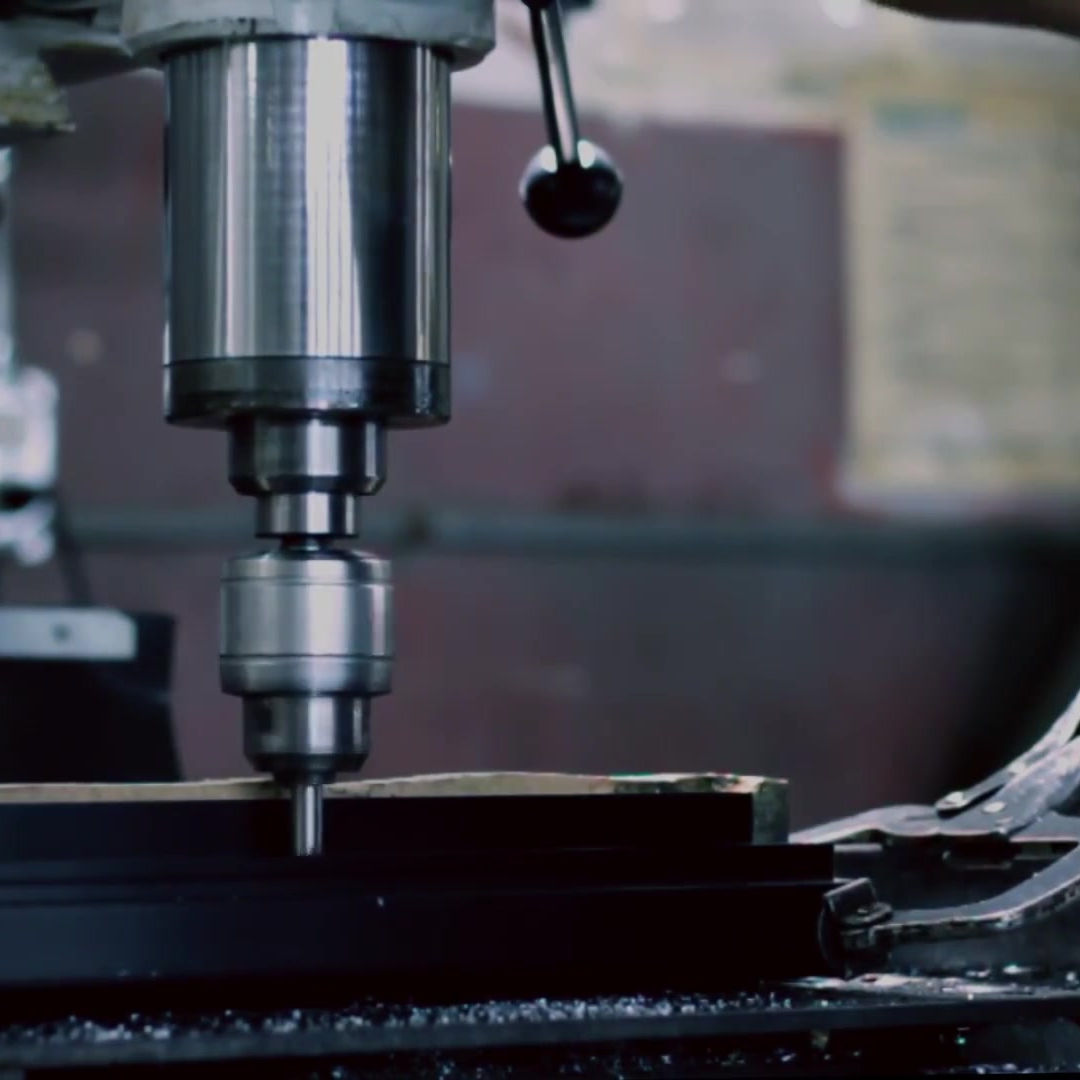
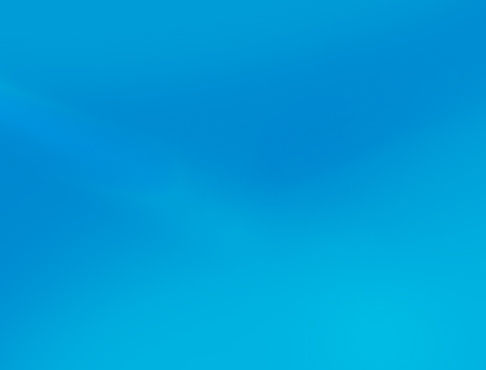
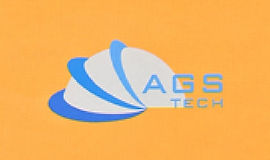
Globálny vlastný výrobca, integrátor, konsolidátor, partner outsourcingu pre širokú škálu produktov a služieb.
Sme váš komplexný zdroj pre výrobu, výrobu, inžinierstvo, konsolidáciu, integráciu, outsourcing zákazkovo vyrábaných a voľne predajných produktov a služieb.
Vyberte si jazyk
-
Zákazková výroba
-
Domáca a globálna zmluvná výroba
-
Outsourcing výroby
-
Domáce a globálne obstarávanie
-
Konsolidácia
-
Engineering Integration
-
Inžinierske služby
Spomedzi mnohých techník SPÁJANIA, ktoré používame vo výrobe, sa osobitný dôraz kladie na ZVÁRANIE, SPÁJKOVANIE, SPÁJOVANIE, LEPENIE a MECHANICKÁ MONTÁŽ NA MIERU, pretože tieto techniky sa široko používajú v aplikáciách, ako je výroba hermetických zostáv, výroba špičkových produktov a špecializované tesnenie. Tu sa zameriame na špecializovanejšie aspekty týchto spájacích techník, keďže súvisia s výrobou pokročilých produktov a zostáv.
FÚZNE ZVÁRANIE: Na roztavenie a spájanie materiálov využívame teplo. Teplo je dodávané elektrinou alebo vysokoenergetickými lúčmi. Typy tavného zvárania, ktoré nasadzujeme, sú ZVÁRANIE PLYNOVÝM PLYNOM, OBUKOVÉ ZVÁRANIE, VYSOKOENERGETICKÉ ZVÁRANIE LÚČOM.
PEVNÉ ZVÁRANIE: Diely spájame bez tavenia a tavenia. Naše metódy zvárania v tuhom stave sú ZVÁRANIE STUDENÉ, ULTRAZVUKOVÉ, ODPOROVÉ, TRENÉ, EXPLOZNÉ ZVÁRANIE a DIFÚZNE ZVÁRANIE.
SPÁJKOVANIE A SPÁJKOVANIE: Používajú prídavné kovy a poskytujú nám výhodu práce pri nižších teplotách ako pri zváraní, čím sa znižuje štrukturálne poškodenie výrobkov. Informácie o našom zariadení na spájkovanie, ktoré vyrába armatúry z keramiky na kov, hermetické tesnenia, vákuové priechodky, komponenty na riadenie vysokého a ultravysokého vákua a tekutiny nájdete tu:Brožúra továrne na spájkovanie
LEPENIE LEPIDLA: Kvôli rôznorodosti lepidiel používaných v priemysle a tiež rôznorodosti aplikácií máme na to vyhradenú stránku. Ak chcete prejsť na našu stránku o lepení, kliknite sem.
MECHANICKÁ MONTÁŽ NA MIERU: Používame rôzne upevňovacie prvky, ako sú skrutky, skrutky, matice, nity. Naše spojovacie prvky nie sú obmedzené na štandardné spojovacie prvky. Navrhujeme, vyvíjame a vyrábame špeciálne spojovacie prvky, ktoré sú vyrobené z neštandardných materiálov tak, aby spĺňali požiadavky pre špeciálne aplikácie. Niekedy je požadovaná elektrická alebo tepelná nevodivosť, zatiaľ čo niekedy vodivosť. Pre niektoré špeciálne aplikácie môže zákazník chcieť špeciálne spojovacie prvky, ktoré nemožno odstrániť bez zničenia produktu. Nápadov a aplikácií je nekonečne veľa. Máme to všetko pre vás, ak nie zo skladu, môžeme to rýchlo vyvinúť. Ak chcete prejsť na našu stránku o mechanickej montáži, kliknite sem. Preskúmajte naše rôzne techniky spájania podrobnejšie.
ZVÁRANIE OXYFUEL GAS (OFW): Na vytvorenie zváracieho plameňa používame palivový plyn zmiešaný s kyslíkom. Keď používame acetylén ako palivo a kyslík, nazývame to zváranie kyslíkom a acetylénom. V procese spaľovania kyslíka a paliva prebiehajú dve chemické reakcie:
C2H2 + O2 ------» 2CO + H2 + Teplo
2CO + H2 + 1,5 O2--------» 2 CO2 + H2O + teplo
Prvá reakcia rozdeľuje acetylén na oxid uhoľnatý a vodík, pričom produkuje asi 33 % celkového vytvoreného tepla. Druhý vyššie uvedený proces predstavuje ďalšie spaľovanie vodíka a oxidu uhoľnatého pri výrobe asi 67 % celkového tepla. Teploty v plameni sú medzi 1533 až 3573 Kelvinmi. Percento kyslíka v zmesi plynov je dôležité. Ak je obsah kyslíka viac ako polovica, plameň sa stáva oxidačným činidlom. To je nežiaduce pre niektoré kovy, ale žiaduce pre iné. Príkladom, kedy je žiaduci oxidačný plameň, sú zliatiny na báze medi, pretože tvorí pasivačnú vrstvu na kovom. Na druhej strane pri znížení obsahu kyslíka nie je možné plné spaľovanie a plameň sa stáva redukčným (karburizačným) plameňom. Teploty v redukčnom plameni sú nižšie a preto je vhodný pre procesy ako spájkovanie a tvrdé spájkovanie. Iné plyny sú tiež potenciálne palivá, ale oproti acetylénu majú určité nevýhody. Prídavné kovy do zvarovej zóny príležitostne dodávame vo forme prídavných tyčí alebo drôtu. Niektoré z nich sú potiahnuté tavivom na spomalenie oxidácie povrchov a tým na ochranu roztaveného kovu. Ďalšou výhodou, ktorú nám tavidlo poskytuje, je odstránenie oxidov a iných látok zo zóny zvaru. To vedie k silnejšiemu spojeniu. Variantom zvárania kyslíkom a palivom je zváranie TLAKOVÝM PLYNOM, kde sa dva komponenty zahrievajú na svojom rozhraní pomocou horáka s kyslíkom a acetylénom a keď sa rozhranie začne topiť, horák sa stiahne a na stlačenie dvoch častí sa použije axiálna sila. kým rozhranie nestuhne.
OBlúKOVÉ ZVÁRANIE: Používame elektrickú energiu na vytvorenie oblúka medzi špičkou elektródy a časťami, ktoré sa majú zvárať. Napájací zdroj môže byť striedavý alebo jednosmerný, pričom elektródy sú buď spotrebné alebo nespotrebiteľné. Prenos tepla pri oblúkovom zváraní možno vyjadriť nasledujúcou rovnicou:
H / l = ex VI / v
Tu H je tepelný príkon, l je dĺžka zvaru, V a I sú použité napätie a prúd, v je rýchlosť zvárania a e je účinnosť procesu. Čím vyššia je účinnosť „e“, tým výhodnejšie sa využíva dostupná energia na roztavenie materiálu. Tepelný príkon môže byť vyjadrený aj ako:
H = ux (objem) = ux A xl
Tu u je merná energia na roztavenie, A prierez zvaru a l dĺžka zvaru. Z dvoch vyššie uvedených rovníc môžeme získať:
v = ex VI / u A
Variantom oblúkového zvárania je SHIELDED METAL ARC WELDING (SMAW), ktoré predstavuje asi 50 % všetkých priemyselných a údržbárskych zváracích procesov. ZVÁRANIE ELEKTRICKÝM OBLÚKOM (ZVÁRANIE TYČOM) sa vykonáva tak, že sa špička obalenej elektródy dotkne obrobku a rýchlo sa odtiahne na vzdialenosť dostatočnú na udržanie oblúka. Tento proces nazývame aj zváraním tyčinkou, pretože elektródy sú tenké a dlhé tyčinky. Počas procesu zvárania sa hrot elektródy roztaví spolu s jej povlakom a základným kovom v blízkosti oblúka. Zmes základného kovu, elektródového kovu a látok z elektródového povlaku tuhne v oblasti zvaru. Povlak elektródy deoxiduje a poskytuje ochranný plyn v oblasti zvaru, čím ju chráni pred kyslíkom v prostredí. Preto sa tento proces nazýva oblúkové zváranie v tienidle. Pre optimálny výkon zvárania používame prúdy medzi 50 a 300 ampérmi a úrovne výkonu zvyčajne menšie ako 10 kW. Dôležitá je aj polarita jednosmerného prúdu (smer toku prúdu). Pri zváraní plechov sa uprednostňuje priama polarita, kde je obrobok kladný a elektróda záporná, pretože má plytký prienik a tiež pre spoje s veľmi širokými medzerami. Keď máme opačnú polaritu, tj elektróda je kladná a obrobok záporná, môžeme dosiahnuť hlbšie prieniky zvaru. So striedavým prúdom, keďže máme pulzujúce oblúky, môžeme zvárať hrubé časti pomocou elektród s veľkým priemerom a maximálnymi prúdmi. Metóda zvárania SMAW je vhodná pre hrúbku obrobku 3 až 19 mm a ešte viac s použitím viacprechodových techník. Troska vytvorená na povrchu zvaru sa musí odstrániť pomocou drôtenej kefy, aby nedochádzalo ku korózii a poruchám v oblasti zvaru. To samozrejme zvyšuje náklady na oblúkové zváranie kovov v tieni. Napriek tomu je SMAW najpopulárnejšou zváracou technikou v priemysle a opravárenských prácach.
ZVÁRANIE POD BLOKOM (PÍLA): V tomto procese chránime zvarový oblúk použitím materiálov s granulovaným tavivom, ako je vápno, oxid kremičitý, fluorid vápenatý, oxid mangánu... atď. Granulované tavivo sa privádza do zóny zvaru gravitačne cez trysku. Tavidlo pokrývajúce zónu roztaveného zvaru výrazne chráni pred iskrami, výparmi, UV žiarením atď. a pôsobí ako tepelný izolátor, čím umožňuje prenikaniu tepla hlboko do obrobku. Netavené tavidlo sa získa, spracuje a znovu použije. Holá cievka sa používa ako elektróda a vedie cez rúrku do oblasti zvaru. Používame prúdy medzi 300 a 2000 ampérmi. Proces zvárania pod tavivom (SAW) je obmedzený na horizontálne a ploché polohy a kruhové zvary, ak je počas zvárania možná rotácia kruhovej konštrukcie (napríklad rúr). Rýchlosť môže dosiahnuť 5 m/min. Proces SAW je vhodný pre hrubé plechy a výsledkom sú vysokokvalitné, húževnaté, tvárne a rovnomerné zvary. Produktivita, to znamená množstvo zvarového materiálu uloženého za hodinu, je 4 až 10-násobok množstva v porovnaní s procesom SMAW.
Iný proces oblúkového zvárania, menovite GAS METAL ARC WELDING (GMAW) alebo alternatívne označovaný ako METAL INERT GAS WELDING (MIG) je založený na tom, že oblasť zvaru je chránená vonkajšími zdrojmi plynov ako hélium, argón, oxid uhličitý... atď. V kove elektródy môžu byť prítomné ďalšie deoxidačné činidlá. Spotrebný drôt sa privádza cez trysku do zvarovej zóny. Výroba zahŕňajúca železné aj neželezné kovy sa vykonáva pomocou plynového oblúkového zvárania kovov (GMAW). Produktivita zvárania je približne 2-krát vyššia ako pri procese SMAW. Používa sa automatizované zváracie zariadenie. Kov sa v tomto procese prenáša jedným z troch spôsobov: „Prenos rozprašovaním“ zahŕňa prenos niekoľkých stoviek malých kovových kvapiek za sekundu z elektródy do oblasti zvaru. Na druhej strane pri „Globulárnom prenose“ sa používajú plyny bohaté na oxid uhličitý a guľôčky roztaveného kovu sú poháňané elektrickým oblúkom. Zváracie prúdy sú vysoké a zvar preniká hlbšie, rýchlosť zvárania je vyššia ako pri prenose sprejom. Guľový prenos je teda lepší pre zváranie ťažších profilov. Nakoniec, pri metóde „Short Circuiting“ sa hrot elektródy dotkne roztaveného zvarového kúpeľa, pričom ho skratuje ako kov rýchlosťou vyššou ako 50 kvapiek za sekundu sa prenáša v jednotlivých kvapkách. Používajú sa nízke prúdy a napätia spolu s tenším drôtom. Používané výkony sú približne 2 kW a relatívne nízke teploty, vďaka čomu je táto metóda vhodná pre tenké plechy s hrúbkou menšou ako 6 mm.
Ďalšia variácia procesu FLUX-CORED ARC WELDING (FCAW) je podobná oblúkovému zváraniu plynom, s výnimkou toho, že elektróda je trubica naplnená tavivom. Výhodou použitia elektród s jadrom je, že vytvárajú stabilnejšie oblúky, dávajú nám možnosť zlepšiť vlastnosti zvarových kovov, menej krehký a flexibilný charakter jeho toku v porovnaní so zváraním SMAW, zlepšené obrysy zvárania. Samotienené elektródy obsahujú materiály, ktoré chránia zvarovú zónu pred atmosférou. Používame výkon cca 20 kW. Podobne ako proces GMAW, aj proces FCAW ponúka možnosť automatizácie procesov pre kontinuálne zváranie a je ekonomický. Pridaním rôznych zliatin do jadra taviva je možné vyvinúť rôzne chemické vlastnosti zvarových kovov.
Pri ELEKTROPLYNOVOM ZVÁRANÍ (EGW) zvárame kusy umiestnené od okraja k okraju. Niekedy sa nazýva aj ZVÁRANIE NA TUPA. Zvarový kov sa vloží do zvarovej dutiny medzi dva kusy, ktoré sa majú spojiť. Priestor je uzavretý dvoma vodou chladenými priehradami, aby sa zabránilo vylievaniu roztavenej trosky. Hrádze sa pohybujú nahor mechanickými pohonmi. Keď je možné obrobok otáčať, môžeme použiť techniku elektroplynového zvárania aj na obvodové zváranie rúr. Elektródy sú vedené cez potrubie, aby sa udržal súvislý oblúk. Prúdy môžu byť okolo 400 ampérov alebo 750 ampérov a úrovne výkonu okolo 20 kW. Inertné plyny pochádzajúce buď z elektródy s tokom alebo z externého zdroja poskytujú tienenie. Elektroplynové zváranie (EGW) používame pre kovy ako sú ocele, titán….atď s hrúbkami od 12 mm do 75 mm. Táto technika je vhodná pre veľké konštrukcie.
Pri inej technike nazývanej ELEKTROSLAGOVÉ ZVÁRANIE (ESW) sa oblúk zapáli medzi elektródou a spodkom obrobku a pridá sa tavidlo. Keď roztavená troska dosiahne hrot elektródy, oblúk zhasne. Energia je nepretržite dodávaná prostredníctvom elektrického odporu roztavenej trosky. Dokážeme zvárať plechy s hrúbkami od 50 mm do 900 mm a dokonca aj vyššie. Prúdy sú okolo 600 ampérov, zatiaľ čo napätia sú medzi 40 – 50 V. Rýchlosti zvárania sú okolo 12 až 36 mm/min. Aplikácie sú podobné zváraniu elektroplynom.
Jeden z našich nekonzumovateľných elektródových procesov, GAS TUNGSTEN ARC WELDING (GTAW), tiež známy ako TUNGSTEN INERT GAS WELDING (TIG), zahŕňa dodávanie prídavného kovu drôtom. Na tesne priliehajúce spoje niekedy prídavný kov nepoužívame. V procese TIG nepoužívame tavivo, ale na tienenie používame argón a hélium. Volfrám má vysoký bod topenia a pri zváraní TIG sa nespotrebováva, preto je možné udržiavať konštantný prúd, ako aj medzery medzi oblúkmi. Úrovne výkonu sú medzi 8 až 20 kW a prúdy buď 200 ampérov (DC) alebo 500 ampérov (AC). Pre hliník a horčík používame striedavý prúd pre jeho funkciu čistenia oxidov. Aby sa zabránilo kontaminácii volfrámovej elektródy, vyhýbame sa jej kontaktu s roztavenými kovmi. Gas Tungsten Arc Welding (GTAW) je obzvlášť užitočné na zváranie tenkých kovov. Zvary GTAW sú veľmi kvalitné s dobrou povrchovou úpravou.
Kvôli vyššej cene vodíkového plynu je menej často používanou technikou ATOMIC HYDROGEN WELDING (AHW), kde generujeme oblúk medzi dvoma volfrámovými elektródami v tieniacej atmosfére prúdiaceho vodíkového plynu. AHW je tiež proces zvárania elektródou bez spotrebováva. Dvojatómový vodíkový plyn H2 sa rozkladá na svoju atómovú formu v blízkosti zváracieho oblúka, kde sú teploty vyššie ako 6273 Kelvinov. Pri lámaní absorbuje veľké množstvo tepla z oblúka. Keď atómy vodíka zasiahnu zvarovú zónu, ktorá je relatívne studeným povrchom, rekombinujú sa do dvojatómovej formy a uvoľnia uložené teplo. Energiu je možné meniť zmenou vzdialenosti obrobku na oblúk.
V ďalšom procese s nespotrebovateľnými elektródami, PLASMA ARC WELDING (PAW), máme koncentrovaný plazmový oblúk nasmerovaný do zóny zvaru. Teploty dosahujú 33 273 Kelvinov v PAW. Plazmový plyn tvorí takmer rovnaký počet elektrónov a iónov. Nízkoprúdový pilotný oblúk iniciuje plazmu, ktorá je medzi volfrámovou elektródou a otvorom. Prevádzkové prúdy sú zvyčajne okolo 100 ampérov. Môže sa privádzať prídavný kov. Pri zváraní plazmovým oblúkom sa tienenie dosiahne vonkajším tieniacim krúžkom a použitím plynov, ako je argón a hélium. Pri zváraní plazmovým oblúkom môže byť oblúk medzi elektródou a obrobkom alebo medzi elektródou a tryskou. Táto zváracia technika má oproti iným metódam výhody vyššej koncentrácie energie, hlbšej a užšej zváracej schopnosti, lepšej stability oblúka, vyššej rýchlosti zvárania až 1 meter/min, menšieho tepelného skreslenia. Vo všeobecnosti používame zváranie plazmovým oblúkom pre hrúbky menšie ako 6 mm a niekedy až do 20 mm pre hliník a titán.
VYSOKOENERGETICKÉ ZVÁRANIE: Ďalší typ metódy tavného zvárania so zváraním elektrónovým lúčom (EBW) a laserovým zváraním (LBW) v dvoch variantoch. Tieto techniky majú mimoriadnu hodnotu pre našu prácu pri výrobe high-tech produktov. Pri zváraní elektrónovým lúčom dopadajú vysokorýchlostné elektróny na obrobok a ich kinetická energia sa premieňa na teplo. Úzky zväzok elektrónov sa ľahko pohybuje vo vákuovej komore. Vo všeobecnosti používame vysoké vákuum pri zváraní elektrickým lúčom. Je možné zvárať plechy s hrúbkou až 150 mm. Nie sú potrebné žiadne ochranné plyny, tavivo ani výplňový materiál. Elektrónové lúče majú výkon 100 kW. Možné sú hlboké a úzke zvary s vysokým pomerom strán až 30 a malými tepelne ovplyvnenými zónami. Rýchlosť zvárania môže dosiahnuť 12 m/min. Pri zváraní laserovým lúčom využívame ako zdroj tepla vysokovýkonné lasery. Laserové lúče už od 10 mikrónov s vysokou hustotou umožňujú hlboký prienik do obrobku. Pri zváraní laserovým lúčom je možný pomer hĺbky k šírke až 10. Používame tak pulzné, ako aj kontinuálne vlnové lasery, pričom prvý v aplikáciách pre tenké materiály a druhý väčšinou pre hrubé obrobky do cca 25 mm. Výkony sú do 100 kW. Zváranie laserovým lúčom nie je vhodné pre opticky veľmi reflexné materiály. Pri zváraní sa môžu použiť aj plyny. Metóda zvárania laserovým lúčom je vhodná pre automatizáciu a veľkoobjemovú výrobu a môže ponúknuť rýchlosť zvárania medzi 2,5 m/min a 80 m/min. Jednou z hlavných výhod, ktoré táto zváracia technika ponúka, je prístup do oblastí, kde nie je možné použiť iné techniky. Laserové lúče môžu ľahko cestovať do takýchto zložitých oblastí. Nie je potrebné žiadne vákuum ako pri zváraní elektrónovým lúčom. Zvary s dobrou kvalitou a pevnosťou, nízkym zmršťovaním, nízkym skreslením a nízkou pórovitosťou možno dosiahnuť zváraním laserovým lúčom. Laserové lúče možno ľahko manipulovať a tvarovať pomocou káblov z optických vlákien. Technika je teda vhodná na zváranie presných hermetických zostáv, elektronických obalov atď.
Pozrime sa na naše techniky PEVNÉHO ZVÁRANIA. COLD WELDING (CW) je proces, pri ktorom sa namiesto tepla aplikuje tlak pomocou lisovníc alebo valcov na diely, ktoré sú spojené. Pri zváraní za studena musí byť aspoň jedna z protiľahlých častí tvárna. Najlepšie výsledky sa dosiahnu s dvoma podobnými materiálmi. Ak sú dva kovy, ktoré sa majú spojiť zváraním za studena, rozdielne, môžu vzniknúť slabé a krehké spoje. Metóda zvárania za studena je vhodná pre mäkké, tvárne a malé obrobky, ako sú elektrické spoje, okraje nádob citlivé na teplo, bimetalové pásy pre termostaty atď. Jednou z variácií studeného zvárania je spájanie valcovaním (alebo zváranie valcami), kde sa tlak aplikuje cez pár valcov. Niekedy vykonávame zváranie valcami pri zvýšených teplotách pre lepšiu medzipovrchovú pevnosť.
Ďalší proces zvárania v tuhom stave, ktorý používame, je ULTRASONIC WELDING (USW), kde sú obrobky vystavené statickej normálovej sile a oscilačným šmykovým napätiam. Oscilačné šmykové napätia sú aplikované cez hrot prevodníka. Ultrazvukové zváranie využíva oscilácie s frekvenciami od 10 do 75 kHz. V niektorých aplikáciách, ako je švové zváranie, používame ako hrot rotujúci zvárací kotúč. Šmykové napätia pôsobiace na obrobky spôsobujú malé plastické deformácie, rozrušujú vrstvy oxidov, kontaminanty a vedú k lepeniu v tuhom stave. Teploty používané pri ultrazvukovom zváraní sú hlboko pod teplotou topenia kovov a nedochádza k žiadnej fúzii. Často používame proces ultrazvukového zvárania (USW) pre nekovové materiály, ako sú plasty. V termoplastoch však teploty dosahujú teploty topenia.
Ďalšou populárnou technikou je pri FRICTION WELDING (FRW) teplo generované trením na rozhraní spájaných obrobkov. Pri zváraní trením udržujeme jeden z obrobkov nehybný, zatiaľ čo druhý obrobok je držaný v prípravku a otáča sa konštantnou rýchlosťou. Obrobky sa potom dostanú do kontaktu pôsobením axiálnej sily. Povrchová rýchlosť otáčania pri zváraní trením môže v niektorých prípadoch dosiahnuť 900 m/min. Po dostatočnom medziplošnom kontakte sa rotujúci obrobok náhle zastaví a axiálna sila sa zvýši. Zóna zvaru je vo všeobecnosti úzka oblasť. Technika zvárania trením sa môže použiť na spájanie pevných a rúrkových častí vyrobených z rôznych materiálov. Na rozhraní vo FRW sa môže vyvinúť nejaký záblesk, ale tento záblesk možno odstrániť sekundárnym obrábaním alebo brúsením. Existujú variácie procesu trecieho zvárania. Napríklad „zotrvačné trecie zváranie“ zahŕňa zotrvačník, ktorého rotačná kinetická energia sa využíva na zváranie dielov. Zvar je dokončený, keď sa zotrvačník zastaví. Rotujúca hmotnosť sa môže meniť a tým aj rotačná kinetická energia. Ďalšou variáciou je „lineárne trecie zváranie“, kde je lineárny vratný pohyb vnútený aspoň jednému z komponentov, ktoré sa majú spojiť. Pri lineárnom trecom zváraní časti nemusia byť kruhové, môžu byť pravouhlé, štvorcové alebo iného tvaru. Frekvencie môžu byť v desiatkach Hz, amplitúdy v rozsahu milimetrov a tlaky v desiatkach alebo stovkách MPa. Nakoniec „trecie zváranie s premiešavaním“ je trochu odlišné od ostatných dvoch vysvetlených vyššie. Zatiaľ čo pri zotrvačnom trecom zváraní a lineárnom trecom zváraní sa zahrievanie rozhraní dosahuje trením trením dvoch kontaktných povrchov, pri metóde trecieho miešania sa tretie teleso otiera o dva povrchy, ktoré sa majú spojiť. Do spoja sa privedie rotačný nástroj s priemerom 5 až 6 mm. Teploty sa môžu zvýšiť na hodnoty medzi 503 až 533 Kelvinmi. Dochádza k zahrievaniu, miešaniu a miešaniu hmoty v spoji. Zváranie trením používame na rôzne materiály vrátane hliníka, plastov a kompozitov. Zvary sú rovnomerné a kvalita je vysoká s minimálnymi pórmi. Pri trecom zváraní s premiešavaním nevznikajú žiadne výpary ani rozstreky a proces je dobre automatizovaný.
ODPOROVÉ ZVÁRANIE (RW): Teplo potrebné na zváranie vzniká elektrickým odporom medzi dvomi spájanými dielmi. Pri odporovom zváraní sa nepoužívajú žiadne tavidlá, ochranné plyny ani spotrebné elektródy. Joule zahrievanie prebieha pri odporovom zváraní a možno ho vyjadriť ako:
H = (štvorec I) x R xtx K
H je teplo generované v jouloch (wattsekundách), prúd I v ampéroch, odpor R v ohmoch, t je čas v sekundách, ktorým prúd preteká. Faktor K je menší ako 1 a predstavuje časť energie, ktorá sa nestratí žiarením a vedením. Prúdy v procesoch odporového zvárania môžu dosiahnuť úrovne až 100 000 A, ale napätia sú zvyčajne 0,5 až 10 voltov. Elektródy sú zvyčajne vyrobené zo zliatin medi. Odporovým zváraním je možné spájať podobné aj rozdielne materiály. Pre tento proces existuje niekoľko variácií: „Odporové bodové zváranie“ zahŕňa dve protiľahlé okrúhle elektródy, ktoré sa dotýkajú povrchov preplátovaného spoja dvoch plechov. Tlak sa aplikuje, kým sa prúd nevypne. Zvarový nuget má spravidla priemer do 10 mm. Odporové bodové zváranie zanecháva na miestach zvaru mierne zafarbené vrúbkované stopy. Bodové zváranie je naša najobľúbenejšia technika odporového zvárania. Pri bodovom zváraní sa používajú rôzne tvary elektród, aby sa dosiahli ťažké miesta. Naše zariadenie na bodové zváranie je riadené CNC a má viacero elektród, ktoré možno použiť súčasne. Ďalšia variácia „odporového švového zvárania“ sa vykonáva pomocou kotúčových alebo valčekových elektród, ktoré vytvárajú súvislé bodové zvary vždy, keď prúd dosiahne dostatočne vysokú úroveň v striedavom napájacom cykle. Spoje vyrobené odporovým švovým zváraním sú vodotesné a plynotesné. Rýchlosť zvárania okolo 1,5 m/min je normálna pre tenké plechy. Je možné použiť prerušované prúdy, takže bodové zvary sa vytvárajú v požadovaných intervaloch pozdĺž švu. Pri „odporovom zváraní výstupkov“ razíme jeden alebo viac výstupkov (jamkov) na jeden z povrchov obrobku, ktorý sa má zvárať. Tieto výstupky môžu byť okrúhle alebo oválne. Na týchto vyrazených miestach, ktoré prichádzajú do kontaktu s protiľahlou časťou, sa dosahujú vysoké lokalizované teploty. Elektródy vyvíjajú tlak na stlačenie týchto výstupkov. Elektródy pri odporovom projekčnom zváraní majú ploché hroty a sú to vodou chladené zliatiny medi. Výhodou odporového premietacieho zvárania je naša schopnosť zvariť množstvo zvarov jedným ťahom, tým predĺžená životnosť elektródy, schopnosť zvárať plechy rôznych hrúbok, schopnosť zvárať matice a skrutky na plechy. Nevýhodou odporového projekčného zvárania sú dodatočné náklady na razenie jamiek. Ešte ďalšou technikou je pri „bleskovom zváraní“ teplo generované oblúkom na koncoch dvoch obrobkov, keď sa začnú dotýkať. Tento spôsob možno alternatívne považovať aj za oblúkové zváranie. Teplota na rozhraní stúpa a materiál mäkne. Aplikuje sa axiálna sila a v zmäkčenej oblasti sa vytvorí zvar. Po dokončení bleskového zvárania môže byť spoj opracovaný pre lepší vzhľad. Kvalita zvaru získaná bleskovým zváraním je dobrá. Výkonové stupne sú 10 až 1500 kW. Bleskové zváranie je vhodné na spájanie podobných alebo rozdielnych kovov do priemeru 75 mm a plechov s hrúbkou od 0,2 mm do 25 mm. „Zváranie pod oblúkom“ je veľmi podobné bleskovému zváraniu. Čap, ako je skrutka alebo závitová tyč, slúži ako jedna elektróda, zatiaľ čo je pripojený k obrobku, ako je doska. Na sústredenie vytvoreného tepla, zabránenie oxidácii a zadržanie roztaveného kovu v zóne zvaru je okolo spoja umiestnený jednorazový keramický krúžok. Nakoniec „príklepové zváranie“ ďalší proces odporového zvárania, ktorý využíva kondenzátor na dodávanie elektrickej energie. Pri príklepovom zváraní sa energia vybije v priebehu milisekúnd veľmi rýchlo, čím sa v spoji vytvorí vysoké lokalizované teplo. Nárazové zváranie široko používame v elektronickom výrobnom priemysle, kde je potrebné zabrániť zahrievaniu citlivých elektronických komponentov v blízkosti spoja.
Technika nazývaná EXPLOSION WELDING zahŕňa detonáciu vrstvy výbušniny, ktorá sa položí na jeden z obrobkov, ktoré sa majú spojiť. Veľmi vysoký tlak vyvíjaný na obrobok vytvára turbulentné a zvlnené rozhranie a dochádza k mechanickému blokovaniu. Pevnosť spoja pri výbušnom zváraní je veľmi vysoká. Výbušné zváranie je dobrou metódou na opláštenie plechov odlišnými kovmi. Po opláštení môžu byť dosky valcované na tenšie časti. Niekedy používame zváranie výbuchom na roztiahnutie rúrok tak, aby boli tesne prilepené k doske.
Našou poslednou metódou v oblasti spájania v tuhom stave je DIFFUSION BONDING alebo DIFFUSION WELDING (DFW), pri ktorej sa dobrý spoj dosiahne hlavne difúziou atómov cez rozhranie. K zváraniu prispieva aj určitá plastická deformácia na rozhraní. Príslušné teploty sú okolo 0,5 Tm, kde Tm je teplota topenia kovu. Pevnosť spoja pri difúznom zváraní závisí od tlaku, teploty, času kontaktu a čistoty kontaktných povrchov. Niekedy na rozhraní používame prídavné kovy. Teplo a tlak sú potrebné pri difúznom spájaní a sú dodávané elektrickým odporom alebo pecou a závažím, lisom alebo iným spôsobom. Podobné a rozdielne kovy je možné spájať difúznym zváraním. Proces je relatívne pomalý kvôli času, ktorý trvá migrácia atómov. DFW je možné automatizovať a široko sa používa pri výrobe zložitých dielov pre letecký, elektronický a medicínsky priemysel. Vyrábané produkty zahŕňajú ortopedické implantáty, senzory, letecké konštrukčné prvky. Difúzne spájanie je možné kombinovať so SUPERPLASTICKÝM TVÁRNÍM na výrobu zložitých plechov. Vybrané miesta na listoch sa najskôr spoja difúzne a potom sa nespojené oblasti roztiahnu do formy pomocou tlaku vzduchu. Pomocou tejto kombinácie metód sa vyrábajú letecké konštrukcie s vysokým pomerom tuhosti k hmotnosti. Kombinovaný proces difúzneho zvárania/superplastického tvarovania znižuje počet požadovaných dielov elimináciou potreby spojovacích prvkov, výsledkom čoho sú nízkonapäťové vysoko presné diely ekonomicky as krátkymi dodacími lehotami.
SPÁJKOVANIE: Techniky spájkovania a spájkovania zahŕňajú nižšie teploty, ako sú teploty potrebné na zváranie. Teploty spájkovania sú však vyššie ako teploty spájkovania. Pri spájkovaní sa medzi povrchy, ktoré sa majú spojiť, vloží prídavný kov a teploty sa zvýšia na teplotu topenia prídavného materiálu nad 723 Kelvinov, ale pod teplotu tavenia obrobkov. Roztavený kov vypĺňa tesne priliehajúci priestor medzi obrobkami. Ochladzovanie a následné tuhnutie kovu pilníka má za následok pevné spoje. Pri spájkovaní natvrdo sa prídavný kov nanáša na spoj. Pri spájkovaní natvrdo sa používa podstatne viac prídavného kovu v porovnaní so spájkovaním. Oxyacetylénový horák s oxidačným plameňom sa používa na nanášanie prídavného kovu pri spájkovaní natvrdo. V dôsledku nižších teplôt pri spájkovaní sú problémy v oblastiach ovplyvnených teplom, ako sú deformácie a zvyškové napätia, menšie. Čím menšia je medzera pri spájkovaní, tým vyššia je pevnosť spoja v šmyku. Maximálna pevnosť v ťahu sa však dosiahne pri optimálnej medzere (špičková hodnota). Pod a nad touto optimálnou hodnotou sa pevnosť v ťahu pri spájkovaní znižuje. Typické vôle pri spájkovaní môžu byť medzi 0,025 a 0,2 mm. Používame rôzne spájkovacie materiály s rôznymi tvarmi, ako sú perá, prášok, krúžky, drôty, pásy... atď. a dokáže vyrobiť tieto prvky špeciálne pre váš dizajn alebo geometriu produktu. Tiež určujeme obsah spájkovacích materiálov podľa vašich základných materiálov a použitia. Na odstránenie nežiaducich oxidových vrstiev a zabránenie oxidácii často používame tavivá pri operáciách spájkovania. Aby sa predišlo následnej korózii, tavivá sa vo všeobecnosti odstránia po operácii spájania. AGS-TECH Inc. používa rôzne metódy spájkovania, vrátane:
- Spájkovanie horákom
- Spájkovanie v peci
- Indukčné spájkovanie
- Odporové spájkovanie
- Spájkovanie ponorením
- Infračervené spájkovanie
- Difúzne spájkovanie
- Vysokoenergetický lúč
Naše najbežnejšie príklady spájkovaných spojov sú vyrobené z rôznych kovov s dobrou pevnosťou, ako sú karbidové vrtáky, vložky, optoelektronické hermetické obaly, tesnenia.
SPÁJKOVANIE: Toto je jedna z našich najčastejšie používaných techník, pri ktorej spájka (výplňový kov) vypĺňa spoj ako pri spájkovaní medzi tesne priliehajúcimi komponentmi. Naše spájky majú bod topenia pod 723 Kelvinov. Vo výrobných prevádzkach nasadzujeme ručné aj automatizované spájkovanie. V porovnaní s tvrdým spájkovaním sú teploty spájkovania nižšie. Spájkovanie nie je veľmi vhodné pre vysokoteplotné alebo vysokopevnostné aplikácie. Na spájkovanie používame okrem iného bezolovnaté spájky, ako aj zliatiny cín-olovo, cín-zinok, olovo-striebro, kadmium-striebro, zinok-hliník. Ako tavidlo pri spájkovaní sa používajú nekorozívne živice, ako aj anorganické kyseliny a soli. Na spájkovanie kovov s nízkou spájkovateľnosťou používame špeciálne tavivá. V aplikáciách, kde musíme spájkovať keramické materiály, sklo alebo grafit, diely najskôr pokovujeme vhodným kovom pre zvýšenú spájkovateľnosť. Naše obľúbené techniky spájkovania sú:
- Pretavenie alebo pastové spájkovanie
- Spájkovanie vlnou
- Spájkovanie v peci
- spájkovanie horákom
- Indukčné spájkovanie
- Spájkovanie železa
- Odporové spájkovanie
- Spájkovanie ponorením
- Ultrazvukové spájkovanie
- Infračervené spájkovanie
Ultrazvukové spájkovanie nám ponúka jedinečnú výhodu, kedy je eliminovaná potreba tavív vďaka ultrazvukovému kavitačnému efektu, ktorý odstraňuje oxidové filmy zo spájaných povrchov. Spájkovanie pretavením a vlnou sú naše priemyselne vynikajúce techniky pre veľkoobjemovú výrobu v elektronike, a preto stojí za to ich podrobnejšie vysvetliť. Pri spájkovaní pretavením používame polotuhé pasty, ktoré obsahujú častice spájkovacieho kovu. Pasta sa nanáša na spoj pomocou procesu sitovania alebo šablónovania. V doskách plošných spojov (PCB) túto techniku často používame. Keď sú elektrické komponenty umiestnené na tieto podložky z pasty, povrchové napätie udržuje obaly na povrchovú montáž zarovnané. Po umiestnení komponentov zohrejeme zostavu v peci, aby prebehlo spájkovanie pretavením. Počas tohto procesu sa rozpúšťadlá v paste odparia, tavidlo v paste sa aktivuje, komponenty sa predhrejú, častice spájky sa roztavia a zmáčajú spoj a nakoniec sa zostava DPS pomaly ochladí. Naša druhá populárna technika pre veľkoobjemovú výrobu dosiek plošných spojov, menovite vlnové spájkovanie, spočíva v tom, že roztavené spájky zmáčajú kovové povrchy a vytvárajú dobré spoje iba vtedy, keď je kov predhriaty. Stojatá laminárna vlna roztavenej spájky je najprv generovaná čerpadlom a predhriate a predtavené PCB sú dopravované cez túto vlnu. Spájka zmáča iba exponované kovové povrchy, ale nezmáča polymérové obaly IC ani dosky plošných spojov potiahnuté polymérom. Vysokorýchlostný prúd horúcej vody vyfukuje prebytočnú spájku zo spoja a zabraňuje premosteniu medzi susednými vodičmi. Pri vlnovom spájkovaní obalov na povrchovú montáž ich pred spájkovaním najskôr prilepíme na dosku plošných spojov. Opäť sa používa tienenie a šablóna, ale tentoraz pre epoxid. Po umiestnení komponentov na správne miesta sa epoxid vytvrdí, dosky sa obrátia a uskutoční sa spájkovanie vlnou.