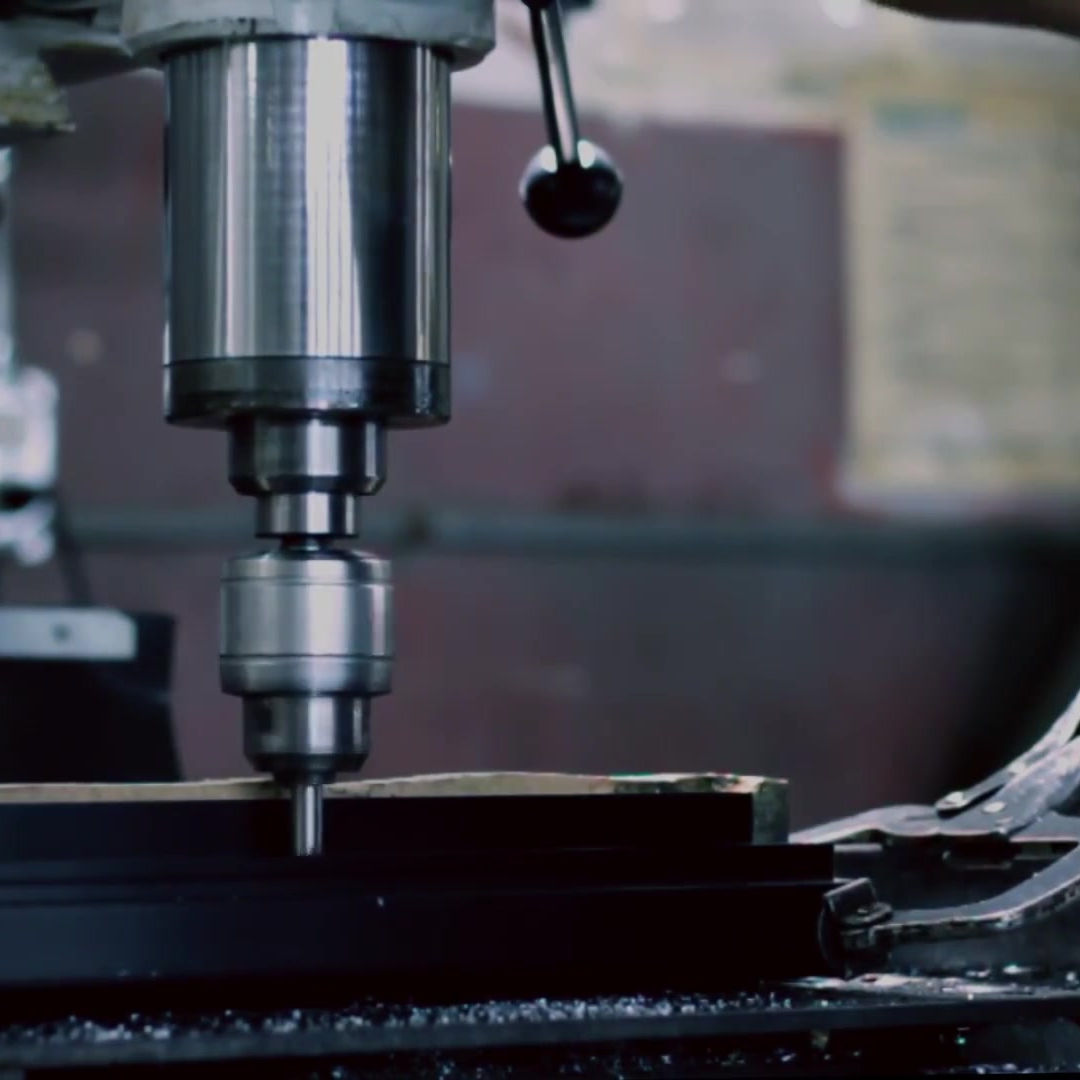
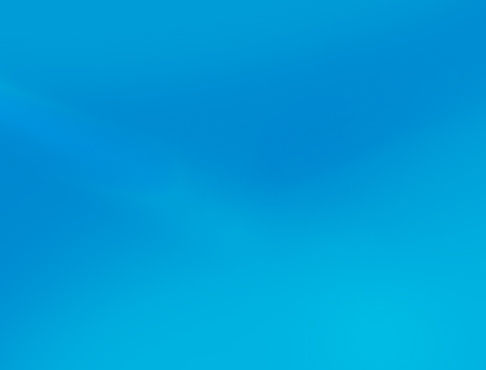
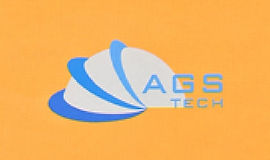
Global Custom Manufacturer, Integrator, Consolidator, Products & Services හි පුළුල් විවිධත්වයක් සඳහා බාහිරින් ලබා ගැනීමේ හවුල්කරු.
අභිරුචි නිෂ්පාදනය කරන ලද සහ රාක්කයෙන් බැහැර නිෂ්පාදන සහ සේවා නිෂ්පාදනය කිරීම, සැකසීම, ඉංජිනේරු විද්යාව, ඒකාබද්ධ කිරීම, ඒකාබද්ධ කිරීම, බාහිරින් ලබා ගැනීම සඳහා අපි ඔබේ එක-නැවතුම් මූලාශ්රය වේ.
ඔබේ භාෂාව තෝරන්න
-
අභිරුචි නිෂ්පාදනය
-
දේශීය සහ ගෝලීය ගිවිසුම් නිෂ්පාදනය
-
නිෂ්පාදන බාහිරකරණය
-
දේශීය සහ ගෝලීය ප්රසම්පාදන
-
Consolidation
-
ඉංජිනේරු අනුකලනය
-
ඉංජිනේරු සේවාවන්
අපි පිරිනමන වීදුරු නිෂ්පාදන වර්ගය වන්නේ බහාලුම් වීදුරු, වීදුරු පිඹීම, වීදුරු කෙඳි සහ නල සහ සැරයටිය, ගෘහස්ත සහ කාර්මික වීදුරු භාණ්ඩ, ලාම්පු සහ බල්බ, නිරවද්ය වීදුරු අච්චු, දෘශ්ය සංරචක සහ එකලස් කිරීම්, පැතලි සහ තහඩු සහ පාවෙන වීදුරු ය. අපි අතින් සෑදීම මෙන්ම යන්ත්ර සෑදීම යන දෙකම සිදු කරයි.
අපගේ ජනප්රිය තාක්ෂණික සෙරමික් නිෂ්පාදන ක්රියාවලීන් වන්නේ ඩයි එබීම, සමස්ථිතික එබීම, උණුසුම් සමස්ථානික එබීම, උණුසුම් එබීම, ස්ලිප් වාත්තු කිරීම, ටේප් වාත්තු කිරීම, නිස්සාරණය, එන්නත් අච්චු ගැසීම, හරිත යන්ත්රකරණය, සින්ටර් කිරීම හෝ වෙඩි තැබීම, දියමන්ති ඇඹරීම, හර්මෙටික් එකලස් කිරීමයි.
ඔබ මෙහි ක්ලික් කරන ලෙස අපි නිර්දේශ කරමු
AGS-TECH Inc මගින් වීදුරු සෑදීම සහ හැඩ ගැන්වීමේ ක්රියාවලීන් පිළිබඳ අපගේ ක්රමානුකූල නිදර්ශන බාගන්න.
ඡායාරූප සහ කටු සටහන් සහිත මෙම බාගත කළ හැකි ගොනු අප ඔබට පහතින් සපයන තොරතුරු වඩාත් හොඳින් අවබෝධ කර ගැනීමට උපකාරී වනු ඇත.
• බහාලුම් වීදුරු නිෂ්පාදනය: අපි නිෂ්පාදනය සඳහා ස්වයංක්රීය මුද්රණ සහ පහර මෙන්ම බ්ලෝ සහ බ්ලෝ රේඛා ඇත. පහර සහ පිඹීමේ ක්රියාවලියේදී අපි ගොබ් එකක් හිස් අච්චුවකට දමා ඉහළ සිට සම්පීඩිත වාතය පහරක් යෙදීමෙන් බෙල්ල සාදමු. මෙය ඉක්බිතිව, බෝතලයේ පූර්ව ආකෘතිය සෑදීම සඳහා සම්පීඩිත වාතය කන්ටේනර් බෙල්ල හරහා අනෙක් දිශාවෙන් දෙවන වරටත් පිඹිනු ලැබේ. මෙම පූර්ව ආකෘතිය පසුව සැබෑ අච්චුව වෙත මාරු කරනු ලැබේ, මෘදු කිරීම සඳහා නැවත රත් කර සම්පීඩිත වාතය පෙර ආකෘතියට එහි අවසාන බහාලුම් හැඩය ලබා දීම සඳහා යොදනු ලැබේ. වඩාත් පැහැදිලිව කිවහොත්, එය පීඩනයට ලක් කර එහි අපේක්ෂිත හැඩය ගැනීමට පිඹින අච්චු කුහරයේ බිත්තිවලට තල්ලු කරයි. අවසාන වශයෙන්, නිෂ්පාදනය කරන ලද වීදුරු බහාලුම පසුව නැවත රත් කිරීම සහ අච්චු ගැසීමේදී නිපදවන ආතතීන් ඉවත් කිරීම සඳහා නිර්වින්දන උඳුනකට මාරු කර පාලිත ආකාරයෙන් සිසිල් කරනු ලැබේ. මුද්රණ සහ පිඹීමේ ක්රමයේදී, උණු කළ ගොබ්ස් පැරිසන් අච්චුවකට (හිස් අච්චුවකට) දමා පැරිසන් හැඩයට (හිස් හැඩයට) තද කරනු ලැබේ. ඉන්පසු හිස් තැන් පිඹින අච්චු වලට මාරු කර "Blow and Blow Process" යටතේ ඉහත විස්තර කර ඇති ක්රියාවලියට සමානව පිඹිනු ලැබේ. සමනය කිරීම සහ ආතතිය සමනය කිරීම වැනි පසුකාලීන පියවර සමාන හෝ සමාන වේ.
• වීදුරු පිඹීම: අපි සාම්ප්රදායික අතින් පිඹීම මෙන්ම ස්වයංක්රීය උපකරණ සමඟ සම්පීඩිත වාතය භාවිතා කරමින් වීදුරු නිෂ්පාදන නිෂ්පාදනය කර ඇත. සමහර ඇණවුම් සඳහා වීදුරු කලා කටයුතු සම්බන්ධ ව්යාපෘති, හෝ ලිහිල් ඉවසීම් සහිත කොටස් කුඩා ප්රමාණයක් අවශ්ය වන ව්යාපෘති, මූලාකෘතිකරණය / ආදර්ශන ව්යාපෘති.... යනාදී ලෙස සම්ප්රදායික පිඹීම අවශ්ය වේ. සාම්ප්රදායික වීදුරු පිඹීම යනු කුහර ලෝහ පයිප්පයක් උණු කළ වීදුරු බඳුනකට ගිල්වා වීදුරු ද්රව්යවලින් යම් ප්රමාණයක් එකතු කිරීම සඳහා නළය කරකැවීමයි. පයිප්පයේ කෙළවරේ එකතු කරන ලද වීදුරුව පැතලි යකඩ මත රෝල් කර, අවශ්ය පරිදි හැඩගස්වා, දිගු කර, නැවත රත් කර වාතය පිඹිනු ලැබේ. සූදානම් වන විට, එය අච්චුවකට ඇතුල් කර වාතය පුපුරවා හරිනු ලැබේ. ලෝහ සමග වීදුරුව ස්පර්ශ නොකිරීමට අච්චු කුහරය තෙත් වේ. ජල චිත්රපටය ඔවුන් අතර කොට්ටයක් ලෙස ක්රියා කරයි. අතින් පිඹීම ශ්රම තීව්ර මන්දගාමී ක්රියාවලියක් වන අතර මූලාකෘතිකරණයට හෝ ඉහළ වටිනාකමක් ඇති අයිතම සඳහා පමණක් සුදුසු වන අතර, එක් කැබැල්ලකට මිල අඩු ඉහළ වෙළුම් ඇණවුම් සඳහා සුදුසු නොවේ.
• ගෘහස්ත සහ කාර්මික වීදුරු භාණ්ඩ නිෂ්පාදනය : විවිධ වර්ගයේ වීදුරු ද්රව්ය භාවිතා කරමින් විශාල වීදුරු භාණ්ඩ විශාල ප්රමාණයක් නිෂ්පාදනය කෙරේ. සමහර වීදුරු තාප ප්රතිරෝධී වන අතර රසායනාගාර වීදුරු භාණ්ඩ සඳහා සුදුසු වන අතර සමහර වීදුරු පිඟන් සෝදන යන්ත්රවලට බොහෝ වාර ගණනක් ඔරොත්තු දීමට ප්රමාණවත් වන අතර දේශීය නිෂ්පාදන සෑදීමට සුදුසු වේ. වෙස්ට්ලේක් යන්ත්ර භාවිතයෙන් දිනකට බීම වීදුරු කැබලි දස දහස් ගණනක් නිෂ්පාදනය කෙරේ. සරල කිරීම සඳහා, උණු කළ වීදුරු රික්තයක් මගින් එකතු කර පූර්ව ආකෘති සෑදීම සඳහා අච්චු වලට ඇතුල් කරනු ලැබේ. එවිට අච්චු වලට වාතය ගසා, මේවා වෙනත් අච්චුවකට මාරු කර නැවත වාතය පිඹින අතර වීදුරුව එහි අවසාන හැඩය ගනී. අතින් පිඹීමේදී මෙන්, මෙම අච්චු ජලයෙන් තෙත් කර තබා ඇත. තවදුරටත් දිගු කිරීම ගෙල සාදනු ලබන නිම කිරීමේ මෙහෙයුමේ කොටසකි. අතිරික්ත වීදුරුව පුළුස්සා දමනු ලැබේ. ඉන්පසු ඉහත විස්තර කර ඇති පාලිත නැවත උනුසුම් කිරීම සහ සිසිලනය කිරීමේ ක්රියාවලිය පහත දැක්වේ.
• GLASS TUBE & ROD FORMING : වීදුරු බට නිෂ්පාදනය සඳහා අප භාවිතා කරන ප්රධාන ක්රියාවලි වන්නේ DANNER සහ VELLO ක්රියාවලි ය. ඩැනර් ක්රියාවලියේදී, උදුනකින් වීදුරු ගලා යන අතර පරාවර්තක ද්රව්ය වලින් සාදන ලද ආනත කමිසයක් මතට වැටේ. කමිසය භ්රමණය වන හිස් පතුවළක් හෝ පිඹින නළයක් මත ගෙන යනු ලැබේ. එවිට වීදුරුව කමිසය වටා ඔතා, අත් දිගේ පහළට සහ පතුවළ කෙළවරට ඉහළින් ගලා යන සිනිඳු තට්ටුවක් සාදයි. නල සෑදීමේදී, හිස් තුඩ සහිත පිඹින නලයක් හරහා වාතය පිඹින අතර, සැරයටිය සෑදීමේදී අපි පතුවළ මත ඝන ඉඟි භාවිතා කරමු. නල හෝ සැරයටි පසුව රැගෙන යන රෝලර් මත ඇදගෙන යනු ලැබේ. වීදුරු බටවල බිත්ති ඝණත්වය සහ විෂ්කම්භය වැනි මානයන් කමිසයේ විෂ්කම්භය සකසා වායු පීඩනය අවශ්ය අගයකට පිඹීම, උෂ්ණත්වය, වීදුරු ගලායාමේ වේගය සහ ඇඳීමේ වේගය සකස් කිරීම මගින් අවශ්ය අගයන්ට සකසනු ලැබේ. අනෙක් අතට Vello වීදුරු නල නිෂ්පාදන ක්රියාවලියට උදුනකින් පිටතට ගමන් කරන වීදුරු සහ හිස් මැන්ඩල් හෝ සීනුවක් සහිත බඳුනකට ඇතුළත් වේ. එවිට වීදුරුව මැන්ඩලය සහ පාත්රය අතර ඇති වායු අවකාශය හරහා ගොස් නලයක හැඩය ගනී. ඉන් පසුව එය රෝලර් හරහා ඇඳීම් යන්ත්රයකට ගමන් කර සිසිල් කරනු ලැබේ. සිසිලන රේඛාව අවසානයේ කැපීම සහ අවසන් සැකසුම් සිදු වේ. ඩැනර් ක්රියාවලියේදී මෙන් නල මානයන් සකස් කළ හැක. Danner to Vello ක්රියාවලිය සංසන්දනය කරන විට, විශාල ප්රමාණයේ නිෂ්පාදනය සඳහා Vello ක්රියාවලිය වඩා සුදුසු බව අපට පැවසිය හැකි අතර Danner ක්රියාවලිය නිශ්චිත කුඩා පරිමා නල ඇණවුම් සඳහා වඩාත් සුදුසු විය හැක.
• ෂීට් සහ පැතලි සහ පාවෙන වීදුරු සැකසීම : අප සතුව විශාල පැතලි වීදුරු විශාල ප්රමාණයක් ඇත. අපගේ පැතලි වීදුරු පාහේ දෘශ්ය පරිපූර්ණයි. අපි දෘශ්ය ආලේපන වැනි විශේෂ ආෙල්පන සහිත වීදුරු පිරිනමන්නෙමු, එහිදී රසායනික වාෂ්ප තැන්පත් කිරීමේ තාක්ෂණය ප්රති-ප්රතිවිකුණුම් හෝ දර්පණ ආලේපනය වැනි ආලේපන තැබීමට භාවිතා කරයි. එසේම විනිවිද පෙනෙන සන්නායක ආලේපන පොදු වේ. වීදුරු මත ඇති ජලභීතික හෝ ජලභීතික ආලේපන සහ වීදුරු ස්වයං-පිරිසිදු කරන ආලේපනය ද පවතී. මෘදු, වෙඩි නොවදින සහ ලැමිෙන්ටඩ් වීදුරු තවමත් ජනප්රිය භාණ්ඩ වේ. අපි අපේක්ෂිත ඉවසීම සහිත අපේක්ෂිත හැඩයට වීදුරු කපා. පැතලි වීදුරුව නැමීම හෝ නැමීම වැනි වෙනත් ද්විතියික මෙහෙයුම් තිබේ.
• PRECISION GLASS MOLDING : අපි මෙම තාක්ෂණය වැඩිපුරම භාවිතා කරන්නේ ඇඹරීම, ලැප් කිරීම සහ ඔප දැමීම වැනි මිල අධික සහ කාලය ගතවන තාක්ෂණික ක්රම අවශ්ය නොවී නිරවද්ය දෘශ්ය සංරචක නිෂ්පාදනය සඳහා ය. මෙම තාක්ෂණය හොඳම දෘෂ්ටි විද්යාවෙන් උපරිම ප්රයෝජන ගැනීම සඳහා සැමවිටම ප්රමාණවත් නොවේ, නමුත් පාරිභෝගික නිෂ්පාදන, ඩිජිටල් කැමරා, වෛද්ය දෘෂ්ටි විද්යාව වැනි සමහර අවස්ථාවල දී එය ඉහළ පරිමාවක් නිෂ්පාදනය කිරීම සඳහා මිලෙන් අඩු හොඳ විකල්පයක් විය හැකිය. එමෙන්ම ගෝලාකාර ජ්යාමිතිය අවශ්ය වන අනෙකුත් වීදුරු සෑදීමේ ක්රමවලට වඩා එය වාසියක් ඇත. මූලික ක්රියාවලියට ඇතුළත් වන්නේ අපගේ අච්චුවේ පහළ පැත්ත හිස් වීදුරුවකින් පැටවීම, ඔක්සිජන් ඉවත් කිරීම සඳහා ක්රියාවලි කුටිය ඉවත් කිරීම, අච්චුව වැසීමට ආසන්නව, අධෝරක්ත ආලෝකයෙන් ඩයි සහ වීදුරු වේගවත් හා සමෝෂ්ණ තාපනය කිරීම, අච්චු අර්ධ තවදුරටත් වසා දැමීමයි. අවශ්ය ඝනකමට පාලනය කළ ආකාරයෙන් මෘදු වූ වීදුරුව සෙමින් තද කර අවසානයේ වීදුරුව සිසිල් කර නයිට්රජන්වලින් කුටිය පුරවා නිෂ්පාදනය ඉවත් කිරීම. නිරවද්ය උෂ්ණත්ව පාලනය, අච්චු වසා දැමීමේ දුර, අච්චු වසා දැමීමේ බලය, අච්චුවේ සහ වීදුරු ද්රව්යවල ප්රසාරණ සංගුණකවලට ගැලපීම මෙම ක්රියාවලියේදී ප්රධාන වේ.
• වීදුරු ඔප්ටිකල් සංරචක සහ එකලස්කිරීම් නිෂ්පාදනය: නිරවද්ය වීදුරු අච්චු වලට අමතරව, ඉල්ලුමට සරිලන යෙදුම් සඳහා උසස් තත්ත්වයේ දෘශ්ය සංරචක සහ එකලස් කිරීම් සඳහා අප භාවිතා කරන වටිනා ක්රියාවලි ගණනාවක් තිබේ. දෘෂ්ය ශ්රේණියේ වීදුරු සියුම් විශේෂ උල්ෙල්ඛ පොහොරවල ඇඹරීම, ලැප් කිරීම සහ ඔප දැමීම දෘශ්ය කාච, ප්රිස්ම, තට්ටු සහ තවත් දේ සෑදීම සඳහා කලාවක් සහ විද්යාවකි. මතුපිට සමතලා බව, රැළි බව, සුමට බව සහ දෝෂ රහිත දෘශ්ය පෘෂ්ඨ සඳහා එවැනි ක්රියාවලීන් පිළිබඳ බොහෝ අත්දැකීම් අවශ්ය වේ. පරිසරයේ කුඩා වෙනස්කම් පිරිවිතර නිෂ්පාදන වලින් බැහැර වීමට සහ නිෂ්පාදන රේඛාව නැවත්වීමට හේතු විය හැක. පිරිසිදු රෙද්දකින් ඔප්ටිකල් මතුපිට තනි පිසදැමීමකින් නිෂ්පාදනයක් පිරිවිතරයන් සපුරාලීමට හෝ පරීක්ෂණයෙන් අසමත් වන අවස්ථා තිබේ. භාවිතා කරන සමහර ජනප්රිය වීදුරු ද්රව්ය වන්නේ විලයනය කරන ලද සිලිකා, ක්වාර්ට්ස්, BK7 ය. එසේම එවැනි සංරචක එකලස් කිරීම සඳහා විශේෂිත වූ අත්දැකීම් අවශ්ය වේ. සමහර විට විශේෂ මැලියම් භාවිතා වේ. කෙසේ වෙතත්, සමහර විට ඔප්ටිකල් ස්පර්ශ කිරීම නම් තාක්ෂණය හොඳම තේරීම වන අතර අමුණා ඇති දෘශ්ය වීදුරු අතර කිසිදු ද්රව්යයක් ඇතුළත් නොවේ. එය මැලියම් නොමැතිව එකිනෙකට සම්බන්ධ කිරීම සඳහා භෞතිකව සම්බන්ධ වන පැතලි මතුපිටකින් සමන්විත වේ. සමහර අවස්ථාවල දී යාන්ත්රික ස්පේසර්, නිරවද්ය වීදුරු දඬු හෝ බෝල, කලම්ප හෝ යන්ත්රගත ලෝහ සංරචක යම් දුරකින් සහ යම් ජ්යාමිතික දිශානතියකින් එකලස් කිරීමට භාවිත කෙරේ. ඉහළ ප්රකාශන නිෂ්පාදනය සඳහා අපගේ ජනප්රිය තාක්ෂණික ක්රම කිහිපයක් අපි විමසා බලමු.
GRINDING & LAPPING & POLISHING : ඔප්ටිකල් සංරචකයේ රළු හැඩය වීදුරු හිස් ඇඹරීමෙන් ලබා ගනී. ඉන්පසුව ඔප දැමීම සහ ඔප දැමීම සිදු කරනු ලබන්නේ දෘෂ්ය සංරචකවල රළු පෘෂ්ඨ අපේක්ෂිත මතුපිට හැඩතල සහිත මෙවලම්වලට එරෙහිව කරකැවීමෙන් සහ අතුල්ලමිනි. දෘෂ්ය විද්යාව සහ හැඩගැන්වීමේ මෙවලම් අතර කුඩා උල්ෙල්ඛ අංශු සහ තරල සහිත ස්ලරි වත් කරනු ලැබේ. එවැනි පොහොරවල ඇති උල්ෙල්ඛ අංශු ප්රමාණය අපේක්ෂිත සමතලා ප්රමාණය අනුව තෝරා ගත හැකිය. අවශ්ය හැඩතලවලින් තීරණාත්මක දෘශ්ය පෘෂ්ඨවල අපගමනය භාවිතා වන ආලෝකයේ තරංග ආයාමය අනුව ප්රකාශ වේ. අපගේ ඉහළ නිරවද්ය දෘෂ්ටි විද්යාවට තරංග ආයාමයෙන් දහයෙන් පංගුවක් (තරංග ආයාම/10) ඉවසීමක් හෝ ඊටත් වඩා දැඩි විය හැකිය. මතුපිට පැතිකඩට අමතරව, තීරනාත්මක පෘෂ්ඨයන් පරිලෝකනය කර අනෙකුත් මතුපිට ලක්ෂණ සහ මානයන්, සීරීම්, චිප්ස්, වලවල්, පැල්ලම්... යනාදී දෝෂ සඳහා ඇගයීමට ලක් කෙරේ. දෘශ්ය නිෂ්පාදන තට්ටුවේ පාරිසරික තත්ත්වයන් දැඩි ලෙස පාලනය කිරීම සහ අති නවීන උපකරණ සමඟ පුළුල් මිනුම් විද්යාව සහ පරීක්ෂණ අවශ්යතා මෙය කර්මාන්තයේ අභියෝගාත්මක ශාඛාවක් බවට පත් කරයි.
• වීදුරු නිෂ්පාදනයේ ද්විතීයික ක්රියාවලි: නැවතත්, වීදුරු වල ද්විතියික සහ නිම කිරීමේ ක්රියාවලීන් සම්බන්ධයෙන් අපි ඔබේ පරිකල්පනයෙන් පමණක් සීමා වෙමු. මෙන්න අපි ඒවායින් සමහරක් ලැයිස්තුගත කරමු:
වීදුරු මත ආලේපන (දෘශ්ය, විද්යුත්, ට්රිබොලොජිකල්, තාප, ක්රියාකාරී, යාන්ත්රික...). උදාහරණයක් ලෙස, අපට වීදුරු වල මතුපිට ගුණාංග වෙනස් කළ හැකිය, උදාහරණයක් ලෙස එය තාපය පරාවර්තනය කරයි, එවිට එය ගොඩනැගිලි අභ්යන්තරය සිසිල්ව තබා ගනී, නැතහොත් නැනෝ තාක්ෂණය භාවිතයෙන් එක් පැත්තක් අධෝරක්ත අවශෝෂණය කරයි. මෙය ගොඩනැඟිලි ඇතුළත උණුසුම්ව තබා ගැනීමට උපකාරී වේ මන්ද යත් පිටත මතුපිට වීදුරු තට්ටුව ගොඩනැගිල්ල තුළ ඇති අධෝරක්ත කිරණ අවශෝෂණය කර එය නැවත ඇතුළතට විකිරණය කරන බැවිනි.
-Etching on glass
- ව්යවහාරික සෙරමික් ලේබල් කිරීම (ACL)
- කැටයම්
- දැල්ල ඔප දැමීම
-රසායනික ඔප දැමීම
- පැල්ලම්
තාක්ෂණික පිඟන් මැටි නිෂ්පාදනය
• DIE Pressing : ඩයි එකක සීමා කර ඇති කැටිති කුඩු වල ඒක අක්ෂීය සම්පිණ්ඩනයකින් සමන්විත වේ
• HOT Pressing : ඝණත්වය වැඩි දියුණු කිරීම සඳහා උෂ්ණත්වය එකතු කිරීමත් සමග, තද කිරීම හා සමාන වේ. කුඩු හෝ සම්පිණ්ඩනය කරන ලද පූර්ව ආකෘතිය ග්රැෆයිට් ඩයි එකට දමා ඒකීය පීඩනය යොදනු ලබන අතර ඩයි එක 2000 C වැනි ඉහළ උෂ්ණත්වවල තබා ඇත. සැකසෙන සෙරමික් කුඩු වර්ගය අනුව උෂ්ණත්වය වෙනස් විය හැක. සංකීර්ණ හැඩතල සහ ජ්යාමිතිය සඳහා දියමන්ති ඇඹරීම වැනි වෙනත් පසුකාලීන සැකසුම් අවශ්ය විය හැකිය.
• ISOSTATIC Pressing : කැටිති කුඩු හෝ ඩයි පීරන ලද සංයුක්ත වාතය රහිත බහාලුම්වල තබා පසුව ඇතුළත දියර සහිත සංවෘත පීඩන භාජනයකට දමනු ලැබේ. ඉන් පසුව පීඩන යාත්රාවේ පීඩනය වැඩි කිරීමෙන් ඒවා සංයුක්ත වේ. යාත්රාව තුළ ඇති ද්රව වායු රහිත භාජනයේ මුළු මතුපිට ප්රදේශය පුරා ඒකාකාරව පීඩන බලවේග මාරු කරයි. ද්රව්යය මෙලෙස ඒකාකාරව සංයුක්ත කර එහි නම්යශීලී බහාලුම්වල හැඩය සහ එහි අභ්යන්තර පැතිකඩ සහ විශේෂාංග ලබා ගනී.
• උණුසුම් සමස්ථිතික එබීම : සමස්ථානික පීඩනයට සමාන නමුත් පීඩන වායු වායුගෝලයට අමතරව, අපි අධික උෂ්ණත්වයේ දී සංයුක්ත සින්ටර් කරමු. උණුසුම් සමස්ථානික පීඩනය අතිරේක ඝනත්වය සහ ශක්තිය වැඩි කරයි.
• ස්ලිප් වාත්තු කිරීම / ජලාපවහන වාත්තු කිරීම : අපි මයික්රොමීටර ප්රමාණයේ සෙරමික් අංශු සහ වාහක ද්රව අත්හිටුවීමකින් අච්චුව පුරවන්නෙමු. මෙම මිශ්රණය "ස්ලිප්" ලෙස හැඳින්වේ. අච්චුවේ සිදුරු ඇති අතර එම නිසා මිශ්රණයේ ඇති දියර අච්චුව තුළට පෙරීම සිදු කරයි. එහි ප්රතිඵලයක් වශයෙන්, අච්චුවේ අභ්යන්තර පෘෂ්ඨයන් මත වාත්තුවක් සෑදී ඇත. සින්ටර් කිරීමෙන් පසු කොටස් අච්චුවෙන් පිටතට ගත හැකිය.
• ටේප් වාත්තු කිරීම : අපි සෙරමික් පටි නිෂ්පාදනය කරන්නේ පැතලි චලනය වන වාහක මතුපිටට සෙරමික් පොහොර දැමීමෙනි. බන්ධන සහ රැගෙන යාමේ අරමුණු සඳහා වෙනත් රසායනික ද්රව්ය සමඟ මිශ්ර කරන ලද සෙරමික් කුඩු මෙම පොහොරවල අඩංගු වේ. ද්රාවක වාෂ්ප වන විට ඝන සහ නම්යශීලී සෙරමික් තහඩු ඉතිරි වන අතර ඒවා අවශ්ය පරිදි කපා හෝ රෝල් කළ හැකිය.
• නිස්සාරණය සැකසීම : අනෙකුත් නිස්සාරණ ක්රියාවලීන්හිදී මෙන්, බන්ධක සහ අනෙකුත් රසායනික ද්රව්ය සහිත සෙරමික් කුඩු මෘදු මිශ්රණයක් එහි හරස්කඩ හැඩය ලබා ගැනීම සඳහා ඩයි එකක් හරහා යවන අතර පසුව අපේක්ෂිත දිගට කපා ඇත. මෙම ක්රියාවලිය සීතල හෝ රත් වූ සෙරමික් මිශ්රණ සමඟ සිදු කෙරේ.
• අඩු පීඩන එන්නත් මෝල්ඩින්: අපි බන්ධන සහ ද්රාවක සහිත සෙරමික් කුඩු මිශ්රණයක් සකස් කර එය පහසුවෙන් තද කළ හැකි සහ මෙවලම් කුහරයට බල කළ හැකි උෂ්ණත්වයකට රත් කරමු. අච්චු චක්රය අවසන් වූ පසු, එම කොටස ඉවත දමන අතර බන්ධන රසායනිකය පුළුස්සා දමනු ලැබේ. ඉන්ජෙක්ෂන් මෝල්ඩින් භාවිතා කිරීමෙන් අපට ආර්ථික වශයෙන් ඉහළ පරිමාවකින් සංකීර්ණ කොටස් ලබා ගත හැකිය. සිදුරු එනම් 10mm ඝන බිත්තියක් මත මිලිමීටරයක කුඩා කොටසක් හැකි ය, ඉදිරියට යන්ත්ර කිරීමකින් තොරව නූල් කළ හැකිය, +/- යන්ත්රය තරම් තද ඉවසීම 0.5% හැකි විට ඊටත් වඩා අඩු වේ. , බිත්ති ඝණත්වය 0.5mm සිට 12.5 mm දක්වා අනුපිළිවෙලට මෙන්ම බිත්ති ඝණත්වය 6.5mm සිට 150mm දක්වා දිග විය හැක.
• හරිත යන්ත්රකරණය : එම ලෝහ යන්ත්රෝපකරණ මෙවලම් භාවිතා කරමින්, හුණු මෙන් මෘදු වන අතරම, අපට යන්ත්රයෙන් තද කළ පිඟන් මැටි ද්රව්ය යන්ත්රගත කළ හැක. +/- 1% ක ඉවසීම හැකි ය. වඩා හොඳ ඉවසීමක් සඳහා අපි දියමන්ති ඇඹරීම භාවිතා කරමු.
• SINTERING හෝ FIRING : සින්ටර් කිරීම මගින් සම්පූර්ණ ඝනත්වය හැකි වේ. හරිත සංයුක්ත කොටස් මත සැලකිය යුතු හැකිලීමක් සිදු වේ, නමුත් අපි කොටස සහ මෙවලම් සැලසුම් කිරීමේදී මෙම මාන වෙනස්කම් සැලකිල්ලට ගන්නා බැවින් මෙය විශාල ගැටළුවක් නොවේ. කුඩු අංශු එකට බන්ධනය වී ඇති අතර සංකෝචන ක්රියාවලිය මගින් ඇති වන සිදුරු විශාල ප්රමාණයකට ඉවත් කරනු ලැබේ.
• දියමන්ති ඇඹරීම: ලෝකයේ අමාරුම ද්රව්යය වන “දියමන්ති” සෙරමික් වැනි දෘඩ ද්රව්ය ඇඹරීමට භාවිතා කරන අතර නිරවද්ය කොටස් ලබා ගනී. මයික්රොමීටර පරාසයේ ඉවසීම සහ ඉතා සුමට මතුපිට සාක්ෂාත් වෙමින් පවතී. එහි වියදම නිසා, අපි මෙම තාක්ෂණය සලකා බලන්නේ අපට එය සැබවින්ම අවශ්ය විට පමණි.
• හර්මෙටික් එකලස් කිරීම් යනු ප්රායෝගිකව කථා කරන විට අතුරු මුහුණත් අතර ද්රව්ය, ඝන, ද්රව හෝ වායු හුවමාරු වීමට ඉඩ නොදෙන ඒවා වේ. හර්මෙටික් මුද්රා තැබීම වාතය රහිත ය. නිදසුනක් ලෙස හර්මෙටික් ඉලෙක්ට්රොනික ආවරණ යනු ඇසුරුම් කරන ලද උපාංගයක ඇති සංවේදී අභ්යන්තර අන්තර්ගතය තෙතමනය, දූෂක හෝ වායූන් මගින් හානියට පත් නොවන ලෙස තබා ගැනීමයි. කිසිවක් 100% හර්මෙටික් නොවේ, නමුත් අපි හර්මෙටික් බව ගැන කතා කරන විට අපි අදහස් කරන්නේ ප්රායෝගිකව, කාන්දු වීමේ අනුපාතය ඉතා අඩු වන තරමට හර්මෙටික් ඇති බවත්, සාමාන්ය පාරිසරික තත්ත්වයන් යටතේ උපාංග ඉතා දිගු කාලයක් ආරක්ෂිතව පවතින බවත්ය. අපගේ හර්මෙටික් එකලස්කිරීම් සමන්විත වන්නේ ලෝහ, වීදුරු සහ සෙරමික් සංරචක, ලෝහ-සෙරමික්, සෙරමික්-ලෝහ-සෙරමික්, ලෝහ-සෙරමික්-ලෝහ, ලෝහ සිට ලෝහ, ලෝහ-වීදුරු, ලෝහ-වීදුරු-ලෝහ, වීදුරු-ලෝහ-වීදුරු, වීදුරු- ලෝහ සහ වීදුරු සිට වීදුරු සහ අනෙකුත් සියලුම ලෝහ-වීදුරු-සෙරමික් බන්ධන සංයෝජන. උදාහරණයක් ලෙස අපට සෙරමික් සංරචක ලෝහ ආලේප කළ හැකි අතර එමඟින් ඒවා එකලස් කිරීමේදී අනෙකුත් සංරචක වලට තදින් බැඳී ඇති අතර විශිෂ්ට මුද්රා තැබීමේ හැකියාව ඇත. ඔප්ටිකල් තන්තු හෝ පෝෂක ලෝහවලින් ආලේප කිරීම සහ ඒවා පෑස්සීමට හෝ ඒවා ආවරණවලට බ්රේස් කිරීමට අපට දැනුමක් ඇත, එම නිසා වායූන් ඇතුළු වීම හෝ කාන්දු වීම සිදු නොවේ. එබැවින් සංවේදී උපාංග ආවරණය කිරීම සහ බාහිර වායුගෝලයෙන් ඒවා ආරක්ෂා කිරීම සඳහා ඉලෙක්ට්රොනික ආවරණ නිෂ්පාදනය සඳහා ඒවා භාවිතා කරනු ලැබේ. ඒවායේ විශිෂ්ට මුද්රා තැබීමේ ලක්ෂණ වලට අමතරව, තාප ප්රසාරණ සංගුණකය, විරූපණ ප්රතිරෝධය, වායුව බැහැර නොවන ස්වභාවය, ඉතා දිගු ආයු කාලය, සන්නායක නොවන ස්වභාවය, තාප පරිවාරක ගුණ, ප්රති-ස්ථිතික ස්වභාවය... යනාදී අනෙකුත් ගුණාංග. ඇතැම් යෙදුම් සඳහා වීදුරු සහ සෙරමික් ද්රව්ය තෝරා ගැනීම. සෙරමික් සිට ලෝහ සවි කිරීම්, හර්මෙටික් මුද්රා තැබීම, රික්ත පෝෂක, ඉහළ සහ අතිශය ඉහළ රික්තක සහ තරල පාලන සංරචක නිෂ්පාදනය කරන අපගේ පහසුකම පිළිබඳ තොරතුරු මෙතැනින් සොයා ගත හැක:හර්මෙටික් සංරචක කර්මාන්තශාලා අත් පත්රිකාව