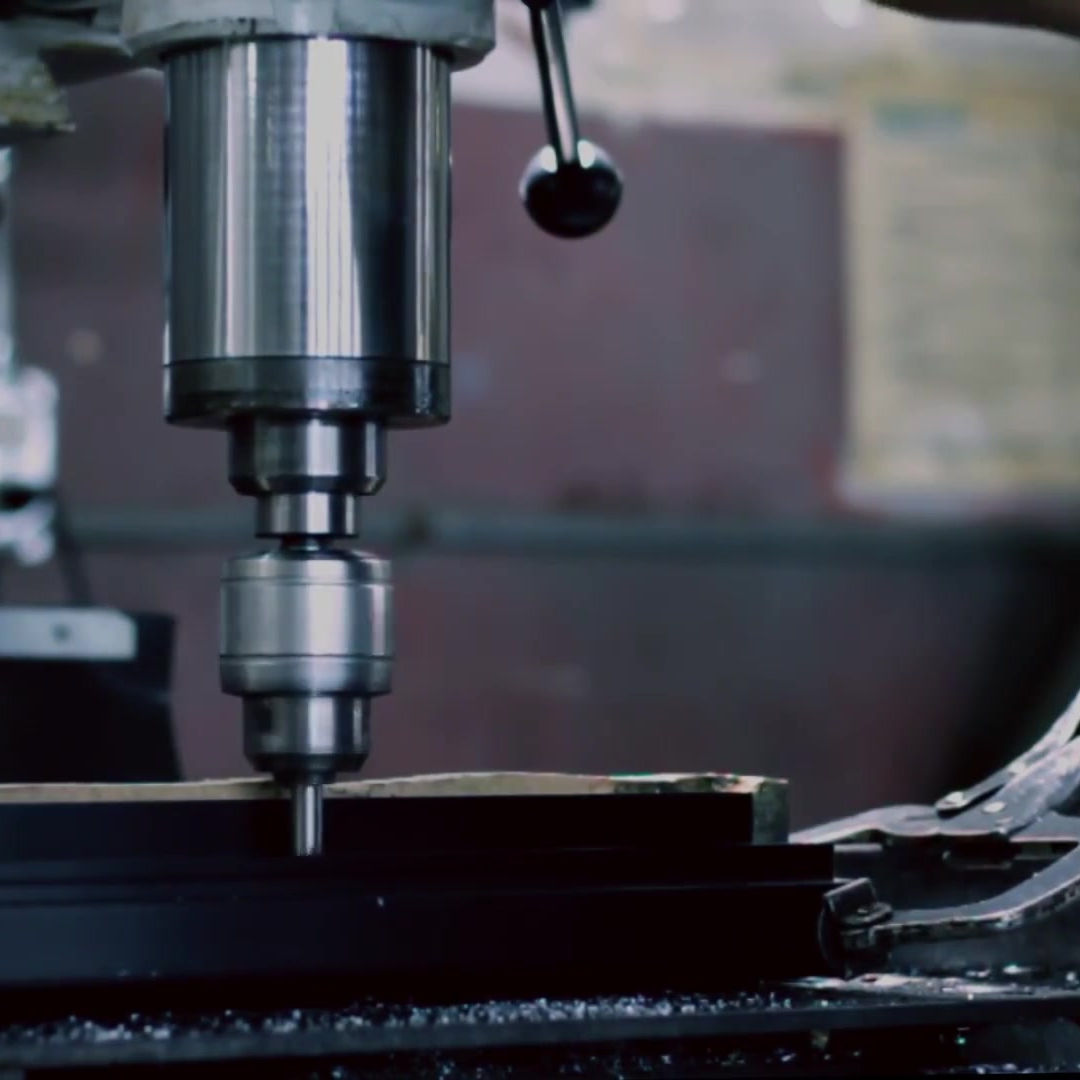
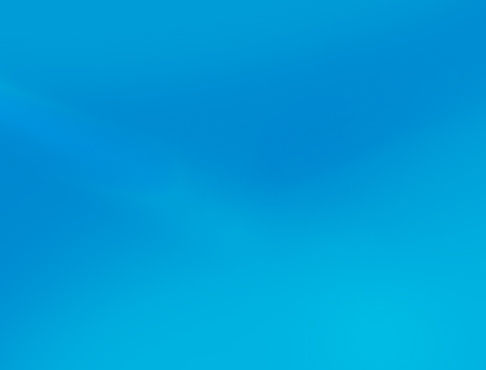
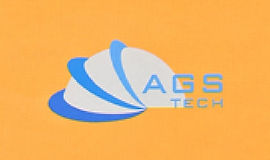
Глобальный производитель на заказ, интегратор, консолидатор, партнер по аутсорсингу широкого спектра продуктов и услуг.
Мы являемся вашим универсальным источником для производства, изготовления, проектирования, консолидации, интеграции, аутсорсинга изготовленных на заказ и готовых продуктов и услуг.
Choose your Language
-
Изготовление на заказ
-
Внутреннее и глобальное контрактное производство
-
Производственный аутсорсинг
-
Внутренние и глобальные закупки
-
Консолидация
-
Инженерная интеграция
-
Инженерные услуги
Типы производства стекла, которые мы предлагаем, включают тарное стекло, выдувание стекла, стекловолокно, трубы и стержни, бытовую и промышленную посуду, лампы и колбы, прецизионное литье стекла, оптические компоненты и сборки, плоское и листовое и флоат-стекло. Мы выполняем как ручную, так и машинную формовку.
Нашими популярными процессами производства технической керамики являются штамповка, изостатическое прессование, горячее изостатическое прессование, горячее прессование, шликерное литье, ленточное литье, экструзия, литье под давлением, необработанная обработка, спекание или обжиг, алмазное шлифование, герметичные сборки.
Мы рекомендуем вам нажать здесь, чтобы
СКАЧАТЬ наши схематические иллюстрации процессов формовки и обработки стекла от AGS-TECH Inc.
СКАЧАТЬ наши схематические иллюстрации процессов производства технической керамики от AGS-TECH Inc.
Эти загружаемые файлы с фотографиями и эскизами помогут вам лучше понять информацию, которую мы предоставляем вам ниже.
• ПРОИЗВОДСТВО СТЕКЛЯННОЙ ТАРЫ: У нас есть автоматизированные линии ПРЕСС-ВДУВ, а также линии ВДУВ-ВЫДУВ для производства. В процессе выдува и выдувания мы бросаем каплю в заготовку и формируем горловину, применяя удар сжатым воздухом сверху. Сразу после этого сжатый воздух продувают второй раз в другом направлении через горлышко контейнера, чтобы сформировать заготовку бутылки. Эта заготовка затем переносится в фактическую форму, повторно нагревается для смягчения и подается сжатый воздух, чтобы придать заготовке окончательную форму контейнера. Точнее говоря, он находится под давлением и прижимается к стенкам полости выдувной формы, чтобы принять желаемую форму. Наконец, изготовленная стеклянная тара переносится в печь отжига для последующего повторного нагрева и снятия напряжений, возникающих при формовании, и охлаждается контролируемым образом. В методе прессования и выдувания расплавленные капли помещаются в форму для изготовления заготовок (заготовка) и прессуются в форму для заготовок (заготовка). Затем заготовки переносятся в формы для выдувания и выдуваются аналогично процессу, описанному выше в разделе «Процесс выдувания и выдувания». Последующие шаги, такие как отжиг и снятие напряжения, аналогичны или одинаковы.
• ВЫДУВАНИЕ СТЕКЛА: Мы производим изделия из стекла, используя как обычное ручное выдувание, так и использование сжатого воздуха на автоматизированном оборудовании. Для некоторых заказов требуется обычное выдувание, например, проекты, связанные со стеклянными изделиями, или проекты, требующие меньшего количества деталей с небольшими допусками, прототипы / демонстрационные проекты и т. д. Обычное выдувание стекла включает погружение полой металлической трубы в кастрюлю с расплавленным стеклом и вращение трубы для сбора некоторого количества стеклянного материала. Стекло, собранное на конце трубы, прокатывается на плоском железе, придается желаемая форма, удлиняется, повторно нагревается и продувается воздухом. Когда он готов, он вставляется в форму и продувается воздухом. Полость формы мокрая, чтобы избежать контакта стекла с металлом. Водяная пленка действует как подушка между ними. Ручное выдувание — это трудоемкий медленный процесс, который подходит только для прототипирования или изделий высокой стоимости, не подходит для недорогих заказов в больших объемах.
• ПРОИЗВОДСТВО БЫТОВОЙ И ПРОМЫШЛЕННОЙ СТЕКЛЯННОЙ ПОСУДА: Используя различные типы стеклянных материалов, производится большое разнообразие стеклянной посуды. Некоторые стекла термостойкие и подходят для лабораторной посуды, а некоторые достаточно хороши для того, чтобы выдерживать многократное мытье в посудомоечной машине и пригодны для изготовления бытовых изделий. На машинах Westlake производятся десятки тысяч стаканов в день. Для упрощения расплавленное стекло собирается вакуумом и помещается в формы для изготовления заготовок. Затем в формы вдувается воздух, они переносятся в другую форму, снова вдувается воздух, и стекло принимает окончательную форму. Как и при ручном выдувании, эти формы увлажняются водой. Дальнейшее растяжение является частью завершающей операции по формированию грифа. Лишнее стекло сгорает. После этого следует контролируемый процесс повторного нагрева и охлаждения, описанный выше.
• ФОРМОВАНИЕ СТЕКЛЯННЫХ ТРУБ И СТЕРЖНЕЙ: Основными процессами, которые мы используем для производства стеклянных труб, являются процессы DANNER и VELLO. В процессе Даннера стекло из печи течет и падает на наклонную втулку из огнеупорных материалов. Гильза закреплена на вращающемся полом валу или паяльной трубке. Затем стекло оборачивается вокруг рукава и образует гладкий слой, стекающий по рукаву и на кончик стержня. При формовании труб воздух продувается через нагнетательную трубку с полым наконечником, а при формовании стержней используются сплошные наконечники на валу. Затем трубы или стержни протягиваются по несущим роликам. Размеры, такие как толщина стенок и диаметр стеклянных трубок, регулируются до желаемых значений путем установки диаметра рукава и давления продувочного воздуха до желаемого значения, регулировки температуры, скорости потока стекла и скорости вытягивания. С другой стороны, процесс производства стеклянных трубок Vello включает в себя перемещение стекла из печи в чашу с помощью полой оправки или колокола. Затем стекло проходит через воздушное пространство между оправкой и чашей и принимает форму трубки. После этого он перемещается по роликам на волочильную машину и охлаждается. В конце линии охлаждения происходит резка и окончательная обработка. Размеры трубы можно регулировать так же, как и в процессе Даннера. Сравнивая процесс Даннера с процессом Велло, мы можем сказать, что процесс Велло лучше подходит для крупносерийного производства, тогда как процесс Даннера может лучше подходить для точных заказов труб меньшего объема.
• ПЕРЕРАБОТКА ЛИСТОВОГО, ПЛОСКОГО И ФЛОАТ-СТЕКЛА: У нас есть большое количество листового стекла толщиной от субмиллиметров до нескольких сантиметров. Наши плоские очки почти оптически совершенны. Мы предлагаем стекло со специальными покрытиями, такими как оптические покрытия, где метод химического осаждения из паровой фазы используется для нанесения покрытий, таких как просветляющее или зеркальное покрытие. Также распространены прозрачные проводящие покрытия. Также доступны гидрофобные или гидрофильные покрытия на стекле, а также покрытия, обеспечивающие самоочищение стекла. Закаленное, пуленепробиваемое и ламинированное стекло — еще одна популярная вещь. Мы режем стекло нужной формы с заданными допусками. Доступны и другие вторичные операции, такие как изгибание или гибка плоского стекла.
• ПРЕЦИЗИОННОЕ ФОРМОВАНИЕ СТЕКЛА: мы используем эту технику в основном для изготовления прецизионных оптических компонентов без необходимости использования более дорогих и трудоемких методов, таких как шлифовка, притирка и полировка. Этот метод не всегда достаточен для изготовления лучшей из лучших оптических систем, но в некоторых случаях, таких как потребительские товары, цифровые камеры, медицинская оптика, он может быть менее дорогим хорошим вариантом для крупносерийного производства. Кроме того, он имеет преимущество перед другими методами формования стекла, когда требуется сложная геометрия, например, в случае асфер. Основной процесс включает в себя загрузку нижней стороны нашей формы стеклянной заготовкой, вакуумирование технологической камеры для удаления кислорода, близкое закрытие формы, быстрый и изотермический нагрев матрицы и стекла инфракрасным светом, дальнейшее закрытие половинок формы. медленное контролируемое прессование размягченного стекла до желаемой толщины и, наконец, охлаждение стекла, заполнение камеры азотом и удаление продукта. Точный контроль температуры, расстояние закрытия формы, усилие закрытия формы, соответствие коэффициентов расширения формы и материала стекла являются ключевыми в этом процессе.
• ПРОИЗВОДСТВО СТЕКЛЯННЫХ ОПТИЧЕСКИХ КОМПОНЕНТОВ И СБОРОК: Помимо прецизионного формования стекла, мы используем ряд ценных процессов для изготовления высококачественных оптических компонентов и сборок для требовательных приложений. Шлифовка, притирка и полировка оптических стекол в мелкозернистых специальных абразивных суспензиях — это искусство и наука для изготовления оптических линз, призм, плоскостей и многого другого. Плоскостность поверхности, волнистость, гладкость и бездефектность оптических поверхностей требуют большого опыта работы с такими процессами. Небольшие изменения в окружающей среде могут привести к выпуску продукции, не соответствующей спецификации, и остановке производственной линии. Бывают случаи, когда однократное протирание оптической поверхности чистой тканью может привести к тому, что продукт будет соответствовать спецификациям или не пройти тест. Некоторые популярные стеклянные материалы: плавленый кварц, кварц, BK7. Также сборка таких компонентов требует специализированного опыта ниши. Иногда используются специальные клеи. Однако иногда метод, называемый оптическим контактом, является лучшим выбором и не требует использования материала между прикрепленными оптическими стеклами. Он состоит из физического контакта плоских поверхностей для соединения друг с другом без клея. В некоторых случаях для сборки оптических компонентов на определенных расстояниях и с определенной геометрической ориентацией друг к другу используются механические прокладки, прецизионные стеклянные стержни или шарики, зажимы или механически обработанные металлические компоненты. Давайте рассмотрим некоторые из наших популярных методов изготовления высококачественной оптики.
ШЛИФОВКА И ПРИТРОЙКА И ПОЛИРОВКА: Грубая форма оптического компонента получается путем шлифовки стеклянной заготовки. После этого осуществляют притирку и полировку путем вращения и трения шероховатых поверхностей оптических компонентов об инструменты с желаемой формой поверхности. Между оптикой и формовочными инструментами заливается суспензия с мельчайшими абразивными частицами и жидкостью. Размеры абразивных частиц в таких суспензиях можно выбирать в соответствии с желаемой степенью плоскостности. Отклонения критических оптических поверхностей от желаемой формы выражаются в терминах длины волны используемого света. Наша высокоточная оптика имеет допуски в десятые доли длины волны (длина волны/10) или даже более жесткие. Помимо профиля поверхности, критические поверхности сканируются и оцениваются на наличие других особенностей поверхности и дефектов, таких как размеры, царапины, сколы, ямки, пятна и т. д. Жесткий контроль условий окружающей среды в цехе оптического производства и обширные требования к метрологии и испытаниям с использованием самого современного оборудования делают эту отрасль промышленности сложной задачей.
• ВТОРИЧНЫЕ ПРОЦЕССЫ В ПРОИЗВОДСТВЕ СТЕКЛА: Опять же, мы ограничены только вашим воображением, когда речь идет о вторичных и чистовых процессах обработки стекла. Здесь мы перечислим некоторые из них:
-Покрытия на стекле (оптические, электрические, трибологические, термические, функциональные, механические...). Например, мы можем изменить свойства поверхности стекла, заставив его, например, отражать тепло, чтобы оно сохраняло прохладу внутри здания, или сделать одну сторону поглощающей инфракрасное излучение с помощью нанотехнологий. Это помогает сохранять тепло внутри зданий, потому что самый внешний поверхностный слой стекла поглощает инфракрасное излучение внутри здания и излучает его обратно внутрь.
-Травление на стекле
-Прикладная керамическая маркировка (ACL)
-Гравировка
- Пламенная полировка
-Химическая полировка
-Окрашивание
ПРОИЗВОДСТВО ТЕХНИЧЕСКОЙ КЕРАМИКИ
• ПРЕССОВАНИЕ В МАСШТАБЕ: Состоит из одноосного прессования гранулированных порошков, заключенных в пресс-форму.
• ГОРЯЧЕЕ ПРЕССОВАНИЕ: Подобно прессованию под давлением, но с добавлением температуры для повышения уплотнения. Порошок или прессованная заготовка помещается в графитовую матрицу и прикладывается одноосное давление, в то время как матрица выдерживается при высоких температурах, таких как 2000 C. Температуры могут быть разными в зависимости от типа обрабатываемого керамического порошка. Для сложных форм и геометрии может потребоваться другая последующая обработка, такая как алмазная шлифовка.
• ИЗОСТАТИЧЕСКОЕ ПРЕССОВАНИЕ: Гранулированный порошок или штампованные прессованные прессовки помещаются в герметичные контейнеры, а затем в закрытый сосуд высокого давления с жидкостью внутри. После этого они уплотняются за счет увеличения давления в сосуде высокого давления. Жидкость внутри сосуда передает силы давления равномерно по всей площади поверхности герметичного сосуда. Таким образом, материал равномерно уплотняется и принимает форму гибкого контейнера, внутренний профиль и характеристики.
• ГОРЯЧОЕ ИЗОСТАТИЧЕСКОЕ ПРЕССОВАНИЕ: Аналогично изостатическому прессованию, но в дополнение к атмосфере сжатого газа мы спекаем прессовку при высокой температуре. Горячее изостатическое прессование приводит к дополнительному уплотнению и повышению прочности.
• ШЛИКОВАЯ ЛИТЬЕ / ДРЕЙН ЛИТЬЕ: Мы заполняем форму суспензией керамических частиц микрометрового размера и несущей жидкостью. Эта смесь называется «слип». Форма имеет поры, поэтому жидкость в смеси фильтруется в форму. В результате на внутренних поверхностях формы образуется отлив. После спекания детали можно вынимать из формы.
• ЛИТЬЕ ЛЕНТЫ: Мы производим керамические ленты, заливая керамические суспензии на плоские движущиеся поверхности носителя. Суспензии содержат керамические порошки, смешанные с другими химическими веществами для связывания и переноски. Когда растворители испаряются, остаются плотные и гибкие листы керамики, которые можно разрезать или свернуть по желанию.
• ЭКСТРУЗИОННОЕ ФОРМОВАНИЕ: Как и в других процессах экструзии, мягкая смесь керамического порошка со связующими веществами и другими химическими веществами пропускается через головку для получения формы поперечного сечения, а затем нарезается на желаемую длину. Процесс выполняется с использованием холодных или нагретых керамических смесей.
• ЛИТЬЕ ПОД НИЗКИМ ДАВЛЕНИЕМ: мы готовим смесь керамического порошка со связующими веществами и растворителями и нагреваем ее до температуры, при которой ее можно легко прессовать и вдавливать в полость инструмента. После завершения цикла формования деталь выбрасывается, а связывающий химикат выжигается. Используя литье под давлением, мы можем экономично получать сложные детали в больших объемах. Возможны отверстия , которые составляют крошечную долю миллиметра на стенке толщиной 10 мм, возможно нарезание резьбы без дополнительной обработки, возможны допуски до +/- 0,5% и даже меньше, когда детали подвергаются механической обработке. , возможна толщина стенки порядка 0,5 мм до длины 12,5 мм, а также толщина стенки от 6,5 мм до длины 150 мм.
• ЭКОЛОГИЧНАЯ ОБРАБОТКА: Используя те же инструменты для обработки металлов, мы можем обрабатывать прессованные керамические материалы, пока они еще мягкие, как мел. Возможны допуски +/- 1%. Для лучшей точности мы используем алмазное шлифование.
• СПЕКАНИЕ или ОБЖИГ: Спекание делает возможным полное уплотнение. У сырых компактных деталей происходит значительная усадка, но это не является большой проблемой, поскольку мы учитываем эти изменения размеров при проектировании детали и оснастки. Частицы порошка связываются вместе, и пористость, вызванная процессом уплотнения, в значительной степени удаляется.
• АЛМАЗНАЯ ШЛИФОВКА: самый твердый в мире материал «алмаз» используется для шлифовки таких твердых материалов, как керамика, и для получения прецизионных деталей. Достигаются допуски в диапазоне микрометров и очень гладкие поверхности. Из-за его дороговизны мы рассматриваем эту технику только тогда, когда она нам действительно нужна.
• ГЕРМЕТИЧНЫЕ СБОРКИ практически не допускают обмена веществами, твердыми телами, жидкостями или газами между поверхностями. Герметичность герметична. Например, герметичные электронные корпуса защищают чувствительное внутреннее содержимое упакованного устройства от влаги, загрязняющих веществ или газов. Ничто не является 100% герметичным, но когда мы говорим о герметичности, мы имеем в виду, что с практической точки зрения герметичность существует в той степени, в которой скорость утечки настолько мала, что устройства безопасны в нормальных условиях окружающей среды в течение очень долгого времени. Наши герметичные узлы состоят из металлических, стеклянных и керамических компонентов, металлокерамики, керамики-металлокерамики, металлокерамики-металла, металл-металл, металл-стекло, металл-стекло-металл, стекло-металл-стекло, стекло-металл. металл и стекло к стеклу и все другие комбинации склеивания металл-стекло-керамика. Например, мы можем покрыть металлом керамические компоненты, чтобы они были прочно соединены с другими компонентами в сборке и обладали отличной герметизирующей способностью. У нас есть ноу-хау покрытия оптических волокон или вводов металлом и их пайки или припайки к корпусам, чтобы газы не проходили и не просачивались внутрь корпусов. Поэтому они используются для изготовления электронных корпусов для герметизации чувствительных устройств и защиты их от внешней атмосферы. Помимо превосходных герметизирующих характеристик, другие свойства, такие как коэффициент теплового расширения, устойчивость к деформации, отсутствие газовыделения, очень долгий срок службы, непроводимость, теплоизоляционные свойства, антистатичность и т. д. сделать стеклянные и керамические материалы предпочтительными для определенных применений. Информацию о нашем предприятии, производящем металлокерамические фитинги, герметики, вакуумные вводы, компоненты для высокого и сверхвысокого вакуума и системы контроля жидкости , можно найти здесь:Брошюра о заводе герметичных компонентов