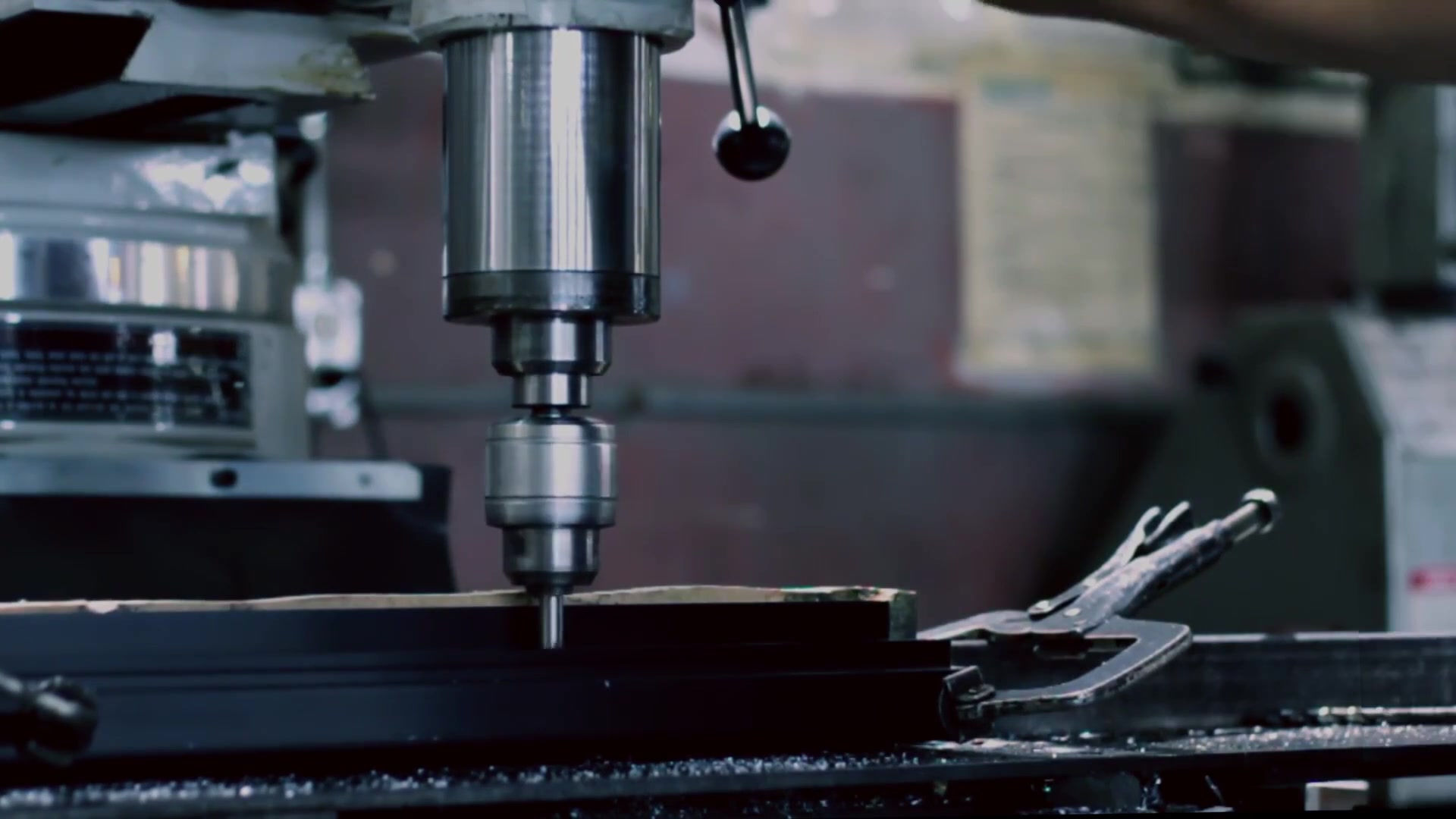
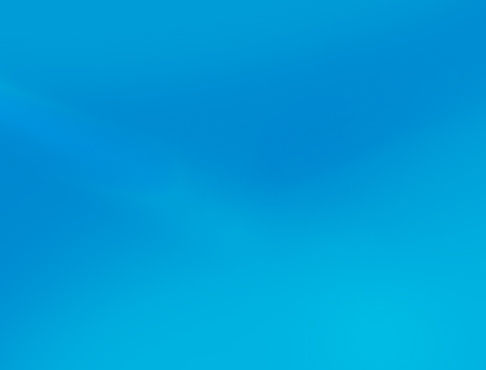
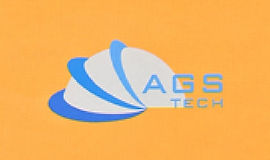
Globálny vlastný výrobca, integrátor, konsolidátor, partner outsourcingu pre širokú škálu produktov a služieb.
Sme váš komplexný zdroj pre výrobu, výrobu, inžinierstvo, konsolidáciu, integráciu, outsourcing zákazkovo vyrábaných a voľne predajných produktov a služieb.
Vyberte si jazyk
-
Zákazková výroba
-
Domáca a globálna zmluvná výroba
-
Outsourcing výroby
-
Domáce a globálne obstarávanie
-
Konsolidácia
-
Engineering Integration
-
Inžinierske služby
ELECTRICAL DISCHARGE MACHINING (EDM), also referred to as SPARK-EROSION or ELECTRODISCHARGE MACHINING, SPARK ERODING, DIE SINKING_cc781905-5cde-3194-bb3b -136bad5cf58d_or WIRE EROSION, is a NON-CONVENTIONAL MANUFACTURING process where erosion of metals takes place and desired shape is obtained using electrical discharges in the form iskier. Ponúkame aj niektoré druhy EDM, menovite NO-WEAR EDM, EDM EDM (WEDM), EDM BRÚSENIE (EDG), DIE-DIE-SNKING EDM, ELEKTRICKÉ VYBITIE FRÉZOVANIA, micro-EDM_7900 -5cde-3194-bb3b-136bad5cf58d_and ELEKTROCHEMICKÉ-VYBITOVÉ BRÚSENIE (ECDG). Naše EDM systémy pozostávajú z tvarovaných nástrojov/elektródy a obrobku pripojeného k jednosmernému napájaniu a vloženého do elektricky nevodivej dielektrickej kvapaliny. Po roku 1940 sa elektroerozívne obrábanie stalo jednou z najdôležitejších a najobľúbenejších výrobných technológií vo výrobnom priemysle.
Keď sa vzdialenosť medzi dvoma elektródami zníži, intenzita elektrického poľa v objeme medzi elektródami sa v niektorých bodoch stane väčšou ako sila dielektrika, ktoré sa zlomí a prípadne vytvorí mostík pre prúdenie prúdu medzi dvoma elektródami. Vytvorí sa intenzívny elektrický oblúk, ktorý spôsobí značné zahrievanie na roztavenie časti obrobku a časti nástrojového materiálu. Výsledkom je odstránenie materiálu z oboch elektród. Súčasne sa dielektrická kvapalina rýchlo zahrieva, čo vedie k odparovaniu kvapaliny v oblúkovej medzere. Akonáhle sa tok prúdu zastaví alebo je zastavený, je teplo odvádzané z plynovej bubliny okolitou dielektrickou tekutinou a bublina kavituje (skolabuje). Rázová vlna vytvorená zrútením bubliny a prúdom dielektrickej tekutiny spláchne úlomky z povrchu obrobku a strháva akýkoľvek roztavený materiál obrobku do dielektrickej tekutiny. Frekvencia opakovania týchto výbojov je medzi 50 až 500 kHz, napätie medzi 50 a 380 V a prúdy medzi 0,1 a 500 ampérov. Nové kvapalné dielektrikum, ako sú minerálne oleje, petrolej alebo destilovaná a deionizovaná voda, sa zvyčajne dopraví do medzielektródového objemu a odnesie pevné častice (vo forme úlomkov) a obnovia sa izolačné vlastnosti dielektrika. Po prietoku prúdu sa potenciálny rozdiel medzi dvoma elektródami obnoví na hodnotu, ktorá bola pred prierazom, takže môže dôjsť k novému prierazu tekutého dielektrika. Naše moderné elektrické výbojové stroje (EDM) ponúkajú numericky riadené pohyby a sú vybavené čerpadlami a filtračnými systémami pre dielektrické kvapaliny.
Elektroerozívne obrábanie (EDM) je metóda obrábania používaná hlavne pre tvrdé kovy alebo také, ktoré by bolo veľmi ťažké obrábať konvenčnými technikami. EDM zvyčajne pracuje s akýmikoľvek materiálmi, ktoré sú elektrickými vodičmi, aj keď boli navrhnuté aj spôsoby obrábania izolačnej keramiky pomocou EDM. Teplota topenia a latentné teplo topenia sú vlastnosti, ktoré určujú objem kovu odstráneného na jeden výboj. Čím sú tieto hodnoty vyššie, tým je rýchlosť úberu materiálu nižšia. Pretože proces obrábania elektrickým výbojom nezahŕňa žiadnu mechanickú energiu, tvrdosť, pevnosť a húževnatosť obrobku neovplyvňuje rýchlosť úberu. Frekvencia výboja alebo energia na výboj, napätie a prúd sa menia, aby sa riadili rýchlosti odstraňovania materiálu. Rýchlosť úberu materiálu a drsnosť povrchu sa zvyšujú so zvyšujúcou sa hustotou prúdu a klesajúcou frekvenciou iskier. Pomocou EDM dokážeme vyrezať zložité kontúry alebo dutiny v predkalenej oceli bez potreby tepelného spracovania na ich zmäkčenie a opätovné vytvrdnutie. Túto metódu môžeme použiť s akýmkoľvek kovom alebo kovovými zliatinami, ako je titán, hastelloy, kovar a inconel. Aplikácie procesu EDM zahŕňajú tvarovanie nástrojov z polykryštalických diamantov. EDM sa považuje za netradičnú alebo nekonvenčnú metódu obrábania spolu s procesmi ako elektrochemické obrábanie (ECM), rezanie vodným lúčom (WJ, AWJ), rezanie laserom. Na druhej strane konvenčné spôsoby obrábania zahŕňajú sústruženie, frézovanie, brúsenie, vŕtanie a iné procesy, ktorých mechanizmus úberu materiálu je v podstate založený na mechanických silách. Elektródy pre elektroerozívne obrábanie (EDM) sú vyrobené z grafitu, mosadze, medi a zliatiny medi a volfrámu. Možné sú priemery elektród do 0,1 mm. Keďže opotrebovanie nástroja je nežiaducim javom, ktorý nepriaznivo ovplyvňuje rozmerovú presnosť pri EDM, využívame proces s názvom NO-WEAR EDM, a to obrátením polarity a použitím medených nástrojov na minimalizáciu opotrebovania nástroja.
V ideálnom prípade možno elektroerozívne obrábanie (EDM) považovať za sériu rozpadu a obnovy dielektrickej kvapaliny medzi elektródami. V skutočnosti je však odstránenie úlomkov z medzielektródovej oblasti takmer vždy čiastočné. To spôsobuje, že elektrické vlastnosti dielektrika v oblasti medzi elektródami sú odlišné od ich nominálnych hodnôt a menia sa s časom. Medzielektródová vzdialenosť (iskrisko) je nastavená riadiacimi algoritmami konkrétneho použitého stroja. Žiaľ, iskrisko v EDM môže byť niekedy skratované úlomkami. Riadiaci systém elektródy nemusí reagovať dostatočne rýchlo, aby zabránil skratu dvoch elektród (nástroja a obrobku). Tento nežiaduci skrat prispieva k úberu materiálu inak ako v ideálnom prípade. Maximálnu dôležitosť venujeme preplachovaniu, aby sa obnovili izolačné vlastnosti dielektrika tak, aby prúd prebiehal vždy v mieste medzielektródovej oblasti, čím sa minimalizuje možnosť neželanej zmeny tvaru (poškodenia) nástrojovej elektródy. a obrobok. Na získanie špecifickej geometrie je nástroj EDM vedený po požadovanej dráhe veľmi blízko k obrobku bez toho, aby sa ho dotýkal. Maximálnu pozornosť venujeme výkonu ovládania pohybu pri používaní. Týmto spôsobom dochádza k veľkému počtu prúdových výbojov / iskier a každý prispieva k odstráneniu materiálu z nástroja aj obrobku, kde sa tvoria malé krátery. Veľkosť kráterov je funkciou technologických parametrov stanovených pre konkrétnu úlohu a rozmery sa môžu pohybovať od nanometrov (ako v prípade mikro-EDM operácií) až po niekoľko stoviek mikrometrov v podmienkach hrubovania. Tieto malé krátery na nástroji spôsobujú postupnú eróziu elektródy nazývanú „opotrebenie nástroja“. Aby sme eliminovali škodlivý vplyv opotrebenia na geometriu obrobku, priebežne vymieňame nástroj-elektródu počas obrábania. Niekedy to dosiahneme použitím priebežne vymieňaného drôtu ako elektródy (tento proces EDM sa tiež nazýva WIRE EDM ). Niekedy používame nástroj-elektródu tak, že len malá časť je skutočne zapojená do procesu obrábania a táto časť sa pravidelne mení. To je napríklad prípad použitia rotujúceho kotúča ako nástrojovej elektródy. Tento proces sa nazýva EDM BRÚSENIE. Ďalšia technika, ktorú používame, pozostáva z použitia sady elektród s rôznymi veľkosťami a tvarmi počas rovnakej operácie EDM na kompenzáciu opotrebenia. Nazývame túto techniku viacerých elektród a najčastejšie sa používa, keď nástrojová elektróda negatívne kopíruje požadovaný tvar a postupuje smerom k polotovaru v jednom smere, zvyčajne vo vertikálnom smere (tj os z). Toto sa podobá ponoreniu nástroja do dielektrickej kvapaliny, v ktorej je obrobok ponorený, a preto je označovaný ako DIE-SINKING EDM_cc781905-5cde-3194-bb3b755136 3194-bb3b-136bad5cf58d_CONVENTIONAL EDM or RAM EDM). Stroje na túto operáciu sa nazývajú SINKER EDM. Elektródy pre tento typ EDM majú zložité tvary. Ak sa konečná geometria získa pomocou elektródy obyčajného jednoduchého tvaru, ktorá sa pohybuje v niekoľkých smeroch a zároveň podlieha rotácii, nazývame ju EDM MILLING. Miera opotrebenia je striktne závislá od technologických parametrov použitých pri prevádzke (polarita, maximálny prúd, napätie naprázdno). Napríklad in micro-EDM, tiež známy ako m-EDM, sú tieto parametre zvyčajne nastavené na hodnoty, ktoré spôsobujú vážne opotrebovanie. Preto je opotrebenie hlavným problémom v tejto oblasti, ktorý minimalizujeme pomocou nášho nahromadeného know-how. Napríklad, aby sa minimalizovalo opotrebovanie grafitových elektród, digitálny generátor, ovládateľný v priebehu milisekúnd, obracia polaritu, keď dochádza k elektroerózii. Výsledkom je efekt podobný galvanickému pokovovaniu, pri ktorom sa erodovaný grafit kontinuálne ukladá späť na elektródu. V inom spôsobe, takzvanom obvode ''Zero Wear'', minimalizujeme frekvenciu spúšťania a zastavovania výboja a udržiavame ho tak dlho, ako je to len možné. Rýchlosť úberu materiálu pri obrábaní elektrickým výbojom možno odhadnúť z:
MRR = 4 x 10 exp (4) x I x T t exp (-1,23)
Tu je MRR v mm3/min, I je prúd v ampéroch, Tw je bod tavenia obrobku v K-273,15K. Exp znamená exponent.
Na druhej strane rýchlosť opotrebenia Wt elektródy možno získať z:
Hmotnosť = (1,1 x 10exp(11) ) x I x Ttexp(-2,38)
Tu je Wt v mm3/min a Tt je teplota topenia materiálu elektródy v K-273,15K
Nakoniec pomer opotrebenia obrobku k elektróde R možno získať z:
R = 2,25 x Trexp (-2,38)
Tr je tu pomer bodov topenia obrobku k elektróde.
SINKER EDM :
Sinker EDM, tiež označovaný ako CAVITY TYP EDM or_cc781905-95cde-piece-electro_cc781905-915cde-6d sa skladá z elektródy, z tekutého dielu EDMfDM781905-95cd-in. Elektróda a obrobok sú pripojené k napájaciemu zdroju. Napájací zdroj generuje elektrický potenciál medzi nimi. Keď sa elektróda priblíži k obrobku, v tekutine nastane dielektrický rozpad, ktorý vytvorí plazmový kanál a preskočí malá iskra. Iskry zvyčajne zasahujú jednu po druhej, pretože je vysoko nepravdepodobné, že by rôzne miesta v medzielektródovom priestore mali identické lokálne elektrické charakteristiky, ktoré by umožnili vznik iskry na všetkých takýchto miestach súčasne. Státisíce týchto iskier vznikajú v náhodných bodoch medzi elektródou a obrobkom za sekundu. Keď základný kov eroduje a iskriská sa následne zväčšuje, náš CNC stroj automaticky spustí elektródu, aby proces mohol pokračovať bez prerušenia. Naše zariadenie má kontrolné cykly známe ako ''čas zapnutia'' a ''čas vypnutia''. Nastavenie času zapnutia určuje dĺžku alebo trvanie iskry. Dlhší čas vytvára hlbšiu dutinu pre túto iskru a všetky nasledujúce iskry pre tento cyklus, čím sa vytvorí hrubší povrch na obrobku a naopak. Čas vypnutia je časový úsek, počas ktorého je jedna iskra nahradená inou. Dlhší čas vypnutia umožňuje dielektrickej kvapaline prepláchnuť tryskou, aby sa vyčistili erodované nečistoty, čím sa zabráni skratu. Tieto nastavenia sa upravia v priebehu mikrosekúnd.
WIRE EDM :
In WIRE ELECTRICAL DISCHARGE MACHINING (WEDM), also called WIRE-CUT EDM or WIRE CUTTING, we feed a tenký jednovláknový kovový drôt z mosadze cez obrobok, ktorý je ponorený v nádrži s dielektrickou kvapalinou. Wire EDM je dôležitou variáciou EDM. Príležitostne používame EDM rezanie drôtom na rezanie dosiek s hrúbkou až 300 mm a na výrobu razidiel, nástrojov a lisovníc z tvrdých kovov, ktoré sa ťažko opracujú inými výrobnými metódami. V tomto procese, ktorý sa podobá na obrysové rezanie pásovou pílou, je drôt, ktorý je neustále podávaný z cievky, držaný medzi hornými a spodnými diamantovými vodidlami. CNC riadené vodiace lišty sa pohybujú v rovine x–y a horné vodiace lišty sa môžu pohybovať aj nezávisle v osi z–u–v, čím vzniká možnosť rezať skosené a prechodné tvary (ako je kruh na dne a štvorec na vrch). Horné vedenie môže ovládať pohyby osí v x–y–u–v–i–j–k–l–. To umožňuje WEDM rezať veľmi zložité a jemné tvary. Priemerná rezná štrbina nášho zariadenia, ktorá dosahuje najlepšie ekonomické náklady a čas obrábania, je 0,335 mm pri použití mosadzného, medeného alebo volfrámového drôtu Ø 0,25. Avšak horné a dolné diamantové vodiace lišty nášho CNC zariadenia sú presné na približne 0,004 mm a môžu mať dráhu rezu alebo zárez len 0,021 mm pri použití drôtu Ø 0,02 mm. Sú teda možné naozaj úzke strihy. Šírka rezu je väčšia ako šírka drôtu, pretože zo strán drôtu k obrobku dochádza k iskreniu, čo spôsobuje eróziu. Toto „prerezanie“ je nevyhnutné, pre mnohé aplikácie je predvídateľné, a preto sa dá kompenzovať (v mikro-EDM sa to často nestáva). Cievky drôtu sú dlhé – 8 kg cievka 0,25 mm drôtu má dĺžku niečo vyše 19 kilometrov. Priemer drôtu môže byť len 20 mikrometrov a presnosť geometrie je v blízkosti +/- 1 mikrometer. Drôt vo všeobecnosti používame iba raz a recyklujeme ho, pretože je relatívne lacný. Pohybuje sa konštantnou rýchlosťou 0,15 až 9 m/min a počas rezu sa udržiava konštantná štrbina (štrbina). V procese drôtového rezania EDM používame vodu ako dielektrickú kvapalinu, ktorá riadi jej odpor a ďalšie elektrické vlastnosti pomocou filtrov a deionizérových jednotiek. Voda spláchne rezaný odpad zo zóny rezu. Preplachovanie je dôležitým faktorom pri určovaní maximálnej rýchlosti posuvu pre danú hrúbku materiálu a preto ho udržiavame konzistentné. Rezná rýchlosť v drôtovom EDM sa udáva ako prierezová plocha rezu za jednotku času, napríklad 18 000 mm2/h pre nástrojovú oceľ D2 s hrúbkou 50 mm. Lineárna rezná rýchlosť v tomto prípade by bola 18 000/50 = 360 mm/h Rýchlosť úberu materiálu pri EDM drôte je:
MRR = Vf xhxb
Tu je MRR v mm3/min, Vf je rýchlosť posuvu drôtu do obrobku v mm/min, h je hrúbka alebo výška v mm a b je rez, čo je:
b = dw + 2 s
Tu dw je priemer drôtu a s je medzera medzi drôtom a obrobkom v mm.
Spolu s užšími toleranciami majú naše moderné viacosové EDM obrábacie centrá na drôtové rezanie pridané funkcie, ako sú viachlavy na rezanie dvoch častí súčasne, ovládacie prvky na zabránenie pretrhnutiu drôtu, automatické samonavliekacie funkcie v prípade pretrhnutia drôtu a programovanie stratégie obrábania na optimalizáciu prevádzky, možnosti priameho a uhlového rezu.
Wire-EDM nám ponúka nízke zvyškové napätia, pretože nevyžaduje vysoké rezné sily na úber materiálu. Keď je energia/výkon na impulz relatívne nízka (ako pri dokončovacích operáciách), očakáva sa malá zmena mechanických vlastností materiálu v dôsledku nízkych zvyškových napätí.
ELEKTRICKÉ VÝBOJOVÉ BRÚSENIE (EDG) : Brúsne kotúče neobsahujú abrazíva, sú vyrobené z grafitu alebo mosadze. Opakujúce sa iskry medzi rotujúcim kotúčom a obrobkom odstraňujú materiál z povrchu obrobku. Rýchlosť úberu materiálu je:
MRR = K x I
Tu je MRR v mm3/min, I je prúd v ampéroch a K je súčiniteľ materiálu obrobku v mm3/A-min. Na rezanie úzkych štrbín na komponentoch často používame brúsenie elektrickým výbojom. Niekedy kombinujeme proces EDG (elektrické brúsenie) s procesom EKG (elektrochemické brúsenie), kde sa materiál odstraňuje chemickým pôsobením, elektrické výboje z grafitového kotúča rozbijú oxidový film a odplavia sa elektrolytom. Proces sa nazýva ELECTROCHEMICAL-DCHARGE GRINDING (ECDG). Aj keď proces ECDG spotrebuje relatívne viac energie, je rýchlejší ako proces EDG. Touto technikou brúsime prevažne tvrdokovové nástroje.
Aplikácie elektroenergetického obrábania:
Výroba prototypu:
Proces EDM používame pri výrobe foriem, nástrojov a lisovníc, ako aj pri výrobe prototypov a výrobných dielov, najmä pre letecký, automobilový a elektronický priemysel, v ktorom sú výrobné množstvá relatívne nízke. V Sinker EDM sa grafitová, medená volfrámová alebo čistá medená elektróda opracúva do požadovaného (negatívneho) tvaru a privádza sa do obrobku na konci vertikálneho barana.
Výroba razidiel:
Na výrobu razidiel na výrobu šperkov a odznakov procesom razenia mincí (razením) môže byť pozitívna predloha vyrobená zo striebra, pretože pri vhodnom nastavení stroja je predloha značne erodovaná a používa sa len raz. Výsledná negatívna matrica sa potom vytvrdí a použije sa v kladive na výrobu razených plošín z vyrezaných plechových polotovarov z bronzu, striebra alebo zliatiny zlata s nízkou odolnosťou. Pre odznaky môžu byť tieto plôšky ďalej tvarované do zakriveného povrchu inou matricou. Tento typ EDM sa zvyčajne vykonáva ponorený do dielektrika na báze oleja. Hotový predmet môže byť ďalej zušľachtený tvrdým (sklo) alebo mäkkým (farba) smaltovaním a/alebo galvanickým pokovovaním čistým zlatom alebo niklom. Mäkšie materiály, ako je striebro, môžu byť ručne vyryté ako vylepšenie.
Vŕtanie malých otvorov:
Na našich strojoch na drôtové rezanie EDM používame EDM vŕtanie malých otvorov na vytvorenie priechodného otvoru v obrobku, cez ktorý prevlečieme drôt na operáciu EDM rezania drôtom. Samostatné EDM hlavy špeciálne pre vŕtanie malých otvorov sú namontované na našich strojoch na rezanie drôtom, ktoré umožňujú, aby sa na veľkých kalených doskách podľa potreby a bez predvŕtania erodovali hotové diely. EDM s malými otvormi používame aj na vŕtanie radov otvorov do okrajov lopatiek turbín používaných v prúdových motoroch. Prúdenie plynu cez tieto malé otvory umožňuje motorom používať vyššie teploty, než by bolo inak možné. Vysokoteplotné, veľmi tvrdé, monokryštálové zliatiny, z ktorých sú čepele vyrobené, robí konvenčné obrábanie týchto otvorov s vysokým pomerom strán extrémne náročným a dokonca nemožným. Ďalšou oblasťou použitia EDM s malými otvormi je vytváranie mikroskopických otvorov pre komponenty palivového systému. Okrem integrovaných EDM hláv nasadzujeme aj samostatné EDM stroje na vŕtanie malých otvorov s osami x–y na obrábanie slepých alebo priechodných otvorov. EDM vŕtanie otvorov s dlhou mosadznou alebo medenou trubicovou elektródou, ktorá sa otáča v skľučovadle s konštantným prietokom destilovanej alebo deionizovanej vody prúdiacej cez elektródu ako preplachovacie činidlo a dielektrikum. Niektoré EDM na vŕtanie malých otvorov sú schopné prevŕtať 100 mm mäkkej alebo dokonca kalenej ocele za menej ako 10 sekúnd. Pri tomto vŕtaní je možné dosiahnuť otvory od 0,3 mm do 6,1 mm.
Dezintegračné obrábanie kovov:
Máme tiež špeciálne EDM stroje na špecifické účely odstraňovania zlomených nástrojov (vrtákov alebo závitníkov) z obrobkov. Tento proces sa nazýva ''obrábanie s dezintegráciou kovu''.
Výhody a nevýhody elektroenergetického obrábania:
Medzi výhody EDM patrí obrábanie:
- Komplexné tvary, ktoré by sa inak ťažko vyrábali bežnými reznými nástrojmi
- Extrémne tvrdý materiál s veľmi blízkymi toleranciami
- Veľmi malé obrobky, kde konvenčné rezné nástroje môžu poškodiť diel nadmerným tlakom rezného nástroja.
- Neexistuje žiadny priamy kontakt medzi nástrojom a obrobkom. Preto môžu byť jemné časti a slabé materiály obrábané bez akéhokoľvek skreslenia.
- Je možné dosiahnuť dobrú povrchovú úpravu.
- Veľmi jemné otvory sa dajú ľahko vyvŕtať.
Nevýhody EDM zahŕňajú:
- Pomalá rýchlosť úberu materiálu.
- Dodatočný čas a náklady vynaložené na vytvorenie elektród pre EDM s piestom a ponorom.
- Reprodukcia ostrých rohov na obrobku je náročná z dôvodu opotrebovania elektródy.
- Spotreba energie je vysoká.
- Vytvorí sa ''Overcut''.
- Pri obrábaní dochádza k nadmernému opotrebovaniu nástroja.
- Elektricky nevodivé materiály je možné obrábať len so špecifickým nastavením procesu.