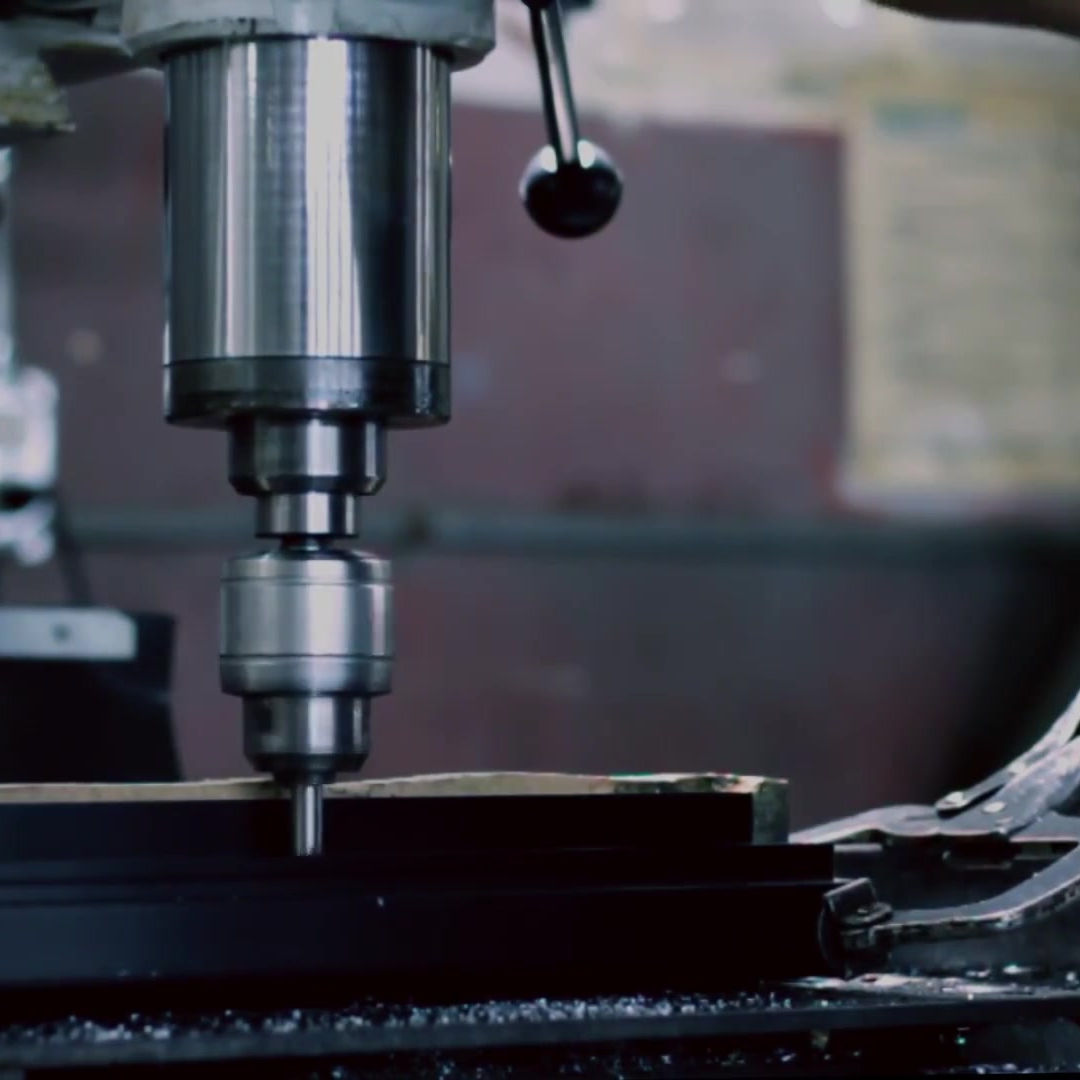
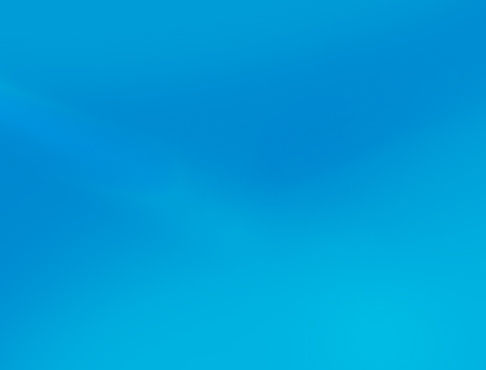
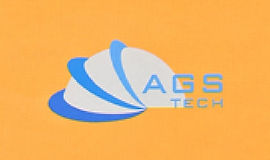
Global Custom Manufacturer, Integrator, Consolidator, Outsourcing Partner for a Wide Variety of Products & Services.
We are your one-stop source for manufacturing, fabrication, engineering, consolidation, integration, outsourcing of custom manufactured and off-shelf products & services. We also private label / white label your products with your brand name if you wish.
Choose your Language
-
Custom Manufacturing of Parts, Components, Assemblies, Finished Products, Machines and Industrial Equipment
-
Domestic & Global Contract Manufacturing
-
Manufacturing Outsourcing
-
Domestic, Global Procurement of Industrial Products
-
Private labeling / White Labeling your Products with your Brand Name
-
Product Finding & Locating Services
-
Global Design and Channel Partnership
-
Engineering Integration
-
Engineering Services
-
Global Consolidation, Warehousing, Logistics
New designs of hydraulic and pneumatic systems require smaller and smaller RESERVOIRS than the traditional ones. We specialize in reservoirs that will meet your industrial needs and standards and are as compact as possible. High vacuum is expensive, and therefore the smallest VACUUM CHAMBERS that will fulfill your needs are the most appealing in most cases. We specialize in modular vacuum chambers and equipment and can offer you solutions on an ongoing basis as your business grows.
HYDRAULIC & PNEUMATIC RESERVOIRS: Fluid power systems require air or liquid to transmit energy. Pneumatic systems use the air as the source for reservoirs. A compressor takes in atmospheric air, compresses it and then stores it in a receiver tank. A receiver tank is similar to a hydraulic system’s accumulator. A receiver tank stores energy for future use similar to a hydraulic accumulator. This is possible because air is a gas and is compressible. At the end of the work cycle the air is simply returned to the atmosphere. Hydraulic systems, on the other hand, need a finite amount of liquid fluid that must be stored and reused continually as the circuit works. Reservoirs are therefore part of almost any hydraulic circuit. Hydraulic reservoirs or tanks may be part of the machine framework or a separate stand-alone unit. The design and application of reservoirs is very important. The efficiency of a well-designed hydraulic circuit can be greatly reduced by poor reservoir design. Hydraulic reservoirs do much more than just providing a place to store fluid.
FUNCTIONS OF PNEUMATIC & HYDRAULIC RESERVOIRS: In addition to holding in reserve enough fluid to supply a system's varying needs, a reservoir provides:
-A large surface area for transferring heat from the fluid to the surrounding environment.
-Sufficient volume to let returning fluid slow down from a high velocity. This allows heavier contaminants to settle down and facilitates air escape. Air space above the fluid can accept air that bubbles out of the fluid. Users get access to remove used fluid and contaminants from the system and can add new fluid.
-A physical barrier separating fluid entering the reservoir from fluid entering the pump suction line.
-Space for hot-fluid expansion, gravity drain-back from a system during shutdown, and storage of large volumes needed intermittently during peak periods of operation
-In some cases, a convenient surface to mount other system components and components.
COMPONENTS OF RESERVOIRS: The filler-breather cap should include a filter media to block contaminants as the fluid level lowers and rises during a cycle. If the cap is used for filling, it should have a filter screen in its neck to catch large particles. It is best to pre-filter any fluid entering reservoirs. The drain plug is removed and tank emptied when the fluid needs to be changed. At this time, the clean-out covers should be removed to provide access to clean out all stubborn residue, rust, and flaking that may have accumulated in the reservoir. The clean-out covers and internal baffle are assembled together, with some brackets to keep the baffle upright. Rubber gaskets seal the clean-out covers to prevent leaks. If the system is seriously contaminated, one must flush all pipes and actuators while changing the tank fluid. This can be done by disconnecting the return line and placing its end in a drum, then cycling the machine. Sight glasses on reservoirs make it easy to visually check fluid levels. Calibrated sight gauges provide even more accuracy. Some sight gauges include a fluid-temperature gauge. The return line should be located in the same end of the reservoir as the inlet line and on the opposite side of the baffle. Return lines should terminate below fluid level to reduce turbulence and aeration in reservoirs. The open end of the return line should be cut at 45 degrees to eliminate the chances of stopping flow if it gets pushed to the bottom. Alternatively the opening can be pointed toward the side wall to get the maximum heat-transfer surface contact possible. In cases where hydraulic reservoirs are part of the machine base or body, it may not be possible to incorporate some of these features. Reservoirs are occasionally pressurized because pressurized reservoirs provide the positive inlet pressure required by some pumps, usually in line piston types. Also pressurized reservoirs force fluid into a cylinder through an undersized pre-fill valve. This may require pressures between 5 and 25 psi and one cannot use conventional rectangular reservoirs. Pressurizing reservoirs keeps out contaminates. If the reservoir always has a positive pressure in it there is no way for atmospheric air with its contaminants to enter. Pressure for this application is very low, between 0.1 to 1.0 psi, and may be acceptable even in rectangular model reservoirs. In a hydraulic circuit, wasted horsepower needs to be calculated in order to determine heat generation. In highly efficient circuits the wasted horsepower could be low enough to use the reservoirs cooling capacities to keep maximum operating temperatures below 130 F. If heat generation is slightly higher than what standard reservoirs can handle, it may be best to oversize the reservoirs rather than adding heat exchangers. Oversized reservoirs are less expensive than heat exchangers; and avoid the cost of installing water lines. Most industrial hydraulic units operate in warm indoor environments and therefore low temperatures are not a problem. For circuits that see temperatures below 65 to 70 F., some sort of fluid heater is recommended. The most common reservoir heater is an electric-powered immersion type unit. These reservoir heaters consist of resistive wires in a steel housing with a mounting option. Integral thermostatic control is available. Another way to electrically heat reservoirs is with a mat that has heating elements like electric blankets. This type heaters require no ports in the reservoirs for insertion. They evenly heat the fluid during times of low or no fluid circulation. Heat can be introduced through a heat exchanger by using hot water or steam The exchanger becomes a temperature controller when it also uses cooling water to take away heat when needed. Temperature controllers are not a common option in most climates because the majority of industrial applications operate in controlled environments. Always consider first if there is any way to reduce or eliminate unnecessarily generated heat, so it does not have to be paid for twice. It is costly to produce the unused heat and it is also expensive to get rid of it after it enters the system. Heat exchangers are costly, the water running through them is not free, and maintenance of this cooling system can be high. Components such as flow controls, sequence valves, reducing valves, and undersized directional control valves can add heat to any circuit and should be carefully thought about when designing. After calculating wasted horsepower, review catalogs that include charts for given size heat exchangers showing the amount of horsepower and/or BTU they can remove at different flows, oil temperatures, and ambient air temperatures. Some systems use a water-cooled heat exchanger in the summer and an air-cooled one in the winter. Such arrangements eliminate plant heating in summer weather and save on heating costs in the winter.
SIZING OF RESERVOIRS: The volume of a reservoir is a very important consideration . A rule of thumb for sizing a hydraulic reservoir is that its volume should equal three times the rated output of the system's fixed-displacement pump or mean flow rate of its variable-displacement pump. As an example, a system using a 10 gpm pump should have a 30 gal reservoir. This is nevertheless only a guideline for initial sizing. Due to modern day system technology, design objectives have changed for economic reasons, such as space saving, minimizing oil usage, and overall system cost reductions. Regardless of whether you choose to follow the traditional rule of thumb or follow the trend toward smaller reservoirs, be aware of parameters that may influence the reservoir size required. As an example, some circuit components such as large accumulators or cylinders may involve large volumes of fluid. Therefore, larger reservoirs may be needed so that fluid level does not drop below the pump inlet regardless of pump flow. Systems exposed to high ambient temperatures also require larger reservoirs unless they incorporate heat exchangers. Be sure to consider the substantial heat that can be generated within a hydraulic system. This heat is generated when the hydraulic system produces more power than is consumed by the load. The size of reservoirs, therefore, is determined primarily by the combination of highest fluid temperature and highest ambient temperature. All other factors being equal, the smaller the temperature difference between the two temperatures, the larger the surface area and hence the volume needed to dissipate heat from fluid to the surrounding environment. If the ambient temperature exceeds the fluid temperature, a heat exchanger will be needed to cool the fluid. For applications where space conservation is important, heat exchangers can reduce reservoir size and cost significantly. If reservoirs are not full at all times, they may not be dissipating heat through their full surface area. Reservoirs should contain at least 10% additional space of fluid capacity. This allows for thermal expansion of the fluid and gravity drain-back during shutdown, yet still provides a free fluid surface for deaeration. Maximum fluid capacity of reservoirs are marked permanently on their top plate. Smaller reservoirs are lighter, more compact, and less expensive to manufacture and maintain than one of traditional size and they are environmentally more friendly by reducing the total amount of fluid that can leak from a system. However specifying smaller reservoirs for a system must be accompanied by modifications that compensate for the lower volumes of fluid contained in the reservoirs. Smaller reservoirs have less surface area for heat transfer, and therefore heat exchangers may be necessary to maintain fluid temperatures within requirements. Also, in smaller reservoirs contaminants will not have as much opportunity for settling, so high-capacity filters will be required to trap contaminants. Traditional reservoirs provide the opportunity for air to escape from fluid before it is drawn into the pump inlet. Providing too small reservoirs could result in aerated fluid being drawn into the pump. This could damage the pump. When specifying a small reservoir, consider installing a flow diffuser, which reduces the velocity of return fluid, and helps prevent foaming and agitation, thus reducing potential pump cavitation from flow disturbances at the inlet. Another method you can use is to install a screen at an angle in the reservoirs. The screen collects small bubbles, which join with others to form large bubbles that rise to the fluid's surface. Nevertheless the most efficient and economical method to prevent aerated fluid from being drawn into the pump is to prevent aeration of fluid in the first place by paying careful attention to fluid flow paths, velocities, and pressures when designing a hydraulic system.
VACUUM CHAMBERS: While it is sufficient to manufacture most of our hydraulic and pneumatic reservoirs by sheet metal forming due to the relatively low pressures involved, some or even most of our vacuum chambers are machined from metals. Very low pressure vacuum systems must endure high external pressures from the atmosphere and cannot be made of sheet metals, plastic moulds or other fabrication techniques that reservoirs are made of. Therefore vacuum chambers are relatively more expensive than reservoirs in most cases. Also sealing of vacuum chambers is a greater challenge as compared to reservoirs in most cases because gas leaks into the chamber is hard to control. Even minute amounts of air leak into some vacuum chambers can be disastrous while most pneumatic and hydraulic reservoirs can tolerate some leakage easily. AGS-TECH is a specialist in high and ultra high vacuum chambers and equipment. We provide our clients the highest quality in engineering and fabrication of high vacuum and ultra high vacuum chambers and equipment. Excellence is assured through control of the entire process from; CAD design, fabrication, leak-testing, UHV cleaning and bake-out with RGA scan when required. We do provide off the shelf catalogue items, as well as work closely with clients to provide custom vacuum equipment and chambers. Vacuum Chambers can be manufactured in Stainless steel 304L/ 316L & 316LN or machined from Aluminum. High vacuum can accommodate small vacuum housings as well as large vacuum chambers with several meters of dimensions. We offer fully integrated vacuum systems-manufactured to your specifications, or designed & built to your requirements. Our vacuum chamber manufacturing lines deploy TIG welding and extensive machine shop facilities with 3, 4 & 5 axis machining to process hard to machine refractory material such as tantalum, molybdenum to high temperature ceramics such as boron and macor. In addition to these complex chambers we are always ready to consider your requests for smaller vacuum reservoirs. Reservoirs and canisters for both low and high vacuum can be designed and supplied.
As we are the most diverse custom manufacturer, engineering integrator, consolidator and outsourcing partner; you can contact us for any of your standard as well as complicated new projects involving reservoirs and chambers for hydraulics, pneumatics and vacuum applications. We can design reservoirs and chambers for you or use your existing designs and turn them into products. In any case, getting our opinion on hydraulic and pneumatic reservoirs and vacuum chambers and accessories for your projects will only be to your benefit.
- Hydraulic Reservoirs with Private Label (We can put your company name as the brand and your company logo on these. This way you can market your brand name when selling or using these)