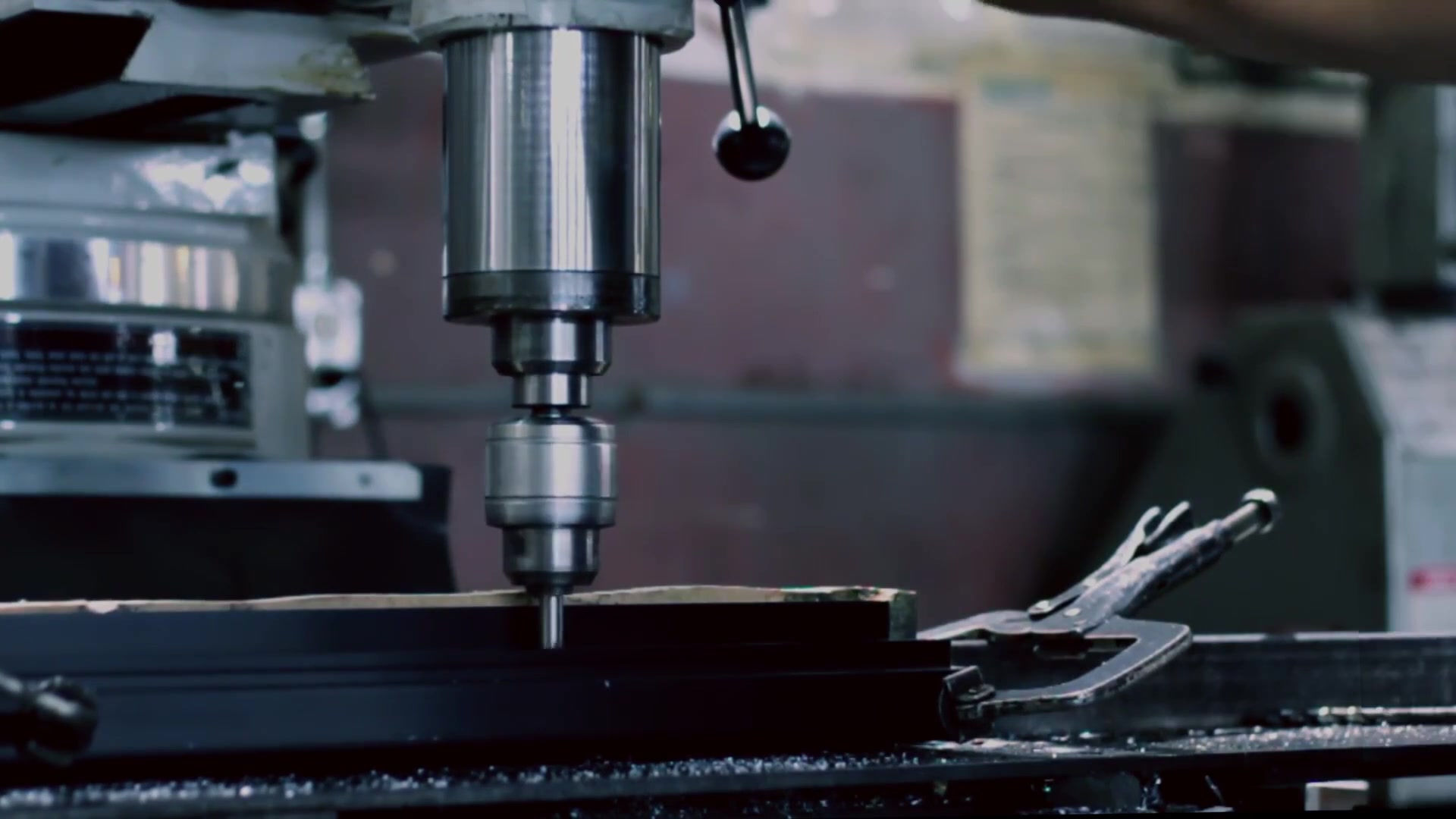
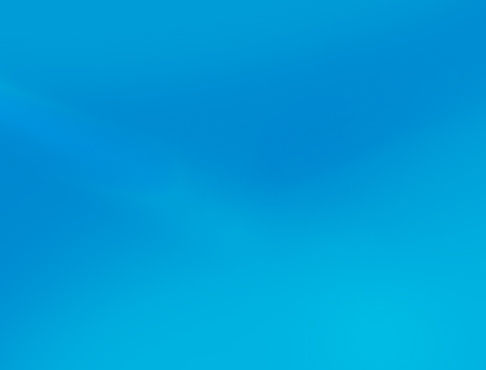
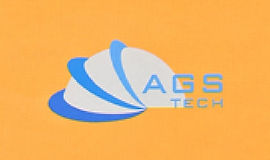
Fabricante personalizado global, integrador, consolidador, parceiro de terceirização para uma ampla variedade de produtos e serviços.
Somos sua fonte única para fabricação, fabricação, engenharia, consolidação, integração, terceirização de produtos e serviços fabricados sob encomenda e prontos para uso.
Choose your Language
-
Fabricação personalizada
-
Fabricação por contrato doméstica e global
-
Terceirização de Manufatura
-
Compras domésticas e globais
-
Consolidação
-
Integração de Engenharia
-
Serviços de engenharia
Search Results
161 resultados encontrados com uma busca vazia
- Processos de junção e montagem e fixação, soldagem, brasagem
Processos de junção e montagem e fixação, soldagem, brasagem, soldagem, sinterização, colagem adesiva, encaixe por pressão, processo de solda por onda e refluxo, forno de tocha Processos de Junção e Montagem e Fixação Unimos, montamos e fixamos suas peças fabricadas e as transformamos em produtos acabados ou semi-acabados por meio de SOLDAGEM, BRASILAGEM, SOLDAGEM, SINTERNIZAÇÃO, COLAGEM ADESIVA, FIXAÇÃO, PRESS FITTING. Alguns de nossos processos de soldagem mais populares são arco, gás oxicorte, resistência, projeção, costura, rebordo, percussão, estado sólido, feixe de elétrons, laser, termita, soldagem por indução. Nossos processos de brasagem populares são tocha, indução, forno e brasagem por imersão. Nossos métodos de solda são ferro, placa quente, forno, indução, mergulho, onda, refluxo e solda ultra-sônica. Para a colagem adesiva, usamos frequentemente termoplásticos e termofixos, epóxis, fenólicos, poliuretano, ligas adesivas, bem como alguns outros produtos químicos e fitas. Finalmente, nossos processos de fixação consistem em pregar, aparafusar, porcas e parafusos, rebitar, rebitar, fixar, costurar e grampear e encaixar. • SOLDAGEM: A soldagem envolve a união de materiais através da fusão das peças de trabalho e introdução de materiais de enchimento, que também une a poça de fusão fundida. Quando a área esfria, obtemos uma junta forte. A pressão é aplicada em alguns casos. Ao contrário da soldagem, as operações de brasagem e soldagem envolvem apenas a fusão de um material com menor ponto de fusão entre as peças, e as peças não derretem. Recomendamos que você clique aqui paraBAIXE nossas Ilustrações Esquemáticas de Processos de Soldagem da AGS-TECH Inc. Isso ajudará você a entender melhor as informações que fornecemos abaixo. Em ARC WELDING, usamos uma fonte de alimentação e um eletrodo para criar um arco elétrico que derrete os metais. O ponto de soldagem é protegido por um gás ou vapor de proteção ou outro material. Este processo é popular para soldagem de peças automotivas e estruturas de aço. Na soldagem a arco de metal blindado (SMAW) ou também conhecida como soldagem por bastão, um bastão de eletrodo é aproximado do material base e um arco elétrico é gerado entre eles. A haste do eletrodo derrete e atua como material de enchimento. O eletrodo também contém fluxo que atua como uma camada de escória e libera vapores que atuam como gás de proteção. Estes protegem a área de solda da contaminação ambiental. Nenhum outro enchimento está sendo usado. As desvantagens deste processo são a sua lentidão, necessidade de substituição frequente dos eletrodos, necessidade de cavar a escória residual proveniente do fluxo. Uma série de metais como ferro, aço, níquel, alumínio, cobre...etc. Pode ser soldado. Suas vantagens são suas ferramentas baratas e facilidade de uso. Soldagem a arco de metal a gás (GMAW) também conhecida como gás metal-inerte (MIG), temos alimentação contínua de um eletrodo consumível de enchimento de arame e um gás inerte ou parcialmente inerte que flui ao redor do arame contra a contaminação ambiental da região de solda. Aço, alumínio e outros metais não ferrosos podem ser soldados. As vantagens do MIG são altas velocidades de soldagem e boa qualidade. As desvantagens são seus equipamentos complicados e desafios enfrentados em ambientes externos ventosos porque temos que manter o gás de proteção ao redor da área de soldagem estável. Uma variação do GMAW é a soldagem a arco com núcleo de fluxo (FCAW), que consiste em um tubo de metal fino preenchido com materiais de fluxo. Às vezes, o fluxo dentro do tubo é suficiente para proteção contra contaminação ambiental. A soldagem por arco submerso (SAW) amplamente um processo automatizado, envolve alimentação contínua de arame e arco que é atingido sob uma camada de cobertura de fluxo. As taxas de produção e qualidade são altas, a escória de soldagem sai facilmente e temos um ambiente de trabalho livre de fumaça. A desvantagem é que ele só pode ser usado para soldar parts em determinadas posições. Na soldagem a arco de tungstênio a gás (GTAW) ou soldagem a gás inerte de tungstênio (TIG), usamos um eletrodo de tungstênio junto com um enchimento separado e gases inertes ou quase inertes. Como sabemos, o tungstênio tem um alto ponto de fusão e é um metal muito adequado para temperaturas muito altas. O Tungstênio em TIG não é consumido ao contrário dos outros métodos explicados acima. Uma técnica de soldagem lenta, mas de alta qualidade, vantajosa sobre outras técnicas de soldagem de materiais finos. Adequado para muitos metais. A soldagem a arco de plasma é semelhante, mas usa gás de plasma para criar o arco. O arco na soldagem a arco plasma é relativamente mais concentrado em comparação ao GTAW e pode ser usado para uma ampla faixa de espessuras de metal em velocidades muito mais altas. A soldagem GTAW e a arco plasma podem ser aplicadas a mais ou menos os mesmos materiais. OXY-FUEL / OXYFUEL WELDING também chamada de soldagem oxiacetileno, soldagem oxi, soldagem a gás é realizada usando combustíveis gasosos e oxigênio para soldagem. Como não há energia elétrica, é portátil e pode ser usado onde não há eletricidade. Usando uma tocha de solda, aquecemos as peças e o material de enchimento para produzir uma piscina de metal fundido compartilhada. Vários combustíveis podem ser usados, como acetileno, gasolina, hidrogênio, propano, butano, etc. Na soldagem oxi-combustível usamos dois recipientes, um para o combustível e outro para o oxigênio. O oxigênio oxida o combustível (queima). SOLDAGEM POR RESISTÊNCIA: Este tipo de soldagem aproveita o aquecimento joule e o calor é gerado no local onde a corrente elétrica é aplicada por um determinado tempo. Altas correntes são passadas através do metal. Poças de metal fundido são formadas neste local. Os métodos de soldagem por resistência são populares devido à sua eficiência, pouco potencial de poluição. No entanto, as desvantagens são os custos do equipamento serem relativamente significativos e a limitação inerente a peças de trabalho relativamente finas. A SOLDAGEM POR PONTO é um tipo importante de soldagem por resistência. Aqui nós juntamos duas ou mais folhas sobrepostas ou peças de trabalho usando dois eletrodos de cobre para prender as folhas e passar uma alta corrente através delas. O material entre os eletrodos de cobre aquece e uma poça de fusão é gerada nesse local. A corrente é então interrompida e as pontas dos eletrodos de cobre resfriam o local da solda porque os eletrodos são resfriados a água. Aplicar a quantidade certa de calor ao material e espessura corretos é fundamental para esta técnica, porque se aplicado incorretamente a junta ficará fraca. A soldagem a ponto tem as vantagens de não causar deformações significativas nas peças de trabalho, eficiência energética, facilidade de automação e excelentes taxas de produção, além de não exigir enchimentos. A desvantagem é que, como a soldagem ocorre em pontos em vez de formar uma costura contínua, a resistência geral pode ser relativamente menor em comparação com outros métodos de soldagem. SEAM WELDING, por outro lado, produz soldas nas superfícies de contato de materiais semelhantes. A costura pode ser de topo ou de sobreposição. A soldagem da costura começa em uma extremidade e se move progressivamente para a outra. Este método também utiliza dois eletrodos de cobre para aplicar pressão e corrente na região da solda. Os eletrodos em forma de disco giram com contato constante ao longo da linha de costura e fazem uma solda contínua. Aqui também, os eletrodos são resfriados por água. As soldas são muito fortes e confiáveis. Outros métodos são as técnicas de soldagem por projeção, flash e rebordo. A SOLDAGEM EM ESTADO SÓLIDO é um pouco diferente dos métodos anteriores explicados acima. A coalescência ocorre em temperaturas abaixo da temperatura de fusão dos metais unidos e sem uso de carga metálica. A pressão pode ser usada em alguns processos. Vários métodos são SOLDAGEM POR COEXTRUSÃO onde metais diferentes são extrudados através da mesma matriz, SOLDAGEM POR PRESSÃO A FRIO onde unimos ligas macias abaixo de seus pontos de fusão, SOLDAGEM POR DIFUSÃO uma técnica sem linhas de solda visíveis, SOLDAGEM POR EXPLOSÃO para unir materiais diferentes, por exemplo, ligas resistentes à corrosão a estruturas aços, SOLDAGEM POR PULSO ELETROMAGNÉTICO onde aceleramos tubos e chapas por forças eletromagnéticas, SOLDAGEM DE FORJA que consiste em aquecer os metais a altas temperaturas e martelá-los juntos, SOLDAGEM POR FRICÇÃO onde se realiza com suficiente soldagem por fricção, SOLDAGEM POR FRICTION STIR que envolve um processo rotativo não ferramenta consumível que atravessa a linha de junção, HOT PRESSURE WELDING onde pressionamos metais juntos em temperaturas elevadas abaixo da temperatura de fusão em vácuo ou gases inertes, HOT ISOSTATIC PRESSURE WELDING um processo onde aplicamos pressão usando gases inertes dentro de um recipiente, ROLL WELDING onde unimos materiais diferentes, forçando-os entre duas rodas giratórias, SOLDAGEM ULTRA-SÔNICA onde são soldadas chapas finas de metal ou plástico usando energia vibracional de alta frequência. Nossos outros processos de soldagem são ELECTRON BEAM WELDING com penetração profunda e processamento rápido, mas sendo um método caro, o consideramos para casos especiais, ELECTROSLAG WELDING um método adequado apenas para chapas grossas pesadas e peças de aço, SOLDAGEM POR INDUÇÃO onde usamos indução eletromagnética e aquecer nossas peças eletricamente condutoras ou ferromagnéticas, LASER BEAM WELDING também com penetração profunda e processamento rápido, mas um método caro, LASER HYBRID WELDING que combina LBW com GMAW no mesmo cabeçote de soldagem e capaz de preencher folgas de 2 mm entre placas, PERCUSSION WELDING que envolve uma descarga elétrica seguida de forjamento dos materiais com pressão aplicada, THERMIT WELDING envolvendo reação exotérmica entre pós de alumínio e óxido de ferro., ELECTROGAS WELDING com eletrodos consumíveis e usado apenas com aço na posição vertical, e finalmente STUD ARC WELDING para unir pino à base material com calor e pressão. Recomendamos que você clique aqui paraBAIXE nossas ilustrações esquemáticas de processos de brasagem, soldagem e colagem adesiva pela AGS-TECH Inc Isso ajudará você a entender melhor as informações que fornecemos abaixo. • BRASAGEM : Nós unimos dois ou mais metais aquecendo metais de adição entre eles acima de seus pontos de fusão e usando ação capilar para espalhar. O processo é semelhante à soldagem, mas as temperaturas envolvidas para derreter o enchimento são mais altas na brasagem. Como na soldagem, o fluxo protege o material de enchimento da contaminação atmosférica. Após o resfriamento, as peças de trabalho são unidas. O processo envolve as seguintes etapas principais: Bom ajuste e folga, limpeza adequada dos materiais de base, fixação adequada, seleção adequada de fluxo e atmosfera, aquecimento do conjunto e, finalmente, limpeza do conjunto brasado. Alguns de nossos processos de brasagem são TORCH BRAZING, um método popular realizado manualmente ou de forma automatizada. É adequado para pedidos de produção de baixo volume e casos especializados. O calor é aplicado usando chamas de gás perto da junta que está sendo brasada. A BRAÇADURA DE FORNO requer menos habilidade do operador e é um processo semiautomático adequado para produção industrial em massa. Tanto o controle da temperatura quanto o controle da atmosfera no forno são vantagens desta técnica, pois o primeiro permite ter ciclos de calor controlados e eliminar o aquecimento local como é o caso da brasagem com maçarico, e o segundo protege a peça da oxidação. Usando jigging, somos capazes de reduzir ao mínimo os custos de fabricação. As desvantagens são o alto consumo de energia, custos de equipamentos e considerações de projeto mais desafiadoras. A BRASAGEM A VÁCUO ocorre em um forno de vácuo. A uniformidade da temperatura é mantida e obtemos juntas sem fluxo, muito limpas e com muito poucas tensões residuais. Os tratamentos térmicos podem ocorrer durante a brasagem a vácuo, devido às baixas tensões residuais presentes durante os ciclos lentos de aquecimento e resfriamento. A principal desvantagem é seu alto custo, pois a criação de ambiente de vácuo é um processo caro. Ainda outra técnica DIP BRAZING une peças fixas onde o composto de brasagem é aplicado em superfícies de contato. Em seguida, as peças fixtured são mergulhadas em um banho de um sal fundido, como cloreto de sódio (sal de mesa), que atua como um meio de transferência de calor e fluxo. O ar é excluído e, portanto, não ocorre a formação de óxido. Na BRAÇADURA POR INDUÇÃO unimos materiais por um metal de adição que tem um ponto de fusão mais baixo do que os materiais de base. A corrente alternada da bobina de indução cria um campo eletromagnético que induz o aquecimento por indução em materiais magnéticos principalmente ferrosos. O método fornece aquecimento seletivo, boas juntas com enchimentos fluindo apenas nas áreas desejadas, pouca oxidação porque não há chamas e o resfriamento é rápido, aquecimento rápido, consistência e adequação para fabricação de alto volume. Para agilizar nossos processos e garantir a consistência, usamos frequentemente pré-formas. Informações sobre nossas instalações de brasagem que produzem conexões de cerâmica para metal, vedação hermética, passagens a vácuo, componentes de controle de fluido e alto e ultra-alto vácuo podem ser encontradas aqui: Brochura da Fábrica de Brasagem • SOLDA: Na solda não temos a fusão das peças de trabalho, mas sim um metal de adição com ponto de fusão mais baixo do que as peças de união que desembocam na junta. O metal de adição na solda derrete a uma temperatura mais baixa do que na brasagem. Usamos ligas isentas de chumbo para soldagem e temos conformidade com RoHS e para diferentes aplicações e requisitos temos ligas diferentes e adequadas, como liga de prata. A soldagem nos oferece juntas que são estanques a gases e líquidos. Em SOFT SOLDERING, nosso metal de adição tem um ponto de fusão abaixo de 400 Centígrados, enquanto em SILVER SOLDERING e BRAZING precisamos de temperaturas mais altas. A soldagem suave usa temperaturas mais baixas, mas não resulta em juntas fortes para aplicações exigentes em temperaturas elevadas. A soldagem de prata, por outro lado, requer altas temperaturas fornecidas pela tocha e nos dá juntas fortes adequadas para aplicações de alta temperatura. A brasagem requer as temperaturas mais altas e geralmente uma tocha está sendo usada. Como as juntas de brasagem são muito fortes, elas são boas candidatas para reparar objetos pesados de ferro. Em nossas linhas de fabricação, usamos tanto a solda manual manual quanto as linhas de solda automatizadas. INDUCTION SOLDERING usa corrente CA de alta frequência em uma bobina de cobre para facilitar o aquecimento por indução. As correntes são induzidas na parte soldada e, como resultado, o calor é gerado na alta resistência joint. Este calor derrete o metal de adição. O fluxo também é usado. A soldagem por indução é um bom método para soldar cilindros e tubos em um processo contínuo envolvendo as bobinas em torno deles. A soldagem de alguns materiais como grafite e cerâmica é mais difícil, pois requer o chapeamento das peças com um metal adequado antes da soldagem. Isso facilita a ligação interfacial. Soldamos esses materiais especialmente para aplicações de embalagens herméticas. Fabricamos nossas placas de circuito impresso (PCB) em alto volume principalmente usando SOLDA ONDA. Apenas para pequenas quantidades de prototipagem, usamos solda manual usando ferro de solda. Usamos solda por onda para montagens de PCB de passagem e montagem em superfície (PCBA). Uma cola temporária mantém os componentes presos à placa de circuito e o conjunto é colocado em uma esteira e se desloca por um equipamento que contém solda derretida. Primeiro o PCB é fluxado e então entra na zona de pré-aquecimento. A solda derretida está em uma panela e tem um padrão de ondas estacionárias em sua superfície. Quando o PCB se move sobre essas ondas, essas ondas entram em contato com a parte inferior do PCB e grudam nas almofadas de solda. A solda fica apenas nos pinos e pads e não na própria PCB. As ondas na solda derretida devem ser bem controladas para que não haja respingos e os topos das ondas não toquem e contaminem áreas indesejadas das placas. Em REFLOW SOLDERING, utilizamos uma pasta de solda adesiva para fixar temporariamente os componentes eletrônicos nas placas. Em seguida, as placas são colocadas em um forno de refluxo com controle de temperatura. Aqui a solda derrete e conecta os componentes permanentemente. Usamos essa técnica tanto para componentes de montagem em superfície quanto para componentes de furos passantes. O controle adequado da temperatura e o ajuste das temperaturas do forno são essenciais para evitar a destruição dos componentes eletrônicos da placa por superaquecimento dos mesmos acima de seus limites máximos de temperatura. No processo de soldagem por refluxo, na verdade, temos várias regiões ou estágios, cada um com um perfil térmico distinto, como etapa de pré-aquecimento, etapa de imersão térmica, etapas de refluxo e resfriamento. Essas diferentes etapas são essenciais para uma soldagem por refluxo sem danos de conjuntos de placas de circuito impresso (PCBA). ULTRASONIC SOLDERING é outra técnica frequentemente usada com capacidades únicas - pode ser usada para soldar vidro, cerâmica e materiais não metálicos. Por exemplo, painéis fotovoltaicos que não são metálicos precisam de eletrodos que podem ser fixados usando esta técnica. Na soldagem ultrassônica, implantamos uma ponta de solda aquecida que também emite vibrações ultrassônicas. Essas vibrações produzem bolhas de cavitação na interface do substrato com o material de solda fundido. A energia implosiva da cavitação modifica a superfície do óxido e remove a sujeira e os óxidos. Durante este tempo, uma camada de liga também é formada. A solda na superfície de ligação incorpora oxigênio e permite a formação de uma forte ligação compartilhada entre o vidro e a solda. A SOLDA DIP pode ser considerada como uma versão mais simples da solda por onda adequada apenas para produção em pequena escala. O primeiro fluxo de limpeza é aplicado como em outros processos. PCBs com componentes montados são mergulhados manualmente ou de forma semi-automática em um tanque contendo solda derretida. A solda derretida adere às áreas metálicas expostas desprotegidas pela máscara de solda na placa. O equipamento é simples e barato. • COLAGEM ADESIVA : Esta é outra técnica popular que usamos com frequência e envolve a colagem de superfícies usando colas, epóxis, agentes plásticos ou outros produtos químicos. A ligação é realizada por evaporação do solvente, por cura por calor, por cura por luz UV, por cura por pressão ou esperando um certo tempo. Várias colas de alto desempenho são usadas em nossas linhas de produção. Com processos de aplicação e cura projetados adequadamente, a colagem adesiva pode resultar em ligações de tensão muito baixas que são fortes e confiáveis. As ligações adesivas podem ser bons protetores contra fatores ambientais como umidade, contaminantes, corrosivos, vibração...etc. As vantagens da colagem adesiva são: elas podem ser aplicadas a materiais que de outra forma seriam difíceis de soldar, soldar ou brasar. Também pode ser preferível para materiais sensíveis ao calor que seriam danificados por soldagem ou outros processos de alta temperatura. Outras vantagens dos adesivos são que eles podem ser aplicados em superfícies de formato irregular e aumentar o peso da montagem em quantidades muito pequenas quando comparado a outros métodos. Também as mudanças dimensionais nas peças são muito mínimas. Algumas colas têm propriedades de correspondência de índice e podem ser usadas entre componentes ópticos sem diminuir significativamente a intensidade da luz ou do sinal óptico. As desvantagens, por outro lado, são os tempos de cura mais longos que podem retardar as linhas de fabricação, requisitos de fixação, requisitos de preparação de superfície e dificuldade de desmontagem quando o retrabalho é necessário. A maioria de nossas operações de colagem adesiva envolve as seguintes etapas: -Tratamento de superfície: Procedimentos especiais de limpeza, como limpeza com água deionizada, limpeza com álcool, limpeza com plasma ou corona, são comuns. Após a limpeza, podemos aplicar promotores de adesão nas superfícies para garantir as melhores juntas possíveis. - Fixação de peças: Tanto para aplicação de adesivos quanto para cura, projetamos e usamos fixações personalizadas. -Aplicação de adesivos: Às vezes usamos sistemas manuais e, às vezes, dependendo do caso, sistemas automatizados, como robótica, servomotores, atuadores lineares para entregar os adesivos no local certo e usamos dispensadores para entregá-los no volume e quantidade certos. -Cura: Dependendo do adesivo, podemos usar secagem e cura simples, bem como cura sob luz UV que atua como catalisador ou cura térmica em um forno ou usando elementos de aquecimento resistivos montados em gabaritos e acessórios. Recomendamos que você clique aqui paraBAIXE nossas ilustrações esquemáticas de processos de fixação da AGS-TECH Inc. Isso ajudará você a entender melhor as informações que fornecemos abaixo. • PROCESSOS DE FIXAÇÃO: Nossos processos de união mecânica se dividem em duas categorias: FIXADORES e JUNTAS INTEGRAL. Exemplos de fixadores que usamos são parafusos, pinos, porcas, parafusos, rebites. Exemplos de juntas integrais que usamos são encaixes de pressão e contração, costuras, crimpagens. Usando uma variedade de métodos de fixação, garantimos que nossas juntas mecânicas sejam fortes e confiáveis por muitos anos de uso. PARAFUSOS e PARAFUSOS são alguns dos fixadores mais comumente usados para manter objetos juntos e posicionamento. Nossos parafusos e cavilhas atendem aos padrões ASME. Vários tipos de parafusos e cavilhas são implantados, incluindo parafusos sextavados e parafusos sextavados, parafusos e parafusos de retenção, parafuso de extremidade dupla, parafuso de bucha, parafuso de olhal, parafuso de espelho, parafuso de chapa metálica, parafuso de ajuste fino, parafusos autoperfurantes e auto-roscantes , parafuso de fixação, parafusos com arruelas embutidas... e muito mais. Temos vários tipos de cabeça de parafuso, como cabeça escareada, cúpula, redonda, flangeada e vários tipos de acionamento de parafuso, como slot, phillips, quadrado, soquete hexagonal. Um RIVET por outro lado é um fixador mecânico permanente que consiste em um eixo cilíndrico liso e uma cabeça por um lado. Após a inserção, a outra extremidade do rebite é deformada e seu diâmetro é ampliado para que permaneça no lugar. Em outras palavras, antes da instalação um rebite tem uma cabeça e após a instalação tem duas. Instalamos vários tipos de rebites dependendo da aplicação, resistência, acessibilidade e custo, como rebites de cabeça sólida/redonda, rebites estruturais, semi-tubulares, cegos, oscar, drive, flush, friction-lock, rebites autoperfurantes. A rebitagem pode ser preferida nos casos em que a deformação térmica e a mudança nas propriedades do material devido ao calor da soldagem precisam ser evitadas. A rebitagem também oferece peso leve e especialmente boa resistência e resistência contra forças de cisalhamento. Contra cargas de tração, no entanto, parafusos, porcas e parafusos podem ser mais adequados. No processo de CLINCHING utilizamos punções e matrizes especiais para formar um intertravamento mecânico entre as chapas metálicas que estão sendo unidas. O punção empurra as camadas de chapa metálica para dentro da cavidade da matriz e resulta na formação de uma junta permanente. Nenhum aquecimento e nenhum resfriamento é necessário no clinching e é um processo de trabalho a frio. É um processo econômico que pode substituir a soldagem a ponto em alguns casos. No PINNING usamos pinos que são elementos de máquina usados para fixar posições de peças de máquinas em relação umas às outras. Os principais tipos são pinos de forquilha, contrapino, pino de mola, pinos de cavilha, and split pin. No STAPLING usamos pistolas e grampos de grampeamento que são fixadores de duas pontas usados para unir ou encadernar materiais. O grampeamento tem as seguintes vantagens: Econômico, simples e rápido de usar, a coroa dos grampos pode ser usada para unir materiais unidos, A coroa do grampo pode facilitar a ligação de uma peça como um cabo e a fixação em uma superfície sem perfurar ou remoção prejudicial e relativamente fácil. O PRESS FITTING é realizado empurrando as peças juntas e o atrito entre elas prende as peças. As peças de encaixe por pressão que consistem em um eixo superdimensionado e um furo subdimensionado geralmente são montadas por um dos dois métodos: aplicando força ou aproveitando a expansão ou contração térmica das peças. Quando um encaixe de pressão é estabelecido pela aplicação de uma força, usamos uma prensa hidráulica ou uma prensa manual. Por outro lado, quando o encaixe de pressão é estabelecido por expansão térmica, aquecemos as partes envolventes e as montamos em seus lugares enquanto quentes. Quando esfriam, eles se contraem e voltam às suas dimensões normais. Isso resulta em um bom ajuste de pressão. Chamamos isso alternativamente de SHRINK-FITTING. A outra maneira de fazer isso é resfriando as peças envelopadas antes da montagem e, em seguida, deslizando-as em suas peças correspondentes. Quando o conjunto aquece, eles se expandem e obtemos um ajuste apertado. Este último método pode ser preferível nos casos em que o aquecimento apresenta o risco de alterar as propriedades do material. O resfriamento é mais seguro nesses casos. Componentes e conjuntos pneumáticos e hidráulicos • Válvulas, componentes hidráulicos e pneumáticos como O-ring, arruela, vedações, gaxeta, anel, calço. Como as válvulas e os componentes pneumáticos vêm em uma grande variedade, não podemos listar tudo aqui. Dependendo dos ambientes físicos e químicos de sua aplicação, temos produtos especiais para você. Por favor, especifique-nos a aplicação, tipo de componente, especificações, condições ambientais como pressão, temperatura, líquidos ou gases que estarão em contato com suas válvulas e componentes pneumáticos; e nós escolheremos o produto mais adequado para você ou fabricaremos especialmente para sua aplicação. CLICK Product Finder-Locator Service PÁGINA ANTERIOR
- Prototipagem Rápida, Manufatura Desktop, Manufatura Aditiva, FDM
Prototipagem Rápida, Fabricação de Desktop, Fabricação Aditiva, Estereolitografia, Polyjet, Modelagem de Deposição Fundida, Sinterização Seletiva a Laser, FDM, SLS Fabricação Aditiva e Rápida Nos últimos anos, temos visto um aumento na demanda por FABRICAÇÃO RÁPIDA ou PROTOTIPAGEM RÁPIDA. Este processo também pode ser chamado de FABRICAÇÃO DE DESKTOP ou FABRICAÇÃO DE FORMA LIVRE. Basicamente, um modelo físico sólido de uma peça é feito diretamente de um desenho CAD tridimensional. Usamos o termo FABRICAÇÃO ADICIONAL para essas várias técnicas onde construímos peças em camadas. Usando hardware e software controlados por computador integrados, realizamos manufatura aditiva. Nossas técnicas de prototipagem e fabricação rápidas são ESTEREOLITOGRAFIA, POLYJET, MODELAGEM DE DEPOSIÇÃO FUNDIDA, SINTERAÇÃO LASER SELETIVA, FUSÃO DE FEIXE DE ELÉTRONS, IMPRESSÃO TRIDIMENSIONAL, FABRICAÇÃO DIRETA, FERRAMENTA RÁPIDA. Recomendamos que você clique aqui paraBAIXE nossas ilustrações esquemáticas de manufatura aditiva e processos de manufatura rápida pela AGS-TECH Inc. Isso ajudará você a entender melhor as informações que fornecemos abaixo. A prototipagem rápida nos fornece: 1.) O projeto conceitual do produto é visto de diferentes ângulos em um monitor usando um sistema 3D/CAD. 2.) Protótipos de materiais não metálicos e metálicos são fabricados e estudados nos aspectos funcional, técnico e estético. 3.) Prototipagem de baixo custo em um tempo muito curto é realizada. A fabricação aditiva pode ser comparada à construção de um pão, empilhando e colando fatias individuais umas sobre as outras. Em outras palavras, o produto é fabricado fatia por fatia, ou camada por camada depositada uma sobre a outra. A maioria das peças pode ser produzida em poucas horas. A técnica é boa se as peças forem necessárias muito rapidamente ou se as quantidades necessárias forem baixas e fazer um molde e ferramentas for muito caro e demorado. No entanto, o custo de uma peça é caro devido às matérias-primas caras. • ESTEREOLITOGRAFIA: Esta técnica também abreviada como STL, baseia-se na cura e endurecimento de um fotopolímero líquido em uma forma específica, focando um feixe de laser sobre ele. O laser polimeriza o fotopolímero e o cura. Ao escanear o feixe de laser UV de acordo com a forma programada ao longo da superfície da mistura de fotopolímeros, a peça é produzida de baixo para cima em fatias individuais em cascata umas sobre as outras. A varredura do ponto do laser é repetida várias vezes para atingir as geometrias programadas no sistema. Depois que a peça é totalmente fabricada, ela é removida da plataforma, enxugada e limpa por ultra-som e com banho de álcool. Em seguida, ele é exposto à irradiação UV por algumas horas para garantir que o polímero esteja totalmente curado e endurecido. Para resumir o processo, uma plataforma que é mergulhada em uma mistura de fotopolímero e um feixe de laser UV são controlados e movidos através de um sistema de servocontrole de acordo com o formato da peça desejada e a peça é obtida por fotopolimerização do polímero camada por camada. Claro que as dimensões máximas da peça produzida são determinadas pelo equipamento de estereolitografia. • POLYJET : Semelhante à impressão a jato de tinta, em polyjet temos oito cabeças de impressão que depositam fotopolímero na bandeja de construção. A luz ultravioleta colocada ao lado dos jatos cura e endurece imediatamente cada camada. Dois materiais são usados em polyjet. O primeiro material é para fabricar o modelo real. O segundo material, uma resina tipo gel, é usada para suporte. Ambos os materiais são depositados camada por camada e simultaneamente curados. Após a conclusão do modelo, o material de suporte é removido com uma solução aquosa. As resinas utilizadas são semelhantes à estereolitografia (STL). O polyjet apresenta as seguintes vantagens em relação à estereolitografia: 1.) Não há necessidade de limpeza das peças. 2.) Não há necessidade de cura pós-processo 3.) Espessuras de camada menores são possíveis e assim obtemos melhor resolução e podemos fabricar peças mais finas. • MODELAGEM DE DEPOSIÇÃO FUSADA: Também abreviada como FDM, neste método uma cabeça de extrusora controlada por robô se move em duas direções principais sobre uma mesa. O cabo é abaixado e levantado conforme necessário. A partir do orifício de uma matriz aquecida na cabeça, um filamento termoplástico é extrudado e uma camada inicial é depositada sobre uma base de espuma. Isso é realizado pela cabeça da extrusora que segue um caminho pré-determinado. Após a camada inicial, a mesa é abaixada e as camadas subsequentes são depositadas umas sobre as outras. Às vezes, ao fabricar uma peça complicada, são necessárias estruturas de suporte para que a deposição possa continuar em determinadas direções. Nestes casos, um material de suporte é extrudado com um espaçamento de filamento menos denso em uma camada, de modo que seja mais fraco que o material do modelo. Essas estruturas de suporte podem ser dissolvidas ou quebradas posteriormente após a conclusão da peça. As dimensões da matriz da extrusora determinam a espessura das camadas extrudadas. O processo FDM produz peças com superfícies escalonadas em planos externos oblíquos. Se esta rugosidade for inaceitável, o polimento a vapor químico ou uma ferramenta aquecida podem ser usados para alisá-los. Até mesmo uma cera de polimento está disponível como material de revestimento para eliminar essas etapas e alcançar tolerâncias geométricas razoáveis. • SINTERING SELETIVO A LASER: Também denominado SLS, o processo é baseado na sinterização de um polímero, pó cerâmico ou metálico seletivamente em um objeto. A parte inferior da câmara de processamento tem dois cilindros: um cilindro de construção parcial e um cilindro de alimentação de pó. O primeiro é abaixado incrementalmente até onde a peça sinterizada está sendo formada e o último é elevado incrementalmente para fornecer pó ao cilindro de construção parcial através de um mecanismo de rolete. Primeiro, uma fina camada de pó é depositada no cilindro de construção parcial, em seguida, um feixe de laser é focado nessa camada, traçando e fundindo/sinterizando uma seção transversal específica, que então se solidifica em um sólido. O pó é áreas que não são atingidas pelo feixe de laser permanecem soltos, mas ainda suporta a parte sólida. Em seguida, outra camada de pó é depositada e o processo é repetido várias vezes para obter a peça. No final, as partículas de pó soltas são sacudidas. Tudo isso é realizado por um computador de controle de processo usando instruções geradas pelo programa CAD 3D da peça que está sendo fabricada. Vários materiais como polímeros (como ABS, PVC, poliéster), ceras, metais e cerâmicas com ligantes poliméricos apropriados podem ser depositados. • ELECTRON-BEAM MELTING : Semelhante à sinterização seletiva a laser, mas usando feixe de elétrons para fundir titânio ou pós de cromo-cobalto para fazer protótipos no vácuo. Alguns desenvolvimentos foram feitos para realizar este processo em aços inoxidáveis, alumínio e ligas de cobre. Se a resistência à fadiga das peças produzidas precisar ser aumentada, usamos a prensagem isostática a quente após a fabricação da peça como um processo secundário. • IMPRESSÃO TRIDIMENSIONAL: Também designada por 3DP, nesta técnica uma cabeça de impressão deposita um aglutinante inorgânico sobre uma camada de pó não metálico ou metálico. Um pistão que transporta o leito de pó é abaixado incrementalmente e em cada etapa o aglutinante é depositado layer por camada e fundido pelo aglutinante. Os materiais em pó utilizados são misturas de polímeros e fibras, areia de fundição, metais. Usando diferentes cabeças de fichário simultaneamente e fichários de cores diferentes, podemos obter várias cores. O processo é semelhante à impressão a jato de tinta, mas em vez de obter uma folha colorida, obtemos um objeto tridimensional colorido. As peças produzidas podem ser porosas e, portanto, podem exigir sinterização e infiltração de metal para aumentar sua densidade e resistência. A sinterização queimará o aglutinante e fundirá os pós metálicos. Metais como aço inoxidável, alumínio, titânio podem ser usados para fazer as peças e como materiais de infiltração geralmente usamos cobre e bronze. A beleza desta técnica é que mesmo montagens complicadas e móveis podem ser fabricadas muito rapidamente. Por exemplo, um conjunto de engrenagem, uma chave inglesa como ferramenta pode ser feita e terá peças móveis e giratórias prontas para serem usadas. Diferentes componentes do conjunto podem ser fabricados com cores diferentes e tudo de uma vez. Baixe nosso folheto em:Noções básicas de impressão 3D de metal • FABRICAÇÃO DIRETA e FERRAMENTA RÁPIDA: Além de avaliação de projeto, solução de problemas, usamos prototipagem rápida para fabricação direta de produtos ou aplicação direta em produtos. Em outras palavras, a prototipagem rápida pode ser incorporada aos processos convencionais para torná-los melhores e mais competitivos. Por exemplo, a prototipagem rápida pode produzir padrões e moldes. Padrões de um polímero de fusão e queima criados por operações de prototipagem rápida podem ser montados para fundição de precisão e investidos. Outro exemplo a ser mencionado é o uso de 3DP para produzir conchas de fundição de cerâmica e usá-lo para operações de fundição de conchas. Mesmo moldes de injeção e inserções de molde podem ser produzidos por prototipagem rápida e pode-se economizar muitas semanas ou meses de tempo de fabricação do molde. Analisando apenas um arquivo CAD da peça desejada, podemos produzir a geometria da ferramenta usando um software. Aqui estão alguns dos nossos métodos populares de ferramentas rápidas: RTV (Room-Temperature Vulcanizing) MOLDAGEM / FUNDIÇÃO DE URETANO : Usando prototipagem rápida pode ser usado para fazer o padrão da peça desejada. Em seguida, esse padrão é revestido com um agente de separação e a borracha RTV líquida é derramada sobre o padrão para produzir as metades do molde. Em seguida, essas metades do molde são usadas para moldar por injeção uretanos líquidos. A vida útil do molde é curta, apenas como 0 ou 30 ciclos, mas suficiente para produção em pequenos lotes. ACES (Acetal Clear Epoxy Solid) MOLDAGEM POR INJEÇÃO : Utilizando técnicas de prototipagem rápida como a estereolitografia, produzimos moldes de injeção. Esses moldes são conchas com uma extremidade aberta para permitir o preenchimento com materiais como epóxi, epóxi preenchido com alumínio ou metais. Novamente, a vida útil do molde é limitada a dezenas ou no máximo centenas de peças. PROCESSO DE FERRAMENTA DE METAL SPRAYED: Usamos prototipagem rápida e fazemos um padrão. Pulverizamos uma liga de zinco-alumínio na superfície do padrão e a revestimos. O padrão com o revestimento de metal é então colocado dentro de um frasco e envasado com epóxi ou epóxi preenchido com alumínio. Finalmente, ele é removido e, produzindo duas metades de molde, obtemos um molde completo para moldagem por injeção. Esses moldes têm vida útil mais longa, em alguns casos, dependendo do material e das temperaturas, podem produzir peças aos milhares. PROCESSO KEELTOOL: Esta técnica pode produzir moldes com 100.000 a 10 milhões de ciclos de vida. Utilizando prototipagem rápida produzimos um molde RTV. Em seguida, o molde é preenchido com uma mistura que consiste em pó de aço para ferramentas A6, carboneto de tungstênio, aglutinante de polímero e deixa-se curar. Este molde é então aquecido para que o polímero seja queimado e os pós metálicos se fundam. O próximo passo é a infiltração de cobre para produzir o molde final. Se necessário, operações secundárias, como usinagem e polimento, podem ser realizadas no molde para melhores precisões dimensionais. CLICK Product Finder-Locator Service PÁGINA ANTERIOR
- Fabricação de elementos de máquinas, engrenagens, acionamentos de engrenagens, rolamentos, chaves, estrias
Fabricação de elementos de máquinas, engrenagens, acionamentos de engrenagens, rolamentos, chaves, estrias, pinos, eixos, vedações, fixadores, embreagem, cames, seguidores, correias, acoplamentos, eixos Fabricação de Elementos de Máquinas consulte Mais informação Conjunto de correias e correntes e acionamento de cabos consulte Mais informação Engrenagens e Conjunto de Acionamento de Engrenagens consulte Mais informação Fabricação de Acoplamentos e Rolamentos consulte Mais informação Fabricação de chaves e estrias e pinos consulte Mais informação Cames e Seguidores e Articulações e Fabricação de Rodas de Catraca consulte Mais informação Fabricação de Eixos consulte Mais informação Fabricação de selos mecânicos consulte Mais informação Conjunto de embreagem e freio consulte Mais informação Fabricação de fixadores consulte Mais informação Montagem de Máquinas Simples ELEMENTOS DE MÁQUINA são componentes elementares de uma máquina. Esses elementos consistem em três tipos básicos: 1.) Componentes estruturais, incluindo membros da estrutura, rolamentos, eixos, estrias, fixadores, vedações e lubrificantes. 2.) Mecanismos que controlam o movimento de várias maneiras, como trens de engrenagens, acionamentos por correia ou corrente, articulações, sistemas de cames e seguidores, freios e embreagens. 3.) Componentes de controle como botões, interruptores, indicadores, sensores, atuadores e controladores de computador. A maioria dos elementos de máquina que oferecemos são padronizados para tamanhos comuns, mas os elementos de máquina feitos sob medida também estão disponíveis para suas aplicações especializadas. A personalização dos elementos da máquina pode ocorrer em designs existentes que estão em nossos catálogos para download ou em designs totalmente novos. A prototipagem e a fabricação de elementos de máquinas podem ser realizadas uma vez que o projeto seja aprovado por ambas as partes. Se novos elementos de máquina precisam ser projetados e fabricados, nossos clientes nos enviam por e-mail seus próprios projetos e os revisamos para aprovação, ou nos pedem para projetar elementos de máquina para sua aplicação. Neste último caso, usamos todas as informações de nossos clientes e projetamos os elementos da máquina e enviamos os projetos finalizados aos nossos clientes para aprovação. Uma vez aprovado, produzimos os primeiros artigos e posteriormente fabricamos os elementos da máquina de acordo com o projeto final. Em qualquer etapa deste trabalho, caso um determinado projeto de elemento de máquina tenha um desempenho insatisfatório em campo (o que é raro), revisamos todo o projeto e fazemos alterações em conjunto com nossos clientes conforme necessário. É nossa prática padrão assinar acordos de confidencialidade (NDA) com nossos clientes para o projeto de elementos de máquinas ou qualquer outro produto sempre que necessário ou necessário. Uma vez que os elementos da máquina para um determinado cliente são projetados e fabricados sob medida, atribuímos um código de produto a ele e somente os produzimos e vendemos ao nosso cliente que possui o produto. Reproduzimos os elementos da máquina utilizando as ferramentas, moldes e procedimentos desenvolvidos quantas vezes forem necessárias e sempre que nosso cliente os solicitar novamente. Em outras palavras, uma vez que um elemento de máquina personalizado é projetado e produzido para você, a propriedade intelectual, bem como todas as ferramentas e moldes são reservados e estocados indefinidamente por nós para você e os produtos reproduzidos como desejar. Também oferecemos aos nossos clientes serviços de engenharia combinando criativamente elementos de máquinas em um componente ou conjunto que atende a uma aplicação e atende ou supera as expectativas de nossos clientes. As plantas que fabricam nossos elementos de máquina são qualificadas pela ISO9001, QS9000 ou TS16949. Além disso, a maioria dos nossos produtos tem a marca CE ou UL e atendem às normas internacionalmente relevantes, como ISO, SAE, ASME, DIN. Clique nos submenus para obter informações detalhadas sobre nossos elementos de máquina, incluindo: - Correias, Correntes e Acionamentos de Cabos - Engrenagens e Acionamentos de Engrenagens - Acoplamentos e rolamentos - Chaves e Splines e pinos - Cames e Ligações - Veios - Selos Mecânicos - Embreagem e freio industrial - Fixadores - Máquinas simples Preparamos uma brochura de referência para nossos clientes, designers e desenvolvedores de novos produtos, incluindo elementos de máquinas. Você pode se familiarizar com alguns termos comumente usados no projeto de componentes de máquinas: Faça o download do folheto para os termos comuns de engenharia mecânica usados por projetistas e engenheiros Nossos elementos de máquina encontram aplicações em uma variedade de campos, como máquinas industriais, sistemas de automação, equipamentos de teste e metrologia, equipamentos de transporte, máquinas de construção e praticamente em qualquer lugar que você possa imaginar. AGS-TECH desenvolve e fabrica elementos de máquinas de vários materiais, dependendo da aplicação. Os materiais usados para os elementos da máquina podem variar de plásticos moldados usados para brinquedos a aço endurecido e especialmente revestido para máquinas industriais. Nossos projetistas usam software profissional de última geração e ferramentas de projeto para desenvolver elementos de máquinas, levando em consideração detalhes como ângulos nos dentes da engrenagem, tensões envolvidas, taxas de desgaste... etc. Por favor, percorra nossos submenus e baixe nossos folhetos e catálogos de produtos para ver se você pode localizar elementos de máquina prontos para uso para sua aplicação. Se você não encontrar uma boa combinação para sua aplicação, informe-nos e trabalharemos com você para desenvolver e fabricar elementos de máquina que atendam às suas necessidades. Se você estiver mais interessado em nossos recursos de engenharia e pesquisa e desenvolvimento em vez de recursos de fabricação, convidamos você a visitar nosso site http://www.ags-engineering.com where você pode encontrar informações mais detalhadas sobre nosso projeto, desenvolvimento de produtos, desenvolvimento de processos, serviços de consultoria de engenharia e muito mais CLICK Product Finder-Locator Service PÁGINA ANTERIOR
- Componentes de transmissão, correias, correntes, acionamentos de cabos, polias, AGS-TECH
Componentes de Transmissão, Correias, Correntes e Acionamentos de Cabos, Convencionais e Ranhurados ou Serrados, Acionamento Positivo, Polias Conjunto de correias e correntes e acionamento de cabos A AGS-TECH Inc. oferece componentes de transmissão de energia, incluindo Correias e Correntes e Conjunto de Acionamento por Cabo. Com anos de refinamento, nossos acionamentos de borracha, couro e outras correias tornaram-se mais leves e compactos, capazes de transportar cargas maiores a um custo menor. Da mesma forma, nossos acionamentos por corrente passaram por muito desenvolvimento ao longo do tempo e oferecem várias vantagens aos nossos clientes. Algumas vantagens do uso de acionamentos por corrente são suas distâncias de centro de eixo relativamente irrestritas, compacidade, facilidade de montagem, elasticidade em tensão sem deslizamento ou fluência, capacidade de operar em ambientes de alta temperatura. Nossos acionadores de cabo também oferecem vantagens como simplicidade em algumas aplicações em relação a outros tipos de componentes de transmissão. Estão disponíveis acionamentos por correia, corrente e cabo, bem como versões fabricadas e montadas sob medida. Podemos fabricar esses componentes de transmissão no tamanho certo para sua aplicação e com os materiais mais adequados. CORREIAS E ACIONAMENTOS DE CORREIA: - Correias planas convencionais: São correias planas lisas sem dentes, ranhuras ou serrilhas. Os acionamentos por correia plana oferecem flexibilidade, boa absorção de choque, transmissão de potência eficiente em altas velocidades, resistência à abrasão e baixo custo. As correias podem ser emendadas ou conectadas para fazer correias maiores. Outras vantagens das correias planas convencionais são que são finas, não estão sujeitas a altas cargas centrífugas (tornam-nas boas para operações de alta velocidade com polias pequenas). Por outro lado, eles impõem altas cargas de rolamento porque as correias planas exigem alta tensão. Outras desvantagens dos acionamentos por correia plana podem ser escorregamento, operação ruidosa e eficiências relativamente mais baixas em velocidades de operação baixas e moderadas. Temos dois tipos de esteiras convencionais: Reforçadas e Não Reforçadas. As correias reforçadas possuem um elemento de tração em sua estrutura. As correias planas convencionais estão disponíveis como couro, tecido ou cordão emborrachado, borracha ou plástico não reforçado, tecido, couro reforçado. Os cintos de couro oferecem longa vida útil, flexibilidade, excelente coeficiente de atrito, fácil reparo. No entanto, os cintos de couro são relativamente caros, precisam de limpeza e limpeza e, dependendo da atmosfera, podem encolher ou esticar. O tecido emborrachado ou os cintos de cordão são resistentes à umidade, ácido e álcalis. As correias de tecido emborrachado são compostas por lonas de algodão ou pato sintético impregnadas com borracha e são as mais econômicas. As correias de cordas emborrachadas consistem em uma série de camadas de cordas impregnadas de borracha. As correias de cordão emborrachado oferecem alta resistência à tração e tamanho e massa modestos. As correias de borracha ou plástico não reforçadas são adequadas para aplicações de acionamento leves e de baixa velocidade. As correias de borracha e plástico não reforçadas podem ser esticadas no lugar sobre suas polias. Correias não reforçadas de plástico podem transmitir maior potência em comparação com correias de borracha. Cintos de couro reforçado consistem em um membro de tração de plástico imprensado entre as camadas superior e inferior de couro. Por fim, nossos cintos de tecido podem consistir em uma única peça de algodão ou pato dobrada e costurada com fileiras de pontos longitudinais. As correias de tecido são capazes de rastrear uniformemente e operar em alta velocidade. - Correias ranhuradas ou serrilhadas (como as correias em V): São correias planas básicas modificadas para oferecer as vantagens de outro tipo de produto de transmissão. Estas são correias planas com um lado inferior com nervuras longitudinalmente. As correias Poly-V são correias planas ranhuradas longitudinalmente ou serrilhadas com seção de tração e uma série de ranhuras adjacentes em forma de V para fins de rastreamento e compressão. A capacidade de energia depende da largura da correia. A correia em V é o cavalo de batalha da indústria e está disponível em uma variedade de tamanhos e tipos padronizados para transmissão de quase qualquer potência de carga. Acionamentos por correia em V operam bem entre 1.500 a 6.000 pés/min, no entanto, correias em V estreitas operam até 10.000 pés/min. Os acionamentos por correia em V oferecem longa vida útil, como 3 a 5 anos e permitem grandes relações de velocidade, são fáceis de instalar e remover, oferecem operação silenciosa, baixa manutenção, boa absorção de choque entre o acionador da correia e os eixos acionados. A desvantagem das correias trapezoidais é o seu deslizamento e fluência e, portanto, podem não ser a melhor solução onde são necessárias velocidades síncronas. Temos correias industriais, automotivas e agrícolas. Comprimentos padrão em estoque, bem como comprimentos personalizados de correias estão disponíveis. Todas as seções transversais padrão da correia em V estão disponíveis em estoque. Existem tabelas onde você pode calcular parâmetros desconhecidos, como comprimento da correia, seção da correia (largura e espessura), desde que você conheça alguns parâmetros do seu sistema, como diâmetros das polias de acionamento e acionamento, distância central entre as polias e velocidades de rotação das polias. Você pode usar essas tabelas ou nos pedir para escolher a correia em V certa para você. - Correias de Acionamento Positivo (Correia de Distribuição): Estas correias também são do tipo plano com uma série de dentes espaçados uniformemente na circunferência interna. Acionamento positivo ou correias dentadas combinam as vantagens das correias planas com as características de aderência positiva das correntes e engrenagens. As correias de transmissão positiva não revelam deslizamentos ou variações de velocidade. Uma ampla gama de relações de velocidade é possível. As cargas dos rolamentos são baixas porque podem operar em baixa tensão. No entanto, eles são mais suscetíveis a desalinhamentos nas polias. - Polias, Polias, Cubos para Correias: São utilizados diferentes tipos de polias com correias planas, nervuradas (serrilhadas) e positivas. Nós fabricamos todos eles. A maioria de nossas polias de correia plana são feitas por fundição de ferro, mas as versões de aço também estão disponíveis em várias combinações de aro e cubo. Nossas polias planas podem ter cubos maciços, raiados ou bipartidos ou podemos fabricar como você desejar. Correias com nervuras e de acionamento positivo estão disponíveis em vários tamanhos e larguras de estoque. Pelo menos uma polia nos acionamentos por correia dentada deve ser flangeada para manter a correia no acionamento. Para sistemas de acionamento de centro longo, é recomendável ter ambas as polias flangeadas. As polias são as rodas ranhuradas das polias e geralmente são fabricadas por fundição de ferro, conformação de aço ou moldagem de plástico. A conformação de aço é um processo adequado para a fabricação de polias automotivas e agrícolas. Produzimos polias com ranhuras regulares e profundas. As roldanas de sulco profundo são bem adequadas quando a correia em V entra na roldana em um ângulo, como é o caso de acionamentos de um quarto de volta. Ranhuras profundas também são adequadas para acionamentos de eixo vertical e aplicações onde a vibração das correias pode ser um problema. Nossas polias intermediárias são polias ranhuradas ou polias planas que não servem para transmitir energia mecânica. As polias intermediárias são usadas principalmente para apertar as correias. - Acionamentos por correia simples e múltipla: Os acionamentos por correia simples têm uma ranhura única, enquanto os acionamentos por correia múltipla têm ranhuras múltiplas. Ao clicar no texto colorido relevante abaixo, você pode baixar nossos catálogos: - Correias de transmissão de energia (inclui correias em V, correias sincronizadoras, correias de borda bruta, correias enroladas e correias especiais) - Correias transportadoras - Polias em V - Polias de sincronização CORRENTES E ACIONAMENTOS DE CORRENTE: Nossas correntes de transmissão de energia têm algumas vantagens, como distâncias do centro do eixo relativamente irrestritas, fácil montagem, compacidade, elasticidade sob tensão sem deslizamento ou fluência, capacidade de operação sob altas temperaturas. Aqui estão os principais tipos de nossas correntes: - Correntes destacáveis: Nossas correntes destacáveis são feitas em uma variedade de tamanhos, passo e resistência final e geralmente de ferro ou aço maleável. As correntes maleáveis são feitas em uma variedade de tamanhos de 0,902 (23 mm) a 4,063 polegadas (103 mm) de passo e resistência final de 700 a 17.000 lb/polegada quadrada. Nossas correntes de aço destacáveis, por outro lado, são feitas em tamanhos de 0,904 polegada (23 mm) a cerca de 3,00 polegada (76 mm) de passo, com resistência máxima de 760 a 5000 lb/polegada quadrada._cc781905-5cde-3194-bb3b- 136bad5cf58d_ - Correntes Pintle: Estas correntes são usadas para cargas mais pesadas e velocidades ligeiramente superiores a cerca de 450 pés/min (2,2 m/s). As correntes Pintle são feitas de elos fundidos individuais com extremidade de cano cheia e redonda com barras laterais deslocadas. Esses elos de corrente são interligados com pinos de aço. Essas correntes variam em passo de cerca de 1,00 polegada (25 mm) a 6,00 polegada (150 mm) e resistências finais entre 3600 a 30.000 lb/polegada quadrada. - Correntes de barra lateral deslocada: são populares em correntes de acionamento de máquinas de construção. Essas correntes trabalham em velocidades de até 1000 pés/min e transmitem cargas de cerca de 250 hp. Geralmente cada elo tem duas barras laterais deslocadas, uma bucha, um rolete, um pino, uma cupilha. - Correntes de Rolos: Estão disponíveis em passos de 0,25 (6 mm) a 3,00 (75 mm) polegadas. A resistência máxima das correntes de rolos de largura única varia entre 925 a 130.000 lb/polegada quadrada. Versões de múltiplas larguras de correntes de rolos estão disponíveis e transmitem maior potência em velocidades mais altas. As correntes de rolos de largura múltipla também oferecem ação mais suave com ruído reduzido. As correntes de roletes são montadas a partir de elos de roletes e elos de pinos. Contrapinos são usados em correntes de roletes de versão destacável. O projeto de acionamentos por corrente de rolos requer conhecimento no assunto. Enquanto os acionamentos por correia são baseados em velocidades lineares, os acionamentos por corrente são baseados na velocidade de rotação da roda dentada menor, que na maioria das instalações é o membro acionado. Além das classificações de potência e da velocidade de rotação, o design dos acionamentos por corrente é baseado em muitos outros fatores. - Correntes de passo duplo: basicamente o mesmo que as correntes de rolos, exceto que o passo é duas vezes maior. - Correntes de dentes invertidos (silenciosas): Correntes de alta velocidade usadas principalmente para motores primários, acionamentos de tomada de força. Os acionamentos por corrente de dentes invertidos podem transmitir potências de até 1200 hp e são compostos por uma série de elos de dentes, montados alternadamente com pinos ou uma combinação de componentes de junta. A corrente de guia central tem elos de guia para engatar nas ranhuras da roda dentada e a corrente de guia lateral tem guias para engatar nas laterais da roda dentada. - Correntes Bead ou Slider: Estas correntes são utilizadas para acionamentos de baixa velocidade e também em operações manuais. Ao clicar no texto colorido relevante abaixo, você pode baixar nossos catálogos: - Correntes de condução - Correntes Transportadoras - Correntes transportadoras de passo grande - Correntes de rolos de aço inoxidável - Correntes de içamento - Correntes de motocicleta - Correntes de Máquinas Agrícolas - Rodas dentadas: Nossas rodas dentadas padrão estão em conformidade com os padrões ANSI. As rodas dentadas de placa são rodas dentadas planas e sem cubos. Nossas rodas dentadas de cubos de pequeno e médio porte são transformadas de barras ou forjados ou feitas por soldagem de um cubo de barra em uma placa laminada a quente. A AGS-TECH Inc. pode fornecer rodas dentadas usinadas a partir de peças fundidas de ferro cinza, aço fundido e construções de cubos soldados, metal em pó sinterizado, plásticos moldados ou usinados. Para uma operação suave em altas velocidades, a seleção adequada do tamanho das rodas dentadas é essencial. As limitações de espaço são, obviamente, um fator que não podemos ignorar ao escolher uma roda dentada. Recomenda-se que a proporção do acionador para as rodas dentadas acionadas não seja superior a 6:1, e o envoltório da corrente no acionador seja de 120 graus. As distâncias centrais entre as rodas dentadas menores e maiores, os comprimentos da corrente e a tensão da corrente também devem ser escolhidos de acordo com alguns cálculos e diretrizes de engenharia recomendados e não aleatoriamente. Baixe nossos catálogos clicando no texto colorido abaixo: - Rodas dentadas e rodas de placa - Buchas de transmissão - Acoplamento de corrente - Fechaduras de Corrente ACIONAMENTOS DE CABOS: Em alguns casos, têm suas vantagens sobre os acionamentos por correia e corrente. Os acionadores de cabo podem realizar a mesma função que as correias e também podem ser mais simples e econômicos de implementar em algumas aplicações. Por exemplo, uma nova série de acionadores de cabo Synchromesh é projetada para tração positiva para substituir cordas convencionais, cabos simples e acionamentos de engrenagens, especialmente em espaços apertados. O novo acionador de cabo foi projetado para fornecer posicionamento de alta precisão em equipamentos eletrônicos, como copiadoras, plotters, máquinas de escrever, impressoras, etc. desenhos extremamente em miniatura. Os cabos Synchromesh podem ser usados com menor tensão quando comparados com as cordas, reduzindo assim o consumo de energia. Entre em contato com a AGS-TECH para dúvidas e opiniões sobre acionamentos por correias, correntes e cabos. CLICK Product Finder-Locator Service PÁGINA ANTERIOR
- Compósitos, Fabricação de Materiais Compósitos, Reforçados com Fibra
Compósitos, Fabricação de Materiais Compósitos, Reforçado com Partículas e Fibras, Cermets, Cerâmica e Composto de Metal, Polímero Reforçado com Fibra de Vidro, Processo de Lay-Up Fabricação de Compósitos e Materiais Compósitos Simplificando, COMPÓSITOS ou MATERIAIS COMPOSTOS são materiais que consistem em dois ou vários materiais com diferentes propriedades físicas ou químicas, mas quando combinados tornam-se um material diferente dos materiais constituintes. Precisamos salientar que os materiais constituintes permanecem separados e distintos na estrutura. O objetivo na fabricação de um material compósito é obter um produto que seja superior aos seus constituintes e combine as características desejadas de cada constituinte. Como um exemplo; resistência, baixo peso ou preço mais baixo podem ser o motivador por trás do projeto e produção de um compósito. O tipo de compósitos que oferecemos são compósitos reforçados com partículas, compósitos reforçados com fibra, incluindo compósitos de matriz cerâmica / matriz polimérica / matriz metálica / carbono-carbono / híbridos, compósitos estruturais e laminados e estruturados em sanduíche e nanocompósitos. As técnicas de fabricação que implantamos na fabricação de materiais compósitos são: Pultrusão, processos de produção de prepreg, colocação avançada de fibra, enrolamento de filamento, colocação de fibra sob medida, processo de laminação por spray de fibra de vidro, tufting, processo de lanxide, z-pinning. Muitos materiais compósitos são constituídos por duas fases, a matriz, que é contínua e envolve a outra fase; e a fase dispersa que está rodeada pela matriz. Recomendamos que você clique aqui paraBAIXE nossas Ilustrações Esquemáticas de Compósitos e Fabricação de Materiais Compósitos pela AGS-TECH Inc. Isso ajudará você a entender melhor as informações que fornecemos abaixo. • COMPÓSITOS REFORÇADOS COM PARTÍCULAS: Esta categoria consiste em dois tipos: compósitos de partículas grandes e compósitos reforçados por dispersão. No primeiro tipo, as interações partícula-matriz não podem ser tratadas no nível atômico ou molecular. Em vez disso, a mecânica contínua é válida. Por outro lado, em compósitos reforçados por dispersão, as partículas são geralmente muito menores na faixa de dezenas de nanômetros. Um exemplo de compósito de partículas grandes são os polímeros aos quais foram adicionados enchimentos. As cargas melhoram as propriedades do material e podem substituir parte do volume do polímero por um material mais econômico. As frações volumétricas das duas fases influenciam o comportamento do compósito. Compósitos de partículas grandes são usados com metais, polímeros e cerâmicas. Os CERMETS são exemplos de compósitos cerâmicos/metálicos. Nosso cermet mais comum é o metal duro. Consiste em cerâmica de carboneto refratário, como partículas de carboneto de tungstênio em uma matriz de um metal como cobalto ou níquel. Esses compósitos de carboneto são amplamente utilizados como ferramentas de corte para aço endurecido. As partículas de metal duro são responsáveis pela ação de corte e sua tenacidade é reforçada pela matriz metálica dúctil. Assim obtemos as vantagens de ambos os materiais em um único compósito. Outro exemplo comum de um compósito de partículas grandes que usamos são partículas de negro de fumo misturadas com borracha vulcanizada para obter um compósito com alta resistência à tração, tenacidade, rasgo e resistência à abrasão. Um exemplo de compósito reforçado por dispersão são metais e ligas metálicas reforçadas e endurecidas pela dispersão uniforme de partículas finas de um material muito duro e inerte. Quando flocos de óxido de alumínio muito pequenos são adicionados à matriz metálica de alumínio, obtemos pó de alumínio sinterizado que possui uma resistência aprimorada a altas temperaturas. • COMPÓSITOS REFORÇADOS COM FIBRA: Esta categoria de compósitos é de fato a mais importante. O objetivo a atingir é alta resistência e rigidez por unidade de peso. A composição da fibra, comprimento, orientação e concentração nestes compósitos são críticos na determinação das propriedades e utilidade destes materiais. Existem três grupos de fibras que usamos: bigodes, fibras e fios. Os bigodes são cristais únicos muito finos e longos. Eles estão entre os materiais mais fortes. Alguns exemplos de materiais de bigode são grafite, nitreto de silício, óxido de alumínio. FIBERS por outro lado são principalmente polímeros ou cerâmicas e estão em estado policristalino ou amorfo. O terceiro grupo são os FIOS finos que possuem diâmetros relativamente grandes e consistem frequentemente em aço ou tungstênio. Um exemplo de compósito reforçado com arame são os pneus de carro que incorporam arame de aço dentro da borracha. Dependendo do material da matriz, temos os seguintes compósitos: COMPOSTOS DE MATRIZ POLÍMERO: São compostos de resina polimérica e fibras como ingrediente de reforço. Um subgrupo desses chamados compósitos de polímero reforçado com fibra de vidro (GFRP) contém fibras de vidro contínuas ou descontínuas dentro de uma matriz polimérica. O vidro oferece alta resistência, é econômico, fácil de fabricar em fibras e é quimicamente inerte. As desvantagens são sua rigidez e rigidez limitadas, sendo as temperaturas de serviço apenas de 200 a 300 centígrados. A fibra de vidro é adequada para carrocerias automotivas e equipamentos de transporte, carrocerias de veículos marítimos, contêineres de armazenamento. Eles não são adequados para aeroespacial nem para construção de pontes devido à rigidez limitada. O outro subgrupo é chamado de Composto de Polímero Reforçado com Fibra de Carbono (CFRP). Aqui, o carbono é nosso material de fibra na matriz polimérica. O carbono é conhecido por seu alto módulo específico e resistência e sua capacidade de mantê-los em altas temperaturas. As fibras de carbono podem nos oferecer módulos de tração padrão, intermediários, altos e ultraelevados. Além disso, as fibras de carbono oferecem diversas características físicas e mecânicas e, portanto, adequadas para várias aplicações de engenharia personalizadas. Os compósitos de CFRP podem ser considerados para fabricar equipamentos esportivos e recreativos, vasos de pressão e componentes estruturais aeroespaciais. Ainda, outro subgrupo, os Compósitos Poliméricos Reforçados com Fibra de Aramida também são materiais de alta resistência e módulo. Suas relações força-peso são extraordinariamente altas. As fibras de aramida também são conhecidas pelos nomes comerciais KEVLAR e NOMEX. Sob tensão, eles têm um desempenho melhor do que outros materiais de fibra polimérica, mas são fracos em compressão. As fibras de aramida são resistentes, resistentes ao impacto, à fluência e à fadiga, estáveis em altas temperaturas, quimicamente inertes, exceto contra ácidos e bases fortes. As fibras de aramida são amplamente utilizadas em artigos esportivos, coletes à prova de balas, pneus, cordas, revestimentos de cabos de fibra óptica. Existem outros materiais de reforço de fibra, mas são usados em menor grau. Estes são boro, carboneto de silício, óxido de alumínio principalmente. O material da matriz polimérica, por outro lado, também é crítico. Ela determina a temperatura máxima de serviço do compósito porque o polímero tem geralmente uma temperatura de fusão e degradação mais baixa. Poliésteres e ésteres vinílicos são amplamente utilizados como matriz polimérica. Resinas também são utilizadas e possuem excelente resistência à umidade e propriedades mecânicas. Por exemplo, a resina de poliimida pode ser usada até cerca de 230 graus Celsius. COMPOSTOS DE METAL-MATRIZ : Nestes materiais utilizamos uma matriz metálica dúctil e as temperaturas de serviço são geralmente superiores aos seus componentes constituintes. Quando comparados aos compósitos de matriz polimérica, estes podem ter temperaturas de operação mais altas, ser não inflamáveis e podem ter melhor resistência à degradação contra fluidos orgânicos. No entanto são mais caros. Materiais de reforço como bigodes, partículas, fibras contínuas e descontínuas; e materiais de matriz como cobre, alumínio, magnésio, titânio, superligas estão sendo comumente usados. Exemplos de aplicações são componentes do motor feitos de matriz de liga de alumínio reforçada com óxido de alumínio e fibras de carbono. COMPOSTOS DE MATRIZ CERÂMICA: Os materiais cerâmicos são conhecidos por sua excelente confiabilidade em altas temperaturas. No entanto, são muito frágeis e apresentam baixos valores de tenacidade à fratura. Ao incorporar partículas, fibras ou whiskers de uma cerâmica na matriz de outra, podemos obter compósitos com maior tenacidade à fratura. Esses materiais embutidos basicamente inibem a propagação de trincas dentro da matriz por meio de alguns mecanismos, como desviar as pontas das trincas ou formar pontes entre as faces das trincas. Como exemplo, as aluminas que são reforçadas com whiskers de SiC são usadas como insertos de ferramentas de corte para usinagem de ligas de metal duro. Estes podem revelar melhores desempenhos em comparação com os carbonetos cimentados. COMPOSTOS DE CARBONO-CARBONO: Tanto o reforço como a matriz são de carbono. Eles têm módulos de alta resistência à tração e resistência a altas temperaturas acima de 2000 graus centígrados, resistência à fluência, alta tenacidade à fratura, baixos coeficientes de expansão térmica, alta condutividade térmica. Essas propriedades os tornam ideais para aplicações que exigem resistência ao choque térmico. A fraqueza dos compósitos carbono-carbono é, no entanto, sua vulnerabilidade à oxidação em altas temperaturas. Exemplos típicos de uso são moldes de prensagem a quente, fabricação avançada de componentes de motores de turbina. COMPOSTOS HÍBRIDOS: Dois ou mais tipos diferentes de fibras são misturados em uma única matriz. Assim, pode-se adaptar um novo material com uma combinação de propriedades. Um exemplo é quando ambas as fibras de carbono e de vidro são incorporadas em uma resina polimérica. As fibras de carbono fornecem rigidez e resistência de baixa densidade, mas são caras. O vidro, por outro lado, é barato, mas não tem a rigidez das fibras de carbono. O compósito híbrido vidro-carbono é mais forte e resistente e pode ser fabricado a um custo menor. PROCESSAMENTO DE COMPÓSITOS REFORÇADOS COM FIBRA: Para plásticos reforçados com fibra contínuos com fibras uniformemente distribuídas orientadas na mesma direção, usamos as seguintes técnicas. PULTRUSÃO: São fabricados varões, vigas e tubos de comprimentos contínuos e seções transversais constantes. As mechas contínuas de fibra são impregnadas com uma resina termofixa e são puxadas através de uma matriz de aço para preformá-las na forma desejada. Em seguida, eles passam por uma matriz de cura usinada com precisão para atingir sua forma final. Como o molde de cura é aquecido, ele cura a matriz de resina. Os extratores puxam o material através das matrizes. Utilizando núcleos ocos inseridos, conseguimos obter tubos e geometrias ocas. O método de pultrusão é automatizado e nos oferece altas taxas de produção. Qualquer comprimento de produto é possível produzir. PROCESSO DE PRODUÇÃO PREPREG: Prepreg é um reforço de fibra contínua pré-impregnado com uma resina polimérica parcialmente curada. É amplamente utilizado para aplicações estruturais. O material vem em forma de fita e é enviado como uma fita. O fabricante o molda diretamente e o cura totalmente sem a necessidade de adicionar qualquer resina. Como os pré-impregnados sofrem reações de cura à temperatura ambiente, eles são armazenados a 0 graus centígrados ou temperaturas inferiores. Após o uso, as fitas restantes são armazenadas de volta em baixas temperaturas. Resinas termoplásticas e termofixas são usadas e fibras de reforço de carbono, aramida e vidro são comuns. Para usar prepregs, o papel de suporte do suporte é primeiro removido e, em seguida, a fabricação é realizada colocando a fita prepreg em uma superfície moldada (o processo de lay-up). Várias camadas podem ser colocadas para obter as espessuras desejadas. A prática frequente é alternar a orientação da fibra para produzir um laminado de dobra cruzada ou dobrada. Finalmente, calor e pressão são aplicados para a cura. Tanto o processamento manual quanto os processos automatizados são usados para cortar prepregs e lay-up. ENROLAMENTO DE FILAMENTO: As fibras de reforço contínuas são posicionadas com precisão em um padrão predeterminado para seguir uma forma oca e geralmente cilíndrica. As fibras passam primeiro por um banho de resina e depois são enroladas em um mandril por um sistema automatizado. Após várias repetições de enrolamento, as espessuras desejadas são obtidas e a cura é realizada à temperatura ambiente ou dentro de um forno. Agora o mandril é removido e o produto é desmoldado. O enrolamento do filamento pode oferecer relações resistência-peso muito altas ao enrolar as fibras em padrões circunferenciais, helicoidais e polares. Tubos, tanques, invólucros são fabricados usando esta técnica. • COMPÓSITOS ESTRUTURAIS: Geralmente são compostos por materiais homogêneos e compostos. Portanto, as propriedades destes são determinadas pelos materiais constituintes e desenho geométrico de seus elementos. Aqui estão os principais tipos: COMPOSTOS LAMINAR: Estes materiais estruturais são feitos de chapas ou painéis bidimensionais com direções de alta resistência preferidas. As camadas são empilhadas e cimentadas juntas. Alternando as direções de alta resistência nos dois eixos perpendiculares, obtemos um compósito que possui alta resistência em ambas as direções no plano bidimensional. Ajustando os ângulos das camadas pode-se fabricar um compósito com resistência nas direções preferidas. O esqui moderno é fabricado dessa maneira. PAINÉIS SANDWICH : Esses compósitos estruturais são leves, mas possuem alta rigidez e resistência. Os painéis sanduíche consistem em duas folhas externas feitas de um material rígido e forte, como ligas de alumínio, plásticos reforçados com fibra ou aço e um núcleo entre as folhas externas. O núcleo precisa ser leve e na maioria das vezes ter um baixo módulo de elasticidade. Os materiais de núcleo populares são espumas poliméricas rígidas, madeira e favos de mel. Os painéis sanduíche são amplamente utilizados na indústria da construção como material de cobertura, piso ou parede, e também nas indústrias aeroespaciais. • NANOCOMPÓSITOS: Esses novos materiais consistem em partículas nanométricas embutidas em uma matriz. Usando nanocompósitos, podemos fabricar materiais de borracha que são barreiras muito boas à penetração do ar, mantendo suas propriedades de borracha inalteradas. CLICK Product Finder-Locator Service PÁGINA ANTERIOR
- Fabricação de vidro e cerâmica, embalagens herméticas, vedações, colagem
Fabricação de vidro e cerâmica, selos e colagem de embalagens herméticas, vidro temperado à prova de balas, moldagem por sopro, vidro de grau óptico, vidro condutivo, moldagem Moldagem e modelagem de vidro e cerâmica O tipo de fabricação de vidro que oferecemos são vidro de recipiente, sopro de vidro, fibra de vidro e tubos e haste, vidraria doméstica e industrial, lâmpada e lâmpada, moldagem de vidro de precisão, componentes e conjuntos ópticos, vidro plano e folha e float. Executamos a conformação manual e à máquina. Nossos processos de fabricação de cerâmica técnica populares são prensagem, prensagem isostática, prensagem isostática a quente, prensagem a quente, fundição por deslizamento, fundição de fita, extrusão, moldagem por injeção, usinagem verde, sinterização ou queima, moagem de diamante, montagens herméticas. Recomendamos que você clique aqui para BAIXE nossas ilustrações esquemáticas de processos de formação e modelagem de vidro pela AGS-TECH Inc. BAIXE nossas ilustrações esquemáticas de processos técnicos de fabricação de cerâmica pela AGS-TECH Inc. Esses arquivos para download com fotos e esboços ajudarão você a entender melhor as informações que fornecemos abaixo. • FABRICAÇÃO DE VIDRO DE CONTÊINER: Temos linhas automatizadas de PRESS AND BLOW e BLOW AND BLOW para fabricação. No processo de sopro e sopro, colocamos uma gota no molde em branco e formamos o gargalo aplicando um sopro de ar comprimido de cima. Imediatamente após isso, o ar comprimido é soprado uma segunda vez da outra direção através do gargalo do recipiente para formar a pré-forma da garrafa. Este pré-molde é então transferido para o molde real, reaquecido para amolecer e ar comprimido é aplicado para dar ao pré-molde sua forma final de recipiente. Mais explicitamente, é pressurizado e empurrado contra as paredes da cavidade do molde de sopro para tomar a forma desejada. Finalmente, o recipiente de vidro fabricado é transferido para um forno de recozimento para posterior reaquecimento e remoção de tensões produzidas durante a moldagem e é resfriado de forma controlada. No método de prensagem e sopro, as gotas derretidas são colocadas em um molde de forma preliminar (molde em branco) e pressionadas na forma de forma preliminar (forma em branco). Os blanks são então transferidos para moldes de sopro e soprados de forma semelhante ao processo descrito acima em “Processo de sopro e sopro”. As etapas subsequentes, como recozimento e alívio de tensão, são semelhantes ou iguais. • SOPRO DE VIDRO: Fabricamos produtos de vidro com sopro manual convencional, bem como com ar comprimido com equipamentos automatizados. Para alguns pedidos é necessário sopro convencional, como projetos que envolvam trabalhos de arte em vidro, ou projetos que exijam um número menor de peças com tolerâncias soltas, projetos de prototipagem/demonstração….etc. O sopro de vidro convencional envolve a imersão de um tubo de metal oco em um pote de vidro fundido e a rotação do tubo para coletar uma certa quantidade do material de vidro. O vidro coletado na ponta do tubo é enrolado em chapinha, moldado conforme desejado, alongado, reaquecido e soprado com ar. Quando estiver pronto, é inserido em um molde e o ar é soprado. A cavidade do molde é molhada para evitar o contato do vidro com o metal. O filme de água atua como uma almofada entre eles. O sopro manual é um processo lento de trabalho intensivo e adequado apenas para prototipagem ou itens de alto valor, não adequado para pedidos de alto volume por peça de baixo custo. • FABRICAÇÃO DE VIDROS DOMÉSTICOS E INDUSTRIAIS: Usando vários tipos de material de vidro, uma grande variedade de vidraria está sendo produzida. Alguns copos são resistentes ao calor e adequados para vidraria de laboratório, enquanto alguns são bons o suficiente para resistir a lava-louças por muitas vezes e são adequados para fazer produtos domésticos. Usando as máquinas Westlake, dezenas de milhares de copos são produzidos por dia. Para simplificar, o vidro fundido é coletado a vácuo e inserido em moldes para fazer as pré-formas. Em seguida, o ar é soprado nos moldes, estes são transferidos para outro molde e o ar é soprado novamente e o vidro toma sua forma final. Como no sopro manual, esses moldes são mantidos molhados com água. O alongamento adicional faz parte da operação de acabamento onde o gargalo está sendo formado. O excesso de vidro está queimado. Em seguida, segue-se o processo controlado de reaquecimento e arrefecimento descrito acima. • FORMAÇÃO DE TUBO E HASTE DE VIDRO: Os principais processos que utilizamos para a fabricação de tubos de vidro são os processos DANNER e VELLO. No Processo Danner, o vidro de um forno flui e cai sobre uma manga inclinada feita de materiais refratários. A luva é transportada em um eixo oco rotativo ou maçarico. O vidro é então enrolado ao redor da luva e forma uma camada lisa que flui pela luva e sobre a ponta do eixo. No caso de formação de tubo, o ar é soprado através de um maçarico com ponta oca, e no caso de formação de haste utilizamos pontas sólidas no eixo. Os tubos ou hastes são então puxados sobre rolos de transporte. As dimensões como espessura de parede e diâmetro dos tubos de vidro são ajustadas para valores desejados, definindo o diâmetro da luva e soprando a pressão do ar para um valor desejado, ajustando a temperatura, a taxa de fluxo do vidro e a velocidade de trefilação. O processo de fabricação do tubo de vidro Vello, por outro lado, envolve o vidro que sai de um forno e entra em uma tigela com um mandril oco ou sino. O vidro então passa pelo espaço de ar entre o mandril e a tigela e toma a forma de um tubo. Em seguida, ele viaja sobre rolos para uma máquina de trefilação e é resfriado. No final da linha de resfriamento ocorre o corte e o processamento final. As dimensões do tubo podem ser ajustadas como no processo Danner. Ao comparar o processo Danner com o Vello, podemos dizer que o processo Vello é mais adequado para produção em grande quantidade, enquanto o processo Danner pode ser mais adequado para pedidos precisos de tubos de menor volume. • PROCESSAMENTO DE CHAPA E VIDRO FLAT & FLOAT : Temos grandes quantidades de vidro plano em espessuras que variam de espessuras submilimétricas a vários centímetros. Nossos vidros planos são de quase perfeição ótica. Oferecemos vidros com revestimentos especiais como revestimentos ópticos, onde a técnica de deposição química de vapor é utilizada para colocar revestimentos como antirreflexo ou revestimento espelhado. Também são comuns os revestimentos condutores transparentes. Também estão disponíveis revestimentos hidrofóbicos ou hidrofílicos em vidro e revestimento que torna o vidro autolimpante. Vidros temperados, à prova de balas e laminados são outros itens populares. Cortamos o vidro na forma desejada com as tolerâncias desejadas. Outras operações secundárias, como curvar ou dobrar vidro plano, estão disponíveis. • MOLDAGEM DE VIDRO DE PRECISÃO: Usamos esta técnica principalmente para a fabricação de componentes ópticos de precisão sem a necessidade de técnicas mais caras e demoradas como retificação, lapidação e polimento. Essa técnica nem sempre é suficiente para fazer o melhor da melhor ótica, mas em alguns casos, como produtos de consumo, câmeras digitais, ótica médica, pode ser uma boa opção menos dispendiosa para fabricação de alto volume. Também tem uma vantagem sobre as outras técnicas de formação de vidro onde são necessárias geometrias complexas, como no caso de aspheres. O processo básico envolve o carregamento do lado inferior do nosso molde com o blank de vidro, evacuação da câmara de processo para remoção de oxigênio, fechamento próximo do molde, aquecimento rápido e isotérmico da matriz e vidro com luz infravermelha, fechamento adicional das metades do molde prensar o vidro amolecido lentamente de forma controlada até a espessura desejada e, finalmente, resfriar o vidro e encher a câmara com nitrogênio e remoção do produto. Controle preciso de temperatura, distância de fechamento do molde, força de fechamento do molde, combinando os coeficientes de expansão do molde e do material de vidro são fundamentais neste processo. • FABRICAÇÃO DE COMPONENTES E CONJUNTOS ÓPTICOS DE VIDRO: Além da moldagem de vidro de precisão, existem vários processos valiosos que usamos para fabricar componentes e conjuntos ópticos de alta qualidade para aplicações exigentes. Lixar, lapidar e polir vidros de grau óptico em pastas abrasivas especiais finas é uma arte e ciência para fazer lentes ópticas, prismas, planos e muito mais. Planicidade da superfície, ondulação, suavidade e superfícies ópticas livres de defeitos requerem muita experiência com tais processos. Pequenas mudanças no ambiente podem resultar em produtos fora de especificação e interromper a linha de fabricação. Há casos em que uma única limpeza na superfície óptica com um pano limpo pode fazer com que um produto atenda às especificações ou falhe no teste. Alguns materiais de vidro populares usados são sílica fundida, quartzo, BK7. Além disso, a montagem de tais componentes requer experiência especializada em nichos. Às vezes, colas especiais estão sendo usadas. No entanto, às vezes, uma técnica chamada de contato óptico é a melhor escolha e não envolve nenhum material entre os vidros ópticos acoplados. Consiste em entrar em contato físico com superfícies planas para fixar umas às outras sem cola. Em alguns casos, espaçadores mecânicos, varetas ou esferas de vidro de precisão, grampos ou componentes metálicos usinados estão sendo usados para montar os componentes ópticos a certas distâncias e com certas orientações geométricas entre si. Vamos examinar algumas de nossas técnicas populares para a fabricação de óptica de ponta. RETIFICAÇÃO E LAPAGEM E POLIMENTO : A forma áspera do componente óptico é obtida com a retificação de uma peça de vidro. Em seguida, a lapidação e o polimento são realizados girando e esfregando as superfícies ásperas dos componentes ópticos contra ferramentas com formas de superfície desejadas. Pastas com pequenas partículas abrasivas e fluido estão sendo despejadas entre a ótica e as ferramentas de modelagem. Os tamanhos de partículas abrasivas em tais pastas podem ser escolhidos de acordo com o grau de planicidade desejado. Os desvios das superfícies ópticas críticas das formas desejadas são expressos em termos de comprimentos de onda da luz que está sendo usada. Nossas ópticas de alta precisão têm tolerâncias de décimo de comprimento de onda (comprimento de onda/10) ou ainda mais apertadas. Além do perfil da superfície, as superfícies críticas são escaneadas e avaliadas quanto a outras características e defeitos da superfície, como dimensões, arranhões, lascas, buracos, manchas... etc. O controle rigoroso das condições ambientais no piso de fabricação óptica e os extensos requisitos de metrologia e teste com equipamentos de última geração tornam este um ramo desafiador da indústria. • PROCESSOS SECUNDÁRIOS NA FABRICAÇÃO DE VIDRO: Mais uma vez, estamos limitados apenas à sua imaginação quando se trata de processos secundários e de acabamento de vidro. Aqui listamos alguns deles: -Revestimentos em vidro (ópticos, eléctricos, tribológicos, térmicos, funcionais, mecânicos...). Como exemplo, podemos alterar as propriedades da superfície do vidro, fazendo-o, por exemplo, refletir o calor para manter os interiores dos edifícios frescos, ou fazer com que um lado absorva o infravermelho usando a nanotecnologia. Isso ajuda a manter o interior dos edifícios aquecido porque a camada de vidro da superfície mais externa absorverá a radiação infravermelha dentro do edifício e a irradiará de volta para o interior. -Gravação on vidro - Rotulagem de Cerâmica Aplicada (ACL) -Gravação -Polimento de chama -Polimento químico - Coloração FABRICAÇÃO DE CERÂMICA TÉCNICA • PRENSA DE ESTAMPA: Consiste na compactação uniaxial de pós granulares confinados em uma matriz • PRENSA A QUENTE: Semelhante à prensagem, mas com adição de temperatura para aumentar a densificação. Pó ou pré-forma compactada é colocada na matriz de grafite e pressão uniaxial é aplicada enquanto a matriz é mantida em altas temperaturas, como 2000 C. As temperaturas podem ser diferentes dependendo do tipo de pó cerâmico que está sendo processado. Para formas e geometrias complicadas, outros processamentos subsequentes, como retificação de diamante, podem ser necessários. • PRESSÃO ISOSTÁTICA: Pó granulado ou compactos prensados são colocados em recipientes herméticos e depois em um recipiente de pressão fechado com líquido dentro. Em seguida, eles são compactados aumentando a pressão do vaso de pressão. O líquido dentro do recipiente transfere as forças de pressão uniformemente sobre toda a área da superfície do recipiente hermético. O material é assim compactado uniformemente e assume a forma de seu recipiente flexível e seu perfil interno e recursos. • PRESSÃO ISOSTÁTICA A QUENTE: Semelhante à prensagem isostática, mas além da atmosfera de gás pressurizado, sinterizamos o compacto em alta temperatura. A prensagem isostática a quente resulta em densificação adicional e maior resistência. • SLIP CASTING / DRAIN CASTING: Enchemos o molde com uma suspensão de partículas de cerâmica de tamanho micrométrico e líquido transportador. Essa mistura é chamada de “deslizamento”. O molde tem poros e, portanto, o líquido na mistura é filtrado para dentro do molde. Como resultado, um molde é formado nas superfícies internas do molde. Após a sinterização, as peças podem ser retiradas do molde. • FUNDIÇÃO DE FITA: Fabricamos fitas cerâmicas por vazamento de pastas cerâmicas em superfícies planas de suporte móvel. As pastas contêm pós cerâmicos misturados com outros produtos químicos para fins de ligação e transporte. À medida que os solventes evaporam, folhas densas e flexíveis de cerâmica são deixadas para trás, que podem ser cortadas ou enroladas conforme desejado. • FORMAÇÃO POR EXTRUSÃO: Como em outros processos de extrusão, uma mistura macia de pó cerâmico com ligantes e outros produtos químicos é passada por uma matriz para adquirir sua forma de seção transversal e depois cortada nos comprimentos desejados. O processo é realizado com misturas cerâmicas frias ou aquecidas. • MOLDAGEM POR INJEÇÃO DE BAIXA PRESSÃO: Preparamos uma mistura de pó cerâmico com ligantes e solventes e aquecemos a uma temperatura onde pode ser facilmente prensada e forçada na cavidade da ferramenta. Uma vez que o ciclo de moldagem é concluído, a peça é ejetada e o produto químico de ligação é queimado. Usando moldagem por injeção, podemos obter peças complexas em grandes volumes economicamente. Furos que são uma pequena fração de milímetro em uma parede de 10 mm de espessura são possíveis, roscas são possíveis sem usinagem posterior, tolerâncias tão apertadas quanto +/- 0,5% são possíveis e ainda menores quando as peças são usinadas , são possíveis espessuras de parede da ordem de 0,5 mm a um comprimento de 12,5 mm, bem como espessuras de parede de 6,5 mm a um comprimento de 150 mm. • USINAGEM VERDE: Utilizando as mesmas ferramentas de usinagem de metal, podemos usinar materiais cerâmicos prensados enquanto ainda estão macios como giz. Tolerâncias de +/- 1% são possíveis. Para melhores tolerâncias, usamos retificação de diamante. • Sinterização ou queima: A sinterização possibilita a densificação total. Ocorre um encolhimento significativo nas peças compactas verdes, mas isso não é um grande problema, pois levamos em consideração essas mudanças dimensionais quando projetamos a peça e o ferramental. As partículas de pó são unidas e a porosidade induzida pelo processo de compactação é removida em grande parte. • MOAGEM DE DIAMANTE: O material mais duro do mundo “diamante” está sendo usado para moer materiais duros como cerâmica e peças de precisão são obtidas. Tolerâncias na faixa de micrômetros e superfícies muito lisas estão sendo alcançadas. Devido ao seu custo, só consideramos esta técnica quando realmente precisamos dela. • CONJUNTOS HERMÉTICOS são aqueles que praticamente não permitem qualquer troca de matéria, sólidos, líquidos ou gases entre interfaces. A vedação hermética é hermética. Por exemplo, invólucros eletrônicos herméticos são aqueles que mantêm o conteúdo interno sensível de um dispositivo embalado ileso por umidade, contaminantes ou gases. Nada é 100% hermético, mas quando falamos de hermeticidade queremos dizer que em termos práticos, que há hermeticidade na medida em que a taxa de vazamento é tão baixa que os dispositivos são seguros em condições ambientais normais por muito tempo. Nossos conjuntos herméticos consistem em componentes de metal, vidro e cerâmica, metal-cerâmica, cerâmica-metal-cerâmica, metal-cerâmica-metal, metal com metal, metal-vidro, metal-vidro-metal, vidro-metal-vidro, vidro- metal e vidro com vidro e todas as outras combinações de ligação metal-vidro-cerâmica. Podemos, por exemplo, revestir com metal os componentes cerâmicos para que possam ser fortemente ligados a outros componentes da montagem e tenham excelente capacidade de vedação. Temos o know-how para revestir fibras ópticas ou passagens com metal e soldá-las ou brasá-las nos invólucros, para que nenhum gás passe ou vaze para os invólucros. Portanto, eles são usados para fabricar gabinetes eletrônicos para encapsular dispositivos sensíveis e protegê-los da atmosfera externa. Além de suas excelentes características de vedação, outras propriedades como o coeficiente de expansão térmica, resistência à deformação, natureza não desgaseificada, vida útil muito longa, natureza não condutora, propriedades de isolamento térmico, natureza antiestática...etc. tornam os materiais de vidro e cerâmica a escolha para determinadas aplicações. Informações sobre nossas instalações que produzem conexões de cerâmica para metal, vedação hermética, passagens a vácuo, componentes de controle de fluido e alto e ultra-alto vácuo podem ser encontradas aqui:Folheto da Fábrica de Componentes Herméticos CLICK Product Finder-Locator Service PÁGINA ANTERIOR
- Conformação de fios e molas, modelagem, soldagem, montagem de fios, bobinas, CNC
Formação de fios e molas, modelagem, soldagem, montagem de fios, molas planas de torção de extensão de compressão de bobina, fios personalizados, molas helicoidais na AGS-TECH Inc. Formação de arame e mola Fabricamos arames personalizados, montagem de arames, arames formados nas formas 2D e 3D desejadas, redes de arame, malhas, cercas, cestas, cercas, molas de arame, molas planas; torção, compressão, tensão, molas planas e muito mais. Nossos processos são formação de arame e mola, trefilação, modelagem, dobra, soldagem, brasagem, solda, perfuração, estampagem, perfuração, chanfradura, retificação, rosqueamento, revestimento, fourslide, slide formando, enrolamento, enrolamento, perturbação. Recomendamos que você clique aqui para BAIXE nossas ilustrações esquemáticas de processos de formação de fios e molas pela AGS-TECH Inc. Este arquivo para download com fotos e esboços ajudará você a entender melhor as informações que fornecemos abaixo. • ESTIRAGEM DO FIO: Usando forças de tração, esticamos o estoque de metal e o puxamos através de uma matriz para reduzir o diâmetro e aumentar seu comprimento. Às vezes usamos uma série de matrizes. Somos capazes de fazer matrizes para cada bitola de fio. Utilizando material de alta resistência à tração desenhamos fios muito finos. Oferecemos fios trabalhados a frio e a quente. • FORMAÇÃO DE ARAME: Um rolo de arame calibrado é dobrado e moldado em um produto útil. Temos a capacidade de formar fios de todas as bitolas, desde filamentos finos até fios grossos como os usados como molas sob chassis de automóveis. Os equipamentos que usamos para a formação de arame são formadores de arame manuais e CNC, bobinadeira, prensas elétricas, fourslide, multi-slide. Nossos processos são trefilação, dobra, endireitamento, achatamento, estiramento, corte, recalque, solda e soldagem e brasagem, montagem, bobinamento, estampagem (ou asa), perfuração, rosqueamento de fio, perfuração, chanfradura, retificação, revestimento e tratamentos de superfície. Nossos equipamentos de última geração podem ser configurados para desenvolver projetos muito complexos de qualquer formato e tolerâncias apertadas. Oferecemos vários tipos de extremidade like extremidades esféricas, pontiagudas ou chanfradas para seus fios. A maioria dos nossos projetos de conformação de arame tem custos de ferramental mínimos a zero. Os tempos de resposta da amostra são geralmente dias. Alterações no design/configuração de formas de arame podem ser feitas muito rapidamente. • FORMAÇÃO DE MOLAS: AGS-TECH fabrica uma grande variedade de molas, incluindo: -Mola de torção / dupla torção -Mola de tensão/compressão -Mola constante/variável - Bobina e Mola Helicoidal -Flat & Leaf Spring -Mola Equilíbrio - Lavadora Belleville -Mola Negadora -Mola helicoidal de taxa progressiva -Mola Onda -Mola Voluta -Molas Cônicas -Anéis de mola -Molas do Relógio -Clipes Fabricamos molas a partir de diversos materiais e podemos orientá-lo de acordo com sua aplicação. Os materiais mais comuns são aço inoxidável, silício cromo, aço de alto carbono, baixo teor de carbono temperado a óleo, cromo vanádio, bronze fosforoso, titânio, liga de cobre berílio, cerâmica de alta temperatura. Utilizamos diversas técnicas na fabricação de molas, incluindo bobinagem CNC, bobinagem a frio, bobinagem a quente, têmpera, acabamento. Outras técnicas já mencionadas acima na formação de arame também são comuns em nossas operações de fabricação de molas. • SERVIÇOS DE ACABAMENTO PARA FIOS E MOLAS: Podemos finalizar seus produtos de várias maneiras, dependendo de sua escolha e necessidade. Alguns processos comuns que oferecemos são: pintura, revestimento em pó, chapeamento, imersão de vinil, anodização, alívio de tensão, tratamento térmico, shot peen, tumble, cromato, electroless níquel, passivação, esmalte cozido, revestimento plástico , limpeza de plasma. CLICK Product Finder-Locator Service PÁGINA ANTERIOR
- Fabricação de conformação de chapa metálica, estampagem, puncionamento, estampagem profunda, CNC
Conformação e fabricação de chapas metálicas, estampagem, puncionamento, dobra, matriz progressiva, soldagem a ponto, estampagem profunda, estampagem e corte de metal na AGS-TECH Inc. Estampagens e fabricação de chapas metálicas Oferecemos estampagem, modelagem, conformação, dobra, puncionamento, corte, corte, perfuração, entalhe, corte, corte, prensagem, fabricação, estampagem profunda usando matrizes de punção única / curso único, bem como matrizes progressivas e fiação, formação de borracha e hidroformagem; corte de chapas metálicas com jato de água, plasma, laser, serra, chama; montagem de chapas metálicas usando soldagem, soldagem a ponto; abaulamento e flexão do tubo de chapa metálica; acabamento de superfícies de chapas metálicas, incluindo pintura por imersão ou spray, revestimento eletrostático em pó, anodização, chapeamento, pulverização catódica e muito mais. Nossos serviços vão desde a prototipagem rápida de chapas metálicas até a fabricação de alto volume. Recomendamos que você clique aqui paraBAIXE nossas ilustrações esquemáticas de processos de fabricação e estampagem de chapas metálicas pela AGS-TECH Inc. Isso ajudará você a entender melhor as informações que estamos fornecendo abaixo. • CORTE DE CHAPAS : Oferecemos CORTES e DESENHOS. Os cortes cortam a chapa de metal em um caminho de cada vez e basicamente não há desperdício de material, enquanto que com cortes a forma não pode ser aninhada com precisão e, portanto, certa quantidade de material é desperdiçada. Um dos nossos processos mais populares é o PUNCHING, onde um pedaço de material redondo ou de outra forma é cortado da chapa de metal. A peça cortada é um desperdício. Outra versão de puncionamento é o SLOTTING, onde são perfurados furos retangulares ou alongados. BLANKING por outro lado é o mesmo processo que o puncionamento, com a distinção da peça a ser cortada é o trabalho e é mantido. FINE BLANKING, uma versão superior do blanking, cria cortes com tolerâncias estreitas e bordas retas e lisas e não requer operações secundárias para a perfeição da peça. Outro processo que utilizamos com frequência é o SLITTING, que é um processo de cisalhamento onde a chapa metálica é cortada por duas lâminas circulares opostas em um caminho reto ou curvo. O abridor de latas é um exemplo simples do processo de corte. Outro popular process para nós é PERFURAÇÃO, onde muitos furos redondos ou de outra forma são perfurados em chapas de metal em um determinado padrão. Um exemplo típico de produto perfurado são os filtros metálicos com muitos orifícios para fluidos. Em NOTCHING, outro processo de corte de chapa, removemos o material de uma peça de trabalho, começando pela borda ou em outro lugar e cortamos para dentro até obter a forma desejada. É um processo progressivo onde cada operação retira outra peça até obter o contorno desejado. Para pequenas tiragens de produção, às vezes usamos um processo relativamente mais lento chamado NIBBLING, que consiste em muitas punções rápidas de furos sobrepostos para fazer um corte maior e mais complexo. No CORTE PROGRESSIVO utilizamos uma série de diferentes operações para obter um único corte ou uma determinada geometria. Finalmente SHAVING um processo secundário nos ajuda a melhorar as arestas dos cortes que já foram feitos. É usado para cortar as lascas, bordas ásperas em chapas de metal. • DOBRAGEM DE CHAPAS : Além do corte, o dobramento é um processo essencial sem o qual não seríamos capazes de produzir a maioria dos produtos. Principalmente uma operação de trabalho a frio, mas às vezes também realizada quando quente ou quente. Usamos matrizes e prensas na maioria das vezes para esta operação. Em PROGRESSIVE BENDING usamos uma série de diferentes operações de punção e matriz para obter uma única dobra ou uma determinada geometria. A AGS-TECH utiliza uma variedade de processos de dobra e faz a escolha dependendo do material da peça, seu tamanho, espessura, tamanho desejado de dobra, raio, curvatura e ângulo de dobra, localização da dobra, economia de operação, quantidades a serem fabricadas… etc. Nós usamos V-BENDING onde um punção em forma de V força a chapa de metal na matriz em forma de V e a dobra. Bom para ângulos muito agudos e obtusos e intermediários, incluindo 90 graus. Usando matrizes de limpeza, realizamos EDGE BENDING. Nosso equipamento nos permite obter ângulos ainda maiores que 90 graus. Na dobra de borda, a peça de trabalho é ensanduichada entre uma almofada de pressão e a matriz, a área para dobra está localizada na borda da matriz e o restante da peça de trabalho é mantido sobre space como uma viga cantilever. Quando o punção atua na parte do cantilever, ele é dobrado sobre a borda da matriz. FLANGING é um processo de dobra de bordas que resulta em um ângulo de 90 graus. Os principais objetivos da operação são a eliminação de arestas vivas e a obtenção de superfícies geométricas para facilitar a união das peças. BEADING, outro processo comum de dobra de borda, forma uma curva sobre a borda de uma peça. O HEMMING, por outro lado, resulta em uma borda da folha que é completamente dobrada sobre si mesma. Em SEAMING, as bordas de duas partes são dobradas uma sobre a outra e unidas. A COSTURA DUPLA, por outro lado, fornece juntas de chapa metálica estanques à água e ao ar. Semelhante à dobra de borda, um processo chamado ROTARY BENDING implanta um cilindro com o ângulo desejado cortado e servindo como punção. À medida que a força é transmitida ao punção, ele se fecha com a peça de trabalho. A ranhura do cilindro dá à porção do cantilever o ângulo desejado. A ranhura pode ter um ângulo menor ou maior que 90 graus. Em AIR BENDING, não precisamos que a matriz inferior tenha um sulco angulado. A chapa metálica é suportada por duas superfícies em lados opostos e a uma certa distância. O punção então aplica uma força no local certo e dobra a peça de trabalho. O CHANNEL BENDING é realizado usando um punção e matriz em forma de canal, e o U-BEND é obtido com um punção em forma de U. OFFSET BENDING produz deslocamentos na chapa metálica. ROLL BENDING, uma técnica boa para trabalhos grossos e dobra de grandes peças de chapas de metal, usa três rolos para alimentar e dobrar as chapas nas curvaturas desejadas. Os rolos são dispostos de modo que a curvatura desejada do trabalho seja obtida. A distância e o ângulo entre os rolos são controlados para obter o resultado desejado. Um rolo móvel permite controlar a curvatura. TUBE FORMING é outra operação popular de dobra de chapas metálicas envolvendo múltiplas matrizes. Os tubos são obtidos após várias ações. A CORRUGAÇÃO também é realizada por operações de dobra. Basicamente, é a flexão simétrica em intervalos regulares em uma peça inteira de chapa metálica. Várias formas podem ser usadas para ondulação. A chapa corrugada é mais rígida e tem melhor resistência à flexão e, portanto, tem aplicações na construção civil. SHEET METAL ROLL FORMING, um processo de fabricação continuous manufacturing é implantado para dobrar seções transversais de uma determinada geometria usando rolos e o trabalho é dobrado em etapas sequenciais, com o rolo final completando o trabalho. Em alguns casos, um único lançamento e, em alguns casos, uma série de lançamentos são empregados. • PROCESSOS COMBINADOS DE CORTE E DOBRA DE CHAPAS : Estes são os processos que cortam e dobram ao mesmo tempo. No PIERCING, um furo é criado usando um punção pontiagudo. À medida que o punção alarga o furo na chapa, o material é dobrado simultaneamente em um flange interno para o furo. O flange obtido pode ter funções importantes. A operação LANCING, por outro lado, corta e dobra a folha para criar uma geometria elevada. • BULGAMENTO E DOBRAGEM DO TUBO DE METAL: No BULGING, alguma parte interna de um tubo oco é pressurizada, fazendo com que o tubo se projete para fora. Como o tubo está dentro de uma matriz, a geometria da protuberância é controlada pela forma da matriz. Em STRETCH BENDING, um tubo de metal é esticado usando forças paralelas ao eixo do tubo e forças de flexão para puxar o tubo sobre um bloco de forma. Em DRAW BENDING, prendemos o tubo perto de sua extremidade a um bloco de forma rotativa que dobra o tubo enquanto gira. Por fim, na CURVATURA POR COMPRESSÃO o tubo é preso à força a um bloco de forma fixo, e uma matriz o dobra sobre o bloco de forma. • DEEP DRAWING: Em uma de nossas operações mais populares, são usados um punção, uma matriz correspondente e um suporte de blank. A peça em bruto de folha de metal é colocada sobre a abertura da matriz e o punção se move em direção à peça em bruto mantida pelo suporte da peça. Uma vez que eles entram em contato, o punção força a chapa de metal na cavidade da matriz para formar o produto. A operação de estampagem profunda assemelha-se ao corte, porém a folga entre o punção e a matriz impede que a chapa seja cortada. Outro fator que garante que a chapa seja estampada em profundidade e não cortada são os cantos arredondados na matriz e punção que evitam o cisalhamento e o corte. Para alcançar uma maior magnitude de estampagem profunda, um processo de REDESENHO está sendo implantado onde uma estampagem profunda subsequente ocorre em uma peça que já passou por um processo de estampagem profunda. No REDESENHO REVERSO, a parte desenhada em profundidade é virada e desenhada na direção oposta. O desenho profundo pode fornecer objetos de formas irregulares, como copos abobadados, cônicos ou escalonados, Em EMBOSSING usamos um par de matrizes macho e fêmea para impressionar a chapa de metal com um desenho ou script. • SPINNING : Uma operação em que uma peça de trabalho plana ou pré-formada é mantida entre um mandril rotativo e o cabeçote traseiro e uma ferramenta aplica pressão localizada ao trabalho à medida que se move gradualmente para cima no mandril. Como resultado, a peça de trabalho é enrolada sobre o mandril e toma sua forma. Utilizamos esta técnica como alternativa ao desenho profundo onde a quantidade de um pedido é pequena, as peças são grandes (diâmetros de até 20 pés) e possuem curvas únicas. Embora os preços por peça sejam geralmente mais altos, os custos de preparação para a operação de fiação CNC são baixos em comparação com a estampagem profunda. Ao contrário, a estampagem profunda requer alto investimento inicial para configuração, mas os custos por peça são baixos quando são produzidas grandes quantidades de peças. Outra versão deste processo é SHEAR SPINNING, onde também há fluxo de metal dentro da peça. O fluxo de metal reduzirá a espessura da peça de trabalho à medida que o processo é realizado. Ainda outro processo relacionado é o TUBE SPINNING, que é aplicado em peças cilíndricas. Também neste processo há fluxo de metal dentro da peça de trabalho. A espessura é assim reduzida e o comprimento do tubo é aumentado. A ferramenta pode ser movida para criar recursos dentro ou fora do tubo. • FORMAÇÃO DE BORRACHA DE CHAPA : Material de borracha ou poliuretano é colocado em um molde de recipiente e a peça de trabalho é colocada na superfície da borracha. Um punção é então aplicado sobre a peça de trabalho e a força na borracha. Como a pressão gerada pela borracha é baixa, a profundidade das peças produzidas é limitada. Como os custos de ferramentas são baixos, o processo é adequado para produção em baixa quantidade. • HIDROFORMAÇÃO : Semelhante à conformação da borracha, neste processo a chapa metálica é prensada por um punção em um líquido pressurizado dentro de uma câmara. O trabalho de chapa metálica é imprensado entre o punção e um diafragma de borracha. O diafragma envolve completamente a peça de trabalho e a pressão do fluido a força a se formar no punção. Desenhos muito profundos ainda mais profundos do que no processo de desenho profundo podem ser obtidos com esta técnica. Fabricamos matrizes de punção única, bem como matrizes progressivas, dependendo da sua peça. As matrizes de estampagem de curso único são um método econômico para produzir rapidamente grandes quantidades de peças simples de chapa metálica, como arruelas. Matrizes progressivas ou a técnica de estampagem profunda são usadas para fabricar geometrias mais complexas. Dependendo do seu caso, o corte por jato de água, laser ou plasma pode ser usado para produzir suas peças de chapa de forma econômica, rápida e precisa. Muitos fornecedores não têm idéia sobre essas técnicas alternativas ou não as têm e, portanto, passam por longas e caras maneiras de fazer matrizes e ferramentas que apenas desperdiçam tempo e dinheiro dos clientes. Se você precisar de componentes de chapa metálica personalizados, como gabinetes, caixas eletrônicas, etc., em poucos dias, entre em contato conosco para obter nosso serviço de PROTOTIPAGEM RÁPIDA DE CHAPA METÁLICA. CLICK Product Finder-Locator Service MENU ANTERIOR
- Forjamento e Metalurgia do Pó, Forjamento em Matriz, Desbaste, Forjamento a Quente
Forjamento e metalurgia em pó, forjamento de matriz, cabeçote, forjamento a quente, matriz de impressão, formato líquido próximo, estampagem, fresamento de metal, rebitagem, cunhagem da AGS-TECH Inc. Forjamento de metais e metalurgia do pó O tipo de processos de FORJAGEM DE METAL que oferecemos são matrizes quentes e frias, matrizes abertas e matrizes fechadas, matrizes de impressão e forjamentos sem rebarbas, cogging, fullering, afiação e forjamento de precisão, forma próxima à rede, cabeçalho , estampagem, forjamento chato, fresagem de metal, prensa e rolo e radial e orbital e anel e forjado isotérmico, cunhagem, rebitagem, forjamento de bola de metal, perfuração de metal, dimensionamento, forjamento de alta taxa de energia. Nossas técnicas de METALURGIA DO PÓ e PROCESSAMENTO DO PÓ são prensagem e sinterização de pó, impregnação, infiltração, prensagem isostática a quente e a frio, moldagem por injeção de metal, compactação de rolo, laminação de pó, extrusão de pó, sinterização solta, sinterização por faísca, prensagem a quente. Recomendamos que você clique aqui para BAIXE nossas ilustrações esquemáticas de processos de forjamento por AGS-TECH Inc. BAIXE nossas ilustrações esquemáticas de processos de metalurgia do pó por AGS-TECH Inc. Esses arquivos para download com fotos e esboços ajudarão você a entender melhor as informações que fornecemos abaixo. No forjamento de metal, forças de compressão são aplicadas e o material é deformado e a forma desejada é obtida. Os materiais forjados mais comuns na indústria são ferro e aço, mas muitos outros como alumínio, cobre, titânio e magnésio também são amplamente forjados. As peças metálicas forjadas possuem estrutura de grãos melhorada, além de trincas vedadas e espaços vazios fechados, portanto, a resistência das peças obtidas por este processo é maior. O forjamento produz peças que são significativamente mais fortes para seu peso do que peças feitas por fundição ou usinagem. Como as peças forjadas são moldadas fazendo o metal fluir em sua forma final, o metal assume uma estrutura de grão direcional que explica a resistência superior das peças. Em outras palavras, as peças obtidas pelo processo de forjamento apresentam melhores propriedades mecânicas em relação às peças fundidas ou usinadas simples. O peso de peças forjadas de metal pode variar de pequenas peças leves a centenas de milhares de libras. Fabricamos peças forjadas principalmente para aplicações mecanicamente exigentes onde são aplicadas altas tensões em peças como peças automotivas, engrenagens, ferramentas de trabalho, ferramentas manuais, eixos de turbinas, engrenagens de motocicletas. Como os custos de ferramentas e configuração são relativamente altos, recomendamos esse processo de fabricação apenas para produção de alto volume e para componentes críticos de baixo volume, mas de alto valor, como trem de pouso aeroespacial. Além do custo do ferramental, os prazos de fabricação para peças forjadas em grande quantidade podem ser maiores em comparação com algumas peças usinadas simples, mas a técnica é crucial para peças que exigem força extraordinária, como parafusos, porcas, aplicações especiais fixadores, automotivo, empilhadeira, peças de guindaste. • FORJAMENTO A QUENTE E A FRIO: O forjamento a quente, como o nome indica, é realizado a altas temperaturas, portanto, a ductilidade é alta e a resistência do material baixa. Isso facilita a deformação e o forjamento fáceis. Ao contrário, o forjamento a frio é realizado em temperaturas mais baixas e requer forças mais altas, o que resulta em encruamento, melhor acabamento superficial e precisão das peças fabricadas. • FORJAMENTO ABERTO E IMPRESSORA: No forjamento em matriz aberta, as matrizes não restringem o material que está sendo comprimido, enquanto no forjamento em matriz de impressão as cavidades dentro das matrizes restringem o fluxo de material enquanto ele é forjado na forma desejada. FORJAGEM DE INVERSÃO ou também chamado de INVERSÃO, que na verdade não é o mesmo, mas um processo muito semelhante, é um processo de matriz aberta onde a peça de trabalho é imprensada entre duas matrizes planas e uma força de compressão reduz sua altura. À medida que a altura é reduced, a largura da peça de trabalho aumenta. HEADING, um processo de forjamento retorcido envolve um estoque cilíndrico que é revolvido em sua extremidade e sua seção transversal é aumentada localmente. No cabeçalho, o estoque é alimentado através da matriz, forjado e depois cortado no comprimento. A operação é capaz de produzir rapidamente grandes quantidades de fixadores. Principalmente é uma operação de trabalho a frio porque é usado para fazer pontas de pregos, pontas de parafusos, porcas e parafusos onde o material precisa ser reforçado. Outro processo de matriz aberta é o COGGING, onde a peça de trabalho é forjada em uma série de etapas, com cada etapa resultando na compressão do material e no movimento subsequente da matriz aberta ao longo do comprimento da peça de trabalho. Em cada etapa, a espessura é reduzida e o comprimento é aumentado em uma pequena quantidade. O processo se assemelha a um estudante nervoso mordendo seu lápis o tempo todo em pequenos passos. Um processo chamado FULLERING é outro método de forjamento em matriz aberta que geralmente implantamos como uma etapa anterior para distribuir o material na peça de trabalho antes que outras operações de forjamento de metal ocorram. Usamos quando a peça de trabalho requer várias forging operations. Na operação, matrizes com superfícies convexas se deformam e fazem com que o metal flua para os dois lados. Um processo semelhante ao fullering, EDGING, por outro lado, envolve matriz aberta com superfícies côncavas para deformar a peça de trabalho. A orla também é um processo preparatório para operações de forjamento subsequentes, faz com que o material flua de ambos os lados para uma área no centro. IMPRESSION DIE FORGING ou CLOSED DIE FORGING como também é chamado utiliza uma matriz/molde que comprime o material e restringe seu fluxo dentro de si. A matriz fecha e o material assume a forma da cavidade da matriz/molde. O FORJAMENTO DE PRECISÃO, processo que requer equipamentos e moldes especiais, produz peças com pouca ou nenhuma rebarba. Em outras palavras, as peças terão dimensões quase finais. Neste processo uma quantidade bem controlada de material é cuidadosamente inserida e posicionada dentro do molde. Implementamos este método para formas complexas com seções finas, pequenas tolerâncias e ângulos de inclinação e quando as quantidades são grandes o suficiente para justificar os custos do molde e do equipamento. • FORJAMENTO FLASHLESS: A peça de trabalho é colocada na matriz de forma que nenhum material possa sair da cavidade para formar rebarba. Nenhum corte de flash indesejado é, portanto, necessário. É um processo de forjamento de precisão e, portanto, requer um controle rigoroso da quantidade de material usado. • SWAGING DE METAL ou FORJAGEM RADIAL: Uma peça de trabalho é atuada circunferencialmente por matriz e forjada. Um mandril também pode ser usado para forjar a geometria da peça de trabalho interna. Na operação de estampagem, a peça de trabalho normalmente recebe vários golpes por segundo. Os itens típicos produzidos por estampagem são ferramentas de ponta pontiaguda, barras cônicas, chaves de fenda. • METAL PIERCING : Utilizamos esta operação frequentemente como uma operação adicional na fabricação de peças. Um furo ou cavidade é criado com perfuração na superfície da peça de trabalho sem quebrá-la. Observe que perfurar é diferente de perfurar, o que resulta em um furo passante. • HOBBING : Um punção com a geometria desejada é pressionado na peça de trabalho e cria uma cavidade com a forma desejada. Chamamos esse soco de HOB. A operação envolve altas pressões e é realizada a frio. Como resultado, o material é trabalhado a frio e endurecido por deformação. Portanto, este processo é muito adequado para a fabricação de moldes, matrizes e cavidades para outros processos de fabricação. Uma vez que a placa é fabricada, pode-se fabricar facilmente muitas cavidades idênticas sem a necessidade de usinar uma a uma. • ROLL FORGING ou ROLL FORMING: Dois rolos opostos são usados para moldar a peça metálica. A peça de trabalho é alimentada nos rolos, os rolos giram e puxam o trabalho para a abertura, o trabalho é então alimentado através da porção ranhurada dos rolos e as forças de compressão dão ao material a forma desejada. Não é um processo de laminação, mas um processo de forjamento, porque é uma operação discreta e não contínua. A geometria nas ranhuras dos rolos forja o material para a forma e geometria necessárias. É realizado a quente. Por ser um processo de forjamento, produz peças com excelentes propriedades mecânicas e, portanto, usamos para fabricação de peças automotivas, como eixos, que precisam ter uma resistência extraordinária em ambientes de trabalho difíceis. • FORJAGEM ORBITAL: A peça de trabalho é colocada em uma cavidade da matriz de forjamento e forjada por uma matriz superior que percorre um caminho orbital conforme gira em um eixo inclinado. A cada revolução, a matriz superior completa exercendo forças de compressão em toda a peça de trabalho. Repetindo essas revoluções várias vezes, o forjamento suficiente é realizado. As vantagens desta técnica de fabricação são sua operação de baixo ruído e menores forças necessárias. Em outras palavras, com pequenas forças, pode-se girar uma matriz pesada em torno de um eixo para aplicar grandes pressões em uma seção da peça de trabalho que está em contato com a matriz. As peças em forma de disco ou cônica às vezes são uma boa opção para esse processo. • FORJAGEM DE ANEL: Usamos frequentemente para fabricar anéis sem costura. O estoque é cortado no comprimento, virado e perfurado até o fim para criar um orifício central. Em seguida, ele é colocado em um mandril e uma matriz de forjamento o martela de cima, enquanto o anel é girado lentamente até que as dimensões desejadas sejam obtidas. • REBITAGEM: Processo comum de união de peças, inicia-se com uma peça metálica reta inserida em furos pré-fabricados através das peças. Depois disso, as duas extremidades da peça de metal são forjadas apertando a junta entre uma matriz superior e inferior. • COINING : Outro processo popular realizado por prensa mecânica, exercendo grandes forças em uma curta distância. O nome “cunhagem” vem dos detalhes finos que são forjados nas superfícies das moedas de metal. É principalmente um processo de acabamento de um produto onde são obtidos detalhes finos nas superfícies como resultado da grande força aplicada pela matriz que transfere esses detalhes para a peça de trabalho. • FORJAMENTO DE ESFERAS DE METAL: Produtos como rolamentos de esferas requerem esferas de metal fabricadas com precisão de alta qualidade. Em uma técnica chamada SKEW ROLLING, usamos dois rolos opostos que giram continuamente à medida que o material é continuamente alimentado nos rolos. Em uma extremidade dos dois rolos, esferas de metal são ejetadas como produto. Um segundo método para forjamento de bolas de metal é o uso de matrizes que comprimem o estoque de material colocado entre elas, tomando a forma esférica da cavidade do molde. Muitas vezes as bolas produzidas requerem algumas etapas adicionais, como acabamento e polimento, para se tornarem um produto de alta qualidade. • FORJAMENTO ISOTÉRMICO / FORJAMENTO A QUENTE: Processo caro realizado somente quando o valor benefício/custo é justificado. Um processo de trabalho a quente onde a matriz é aquecida aproximadamente à mesma temperatura que a peça de trabalho. Uma vez que tanto a matriz quanto a peça têm aproximadamente a mesma temperatura, não há resfriamento e as características de fluxo do metal são melhoradas. A operação é adequada para superligas e materiais com forjabilidade inferior e materiais cujo propriedades mecânicas são muito sensíveis a pequenos gradientes e mudanças de temperatura. • ENTALHE DO METAL: É um processo de acabamento a frio. O fluxo de material é irrestrito em todas as direções, com exceção da direção em que a força é aplicada. Como resultado, obtém-se um acabamento superficial muito bom e dimensões precisas. • FORJAMENTO DE ALTA TAXA DE ENERGIA: A técnica envolve um molde superior preso ao braço de um pistão que é rapidamente empurrado à medida que uma mistura ar-combustível é inflamada por uma vela de ignição. Assemelha-se à operação de pistões em um motor de carro. O molde atinge a peça de trabalho muito rapidamente e depois retorna à sua posição original muito rapidamente graças à contrapressão. O trabalho é forjado em poucos milissegundos e, portanto, não há tempo para o trabalho esfriar. Isso é útil para peças difíceis de forjar que possuem propriedades mecânicas muito sensíveis à temperatura. Em outras palavras, o processo é tão rápido que a peça é formada sob temperatura constante e não haverá gradientes de temperatura nas interfaces molde/peça. • Em DIE FORGING, o metal é batido entre dois blocos de aço correspondentes com formas especiais neles, chamados de matrizes. Quando o metal é martelado entre as matrizes, ele assume a mesma forma que as formas da matriz. Quando atinge sua forma final, é retirado para esfriar. Este processo produz peças fortes e de formato preciso, mas requer um investimento maior para as matrizes especializadas. O forjamento invertido aumenta o diâmetro de um pedaço de metal ao aplainá-lo. Geralmente é usado para fazer peças pequenas, especialmente para formar cabeças em fixadores como parafusos e pregos. • METALURGIA DO PÓ / PROCESSAMENTO DO PÓ: Como o nome indica, envolve processos de fabricação para a fabricação de peças sólidas de determinadas geometrias e formas a partir de pós. Se pós metálicos são usados para este fim, é o domínio da metalurgia do pó e se pós não metálicos são usados, é o processamento de pó. As peças sólidas são produzidas a partir de pós por prensagem e sinterização. PÓ PRENSA é usado para compactar pós em formas desejadas. Primeiro, o material primário é fisicamente pulverizado, dividindo-o em muitas pequenas partículas individuais. A mistura de pó é preenchida no molde e um punção se move em direção ao pó e o compacta na forma desejada. Realizado principalmente à temperatura ambiente, com a prensagem do pó obtém-se uma parte sólida e é chamado de compacto verde. Aglutinantes e lubrificantes são comumente usados para aumentar a compactabilidade. Somos capazes de formar prensas de pó usando prensas hidráulicas com vários milhares de toneladas de capacidade. Também temos prensas de dupla ação com punções superiores e inferiores opostas, bem como prensas de ação múltipla para geometrias de peças altamente complexas. A uniformidade, que é um desafio importante para muitas usinas de metalurgia do pó/processamento de pó, não é um grande problema para a AGS-TECH devido à nossa vasta experiência na fabricação personalizada dessas peças por muitos anos. Mesmo com peças mais grossas, onde a uniformidade representa um desafio, conseguimos. Se nos comprometermos com o seu projeto, faremos suas peças. Se virmos algum risco potencial, informaremos em advance. A SINTERIZAÇÃO DO PÓ, que é a segunda etapa, envolve o aumento da temperatura até certo grau e a manutenção da temperatura nesse nível por um certo tempo para que as partículas de pó na peça prensada possam se unir. Isso resulta em ligações muito mais fortes e fortalecimento da peça de trabalho. A sinterização ocorre próximo à temperatura de fusão do pó. Durante a sinterização, a contração ocorrerá, a resistência do material, a densidade, a ductilidade, a condutividade térmica e a condutividade elétrica são aumentadas. Temos fornos descontínuos e contínuos para sinterização. Uma de nossas capacidades é ajustar o nível de porosidade das peças que produzimos. Por exemplo, podemos produzir filtros de metal mantendo as peças porosas até certo ponto. Usando uma técnica chamada IMPREGNAÇÃO, preenchemos os poros do metal com um fluido como o óleo. Produzimos, por exemplo, rolamentos impregnados de óleo que são autolubrificantes. No processo de INFILTRAÇÃO preenchemos os poros de um metal com outro metal de ponto de fusão inferior ao material base. A mistura é aquecida a uma temperatura entre as temperaturas de fusão dos dois metais. Como resultado, algumas propriedades especiais podem ser obtidas. Também realizamos frequentemente operações secundárias, como usinagem e forjamento em peças fabricadas em pó, quando características ou propriedades especiais precisam ser obtidas ou quando a peça pode ser fabricada com menos etapas de processo. PRESSÃO ISOSTÁTICA: Neste processo a pressão do fluido está sendo usada para compactar a peça. Os pós metálicos são colocados em um molde feito de um recipiente flexível selado. Na prensagem isostática, a pressão é aplicada de todos os lados, ao contrário da pressão axial vista na prensagem convencional. As vantagens da prensagem isostática são densidade uniforme dentro da peça, especialmente para peças maiores ou mais grossas, propriedades superiores. Sua desvantagem são os longos tempos de ciclo e as precisões geométricas relativamente baixas. A PRESSÃO ISOSTÁTICA A FRIO é realizada à temperatura ambiente e o molde flexível é feito de borracha, PVC ou uretano ou materiais similares. O fluido usado para pressurização e compactação é óleo ou água. A sinterização convencional do compacto verde segue isso. A PRESSÃO ISOSTÁTICA A QUENTE, por outro lado, é realizada em altas temperaturas e o material do molde é chapa ou cerâmica com ponto de fusão alto o suficiente para resistir às temperaturas. O fluido pressurizado é geralmente um gás inerte. As operações de prensagem e sinterização são realizadas em uma única etapa. A porosidade é quase completamente eliminada, uma estrutura uniform grain é obtida. A vantagem da prensagem isostática a quente é que ela pode produzir peças comparáveis à fundição e forjamento combinados, ao mesmo tempo em que torna possível o uso de materiais que não são adequados para fundição e forjamento. A desvantagem da prensagem isostática a quente é o seu alto tempo de ciclo e, portanto, o custo. É adequado para peças críticas de baixo volume. MOLDAGEM POR INJEÇÃO DE METAL: Processo muito adequado para a produção de peças complexas com paredes finas e geometrias detalhadas. Mais adequado para peças menores. Pós e ligante de polímero são misturados, aquecidos e injetados em um molde. O aglutinante de polímero reveste as superfícies das partículas de pó. Após a moldagem, o aglutinante é removido por aquecimento a baixa temperatura ou dissolvido usando um solvente. COMPACTAÇÃO DE ROLOS / ROLAMENTO DE PÓ: Os pós são usados para produzir tiras ou folhas contínuas. O pó é alimentado a partir de um alimentador e compactado por dois rolos rotativos em folhas ou tiras. A operação é realizada a frio. A folha é transportada para um forno de sinterização. O processo de sinterização pode ser repetido uma segunda vez. EXTRUSÃO DE PÓ: As peças com grande relação comprimento/diâmetro são fabricadas por extrusão de um recipiente de chapa fina com pó. SINTERING LOOSE: Como o nome indica, é um método de compactação e sinterização sem pressão, adequado para a produção de peças muito porosas, como filtros metálicos. O pó é alimentado na cavidade do molde sem compactação. SINTERING LOOSE: Como o nome indica, é um método de compactação e sinterização sem pressão, adequado para a produção de peças muito porosas, como filtros metálicos. O pó é alimentado na cavidade do molde sem compactação. SINTERIZAÇÃO DE FAÍSCAS: O pó é comprimido no molde por dois punções opostos e uma corrente elétrica de alta potência é aplicada ao punção e passa pelo pó compactado entre eles. A alta corrente queima os filmes superficiais das partículas de pó e os sinteriza com o calor gerado. O processo é rápido porque o calor não é aplicado de fora, mas sim gerado de dentro do molde. PRENSA A QUENTE: Os pós são prensados e sinterizados em uma única etapa em um molde que resiste às altas temperaturas. À medida que a matriz compacta, o calor do pó é aplicado a ela. Boas precisões e propriedades mecânicas alcançadas por este método o tornam uma opção atraente. Mesmo metais refratários podem ser processados usando materiais de molde como grafite. CLICK Product Finder-Locator Service MENU ANTERIOR
- Extrusões de metal de borracha plástica, matrizes de extrusão, extrusão de alumínio
Extrusões de metal de borracha plástica, matrizes de extrusão, extrusão de alumínio, conformação de tubos de tubos, perfis de plástico, fabricação de perfis de metal, PVC na AGS-TECH Inc. Extrusões, Produtos Extrudados, Extrudados Usamos o processo EXTRUSION process para fabricar produtos com perfil de seção transversal fixo, como tubos, tubulações e dissipadores de calor. Embora muitos materiais possam ser extrudados, nossas extrusões mais comuns são feitas de metal, polímeros/plásticos, cerâmica obtida pelo método de extrusão a frio, morno ou quente. Chamamos as partes extrudadas de extrudadas ou extrudadas se no plural. Algumas versões especializadas do processo que também realizamos são overjacketing, coextrusão e extrusão composta. Recomendamos que você clique aqui para BAIXE nossas ilustrações esquemáticas de processos de extrusão de metalocerâmica e plástico pela AGS-TECH Inc. Isso ajudará você a entender melhor as informações que estamos fornecendo abaixo. Na extrusão o material a ser extrudado é empurrado ou trefilado através de uma matriz que possui o perfil de seção transversal desejado. O processo pode ser usado para fabricar seções transversais complexas com excelente acabamento superficial e para trabalhar em materiais frágeis. Pode-se produzir qualquer comprimento de peças usando este processo. Para simplificar as etapas do processo: 1.) Nas extrusões a quente ou a quente o material é aquecido e carregado em um recipiente na prensa. O material é pressionado e empurrado para fora da matriz. 2.) O extrudado produzido é esticado para alisamento, tratado termicamente ou trabalhado a frio para aumentar suas propriedades. Por outro lado COLD EXTRUSION ocorre em torno da temperatura ambiente e tem as vantagens de menos oxidação, alta resistência, tolerâncias mais estreitas, bom acabamento superficial e solidez. WARM EXTRUSION é realizado acima da temperatura ambiente, mas abaixo do ponto de recristalização. Oferece um compromisso e equilíbrio para as forças necessárias, ductilidade e propriedades do material e, portanto, é a escolha para algumas aplicações. HOT EXTRUSION ocorre acima da temperatura de recristalização do material. Desta forma é mais fácil empurrar o material através da matriz. No entanto, o custo do equipamento é alto. Quanto mais complexo um perfil extrudado, mais caro é o molde (ferramenta) e menor é a taxa de produção. As seções transversais da matriz, bem como as espessuras, possuem limitações que dependem do material a ser extrudado. Cantos afiados em matrizes de extrusão são sempre indesejáveis e devem ser evitados, a menos que seja necessário. De acordo com o material que está sendo extrudado, oferecemos: • METAL EXTRUSIONS : Os mais comuns que produzimos são alumínio, latão, zinco, cobre, aço, titânio, magnésio • EXTRUSÃO DE PLÁSTICO : O plástico é fundido e formado em um perfil contínuo. Nossos materiais comuns processados são polietileno, nylon, poliestireno, cloreto de polivinila, polipropileno, plástico ABS, policarbonato, acrílico. Os produtos típicos que fabricamos incluem tubos e tubulações, armações de plástico. No processo, pequenos grânulos de plástico/resina são alimentados por gravidade do funil para o barril da máquina de extrusão. Freqüentemente também misturamos corantes ou outros aditivos na tremonha para dar ao produto as especificações e propriedades necessárias. O material que entra no barril aquecido é forçado pelo parafuso giratório a sair do barril na extremidade e se mover através do pacote de tela para remoção de contaminantes no plástico fundido. Depois de passar o pacote de tela, o plástico entra na matriz de extrusão. A matriz dá ao plástico macio em movimento sua forma de perfil à medida que passa. Agora o extrudado passa por um banho-maria para resfriamento. Outras técnicas que a AGS-TECH Inc. vem usando há muitos anos são: • EXTRUSÃO DE TUBOS E TUBOS : Os tubos e tubos de plástico são formados quando o plástico é extrudado através de uma matriz de modelagem redonda e resfriado em banho-maria, depois cortado no comprimento ou enrolado/enrolado. Transparente ou colorido, listrado, parede simples ou dupla, flexível ou rígido, PE, PP, poliuretano, PVC, nylon, PC, silicone, vinil ou então, temos tudo. Dispomos de tubos abastecidos, bem como a capacidade de produzir de acordo com as suas especificações. A AGS-TECH fabrica tubos de acordo com os requisitos da FDA, UL e LE para aplicações médicas, elétricas e eletrônicas, industriais e outras. • OVERJACKETING / OVER JACKETING EXTRUSION : Esta técnica aplica uma camada externa de plástico no fio ou cabo existente. Nossos fios de isolamento são fabricados com este método. • COEXTRUSION : Várias camadas de material são extrudadas simultaneamente. As várias camadas são entregues por várias extrusoras. As várias espessuras de camada podem ser ajustadas para atender às especificações do cliente. Esse processo possibilita o uso de vários polímeros, cada um com uma funcionalidade diferente no produto. Como resultado, pode-se otimizar uma gama de propriedades. • EXTRUSÃO DE COMPOSTOS: Um único ou vários polímeros são misturados com aditivos para obter um composto plástico. Nossas extrusoras de dupla rosca produzem extrusões compostas. As matrizes de extrusão são geralmente baratas em comparação com os moldes de metal. Se você está pagando muito mais do que alguns milhares de dólares por uma matriz de extrusão de tamanho pequeno ou médio que extrusa alumínio, provavelmente está pagando demais. Somos especialistas em determinar qual técnica é a mais econômica, mais rápida e mais adequada para sua aplicação. Às vezes, extrudar e usinar uma peça pode economizar muito dinheiro. Antes de tomar uma decisão firme, peça-nos primeiro a nossa opinião. Ajudamos muitos clientes a tomar as decisões certas. Para algumas extrusões de metal amplamente utilizadas, você pode baixar nossos folhetos e catálogos clicando no texto colorido abaixo. Se for um produto de prateleira que atenda às suas necessidades, será mais econômico. Baixe nossos recursos de extrusão de tubos e tubos médicos Baixe nossos dissipadores de calor extrudados • PROCESSOS SECUNDÁRIOS DE MANUFATURA E FABRICAÇÃO PARA EXTRUSIONS : Entre os processos de valor agregado que oferecemos para produtos extrudados estão: -Tubo personalizado e dobra de tubo, formação e modelagem, corte de tubo, formação de extremidade de tubo, enrolamento de tubo, usinagem e acabamento, perfuração e perfuração e perfuração, -Conjuntos de tubos e tubos personalizados, montagem tubular, soldagem, brasagem e solda -Dobragem de extrusão personalizada, formando e moldando -Limpeza, desengorduramento, decapagem, passivação, polimento, anodização, galvanização, pintura, tratamento térmico, recozimento e endurecimento, marcação, gravação e rotulagem, embalagem personalizada. CLICK Product Finder-Locator Service PÁGINA ANTERIOR
- Peças fundidas e usinadas, fabricação CNC, fresagem, torneamento, suíço
Peças fundidas e usinadas, fabricação CNC, fresagem, torneamento, usinagem tipo suíço, fundição sob pressão, fundição de investimento, peças fundidas com espuma perdida da AGS-TECH Inc. Fundição e Usinagem Nossas técnicas de fundição e usinagem personalizadas são fundições descartáveis e não descartáveis, fundição ferrosa e não ferrosa, areia, matriz, centrífuga, contínua, molde cerâmico, investimento, espuma perdida, forma próxima à rede, molde permanente (fundição por gravidade), gesso molde (fundição de gesso) e carcaça, peças usinadas produzidas por fresamento e torneamento usando equipamentos convencionais e CNC, usinagem tipo suíça para peças de pequena precisão baratas de alto rendimento, usinagem de parafusos para fixadores, usinagem não convencional. Por favor, tenha em mente que além de metais e ligas metálicas, nós usinamos componentes de cerâmica, vidro e plástico também em alguns casos quando a fabricação de um molde não é atraente ou não é a opção. A usinagem de materiais poliméricos requer a experiência especializada que temos devido ao desafio que os plásticos e a borracha apresentam devido à sua maciez, não rigidez...etc. Para usinagem de cerâmica e vidro, consulte nossa página sobre Fabricação Não Convencional. AGS-TECH Inc. fabrica e fornece peças fundidas leves e pesadas. Fornecemos peças fundidas de metal e peças usinadas para caldeiras, trocadores de calor, automóveis, micromotores, turbinas eólicas, equipamentos de embalagem de alimentos e muito mais. Recomendamos que você clique aqui para BAIXE nossas ilustrações esquemáticas de processos de usinagem e fundição da AGS-TECH Inc. Isso ajudará você a entender melhor as informações que estamos fornecendo abaixo. Vejamos algumas das várias técnicas que oferecemos em detalhes: • FUNDIÇÃO DE MOLDE DESCARREGÁVEL: Esta ampla categoria refere-se a métodos que envolvem moldes temporários e não reutilizáveis. Exemplos são areia, gesso, concha, investimento (também chamado de cera perdida) e fundição de gesso. • FUNDIÇÃO EM AREIA: Processo em que se utiliza areia como material do molde. Um método muito antigo e ainda muito popular na medida em que a maioria das peças fundidas de metal produzidas são feitas por esta técnica. Baixo custo mesmo na produção de baixa quantidade. Adequado para fabricação de peças pequenas e grandes. A técnica pode ser usada para fabricar peças em dias ou semanas com muito pouco investimento. A areia úmida é colada com argila, aglutinantes ou óleos especiais. A areia é geralmente contida em caixas de molde e o sistema de cavidade e porta é criado pela compactação da areia ao redor dos modelos. Os processos são: 1.) Colocação do modelo na areia para fazer o molde 2.) Incorporação de modelo e areia em um sistema de gating 3.) Remoção do modelo 4.) Preenchimento da cavidade do molde com metal fundido 5.) Resfriamento do metal 6.) Quebra do molde de areia e remoção da fundição • FUNDIÇÃO DE MOLDE DE GESSO: Semelhante à fundição de areia, e em vez de areia, gesso de paris está sendo usado como material de molde. Prazos de produção curtos, como fundição em areia e baratos. Boas tolerâncias dimensionais e acabamento superficial. Sua principal desvantagem é que só pode ser usado com metais de baixo ponto de fusão, como alumínio e zinco. • FUNDIÇÃO EM MOLDE SHELL: Também semelhante à fundição em areia. Cavidade do molde obtida por casca endurecida de areia e resina termoendurecível em vez de frasco preenchido com areia como no processo de fundição em areia. Quase qualquer metal adequado para ser fundido por areia pode ser fundido por moldagem em concha. O processo pode ser resumido como: 1.) Fabricação do molde de concha. A areia usada tem um tamanho de grão muito menor quando comparada à areia usada na fundição de areia. A areia fina é misturada com resina termofixa. O padrão de metal é revestido com um agente de separação para facilitar a remoção da casca. Em seguida, o padrão de metal é aquecido e a mistura de areia é porosa ou soprada sobre o padrão de fundição a quente. Uma casca fina se forma na superfície do padrão. A espessura desta casca pode ser ajustada variando o tempo que a mistura de resina de areia está em contato com o padrão de metal. A areia solta é então removida com o padrão coberto de casca restante. 2.) Em seguida, a casca e o padrão são aquecidos em um forno para que a casca endureça. Após a conclusão do endurecimento, a casca é ejetada do padrão usando pinos embutidos no padrão. 3.) Duas dessas conchas são montadas por colagem ou fixação e formam o molde completo. Agora o molde de concha é inserido em um recipiente no qual é suportado por granalha de areia ou metal durante o processo de fundição. 4.) Agora o metal quente pode ser derramado no molde de concha. As vantagens do shell casting são produtos com muito bom acabamento superficial, possibilidade de fabricação de peças complexas com alta precisão dimensional, processo fácil de automatizar, econômico para produção de grande volume. As desvantagens são os moldes necessitarem de boa ventilação devido aos gases que são criados quando o metal fundido entra em contato com o produto químico ligante, as resinas termofixas e os padrões de metal são caros. Devido ao custo dos padrões de metal, a técnica pode não ser adequada para execuções de produção de baixa quantidade. • INVESTMENT CASTING (também conhecido como LOST-WAX CASTING): Também uma técnica muito antiga e adequada para a fabricação de peças de qualidade com alta precisão, repetibilidade, versatilidade e integridade de diversos metais, materiais refratários e ligas especiais de alto desempenho. Peças pequenas e grandes podem ser produzidas. Um processo caro quando comparado a alguns dos outros métodos, mas a grande vantagem é a possibilidade de produzir peças com formato próximo ao líquido, contornos e detalhes intrincados. Assim, o custo é um pouco compensado pela eliminação de retrabalho e usinagem em alguns casos. Embora possa haver variações, aqui está um resumo do processo geral de fundição de investimento: 1.) Criação do padrão mestre original de cera ou plástico. Cada fundição precisa de um padrão, pois eles são destruídos no processo. O molde a partir do qual os padrões são fabricados também é necessário e na maioria das vezes o molde é fundido ou usinado. Como o molde não precisa ser aberto, fundições complexas podem ser obtidas, muitos padrões de cera podem ser conectados como os galhos de uma árvore e despejados juntos, permitindo assim a produção de várias peças a partir de um único vazamento do metal ou liga metálica. 2.) Em seguida, o padrão é mergulhado ou derramado com uma pasta refratária composta de sílica de grão muito fino, água e ligantes. Isso resulta em uma camada de cerâmica sobre a superfície do padrão. O revestimento refratário no padrão é deixado para secar e endurecer. Esta etapa é de onde vem o nome de fundição de investimento: pasta refratária é investida sobre o padrão de cera. 3.) Nesta etapa, o molde cerâmico endurecido é virado de cabeça para baixo e aquecido para que a cera derreta e saia do molde. Uma cavidade é deixada para trás para a fundição do metal. 4.) Após a saída da cera, o molde cerâmico é aquecido a uma temperatura ainda mais alta, o que resulta no fortalecimento do molde. 5.) A fundição de metal é derramada no molde quente preenchendo todas as seções intrincadas. 6.) A fundição pode solidificar 7.) Finalmente, o molde cerâmico é quebrado e as peças fabricadas são cortadas da árvore. Aqui está um link para o folheto da planta de fundição por investimento • FUNDIÇÃO DE PADRÃO EVAPORATIVO: O processo usa um padrão feito de um material como espuma de poliestireno que evaporará quando o metal fundido quente for derramado no molde. Existem dois tipos deste processo: LOST FOAM CASTING que utiliza areia não aderente e FULL MOLD CASTING que utiliza areia aderente. Aqui estão as etapas gerais do processo: 1.) Fabrique o molde a partir de um material como poliestireno. Quando grandes quantidades serão fabricadas, o padrão é moldado. Se a peça tiver uma forma complexa, várias seções desse material de espuma podem precisar ser coladas para formar o padrão. Costumamos revestir o padrão com um composto refratário para criar um bom acabamento superficial na peça fundida. 2.) O padrão é então colocado em areia de moldagem. 3.) O metal fundido é derramado no molde, evaporando o padrão de espuma, ou seja, poliestireno na maioria dos casos, à medida que flui através da cavidade do molde. 4.) O metal fundido é deixado no molde de areia para endurecer. 5.) Depois de endurecido, removemos a fundição. Em alguns casos, o produto que fabricamos requer um núcleo dentro do padrão. Na fundição evaporativa, não há necessidade de colocar e fixar um macho na cavidade do molde. A técnica é adequada para a fabricação de geometrias muito complexas, pode ser facilmente automatizada para produção de alto volume e não há linhas de partição na peça fundida. O processo básico é simples e econômico de implementar. Para produção de grande volume, uma vez que é necessária uma matriz ou molde para produzir os padrões de poliestireno, isso pode ser um pouco caro. • FUNDIÇÃO DE MOLDE NÃO EXPANDÍVEL: Esta ampla categoria refere-se a métodos onde o molde não precisa ser reformado após cada ciclo de produção. Exemplos são fundição permanente, matriz, contínua e centrífuga. A repetibilidade é obtida e as peças podem ser caracterizadas como NEAR NET SHAPE. • FUNDIÇÃO DE MOLDE PERMANENTE: Os moldes reutilizáveis feitos de metal são usados para múltiplas fundições. Um molde permanente geralmente pode ser usado por dezenas de milhares de vezes antes de se desgastar. Gravidade, pressão de gás ou vácuo são geralmente usados para encher o molde. Os moldes (também chamados de matrizes) geralmente são feitos de ferro, aço, cerâmica ou outros metais. O processo geral é: 1.) Usinar e criar o molde. É comum usinar o molde a partir de dois blocos metálicos que se encaixam e podem ser abertos e fechados. Tanto as características da peça quanto o sistema de abertura são geralmente usinados no molde de fundição. 2.) As superfícies internas do molde são revestidas com uma pasta que incorpora materiais refratários. Isso ajuda a controlar o fluxo de calor e atua como lubrificante para facilitar a remoção da peça fundida. 3.) Em seguida, as metades do molde permanente são fechadas e o molde é aquecido. 4.) O metal fundido é derramado no molde e deixado para solidificação. 5.) Antes que ocorra muito resfriamento, removemos a peça do molde permanente usando ejetores quando as metades do molde são abertas. Frequentemente usamos fundição em molde permanente para metais de baixo ponto de fusão, como zinco e alumínio. Para fundições de aço, usamos grafite como material de molde. Algumas vezes obtemos geometrias complexas usando machos dentro de moldes permanentes. As vantagens desta técnica são fundidos com boas propriedades mecânicas obtidas por resfriamento rápido, uniformidade nas propriedades, boa precisão e acabamento superficial, baixas taxas de rejeito, possibilidade de automatizar o processo e produzir grandes volumes economicamente. As desvantagens são os altos custos de configuração inicial que o tornam inadequado para operações de baixo volume e limitações no tamanho das peças fabricadas. • DIE CASTING: Uma matriz é usinada e o metal fundido é empurrado sob alta pressão para dentro das cavidades do molde. Tanto fundições de metais não ferrosos como ferrosos são possíveis. O processo é adequado para produções de alta quantidade de peças pequenas e médias com detalhes, paredes extremamente finas, consistência dimensional e bom acabamento superficial. A AGS-TECH Inc. é capaz de fabricar espessuras de parede tão pequenas quanto 0,5 mm usando esta técnica. Assim como na fundição em molde permanente, o molde precisa ser composto por duas metades que podem abrir e fechar para a retirada da peça produzida. Um molde de fundição pode ter várias cavidades para permitir a produção de vários fundidos com cada ciclo. Os moldes de fundição sob pressão são muito pesados e muito maiores do que as peças que produzem, portanto, também caros. Reparamos e substituímos matrizes desgastadas gratuitamente para nossos clientes, desde que eles repediram suas peças de nós. Nossas matrizes têm longa vida útil na faixa de várias centenas de milhares de ciclos. Aqui estão as etapas básicas do processo simplificado: 1.) Produção do molde geralmente em aço 2.) Molde instalado na máquina de fundição 3.) O pistão força o metal fundido a fluir nas cavidades da matriz, preenchendo as características intrincadas e as paredes finas 4.) Depois de encher o molde com o metal fundido, o fundido é endurecido sob pressão 5.) O molde é aberto e a fundição é removida com a ajuda de pinos ejetores. 6.) Agora as matrizes vazias são lubrificadas novamente e fixadas para o próximo ciclo. Na fundição sob pressão, frequentemente usamos moldagem por inserção, onde incorporamos uma peça adicional no molde e fundimos o metal ao redor dela. Após a solidificação, essas peças passam a fazer parte do produto fundido. As vantagens da fundição sob pressão são boas propriedades mecânicas das peças, possibilidade de recursos intrincados, detalhes finos e bom acabamento superficial, altas taxas de produção, fácil automação. As desvantagens são: Não muito adequado para baixo volume devido ao alto custo do molde e do equipamento, limitações nas formas que podem ser fundidas, pequenas marcas redondas nas peças fundidas resultantes do contato dos pinos ejetores, rebarbas finas de metal espremido na linha de partição, necessidade para respiros ao longo da linha de separação entre a matriz, necessidade de manter baixas as temperaturas do molde usando circulação de água. • FUNDIÇÃO CENTRÍFUGA: O metal fundido é vazado no centro do molde rotativo no eixo de rotação. As forças centrífugas jogam o metal para a periferia e ele se solidifica à medida que o molde continua girando. As rotações do eixo horizontal e vertical podem ser usadas. Peças com superfícies internas redondas, bem como outras formas não redondas, podem ser fundidas. O processo pode ser resumido como: 1.) O metal fundido é derramado no molde centrífugo. O metal é então forçado para as paredes externas devido à fiação do molde. 2.) À medida que o molde gira, o metal fundido endurece A fundição centrífuga é uma técnica adequada para a produção de peças cilíndricas ocas como tubos, sem necessidade de sprues, risers e elementos de canal, bom acabamento superficial e recursos detalhados, sem problemas de retração, possibilidade de produzir tubos longos com diâmetros muito grandes, capacidade de produção de alta taxa . • FUNDIÇÃO CONTÍNUA ( STRAND CASTING ) : Usada para fundir um comprimento contínuo de metal. Basicamente, o metal fundido é vazado no perfil bidimensional do molde, mas seu comprimento é indeterminado. O novo metal fundido é constantemente alimentado no molde à medida que o fundido se desloca para baixo, com seu comprimento aumentando com o tempo. Metais como cobre, aço, alumínio são fundidos em longos fios usando o processo de fundição contínua. O processo pode ter várias configurações, mas a comum pode ser simplificada como: 1.) O metal fundido é derramado em um recipiente localizado acima do molde em quantidades e taxas de fluxo bem calculadas e flui através do molde resfriado a água. A fundição de metal despejada no molde se solidifica em uma barra inicial colocada na parte inferior do molde. Esta barra inicial dá aos rolos algo para agarrar inicialmente. 2.) A longa corda de metal é transportada por rolos a uma velocidade constante. Os rolos também mudam a direção do fluxo do fio de metal de vertical para horizontal. 3.) Após o lingotamento contínuo ter percorrido uma certa distância horizontal, uma tocha ou serra que se move com o lingotamento corta-o rapidamente nos comprimentos desejados. O processo de fundição contínua pode ser integrado com o PROCESSO DE ROLAGEM, onde o metal fundido continuamente pode ser alimentado diretamente em um laminador para produzir vigas em I, vigas em T... etc. A fundição contínua produz propriedades uniformes em todo o produto, tem uma alta taxa de solidificação, reduz o custo devido à perda muito baixa de material, oferece um processo onde o carregamento de metal, vazamento, solidificação, corte e remoção da fundição ocorrem em uma operação contínua e resultando assim em alta taxa de produtividade e alta qualidade. Uma consideração importante é, no entanto, o alto investimento inicial, custos de instalação e requisitos de espaço. • SERVIÇOS DE USINAGEM: Oferecemos usinagem de três, quatro e cinco eixos. Os tipos de processos de usinagem que utilizamos são TORNEAMENTO, FRESAGEM, FURAÇÃO, FURAÇÃO, BROCHAGEM, PLANEAMENTO, SERRAGEM, RETIFICAÇÃO, LAPAGEM, POLIMENTO e USINAGEM NÃO TRADICIONAL que é elaborada em um menu diferente do nosso site. Para a maior parte de nossa fabricação, usamos máquinas CNC. No entanto, para algumas operações, as técnicas convencionais são mais adequadas e, portanto, também confiamos nelas. Nossas capacidades de usinagem atingem o nível mais alto possível e algumas peças mais exigentes são fabricadas em uma fábrica certificada AS9100. As lâminas de motores a jato exigem experiência de fabricação altamente especializada e o equipamento certo. A indústria aeroespacial tem padrões muito rígidos. Alguns componentes com estruturas geométricas complexas são mais facilmente fabricados por usinagem de cinco eixos, que é encontrada apenas em algumas usinas, incluindo a nossa. Nossa fábrica certificada aeroespacial tem a experiência necessária em conformidade com os extensos requisitos de documentação da indústria aeroespacial. Nas operações de TORNEAMENTO, uma peça de trabalho é girada e movida contra uma ferramenta de corte. Para este processo está sendo utilizada uma máquina chamada torno. Em FRESAMENTO, uma máquina chamada fresadora possui uma ferramenta rotativa para trazer as arestas de corte para apoiar uma peça de trabalho. As operações de PERFURAÇÃO envolvem uma fresa rotativa com arestas de corte que produz furos ao entrar em contato com a peça de trabalho. Prensas de furadeira, tornos ou moinhos são geralmente usados. Nas operações de FURAÇÃO, uma ferramenta com uma única ponta dobrada é movida para um furo áspero em uma peça de trabalho giratória para aumentar um pouco o furo e melhorar a precisão. É usado para fins de acabamento fino. BROACHING envolve uma ferramenta dentada para remover o material de uma peça de trabalho em uma passagem da brocha (ferramenta dentada). No brochamento linear, a brocha corre linearmente contra uma superfície da peça de trabalho para efetuar o corte, enquanto que no brochamento rotativo, a brocha é girada e pressionada na peça de trabalho para cortar uma forma simétrica do eixo. A USINAGEM DO TIPO SUÍÇO é uma de nossas técnicas valiosas que usamos para a fabricação de alto volume de pequenas peças de alta precisão. Usando torno tipo suíço, tornamos peças pequenas, complexas e de precisão de forma econômica. Ao contrário dos tornos convencionais onde a peça de trabalho é mantida estacionária e a ferramenta em movimento, nos centros de torneamento do tipo suíço, a peça de trabalho pode se mover no eixo Z e a ferramenta fica estacionária. Na usinagem tipo suíça, o estoque da barra é retido na máquina e avançado através de uma bucha guia no eixo z, expondo apenas a parte a ser usinada. Desta forma, um aperto firme é garantido e a precisão é muito alta. A disponibilidade de ferramentas motorizadas oferece a oportunidade de fresar e perfurar à medida que o material avança da bucha guia. O eixo Y do equipamento tipo suíço oferece recursos completos de fresamento e economiza muito tempo na fabricação. Além disso, nossas máquinas possuem furadeiras e ferramentas de mandrilamento que atuam na peça quando esta é mantida no subfuso. Nossa capacidade de usinagem do tipo suíço nos dá uma oportunidade de usinagem completa totalmente automatizada em uma única operação. A usinagem é um dos maiores segmentos de negócios da AGS-TECH Inc.. Nós a usamos como uma operação primária ou uma operação secundária após a fundição ou extrusão de uma peça para que todas as especificações de desenho sejam atendidas. • SERVIÇOS DE ACABAMENTO DE SUPERFÍCIE: Oferecemos uma grande variedade de tratamentos de superfície e acabamento de superfície, como condicionamento de superfície para aumentar a adesão, deposição de fina camada de óxido para aumentar a adesão do revestimento, jateamento de areia, chem-film, anodização, nitretação, revestimento em pó, revestimento em spray , várias técnicas avançadas de metalização e revestimento, incluindo pulverização catódica, feixe de elétrons, evaporação, chapeamento, revestimentos duros, como diamante como carbono (DLC) ou revestimento de titânio para ferramentas de perfuração e corte. • SERVIÇOS DE MARCAÇÃO E ETIQUETAGEM DE PRODUTOS: Muitos de nossos clientes exigem marcação e etiquetagem, marcação a laser, gravação em peças metálicas. Se você tiver alguma necessidade, deixe-nos discutir qual opção será a melhor para você. Aqui estão alguns dos produtos fundidos de metal comumente usados. Uma vez que estes são prontos para uso, você pode economizar nos custos do molde caso algum deles atenda às suas necessidades: CLIQUE AQUI PARA BAIXAR nossas caixas de alumínio fundido da série 11 da AGS-Electronics CLICK Product Finder-Locator Service PÁGINA ANTERIOR
- Peças fabricadas sob encomenda, montagens, moldes de plástico, fundição, usinagem
Peças fabricadas sob medida, montagens, molde de plástico, moldagem de borracha, fundição de metal, usinagem CNC, torneamento, fresamento, montagem óptica eletrônica elétrica, PCBA Peças fabricadas sob encomenda, Montagens, Produtos consulte Mais informação Moldes e Moldagem de Plástico e Borracha consulte Mais informação Fundição e Usinagem consulte Mais informação Extrusões, Produtos Extrudados consulte Mais informação Estampagens e fabricação de chapas metálicas consulte Mais informação Forjamento de metais e metalurgia do pó consulte Mais informação Formação de arame e mola consulte Mais informação Moldagem e modelagem de vidro e cerâmica consulte Mais informação Fabricação Aditiva e Rápida consulte Mais informação Fabricação de Compósitos e Materiais Compósitos consulte Mais informação Processos de Junção e Montagem e Fixação Produzimos peças e conjuntos para você e oferecemos os seguintes processos de fabricação: • Moldes de plástico e borracha e peças moldadas. Moldagem por injeção, termoformagem, moldagem termofixa, moldagem a vácuo, moldagem por sopro, moldagem rotacional, moldagem por vazamento, moldagem por inserção e outros. • Extrusões de plástico, borracha e metal • Fundidos ferrosos e não ferrosos e peças usinadas produzidas por técnicas de fresamento e torneamento, usinagem tipo suíço. • Peças de metalurgia do pó • Estampagens metálicas e não metálicas, conformação de chapas metálicas, conjuntos de chapas metálicas soldadas • Forjamento a frio e a quente • Fios, conjuntos de fios soldados, formação de fios • Vários tipos de molas, formação de mola • Fabricação de engrenagens, caixa de engrenagens, acoplamento, sem-fim, redutor de velocidade, cilindro, correias de transmissão, correntes de transmissão, componentes de transmissão • Vidro temperado e à prova de balas personalizado em conformidade com os padrões militares e da OTAN • Esferas, rolamentos, polias e conjuntos de polias • Válvulas e componentes pneumáticos, como O-ring, arruela e vedações • Peças e conjuntos de vidro e cerâmica, componentes à prova de vácuo e herméticos, colagem metalo-cerâmica e cerâmica-cerâmica. • Vários tipos de montagens mecânicas, optomecânicas, eletromecânicas, optoeletrônicas. • Ligação metal-borracha, metal-plástico • Tubos e tubos, formação de tubos, dobras e conjuntos de tubos personalizados, fabricação de foles. • Fabricação de fibra de vidro • Soldagem utilizando diversas técnicas como solda a ponto, solda a laser, MIG, TIG. Soldagem ultrassônica para peças plásticas. • Vasta variedade de tratamentos de superfície e acabamentos de superfície, como condicionamento de superfície para aumentar a adesão, depósito de fina camada de óxido para aumentar a adesão do revestimento, jateamento de areia, filme químico, anodização, nitretação, revestimento em pó, revestimento por pulverização, várias técnicas avançadas de metalização e revestimento incluindo sputtering, feixe de elétrons, evaporação, chapeamento, revestimentos duros como diamante como carbono (DLC) ou titânio para ferramentas de corte e perfuração. • Marcação e rotulagem, marcação a laser em peças metálicas, impressão em peças plásticas e de borracha Faça o download do folheto para os termos comuns de engenharia mecânica usados por projetistas e engenheiros Construímos produtos de acordo com suas especificações e requisitos particulares. Para oferecer a melhor qualidade, entrega e preços, fabricamos produtos globalmente na China, Índia, Taiwan, Filipinas, Coréia do Sul, Malásia, Sri Lanka, Turquia, EUA, Canadá, Alemanha, Reino Unido e Japão. Isso nos torna muito mais fortes e globalmente mais competitivos do que qualquer outro custom manufacturer. Nossos produtos são fabricados em ambientes certificados ISO9001:2000, QS9000, ISO14001, TS16949 e possuem marca CE, UL e atendem a outros padrões da indústria. Assim que formos designados para o seu projeto, podemos cuidar de toda a fabricação, montagem, teste, qualificação, envio e alfândega como desejar. Se preferir, podemos armazenar suas peças, montar kits personalizados, imprimir e etiquetar o nome e marca da sua empresa e enviar para seus clientes. Em outras palavras, também podemos ser seu centro de armazenamento e distribuição, se preferir. Como nossos armazéns estão localizados perto dos principais portos marítimos, isso nos dá uma vantagem logística. Por exemplo, quando seus produtos chegam a um grande porto marítimo dos EUA, podemos transportá-los diretamente para um armazém próximo, onde podemos armazenar, montar, fazer kits, rotular, imprimir, embalar de acordo com sua escolha e enviar enviar para seus clientes. Não fornecemos apenas produtos. Nossa empresa trabalha em contratos personalizados, onde vamos ao seu site, avaliamos seu projeto no local e desenvolvemos uma proposta de projeto personalizada para você. Em seguida, enviamos nossa equipe experiente para implementar o projeto. Mais informações sobre nosso trabalho de engenharia podem ser encontradas em http://www.ags-engineering.com - Aceitamos projetos pequenos e grandes em escala industrial. Como primeiro passo, podemos conectá-lo por telefone, teleconferência ou MSN Messenger aos membros de nossa equipe de especialistas, para que você possa se comunicar diretamente com um especialista, fazer perguntas e discutir seu projeto. Ligue para nós e, se necessário, iremos visitá-lo. PÁGINA ANTERIOR