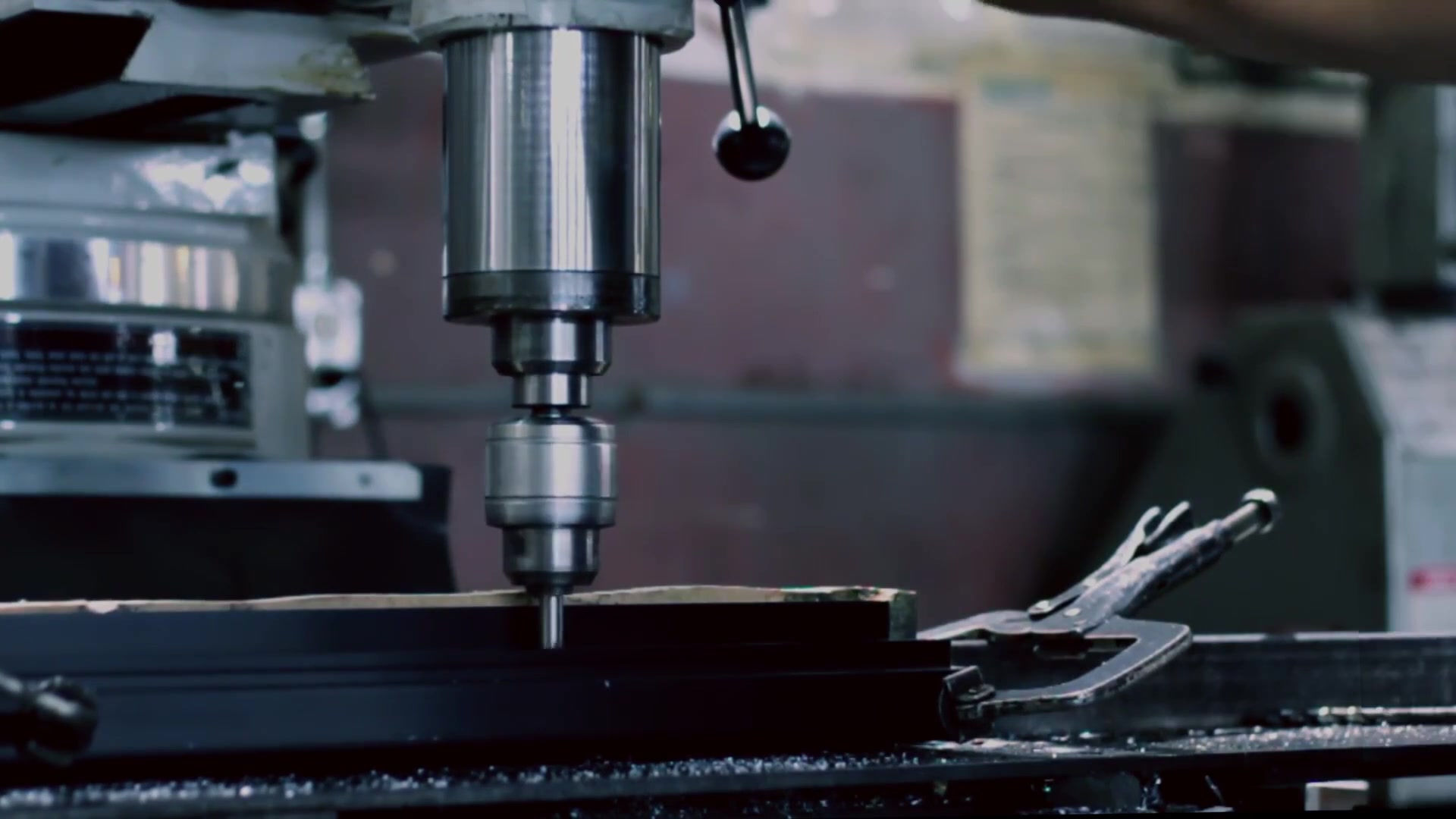
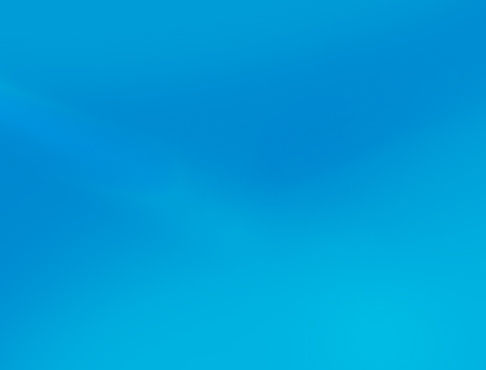
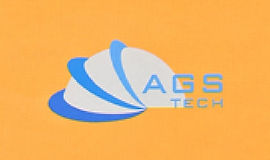
Global Custom Manufacturer, Integrator, Consolidator, Outsourcing Partner for a Wide Variety of Products & Services.
We are your one-stop source for manufacturing, fabrication, engineering, consolidation, integration, outsourcing of custom manufactured and off-shelf products & services. We also private label / white label your products with your brand name if you wish.
Choose your Language
-
Custom Manufacturing of Parts, Components, Assemblies, Finished Products, Machines and Industrial Equipment
-
Domestic & Global Contract Manufacturing
-
Manufacturing Outsourcing
-
Domestic, Global Procurement of Industrial Products
-
Private labeling / White Labeling your Products with your Brand Name
-
Product Finding & Locating Services
-
Global Design and Channel Partnership
-
Engineering Integration
-
Engineering Services
-
Global Consolidation, Warehousing, Logistics
Vital components in pneumatic, hydraulic and vacuum systems are SEALS, FITTINGS, CONNECTIONS, ADAPTERS, QUICK COUPLINGS, CLAMPS, FLANGES. Depending on the application environment, standards requirements, and geometry of the application area there are a wide spectrum of these products readily available from our stock. On the other hand, for customers with special needs and requirements we are custom manufacturing seals, fittings, connections, adaptors, clamps and flanges for every possible pneumatics, hydraulics and vacuum application.
If components within hydraulic systems never needed to be removed, we could simply braze or weld connections. However, it is inevitable that connections must be broken to allow servicing and replacing, so removable fittings and connections are a necessity for hydraulic, pneumatic and vacuum systems. Fittings seal fluids within hydraulic systems by one of two techniques: ALL-METAL FITTINGS rely on metal-to-metal contact, while O-RING TYPE FITTINGS rely on compressing an elastomeric seal. In both cases, tightening threads between mating halves of the fitting or between fitting and component forces two mating surfaces come together to form a high-pressure seal.
ALL-METAL FITTINGS: Threads on pipe fittings are tapered and rely on the stress generated by forcing the tapered threads of the male half of the fittings into the female half of fittings. Pipe threads are prone to leakage because they are torque-sensitive. Over-tightening all-metal fittings distorts the threads too much and creates a path for leakage around the fittings threads. Pipe threads on all-metal fittings are also prone to loosening when exposed to vibration and wide temperature fluctuations. Pipe threads on fittings are tapered, and therefore repeated assembly and disassembly of the fittings aggravate the leakage problems by distorting the threads. Flare-type fittings are superior to pipe fittings and likely will remain the design of choice used in hydraulic systems. Tightening the nut draws the fittings into the flared end of the tubing, resulting in a positive seal between the flared tube face and the fitting body. The 37 degree flare fittings are designed for use with thin-wall to medium-thickness tubing in systems with operating pressures up to 3,000 psi and temperatures from -65 to 400 F. Because thick-wall tubing is difficult to form to produce the flare, it is not recommended for use with flare fittings. It is more compact than most other fittings and can easily be adapted to metric tubing. It is readily available and one of the most economical. The flareless fittings, gradually are gaining wider acceptance, because they require minimal tube preparation. Flareless fittings handle average fluid working pressures up to 3,000 psi and are more tolerant of vibration than other types of all-metal fittings. Tightening the fitting's nut onto the body draws a ferrule into the body. This compresses the ferrule around the tube, causing the ferrule to contact, then penetrate the outer circumference of the tube, creating a positive seal. Flareless fittings need to be used with medium or thick-walled tubing.
O-RING TYPE FITTINGS: Fittings using O-rings for leak-tight connections continue to gain acceptance by equipment designers. Three basic types are available: SAE straight-thread O-ring boss fittings, face seal or flat-face O-ring (FFOR) fittings, and O-ring flange fittings. The choice between O-ring boss and FFOR fittings usually depends on such factors as fitting location, wrench clearance…etc. Flange connections generally are used with tubing that have an outer diameter greater than 7/8-inch or for applications involving extremely high pressures. O-ring boss fittings seat an O-ring between threads and wrench flats around the outer diameter (OD) of the male half of the connector. A leak-tight seal is formed against a machined seat on the female port. There are two groups of O-ring boss fittings: adjustable and non-adjustable fittings. Non-adjustable or non-orientable O-ring boss fittings include plugs and connectors. These are simply screwed into a port, and no alignment is needed. Adjustable fittings on the other hand, such as elbows and tees, need to be oriented in a specific direction. The basic design difference between the two types of O-ring boss fittings is that plugs and connectors have no locknuts and require no back-up washer to effectively seal a joint. They depend on their flanged annular area to push the O-ring into the port's tapered seal cavity and squeeze the O-ring for sealing the connection. On the other hand, adjustable fittings are screwed into the mating member, oriented in the required direction, and locked in place when a locknut is tightened. Tightening the locknut also forces a captive backup washer onto the O-ring, which forms the leak-tight seal. Assembly is always predictable, technicians need only make sure that the backup washer is firmly seated on the port's spot face surface when the assembly is completed and that it is tightened properly. The FFOR fittings form a seal between a flat and finished surface on the female half and an O-ring held in a recessed circular groove in the male half. Turning a captive threaded nut on the female half draws the two halves together while compressing the O-ring. Fittings with O-ring seals offer some advantages over metal-to-metal fittings. All-metal fittings are more susceptible to leakage because they must be tightened to within a higher, yet narrower torque range. This makes it easier to strip threads or crack or distort fitting components, which prevents proper sealing. The rubber-to-metal seal in O-ring fittings does not distort any metal parts and provides a feel on our fingers when the connection is tight. All-metal fittings tighten more gradually, so technicians may find it more difficult detecting when a connection is tight enough but not too tight. Disadvantages are that O-ring fittings are more expensive than all-metal fittings, and care must be exercised during installation to ensure that the O-ring doesn't fall out or get damaged when the assemblies are connected. In addition, O-rings are not interchangeable among all couplings. Selecting the wrong O-ring or reusing one that has been deformed or damaged can result in leakage in fittings. Once an O-ring has been used in a fitting, it is not reusable, even though it may appear free of distortions.
FLANGES: We offer flanges individually or as a complete set for a number of applications in a range of sizes and types. Stock is kept of Flanges, Counter-flanges, 90 degree flanges, Split flanges, Threaded flanges. Fittings for tubing larger than 1-in. OD have to be tightened with large hexnuts which requires a large wrench to apply sufficient torque to tighten the fittings properly. To install such large fittings, the necessary space needs to be given to workers to swing large wrenches. Worker strength and fatigue could also affect proper assembly. Wrench extensions may be needed for some workers to exert an applicable amount of torque. Split-flange fittings are available so that they overcome these problems. Split-flange fittings use an O-ring to seal a joint and contain pressurized fluid. An elastomeric O-ring sits in a groove on a flange and mates with a flat surface on a port - an arrangement similar to the FFOR fitting. The O-ring flange is attached to the port using four mounting bolts that tighten down onto flange clamps. This eliminates the need for large wrenches when connecting large-diameter components. When installing flange connections, it is important to apply even torque on the four flange bolts to avoid creating a gap through which the O-ring can extrude under high pressure. A split-flange fitting consists generally of four elements: a flanged head connected permanently (generally welded or brazed) to the tube, an O-ring that fits into a groove machined into the end face of the flange, and two mating clamp halves with appropriate bolts to connect the split-flange assembly to a mating surface. The clamp halves do not actually contact the mating surfaces. A critical operation during assembly of a split-flange fitting to its mating surface is to make sure that the four fastening bolts are tightened gradually and evenly in a cross pattern.
CLAMPS: A variety of clamping solutions for hose and tube are available, with either a profiled or smooth inner surface in a wide range of sizes. All necessary components can be supplied according to the specific application including, Clamp jaws, Bolts, Stacking bolts, Weld plates, Top plates, Rail. Our hydraulic and pneumatic clamps enable a more efficient installation, resulting in a clean pipe layout, with effective vibration and noise reduction. AGS-TECH hydraulic and pneumatic clamping products ensure repeatability of clamping and consistent clamping forces to avoid part movement and tool breakage. We stock a wide variety of clamping components (inch and metric-based), precision 7 MPa (70 bar) hydraulic clamping systems and professional-grade pneumatic work-holding devices. Our hydraulic clamping products are rated up to 5,000 psi operating pressure that can securely clamp parts in many applications ranging from automotive to welding, and from consumer to industrial markets. Our selection of pneumatic clamping systems provide air-operated holding for high-production environments and applications that require consistent clamping forces. Pneumatic clamps are used for holding and fixturing in assembly, machining, plastics manufacturing, automation and welding applications. We can help you determine work-holding solutions based on your part size, amount of clamp forces needed and other factors. As the World’s most diverse custom manufacturer, outsourcing partner and engineering integrator, we can design and manufacture custom pneumatic and hydraulic clamps for you.
ADAPTERS: AGS-TECH offers adapters that provide leak free solutions. Adapters include hydraulic, pneumatic & instrumentation. Our adapters are manufactured to meet or exceed the industrial standards requirements of SAE, ISO, DIN, DOT and JIS. A wide range of adapter styles are available including: Swivel Adapters, Steel and Stainless Steel Pipe Adapters and Industrial Fittings, Brass Pipe Adapters, Brass and Plastic Industrial Fittings, High Purity and Process Adapters, Angled Flare Adapters.
QUICK COUPLINGS: We offer quick connect / disconnect couplings for hydraulic, pneumatic and medical applications. Quick disconnect couplings are used to connect and disconnect hydraulic or pneumatic lines quickly and easily without using any tools. Various models are available: Non spill and double-shut-off quick couplings, Connect under pressure quick couplings, Thermoplastic quick couplings, Test port quick couplings, agricultural quick couplings,….and more.
SEALS: Hydraulic and pneumatic seals are designed for the reciprocating motion which is common in hydraulic and pneumatic applications, such as cylinders. Hydraulic and pneumatic seals include Piston seals, Rod seals, U-cups, Vee, Cup, W, Piston, Flange packings. Hydraulic seals are designed for high-pressure dynamic applications such as hydraulic cylinders. Pneumatic seals are used in pneumatic cylinders and valves and are usually designed for lower operating pressures compared to hydraulic seals. Pneumatic applications demand however higher operating speeds and lower friction seals compared to hydraulic applications. Seals may be used for rotary and reciprocating motion. Some hydraulic seals and pneumatic seals are composite and are two-or multi-part manufactured as an integral unit. A typical composite seal consists of an integral PTFE ring and an elastomer ring, providing the properties of an elastomeric ring with a rigid, low friction (PTFE) working face. Our seals can have a variety of different cross sections. Common sealing orientation and directions for hydraulic and pneumatic seals include 1.) Rod Seals which are radial seals. The seal is press-fit into a housing bore with the sealing lip contacting the shaft. Also referred to as a shaft seal. 2.) Piston seals which are radial seals. The seal is fit onto a shaft with the sealing lip contacting the housing bore. V-rings are considered external lip seals, 3.) Symmetric seals are symmetrical and work equally well as a rod or piston seal, 4.) An axial seal seals axially against a housing or machine component. Sealing direction is relevant to hydraulic and pneumatic seals used in applications with axial motion, such as cylinders and pistons. The action can be single or double. Single acting, or unidirectional seals, offer an effective seal in one axial direction only, whereas double acting, or bi-directional seals, are effective when sealing in both directions. In order to seal in both directions for a reciprocating motion, more than one seal must be used. Features for hydraulic and pneumatic seals include spring loaded, integral wiper, and split seal.
Some important dimensions to consider when you specify hydraulic and pneumatic seals are:
• Shaft outer diameter or seal inner diameter
• Housing bore diameter or seal outer diameter
• Axial cross section or thickness
• Radial cross section
Important service limit parameters to consider when purchasing seals are:
• Maximum operating speed
• Maximum operating pressure
• Vacuum rating
• Operation temperature
Popular material choices for rubber sealing elements for hydraulics and pneumatics include:
• Ethylene Acrylic
• EDPM Rubber
• Fluoroelastomer and Fluorosilicone
• Nitrile
• Nylon or Polyamide
• Polychloroprene
• Polyoxymethylene
• Polytetrafluoroethylene (PTFE)
• Polyurethane / Urethane
• Natural Rubber
Some seal material choices are:
• Sintered Bronze
• Stainless Steel
• Cast Iron
• Felt
• Leather
Standards related to seals are:
BS 6241 - Specifications for dimensions of housing for hydraulic seals incorporating bearing rings for reciprocating applications
ISO 7632 - Road vehicles - elastomeric seals
GOST 14896 - Rubber U-packing seals for hydraulic devices
You can download relevant product brochures from the links below:
Pneumatic Air Tubing Connectors Adapters Couplings Splitters and Accessories
Private Label Pneumatic Compressed Air Hoses Fittings (We private label these with your brand name and logo if you wish)
Private Label Pneumatic Quick Couplings, Plugs and Nipples (We private label these with your brand name and logo if you wish)
Information on our facility producing ceramic to metal fittings, hermetic sealing, vacuum feedthroughs, high and ultrahigh vacuum and fluid control components can be found here: Fluid Control Factory Brochure