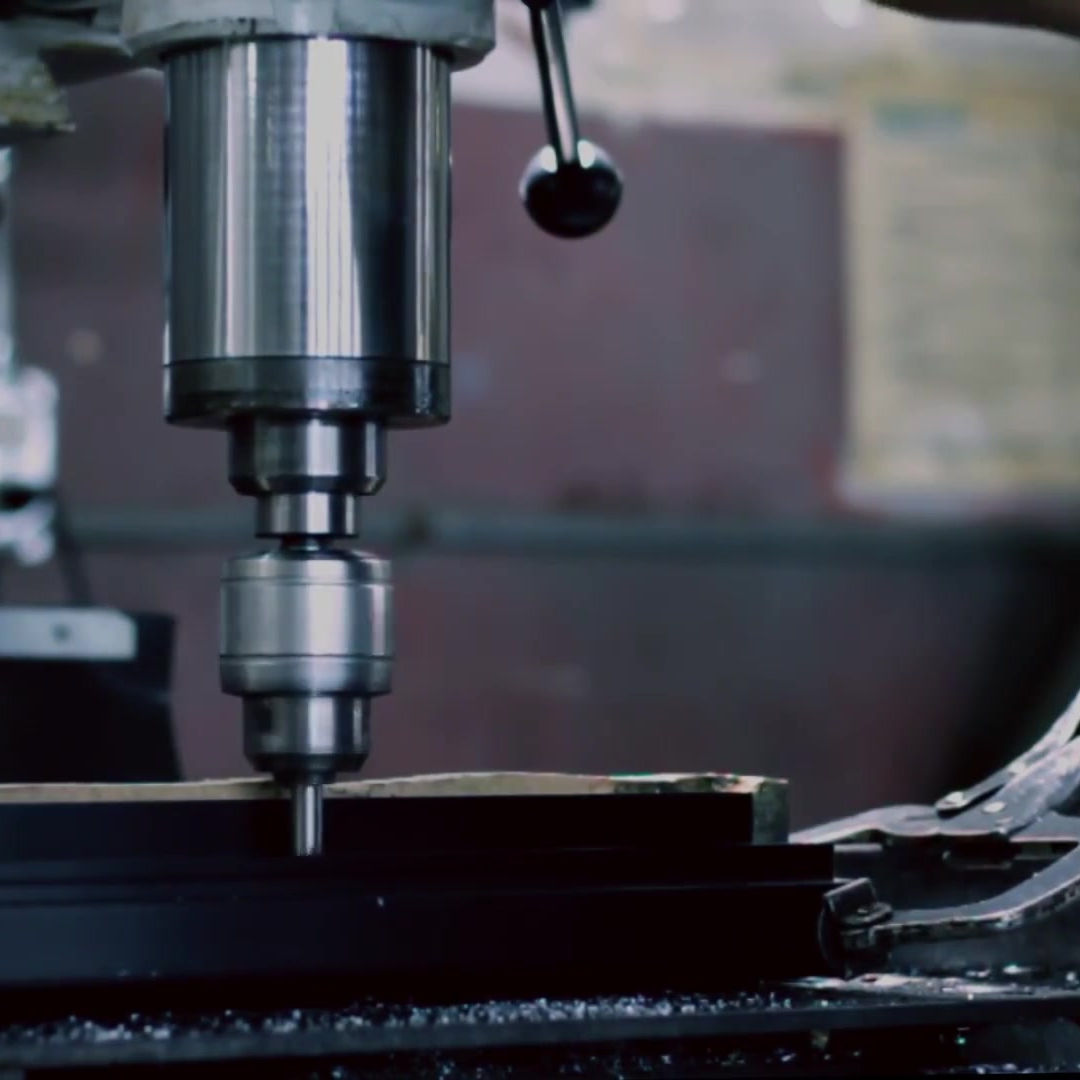
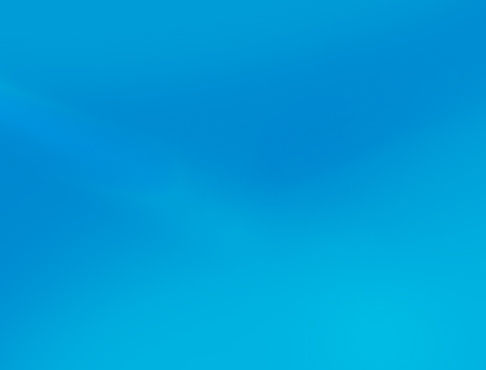
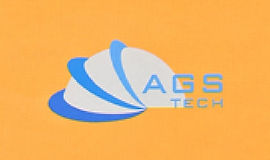
Producător global personalizat, integrator, consolidator, partener de outsourcing pentru o gamă largă de produse și servicii.
Suntem sursa dvs. unică pentru producția, fabricarea, inginerie, consolidare, integrare, externalizare a produselor și serviciilor fabricate la comandă și de pe raft.
Choose your Language
-
Fabricare la comandă
-
Producție pe bază de contract intern și global
-
Externalizarea producției
-
Achiziții interne și globale
-
Consolidation
-
Integrare inginerie
-
Servicii de inginerie
Search Results
164 de rezultate găsite cu o căutare fără conținut
- Composites, Composite Materials Manufacturing, Fiber Reinforced
Composites, Composite Materials Manufacturing, Particle and Fiber Reinforced, Cermets, Ceramic & Metal Composite, Glass Fiber Reinforced Polymer, Lay-Up Process Producția de materiale compozite și compozite Simplu definite, COMPOZITE sau MATERIALE COMPOZITE sunt materiale formate din două sau mai multe materiale cu proprietăți fizice sau chimice diferite, dar atunci când sunt combinate devin un material care este diferit de materialele constitutive. Trebuie să subliniem că materialele constitutive rămân separate și distincte în structură. Scopul fabricării unui material compozit este de a obține un produs care este superior constituenților săi și combină caracteristicile dorite ale fiecărui constituent. Ca exemplu; rezistența, greutatea redusă sau prețul mai mic pot fi motivația din spatele proiectării și producerii unui compozit. Tipurile de compozite pe care le oferim sunt compozite armate cu particule, compozite armate cu fibre, inclusiv compozite cu matrice ceramică / matrice polimerică / cu matrice metalică / carbon-carbon / compozite hibride, compozite structurale și laminate și cu structură sandwich și nanocompozite. Tehnicile de fabricație pe care le implementăm în fabricarea materialelor compozite sunt: pultruziune, procese de producție preimpregnate, plasare avansată a fibrelor, înfășurare a filamentului, plasare personalizată a fibrelor, procesul de întindere prin pulverizare fibră de sticlă, tufting, proces lanxide, z-pinning. Multe materiale compozite sunt formate din două faze, matricea, care este continuă și înconjoară cealaltă fază; și faza dispersată care este înconjurată de matrice. Vă recomandăm să faceți clic aici pentruDESCARCĂ Ilustrațiile noastre schematice ale producției de compozite și materiale compozite de către AGS-TECH Inc. Acest lucru vă va ajuta să înțelegeți mai bine informațiile pe care vi le oferim mai jos. • COMPOZITE ÎNFORTATE CU PARTICULE: Această categorie constă din două tipuri: compozite cu particule mari și compozite întărite cu dispersie. În primul tip, interacțiunile particule-matrice nu pot fi tratate la nivel atomic sau molecular. În schimb, mecanica continuului este valabilă. Pe de altă parte, în compozitele întărite cu dispersie, particulele sunt în general mult mai mici în intervalele de zeci de nanometri. Un exemplu de compozit cu particule mari sunt polimerii cărora li s-au adăugat materiale de umplutură. Materialele de umplutură îmbunătățesc proprietățile materialului și pot înlocui o parte din volumul polimerului cu un material mai economic. Fracțiile de volum ale celor două faze influențează comportamentul compozitului. Compozitele cu particule mari sunt utilizate cu metale, polimeri și ceramică. CERMETS-urile sunt exemple de compozite ceramice/metalice. Cel mai comun cermet al nostru este carbura cimentată. Este alcătuit din ceramică de carbură refractară, cum ar fi particule de carbură de tungsten, într-o matrice de metal, cum ar fi cobaltul sau nichelul. Aceste compozite din carbură sunt utilizate pe scară largă ca instrumente de tăiere pentru oțel călit. Particulele de carbură dură sunt responsabile pentru acțiunea de tăiere, iar duritatea lor este îmbunătățită de matricea metalică ductilă. Astfel obținem avantajele ambelor materiale într-un singur compozit. Un alt exemplu comun de compozit cu particule mari pe care îl folosim sunt particulele de negru de fum amestecate cu cauciuc vulcanizat pentru a obține un compozit cu rezistență ridicată la tracțiune, tenacitate, rezistență la rupere și abraziune. Un exemplu de compozit întărit prin dispersie este metalele și aliajele metalice întărite și întărite prin dispersia uniformă a particulelor fine dintr-un material foarte dur și inert. Când se adaugă fulgi foarte mici de oxid de aluminiu la matricea metalică de aluminiu, obținem pulbere de aluminiu sinterizat care are o rezistență îmbunătățită la temperatură ridicată. • COMPOZITE RĂMĂTATE CU FIBRĂ: Această categorie de compozite este de fapt cea mai importantă. Scopul de atins este rezistența și rigiditatea ridicate pe unitate de greutate. Compoziția fibrelor, lungimea, orientarea și concentrația din aceste compozite sunt critice în determinarea proprietăților și utilității acestor materiale. Sunt trei grupuri de fibre pe care le folosim: mustăți, fibre și fire. WHISKERS sunt monocristale foarte subțiri și lungi. Sunt printre cele mai rezistente materiale. Unele exemple de materiale pentru mustață sunt grafitul, nitrura de siliciu, oxidul de aluminiu. FIBRE, pe de altă parte, sunt în mare parte polimeri sau ceramice și sunt în stare policristalină sau amorfă. Al treilea grup este Sârmele fine care au diametre relativ mari și constau frecvent din oțel sau wolfram. Un exemplu de compozit armat cu sârmă sunt anvelopele auto care încorporează sârmă de oțel în interiorul cauciucului. În funcție de materialul matricei, avem următoarele compozite: COMPOZITE POLIMER-MATRICE: Acestea sunt realizate dintr-o rășină polimerică și fibre ca ingredient de întărire. Un subgrup dintre acestea, numite compozite polimere armate cu fibre de sticlă (GFRP), conțin fibre de sticlă continue sau discontinue într-o matrice polimerică. Sticla oferă o rezistență ridicată, este economică, ușor de fabricat în fibre și este inertă din punct de vedere chimic. Dezavantajele sunt rigiditatea și rigiditatea lor limitată, temperaturile de serviciu fiind de doar până la 200 – 300 de grade Celsius. Fibra de sticlă este potrivită pentru caroserii auto și echipamente de transport, caroserii vehiculelor marine, containere de depozitare. Nu sunt potrivite pentru industria aerospațială și nici pentru realizarea de poduri din cauza rigidității limitate. Celălalt subgrup se numește compozit polimer întărit cu fibră de carbon (CFRP). Aici, carbonul este materialul nostru de fibre din matricea polimerică. Carbonul este cunoscut pentru modulul specific ridicat și rezistența și capacitatea sa de a le menține la temperaturi ridicate. Fibrele de carbon ne pot oferi module de tracțiune standard, intermediare, înalte și ultraînalte. În plus, fibrele de carbon oferă diverse caracteristici fizice și mecanice și, prin urmare, sunt potrivite pentru diverse aplicații de inginerie personalizate. Compozitele CFRP pot fi considerate pentru a produce echipamente sportive și recreative, vase sub presiune și componente structurale aerospațiale. Totuși, un alt subgrup, compozitele polimerice armate cu fibre de aramidă sunt, de asemenea, materiale de înaltă rezistență și modul. Raporturile dintre rezistență și greutate sunt remarcabil de ridicate. Fibrele de aramidă sunt cunoscute și sub denumirile comerciale KEVLAR și NOMEX. Sub tensiune au rezultate mai bune decât alte materiale din fibre polimerice, dar sunt slabe la compresie. Fibrele de aramidă sunt dure, rezistente la impact, rezistente la fluaj și oboseală, stabile la temperaturi ridicate, inerte chimic, cu excepția acizilor și bazelor puternice. Fibrele de aramidă sunt utilizate pe scară largă în articole sportive, veste antiglonț, anvelope, frânghii, învelișuri pentru cabluri cu fibră optică. Există și alte materiale de armare cu fibre, dar sunt utilizate într-o măsură mai mică. Acestea sunt în principal bor, carbură de siliciu, oxid de aluminiu. Pe de altă parte, materialul matricei polimerice este, de asemenea, critic. Acesta determină temperatura maximă de serviciu a compozitului deoarece polimerul are în general o temperatură de topire și degradare mai scăzută. Poliesterii și esterii vinilici sunt utilizați pe scară largă ca matrice polimerică. De asemenea, sunt folosite rășini și au o rezistență excelentă la umiditate și proprietăți mecanice. De exemplu, rășina poliimidă poate fi folosită până la aproximativ 230 de grade Celsius. COMPOZITE METAL-MATRICE: În aceste materiale folosim o matrice metalică ductilă, iar temperaturile de serviciu sunt în general mai mari decât componentele lor constitutive. În comparație cu compozitele cu matrice polimerică, acestea pot avea temperaturi de funcționare mai ridicate, pot fi neinflamabile și pot avea o rezistență mai bună la degradare împotriva fluidelor organice. Cu toate acestea, sunt mai scumpe. Materiale de ranforsare precum mustati, particule, fibre continue si discontinue; iar materialele matricei cum ar fi cuprul, aluminiul, magneziul, titanul, superaliaje sunt utilizate în mod obișnuit. Exemple de aplicații sunt componentele motorului realizate din matrice de aliaj de aluminiu ranforsată cu oxid de aluminiu și fibre de carbon. COMPOZITE CERAMIC-MATRIX: Materialele ceramice sunt cunoscute pentru fiabilitatea lor remarcabil de bună la temperaturi ridicate. Cu toate acestea, sunt foarte fragile și au valori scăzute pentru duritatea la rupere. Prin încorporarea particulelor, fibrelor sau mustăților unei ceramice în matricea alteia, putem obține compozite cu rezistențe mai mari la rupere. Aceste materiale încorporate inhibă practic propagarea fisurilor în interiorul matricei prin unele mecanisme, cum ar fi devierea vârfurilor fisurilor sau formarea de punți peste fețele fisurilor. De exemplu, aluminele care sunt întărite cu mustăți de SiC sunt folosite ca inserții de scule de tăiere pentru prelucrarea aliajelor de metal dur. Acestea pot dezvălui performanțe mai bune în comparație cu carburile cimentate. COMPOZITE CARBON-CARBON: Atât armătura, cât și matricea sunt din carbon. Au module mari de tracțiune și rezistențe la temperaturi ridicate peste 2000 de grade Celsius, rezistență la fluaj, tenacitate mare la rupere, coeficienți de dilatare termică scăzuti, conductivitati termice ridicate. Aceste proprietăți le fac ideale pentru aplicații care necesită rezistență la șocuri termice. Slăbiciunea compozitelor carbon-carbon este totuși vulnerabilitatea lor împotriva oxidării la temperaturi ridicate. Exemple tipice de utilizare sunt matrițele de presare la cald, fabricarea avansată a componentelor motoarelor cu turbină. COMPOZITE HIBRIDE: Două sau mai multe tipuri diferite de fibre sunt amestecate într-o singură matrice. Astfel, se poate personaliza un nou material cu o combinație de proprietăți. Un exemplu este atunci când atât fibrele de carbon, cât și cele de sticlă sunt încorporate într-o rășină polimerică. Fibrele de carbon oferă rigiditate și rezistență de densitate scăzută, dar sunt scumpe. Pe de altă parte, sticla este ieftină, dar nu are rigiditatea fibrelor de carbon. Compozitul hibrid sticlă-carbon este mai puternic și mai dur și poate fi fabricat la un cost mai mic. PRELUCRAREA COMPOZITELOR ARMATE CU FIBRE: Pentru materialele plastice armate cu fibre continue cu fibre uniform distribuite orientate in aceeasi directie folosim urmatoarele tehnici. PULTRUZIE: Sunt fabricate tije, grinzi și tuburi de lungimi continue și secțiuni transversale constante. Rovingurile de fibre continue sunt impregnate cu o rășină termorezistabilă și sunt trase printr-o matriță de oțel pentru a le preforma la forma dorită. Apoi, trec printr-o matriță de întărire prelucrată cu precizie pentru a obține forma sa finală. Deoarece matrița de întărire este încălzită, se întărește matricea de rășină. Extractoarele trag materialul prin matrițe. Folosind miezuri goale introduse, putem obține tuburi și geometrii goale. Metoda de pultruziune este automatizată și ne oferă rate de producție ridicate. Este posibil să se producă orice lungime de produs. PROCESUL DE PRODUCȚIE PREPREG: Prepreg este o armătură cu fibre continue preimpregnată cu o rășină polimerică parțial întărită. Este utilizat pe scară largă pentru aplicații structurale. Materialul vine sub formă de bandă și este expediat ca bandă. Producătorul îl modelează direct și îl întărește complet fără a fi nevoie să adăugați rășină. Deoarece preimpregnatele suferă reacții de întărire la temperatura camerei, acestea sunt depozitate la 0 °C sau la temperaturi mai mici. După utilizare, benzile rămase sunt depozitate înapoi la temperaturi scăzute. Se folosesc rășini termoplastice și termorigide, iar fibrele de armare din carbon, aramid și sticlă sunt comune. Pentru a utiliza materiale preimpregnate, hârtia de suport este mai întâi îndepărtată și apoi fabricarea este realizată prin așezarea benzii preimpregnate pe o suprafață prelucrată (procesul de întindere). Se pot așeza mai multe straturi pentru a obține grosimile dorite. Practica frecventă este alternarea orientării fibrei pentru a produce un strat încrucișat sau laminat în unghi. În cele din urmă, se aplică căldură și presiune pentru întărire. Atât procesarea manuală, cât și procesele automate sunt utilizate pentru tăierea preimpregnate și lay-up. BOBINAREA FILAMENTULUI: Fibrele de armare continue sunt poziționate cu precizie într-un model predeterminat pentru a urma o formă goală și, de obicei, ciclindiric. Fibrele trec mai întâi printr-o baie de rășină și apoi sunt înfășurate pe un dorn printr-un sistem automat. După mai multe repetări de înfășurare se obțin grosimile dorite și întărirea se efectuează fie la temperatura camerei, fie în interiorul cuptorului. Acum dornul este îndepărtat și produsul este deformat. Înfășurarea filamentului poate oferi rapoarte rezistență-greutate foarte ridicate prin înfășurarea fibrelor în modele circumferențiale, elicoidale și polare. Conductele, rezervoarele, carcasele sunt fabricate folosind această tehnică. • COMPOZITE STRUCTURALE: În general, acestea sunt alcătuite atât din materiale omogene, cât și din materiale compozite. Prin urmare, proprietățile acestora sunt determinate de materialele constitutive și de designul geometric al elementelor sale. Iată principalele tipuri: COMPOZITE LAMINARE: Aceste materiale structurale sunt realizate din foi sau panouri bidimensionale cu direcții de înaltă rezistență preferate. Straturile sunt stivuite și cimentate împreună. Alternând direcțiile de mare rezistență în cele două axe perpendiculare, obținem un compozit care are rezistență mare în ambele direcții în planul bidimensional. Prin reglarea unghiurilor straturilor se poate fabrica un compozit cu rezistență în direcțiile preferate. Schiul modern este fabricat astfel. PANOURI SANDWICH: Aceste compozite structurale sunt ușoare, dar au totuși rigiditate și rezistență ridicate. Panourile sandwich constau din două foi exterioare realizate dintr-un material rigid și puternic, cum ar fi aliaje de aluminiu, materiale plastice armate cu fibre sau oțel și un miez între foile exterioare. Miezul trebuie să fie ușor și de cele mai multe ori să aibă un modul scăzut de elasticitate. Materialele de bază populare sunt spume polimerice rigide, lemn și faguri. Panourile sandwich sunt utilizate pe scară largă în industria construcțiilor ca material de acoperiș, material pentru podea sau pereți, precum și în industria aerospațială. • NANOCOMPOZITE: Aceste noi materiale constau din particule nanocompozite încorporate într-o matrice. Folosind nanocompozite putem fabrica materiale cauciucate care constituie bariere foarte bune în calea pătrunderii aerului, păstrând în același timp proprietățile cauciucului neschimbate. CLICK Product Finder-Locator Service PAGINA ANTERIOARĂ
- Machine Elements Manufacturing, Gears, Gear Drives, Bearings, Keys, Splines
Machine Elements Manufacturing, Gears, Gear Drives, Bearings, Keys, Splines, Pins, Shafts, Seals, Fasteners, Clutch, Cams, Followers, Belts, Couplings, Shafts Fabricarea elementelor de mașini Citeste mai mult Curele și lanțuri și ansamblu de transmisie prin cablu Citeste mai mult Angrenaje și ansamblu de transmisie Citeste mai mult Producție de cuplaje și rulmenți Citeste mai mult Producție chei și caneluri și știfturi Citeste mai mult Came și urmăritori și legături și producție de roți cu clichet Citeste mai mult Fabricarea arborilor Citeste mai mult Fabricare Sigilii Mecanice Citeste mai mult Ansamblu ambreiaj și frână Citeste mai mult Fabricarea elementelor de fixare Citeste mai mult Asamblare simplă a mașinilor ELEMENTELE MAȘINII sunt componente elementare ale unei mașini. Aceste elemente constau din trei tipuri de bază: 1.) Componente structurale, inclusiv elemente de cadru, rulmenți, osii, caneluri, elemente de fixare, etanșări și lubrifianți. 2.) Mecanisme care controlează mișcarea în diferite moduri, cum ar fi trenuri de viteze, transmisii prin curea sau cu lanț, legături, sisteme cu came și urmăritori, frâne și ambreiaje. 3.) Componente de control cum ar fi butoane, comutatoare, indicatoare, senzori, actuatoare și controlere de calculator. Majoritatea elementelor de mașină pe care vi le oferim sunt standardizate la dimensiuni comune, dar elementele de mașină personalizate sunt disponibile și pentru aplicațiile dumneavoastră specializate. Personalizarea elementelor mașinii poate avea loc pe modele existente care se află în cataloagele noastre descărcabile sau pe modele noi. Prototiparea și fabricarea elementelor mașinii pot fi continuate odată ce proiectul este aprobat de ambele părți. Dacă trebuie proiectate și fabricate elemente noi de mașină, clienții noștri fie ne trimit prin e-mail propriile planuri și le revizuim pentru aprobare, fie ne solicită să proiectăm elemente de mașină pentru aplicația lor. În acest din urmă caz, folosim toate contribuțiile clienților noștri și proiectăm elementele mașinii și trimitem proiectele finalizate clienților noștri pentru aprobare. Odată aprobate, producem primele articole și ulterior fabricăm elementele mașinii conform proiectului final. În orice etapă a acestei lucrări, în cazul în care proiectarea unui anumit element de mașină funcționează nesatisfăcător pe teren (ceea ce este rar), revizuim întregul proiect și facem modificări împreună cu clienții noștri, după cum este necesar. Este practica noastră standard să semnăm acorduri de confidențialitate (NDA) cu clienții noștri pentru proiectarea elementelor mașinii sau a oricărui alt produs ori de câte ori este necesar sau necesar. Odată ce elementele mașinii pentru un anumit client sunt proiectate și fabricate la comandă, îi atribuim un cod de produs și le producem și le vindem doar clientului nostru care deține produsul. Reproducem elementele mașinii folosind instrumentele, matrițele și procedurile dezvoltate de câte ori este nevoie și ori de câte ori clientul le recomandă. Cu alte cuvinte, odată ce un element de mașină personalizat este proiectat și produs pentru dvs., proprietatea intelectuală, precum și toate sculele și matrițele sunt rezervate și stocate pe termen nelimitat de către noi pentru dvs. și pentru produsele reproduse după cum doriți. De asemenea, oferim clienților noștri servicii de inginerie prin combinarea creativă a elementelor mașinii într-o componentă sau ansamblu care servește unei aplicații și îndeplinește sau depășește așteptările clienților noștri. Instalațiile care fabrică elementele mașinilor noastre sunt calificate fie prin ISO9001, QS9000 sau TS16949. În plus, majoritatea produselor noastre au marcaj CE sau UL și îndeplinesc standarde relevante la nivel internațional, cum ar fi ISO, SAE, ASME, DIN. Vă rugăm să faceți clic pe submeniuri pentru a obține informații detaliate despre elementele mașinii noastre, inclusiv: - Curele, lanțuri și transmisii prin cablu - Angrenaje și angrenaje - Cuplaje și rulmenți - Chei și spline și știfturi - Came și legături - Arbore - Garnituri mecanice - Ambreiaj și frână industrial - Elemente de fixare - Mașini simple Am pregătit o broșură de referință pentru clienții noștri, proiectanții și dezvoltatorii de produse noi, inclusiv elemente de mașină. Vă puteți familiariza cu câțiva termeni folosiți în mod obișnuit în proiectarea componentelor mașinii: Descărcați broșura pentru Termenii uzuali de inginerie mecanică utilizați de proiectanți și ingineri Elementele noastre de mașini găsesc aplicații într-o varietate de domenii, cum ar fi mașini industriale, sisteme de automatizare, echipamente de testare și metrologie, echipamente de transport, mașini de construcții și practic oriunde vă puteți gândi. AGS-TECH dezvoltă și produce elemente de mașină din diverse materiale în funcție de aplicație. Materialele utilizate pentru elementele mașinii pot varia de la materiale plastice turnate utilizate pentru jucării până la oțel cementat și acoperit special pentru mașinile industriale. Designerii noștri folosesc software profesional de ultimă generație și instrumente de proiectare pentru dezvoltarea elementelor mașinii, ținând cont de detalii precum unghiurile dinților angrenajului, tensiunile implicate, ratele de uzură etc. Vă rugăm să parcurgeți submeniurile noastre și să descărcați broșurile și cataloagele noastre de produse pentru a vedea dacă puteți găsi elemente de mașină disponibile pentru aplicația dvs. Dacă nu puteți găsi o potrivire potrivită pentru aplicația dvs., vă rugăm să ne anunțați și vom colabora cu dvs. pentru a dezvolta și fabrica elemente de mașină care să vă satisfacă nevoile. Dacă sunteți mai ales interesat de capabilitățile noastre de inginerie și cercetare și dezvoltare în loc de capabilitățile de producție, atunci vă invităm să vizitați site-ul nostru web http://www.ags-engineering.com unde puteți găsi informații mai detaliate despre designul nostru, dezvoltarea produselor, dezvoltarea proceselor, serviciile de consultanță în inginerie și multe altele CLICK Product Finder-Locator Service PAGINA ANTERIOARĂ
- Joining & Assembly & Fastening Processes, Welding, Brazing, Soldering
Joining & Assembly & Fastening Processes, Welding, Brazing, Soldering, Sintering, Adhesive Bonding, Press Fitting, Wave and Reflow Solder Process, Torch Furnace Procese de îmbinare și asamblare și fixare Îmbinăm, asamblam și fixăm piesele dumneavoastră fabricate și le transformăm în produse finite sau semifabricate folosind SUDARE, BRAZARE, LIPIERE, SINTERIZARE, LIERE ADEZIVĂ, FIXARE, MONTARE PRESĂ. Unele dintre cele mai populare procese de sudare ale noastre sunt arc, gaz oxicombustibil, rezistență, proiecție, cusătură, supărare, percuție, stare solidă, fascicul de electroni, laser, termit, sudare prin inducție. Procesele noastre populare de lipire sunt pistolul, inducția, cuptorul și lipirea prin scufundare. Metodele noastre de lipit sunt fierul, plita fierbinte, cuptorul, inducția, scufundarea, unda, reflow și lipirea cu ultrasunete. Pentru lipirea cu adeziv folosim frecvent materiale termoplastice și termostabilizate, epoxidici, fenolici, poliuretan, aliaje adezive, precum și alte substanțe chimice și benzi. În cele din urmă, procesele noastre de fixare constau în cuie, înșurubare, piulițe și șuruburi, nituire, strângere, prindere, cusătură și capsare și montare prin presare. • SUDARE: Sudarea implică îmbinarea materialelor prin topirea pieselor de prelucrat și introducerea de materiale de umplutură, care se îmbină și la bazinul de sudură topit. Când zona se răcește, obținem o îmbinare puternică. În unele cazuri se aplică presiune. Spre deosebire de sudare, operațiunile de lipire și lipire implică doar topirea unui material cu punct de topire mai mic între piesele de prelucrat, iar piesele de prelucrat nu se topesc. Vă recomandăm să faceți clic aici pentruDESCARCĂ Ilustrațiile noastre schematice ale proceselor de sudare de la AGS-TECH Inc. Acest lucru vă va ajuta să înțelegeți mai bine informațiile pe care vi le oferim mai jos. În SUDAREA ARC, folosim o sursă de alimentare și un electrod pentru a crea un arc electric care topește metalele. Punctul de sudare este protejat de un gaz de protecție sau vapori sau alt material. Acest proces este popular pentru sudarea pieselor auto și a structurilor din oțel. În sudarea cu arc metalic acoperit (SMAW) sau cunoscută și sub denumirea de sudare cu stick, un stick de electrod este adus aproape de materialul de bază și se generează un arc electric între ele. Tija electrodului se topește și acționează ca material de umplutură. Electrodul conține, de asemenea, flux care acționează ca un strat de zgură și emite vapori care acționează ca gaz de protecție. Acestea protejează zona de sudură de contaminarea mediului. Nu se folosesc alte materiale de umplutură. Dezavantajele acestui proces sunt încetineala, necesitatea înlocuirii frecvente a electrozilor, nevoia de a ciobi zgura reziduală provenită din flux. Un număr de metale precum fier, oțel, nichel, aluminiu, cupru etc. Poate fi sudat. Avantajele sale sunt instrumentele sale ieftine și ușurința în utilizare. Sudarea cu arc metalic cu gaz (GMAW), cunoscută și sub denumirea de gaz metal-inert (MIG), avem alimentare continuă cu un umplutură de sârmă cu electrod consumabil și un gaz inert sau parțial inert care curge în jurul firului împotriva contaminării mediului înconjurător a regiunii de sudare. Oțelul, aluminiul și alte metale neferoase pot fi sudate. Avantajele MIG sunt viteze mari de sudare și calitate bună. Dezavantajele sunt echipamentele sale complicate și provocările cu care se confruntă în mediile exterioare cu vânt, deoarece trebuie să menținem stabil gazul de protecție din jurul zonei de sudare. O variație a GMAW este sudarea cu arc cu miez de flux (FCAW) care constă dintr-un tub de metal fin umplut cu materiale de flux. Uneori, fluxul din interiorul tubului este suficient pentru a proteja împotriva contaminării mediului. Sudarea cu arc submers (SAW) este un proces automatizat, care implică alimentarea continuă a firului și arcul care este lovit sub un strat de acoperire de flux. Ratele de producție și calitatea sunt ridicate, zgura de sudură se desprinde ușor și avem un mediu de lucru fără fum. Dezavantajul este că poate fi folosit doar pentru a suda parts în anumite poziții. În sudarea cu arc de tungsten cu gaz (GTAW) sau sudarea cu gaz tungsten-inert (TIG) folosim un electrod de tungsten împreună cu o umplutură separată și gaze inerte sau aproape inerte. După cum știm, tungstenul are un punct de topire ridicat și este un metal foarte potrivit pentru temperaturi foarte ridicate. Tungstenul din TIG nu se consumă spre deosebire de celelalte metode explicate mai sus. O tehnică de sudare lentă, dar de înaltă calitate, avantajoasă față de alte tehnici de sudare a materialelor subțiri. Potrivit pentru multe metale. Sudarea cu arc cu plasmă este similară, dar utilizează gaz cu plasmă pentru a crea arcul. Arcul în sudarea cu arc cu plasmă este relativ mai concentrat în comparație cu GTAW și poate fi utilizat pentru o gamă mai largă de grosimi de metal la viteze mult mai mari. Sudarea cu arc GTAW și cu plasmă poate fi aplicată mai mult sau mai puțin pe aceleași materiale. SUDAREA OXY-FUEL / OXYFUEL numită și sudare oxiacetilenă, sudarea oxi, sudarea cu gaz se realizează folosind combustibili gazosi și oxigen pentru sudare. Deoarece nu se utilizează energie electrică, este portabil și poate fi folosit acolo unde nu există energie electrică. Folosind o pistoletă de sudură încălzim piesele și materialul de umplutură pentru a produce un bazin de metal topit comun. Pot fi utilizați diferiți combustibili, cum ar fi acetilena, benzina, hidrogenul, propanul, butanul etc. În sudarea oxi-combustibil folosim două recipiente, unul pentru combustibil și celălalt pentru oxigen. Oxigenul oxidează combustibilul (îl arde). SUDARE CU REZISTENTA: Acest tip de sudare profita de incalzirea in joule si caldura este generata in locul in care se aplica curentul electric pentru un anumit timp. Curenții mari trec prin metal. În această locație se formează bazine de metal topit. Metodele de sudare prin rezistență sunt populare datorită eficienței lor, potențialului mic de poluare. Cu toate acestea, dezavantajele sunt costurile echipamentelor relativ semnificative și limitarea inerentă la piesele de lucru relativ subțiri. SUDAREA PUNTURILOR este un tip major de sudare prin rezistență. Aici unim două sau mai multe foi suprapuse sau piese de lucru folosind doi electrozi de cupru pentru a fixa foile împreună și a trece un curent mare prin ele. Materialul dintre electrozii de cupru se încălzește și se generează un bazin topit în acea locație. Curentul este apoi oprit, iar vârfurile electrodului de cupru răcesc locul sudării, deoarece electrozii sunt răciți cu apă. Aplicarea cantității potrivite de căldură pe materialul și grosimea potrivite este cheia pentru această tehnică, deoarece dacă este aplicată greșit îmbinarea va fi slabă. Sudarea prin puncte are avantajele că nu provoacă deformare semnificativă a pieselor de prelucrat, eficiență energetică, ușurință de automatizare și rate de producție remarcabile și nu necesită umpluturi. Dezavantajul este că, deoarece sudarea are loc mai degrabă în puncte decât să formeze o cusătură continuă, rezistența totală poate fi relativ mai mică în comparație cu alte metode de sudare. SUDAREA CUSATURĂ, pe de altă parte, produce suduri la suprafețele de contact ale materialelor similare. Cusătura poate fi cap la cap sau îmbinare suprapusă. Sudarea cusăturii începe de la un capăt și trece progresiv la celălalt. Această metodă folosește și doi electrozi din cupru pentru a aplica presiune și curent în regiunea de sudare. Electrozii în formă de disc se rotesc cu contact constant de-a lungul liniei de cusătură și realizează o sudură continuă. Și aici, electrozii sunt răciți cu apă. Sudurile sunt foarte puternice și fiabile. Alte metode sunt tehnicile de sudură prin proiecție, flash și sudură. SUDAREA în stare solidă este puțin diferită de metodele anterioare explicate mai sus. Coalescența are loc la temperaturi sub temperatura de topire a metalelor îmbinate și fără utilizarea umpluturii metalice. Presiunea poate fi utilizată în unele procese. Diverse metode sunt SUDAREA COEXTRUZIUNE în care metalele diferite sunt extrudate prin aceeași matriță, SUDAREA LA PRESIUNE LA RECE în care îmbinăm aliajele moi sub punctele lor de topire, SUDAREA prin difuzie o tehnică fără linii vizibile de sudură, SUDAREA prin explozie pentru îmbinarea materialelor diferite, de exemplu aliaje rezistente la coroziune la structura oteluri, SUDAREA ELECTROMAGNETICA IMPULS in care se accelereaza tuburile si tablele prin forte electromagnetice, SUDURA FORJA care consta in incalzirea metalelor la temperaturi ridicate si ciocanarea lor intre ele, SUDAREA CU FRACTARE unde se executa cu suficienta sudura cu frecare, SUDAREA FRICTION STIR care presupune o rotatie non- unealtă consumabilă care traversează linia de îmbinare, SUDARE LA PRESIUNE LA CALDE unde presăm metalele împreună la temperaturi ridicate sub temperatura de topire în vid sau gaze inerte, SUDARE LA PRESIUNE ISOSTATICĂ LA CALDE un proces în care aplicăm presiune folosind gaze inerte în interiorul unui vas, SUDARE LA ROLL unde îmbinăm materiale diferite prin forțarea lor între două roți rotative, SUDARE ULTRASONIC la care sunt sudate foi subțiri de metal sau plastic folosind energie vibrațională de înaltă frecvență. Celelalte procedee ale noastre de sudare sunt SUDURA CU GRAND ELECTRONIC cu penetrare profundă și procesare rapidă, dar fiind o metodă costisitoare o considerăm pentru cazuri speciale, SUDURA ELECTROZĂRĂ o metodă potrivită numai pentru plăci groase și piese de oțel de prelucrat, SUDURĂ prin INDUCȚIE unde folosim inducția electromagnetică și încălzește piesele noastre electric conductoare sau feromagnetice, SUDARE LASER FACEȚI, de asemenea, cu penetrare adâncă și procesare rapidă, dar o metodă costisitoare, SUDARE HIBRIDĂ LASER care combină LBW cu GMAW în același cap de sudură și capabilă să depășească golurile de 2 mm între plăci, SUDARE prin percuție care presupune o descărcare electrică urmată de forjarea materialelor cu presiune aplicată, SUDAREA TERMITĂ care implică reacție exotermă între pulberile de oxid de aluminiu și fier., SUDAREA ELECTROGAZ cu electrozi consumabili și utilizată numai cu oțel în poziție verticală, iar în final SUDARE ARC STUD pentru îmbinarea știftului la bază material cu căldură și presiune. Vă recomandăm să faceți clic aici pentruDESCARCĂ Ilustrațiile noastre schematice ale proceselor de lipire, lipire și lipire cu adeziv de la AGS-TECH Inc Acest lucru vă va ajuta să înțelegeți mai bine informațiile pe care vi le oferim mai jos. • BRAZARE: Unim două sau mai multe metale prin încălzirea metalelor de adaos între ele deasupra punctelor de topire și folosind acțiunea capilară pentru a se răspândi. Procesul este similar cu lipirea, dar temperaturile implicate pentru topirea umpluturii sunt mai mari la lipire. Ca și în cazul sudării, fluxul protejează materialul de umplutură de contaminarea atmosferică. După răcire, piesele de prelucrat sunt îmbinate. Procesul implică următorii pași cheie: potrivire și degajare bună, curățarea corespunzătoare a materialelor de bază, fixarea corespunzătoare, selectarea corespunzătoare a fluxului și a atmosferei, încălzirea ansamblului și, în final, curățarea ansamblului lipit. Unele dintre procesele noastre de lipire sunt BRAZARE LA TORȚĂ, o metodă populară efectuată manual sau automat. Este potrivit pentru comenzi de producție cu volum redus și cazuri specializate. Căldura este aplicată folosind flăcări de gaz în apropierea îmbinării care este brazată. BRAZAREA LA FUNNER necesită mai puțină abilități de operator și este un proces semi-automat potrivit pentru producția industrială în masă. Atât controlul temperaturii, cât și controlul atmosferei din cuptor sunt avantaje ale acestei tehnici, deoarece prima ne permite să avem cicluri de căldură controlate și să eliminăm încălzirea locală, așa cum este cazul în cazul lipirii cu torță, iar cea din urmă protejează piesa de oxidare. Folosind jigging, suntem capabili să reducem costurile de producție la minimum. Dezavantajele sunt consumul mare de energie, costurile echipamentelor și considerații de proiectare mai dificile. BRAZAREA ÎN VID are loc într-un cuptor cu vid. Se menține uniformitatea temperaturii și obținem îmbinări fără flux, foarte curate, cu tensiuni reziduale foarte mici. Tratamentele termice pot avea loc în timpul lipirii în vid, din cauza tensiunilor reziduale scăzute prezente în timpul ciclurilor lente de încălzire și răcire. Dezavantajul major este costul său ridicat deoarece crearea unui mediu de vid este un proces costisitor. O altă tehnică DIP BRAZING îmbină părțile fixate în care compusul de lipire este aplicat pe suprafețele de îmbinare. După aceea, piesele fixate fixtured sunt scufundate într-o baie de sare topită, cum ar fi clorura de sodiu (sare de masă), care acționează ca mediu de transfer de căldură și flux. Aerul este exclus și, prin urmare, nu are loc formarea de oxid. La BRAZARE prin INDUCȚIE îmbinăm materialele printr-un metal de umplutură care are un punct de topire mai scăzut decât materialele de bază. Curentul alternativ de la bobina de inducție creează un câmp electromagnetic care induce încălzirea prin inducție pe materialele magnetice mai ales feroase. Metoda oferă încălzire selectivă, îmbinări bune cu materiale de umplutură care curg numai în zonele dorite, oxidare redusă deoarece nu sunt prezente flăcări și răcirea este rapidă, încălzire rapidă, consistență și adecvare pentru producția de volum mare. Pentru a ne accelera procesele și pentru a asigura coerența, folosim frecvent preforme. Informații despre instalația noastră de lipire care produce fitinguri din ceramică pe metal, etanșare ermetică, treceri de vid, vid înalt și ultraînalt și componente de control al fluidelor pot fi găsite aici:_cc781905-5cde-bb319836_bb31944Broșura Fabrica de lipire • LIPIREA: La lipire nu avem topirea pieselor de prelucrat, ci un metal de adaos cu un punct de topire mai mic decât piesele de îmbinare care se varsă în îmbinare. Metalul de umplutură în lipire se topește la temperatură mai scăzută decât în lipire. Folosim aliaje fără plumb pentru lipire și respectăm RoHS și pentru diferite aplicații și cerințe avem aliaje diferite și adecvate, cum ar fi aliajul de argint. Lipirea ne oferă îmbinări care sunt etanșe la gaz și lichide. În lipirea moale, metalul nostru de adaos are un punct de topire sub 400 de grade Celsius, în timp ce în lipirea și lipirea cu argint avem nevoie de temperaturi mai ridicate. Lipirea moale folosește temperaturi mai scăzute, dar nu are ca rezultat îmbinări puternice pentru aplicații solicitante la temperaturi ridicate. Lipirea cu argint, pe de altă parte, necesită temperaturi ridicate furnizate de torță și ne oferă îmbinări puternice, potrivite pentru aplicații la temperaturi înalte. Lipirea necesită cele mai ridicate temperaturi și, de obicei, se folosește o torță. Deoarece îmbinările de lipire sunt foarte puternice, acestea sunt un bun candidat pentru repararea obiectelor grele de fier. În liniile noastre de producție folosim atât lipirea manuală, cât și liniile automate de lipit. LIPIREA INDUCȚIE folosește curent alternativ de înaltă frecvență într-o bobină de cupru pentru a facilita încălzirea prin inducție. Curenții sunt induși în partea lipită și ca rezultat se generează căldură la rezistența mare joint. Această căldură topește metalul de umplutură. Se folosește și flux. Lipirea prin inducție este o metodă bună pentru lipirea cilindrilor și țevilor într-un proces continuu prin înfășurarea bobinelor în jurul lor. Lipirea unor materiale precum grafitul și ceramica este mai dificilă deoarece necesită placarea pieselor de prelucrat cu un metal adecvat înainte de lipire. Acest lucru facilitează legarea interfacială. Lipim astfel de materiale în special pentru aplicații de ambalare ermetică. Producem plăcile noastre de circuite imprimate (PCB) în volum mare, în principal folosind lipirea cu valuri. Numai pentru cantități mici de prototipuri folosim lipirea manuală cu fier de lipit. Folosim lipirea prin val atât pentru ansambluri PCB cu găuri traversante, cât și pentru montare la suprafață (PCBA). Un adeziv temporar menține componentele atașate la placa de circuite, iar ansamblul este plasat pe un transportor și se deplasează printr-un echipament care conține lipire topită. Mai întâi, PCB-ul este fluxat și apoi intră în zona de preîncălzire. Lipitura topită este într-o tigaie și are un model de valuri staționare pe suprafața sa. Când PCB-ul se deplasează peste aceste unde, aceste unde contactează partea inferioară a PCB-ului și se lipesc de plăcuțele de lipit. Lipirea rămâne doar pe pini și plăcuțe și nu pe PCB în sine. Valurile din lipirea topită trebuie să fie bine controlate, astfel încât să nu existe stropire, iar vârfurile undelor să nu atingă și să contamineze zonele nedorite ale plăcilor. În REFLOW SOLDERING, folosim o pastă de lipit lipicioasă pentru a atașa temporar componentele electronice de plăci. Apoi plăcile sunt trecute printr-un cuptor de reflow cu control al temperaturii. Aici lipitura se topește și conectează permanent componentele. Folosim această tehnică atât pentru componentele de montare pe suprafață, cât și pentru componentele cu orificii traversante. Controlul adecvat al temperaturii și reglarea temperaturii cuptorului este esențială pentru a evita distrugerea componentelor electronice de pe placă prin supraîncălzirea acestora peste limitele lor maxime de temperatură. În procesul de lipire prin reflux avem de fapt mai multe regiuni sau etape fiecare cu un profil termic distinct, cum ar fi etapa de preîncălzire, etapa de înmuiere termică, etapa de refluxare și etapa de răcire. Acești pași diferiți sunt esențiali pentru o lipire prin reflow fără deteriorare a ansamblurilor de plăci de circuit imprimat (PCBA). LIPIREA ULTRASONICĂ este o altă tehnică frecvent utilizată cu capacități unice - Poate fi folosită pentru a lipi sticlă, ceramică și materiale nemetalice. De exemplu, panourile fotovoltaice care sunt nemetalice au nevoie de electrozi care pot fi fixați folosind această tehnică. În lipirea cu ultrasunete, implementăm un vârf de lipit încălzit care emite și vibrații ultrasonice. Aceste vibrații produc bule de cavitație la interfața substratului cu materialul de lipit topit. Energia implozivă a cavitației modifică suprafața oxidului și îndepărtează murdăria și oxizii. În acest timp se formează și un strat de aliaj. Lipitura de la suprafața de lipire încorporează oxigen și permite formarea unei legături comune puternice între sticlă și lipire. Lipirea prin scufundare poate fi privită ca o versiune mai simplă a lipirii prin valuri, potrivită numai pentru producția la scară mică. Primul flux de curățare este aplicat ca în alte procese. PCB-urile cu componente montate sunt scufundate manual sau semi-automat într-un rezervor care conține lipitură topită. Lipitura topită se lipește de zonele metalice expuse neprotejate de masca de lipit de pe placă. Echipamentul este simplu și ieftin. • LIPIREA ADEZIVĂ: Aceasta este o altă tehnică populară pe care o folosim frecvent și implică lipirea suprafețelor folosind cleiuri, epoxidici, agenți plastici sau alte substanțe chimice. Lipirea se realizează fie prin evaporarea solventului, prin întărire la căldură, prin polimerizare cu lumină UV, prin întărire sub presiune sau prin așteptare pentru un anumit timp. În liniile noastre de producție sunt utilizați diverse adezivi de înaltă performanță. Cu procese de aplicare și întărire concepute corespunzător, lipirea adeziv poate avea ca rezultat legături de stres foarte scăzute, care sunt puternice și de încredere. Legăturile adezive pot fi buni protectori împotriva factorilor de mediu, cum ar fi umiditatea, contaminanții, corozivii, vibrațiile etc. Avantajele lipirii adezive sunt: pot fi aplicate pe materiale care altfel ar fi greu de lipit, sudat sau lipit. De asemenea, poate fi de preferat pentru materialele sensibile la căldură care ar fi deteriorate prin sudare sau alte procese la temperaturi ridicate. Alte avantaje ale adezivilor sunt că pot fi aplicați pe suprafețe de formă neregulată și pot crește greutatea ansamblului în cantități foarte mici în comparație cu alte metode. De asemenea, modificările dimensionale ale pieselor sunt foarte minime. Unele cleiuri au proprietăți de potrivire a indicelui și pot fi utilizate între componentele optice fără a scădea în mod semnificativ puterea luminii sau a semnalului optic. Pe de altă parte, dezavantajele sunt timpii de întărire mai lungi care pot încetini liniile de producție, cerințele de fixare, cerințele de pregătire a suprafeței și dificultatea de a dezasambla atunci când este nevoie de reprelucrare. Majoritatea operațiunilor noastre de lipire cu adeziv implică următorii pași: -Tratamentul suprafeței: procedurile speciale de curățare, cum ar fi curățarea cu apă deionizată, curățarea cu alcool, curățarea cu plasmă sau corona sunt frecvente. După curățare, putem aplica promotori de aderență pe suprafețe pentru a asigura cele mai bune îmbinări posibile. - Fixarea pieselor: atât pentru aplicarea adezivilor, cât și pentru întărire, proiectăm și folosim dispozitive personalizate. -Aplicare adeziv: Folosim uneori sisteme manuale, iar uneori, in functie de caz, automate precum robotica, servomotoare, actuatoare liniare pentru a livra adezivii la locul potrivit si folosim dozatoare pentru a-i livra la volumul si cantitatea potrivita. - Întărire: În funcție de adeziv, putem folosi uscare și întărire simplă, precum și întărire sub lumini UV care acționează ca catalizator sau întărire la căldură într-un cuptor sau folosind elemente de încălzire rezistive montate pe dispozitive și dispozitive de fixare. Vă recomandăm să faceți clic aici pentruDESCARCĂ Ilustrațiile noastre schematice ale proceselor de fixare de la AGS-TECH Inc. Acest lucru vă va ajuta să înțelegeți mai bine informațiile pe care vi le oferim mai jos. • PROCESE DE FIXARE: Procesele noastre mecanice de îmbinare se încadrează în două categorii de brad: FASTENERS și INTEGRAL JOINTS. Exemple de elemente de fixare pe care le folosim sunt șuruburi, știfturi, piulițe, șuruburi, nituri. Exemple de îmbinări integrale pe care le folosim sunt snap and shrink fits, cusături, sertizare. Folosind o varietate de metode de fixare, ne asigurăm că îmbinările noastre mecanice sunt puternice și fiabile pentru mulți ani de utilizare. Șuruburile și șuruburile sunt unele dintre cele mai utilizate elemente de fixare pentru ținerea și poziționarea obiectelor împreună. Șuruburile și șuruburile noastre respectă standardele ASME. Sunt utilizate diferite tipuri de șuruburi și șuruburi, inclusiv șuruburi hexagonale și șuruburi hexagonale, șuruburi și șuruburi autoblocante, șuruburi cu două capete, șuruburi cu cap, șurub cu ochi, șurub oglindă, șurub pentru tablă, șurub de reglare fină, șuruburi autoforante și autofiletante. , șurub de fixare, șuruburi cu șaibe încorporate și multe altele. Avem diferite tipuri de cap de șurub, cum ar fi cap înecat, cupolă, rotund, cu flanșă și diferite tipuri de șuruburi, cum ar fi slot, Phillips, pătrat, hexagonal. Pe de altă parte, un RIVET este un dispozitiv de fixare mecanic permanent format dintr-un ax cilindric neted și un cap pe de o parte. După introducere, celălalt capăt al nitului este deformat și diametrul acestuia este extins astfel încât să rămână pe loc. Cu alte cuvinte, înainte de instalare un nit are un singur cap, iar după instalare are două. Instalăm diferite tipuri de nituri în funcție de aplicație, rezistență, accesibilitate și cost, cum ar fi nituri cu cap solid/rotund, nituri structurale, semitubulare, oarbe, oscar, drive, flush, cu blocare prin frecare, nituri autoperforante. Nituirea poate fi preferată în cazurile în care trebuie evitată deformarea termică și modificarea proprietăților materialului din cauza căldurii de sudare. Nituirea oferă, de asemenea, greutate redusă și în special rezistență și rezistență bună împotriva forțelor de forfecare. Cu toate acestea, împotriva sarcinilor de tracțiune, șuruburile, piulițele și șuruburile pot fi mai potrivite. În procesul de CLINCHARE folosim poanson și matrițe speciale pentru a forma o interblocare mecanică între foile de metal care se îmbină. Poansonul împinge straturile de tablă în cavitatea matriței și are ca rezultat formarea unei îmbinări permanente. Nu este necesară nicio încălzire și nicio răcire în clinch și este un proces de lucru la rece. Este un proces economic care poate înlocui sudarea în puncte în unele cazuri. În PINNING folosim știfturi care sunt elemente ale mașinii utilizate pentru a asigura pozițiile pieselor mașinii unele față de altele. Tipurile majore sunt știfturi, știfturi, știfturi cu arc, știfturi, și știftul despicat. În CAPSARE folosim pistoale de capsare și capse care sunt elemente de fixare cu două capete folosite pentru a îmbina sau lega materiale. Capsarea are următoarele avantaje: Economică, simplă și rapidă de utilizat, coroana capselor poate fi folosită pentru a lega materialele îmbinate între ele, Coroana capsei poate facilita unirea unei piese ca un cablu și fixarea acesteia pe o suprafață fără perforare sau dăunătoare, îndepărtare relativ ușoară. PRESAREA se realizează prin împingerea pieselor împreună, iar frecarea dintre ele fixează piesele. Piesele de fixare prin presare constând dintr-un arbore supradimensionat și un orificiu subdimensionat sunt, în general, asamblate prin una din două metode: fie prin aplicarea forței, fie profitând de dilatarea sau contracția termică a pieselor. Când se stabilește o racordare prin presare prin aplicarea unei forțe, folosim fie o presă hidraulică, fie o presă manuală. Pe de altă parte, atunci când montarea prin presare este stabilită prin dilatare termică, încălzim părțile învelitoare și le asamblam la locul lor cât timp sunt fierbinți. Când se răcesc, se contractă și revin la dimensiunile lor normale. Acest lucru are ca rezultat o potrivire bună prin presare. Numim asta alternativ MONTARE RETRACTĂ. Cealaltă modalitate de a face acest lucru este răcirea pieselor învelite înainte de asamblare și apoi glisarea lor în părțile lor de împerechere. Când ansamblul se încălzește, se extind și obținem o potrivire strânsă. Această ultimă metodă poate fi de preferat în cazurile în care încălzirea prezintă riscul de modificare a proprietăților materialului. Răcirea este mai sigură în aceste cazuri. Componente și ansambluri pneumatice și hidraulice • Supape, componente hidraulice și pneumatice, cum ar fi inele O, șaibă, garnituri, garnitură, inel, lame. Deoarece supapele și componentele pneumatice vin într-o mare varietate, nu putem enumera totul aici. În funcție de mediile fizice și chimice ale aplicației dvs., avem produse speciale pentru dvs. Vă rugăm să ne specificați aplicația, tipul de componentă, specificațiile, condițiile de mediu precum presiunea, temperatura, lichidele sau gazele care vor intra în contact cu supapele și componentele pneumatice dvs.; și vom alege cel mai potrivit produs pentru dvs. sau îl vom fabrica special pentru aplicația dvs. CLICK Product Finder-Locator Service PAGINA ANTERIOARĂ
- Transmission Components, Belts, Chains, Cable Drives, Pulleys,AGS-TECH
Transmission Components, Belts, Chains and Cable Drives, Conventional & Grooved or Serrated, Positive Drive, Pulleys Curele și lanțuri și ansamblu de transmisie prin cablu AGS-TECH Inc. vă oferă componente de transmisie a puterii, inclusiv curele și lanțuri și ansamblu de transmisie prin cablu. Cu ani de rafinament, transmisiile noastre din cauciuc, piele și alte curele au devenit mai ușoare și mai compacte, capabile să suporte sarcini mai mari la costuri mai mici. În mod similar, transmisiile noastre în lanț au trecut prin multe dezvoltări de-a lungul timpului și oferă clienților noștri mai multe avantaje. Unele avantaje ale utilizării transmisiilor cu lanț sunt distanța relativ nerestricționată între centrele arborelui, compactitatea, ușurința de asamblare, elasticitatea în tensiune fără alunecare sau fluaj, capacitatea de a funcționa în medii cu temperaturi ridicate. Unitățile noastre de cablu oferă, de asemenea, avantaje precum simplitatea în unele aplicații față de alte tipuri de componente de transmisie. Sunt disponibile atât transmisii de curea, lanț și cablu, cât și versiuni fabricate și asamblate la comandă. Putem fabrica aceste componente de transmisie la dimensiunea potrivită aplicației dumneavoastră și din cele mai potrivite materiale. CUREAȘI ȘI TRANSMISĂRI CU CUREA: - Curele plate convenționale: Acestea sunt curele plate simple, fără dinți, șanțuri sau creme. Transmisiile cu curele plate oferă flexibilitate, absorbție bună a șocurilor, transmisie eficientă a puterii la viteze mari, rezistență la abraziune, cost redus. Curelele pot fi îmbinate sau conectate pentru a face curele mai mari. Alte avantaje ale curelelor plate convenționale sunt că sunt subțiri, nu sunt supuse unor sarcini centrifuge mari (le face bune pentru operațiuni de mare viteză cu scripete mici). Pe de altă parte, ele impun sarcini portante mari, deoarece curelele plate necesită o tensiune mare. Alte dezavantaje ale transmisiilor cu curele plate pot fi alunecarea, funcționarea zgomotoasă și eficiența relativ mai scăzută la viteze mici și moderate de funcționare. Avem două tipuri de curele convenționale: întărite și neîntărite. Centurile armate au un element de tracțiune în structura lor. Curele plate convenționale sunt disponibile ca piele, material cauciucat sau snur, cauciuc neîntărit sau plastic, material textil, piele ranforsată. Curelele din piele oferă durată lungă de viață, flexibilitate, coeficient excelent de frecare, reparație ușoară. Cu toate acestea, curelele din piele sunt relativ scumpe, necesită îmbrăcarea și curățarea centurii și, în funcție de atmosferă, se pot micșora sau întinde. Țesăturile cauciucate sau curelele din snur sunt rezistente la umiditate, acid și alcalii. Curelele din material cauciucat sunt formate din straturi de bumbac sau rață sintetică impregnate cu cauciuc și sunt cele mai economice. Curele de cablu cauciucate constau dintr-o serie de straturi de cabluri impregnate cu cauciuc. Curelele cauciucate oferă o rezistență ridicată la tracțiune și o dimensiune și o masă modeste. Curelele de cauciuc sau plastic neîntărite sunt potrivite pentru aplicații ușoare, cu viteză redusă. Curelele de cauciuc și plastic neîntărite pot fi întinse la locul lor peste scripetele lor. Curelele din plastic neîntărite pot transmite o putere mai mare în comparație cu curelele din cauciuc. Centurile de piele ranforsate constau dintr-un element de tracțiune din plastic, plasat între straturile superioare și inferioare de piele. În cele din urmă, curelele noastre din țesătură pot consta dintr-o singură bucată de bumbac sau rață împăturită și cusută cu rânduri de cusături longitudinale. Centurile din material textil pot urmări uniform și funcționează la viteză mare. - Curele canelate sau zimtate (cum ar fi curele trapezoidale): Acestea sunt curele plate de bază modificate pentru a oferi avantajele unui alt tip de produs de transmisie. Acestea sunt curele plate cu o parte inferioară cu nervuri longitudinale. Curelele Poly-V sunt curele plate cu caneluri longitudinale sau zimtate, cu secțiune de tracțiune și o serie de caneluri adiacente în formă de V pentru urmărire și compresie. Capacitatea de putere depinde de lățimea centurii. Cureaua trapezoidală este calul de lucru al industriei și sunt disponibile într-o varietate de dimensiuni și tipuri standardizate pentru transmiterea aproape oricărei puteri de sarcină. Transmisiile cu curele trapezoidale funcționează bine între 1500 și 6000 ft/min, totuși curelele înguste vor funcționa până la 10.000 ft/min. Transmisiile cu curele trapezoidale oferă o durată lungă de viață, cum ar fi 3 până la 5 ani și permit rapoarte mari de viteză, sunt ușor de instalat și demontat, oferă o funcționare silențioasă, întreținere redusă, o bună absorbție a șocurilor între transmisia curelei și arborii antrenați. Dezavantajul curelelor trapezoidale este alunecarea și fluajul lor și, prin urmare, este posibil să nu fie cea mai bună soluție acolo unde sunt necesare viteze sincrone. Avem curele industriale, auto și agricole. Sunt disponibile lungimi standard stocate, precum și lungimi personalizate de curele. Toate secțiunile transversale standard ale curelei trapezoidale sunt disponibile din stoc. Există tabele în care puteți calcula parametri necunoscuți, cum ar fi lungimea curelei, secțiunea curelei (lățimea și grosimea) cu condiția să cunoașteți câțiva parametri ai sistemului dvs., cum ar fi diametrele scripetelor antrenate și antrenate, distanța dintre centrele dintre scripete și vitezele de rotație ale scripetelor. Puteți folosi astfel de tabele sau ne puteți cere să alegem cureaua trapezoială potrivită pentru dvs. - Curele de transmisie pozitivă (Curea de distribuție): Aceste curele sunt, de asemenea, de tip plat, cu o serie de dinți distanțați uniform pe circumferința interioară. Curelele de transmisie pozitivă sau de distribuție combină avantajele curelelor plate cu caracteristicile de prindere pozitivă ale lanțurilor și angrenajelor. Curelele de transmisie pozitive nu evidențiază alunecare sau variații de viteză. Este posibilă o gamă largă de rapoarte de viteză. Sarcinile lagărului sunt scăzute deoarece pot funcționa la tensiune scăzută. Ele sunt totuși mai susceptibile la dezaliniri ale scripetelor. - Scripete, snopi, butuci pentru curele: Se folosesc diferite tipuri de scripete cu curele de transmisie plate, cu nervuri (cretate) și pozitive. Le producem pe toate. Majoritatea scripetelor noastre plate sunt fabricate din fier turnat, dar versiunile din oțel sunt disponibile și în diferite combinații de jante și butuci. Scripeții noștri cu curele plate pot avea butuci solidi, cu spițe sau despicați sau putem produce după cum doriți. Cenelele cu nervuri și cu transmisie pozitivă sunt disponibile într-o varietate de dimensiuni și lățimi stoc. Cel puțin un scripete din transmisiile cu curele de distribuție trebuie să fie cu flanșă pentru a menține cureaua pe transmisie. Pentru sistemele de antrenare centrală lungă, se recomandă să aibă ambele fulii cu flanșă. Snopii sunt roțile canelate ale scripetelor și sunt în general fabricate prin turnare a fierului, formarea oțelului sau turnarea plasticului. Formarea oțelului este un proces potrivit pentru fabricarea snopii auto și agricole. Producem snopi cu caneluri regulate si adanci. Ropii cu canelură adâncă sunt potrivite atunci când cureaua trapezoidală intră în scripeți la un unghi, așa cum este cazul în cazul antrenărilor cu un sfert de tură. Canelurile adânci sunt, de asemenea, potrivite pentru antrenările cu arbore vertical și aplicațiile în care vibrația curelelor poate fi o problemă. Scripetele noastre foloase sunt scripete canelate sau scripete plate care nu servesc la transmiterea puterii mecanice. Roțile de rulare sunt folosite mai ales pentru strângerea curelelor. - Transmisii cu curele simple și multiple: Transmisiile cu curele simple au o singură canelură, în timp ce transmisiile cu curele multiple au mai multe caneluri. Făcând clic pe textul colorat relevant de mai jos, puteți descărca cataloagele noastre: - Curele de transmisie a puterii (include curele trapezoidale, curele de distribuție, curele cu margine brută, curele înfășurate și curele speciale) - Benzi transportoare - Scripeți în V - Scripeți de sincronizare LANȚURI ȘI LANȚURI: Lanțurile noastre de transmisie au câteva avantaje, cum ar fi distanțe relativ nerestricționate între centrele arborelui, asamblare ușoară, compactitate, elasticitate sub tensiune fără alunecare sau fluaj, capacitatea de funcționare la temperaturi ridicate. Iată principalele tipuri de lanțuri noastre: - Lanțuri detașabile: Lanțurile noastre detașabile sunt fabricate într-o gamă largă de dimensiuni, pas și rezistență maximă și, în general, din fontă maleabilă sau oțel. Lanțurile maleabile sunt fabricate într-o gamă de dimensiuni de la 0,902 (23 mm) la 4,063 inchi (103 mm) pas și rezistență maximă de la 700 la 17.000 lb/inch pătrat. Lanțurile noastre detașabile din oțel, pe de altă parte, sunt fabricate în dimensiuni de la 0,904 inchi (23 mm) la aproximativ 3,00 inci (76 mm) în pas, cu rezistență maximă de la 760 la 5000 lb/inch pătrat._cc781905-5cde-3194-bb3b- 136bad5cf58d_ - Lanțuri cu pin: Aceste lanțuri sunt folosite pentru sarcini mai grele și viteze puțin mai mari până la aproximativ 450 de picioare/min (2,2 m/sec). Lanțurile cu țevi sunt realizate din zale turnate individuale, având capătul rotund, plin, cu bare laterale deplasate. Aceste zale sunt intercuplate cu știfturi de oțel. Aceste lanțuri variază în pas de la aproximativ 1,00 inch (25 mm) la 6,00 inch (150 mm) și rezistența maximă între 3600 și 30.000 lb/inch pătrat. - Lanțuri cu bară laterală decalată: acestea sunt populare în lanțurile de transmisie ale mașinilor de construcții. Aceste lanțuri funcționează la viteze de până la 1000 ft/min și transmit sarcini la aproximativ 250 CP. În general, fiecare legătură are două bare laterale decalate, o bucșă, o rolă, un știft, un știft. - Lanțuri cu role: sunt disponibile în pasi de la 0,25 (6 mm) la 3,00 (75 mm) inci. Rezistența maximă a lanțurilor cu role cu o singură lățime variază între 925 și 130.000 lb/inch pătrat. Sunt disponibile versiuni cu lățimi multiple ale lanțurilor cu role și transmit o putere mai mare la viteze mai mari. Lanțurile cu role cu lățimi multiple oferă, de asemenea, o acțiune mai lină cu zgomot redus. Lanțurile cu role sunt asamblate din legături cu role și legături cu știfturi. Știfturile sunt utilizate în lanțurile cu role din versiunea detașabilă. Proiectarea transmisiilor cu lanț cu role necesită experiență în domeniu. În timp ce transmisiile cu curea se bazează pe viteze liniare, transmisiile cu lanț se bazează pe viteza de rotație a pinionului mai mic, care este în majoritatea instalațiilor elementul antrenat. Pe lângă puterea nominală și viteza de rotație, designul transmisiilor cu lanț se bazează pe mulți alți factori. - Lanțuri cu pas dublu: practic la fel ca și lanțurile cu role, cu excepția faptului că pasul este de două ori mai lung. - Lanțuri cu dinți inversați (silențioase): lanțuri de mare viteză utilizate în principal pentru motoare primare, acționări cu priză de putere. Transmisiile cu lanț cu dinți inversați pot transmite puteri de până la 1200 CP și sunt formate dintr-o serie de zale dentare, asamblate alternativ fie cu știfturi, fie cu o combinație de componente de îmbinare. Lanțul de ghidare central are legături de ghidare pentru a cupla canelurile din pinion, iar lanțul de ghidare lateral are ghidaje pentru a cupla părțile laterale ale pinionului. - Lanțuri cu mărgele sau glisare: Aceste lanțuri sunt folosite pentru viteze mici și, de asemenea, în operațiuni manuale. Făcând clic pe textul colorat relevant de mai jos, puteți descărca cataloagele noastre: - Lanțuri de conducere - Lanțuri transportoare - Lanțuri transportoare cu pas mare - Lanțuri cu role din oțel inoxidabil - Lanțuri de ridicare - Lanțuri pentru motociclete - Lanțuri de mașini agricole - pinioane: pinioanele noastre standard sunt conforme cu standardele ANSI. Pinionii cu plăci sunt pinioane plate, fără butuc. Pinionii noștri butuci de dimensiuni mici și mijlocii sunt transformați din bară sau din piese forjate sau sunt realizate prin sudarea unui butuc de bară pe o placă laminată la cald. AGS-TECH Inc. poate furniza pinioane prelucrate din piese turnate din fontă gri, oțel turnat și construcții de butuci sudate, pulbere metalică sinterizată, materiale plastice turnate sau prelucrate. Pentru o funcționare lină la viteze mari, este esențială alegerea corectă a dimensiunii pinioanelor. Limitările de spațiu este, desigur, un factor pe care nu îl putem ignora atunci când alegem un pinion. Se recomandă ca raportul dintre șofer și pinioanele antrenate să nu fie mai mare de 6:1, iar învelișul lanțului pe șofer să fie de 120 de grade. Distanțele dintre centrele dintre pinioanele mai mici și cele mai mari, lungimile lanțului și tensiunea lanțului trebuie, de asemenea, alese conform unor calcule și linii directoare de inginerie recomandate și nu aleatoriu. Descărcați cataloagele noastre făcând clic pe textul colorat de mai jos: - Pinioane și roți cu plăci - Bucșe de transmisie - Cuplaj cu lanț - Încuietori cu lanț TRANSMISĂRI DE CABLURI: Acestea au avantajele lor față de curele și transmisii cu lanț în unele cazuri. Transmisiile prin cablu pot îndeplini aceeași funcție ca curelele și pot fi, de asemenea, mai simplu și mai economic de implementat în unele aplicații. De exemplu, o nouă serie de unități de cablu Synchromesh sunt proiectate pentru tracțiune pozitivă, pentru a înlocui frânghiile convenționale, cablurile simple și transmisiile cu roți dinți, în special în spațiile înguste. Noua unitate de cablu este concepută pentru a oferi o poziționare de înaltă precizie în echipamente electronice, cum ar fi mașini de copiat, plotere, mașini de scris, imprimante, etc. O caracteristică cheie a noii unități de cablu este capacitatea sa de a fi utilizată în configurații serpentine 3D care permit desene extrem de miniaturale. Cablurile sincronizate pot fi utilizate cu o tensiune mai mică în comparație cu cablurile, reducând astfel consumul de energie. Contactați AGS-TECH pentru întrebări și opinii despre curele, lanțuri și transmisii prin cablu. CLICK Product Finder-Locator Service PAGINA ANTERIOARĂ
- Rapid Prototyping, Desktop Manufacturing, Additive Manufacturing, FDM
Rapid Prototyping, Desktop Manufacturing, Additive Manufacturing, Stereolithography, Polyjet, Fused Deposition Modeling, Selective Laser Sintering, FDM, SLS Producție aditivă și rapidă În ultimii ani, am observat o creștere a cererii pentru RAPID MANUFACTURING sau RAPID PROTOTIPING. Acest proces poate fi numit și DESKTOP MANUFACTURING sau FABRICARE ÎN FORME LIBERE. Practic, un model fizic solid al unei piese este realizat direct dintr-un desen CAD tridimensional. Folosim termenul de FABRICARE ADITIVĂ pentru aceste tehnici diferite în care construim piese în straturi. Folosind hardware și software integrat, condus de computer, realizăm fabricarea aditivă. Tehnicile noastre rapide de prototipare și fabricație sunt STEREOLITOGRAFIA, POLYJET, MODELAREA DEPOZITĂ FUNZIONATĂ, SINTERIZAREA SELECTIVĂ LASER, TOPIREA PRINCIPALA DE ELECTRONI, IMPRIMARE TRIDIMENSIONALĂ, FABRICAȚIE DIRECTĂ, UTILIZARE RAPIDĂ. Vă recomandăm să faceți clic aici pentruDESCARCĂ Ilustrațiile noastre schematice ale proceselor de fabricație aditivă și de producție rapidă de AGS-TECH Inc. Acest lucru vă va ajuta să înțelegeți mai bine informațiile pe care vi le oferim mai jos. Prototiparea rapidă ne oferă: 1.) Designul conceptual al produsului este vizualizat din diferite unghiuri pe un monitor folosind un sistem 3D/CAD. 2.) Prototipurile din materiale nemetalice și metalice sunt fabricate și studiate din aspecte funcționale, tehnice și estetice. 3.) Se realizează prototipuri cu costuri reduse într-un timp foarte scurt. Fabricarea aditivă poate fi asemănată cu construcția unei bucăți de pâine prin stivuirea și lipirea feliilor individuale una peste alta. Cu alte cuvinte, produsul este fabricat felie cu felie, sau strat cu strat depus unul pe celălalt. Majoritatea pieselor pot fi produse în câteva ore. Tehnica este bună dacă piesele sunt necesare foarte repede sau dacă cantitățile necesare sunt mici, iar realizarea unei matrițe și unelte este prea costisitoare și necesită timp. Cu toate acestea, costul unei piese este scump din cauza materiilor prime scumpe. • STEREOLITOGRAFIE: Această tehnică, abreviată și STL, se bazează pe întărirea și întărirea unui fotopolimer lichid într-o formă specifică prin focalizarea unui fascicul laser asupra acestuia. Laserul polimerizează fotopolimerul și îl întărește. Prin scanarea fasciculului laser UV în funcție de forma programată de-a lungul suprafeței amestecului de fotopolimeri, piesa este produsă de jos în sus în felii individuale în cascadă una peste alta. Scanarea punctului laser se repetă de mai multe ori pentru a obține geometriile programate în sistem. După ce piesa este complet fabricată, aceasta este scoasă de pe platformă, șters și curățată cu ultrasunete și cu baie de alcool. Apoi, este expus la iradiere UV timp de câteva ore pentru a vă asigura că polimerul este complet întărit și întărit. Pentru a rezuma procesul, o platformă care este scufundată într-un amestec de fotopolimer și un fascicul laser UV sunt controlate și deplasate printr-un sistem de servocontrol în funcție de forma piesei dorite, iar piesa este obținută prin fotopolimerizarea strat cu strat de polimer. Desigur dimensiunile maxime ale piesei produse sunt determinate de echipamentul de stereolitografie. • POLYJET: Similar cu imprimarea cu jet de cerneală, în polyjet avem opt capete de imprimare care depun fotopolimer pe tava de construcție. Lumina ultravioletă plasată lângă jeturi întărește și întărește imediat fiecare strat. În polijet sunt utilizate două materiale. Primul material este pentru fabricarea modelului propriu-zis. Al doilea material, o rășină asemănătoare gelului este utilizată pentru sprijin. Ambele materiale sunt depuse strat cu strat și întărite simultan. După finalizarea modelului, materialul suport este îndepărtat cu o soluție apoasă. Rășinile utilizate sunt similare cu stereolitografia (STL). Polyjet-ul are următoarele avantaje față de stereolitografia: 1.) Nu este nevoie de curățarea pieselor. 2.) Nu este nevoie de întărire post-proces 3.) Sunt posibile grosimi mai mici ale stratului și astfel obținem o rezoluție mai bună și putem produce piese mai fine. • MODELARE DEPOZITĂ FUNZIONATĂ: Abreviat și ca FDM, în această metodă un cap de extruder controlat de robot se mișcă în două direcții principale peste o masă. Cablul este coborât și ridicat după cum este necesar. Din orificiul unei matrițe încălzite de pe cap, se extruda un filament termoplastic și se depune un strat inițial pe o fundație de spumă. Acest lucru se realizează prin capul extruderului care urmează o cale predeterminată. După stratul inițial, masa este coborâtă și straturile ulterioare sunt depuse unul peste altul. Uneori, la fabricarea unei piese complicate, sunt necesare structuri de susținere, astfel încât depunerea să poată continua în anumite direcții. În aceste cazuri, un material suport este extrudat cu o distanță mai puțin densă a filamentului pe un strat, astfel încât să fie mai slab decât materialul model. Aceste structuri de susținere pot fi ulterior dizolvate sau rupte după finalizarea piesei. Dimensiunile matriței extruder determină grosimea straturilor extrudate. Procesul FDM produce piese cu suprafete trepte pe planuri exterioare oblice. Dacă această rugozitate este inacceptabilă, se poate folosi lustruire cu vapori chimici sau o unealtă încălzită pentru netezirea acestora. Chiar și o ceară de lustruit este disponibilă ca material de acoperire pentru a elimina acești pași și pentru a obține toleranțe geometrice rezonabile. • SINTERIZAREA SELECTIVĂ LASER: Denumit și SLS, procesul se bazează pe sinterizarea selectivă a unui polimer, a pulberilor ceramice sau metalice într-un obiect. Partea inferioară a camerei de procesare are doi cilindri: un cilindru parțial și un cilindru de alimentare cu pulbere. Prima este coborâtă treptat până la locul în care se formează partea sinterizată, iar cea din urmă este ridicată treptat pentru a furniza pulbere cilindrului de construcție a părții printr-un mecanism cu role. Mai întâi, un strat subțire de pulbere este depus în cilindrul de construcție parțială, apoi un fascicul laser este focalizat pe acel strat, urmărind și topind/sinterind o anumită secțiune transversală, care apoi se resolidifică într-un solid. Pulberea este zonele care nu sunt lovite de raza laser rămân libere, dar susține totuși porțiunea solidă. Apoi se depune un alt strat de pulbere și procesul se repetă de multe ori pentru a obține piesa. La sfârșit, particulele de pulbere libere sunt scuturate. Toate acestea sunt realizate de un computer de control al procesului folosind instrucțiuni generate de programul CAD 3D al piesei fabricate. Pot fi depuse diverse materiale precum polimeri (cum ar fi ABS, PVC, poliester), ceară, metale și ceramică cu lianți polimerici corespunzători. • ELECTRON-BEAM MELTING : Similar cu sinterizarea selectivă cu laser, dar folosind fascicul de electroni pentru a topi pulberile de titan sau crom cobalt pentru a realiza prototipuri în vid. Au fost făcute unele dezvoltări pentru a efectua acest proces pe oțeluri inoxidabile, aluminiu și aliaje de cupru. În cazul în care rezistența la oboseală a pieselor produse trebuie crescută, folosim presarea izostatică la cald după fabricarea pieselor ca proces secundar. • IMPRIMARE TRIDIMENSIONALĂ: Notat și cu 3DP, în această tehnică un cap de imprimare depune un liant anorganic pe un strat de pulbere nemetalic sau metalică. Un piston care poartă patul de pulbere este coborât treptat și la fiecare pas liantul este depus strat cu strat și fuzionat de liant. Materialele pulbere utilizate sunt amestecuri de polimeri și fibre, nisip de turnătorie, metale. Folosind simultan diferite capete de legare și lianți de culoare diferite putem obține diferite culori. Procesul este similar cu imprimarea cu jet de cerneală, dar în loc să obținem o foaie colorată obținem un obiect tridimensional colorat. Piesele produse pot fi poroase și, prin urmare, pot necesita sinterizare și infiltrare de metal pentru a crește densitatea și rezistența. Sinterizarea va arde liantul și va topi pulberile metalice împreună. Metale precum oțel inoxidabil, aluminiu, titan pot fi folosite pentru a face piesele și ca materiale de infiltrare folosim în mod obișnuit cuprul și bronzul. Frumusețea acestei tehnici este că chiar și ansamblurile complicate și în mișcare pot fi fabricate foarte rapid. De exemplu, un ansamblu de angrenaje, o cheie ca unealtă poate fi realizat și va avea piese mobile și rotitoare gata de a fi utilizate. Diferitele componente ale ansamblului pot fi fabricate cu diferite culori și toate într-o singură lovitură. Descărcați broșura noastră pe:Bazele imprimării 3D din metal • PRODUCEREA DIRECTA si UTILIZARE RAPIDA: Pe langa evaluarea designului, depanare, folosim prototipuri rapide pentru fabricarea directa a produselor sau aplicarea directa in produse. Cu alte cuvinte, prototiparea rapidă poate fi încorporată în procesele convenționale pentru a le face mai bune și mai competitive. De exemplu, prototiparea rapidă poate produce modele și matrițe. Modelele unui polimer de topire și ardere create prin operațiuni de prototipare rapidă pot fi asamblate pentru turnare și investite. Un alt exemplu de menționat este utilizarea 3DP pentru a produce carcasa de turnare ceramică și utilizarea acestuia pentru operațiunile de turnare a carcasei. Chiar și matrițele de injecție și inserțiile de matriță pot fi produse prin prototipare rapidă și se pot economisi multe săptămâni sau luni de timp pentru realizarea matriței. Doar analizând un fișier CAD al piesei dorite, putem produce geometria sculei folosind software. Iată câteva dintre metodele noastre populare de scule rapide: RTV (Room-Temperature Vulcanizing) MULTARE / TURNARE URETAN: Utilizarea prototipului rapid poate fi folosită pentru a realiza modelul piesei dorite. Apoi, acest model este acoperit cu un agent de despărțire și cauciuc RTV lichid este turnat peste model pentru a produce jumătățile de matriță. Apoi, aceste jumătăți de matriță sunt folosite pentru a injecta uretani lichidi. Durata de viață a matriței este scurtă, doar ca 0 sau 30 de cicluri, dar suficientă pentru producția de loturi mici. ACES (Acetal Clear Epoxy Solid) MULTARE prin injectare: Utilizând tehnici de prototipare rapidă, cum ar fi stereolitografia, producem matrițe de injecție. Aceste matrițe sunt cochilii cu un capăt deschis pentru a permite umplerea cu materiale precum epoxidice, epoxidice umplut cu aluminiu sau metale. Din nou, durata de viață a matriței este limitată la zeci sau maxim sute de piese. PROCES DE UTILIZARE METAL PULVIZAT: Folosim prototipuri rapide și realizăm un model. Pulverizăm un aliaj de zinc-aluminiu pe suprafața modelului și o acoperim. Modelul cu înveliș metalic este apoi plasat în interiorul unui balon și ghiveci cu un epoxidic sau epoxidic umplut cu aluminiu. În cele din urmă, este îndepărtat și prin producerea a două astfel de jumătăți de matriță obținem o matriță completă pentru turnarea prin injecție. Aceste matrițe au o durată de viață mai mare, în unele cazuri în funcție de material și temperaturi pot produce piese în mii. PROCESUL KEELTOOL: Această tehnică poate produce matrițe cu cicluri de viață de 100.000 până la 10 milioane. Folosind prototiparea rapidă, producem o matriță RTV. Forma se umple apoi cu un amestec format din pulbere de oțel pentru scule A6, carbură de tungsten, liant polimeric și se lasă să se întărească. Această matriță este apoi încălzită pentru ca polimerul să se ardă și pulberile metalice să topească. Următorul pas este infiltrarea cuprului pentru a produce matrița finală. Dacă este necesar, pe matriță pot fi efectuate operațiuni secundare precum prelucrarea și lustruirea pentru o mai bună acuratețe dimensională. CLICK Product Finder-Locator Service PAGINA ANTERIOARĂ
- Glass and Ceramic Manufacturing, Hermetic Packages, Seals, Bonding
Glass and Ceramic Manufacturing, Hermetic Packages Seals and Bonding, Tempered Bulletproof Glass, Blow Moulding, Optical Grade Glass, Conductive Glass, Molding Formare și modelare sticle și ceramică Tipurile de producție de sticlă pe care le oferim sunt sticlă pentru containere, sticlă suflată, fibră de sticlă și tuburi și tijă, sticlă casnică și industrială, lămpi și becuri, turnare de precizie din sticlă, componente și ansambluri optice, sticlă plată și tablă și float. Executăm atât modelarea manuală, cât și modelarea la mașină. Procesele noastre populare de fabricare a ceramicii tehnice sunt presarea cu matriță, presarea izostatică, presarea izostatică la cald, presarea la cald, turnarea cu alunecare, turnarea cu bandă, extrudarea, turnarea prin injecție, prelucrarea verde, sinterizarea sau arderea, șlefuirea cu diamant, ansamblurile ermetice. Vă recomandăm să faceți clic aici pentru DESCARCĂ Ilustrațiile noastre schematice ale proceselor de formare și modelare a sticlei de la AGS-TECH Inc. DESCARCĂ Ilustrațiile noastre schematice ale proceselor tehnice de fabricație a ceramicii de la AGS-TECH Inc. Aceste fișiere descărcabile cu fotografii și schițe vă vor ajuta să înțelegeți mai bine informațiile pe care vi le oferim mai jos. • FABRICAȚIE DE STICLĂ DE RECIPIENTĂ: Avem linii automate de PRESARE ȘI SUFLARE, precum și linii de suflare și suflare pentru producție. În procesul de suflare și suflare aruncăm o gură în matriță goală și formăm gâtul aplicând o lovitură de aer comprimat de sus. Imediat după aceasta, aer comprimat este suflat a doua oară din cealaltă direcție prin gâtul recipientului pentru a forma preforma sticlei. Această preformă este apoi transferată în matrița propriu-zisă, reîncălzită pentru a se înmuia și se aplică aer comprimat pentru a da preformei forma finală a recipientului. Mai explicit, este presurizat și împins pe pereții cavității matriței de suflare pentru a lua forma dorită. În cele din urmă, recipientul din sticlă fabricat este transferat într-un cuptor de recoacere pentru reîncălzirea ulterioară și îndepărtarea tensiunilor produse în timpul turnării și este răcit într-un mod controlat. În metoda prin presare și suflare, bucățile topite sunt introduse într-o matriță paraison (forma semifabricată) și presate în forma paraison (forma semifabricată). Semifabricatele sunt apoi transferate în matrițe de suflare și suflate similar cu procesul descris mai sus în „Procesul de suflare și suflare”. Etapele ulterioare, cum ar fi recoacerea și eliberarea tensiunii, sunt similare sau la fel. • SUFLARE STICLĂ: Producem produse din sticlă folosind suflarea manuală convențională, precum și aer comprimat cu echipamente automate. Pentru unele comenzi este necesară suflarea convențională, cum ar fi proiectele care implică lucrări de artă pe sticlă sau proiecte care necesită un număr mai mic de piese cu toleranțe slabe, proiecte de prototipare/demo….etc. Suflarea convențională a sticlei implică scufundarea unei țevi metalice goale într-un vas de sticlă topită și rotirea țevii pentru colectarea unei cantități de material din sticlă. Sticla colectată pe vârful țevii este rulată pe fier plat, modelată după dorință, alungită, reîncălzită și suflată cu aer. Când este gata, se introduce într-o matriță și se sufla aer. Cavitatea matriței este umedă pentru a evita contactul sticlei cu metalul. Pelicula de apă acționează ca o pernă între ele. Suflarea manuală este un proces lent care necesită multă muncă și este potrivit doar pentru prototipare sau articole de mare valoare, nu este potrivit pentru comenzi de volum mare ieftine pe bucată. • PRODUCEREA DE STICLURII DOMESTICE ȘI INDUSTRIALE: Folosind diferite tipuri de materiale din sticlă se produce o mare varietate de articole din sticlă. Unele pahare sunt rezistente la căldură și sunt potrivite pentru sticlăria de laborator, în timp ce unele sunt suficient de bune pentru a rezista la mașinile de spălat vase de mai multe ori și sunt potrivite pentru fabricarea produselor casnice. Utilizând aparatele Westlake, se produc zeci de mii de bucăți de pahare pe zi. Pentru a simplifica, sticla topită este colectată prin vid și introdusă în matrițe pentru a face preformele. Apoi aerul este suflat în matrițe, acestea sunt transferate într-o altă matriță și aerul este suflat din nou și sticla capătă forma finală. Ca și în suflarea manuală, aceste matrițe sunt ținute umede cu apă. Întinderea ulterioară face parte din operația de finisare în care se formează gâtul. Excesul de sticlă este ars. După aceea, urmează procesul controlat de reîncălzire și răcire descris mai sus. • FORMAREA TUBILOR DE STICLĂ ȘI TIGELOR: Principalele procese pe care le folosim pentru fabricarea tuburilor de sticlă sunt procesele DANNER și VELLO. În procesul Danner, sticla dintr-un cuptor curge și cade pe un manșon înclinat din materiale refractare. Manșonul este transportat pe un arbore tubular rotativ sau suflantă. Sticla este apoi înfășurată în jurul manșonului și formează un strat neted care curge în jos pe manșon și peste vârful tijei. În cazul formării tuburilor, aerul este suflat printr-o suflantă cu vârf gol, iar în cazul formării tijei folosim vârfuri solide pe arbore. Tuburile sau tijele sunt apoi trase peste role de transport. Dimensiunile precum grosimea peretelui și diametrul tuburilor de sticlă sunt ajustate la valorile dorite prin setarea diametrului manșonului și suflarea presiunii aerului la o valoare dorită, ajustând temperatura, viteza de curgere a sticlei și viteza de tragere. Procesul de fabricare a tubului de sticlă Vello, pe de altă parte, implică sticlă care se deplasează dintr-un cuptor și într-un vas cu un dorn sau un clopot gol. Sticla trece apoi prin spațiul de aer dintre dorn și bol și ia forma unui tub. După aceea, se deplasează peste role la o mașină de desenat și este răcită. La sfârșitul liniei de răcire are loc tăierea și prelucrarea finală. Dimensiunile tubului pot fi ajustate la fel ca în procesul Danner. Când comparăm procesul Danner cu procesul Vello, putem spune că procesul Vello se potrivește mai bine pentru producția în cantități mari, în timp ce procesul Danner poate fi mai potrivit pentru comenzi precise de tuburi de volum mai mic. • PRELUCRARE PLĂCI ȘI STICLĂ PLATĂ și FLOTĂ: Avem cantități mari de sticlă plată în grosimi variind de la grosimi submilimetrice până la câțiva centimetri. Ochelarii noștri plati sunt aproape de perfecțiune optică. Oferim sticlă cu acoperiri speciale, cum ar fi acoperiri optice, în care tehnica de depunere chimică a vaporilor este utilizată pentru a pune acoperiri precum acoperirea antireflex sau oglindă. De asemenea, sunt comune acoperirile conductoare transparente. De asemenea, sunt disponibile acoperiri hidrofobe sau hidrofile pe sticlă și acoperiri care fac sticla auto-curățată. Ochelarii căliți, antiglonț și laminati sunt încă alte articole populare. Tăiem sticla în forma dorită cu toleranțele dorite. Sunt disponibile și alte operațiuni secundare, cum ar fi curbarea sau îndoirea sticlei plane. • MULTARE DE PRECIZIE A STICLEI: Folosim aceasta tehnica mai ales pentru fabricarea componentelor optice de precizie, fara a fi nevoie de tehnici mai costisitoare si consumatoare de timp, cum ar fi slefuirea, slefuirea si lustruirea. Această tehnică nu este întotdeauna suficientă pentru a obține cele mai bune optice, dar în unele cazuri, cum ar fi produsele de larg consum, camerele digitale, optica medicală, poate fi o opțiune bună mai puțin costisitoare pentru producția de volum mare. De asemenea, are un avantaj față de celelalte tehnici de formare a sticlei în care sunt necesare geometrii complexe, cum ar fi în cazul asferelor. Procesul de bază presupune încărcarea părții inferioare a matriței noastre cu semifabricatul de sticlă, evacuarea camerei de proces pentru îndepărtarea oxigenului, aproape închiderea matriței, încălzirea rapidă și izotermă a matriței și a sticlei cu lumină infraroșie, închiderea ulterioară a jumătăților de matriță. se presează încet sticla înmuiată, într-un mod controlat, până la grosimea dorită și, în final, se răcește sticla și se umple camera cu azot și se îndepărtează produsul. Controlul precis al temperaturii, distanța de închidere a matriței, forța de închidere a matriței, potrivirea coeficienților de expansiune a matriței și a materialului din sticlă sunt cheia în acest proces. • FABRICAREA COMPONENTELOR ȘI ASAMBLELOR OPTICE STICLĂ: Pe lângă turnarea de precizie a sticlei, există o serie de procese valoroase pe care le folosim pentru a realiza componente și ansambluri optice de înaltă calitate pentru aplicații solicitante. Slefuirea, șlefuirea și lustruirea sticlelor de calitate optică în șlamuri abrazive speciale fine este o artă și o știință pentru realizarea de lentile optice, prisme, plate și multe altele. Planeitatea suprafeței, ondularea, netezimea și suprafețele optice fără defecte necesită multă experiență în astfel de procese. Micile modificări ale mediului pot duce la produse care nu corespund specificațiilor și pot opri linia de producție. Există cazuri în care o singură ștergere pe suprafața optică cu o cârpă curată poate face ca un produs să îndeplinească specificațiile sau să eșueze testul. Unele materiale populare din sticlă utilizate sunt silice topită, cuarț, BK7. De asemenea, asamblarea unor astfel de componente necesită experiență de nișă specializată. Uneori se folosesc cleiuri speciale. Cu toate acestea, uneori, o tehnică numită contact optic este cea mai bună alegere și nu implică niciun material între ochelarii optici atașați. Constă în contactul fizic cu suprafețe plane pentru a se atașa între ele fără adeziv. În unele cazuri, distanțiere mecanice, tije sau bile de sticlă de precizie, cleme sau componente metalice prelucrate sunt folosite pentru a asambla componentele optice la anumite distanțe și cu anumite orientări geometrice unele față de altele. Să examinăm câteva dintre tehnicile noastre populare pentru fabricarea opticii de înaltă calitate. Șlefuire, șlefuire și lustruire: Forma brută a componentei optice este obținută prin șlefuirea unui semifabricat de sticlă. După aceea, șlefuirea și lustruirea sunt efectuate prin rotirea și frecarea suprafețelor aspre ale componentelor optice de unelte cu formele de suprafață dorite. Suspensii cu particule abrazive minuscule și fluide sunt turnate între optică și instrumentele de modelare. Dimensiunile particulelor abrazive din astfel de suspensii pot fi alese în funcție de gradul de planeitate dorit. Abaterile suprafețelor optice critice de la formele dorite sunt exprimate în termeni de lungimi de undă ale luminii utilizate. Optica noastră de înaltă precizie are toleranțe ale unei zecimi de lungime de undă (lungime de undă/10) sau chiar mai strâns este posibil. Pe lângă profilul suprafeței, suprafețele critice sunt scanate și evaluate pentru alte caracteristici și defecte ale suprafeței, cum ar fi dimensiuni, zgârieturi, așchii, gropi, pete... etc. Controlul strict al condițiilor de mediu în producția optică și cerințele extinse de metrologie și testare cu echipamente de ultimă generație fac din aceasta o ramură provocatoare a industriei. • PROCESE SECUNDARE ÎN FABRICAREA STICLEI: Din nou, suntem limitați doar cu imaginația dumneavoastră atunci când vine vorba de procesele secundare și de finisare ale sticlei. Iată câteva dintre ele: -Acoperiri pe sticla (optice, electrice, tribologice, termice, functionale, mecanice...). De exemplu, putem modifica proprietățile suprafeței sticlei făcându-l, de exemplu, să reflecte căldura, astfel încât să mențină răcoare interioarele clădirii, sau să facem ca o parte să absoarbă infraroșu folosind nanotehnologia. Acest lucru ajută la menținerea caldă a interiorului clădirilor, deoarece stratul exterior de sticlă va absorbi radiația infraroșie din interiorul clădirii și o va radia înapoi în interior. -Gravare pe sticla -Etichetare ceramică aplicată (ACL) -Gravare -Lustruire cu flacără -Lustruire chimica -Patarea FABRICAREA CERAMICII TEHNICE • PRESARE CU STILĂ: Constă în compactarea uniaxială a pulberilor granulare limitate într-o matriță • PRESARE LA CALDE: Similar cu presarea cu matriță, dar cu adăugare de temperatură pentru a îmbunătăți densificarea. Pulberea sau preforma compactată este plasată în matriță de grafit și se aplică presiune uniaxială în timp ce matrița este menținută la temperaturi ridicate, cum ar fi 2000 C. Temperaturile pot fi diferite în funcție de tipul de pulbere ceramică care este prelucrată. Pentru forme și geometrii complicate pot fi necesare alte procesări ulterioare, cum ar fi șlefuirea cu diamant. • PRESARE ISOSTATICĂ: Pulbere granulară sau compacte presate cu matriță sunt plasate în recipiente etanșe și apoi într-un vas sub presiune închis, cu lichid în interior. După aceea, acestea sunt compactate prin creșterea presiunii vasului sub presiune. Lichidul din interiorul vasului transferă forțele de presiune în mod uniform pe întreaga suprafață a recipientului etanș. Materialul este astfel compactat uniform și ia forma recipientului său flexibil și profilul și caracteristicile sale interne. • PRESARE ISOSTATICĂ LA CALDE: Similar cu presarea izostatică, dar pe lângă atmosfera de gaz sub presiune, sinterăm compactul la temperatură ridicată. Presarea izostatică la cald are ca rezultat o densificare suplimentară și o rezistență crescută. • turnare cu alunecare / turnare cu scurgere: umplem matrița cu o suspensie de particule ceramice de dimensiuni micrometrice și lichid purtător. Acest amestec se numește „alunecare”. Forma are pori și, prin urmare, lichidul din amestec este filtrat în matriță. Ca rezultat, se formează o turnare pe suprafețele interioare ale matriței. După sinterizare, piesele pot fi scoase din matriță. • TURNAREA BANDELOR: Producem benzi ceramice prin turnarea suspensiilor ceramice pe suprafete plane mobile. Suspensiile conțin pulberi ceramice amestecate cu alte substanțe chimice pentru legare și transport. Pe măsură ce solvenții se evaporă, se lasă în urmă foi dense și flexibile de ceramică care pot fi tăiate sau rulate după cum se dorește. • FORMARE prin extrudare: Ca și în alte procese de extrudare, un amestec moale de pulbere ceramică cu lianți și alte substanțe chimice este trecut printr-o matriță pentru a dobândi forma în secțiune transversală și apoi este tăiat la lungimile dorite. Procesul se realizează cu amestecuri ceramice reci sau încălzite. • MULTARE CU INJECȚIE LA PRESIUNE JUSĂ: Pregătim un amestec de pulbere ceramică cu lianți și solvenți și îl încălzim la o temperatură în care poate fi ușor presat și forțat în cavitatea sculei. Odată ce ciclul de turnare este complet, piesa este ejectată și substanța chimică de legare este arsă. Utilizând turnarea prin injecție, putem obține piese complicate la volume mari din punct de vedere economic. Sunt posibile găuri care sunt o mică fracțiune de milimetru pe un perete de 10 mm grosime, sunt posibile filete fără prelucrare ulterioară, toleranțe cât de strânse de +/- 0,5% sunt posibile și chiar mai mici atunci când piesele sunt prelucrate. , sunt posibile grosimi de perete de ordinul de la 0,5 mm la o lungime de 12,5 mm, precum și grosimi de perete de la 6,5 mm la o lungime de 150 mm. • PRELUCRARE VERDE: Folosind aceleași scule de prelucrare a metalelor, putem prelucra materiale ceramice presate cât timp sunt încă moi ca creta. Sunt posibile toleranțe de +/- 1%. Pentru toleranțe mai bune folosim șlefuirea cu diamant. • SINTERIZAREA sau ARDEREA: Sinterizarea face posibilă densificarea completă. Pe piesele compacte verzi apare o contracție semnificativă, dar aceasta nu este o problemă mare, deoarece luăm în considerare aceste modificări dimensionale atunci când proiectăm piesa și sculele. Particulele de pulbere sunt legate între ele și porozitatea indusă de procesul de compactare este îndepărtată în mare măsură. • Șlefuirea cu diamante: Cel mai dur material „diamant” din lume este folosit pentru șlefuirea materialelor dure precum ceramica și se obțin piese de precizie. Se realizează toleranțe în intervalul micrometric și suprafețe foarte netede. Datorită costului ei, luăm în considerare această tehnică doar atunci când avem cu adevărat nevoie de ea. • ANSAMBLE ERMETICE sunt cele care practic nu permit nici un schimb de materie, solide, lichide sau gaze intre interfete. Etanșarea ermetică este etanșă. De exemplu, carcasele electronice ermetice sunt cele care păstrează conținutul interior sensibil al unui dispozitiv ambalat nevătămat de umiditate, contaminanți sau gaze. Nimic nu este 100% ermetic, dar atunci când vorbim de ermeticitate ne referim la faptul că în termeni practici, că există ermeticitate în măsura în care rata de scurgere este atât de scăzută încât dispozitivele sunt sigure în condiții normale de mediu timp foarte lung. Ansamblurile noastre ermetice constau din componente metalice, sticla si ceramica, metal-ceramica, ceramica-metal-ceramica, metal-ceramica-metal, metal pe metal, metal-sticlă, metal-sticlă-metal, sticlă-metal-sticlă, sticlă- metal și sticlă la sticlă și toate celelalte combinații de lipire metal-sticlă-ceramică. De exemplu, putem acoperi componentele ceramice cu metal, astfel încât acestea să poată fi lipite puternic de alte componente ale ansamblului și să aibă o capacitate excelentă de etanșare. Avem cunoștințele de a acoperi fibrele optice sau traversele cu metal și de a le lipi sau lipi pe carcase, astfel încât să nu treacă sau să nu se scurgă gaze în carcase. Prin urmare, ele sunt utilizate pentru fabricarea carcasei electronice pentru a încapsula dispozitive sensibile și pentru a le proteja de atmosfera exterioară. Pe langa caracteristicile lor excelente de etansare, alte proprietati precum coeficientul de dilatare termica, rezistenta la deformare, natura fara gazare, durata de viata foarte lunga, natura neconductiva, proprietati de izolare termica, natura antistatica...etc. face din materialele din sticlă și ceramică alegerea pentru anumite aplicații. Informații despre unitatea noastră de producție de fitinguri ceramice până la metal, etanșare ermetică, treceri de vid, vid înalt și ultraînalt și componente de control al fluidelor pot fi găsite aici:Broșura fabricii de componente ermetice CLICK Product Finder-Locator Service PAGINA ANTERIOARĂ
- Wire & Spring Forming, Shaping, Welding, Assembly of Wires, Coil, CNC
Wire & Spring Forming, Shaping, Welding, Assembly of Wires, Coil Compression Extension Torsion Flat Springs, Custom Wires, Helical Springs at AGS-TECH Inc. Formare cu sârmă și arc Producem fire personalizate, ansamblu de sârmă, fire formate în formele 2D și 3D dorite, plase de sârmă, plasă, carcase, coș, gard, arc de sârmă, arc plat; torsiune, compresie, tensiune, arcuri plate și multe altele. Procesele noastre sunt formarea cu sârmă și arc, trefilarea sârmei, modelarea, îndoirea, sudarea, lipirea, lipirea, găurirea, ștergerea, găurirea, teșirea, șlefuirea, filetarea, acoperirea, formarea cu alunecare, înfășurarea, bobinarea, răsturnarea. Vă recomandăm să faceți clic aici pentru DESCARCĂ Ilustrațiile noastre schematice ale proceselor de formare a sârmei și arcurilor de la AGS-TECH Inc. Acest fișier descărcabil cu fotografii și schițe vă va ajuta să înțelegeți mai bine informațiile pe care vi le oferim mai jos. • TRESARE: Folosind forțele de tracțiune, întindem materialul metalic și îl tragem printr-o matriță pentru a reduce diametrul și a crește lungimea acestuia. Uneori folosim o serie de matrițe. Suntem capabili să facem matrițe pentru fiecare calibre de sârmă. Folosind material cu rezistență ridicată la tracțiune, desenăm fire foarte subțiri. Oferim atat fire lucrate la rece cat si la cald. • FORMAREA SÂRMULUI: O rolă de sârmă calibrată este îndoită și modelată într-un produs util. Avem capacitatea de a forma fire din toate calibrele, inclusiv filamente subțiri, precum și fire groase, cum ar fi cele folosite ca arcuri sub șasiul automobilului. Echipamentele pe care le folosim pentru formarea sârmei sunt formatoare de sârmă manuale și CNC, bobinatoare, prese electrice, fourslide, multi-slide. Procesele noastre sunt tragerea, îndoirea, îndreptarea, aplatizarea, întinderea, tăierea, răsturnarea, lipirea și sudarea și lipirea, asamblarea, bobinarea, ștergerea (sau aripile), perforarea, filetarea sârmei, găurirea, teșirea, șlefuirea, acoperirea și tratamentele de suprafață. Echipamentele noastre de ultimă generație pot fi configurate pentru a dezvolta modele foarte complexe de orice formă și toleranțe strânse. Oferim diferite tipuri de capete like capete sferice, ascuțite sau teșite pentru firele dumneavoastră. Majoritatea proiectelor noastre de formare a sârmei au costuri minime până la zero cu scule. Timpul de livrare a mostrelor este în general de zile. Modificările la proiectarea/configurarea formelor de sârmă pot fi făcute foarte rapid. • FORMAREA ARCOLOR: AGS-TECH produce o mare varietate de arcuri, inclusiv: -Torsiune/Arc dublu de torsiune -Arc de tensiune / compresie -Arac constant/variabil -Elicoidal și arc elicoidal -Arcuri plat și lamelă -Arac de echilibru -Masina de spalat Belleville - Negator Spring -Arc elicoidal cu viteză progresivă -Wave Spring -Volute Spring -Arcuri conice -Inele de primăvară -Clock Springs - Clipuri Producem arcuri dintr-o varietate de materiale și vă putem ghida în funcție de aplicația dvs. Cele mai comune materiale sunt oțel inoxidabil, siliciu crom, oțel cu conținut ridicat de carbon, temperat în ulei cu conținut scăzut de carbon, crom vanadiu, bronz fosfor, titan, aliaj de cupru beriliu, ceramică la temperatură înaltă. Folosim diverse tehnici la fabricarea arcurilor, inclusiv bobinaj CNC, bobinaj la rece, bobinare la cald, calire, finisare. Alte tehnici deja menționate mai sus la formarea sârmei sunt, de asemenea, comune în operațiunile noastre de fabricare a arcurilor. • SERVICII DE FINISARE pentru SIRME ȘI ARCOURI: Vă putem finisa produsele în mai multe moduri, în funcție de alegerea și nevoile dumneavoastră. Unele procese obișnuite pe care le oferim sunt: vopsire, vopsire cu pulbere, placare, scufundare cu vinil, anodizare, eliberare de stres, tratament termic, șlefuire, cromat, nichel fără electros, pasivare, email copt, plastic acoperit, , curatare plasma. CLICK Product Finder-Locator Service PAGINA ANTERIOARĂ
- Forging and Powdered Metallurgy, Die Forging, Heading, Hot Forging
Forging and Powdered Metallurgy, Die Forging, Heading, Hot Forging, Impression Die, Near Net Shape, Swaging, Metal Hobbing, Riveting, Coining from AGS-TECH Inc. Forjare metale și metalurgie a pulberilor Tipul de procese de FORJARE METALĂ pe care le oferim sunt matrițe la cald și la rece, matriță deschisă și închisă, matriță de amprentare și forjare fără eșantionare, cogging, pliare, canturi și forjare de precizie, formă aproape netă, antet , presărare, forjare deformată, frezare metalică, presare și rulare și forjare radială și orbitală și inelară și izotermă, monetare, nituire, forjare cu bile de metal, perforare metal, dimensionare, forjare cu rată ridicată de energie. Tehnicile noastre de METALURGIA PULBEREI și PRELUCRAREA PULBEREI sunt presarea și sinterizarea pulberilor, impregnarea, infiltrarea, presarea izostatică la cald și la rece, turnarea prin injecție a metalelor, compactarea cu role, laminarea pulberii, extrudarea pulberii, sinterizarea în vrac, sinterizarea prin scânteie, presarea la cald. Vă recomandăm să faceți clic aici pentru DESCARCĂ Ilustrațiile noastre schematice ale proceselor de forjare de la AGS-TECH Inc. DESCARCĂ Ilustrațiile noastre schematice ale proceselor de metalurgie a pulberilor de la AGS-TECH Inc. Aceste fișiere descărcabile cu fotografii și schițe vă vor ajuta să înțelegeți mai bine informațiile pe care vi le oferim mai jos. În forjarea metalelor se aplică forțe de compresiune și materialul este deformat și se obține forma dorită. Cele mai comune materiale forjate în industrie sunt fierul și oțelul, dar multe altele, cum ar fi aluminiul, cuprul, titanul, magneziul sunt, de asemenea, forjate pe scară largă. Piesele metalice forjate au structuri de cereale îmbunătățite pe lângă fisurile sigilate și spațiile goale închise, astfel rezistența pieselor obținute prin acest proces este mai mare. Forjarea produce piese care sunt semnificativ mai puternice pentru greutatea lor decât piesele realizate prin turnare sau prelucrare. Deoarece piesele forjate sunt modelate făcând ca metalul să curgă în forma sa finală, metalul capătă o structură de granulație direcțională care explică rezistența superioară a pieselor. Cu alte cuvinte, piesele obținute prin procesul de forjare dezvăluie proprietăți mecanice mai bune în comparație cu piesele simple turnate sau prelucrate. Greutatea pieselor forjate din metal poate varia de la piese mici și ușoare până la sute de mii de lire sterline. Producem piese forjate în cea mai mare parte pentru aplicații solicitante din punct de vedere mecanic, în care solicitările mari sunt aplicate pe piese precum piese de automobile, roți dințate, unelte de lucru, unelte de mână, arbori turbine, angrenaje pentru motociclete. Deoarece costurile de scule și de instalare sunt relativ mari, recomandăm acest proces de fabricație numai pentru producția de volum mare și pentru componente critice de volum redus, dar de mare valoare, cum ar fi trenul de aterizare aerospațial. Pe lângă costul sculelor, timpii de producție pentru piese forjate în cantități mari pot fi mai lungi în comparație cu unele piese simple prelucrate, dar tehnica este crucială pentru piesele care necesită o rezistență extraordinară, cum ar fi șuruburi, piulițe, aplicații speciale. elemente de fixare, auto, stivuitoare, piese de macara. • FORJAREA LA FERINȚĂ și LA RECE: Forjarea la cald, după cum sugerează și numele, se realizează la temperaturi ridicate, ductilitatea este prin urmare ridicată și rezistența materialului scăzută. Acest lucru facilitează deformarea și forjarea ușoară. Dimpotrivă, forjarea la rece se realizează la temperaturi mai scăzute și necesită forțe mai mari, ceea ce are ca rezultat întărirea prin deformare, finisarea suprafeței mai bună și precizia pieselor fabricate. • FORJAREA MATRICE DESCHISĂ și FORJAREA MATRIZĂ: În forjarea cu matriță deschisă, matrițele nu constrâng materialul care este comprimat, în timp ce în forjarea cu matriță de imprimare, cavitățile din matrițe restricționează fluxul materialului în timp ce acesta este forjat în forma dorită. FORJAREA SUPARATĂ sau numită și SUPARARE, care de fapt nu este același, dar un proces foarte asemănător, este un proces de matriță deschisă în care piesa de prelucrat este prinsă între două matrițe plate și o forță de compresiune îi reduce înălțimea. Pe măsură ce înălțimea este reduced, lățimea piesei de prelucrat crește. HEADING, un proces de forjare deformată implică un material cilindric care este răsturnat la capăt și secțiunea transversală a acestuia este mărită local. În poziție, stocul este alimentat prin matriță, forjat și apoi tăiat la lungime. Operația este capabilă să producă rapid cantități mari de elemente de fixare. În cea mai mare parte, este o operațiune de lucru la rece, deoarece este folosită pentru a face capete de cuie, capete de șuruburi, piulițe și șuruburi unde materialul trebuie întărit. Un alt proces de matriță deschisă este COGGING, în care piesa de prelucrat este forjată într-o serie de etape, fiecare pas având ca rezultat comprimarea materialului și mișcarea ulterioară a matriței deschise de-a lungul lungimii piesei de prelucrat. La fiecare pas, grosimea este redusă și lungimea este mărită cu o cantitate mică. Procesul seamănă cu un student nervos care își mușcă creionul în pași mici. Un proces numit FULLERING este o altă metodă de forjare cu matriță deschisă pe care o desfășurăm adesea ca pas anterior pentru a distribui materialul în piesa de prelucrat înainte de a avea loc alte operațiuni de forjare a metalului. Îl folosim atunci când piesa de prelucrat necesită mai multe forjare operations. În operațiune, matrița cu suprafețele convexe se deformează și provoacă curgerea metalului pe ambele părți. Un proces asemănător cu plinizarea, TINCILE, pe de altă parte, implică matriță deschisă cu suprafețe concave pentru a deforma piesa de prelucrat. Tijirea, de asemenea, un proces pregătitor pentru operațiunile ulterioare de forjare face ca materialul să curgă din ambele părți într-o zonă din centru. FORJAREA MATRICE DE IMPRESIUNE sau FORJAREA MATRICE ÎNCHIS, așa cum este numită și, utilizează o matriță / matriță care comprimă materialul și restricționează curgerea acestuia în interiorul său. Matrița se închide și materialul ia forma matriței/cavității matriței. FORJAREA DE PRECIZIE, un proces care necesită echipamente și matrițe speciale, produce piese fără fulger sau foarte puțin. Cu alte cuvinte, piesele vor avea dimensiuni aproape finale. În acest proces, o cantitate bine controlată de material este introdusă cu atenție și poziționată în interiorul matriței. Implementăm această metodă pentru forme complexe cu secțiuni subțiri, toleranțe mici și unghiuri de tragere și atunci când cantitățile sunt suficient de mari pentru a justifica costurile matriței și echipamentelor. • FORJAREA FĂRĂ FLASH: Piesa de prelucrat este plasată în matriță astfel încât niciun material să nu poată curge din cavitate pentru a forma fulger. Prin urmare, nu este necesară tăierea nedorită a blițului. Este un proces de forjare de precizie și, prin urmare, necesită un control atent al cantității de material utilizat. • PRELUCRARE METAL sau FORJAREA RADIALĂ: O piesă de prelucrat este acționată circumferențial prin matriță și forjată. Un dorn poate fi folosit la fel de bine pentru a forja geometria interioară a piesei de prelucrat. În operația de presărare, piesa de prelucrat primește de obicei mai multe curse pe secundă. Articolele tipice produse prin presărare sunt unelte cu vârf ascuțit, bare conice, șurubelnițe. • PIERCING METAL: Folosim frecvent aceasta operatie ca o operatiune suplimentara in fabricarea pieselor. O gaură sau o cavitate este creată cu perforarea pe suprafața piesei de prelucrat fără a se sparge prin aceasta. Vă rugăm să rețineți că perforarea este diferită de găurire, ceea ce are ca rezultat o gaură de trecere. • HOBBING: Un poanson cu geometria dorită este presat în piesa de prelucrat și creează o cavitate cu forma dorită. Numim acest pumn plită. Operatia presupune presiuni mari si se desfasoara la rece. Ca rezultat, materialul este prelucrat la rece și întărit. Prin urmare, acest proces este foarte potrivit pentru fabricarea matrițelor, matrițelor și cavităților pentru alte procese de fabricație. Odată fabricată plita, se pot fabrica cu ușurință multe cavități identice, fără a fi nevoie să le prelucrați una câte una. • FORJAREA LAMINĂRII sau FORMAREA LAMINĂRII: Pentru modelarea piesei metalice se folosesc două role opuse. Piesa de prelucrat este alimentată în role, rolele se întorc și trag lucrarea în gol, lucrul este apoi alimentat prin porțiunea canelată a rolelor și forțele de compresiune dau materialului forma dorită. Nu este un proces de laminare, ci un proces de forjare, deoarece este o operațiune mai degrabă discretă decât continuă. Geometria arborilor de rulouri forjează materialul la forma și geometria necesară. Se execută la cald. Datorită faptului că este un proces de forjare, produce piese cu proprietăți mecanice remarcabile și, prin urmare, îl folosim pentru manufacturing piese auto, cum ar fi arbori, care trebuie să aibă o rezistență extraordinară în medii de lucru dificile. • FORJAREA ORBITALĂ: Piesa de prelucrat este introdusă într-o cavitate a matriței de forjare și forjată de o matriță superioară care se deplasează pe o cale orbitală în timp ce se rotește pe o axă înclinată. La fiecare rotație, matrița superioară se completează exercitând forțe de compresiune asupra întregii piese de prelucrat. Repetând aceste rotații de mai multe ori, se realizează suficient forjare. Avantajele acestei tehnici de fabricație sunt funcționarea cu zgomot redus și forțele mai mici necesare. Cu alte cuvinte, cu forțe mici, se poate roti o matriță grea în jurul unei axe pentru a aplica presiuni mari asupra unei secțiuni a piesei de prelucrat care este în contact cu matrița. Piesele în formă de disc sau conic sunt uneori potrivite pentru acest proces. • FORJAREA INELELOR: Folosim frecvent pentru a produce inele fără sudură. Stocul este tăiat la lungime, răsturnat și apoi străpuns până la capăt pentru a crea o gaură centrală. Apoi este pus pe un dorn și o matriță de forjare îl lovește de sus, în timp ce inelul este rotit încet până se obține dimensiunile dorite. • NITARE: Un proces comun de îmbinare a pieselor, începe cu o piesă metalică dreaptă introdusă în găuri prefabricate prin piese. După aceea, cele două capete ale piesei metalice sunt forjate prin strângerea îmbinării dintre o matriță superioară și cea inferioară. • MONETAREA: Un alt proces popular realizat prin presa mecanică, care exercită forțe mari pe distanțe scurte. Denumirea „coining” provine de la detaliile fine care sunt forjate pe suprafețele monedelor metalice. Este în mare parte un proces de finisare pentru un produs în care detaliile fine sunt obținute pe suprafețe ca urmare a forței mari aplicate de matriță care transferă aceste detalii pe piesa de prelucrat. • FORJAREA BILELE METALICE: Produse precum rulmenții cu bile necesită bile metalice de înaltă calitate, fabricate cu precizie. Într-o tehnică numită SKEW ROLLING, folosim două role opuse care se rotesc continuu pe măsură ce stocul este alimentat continuu în role. La un capăt al celor două role sunt aruncate sfere metalice ca produs. O a doua metodă de forjare cu bile metalice este utilizarea matrițelor care stoarce materialul plasat între ele luând forma sferică a cavității matriței. Adesea, bilele produse necesită câțiva pași suplimentari, cum ar fi finisarea și lustruirea, pentru a deveni un produs de înaltă calitate. • FORJAREA IZOTERMICĂ / FORJAREA LA CALDE: Un proces costisitor efectuat numai atunci când valoarea beneficiului / costului este justificată. Un proces de lucru la cald în care matrița este încălzită la aproximativ aceeași temperatură ca și piesa de prelucrat. Deoarece atât matrița, cât și lucrarea au aproximativ aceeași temperatură, nu există răcire și caracteristicile de curgere ale metalului sunt îmbunătățite. Operația este potrivită pentru super aliaje și materiale cu forjabilitate inferioară și materiale ale căror proprietățile mecanice sunt foarte sensibile la gradienți și modificări mici de temperatură. • DIMENSIONAREA METALULUI: Este un proces de finisare la rece. Fluxul materialului este nerestricționat în toate direcțiile, cu excepția direcției în care se aplică forța. Ca rezultat, se obține un finisaj foarte bun al suprafeței și dimensiuni precise. • Forjare cu rată ridicată de energie: Tehnica implică o matriță superioară atașată la brațul unui piston care este împins rapid pe măsură ce amestecul combustibil-aer este aprins de o bujie. Seamănă cu funcționarea pistoanelor într-un motor de mașină. Matrița lovește piesa de lucru foarte repede și apoi revine la poziția inițială foarte repede datorită contrapresiunii. Lucrarea este falsificată în câteva milisecunde și, prin urmare, nu există timp pentru ca munca să se răcească. Acest lucru este util pentru piese greu de forjat care au proprietăți mecanice foarte sensibile la temperatură. Cu alte cuvinte, procesul este atât de rapid încât piesa se formează la o temperatură constantă și nu vor exista gradienți de temperatură la interfețele matriță/piesa de prelucrat. • În FORJAREA STILĂ, metalul este bătut între două blocuri de oțel potrivite cu forme speciale în ele, numite matrițe. Când metalul este ciocănit între matrițe, acesta capătă aceeași formă ca și formele din matriță. Când atinge forma finală, se scoate la răcit. Acest proces produce piese puternice care au o formă precisă, dar necesită o investiție mai mare pentru matrițele specializate. Forjarea supărată crește diametrul unei piese de metal prin aplatizarea acesteia. În general, este folosit pentru a face piese mici, în special pentru a forma capete pe elemente de fixare precum șuruburi și cuie. • METALURGIA PULBEREI / PRELUCRAREA PUDREI: După cum sugerează și numele, implică procese de fabricație pentru fabricarea pieselor solide din anumite geometrii și forme din pulberi. Dacă în acest scop se folosesc pulberi metalice, este domeniul metalurgiei pulberilor, iar dacă se folosesc pulberi nemetalice este vorba de prelucrarea pulberilor. Piesele solide sunt produse din pulberi prin presare și sinterizare. PRESAREA PUDREI este folosită pentru a compacta pulberile în formele dorite. În primul rând, materialul primar este fizic sub formă de pulbere, împărțindu-l în multe particule individuale mici. Amestecul de pulbere este umplut în matriță și un pumn se deplasează spre pulbere și o compactează în forma dorită. Se realizează în cea mai mare parte la temperatura camerei, prin presarea pulberii se obține o parte solidă și se numește compact verde. Lianții și lubrifianții sunt utilizați în mod obișnuit pentru a îmbunătăți compactabilitatea. Suntem capabili de formare prin presare a pulberii folosind prese hidraulice cu o capacitate de câteva mii de tone. De asemenea, avem prese cu acțiune dublă cu poansonuri opuse de sus și de jos, precum și prese cu acțiune multiplă pentru geometrii de piese extrem de complexe. Uniformitatea, care este o provocare importantă pentru multe fabrici de metalurgie/prelucrare a pulberilor, nu reprezintă o problemă mare pentru AGS-TECH, datorită experienței noastre vaste în fabricarea la comandă a unor astfel de piese de mulți ani. Chiar și cu părți mai groase în care uniformitatea reprezintă o provocare, am reușit. Dacă ne angajăm în proiectul dumneavoastră, vă vom realiza piesele. Dacă vedem riscuri potențiale, vă vom informa în avans. SINTERIZAREA PULBEREI, care este a doua etapă, implică creșterea temperaturii până la un anumit grad și menținerea temperaturii la acel nivel pentru un anumit timp, astfel încât particulele de pulbere din partea presată să se poată lega între ele. Acest lucru duce la legături mult mai puternice și la întărirea piesei de prelucrat. Sinterizarea are loc aproape de temperatura de topire a pulberii. În timpul sinterizării va avea loc contracția, rezistența materialului, densitatea, ductilitatea, conductibilitatea termică, conductivitatea electrică sunt crescute. Avem cuptoare discontinue și continue pentru sinterizare. Una dintre capacitățile noastre este ajustarea nivelului de porozitate al pieselor pe care le producem. De exemplu, putem produce filtre metalice menținând piesele poroase într-o oarecare măsură. Folosind o tehnică numită IMPREGNARE, umplem porii metalului cu un fluid precum uleiul. Producem, de exemplu, rulmenți impregnați cu ulei, care sunt auto-lubrifianți. În procesul de INFILTRARE umplem porii unui metal cu un alt metal cu punct de topire mai mic decât materialul de bază. Amestecul este încălzit la o temperatură între temperaturile de topire ale celor două metale. Ca urmare, pot fi obținute unele proprietăți speciale. De asemenea, efectuăm frecvent operații secundare, cum ar fi prelucrarea și forjarea pieselor fabricate cu pulbere, atunci când trebuie obținute caracteristici sau proprietăți speciale sau când piesa poate fi fabricată cu mai puțini pași de proces. PRESARE ISOSTATICĂ: În acest proces, presiunea fluidului este utilizată pentru compactarea piesei. Pulberile metalice sunt plasate într-o matriță realizată dintr-un recipient flexibil sigilat. În presarea izostatică, presiunea este aplicată din jur, spre deosebire de presiunea axială observată în presarea convențională. Avantajele presării izostatice sunt densitatea uniformă în interiorul piesei, în special pentru piese mai mari sau mai groase, proprietăți superioare. Dezavantajul său este ciclul lung și precizia geometrică relativ scăzută. PRESAREA ISOSTATICĂ LA RECE se efectuează la temperatura camerei iar matrița flexibilă este realizată din cauciuc, PVC sau uretan sau materiale similare. Fluidul folosit pentru presurizare și compactare este uleiul sau apa. Urmează sinterizarea convențională a compactului verde. PRESAREA ISOSTATICĂ LA CALDO, pe de altă parte, se realizează la temperaturi ridicate, iar materialul matriței este tablă sau ceramică cu un punct de topire suficient de ridicat pentru a rezista la temperaturi. Fluidul de presurizare este de obicei un gaz inert. Operatiile de presare si sinterizare se realizeaza intr-un singur pas. Porozitatea este aproape complet eliminată, se obține o structură uniform grain. Avantajul presării izostatice la cald este că poate produce piese comparabile cu turnarea și forjarea combinate, făcând posibilă utilizarea materialelor care nu sunt potrivite pentru turnare și forjare. Dezavantajul presării izostatice la cald este timpul mare de ciclu și, prin urmare, costul. Este potrivit pentru părți critice cu volum redus. MATURARE INJECȚIE DE METAL: Proces foarte potrivit pentru producerea de piese complexe cu pereți subțiri și geometrii detaliate. Cel mai potrivit pentru piese mai mici. Pulberile și liantul polimeric sunt amestecate, încălzite și injectate într-o matriță. Liantul polimeric acoperă suprafețele particulelor de pulbere. După turnare, liantul este îndepărtat fie prin încălzire la temperatură joasă, fie prin dizolvare folosind un solvent. COMPACTARE ROLA / LAMINARE PULBERE: Pulberile sunt folosite pentru a produce benzi sau foi continue. Pulberea este alimentată dintr-un alimentator și compactată de două role rotative în foaie sau benzi. Operația se efectuează la rece. Foaia este transportată într-un cuptor de sinterizare. Procesul de sinterizare poate fi repetat a doua oară. EXTRUDEA PULBEREI: Piesele cu rapoarte mari lungime/diametru sunt fabricate prin extrudarea unui recipient din tablă subțire cu pulbere. SINTERIZAREA LOTĂ: După cum sugerează și numele, este o metodă de compactare și sinterizare fără presiune, potrivită pentru producerea de piese foarte poroase, cum ar fi filtrele metalice. Pulberea este introdusă în cavitatea matriței fără compactare. SINTERIZAREA LOTĂ: După cum sugerează și numele, este o metodă de compactare și sinterizare fără presiune, potrivită pentru producerea de piese foarte poroase, cum ar fi filtrele metalice. Pulberea este introdusă în cavitatea matriței fără compactare. SINTERIZAREA SCÂNTEII: Pulberea este comprimată în matriță cu două poanson opuse și un curent electric de mare putere este aplicat pe poanson și trece prin pulberea compactată, introdusă între ele. Curentul mare arde peliculele de suprafață din particulele de pulbere și le sinterizează cu căldura generată. Procesul este rapid deoarece căldura nu este aplicată din exterior, ci este generată din interiorul matriței. PRESARE LA CALD: Pulberile sunt presate și sinterizate într-o singură etapă într-o matriță care poate rezista la temperaturi ridicate. Pe măsură ce matrița se compactează, i se aplică căldură pulberii. Preciziile bune și proprietățile mecanice obținute prin această metodă o fac o opțiune atractivă. Chiar și metalele refractare pot fi prelucrate folosind materiale de matriță, cum ar fi grafitul. CLICK Product Finder-Locator Service MENIU ANTERIOR
- Sheet Metal Forming Fabrication, Stamping, Punching, Deep Drawing, CNC
Sheet Metal Forming and Fabrication, Stamping, Punching, Bending, Progressive Die, Spot Welding, Deep Drawing, Metal Blanking and Slitting at AGS-TECH Inc. Ștanțare și fabricație de tablă Oferim ștanțare, modelare, formare, îndoire, ștanțare, ștanțare, tăiere, perforare, crestare, ronțăit, bărbierit, prelucrare prin presare, fabricare, ambutisare adâncă folosind matrițe cu un singur poanson / cu o singură cursă, precum și matrițe progresive și filare, formare cauciuc și hidroformare; tăierea tablei cu jet de apă, plasmă, laser, ferăstrău, flacără; asamblare table folosind sudare, sudare în puncte; tubul de tablă bombat și îndoit; Finisarea suprafeței tablei, inclusiv vopsirea prin scufundare sau pulverizare, acoperire cu pulbere electrostatică, anodizare, placare, pulverizare și multe altele. Serviciile noastre variază de la prototiparea rapidă a tablei până la producția de volum mare. Vă recomandăm să faceți clic aici pentruDESCARCĂ Ilustrațiile noastre schematice ale proceselor de fabricare și ștanțare a tablei de către AGS-TECH Inc. Acest lucru vă va ajuta să înțelegeți mai bine informațiile pe care vi le oferim mai jos. • TĂIERE TĂBLĂ: Oferim TĂIEȚI și DESPĂRȚI. Tăierea taie tabla pe o singură cale la un moment dat și practic nu există nicio risipă de material, în timp ce cu despărțiri forma nu poate fi așezată cu precizie și, prin urmare, se irosește o anumită cantitate de material. Unul dintre cele mai populare procese ale noastre este ȘUNTAREA, în care o bucată de material rotundă sau de altă formă este tăiată din tablă. Piesa care este tăiată este deșeuri. O altă versiune de perforare este SLOTTING, unde sunt perforate găuri dreptunghiulare sau alungite. DEBILARE, pe de altă parte, este același proces ca și ștanțare, cu distincția piesei decupate este lucrul și se păstrează. FINE BLANKING, o versiune superioară a decupării, creează tăieturi cu toleranțe strânse și margini netede drepte și nu necesită operații secundare pentru perfecțiunea piesei de prelucrat. Un alt proces pe care îl folosim frecvent este TENDEREA, care este un proces de forfecare în care tabla este tăiată de două lame circulare opuse pe o cale dreaptă sau curbă. Deschizătorul de conserve este un exemplu simplu al procesului de tăiere. Un alt proces process pentru noi este PERFORAREA, unde multe găuri rotunde sau de altă formă sunt perforate în tablă într-un anumit model. Un exemplu tipic pentru un produs perforat sunt filtrele metalice cu multe orificii pentru fluide. În NOTCHING, un alt proces de tăiere a tablei, scoatem materialul dintr-o piesă de prelucrat, începând de la margine sau în altă parte și tăiem spre interior până se obține forma dorită. Este un proces progresiv in care fiecare operatie indeparteaza o alta bucata pana se obtine conturul dorit. Pentru producții mici, folosim uneori un proces relativ mai lent numit NIBBLING, care constă în multe perforații rapide de găuri suprapuse pentru a face o tăietură mai mare și mai complexă. În TĂIEREA PROGRESIVĂ folosim o serie de operații diferite pentru a obține o singură tăietură sau o anumită geometrie. În cele din urmă, BARNIERUL un proces secundar ne ajută să îmbunătățim marginile tăierilor care au fost deja făcute. Este folosit pentru tăierea așchiilor, a marginilor aspre pe lucrări de tablă. • Îndoirea tablei: Pe lângă tăiere, îndoirea este un proces esențial fără de care nu am putea produce majoritatea produselor. De cele mai multe ori o operație de lucru la rece, dar uneori efectuată și când este cald sau cald. Folosim matrițe și presam de cele mai multe ori pentru această operație. În PROGRESSIVE BENDING folosim o serie de operații diferite de perforare și matriță pentru a obține o singură îndoire sau o anumită geometrie. AGS-TECH utilizează o varietate de procese de îndoire și face alegerea în funcție de materialul piesei de prelucrat, dimensiunea acestuia, grosimea acestuia, dimensiunea dorită a îndoirii, raza, curbura și unghiul de îndoire, locația îndoirii, economia de funcționare, cantitățile de fabricat... etc. Folosim V-BENDING unde un poanson în formă de V forțează tabla în matrița în formă de V și o îndoaie. Bun atât pentru unghiuri foarte acute, cât și pentru unghiuri obtuze și între ele, inclusiv 90 de grade. Folosind matrițe de ștergere, efectuăm îndoirea marginilor. Echipamentul nostru ne permite să obținem unghiuri chiar mai mari de 90 de grade. La îndoirea pe margine, piesa de prelucrat este plasată între un tampon de presiune și matriță, zona pentru îndoire este situată pe marginea matriței, iar restul piesei de prelucrat este ținută peste spațiu ca o grindă cantilever. Când poansonul acționează asupra porțiunii în consolă, acesta este îndoit peste marginea matriței. FLANGAREA este un proces de îndoire a marginilor care are ca rezultat un unghi de 90 de grade. Obiectivele principale ale operațiunii sunt eliminarea muchiilor ascuțite și obținerea suprafețelor geometrice pentru a ușura îmbinarea pieselor. BEADING, un alt proces comun de îndoire a marginilor formează o buclă peste marginea unei piese. HEMMING pe de altă parte are ca rezultat o margine a foii care este complet îndoită pe ea însăși. În SEAMING, marginile a două părți sunt îndoite una peste alta și îmbinate. CUNSĂTURA DUBLĂ, pe de altă parte, asigură îmbinări etanșe la apă și la aer. Similar cu îndoirea marginilor, un proces numit ROTARY BENDING desfășoară un cilindru cu unghiul dorit tăiat și servind drept perforator. Pe măsură ce forța este transmisă poansonului, acesta se închide cu piesa de prelucrat. Canelura cilindrului oferă porțiunii în consolă unghiul dorit. Canelura poate avea un unghi mai mic sau mai mare de 90 de grade. În AIR BENDING, nu avem nevoie ca matrița inferioară să aibă o canelură în unghi. Tabla este susținută de două suprafețe pe laturi opuse și la o anumită distanță. Poansonul aplică apoi o forță în locul potrivit și îndoaie piesa de prelucrat. CHANNEL BENDING se realizează folosind un poanson și o matriță în formă de canal, iar U-BEND se realizează cu un poanson în formă de U. OFFSET BENDING produce decalaje pe tablă. ROLL BENDING, o tehnică bună pentru lucrul gros și îndoirea bucăților mari de plăci metalice, folosește trei role pentru a alimenta și îndoi plăcile la curbura dorită. Rolele sunt aranjate astfel încât să se obțină îndoirea dorită a lucrării. Distanța și unghiul dintre role sunt controlate pentru a obține rezultatul dorit. O rolă mobilă face posibilă controlul curburii. FORMAREA TUBILOR este o altă operație populară de îndoire a tablei care implică mai multe matrițe. Tuburile sunt obținute după mai multe acțiuni. CORRUGAREA se realizează și prin operații de îndoire. Practic, este îndoirea simetrică la intervale regulate de-a lungul unei întregi piese de tablă. Pentru ondulare pot fi folosite diferite forme. Tabla ondulata este mai rigida si are o rezistenta mai buna la incovoiere si de aceea are aplicatii in industria constructiilor. FORMAREA TĂBLĂRILOR, un proces continuu manufacturing este desfășurat pentru a îndoi secțiuni transversale de o anumită geometrie folosind role și lucrarea este îndoită în pași succesivi, cu rola finală completând lucrarea. În unele cazuri se utilizează o singură rolă și în unele cazuri o serie de role. • PROCESE COMBINATE DE TĂIERE ȘI DE ÎNDOIRE TĂBLI: Acestea sunt procesele care taie și îndoaie în același timp. În PIERCING, se creează o gaură folosind un pumn ascuțit. Pe măsură ce perforatorul lărgește orificiul din foaie, materialul este îndoit simultan într-o flanșă interioară pentru gaură. Flanșa obținută poate avea funcții importante. Pe de altă parte, operația de LANȚARE taie și îndoaie tabla pentru a crea o geometrie înălțată. • BOMBARE ȘI ÎNDOIRE TUBUL METAL: În BUFING, o parte interioară a unui tub tubular este presurizată, determinând umflarea tubului spre exterior. Deoarece tubul se află în interiorul unei matrițe, geometria umflăturii este controlată de forma matriței. În STRETCH BENDING, un tub de metal este întins folosind forțe paralele cu axa tubului și forțe de îndoire pentru a trage tubul peste un bloc de formă. În DRAW BENDING, prindem tubul aproape de capătul său de un bloc de formă rotativ care îndoaie tubul în timp ce se rotește. În cele din urmă, la îndoirea prin compresie tubul este ținut cu forță de un bloc de formă fix, iar o matriță îl îndoaie peste blocul de formă. • DEEP DRAWING: Într-una dintre cele mai populare operațiuni ale noastre, se folosesc un poanson, o matriță potrivită și un suport pentru semifabricat. Semifabricatul din tablă este plasat peste deschiderea matriței și poansonul se deplasează către semifabricatul ținut de suportul semifabricatului. Odată ce intră în contact, poansonul forțează tabla în cavitatea matriței pentru a forma produsul. Operația de embotire adâncă seamănă cu tăierea, cu toate acestea, spațiul dintre poanson și matriță împiedică tăierea foii. Un alt factor care asigură ca foaia să fie îngroșată și nu tăiată sunt colțurile rotunjite de pe matriță și poanson care împiedică forfecarea și tăierea. Pentru a obține o amploare mai mare a ambutisării adânci, este desfășurat un proces de REDENSARE, în care are loc o ambugare ulterioară pe o piesă care a suferit deja un proces de ambutisare. În REDESENAREA INVERSĂ, partea trasă adânc este răsturnată și desenată în direcția opusă. Embutarea adâncă poate oferi obiecte de formă neregulată, cum ar fi cupe bombate, conice sau trepte, În embosing folosim o pereche de matrițe masculin și feminin pentru a impresiona tabla cu un design sau un script. • SPINNING : O operație în care o piesă de prelucrat plată sau preformată este ținută între un dorn rotativ și un material de coadă și o unealtă aplică presiune localizată asupra lucrării pe măsură ce aceasta se deplasează treptat în sus pe dorn. Ca rezultat, piesa de prelucrat este înfășurată peste dorn și își ia forma. Folosim această tehnică ca alternativă la embotirea adâncă, unde cantitatea unei comenzi este mică, piesele sunt mari (diametre de până la 20 de picioare) și au curbe unice. Chiar dacă prețurile pe bucată sunt în general mai mari, costurile de instalare pentru operația de filare CNC sunt scăzute în comparație cu ambutisarea adâncă. Dimpotrivă, ambutisarea adâncă necesită investiții inițiale mari pentru montaj, dar costurile pe bucată sunt mici atunci când sunt produse cantități mari de piese. O altă versiune a acestui proces este STRINGAREA prin forfecare, unde există și un flux de metal în interiorul piesei de prelucrat. Fluxul de metal va reduce grosimea piesei de prelucrat pe măsură ce procesul este efectuat. Un alt proces înrudit este TUBE SPINNING, care se aplică pe piesele cilindrice. De asemenea, în acest proces există un flux de metal în interiorul piesei de prelucrat. Grosimea este astfel redusă și lungimea tubului este mărită. Instrumentul poate fi mutat pentru a crea caracteristici în interiorul sau în exteriorul tubului. • FORMAREA TABILELOR DE CAUciuC: Materialul de cauciuc sau poliuretan este pus într-o matriță de container și piesa de prelucrat este plasată pe suprafața cauciucului. Apoi se acționează un pumn asupra piesei de prelucrat și o forțează în cauciuc. Deoarece presiunea generată de cauciuc este scăzută, adâncimea pieselor produse este limitată. Deoarece costurile cu scule sunt mici, procesul este potrivit pentru producția în cantități mici. • HIDROFORMARE: Similar cu formarea cauciucului, în acest proces prelucrarea tablei este presată cu un poanson într-un lichid sub presiune în interiorul unei camere. Materialul din tablă este prins între poanson și o diafragmă de cauciuc. Diafragma înconjoară complet piesa de prelucrat, iar presiunea fluidului o forțează să se formeze pe poanson. Cu această tehnică se pot obține trage foarte adânc și mai profund decât în procesul de embotire adâncă. Producem matrițe cu o singură perforare, precum și matrițe progresive, în funcție de partea dvs. Matrițele de ștanțare cu o singură cursă sunt o metodă rentabilă pentru a produce rapid cantități mari de piese simple din tablă, cum ar fi șaibe. Matrițele progresive sau tehnica de ambutisare adâncă sunt utilizate pentru fabricarea de geometrii mai complexe. În funcție de cazul dvs., tăierea cu jet de apă, cu laser sau cu plasmă poate fi utilizată pentru a vă produce piesele din tablă ieftin, rapid și precis. Mulți furnizori nu au nicio idee despre aceste tehnici alternative sau nu le au și, prin urmare, trec prin modalități lungi și costisitoare de a face matrițe și unelte care doar pierd clienții timp și bani. Dacă aveți nevoie de componente din tablă construite la comandă, cum ar fi carcase, carcase electronice... etc, la fel de repede în câteva zile, atunci contactați-ne pentru serviciul nostru de PROTOTIPARE RAPIDĂ DE TĂBLĂ. CLICK Product Finder-Locator Service MENIU ANTERIOR
- Plastic Rubber Metal Extrusions, Extrusion Dies, Aluminum Extruding
Plastic Rubber Metal Extrusions, Extrusion Dies, Aluminum Extruding, Pipe Tube Forming, Plastic Profiles, Metal Profiles Manufacturing, PVC at AGS-TECH Inc. Extrudari, Produse Extrudate, Extrudate Folosim procesul EXTRUSION process pentru a fabrica produse cu un profil de secțiune transversală fix, cum ar fi tuburi, țevi și radiatoare. Chiar dacă multe materiale pot fi extrudate, extrudarile noastre cele mai obișnuite sunt realizate din metal, polimeri/plastic, ceramică obținută fie prin metoda de extrudare la rece, la cald sau la cald. Numim părțile extrudate extrudat sau extrudate dacă sunt la plural. Unele versiuni specializate ale procesului pe care le efectuăm, de asemenea, sunt suprajacketingul, coextrudarea și extrudarea compusă. Vă recomandăm să faceți clic aici pentru a DESCARCĂ Ilustrațiile noastre schematice ale proceselor de extrudare a metalelor, ceramicii și plasticului, realizate de AGS-TECH Inc. Acest lucru vă va ajuta să înțelegeți mai bine informațiile pe care vi le oferim mai jos. În extrudare, materialul de extrudat este împins sau tras printr-o matriță care are profilul în secțiune transversală dorit. Procesul poate fi utilizat pentru a produce secțiuni transversale complexe cu finisare excelentă a suprafeței și pentru a lucra pe material fragil. Se poate produce orice lungime de piese folosind acest proces. Pentru a simplifica pașii procesului: 1.) În extrudările calde sau fierbinți, materialul este încălzit și încărcat într-un recipient în presă. Materialul este presat și împins afară din matriță. 2.) Extrudatul produs este întins pentru îndreptare, tratat termic sau prelucrat la rece pentru îmbunătățirea proprietăților sale. Pe de altă parte COLD EXTRUSION se desfășoară la temperatura camerei și are avantajele unei oxidari mai puține, toleranțe ridicate, rapiditate, rezistență la suprafață și finisare mai apropiată. EXTRUZIUNEA CALDE se realizează peste temperatura camerei, dar sub punctul de recristalizare. Oferă un compromis și un echilibru pentru forțele, ductilitatea și proprietățile materialelor necesare și, prin urmare, este alegerea pentru unele aplicații. HOT EXTRRUSION are loc peste temperatura de recristalizare a materialului. În acest fel, este mai ușor să împingeți materialul prin matriță. Cu toate acestea, costul echipamentului este mare. Cu cât un profil extrudat este mai complex, cu atât matrița (uneltele) este mai costisitoare și cu atât rata de producție este mai mică. Secțiunile transversale ale matriței, precum și grosimile au limitări care depind de materialul care trebuie extrudat. Colțurile ascuțite în matrițele de extrudare sunt întotdeauna nedorite și trebuie evitate dacă nu este necesar. În funcție de materialul care este extrudat, oferim: • METAL EXTRUSIONS : Cele mai comune produse pe care le producem sunt aluminiu, alamă, zinc, cupru, oțel, titan, magneziu • EXTRUZIA PLASTICĂ : Plasticul este topit și format într-un profil continuu. Materialele noastre obișnuite procesate sunt polietilena, nailonul, polistirenul, clorura de polivinil, polipropilena, plasticul ABS, policarbonatul, acrilul. Produsele tipice pe care le fabricăm includ țevi și tuburi, rame din plastic. În acest proces, micile margele/rășină de plastic sunt introduse prin gravitație din buncăr în butoiul mașinii de extrudare. Frecvent amestecăm coloranți sau alți aditivi în buncăr pentru a oferi produsului specificațiile și proprietățile necesare. Materialul care intră în butoiul încălzit este forțat de șurubul rotativ să părăsească butoiul la capăt și să se deplaseze prin pachetul de ecran pentru îndepărtarea contaminanților din plasticul topit. După trecerea pachetului de ecran, plasticul intră în matrița de extrudare. Matrița conferă plasticului moale în mișcare forma sa de profil pe măsură ce trece prin el. Acum extrudatul trece printr-o baie de apă pentru răcire. Alte tehnici pe care AGS-TECH Inc. le folosește de mulți ani sunt: • PIPE & TUBING EXTRUSION : Țevile și tuburile din plastic se formează atunci când plasticul este extrudat printr-o matriță de formare rotundă și răcit într-o baie de apă, apoi tăiat la lungime sau bobinat / bobinat. Transparente sau colorate, dungi, perete simplu sau dublu, flexibile sau rigide, PE, PP, poliuretan, PVC, nailon, PC, silicon, vinil sau altceva, le avem pe toate. Avem tuburi stocate, precum și capacitatea de a produce conform specificațiilor dumneavoastră. AGS-TECH produce tuburi conform cerințelor FDA, UL și LE pentru aplicații medicale, electrice și electronice, industriale și alte aplicații. • OVERJACKETING / OVER JACKETING EXTRUSION : Această tehnică aplică un strat exterior de plastic pe firul sau cablul existent. Firele noastre de izolație sunt fabricate cu această metodă. • COEXTRUSION : sunt extrudate simultan mai multe straturi de material. Straturile multiple sunt livrate de mai multe extrudere. Diferitele grosimi ale stratului pot fi ajustate pentru a satisface specificațiile clientului. Acest proces face posibilă utilizarea mai multor polimeri, fiecare având o funcționalitate diferită în produs. Ca rezultat, se poate optimiza o serie de proprietăți. • EXTRUDERE COMPUSĂ: Un singur polimer sau mai mulți polimeri sunt amestecați cu aditivi pentru a obține un compus plastic. Extruderele noastre cu două șuruburi produc extrudere de amestecare. Motoarele de extrudare sunt, în general, ieftine în comparație cu matrițele metalice. Dacă plătiți mult mai mult de câteva mii de dolari pentru o matriță de extrudare de dimensiuni mici sau medii din aluminiu, probabil că plătiți prea mult. Suntem experți în a determina care tehnică este cea mai rentabilă, cea mai rapidă și cea mai potrivită pentru aplicația dvs. Uneori, extrudarea și apoi prelucrarea unei piese vă poate economisi mulți bani. Înainte de a lua o decizie fermă, cere-ne mai întâi părerea noastră. Am ajutat mulți clienți să ia deciziile corecte. Pentru unele extrudate metalice utilizate pe scară largă, puteți descărca broșurile și cataloagele noastre făcând clic pe textul colorat de mai jos. Dacă este un produs disponibil la raft care îndeplinește cerințele dvs., va fi mai economic. Descărcați capacitățile noastre de extrudare a tuburilor și conductelor medicale Descărcați radiatoarele noastre extrudate • PROCESE SECUNDARE DE FABRICAȚIE ȘI DE FABRICARE PENTRU EXTRUZII : Printre procesele cu valoare adăugată pe care le oferim pentru produsele extrudate se numără: - Îndoirea, formarea și modelarea țevilor și a țevilor personalizate, tăierea tubului, formarea capătului tubului, bobinarea tubului, prelucrare și finisare, găurire și perforare și perforare, - Ansambluri personalizate de țevi și tuburi, ansamblu tubular, sudare, lipire și lipire - Îndoire, formare și modelare prin extrudare personalizată -Curatare, degresare, decapare, pasivare, lustruire, anodizare, placare, vopsire, tratare termica, recoacere si calire, marcare, gravare si etichetare, ambalare la comanda. CLICK Product Finder-Locator Service PAGINA ANTERIOARĂ
- Casting and Machined Parts, CNC Manufacturing, Milling, Turning, Swiss
Casting and Machined Parts, CNC Manufacturing, Milling, Turning, Swiss Type Machining, Die Casting, Investment Casting, Lost Foam Cast Parts from AGS-TECH Inc. Turnare și prelucrare Tehnicile noastre personalizate de turnare și prelucrare sunt piese turnate consumabile și neutilizabile, turnare feroasă și neferoasă, nisip, matriță, matriță centrifugă, continuă, matriță ceramică, investiție, spumă pierdută, formă aproape netă, matriță permanentă (turnare prin gravitație), ipsos. turnare (turnare din ipsos) și piese turnate în carcasă, piese prelucrate produse prin frezare și strunjire folosind echipamente convenționale, precum și CNC, prelucrare de tip elvețian pentru piese mici de precizie, ieftine, prelucrare mare, prelucrare cu șuruburi pentru elemente de fixare, prelucrare neconvențională. Vă rugăm să rețineți că, pe lângă metale și aliaje metalice, prelucram componente ceramice, sticlă și plastic, de asemenea, în unele cazuri când fabricarea unei matrițe nu este atrăgătoare sau nu este opțiunea. Prelucrarea materialelor polimerice necesită experiența de specialitate pe care o avem din cauza provocărilor pe care o prezintă plasticul și cauciucul datorită moliciunii, nerigidității...etc. Pentru prelucrarea ceramicii și sticlei, vă rugăm să consultați pagina noastră despre Fabricarea neconvențională. AGS-TECH Inc. produce și furnizează piese turnate atât ușoare, cât și grele. Furnizăm piese turnate metalice și piese prelucrate pentru cazane, schimbătoare de căldură, automobile, micromotoare, turbine eoliene, echipamente de ambalare a alimentelor și multe altele. Vă recomandăm să faceți clic aici pentru a DESCARCĂ Ilustrațiile noastre schematice ale proceselor de prelucrare și turnare de la AGS-TECH Inc. Acest lucru vă va ajuta să înțelegeți mai bine informațiile pe care vi le oferim mai jos. Să ne uităm la câteva dintre diferitele tehnici pe care le oferim în detaliu: • Turnarea matrițelor uzabile: Această categorie largă se referă la metode care implică matrițe temporare și nereutilizabile. Exemple sunt nisipul, ipsosul, cochilia, investiția (numită și ceară pierdută) și turnarea în ipsos. • Turnarea cu nisip: un proces în care nisipul este folosit ca material de matriță. O metodă foarte veche și încă foarte populară în măsura în care majoritatea pieselor metalice produse sunt realizate prin această tehnică. Cost redus chiar și la producție în cantitate mică. Potrivit pentru fabricarea de piese mici și mari. Tehnica poate fi folosită pentru a fabrica piese în câteva zile sau săptămâni, cu investiții foarte mici. Nisipul umed este lipit împreună cu argilă, lianți sau uleiuri speciale. Nisipul este în general conținut în cutiile de matriță, iar sistemul de cavitate și poartă sunt create prin compactarea nisipului din jurul modelelor. Procesele sunt: 1.) Plasarea modelului in nisip pentru realizarea matritei 2.) Incorporarea modelului si nisipului intr-un sistem de gating 3.) Îndepărtarea modelului 4.) Umplerea cavității matriței cu metal topit 5.) Răcirea metalului 6.) Ruperea matriței de nisip și îndepărtarea turnării • Turnarea matriței de ipsos: Similar cu turnarea cu nisip și, în loc de nisip, ca material de matriță se folosește tencuiala de Paris. Timp de producție scurt, cum ar fi turnarea cu nisip și ieftin. Tolerante dimensionale bune si finisare a suprafetei. Dezavantajul său major este că poate fi utilizat numai cu metale cu punct de topire scăzut precum aluminiul și zincul. • TURNAREA MATRICE DE COCAJĂ: De asemenea, asemănătoare cu turnarea cu nisip. Cavitatea matriței obținută prin înveliș de nisip întărit și liant de rășină termorigide în loc de balon umplut cu nisip ca în procesul de turnare cu nisip. Aproape orice metal potrivit pentru a fi turnat cu nisip poate fi turnat prin turnare coajă. Procesul poate fi rezumat astfel: 1.) Fabricarea matriței de coajă. Nisipul folosit are o dimensiune mult mai mică a granulelor în comparație cu nisipul folosit la turnarea cu nisip. Nisipul fin este amestecat cu rasina termorezistenta. Modelul metalic este acoperit cu un agent de despărțire pentru a facilita îndepărtarea carcasei. După aceea, modelul de metal este încălzit și amestecul de nisip este poros sau suflat pe modelul de turnare la cald. Pe suprafața modelului se formează o coajă subțire. Grosimea acestui înveliș poate fi ajustată variind perioada de timp în care amestecul de rășini de nisip este în contact cu modelul metalic. Nisipul liber este apoi îndepărtat, rămânând modelul acoperit cu coajă. 2.) Apoi, coaja și modelul sunt încălzite într-un cuptor, astfel încât coaja să se întărească. După ce întărirea este completă, carcasa este scoasă din model folosind știfturi încorporați în model. 3.) Două astfel de cochilii sunt asamblate împreună prin lipire sau prindere și alcătuiesc matrița completă. Acum matrița de coajă este introdusă într-un recipient în care este susținută de nisip sau împușcătură de metal în timpul procesului de turnare. 4.) Acum metalul fierbinte poate fi turnat în matrița de coajă. Avantajele turnării în carcasă sunt produse cu finisare foarte bună a suprafeței, posibilitatea de fabricare a pieselor complexe cu precizie dimensională ridicată, proces ușor de automatizat, economic pentru producția de volum mare. Dezavantajele sunt că matrițele necesită o bună ventilație din cauza gazelor care sunt create atunci când metalul topit intră în contact cu substanța chimică de liant, rășinile termorigide și modelele metalice sunt scumpe. Datorită costului modelelor metalice, este posibil ca tehnica să nu se potrivească bine pentru serii de producție în cantitate mică. • TURNAREA INVESTMENT (cunoscută și sub denumirea de LOST-WAX CASTING): De asemenea, o tehnică foarte veche și potrivită pentru fabricarea pieselor de calitate, cu precizie ridicată, repetabilitate, versatilitate și integritate din multe metale, materiale refractare și aliaje speciale de înaltă performanță. Pot fi produse piese de dimensiuni mici și mari. Un proces costisitor în comparație cu unele dintre celelalte metode, dar avantajul major este posibilitatea de a produce piese cu formă aproape netă, contururi complicate și detalii. Deci costul este oarecum compensat de eliminarea reprelucrării și prelucrării în unele cazuri. Chiar dacă pot exista variații, iată un rezumat al procesului general de turnare a investițiilor: 1.) Crearea modelului principal original din ceară sau plastic. Fiecare turnare are nevoie de un model, deoarece acestea sunt distruse în acest proces. Este necesară și matriță din care sunt fabricate modele și de cele mai multe ori matrița este turnată sau prelucrată. Deoarece matrița nu trebuie să fie deschisă, pot fi realizate turnări complexe, multe modele de ceară pot fi conectate ca ramurile unui copac și turnate împreună, permițând astfel producția de piese multiple dintr-o singură turnare a metalului sau a aliajului metalic. 2.) Apoi, modelul este scufundat sau turnat peste cu o suspensie refractară compusă din silice cu granulație foarte fină, apă, lianți. Acest lucru are ca rezultat un strat ceramic pe suprafața modelului. Stratul refractar de pe model este lăsat să se usuce și să se întărească. Acest pas este de unde provine denumirea de turnare de investiții: șlam refractar este plasat peste modelul de ceară. 3.) La acest pas, matrița ceramică întărită este răsturnată și încălzită astfel încât ceara să se topească și să se toarne din matriță. O cavitate este lăsată în urmă pentru turnarea metalului. 4.) După ce ceara este scoasă, matrița ceramică este încălzită la o temperatură chiar mai mare, ceea ce are ca rezultat întărirea matriței. 5.) Turnarea metalului este turnată în matrița fierbinte umplând toate secțiunile complicate. 6.) Turnarea este lăsată să se solidifice 7.) În cele din urmă matrița ceramică este spartă și piesele fabricate sunt tăiate din copac. Iată un link către broșura Investment Casting Plant • TURNAREA MODELUL EVAPORATIV: Procesul folosește un model realizat dintr-un material, cum ar fi spuma de polistiren, care se va evapora atunci când metalul topit fierbinte este turnat în matriță. Există două tipuri de acest proces: turnarea cu spumă pierdută, care folosește nisip nelegat și turnarea cu mucegai complet, care utilizează nisip lipit. Iată pașii generali ai procesului: 1.) Fabricați modelul dintr-un material precum polistirenul. Când se vor fabrica cantități mari, modelul este modelat. Dacă o parte are o formă complexă, mai multe secțiuni ale unui astfel de material spumant ar putea fi nevoie să fie lipite împreună pentru a forma modelul. Adesea acoperim modelul cu un compus refractar pentru a crea un finisaj bun al suprafeței turnării. 2.) Modelul este apoi pus în nisip de turnare. 3.) Metalul topit este turnat în matriță, evaporând modelul de spumă, adică polistiren în cele mai multe cazuri pe măsură ce curge prin cavitatea matriței. 4.) Metalul topit este lăsat în matrița de nisip pentru a se întări. 5.) După ce se întărește, scoatem turnarea. În unele cazuri, produsul pe care îl fabricăm necesită un miez în cadrul modelului. În turnarea evaporativă, nu este nevoie să plasați și să fixați un miez în cavitatea matriței. Tehnica este potrivită pentru fabricarea de geometrii foarte complexe, poate fi automatizată cu ușurință pentru producția de volum mare și nu există linii de despărțire în piesa turnată. Procesul de bază este simplu și economic de implementat. Pentru producția de volum mare, deoarece este necesară o matriță sau o matriță pentru a produce modelele din polistiren, acest lucru poate fi oarecum costisitor. • Turnarea matriței NEEXPANDIBILE: Această categorie largă se referă la metodele în care matrița nu trebuie reformată după fiecare ciclu de producție. Exemple sunt turnarea permanentă, matriță, continuă și centrifugă. Se obține repetabilitate și piesele pot fi caracterizate ca FORMA APROAPE NETĂ. • TURNARE PERMANENTĂ DE MULTE: Formele reutilizabile din metal sunt utilizate pentru turnări multiple. O matriță permanentă poate fi folosită în general de zeci de mii de ori înainte de a se uza. Gravitația, presiunea gazului sau vidul sunt în general folosite pentru a umple matrița. Matrite (numite si matrita) sunt in general realizate din fier, otel, ceramica sau alte metale. Procesul general este: 1.) Mașinați și creați matrița. Este obișnuit să prelucrați matrița din două blocuri metalice care se potrivesc împreună și pot fi deschise și închise. Atât caracteristicile piesei, cât și sistemul de închidere sunt în general prelucrate în matrița de turnare. 2.) Suprafețele interne ale matriței sunt acoperite cu o suspensie care încorporează materiale refractare. Acest lucru ajută la controlul fluxului de căldură și acționează ca un lubrifiant pentru îndepărtarea ușoară a piesei turnate. 3.) Apoi, jumătățile de matriță permanente sunt închise și matrița este încălzită. 4.) Metalul topit este turnat în matriță și lăsat să se solidifice. 5.) Înainte de a avea loc o răcire intensă, scoatem piesa din matrița permanentă folosind ejectoare atunci când jumătățile de matriță sunt deschise. Folosim frecvent turnarea permanentă pentru metale cu punct de topire scăzut, cum ar fi zincul și aluminiul. Pentru turnarea din oțel, folosim grafit ca material de matriță. Obținem uneori geometrii complexe folosind miezuri în matrițe permanente. Avantajele acestei tehnici sunt piese turnate cu proprietăți mecanice bune obținute prin răcire rapidă, uniformitate în proprietăți, precizie bună și finisare a suprafeței, rate scăzute de respingere, posibilitatea de automatizare a procesului și de a produce volume mari economic. Dezavantajele sunt costurile mari de configurare inițială care îl fac nepotrivit pentru operațiuni cu volum redus și limitările privind dimensiunea pieselor fabricate. • TURNAREA sub presiune: O matriță este prelucrată și metalul topit este împins sub presiune înaltă în cavitățile matriței. Sunt posibile atât turnarea sub presiune a metalelor neferoase, cât și a celor feroase. Procesul este potrivit pentru serii de producție în cantități mari de piese de dimensiuni mici și medii cu detalii, pereți extrem de subțiri, consistență dimensională și finisare bună a suprafeței. AGS-TECH Inc. este capabilă să producă grosimi de pereți de până la 0,5 mm folosind această tehnică. Ca și în turnarea permanentă a matriței, matrița trebuie să fie formată din două jumătăți care se pot deschide și închide pentru îndepărtarea părții produse. O matriță de turnare sub presiune poate avea mai multe cavități pentru a permite producția de mai multe piese turnate cu fiecare ciclu. Formele de turnare sub presiune sunt foarte grele și mult mai mari decât piesele pe care le produc, prin urmare și costisitoare. Reparăm și înlocuim matrițele uzate gratuit pentru clienții noștri, atâta timp cât își comandă din nou piesele de la noi. Motele noastre au durate de viață lungi în intervalul de câteva sute de mii de cicluri. Iată pașii de bază simplificați ai procesului: 1.) Producția matriței în general din oțel 2.) matriță instalată pe mașina de turnare sub presiune 3.) Pistonul forțează metalul topit să curgă în cavitățile matriței, completând caracteristicile complicate și pereții subțiri 4.) După umplerea matriței cu metalul topit, turnarea este lăsată să se întărească sub presiune 5.) Se deschide matrița și se îndepărtează turnarea cu ajutorul știfturilor de evacuare. 6.) Acum matrițele goale sunt lubrifiate din nou și sunt prinse pentru următorul ciclu. În turnarea sub presiune, folosim frecvent turnarea cu inserție în care încorporăm o piesă suplimentară în matriță și turnăm metalul în jurul acesteia. După solidificare, aceste părți devin parte a produsului turnat. Avantajele turnării sub presiune sunt proprietățile mecanice bune ale pieselor, posibilitatea unor caracteristici complexe, detalii fine și finisare bună a suprafeței, rate ridicate de producție, automatizare ușoară. Dezavantajele sunt: nu foarte potrivit pentru volum redus din cauza costului ridicat al matriței și al echipamentului, limitări ale formelor care pot fi turnate, mici semne rotunde pe piesele turnate rezultate din contactul cu știfturile ejectorului, fulger subțire de metal stors la linia de despărțire, nevoie pentru orificiile de aerisire de-a lungul liniei de separare dintre matriță, necesitatea de a menține temperaturile matriței scăzute folosind circulația apei. • TURNARE CENTRIFUGĂ: Metalul topit este turnat în centrul matriței rotative la axa de rotație. Forțele centrifuge aruncă metalul spre periferie și este lăsat să se solidifice pe măsură ce matrița continuă să se rotească. Pot fi utilizate atât rotațiile pe axă orizontală, cât și pe cea verticală. Piesele cu suprafețe interioare rotunde, precum și alte forme nerotunde pot fi turnate. Procesul poate fi rezumat astfel: 1.) Metalul topit este turnat în matriță centrifugă. Metalul este apoi forțat spre pereții exteriori din cauza rotării matriței. 2.) Pe măsură ce matrița se rotește, turnarea metalică se întărește Turnarea centrifugală este o tehnică potrivită pentru producția de piese cilindrice goale, cum ar fi țevile, nu este nevoie de coloane, coloane și elemente de deschidere, finisare bună a suprafeței și caracteristici detaliate, fără probleme de contracție, posibilitatea de a produce țevi lungi cu diametre foarte mari, capacitate de producție cu viteză ridicată . • TURNARE CONTINUĂ ( TORRE TORNI ) : Folosit pentru turnarea unei lungimi continue de metal. Practic, metalul topit este turnat în profilul bidimensional al matriței, dar lungimea sa este nedeterminată. Noul metal topit este alimentat în mod constant în matriță pe măsură ce turnarea se deplasează în jos, lungimea sa crescând în timp. Metalele precum cuprul, oțelul, aluminiul sunt turnate în fire lungi prin procesul de turnare continuă. Procesul poate avea diverse configurații, dar cea comună poate fi simplificată astfel: 1.) Metalul topit este turnat într-un recipient situat deasupra matriței la cantități și debite bine calculate și curge prin matrița răcită cu apă. Turnarea metalică turnată în matriță se solidifică într-o bară de pornire plasată în partea de jos a matriței. Această bară de pornire oferă rolelor ceva de care să se apuce inițial. 2.) Șuvița lungă de metal este purtată de role cu o viteză constantă. Rolele schimbă, de asemenea, direcția fluxului de șuvițe metalice de la vertical la orizontal. 3.) După ce turnarea continuă a parcurs o anumită distanță orizontală, o lanternă sau un ferăstrău care se mișcă odată cu turnarea o taie rapid la lungimile dorite. Procesul de turnare continuă poate fi integrat cu PROCESUL DE LAMINARE, în care metalul turnat continuu poate fi alimentat direct într-un laminor pentru a produce grinzi în I, grinzi în T….etc. Turnarea continuă produce proprietăți uniforme în întregul produs, are o viteză mare de solidificare, reduce costurile datorită pierderii foarte mici de material, oferă un proces în care încărcarea metalului, turnarea, solidificarea, tăierea și îndepărtarea turnării au loc într-o operațiune continuă și rezultând astfel o rată de productivitate ridicată și o calitate înaltă. O considerație majoră este însă investiția inițială ridicată, costurile de instalare și cerințele de spațiu. • SERVICII DE PRELUCRARE: Oferim prelucrare pe trei, patru și cinci axe. Tipul de procese de prelucrare pe care le folosim sunt strunjirea, frezarea, găurirea, alezarea, broșarea, rindeaua, tăierea, șlefuirea, șlefuirea, lustruirea și prelucrările NETRADIȚIONALE care sunt elaborate în continuare într-un meniu diferit al site-ului nostru. Pentru cea mai mare parte a producției noastre, folosim mașini CNC. Cu toate acestea, pentru unele operațiuni, tehnicile convenționale se potrivesc mai bine și, prin urmare, ne bazăm și pe ele. Capacitățile noastre de prelucrare ating cel mai înalt nivel posibil și unele piese cele mai solicitante sunt fabricate într-o fabrică certificată AS9100. Paletele motoarelor cu reacție necesită experiență de producție foarte specializată și echipamentul potrivit. Industria aerospațială are standarde foarte stricte. Unele componente cu structuri geometrice complexe sunt cel mai ușor fabricate prin prelucrare pe cinci axe, care se găsește doar în unele fabrici de prelucrare, inclusiv la noi. Fabrica noastră certificată aerospațială are experiența necesară în conformitate cu cerințele extinse de documentare din industria aerospațială. În operațiunile de strunjire, o piesă de prelucrat este rotită și deplasată împotriva unei scule de tăiere. Pentru acest proces se folosește o mașină numită strung. În FRAZARE, o mașină numită mașină de frezat are o unealtă rotativă pentru a aduce marginile de tăiere în sprijinul unei piese de prelucrat. Operațiunile de găurire implică o freză rotativă cu muchii tăietoare care produce găuri la contactul cu piesa de prelucrat. In general se folosesc prese de gaurit, strunguri sau mori. În operațiunile de găurire, o unealtă cu un singur vârf ascuțit îndoit este mutată într-o gaură brută dintr-o piesa de prelucrat care se rotește pentru a mări ușor gaura și pentru a îmbunătăți precizia. Este folosit pentru finisaje fine. BROȘAREA implică o unealtă dințată pentru a îndepărta materialul dintr-o piesă de prelucrat într-o singură trecere a broșei (uneltă dințată). La broșarea liniară, broșa rulează liniar pe o suprafață a piesei de prelucrat pentru a efectua tăierea, în timp ce la broșarea rotativă, broșa este rotită și presată în piesa de prelucrat pentru a tăia o formă simetrică a axei. SWISS TYPE MACHINING este una dintre tehnicile noastre valoroase pe care le folosim pentru fabricarea de volum mare a pieselor mici de mare precizie. Folosind strung de tip elvețian, transformăm piese mici, complexe și de precizie la preț redus. Spre deosebire de strungurile convenționale în care piesa de prelucrat este menținută staționară și scula în mișcare, în centrele de strunjire de tip elvețian, piesa de prelucrat este lăsată să se miște pe axa Z, iar unealta este staționară. La prelucrarea de tip elvețian, materialul de bară este ținut în mașină și avansat printr-o bucșă de ghidare în axa Z, expunând doar porțiunea de prelucrat. În acest fel, se asigură o prindere strânsă, iar precizia este foarte mare. Disponibilitatea sculelor sub tensiune oferă posibilitatea de a freza și găuri pe măsură ce materialul avansează din bucșa de ghidare. Axa Y a echipamentului de tip elvețian oferă capabilități complete de frezare și economisește o cantitate mare de timp în producție. În plus, mașinile noastre au burghie și scule de alezat care funcționează asupra piesei atunci când aceasta este ținută în sub-ax. Capacitatea noastră de prelucrare de tip elvețian ne oferă o oportunitate de prelucrare complet automatizată într-o singură operațiune. Prelucrarea mecanică este unul dintre cele mai mari segmente ale afacerii AGS-TECH Inc. Îl folosim fie ca operație primară, fie ca operație secundară după turnarea sau extrudarea unei piese, astfel încât toate specificațiile de desen să fie îndeplinite. • SERVICII DE FINISARE A SUPRAFEȚEI: Oferim o mare varietate de tratamente de suprafață și finisare a suprafețelor, cum ar fi condiționarea suprafețelor pentru a îmbunătăți aderența, depunerea unui strat subțire de oxid pentru a îmbunătăți aderența acoperirii, sablare, film chimic, anodizare, nitrurare, acoperire cu pulbere, acoperire prin pulverizare. , diverse tehnici avansate de metalizare și acoperire, inclusiv pulverizare, fascicul de electroni, evaporare, placare, acoperiri dure, cum ar fi carbonul diamant (DLC) sau acoperirea cu titan pentru unelte de găurit și tăiere. • SERVICII DE MARCARE ȘI ETICHETARE PRODUSE: Mulți dintre clienții noștri necesită marcare și etichetare, marcare cu laser, gravare pe piesele metalice. Dacă aveți o astfel de nevoie, permiteți-ne să discutăm care opțiune va fi cea mai bună pentru dvs. Iată câteva dintre produsele turnate metalice utilizate în mod obișnuit. Deoarece acestea sunt disponibile pe raft, puteți economisi costurile matriței în cazul în care oricare dintre acestea se potrivește cerințelor dvs.: CLICK AICI PENTRU A DESCARCĂ cutiile noastre din aluminiu turnat din seria 11 de la AGS-Electronics CLICK Product Finder-Locator Service PAGINA ANTERIOARĂ
- Custom Manufactured Parts, Assemblies, Plastic Mold, Casting,Machining
Custom Manufactured Parts, Assemblies, Plastic Mold, Rubber Molding, Metal Casting, CNC Machining, Turning, Milling, Electrical Electronic Optical Assembly PCBA Piese fabricate la comandă & Ansambluri și produse Citeste mai mult Matrite din plastic si cauciuc si turnare Citeste mai mult Turnare și prelucrare Citeste mai mult Extrudari, Produse extrudate Citeste mai mult Ștanțare și fabricație de tablă Citeste mai mult Forjare metale și metalurgie a pulberilor Citeste mai mult Formare cu sârmă și arc Citeste mai mult Formare și modelare sticle și ceramică Citeste mai mult Producție aditivă și rapidă Citeste mai mult Producția de materiale compozite și compozite Citeste mai mult Procese de îmbinare și asamblare și fixare Producem piese și ansambluri pentru dvs. și vă oferim următoarele procese de fabricație: • Matrite din plastic si cauciuc si piese turnate. Turnare prin injecție, termoformare, turnare termostată, formare în vid, turnare prin suflare, turnare rotațională, turnare turnare, turnare prin inserție și altele. • Extrudari din plastic, cauciuc și metal • Piese turnate feroase și neferoase și piese prelucrate produse prin tehnici de frezare și strunjire, prelucrare de tip elvețian. • Piese de metalurgie a pulberilor • Ștanțare metalice și nemetalice, formare tablă, ansambluri din tablă sudate • Forjare la rece și la cald • Sârme, ansambluri de sârmă sudate, formarea sârmei • Diverse tipuri de arcuri, formând arc • Fabricare angrenaje, cutie de viteze, cuplaj, melcat, reductor de viteză, cilindru, curele de transmisie, lanțuri de transmisie, componente de transmisie • Sticlă securizată și antiglonț, conformă cu standardele NATO și militare • Bile, rulmenți, scripete și ansambluri de scripete • Supape și componente pneumatice, cum ar fi inele O, șaibă și garnituri • Piese si ansambluri din sticla si ceramica, componente rezistente la vid si ermetice, lipire metal-ceramica si ceramica-ceramica. • Diverse tipuri de ansambluri mecanice, optomecanice, electromecanice, optoelectronice. • Lipire metal-cauciuc, metal-plastic • Țevi și țevi, formarea țevilor, îndoirea și ansamblurile de țevi personalizate, fabricarea de burduf. • Fabricarea fibrei de sticla • Sudarea folosind diverse tehnici precum sudarea în puncte, sudarea cu laser, MIG, TIG. Sudare cu ultrasunete pentru piese din plastic. • O mare varietate de tratamente de suprafață și finisaje de suprafață, cum ar fi condiționarea suprafeței pentru a îmbunătăți aderența, depunerea unui strat subțire de oxid pentru a îmbunătăți aderența acoperirii, sablare, film chimic, anodizare, nitrurare, acoperire cu pulbere, acoperire prin pulverizare, diverse tehnici avansate de metalizare și acoperire inclusiv pulverizare, fascicul de electroni, evaporare, placare, acoperiri dure, cum ar fi carbonul de tip diamant (DLC) sau titan pentru unelte de tăiere și găurire. • Marcare si etichetare, marcare laser pe piese metalice, imprimare pe piese din plastic si cauciuc Descărcați broșura pentru Termenii uzuali de inginerie mecanică utilizați de proiectanți și ingineri Construim produse conform specificațiilor și cerințelor dumneavoastră specifice. Pentru a vă oferi cea mai bună calitate, livrare și prețuri, producem produse la nivel global în China, India, Taiwan, Filipine, Coreea de Sud, Malaezia, Sri Lanka, Turcia, SUA, Canada, Germania, Marea Britanie și Japonia. Acest lucru ne face mult mai puternici și mai competitivi la nivel global decât orice alt custom manufacturer. Produsele noastre sunt fabricate în medii certificate ISO9001:2000, QS9000, ISO14001, TS16949 și au marcaj CE, UL și îndeplinesc alte standarde industriale. Odată ce suntem desemnați pentru proiectul dvs., ne putem ocupa de întreaga producție, asamblare, testare, calificare, expediere și vamă după cum doriți. Dacă preferați, vă putem depozita piesele, asambla kituri personalizate, imprimăm și etichetăm numele și marca companiei dvs. și putem livra clienților dumneavoastră. Cu alte cuvinte, putem fi și centrul dvs. de depozitare și distribuție, dacă doriți. Deoarece depozitele noastre sunt situate în apropiere de porturi maritime importante, ne oferă un avantaj logistic. De exemplu, când produsele dvs. ajung într-un port maritim important din SUA, le putem transporta direct la un depozit din apropiere unde putem stoca, asambla, realiza kituri, reeticheta, imprima, ambalăm în funcție de alegerea dvs. expediați clienților dvs. Nu furnizăm doar produse. Compania noastră lucrează pe contracte la comandă, unde venim pe site-ul dvs., vă evaluăm proiectul la fața locului și dezvoltăm o propunere de proiect personalizată pentru dvs. Apoi trimitem echipa noastră experimentată să implementeze proiectul. Mai multe informații despre lucrările noastre de inginerie pot fi găsite pe http://www.ags-engineering.com -Preluăm proiecte mici, precum și proiecte mari la scară industrială. Ca prim pas, vă putem conecta fie prin telefon, teleconferință sau MSN Messenger cu membrii echipei noastre de experți, astfel încât să puteți comunica direct cu un expert, să puneți întrebări și să discutați despre proiectul dvs. Sună-ne și dacă este nevoie venim să te vizităm. PAGINA ANTERIOARĂ