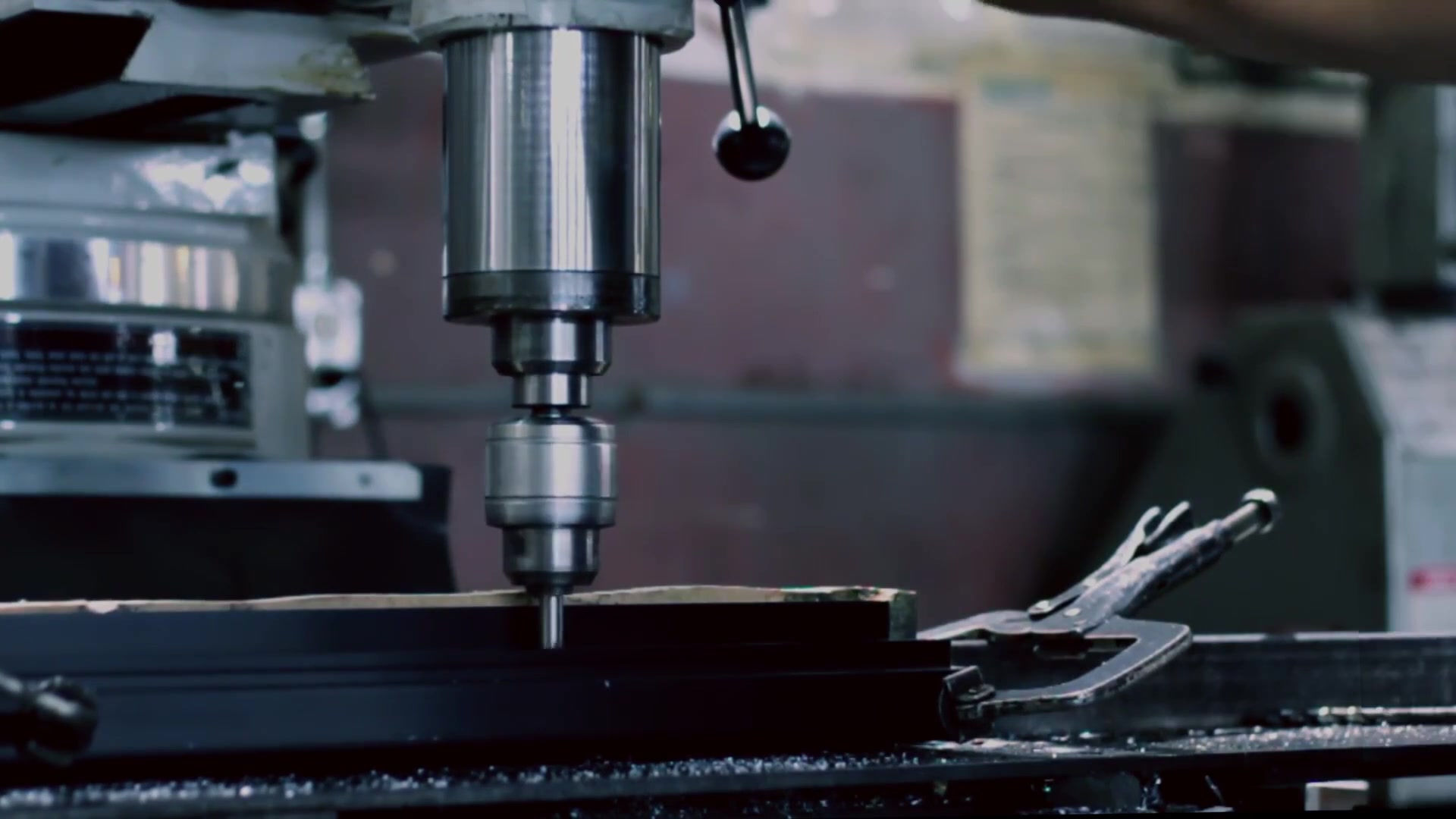
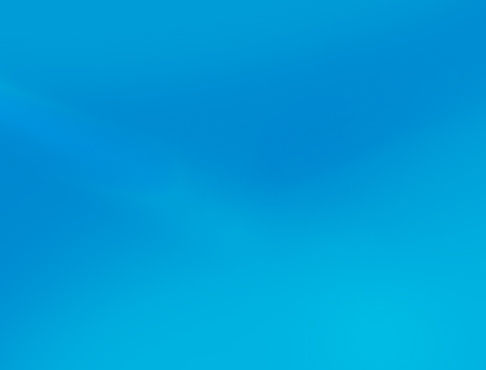
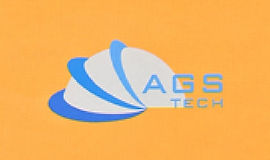
Producător global personalizat, integrator, consolidator, partener de outsourcing pentru o gamă largă de produse și servicii.
Suntem sursa dvs. unică pentru producția, fabricarea, inginerie, consolidare, integrare, externalizare a produselor și serviciilor fabricate la comandă și de pe raft.
Choose your Language
-
Fabricare la comandă
-
Producție pe bază de contract intern și global
-
Externalizarea producției
-
Achiziții interne și globale
-
Consolidation
-
Integrare inginerie
-
Servicii de inginerie
ELECTRICAL DISCHARGE MACHINING (EDM), also referred to as SPARK-EROSION or ELECTRODISCHARGE MACHINING, SPARK ERODING, DIE SINKING_cc781905-5cde-3194-bb3b -136bad5cf58d_or WIRE EROSION, is a NON-CONVENTIONAL MANUFACTURING process where erosion of metals takes place and desired shape is obtained using electrical discharges in the form de scântei. Oferim, de asemenea, câteva varietăți de EDM, și anume NO-WEAR EDM, WIRE EDM (WEDM), EDM GRRINDING (EDG), DIE-SINKING EDM, ELECTRICAL-DESCHARGE MILLING, micro-EDMcc7, m81900_5 -5cde-3194-bb3b-136bad5cf58d_and POLITIFICARE ELECTROCHIMICĂ-DESCARCARE (ECDG). Sistemele noastre EDM constau din scule/electrod modelate și piesa de prelucrat conectată la surse de curent continuu și introdusă într-un fluid dielectric neconductor electric. După 1940, prelucrarea cu descărcare electrică a devenit una dintre cele mai importante și populare tehnologii de producție în industriile prelucrătoare.
Când distanța dintre cei doi electrozi este redusă, intensitatea câmpului electric în volumul dintre electrozi devine mai mare decât puterea dielectricului în unele puncte, care se rupe, formând în cele din urmă o punte de curgere a curentului între cei doi electrozi. Se generează un arc electric intens care determină încălzirea semnificativă pentru a topi o parte a piesei de prelucrat și o parte din materialul de scule. Ca rezultat, materialul este îndepărtat din ambii electrozi. În același timp, fluidul dielectric este încălzit rapid, ducând la evaporarea fluidului în spațiul arcului. Odată ce fluxul de curent se oprește sau este oprit, căldura este îndepărtată din bula de gaz de către fluidul dielectric din jur și bula cavitată (se prăbușește). Unda de șoc creată de prăbușirea bulei și fluxul de fluid dielectric scoate resturile de pe suprafața piesei de prelucrat și antrenează orice material topit al piesei de prelucrat în fluidul dielectric. Rata de repetiție pentru aceste descărcări este între 50 și 500 kHz, tensiuni între 50 și 380 V și curenți între 0,1 și 500 de amperi. Noul dielectric lichid, cum ar fi uleiurile minerale, kerosenul sau apa distilată și deionizată, este de obicei transportat în volumul inter-electrod, purtând particulele solide (sub formă de resturi) și proprietățile izolante ale dielectricului sunt restaurate. După un flux de curent, diferența de potențial dintre cei doi electrozi este restabilită la ceea ce era înainte de defectare, astfel încât poate apărea o nouă defalcare dielectrică lichidă. Mașinile noastre moderne de descărcare electrică (EDM) oferă mișcări controlate numeric și sunt echipate cu pompe și sisteme de filtrare pentru fluidele dielectrice.
Prelucrarea cu descărcare electrică (EDM) este o metodă de prelucrare utilizată în principal pentru metale dure sau pentru cele care ar fi foarte greu de prelucrat cu tehnici convenționale. EDM funcționează de obicei cu orice materiale care sunt conductori electrici, deși au fost propuse și metode de prelucrare a ceramicii izolatoare cu EDM. Punctul de topire și căldura latentă de topire sunt proprietăți care determină volumul de metal îndepărtat per descărcare. Cu cât aceste valori sunt mai mari, cu atât rata de îndepărtare a materialului este mai lentă. Deoarece procesul de prelucrare cu descărcare electrică nu implică nicio energie mecanică, duritatea, rezistența și duritatea piesei de prelucrat nu afectează rata de îndepărtare. Frecvența de descărcare sau energia per descărcare, tensiunea și curentul sunt variate pentru a controla ratele de îndepărtare a materialului. Rata de îndepărtare a materialului și rugozitatea suprafeței cresc odată cu creșterea densității curentului și scăderea frecvenței scânteilor. Putem tăia contururi sau cavități complicate din oțel preîntărit folosind EDM fără a fi nevoie de tratament termic pentru a le înmuia și a le reîntări. Putem folosi această metodă cu orice metal sau aliaje metalice precum titanul, hastelloy, kovar și inconel. Aplicațiile procesului EDM includ modelarea sculelor cu diamant policristalin. EDM este considerată o metodă de prelucrare netradițională sau neconvențională, împreună cu procese precum prelucrarea electrochimică (ECM), tăierea cu jet de apă (WJ, AWJ), tăierea cu laser. Pe de altă parte, metodele convenționale de prelucrare includ strunjirea, frezarea, șlefuirea, găurirea și alte procese al căror mecanism de îndepărtare a materialului se bazează în principal pe forțe mecanice. Electrozii pentru prelucrarea cu descărcare electrică (EDM) sunt fabricați din aliaj de grafit, alamă, cupru și cupru-tungsten. Diametrele electrodului de până la 0,1 mm sunt posibile. Deoarece uzura sculelor este un fenomen nedorit care afectează negativ acuratețea dimensională în EDM, profităm de un proces numit NO-WEAR EDM, prin inversarea polarității și utilizarea sculelor din cupru pentru a minimiza uzura sculei.
În mod ideal, prelucrarea cu descărcare electrică (EDM) poate fi considerată o serie de defalcări și refaceri a lichidului dielectric între electrozi. În realitate însă, îndepărtarea resturilor din zona inter-electrodului este aproape întotdeauna parțială. Acest lucru face ca proprietățile electrice ale dielectricului din zona inter-electrozilor să fie diferite de valorile lor nominale și să varieze în timp. Distanța inter-electrod, (spark-gap), este ajustată de algoritmii de control ai mașinii specifice utilizate. Scânteia din EDM poate fi, din păcate, uneori scurtcircuitată de resturi. Este posibil ca sistemul de control al electrodului să nu reacționeze suficient de rapid pentru a preveni scurtcircuitarea celor doi electrozi (unealta și piesa de prelucrat). Acest scurtcircuit nedorit contribuie la îndepărtarea materialului diferit de cazul ideal. Acordăm cea mai mare importanță acțiunii de spălare pentru a restabili proprietățile izolatoare ale dielectricului, astfel încât curentul să aibă loc întotdeauna în punctul din zona inter-electrodului, reducând astfel la minimum posibilitatea modificării nedorite a formei (deteriorării) sculei-electrod. și piesa de prelucrat. Pentru a obține o geometrie specifică, unealta EDM este ghidată de-a lungul traseului dorit foarte aproape de piesa de prelucrat fără a o atinge. Acordăm o atenție deosebită performanței controlului mișcării în utilizare. În acest fel, au loc un număr mare de descărcări de curent/scântei și fiecare contribuie la îndepărtarea materialului atât din sculă, cât și din piesa de prelucrat, unde se formează mici cratere. Dimensiunea craterelor este o funcție a parametrilor tehnologici stabiliți pentru munca specifică în cauză, iar dimensiunile pot varia de la scară nanometrică (cum ar fi în cazul operațiunilor de micro-EDM) la câteva sute de micrometri în condiții de degroșare. Aceste mici cratere de pe unealtă provoacă eroziunea treptată a electrodului numită „uzură a sculei”. Pentru a contracara efectul dăunător al uzurii asupra geometriei piesei de prelucrat înlocuim continuu electrodul-scula în timpul unei operațiuni de prelucrare. Uneori reușim acest lucru prin utilizarea unui fir înlocuit continuu ca electrod (acest proces EDM se mai numește și WIRE EDM ). Uneori folosim electrodul-scula în așa fel încât doar o mică parte a acestuia este efectiv angajată în procesul de prelucrare și această porțiune este schimbată în mod regulat. Acesta este, de exemplu, cazul când se folosește un disc rotativ ca electrod de sculă. Acest proces se numește EDM GRINDING. O altă tehnică pe care o implementăm constă în folosirea unui set de electrozi cu dimensiuni și forme diferite în timpul aceleiași operațiuni EDM pentru a compensa uzura. Numim această tehnică cu electrozi multiplu și este folosită cel mai frecvent atunci când electrodul sculei reproduce în negativ forma dorită și este avansat către semifabricat de-a lungul unei singure direcții, de obicei direcția verticală (adică axa z). Aceasta seamănă cu chiuveta sculei în lichidul dielectric în care este scufundată piesa de prelucrat și, prin urmare, este denumită DIE-SINKING EDM_cc781905-5cde-3194-bb3b5cf58d6_bad5c781905-5cde-3194 3194-bb3b-136bad5cf58d_CONVENTIONAL EDM or RAM EDM). Mașinile pentru această operațiune se numesc SINKER EDM. Electrozii pentru acest tip de EDM au forme complexe. Dacă geometria finală este obținută folosind un electrod de obicei de formă simplă deplasat pe mai multe direcții și este, de asemenea, supus rotațiilor, îl numim EDM MILLING. Gradul de uzură depinde strict de parametrii tehnologici utilizați în funcționare (polaritate, curent maxim, tensiune în circuit deschis). De exemplu, in micro-EDM, cunoscut și ca m-EDM, acești parametri sunt de obicei setați la valori care generează uzură severă. Prin urmare, uzura este o problemă majoră în acea zonă pe care o minimizăm folosind know-how-ul acumulat. De exemplu, pentru a minimiza uzura electrozilor de grafit, un generator digital, controlabil în milisecunde, inversează polaritatea pe măsură ce are loc electroeroziunea. Acest lucru are ca rezultat un efect similar cu placarea galvanică, care depune continuu grafitul erodat înapoi pe electrod. Într-o altă metodă, așa-numitul circuit „Zero Wear”, minimizăm cât de des pornește și se oprește descărcarea, menținând-o cât mai mult timp posibil. Rata de îndepărtare a materialului în prelucrarea cu descărcare electrică poate fi estimată din:
MRR = 4 x 10 exp(4) x I x Tw exp (-1,23)
Aici MRR este în mm3/min, I este curent în Amperi, Tw este punctul de topire al piesei de prelucrat în K-273.15K. Exp înseamnă exponent.
Pe de altă parte, rata de uzură Wt a electrodului poate fi obținută din:
Wt = ( 1,1 x 10exp(11) ) x I x Ttexp(-2,38)
Aici Wt este în mm3/min și Tt este punctul de topire al materialului electrodului în K-273.15K
În cele din urmă, raportul de uzură al piesei de prelucrat față de electrodul R poate fi obținut din:
R = 2,25 x Trexp(-2,38)
Aici Tr este raportul dintre punctele de topire ale piesei de prelucrat la electrod.
SINKER EDM :
Sinker EDM, denumit și CAVITY TYPE EDM or_cc781905-5cde-bad5cf58d_cavity TYPE EDM or_cc781905-5cde-bad5cf58d-3cde-izolație-3cf18194-5cde-emerge-3cf5805-5cde-emerge-3cf5805-5cde-i-3cde-3cf58-3cde Electrodul și piesa de prelucrat sunt conectate la o sursă de alimentare. Sursa de alimentare generează un potențial electric între cele două. Pe măsură ce electrodul se apropie de piesa de prelucrat, în fluid are loc o defalcare dielectrică, formând un canal de plasmă și o mică scânteie sare. De obicei, scânteile lovesc una câte una, deoarece este foarte puțin probabil ca diferite locații din spațiul inter-electrod să aibă caracteristici electrice locale identice, care ar permite ca o scânteie să apară în toate astfel de locații simultan. Sute de mii de aceste scântei apar în puncte aleatorii între electrod și piesa de prelucrat pe secundă. Pe măsură ce metalul de bază se erodează, iar eclatorul crește ulterior, electrodul este coborât automat de mașina noastră CNC, astfel încât procesul să poată continua neîntrerupt. Echipamentul nostru are cicluri de control cunoscute sub denumirea de ''on time'' și ''off time''. Setarea timpului de pornire determină durata sau durata scânteii. Un timp mai lung produce o cavitate mai adâncă pentru acea scânteie și pentru toate scânteile ulterioare pentru acel ciclu, creând un finisaj mai dur pe piesa de prelucrat și invers. Timpul de oprire este perioada de timp în care o scânteie este înlocuită cu alta. Un timp de oprire mai lung permite lichidului dielectric să curgă printr-o duză pentru a curăța resturile erodate, evitând astfel un scurtcircuit. Aceste setări sunt ajustate în microsecunde.
WIRE EDM :
In WIRE ELECTRICAL DISCHARGE MACHINING (WEDM), also called WIRE-CUT EDM or WIRE CUTTING, we feed a sârmă metalică subțire dintr-un singur fir de alamă prin piesa de prelucrat, care este scufundată într-un rezervor de fluid dielectric. EDM cu sârmă este o variație importantă a EDM. Folosim ocazional EDM tăiat cu sârmă pentru a tăia plăci groase de 300 mm și pentru a face poanson, unelte și matrițe din metale dure care sunt greu de prelucrat cu alte metode de fabricație. În acest proces care seamănă cu tăierea conturului cu un ferăstrău cu bandă, sârma, care este alimentată constant dintr-o bobină, este ținută între ghidajele diamantate superioare și inferioare. Ghidajele controlate de CNC se deplasează în planul x–y, iar ghidajul superior se poate deplasa, de asemenea, independent în axa z–u–v, dând naștere capacității de a tăia forme conice și de tranziție (cum ar fi cerc în partea de jos și pătrat la topul). Ghidajul superior poate controla mișcările axei în x–y–u–v–i–j–k–l–. Acest lucru permite WEDM să taie forme foarte complicate și delicate. Intervalul mediu de tăiere al echipamentului nostru care realizează cel mai bun cost economic și timp de prelucrare este de 0,335 mm folosind sârmă de alamă, cupru sau wolfram de Ø 0,25. Cu toate acestea, ghidajele diamantate superioare și inferioare ale echipamentelor noastre CNC au o precizie de aproximativ 0,004 mm și pot avea o cale de tăiere sau o tăietură de până la 0,021 mm folosind un fir de Ø 0,02 mm. Deci sunt posibile tăieturi cu adevărat înguste. Lățimea de tăiere este mai mare decât lățimea firului, deoarece apar scântei de pe părțile laterale ale firului către piesa de prelucrat, provocând eroziune. Această „depășire” este necesară, pentru multe aplicații este previzibilă și, prin urmare, poate fi compensată (în micro-EDM acest lucru nu este adesea cazul). Bobinele de sârmă sunt lungi – o bobină de 8 kg de sârmă de 0,25 mm are puțin peste 19 kilometri lungime. Diametrul firului poate fi de până la 20 de micrometri, iar precizia geometriei este de aproximativ +/- 1 micrometru. În general, folosim firul o singură dată și îl reciclăm pentru că este relativ ieftin. Se deplasează cu o viteză constantă de 0,15 până la 9 m/min și se menține o tăietură constantă (slot) în timpul tăierii. În procesul de electroeroziune prin tăiere cu sârmă folosim apa ca fluid dielectric, controlându-i rezistivitatea și alte proprietăți electrice cu filtre și unități de deionizare. Apa spăla resturile tăiate departe de zona de tăiere. Spălarea este un factor important în determinarea vitezei maxime de avans pentru o anumită grosime a materialului și, prin urmare, o menținem consecventă. Viteza de tăiere în EDM cu sârmă este stabilită în termeni de suprafață transversală tăiată pe unitatea de timp, cum ar fi 18.000 mm2/h pentru oțel de scule D2 de 50 mm grosime. Viteza de tăiere liniară pentru acest caz ar fi 18.000/50 = 360 mm/h. Rata de îndepărtare a materialului în electroeroziune cu sârmă este:
MRR = Vf xhxb
Aici MRR este în mm3/min, Vf este viteza de avans a firului în piesa de prelucrat în mm/min, h este grosimea sau înălțimea în mm și b este tăietura, care este:
b = dw + 2s
Aici dw este diametrul firului și s este distanța dintre fir și piesa de prelucrat în mm.
Pe lângă toleranțe mai strânse, centrele noastre moderne de prelucrare cu sârmă EDM cu mai multe axe au adăugat caracteristici, cum ar fi capete multiple pentru tăierea a două piese în același timp, controale pentru prevenirea ruperii sârmei, caracteristici automate de auto-filetare în cazul ruperii sârmei și programare. strategii de prelucrare pentru a optimiza funcționarea, capacitățile de tăiere dreaptă și unghiulară.
Wire-EDM ne oferă tensiuni reziduale reduse, deoarece nu necesită forțe mari de tăiere pentru îndepărtarea materialului. Când energia/puterea per impuls este relativ scăzută (ca și în operațiunile de finisare), se așteaptă o mică modificare a proprietăților mecanice ale unui material din cauza tensiunilor reziduale scăzute.
POLITIRE ELECTRICA-DESCARCARE (EDG) : Rotile de polizare nu contin abrazivi, sunt din grafit sau alama. Scânteile repetitive dintre roata rotativă și piesa de prelucrat îndepărtează materialul de pe suprafețele piesei de prelucrat. Rata de îndepărtare a materialului este:
MRR = K x I
Aici MRR este în mm3/min, I este curent în Amperi și K este factorul material al piesei de prelucrat în mm3/A-min. Folosim frecvent șlefuirea cu descărcare electrică pentru a tăia fante înguste pe componente. Uneori combinăm procesul EDG (Electrical-Discharge Grinding) cu procesul ECG (Electrochemical Grinding) în care materialul este îndepărtat prin acțiune chimică, descărcările electrice de la roata de grafit rupând pelicula de oxid și spălate de electrolit. Procesul se numește ELECTROCHEMICAL-DISCHARGE GRINDING (ECDG). Chiar dacă procesul ECDG consumă relativ mai multă energie, este un proces mai rapid decât EDG. În mare parte, șlefuim sculele din carbură folosind această tehnică.
Aplicații ale prelucrării cu descărcare electrică:
Productie prototip:
Folosim procesul EDM în fabricarea matrițelor, a sculelor și a matrițelor, precum și pentru realizarea de prototipuri și piese de producție, în special pentru industria aerospațială, auto și electronică în care cantitățile de producție sunt relativ scăzute. În Sinker EDM, un electrod de grafit, tungsten de cupru sau cupru pur este prelucrat în forma dorită (negativă) și introdus în piesa de prelucrat la capătul unui berbec vertical.
Fabricarea matrițelor de monedă:
Pentru crearea matrițelor pentru producerea de bijuterii și insigne prin procesul de monedare (ștanțare), masterul pozitiv poate fi realizat din argint sterlină, deoarece (cu setări adecvate ale mașinii) masterul este erodat semnificativ și este folosit o singură dată. Matrița negativă rezultată este apoi întărită și utilizată într-un ciocan de picătură pentru a produce plăci ștanțate din semifabricate de tablă decupată din bronz, argint sau aliaj de aur cu rezistență redusă. Pentru insigne, aceste plăci pot fi modelate în continuare la o suprafață curbată printr-o altă matriță. Acest tip de electroeroziune se realizează de obicei scufundat într-un dielectric pe bază de ulei. Obiectul finit poate fi rafinat în continuare prin emailare dură (sticlă) sau moale (vopsea) și/sau galvanizat cu aur pur sau nichel. Materialele mai moi, cum ar fi argintul, pot fi gravate manual ca rafinament.
Forarea gaurilor mici:
La mașinile noastre de electroeroziune cu sârmă, folosim EDM cu găuri mici pentru a face un orificiu traversant într-o piesa de prelucrat prin care să filem sârma pentru operația de electroeroziune cu sârmă. Capete EDM separate, special pentru găurirea găurilor mici, sunt montate pe mașinile noastre de tăiat cu sârmă, ceea ce permite plăcilor mari întărite să aibă piesele finite erodate după cum este necesar și fără găurire prealabilă. De asemenea, folosim EDM cu găuri mici pentru a găuri șiruri de găuri în marginile palelor turbinei utilizate la motoarele cu reacție. Fluxul de gaz prin aceste orificii mici permite motoarelor să utilizeze temperaturi mai ridicate decât ar fi posibil. Aliajele cu un singur cristal la temperatură înaltă, foarte dure, din care sunt fabricate aceste lame, prelucrarea convențională a acestor găuri cu raport de aspect ridicat face extrem de dificilă și chiar imposibilă. Alte domenii de aplicare pentru EDM cu orificii mici este crearea orificiilor microscopice pentru componentele sistemului de combustibil. Pe lângă capetele EDM integrate, implementăm mașini EDM de găurit mici de sine stătătoare cu axe x–y pentru a prelucra găurile oarbe sau traversante. EDM forează găuri cu un electrod lung din alamă sau cu tub care se rotește într-un mandrina cu un flux constant de apă distilată sau deionizată care curge prin electrod ca agent de spălare și dielectric. Unele electroerozoare cu găuri mici pot găuri 100 mm de oțel moale sau chiar călit în mai puțin de 10 secunde. În această operațiune de găurire pot fi realizate găuri între 0,3 mm și 6,1 mm.
Prelucrare prin dezintegrare a metalelor:
De asemenea, avem mașini speciale de electroeroziune cu scopul specific de a îndepărta uneltele sparte (burghii sau robinete) de pe piesele de prelucrat. Acest proces se numește „prelucrare prin dezintegrare a metalelor”.
Avantaje și dezavantaje Prelucrarea cu descărcare electrică:
Avantajele EDM includ prelucrarea:
- Forme complexe care altfel ar fi dificil de produs cu unelte de tăiere convenționale
- Material extrem de dur la toleranțe foarte strânse
- Piese de lucru foarte mici în care uneltele convenționale de tăiere pot deteriora piesa din cauza presiunii excesive a sculei de tăiere.
- Nu există contact direct între unealtă și piesa de prelucrat. Prin urmare, secțiunile delicate și materialele slabe pot fi prelucrate fără nicio distorsiune.
- Se poate obține un finisaj bun al suprafeței.
- Găurile foarte fine pot fi găurite cu ușurință.
Dezavantajele EDM includ:
- Rata lentă de îndepărtare a materialului.
- Timpul și costul suplimentar utilizat pentru crearea electrozilor pentru electroeroziune cu ram/sinker.
- Reproducerea colțurilor ascuțite pe piesa de prelucrat este dificilă din cauza uzurii electrodului.
- Consumul de energie este mare.
- Se formează ''Overcut''.
- Uzura excesivă a sculei apare în timpul prelucrării.
- Materialele neconductoare din punct de vedere electric pot fi prelucrate numai cu o configurație specifică a procesului.