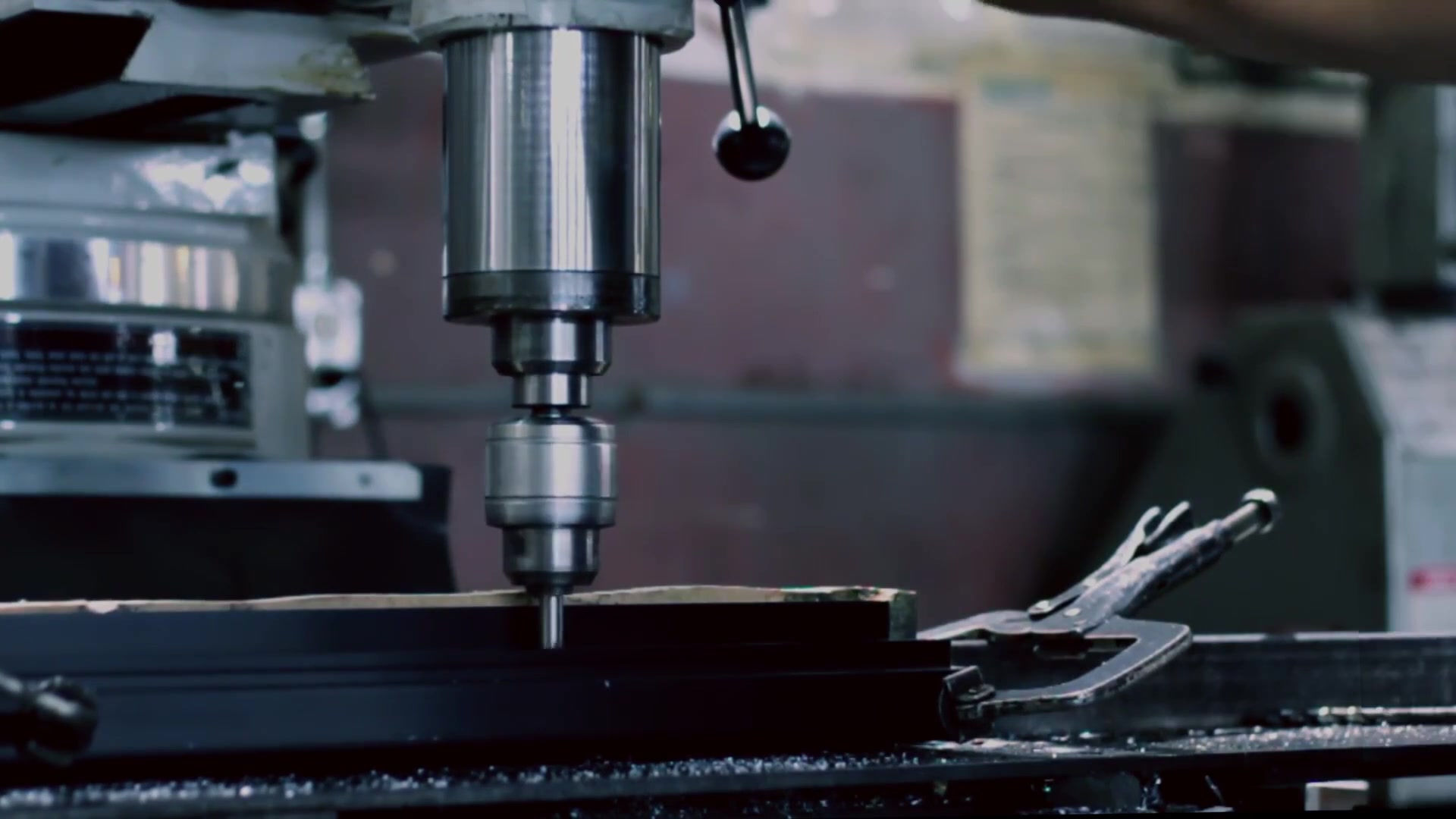
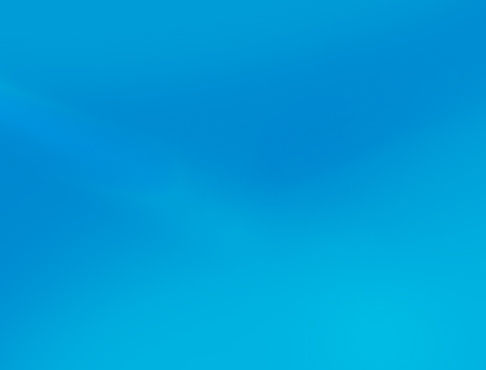
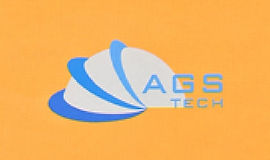
Глобальный производитель на заказ, интегратор, консолидатор, партнер по аутсорсингу широкого спектра продуктов и услуг.
Мы являемся вашим универсальным источником для производства, изготовления, проектирования, консолидации, интеграции, аутсорсинга изготовленных на заказ и готовых продуктов и услуг.
Choose your Language
-
Изготовление на заказ
-
Внутреннее и глобальное контрактное производство
-
Производственный аутсорсинг
-
Внутренние и глобальные закупки
-
Консолидация
-
Инженерная интеграция
-
Инженерные услуги
В последние годы мы наблюдаем рост спроса на БЫСТРОЕ ПРОИЗВОДСТВО или БЫСТРОЕ ПРОТОТИПИРОВАНИЕ. Этот процесс также может называться НАСТОЛЬНЫМ ПРОИЗВОДСТВОМ или ПРОИЗВОДСТВОМ СВОБОДНОЙ ФОРМЫ. В основном твердая физическая модель детали создается непосредственно из трехмерного чертежа САПР. Мы используем термин АДДИТИВНОЕ ПРОИЗВОДСТВО для этих различных методов, когда мы строим детали слоями. Используя интегрированное компьютерное оборудование и программное обеспечение, мы осуществляем аддитивное производство. Нашими методами быстрого прототипирования и производства являются СТЕРЕОЛИТОГРАФИЯ, ПОЛИФРАГМЕНТ, МОДЕЛИРОВАНИЕ НАПЛАВЛЕНИЕМ, СЕЛЕКТИВНОЕ ЛАЗЕРНОЕ СПЕКАНИЕ, ЭЛЕКТРОННО-ЛУЧЕВОЕ ПЛАВЛЕНИЕ, ТРЕХМЕРНАЯ ПЕЧАТЬ, ПРЯМОЕ ПРОИЗВОДСТВО, БЫСТРОЕ ОБОРУДОВАНИЕ. Мы рекомендуем вам нажать здесь, чтобыЗАГРУЗИТЕ наши схематические иллюстрации процессов аддитивного и быстрого производства от AGS-TECH Inc.
Это поможет вам лучше понять информацию, которую мы предоставляем вам ниже.
Быстрое прототипирование обеспечивает нам: 1.) Концептуальный дизайн продукта просматривается с разных сторон на мониторе с помощью системы 3D/CAD. 2.) Прототипы из неметаллических и металлических материалов изготавливаются и исследуются с функциональной, технической и эстетической точек зрения. 3.) Недорогое прототипирование в очень короткие сроки. Аддитивное производство можно сравнить с изготовлением буханки хлеба путем укладки и соединения отдельных ломтиков друг с другом. Другими словами, продукт изготавливается ломтик за ломтиком или слой за слоем накладывается друг на друга. Большинство деталей может быть изготовлено в течение нескольких часов. Этот метод хорош, если детали нужны очень быстро или если необходимое количество невелико, а изготовление формы и оснастки слишком дорого и занимает много времени. Однако стоимость детали высока из-за дорогого сырья.
• СТЕРЕОЛИТОГРАФИЯ: Этот метод, также сокращенно называемый STL, основан на отверждении и отверждении жидкого фотополимера до определенной формы путем фокусировки на нем лазерного луча. Лазер полимеризует фотополимер и отверждает его. Путем сканирования УФ-лазерным лучом по запрограммированной форме вдоль поверхности фотополимерной смеси деталь изготавливается снизу вверх в виде отдельных срезов, расположенных каскадом друг над другом. Сканирование лазерного пятна повторяется много раз для достижения геометрии, запрограммированной в системе. После того, как деталь полностью изготовлена, ее снимают с платформы, промокают и очищают ультразвуком и спиртовой ванной. Затем он подвергается воздействию УФ-излучения в течение нескольких часов, чтобы убедиться, что полимер полностью отвердел и затвердел. Подводя итог процессу, платформа, которая погружается в фотополимерную смесь, и УФ-лазерный луч контролируются и перемещаются через систему сервоуправления в соответствии с формой желаемой детали, и деталь получается путем фотоотверждения полимера слой за слоем. Разумеется, максимальные размеры изготавливаемой детали определяются стереолитографическим оборудованием.
• POLYJET: Подобно струйной печати, в Polyjet у нас есть восемь печатающих головок, которые наносят фотополимер на модельный лоток. Ультрафиолетовый свет, помещенный рядом с форсунками, мгновенно отверждает и укрепляет каждый слой. В Polyjet используются два материала. Первый материал предназначен для изготовления самой модели. Второй материал, гелеобразная смола, используется для поддержки. Оба эти материала наносятся послойно и одновременно отверждаются. После завершения модели вспомогательный материал удаляется водным раствором. Используемые смолы аналогичны стереолитографии (STL). Polyjet имеет следующие преимущества перед стереолитографией: 1) Нет необходимости в очистке деталей. 2.) Нет необходимости в отверждении после обработки. 3.) Возможна меньшая толщина слоя, и, таким образом, мы получаем лучшее разрешение и можем изготавливать более тонкие детали.
• МОДЕЛИРОВАНИЕ НАПЛАВЛЕНИЕМ: также сокращенно FDM, в этом методе головка экструдера, управляемая роботом, перемещается по столу в двух основных направлениях. Трос опускается и поднимается по мере необходимости. Из отверстия нагретой головки на головке выдавливается термопластичная нить и наносится начальный слой на пенопластовую основу. Это достигается за счет того, что головка экструдера движется по заданной траектории. После начального слоя стол опускают и последующие слои накладывают друг на друга. Иногда при изготовлении сложной детали необходимы опорные конструкции, чтобы наплавка могла продолжаться в определенных направлениях. В этих случаях материал-подложка экструдируется с менее плотным расположением нитей на слое, так что он слабее материала модели. Эти опорные конструкции могут быть впоследствии растворены или разорваны после завершения изготовления детали. Размеры головки экструдера определяют толщину экструдируемых слоев. Процесс FDM производит детали со ступенчатыми поверхностями на наклонных внешних плоскостях. Если эта шероховатость неприемлема, для ее сглаживания можно использовать химическую полировку в парах или нагретый инструмент. Даже полировальный воск доступен в качестве материала покрытия, чтобы исключить эти этапы и добиться разумных геометрических допусков.
• ВЫБОРОЧНОЕ ЛАЗЕРНОЕ СПЕКАНИЕ: Также обозначаемый как SLS, процесс основан на выборочном спекании полимерных, керамических или металлических порошков в объект. В нижней части рабочей камеры есть два цилиндра: цилиндр для частичной сборки и цилиндр для подачи порошка. Первый постепенно опускается туда, где формируется спеченная деталь, а второй постепенно поднимается для подачи порошка в формовочный цилиндр через роликовый механизм. Сначала тонкий слой порошка осаждается в формовочном цилиндре, затем лазерный луч фокусируется на этом слое, отслеживая и расплавляя/спекая определенное поперечное сечение, которое затем снова затвердевает в твердое тело. Порошок — это участки, на которые не попадает лазерный луч, остаются рыхлыми, но все еще поддерживают твердую часть. Затем наносится еще один слой порошка, и процесс многократно повторяется для получения детали. В конце рыхлые частицы порошка стряхивают. Все это выполняется компьютером управления технологическим процессом с использованием инструкций, сгенерированных программой 3D CAD изготавливаемой детали. Различные материалы, такие как полимеры (например, АБС, ПВХ, полиэстер), воск, металлы и керамика, могут быть нанесены на соответствующие полимерные связующие.
• ЭЛЕКТРОННЫЙ ЛУЧ MELTING: Аналогично избирательному лазерному спеканию, но с использованием электронного луча для плавления порошков титана или кобальта и хрома для изготовления прототипов в вакууме. Были сделаны некоторые разработки для выполнения этого процесса на нержавеющих сталях, алюминиевых и медных сплавах. Если необходимо повысить усталостную прочность изготовленных деталей, мы используем горячее изостатическое прессование после изготовления детали в качестве вторичного процесса.
• ТРЕХМЕРНАЯ ПЕЧАТЬ: Также обозначается как 3DP, в этом методе печатающая головка наносит неорганическое связующее на слой неметаллического или металлического порошка. Поршень, несущий слой порошка, постепенно опускается, и на каждом этапе связующее наносится слой за слоем и сплавляется со связующим. В качестве порошковых материалов используются смеси полимеров и волокна, формовочный песок, металлы. Используя одновременно разные связующие головки и связующие вещества разных цветов, мы можем получить различные цвета. Процесс аналогичен струйной печати, но вместо цветного листа мы получаем цветной трехмерный объект. Изготовленные детали могут быть пористыми и, следовательно, могут потребовать спекания и пропитки металлом для увеличения их плотности и прочности. Спекание выжигает связующее и сплавляет металлические порошки. Для изготовления деталей можно использовать такие металлы, как нержавеющая сталь, алюминий, титан, а в качестве материалов для инфильтрации мы обычно используем медь и бронзу. Прелесть этой техники в том, что даже сложные и подвижные узлы могут быть изготовлены очень быстро. Например, зубчатая передача в сборе, гаечный ключ в качестве инструмента могут быть изготовлены с движущимися и вращающимися частями, готовыми к использованию. Различные компоненты сборки могут быть изготовлены в разных цветах и в одном кадре. Загрузите нашу брошюру:Основы 3D-печати металлом
• ПРЯМОЕ ПРОИЗВОДСТВО и БЫСТРАЯ ИНСТРУМЕНТАЦИЯ: Помимо оценки конструкции и устранения неполадок, мы используем быстрое прототипирование для непосредственного производства продуктов или непосредственного применения в продуктах. Другими словами, быстрое прототипирование можно включить в обычные процессы, чтобы сделать их лучше и конкурентоспособнее. Например, быстрое прототипирование позволяет создавать шаблоны и формы. Образцы плавящегося и горящего полимера, созданные с помощью операций быстрого прототипирования, могут быть собраны для литья по выплавляемым моделям и вложены. Другим примером, который следует упомянуть, является использование 3DP для производства керамических литейных оболочек и его использования для операций литья оболочек. Даже пресс-формы для литья под давлением и вкладыши для пресс-форм могут быть изготовлены путем быстрого прототипирования, что позволяет сэкономить многие недели или месяцы времени на изготовление пресс-форм. Только анализируя файл САПР нужной детали, мы можем создать геометрию инструмента с помощью программного обеспечения. Вот некоторые из наших популярных методов быстрой обработки:
RTV (вулканизация при комнатной температуре) ФОРМОВАНИЕ / ЛИТЬЕ УРЕТАНА: Для изготовления модели желаемой детали можно использовать быстрое прототипирование. Затем этот образец покрывают разделительным составом и заливают жидким каучуком RTV для изготовления половинок пресс-формы. Затем эти половинки формы используются для литья под давлением жидких уретанов. Срок службы пресс-формы короткий, всего около 0 или 30 циклов, но этого достаточно для мелкосерийного производства.
ACES (Acetal Clear Epoxy Solid) ЛИТЬЕ ДЛЯ ИНСТРУМЕНТА: Используя методы быстрого прототипирования, такие как стереолитография, мы производим пресс-формы для литья под давлением. Эти формы представляют собой оболочки с открытым концом для заполнения такими материалами, как эпоксидная смола, эпоксидная смола с алюминиевым наполнителем или металлы. Опять же, срок службы пресс-формы ограничен десятками или максимум сотнями деталей.
ПРОЦЕСС ИЗГОТОВЛЕНИЯ ИНСТРУМЕНТА НАПЫЛЕННЫМ МЕТАЛЛОМ: Мы используем быстрое прототипирование и делаем шаблон. Мы распыляем сплав цинка с алюминием на поверхность рисунка и покрываем его. Затем шаблон с металлическим покрытием помещают внутрь колбы и заливают эпоксидной смолой или эпоксидной смолой с алюминиевым наполнителем. Наконец, он удаляется, и, изготовив две такие половинки формы, мы получаем готовую форму для литья под давлением. Эти пресс-формы имеют более длительный срок службы, в некоторых случаях, в зависимости от материала и температуры, они могут производить тысячи деталей.
ПРОЦЕСС KEELTOOL: Этот метод позволяет производить пресс-формы со сроком службы от 100 000 до 10 миллионов циклов. Используя быстрое прототипирование, мы изготавливаем пресс-форму RTV. Затем форму заполняют смесью, состоящей из порошка инструментальной стали А6, карбида вольфрама, полимерного связующего, и оставляют для отверждения. Затем эту форму нагревают, чтобы полимер выгорел, а металлические порошки расплавились. Следующим шагом является пропитка медью для изготовления окончательной формы. При необходимости на пресс-форме могут быть выполнены вторичные операции, такие как механическая обработка и полировка, для повышения точности размеров.