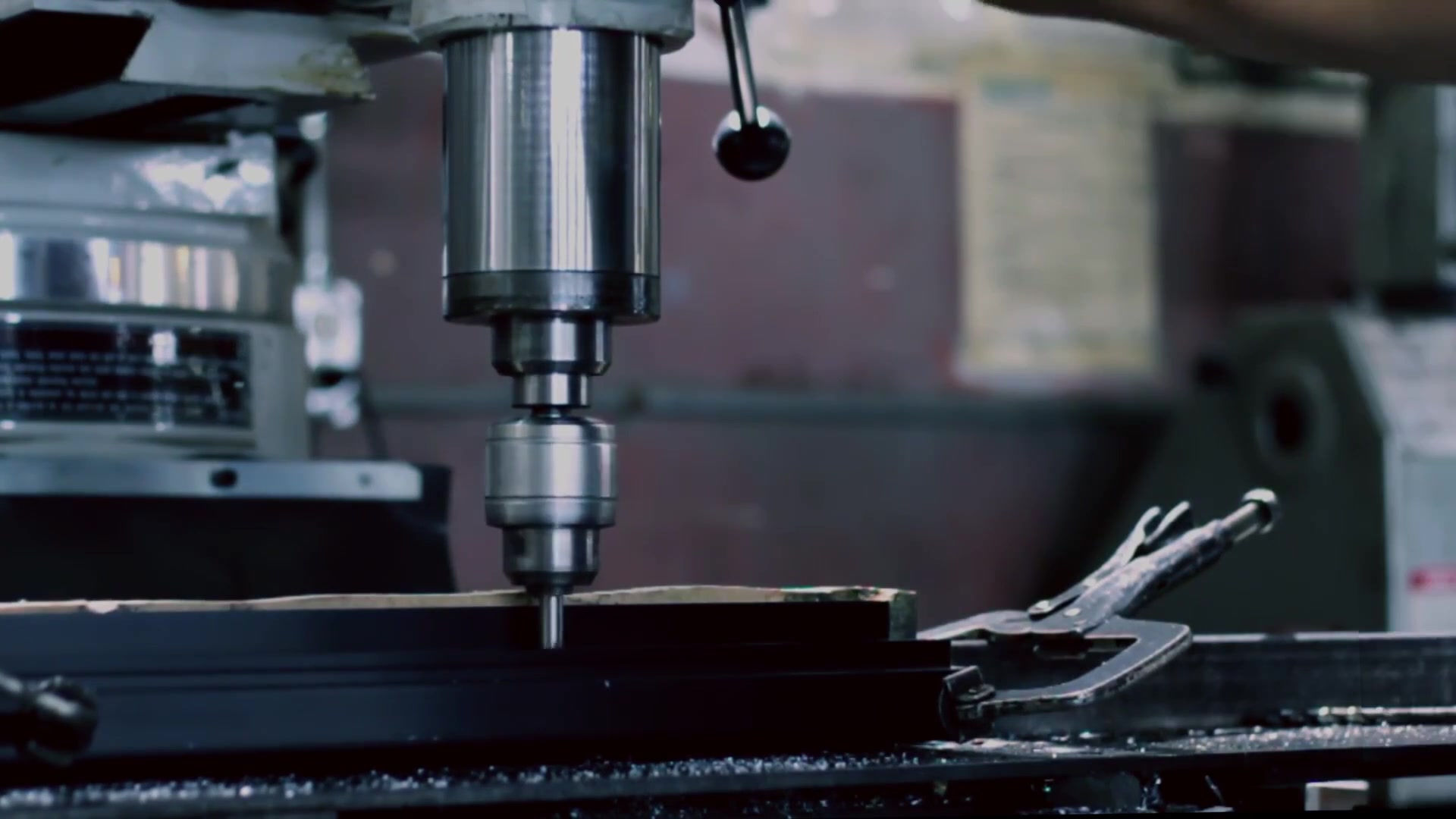
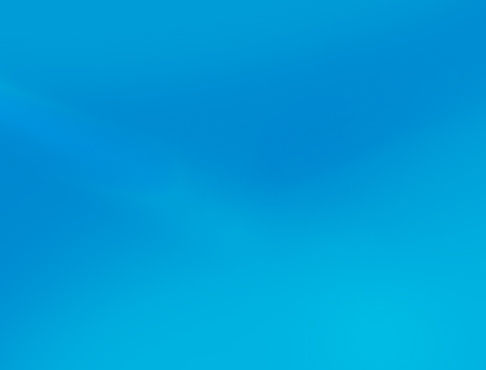
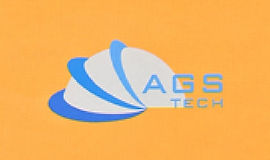
Globálny vlastný výrobca, integrátor, konsolidátor, partner outsourcingu pre širokú škálu produktov a služieb.
Sme váš komplexný zdroj pre výrobu, výrobu, inžinierstvo, konsolidáciu, integráciu, outsourcing zákazkovo vyrábaných a voľne predajných produktov a služieb.
Vyberte si jazyk
-
Zákazková výroba
-
Domáca a globálna zmluvná výroba
-
Outsourcing výroby
-
Domáce a globálne obstarávanie
-
Konsolidácia
-
Engineering Integration
-
Inžinierske služby
Search Results
Počet nájdených výsledkov s prázdnym vyhľadávaním: 164
- Rapid Prototyping, Desktop Manufacturing, Additive Manufacturing, FDM
Rapid Prototyping, Desktop Manufacturing, Additive Manufacturing, Stereolithography, Polyjet, Fused Deposition Modeling, Selective Laser Sintering, FDM, SLS Aditívna a rýchla výroba V posledných rokoch sme zaznamenali nárast dopytu po RAPID MANUFACTURING alebo RAPID PROTOTYPING. Tento proces môže byť tiež nazývaný STOLOVÁ VÝROBA alebo VOĽNÁ VÝROBA. V zásade je pevný fyzický model dielu vyrobený priamo z trojrozmerného výkresu CAD. Pre tieto rôzne techniky, kde staviame diely vo vrstvách, používame termín ADItívna výroba. Pomocou integrovaného počítačom riadeného hardvéru a softvéru vykonávame aditívnu výrobu. Naše rýchle prototypové a výrobné techniky sú STEREOLITOGRAFIA, POLYJET, FUSED-DEPOZIČNÉ MODELOVANIE, SELEKTÍVNE LASEROVÉ SINTROVANIE, TAVENIE ELEKTRONOVÝM LÚČOM, TROJROZMERNÁ TLAČ, PRIAMA VÝROBA, RÝCHLE NÁSTROJE. Odporúčame vám kliknúť semSTIAHNITE si naše schematické ilustrácie aditívnej výroby a rýchlych výrobných procesov od AGS-TECH Inc. Pomôže vám to lepšie porozumieť informáciám, ktoré vám poskytujeme nižšie. Rapid prototyping nám poskytuje: 1.) Koncepčný dizajn produktu je sledovaný z rôznych uhlov na monitore pomocou 3D / CAD systému. 2.) Prototypy z nekovových a kovových materiálov sa vyrábajú a skúmajú z funkčného, technického a estetického hľadiska. 3.) Nízkonákladové prototypovanie je zrealizované vo veľmi krátkom čase. Aditívna výroba sa môže podobať konštrukcii bochníka chleba naskladaním a spájaním jednotlivých plátkov na seba. Inými slovami, výrobok sa vyrába plátok po plátku alebo vrstva po vrstve nanesená jedna na druhú. Väčšinu dielov je možné vyrobiť do niekoľkých hodín. Táto technika je dobrá, ak sú diely potrebné veľmi rýchlo alebo ak sú potrebné množstvá nízke a výroba formy a nástrojov je príliš drahá a časovo náročná. Náklady na diel sú však drahé kvôli drahým surovinám. • STEREOLITOGRAFIA : Táto technika, tiež skrátená ako STL, je založená na vytvrdzovaní a vytvrdzovaní tekutého fotopolyméru do špecifického tvaru zaostrením laserového lúča naň. Laser polymerizuje fotopolymér a vytvrdzuje ho. Skenovaním UV laserového lúča podľa naprogramovaného tvaru pozdĺž povrchu zmesi fotopolymérov je dielec vyrábaný zdola nahor v jednotlivých na sebe kaskádových rezoch. Skenovanie laserového bodu sa mnohokrát opakuje, aby sa dosiahli geometrie naprogramované v systéme. Po úplnom vyrobení dielu sa tento vyberie z plošiny, odsaje a vyčistí ultrazvukom a alkoholovým kúpeľom. Potom sa na niekoľko hodín vystaví UV žiareniu, aby sa zabezpečilo úplné vytvrdenie a vytvrdnutie polyméru. Aby sme to zhrnuli, platforma, ktorá je ponorená do zmesi fotopolymérov a UV laserový lúč sa riadia a pohybujú cez servoriadiaci systém podľa tvaru požadovaného dielu a diel sa získava fototvrdnutím polymérnej vrstvy po vrstve. Samozrejme maximálne rozmery vyrobeného dielu sú určené stereolitografickým zariadením. • POLYJET : Podobne ako pri atramentovej tlači, v polyjet máme osem tlačových hláv, ktoré ukladajú fotopolymér na stavebný zásobník. Ultrafialové svetlo umiestnené vedľa trysiek okamžite vytvrdzuje a vytvrdzuje každú vrstvu. V polyjete sa používajú dva materiály. Prvý materiál je na výrobu skutočného modelu. Druhý materiál, gélovitá živica, sa používa na podporu. Oba tieto materiály sa nanášajú vrstva po vrstve a súčasne sa vytvrdzujú. Po dokončení modelu sa nosný materiál odstráni vodným roztokom. Použité živice sú podobné stereolitografii (STL). Polyjet má oproti stereolitografii nasledujúce výhody: 1.) Nie je potrebné čistenie častí. 2.) Nie je potrebné následné vytvrdzovanie 3.) Menšie hrúbky vrstiev sú možné, a tak získame lepšie rozlíšenie a môžeme vyrábať jemnejšie diely. • MODELOVANIE FUSED DEPOSITION MODELING: Tiež skrátené ako FDM, pri tejto metóde sa robotom riadená hlava extrudéra pohybuje nad stolom v dvoch hlavných smeroch. Kábel sa spúšťa a zdvíha podľa potreby. Z otvoru vyhrievanej matrice na hlave sa vytlačí termoplastické vlákno a na penový základ sa nanesie počiatočná vrstva. To sa dosiahne pomocou hlavy extrudéra, ktorá sleduje vopred stanovenú dráhu. Po počiatočnej vrstve sa stôl spustí a ďalšie vrstvy sa ukladajú na seba. Niekedy pri výrobe komplikovaného dielu sú potrebné podporné konštrukcie, aby nanášanie mohlo pokračovať v určitých smeroch. V týchto prípadoch je nosný materiál extrudovaný s menšou hustotou rozmiestnenia filamentu na vrstve, takže je slabší ako modelový materiál. Tieto nosné konštrukcie možno neskôr po dokončení dielca rozpustiť alebo odlomiť. Rozmery vytláčacej hubice určujú hrúbku vytláčaných vrstiev. Proces FDM produkuje diely so stupňovitými povrchmi na šikmých vonkajších rovinách. Ak je táto drsnosť neprijateľná, na ich vyhladenie možno použiť chemické leštenie parou alebo vyhrievaný nástroj. Dokonca aj leštiaci vosk je dostupný ako náterový materiál, aby sa eliminovali tieto kroky a dosiahli sa primerané geometrické tolerancie. • SELEKTÍVNE LASEROVÉ SINTROVANIE: Proces označovaný aj ako SLS je založený na selektívnom spekaní polymérnych, keramických alebo kovových práškov do predmetu. Spodná časť spracovacej komory má dva valce: čiastočne zostavený valec a valec na podávanie prášku. Prvý sa postupne spúšťa do miesta, kde sa vytvára spekaná časť, a druhý sa postupne zdvíha, aby dodával prášok do valcového valca prostredníctvom valčekového mechanizmu. Najprv sa tenká vrstva prášku nanesie do valca s čiastočnou konštrukciou, potom sa na túto vrstvu zameria laserový lúč, pričom sa obkreslí a roztopí/sintruje konkrétny prierez, ktorý potom znova stuhne na pevnú látku. Prášok sú oblasti, ktoré nie sú zasiahnuté laserovým lúčom, zostávajú voľné, ale stále podporujú pevnú časť. Potom sa nanesie ďalšia vrstva prášku a proces sa mnohokrát opakuje, aby sa získala časť. Na konci sa vytrasú voľné častice prášku. Všetky tieto činnosti vykonáva počítač na riadenie procesu pomocou inštrukcií generovaných 3D CAD programom vyrábaného dielu. Môžu sa nanášať rôzne materiály, ako sú polyméry (ako ABS, PVC, polyester), vosk, kovy a keramika s vhodnými polymérnymi spojivami. • ELEKTRONOVÝ BEAM MELTING : Podobné ako selektívne laserové spekanie, ale s použitím elektrónového lúča na roztavenie práškov titánu alebo kobaltu a chrómu na výrobu prototypov vo vákuu. Na vykonanie tohto procesu na nehrdzavejúcej oceli, hliníku a zliatinách medi sa urobil určitý vývoj. Ak je potrebné zvýšiť únavovú pevnosť vyrábaných dielov, používame ako sekundárny proces po výrobe dielu izostatické lisovanie za tepla. • TROJROZMERNÁ TLAČ: Pri tejto technike označovaná aj ako 3DP nanáša tlačová hlava anorganické spojivo na vrstvu buď nekovového alebo kovového prášku. Piest nesúci práškové lôžko sa postupne znižuje a v každom kroku sa spojivo nanáša vrstva po vrstve a spája sa spojivom. Použité práškové materiály sú polymérne zmesi a vlákna, zlievarenský piesok, kovy. Použitím rôznych hláv spojiva súčasne a rôznych farieb spojív môžeme získať rôzne farby. Proces je podobný atramentovej tlači, ale namiesto farebného listu získame farebný trojrozmerný objekt. Vyrobené diely môžu byť porézne, a preto môžu vyžadovať spekanie a infiltráciu kovu, aby sa zvýšila ich hustota a pevnosť. Spekaním sa spojivo spáli a kovové prášky sa spoja. Na výrobu dielov je možné použiť kovy ako nehrdzavejúca oceľ, hliník, titán a ako infiltračné materiály bežne používame meď a bronz. Krása tejto techniky je v tom, že aj komplikované a pohyblivé zostavy sa dajú vyrobiť veľmi rýchlo. Napríklad je možné vyrobiť ozubené koleso, kľúč ako nástroj a budú mať pohyblivé a otáčavé časti pripravené na použitie. Rôzne komponenty zostavy je možné vyrobiť v rôznych farbách a to všetko naraz. Stiahnite si našu brožúru na:Základy 3D tlače kovov • PRIAMA VÝROBA a RAPID TOOLING: Okrem hodnotenia dizajnu, riešenia problémov používame rýchle prototypovanie na priamu výrobu produktov alebo priamu aplikáciu do produktov. Inými slovami, rýchle prototypovanie môže byť začlenené do konvenčných procesov, aby boli lepšie a konkurencieschopnejšie. Napríklad rýchle prototypovanie môže produkovať vzory a formy. Vzory taviaceho sa a horiaceho polyméru vytvorené operáciami rýchleho prototypovania možno zostaviť na investičné liatie a zataviť. Ďalším príkladom, ktorý treba spomenúť, je použitie 3DP na výrobu keramického odlievacieho plášťa a jeho použitie na operácie odlievania plášťa. Dokonca aj vstrekovacie formy a vložky do foriem je možné vyrábať rýchlym prototypovaním a možno ušetriť mnoho týždňov alebo mesiacov času na výrobu foriem. Iba analýzou CAD súboru požadovaného dielu môžeme pomocou softvéru vytvoriť geometriu nástroja. Tu sú niektoré z našich populárnych metód rýchleho obrábania: RTV (Vulkanizácia pri izbovej teplote) LIETANIE / ODLIATOK URETÁNU: Pomocou rýchleho prototypovania je možné vytvoriť vzor požadovaného dielu. Potom sa tento vzor potiahne separačným prostriedkom a na vzor sa naleje tekutá RTV guma, aby sa vytvorili polovice formy. Ďalej sa tieto polovice formy použijú na vstrekovanie tekutých uretánov. Životnosť formy je krátka, len 0 alebo 30 cyklov, ale dosť na výrobu malých sérií. VSTREKOVANIE ACES (Acetal Clear Epoxy Solid) : Pomocou techník rýchleho prototypovania, ako je stereolitografia, vyrábame vstrekovacie formy. Tieto formy sú škrupiny s otvoreným koncom, ktoré umožňujú plnenie materiálmi, ako je epoxid, epoxid plnený hliníkom alebo kovy. Životnosť formy je opäť obmedzená na desiatky alebo maximálne stovky dielov. PROCES STRIEKANÝCH KOVOVÝCH NÁSTROJOV: Používame rýchle prototypovanie a vytvárame vzor. Na povrch vzoru nastriekame zinkovo-hliníkovú zliatinu a natrieme. Vzor s kovovým povlakom sa potom umiestni do banky a zaleje sa epoxidom alebo epoxidom naplneným hliníkom. Nakoniec sa odstráni a výrobou dvoch takýchto polovíc formy získame kompletnú formu na vstrekovanie. Tieto formy majú dlhšiu životnosť, v niektorých prípadoch v závislosti od materiálu a teplôt dokážu vyrobiť diely v tisíckach. PROCES KEELTOOL: Táto technika môže produkovať formy so životnosťou 100 000 až 10 miliónov cyklov. Pomocou rýchleho prototypovania vyrábame formu RTV. Forma sa potom naplní zmesou pozostávajúcou z prášku nástrojovej ocele A6, karbidu volfrámu, polymérneho spojiva a nechá sa vytvrdnúť. Táto forma sa potom zahrieva, aby sa polymér spálil a kovové prášky sa spojili. Ďalším krokom je infiltrácia medi na výrobu konečnej formy. V prípade potreby je možné na forme vykonať sekundárne operácie, ako je obrábanie a leštenie, aby sa dosiahla lepšia rozmerová presnosť. _cc781905-5cde-3194-bb3b-136d_5c CLICK Product Finder-Locator Service PREDCHÁDZAJÚCA STRANA
- Transmission Components, Belts, Chains, Cable Drives, Pulleys,AGS-TECH
Transmission Components, Belts, Chains and Cable Drives, Conventional & Grooved or Serrated, Positive Drive, Pulleys Zostava remeňov a reťazí a káblového pohonu AGS-TECH Inc. vám ponúka komponenty na prenos energie vrátane remeňov a reťazí a zostavy káblového pohonu. Rokmi zdokonaľovania sa naše gumené, kožené a iné remeňové pohony stali ľahšími a kompaktnejšími, schopné uniesť vyššie zaťaženie pri nižších nákladoch. Podobne aj naše reťazové pohony prešli postupom času veľkým vývojom a našim zákazníkom ponúkajú viacero výhod. Niektoré výhody použitia reťazových pohonov sú ich relatívne neobmedzené osové vzdialenosti hriadeľov, kompaktnosť, ľahká montáž, elasticita v ťahu bez prekĺznutia alebo tečenia, schopnosť pracovať v prostredí s vysokou teplotou. Naše káblové pohony tiež ponúkajú výhody, ako je jednoduchosť v niektorých aplikáciách oproti iným typom prevodových komponentov. K dispozícii sú štandardné remeňové, reťazové a káblové pohony, ako aj na mieru vyrobené a zmontované verzie. Tieto komponenty prevodovky vieme vyrobiť v správnej veľkosti pre vašu aplikáciu a z najvhodnejších materiálov. REMEŇA A REMEŇOVÉ POHONY: - Bežné ploché remene: Sú to hladké ploché remene bez zubov, drážok alebo zúbkov. Ploché remeňové pohony ponúkajú flexibilitu, dobré tlmenie nárazov, efektívny prenos sily pri vysokých rýchlostiach, odolnosť proti oderu, nízke náklady. Pásy môžu byť spojené alebo spojené, aby sa vytvorili väčšie pásy. Ďalšie výhody bežných plochých remeňov sú tenké, nie sú vystavené vysokému odstredivému zaťaženiu (vhodné pre vysokorýchlostné operácie s malými kladkami). Na druhej strane kladú vysoké zaťaženie ložísk, pretože ploché remene vyžadujú vysoké napätie. Ďalšími nevýhodami pohonov s plochým remeňom môže byť preklzávanie, hlučná prevádzka a relatívne nižšia účinnosť pri nízkych a stredných rýchlostiach prevádzky. Máme dva typy konvenčných pásov: vystužené a nevystužené. Vystužené pásy majú vo svojej štruktúre ťažný prvok. Bežné ploché opasky sú dostupné ako koža, pogumovaná tkanina alebo šnúra, nevystužená guma alebo plast, tkanina, vystužená koža. Kožené remene ponúkajú dlhú životnosť, pružnosť, výborný koeficient trenia, jednoduchú opravu. Kožené opasky sú však relatívne drahé, vyžadujú úpravu a čistenie opasku a v závislosti od atmosféry sa môžu zmenšiť alebo natiahnuť. Pogumované tkaninové alebo kordové pásy sú odolné voči vlhkosti, kyselinám a zásadám. Pogumované látkové pásy sú vyrobené z vrstiev bavlny alebo syntetickej kačice impregnovanej gumou a sú najekonomickejšie. Pogumované kordové pásy pozostávajú zo série vrstiev gumou impregnovaných kordov. Pogumované kordové pásy ponúkajú vysokú pevnosť v ťahu a skromnú veľkosť a hmotnosť. Nevystužené gumové alebo plastové remene sú vhodné pre ľahké aplikácie s nízkymi otáčkami. Nevystužené gumové a plastové remene môžu byť natiahnuté na svoje miesto cez ich kladky. Plastové nevystužené pásy môžu prenášať vyšší výkon v porovnaní s gumenými pásmi. Vystužené kožené opasky pozostávajú z plastového ťažného člena vloženého medzi hornú a spodnú vrstvu kože. Nakoniec, naše látkové pásy môžu pozostávať z jedného kusu bavlny alebo kačice poskladaného a zošitého radmi pozdĺžnych stehov. Látkové pásy sú schopné rovnomerne sledovať a pracovať pri vysokej rýchlosti. - Drážkované alebo zúbkované remene (ako sú klinové remene): Ide o základné ploché remene upravené tak, aby poskytovali výhody iného typu prevodového produktu. Ide o ploché pásy s pozdĺžne rebrovanou spodnou stranou. Poly-V remene sú pozdĺžne drážkované alebo zúbkované ploché remene s ťahovou časťou a sériou susediacich drážok v tvare V na účely sledovania a stláčania. Výkon závisí od šírky pásu. Klinový remeň je ťahúňom priemyslu a je dostupný v rôznych štandardizovaných veľkostiach a typoch na prenos takmer akéhokoľvek zaťaženia. Pohony klinovými remeňmi fungujú dobre medzi 1500 až 6000 stôp/min, avšak úzke klinové remene budú fungovať až do 10 000 stôp/min. Pohony s klinovým remeňom ponúkajú dlhú životnosť 3 až 5 rokov a umožňujú veľké rýchlostné pomery, ľahko sa inštalujú a demontujú, ponúkajú tichý chod, nízke nároky na údržbu, dobré tlmenie nárazov medzi remeňovým pohonom a hnaným hriadeľom. Nevýhodou klinových remeňov je ich určitý sklz a dotvarovanie, a preto nemusia byť najlepším riešením tam, kde sa vyžadujú synchrónne otáčky. Máme priemyselné, automobilové a poľnohospodárske pásy. K dispozícii sú skladové štandardné dĺžky, ako aj vlastné dĺžky opaskov. Všetky štandardné prierezy klinových remeňov sú dostupné zo skladu. Existujú tabuľky, v ktorých môžete vypočítať neznáme parametre, ako je dĺžka remeňa, časť remeňa (šírka a hrúbka), za predpokladu, že poznáte niektoré parametre vášho systému, ako sú priemery hnacej a hnanej remenice, stredová vzdialenosť medzi remenicami a rýchlosť otáčania remeníc. Môžete použiť takéto tabuľky alebo nás požiadať, aby sme pre vás vybrali ten správny klinový remeň. - Pozitívny hnací remeň (rozvodový remeň): Tieto remene sú tiež plochého typu so sériou rovnomerne rozmiestnených zubov na vnútornom obvode. Pozitívne hnacie alebo rozvodové remene kombinujú výhody plochých remeňov s pozitívnym záberom reťazí a ozubených kolies. Pozitívne hnacie remene neodhalia žiadne preklzávanie ani zmeny rýchlosti. Je možný široký rozsah rýchlostných pomerov. Zaťaženia ložísk sú nízke, pretože môžu pracovať pri nízkom napätí. Sú však náchylnejšie na nesúosovosť remeníc. - Remenice, kladky, náboje pre remene: Používajú sa rôzne typy remeníc s plochými, rebrovanými (zúbkovanými) a pozitívnymi hnacími remeňmi. Vyrábame ich všetky. Väčšina našich plochých remeníc je vyrobená liatím zo železa, ale oceľové verzie sú dostupné aj v rôznych kombináciách ráfikov a nábojov. Naše kladky s plochým remeňom môžu mať plné, lúčové alebo delené náboje alebo ich môžeme vyrobiť podľa vášho želania. Rebrované remene a remene s pozitívnym pohonom sú dostupné v rôznych veľkostiach a šírkach. Najmenej jedna remenica v pohonoch s ozubeným remeňom musí mať prírubu, aby sa remeň udržal na pohone. Pre systémy s dlhým stredovým pohonom sa odporúča mať obe remenice s prírubou. Kladky sú drážkované kolesá remeníc a vo všeobecnosti sa vyrábajú odlievaním železa, tvárnením ocele alebo lisovaním plastov. Tvárnenie ocele je vhodný proces na výrobu automobilových a poľnohospodárskych kladiek. Vyrábame kladky s pravidelnými a hlbokými drážkami. Kladky s hlbokými drážkami sú vhodné, keď klinový remeň vstupuje do kladky pod uhlom, ako je to v prípade štvrťotáčkových pohonov. Hlboké drážky sú tiež vhodné pre pohony s vertikálnym hriadeľom a aplikácie, kde môžu byť problémom vibrácie remeňov. Naše napínacie kladky sú drážkované kladky alebo ploché kladky, ktoré neslúžia na prenos mechanickej sily. Napínacie kladky sa používajú väčšinou na napínanie remeňov. - Pohony s jedným a viacerými remeňmi: Pohony s jedným remeňom majú jednu drážku, zatiaľ čo pohony s viacerými remeňmi majú viacero drážok. Kliknutím na príslušný farebný text nižšie si môžete stiahnuť naše katalógy: - Remene na prenos energie (zahŕňa klinové remene, rozvodové remene, remene s hrubým okrajom, obalené remene a špeciálne remene) - Dopravné pásy - V-kladky - Rozvodové kladky REŤAZE A REŤAZOVÉ POHONY: Naše reťaze na prenos sily majú niektoré výhody, ako sú relatívne neobmedzené vzdialenosti osov hriadeľov, jednoduchá montáž, kompaktnosť, pružnosť v ťahu bez prekĺznutia alebo tečenia, schopnosť prevádzky pri vysokých teplotách. Tu sú hlavné typy našich reťazí: - Odnímateľné reťaze: Naše odnímateľné reťaze sa vyrábajú v rôznych veľkostiach, rozstupe a maximálnej pevnosti a vo všeobecnosti z kujného železa alebo ocele. Kujné reťaze sa vyrábajú v rozsahu veľkostí od 0,902 (23 mm) do 4,063 palca (103 mm) a medznej pevnosti od 700 do 17 000 lb/štvorcový palec. Naše odnímateľné oceľové reťaze sa na druhej strane vyrábajú vo veľkostiach od 0,904 palca (23 mm) do približne 3,00 palca (76 mm) v rozstupe, s maximálnou pevnosťou od 760 do 5 000 lb/štvorcový palec._cc781905-5cde-3194-bb3b- 136bad5cf58d_ - Čepové reťaze: Tieto reťaze sa používajú pre väčšie bremená a mierne vyššie rýchlosti do približne 450 stôp/min (2,2 m/s). Čapové reťaze sú vyrobené z jednotlivých liatych článkov s plným, okrúhlym hlavňovým koncom s odsadenými bočnicami. Tieto reťazové články sú prepojené s oceľovými čapmi. Tieto reťaze majú rozstup od približne 1,00 palca (25 mm) do 6,00 palca (150 mm) a konečnú pevnosť medzi 3 600 až 30 000 lb/palec štvorcový. - Reťaze s offsetovou bočnou lištou: Sú obľúbené v hnacích reťaziach stavebných strojov. Tieto reťaze pracujú pri rýchlostiach do 1000 stôp/min a prenášajú zaťaženie do približne 250 koní. Vo všeobecnosti má každý článok dve odsadené bočnice, jedno puzdro, jeden valec, jeden kolík, závlačku. - Valčekové reťaze: Sú dostupné v rozstupoch od 0,25 (6 mm) do 3,00 (75 mm) palca. Konečná pevnosť valčekových reťazí s jednou šírkou sa pohybuje medzi 925 až 130 000 lb/štvorcový palec. Dostupné sú verzie valčekových reťazí s viacerými šírkami, ktoré prenášajú väčší výkon pri vyšších rýchlostiach. Valčekové reťaze s viacerými šírkami tiež ponúkajú hladší chod so zníženou hlučnosťou. Valčekové reťaze sú zostavené z valčekových a čapových článkov. Závlačky sa používajú v odnímateľných verziách valčekových reťazí. Konštrukcia valčekových reťazových pohonov si vyžaduje odborné znalosti. Zatiaľ čo remeňové pohony sú založené na lineárnych rýchlostiach, reťazové pohony sú založené na rýchlosti otáčania menšieho reťazového kolesa, ktoré je vo väčšine inštalácií hnaným členom. Okrem menovitého výkonu a rýchlosti otáčania je konštrukcia reťazových pohonov založená na mnohých ďalších faktoroch. - Dvojité reťaze: V podstate rovnaké ako valčekové reťaze s tým rozdielom, že rozstup je dvakrát dlhší. - Reťaze s obrátenými zubami (tiché): Vysokorýchlostné reťaze používané väčšinou pre pohony s vývodovým hriadeľom. Pohony s obrátenou ozubenou reťazou môžu prenášať výkon až 1200 koní a sú tvorené radom ozubených článkov, striedavo zostavených buď s čapmi, alebo kombináciou komponentov kĺbov. Stredová vodiaca reťaz má vodiace články na zapadnutie do drážok v ozubenom kolese a bočná vodiaca reťaz má vodiace lišty na zapojenie strán ozubeného kolesa. - Guľôčkové alebo posuvné reťaze: Tieto reťaze sa používajú pre pomalé jazdy a tiež pri manuálnych operáciách. Kliknutím na príslušný farebný text nižšie si môžete stiahnuť naše katalógy: - Hnacie reťaze - Dopravné reťaze - Dopravné reťaze s veľkým rozstupom - Valčekové reťaze z nehrdzavejúcej ocele - Zdvíhacie reťaze - Motocyklové reťaze - Reťaze poľnohospodárskych strojov - Ozubené kolesá: Naše štandardné ozubené kolesá zodpovedajú normám ANSI. Doskové ozubené kolesá sú ploché ozubené kolesá bez náboja. Naše malé a stredne veľké ozubené kolesá sú sústružené z tyčového materiálu alebo výkovkov alebo vyrobené zváraním náboja tyčového materiálu na plech valcovaný za tepla. AGS-TECH Inc. môže dodať reťazové kolesá opracované z odliatkov zo šedej liatiny, oceľovej liatiny a zváraných konštrukcií nábojov, spekaného práškového kovu, lisovaných alebo opracovaných plastov. Pre hladkú prevádzku pri vysokých rýchlostiach je nevyhnutný správny výber veľkosti ozubených kolies. Priestorové obmedzenia sú samozrejme faktorom, ktorý nemôžeme ignorovať pri výbere ozubeného kolesa. Odporúča sa, aby pomer hnacích a hnaných ozubených kolies nebol väčší ako 6:1 a navinutie reťaze na unášači bolo 120 stupňov. Stredové vzdialenosti medzi menšími a väčšími ozubenými kolesami, dĺžky reťaze a napnutie reťaze musia byť tiež zvolené podľa niektorých odporúčaných technických výpočtov a pokynov a nie náhodne. Stiahnite si naše katalógy kliknutím na farebný text nižšie: - Ozubené kolesá a tanierové kolesá - Prevodové puzdrá - Reťazová spojka - Reťazové zámky KÁBLOVÉ POHONY: Tieto majú v niektorých prípadoch svoje výhody oproti remeňovým a reťazovým pohonom. Káblové pohony môžu vykonávať rovnakú funkciu ako remene a môžu byť tiež jednoduchšie a ekonomickejšie na implementáciu v niektorých aplikáciách. Napríklad nová séria Synchromesh Cable Drives je navrhnutá pre pozitívnu trakciu, aby nahradila konvenčné laná, jednoduché káble a ozubené pohony, najmä v stiesnených priestoroch. Nový káblový pohon je navrhnutý tak, aby poskytoval vysoko presné polohovanie v elektronických zariadeniach, ako sú kopírovacie stroje, plotre, písacie stroje, tlačiarne,….. atď. Kľúčovou vlastnosťou nového káblového pohonu je jeho schopnosť použitia v 3D serpentínových konfiguráciách, ktoré umožňujú extrémne miniatúrne vzory. Synchromované káble je možné použiť s nižším napätím v porovnaní s lanami, čím sa znižuje spotreba energie. Pre otázky a názory na remene, reťazové a káblové pohony kontaktujte AGS-TECH. CLICK Product Finder-Locator Service PREDCHÁDZAJÚCA STRANA
- Composites, Composite Materials Manufacturing, Fiber Reinforced
Composites, Composite Materials Manufacturing, Particle and Fiber Reinforced, Cermets, Ceramic & Metal Composite, Glass Fiber Reinforced Polymer, Lay-Up Process Výroba kompozitov a kompozitných materiálov Jednoducho definované, KOMPOZITY alebo KOMPOZITNÉ MATERIÁLY sú materiály pozostávajúce z dvoch alebo viacerých materiálov s rôznymi fyzikálnymi alebo chemickými vlastnosťami, ale keď sa skombinujú, stanú sa materiálom, ktorý je odlišný od základných materiálov. Musíme zdôrazniť, že základné materiály zostávajú oddelené a odlišné v štruktúre. Cieľom pri výrobe kompozitného materiálu je získať produkt, ktorý je lepší ako jeho zložky a kombinuje požadované vlastnosti každej zložky. Ako príklad; pevnosť, nízka hmotnosť alebo nižšia cena môžu byť motiváciou pri navrhovaní a výrobe kompozitu. Typy kompozitov, ktoré ponúkame, sú časticami vystužené kompozity, vláknami vystužené kompozity vrátane kompozitov s keramickou matricou / polymérnou matricou / kovovou matricou / uhlík-uhlík / hybridných kompozitov, štruktúrne a laminované a sendvičové kompozity a nanokompozity. Výrobné techniky, ktoré používame pri výrobe kompozitných materiálov, sú: Pultrúzia, výrobné procesy predimpregnovaných laminátov, pokročilé umiestňovanie vlákien, navíjanie vlákien, umiestňovanie vlákien na mieru, proces kladenia sklenených vlákien sprejom, všívanie, lanxidový proces, z-pinning. Mnohé kompozitné materiály sa skladajú z dvoch fáz, matrice, ktorá je spojitá a obklopuje druhú fázu; a dispergovaná fáza, ktorá je obklopená matricou. Odporúčame vám kliknúť semSTIAHNITE si naše schematické ilustrácie výroby kompozitov a kompozitných materiálov spoločnosťou AGS-TECH Inc. Pomôže vám to lepšie porozumieť informáciám, ktoré vám poskytujeme nižšie. • KOMPOZITY VYZTUŽENÉ ČASTICAMI: Táto kategória pozostáva z dvoch typov: kompozity s veľkými časticami a kompozity spevnené disperziou. V prvom type interakcie častica-matrica nemôžu byť ošetrené na atómovej alebo molekulárnej úrovni. Namiesto toho platí mechanika kontinua. Na druhej strane v disperzne spevnených kompozitoch sú častice vo všeobecnosti oveľa menšie v rozsahu desiatok nanometrov. Príkladom kompozitu s veľkými časticami sú polyméry, do ktorých boli pridané plnivá. Plnivá zlepšujú vlastnosti materiálu a môžu nahradiť časť objemu polyméru ekonomickejším materiálom. Objemové podiely dvoch fáz ovplyvňujú správanie kompozitu. Kompozity s veľkými časticami sa používajú s kovmi, polymérmi a keramikou. CERMETY sú príklady keramických / kovových kompozitov. Náš najbežnejší cermet je slinutý karbid. Pozostáva zo žiaruvzdornej karbidovej keramiky, ako sú častice karbidu volfrámu v matrici z kovu, ako je kobalt alebo nikel. Tieto karbidové kompozity sú široko používané ako rezné nástroje pre kalenú oceľ. Častice tvrdého karbidu sú zodpovedné za rezný účinok a ich húževnatosť je zvýšená tvárnou kovovou matricou. Takto získame výhody oboch materiálov v jednom kompozite. Ďalším bežným príkladom kompozitu s veľkými časticami, ktorý používame, sú častice sadzí zmiešané s vulkanizovanou gumou na získanie kompozitu s vysokou pevnosťou v ťahu, húževnatosťou, odolnosťou proti roztrhnutiu a oderu. Príkladom disperzne spevneného kompozitu sú kovy a kovové zliatiny spevnené a vytvrdené rovnomernou disperziou jemných častíc veľmi tvrdého a inertného materiálu. Keď sa do hliníkovej kovovej matrice pridajú veľmi malé vločky oxidu hlinitého, získame spekaný hliníkový prášok, ktorý má zvýšenú pevnosť pri vysokých teplotách. • KOMPOZITY VYZTUŽENÉ VLÁKNAMI: Táto kategória kompozitov je v skutočnosti najdôležitejšia. Cieľom je dosiahnuť vysokú pevnosť a tuhosť na jednotku hmotnosti. Zloženie vlákien, dĺžka, orientácia a koncentrácia v týchto kompozitoch sú rozhodujúce pri určovaní vlastností a užitočnosti týchto materiálov. Používame tri skupiny vlákien: fúzy, vlákna a drôty. FÚZY sú veľmi tenké a dlhé monokryštály. Patria medzi najpevnejšie materiály. Niektoré príklady fúznych materiálov sú grafit, nitrid kremíka, oxid hlinitý. FIBERS na druhej strane sú väčšinou polyméry alebo keramika a sú v polykryštalickom alebo amorfnom stave. Treťou skupinou sú jemné DRÔTY, ktoré majú relatívne veľké priemery a často pozostávajú z ocele alebo volfrámu. Príkladom drôtom vystuženého kompozitu sú pneumatiky automobilov, ktoré obsahujú oceľový drôt vo vnútri gumy. V závislosti od materiálu matrice máme nasledujúce kompozity: KOMPOZITY POLYMER-MATRIX: Sú vyrobené z polymérovej živice a vlákien ako výstužnej zložky. Podskupina týchto kompozitov nazývaných polyméry vystužené sklenenými vláknami (GFRP) obsahuje kontinuálne alebo diskontinuálne sklenené vlákna v polymérnej matrici. Sklo ponúka vysokú pevnosť, je ekonomické, ľahko sa spracováva na vlákna a je chemicky inertné. Nevýhodou je ich obmedzená tuhosť a tuhosť, prevádzkové teploty len do 200 – 300 °C. Sklolaminát je vhodný pre automobilové karosérie a dopravné zariadenia, karosérie námorných vozidiel, skladovacie kontajnery. Nie sú vhodné pre kozmonautiku ani výrobu mostov kvôli obmedzenej tuhosti. Druhá podskupina sa nazýva kompozit polyméru vystuženého uhlíkovými vláknami (CFRP). Tu je uhlík naším vláknitým materiálom v polymérnej matrici. Uhlík je známy svojim vysokým špecifickým modulom a pevnosťou a schopnosťou udržiavať ich pri vysokých teplotách. Uhlíkové vlákna nám môžu ponúknuť moduly štandardnej, strednej, vysokej a ultravysokej pevnosti v ťahu. Okrem toho uhlíkové vlákna ponúkajú rôzne fyzikálne a mechanické vlastnosti, a preto sú vhodné pre rôzne zákazkové inžinierske aplikácie. Kompozity CFRP možno považovať za výrobu športových a rekreačných zariadení, tlakových nádob a konštrukčných komponentov letectva. Ďalšia podskupina, polymérne kompozity vystužené aramidovými vláknami, sú tiež materiály s vysokou pevnosťou a modulom. Ich pomer pevnosti k hmotnosti je mimoriadne vysoký. Aramidové vlákna sú známe aj pod obchodnými názvami KEVLAR a NOMEX. Pod napätím fungujú lepšie ako iné materiály z polymérnych vlákien, ale sú slabé v kompresii. Aramidové vlákna sú húževnaté, odolné voči nárazu, tečeniu a únave, stabilné pri vysokých teplotách, chemicky inertné okrem silných kyselín a zásad. Aramidové vlákna sú široko používané v športovom tovare, nepriestrelných vestách, pneumatikách, lanách, plášťoch káblov z optických vlákien. Existujú aj iné vláknité výstužné materiály, ale používajú sa v menšej miere. Sú to hlavne bór, karbid kremíka, oxid hlinitý. Materiál polymérnej matrice je na druhej strane tiež kritický. Určuje maximálnu prevádzkovú teplotu kompozitu, pretože polymér má vo všeobecnosti nižšiu teplotu topenia a degradácie. Polyestery a vinylestery sa široko používajú ako polymérna matrica. Používajú sa aj živice, ktoré majú vynikajúcu odolnosť proti vlhkosti a mechanické vlastnosti. Napríklad polyimidová živica sa môže použiť až do približne 230 stupňov Celzia. KOMPOZITY KOVOVEJ MATRICE: V týchto materiáloch používame tvárnu kovovú matricu a prevádzkové teploty sú vo všeobecnosti vyššie ako ich základné zložky. V porovnaní s kompozitmi s polymérnou matricou môžu mať vyššie prevádzkové teploty, byť nehorľavé a môžu mať lepšiu odolnosť voči degradácii voči organickým kvapalinám. Sú však drahšie. Vystužovacie materiály, ako sú fúzy, častice, kontinuálne a nespojité vlákna; a bežne sa používajú matricové materiály ako meď, hliník, horčík, titán a superzliatiny. Príkladmi aplikácií sú komponenty motora vyrobené z matrice z hliníkovej zliatiny vystuženej oxidom hlinitým a uhlíkovými vláknami. KOMPOZITY KERAMIC-MATRIX: Keramické materiály sú známe svojou mimoriadne dobrou spoľahlivosťou pri vysokých teplotách. Sú však veľmi krehké a majú nízke hodnoty lomovej húževnatosti. Zapustením častíc, vlákien alebo whiskerov jednej keramiky do matrice druhej sme schopní dosiahnuť kompozity s vyššou lomovou húževnatosťou. Tieto vložené materiály v podstate inhibujú šírenie trhlín vo vnútri matrice niektorými mechanizmami, ako je vychyľovanie špičiek trhlín alebo vytváranie mostíkov cez čelá trhlín. Napríklad oxidy hlinité, ktoré sú vystužené fúzmi SiC, sa používajú ako vložky rezných nástrojov na obrábanie zliatin tvrdých kovov. Tieto môžu odhaliť lepšie výkony v porovnaní so slinutými karbidmi. KOMPOZITY UHLÍK-UHLÍK: Výstuž aj matrica sú uhlíkové. Majú vysoké moduly v ťahu a pevnosti pri vysokých teplotách nad 2000 stupňov Celzia, odolnosť proti tečeniu, vysokú lomovú húževnatosť, nízke koeficienty tepelnej rozťažnosti, vysokú tepelnú vodivosť. Vďaka týmto vlastnostiam sú ideálne pre aplikácie vyžadujúce odolnosť proti tepelným šokom. Slabinou uhlíkovo-uhlíkových kompozitov je však ich zraniteľnosť voči oxidácii pri vysokých teplotách. Typickými príkladmi použitia sú formy na lisovanie za tepla, pokročilá výroba komponentov turbínových motorov. HYBRIDNÉ KOMPOZITY: Dva alebo viac rôznych typov vlákien sú zmiešané v jednej matrici. Dá sa tak prispôsobiť nový materiál s kombináciou vlastností. Príkladom je, keď sú uhlíkové aj sklenené vlákna začlenené do polymérnej živice. Uhlíkové vlákna poskytujú tuhosť a pevnosť s nízkou hustotou, ale sú drahé. Sklo je na druhej strane lacné, ale chýba mu tuhosť uhlíkových vlákien. Hybridný kompozit sklo-uhlík je pevnejší a odolnejší a dá sa vyrobiť za nižšiu cenu. SPRACOVANIE KOMPOZITOV VYZTUŽENÝCH VLÁKNAMI: Pre súvislé plasty vystužené vláknami s rovnomerne rozloženými vláknami orientovanými v rovnakom smere používame nasledujúce techniky. PULTRUSION: Vyrábajú sa tyče, nosníky a rúry priebežných dĺžok a konštantných prierezov. Nepretržité vlákna sú impregnované termosetovou živicou a ťahané cez oceľovú matricu, aby sa predtvarovali do požadovaného tvaru. Potom prechádzajú cez presne opracovanú vytvrdzovaciu formu, aby dosiahli konečný tvar. Pretože sa vytvrdzovacia hubica zahrieva, vytvrdzuje živicovú matricu. Sťahováky ťahajú materiál cez matrice. Pomocou vložených dutých jadier sme schopní získať rúrky a duté geometrie. Metóda pultrúzie je automatizovaná a ponúka nám vysoké výrobné rýchlosti. Je možné vyrobiť akúkoľvek dĺžku produktu. PROCES VÝROBY PREPREG: Predimpregnovaný laminát je výstuž z nekonečných vlákien predimpregnovaná čiastočne vytvrdenou polymérovou živicou. Je široko používaný pre konštrukčné aplikácie. Materiál je dodávaný vo forme pásky a je dodávaný ako páska. Výrobca ho priamo formuje a úplne vytvrdzuje bez potreby pridávania akejkoľvek živice. Pretože predimpregnované lamináty podliehajú vytvrdzovacím reakciám pri teplote miestnosti, skladujú sa pri teplote 0 °C alebo nižšej. Po použití sa zostávajúce pásky skladujú pri nízkych teplotách. Používajú sa termoplastické a termosetové živice a bežné sú výstužné vlákna z uhlíka, aramidu a skla. Na použitie predimpregnovaných laminátov sa najskôr odstráni nosný podkladový papier a potom sa uskutoční výroba položením predimpregnovanej pásky na upravený povrch (proces kladenia). Na získanie požadovaných hrúbok je možné položiť niekoľko vrstiev. Častou praxou je striedanie orientácie vlákien, aby sa vytvoril laminát s priečnymi alebo uhlovými vrstvami. Nakoniec sa na vytvrdenie aplikuje teplo a tlak. Na rezanie predimpregnovaných laminátov a kladenie sa používa ako ručné spracovanie, tak aj automatizované procesy. NAVINUTIE VLÁKNA: Súvislé výstužné vlákna sú presne umiestnené vo vopred určenom vzore tak, aby sledovali dutý a zvyčajne cyklický tvar. Vlákna najskôr prechádzajú cez živicový kúpeľ a potom sú automatizovaným systémom navinuté na tŕň. Po niekoľkých opakovaniach navíjania sa získajú požadované hrúbky a vytvrdzovanie sa vykonáva buď pri izbovej teplote alebo v peci. Teraz sa tŕň odstráni a výrobok sa vyberie z formy. Vinutie vlákna môže ponúknuť veľmi vysoké pomery pevnosti k hmotnosti navíjaním vlákien v obvodových, špirálových a polárnych vzoroch. Rúry, nádrže, plášte sa vyrábajú touto technikou. • KONŠTRUKČNÉ KOMPOZITY: Vo všeobecnosti sú vyrobené z homogénnych aj kompozitných materiálov. Preto sú ich vlastnosti určené materiálmi a geometrickým dizajnom ich prvkov. Tu sú hlavné typy: LAMINÁRNE KOMPOZITY: Tieto konštrukčné materiály sú vyrobené z dvojrozmerných plechov alebo panelov s preferovanými smermi vysokej pevnosti. Vrstvy sú naskladané a spojené dohromady. Striedaním smerov vysokej pevnosti v dvoch kolmých osiach získame kompozit, ktorý má vysokú pevnosť v oboch smeroch v dvojrozmernej rovine. Nastavením uhlov vrstiev je možné vyrobiť kompozit s pevnosťou vo výhodných smeroch. Moderné lyže sa vyrábajú týmto spôsobom. SANDWICH PANELY: Tieto konštrukčné kompozity sú ľahké, ale napriek tomu majú vysokú tuhosť a pevnosť. Sendvičové panely pozostávajú z dvoch vonkajších plechov vyrobených z tuhého a pevného materiálu, ako sú hliníkové zliatiny, vláknami vystužené plasty alebo oceľ, a jadro medzi vonkajšími plechmi. Jadro musí byť ľahké a väčšinou musí mať nízky modul pružnosti. Obľúbenými materiálmi jadra sú tuhé polymérne peny, drevo a voštiny. Sendvičové panely sú široko používané v stavebníctve ako strešný materiál, materiál na podlahy alebo steny a tiež v leteckom priemysle. • NANOKOMPOZITY : Tieto nové materiály pozostávajú z častíc s nanočasticou uložených v matrici. Pomocou nanokompozitov dokážeme vyrobiť gumené materiály, ktoré sú veľmi dobrými bariérami proti prenikaniu vzduchu pri zachovaní ich gumových vlastností nezmenených. CLICK Product Finder-Locator Service PREDCHÁDZAJÚCA STRANA
- Joining & Assembly & Fastening Processes, Welding, Brazing, Soldering
Joining & Assembly & Fastening Processes, Welding, Brazing, Soldering, Sintering, Adhesive Bonding, Press Fitting, Wave and Reflow Solder Process, Torch Furnace Procesy spájania a montáže a upevnenia Vaše vyrobené diely spájame, montujeme a upevňujeme a premieňame na hotové alebo polotovary pomocou ZVÁRANIA, SPÁJOVANIA, SPÁJKOVANIA, SPEKANIA, LEPENIA, UPEVŇOVANIA, LISOVANIA. Niektoré z našich najobľúbenejších zváracích procesov sú oblúkové, kyslíko-palivové, odporové, projekčné, ševové, upchaté, príklepové, pevné, elektrónovým lúčom, laserové, termitové, indukčné zváranie. Naše obľúbené procesy spájkovania sú spájkovanie horákom, indukcia, pec a ponorné spájkovanie. Naše metódy spájkovania sú železo, horúca platňa, rúra, indukcia, ponorenie, vlnenie, pretavenie a ultrazvukové spájkovanie. Na lepenie často používame termoplasty a termosety, epoxidy, fenoly, polyuretán, lepiace zliatiny ako aj niektoré ďalšie chemikálie a pásky. Nakoniec naše upevňovacie procesy pozostávajú z pribíjania klincov, skrutkovania, matíc a skrutiek, nitovania, klinčovania, špendlíkovania, zošívania a zošívania a lisovania. • ZVÁRANIE: Zváranie zahŕňa spájanie materiálov tavením obrobkov a zavádzaním prídavných materiálov, ktoré tiež spájajú roztavený zvarový kúpeľ. Keď sa oblasť ochladí, získame pevný spoj. V niektorých prípadoch sa používa tlak. Na rozdiel od zvárania operácie tvrdého spájkovania zahŕňajú iba tavenie materiálu s nižšou teplotou tavenia medzi obrobkami a obrobky sa netavia. Odporúčame vám kliknúť semSTIAHNITE si naše schematické ilustrácie zváracích procesov od AGS-TECH Inc. Pomôže vám to lepšie porozumieť informáciám, ktoré vám poskytujeme nižšie. Pri ARCH WELDING používame napájací zdroj a elektródu na vytvorenie elektrického oblúka, ktorý roztaví kovy. Miesto zvárania je chránené ochranným plynom alebo parou alebo iným materiálom. Tento proces je obľúbený pri zváraní automobilových dielov a oceľových konštrukcií. Pri oblúkovom zváraní v obale (SMAW) alebo tiež známom ako zváranie tyčou sa tyč elektródy priblíži k základnému materiálu a medzi nimi sa vytvorí elektrický oblúk. Tyč elektródy sa roztaví a pôsobí ako výplňový materiál. Elektróda tiež obsahuje tavivo, ktoré pôsobí ako vrstva trosky a vydáva výpary, ktoré pôsobia ako ochranný plyn. Tie chránia oblasť zvaru pred kontamináciou z prostredia. Nepoužívajú sa žiadne iné plnivá. Nevýhodou tohto procesu je jeho pomalosť, potreba častej výmeny elektród, potreba odštiepenia zvyškovej trosky pochádzajúcej z taviva. Množstvo kovov, ako je železo, oceľ, nikel, hliník, meď atď. Dá sa zvárať. Jeho výhodou sú lacné nástroje a jednoduché použitie. Plynové oblúkové zváranie kovov (GMAW), tiež známe ako kov-inertný plyn (MIG), máme kontinuálne privádzanie tavnej elektródovej výplne drôtu a inertného alebo čiastočne inertného plynu, ktorý prúdi okolo drôtu proti kontaminácii oblasti zvaru prostredím. Je možné zvárať oceľ, hliník a iné neželezné kovy. Výhodou MIG je vysoká rýchlosť zvárania a dobrá kvalita. Nevýhodou je komplikované vybavenie a problémy, ktorým čelíme vo veternom vonkajšom prostredí, pretože musíme udržiavať ochranný plyn okolo oblasti zvárania stabilný. Variáciou GMAW je oblúkové zváranie s tavivom (FCAW), ktoré pozostáva z jemnej kovovej rúrky naplnenej tavivovým materiálom. Niekedy je tok vo vnútri trubice dostatočný na ochranu pred kontamináciou životného prostredia. Zváranie pod tavivom (SAW) je široko automatizovaný proces, ktorý zahŕňa nepretržité podávanie drôtu a oblúk, ktorý sa vytvára pod vrstvou taviva. Výrobné rýchlosti a kvalita sú vysoké, troska zo zvárania sa ľahko odstraňuje a máme pracovné prostredie bez dymu. Nevýhodou je, že sa dá použiť len na zváranie dielov parts v určitých polohách. Pri oblúkovom zváraní plynovým volfrámom (GTAW) alebo zváraní volfrámovým inertným plynom (TIG) používame volfrámovú elektródu spolu so samostatnou výplňou a inertnými alebo takmer inertnými plynmi. Ako vieme, volfrám má vysoký bod topenia a je to veľmi vhodný kov pre veľmi vysoké teploty. Volfrám sa pri TIG nespotrebováva na rozdiel od iných metód vysvetlených vyššie. Pomalá, ale vysokokvalitná zváracia technika výhodnejšia oproti iným technikám pri zváraní tenkých materiálov. Vhodné pre mnoho kovov. Zváranie plazmovým oblúkom je podobné, ale na vytvorenie oblúka sa používa plazmový plyn. Oblúk pri zváraní plazmovým oblúkom je relatívne koncentrovanejší v porovnaní s GTAW a môže byť použitý pre širší rozsah hrúbok kovu pri oveľa vyšších rýchlostiach. GTAW a plazmové oblúkové zváranie je možné aplikovať na viac-menej rovnaké materiály. OXY-FUEL / OXYFUEL WELDING tiež nazývané oxyacetylénové zváranie, oxyzváranie, zváranie plynom sa vykonáva pomocou plynných palív a kyslíka na zváranie. Keďže sa nepoužíva žiadna elektrická energia, je prenosný a môže byť použitý tam, kde nie je elektrina. Pomocou zváracieho horáka zohrievame kusy a prídavný materiál, aby sa vytvoril spoločný kúpeľ roztaveného kovu. Môžu sa použiť rôzne palivá, ako je acetylén, benzín, vodík, propán, bután atď. Pri kyslíkovo-palivovom zváraní používame dve nádoby, jednu na palivo a druhú na kyslík. Kyslík okysličuje palivo (spaľuje ho). ODPOROVÉ ZVÁRANIE: Tento typ zvárania využíva joulové zahrievanie a teplo sa vytvára v mieste, kde sa po určitú dobu aplikuje elektrický prúd. Cez kov prechádzajú vysoké prúdy. Na tomto mieste sa tvoria kaluže roztaveného kovu. Metódy odporového zvárania sú obľúbené pre svoju účinnosť, malý potenciál znečistenia. Nevýhodou sú však relatívne značné náklady na vybavenie a inherentné obmedzenie na relatívne tenké obrobky. BODOVÉ ZVÁRANIE je jedným z hlavných typov odporového zvárania. Tu spájame dva alebo viac prekrývajúcich sa plátov alebo obrobkov pomocou dvoch medených elektród na zovretie plátov k sebe a prechod cez ne vysoký prúd. Materiál medzi medenými elektródami sa zahrieva a na tomto mieste sa vytvára roztavený kúpeľ. Prúd sa potom zastaví a hroty medených elektród ochladzujú miesto zvaru, pretože elektródy sú chladené vodou. Aplikovanie správneho množstva tepla na správny materiál a hrúbku je pre túto techniku kľúčové, pretože pri nesprávnom použití bude spoj slabý. Bodové zváranie má výhody v tom, že nespôsobuje žiadne významné deformácie obrobkov, energetickú účinnosť, jednoduchú automatizáciu a vynikajúce výrobné rýchlosti a nevyžaduje žiadne plnivá. Nevýhodou je, že keďže zváranie prebieha v bodoch a nie pri vytváraní súvislého švu, celková pevnosť môže byť relatívne nižšia v porovnaní s inými spôsobmi zvárania. ŠVOVÉ ZVÁRANIE na druhej strane vytvára zvary na lícujúcich povrchoch podobných materiálov. Šev môže byť tupý alebo prekrytý. Švové zváranie začína na jednom konci a postupne sa presúva na druhý. Táto metóda tiež používa dve elektródy z medi na aplikáciu tlaku a prúdu na oblasť zvaru. Elektródy v tvare kotúča sa otáčajú s konštantným kontaktom pozdĺž línie švu a vytvárajú súvislý zvar. Aj tu sú elektródy chladené vodou. Zvary sú veľmi pevné a spoľahlivé. Ďalšími metódami sú projekčné, bleskové a upchavé zváracie techniky. PEVNÉ ZVÁRANIE je trochu iné ako predchádzajúce metódy vysvetlené vyššie. Koalescencia prebieha pri teplotách pod teplotou topenia spojených kovov a bez použitia kovového plniva. V niektorých procesoch sa môže použiť tlak. Rôzne metódy sú KOEXTRÚZNE ZVÁRANIE, kde sa rozdielne kovy vytláčajú cez rovnakú matricu, ZVÁRANIE TLAKOM STUDENÝM, kde spájame mäkké zliatiny pod ich bodmi tavenia, DIFÚZNE ZVÁRANIE technika bez viditeľných línií zvaru, EXPLOZNÉ ZVÁRANIE na spájanie rôznych materiálov, napr. zliatin odolných voči korózii ku konštrukčným ocele, ELEKTROMAGNETICKÉ PULZNÉ ZVÁRANIE, kde urýchľujeme rúry a plechy elektromagnetickými silami, KOVACIE ZVÁRANIE spočívajúce v zahriatí kovov na vysoké teploty a ich zbití, TRENÉ ZVÁRANIE, kde sa vykonáva zváranie s dostatočným trením, TRECIE ZVÁRANIE, ktoré zahŕňa rotačný ne spotrebný nástroj prechádzajúci spojovacou líniou, TEPLOVÉ ZVÁRANIE, kde lisujeme kovy k sebe pri zvýšených teplotách pod teplotou topenia vo vákuu alebo v inertných plynoch, HORÚCE IZSTATICKÉ TLAKOVÉ ZVÁRANIE proces, pri ktorom aplikujeme tlak pomocou inertných plynov vo vnútri nádoby, VALCOVÉ ZVÁRANIE, kde spájame rozdielne materiály ich vtláčaním medzi seba dve rotujúce kolesá, ULTRAZVUKOVÉ ZVÁRANIE, kde sa pomocou vysokofrekvenčnej vibračnej energie zvárajú tenké kovové alebo plastové plechy. Ďalšími našimi zváracími procesmi sú ZVÁRANIE ELEKTRONOVÝM LÚČOM s hlbokým prienikom a rýchlym spracovaním, ale ako nákladná metóda ju považujeme pre špeciálne prípady, ELEKTROSLAGOVÉ ZVÁRANIE metóda vhodná len pre ťažké hrubé plechy a obrobky z ocele, INDUKČNÉ ZVÁRANIE, kde využívame elektromagnetickú indukciu a ohrievajte naše elektricky vodivé alebo feromagnetické obrobky, ZVÁRANIE LASEROVÝM LÚČOM aj s hlbokým prienikom a rýchlym spracovaním, ale nákladná metóda, LASEROVÉ HYBRIDNÉ ZVÁRANIE, ktoré kombinuje LBW s GMAW v tej istej zváracej hlave a schopné premostiť medzery 2 mm medzi doskami, NÁBOJOVÉ ZVÁRANIE, ktoré zahŕňa elektrický výboj, po ktorom nasleduje kovanie materiálov aplikovaným tlakom, TERMITOVÉ ZVÁRANIE zahŕňajúce exotermickú reakciu medzi práškom oxidu hliníka a železa, ELEKTROPLYNOVÉ ZVÁRANIE s tavnými elektródami a používa sa len s oceľou vo vertikálnej polohe a nakoniec STUD ARC WELDING na spojenie kolíka so základňou materiál s teplom a tlakom. Odporúčame vám kliknúť semSTIAHNITE si naše schematické ilustrácie procesov spájkovania, spájkovania a lepenia od AGS-TECH Inc Pomôže vám to lepšie porozumieť informáciám, ktoré vám poskytujeme nižšie. • SPÁJOVANIE: Dva alebo viac kovov spájame zahrievaním prídavných kovov medzi nimi nad ich bod topenia a pomocou kapilárneho pôsobenia na šírenie. Proces je podobný spájkovaniu, ale teploty spojené s roztavením plniva sú vyššie pri spájkovaní. Podobne ako pri zváraní, tavivo chráni prídavný materiál pred atmosférickou kontamináciou. Po ochladení sa obrobky spoja. Proces zahŕňa nasledujúce kľúčové kroky: Dobré lícovanie a vôľa, správne čistenie základných materiálov, správne upevnenie, správny výber taviva a atmosféry, ohrev zostavy a nakoniec čistenie spájkovanej zostavy. Niektoré z našich procesov spájkovania sú HORÁKOVÉ SPÁJOVANIE, populárna metóda vykonávaná ručne alebo automatizovaným spôsobom. Je vhodný pre zákazky s malým objemom výroby a špecializované prípady. Teplo sa aplikuje pomocou plynových plameňov v blízkosti spájkovaného spoja. SPÁJKOVANIE V PECI vyžaduje menšiu zručnosť operátora a je to poloautomatický proces vhodný pre priemyselnú hromadnú výrobu. Regulácia teploty aj regulácia atmosféry v peci sú výhodami tejto techniky, pretože prvá umožňuje mať riadené tepelné cykly a eliminovať lokálne zahrievanie, ako je to v prípade spájkovania horákom, a druhá chráni diel pred oxidáciou. Pomocou jiggingu sme schopní znížiť výrobné náklady na minimum. Nevýhodou je vysoká spotreba energie, náklady na vybavenie a náročnejšie konštrukčné úvahy. VÁKUOVÉ SPÁJOVANIE prebieha vo vákuovej peci. Rovnomernosť teplôt je zachovaná a získavame veľmi čisté spoje bez taviva s veľmi malým zvyškovým napätím. Tepelné spracovanie môže prebiehať počas vákuového spájkovania kvôli nízkym zvyškovým napätiam prítomným počas pomalých cyklov zahrievania a chladenia. Hlavnou nevýhodou je jeho vysoká cena, pretože vytvorenie vákuového prostredia je nákladný proces. Ďalšia technika DIP BRAZING spája upevnené časti, kde sa spájkovacia hmota nanáša na spájané povrchy. Potom sa časti fixtured ponoria do kúpeľa s roztavenou soľou, ako je chlorid sodný (stolová soľ), ktorý pôsobí ako teplonosné médium a tavivo. Vzduch je vylúčený a preto nedochádza k tvorbe oxidu. Pri INDUKČNOM SPÁJOVANÍ spájame materiály prídavným kovom, ktorý má nižšiu teplotu topenia ako základné materiály. Striedavý prúd z indukčnej cievky vytvára elektromagnetické pole, ktoré indukuje indukčný ohrev na prevažne železných magnetických materiáloch. Metóda poskytuje selektívny ohrev, dobré spoje s plnivami prúdiacimi len v požadovaných oblastiach, malú oxidáciu, pretože nie sú prítomné žiadne plamene a chladenie je rýchle, rýchly ohrev, konzistencia a vhodnosť pre veľkoobjemovú výrobu. Aby sme urýchlili naše procesy a zabezpečili konzistentnosť, často používame predlisky. Informácie o našom spájkovacom zariadení, ktoré vyrába armatúry z keramiky na kov, hermetické tesnenia, vákuové priechodky, vysoko a ultravysoké vákuum a komponenty na reguláciu tekutín nájdete tu:_cc781905-5cde-3194-bb3b_136Brožúra továrne na spájkovanie • SPÁJKOVANIE : Pri spájkovaní nedochádza k roztaveniu obrobkov, ale prídavného kovu s nižším bodom tavenia ako majú spojovacie časti, ktorý steká do spoja. Prídavný kov sa pri spájkovaní topí pri nižšej teplote ako pri spájkovaní. Na spájkovanie používame bezolovnaté zliatiny a spĺňame RoHS a pre rôzne aplikácie a požiadavky máme rôzne a vhodné zliatiny, ako je zliatina striebra. Spájkovanie nám ponúka spoje, ktoré sú plynotesné a vodotesné. Pri MÄKKOM SPÁJKOVANÍ má náš prídavný kov bod topenia pod 400 stupňov Celzia, zatiaľ čo pri STRIEBORNOM SPÁJKOVANÍ A SPÁJKOVANÍM STRIEBOROM potrebujeme vyššie teploty. Mäkké spájkovanie využíva nižšie teploty, ale nevedie k pevným spojom pre náročné aplikácie pri zvýšených teplotách. Strieborné spájkovanie na druhej strane vyžaduje vysoké teploty poskytované horákom a poskytuje nám pevné spoje vhodné pre vysokoteplotné aplikácie. Spájkovanie vyžaduje najvyššie teploty a zvyčajne sa používa horák. Pretože spájkované spoje sú veľmi pevné, sú dobrými kandidátmi na opravu ťažkých železných predmetov. V našich výrobných linkách používame ako ručné ručné spájkovanie, tak aj automatizované spájkovacie linky. INDUCTIONSOLDERING využíva vysokofrekvenčný striedavý prúd v medenej cievke na uľahčenie indukčného ohrevu. V spájkovanej časti sa indukujú prúdy a v dôsledku toho vzniká teplo pri vysokom odpore joint. Toto teplo roztaví prídavný kov. Používa sa aj tavivo. Indukčné spájkovanie je dobrou metódou na spájkovanie valcov a rúr v nepretržitom procese ovíjaním cievok okolo nich. Spájkovanie niektorých materiálov, ako je grafit a keramika, je náročnejšie, pretože si vyžaduje pokovovanie obrobkov pred spájkovaním vhodným kovom. To uľahčuje medzifázové spojenie. Spájkujeme tieto materiály špeciálne pre aplikácie hermetické balenie. Naše dosky plošných spojov (PCB) vyrábame vo veľkom objeme prevažne pomocou VLNOVÉHO SPÁJANIA. Len pre malé množstvo prototypových účelov používame ručné spájkovanie pomocou spájkovačky. Spájkovanie vlnou používame ako pre priechodné otvory, tak aj pre povrchovú montáž PCB zostáv (PCBA). Dočasné lepidlo udržuje komponenty pripojené k doske plošných spojov a zostava je umiestnená na dopravníku a pohybuje sa cez zariadenie, ktoré obsahuje roztavenú spájku. Najprv sa doska plošných spojov roztaví a potom vstúpi do zóny predhrievania. Roztavená spájka je v panvici a na svojom povrchu má vzor stojatých vĺn. Keď sa DPS pohybuje cez tieto vlny, tieto vlny sa dotknú spodnej časti DPS a prilepia sa na spájkovacie podložky. Spájka zostáva iba na kolíkoch a podložkách a nie na samotnej DPS. Vlny v roztavenej spájke musia byť dobre kontrolované, aby nedochádzalo k rozstrekovaniu a vrchné časti vĺn sa nedotýkali a nekontaminovali nežiaduce oblasti dosiek. V REFLOW SOLDERING používame lepivú spájkovaciu pastu na dočasné pripevnenie elektronických súčiastok k doskám. Potom sa dosky vložia do reflow pece s reguláciou teploty. Tu sa spájka roztaví a natrvalo spojí súčiastky. Túto techniku používame pre komponenty na povrchovú montáž, ako aj pre komponenty s priechodnými otvormi. Správna kontrola teploty a nastavenie teplôt pece je nevyhnutné, aby sa predišlo zničeniu elektronických komponentov na doske ich prehriatím nad ich maximálne teplotné limity. V procese spájkovania pretavením máme v skutočnosti niekoľko oblastí alebo stupňov, z ktorých každý má odlišný tepelný profil, ako je krok predhrievania, krok tepelného namáčania, kroky pretavenia a chladenia. Tieto rôzne kroky sú nevyhnutné pre bezškodové spájkovanie zostáv dosiek s plošnými spojmi (PCBA). ULTRAZVUKOVÉ SPÁJKOVANIE je ďalšou často používanou technikou s jedinečnými schopnosťami- Dá sa použiť na spájkovanie sklenených, keramických a nekovových materiálov. Napríklad fotovoltaické panely, ktoré sú nekovové, potrebujú elektródy, ktoré je možné pripevniť pomocou tejto techniky. Pri ultrazvukovom spájkovaní používame vyhrievaný spájkovací hrot, ktorý tiež vydáva ultrazvukové vibrácie. Tieto vibrácie vytvárajú kavitačné bubliny na rozhraní substrátu s roztaveným spájkovacím materiálom. Implozívna energia kavitácie upravuje povrch oxidu a odstraňuje nečistoty a oxidy. Počas tejto doby sa tiež vytvorí vrstva zliatiny. Spájka na spojovacom povrchu obsahuje kyslík a umožňuje vytvorenie silnej zdieľanej väzby medzi sklom a spájkou. PÁJKOVANIE PÁKANÍM možno považovať za jednoduchšiu verziu vlnového spájkovania, ktorá je vhodná len pre výrobu v malom meradle. Ako pri iných procesoch sa aplikuje prvé čistiace tavidlo. Dosky plošných spojov s osadenými súčiastkami sú ponorené ručne alebo poloautomatickým spôsobom do nádrže obsahujúcej roztavenú spájku. Roztavená spájka sa prilepí na odkryté kovové oblasti nechránené spájkovacou maskou na doske. Zariadenie je jednoduché a lacné. • LEPENIE : Toto je ďalšia populárna technika, ktorú často používame a zahŕňa spájanie povrchov pomocou lepidiel, epoxidov, plastov alebo iných chemikálií. Lepenie sa dosiahne buď odparením rozpúšťadla, tepelným vytvrdzovaním, vytvrdzovaním UV svetlom, tlakovým vytvrdzovaním alebo čakaním na určitý čas. V našich výrobných linkách sa používajú rôzne vysokovýkonné lepidlá. Pri správne navrhnutej aplikácii a procesoch vytvrdzovania môže lepenie viesť k spojom s veľmi nízkym napätím, ktoré sú pevné a spoľahlivé. Lepené spoje môžu byť dobrou ochranou proti environmentálnym faktorom, ako je vlhkosť, kontaminanty, korózie, vibrácie atď. Výhody lepenia sú: možno ich aplikovať na materiály, ktoré by sa inak ťažko spájkovali, zvárali alebo spájkovali. Tiež to môže byť výhodné pre materiály citlivé na teplo, ktoré by sa poškodili zváraním alebo inými vysokoteplotnými procesmi. Ďalšími výhodami lepidiel je, že sa dajú aplikovať na povrchy nepravidelného tvaru a v porovnaní s inými metódami zvyšujú hmotnosť zostavy o veľmi malé množstvá. Tiež rozmerové zmeny dielov sú veľmi minimálne. Niektoré lepidlá majú vlastnosti zodpovedajúce indexu a možno ich použiť medzi optickými komponentmi bez výrazného zníženia intenzity svetla alebo optického signálu. Nevýhodami na druhej strane sú dlhšie časy vytvrdzovania, ktoré môžu spomaliť výrobné linky, požiadavky na upevnenie, požiadavky na prípravu povrchu a ťažkosti pri rozoberaní, keď je potrebné prepracovať. Väčšina našich operácií lepenia zahŕňa nasledujúce kroky: -Povrchová úprava: Bežné sú špeciálne čistiace postupy ako čistenie deionizovanou vodou, čistenie alkoholom, plazmové alebo korónové čistenie. Po očistení môžeme na povrchy naniesť prostriedky na zlepšenie priľnavosti, aby sme zabezpečili čo najlepšie spoje. -Upevnenie dielov: Na nanášanie lepidla, ako aj na vytvrdzovanie navrhujeme a používame vlastné prípravky. -Aplikácia lepidla: Niekedy používame manuálne a niekedy v závislosti od prípadu automatizované systémy, ako je robotika, servomotory, lineárne pohony na dodávanie lepidiel na správne miesto a na dodávanie lepidiel v správnom objeme a množstve používame dávkovače. -Vytvrdzovanie: V závislosti od lepidla môžeme použiť jednoduché sušenie a vytvrdzovanie, ako aj vytvrdzovanie pod UV svetlom, ktoré pôsobí ako katalyzátor alebo vytvrdzovanie teplom v peci alebo pomocou odporových vykurovacích prvkov namontovaných na prípravkoch a prípravkoch. Odporúčame vám kliknúť semSTIAHNITE si naše schematické ilustrácie upevňovacích procesov od AGS-TECH Inc. Pomôže vám to lepšie porozumieť informáciám, ktoré vám poskytujeme nižšie. • SPOJOVACIE PROCESY: Naše procesy mechanického spájania spadajú do dvoch hlavných kategórií: SPOJOVACIE PRVKY a INTEGRÁLNE SPOJKY. Príklady spojovacích prvkov, ktoré používame, sú skrutky, kolíky, matice, svorníky, nity. Príklady integrálnych spojov, ktoré používame, sú zacvakávacie a zmršťovacie spoje, švy, lemy. Pomocou rôznych spôsobov upevnenia zaisťujeme, že naše mechanické spoje sú pevné a spoľahlivé po mnoho rokov používania. SKRUTKY a SKRUTKY sú niektoré z najbežnejšie používaných spojovacích prvkov na držanie predmetov pohromade a ich umiestnenie. Naše skrutky a svorníky spĺňajú normy ASME. Používajú sa rôzne typy skrutiek a skrutiek vrátane skrutiek so šesťhrannou hlavou a šesťhranných skrutiek, pozdržaných skrutiek a skrutiek, skrutiek s dvojitým koncom, hmoždinkovej skrutky, skrutky s okom, zrkadlovej skrutky, skrutky do plechu, skrutky pre jemné nastavenie, samorezných a samorezných skrutiek , nastavovacia skrutka, skrutky so vstavanými podložkami,...a ďalšie. Máme rôzne typy hláv skrutiek, ako sú zápustná, kupolová, okrúhla, prírubová hlava a rôzne typy skrutkových pohonov, ako sú drážkové, krížové, štvorcové, šesťhranné. RIVET na druhej strane je trvalý mechanický spojovací prvok pozostávajúci z hladkého valcového drieku a hlavy na jednej strane. Po vložení sa druhý koniec nitu zdeformuje a jeho priemer sa roztiahne tak, aby zostal na mieste. Inými slovami, pred inštaláciou má nit jednu hlavu a po inštalácii dve. Inštalujeme rôzne typy nitov v závislosti od použitia, sily, dostupnosti a ceny, ako sú nity s pevnou/guľatou hlavou, konštrukčné, polotrubkové, slepé, oscarové, hnacie, lícované, s trecím zámkom, samorezné nity. Nitovanie môže byť preferované v prípadoch, keď je potrebné zabrániť tepelnej deformácii a zmene vlastností materiálu v dôsledku zváracieho tepla. Nitovanie tiež ponúka nízku hmotnosť a najmä dobrú pevnosť a odolnosť voči šmykovým silám. Proti ťahovým zaťaženiam však môžu byť vhodnejšie skrutky, matice a skrutky. V procese CLINCHING používame špeciálny razník a matrice na vytvorenie mechanického spojenia medzi spájanými plechmi. Razník tlačí vrstvy plechu do dutiny matrice a výsledkom je vytvorenie trvalého spoja. Clinching nevyžaduje žiadne zahrievanie ani chladenie a je to proces spracovania za studena. Ide o ekonomický proces, ktorý môže v niektorých prípadoch nahradiť bodové zváranie. V ČIPOVANÍ používame čapy, ktoré sú strojnými prvkami, ktoré sa používajú na zaistenie vzájomnej polohy častí stroja. Hlavné typy sú vidlicové kolíky, závlačky, pružinové kolíky, kolíky, a závlačka. V ZOŠÍVANÍ používame zošívacie pištole a sponky, čo sú dvojzubové spojovacie prvky používané na spájanie alebo viazanie materiálov. Zošívanie má nasledujúce výhody: Ekonomické, jednoduché a rýchle použitie, korunka sponiek môže byť použitá na premostenie materiálov natupo, Korunka sponky môže uľahčiť premostenie kusu ako je kábel a jeho upevnenie k povrchu bez prepichnutia alebo poškodenie, relatívne ľahké odstránenie. LISOVANIA sa vykonáva zatlačením dielov k sebe a trenie medzi nimi diely spojí. Lisované diely pozostávajúce z nadrozmerného hriadeľa a poddimenzovaného otvoru sa vo všeobecnosti montujú jedným z dvoch spôsobov: Buď pôsobením sily, alebo využitím tepelnej rozťažnosti alebo kontrakcie dielov. Keď je lisovacia tvarovka vytvorená pôsobením sily, používame buď hydraulický lis, alebo ručný lis. Na druhej strane, keď sa lisovacia tvarovka upevňuje tepelnou rozťažnosťou, ohrievame obalové diely a za horúca ich zostavujeme na svoje miesto. Keď vychladnú, stiahnu sa a vrátia sa do svojich normálnych rozmerov. Výsledkom je dobré lisovanie. Alternatívne tomu hovoríme SHRINK-FITTING. Iný spôsob, ako to urobiť, je ochladzovať zabalené časti pred montážou a potom ich zasunúť do príslušných častí. Keď sa zostava zahreje, roztiahnu sa a získame pevné uchytenie. Táto posledná metóda môže byť výhodnejšia v prípadoch, keď zahrievanie predstavuje riziko zmeny vlastností materiálu. Chladenie je v takýchto prípadoch bezpečnejšie. Pneumatické a hydraulické komponenty a zostavy • Ventily, hydraulické a pneumatické komponenty ako O-krúžok, podložka, tesnenia, tesnenie, krúžok, podložka. Keďže ventily a pneumatické komponenty sú vo veľkom množstve, nemôžeme tu vymenovať všetko. V závislosti od fyzikálneho a chemického prostredia vašej aplikácie máme pre vás špeciálne produkty. Uveďte, prosím, aplikáciu, typ komponentu, špecifikácie, podmienky prostredia, ako je tlak, teplota, kvapaliny alebo plyny, ktoré budú v kontakte s vašimi ventilmi a pneumatickými komponentmi; a vyberieme pre vás najvhodnejší produkt alebo ho vyrobíme špeciálne pre vašu aplikáciu. CLICK Product Finder-Locator Service PREDCHÁDZAJÚCA STRANA
- Machine Elements Manufacturing, Gears, Gear Drives, Bearings, Keys, Splines
Machine Elements Manufacturing, Gears, Gear Drives, Bearings, Keys, Splines, Pins, Shafts, Seals, Fasteners, Clutch, Cams, Followers, Belts, Couplings, Shafts Výroba strojných prvkov Čítaj viac Zostava remeňov a reťazí a káblového pohonu Čítaj viac Zostava ozubených kolies a pohonu ozubených kolies Čítaj viac Výroba spojok a ložísk Čítaj viac Výroba kľúčov a drážok a kolíkov Čítaj viac Výroba vačiek a unášačov a spojok a račňových kolies Čítaj viac Výroba hriadeľov Čítaj viac Výroba mechanických tesnení Čítaj viac Zostava spojky a brzdy Čítaj viac Výroba spojovacích materiálov Čítaj viac Montáž jednoduchých strojov PRVKY STROJA sú základné komponenty stroja. Tieto prvky pozostávajú z troch základných typov: 1.) Konštrukčné komponenty vrátane rámových prvkov, ložísk, náprav, drážok, upevňovacích prvkov, tesnení a mazív. 2.) Mechanizmy ovládajúce pohyb rôznymi spôsobmi, ako sú ozubené prevody, remeňové alebo reťazové pohony, spojenia, vačkové a kladkové systémy, brzdy a spojky. 3.) Ovládacie komponenty ako tlačidlá, spínače, indikátory, senzory, akčné členy a počítačové ovládače. Väčšina strojových prvkov, ktoré vám ponúkame, je štandardizovaná na bežné veľkosti, ale sú k dispozícii aj strojové prvky vyrobené na mieru pre vaše špecializované aplikácie. Prispôsobenie prvkov stroja sa môže uskutočniť na existujúcich dizajnoch, ktoré sú v našich katalógoch na stiahnutie, alebo na úplne nových dizajnoch. Prototypovanie a výroba prvkov stroja môže pokračovať po schválení návrhu oboma stranami. Ak je potrebné navrhnúť a vyrobiť nové prvky stroja, naši zákazníci nám buď e-mailom pošlú svoje vlastné plány a my ich posúdime na schválenie, alebo nás požiadajú o navrhnutie prvkov stroja pre ich aplikáciu. V druhom prípade využívame všetky vstupy od našich zákazníkov a navrhujeme prvky stroja a posielame hotové plány našim klientom na schválenie. Po schválení vyrobíme prvé výrobky a následne vyrobíme prvky stroja podľa finálneho návrhu. V ktorejkoľvek fáze tejto práce, v prípade, že konkrétny návrh strojového prvku funguje v teréne neuspokojivo (čo je zriedkavé), posúdime celý projekt a spoločne s našimi klientmi vykonáme úpravy podľa potreby. Našou štandardnou praxou je podpisovanie zmlúv o mlčanlivosti (NDA) s našimi zákazníkmi na návrh strojných prvkov alebo akéhokoľvek iného produktu, kedykoľvek je to potrebné alebo požadované. Keď sú prvky stroja pre konkrétneho zákazníka navrhnuté a vyrobené na mieru, pridelíme im kód produktu a vyrobíme a predáme ich len zákazníkovi, ktorý produkt vlastní. Strojové prvky reprodukujeme pomocou vyvinutých nástrojov, foriem a postupov toľkokrát, koľkokrát je to potrebné a kedykoľvek si ich zákazník objedná. Inými slovami, akonáhle je pre vás navrhnutý a vyrobený prvok stroja na mieru, duševné vlastníctvo, ako aj všetky nástroje a formy sú u nás rezervované a na dobu neurčitú skladované pre vás a produkty reprodukované podľa vášho želania. Našim klientom tiež ponúkame inžinierske služby kreatívnym kombinovaním strojových prvkov do komponentu alebo zostavy, ktorá slúži aplikácii a spĺňa alebo prekračuje očakávania našich zákazníkov. Závody vyrábajúce naše strojové prvky sú kvalifikované buď podľa ISO9001, QS9000 alebo TS16949. Navyše väčšina našich produktov má označenie CE alebo UL a spĺňa medzinárodne relevantné normy, ako sú ISO, SAE, ASME, DIN. Kliknutím na podponuky získate podrobné informácie o našich strojových prvkoch vrátane: - Remene, reťaze a káblové pohony - Ozubené kolesá a ozubené prevody - Spojky a ložiská - Klávesy a drážky a kolíky - Vačky a prepojenia - Hriadele - Mechanické tesnenia - Priemyselná spojka a brzda - Spojovacie prvky - Jednoduché stroje Pre našich zákazníkov, dizajnérov a vývojárov nových produktov vrátane strojných prvkov sme pripravili referenčnú brožúru. Môžete sa zoznámiť s niektorými bežne používanými pojmami v dizajne strojových komponentov: Stiahnite si brožúru s bežnými pojmami strojárskeho inžinierstva, ktoré používajú dizajnéri a inžinieri Naše strojové prvky nachádzajú uplatnenie v rôznych oblastiach, ako sú priemyselné stroje, automatizačné systémy, testovacie a metrologické zariadenia, dopravné zariadenia, stavebné stroje a prakticky kdekoľvek si spomeniete. AGS-TECH vyvíja a vyrába prvky strojov z rôznych materiálov v závislosti od použitia. Materiály používané na strojové prvky môžu siahať od lisovaných plastov používaných na hračky až po cementovanú a špeciálne potiahnutú oceľ pre priemyselné stroje. Naši dizajnéri používajú najmodernejší profesionálny softvér a konštrukčné nástroje na vývoj strojných prvkov, pričom berú do úvahy detaily, ako sú uhly v zuboch ozubených kolies, príslušné napätia, miery opotrebovania... atď. Prejdite si naše podponuky a stiahnite si naše produktové brožúry a katalógy, aby ste zistili, či môžete nájsť bežné prvky stroja pre vašu aplikáciu. Ak nemôžete nájsť vhodnú zhodu pre vašu aplikáciu, dajte nám vedieť a my s vami budeme spolupracovať na vývoji a výrobe strojných prvkov, ktoré budú spĺňať vaše potreby. Ak vás namiesto výrobných kapacít väčšinou zaujímajú naše inžinierske a výskumné a vývojové kapacity, pozývame vás na návštevu našej webovej stránky http://www.ags-engineering.com kde môžete nájsť podrobnejšie informácie o našom dizajne, vývoji produktov, vývoji procesov, inžinierskych konzultačných službách a ďalšie CLICK Product Finder-Locator Service PREDCHÁDZAJÚCA STRANA
- Glass and Ceramic Manufacturing, Hermetic Packages, Seals, Bonding
Glass and Ceramic Manufacturing, Hermetic Packages Seals and Bonding, Tempered Bulletproof Glass, Blow Moulding, Optical Grade Glass, Conductive Glass, Molding Tvarovanie a tvarovanie skla a keramiky Typy výroby skla, ktoré ponúkame, sú obalové sklo, fúkanie skla, sklenené vlákna a rúrky a tyče, domáce a priemyselné sklo, lampy a žiarovky, presné lisovanie skla, optické komponenty a zostavy, ploché a tabuľové a plavené sklo. Vykonávame ručné tvarovanie aj strojové tvarovanie. Naše obľúbené výrobné procesy technickej keramiky sú lisovanie, izostatické lisovanie, izostatické lisovanie za tepla, lisovanie za tepla, liatie sklzu, odlievanie pásky, extrúzia, vstrekovanie, surové obrábanie, spekanie alebo vypaľovanie, diamantové brúsenie, hermetické zostavy. Odporúčame vám kliknúť sem STIAHNITE si naše schematické ilustrácie procesov tvarovania a tvarovania skla od AGS-TECH Inc. STIAHNITE si naše schematické ilustrácie technologických procesov výroby keramiky od AGS-TECH Inc. Tieto súbory na stiahnutie s fotografiami a náčrtmi vám pomôžu lepšie porozumieť informáciám, ktoré vám poskytujeme nižšie. • VÝROBA KONTAJNEROVÉHO SKLA: Na výrobu sme zautomatizovali linky PRESS AND FLOW, ako aj BLOW AND BLOW. V procese vyfukovania a vyfukovania vhodíme dávku do prednej formy a vytvarujeme hrdlo fúkaním stlačeného vzduchu zhora. Bezprostredne potom sa stlačený vzduch fúka druhýkrát z druhého smeru cez hrdlo nádoby, aby sa vytvoril predtvar fľaše. Tento predlisok sa potom prenesie do skutočnej formy, znova sa zahreje na zmäknutie a aplikuje sa stlačený vzduch, aby sa predlisku získal konečný tvar nádoby. Presnejšie povedané, je natlakovaný a tlačený proti stenám dutiny vyfukovacej formy, aby získal požadovaný tvar. Nakoniec sa vyrobený sklenený obal premiestni do žíhacej pece na následné ohriatie a odstránenie pnutia vznikajúceho počas tvarovania a kontrolovane sa ochladí. Pri metóde lisovania a vyfukovania sa roztavené dávky vkladajú do predliatkovej formy (predliska) a lisujú sa do tvaru predlisku (tvar predlisku). Polotovary sa potom prenesú do vyfukovacích foriem a vyfukujú sa podobne ako v procese opísanom vyššie v časti „Proces vyfukovania a vyfukovania“. Následné kroky ako žíhanie a odbúranie stresu sú podobné alebo rovnaké. • FÚKANIE SKLA : Výrobky zo skla vyrábame konvenčným ručným fúkaním, ako aj stlačeným vzduchom s automatizovaným zariadením. Pre niektoré zákazky je potrebné konvenčné fúkanie, ako sú projekty zahŕňajúce umelecké diela zo skla alebo projekty, ktoré vyžadujú menší počet dielov s voľnými toleranciami, prototypové / demo projekty... atď. Bežné fúkanie skla zahŕňa ponorenie dutej kovovej rúrky do nádoby s roztaveným sklom a otáčanie rúrky na zhromaždenie určitého množstva skleneného materiálu. Sklo zhromaždené na špičke fajky sa navalí na ploché železo, vytvaruje sa podľa potreby, predĺži sa, znovu sa zohreje a vyfúkne vzduchom. Keď je pripravený, vloží sa do formy a fúka sa vzduch. Dutina formy je mokrá, aby sa zabránilo kontaktu skla s kovom. Vodný film medzi nimi pôsobí ako vankúš. Ručné fúkanie je pomalý proces náročný na prácu a je vhodný len na prototypovanie alebo položky vysokej hodnoty, nie je vhodný pre lacné veľkoobjemové objednávky za kus. • VÝROBA DOMÁCEHO A PRIEMYSELNÉHO SKLA: S použitím rôznych druhov sklenených materiálov sa vyrába veľké množstvo rôznych druhov skla. Niektoré poháre sú odolné voči teplu a sú vhodné na laboratórne sklo, zatiaľ čo niektoré sú dostatočne dobré na to, aby odolali umývaniu riadu mnohokrát a sú vhodné na výrobu domácich výrobkov. Na strojoch Westlake sa denne vyrobia desiatky tisíc kusov nápojového skla. Pre zjednodušenie sa roztavené sklo zhromažďuje pomocou vákua a vkladá sa do foriem na výrobu predliskov. Potom sa do foriem vháňa vzduch, tie sa prenesú do inej formy a opäť sa vháňa vzduch a sklo získa svoj konečný tvar. Podobne ako pri ručnom fúkaní sa tieto formy udržiavajú vlhké vodou. Ďalšie naťahovanie je súčasťou dokončovacej operácie, kde sa tvorí krk. Prebytočné sklo je spálené. Potom nasleduje riadený proces opätovného ohrevu a chladenia opísaný vyššie. • TVÁRENIE SKLENÝCH RÚR A TYČOV: Hlavné procesy, ktoré používame na výrobu sklenených rúr, sú procesy DANNER a VELLO. V Dannerovom procese sklo z pece tečie a padá na naklonenú manžetu vyrobenú zo žiaruvzdorných materiálov. Objímka je nesená na otočnom dutom hriadeli alebo fúkačke. Sklo sa potom omotá okolo objímky a vytvorí hladkú vrstvu stekajúcu po objímke a cez špičku drieku. V prípade tvarovania rúr je vzduch fúkaný cez fúkačku s dutým hrotom a v prípade tvarovania tyče používame pevné hroty na hriadeli. Rúry alebo tyče sa potom ťahajú cez nosné valčeky. Rozmery, ako je hrúbka steny a priemer sklenených trubíc, sa upravia na požadované hodnoty nastavením priemeru objímky a fúkaním tlaku vzduchu na požadovanú hodnotu, nastavením teploty, rýchlosti prúdenia skla a rýchlosti ťahania. Proces výroby sklenených trubíc Vello na druhej strane zahŕňa sklo, ktoré putuje z pece do misy s dutým tŕňom alebo zvonom. Sklo potom prechádza vzduchovým priestorom medzi tŕňom a miskou a nadobúda tvar trubice. Potom putuje cez valce do ťažného stroja a chladí sa. Na konci chladiacej linky prebieha rezanie a konečné spracovanie. Rozmery trubice je možné upraviť rovnako ako v procese Danner. Keď porovnáme proces Danner s procesom Vello, môžeme povedať, že proces Vello je vhodnejší pre výrobu veľkého množstva, zatiaľ čo proces Danner môže byť vhodnejší pre presné objednávky menších objemov rúr. • SPRACOVANIE PLACHTOVÉHO A PLOCHÉHO A PLAVÉHO SKLA: Máme veľké množstvá plochého skla v hrúbkach od submilimetrových až po niekoľko centimetrov. Naše ploché sklá sú takmer optickej dokonalosti. Ponúkame sklá so špeciálnymi povlakmi, ako sú optické povlaky, kde sa používa technika chemického naparovania na nanášanie povlakov, ako je antireflexný alebo zrkadlový povlak. Bežné sú tiež priehľadné vodivé povlaky. K dispozícii sú tiež hydrofóbne alebo hydrofilné povlaky na skle a povlak, ktorý umožňuje samočistenie skla. Tvrdené, nepriestrelné a vrstvené sklá sú ďalšie obľúbené položky. Sklo vyrežeme do požadovaného tvaru s požadovanými toleranciami. K dispozícii sú ďalšie sekundárne operácie, ako je zakrivenie alebo ohýbanie plochého skla. • PRESNÉ LIŠOVANIE SKLA: Túto techniku používame väčšinou na výrobu presných optických komponentov bez potreby drahších a časovo náročných techník, ako je brúsenie, lapovanie a leštenie. Táto technika nie je vždy dostatočná na výrobu najlepšej optiky, ale v niektorých prípadoch, ako sú spotrebné výrobky, digitálne fotoaparáty, lekárska optika, môže byť lacnejšou dobrou voľbou pre veľkoobjemovú výrobu. Výhodu má aj oproti iným technikám tvarovania skla, kde sa vyžadujú zložité geometrie, ako napríklad v prípade asfér. Základný proces zahŕňa naplnenie spodnej strany našej formy skleneným polotovarom, evakuáciu procesnej komory na odstránenie kyslíka, blízke uzavretie formy, rýchle a izotermické zahrievanie formy a skla infračerveným svetlom, ďalšie uzavretie polovíc formy pomalé stláčanie zmäkčeného skla kontrolovaným spôsobom na požadovanú hrúbku a nakoniec ochladenie skla a naplnenie komory dusíkom a odstránenie produktu. Presná regulácia teploty, vzdialenosť zatvárania formy, sila zatvárania formy, prispôsobenie koeficientov rozťažnosti formy a skleneného materiálu sú v tomto procese kľúčové. • VÝROBA SKLENENÝCH OPTICKÝCH KOMPONENTOV A ZOSTAVOV: Okrem presného lisovania skla existuje množstvo cenných procesov, ktoré používame na výrobu vysoko kvalitných optických komponentov a zostáv pre náročné aplikácie. Brúsenie, lapovanie a leštenie optických skiel v jemných špeciálnych brúsnych suspenziách je umenie a veda pri výrobe optických šošoviek, hranolov, plošiek a ďalších. Plochosť povrchu, zvlnenie, hladkosť a optické povrchy bez defektov vyžadujú veľa skúseností s takýmito procesmi. Malé zmeny v prostredí môžu viesť k tomu, že produkty nespĺňajú špecifikácie a môžu zastaviť výrobnú linku. Existujú prípady, keď jediné utretie optického povrchu čistou handričkou môže spôsobiť, že výrobok spĺňa špecifikácie alebo zlyhá v teste. Niektoré obľúbené sklenené materiály sú tavený oxid kremičitý, kremeň, BK7. Aj montáž takýchto komponentov si vyžaduje špecializované špecializované skúsenosti. Niekedy sa používajú špeciálne lepidlá. Niekedy je však najlepšou voľbou technika nazývaná optický kontakt a nezahŕňa žiadny materiál medzi pripevnenými optickými sklami. Pozostáva z fyzického kontaktu plochých povrchov, ktoré sa k sebe pripájajú bez lepidla. V niektorých prípadoch sa na zostavenie optických komponentov v určitých vzdialenostiach as určitými geometrickými orientáciami používajú mechanické rozpery, presné sklenené tyčinky alebo guľôčky, svorky alebo opracované kovové komponenty. Pozrime sa na niektoré z našich populárnych techník na výrobu špičkovej optiky. BRÚSENIE A LAPOVANIE A LEŠTENIE: Hrubý tvar optického komponentu sa získa brúsením skleneného polotovaru. Potom sa vykoná lapovanie a leštenie otáčaním a trením drsných povrchov optických komponentov o nástroje s požadovanými tvarmi povrchu. Medzi optiku a tvarovacie nástroje sa nalievajú kaly s drobnými abrazívnymi časticami a tekutinou. Veľkosti abrazívnych častíc v takýchto suspenziách môžu byť zvolené podľa požadovaného stupňa rovinnosti. Odchýlky kritických optických povrchov od požadovaných tvarov sú vyjadrené pomocou vlnových dĺžok použitého svetla. Naša vysoko presná optika má toleranciu desatiny vlnovej dĺžky (vlnová dĺžka/10) alebo je možná ešte prísnejšia. Okrem profilu povrchu sú kritické povrchy skenované a vyhodnocované na ďalšie povrchové vlastnosti a chyby, ako sú rozmery, škrabance, triesky, jamky, škvrny... atď. Prísna kontrola podmienok prostredia v oblasti výroby optiky a rozsiahle požiadavky na metrológiu a testovanie s najmodernejším vybavením robia z tohto odvetvia náročné priemyselné odvetvie. • SEKUNDÁRNE PROCESY VO VÝROBE SKLA: Opäť sme obmedzení iba vašou predstavivosťou, pokiaľ ide o sekundárne a dokončovacie procesy skla. Tu uvádzame niektoré z nich: -Povlaky na sklách (optické, elektrické, tribologické, tepelné, funkčné, mechanické...). Ako príklad môžeme zmeniť povrchové vlastnosti skla tak, aby napríklad odrážalo teplo, aby udržalo interiéry v budovách chladné, alebo aby jedna strana absorbovala infračervené žiarenie pomocou nanotechnológie. To pomáha udržiavať vnútro budov v teple, pretože vonkajšia povrchová vrstva skla absorbuje infračervené žiarenie vo vnútri budovy a vyžaruje ho späť dovnútra. - Leptanie on sklo - Aplikované keramické označovanie (ACL) -Gravírovanie - Leštenie plameňom - Chemické leštenie - Farbenie VÝROBA TECHNICKEJ KERAMIKA • LIŠOVANIE V MATICE: Pozostáva z jednoosového zhutňovania zrnitých práškov uzavretých v matrici • LISOVANIE ZA HORÚCA: Podobné ako lisovanie, ale s pridaním teploty na zvýšenie zahustenia. Prášok alebo zhutnený predlisok sa umiestni do grafitovej matrice a aplikuje sa jednoosový tlak, pričom sa matrica udržiava pri vysokých teplotách, ako je 2000 C. Teploty sa môžu líšiť v závislosti od typu spracovávaného keramického prášku. Pre komplikované tvary a geometrie môže byť potrebné ďalšie následné spracovanie, ako je brúsenie diamantom. • IZOSTATICKÉ LISOVANIE: Granulovaný prášok alebo lisované výlisky sa umiestnia do vzduchotesných nádob a potom do uzavretej tlakovej nádoby s kvapalinou vo vnútri. Potom sa zhutnia zvýšením tlaku v tlakovej nádobe. Kvapalina vo vnútri nádoby prenáša tlakové sily rovnomerne po celej ploche vzduchotesnej nádoby. Materiál je tak rovnomerne zhutnený a nadobúda tvar svojej flexibilnej nádoby a jej vnútorného profilu a vlastností. • IZOSTATICKÉ LISOVANIE ZA HORÚCA : Podobne ako pri izostatickom lisovaní, ale okrem atmosféry stlačeného plynu výlisky spekáme pri vysokej teplote. Izostatické lisovanie za tepla má za následok dodatočné zhutnenie a zvýšenú pevnosť. • ODLIATOK ODTOKOV : Formu naplníme suspenziou mikrometrových keramických častíc a nosnou kvapalinou. Táto zmes sa nazýva „slip“. Forma má póry a preto sa kvapalina v zmesi filtruje do formy. V dôsledku toho sa na vnútorných plochách formy vytvorí odliatok. Po spekaní je možné diely vybrať z formy. • ODLIEVANIE PÁSKY: Keramické pásky vyrábame odlievaním keramických kalov na ploché pohyblivé povrchy nosiča. Kaše obsahujú keramické prášky zmiešané s inými chemikáliami na účely viazania a prenášania. Keď sa rozpúšťadlá odparujú, zanechávajú sa husté a ohybné keramické dosky, ktoré je možné podľa potreby rezať alebo valcovať. • VYTVÁRANIE VYTLAČOVANÍM: Rovnako ako pri iných procesoch vytláčania, mäkká zmes keramického prášku so spojivami a inými chemikáliami prechádza cez matricu, aby získala svoj prierezový tvar a potom sa reže na požadované dĺžky. Proces sa vykonáva so studenými alebo zahrievanými keramickými zmesami. • NÍZKOTLAKOVÉ VSTREKOVANIE : Pripravíme zmes keramického prášku so spojivami a rozpúšťadlami a zahrejeme ju na teplotu, pri ktorej sa dá ľahko vtlačiť a vytlačiť do dutiny nástroja. Po dokončení lisovacieho cyklu sa diel vysunie a spojovacia chemikália sa spáli. Pomocou vstrekovania môžeme ekonomicky získať zložité diely vo veľkých objemoch. Otvory , ktoré sú nepatrným zlomkom milimetra na stene s hrúbkou 10 mm, sú možné, závity sú možné bez ďalšieho opracovania, tolerancie až +/- 0,5 % sú možné a ešte nižšie pri obrábaní dielov sú možné hrúbky steny rádovo od 0,5 mm do dĺžky 12,5 mm, ako aj hrúbky steny od 6,5 mm do dĺžky 150 mm. • ZELENÉ OBRÁBENIE : Pomocou rovnakých nástrojov na obrábanie kovov môžeme obrábať lisované keramické materiály, kým sú ešte mäkké ako krieda. Možné sú tolerancie +/- 1 %. Pre lepšiu toleranciu používame diamantové brúsenie. • SPIEVANIE alebo VYPALOVANIE: Spekanie umožňuje úplné zahustenie. Na zelených kompaktných dieloch dochádza k výraznému zmršťovaniu, ale to nie je veľký problém, pretože tieto rozmerové zmeny berieme do úvahy pri navrhovaní dielu a nástrojov. Častice prášku sú navzájom spojené a pórovitosť spôsobená procesom zhutňovania je do značnej miery odstránená. • BRÚSENIE DIAMANTOV: Najtvrdší materiál na svete „diamant“ sa používa na brúsenie tvrdých materiálov, ako je keramika, a získavajú sa presné diely. Dosahujú sa tolerancie v oblasti mikrometrov a veľmi hladké povrchy. Vzhľadom na jej náklady uvažujeme o tejto technike len vtedy, keď ju skutočne potrebujeme. • HERMETICKÉ ZOSTAVY sú také, ktoré prakticky neumožňujú žiadnu výmenu látok, pevných látok, kvapalín alebo plynov medzi rozhraniami. Hermetické tesnenie je vzduchotesné. Napríklad hermetické elektronické kryty sú tie, ktoré udržujú citlivý vnútorný obsah zabaleného zariadenia bez poškodenia vlhkosťou, kontaminantmi alebo plynmi. Nič nie je 100% hermetické, ale keď hovoríme o hermetickosti, v praxi to znamená, že hermetickosť existuje do takej miery, že miera úniku je taká nízka, že zariadenia sú za normálnych podmienok prostredia bezpečné po veľmi dlhú dobu. Naše hermetické zostavy pozostávajú z kovových, sklenených a keramických komponentov, kovokeramických, keramicko-kovovo-keramických, kovokeramických-kovových, kov na kov, kov-sklo, kov-sklo-kov, sklo-kov-sklo, sklo- kov a sklo na sklo a všetky ostatné kombinácie spájania kov-sklo-keramika. Môžeme napríklad pokovovať keramické komponenty, aby mohli byť pevne spojené s ostatnými komponentmi v zostave a mali vynikajúcu tesniacu schopnosť. Máme know-how na poťahovanie optických vlákien alebo priechodiek kovom a ich spájkovanie alebo spájkovanie na kryty, takže do krytov neprechádzajú ani neunikajú žiadne plyny. Preto sa používajú na výrobu elektronických krytov na zapuzdrenie citlivých zariadení a ich ochranu pred vonkajšou atmosférou. Okrem vynikajúcich tesniacich vlastností sú k dispozícii aj ďalšie vlastnosti, ako sú koeficient tepelnej rozťažnosti, deformačná odolnosť, bezodplynivosť, veľmi dlhá životnosť, nevodivosť, tepelnoizolačné vlastnosti, antistatická povaha...atď. urobiť zo skla a keramiky výber pre určité aplikácie. Informácie o našom zariadení, ktoré vyrába armatúry z keramiky na kov, hermetické tesnenia, vákuové priechodky, vysoko a ultravysoké vákuum a komponenty na riadenie tekutín nájdete tu:Brožúra továrne na hermetické komponenty CLICK Product Finder-Locator Service PREDCHÁDZAJÚCA STRANA
- Wire & Spring Forming, Shaping, Welding, Assembly of Wires, Coil, CNC
Wire & Spring Forming, Shaping, Welding, Assembly of Wires, Coil Compression Extension Torsion Flat Springs, Custom Wires, Helical Springs at AGS-TECH Inc. Drôtové a pružinové tvarovanie Vyrábame drôty na mieru, drôtené montáže, drôty tvarované do požadovaných 2D a 3D tvarov, drôtené siete, pletivá, ohrádky, košíky, ploty, drôtené pružiny, ploché pružiny; krútenie, stláčanie, ťah, ploché pružiny a iné. Naše procesy sú tvárnenie drôtu a pružín, ťahanie drôtu, tvarovanie, ohýbanie, zváranie, tvrdé spájkovanie, spájkovanie, dierovanie, kovania, vŕtanie, zrážanie hrán, brúsenie, závitovanie, nanášanie, tvarovanie sklzom, navíjanie, navíjanie, utláčanie. Odporúčame vám kliknúť sem STIAHNITE si naše schematické ilustrácie procesov tvárnenia drôtu a pružiny od AGS-TECH Inc. Tento súbor na stiahnutie s fotografiami a náčrtmi vám pomôže lepšie porozumieť informáciám, ktoré vám poskytujeme nižšie. • ŤAHANIE DRÔTU: Pomocou ťahových síl naťahujeme kovový materiál a ťaháme ho cez matricu, aby sa zmenšil priemer a zväčšila jeho dĺžka. Niekedy používame sériu matríc. Sme schopní vyrobiť zápustky pre každý rozmer drôtu. Pomocou materiálu s vysokou pevnosťou v ťahu ťaháme veľmi tenké drôty. Ponúkame drôty opracované za studena aj za tepla. • TVORBA DRÔTU: Kotúč kalibrovaného drôtu sa ohne a vytvaruje do užitočného produktu. Máme schopnosť vytvárať drôty zo všetkých kalibrov, vrátane tenkých vlákien, ako aj hrubých drôtov, ako sú tie, ktoré sa používajú ako pružiny pod podvozky automobilov. Zariadenia, ktoré používame na tvárnenie drôtu sú ručné a CNC formovače drôtu, navíjačka, silové lisy, štvorsúpravové, viaczásuvkové. Naše procesy sú ťahanie, ohýbanie, vyrovnávanie, sploštenie, naťahovanie, rezanie, utláčanie, spájkovanie a zváranie a tvrdé spájkovanie, montáž, navíjanie, kovania (alebo krídlovanie), dierovanie, závitovanie drôtu, vŕtanie, zrážanie hrán, brúsenie, poťahovanie a povrchové úpravy. Naše najmodernejšie vybavenie je možné nastaviť tak, aby vyvíjalo veľmi zložité návrhy akéhokoľvek tvaru a úzkych tolerancií. Ponúkame rôzne typy koncoviek ako guľovité, špicaté alebo skosené konce pre vaše drôty. Väčšina našich projektov na tvarovanie drôtu má minimálne až nulové náklady na nástroje. Vzorové časy obrátky sú zvyčajne dni. Zmeny v dizajne/konfigurácii drôtených foriem je možné vykonať veľmi rýchlo. • TVORENIE PRUŽÍN: AGS-TECH vyrába veľké množstvo pružín vrátane: -Torzná / Dvojitá torzná pružina - Napínacia / tlačná pružina - Konštantná / variabilná pružina - Vinutá a špirálová pružina -Plochá a listová pružina - Vyvážiť jar - Belleville Washer - Negator Spring - Vinutá pružina s progresívnou rýchlosťou - Pružina vlny -Volute Spring - Kužeľové pružiny - Pružinové prstene - Hodinové pružiny -Klipy Vyrábame pružiny z rôznych materiálov a môžeme vás viesť podľa vašej aplikácie. Najbežnejšie materiály sú nehrdzavejúca oceľ, chrómový kremík, vysoko uhlíková oceľ, v oleji temperovaná nízkouhlíková, chrómvanád, fosforový bronz, titán, zliatina berýlia a medi, vysokoteplotná keramika. Pri výrobe pružín používame rôzne techniky, vrátane CNC navíjania, navíjania za studena, navíjania za tepla, kalenia, konečnej úpravy. Ďalšie techniky, ktoré už boli spomenuté vyššie pri tvarovaní drôtu, sú tiež bežné v našich operáciách výroby pružín. • DOKONČOVACIE SLUŽBY PRE DRÔTY A PRUŽINY: Vaše produkty môžeme dokončiť mnohými spôsobmi v závislosti od vášho výberu a potrieb. Niektoré bežné procesy, ktoré ponúkame, sú: lakovanie, práškové lakovanie, pokovovanie, máčanie vinylu, eloxovanie, odľahčenie, tepelné spracovanie, brokovanie, bubnovanie, chrómovanie, elektrický nikel, pasivácia, vypaľovaný smalt, plastový povlak , čistenie plazmou. CLICK Product Finder-Locator Service PREDCHÁDZAJÚCA STRANA
- Sheet Metal Forming Fabrication, Stamping, Punching, Deep Drawing, CNC
Sheet Metal Forming and Fabrication, Stamping, Punching, Bending, Progressive Die, Spot Welding, Deep Drawing, Metal Blanking and Slitting at AGS-TECH Inc. Lisovanie a výroba plechov Ponúkame lisovanie plechov, tvarovanie, tvárnenie, ohýbanie, dierovanie, vysekávanie, rezanie, dierovanie, vrúbkovanie, vysekávanie, strihanie, lisovanie, výrobu, hlboké ťahanie pomocou jednorazových/jednoťahových razidiel, ako aj progresívne matrice a spriadanie, tvarovanie gumy a hydroformovanie; rezanie plechu vodným lúčom, plazmou, laserom, pílou, plameňom; montáž plechu pomocou zvárania, bodového zvárania; vydutie a ohýbanie plechových rúr; povrchová úprava plechu vrátane lakovania ponorom alebo striekaním, elektrostatického práškového lakovania, eloxovania, pokovovania, naprašovania a ďalších. Naše služby siahajú od rýchleho prototypovania plechu až po veľkoobjemovú výrobu. Odporúčame vám kliknúť semSTIAHNITE si naše schematické ilustrácie procesov výroby a lisovania plechov od spoločnosti AGS-TECH Inc. Pomôže vám to lepšie porozumieť informáciám, ktoré vám poskytujeme nižšie. • STRIHANIE PLECHOV : Ponúkame ODREZÁVANIE a DELENIE. Odrezky režú plech po jednej dráhe a v podstate nedochádza k plytvaniu materiálom, zatiaľ čo pri upichovaní sa tvar nedá presne do seba zasunúť a tým sa určité množstvo materiálu plytvá. Jedným z našich najobľúbenejších procesov je DIEROVANIE, kedy sa z plechu vyreže kus materiálu okrúhleho alebo iného tvaru. Vystrihnutý kus je odpad. Ďalšou verziou dierovania je DRÁŽKOVANIE, kde sa dierujú pravouhlé alebo podlhovasté otvory. BLANKING na druhej strane je rovnaký proces ako dierovanie, s rozlíšením vyrezaného kusu je práca a je zachovaná. FINE BLANKING, špičková verzia blankovania, vytvára rezy s úzkymi toleranciami a rovnými hladkými hranami a nevyžaduje sekundárne operácie na dokonalosť obrobku. Ďalším procesom, ktorý často používame, je DEZANIE, čo je proces strihania, pri ktorom sa plech reže dvoma protiľahlými kruhovými čepeľami v priamej alebo zakrivenej dráhe. Otvárač na konzervy je jednoduchým príkladom procesu rezania. Ďalším obľúbeným procesom je pre nás PERFOROVANIE, pri ktorom je do plechu vyrazených veľa otvorov okrúhleho alebo iného tvaru v určitom vzore. Typickým príkladom pre perforovaný výrobok sú kovové filtre s mnohými otvormi pre tekutiny. V REZAČOVANÍ, inom procese rezania plechu, odoberáme materiál z obrobku, začínajúc od okraja alebo inde a režeme dovnútra, kým nezískame požadovaný tvar. Ide o progresívny proces, pri ktorom sa pri každej operácii odstraňuje ďalší kus, kým sa nedosiahne požadovaný obrys. Pre malé výrobné série niekedy používame relatívne pomalší proces nazývaný NIBBLING, ktorý pozostáva z mnohých rýchlych razníc prekrývajúcich sa otvorov na vytvorenie väčšieho a komplexnejšieho rezu. V PROGRESÍVNOM REZANÍ používame sériu rôznych operácií na získanie jedného rezu alebo určitej geometrie. Sekundárny proces HOLENIE nám nakoniec pomáha vylepšiť hrany už urobených rezov. Používa sa na odrezávanie triesok, hrubovanie hrán pri opracovaní plechu. • OHÝBANIE PLECHU: Okrem rezania je ohýbanie nevyhnutným procesom, bez ktorého by sme nedokázali vyrobiť väčšinu produktov. Väčšinou je to operácia za studena, ale niekedy sa vykonáva aj za tepla alebo za tepla. Na túto operáciu väčšinou používame matrice a lisy. Pri POSTUPNOM OHÝBANÍ používame sériu rôznych raziacich a lisovacích operácií na získanie jediného ohybu alebo určitej geometrie. AGS-TECH používa rôzne ohýbacie procesy a robí výber v závislosti od materiálu obrobku, jeho veľkosti, hrúbky, požadovanej veľkosti ohybu, polomeru, zakrivenia a uhla ohybu, umiestnenia ohybu, ekonomiky prevádzky, vyrábaného množstva… atď. Používame Ohýbanie do V, kde razník v tvare V vtlačí plech do matrice v tvare V a ohne ho. Dobré pre veľmi ostré aj tupé uhly a medzi nimi, vrátane 90 stupňov. Pomocou stieracích matríc vykonávame OHÝBANIE HRAN. Naše vybavenie nám umožňuje získať uhly aj väčšie ako 90 stupňov. Pri ohýbaní hrán je obrobok vložený medzi prítlačnú podložku a matricu, oblasť ohýbania je umiestnená na okraji matrice a zvyšok obrobku je držaný nad space ako konzolový nosník. Keď razník pôsobí na konzolovú časť, je ohnutá cez okraj matrice. FLANGING je proces ohýbania hrán, ktorého výsledkom je uhol 90 stupňov. Hlavným cieľom operácie je eliminácia ostrých hrán a získanie geometrických povrchov na uľahčenie spájania dielov. BEADING, ďalší bežný proces ohýbania hrán vytvára zvlnenie cez hranu dielu. LEMOVANIE na druhej strane vedie k okraju listu, ktorý je úplne ohnutý. V SEAMINGU sa okraje dvoch dielov prehnú na seba a spoja. Na druhej strane DVOJITÝ ŠIVOK poskytuje vodotesné a vzduchotesné spoje plechov. Podobne ako pri ohýbaní hrán, proces nazývaný OTOČNÉ OHYBOVANIE rozmiestňuje valec s vyrezaným požadovaným uhlom a slúži ako razník. Keď je sila prenášaná na razník, uzatvára sa s obrobkom. Drážka valca dáva konzolovej časti požadovaný uhol. Drážka môže mať uhol menší alebo väčší ako 90 stupňov. Pri VZDUCHOVOM OHÝBANÍ nepotrebujeme, aby mala spodná matrica lomenú drážku. Plech je podopretý dvoma plochami na protiľahlých stranách a v určitej vzdialenosti. Razník potom pôsobí silou na správnom mieste a ohýba obrobok. KANÁLOVÉ OHÝBANIE sa vykonáva pomocou razníka a matrice v tvare kanála a Ohýbanie do U sa dosahuje razníkom v tvare U. OFFSET BENDING vytvára ofsety na plechu. ROLL BENDING, technika vhodná na hrubé práce a ohýbanie veľkých kusov kovových plátov, používa tri valce na podávanie a ohýbanie plátov do požadovaných zakrivení. Kotúče sú usporiadané tak, aby sa dosiahol požadovaný ohyb diela. Vzdialenosť a uhol medzi valcami sú riadené tak, aby sa dosiahol požadovaný výsledok. Pohyblivý valec umožňuje ovládať zakrivenie. TVÁRENIE RÚR je ďalšou populárnou operáciou ohýbania plechu, ktorá zahŕňa viacero foriem. Rúry sa získajú po viacerých akciách. Zvlnenie sa vykonáva aj ohýbaním. V podstate ide o symetrické ohýbanie v pravidelných intervaloch po celom kuse plechu. Na zvlnenie je možné použiť rôzne tvary. Vlnitý plech je pevnejší a má lepšiu odolnosť proti ohybu, a preto má uplatnenie v stavebníctve. TVORENIE PLECHU ROLOVANÍM, kontinuálny manufacturing proces sa používa na ohýbanie prierezov určitej geometrie pomocou valcov a dielo sa ohýba v sekvenčných krokoch, pričom konečný valec dokončí prácu. V niektorých prípadoch sa používa jeden kotúč av niektorých prípadoch séria kotúčov. • KOMBINOVANÉ PROCESY REZANIE A OHÝBANIE PLECHU: Sú to procesy, ktoré režú a ohýbajú súčasne. V PIERCINGU sa vytvorí otvor pomocou špicaté raznice. Keď priebojník rozširuje otvor v plechu, materiál sa súčasne ohýba do vnútornej príruby pre otvor. Získaná príruba môže mať dôležité funkcie. Operácia LNCING na druhej strane reže a ohýba plech, aby sa vytvorila zvýšená geometria. • VYHNUTIE A OHNUTIE KOVOVEJ RÚRY: Pri VYDUBENÍ je niektorá vnútorná časť dutej rúrky pod tlakom, čo spôsobuje vydutie rúrky smerom von. Pretože rúrka je vo vnútri matrice, geometria vydutia je riadená tvarom matrice. Pri STRETCH BENDING sa kovová rúrka naťahuje pomocou síl rovnobežných s osou rúrky a ohybových síl na pretiahnutie rúrky cez debniaci blok. Pri DRAW BENDING upíname rúrku blízko jej konca k otočnému bloku formy, ktorý rúrku pri otáčaní ohýba. Nakoniec, pri KOMPRESNOM OHÝBANÍ je rúrka držaná silou na pevnom debnenom bloku a matrica ju ohýba cez debniaci blok. • HĹBKOVÉ ŤAHANIE : V jednej z našich najobľúbenejších operácií sa používa razník, vhodná matrica a držiak polotovaru. Plechový polotovar sa umiestni nad otvor matrice a razník sa pohybuje smerom k polotovaru držanému držiakom polotovaru. Akonáhle sa dostanú do kontaktu, razník vtlačí plech do dutiny formy, aby vytvoril produkt. Operácia hlbokého ťahania pripomína rezanie, avšak vôľa medzi razníkom a matricou zabraňuje odrezaniu plechu. Ďalším faktorom, ktorý zaisťuje, že plech je hlboko ťahaný a nerezaný, sú zaoblené rohy na razidle a razidle, ktoré bránia strihaniu a rezaniu. Na dosiahnutie väčšieho rozsahu hlbokého ťahania sa používa proces REDRAWING, pri ktorom sa následné hlboké ťahanie uskutočňuje na dielci, ktorý už prešiel procesom hlbokého ťahania. V REVERSE PREDRAWING sa hlboko ťahaná časť prevráti a nakreslí v opačnom smere. Hlboké kreslenie môže poskytnúť predmety nepravidelného tvaru, ako sú kupolovité, kužeľovité alebo stupňovité poháre, Pri RAZENÍ používame dvojicu samčích a samičích razníc, aby sme plechu vtlačili dizajn alebo písmo. • SPINNING : Operácia, pri ktorej je plochý alebo predtvarovaný obrobok držaný medzi rotujúcim tŕňom a chvostom a nástroj vyvíja lokalizovaný tlak na obrobok, keď sa postupne posúva nahor po tŕni. V dôsledku toho je obrobok obalený cez tŕň a nadobúda svoj tvar. Túto techniku používame ako alternatívu k hlbokému ťahaniu, kde je množstvo zákazky malé, diely sú veľké (priemery do 20 stôp) a majú jedinečné krivky. Aj keď sú ceny za kus vo všeobecnosti vyššie, zriaďovacie náklady na CNC spriadanie sú v porovnaní s hlbokým ťahaním nízke. Naopak, hlboké ťahanie vyžaduje vysoké počiatočné investície na nastavenie, ale náklady na kus sú nízke, keď sa vyrába veľké množstvo dielov. Ďalšou verziou tohto procesu je SHEAR SPINNING, kde tiež dochádza k prúdeniu kovu v obrobku. Prúd kovu zníži hrúbku obrobku počas procesu. Ďalším súvisiacim procesom je SPODENIE RÚR, ktoré sa aplikuje na valcové časti. Aj pri tomto procese dochádza v obrobku k toku kovu. Hrúbka sa tým zníži a dĺžka rúrky sa zväčší. Nástroj je možné presúvať a vytvárať prvky na vnútornej alebo vonkajšej strane trubice. • TVÁRENIE PLECHU GUMOU : Gumový alebo polyuretánový materiál sa vloží do matrice nádoby a obrobok sa položí na povrch gumy. Potom sa na obrobok pôsobí razníkom a vtlačí ho do gumy. Pretože tlak generovaný gumou je nízky, hĺbka vyrobených dielov je obmedzená. Keďže náklady na nástroje sú nízke, proces je vhodný na výrobu malého množstva. • HYDROFORMOVANIE: Podobne ako pri tvárnení gumy sa pri tomto procese plech lisuje razníkom do stlačenej kvapaliny vo vnútri komory. Plechové dielo je vložené medzi razidlo a gumovú membránu. Membrána úplne obklopuje obrobok a tlak tekutiny ho núti, aby sa vytvoril na razidle. Pomocou tejto techniky možno dosiahnuť veľmi hlboké ťahy ešte hlbšie ako pri procese hlbokého ťahania. Vyrábame jednorazové matrice, ako aj progresívne matrice v závislosti od vašej časti. Jednotaktné razidlá sú nákladovo efektívnou metódou na rýchlu výrobu veľkého množstva jednoduchých plechových dielov, ako sú podložky. Na výrobu zložitejších geometrií sa používajú progresívne matrice alebo technika hlbokého ťahania. V závislosti od vášho prípadu je možné použiť rezanie vodným lúčom, laserom alebo plazmou na výrobu vašich plechových dielov lacno, rýchlo a presne. Mnohí dodávatelia o týchto alternatívnych technikách nemajú ani potuchy, a preto prechádzajú zdĺhavými a drahými spôsobmi výroby matríc a nástrojov, ktoré len strácajú čas a peniaze zákazníkov. Ak požadujete na mieru vyrobené plechové komponenty, ako sú kryty, elektronické kryty... atď. tak rýchlo ako do niekoľkých dní, potom nás kontaktujte pre našu službu RAPID PLECH PROTOTYPING. CLICK Product Finder-Locator Service PREDCHÁDZAJÚCE MENU
- Forging and Powdered Metallurgy, Die Forging, Heading, Hot Forging
Forging and Powdered Metallurgy, Die Forging, Heading, Hot Forging, Impression Die, Near Net Shape, Swaging, Metal Hobbing, Riveting, Coining from AGS-TECH Inc. Kovanie kovov a prášková metalurgia Typy procesov KOVANIA KOVOV, ktoré ponúkame, sú zápustka za tepla a za studena, otvorená zápustka a uzavretá zápustka, zápustka a výkovky bez výliskov, cogging, valcovanie, lemovanie a presné kovanie, tvar takmer siete, hlavička , kovanie, upchaté kovanie, kovové odvalovacie frézy, lisovacie a valčekové & radiálne & orbitálne & prstencové & izotermické výkovky, razenie, nitovanie, kovanie kovových guľôčok, kovové dierovanie, dimenzovanie, vysokoenergetické kovanie. Naše techniky PRÁŠKOVÁ METALURGIA a PRÁŠKOVÉ SPRACOVANIE sú práškové lisovanie a spekanie, impregnácia, infiltrácia, izostatické lisovanie za tepla a za studena, vstrekovanie kovov, zhutňovanie valcovaním, valcovanie prášku, vytláčanie prášku, voľné spekanie, iskrové spekanie, lisovanie za tepla. Odporúčame vám kliknúť sem STIAHNITE si naše schematické ilustrácie procesov kovania od AGS-TECH Inc. STIAHNITE si naše schematické ilustrácie procesov práškovej metalurgie od AGS-TECH Inc. Tieto súbory na stiahnutie s fotografiami a náčrtmi vám pomôžu lepšie porozumieť informáciám, ktoré vám poskytujeme nižšie. Pri kovaní kovov sa aplikujú tlakové sily a materiál sa deformuje a získa sa požadovaný tvar. Najbežnejšími kovanými materiálmi v priemysle sú železo a oceľ, ale mnohé ďalšie, ako je hliník, meď, titán, horčík, sú tiež široko kované. Kované kovové diely majú okrem utesnených trhlín a uzavretých prázdnych priestorov vylepšenú štruktúru zŕn, takže pevnosť dielov získaných týmto procesom je vyššia. Kovaním sa vyrábajú diely, ktoré sú výrazne pevnejšie vzhľadom na svoju hmotnosť ako diely vyrobené odlievaním alebo obrábaním. Pretože kované diely sú tvarované tak, že kov tečie do svojho konečného tvaru, kov nadobúda štruktúru smerového zrna, ktorá zodpovedá za vynikajúcu pevnosť dielov. Inými slovami, diely získané kovaním vykazujú lepšie mechanické vlastnosti v porovnaní s jednoduchými odlievanými alebo opracovanými dielmi. Hmotnosť kovových výkovkov sa môže pohybovať od malých ľahkých častí až po stovky tisíc libier. Vyrábame výkovky prevažne pre mechanicky náročné aplikácie, kde je veľké namáhanie dielov ako sú automobilové diely, ozubené kolesá, pracovné nástroje, ručné náradie, hriadele turbín, výstroj motocyklov. Pretože náklady na nástroje a nastavenie sú relatívne vysoké, odporúčame tento výrobný proces iba pre veľkoobjemovú výrobu a pre nízkoobjemové, ale vysoko hodnotné kritické komponenty, ako sú letecké podvozky. Okrem nákladov na nástroje môžu byť výrobné časy pre veľké množstvo kovaných dielov dlhšie v porovnaní s niektorými jednoduchými obrábanými dielmi, ale táto technika je rozhodujúca pre diely, ktoré vyžadujú mimoriadnu pevnosť, ako sú skrutky, matice, špeciálne aplikácie spojovacie prvky, automobilový priemysel, vysokozdvižné vozíky, diely žeriavov. • KOVANIE ZA HORÚCU a STUDENÉ KOVANIE: Kovanie za tepla, ako už názov napovedá, sa vykonáva pri vysokých teplotách, ťažnosť je preto vysoká a pevnosť materiálu nízka. To uľahčuje ľahkú deformáciu a kovanie. Naopak, zápustkové kovanie za studena sa vykonáva pri nižších teplotách a vyžaduje vyššie sily, čo má za následok deformačné spevnenie, lepšiu povrchovú úpravu a presnosť vyrábaných dielov. • OTVORENÉ ZÁVERKOVÉ KOVANIE a KOVANIE V OTLAKU: Pri voľnom kovaní zápustky neobmedzujú materiál, ktorý sa má stláčať, zatiaľ čo pri kovaní v zápustke dutiny v zápustkách obmedzujú tok materiálu pri kovaní do požadovaného tvaru. KOVANIE NAPÁJENÍM alebo tiež nazývané PREPÄŤOVANIE, čo v skutočnosti nie je rovnaký, ale veľmi podobný proces, je proces s otvorenou matricou, kde je obrobok vložený medzi dve ploché matrice a tlaková sila znižuje jeho výšku. Keď je výška reduced, šírka obrobku sa zväčšuje. HLAVA, proces upchatého kovania zahŕňa valcový materiál, ktorý je na svojom konci upnutý a jeho prierez sa lokálne zväčší. V hlavičke je materiál vedený cez matricu, kovaný a potom narezaný na dĺžku. Prevádzka je schopná rýchlo vyrábať veľké množstvá spojovacích prvkov. Väčšinou ide o prácu za studena, pretože sa používa na výrobu koncov klincov, koncov skrutiek, matíc a skrutiek, kde je potrebné materiál spevniť. Ďalším procesom otvorenej formy je COGGING, kde je obrobok kovaný v sérii krokov, pričom každý krok vedie k stlačeniu materiálu a následnému pohybu otvorenej formy po dĺžke obrobku. Pri každom kroku sa hrúbka zmenšuje a dĺžka sa o malé množstvo zväčšuje. Tento proces sa podobá nervóznemu študentovi, ktorý si celý čas obhrýza ceruzku v malých krokoch. Proces nazývaný FULLERING je ďalšou metódou kovania v zápustke, ktorú často používame ako skorší krok na distribúciu materiálu v obrobku pred uskutočnením iných operácií kovania. Používame ho, keď obrobok vyžaduje niekoľko operácií kovania operations. Pri prevádzke sa matrica s konvexnými povrchmi deformuje a spôsobuje vytekanie kovu na obe strany. Na druhej strane, podobný proces ako valcovanie, HRANOVANIE zahŕňa otvorenú matricu s konkávnymi povrchmi na deformáciu obrobku. Okrajovanie je tiež prípravným procesom pre následné operácie kovania, vďaka čomu materiál prúdi z oboch strán do oblasti v strede. TLAČOVÉ KOVANIE alebo ZATVORENÉ ZÁVERKOVÉ KOVANIE, ako sa tiež nazýva, používa zápustku / formu, ktorá stláča materiál a obmedzuje jeho tok v sebe. Forma sa uzavrie a materiál nadobudne tvar dutiny formy / formy. PRESNÉ KOVANIE, proces vyžadujúci špeciálne vybavenie a formu, produkuje diely bez alebo len s veľmi malým zábleskom. Inými slovami, diely budú mať takmer konečné rozmery. V tomto procese sa do formy opatrne vloží a umiestni dobre kontrolované množstvo materiálu. Túto metódu používame pre zložité tvary s tenkými časťami, malými toleranciami a uhlmi úkosu a keď sú množstvá dostatočne veľké na to, aby odôvodnili náklady na formu a vybavenie. • BEZPROBLÉKOVÉ KOVANIE: Obrobok je umiestnený v zápustke tak, aby žiadny materiál nemohol vytiecť z dutiny a vytvoriť záblesk. Nie je teda potrebné žiadne nežiaduce orezávanie bleskom. Ide o presný proces kovania, a preto si vyžaduje dôkladnú kontrolu množstva použitého materiálu. • KOVOVÉ KÚVANIE alebo RADIÁLNE KOVANIE: Na obrobok sa po obvode pôsobí zápustkou a je vykovaný. Na kovanie vnútornej geometrie obrobku sa môže použiť aj tŕň. Pri operácii kovania obrobok typicky dostáva niekoľko zdvihov za sekundu. Typickými predmetmi vyrábanými kovaním sú špičaté nástroje, kužeľové tyče, skrutkovače. • PREBERANIE KOVU: Túto operáciu používame často ako doplnkovú operáciu pri výrobe dielov. Otvor alebo dutina sa vytvorí dierovaním na povrchu obrobku bez toho, aby sa cez neho prerazilo. Upozorňujeme, že piercing je iný ako vŕtanie, ktorého výsledkom je priechodný otvor. • HOBBING: Razník s požadovanou geometriou sa vtlačí do obrobku a vytvorí dutinu požadovaného tvaru. Tomuto punču hovoríme HOB. Operácia zahŕňa vysoké tlaky a vykonáva sa za studena. Výsledkom je, že materiál je opracovaný za studena a deformovaný. Preto je tento proces veľmi vhodný na výrobu foriem, razníc a dutín pre iné výrobné procesy. Keď je varná doska vyrobená, je možné jednoducho vyrobiť mnoho rovnakých dutín bez toho, aby ste ich museli opracovávať jednu po druhej. • VALCOVANIE alebo TVAROVANIE VALCOV: Na tvarovanie kovovej časti sa používajú dva protiľahlé valce. Obrobok sa privádza do valcov, valce sa otáčajú a ťahajú obrobok do medzery, obrobok sa potom posúva cez drážkovanú časť valcov a tlakové sily dávajú materiálu požadovaný tvar. Nie je to proces valcovania, ale proces kovania, pretože je to skôr diskrétna ako nepretržitá operácia. Geometria na drážkach valcov vykováva materiál do požadovaného tvaru a geometrie. Vykonáva sa za tepla. Keďže ide o proces kovania, vyrába diely s vynikajúcimi mechanickými vlastnosťami, a preto ho používame na výrobu automobilových dielov, ako sú hriadele, ktoré musia mať mimoriadnu odolnosť v náročných pracovných prostrediach. • ORBITÁLNE KOVANIE: Obrobok sa vloží do dutiny kovacej zápustky a vykuje hornou zápustkou, ktorá sa pohybuje po orbitálnej dráhe, keď sa otáča na naklonenej osi. Pri každej otáčke dokončí horná matrica vyvíjanie tlakových síl na celý obrobok. Viacnásobným opakovaním týchto otáčok sa vykoná dostatočné kovanie. Výhodou tejto výrobnej techniky je jej nízka hlučnosť a menšie potrebné sily. Inými slovami s malými silami je možné otáčať ťažkou matricou okolo osi, aby sa vyvinul veľký tlak na časť obrobku, ktorá je v kontakte s matricou. Diskové alebo kužeľovité časti sú niekedy vhodné pre tento proces. • KOVANIE PRSTENOV: Často používame na výrobu bezšvíkových prsteňov. Pažba sa nareže na požadovanú dĺžku, upevní sa a potom sa celá prepichne, aby sa vytvoril stredový otvor. Potom sa nasadí na tŕň a kováčska zápustka naň pri pomalom otáčaní prstenca pribíja kladivom, kým sa nedosiahnu požadované rozmery. • NITOVANIE: Bežný proces spájania dielov sa začína priamym kovovým kusom vloženým do vopred pripravených otvorov cez diely. Potom sa dva konce kovového kusu vykujú stlačením spoja medzi hornou a spodnou matricou. • RAŽENIE : Ďalší populárny proces vykonávaný mechanickým lisom, pri ktorom sa na krátku vzdialenosť vyvíjajú veľké sily. Názov „mince“ pochádza z jemných detailov, ktoré sú vykované na povrchu kovových mincí. Je to väčšinou proces dokončovania produktu, kde sa jemné detaily získavajú na povrchoch v dôsledku veľkej sily vyvíjanej matricou, ktorá tieto detaily prenáša na obrobok. • KOVANIE KOVOVÝCH GULIČIEK: Výrobky ako guľôčkové ložiská vyžadujú vysokokvalitné presne vyrobené kovové guľôčky. V jednej technike nazývanej SKEW ROLLING používame dva protiľahlé valce, ktoré sa nepretržite otáčajú, keď sa materiál nepretržite podáva do valcov. Na jednom konci dvoch valcov sa kovové guľôčky vysunú ako produkt. Druhým spôsobom na kovanie kovových guľôčok je použitie matrice, ktorá stlačí materiál umiestnený medzi nimi, pričom má guľový tvar dutiny formy. Vyrábané gule často vyžadujú niektoré ďalšie kroky, ako je konečná úprava a leštenie, aby sa stali vysokokvalitným produktom. • IZOTERMICKÉ KOVANIE / KOVANIE V ZÁVERE : Nákladný proces vykonávaný len vtedy, keď je opodstatnená hodnota prínosu / nákladov. Proces spracovania za tepla, pri ktorom sa matrica zahrieva na približne rovnakú teplotu ako obrobok. Pretože matrica aj obrobok majú približne rovnakú teplotu, nedochádza k ochladzovaniu a zlepšujú sa charakteristiky toku kovu. Operácia je vhodná pre superzliatiny a materiály s horšou kujnosťou a materiály, ktorých mechanické vlastnosti sú veľmi citlivé na malé teplotné gradienty a zmeny. • VELIKOSTI KOVOV: Je to proces dokončovania za studena. Tok materiálu je neobmedzený vo všetkých smeroch s výnimkou smeru, v ktorom pôsobí sila. Výsledkom je veľmi dobrá povrchová úprava a presné rozmery. • KOVANIE S VYSOKOU ENERGIOU: Táto technika zahŕňa hornú formu pripevnenú k ramenu piestu, ktorý sa rýchlo zatlačí, keď sa zapaľovacou sviečkou zapáli zmes paliva a vzduchu. Pripomína činnosť piestov v motore auta. Forma veľmi rýchlo zasiahne obrobok a vďaka spätnému tlaku sa veľmi rýchlo vráti do pôvodnej polohy. Dielo je vykované v priebehu niekoľkých milisekúnd a preto nie je čas na vychladnutie diela. To je užitočné pre ťažko kovateľné diely, ktoré majú mechanické vlastnosti veľmi citlivé na teplotu. Inými slovami, proces je taký rýchly, že súčiastka sa formuje pri konštantnej teplote a na rozhraní formy a obrobku nebudú žiadne teplotné gradienty. • Pri ZÁVEREČNOM KOVANÍ sa kov bije medzi dva zhodné oceľové bloky so špeciálnymi tvarmi, ktoré sa nazývajú zápustky. Keď sa kov vrazí medzi matrice, získa rovnaký tvar ako tvary v matrici. Keď dosiahne svoj konečný tvar, vyberie sa, aby vychladol. Tento proces produkuje pevné diely, ktoré majú presný tvar, ale vyžadujú si väčšie investície do špecializovaných lisovníc. Upchaté kovanie zväčšuje priemer kusu kovu jeho sploštením. Vo všeobecnosti sa používa na výrobu malých častí, najmä na vytváranie hláv na spojovacích materiáloch, ako sú skrutky a klince. • PRÁŠKOVÁ METALURGIA / PRÁŠKOVÉ SPRACOVANIE: Ako už názov napovedá, zahŕňa výrobné procesy na výrobu pevných častí určitých geometrií a tvarov z práškov. Ak sa na tento účel používajú kovové prášky, ide o oblasť práškovej metalurgie a ak sa používajú nekovové prášky, ide o práškové spracovanie. Pevné diely sa vyrábajú z práškov lisovaním a spekaním. POWDER PRESSING sa používa na lisovanie práškov do požadovaných tvarov. Po prvé, primárny materiál sa fyzikálne rozpráši, čím sa rozdelí na mnoho malých jednotlivých častíc. Prášková zmes sa naplní do formy a razidlo sa pohybuje smerom k prášku a zhutňuje ho do požadovaného tvaru. Väčšinou sa vykonáva pri izbovej teplote, lisovaním prášku sa získa tuhá časť, ktorá sa nazýva zelený výlisok. Spojivá a lubrikanty sa bežne používajú na zlepšenie zhutniteľnosti. Sme schopní lisovať prášok na hydraulických lisoch s kapacitou niekoľko tisíc ton. Máme tiež dvojčinné lisy s protiľahlými hornými a spodnými razníkmi, ako aj viacčinné lisy pre vysoko zložité geometrie dielov. Rovnomernosť, ktorá je dôležitou výzvou pre mnohé závody na práškovú metalurgiu / spracovanie práškov, nie je pre AGS-TECH žiadnym veľkým problémom, pretože máme dlhoročné skúsenosti s výrobou takýchto dielov na zákazku. Uspeli sme aj pri hrubších častiach, kde jednotnosť predstavuje výzvu. Ak sa zaviažeme k vášmu projektu, vyrobíme vaše diely. Ak uvidíme akékoľvek potenciálne riziká, budeme vás informovať in záloha. SPIEVANIE PRÁŠKA, čo je druhý krok, zahŕňa zvýšenie teploty na určitý stupeň a udržiavanie teploty na tejto úrovni po určitý čas, aby sa častice prášku v lisovanom diele mohli spojiť. Výsledkom sú oveľa pevnejšie väzby a spevnenie obrobku. Spekanie prebieha blízko teploty topenia prášku. Počas spekania dôjde k zmršteniu, zvýši sa pevnosť materiálu, hustota, ťažnosť, tepelná vodivosť a elektrická vodivosť. Máme vsádzkové a kontinuálne pece na spekanie. Jednou z našich možností je úprava úrovne pórovitosti dielov, ktoré vyrábame. Napríklad sme schopní vyrábať kovové filtre tak, že časti do určitej miery udržiavame porézne. Pomocou techniky nazývanej IMPREGNÁCIA vyplníme póry v kove tekutinou, ako je olej. Vyrábame napríklad ložiská impregnované olejom, ktoré sú samomazné. V procese INFILTRÁCIE vypĺňame póry kovu iným kovom s nižšou teplotou topenia ako je základný materiál. Zmes sa zahreje na teplotu medzi teplotami topenia dvoch kovov. V dôsledku toho je možné získať niektoré špeciálne vlastnosti. Často tiež vykonávame sekundárne operácie, ako je obrábanie a kovanie dielov vyrobených z prášku, keď je potrebné získať špeciálne vlastnosti alebo vlastnosti alebo keď je možné diel vyrobiť s menším počtom procesných krokov. IZSTATICKÉ LISOVANIE: V tomto procese sa na zhutnenie dielu používa tlak tekutiny. Kovové prášky sú umiestnené vo forme vyrobenej z uzavretej flexibilnej nádoby. Pri izostatickom lisovaní je tlak aplikovaný zo všetkých strán, na rozdiel od axiálneho tlaku pozorovaného pri bežnom lisovaní. Výhody izostatického lisovania sú rovnomerná hustota v rámci dielu, najmä pre väčšie alebo hrubšie diely, vynikajúce vlastnosti. Jeho nevýhodou sú dlhé doby cyklu a relatívne nízka geometrická presnosť. IZOSTATICKÉ LISOVANIE ZA STUDENA sa vykonáva pri izbovej teplote a pružná forma je vyrobená z gumy, PVC alebo uretánu alebo podobných materiálov. Kvapalinou používanou na tlakovanie a zhutňovanie je olej alebo voda. Nasleduje konvenčné spekanie zeleného výlisku. IZOSTATICKÉ LISOVANIE za horúca sa na druhej strane vykonáva pri vysokých teplotách a materiálom formy je plech alebo keramika s dostatočne vysokým bodom tavenia, ktorý teplotám odoláva. Tlaková kvapalina je zvyčajne inertný plyn. Operácie lisovania a spekania sa vykonávajú v jednom kroku. Pórovitosť je takmer úplne eliminovaná, získa sa uniform grain štruktúra. Výhodou izostatického lisovania za tepla je, že je možné vyrábať diely porovnateľné s odlievaním a kovaním v kombinácii, pričom je možné použiť materiály, ktoré nie sú vhodné na odlievanie a kovanie. Nevýhodou izostatického lisovania za horúca je jeho dlhá doba cyklu a tým aj cena. Je vhodný pre kritické časti s malým objemom. VSTREKOVANIE KOVOV: Veľmi vhodný proces na výrobu zložitých dielov s tenkými stenami a detailnou geometriou. Najvhodnejšie na menšie diely. Prášky a polymérne spojivo sa zmiešajú, zahrievajú a vstrekujú do formy. Polymérne spojivo pokrýva povrchy práškových častíc. Po formovaní sa spojivo odstráni buď zahrievaním pri nízkej teplote alebo rozpustením pomocou rozpúšťadla. HUTNENIE ROLKA / VÁLCOVANIE PRÁŠKA : Prášky sa používajú na výrobu súvislých pásov alebo plechov. Prášok je podávaný z podávača a zhutňovaný dvoma rotujúcimi valcami do listov alebo pásov. Operácia sa vykonáva za studena. Plech sa prenáša do spekacej pece. Proces spekania sa môže opakovať druhýkrát. EXTRÚZIA PRÁŠKA: Diely s veľkými pomermi dĺžky k priemeru sa vyrábajú vytláčaním tenkej plechovej nádoby s práškom. VOĽNÉ SPEKÁVANIE: Ako už názov napovedá, ide o beztlakovú metódu zhutňovania a spekania, ktorá je vhodná na výrobu veľmi poréznych dielov, ako sú kovové filtre. Prášok sa privádza do dutiny formy bez zhutňovania. VOĽNÉ SPEKÁVANIE: Ako už názov napovedá, ide o beztlakovú metódu zhutňovania a spekania, ktorá je vhodná na výrobu veľmi poréznych dielov, ako sú kovové filtre. Prášok sa privádza do dutiny formy bez zhutňovania. IZKROVÉ SPIENUTIE: Prášok je stlačený vo forme dvoma protiľahlými razníkmi a na razidlo sa aplikuje vysokovýkonný elektrický prúd a prechádza cez zhutnený prášok vložený medzi nimi. Vysoký prúd spáli povrchové filmy z častíc prášku a vzniknutým teplom ich speká. Proces je rýchly, pretože teplo nie je aplikované zvonku, ale vytvára sa zvnútra formy. LISOVANIE ZA HORÚCA : Prášky sa lisujú a spekajú v jednom kroku vo forme, ktorá odolá vysokým teplotám. Keď sa forma zhutňuje, aplikuje sa na ňu práškové teplo. Dobrá presnosť a mechanické vlastnosti dosiahnuté touto metódou z nej robia atraktívnu možnosť. Dokonca aj žiaruvzdorné kovy môžu byť spracované použitím formovacích materiálov, ako je grafit. CLICK Product Finder-Locator Service PREDCHÁDZAJÚCE MENU
- Plastic Rubber Metal Extrusions, Extrusion Dies, Aluminum Extruding
Plastic Rubber Metal Extrusions, Extrusion Dies, Aluminum Extruding, Pipe Tube Forming, Plastic Profiles, Metal Profiles Manufacturing, PVC at AGS-TECH Inc. Extrúzie, extrudované výrobky, extrudáty Proces EXTRUSION process používame na výrobu produktov s pevným profilom prierezu, ako sú rúry, rúrky a chladiče. Aj keď je možné extrudovať mnoho materiálov, naše najbežnejšie extrúzie sú vyrobené z kovu, polymérov / plastov, keramiky získanej metódou extrúzie za studena, za tepla alebo za tepla. Vytlačené časti nazývame extrudát alebo extrudáty, ak je množné číslo. Niektoré špecializované verzie procesu, ktoré tiež vykonávame, sú opláštenie, koextrúzia a kombinovaná extrúzia. Odporúčame vám kliknúť sem na STIAHNITE si naše schematické ilustrácie procesov vytláčania kovov, keramiky a plastov od AGS-TECH Inc. Pomôže vám to lepšie porozumieť informáciám, ktoré vám poskytujeme nižšie. Pri vytláčaní sa materiál, ktorý sa má vytlačiť, pretláča alebo ťahá cez matricu, ktorá má požadovaný profil prierezu. Proces je možné použiť na výrobu zložitých prierezov s vynikajúcou povrchovou úpravou a na opracovanie krehkého materiálu. Pomocou tohto procesu je možné vyrábať diely ľubovoľnej dĺžky. Na zjednodušenie krokov procesu: 1.) Pri vytláčaní za tepla alebo za tepla sa materiál ohrieva a vkladá do nádoby v lise. Materiál sa lisuje a vytláča z matrice. 2.) Vyrobený extrudát je tiahnutý na rovnanie, tepelne spracovaný alebo opracovaný za studena pre zlepšenie jeho vlastností. Na druhej strane COLD EXTRUSION prebieha približne pri izbovej teplote a má výhody menšej tolerancie, vysokej pevnosti a povrchovej úpravy. WARM EXTRUSION sa vykonáva nad izbovou teplotou, ale pod bodom rekryštalizácie. Ponúka kompromis a rovnováhu pre požadované sily, ťažnosť a vlastnosti materiálu, a preto je voľbou pre niektoré aplikácie. HOT EXTRUSION prebieha nad teplotou rekryštalizácie materiálu. Týmto spôsobom je jednoduchšie pretláčať materiál cez matricu. Náklady na vybavenie sú však vysoké. Čím je vytláčaný profil zložitejší, tým je nástroj (nástroj) nákladnejší a tým nižšia je rýchlosť výroby. Prierezy matrice, ako aj hrúbky majú obmedzenia, ktoré závisia od materiálu, ktorý sa má vytláčať. Ostré rohy vo vytláčacích nástrojoch sú vždy nežiaduce a ak to nie je nevyhnutné, je potrebné sa im vyhnúť. Podľa materiálu, ktorý sa vytláča, ponúkame: • METAL EXTRUSIONS : Najčastejšie vyrábame hliník, mosadz, zinok, meď, oceľ, titán, horčík • VYTLAČOVANIE PLASTU : Plast sa roztaví a vytvaruje do súvislého profilu. Naše bežné spracovávané materiály sú polyetylén, nylon, polystyrén, polyvinylchlorid, polypropylén, ABS plast, polykarbonát, akryl. Medzi typické produkty, ktoré vyrábame patria rúry a rúrky, plastové rámy. V procese sú malé plastové guľôčky / živica gravitačne privádzané z násypky do valca extrúzneho stroja. Často do násypky primiešavame aj farbivá alebo iné prísady, aby produkt získal požadované špecifikácie a vlastnosti. Materiál vstupujúci do vyhrievaného valca je nútený otáčajúcou sa skrutkou opustiť valec na konci a pohybovať sa cez sito, aby sa odstránili kontaminanty v roztavenom plaste. Po prechode cez sito sa plast dostane do vytláčacej hubice. Forma dodáva pohyblivému mäkkému plastu jeho profilový tvar, keď ním prechádza. Teraz extrudát prechádza vodným kúpeľom na chladenie. Ďalšie techniky, ktoré AGS-TECH Inc. používa už mnoho rokov, sú: • VYTLAČOVANIE RÚR A RÚRiek : Plastové rúrky a rúrky sa formujú, keď sa plasty vytláčajú cez okrúhlu tvarovaciu matricu a chladia sa vo vodnom kúpeli, potom sa krájajú na dĺžku alebo zvíjajú/navíjajú. Číre alebo farebné, pruhované, s jednou alebo dvojitou stenou, flexibilné alebo tuhé, PE, PP, polyuretán, PVC, nylon, PC, silikón, vinyl alebo iné, máme všetko. Máme skladované rúrky, ako aj schopnosť vyrábať podľa vašich špecifikácií. AGS-TECH vyrába hadičky podľa požiadaviek FDA, UL a LE pre medicínske, elektrické a elektronické, priemyselné a iné aplikácie. • PREVNÁŠANIE / PREVNÁŠANIE PLÁŠŤANIE : Táto technika aplikuje vonkajšiu vrstvu plastu na existujúci drôt alebo kábel. Naše izolačné drôty sa vyrábajú touto metódou. • COEXTRUSION : Súčasne sa extruduje viacero vrstiev materiálu. Viacnásobné vrstvy sú dodávané viacerými extrudérmi. Rôzne hrúbky vrstiev je možné upraviť podľa požiadaviek zákazníka. Tento proces umožňuje použiť viacero polymérov, z ktorých každý má v produkte inú funkčnosť. V dôsledku toho je možné optimalizovať celý rad vlastností. • EXTRÚZIA ZLOŽIEK: Jeden alebo viacero polymérov sa zmieša s prísadami, aby sa získala plastická zmes. Naše dvojzávitovkové extrudéry vyrábajú zmiešavacie výlisky. Vytláčacie formy sú vo všeobecnosti lacné v porovnaní s kovovými formami. Ak platíte oveľa viac ako niekoľko tisíc dolárov za malú alebo strednú vytláčaciu matricu na vytláčanie hliníka, pravdepodobne platíte príliš veľa. Sme odborníci na určenie, ktorá technika je cenovo najefektívnejšia, najrýchlejšia a najvhodnejšia pre vašu aplikáciu. Niekedy vám vytlačenie a následné opracovanie dielu môže ušetriť veľa peňazí. Skôr ako sa rozhodneš, opýtaj sa nás najprv na náš názor. Mnohým zákazníkom sme pomohli urobiť správne rozhodnutia. Pre niektoré široko používané kovové výlisky si môžete stiahnuť naše brožúry a katalógy kliknutím na farebný text nižšie. Ak ide o bežný produkt, ktorý spĺňa vaše požiadavky, bude to ekonomickejšie. Stiahnite si naše možnosti vytláčania lekárskych rúr a rúrok Stiahnite si naše extrudované chladiče • SEKUNDÁRNE VÝROBNÉ A VÝROBNÉ PROCESY PRE EXTRÚZIE : Medzi procesy s pridanou hodnotou, ktoré ponúkame pre extrudované produkty, patria: -Ohýbanie, tvarovanie a tvarovanie rúr a rúr na mieru, odrezávanie rúr, tvarovanie koncov rúr, navíjanie rúr, obrábanie a konečná úprava, vŕtanie a dierovanie a dierovanie, -Zakázkové zostavy rúr a rúrok, montáž rúr, zváranie, tvrdé spájkovanie a spájkovanie -Vlastné vytláčanie ohýbanie, tvarovanie a tvarovanie -Čistenie, odmasťovanie, morenie, pasivácia, leštenie, eloxovanie, pokovovanie, lakovanie, tepelné spracovanie, žíhanie a kalenie, značenie, gravírovanie a etiketovanie, balenie na mieru. CLICK Product Finder-Locator Service PREDCHÁDZAJÚCA STRANA
- Casting and Machined Parts, CNC Manufacturing, Milling, Turning, Swiss
Casting and Machined Parts, CNC Manufacturing, Milling, Turning, Swiss Type Machining, Die Casting, Investment Casting, Lost Foam Cast Parts from AGS-TECH Inc. Odlievanie a obrábanie Naše zákazkové odlievacie a obrábacie techniky sú spotrebné a nepotrebné odliatky, železné a neželezné odliatky, piesok, matrica, odstredivá, kontinuálna, keramická forma, investícia, stratená pena, takmer sieťový tvar, trvalá forma (gravitačné liatie), sadra formy (odliatky zo sadry) a škrupinové odliatky, opracované diely vyrábané frézovaním a sústružením na konvenčných aj CNC zariadeniach, obrábanie švajčiarskym typom pre vysokovýkonné lacné malé presné diely, skrutkové obrábanie spojovacích prvkov, nekonvenčné obrábanie. Prosím, majte na pamäti, že okrem kovov a kovových zliatin obrábame aj keramické, sklenené a plastové komponenty v niektorých prípadoch, keď výroba formy nie je príťažlivá alebo nie je vhodná. Obrábanie polymérnych materiálov si vyžaduje špecializované skúsenosti, ktoré máme kvôli problémom, ktoré plasty a guma predstavujú kvôli ich mäkkosti, nepevnosti... atď. Informácie o obrábaní keramiky a skla nájdete na našej stránke Nekonvenčná výroba. AGS-TECH Inc. vyrába a dodáva ľahké aj ťažké odliatky. Dodávame kovové odliatky a opracované diely pre kotly, výmenníky tepla, automobily, mikromotory, veterné turbíny, zariadenia na balenie potravín a ďalšie. Odporúčame vám kliknúť sem na STIAHNITE si naše schematické ilustrácie procesov obrábania a odlievania od AGS-TECH Inc. Pomôže vám to lepšie porozumieť informáciám, ktoré vám poskytujeme nižšie. Pozrime sa podrobne na niektoré z rôznych techník, ktoré ponúkame: • ODLIETANIE FORMÍ: Táto široká kategória sa týka metód, ktoré zahŕňajú dočasné a jednorazové formy. Príkladmi sú piesok, sadra, škrupina, investícia (tiež nazývaná stratený vosk) a sadrový odliatok. • LIATIE DO PIESKU: Proces, pri ktorom sa ako materiál formy používa piesok. Veľmi stará metóda a stále veľmi populárna do tej miery, že väčšina vyrábaných kovových odliatkov je vyrobená touto technikou. Nízke náklady aj pri malom množstve výroby. Vhodné na výrobu malých a veľkých dielov. Táto technika môže byť použitá na výrobu dielov v priebehu niekoľkých dní alebo týždňov s veľmi malými investíciami. Vlhký piesok sa spája pomocou hliny, spojív alebo špeciálnych olejov. Piesok je vo všeobecnosti obsiahnutý vo formovacích boxoch a systém dutín a vrát sa vytvára zhutňovaním piesku okolo modelov. Procesy sú: 1.) Uloženie modelu do piesku na výrobu formy 2.) Začlenenie modelu a piesku do vtokového systému 3.) Odstránenie modelu 4.) Vyplnenie dutiny formy roztaveným kovom 5.) Chladenie kovu 6.) Rozbitie pieskovej formy a vybratie odliatku • ODLIEVANIE SADRY: Podobne ako pri odlievaní do piesku a namiesto piesku sa ako materiál formy používa sadra z Paríža. Krátke výrobné časy, ako je liatie do piesku a lacné. Dobré rozmerové tolerancie a povrchová úprava. Jeho hlavnou nevýhodou je, že ho možno použiť iba s kovmi s nízkou teplotou topenia, ako je hliník a zinok. • ODLIATOK škrupín: Tiež podobné odlievaniu do piesku. Dutina formy získaná vytvrdeným plášťom piesku a termosetovým živicovým spojivom namiesto banky naplnenej pieskom ako pri procese odlievania do piesku. Takmer každý kov vhodný na odlievanie do piesku možno odlievať škrupinovým odlievaním. Proces možno zhrnúť takto: 1.) Výroba škrupinovej formy. Použitý piesok má oveľa menšiu zrnitosť v porovnaní s pieskom používaným pri liatí do piesku. Jemný piesok sa zmieša s termosetovou živicou. Kovový vzor je potiahnutý separačným prostriedkom, aby sa uľahčilo odstránenie škrupiny. Potom sa kovový vzor zahreje a piesková zmes sa póruje alebo fúka na horúci odlievaný vzor. Na povrchu vzoru sa vytvorí tenká škrupina. Hrúbku tejto škrupiny je možné nastaviť zmenou dĺžky času, počas ktorého je zmes pieskovej živice v kontakte s kovovým vzorom. Voľný piesok sa potom odstráni, pričom zostane vzor pokrytý škrupinou. 2.) Ďalej sa škrupina a vzor zohrievajú v rúre, aby škrupina stuhla. Po dokončení vytvrdnutia sa škrupina vysunie zo vzoru pomocou kolíkov zabudovaných do vzoru. 3.) Dve takéto škrupiny sa spoja dohromady lepením alebo zovretím a tvoria kompletnú formu. Teraz je škrupinová forma vložená do nádoby, v ktorej je počas procesu odlievania podopretá pieskom alebo kovovými brokmi. 4.) Teraz môžeme horúci kov naliať do formy na škrupinu. Výhodou škrupinového odlievania sú výrobky s veľmi dobrou povrchovou úpravou, možnosť výroby zložitých dielov s vysokou rozmerovou presnosťou, proces ľahko automatizovateľný, ekonomický pre veľkosériovú výrobu. Nevýhody sú, že formy vyžadujú dobré vetranie, pretože plyny vznikajú pri kontakte roztaveného kovu so spojivom, termosetové živice a kovové vzory sú drahé. Kvôli nákladom na kovové vzory nemusí táto technika dobre vyhovovať pre malé množstvo výroby. • INVESTIČNÉ ODLIATIE (známe aj ako LOST-WAX CASTING): Tiež veľmi stará technika a vhodná na výrobu kvalitných dielov s vysokou presnosťou, opakovateľnosťou, všestrannosťou a integritou z mnohých kovov, žiaruvzdorných materiálov a špeciálnych vysokovýkonných zliatin. Je možné vyrábať malé aj veľké diely. Nákladný proces v porovnaní s niektorými inými metódami, ale hlavnou výhodou je možnosť vyrábať diely s takmer čistým tvarom, zložitými obrysmi a detailmi. Takže náklady sú v niektorých prípadoch do istej miery kompenzované elimináciou prepracovania a obrábania. Aj keď môžu existovať odchýlky, tu je zhrnutie všeobecného procesu investičného liatia: 1.) Vytvorenie originálnej predlohy z vosku alebo plastu. Každý odliatok potrebuje jeden vzor, pretože tieto sa pri tomto procese zničia. Potrebná je aj forma, z ktorej sa vyrábajú vzory a väčšinou sa forma odlieva alebo opracúva. Pretože formu nie je potrebné otvárať, je možné docieliť zložité odliatky, mnohé voskové vzory je možné spájať ako konáre stromu a zlievať dohromady, čo umožňuje výrobu viacerých dielov z jedného odliatia kovu alebo kovovej zliatiny. 2.) Ďalej sa vzor ponorí alebo preleje žiaruvzdornou kašou zloženou z veľmi jemnozrnného oxidu kremičitého, vody, spojív. Výsledkom je keramická vrstva na povrchu vzoru. Žiaruvzdorný náter na vzore sa nechá zaschnúť a vytvrdnúť. Od tohto kroku pochádza názov zatavovacie liatie: Žiaruvzdorná kaša sa zaleje cez voskový vzor. 3.) V tomto kroku vytvrdnutú keramickú formu otočíme hore dnom a nahrejeme, aby sa vosk roztopil a vylial z formy. Pre kovový odliatok zostáva dutina. 4.) Po vypustení vosku sa keramická forma zahreje na ešte vyššiu teplotu, čo má za následok spevnenie formy. 5.) Kovový odliatok sa naleje do horúcej formy a vyplní všetky zložité časti. 6.) Odliatok sa nechá stuhnúť 7.) Nakoniec sa keramická forma rozbije a vyrobené diely sa odrežú zo stromu. Tu je odkaz na brožúru o závode na investičné odlievanie • ODLIEVANIE VZORU ODPAĽOVANIA: Proces využíva vzor vyrobený z materiálu, akým je polystyrénová pena, ktorá sa odparí, keď sa do formy naleje horúci roztavený kov. Existujú dva typy tohto procesu: LOST FOAM CASTING, pri ktorom sa používa nespojený piesok, a ODLIATOK PLNEJ MULTI, pri ktorom sa používa viazaný piesok. Tu sú všeobecné kroky procesu: 1.) Vzor vyrobte z materiálu ako je polystyrén. Keď sa budú vyrábať veľké množstvá, vzor sa formuje. Ak má časť zložitý tvar, na vytvorenie vzoru môže byť potrebné zlepiť niekoľko častí takéhoto penového materiálu. Vzor často natierame žiaruvzdornou zmesou, aby sme vytvorili dobrú povrchovú úpravu odliatku. 2.) Vzor sa potom vloží do formovacieho piesku. 3.) Roztavený kov sa naleje do formy, pričom sa pri prúdení cez dutinu formy odparí penový vzor, teda vo väčšine prípadov polystyrén. 4.) Roztavený kov sa nechá vytvrdnúť v pieskovej forme. 5.) Po vytvrdnutí odliatok stiahneme. V niektorých prípadoch produkt, ktorý vyrábame, vyžaduje jadro vo vzore. Pri odparovacom odlievaní nie je potrebné umiestňovať a upevňovať jadro v dutine formy. Technika je vhodná na výrobu veľmi zložitých geometrií, dá sa ľahko automatizovať pre veľkoobjemovú výrobu a v odliatku nie sú žiadne deliace linky. Implementácia základného procesu je jednoduchá a hospodárna. Pri veľkoobjemovej výrobe, keďže na výrobu vzorov z polystyrénu je potrebná forma alebo forma, to môže byť trochu nákladné. • ODLIATIE NEEXPANDOVATEĽNÝCH FORIEM: Táto široká kategória sa týka metód, pri ktorých nie je potrebné formu po každom výrobnom cykle reformovať. Príkladmi sú trvalé, zápustkové, kontinuálne a odstredivé liatie. Získa sa opakovateľnosť a časti možno charakterizovať ako NEAR NET SHAPE. • TRVALÉ ODLIATIE FORMY: Opakovane použiteľné formy vyrobené z kovu sa používajú na viacnásobné odlievanie. Trvalá forma môže byť vo všeobecnosti použitá desaťtisíckrát, kým sa neopotrebuje. Na plnenie formy sa vo všeobecnosti používa gravitácia, tlak plynu alebo vákuum. Formy (tiež nazývané matrice) sú zvyčajne vyrobené zo železa, ocele, keramiky alebo iných kovov. Všeobecný proces je: 1.) Opracujte a vytvorte formu. Je bežné, že sa forma vyrába z dvoch kovových blokov, ktoré do seba zapadajú a dajú sa otvárať a zatvárať. Obidve vlastnosti dielu, ako aj vtokový systém sú spravidla opracované do odlievacej formy. 2.) Vnútorné povrchy formy sú potiahnuté kašou obsahujúcou žiaruvzdorné materiály. To pomáha kontrolovať tepelný tok a pôsobí ako mazivo pre ľahké odstránenie odliatkov. 3.) Ďalej sa polovice trvalej formy uzavrú a forma sa zahreje. 4.) Roztavený kov sa naleje do formy a nechá sa ešte stuhnúť. 5.) Skôr ako dôjde k väčšiemu ochladeniu, vyberieme diel z trvalej formy pomocou vyhadzovačov pri otvorení polovíc formy. Často používame trvalé odlievanie kovov s nízkou teplotou topenia, ako je zinok a hliník. Pre oceľové odliatky používame ako formovací materiál grafit. Niekedy získavame zložité geometrie pomocou jadier v trvalých formách. Výhodou tejto techniky sú odliatky s dobrými mechanickými vlastnosťami získanými rýchlym ochladením, jednotnosť vlastností, dobrá presnosť a povrchová úprava, nízka miera nepodarkovosti, možnosť automatizácie procesu a ekonomická výroba veľkých objemov. Nevýhodami sú vysoké počiatočné náklady na nastavenie, ktoré ho robia nevhodným pre operácie s malým objemom, a obmedzenia veľkosti vyrábaných dielov. • ODLIATOK : Forma je opracovaná a roztavený kov je tlačený pod vysokým tlakom do dutín formy. Možné sú tlakové odliatky z neželezných aj železných kovov. Proces je vhodný pre veľké série výroby malých až stredne veľkých dielov s detailmi, extrémne tenkými stenami, rozmerovou stálosťou a dobrou povrchovou úpravou. AGS-TECH Inc. je schopná touto technikou vyrábať steny s hrúbkou len 0,5 mm. Podobne ako pri odlievaní stálej formy, forma musí pozostávať z dvoch polovíc, ktoré sa môžu otvárať a zatvárať na odstránenie vyrobeného dielu. Forma na tlakové liatie môže mať viacero dutín na umožnenie výroby viacerých odliatkov v každom cykle. Formy na tlakové liatie sú veľmi ťažké a oveľa väčšie ako diely, ktoré vyrábajú, a preto sú tiež drahé. Našim zákazníkom bezplatne opravujeme a vymieňame opotrebované matrice, pokiaľ si u nás objednajú svoje diely. Naše matrice majú dlhú životnosť v rozsahu niekoľko stoviek tisíc cyklov. Tu sú základné zjednodušené kroky procesu: 1.) Výroba formy spravidla z ocele 2.) Forma inštalovaná na stroji na tlakové liatie 3.) Piest núti roztavený kov prúdiť v dutinách matrice, čím vypĺňa zložité prvky a tenké steny 4.) Po naplnení formy roztaveným kovom sa odliatok nechá vytvrdnúť pod tlakom 5.) Forma sa otvorí a odliatok sa vyberie pomocou vyhadzovacích kolíkov. 6.) Teraz je prázdna matrica opäť namazaná a upnutá na ďalší cyklus. Pri tlakovom liatí často používame vložkové odlievanie, pri ktorom do formy začleňujeme ďalšiu časť a okolo nej odlievame kov. Po stuhnutí sa tieto časti stanú súčasťou odlievaného výrobku. Výhodou tlakového liatia sú dobré mechanické vlastnosti dielov, možnosť zložitých prvkov, jemné detaily a dobrá povrchová úprava, vysoká produktivita, jednoduchá automatizácia. Nevýhody sú: Nie je veľmi vhodný pre malý objem kvôli vysokým nákladom na lisovnicu a vybavenie, obmedzenia v tvaroch, ktoré je možné odlievať, malé okrúhle stopy na odlievaných častiach spôsobené kontaktom vyhadzovacích kolíkov, tenký záblesk kovu vytlačený na deliacej čiare, potreba pre vetracie otvory pozdĺž deliacej čiary medzi matricou nutnosť udržiavať nízke teploty formy pomocou cirkulácie vody. • ODSTREDIVÉ LIETANIE: Roztavený kov sa naleje do stredu rotujúcej formy v osi otáčania. Odstredivé sily vrhajú kov smerom k okraju a nechá sa stuhnúť, keď sa forma stále otáča. Je možné použiť otáčanie horizontálnej aj vertikálnej osi. Je možné odlievať diely s oblými vnútornými povrchmi, ako aj iné neokrúhle tvary. Proces možno zhrnúť takto: 1.) Roztavený kov sa naleje do odstredivej formy. Kov je potom tlačený k vonkajším stenám v dôsledku otáčania formy. 2.) Ako sa forma otáča, kovový odliatok tuhne Odstredivé liatie je vhodná technika na výrobu dutých valcových dielov, ako sú rúry, nie sú potrebné vtoky, stúpačky a vtokové prvky, dobrá povrchová úprava a detailné vlastnosti, žiadne problémy so zmršťovaním, možnosť výroby dlhých rúr s veľmi veľkými priemermi, vysoká rýchlosť výroby . • KONTINUÁLNE ODLIEVANIE ( LIATIE PLÁNOV ): Používa sa na odlievanie súvislej dĺžky kovu. V podstate sa roztavený kov odlieva do dvojrozmerného profilu formy, ale jeho dĺžka je neurčitá. Nový roztavený kov sa neustále privádza do formy, keď sa odliatok pohybuje smerom nadol, pričom jeho dĺžka sa s časom zvyšuje. Kovy ako meď, oceľ, hliník sa odlievajú do dlhých prameňov pomocou procesu kontinuálneho odlievania. Proces môže mať rôzne konfigurácie, ale ten spoločný možno zjednodušiť ako: 1.) Roztavený kov sa naleje do nádoby umiestnenej vysoko nad formou v dobre vypočítaných množstvách a prietokoch a preteká vodou chladenou formou. Kovový odliatok naliaty do formy stuhne na štartovaciu tyč umiestnenú na dne formy. Táto štartovacia lišta dáva valcom niečo, čoho sa môžu na začiatku chytiť. 2.) Dlhý kovový prameň je unášaný valčekmi konštantnou rýchlosťou. Valce tiež menia smer toku kovového pásu z vertikálneho na horizontálny. 3.) Potom, čo plynulý odliatok prejde určitú vodorovnú vzdialenosť, horák alebo píla, ktorá sa pohybuje s odliatkom, ho rýchlo odreže na požadované dĺžky. Proces kontinuálneho odlievania môže byť integrovaný s ROLLING PROCESS, kde kontinuálne odlievaný kov môže byť privádzaný priamo do valcovacej stolice na výrobu I-nosníkov, T-nosníkov... atď. Kontinuálne odlievanie vytvára jednotné vlastnosti v celom výrobku, má vysokú rýchlosť tuhnutia, znižuje náklady vďaka veľmi nízkym stratám materiálu, ponúka proces, pri ktorom nakladanie kovu, liatie, tuhnutie, rezanie a vyberanie odliatkov prebieha v kontinuálnej prevádzke a čo vedie k vysokej produktivite a vysokej kvalite. Hlavným hľadiskom sú však vysoké počiatočné investície, náklady na inštaláciu a priestorové požiadavky. • OBRÁBACIE SLUŽBY : Ponúkame troj, štvor a päťosové obrábanie. Typy procesov obrábania, ktoré používame sú SÚSTRUŽENIE, FRÉZOVANIE, VŔTANIE, VYVRTÁVANIE, PRETAHOVANIE, HOBLOVANIE, PÍLENIE, BRÚSENIE, LAPOVANIE, LEŠTENIE a NETRADIČNÉ OBRÁBENIE, ktoré je bližšie rozpracované v inej ponuke našej webovej stránky. Pre väčšinu našej výroby používame CNC stroje. Pre niektoré operácie sú však konvenčné techniky vhodnejšie, a preto sa na ne spoliehame tiež. Naše možnosti obrábania dosahujú najvyššiu možnú úroveň a niektoré najnáročnejšie diely sa vyrábajú v závode s certifikátom AS9100. Lopatky prúdových motorov vyžadujú vysoko špecializované výrobné skúsenosti a správne vybavenie. Letecký priemysel má veľmi prísne normy. Niektoré súčiastky so zložitými geometrickými štruktúrami sa najľahšie vyrábajú päťosovým obrábaním, ktoré sa nachádza len v niektorých obrábacích závodoch vrátane našej. Náš závod s certifikáciou pre letecký priemysel má potrebné skúsenosti v súlade s požiadavkami rozsiahlej dokumentácie leteckého priemyslu. V operáciách SÚSTRUŽENIA sa obrobok otáča a pohybuje proti reznému nástroju. Na tento proces sa používa stroj nazývaný sústruh. Pri FRÉZOVANÍ má stroj nazývaný frézka rotačný nástroj, ktorý privádza rezné hrany do styku s obrobkom. Operácie VŔTANIE zahŕňajú rotačnú frézu s reznými hranami, ktorá pri kontakte s obrobkom vytvára otvory. Vo všeobecnosti sa používajú vŕtacie lisy, sústruhy alebo frézy. Pri operáciách VYVRTÁVANIA sa nástroj s jednou zahnutou špičkou presunie do hrubého otvoru v rotujúcom obrobku, aby sa otvor mierne zväčšil a zlepšila sa presnosť. Používa sa na jemné dokončovacie účely. PRETAHOVANIE zahŕňa ozubený nástroj na odstránenie materiálu z obrobku jedným prechodom preťahovača (ozubený nástroj). Pri lineárnom preťahovaní prebieha preťahovanie lineárne proti povrchu obrobku na uskutočnenie rezu, zatiaľ čo pri rotačnom preťahovaní sa preťahovač otáča a vtláča do obrobku, aby vyrezal osovo symetrický tvar. SWISS TYPE MACHINING je jednou z našich cenných techník, ktoré používame na veľkoobjemovú výrobu malých a vysoko presných dielov. Pomocou sústruhu švajčiarskeho typu sústružíme malé, zložité a presné diely lacno. Na rozdiel od bežných sústruhov, kde je obrobok nehybný a nástroj sa pohybuje, v sústružníckych centrách švajčiarskeho typu sa obrobok môže pohybovať v osi Z a nástroj je nehybný. Pri obrábaní švajčiarskeho typu je tyčový materiál držaný v stroji a posúvaný cez vodiace puzdro v osi z, čím sa odhaľuje iba časť, ktorá sa má obrábať. Týmto spôsobom je zaistené pevné uchopenie a presnosť je veľmi vysoká. Dostupnosť nástrojov pod napätím poskytuje možnosť frézovať a vŕtať, keď materiál postupuje z vodiaceho puzdra. Os Y zariadenia švajčiarskeho typu poskytuje plné možnosti frézovania a šetrí veľké množstvo času pri výrobe. Okrem toho naše stroje majú vŕtačky a vyvrtávacie nástroje, ktoré pracujú na diele, keď je držaný v pomocnom vretene. Naša schopnosť obrábania švajčiarskeho typu nám dáva možnosť plne automatizovaného kompletného obrábania v jedinej operácii. Obrábanie je jedným z najväčších segmentov podnikania AGS-TECH Inc. Používame ho buď ako primárnu operáciu alebo sekundárnu operáciu po odliatí alebo vytlačení dielu tak, aby boli splnené všetky špecifikácie výkresu. • SLUŽBY POVRCHOVEJ ÚPRAVY: Ponúkame širokú škálu povrchových úprav a povrchových úprav, ako je úprava povrchu na zvýšenie priľnavosti, nanášanie tenkej oxidovej vrstvy na zvýšenie priľnavosti náteru, pieskovanie, chemický film, eloxovanie, nitridovanie, práškové lakovanie, striekanie , rôzne pokročilé techniky pokovovania a povlakovania vrátane naprašovania, elektrónového lúča, odparovania, pokovovania, tvrdých povlakov, ako je napríklad diamantový uhlík (DLC) alebo titánový povlak pre vŕtacie a rezné nástroje. • SLUŽBY ZNAČENIA A OZNAČOVANIA VÝROBKOV: Mnoho našich zákazníkov vyžaduje značenie a označovanie, laserové značenie, gravírovanie na kovové časti. Ak máte takúto potrebu, dovoľte nám prediskutovať, ktorá možnosť bude pre vás najlepšia. Tu sú niektoré z bežne používaných kovových odliatkov. Keďže sú bežne dostupné, môžete ušetriť na nákladoch na formy, ak niektorý z nich vyhovuje vašim požiadavkám: KLIKNITE SEM, ABY SI STIAHNULI naše hliníkové boxy radu 11 odlievané pod tlakom od AGS-Electronics CLICK Product Finder-Locator Service PREDCHÁDZAJÚCA STRANA
- Custom Manufactured Parts, Assemblies, Plastic Mold, Casting,Machining
Custom Manufactured Parts, Assemblies, Plastic Mold, Rubber Molding, Metal Casting, CNC Machining, Turning, Milling, Electrical Electronic Optical Assembly PCBA Diely, zostavy a produkty vyrobené na mieru Čítaj viac Plastové a gumové formy a lisovanie Čítaj viac Odlievanie a obrábanie Čítaj viac Výlisky, Extrudované výrobky Čítaj viac Lisovanie a výroba plechov Čítaj viac Kovanie kovov a prášková metalurgia Čítaj viac Drôtové a pružinové tvarovanie Čítaj viac Tvarovanie a tvarovanie skla a keramiky Čítaj viac Aditívna a rýchla výroba Čítaj viac Výroba kompozitov a kompozitných materiálov Čítaj viac Procesy spájania a montáže a upevnenia Vyrábame pre Vás diely a zostavy a ponúkame nasledovné výrobné procesy: • Plastové a gumené formy a lisované diely. Vstrekovanie, tvarovanie za tepla, tvarovanie termosetom, vákuové tvarovanie, vyfukovanie, rotačné tvarovanie, odlievanie, vstrekovanie a iné. • Plastové, gumené a kovové výlisky • Železné a neželezné odliatky a opracované diely vyrábané technikou frézovania a sústruženia, obrábaním švajčiarskeho typu. • Diely z práškovej metalurgie • Kovové a nekovové výlisky, tvárnenie plechov, zvárané plechové zostavy • Kovanie za studena a za tepla • Drôty, zvárané zostavy drôtov, tvarovanie drôtov • Rôzne typy pružín, tvarovanie pružín • Výroba ozubených kolies, prevodoviek, spojok, závitoviek, reduktorov rýchlosti, valcov, prevodových remeňov, prevodových reťazí, prevodových komponentov • Vlastné tvrdené a nepriestrelné sklo v súlade s NATO a vojenskými normami • Guľôčky, ložiská, remenice a zostavy remeníc • Ventily a pneumatické komponenty ako O-krúžok, podložky a tesnenia • Sklenené a keramické diely a zostavy, vákuovo odolné a hermetické komponenty, kovo-keramické a keramicko-keramické lepenie. • Rôzne typy mechanických, optomechanických, elektromechanických, optoelektronických zostáv. • Spojenie kov-guma, kov-plast • Rúry a rúry, tvarovanie rúr, ohýbanie a zostavy rúr na zákazku, výroba vlnovcov. • Výroba sklenených vlákien • Zváranie rôznymi technikami ako bodové zváranie, laserové zváranie, MIG, TIG. Ultrazvukové zváranie plastových dielov. • Široká škála povrchových úprav a povrchových úprav, ako je úprava povrchu na zvýšenie priľnavosti, nanášanie tenkej oxidovej vrstvy na zvýšenie priľnavosti povlaku, pieskovanie, chemický film, eloxovanie, nitridovanie, práškové lakovanie, striekanie, rôzne pokročilé metalizačné a lakovacie techniky vrátane naprašovania, elektrónového lúča, naparovania, pokovovania, tvrdých povlakov, ako je diamant ako uhlík (DLC) alebo titán pre rezné a vŕtacie nástroje. • Značenie a etiketovanie, laserové značenie na kovové časti, tlač na plastové a gumené časti Stiahnite si brožúru s bežnými pojmami strojárskeho inžinierstva, ktoré používajú dizajnéri a inžinieri Vyrábame produkty podľa vašich konkrétnych špecifikácií a požiadaviek. Aby sme vám mohli ponúknuť najlepšiu kvalitu, dodanie a ceny, vyrábame produkty po celom svete v Číne, Indii, Taiwane, Filipínach, Južnej Kórei, Malajzii, Srí Lanke, Turecku, USA, Kanade, Nemecku, Veľkej Británii a Japonsku. To nás robí oveľa silnejšími a globálne konkurencieschopnejšími než ktorýkoľvek iný custom manufacturer. Naše produkty sú vyrábané v certifikovaných prostrediach ISO9001:2000, QS9000, ISO14001, TS16949 a majú značku CE, UL a spĺňajú ďalšie priemyselné normy. Akonáhle sme menovaní pre váš projekt, môžeme sa postarať o celú výrobu, montáž, testovanie, kvalifikáciu, expedíciu a clo podľa vášho želania. Ak chcete, môžeme skladovať vaše diely, zostaviť vlastné súpravy, vytlačiť a označiť názov a značku vašej spoločnosti a poslať zásielku vašim zákazníkom. Inými slovami, môžeme byť aj vašim skladovým a distribučným centrom, ak si to želáte. Keďže naše sklady sa nachádzajú v blízkosti veľkých námorných prístavov, poskytuje nám to logistickú výhodu. Napríklad, keď vaše produkty dorazia do veľkého námorného prístavu v USA, môžeme dopraviť ich priamo do blízkeho skladu, kde ich môžeme uložiť, zostaviť, vyrobiť súpravy, preznačiť, vytlačiť, zabaliť podľa vášho výberu a nechať ich poslať doručiť svojim zákazníkom. Dodávame nielen produkty. Naša spoločnosť pracuje na zákazkách na mieru, kedy prídeme na vašu stránku, zhodnotíme váš projekt na mieste a vypracujeme návrh projektu na mieru. Následne pošleme náš skúsený tím na realizáciu projektu. Viac informácií o našej inžinierskej činnosti nájdete na http://www.ags-engineering.com - Berieme malé projekty aj veľké projekty v priemyselnom meradle. Ako prvý krok vás môžeme spojiť buď telefonicky, telekonferenciou alebo službou MSN messenger s členmi nášho tímu odborníkov, takže môžete komunikovať priamo s odborníkom, klásť otázky a diskutovať o svojom projekte. Zavolajte nám a v prípade potreby vás prídeme navštíviť. PREDCHÁDZAJÚCA STRANA