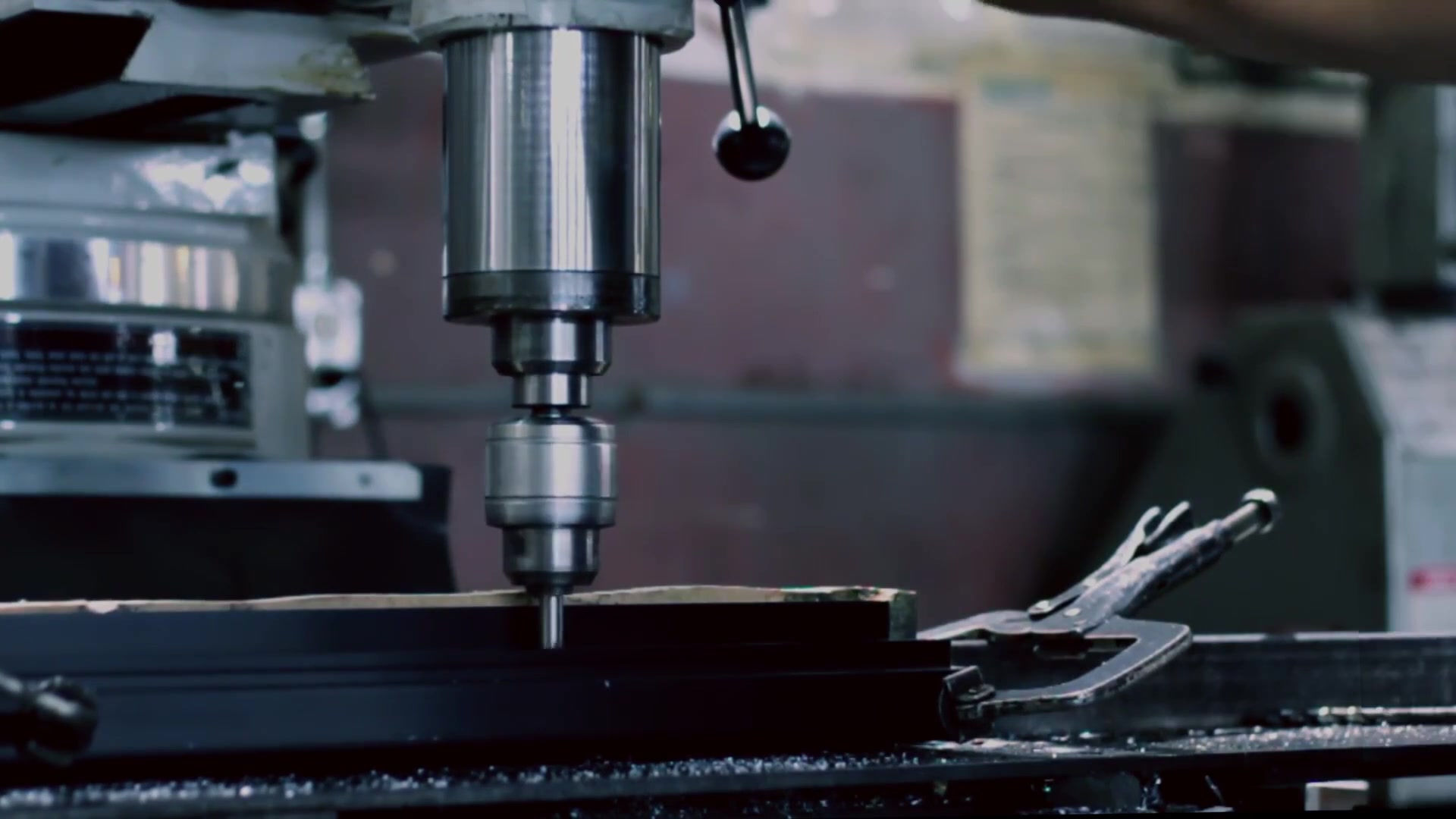
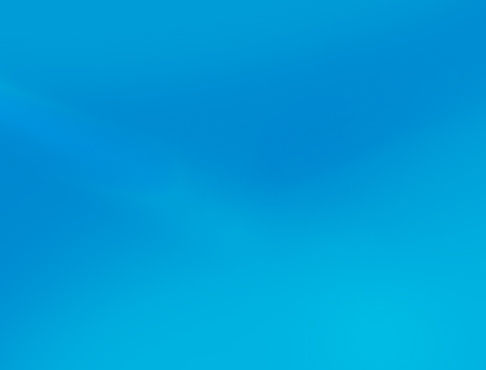
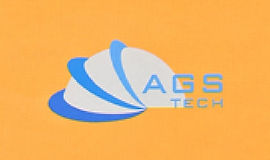
Fabricante personalizado global, integrador, consolidador, parceiro de terceirização para uma ampla variedade de produtos e serviços.
Somos sua fonte única para fabricação, fabricação, engenharia, consolidação, integração, terceirização de produtos e serviços fabricados sob encomenda e prontos para uso.
Choose your Language
-
Fabricação personalizada
-
Fabricação por contrato doméstica e global
-
Terceirização de Manufatura
-
Compras domésticas e globais
-
Consolidação
-
Integração de Engenharia
-
Serviços de engenharia
Nossas técnicas de fundição e usinagem personalizadas são fundições descartáveis e não descartáveis, fundição ferrosa e não ferrosa, areia, matriz, centrífuga, contínua, molde cerâmico, investimento, espuma perdida, forma próxima à rede, molde permanente (fundição por gravidade), gesso molde (fundição de gesso) e carcaça, peças usinadas produzidas por fresamento e torneamento usando equipamentos convencionais e CNC, usinagem tipo suíça para peças de pequena precisão baratas de alto rendimento, usinagem de parafusos para fixadores, usinagem não convencional. Por favor, tenha em mente que além de metais e ligas metálicas, nós usinamos componentes de cerâmica, vidro e plástico também em alguns casos quando a fabricação de um molde não é atraente ou não é a opção. A usinagem de materiais poliméricos requer a experiência especializada que temos devido ao desafio que os plásticos e a borracha apresentam devido à sua maciez, não rigidez...etc. Para usinagem de cerâmica e vidro, consulte nossa página sobre Fabricação Não Convencional. AGS-TECH Inc. fabrica e fornece peças fundidas leves e pesadas. Fornecemos peças fundidas de metal e peças usinadas para caldeiras, trocadores de calor, automóveis, micromotores, turbinas eólicas, equipamentos de embalagem de alimentos e muito mais. Recomendamos que você clique aqui para BAIXE nossas ilustrações esquemáticas de processos de usinagem e fundição da AGS-TECH Inc.
Isso ajudará você a entender melhor as informações que estamos fornecendo abaixo. Vejamos algumas das várias técnicas que oferecemos em detalhes:
• FUNDIÇÃO DE MOLDE DESCARREGÁVEL: Esta ampla categoria refere-se a métodos que envolvem moldes temporários e não reutilizáveis. Exemplos são areia, gesso, concha, investimento (também chamado de cera perdida) e fundição de gesso.
• FUNDIÇÃO EM AREIA: Processo em que se utiliza areia como material do molde. Um método muito antigo e ainda muito popular na medida em que a maioria das peças fundidas de metal produzidas são feitas por esta técnica. Baixo custo mesmo na produção de baixa quantidade. Adequado para fabricação de peças pequenas e grandes. A técnica pode ser usada para fabricar peças em dias ou semanas com muito pouco investimento. A areia úmida é colada com argila, aglutinantes ou óleos especiais. A areia é geralmente contida em caixas de molde e o sistema de cavidade e porta é criado pela compactação da areia ao redor dos modelos. Os processos são:
1.) Colocação do modelo na areia para fazer o molde
2.) Incorporação de modelo e areia em um sistema de gating
3.) Remoção do modelo
4.) Preenchimento da cavidade do molde com metal fundido
5.) Resfriamento do metal
6.) Quebra do molde de areia e remoção da fundição
• FUNDIÇÃO DE MOLDE DE GESSO: Semelhante à fundição de areia, e em vez de areia, gesso de paris está sendo usado como material de molde. Prazos de produção curtos, como fundição em areia e baratos. Boas tolerâncias dimensionais e acabamento superficial. Sua principal desvantagem é que só pode ser usado com metais de baixo ponto de fusão, como alumínio e zinco.
• FUNDIÇÃO EM MOLDE SHELL: Também semelhante à fundição em areia. Cavidade do molde obtida por casca endurecida de areia e resina termoendurecível em vez de frasco preenchido com areia como no processo de fundição em areia. Quase qualquer metal adequado para ser fundido por areia pode ser fundido por moldagem em concha. O processo pode ser resumido como:
1.) Fabricação do molde de concha. A areia usada tem um tamanho de grão muito menor quando comparada à areia usada na fundição de areia. A areia fina é misturada com resina termofixa. O padrão de metal é revestido com um agente de separação para facilitar a remoção da casca. Em seguida, o padrão de metal é aquecido e a mistura de areia é porosa ou soprada sobre o padrão de fundição a quente. Uma casca fina se forma na superfície do padrão. A espessura desta casca pode ser ajustada variando o tempo que a mistura de resina de areia está em contato com o padrão de metal. A areia solta é então removida com o padrão coberto de casca restante.
2.) Em seguida, a casca e o padrão são aquecidos em um forno para que a casca endureça. Após a conclusão do endurecimento, a casca é ejetada do padrão usando pinos embutidos no padrão.
3.) Duas dessas conchas são montadas por colagem ou fixação e formam o molde completo. Agora o molde de concha é inserido em um recipiente no qual é suportado por granalha de areia ou metal durante o processo de fundição.
4.) Agora o metal quente pode ser derramado no molde de concha.
As vantagens do shell casting são produtos com muito bom acabamento superficial, possibilidade de fabricação de peças complexas com alta precisão dimensional, processo fácil de automatizar, econômico para produção de grande volume.
As desvantagens são os moldes necessitarem de boa ventilação devido aos gases que são criados quando o metal fundido entra em contato com o produto químico ligante, as resinas termofixas e os padrões de metal são caros. Devido ao custo dos padrões de metal, a técnica pode não ser adequada para execuções de produção de baixa quantidade.
• INVESTMENT CASTING (também conhecido como LOST-WAX CASTING): Também uma técnica muito antiga e adequada para a fabricação de peças de qualidade com alta precisão, repetibilidade, versatilidade e integridade de diversos metais, materiais refratários e ligas especiais de alto desempenho. Peças pequenas e grandes podem ser produzidas. Um processo caro quando comparado a alguns dos outros métodos, mas a grande vantagem é a possibilidade de produzir peças com formato próximo ao líquido, contornos e detalhes intrincados. Assim, o custo é um pouco compensado pela eliminação de retrabalho e usinagem em alguns casos. Embora possa haver variações, aqui está um resumo do processo geral de fundição de investimento:
1.) Criação do padrão mestre original de cera ou plástico. Cada fundição precisa de um padrão, pois eles são destruídos no processo. O molde a partir do qual os padrões são fabricados também é necessário e na maioria das vezes o molde é fundido ou usinado. Como o molde não precisa ser aberto, fundições complexas podem ser obtidas, muitos padrões de cera podem ser conectados como os galhos de uma árvore e despejados juntos, permitindo assim a produção de várias peças a partir de um único vazamento do metal ou liga metálica.
2.) Em seguida, o padrão é mergulhado ou derramado com uma pasta refratária composta de sílica de grão muito fino, água e ligantes. Isso resulta em uma camada de cerâmica sobre a superfície do padrão. O revestimento refratário no padrão é deixado para secar e endurecer. Esta etapa é de onde vem o nome de fundição de investimento: pasta refratária é investida sobre o padrão de cera.
3.) Nesta etapa, o molde cerâmico endurecido é virado de cabeça para baixo e aquecido para que a cera derreta e saia do molde. Uma cavidade é deixada para trás para a fundição do metal.
4.) Após a saída da cera, o molde cerâmico é aquecido a uma temperatura ainda mais alta, o que resulta no fortalecimento do molde.
5.) A fundição de metal é derramada no molde quente preenchendo todas as seções intrincadas.
6.) A fundição pode solidificar
7.) Finalmente, o molde cerâmico é quebrado e as peças fabricadas são cortadas da árvore.
Aqui está um link para o folheto da planta de fundição por investimento
• FUNDIÇÃO DE PADRÃO EVAPORATIVO: O processo usa um padrão feito de um material como espuma de poliestireno que evaporará quando o metal fundido quente for derramado no molde. Existem dois tipos deste processo: LOST FOAM CASTING que utiliza areia não aderente e FULL MOLD CASTING que utiliza areia aderente. Aqui estão as etapas gerais do processo:
1.) Fabrique o molde a partir de um material como poliestireno. Quando grandes quantidades serão fabricadas, o padrão é moldado. Se a peça tiver uma forma complexa, várias seções desse material de espuma podem precisar ser coladas para formar o padrão. Costumamos revestir o padrão com um composto refratário para criar um bom acabamento superficial na peça fundida.
2.) O padrão é então colocado em areia de moldagem.
3.) O metal fundido é derramado no molde, evaporando o padrão de espuma, ou seja, poliestireno na maioria dos casos, à medida que flui através da cavidade do molde.
4.) O metal fundido é deixado no molde de areia para endurecer.
5.) Depois de endurecido, removemos a fundição.
Em alguns casos, o produto que fabricamos requer um núcleo dentro do padrão. Na fundição evaporativa, não há necessidade de colocar e fixar um macho na cavidade do molde. A técnica é adequada para a fabricação de geometrias muito complexas, pode ser facilmente automatizada para produção de alto volume e não há linhas de partição na peça fundida. O processo básico é simples e econômico de implementar. Para produção de grande volume, uma vez que é necessária uma matriz ou molde para produzir os padrões de poliestireno, isso pode ser um pouco caro.
• FUNDIÇÃO DE MOLDE NÃO EXPANDÍVEL: Esta ampla categoria refere-se a métodos onde o molde não precisa ser reformado após cada ciclo de produção. Exemplos são fundição permanente, matriz, contínua e centrífuga. A repetibilidade é obtida e as peças podem ser caracterizadas como NEAR NET SHAPE.
• FUNDIÇÃO DE MOLDE PERMANENTE: Os moldes reutilizáveis feitos de metal são usados para múltiplas fundições. Um molde permanente geralmente pode ser usado por dezenas de milhares de vezes antes de se desgastar. Gravidade, pressão de gás ou vácuo são geralmente usados para encher o molde. Os moldes (também chamados de matrizes) geralmente são feitos de ferro, aço, cerâmica ou outros metais. O processo geral é:
1.) Usinar e criar o molde. É comum usinar o molde a partir de dois blocos metálicos que se encaixam e podem ser abertos e fechados. Tanto as características da peça quanto o sistema de abertura são geralmente usinados no molde de fundição.
2.) As superfícies internas do molde são revestidas com uma pasta que incorpora materiais refratários. Isso ajuda a controlar o fluxo de calor e atua como lubrificante para facilitar a remoção da peça fundida.
3.) Em seguida, as metades do molde permanente são fechadas e o molde é aquecido.
4.) O metal fundido é derramado no molde e deixado para solidificação.
5.) Antes que ocorra muito resfriamento, removemos a peça do molde permanente usando ejetores quando as metades do molde são abertas.
Frequentemente usamos fundição em molde permanente para metais de baixo ponto de fusão, como zinco e alumínio. Para fundições de aço, usamos grafite como material de molde. Algumas vezes obtemos geometrias complexas usando machos dentro de moldes permanentes. As vantagens desta técnica são fundidos com boas propriedades mecânicas obtidas por resfriamento rápido, uniformidade nas propriedades, boa precisão e acabamento superficial, baixas taxas de rejeito, possibilidade de automatizar o processo e produzir grandes volumes economicamente. As desvantagens são os altos custos de configuração inicial que o tornam inadequado para operações de baixo volume e limitações no tamanho das peças fabricadas.
• DIE CASTING: Uma matriz é usinada e o metal fundido é empurrado sob alta pressão para dentro das cavidades do molde. Tanto fundições de metais não ferrosos como ferrosos são possíveis. O processo é adequado para produções de alta quantidade de peças pequenas e médias com detalhes, paredes extremamente finas, consistência dimensional e bom acabamento superficial. A AGS-TECH Inc. é capaz de fabricar espessuras de parede tão pequenas quanto 0,5 mm usando esta técnica. Assim como na fundição em molde permanente, o molde precisa ser composto por duas metades que podem abrir e fechar para a retirada da peça produzida. Um molde de fundição pode ter várias cavidades para permitir a produção de vários fundidos com cada ciclo. Os moldes de fundição sob pressão são muito pesados e muito maiores do que as peças que produzem, portanto, também caros. Reparamos e substituímos matrizes desgastadas gratuitamente para nossos clientes, desde que eles repediram suas peças de nós. Nossas matrizes têm longa vida útil na faixa de várias centenas de milhares de ciclos.
Aqui estão as etapas básicas do processo simplificado:
1.) Produção do molde geralmente em aço
2.) Molde instalado na máquina de fundição
3.) O pistão força o metal fundido a fluir nas cavidades da matriz, preenchendo as características intrincadas e as paredes finas
4.) Depois de encher o molde com o metal fundido, o fundido é endurecido sob pressão
5.) O molde é aberto e a fundição é removida com a ajuda de pinos ejetores.
6.) Agora as matrizes vazias são lubrificadas novamente e fixadas para o próximo ciclo.
Na fundição sob pressão, frequentemente usamos moldagem por inserção, onde incorporamos uma peça adicional no molde e fundimos o metal ao redor dela. Após a solidificação, essas peças passam a fazer parte do produto fundido. As vantagens da fundição sob pressão são boas propriedades mecânicas das peças, possibilidade de recursos intrincados, detalhes finos e bom acabamento superficial, altas taxas de produção, fácil automação. As desvantagens são: Não muito adequado para baixo volume devido ao alto custo do molde e do equipamento, limitações nas formas que podem ser fundidas, pequenas marcas redondas nas peças fundidas resultantes do contato dos pinos ejetores, rebarbas finas de metal espremido na linha de partição, necessidade para respiros ao longo da linha de separação entre a matriz, necessidade de manter baixas as temperaturas do molde usando circulação de água.
• FUNDIÇÃO CENTRÍFUGA: O metal fundido é vazado no centro do molde rotativo no eixo de rotação. As forças centrífugas jogam o metal para a periferia e ele se solidifica à medida que o molde continua girando. As rotações do eixo horizontal e vertical podem ser usadas. Peças com superfícies internas redondas, bem como outras formas não redondas, podem ser fundidas. O processo pode ser resumido como:
1.) O metal fundido é derramado no molde centrífugo. O metal é então forçado para as paredes externas devido à fiação do molde.
2.) À medida que o molde gira, o metal fundido endurece
A fundição centrífuga é uma técnica adequada para a produção de peças cilíndricas ocas como tubos, sem necessidade de sprues, risers e elementos de canal, bom acabamento superficial e recursos detalhados, sem problemas de retração, possibilidade de produzir tubos longos com diâmetros muito grandes, capacidade de produção de alta taxa .
• FUNDIÇÃO CONTÍNUA ( STRAND CASTING ) : Usada para fundir um comprimento contínuo de metal. Basicamente, o metal fundido é vazado no perfil bidimensional do molde, mas seu comprimento é indeterminado. O novo metal fundido é constantemente alimentado no molde à medida que o fundido se desloca para baixo, com seu comprimento aumentando com o tempo. Metais como cobre, aço, alumínio são fundidos em longos fios usando o processo de fundição contínua. O processo pode ter várias configurações, mas a comum pode ser simplificada como:
1.) O metal fundido é derramado em um recipiente localizado acima do molde em quantidades e taxas de fluxo bem calculadas e flui através do molde resfriado a água. A fundição de metal despejada no molde se solidifica em uma barra inicial colocada na parte inferior do molde. Esta barra inicial dá aos rolos algo para agarrar inicialmente.
2.) A longa corda de metal é transportada por rolos a uma velocidade constante. Os rolos também mudam a direção do fluxo do fio de metal de vertical para horizontal.
3.) Após o lingotamento contínuo ter percorrido uma certa distância horizontal, uma tocha ou serra que se move com o lingotamento corta-o rapidamente nos comprimentos desejados.
O processo de fundição contínua pode ser integrado com o PROCESSO DE ROLAGEM, onde o metal fundido continuamente pode ser alimentado diretamente em um laminador para produzir vigas em I, vigas em T... etc. A fundição contínua produz propriedades uniformes em todo o produto, tem uma alta taxa de solidificação, reduz o custo devido à perda muito baixa de material, oferece um processo onde o carregamento de metal, vazamento, solidificação, corte e remoção da fundição ocorrem em uma operação contínua e resultando assim em alta taxa de produtividade e alta qualidade. Uma consideração importante é, no entanto, o alto investimento inicial, custos de instalação e requisitos de espaço.
• SERVIÇOS DE USINAGEM: Oferecemos usinagem de três, quatro e cinco eixos. Os tipos de processos de usinagem que utilizamos são TORNEAMENTO, FRESAGEM, FURAÇÃO, FURAÇÃO, BROCHAGEM, PLANEAMENTO, SERRAGEM, RETIFICAÇÃO, LAPAGEM, POLIMENTO e USINAGEM NÃO TRADICIONAL que é elaborada em um menu diferente do nosso site. Para a maior parte de nossa fabricação, usamos máquinas CNC. No entanto, para algumas operações, as técnicas convencionais são mais adequadas e, portanto, também confiamos nelas. Nossas capacidades de usinagem atingem o nível mais alto possível e algumas peças mais exigentes são fabricadas em uma fábrica certificada AS9100. As lâminas de motores a jato exigem experiência de fabricação altamente especializada e o equipamento certo. A indústria aeroespacial tem padrões muito rígidos. Alguns componentes com estruturas geométricas complexas são mais facilmente fabricados por usinagem de cinco eixos, que é encontrada apenas em algumas usinas, incluindo a nossa. Nossa fábrica certificada aeroespacial tem a experiência necessária em conformidade com os extensos requisitos de documentação da indústria aeroespacial.
Nas operações de TORNEAMENTO, uma peça de trabalho é girada e movida contra uma ferramenta de corte. Para este processo está sendo utilizada uma máquina chamada torno.
Em FRESAMENTO, uma máquina chamada fresadora possui uma ferramenta rotativa para trazer as arestas de corte para apoiar uma peça de trabalho.
As operações de PERFURAÇÃO envolvem uma fresa rotativa com arestas de corte que produz furos ao entrar em contato com a peça de trabalho. Prensas de furadeira, tornos ou moinhos são geralmente usados.
Nas operações de FURAÇÃO, uma ferramenta com uma única ponta dobrada é movida para um furo áspero em uma peça de trabalho giratória para aumentar um pouco o furo e melhorar a precisão. É usado para fins de acabamento fino.
BROACHING envolve uma ferramenta dentada para remover o material de uma peça de trabalho em uma passagem da brocha (ferramenta dentada). No brochamento linear, a brocha corre linearmente contra uma superfície da peça de trabalho para efetuar o corte, enquanto que no brochamento rotativo, a brocha é girada e pressionada na peça de trabalho para cortar uma forma simétrica do eixo.
A USINAGEM DO TIPO SUÍÇO é uma de nossas técnicas valiosas que usamos para a fabricação de alto volume de pequenas peças de alta precisão. Usando torno tipo suíço, tornamos peças pequenas, complexas e de precisão de forma econômica. Ao contrário dos tornos convencionais onde a peça de trabalho é mantida estacionária e a ferramenta em movimento, nos centros de torneamento do tipo suíço, a peça de trabalho pode se mover no eixo Z e a ferramenta fica estacionária. Na usinagem tipo suíça, o estoque da barra é retido na máquina e avançado através de uma bucha guia no eixo z, expondo apenas a parte a ser usinada. Desta forma, um aperto firme é garantido e a precisão é muito alta. A disponibilidade de ferramentas motorizadas oferece a oportunidade de fresar e perfurar à medida que o material avança da bucha guia. O eixo Y do equipamento tipo suíço oferece recursos completos de fresamento e economiza muito tempo na fabricação. Além disso, nossas máquinas possuem furadeiras e ferramentas de mandrilamento que atuam na peça quando esta é mantida no subfuso. Nossa capacidade de usinagem do tipo suíço nos dá uma oportunidade de usinagem completa totalmente automatizada em uma única operação.
A usinagem é um dos maiores segmentos de negócios da AGS-TECH Inc.. Nós a usamos como uma operação primária ou uma operação secundária após a fundição ou extrusão de uma peça para que todas as especificações de desenho sejam atendidas.
• SERVIÇOS DE ACABAMENTO DE SUPERFÍCIE: Oferecemos uma grande variedade de tratamentos de superfície e acabamento de superfície, como condicionamento de superfície para aumentar a adesão, deposição de fina camada de óxido para aumentar a adesão do revestimento, jateamento de areia, chem-film, anodização, nitretação, revestimento em pó, revestimento em spray , várias técnicas avançadas de metalização e revestimento, incluindo pulverização catódica, feixe de elétrons, evaporação, chapeamento, revestimentos duros, como diamante como carbono (DLC) ou revestimento de titânio para ferramentas de perfuração e corte.
• SERVIÇOS DE MARCAÇÃO E ETIQUETAGEM DE PRODUTOS: Muitos de nossos clientes exigem marcação e etiquetagem, marcação a laser, gravação em peças metálicas. Se você tiver alguma necessidade, deixe-nos discutir qual opção será a melhor para você.
Aqui estão alguns dos produtos fundidos de metal comumente usados. Uma vez que estes são prontos para uso, você pode economizar nos custos do molde caso algum deles atenda às suas necessidades:
CLIQUE AQUI PARA BAIXAR nossas caixas de alumínio fundido da série 11 da AGS-Electronics