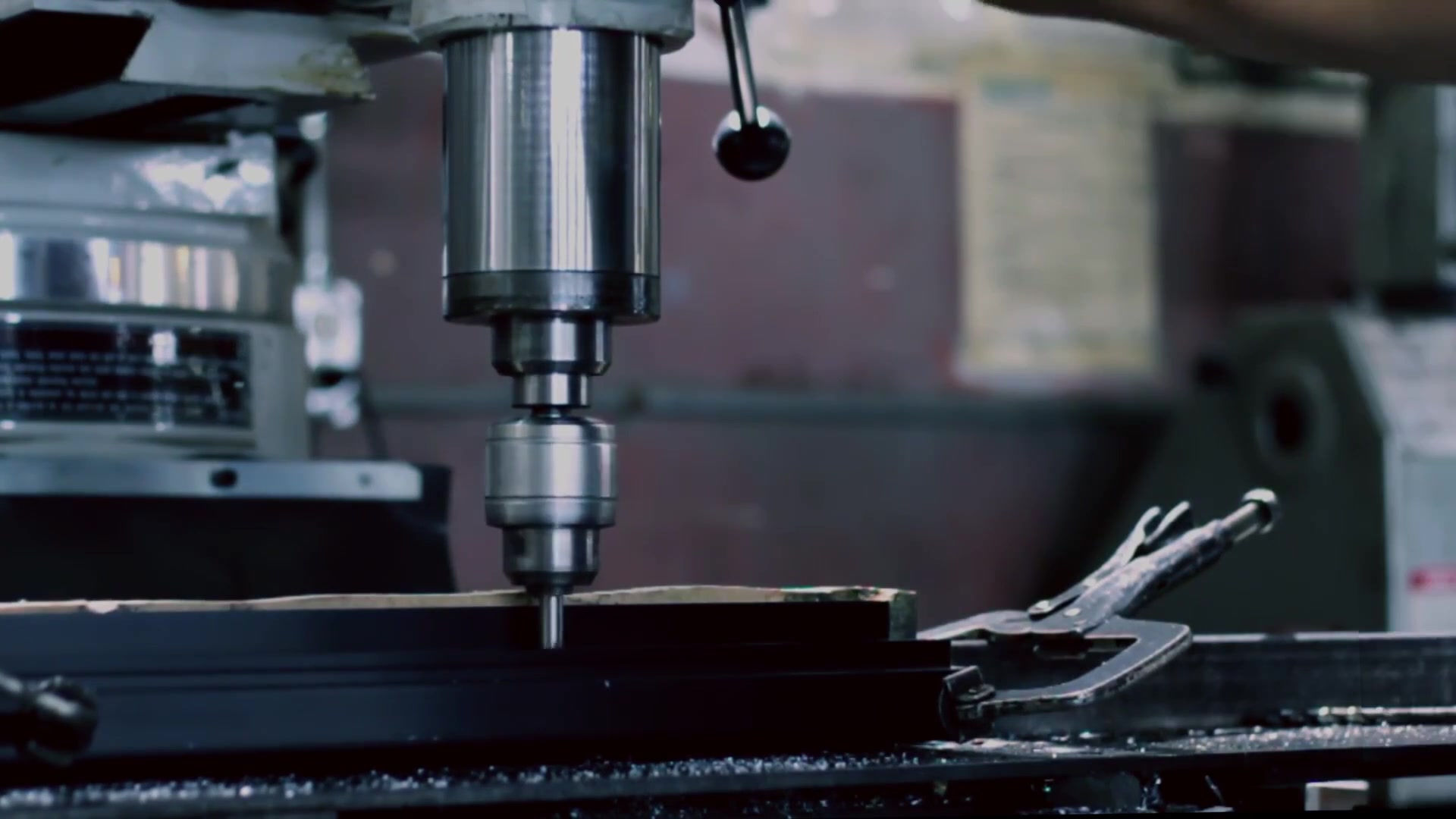
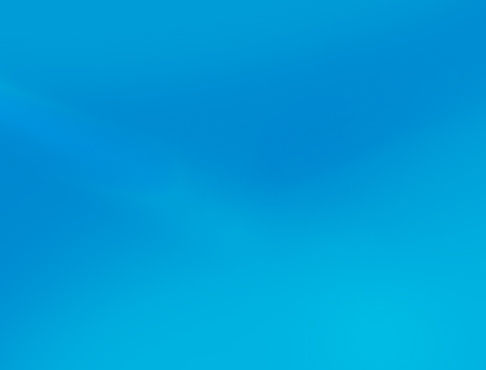
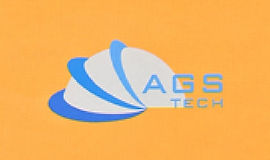
Fabricante personalizado global, integrador, consolidador, parceiro de terceirização para uma ampla variedade de produtos e serviços.
Somos sua fonte única para fabricação, fabricação, engenharia, consolidação, integração, terceirização de produtos e serviços fabricados sob encomenda e prontos para uso.
Choose your Language
-
Fabricação personalizada
-
Fabricação por contrato doméstica e global
-
Terceirização de Manufatura
-
Compras domésticas e globais
-
Consolidação
-
Integração de Engenharia
-
Serviços de engenharia
Search Results
161 resultados encontrados com uma busca vazia
- Fabricação de eletrônicos elétricos personalizados, iluminação, exibição, PCB, PCBA
Fabricação de eletrônicos elétricos personalizados, iluminação, display, tela sensível ao toque, montagem de cabos, PCB, PCBA, dispositivos sem fio, chicote de fios, componentes de micro-ondas Elétricos e eletrônicos personalizados Products Manufacturing consulte Mais informação Montagem e interconexões de cabos elétricos e eletrônicos consulte Mais informação Fabricação e montagem de PCB e PCBA consulte Mais informação Fabricação e montagem de componentes e sistemas de energia elétrica e energia consulte Mais informação Fabricação e montagem de dispositivos de RF e sem fio consulte Mais informação Fabricação e Montagem de Componentes e Sistemas de Microondas consulte Mais informação Fabricação e Montagem de Sistemas de Iluminação e Iluminação consulte Mais informação Solenóides e componentes e conjuntos eletromagnéticos consulte Mais informação Componentes e conjuntos elétricos e eletrônicos consulte Mais informação Fabricação e montagem de monitores e telas sensíveis ao toque e monitores consulte Mais informação Fabricação e Montagem de Sistemas de Automação e Robótica consulte Mais informação Sistemas Embarcados e Computadores Industriais e Painel PC consulte Mais informação Equipamento de Teste Industrial Nós oferecemos: • Montagem de Cabo Personalizado, PCB, Display e Tela Touchscreen (como iPod), Componentes de Energia e Energia, Wireless, Microondas, Componentes de Controle de Movimento, Produtos de Iluminação, Componentes Eletromagnéticos e Eletrônicos. Construímos produtos de acordo com suas especificações e requisitos particulares. Nossos produtos são fabricados em ambientes certificados ISO9001:2000, QS9000, ISO14001, TS16949 e possuem a marca CE, UL e atendem a outros padrões da indústria, como IEEE, ANSI. Uma vez nomeados para o seu projeto, podemos cuidar de toda a fabricação, montagem, testes, qualificação, envio e alfândega. Se preferir, podemos armazenar suas peças, montar kits personalizados, imprimir e etiquetar o nome e marca da sua empresa e enviar para seus clientes. Ou seja, podemos ser o seu centro de armazenamento e distribuição se assim o preferir. Como nossos armazéns estão localizados perto dos principais portos marítimos, isso nos dá uma vantagem logística. Por exemplo, quando seus produtos chegam a um grande porto marítimo dos EUA, podemos transportá-los diretamente para um armazém próximo, onde podemos armazenar, montar, fazer kits, rotular, imprimir, embalar de acordo com sua escolha e enviar para seus clientes, se desejar . Não fornecemos apenas produtos. Nossa empresa trabalha em contratos personalizados, onde vamos ao seu site, avaliamos seu projeto no local e desenvolvemos uma proposta de projeto personalizada para você. Em seguida, enviamos nossa equipe experiente para implementar o projeto. Exemplos de trabalhos contratados incluem a instalação de módulos solares, geradores eólicos, iluminação LED e sistemas de automação de economia de energia em suas instalações industriais para reduzir suas contas de energia, instalação de sistema de detecção de fibra óptica para detectar quaisquer danos em suas tubulações ou detectar possíveis intrusos invadindo sua instalações. Aceitamos pequenos projetos, bem como grandes projetos em escala industrial. Como primeiro passo, podemos conectá-lo por telefone, teleconferência ou MSN Messenger aos membros de nossa equipe de especialistas, para que você possa se comunicar diretamente com um especialista, fazer perguntas e discutir seu projeto. Se precisar iremos até você. Se você precisar de algum desses produtos ou tiver dúvidas, ligue para +1-505-550-6501 ou envie um e-mail para vendas@agstech.net Se você estiver mais interessado em nossos recursos de engenharia e pesquisa e desenvolvimento em vez de recursos de fabricação, convidamos você a visitar nosso site de engenharia http://www.ags-engineering.com CLICK Product Finder-Locator Service PÁGINA ANTERIOR
- Micromontagem e Embalagem - Fixadores Micromecânicos - Automontagem
Micromontagem e embalagem - Fixadores micromecânicos - Automontagem - Fixação micromecânica adesiva - AGS-TECH Inc. Micromontagem e Embalagem Já resumimos nossos MICRO ASSEMBLY & PACKAGING services e produtos relacionados especificamente à microeletrônica em nossa página_cc781905-5cde_3194-bb3b-136bad5cf58dFabricação de Microeletrônicos / Fabricação de Semicondutores. Aqui vamos nos concentrar em técnicas de micromontagem e embalagem mais genéricas e universais que usamos para todos os tipos de produtos, incluindo sistemas mecânicos, ópticos, microeletrônicos, optoeletrônicos e híbridos que consistem em uma combinação destes. As técnicas que discutimos aqui são mais versáteis e podem ser consideradas usadas em aplicações mais incomuns e fora do padrão. Em outras palavras, as técnicas de micro montagem e embalagem discutidas aqui são nossas ferramentas que nos ajudam a pensar “fora da caixa”. Aqui estão alguns dos nossos métodos extraordinários de micro montagem e embalagem: - Micro montagem e embalagem manual - Micromontagem e embalagem automatizadas - Métodos de automontagem, como automontagem fluídica - Micromontagem estocástica por vibração, forças gravitacionais ou eletrostáticas ou outras. - Uso de fixadores micromecânicos - Fixação micromecânica adesiva Vamos explorar algumas de nossas extraordinárias técnicas versáteis de micromontagem e embalagem com mais detalhes. MONTAGEM E EMBALAGEM MANUAL DE MICRO: As operações manuais podem ter um custo proibitivo e exigir um nível de precisão que pode ser impraticável para um operador devido à tensão que causa nos olhos e às limitações de destreza associadas à montagem dessas peças em miniatura sob um microscópio. No entanto, para aplicações especiais de baixo volume, a micromontagem manual pode ser a melhor opção, pois não requer necessariamente o projeto e a construção de sistemas automatizados de micromontagem. MICRO MONTAGEM E EMBALAGEM AUTOMATIZADA: Nossos sistemas de micromontagem são projetados para tornar a montagem mais fácil e econômica, permitindo o desenvolvimento de novas aplicações para tecnologias de micromáquinas. Podemos micromontar dispositivos e componentes nas dimensões de nível de mícrons usando sistemas robóticos. Aqui estão alguns dos nossos equipamentos e capacidades de micromontagem e embalagem automatizados: • Equipamento de controle de movimento de alto nível, incluindo uma célula de trabalho robótica com resolução de posição nanométrica • Células de trabalho orientadas por CAD totalmente automatizadas para micromontagem • Métodos de óptica de Fourier para gerar imagens sintéticas de microscópio a partir de desenhos CAD para testar rotinas de processamento de imagem sob várias ampliações e profundidades de campo (DOF) • Design personalizado e capacidade de produção de micropinças, manipuladores e atuadores para micromontagem e embalagem de precisão • Interferômetros a laser • Strain gages para feedback de força • Visão computacional em tempo real para controlar servomecanismos e motores para o microalinhamento e micromontagem de peças com tolerâncias submicrométricas • Microscópios Eletrônicos de Varredura (SEM) e Microscópios Eletrônicos de Transmissão (TEM) • Manipulador nano de 12 graus de liberdade Nosso processo de micromontagem automatizado pode colocar várias engrenagens ou outros componentes em vários postes ou locais em uma única etapa. Nossas capacidades de micromanipulação são enormes. Estamos aqui para ajudá-lo com ideias extraordinárias fora do padrão. MÉTODOS DE AUTO-MONTAGEM DE MICRO E NANO: Em processos de auto-montagem, um sistema desordenado de componentes pré-existentes forma uma estrutura ou padrão organizado como consequência de interações locais específicas entre os componentes, sem direção externa. Os componentes de automontagem experimentam apenas interações locais e normalmente obedecem a um conjunto simples de regras que governam como eles se combinam. Embora esse fenômeno seja independente de escala e possa ser utilizado para sistemas de autoconstrução e fabricação em quase todas as escalas, nosso foco está na micro automontagem e na nano automontagem. Para a construção de dispositivos microscópicos, uma das ideias mais promissoras é explorar o processo de automontagem. Estruturas complexas podem ser criadas combinando blocos de construção em circunstâncias naturais. Para dar um exemplo, é estabelecido um método para micromontagem de vários lotes de microcomponentes em um único substrato. O substrato é preparado com sítios de ligação de ouro revestidos hidrofóbicos. Para realizar a micromontagem, um óleo de hidrocarboneto é aplicado ao substrato e umedece exclusivamente os sítios de ligação hidrofóbica em água. Os microcomponentes são então adicionados à água e montados nos locais de ligação umedecidos com óleo. Ainda mais, a micromontagem pode ser controlada para ocorrer em locais de ligação desejados usando um método eletroquímico para desativar locais de ligação de substrato específicos. Ao aplicar repetidamente esta técnica, diferentes lotes de microcomponentes podem ser montados sequencialmente em um único substrato. Após o procedimento de micromontagem, ocorre a galvanoplastia para estabelecer as conexões elétricas dos componentes micromontados. MICROMONTAGEM ESTOCÁSTICA: Na micromontagem paralela, onde as peças são montadas simultaneamente, há micromontagem determinística e estocástica. Na micromontagem determinística, a relação entre a peça e seu destino no substrato é conhecida antecipadamente. Na micromontagem estocástica, por outro lado, essa relação é desconhecida ou aleatória. As peças se automontam em processos estocásticos impulsionados por alguma força motriz. Para que a micro automontagem ocorra, é necessário que haja forças de ligação, a ligação precisa ocorrer de forma seletiva e as peças de micromontagem precisam ser capazes de se mover para que possam se juntar. A micromontagem estocástica é muitas vezes acompanhada de vibrações, forças eletrostáticas, microfluídicas ou outras que atuam sobre os componentes. A micromontagem estocástica é especialmente útil quando os blocos de construção são menores, porque o manuseio dos componentes individuais se torna um desafio maior. A automontagem estocástica também pode ser observada na natureza. FIXADORES MICROMECÂNICOS: Na escala micro, os tipos convencionais de fixadores como parafusos e dobradiças não funcionarão facilmente devido às atuais restrições de fabricação e grandes forças de atrito. Por outro lado, os fechos micro snap funcionam mais facilmente em aplicações de micromontagem. Os prendedores de micro snap são dispositivos deformáveis que consistem em pares de superfícies de contato que se encaixam durante a micromontagem. Devido ao movimento de montagem simples e linear, os fechos de encaixe têm uma ampla gama de aplicações em operações de micromontagem, como dispositivos com componentes múltiplos ou em camadas, ou plugues micro opto-mecânicos, sensores com memória. Outros fixadores de micromontagem são as juntas “chave-bloqueio” e as juntas “intertravadas”. As juntas de travamento por chave consistem na inserção de uma “chave” em uma micropeça, em uma ranhura de encaixe em outra micropeça. O travamento na posição é obtido pela translação da primeira microparte dentro da outra. As juntas de travamento são criadas pela inserção perpendicular de uma micropeça com uma fenda em outra micropeça com uma fenda. As fendas criam um ajuste de interferência e são permanentes quando as micropeças são unidas. FIXAÇÃO MICROMECÂNICA ADESIVA: A fixação mecânica adesiva é usada para construir microdispositivos 3D. O processo de fixação inclui mecanismos de auto-alinhamento e colagem adesiva. Mecanismos de auto-alinhamento são implantados em micromontagem adesiva para aumentar a precisão do posicionamento. Uma micro sonda ligada a um micromanipulador robótico coleta e deposita com precisão o adesivo nos locais de destino. A luz de cura endurece o adesivo. O adesivo curado mantém as peças micro montadas em suas posições e fornece juntas mecânicas fortes. Usando adesivo condutor, uma conexão elétrica confiável pode ser obtida. A fixação mecânica adesiva requer apenas operações simples, podendo resultar em conexões confiáveis e alta precisão de posicionamento, que são importantes na micromontagem automática. Para demonstrar a viabilidade deste método, muitos dispositivos MEMS tridimensionais foram micromontados, incluindo um interruptor óptico rotativo 3D. CLICK Product Finder-Locator Service PÁGINA ANTERIOR
- Produtos industriais de couro, AGS-TECH Inc.
Produtos industriais de couro, incluindo correias de afiação e afiação, correias de transmissão de couro, correias de pedal de couro para máquinas de costura, organizadores e suportes de ferramentas de couro, coldres de armas de couro, capas de volante de couro e muito mais. Produtos Industriais de Couro Os produtos de couro industrial fabricados incluem: - Cintos de afiação e afiação de couro - Correias de transmissão de couro - Máquina de costura cinto de pedal de couro - Organizadores e suportes de ferramentas de couro - Coldres de couro para armas O couro é um produto natural com excelentes propriedades que o tornam adequado para muitas aplicações. As correias industriais de couro são utilizadas em transmissões de potência, como correias de pedal de couro para máquinas de costura, bem como na fixação, fixação, afiação e afiação de lâminas de metal, entre muitos outros. Além de nossas correias de couro industrial disponíveis em nossos folhetos, também podem ser produzidas para você correias sem fim e comprimentos/larguras especiais. As aplicações de couro industrial incluem Correia de couro plana para transmissão de energia e correia de couro redonda para máquinas de costura industriais. Industrial leather is one of the oldest types of manufactured products. Our Vegetable Tanned Industrial leathers are pit tanned for muitos meses e fortemente revestidos com uma mistura de óleos e engraxados para dar sua resistência máxima. Nossos couros industriais cromados podem ser fabricados de várias maneiras, encerado, oleado ou seco para moldagem. cc781905-5cde-3194-bb3b-136bad5cf58d_We oferece um couro chrome-retanned fabricado para suportar temperaturas muito altas e pode ser usado para aplicações hidráulicas_cc78190 3194-bb3b-136bad5cf58d_and packings. Our Chrome ed para ter propriedades de abrasão extraordinárias. Várias durezas Shore estão disponíveis. Existem muitas outras aplicações de produtos de couro industrial, incluindo organizadores de ferramentas vestíveis, porta-ferramentas, fios de couro, capas de volante... etc. Estamos aqui para ajudá-lo em seus projetos. Uma planta, um esboço, uma foto ou amostra podem servir para nos fazer entender as necessidades do seu produto. Podemos fabricar o produto de couro industrial de acordo com seu design ou podemos ajudá-lo em seu trabalho de design e, assim que você aprovar o design final, podemos fabricar o produto para você. Desde que fornecemos uma grande variedade de produtos de couro industrial com diferentes dimensões, aplicações e grau de material; é impossível listá-los todos aqui. Recomendamos que você envie um e-mail ou ligue para nós para que possamos determinar qual produto é o mais adequado para você. Ao entrar em contato conosco, certifique-se de nos informar sobre: - Sua aplicação para os produtos industriais de couro - Grau de material desejado e necessário - Dimensões - Terminar - Requisitos de embalagem - Requisitos de rotulagem - Quantidade PÁGINA ANTERIOR
- Fabricação de microeletrônica, Fabricação de semicondutores, Fundição, IC
Fabricação de microeletrônica, Fabricação de semicondutores - Fundição - FPGA - Embalagem de montagem de IC - AGS-TECH Inc. Fabricação e fabricação de microeletrônicos e semicondutores Muitas de nossas técnicas e processos de nanomanufatura, micromanufatura e mesomanufatura explicados nos outros menus podem ser usados para MICROELECTRONICS MANUFACTURING too. No entanto, devido à importância da microeletrônica em nossos produtos, vamos nos concentrar no assunto aplicações específicas desses processos aqui. Os processos relacionados à microeletrônica também são amplamente referidos como SEMICONDUCTOR FABRICATION processes. Nossos serviços de projeto e fabricação de engenharia de semicondutores incluem: - FPGA projeto, desenvolvimento e programação da placa - Microelectronics serviços de fundição: Design, prototipagem e fabricação, serviços de terceiros - Semiconductor wafer preparação: Dicing, backgrinding, desbaste, colocação de retículo, classificação de matrizes, pick and place, inspeção - Microelectronic pacote design e fabricação: Ambos off-shelf e design personalizado e fabricação - Semiconductor IC montagem e embalagem e teste: Die, ligação de fio e chip, encapsulamento, montagem, marcação e branding - Quadros de chumbo para dispositivos semicondutores: Projeto e fabricação prontos e personalizados - Design e fabricação de dissipadores de calor para microeletrônica: design e fabricação prontos e personalizados - Projeto e fabricação de sensores e atuadores: Projeto e fabricação prontos e personalizados - Projeto e fabricação de circuitos optoeletrônicos e fotônicos Vamos examinar as tecnologias de teste e fabricação de microeletrônicos e semicondutores com mais detalhes para que você possa entender melhor os serviços e produtos que oferecemos. FPGA Board Design, Desenvolvimento e Programação: Field-programmable gate arrays (FPGAs) são chips de silício reprogramáveis. Ao contrário dos processadores encontrados em computadores pessoais, a programação de um FPGA reconecta o próprio chip para implementar a funcionalidade do usuário em vez de executar um aplicativo de software. Usando blocos lógicos pré-construídos e recursos de roteamento programáveis, os chips FPGA podem ser configurados para implementar a funcionalidade de hardware personalizada sem usar uma placa de ensaio e um ferro de solda. As tarefas de computação digital são realizadas em software e compiladas em um arquivo de configuração ou fluxo de bits que contém informações sobre como os componentes devem ser conectados. Os FPGAs podem ser usados para implementar qualquer função lógica que um ASIC possa executar e são completamente reconfiguráveis e podem receber uma “personalidade” completamente diferente pela recompilação de uma configuração de circuito diferente. FPGAs combinam as melhores partes de circuitos integrados específicos de aplicação (ASICs) e sistemas baseados em processador. Esses benefícios incluem o seguinte: • Tempos de resposta de E/S mais rápidos e funcionalidade especializada • Excedendo o poder de computação dos processadores de sinal digital (DSPs) • Prototipagem e verificação rápidas sem o processo de fabricação de ASIC personalizado • Implementação de funcionalidade personalizada com a confiabilidade de hardware determinístico dedicado • Atualizável em campo, eliminando a despesa de reprojeto e manutenção personalizados do ASIC Os FPGAs fornecem velocidade e confiabilidade, sem exigir grandes volumes para justificar a grande despesa inicial do design ASIC personalizado. O silício reprogramável também tem a mesma flexibilidade do software executado em sistemas baseados em processador e não é limitado pelo número de núcleos de processamento disponíveis. Ao contrário dos processadores, os FPGAs são verdadeiramente paralelos por natureza, de modo que diferentes operações de processamento não precisam competir pelos mesmos recursos. Cada tarefa de processamento independente é atribuída a uma seção dedicada do chip e pode funcionar de forma autônoma sem qualquer influência de outros blocos lógicos. Como resultado, o desempenho de uma parte do aplicativo não é afetado quando mais processamento é adicionado. Alguns FPGAs possuem recursos analógicos além de funções digitais. Alguns recursos analógicos comuns são a taxa de variação programável e a força de acionamento em cada pino de saída, permitindo que o engenheiro defina taxas lentas em pinos levemente carregados que de outra forma tocariam ou acoplariam inaceitavelmente e definir taxas mais fortes e rápidas em pinos muito carregados em alta velocidade canais que de outra forma funcionariam muito lentamente. Outro recurso analógico relativamente comum são os comparadores diferenciais nos pinos de entrada projetados para serem conectados a canais de sinalização diferencial. Alguns FPGAs de sinal misto têm integrados conversores analógico-digital (ADCs) periféricos e conversores digital-analógico (DACs) com blocos de condicionamento de sinal analógico que lhes permitem operar como um sistema em um chip. Resumidamente, os 5 principais benefícios dos chips FPGA são: 1. Bom desempenho 2. Curto prazo de comercialização 3. Baixo custo 4. Alta confiabilidade 5. Capacidade de manutenção a longo prazo Bom desempenho – Com sua capacidade de acomodar processamento paralelo, os FPGAs têm melhor poder computacional do que os processadores de sinal digital (DSPs) e não requerem execução sequencial como DSPs e podem realizar mais por ciclos de clock. O controle de entradas e saídas (E/S) no nível do hardware fornece tempos de resposta mais rápidos e funcionalidade especializada para atender aos requisitos do aplicativo. Short Time to Market - FPGAs oferecem flexibilidade e capacidade de prototipagem rápida e, portanto, menor tempo de colocação no mercado. Nossos clientes podem testar uma ideia ou conceito e verificá-lo em hardware sem passar pelo longo e caro processo de fabricação do design ASIC personalizado. Podemos implementar mudanças incrementais e iterar em um projeto de FPGA em horas em vez de semanas. O hardware comercial de prateleira também está disponível com diferentes tipos de E/S já conectados a um chip FPGA programável pelo usuário. A crescente disponibilidade de ferramentas de software de alto nível oferece núcleos IP valiosos (funções pré-construídas) para controle avançado e processamento de sinal. Baixo custo—As despesas de engenharia não recorrente (NRE) de projetos ASIC personalizados excedem as de soluções de hardware baseadas em FPGA. O grande investimento inicial em ASICs pode ser justificado para OEMs que produzem muitos chips por ano, porém muitos usuários finais precisam de funcionalidades de hardware personalizadas para os muitos sistemas em desenvolvimento. Nosso FPGA de silício programável oferece algo sem custos de fabricação ou longos prazos de montagem. Os requisitos do sistema mudam frequentemente ao longo do tempo, e o custo de fazer alterações incrementais nos projetos de FPGA é insignificante quando comparado com a grande despesa de refazer um ASIC. Alta Confiabilidade - As ferramentas de software fornecem o ambiente de programação e os circuitos FPGA são uma verdadeira implementação da execução do programa. Os sistemas baseados em processador geralmente envolvem várias camadas de abstração para ajudar no agendamento de tarefas e compartilhar recursos entre vários processos. A camada de driver controla os recursos de hardware e o SO gerencia a memória e a largura de banda do processador. Para qualquer núcleo de processador, apenas uma instrução pode ser executada por vez, e os sistemas baseados em processador correm continuamente o risco de tarefas de tempo crítico se anteciparem umas às outras. FPGAs, não usam SOs, apresentam preocupações mínimas de confiabilidade com sua verdadeira execução paralela e hardware determinístico dedicado a cada tarefa. Capacidade de manutenção de longo prazo - os chips FPGA podem ser atualizados em campo e não exigem o tempo e o custo envolvidos no redesenho do ASIC. Os protocolos de comunicação digital, por exemplo, têm especificações que podem mudar ao longo do tempo, e as interfaces baseadas em ASIC podem causar desafios de manutenção e compatibilidade futura. Pelo contrário, os chips FPGA reconfiguráveis podem acompanhar as modificações futuras potencialmente necessárias. À medida que os produtos e sistemas amadurecem, nossos clientes podem fazer melhorias funcionais sem perder tempo redesenhando o hardware e modificando os layouts das placas. Serviços de fundição de microeletrônicos: Nossos serviços de fundição de microeletrônicos incluem design, prototipagem e fabricação, serviços de terceiros. Oferecemos assistência aos nossos clientes durante todo o ciclo de desenvolvimento do produto - desde o suporte ao projeto até a prototipagem e suporte à fabricação de chips semicondutores. Nosso objetivo em serviços de suporte de projeto é permitir uma abordagem correta de primeira para projetos digitais, analógicos e de sinais mistos de dispositivos semicondutores. Por exemplo, ferramentas de simulação específicas de MEMS estão disponíveis. Fabs que podem lidar com wafers de 6 e 8 polegadas para CMOS e MEMS integrados estão à sua disposição. Oferecemos aos nossos clientes suporte de projeto para todas as principais plataformas de automação de projeto eletrônico (EDA), fornecendo modelos corretos, kits de projeto de processo (PDK), bibliotecas analógicas e digitais e suporte de projeto para fabricação (DFM). Oferecemos duas opções de prototipagem para todas as tecnologias: o serviço Multi Product Wafer (MPW), onde vários dispositivos são processados em paralelo em um wafer, e o serviço Multi Level Mask (MLM) com quatro níveis de máscara desenhados no mesmo retículo. Estes são mais econômicos do que o conjunto completo de máscaras. O serviço MLM é altamente flexível em comparação com as datas fixas do serviço MPW. As empresas podem preferir a terceirização de produtos semicondutores a uma fundição de microeletrônicos por vários motivos, incluindo a necessidade de uma segunda fonte, uso de recursos internos para outros produtos e serviços, disposição de não fabricar e diminuir o risco e a carga de executar uma fábrica de semicondutores etc. A AGS-TECH oferece processos de fabricação de microeletrônica de plataforma aberta que podem ser reduzidos para pequenas execuções de wafer, bem como para fabricação em massa. Sob certas circunstâncias, suas ferramentas de fabricação de microeletrônicos ou MEMS existentes ou conjuntos de ferramentas completos podem ser transferidos como ferramentas consignadas ou ferramentas vendidas de sua fábrica para nosso site de fabricação, ou seus produtos microeletrônicos e MEMS existentes podem ser redesenhados usando tecnologias de processo de plataforma aberta e portados para um processo disponível em nossa fábrica. Isso é mais rápido e econômico do que uma transferência de tecnologia personalizada. Se desejado, no entanto, os processos de fabricação de microeletrônicos / MEMS existentes do cliente podem ser transferidos. Preparação de wafer semicondutor: Se desejado pelos clientes depois que os wafers são microfabricados, realizamos corte em cubos, backgrinding, desbaste, colocação de retículo, classificação de matrizes, pick and place, operações de inspeção em wafers semicondutores. O processamento de wafer semicondutor envolve metrologia entre as várias etapas de processamento. Por exemplo, métodos de teste de filme fino baseados em elipsometria ou reflectometria são usados para controlar rigidamente a espessura do óxido de porta, bem como a espessura, índice de refração e coeficiente de extinção de fotorresistência e outros revestimentos. Usamos equipamentos de teste de wafer de semicondutores para verificar se os wafers não foram danificados por etapas de processamento anteriores até o teste. Uma vez que os processos front-end tenham sido concluídos, os dispositivos microeletrônicos semicondutores são submetidos a uma variedade de testes elétricos para determinar se eles funcionam corretamente. Referimo-nos à proporção de dispositivos microeletrônicos no wafer que funcionam adequadamente como o “rendimento”. Os testes de chips microeletrônicos no wafer são realizados com um testador eletrônico que pressiona pequenas sondas contra o chip semicondutor. A máquina automatizada marca cada chip microeletrônico ruim com uma gota de corante. Os dados de teste de wafer são registrados em um banco de dados de computador central e os chips semicondutores são classificados em caixas virtuais de acordo com limites de teste predeterminados. Os dados de binning resultantes podem ser representados graficamente ou registrados em um mapa de wafer para rastrear defeitos de fabricação e marcar chips defeituosos. Este mapa também pode ser usado durante a montagem e embalagem do wafer. Nos testes finais, os chips microeletrônicos são testados novamente após a embalagem, porque os fios de ligação podem estar faltando ou o desempenho analógico pode ser alterado pela embalagem. Depois que um wafer semicondutor é testado, ele normalmente é reduzido em espessura antes que o wafer seja marcado e depois quebrado em matrizes individuais. Este processo é chamado de corte de wafer semicondutor. Usamos máquinas automáticas pick-and-place especialmente fabricadas para a indústria de microeletrônica para separar as matrizes de semicondutores boas e ruins. Apenas os chips semicondutores bons e não marcados são embalados. Em seguida, no processo de embalagem microeletrônica de plástico ou cerâmica, montamos a matriz semicondutora, conectamos as almofadas da matriz aos pinos da embalagem e selamos a matriz. Pequenos fios de ouro são usados para conectar as almofadas aos pinos usando máquinas automatizadas. O pacote de escala de chip (CSP) é outra tecnologia de embalagem microeletrônica. Um pacote em linha duplo de plástico (DIP), como a maioria dos pacotes, é várias vezes maior do que a matriz semicondutora real colocada dentro, enquanto os chips CSP são quase do tamanho da matriz microeletrônica; e um CSP pode ser construído para cada matriz antes que a pastilha semicondutora seja cortada em cubos. Os chips microeletrônicos embalados são testados novamente para garantir que não sejam danificados durante o empacotamento e que o processo de interconexão entre matriz e pino tenha sido concluído corretamente. Usando lasers, gravamos os nomes e números dos chips na embalagem. Projeto e fabricação de pacotes microeletrônicos: Oferecemos design e fabricação personalizados e prontos para uso de pacotes microeletrônicos. Como parte deste serviço, também é realizada a modelagem e simulação de pacotes microeletrônicos. A modelagem e a simulação garantem o Design de Experimentos (DoE) virtual para alcançar a solução ideal, em vez de testar pacotes em campo. Isso reduz o custo e o tempo de produção, principalmente para o desenvolvimento de novos produtos em microeletrônica. Este trabalho também nos dá a oportunidade de explicar aos nossos clientes como a montagem, confiabilidade e testes afetarão seus produtos microeletrônicos. O objetivo principal da embalagem microeletrônica é projetar um sistema eletrônico que satisfaça os requisitos de uma aplicação particular a um custo razoável. Devido às muitas opções disponíveis para interconectar e abrigar um sistema microeletrônico, a escolha de uma tecnologia de embalagem para uma determinada aplicação necessita de avaliação especializada. Os critérios de seleção para pacotes de microeletrônica podem incluir alguns dos seguintes drivers de tecnologia: -Fiabilidade -Colheita -Custo -Propriedades de dissipação de calor - Desempenho de blindagem eletromagnética -Resistência mecânica -Confiabilidade Essas considerações de projeto para pacotes microeletrônicos afetam a velocidade, funcionalidade, temperaturas de junção, volume, peso e muito mais. O objetivo principal é selecionar a tecnologia de interconexão mais econômica e confiável. Usamos métodos e softwares de análise sofisticados para projetar pacotes de microeletrônica. A embalagem de microeletrônicos lida com o projeto de métodos para a fabricação de sistemas eletrônicos em miniatura interconectados e a confiabilidade desses sistemas. Especificamente, o empacotamento de microeletrônicos envolve o roteamento de sinais, mantendo a integridade do sinal, distribuindo terra e energia para circuitos integrados de semicondutores, dispersando o calor dissipado, mantendo a integridade estrutural e do material e protegendo o circuito contra riscos ambientais. Geralmente, os métodos para empacotar CIs microeletrônicos envolvem o uso de um PWB com conectores que fornecem as E/S do mundo real para um circuito eletrônico. As abordagens tradicionais de empacotamento de microeletrônica envolvem o uso de pacotes únicos. A principal vantagem de um pacote de chip único é a capacidade de testar completamente o IC microeletrônico antes de interconectar ao substrato subjacente. Esses dispositivos semicondutores embalados são montados em orifícios ou montados em superfície no PWB. Os pacotes de microeletrônicos montados na superfície não requerem orifícios para atravessar toda a placa. Em vez disso, os componentes microeletrônicos montados na superfície podem ser soldados em ambos os lados do PWB, permitindo maior densidade do circuito. Essa abordagem é chamada de tecnologia de montagem em superfície (SMT). A adição de pacotes estilo array de área, como arrays ball-grid (BGAs) e pacotes de escala de chip (CSPs), está tornando o SMT competitivo com as tecnologias de empacotamento de microeletrônica de semicondutores de alta densidade. Uma tecnologia de embalagem mais recente envolve a conexão de mais de um dispositivo semicondutor em um substrato de interconexão de alta densidade, que é então montado em um pacote grande, fornecendo pinos de E/S e proteção ambiental. Essa tecnologia de módulo multichip (MCM) é caracterizada ainda pelas tecnologias de substrato usadas para interconectar os ICs conectados. MCM-D representa metal de filme fino depositado e multicamadas dielétricas. Os substratos MCM-D têm as densidades de fiação mais altas de todas as tecnologias MCM, graças às sofisticadas tecnologias de processamento de semicondutores. MCM-C refere-se a substratos “cerâmicos” multicamadas, disparados de camadas alternadas empilhadas de tintas metálicas peneiradas e folhas de cerâmica não queimadas. Usando o MCM-C obtemos uma capacidade de fiação moderadamente densa. MCM-L refere-se a substratos multicamadas feitos de “laminados” de PWB metalizados empilhados, que são padronizados individualmente e depois laminados. Costumava ser uma tecnologia de interconexão de baixa densidade, mas agora o MCM-L está se aproximando rapidamente da densidade das tecnologias de embalagem microeletrônica MCM-C e MCM-D. A tecnologia de empacotamento de microeletrônicos de conexão direta de chip (DCA) ou chip-on-board (COB) envolve a montagem dos CIs de microeletrônicos diretamente no PWB. Um encapsulante de plástico, que é “globbed” sobre o IC nu e depois curado, fornece proteção ambiental. Os CIs de microeletrônica podem ser interconectados ao substrato usando métodos de flip-chip ou de ligação por fio. A tecnologia DCA é particularmente econômica para sistemas limitados a 10 ou menos CIs semicondutores, pois um número maior de chips pode afetar o rendimento do sistema e os conjuntos DCA podem ser difíceis de retrabalhar. Uma vantagem comum às opções de empacotamento DCA e MCM é a eliminação do nível de interconexão do pacote IC semicondutor, que permite maior proximidade (atrasos de transmissão de sinal mais curtos) e indutância de chumbo reduzida. A principal desvantagem de ambos os métodos é a dificuldade em adquirir CIs microeletrônicos totalmente testados. Outras desvantagens das tecnologias DCA e MCM-L incluem má gestão térmica graças à baixa condutividade térmica dos laminados PWB e um coeficiente de expansão térmica pobre entre a matriz semicondutora e o substrato. Resolver o problema de incompatibilidade de expansão térmica requer um substrato de interposição, como molibdênio para matrizes ligadas por fio e um epóxi de preenchimento insuficiente para matrizes flip-chip. O módulo de portadora multichip (MCCM) combina todos os aspectos positivos do DCA com a tecnologia MCM. O MCCM é simplesmente um pequeno MCM em um suporte de metal fino que pode ser colado ou mecanicamente conectado a um PWB. O fundo de metal atua tanto como um dissipador de calor quanto como um intermediário de tensão para o substrato MCM. O MCCM possui terminais periféricos para ligação de fios, solda ou ligação de guias a um PWB. CIs semicondutores nus são protegidos usando um material glob-top. Quando você entrar em contato conosco, discutiremos sua aplicação e requisitos para escolher a melhor opção de embalagem microeletrônica para você. Montagem, embalagem e teste de IC de semicondutores: Como parte de nossos serviços de fabricação de microeletrônicos, oferecemos colagem de matrizes, fios e chips, encapsulamento, montagem, marcação e branding, testes. Para que um chip semicondutor ou circuito integrado de microeletrônica funcione, ele precisa estar conectado ao sistema que ele controlará ou fornecerá instruções. O conjunto de IC da Microeletrônica fornece as conexões para transferência de energia e informações entre o chip e o sistema. Isso é feito conectando o chip microeletrônico a um pacote ou conectando-o diretamente ao PCB para essas funções. As conexões entre o chip e o pacote ou placa de circuito impresso (PCB) são por meio de ligação de fio, através de furo ou conjunto de chip flip. Somos líderes do setor na busca de soluções de empacotamento de microeletrônicos IC para atender aos complexos requisitos dos mercados sem fio e de internet. Oferecemos milhares de formatos e tamanhos de pacotes diferentes, desde os tradicionais pacotes IC microeletrônicos de leadframe para montagem em orifício e superfície, até as mais recentes soluções de escala de chip (CSP) e matriz de grade de esferas (BGA) necessárias em aplicações de alta contagem de pinos e alta densidade . Uma grande variedade de pacotes estão disponíveis em estoque, incluindo CABGA (Chip Array BGA), CQFP, CTBGA (Chip Array Thin Core BGA), CVBGA (Very Thin Chip Array BGA), Flip Chip, LCC, LGA, MQFP, PBGA, PDIP, PLCC, PoP - Package on Package, PoP TMV - Via Molde, SOIC / SOJ, SSOP, TQFP, TSOP, WLP (Wafer Level Package)…..etc. A ligação de fios usando cobre, prata ou ouro está entre as mais populares em microeletrônica. O fio de cobre (Cu) tem sido um método de conexão de matrizes semicondutoras de silício aos terminais do pacote microeletrônico. Com o recente aumento no custo do fio de ouro (Au), o fio de cobre (Cu) é uma maneira atraente de gerenciar o custo geral do pacote em microeletrônica. Também se assemelha ao fio de ouro (Au) devido às suas propriedades elétricas semelhantes. A autoindutância e a autocapacitância são quase as mesmas para fios de ouro (Au) e cobre (Cu) com fios de cobre (Cu) com menor resistividade. Em aplicações de microeletrônica onde a resistência devido ao fio de ligação pode afetar negativamente o desempenho do circuito, o uso de fio de cobre (Cu) pode oferecer melhorias. Os fios de liga de cobre, cobre revestido com paládio (PCC) e prata (Ag) surgiram como alternativas aos fios de ligação de ouro devido ao custo. Os fios à base de cobre são baratos e têm baixa resistividade elétrica. No entanto, a dureza do cobre dificulta o uso em muitas aplicações, como aquelas com estruturas frágeis de pastilhas adesivas. Para essas aplicações, o Ag-Alloy oferece propriedades semelhantes às do ouro enquanto seu custo é semelhante ao do PCC. O fio Ag-Alloy é mais macio que o PCC, resultando em menor Al-Splash e menor risco de danos na almofada de ligação. O fio Ag-Alloy é o melhor substituto de baixo custo para aplicações que precisam de ligação die-to-die, ligação em cascata, passo de almofada de ligação ultrafina e pequenas aberturas de almofada de ligação, altura de loop ultra baixa. Fornecemos uma gama completa de serviços de teste de semicondutores, incluindo teste de wafer, vários tipos de teste final, teste de nível de sistema, teste de tira e serviços completos de fim de linha. Testamos uma variedade de tipos de dispositivos semicondutores em todas as nossas famílias de pacotes, incluindo radiofrequência, sinal analógico e misto, digital, gerenciamento de energia, memória e várias combinações, como ASIC, módulos com vários chips, System-in-Package (SiP) e embalagens 3D empilhadas, sensores e dispositivos MEMS, como acelerômetros e sensores de pressão. Nosso hardware de teste e equipamentos de contato são adequados para tamanho de pacote personalizado SiP, soluções de contato de dupla face para Package on Package (PoP), TMV PoP, soquetes FusionQuad, MicroLeadFrame de várias linhas, Pilar de cobre de passo fino. Os equipamentos de teste e os pisos de teste são integrados com ferramentas CIM/CAM, análise de rendimento e monitoramento de desempenho para fornecer rendimento de eficiência muito alto na primeira vez. Oferecemos vários processos de teste de microeletrônica adaptável para nossos clientes e oferecemos fluxos de teste distribuídos para SiP e outros fluxos de montagem complexos. A AGS-TECH fornece uma gama completa de serviços de consultoria, desenvolvimento e engenharia de testes em todo o ciclo de vida de seus produtos de semicondutores e microeletrônicos. Entendemos os mercados exclusivos e os requisitos de teste para SiP, automotivo, rede, jogos, gráficos, computação, RF/sem fio. Os processos de fabricação de semicondutores exigem soluções de marcação rápidas e controladas com precisão. Velocidades de marcação acima de 1.000 caracteres/segundo e profundidades de penetração de material inferiores a 25 mícrons são comuns na indústria de microeletrônica de semicondutores usando lasers avançados. Somos capazes de marcar compostos de moldes, wafers, cerâmicas e muito mais com entrada de calor mínima e repetibilidade perfeita. Usamos lasers com alta precisão para marcar até as peças menores sem danos. Estruturas de chumbo para dispositivos semicondutores: São possíveis projetos e fabricação prontos e personalizados. As estruturas de chumbo são utilizadas nos processos de montagem de dispositivos semicondutores e são essencialmente camadas finas de metal que conectam a fiação de minúsculos terminais elétricos na superfície da microeletrônica semicondutora aos circuitos de grande escala em dispositivos elétricos e PCBs. Quadros de chumbo são usados em quase todos os pacotes de microeletrônica de semicondutores. A maioria dos pacotes de microeletrônicos IC são feitos colocando o chip de silício semicondutor em uma estrutura de chumbo, depois ligando o chip aos fios de metal dessa estrutura de chumbo e, posteriormente, cobrindo o chip microeletrônico com uma cobertura plástica. Esta embalagem microeletrônica simples e de custo relativamente baixo ainda é a melhor solução para muitas aplicações. Os quadros de chumbo são produzidos em tiras longas, o que permite que sejam processados rapidamente em máquinas de montagem automatizadas, e geralmente são utilizados dois processos de fabricação: fotogravação de algum tipo e estampagem. Na microeletrônica, o projeto de estrutura de chumbo geralmente exige especificações e recursos personalizados, projetos que melhorem as propriedades elétricas e térmicas e requisitos específicos de tempo de ciclo. Temos uma experiência profunda na fabricação de quadros de chumbo de microeletrônica para uma variedade de clientes diferentes usando gravação e estampagem de fotos assistidas a laser. Projeto e fabricação de dissipadores de calor para microeletrônica: Projeto e fabricação prontos e personalizados. Com o aumento da dissipação de calor dos dispositivos microeletrônicos e a redução nos fatores de forma gerais, o gerenciamento térmico se torna um elemento mais importante do design de produtos eletrônicos. A consistência no desempenho e a expectativa de vida dos equipamentos eletrônicos estão inversamente relacionadas à temperatura dos componentes do equipamento. A relação entre a confiabilidade e a temperatura de operação de um dispositivo semicondutor de silício típico mostra que uma redução na temperatura corresponde a um aumento exponencial na confiabilidade e expectativa de vida do dispositivo. Portanto, a longa vida útil e o desempenho confiável de um componente microeletrônico semicondutor podem ser alcançados controlando efetivamente a temperatura de operação do dispositivo dentro dos limites estabelecidos pelos projetistas. Dissipadores de calor são dispositivos que aumentam a dissipação de calor de uma superfície quente, geralmente a caixa externa de um componente gerador de calor, para um ambiente mais frio, como o ar. Para as discussões a seguir, assume-se que o ar é o fluido de resfriamento. Na maioria das situações, a transferência de calor através da interface entre a superfície sólida e o ar refrigerante é a menos eficiente dentro do sistema, e a interface sólido-ar representa a maior barreira para a dissipação de calor. Um dissipador de calor reduz essa barreira principalmente aumentando a área da superfície que está em contato direto com o refrigerante. Isso permite que mais calor seja dissipado e/ou reduza a temperatura de operação do dispositivo semicondutor. O objetivo principal de um dissipador de calor é manter a temperatura do dispositivo microeletrônico abaixo da temperatura máxima permitida especificada pelo fabricante do dispositivo semicondutor. Podemos classificar os dissipadores de calor em termos de métodos de fabricação e suas formas. Os tipos mais comuns de dissipadores de calor refrigerados a ar incluem: - Estampagem: As chapas de cobre ou alumínio são estampadas nas formas desejadas. eles são usados no resfriamento a ar tradicional de componentes eletrônicos e oferecem uma solução econômica para problemas térmicos de baixa densidade. Eles são adequados para produção de alto volume. - Extrusão: Estes dissipadores de calor permitem a formação de elaboradas formas bidimensionais capazes de dissipar grandes cargas de calor. Eles podem ser cortados, usinados e opcionais adicionados. Um corte transversal produzirá dissipadores de calor de aletas retangulares e omnidirecionais, e a incorporação de aletas serrilhadas melhora o desempenho em aproximadamente 10 a 20%, mas com uma taxa de extrusão mais lenta. Os limites de extrusão, como a altura da aleta até a espessura da aleta, geralmente determinam a flexibilidade nas opções de projeto. A relação de aspecto altura/espaço da aleta típica de até 6 e uma espessura mínima da aleta de 1,3 mm são atingíveis com técnicas de extrusão padrão. Uma proporção de 10 para 1 e uma espessura de aleta de 0,8″ podem ser obtidas com recursos especiais de design de matriz. No entanto, à medida que a proporção aumenta, a tolerância de extrusão é comprometida. - Aletas coladas/fabricadas: A maioria dos dissipadores de calor resfriados a ar é limitada por convecção, e o desempenho térmico geral de um dissipador de calor resfriado a ar pode ser melhorado significativamente se mais área de superfície puder ser exposta ao fluxo de ar. Esses dissipadores de calor de alto desempenho utilizam epóxi preenchido com alumínio termicamente condutor para unir aletas planas em uma placa de base de extrusão ranhurada. Esse processo permite uma relação de aspecto entre altura e folga da aleta muito maior de 20 a 40, aumentando significativamente a capacidade de resfriamento sem aumentar a necessidade de volume. - Fundições: Os processos de areia, cera perdida e fundição sob pressão para alumínio ou cobre/bronze estão disponíveis com ou sem assistência a vácuo. Usamos essa tecnologia para a fabricação de dissipadores de calor de aletas de pino de alta densidade que proporcionam o máximo desempenho ao usar o resfriamento de impacto. - Aletas Dobradas: A chapa corrugada de alumínio ou cobre aumenta a área superficial e o desempenho volumétrico. O dissipador de calor é então fixado a uma placa de base ou diretamente à superfície de aquecimento por meio de epóxi ou brasagem. Não é adequado para dissipadores de calor de alto perfil devido à disponibilidade e eficiência das aletas. Assim, permite a fabricação de dissipadores de calor de alto desempenho. Ao selecionar um dissipador de calor adequado que atenda aos critérios térmicos necessários para suas aplicações de microeletrônica, precisamos examinar vários parâmetros que afetam não apenas o desempenho do dissipador de calor em si, mas também o desempenho geral do sistema. A escolha de um tipo particular de dissipador de calor em microeletrônica depende em grande parte do balanço térmico permitido para o dissipador de calor e das condições externas ao redor do dissipador de calor. Nunca há um único valor de resistência térmica atribuído a um determinado dissipador de calor, pois a resistência térmica varia com as condições externas de resfriamento. Projeto e fabricação de sensores e atuadores: Estão disponíveis projetos e fabricação prontos e personalizados. Oferecemos soluções com processos prontos para uso para sensores inerciais, sensores de pressão e pressão relativa e dispositivos sensores de temperatura IR. Usando nossos blocos IP para acelerômetros, sensores IR e de pressão ou aplicando seu projeto de acordo com as especificações e regras de projeto disponíveis, podemos ter dispositivos de sensores baseados em MEMS entregues a você dentro de semanas. Além do MEMS, outros tipos de estruturas de sensores e atuadores podem ser fabricados. Projeto e fabricação de circuitos optoeletrônicos e fotônicos: Um circuito integrado fotônico ou óptico (PIC) é um dispositivo que integra várias funções fotônicas. Pode ser semelhante a circuitos integrados eletrônicos em microeletrônica. A principal diferença entre os dois é que um circuito integrado fotônico fornece funcionalidade para sinais de informação impostos em comprimentos de onda ópticos no espectro visível ou infravermelho próximo 850 nm-1650 nm. As técnicas de fabricação são semelhantes às usadas em circuitos integrados de microeletrônica, onde a fotolitografia é usada para padronizar wafers para gravação e deposição de material. Ao contrário da microeletrônica de semicondutores, onde o dispositivo primário é o transistor, não há um único dispositivo dominante na optoeletrônica. Os chips fotônicos incluem guias de onda de interconexão de baixa perda, divisores de potência, amplificadores ópticos, moduladores ópticos, filtros, lasers e detectores. Esses dispositivos requerem uma variedade de materiais e técnicas de fabricação diferentes e, portanto, é difícil realizar todos eles em um único chip. Nossas aplicações de circuitos integrados fotônicos são principalmente nas áreas de comunicação por fibra óptica, computação biomédica e fotônica. Alguns exemplos de produtos optoeletrônicos que podemos projetar e fabricar para você são LEDs (diodos emissores de luz), lasers de diodo, receptores optoeletrônicos, fotodiodos, módulos de distância a laser, módulos de laser personalizados e muito mais. CLICK Product Finder-Locator Service PÁGINA ANTERIOR
- Usinagem por jato de água, corte WJ, jato de água abrasivo, WJM, AWJM, AJM
Usinagem por Jato de Água - Corte WJ - Jato de Água Abrasivo - Usinagem Hidrodinâmica - WJM - AWJM - AJM - AGS-TECH Inc. Usinagem com Jato de Água e Jato de Água Abrasivo e Usinagem e Corte com Jato de Água The principle of operation of WATER-JET, ABRASIVE WATER-JET and ABRASIVE-JET MACHINING & CUTTING is based na mudança de impulso do fluxo rápido que atinge a peça de trabalho. Durante esta mudança de momento, uma forte força atua e corta a peça de trabalho. Estas WATERJET CUTTING & USINING (WJM) techniques são baseadas em água e abrasivos altamente refinados, impulsionados a três vezes a velocidade do som, para fazer cortes incrivelmente precisos e precisos em praticamente qualquer material. Para alguns materiais como couro e plástico, um abrasivo pode ser omitido e o corte pode ser feito apenas com água. A usinagem com jato de água pode fazer coisas que outras técnicas não podem, desde o corte de detalhes intrincados e muito finos em pedra, vidro e metais; para furação rápida de titânio. Nossas máquinas de corte por jato de água podem manusear grandes materiais planos com muitos pés de dimensões sem limite para o tipo de material. Para fazer cortes e fabricar peças, podemos digitalizar imagens de arquivos para o computador ou um Desenho Auxiliado por Computador (CAD) do seu projeto pode ser preparado por nossos engenheiros. Precisamos determinar o tipo de material a ser cortado, sua espessura e a qualidade de corte desejada. Projetos intrincados não apresentam problemas, pois o bico simplesmente segue o padrão da imagem renderizada. Os designs são limitados apenas pela sua imaginação. Contacte-nos hoje com o seu projeto e deixe-nos dar-lhe as nossas sugestões e orçamento. Vamos examinar esses três tipos de processos em detalhes. USINAGEM A JATO DE ÁGUA (WJM): O processo também pode ser chamado HYDRODYNAMIC USINING. As forças altamente localizadas do jato de água são usadas para operações de corte e rebarbação. Em palavras mais simples, o jato de água age como uma serra que corta um sulco estreito e liso no material. Os níveis de pressão na usinagem com jato de água são de cerca de 400 MPa, o que é bastante suficiente para uma operação eficiente. Se necessário, podem ser geradas pressões que sejam algumas vezes este valor. Os diâmetros dos bicos de jato estão na vizinhança de 0,05 a 1 mm. Cortamos uma variedade de materiais não metálicos, como tecidos, plásticos, borracha, couro, materiais isolantes, papel, materiais compostos usando os cortadores de jato de água. Mesmo formas complicadas, como revestimentos de painéis automotivos feitos de vinil e espuma, podem ser cortadas usando equipamentos de usinagem a jato de água controlados por CNC de vários eixos. A usinagem por jato de água é um processo eficiente e limpo quando comparado a outros processos de corte. Algumas das principais vantagens desta técnica são: -Os cortes podem ser iniciados em qualquer local da peça de trabalho sem a necessidade de pré-perfuração. -Nenhum calor significativo é produzido -O processo de usinagem e corte por jato de água é adequado para materiais flexíveis porque não ocorre deflexão e dobra da peça de trabalho. -As rebarbas produzidas são mínimas -Corte e usinagem com jato de água é um processo ambientalmente amigável e seguro que usa água. USINAGEM A JATO DE ÁGUA ABRASIVO (AWJM): Neste processo, partículas abrasivas como carbeto de silício ou óxido de alumínio são contidas no jato de água. Isso aumenta a taxa de remoção de material em relação à usinagem puramente com jato de água. Materiais metálicos, não metálicos, compostos e outros podem ser cortados usando AWJM. A técnica é particularmente útil para nós no corte de materiais sensíveis ao calor que não podemos cortar usando outras técnicas que produzem calor. Podemos produzir furos de tamanho mínimo de 3 mm e profundidades máximas de cerca de 25 mm. A velocidade de corte pode chegar a vários metros por minuto, dependendo do material que está sendo usinado. Para metais, a velocidade de corte em AWJM é menor em comparação com plásticos. Usando nossas máquinas de controle robótico de múltiplos eixos, podemos usinar peças tridimensionais complexas para terminar as dimensões sem a necessidade de um segundo processo. Para manter as dimensões e o diâmetro do bico constantes, usamos bicos de safira, o que é importante para manter a precisão e a repetibilidade das operações de corte. USINAGEM A JATO ABRASIVO (AJM) : Neste processo, um jato de ar seco, nitrogênio ou dióxido de carbono contendo partículas abrasivas em alta velocidade atinge e corta a peça sob condições controladas. A Usinagem a Jato Abrasivo é usada para cortar pequenos furos, ranhuras e padrões intrincados em materiais metálicos e não metálicos muito duros e quebradiços, rebarbar e remover rebarbas de peças, aparar e chanfrar, remover filmes superficiais como óxidos, limpeza de componentes com superfícies irregulares. As pressões do gás são em torno de 850 kPa e as velocidades do jato abrasivo em torno de 300 m/s. As partículas abrasivas têm diâmetros em torno de 10 a 50 mícrons. As partículas abrasivas de alta velocidade arredondam os cantos afiados e os furos feitos tendem a ser cônicos. Portanto, projetistas de peças que serão usinadas por jato abrasivo devem levar isso em consideração e certificar-se de que as peças produzidas não necessitem de cantos e furos afiados. Os processos de usinagem por jato de água, jato de água abrasivo e jato abrasivo podem ser usados de forma eficaz para operações de corte e rebarbação. Estas técnicas têm uma flexibilidade inerente graças ao facto de não utilizarem ferramentas duras. CLICK Product Finder-Locator Service PÁGINA ANTERIOR
- Usinagem a Plasma, Corte a Plasma HF, Goivagem a Plasma, CNC, Soldagem a Arco
Usinagem a plasma - Corte a plasma HF - Goivagem a plasma - CNC - Soldagem a arco plasma - PAW - GTAW - AGS-TECH Inc. Usinagem e corte a plasma We use the PLASMA CUTTING and PLASMA MACHINING processes to cut and machine steel, aluminum, metals and other materials of espessuras diferentes usando uma tocha de plasma. No corte a plasma (também chamado às vezes PLASMA-ARC CUTTING), um gás inerte ou ar comprimido é soprado em alta velocidade de um bocal e simultaneamente um arco elétrico é formado através desse gás do bocal para a superfície sendo cortada, transformando uma parte desse gás em plasma. Para simplificar, o plasma pode ser descrito como o quarto estado da matéria. Os três estados da matéria são sólido, líquido e gasoso. Para um exemplo comum, a água, esses três estados são gelo, água e vapor. A diferença entre esses estados está relacionada aos seus níveis de energia. Quando adicionamos energia na forma de calor ao gelo, ele derrete e forma água. Quando adicionamos mais energia, a água vaporiza na forma de vapor. Ao adicionar mais energia ao vapor, esses gases tornam-se ionizados. Este processo de ionização faz com que o gás se torne eletricamente condutor. Chamamos esse gás ionizado eletricamente condutor de “plasma”. O plasma é muito quente e derrete o metal que está sendo cortado e, ao mesmo tempo, sopra o metal fundido para longe do corte. Usamos plasma para cortar materiais finos e grossos, ferrosos e não ferrosos. Nossas tochas manuais geralmente podem cortar chapas de aço de até 2 polegadas de espessura, e nossas tochas mais fortes controladas por computador podem cortar aço de até 6 polegadas de espessura. Os cortadores de plasma produzem um cone muito quente e localizado para cortar e, portanto, são muito adequados para cortar chapas de metal em formas curvas e angulares. As temperaturas geradas no corte a plasma são muito altas e em torno de 9673 Kelvin na tocha de plasma de oxigênio. Isso nos oferece um processo rápido, pequena largura de corte e bom acabamento superficial. Em nossos sistemas usando eletrodos de tungstênio, o plasma é inerte, formado usando gases de argônio, argônio-H2 ou nitrogênio. No entanto, às vezes também usamos gases oxidantes, como ar ou oxigênio, e nesses sistemas o eletrodo é de cobre com háfnio. A vantagem de uma tocha de plasma de ar é que ela usa ar em vez de gases caros, reduzindo potencialmente o custo total de usinagem. Nossas máquinas HF-TYPE PLASMA CUTTING machines usam uma faísca de alta frequência e alta tensão para ionizar o ar através da cabeça da tocha e iniciar arcos. Nossos cortadores a plasma HF não exigem que a tocha esteja em contato com o material da peça de trabalho no início e são adequados para aplicações envolvendo COMPUTER NUMERICAL CONTROL (CNC) cutting. Outros fabricantes estão usando máquinas primitivas que exigem contato da ponta com o metal original para iniciar e, em seguida, ocorre a separação do intervalo. Esses cortadores de plasma mais primitivos são mais suscetíveis a danos na ponta de contato e no escudo na partida. Nossas PILOT-ARC TIPO PLASMA machines usam um processo de duas etapas para produzir plasma, sem a necessidade de contato inicial. Na primeira etapa, um circuito de alta tensão e baixa corrente é usado para inicializar uma faísca de alta intensidade muito pequena dentro do corpo da tocha, gerando uma pequena bolsa de gás de plasma. Isso é chamado de arco piloto. O arco piloto tem um caminho elétrico de retorno embutido na cabeça da tocha. O arco piloto é mantido e preservado até que seja aproximado da peça de trabalho. Lá, o arco piloto acende o arco principal de corte a plasma. Os arcos de plasma são extremamente quentes e estão na faixa de 25.000 °C = 45.000 °F. Um método mais tradicional que também implantamos é OXYFUEL-GAS CUTTING (OFC) onde usamos uma tocha como na soldagem. A operação é utilizada no corte de aço, ferro fundido e aço fundido. O princípio de corte no corte oxicombustível é baseado na oxidação, queima e fusão do aço. As larguras de corte no corte a oxicorte estão em torno de 1,5 a 10 mm. O processo de arco de plasma tem sido visto como uma alternativa ao processo de oxi-combustível. O processo de arco de plasma difere do processo de oxi-combustível, pois opera usando o arco para derreter o metal, enquanto no processo de oxi-combustível, o oxigênio oxida o metal e o calor da reação exotérmica derrete o metal. Portanto, ao contrário do processo de oxi-combustível, o processo de plasma pode ser aplicado para cortar metais que formam óxidos refratários, como aço inoxidável, alumínio e ligas não ferrosas. GOUGING PLASMA um processo semelhante ao corte a plasma, normalmente é realizado com o mesmo equipamento que o corte a plasma. Em vez de cortar o material, a goivagem a plasma usa uma configuração de tocha diferente. O bico da tocha e o difusor de gás são geralmente diferentes, e uma distância maior da tocha à peça de trabalho é mantida para soprar o metal. A goivagem a plasma pode ser usada em várias aplicações, incluindo a remoção de uma solda para retrabalho. Alguns dos nossos cortadores de plasma são embutidos na mesa CNC. As mesas CNC têm um computador para controlar a cabeça da tocha para produzir cortes limpos e precisos. Nosso moderno equipamento de plasma CNC é capaz de cortar materiais espessos em vários eixos e permite oportunidades para costuras de soldagem complexas que não são possíveis de outra forma. Nossos cortadores de arco de plasma são altamente automatizados através do uso de controles programáveis. Para materiais mais finos, preferimos o corte a laser ao corte a plasma, principalmente devido às habilidades superiores de corte de furos do nosso cortador a laser. Também implantamos máquinas de corte a plasma CNC verticais, oferecendo-nos um espaço menor, maior flexibilidade, melhor segurança e operação mais rápida. A qualidade da aresta de corte a plasma é semelhante à obtida com os processos de corte oxi-combustível. No entanto, como o processo de plasma corta por fusão, uma característica é o maior grau de fusão em direção ao topo do metal, resultando em arredondamento da borda superior, baixa esquadria da borda ou um chanfro na borda cortada. Usamos novos modelos de tochas de plasma com um bico menor e um arco de plasma mais fino para melhorar a constrição do arco e produzir um aquecimento mais uniforme na parte superior e inferior do corte. Isso nos permite obter precisão próxima do laser no corte a plasma e nas bordas usinadas. Nossos CORTE A ARCO DE PLASMA DE ALTA TOLERÂNCIA (HTPAC) systems operam com um plasma altamente restrito. A focagem do plasma é obtida forçando o plasma gerado pelo oxigênio a girar à medida que entra no orifício do plasma e um fluxo secundário de gás é injetado a jusante do bocal de plasma. Temos um campo magnético separado em torno do arco. Isso estabiliza o jato de plasma, mantendo a rotação induzida pelo gás em turbilhão. Ao combinar o controle CNC de precisão com essas tochas menores e mais finas, somos capazes de produzir peças que exigem pouco ou nenhum acabamento. As taxas de remoção de material na usinagem a plasma são muito maiores do que nos processos de Usinagem por Descarga Elétrica (EDM) e Usinagem por Feixe de Laser (LBM), e as peças podem ser usinadas com boa reprodutibilidade. SOLDA A ARCO PLASMA (PAW) é um processo semelhante à soldagem a arco de tungstênio a gás (GTAW). O arco elétrico é formado entre um eletrodo geralmente feito de tungstênio sinterizado e a peça de trabalho. A principal diferença do GTAW é que no PAW, ao posicionar o eletrodo dentro do corpo da tocha, o arco de plasma pode ser separado do invólucro do gás de proteção. O plasma é então forçado através de um bocal de cobre de furo fino que contrai o arco e o plasma que sai do orifício em altas velocidades e temperaturas próximas de 20.000 °C. A soldagem a arco de plasma é um avanço em relação ao processo GTAW. O processo de soldagem PAW utiliza um eletrodo de tungstênio não consumível e um arco constrito através de um bico de cobre de furo fino. PAW pode ser usado para unir todos os metais e ligas que são soldáveis com GTAW. Várias variações básicas do processo PAW são possíveis variando a corrente, a taxa de fluxo de gás de plasma e o diâmetro do orifício, incluindo: Microplasma (< 15 Amperes) Modo de fusão (15–400 Amperes) Modo Keyhole (>100 Amperes) Na soldagem a arco plasma (PAW) obtemos uma maior concentração de energia em relação à GTAW. A penetração profunda e estreita é possível, com uma profundidade máxima de 12 a 18 mm (0,47 a 0,71 pol.), dependendo do material. A maior estabilidade do arco permite um comprimento de arco muito maior (stand-off) e uma tolerância muito maior a mudanças no comprimento do arco. Como desvantagem, no entanto, o PAW requer equipamentos relativamente caros e complexos em comparação com o GTAW. Além disso, a manutenção da tocha é crítica e mais desafiadora. Outras desvantagens do PAW são: Os procedimentos de soldagem tendem a ser mais complexos e menos tolerantes a variações no ajuste, etc. A habilidade do operador exigida é um pouco mais do que para GTAW. A substituição do orifício é necessária. CLICK Product Finder-Locator Service PÁGINA ANTERIOR
- Optical Displays, Screen, Monitors Manufacturing - AGS-TECH Inc.
Visores ópticos, telas, monitores, fabricação de painéis de toque Fabricação e montagem de displays ópticos, telas, monitores Faça o download do folheto para o nosso PROGRAMA DE PARCERIA DE DESIGN CLICK Product Finder-Locator Service PÁGINA ANTERIOR
- Sistemas embarcados, Computador embarcado, Computadores industriais, Janz Tec
Sistemas embarcados - Computador embarcado - Computadores industriais - Janz Tec - Korenix - AGS-TECH Inc. Sistemas e Computadores Embarcados Um SISTEMA EMBARCADO é um sistema de computador projetado para funções de controle específicas dentro de um sistema maior, geralmente com restrições de computação em tempo real. Ele é incorporado como parte de um dispositivo completo, muitas vezes incluindo hardware e peças mecânicas. Por outro lado, um computador de uso geral, como um computador pessoal (PC), é projetado para ser flexível e atender a uma ampla gama de necessidades do usuário final. A arquitetura do sistema embarcado é orientada em um PC padrão, sendo que o PC EMBARCADO consiste apenas nos componentes que ele realmente precisa para a aplicação em questão. Os sistemas embarcados controlam muitos dispositivos de uso comum atualmente. Entre os COMPUTADORES EMBARCADOS que oferecemos estão ATOP TECHNOLOGIES, JANZ TEC, KORENIX TECHNOLOGY, DFI-ITOX e outros modelos de produtos. Nossos computadores embarcados são sistemas robustos e confiáveis para uso industrial onde o tempo de inatividade pode ser desastroso. Eles são energeticamente eficientes, muito flexíveis em uso, construídos modularmente, compactos, poderosos como um computador completo, sem ventoinha e sem ruído. Nossos computadores embarcados têm excelente resistência à temperatura, estanqueidade, choque e vibração em ambientes agressivos e são amplamente utilizados na construção de máquinas e fábricas, usinas de energia e energia, indústrias de tráfego e transporte, médica, biomédica, bioinstrumentação, indústria automotiva, militar, mineração, marinha , marinha, aeroespacial e muito mais. Faça o download do nosso folheto compacto de produtos ATOP TECHNOLOGIES (Baixe o produto ATOP Technologies List 2021) Faça o download da nossa brochura de produtos compactos do modelo JANZ TEC Faça o download do nosso folheto de produtos compactos do modelo KORENIX Baixe nosso folheto de sistemas embarcados do modelo DFI-ITOX Faça o download do nosso folheto de computadores de placa única incorporados modelo DFI-ITOX Faça o download do nosso folheto de módulos de computador a bordo do modelo DFI-ITOX Baixe nosso folheto ICP DAS modelo PACs Embedded Controllers & DAQ Para ir à nossa loja de informática industrial, CLIQUE AQUI. Aqui estão alguns dos computadores embarcados mais populares que oferecemos: PC embarcado com tecnologia Intel ATOM Z510/530 PC embarcado sem ventoinha Sistema de PC embutido com Freescale i.MX515 Sistemas de PC embutidos robustos Sistemas modulares de PC embutido Sistemas IHM e Soluções de Display Industrial sem Ventilador Lembre-se sempre que a AGS-TECH Inc. é um INTEGRADOR DE ENGENHARIA estabelecido e FABRICANTE PERSONALIZADO. Portanto, caso você precise de algo fabricado sob medida, informe-nos e ofereceremos uma solução chave na mão que tira o quebra-cabeça da sua mesa e facilita seu trabalho. Faça o download do folheto para o nosso PROGRAMA DE PARCERIA DE DESIGN Vamos apresentar brevemente nossos parceiros que constroem esses computadores incorporados: JANZ TEC AG: Janz Tec AG, é um fabricante líder de montagens eletrônicas e sistemas completos de computadores industriais desde 1982. A empresa desenvolve produtos de computação embarcada, computadores industriais e dispositivos de comunicação industrial de acordo com as necessidades do cliente. Todos os produtos JANZ TEC são produzidos exclusivamente na Alemanha com a mais alta qualidade. Com mais de 30 anos de experiência no mercado, a Janz Tec AG é capaz de atender às necessidades individuais dos clientes – isso começa desde a fase de conceito e continua através do desenvolvimento e produção dos componentes até a entrega. A Janz Tec AG está definindo os padrões nas áreas de computação embarcada, PC industrial, comunicação industrial, design personalizado. Os funcionários da Janz Tec AG concebem, desenvolvem e produzem componentes e sistemas de computador incorporados com base em padrões mundiais que são adaptados individualmente às necessidades específicas do cliente. Os computadores embarcados Janz Tec têm os benefícios adicionais de disponibilidade a longo prazo e a mais alta qualidade possível, juntamente com uma ótima relação preço/desempenho. Os computadores embarcados Janz Tec são sempre utilizados quando são necessários sistemas extremamente robustos e confiáveis devido aos requisitos neles realizados. Os computadores industriais Janz Tec compactos e de construção modular são de baixa manutenção, energeticamente eficientes e extremamente flexíveis. A arquitetura de computador dos sistemas embarcados Janz Tec é orientada em um PC padrão, onde o PC embarcado consiste apenas nos componentes que ele realmente precisa para a aplicação relevante. Isso facilita o uso completamente independente em ambientes nos quais o serviço seria extremamente caro. Apesar de serem computadores embarcados, muitos produtos da Janz Tec são tão poderosos que podem substituir um computador completo. Os benefícios dos computadores embarcados da marca Janz Tec são operação sem ventilador e baixa manutenção. Os computadores embarcados Janz Tec são usados na construção de máquinas e plantas, produção de energia e energia, transporte e tráfego, tecnologia médica, indústria automotiva, engenharia de produção e fabricação e muitas outras aplicações industriais. Os processadores, que estão se tornando cada vez mais poderosos, permitem o uso de um PC embarcado Janz Tec mesmo quando são confrontados requisitos particularmente complexos dessas indústrias. Uma vantagem disso é o ambiente de hardware familiar a muitos desenvolvedores e a disponibilidade de ambientes de desenvolvimento de software apropriados. A Janz Tec AG vem adquirindo a experiência necessária no desenvolvimento de seus próprios sistemas computacionais embarcados, que podem ser adaptados às necessidades do cliente sempre que necessário. O foco dos projetistas da Janz Tec no setor de computação embarcada está na solução ideal adequada à aplicação e aos requisitos individuais do cliente. Sempre foi o objetivo da Janz Tec AG fornecer alta qualidade para os sistemas, design sólido para uso a longo prazo e excepcional relação preço/desempenho. Os processadores modernos usados atualmente em sistemas de computadores embarcados são Freescale Intel Core i3/i5/i7, i.MX5x e Intel Atom, Intel Celeron e Core2Duo. Além disso, os computadores industriais Janz Tec não são apenas equipados com interfaces padrão como ethernet, USB e RS 232, mas uma interface CANbus também está disponível para o usuário como um recurso. O PC embarcado Janz Tec geralmente não possui ventilador e, portanto, pode ser usado com mídia CompactFlash na maioria dos casos para que não precise de manutenção. CLICK Product Finder-Locator Service PÁGINA ANTERIOR
- Fabricação de mesoma, fabricação de mesoescala, fabricação de dispositivos em miniatura
Mesomamanufatura - Fabricação em mesoescala - Fabricação de dispositivos em miniatura - Motores minúsculos - AGS-TECH Inc. Fabricação em Mesoescala / Mesomanufatura Com as técnicas de produção convencionais, produzimos estruturas em “macroescala” relativamente grandes e visíveis a olho nu. With MESOMANUFACTURING no entanto, produzimos componentes para dispositivos em miniatura. A mesomanufatura também é chamada de MESOSCALE MANUFACTURING or MESO-MACHINING. A mesomanufatura se sobrepõe tanto à macro quanto à micromanufatura. Exemplos de mesofabricação são aparelhos auditivos, stents, motores muito pequenos. A primeira abordagem na mesomanufatura é reduzir os processos de macromanufatura. Por exemplo, um pequeno torno com dimensões de algumas dezenas de milímetros e um motor de 1,5 W pesando 100 gramas é um bom exemplo de mesomanufatura onde o downscaling ocorreu. A segunda abordagem é aumentar os processos de micromanufatura. Como exemplo, os processos LIGA podem ser ampliados e entrar no domínio da mesomanufatura. Nossos processos de mesomanufatura estão preenchendo a lacuna entre os processos MEMS baseados em silício e a usinagem convencional em miniatura. Os processos de mesoescala podem fabricar peças bidimensionais e tridimensionais com características de tamanho mícron em materiais tradicionais, como aços inoxidáveis, cerâmicas e vidro. Os processos de mesomanufatura que estão atualmente disponíveis para nós incluem pulverização por feixe de íons focado (FIB), microfresagem, microtorneamento, ablação a laser excimer, ablação a laser de femto-segundo e usinagem de micro eletro-descarga (EDM). Esses processos de mesoescala empregam tecnologias de usinagem subtrativas (ou seja, remoção de material), enquanto o processo LIGA é um processo aditivo de mesoescala. Os processos de mesomanufatura possuem diferentes capacidades e especificações de desempenho. As especificações de desempenho de usinagem de interesse incluem tamanho mínimo do recurso, tolerância do recurso, precisão da localização do recurso, acabamento da superfície e taxa de remoção de material (MRR). Temos a capacidade de mesofabricar componentes eletromecânicos que requerem peças de mesoescala. As peças de mesoescala fabricadas por processos de mesomanufatura subtrativos têm propriedades tribológicas únicas devido à variedade de materiais e às condições de superfície produzidas pelos diferentes processos de mesomanufatura. Essas tecnologias de usinagem subtrativa de mesoescala nos trazem preocupações relacionadas à limpeza, montagem e tribologia. A limpeza é vital na mesomanufatura porque a sujeira de mesoescala e o tamanho das partículas de detritos criados durante o processo de mesousinagem podem ser comparáveis aos recursos de mesoescala. Fresamento e torneamento de mesoescala podem criar cavacos e rebarbas que podem bloquear furos. A morfologia da superfície e as condições de acabamento da superfície variam muito dependendo do método de mesofabricação. As peças de mesoescala são difíceis de manusear e alinhar, o que torna a montagem um desafio que a maioria de nossos concorrentes não consegue superar. Nossas taxas de rendimento na mesomanufatura são muito superiores aos nossos concorrentes, o que nos dá a vantagem de poder oferecer melhores preços. PROCESSOS DE USINAGEM DE MESOESCALA: Nossas principais técnicas de mesomanufatura são Feixe de Íons Focados (FIB), Microfresamento e Microtorneamento, meso-usinagem a laser, Micro-EDM (usinagem por eletro-descarga) Mesomanufatura usando feixe de íons focado (FIB), microfresamento e microtorneamento: O FIB pulveriza o material de uma peça de trabalho por bombardeamento de feixe de íons de gálio. A peça de trabalho é montada em um conjunto de estágios de precisão e é colocada em uma câmara de vácuo sob a fonte de gálio. Os estágios de translação e rotação na câmara de vácuo disponibilizam vários locais na peça de trabalho para o feixe de íons de gálio para a mesofabricação de FIB. Um campo elétrico ajustável varre o feixe para cobrir uma área projetada pré-definida. Um potencial de alta tensão faz com que uma fonte de íons de gálio acelere e colida com a peça de trabalho. As colisões retiram os átomos da peça de trabalho. O resultado do processo de meso-usinagem FIB pode ser a criação de facetas quase verticais. Alguns FIBs disponíveis para nós têm diâmetros de feixe tão pequenos quanto 5 nanômetros, tornando o FIB uma máquina capaz de mesoescala e até microescala. Montamos ferramentas de microfresagem em fresadoras de alta precisão para usinar canais em alumínio. Usando FIB, podemos fabricar ferramentas de microtorneamento que podem ser usadas em um torno para fabricar hastes com rosca fina. Em outras palavras, o FIB pode ser usado para usinar ferramentas duras, além de meso-usinar diretamente na peça final. A baixa taxa de remoção de material tornou o FIB impraticável para usinagem direta de grandes recursos. As ferramentas duras, no entanto, podem remover material a uma taxa impressionante e são duráveis o suficiente para várias horas de usinagem. No entanto, o FIB é prático para meso-usinagem direta de formas tridimensionais complexas que não requerem uma taxa de remoção de material substancial. O comprimento de exposição e o ângulo de incidência podem afetar muito a geometria de recursos usinados diretamente. Laser Mesomanufacturing: Excimer lasers são usados para mesomanufacturing. O excimer laser usina o material pulsando-o com pulsos de nanossegundos de luz ultravioleta. A peça de trabalho é montada em estágios de translação de precisão. Um controlador coordena o movimento da peça de trabalho em relação ao feixe de laser UV estacionário e coordena o disparo dos pulsos. Uma técnica de projeção de máscara pode ser usada para definir geometrias de meso-usinagem. A máscara é inserida na parte expandida do feixe onde a fluência do laser é muito baixa para remover a máscara. A geometria da máscara é reduzida através da lente e projetada na peça de trabalho. Essa abordagem pode ser usada para usinar vários furos (matrizes) simultaneamente. Nossos lasers excimer e YAG podem ser usados para usinar polímeros, cerâmicas, vidro e metais com tamanhos de recursos tão pequenos quanto 12 mícrons. O bom acoplamento entre o comprimento de onda UV (248 nm) e a peça de trabalho na mesomanufatura/meso-usinagem a laser resulta em paredes de canal verticais. Uma abordagem de meso-usinagem a laser mais limpa é usar um laser de femtosegundo de Ti-safira. Os detritos detectáveis de tais processos de mesomanufatura são partículas nanométricas. Características profundas de um mícron podem ser microfabricadas usando o laser de femtossegundos. O processo de ablação a laser de femtosegundo é único, pois quebra as ligações atômicas em vez do material de ablação térmica. O processo de meso-usinagem / microusinagem a laser de femtossegundos tem um lugar especial na mesomanufatura porque é mais limpo, capaz de mícrons e não é específico do material. Mesofabricação usando Micro-EDM (usinagem por eletro-descarga): A usinagem por eletro-descarga remove o material através de um processo de erosão por faísca. Nossas máquinas de micro-EDM podem produzir recursos tão pequenos quanto 25 mícrons. Para a máquina de micro-EDM de chumbada e de fio, as duas principais considerações para determinar o tamanho do recurso são o tamanho do eletrodo e a folga do excesso. Estão sendo usados eletrodos com pouco mais de 10 mícrons de diâmetro e excesso de queima de apenas alguns mícrons. A criação de um eletrodo com geometria complexa para a máquina de eletroerosão por chumbada requer know-how. Tanto o grafite quanto o cobre são populares como materiais de eletrodo. Uma abordagem para fabricar um eletrodo EDM de chumbada complicado para uma peça de mesoescala é usar o processo LIGA. O cobre, como material do eletrodo, pode ser revestido em moldes LIGA. O eletrodo de cobre LIGA pode então ser montado na máquina de eletroerosão chumbada para mesofabricar uma peça em um material diferente, como aço inoxidável ou kovar. Nenhum processo de mesomanufatura é suficiente para todas as operações. Alguns processos de mesoescala são mais abrangentes do que outros, mas cada processo tem seu nicho. Na maioria das vezes, precisamos de uma variedade de materiais para otimizar o desempenho dos componentes mecânicos e nos sentimos confortáveis com materiais tradicionais, como o aço inoxidável, porque esses materiais têm uma longa história e foram muito bem caracterizados ao longo dos anos. Os processos de mesomanufatura nos permitem utilizar materiais tradicionais. As tecnologias de usinagem de mesoescala subtrativas expandem nossa base de materiais. O desgaste pode ser um problema com algumas combinações de materiais na mesomanufatura. Cada processo de usinagem de mesoescala em particular afeta exclusivamente a rugosidade e a morfologia da superfície. O microfresamento e o microtorneamento podem gerar rebarbas e partículas que podem causar problemas mecânicos. Micro-EDM pode deixar uma camada de refundição que pode ter características particulares de desgaste e fricção. Efeitos de atrito entre peças de mesoescala podem ter pontos de contato limitados e não são modelados com precisão por modelos de contato de superfície. Algumas tecnologias de usinagem de mesoescala, como micro-EDM, são bastante maduras, ao contrário de outras, como meso-usinagem a laser de femtosegundo, que ainda requerem desenvolvimento adicional. CLICK Product Finder-Locator Service PÁGINA ANTERIOR
- Micro-Óptica - Micro-Óptica - Micro-Óptica - Óptica de Nível Wafer
Micro-Óptica, Micro-Óptica, Micro-Óptica, Óptica de Nível Wafer, Grades, Lentes Fresnel, Matriz de Lentes, Microespelhos, Micro-Refletores, Colimadores, Esferas, LED Fabricação de micro-óptica Um dos campos de microfabricação em que estamos envolvidos é MICRO-OPTICS MANUFACTURING. A micro-ótica permite a manipulação da luz e o gerenciamento de fótons com estruturas e componentes em escala de mícron e sub-mícron. Algumas aplicações de MICRO-OPTICAL COMPONENTS e SUBSYSTEMS são: Tecnologia da informação: Em micro-displays, microprojetores, armazenamento óptico de dados, microcâmeras, scanners, impressoras, copiadoras…etc. Biomedicina: Diagnóstico minimamente invasivo/ponto de atendimento, monitoramento de tratamento, sensores de microimagem, implantes de retina, microendoscópios. Iluminação: Sistemas baseados em LEDs e outras fontes de luz eficientes Sistemas de segurança e proteção: Sistemas de visão noturna infravermelha para aplicações automotivas, sensores ópticos de impressão digital, scanners de retina. Comunicação Óptica e Telecomunicações: Em comutadores fotônicos, componentes de fibra óptica passiva, amplificadores ópticos, mainframe e sistemas de interconexão de computadores pessoais Estruturas inteligentes: Em sistemas de detecção baseados em fibra óptica e muito mais Os tipos de componentes e subsistemas micro-ópticos que fabricamos e fornecemos são: - Óptica de nível de bolacha - Óptica Refrativa - Óptica Difrativa - Filtros - Grades - Hologramas gerados por computador - Componentes Microópticos Híbridos - Micro-óptica infravermelha - Micro-Óptica de Polímero - MEMS Ópticos - Sistemas Micro-Ópticos Monoliticamente e Discretamente Integrados Alguns dos nossos produtos micro-ópticos mais utilizados são: - Lentes biconvexas e plano-convexas - Lentes acromáticas - Lentes de bola - Lentes Vortex - Lentes Fresnel - Lente multifocal - Lentes Cilíndricas - Lentes Graded Index (GRIN) - Prismas Micro-ópticos - Asferas - Matrizes de Aspheres - Colimadores - Matrizes de micro-lentes - Grades de Difração - Polarizadores Wire-Grid - Filtros digitais micro-ópticos - Grades de Compressão de Pulso - Módulos de LED - Moldadores de Feixe - Amostrador de Feixe - Gerador de Anel - Homogeneizadores / Difusores Micro-ópticos - Divisores de feixe multiponto - Combinadores de feixe de comprimento de onda duplo - Interconexões micro-ópticas - Sistemas Inteligentes de Micro-Óptica - Microlentes de imagem - Microespelhos - Micro refletores - Janelas micro-ópticas - Máscara Dielétrica - Diafragmas de íris Deixe-nos fornecer algumas informações básicas sobre esses produtos micro-ópticos e suas aplicações: LENTES ESFERA: As lentes esféricas são lentes micro-ópticas completamente esféricas mais comumente usadas para acoplar a luz dentro e fora das fibras. Nós fornecemos uma variedade de lentes micro-ópticas e podemos fabricar também de acordo com suas próprias especificações. Nossas lentes esféricas de quartzo têm excelente transmissão UV e IR entre 185nm a >2000nm, e nossas lentes de safira têm um índice de refração mais alto, permitindo uma distância focal muito curta para excelente acoplamento de fibra. Estão disponíveis lentes micro-ópticas de outros materiais e diâmetros. Além das aplicações de acoplamento de fibra, as lentes micro-ópticas esféricas são usadas como lentes objetivas em endoscopia, sistemas de medição a laser e leitura de código de barras. Por outro lado, as lentes de meia esfera micro-ópticas oferecem uma dispersão uniforme da luz e são amplamente utilizadas em displays de LED e semáforos. ASFERAS MICRO-ÓPTICAS e ARRAYS: As superfícies asféricas têm um perfil não esférico. O uso de aspheres pode reduzir o número de ópticas necessárias para alcançar um desempenho óptico desejado. Aplicações populares para matrizes de lentes micro-ópticas com curvatura esférica ou asférica são geração de imagens e iluminação e a colimação efetiva da luz do laser. A substituição de um único conjunto de microlentes asféricas por um sistema multilente complexo resulta não apenas em tamanho menor, peso mais leve, geometria compacta e menor custo de um sistema óptico, mas também em melhoria significativa de seu desempenho óptico, como melhor qualidade de imagem. No entanto, a fabricação de microlentes asféricas e matrizes de microlentes é um desafio, porque as tecnologias convencionais usadas para aspheres de tamanho macro, como fresagem de diamante de ponto único e refluxo térmico, não são capazes de definir um perfil de lente micro-óptica complicado em uma área tão pequena quanto vários a dezenas de micrômetros. Possuímos o know-how de produzir tais estruturas micro-ópticas usando técnicas avançadas como lasers de femtossegundos. LENTES ACHROMAT MICRO-ÓPTICAS: Essas lentes são ideais para aplicações que exigem correção de cor, enquanto as lentes asféricas são projetadas para corrigir aberrações esféricas. Uma lente acromática ou acromática é uma lente projetada para limitar os efeitos da aberração cromática e esférica. As lentes acromáticas micro-ópticas fazem correções para focar dois comprimentos de onda (como as cores vermelha e azul) no mesmo plano. LENTES CILÍNDRICAS: Essas lentes focalizam a luz em uma linha em vez de um ponto, como faria uma lente esférica. A face ou faces curvas de uma lente cilíndrica são seções de um cilindro e focam a imagem que passa por ela em uma linha paralela à interseção da superfície da lente e um plano tangente a ela. A lente cilíndrica comprime a imagem na direção perpendicular a essa linha, e a deixa inalterada na direção paralela a ela (no plano tangente). Estão disponíveis versões micro-ópticas minúsculas que são adequadas para uso em ambientes micro-ópticos, exigindo componentes de fibra óptica de tamanho compacto, sistemas de laser e dispositivos micro-ópticos. JANELAS MICRO-ÓPTICAS E APARTAMENTOS: Estão disponíveis janelas micro-ópticas milimétricas que atendem a requisitos de tolerância apertados. Podemos fabricá-los de acordo com suas especificações a partir de qualquer um dos óculos de grau óptico. Oferecemos uma variedade de janelas micro-ópticas feitas de diferentes materiais, como sílica fundida, BK7, safira, sulfeto de zinco….etc. com transmissão de UV para faixa intermediária de IR. MICROLENTES DE IMAGEM: As microlentes são lentes pequenas, geralmente com diâmetro inferior a um milímetro (mm) e tão pequenas quanto 10 micrômetros. Lentes de imagem são usadas para visualizar objetos em sistemas de imagem. Lentes de imagem são usadas em sistemas de imagem para focalizar uma imagem de um objeto examinado em um sensor de câmera. Dependendo da lente, as lentes de imagem podem ser usadas para remover paralaxe ou erro de perspectiva. Eles também podem oferecer ampliações ajustáveis, campo de visão e distâncias focais. Essas lentes permitem que um objeto seja visto de várias maneiras para ilustrar certos recursos ou características que podem ser desejáveis em determinadas aplicações. MICROMESPELHOS: Os dispositivos de microespelhos são baseados em espelhos microscopicamente pequenos. Os espelhos são sistemas microeletromecânicos (MEMS). Os estados desses dispositivos micro-ópticos são controlados pela aplicação de uma tensão entre os dois eletrodos ao redor das matrizes de espelhos. Dispositivos de microespelhos digitais são usados em projetores de vídeo e dispositivos ópticos e microespelhos são usados para deflexão e controle da luz. COLIMADORES MICRO-ÓPTICOS E MATRIZ DE COLIMADORES: Uma variedade de colimadores micro-ópticos está disponível no mercado. Os colimadores micro-ópticos de feixe pequeno para aplicações exigentes são produzidos usando a tecnologia de fusão a laser. A extremidade da fibra é fundida diretamente ao centro óptico da lente, eliminando assim o epóxi dentro do caminho óptico. A superfície da lente do colimador micro-óptico é então polida a laser até um milionésimo de polegada da forma ideal. Os colimadores Small Beam produzem feixes colimados com cinturas de feixe abaixo de um milímetro. Os colimadores micro-ópticos de feixe pequeno são normalmente usados em comprimentos de onda de 1064, 1310 ou 1550 nm. Os colimadores micro-ópticos baseados em lentes GRIN também estão disponíveis, bem como conjuntos de matrizes de colimadores e matrizes de fibras de colimadores. LENTES FRESNEL MICROÓPTICAS: Uma lente Fresnel é um tipo de lente compacta projetada para permitir a construção de lentes de grande abertura e distância focal curta sem a massa e volume de material que seriam exigidos por uma lente de design convencional. Uma lente Fresnel pode ser muito mais fina do que uma lente convencional comparável, às vezes assumindo a forma de uma folha plana. Uma lente Fresnel pode capturar mais luz oblíqua de uma fonte de luz, permitindo assim que a luz seja visível em distâncias maiores. A lente Fresnel reduz a quantidade de material necessária em comparação com uma lente convencional, dividindo a lente em um conjunto de seções anulares concêntricas. Em cada seção, a espessura total é diminuída em comparação com uma lente simples equivalente. Isso pode ser visto como a divisão da superfície contínua de uma lente padrão em um conjunto de superfícies de mesma curvatura, com descontinuidades graduais entre elas. As lentes micro-ópticas Fresnel focam a luz por refração em um conjunto de superfícies curvas concêntricas. Essas lentes podem ser feitas muito finas e leves. As lentes micro-ópticas Fresnel oferecem oportunidades em óptica para aplicações de raios X de alta resolução, recursos de interconexão óptica por meio de placa. Temos vários métodos de fabricação, incluindo micromoldagem e microusinagem para fabricar lentes e matrizes micro-ópticas de Fresnel especificamente para suas aplicações. Podemos projetar uma lente Fresnel positiva como colimador, coletor ou com dois conjugados finitos. As lentes Micro-Optical Fresnel são geralmente corrigidas para aberrações esféricas. As lentes micro-ópticas positivas podem ser metalizadas para uso como um segundo refletor de superfície e as lentes negativas podem ser metalizadas para uso como um primeiro refletor de superfície. PRISMAS MICRO-ÓPTICOS: Nossa linha de micro-óptica de precisão inclui microprismas revestidos e não revestidos padrão. Eles são adequados para uso com fontes de laser e aplicações de imagem. Nossos prismas micro-ópticos têm dimensões submilimétricas. Nossos prismas micro-ópticos revestidos também podem ser usados como refletores de espelho em relação à luz recebida. Prismas não revestidos atuam como espelhos para a luz incidente em um dos lados curtos, uma vez que a luz incidente é totalmente refletida internamente na hipotenusa. Exemplos de nossos recursos de prisma micro-óptico incluem prismas de ângulo reto, conjuntos de cubos de divisão de feixes, prismas Amici, prismas K, prismas Dove, prismas Roof, Cornercubes, Pentaprismas, prismas romboides, prismas Bauernfeind, prismas de dispersão, prismas refletores. Também oferecemos microprismas ópticos guiadores de luz e antirreflexo feitos de acrílico, policarbonato e outros materiais plásticos pelo processo de fabricação de estampagem a quente para aplicações em lâmpadas e luminárias, LEDs. São superfícies de prisma altamente eficientes e fortes que guiam a luz com precisão, suportam luminárias para cumprir os regulamentos do escritório para deslumbramento. Estruturas de prisma personalizadas adicionais são possíveis. Microprismas e matrizes de microprismas em nível de wafer também são possíveis usando técnicas de microfabricação. GRADES DE DIFRAÇÃO: Oferecemos projeto e fabricação de elementos micro-ópticos difrativos (DOEs). Uma rede de difração é um componente óptico com uma estrutura periódica, que divide e difrata a luz em vários feixes que viajam em diferentes direções. As direções desses feixes dependem do espaçamento da grade e do comprimento de onda da luz para que a grade atue como elemento dispersivo. Isso torna a grade um elemento adequado para ser usado em monocromadores e espectrômetros. Usando litografia baseada em wafer, produzimos elementos micro-ópticos difrativos com características de desempenho térmico, mecânico e óptico excepcionais. O processamento de micro-óptica em nível de wafer oferece excelente repetibilidade de fabricação e saída econômica. Alguns dos materiais disponíveis para elementos micro-ópticos difrativos são cristal-quartzo, sílica fundida, vidro, silício e substratos sintéticos. As grades de difração são úteis em aplicações como análise espectral/espectroscopia, MUX/DEMUX/DWDM, controle de movimento de precisão, como em codificadores ópticos. As técnicas de litografia possibilitam a fabricação de grades micro-óticas de precisão com espaçamentos de sulcos rigidamente controlados. A AGS-TECH oferece designs personalizados e de estoque. LENTES VORTEX: Em aplicações de laser há a necessidade de converter um feixe gaussiano em um anel de energia em forma de rosquinha. Isto é conseguido usando lentes Vortex. Algumas aplicações são em litografia e microscopia de alta resolução. Polímero em placas de fase Vortex de vidro também estão disponíveis. HOMOGENIZADORES/DIFUSORES MICRO-ÓTICOS: Uma variedade de tecnologias é usada para fabricar nossos homogeneizadores e difusores micro-ópticos, incluindo gravação em relevo, filmes difusores projetados, difusores gravados, difusores HiLAM. Laser Speckle é o fenômeno óptico resultante da interferência aleatória de luz coerente. Este fenômeno é utilizado para medir a Função de Transferência de Modulação (MTF) de matrizes de detectores. Difusores de microlentes são dispositivos micro-ópticos eficientes para geração de speckle. BEAM SHAPERS: Um micro-optic beam shaper é uma óptica ou um conjunto de ópticas que transforma tanto a distribuição de intensidade quanto a forma espacial de um feixe de laser em algo mais desejável para uma determinada aplicação. Freqüentemente, um feixe de laser tipo gaussiano ou não uniforme é transformado em um feixe de topo plano. A micro-óptica do modelador de feixe é usada para moldar e manipular feixes de laser monomodo e multimodo. Nossas micro-óticas modeladoras de feixe fornecem formas circulares, quadradas, retilíneas, hexagonais ou de linha e homogeneizam o feixe (topo plano) ou fornecem um padrão de intensidade personalizado de acordo com os requisitos da aplicação. Foram fabricados elementos micro-ópticos refrativos, difrativos e refletivos para modelagem e homogeneização de feixes de laser. Elementos micro-ópticos multifuncionais são usados para moldar perfis de feixe de laser arbitrários em uma variedade de geometrias, como uma matriz de pontos homogênea ou padrão de linha, uma folha de luz de laser ou perfis de intensidade de topo plano. Exemplos de aplicação de vigas finas são corte e soldagem keyhole. Exemplos de aplicação de feixe amplo são soldagem por condução, brasagem, soldagem, tratamento térmico, ablação de filme fino, laser peening. GRADES DE COMPRESSÃO DE PULSO: A compressão de pulso é uma técnica útil que aproveita a relação entre a duração do pulso e a largura espectral de um pulso. Isso permite a amplificação de pulsos de laser acima dos limites normais de limite de dano impostos pelos componentes ópticos no sistema de laser. Existem técnicas lineares e não lineares para reduzir as durações dos pulsos ópticos. Há uma variedade de métodos para comprimir/encurtar temporalmente os pulsos ópticos, ou seja, reduzir a duração do pulso. Esses métodos geralmente começam na região de picossegundos ou femtossegundos, ou seja, já no regime de pulsos ultracurtos. DIvisores de feixes multipontos: A divisão de feixes por meio de elementos difrativos é desejável quando um elemento é necessário para produzir vários feixes ou quando é necessária uma separação de potência óptica muito exata. O posicionamento preciso também pode ser alcançado, por exemplo, para criar furos em distâncias claramente definidas e precisas. Temos elementos multiponto, elementos amostradores de feixe, elemento multifoco. Usando um elemento difrativo, os feixes incidentes colimados são divididos em vários feixes. Esses feixes ópticos têm igual intensidade e ângulos iguais entre si. Temos elementos unidimensionais e bidimensionais. Os elementos 1D dividem as vigas ao longo de uma linha reta, enquanto os elementos 2D produzem vigas dispostas em uma matriz de, por exemplo, 2 x 2 ou 3 x 3 pontos e elementos com pontos dispostos hexagonalmente. Versões micro-ópticas estão disponíveis. ELEMENTOS DE AMOSTRAGEM DE FEIXE: Esses elementos são grades que são usadas para monitoramento em linha de lasers de alta potência. A primeira ordem de difração ± pode ser usada para medições de feixe. Sua intensidade é significativamente menor que a do feixe principal e pode ser projetada sob medida. Ordens de difração mais altas também podem ser usadas para medições com intensidade ainda menor. Variações na intensidade e mudanças no perfil do feixe de lasers de alta potência podem ser monitoradas de forma confiável em linha usando este método. ELEMENTOS MULTI-FOCUS: Com este elemento difrativo vários pontos focais podem ser criados ao longo do eixo óptico. Esses elementos ópticos são usados em sensores, oftalmologia, processamento de materiais. Versões micro-ópticas estão disponíveis. INTERCONEXÕES MICROÓPTICAS: As interconexões ópticas vêm substituindo os fios elétricos de cobre nos diferentes níveis da hierarquia de interconexão. Uma das possibilidades de trazer as vantagens das telecomunicações micro-ópticas para o backplane do computador, a placa de circuito impresso, o nível de interconexão entre chip e on-chip, é usar módulos de interconexão micro-óptica de espaço livre feitos de plástico. Esses módulos são capazes de transportar alta largura de banda de comunicação agregada através de milhares de links ópticos ponto a ponto em um espaço de um centímetro quadrado. Entre em contato conosco para interconexões micro-ópticas personalizadas e personalizadas para o backplane do computador, a placa de circuito impresso, os níveis de interconexão entre chip e on-chip. SISTEMAS DE MICRO-ÓPTICA INTELIGENTES: Módulos de luz micro-óptica inteligentes são usados em telefones inteligentes e dispositivos inteligentes para aplicações de flash LED, em interconexões ópticas para transporte de dados em supercomputadores e equipamentos de telecomunicações, como soluções miniaturizadas para modelagem de feixe de infravermelho próximo, detecção em jogos aplicativos e para suportar o controle de gestos em interfaces de usuário naturais. Os módulos optoeletrônicos de detecção são usados para várias aplicações de produtos, como luz ambiente e sensores de proximidade em telefones inteligentes. Sistemas micro-óticos de imagem inteligente são usados para câmeras primárias e frontais. Oferecemos também sistemas micro-ópticos inteligentes personalizados com alto desempenho e capacidade de fabricação. MÓDULOS DE LED: Você pode encontrar nossos chips de LED, matrizes e módulos em nossa página Fabricação de componentes de iluminação e iluminação clicando aqui. POLARIZADORES DE FIO-GRADE: Consistem em um arranjo regular de finos fios metálicos paralelos, colocados em um plano perpendicular ao feixe incidente. A direção de polarização é perpendicular aos fios. Os polarizadores padronizados têm aplicações em polarimetria, interferometria, displays 3D e armazenamento de dados ópticos. Polarizadores de grade de fio são amplamente utilizados em aplicações de infravermelho. Por outro lado, os polarizadores de malha de fios micropadrões têm resolução espacial limitada e baixo desempenho em comprimentos de onda visíveis, são suscetíveis a defeitos e não podem ser facilmente estendidos para polarizações não lineares. Os polarizadores pixelados usam uma matriz de grades de nanofios com micropadrões. Os polarizadores micro-óticos pixelados podem ser alinhados com câmeras, matrizes de planos, interferômetros e microbolômetros sem a necessidade de interruptores polarizadores mecânicos. Imagens vibrantes que distinguem entre múltiplas polarizações nos comprimentos de onda visíveis e IR podem ser capturadas simultaneamente em tempo real, permitindo imagens rápidas e de alta resolução. Os polarizadores micro-ópticos pixelados também permitem imagens nítidas em 2D e 3D, mesmo em condições de pouca luz. Oferecemos polarizadores padronizados para dispositivos de imagem de dois, três e quatro estados. Versões micro-ópticas estão disponíveis. LENTES GRADED INDEX (GRIN): A variação gradual do índice de refração (n) de um material pode ser usada para produzir lentes com superfícies planas, ou lentes que não apresentam as aberrações normalmente observadas com lentes esféricas tradicionais. As lentes de índice de gradiente (GRIN) podem ter um gradiente de refração esférico, axial ou radial. Versões micro-ópticas muito pequenas estão disponíveis. FILTROS DIGITAIS MICROÓPTICOS: Filtros digitais de densidade neutra são usados para controlar os perfis de intensidade dos sistemas de iluminação e projeção. Esses filtros micro-ópticos contêm microestruturas absorventes de metal bem definidas que são distribuídas aleatoriamente em um substrato de sílica fundida. As propriedades desses componentes micro-ópticos são alta precisão, grande abertura clara, alto limite de dano, atenuação de banda larga para comprimentos de onda DUV a IR, perfis de transmissão unidimensionais ou bidimensionais bem definidos. Algumas aplicações são aberturas de borda suave, correção precisa de perfis de intensidade em sistemas de iluminação ou projeção, filtros de atenuação variável para lâmpadas de alta potência e feixes de laser expandidos. Podemos personalizar a densidade e o tamanho das estruturas para atender com precisão aos perfis de transmissão exigidos pela aplicação. COMBINADORES DE FEIXE DE MÚLTIPLOS COMPRIMENTOS DE ONDA: Os combinadores de feixes de vários comprimentos de onda combinam dois colimadores de LED de diferentes comprimentos de onda em um único feixe colimado. Vários combinadores podem ser conectados em cascata para combinar mais de duas fontes de colimador de LED. Os combinadores de feixe são feitos de divisores de feixe dicróicos de alto desempenho que combinam dois comprimentos de onda com eficiência > 95%. Versões micro-ópticas muito pequenas estão disponíveis. CLICK Product Finder-Locator Service PÁGINA ANTERIOR
- Instrumentos de teste mecânico - testador de tensão - máquina de teste de torção
Instrumentos de teste mecânico - testador de tensão - máquina de teste de torção - testador de flexão - dispositivo de teste de impacto - testador de concreto - máquina de teste de compressão Instrumentos de Teste Mecânico Entre o grande número de MECHANICAL TEST INSTRUMENTS focamos nossa atenção para os mais essenciais e populares:_cc781905-5cde-3194-bb3b-136bad5cf58DT_IMPACTERS , TESTES DE TENSÃO, MÁQUINAS DE TESTE DE COMPRESSÃO, EQUIPAMENTO DE TESTE DE TORÇÃO, MÁQUINA DE TESTE DE FADIGA, TESTADORES DE FLEXÃO DE TRÊS E QUATRO PONTOS, COEFICIENTE DE TESTES DE FRICÇÃO, TESTES DE DUREZA E ESPESSURA, TESTES DE RUGOSIDADE DE SUPERFÍCIE, MEDIDORES DE VIBRAÇÃO, PRECISION BALANCE ANALÍTICO. Oferecemos aos nossos clientes marcas de qualidade como SADT, SINOAGE for sob preços de tabela. Para baixar o catálogo de nossos equipamentos de metrologia e teste da marca SADT, CLIQUE AQUI. Aqui você encontrará alguns desses equipamentos de teste, como testadores de concreto e testador de rugosidade de superfície. Vamos examinar esses dispositivos de teste com algum detalhe: SCHMIDT HAMMER / CONCRETE TESTER : This test instrument, also sometimes called a SWISS HAMMER or a REBOUND HAMMER, é um dispositivo para medir as propriedades elásticas ou resistência de concreto ou rocha, principalmente dureza superficial e resistência à penetração. O martelo mede o rebote de uma massa carregada por mola impactando contra a superfície da amostra. O martelo de teste atingirá o concreto com uma energia predeterminada. O rebote do martelo depende da dureza do concreto e é medido pelo equipamento de teste. Tomando um gráfico de conversão como referência, o valor de rebote pode ser usado para determinar a resistência à compressão. O martelo Schmidt é uma escala arbitrária que varia de 10 a 100. Os martelos Schmidt vêm com várias faixas de energia diferentes. Suas faixas de energia são: (i) Energia de impacto Tipo L-0,735 Nm, (ii) Energia de impacto Tipo N-2,207 Nm; e (iii) Energia de impacto Tipo M-29,43 Nm. Variação local na amostra. Para minimizar a variação local nas amostras, é recomendável fazer uma seleção de leituras e obter seu valor médio. Antes do teste, o martelo Schmidt precisa ser calibrado usando uma bigorna de teste de calibração fornecida pelo fabricante. Devem ser feitas 12 leituras, eliminando a mais alta e a mais baixa, e depois fazendo a média das dez leituras restantes. Este método é considerado uma medida indireta da resistência do material. Ele fornece uma indicação baseada nas propriedades da superfície para comparação entre amostras. Este método de teste para testar concreto é regido pela ASTM C805. Por outro lado, a norma ASTM D5873 descreve o procedimento para ensaio de rocha. Dentro do nosso catálogo de marcas SADT você encontrará os seguintes produtos: DIGITAL CONCRETE TEST HAMMER Modelos SADT HT-225D/HT-75D/HT-20D - O modelo SADT O HT-225D é um martelo de teste de concreto digital integrado que combina processador de dados e martelo de teste em uma única unidade. É amplamente utilizado para testes de qualidade não destrutivos de concreto e materiais de construção. A partir de seu valor de rebote, a resistência à compressão do concreto pode ser calculada automaticamente. Todos os dados de teste podem ser armazenados na memória e transferidos para o PC por cabo USB ou sem fio por Bluetooth. Os modelos HT-225D e HT-75D possuem faixa de medição de 10 – 70N/mm2, enquanto o modelo HT-20D possui apenas 1 – 25N/mm2. A energia de impacto do HT-225D é de 0,225 Kgm e é adequada para testar construções comuns e de pontes, a energia de impacto do HT-75D é de 0,075 Kgm e é adequada para testar peças pequenas e sensíveis ao impacto de concreto e tijolos artificiais e, finalmente, a energia de impacto do HT-20D é de 0,020Kgm e é adequada para testar produtos de argamassa ou argila. TESTADORES DE IMPACTO: Em muitas operações de fabricação e durante sua vida útil, muitos componentes precisam ser submetidos a cargas de impacto. No teste de impacto, a amostra entalhada é colocada em um testador de impacto e quebrada com um pêndulo oscilante. Existem dois tipos principais deste teste: The CHARPY TEST and the IZOD TEST. Para o ensaio Charpy os corpos de prova são apoiados em ambas as extremidades, enquanto que para o ensaio Izod eles são apoiados apenas em uma extremidade como uma viga em balanço. A partir da quantidade de oscilação do pêndulo, obtém-se a energia dissipada na quebra do corpo de prova, esta energia é a tenacidade ao impacto do material. Usando os testes de impacto, podemos determinar as temperaturas de transição dúctil-frágil dos materiais. Materiais com alta resistência ao impacto geralmente têm alta resistência e ductilidade. Esses testes também revelam a sensibilidade da tenacidade ao impacto de um material a defeitos de superfície, porque o entalhe no corpo de prova pode ser considerado um defeito de superfície. TENSION TESTER : As características de resistência-deformação dos materiais são determinadas usando este teste. As amostras de teste são preparadas de acordo com as normas ASTM. Normalmente, amostras sólidas e redondas são testadas, mas folhas planas e amostras tubulares também podem ser testadas usando o teste de tensão. O comprimento original de um corpo de prova é a distância entre as marcas de medição nele e normalmente tem 50 mm de comprimento. É indicado como lo. Comprimentos maiores ou menores podem ser usados dependendo das amostras e produtos. A área da seção transversal original é denotada como Ao. A tensão de engenharia ou também chamada tensão nominal é então dada como: Sigma = P / Ao E a deformação de engenharia é dada como: e = (l – l) / l Na região elástica linear, o corpo de prova se alonga proporcionalmente à carga até o limite de proporcionalidade. Além deste limite, ainda que não linearmente, o corpo de prova continuará a se deformar elasticamente até o limite de escoamento Y. Nessa região elástica, o material retornará ao seu comprimento original se retirarmos a carga. A Lei de Hooke se aplica nesta região e nos dá o Módulo de Young: E = Sigma / e Se aumentarmos a carga e ultrapassarmos o ponto de escoamento Y, o material começa a ceder. Em outras palavras, o corpo de prova começa a sofrer deformação plástica. Deformação plástica significa deformação permanente. A área da seção transversal do corpo de prova diminui de forma permanente e uniforme. Se o corpo de prova é descarregado neste ponto, a curva segue uma linha reta descendente e paralela à linha original na região elástica. Se a carga for aumentada ainda mais, a curva atinge um máximo e começa a diminuir. O ponto de tensão máxima é chamado de resistência à tração ou resistência à tração final e é denotado como UTS. O UTS pode ser interpretado como a resistência geral dos materiais. Quando a carga é maior do que o UTS, ocorre o estreitamento no corpo de prova e o alongamento entre as marcas do medidor não é mais uniforme. Em outras palavras, a amostra torna-se muito fina no local onde ocorre o estrangulamento. Durante o estrangulamento, a tensão elástica diminui. Se o teste for continuado, a tensão de engenharia cai ainda mais e o corpo de prova fratura na região do pescoço. O nível de tensão na fratura é a tensão de fratura. A deformação no ponto de fratura é um indicador de ductilidade. A deformação até o UTS é chamada de deformação uniforme, e o alongamento na fratura é chamado de alongamento total. Alongamento = ((lf – lo) / lo) x 100 Redução de Área = ((Ao – Af) / Ao) x 100 O alongamento e a redução da área são bons indicadores de ductilidade. MÁQUINA DE TESTE DE COMPRESSÃO ( COMPRESSION TESTER ) : Neste teste, o corpo de prova é submetido a uma carga de compressão contrária ao teste de tração onde a carga é de tração. Geralmente, uma amostra cilíndrica sólida é colocada entre duas placas planas e comprimida. Usando lubrificantes nas superfícies de contato, um fenômeno conhecido como barril é evitado. A taxa de deformação de engenharia na compressão é dada por: de / dt = - v / ho, onde v é a velocidade da matriz, ho altura original do corpo de prova. A taxa de deformação verdadeira, por outro lado, é: de = dt = - v/ h, sendo h a altura instantânea do corpo de prova. Para manter a taxa de deformação verdadeira constante durante o teste, um plastômetro de came através de uma ação de came reduz a magnitude de v proporcionalmente à medida que a altura do corpo de prova h diminui durante o teste. Usando o teste de compressão, as ductilidades dos materiais são determinadas pela observação de trincas formadas em superfícies cilíndricas de barril. Outro teste com algumas diferenças nas geometrias da matriz e da peça é the PLANE-STRAIN COMPRESSION TEST, que nos dá a tensão de escoamento do material em deformação plana denotada amplamente como Y'. A tensão de escoamento de materiais em deformação plana pode ser estimada como: Y' = 1,15 Y MÁQUINAS DE TESTE DE TORÇÃO (TESTADORES DE TORÇÃO) : The TORSION TEST é outro método amplamente utilizado para determinar as propriedades do material. Um corpo de prova tubular com uma seção média reduzida é usado neste teste. Tensão de cisalhamento, T é dado por: T = T/2 (Pi) (quadrado de r) t Aqui, T é o torque aplicado, r é o raio médio e t é a espessura da seção reduzida no meio do tubo. A tensão de cisalhamento, por outro lado, é dada por: ß = r Ø / l Aqui l é o comprimento da seção reduzida e Ø é o ângulo de torção em radianos. Dentro da faixa elástica, o módulo de cisalhamento (módulo de rigidez) é expresso como: G = T / ß A relação entre o módulo de cisalhamento e o módulo de elasticidade é: G = E / 2( 1 + V ) O teste de torção é aplicado a barras redondas sólidas em temperaturas elevadas para estimar a forjabilidade dos metais. Quanto mais torções o material pode suportar antes da falha, mais forjável ele é. THREE & FOUR POINT BENDING TESTERS : For brittle materials, the BEND TEST (also called FLEXURE TEST) é apropriado. Um corpo de prova retangular é apoiado em ambas as extremidades e uma carga é aplicada verticalmente. A força vertical é aplicada em um ponto, como no caso de um testador de flexão de três pontos, ou em dois pontos, como no caso de uma máquina de teste de quatro pontos. A tensão na fratura na flexão é referida como o módulo de ruptura ou resistência à ruptura transversal. É dado como: Sigma = M c / I Aqui, M é o momento fletor, c é a metade da profundidade do corpo de prova e I é o momento de inércia da seção transversal. A magnitude da tensão é a mesma na flexão de três e quatro pontos quando todos os outros parâmetros são mantidos constantes. O teste de quatro pontos provavelmente resultará em um módulo de ruptura menor em comparação com o teste de três pontos. Outra superioridade do teste de flexão de quatro pontos sobre o teste de flexão de três pontos é que seus resultados são mais consistentes com menor dispersão estatística dos valores. MÁQUINA DE TESTE DE FADIGA: Em TESTE DE FADIGA, uma amostra é submetida repetidamente a vários estados de tensão. As tensões são geralmente uma combinação de tensão, compressão e torção. O processo de teste pode ser semelhante a dobrar um pedaço de fio alternadamente em uma direção e depois na outra até que ele se quebre. A amplitude de tensão pode ser variada e é indicada como “S”. O número de ciclos para causar a falha total da amostra é registrado e é indicado como “N”. A amplitude de tensão é o valor máximo de tensão em tração e compressão ao qual o corpo de prova é submetido. Uma variação do teste de fadiga é realizada em um eixo giratório com uma carga descendente constante. O limite de resistência (limite de fadiga) é definido como o máx. valor de tensão que o material pode suportar sem falha por fadiga, independentemente do número de ciclos. A resistência à fadiga dos metais está relacionada à sua resistência à tração final UTS. COEFICIENTE DE FRICTION TESTER : Este equipamento de teste mede a facilidade com que duas superfícies em contato podem deslizar uma sobre a outra. Existem dois valores diferentes associados ao coeficiente de atrito, ou seja, o coeficiente de atrito estático e cinético. O atrito estático aplica-se à força necessária para iniciar o movimento entre as duas superfícies e o atrito cinético é a resistência ao deslizamento quando as superfícies estão em movimento relativo. Medidas apropriadas precisam ser tomadas antes do teste e durante o teste para garantir a ausência de sujeira, graxa e outros contaminantes que possam afetar adversamente os resultados do teste. ASTM D1894 é o principal padrão de teste de coeficiente de atrito e é usado por muitas indústrias com diferentes aplicações e produtos. Estamos aqui para lhe oferecer o equipamento de teste mais adequado. Se você precisar de uma configuração personalizada projetada especificamente para sua aplicação, podemos modificar o equipamento existente de acordo com seus requisitos e necessidades. TESTADORES DE DUREZA : Acesse nossa página relacionada clicando aqui TESTADORES DE ESPESSURA : Acesse nossa página relacionada clicando aqui TESTADORES DE RUGOSIDADE DE SUPERFÍCIE : Acesse nossa página relacionada clicando aqui MEDIDORES DE VIBRAÇÃO : Acesse nossa página relacionada clicando aqui TACÔMETROS : Acesse nossa página relacionada clicando aqui Para obter detalhes e outros equipamentos semelhantes, visite nosso site de equipamentos: http://www.sourceindustrialsupply.com CLICK Product Finder-Locator Service PÁGINA ANTERIOR
- Usinagem por feixe de elétrons, EBM, usinagem e corte e mandrilamento E-Beam
Usinagem por feixe de elétrons, EBM, usinagem e corte e mandrilamento de vigas E, fabricação personalizada de peças - AGS-TECH Inc. Usinagem EBM e Usinagem de Feixe de Elétrons Em ELECTRON-BEAM MACHINING (EBM) temos elétrons de alta velocidade concentrados em um feixe estreito que são direcionados para a peça de trabalho, criando calor e vaporizando o material. Assim EBM é um tipo de HIGH-ENERGY-BEAM MACHINING technique. A usinagem por feixe de elétrons (EBM) pode ser usada para corte ou mandrilamento muito preciso de uma variedade de metais. O acabamento da superfície é melhor e a largura do corte é mais estreita em comparação com outros processos de corte térmico. Os feixes de elétrons em equipamentos de usinagem EBM são gerados em um canhão de feixe de elétrons. As aplicações da usinagem por feixe de elétrons são semelhantes às da usinagem por feixe de laser, exceto que o EBM requer um bom vácuo. Assim, esses dois processos são classificados como processos eletro-óptico-térmicos. A peça a ser usinada com o processo EBM está localizada sob o feixe de elétrons e é mantida sob vácuo. As pistolas de feixe de elétrons em nossas máquinas EBM também são fornecidas com sistemas de iluminação e telescópios para alinhamento do feixe com a peça de trabalho. A peça de trabalho é montada em uma mesa CNC para que furos de qualquer formato possam ser usinados usando o controle CNC e a funcionalidade de deflexão do feixe da pistola. Para conseguir a evaporação rápida do material, a densidade planar da potência no feixe deve ser a mais alta possível. Valores de até 10exp7 W/mm2 podem ser alcançados no ponto de impacto. Os elétrons transferem sua energia cinética em calor em uma área muito pequena, e o material impactado pelo feixe é evaporado em um tempo muito curto. O material fundido na parte superior da frente é expelido da zona de corte pela alta pressão de vapor nas partes inferiores. O equipamento EBM é construído de forma semelhante às máquinas de solda por feixe de elétrons. Máquinas de feixe de elétrons geralmente utilizam voltagens na faixa de 50 a 200 kV para acelerar elétrons a cerca de 50 a 80% da velocidade da luz (200.000 km/s). Lentes magnéticas cuja função é baseada nas forças de Lorentz são usadas para focar o feixe de elétrons na superfície da peça de trabalho. Com a ajuda de um computador, o sistema de deflexão eletromagnética posiciona o feixe conforme necessário para que os furos de qualquer formato possam ser perfurados. Em outras palavras, as lentes magnéticas do equipamento Electron-Beam-Machining moldam o feixe e reduzem a divergência. As aberturas, por outro lado, permitem que apenas os elétrons convergentes passem e capturem os elétrons divergentes de baixa energia das franjas. A abertura e as lentes magnéticas nas máquinas EBM melhoram assim a qualidade do feixe de elétrons. A pistola no EBM é usada no modo pulsado. Os furos podem ser perfurados em folhas finas usando um único pulso. No entanto, para placas mais espessas, vários pulsos seriam necessários. Geralmente são usadas durações de pulso de comutação tão baixas quanto 50 microssegundos até 15 milissegundos. Para minimizar as colisões de elétrons com moléculas de ar, resultando em dispersão e manter a contaminação ao mínimo, o vácuo é usado no EBM. O vácuo é difícil e caro de produzir. Especialmente obter um bom vácuo em grandes volumes e câmaras é muito exigente. Portanto, o EBM é mais adequado para peças pequenas que se encaixam em câmaras de vácuo compactas de tamanho razoável. O nível de vácuo dentro da arma do EBM é da ordem de 10EXP(-4) a 10EXP(-6) Torr. A interação do feixe de elétrons com a peça de trabalho produz raios X que representam perigo para a saúde e, portanto, pessoal bem treinado deve operar o equipamento EBM. De um modo geral, o EBM-Machining é usado para cortar furos tão pequenos quanto 0,001 polegada (0,025 milímetros) de diâmetro e ranhuras tão estreitas quanto 0,001 polegada em materiais de até 0,250 polegada (6,25 milímetros) de espessura. O comprimento característico é o diâmetro sobre o qual o feixe está ativo. O feixe de elétrons no EBM pode ter um comprimento característico de dezenas de mícrons a mm, dependendo do grau de focalização do feixe. Geralmente, o feixe de elétrons focado em alta energia é feito para colidir com a peça de trabalho com um tamanho de ponto de 10 a 100 mícrons. O EBM pode fornecer furos de diâmetros na faixa de 100 mícrons a 2 mm com profundidade de até 15 mm, ou seja, com uma relação profundidade/diâmetro em torno de 10. No caso de feixes de elétrons desfocados, as densidades de potência cairiam até 1 Watt/mm2. No entanto, no caso de feixes focados, as densidades de potência podem ser aumentadas para dezenas de kW/mm2. Como comparação, os feixes de laser podem ser focados em um tamanho de ponto de 10 – 100 mícrons com uma densidade de potência tão alta quanto 1 MW/mm2. A descarga elétrica normalmente fornece as densidades de potência mais altas com tamanhos de pontos menores. A corrente do feixe está diretamente relacionada ao número de elétrons disponíveis no feixe. A corrente do feixe na usinagem de feixe de elétrons pode ser tão baixa quanto 200 microamperes a 1 ampere. Aumentar a corrente do feixe e/ou a duração do pulso do EBM aumenta diretamente a energia por pulso. Usamos pulsos de alta energia acima de 100 J/pulso para usinar furos maiores em chapas mais grossas. Em condições normais, a usinagem EBM nos oferece a vantagem de produtos sem rebarbas. Os parâmetros de processo que afetam diretamente as características de usinagem na usinagem de feixe de elétrons são: • Tensão de aceleração • Corrente do feixe • Duração do pulso • Energia por pulso • Potência por pulso • Corrente da lente • Tamanho do ponto • Densidade de potência Algumas estruturas extravagantes também podem ser obtidas usando o Electron-Beam-Machining. Os furos podem ser afunilados ao longo da profundidade ou em forma de barril. Focalizando o feixe abaixo da superfície, pode-se obter afunilamento reverso. Uma ampla gama de materiais como aço, aço inoxidável, titânio e superligas de níquel, alumínio, plásticos e cerâmicas podem ser usinados usando a usinagem de vigas eletrônicas. Pode haver danos térmicos associados ao EBM. No entanto, a zona afetada pelo calor é estreita devido a curtas durações de pulso na EBM. As zonas afetadas pelo calor são geralmente em torno de 20 a 30 mícrons. Alguns materiais, como ligas de alumínio e titânio, são mais facilmente usinados em comparação com o aço. Além disso, a usinagem EBM não envolve forças de corte nas peças de trabalho. Isso permite a usinagem de materiais frágeis e quebradiços por EBM sem nenhuma fixação ou fixação significativa, como é o caso das técnicas de usinagem mecânica. Os furos também podem ser perfurados em ângulos muito rasos, como 20 a 30 graus. As vantagens da usinagem de feixe de elétrons: EBM fornece taxas de perfuração muito altas quando pequenos furos com alta proporção são perfurados. A EBM pode usinar praticamente qualquer material, independentemente de suas propriedades mecânicas. Nenhuma força de corte mecânica está envolvida, portanto, os custos de fixação, fixação e fixação do trabalho são ignoráveis, e materiais frágeis/frágeis podem ser processados sem problemas. As zonas afetadas pelo calor na EBM são pequenas devido aos pulsos curtos. O EBM é capaz de fornecer qualquer formato de furo com precisão usando bobinas eletromagnéticas para desviar os feixes de elétrons e a mesa CNC. As desvantagens da usinagem por feixe de elétrons: O equipamento é caro e a operação e manutenção de sistemas de vácuo requer técnicos especializados. O EBM requer períodos significativos de inatividade da bomba de vácuo para atingir as baixas pressões necessárias. Embora a zona afetada pelo calor seja pequena na EBM, a formação da camada de refusão ocorre com frequência. Nossos muitos anos de experiência e know-how nos ajudam a aproveitar este valioso equipamento em nosso ambiente de fabricação. CLICK Product Finder-Locator Service PÁGINA ANTERIOR