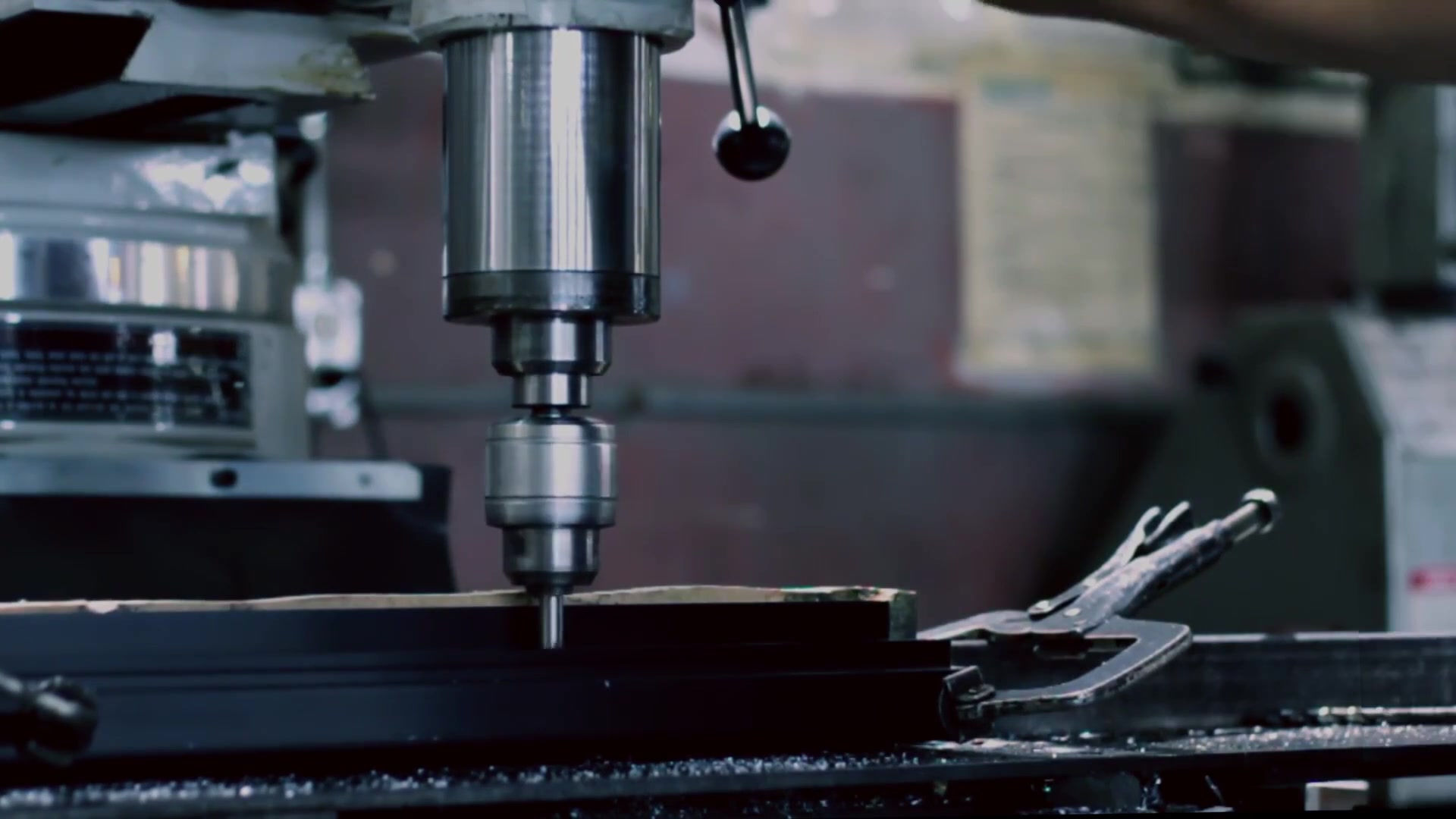
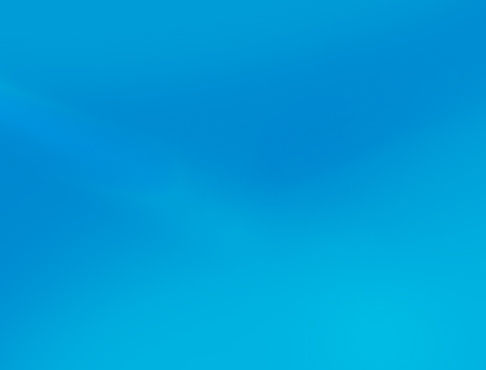
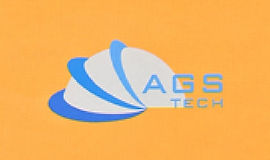
Globalny producent na zamówienie, integrator, konsolidator, partner outsourcingowy w zakresie szerokiej gamy produktów i usług.
Jesteśmy Twoim źródłem kompleksowej obsługi w zakresie produkcji, wytwarzania, inżynierii, konsolidacji, integracji, outsourcingu produktów i usług produkowanych na zamówienie oraz gotowych.
Choose your Language
-
Produkcja na zamówienie
-
Produkcja kontraktowa w kraju i na świecie
-
Outsourcing produkcji
-
Zamówienia krajowe i globalne
-
Konsolidacja
-
Integracja inżynierska
-
Usługi inżynieryjne
Search Results
Znaleziono 164 wyniki za pomocą pustego wyszukiwania
- Test Equipment for Furniture Testing
Test Equipment for Furniture Testing, Sofa Durability Tester, Chair Base Static Tester, Chair Drop Impact Tester, Mattress Firmness Tester Testery elektroniczne Termin TESTER ELEKTRONICZNY odnosi się do sprzętu testowego, który jest używany głównie do testowania, kontroli i analizy elementów i systemów elektrycznych i elektronicznych. Oferujemy najpopularniejsze w branży: ZASILACZE I URZĄDZENIA GENERUJĄCE SYGNAŁ: ZASILACZ, GENERATOR SYGNAŁU, SYNTEZATOR CZĘSTOTLIWOŚCI, GENERATOR FUNKCJI, GENERATOR WZORÓW CYFROWYCH, GENERATOR IMPULSÓW, WTRYSKIWACZ SYGNAŁU MIERNIKI: MULTIMETRY CYFROWE, MIERNIK LCR, MIERNIK EMF, MIERNIK POJEMNOŚCI, PRZYRZĄD MOSTKOWY, MIERNIK CĘGOWY, GAUSMETR/TESLAMETR/MAGNETOMIER, MIERNIK REZYSTANCJI UZIEMIENIA ANALIZATORY: OSCYLOSKOPY, ANALIZATOR LOGIKI, ANALIZATOR WIDMA, ANALIZATOR PROTOKOŁÓW, ANALIZATOR SYGNAŁÓW WEKTOROWYCH, REFLEKTOMETR W DZIEDZINIE CZASU, PÓŁPRZEWODNIK ŚLEDZENIE KRZYWEJ, ANALIZATOR SIECI, OBRACANIE FAZ, ROTACJA FAZY Aby uzyskać szczegółowe informacje i podobny sprzęt, odwiedź naszą stronę internetową poświęconą sprzętowi: http://www.sourceindustrialsupply.com Przyjrzyjmy się pokrótce niektórym z tych urządzeń, które są używane na co dzień w całej branży: Dostarczane przez nas zasilacze elektryczne do celów metrologicznych są urządzeniami dyskretnymi, stacjonarnymi i wolnostojącymi. REGULOWANE ZASILACZE ELEKTRYCZNE są jednymi z najpopularniejszych, ponieważ ich wartości wyjściowe można regulować, a ich napięcie wyjściowe lub prąd są utrzymywane na stałym poziomie, nawet przy wahaniach napięcia wejściowego lub prądu obciążenia. IZOLOWANE ZASILACZE mają wyjścia mocy, które są elektrycznie niezależne od ich mocy wejściowych. W zależności od metody konwersji mocy istnieją ZASILACZE LINIOWE i PRZEŁĄCZALNE. Zasilacze liniowe przetwarzają moc wejściową bezpośrednio ze wszystkimi aktywnymi komponentami konwersji mocy pracującymi w obszarach liniowych, podczas gdy zasilacze impulsowe mają komponenty pracujące głównie w trybach nieliniowych (takich jak tranzystory) i konwertują moc na impulsy AC lub DC przed przetwarzanie. Zasilacze impulsowe są generalnie bardziej wydajne niż zasilacze liniowe, ponieważ tracą mniej energii ze względu na krótszy czas, jaki ich komponenty spędzają w liniowych obszarach działania. W zależności od zastosowania używane jest zasilanie prądem stałym lub zmiennym. Inne popularne urządzenia to ZASILACZE PROGRAMOWALNE, w których napięcie, prąd lub częstotliwość mogą być zdalnie sterowane poprzez wejście analogowe lub interfejs cyfrowy, taki jak RS232 lub GPIB. Wiele z nich posiada wbudowany mikrokomputer do monitorowania i kontrolowania operacji. Takie instrumenty są niezbędne do celów zautomatyzowanego testowania. Niektóre zasilacze elektroniczne wykorzystują ograniczenie prądu zamiast odcinania zasilania w przypadku przeciążenia. Ograniczenie elektroniczne jest powszechnie stosowane w instrumentach typu laboratoryjnego. GENERATORY SYGNAŁU to kolejne szeroko stosowane przyrządy w laboratoriach i przemyśle, generujące powtarzające się lub nie powtarzające się sygnały analogowe lub cyfrowe. Alternatywnie nazywane są również GENERATORAMI FUNKCYJNYMI, GENERATORAMI WZORÓW CYFROWYCH lub GENERATORAMI CZĘSTOTLIWOŚCI. Generatory funkcji generują proste, powtarzalne przebiegi, takie jak fale sinusoidalne, impulsy schodkowe, przebiegi kwadratowe i trójkątne oraz przebiegi arbitralne. Dzięki generatorom przebiegów arbitralnych użytkownik może generować dowolne przebiegi, w opublikowanych granicach zakresu częstotliwości, dokładności i poziomu wyjściowego. W przeciwieństwie do generatorów funkcyjnych, które są ograniczone do prostego zestawu przebiegów, generator przebiegów arbitralnych pozwala użytkownikowi określić przebieg źródłowy na wiele różnych sposobów. GENERATORY SYGNAŁU RF i MIKROFALOWEGO służą do testowania komponentów, odbiorników i systemów w aplikacjach takich jak komunikacja komórkowa, WiFi, GPS, radiodyfuzja, komunikacja satelitarna i radary. Generatory sygnału RF zwykle pracują w zakresie od kilku kHz do 6 GHz, podczas gdy generatory sygnału mikrofalowego działają w znacznie szerszym zakresie częstotliwości, od mniej niż 1 MHz do co najmniej 20 GHz, a nawet do setek zakresów GHz przy użyciu specjalnego sprzętu. Generatory sygnałów RF i mikrofalowych można dalej klasyfikować jako generatory sygnałów analogowych lub wektorowych. GENERATORY SYGNAŁU CZĘSTOTLIWOŚCI AUDIO generują sygnały w zakresie częstotliwości audio i powyżej. Posiadają elektroniczne aplikacje laboratoryjne sprawdzające charakterystykę częstotliwościową sprzętu audio. GENERATORY SYGNAŁU WEKTOROWEGO, czasami nazywane również GENERATORAMI SYGNAŁU CYFROWEGO, są zdolne do generowania cyfrowo modulowanych sygnałów radiowych. Generatory sygnałów wektorowych mogą generować sygnały w oparciu o standardy branżowe, takie jak GSM, W-CDMA (UMTS) i Wi-Fi (IEEE 802.11). GENERATORY SYGNAŁÓW LOGICZNYCH nazywane są również CYFROWYMI GENERATORAMI WZORÓW. Generatory te wytwarzają sygnały logiczne, czyli logiczne jedynki i zera w postaci konwencjonalnych poziomów napięcia. Generatory sygnałów logicznych są wykorzystywane jako źródła bodźców do funkcjonalnej walidacji i testowania cyfrowych układów scalonych i systemów wbudowanych. Wyżej wymienione urządzenia są przeznaczone do użytku ogólnego. Istnieje jednak wiele innych generatorów sygnałów zaprojektowanych do niestandardowych, specyficznych zastosowań. WTRYSKIWACZ SYGNAŁU jest bardzo przydatnym i szybkim narzędziem do rozwiązywania problemów do śledzenia sygnału w obwodzie. Technicy mogą bardzo szybko określić wadliwy stan urządzenia, takiego jak odbiornik radiowy. Wtryskiwacz sygnału można podać na wyjście głośnikowe, a jeśli sygnał jest słyszalny można przejść do poprzedniego etapu obwodu. W tym przypadku wzmacniacz audio, a jeśli wprowadzony sygnał jest słyszany ponownie, można przesuwać wstrzykiwany sygnał w górę stopni obwodu, aż sygnał przestanie być słyszalny. Pomoże to zlokalizować lokalizację problemu. MULTIMETR to elektroniczny przyrząd pomiarowy łączący kilka funkcji pomiarowych w jednej jednostce. Ogólnie rzecz biorąc, multimetry mierzą napięcie, prąd i rezystancję. Dostępna jest zarówno wersja cyfrowa, jak i analogowa. Oferujemy przenośne multimetry ręczne oraz modele laboratoryjne z certyfikowaną kalibracją. Nowoczesne multimetry mogą mierzyć wiele parametrów takich jak: napięcie (zarówno AC/DC), w woltach, prąd (zarówno AC/DC), w amperach, rezystancja w omach. Dodatkowo niektóre multimetry mierzą: pojemność w faradach, przewodność w siemensach, decybelach, cykl pracy w procentach, częstotliwość w hercach, indukcyjność w henrach, temperaturę w stopniach Celsjusza lub Fahrenheita za pomocą sondy do pomiaru temperatury. Niektóre multimetry obejmują również: tester ciągłości; dźwięki podczas przewodzenia obwodu, diody (pomiar spadku w przód złącz diod), tranzystory (pomiar wzmocnienia prądu i innych parametrów), funkcja sprawdzania baterii, funkcja pomiaru poziomu światła, funkcja pomiaru kwasowości i zasadowości (pH) oraz funkcja pomiaru wilgotności względnej. Nowoczesne multimetry są często cyfrowe. Nowoczesne multimetry cyfrowe często mają wbudowany komputer, dzięki czemu są bardzo potężnymi narzędziami w metrologii i testowaniu. Obejmują one takie funkcje, jak: • Auto-zakres, który wybiera właściwy zakres dla badanej wielkości, tak aby pokazywane były najbardziej znaczące cyfry. • Automatyczna polaryzacja dla odczytów prądu stałego pokazuje, czy przyłożone napięcie jest dodatnie czy ujemne. • Próbkowanie i wstrzymanie, które zablokuje ostatni odczyt do badania po wyjęciu przyrządu z testowanego obwodu. • Ograniczone prądem testy spadku napięcia na złączach półprzewodnikowych. Chociaż nie jest to zamiennik testera tranzystorów, ta cecha multimetrów cyfrowych ułatwia testowanie diod i tranzystorów. • Wykres słupkowy przedstawiający badaną wielkość dla lepszej wizualizacji szybkich zmian mierzonych wartości. • Oscyloskop o małej przepustowości. •Testery obwodów samochodowych z testami synchronizacji samochodowej i sygnałów zatrzymania. •Funkcja akwizycji danych do rejestrowania maksymalnych i minimalnych odczytów w danym okresie oraz do pobierania wielu próbek w stałych odstępach czasu. • Połączony miernik LCR. Niektóre multimetry mogą być połączone z komputerami, a niektóre mogą przechowywać pomiary i przesyłać je do komputera. Jeszcze inne bardzo przydatne narzędzie, LCR METER to przyrząd pomiarowy do pomiaru indukcyjności (L), pojemności (C) i rezystancji (R) elementu. Impedancja jest mierzona wewnętrznie i konwertowana do wyświetlania na odpowiednią wartość pojemności lub indukcyjności. Odczyty będą dość dokładne, jeśli testowany kondensator lub cewka indukcyjna nie mają znaczącej składowej rezystancyjnej impedancji. Zaawansowane mierniki LCR mierzą rzeczywistą indukcyjność i pojemność, a także równoważną rezystancję szeregową kondensatorów i współczynnik dobroci elementów indukcyjnych. Badane urządzenie jest poddawane działaniu źródła napięcia przemiennego, a miernik mierzy napięcie w poprzek oraz prąd płynący przez badane urządzenie. Na podstawie stosunku napięcia do prądu miernik może określić impedancję. W niektórych przyrządach mierzony jest również kąt fazowy między napięciem a prądem. W połączeniu z impedancją można obliczyć i wyświetlić równoważną pojemność lub indukcyjność oraz rezystancję testowanego urządzenia. Mierniki LCR mają wybieralne częstotliwości testowe 100 Hz, 120 Hz, 1 kHz, 10 kHz i 100 kHz. Mierniki laboratoryjne LCR mają zwykle wybieralne częstotliwości testowe powyżej 100 kHz. Często zawierają one możliwość nałożenia napięcia lub prądu stałego na sygnał pomiarowy prądu przemiennego. Podczas gdy niektóre mierniki oferują możliwość zewnętrznego zasilania tych napięć lub prądów DC, inne urządzenia zasilają je wewnętrznie. MIERNIK PEM jest przyrządem testowo-metrologicznym do pomiaru pól elektromagnetycznych (EMF). Większość z nich mierzy gęstość strumienia promieniowania elektromagnetycznego (pola DC) lub zmianę pola elektromagnetycznego w czasie (pola AC). Istnieją wersje przyrządów jednoosiowych i trójosiowych. Mierniki jednoosiowe kosztują mniej niż mierniki trójosiowe, ale wykonanie testu zajmuje więcej czasu, ponieważ miernik mierzy tylko jeden wymiar pola. Jednoosiowe mierniki EMF muszą być przechylane i obracane we wszystkich trzech osiach, aby zakończyć pomiar. Z drugiej strony mierniki trójosiowe mierzą wszystkie trzy osie jednocześnie, ale są droższe. Miernik EMF może mierzyć pola elektromagnetyczne prądu przemiennego, które pochodzą ze źródeł takich jak przewody elektryczne, podczas gdy GAUSMETRY / TESLAMETRY lub MAGNETOMETRY mierzą pola prądu stałego emitowane ze źródeł, w których występuje prąd stały. Większość mierników EMF jest skalibrowana do pomiaru pól przemiennych 50 i 60 Hz odpowiadających częstotliwości prądu w sieci elektrycznej w USA i Europie. Istnieją inne mierniki, które mogą mierzyć pola zmieniające się z częstotliwością nawet 20 Hz. Pomiary EMF mogą być szerokopasmowe w szerokim zakresie częstotliwości lub selektywnie monitorować tylko interesujący zakres częstotliwości. MIERNIK POJEMNOŚCI jest przyrządem testowym służącym do pomiaru pojemności w większości dyskretnych kondensatorów. Niektóre mierniki wyświetlają tylko pojemność, podczas gdy inne pokazują również upływ, równoważną rezystancję szeregową i indukcyjność. Przyrządy testowe wyższej klasy wykorzystują techniki, takie jak wprowadzenie testowanego kondensatora do obwodu mostkowego. Zmieniając wartości pozostałych odgałęzień mostka, tak aby doprowadzić mostek do równowagi, określa się wartość nieznanego kondensatora. Ta metoda zapewnia większą precyzję. Mostek może być również zdolny do pomiaru rezystancji szeregowej i indukcyjności. Można mierzyć kondensatory w zakresie od pikofaradów do faradów. Obwody mostkowe nie mierzą prądu upływu, ale można przyłożyć napięcie polaryzacji DC i bezpośrednio mierzyć upływ. Wiele INSTRUMENTÓW BRIDGE można podłączyć do komputerów i dokonywać wymiany danych w celu pobierania odczytów lub zewnętrznego sterowania mostem. Takie przyrządy pomostowe oferują również testy typu „go / no go” w celu automatyzacji testów w szybkim środowisku produkcyjnym i kontroli jakości. Jeszcze innym przyrządem testowym, CLAMP METER, jest tester elektryczny łączący woltomierz z cęgowym miernikiem prądu. Większość nowoczesnych wersji mierników cęgowych jest cyfrowa. Nowoczesne mierniki cęgowe mają większość podstawowych funkcji multimetru cyfrowego, ale mają dodatkową funkcję przekładnika prądowego wbudowanego w produkt. Kiedy zaciśniesz „szczęki” przyrządu wokół przewodnika przewodzącego duży prąd przemienny, prąd ten jest przekazywany przez szczęki, podobnie jak żelazny rdzeń transformatora mocy, do uzwojenia wtórnego, które jest połączone z bocznikiem wejścia miernika , zasada działania bardzo zbliżona do transformatora. Na wejście miernika podawany jest znacznie mniejszy prąd ze względu na stosunek liczby uzwojeń wtórnych do liczby uzwojeń pierwotnych owiniętych wokół rdzenia. Pierwotny jest reprezentowany przez jeden przewodnik, wokół którego zaciskane są szczęki. Jeśli wtórne ma 1000 uzwojeń, to prąd wtórny wynosi 1/1000 prądu płynącego w pierwotnym, lub w tym przypadku mierzonym przewodzie. Zatem 1 amper prądu w mierzonym przewodniku wytworzy 0,001 ampera prądu na wejściu miernika. Za pomocą mierników cęgowych można łatwo mierzyć znacznie większe prądy, zwiększając liczbę zwojów w uzwojeniu wtórnym. Podobnie jak w przypadku większości naszych urządzeń testowych, zaawansowane mierniki cęgowe oferują możliwość rejestrowania. TESTERY REZYSTANCJI UZIEMIENIA służą do badania uziomów oraz rezystywności gruntu. Wymagania dotyczące przyrządu zależą od zakresu zastosowań. Nowoczesne przyrządy do testowania uziemienia cęgowego upraszczają testowanie pętli uziemienia i umożliwiają nieinwazyjne pomiary prądu upływu. Wśród sprzedawanych przez nas ANALIZATORÓW są bez wątpienia OSCYLOSKOPY jeden z najczęściej używanych urządzeń. Oscyloskop, zwany również OSCILLOGRAPHEM, jest rodzajem elektronicznego przyrządu testowego, który umożliwia obserwację stale zmieniających się napięć sygnału jako dwuwymiarowy wykres jednego lub więcej sygnałów w funkcji czasu. Sygnały nieelektryczne, takie jak dźwięk i wibracje, mogą być również przekształcane na napięcia i wyświetlane na oscyloskopach. Oscyloskopy służą do obserwowania zmian sygnału elektrycznego w czasie, napięcie i czas opisują kształt, który jest stale wykreślany na skalibrowanej skali. Obserwacja i analiza przebiegu ujawnia nam takie właściwości, jak amplituda, częstotliwość, interwał czasowy, czas narastania i zniekształcenia. Oscyloskopy można regulować tak, aby powtarzające się sygnały były obserwowane jako ciągły kształt na ekranie. Wiele oscyloskopów ma funkcję przechowywania, która umożliwia przechwytywanie pojedynczych zdarzeń przez przyrząd i wyświetlanie ich przez stosunkowo długi czas. To pozwala nam obserwować wydarzenia zbyt szybko, aby były bezpośrednio dostrzegalne. Nowoczesne oscyloskopy to lekkie, kompaktowe i przenośne przyrządy. Istnieją również miniaturowe przyrządy zasilane bateryjnie do zastosowań terenowych. Oscyloskopy laboratoryjne są zazwyczaj urządzeniami stacjonarnymi. Istnieje szeroka gama sond i kabli wejściowych do użytku z oscyloskopami. Skontaktuj się z nami, jeśli potrzebujesz porady, który z nich zastosować w swojej aplikacji. Oscyloskopy z dwoma wejściami pionowymi nazywane są oscyloskopami dwuścieżkowymi. Używając jednowiązkowego CRT, multipleksują wejścia, zwykle przełączając się między nimi wystarczająco szybko, aby wyświetlić dwa ślady naraz. Są też oscyloskopy z większą ilością śladów; cztery wejścia są wśród nich wspólne. Niektóre oscyloskopy wielościeżkowe wykorzystują zewnętrzne wejście wyzwalające jako opcjonalne wejście pionowe, a niektóre mają trzeci i czwarty kanał z minimalną kontrolą. Nowoczesne oscyloskopy mają kilka wejść dla napięć, dzięki czemu można je wykorzystać do wykreślenia jednego zmiennego napięcia względem drugiego. Jest to używane na przykład do tworzenia wykresów krzywych IV (charakterystyka prądu w funkcji napięcia) dla komponentów takich jak diody. W przypadku wysokich częstotliwości i szybkich sygnałów cyfrowych szerokość pasma wzmacniaczy pionowych i częstotliwość próbkowania muszą być wystarczająco wysokie. Do ogólnego użytku zwykle wystarcza szerokość pasma co najmniej 100 MHz. Znacznie mniejsza przepustowość jest wystarczająca tylko do zastosowań związanych z częstotliwością dźwięku. Przydatny zakres przemiatania wynosi od jednej sekundy do 100 nanosekund, z odpowiednim wyzwalaniem i opóźnieniem przemiatania. Do stabilnego wyświetlania wymagany jest dobrze zaprojektowany, stabilny obwód wyzwalający. Jakość obwodu wyzwalającego jest kluczowa dla dobrych oscyloskopów. Innym kluczowym kryterium wyboru jest głębokość pamięci próbki i częstotliwość próbkowania. Nowoczesne DSO na poziomie podstawowym mają teraz 1 MB lub więcej pamięci próbek na kanał. Często ta pamięć próbek jest współdzielona przez kanały i czasami może być w pełni dostępna tylko przy niższych częstotliwościach próbkowania. Przy najwyższych częstotliwościach próbkowania pamięć może być ograniczona do kilku dziesiątek KB. Każdy nowoczesny DSO z częstotliwością próbkowania „w czasie rzeczywistym” będzie miał zazwyczaj 5-10 razy większą przepustowość wejściową w częstotliwości próbkowania. Tak więc DSO o szerokości pasma 100 MHz miałby częstotliwość próbkowania 500 Ms/s - 1 Gs/s. Znacznie zwiększona częstotliwość próbkowania w dużej mierze wyeliminowała wyświetlanie nieprawidłowych sygnałów, które czasami występowały w pierwszej generacji oscyloskopów cyfrowych. Większość nowoczesnych oscyloskopów zapewnia jeden lub więcej zewnętrznych interfejsów lub magistral, takich jak GPIB, Ethernet, port szeregowy i USB, aby umożliwić zdalną kontrolę przyrządu za pomocą zewnętrznego oprogramowania. Oto lista różnych typów oscyloskopów: OSCYLOSKOP PROMIENIU KATODOWEGO OSCYLOSKOP DWUWIĄZKOWY ANALOGOWY OSCYLOSKOP PRZECHOWYWANIA OSCYLOSKOPY CYFROWE OSCYLOSKOPY MIESZANE OSCYLOSKOPY RĘCZNE OSCYLOSKOPY NA PC ANALIZATOR LOGICZNY to przyrząd, który przechwytuje i wyświetla wiele sygnałów z systemu cyfrowego lub obwodu cyfrowego. Analizator logiczny może konwertować przechwycone dane na diagramy czasowe, dekodowanie protokołów, ślady maszyny stanowej, język asemblera. Analizatory stanów logicznych mają zaawansowane możliwości wyzwalania i są przydatne, gdy użytkownik musi zobaczyć zależności czasowe między wieloma sygnałami w systemie cyfrowym. MODUŁOWE ANALIZATORY LOGICZNE składają się zarówno z obudowy lub ramy głównej, jak i modułów analizatorów stanów logicznych. Obudowa lub rama główna zawiera wyświetlacz, elementy sterujące, komputer sterujący i wiele gniazd, w których zainstalowany jest sprzęt do przechwytywania danych. Każdy moduł ma określoną liczbę kanałów, a wiele modułów można łączyć w celu uzyskania bardzo dużej liczby kanałów. Możliwość łączenia wielu modułów w celu uzyskania dużej liczby kanałów oraz ogólnie wyższa wydajność modułowych analizatorów logicznych powoduje, że są one droższe. W przypadku bardzo wysokiej klasy modułowych analizatorów stanów logicznych, użytkownicy mogą potrzebować zapewnić własny komputer nadrzędny lub zakupić wbudowany sterownik kompatybilny z systemem. PRZENOŚNE ANALIZATORY LOGICZNE integrują wszystko w jednym pakiecie z opcjami zainstalowanymi fabrycznie. Zwykle mają niższą wydajność niż modułowe, ale są ekonomicznymi narzędziami metrologicznymi do ogólnego debugowania. W PC-BASED LOGIC ANALYZERS sprzęt łączy się z komputerem przez połączenie USB lub Ethernet i przekazuje przechwycone sygnały do oprogramowania na komputerze. Urządzenia te są na ogół znacznie mniejsze i tańsze, ponieważ wykorzystują istniejącą klawiaturę, wyświetlacz i procesor komputera osobistego. Analizatory stanów logicznych mogą być wyzwalane przez skomplikowaną sekwencję zdarzeń cyfrowych, a następnie przechwytywać duże ilości danych cyfrowych z testowanych systemów. Obecnie w użyciu są specjalistyczne złącza. Ewolucja sond analizatorów stanów logicznych doprowadziła do powstania wspólnego śladu obsługiwanego przez wielu dostawców, co zapewnia dodatkową swobodę użytkownikom końcowym: Technologia bezzłączy oferowana pod różnymi nazwami handlowymi producentów, takimi jak sondy kompresji; Miękki dotyk; Używany jest D-Max. Sondy te zapewniają trwałe, niezawodne połączenie mechaniczne i elektryczne między sondą a płytką drukowaną. ANALIZATOR WIDMA mierzy wielkość sygnału wejściowego w funkcji częstotliwości w pełnym zakresie częstotliwości przyrządu. Podstawowym zastosowaniem jest pomiar mocy widma sygnałów. Istnieją również analizatory widma optycznego i akustycznego, ale tutaj omówimy tylko analizatory elektroniczne, które mierzą i analizują elektryczne sygnały wejściowe. Widma uzyskane z sygnałów elektrycznych dostarczają nam informacji o częstotliwości, mocy, harmonicznych, szerokości pasma… itd. Częstotliwość jest wyświetlana na osi poziomej, a amplituda sygnału na pionowej. Analizatory widma są szeroko stosowane w przemyśle elektronicznym do analizy widma częstotliwości radiowych, sygnałów RF i audio. Patrząc na widmo sygnału, jesteśmy w stanie ujawnić elementy sygnału i działanie układu je wytwarzającego. Analizatory widma są w stanie wykonać dużą różnorodność pomiarów. Patrząc na metody wykorzystywane do uzyskania widma sygnału, możemy kategoryzować typy analizatorów widma. - SWEPT-TUNED SPECTRUM ANALYZER wykorzystuje odbiornik superheterodynowy do konwersji w dół części widma sygnału wejściowego (za pomocą oscylatora sterowanego napięciem i miksera) do częstotliwości środkowej filtra pasmowego. Dzięki architekturze superheterodynowej oscylator sterowany napięciem jest przemiatany przez szereg częstotliwości, wykorzystując pełny zakres częstotliwości instrumentu. Analizatory widma ze strojeniem przesuniętym pochodzą z odbiorników radiowych. W związku z tym analizatory z skośnym strojeniem są albo analizatorami z dostrojonym filtrem (analogicznie do radia TRF) lub analizatorami superheterodynowymi. W rzeczywistości, w swojej najprostszej postaci, można by pomyśleć o analizatorze widma z przesuniętym strojeniem jako o woltomierzu z selektywnością częstotliwości z zakresem częstotliwości, który jest dostrajany (przesuwany) automatycznie. Jest to zasadniczo woltomierz selektywny względem częstotliwości, reagujący na wartości szczytowe, skalibrowany do wyświetlania wartości skutecznej fali sinusoidalnej. Analizator widma może pokazać poszczególne składowe częstotliwości, które składają się na złożony sygnał. Jednak nie dostarcza informacji o fazie, tylko informacje o amplitudzie. Nowoczesne analizatory z przestrajaniem (w szczególności analizatory superheterodynowe) to precyzyjne urządzenia, które mogą wykonywać różnorodne pomiary. Są one jednak używane przede wszystkim do pomiaru sygnałów w stanie ustalonym lub powtarzalnych, ponieważ nie mogą jednocześnie oceniać wszystkich częstotliwości w danym przedziale. Możliwość jednoczesnej oceny wszystkich częstotliwości jest możliwa tylko przy użyciu analizatorów czasu rzeczywistego. - ANALIZATORY WIDMA W CZASIE RZECZYWISTYM: ANALIZATOR WIDMA FFT oblicza dyskretną transformatę Fouriera (DFT), matematyczny proces, który przekształca przebieg na składowe jego widma sygnału wejściowego. Analizator widma Fouriera lub FFT to kolejna implementacja analizatora widma w czasie rzeczywistym. Analizator Fouriera wykorzystuje cyfrowe przetwarzanie sygnału do próbkowania sygnału wejściowego i przekształcenia go w domenę częstotliwości. Ta konwersja jest wykonywana przy użyciu szybkiej transformacji Fouriera (FFT). FFT jest implementacją dyskretnej transformacji Fouriera, algorytmu matematycznego używanego do przekształcania danych z domeny czasu do domeny częstotliwości. Inny rodzaj analizatorów widma w czasie rzeczywistym, a mianowicie PARALLEL FILTER ANALYZERS łączy kilka filtrów pasmowoprzepustowych, każdy o innej częstotliwości pasmowoprzepustowej. Każdy filtr pozostaje cały czas podłączony do wejścia. Po początkowym czasie ustalania, analizator z filtrem równoległym może natychmiast wykryć i wyświetlić wszystkie sygnały w zakresie pomiarowym analizatora. Dlatego analizator z filtrem równoległym zapewnia analizę sygnału w czasie rzeczywistym. Analizator z filtrem równoległym jest szybki, mierzy sygnały przejściowe i zmienne w czasie. Jednak rozdzielczość częstotliwości analizatora z filtrem równoległym jest znacznie niższa niż w przypadku większości analizatorów z przesuniętym strojeniem, ponieważ rozdzielczość jest określana przez szerokość filtrów pasmowoprzepustowych. Aby uzyskać dobrą rozdzielczość w szerokim zakresie częstotliwości, potrzeba wielu pojedynczych filtrów, co czyni to kosztownym i złożonym. Dlatego większość analizatorów z filtrem równoległym, z wyjątkiem najprostszych dostępnych na rynku, jest droga. - WEKTOROWA ANALIZA SYGNAŁU (VSA): W przeszłości analizatory widma z przestrajaniem i superheterodynami obejmowały szerokie zakresy częstotliwości od audio, poprzez mikrofale, do częstotliwości milimetrowych. Ponadto analizatory z szybką transformatą Fouriera (FFT) intensywnie wykorzystującą cyfrowe przetwarzanie sygnału (DSP) zapewniały analizę widma i sieci o wysokiej rozdzielczości, ale ograniczały się do niskich częstotliwości ze względu na ograniczenia technologii konwersji analogowo-cyfrowej i przetwarzania sygnału. Dzisiejsze szerokopasmowe, modulowane wektorowo, zmienne w czasie sygnały w dużym stopniu korzystają z możliwości analizy FFT i innych technik DSP. Analizatory sygnałów wektorowych łączą technologię superheterodynową z szybkimi przetwornikami ADC i innymi technologiami DSP, oferując szybkie pomiary widma o wysokiej rozdzielczości, demodulację i zaawansowaną analizę w dziedzinie czasu. VSA jest szczególnie przydatny do charakteryzowania złożonych sygnałów, takich jak sygnały impulsowe, przejściowe lub modulowane używane w aplikacjach komunikacyjnych, wideo, transmisji, sonarze i obrazowaniu ultradźwiękowym. W zależności od kształtu analizatory widma są pogrupowane jako stacjonarne, przenośne, ręczne i sieciowe. Modele stołowe są przydatne w zastosowaniach, w których analizator widma można podłączyć do zasilania prądem przemiennym, na przykład w laboratorium lub w obszarze produkcyjnym. Najwyższej klasy analizatory widma zazwyczaj oferują lepszą wydajność i specyfikacje niż wersje przenośne lub podręczne. Są one jednak na ogół cięższe i mają kilka wentylatorów do chłodzenia. Niektóre BENCHTOP SPECTRUM ANALYZERS oferują opcjonalne zestawy akumulatorów, co pozwala na używanie ich z dala od gniazdka sieciowego. Są one określane jako PRZENOŚNE ANALIZATORY WIDMA. Modele przenośne są przydatne w zastosowaniach, w których analizator widma musi być wyniesiony na zewnątrz w celu wykonania pomiarów lub noszony podczas użytkowania. Oczekuje się, że dobry przenośny analizator widma będzie oferował opcjonalne zasilanie bateryjne, aby umożliwić użytkownikowi pracę w miejscach bez gniazdek elektrycznych, czytelny wyświetlacz, aby umożliwić odczyt ekranu w jasnym świetle słonecznym, ciemności lub zakurzonych warunkach, przy niewielkiej wadze. Ręczne analizatory widma są przydatne w zastosowaniach, w których analizator widma musi być bardzo lekki i mały. Analizatory ręczne oferują ograniczone możliwości w porównaniu z większymi systemami. Zaletami ręcznych analizatorów widma jest jednak ich bardzo niski pobór mocy, zasilanie bateryjne w terenie, co pozwala użytkownikowi na swobodne poruszanie się na zewnątrz, bardzo mały rozmiar i niewielka waga. Wreszcie, SIECIOWE ANALIZATORY SPEKTRUM nie zawierają wyświetlacza i zostały zaprojektowane, aby umożliwić nową klasę geograficznie rozproszonych aplikacji do monitorowania i analizy widma. Kluczowym atrybutem jest możliwość podłączenia analizatora do sieci i monitorowania takich urządzeń przez sieć. Chociaż wiele analizatorów widma ma port Ethernet do sterowania, zazwyczaj brakuje im wydajnych mechanizmów przesyłania danych i są zbyt nieporęczne i/lub drogie, aby można je było wdrożyć w taki sposób rozproszony. Rozproszony charakter takich urządzeń umożliwia geolokalizację nadajników, monitorowanie widma dla dynamicznego dostępu do widma i wiele innych tego typu zastosowań. Urządzenia te są w stanie synchronizować przechwytywane dane w sieci analizatorów i umożliwiają wydajny transfer danych w sieci przy niskich kosztach. ANALIZATOR PROTOKOŁÓW to narzędzie zawierające sprzęt i/lub oprogramowanie służące do przechwytywania i analizowania sygnałów i ruchu danych w kanale komunikacyjnym. Analizatory protokołów są najczęściej używane do pomiaru wydajności i rozwiązywania problemów. Łączą się z siecią, aby obliczyć kluczowe wskaźniki wydajności, monitorować sieć i przyspieszać działania związane z rozwiązywaniem problemów. ANALIZATOR PROTOKOŁÓW SIECIOWYCH jest istotną częścią zestawu narzędzi administratora sieci. Analiza protokołu sieciowego służy do monitorowania stanu komunikacji sieciowej. Aby dowiedzieć się, dlaczego urządzenie sieciowe działa w określony sposób, administratorzy używają analizatora protokołów do wykrywania ruchu i ujawniania danych i protokołów przesyłanych przez sieć. Analizatory protokołów sieciowych służą do - Rozwiązywanie trudnych do rozwiązania problemów - Wykrywaj i identyfikuj złośliwe oprogramowanie / złośliwe oprogramowanie. Pracuj z systemem wykrywania włamań lub pułapką miodu. - Zbierz informacje, takie jak podstawowe wzorce ruchu i wskaźniki wykorzystania sieci - Zidentyfikuj nieużywane protokoły, aby usunąć je z sieci - Generuj ruch do testów penetracyjnych - Podsłuchiwanie ruchu (np. lokalizowanie nieautoryzowanego ruchu w komunikatorach lub bezprzewodowych punktach dostępowych) REFLEKTOMETR W DZIEDZINIE CZASU (TDR) to przyrząd, który wykorzystuje reflektometrię w dziedzinie czasu do charakteryzowania i lokalizowania uszkodzeń w kablach metalowych, takich jak skrętki dwużyłowe i kable koncentryczne, złącza, płytki drukowane itp. Reflektometry w dziedzinie czasu mierzą odbicia wzdłuż przewodnika. Aby je zmierzyć, TDR przesyła sygnał padający na przewodnik i obserwuje jego odbicia. Jeśli przewodnik ma jednakową impedancję i jest prawidłowo zakończony, nie będzie odbić, a pozostały sygnał padający zostanie pochłonięty na drugim końcu przez zakończenie. Jeśli jednak gdzieś występuje zmiana impedancji, część padającego sygnału zostanie odbita z powrotem do źródła. Odbicia będą miały taki sam kształt jak sygnał padający, ale ich znak i wielkość zależą od zmiany poziomu impedancji. Jeśli występuje skokowy wzrost impedancji, odbicie będzie miało taki sam znak jak sygnał padający, a jeśli nastąpi skokowy spadek impedancji, odbicie będzie miało znak przeciwny. Odbicia są mierzone na wyjściu/wejściu reflektometru w dziedzinie czasu i wyświetlane jako funkcja czasu. Alternatywnie wyświetlacz może pokazywać transmisję i odbicia w funkcji długości kabla, ponieważ prędkość propagacji sygnału jest prawie stała dla danego medium transmisyjnego. Rejestratory TDR mogą być używane do analizy impedancji i długości kabli, strat w złączach i spawach oraz ich lokalizacji. Pomiary impedancji TDR zapewniają projektantom możliwość przeprowadzenia analizy integralności sygnału połączeń systemu i dokładnego przewidzenia wydajności systemu cyfrowego. Pomiary TDR są szeroko stosowane w pracach nad charakteryzacją płyt. Projektant płytek drukowanych może określić impedancje charakterystyczne ścieżek płytki, obliczyć dokładne modele komponentów płytki i dokładniej przewidzieć wydajność płytki. Istnieje wiele innych obszarów zastosowań reflektometrów w dziedzinie czasu. SEMICONDUCTOR CURVE TRACER to sprzęt testowy używany do analizy charakterystyk dyskretnych urządzeń półprzewodnikowych, takich jak diody, tranzystory i tyrystory. Przyrząd oparty jest na oscyloskopie, ale zawiera również źródła napięcia i prądu, które można wykorzystać do stymulowania badanego urządzenia. Do dwóch zacisków testowanego urządzenia przykładane jest napięcie skokowe i mierzona jest wielkość prądu, jaki urządzenie pozwala na przepływ przy każdym napięciu. Na ekranie oscyloskopu wyświetlany jest wykres o nazwie VI (napięcie w funkcji prądu). Konfiguracja obejmuje maksymalne przyłożone napięcie, polaryzację przyłożonego napięcia (w tym automatyczne przyłożenie biegunowości dodatniej i ujemnej) oraz rezystancję wstawioną szeregowo z urządzeniem. W przypadku dwóch urządzeń końcowych, takich jak diody, wystarczy to, aby w pełni scharakteryzować urządzenie. Wskaźnik krzywej może wyświetlać wszystkie interesujące parametry, takie jak napięcie przewodzenia diody, prąd upływu wstecznego, napięcie przebicia wstecznego itp. Urządzenia z trzema zaciskami, takie jak tranzystory i FET, również wykorzystują połączenie z zaciskiem kontrolnym testowanego urządzenia, takim jak zacisk Base lub Gate. W przypadku tranzystorów i innych urządzeń opartych na prądzie, prąd bazy lub innego zacisku sterującego jest schodkowy. W przypadku tranzystorów polowych (FET) zamiast prądu schodkowego stosuje się napięcie schodkowe. Przesuwając napięcie przez skonfigurowany zakres napięć na zaciskach głównych, dla każdego skoku napięcia sygnału sterującego automatycznie generowana jest grupa krzywych VI. Ta grupa krzywych bardzo ułatwia określenie wzmocnienia tranzystora lub napięcia wyzwalającego tyrystora lub TRIAC. Nowoczesne półprzewodnikowe znaczniki krzywych oferują wiele atrakcyjnych funkcji, takich jak intuicyjne interfejsy użytkownika oparte na systemie Windows, generowanie IV, CV i impulsów oraz pulse IV, biblioteki aplikacji dołączone do każdej technologii… itd. TESTER / WSKAŹNIK OBROTU FAZY: Są to kompaktowe i wytrzymałe przyrządy testowe do identyfikacji kolejności faz w systemach trójfazowych i fazach otwartych/bez napięcia. Idealnie nadają się do montażu maszyn wirujących, silników oraz do sprawdzania mocy generatora. Wśród zastosowań znajduje się identyfikacja właściwej kolejności faz, wykrywanie brakujących faz przewodów, określanie właściwych połączeń maszyn wirujących, wykrywanie obwodów pod napięciem. LICZNIK CZĘSTOTLIWOŚCI jest przyrządem testowym używanym do pomiaru częstotliwości. Liczniki częstotliwości zazwyczaj używają licznika, który gromadzi liczbę zdarzeń występujących w określonym przedziale czasu. Jeśli zdarzenie, które ma być liczone, ma formę elektroniczną, wystarczy proste połączenie z instrumentem. Sygnały o większej złożoności mogą wymagać pewnego uwarunkowania, aby nadawały się do zliczania. Większość liczników częstotliwości ma na wejściu jakąś formę wzmacniacza, obwodów filtrujących i kształtujących. Cyfrowe przetwarzanie sygnału, kontrola czułości i histereza to inne techniki poprawiające wydajność. Inne rodzaje zdarzeń okresowych, które z natury nie mają charakteru elektronicznego, będą musiały zostać przekształcone za pomocą przetworników. Liczniki częstotliwości RF działają na tych samych zasadach, co liczniki niższych częstotliwości. Mają większy zasięg przed przepełnieniem. W przypadku bardzo wysokich częstotliwości mikrofalowych wiele projektów wykorzystuje szybki preskaler, aby obniżyć częstotliwość sygnału do punktu, w którym mogą działać normalne obwody cyfrowe. Liczniki częstotliwości mikrofalowych mogą mierzyć częstotliwości do prawie 100 GHz. Powyżej tych wysokich częstotliwości mierzony sygnał jest łączony w mikserze z sygnałem z lokalnego oscylatora, wytwarzając sygnał o częstotliwości różnicowej, która jest wystarczająco niska do bezpośredniego pomiaru. Popularne interfejsy w licznikach częstotliwości to RS232, USB, GPIB i Ethernet, podobnie jak inne nowoczesne przyrządy. Oprócz wysyłania wyników pomiarów, licznik może powiadamiać użytkownika o przekroczeniu zdefiniowanych przez użytkownika limitów pomiarowych. Aby uzyskać szczegółowe informacje i podobny sprzęt, odwiedź naszą stronę internetową poświęconą sprzętowi: http://www.sourceindustrialsupply.com For other similar equipment, please visit our equipment website: http://www.sourceindustrialsupply.com CLICK Product Finder-Locator Service POPRZEDNIA STRONA
- Electric Discharge Machining, EDM, Spark Machining, Die Sinking
Electric Discharge Machining - EDM - Spark Machining - Die Sinking - Wire Erosion - Custom Manufacturing - AGS-TECH Inc. Obróbka elektroiskrowa, frezowanie elektroerozyjne i szlifowanie OBRÓBKA WYŁADOWNICZA ELEKTRYCZNEGO (EDM), określana również jako SPARK-EROSION or SPARK-EROSION or_cc781905-5cde-3194-bb3b-136bad5c- -136bad5cf58d_or EROZJA DRUTU, to a NON-CONVENTIONAL MANUFACTURING_cc781905-5cde-3194-bb3b-136proces, w którym uzyskuje się pożądany kształt i wyładowanie elektryczne iskier. Oferujemy również niektóre odmiany EDM, a mianowicie NO-WEAR EDM, DRUT EDM (WEDM), EDM GRINDING (EDG), EDM EDM, ELEKTRYCZNO-WYŁADOWCZE FREZOWANIE, micro-EDM, m-EDM_cc781905 -5cde-3194-bb3b-136bad5cf58d_and SZLIFOWANIE ELEKTROCHEMICZNE (ECDG). Nasze systemy EDM składają się z ukształtowanych narzędzi/elektrody i przedmiotu obrabianego podłączonych do zasilaczy prądu stałego i umieszczonych w nieprzewodzącym elektrycznie płynie dielektrycznym. Po 1940 r. obróbka elektroerozyjna stała się jedną z najważniejszych i najbardziej popularnych technologii produkcyjnych w przemyśle wytwórczym. Gdy odległość między dwiema elektrodami jest zmniejszona, natężenie pola elektrycznego w objętości między elektrodami staje się w niektórych punktach większe niż siła dielektryka, który pęka, ostatecznie tworząc mostek dla przepływu prądu między dwiema elektrodami. Generowany jest intensywny łuk elektryczny, który powoduje znaczne nagrzewanie się części obrabianego przedmiotu i części materiału oprzyrządowania. W rezultacie materiał jest usuwany z obu elektrod. Jednocześnie płyn dielektryczny jest szybko podgrzewany, co powoduje odparowanie płynu w szczelinie łukowej. Gdy przepływ prądu ustaje lub jest zatrzymany, ciepło jest usuwane z pęcherzyka gazu przez otaczający płyn dielektryczny i pęcherzyk ulega kawitacji (zapada się). Fala uderzeniowa wytworzona przez zapadnięcie się bańki i przepływ płynu dielektrycznego wypłukuje zanieczyszczenia z powierzchni przedmiotu obrabianego i porywa stopiony materiał przedmiotu obrabianego do płynu dielektrycznego. Częstotliwość powtarzania tych wyładowań wynosi od 50 do 500 kHz, napięcia od 50 do 380 V i prądy od 0,1 do 500 amperów. Nowy ciekły dielektryk, taki jak oleje mineralne, nafta lub woda destylowana i dejonizowana, jest zwykle przenoszony do objętości międzyelektrodowej, unosząc cząstki stałe (w postaci gruzu) i przywracane są właściwości izolacyjne dielektryka. Po przepływie prądu różnica potencjałów między dwiema elektrodami zostaje przywrócona do wartości sprzed przebicia, więc może nastąpić nowe przebicie dielektryka ciekłego. Nasze nowoczesne maszyny elektroerozyjne (EDM) oferują ruchy sterowane numerycznie i są wyposażone w pompy i systemy filtrowania płynów dielektrycznych. Obróbka elektroerozyjne (EDM) to metoda obróbki stosowana głównie w przypadku metali twardych lub tych, które byłyby bardzo trudne do obróbki konwencjonalnymi technikami. EDM zwykle pracuje z dowolnymi materiałami, które są przewodnikami elektrycznymi, chociaż zaproponowano również metody obróbki ceramiki izolacyjnej za pomocą EDM. Temperatura topnienia i utajone ciepło topnienia to właściwości, które determinują objętość usuwanego metalu podczas wyładowania. Im wyższe te wartości, tym wolniejsze tempo usuwania materiału. Ponieważ proces obróbki elektroerozyjnej nie wymaga żadnej energii mechanicznej, twardość, wytrzymałość i wytrzymałość przedmiotu obrabianego nie mają wpływu na szybkość usuwania. Częstotliwość rozładowania lub energia na wyładowanie, napięcie i prąd są zmieniane w celu kontrolowania szybkości usuwania materiału. Szybkość usuwania materiału i chropowatość powierzchni rosną wraz ze wzrostem gęstości prądu i spadkiem częstotliwości iskry. Możemy wycinać skomplikowane kontury lub wgłębienia we wstępnie utwardzonej stali za pomocą EDM bez konieczności obróbki cieplnej w celu ich zmiękczenia i ponownego utwardzenia. Metodę tę możemy zastosować z dowolnym metalem lub stopami metali, takimi jak tytan, hastelloy, kovar i inconel. Zastosowania procesu EDM obejmują kształtowanie narzędzi z polikrystalicznego diamentu. EDM jest uważany za nietradycyjną lub niekonwencjonalną metodę obróbki wraz z procesami takimi jak obróbka elektrochemiczna (ECM), cięcie strumieniem wody (WJ, AWJ), cięcie laserowe. Z drugiej strony konwencjonalne metody obróbki obejmują toczenie, frezowanie, szlifowanie, wiercenie i inne procesy, których mechanizm usuwania materiału opiera się zasadniczo na siłach mechanicznych. Elektrody do obróbki elektroerozyjnej (EDM) wykonane są ze stopów grafitu, mosiądzu, miedzi i miedzi z wolframem. Możliwe są średnice elektrod do 0,1 mm. Ponieważ zużycie narzędzia jest niepożądanym zjawiskiem, które ma negatywny wpływ na dokładność wymiarową w EDM, wykorzystujemy proces o nazwie NO-WEAR EDM, odwracając biegunowość i używając narzędzi miedzianych w celu zminimalizowania zużycia narzędzia. Idealnie mówiąc, obróbkę elektroerozyjne (EDM) można uznać za serię przebicia i przywrócenia cieczy dielektrycznej między elektrodami. W rzeczywistości jednak usuwanie gruzu z obszaru międzyelektrodowego jest prawie zawsze częściowe. Powoduje to, że właściwości elektryczne dielektryka w obszarze międzyelektrodowym różnią się od ich wartości nominalnych i zmieniają się w czasie. Odległość między elektrodami (iskiernik) jest regulowana przez algorytmy sterowania używanej maszyny. Iskiernik w EDM może niestety czasami zostać zwarty przez zanieczyszczenia. System sterowania elektrody może nie reagować wystarczająco szybko, aby zapobiec zwarciu dwóch elektrod (narzędzia i przedmiotu obrabianego). To niepożądane zwarcie przyczynia się do usuwania materiału inaczej niż w idealnym przypadku. Przykładamy ogromną wagę do działania płukania w celu przywrócenia właściwości izolacyjnych dielektryka tak, aby prąd zawsze płynął w punkcie obszaru międzyelektrodowego, minimalizując tym samym możliwość niepożądanej zmiany kształtu (uszkodzenia) narzędzia-elektrody i obrabiany przedmiot. Aby uzyskać określoną geometrię, narzędzie EDM jest prowadzone po pożądanej ścieżce bardzo blisko obrabianego przedmiotu, bez dotykania go. Przywiązujemy najwyższą wagę do wydajności sterowania ruchem podczas użytkowania. W ten sposób ma miejsce duża liczba wyładowań prądowych/iskier, a każde z nich przyczynia się do usuwania materiału zarówno z narzędzia, jak i przedmiotu obrabianego, gdzie powstają małe kratery. Rozmiar kraterów jest funkcją parametrów technologicznych ustalonych dla konkretnego zadania, a wymiary mogą wahać się od nanoskali (tak jak w przypadku operacji mikro-EDM) do kilkuset mikrometrów w warunkach obróbki zgrubnej. Te małe kratery na narzędziu powodują stopniową erozję elektrody zwaną „zużyciem narzędzia”. Aby przeciwdziałać szkodliwemu wpływowi zużycia na geometrię przedmiotu obrabianego, stale wymieniamy narzędzie-elektrodę podczas obróbki. Czasami osiągamy to za pomocą stale wymienianego drutu jako elektrody (ten proces EDM jest również nazywany WIRE EDM ). Czasami używamy narzędzia-elektrody w taki sposób, że tylko niewielka jej część jest faktycznie zaangażowana w proces obróbki i ta część jest zmieniana na bieżąco. Tak jest na przykład w przypadku użycia wirującego dysku jako elektrody narzędziowej. Proces ten nazywa się EDM SZLIFOWANIE. Jeszcze inna technika, którą stosujemy, polega na użyciu zestawu elektrod o różnych rozmiarach i kształtach podczas tej samej operacji EDM, aby skompensować zużycie. Nazywamy tę technikę wieloelektrodową i jest ona najczęściej stosowana, gdy elektroda narzędziowa replikuje w negatywie pożądany kształt i jest przesuwana w kierunku półfabrykatu wzdłuż jednego kierunku, zwykle kierunku pionowego (tj. osi Z). Przypomina to zanurzenie narzędzia w cieczy dielektrycznej, w której zanurzony jest obrabiany przedmiot, i dlatego jest określane jako DIE-SINKING EDM (czasami nazywane_cc781905-5cde- 3194-bb3b-136bad5cf58d_CONVENTIONAL EDM or RAM EDM). Maszyny do tej operacji nazywają się SINKER EDM. Elektrody do tego typu EDM mają złożone formy. Jeśli ostateczną geometrię uzyskuje się za pomocą zwykle prostej elektrody poruszanej w kilku kierunkach i również podlega ona obrotom, nazywamy to EDM FREZOWANIE. Stopień zużycia jest ściśle uzależniony od parametrów technologicznych zastosowanych w operacji (biegunowość, prąd maksymalny, napięcie w obwodzie otwartym). Na przykład in micro-EDM, znany również jako m-EDM, parametry te są zwykle ustawiane na wartości, które powodują poważne zużycie. Dlatego zużycie jest poważnym problemem w tym obszarze, który minimalizujemy korzystając z naszego zgromadzonego know-how. Na przykład, aby zminimalizować zużycie elektrod grafitowych, generator cyfrowy, sterowany w ciągu milisekund, odwraca polaryzację podczas elektroerozji. Daje to efekt podobny do galwanizacji, która w sposób ciągły osadza zerodowany grafit z powrotem na elektrodzie. W innej metodzie, tak zwanym obwodzie „Zero Wear”, minimalizujemy częstotliwość rozpoczynania i zatrzymywania wyładowania, utrzymując je tak długo, jak to możliwe. Szybkość usuwania materiału w obróbce elektroerozyjnej można oszacować na podstawie: MRR = 4 x 10 exp(4) x I x Tw exp (-1,23) Tutaj MRR jest w mm3/min, I to prąd w amperach, Tw to temperatura topnienia obrabianego przedmiotu w K-273,15K. Exp oznacza wykładnik. Z drugiej strony wskaźnik zużycia Wt elektrody można uzyskać z: Wt = ( 1,1 x 10exp(11)) x I x Ttexp(-2,38) Tutaj Wt jest w mm3/min, a Tt jest temperaturą topnienia materiału elektrody w K-273,15K Ostatecznie stosunek zużycia przedmiotu obrabianego do elektrody R można uzyskać z: R = 2,25 x Trex (-2,38) Tutaj Tr jest stosunkiem temperatur topnienia przedmiotu obrabianego do elektrody. SINKER EDM : Elektrodrążarka wgłębna, określana również jako TYP WNĘKI EDM or VOLUME EDM, składa się z elektrody zanurzonej w płynie i przedmiocie obrabianym Elektroda i obrabiany przedmiot są podłączone do zasilania. Zasilacz generuje potencjał elektryczny między nimi. Gdy elektroda zbliża się do przedmiotu obrabianego, w płynie dochodzi do przebicia dielektryka, tworząc kanał plazmowy i przeskakuje mała iskra. Iskry zwykle uderzają pojedynczo, ponieważ jest wysoce nieprawdopodobne, aby różne miejsca w przestrzeni międzyelektrodowej miały identyczne lokalne właściwości elektryczne, które umożliwiłyby jednoczesne występowanie iskry we wszystkich takich miejscach. Setki tysięcy takich iskier wydarzają się w przypadkowych punktach między elektrodą a przedmiotem obrabianym na sekundę. Ponieważ metal nieszlachetny ulega erozji, a następnie zwiększa się szczelina iskrowa, elektroda jest automatycznie obniżana przez naszą maszynę CNC, dzięki czemu proces może być kontynuowany bez zakłóceń. Nasz sprzęt posiada cykle kontrolne znane jako „na czas” i „czas wolny”. Ustawienie czasu określa długość lub czas trwania iskry. Dłuższy czas wytwarza głębsze wgłębienie dla tej iskry i wszystkich kolejnych iskier dla tego cyklu, tworząc bardziej chropowate wykończenie przedmiotu obrabianego i odwrotnie. Czas wyłączenia to czas, w którym jedna iskra jest zastępowana przez inną. Dłuższy czas przestoju umożliwia przepłukanie płynu dielektrycznego przez dyszę w celu oczyszczenia zerodowanych zanieczyszczeń, unikając w ten sposób zwarcia. Te ustawienia są regulowane w mikrosekundach. DRUT EDM : In WIRE OBRÓBKA ELEKTRYCZNA (WEDM), zwana także WIRE-CUT EDM_cc781905-5cde-3194-bb3b-136bad5-336WIRE-bb5cF5cde-3194-bb3b-136bad5cf58d_WIRE-CUT EDM_cc781905-5cde-3194-bb3b-136bad5-336WIRE-bb5f5 cienki jednożyłowy metalowy drut z mosiądzu przechodzący przez obrabiany przedmiot, który jest zanurzony w zbiorniku z płynem dielektrycznym. Drut EDM jest ważną odmianą EDM. Czasami używamy elektrodrążarki drutowej do cięcia płyt o grubości do 300 mm oraz do wykonywania stempli, narzędzi i matryc z twardych metali, które są trudne do obróbki innymi metodami produkcyjnymi. W tym procesie, który przypomina cięcie konturowe piłą taśmową, drut, który jest stale podawany ze szpuli, jest utrzymywany pomiędzy górną i dolną prowadnicą diamentową. Sterowane CNC prowadnice poruszają się w płaszczyźnie x–y, a górna prowadnica może również poruszać się niezależnie w osi z–u–v, co daje możliwość wycinania stożkowych i przejściowych kształtów (takich jak okrąg na dole i kwadrat przy szczyt). Górna prowadnica może kontrolować ruchy osi w x–y–u–v–i–j–k–l–. Dzięki temu WEDM wycina bardzo skomplikowane i delikatne kształty. Przeciętny rzaz naszego sprzętu, który osiąga najlepszy koszt i czas obróbki, wynosi 0,335 mm przy użyciu drutu mosiężnego, miedzianego lub wolframowego Ø 0,25. Jednak górna i dolna prowadnica diamentowa naszego sprzętu CNC mają dokładność około 0,004 mm i mogą mieć ścieżkę cięcia lub szczelinę o wielkości zaledwie 0,021 mm przy użyciu drutu o średnicy 0,02 mm. Tak więc możliwe są naprawdę wąskie cięcia. Szerokość cięcia jest większa niż szerokość drutu, ponieważ iskrzenie występuje od boków drutu do przedmiotu obrabianego, powodując erozję. To „nacięcie” jest konieczne, w wielu zastosowaniach jest przewidywalne i dlatego można je skompensować (w mikro-EDM nie zdarza się to często). Szpule drutu są długie — 8 kg szpula drutu 0,25 mm ma nieco ponad 19 kilometrów długości. Średnica drutu może wynosić nawet 20 mikrometrów, a dokładność geometrii jest w okolicach +/- 1 mikrometra. Zazwyczaj używamy drutu tylko raz i poddajemy go recyklingowi, ponieważ jest stosunkowo niedrogi. Porusza się ze stałą prędkością od 0,15 do 9 m/min, a podczas cięcia utrzymywany jest stały rzaz (szczelina). W procesie wycinania drutem EDM używamy wody jako płynu dielektrycznego, kontrolując jego rezystywność i inne właściwości elektryczne za pomocą filtrów i jednostek dejonizujących. Woda wypłukuje cięte odpady ze strefy cięcia. Płukanie jest ważnym czynnikiem przy określaniu maksymalnej prędkości posuwu dla danej grubości materiału i dlatego utrzymujemy ją na stałym poziomie. Prędkość skrawania w drążeniu drutowym jest określana jako pole przekroju poprzecznego cięcia w jednostce czasu, np. 18 000 mm2/h dla stali narzędziowej D2 o grubości 50 mm. Liniowa prędkość skrawania w tym przypadku wynosiłaby 18 000/50 = 360 mm/godz. Szybkość usuwania materiału w drucianym EDM wynosi: MRR = Vf xhxb Tutaj MRR jest w mm3/min, Vf jest szybkością podawania drutu do przedmiotu obrabianego w mm/min, h jest grubością lub wysokością w mm, a b jest szczeliną, która wynosi: b = dw + 2s Tutaj dw jest średnicą drutu, a s jest odstępem między drutem a przedmiotem obrabianym w mm. Wraz z węższymi tolerancjami, nasze nowoczesne wieloosiowe centra obróbkowe EDM do cięcia drutu posiadają dodatkowe funkcje, takie jak wiele głowic do jednoczesnego cięcia dwóch części, elementy sterujące zapobiegające zerwaniu drutu, automatyczne funkcje samogwintowania w przypadku zerwania drutu oraz zaprogramowane strategie obróbki w celu optymalizacji operacji, możliwości cięcia prostego i kątowego. Wire-EDM oferuje nam niskie naprężenia szczątkowe, ponieważ nie wymaga dużych sił skrawania do usuwania materiału. Gdy energia/moc na impuls jest stosunkowo niska (jak w operacjach wykańczających), oczekuje się niewielkiej zmiany właściwości mechanicznych materiału ze względu na niskie naprężenia szczątkowe. SZLIFOWANIE ELEKTRYCZNO-ELEKTRYCZNE (EDG) : Ściernice nie zawierają materiałów ściernych, są wykonane z grafitu lub mosiądzu. Powtarzające się iskry między obracającym się kołem a przedmiotem obrabianym usuwają materiał z powierzchni przedmiotu obrabianego. Szybkość usuwania materiału wynosi: MRR = K x I Tutaj MRR jest w mm3/min, I jest prądem w amperach, a K jest współczynnikiem materiału przedmiotu obrabianego w mm3/A-min. Często używamy szlifowania elektroerozyjnego do cięcia wąskich szczelin na elementach. Czasami łączymy proces EDG (Electrical-Discharge Grinding) z procesem EKG (Electrochemical Grinding), w którym materiał jest usuwany przez działanie chemiczne, wyładowania elektryczne z tarczy grafitowej rozbijają warstwę tlenku i są wypłukiwane przez elektrolit. Proces ten nazywa się ELEKTROCHEMICZNO-WYŁADOWCZE SZLIFOWANIE (ECDG). Mimo że proces ECDG zużywa stosunkowo więcej energii, jest procesem szybszym niż EDG. Tą techniką szlifujemy głównie narzędzia z węglików spiekanych. Zastosowania obróbki elektroerozyjnej: Produkcja prototypu: Proces EDM wykorzystujemy w produkcji form, narzędzi i matryc, a także przy wykonywaniu prototypów i części produkcyjnych, szczególnie dla przemysłu lotniczego, samochodowego i elektronicznego, w których wielkość produkcji jest stosunkowo niewielka. W Sinker EDM elektroda grafitowa, miedziana wolframowa lub czysta miedź jest obrabiana w pożądany (negatywny) kształt i wprowadzana do przedmiotu obrabianego na końcu pionowego suwaka. Wykonywanie wykrojników monet: Do tworzenia matryc do produkcji biżuterii i odznak w procesie monet (stemplowania) matryca pozytywowa może być wykonana ze srebra próby 925, ponieważ (przy odpowiednich ustawieniach maszyny) matryca ulega znacznej erozji i jest używana tylko raz. Powstała matryca negatywowa jest następnie hartowana i używana w młotku spadowym do wytwarzania wytłoczonych płaskowników z wykrojów z brązu, srebra lub niskoodpornego stopu złota. W przypadku odznak te spłaszczenia mogą być dalej kształtowane do zakrzywionej powierzchni za pomocą innej matrycy. Ten typ EDM jest zwykle wykonywany zanurzony w dielektryku na bazie oleju. Gotowy przedmiot może być dalej uszlachetniany przez twarde (szkło) lub miękkie (farba) emaliowanie i/lub galwanicznie pokrywane czystym złotem lub niklem. Bardziej miękkie materiały, takie jak srebro, mogą być ręcznie grawerowane jako uszlachetnienie. Wiercenie małych otworów: W naszych wycinarkach drutowych EDM używamy EDM do wiercenia małych otworów, aby wykonać otwór przelotowy w obrabianym przedmiocie, przez który należy przewlec drut do operacji wycinania drutowego. Oddzielne głowice EDM przeznaczone specjalnie do wiercenia małych otworów są montowane na naszych wycinarkach drutowych, które umożliwiają erozję gotowych części dużych płyt hartowanych w razie potrzeby bez wstępnego wiercenia. Stosujemy również elektroerozyjne małe otwory do wiercenia rzędów otworów w krawędziach łopatek turbin stosowanych w silnikach odrzutowych. Przepływ gazu przez te małe otwory umożliwia silnikom stosowanie wyższych temperatur, niż byłoby to możliwe w innym przypadku. Wysokotemperaturowe, bardzo twarde, monokrystaliczne stopy, z których wykonane są te ostrza, sprawiają, że konwencjonalna obróbka tych otworów o wysokim wydłużeniu jest niezwykle trudna, a nawet niemożliwa. Inne obszary zastosowań EDM z małymi otworami to tworzenie mikroskopijnych otworów dla elementów układu paliwowego. Oprócz zintegrowanych głowic EDM wdrażamy samodzielne maszyny EDM do wiercenia małych otworów z osiami x–y do obróbki otworów nieprzelotowych lub przelotowych. EDM wierci otwory za pomocą długiej mosiężnej lub miedzianej elektrody rurowej, która obraca się w uchwycie przy stałym przepływie wody destylowanej lub dejonizowanej przepływającej przez elektrodę jako środek płuczący i dielektryk. Niektóre elektrodrążarki EDM do wiercenia małych otworów są w stanie przewiercić 100 mm miękkiej lub nawet hartowanej stali w czasie krótszym niż 10 sekund. W tej operacji wiercenia można wykonać otwory od 0,3 mm do 6,1 mm. Obróbka z dezintegracją metalu: Posiadamy również specjalne maszyny EDM przeznaczone do usuwania złamanych narzędzi (wierteł lub gwintowników) z obrabianych elementów. Proces ten nazywany jest „obróbką z dezintegracją metalu”. Zalety i wady Obróbka elektroerozyjna: Zalety EDM obejmują obróbkę: - Złożone kształty, które w innym przypadku byłyby trudne do wykonania przy użyciu konwencjonalnych narzędzi skrawających - Niezwykle twardy materiał z bardzo wąskimi tolerancjami - Bardzo małe elementy obrabiane, w przypadku których konwencjonalne narzędzia tnące mogą uszkodzić część w wyniku nadmiernego nacisku narzędzia tnącego. - Nie ma bezpośredniego kontaktu między narzędziem a obrabianym przedmiotem. Dzięki temu delikatne sekcje i słabe materiały mogą być obrabiane bez zniekształceń. - Można uzyskać dobre wykończenie powierzchni. - Bardzo drobne otwory można łatwo wywiercić. Wady EDM obejmują: - Wolne tempo usuwania materiału. - Dodatkowy czas i koszt zużyty na wykonanie elektrod do EDM nurnika/nurnika. - Odtworzenie ostrych narożników na obrabianym przedmiocie jest trudne ze względu na zużycie elektrody. - Pobór mocy jest wysoki. - Powstaje „Przecięcie”. - Podczas obróbki dochodzi do nadmiernego zużycia narzędzia. - Materiały nieprzewodzące elektrycznie mogą być obrabiane tylko przy określonej konfiguracji procesu. CLICK Product Finder-Locator Service POPRZEDNIA STRONA
- Active Optical Components, Lasers, Photodetectors, LED Dies, Laser
Active Optical Components - Lasers - Photodetectors - LED Dies - Photomicrosensor - Fiber Optic - AGS-TECH Inc. - USA Produkcja i montaż aktywnych elementów optycznych The ACTIVE OPTICAL COMPONENTS we produkujemy i dostarczamy: • Lasery i fotodetektory, PSD (Position Sensitive Detectors), poczwórne komórki. Nasze aktywne komponenty optyczne obejmują szerokie spektrum regionów długości fal. Niezależnie od tego, czy Twoim zastosowaniem są lasery dużej mocy do cięcia przemysłowego, wiercenia, spawania itp., czy też lasery medyczne do chirurgii lub diagnostyki, czy też lasery telekomunikacyjne lub detektory odpowiednie dla sieci ITU, jesteśmy Twoim źródłem kompleksowej obsługi. Poniżej znajdują się broszury do pobrania dotyczące niektórych z naszych gotowych aktywnych komponentów optycznych i urządzeń. Jeśli nie możesz znaleźć tego, czego szukasz, skontaktuj się z nami, a będziemy mieli coś do zaoferowania. Zajmujemy się również produkcją na zamówienie aktywnych elementów i zespołów optycznych zgodnie z Państwa zastosowaniem i wymaganiami. • Wśród wielu osiągnięć naszych inżynierów optycznych znajduje się koncepcja, projekt optyczny i optomechaniczny optycznej głowicy skanującej dla SYSTEMU WIERCENIA LASEROWEGO GS 600 z podwójnymi skanerami galvo i samokompensującym ustawieniem. Od momentu wprowadzenia rodzina GS600 stała się systemem wybieranym przez wielu wiodących producentów masowych na całym świecie. Korzystając z narzędzi do projektowania optycznego, takich jak ZEMAX i CodeV, nasi inżynierowie optyki są gotowi zaprojektować niestandardowe systemy. Jeśli posiadasz tylko pliki SOLIDWORKS do swojego projektu, nie martw się, wyślij je, a my opracujemy i stworzymy pliki projektu optycznego, zoptymalizujemy i zasymulujemy oraz zatwierdzimy ostateczny projekt. Nawet odręczny szkic, makieta, prototyp lub próbka w większości przypadków wystarczają nam do zaspokojenia potrzeb związanych z rozwojem produktu. Pobierz nasz katalog aktywnych produktów światłowodowych Pobierz nasz katalog fotosensorów Pobierz nasz katalog fotomikrosensorów Pobierz nasz katalog gniazd i akcesoriów do fotoczujników i fotomikrosensorów Pobierz katalog naszych matryc i chipów LED Pobierz nasz obszerny katalog komponentów elektrycznych i elektronicznych dla produktów z półki sklepowej Pobierz broszurę dla naszego PROGRAM PARTNERSKI W PROJEKTOWANIU R mi Kod referencyjny: OICASANLY CLICK Product Finder-Locator Service POPRZEDNIA STRONA
- Holography - Holographic Glass Grating - AGS-TECH Inc. - New Mexico
Holography - Holographic Glass Grating - AGS-TECH Inc. - New Mexico - USA Produkcja produktów i systemów holograficznych Dostarczamy produkty z półki, jak również zaprojektowane i wyprodukowane na zamówienie HOLOGRAPHY PRODUCTS, w tym: • Wyświetlacze hologramowe 180, 270, 360 stopni / projekcja wizualna oparta na holografii • Samoprzylepne wyświetlacze z hologramem 360 stopni • Folia okienna 3D do reklam displayowych • Prezentacja hologramów Full HD i wyświetlacz holograficzny Piramida 3D do reklam holograficznych • Holocube z wyświetlaczem holograficznym 3D do reklamy holograficznej • System projekcji holograficznej 3D • Ekran holograficzny 3D Mesh Screen • Film do projekcji tylnej / Film do projekcji przedniej (z rolki) • Interaktywny wyświetlacz dotykowy • Zakrzywiony ekran projekcyjny: Zakrzywiony ekran projekcyjny to spersonalizowany produkt wykonywany na zamówienie dla każdego klienta. Produkujemy ekrany zakrzywione, ekrany do aktywnych i pasywnych ekranów symulatorów 3D oraz wyświetlacze symulacyjne. • Holograficzne produkty optyczne, takie jak naklejki zabezpieczające i potwierdzające autentyczność produktu (nadruk niestandardowy zgodnie z życzeniem klienta) • Szklane kraty holograficzne do zastosowań ozdobnych lub ilustracyjnych i edukacyjnych. Aby dowiedzieć się o naszych możliwościach inżynieryjnych i badawczo-rozwojowych, zapraszamy do odwiedzenia naszej strony inżynierskiej http://www.ags-engineering.com CLICK Product Finder-Locator Service POPRZEDNIA STRONA
- Customized Optomechanical Assemblies | agstech
Optomechanical Components & Assemblies, Beam Expander, Interferometers, Polarizers, Prism and Cube Assembly, Medical & Industrial Video Coupler, Optic Mounts Dostosowane zespoły optomechaniczne AGS-TECH jest dostawcą: • Niestandardowe zespoły optomechaniczne, takie jak ekspander wiązki, rozdzielacz wiązki, interferometria, etalon, filtr, izolator, polaryzator, montaż pryzmatu i sześcianu, mocowania optyczne, teleskop, lornetka, mikroskop metalurgiczny, adaptery kamery cyfrowej do mikroskopu i teleskopu, medyczne i przemysłowe złącza wideo, specjalne indywidualnie zaprojektowane systemy oświetlenia. Wśród produktów optomechanicznych opracowanych przez naszych inżynierów znajdują się: - Przenośny mikroskop metalurgiczny, który można ustawić w pozycji pionowej lub odwróconej. - Mikroskop do wklęsłodruku. - Adaptery do aparatów cyfrowych do mikroskopu i teleskopu. Standardowe adaptery pasują do wszystkich popularnych modeli aparatów cyfrowych i można je dostosować w razie potrzeby. - Wideozłącza medyczne i przemysłowe. Wszystkie medyczne złącza wideo pasują do standardowych okularów endoskopowych i są całkowicie uszczelnione i nasiąkające. - Gogle noktowizyjne - Lusterka samochodowe Broszura dotycząca komponentów optycznych (Kliknij na lewy niebieski link, aby pobrać) - w tym miejscu znajdziesz nasze komponenty optyczne i podzespoły w wolnej przestrzeni, które wykorzystujemy przy projektowaniu i produkcji zespołów optomechanicznych do zastosowań specjalnych. Łączymy i montujemy te elementy optyczne z precyzyjnie obrobionymi częściami metalowymi, aby budować produkty optomechaniczne naszych klientów. Stosujemy specjalne techniki klejenia i mocowania oraz materiały do sztywnego, niezawodnego i trwałego montażu. W niektórych przypadkach stosujemy technikę „kontaktowania optycznego”, w której łączymy ze sobą wyjątkowo płaskie i czyste powierzchnie i łączymy je bez użycia klejów lub epoksydów. Nasze zespoły optomechaniczne są czasami montowane pasywnie, a czasami montaż aktywny ma miejsce, gdzie używamy laserów i detektorów, aby upewnić się, że części są odpowiednio wyrównane przed ich zamocowaniem. Nawet przy intensywnych cyklach środowiskowych w specjalnych komorach, takich jak wysoka/niska temperatura; komory o wysokiej/niskiej wilgotności, nasze zespoły pozostają nienaruszone i działają dalej. Wszystkie nasze surowce do montażu optomechanicznego są pozyskiwane ze znanych na całym świecie źródeł, takich jak Corning i Schott. Broszura dotycząca luster samochodowych (Kliknij na lewy niebieski link, aby pobrać) CLICK Product Finder-Locator Service POPRZEDNIA STRONA
- Hardness Tester - Rockwell - Brinell - Vickers - Leeb - Microhardness
Hardness Tester - Rockwell - Brinell - Vickers - Leeb - Microhardness - Universal - AGS-TECH Inc. - New Mexico - USA Twardościomierze AGS-TECH Inc. posiada w ofercie szeroką gamę testerów twardości, w tym ROCKWELL, BRINELL, VICKERS, LEEB, KNOOP, MIKROWARSTWOŚCI, UNIWERSALNY TESTER TWARDOŚCI, PRZENOŚNE TESTOWANIE TWARDOŚCI, OPTYCZNE PRZYRZĄDY DO POMIARÓW I OPROGRAMOWANIA akwizycja i analiza, bloki testowe, wgłębniki, kowadła i powiązane akcesoria. Niektóre ze sprzedawanych przez nas markowych testerów twardości to SADT, SINOAGE and MITECH. Aby pobrać katalog naszych urządzeń metrologicznych i badawczych marki SADT, KLIKNIJ TUTAJ. Aby pobrać broszurę dotyczącą naszego przenośnego twardościomierza MITECH MH600, KLIKNIJ TUTAJ KLIKNIJ TUTAJ, aby pobrać tabelę porównawczą produktów między twardościomierzami MITECH Jednym z najczęstszych testów do oceny właściwości mechanicznych materiałów jest test twardości. Twardość materiału to jego odporność na trwałe wgniecenia. Można też powiedzieć, że twardość to odporność materiału na zarysowania i ścieranie. Istnieje kilka technik pomiaru twardości materiałów przy użyciu różnych geometrii i materiałów. Wyniki pomiarów nie są bezwzględne, są raczej względnym wskaźnikiem porównawczym, ponieważ wyniki zależą od kształtu wgłębnika i przyłożonego obciążenia. Nasze przenośne twardościomierze mogą generalnie przeprowadzić dowolny test twardości wymieniony powyżej. Można je skonfigurować pod kątem określonych cech geometrycznych i materiałów, takich jak wnętrza otworów, zęby kół zębatych… itp. Przyjrzyjmy się pokrótce różnym metodom badania twardości. TEST BRINELLA : W tym teście kulka ze stali lub węglika wolframu o średnicy 10 mm jest dociskana do powierzchni siłą 500, 1500 lub 3000 kg. Liczba twardości Brinella to stosunek obciążenia do zakrzywionego obszaru wgniecenia. Test Brinella pozostawia na powierzchni różnego rodzaju odciski w zależności od stanu badanego materiału. Na przykład na materiałach wyżarzanych pozostawia się zaokrąglony profil, podczas gdy na materiałach obrabianych na zimno obserwujemy ostry profil. Kulki wgłębnika z węglika wolframu są zalecane dla twardości Brinella wyższych niż 500. W przypadku twardszych materiałów obrabianych zaleca się obciążenie 1500 kg lub 3000 kg, aby pozostawione odciski były wystarczająco duże do dokładnego pomiaru. Z uwagi na fakt, że odciski wykonane tym samym wgłębnikiem przy różnych obciążeniach nie są geometrycznie podobne, liczba twardości Brinella zależy od zastosowanego obciążenia. Dlatego zawsze należy zwracać uwagę na zastosowane obciążenie wyników testu. Test Brinella dobrze nadaje się do materiałów od niskiej do średniej twardości. ROCKWELL TEST : W tym teście mierzona jest głębokość penetracji. Wgłębnik jest dociskany do powierzchni początkowo z niewielkim obciążeniem, a następnie z dużym obciążeniem. Różnica w zadłużeniu penetracyjnym jest miarą twardości. Istnieje kilka skal twardości Rockwella wykorzystujących różne obciążenia, materiały wgłębnika i geometrie. Numer twardości Rockwella jest odczytywany bezpośrednio z tarczy na maszynie wytrzymałościowej. Na przykład, jeśli liczba twardości wynosi 55 w skali C, jest zapisywana jako 55 HRC. TEST VICKERS : Czasami określany również jako TEST TWARDOŚCI DIAMENTOWEJ PIRAMIDY, wykorzystuje wgłębnik diamentowy w kształcie piramidy z obciążeniem od 1 do 120 kg. Liczba twardości Vickersa jest określona przez HV=1,854P / kwadrat L. L tutaj jest długością przekątnej piramidy diamentowej. Test Vickersa daje w zasadzie tę samą wartość twardości niezależnie od obciążenia. Test Vickersa nadaje się do testowania materiałów o szerokim zakresie twardości, w tym bardzo twardych materiałów. KNOOP TEST : W tym teście używamy wgłębnika diamentowego w kształcie wydłużonej piramidy i ładuje od 25g do 5 kg. Liczba twardości Knoopa jest podana jako HK=14,2P / kwadrat L. Tutaj litera L jest długością wydłużonej przekątnej. Wielkość wgłębień w testach Knoopa jest stosunkowo niewielka, w zakresie od 0,01 do 0,10 mm. Ze względu na tę niewielką liczbę bardzo ważne jest przygotowanie powierzchni pod materiał. Wyniki badań powinny odnosić się do przyłożonego obciążenia, ponieważ uzyskana twardość zależy od przyłożonego obciążenia. Ponieważ używane są lekkie obciążenia, test Knoopa jest uważany za a MICROHARDNESS TEST. Test Knoopa nadaje się zatem do bardzo małych, cienkich próbek, kruchych materiałów, takich jak kamienie szlachetne, szkło i węgliki, a nawet do pomiaru twardości pojedynczych ziaren w metalu. TEST TWARDOŚCI LEEB : Opiera się na technice odbicia mierzącej twardość Leeba. Jest to łatwa i popularna w przemyśle metoda. Ta przenośna metoda jest najczęściej używana do testowania wystarczająco dużych detali o masie powyżej 1 kg. Korpus udarowy z końcówką testową z twardego metalu jest napędzany siłą sprężyny na powierzchnię przedmiotu obrabianego. Gdy korpus udarowy uderza w przedmiot obrabiany, następuje odkształcenie powierzchni, które powoduje utratę energii kinetycznej. Pomiary prędkości ujawniają tę utratę energii kinetycznej. Gdy korpus uderzający przechodzi przez cewkę w dokładnej odległości od powierzchni, podczas fazy zderzenia i odbicia indukowane jest napięcie sygnału. Te napięcia są proporcjonalne do prędkości. Wykorzystując elektroniczne przetwarzanie sygnału, uzyskuje się z wyświetlacza wartość twardości Leeba. Nasze PRZENOŚNE TESTERY TWARDOŚCI TWARDOŚCI from SADT_cc781905-5cde-3194-cccf318b-136bad5 SADT HARTIP2000/HARTIP2000 D&DL : Jest to innowacyjny przenośny twardościomierz Leeb z nowo opatentowaną technologią, która sprawia, że HARTIP 2000 jest uniwersalnym testerem twardości pod kątem (UA). Nie ma potrzeby ustawiania kierunku uderzenia podczas wykonywania pomiarów pod dowolnym kątem. Dlatego HARTIP 2000 oferuje dokładność liniową w porównaniu z metodą kompensacji kąta. HARTIP 2000 jest również twardościomierzem pozwalającym zaoszczędzić pieniądze i posiada wiele innych funkcji. HARTIP2000 DL jest wyposażony w unikalną sondę SADT D i DL 2-w-1. SADT HARTIP1800 Plus/1800 Plus D&DL : To urządzenie jest zaawansowanym, najnowocześniejszym testerem twardości metalu wielkości dłoni z wieloma nowymi funkcjami. Wykorzystując opatentowaną technologię, SADT HARTIP1800 Plus to produkt nowej generacji. Ma wysoką dokładność +/-2 HL (lub 0,3% @HL800) z wyświetlaczem OLED o wysokim kontrakcie i szerokim zakresie temperatur otoczenia (-40ºC~60ºC). Oprócz ogromnych pamięci w 400 blokach z danymi 360k, HARTIP1800 Plus może pobierać zmierzone dane do komputera i drukować na mini-drukarce przez port USB i bezprzewodowo za pomocą wewnętrznego modułu niebieskiego zęba. Akumulator można ładować po prostu z portu USB. Posiada funkcję ponownej kalibracji klienta i statyki. HARTIP 1800 plus D&DL jest wyposażony w sondę „dwa w jednym”. Dzięki unikalnej sondzie „dwa w jednym”, HARTIP1800plus D&DL może konwertować pomiędzy sondą D i sondą DL po prostu poprzez zmianę korpusu udarowego. Jest to bardziej ekonomiczne niż kupowanie ich pojedynczo. Ma taką samą konfigurację jak HARTIP1800 plus, z wyjątkiem sondy „dwa w jednym”. SADT HARTIP1800 Basic/1800 Basic D&DL : Jest to podstawowy model dla HARTIP1800plus. Z większością podstawowych funkcji HARTIP1800 plus i niższą ceną, HARTIP1800 Basic jest dobrym wyborem dla klientów z ograniczonym budżetem. HARTIP1800 Basic może być również wyposażony w nasze wyjątkowe urządzenie udarowe D/DL „dwa w jednym”. SADT HARTIP 3000 : Jest to zaawansowany ręczny cyfrowy tester twardości metalu o wysokiej dokładności, szerokim zakresie pomiarowym i łatwości obsługi. Nadaje się do badania twardości wszystkich metali, zwłaszcza na miejscu, w przypadku dużych elementów konstrukcyjnych i zmontowanych, które są szeroko stosowane w przemyśle energetycznym, petrochemicznym, lotniczym, motoryzacyjnym i maszynowym. SADT HARTIP1500/HARTIP1000 : Jest to zintegrowany ręczny twardościomierz metalu, który łączy urządzenie udarowe (sonda) i procesor w jednym urządzeniu. Rozmiar jest znacznie mniejszy niż standardowe urządzenie udarowe, dzięki czemu HARTIP 1500/1000 spełnia nie tylko normalne warunki pomiarowe, ale także może wykonywać pomiary w wąskich przestrzeniach. HARTIP 1500/1000 nadaje się do badania twardości prawie wszystkich materiałów żelaznych i nieżelaznych. Dzięki nowej technologii jego dokładność jest wyższa niż w przypadku standardowego typu. HARTIP 1500/1000 to jeden z najbardziej ekonomicznych twardościomierzy w swojej klasie. AUTOMATYCZNY SYSTEM POMIAROWY ODCZYTU TWARDOŚCI BRINELL / SADT HB SCALER : HB Scaler to optyczny system pomiarowy, który może automatycznie mierzyć wielkość wgłębienia z twardościomierza Brinella i podaje odczyty twardości Brinella. Wszystkie wartości i obrazy wcięć można zapisać na komputerze. Dzięki oprogramowaniu wszystkie wartości mogą być przetwarzane i drukowane w formie raportu. Nasz TESTER TWARDOŚCI STOŁU products from SADT_cc781905-5cde-336bad-bb358b SADT HR-150A TWARDOŚCIOMIERZ ROCKWELL : Ręcznie obsługiwany twardościomierz Rockwell HR-150A jest znany ze swojej perfekcji i łatwości obsługi. Ta maszyna wykorzystuje standardową siłę wstępnego testu wynoszącą 10 kgf i główne obciążenia 60/100/150 kilogramów, przy zachowaniu zgodności z międzynarodowym standardem Rockwella. Po każdym teście HR-150A pokazuje wartość twardości Rockwell B lub Rockwell C bezpośrednio na czujniku zegarowym. Wstępną siłę testową należy przyłożyć ręcznie, a następnie przyłożyć główne obciążenie za pomocą dźwigni po prawej stronie twardościomierza. Po odciążeniu tarcza wskazuje żądaną wartość twardości bezpośrednio z dużą dokładnością i powtarzalnością. SADT HR-150DT ZMOTORYZOWANY TESTER TWARDOŚCI ROCKWELL : Ta seria twardościomierzy jest znana ze swojej dokładności i łatwości obsługi, działa w pełni zgodnie z międzynarodowym standardem Rockwell. W zależności od kombinacji typu wgłębnika i przyłożonej całkowitej siły testowej, każdej skali Rockwella nadawany jest unikalny symbol. HR-150DT i HRM-45DT mają na tarczy określone skale Rockwella HRC i HRB. Odpowiednią siłę należy wyregulować ręcznie za pomocą pokrętła znajdującego się po prawej stronie maszyny. Po przyłożeniu siły wstępnej, HR150DT i HRM-45DT przejdą w pełni zautomatyzowane testy: ładowanie, oczekiwanie, rozładowywanie, a na końcu pokażą twardość. SADT HRS-150 CYFROWY TESTER TWARDOŚCI ROCKWELL : Cyfrowy twardościomierz Rockwell HRS-150 został zaprojektowany z myślą o łatwości użytkowania i bezpieczeństwie pracy. Jest zgodny z międzynarodowym standardem Rockwell. W zależności od kombinacji typu wgłębnika i przyłożonej całkowitej siły testowej, każdej skali Rockwella nadawany jest unikalny symbol. HRS-150 automatycznie pokaże wybór określonej skali Rockwella na wyświetlaczu LCD i wskaże, które obciążenie jest używane. Zintegrowany mechanizm automatycznego hamowania umożliwia ręczne przyłożenie wstępnej siły testowej bez możliwości popełnienia błędu. Po przyłożeniu siły wstępnej HRS-150 przeprowadzi w pełni automatyczny test: obciążenie, czas przebywania, odciążenie oraz obliczenie wartości twardości i jej wyświetlenie. Po podłączeniu do dołączonej drukarki przez wyjście RS232, możliwe jest wydrukowanie wszystkich wyników. Nasz STOŁOWY TESTER TWARDOŚCI POWIERZCHNIOWEJ TYPU ROCKWELL products from bb3b3cdecc7819: SADT HRM-45DT Zmotoryzowany tester twardości powierzchniowej Rockwella : Ta seria twardościomierzy jest uznana za dokładność i łatwość obsługi, działa całkowicie zgodnie z międzynarodowym standardem Rockwell. W zależności od kombinacji typu wgłębnika i przyłożonej całkowitej siły testowej, każdej skali Rockwella nadawany jest unikalny symbol. HR-150DT i HRM-45DT są wyposażone w obie specyficzne skale Rockwella HRC i HRB na tarczy. Odpowiednią siłę należy wyregulować ręcznie za pomocą pokrętła znajdującego się po prawej stronie maszyny. Po przyłożeniu siły wstępnej, HR150DT i HRM-45DT przejdą w pełni automatyczny proces testowy: ładowanie, przebywanie, rozładowywanie, a na końcu wyświetlają twardość. SADT HRMS-45 TWARDOŚCIOMIERZ POWIERZCHNIOWY ROCKWELLA : Cyfrowy twardościomierz Rockwell HRMS-45 jest nowatorskim produktem integrującym zaawansowane technologie mechaniczne i elektroniczne. Podwójny wyświetlacz diod cyfrowych LCD i LED sprawia, że jest to ulepszona wersja produktu standardowego testera powierzchniowego Rockwell. Mierzy twardość metali żelaznych, nieżelaznych i materiałów twardych, warstw nawęglanych i azotowanych oraz innych warstw poddanych obróbce chemicznej. Służy również do pomiaru twardości cienkich elementów. SADT XHR-150 PLASTIKOWY TESTER TWARDOŚCI ROCKWELLA : XHR-150 tworzyw sztucznych Twardościomierz Rockwella przyjmuje zmotoryzowaną metodę testowania, siła testowa może być obciążana, utrzymywana w miejscu i automatycznie rozładowywana. Błąd ludzki jest zminimalizowany i łatwy w obsłudze. Służy do pomiaru twardych tworzyw sztucznych, twardych gum, aluminium, cyny, miedzi, miękkiej stali, żywic syntetycznych, materiałów tribologicznych itp. Nasz TESTER TWARDOŚCI STOŁOWYCH VICKERS products from SADT_cc781905-558cde-3194 SADT HVS-10/50 NISKO OBCIĄŻONY TESTER TWARDOŚCI VICKERS : Ten niskoobciążony twardościomierz Vickersa z cyfrowym wyświetlaczem jest nowym, zaawansowanym technologicznie produktem łączącym technologie mechaniczne i fotoelektryczne. Jako substytut tradycyjnych twardościomierzy Vickera o małym obciążeniu, charakteryzuje się łatwą obsługą i dobrą niezawodnością, która jest specjalnie zaprojektowana do testowania małych, cienkich próbek lub części po pokryciu powierzchni. Nadaje się do instytutów badawczych, laboratoriów przemysłowych i działów kontroli jakości, jest to idealny przyrząd do testowania twardości do celów badawczych i pomiarowych. Oferuje integrację technologii programowania komputerowego, optyczny system pomiarowy o wysokiej rozdzielczości i technikę fotoelektryczną, wprowadzanie klawiszy programowalnych, regulację źródła światła, wybór modelu testowego, tabele konwersji, czas utrzymywania ciśnienia, wprowadzanie numeru pliku i funkcje zapisywania danych. Posiada duży ekran LCD do wyświetlania modelu testowego, ciśnienia testowego, długości wcięcia, wartości twardości, czasu utrzymywania ciśnienia i liczby testów. Oferuje również rejestrację daty, rejestrację wyników badań i przetwarzanie danych, funkcję wydruku, poprzez interfejs RS232. SADT HV-10/50 NISKO OBCIĄŻENIOWY TESTER TWARDOŚCI Vickersa : Te niskoobciążeniowe twardościomierze Vickersa to nowe, zaawansowane technologicznie produkty integrujące technologie mechaniczne i fotoelektryczne. Testery te są specjalnie zaprojektowane do testowania małych i cienkich próbek oraz części po pokryciu powierzchni. Nadaje się do instytutów badawczych, laboratoriów przemysłowych i działów kontroli jakości. Kluczowe cechy i funkcje to sterowanie mikrokomputerem, regulacja źródła światła za pomocą klawiszy programowalnych, regulacja czasu utrzymywania nacisku i wyświetlacza LED/LCD, unikalne urządzenie do konwersji pomiarów i unikalne urządzenie do jednorazowego odczytu pomiaru mikrookularu, które zapewnia łatwą obsługę i wysoką dokładność. SADT HV-30 TESTER TWARDOŚCI VICKERS : Twardościomierz Vickers model HV-30 jest specjalnie zaprojektowany do testowania małych, cienkich próbek i części po pokryciu powierzchni. Odpowiednie dla instytutów badawczych, laboratoriów fabrycznych i działów kontroli jakości, są to idealne przyrządy do testowania twardości do celów badawczych i testowych. Kluczowe cechy i funkcje to sterowanie mikrokomputerem, automatyczny mechanizm ładowania i rozładowywania, regulacja źródła światła za pomocą sprzętu, regulacja czasu utrzymywania ciśnienia (0~30s), unikalne urządzenie do konwersji pomiaru i unikalne urządzenie do jednorazowego odczytu pomiaru mikrookularu, zapewniające łatwe wykorzystanie i wysoka dokładność. Nasz MIKRO TWARDOŚCI TYPU STOŁOWEGO products from SADT_cc781905-5cde-3194 SADT HV-1000 MIKRO TESTER TWARDOŚCI / HVS-1000 CYFROWY MIKRO TESTER TWARDOŚCI : Ten produkt jest szczególnie odpowiedni do precyzyjnego badania twardości małych i cienkich próbek, takich jak arkusze, folie, powłoki, wyroby ceramiczne i utwardzone warstwy. Aby zapewnić zadowalające wcięcie, HV1000 / HVS1000 oferuje automatyczne operacje załadunku i rozładunku, bardzo dokładny mechanizm ładowania i solidny system dźwigni. System sterowany mikrokomputerem zapewnia absolutnie precyzyjny pomiar twardości z regulowanym czasem przebywania. SADT DHV-1000 MICRO TESTER TWARDOŚCI / DHV-1000Z CYFROWY TESTER TWARDOŚCI VICKERS : Te mikro twardościomierze Vickersa o unikalnej i precyzyjnej konstrukcji są w stanie uzyskać wyraźniejsze wgłębienie, a tym samym dokładniejsze pomiary. Dzięki soczewce 20x i soczewce 40x przyrząd ma szersze pole pomiarowe i szerszy zakres zastosowań. Wyposażony w mikroskop cyfrowy, na ekranie LCD pokazuje metody pomiaru, siłę testową, długość wgłębienia, wartość twardości, czas przebywania siły testowej oraz liczbę pomiarów. Dodatkowo jest wyposażony w interfejs połączony z kamerą cyfrową i kamerą CCD. Ten tester jest szeroko stosowany do pomiaru metali żelaznych, metali nieżelaznych, cienkich przekrojów IC, powłok, szkła, ceramiki, kamieni szlachetnych, warstw hartowanych i innych. SADT DXHV-1000 CYFROWY MIKRO TWARDOŚCIOMIERZ : Te mikrotwardościomierze Vickers wykonane z unikalnym i precyzyjnym są w stanie uzyskać wyraźniejsze wgłębienie, a tym samym dokładniejsze pomiary. Dzięki soczewce 20x i soczewce 40x tester ma szersze pole pomiarowe i szerszy zakres zastosowań. Dzięki automatycznemu obracającemu urządzeniu (automatycznie obracającej się wieży) operacja stała się łatwiejsza; a dzięki interfejsowi gwintowanemu można go połączyć z aparatem cyfrowym i kamerą wideo CCD. Po pierwsze, urządzenie umożliwia korzystanie z ekranu dotykowego LCD, co pozwala na większą kontrolę nad operacją przez człowieka. Urządzenie posiada takie możliwości jak bezpośredni odczyt pomiarów, łatwa zmiana skali twardości, zapisywanie danych, drukowanie oraz połączenie z interfejsem RS232. Ten tester jest szeroko stosowany do pomiaru metali żelaznych, metali nieżelaznych, cienkich przekrojów IC, powłok, szkła, ceramiki, kamieni szlachetnych; cienkie elementy z tworzywa sztucznego, hartowanie warstw utwardzonych i nie tylko. Nasz STOŁOWY TESTER TWARDOŚCI BRINELLA / WIELOFUNKCYJNY TESTER TWARDOŚCI TWARDOŚCI products from_cc781905-5cde-3194-bb378d- SADT HD9-45 SUPERFICIAL TESTER TWARDOŚCI OPTYCZNEJ ROCKWELL & VICKERS : To urządzenie służy do pomiaru twardości metali żelaznych, nieżelaznych, twardych metali, warstw nawęglanych i azotowanych oraz warstw i cienkich elementów poddanych obróbce chemicznej. SADT HBRVU-187.5 TESTER TWARDOŚCI OPTYCZNEJ BRINELL'A ROCKWELL & VICKERS : Ten przyrząd służy do określania twardości Brinella, Rockwella i Vickersa metali żelaznych, nieżelaznych, twardych metali, warstw nawęglanych i warstw poddanych obróbce chemicznej. Może być stosowany w zakładach, instytutach naukowo-badawczych, laboratoriach i uczelniach. SADT HBRV-187.5 TESTER TWARDOŚCI BRINELLA ROCKWELL & VICKERS (NIEOPTYCZNY) : Ten przyrząd służy do określania twardości Brinella, Rockwella i Vickersa metali żelaznych, nieżelaznych, twardych, nawęglanych i warstwy poddane obróbce chemicznej. Może być stosowany w fabrykach, instytutach naukowo-badawczych, laboratoriach i uczelniach. To nie jest twardościomierz optyczny. SADT HBE-3000A TESTER TWARDOŚCI BRINELLA : Ten automatyczny twardościomierz Brinella oferuje szeroki zakres pomiarowy do 3000 Kgf z wysoką dokładnością zgodną z normą DIN 51225/1. Podczas automatycznego cyklu testowego przyłożona siła będzie kontrolowana przez system zamkniętej pętli, gwarantujący stałą siłę na obrabianym elemencie, zgodnie z normą DIN 50351. HBE-3000A jest w całości wyposażony w mikroskop do czytania z 20-krotnym powiększeniem i rozdzielczością mikrometra 0,005 mm. SADT HBS-3000 CYFROWY TESTER TWARDOŚCI BRINELLA : Ten cyfrowy twardościomierz Brinella to najnowocześniejsze urządzenie nowej generacji. Może służyć do określania twardości Brinella metali żelaznych i nieżelaznych. Tester oferuje elektroniczne automatyczne ładowanie, programowanie oprogramowania komputerowego, pomiar optyczny dużej mocy, fotosensor i inne funkcje. Każdy proces operacyjny i wynik testu można wyświetlić na dużym ekranie LCD. Wyniki testu można wydrukować. Urządzenie nadaje się do środowisk produkcyjnych, uczelni i instytucji naukowych. SADT MHB-3000 CYFROWY ELEKTRONICZNY TESTER TWARDOŚCI BRINELLA : Ten instrument jest zintegrowanym produktem łączącym techniki optyczne, mechaniczne i elektroniczne, przyjmując precyzyjną strukturę mechaniczną i sterowany komputerowo układ zamknięty. Przyrząd ładuje i rozładowuje siłę testową za pomocą swojego silnika. Wykorzystując czujnik kompresji o dokładności 0,5% do sprzężenia zwrotnego informacji i procesora do sterowania, przyrząd automatycznie kompensuje zmieniające się siły testowe. Wyposażony w cyfrowy mikrookular na instrumencie, długość wgłębienia może być mierzona direct. Wszystkie dane testowe, takie jak metoda testowa, wartość siły testowej, długość wgłębienia testowego, wartość twardości i czas przebywania siły testowej, można wyświetlić na ekranie LCD. Nie ma potrzeby wprowadzania wartości długości przekątnej dla wcięcia i nie ma potrzeby wyszukiwania wartości twardości z tabeli twardości. Dzięki temu odczytywane dane są dokładniejsze, a obsługa tego przyrządu łatwiejsza. Aby uzyskać szczegółowe informacje i podobny sprzęt, odwiedź naszą stronę internetową poświęconą sprzętowi: http://www.sourceindustrialsupply.com CLICK Product Finder-Locator Service POPRZEDNIA STRONA
- Functional Decorative Coatings - Thin Film - Thick Films - AR Coating
Functional & Decorative Coatings, Thin Film, Thick Films, Antireflective and Reflective Mirror Coating - AGS-TECH Inc. Powłoki funkcjonalne / Powłoki dekoracyjne / Cienka folia / Gruba folia A COATING to pokrycie nakładane na powierzchnię przedmiotu. Powłoki mogą mieć postać THIN FILM (grubość poniżej 1 mikrona) lub THICK FILM_3bdecc7805( o grubości powyżej 1 mikrona). W zależności od przeznaczenia powłoki możemy zaoferować Ci POWŁOKI DEKORACYJNE and/or POWŁOKI FUNKCJONALNE Czasami stosujemy powłoki funkcjonalne, aby zmienić właściwości powierzchni podłoża, takie jak przyczepność, zwilżalność, odporność na korozję lub odporność na zużycie. W niektórych innych przypadkach, takich jak wytwarzanie urządzeń półprzewodnikowych, nakładamy powłoki funkcjonalne, aby dodać zupełnie nową właściwość, taką jak namagnesowanie lub przewodność elektryczna, które stają się istotną częścią gotowego produktu. Nasze najpopularniejsze POWŁOKI FUNKCJONALNE są: Powłoki klejące: Przykładami są taśma klejąca, tkanina do naprasowania. Inne funkcjonalne powłoki klejące są stosowane w celu zmiany właściwości adhezyjnych, takie jak nieprzywierające garnki powlekane PTFE, podkłady, które zachęcają do dobrego przylegania kolejnych powłok. Powłoki trybologiczne: Te powłoki funkcjonalne odnoszą się do zasad tarcia, smarowania i zużycia. Każdy produkt, w którym jeden materiał ślizga się lub ociera o inny, podlega złożonym interakcjom trybologicznym. Produkty takie jak implanty biodrowe i inne sztuczne protezy są smarowane w określony sposób, podczas gdy inne produkty nie są smarowane, jak w przypadku elementów ślizgowych o wysokiej temperaturze, w których nie można stosować konwencjonalnych smarów. Udowodniono, że tworzenie się zagęszczonych warstw tlenkowych chroni przed zużyciem takich ślizgowych części mechanicznych. Powłoki funkcjonalne trybologiczne mają ogromne zalety w przemyśle, minimalizując zużycie elementów maszyn, minimalizując zużycie i odchylenia tolerancji w narzędziach produkcyjnych, takich jak matryce i formy, minimalizując wymagania dotyczące mocy oraz zwiększając efektywność energetyczną maszyn i urządzeń. Powłoki optyczne: Przykładami są powłoki antyrefleksyjne (AR), powłoki odblaskowe do luster, powłoki absorbujące promieniowanie UV do ochrony oczu lub do wydłużenia żywotności podłoża, przyciemnianie stosowane w niektórych barwnych światłach, przyciemniane szyby i okulary przeciwsłoneczne. Powłoki katalityczne takie jak nakładane na szkło samoczyszczące. Powłoki światłoczułe używane do wytwarzania produktów takich jak filmy fotograficzne Powłoki ochronne: Farby mogą być uważane za chroniące produkty, a nie tylko jako dekoracyjne. Twarde powłoki zapobiegające zarysowaniom na tworzywach sztucznych i innych materiałach są jedną z naszych najczęściej stosowanych powłok funkcjonalnych, które zmniejszają zarysowania, poprawiają odporność na zużycie itp. Dużą popularnością cieszą się również powłoki antykorozyjne, takie jak galwanizacja. Inne ochronne powłoki funkcjonalne nakładane są na wodoodporną tkaninę i papier, antybakteryjne powłoki powierzchniowe na narzędziach chirurgicznych i implantach. Powłoki hydrofilowe / hydrofobowe: funkcjonalne cienkie i grube warstwy zwilżające (hydrofilowe) i niezwilżające (hydrofobowe) są ważne w zastosowaniach, w których absorpcja wody jest pożądana lub niepożądana. Korzystając z zaawansowanej technologii, możemy zmienić powierzchnie Twoich produktów, aby były łatwo zwilżalne lub niezwilżalne. Typowe zastosowania to tekstylia, opatrunki, skórzane buty, produkty farmaceutyczne lub chirurgiczne. Natura hydrofilowa odnosi się do fizycznej właściwości cząsteczki, która może przejściowo wiązać się z wodą (H2O) poprzez wiązanie wodorowe. Jest to korzystne termodynamicznie i sprawia, że cząsteczki te są rozpuszczalne nie tylko w wodzie, ale także w innych rozpuszczalnikach polarnych. Cząsteczki hydrofilowe i hydrofobowe są również znane odpowiednio jako cząsteczki polarne i cząsteczki niepolarne. Powłoki magnetyczne: Te funkcjonalne powłoki dodają właściwości magnetyczne, takie jak w przypadku dyskietek magnetycznych, kaset, pasków magnetycznych, nośników magnetooptycznych, indukcyjnych nośników zapisu, czujników magnetorezystancyjnych i cienkowarstwowych głowic w produktach. Cienkie folie magnetyczne to arkusze materiału magnetycznego o grubości kilku mikrometrów lub mniejszej, stosowane głównie w przemyśle elektronicznym. Cienkie warstwy magnetyczne mogą być powłokami funkcjonalnymi monokrystalicznymi, polikrystalicznymi, amorficznymi lub wielowarstwowymi w układzie ich atomów. Stosowane są zarówno folie ferro- jak i ferrimagnetyczne. Funkcjonalne powłoki ferromagnetyczne są zwykle stopami metali przejściowych. Na przykład permalloy jest stopem niklowo-żelaznym. Funkcjonalne powłoki ferrimagnetyczne, takie jak granaty lub folie amorficzne, zawierają metale przejściowe, takie jak żelazo lub kobalt oraz pierwiastki ziem rzadkich, a właściwości ferrimagnetyczne są korzystne w zastosowaniach magnetooptycznych, w których można osiągnąć niski całkowity moment magnetyczny bez znaczącej zmiany temperatury Curie . Niektóre elementy czujnika działają na zasadzie zmiany właściwości elektrycznych, takich jak rezystancja elektryczna, za pomocą pola magnetycznego. W technologii półprzewodnikowej głowica magnetorezystyczna stosowana w technologii pamięci dyskowej działa zgodnie z tą zasadą. W wielowarstwach magnetycznych i kompozytach zawierających materiał magnetyczny i niemagnetyczny obserwuje się bardzo duże sygnały magnetorezystancyjne (gigantyczny magnetorezystancja). Powłoki elektryczne lub elektroniczne: Te powłoki funkcjonalne dodają właściwości elektryczne lub elektroniczne, takie jak przewodność, do wytwarzania produktów, takich jak rezystory, właściwości izolacyjne, takie jak w przypadku powłok drutów magnetycznych stosowanych w transformatorach. POWŁOKI DEKORACYJNE: Kiedy mówimy o powłokach dekoracyjnych, możliwości ogranicza tylko Twoja wyobraźnia. Zarówno powłoki grubo jak i cienkowarstwowe zostały z powodzeniem opracowane i zastosowane w przeszłości na produktach naszych klientów. Niezależnie od trudności związanych z geometrycznym kształtem i materiałem podłoża oraz warunków aplikacji, zawsze jesteśmy w stanie sformułować chemię, aspekty fizyczne, takie jak dokładny kod koloru Pantone i metodę nakładania żądanych powłok dekoracyjnych. Możliwe są również złożone wzory obejmujące kształty lub różne kolory. Możemy sprawić, by Twoje plastikowe części polimerowe wyglądały na metaliczne. Możemy anodować profile anodowane różnymi wzorami i nawet nie będą wyglądać na anodowane. Możemy nanieść lustrzaną powłokę na część o dziwnym kształcie. Ponadto można formułować powłoki dekoracyjne, które będą jednocześnie działać jako powłoki funkcjonalne. Każda z wymienionych poniżej technik osadzania cienkich i grubych warstw stosowanych do powłok funkcjonalnych może być zastosowana do powłok dekoracyjnych. Oto niektóre z naszych popularnych powłok dekoracyjnych: - Powłoki dekoracyjne cienkowarstwowe PVD - Galwaniczne powłoki dekoracyjne - Powłoki dekoracyjne cienkowarstwowe CVD i PECVD - Powłoki dekoracyjne z odparowaniem termicznym - Powłoka dekoracyjna Roll-to-Roll - Powłoki dekoracyjne z interferencją tlenków E-Beam -Poszycie jonowe - Odparowywanie łukiem katodowym dla powłok dekoracyjnych - PVD + fotolitografia, ciężkie złocenie na PVD - Powłoki aerozolowe do barwienia szkła - Powłoka przeciw matowieniu - Dekoracyjne systemy miedziano-niklowo-chromowe -Dekoracyjna powłoka proszkowa - Malowanie dekoracyjne, niestandardowe formuły farb przy użyciu pigmentów, wypełniaczy, dyspergatora koloidalnej krzemionki ... itp. Jeśli skontaktujesz się z nami ze swoimi wymaganiami dotyczącymi powłok dekoracyjnych, możemy dostarczyć Ci naszą ekspercką opinię. Dysponujemy zaawansowanymi narzędziami, takimi jak czytniki kolorów, komparatory kolorów… itd. aby zagwarantować stałą jakość Twoich powłok. PROCESY POWLEKANIA CIENKIEM I GRUBYM FILMEM: Oto najszerzej stosowane z naszych technik. Galwanizacja / Galwanizacja chemiczna (twardy chrom, nikiel chemiczny) Galwanizacja to proces powlekania jednego metalu na drugim przez hydrolizę, w celach dekoracyjnych, zapobieganiu korozji metalu lub w innych celach. Galwanizacja pozwala nam na użycie niedrogich metali, takich jak stal, cynk lub tworzywa sztuczne do masy produktu, a następnie nakładanie różnych metali na zewnątrz w postaci folii dla lepszego wyglądu, ochrony i innych pożądanych dla produktu właściwości. Powlekanie bezprądowe, znane również jako powlekanie chemiczne, to niegalwaniczna metoda powlekania, która obejmuje kilka jednoczesnych reakcji w roztworze wodnym, które zachodzą bez użycia zewnętrznej energii elektrycznej. Reakcja zachodzi, gdy wodór jest uwalniany przez środek redukujący i utleniany, tworząc w ten sposób ładunek ujemny na powierzchni części. Zaletami tych cienkich i grubych powłok jest dobra odporność na korozję, niska temperatura obróbki, możliwość osadzania się w otworach, szczelinach… itp. Wady to ograniczony wybór materiałów powłokowych, stosunkowo miękki charakter powłok, niezbędne dla środowiska kąpiele do obróbki w tym chemikalia, takie jak cyjanek, metale ciężkie, fluorki, oleje, ograniczona dokładność replikacji powierzchni. Procesy dyfuzji (azotowanie, węgloazotowanie, borowanie, fosforanowanie itp.) W piecach do obróbki cieplnej rozproszone elementy zwykle pochodzą z gazów reagujących w wysokich temperaturach z metalowymi powierzchniami. Może to być czysta reakcja termiczna i chemiczna w wyniku termicznej dysocjacji gazów. W niektórych przypadkach rozproszone elementy pochodzą z brył. Zaletami tych procesów powlekania termochemicznego są dobra odporność na korozję, dobra powtarzalność. Ich wadą są stosunkowo miękkie powłoki, ograniczony wybór materiału bazowego (który musi nadawać się do azotowania), długi czas obróbki, związane z tym zagrożenia dla środowiska i zdrowia, konieczność dalszej obróbki. CVD (chemiczne osadzanie z fazy gazowej) CVD to proces chemiczny stosowany do wytwarzania wysokiej jakości, wysokowydajnych, trwałych powłok. W procesie powstają również cienkie folie. W typowym CVD podłoża są wystawiane na działanie jednego lub więcej lotnych prekursorów, które reagują i/lub rozkładają się na powierzchni podłoża z wytworzeniem pożądanej cienkiej błony. Zaletami tych cienkich i grubych folii jest ich wysoka odporność na zużycie, możliwość ekonomicznego wytwarzania grubszych powłok, przydatność do otworów wiertniczych, szczelin… itd. Wadami procesów CVD są ich wysokie temperatury przetwarzania, trudność lub niemożność nakładania powłok wieloma metalami (np. TiAlN), zaokrąglanie krawędzi, stosowanie niebezpiecznych dla środowiska chemikaliów. PACVD / PECVD (chemiczne osadzanie z fazy gazowej wspomagane plazmowo) PACVD jest również nazywany PECVD, co oznacza CVD wzmocnione plazmą. Podczas gdy w procesie powlekania PVD materiały cienkie i grube warstwy są odparowywane z postaci stałej, w PECVD powłoka powstaje w fazie gazowej. Gazy prekursorowe pękają w plazmie, aby stać się dostępne dla powłoki. Zaletą tej techniki osadzania cienkich i grubych warstw jest to, że możliwe są znacznie niższe temperatury procesu w porównaniu z CVD, nakładane są precyzyjne powłoki. Wadą PACVD jest to, że ma tylko ograniczoną przydatność do otworów wiertniczych, szczelin itp. PVD (fizyczne osadzanie z fazy gazowej) Procesy PVD to różnorodne czysto fizyczne metody osadzania próżniowego stosowane do osadzania cienkich warstw poprzez kondensację odparowanej postaci pożądanego materiału folii na powierzchniach obrabianego przedmiotu. Powłoki napylające i odparowujące są przykładami PVD. Zaletą jest to, że nie powstają żadne szkodliwe dla środowiska materiały i emisje, można wytwarzać wiele różnych powłok, temperatury powłok są poniżej końcowej temperatury obróbki cieplnej większości stali, precyzyjnie odtwarzalne cienkie powłoki, wysoka odporność na zużycie, niski współczynnik tarcia. Wadami są otwory, szczeliny ...itd. może być powlekany tylko do głębokości równej średnicy lub szerokości otworu, odporny na korozję tylko w określonych warunkach, a w celu uzyskania jednolitej grubości powłoki części muszą być obracane podczas nakładania. Przyczepność powłok funkcjonalnych i dekoracyjnych jest zależna od podłoża. Ponadto żywotność powłok cienko i grubopowłokowych zależy od parametrów środowiskowych, takich jak wilgotność, temperatura itp. Dlatego przed rozważeniem powłoki funkcjonalnej lub dekoracyjnej skontaktuj się z nami w celu uzyskania opinii. Możemy wybrać najbardziej odpowiednie materiały powłokowe i technikę powlekania, które pasują do Twoich podłoży i aplikacji, a następnie nałożyć je zgodnie z najsurowszymi normami jakości. Skontaktuj się z AGS-TECH Inc. w celu uzyskania szczegółowych informacji na temat możliwości osadzania cienkich i grubych warstw. Potrzebujesz pomocy projektowej? Potrzebujesz prototypów ? Potrzebujesz masowej produkcji? Jesteśmy tutaj, aby Ci pomóc. CLICK Product Finder-Locator Service POPRZEDNIA STRONA
- Electronic Testers, Electrical Properties Testing, Oscilloscope, Pulse
Electronic Testers - Electrical Test Equipment - Electrical Properties Testing - Oscilloscope - Signal Generator - Function Generator - Pulse Generator - Frequency Synthesizer - Multimeter Testery elektroniczne Termin TESTER ELEKTRONICZNY odnosi się do sprzętu testowego, który jest używany głównie do testowania, kontroli i analizy elementów i systemów elektrycznych i elektronicznych. Oferujemy najpopularniejsze w branży: ZASILACZE I URZĄDZENIA GENERUJĄCE SYGNAŁ: ZASILACZ, GENERATOR SYGNAŁU, SYNTEZATOR CZĘSTOTLIWOŚCI, GENERATOR FUNKCJI, GENERATOR WZORÓW CYFROWYCH, GENERATOR IMPULSÓW, WTRYSKIWACZ SYGNAŁU MIERNIKI: MULTIMETRY CYFROWE, MIERNIK LCR, MIERNIK EMF, MIERNIK POJEMNOŚCI, PRZYRZĄD MOSTKOWY, MIERNIK CĘGOWY, GAUSMETR/TESLAMETR/MAGNETOMIER, MIERNIK REZYSTANCJI UZIEMIENIA ANALIZATORY: OSCYLOSKOPY, ANALIZATOR LOGIKI, ANALIZATOR WIDMA, ANALIZATOR PROTOKOŁÓW, ANALIZATOR SYGNAŁÓW WEKTOROWYCH, REFLEKTOMETR W DZIEDZINIE CZASU, PÓŁPRZEWODNIK ŚLEDZENIE KRZYWEJ, ANALIZATOR SIECI, OBRACANIE FAZ, ROTACJA FAZY Aby uzyskać szczegółowe informacje i podobny sprzęt, odwiedź naszą stronę internetową poświęconą sprzętowi: http://www.sourceindustrialsupply.com Przyjrzyjmy się pokrótce niektórym z tych urządzeń, które są używane na co dzień w całej branży: Dostarczane przez nas zasilacze elektryczne do celów metrologicznych są urządzeniami dyskretnymi, stacjonarnymi i wolnostojącymi. REGULOWANE ZASILACZE ELEKTRYCZNE są jednymi z najpopularniejszych, ponieważ ich wartości wyjściowe można regulować, a ich napięcie wyjściowe lub prąd są utrzymywane na stałym poziomie, nawet przy wahaniach napięcia wejściowego lub prądu obciążenia. IZOLOWANE ZASILACZE mają wyjścia mocy, które są elektrycznie niezależne od ich mocy wejściowych. W zależności od metody konwersji mocy istnieją ZASILACZE LINIOWE i PRZEŁĄCZALNE. Zasilacze liniowe przetwarzają moc wejściową bezpośrednio ze wszystkimi aktywnymi komponentami konwersji mocy pracującymi w obszarach liniowych, podczas gdy zasilacze impulsowe mają komponenty pracujące głównie w trybach nieliniowych (takich jak tranzystory) i konwertują moc na impulsy AC lub DC przed przetwarzanie. Zasilacze impulsowe są generalnie bardziej wydajne niż zasilacze liniowe, ponieważ tracą mniej energii ze względu na krótszy czas, jaki ich komponenty spędzają w liniowych obszarach działania. W zależności od zastosowania używane jest zasilanie prądem stałym lub zmiennym. Inne popularne urządzenia to ZASILACZE PROGRAMOWALNE, w których napięcie, prąd lub częstotliwość mogą być zdalnie sterowane poprzez wejście analogowe lub interfejs cyfrowy, taki jak RS232 lub GPIB. Wiele z nich posiada wbudowany mikrokomputer do monitorowania i kontrolowania operacji. Takie instrumenty są niezbędne do celów zautomatyzowanego testowania. Niektóre zasilacze elektroniczne wykorzystują ograniczenie prądu zamiast odcinania zasilania w przypadku przeciążenia. Ograniczenie elektroniczne jest powszechnie stosowane w instrumentach typu laboratoryjnego. GENERATORY SYGNAŁU to kolejne szeroko stosowane przyrządy w laboratoriach i przemyśle, generujące powtarzające się lub nie powtarzające się sygnały analogowe lub cyfrowe. Alternatywnie nazywane są również GENERATORAMI FUNKCYJNYMI, GENERATORAMI WZORÓW CYFROWYCH lub GENERATORAMI CZĘSTOTLIWOŚCI. Generatory funkcji generują proste, powtarzalne przebiegi, takie jak fale sinusoidalne, impulsy schodkowe, przebiegi kwadratowe i trójkątne oraz przebiegi arbitralne. Dzięki generatorom przebiegów arbitralnych użytkownik może generować dowolne przebiegi, w opublikowanych granicach zakresu częstotliwości, dokładności i poziomu wyjściowego. W przeciwieństwie do generatorów funkcyjnych, które są ograniczone do prostego zestawu przebiegów, generator przebiegów arbitralnych pozwala użytkownikowi określić przebieg źródłowy na wiele różnych sposobów. GENERATORY SYGNAŁU RF i MIKROFALOWEGO służą do testowania komponentów, odbiorników i systemów w aplikacjach takich jak komunikacja komórkowa, WiFi, GPS, radiodyfuzja, komunikacja satelitarna i radary. Generatory sygnału RF zwykle pracują w zakresie od kilku kHz do 6 GHz, podczas gdy generatory sygnału mikrofalowego działają w znacznie szerszym zakresie częstotliwości, od mniej niż 1 MHz do co najmniej 20 GHz, a nawet do setek zakresów GHz przy użyciu specjalnego sprzętu. Generatory sygnałów RF i mikrofalowych można dalej klasyfikować jako generatory sygnałów analogowych lub wektorowych. GENERATORY SYGNAŁU CZĘSTOTLIWOŚCI AUDIO generują sygnały w zakresie częstotliwości audio i powyżej. Posiadają elektroniczne aplikacje laboratoryjne sprawdzające charakterystykę częstotliwościową sprzętu audio. GENERATORY SYGNAŁU WEKTOROWEGO, czasami nazywane również GENERATORAMI SYGNAŁU CYFROWEGO, są zdolne do generowania cyfrowo modulowanych sygnałów radiowych. Generatory sygnałów wektorowych mogą generować sygnały w oparciu o standardy branżowe, takie jak GSM, W-CDMA (UMTS) i Wi-Fi (IEEE 802.11). GENERATORY SYGNAŁÓW LOGICZNYCH nazywane są również CYFROWYMI GENERATORAMI WZORÓW. Generatory te wytwarzają sygnały logiczne, czyli logiczne jedynki i zera w postaci konwencjonalnych poziomów napięcia. Generatory sygnałów logicznych są wykorzystywane jako źródła bodźców do funkcjonalnej walidacji i testowania cyfrowych układów scalonych i systemów wbudowanych. Wyżej wymienione urządzenia są przeznaczone do użytku ogólnego. Istnieje jednak wiele innych generatorów sygnałów zaprojektowanych do niestandardowych, specyficznych zastosowań. WTRYSKIWACZ SYGNAŁU jest bardzo przydatnym i szybkim narzędziem do rozwiązywania problemów do śledzenia sygnału w obwodzie. Technicy mogą bardzo szybko określić wadliwy stan urządzenia, takiego jak odbiornik radiowy. Wtryskiwacz sygnału można podać na wyjście głośnikowe, a jeśli sygnał jest słyszalny można przejść do poprzedniego etapu obwodu. W tym przypadku wzmacniacz audio, a jeśli wprowadzony sygnał jest słyszany ponownie, można przesuwać wstrzykiwany sygnał w górę stopni obwodu, aż sygnał przestanie być słyszalny. Pomoże to zlokalizować lokalizację problemu. MULTIMETR to elektroniczny przyrząd pomiarowy łączący kilka funkcji pomiarowych w jednej jednostce. Ogólnie rzecz biorąc, multimetry mierzą napięcie, prąd i rezystancję. Dostępna jest zarówno wersja cyfrowa, jak i analogowa. Oferujemy przenośne multimetry ręczne oraz modele laboratoryjne z certyfikowaną kalibracją. Nowoczesne multimetry mogą mierzyć wiele parametrów takich jak: napięcie (zarówno AC/DC), w woltach, prąd (zarówno AC/DC), w amperach, rezystancja w omach. Dodatkowo niektóre multimetry mierzą: pojemność w faradach, przewodność w siemensach, decybelach, cykl pracy w procentach, częstotliwość w hercach, indukcyjność w henrach, temperaturę w stopniach Celsjusza lub Fahrenheita za pomocą sondy do pomiaru temperatury. Niektóre multimetry obejmują również: tester ciągłości; dźwięki podczas przewodzenia obwodu, diody (pomiar spadku w przód złącz diod), tranzystory (pomiar wzmocnienia prądu i innych parametrów), funkcja sprawdzania baterii, funkcja pomiaru poziomu światła, funkcja pomiaru kwasowości i zasadowości (pH) oraz funkcja pomiaru wilgotności względnej. Nowoczesne multimetry są często cyfrowe. Nowoczesne multimetry cyfrowe często mają wbudowany komputer, dzięki czemu są bardzo potężnymi narzędziami w metrologii i testowaniu. Obejmują one takie funkcje, jak: • Auto-zakres, który wybiera właściwy zakres dla badanej wielkości, tak aby pokazywane były najbardziej znaczące cyfry. • Automatyczna polaryzacja dla odczytów prądu stałego pokazuje, czy przyłożone napięcie jest dodatnie czy ujemne. • Próbkowanie i wstrzymanie, które zablokuje ostatni odczyt do badania po wyjęciu przyrządu z testowanego obwodu. • Ograniczone prądem testy spadku napięcia na złączach półprzewodnikowych. Chociaż nie jest to zamiennik testera tranzystorów, ta cecha multimetrów cyfrowych ułatwia testowanie diod i tranzystorów. • Wykres słupkowy przedstawiający badaną wielkość dla lepszej wizualizacji szybkich zmian mierzonych wartości. • Oscyloskop o małej przepustowości. •Testery obwodów samochodowych z testami synchronizacji samochodowej i sygnałów zatrzymania. •Funkcja akwizycji danych do rejestrowania maksymalnych i minimalnych odczytów w danym okresie oraz do pobierania wielu próbek w stałych odstępach czasu. • Połączony miernik LCR. Niektóre multimetry mogą być połączone z komputerami, a niektóre mogą przechowywać pomiary i przesyłać je do komputera. Jeszcze inne bardzo przydatne narzędzie, LCR METER to przyrząd pomiarowy do pomiaru indukcyjności (L), pojemności (C) i rezystancji (R) elementu. Impedancja jest mierzona wewnętrznie i konwertowana do wyświetlania na odpowiednią wartość pojemności lub indukcyjności. Odczyty będą dość dokładne, jeśli testowany kondensator lub cewka indukcyjna nie mają znaczącej składowej rezystancyjnej impedancji. Zaawansowane mierniki LCR mierzą rzeczywistą indukcyjność i pojemność, a także równoważną rezystancję szeregową kondensatorów i współczynnik dobroci elementów indukcyjnych. Badane urządzenie jest poddawane działaniu źródła napięcia przemiennego, a miernik mierzy napięcie w poprzek oraz prąd płynący przez badane urządzenie. Na podstawie stosunku napięcia do prądu miernik może określić impedancję. W niektórych przyrządach mierzony jest również kąt fazowy między napięciem a prądem. W połączeniu z impedancją można obliczyć i wyświetlić równoważną pojemność lub indukcyjność oraz rezystancję testowanego urządzenia. Mierniki LCR mają wybieralne częstotliwości testowe 100 Hz, 120 Hz, 1 kHz, 10 kHz i 100 kHz. Mierniki laboratoryjne LCR mają zwykle wybieralne częstotliwości testowe powyżej 100 kHz. Często zawierają one możliwość nałożenia napięcia lub prądu stałego na sygnał pomiarowy prądu przemiennego. Podczas gdy niektóre mierniki oferują możliwość zewnętrznego zasilania tych napięć lub prądów DC, inne urządzenia zasilają je wewnętrznie. MIERNIK PEM jest przyrządem testowo-metrologicznym do pomiaru pól elektromagnetycznych (EMF). Większość z nich mierzy gęstość strumienia promieniowania elektromagnetycznego (pola DC) lub zmianę pola elektromagnetycznego w czasie (pola AC). Istnieją wersje przyrządów jednoosiowych i trójosiowych. Mierniki jednoosiowe kosztują mniej niż mierniki trójosiowe, ale wykonanie testu zajmuje więcej czasu, ponieważ miernik mierzy tylko jeden wymiar pola. Jednoosiowe mierniki EMF muszą być przechylane i obracane we wszystkich trzech osiach, aby zakończyć pomiar. Z drugiej strony mierniki trójosiowe mierzą wszystkie trzy osie jednocześnie, ale są droższe. Miernik EMF może mierzyć pola elektromagnetyczne prądu przemiennego, które pochodzą ze źródeł takich jak przewody elektryczne, podczas gdy GAUSMETRY / TESLAMETRY lub MAGNETOMETRY mierzą pola prądu stałego emitowane ze źródeł, w których występuje prąd stały. Większość mierników EMF jest skalibrowana do pomiaru pól przemiennych 50 i 60 Hz odpowiadających częstotliwości prądu w sieci elektrycznej w USA i Europie. Istnieją inne mierniki, które mogą mierzyć pola zmieniające się z częstotliwością nawet 20 Hz. Pomiary EMF mogą być szerokopasmowe w szerokim zakresie częstotliwości lub selektywnie monitorować tylko interesujący zakres częstotliwości. MIERNIK POJEMNOŚCI jest przyrządem testowym służącym do pomiaru pojemności w większości dyskretnych kondensatorów. Niektóre mierniki wyświetlają tylko pojemność, podczas gdy inne pokazują również upływ, równoważną rezystancję szeregową i indukcyjność. Przyrządy testowe wyższej klasy wykorzystują techniki, takie jak wprowadzenie testowanego kondensatora do obwodu mostkowego. Zmieniając wartości pozostałych odgałęzień mostka, tak aby doprowadzić mostek do równowagi, określa się wartość nieznanego kondensatora. Ta metoda zapewnia większą precyzję. Mostek może być również zdolny do pomiaru rezystancji szeregowej i indukcyjności. Można mierzyć kondensatory w zakresie od pikofaradów do faradów. Obwody mostkowe nie mierzą prądu upływu, ale można przyłożyć napięcie polaryzacji DC i bezpośrednio mierzyć upływ. Wiele INSTRUMENTÓW BRIDGE można podłączyć do komputerów i dokonywać wymiany danych w celu pobierania odczytów lub zewnętrznego sterowania mostem. Takie przyrządy pomostowe oferują również testy typu „go / no go” w celu automatyzacji testów w szybkim środowisku produkcyjnym i kontroli jakości. Jeszcze innym przyrządem testowym, CLAMP METER, jest tester elektryczny łączący woltomierz z cęgowym miernikiem prądu. Większość nowoczesnych wersji mierników cęgowych jest cyfrowa. Nowoczesne mierniki cęgowe mają większość podstawowych funkcji multimetru cyfrowego, ale mają dodatkową funkcję przekładnika prądowego wbudowanego w produkt. Kiedy zaciśniesz „szczęki” przyrządu wokół przewodnika przewodzącego duży prąd przemienny, prąd ten jest przekazywany przez szczęki, podobnie jak żelazny rdzeń transformatora mocy, do uzwojenia wtórnego, które jest połączone z bocznikiem wejścia miernika , zasada działania bardzo zbliżona do transformatora. Na wejście miernika podawany jest znacznie mniejszy prąd ze względu na stosunek liczby uzwojeń wtórnych do liczby uzwojeń pierwotnych owiniętych wokół rdzenia. Pierwotny jest reprezentowany przez jeden przewodnik, wokół którego zaciskane są szczęki. Jeśli wtórne ma 1000 uzwojeń, to prąd wtórny wynosi 1/1000 prądu płynącego w pierwotnym, lub w tym przypadku mierzonym przewodzie. Zatem 1 amper prądu w mierzonym przewodniku wytworzy 0,001 ampera prądu na wejściu miernika. Za pomocą mierników cęgowych można łatwo mierzyć znacznie większe prądy, zwiększając liczbę zwojów w uzwojeniu wtórnym. Podobnie jak w przypadku większości naszych urządzeń testowych, zaawansowane mierniki cęgowe oferują możliwość rejestrowania. TESTERY REZYSTANCJI UZIEMIENIA służą do badania uziomów oraz rezystywności gruntu. Wymagania dotyczące przyrządu zależą od zakresu zastosowań. Nowoczesne przyrządy do testowania uziemienia cęgowego upraszczają testowanie pętli uziemienia i umożliwiają nieinwazyjne pomiary prądu upływu. Wśród sprzedawanych przez nas ANALIZATORÓW są bez wątpienia OSCYLOSKOPY jeden z najczęściej używanych urządzeń. Oscyloskop, zwany również OSCILLOGRAPHEM, jest rodzajem elektronicznego przyrządu testowego, który umożliwia obserwację stale zmieniających się napięć sygnału jako dwuwymiarowy wykres jednego lub więcej sygnałów w funkcji czasu. Sygnały nieelektryczne, takie jak dźwięk i wibracje, mogą być również przekształcane na napięcia i wyświetlane na oscyloskopach. Oscyloskopy służą do obserwowania zmian sygnału elektrycznego w czasie, napięcie i czas opisują kształt, który jest stale wykreślany na skalibrowanej skali. Obserwacja i analiza przebiegu ujawnia nam takie właściwości, jak amplituda, częstotliwość, interwał czasowy, czas narastania i zniekształcenia. Oscyloskopy można regulować tak, aby powtarzające się sygnały były obserwowane jako ciągły kształt na ekranie. Wiele oscyloskopów ma funkcję przechowywania, która umożliwia przechwytywanie pojedynczych zdarzeń przez przyrząd i wyświetlanie ich przez stosunkowo długi czas. To pozwala nam obserwować wydarzenia zbyt szybko, aby były bezpośrednio dostrzegalne. Nowoczesne oscyloskopy to lekkie, kompaktowe i przenośne przyrządy. Istnieją również miniaturowe przyrządy zasilane bateryjnie do zastosowań terenowych. Oscyloskopy laboratoryjne są zazwyczaj urządzeniami stacjonarnymi. Istnieje szeroka gama sond i kabli wejściowych do użytku z oscyloskopami. Skontaktuj się z nami, jeśli potrzebujesz porady, który z nich zastosować w swojej aplikacji. Oscyloskopy z dwoma wejściami pionowymi nazywane są oscyloskopami dwuścieżkowymi. Używając jednowiązkowego CRT, multipleksują wejścia, zwykle przełączając się między nimi wystarczająco szybko, aby wyświetlić dwa ślady naraz. Są też oscyloskopy z większą ilością śladów; cztery wejścia są wśród nich wspólne. Niektóre oscyloskopy wielościeżkowe wykorzystują zewnętrzne wejście wyzwalające jako opcjonalne wejście pionowe, a niektóre mają trzeci i czwarty kanał z minimalną kontrolą. Nowoczesne oscyloskopy mają kilka wejść dla napięć, dzięki czemu można je wykorzystać do wykreślenia jednego zmiennego napięcia względem drugiego. Jest to używane na przykład do tworzenia wykresów krzywych IV (charakterystyka prądu w funkcji napięcia) dla komponentów takich jak diody. W przypadku wysokich częstotliwości i szybkich sygnałów cyfrowych szerokość pasma wzmacniaczy pionowych i częstotliwość próbkowania muszą być wystarczająco wysokie. Do ogólnego użytku zwykle wystarcza szerokość pasma co najmniej 100 MHz. Znacznie mniejsza przepustowość jest wystarczająca tylko do zastosowań związanych z częstotliwością dźwięku. Przydatny zakres przemiatania wynosi od jednej sekundy do 100 nanosekund, z odpowiednim wyzwalaniem i opóźnieniem przemiatania. Do stabilnego wyświetlania wymagany jest dobrze zaprojektowany, stabilny obwód wyzwalający. Jakość obwodu wyzwalającego jest kluczowa dla dobrych oscyloskopów. Innym kluczowym kryterium wyboru jest głębokość pamięci próbki i częstotliwość próbkowania. Nowoczesne DSO na poziomie podstawowym mają teraz 1 MB lub więcej pamięci próbek na kanał. Często ta pamięć próbek jest współdzielona przez kanały i czasami może być w pełni dostępna tylko przy niższych częstotliwościach próbkowania. Przy najwyższych częstotliwościach próbkowania pamięć może być ograniczona do kilku dziesiątek KB. Każdy nowoczesny DSO z częstotliwością próbkowania „w czasie rzeczywistym” będzie miał zazwyczaj 5-10 razy większą przepustowość wejściową w częstotliwości próbkowania. Tak więc DSO o szerokości pasma 100 MHz miałby częstotliwość próbkowania 500 Ms/s - 1 Gs/s. Znacznie zwiększona częstotliwość próbkowania w dużej mierze wyeliminowała wyświetlanie nieprawidłowych sygnałów, które czasami występowały w pierwszej generacji oscyloskopów cyfrowych. Większość nowoczesnych oscyloskopów zapewnia jeden lub więcej zewnętrznych interfejsów lub magistral, takich jak GPIB, Ethernet, port szeregowy i USB, aby umożliwić zdalną kontrolę przyrządu za pomocą zewnętrznego oprogramowania. Oto lista różnych typów oscyloskopów: OSCYLOSKOP PROMIENIU KATODOWEGO OSCYLOSKOP DWUWIĄZKOWY ANALOGOWY OSCYLOSKOP PRZECHOWYWANIA OSCYLOSKOPY CYFROWE OSCYLOSKOPY MIESZANE OSCYLOSKOPY RĘCZNE OSCYLOSKOPY NA PC ANALIZATOR LOGICZNY to przyrząd, który przechwytuje i wyświetla wiele sygnałów z systemu cyfrowego lub obwodu cyfrowego. Analizator logiczny może konwertować przechwycone dane na diagramy czasowe, dekodowanie protokołów, ślady maszyny stanowej, język asemblera. Analizatory stanów logicznych mają zaawansowane możliwości wyzwalania i są przydatne, gdy użytkownik musi zobaczyć zależności czasowe między wieloma sygnałami w systemie cyfrowym. MODUŁOWE ANALIZATORY LOGICZNE składają się zarówno z obudowy lub ramy głównej, jak i modułów analizatorów stanów logicznych. Obudowa lub rama główna zawiera wyświetlacz, elementy sterujące, komputer sterujący i wiele gniazd, w których zainstalowany jest sprzęt do przechwytywania danych. Każdy moduł ma określoną liczbę kanałów, a wiele modułów można łączyć w celu uzyskania bardzo dużej liczby kanałów. Możliwość łączenia wielu modułów w celu uzyskania dużej liczby kanałów oraz ogólnie wyższa wydajność modułowych analizatorów logicznych powoduje, że są one droższe. W przypadku bardzo wysokiej klasy modułowych analizatorów stanów logicznych, użytkownicy mogą potrzebować zapewnić własny komputer nadrzędny lub zakupić wbudowany sterownik kompatybilny z systemem. PRZENOŚNE ANALIZATORY LOGICZNE integrują wszystko w jednym pakiecie z opcjami zainstalowanymi fabrycznie. Zwykle mają niższą wydajność niż modułowe, ale są ekonomicznymi narzędziami metrologicznymi do ogólnego debugowania. W PC-BASED LOGIC ANALYZERS sprzęt łączy się z komputerem przez połączenie USB lub Ethernet i przekazuje przechwycone sygnały do oprogramowania na komputerze. Urządzenia te są na ogół znacznie mniejsze i tańsze, ponieważ wykorzystują istniejącą klawiaturę, wyświetlacz i procesor komputera osobistego. Analizatory stanów logicznych mogą być wyzwalane przez skomplikowaną sekwencję zdarzeń cyfrowych, a następnie przechwytywać duże ilości danych cyfrowych z testowanych systemów. Obecnie w użyciu są specjalistyczne złącza. Ewolucja sond analizatorów stanów logicznych doprowadziła do powstania wspólnego śladu obsługiwanego przez wielu dostawców, co zapewnia dodatkową swobodę użytkownikom końcowym: Technologia bezzłączy oferowana pod różnymi nazwami handlowymi producentów, takimi jak sondy kompresji; Miękki dotyk; Używany jest D-Max. Sondy te zapewniają trwałe, niezawodne połączenie mechaniczne i elektryczne między sondą a płytką drukowaną. ANALIZATOR WIDMA mierzy wielkość sygnału wejściowego w funkcji częstotliwości w pełnym zakresie częstotliwości przyrządu. Podstawowym zastosowaniem jest pomiar mocy widma sygnałów. Istnieją również analizatory widma optycznego i akustycznego, ale tutaj omówimy tylko analizatory elektroniczne, które mierzą i analizują elektryczne sygnały wejściowe. Widma uzyskane z sygnałów elektrycznych dostarczają nam informacji o częstotliwości, mocy, harmonicznych, szerokości pasma… itd. Częstotliwość jest wyświetlana na osi poziomej, a amplituda sygnału na pionowej. Analizatory widma są szeroko stosowane w przemyśle elektronicznym do analizy widma częstotliwości radiowych, sygnałów RF i audio. Patrząc na widmo sygnału, jesteśmy w stanie ujawnić elementy sygnału i działanie układu je wytwarzającego. Analizatory widma są w stanie wykonać dużą różnorodność pomiarów. Patrząc na metody wykorzystywane do uzyskania widma sygnału, możemy kategoryzować typy analizatorów widma. - SWEPT-TUNED SPECTRUM ANALYZER wykorzystuje odbiornik superheterodynowy do konwersji w dół części widma sygnału wejściowego (za pomocą oscylatora sterowanego napięciem i miksera) do częstotliwości środkowej filtra pasmowego. Dzięki architekturze superheterodynowej oscylator sterowany napięciem jest przemiatany przez szereg częstotliwości, wykorzystując pełny zakres częstotliwości instrumentu. Analizatory widma ze strojeniem przesuniętym pochodzą z odbiorników radiowych. W związku z tym analizatory z skośnym strojeniem są albo analizatorami z dostrojonym filtrem (analogicznie do radia TRF) lub analizatorami superheterodynowymi. W rzeczywistości, w swojej najprostszej postaci, można by pomyśleć o analizatorze widma z przesuniętym strojeniem jako o woltomierzu z selektywnością częstotliwości z zakresem częstotliwości, który jest dostrajany (przesuwany) automatycznie. Jest to zasadniczo woltomierz selektywny względem częstotliwości, reagujący na wartości szczytowe, skalibrowany do wyświetlania wartości skutecznej fali sinusoidalnej. Analizator widma może pokazać poszczególne składowe częstotliwości, które składają się na złożony sygnał. Jednak nie dostarcza informacji o fazie, tylko informacje o amplitudzie. Nowoczesne analizatory z przestrajaniem (w szczególności analizatory superheterodynowe) to precyzyjne urządzenia, które mogą wykonywać różnorodne pomiary. Są one jednak używane przede wszystkim do pomiaru sygnałów w stanie ustalonym lub powtarzalnych, ponieważ nie mogą jednocześnie oceniać wszystkich częstotliwości w danym przedziale. Możliwość jednoczesnej oceny wszystkich częstotliwości jest możliwa tylko przy użyciu analizatorów czasu rzeczywistego. - ANALIZATORY WIDMA W CZASIE RZECZYWISTYM: ANALIZATOR WIDMA FFT oblicza dyskretną transformatę Fouriera (DFT), matematyczny proces, który przekształca przebieg na składowe jego widma sygnału wejściowego. Analizator widma Fouriera lub FFT to kolejna implementacja analizatora widma w czasie rzeczywistym. Analizator Fouriera wykorzystuje cyfrowe przetwarzanie sygnału do próbkowania sygnału wejściowego i przekształcenia go w domenę częstotliwości. Ta konwersja jest wykonywana przy użyciu szybkiej transformacji Fouriera (FFT). FFT jest implementacją dyskretnej transformacji Fouriera, algorytmu matematycznego używanego do przekształcania danych z domeny czasu do domeny częstotliwości. Inny rodzaj analizatorów widma w czasie rzeczywistym, a mianowicie PARALLEL FILTER ANALYZERS łączy kilka filtrów pasmowoprzepustowych, każdy o innej częstotliwości pasmowoprzepustowej. Każdy filtr pozostaje cały czas podłączony do wejścia. Po początkowym czasie ustalania, analizator z filtrem równoległym może natychmiast wykryć i wyświetlić wszystkie sygnały w zakresie pomiarowym analizatora. Dlatego analizator z filtrem równoległym zapewnia analizę sygnału w czasie rzeczywistym. Analizator z filtrem równoległym jest szybki, mierzy sygnały przejściowe i zmienne w czasie. Jednak rozdzielczość częstotliwości analizatora z filtrem równoległym jest znacznie niższa niż w przypadku większości analizatorów z przesuniętym strojeniem, ponieważ rozdzielczość jest określana przez szerokość filtrów pasmowoprzepustowych. Aby uzyskać dobrą rozdzielczość w szerokim zakresie częstotliwości, potrzeba wielu pojedynczych filtrów, co czyni to kosztownym i złożonym. Dlatego większość analizatorów z filtrem równoległym, z wyjątkiem najprostszych dostępnych na rynku, jest droga. - WEKTOROWA ANALIZA SYGNAŁU (VSA): W przeszłości analizatory widma z przestrajaniem i superheterodynami obejmowały szerokie zakresy częstotliwości od audio, poprzez mikrofale, do częstotliwości milimetrowych. Ponadto analizatory z szybką transformatą Fouriera (FFT) intensywnie wykorzystującą cyfrowe przetwarzanie sygnału (DSP) zapewniały analizę widma i sieci o wysokiej rozdzielczości, ale ograniczały się do niskich częstotliwości ze względu na ograniczenia technologii konwersji analogowo-cyfrowej i przetwarzania sygnału. Dzisiejsze szerokopasmowe, modulowane wektorowo, zmienne w czasie sygnały w dużym stopniu korzystają z możliwości analizy FFT i innych technik DSP. Analizatory sygnałów wektorowych łączą technologię superheterodynową z szybkimi przetwornikami ADC i innymi technologiami DSP, oferując szybkie pomiary widma o wysokiej rozdzielczości, demodulację i zaawansowaną analizę w dziedzinie czasu. VSA jest szczególnie przydatny do charakteryzowania złożonych sygnałów, takich jak sygnały impulsowe, przejściowe lub modulowane używane w aplikacjach komunikacyjnych, wideo, transmisji, sonarze i obrazowaniu ultradźwiękowym. W zależności od kształtu analizatory widma są pogrupowane jako stacjonarne, przenośne, ręczne i sieciowe. Modele stołowe są przydatne w zastosowaniach, w których analizator widma można podłączyć do zasilania prądem przemiennym, na przykład w laboratorium lub w obszarze produkcyjnym. Najwyższej klasy analizatory widma zazwyczaj oferują lepszą wydajność i specyfikacje niż wersje przenośne lub podręczne. Są one jednak na ogół cięższe i mają kilka wentylatorów do chłodzenia. Niektóre BENCHTOP SPECTRUM ANALYZERS oferują opcjonalne zestawy akumulatorów, co pozwala na używanie ich z dala od gniazdka sieciowego. Są one określane jako PRZENOŚNE ANALIZATORY WIDMA. Modele przenośne są przydatne w zastosowaniach, w których analizator widma musi być wyniesiony na zewnątrz w celu wykonania pomiarów lub noszony podczas użytkowania. Oczekuje się, że dobry przenośny analizator widma będzie oferował opcjonalne zasilanie bateryjne, aby umożliwić użytkownikowi pracę w miejscach bez gniazdek elektrycznych, czytelny wyświetlacz, aby umożliwić odczyt ekranu w jasnym świetle słonecznym, ciemności lub zakurzonych warunkach, przy niewielkiej wadze. Ręczne analizatory widma są przydatne w zastosowaniach, w których analizator widma musi być bardzo lekki i mały. Analizatory ręczne oferują ograniczone możliwości w porównaniu z większymi systemami. Zaletami ręcznych analizatorów widma jest jednak ich bardzo niski pobór mocy, zasilanie bateryjne w terenie, co pozwala użytkownikowi na swobodne poruszanie się na zewnątrz, bardzo mały rozmiar i niewielka waga. Wreszcie, SIECIOWE ANALIZATORY SPEKTRUM nie zawierają wyświetlacza i zostały zaprojektowane, aby umożliwić nową klasę geograficznie rozproszonych aplikacji do monitorowania i analizy widma. Kluczowym atrybutem jest możliwość podłączenia analizatora do sieci i monitorowania takich urządzeń przez sieć. Chociaż wiele analizatorów widma ma port Ethernet do sterowania, zazwyczaj brakuje im wydajnych mechanizmów przesyłania danych i są zbyt nieporęczne i/lub drogie, aby można je było wdrożyć w taki sposób rozproszony. Rozproszony charakter takich urządzeń umożliwia geolokalizację nadajników, monitorowanie widma dla dynamicznego dostępu do widma i wiele innych tego typu zastosowań. Urządzenia te są w stanie synchronizować przechwytywane dane w sieci analizatorów i umożliwiają wydajny transfer danych w sieci przy niskich kosztach. ANALIZATOR PROTOKOŁÓW to narzędzie zawierające sprzęt i/lub oprogramowanie służące do przechwytywania i analizowania sygnałów i ruchu danych w kanale komunikacyjnym. Analizatory protokołów są najczęściej używane do pomiaru wydajności i rozwiązywania problemów. Łączą się z siecią, aby obliczyć kluczowe wskaźniki wydajności, monitorować sieć i przyspieszać działania związane z rozwiązywaniem problemów. ANALIZATOR PROTOKOŁÓW SIECIOWYCH jest istotną częścią zestawu narzędzi administratora sieci. Analiza protokołu sieciowego służy do monitorowania stanu komunikacji sieciowej. Aby dowiedzieć się, dlaczego urządzenie sieciowe działa w określony sposób, administratorzy używają analizatora protokołów do wykrywania ruchu i ujawniania danych i protokołów przesyłanych przez sieć. Analizatory protokołów sieciowych służą do - Rozwiązywanie trudnych do rozwiązania problemów - Wykrywaj i identyfikuj złośliwe oprogramowanie / złośliwe oprogramowanie. Pracuj z systemem wykrywania włamań lub pułapką miodu. - Zbierz informacje, takie jak podstawowe wzorce ruchu i wskaźniki wykorzystania sieci - Zidentyfikuj nieużywane protokoły, aby usunąć je z sieci - Generuj ruch do testów penetracyjnych - Podsłuchiwanie ruchu (np. lokalizowanie nieautoryzowanego ruchu w komunikatorach lub bezprzewodowych punktach dostępowych) REFLEKTOMETR W DZIEDZINIE CZASU (TDR) to przyrząd, który wykorzystuje reflektometrię w dziedzinie czasu do charakteryzowania i lokalizowania uszkodzeń w kablach metalowych, takich jak skrętki dwużyłowe i kable koncentryczne, złącza, płytki drukowane itp. Reflektometry w dziedzinie czasu mierzą odbicia wzdłuż przewodnika. Aby je zmierzyć, TDR przesyła sygnał padający na przewodnik i obserwuje jego odbicia. Jeśli przewodnik ma jednakową impedancję i jest prawidłowo zakończony, nie będzie odbić, a pozostały sygnał padający zostanie pochłonięty na drugim końcu przez zakończenie. Jeśli jednak gdzieś występuje zmiana impedancji, część padającego sygnału zostanie odbita z powrotem do źródła. Odbicia będą miały taki sam kształt jak sygnał padający, ale ich znak i wielkość zależą od zmiany poziomu impedancji. Jeśli występuje skokowy wzrost impedancji, odbicie będzie miało taki sam znak jak sygnał padający, a jeśli nastąpi skokowy spadek impedancji, odbicie będzie miało znak przeciwny. Odbicia są mierzone na wyjściu/wejściu reflektometru w dziedzinie czasu i wyświetlane jako funkcja czasu. Alternatywnie wyświetlacz może pokazywać transmisję i odbicia w funkcji długości kabla, ponieważ prędkość propagacji sygnału jest prawie stała dla danego medium transmisyjnego. Rejestratory TDR mogą być używane do analizy impedancji i długości kabli, strat w złączach i spawach oraz ich lokalizacji. Pomiary impedancji TDR zapewniają projektantom możliwość przeprowadzenia analizy integralności sygnału połączeń systemu i dokładnego przewidzenia wydajności systemu cyfrowego. Pomiary TDR są szeroko stosowane w pracach nad charakteryzacją płyt. Projektant płytek drukowanych może określić impedancje charakterystyczne ścieżek płytki, obliczyć dokładne modele komponentów płytki i dokładniej przewidzieć wydajność płytki. Istnieje wiele innych obszarów zastosowań reflektometrów w dziedzinie czasu. SEMICONDUCTOR CURVE TRACER to sprzęt testowy używany do analizy charakterystyk dyskretnych urządzeń półprzewodnikowych, takich jak diody, tranzystory i tyrystory. Przyrząd oparty jest na oscyloskopie, ale zawiera również źródła napięcia i prądu, które można wykorzystać do stymulowania badanego urządzenia. Do dwóch zacisków testowanego urządzenia przykładane jest napięcie skokowe i mierzona jest wielkość prądu, jaki urządzenie pozwala na przepływ przy każdym napięciu. Na ekranie oscyloskopu wyświetlany jest wykres o nazwie VI (napięcie w funkcji prądu). Konfiguracja obejmuje maksymalne przyłożone napięcie, polaryzację przyłożonego napięcia (w tym automatyczne przyłożenie biegunowości dodatniej i ujemnej) oraz rezystancję wstawioną szeregowo z urządzeniem. W przypadku dwóch urządzeń końcowych, takich jak diody, wystarczy to, aby w pełni scharakteryzować urządzenie. Wskaźnik krzywej może wyświetlać wszystkie interesujące parametry, takie jak napięcie przewodzenia diody, prąd upływu wstecznego, napięcie przebicia wstecznego itp. Urządzenia z trzema zaciskami, takie jak tranzystory i FET, również wykorzystują połączenie z zaciskiem kontrolnym testowanego urządzenia, takim jak zacisk Base lub Gate. W przypadku tranzystorów i innych urządzeń opartych na prądzie, prąd bazy lub innego zacisku sterującego jest schodkowy. W przypadku tranzystorów polowych (FET) zamiast prądu schodkowego stosuje się napięcie schodkowe. Przesuwając napięcie przez skonfigurowany zakres napięć na zaciskach głównych, dla każdego skoku napięcia sygnału sterującego automatycznie generowana jest grupa krzywych VI. Ta grupa krzywych bardzo ułatwia określenie wzmocnienia tranzystora lub napięcia wyzwalającego tyrystora lub TRIAC. Nowoczesne półprzewodnikowe znaczniki krzywych oferują wiele atrakcyjnych funkcji, takich jak intuicyjne interfejsy użytkownika oparte na systemie Windows, generowanie IV, CV i impulsów oraz pulse IV, biblioteki aplikacji dołączone do każdej technologii… itd. TESTER / WSKAŹNIK OBROTU FAZY: Są to kompaktowe i wytrzymałe przyrządy testowe do identyfikacji kolejności faz w systemach trójfazowych i fazach otwartych/bez napięcia. Idealnie nadają się do montażu maszyn wirujących, silników oraz do sprawdzania mocy generatora. Wśród zastosowań znajduje się identyfikacja właściwej kolejności faz, wykrywanie brakujących faz przewodów, określanie właściwych połączeń maszyn wirujących, wykrywanie obwodów pod napięciem. LICZNIK CZĘSTOTLIWOŚCI jest przyrządem testowym używanym do pomiaru częstotliwości. Liczniki częstotliwości zazwyczaj używają licznika, który gromadzi liczbę zdarzeń występujących w określonym przedziale czasu. Jeśli zdarzenie, które ma być liczone, ma formę elektroniczną, wystarczy proste połączenie z instrumentem. Sygnały o większej złożoności mogą wymagać pewnego uwarunkowania, aby nadawały się do zliczania. Większość liczników częstotliwości ma na wejściu jakąś formę wzmacniacza, obwodów filtrujących i kształtujących. Cyfrowe przetwarzanie sygnału, kontrola czułości i histereza to inne techniki poprawiające wydajność. Inne rodzaje zdarzeń okresowych, które z natury nie mają charakteru elektronicznego, będą musiały zostać przekształcone za pomocą przetworników. Liczniki częstotliwości RF działają na tych samych zasadach, co liczniki niższych częstotliwości. Mają większy zasięg przed przepełnieniem. W przypadku bardzo wysokich częstotliwości mikrofalowych wiele projektów wykorzystuje szybki preskaler, aby obniżyć częstotliwość sygnału do punktu, w którym mogą działać normalne obwody cyfrowe. Liczniki częstotliwości mikrofalowych mogą mierzyć częstotliwości do prawie 100 GHz. Powyżej tych wysokich częstotliwości mierzony sygnał jest łączony w mikserze z sygnałem z lokalnego oscylatora, wytwarzając sygnał o częstotliwości różnicowej, która jest wystarczająco niska do bezpośredniego pomiaru. Popularne interfejsy w licznikach częstotliwości to RS232, USB, GPIB i Ethernet, podobnie jak inne nowoczesne przyrządy. Oprócz wysyłania wyników pomiarów, licznik może powiadamiać użytkownika o przekroczeniu zdefiniowanych przez użytkownika limitów pomiarowych. Aby uzyskać szczegółowe informacje i podobny sprzęt, odwiedź naszą stronę internetową poświęconą sprzętowi: http://www.sourceindustrialsupply.com CLICK Product Finder-Locator Service POPRZEDNIA STRONA
- PCB, PCBA, Printed Circuit Board Assembly, Surface Mount Assembly, SMA
PCB - PCBA - Printed Circuit Board Assembly - Rigid Flexible Multilayer - Surface Mount Assembly - SMA - AGS-TECH Inc. Produkcja i montaż PCB i PCBA Oferujemy: PCB: Płytka drukowana PCBA: Zespół płytki drukowanej • Zespoły płytek drukowanych wszystkich typów (PCB, sztywne, elastyczne i wielowarstwowe) • Podłoża lub kompletny montaż PCBA w zależności od potrzeb. • Montaż przelotowy i montaż powierzchniowy (SMA) Prześlij nam swoje pliki Gerber, BOM, specyfikacje komponentów. Możemy albo zmontować twoje PCB i PCBA używając dokładnie określonych komponentów, albo możemy zaoferować pasujące alternatywy. Mamy doświadczenie w wysyłce PCB i PCBA i upewnimy się, że zapakujemy je w torby antystatyczne, aby uniknąć uszkodzeń elektrostatycznych. Obwody drukowane przeznaczone do pracy w ekstremalnych warunkach często mają powłokę konforemną, którą nakłada się przez zanurzanie lub natryskiwanie po lutowaniu elementów. Powłoka zapobiega korozji i prądom upływowym lub zwarciom spowodowanym kondensacją. Nasze powłoki konformalne to zazwyczaj zanurzenia rozcieńczonych roztworów gumy silikonowej, poliuretanu, akrylu lub epoksydu. Niektóre z nich to inżynieryjne tworzywa sztuczne napylane na płytkę drukowaną w komorze próżniowej. Norma bezpieczeństwa UL 796 obejmuje wymagania dotyczące bezpieczeństwa komponentów dla płytek drukowanych do użytku jako komponenty w urządzeniach lub urządzeniach. Nasze testy analizują takie cechy, jak palność, maksymalna temperatura pracy, śledzenie elektryczne, ugięcie cieplne i bezpośrednie podparcie części elektrycznych pod napięciem. Płytki PCB mogą wykorzystywać organiczne lub nieorganiczne materiały bazowe w postaci jedno lub wielowarstwowej, sztywnej lub elastycznej. Konstrukcja obwodów może obejmować techniki wytrawiania, tłoczenia matrycowego, wycinania wstępnego, spłukiwania, dodatków i platerowanych przewodów. Można stosować drukowane części składowe. Przydatność parametrów wzoru, temperatury i maksymalnych limitów lutowania należy określić zgodnie z odpowiednią konstrukcją i wymaganiami produktu końcowego. Nie czekaj, zadzwoń po więcej informacji, pomoc projektową, prototypy i produkcję masową. Jeśli potrzebujesz, zajmiemy się etykietowaniem, pakowaniem, wysyłką, importem i odprawą celną, magazynowaniem i dostawą. Poniżej możesz pobrać nasze odpowiednie broszury i katalogi dotyczące montażu PCB i PCBA: Ogólne możliwości procesu i tolerancje dla produkcji sztywnych płytek drukowanych Ogólne możliwości procesu i tolerancje dla produkcji aluminiowych płytek drukowanych Ogólne możliwości procesu i tolerancje dla elastycznej i sztywnej, elastycznej produkcji PCB Ogólne procesy wytwarzania PCB Ogólne podsumowanie procesu produkcji zespołu obwodów drukowanych PCBA Przegląd Zakładu Produkcji Obwodów Drukowanych Kilka innych broszur naszych produktów, które możemy wykorzystać w projektach montażu PCB i PCBA: Aby pobrać nasz katalog komponentów i sprzętu interkonektowego z półki, takich jak szybkozłącza, wtyczki i gniazda USB, wtyki i gniazda micro oraz wiele innych, KLIKNIJ TUTAJ Bloki zaciskowe i złącza Katalog ogólny łączówek Radiatory standardowe Wytłaczane radiatory Radiatory Easy Click to idealny produkt do montażu PCB Radiatory Super Power do układów elektronicznych średniej - dużej mocy Radiatory z Super Fins Moduły LCD Katalog gniazd-zasilanie-złącza wejściowe Pobierz broszurę dla naszego PROGRAM PARTNERSKI W PROJEKTOWANIU Jeśli są Państwo zainteresowani naszymi możliwościami inżynieryjnymi i badawczo-rozwojowymi, a nie operacjami i możliwościami produkcyjnymi, zapraszamy do odwiedzenia naszej strony inżynierskiej http://www.ags-engineering.com CLICK Product Finder-Locator Service POPRZEDNIA STRONA
- Cable & Connector Assembly, Wire Harness, Cable Management Accessories
Cable Assembly - Wire Harness - Cable Management Accessories - Connectorization - Cable Fan Out - Interconnects Zespół kabli elektrycznych i elektronicznych oraz łączniki Oferujemy: • Różnego rodzaju przewody, kable, akcesoria do montażu kabli i zarządzania kablami, nieekranowane lub ekranowane kable do dystrybucji zasilania, wysokiego napięcia, niskiego sygnału, telekomunikacji… itd., łączników i elementów łączących. • Złącza, wtyki, adaptery i tuleje współpracujące, łączony panel krosowy, obudowa spawów. - Aby pobrać nasz katalog komponentów i sprzętu interkonektów z półki, KLIKNIJ TUTAJ. - Bloki zaciskowe i złącza - Katalog ogólny łączówek - Katalog gniazd-zasilanie-złącza wejściowe - Broszura dotycząca produktów do zakańczania kabli (Rury, izolacje, ochrona, termokurczliwe, naprawy kabli, osłony zabezpieczające, zaciski, opaski kablowe i klipsy, znaczniki przewodów, taśmy, zaślepki kabli, szczeliny dystrybucyjne) - Informacje o naszym zakładzie produkującym złączki ceramiczno-metalowe, hermetyczne uszczelnienia, przepusty próżniowe, elementy wysokiej i ultrawysokiej próżni, adaptery i złącza BNC, SHV, przewody i styki stykowe, końcówki złączy można znaleźć tutaj:_cc781905-5cde-3194-bb3b- 136bad5cf58d_ Broszura fabryczna Pobierz broszurę dla naszegoPROGRAM PARTNERSKI W PROJEKTOWANIU Interkonekty i produkty do montażu kabli są dostępne w szerokiej gamie. Podaj nam typ, zastosowanie, arkusze specyfikacji, jeśli są dostępne, a my zaproponujemy najbardziej odpowiedni produkt. Możemy dostosować je dla Ciebie, jeśli nie jest to produkt z półki. Nasze zestawy kabli i połączenia są oznaczone znakiem CE lub UL przez autoryzowane organizacje i są zgodne z przepisami i normami branżowymi, takimi jak IEEE, IEC, ISO...itd. Aby dowiedzieć się więcej o naszych możliwościach inżynieryjnych i badawczo-rozwojowych zamiast o operacjach produkcyjnych, zapraszamy do odwiedzenia naszej strony inżynierskiej http://www.ags-engineering.com CLICK Product Finder-Locator Service POPRZEDNIA STRONA
- Wireless Components, Antenna, Radio Frequency Devices, RF Devices, HF
Wireless Components - Antenna - Radio Frequency Devices - RF Devices - Remote Sensing and Control - High Frequency Produkcja i montaż urządzeń radiowych i bezprzewodowych • Bezprzewodowe komponenty, urządzenia i zespoły do teledetekcji, zdalnego sterowania i komunikacji. Służymy pomocą podczas projektowania, rozwoju, prototypowania lub masowej produkcji różnego rodzaju radiotelefonów stacjonarnych, mobilnych i przenośnych, telefonów komórkowych, odbiorników GPS, palmtopów, sprzętu inteligentnego i zdalnego sterowania oraz urządzeń sieci bezprzewodowej i instrumenty. Posiadamy również gotowe komponenty i urządzenia bezprzewodowe, które możesz wybrać z poniższych broszur. Urządzenia RF i cewki indukcyjne wysokiej częstotliwości Tabela przeglądu produktów RF Linia produktów urządzeń wysokiej częstotliwości 5G - LTE 4G - LPWA 3G - 2G - GPS - GNSS - WLAN - BT - Combo - ISM Antena-Broszura Ferryty miękkie - Rdzenie - Toroidy - Produkty przeciwzakłóceniowe - Broszura dotycząca transponderów i akcesoriów RFID Informacje o naszym zakładzie produkującym złączki ceramiczne na metalowe, hermetyczne uszczelnienia, przepusty próżniowe, komponenty wysokiej i ultrawysokiej próżni, adaptery i złącza BNC, SHV, przewody i styki stykowe, końcówki złączy można znaleźć tutaj: Broszura fabryczna Pobierz broszurę dla naszego PROGRAM PARTNERSKI W PROJEKTOWANIU Uczestniczymy również w programie zasobów stron trzecich i jesteśmy odsprzedawcą produktów oferowanych przez RF Digital ( Witryna internetowa: http://www.rfdigital.com ) , firma produkująca szeroką linię w pełni zintegrowanych, tanich, wysokiej jakości, wysokiej jakości, konfigurowalnych bezprzewodowych modułów nadajnika, odbiornika i nadajnika RF, odpowiednich do szerokiego zakresu zastosowań. Uczestniczymy w programie poleceń RF Digital jako firma zajmująca się projektowaniem i rozwojem produktów. Skontaktuj się z nami, aby skorzystać z naszych w pełni zintegrowanych, konfigurowalnych bezprzewodowych modułów nadawczo-odbiorczych i nadawczo-odbiorczych, urządzeń RF wysokiej częstotliwości, a przede wszystkim z naszych usług doradczych dotyczących wdrażania i stosowania tych bezprzewodowych komponentów i urządzeń oraz naszych usług integracji inżynierskiej. Możemy sprawić, że zrealizujesz nowy cykl rozwoju produktu, pomagając Ci na każdym etapie procesu, od koncepcji przez projekt, prototypowanie, produkcję pierwszego artykułu, aż po produkcję masową. • Niektóre zastosowania technologii bezprzewodowej, w których możemy Ci pomóc, to: - Bezprzewodowe systemy bezpieczeństwa - Zdalne sterowanie konsumenckimi urządzeniami elektronicznymi lub sprzętem komercyjnym. - Telefonia komórkowa (telefony i modemy): - WiFi - Bezprzewodowe przesyłanie energii - Urządzenia komunikacji radiowej - Urządzenia komunikacyjne bliskiego zasięgu typu punkt-punkt, takie jak mikrofony bezprzewodowe, piloty, IrDA, RFID (identyfikacja częstotliwości radiowej), bezprzewodowe USB, DSRC (dedykowana komunikacja bliskiego zasięgu), EnOcean, komunikacja bliskiego zasięgu, bezprzewodowe sieci czujników: ZigBee , EnOcean; Sieci osobiste, Bluetooth, ultraszerokopasmowe, bezprzewodowe sieci komputerowe: bezprzewodowe sieci lokalne (WLAN), bezprzewodowe sieci metropolitalne (WMAN)... itd. Więcej informacji na temat naszych możliwości w zakresie inżynierii oraz badań i rozwoju można znaleźć w naszej witrynie poświęconej inżynierii http://www.ags-engineering.com CLICK Product Finder-Locator Service POPRZEDNIA STRONA
- Computer Chassis, Racks, Shelves, 19 inch Rack, 23 inch Rack, Case
Computer Chassis - Racks - Shelves - 19 inch Rack - 23 inch Rack - Computer and Instrument Case Manufacturing - AGS-TECH Inc. - New Mexico - USA Obudowa, stojaki, uchwyty do komputerów przemysłowych Oferujemy najbardziej trwałe i niezawodne PODWOZIA KOMPUTERÓW PRZEMYSŁOWYCH, STOJAKI, UCHWYTY, INSTRUMENTY DO MONTAŻU W RACK and_cc781905-5cde-336bad-bb358b REGAŁY CALOWE I 23-CALOWE, PEŁNE ROZMIARY and HALF, OPEN and_ccUN_336bad5cde-3194-bb3b-136bad5cf58d_HALF, OPEN and_ccUN_336bad- KOMPONENTY WSPIERAJĄCE, SZYNY and SLIDES, DWA and_and SLIDES, DWA and_and_cc781905-5cde-3cf5spełniające międzynarodowe standardy branżowe Oprócz naszych produktów z półki jesteśmy w stanie zbudować dla Ciebie dowolne specjalnie dopasowane podwozia, stojaki i mocowania. Niektóre z marek, które mamy w magazynie, to BELKIN, HEWLETT PACKARD, KENDALL HOWARD, GREAT LAKES, APC, RITTAL, LIEBERT, RALOY, SHARK RACK, UPSITE TECHNOLOGIES. Kliknij tutaj, aby pobrać nasze podwozia przemysłowe marki DFI-ITOX Kliknij tutaj, aby pobrać obudowę wtykową serii 06 firmy AGS-Electronics Kliknij tutaj, aby pobrać nasz system walizkowy serii 01 Instrument Case System-I firmy AGS-Electronics Kliknij tutaj, aby pobrać naszą skrzynkę przyrządów serii 05 System-V firmy AGS-Electronics Aby wybrać odpowiednią obudowę, stelaż lub uchwyt klasy przemysłowej, przejdź do naszego sklepu z komputerami przemysłowymi, KLIKNIJ TUTAJ. Pobierz broszurę dla naszego PROGRAM PARTNERSKI W PROJEKTOWANIU Oto kilka kluczowych terminów, które powinny być przydatne w celach informacyjnych: A RACK UNIT or U (rzadziej określane jako RU) to jednostka miary używana do opisania wysokości sprzętu przeznaczonego do montażu w a_cc781905-5cde-3194-bb3b -136bad5cf58d_19-calowa stelaż lub a 23-calowa stelaż (Wymiary 19- lub 23-calowe odnoszą się do rama montażowa w stelażu, czyli szerokość sprzętu, który można zamontować w stelażu). Jedna jednostka szafy ma wysokość 1,75 cala (44,45 mm). Rozmiar urządzenia montowanego w stelażu jest często określany jako liczba w „U”. Na przykład jedna jednostka rack jest często określana jako „1U”, 2 jednostki rack jako „2U” i tak dalej. Typowy full size rack is 44U, co oznacza, że mieści nieco ponad 6 stóp sprzętu. Jednak w informatyce i informatyce half-rack zazwyczaj opisuje jednostkę o wysokości 1U i połowę głębokości szafy 4-słupkowej (np. przełącznik sieciowy). , router, przełącznik KVM lub serwer), tak aby na przestrzeni 1U można było zamontować dwie jednostki (jedna z przodu szafy, a druga z tyłu). W odniesieniu do samej obudowy stelaża termin pół stelaża oznacza zazwyczaj obudowę stelaża o wysokości 24U. Panel przedni lub panel wypełniający w stelażu nie jest dokładną wielokrotnością 1,75 cala (44,45 mm). Aby zapewnić przestrzeń między sąsiednimi komponentami montowanymi w szafie, panel ma 1⁄32 cala (0,031 cala lub 0,79 mm) mniej niż wynika to z pełnej liczby jednostek szafy. W ten sposób panel przedni 1U miałby wysokość 1,719 cala (43,66 mm). Szafa 19-calowa to znormalizowana rama lub obudowa do montażu wielu modułów sprzętu. Każdy moduł ma panel przedni o szerokości 19 cali (482,6 mm) wraz z krawędziami lub uszami wystającymi z każdej strony, które umożliwiają przymocowanie modułu do ramy szafy za pomocą śrub. Sprzęt przeznaczony do umieszczenia w stelażu jest zwykle opisywany jako montaż w stelażu, przyrząd do montażu w stelażu, system montowany w stelażu, obudowa montowana w stelażu, subrack, montowana w stelażu lub czasami po prostu półka. Szafa 23-calowa służy do przechowywania telefonu (przede wszystkim), komputera, sprzętu audio i innego sprzętu, chociaż jest mniej powszechna niż szafa 19-calowa. Rozmiar uwzględnia szerokość płyty czołowej dla zainstalowanego sprzętu. Jednostka szafy jest miarą odstępu w pionie i jest wspólna dla szaf 19 i 23-calowych (580 mm). Rozstaw otworów jest rozstawiany co 1 cal (25 mm) (standard Western Electric) lub taki sam jak w przypadku szaf 19-calowych (480 mm) (rozstaw 0,625 cala / 15,9 mm). CLICK Product Finder-Locator Service POPRZEDNIA STRONA