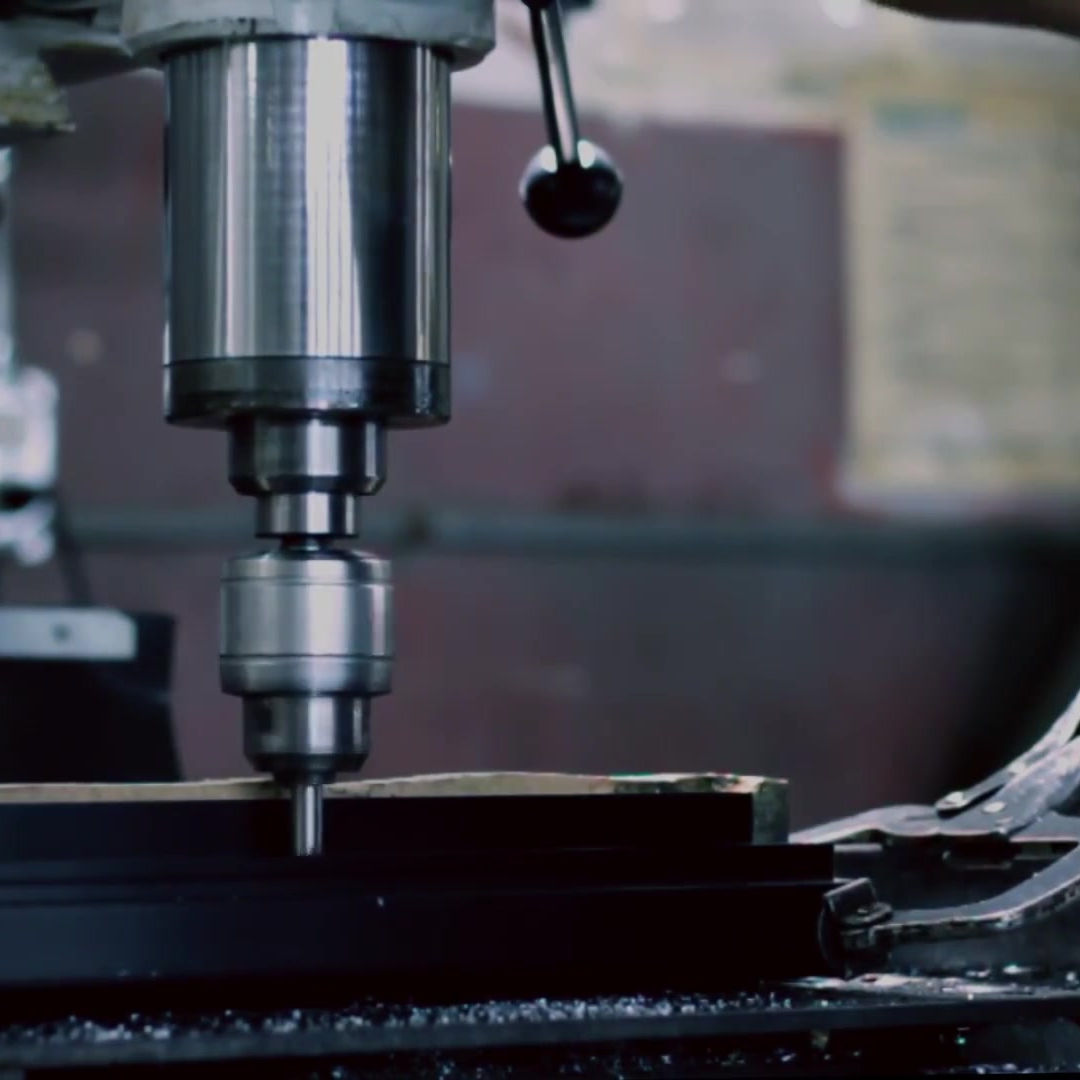
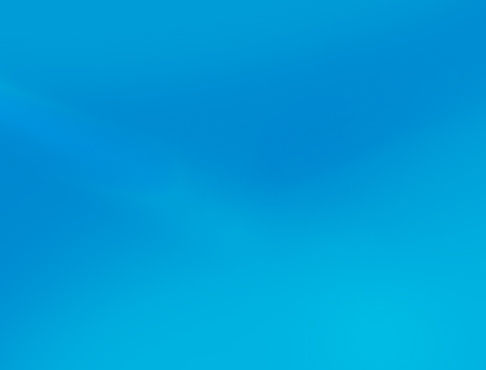
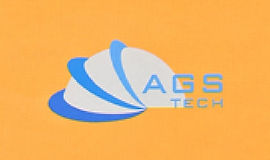
Глобальный производитель на заказ, интегратор, консолидатор, партнер по аутсорсингу широкого спектра продуктов и услуг.
Мы являемся вашим универсальным источником для производства, изготовления, проектирования, консолидации, интеграции, аутсорсинга изготовленных на заказ и готовых продуктов и услуг.
Choose your Language
-
Изготовление на заказ
-
Внутреннее и глобальное контрактное производство
-
Производственный аутсорсинг
-
Внутренние и глобальные закупки
-
Консолидация
-
Инженерная интеграция
-
Инженерные услуги
ELECTRICAL DISCHARGE MACHINING (EDM), also referred to as SPARK-EROSION or ELECTRODISCHARGE MACHINING, SPARK ERODING, DIE SINKING_cc781905-5cde-3194-bb3b -136bad5cf58d_or WIRE EROSION, is a NON-CONVENTIONAL MANUFACTURING process where erosion of metals takes place and desired shape is obtained using electrical discharges in the form искр. Мы также предлагаем некоторые разновидности электроэрозионной обработки, а именно БЕЗИЗНОСНАЯ ЭЭО, ПРОВОЛОЧНО-ЭЭО (ЭЭО), ЭЭО-ШЛИФОВАЛЬНАЯ (ЭЭО), ЭЭО-ПРОМЫВНАЯ, ЭЛЕКТРОРАЗРЯДНАЯ ФРЕЗЕРОВКА, микро-ЭЭО, М-ЭЭО_cc781905 -5cde-3194-bb3b-136bad5cf58d_and ЭЛЕКТРОХИМИЧЕСКО-РАЗРЯДНОЕ ШЛИФОВАНИЕ (ECDG). Наши системы электроэрозионной обработки состоят из фасонных инструментов/электрода и заготовки, подключенных к источникам питания постоянного тока и помещенных в электрически непроводящую диэлектрическую жидкость. После 1940 года электроэрозионная обработка стала одной из самых важных и популярных производственных технологий в обрабатывающей промышленности.
Когда расстояние между двумя электродами уменьшается, напряженность электрического поля в объеме между электродами становится больше, чем прочность диэлектрика в некоторых точках, который разрывается, в конечном итоге образуя мост для протекания тока между двумя электродами. Возникает интенсивная электрическая дуга, вызывающая значительный нагрев, расплавляющий часть заготовки и часть материала инструмента. В результате материал удаляется с обоих электродов. В то же время диэлектрическая жидкость быстро нагревается, что приводит к испарению жидкости в дуговом промежутке. Как только ток прекращается или он останавливается, тепло от газового пузыря отводится окружающей диэлектрической жидкостью, и пузырек кавитирует (схлопывается). Ударная волна, создаваемая схлопыванием пузырька, и поток диэлектрической жидкости смывают мусор с поверхности заготовки и уносят любой расплавленный материал заготовки в диэлектрическую жидкость. Частота повторения этих разрядов составляет от 50 до 500 кГц, напряжения от 50 до 380 В и токи от 0,1 до 500 ампер. Новый жидкий диэлектрик, такой как минеральные масла, керосин или дистиллированная и деионизированная вода, обычно подается в межэлектродный объем, унося с собой твердые частицы (в виде мусора), и изолирующие свойства диэлектрика восстанавливаются. После протекания тока разность потенциалов между двумя электродами восстанавливается до того, что было до пробоя, поэтому может произойти новый пробой жидкого диэлектрика. Наши современные электроэрозионные машины (EDM) предлагают движения с числовым программным управлением и оснащены насосами и системами фильтрации для диэлектрических жидкостей.
Электроэрозионная обработка (EDM) — это метод обработки, используемый в основном для твердых металлов или тех, которые было бы очень трудно обрабатывать обычными методами. Электроэрозионная обработка обычно работает с любыми материалами, которые являются электрическими проводниками, хотя также были предложены методы обработки изоляционной керамики с помощью электроэрозионной обработки. Температура плавления и скрытая теплота плавления являются свойствами, определяющими объем удаляемого металла за один разряд. Чем выше эти значения, тем медленнее скорость съема материала. Поскольку в процессе электроэрозионной обработки не используется механическая энергия, твердость, прочность и ударная вязкость заготовки не влияют на скорость съема. Частота разряда или энергия на разряд, напряжение и ток изменяются для контроля скорости съема материала. Скорость съема материала и шероховатость поверхности увеличиваются с увеличением плотности тока и уменьшением частоты искры. Мы можем вырезать сложные контуры или полости в предварительно закаленной стали с помощью электроэрозионной обработки без необходимости термической обработки для их размягчения и повторного упрочнения. Мы можем использовать этот метод с любым металлом или металлическими сплавами, такими как титан, хастеллой, ковар и инконель. Применение процесса электроэрозионной обработки включает формирование поликристаллических алмазных инструментов. Электроэрозионная обработка считается нетрадиционным или нетрадиционным методом обработки наряду с такими процессами, как электрохимическая обработка (ЭХО), гидроабразивная резка (WJ, AWJ), лазерная резка. С другой стороны, обычные методы механической обработки включают точение, фрезерование, шлифование, сверление и другие процессы, механизм удаления материала которых по существу основан на механических силах. Электроды для электроэрозионной обработки (ЭЭО) изготавливают из графита, латуни, меди и медно-вольфрамового сплава. Возможны диаметры электродов до 0,1 мм. Поскольку износ инструмента является нежелательным явлением, отрицательно влияющим на точность размеров при электроэрозионной обработке, мы используем процесс, называемый NO-WEAR EDM, путем изменения полярности и использования медных инструментов для минимизации износа инструмента.
В идеале электроэрозионную обработку (ЭЭО) можно рассматривать как серию пробоев и восстановления диэлектрической жидкости между электродами. Однако в действительности удаление мусора из межэлектродной области почти всегда частичное. Это приводит к тому, что электрические свойства диэлектрика в межэлектродной области отличаются от номинальных значений и изменяются во времени. Межэлектродное расстояние (искровой разрядник) регулируется алгоритмами управления конкретной используемой машиной. К сожалению, искровой разрядник в EDM иногда может быть закорочен осколками. Система управления электродом может не среагировать достаточно быстро, чтобы предотвратить короткое замыкание двух электродов (инструмента и заготовки). Это нежелательное короткое замыкание способствует удалению материала иначе, чем в идеальном случае. Мы придаем первостепенное значение промывочному действию для восстановления изолирующих свойств диэлектрика, чтобы ток всегда протекал в точке межэлектродной зоны, тем самым сводя к минимуму возможность нежелательного изменения формы (повреждения) инструмента-электрода. и заготовка. Для получения определенной геометрии электроэрозионный инструмент направляется по желаемой траектории очень близко к заготовке, не касаясь ее. Мы уделяем особое внимание эффективности управления движением при использовании. Таким образом, происходит большое количество токовых разрядов/искр, и каждый из них способствует удалению материала как с инструмента, так и с заготовки, где образуются небольшие кратеры. Размер кратеров зависит от технологических параметров, установленных для конкретной выполняемой работы, и размеры могут варьироваться от наномасштаба (например, в случае операций микроэрозионной обработки) до нескольких сотен микрометров в черновых условиях. Эти маленькие кратеры на инструменте вызывают постепенную эрозию электрода, называемую «износом инструмента». Чтобы противодействовать пагубному влиянию износа на геометрию заготовки, мы постоянно заменяем электрод-инструмент во время операции обработки. Иногда мы достигаем этого, используя постоянно заменяемую проволоку в качестве электрода (этот процесс EDM также называется WIRE EDM ). Иногда мы используем инструмент-электрод таким образом, что в процессе обработки фактически задействована лишь небольшая его часть, и эта часть регулярно меняется. Так обстоит дело, например, при использовании вращающегося диска в качестве электрода-инструмента. Этот процесс называется EDM GRINDING. Еще одна технология, которую мы используем, состоит в использовании набора электродов разных размеров и форм во время одной и той же операции электроэрозионной обработки для компенсации износа. Мы называем это методом нескольких электродов, и он чаще всего используется, когда электрод-инструмент повторяет в отрицательном направлении желаемую форму и продвигается к заготовке в одном направлении, обычно в вертикальном направлении (т.е. по оси z). Это напоминает погружение инструмента в диэлектрическую жидкость, в которую погружена заготовка, и поэтому обозначается как DIE-SINKING EDM (иногда называется_cc781905-5cde- 3194-bb3b-136bad5cf58d_CONVENTIONAL EDM or RAM EDM). Машины для этой операции называются SINKER EDM. Электроды для этого вида электроэрозионной обработки имеют сложную форму. Если окончательная геометрия получается с помощью электрода обычно простой формы, перемещаемого по нескольким направлениям и также подверженного вращениям, мы называем это EDM ФРЕЗЕРОВАНИЕМ. Величина износа находится в строгой зависимости от используемых при эксплуатации технологических параметров (полярность, максимальный ток, напряжение холостого хода). Например, в micro-EDM, также известном как m-EDM, эти параметры обычно устанавливаются на значения, вызывающие сильный износ. Поэтому износ является серьезной проблемой в той области, которую мы сводим к минимуму, используя накопленные ноу-хау. Например, чтобы свести к минимуму износ графитовых электродов, цифровой генератор, управляемый в течение миллисекунд, меняет полярность, когда происходит электроэрозия. Это приводит к эффекту, аналогичному гальванике, когда эродированный графит непрерывно осаждается обратно на электрод. В другом методе, так называемой схеме «Нулевого износа», мы минимизируем частоту запуска и прекращения разряда, поддерживая его как можно дольше. Скорость съема материала при электроэрозионной обработке можно оценить по формуле:
MRR = 4 x 10 exp(4) x I x Tw exp (-1,23)
Здесь MRR – в мм3/мин, I – сила тока в Амперах, Tw – температура плавления заготовки в К-273,15К. exp означает экспоненту.
С другой стороны, скорость износа Wt электрода может быть получена из:
Wt = (1,1 x 10exp(11)) x I x Ttexp(-2,38)
Здесь Wt в мм3/мин, а Tt – температура плавления электродного материала в K-273,15K.
Наконец, отношение износа заготовки к электроду R может быть получено из:
R = 2,25 x Treexp (-2,38)
Здесь Tr – отношение температур плавления заготовки к электроду.
ГРУЗИЛО EDM :
Электроэрозионный электроэрозионный станок, также называемый CAVITY TYPE EDM or VOLUME EDM, состоит из погруженной в жидкость электроэрозионной заготовки и электроэрозионной сварки. Электрод и заготовка подключаются к источнику питания. Источник питания генерирует электрический потенциал между ними. По мере приближения электрода к заготовке в жидкости происходит пробой диэлектрика, образующий плазменный канал, и проскакивает небольшая искра. Искры обычно бьют по одной, потому что очень маловероятно, чтобы разные места в межэлектродном пространстве имели одинаковые локальные электрические характеристики, которые позволили бы искре возникнуть во всех таких местах одновременно. Сотни тысяч таких искр возникают в случайных точках между электродом и заготовкой в секунду. По мере эрозии основного металла и последующего увеличения искрового промежутка электрод автоматически опускается нашим станком с ЧПУ, так что процесс может продолжаться непрерывно. Наше оборудование имеет контрольные циклы, известные как «время включения» и «время отключения». Настройка времени включения определяет длину или продолжительность искры. Более длительное время создает более глубокую полость для этой искры и всех последующих искр для этого цикла, создавая более грубую поверхность на заготовке, и наоборот. Время выключения – это период времени, когда одна искра сменяется другой. Более длительное время отключения позволяет диэлектрической жидкости промываться через сопло, чтобы очистить эродированный мусор, тем самым избегая короткого замыкания. Эти настройки регулируются за микросекунды.
ПРОВОД EDM :
In WIRE ELECTRICAL DISCHARGE MACHINING (WEDM), also called WIRE-CUT EDM or WIRE CUTTING, we feed a тонкую однопроволочную металлическую проволоку из латуни пропускают через заготовку, которая погружена в емкость с диэлектрической жидкостью. Проволочный электроэрозионный станок является важной разновидностью электроэрозионного станка. Иногда мы используем проволочную электроэрозионную резку для резки пластин толщиной до 300 мм и изготовления пуансонов, инструментов и штампов из твердых металлов, которые трудно обрабатывать другими методами производства. В этом процессе, напоминающем контурную резку ленточной пилой, проволока, постоянно сматываемая с катушки, удерживается между верхней и нижней алмазными направляющими. Направляющие с ЧПУ перемещаются в плоскости x–y, а верхняя направляющая также может независимо перемещаться по оси z–u–v, что дает возможность вырезать конические и переходные формы (например, круг внизу и квадрат внизу). вершина). Верхняя направляющая может управлять перемещениями осей в x–y–u–v–i–j–k–l–. Это позволяет станку WEDM вырезать очень сложные и тонкие формы. Средний пропил на нашем оборудовании, обеспечивающий наилучшие экономические затраты и время обработки, составляет 0,335 мм при использовании латунной, медной или вольфрамовой проволоки диаметром 0,25. Однако верхняя и нижняя алмазные направляющие нашего оборудования с ЧПУ имеют точность около 0,004 мм и могут иметь траекторию реза или пропил всего 0,021 мм при использовании проволоки диаметром 0,02 мм. Так что возможны действительно узкие разрезы. Ширина реза больше, чем ширина проволоки, потому что от боковых сторон проволоки к заготовке возникает искрообразование, вызывающее эрозию. Этот «перерез» необходим, для многих применений он предсказуем и поэтому может быть компенсирован (в микро-ЭДМ это бывает нечасто). Катушки проволоки длинные — 8-килограммовая катушка с проволокой 0,25 мм имеет длину чуть более 19 километров. Диаметр проволоки может составлять всего 20 микрометров, а точность геометрии составляет около +/- 1 микрометра. Обычно мы используем проволоку только один раз и перерабатываем ее, потому что она относительно недорогая. Он перемещается с постоянной скоростью от 0,15 до 9 м/мин, и во время резки сохраняется постоянный пропил (паз). В процессе электроэрозионной резки мы используем воду в качестве диэлектрической жидкости, контролируя ее удельное сопротивление и другие электрические свойства с помощью фильтров и деионизаторов. Вода вымывает срезанный мусор из зоны резания. Промывка является важным фактором при определении максимальной скорости подачи для данной толщины материала, поэтому мы поддерживаем ее неизменной. Скорость резания в проволочной электроэрозионной обработке выражается в виде площади поперечного сечения, разрезаемой в единицу времени, например, 18 000 мм2/час для инструментальной стали D2 толщиной 50 мм. Линейная скорость резки для этого случая будет 18 000/50 = 360 мм/ч. Скорость съема материала при проволочной электроэрозионной обработке составляет:
МРР = Vf xhxb
Здесь MRR выражается в мм3/мин, Vf — скорость подачи проволоки в заготовку в мм/мин, h — толщина или высота в мм, а b — ширина пропила, которая равна:
б = дв + 2с
Здесь dw — диаметр проволоки, s — зазор между проволокой и заготовкой в мм.
Наряду с более жесткими допусками, наши современные многоосевые электроэрозионные обрабатывающие центры для резки проволоки имеют дополнительные функции, такие как несколько головок для одновременной резки двух деталей, элементы управления для предотвращения обрыва проволоки, функции автоматической самозаправки в случае обрыва проволоки и запрограммированные стратегии обработки для оптимизации работы, возможности прямой и угловой резки.
Wire-EDM предлагает нам низкие остаточные напряжения, потому что не требует больших усилий резания для удаления материала. Когда энергия/мощность на импульс относительно невелика (как при чистовых операциях), ожидается незначительное изменение механических свойств материала из-за низких остаточных напряжений.
ЭЛЕКТРОГРАФНЫЙ ШЛИФОВАЛЬНЫЙ (ЭДГ) : Шлифовальные круги не содержат абразивов, они изготовлены из графита или латуни. Повторяющиеся искры между вращающимся колесом и заготовкой удаляют материал с поверхности заготовки. Скорость съема материала составляет:
МРР = К х I
Здесь MRR выражается в мм3/мин, I — сила тока в амперах, а K — коэффициент материала заготовки в мм3/А-мин. Мы часто используем электроэрозионную шлифовку, чтобы сделать узкие прорези на компонентах. Иногда мы комбинируем процесс EDG (электроразрядное шлифование) с процессом ECG (электрохимическое шлифование), при котором материал удаляется химическим воздействием, электрические разряды от графитового круга разрушают оксидную пленку и вымываются электролитом. Процесс называется ЭЛЕКТРОХИМИЧЕСКО-РАЗРЯДНОЕ ШЛИФОВАНИЕ (ECDG). Несмотря на то, что процесс ECDG потребляет относительно больше энергии, это более быстрый процесс, чем EDG. Мы в основном точим твердосплавные инструменты, используя эту технику.
Применение электроэрозионной обработки:
Изготовление прототипа:
Мы используем процесс электроэрозионной обработки в производстве пресс-форм, инструментов и штампов, а также для изготовления прототипов и серийных деталей, особенно для аэрокосмической, автомобильной и электронной промышленности, где объемы производства относительно невелики. В Sinker EDM графитовому, медно-вольфрамовому или чисто медному электроду придают желаемую (негативную) форму и подают в заготовку на конце вертикального ползуна.
Изготовление штампа для монет:
Для изготовления штампов для изготовления украшений и значков методом чеканки (штамповки) позитивный мастер может быть изготовлен из стерлингового серебра, так как (при соответствующих настройках станка) мастер значительно выветривается и используется только один раз. Полученный негативный штамп затем закаливается и используется в ударном молоте для изготовления штампованных плоских деталей из вырезанных листовых заготовок из бронзы, серебра или низкопробного золотого сплава. Для значков этим плоскостям может быть дополнительно придана криволинейная поверхность с помощью другой матрицы. Этот тип электроэрозионной обработки обычно выполняется погруженным в диэлектрик на масляной основе. Готовый объект может быть дополнительно обработан твердой (стекло) или мягкой (краска) эмалью и/или гальваническим покрытием чистым золотом или никелем. Более мягкие материалы, такие как серебро, могут быть украшены ручной гравировкой.
Сверление небольших отверстий:
На наших электроэрозионных станках с проволочной резкой мы используем электроэрозионное сверление небольших отверстий, чтобы сделать сквозное отверстие в заготовке, через которое продевается проволока для операции электроэрозионной резки с проволокой. Отдельные электроэрозионные головки, специально предназначенные для сверления небольших отверстий, устанавливаются на наши проволочные станки, которые позволяют вырезать из больших закаленных пластин готовые детали по мере необходимости и без предварительного сверления. Мы также используем электроэрозионный станок с малыми отверстиями для сверления рядов отверстий в кромках лопаток турбин, используемых в реактивных двигателях. Поток газа через эти маленькие отверстия позволяет двигателям использовать более высокие температуры, чем это возможно в противном случае. Жаропрочные, очень твердые монокристаллические сплавы, из которых изготовлены эти лезвия, делают обычную обработку этих отверстий с высоким коэффициентом удлинения чрезвычайно сложной и даже невозможной. Другой областью применения электроэрозионной обработки с малыми отверстиями является создание микроскопических отверстий для компонентов топливной системы. Помимо встроенных электроэрозионных головок, мы используем автономные электроэрозионные станки для сверления небольших отверстий с осями x–y для обработки глухих или сквозных отверстий. Электроэрозионные сверла просверливают отверстия с помощью длинного латунного или медного трубчатого электрода, который вращается в патроне с постоянным потоком дистиллированной или деионизированной воды, протекающей через электрод в качестве промывочного агента и диэлектрика. Некоторые электроэрозионные станки для сверления небольших отверстий способны просверливать 100 мм мягкой или даже закаленной стали менее чем за 10 секунд. С помощью этой операции сверления можно получить отверстия диаметром от 0,3 мм до 6,1 мм.
Металлоразрушающая обработка:
У нас также есть специальные электроэрозионные станки для удаления сломанных инструментов (сверл или метчиков) с заготовок. Этот процесс называется «обработка дезинтеграцией металла».
Преимущества и недостатки электроэрозионной обработки:
К преимуществам электроэрозионной обработки относятся:
- Сложные формы, которые в противном случае было бы трудно изготовить с помощью обычных режущих инструментов
- Чрезвычайно твердый материал с очень жесткими допусками
- Очень маленькие детали, где обычные режущие инструменты могут повредить деталь из-за избыточного давления режущего инструмента.
- Нет прямого контакта между инструментом и заготовкой. Поэтому тонкие секции и слабые материалы могут быть обработаны без каких-либо искажений.
- Может быть получена хорошая отделка поверхности.
- Можно легко просверлить очень тонкие отверстия.
К недостаткам ЭДМ относятся:
- Низкая скорость съема материала.
- Дополнительные затраты времени и средств на создание электродов для электроэрозионной обработки плашкой/грузином.
- Воспроизведение острых углов на заготовке затруднено из-за износа электрода.
- Высокое энергопотребление.
- Образуется «перерез».
- Во время обработки происходит чрезмерный износ инструмента.
- Электрически непроводящие материалы можно обрабатывать только при определенной настройке процесса.