy AGS-Electronics
Kliknij tutaj, aby pobrać nasze plastikowe obudowy serii 08 firmy AGS-Electronics
Kliknij tutaj, aby pobrać nasze specjalne plastikowe obudowy serii 18 firmy AGS-Electronics
Kliknij tutaj, aby pobrać nasze obudowy plastikowe z serii 24 DIN firmy AGS-Electronics
Kliknij tutaj, aby pobrać nasze plastikowe walizki do urządzeń serii 37 firmy AGS-Electronics
Kliknij tutaj, aby pobrać nasze modułowe obudowy plastikowe z serii 15 firmy AGS-Electronics
Kliknij tutaj, aby pobrać nasze obudowy PLC serii 14 firmy AGS-Electronics
Kliknij tutaj, aby pobrać nasze obudowy do zalewania i zasilania serii 31 firmy AGS-Electronics
Kliknij tutaj, aby pobrać nasze obudowy naścienne serii 20 firmy AGS-Electronics
Kliknij tutaj, aby pobrać nasze obudowy plastikowe i stalowe serii 03 firmy AGS-Electronics
Kliknij tutaj, aby pobrać nasze modułowe obudowy na szynę DIN serii 16 firmy AGS-Electronics
Kliknij tutaj, aby pobrać nasze obudowy do komputerów stacjonarnych serii 19 firmy AGS-Electronics
Kliknij tutaj, aby pobrać nasze obudowy czytników kart serii 21 firmy AGS-Electronics