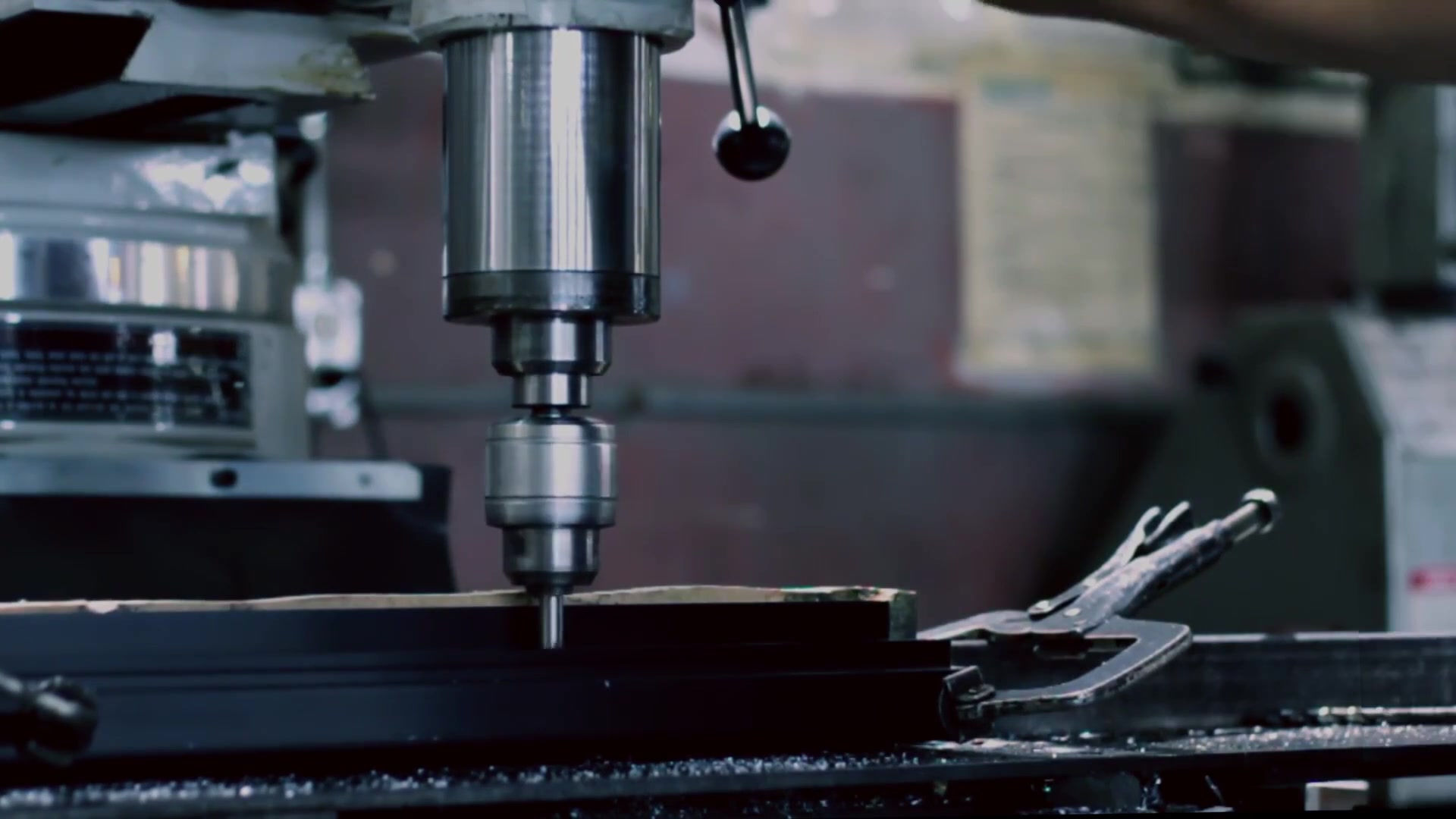
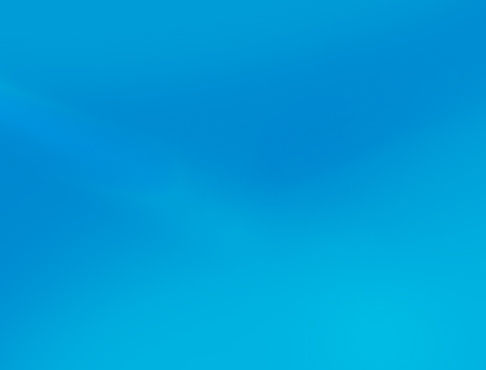
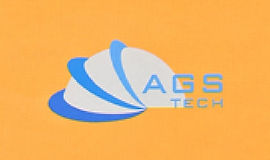
Globalny producent na zamówienie, integrator, konsolidator, partner outsourcingowy w zakresie szerokiej gamy produktów i usług.
Jesteśmy Twoim źródłem kompleksowej obsługi w zakresie produkcji, wytwarzania, inżynierii, konsolidacji, integracji, outsourcingu produktów i usług produkowanych na zamówienie oraz gotowych.
Choose your Language
-
Produkcja na zamówienie
-
Produkcja kontraktowa w kraju i na świecie
-
Outsourcing produkcji
-
Zamówienia krajowe i globalne
-
Konsolidacja
-
Integracja inżynierska
-
Usługi inżynieryjne
Search Results
Znaleziono 164 wyniki za pomocą pustego wyszukiwania
- Machine Elements Manufacturing, Gears, Gear Drives, Bearings, Keys, Splines
Machine Elements Manufacturing, Gears, Gear Drives, Bearings, Keys, Splines, Pins, Shafts, Seals, Fasteners, Clutch, Cams, Followers, Belts, Couplings, Shafts Produkcja elementów maszyn Czytaj więcej Pasy i łańcuchy oraz zespół napędu kablowego Czytaj więcej Koła zębate i zespół napędu zębatego Czytaj więcej Produkcja sprzęgieł i łożysk Czytaj więcej Produkcja kluczy, wypustów i szpilek Czytaj więcej Produkcja krzywek i popychaczy, połączeń i kół zapadkowych Czytaj więcej Produkcja wałów Czytaj więcej Produkcja uszczelnień mechanicznych Czytaj więcej Zespół sprzęgła i hamulca Czytaj więcej Produkcja elementów złącznych Czytaj więcej Prosty montaż maszyn ELEMENTY MASZYNY są podstawowymi elementami maszyny. Elementy te składają się z trzech podstawowych typów: 1.) Elementy konstrukcyjne, w tym elementy ramy, łożyska, osie, wielowypusty, elementy złączne, uszczelnienia i smary. 2.) Mechanizmy kontrolujące ruch na różne sposoby, takie jak przekładnie zębate, napędy pasowe lub łańcuchowe, połączenia, systemy krzywkowe i popychacze, hamulce i sprzęgła. 3.) Elementy sterujące, takie jak przyciski, przełączniki, wskaźniki, czujniki, siłowniki i sterowniki komputerowe. Większość oferowanych przez nas elementów maszyn jest znormalizowana do typowych rozmiarów, ale dostępne są również elementy maszyn na zamówienie dla Twoich specjalistycznych zastosowań. Dostosowanie elementów maszyn może odbywać się na istniejących projektach, które znajdują się w naszych katalogach do pobrania lub na zupełnie nowych projektach. Prototypowanie i produkcja elementów maszyn może być kontynuowana po zatwierdzeniu projektu przez obie strony. Jeśli trzeba zaprojektować i wyprodukować nowe elementy maszyn, nasi klienci albo wysyłają nam e-mailem własne projekty, a my sprawdzamy je do zatwierdzenia, albo proszą nas o zaprojektowanie elementów maszyn do ich zastosowania. W tym drugim przypadku wykorzystujemy cały wkład naszych klientów i projektujemy elementy maszyn, a gotowe projekty przesyłamy naszym klientom do akceptacji. Po zatwierdzeniu produkujemy pierwsze artykuły, a następnie wykonujemy elementy maszyn według ostatecznego projektu. Na każdym etapie tych prac, w przypadku, gdy dany projekt elementu maszyny wypada w warunkach polowych niezadowalająco (co jest rzadkością), weryfikujemy cały projekt i w razie potrzeby wspólnie z naszymi klientami dokonujemy przeróbek. Naszą standardową praktyką jest podpisywanie umów o zachowaniu poufności (NDA) z naszymi klientami na projektowanie elementów maszyn lub innych produktów, gdy jest to potrzebne lub wymagane. Gdy elementy maszyny dla konkretnego klienta są zaprojektowane i wykonane na zamówienie, przypisujemy do niego kod produktu i produkujemy je i sprzedajemy tylko naszemu klientowi, który jest właścicielem produktu. Odtwarzamy elementy maszyn za pomocą opracowanych narzędzi, form i procedur tyle razy, ile jest to potrzebne i ilekroć nasz klient ponownie je zamówi. Innymi słowy, po zaprojektowaniu i wyprodukowaniu dla Ciebie niestandardowego elementu maszyny, własność intelektualna, jak również wszystkie narzędzia i formy są przez nas zarezerwowane i przechowywane przez nas na czas nieokreślony dla Ciebie i produktów odtwarzanych zgodnie z Twoimi życzeniami. Naszym klientom oferujemy również usługi inżynieryjne poprzez kreatywne łączenie elementów maszyn w komponent lub zespół, który służy aplikacji i spełnia lub przekracza oczekiwania naszych klientów. Zakłady produkujące nasze elementy maszyn są kwalifikowane przez ISO9001, QS9000 lub TS16949. Ponadto większość naszych produktów posiada znak CE lub UL i spełnia międzynarodowe normy, takie jak ISO, SAE, ASME, DIN. Proszę kliknąć w podmenu, aby uzyskać szczegółowe informacje o naszych elementach maszyn, w tym: - Pasy, Łańcuchy i Napędy Kablowe - Koła zębate i napędy zębate - Sprzęgła i łożyska -Klucze i splajny i szpilki - Krzywki i powiązania - Wały - Uszczelnienia mechaniczne - Przemysłowe sprzęgło i hamulec - Łączniki - Proste maszyny Przygotowaliśmy broszurę referencyjną dla naszych klientów, projektantów i twórców nowych produktów, w tym elementów maszyn. Możesz zapoznać się z niektórymi powszechnie używanymi terminami w projektowaniu elementów maszyn: Pobierz broszurę dotyczącą wspólnych terminów inżynierii mechanicznej używanych przez projektantów i inżynierów Nasze elementy maszyn znajdują zastosowanie w różnych dziedzinach, takich jak maszyny przemysłowe, systemy automatyki, urządzenia testujące i metrologiczne, sprzęt transportowy, maszyny budowlane i praktycznie wszędzie, o czym tylko pomyślisz. AGS-TECH opracowuje i produkuje elementy maszyn z różnych materiałów w zależności od zastosowania. Materiały stosowane na elementy maszyn mogą obejmować od formowanych tworzyw sztucznych używanych do zabawek po nawęglaną i specjalnie powlekaną stal do maszyn przemysłowych. Nasi projektanci używają najnowocześniejszego profesjonalnego oprogramowania i narzędzi projektowych do projektowania elementów maszyn, biorąc pod uwagę takie szczegóły, jak kąty uzębienia kół zębatych, występujące naprężenia, wskaźniki zużycia… itd. Przewiń nasze podmenu i pobierz nasze broszury i katalogi produktów, aby sprawdzić, czy możesz znaleźć gotowe elementy maszyn do swojego zastosowania. Jeśli nie możesz znaleźć odpowiedniego dopasowania do swojej aplikacji, daj nam znać, a wspólnie opracujemy i wyprodukujemy elementy maszyn, które spełnią Twoje potrzeby. Jeśli interesują Cię przede wszystkim nasze możliwości inżynieryjne i badawczo-rozwojowe, a nie możliwości produkcyjne, zapraszamy do odwiedzenia naszej strony internetowej http://www.ags-engineering.com gdzie można znaleźć bardziej szczegółowe informacje na temat naszego projektu, rozwoju produktu, rozwoju procesów, usług doradztwa inżynieryjnego i nie tylko CLICK Product Finder-Locator Service POPRZEDNIA STRONA
- Joining & Assembly & Fastening Processes, Welding, Brazing, Soldering
Joining & Assembly & Fastening Processes, Welding, Brazing, Soldering, Sintering, Adhesive Bonding, Press Fitting, Wave and Reflow Solder Process, Torch Furnace Procesy łączenia, montażu i mocowania Łączymy, montujemy i mocujemy wyprodukowane przez Państwa części i przekształcamy je w gotowe lub półfabrykaty za pomocą SPAWANIA, LUTOWANIA, LUTOWANIA, SPIEKANIA, KLEJENIA KLEJEM, ŁĄCZENIA, ZACISKANIA. Niektóre z naszych najpopularniejszych procesów spawalniczych to spawanie łukowe, gazowo-tlenowe, oporowe, rzutowe, spawowe, spęczane, udarowe, półprzewodnikowe, wiązką elektronów, laserowe, termitowe, indukcyjne. Nasze popularne procesy lutowania to lutowanie palnikowe, indukcyjne, piecowe i zanurzeniowe. Nasze metody lutowania to lutowanie żelazne, płytowe, piecowe, indukcyjne, zanurzeniowe, falowe, rozpływowe i ultradźwiękowe. Do klejenia często używamy tworzyw termoplastycznych i termoutwardzalnych, epoksydów, fenoli, poliuretanów, stopów klejących oraz niektórych innych chemikaliów i taśm. Wreszcie nasze procesy mocowania obejmują wbijanie gwoździ, wkręcanie, nakrętki i śruby, nitowanie, zaciskanie, przypinanie, zszywanie i zszywanie oraz pasowanie wtłaczane. • SPAWANIE: Spawanie obejmuje łączenie materiałów poprzez topienie obrabianych elementów i wprowadzanie materiałów wypełniających, które również łączą się ze stopionym jeziorkiem spawalniczym. Gdy okolica się ochłodzi, uzyskujemy mocne połączenie. W niektórych przypadkach stosowany jest nacisk. W przeciwieństwie do spawania, operacje lutowania i lutowania polegają jedynie na topieniu materiału o niższej temperaturze topnienia pomiędzy detalami, a detale nie topią się. Zalecamy kliknięcie tutaj, abyPOBIERZ nasze schematyczne ilustracje procesów spawania opracowane przez AGS-TECH Inc. Pomoże Ci to lepiej zrozumieć informacje, które udostępniamy poniżej. W spawaniu łukowym używamy zasilacza i elektrody do wytworzenia łuku elektrycznego, który topi metale. Miejsce spawania jest chronione gazem osłonowym lub parą lub innym materiałem. Proces ten jest popularny przy spawaniu części samochodowych i konstrukcji stalowych. W spawaniu łukowym w osłonie metalowej (SMAW) lub znanym również jako spawanie kijem, pałeczka elektrody jest zbliżana do materiału podstawowego, a między nimi powstaje łuk elektryczny. Pręt elektrody topi się i działa jako materiał wypełniający. Elektroda zawiera również topnik, który działa jak warstwa żużla i wydziela opary, które działają jak gaz osłonowy. Chronią one obszar spawania przed zanieczyszczeniem środowiska. Żadne inne wypełniacze nie są używane. Wadą tego procesu jest jego powolność, konieczność częstej wymiany elektrod, konieczność rozdrobnienia resztkowego żużla pochodzącego z topnika. Szereg metali, takich jak żelazo, stal, nikiel, aluminium, miedź… itd. Możliwość spawania. Jego zaletami są niedrogie narzędzia i łatwość obsługi. Spawanie łukiem metalowym w osłonie gazu (GMAW), znane również jako gaz obojętny metal (MIG), mamy ciągłe podawanie zużywalnego wypełniacza drutu elektrodowego i gazu obojętnego lub częściowo obojętnego, który przepływa wokół drutu, chroniąc przed zanieczyszczeniem środowiska w obszarze spawania. Można spawać stal, aluminium i inne metale nieżelazne. Zaletami MIG są wysokie prędkości spawania i dobra jakość. Wadą jest skomplikowany sprzęt i wyzwania, z jakimi mierzy się w wietrznych środowiskach zewnętrznych, ponieważ musimy utrzymywać stabilny gaz osłonowy wokół obszaru spawania. Odmianą GMAW jest spawanie łukowe z rdzeniem topnikowym (FCAW), które składa się z cienkiej metalowej rury wypełnionej materiałami topnikowymi. Czasami strumień wewnątrz rurki wystarcza do ochrony przed zanieczyszczeniem środowiska. Spawanie łukiem krytym (SAW) jest szeroko zautomatyzowanym procesem, obejmującym ciągłe podawanie drutu i zajarzenie łuku pod warstwą otuliny topnika. Szybkość produkcji i jakość są wysokie, żużel spawalniczy łatwo schodzi, a środowisko pracy jest wolne od dymu. Wadą jest to, że można go używać tylko do spawania parts w określonych pozycjach. W spawaniu łukiem wolframowym (GTAW) lub spawaniu wolframowym w gazie obojętnym (TIG) używamy elektrody wolframowej wraz z oddzielnym wypełniaczem i gazami obojętnymi lub zbliżonymi do obojętnych. Jak wiemy, wolfram ma wysoką temperaturę topnienia i jest bardzo odpowiednim metalem do bardzo wysokich temperatur. Wolfram w TIG nie jest zużywany w przeciwieństwie do innych metod wyjaśnionych powyżej. Powolna, ale wysokiej jakości technika spawania, przewyższająca inne techniki spawania cienkich materiałów. Nadaje się do wielu metali. Spawanie łukiem plazmowym jest podobne, ale do tworzenia łuku wykorzystuje się gaz plazmowy. Łuk podczas spawania łukiem plazmowym jest stosunkowo bardziej skoncentrowany w porównaniu do spawania metodą GTAW i może być stosowany do szerszego zakresu grubości metalu przy znacznie wyższych prędkościach. Spawanie metodą GTAW i łukiem plazmowym może być stosowane do mniej więcej takich samych materiałów. SPAWANIE TLENOWE / TLENOWE zwane również spawaniem tlenowo-acetylenowym, spawanie tlenowe, spawanie gazowe odbywa się przy użyciu paliw gazowych i tlenu do spawania. Ponieważ nie jest używana energia elektryczna, jest przenośny i może być używany tam, gdzie nie ma elektryczności. Za pomocą palnika spawalniczego podgrzewamy elementy i materiał wypełniający, aby wytworzyć wspólny basen stopionego metalu. Można stosować różne paliwa, takie jak acetylen, benzyna, wodór, propan, butan… itd. W spawaniu tlenowo-paliwowym używamy dwóch zbiorników, jednego na paliwo, a drugiego na tlen. Tlen utlenia paliwo (spala je). ZGRZEWANIE REZYSTANCYJNE: Ten rodzaj zgrzewania wykorzystuje ogrzewanie Joule'a, a ciepło jest wytwarzane w miejscu, w którym przez określony czas działa prąd elektryczny. Przez metal przechodzą wysokie prądy. W tym miejscu tworzą się kałuże stopionego metalu. Metody zgrzewania oporowego są popularne ze względu na ich wydajność, niewielki potencjał zanieczyszczeń. Wadami są jednak stosunkowo znaczne koszty sprzętu i nieodłączne ograniczenie stosunkowo cienkich elementów obrabianych. ZGRZEWANIE PUNKTOWE jest jednym z głównych rodzajów zgrzewania oporowego. Tutaj łączymy dwa lub więcej zachodzących na siebie arkuszy lub elementów roboczych, używając dwóch miedzianych elektrod do zaciskania arkuszy i przepuszczania przez nie wysokiego prądu. Materiał pomiędzy miedzianymi elektrodami nagrzewa się i w tym miejscu powstaje roztopiona kałuża. Prąd jest następnie zatrzymywany, a miedziane końcówki elektrod chłodzą miejsce spoiny, ponieważ elektrody są chłodzone wodą. Doprowadzenie odpowiedniej ilości ciepła do właściwego materiału i odpowiedniej grubości jest kluczowe dla tej techniki, ponieważ w przypadku niewłaściwego zastosowania połączenie będzie słabe. Zgrzewanie punktowe ma tę zaletę, że nie powoduje znaczących odkształceń elementów obrabianych, jest energooszczędne, łatwość automatyzacji i doskonałe tempo produkcji oraz nie wymaga żadnych wypełniaczy. Wadą jest to, że ponieważ spawanie odbywa się punktowo, a nie tworzy ciągły szew, całkowita wytrzymałość może być stosunkowo niższa w porównaniu z innymi metodami spawania. Z kolei SEAM WELDING tworzy spoiny na stykających się powierzchniach podobnych materiałów. Szew może być łączony na styk lub na zakładkę. Spawanie spoin zaczyna się na jednym końcu i przesuwa się stopniowo do drugiego. W tej metodzie stosuje się również dwie elektrody miedziane do przykładania ciśnienia i prądu do obszaru spoiny. Elektrody w kształcie tarczy obracają się ze stałym kontaktem wzdłuż linii szwu i wykonują ciągłą spoinę. Tutaj również elektrody są chłodzone wodą. Spoiny są bardzo mocne i niezawodne. Inne metody to spawanie rzutowe, błyskowe i spęczające. SPAWANIE SOLIDNE jest nieco inne niż poprzednie metody wyjaśnione powyżej. Koalescencja zachodzi w temperaturach poniżej temperatury topnienia łączonych metali i bez użycia wypełniacza metalowego. W niektórych procesach może być stosowane ciśnienie. Różne metody to ZGRZEWANIE KOEKTRUZYJNE gdzie różne metale są wytłaczane przez tę samą matrycę, ZGRZEWANIE NA ZIMNO gdzie łączymy miękkie stopy poniżej ich temperatury topnienia, ZGRZEWANIE DYFUZYJNE techniką bez widocznych linii zgrzewów, ZGRZEWANIE WYBUCHOWE do łączenia materiałów odmiennych, np. stopów odpornych na korozję z konstrukcją. stali, ZGRZEWANIA IMPULSOWEGO ELEKTROMAGNETYCZNEGO, w którym przyspieszamy rury i blachy siłami elektromagnetycznymi, ZGRZEWANIA KUŻOWEGO polegającego na podgrzaniu metali do wysokich temperatur i zbijaniu ich ze sobą młotkiem, ZGRZEWANIA TARCIOWEGO, w którym wykonuje się odpowiednie zgrzewanie tarciowe, ZGRZEWANIA TARCZOWEGO Z PRZESYŁANIEM, które polega na narzędzie zużywalne przechodzące przez linię złącza, ZGRZEWANIE NA GORĄCO, gdzie ściskamy metale w podwyższonych temperaturach poniżej temperatury topnienia w próżni lub w gazach obojętnych, ZGRZEWANIE NA GORĄCO IZOSTATYCZNE ZGRZEWANIE CIŚNIENIOWE proces, w którym stosujemy ciśnienie za pomocą gazów obojętnych wewnątrz naczynia, ZGRZEWANIE WALCOWE, w którym łączymy odmiennych materiałów, wymuszając je między dwa obrotowe koła, ZGRZEW ULTRADŹWIĘKOWY, gdzie cienkie arkusze metalu lub tworzywa sztucznego są spawane przy użyciu energii wibracyjnej o wysokiej częstotliwości. Inne nasze procesy spawalnicze to SPAWANIE WIĄZKAMI ELEKTRONICZNYMI z głębokim wtopieniem i szybką obróbką, ale jako metodą kosztowną, uważamy ją za szczególną w szczególnych przypadkach, SPAWANIE ELEKTROŻUŻOWE metodą odpowiednią tylko dla grubych blach i elementów stalowych, SPAWANIE INDUKCYJNE gdzie stosujemy indukcję elektromagnetyczną oraz nagrzewanie naszych elementów przewodzących prąd elektryczny lub ferromagnetycznych, SPAWANIE WIĄZKAMI LASEROWYMI również z głębokim wtopieniem i szybką obróbką, ale kosztowną metodą, SPAWANIE HYBRYDOWE LASEROWE, które łączy LBW z GMAW w tej samej głowicy spawalniczej i jest w stanie wypełnić szczeliny 2 mm między płytami, ZGRZEWANIE PERKUSYJNE, które polega na wyładowaniu elektrycznym, po którym następuje kucie materiałów pod przyłożonym ciśnieniem, ZGRZEWANIE TERMITOWE polegające na reakcji egzotermicznej pomiędzy proszkami aluminium i tlenku żelaza, ZGRZEWANIE ELEKTROGAZOWE z użyciem elektrod topliwych i stosowane wyłącznie ze stali w pozycji pionowej, a na koniec ZGRZEWANIE ŁUKOWE DO ŁĄCZENIA kołka z podstawą materiał z ciepłem i ciśnieniem. Zalecamy kliknięcie tutaj, abyPOBIERZ nasze schematyczne ilustracje procesów lutowania, lutowania i klejenia opracowane przez AGS-TECH Inc Pomoże Ci to lepiej zrozumieć informacje, które udostępniamy poniżej. • LUTOWANIE: Łączymy dwa lub więcej metali przez podgrzewanie spoiw pomiędzy nimi powyżej ich temperatur topnienia i rozprowadzanie metodą kapilarną. Proces jest podobny do lutowania, ale temperatury potrzebne do stopienia wypełniacza są wyższe podczas lutowania. Podobnie jak w przypadku spawania, topnik chroni materiał wypełniający przed zanieczyszczeniami atmosferycznymi. Po schłodzeniu detale są łączone. Proces obejmuje następujące kluczowe etapy: dobre dopasowanie i luz, właściwe czyszczenie materiałów bazowych, właściwe mocowanie, właściwy dobór topnika i atmosfery, podgrzewanie zespołu i wreszcie czyszczenie zespołu lutowanego. Niektóre z naszych procesów lutowania to TORCH BRAZING, popularna metoda wykonywana ręcznie lub w sposób zautomatyzowany. Nadaje się do małych zleceń produkcyjnych i specjalistycznych przypadków. Ciepło jest dostarczane za pomocą płomieni gazowych w pobliżu lutowanego złącza. LUTOWANIE PIECE wymaga mniejszych umiejętności operatora i jest procesem półautomatycznym, nadającym się do masowej produkcji przemysłowej. Zaletą tej techniki jest zarówno kontrola temperatury, jak i atmosfery w piecu, ponieważ ta pierwsza umożliwia nam kontrolowanie cykli cieplnych i eliminację miejscowego nagrzewania, jak ma to miejsce w przypadku lutowania palnikowego, a ta druga chroni część przed utlenianiem. Stosując jigging jesteśmy w stanie zredukować koszty produkcji do minimum. Wadami są wysokie zużycie energii, koszty sprzętu i trudniejsze względy projektowe. LUTOWANIE PRÓŻNIOWE odbywa się w piecu próżniowym. Utrzymuje się równomierność temperatury i uzyskujemy wolne od topników, bardzo czyste połączenia z bardzo małymi naprężeniami szczątkowymi. Obróbka cieplna może odbywać się podczas lutowania próżniowego ze względu na niewielkie naprężenia szczątkowe występujące podczas powolnych cykli ogrzewania i chłodzenia. Główną wadą jest wysoki koszt, ponieważ tworzenie środowiska próżniowego jest procesem kosztownym. Jeszcze inna technika DIP BRAZING łączy mocowane części, w których masa lutownicza jest nakładana na współpracujące powierzchnie. Następnie zamocowane części są zanurzane w kąpieli ze stopionej soli, takiej jak chlorek sodu (sól kuchenna), która działa jako nośnik ciepła i topnik. Powietrze jest wykluczone i dlatego nie dochodzi do tworzenia się tlenków. W LUTOWANIU INDUKCYJNYM łączymy materiały spoiwem o niższej temperaturze topnienia niż materiały bazowe. Prąd przemienny z cewki indukcyjnej wytwarza pole elektromagnetyczne, które indukuje nagrzewanie indukcyjne na przeważnie żelaznych materiałach magnetycznych. Metoda zapewnia selektywne ogrzewanie, dobre połączenia z wypełniaczami płynącymi tylko w pożądanych obszarach, niewielkie utlenianie, ponieważ nie ma płomienia, a chłodzenie jest szybkie, szybkie nagrzewanie, konsystencja i przydatność do produkcji wielkoseryjnej. Aby przyspieszyć nasze procesy i zapewnić spójność, często korzystamy z preform. Informacje na temat naszego zakładu produkującego złączki ceramiczne do metalowych, hermetyczne uszczelnienia, przepusty próżniowe, komponenty do kontroli wysokiego i ultrawysokiego podciśnienia i płynów można znaleźć tutaj: Broszura dotycząca fabryki lutów twardych • LUTOWANIE : W lutowaniu nie mamy do czynienia z topieniem się elementów obrabianych, ale ze spoiwem o niższej temperaturze topnienia niż części łączące, które wpływają do złącza. Spoiwo w lutowaniu topi się w niższej temperaturze niż w lutowaniu. Do lutowania używamy stopów bezołowiowych i spełniamy wymagania RoHS, a dla różnych zastosowań i wymagań mamy różne i odpowiednie stopy, takie jak stop srebra. Lutowanie oferuje nam złącza, które są gazo i cieczoszczelne. W LUTOWANIU MIĘKKIM nasz lut ma temperaturę topnienia poniżej 400 stopni Celsjusza, podczas gdy w LUTOWANIU SREBRNYM i LUTOWANIU LUTYMOWYM potrzebujemy wyższych temperatur. Lutowanie miękkie wykorzystuje niższe temperatury, ale nie daje mocnych połączeń w wymagających zastosowaniach w podwyższonych temperaturach. Z drugiej strony lutowanie srebrem wymaga wysokich temperatur zapewnianych przez palnik i daje nam mocne połączenia odpowiednie do zastosowań w wysokich temperaturach. Lutowanie wymaga najwyższych temperatur i zwykle używa się palnika. Ponieważ połączenia lutowane są bardzo mocne, są dobrymi kandydatami do naprawy ciężkich przedmiotów żelaznych. W naszych liniach produkcyjnych stosujemy zarówno ręczne lutowanie ręczne, jak i automatyczne linie lutownicze. INDUCTION LUDERING wykorzystuje prąd przemienny wysokiej częstotliwości w cewce miedzianej w celu ułatwienia nagrzewania indukcyjnego. W części lutowanej indukowane są prądy, w wyniku czego na złączu o dużej rezystancji joint generowane jest ciepło. To ciepło topi metal wypełniający. Stosowany jest również topnik. Lutowanie indukcyjne jest dobrą metodą do lutowania cylindrów i rur w procesie ciągłym poprzez owijanie cewek wokół nich. Lutowanie niektórych materiałów, takich jak grafit i ceramika, jest trudniejsze, ponieważ przed lutowaniem wymaga powlekania elementów odpowiednim metalem. Ułatwia to wiązanie międzyfazowe. Lutujemy takie materiały specjalnie do zastosowań w opakowaniach hermetycznych. Nasze płytki drukowane (PCB) produkujemy w dużych ilościach, głównie przy użyciu LUTY WAVE. Tylko dla niewielkich ilości celów prototypowych stosujemy lutowanie ręczne za pomocą lutownicy lutowniczej. Używamy lutowania na fali zarówno do montażu przewlekanego, jak i montażu powierzchniowego PCB (PCBA). Tymczasowy klej utrzymuje komponenty przymocowane do płytki drukowanej, a zespół jest umieszczany na przenośniku i przechodzi przez sprzęt zawierający stopiony lut. Najpierw PCB jest topiony, a następnie wchodzi do strefy podgrzewania. Stopiony lut znajduje się na patelni i ma na swojej powierzchni wzór fal stojących. Kiedy PCB porusza się po tych falach, fale te stykają się z dnem PCB i przyklejają się do pól lutowniczych. Lut pozostaje tylko na pinach i padach, a nie na samej płytce drukowanej. Fale w stopionym lutowiu muszą być dobrze kontrolowane, aby nie było rozpryskiwania, a wierzchołki fal nie dotykały i nie zanieczyszczały niepożądanych obszarów płytek. W lutowaniu rozpływowym używamy lepkiej pasty lutowniczej, aby tymczasowo przymocować elementy elektroniczne do płytek. Następnie deski trafiają do pieca rozpływowego z kontrolą temperatury. Tutaj lut topi się i trwale łączy elementy. Stosujemy tę technikę zarówno w przypadku elementów do montażu powierzchniowego, jak i elementów przewlekanych. Właściwa kontrola temperatury i dostosowanie temperatury piekarnika jest niezbędne, aby uniknąć zniszczenia elementów elektronicznych na płycie poprzez przegrzanie ich powyżej maksymalnych limitów temperatury. W procesie lutowania rozpływowego mamy w rzeczywistości kilka obszarów lub etapów, z których każdy ma odrębny profil termiczny, taki jak etap podgrzewania, etap wygrzewania termicznego, etapy ponownego rozpływu i chłodzenia. Te różne etapy są niezbędne do bezawaryjnego lutowania rozpływowego zespołów obwodów drukowanych (PCBA). LUTOWANIE ULTRADŹWIĘKOWE to kolejna często stosowana technika o wyjątkowych możliwościach – może być stosowana do lutowania materiałów szklanych, ceramicznych i niemetalicznych. Na przykład panele fotowoltaiczne, które są niemetalowe, wymagają elektrod, które można przymocować tą techniką. W lutowaniu ultradźwiękowym stosujemy podgrzewany grot lutowniczy, który również emituje wibracje ultradźwiękowe. Wibracje te wytwarzają pęcherzyki kawitacyjne na styku podłoża ze stopionym materiałem lutowniczym. Implozyjna energia kawitacji modyfikuje powierzchnię tlenku i usuwa brud i tlenki. W tym czasie tworzy się również warstwa stopu. Lut na powierzchni łączenia zawiera tlen i umożliwia tworzenie silnego wspólnego wiązania między szkłem a lutowiem. DIP SOLDERING można uznać za prostszą wersję lutowania na fali, odpowiednią tylko do produkcji na małą skalę. Pierwszy topnik czyszczący nakładany jest podobnie jak w innych procesach. Obwody drukowane z zamontowanymi elementami są zanurzane ręcznie lub w sposób półautomatyczny w zbiorniku zawierającym stopiony lut. Stopiony lut przykleja się do odsłoniętych obszarów metalowych niezabezpieczonych maską lutowniczą na płytce. Sprzęt jest prosty i niedrogi. • KLEJENIE KLEJEM : Jest to kolejna popularna technika, którą często stosujemy i polega na sklejaniu powierzchni za pomocą klejów, żywic epoksydowych, środków plastycznych lub innych chemikaliów. Klejenie uzyskuje się przez odparowanie rozpuszczalnika, utwardzanie na gorąco, utwardzanie światłem UV, utwardzanie ciśnieniowe lub odczekanie przez pewien czas. W naszych liniach produkcyjnych stosowane są różne kleje o wysokiej wydajności. Przy odpowiednio zaprojektowanych procesach nakładania i utwardzania, łączenie adhezyjne może skutkować bardzo niskimi naprężeniami, które są mocne i niezawodne. Wiązania klejowe mogą być dobrą ochroną przed czynnikami środowiskowymi, takimi jak wilgoć, zanieczyszczenia, korozje, wibracje… itp. Zaletami klejenia są: można je nakładać na materiały, które w innym przypadku byłyby trudne do lutowania, spawania lub lutowania. Może być również preferowane w przypadku materiałów wrażliwych na ciepło, które zostałyby uszkodzone przez spawanie lub inne procesy wysokotemperaturowe. Inne zalety klejów to możliwość ich nakładania na powierzchnie o nieregularnych kształtach i bardzo niewielkie zwiększenie ciężaru montażu w porównaniu z innymi metodami. Również zmiany wymiarowe części są bardzo minimalne. Niektóre kleje mają właściwości dopasowania indeksu i mogą być stosowane pomiędzy elementami optycznymi bez znacznego zmniejszania siły światła lub sygnału optycznego. Z drugiej strony wadami są dłuższe czasy utwardzania, które mogą spowolnić linie produkcyjne, wymagania dotyczące mocowania, wymagania dotyczące przygotowania powierzchni i trudności z demontażem, gdy konieczna jest przeróbka. Większość naszych operacji klejenia obejmuje następujące etapy: -Obróbka powierzchni: Powszechne są specjalne procedury czyszczenia, takie jak czyszczenie wodą dejonizowaną, czyszczenie alkoholem, czyszczenie plazmowe lub koronowe. Po oczyszczeniu możemy nanieść na powierzchnie promotory przyczepności, aby zapewnić jak najlepsze połączenia. - Mocowanie części: zarówno do aplikacji kleju, jak i do utwardzania projektujemy i stosujemy niestandardowe mocowania. -Nakładanie kleju: Czasami używamy ręcznych, a czasami, w zależności od przypadku, zautomatyzowanych systemów, takich jak robotyka, serwomotory, siłowniki liniowe w celu dostarczenia kleju we właściwe miejsce i używamy dozowników, aby dostarczyć go w odpowiedniej objętości i ilości. -Utwardzanie: W zależności od kleju możemy zastosować proste suszenie i utwardzanie, a także utwardzanie pod lampami UV, które działają jako katalizator lub utwardzanie na gorąco w piecu lub przy użyciu oporowych elementów grzejnych montowanych na przyrządach i uchwytach. Zalecamy kliknięcie tutaj, abyPOBIERZ nasze schematyczne ilustracje procesów mocowania autorstwa AGS-TECH Inc. Pomoże Ci to lepiej zrozumieć informacje, które udostępniamy poniżej. • PROCESY ŁĄCZENIA: Nasze procesy łączenia mechanicznego dzielą się na dwie kategorie: MOCOWANIA i POŁĄCZENIA INTEGRALNE. Przykładami stosowanych przez nas elementów złącznych są śruby, kołki, nakrętki, śruby, nity. Przykładami stosowanych przez nas połączeń integralnych są połączenia zatrzaskowe i skurczowe, szwy, zaciski. Stosując różnorodne metody mocowania zapewniamy, że nasze połączenia mechaniczne są mocne i niezawodne przez wiele lat użytkowania. ŚRUBY i ŚRUBY to jedne z najczęściej używanych elementów złącznych do trzymania przedmiotów razem i pozycjonowania. Nasze śruby i wkręty spełniają normy ASME. Stosowane są różne rodzaje śrub i śrub, w tym śruby z łbem sześciokątnym i śruby z łbem sześciokątnym, śruby i śruby do drewna, śruba dwustronna, śruba kołkowa, śruba oczkowa, śruba lustrzana, śruba do blachy, śruba do precyzyjnej regulacji, śruby samowiercące i samogwintujące , wkręt dociskowy, wkręty z wbudowanymi podkładkami,… i nie tylko. Posiadamy różne typy łbów śrub, takie jak łeb stożkowy, kopułkowy, okrągły, kołnierzowy oraz różne typy napędów śrubowych, takie jak rowek, krzyżakowy, kwadratowy, sześciokątny. Z drugiej strony RIVET jest trwałym łącznikiem mechanicznym składającym się z gładkiego cylindrycznego wału i łba z jednej strony. Po włożeniu drugi koniec nitu ulega deformacji, a jego średnica jest rozszerzana tak, aby pozostał na swoim miejscu. Innymi słowy, przed montażem nit ma jeden łeb, a po montażu dwa. Montujemy różne rodzaje nitów w zależności od zastosowania, wytrzymałości, dostępności i kosztu, takie jak nity z łbem pełnym/okrągłym, konstrukcyjne, półrurowe, zrywalne, oscarowe, wbijane, wpuszczane, samozaciskowe, samowtłaczające. Nitowanie może być preferowane w przypadkach, w których należy unikać odkształceń termicznych i zmian właściwości materiału spowodowanych ciepłem spawania. Nitowanie zapewnia również niewielką wagę oraz szczególnie dobrą wytrzymałość i odporność na siły ścinające. Jednak w przypadku obciążeń rozciągających bardziej odpowiednie mogą być śruby, nakrętki i śruby. W procesie CLINCHING wykorzystujemy specjalne stemple i matryce, które tworzą mechaniczną blokadę pomiędzy łączonymi blachami. Stempel wpycha warstwy blachy do wnęki matrycy i powoduje powstanie trwałego połączenia. W klinczowaniu nie jest wymagane ogrzewanie ani chłodzenie i jest to proces obróbki na zimno. Jest to ekonomiczny proces, który w niektórych przypadkach może zastąpić zgrzewanie punktowe. W PINNING wykorzystujemy kołki, które są elementami maszyn służącymi do zabezpieczenia położenia części maszyny względem siebie. Główne typy to zawleczki, zawleczki, zawleczki, zawleczki, i zawleczka. W ZSZYWANIU używamy zszywaczy i zszywek, które są dwuzębnymi łącznikami służącymi do łączenia lub wiązania materiałów. Zszywanie ma następujące zalety: ekonomiczne, proste i szybkie w użyciu, korona zszywek może być używana do łączenia materiałów połączonych ze sobą, korona zszywki może ułatwić połączenie elementu jak kabel i przymocowanie go do powierzchni bez przebijania lub szkodliwe, stosunkowo łatwe usuwanie. ZŁĄCZANIE ZACISKOWE odbywa się poprzez dociskanie części do siebie, a tarcie między nimi mocuje części. Części pasowane wtłaczane składające się z nadwymiarowego wałka i podwymiarowego otworu są zazwyczaj montowane jedną z dwóch metod: albo poprzez przyłożenie siły, albo wykorzystanie rozszerzalności lub kurczenia się części pod wpływem temperatury. Gdy złączka zaciskowa jest ustalana przez przyłożenie siły, używamy prasy hydraulicznej lub prasy ręcznej. Z drugiej strony, gdy pasowanie wtłaczane jest ustalane przez rozszerzalność cieplną, podgrzewamy części otaczające i montujemy je na swoje miejsce na gorąco. Kiedy ostygną, kurczą się i wracają do swoich normalnych wymiarów. Daje to dobre pasowanie wtłaczane. Nazywamy to alternatywnie DOPASOWANIEM KURCZLIWYM. Innym sposobem na zrobienie tego jest schłodzenie owiniętych części przed montażem, a następnie wsunięcie ich w ich współpracujące części. Gdy montaż się rozgrzeje, rozszerzają się i uzyskujemy ciasne dopasowanie. Ta ostatnia metoda może być preferowana w przypadkach, gdy ogrzewanie stwarza ryzyko zmiany właściwości materiału. W takich przypadkach chłodzenie jest bezpieczniejsze. Podzespoły i zespoły pneumatyczne i hydrauliczne • Zawory, elementy hydrauliczne i pneumatyczne takie jak O-ring, podkładka, uszczelki, uszczelka, pierścień, podkładka. Ponieważ zawory i elementy pneumatyczne są bardzo różnorodne, nie możemy tutaj wszystkiego wymienić. W zależności od środowiska fizycznego i chemicznego Twojej aplikacji mamy dla Ciebie specjalne produkty. Proszę podać nam zastosowanie, rodzaj komponentu, specyfikacje, warunki środowiskowe, takie jak ciśnienie, temperatura, ciecze lub gazy, które będą miały kontakt z Państwa zaworami i komponentami pneumatycznymi; a my dobierzemy dla Ciebie najbardziej odpowiedni produkt lub wyprodukujemy go specjalnie do Twojego zastosowania. CLICK Product Finder-Locator Service POPRZEDNIA STRONA
- Rapid Prototyping, Desktop Manufacturing, Additive Manufacturing, FDM
Rapid Prototyping, Desktop Manufacturing, Additive Manufacturing, Stereolithography, Polyjet, Fused Deposition Modeling, Selective Laser Sintering, FDM, SLS Produkcja przyrostowa i szybka W ostatnich latach obserwujemy wzrost zapotrzebowania na RAPID MANUFACTURING lub RAPID PROTOTYPING. Proces ten można również nazwać DESKTOP MANUFACTURINGEM lub FABRICATION FABRICATION. Zasadniczo solidny fizyczny model części jest tworzony bezpośrednio z trójwymiarowego rysunku CAD. Używamy terminu ADDITIVE MANUFACTURING dla tych różnych technik, w których budujemy części warstwami. Wykorzystując zintegrowany sprzęt komputerowy i oprogramowanie, wykonujemy produkcję addytywną. Nasze techniki szybkiego prototypowania i produkcji to: STEREOLITOGRAFIA, POLYJET, MODELOWANIE STOSOWANE, SELEKTYWNE SPIEKANIE LASEROWE, TOPIENIE WIĄZKĄ ELEKTRONOWĄ, DRUK TRÓJWYMIAROWY, BEZPOŚREDNIA PRODUKCJA, SZYBKIE NARZĘDZIA. Zalecamy kliknięcie tutaj, abyPOBIERZ nasze schematyczne ilustracje wytwarzania przyrostowego i procesów szybkiego wytwarzania opracowane przez AGS-TECH Inc. Pomoże Ci to lepiej zrozumieć informacje, które udostępniamy poniżej. Szybkie prototypowanie zapewnia nam: 1.) Projekt koncepcyjny produktu jest oglądany pod różnymi kątami na monitorze za pomocą systemu 3D/CAD. 2.) Prototypy z materiałów niemetalicznych i metalowych są produkowane i badane pod kątem funkcjonalnym, technicznym i estetycznym. 3.) Prototypowanie niskokosztowe w bardzo krótkim czasie. Produkcja przyrostowa może być podobna do budowy bochenka chleba poprzez układanie i łączenie poszczególnych kromek jeden na drugim. Innymi słowy, produkt jest wytwarzany kawałek po kawałku lub nakładany na siebie warstwa po warstwie. Większość części można wyprodukować w ciągu kilku godzin. Technika jest dobra, jeśli części są potrzebne bardzo szybko lub jeśli potrzebne ilości są małe, a wykonanie formy i oprzyrządowania jest zbyt kosztowne i czasochłonne. Jednak koszt części jest wysoki ze względu na drogie surowce. • STEREOLITOGRAFIA: Technika ta, określana również skrótem STL, polega na utwardzaniu i utwardzeniu ciekłego fotopolimeru do określonego kształtu poprzez skupienie na nim wiązki laserowej. Laser polimeryzuje fotopolimer i utwardza go. Dzięki skanowaniu wiązką lasera UV zgodnie z zaprogramowanym kształtem wzdłuż powierzchni mieszanki fotopolimerowej, część wytwarzana jest od dołu do góry w pojedynczych warstwach ułożonych kaskadowo jeden na drugim. Skanowanie plamki laserowej jest powtarzane wiele razy, aby uzyskać geometrie zaprogramowane w systemie. Po całkowitym wykonaniu części zdejmuje się ją z platformy, wyciera i czyści ultradźwiękowo oraz w kąpieli alkoholowej. Następnie przez kilka godzin jest wystawiony na działanie promieniowania UV, aby upewnić się, że polimer jest w pełni utwardzony i utwardzony. Podsumowując proces, platforma zanurzona w mieszaninie fotopolimerów i wiązka lasera UV są sterowane i przesuwane przez system serwosterowania zgodnie z kształtem pożądanej części, a część uzyskuje się poprzez fotoutwardzanie polimeru warstwa po warstwie. Oczywiście maksymalne wymiary produkowanej części określa sprzęt stereolitografii. • POLYJET : Podobnie jak w przypadku druku atramentowego, w Polyjet mamy osiem głowic drukujących, które umieszczają fotopolimer na tacy roboczej. Światło ultrafioletowe umieszczone obok dysz natychmiast utwardza i utwardza każdą warstwę. W polyjet stosowane są dwa materiały. Pierwszy materiał służy do wykonania rzeczywistego modelu. Drugi materiał, żelowata żywica, służy do podparcia. Oba te materiały są nakładane warstwa po warstwie i jednocześnie utwardzane. Po ukończeniu modelu materiał nośnika usuwa się roztworem wodnym. Stosowane żywice są podobne do stereolitografii (STL). Polyjet ma następujące zalety w porównaniu ze stereolitografią: 1.) Nie ma potrzeby czyszczenia części. 2.) Nie ma potrzeby utwardzania po procesie 3.) Możliwe są mniejsze grubości warstw, dzięki czemu uzyskujemy lepszą rozdzielczość i możemy produkować drobniejsze części. • MODELOWANIE STOSOWANEGO STANOWISKA: W tej metodzie, w skrócie FDM, głowica wytłaczarki sterowana przez robota porusza się w dwóch zasadniczych kierunkach po stole. W razie potrzeby lina jest opuszczana i podnoszona. Z otworu nagrzanej matrycy na głowicy wytłaczane jest włókno termoplastyczne i nakładana jest warstwa początkowa na podkład piankowy. Odbywa się to dzięki głowicy wytłaczarki, która porusza się z góry określoną ścieżką. Po pierwszej warstwie stół jest opuszczany, a kolejne warstwy układane są jedna na drugiej. Czasami przy wytwarzaniu skomplikowanej części potrzebne są struktury wspierające, aby osadzanie mogło być kontynuowane w określonych kierunkach. W takich przypadkach materiał podporowy jest wytłaczany z mniej gęstym odstępem filamentu na warstwie, dzięki czemu jest słabszy niż materiał modelowy. Te konstrukcje wsporcze można później rozpuścić lub odłamać po zakończeniu części. Wymiary matrycy wytłaczarki określają grubość wytłaczanych warstw. Proces FDM wytwarza części o stopniowanych powierzchniach na ukośnych płaszczyznach zewnętrznych. Jeśli ta chropowatość jest niedopuszczalna, do ich wygładzenia można użyć chemicznego polerowania parowego lub rozgrzanego narzędzia. Dostępny jest nawet wosk do polerowania jako materiał powlekający, aby wyeliminować te etapy i osiągnąć rozsądne tolerancje geometryczne. • SELEKTYWNE SPIEKANIE LASEROWE: Proces ten, określany również jako SLS, opiera się na selektywnym spiekaniu proszków polimerowych, ceramicznych lub metalicznych w obiekcie. Dno komory przetwarzania ma dwa cylindry: cylinder częściowy i cylinder podający proszek. Pierwsza jest stopniowo obniżana do miejsca, w którym jest formowana spiekana część, a druga jest stopniowo podnoszona w celu dostarczenia proszku do cylindra do wytwarzania części poprzez mechanizm wałka. Najpierw cienka warstwa proszku jest osadzana w cylindrze do obróbki częściowej, a następnie wiązka lasera jest skupiana na tej warstwie, śledząc i topiąc/spiekając określony przekrój, który następnie zestala się w ciało stałe. Proszek to obszary, na które nie uderza wiązka laserowa, pozostają luźne, ale nadal podpierają twardą część. Następnie nakładana jest kolejna warstwa proszku i proces jest wielokrotnie powtarzany w celu uzyskania części. Na koniec strząsa się luźne cząsteczki proszku. Wszystko to realizowane jest przez komputer sterujący procesem za pomocą instrukcji generowanych przez program 3D CAD produkowanej części. Można osadzać różne materiały, takie jak polimery (takie jak ABS, PVC, poliester), wosk, metale i ceramikę z odpowiednimi spoiwami polimerowymi. • ELECTRON-BEAM MELTING : Podobny do selektywnego spiekania laserowego, ale wykorzystujący wiązkę elektronów do topienia proszków tytanu lub chromu kobaltowego w celu wykonania prototypów w próżni. Wprowadzono pewne udoskonalenia, aby przeprowadzić ten proces na stalach nierdzewnych, aluminium i stopach miedzi. Jeśli trzeba zwiększyć wytrzymałość zmęczeniową produkowanych części, stosujemy prasowanie izostatyczne na gorąco po produkcji części jako proces wtórny. • DRUK TRÓJWYMIAROWY: określany również jako 3DP, w tej technice głowica drukująca osadza nieorganiczne spoiwo na warstwie niemetalicznego lub metalicznego proszku. Tłok podtrzymujący złoże proszku jest stopniowo obniżany i na każdym etapie osadzane jest spoiwo warstwa po warstwie i stapiane przez spoiwo. Stosowane materiały proszkowe to mieszanki i włókna polimerów, piasek odlewniczy, metale. Stosując jednocześnie różne głowice bindujące i różne kolory binderów możemy uzyskać różne kolory. Proces ten jest podobny do drukowania atramentowego, ale zamiast kolorowego arkusza otrzymujemy kolorowy obiekt trójwymiarowy. Wytwarzane części mogą być porowate i dlatego mogą wymagać spiekania i infiltracji metalem w celu zwiększenia ich gęstości i wytrzymałości. Spiekanie spowoduje spalenie spoiwa i stopienie ze sobą proszków metali. Metale takie jak stal nierdzewna, aluminium, tytan mogą być używane do produkcji części, a jako materiały infiltracyjne powszechnie używamy miedzi i brązu. Piękno tej techniki polega na tym, że nawet skomplikowane i ruchome zespoły mogą być produkowane bardzo szybko. Na przykład zespół przekładni, klucz jako narzędzie może być wykonany i będzie miał części ruchome i obrotowe gotowe do użycia. Różne elementy zestawu mogą być wyprodukowane w różnych kolorach i wszystko w jednym ujęciu. Pobierz naszą broszurę na:Podstawy drukowania 3D w metalu • BEZPOŚREDNIA PRODUKCJA i SZYBKIE NARZĘDZIA: Oprócz oceny projektu i rozwiązywania problemów stosujemy szybkie prototypowanie do bezpośredniego wytwarzania produktów lub bezpośredniego stosowania w produktach. Innymi słowy, szybkie prototypowanie można włączyć do konwencjonalnych procesów, aby uczynić je lepszymi i bardziej konkurencyjnymi. Na przykład szybkie prototypowanie może tworzyć wzory i formy. Wzory topniejącego i płonącego polimeru utworzonego w operacjach szybkiego prototypowania mogą być montowane do odlewania metodą traconego wosku i zainwestowane. Innym przykładem, o którym warto wspomnieć, jest zastosowanie 3DP do produkcji ceramicznej skorupy odlewniczej i wykorzystanie jej do operacji odlewania skorupy. Nawet formy wtryskowe i wkładki do form można wytwarzać za pomocą szybkiego prototypowania, co pozwala zaoszczędzić wiele tygodni lub miesięcy czasu realizacji formy. Analizując tylko plik CAD żądanej części, możemy wytworzyć geometrię narzędzia za pomocą oprogramowania. Oto niektóre z naszych popularnych metod szybkiego oprzyrządowania: RTV (Wulkanizacja w temperaturze pokojowej) FORMOWANIE / ODLEWANIE URETANU: Przy użyciu szybkiego prototypowania można wykonać wzór żądanej części. Następnie ten wzór jest powlekany środkiem rozdzielającym i płynna guma RTV jest wylewana na wzór w celu wytworzenia połówek formy. Następnie te połówki formy są wykorzystywane do formowania wtryskowego ciekłych uretanów. Żywotność formy jest krótka, tylko 0 lub 30 cykli, ale wystarcza do produkcji małych partii. ACES (Acetal Clear Epoxy Solid) FORMOWANIE WTRYSKOWE: Wykorzystując techniki szybkiego prototypowania, takie jak stereolitografia, produkujemy formy wtryskowe. Formy te to skorupy z otwartym końcem, aby umożliwić wypełnienie materiałami takimi jak żywica epoksydowa, żywica epoksydowa wypełniona aluminium lub metale. Ponownie żywotność formy jest ograniczona do dziesiątek lub maksymalnie setek części. PROCES NATRYSKIWANIA METALI: Stosujemy szybkie prototypowanie i wykonujemy wzór. Na powierzchnię modelu natryskujemy stop cynkowo-aluminiowy i powlekamy go. Wzór z metalową powłoką jest następnie umieszczany w kolbie i zalewany żywicą epoksydową lub epoksydową wypełnioną aluminium. Na koniec zostaje ona usunięta i wytwarzając dwie takie połówki formy otrzymujemy kompletną formę do wtrysku. Formy te mają dłuższą żywotność, w niektórych przypadkach, w zależności od materiału i temperatury, mogą produkować tysiące części. PROCES KEELTOOL: Ta technika umożliwia produkcję form o żywotności od 100 000 do 10 milionów cykli. Korzystając z szybkiego prototypowania produkujemy formę RTV. Forma jest następnie wypełniana mieszaniną składającą się z proszku stali narzędziowej A6, węglika wolframu, spoiwa polimerowego i pozostawiana do utwardzenia. Ta forma jest następnie podgrzewana, aby wypalić polimer i stopić proszki metalu. Następnym krokiem jest infiltracja miedzią w celu wytworzenia ostatecznej formy. W razie potrzeby na formie można wykonać dodatkowe operacje, takie jak obróbka skrawaniem i polerowanie, aby uzyskać lepszą dokładność wymiarową. CLICK Product Finder-Locator Service POPRZEDNIA STRONA
- Composites, Composite Materials Manufacturing, Fiber Reinforced
Composites, Composite Materials Manufacturing, Particle and Fiber Reinforced, Cermets, Ceramic & Metal Composite, Glass Fiber Reinforced Polymer, Lay-Up Process Produkcja kompozytów i materiałów kompozytowych W uproszczeniu, KOMPOZYTY lub MATERIAŁY KOMPOZYTOWE to materiały składające się z dwóch lub wielu materiałów o różnych właściwościach fizycznych lub chemicznych, ale po połączeniu stają się materiałem innym niż materiały składowe. Należy zaznaczyć, że materiały składowe pozostają odrębne i odrębne w strukturze. Celem wytwarzania materiału kompozytowego jest uzyskanie produktu, który jest lepszy niż jego składniki i łączy pożądane cechy każdego składnika. Jako przykład; wytrzymałość, niska waga czy niższa cena mogą być motywacją do zaprojektowania i wyprodukowania kompozytu. Rodzaje oferowanych przez nas kompozytów to kompozyty wzmacniane cząsteczkami, kompozyty wzmacniane włóknami, w tym kompozyty z osnową ceramiczną/polimerową/metalową/węglowo-węglową/hybrydową, kompozyty strukturalne, laminowane i warstwowe oraz nanokompozyty. Techniki wytwarzania, które stosujemy w produkcji materiałów kompozytowych, to: Pultruzja, procesy produkcji prepregów, zaawansowane umieszczanie włókien, nawijanie włókien, dopasowane umieszczanie włókien, proces nakładania natryskowego włókna szklanego, tuftowanie, proces lanxide, z-pinning. Wiele materiałów kompozytowych składa się z dwóch faz, matrycy, która jest ciągła i otacza drugą fazę; oraz fazę rozproszoną, która jest otoczona przez matrycę. Zalecamy kliknięcie tutaj, abyPOBIERZ nasze schematyczne ilustracje produkcji kompozytów i materiałów kompozytowych przez AGS-TECH Inc. Pomoże Ci to lepiej zrozumieć informacje, które udostępniamy poniżej. • KOMPOZYTY WZMOCNIONE CZĄSTECZKAMI: Ta kategoria obejmuje dwa typy: kompozyty wielkocząsteczkowe i kompozyty wzmocnione dyspersyjnie. W pierwszym typie oddziaływań cząstka-matryca nie można traktować na poziomie atomowym lub molekularnym. Zamiast tego obowiązuje mechanika kontinuum. Z drugiej strony, w kompozytach wzmocnionych dyspersyjnie cząstki są na ogół znacznie mniejsze w zakresie kilkudziesięciu nanometrów. Przykładem kompozytu wielkocząsteczkowego są polimery, do których dodano wypełniacze. Wypełniacze poprawiają właściwości materiału i mogą zastąpić część objętości polimeru bardziej ekonomicznym materiałem. Udziały objętościowe dwóch faz wpływają na zachowanie kompozytu. Kompozyty wielkocząsteczkowe są stosowane z metalami, polimerami i ceramiką. CERMETS są przykładami kompozytów ceramiczno-metalowych. Naszym najczęstszym cermetalem jest węglik spiekany. Składa się z ogniotrwałej ceramiki węglikowej, takiej jak cząstki węglika wolframu w osnowie z metalu, takiego jak kobalt lub nikiel. Te kompozyty węglikowe są szeroko stosowane jako narzędzia skrawające do stali hartowanej. Cząstki twardego węglika są odpowiedzialne za cięcie, a ich ciągliwość jest wzmocniona przez plastyczną osnowę metalową. W ten sposób uzyskujemy zalety obu materiałów w jednym kompozycie. Innym powszechnym przykładem stosowanego przez nas kompozytu wielkocząsteczkowego są cząstki sadzy zmieszane z wulkanizowaną gumą w celu uzyskania kompozytu o wysokiej wytrzymałości na rozciąganie, twardości, rozdzieraniu i ścieraniu. Przykładem kompozytu wzmocnionego dyspersyjnie są metale i stopy metali wzmocnione i utwardzone równomierną dyspersją drobnych cząstek bardzo twardego i obojętnego materiału. Po dodaniu bardzo małych płatków tlenku glinu do aluminiowej matrycy metalowej otrzymujemy spiekany proszek aluminiowy, który ma zwiększoną wytrzymałość w wysokich temperaturach. • KOMPOZYTY WZMOCNIONE WŁÓKNEM: Ta kategoria kompozytów jest w rzeczywistości najważniejsza. Celem do osiągnięcia jest wysoka wytrzymałość i sztywność na jednostkę masy. Skład włókien, długość, orientacja i koncentracja w tych kompozytach ma kluczowe znaczenie dla określenia właściwości i przydatności tych materiałów. Stosowane są trzy grupy włókien: wiskery, włókna i druty. WĄSY to bardzo cienkie i długie monokryształy. Są jednymi z najmocniejszych materiałów. Niektóre przykładowe materiały typu wiskery to grafit, azotek krzemu, tlenek glinu. FIBERS z drugiej strony to głównie polimery lub ceramika i występują w stanie polikrystalicznym lub amorficznym. Trzecia grupa to cienkie DRUTY, które mają stosunkowo duże średnice i często składają się ze stali lub wolframu. Przykładem kompozytu zbrojonego drutem są opony samochodowe, które zawierają stalowy drut wewnątrz gumy. W zależności od materiału osnowy mamy kompozyty: KOMPOZYTY POLIMER-MATRIX: są wykonane z żywicy polimerowej i włókien jako składnika wzmacniającego. Podgrupa tych, zwana kompozytami polimerowymi wzmacnianymi włóknem szklanym (GFRP), zawiera ciągłe lub nieciągłe włókna szklane w matrycy polimerowej. Szkło oferuje wysoką wytrzymałość, jest ekonomiczne, łatwe do przetworzenia na włókna i jest chemicznie obojętne. Wadą jest ich ograniczona sztywność i sztywność, a temperatury pracy wynoszą tylko do 200 – 300 stopni Celsjusza. Włókno szklane nadaje się do nadwozi samochodowych i sprzętu transportowego, nadwozi pojazdów morskich, pojemników magazynowych. Ze względu na ograniczoną sztywność nie nadają się do przemysłu lotniczego ani mostów. Druga podgrupa nosi nazwę kompozyt polimerowy wzmocniony włóknem węglowym (CFRP). Tutaj węgiel jest naszym materiałem włóknistym w matrycy polimerowej. Węgiel znany jest z wysokiego modułu właściwego i wytrzymałości oraz zdolności do utrzymywania ich w wysokich temperaturach. Włókna węglowe oferują nam standardowe, pośrednie, wysokie i ultrawysokie moduły rozciągania. Ponadto włókna węglowe oferują różnorodne właściwości fizyczne i mechaniczne, a zatem nadają się do różnych niestandardowych zastosowań inżynierskich. Kompozyty CFRP mogą być brane pod uwagę do produkcji sprzętu sportowego i rekreacyjnego, zbiorników ciśnieniowych i lotniczych elementów konstrukcyjnych. Jeszcze inna podgrupa, kompozyty polimerowe wzmocnione włóknem aramidowym, to również materiały o wysokiej wytrzymałości i module. Ich stosunek wytrzymałości do masy jest wyjątkowo wysoki. Włókna aramidowe znane są również pod nazwami handlowymi KEVLAR i NOMEX. Pod napięciem zachowują się lepiej niż inne materiały z włókien polimerowych, ale są słabe w ściskaniu. Włókna aramidowe są wytrzymałe, odporne na uderzenia, pełzanie i zmęczenie, stabilne w wysokich temperaturach, chemicznie obojętne, z wyjątkiem silnych kwasów i zasad. Włókna aramidowe są szeroko stosowane w artykułach sportowych, kamizelkach kuloodpornych, oponach, linach, osłonach kabli światłowodowych. Istnieją inne materiały wzmacniające włókna, ale są stosowane w mniejszym stopniu. Są to głównie bor, węglik krzemu, głównie tlenek glinu. Z drugiej strony, materiał matrycy polimerowej jest również krytyczny. Określa maksymalną temperaturę pracy kompozytu, ponieważ polimer ma na ogół niższą temperaturę topnienia i degradacji. Jako matrycę polimerową szeroko stosuje się poliestry i estry winylowe. Stosowane są również żywice, które mają doskonałą odporność na wilgoć i właściwości mechaniczne. Na przykład żywica poliimidowa może być używana do około 230 stopni Celsjusza. KOMPOZYTY METAL-MATRIX : W tych materiałach stosujemy ciągliwą osnowę metalową, a temperatury pracy są generalnie wyższe niż ich składników. W porównaniu z kompozytami z matrycą polimerową mogą one mieć wyższe temperatury robocze, być niepalne i mogą mieć lepszą odporność na degradację w stosunku do płynów organicznych. Są jednak droższe. Materiały wzmacniające, takie jak wiskery, cząstki stałe, włókna ciągłe i nieciągłe; oraz powszechnie stosowane są materiały osnowy, takie jak miedź, aluminium, magnez, tytan, nadstopy. Przykładowe zastosowania to elementy silnika wykonane z matrycy ze stopu aluminium wzmocnionego tlenkiem aluminium i włóknami węglowymi. KOMPOZYTY CERAMIC-MATRIX : Materiały ceramiczne są znane ze swojej wyjątkowo dobrej niezawodności w wysokich temperaturach. Są jednak bardzo kruche i mają niskie wartości odporności na pękanie. Osadzając cząstki, włókna lub wiskery jednej ceramiki w osnowie drugiej jesteśmy w stanie uzyskać kompozyty o wyższej odporności na pękanie. Te osadzone materiały zasadniczo hamują propagację pęknięć wewnątrz matrycy przez pewne mechanizmy, takie jak odchylanie wierzchołków pęknięć lub tworzenie mostków na powierzchniach pęknięć. Na przykład tlenki glinu wzmocnione wiskerami SiC są stosowane jako płytki narzędzi skrawających do obróbki stopów metali twardych. Mogą one wykazywać lepsze osiągi w porównaniu do węglików spiekanych. KOMPOZYTY WĘGLOWE-WĘGLOWE: Zarówno wzmocnienie, jak i matryca są wykonane z węgla. Charakteryzują się wysokimi modułami rozciągania i wytrzymałościami w wysokich temperaturach powyżej 2000 stopni Celsjusza, odpornością na pełzanie, wysoką odpornością na pękanie, niskimi współczynnikami rozszerzalności cieplnej, wysoką przewodnością cieplną. Te właściwości czynią je idealnymi do zastosowań wymagających odporności na szok termiczny. Słabością kompozytów węglowo-węglowych jest jednak ich podatność na utlenianie w wysokich temperaturach. Typowymi przykładami zastosowania są formy do prasowania na gorąco, produkcja zaawansowanych podzespołów silników turbinowych. KOMPOZYTY HYBRYDOWE: W jednej matrycy miesza się dwa lub więcej różnych rodzajów włókien. W ten sposób można dostosować nowy materiał z kombinacją właściwości. Przykładem jest wprowadzenie do żywicy polimerowej zarówno włókien węglowych, jak i szklanych. Włókna węglowe zapewniają sztywność i wytrzymałość o niskiej gęstości, ale są drogie. Z drugiej strony szkło jest niedrogie, ale brakuje mu sztywności włókien węglowych. Hybrydowy kompozyt szklano-węglowy jest mocniejszy i twardszy i może być wytwarzany po niższych kosztach. OBRÓBKA KOMPOZYTÓW WZMOCNIONYCH WŁÓKNAMI: W przypadku ciągłych tworzyw sztucznych wzmocnionych włóknami z równomiernie rozłożonymi włóknami zorientowanymi w tym samym kierunku stosujemy następujące techniki. PULTRUZJA: Produkowane są pręty, belki i rury o ciągłych długościach i stałych przekrojach. Rowingi z włókien ciągłych są impregnowane żywicą termoutwardzalną i przeciągane przez stalową matrycę, aby wstępnie uformować je w pożądany kształt. Następnie przechodzą przez precyzyjnie obrobioną matrycę utwardzającą, aby uzyskać ostateczny kształt. Ponieważ matryca utwardzająca jest podgrzewana, utwardza matrycę żywiczną. Ściągacze przeciągają materiał przez matryce. Dzięki wstawianym pustym rdzeniom jesteśmy w stanie uzyskać rury i puste geometrie. Metoda pultruzji jest zautomatyzowana i oferuje nam wysokie tempo produkcji. Można wyprodukować dowolną długość produktu. PROCES PRODUKCJI PREPREGU: Prepreg to zbrojenie z włókien ciągłych wstępnie impregnowane częściowo utwardzoną żywicą polimerową. Jest szeroko stosowany do zastosowań konstrukcyjnych. Materiał jest dostarczany w formie taśmy i wysyłany jako taśma. Producent formuje go bezpośrednio i całkowicie utwardza bez konieczności dodawania żywicy. Ponieważ prepregi ulegają reakcjom utwardzania w temperaturze pokojowej, przechowuje się je w temperaturze 0 stopni Celsjusza lub niższej. Po użyciu pozostałe taśmy są przechowywane z powrotem w niskich temperaturach. Stosowane są żywice termoplastyczne i termoutwardzalne, a powszechnie stosowane są włókna wzmacniające z węgla, aramidu i szkła. Aby użyć prepregów, najpierw usuwa się papier podkładowy nośnika, a następnie wykonuje się produkcję poprzez nałożenie taśmy prepregowej na obrabianą powierzchnię (proces układania). Można ułożyć kilka warstw, aby uzyskać żądaną grubość. Częstą praktyką jest zmiana orientacji włókien w celu wytworzenia laminatu warstwowego lub warstwowego. Na koniec do utwardzania stosuje się ciepło i ciśnienie. Zarówno obróbka ręczna, jak i procesy zautomatyzowane są stosowane do cięcia prepregów i lay-upów. NAWIJANIE WŁÓKNA: Ciągłe włókna wzmacniające są dokładnie rozmieszczone we wcześniej ustalonym wzorze, podążając za wydrążonym i zwykle o kształcie cyklindycznym. Włókna najpierw przechodzą przez kąpiel w żywicy, a następnie są nawijane na trzpień przez zautomatyzowany system. Po kilku powtórzeniach nawijania uzyskuje się żądaną grubość, a utwardzanie przeprowadza się albo w temperaturze pokojowej, albo w piecu. Teraz trzpień jest usuwany, a produkt jest zdejmowany. Nawijanie włókien może oferować bardzo wysoki stosunek wytrzymałości do masy dzięki nawijaniu włókien we wzory obwodowe, śrubowe i biegunowe. Rury, zbiorniki, obudowy są produkowane tą techniką. • KOMPOZYTY STRUKTURALNE: Generalnie składają się z materiałów jednorodnych i kompozytowych. Dlatego ich właściwości są determinowane przez materiały składowe i konstrukcję geometryczną jej elementów. Oto główne typy: KOMPOZYTY LAMINARNE: Te materiały konstrukcyjne są wykonane z dwuwymiarowych arkuszy lub paneli o preferowanych kierunkach o wysokiej wytrzymałości. Warstwy są układane i klejone razem. Zmieniając kierunki o wysokiej wytrzymałości w dwóch prostopadłych osiach, otrzymujemy kompozyt o wysokiej wytrzymałości w obu kierunkach w płaszczyźnie dwuwymiarowej. Dopasowując kąty warstw można wytworzyć kompozyt o wytrzymałości w preferowanych kierunkach. W ten sposób powstają nowoczesne narty. PANELE WARSTWOWE: Te kompozyty strukturalne są lekkie, ale mają wysoką sztywność i wytrzymałość. Panele warstwowe składają się z dwóch zewnętrznych arkuszy wykonanych ze sztywnego i wytrzymałego materiału, takiego jak stopy aluminium, tworzywa sztuczne wzmocnione włóknami lub stal oraz rdzeń pomiędzy arkuszami zewnętrznymi. Rdzeń musi być lekki i przez większość czasu mieć niski moduł sprężystości. Popularne materiały rdzeniowe to sztywne pianki polimerowe, drewno i plastry miodu. Płyty warstwowe są szeroko stosowane w budownictwie jako materiał na pokrycia dachowe, materiał podłogowy lub ścienny, a także w przemyśle lotniczym. • NANOKOMPOZYTY: Te nowe materiały składają się z cząstek o rozmiarach nanometrowych osadzonych w matrycy. Używając nanokompozytów możemy wytwarzać materiały gumowe, które są bardzo dobrą barierą dla przenikania powietrza, zachowując przy tym niezmienione właściwości gumy. CLICK Product Finder-Locator Service POPRZEDNIA STRONA
- Transmission Components, Belts, Chains, Cable Drives, Pulleys,AGS-TECH
Transmission Components, Belts, Chains and Cable Drives, Conventional & Grooved or Serrated, Positive Drive, Pulleys Pasy i łańcuchy oraz zespół napędu kablowego AGS-TECH Inc. oferuje komponenty do przenoszenia mocy, w tym paski i łańcuchy oraz zespół napędowy kabla. Dzięki wieloletnim udoskonaleniom nasze gumowe, skórzane i inne napędy pasowe stały się lżejsze i bardziej kompaktowe, zdolne do przenoszenia większych obciążeń przy niższych kosztach. Podobnie nasze napędy łańcuchowe przeszły z biegiem czasu wiele zmian i oferują naszym klientom wiele korzyści. Niektóre zalety stosowania napędów łańcuchowych to stosunkowo nieograniczona odległość między osiami wałów, zwartość, łatwość montażu, elastyczność przy rozciąganiu bez poślizgu lub pełzania, zdolność do pracy w środowiskach o wysokiej temperaturze. Nasze napędy kablowe mają również zalety, takie jak prostota w niektórych zastosowaniach, w porównaniu z innymi typami komponentów transmisyjnych. Dostępne są zarówno standardowe napędy taśmowe, łańcuchowe i kablowe, jak i niestandardowe wersje wyprodukowane i zmontowane. Możemy wyprodukować te elementy przekładni w odpowiednim rozmiarze dla danego zastosowania i z najbardziej odpowiednich materiałów. PASY I NAPĘDY PASKOWE: - Konwencjonalne płaskie pasy: są to zwykłe płaskie pasy bez zębów, rowków i ząbków. Napędy z paskiem płaskim oferują elastyczność, dobrą amortyzację, wydajne przenoszenie mocy przy dużych prędkościach, odporność na ścieranie, niski koszt. Pasy można splatać lub łączyć w większe pasy. Kolejnymi zaletami konwencjonalnych pasów płaskich są to, że są cienkie, nie podlegają dużym obciążeniom odśrodkowym (dzięki czemu nadają się do pracy przy dużych prędkościach z małymi kołami pasowymi). Z drugiej strony nakładają duże obciążenia na łożyska, ponieważ pasy płaskie wymagają dużego naprężenia. Innymi wadami napędów z paskiem płaskim mogą być poślizgi, głośna praca i stosunkowo niższe sprawności przy niskich i umiarkowanych prędkościach pracy. Posiadamy dwa rodzaje pasów konwencjonalnych: Wzmocnione i Niewzmocnione. Wzmocnione pasy mają w swojej strukturze element rozciągliwy. Konwencjonalne płaskie pasy są dostępne jako skóra, gumowana tkanina lub sznurek, niewzmocniona guma lub plastik, tkanina, wzmocniona skóra. Pasy skórzane oferują długą żywotność, elastyczność, doskonały współczynnik tarcia, łatwą naprawę. Pasy skórzane są jednak stosunkowo drogie, wymagają ubierania i czyszczenia pasów, aw zależności od atmosfery mogą się kurczyć lub rozciągać. Gumowane paski z tkaniny lub kordu są odporne na wilgoć, kwasy i zasady. Pasy z gumowanej tkaniny składają się z warstw bawełny lub syntetycznej kaczki impregnowanej gumą i są najbardziej ekonomiczne. Gumowane pasy kordowe składają się z szeregu warstw kordów impregnowanych gumą. Gumowane pasy kordowe zapewniają wysoką wytrzymałość na rozciąganie oraz niewielki rozmiar i masę. Niewzmocnione pasy gumowe lub plastikowe nadają się do lekkich, wolnoobrotowych zastosowań napędowych. Niewzmocnione pasy gumowe i plastikowe można naciągnąć na swoje koła pasowe. Niewzmocnione plastikowe pasy mogą przenosić większą moc w porównaniu do pasów gumowych. Pasy ze wzmocnionej skóry składają się z plastikowego elementu rozciągliwego umieszczonego pomiędzy górną i dolną warstwą skóry. Wreszcie nasze pasy tkaninowe mogą składać się z jednego kawałka bawełny lub kaczki złożonej i zszytej rzędami ściegów wzdłużnych. Taśmy materiałowe są w stanie toczyć się równomiernie i działać z dużą prędkością. - Pasy rowkowane lub ząbkowane (takie jak paski klinowe): Są to podstawowe płaskie pasy zmodyfikowane w celu zapewnienia zalet innego rodzaju produktów przekładniowych. Są to płaskie paski z podłużnie prążkowanym spodem. Pasy Poly-V są podłużnie rowkowanymi lub ząbkowanymi płaskimi pasami o przekroju rozciąganym i szeregiem sąsiednich rowków w kształcie litery V do celów śledzenia i ściskania. Moc zależy od szerokości taśmy. Pasy klinowe to koń pociągowy przemysłu i są dostępne w różnych standardowych rozmiarach i typach do przenoszenia prawie każdej mocy obciążenia. Napędy z paskiem klinowym działają dobrze w zakresie od 1500 do 6000 stóp/min, jednak wąskie paski klinowe będą działać z prędkością do 10 000 stóp/min. Napędy z paskiem klinowym zapewniają długą żywotność, od 3 do 5 lat i pozwalają na duże przełożenia prędkości, są łatwe w montażu i demontażu, zapewniają cichą pracę, niskie koszty utrzymania, dobrą amortyzację między napędem pasowym a napędzanymi wałami. Wadą pasów klinowych jest ich pewien poślizg i pełzanie, dlatego mogą nie być najlepszym rozwiązaniem tam, gdzie wymagane są prędkości synchroniczne. Posiadamy pasy przemysłowe, motoryzacyjne i rolnicze. Dostępne są standardowe długości magazynowe oraz niestandardowe długości pasów. Wszystkie standardowe przekroje pasów klinowych są dostępne z magazynu. Istnieją tabele, w których można obliczyć nieznane parametry, takie jak długość pasa, przekrój pasa (szerokość i grubość), pod warunkiem, że znasz niektóre parametry systemu, takie jak średnice napędzającego i napędzanego koła pasowego, odległość osi między kołami pasowymi i prędkości obrotowe kół pasowych. Możesz skorzystać z takich tabel lub poprosić nas o dobranie odpowiedniego paska klinowego. - Pasy napędowe dodatnie (paski rozrządu): Pasy te są również płaskie z szeregiem równomiernie rozmieszczonych zębów na obwodzie wewnętrznym. Pasy napędowe lub zębate łączą zalety pasów płaskich z właściwościami chwytu dodatniego łańcuchów i kół zębatych. Pasy napędowe z napędem dodatnim nie wykazują poślizgów ani zmian prędkości. Możliwy jest szeroki zakres przełożeń prędkości. Obciążenia łożysk są niskie, ponieważ mogą pracować przy niskim napięciu. Są jednak bardziej podatne na niewspółosiowość kół pasowych. - Koła pasowe, koła pasowe, piasty do pasów: Różne typy kół pasowych są używane z płaskimi, żebrowanymi (ząbkowanymi) i dodatnimi paskami napędowymi. Produkujemy je wszystkie. Większość naszych płaskich kół pasowych jest wykonywana przez odlewanie z żelaza, ale wersje stalowe są również dostępne w różnych kombinacjach obręczy i piast. Nasze koła pasowe z płaskimi paskami mogą mieć piasty pełne, szprychowe lub dzielone lub możemy produkować według życzenia. Pasy żebrowane i przymusowe są dostępne w różnych rozmiarach i szerokościach. Co najmniej jedno koło pasowe w napędach z paskiem rozrządu musi być wyposażone w kołnierz, aby utrzymać pasek na napędzie. W przypadku długich centralnych układów napędowych zaleca się, aby oba koła pasowe były kołnierzowe. Krążki są rowkowanymi kołami kół pasowych i są zwykle wytwarzane przez odlewanie żeliwa, formowanie stali lub formowanie tworzyw sztucznych. Formowanie stali jest odpowiednim procesem do produkcji kół samochodowych i rolniczych. Produkujemy krążki z rowkami regularnymi i głębokimi. Koła z głębokim rowkiem są odpowiednie, gdy pasek klinowy wchodzi w koło pod kątem, tak jak ma to miejsce w napędach ćwierćobrotowych. Głębokie rowki doskonale nadają się również do napędów z wałem pionowym i zastosowań, w których wibracje pasów mogą stanowić problem. Nasze koła napinające to rowkowane koła pasowe lub płaskie, które nie służą do przenoszenia mocy mechanicznej. Rolki napinające służą głównie do napinania pasów. - Napędy z pojedynczym i wieloma paskami: Napędy z pojedynczym paskiem mają pojedynczy rowek, podczas gdy napędy z wieloma paskami mają wiele rowków. Klikając poniżej w odpowiedni kolorowy tekst, możesz pobrać nasze katalogi: - Pasy przeniesienia napędu (w tym paski klinowe, paski rozrządu, paski surowej krawędzi, paski owijane i paski specjalne) - Przenośniki taśmowe - koła pasowe w kształcie litery V - koła pasowe rozrządu ŁAŃCUCHY I NAPĘDY ŁAŃCUCHOWE: Nasze łańcuchy napędowe mają pewne zalety, takie jak stosunkowo nieograniczona odległość między osiami wałów, łatwy montaż, zwartość, elastyczność przy rozciąganiu bez poślizgu i pełzania, zdolność do pracy w wysokich temperaturach. Oto główne rodzaje naszych łańcuchów: - Odpinane łańcuchy: Nasze odłączane łańcuchy są wykonane w różnych rozmiarach, skoku i najwyższej wytrzymałości i ogólnie z żeliwa ciągliwego lub stali. Łańcuchy ciągliwe są produkowane w różnych rozmiarach od podziałki 0,902 (23 mm) do 4,063 cala (103 mm) i wytrzymałości od 700 do 17 000 funtów/cal kwadratowy. Z drugiej strony nasze odłączane stalowe łańcuchy są produkowane w rozmiarach od 0,904 cala (23 mm) do około 3,00 cala (76 mm) w skoku, o maksymalnej wytrzymałości od 760 do 5000 funtów/cal kwadratowy._cc781905-5cde-3194-bb3b- 136bad5cf58d_ - Łańcuchy czopowe: Te łańcuchy są używane do cięższych ładunków i nieco wyższych prędkości do około 450 stóp/min (2,2 m/s). Łańcuchy czopowe wykonane są z pojedynczych ogniw odlewanych z pełnym, okrągłym zakończeniem lufy z przesuniętymi poprzeczkami. Te ogniwa łańcucha są sprzężone stalowymi kołkami. Łańcuchy te mają podziałkę od około 1,00 cala (25 mm) do 6,00 cala (150 mm) i wytrzymałość końcową od 3600 do 30 000 funtów/cal kwadratowy. - Łańcuchy z przesuniętymi paskami bocznymi: są popularne w łańcuchach napędowych maszyn budowlanych. Łańcuchy te pracują z prędkością do 1000 stóp/min i przenoszą obciążenia do około 250 KM. Generalnie każde ogniwo ma dwa przesunięte listwy boczne, jedną tuleję, jedną rolkę, jeden sworzeń, zawleczkę. - Łańcuchy rolkowe: są dostępne w podziałkach od 0,25 (6 mm) do 3,00 (75 mm) cali. Najwyższa wytrzymałość łańcuchów rolkowych o pojedynczej szerokości mieści się w zakresie od 925 do 130 000 funtów/cal kwadratowy. Dostępne są wersje łańcuchów rolkowych o wielu szerokościach, które przekazują większą moc przy wyższych prędkościach. Łańcuchy rolkowe o wielu szerokościach zapewniają również płynniejszą pracę przy niższym poziomie hałasu. Łańcuchy rolkowe składają się z ogniw rolkowych i ogniw sworzniowych. Zawleczki stosowane są w wersji odpinanej łańcuchów rolkowych. Konstrukcja napędów rolkowo-łańcuchowych wymaga specjalistycznej wiedzy. Podczas gdy napędy pasowe bazują na prędkościach liniowych, napędy łańcuchowe bazują na prędkości obrotowej mniejszego koła zębatego, które w większości instalacji jest elementem napędzanym. Oprócz mocy znamionowych i prędkości obrotowej, konstrukcja napędów łańcuchowych opiera się na wielu innych czynnikach. - Łańcuchy o podwójnej podziałce: Zasadniczo takie same jak łańcuchy rolkowe, z wyjątkiem tego, że podziałka jest dwa razy dłuższa. - Łańcuchy z odwróconym zębem (ciche): Łańcuchy o dużej prędkości stosowane głównie w napędach głównych i napędach odbioru mocy. Napędy z odwróconymi zębami mogą przenosić moc do 1200 KM i składają się z szeregu ogniw zębatych, naprzemiennie montowanych za pomocą sworzni lub kombinacji elementów przegubowych. Łańcuch prowadnicy środkowej ma ogniwa prowadzące, które zaczepiają się o rowki w kole zębatym, a łańcuch prowadnicy bocznej ma prowadnice, które zaczepiają boki koła zębatego. - Łańcuchy kulkowe lub suwakowe: Te łańcuchy są używane do napędów wolnoobrotowych, a także do operacji ręcznych. Klikając poniżej w odpowiedni kolorowy tekst, możesz pobrać nasze katalogi: - Łańcuchy napędowe - Łańcuchy przenośnikowe - Łańcuchy przenośników o dużym skoku - Łańcuchy rolkowe ze stali nierdzewnej - Łańcuchy do podnoszenia - Łańcuchy motocyklowe - Łańcuchy maszyn rolniczych - Koła zębate: Nasze standardowe koła zębate są zgodne z normami ANSI. Zębatki płytowe to płaskie, bez piasty. Nasze małe i średnie koła łańcuchowe piasty są toczone z prętów lub odkuwek lub wykonywane przez spawanie piasty prętów z blachą gorącowalcowaną. Firma AGS-TECH Inc. może dostarczyć koła zębate wykonane z odlewów z żeliwa szarego, staliwa i konstrukcji spawanych piast, spiekany metal proszkowy, formowane lub obrabiane tworzywa sztuczne. Do płynnej pracy przy dużych prędkościach niezbędny jest odpowiedni dobór wielkości kół zębatych. Ograniczenia przestrzeni to oczywiście czynnik, którego nie możemy pominąć przy wyborze zębatki. Zaleca się, aby stosunek zabieraka do napędzanych kół łańcuchowych nie przekraczał 6:1, a owinięcie łańcucha na zabieraku wynosiło 120 stopni. Odległości osi między mniejszymi i większymi zębatkami, długość łańcucha i napięcie łańcucha również należy dobierać zgodnie z niektórymi zalecanymi obliczeniami inżynierskimi i wytycznymi, a nie losowo. Pobierz nasze katalogi, klikając kolorowy tekst poniżej: - Zębatki i Koła Płytowe - Tuleje skrzyni biegów -Sprzęgło łańcuchowe - Zamki łańcuchowe NAPĘDY KABLOWE: W niektórych przypadkach mają one przewagę nad napędami pasowymi i łańcuchowymi. Napędy kablowe mogą pełnić tę samą funkcję co pasy, a także mogą być prostsze i bardziej ekonomiczne do wdrożenia w niektórych zastosowaniach. Na przykład nowa seria napędów kablowych Synchromesh została zaprojektowana z myślą o pozytywnej przyczepności, aby zastąpić konwencjonalne liny, proste kable i napędy zębate, szczególnie w ciasnych przestrzeniach. Nowy napęd kablowy został zaprojektowany w celu zapewnienia wysokiej precyzji pozycjonowania w sprzęcie elektronicznym, takim jak kopiarki, plotery, maszyny do pisania, drukarki,….. itd. Kluczową cechą nowego napędu kablowego jest jego możliwość użycia w konfiguracjach serpentyn 3D, które umożliwiają niezwykle miniaturowe projekty. Kable synchroniczne mogą być używane z mniejszym napięciem w porównaniu z linami, co zmniejsza zużycie energii. Skontaktuj się z AGS-TECH w przypadku pytań i opinii na temat napędów pasowych, łańcuchowych i linowych. CLICK Product Finder-Locator Service POPRZEDNIA STRONA
- Glass and Ceramic Manufacturing, Hermetic Packages, Seals, Bonding
Glass and Ceramic Manufacturing, Hermetic Packages Seals and Bonding, Tempered Bulletproof Glass, Blow Moulding, Optical Grade Glass, Conductive Glass, Molding Formowanie i kształtowanie szkła i ceramiki Proponowane przez nas rodzaje produkcji szkła to szkło opakowaniowe, dmuchanie szkła, włókno szklane i pręty, szkło domowe i przemysłowe, lampy i bańki, precyzyjne formowanie szkła, elementy i zespoły optyczne, szkło płaskie i arkuszowe oraz float. Wykonujemy zarówno formowanie ręczne jak i maszynowe. Nasze popularne procesy produkcji ceramiki technicznej to: prasowanie matrycowe, prasowanie izostatyczne, prasowanie izostatyczne na gorąco, prasowanie na gorąco, odlewanie z gęstwy, odlewanie taśmowe, wytłaczanie, formowanie wtryskowe, obróbka mechaniczna, spiekanie lub wypalanie, szlifowanie diamentowe, hermetyczne zespoły. Zalecamy kliknięcie tutaj, aby POBIERZ nasze schematyczne ilustracje procesów formowania i kształtowania szkła autorstwa AGS-TECH Inc. POBIERZ nasze schematyczne ilustracje technicznych procesów produkcji ceramiki autorstwa AGS-TECH Inc. Te pliki do pobrania ze zdjęciami i szkicami pomogą Ci lepiej zrozumieć informacje, które udostępniamy poniżej. • PRODUKCJA SZKŁA KONTENEROWEGO: Posiadamy zautomatyzowane linie PRESS AND BLOW oraz BLOW AND BLOW do produkcji. W procesie wydmuchu i rozdmuchu wrzucamy kroplę do pustej formy i formujemy szyjkę poprzez nadmuch sprężonego powietrza od góry. Bezpośrednio po tym sprężone powietrze jest przedmuchiwane po raz drugi z drugiego kierunku przez szyjkę pojemnika w celu uformowania preformy butelki. Ta preforma jest następnie przenoszona do właściwej formy, ponownie podgrzewana w celu zmiękczenia i aplikowane jest sprężone powietrze, aby nadać preformie ostateczny kształt pojemnika. Mówiąc dokładniej, jest on pod ciśnieniem i dociskany do ścianek wnęki formy do rozdmuchiwania, aby przybrał pożądany kształt. Na koniec wytworzony szklany pojemnik jest przenoszony do pieca do wyżarzania w celu późniejszego ponownego podgrzania i usunięcia naprężeń powstałych podczas formowania i jest chłodzony w kontrolowany sposób. W metodzie tłoczenia i rozdmuchiwania roztopione krople są umieszczane w formie wstępnej (forma wstępna) i prasowana w kształt wstępny (forma wstępna). Półfabrykaty są następnie przenoszone do form do rozdmuchiwania i rozdmuchiwane podobnie do procesu opisanego powyżej w części „Proces rozdmuchu i rozdmuchu”. Kolejne kroki, takie jak wyżarzanie i odprężanie, są podobne lub takie same. • DMUCHANIE SZKŁA : Wytwarzamy wyroby szklane stosując konwencjonalne dmuchanie ręczne oraz sprężone powietrze za pomocą zautomatyzowanych urządzeń. W przypadku niektórych zamówień konieczne jest konwencjonalne rozdmuchiwanie, np. projekty obejmujące prace ze szkła lub projekty wymagające mniejszej liczby części o luźnych tolerancjach, projekty prototypowe / demonstracyjne… itd. Konwencjonalne dmuchanie szkła polega na zanurzeniu pustej w środku metalowej rury w naczyniu ze stopionym szkłem i obróceniu rury w celu zebrania pewnej ilości materiału szklanego. Szkło zebrane na czubku rury jest zwijane na płaskowniku, dowolnie ukształtowane, wydłużone, ponownie nagrzane i nadmuchane powietrzem. Gdy jest gotowy, wkłada się go do formy i wdmuchuje powietrze. Wnęka formy jest wilgotna, aby uniknąć kontaktu szkła z metalem. Folia wodna działa między nimi jak poduszka. Ręczne rozdmuchiwanie jest powolnym procesem pracochłonnym i nadaje się tylko do tworzenia prototypów lub przedmiotów o wysokiej wartości, nie nadaje się do niedrogich zamówień o dużej objętości na sztukę. • PRODUKCJA SZKŁA DOMOWEGO I PRZEMYSŁOWEGO : Używając różnych rodzajów materiałów szklanych, wytwarzana jest duża różnorodność wyrobów szklanych. Niektóre szklanki są odporne na ciepło i nadają się do szkła laboratoryjnego, podczas gdy niektóre są wystarczająco dobre, aby wytrzymać wiele razy zmywanie w zmywarce i nadają się do wytwarzania produktów domowych. Za pomocą maszyn Westlake produkuje się dziesiątki tysięcy sztuk szklanek dziennie. Aby uprościć, stopione szkło jest zbierane próżniowo i wkładane do form w celu wykonania preform. Następnie do form wdmuchiwane jest powietrze, które przenoszone jest do innej formy i ponownie wdmuchiwane jest powietrze i szkło nabiera ostatecznego kształtu. Podobnie jak w przypadku ręcznego rozdmuchiwania, formy te są utrzymywane w stanie wilgotnym wodą. Dalsze rozciąganie jest częścią operacji wykańczającej, podczas której formowana jest szyjka. Nadmiar szkła jest spalony. Następnie następuje opisany powyżej kontrolowany proces ponownego ogrzewania i chłodzenia. • FORMOWANIE RUR I PRĘTÓW SZKLANYCH: Głównymi procesami stosowanymi do produkcji rur szklanych są procesy DANNER i VELLO. W procesie Dannera szkło z pieca przepływa i spada na pochyloną tuleję wykonaną z materiałów ogniotrwałych. Tuleja jest prowadzona na obracającym się wale drążonym lub palniku. Szkło jest następnie owijane wokół tulei i tworzy gładką warstwę spływającą w dół tulei i na czubek wału. W przypadku formowania rur powietrze wdmuchiwane jest przez cybuch z wydrążoną końcówką, a w przypadku formowania prętów stosujemy pełne końcówki na wale. Rury lub pręty są następnie przeciągane przez rolki nośne. Wymiary takie jak grubość ścianki i średnica rurek szklanych są dopasowywane do żądanych wartości poprzez ustawienie średnicy tulei i ciśnienia powietrza nadmuchowego na żądaną wartość, regulację temperatury, szybkości przepływu szkła i prędkości wyciągania. Z drugiej strony proces produkcji szklanych rurek Vello obejmuje szkło, które przemieszcza się z pieca do miski z wydrążonym trzpieniem lub dzwonem. Szkło przechodzi następnie przez przestrzeń powietrzną między trzpieniem a miską i przybiera kształt rury. Następnie przemieszcza się po rolkach do ciągarki i jest chłodzony. Na końcu linii chłodzenia następuje cięcie i obróbka końcowa. Wymiary rur można regulować tak jak w procesie Danner. Porównując proces Danner z Vello, możemy powiedzieć, że proces Vello lepiej nadaje się do produkcji wielkoseryjnej, podczas gdy proces Danner może lepiej pasować do precyzyjnych zamówień na rury o mniejszej objętości. • OBRÓBKA SZKŁA ARKUSZOWEGO I PŁASKIEGO I FLOAT : Posiadamy duże ilości szkła płaskiego o grubościach od submilimetrowych do kilku centymetrów. Nasze płaskie okulary charakteryzują się niemal optyczną perfekcją. Oferujemy szkło ze specjalnymi powłokami, takimi jak powłoki optyczne, gdzie do nakładania powłok antyodbiciowych lub lustrzanych stosowana jest technika naparowywania chemicznego. Powszechne są również przezroczyste powłoki przewodzące. Dostępne są również powłoki hydrofobowe lub hydrofilowe na szkle oraz powłoka, która sprawia, że szkło jest samoczyszczące. Kolejnymi popularnymi przedmiotami są szkła hartowane, kuloodporne i laminowane. Docinamy szkło do pożądanego kształtu z pożądanymi tolerancjami. Dostępne są inne operacje drugorzędne, takie jak wyginanie lub gięcie płaskiego szkła. • PRECYZYJNE FORMOWANIE SZKŁA: Używamy tej techniki głównie do produkcji precyzyjnych elementów optycznych bez potrzeby stosowania droższych i czasochłonnych technik, takich jak szlifowanie, docieranie i polerowanie. Ta technika nie zawsze jest wystarczająca do uzyskania najlepszej optyki, ale w niektórych przypadkach, takich jak produkty konsumenckie, aparaty cyfrowe, optyka medyczna, może to być tańsza dobra opcja w przypadku produkcji wielkoseryjnej. Ponadto ma przewagę nad innymi technikami formowania szkła, w których wymagane są złożone geometrie, na przykład w przypadku kul. Podstawowy proces obejmuje załadowanie dolnej strony formy półfabrykatem szklanym, opróżnienie komory procesowej w celu usunięcia tlenu, przy zamknięciu formy, szybkie i izotermiczne nagrzewanie matrycy i szkła światłem podczerwonym, dalsze zamykanie połówek formy dociskanie zmiękczonego szkła powoli w sposób kontrolowany do pożądanej grubości, a na koniec schłodzenie szkła i wypełnienie komory azotem oraz usunięcie produktu. Precyzyjna kontrola temperatury, odległość zamknięcia formy, siła zamykania formy, dopasowanie współczynników rozszerzalności formy i materiału szklanego są w tym procesie kluczowe. • PRODUKCJA SZKLANYCH KOMPONENTÓW I ZESPOŁÓW OPTYCZNYCH: Oprócz precyzyjnego formowania szkła istnieje szereg cennych procesów, których używamy do wytwarzania wysokiej jakości elementów i zespołów optycznych do wymagających zastosowań. Szlifowanie, docieranie i polerowanie szkieł optycznych w drobnych specjalnych zawiesinach ściernych jest sztuką i nauką przy wytwarzaniu soczewek optycznych, pryzmatów, płaskich i innych. Płaskość powierzchni, falistość, gładkość i wolne od wad powierzchnie optyczne wymagają dużego doświadczenia z takimi procesami. Niewielkie zmiany w środowisku mogą spowodować, że produkty będą niezgodne ze specyfikacją i zatrzymają linię produkcyjną. Zdarzają się przypadki, w których pojedyncze przetarcie powierzchni optycznej czystą szmatką może sprawić, że produkt spełni wymagania lub nie przejdzie testu. Niektóre popularne materiały szklane to topiona krzemionka, kwarc, BK7. Również montaż takich komponentów wymaga specjalistycznego doświadczenia niszowego. Czasami używa się specjalnych klejów. Czasami jednak najlepszym wyborem jest technika zwana kontaktowaniem optycznym, która nie zawiera materiału pomiędzy przymocowanymi szkłami optycznymi. Składa się z fizycznego kontaktu płaskich powierzchni, które łączą się ze sobą bez kleju. W niektórych przypadkach do montażu elementów optycznych w określonych odległościach i przy określonych orientacjach geometrycznych stosuje się mechaniczne przekładki dystansowe, precyzyjne szklane pręty lub kulki, zaciski lub obrabiane elementy metalowe. Przyjrzyjmy się niektórym z naszych popularnych technik produkcji wysokiej klasy optyki. SZLIFOWANIE I DOCIERANIE I POLEROWANIE: Szorstki kształt elementu optycznego uzyskuje się poprzez szlifowanie półfabrykatu szklanego. Następnie przeprowadza się docieranie i polerowanie przez obracanie i pocieranie szorstkich powierzchni elementów optycznych o narzędzia o pożądanych kształtach powierzchni. Zawiesiny z drobnymi cząstkami ściernymi i płynem są wlewane między optykę a narzędzia kształtujące. Rozmiary cząstek ściernych w takich zawiesinach można dobierać w zależności od pożądanego stopnia płaskości. Odchylenia krytycznych powierzchni optycznych od pożądanych kształtów są wyrażane w postaci długości fal stosowanego światła. Nasza optyka o wysokiej precyzji ma tolerancje jednej dziesiątej długości fali (Długość fali/10) lub nawet węższe. Oprócz profilu powierzchni, krytyczne powierzchnie są skanowane i oceniane pod kątem innych cech powierzchni i wad, takich jak wymiary, rysy, odpryski, wgłębienia, plamki... itd. Ścisła kontrola warunków środowiskowych w produkcji optycznej oraz rozbudowane wymagania metrologiczne i testowe przy użyciu najnowocześniejszego sprzętu sprawiają, że jest to wymagająca gałąź przemysłu. • WTÓRNE PROCESY W PRODUKCJI SZKŁA: Ponownie ograniczamy się jedynie do Twojej wyobraźni, jeśli chodzi o wtórne i wykańczające procesy szkła. Oto lista niektórych z nich: -Powłoki na szkle (optyczne, elektryczne, trybologiczne, termiczne, funkcjonalne, mechaniczne...). Jako przykład możemy zmienić właściwości powierzchni szkła tak, aby np. odbijało ciepło, dzięki czemu utrzymuje chłód we wnętrzach budynku, lub aby jednostronnie pochłaniało promieniowanie podczerwone za pomocą nanotechnologii. Pomaga to utrzymać ciepło wewnątrz budynków, ponieważ najbardziej zewnętrzna warstwa szkła pochłania promieniowanie podczerwone wewnątrz budynku i promieniuje je z powrotem do środka. - Wytrawianie na szkle -Applied Ceramic Labeling (ACL) -Rytownictwo -Polerowanie płomieniowe -Polerowanie chemiczne -Barwiący PRODUKCJA CERAMIKI TECHNICZNEJ • TŁOCZENIE MATRYCOWE: Składa się z jednoosiowego zagęszczania granulowanych proszków zamkniętych w matrycy • TŁOCZENIE NA GORĄCO: Podobne do tłoczenia matrycowego, ale z dodatkiem temperatury w celu zwiększenia zagęszczenia. Proszek lub zagęszczoną preformę umieszcza się w matrycy grafitowej i przykłada się jednoosiowe ciśnienie, podczas gdy matryca jest utrzymywana w wysokich temperaturach, takich jak 2000 C. Temperatury mogą się różnić w zależności od rodzaju przetwarzanego proszku ceramicznego. W przypadku skomplikowanych kształtów i geometrii może być potrzebna inna dalsza obróbka, taka jak szlifowanie diamentem. • PRASOWANIE IZOSTATYCZNE: Granulowany proszek lub prasowane ciśnieniowo kompakty są umieszczane w hermetycznych pojemnikach, a następnie w zamkniętym zbiorniku ciśnieniowym z płynem w środku. Następnie są zagęszczane poprzez zwiększenie ciśnienia w zbiorniku ciśnieniowym. Ciecz wewnątrz naczynia przenosi siły ciśnienia równomiernie na całej powierzchni hermetycznego pojemnika. W ten sposób materiał jest sprasowany równomiernie i przyjmuje kształt elastycznego pojemnika oraz jego wewnętrzny profil i cechy. • PRASOWANIE IZOSTATYCZNE NA GORĄCO: Podobnie jak prasowanie izostatyczne, ale oprócz sprężonej atmosfery gazowej spiekamy wypraską w wysokiej temperaturze. Prasowanie izostatyczne na gorąco powoduje dodatkowe zagęszczenie i zwiększenie wytrzymałości. • ODLEWANIE SLIPOWE / ODLEWANIE DRENAŻOWE : Wypełniamy formę zawiesiną cząstek ceramicznych o wielkości mikrometrów i płynem nośnym. Ta mieszanka nazywa się „poślizgiem”. Forma ma pory i dlatego płyn w mieszaninie jest filtrowany do formy. W rezultacie na wewnętrznych powierzchniach formy powstaje odlew. Po spiekaniu części można wyjąć z formy. • ODLEWANIE TAŚM: Produkujemy taśmy ceramiczne poprzez odlewanie zawiesin ceramicznych na płaskie ruchome powierzchnie nośne. Zawiesiny zawierają proszki ceramiczne zmieszane z innymi chemikaliami w celu wiązania i przenoszenia. Gdy rozpuszczalniki odparowują, pozostają gęste i elastyczne arkusze ceramiki, które można dowolnie ciąć lub zwijać. • FORMOWANIE PRZEZ WYTŁACZANIE: Podobnie jak w innych procesach wyciskania, miękka mieszanina proszku ceramicznego ze spoiwami i innymi chemikaliami jest przepuszczana przez matrycę w celu uzyskania jej kształtu przekroju, a następnie jest cięta na żądaną długość. Proces jest wykonywany z użyciem zimnych lub podgrzewanych mieszanek ceramicznych. • FORMOWANIE WTRYSKOWE NISKOCIŚNIENIOWE: Przygotowujemy mieszankę proszku ceramicznego ze spoiwami i rozpuszczalnikami i podgrzewamy ją do temperatury, w której można ją łatwo wcisnąć i wcisnąć do gniazda narzędzia. Po zakończeniu cyklu formowania część jest wyrzucana, a wiążąca substancja chemiczna jest spalana. Dzięki formowaniu wtryskowemu możemy ekonomicznie uzyskać skomplikowane części w dużych ilościach. Możliwe są otwory , które są maleńkim ułamkiem milimetra na ściance o grubości 10 mm, gwinty są możliwe bez dalszej obróbki, możliwe są tolerancje tak wąskie jak +/- 0,5%, a nawet niższe, gdy części są obrabiane , możliwe są grubości ścianek od 0,5mm do długości 12,5mm oraz grubości ścianek od 6,5mm do długości 150mm. • OBRÓBKA ZIELONA: Używając tych samych narzędzi do obróbki metalu, możemy obrabiać prasowane materiały ceramiczne, gdy są jeszcze miękkie jak kreda. Możliwe są tolerancje +/- 1%. Dla lepszych tolerancji stosujemy szlifowanie diamentowe. • SPIEKANIE lub WYPALANIE : Spiekanie umożliwia pełne zagęszczenie. Na zielonych, kompaktowych częściach występuje znaczny skurcz, ale nie jest to duży problem, ponieważ uwzględniamy te zmiany wymiarowe podczas projektowania części i oprzyrządowania. Cząsteczki proszku są ze sobą połączone, a porowatość wywołana procesem zagęszczania zostaje w znacznym stopniu usunięta. • SZLIFOWANIE DIAMENTEM: Najtwardszy na świecie materiał „diament” jest używany do szlifowania twardych materiałów, takich jak ceramika i uzyskiwane są części precyzyjne. Uzyskuje się tolerancje w zakresie mikrometrów i bardzo gładkie powierzchnie. Ze względu na koszt rozważamy tę technikę tylko wtedy, gdy naprawdę jej potrzebujemy. • ZESPOŁY HERMETYCZNE to takie, które praktycznie mówiąc nie pozwalają na jakąkolwiek wymianę materii, ciał stałych, cieczy lub gazów między interfejsami. Hermetyczne uszczelnienie jest hermetyczne. Na przykład hermetyczne obudowy elektroniczne to takie, które chronią wrażliwą zawartość wnętrza zapakowanego urządzenia przed wilgocią, zanieczyszczeniami lub gazami. Nic nie jest w 100% hermetyczne, ale kiedy mówimy o hermetyczności, to w praktyce mamy na myśli hermetyczność do tego stopnia, że wskaźnik nieszczelności jest tak niski, że urządzenia są bezpieczne w normalnych warunkach środowiskowych przez bardzo długi czas. Nasze hermetyczne zestawy składają się z elementów metalowych, szklanych i ceramicznych, metal-ceramika, ceramika-metal-ceramika, metal-ceramika-metal, metal-metal, metal-szkło, metal-szkło-metal, szkło-metal-szkło, szkło- metal i szkło do szkła oraz wszelkie inne kombinacje łączenia metal-szkło-ceramika. Możemy na przykład pokryć metalem elementy ceramiczne, aby mogły być silnie połączone z innymi elementami w zespole i miały doskonałe właściwości uszczelniające. Posiadamy wiedzę na temat pokrywania światłowodów lub przepustów metalem oraz lutowania lub lutowania ich do obudów, dzięki czemu żadne gazy nie przedostają się do obudowy. Dlatego są wykorzystywane do produkcji obudów elektronicznych do hermetyzacji wrażliwych urządzeń i ochrony ich przed atmosferą zewnętrzną. Oprócz doskonałych właściwości uszczelniających, inne właściwości, takie jak współczynnik rozszerzalności cieplnej, odporność na odkształcenia, charakter nieodgazowujący, bardzo długa żywotność, charakter nieprzewodzący, właściwości termoizolacyjne, charakter antystatyczny itp. sprawiają, że materiały szklane i ceramiczne są dobrym wyborem do określonych zastosowań. Informacje na temat naszego zakładu produkującego złączki ceramiczno-metalowe, hermetyczne uszczelnienia, przepusty próżniowe, komponenty wysokiego i ultrawysokiego podciśnienia oraz kontroli płynów można znaleźć tutaj:Broszura dotycząca fabryki komponentów hermetycznych CLICK Product Finder-Locator Service POPRZEDNIA STRONA
- Wire & Spring Forming, Shaping, Welding, Assembly of Wires, Coil, CNC
Wire & Spring Forming, Shaping, Welding, Assembly of Wires, Coil Compression Extension Torsion Flat Springs, Custom Wires, Helical Springs at AGS-TECH Inc. Formowanie drutu i sprężyn Produkujemy niestandardowe druty, montaż drutu, druty uformowane w pożądane kształty 2D i 3D, siatki druciane, siatki, obudowy, kosz, ogrodzenie, sprężynę drucianą, sprężynę płaską; skręcanie, ściskanie, rozciąganie, sprężyny płaskie i inne. Nasze procesy to formowanie drutu i sprężyn, ciągnienie drutu, kształtowanie, gięcie, spawanie, lutowanie, lutowanie, przebijanie, kształtowanie, wiercenie, fazowanie, szlifowanie, gwintowanie, powlekanie, czterosuwowe, formowanie ślizgowe, nawijanie, zwijanie, spęczanie. Zalecamy kliknięcie tutaj, aby POBIERZ nasze schematyczne ilustracje procesów formowania drutu i sprężyn autorstwa AGS-TECH Inc. Ten plik do pobrania ze zdjęciami i szkicami pomoże Ci lepiej zrozumieć informacje, które udostępniamy poniżej. • CIĄGANIE DRUTU: Używając sił rozciągających rozciągamy metalowy materiał i przeciągamy go przez matrycę, aby zmniejszyć średnicę i zwiększyć jej długość. Czasami używamy serii wykrojników. Jesteśmy w stanie wykonać matryce do każdego przekroju drutu. Używając materiału o dużej wytrzymałości na rozciąganie ciągniemy bardzo cienkie druty. Oferujemy druty obrabiane zarówno na zimno jak i na gorąco. • FORMOWANIE DRUTU : Rolka kalibrowanego drutu jest wygięta i ukształtowana w użyteczny produkt. Posiadamy możliwość formowania drutów o dowolnym przekroju, zarówno cienkich włókien jak i grubych drutów, takich jak te używane jako sprężyny pod podwoziem samochodów. Urządzenia, których używamy do formowania drutu to formowacze drutu ręczne i CNC, zwijarki, prasy mechaniczne, czterosuwowe, wieloślizgowe. Nasze procesy to ciągnienie, gięcie, prostowanie, spłaszczanie, rozciąganie, cięcie, spęczanie, lutowanie i spawanie, montaż, zwijanie, kształtowanie (lub skrzydlenie), przebijanie, gwintowanie drutu, wiercenie, fazowanie, szlifowanie, powlekanie i obróbka powierzchni. Nasz najnowocześniejszy sprzęt można skonfigurować do opracowywania bardzo złożonych projektów o dowolnym kształcie i wąskich tolerancjach. Oferujemy różne typy końcówek like sferyczne, spiczaste lub sfazowane dla Twoich przewodów. Większość naszych projektów formowania drutu ma minimalne lub zerowe koszty oprzyrządowania. Przykładowe czasy realizacji to zazwyczaj dni. Zmiany w projekcie/konfiguracji form przewodów można wprowadzić bardzo szybko. • FORMOWANIE SPRĘŻYN: AGS-TECH produkuje szeroką gamę sprężyn, w tym: -Sprężyna skrętna/podwójna skrętna -Sprężyna napinająca/ściskana -Sprężyna stała / zmienna -Cewka i sprężyna śrubowa -Sprężyna płaska i piórowa -Wiosna równowagi -Podkładka Belleville -Negator Wiosna -Sprężyna śrubowa o progresywnym tempie -Wiosna fali -Wolta Wiosna -Sprężyny stożkowe -Pierścienie wiosenne -Sprężyny zegarowe -Klipy Produkujemy sprężyny z różnych materiałów i możemy poprowadzić Cię zgodnie z Twoim zastosowaniem. Najczęstsze materiały to stal nierdzewna, chrom krzemowy, stal wysokowęglowa, niskowęglowa hartowana olejem, chromowo-wanadowa, brąz fosforowy, tytan, stop miedzi berylowej, ceramika wysokotemperaturowa. W produkcji sprężyn stosujemy różne techniki, w tym zwijanie CNC, nawijanie na zimno, nawijanie na gorąco, hartowanie, wykańczanie. Inne techniki wymienione powyżej w ramach formowania drutu są również powszechne w naszych operacjach produkcji sprężyn. • USŁUGI WYKOŃCZENIOWE DLA PRZEWODÓW I SPRĘŻYN: Możemy wykończyć Twoje produkty na wiele sposobów w zależności od Twojego wyboru i potrzeb. Niektóre typowe procesy, które oferujemy to: malowanie, malowanie proszkowe, powlekanie, zanurzanie winylu, anodowanie, odprężanie, obróbka cieplna, śrutowanie, bębnowanie, chromianowanie, nikiel bezelektrodowy, pasywacja, wypalana emalia, powłoka z tworzywa sztucznego , czyszczenie plazmowe. CLICK Product Finder-Locator Service POPRZEDNIA STRONA
- Sheet Metal Forming Fabrication, Stamping, Punching, Deep Drawing, CNC
Sheet Metal Forming and Fabrication, Stamping, Punching, Bending, Progressive Die, Spot Welding, Deep Drawing, Metal Blanking and Slitting at AGS-TECH Inc. Tłoczenie i obróbka blach Oferujemy tłoczenie blach, kształtowanie, formowanie, gięcie, wykrawanie, wykrawanie, cięcie wzdłużne, perforowanie, nacinanie, wycinanie, skrawanie, prasowanie, obróbkę, głębokie tłoczenie za pomocą wykrojników jednopunktowych / jednosuwowych, a także wykrojniki progresywne i przędzenie, formowanie gumy i hydroformowanie; cięcie blach strumieniem wody, plazmą, laserem, piłą, płomieniem; montaż blach metodą spawania, zgrzewania punktowego; wybrzuszanie i gięcie rur z blachy; wykańczanie powierzchni blach, w tym malowanie zanurzeniowe lub natryskowe, elektrostatyczne malowanie proszkowe, anodowanie, powlekanie galwaniczne, napylanie i inne. Nasze usługi obejmują zarówno szybkie prototypowanie blach, jak i produkcję wielkoseryjną. Zalecamy kliknięcie tutaj, abyPOBIERZ nasze schematyczne ilustracje procesów wytwarzania i tłoczenia blach autorstwa AGS-TECH Inc. Pomoże to lepiej zrozumieć informacje, które przekazujemy poniżej. • CIĘCIE BLACH: Oferujemy PRZYCIĘCIA i PRZECINKI. Odcięcia tną blachę po jednej ścieżce na raz i w zasadzie nie ma marnowania materiału, podczas gdy przy rozcięciach kształt nie może być precyzyjnie ułożony i dlatego pewna ilość materiału jest marnowana. Jednym z naszych najpopularniejszych procesów jest WYKRAWANIE, w którym z blachy wycinany jest kawałek materiału o okrągłym lub innym kształcie. Wycięty kawałek jest odpadem. Inną wersją wykrawania jest SLOTTING, gdzie wycinane są otwory prostokątne lub podłużne. Z drugiej strony WYKRAWANIE jest tym samym procesem co wykrawanie, z wyróżnieniem wycinanego kawałka, który jest pracą i jest zachowywany. FINE BLANKING, doskonała wersja wykrawania, tworzy cięcia z wąskimi tolerancjami i prostymi, gładkimi krawędziami i nie wymaga dodatkowych operacji w celu udoskonalenia obrabianego przedmiotu. Innym często stosowanym przez nas procesem jest SLITTING, czyli proces ścinania, w którym blacha jest cięta dwoma przeciwstawnymi okrągłymi ostrzami po prostej lub zakrzywionej ścieżce. Otwieracz do puszek to prosty przykład procesu cięcia. Innym popularnym dla nas procesem jest PERFORACJA, w której wiele otworów okrągłych lub o innym kształcie jest wybijanych w blasze w określony wzór. Typowym przykładem produktu perforowanego są metalowe filtry z wieloma otworami na płyny. W nacinaniu, kolejnym procesie cięcia blachy, usuwamy materiał z obrabianego przedmiotu, zaczynając od krawędzi lub w innym miejscu i tniemy do wewnątrz, aż do uzyskania pożądanego kształtu. Jest to progresywny proces, w którym każda operacja usuwa kolejny element, aż do uzyskania pożądanego konturu. W przypadku małych serii produkcyjnych czasami stosujemy stosunkowo wolniejszy proces zwany NIBBLING, który składa się z wielu szybkich wykrojów nakładających się otworów, aby wykonać większe, bardziej złożone cięcie. W PROGRESYWNYM CIĘCIU wykorzystujemy szereg różnych operacji, aby uzyskać pojedyncze cięcie lub określoną geometrię. Wreszcie GOLENIE wtórny proces pomaga nam poprawić krawędzie już wykonanych cięć. Służy do odcinania wiórów, szorstkich krawędzi na obróbce blach. • GIĘCIE BLACH : Oprócz cięcia, gięcie jest podstawowym procesem, bez którego nie bylibyśmy w stanie wyprodukować większości produktów. Przeważnie operacja na zimno, ale czasami również na ciepło lub na gorąco. Do tej operacji najczęściej używamy matryc i prasy. W PROGRESYWNYM GIĘCIU wykorzystujemy szereg różnych operacji stempla i matrycy w celu uzyskania pojedynczego gięcia lub określonej geometrii. AGS-TECH wykorzystuje różnorodne procesy gięcia i dokonuje wyboru w zależności od materiału przedmiotu obrabianego, jego wielkości, grubości, pożądanego rozmiaru gięcia, promienia, krzywizny i kąta gięcia, lokalizacji gięcia, ekonomii eksploatacji, ilości do wyprodukowania… itp. Używamy GIĘCIA V, gdzie stempel w kształcie litery V wciska blachę do matrycy w kształcie litery V i wygina ją. Dobry zarówno do bardzo ostrych, jak i rozwartych kątów oraz pomiędzy, w tym 90 stopni. Za pomocą wykrojników wykonujemy GIĘCIE KRAWĘDZI. Nasz sprzęt pozwala nam na uzyskanie kątów nawet większych niż 90 stopni. Podczas gięcia krawędzi obrabiany przedmiot jest umieszczony pomiędzy podkładką dociskową a matrycą, obszar do gięcia znajduje się na krawędzi matrycy, a reszta obrabianego przedmiotu jest utrzymywana nad przestrzenią jak belka wspornikowa. Kiedy stempel działa na część wspornikową, jest wyginany nad krawędzią matrycy. FLANGING to proces gięcia krawędzi, w wyniku którego powstaje kąt 90 stopni. Główne cele operacji to eliminacja ostrych krawędzi oraz uzyskanie geometrycznych powierzchni ułatwiających łączenie części. FREZOWANIE, inny powszechny proces gięcia krawędzi, tworzy zawinięcie na krawędzi części. Z drugiej strony podwijanie powoduje, że krawędź arkusza jest całkowicie zagięta na sobie. W SEAMING krawędzie dwóch części są zagięte i połączone. Z kolei DOUBLE SEAMING zapewnia wodoszczelne i hermetyczne połączenia blach. Podobnie jak w przypadku gięcia krawędzi, proces zwany GIĘCIEM OBROTOWYM wykorzystuje cylinder z wycięciem pod żądanym kątem i służy jako stempel. Gdy siła jest przenoszona na stempel, zamyka się on wraz z obrabianym przedmiotem. Rowek cylindra nadaje części wspornikowej pożądany kąt. Rowek może mieć kąt mniejszy lub większy niż 90 stopni. W AIR BENDING nie potrzebujemy, aby dolna matryca miała skośny rowek. Blacha jest podtrzymywana przez dwie powierzchnie po przeciwnych stronach iw pewnej odległości. Stempel następnie przykłada siłę we właściwym miejscu i wygina obrabiany przedmiot. GIĘCIE KANAŁU wykonuje się za pomocą stempla i matrycy w kształcie kanału, a U-BEND uzyskuje się za pomocą stempla w kształcie litery U. GIĘCIE PRZESUNIĘTE tworzy przesunięcia na arkuszu blachy. GIĘCIE ROLKOWE, technika dobra do grubej obróbki i gięcia dużych kawałków metalowych płyt, wykorzystuje trzy rolki do podawania i gięcia płyt do pożądanych krzywizn. Rolki są ułożone tak, aby uzyskać pożądane wygięcie pracy. Odległość i kąt między rolkami jest kontrolowany w celu uzyskania pożądanego rezultatu. Ruchoma rolka umożliwia kontrolę krzywizny. FORMOWANIE RUR to kolejna popularna operacja gięcia blach z wykorzystaniem wielu matryc. Rurki uzyskuje się po wielu czynnościach. FARBOWANIE wykonuje się również poprzez operacje gięcia. Zasadniczo jest to symetryczne zginanie w regularnych odstępach na całym kawałku blachy. Do karbowania można stosować różne kształty. Blacha falista jest sztywniejsza i ma lepszą odporność na zginanie, dzięki czemu znajduje zastosowanie w przemyśle budowlanym. FORMOWANIE ROLKI BLACHY, proces ciągły manufacturing jest stosowany do gięcia przekrojów poprzecznych o określonej geometrii za pomocą rolek, a praca jest wyginana w kolejnych krokach, a ostatnia rolka kończy pracę. W niektórych przypadkach stosuje się pojedynczą rolkę, a w niektórych przypadkach serię rolek. • POŁĄCZONE PROCESY CIĘCIA I GIĘCIA BLACH: Są to procesy, które jednocześnie tną i zginają. W PIERCING otwór jest tworzony za pomocą ostrego stempla. Gdy stempel poszerza otwór w blasze, materiał jest jednocześnie wyginany w wewnętrzny kołnierz otworu. Otrzymany kołnierz może pełnić ważne funkcje. Z drugiej strony operacja NACINANIA tnie i wygina arkusz, aby utworzyć podniesioną geometrię. • WYPĘDZANIE I ZGINANIE RUR METALOWYCH: W WYDŁUŻANIU pewna wewnętrzna część pustej rury jest poddawana działaniu ciśnienia, co powoduje wybrzuszenie rury na zewnątrz. Ponieważ rura znajduje się wewnątrz matrycy, geometria wybrzuszenia jest kontrolowana przez kształt matrycy. W GIĘCIE ROZCIĄGAJĄCYM metalowa rura jest rozciągana za pomocą sił równoległych do osi rury i sił zginających, aby naciągnąć rurę na blok szalunkowy. W DRAW BENDING zaciskamy rurę blisko jej końca do obrotowego bloku formującego, który wygina rurę podczas obracania. Wreszcie, podczas GIĘCIA KOMPRESYJNEGO rura jest przytrzymywana siłą do nieruchomego bloku formy, a matryca wygina ją nad blokiem formy. • GŁĘBOKIE CIĄGNIĘCIE : W jednej z naszych najpopularniejszych operacji używa się stempla, pasującej matrycy i pustego uchwytu. Półfabrykat z blachy jest umieszczany nad otworem matrycy, a stempel przesuwa się w kierunku półwyrobu trzymanego przez uchwyt półwyrobu. Po zetknięciu się, stempel wpycha blachę do wnęki matrycy, aby uformować produkt. Operacja głębokiego tłoczenia przypomina cięcie, jednak prześwit pomiędzy stemplem a matrycą uniemożliwia cięcie blachy. Kolejnym czynnikiem zapewniającym, że blacha jest głęboko ciągniona, a nie cięta, są zaokrąglone rogi matrycy i stempla, które zapobiegają ścinaniu i cięciu. Aby osiągnąć większy stopień głębokiego tłoczenia, wdrażany jest proces PRZERYWANIA, w którym kolejne głębokie tłoczenie odbywa się na części, która została już poddana procesowi głębokiego tłoczenia. W ODWROTNYM PRZERYSOWANIU głęboko rysowana część jest odwracana i rysowana w przeciwnym kierunku. Głębokie tłoczenie może zapewnić obiekty o nieregularnych kształtach, takie jak wypukłe, zwężające się lub schodkowe miseczki. W WYTŁACZANIU używamy pary matrycy męskiej i żeńskiej, aby odcisnąć na blasze projekt lub skrypt. • SPINNING : Operacja, w której płaski lub wstępnie uformowany przedmiot obrabiany jest utrzymywany między obracającym się trzpieniem a konikiem, a narzędzie wywiera lokalny nacisk na obrabiany przedmiot, stopniowo przesuwając się w górę trzpienia. W rezultacie przedmiot obrabiany jest owijany na trzpieniu i nabiera swojego kształtu. Używamy tej techniki jako alternatywy dla głębokiego rysowania, gdzie ilość zamówienia jest niewielka, części są duże (średnice do 20 stóp) i mają unikalne krzywe. Chociaż ceny za sztukę są ogólnie wyższe, koszty konfiguracji operacji przędzenia CNC są niskie w porównaniu do głębokiego tłoczenia. Wręcz przeciwnie, głębokie tłoczenie wymaga dużych nakładów początkowych na ustawienie, ale koszty jednostkowe są niskie, gdy wytwarzana jest duża ilość części. Inną wersją tego procesu jest OBRÓBKA TNĄCĄ, w której w obrabianym przedmiocie występuje również przepływ metalu. Przepływ metalu zmniejszy grubość obrabianego przedmiotu w trakcie trwania procesu. Jeszcze innym pokrewnym procesem jest TUBE SPINNING, który jest stosowany na częściach cylindrycznych. Również w tym procesie następuje przepływ metalu w przedmiocie obrabianym. Grubość jest w ten sposób zmniejszona, a długość rury zwiększona. Narzędzie można przesuwać, aby tworzyć elementy wewnątrz lub na zewnątrz rury. • GUMA FORMOWANIE BLACHY: Materiał gumowy lub poliuretanowy umieszcza się w wykrojniku pojemnika, a obrabiany przedmiot umieszcza się na powierzchni gumy. Następnie na obrabiany przedmiot działa stempel i wciska go w gumę. Ponieważ ciśnienie wytwarzane przez gumę jest niskie, głębokość wytwarzanych części jest ograniczona. Ponieważ koszty oprzyrządowania są niskie, proces ten nadaje się do produkcji małoseryjnej. • HYDROFORMOWANIE: Podobnie do formowania gumy, w tym procesie blacha jest wciskana przez stempel do cieczy pod ciśnieniem wewnątrz komory. Blacha jest umieszczona pomiędzy stemplem a gumową membraną. Membrana całkowicie otacza obrabiany przedmiot, a ciśnienie płynu wymusza jego formowanie na stemplu. Dzięki tej technice można uzyskać bardzo głębokie rysunki, nawet głębsze niż w procesie głębokiego rysowania. Produkujemy wykrojniki jednowykrojnikowe, jak również wykrojniki progresywne w zależności od Państwa części. Wykrojniki jednoskokowe są opłacalną metodą szybkiego wytwarzania dużych ilości prostych części blaszanych, takich jak podkładki. Do wytwarzania bardziej złożonych geometrii stosuje się matryce progresywne lub technikę głębokiego tłoczenia. W zależności od przypadku, cięcie strumieniem wody, laserem lub plazmą może być wykorzystane do niedrogiej, szybkiej i dokładnej produkcji części z blachy. Wielu dostawców nie ma pojęcia o tych alternatywnych technikach lub ich nie ma i dlatego przechodzą przez długie i kosztowne sposoby wytwarzania matryc i narzędzi, które tylko marnują czas i pieniądze klientów. Jeśli potrzebujesz niestandardowych elementów blaszanych, takich jak obudowy, obudowy elektroniczne itp. w ciągu kilku dni, skontaktuj się z nami, aby uzyskać usługę SZYBKIEGO PROTOTYPOWANIA BLACH. CLICK Product Finder-Locator Service POPRZEDNIE MENU
- Forging and Powdered Metallurgy, Die Forging, Heading, Hot Forging
Forging and Powdered Metallurgy, Die Forging, Heading, Hot Forging, Impression Die, Near Net Shape, Swaging, Metal Hobbing, Riveting, Coining from AGS-TECH Inc. Kucie metali i metalurgia proszków Rodzaje oferowanych przez nas procesów KUCIA METALU to kucie matrycowe na gorąco i na zimno, matryce otwarte i matrycowe zamknięte, matrycowe i odkuwki bezwypływowe, cogging, fulering, obrzeża i kucie precyzyjne, kształt zbliżony do siatki, kłos , kucie, kucie spęczane, kucie obwiedniowe do metalu, prasowanie i walcowanie, odkuwki promieniowe, orbitalne, pierścieniowe i izotermiczne, wybijanie, nitowanie, kucie kulek metalowych, przebijanie metali, zaklejanie, kucie wysokoenergetyczne. Nasze techniki METALURGII PROSZKÓW i PRZETWARZANIA PROSZKÓW to prasowanie i spiekanie proszków, impregnacja, infiltracja, prasowanie izostatyczne na gorąco i na zimno, formowanie wtryskowe metali, zagęszczanie na walcach, walcowanie proszków, wytłaczanie proszków, spiekanie sypkie, spiekanie iskrowe, prasowanie na gorąco. Zalecamy kliknięcie tutaj, aby POBIERZ nasze schematyczne ilustracje procesów kucia autorstwa AGS-TECH Inc. POBIERZ nasze schematyczne ilustracje procesów metalurgii proszków autorstwa AGS-TECH Inc. Te pliki do pobrania ze zdjęciami i szkicami pomogą Ci lepiej zrozumieć informacje, które udostępniamy poniżej. Przy kuciu metalu przykładane są siły ściskające i materiał jest odkształcany i uzyskuje się pożądany kształt. Najpopularniejszymi materiałami kutymi w przemyśle są żelazo i stal, ale wiele innych, takich jak aluminium, miedź, tytan, magnez, jest również szeroko kutych. Odkuwane elementy metalowe oprócz uszczelnionych pęknięć i zamkniętych pustych przestrzeni posiadają ulepszoną strukturę ziarna, dzięki czemu wytrzymałość części uzyskiwanych w tym procesie jest wyższa. Kucie wytwarza części, które są znacznie mocniejsze ze względu na swoją wagę niż części wykonane przez odlewanie lub obróbkę skrawaniem. Ponieważ części kute są kształtowane przez nadanie metalowi ostatecznego kształtu, metal nabiera kierunkowej struktury ziarnistej, która zapewnia doskonałą wytrzymałość części. Innymi słowy, części otrzymane w procesie kucia wykazują lepsze właściwości mechaniczne w porównaniu do prostych części odlewanych lub obrabianych. Waga metalowych odkuwek może wahać się od małych lekkich części do setek tysięcy funtów. Produkujemy odkuwki głównie do wymagających zastosowań mechanicznych, w których występują duże naprężenia na takie części jak części samochodowe, koła zębate, narzędzia robocze, narzędzia ręczne, wały turbin, przekładnie motocyklowe. Ponieważ koszty oprzyrządowania i ustawienia są stosunkowo wysokie, zalecamy ten proces produkcyjny tylko w przypadku produkcji wielkoseryjnej oraz w przypadku małoseryjnych, ale o wysokiej wartości elementów o znaczeniu krytycznym, takich jak podwozie lotnicze. Poza kosztem oprzyrządowania, czas realizacji produkcji dużych ilości części kutych może być dłuższy w porównaniu do niektórych prostych części obrabianych, ale technika ma kluczowe znaczenie dla części, które wymagają nadzwyczajnej wytrzymałości, takich jak śruby, nakrętki, specjalne zastosowanie elementy złączne, samochodowe, do wózków widłowych, części do dźwigów. • KUCIE NA GORĄCO i NA ZIMNO : Kucie matrycowe na gorąco, jak sama nazwa wskazuje, odbywa się w wysokich temperaturach, dlatego ciągliwość jest wysoka, a wytrzymałość materiału niska. Ułatwia to łatwe odkształcanie i kucie. Wręcz przeciwnie, kucie matrycowe na zimno odbywa się w niższych temperaturach i wymaga większych sił, co skutkuje umocnieniem przez zgniot, lepszym wykończeniem powierzchni i dokładnością wytwarzanych części. • KUCIE MATRYCOWE OTWARTE i WCISKOWE: W kuciu matrycowym matryce nie ograniczają ściskanego materiału, podczas gdy w kuciu matrycowym wnęki w matrycach ograniczają przepływ materiału podczas kucia do pożądanego kształtu. KUCIE PLASTIKOWE lub zwane również USTALANIEM, które w rzeczywistości nie jest tym samym, ale bardzo podobnym procesem, to proces otwartej matrycy, w którym obrabiany przedmiot jest umieszczony pomiędzy dwoma płaskimi matrycami, a siła ściskająca zmniejsza jego wysokość. Gdy wysokość wynosi reduced, zwiększa się szerokość obrabianego przedmiotu. HEADING, proces kucia spęczanego obejmuje cylindryczny materiał, który jest spęczany na swoim końcu, a jego przekrój jest lokalnie zwiększany. W główce materiał jest podawany przez matrycę, kuty, a następnie cięty na długość. Operacja jest w stanie szybko wyprodukować duże ilości elementów złącznych. Przeważnie jest to operacja obróbki na zimno, ponieważ jest wykorzystywana do wykonywania końcówek gwoździ, końcówek śrub, nakrętek i śrub tam, gdzie materiał wymaga wzmocnienia. Innym procesem otwartej matrycy jest COGGING, w którym obrabiany przedmiot jest kuty w serii kroków, z których każdy powoduje ściskanie materiału, a następnie ruch otwartej matrycy wzdłuż długości przedmiotu obrabianego. Na każdym kroku grubość jest zmniejszana, a długość nieznacznie zwiększana. Proces przypomina nerwowego ucznia gryzienie ołówka małymi krokami. Proces o nazwie FULLERING to kolejna metoda kucia matrycowego, którą często stosujemy jako wcześniejszy krok w celu rozprowadzenia materiału w elemencie obrabianym przed rozpoczęciem innych operacji kucia metalu. Używamy go, gdy obrabiany przedmiot wymaga kilku operacji kucia operations. Podczas pracy matryca o wypukłych powierzchniach odkształca się i powoduje wypływ metalu w obie strony. Podobny proces do fulerowania, EDGING z drugiej strony obejmuje otwartą matrycę z wklęsłymi powierzchniami, aby odkształcić obrabiany przedmiot. Obrzeża są również procesem przygotowawczym do kolejnych operacji kucia, dzięki czemu materiał przepływa z obu stron do obszaru pośrodku. KUCIE WCISKOWE lub KUCIE WKLEJOWE ZAMKNIĘTE, jak to się nazywa, wykorzystuje matrycę / formę, która ściska materiał i ogranicza jego przepływ w sobie. Matryca zamyka się, a materiał przyjmuje kształt wnęki matrycy/formy. PRECYZYJNE KUCIE, proces wymagający specjalnego sprzętu i formy, wytwarza części bez lub z bardzo małą ilością wypływu. Innymi słowy, części będą miały wymiary zbliżone do ostatecznych. W tym procesie dokładnie kontrolowana ilość materiału jest ostrożnie wkładana i umieszczana wewnątrz formy. Wdrażamy tę metodę w przypadku skomplikowanych kształtów o cienkich przekrojach, małych tolerancjach i kątach pochylenia oraz gdy ilości są wystarczająco duże, aby uzasadnić koszty formy i sprzętu. • KUCIE BEZWYBUCHOWE: Obrabiany przedmiot jest umieszczany w matrycy w taki sposób, że żaden materiał nie może wypłynąć z wnęki, tworząc wypływkę. Dzięki temu nie jest potrzebne żadne niepożądane przycinanie lampy błyskowej. Jest to precyzyjny proces kucia, a zatem wymaga ścisłej kontroli ilości użytego materiału. • KLUCZOWANIE METALU lub KUCIE PROMIENIOWE : Obrabiany przedmiot jest obrabiany obwodowo przez matrycę i kuty. Do wykucia wewnętrznej geometrii przedmiotu obrabianego można również użyć trzpienia. W operacji kształtowania obrabiany przedmiot zazwyczaj otrzymuje kilka suwów na sekundę. Typowymi przedmiotami wytwarzanymi przez kształtowanie są narzędzia o ostrych końcówkach, stożkowe pręty, śrubokręty. • PRZEBICIE METALU: Często używamy tej operacji jako dodatkowej operacji w produkcji części. Otwór lub wnęka jest tworzona przez przebijanie na powierzchni obrabianego przedmiotu bez przebijania się przez nią. Należy pamiętać, że przebijanie różni się od wiercenia, w wyniku którego powstaje otwór przelotowy. • WKRĘTANIE: Stempel o pożądanej geometrii jest wciskany w obrabiany przedmiot i tworzy wgłębienie o pożądanym kształcie. Nazywamy to ciosem HOB. Operacja wymaga wysokiego ciśnienia i jest przeprowadzana na zimno. W rezultacie materiał jest obrabiany na zimno i utwardzany zgniotowo. Dlatego proces ten jest bardzo odpowiedni do wytwarzania form, matryc i wnęk do innych procesów produkcyjnych. Po wyprodukowaniu płyty można z łatwością wyprodukować wiele identycznych wnęk bez konieczności obróbki ich pojedynczo. • KUCIE WALCOWE lub FORMOWANIE WALCOWE: Do kształtowania części metalowej używa się dwóch przeciwstawnych walców. Obrabiany przedmiot jest podawany do rolek, rolki obracają się i wciągają pracę do szczeliny, następnie obrabiana jest podawana przez rowkowaną część rolek, a siły ściskające nadają materiałowi pożądany kształt. Nie jest to proces walcowania, ale proces kucia, ponieważ jest to operacja dyskretna, a nie ciągła. Geometria na rowkach walców wykuwa materiał do wymaganego kształtu i geometrii. Wykonywany jest na gorąco. Ponieważ jest procesem kucia, wytwarza części o wyjątkowych właściwościach mechanicznych, dlatego używamy go do produkcji części samochodowych, takich jak wały, które muszą mieć wyjątkową wytrzymałość w trudnych warunkach pracy. • KUCIE ORBITALNE: Obrabiany przedmiot jest umieszczany we wnęce matrycy kuźniczej i kuty przez górną matrycę, która porusza się po ścieżce orbitalnej, obracając się po nachylonej osi. Przy każdym obrocie górna matryca kończy wywieranie sił ściskających na cały obrabiany przedmiot. Powtarzając te obroty kilka razy, wykonuje się wystarczające kucie. Zaletami tej techniki wytwarzania jest cicha praca i mniejsze potrzebne siły. Innymi słowy, przy niewielkich siłach można obracać ciężką matrycę wokół osi, aby wywrzeć duże naciski na część obrabianego przedmiotu, która styka się z matrycą. Części w kształcie dysku lub stożka są czasami dobrze dopasowane do tego procesu. • KUCIE PIERŚCIENIA: Często używamy do produkcji pierścieni bez szwu. Kolba jest przycinana na długość, spęczana, a następnie przebijana na wylot, aby utworzyć centralny otwór. Następnie nakłada się go na trzpień i matryca kuźnicza wbija go od góry, powoli obracając pierścień, aż do uzyskania żądanych wymiarów. • NITOWANIE: Powszechny proces łączenia części, rozpoczyna się od prostego kawałka metalu włożonego w uprzednio wykonane otwory przez części. Następnie dwa końce kawałka metalu są kute przez ściśnięcie połączenia między górną i dolną matrycą. • COINING: Inny popularny proces wykonywany przez prasę mechaniczną, wywierającą duże siły na niewielką odległość. Nazwa „coining” pochodzi od drobnych detali wykutych na powierzchni metalowych monet. Jest to głównie proces wykańczania produktu, w którym drobne szczegóły są uzyskiwane na powierzchniach w wyniku dużej siły przyłożonej przez matrycę, która przenosi te szczegóły na obrabiany przedmiot. • KUCIE KUL METALOWYCH: Produkty takie jak łożyska kulkowe wymagają wysokiej jakości precyzyjnie wykonanych kulek metalowych. W jednej technice zwanej SKEW ROLLING używamy dwóch przeciwstawnych rolek, które obracają się w sposób ciągły podczas ciągłego podawania materiału do rolek. Na jednym końcu dwóch rolek wyrzucane są metalowe kulki jako produkt. Drugą metodą kucia kulek metalowych jest użycie matrycy, która ściska wsad materiału umieszczony pomiędzy nimi, przyjmując kulisty kształt gniazda formy. Często produkowane kulki wymagają dodatkowych czynności, takich jak wykończenie i polerowanie, aby stać się produktem wysokiej jakości. • KUCIE IZOTERMICZNE / KUCIE matrycowe na gorąco: kosztowny proces wykonywany tylko wtedy, gdy stosunek korzyści do kosztów jest uzasadniony. Proces obróbki na gorąco, w którym matryca jest podgrzewana do mniej więcej tej samej temperatury co obrabiany przedmiot. Ponieważ zarówno matryca, jak i praca mają mniej więcej tę samą temperaturę, nie ma chłodzenia, a właściwości płynięcia metalu ulegają poprawie. Operacja dobrze pasuje do superstopów i materiałów o gorszej podatności na kowalność oraz materiałów, których właściwości mechaniczne są bardzo wrażliwe na małe gradienty i zmiany temperatury. • ROZMIAR METALU: Jest to proces wykańczania na zimno. Przepływ materiału jest nieograniczony we wszystkich kierunkach z wyjątkiem kierunku przyłożenia siły. W efekcie uzyskuje się bardzo dobre wykończenie powierzchni i dokładne wymiary. • KUCIE WYSOKIEJ ENERGII : Technika obejmuje górną formę przymocowaną do ramienia tłoka, która jest szybko popychana, gdy mieszanina paliwowo-powietrzna jest zapalana przez świecę zapłonową. Przypomina to działanie tłoków w silniku samochodowym. Forma bardzo szybko uderza w obrabiany przedmiot, a następnie dzięki przeciwciśnieniu bardzo szybko powraca do swojej pierwotnej pozycji. Praca jest kuta w ciągu kilku milisekund i dlatego nie ma czasu na ostygnięcie pracy. Jest to przydatne w przypadku trudnych do kucia części, które mają bardzo wrażliwe na temperaturę właściwości mechaniczne. Innymi słowy, proces jest tak szybki, że część jest formowana w stałej temperaturze przez cały czas i nie będzie gradientów temperatury na styku formy/elementu obrabianego. • W KUCIE MATRYCOWE metal jest ubijany pomiędzy dwoma dopasowanymi do siebie stalowymi blokami o specjalnych kształtach, zwanych matrycami. Kiedy metal jest wbijany między matryce, przybiera taki sam kształt jak kształty w matrycy. Gdy osiągnie swój ostateczny kształt, jest wyjmowany do ostygnięcia. Proces ten wytwarza mocne części o precyzyjnym kształcie, ale wymaga większej inwestycji w specjalistyczne matryce. Kucie spęczane zwiększa średnicę kawałka metalu poprzez jego spłaszczenie. Jest zwykle używany do wytwarzania małych części, zwłaszcza do formowania łbów elementów złącznych, takich jak śruby i gwoździe. • METALURGIA PROSZKÓW / PRZETWARZANIE PROSZKU: Jak sama nazwa wskazuje, obejmuje procesy produkcyjne do wytwarzania części stałych o określonej geometrii i kształtach z proszków. Jeśli do tego celu stosuje się proszki metali, jest to dziedzina metalurgii proszków, a jeśli stosuje się proszki niemetaliczne, to obróbka proszków. Części stałe są produkowane z proszków poprzez prasowanie i spiekanie. TŁOCZENIE PROSZKU służy do prasowania proszków w pożądane kształty. Najpierw materiał pierwotny jest fizycznie sproszkowany, dzieląc go na wiele małych pojedynczych cząstek. Mieszanka proszkowa jest napełniana do matrycy, a stempel przesuwa się w kierunku proszku i zagęszcza go do pożądanego kształtu. Przeważnie wykonywany w temperaturze pokojowej, przy prasowaniu proszku uzyskuje się stałą część i nazywa się ją zieloną wypraską. Spoiwa i smary są powszechnie stosowane w celu zwiększenia zagęszczalności. Jesteśmy zdolni do formowania na prasie proszkowej na prasach hydraulicznych o wydajności kilku tysięcy ton. Posiadamy również prasy o podwójnym działaniu z przeciwstawnymi stemplami górnymi i dolnymi, a także prasy o działaniu wielozadaniowym do bardzo złożonych geometrii części. Jednorodność, która jest ważnym wyzwaniem dla wielu zakładów metalurgii proszków / przetwórstwa proszków, nie stanowi dużego problemu dla AGS-TECH ze względu na nasze wieloletnie doświadczenie w produkcji takich części na zamówienie. Nawet w przypadku grubszych części, w których jednolitość stanowi wyzwanie, udało nam się. Jeśli zaangażujemy się w Twój projekt, wykonamy Twoje części. Jeśli zauważymy jakiekolwiek potencjalne zagrożenia, poinformujemy Cię in zaliczka. SPIEKANIE PROSZKU, które jest drugim etapem, polega na podniesieniu temperatury do pewnego stopnia i utrzymywaniu jej na tym poziomie przez określony czas, aby cząsteczki proszku w sprasowanej części mogły się ze sobą związać. Skutkuje to znacznie silniejszymi wiązaniami i wzmocnieniem obrabianego przedmiotu. Spiekanie odbywa się w temperaturze zbliżonej do temperatury topnienia proszku. Podczas spiekania nastąpi skurcz, wytrzymałość materiału, gęstość, ciągliwość, przewodność cieplna, przewodność elektryczna wzrastają. Posiadamy piece okresowe i ciągłe do spiekania. Jedną z naszych możliwości jest dostosowanie poziomu porowatości produkowanych przez nas części. Na przykład jesteśmy w stanie produkować filtry metalowe, utrzymując części do pewnego stopnia porowate. Stosując technikę o nazwie IMPREGNACJA wypełniamy pory w metalu płynem takim jak olej. Produkujemy np. łożyska impregnowane olejem, które są samosmarujące. W procesie INFILTRACJI pory metalu wypełniamy innym metalem o niższej temperaturze topnienia niż materiał bazowy. Mieszaninę ogrzewa się do temperatury pomiędzy temperaturami topnienia dwóch metali. W rezultacie można uzyskać pewne specjalne właściwości. Często wykonujemy również operacje drugorzędne, takie jak obróbka skrawaniem i kucie na częściach produkowanych proszkowo, gdy trzeba uzyskać specjalne cechy lub właściwości lub gdy część można wyprodukować przy mniejszej liczbie etapów procesu. PRASOWANIE IZOSTATYCZNE: W tym procesie do zagęszczania części wykorzystywane jest ciśnienie płynu. Proszki metali są umieszczane w formie wykonanej ze szczelnego elastycznego pojemnika. W prasowaniu izostatycznym nacisk wywierany jest z całego otoczenia, w przeciwieństwie do nacisku osiowego obserwowanego w konwencjonalnym prasowaniu. Zaletą prasowania izostatycznego jest jednolita gęstość w części, szczególnie w przypadku większych lub grubszych części, doskonałe właściwości. Jego wadą są długie czasy cyklu i stosunkowo niska dokładność geometryczna. TŁOCZENIE IZOSTATYCZNE NA ZIMNO odbywa się w temperaturze pokojowej, a elastyczna forma wykonana jest z gumy, PVC lub uretanu lub podobnych materiałów. Płyn używany do sprężania i zagęszczania to olej lub woda. Następuje konwencjonalne spiekanie zielonego wypraski. Z drugiej strony, prasowanie izostatyczne na gorąco odbywa się w wysokich temperaturach, a materiałem formy jest blacha lub ceramika o wystarczająco wysokiej temperaturze topnienia, która jest odporna na temperatury. Płyn pod ciśnieniem jest zwykle gazem obojętnym. Prasowanie i spiekanie wykonywane są w jednym kroku. Porowatość jest prawie całkowicie wyeliminowana, uzyskuje się jednolitą strukturę grain. Zaletą prasowania izostatycznego na gorąco jest możliwość wytwarzania części porównywalnych z połączeniem odlewania i kucia, przy jednoczesnym umożliwieniu stosowania materiałów nienadających się do odlewania i kucia. Wadą prasowania izostatycznego na gorąco jest długi czas cyklu, a co za tym idzie koszt. Nadaje się do krytycznych części o małej objętości. FORMOWANIE WTRYSKOWE METALU: Bardzo odpowiedni proces do produkcji skomplikowanych części o cienkich ściankach i szczegółowej geometrii. Najbardziej odpowiedni do mniejszych części. Proszki i spoiwo polimerowe są mieszane, podgrzewane i wtryskiwane do formy. Spoiwo polimerowe pokrywa powierzchnię cząstek proszku. Po formowaniu spoiwo jest usuwane przez ogrzewanie w niskiej temperaturze lub rozpuszczone za pomocą rozpuszczalnika. ZAGĘSZCZANIE WALCAMI / WALCOWANIE PROSZKU: Proszki są używane do produkcji ciągłych pasków lub arkuszy. Proszek podawany jest z podajnika i zagęszczany za pomocą dwóch obracających się rolek w arkusz lub paski. Operacja przeprowadzana jest na zimno. Blacha jest przenoszona do pieca do spiekania. Proces spiekania można powtórzyć po raz drugi. WYTŁACZANIE PROSZKU: Części o dużym stosunku długości do średnicy są wytwarzane przez wytłaczanie cienkiego pojemnika z blachy z proszkiem. SPIEKANIE LUZEM: Jak sama nazwa wskazuje, jest to bezciśnieniowa metoda zagęszczania i spiekania, odpowiednia do produkcji bardzo porowatych części, takich jak filtry metalowe. Proszek jest podawany do gniazda formy bez zagęszczania. SPIEKANIE LUZEM: Jak sama nazwa wskazuje, jest to bezciśnieniowa metoda zagęszczania i spiekania, odpowiednia do produkcji bardzo porowatych części, takich jak filtry metalowe. Proszek jest podawany do gniazda formy bez zagęszczania. Spiekanie iskrowe: Proszek jest prasowany w formie przez dwa przeciwstawne stemple, a do stempla doprowadzany jest prąd elektryczny o dużej mocy, który przechodzi przez sprasowany proszek umieszczony pomiędzy nimi. Wysoki prąd wypala warstwy powierzchniowe z cząstek proszku i spieka je pod wpływem wytworzonego ciepła. Proces jest szybki, ponieważ ciepło nie jest doprowadzane z zewnątrz, lecz jest generowane z wnętrza formy. TŁOCZENIE NA GORĄCO: Proszki są prasowane i spiekane w jednym kroku w formie, która może wytrzymać wysokie temperatury. Gdy matryca zagęszcza się, ciepło proszku jest do niego przykładane. Dobre dokładności i właściwości mechaniczne uzyskane tą metodą sprawiają, że jest to atrakcyjna opcja. Nawet metale ogniotrwałe mogą być przetwarzane przy użyciu materiałów do form, takich jak grafit. CLICK Product Finder-Locator Service POPRZEDNIE MENU
- Plastic Rubber Metal Extrusions, Extrusion Dies, Aluminum Extruding
Plastic Rubber Metal Extrusions, Extrusion Dies, Aluminum Extruding, Pipe Tube Forming, Plastic Profiles, Metal Profiles Manufacturing, PVC at AGS-TECH Inc. Wytłoczki, Produkty Wyciskane, Wytłaczane Używamy procesu EXTRUSION do wytwarzania produktów o stałym profilu przekroju, takich jak rury, rury i radiatory. Mimo, że można wytłaczać wiele materiałów, nasze najpopularniejsze profile są wykonane z metalu, polimerów/plastiku, ceramiki otrzymywanej metodą wytłaczania na zimno, ciepło lub na gorąco. Wytłoczone części nazywamy ekstrudatami lub ekstrudatami, jeśli liczba mnoga. Niektóre wyspecjalizowane wersje procesu, który wykonujemy, to obciąganie, współwytłaczanie i wytłaczanie złożone. Zalecamy kliknięcie tutaj, aby POBIERZ nasze schematyczne ilustracje procesów wytłaczania ceramiki metalowej i tworzyw sztucznych autorstwa AGS-TECH Inc. Pomoże to lepiej zrozumieć informacje, które przekazujemy poniżej. W wytłaczaniu materiał, który ma zostać wytłoczony, jest przepychany lub przeciągany przez matrycę, która ma żądany profil przekroju poprzecznego. Proces ten może być wykorzystany do wytwarzania skomplikowanych przekrojów z doskonałym wykończeniem powierzchni oraz do pracy na kruchym materiale. Za pomocą tego procesu można wyprodukować części o dowolnej długości. Aby uprościć etapy procesu: 1.) W ciepłych lub gorących ekstruzjach materiał jest podgrzewany i ładowany do pojemnika w prasie. Materiał jest prasowany i wypychany z matrycy. 2.) Wyprodukowany ekstrudat jest rozciągany w celu prostowania, poddawany obróbce cieplnej lub obróbce na zimno w celu polepszenia jego właściwości. Z drugiej strony COLD EXTRUSION odbywa się w temperaturze zbliżonej do pokojowej i ma zalety w postaci mniejszego utleniania, wysokiej wytrzymałości, bliższych tolerancji, dobrego wykończenia powierzchni i trwałości. WYTŁACZANIE NA CIEPŁO jest przeprowadzane powyżej temperatury pokojowej, ale poniżej temperatury rekrystalizacji. Oferuje kompromis i równowagę dla wymaganych sił, plastyczności i właściwości materiału, dlatego jest wyborem do niektórych zastosowań. WYTŁACZANIE NA GORĄCO odbywa się powyżej temperatury rekrystalizacji materiału. W ten sposób łatwiej jest przepchnąć materiał przez matrycę. Jednak koszt sprzętu jest wysoki. Im bardziej złożony profil wytłaczany, tym droższa jest matryca (oprzyrządowanie) i mniejsza jest wydajność produkcji. Przekroje matrycy oraz grubości mają ograniczenia zależne od materiału, który ma być wytłaczany. Ostre narożniki w matrycach są zawsze niepożądane i należy ich unikać, jeśli nie jest to konieczne. W zależności od wytłaczanego materiału oferujemy: • WYCISKI METALOWE : Najczęściej produkowane przez nas to aluminium, mosiądz, cynk, miedź, stal, tytan, magnez • WYTŁACZANIE TWORZYWA SZTUCZNEGO : Plastik jest topiony i formowany w ciągły profil. Nasze wspólne materiały przetwarzane to polietylen, nylon, polistyren, polichlorek winylu, polipropylen, plastik ABS, poliwęglan, akryl. Typowe produkty, które produkujemy to rury i przewody rurowe, ramy z tworzyw sztucznych. W tym procesie małe plastikowe kulki / żywica są podawane grawitacyjnie z leja do beczki wytłaczarki. Często mieszamy również barwniki lub inne dodatki do leja, aby nadać produktowi wymagane specyfikacje i właściwości. Materiał wchodzący do ogrzewanej beczki jest zmuszany przez obracającą się śrubę, aby opuścić beczkę na końcu i przejść przez pakiet sit w celu usunięcia zanieczyszczeń ze stopionego tworzywa sztucznego. Po przejściu pakietu sit plastik wchodzi do matrycy wytłaczarki. Matryca nadaje ruchomemu miękkiemu plastikowi kształt profilu podczas jego przechodzenia. Teraz ekstrudat przechodzi przez łaźnię wodną w celu schłodzenia. Inne techniki stosowane przez AGS-TECH Inc. od wielu lat to: • WYTŁACZANIE RUR I PRZEWODÓW : Rury i rurki z tworzyw sztucznych są formowane, gdy tworzywo sztuczne jest wytłaczane przez okrągłą matrycę kształtującą i chłodzone w łaźni wodnej, a następnie cięte na długość lub zwijane. Przezroczyste lub kolorowe, w paski, jedno lub dwuścienne, elastyczne lub sztywne, PE, PP, poliuretan, PVC, nylon, PC, silikon, winyl lub inne, mamy to wszystko. Posiadamy zapasy rur, a także możliwość produkcji zgodnie z Twoimi specyfikacjami. AGS-TECH produkuje rury spełniające wymagania FDA, UL i LE do zastosowań medycznych, elektrycznych i elektronicznych, przemysłowych i innych. • OVERJACKETING / OVERJACKETING EXTRUSION : Ta technika nakłada zewnętrzną warstwę tworzywa sztucznego na istniejący przewód lub kabel. Tą metodą produkowane są nasze przewody izolacyjne. • COEXTRUSION : jednocześnie wytłaczanych jest wiele warstw materiału. Wiele warstw jest dostarczanych przez wiele wytłaczarek. Różne grubości warstw można dostosować do wymagań klienta. Proces ten umożliwia użycie wielu polimerów, z których każdy ma inną funkcjonalność w produkcie. Dzięki temu można zoptymalizować szereg właściwości. • WYTŁACZANIE MIESZANKI: Pojedynczy lub wiele polimerów miesza się z dodatkami w celu uzyskania związku plastycznego. Nasze wytłaczarki dwuślimakowe wytwarzają wytłoczki mieszające. Matryce do wytłaczania są generalnie niedrogie w porównaniu do form metalowych. Jeśli płacisz znacznie więcej niż kilka tysięcy dolarów za małą lub średnią wielkość matrycy do wytłaczania aluminium, prawdopodobnie płacisz za dużo. Jesteśmy ekspertami w określaniu, która technika jest najbardziej opłacalna, najszybsza i najbardziej odpowiednia dla Twojej aplikacji. Czasami wyciskanie, a następnie obróbka części może zaoszczędzić sporo pieniędzy. Przed podjęciem zdecydowanej decyzji zapytaj nas najpierw o naszą opinię. Pomogliśmy wielu klientom w podjęciu właściwych decyzji. W przypadku niektórych powszechnie stosowanych profili metalowych możesz pobrać nasze broszury i katalogi, klikając kolorowy tekst poniżej. Jeśli jest to produkt z półki, który spełnia Twoje wymagania, będzie bardziej ekonomiczny. Pobierz nasze możliwości wytłaczania rur i rurek medycznych Pobierz nasze ekstrudowane radiatory • WTÓRNE PROCESY PRODUKCJI I WYTWARZANIA DO WYTŁACZANIA : Wśród procesów o wartości dodanej, które oferujemy dla produktów ekstrudowanych, są: -Niestandardowe gięcie rur i rur, formowanie i kształtowanie, odcinanie rur, formowanie końcówek rur, zwijanie rur, obróbka i wykańczanie, wiercenie i przebijanie otworów oraz wykrawanie, -Niestandardowe zespoły rur i rurek, montaż rur, spawanie, lutowanie i lutowanie -Gięcie, formowanie i kształtowanie na zamówienie; - Czyszczenie, odtłuszczanie, wytrawianie, pasywacja, polerowanie, anodowanie, galwanizacja, malowanie, obróbka cieplna, wyżarzanie i hartowanie, znakowanie, grawerowanie i etykietowanie, pakowanie na zamówienie. CLICK Product Finder-Locator Service POPRZEDNIA STRONA
- Casting and Machined Parts, CNC Manufacturing, Milling, Turning, Swiss
Casting and Machined Parts, CNC Manufacturing, Milling, Turning, Swiss Type Machining, Die Casting, Investment Casting, Lost Foam Cast Parts from AGS-TECH Inc. Odlewanie i obróbka Nasze niestandardowe techniki odlewania i obróbki to odlewy jednorazowe i jednorazowe, odlewy żelazne i nieżelazne, piasek, matryca, odśrodkowa, ciągła, ceramiczna forma, inwestycja, tracona pianka, kształt zbliżony do netto, stała forma (odlewanie ciśnieniowe grawitacyjne), gips odlewy formowe (odlewy gipsowe) i łupinowe, części obrabiane metodą frezowania i toczenia przy użyciu urządzeń konwencjonalnych i CNC, obróbka szwajcarska zapewniająca dużą przepustowość niedrogich drobnych elementów precyzyjnych, obróbka śrub pod elementy złączne, obróbka niekonwencjonalna. Należy pamiętać, że oprócz metali i stopów metali obrabiamy elementy ceramiczne, szklane i plastikowe, a także w niektórych przypadkach, gdy wykonanie formy nie jest atrakcyjne lub nie jest możliwe. Obróbka materiałów polimerowych wymaga specjalistycznego doświadczenia, które posiadamy ze względu na wyzwania, jakie stawiają tworzywa sztuczne i guma ze względu na ich miękkość, brak sztywności... itd. Informacje na temat obróbki ceramiki i szkła można znaleźć na naszej stronie poświęconej obróbce niekonwencjonalnej. AGS-TECH Inc. produkuje i dostarcza zarówno lekkie, jak i ciężkie odlewy. Dostarczamy odlewy metalowe i obrabiane części do kotłów, wymienników ciepła, samochodów, mikrosilników, turbin wiatrowych, urządzeń do pakowania żywności i innych. Zalecamy kliknięcie tutaj, aby POBIERZ nasze schematyczne ilustracje procesów obróbki i odlewania opracowane przez firmę AGS-TECH Inc. Pomoże to lepiej zrozumieć informacje, które przekazujemy poniżej. Przyjrzyjmy się szczegółowo niektórym z różnych technik, które oferujemy: • ODLEWANIE EKSPLOATACYJNYCH FORM: Ta szeroka kategoria odnosi się do metod, które obejmują formy tymczasowe i jednorazowe. Przykładami są piasek, gips, muszla, inwestycja (zwana również woskiem traconym) i odlewanie gipsu. • ODLEWANIE PIASKOWE: proces, w którym jako materiał formy używany jest piasek. Metoda bardzo stara i wciąż bardzo popularna do tego stopnia, że większość produkowanych odlewów metalowych jest wykonywana tą techniką. Niski koszt nawet przy produkcji małoseryjnej. Nadaje się do produkcji małych i dużych części. Technikę tę można wykorzystać do produkcji części w ciągu dni lub tygodni przy bardzo niewielkich nakładach inwestycyjnych. Wilgotny piasek jest spajany gliną, spoiwami lub specjalnymi olejami. Piasek jest zwykle zawarty w skrzynkach formierskich, a system wnęki i bramy jest tworzony przez zagęszczanie piasku wokół modeli. Procesy to: 1.) Umieszczenie modelu w piasku w celu wykonania formy 2.) Włączenie modelu i piasku do systemu bramkowania 3.) Usunięcie modelu 4.) Wypełnienie wnęki formy stopionym metalem 5.) Chłodzenie metalu 6.) Łamanie formy piaskowej i usuwanie odlewu • ODLEWANIE W FORMIE TYNKOWEJ: Podobnie jak w przypadku odlewania piaskowego, zamiast piasku, jako materiał formy stosuje się gips modelarski. Krótkie czasy realizacji produkcji, takie jak odlewanie w piasku i niedrogie. Dobre tolerancje wymiarowe i wykończenie powierzchni. Jego główną wadą jest to, że może być stosowany tylko z metalami o niskiej temperaturze topnienia, takimi jak aluminium i cynk. • ODLEWANIE W FORMIE POWŁOKI: Podobnie jak w przypadku odlewania w formach piaskowych. Gniazdo formy uzyskane przez utwardzoną skorupę z piasku i spoiwa z żywicy termoutwardzalnej zamiast kolby wypełnionej piaskiem jak w procesie odlewania w piasku. Prawie każdy metal nadający się do odlewania w piasku można odlewać metodą skorupową. Proces można podsumować jako: 1.) Produkcja formy skorupowej. Zastosowany piasek ma znacznie mniejszy rozmiar ziarna w porównaniu z piaskiem używanym do odlewania w piasku. Drobny piasek miesza się z żywicą termoutwardzalną. Metalowy wzór jest pokryty środkiem antyadhezyjnym, aby ułatwić zdejmowanie skorupy. Następnie model metalowy jest podgrzewany i mieszanina piasku jest porowata lub nadmuchana na model odlewania na gorąco. Na powierzchni wzoru tworzy się cienka powłoka. Grubość tej skorupy można regulować, zmieniając czas, w którym mieszanina piasku i żywicy styka się z metalowym wzorem. Luźny piasek jest następnie usuwany z pozostawionym wzorem pokrytym muszlą. 2.) Następnie skorupa i wzór są podgrzewane w piecu, aby skorupa stwardniała. Po całkowitym utwardzeniu skorupa jest wyrzucana z wzoru za pomocą szpilek wbudowanych we wzór. 3.) Dwie takie skorupy są łączone ze sobą przez sklejenie lub zaciśnięcie i tworzą kompletną formę. Teraz forma skorupowa jest wkładana do pojemnika, w którym podczas procesu odlewania jest podtrzymywana piaskiem lub śrutem metalowym. 4.) Teraz gorący metal można wlać do formy skorupowej. Zaletami odlewania skorupowego są produkty o bardzo dobrym wykończeniu powierzchni, możliwość wykonania skomplikowanych części z dużą dokładnością wymiarową, łatwość automatyzacji procesu, ekonomiczność przy produkcji wielkoseryjnej. Wadą jest to, że formy wymagają dobrej wentylacji ze względu na gazy, które powstają, gdy stopiony metal styka się ze spoiwem chemicznym, żywice termoutwardzalne i metalowe modele są drogie. Ze względu na koszt wzorów metalowych, technika ta może nie pasować do małych serii produkcyjnych. • ODLEWANIE INWESTYCYJNE (znane również jako ODLEWANIE LOST-WAX): Również bardzo stara technika, odpowiednia do wytwarzania wysokiej jakości części z dużą dokładnością, powtarzalnością, wszechstronnością i integralnością z wielu metali, materiałów ogniotrwałych i specjalnych stopów o wysokiej wydajności. Można wytwarzać zarówno małe, jak i duże części. Jest to kosztowny proces w porównaniu z niektórymi innymi metodami, ale główną zaletą jest możliwość wytwarzania części o zbliżonym kształcie, skomplikowanych konturach i szczegółach. Tak więc koszt jest w pewnym stopniu równoważony przez eliminację poprawek i obróbki w niektórych przypadkach. Chociaż mogą występować różnice, oto podsumowanie ogólnego procesu odlewania metodą traconego wosku: 1.) Tworzenie oryginalnego wzorca z wosku lub plastiku. Każdy odlew wymaga jednego wzoru, ponieważ są one niszczone w procesie. Potrzebna jest również forma, z której wykonywane są wzory i przez większość czasu forma jest odlewana lub obrabiana. Ponieważ forma nie musi być otwierana, można uzyskać skomplikowane odlewy, wiele modeli woskowych można połączyć jak gałęzie drzewa i zlać razem, umożliwiając w ten sposób produkcję wielu części z jednego wylania metalu lub stopu metalu. 2.) Następnie model zanurza się lub wylewa ogniotrwałą zawiesiną składającą się z bardzo drobnoziarnistej krzemionki, wody, spoiw. Powoduje to powstanie warstwy ceramicznej na powierzchni wzoru. Powłokę ogniotrwałą na wzorze pozostawia się do wyschnięcia i utwardzenia. Od tego etapu pochodzi nazwa odlewania metodą traconego wosku: Zawiesina ogniotrwała jest nakładana na wzór woskowy. 3.) Na tym etapie utwardzona forma ceramiczna jest odwracana do góry nogami i podgrzewana, aby wosk stopił się i wylał z formy. Pozostawia się wnękę do odlewania metalu. 4.) Po wyjęciu wosku forma ceramiczna jest podgrzewana do jeszcze wyższej temperatury, co powoduje jej wzmocnienie. 5.) Odlew metalu wlewa się do gorącej formy wypełniającej wszystkie skomplikowane sekcje. 6.) Odlew może się zestalić 7.) Na koniec forma ceramiczna jest łamana, a wyprodukowane części są wycinane z drzewa. Oto link do Broszury Odlewnictwa Inwestycyjnego • ODLEWANIE WZORÓW ODPAROWANYCH: Proces wykorzystuje wzór wykonany z materiału takiego jak pianka polistyrenowa, który odparowuje, gdy gorący stopiony metal jest wlewany do formy. Istnieją dwa rodzaje tego procesu: LOST FOAM CASTING, który wykorzystuje piasek niezwiązany oraz FULL MOLD CASTING, który wykorzystuje piasek związany. Oto ogólne etapy procesu: 1.) Wyprodukuj wzór z materiału takiego jak polistyren. Gdy będą produkowane duże ilości, wzór jest formowany. Jeżeli część ma złożony kształt, może być konieczne sklejenie kilku odcinków takiego materiału piankowego w celu utworzenia wzoru. Często pokrywamy wzór masą ogniotrwałą, aby uzyskać dobre wykończenie powierzchni odlewu. 2.) Wzór jest następnie umieszczany w piasku formierskim. 3.) Stopiony metal jest wlewany do formy, odparowując wzór piankowy, tj. w większości przypadków polistyren przepływający przez gniazdo formy. 4.) Stopiony metal pozostaje w formie piaskowej do stwardnienia. 5.) Po stwardnieniu usuwamy odlew. W niektórych przypadkach wytwarzany przez nas produkt wymaga rdzenia we wzorze. W odlewaniu wyparnym nie ma potrzeby umieszczania i zabezpieczania rdzenia we wnęce formy. Technika ta jest odpowiednia do wytwarzania bardzo złożonych geometrii, można ją łatwo zautomatyzować do produkcji wielkoseryjnej, a w odlewie nie ma linii podziału. Podstawowy proces jest prosty i ekonomiczny w realizacji. W przypadku produkcji wielkoseryjnej, ponieważ do wytworzenia wzorów z polistyrenu potrzebna jest matryca lub forma, może to być nieco kosztowne. • ODLEWANIE FORM NIEROZPRĘŻALNYCH: Ta szeroka kategoria odnosi się do metod, w których forma nie musi być ponownie przetwarzana po każdym cyklu produkcyjnym. Przykładami są odlewanie trwałe, ciśnieniowe, ciągłe i odśrodkowe. Uzyskuje się powtarzalność, a części można scharakteryzować jako KSZTAŁT BLISKO NETTO. • TRWAŁE ODLEWANIE FORM: Formy wielokrotnego użytku wykonane z metalu są używane do odlewania wielokrotnego. Forma stała może być używana dziesiątki tysięcy razy, zanim się zużyje. Do napełniania formy stosuje się zwykle grawitację, ciśnienie gazu lub próżnię. Formy (zwane również matrycami) są zwykle wykonane z żelaza, stali, ceramiki lub innych metali. Ogólny proces to: 1.) Obrabiaj i stwórz formę. Formę często wykonuje się z dwóch pasujących do siebie metalowych bloków, które można otwierać i zamykać. Zarówno elementy części, jak i system bramkowania są zazwyczaj obrabiane w formie odlewniczej. 2.) Wewnętrzne powierzchnie formy są pokryte zawiesiną zawierającą materiały ogniotrwałe. Pomaga to kontrolować przepływ ciepła i działa jak smar ułatwiający usuwanie odlewu. 3.) Następnie stałe połówki formy są zamykane i forma jest podgrzewana. 4.) Stopiony metal wlewa się do formy i pozostawia do zestalenia. 5.) Zanim nastąpi duże schłodzenie, wyjmujemy część z formy stałej za pomocą wypychaczy, gdy połówki formy są otwarte. Często stosujemy odlewanie w formach trwałych do metali o niskiej temperaturze topnienia, takich jak cynk i aluminium. Do odlewów staliwnych używamy grafitu jako materiału do formowania. Niekiedy uzyskujemy złożone geometrie za pomocą rdzeni w formach trwałych. Zaletami tej techniki są odlewy o dobrych właściwościach mechanicznych uzyskiwanych dzięki szybkiemu chłodzeniu, jednorodność właściwości, dobra dokładność i wykończenie powierzchni, niskie współczynniki odrzutów, możliwość automatyzacji procesu i ekonomiczne wytwarzanie dużych ilości. Wadą są wysokie koszty początkowej konfiguracji, które sprawiają, że nie nadaje się do operacji o małej objętości oraz ograniczenia wielkości produkowanych części. • ODLEWANIE MATRYC: Matryca jest obrabiana maszynowo, a stopiony metal jest wpychany pod wysokim ciśnieniem do wnęk formy. Możliwe są zarówno odlewy ciśnieniowe z metali nieżelaznych, jak i metali żelaznych. Proces nadaje się do dużych serii produkcyjnych małych i średnich części z detalami, wyjątkowo cienkimi ściankami, spójnością wymiarową i dobrym wykończeniem powierzchni. AGS-TECH Inc. jest w stanie wyprodukować tą techniką ściany o grubości nawet 0,5 mm. Podobnie jak w przypadku odlewania w formach trwałych, forma musi składać się z dwóch połówek, które mogą się otwierać i zamykać w celu usunięcia wyprodukowanej części. Forma odlewnicza może mieć wiele wnęk, aby umożliwić produkcję wielu odlewów w każdym cyklu. Formy do odlewania ciśnieniowego są bardzo ciężkie i znacznie większe niż produkowane przez nie części, a zatem również drogie. Bezpłatnie naprawiamy i wymieniamy zużyte matryce dla naszych klientów, o ile ponownie zamówią u nas swoje części. Nasze matryce mają długą żywotność w zakresie kilkuset tysięcy cykli. Oto podstawowe uproszczone etapy procesu: 1.) Produkcja formy ogólnie ze stali 2.) Forma zainstalowana na maszynie do odlewania ciśnieniowego 3.) Tłok wymusza przepływ stopionego metalu w zagłębieniach matrycy, wypełniając zawiłe rysy i cienkie ścianki 4.) Po napełnieniu formy stopionym metalem odlew pozostawia się do utwardzenia pod ciśnieniem 5.) Forma jest otwierana, a odlew usuwany za pomocą kołków wypychaczy. 6.) Teraz pusta matryca jest ponownie nasmarowana i zaciśnięta do następnego cyklu. W odlewaniu ciśnieniowym często stosujemy formowanie wkładek, w którym do formy wbudowujemy dodatkową część i odlewamy wokół niej metal. Po zestaleniu części te stają się częścią odlewanego produktu. Zaletami odlewania ciśnieniowego są dobre właściwości mechaniczne części, możliwość tworzenia skomplikowanych detali, drobne szczegóły i dobre wykończenie powierzchni, wysokie tempo produkcji, łatwa automatyzacja. Wady to: Niezbyt odpowiednia dla małych objętości ze względu na wysoki koszt matrycy i sprzętu, ograniczenia w kształtach, które można odlewać, małe okrągłe ślady na odlewanych częściach wynikające ze styku kołków wypychaczy, cienka wypływka metalu wyciskanego na linii podziału, potrzeba w przypadku otworów wentylacyjnych wzdłuż linii podziału między matrycą, konieczność utrzymania niskiej temperatury formy przy użyciu cyrkulacji wody. • ODLEWANIE ODŚRODKOWE: Stopiony metal jest wlewany do środka formy obrotowej na osi obrotu. Siły odśrodkowe wyrzucają metal w kierunku obrzeża i pozwala na krzepnięcie, gdy forma nadal się obraca. Można stosować zarówno obroty osi poziomej, jak i pionowej. Odlewane mogą być zarówno części o okrągłych powierzchniach wewnętrznych, jak i inne nieokrągłe kształty. Proces można podsumować jako: 1.) Stopiony metal wlewa się do formy odśrodkowej. Metal jest następnie dociskany do ścian zewnętrznych w wyniku wirowania formy. 2.) Gdy forma się obraca, odlew metalu twardnieje Odlewanie odśrodkowe jest odpowiednią techniką do produkcji wydrążonych części cylindrycznych, takich jak rury, nie ma potrzeby stosowania wlewów, pionów i elementów zamykających, dobre wykończenie powierzchni i szczegółowe cechy, brak problemów ze skurczem, możliwość produkcji długich rur o bardzo dużych średnicach, wysoka wydajność produkcyjna . • ODLEWANIE CIĄGŁE (ODLEWANIE PASEM): Stosowane do odlewania ciągłej długości metalu. Zasadniczo stopiony metal jest odlewany w dwuwymiarowy profil formy, ale jego długość jest nieokreślona. Nowy stopiony metal jest stale podawany do formy, gdy odlew przesuwa się w dół, a jego długość wzrasta wraz z upływem czasu. Metale takie jak miedź, stal, aluminium odlewane są w długie pasma w procesie ciągłego odlewania. Proces może mieć różne konfiguracje, ale wspólną można uprościć jako: 1.) Stopiony metal jest wlewany do pojemnika znajdującego się wysoko nad formą w dobrze obliczonych ilościach i szybkościach przepływu i przepływa przez formę chłodzoną wodą. Metalowy odlew wlany do formy krzepnie do listwy startowej umieszczonej na dnie formy. Ta listwa startowa daje rolkom coś, za co mogą się początkowo chwycić. 2.) Długie metalowe pasmo jest przenoszone na rolkach ze stałą prędkością. Rolki zmieniają również kierunek przepływu metalowego pasma z pionowego na poziomy. 3.) Po przebyciu pewnej odległości przez odlewanie ciągłe, palnik lub piła poruszająca się wraz z odlewem szybko przycina go do żądanej długości. Proces ciągłego odlewania można zintegrować z ROLLING PROCESS, w którym metal odlewany w sposób ciągły może być podawany bezpośrednio do walcarki w celu wytworzenia belek dwuteowych, belek teowych… itd. Odlewanie ciągłe zapewnia jednolite właściwości w całym produkcie, charakteryzuje się wysokim stopniem krzepnięcia, zmniejsza koszty ze względu na bardzo niskie straty materiału, oferuje proces, w którym ładowanie metalu, wylewanie, krzepnięcie, cięcie i usuwanie odlewu odbywa się w trybie ciągłym i co skutkuje wysoką wydajnością i wysoką jakością. Głównym czynnikiem jest jednak wysoka inwestycja początkowa, koszty instalacji i wymagania przestrzenne. • USŁUGI OBRÓBCZE : Oferujemy obróbkę trzy-, cztero- i pięcioosiową. Rodzaje stosowanych przez nas procesów obróbki to TOCZENIE, FREZOWANIE, WIERCENIE, WYTACZANIE, PRZECIĄGANIE, STRUGANIE, PIŁOWANIE, SZLIFOWANIE, DOCIERANIE, POLEROWANIE i OBRÓBKA NIETRADYCYJNA, która jest dalej rozwijana w innym menu naszej strony internetowej. Do większości naszej produkcji używamy maszyn CNC. Jednak w przypadku niektórych operacji konwencjonalne techniki są lepiej dopasowane i dlatego również na nich polegamy. Nasze możliwości obróbki osiągają najwyższy możliwy poziom, a niektóre najbardziej wymagające części są produkowane w zakładzie posiadającym certyfikat AS9100. Łopatki do silników odrzutowych wymagają wysoce specjalistycznego doświadczenia produkcyjnego i odpowiedniego sprzętu. Przemysł lotniczy ma bardzo surowe standardy. Niektóre elementy o złożonej strukturze geometrycznej najłatwiej wytwarza się za pomocą obróbki pięcioosiowej, która występuje tylko w niektórych zakładach obróbczych, w tym w naszej. Nasz certyfikowany zakład lotniczy posiada niezbędne doświadczenie spełniające obszerne wymagania dotyczące dokumentacji przemysłu lotniczego. W operacjach TOCZENIA przedmiot obrabiany jest obracany i przesuwany względem narzędzia skrawającego. Do tego procesu używana jest maszyna zwana tokarką. W FREZOWANIU maszyna zwana frezarką ma obrotowe narzędzie, które powoduje, że krawędzie tnące opierają się o obrabiany przedmiot. Operacje WIERCENIA obejmują obrotowy nóż z krawędziami tnącymi, który wytwarza otwory w kontakcie z obrabianym przedmiotem. Zwykle stosuje się wiertarki, tokarki lub młyny. W operacjach WYTACZANIA narzędzie z pojedynczą zagiętą, spiczastą końcówką jest przesuwane do zgrubnego otworu w obracającym się przedmiocie obrabianym, aby nieznacznie powiększyć otwór i poprawić dokładność. Służy do precyzyjnego wykańczania. PRZECIĄGANIE polega na użyciu narzędzia zębatego do usuwania materiału z przedmiotu obrabianego w jednym przejściu przeciągania (narzędzie zębate). W przeciąganiu liniowym przeciąganie przebiega liniowo po powierzchni przedmiotu obrabianego, aby wykonać cięcie, podczas gdy w przeciąganiu obrotowym przeciąganie jest obracane i wciskane w przedmiot obrabiany, aby wyciąć kształt symetryczny względem osi. OBRÓBKA TYPU SZWAJCARSKIEGO jest jedną z naszych cennych technik, których używamy do wielkoseryjnej produkcji małych, precyzyjnych części. Na tokarce typu szwajcarskiego niedrogo toczymy małe, złożone, precyzyjne części. W przeciwieństwie do konwencjonalnych tokarek, w których przedmiot obrabiany jest nieruchomy, a narzędzie jest w ruchu, w centrach tokarskich typu Swiss przedmiot obrabiany może poruszać się w osi Z, a narzędzie jest nieruchome. W obróbce typu szwajcarskiego półfabrykat jest utrzymywany w maszynie i przesuwany przez tuleję prowadzącą w osi Z, odsłaniając tylko część do obróbki. W ten sposób zapewniony jest mocny chwyt i bardzo wysoka dokładność. Dostępność narzędzi pod napięciem umożliwia frezowanie i wiercenie w miarę przesuwania się materiału z tulei prowadzącej. Oś Y urządzeń typu szwajcarskiego zapewnia pełne możliwości frezowania i oszczędza dużą ilość czasu w produkcji. Ponadto nasze maszyny posiadają wiertła i narzędzia wytaczarskie, które działają na części, gdy jest ona trzymana we wrzecionie pomocniczym. Nasze możliwości obróbki Swiss-Type dają nam w pełni zautomatyzowaną, kompletną obróbkę w jednej operacji. Obróbka skrawaniem jest jednym z największych segmentów działalności AGS-TECH Inc. Używamy go jako operacji podstawowej lub operacji drugorzędnej po odlewaniu lub wytłaczaniu części, aby wszystkie specyfikacje rysunkowe były spełnione. • USŁUGI WYKOŃCZENIA POWIERZCHNI: Oferujemy szeroką gamę obróbki powierzchni i wykańczania powierzchni, takich jak kondycjonowanie powierzchni w celu zwiększenia przyczepności, osadzanie cienkiej warstwy tlenku w celu zwiększenia przyczepności powłoki, piaskowanie, chem-film, anodowanie, azotowanie, malowanie proszkowe, powlekanie natryskowe , różne zaawansowane techniki metalizacji i powlekania, w tym rozpylanie, wiązka elektronów, odparowanie, powlekanie, twarde powłoki, takie jak diamentopodobny węgiel (DLC) lub powłoka tytanowa do narzędzi wiertniczych i skrawających. • USŁUGI ZNAKOWANIA I ETYKIETOWANIA PRODUKTÓW: Wielu naszych klientów wymaga znakowania i etykietowania, znakowania laserowego, grawerowania na częściach metalowych. Jeśli masz taką potrzebę, porozmawiajmy, która opcja będzie dla Ciebie najlepsza. Oto niektóre z powszechnie stosowanych produktów odlewanych z metalu. Ponieważ są one gotowe, możesz zaoszczędzić na kosztach form, jeśli którykolwiek z nich spełni Twoje wymagania: KLIKNIJ TUTAJ, ABY POBRAĆ nasze pudełka z odlewanego ciśnieniowo aluminium serii 11 firmy AGS-Electronics CLICK Product Finder-Locator Service POPRZEDNIA STRONA
- Custom Manufactured Parts, Assemblies, Plastic Mold, Casting,Machining
Custom Manufactured Parts, Assemblies, Plastic Mold, Rubber Molding, Metal Casting, CNC Machining, Turning, Milling, Electrical Electronic Optical Assembly PCBA Części produkowane na zamówienie & Zespoły i produkty Czytaj więcej Formy i formy z tworzyw sztucznych i gumy Czytaj więcej Odlewanie i obróbka Czytaj więcej Wytłaczanie, produkty wyciskane Czytaj więcej Tłoczenie i obróbka blach Czytaj więcej Kucie metali i metalurgia proszków Czytaj więcej Formowanie drutu i sprężyn Czytaj więcej Formowanie i kształtowanie szkła i ceramiki Czytaj więcej Produkcja przyrostowa i szybka Czytaj więcej Produkcja kompozytów i materiałów kompozytowych Czytaj więcej Procesy łączenia, montażu i mocowania Produkujemy dla Państwa części i zespoły oraz oferujemy następujące procesy produkcyjne: • Formy i części z tworzyw sztucznych i gumy. Formowanie wtryskowe, termoformowanie, formowanie termoutwardzalne, formowanie próżniowe, formowanie z rozdmuchem, formowanie rotacyjne, formowanie przez odlewanie, formowanie wkładek i inne. • Profile plastikowe, gumowe i metalowe • Odlewy żelazne i nieżelazne oraz elementy obrabiane wykonane technikami frezowania i toczenia, obróbka typu szwajcarskiego. • Części do metalurgii proszków • Tłoczenie metali i niemetali, formowanie blach, spawane zestawy blach • Kucie na zimno i na gorąco • Druty, spawane zespoły drutów, formowanie drutu • Różne rodzaje sprężyn, formowanie sprężyn • Produkcja kół zębatych, skrzynia biegów, sprzęgło, ślimak, reduktor prędkości, cylinder, pasy transmisyjne, łańcuchy transmisyjne, elementy skrzyni biegów • Niestandardowe hartowane i kuloodporne szkło zgodne ze standardami NATO i wojskowymi • Kulki, łożyska, koła pasowe i zespoły kół pasowych • Zawory i elementy pneumatyczne, takie jak O-ring, podkładka i uszczelki • Części i podzespoły szklane i ceramiczne, elementy odporne na próżnię i hermetyczne, łączenie metal-ceramika i ceramika-ceramika. • Różne typy zespołów mechanicznych, optomechanicznych, elektromechanicznych, optoelektronicznych. • Łączenie metal-guma, metal-plastik • Rury i przewody rurowe, formowanie rur, gięcie i niestandardowe zespoły rur, produkcja mieszków. • Produkcja włókna szklanego • Spawanie różnymi technikami np. spawanie punktowe, spawanie laserowe, MIG, TIG. Zgrzewanie ultradźwiękowe części z tworzyw sztucznych. • Szeroki wybór obróbki powierzchni i wykończeń powierzchni, takich jak kondycjonowanie powierzchni w celu zwiększenia przyczepności, osadzanie cienkiej warstwy tlenku w celu zwiększenia przyczepności powłoki, piaskowanie, chem-film, anodowanie, azotowanie, malowanie proszkowe, powlekanie natryskowe, różne zaawansowane techniki metalizacji i powlekania w tym rozpylanie, wiązka elektronów, odparowanie, platerowanie, twarde powłoki, takie jak diamentopodobny węgiel (DLC) lub tytan do narzędzi tnących i wiertniczych. • Znakowanie i etykietowanie, znakowanie laserowe na częściach metalowych, drukowanie na częściach plastikowych i gumowych Pobierz broszurę dotyczącą wspólnych terminów inżynierii mechanicznej używanych przez projektantów i inżynierów Tworzymy produkty zgodnie z Twoimi konkretnymi specyfikacjami i wymaganiami. Aby zaoferować Państwu najwyższą jakość, dostawę i ceny, produkujemy produkty na całym świecie w Chinach, Indiach, Tajwanie, Filipinach, Korei Południowej, Malezji, Sri Lance, Turcji, USA, Kanadzie, Niemczech, Wielkiej Brytanii i Japonii. To sprawia, że jesteśmy znacznie silniejsi i bardziej konkurencyjni na całym świecie niż jakikolwiek inny niestandardowy manufacturer. Nasze produkty są wytwarzane w środowiskach posiadających certyfikaty ISO9001:2000, QS9000, ISO14001, TS16949 i posiadają znak CE, UL oraz spełniają inne standardy branżowe. Gdy zostaniemy wyznaczeni do Twojego projektu, możemy zająć się całą produkcją, montażem, testowaniem, kwalifikacją, wysyłką i odprawą celną, jak chcesz. Jeśli wolisz, możemy magazynować Twoje części, montować niestandardowe zestawy, drukować i oznaczać nazwę i markę Twojej firmy oraz dostarczać do Twoich klientów. Innymi słowy, w razie potrzeby możemy być również Twoim centrum magazynowym i dystrybucyjnym. Ponieważ nasze magazyny znajdują się w pobliżu głównych portów morskich, daje nam to przewagę logistyczną. Na przykład, gdy Twoje produkty dotrą do dużego portu morskiego w USA, możemy transportować je bezpośrednio do pobliskiego magazynu, gdzie możemy przechowywać, montować, tworzyć zestawy, ponownie oznaczać, drukować, pakować zgodnie z Twoim wyborem i upuszczać wysyłaj do swoich klientów. Dostarczamy nie tylko produkty. Nasza firma pracuje na niestandardowych umowach, w których przychodzimy do Twojej witryny, oceniamy Twój projekt na miejscu i opracowujemy propozycję projektu specjalnie zaprojektowaną dla Ciebie. Następnie wysyłamy nasz doświadczony zespół do realizacji projektu. Więcej informacji o naszej pracy inżynierskiej można znaleźć na http://www.ags-engineering.com - Podejmujemy się małych projektów jak i dużych projektów na skalę przemysłową. W pierwszej kolejności możemy połączyć Cię przez telefon, telekonferencję lub komunikator MSN z członkami naszego zespołu ekspertów, dzięki czemu możesz komunikować się bezpośrednio z ekspertem, zadawać pytania i omawiać swój projekt. Zadzwoń do nas, a w razie potrzeby przyjedziemy i Cię odwiedzimy. POPRZEDNIA STRONA