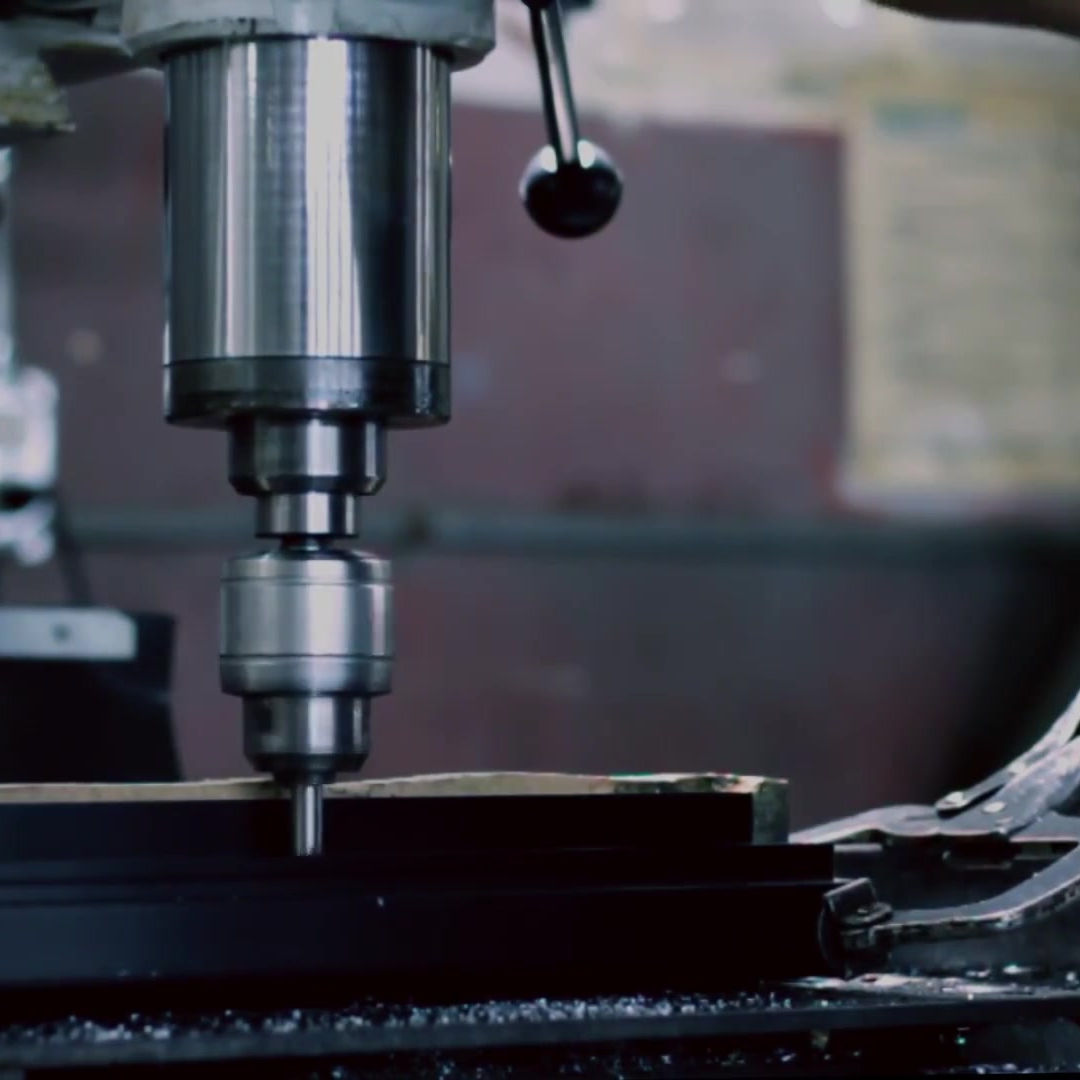
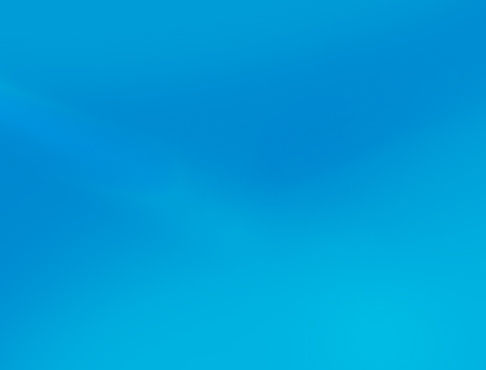
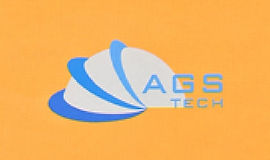
Глобальный производитель на заказ, интегратор, консолидатор, партнер по аутсорсингу широкого спектра продуктов и услуг.
Мы являемся вашим универсальным источником для производства, изготовления, проектирования, консолидации, интеграции, аутсорсинга изготовленных на заказ и готовых продуктов и услуг.
Choose your Language
-
Изготовление на заказ
-
Внутреннее и глобальное контрактное производство
-
Производственный аутсорсинг
-
Внутренние и глобальные закупки
-
Консолидация
-
Инженерная интеграция
-
Инженерные услуги
Search Results
Найден 161 результат с пустым поисковым запросом
- Производство элементов машин, шестерни, зубчатые передачи, подшипники, шпонки, шлицы
Производство элементов машин, Шестерни, Зубчатые передачи, Подшипники, Шпонки, Шлицы, Шпильки, Валы, Уплотнения, Крепежные детали, Сцепления, Кулачки, толкатели, Ремни, Муфты, Валы Производство деталей машин Читать далее Ремни, цепи и кабельный привод в сборе Читать далее Шестерни и зубчатая передача в сборе Читать далее Производство муфт и подшипников Читать далее Изготовление ключей, шлицов и штифтов Читать далее Производство кулачков, толкателей, тяг и храповых колес Читать далее Производство валов Читать далее Производство механических уплотнений Читать далее Сцепление и тормоз в сборе Читать далее Производство крепежа Читать далее Сборка простых машин ЭЛЕМЕНТЫ МАШИНЫ являются элементарными компонентами машины. Эти элементы состоят из трех основных типов: 1.) Компоненты конструкции, включая элементы рамы, подшипники, оси, шлицы, крепежные детали, уплотнения и смазочные материалы. 2.) Механизмы, управляющие движением различными способами, такие как зубчатые передачи, ременные или цепные передачи, рычажные механизмы, кулачковые и следящие системы, тормоза и муфты. 3.) Компоненты управления, такие как кнопки, переключатели, индикаторы, датчики, приводы и компьютерные контроллеры. Большинство элементов машин, которые мы предлагаем вам, стандартизированы по стандартным размерам, но также доступны элементы машин, изготовленные по индивидуальному заказу для ваших специализированных приложений. Индивидуальная настройка элементов машин может выполняться на существующих проектах, которые есть в наших загружаемых каталогах, или на совершенно новых проектах. Прототипирование и производство элементов машин могут быть продолжены после утверждения проекта обеими сторонами. Если необходимо спроектировать и изготовить новые элементы машин, наши клиенты либо отправляют нам по электронной почте свои собственные чертежи, и мы рассматриваем их для утверждения, либо они просят нас спроектировать элементы машин для их применения. В последнем случае мы используем всю информацию от наших клиентов и проектируем элементы машины и отправляем окончательные чертежи нашим клиентам для утверждения. После утверждения мы производим первые изделия, а затем изготавливаем элементы машин в соответствии с окончательным проектом. На любом этапе этой работы, в случае неудовлетворительной работы той или иной конструкции элемента машины в полевых условиях (что бывает редко), мы пересматриваем весь проект и при необходимости вносим изменения совместно с нашими заказчиками. Нашей стандартной практикой является подписание соглашений о неразглашении информации (NDA) с нашими клиентами для проектирования элементов машин или любого другого продукта, когда это необходимо или требуется. После того, как элементы машин разработаны и изготовлены по индивидуальному заказу для конкретного клиента, мы присваиваем им код продукта и производим и продаем их только нашему клиенту, которому принадлежит продукт. Мы воспроизводим элементы машин, используя разработанные инструменты, формы и процедуры столько раз, сколько необходимо и всякий раз, когда наш клиент повторно заказывает их. Другими словами, после того, как для вас разработан и изготовлен нестандартный элемент машины, интеллектуальная собственность, а также все инструменты и пресс-формы зарезервированы и хранятся нами на неопределенный срок для вас, а продукты воспроизводятся по вашему желанию. Мы также предлагаем нашим клиентам инжиниринговые услуги, творчески объединяя элементы машин в компонент или сборку, которые служат применению и соответствуют или превосходят ожидания наших клиентов. Заводы, производящие элементы наших машин, сертифицированы по стандартам ISO9001, QS9000 или TS16949. Кроме того, большинство наших продуктов имеют маркировку CE или UL и соответствуют международным стандартам, таким как ISO, SAE, ASME, DIN. Пожалуйста, нажмите на подменю, чтобы получить подробную информацию о наших элементах машины, включая: - Ремни, цепи и тросовые приводы - Шестерни и зубчатые передачи - Муфты и подшипники - Ключи, шлицы и штифты - Кулачки и связи - Валы - Механические уплотнения - Промышленное сцепление и тормоз - Крепеж - Простые машины Мы подготовили справочную брошюру для наших клиентов, дизайнеров и разработчиков новых продуктов, включая элементы машин. Вы можете ознакомиться с некоторыми общеупотребительными терминами при проектировании компонентов машин: Загрузите брошюру об общих терминах в области машиностроения, используемых конструкторами и инженерами Наши элементы машин находят применение в различных областях, таких как промышленное оборудование, системы автоматизации, испытательное и метрологическое оборудование, транспортное оборудование, строительные машины и практически везде, о чем вы только можете подумать. АГС-ТЕХ разрабатывает и производит элементы машин из различных материалов в зависимости от области применения. Материалы, используемые для элементов машин, могут варьироваться от формованных пластиков, используемых для игрушек, до закаленной стали со специальным покрытием для промышленного оборудования. Наши конструкторы используют современное профессиональное программное обеспечение и средства проектирования для разработки элементов машин с учетом таких деталей, как углы зубьев шестерен, возникающие напряжения, скорость износа и т. д. Пожалуйста, просмотрите наши подменю и загрузите брошюры и каталоги нашей продукции, чтобы узнать, можете ли вы найти готовые элементы машин для вашего применения. Если вы не можете найти подходящий вариант для своего применения, сообщите нам об этом, и мы будем работать с вами над разработкой и производством элементов машин, которые будут соответствовать вашим потребностям. Если вас больше интересуют наши инженерные и научно-исследовательские возможности, а не производственные возможности, мы приглашаем вас посетить наш веб-сайт http://www.ags-engineering.com где вы можете найти более подробную информацию о нашем дизайне, разработке продуктов, разработке процессов, инженерно-консультационных услугах и многом другом CLICK Product Finder-Locator Service ПРЕДЫДУЩАЯ СТРАНИЦА
- Композиты, Производство композитных материалов, Армированные волокном
Композиты, Производство композиционных материалов, Армирование частицами и волокнами, Керметы, Керамические и металлические композиты, Полимер, армированный стекловолокном, Процесс укладки Производство композитов и композитных материалов Проще говоря, КОМПОЗИТЫ или КОМПОЗИТНЫЕ МАТЕРИАЛЫ - это материалы, состоящие из двух или нескольких материалов с разными физическими или химическими свойствами, но при объединении они становятся материалом, который отличается от составляющих материалов. Мы должны отметить, что составляющие материалы остаются отдельными и отчетливыми в структуре. Целью производства композитного материала является получение продукта, который превосходит входящие в его состав компоненты и сочетает в себе желаемые свойства каждого из них. В качестве примера; прочность, малый вес или более низкая цена могут быть мотивом для разработки и производства композита. Композиты, которые мы предлагаем, представляют собой армированные частицами композиты, армированные волокнами композиты, в том числе композиты с керамической матрицей / полимерной матрицей / металлической матрицей / углерод-углерод / гибридные композиты, конструкционные, ламинированные и сэндвич-структурированные композиты и нанокомпозиты. Методы изготовления, которые мы используем в производстве композитных материалов: пултрузия, процессы производства препрега, усовершенствованная укладка волокна, намотка нити, индивидуальная укладка волокна, процесс напыления стекловолокна, тафтинг, процесс ланоксида, z-пиннинг. Многие композиционные материалы состоят из двух фаз: матрицы, которая является непрерывной и окружает другую фазу; и дисперсная фаза, окруженная матрицей. Мы рекомендуем вам нажать здесь, чтобыСКАЧАТЬ наши схематические иллюстрации производства композитов и композитных материалов от AGS-TECH Inc. Это поможет вам лучше понять информацию, которую мы предоставляем вам ниже. • КОМПОЗИТЫ, УСИЛЕННЫЕ ЧАСТИЦАМИ: Эта категория состоит из двух типов: композиты с крупными частицами и композиты, упрочненные дисперсией. В первом типе взаимодействие частицы с матрицей нельзя рассматривать на атомном или молекулярном уровне. Вместо этого действует механика сплошных сред. С другой стороны, в дисперсионно-упрочненных композитах частицы обычно намного меньше в диапазоне десятков нанометров. Примером композита с крупными частицами являются полимеры, к которым добавлены наполнители. Наполнители улучшают свойства материала и могут заменить часть объема полимера более экономичным материалом. Объемные доли двух фаз влияют на поведение композита. Композиты с крупными частицами используются с металлами, полимерами и керамикой. CERMETS являются примерами керамических/металлических композитов. Самый распространенный кермет – это цементированный карбид. Он состоит из тугоплавкой карбидной керамики, такой как частицы карбида вольфрама, в матрице из металла, такого как кобальт или никель. Эти карбидные композиты широко используются в качестве режущих инструментов для закаленной стали. Твердые частицы карбида отвечают за режущее действие, а их ударная вязкость повышается за счет пластичной металлической матрицы. Таким образом, мы получаем преимущества обоих материалов в одном композите. Другим распространенным примером композита с крупными частицами, который мы используем, являются частицы сажи, смешанные с вулканизированной резиной для получения композита с высокой прочностью на растяжение, ударной вязкостью, сопротивлением разрыву и истиранию. Примером дисперсно-упрочненного композита являются металлы и сплавы металлов, упрочняемые и упрочняемые за счет равномерного диспергирования мелких частиц очень твердого и инертного материала. При добавлении очень мелких чешуек оксида алюминия к металлической алюминиевой матрице мы получаем спеченный алюминиевый порошок, обладающий повышенной жаропрочностью. • КОМПОЗИТЫ, АРМИРОВАННЫЕ ВОЛОКНОМ: Эта категория композитов на самом деле является самой важной. Целью достижения является высокая прочность и жесткость на единицу веса. Состав, длина, ориентация и концентрация волокон в этих композитах имеют решающее значение для определения свойств и полезности этих материалов. Мы используем три группы волокон: усы, волокна и проволоки. УИСКЕРЫ представляют собой очень тонкие и длинные монокристаллы. Они относятся к самым прочным материалам. Некоторыми примерами нитевидных материалов являются графит, нитрид кремния, оксид алюминия. ВОЛОКОНЫ, с другой стороны, представляют собой в основном полимеры или керамику и находятся в поликристаллическом или аморфном состоянии. Третья группа — это тонкие ПРОВОЛОКИ, которые имеют относительно большие диаметры и часто состоят из стали или вольфрама. Примером композитного материала, армированного проволокой, являются автомобильные шины, в которых стальная проволока находится внутри резины. В зависимости от материала матрицы, мы имеем следующие композиты: ПОЛИМЕРНО-МАТРИЧНЫЕ КОМПОЗИТЫ: изготавливаются из полимерной смолы и волокон в качестве армирующего компонента. Подгруппа из них, называемая композитами из полимера, армированного стекловолокном (GFRP), содержит непрерывные или прерывистые стекловолокна в полимерной матрице. Стекло обладает высокой прочностью, экономично, легко превращается в волокна и химически инертно. Недостатками являются их ограниченная жесткость и жесткость, температура эксплуатации только до 200 – 300 градусов по Цельсию. Стекловолокно подходит для автомобильных кузовов и транспортного оборудования, кузовов морских транспортных средств, контейнеров для хранения. Они не подходят для аэрокосмической промышленности и изготовления мостов из-за ограниченной жесткости. Другая подгруппа называется Композитный полимер, армированный углеродным волокном (CFRP). Здесь углерод — это наш волокнистый материал в полимерной матрице. Углерод известен своим высоким удельным модулем и прочностью, а также способностью сохранять их при высоких температурах. Углеродные волокна могут предложить нам стандартные, промежуточные, высокие и сверхвысокие модули растяжения. Кроме того, углеродные волокна обладают разнообразными физическими и механическими характеристиками и, следовательно, подходят для различных индивидуальных инженерных приложений. Композиты из углепластика можно рассматривать для производства спортивного и развлекательного оборудования, сосудов под давлением и компонентов аэрокосмической конструкции. Тем не менее, другая подгруппа, полимерные композиты, армированные арамидным волокном, также являются высокопрочными и модульными материалами. Соотношение прочности и веса у них исключительно высокое. Арамидные волокна также известны под торговыми названиями KEVLAR и NOMEX. При растяжении они работают лучше, чем другие полимерные волокнистые материалы, но слабы при сжатии. Арамидные волокна прочны, ударопрочны, устойчивы к ползучести и усталости, стабильны при высоких температурах, химически инертны, за исключением воздействия сильных кислот и щелочей. Арамидные волокна широко используются в спортивных товарах, бронежилетах, шинах, канатах, оболочках оптоволоконных кабелей. Существуют и другие армирующие волокна материалы, но они используются в меньшей степени. В основном это бор, карбид кремния, оксид алюминия. С другой стороны, материал полимерной матрицы также имеет решающее значение. Он определяет максимальную рабочую температуру композита, поскольку полимер обычно имеет более низкую температуру плавления и разложения. Полиэфиры и виниловые эфиры широко используются в качестве полимерной матрицы. Также используются смолы, обладающие отличной влагостойкостью и механическими свойствами. Например, полиимидная смола может использоваться при температуре до 230 градусов Цельсия. КОМПОЗИТЫ С МЕТАЛЛИЧЕСКОЙ МАТРИЦЕЙ: В этих материалах мы используем пластичную металлическую матрицу, а рабочие температуры, как правило, выше, чем у составляющих их компонентов. По сравнению с композитами с полимерной матрицей они могут иметь более высокие рабочие температуры, быть негорючими и могут иметь лучшую стойкость к разложению органическими жидкостями. Однако они дороже. Армирующие материалы, такие как вискеры, частицы, непрерывные и прерывистые волокна; и обычно используются матричные материалы, такие как медь, алюминий, магний, титан, суперсплавы. Примерами применения являются компоненты двигателя, изготовленные из матрицы из алюминиевого сплава, армированной оксидом алюминия и углеродными волокнами. КЕРАМИЧЕСКИЕ МАТРИЧНЫЕ КОМПОЗИТЫ: Керамические материалы известны своей исключительно хорошей надежностью при высоких температурах. Однако они очень хрупкие и имеют низкие значения вязкости разрушения. Встраивая частицы, волокна или нитевидные кристаллы одной керамики в матрицу другой, мы можем получить композиты с более высокой стойкостью к разрушению. Эти встроенные материалы в основном препятствуют распространению трещины внутри матрицы с помощью некоторых механизмов, таких как отклонение вершины трещины или образование перемычек через поверхности трещины. Например, оксиды алюминия, армированные нитевидными кристаллами SiC, используются в качестве режущих пластин для обработки твердых сплавов. Они могут показать лучшие характеристики по сравнению с цементированными карбидами. УГЛЕРОД-УГЛЕРОДНЫЕ КОМПОЗИТЫ: как армирование, так и матрица изготовлены из углерода. Они обладают высокими модулями растяжения и прочностью при высоких температурах свыше 2000°С, сопротивлением ползучести, высокой вязкостью разрушения, низким коэффициентом теплового расширения, высокой теплопроводностью. Эти свойства делают их идеальными для применений, требующих устойчивости к тепловому удару. Однако слабостью углерод-углеродных композитов является их уязвимость к окислению при высоких температурах. Типичными примерами использования являются пресс-формы для горячего прессования, производство современных компонентов газотурбинных двигателей. ГИБРИДНЫЕ КОМПОЗИТЫ: два или более разных типа волокон смешаны в одной матрице. Таким образом, можно адаптировать новый материал с комбинацией свойств. Например, когда в полимерную смолу включены и углеродные, и стеклянные волокна. Углеродные волокна обеспечивают жесткость и прочность низкой плотности, но они дороги. С другой стороны, стекло недорогое, но ему не хватает жесткости углеродного волокна. Гибридный стеклоуглеродный композит прочнее и жестче, и его можно производить с меньшими затратами. ПЕРЕРАБОТКА АРМИРОВАННЫХ ВОЛОКНОМ КОМПОЗИТОВ: Для непрерывных армированных волокном пластиков с равномерно распределенными волокнами, ориентированными в одном направлении, мы используем следующие методы. ПУЛЬТРУЗИЯ: Изготавливаются стержни, балки и трубы непрерывных длин и постоянных сечений. Ровинги из непрерывных волокон пропитывают термореактивной смолой и протягивают через стальную фильеру, чтобы предварительно придать им желаемую форму. Затем они проходят через прецизионную матрицу для отверждения, чтобы получить окончательную форму. Так как отверждающая головка нагревается, она отверждает полимерную матрицу. Съемники протягивают материал через матрицы. Используя вставленные полые стержни, мы можем получить трубы и полые геометрические формы. Метод пултрузии автоматизирован и обеспечивает высокую производительность. Возможно изготовление изделия любой длины. ПРОЦЕСС ПРОИЗВОДСТВА ПРЕПРЕГА: Препрег представляет собой арматуру из непрерывных волокон, предварительно пропитанную частично отвержденной полимерной смолой. Он широко используется для структурных приложений. Материал поставляется в виде ленты и поставляется в виде ленты. Производитель формирует его напрямую и полностью отверждает без добавления смолы. Поскольку препреги подвергаются реакциям отверждения при комнатной температуре, их хранят при 0°С или более низких температурах. После использования оставшиеся ленты хранятся обратно при низких температурах. Используются термопластичные и термореактивные смолы, широко распространены армирующие волокна из углерода, арамида и стекла. Чтобы использовать препреги, сначала удаляют бумажную подложку, а затем осуществляют изготовление, укладывая ленту препрега на обработанную поверхность (процесс укладки). Для получения желаемой толщины можно уложить несколько слоев. Частой практикой является чередование ориентации волокон для получения ламината с поперечными или угловыми слоями. Наконец, для отверждения применяются тепло и давление. Для резки препрегов и укладки используются как ручная обработка, так и автоматизированные процессы. НАМОТКА ВОЛОТА: Непрерывные армирующие волокна точно располагаются по заданному шаблону, чтобы следовать полой и обычно циклокруглой форме. Волокна сначала проходят через ванну со смолой, а затем автоматически наматываются на оправку. После нескольких повторений намотки получают желаемую толщину и отверждение проводят либо при комнатной температуре, либо в печи. Теперь оправку снимают и изделие извлекают из формы. Намотка нитей может обеспечить очень высокое отношение прочности к весу за счет намотки волокон по окружности, спирали и полярным узорам. По этой технологии изготавливаются трубы, резервуары, кожухи. • КОНСТРУКЦИОННЫЕ КОМПОЗИТЫ: Обычно они состоят как из гомогенных, так и из композиционных материалов. Поэтому их свойства определяются составляющими материалами и геометрическим рисунком его элементов. Вот основные типы: ЛАМИНАРНЫЕ КОМПОЗИТЫ: Эти конструкционные материалы изготавливаются из двумерных листов или панелей с предпочтительными направлениями высокой прочности. Слои укладываются и цементируются вместе. Чередуя направления высокой прочности в двух перпендикулярных осях, мы получаем композит, обладающий высокой прочностью в обоих направлениях в двумерной плоскости. Регулируя углы слоев, можно изготовить композит с прочностью в предпочтительных направлениях. Так производятся современные лыжи. СЭНДВИЧ-ПАНЕЛИ: Эти конструкционные композиты легкие, но при этом обладают высокой жесткостью и прочностью. Сэндвич-панели состоят из двух внешних листов, изготовленных из жесткого и прочного материала, такого как алюминиевые сплавы, армированный волокном пластик или сталь, и сердцевины между внешними листами. Сердечник должен быть легким и в большинстве случаев иметь низкий модуль упругости. Популярными материалами сердцевины являются жесткие полимерные пены, дерево и соты. Сэндвич-панели широко используются в строительной отрасли в качестве кровельного, напольного или стенового материала, а также в аэрокосмической промышленности. • НАНОКОМПОЗИТЫ: Эти новые материалы состоят из частиц наноразмеров, встроенных в матрицу. Используя нанокомпозиты, мы можем производить каучуковые материалы, которые являются очень хорошими барьерами для проникновения воздуха, сохраняя при этом свои каучуковые свойства неизменными. CLICK Product Finder-Locator Service ПРЕДЫДУЩАЯ СТРАНИЦА
- Компоненты трансмиссии, ремни, цепи, тросовые приводы, шкивы
Компоненты трансмиссии, ремни, цепи и тросовые приводы, обычные и рифленые или зубчатые, принудительная передача, шкивы Ремни, цепи и кабельный привод в сборе AGS-TECH Inc. предлагает вам компоненты силовой передачи, включая ремни, цепи и тросовый привод в сборе. Благодаря многолетнему совершенствованию наши резиновые, кожаные и другие ременные приводы стали легче и компактнее, способными выдерживать более высокие нагрузки при меньших затратах. Точно так же наши цепные приводы со временем претерпели значительные изменения и предлагают нашим клиентам ряд преимуществ. Некоторыми преимуществами использования цепных передач являются их относительно неограниченные расстояния между центрами валов, компактность, простота сборки, эластичность при растяжении без проскальзывания и проскальзывания, возможность работы в высокотемпературных средах. Наши кабельные приводы также обладают такими преимуществами, как простота некоторых приложений по сравнению с другими типами компонентов передачи. Доступны как стандартные ременные, цепные и тросовые приводы, так и версии, изготовленные и собранные по индивидуальному заказу. Мы можем изготовить эти компоненты трансмиссии нужного размера для вашего применения и из наиболее подходящих материалов. РЕМНИ И РЕМЕННЫЕ ПРИВОДЫ: - Обычные плоские ремни: это простые плоские ремни без зубцов, канавок или зазубрин. Приводы с плоским ремнем обеспечивают гибкость, хорошее поглощение ударов, эффективную передачу мощности на высоких скоростях, стойкость к истиранию и низкую стоимость. Ремни можно сращивать или соединять, чтобы получились ремни большего размера. Другими преимуществами обычных плоских ремней являются то, что они тонкие, не подвержены высоким центробежным нагрузкам (что делает их подходящими для высокоскоростных операций с небольшими шкивами). С другой стороны, они создают высокие нагрузки на подшипники, поскольку плоские ремни требуют высокого натяжения. Другими недостатками плоских ременных передач могут быть проскальзывание, шумная работа и относительно более низкий КПД при низких и средних скоростях работы. У нас есть два типа обычных ремней: армированные и неармированные. Армированные ремни имеют в своей конструкции натяжной элемент. Обычные плоские ремни бывают из кожи, прорезиненной ткани или корда, неармированной резины или пластика, ткани, армированной кожи. Кожаные ремни отличаются долговечностью, гибкостью, отличным коэффициентом трения, простотой ремонта. Однако кожаные ремни относительно дороги, их необходимо чистить и чистить, и в зависимости от атмосферы они могут сжиматься или растягиваться. Ремни из прорезиненной ткани или корда устойчивы к воздействию влаги, кислот и щелочей. Прорезиненные тканевые ремни состоят из слоев хлопчатобумажной или синтетической ткани, пропитанной каучуком, и являются наиболее экономичными. Ремни из прорезиненного корда состоят из ряда слоев корда, пропитанного резиной. Ремни из прорезиненного корда отличаются высокой прочностью на растяжение и небольшими размерами и массой. Неармированные резиновые или пластмассовые ремни подходят для маломощных низкоскоростных приводов. Неармированные резиновые и пластмассовые ремни можно натягивать на их шкивы. Пластиковые неармированные ремни могут передавать большую мощность по сравнению с резиновыми ремнями. Армированные кожаные ремни состоят из эластичного пластикового элемента, зажатого между верхним и нижним слоями кожи. Наконец, наши тканевые ремни могут состоять из цельного куска хлопка или утки, сложенного и сшитого рядами продольных стежков. Тканевые ремни способны равномерно двигаться и работать на высокой скорости. - Рифленые или зубчатые ремни (например, клиновые ремни): это базовые плоские ремни, модифицированные для обеспечения преимуществ другого типа трансмиссии. Это плоские ремни с продольно ребристой нижней стороной. Поликлиновые ремни представляют собой плоские ремни с продольными или зубчатыми канавками, с секцией растяжения и рядом смежных V-образных канавок для отслеживания и сжатия. Мощность зависит от ширины ремня. Клиновые ремни являются рабочей лошадкой в промышленности и доступны в различных стандартных размерах и типах для передачи практически любой нагрузки. Клиновые ремни хорошо работают на скоростях от 1500 до 6000 футов/мин, однако узкие клиновые ремни могут работать со скоростью до 10 000 футов/мин. Клиновые ременные приводы обеспечивают длительный срок службы, например от 3 до 5 лет, и допускают большие передаточные числа, их легко устанавливать и снимать, они обеспечивают бесшумную работу, низкие эксплуатационные расходы, хорошее поглощение ударов между приводным ремнем и ведомыми валами. Недостатком клиновых ремней является их определенное проскальзывание и проскальзывание, и поэтому они могут быть не лучшим решением там, где требуются синхронные скорости. У нас есть промышленные, автомобильные и сельскохозяйственные ремни. В наличии имеются стандартные длины ремней, а также нестандартные длины ремней. Все стандартные поперечные сечения клиновых ремней доступны со склада. Существуют таблицы, в которых вы можете рассчитать неизвестные параметры, такие как длина ремня, сечение ремня (ширина и толщина), при условии, что вы знаете некоторые параметры вашей системы, такие как диаметры ведущего и ведомого шкивов, межцентровое расстояние между шкивами и скорости вращения шкивов. Вы можете воспользоваться этими таблицами или попросить нас подобрать для вас правильный клиновой ремень. - Приводные ремни (ремни ГРМ): эти ремни также плоского типа с рядом равномерно расположенных зубьев по внутренней окружности. Приводные или зубчатые ремни с принудительным приводом сочетают в себе преимущества плоских ремней с характеристиками положительного сцепления цепей и шестерен. Приводные ремни не обнаруживают проскальзывания или колебаний скорости. Возможен широкий диапазон скоростей. Нагрузки на подшипники низкие, потому что они могут работать при низком натяжении. Однако они более подвержены смещению шкивов. - Шкивы, шкивы, ступицы для ремней: различные типы шкивов используются с плоскими, ребристыми (зубчатыми) и принудительными приводными ремнями. Мы производим их все. Большинство наших шкивов с плоским ремнем изготавливаются методом литья из чугуна, но также доступны версии из стали с различными комбинациями обода и ступицы. Наши шкивы с плоским ремнем могут иметь цельные, со спицами или разъемные ступицы, или мы можем изготовить их по вашему желанию. Поликлиновые ремни и ремни с принудительным приводом доступны в различных размерах и ширине. По крайней мере, один шкив в ременных приводах должен иметь фланцы, чтобы ремень оставался на приводе. Для систем с длинным центральным приводом рекомендуется, чтобы оба шкива были фланцевыми. Шкивы представляют собой рифленые колеса шкивов и обычно изготавливаются путем литья чугуна, формовки стали или литья пластмассы. Формовка стали подходит для производства автомобильных и сельскохозяйственных шкивов. Мы производим шкивы с регулярными и глубокими канавками. Шкивы с глубокими канавками хорошо подходят, когда клиновой ремень входит в шкив под углом, как в случае четвертьоборотных приводов. Глубокие канавки также хорошо подходят для приводов с вертикальными валами и приложений, где вибрация ремней может быть проблемой. Наши натяжные шкивы представляют собой шкивы с желобками или плоские шкивы, которые не служат для передачи механической энергии. Натяжные ролики используются в основном для натяжения ремней. - Приводы с одним и несколькими ремнями: приводы с одним ремнем имеют одну канавку, тогда как приводы с несколькими ремнями имеют несколько канавок. Нажав на соответствующий цветной текст ниже, вы можете скачать наши каталоги: - Ремни силовой передачи (включая клиновые ремни, зубчатые ремни, ремни с необработанными краями, обернутые ремни и специальные ремни) - Конвейерные ленты - V-образные шкивы - Зубчатые шкивы ЦЕПИ И ЦЕПНЫЕ ПЕРЕДАЧИ: Наши приводные цепи имеют ряд преимуществ, таких как относительно неограниченные расстояния между центрами валов, простота сборки, компактность, эластичность при растяжении без проскальзывания и проскальзывания, способность работать при высоких температурах. Вот основные типы наших цепей: - Съемные цепи: Наши съемные цепи изготавливаются различных размеров, с разным шагом и предельной прочностью и, как правило, из ковкого железа или стали. Гибкие цепи изготавливаются с шагом от 0,902 (23 мм) до 4,063 дюйма (103 мм) и пределом прочности от 700 до 17 000 фунтов на квадратный дюйм. С другой стороны, наши съемные стальные цепи изготавливаются с шагом от 0,904 дюйма (23 мм) до примерно 3,00 дюйма (76 мм) с пределом прочности от 760 до 5000 фунтов/кв. дюйм._cc781905-5cde-3194-bb3b- 136bad5cf58d_ - Игольчатые цепи: эти цепи используются для более тяжелых грузов и немного более высоких скоростей, примерно до 450 футов/мин (2,2 м/сек). Игольчатые цепи состоят из отдельных литых звеньев, имеющих цельный круглый ствол со смещенными боковыми звеньями. Эти звенья цепи соединены между собой стальными штифтами. Эти цепи имеют шаг от 1,00 дюйма (25 мм) до 6,00 дюймов (150 мм) и предел прочности от 3600 до 30 000 фунтов на квадратный дюйм. - Цепи со смещением боковых стержней: они популярны в приводных цепях строительной техники. Эти цепи работают на скоростях до 1000 футов/мин и передают нагрузки примерно до 250 л.с. Как правило, каждое звено имеет две смещенные боковые планки, одну втулку, один ролик, один штифт и шплинт. - Роликовые цепи: они доступны с шагом от 0,25 (6 мм) до 3,00 (75 мм) дюймов. Предельная прочность роликовых цепей одинарной ширины находится в диапазоне от 925 до 130 000 фунтов на квадратный дюйм. Доступны версии роликовых цепей с разной шириной, которые передают большую мощность на более высоких скоростях. Роликовые цепи разной ширины также обеспечивают более плавное движение и меньший уровень шума. Роликовые цепи собираются из роликовых звеньев и штифтовых звеньев. Шплинты используются в роликовых цепях разъемного исполнения. Проектирование приводов с роликовыми цепями требует специальных знаний. В то время как ременные передачи основаны на линейных скоростях, цепные передачи основаны на скорости вращения меньшей звездочки, которая в большинстве установок является ведомым элементом. Помимо номинальной мощности и скорости вращения, конструкция цепных приводов зависит от многих других факторов. - Цепи с двойным шагом: в основном такие же, как и роликовые цепи, за исключением того, что шаг в два раза длиннее. - Цепи с перевернутыми зубьями (бесшумные): высокоскоростные цепи, используемые в основном для первичных двигателей и приводов отбора мощности. Цепные передачи с перевернутыми зубьями могут передавать мощность до 1200 л.с. и состоят из ряда зубчатых звеньев, попеременно собранных либо со штифтами, либо с комбинацией соединительных компонентов. Цепь с центральной направляющей имеет направляющие звенья для зацепления с пазами звездочки, а цепь с боковой направляющей имеет направляющие для зацепления с боковыми сторонами звездочки. - Бортовые или ползунковые цепи: эти цепи используются для низкоскоростных приводов, а также для ручных операций. Нажав на соответствующий цветной текст ниже, вы можете скачать наши каталоги: - Приводные цепи - Конвейерные цепи - Конвейерные цепи с большим шагом - Роликовые цепи из нержавеющей стали - Подъемные цепи - Мотоциклетные цепи - Цепи сельскохозяйственных машин - Звездочки: наши стандартные звездочки соответствуют стандартам ANSI. Дисковые звездочки представляют собой плоские бесступичные звездочки. Наши ступичные звездочки малого и среднего размера вытачиваются из пруткового проката или поковок или изготавливаются путем приваривания ступицы пруткового проката к горячекатаному листу. AGS-TECH Inc. может поставлять звездочки, изготовленные из отливок из серого чугуна, литой стали и сварных конструкций ступиц, спеченного порошкового металла, формованных или обработанных пластиков. Для плавной работы на высоких скоростях очень важен правильный выбор размера звездочек. Ограничения по пространству, конечно же, фактор, который мы не можем игнорировать при выборе звездочки. Рекомендуется, чтобы соотношение ведущей и ведомой звездочек было не более 6:1, а намотка цепи на ведущую составляла 120 градусов. Межцентровые расстояния между меньшей и большей звездочками, длина цепи и натяжение цепи также должны быть выбраны в соответствии с некоторыми рекомендуемыми инженерными расчетами и рекомендациями, а не случайным образом. Загрузите наши каталоги, щелкнув цветной текст ниже: - Звездочки и пластинчатые колеса - Втулки трансмиссии - Цепная муфта - Цепные замки ТРОСОВЫЕ ПРИВОДЫ: в некоторых случаях они имеют свои преимущества перед ременными и цепными приводами. Тросовые приводы могут выполнять ту же функцию, что и ремни, а также могут быть проще и экономичнее в реализации в некоторых приложениях. Например, новая серия синхронизированных тросовых приводов предназначена для положительного натяжения и заменяет обычные тросы, простые тросы и зубчатые приводы, особенно в ограниченном пространстве. Новый тросовый привод предназначен для обеспечения высокоточного позиционирования в электронном оборудовании, таком как копировальные машины, плоттеры, пишущие машинки, принтеры и т. д. Ключевой особенностью нового тросового привода является его способность использоваться в трехмерных змеевидных конфигурациях, которые позволяют чрезвычайно миниатюрные конструкции. Тросы синхронизатора могут использоваться с меньшим натяжением по сравнению с канатами, что снижает потребление энергии. Свяжитесь с AGS-TECH, если у вас есть вопросы и мнения о ременных, цепных и тросовых приводах. CLICK Product Finder-Locator Service ПРЕДЫДУЩАЯ СТРАНИЦА
- Быстрое прототипирование, настольное производство, аддитивное производство, моделирование наплавлением
Быстрое прототипирование, настольное производство, аддитивное производство, стереолитография, Polyjet, моделирование наплавлением, селективное лазерное спекание, FDM, SLS Аддитивное и быстрое производство В последние годы мы наблюдаем рост спроса на БЫСТРОЕ ПРОИЗВОДСТВО или БЫСТРОЕ ПРОТОТИПИРОВАНИЕ. Этот процесс также может называться НАСТОЛЬНЫМ ПРОИЗВОДСТВОМ или ПРОИЗВОДСТВОМ СВОБОДНОЙ ФОРМЫ. В основном твердая физическая модель детали создается непосредственно из трехмерного чертежа САПР. Мы используем термин АДДИТИВНОЕ ПРОИЗВОДСТВО для этих различных методов, когда мы строим детали слоями. Используя интегрированное компьютерное оборудование и программное обеспечение, мы осуществляем аддитивное производство. Нашими методами быстрого прототипирования и производства являются СТЕРЕОЛИТОГРАФИЯ, ПОЛИФРАГМЕНТ, МОДЕЛИРОВАНИЕ НАПЛАВЛЕНИЕМ, СЕЛЕКТИВНОЕ ЛАЗЕРНОЕ СПЕКАНИЕ, ЭЛЕКТРОННО-ЛУЧЕВОЕ ПЛАВЛЕНИЕ, ТРЕХМЕРНАЯ ПЕЧАТЬ, ПРЯМОЕ ПРОИЗВОДСТВО, БЫСТРОЕ ОБОРУДОВАНИЕ. Мы рекомендуем вам нажать здесь, чтобыЗАГРУЗИТЕ наши схематические иллюстрации процессов аддитивного и быстрого производства от AGS-TECH Inc. Это поможет вам лучше понять информацию, которую мы предоставляем вам ниже. Быстрое прототипирование обеспечивает нам: 1.) Концептуальный дизайн продукта просматривается с разных сторон на мониторе с помощью системы 3D/CAD. 2.) Прототипы из неметаллических и металлических материалов изготавливаются и исследуются с функциональной, технической и эстетической точек зрения. 3.) Недорогое прототипирование в очень короткие сроки. Аддитивное производство можно сравнить с изготовлением буханки хлеба путем укладки и соединения отдельных ломтиков друг с другом. Другими словами, продукт изготавливается ломтик за ломтиком или слой за слоем накладывается друг на друга. Большинство деталей может быть изготовлено в течение нескольких часов. Этот метод хорош, если детали нужны очень быстро или если необходимое количество невелико, а изготовление формы и оснастки слишком дорого и занимает много времени. Однако стоимость детали высока из-за дорогого сырья. • СТЕРЕОЛИТОГРАФИЯ: Этот метод, также сокращенно называемый STL, основан на отверждении и отверждении жидкого фотополимера до определенной формы путем фокусировки на нем лазерного луча. Лазер полимеризует фотополимер и отверждает его. Путем сканирования УФ-лазерным лучом по запрограммированной форме вдоль поверхности фотополимерной смеси деталь изготавливается снизу вверх в виде отдельных срезов, расположенных каскадом друг над другом. Сканирование лазерного пятна повторяется много раз для достижения геометрии, запрограммированной в системе. После того, как деталь полностью изготовлена, ее снимают с платформы, промокают и очищают ультразвуком и спиртовой ванной. Затем он подвергается воздействию УФ-излучения в течение нескольких часов, чтобы убедиться, что полимер полностью отвердел и затвердел. Подводя итог процессу, платформа, которая погружается в фотополимерную смесь, и УФ-лазерный луч контролируются и перемещаются через систему сервоуправления в соответствии с формой желаемой детали, и деталь получается путем фотоотверждения полимера слой за слоем. Разумеется, максимальные размеры изготавливаемой детали определяются стереолитографическим оборудованием. • POLYJET: Подобно струйной печати, в Polyjet у нас есть восемь печатающих головок, которые наносят фотополимер на модельный лоток. Ультрафиолетовый свет, помещенный рядом с форсунками, мгновенно отверждает и укрепляет каждый слой. В Polyjet используются два материала. Первый материал предназначен для изготовления самой модели. Второй материал, гелеобразная смола, используется для поддержки. Оба эти материала наносятся послойно и одновременно отверждаются. После завершения модели вспомогательный материал удаляется водным раствором. Используемые смолы аналогичны стереолитографии (STL). Polyjet имеет следующие преимущества перед стереолитографией: 1) Нет необходимости в очистке деталей. 2.) Нет необходимости в отверждении после обработки. 3.) Возможна меньшая толщина слоя, и, таким образом, мы получаем лучшее разрешение и можем изготавливать более тонкие детали. • МОДЕЛИРОВАНИЕ НАПЛАВЛЕНИЕМ: также сокращенно FDM, в этом методе головка экструдера, управляемая роботом, перемещается по столу в двух основных направлениях. Трос опускается и поднимается по мере необходимости. Из отверстия нагретой головки на головке выдавливается термопластичная нить и наносится начальный слой на пенопластовую основу. Это достигается за счет того, что головка экструдера движется по заданной траектории. После начального слоя стол опускают и последующие слои накладывают друг на друга. Иногда при изготовлении сложной детали необходимы опорные конструкции, чтобы наплавка могла продолжаться в определенных направлениях. В этих случаях материал-подложка экструдируется с менее плотным расположением нитей на слое, так что он слабее материала модели. Эти опорные конструкции могут быть впоследствии растворены или разорваны после завершения изготовления детали. Размеры головки экструдера определяют толщину экструдируемых слоев. Процесс FDM производит детали со ступенчатыми поверхностями на наклонных внешних плоскостях. Если эта шероховатость неприемлема, для ее сглаживания можно использовать химическую полировку в парах или нагретый инструмент. Даже полировальный воск доступен в качестве материала покрытия, чтобы исключить эти этапы и добиться разумных геометрических допусков. • ВЫБОРОЧНОЕ ЛАЗЕРНОЕ СПЕКАНИЕ: Также обозначаемый как SLS, процесс основан на выборочном спекании полимерных, керамических или металлических порошков в объект. В нижней части рабочей камеры есть два цилиндра: цилиндр для частичной сборки и цилиндр для подачи порошка. Первый постепенно опускается туда, где формируется спеченная деталь, а второй постепенно поднимается для подачи порошка в формовочный цилиндр через роликовый механизм. Сначала тонкий слой порошка осаждается в формовочном цилиндре, затем лазерный луч фокусируется на этом слое, отслеживая и расплавляя/спекая определенное поперечное сечение, которое затем снова затвердевает в твердое тело. Порошок — это участки, на которые не попадает лазерный луч, остаются рыхлыми, но все еще поддерживают твердую часть. Затем наносится еще один слой порошка, и процесс многократно повторяется для получения детали. В конце рыхлые частицы порошка стряхивают. Все это выполняется компьютером управления технологическим процессом с использованием инструкций, сгенерированных программой 3D CAD изготавливаемой детали. Различные материалы, такие как полимеры (например, АБС, ПВХ, полиэстер), воск, металлы и керамика, могут быть нанесены на соответствующие полимерные связующие. • ЭЛЕКТРОННЫЙ ЛУЧ MELTING: Аналогично избирательному лазерному спеканию, но с использованием электронного луча для плавления порошков титана или кобальта и хрома для изготовления прототипов в вакууме. Были сделаны некоторые разработки для выполнения этого процесса на нержавеющих сталях, алюминиевых и медных сплавах. Если необходимо повысить усталостную прочность изготовленных деталей, мы используем горячее изостатическое прессование после изготовления детали в качестве вторичного процесса. • ТРЕХМЕРНАЯ ПЕЧАТЬ: Также обозначается как 3DP, в этом методе печатающая головка наносит неорганическое связующее на слой неметаллического или металлического порошка. Поршень, несущий слой порошка, постепенно опускается, и на каждом этапе связующее наносится слой за слоем и сплавляется со связующим. В качестве порошковых материалов используются смеси полимеров и волокна, формовочный песок, металлы. Используя одновременно разные связующие головки и связующие вещества разных цветов, мы можем получить различные цвета. Процесс аналогичен струйной печати, но вместо цветного листа мы получаем цветной трехмерный объект. Изготовленные детали могут быть пористыми и, следовательно, могут потребовать спекания и пропитки металлом для увеличения их плотности и прочности. Спекание выжигает связующее и сплавляет металлические порошки. Для изготовления деталей можно использовать такие металлы, как нержавеющая сталь, алюминий, титан, а в качестве материалов для инфильтрации мы обычно используем медь и бронзу. Прелесть этой техники в том, что даже сложные и подвижные узлы могут быть изготовлены очень быстро. Например, зубчатая передача в сборе, гаечный ключ в качестве инструмента могут быть изготовлены с движущимися и вращающимися частями, готовыми к использованию. Различные компоненты сборки могут быть изготовлены в разных цветах и в одном кадре. Загрузите нашу брошюру:Основы 3D-печати металлом • ПРЯМОЕ ПРОИЗВОДСТВО и БЫСТРАЯ ИНСТРУМЕНТАЦИЯ: Помимо оценки конструкции и устранения неполадок, мы используем быстрое прототипирование для непосредственного производства продуктов или непосредственного применения в продуктах. Другими словами, быстрое прототипирование можно включить в обычные процессы, чтобы сделать их лучше и конкурентоспособнее. Например, быстрое прототипирование позволяет создавать шаблоны и формы. Образцы плавящегося и горящего полимера, созданные с помощью операций быстрого прототипирования, могут быть собраны для литья по выплавляемым моделям и вложены. Другим примером, который следует упомянуть, является использование 3DP для производства керамических литейных оболочек и его использования для операций литья оболочек. Даже пресс-формы для литья под давлением и вкладыши для пресс-форм могут быть изготовлены путем быстрого прототипирования, что позволяет сэкономить многие недели или месяцы времени на изготовление пресс-форм. Только анализируя файл САПР нужной детали, мы можем создать геометрию инструмента с помощью программного обеспечения. Вот некоторые из наших популярных методов быстрой обработки: RTV (вулканизация при комнатной температуре) ФОРМОВАНИЕ / ЛИТЬЕ УРЕТАНА: Для изготовления модели желаемой детали можно использовать быстрое прототипирование. Затем этот образец покрывают разделительным составом и заливают жидким каучуком RTV для изготовления половинок пресс-формы. Затем эти половинки формы используются для литья под давлением жидких уретанов. Срок службы пресс-формы короткий, всего около 0 или 30 циклов, но этого достаточно для мелкосерийного производства. ACES (Acetal Clear Epoxy Solid) ЛИТЬЕ ДЛЯ ИНСТРУМЕНТА: Используя методы быстрого прототипирования, такие как стереолитография, мы производим пресс-формы для литья под давлением. Эти формы представляют собой оболочки с открытым концом для заполнения такими материалами, как эпоксидная смола, эпоксидная смола с алюминиевым наполнителем или металлы. Опять же, срок службы пресс-формы ограничен десятками или максимум сотнями деталей. ПРОЦЕСС ИЗГОТОВЛЕНИЯ ИНСТРУМЕНТА НАПЫЛЕННЫМ МЕТАЛЛОМ: Мы используем быстрое прототипирование и делаем шаблон. Мы распыляем сплав цинка с алюминием на поверхность рисунка и покрываем его. Затем шаблон с металлическим покрытием помещают внутрь колбы и заливают эпоксидной смолой или эпоксидной смолой с алюминиевым наполнителем. Наконец, он удаляется, и, изготовив две такие половинки формы, мы получаем готовую форму для литья под давлением. Эти пресс-формы имеют более длительный срок службы, в некоторых случаях, в зависимости от материала и температуры, они могут производить тысячи деталей. ПРОЦЕСС KEELTOOL: Этот метод позволяет производить пресс-формы со сроком службы от 100 000 до 10 миллионов циклов. Используя быстрое прототипирование, мы изготавливаем пресс-форму RTV. Затем форму заполняют смесью, состоящей из порошка инструментальной стали А6, карбида вольфрама, полимерного связующего, и оставляют для отверждения. Затем эту форму нагревают, чтобы полимер выгорел, а металлические порошки расплавились. Следующим шагом является пропитка медью для изготовления окончательной формы. При необходимости на пресс-форме могут быть выполнены вторичные операции, такие как механическая обработка и полировка, для повышения точности размеров. CLICK Product Finder-Locator Service ПРЕДЫДУЩАЯ СТРАНИЦА
- Процессы соединения, сборки и крепления, сварка, пайка, пайка
Процессы соединения, сборки и крепления, сварка, пайка, пайка, спекание, клеевое соединение, пресс-фитинг, пайка волной и оплавлением, газовая печь Процессы соединения, сборки и крепления Мы соединяем, собираем и скрепляем ваши изготовленные детали и превращаем их в готовые изделия или полуфабрикаты, используя СВАРКУ, ПАЙКУ, ПАЙКУ, СПЕЧЕНИЕ, СКЛЕИВАНИЕ, КРЕПЛЕНИЕ, ПРЕСС-ФИТИНГ. Некоторыми из наших самых популярных сварочных процессов являются дуговая, газокислородная, контактная, проекционная, шовная, осадочная, ударная, твердотельная, электронно-лучевая, лазерная, термитная, индукционная сварка. Нашими популярными процессами пайки являются горелка, индукционная пайка, печная пайка и пайка погружением. Нашими методами пайки являются железо, горячая плита, печь, индукция, погружение, волна, пайка оплавлением и ультразвуковая пайка. Для клеевого соединения мы часто используем термопласты и термореактивные, эпоксидные, фенольные, полиуретановые, клеевые сплавы, а также некоторые другие химикаты и ленты. Наконец, наши процессы крепления состоят из забивания гвоздей, завинчивания гаек и болтов, заклепывания, зажима, закрепления штифтами, сшивания и скрепления скобами, а также прессовой посадки. • СВАРКА: Сварка включает в себя соединение материалов путем плавления заготовок и введения присадочных материалов, которые также соединяются с расплавленной сварочной ванной. Когда участок остынет, получим прочный стык. В некоторых случаях применяется давление. В отличие от сварки, операции пайки и пайки включают только плавление материала с более низкой температурой плавления между заготовками, а заготовки не плавятся. Мы рекомендуем вам нажать здесь, чтобыСКАЧАТЬ наши схематические иллюстрации сварочных процессов от AGS-TECH Inc. Это поможет вам лучше понять информацию, которую мы предоставляем вам ниже. В ДУГОВОЙ СВАРКЕ мы используем источник питания и электрод для создания электрической дуги, которая плавит металлы. Место сварки защищено защитным газом, паром или другим материалом. Этот процесс популярен для сварки автомобильных деталей и стальных конструкций. При дуговой сварке металлическим электродом (SMAW), также известной как сварка стержнем, стержень электрода подносится близко к основному материалу, и между ними возникает электрическая дуга. Электродный стержень плавится и действует как наполнитель. Электрод также содержит флюс, который действует как слой шлака и выделяет пары, действующие как защитный газ. Они защищают зону сварки от загрязнения окружающей среды. Другие наполнители не используются. Недостатками этого процесса являются его медлительность, необходимость частой замены электродов, необходимость отщепления остаточного шлака от флюса. Ряд металлов, таких как железо, сталь, никель, алюминий, медь и т. д. Можно сваривать. Его преимуществами являются его недорогие инструменты и простота использования. Газовая дуговая сварка металлическим электродом (GMAW), также известная как металл-инертный газ (MIG), у нас есть непрерывная подача наполнителя расходуемой электродной проволоки и инертного или частично инертного газа, который обтекает проволоку, защищая область сварки от загрязнения окружающей средой. Можно сваривать сталь, алюминий и другие цветные металлы. Преимуществами MIG являются высокая скорость сварки и хорошее качество. Недостатками являются его сложное оборудование и проблемы, с которыми приходится сталкиваться в ветреную погоду на открытом воздухе, потому что мы должны поддерживать стабильность защитного газа вокруг зоны сварки. Разновидностью GMAW является дуговая сварка с флюсовой проволокой (FCAW), которая состоит из тонкой металлической трубки, заполненной флюсовыми материалами. Иногда флюса внутри трубки достаточно для защиты от загрязнения окружающей среды. Дуговая сварка под флюсом (SAW) — широко автоматизированный процесс, включающий непрерывную подачу проволоки и дугу, которая зажигается под слоем флюсового покрытия. Производительность и качество высоки, сварочный шлак легко отделяется, и у нас нет дыма на рабочем месте. Недостатком является то, что его можно использовать только для сварки parts в определенных положениях. При дуговой сварке вольфрамовым электродом (GTAW) или сварке вольфрамовым электродом в среде инертного газа (TIG) мы используем вольфрамовый электрод вместе с отдельным наполнителем и инертными или почти инертными газами. Как мы знаем, вольфрам имеет высокую температуру плавления, и это очень подходящий металл для очень высоких температур. Вольфрам в TIG не расходуется, в отличие от других методов, описанных выше. Медленная, но качественная технология сварки, имеющая преимущества перед другими методами сварки тонких материалов. Подходит для многих металлов. Плазменная дуговая сварка аналогична, но для создания дуги используется плазменный газ. Дуга при плазменной дуговой сварке относительно более концентрированная по сравнению с GTAW и может использоваться для более широкого диапазона толщин металла при гораздо более высоких скоростях. GTAW и плазменная дуговая сварка могут применяться к более или менее одинаковым материалам. КИСЛОРОДНО-ТОПЛИВНАЯ / КИСЛОРОДНАЯ СВАРКА, также называемая кислородно-ацетиленовой сваркой, кислородной сваркой, газовой сваркой, осуществляется с использованием газового топлива и кислорода для сварки. Поскольку электроэнергия не используется, он портативный и может использоваться там, где нет электричества. Используя сварочную горелку, мы нагреваем детали и присадочный материал, чтобы получить общую ванну расплавленного металла. Можно использовать различные виды топлива, такие как ацетилен, бензин, водород, пропан, бутан и т. д. При кислородно-топливной сварке мы используем два контейнера, один для топлива, а другой для кислорода. Кислород окисляет топливо (сжигает его). СОПРОТИВНАЯ СВАРКА: Этот тип сварки использует джоулев нагрев, и тепло генерируется в месте, где подается электрический ток в течение определенного времени. Через металл пропускают большие токи. В этом месте образуются лужи расплавленного металла. Методы контактной сварки популярны из-за их эффективности и небольшого потенциала загрязнения. Однако недостатками являются относительно высокие затраты на оборудование и присущие этому способу ограничения относительно тонких заготовок. ТОЧЕЧНАЯ СВАРКА является одним из основных видов контактной сварки. Здесь мы соединяем два или более перекрывающихся листа или заготовки, используя два медных электрода, чтобы сжать листы вместе и пропустить через них сильный ток. Материал между медными электродами нагревается, и в этом месте образуется расплавленная ванна. Затем ток прекращается, и наконечники медных электродов охлаждают место сварки, поскольку электроды охлаждаются водой. Применение нужного количества тепла к нужному материалу и толщине является ключевым моментом для этой техники, потому что при неправильном применении соединение будет слабым. Точечная сварка имеет преимущества, заключающиеся в том, что она не вызывает значительной деформации заготовок, энергоэффективна, проста в автоматизации и обеспечивает выдающуюся производительность, а также не требует использования каких-либо наполнителей. Недостатком является то, что, поскольку сварка происходит точечно, а не образует непрерывный шов, общая прочность может быть относительно ниже по сравнению с другими методами сварки. ШВОВАЯ СВАРКА, с другой стороны, производит сварные швы на поверхностях сходных материалов. Шов может быть встык или внахлест. Сварка швов начинается с одного конца и постепенно переходит к другому. В этом методе также используются два электрода из меди для приложения давления и тока к области сварки. Электроды в форме дисков вращаются с постоянным контактом вдоль линии шва и производят непрерывный шов. Здесь также электроды охлаждаются водой. Сварные швы очень прочные и надежные. Другими методами являются проекционная сварка, сварка оплавлением и сварка с осадкой. СВАРКА ТВЕРДОГО ТЕЛА немного отличается от предыдущих методов, описанных выше. Коалесценция происходит при температурах ниже температуры плавления соединяемых металлов и без использования металлического наполнителя. В некоторых процессах может использоваться давление. Существуют различные методы: СОЭКСТРУЖНАЯ СВАРКА, при которой разнородные металлы выдавливаются через одну и ту же головку, СВАРКА ХОЛОДНЫМ ДАВЛЕНИЕМ, при которой мы соединяем мягкие сплавы при температуре ниже их точки плавления, ДИФФУЗИОННАЯ СВАРКА – метод без видимых линий сварки, СВАРКА ВЗРЫВОМ для соединения разнородных материалов, например, коррозионностойких сплавов с конструкционными. сталей, ЭЛЕКТРОМАГНИТНО-ИМПУЛЬСНАЯ СВАРКА, при которой трубы и листы ускоряются электромагнитными силами, КУЗОВАЯ СВАРКА, заключающаяся в нагреве металлов до высоких температур и сбивании их вместе, СВАРКА ТРЕНИЕМ, при которой выполняется сварка с достаточным трением, СВАРКА ТРЕНИЕМ С ПЕРЕМЕШИВАНИЕМ, при которой вращающийся расходуемый инструмент, пересекающий линию стыка, СВАРКА ГОРЯЧИМ ДАВЛЕНИЕМ, когда мы сжимаем металлы вместе при повышенных температурах ниже температуры плавления в вакууме или инертных газах, СВАРКА ГОРЯЧИМ ИЗОСТАТИЧЕСКИМ ДАВЛЕНИЕМ, процесс, при котором мы применяем давление с использованием инертных газов внутри сосуда, СВАРКА ВАЛКА, где мы соединяем разнородных материалов, помещая их между два вращающихся колеса, УЛЬТРАЗВУКОВАЯ СВАРКА, при которой тонкие листы металла или пластика свариваются с использованием высокочастотной вибрационной энергии. Другими нашими сварочными процессами являются ЭЛЕКТРОННО-ЛУЧЕВАЯ СВАРКА с глубоким проплавлением и быстрой обработкой, но поскольку это дорогостоящий метод, мы рассматриваем его для особых случаев, ЭЛЕКТРОШЛАКОВАЯ СВАРКА, метод, подходящий только для тяжелых толстых листов и заготовок из стали, ИНДУКЦИОННАЯ СВАРКА, где мы используем электромагнитную индукцию и нагрев наших электропроводящих или ферромагнитных заготовок, ЛАЗЕРНАЯ СВАРКА также с глубоким проплавлением и быстрой обработкой, но является дорогостоящим методом, ЛАЗЕРНАЯ ГИБРИДНАЯ СВАРКА, которая сочетает LBW и GMAW в одной сварочной головке и способна перекрыть зазоры 2 мм между пластинами, УДАРНАЯ СВАРКА, которая включает электрический разряд с последующей ковкой материалов под давлением, ТЕРМИТНАЯ СВАРКА, включающая экзотермическую реакцию между порошками алюминия и оксида железа., ЭЛЕКТРОГАЗОВАЯ СВАРКА с плавящимся электродом и используется только со сталью в вертикальном положении, и, наконец, ДУГОВАЯ СВАРКА ШПИЛЬКИ для соединения шпильки с основанием. материала с помощью тепла и давления. Мы рекомендуем вам нажать здесь, чтобыСКАЧАТЬ наши схематические иллюстрации процессов пайки, пайки и склеивания от AGS-TECH Inc. Это поможет вам лучше понять информацию, которую мы предоставляем вам ниже. • ПАЙКА: Мы соединяем два или более металлов, нагревая присадочные металлы между ними до температуры их плавления и используя капиллярное действие для их растекания. Процесс похож на пайку, но температура плавления наполнителя при пайке выше. Как и при сварке, флюс защищает присадочный материал от атмосферного загрязнения. После охлаждения заготовки соединяются между собой. Процесс включает в себя следующие ключевые этапы: хорошая посадка и зазор, правильная очистка основных материалов, правильное крепление, правильный выбор флюса и атмосферы, нагрев сборки и, наконец, очистка паяной сборки. Одним из наших процессов пайки является ГОРЕЛКА, популярный метод, выполняемый вручную или автоматически. Подходит для небольших производственных заказов и особых случаев. Тепло подается с помощью газового пламени вблизи места пайки. ПАЙКА В ПЕЧИ требует меньше навыков оператора и представляет собой полуавтоматический процесс, пригодный для промышленного массового производства. Преимуществом этого метода являются как контроль температуры, так и контроль атмосферы в печи, поскольку первый позволяет нам контролировать циклы нагрева и устранять локальный нагрев, как в случае пайки горелкой, а второй защищает деталь от окисления. Используя отсадочное оборудование, мы можем снизить производственные затраты до минимума. Недостатками являются высокое энергопотребление, стоимость оборудования и более сложные конструктивные решения. ВАКУУМНАЯ ПАЙКА происходит в вакуумной печи. Температурная однородность сохраняется, и мы получаем очень чистые соединения без флюсов с очень небольшими остаточными напряжениями. Термическая обработка может иметь место во время вакуумной пайки из-за низких остаточных напряжений, возникающих во время медленных циклов нагрева и охлаждения. Основным недостатком является его высокая стоимость, поскольку создание вакуумной среды является дорогостоящим процессом. Еще один метод – ПАЯКА ПОГРУЖЕНИЕМ – соединяет неподвижные детали, при этом на сопрягаемые поверхности наносится припой. После этого детали fixtured погружают в ванну с расплавленной солью, такой как хлорид натрия (поваренная соль), которая действует как теплоноситель и флюс. Воздух исключается, и поэтому не происходит образования оксида. При ИНДУКЦИОННОЙ ПАЯКЕ мы соединяем материалы присадочным металлом, температура плавления которого ниже, чем у основных материалов. Переменный ток от индукционной катушки создает электромагнитное поле, которое вызывает индукционный нагрев в основном ферромагнитных материалов. Этот метод обеспечивает избирательный нагрев, хорошие соединения с наполнителями, текущими только в нужных областях, небольшое окисление, поскольку отсутствует пламя, а охлаждение происходит быстро, быстрый нагрев, консистенция и пригодность для крупносерийного производства. Для ускорения наших процессов и обеспечения согласованности мы часто используем преформы. Информацию о нашем предприятии для пайки керамики и металла, герметизации, вакуумных вводов, высоком и сверхвысоком вакууме и компонентах управления подачей жидкости можно найти здесь: Брошюра о паяльном заводе • ПАЯЯ: При пайке мы имеем дело не с плавлением заготовок, а с плавлением присадочного металла с более низкой температурой плавления, чем у соединяемых деталей, который затекает в соединение. Припой при пайке плавится при более низкой температуре, чем при пайке. Мы используем бессвинцовые сплавы для пайки и соответствуют требованиям RoHS, а для различных применений и требований у нас есть различные и подходящие сплавы, такие как серебряный сплав. Пайка предлагает нам соединения, непроницаемые для газа и жидкости. При МЯГКОЙ ПАЙКЕ наш припой имеет температуру плавления ниже 400 градусов по Цельсию, в то время как при ПАЯКЕ СЕРЕБРОМ и ПАЙКЕ нам нужны более высокие температуры. Мягкая пайка использует более низкие температуры, но не дает прочных соединений для требовательных приложений при повышенных температурах. С другой стороны, серебряная пайка требует высоких температур, обеспечиваемых горелкой, и дает нам прочные соединения, подходящие для высокотемпературных применений. Пайка требует самых высоких температур, и обычно используется горелка. Поскольку паяные соединения очень прочные, они хорошо подходят для ремонта тяжелых железных предметов. В наших производственных линиях мы используем как ручную пайку, так и автоматические линии пайки. ИНДУКЦИОННАЯ ПАЙКА использует высокочастотный переменный ток в медной катушке для облегчения индукционного нагрева. В месте пайки индуцируются токи, в результате чего на высоком сопротивлении joint выделяется тепло. Это тепло расплавляет присадочный металл. Также используется флюс. Индукционная пайка является хорошим методом пайки цилиндров и труб в непрерывном процессе путем наматывания на них катушек. Пайка некоторых материалов, таких как графит и керамика, более сложна, поскольку требует покрытия деталей подходящим металлом перед пайкой. Это облегчает межфазное соединение. Мы припаиваем такие материалы специально для герметичных упаковок. Мы производим наши печатные платы (PCB) в больших объемах, в основном, с использованием пайки волной. Только для небольшого количества прототипов мы используем ручную пайку паяльником. Мы используем пайку волной припоя как для сквозных, так и для поверхностного монтажа печатных плат (PCBA). Временный клей удерживает компоненты прикрепленными к печатной плате, а сборка помещается на конвейер и проходит через оборудование, содержащее расплавленный припой. Сначала печатная плата оплавляется, а затем поступает в зону предварительного нагрева. Расплавленный припой находится в поддоне и имеет на своей поверхности узор стоячих волн. Когда печатная плата движется по этим волнам, эти волны касаются нижней части печатной платы и прилипают к контактным площадкам для пайки. Припой остается только на выводах и контактных площадках, но не на самой печатной плате. Волны в расплавленном припое должны хорошо контролироваться, чтобы не было разбрызгивания, а вершины волн не касались и не загрязняли нежелательные участки платы. При пайке оплавлением мы используем липкую паяльную пасту для временного прикрепления электронных компонентов к плате. Затем платы помещают в печь оплавления с контролем температуры. Здесь припой плавится и соединяет компоненты навсегда. Мы используем эту технику как для компонентов поверхностного монтажа, так и для компонентов сквозного монтажа. Надлежащий контроль температуры и регулировка температуры печи необходимы, чтобы избежать разрушения электронных компонентов на плате из-за их перегрева выше их максимальных температурных пределов. В процессе пайки оплавлением у нас фактически есть несколько областей или стадий, каждая из которых имеет свой температурный профиль, например, стадия предварительного нагрева, стадия термической выдержки, стадия оплавления и охлаждения. Эти различные шаги необходимы для безповрежденной пайки оплавлением сборок печатных плат (PCBA). УЛЬТРАЗВУКОВАЯ ПАЯЯ — еще один часто используемый метод с уникальными возможностями. Его можно использовать для пайки стекла, керамики и неметаллических материалов. Например, фотогальванические панели, которые являются неметаллическими, нуждаются в электродах, которые можно прикрепить с помощью этого метода. При ультразвуковой пайке используется нагретое паяльное жало, которое также излучает ультразвуковые колебания. Эти вибрации создают кавитационные пузырьки на границе подложки с расплавленным припоем. Имплозивная энергия кавитации модифицирует оксидную поверхность и удаляет грязь и оксиды. За это время также образуется слой сплава. Припой на склеиваемой поверхности содержит кислород и обеспечивает прочную общую связь между стеклом и припоем. ПАЙКА ПОГРУЖЕНИЕМ может рассматриваться как более простая версия пайки волной припоя, подходящая только для мелкосерийного производства. Первый очищающий флюс применяется, как и в других процессах. Платы с установленными компонентами погружаются вручную или в полуавтоматическом режиме в емкость с расплавленным припоем. Расплавленный припой прилипает к открытым металлическим участкам платы, незащищенным паяльной маской. Оборудование простое и недорогое. • КЛЕЙНОЕ СОЕДИНЕНИЕ: Это еще один популярный метод, который мы часто используем, и он включает в себя склеивание поверхностей с помощью клея, эпоксидных смол, пластификаторов или других химикатов. Склеивание осуществляется путем испарения растворителя, термоотверждения, отверждения УФ-светом, отверждения под давлением или ожидания в течение определенного времени. В наших производственных линиях используются различные высокоэффективные клеи. При правильно спроектированных процессах нанесения и отверждения клеевое соединение может привести к прочным и надежным соединениям с очень низким напряжением. Адгезионные соединения могут быть хорошими защитниками от факторов окружающей среды, таких как влага, загрязняющие вещества, коррозионные вещества, вибрация и т. д. Преимущества клеевого соединения: они могут применяться к материалам, которые в противном случае было бы трудно паять, сваривать или паять. Также это может быть предпочтительнее для термочувствительных материалов, которые могут быть повреждены при сварке или других высокотемпературных процессах. Другие преимущества клея заключаются в том, что его можно наносить на поверхности неправильной формы и очень незначительно увеличивать вес сборки по сравнению с другими методами. Кроме того, размерные изменения деталей очень минимальны. Некоторые клеи обладают свойствами согласования преломления и могут использоваться между оптическими компонентами без значительного снижения силы света или оптического сигнала. Недостатками, с другой стороны, являются более длительное время отверждения, которое может замедлить производственные линии, требования к креплению, требования к подготовке поверхности и трудности с разборкой, когда требуется доработка. Большинство наших операций по склеиванию состоят из следующих этапов: -Обработка поверхности: распространены специальные процедуры очистки, такие как очистка деионизированной водой, очистка спиртом, плазменная очистка или очистка коронным разрядом. После очистки мы можем нанести на поверхности усилители адгезии, чтобы обеспечить наилучшее соединение. - Крепление деталей: как для нанесения клея, так и для отверждения мы разрабатываем и используем специальные приспособления. - Нанесение клея: мы иногда используем ручные, а иногда, в зависимости от случая, автоматизированные системы, такие как робототехника, серводвигатели, линейные приводы, для доставки клея в нужное место, и мы используем диспенсеры для доставки его в нужном объеме и количестве. -Отверждение: в зависимости от клея, мы можем использовать простую сушку и отверждение, а также отверждение под воздействием УФ-излучения, которое действует как катализатор, или отверждение при нагревании в печи или с использованием резистивных нагревательных элементов, установленных на приспособлениях и приспособлениях. Мы рекомендуем вам нажать здесь, чтобыСКАЧАТЬ наши схематические иллюстрации процессов крепления от AGS-TECH Inc. Это поможет вам лучше понять информацию, которую мы предоставляем вам ниже. • ПРОЦЕССЫ КРЕПЛЕНИЯ: Наши процессы механического соединения делятся на две категории: КРЕПЕЖНЫЕ СОЕДИНЕНИЯ и ЦЕЛЬНЫЕ СОЕДИНЕНИЯ. Примеры используемых нами крепежных элементов: винты, штифты, гайки, болты, заклепки. Примерами неразъемных соединений, которые мы используем, являются защелки и термоусадки, швы, гофры. Используя различные методы крепления, мы обеспечиваем прочность и надежность наших механических соединений в течение многих лет эксплуатации. ВИНТЫ и БОЛТЫ являются одними из наиболее часто используемых крепежных элементов для скрепления объектов и их позиционирования. Наши винты и болты соответствуют стандартам ASME. Используются различные типы винтов и болтов, включая винты с шестигранной головкой и болты с шестигранной головкой, винты и болты с запаздыванием, двухсторонний винт, дюбельный винт, винт с проушиной, винт для зеркала, винт для листового металла, винт для точной регулировки, самосверлящие и самонарезающие винты. , установочный винт, винты со встроенными шайбами и многое другое. У нас есть различные типы головок винтов, такие как потайная, купольная, круглая, с фланцевой головкой, а также различные типы винтовых приводов, такие как шлицевые, крестообразные, квадратные, шестигранные. RIVET, с другой стороны, представляет собой постоянное механическое крепление, состоящее из гладкого цилиндрического стержня и головки с одной стороны. После вставки другой конец заклепки деформируется, а ее диаметр увеличивается, чтобы она оставалась на месте. Другими словами, до установки заклепка имеет одну головку, а после установки две. Мы устанавливаем различные типы заклепок в зависимости от области применения, прочности, доступности и стоимости, такие как заклепки со сплошной/круглой головкой, конструкционные, полутрубчатые, глухие, оскарные, приводные, заподлицо, фрикционные, самонарезающие заклепки. Клепка может быть предпочтительнее в тех случаях, когда необходимо избежать тепловой деформации и изменения свойств материала из-за тепла сварки. Клепка также предлагает легкий вес и особенно хорошую прочность и устойчивость к сдвиговым усилиям. Однако при растягивающих нагрузках более подходящими могут быть винты, гайки и болты. В процессе CLINCHING мы используем специальные пуансоны и штампы для создания механического сцепления между соединяемыми листовыми металлами. Пуансон проталкивает слои листового металла в полость штампа, что приводит к образованию неразъемного соединения. При клинче не требуется ни нагрева, ни охлаждения, это холодный рабочий процесс. Это экономичный процесс, который в некоторых случаях может заменить точечную сварку. В СОЕДИНЕНИИ мы используем штифты, которые представляют собой элементы машины, используемые для фиксации положения частей машины относительно друг друга. Основные типы: шплинт, шплинт, пружинный штифт, установочный штифт, и шплинт. В СТЕПЛЕНИИ мы используем степлеры и скобы, которые представляют собой двухсторонние застежки, используемые для соединения или связывания материалов. Сшивание скобами имеет следующие преимущества: экономичность, простота и быстрота в использовании, головка скобы может использоваться для соединения материалов, соединенных встык, головка скобы может облегчить соединение куска, такого как кабель, и крепление его к поверхности без прокалывания или повреждения, относительно легкое удаление. ПРЕСС-ФИТИНГ выполняется путем сближения деталей, а трение между ними скрепляет детали. Детали с прессовой посадкой, состоящие из вала увеличенного размера и отверстия меньшего размера, обычно собираются одним из двух способов: либо путем приложения силы, либо с использованием теплового расширения или сжатия деталей. Когда пресс-фитинг устанавливается с усилием, мы используем либо гидравлический пресс, либо ручной пресс. С другой стороны, когда пресс-фитинг устанавливается за счет теплового расширения, мы нагреваем обволакивающие детали и собираем их на место в горячем виде. При охлаждении они сжимаются и возвращаются к своим нормальным размерам. Это приводит к хорошей прессовой посадке. Альтернативно мы называем это ТЕРМОФИТИНГОМ. Другой способ сделать это - охладить детали в оболочке перед сборкой, а затем вставить их в сопрягаемые детали. Когда сборка прогревается, они расширяются, и мы получаем плотную посадку. Этот последний метод может быть предпочтительнее в тех случаях, когда нагрев создает риск изменения свойств материала. Охлаждение в таких случаях более безопасно. Пневматические и гидравлические компоненты и узлы • Клапаны, гидравлические и пневматические компоненты, такие как уплотнительное кольцо, шайба, уплотнения, прокладка, кольцо, прокладка. Поскольку существует большое разнообразие клапанов и пневматических компонентов, мы не можем перечислить здесь все. В зависимости от физической и химической среды вашего применения у нас есть специальные продукты для вас. Пожалуйста, укажите область применения, тип компонента, технические характеристики, условия окружающей среды, такие как давление, температура, жидкости или газы, которые будут контактировать с вашими клапанами и пневматическими компонентами; и мы подберем для вас наиболее подходящий продукт или изготовим его специально для вашего применения. CLICK Product Finder-Locator Service ПРЕДЫДУЩАЯ СТРАНИЦА
- Производство стекла и керамики, герметическая упаковка, уплотнения, склеивание
Производство стекла и керамики, Уплотнения и склеивание герметичных упаковок, Закаленное пуленепробиваемое стекло, Выдувное формование, Стекло оптического класса, Проводящее стекло, Литье Формование и формование стекла и керамики Типы производства стекла, которые мы предлагаем, включают тарное стекло, выдувание стекла, стекловолокно, трубы и стержни, бытовую и промышленную посуду, лампы и колбы, прецизионное литье стекла, оптические компоненты и сборки, плоское и листовое и флоат-стекло. Мы выполняем как ручную, так и машинную формовку. Нашими популярными процессами производства технической керамики являются штамповка, изостатическое прессование, горячее изостатическое прессование, горячее прессование, шликерное литье, ленточное литье, экструзия, литье под давлением, необработанная обработка, спекание или обжиг, алмазное шлифование, герметичные сборки. Мы рекомендуем вам нажать здесь, чтобы СКАЧАТЬ наши схематические иллюстрации процессов формовки и обработки стекла от AGS-TECH Inc. СКАЧАТЬ наши схематические иллюстрации процессов производства технической керамики от AGS-TECH Inc. Эти загружаемые файлы с фотографиями и эскизами помогут вам лучше понять информацию, которую мы предоставляем вам ниже. • ПРОИЗВОДСТВО СТЕКЛЯННОЙ ТАРЫ: У нас есть автоматизированные линии ПРЕСС-ВДУВ, а также линии ВДУВ-ВЫДУВ для производства. В процессе выдува и выдувания мы бросаем каплю в заготовку и формируем горловину, применяя удар сжатым воздухом сверху. Сразу после этого сжатый воздух продувают второй раз в другом направлении через горлышко контейнера, чтобы сформировать заготовку бутылки. Эта заготовка затем переносится в фактическую форму, повторно нагревается для смягчения и подается сжатый воздух, чтобы придать заготовке окончательную форму контейнера. Точнее говоря, он находится под давлением и прижимается к стенкам полости выдувной формы, чтобы принять желаемую форму. Наконец, изготовленная стеклянная тара переносится в печь отжига для последующего повторного нагрева и снятия напряжений, возникающих при формовании, и охлаждается контролируемым образом. В методе прессования и выдувания расплавленные капли помещаются в форму для изготовления заготовок (заготовка) и прессуются в форму для заготовок (заготовка). Затем заготовки переносятся в формы для выдувания и выдуваются аналогично процессу, описанному выше в разделе «Процесс выдувания и выдувания». Последующие шаги, такие как отжиг и снятие напряжения, аналогичны или одинаковы. • ВЫДУВАНИЕ СТЕКЛА: Мы производим изделия из стекла, используя как обычное ручное выдувание, так и использование сжатого воздуха на автоматизированном оборудовании. Для некоторых заказов требуется обычное выдувание, например, проекты, связанные со стеклянными изделиями, или проекты, требующие меньшего количества деталей с небольшими допусками, прототипы / демонстрационные проекты и т. д. Обычное выдувание стекла включает погружение полой металлической трубы в кастрюлю с расплавленным стеклом и вращение трубы для сбора некоторого количества стеклянного материала. Стекло, собранное на конце трубы, прокатывается на плоском железе, придается желаемая форма, удлиняется, повторно нагревается и продувается воздухом. Когда он готов, он вставляется в форму и продувается воздухом. Полость формы мокрая, чтобы избежать контакта стекла с металлом. Водяная пленка действует как подушка между ними. Ручное выдувание — это трудоемкий медленный процесс, который подходит только для прототипирования или изделий высокой стоимости, не подходит для недорогих заказов в больших объемах. • ПРОИЗВОДСТВО БЫТОВОЙ И ПРОМЫШЛЕННОЙ СТЕКЛЯННОЙ ПОСУДА: Используя различные типы стеклянных материалов, производится большое разнообразие стеклянной посуды. Некоторые стекла термостойкие и подходят для лабораторной посуды, а некоторые достаточно хороши для того, чтобы выдерживать многократное мытье в посудомоечной машине и пригодны для изготовления бытовых изделий. На машинах Westlake производятся десятки тысяч стаканов в день. Для упрощения расплавленное стекло собирается вакуумом и помещается в формы для изготовления заготовок. Затем в формы вдувается воздух, они переносятся в другую форму, снова вдувается воздух, и стекло принимает окончательную форму. Как и при ручном выдувании, эти формы увлажняются водой. Дальнейшее растяжение является частью завершающей операции по формированию грифа. Лишнее стекло сгорает. После этого следует контролируемый процесс повторного нагрева и охлаждения, описанный выше. • ФОРМОВАНИЕ СТЕКЛЯННЫХ ТРУБ И СТЕРЖНЕЙ: Основными процессами, которые мы используем для производства стеклянных труб, являются процессы DANNER и VELLO. В процессе Даннера стекло из печи течет и падает на наклонную втулку из огнеупорных материалов. Гильза закреплена на вращающемся полом валу или паяльной трубке. Затем стекло оборачивается вокруг рукава и образует гладкий слой, стекающий по рукаву и на кончик стержня. При формовании труб воздух продувается через нагнетательную трубку с полым наконечником, а при формовании стержней используются сплошные наконечники на валу. Затем трубы или стержни протягиваются по несущим роликам. Размеры, такие как толщина стенок и диаметр стеклянных трубок, регулируются до желаемых значений путем установки диаметра рукава и давления продувочного воздуха до желаемого значения, регулировки температуры, скорости потока стекла и скорости вытягивания. С другой стороны, процесс производства стеклянных трубок Vello включает в себя перемещение стекла из печи в чашу с помощью полой оправки или колокола. Затем стекло проходит через воздушное пространство между оправкой и чашей и принимает форму трубки. После этого он перемещается по роликам на волочильную машину и охлаждается. В конце линии охлаждения происходит резка и окончательная обработка. Размеры трубы можно регулировать так же, как и в процессе Даннера. Сравнивая процесс Даннера с процессом Велло, мы можем сказать, что процесс Велло лучше подходит для крупносерийного производства, тогда как процесс Даннера может лучше подходить для точных заказов труб меньшего объема. • ПЕРЕРАБОТКА ЛИСТОВОГО, ПЛОСКОГО И ФЛОАТ-СТЕКЛА: У нас есть большое количество листового стекла толщиной от субмиллиметров до нескольких сантиметров. Наши плоские очки почти оптически совершенны. Мы предлагаем стекло со специальными покрытиями, такими как оптические покрытия, где метод химического осаждения из паровой фазы используется для нанесения покрытий, таких как просветляющее или зеркальное покрытие. Также распространены прозрачные проводящие покрытия. Также доступны гидрофобные или гидрофильные покрытия на стекле, а также покрытия, обеспечивающие самоочищение стекла. Закаленное, пуленепробиваемое и ламинированное стекло — еще одна популярная вещь. Мы режем стекло нужной формы с заданными допусками. Доступны и другие вторичные операции, такие как изгибание или гибка плоского стекла. • ПРЕЦИЗИОННОЕ ФОРМОВАНИЕ СТЕКЛА: мы используем эту технику в основном для изготовления прецизионных оптических компонентов без необходимости использования более дорогих и трудоемких методов, таких как шлифовка, притирка и полировка. Этот метод не всегда достаточен для изготовления лучшей из лучших оптических систем, но в некоторых случаях, таких как потребительские товары, цифровые камеры, медицинская оптика, он может быть менее дорогим хорошим вариантом для крупносерийного производства. Кроме того, он имеет преимущество перед другими методами формования стекла, когда требуется сложная геометрия, например, в случае асфер. Основной процесс включает в себя загрузку нижней стороны нашей формы стеклянной заготовкой, вакуумирование технологической камеры для удаления кислорода, близкое закрытие формы, быстрый и изотермический нагрев матрицы и стекла инфракрасным светом, дальнейшее закрытие половинок формы. медленное контролируемое прессование размягченного стекла до желаемой толщины и, наконец, охлаждение стекла, заполнение камеры азотом и удаление продукта. Точный контроль температуры, расстояние закрытия формы, усилие закрытия формы, соответствие коэффициентов расширения формы и материала стекла являются ключевыми в этом процессе. • ПРОИЗВОДСТВО СТЕКЛЯННЫХ ОПТИЧЕСКИХ КОМПОНЕНТОВ И СБОРОК: Помимо прецизионного формования стекла, мы используем ряд ценных процессов для изготовления высококачественных оптических компонентов и сборок для требовательных приложений. Шлифовка, притирка и полировка оптических стекол в мелкозернистых специальных абразивных суспензиях — это искусство и наука для изготовления оптических линз, призм, плоскостей и многого другого. Плоскостность поверхности, волнистость, гладкость и бездефектность оптических поверхностей требуют большого опыта работы с такими процессами. Небольшие изменения в окружающей среде могут привести к выпуску продукции, не соответствующей спецификации, и остановке производственной линии. Бывают случаи, когда однократное протирание оптической поверхности чистой тканью может привести к тому, что продукт будет соответствовать спецификациям или не пройти тест. Некоторые популярные стеклянные материалы: плавленый кварц, кварц, BK7. Также сборка таких компонентов требует специализированного опыта ниши. Иногда используются специальные клеи. Однако иногда метод, называемый оптическим контактом, является лучшим выбором и не требует использования материала между прикрепленными оптическими стеклами. Он состоит из физического контакта плоских поверхностей для соединения друг с другом без клея. В некоторых случаях для сборки оптических компонентов на определенных расстояниях и с определенной геометрической ориентацией друг к другу используются механические прокладки, прецизионные стеклянные стержни или шарики, зажимы или механически обработанные металлические компоненты. Давайте рассмотрим некоторые из наших популярных методов изготовления высококачественной оптики. ШЛИФОВКА И ПРИТРОЙКА И ПОЛИРОВКА: Грубая форма оптического компонента получается путем шлифовки стеклянной заготовки. После этого осуществляют притирку и полировку путем вращения и трения шероховатых поверхностей оптических компонентов об инструменты с желаемой формой поверхности. Между оптикой и формовочными инструментами заливается суспензия с мельчайшими абразивными частицами и жидкостью. Размеры абразивных частиц в таких суспензиях можно выбирать в соответствии с желаемой степенью плоскостности. Отклонения критических оптических поверхностей от желаемой формы выражаются в терминах длины волны используемого света. Наша высокоточная оптика имеет допуски в десятые доли длины волны (длина волны/10) или даже более жесткие. Помимо профиля поверхности, критические поверхности сканируются и оцениваются на наличие других особенностей поверхности и дефектов, таких как размеры, царапины, сколы, ямки, пятна и т. д. Жесткий контроль условий окружающей среды в цехе оптического производства и обширные требования к метрологии и испытаниям с использованием самого современного оборудования делают эту отрасль промышленности сложной задачей. • ВТОРИЧНЫЕ ПРОЦЕССЫ В ПРОИЗВОДСТВЕ СТЕКЛА: Опять же, мы ограничены только вашим воображением, когда речь идет о вторичных и чистовых процессах обработки стекла. Здесь мы перечислим некоторые из них: -Покрытия на стекле (оптические, электрические, трибологические, термические, функциональные, механические...). Например, мы можем изменить свойства поверхности стекла, заставив его, например, отражать тепло, чтобы оно сохраняло прохладу внутри здания, или сделать одну сторону поглощающей инфракрасное излучение с помощью нанотехнологий. Это помогает сохранять тепло внутри зданий, потому что самый внешний поверхностный слой стекла поглощает инфракрасное излучение внутри здания и излучает его обратно внутрь. -Травление на стекле -Прикладная керамическая маркировка (ACL) -Гравировка - Пламенная полировка -Химическая полировка -Окрашивание ПРОИЗВОДСТВО ТЕХНИЧЕСКОЙ КЕРАМИКИ • ПРЕССОВАНИЕ В МАСШТАБЕ: Состоит из одноосного прессования гранулированных порошков, заключенных в пресс-форму. • ГОРЯЧЕЕ ПРЕССОВАНИЕ: Подобно прессованию под давлением, но с добавлением температуры для повышения уплотнения. Порошок или прессованная заготовка помещается в графитовую матрицу и прикладывается одноосное давление, в то время как матрица выдерживается при высоких температурах, таких как 2000 C. Температуры могут быть разными в зависимости от типа обрабатываемого керамического порошка. Для сложных форм и геометрии может потребоваться другая последующая обработка, такая как алмазная шлифовка. • ИЗОСТАТИЧЕСКОЕ ПРЕССОВАНИЕ: Гранулированный порошок или штампованные прессованные прессовки помещаются в герметичные контейнеры, а затем в закрытый сосуд высокого давления с жидкостью внутри. После этого они уплотняются за счет увеличения давления в сосуде высокого давления. Жидкость внутри сосуда передает силы давления равномерно по всей площади поверхности герметичного сосуда. Таким образом, материал равномерно уплотняется и принимает форму гибкого контейнера, внутренний профиль и характеристики. • ГОРЯЧОЕ ИЗОСТАТИЧЕСКОЕ ПРЕССОВАНИЕ: Аналогично изостатическому прессованию, но в дополнение к атмосфере сжатого газа мы спекаем прессовку при высокой температуре. Горячее изостатическое прессование приводит к дополнительному уплотнению и повышению прочности. • ШЛИКОВАЯ ЛИТЬЕ / ДРЕЙН ЛИТЬЕ: Мы заполняем форму суспензией керамических частиц микрометрового размера и несущей жидкостью. Эта смесь называется «слип». Форма имеет поры, поэтому жидкость в смеси фильтруется в форму. В результате на внутренних поверхностях формы образуется отлив. После спекания детали можно вынимать из формы. • ЛИТЬЕ ЛЕНТЫ: Мы производим керамические ленты, заливая керамические суспензии на плоские движущиеся поверхности носителя. Суспензии содержат керамические порошки, смешанные с другими химическими веществами для связывания и переноски. Когда растворители испаряются, остаются плотные и гибкие листы керамики, которые можно разрезать или свернуть по желанию. • ЭКСТРУЗИОННОЕ ФОРМОВАНИЕ: Как и в других процессах экструзии, мягкая смесь керамического порошка со связующими веществами и другими химическими веществами пропускается через головку для получения формы поперечного сечения, а затем нарезается на желаемую длину. Процесс выполняется с использованием холодных или нагретых керамических смесей. • ЛИТЬЕ ПОД НИЗКИМ ДАВЛЕНИЕМ: мы готовим смесь керамического порошка со связующими веществами и растворителями и нагреваем ее до температуры, при которой ее можно легко прессовать и вдавливать в полость инструмента. После завершения цикла формования деталь выбрасывается, а связывающий химикат выжигается. Используя литье под давлением, мы можем экономично получать сложные детали в больших объемах. Возможны отверстия , которые составляют крошечную долю миллиметра на стенке толщиной 10 мм, возможно нарезание резьбы без дополнительной обработки, возможны допуски до +/- 0,5% и даже меньше, когда детали подвергаются механической обработке. , возможна толщина стенки порядка 0,5 мм до длины 12,5 мм, а также толщина стенки от 6,5 мм до длины 150 мм. • ЭКОЛОГИЧНАЯ ОБРАБОТКА: Используя те же инструменты для обработки металлов, мы можем обрабатывать прессованные керамические материалы, пока они еще мягкие, как мел. Возможны допуски +/- 1%. Для лучшей точности мы используем алмазное шлифование. • СПЕКАНИЕ или ОБЖИГ: Спекание делает возможным полное уплотнение. У сырых компактных деталей происходит значительная усадка, но это не является большой проблемой, поскольку мы учитываем эти изменения размеров при проектировании детали и оснастки. Частицы порошка связываются вместе, и пористость, вызванная процессом уплотнения, в значительной степени удаляется. • АЛМАЗНАЯ ШЛИФОВКА: самый твердый в мире материал «алмаз» используется для шлифовки таких твердых материалов, как керамика, и для получения прецизионных деталей. Достигаются допуски в диапазоне микрометров и очень гладкие поверхности. Из-за его дороговизны мы рассматриваем эту технику только тогда, когда она нам действительно нужна. • ГЕРМЕТИЧНЫЕ СБОРКИ практически не допускают обмена веществами, твердыми телами, жидкостями или газами между поверхностями. Герметичность герметична. Например, герметичные электронные корпуса защищают чувствительное внутреннее содержимое упакованного устройства от влаги, загрязняющих веществ или газов. Ничто не является 100% герметичным, но когда мы говорим о герметичности, мы имеем в виду, что с практической точки зрения герметичность существует в той степени, в которой скорость утечки настолько мала, что устройства безопасны в нормальных условиях окружающей среды в течение очень долгого времени. Наши герметичные узлы состоят из металлических, стеклянных и керамических компонентов, металлокерамики, керамики-металлокерамики, металлокерамики-металла, металл-металл, металл-стекло, металл-стекло-металл, стекло-металл-стекло, стекло-металл. металл и стекло к стеклу и все другие комбинации склеивания металл-стекло-керамика. Например, мы можем покрыть металлом керамические компоненты, чтобы они были прочно соединены с другими компонентами в сборке и обладали отличной герметизирующей способностью. У нас есть ноу-хау покрытия оптических волокон или вводов металлом и их пайки или припайки к корпусам, чтобы газы не проходили и не просачивались внутрь корпусов. Поэтому они используются для изготовления электронных корпусов для герметизации чувствительных устройств и защиты их от внешней атмосферы. Помимо превосходных герметизирующих характеристик, другие свойства, такие как коэффициент теплового расширения, устойчивость к деформации, отсутствие газовыделения, очень долгий срок службы, непроводимость, теплоизоляционные свойства, антистатичность и т. д. сделать стеклянные и керамические материалы предпочтительными для определенных применений. Информацию о нашем предприятии, производящем металлокерамические фитинги, герметики, вакуумные вводы, компоненты для высокого и сверхвысокого вакуума и системы контроля жидкости , можно найти здесь:Брошюра о заводе герметичных компонентов CLICK Product Finder-Locator Service ПРЕДЫДУЩАЯ СТРАНИЦА
- Формовка проволоки и пружин, формовка, сварка, сборка проволоки, катушка, ЧПУ
Формовка проволоки и пружин, формовка, сварка, сборка проводов, пружины сжатия, удлинение, торсионные плоские пружины, нестандартная проволока, винтовые пружины Проволочное и пружинное формование Мы производим нестандартные провода, проволочные сборки, проволоку, сформированную в желаемые 2D и 3D формы, проволочные сетки, сетку, ограждения, корзину, забор, проволочную пружину, плоскую пружину; кручение, сжатие, растяжение, плоские пружины и многое другое. Наши процессы включают в себя формование проволоки и пружин, волочение проволоки, формование, гибку, сварку, пайку, пайку, прокалывание, обжимку, сверление, снятие фаски, шлифование, нарезание резьбы, нанесение покрытия, четырехпозиционное скольжение, формование скольжения, намотку, намотку, осадку. Мы рекомендуем вам нажать здесь, чтобы СКАЧАТЬ наши схематические иллюстрации процессов формовки проволоки и пружин от AGS-TECH Inc. Этот загружаемый файл с фотографиями и эскизами поможет вам лучше понять информацию, которую мы предоставляем вам ниже. • ВОЛОЧЕНИЕ ПРОВОЛОКИ: Используя силы растяжения, мы растягиваем металлическую заготовку и протягиваем ее через матрицу, чтобы уменьшить диаметр и увеличить ее длину. Иногда мы используем серию штампов. Мы можем изготовить матрицы для каждого калибра проволоки. Используя материал с высокой прочностью на растяжение, мы протягиваем очень тонкие провода. Мы предлагаем как холодную, так и горячую деформируемую проволоку. • ФОРМОВКА ПРОВОЛОКИ: рулон калиброванной проволоки сгибается и формуется в полезный продукт. У нас есть возможность формовать проволоки всех размеров, включая тонкие нити, а также толстые проволоки, такие как те, которые используются в качестве пружин автомобильного шасси. Оборудование, которое мы используем для формирования проволоки, включает в себя ручные и станки с ЧПУ, моталку, силовые прессы, форслайд, мультислайд. Наши процессы включают волочение, гибку, выпрямление, сплющивание, растяжение, резку, осадку, пайку и сварку и пайку, сборку, намотку, обжимку (или окантовку), прокалывание, нарезание резьбы, сверление, снятие фаски, шлифование, нанесение покрытия и обработку поверхности. Наше современное оборудование может быть настроено для разработки очень сложных конструкций любой формы и жестких допусков. Мы предлагаем различные типы наконечников например, сферические, заостренные или скошенные концы для ваших проводов. Большинство наших проектов по формованию проволоки имеют минимальные или нулевые затраты на инструменты. Срок изготовления образцов обычно составляет несколько дней. Изменения в конструкцию/конфигурацию проволочных профилей можно вносить очень быстро. • ФОРМОВКА ПРУЖИН: AGS-TECH производит широкий ассортимент пружин, включая: - Торсион / Двойная пружина кручения -Пружина растяжения/сжатия -Постоянная/переменная пружина - Катушка и спиральная пружина -Плоская и листовая рессора -Балансовая пружина - Бельвиль Стиральная машина -Отрицательная пружина -Винтовая пружина с прогрессивной скоростью -Волна Весна -Волютная пружина -Конические пружины -Весенние кольца -Часовые пружины -Клипы Мы производим пружины из различных материалов и можем помочь вам в соответствии с вашими потребностями. Наиболее распространенными материалами являются нержавеющая сталь, хромокремний, высокоуглеродистая сталь, закаленная в масле низкоуглеродистая, хромованадиевая, фосфористая бронза, титан, бериллиево-медный сплав, высокотемпературная керамика. Мы используем различные технологии изготовления пружин, в том числе намотку на станке с ЧПУ, холодную навивку, горячую навивку, закалку, чистовую обработку. Другие методы, уже упомянутые выше в разделе «Формование проволоки», также широко используются в наших операциях по производству пружин. • ОТДЕЛОЧНЫЕ УСЛУГИ ДЛЯ ПРОВОДОВ И ПРУЖИН: Мы можем закончить вашу продукцию различными способами в зависимости от вашего выбора и потребностей. Некоторые распространенные процессы, которые мы предлагаем: покраска, порошковое покрытие, гальваническое покрытие, виниловое погружение, анодирование, снятие напряжений, термообработка, дробеструйная обработка, барабанное прессование, хроматирование, химический никель, пассивация, обожженная эмаль, пластиковое покрытие , плазменная очистка. CLICK Product Finder-Locator Service ПРЕДЫДУЩАЯ СТРАНИЦА
- Ковка и порошковая металлургия, штамповка, вырубка, горячая ковка
Ковка и порошковая металлургия, ковка в штампах, вырубка, горячая ковка, штампы, почти чистая форма, обжимка, зубофрезерная обработка металла, клепка, чеканка Ковка металлов и порошковая металлургия Типы процессов КОВКИ МЕТАЛЛА, которые мы предлагаем, включают горячую и холодную штамповку, открытую и закрытую штамповку, штамповку штампов и поковки без облоя, cogging, фуллерование, окантовку и прецизионную ковку, почти чистую форму, рубку. , штамповка, ковка с осадкой, зубофрезерная, прессово-валковая, радиальная, орбитальная, кольцевая и изотермическая поковки, чеканка, клепка, ковка металлических шариков, прокалывание металла, калибрование, ковка с высокой энергоемкостью. Нашими методами ПОРОШКОВОЙ МЕТАЛЛУРГИИ и ОБРАБОТКИ ПОРОШКА являются прессование порошка и спекание, пропитка, инфильтрация, горячее и холодное изостатическое прессование, литье под давлением, прессование валков, прокатка порошка, экструзия порошка, свободное спекание, электроискровое спекание, горячее прессование. Мы рекомендуем вам нажать здесь, чтобы СКАЧАТЬ наши схематические иллюстрации процессов ковки от AGS-TECH Inc. СКАЧАТЬ наши схемы процессов порошковой металлургии от AGS-TECH Inc. Эти загружаемые файлы с фотографиями и эскизами помогут вам лучше понять информацию, которую мы предоставляем вам ниже. При ковке металлов применяются сжимающие силы, материал деформируется и приобретается нужная форма. Наиболее распространенными коваными материалами в промышленности являются железо и сталь, но многие другие, такие как алюминий, медь, титан, магний, также широко подделываются. Кованые металлические детали имеют улучшенную зернистую структуру в дополнение к закрытым трещинам и закрытым пустым пространствам, поэтому прочность деталей, полученных таким способом, выше. Ковка производит детали, которые значительно прочнее для своего веса, чем детали, изготовленные литьем или механической обработкой. Поскольку кованые детали формируются путем придания металлу окончательной формы, металл приобретает направленную структуру зерен, которая обеспечивает превосходную прочность деталей. Другими словами, детали, полученные методом ковки, обладают лучшими механическими свойствами по сравнению с простыми литыми или обработанными деталями. Вес металлических поковок может варьироваться от небольших легких деталей до сотен тысяч фунтов. Мы производим поковки в основном для механических применений, где высокие нагрузки применяются к таким деталям, как автомобильные детали, шестерни, рабочие инструменты, ручные инструменты, валы турбин, шестерни мотоциклов. Поскольку затраты на оснастку и настройку относительно высоки, мы рекомендуем этот производственный процесс только для крупносерийного производства и для небольших, но ценных критически важных компонентов, таких как аэрокосмическое шасси. Помимо стоимости инструментов, время изготовления кованых деталей в больших количествах может быть больше по сравнению с некоторыми простыми механически обработанными деталями, но технология имеет решающее значение для деталей, которые требуют чрезвычайной прочности, таких как болты, гайки, специальные приложения. крепежные, автомобильные, вилочные погрузчики, запчасти для кранов. • ГОРЯЧАЯ И ХОЛОДНАЯ ФОРМОВКА: Горячая штамповка, как следует из названия, выполняется при высоких температурах, поэтому пластичность высокая, а прочность материала низкая. Это облегчает легкую деформацию и ковку. Наоборот, холодная штамповка выполняется при более низких температурах и требует более высоких усилий, что приводит к деформации, улучшению чистоты поверхности и точности изготавливаемых деталей. • КОВКА В ОТКРЫТЫХ МАТЕРИАЛАХ И В ПРЯМЫХ КОВКАХ: При свободной штамповке штампы не ограничивают сжимаемый материал, тогда как при штамповке в штампах полости внутри штампов ограничивают поток материала, пока он выковывается в желаемую форму. ФОРМОВКА ОСАЖДЕНИЯ или также называемая ОСАЖДЕНИЕМ, что на самом деле не то же самое, но очень похожий процесс, представляет собой процесс с открытой штамповкой, при котором заготовка помещается между двумя плоскими штампами, а сила сжатия уменьшает ее высоту. Поскольку высота is reduced, ширина заготовки увеличивается. ГОЛОВКА, процесс ковки с высадкой включает в себя цилиндрическую заготовку, которая высаживается на конце, а ее поперечное сечение увеличивается локально. При высадке заготовка пропускается через матрицу, проковывается, а затем нарезается по длине. Операция способна быстро производить большое количество крепежных изделий. В основном это операция холодной обработки, потому что она используется для изготовления концов гвоздей, концов винтов, гаек и болтов, где материал необходимо укрепить. Другой процесс с открытым штампом - это COGGING, при котором заготовка выковывается в несколько этапов, каждый из которых приводит к сжатию материала и последующему движению открытого штампа по длине заготовки. На каждом этапе толщина уменьшается, а длина увеличивается на небольшую величину. Процесс напоминает нервного студента, который все время маленькими шажками кусает карандаш. Процесс под названием FULLERING — это еще один метод ковки в открытых штампах, который мы часто используем в качестве более раннего шага для распределения материала в заготовке до того, как будут выполнены другие операции ковки металла. Мы используем его, когда заготовка требует нескольких операций forging . В процессе эксплуатации штампы с выпуклыми поверхностями деформируются и вызывают вытекание металла в обе стороны. Процесс, аналогичный фуллеровке, ОБРЕЗКА КРОМКИ, с другой стороны, включает в себя открытую матрицу с вогнутыми поверхностями для деформации заготовки. Кромка также является подготовительным процессом для последующих операций ковки, заставляя материал стекать с обеих сторон в область в центре. ОТПЕЧАТНАЯ ФОРМОВКА, или ЗАКРЫТАЯ ФОРМОВКА, как ее еще называют, использует штамп / пресс-форму, которая сжимает материал и ограничивает его течение внутри себя. Матрица закрывается, и материал принимает форму полости матрицы/формы. ТОЧНАЯ КОВКА, процесс, требующий специального оборудования и пресс-формы, позволяет производить детали без облоя или с очень небольшим облоем. Другими словами, детали будут иметь почти окончательные размеры. В этом процессе хорошо контролируемое количество материала аккуратно вставляется и размещается внутри формы. Мы используем этот метод для сложных форм с тонкими сечениями, небольшими допусками и углами наклона, а также когда количества достаточно велики, чтобы оправдать затраты на пресс-форму и оборудование. • БЕЗПЛЕТЕННАЯ КОВКА: Заготовка помещается в штамп таким образом, что материал не может вытекать из полости и образовывать заусенец. Таким образом, нежелательная обрезка вспышки не требуется. Это точный процесс ковки, поэтому требуется тщательный контроль количества используемого материала. • ОБМАЖКА МЕТАЛЛА или РАДИАЛЬНАЯ КОВКА: Заготовка подвергается воздействию штампа и ковки по окружности. Оправку также можно использовать для ковки внутренней геометрии заготовки. При обжиме заготовка обычно совершает несколько ударов в секунду. Типичными изделиями, производимыми штамповкой, являются остроконечные инструменты, конические стержни, отвертки. • ПРОЖИВАНИЕ МЕТАЛЛА: Мы часто используем эту операцию как дополнительную операцию при изготовлении деталей. Отверстие или полость создают прокалыванием на поверхности заготовки без ее пробития. Обратите внимание, что прокалывание отличается от сверления, в результате которого получается сквозное отверстие. • Зубофрезерование: пуансон нужной геометрии вдавливается в заготовку и создает полость нужной формы. Мы называем этот удар HOB. Операция связана с высоким давлением и проводится на холоду. В результате материал подвергается холодной обработке и деформационному упрочнению. Поэтому этот процесс очень подходит для изготовления пресс-форм, штампов и полостей для других производственных процессов. После изготовления варочной панели можно легко изготовить множество одинаковых полостей без необходимости механической обработки их одну за другой. • ПРОКАТНАЯ ФОРМОВКА или ПРОФИЛИРОВАНИЕ: Два противоположных ролика используются для придания формы металлической детали. Заготовка подается в валки, валки поворачиваются и втягивают заготовку в зазор, затем заготовка подается через рифленую часть валков, и сжимающие силы придают материалу желаемую форму. Это не процесс прокатки, а процесс ковки, потому что это дискретная, а не непрерывная операция. Геометрия на канавках валков выковывает материал до требуемой формы и геометрии. Выполняется в горячем виде. Поскольку это процесс ковки, он позволяет производить детали с выдающимися механическими свойствами, и поэтому мы используем его для производства автомобильных деталей, таких как валы, которые должны иметь исключительную износостойкость в тяжелых условиях работы. • ОРБИТАЛЬНАЯ КОВКА: Заготовка помещается в полость ковочного штампа и выковывается с помощью верхнего штампа, который перемещается по орбитальной траектории, вращаясь вокруг наклонной оси. При каждом обороте верхняя матрица завершает приложение сжимающих усилий ко всей заготовке. Повторяя эти обороты несколько раз, выполняется достаточная ковка. Преимуществом этой технологии производства является ее малошумная работа и меньшие требуемые усилия. Другими словами, с небольшим усилием можно вращать тяжелую матрицу вокруг оси, чтобы оказывать большое давление на часть заготовки, которая находится в контакте с матрицей. Дисковые или конические детали иногда хорошо подходят для этого процесса. • КОВКА КОЛЬЦ: Мы часто используем для изготовления бесшовных колец. Заготовка обрезается по длине, осаживается, а затем прокалывается насквозь, чтобы образовалось центральное отверстие. Затем его надевают на оправку и ковочный штамп забивает его сверху при медленном вращении кольца до получения нужных размеров. • ЗАКЛЕПКА: Обычный процесс соединения деталей начинается с прямого металлического элемента, вставленного в заранее проделанные отверстия в деталях. После этого два конца металлической детали проковываются путем сжатия соединения между верхней и нижней матрицей. • ЧЕканка: еще один популярный процесс, осуществляемый с помощью механического пресса, с приложением больших усилий на небольшом расстоянии. Название «чеканка» происходит от мелких деталей, которые выкованы на поверхности металлических монет. В основном это процесс отделки продукта, при котором мелкие детали получаются на поверхности в результате большого усилия, прикладываемого штампом, который переносит эти детали на заготовку. • КОВКА МЕТАЛЛИЧЕСКИХ ШАРОВ: Для таких изделий, как шарикоподшипники, требуются высококачественные точно изготовленные металлические шарики. В одном методе, называемом СКОСАЯ ПРОКАТКА, мы используем два противоположных вала, которые непрерывно вращаются, поскольку заготовка непрерывно подается в валки. На одном конце двух валков в качестве продукта выбрасываются металлические шарики. Второй метод ковки металлических шаров заключается в использовании штампов, которые сжимают материал, помещенный между ними, принимая сферическую форму полости формы. Часто производимые мячи требуют некоторых дополнительных шагов, таких как отделка и полировка, чтобы стать продуктом высокого качества. • ИЗОТЕРМИЧЕСКАЯ ФОРМОВКА/ГОРЯЧАЯ ФОРМОВКА: Дорогостоящий процесс, выполняемый только в том случае, если соотношение выгоды/стоимости оправдано. Горячий процесс обработки, при котором штамп нагревается примерно до той же температуры, что и заготовка. Поскольку и штамп, и работа имеют примерно одинаковую температуру, охлаждение отсутствует, а характеристики текучести металла улучшаются. Операция хорошо подходит для жаропрочных сплавов и материалов с низкой ковкостью, а также для материалов, механические свойства очень чувствительны к небольшим температурным градиентам и изменениям. • ПРОКЛАДКА МЕТАЛЛА: это процесс холодной отделки. Поток материала неограничен во всех направлениях, за исключением направления приложения силы. В результате получаются очень хорошая чистота поверхности и точные размеры. • ВЫСОКОЭНЕРГЕТИЧЕСКАЯ КОВКА: Этот метод включает в себя верхнюю форму, прикрепленную к плечу поршня, который быстро толкается, когда топливно-воздушная смесь воспламеняется свечой зажигания. Это напоминает работу поршней в двигателе автомобиля. Форма ударяется о заготовку очень быстро, а затем очень быстро возвращается в исходное положение благодаря обратному давлению. Работа выковывается за несколько миллисекунд, поэтому работа не успевает остыть. Это полезно для трудно поддающихся ковке деталей, механические свойства которых очень чувствительны к температуре. Другими словами, процесс настолько быстрый, что деталь формируется при постоянной температуре на всем протяжении, и не будет температурных градиентов на границах раздела форма/заготовка. • В КОВКЕ МЕТАЛЛ забивается между двумя соответствующими стальными блоками с особыми формами в них, называемыми штампами. Когда металл забивается между штампами, он принимает ту же форму, что и формы в штампе. Когда он достигает своей окончательной формы, его вынимают остывать. Этот процесс позволяет производить прочные детали точной формы, но требует больших затрат на специализированные штампы. Ковка с осадкой увеличивает диаметр куска металла за счет его уплощения. Обычно он используется для изготовления мелких деталей, особенно для формирования головок крепежных деталей, таких как болты и гвозди. • ПОРОШКОВАЯ МЕТАЛЛУРГИЯ / ПЕРЕРАБОТКА ПОРОШКОВ: Как следует из названия, она включает в себя производственные процессы для изготовления твердых деталей определенной геометрии и формы из порошков. Если для этой цели используются металлические порошки, то это область порошковой металлургии, а если используются неметаллические порошки, то это порошковая обработка. Твердые детали производятся из порошков методом прессования и спекания. ПРЕССОВАНИЕ ПОРОШКОВ используется для прессования порошков в желаемую форму. Во-первых, первичный материал физически измельчают, разделяя его на множество мелких отдельных частиц. Порошковая смесь засыпается в пресс-форму, и пуансон движется к порошку и уплотняет его до желаемой формы. В основном выполняется при комнатной температуре, при прессовании порошка получается твердая деталь, которую называют сырой прессовкой. Связующие и смазочные материалы обычно используются для улучшения уплотняемости. Мы можем формовать порошковые материалы с помощью гидравлических прессов мощностью в несколько тысяч тонн. Также у нас есть прессы двойного действия с противоположными верхним и нижним пуансонами, а также прессы многократного действия для деталей очень сложной геометрии. Однородность, которая является важной проблемой для многих заводов порошковой металлургии / порошковой обработки, не является большой проблемой для AGS-TECH благодаря нашему многолетнему опыту в изготовлении таких деталей на заказ. Даже с более толстыми деталями, где однородность представляет собой проблему, мы добились успеха. Если мы возьмемся за ваш проект, мы сделаем ваши детали. Если мы увидим какие-либо потенциальные риски, мы сообщим вам in заранее. СПЕКАНИЕ ПОРОШКА, которое является вторым этапом, включает в себя повышение температуры до определенной степени и поддержание температуры на этом уровне в течение определенного времени, чтобы частицы порошка в прессованной детали могли соединиться друг с другом. Это приводит к гораздо более прочным связям и укреплению заготовки. Спекание происходит близко к температуре плавления порошка. При спекании происходит усадка, повышаются прочность материала, плотность, пластичность, теплопроводность, электропроводность. У нас есть печи периодического и непрерывного действия для спекания. Одной из наших возможностей является регулирование уровня пористости производимых нами деталей. Например, мы можем производить металлические фильтры, сохраняя пористость деталей в некоторой степени. Используя технику, называемую ПРОПИТКА, мы заполняем поры в металле жидкостью, такой как масло. Например, мы производим пропитанные маслом подшипники, которые являются самосмазывающимися. В процессе ИНФИЛЬТРАЦИИ мы заполняем поры металла другим металлом с более низкой температурой плавления, чем основной материал. Смесь нагревают до температуры, промежуточной между температурами плавления двух металлов. В результате могут быть получены некоторые особые свойства. Мы также часто выполняем вторичные операции, такие как механическая обработка и ковка, на деталях, изготовленных из порошка, когда необходимо получить особые характеристики или свойства или когда деталь может быть изготовлена с меньшим количеством технологических операций. ИЗОСТАТИЧЕСКОЕ ПРЕССОВАНИЕ: В этом процессе используется давление жидкости для уплотнения детали. Металлические порошки помещают в форму, представляющую собой герметичный гибкий контейнер. При изостатическом прессовании давление прикладывается со всех сторон, в отличие от осевого давления, наблюдаемого при обычном прессовании. Преимуществами изостатического прессования являются равномерная плотность внутри детали, особенно для более крупных или толстых деталей, превосходные свойства. Его недостатком является длительное время цикла и относительно низкая геометрическая точность. ХОЛОДНОЕ ИЗОСТАТИЧЕСКОЕ ПРЕССОВАНИЕ осуществляется при комнатной температуре, а гибкая форма изготавливается из резины, ПВХ, уретана или подобных материалов. Жидкость, используемая для повышения давления и уплотнения, представляет собой масло или воду. Далее следует обычное спекание сырой прессовки. ГОРЯЧОЕ ИЗОСТАТИЧЕСКОЕ ПРЕССОВАНИЕ, с другой стороны, осуществляется при высоких температурах, а материал формы представляет собой листовой металл или керамику с достаточно высокой температурой плавления, которая выдерживает высокие температуры. Рабочая жидкость обычно представляет собой инертный газ. Операции прессования и спекания выполняются в один этап. Практически полностью устраняется пористость, получается равномерная структура зерна. Преимущество горячего изостатического прессования заключается в том, что с его помощью можно производить детали, сравнимые с литьем и ковкой, в то же время делая возможным использование материалов, не подходящих для литья и ковки. Недостатком горячего изостатического прессования является его высокая продолжительность цикла и, следовательно, стоимость. Он подходит для ответственных деталей небольшого объема. ЛИТЬЕ МЕТАЛЛА ПОД ДАВЛЕНИЕМ: Очень подходящий процесс для производства сложных деталей с тонкими стенками и детализированной геометрией. Наиболее подходит для мелких деталей. Порошки и полимерное связующее смешивают, нагревают и впрыскивают в форму. Полимерное связующее покрывает поверхности частиц порошка. После формования связующее удаляют либо низкотемпературным нагреванием, либо растворяют с помощью растворителя. ВАЛОЧНОЕ УПЛОТНЕНИЕ / ПОРОШКОВАЯ ПРОКАТКА: Порошки используются для производства непрерывных полос или листов. Порошок подается из питателя и уплотняется двумя вращающимися валками в листы или полосы. Операция проводится в холодном виде. Лист подается в печь для спекания. Процесс спекания может быть повторен во второй раз. ЭКСТРУЗИЯ ПОРОШКА: Детали с большим отношением длины к диаметру изготавливаются путем экструзии контейнера из тонкого листового металла с порошком. СВОБОДНОЕ СПЕКАНИЕ: Как следует из названия, это метод уплотнения и спекания без давления, подходящий для изготовления очень пористых деталей, таких как металлические фильтры. Порошок подается в полость формы без уплотнения. СВОБОДНОЕ СПЕКАНИЕ: Как следует из названия, это метод уплотнения и спекания без давления, подходящий для изготовления очень пористых деталей, таких как металлические фильтры. Порошок подается в полость формы без уплотнения. ИСКРОВОЕ СПЕЧЕНИЕ: Порошок сжимается в форме двумя противоположными пуансонами, и к пуансону прикладывается электрический ток высокой мощности, который проходит через уплотненный порошок, зажатый между ними. Сильный ток выжигает поверхностные пленки частиц порошка и спекает их за счет выделяемого тепла. Процесс быстрый, потому что тепло не подается извне, а генерируется внутри формы. ГОРЯЧЕЕ ПРЕССОВАНИЕ: Порошки прессуются и спекаются за один этап в форме, способной выдерживать высокие температуры. Когда матрица уплотняется, к ней прикладывается тепло порошка. Хорошая точность и механические свойства, достигаемые этим методом, делают его привлекательным вариантом. Даже тугоплавкие металлы можно обрабатывать с использованием формовочных материалов, таких как графит. CLICK Product Finder-Locator Service ПРЕДЫДУЩЕЕ МЕНЮ
- Изготовление листового металла, штамповка, штамповка, глубокая вытяжка, ЧПУ
Формовка и изготовление листового металла, штамповка, штамповка, гибка, прогрессивная штамповка, точечная сварка, глубокая вытяжка, вырубка и резка металла Штамповки и изготовление листового металла Мы предлагаем штамповку листового металла, формование, формование, гибку, штамповку, вырубку, продольную резку, перфорацию, вырубку, высечку, строгание, штамповку, изготовление, глубокую вытяжку с использованием штампов с одним пуансоном / одиночным ходом, а также прогрессивные штампы и прядение, формование резины и гидроформинг; раскрой листового металла водоструйным, плазменным, лазерным, пильным, пламенным; сборка листового металла с помощью сварки, точечной сварки; выпячивание и изгиб трубы из листового металла; отделка поверхности листового металла, включая покраску погружением или распылением, электростатическое порошковое покрытие, анодирование, гальваническое покрытие, напыление и многое другое. Наши услуги варьируются от быстрого прототипирования листового металла до крупносерийного производства. Мы рекомендуем вам нажать здесь, чтобыСКАЧАТЬ наши схематические иллюстрации процессов изготовления и штамповки листового металла от AGS-TECH Inc. Это поможет вам лучше понять информацию, которую мы предоставляем вам ниже. • РЕЗКА ЛИСТОВОГО МЕТАЛЛА: Мы предлагаем РЕЗКИ и РАЗДЕЛКИ. Отрезки режут листовой металл по одной траектории за раз, и в основном нет отходов материала, тогда как при разрезах форма не может быть точно прижата, и поэтому определенное количество материала теряется. Одним из наших самых популярных процессов является ПРОБИВКА, когда из листового металла вырезается кусок материала круглой или другой формы. Отрезанный кусок - отходы. Другой вариант пробивки – ПРОРЕЗАНИЕ, при котором пробиваются отверстия прямоугольной или удлиненной формы. ЗАГЛУШКА, с другой стороны, - это тот же процесс, что и штамповка, с тем отличием, что вырезаемая деталь является работой и сохраняется. FINE BLANKING, улучшенная версия вырубки, создает резы с жесткими допусками и прямыми гладкими краями и не требует дополнительных операций для идеальной обработки заготовки. Другим процессом, который мы часто используем, является ПРОРЕЗКА, которая представляет собой процесс резки листового металла двумя противоположными круглыми лезвиями по прямой или изогнутой траектории. Консервный нож — это простой пример процесса разрезания. Другой популярный процесс у нас - ПЕРФОРИРОВАНИЕ, при котором в листовом металле по определенному шаблону пробивается множество отверстий круглой или другой формы. Типичным примером перфорированного изделия являются металлические фильтры с множеством отверстий для жидкостей. В НАСЕЧЕНИИ, еще одном процессе резки листового металла, мы удаляем материал с заготовки, начиная с края или в другом месте, и разрезаем внутрь, пока не будет получена желаемая форма. Это прогрессивный процесс, при котором каждая операция удаляет другую деталь, пока не будет получен желаемый контур. Для небольших производственных циклов мы иногда используем относительно более медленный процесс, называемый ВЫСЕЧЕНИЕМ, который состоит из множества быстрых пробивок перекрывающихся отверстий для получения более крупного и сложного разреза. В ПРОГРЕССИВНОЙ РЕЗКЕ мы используем ряд различных операций для получения одного разреза или определенной геометрии. Наконец, ОБРЕЗАНИЕ вторичного процесса помогает нам улучшить края уже сделанных разрезов. Используется для срезания стружки, необработанных кромок на изделиях из листового металла. • ГИБКА ЛИСТОВОГО МЕТАЛЛА: Помимо резки, гибка является важным процессом, без которого мы не смогли бы производить большую часть продукции. В основном операция холодной обработки, но иногда также выполняется в теплом или горячем состоянии. Мы используем штампы и прессование большую часть времени для этой операции. В ПРОГРЕССИВНОЙ ИЗГИБКЕ мы используем серию различных операций штамповки и штамповки для получения одного изгиба или определенной геометрии. AGS-TECH использует различные процессы гибки и делает выбор в зависимости от материала заготовки, ее размера, толщины, желаемого размера изгиба, радиуса, кривизны и угла изгиба, места изгиба, экономичности операции, объемов производства… и т.п. Мы используем V-ОБРАЗНЫЙ ИЗГИБ, когда V-образный пуансон вдавливает листовой металл в V-образную матрицу и изгибает его. Хорошо подходит как для очень острых и тупых углов, так и для промежуточных, включая 90 градусов. С помощью обтирочных плашек выполняем ИЗГИБ КРОМОК. Наше оборудование позволяет получать углы даже больше 90 градусов. При гибке кромок заготовка зажата между прижимной пластиной и матрицей, область для гибки расположена на кромке матрицы, а остальная часть заготовки удерживается над space подобно консольной балке. Когда пуансон воздействует на консольную часть, она изгибается над краем штампа. FLANGING - это процесс гибки кромок, в результате которого получается угол 90 градусов. Основными целями операции являются устранение острых кромок и получение геометрических поверхностей для облегчения соединения деталей. ИЗГОТОВЛЕНИЕ БОКОВ, еще один распространенный процесс гибки кромок, образующий завиток на кромке детали. С другой стороны, ПОДШИВКА приводит к тому, что край листа полностью загибается сам на себя. В ЗАГОТОВКЕ края двух деталей загибаются друг на друга и соединяются. ДВОЙНОЙ ШОВ, с другой стороны, обеспечивает водонепроницаемые и воздухонепроницаемые соединения листового металла. Подобно гибке кромок, процесс, называемый ВРАЩАТЕЛЬНЫМ ИЗГИБОМ, разворачивает цилиндр с вырезом под нужным углом, который служит пуансоном. Когда усилие передается на пуансон, он смыкается с заготовкой. Канавка цилиндра придает консольной части желаемый угол. Канавка может иметь угол меньше или больше 90 градусов. При ГИБКЕ НА ВОЗДУХЕ нам не нужно, чтобы на нижней матрице была угловая канавка. Листовой металл поддерживается двумя поверхностями с противоположных сторон и на определенном расстоянии. Затем пуансон прикладывает усилие в нужном месте и изгибает заготовку. ИЗГИБ КАНАЛА выполняется с помощью пуансона и матрицы в форме канала, а U-ИЗГИБ достигается с помощью пуансона U-образной формы. OFFSET BENDING производит смещения на листовом металле. ИЗГИБ ВАЛЬЦА, метод, подходящий для толстой работы и гибки больших кусков металлических пластин, использует три ролика для подачи и гибки пластин до желаемой кривизны. Валки располагаются так, чтобы получился нужный изгиб работы. Расстояние и угол между валками контролируются для получения желаемого результата. Подвижный ролик позволяет контролировать кривизну. ФОРМОВКА ТРУБ — еще одна популярная операция гибки листового металла с использованием нескольких штампов. Трубки получаются после множественных действий. ГОФР также выполняется операциями гибки. В основном это симметричный изгиб через равные промежутки времени по всему куску листового металла. Для гофрирования можно использовать различные формы. Гофрированный листовой металл более жесткий и имеет лучшую устойчивость к изгибу, поэтому находит применение в строительной отрасли. ПРОФИЛИРОВАНИЕ ЛИСТОВОГО МЕТАЛЛА, непрерывный производственный процесс развертывается для гибки поперечных сечений определенной геометрии с использованием валков, и работа сгибается в последовательных шагах, при этом последний валок завершает работу. В некоторых случаях используется один вал, а в некоторых случаях - серия валков. • КОМБИНИРОВАННЫЕ ПРОЦЕССЫ РЕЗКИ И ГИБКИ ЛИСТОВОГО МЕТАЛЛА: это процессы, которые одновременно режут и гнут. В ПИРСИНГЕ отверстие создается с помощью заостренного пробойника. По мере того как пуансон расширяет отверстие в листе, материал одновременно сгибается во внутренний фланец для отверстия. Полученный фланец может иметь важные функции. Операция LANCING, с другой стороны, разрезает и сгибает лист для создания выпуклой геометрии. • ВЫПОЛНЕНИЕ И ИЗГИБ МЕТАЛЛИЧЕСКОЙ ТРУБЫ: При ВЫПУСКЕ некоторая внутренняя часть полой трубы находится под давлением, в результате чего труба выпячивается наружу. Поскольку трубка находится внутри матрицы, геометрия выпуклости определяется формой матрицы. В ИЗГИБОВОМ РАСТЯЖЕНИИ металлическая труба растягивается с использованием сил, параллельных оси трубы, и сил изгиба, чтобы натянуть трубу на опалубочный блок. В ИЗГИБКЕ ВЫТЯЖИВАНИЕМ мы прижимаем трубу ближе к ее концу к вращающемуся опалубочному блоку, который изгибает трубу при вращении. Наконец, при ИЗГИБЕ С СЖАТИЕМ труба с усилием удерживается на неподвижном опалубочном блоке, и матрица сгибает ее над опалубочным блоком. • ГЛУБОКАЯ ВЫТЯЖКА: В одной из наших самых популярных операций используются пуансон, соответствующий штамп и держатель заготовки. Заготовка из листового металла помещается над отверстием штампа, и пуансон движется к заготовке, удерживаемой держателем заготовки. Как только они соприкасаются, пуансон вдавливает листовой металл в полость штампа, формируя изделие. Операция глубокой вытяжки напоминает резку, однако зазор между пуансоном и матрицей препятствует разрезанию листа. Еще одним фактором, обеспечивающим глубокую вытяжку листа, а не его резку, являются закругленные углы штампа и пуансона, которые предотвращают разрезание и разрезание. Чтобы добиться большей степени глубокой вытяжки, развертывается процесс REDRAWING, при котором последующая глубокая вытяжка выполняется на детали, которая уже подверглась процессу глубокой вытяжки. В REVERSE REDRAWING глубоко нарисованная деталь переворачивается и рисуется в противоположном направлении. Глубокая вытяжка позволяет создавать объекты неправильной формы, такие как куполообразные, конические или ступенчатые чашки. • СПИННИНГ: Операция, при которой плоская или предварительно отформованная заготовка удерживается между вращающейся оправкой и задней бабкой, а инструмент оказывает локализованное давление на заготовку по мере ее постепенного перемещения вверх по оправке. В результате заготовка наматывается на оправку и принимает ее форму. Мы используем эту технику как альтернативу глубокой вытяжке, когда объем заказа небольшой, детали большие (диаметром до 20 футов) и имеют уникальные изгибы. Несмотря на то, что цены за штуку, как правило, выше, затраты на настройку прядильного станка с ЧПУ ниже по сравнению с глубокой вытяжкой. Напротив, глубокая вытяжка требует больших первоначальных инвестиций для настройки, но затраты на единицу продукции низки при производстве большого количества деталей. Другим вариантом этого процесса является СДВИЖНОЕ ПРЯМООБРАБОТАНИЕ, при котором внутри заготовки также происходит течение металла. Поток металла будет уменьшать толщину заготовки по мере выполнения процесса. Еще одним родственным процессом является ПРЯДЕНИЕ ТРУБ, которое применяется к цилиндрическим деталям. Также в этом процессе происходит течение металла внутри заготовки. Таким образом, толщина трубы уменьшается, а длина трубы увеличивается. Инструмент можно перемещать для создания элементов внутри или снаружи трубы. • РЕЗИНОВОЕ ФОРМОВАНИЕ ЛИСТОВОГО МЕТАЛЛА: Резиновый или полиуретановый материал помещается в контейнерную форму, а заготовка помещается на поверхность резины. Затем на заготовку воздействуют ударом, который вдавливает ее в резину. Поскольку давление, создаваемое резиной, низкое, глубина изготавливаемых деталей ограничена. Поскольку затраты на оснастку низкие, этот процесс подходит для мелкосерийного производства. • ГИДРОФОРМОВКА: Подобно формовке резины, в этом процессе листовой металл прессуется пуансоном в жидкость под давлением внутри камеры. Листовой металл зажат между пуансоном и резиновой диафрагмой. Диафрагма полностью окружает заготовку, и давление жидкости заставляет ее формироваться на пуансоне. С помощью этой техники можно получить очень глубокие рисунки, даже более глубокие, чем в процессе глубокого рисования. Мы производим штампы с одним пуансоном, а также прогрессивные штампы в зависимости от вашей детали. Однотактные штампы для штамповки являются экономически эффективным методом быстрого производства большого количества простых деталей из листового металла, таких как шайбы. Для изготовления более сложной геометрии используются прогрессивные штампы или техника глубокой вытяжки. В зависимости от вашего случая, гидроабразивная, лазерная или плазменная резка может использоваться для недорогого, быстрого и точного производства деталей из листового металла. Многие поставщики не имеют ни малейшего представления об этих альтернативных технологиях или не имеют их, и поэтому они прибегают к длительным и дорогостоящим способам изготовления штампов и инструментов, которые только тратят время и деньги клиентов. Если вам требуются изготовленные на заказ компоненты из листового металла, такие как корпуса, корпуса для электронных устройств и т. д., в течение нескольких дней, свяжитесь с нами, чтобы воспользоваться услугой БЫСТРОГО ПРОТОТИПИРОВАНИЯ ИЗ ЛИСТОВОГО МЕТАЛЛА. CLICK Product Finder-Locator Service ПРЕДЫДУЩЕЕ МЕНЮ
- Пластиковые резиновые металлические профили, экструзионные матрицы, экструзия алюминия
Пластиковая резина, экструзия металла, экструзионные матрицы, экструзия алюминия, формовка труб, пластиковые профили, производство металлических профилей, ПВХ Экструзии, экструдированные продукты, экструдаты Мы используем процесс EXTRUSION для производства продуктов с фиксированным профилем поперечного сечения, таких как трубы, трубы и радиаторы. Несмотря на то, что многие материалы могут быть экструдированы, наши наиболее распространенные экструзии изготавливаются из металла, полимеров / пластика, керамики, полученных методом холодной, теплой или горячей экструзии. Мы называем экструдированные детали экструдатом или экструдатом во множественном числе. Некоторые специализированные версии процесса, которые мы также выполняем, включают наружную оболочку, коэкструзию и комбинированную экструзию. Мы рекомендуем вам нажать здесь to СКАЧАТЬ наши схематические иллюстрации процессов экструзии металлокерамики и пластика от AGS-TECH Inc. Это поможет вам лучше понять информацию, которую мы предоставляем вам ниже. При экструзии материал, подлежащий экструзии, проталкивается или вытягивается через головку, имеющую желаемый профиль поперечного сечения. Этот процесс можно использовать для изготовления сложных поперечных сечений с превосходной чистотой поверхности и для обработки хрупких материалов. С помощью этого процесса можно производить детали любой длины. Чтобы упростить этапы процесса: 1.) При теплой или горячей экструзии материал нагревается и загружается в контейнер в прессе. Материал прессуется и выталкивается из матрицы. 2.) Полученный экструдат подвергают вытягиванию для правки, термообработке или холодной обработке для улучшения его свойств. С другой стороны, ХОЛОДНАЯ ЭКСТРУЗИЯ происходит при комнатной температуре и имеет преимущества меньшего окисления, высокой прочности, более жестких допусков, хорошей отделки поверхности и стойкости. ГОРЯЧАЯ ЭКСТРУЗИЯ выполняется при температуре выше комнатной, но ниже точки рекристаллизации. Он предлагает компромисс и баланс требуемых сил, пластичности и свойств материала и поэтому является выбором для некоторых применений. ГОРЯЧАЯ ЭКСТРУЗИЯ происходит при температуре выше температуры рекристаллизации материала. Таким образом легче протолкнуть материал через матрицу. Однако стоимость оборудования высока. Чем сложнее экструдированный профиль, тем дороже штамп (инструмент) и ниже темп производства. Поперечное сечение матрицы, а также ее толщина имеют ограничения, зависящие от экструдируемого материала. Острые углы экструзионных головок всегда нежелательны, и их следует избегать без необходимости. В зависимости от экструдируемого материала мы предлагаем: • МЕТАЛЛИЧЕСКИЕ ПРОФИЛЬНЫЕ ПРОФИЛИ : Наиболее распространенными из которых мы производим, являются алюминий, латунь, цинк, медь, сталь, титан, магний. • ЭКСТРУЗИЯ ПЛАСТИКА : Пластмасса расплавляется и формируется в непрерывный профиль. Наши общие обрабатываемые материалы: полиэтилен, нейлон, полистирол, поливинилхлорид, полипропилен, АБС-пластик, поликарбонат, акрил. Типичные продукты, которые мы производим, включают трубы и шланги, пластиковые рамы. В процессе маленькие пластиковые шарики/смола подаются самотеком из бункера в цилиндр экструзионной машины. Часто мы также смешиваем красители или другие добавки в бункере, чтобы придать продукту требуемые характеристики и свойства. Материал, поступающий в нагретую бочку, под действием вращающегося шнека покидает бочку в конце и проходит через сетку для удаления загрязняющих веществ из расплавленного пластика. После прохождения сетчатого фильтра пластик поступает в экструзионную головку. Матрица придает движущемуся мягкому пластику форму профиля, когда он проходит через него. Теперь экструдат проходит водяную баню для охлаждения. Другие методы, которые AGS-TECH Inc. использует в течение многих лет: • ЭКСТРУЗИЯ ТРУБ И ТРУБОПРОВОДОВ : Пластиковые трубы выдавливаются через круглую формовочную головку и охлаждаются в водяной бане, а затем отрезаются по длине или скручиваются/наматываются. Прозрачные или цветные, полосатые, с одной или двумя стенками, гибкие или жесткие, из полиэтилена, полипропилена, полиуретана, ПВХ, нейлона, поликарбоната, силикона, винила и т. д., у нас есть все. У нас есть запасные трубы, а также возможность производить в соответствии с вашими спецификациями. AGS-TECH производит трубки в соответствии с требованиями FDA, UL и LE для медицинских, электрических и электронных, промышленных и других применений. • НАКЛАДКА / ЭКСТРУЗИЯ НАД ОБОЛОЧКОЙ : Этот метод наносит внешний слой пластика на существующий провод или кабель. Наши изолированные провода изготавливаются по этому методу. • COEXTRUSION : Одновременно экструдируется несколько слоев материала. Несколько слоев доставляются несколькими экструдерами. Различные толщины слоев могут быть отрегулированы в соответствии с требованиями заказчика. Этот процесс позволяет использовать в продукте несколько полимеров, каждый из которых имеет различную функциональность. В результате можно оптимизировать ряд свойств. • ЭКСТРУЗИЯ СОЕДИНЕНИЙ: Один или несколько полимеров смешивают с добавками для получения пластичного соединения. Наши двухшнековые экструдеры производят компаундирующие экструзии. Экструзионные головки обычно недороги по сравнению с металлическими формами. Если вы платите гораздо больше, чем несколько тысяч долларов за экструзионную головку малого или среднего размера для экструзии алюминия, вы, вероятно, переплачиваете. Мы являемся экспертами в определении того, какой метод является наиболее экономичным, быстрым и наиболее подходящим для вашего применения. Иногда выдавливание, а затем механическая обработка детали может сэкономить вам много денег. Прежде чем принять твердое решение, сначала спросите нас о нашем мнении. Мы помогли многим клиентам принять правильное решение. Для некоторых широко используемых металлических профилей вы можете скачать наши брошюры и каталоги, нажав на цветной текст ниже. Если это готовый продукт, отвечающий вашим требованиям, он будет более экономичным. Загрузите наши возможности экструзии медицинских труб и труб Загрузите наши экструдированные радиаторы • ВТОРИЧНЫЕ ПРОИЗВОДСТВЕННЫЕ ПРОЦЕССЫ ДЛЯ ЭКСТРУЗИОННЫХ ПРОФИЛЕЙ : Среди процессов с добавленной стоимостью, которые мы предлагаем для экструдированных продуктов: -Изгиб, формование и формование труб и труб на заказ, обрезка труб, формовка концов труб, намотка труб, механическая обработка и отделка, сверление отверстий, пробивка и штамповка, -Нестандартные трубы и трубы в сборе, трубная сборка, сварка, пайка и пайка -Изгиб экструзии на заказ, формование и формование -Очистка, обезжиривание, травление, пассивация, полировка, анодирование, гальваническое покрытие, покраска, термообработка, отжиг и закалка, маркировка, гравировка и маркировка, индивидуальная упаковка. CLICK Product Finder-Locator Service ПРЕДЫДУЩАЯ СТРАНИЦА
- Литье и обработка деталей, производство с ЧПУ, фрезерование, токарная обработка, швейцарская обработка
Литье и обработка деталей, Производство на станках с ЧПУ, Фрезерование, Токарная обработка, Швейцарская обработка, Литье под давлением, Литье по выплавляемым моделям, Детали, отлитые по выплавляемым моделям Литье и обработка Наши нестандартные методы литья и механической обработки включают одноразовое и многоразовое литье, литье черных и цветных металлов, песчаное, штампованное, центробежное, непрерывное, керамическое литье, инвестиционную форму, выплавляемую пену, форму, близкую к чистой, постоянную форму (литье под давлением), гипс. отливки в формы (гипсовое литье) и отливки в оболочки, обработанные детали, изготовленные фрезерованием и точением на обычном оборудовании, а также на оборудовании с ЧПУ, швейцарская обработка для высокопроизводительных недорогих мелких прецизионных деталей, обработка винтов для крепежа, нетрадиционная обработка. Пожалуйста, имейте в виду, что помимо металлов и металлических сплавов мы также обрабатываем керамические, стеклянные и пластиковые компоненты, а также в некоторых случаях, когда изготовление пресс-формы нецелесообразно или не представляется возможным. Механическая обработка полимерных материалов требует специального опыта, который у нас есть из-за проблем, связанных с пластиками и резиной из-за их мягкости, нежесткости и т. д. Информацию о механической обработке керамики и стекла см. на нашей странице, посвященной нетрадиционному производству. AGS-TECH Inc. производит и поставляет как легкие, так и тяжелые отливки. Мы поставляем металлические отливки и обработанные детали для котлов, теплообменников, автомобилей, микромоторов, ветряных турбин, оборудования для упаковки пищевых продуктов и многого другого. Мы рекомендуем вам нажать здесь to СКАЧАТЬ наши схематические иллюстрации процессов обработки и литья от AGS-TECH Inc. Это поможет вам лучше понять информацию, которую мы предоставляем вам ниже. Давайте подробно рассмотрим некоторые из различных методов, которые мы предлагаем: • ЛИТЬЕ В РАЗНООБРАЗНЫЕ ФОРМЫ: Эта широкая категория относится к методам, в которых используются временные и одноразовые формы. Примерами являются песок, гипс, ракушка, паковочная масса (также называемая выплавляемым воском) и гипсовое литье. • ЛИТЬЕ В ПЕСКИ: Процесс, при котором в качестве материала формы используется песок. Очень старый метод, который до сих пор очень популярен, так как большинство производимых металлических отливок изготавливается по этому методу. Низкая себестоимость даже при небольших объемах производства. Подходит для изготовления мелких и крупных деталей. Этот метод можно использовать для изготовления деталей в течение нескольких дней или недель с очень небольшими инвестициями. Влажный песок связывают вместе с помощью глины, связующих веществ или специальных масел. Песок обычно содержится в ящиках для форм, а система полостей и литников создается путем уплотнения песка вокруг моделей. Процессы: 1.) Помещение модели в песок для изготовления формы. 2.) Включение модели и песка в литниковую систему 3.) Удаление модели 4.) Заполнение полости формы расплавленным металлом 5.) Охлаждение металла 6.) Разбивание песчаной формы и снятие отливки • ЛИТЬЕ В ГИПСОВУЮ ФОРМУ: аналогично литью в песчаные формы, но вместо песка в качестве материала формы используется гипс. Короткие сроки производства, такие как литье в песчаные формы и недорого. Хорошие допуски на размеры и качество поверхности. Его основным недостатком является то, что его можно использовать только с металлами с низкой температурой плавления, такими как алюминий и цинк. • ЛИТЬЕ В ОБОЛОЧКУ: Также похоже на литье в песчаные формы. Полость формы, полученная за счет затвердевшей оболочки из песка и связующего из термореактивной смолы вместо опоки, заполненной песком, как в процессе литья в песчаные формы. Почти любой металл, пригодный для литья в песок, может быть отлит методом оболочкового литья. Процесс можно обобщить следующим образом: 1.) Изготовление оболочковой формы. Используемый песок имеет гораздо меньший размер зерна по сравнению с песком, используемым при литье в песчаные формы. Мелкий песок смешивается с термореактивной смолой. Металлический узор покрыт разделительным составом, чтобы облегчить снятие оболочки. После этого металлическая модель нагревается, и песчаная смесь наносится или выдувается на горячую модель отливки. На поверхности узора образуется тонкая оболочка. Толщину этой оболочки можно регулировать, изменяя продолжительность контакта смеси песка и смолы с металлическим рисунком. Затем рыхлый песок удаляется, а рисунок, покрытый ракушкой, остается. 2.) Далее скорлупу и выкройку прогревают в печи, чтобы скорлупа затвердела. После завершения затвердевания оболочка выталкивается из шаблона с помощью штифтов, встроенных в шаблон. 3.) Две такие оболочки собираются вместе путем склеивания или зажима и составляют полную форму. Теперь оболочковая форма вставляется в емкость, в которой она поддерживается песком или металлической дробью в процессе литья. 4.) Теперь горячий металл можно заливать в форму. Преимущества оболочечного литья – изделия с очень хорошей отделкой поверхности, возможность изготовления сложных деталей с высокой точностью размеров, легкость автоматизации процесса, экономичность при крупносерийном производстве. Недостатки заключаются в том, что формы требуют хорошей вентиляции из-за газов, которые образуются при контакте расплавленного металла со связующим химическим веществом, термореактивные смолы и металлические модели дороги. Из-за стоимости металлических моделей этот метод может не подходить для мелкосерийного производства. • ЛИТЬЕ ПО ИНВЕСТИЦИОННЫМ ОБРАЗЦАМ (также известное как ЛИТЬЕ ПО ВОСКАМ): также очень старая технология, подходящая для изготовления качественных деталей с высокой точностью, повторяемостью, универсальностью и целостностью из многих металлов, тугоплавких материалов и специальных сплавов с высокими эксплуатационными характеристиками. Возможно изготовление как мелких, так и крупногабаритных деталей. Дорогостоящий процесс по сравнению с некоторыми другими методами, но основным преимуществом является возможность изготовления деталей с почти заданной формой, сложными контурами и деталями. Таким образом, стоимость несколько компенсируется устранением переделок и механической обработки в некоторых случаях. Несмотря на то, что могут быть вариации, вот краткое изложение общего процесса литья по выплавляемым моделям: 1.) Создание оригинальной мастер-модели из воска или пластика. Для каждой отливки требуется один шаблон, так как они разрушаются в процессе. Форма, из которой изготавливаются модели, также необходима, и большую часть времени форму отливают или обрабатывают. Поскольку форму открывать не нужно, можно получить сложные отливки, многие восковые модели можно соединить, как ветви дерева, и залить вместе, что позволяет производить несколько деталей из одной заливки металла или металлического сплава. 2.) Затем модель окунают или заливают огнеупорной суспензией, состоящей из очень мелкозернистого кремнезема, воды, связующих. Это приводит к керамическому слою на поверхности рисунка. Огнеупорный слой на шаблоне оставляют сохнуть и затвердевать. Именно на этом этапе происходит название «литье по выплавляемым моделям»: огнеупорная суспензия наносится на восковую модель. 3.) На этом этапе затвердевшую керамическую форму переворачивают вверх дном и нагревают, чтобы воск расплавился и вылился из формы. Оставляют полость для металлической отливки. 4.) После удаления воска керамическая форма нагревается до еще более высокой температуры, что приводит к упрочнению формы. 5.) Металлическая отливка заливается в горячую форму, заполняя все сложные участки. 6.) Отливке дают затвердеть 7.) Наконец, керамическая форма разбивается, а изготовленные детали вырезаются из дерева. Вот ссылка на Брошюру завода литья по выплавляемым моделям • ЛИТЬЕ МОДЕЛИ ИСПАРЕНИЯ: В процессе используется модель, изготовленная из такого материала, как пенополистирол, который испаряется при заливке горячего расплавленного металла в форму. Существует два типа этого процесса: ЛИТЬЕ ПО ПОТЕРЯМ, в котором используется несвязанный песок, и ЛИТЬЕ ПОЛНОЙ ФОРМЫ, в котором используется связанный песок. Вот общие этапы процесса: 1.) Изготовьте выкройку из такого материала, как полистирол. Когда будет производиться большое количество, выкройка формуется. Если деталь имеет сложную форму, может потребоваться склеивание нескольких секций такого вспененного материала для формирования рисунка. Мы часто покрываем шаблон огнеупорным составом, чтобы создать хорошую поверхность отливки. 2.) Затем шаблон помещается в формовочную смесь. 3.) Расплавленный металл заливается в форму, испаряя пенопласт, т.е. в большинстве случаев полистирол, при протекании через полость формы. 4.) Расплавленный металл оставляют в песчаной форме для затвердевания. 5.) После затвердевания снимаем отливку. В некоторых случаях продукт, который мы производим, требует сердцевины в шаблоне. При испарительном литье нет необходимости размещать и закреплять стержень в полости формы. Метод подходит для изготовления деталей очень сложной геометрии, легко автоматизируется для крупносерийного производства, в отливке отсутствуют линии разъема. Основной процесс прост и экономичен в реализации. Для крупносерийного производства, поскольку для изготовления моделей из полистирола требуется штамп или форма, это может быть несколько дорогостоящим. • ЛИТЬЕ В НЕРАСШИРЯЕМУЮ ФОРМУ: Эта широкая категория относится к методам, при которых форму не нужно переделывать после каждого производственного цикла. Примерами являются непрерывное литье, литье под давлением, непрерывное и центробежное литье. Достигается повторяемость, и детали можно охарактеризовать как ПОЧТИ РЕЗУЛЬТАТНУЮ ФОРМУ. • ПОСТОЯННАЯ ОТЛИВКА В ФОРМЫ: Многоразовые формы из металла используются для многократного литья. Как правило, постоянную форму можно использовать десятки тысяч раз, прежде чем она изнашивается. Для заполнения формы обычно используются сила тяжести, давление газа или вакуум. Формы (также называемые штампами) обычно изготавливаются из железа, стали, керамики или других металлов. Общий процесс таков: 1.) Обработайте и создайте форму. Обычно форму изготавливают из двух металлических блоков, которые подходят друг к другу и могут открываться и закрываться. Как детали, так и литниковая система обычно изготавливаются в литейной форме. 2.) Внутренние поверхности формы покрыты суспензией, содержащей огнеупорные материалы. Это помогает контролировать поток тепла и действует как смазка для легкого удаления литой детали. 3.) Затем постоянные половинки пресс-формы закрываются и пресс-форма нагревается. 4.) Расплавленный металл заливают в форму и оставляют до затвердевания. 5.) До того, как произойдет значительное охлаждение, мы извлекаем деталь из постоянной формы с помощью эжекторов, когда половинки формы открыты. Мы часто используем литье в постоянные формы для металлов с низкой температурой плавления, таких как цинк и алюминий. Для стальных отливок мы используем графит в качестве материала формы. Иногда мы получаем сложную геометрию, используя стержни в постоянных формах. Преимуществами этого метода являются отливки с хорошими механическими свойствами, полученными путем быстрого охлаждения, однородность свойств, хорошая точность и чистота поверхности, низкий процент брака, возможность автоматизации процесса и экономичное производство больших объемов. Недостатками являются высокие первоначальные затраты на настройку, которые делают его непригодным для операций с небольшим объемом, и ограничения по размеру изготавливаемых деталей. • ЛИТЬЕ ПОД ДАВЛЕНИЕМ: Обрабатывается форма, и расплавленный металл под высоким давлением вдавливается в полости формы. Возможно литье под давлением как цветных, так и черных металлов. Этот процесс подходит для крупносерийного производства деталей малого и среднего размера с деталями, чрезвычайно тонкими стенками, стабильностью размеров и хорошим качеством поверхности. Компания AGS-TECH Inc. способна производить с использованием этой технологии стенки толщиной всего 0,5 мм. Как и при литье в постоянные формы, форма должна состоять из двух половин, которые могут открываться и закрываться для извлечения изготавливаемой детали. Форма для литья под давлением может иметь несколько полостей, что позволяет производить несколько отливок за каждый цикл. Формы для литья под давлением очень тяжелые и намного больше, чем детали, которые они производят, поэтому они также дороги. Мы бесплатно ремонтируем и заменяем изношенные штампы для наших клиентов, если они повторно заказывают у нас свои детали. Срок службы наших штампов составляет несколько сотен тысяч циклов. Вот основные упрощенные этапы процесса: 1.) Изготовление пресс-формы в основном из стали 2.) Пресс-форма, установленная на машине для литья под давлением 3.) Поршень заставляет расплавленный металл течь в полости матрицы, заполняя сложные элементы и тонкие стенки. 4.) После заполнения формы расплавленным металлом отливка подвергается закалке под давлением. 5.) Форма открывается и отливка удаляется с помощью выталкивающих штифтов. 6.) Теперь пустая матрица снова смазывается и зажимается для следующего цикла. При литье под давлением мы часто используем формование со вставкой, когда мы вставляем дополнительную деталь в форму и отливаем вокруг нее металл. После затвердевания эти детали становятся частью отлитого изделия. Преимуществами литья под давлением являются хорошие механические свойства деталей, возможность получения сложных элементов, мелких деталей и хорошей чистоты поверхности, высокая производительность, простота автоматизации. Недостатки: не очень подходит для небольших объемов из-за высокой стоимости штампа и оборудования, ограничения по формам, которые можно отливать, небольшие круглые следы на литых деталях, возникающие в результате контакта выталкивающих штифтов, тонкий налет металла, выдавленный на линии разъема, необходимость для вентиляционных отверстий вдоль линии разъема между матрицами, необходимость поддержания низкой температуры пресс-формы за счет циркуляции воды. • ЦЕНТРОБЕЖНАЯ ЛИТЬЕ: Расплавленный металл заливается в центр вращающейся формы на оси вращения. Центробежные силы отбрасывают металл к периферии, и он затвердевает, пока форма продолжает вращаться. Можно использовать как горизонтальное, так и вертикальное вращение осей. Можно отливать детали с круглыми внутренними поверхностями, а также другие некруглые формы. Процесс можно обобщить следующим образом: 1.) Расплавленный металл заливают в центробежную форму. Затем металл прижимается к внешним стенкам из-за вращения формы. 2.) Когда форма вращается, металлическая отливка затвердевает. Центробежное литье является подходящим методом для производства полых цилиндрических деталей, таких как трубы, отсутствие необходимости в литниках, стояках и литниковых элементах, хорошее качество поверхности и подробные характеристики, отсутствие проблем с усадкой, возможность производства длинных труб очень большого диаметра, высокая производительность . • НЕПРЕРЫВНАЯ ЛИТЬЕ (МЕТАЛЛИЧЕСКАЯ ЛИТКА): Используется для непрерывной разливки металла. В основном расплавленный металл заливается в двухмерный профиль формы, но его длина не определена. Новый расплавленный металл постоянно подается в форму по мере того, как отливка движется вниз, и ее длина со временем увеличивается. Металлы, такие как медь, сталь, алюминий, отливают в длинные нити с использованием процесса непрерывного литья. Процесс может иметь различные конфигурации, но общий можно упростить следующим образом: 1.) Расплавленный металл заливается в емкость, расположенную высоко над формой, в точно рассчитанных количествах и расходах и течет через форму с водяным охлаждением. Металлическая отливка, залитая в форму, затвердевает до стартового стержня, расположенного на дне формы. Эта стартовая планка дает роликам что-то, за что можно зацепиться изначально. 2.) Длинная металлическая заготовка перемещается роликами с постоянной скоростью. Ролики также меняют направление потока металлической заготовки с вертикального на горизонтальное. 3.) После того, как непрерывная отливка прошла определенное расстояние по горизонтали, горелка или пила, которые перемещаются вместе с отливкой, быстро отрезают ее до нужной длины. Процесс непрерывной разливки можно интегрировать с ПРОЦЕССОМ ПРОКАТКИ, при котором непрерывно разливаемый металл можно подавать непосредственно в прокатный стан для производства двутавровых балок, тавровых балок и т. д. Непрерывное литье обеспечивает однородные свойства всего продукта, имеет высокую скорость затвердевания, снижает стоимость из-за очень низких потерь материала, предлагает процесс, в котором загрузка металла, заливка, затвердевание, резка и удаление отливки происходят в непрерывном режиме и что приводит к высокой производительности и высокому качеству. Однако основным соображением являются высокие первоначальные инвестиции, затраты на установку и требования к пространству. • УСЛУГИ ПО ОБРАБОТКЕ: Мы предлагаем трех-, четырех- и пятиосевую обработку. Используемые нами процессы обработки: ТОКАРНАЯ, ФРЕЗЕРОВАЛЬНАЯ, СВЕРЛИТЕЛЬНАЯ, РАСТОЧНАЯ, ПРОШИВКА, СТРОГООБРАБОТКА, ПИЛКА, ШЛИФОВКА, ПРИТРОЙКА, ПОЛИРОВКА и НЕТРАДИЦИОННАЯ ОБРАБОТКА, которая более подробно описана в другом меню нашего веб-сайта. Для большей части нашего производства мы используем станки с ЧПУ. Однако для некоторых операций лучше подходят традиционные методы, поэтому мы также полагаемся на них. Наши возможности обработки достигают максимально возможного уровня, и некоторые наиболее требовательные детали производятся на заводе, сертифицированном AS9100. Лопасти реактивных двигателей требуют узкоспециализированного производственного опыта и подходящего оборудования. В аэрокосмической отрасли действуют очень строгие стандарты. Некоторые детали со сложной геометрической структурой проще всего изготавливать пятикоординатной обработкой, которая есть только на некоторых механообрабатывающих предприятиях, в том числе и на нашем. Наш завод, сертифицированный для аэрокосмической отрасли, имеет необходимый опыт в соответствии с обширными требованиями документации аэрокосмической отрасли. В токарных операциях заготовка вращается и перемещается относительно режущего инструмента. Для этого процесса используется машина, называемая токарным станком. В ФРЕЗЕРОВАНИИ станок, называемый фрезерным станком, имеет вращающийся инструмент, который прижимает режущие кромки к заготовке. Операции СВЕРЛЕНИЯ включают вращающуюся фрезу с режущими кромками, которая создает отверстия при контакте с заготовкой. Обычно используются сверлильные станки, токарные станки или мельницы. При РАСТОЧНОЙ операции инструмент с одним изогнутым заостренным концом перемещается в черновое отверстие во вращающейся заготовке, чтобы немного увеличить отверстие и повысить точность. Используется для чистовой отделки. ПРОШИВКА включает в себя зубчатый инструмент для удаления материала с заготовки за один проход протяжки (зубчатый инструмент). При линейной протяжке протяжка проходит линейно по поверхности заготовки, чтобы произвести рез, тогда как при вращательной протяжке протяжка вращается и вдавливается в заготовку, чтобы вырезать осесимметричную форму. SWISS TYPE MACHINING — одна из наших ценных технологий, которые мы используем для крупносерийного производства небольших высокоточных деталей. На токарном станке швейцарского типа мы недорого вытачиваем мелкие, сложные, прецизионные детали. В отличие от обычных токарных станков, где заготовка остается неподвижной, а инструмент движется, в токарных центрах швейцарского типа заготовка может перемещаться по оси Z, а инструмент неподвижен. При обработке по швейцарскому типу прутковый материал удерживается в станке и продвигается через направляющую втулку по оси Z, обнажая только часть, подлежащую обработке. Таким образом обеспечивается плотный захват и очень высокая точность. Наличие приводных инструментов обеспечивает возможность фрезерования и сверления по мере продвижения материала из направляющей втулки. Ось Y оборудования швейцарского типа обеспечивает полные возможности фрезерования и значительно экономит время производства. Кроме того, наши станки имеют сверла и расточные инструменты, которые воздействуют на деталь, удерживаемую во вспомогательном шпинделе. Наши возможности обработки швейцарского типа дают нам возможность полностью автоматизированной полной обработки за одну операцию. Механическая обработка является одним из крупнейших сегментов бизнеса AGS-TECH Inc. Мы используем его либо в качестве основной операции, либо в качестве дополнительной операции после литья или выдавливания детали, чтобы были соблюдены все спецификации чертежа. • УСЛУГИ ПО ОБРАБОТКЕ ПОВЕРХНОСТИ: Мы предлагаем широкий спектр услуг по обработке и отделке поверхности, таких как подготовка поверхности для улучшения адгезии, нанесение тонкого оксидного слоя для улучшения адгезии покрытия, пескоструйная обработка, химическая пленка, анодирование, азотирование, порошковое покрытие, напыление. , различные передовые методы металлизации и нанесения покрытий, включая напыление, электронно-лучевое напыление, нанесение покрытия, твердые покрытия, такие как алмазоподобный углерод (DLC) или титановое покрытие для сверлильных и режущих инструментов. • УСЛУГИ ПО МАРКИРОВКЕ И МАРКИРОВКЕ ПРОДУКЦИИ: Многим нашим клиентам требуется маркировка и маркировка, лазерная маркировка, гравировка на металлических деталях. Если у вас есть такая потребность, давайте обсудим, какой вариант будет лучшим для вас. Вот некоторые из наиболее часто используемых металлических литых изделий. Поскольку они есть в наличии, вы можете сэкономить на затратах на пресс-формы, если какой-либо из них соответствует вашим требованиям: НАЖМИТЕ ЗДЕСЬ, ЧТОБЫ СКАЧАТЬ наши литые алюминиевые коробки серии 11 от AGS-Electronics CLICK Product Finder-Locator Service ПРЕДЫДУЩАЯ СТРАНИЦА
- Изготовленные на заказ детали, сборки, пластиковые формы, литье, механическая обработка
Детали, изготовленные на заказ, сборки, пластиковые формы, формование резины, литье металлов, обработка с ЧПУ, токарная обработка, фрезерование, электрические электронные оптические сборки, печатные платы Изготовленные на заказ детали & Сборки и продукты Читать далее Пластиковые и резиновые формы и литье Читать далее Литье и обработка Читать далее Экструзии, экструдированные продукты Читать далее Штамповки и изготовление листового металла Читать далее Ковка металлов и порошковая металлургия Читать далее Проволочное и пружинное формование Читать далее Формование и формование стекла и керамики Читать далее Аддитивное и быстрое производство Читать далее Производство композитов и композитных материалов Читать далее Процессы соединения, сборки и крепления Мы изготавливаем для вас детали и узлы и предлагаем следующие производственные процессы: • Пластмассовые и резиновые формы и фасонные детали. Литье под давлением, термоформование, термореактивное формование, вакуумное формование, выдувное формование, ротационное формование, литье под давлением, литье под давлением и другие. • Пластиковые, резиновые и металлические профили • Отливки и детали из черных и цветных металлов, изготовленные токарно-фрезерными методами, швейцарской механической обработки. • Детали из порошковой металлургии • Металлические и неметаллические штамповки, формовка листового металла, сварные сборки из листового металла • Холодная и горячая ковка • Проволока, сварные проволочные сборки, формовка проволоки • Различные типы пружин, формование пружин • Производство зубчатых колес, редуктора, муфты, червяка, редуктора, цилиндра, приводных ремней, передаточных цепей, компонентов трансмиссии. • Изготовленное на заказ закаленное и пуленепробиваемое стекло, соответствующее стандартам НАТО и военным стандартам. • Шарики, подшипники, шкивы и шкивы в сборе • Клапаны и пневматические компоненты, такие как уплотнительное кольцо, шайба и уплотнения • Детали и узлы из стекла и керамики, вакуумные и герметичные компоненты, металлокерамические и керамико-керамические соединения. • Различные типы механических, оптико-механических, электромеханических, оптоэлектронных узлов. • Связка металл-резина, металл-пластик • Трубы и трубки, формовка труб, гибка и сборка труб на заказ, изготовление сильфонов. • Производство стеклопластика • Сварка различными методами, такими как точечная сварка, лазерная сварка, MIG, TIG. Ультразвуковая сварка пластиковых деталей. • Большое разнообразие способов обработки и отделки поверхности, таких как подготовка поверхности для повышения адгезии, нанесение тонкого оксидного слоя для улучшения адгезии покрытия, пескоструйная обработка, химическая пленка, анодирование, азотирование, порошковое покрытие, напыление, различные передовые технологии металлизации и нанесения покрытий. включая напыление, электронно-лучевое напыление, напыление, нанесение твердых покрытий, таких как алмазоподобный углерод (DLC) или титан, для режущих и сверлильных инструментов. • Маркировка и маркировка, лазерная маркировка металлических деталей, печать на пластиковых и резиновых деталях Загрузите брошюру об общих терминах в области машиностроения, используемых конструкторами и инженерами Мы производим продукцию в соответствии с вашими конкретными спецификациями и требованиями. Чтобы предложить вам лучшее качество, доставку и цены, мы производим продукцию по всему миру в Китае, Индии, Тайване, Филиппинах, Южной Корее, Малайзии, Шри-Ланке, Турции, США, Канаде, Германии, Великобритании и Японии. Это делает нас намного сильнее и конкурентоспособнее в глобальном масштабе, чем любой другой custom производитель. Наша продукция производится в сертифицированных средах ISO9001:2000, QS9000, ISO14001, TS16949 и имеет знак CE, UL и соответствует другим отраслевым стандартам. Как только мы назначаемся для вашего проекта, мы можем позаботиться обо всем производстве, сборке, тестировании, квалификации, доставке и таможне по вашему желанию. Если вы предпочитаете, мы можем хранить ваши детали, собирать индивидуальные комплекты, печатать и маркировать название и бренд вашей компании и отправлять их вашим клиентам. Другими словами, мы можем быть вашим складским и распределительным центром, если это необходимо. Поскольку наши склады расположены вблизи крупных морских портов, это дает нам логистическое преимущество. Например, когда ваша продукция прибывает в крупный морской порт США, мы можем транспортировать ее непосредственно на ближайший склад, где мы можем хранить, собирать, изготавливать комплекты, перемаркировать, печатать, упаковывать по вашему выбору и доставлять. отправить своим клиентам. Мы не только поставляем продукцию. Наша компания работает по индивидуальным контрактам, когда мы приезжаем на ваш объект, оцениваем ваш проект на месте и разрабатываем проектное предложение, разработанное специально для вас. Затем мы отправляем нашу опытную команду для реализации проекта. Более подробную информацию о наших инженерных работах можно найти на http://www.ags-engineering.com -Мы беремся за небольшие проекты, а также крупные проекты в промышленных масштабах. В качестве первого шага мы можем соединить вас по телефону, телеконференции или через мессенджер MSN с членами нашей команды экспертов, чтобы вы могли общаться напрямую с экспертом, задавать вопросы и обсуждать свой проект. Позвоните нам, и если нужно, мы приедем к вам в гости. ПРЕДЫДУЩАЯ СТРАНИЦА